Critical Evaluation of Juran's Quality Management in Organizations
VerifiedAdded on 2023/05/30
|9
|2648
|116
Report
AI Summary
This report critically evaluates Joseph Juran's contributions to quality management practices in contemporary organizations. It explores Juran's philosophy of "fitness for use," emphasizing design quality, conformance, availability, safety, and field use. The report discusses how Juran's approach spans the product life cycle and involves statistical techniques for analysis and improvement. It also highlights Juran's advocacy for cost-of-quality accounting systems, focusing on internal and external failure costs, appraisal costs, and prevention costs. The report uses Nokia as an example to illustrate the application of Juran's principles in a real-world business context, discussing Nokia's quality programs, financial practices, and strategic initiatives. The analysis concludes that understanding and implementing Juran's standards can significantly enhance a company's ability to produce durable and unique products, thereby improving its competitive edge.
Contribute Materials
Your contribution can guide someone’s learning journey. Share your
documents today.
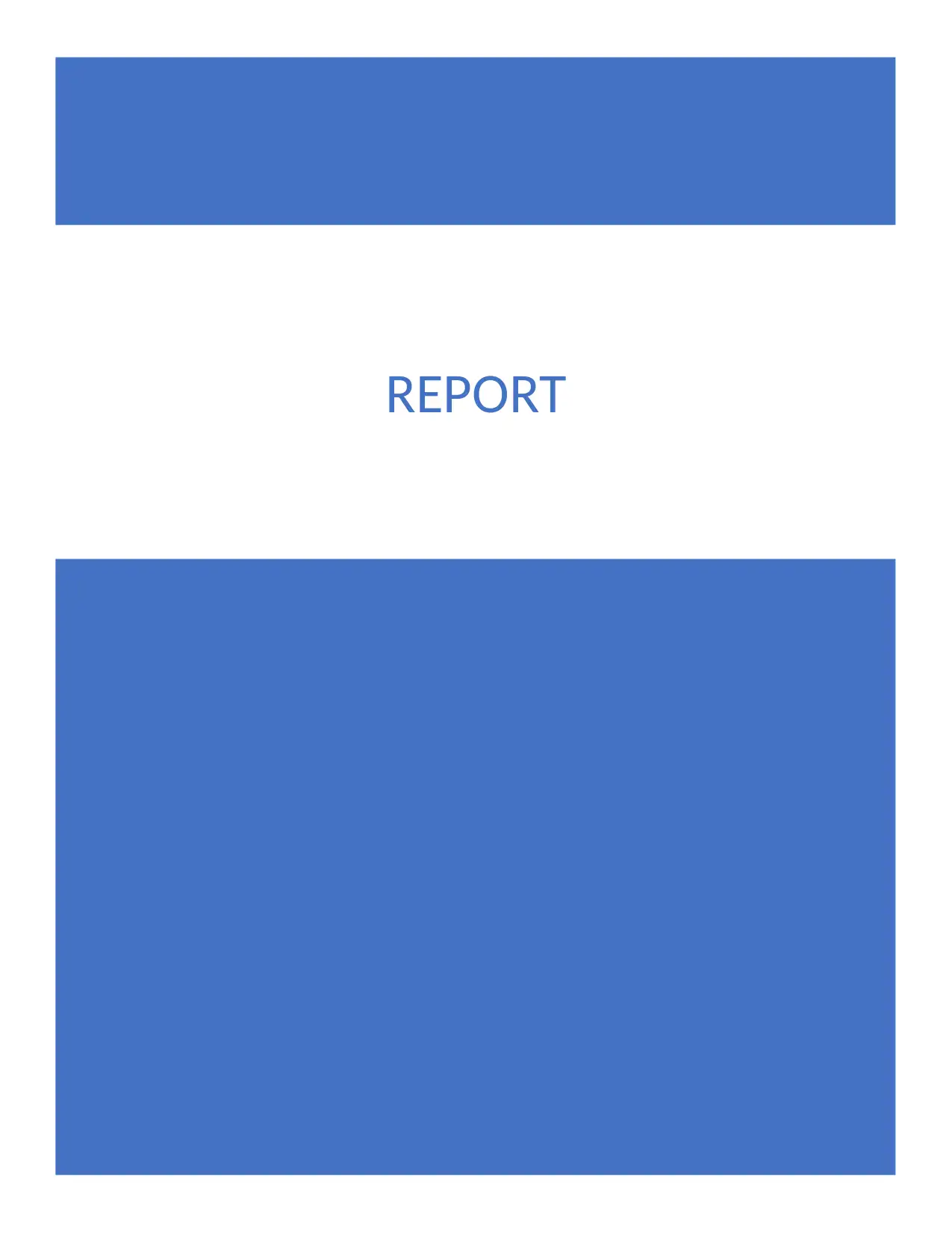
REPORT
Secure Best Marks with AI Grader
Need help grading? Try our AI Grader for instant feedback on your assignments.
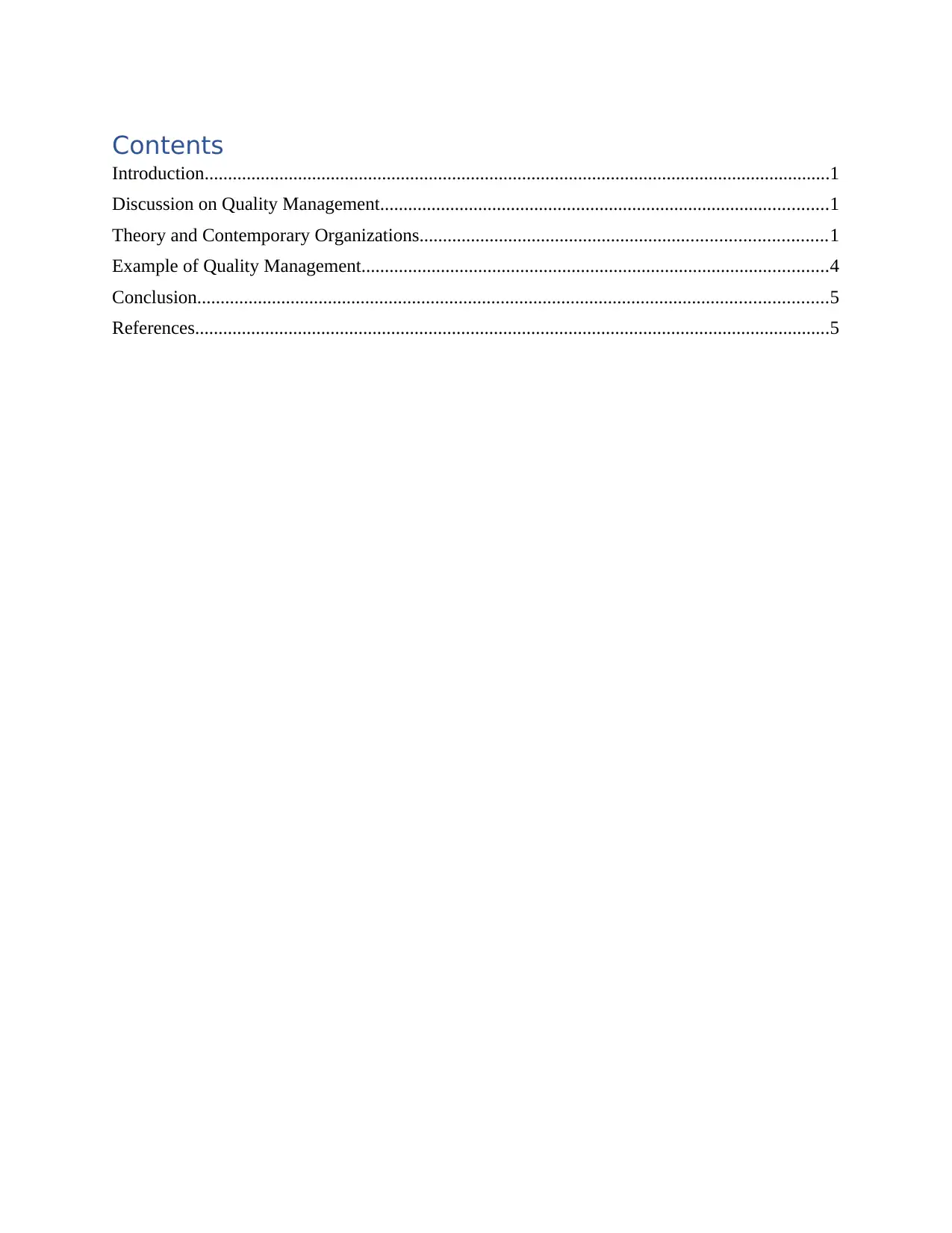
Contents
Introduction......................................................................................................................................1
Discussion on Quality Management................................................................................................1
Theory and Contemporary Organizations.......................................................................................1
Example of Quality Management....................................................................................................4
Conclusion.......................................................................................................................................5
References........................................................................................................................................5
Introduction......................................................................................................................................1
Discussion on Quality Management................................................................................................1
Theory and Contemporary Organizations.......................................................................................1
Example of Quality Management....................................................................................................4
Conclusion.......................................................................................................................................5
References........................................................................................................................................5
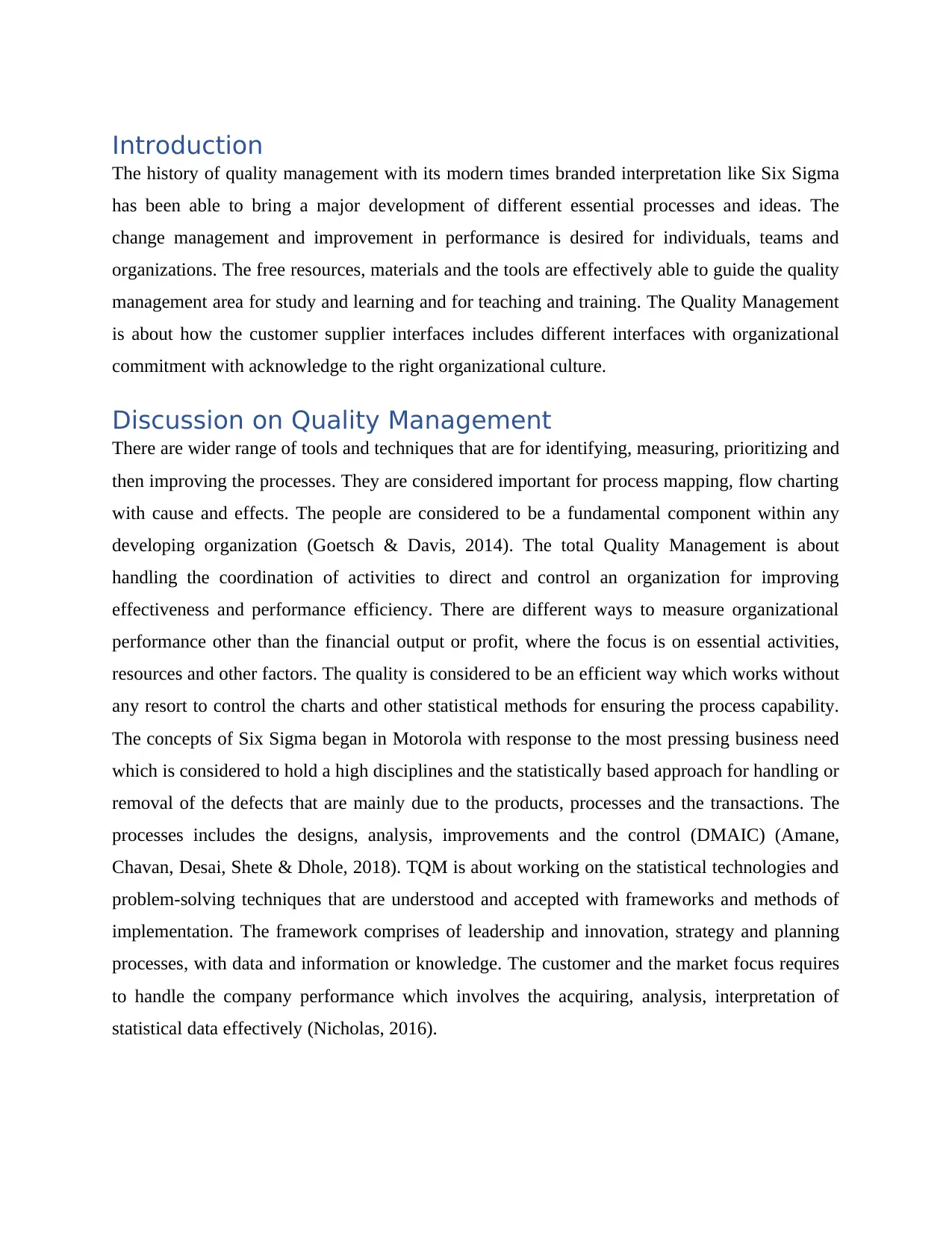
Introduction
The history of quality management with its modern times branded interpretation like Six Sigma
has been able to bring a major development of different essential processes and ideas. The
change management and improvement in performance is desired for individuals, teams and
organizations. The free resources, materials and the tools are effectively able to guide the quality
management area for study and learning and for teaching and training. The Quality Management
is about how the customer supplier interfaces includes different interfaces with organizational
commitment with acknowledge to the right organizational culture.
Discussion on Quality Management
There are wider range of tools and techniques that are for identifying, measuring, prioritizing and
then improving the processes. They are considered important for process mapping, flow charting
with cause and effects. The people are considered to be a fundamental component within any
developing organization (Goetsch & Davis, 2014). The total Quality Management is about
handling the coordination of activities to direct and control an organization for improving
effectiveness and performance efficiency. There are different ways to measure organizational
performance other than the financial output or profit, where the focus is on essential activities,
resources and other factors. The quality is considered to be an efficient way which works without
any resort to control the charts and other statistical methods for ensuring the process capability.
The concepts of Six Sigma began in Motorola with response to the most pressing business need
which is considered to hold a high disciplines and the statistically based approach for handling or
removal of the defects that are mainly due to the products, processes and the transactions. The
processes includes the designs, analysis, improvements and the control (DMAIC) (Amane,
Chavan, Desai, Shete & Dhole, 2018). TQM is about working on the statistical technologies and
problem-solving techniques that are understood and accepted with frameworks and methods of
implementation. The framework comprises of leadership and innovation, strategy and planning
processes, with data and information or knowledge. The customer and the market focus requires
to handle the company performance which involves the acquiring, analysis, interpretation of
statistical data effectively (Nicholas, 2016).
The history of quality management with its modern times branded interpretation like Six Sigma
has been able to bring a major development of different essential processes and ideas. The
change management and improvement in performance is desired for individuals, teams and
organizations. The free resources, materials and the tools are effectively able to guide the quality
management area for study and learning and for teaching and training. The Quality Management
is about how the customer supplier interfaces includes different interfaces with organizational
commitment with acknowledge to the right organizational culture.
Discussion on Quality Management
There are wider range of tools and techniques that are for identifying, measuring, prioritizing and
then improving the processes. They are considered important for process mapping, flow charting
with cause and effects. The people are considered to be a fundamental component within any
developing organization (Goetsch & Davis, 2014). The total Quality Management is about
handling the coordination of activities to direct and control an organization for improving
effectiveness and performance efficiency. There are different ways to measure organizational
performance other than the financial output or profit, where the focus is on essential activities,
resources and other factors. The quality is considered to be an efficient way which works without
any resort to control the charts and other statistical methods for ensuring the process capability.
The concepts of Six Sigma began in Motorola with response to the most pressing business need
which is considered to hold a high disciplines and the statistically based approach for handling or
removal of the defects that are mainly due to the products, processes and the transactions. The
processes includes the designs, analysis, improvements and the control (DMAIC) (Amane,
Chavan, Desai, Shete & Dhole, 2018). TQM is about working on the statistical technologies and
problem-solving techniques that are understood and accepted with frameworks and methods of
implementation. The framework comprises of leadership and innovation, strategy and planning
processes, with data and information or knowledge. The customer and the market focus requires
to handle the company performance which involves the acquiring, analysis, interpretation of
statistical data effectively (Nicholas, 2016).
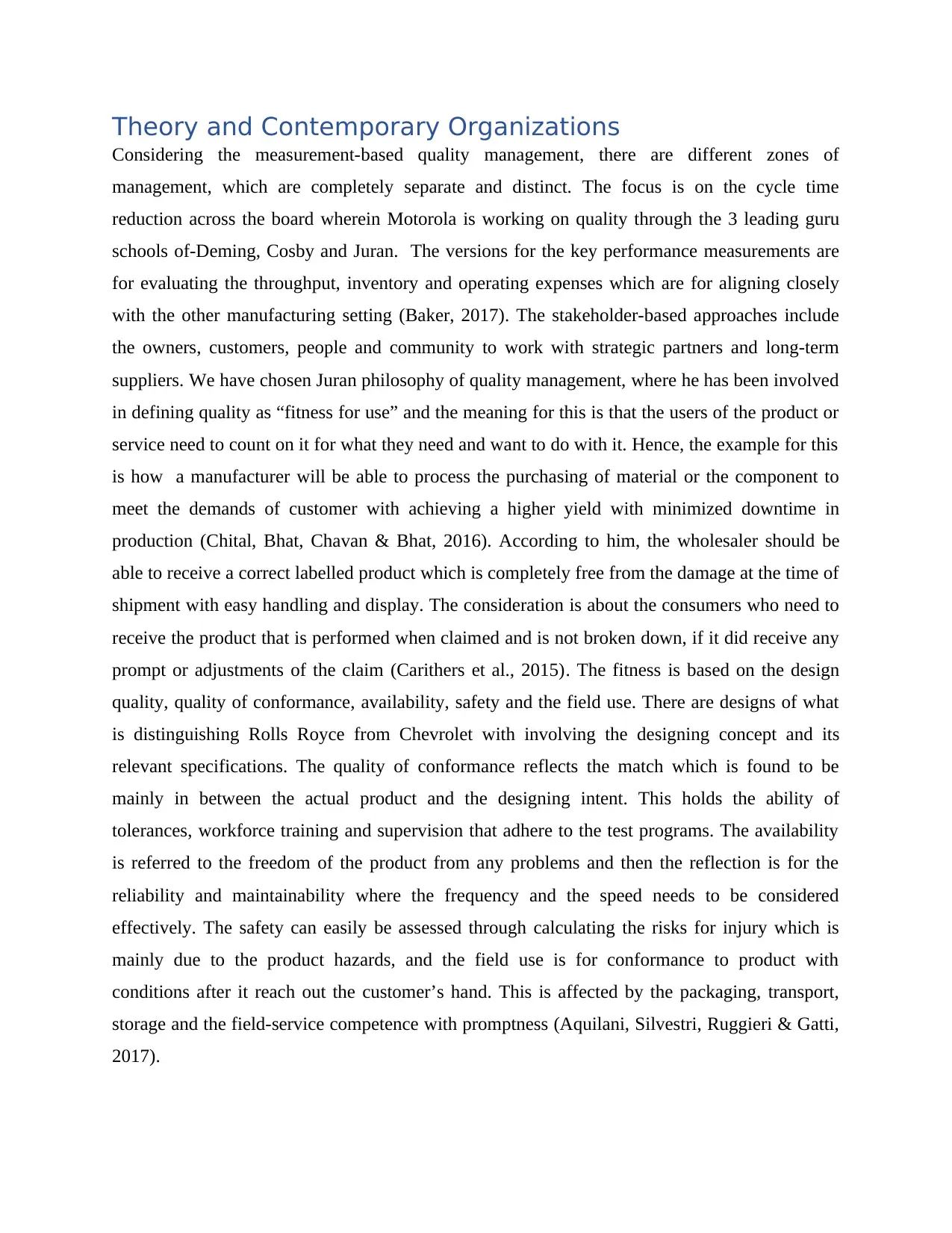
Theory and Contemporary Organizations
Considering the measurement-based quality management, there are different zones of
management, which are completely separate and distinct. The focus is on the cycle time
reduction across the board wherein Motorola is working on quality through the 3 leading guru
schools of-Deming, Cosby and Juran. The versions for the key performance measurements are
for evaluating the throughput, inventory and operating expenses which are for aligning closely
with the other manufacturing setting (Baker, 2017). The stakeholder-based approaches include
the owners, customers, people and community to work with strategic partners and long-term
suppliers. We have chosen Juran philosophy of quality management, where he has been involved
in defining quality as “fitness for use” and the meaning for this is that the users of the product or
service need to count on it for what they need and want to do with it. Hence, the example for this
is how a manufacturer will be able to process the purchasing of material or the component to
meet the demands of customer with achieving a higher yield with minimized downtime in
production (Chital, Bhat, Chavan & Bhat, 2016). According to him, the wholesaler should be
able to receive a correct labelled product which is completely free from the damage at the time of
shipment with easy handling and display. The consideration is about the consumers who need to
receive the product that is performed when claimed and is not broken down, if it did receive any
prompt or adjustments of the claim (Carithers et al., 2015). The fitness is based on the design
quality, quality of conformance, availability, safety and the field use. There are designs of what
is distinguishing Rolls Royce from Chevrolet with involving the designing concept and its
relevant specifications. The quality of conformance reflects the match which is found to be
mainly in between the actual product and the designing intent. This holds the ability of
tolerances, workforce training and supervision that adhere to the test programs. The availability
is referred to the freedom of the product from any problems and then the reflection is for the
reliability and maintainability where the frequency and the speed needs to be considered
effectively. The safety can easily be assessed through calculating the risks for injury which is
mainly due to the product hazards, and the field use is for conformance to product with
conditions after it reach out the customer’s hand. This is affected by the packaging, transport,
storage and the field-service competence with promptness (Aquilani, Silvestri, Ruggieri & Gatti,
2017).
Considering the measurement-based quality management, there are different zones of
management, which are completely separate and distinct. The focus is on the cycle time
reduction across the board wherein Motorola is working on quality through the 3 leading guru
schools of-Deming, Cosby and Juran. The versions for the key performance measurements are
for evaluating the throughput, inventory and operating expenses which are for aligning closely
with the other manufacturing setting (Baker, 2017). The stakeholder-based approaches include
the owners, customers, people and community to work with strategic partners and long-term
suppliers. We have chosen Juran philosophy of quality management, where he has been involved
in defining quality as “fitness for use” and the meaning for this is that the users of the product or
service need to count on it for what they need and want to do with it. Hence, the example for this
is how a manufacturer will be able to process the purchasing of material or the component to
meet the demands of customer with achieving a higher yield with minimized downtime in
production (Chital, Bhat, Chavan & Bhat, 2016). According to him, the wholesaler should be
able to receive a correct labelled product which is completely free from the damage at the time of
shipment with easy handling and display. The consideration is about the consumers who need to
receive the product that is performed when claimed and is not broken down, if it did receive any
prompt or adjustments of the claim (Carithers et al., 2015). The fitness is based on the design
quality, quality of conformance, availability, safety and the field use. There are designs of what
is distinguishing Rolls Royce from Chevrolet with involving the designing concept and its
relevant specifications. The quality of conformance reflects the match which is found to be
mainly in between the actual product and the designing intent. This holds the ability of
tolerances, workforce training and supervision that adhere to the test programs. The availability
is referred to the freedom of the product from any problems and then the reflection is for the
reliability and maintainability where the frequency and the speed needs to be considered
effectively. The safety can easily be assessed through calculating the risks for injury which is
mainly due to the product hazards, and the field use is for conformance to product with
conditions after it reach out the customer’s hand. This is affected by the packaging, transport,
storage and the field-service competence with promptness (Aquilani, Silvestri, Ruggieri & Gatti,
2017).
Secure Best Marks with AI Grader
Need help grading? Try our AI Grader for instant feedback on your assignments.
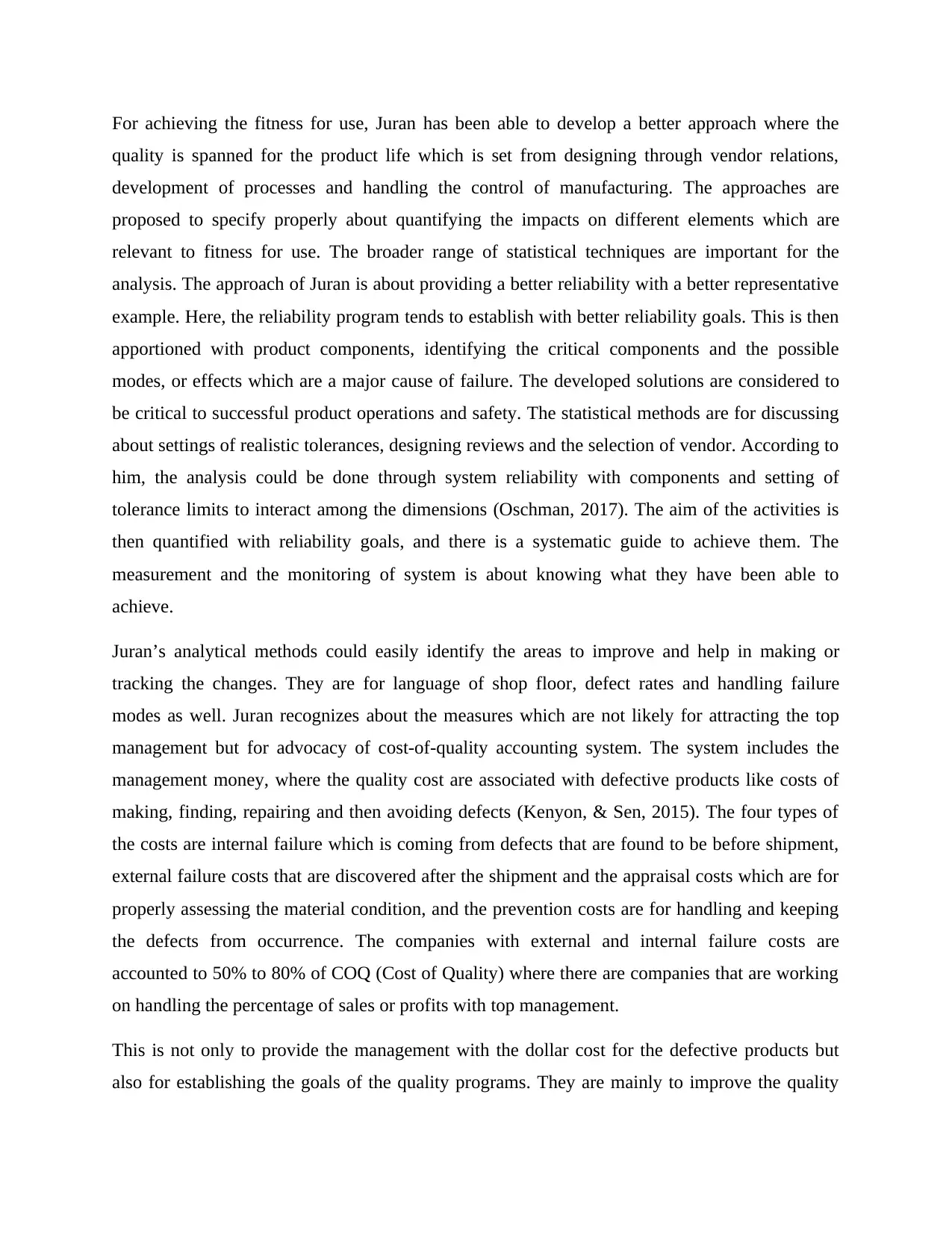
For achieving the fitness for use, Juran has been able to develop a better approach where the
quality is spanned for the product life which is set from designing through vendor relations,
development of processes and handling the control of manufacturing. The approaches are
proposed to specify properly about quantifying the impacts on different elements which are
relevant to fitness for use. The broader range of statistical techniques are important for the
analysis. The approach of Juran is about providing a better reliability with a better representative
example. Here, the reliability program tends to establish with better reliability goals. This is then
apportioned with product components, identifying the critical components and the possible
modes, or effects which are a major cause of failure. The developed solutions are considered to
be critical to successful product operations and safety. The statistical methods are for discussing
about settings of realistic tolerances, designing reviews and the selection of vendor. According to
him, the analysis could be done through system reliability with components and setting of
tolerance limits to interact among the dimensions (Oschman, 2017). The aim of the activities is
then quantified with reliability goals, and there is a systematic guide to achieve them. The
measurement and the monitoring of system is about knowing what they have been able to
achieve.
Juran’s analytical methods could easily identify the areas to improve and help in making or
tracking the changes. They are for language of shop floor, defect rates and handling failure
modes as well. Juran recognizes about the measures which are not likely for attracting the top
management but for advocacy of cost-of-quality accounting system. The system includes the
management money, where the quality cost are associated with defective products like costs of
making, finding, repairing and then avoiding defects (Kenyon, & Sen, 2015). The four types of
the costs are internal failure which is coming from defects that are found to be before shipment,
external failure costs that are discovered after the shipment and the appraisal costs which are for
properly assessing the material condition, and the prevention costs are for handling and keeping
the defects from occurrence. The companies with external and internal failure costs are
accounted to 50% to 80% of COQ (Cost of Quality) where there are companies that are working
on handling the percentage of sales or profits with top management.
This is not only to provide the management with the dollar cost for the defective products but
also for establishing the goals of the quality programs. They are mainly to improve the quality
quality is spanned for the product life which is set from designing through vendor relations,
development of processes and handling the control of manufacturing. The approaches are
proposed to specify properly about quantifying the impacts on different elements which are
relevant to fitness for use. The broader range of statistical techniques are important for the
analysis. The approach of Juran is about providing a better reliability with a better representative
example. Here, the reliability program tends to establish with better reliability goals. This is then
apportioned with product components, identifying the critical components and the possible
modes, or effects which are a major cause of failure. The developed solutions are considered to
be critical to successful product operations and safety. The statistical methods are for discussing
about settings of realistic tolerances, designing reviews and the selection of vendor. According to
him, the analysis could be done through system reliability with components and setting of
tolerance limits to interact among the dimensions (Oschman, 2017). The aim of the activities is
then quantified with reliability goals, and there is a systematic guide to achieve them. The
measurement and the monitoring of system is about knowing what they have been able to
achieve.
Juran’s analytical methods could easily identify the areas to improve and help in making or
tracking the changes. They are for language of shop floor, defect rates and handling failure
modes as well. Juran recognizes about the measures which are not likely for attracting the top
management but for advocacy of cost-of-quality accounting system. The system includes the
management money, where the quality cost are associated with defective products like costs of
making, finding, repairing and then avoiding defects (Kenyon, & Sen, 2015). The four types of
the costs are internal failure which is coming from defects that are found to be before shipment,
external failure costs that are discovered after the shipment and the appraisal costs which are for
properly assessing the material condition, and the prevention costs are for handling and keeping
the defects from occurrence. The companies with external and internal failure costs are
accounted to 50% to 80% of COQ (Cost of Quality) where there are companies that are working
on handling the percentage of sales or profits with top management.
This is not only to provide the management with the dollar cost for the defective products but
also for establishing the goals of the quality programs. They are mainly to improve the quality
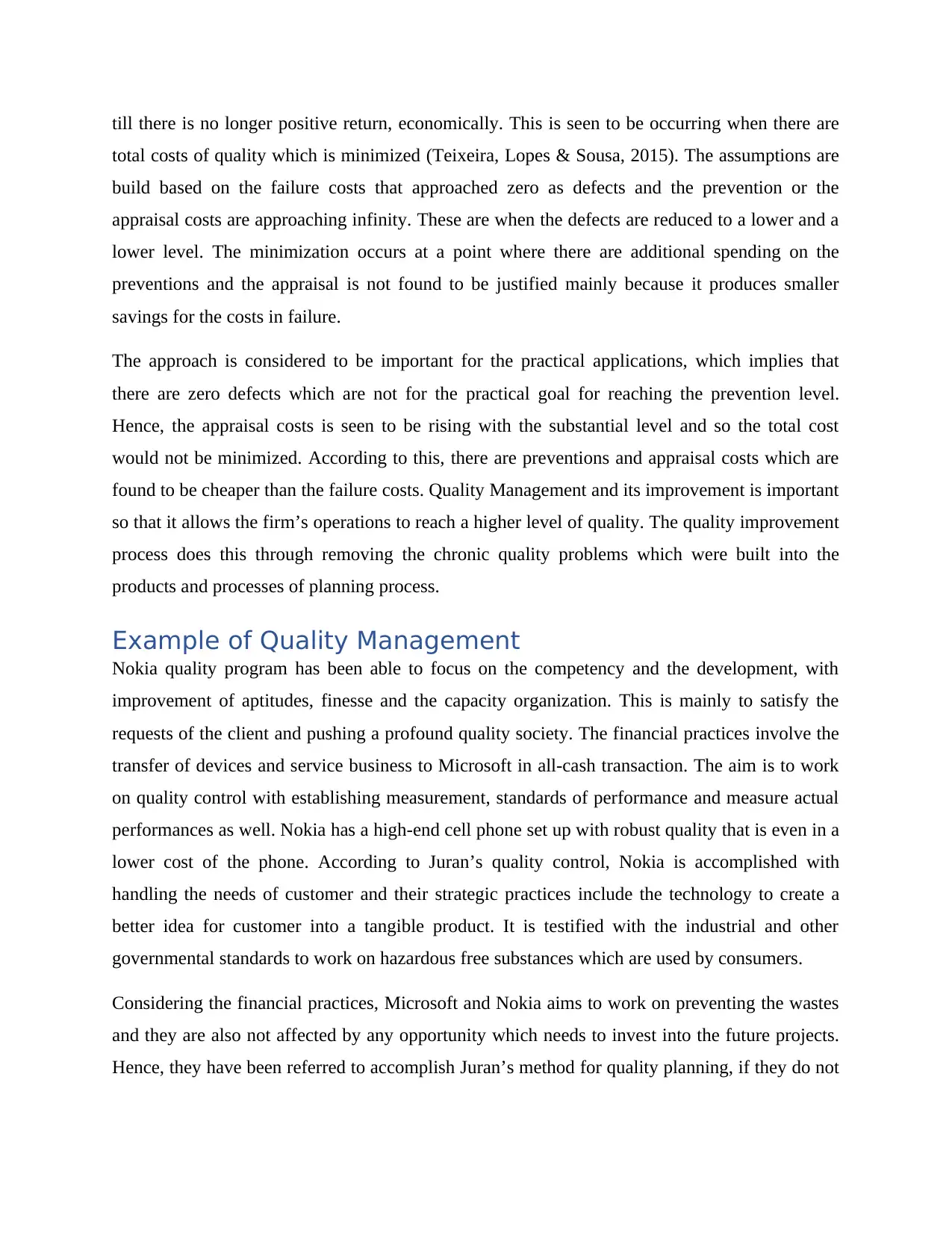
till there is no longer positive return, economically. This is seen to be occurring when there are
total costs of quality which is minimized (Teixeira, Lopes & Sousa, 2015). The assumptions are
build based on the failure costs that approached zero as defects and the prevention or the
appraisal costs are approaching infinity. These are when the defects are reduced to a lower and a
lower level. The minimization occurs at a point where there are additional spending on the
preventions and the appraisal is not found to be justified mainly because it produces smaller
savings for the costs in failure.
The approach is considered to be important for the practical applications, which implies that
there are zero defects which are not for the practical goal for reaching the prevention level.
Hence, the appraisal costs is seen to be rising with the substantial level and so the total cost
would not be minimized. According to this, there are preventions and appraisal costs which are
found to be cheaper than the failure costs. Quality Management and its improvement is important
so that it allows the firm’s operations to reach a higher level of quality. The quality improvement
process does this through removing the chronic quality problems which were built into the
products and processes of planning process.
Example of Quality Management
Nokia quality program has been able to focus on the competency and the development, with
improvement of aptitudes, finesse and the capacity organization. This is mainly to satisfy the
requests of the client and pushing a profound quality society. The financial practices involve the
transfer of devices and service business to Microsoft in all-cash transaction. The aim is to work
on quality control with establishing measurement, standards of performance and measure actual
performances as well. Nokia has a high-end cell phone set up with robust quality that is even in a
lower cost of the phone. According to Juran’s quality control, Nokia is accomplished with
handling the needs of customer and their strategic practices include the technology to create a
better idea for customer into a tangible product. It is testified with the industrial and other
governmental standards to work on hazardous free substances which are used by consumers.
Considering the financial practices, Microsoft and Nokia aims to work on preventing the wastes
and they are also not affected by any opportunity which needs to invest into the future projects.
Hence, they have been referred to accomplish Juran’s method for quality planning, if they do not
total costs of quality which is minimized (Teixeira, Lopes & Sousa, 2015). The assumptions are
build based on the failure costs that approached zero as defects and the prevention or the
appraisal costs are approaching infinity. These are when the defects are reduced to a lower and a
lower level. The minimization occurs at a point where there are additional spending on the
preventions and the appraisal is not found to be justified mainly because it produces smaller
savings for the costs in failure.
The approach is considered to be important for the practical applications, which implies that
there are zero defects which are not for the practical goal for reaching the prevention level.
Hence, the appraisal costs is seen to be rising with the substantial level and so the total cost
would not be minimized. According to this, there are preventions and appraisal costs which are
found to be cheaper than the failure costs. Quality Management and its improvement is important
so that it allows the firm’s operations to reach a higher level of quality. The quality improvement
process does this through removing the chronic quality problems which were built into the
products and processes of planning process.
Example of Quality Management
Nokia quality program has been able to focus on the competency and the development, with
improvement of aptitudes, finesse and the capacity organization. This is mainly to satisfy the
requests of the client and pushing a profound quality society. The financial practices involve the
transfer of devices and service business to Microsoft in all-cash transaction. The aim is to work
on quality control with establishing measurement, standards of performance and measure actual
performances as well. Nokia has a high-end cell phone set up with robust quality that is even in a
lower cost of the phone. According to Juran’s quality control, Nokia is accomplished with
handling the needs of customer and their strategic practices include the technology to create a
better idea for customer into a tangible product. It is testified with the industrial and other
governmental standards to work on hazardous free substances which are used by consumers.
Considering the financial practices, Microsoft and Nokia aims to work on preventing the wastes
and they are also not affected by any opportunity which needs to invest into the future projects.
Hence, they have been referred to accomplish Juran’s method for quality planning, if they do not
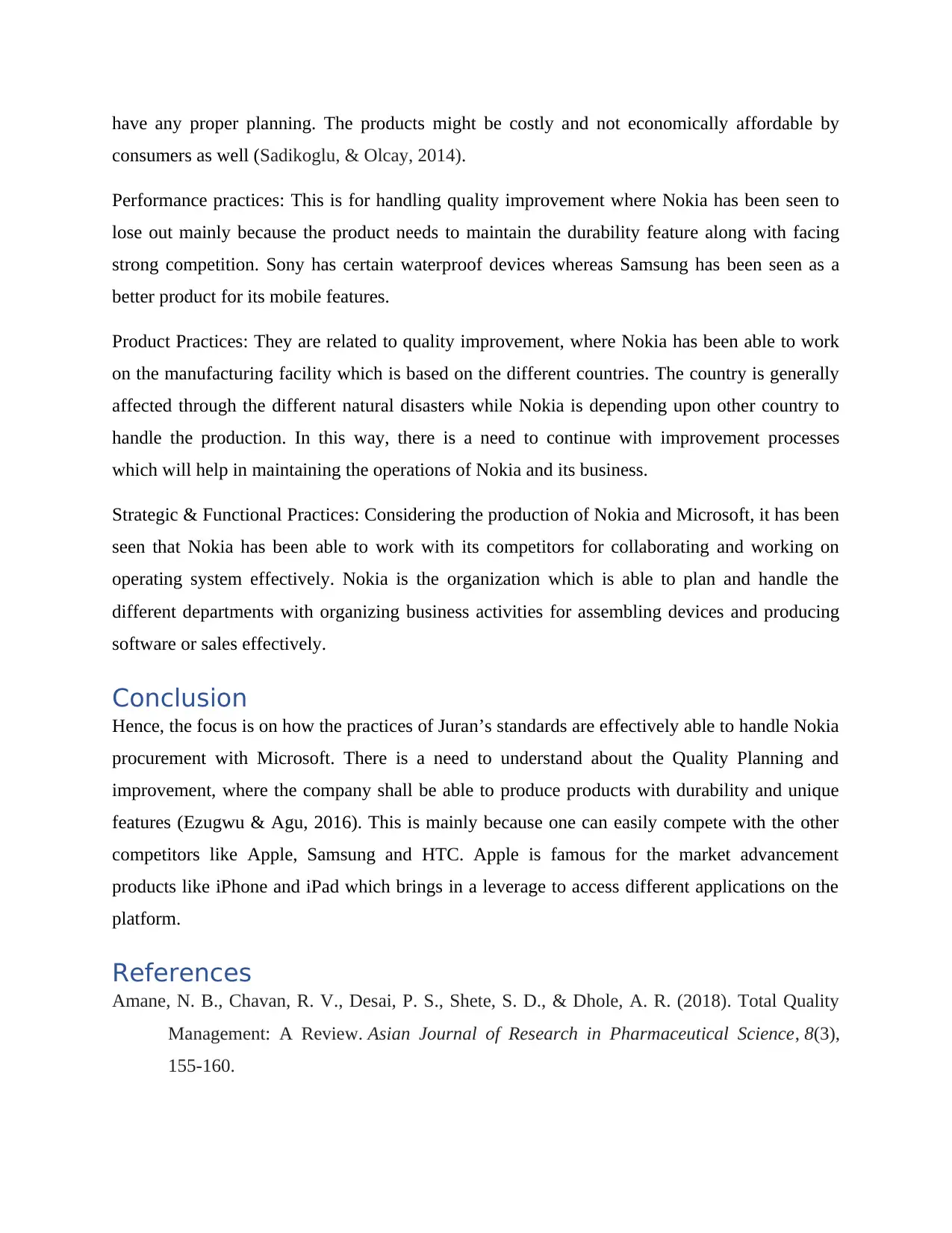
have any proper planning. The products might be costly and not economically affordable by
consumers as well (Sadikoglu, & Olcay, 2014).
Performance practices: This is for handling quality improvement where Nokia has been seen to
lose out mainly because the product needs to maintain the durability feature along with facing
strong competition. Sony has certain waterproof devices whereas Samsung has been seen as a
better product for its mobile features.
Product Practices: They are related to quality improvement, where Nokia has been able to work
on the manufacturing facility which is based on the different countries. The country is generally
affected through the different natural disasters while Nokia is depending upon other country to
handle the production. In this way, there is a need to continue with improvement processes
which will help in maintaining the operations of Nokia and its business.
Strategic & Functional Practices: Considering the production of Nokia and Microsoft, it has been
seen that Nokia has been able to work with its competitors for collaborating and working on
operating system effectively. Nokia is the organization which is able to plan and handle the
different departments with organizing business activities for assembling devices and producing
software or sales effectively.
Conclusion
Hence, the focus is on how the practices of Juran’s standards are effectively able to handle Nokia
procurement with Microsoft. There is a need to understand about the Quality Planning and
improvement, where the company shall be able to produce products with durability and unique
features (Ezugwu & Agu, 2016). This is mainly because one can easily compete with the other
competitors like Apple, Samsung and HTC. Apple is famous for the market advancement
products like iPhone and iPad which brings in a leverage to access different applications on the
platform.
References
Amane, N. B., Chavan, R. V., Desai, P. S., Shete, S. D., & Dhole, A. R. (2018). Total Quality
Management: A Review. Asian Journal of Research in Pharmaceutical Science, 8(3),
155-160.
consumers as well (Sadikoglu, & Olcay, 2014).
Performance practices: This is for handling quality improvement where Nokia has been seen to
lose out mainly because the product needs to maintain the durability feature along with facing
strong competition. Sony has certain waterproof devices whereas Samsung has been seen as a
better product for its mobile features.
Product Practices: They are related to quality improvement, where Nokia has been able to work
on the manufacturing facility which is based on the different countries. The country is generally
affected through the different natural disasters while Nokia is depending upon other country to
handle the production. In this way, there is a need to continue with improvement processes
which will help in maintaining the operations of Nokia and its business.
Strategic & Functional Practices: Considering the production of Nokia and Microsoft, it has been
seen that Nokia has been able to work with its competitors for collaborating and working on
operating system effectively. Nokia is the organization which is able to plan and handle the
different departments with organizing business activities for assembling devices and producing
software or sales effectively.
Conclusion
Hence, the focus is on how the practices of Juran’s standards are effectively able to handle Nokia
procurement with Microsoft. There is a need to understand about the Quality Planning and
improvement, where the company shall be able to produce products with durability and unique
features (Ezugwu & Agu, 2016). This is mainly because one can easily compete with the other
competitors like Apple, Samsung and HTC. Apple is famous for the market advancement
products like iPhone and iPad which brings in a leverage to access different applications on the
platform.
References
Amane, N. B., Chavan, R. V., Desai, P. S., Shete, S. D., & Dhole, A. R. (2018). Total Quality
Management: A Review. Asian Journal of Research in Pharmaceutical Science, 8(3),
155-160.
Paraphrase This Document
Need a fresh take? Get an instant paraphrase of this document with our AI Paraphraser
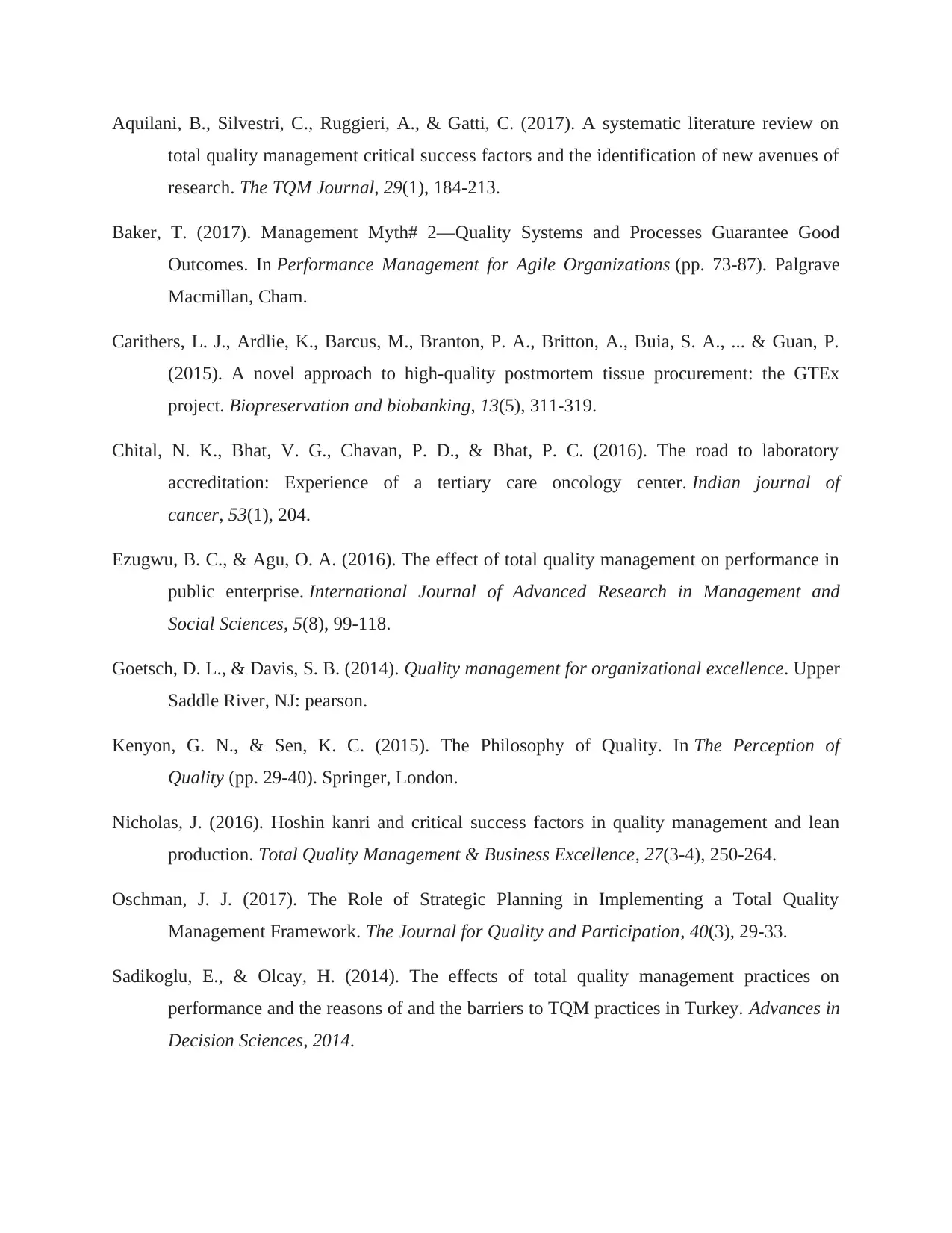
Aquilani, B., Silvestri, C., Ruggieri, A., & Gatti, C. (2017). A systematic literature review on
total quality management critical success factors and the identification of new avenues of
research. The TQM Journal, 29(1), 184-213.
Baker, T. (2017). Management Myth# 2—Quality Systems and Processes Guarantee Good
Outcomes. In Performance Management for Agile Organizations (pp. 73-87). Palgrave
Macmillan, Cham.
Carithers, L. J., Ardlie, K., Barcus, M., Branton, P. A., Britton, A., Buia, S. A., ... & Guan, P.
(2015). A novel approach to high-quality postmortem tissue procurement: the GTEx
project. Biopreservation and biobanking, 13(5), 311-319.
Chital, N. K., Bhat, V. G., Chavan, P. D., & Bhat, P. C. (2016). The road to laboratory
accreditation: Experience of a tertiary care oncology center. Indian journal of
cancer, 53(1), 204.
Ezugwu, B. C., & Agu, O. A. (2016). The effect of total quality management on performance in
public enterprise. International Journal of Advanced Research in Management and
Social Sciences, 5(8), 99-118.
Goetsch, D. L., & Davis, S. B. (2014). Quality management for organizational excellence. Upper
Saddle River, NJ: pearson.
Kenyon, G. N., & Sen, K. C. (2015). The Philosophy of Quality. In The Perception of
Quality (pp. 29-40). Springer, London.
Nicholas, J. (2016). Hoshin kanri and critical success factors in quality management and lean
production. Total Quality Management & Business Excellence, 27(3-4), 250-264.
Oschman, J. J. (2017). The Role of Strategic Planning in Implementing a Total Quality
Management Framework. The Journal for Quality and Participation, 40(3), 29-33.
Sadikoglu, E., & Olcay, H. (2014). The effects of total quality management practices on
performance and the reasons of and the barriers to TQM practices in Turkey. Advances in
Decision Sciences, 2014.
total quality management critical success factors and the identification of new avenues of
research. The TQM Journal, 29(1), 184-213.
Baker, T. (2017). Management Myth# 2—Quality Systems and Processes Guarantee Good
Outcomes. In Performance Management for Agile Organizations (pp. 73-87). Palgrave
Macmillan, Cham.
Carithers, L. J., Ardlie, K., Barcus, M., Branton, P. A., Britton, A., Buia, S. A., ... & Guan, P.
(2015). A novel approach to high-quality postmortem tissue procurement: the GTEx
project. Biopreservation and biobanking, 13(5), 311-319.
Chital, N. K., Bhat, V. G., Chavan, P. D., & Bhat, P. C. (2016). The road to laboratory
accreditation: Experience of a tertiary care oncology center. Indian journal of
cancer, 53(1), 204.
Ezugwu, B. C., & Agu, O. A. (2016). The effect of total quality management on performance in
public enterprise. International Journal of Advanced Research in Management and
Social Sciences, 5(8), 99-118.
Goetsch, D. L., & Davis, S. B. (2014). Quality management for organizational excellence. Upper
Saddle River, NJ: pearson.
Kenyon, G. N., & Sen, K. C. (2015). The Philosophy of Quality. In The Perception of
Quality (pp. 29-40). Springer, London.
Nicholas, J. (2016). Hoshin kanri and critical success factors in quality management and lean
production. Total Quality Management & Business Excellence, 27(3-4), 250-264.
Oschman, J. J. (2017). The Role of Strategic Planning in Implementing a Total Quality
Management Framework. The Journal for Quality and Participation, 40(3), 29-33.
Sadikoglu, E., & Olcay, H. (2014). The effects of total quality management practices on
performance and the reasons of and the barriers to TQM practices in Turkey. Advances in
Decision Sciences, 2014.
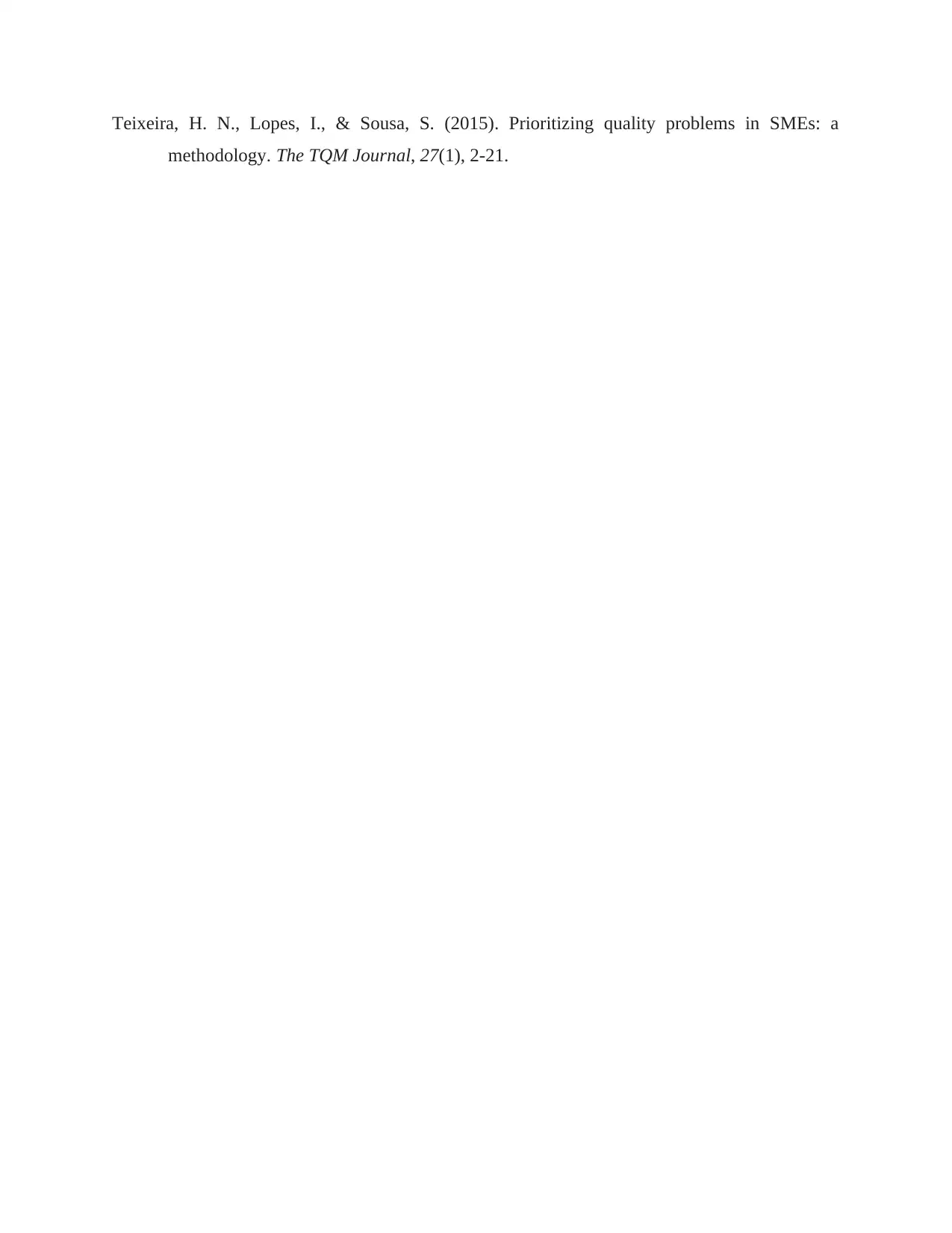
Teixeira, H. N., Lopes, I., & Sousa, S. (2015). Prioritizing quality problems in SMEs: a
methodology. The TQM Journal, 27(1), 2-21.
methodology. The TQM Journal, 27(1), 2-21.
1 out of 9
Related Documents

Your All-in-One AI-Powered Toolkit for Academic Success.
+13062052269
info@desklib.com
Available 24*7 on WhatsApp / Email
Unlock your academic potential
© 2024 | Zucol Services PVT LTD | All rights reserved.