Assessment of a Mobile E-Waste Processing Facility: A Detailed Report
VerifiedAdded on 2020/04/01
|36
|11036
|119
Report
AI Summary
This report provides an in-depth assessment of a mobile e-waste processing facility, focusing on the methodologies used for recycling and metal recovery from electronic waste. The study covers various aspects, including the processing of e-waste, the recovery of valuable metals like gold, platinum, silver, and palladium, as well as the responsible management of toxic substances such as mercury, lead, and beryllium. The report details the e-waste processing stages, from collection and dismantling to end processing, and the use of techniques like pyrometallurgy and hydrometallurgy. It includes preliminary designs for the recycling process, extractive metallurgy, sorting, and dismantling processes. Furthermore, it examines the design of integrated mobile recycling plants, with a focus on the container designs, and the analysis and results obtained from the evaluation. The report also emphasizes the importance of urban mining and the economic and environmental benefits of recycling electronic waste, providing a comprehensive overview of the entire e-waste recycling process.
Contribute Materials
Your contribution can guide someone’s learning journey. Share your
documents today.
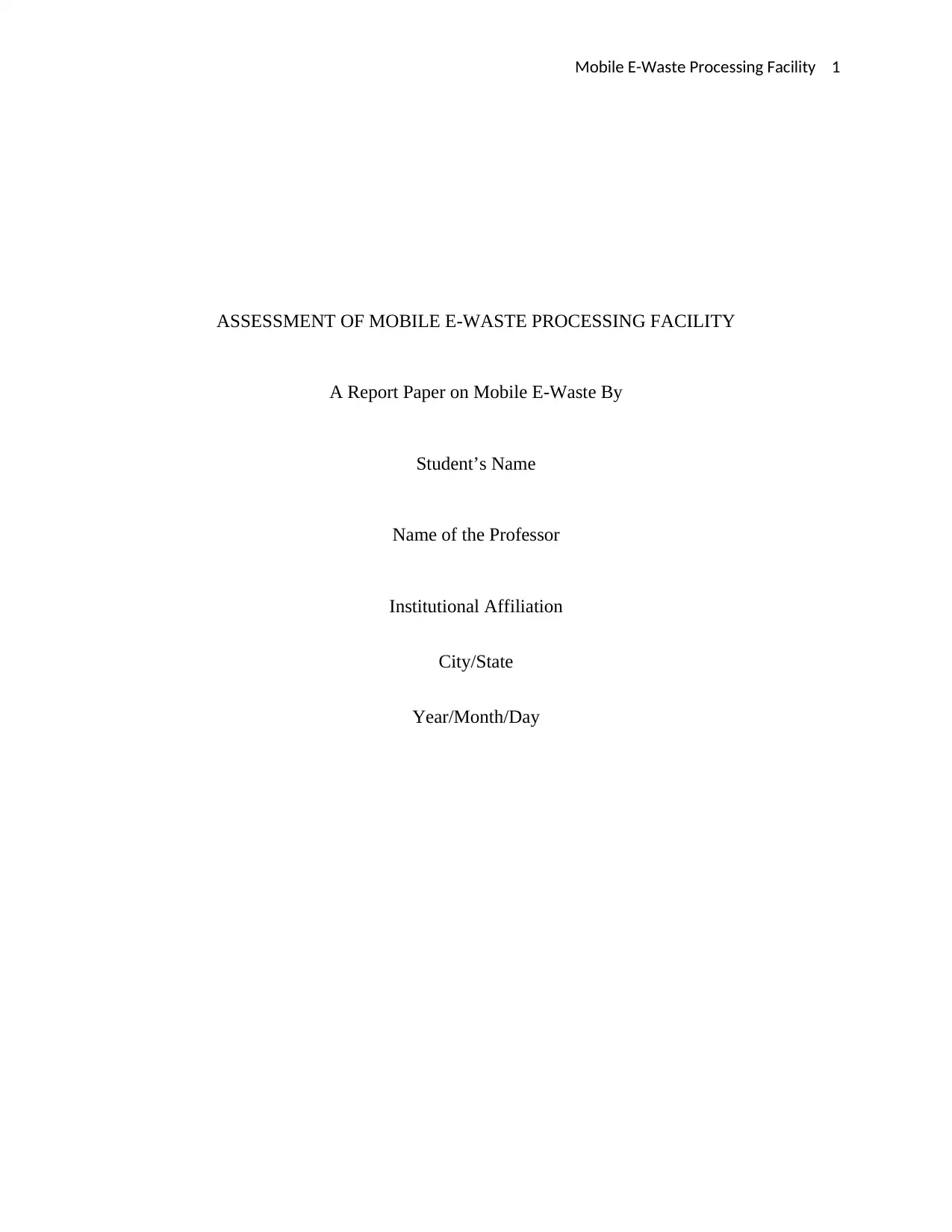
Mobile E-Waste Processing Facility 1
ASSESSMENT OF MOBILE E-WASTE PROCESSING FACILITY
A Report Paper on Mobile E-Waste By
Student’s Name
Name of the Professor
Institutional Affiliation
City/State
Year/Month/Day
ASSESSMENT OF MOBILE E-WASTE PROCESSING FACILITY
A Report Paper on Mobile E-Waste By
Student’s Name
Name of the Professor
Institutional Affiliation
City/State
Year/Month/Day
Secure Best Marks with AI Grader
Need help grading? Try our AI Grader for instant feedback on your assignments.
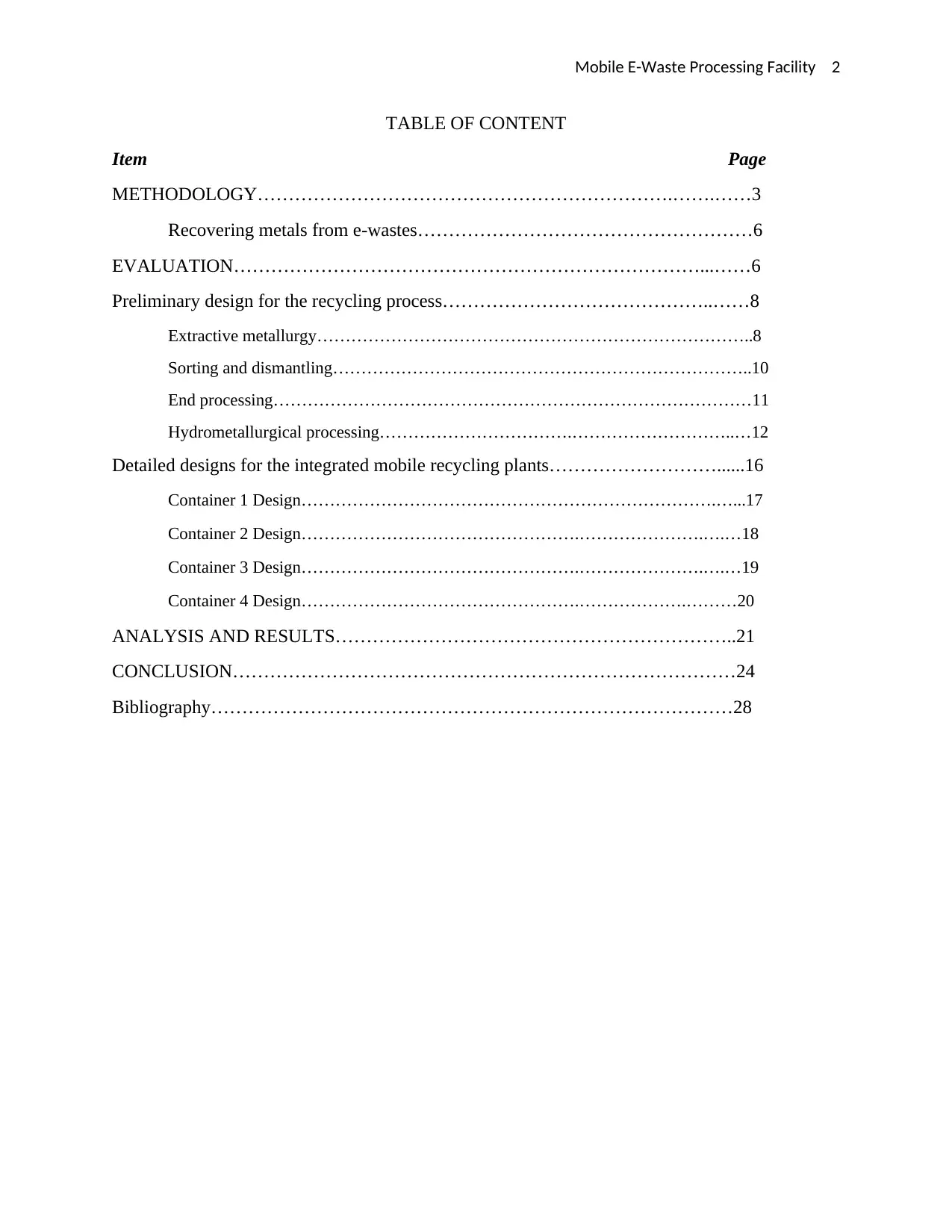
Mobile E-Waste Processing Facility 2
TABLE OF CONTENT
Item Page
METHODOLOGY………………………………………………………….…….……3
Recovering metals from e-wastes………………………………………………6
EVALUATION…………………………………………………………………...……6
Preliminary design for the recycling process……………………………………..……8
Extractive metallurgy…………………………………………………………………..8
Sorting and dismantling………………………………………………………………..10
End processing…………………………………………………………………………11
Hydrometallurgical processing…………………………….………………………..…12
Detailed designs for the integrated mobile recycling plants………………………......16
Container 1 Design……………………………………………………………….…...17
Container 2 Design………………………………………….………………….….…18
Container 3 Design………………………………………….………………….….…19
Container 4 Design………………………………………….……………….………20
ANALYSIS AND RESULTS………………………………………………………..21
CONCLUSION………………………………………………………………………24
Bibliography…………………………………………………………………………28
TABLE OF CONTENT
Item Page
METHODOLOGY………………………………………………………….…….……3
Recovering metals from e-wastes………………………………………………6
EVALUATION…………………………………………………………………...……6
Preliminary design for the recycling process……………………………………..……8
Extractive metallurgy…………………………………………………………………..8
Sorting and dismantling………………………………………………………………..10
End processing…………………………………………………………………………11
Hydrometallurgical processing…………………………….………………………..…12
Detailed designs for the integrated mobile recycling plants………………………......16
Container 1 Design……………………………………………………………….…...17
Container 2 Design………………………………………….………………….….…18
Container 3 Design………………………………………….………………….….…19
Container 4 Design………………………………………….……………….………20
ANALYSIS AND RESULTS………………………………………………………..21
CONCLUSION………………………………………………………………………24
Bibliography…………………………………………………………………………28
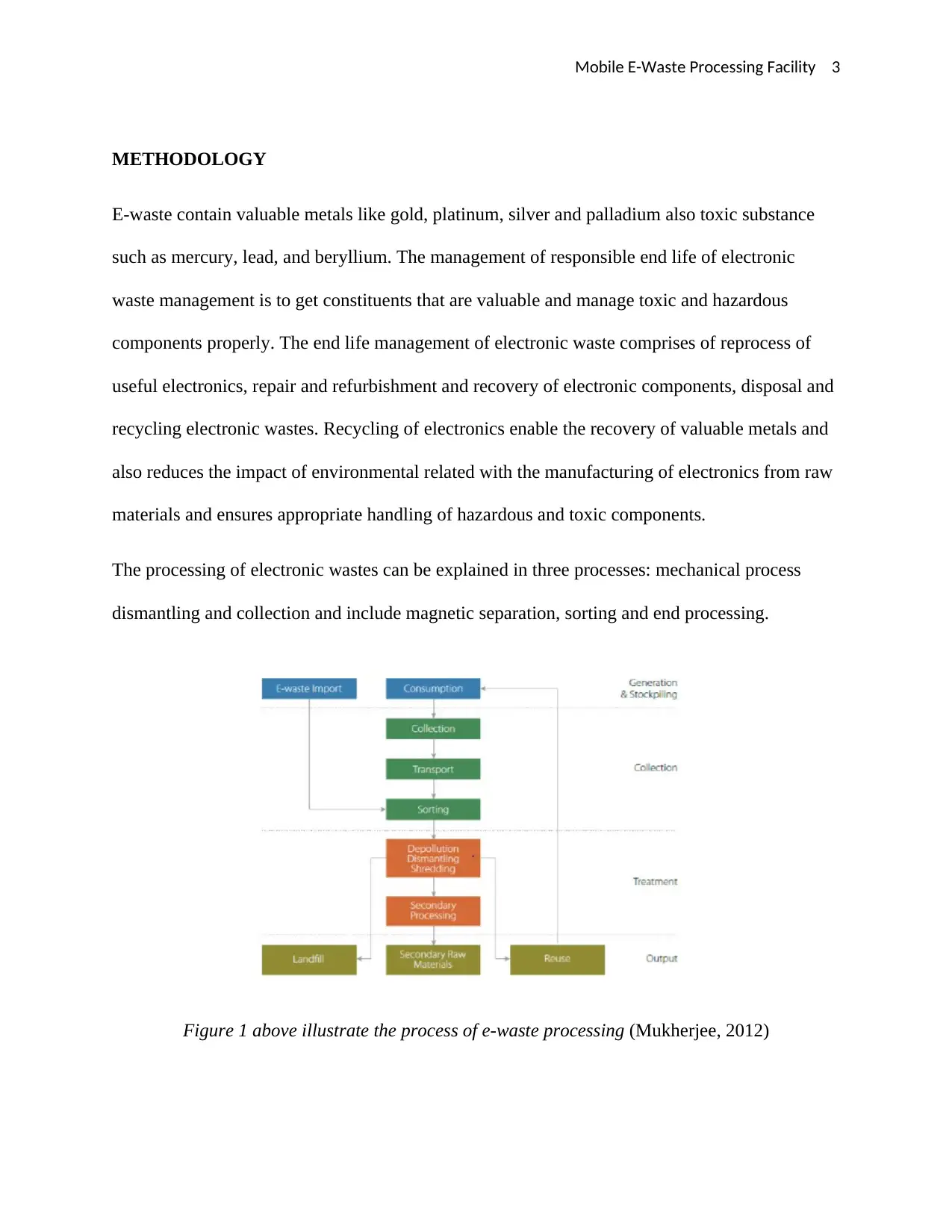
Mobile E-Waste Processing Facility 3
METHODOLOGY
E-waste contain valuable metals like gold, platinum, silver and palladium also toxic substance
such as mercury, lead, and beryllium. The management of responsible end life of electronic
waste management is to get constituents that are valuable and manage toxic and hazardous
components properly. The end life management of electronic waste comprises of reprocess of
useful electronics, repair and refurbishment and recovery of electronic components, disposal and
recycling electronic wastes. Recycling of electronics enable the recovery of valuable metals and
also reduces the impact of environmental related with the manufacturing of electronics from raw
materials and ensures appropriate handling of hazardous and toxic components.
The processing of electronic wastes can be explained in three processes: mechanical process
dismantling and collection and include magnetic separation, sorting and end processing.
Figure 1 above illustrate the process of e-waste processing (Mukherjee, 2012)
METHODOLOGY
E-waste contain valuable metals like gold, platinum, silver and palladium also toxic substance
such as mercury, lead, and beryllium. The management of responsible end life of electronic
waste management is to get constituents that are valuable and manage toxic and hazardous
components properly. The end life management of electronic waste comprises of reprocess of
useful electronics, repair and refurbishment and recovery of electronic components, disposal and
recycling electronic wastes. Recycling of electronics enable the recovery of valuable metals and
also reduces the impact of environmental related with the manufacturing of electronics from raw
materials and ensures appropriate handling of hazardous and toxic components.
The processing of electronic wastes can be explained in three processes: mechanical process
dismantling and collection and include magnetic separation, sorting and end processing.
Figure 1 above illustrate the process of e-waste processing (Mukherjee, 2012)
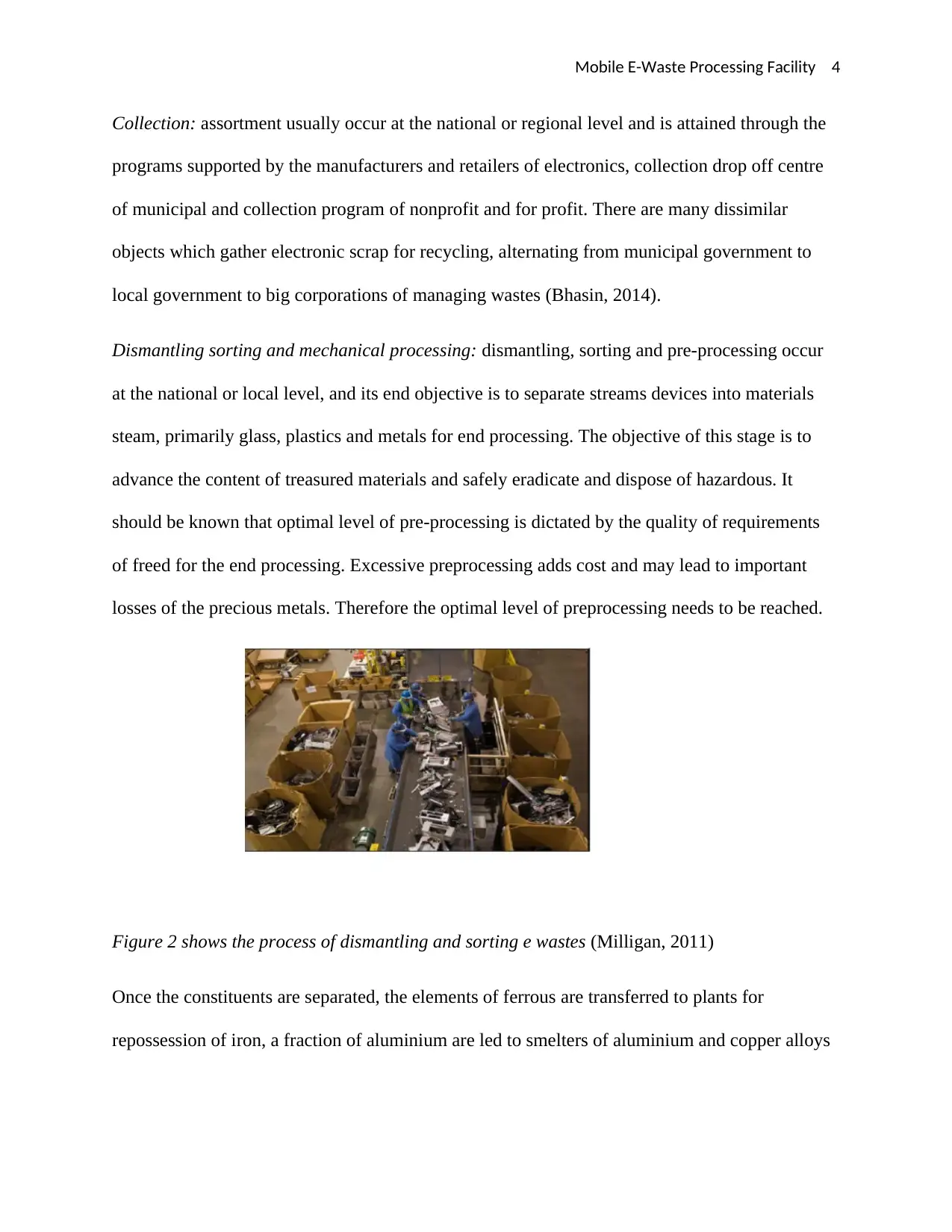
Mobile E-Waste Processing Facility 4
Collection: assortment usually occur at the national or regional level and is attained through the
programs supported by the manufacturers and retailers of electronics, collection drop off centre
of municipal and collection program of nonprofit and for profit. There are many dissimilar
objects which gather electronic scrap for recycling, alternating from municipal government to
local government to big corporations of managing wastes (Bhasin, 2014).
Dismantling sorting and mechanical processing: dismantling, sorting and pre-processing occur
at the national or local level, and its end objective is to separate streams devices into materials
steam, primarily glass, plastics and metals for end processing. The objective of this stage is to
advance the content of treasured materials and safely eradicate and dispose of hazardous. It
should be known that optimal level of pre-processing is dictated by the quality of requirements
of freed for the end processing. Excessive preprocessing adds cost and may lead to important
losses of the precious metals. Therefore the optimal level of preprocessing needs to be reached.
Figure 2 shows the process of dismantling and sorting e wastes (Milligan, 2011)
Once the constituents are separated, the elements of ferrous are transferred to plants for
repossession of iron, a fraction of aluminium are led to smelters of aluminium and copper alloys
Collection: assortment usually occur at the national or regional level and is attained through the
programs supported by the manufacturers and retailers of electronics, collection drop off centre
of municipal and collection program of nonprofit and for profit. There are many dissimilar
objects which gather electronic scrap for recycling, alternating from municipal government to
local government to big corporations of managing wastes (Bhasin, 2014).
Dismantling sorting and mechanical processing: dismantling, sorting and pre-processing occur
at the national or local level, and its end objective is to separate streams devices into materials
steam, primarily glass, plastics and metals for end processing. The objective of this stage is to
advance the content of treasured materials and safely eradicate and dispose of hazardous. It
should be known that optimal level of pre-processing is dictated by the quality of requirements
of freed for the end processing. Excessive preprocessing adds cost and may lead to important
losses of the precious metals. Therefore the optimal level of preprocessing needs to be reached.
Figure 2 shows the process of dismantling and sorting e wastes (Milligan, 2011)
Once the constituents are separated, the elements of ferrous are transferred to plants for
repossession of iron, a fraction of aluminium are led to smelters of aluminium and copper alloys
Secure Best Marks with AI Grader
Need help grading? Try our AI Grader for instant feedback on your assignments.
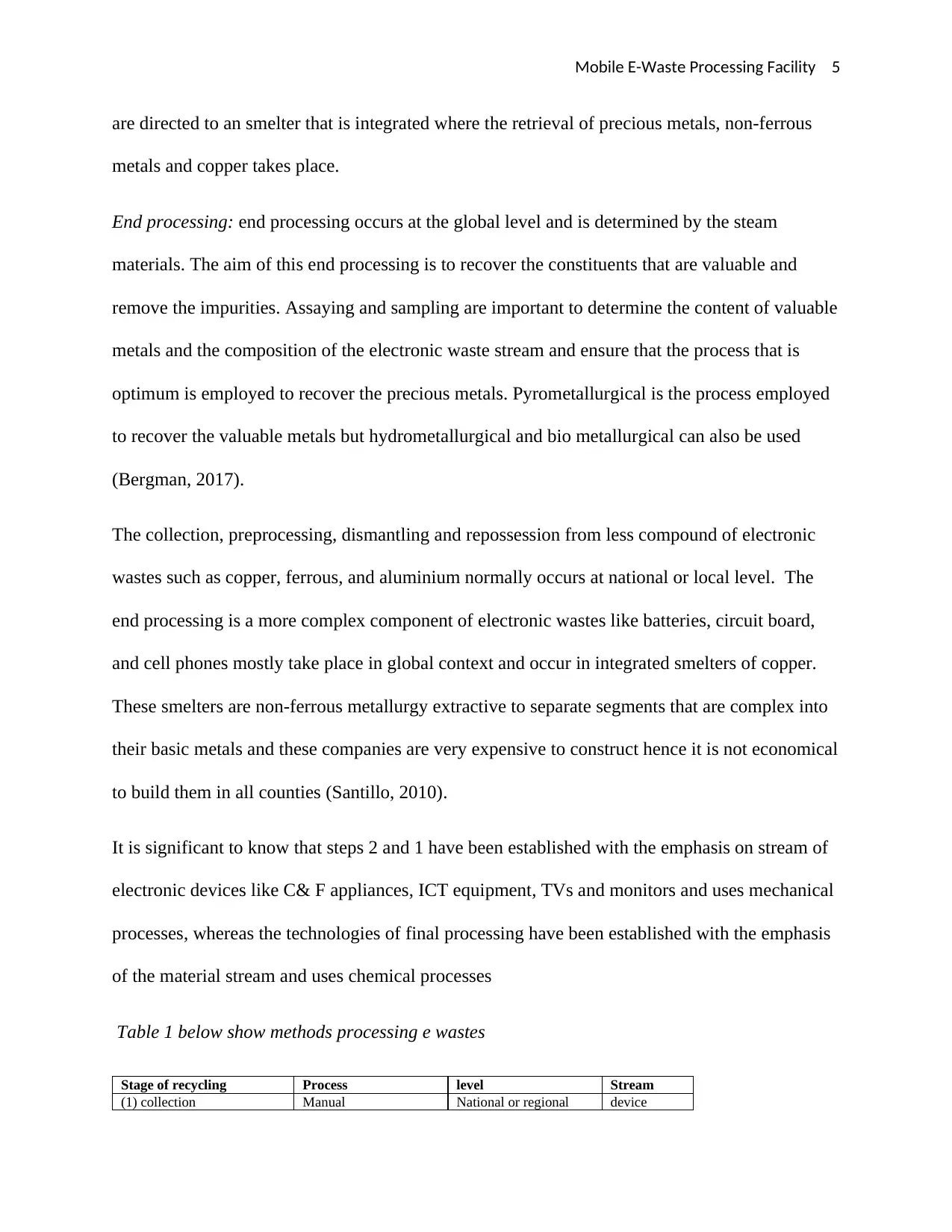
Mobile E-Waste Processing Facility 5
are directed to an smelter that is integrated where the retrieval of precious metals, non-ferrous
metals and copper takes place.
End processing: end processing occurs at the global level and is determined by the steam
materials. The aim of this end processing is to recover the constituents that are valuable and
remove the impurities. Assaying and sampling are important to determine the content of valuable
metals and the composition of the electronic waste stream and ensure that the process that is
optimum is employed to recover the precious metals. Pyrometallurgical is the process employed
to recover the valuable metals but hydrometallurgical and bio metallurgical can also be used
(Bergman, 2017).
The collection, preprocessing, dismantling and repossession from less compound of electronic
wastes such as copper, ferrous, and aluminium normally occurs at national or local level. The
end processing is a more complex component of electronic wastes like batteries, circuit board,
and cell phones mostly take place in global context and occur in integrated smelters of copper.
These smelters are non-ferrous metallurgy extractive to separate segments that are complex into
their basic metals and these companies are very expensive to construct hence it is not economical
to build them in all counties (Santillo, 2010).
It is significant to know that steps 2 and 1 have been established with the emphasis on stream of
electronic devices like C& F appliances, ICT equipment, TVs and monitors and uses mechanical
processes, whereas the technologies of final processing have been established with the emphasis
of the material stream and uses chemical processes
Table 1 below show methods processing e wastes
Stage of recycling Process level Stream
(1) collection Manual National or regional device
are directed to an smelter that is integrated where the retrieval of precious metals, non-ferrous
metals and copper takes place.
End processing: end processing occurs at the global level and is determined by the steam
materials. The aim of this end processing is to recover the constituents that are valuable and
remove the impurities. Assaying and sampling are important to determine the content of valuable
metals and the composition of the electronic waste stream and ensure that the process that is
optimum is employed to recover the precious metals. Pyrometallurgical is the process employed
to recover the valuable metals but hydrometallurgical and bio metallurgical can also be used
(Bergman, 2017).
The collection, preprocessing, dismantling and repossession from less compound of electronic
wastes such as copper, ferrous, and aluminium normally occurs at national or local level. The
end processing is a more complex component of electronic wastes like batteries, circuit board,
and cell phones mostly take place in global context and occur in integrated smelters of copper.
These smelters are non-ferrous metallurgy extractive to separate segments that are complex into
their basic metals and these companies are very expensive to construct hence it is not economical
to build them in all counties (Santillo, 2010).
It is significant to know that steps 2 and 1 have been established with the emphasis on stream of
electronic devices like C& F appliances, ICT equipment, TVs and monitors and uses mechanical
processes, whereas the technologies of final processing have been established with the emphasis
of the material stream and uses chemical processes
Table 1 below show methods processing e wastes
Stage of recycling Process level Stream
(1) collection Manual National or regional device
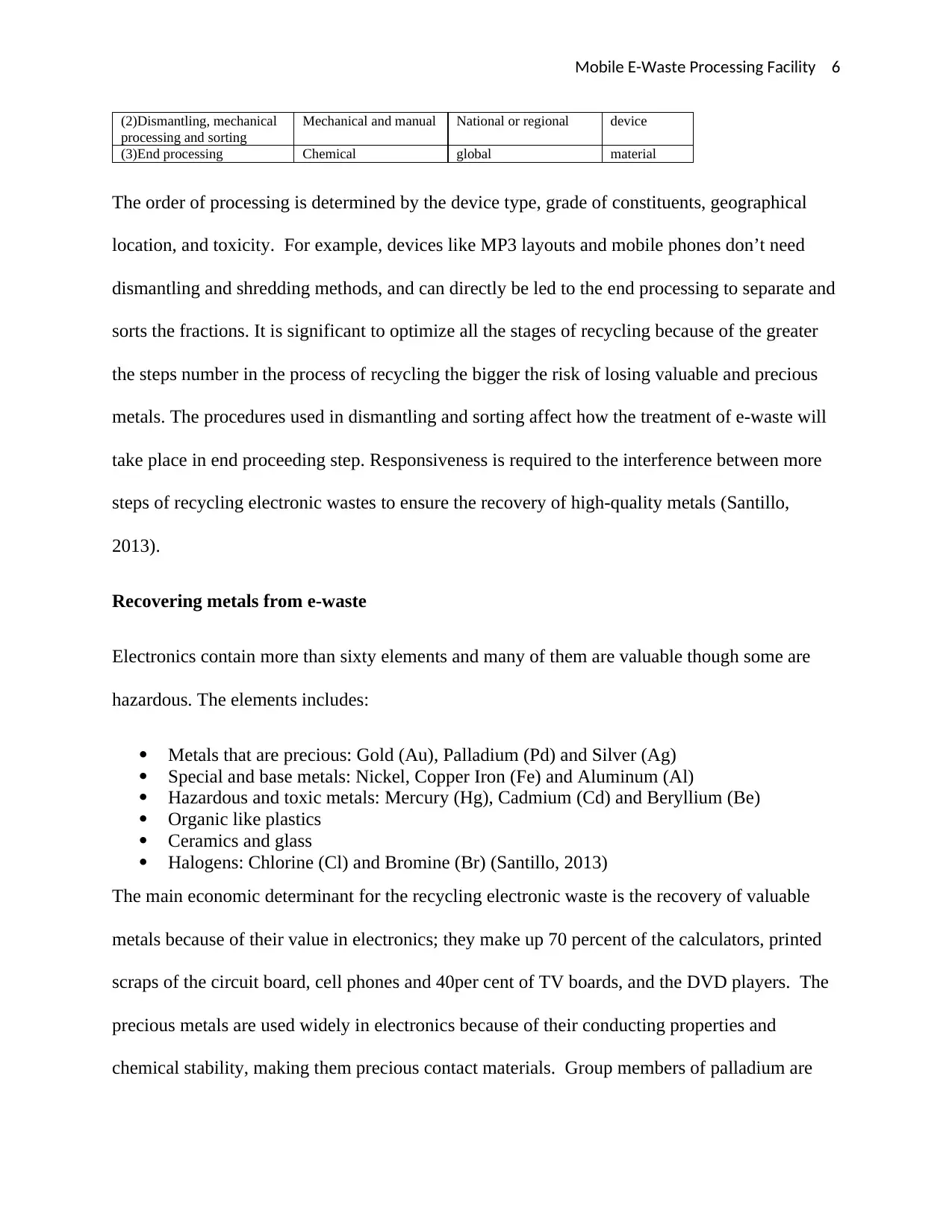
Mobile E-Waste Processing Facility 6
(2)Dismantling, mechanical
processing and sorting
Mechanical and manual National or regional device
(3)End processing Chemical global material
The order of processing is determined by the device type, grade of constituents, geographical
location, and toxicity. For example, devices like MP3 layouts and mobile phones don’t need
dismantling and shredding methods, and can directly be led to the end processing to separate and
sorts the fractions. It is significant to optimize all the stages of recycling because of the greater
the steps number in the process of recycling the bigger the risk of losing valuable and precious
metals. The procedures used in dismantling and sorting affect how the treatment of e-waste will
take place in end proceeding step. Responsiveness is required to the interference between more
steps of recycling electronic wastes to ensure the recovery of high-quality metals (Santillo,
2013).
Recovering metals from e-waste
Electronics contain more than sixty elements and many of them are valuable though some are
hazardous. The elements includes:
Metals that are precious: Gold (Au), Palladium (Pd) and Silver (Ag)
Special and base metals: Nickel, Copper Iron (Fe) and Aluminum (Al)
Hazardous and toxic metals: Mercury (Hg), Cadmium (Cd) and Beryllium (Be)
Organic like plastics
Ceramics and glass
Halogens: Chlorine (Cl) and Bromine (Br) (Santillo, 2013)
The main economic determinant for the recycling electronic waste is the recovery of valuable
metals because of their value in electronics; they make up 70 percent of the calculators, printed
scraps of the circuit board, cell phones and 40per cent of TV boards, and the DVD players. The
precious metals are used widely in electronics because of their conducting properties and
chemical stability, making them precious contact materials. Group members of palladium are
(2)Dismantling, mechanical
processing and sorting
Mechanical and manual National or regional device
(3)End processing Chemical global material
The order of processing is determined by the device type, grade of constituents, geographical
location, and toxicity. For example, devices like MP3 layouts and mobile phones don’t need
dismantling and shredding methods, and can directly be led to the end processing to separate and
sorts the fractions. It is significant to optimize all the stages of recycling because of the greater
the steps number in the process of recycling the bigger the risk of losing valuable and precious
metals. The procedures used in dismantling and sorting affect how the treatment of e-waste will
take place in end proceeding step. Responsiveness is required to the interference between more
steps of recycling electronic wastes to ensure the recovery of high-quality metals (Santillo,
2013).
Recovering metals from e-waste
Electronics contain more than sixty elements and many of them are valuable though some are
hazardous. The elements includes:
Metals that are precious: Gold (Au), Palladium (Pd) and Silver (Ag)
Special and base metals: Nickel, Copper Iron (Fe) and Aluminum (Al)
Hazardous and toxic metals: Mercury (Hg), Cadmium (Cd) and Beryllium (Be)
Organic like plastics
Ceramics and glass
Halogens: Chlorine (Cl) and Bromine (Br) (Santillo, 2013)
The main economic determinant for the recycling electronic waste is the recovery of valuable
metals because of their value in electronics; they make up 70 percent of the calculators, printed
scraps of the circuit board, cell phones and 40per cent of TV boards, and the DVD players. The
precious metals are used widely in electronics because of their conducting properties and
chemical stability, making them precious contact materials. Group members of palladium are
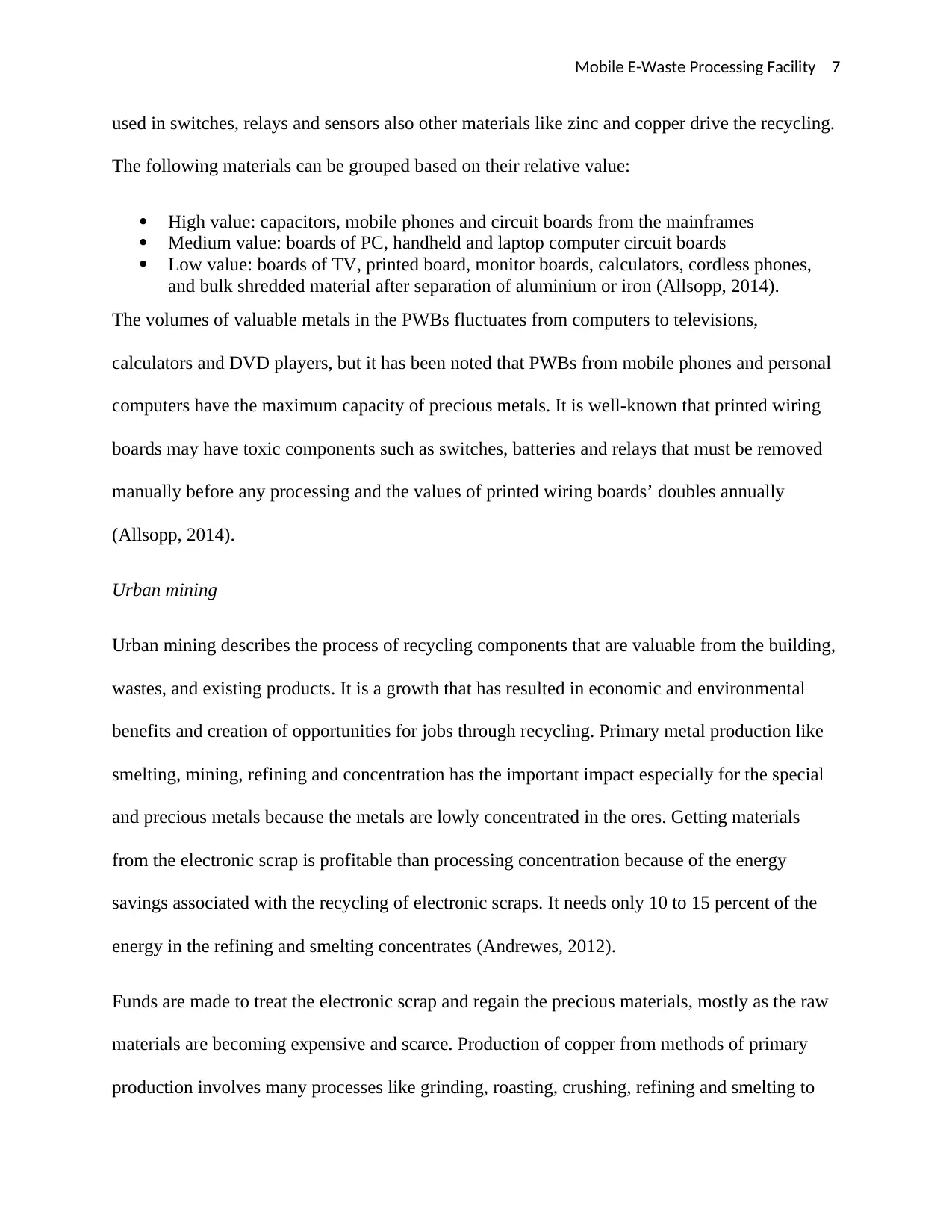
Mobile E-Waste Processing Facility 7
used in switches, relays and sensors also other materials like zinc and copper drive the recycling.
The following materials can be grouped based on their relative value:
High value: capacitors, mobile phones and circuit boards from the mainframes
Medium value: boards of PC, handheld and laptop computer circuit boards
Low value: boards of TV, printed board, monitor boards, calculators, cordless phones,
and bulk shredded material after separation of aluminium or iron (Allsopp, 2014).
The volumes of valuable metals in the PWBs fluctuates from computers to televisions,
calculators and DVD players, but it has been noted that PWBs from mobile phones and personal
computers have the maximum capacity of precious metals. It is well-known that printed wiring
boards may have toxic components such as switches, batteries and relays that must be removed
manually before any processing and the values of printed wiring boards’ doubles annually
(Allsopp, 2014).
Urban mining
Urban mining describes the process of recycling components that are valuable from the building,
wastes, and existing products. It is a growth that has resulted in economic and environmental
benefits and creation of opportunities for jobs through recycling. Primary metal production like
smelting, mining, refining and concentration has the important impact especially for the special
and precious metals because the metals are lowly concentrated in the ores. Getting materials
from the electronic scrap is profitable than processing concentration because of the energy
savings associated with the recycling of electronic scraps. It needs only 10 to 15 percent of the
energy in the refining and smelting concentrates (Andrewes, 2012).
Funds are made to treat the electronic scrap and regain the precious materials, mostly as the raw
materials are becoming expensive and scarce. Production of copper from methods of primary
production involves many processes like grinding, roasting, crushing, refining and smelting to
used in switches, relays and sensors also other materials like zinc and copper drive the recycling.
The following materials can be grouped based on their relative value:
High value: capacitors, mobile phones and circuit boards from the mainframes
Medium value: boards of PC, handheld and laptop computer circuit boards
Low value: boards of TV, printed board, monitor boards, calculators, cordless phones,
and bulk shredded material after separation of aluminium or iron (Allsopp, 2014).
The volumes of valuable metals in the PWBs fluctuates from computers to televisions,
calculators and DVD players, but it has been noted that PWBs from mobile phones and personal
computers have the maximum capacity of precious metals. It is well-known that printed wiring
boards may have toxic components such as switches, batteries and relays that must be removed
manually before any processing and the values of printed wiring boards’ doubles annually
(Allsopp, 2014).
Urban mining
Urban mining describes the process of recycling components that are valuable from the building,
wastes, and existing products. It is a growth that has resulted in economic and environmental
benefits and creation of opportunities for jobs through recycling. Primary metal production like
smelting, mining, refining and concentration has the important impact especially for the special
and precious metals because the metals are lowly concentrated in the ores. Getting materials
from the electronic scrap is profitable than processing concentration because of the energy
savings associated with the recycling of electronic scraps. It needs only 10 to 15 percent of the
energy in the refining and smelting concentrates (Andrewes, 2012).
Funds are made to treat the electronic scrap and regain the precious materials, mostly as the raw
materials are becoming expensive and scarce. Production of copper from methods of primary
production involves many processes like grinding, roasting, crushing, refining and smelting to
Paraphrase This Document
Need a fresh take? Get an instant paraphrase of this document with our AI Paraphraser
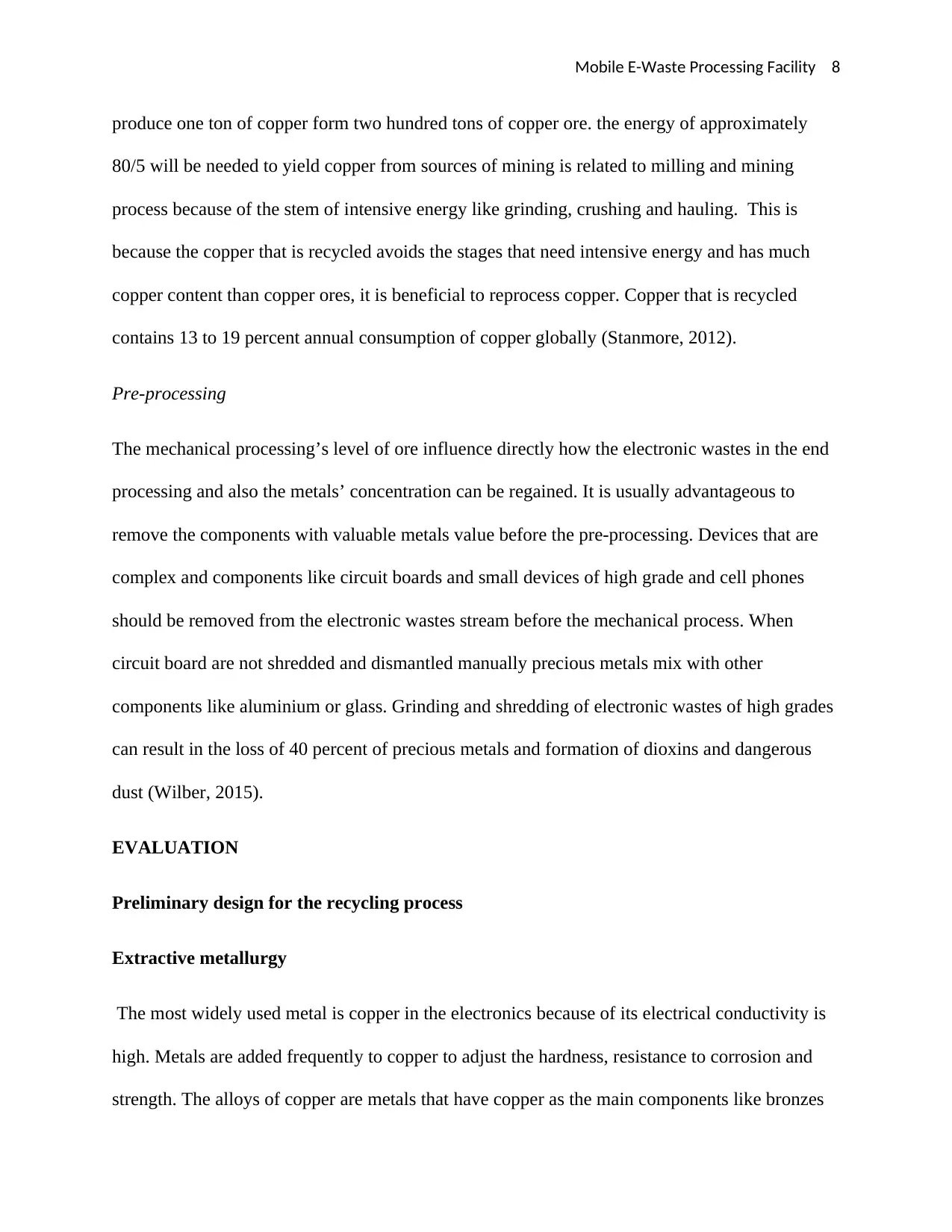
Mobile E-Waste Processing Facility 8
produce one ton of copper form two hundred tons of copper ore. the energy of approximately
80/5 will be needed to yield copper from sources of mining is related to milling and mining
process because of the stem of intensive energy like grinding, crushing and hauling. This is
because the copper that is recycled avoids the stages that need intensive energy and has much
copper content than copper ores, it is beneficial to reprocess copper. Copper that is recycled
contains 13 to 19 percent annual consumption of copper globally (Stanmore, 2012).
Pre-processing
The mechanical processing’s level of ore influence directly how the electronic wastes in the end
processing and also the metals’ concentration can be regained. It is usually advantageous to
remove the components with valuable metals value before the pre-processing. Devices that are
complex and components like circuit boards and small devices of high grade and cell phones
should be removed from the electronic wastes stream before the mechanical process. When
circuit board are not shredded and dismantled manually precious metals mix with other
components like aluminium or glass. Grinding and shredding of electronic wastes of high grades
can result in the loss of 40 percent of precious metals and formation of dioxins and dangerous
dust (Wilber, 2015).
EVALUATION
Preliminary design for the recycling process
Extractive metallurgy
The most widely used metal is copper in the electronics because of its electrical conductivity is
high. Metals are added frequently to copper to adjust the hardness, resistance to corrosion and
strength. The alloys of copper are metals that have copper as the main components like bronzes
produce one ton of copper form two hundred tons of copper ore. the energy of approximately
80/5 will be needed to yield copper from sources of mining is related to milling and mining
process because of the stem of intensive energy like grinding, crushing and hauling. This is
because the copper that is recycled avoids the stages that need intensive energy and has much
copper content than copper ores, it is beneficial to reprocess copper. Copper that is recycled
contains 13 to 19 percent annual consumption of copper globally (Stanmore, 2012).
Pre-processing
The mechanical processing’s level of ore influence directly how the electronic wastes in the end
processing and also the metals’ concentration can be regained. It is usually advantageous to
remove the components with valuable metals value before the pre-processing. Devices that are
complex and components like circuit boards and small devices of high grade and cell phones
should be removed from the electronic wastes stream before the mechanical process. When
circuit board are not shredded and dismantled manually precious metals mix with other
components like aluminium or glass. Grinding and shredding of electronic wastes of high grades
can result in the loss of 40 percent of precious metals and formation of dioxins and dangerous
dust (Wilber, 2015).
EVALUATION
Preliminary design for the recycling process
Extractive metallurgy
The most widely used metal is copper in the electronics because of its electrical conductivity is
high. Metals are added frequently to copper to adjust the hardness, resistance to corrosion and
strength. The alloys of copper are metals that have copper as the main components like bronzes
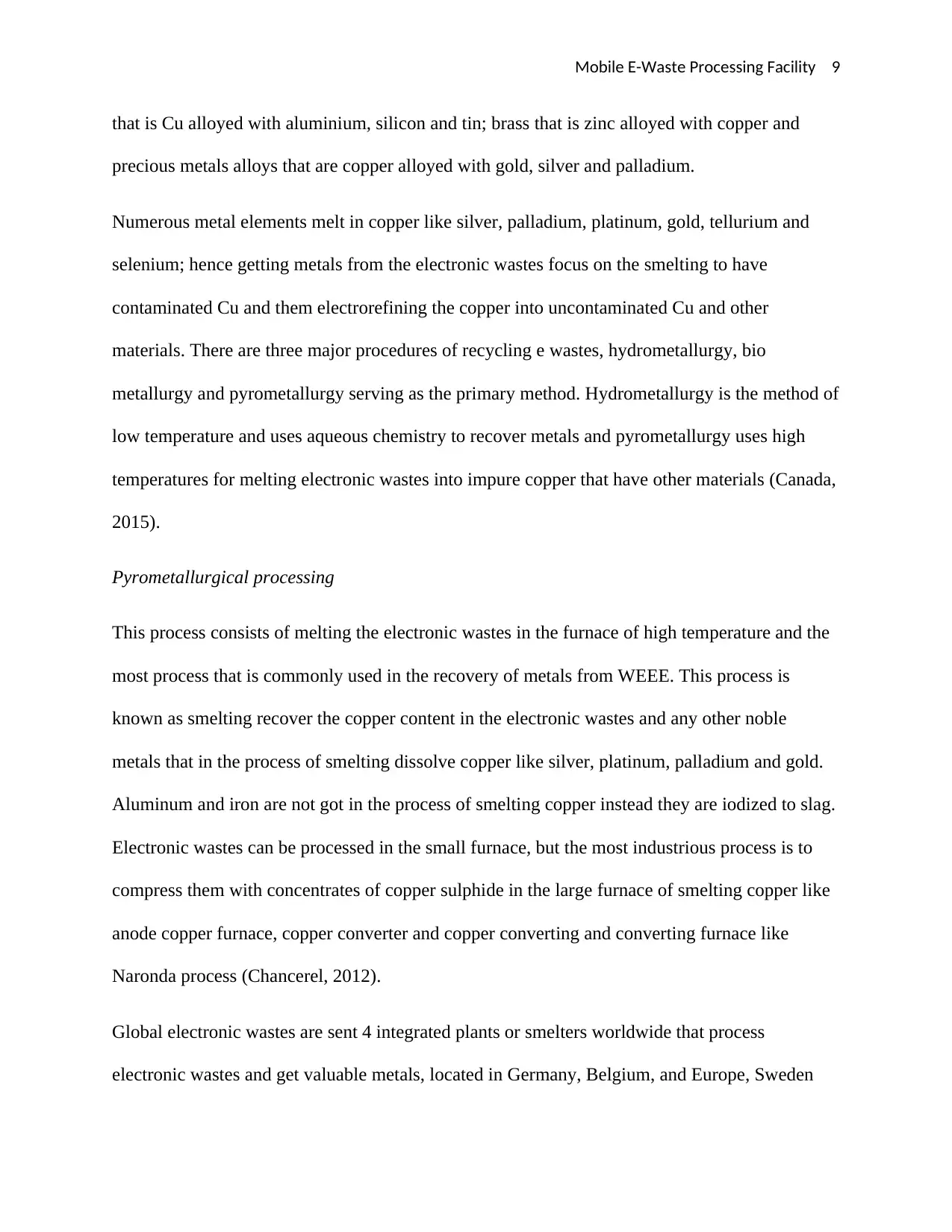
Mobile E-Waste Processing Facility 9
that is Cu alloyed with aluminium, silicon and tin; brass that is zinc alloyed with copper and
precious metals alloys that are copper alloyed with gold, silver and palladium.
Numerous metal elements melt in copper like silver, palladium, platinum, gold, tellurium and
selenium; hence getting metals from the electronic wastes focus on the smelting to have
contaminated Cu and them electrorefining the copper into uncontaminated Cu and other
materials. There are three major procedures of recycling e wastes, hydrometallurgy, bio
metallurgy and pyrometallurgy serving as the primary method. Hydrometallurgy is the method of
low temperature and uses aqueous chemistry to recover metals and pyrometallurgy uses high
temperatures for melting electronic wastes into impure copper that have other materials (Canada,
2015).
Pyrometallurgical processing
This process consists of melting the electronic wastes in the furnace of high temperature and the
most process that is commonly used in the recovery of metals from WEEE. This process is
known as smelting recover the copper content in the electronic wastes and any other noble
metals that in the process of smelting dissolve copper like silver, platinum, palladium and gold.
Aluminum and iron are not got in the process of smelting copper instead they are iodized to slag.
Electronic wastes can be processed in the small furnace, but the most industrious process is to
compress them with concentrates of copper sulphide in the large furnace of smelting copper like
anode copper furnace, copper converter and copper converting and converting furnace like
Naronda process (Chancerel, 2012).
Global electronic wastes are sent 4 integrated plants or smelters worldwide that process
electronic wastes and get valuable metals, located in Germany, Belgium, and Europe, Sweden
that is Cu alloyed with aluminium, silicon and tin; brass that is zinc alloyed with copper and
precious metals alloys that are copper alloyed with gold, silver and palladium.
Numerous metal elements melt in copper like silver, palladium, platinum, gold, tellurium and
selenium; hence getting metals from the electronic wastes focus on the smelting to have
contaminated Cu and them electrorefining the copper into uncontaminated Cu and other
materials. There are three major procedures of recycling e wastes, hydrometallurgy, bio
metallurgy and pyrometallurgy serving as the primary method. Hydrometallurgy is the method of
low temperature and uses aqueous chemistry to recover metals and pyrometallurgy uses high
temperatures for melting electronic wastes into impure copper that have other materials (Canada,
2015).
Pyrometallurgical processing
This process consists of melting the electronic wastes in the furnace of high temperature and the
most process that is commonly used in the recovery of metals from WEEE. This process is
known as smelting recover the copper content in the electronic wastes and any other noble
metals that in the process of smelting dissolve copper like silver, platinum, palladium and gold.
Aluminum and iron are not got in the process of smelting copper instead they are iodized to slag.
Electronic wastes can be processed in the small furnace, but the most industrious process is to
compress them with concentrates of copper sulphide in the large furnace of smelting copper like
anode copper furnace, copper converter and copper converting and converting furnace like
Naronda process (Chancerel, 2012).
Global electronic wastes are sent 4 integrated plants or smelters worldwide that process
electronic wastes and get valuable metals, located in Germany, Belgium, and Europe, Sweden
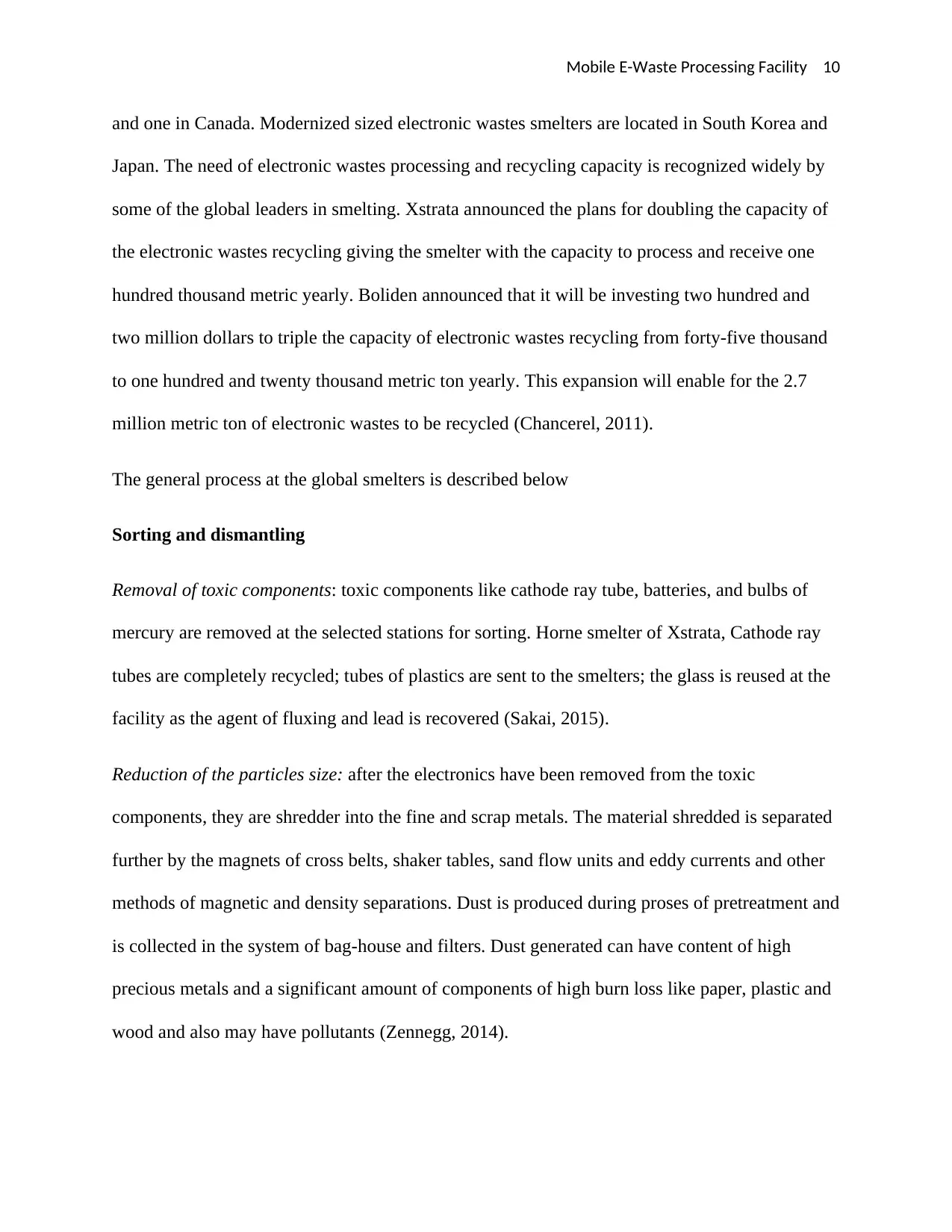
Mobile E-Waste Processing Facility 10
and one in Canada. Modernized sized electronic wastes smelters are located in South Korea and
Japan. The need of electronic wastes processing and recycling capacity is recognized widely by
some of the global leaders in smelting. Xstrata announced the plans for doubling the capacity of
the electronic wastes recycling giving the smelter with the capacity to process and receive one
hundred thousand metric yearly. Boliden announced that it will be investing two hundred and
two million dollars to triple the capacity of electronic wastes recycling from forty-five thousand
to one hundred and twenty thousand metric ton yearly. This expansion will enable for the 2.7
million metric ton of electronic wastes to be recycled (Chancerel, 2011).
The general process at the global smelters is described below
Sorting and dismantling
Removal of toxic components: toxic components like cathode ray tube, batteries, and bulbs of
mercury are removed at the selected stations for sorting. Horne smelter of Xstrata, Cathode ray
tubes are completely recycled; tubes of plastics are sent to the smelters; the glass is reused at the
facility as the agent of fluxing and lead is recovered (Sakai, 2015).
Reduction of the particles size: after the electronics have been removed from the toxic
components, they are shredder into the fine and scrap metals. The material shredded is separated
further by the magnets of cross belts, shaker tables, sand flow units and eddy currents and other
methods of magnetic and density separations. Dust is produced during proses of pretreatment and
is collected in the system of bag-house and filters. Dust generated can have content of high
precious metals and a significant amount of components of high burn loss like paper, plastic and
wood and also may have pollutants (Zennegg, 2014).
and one in Canada. Modernized sized electronic wastes smelters are located in South Korea and
Japan. The need of electronic wastes processing and recycling capacity is recognized widely by
some of the global leaders in smelting. Xstrata announced the plans for doubling the capacity of
the electronic wastes recycling giving the smelter with the capacity to process and receive one
hundred thousand metric yearly. Boliden announced that it will be investing two hundred and
two million dollars to triple the capacity of electronic wastes recycling from forty-five thousand
to one hundred and twenty thousand metric ton yearly. This expansion will enable for the 2.7
million metric ton of electronic wastes to be recycled (Chancerel, 2011).
The general process at the global smelters is described below
Sorting and dismantling
Removal of toxic components: toxic components like cathode ray tube, batteries, and bulbs of
mercury are removed at the selected stations for sorting. Horne smelter of Xstrata, Cathode ray
tubes are completely recycled; tubes of plastics are sent to the smelters; the glass is reused at the
facility as the agent of fluxing and lead is recovered (Sakai, 2015).
Reduction of the particles size: after the electronics have been removed from the toxic
components, they are shredder into the fine and scrap metals. The material shredded is separated
further by the magnets of cross belts, shaker tables, sand flow units and eddy currents and other
methods of magnetic and density separations. Dust is produced during proses of pretreatment and
is collected in the system of bag-house and filters. Dust generated can have content of high
precious metals and a significant amount of components of high burn loss like paper, plastic and
wood and also may have pollutants (Zennegg, 2014).
Secure Best Marks with AI Grader
Need help grading? Try our AI Grader for instant feedback on your assignments.
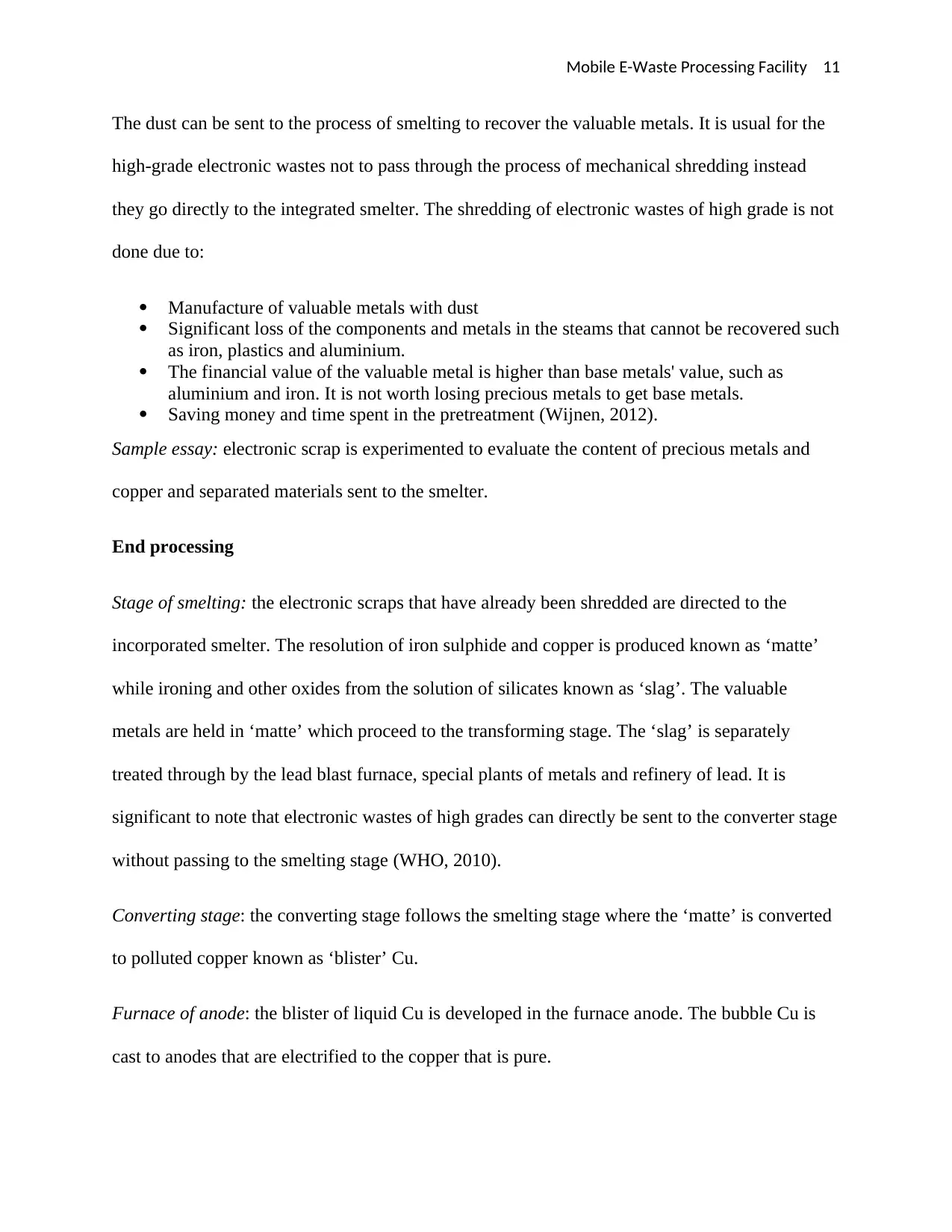
Mobile E-Waste Processing Facility 11
The dust can be sent to the process of smelting to recover the valuable metals. It is usual for the
high-grade electronic wastes not to pass through the process of mechanical shredding instead
they go directly to the integrated smelter. The shredding of electronic wastes of high grade is not
done due to:
Manufacture of valuable metals with dust
Significant loss of the components and metals in the steams that cannot be recovered such
as iron, plastics and aluminium.
The financial value of the valuable metal is higher than base metals' value, such as
aluminium and iron. It is not worth losing precious metals to get base metals.
Saving money and time spent in the pretreatment (Wijnen, 2012).
Sample essay: electronic scrap is experimented to evaluate the content of precious metals and
copper and separated materials sent to the smelter.
End processing
Stage of smelting: the electronic scraps that have already been shredded are directed to the
incorporated smelter. The resolution of iron sulphide and copper is produced known as ‘matte’
while ironing and other oxides from the solution of silicates known as ‘slag’. The valuable
metals are held in ‘matte’ which proceed to the transforming stage. The ‘slag’ is separately
treated through by the lead blast furnace, special plants of metals and refinery of lead. It is
significant to note that electronic wastes of high grades can directly be sent to the converter stage
without passing to the smelting stage (WHO, 2010).
Converting stage: the converting stage follows the smelting stage where the ‘matte’ is converted
to polluted copper known as ‘blister’ Cu.
Furnace of anode: the blister of liquid Cu is developed in the furnace anode. The bubble Cu is
cast to anodes that are electrified to the copper that is pure.
The dust can be sent to the process of smelting to recover the valuable metals. It is usual for the
high-grade electronic wastes not to pass through the process of mechanical shredding instead
they go directly to the integrated smelter. The shredding of electronic wastes of high grade is not
done due to:
Manufacture of valuable metals with dust
Significant loss of the components and metals in the steams that cannot be recovered such
as iron, plastics and aluminium.
The financial value of the valuable metal is higher than base metals' value, such as
aluminium and iron. It is not worth losing precious metals to get base metals.
Saving money and time spent in the pretreatment (Wijnen, 2012).
Sample essay: electronic scrap is experimented to evaluate the content of precious metals and
copper and separated materials sent to the smelter.
End processing
Stage of smelting: the electronic scraps that have already been shredded are directed to the
incorporated smelter. The resolution of iron sulphide and copper is produced known as ‘matte’
while ironing and other oxides from the solution of silicates known as ‘slag’. The valuable
metals are held in ‘matte’ which proceed to the transforming stage. The ‘slag’ is separately
treated through by the lead blast furnace, special plants of metals and refinery of lead. It is
significant to note that electronic wastes of high grades can directly be sent to the converter stage
without passing to the smelting stage (WHO, 2010).
Converting stage: the converting stage follows the smelting stage where the ‘matte’ is converted
to polluted copper known as ‘blister’ Cu.
Furnace of anode: the blister of liquid Cu is developed in the furnace anode. The bubble Cu is
cast to anodes that are electrified to the copper that is pure.
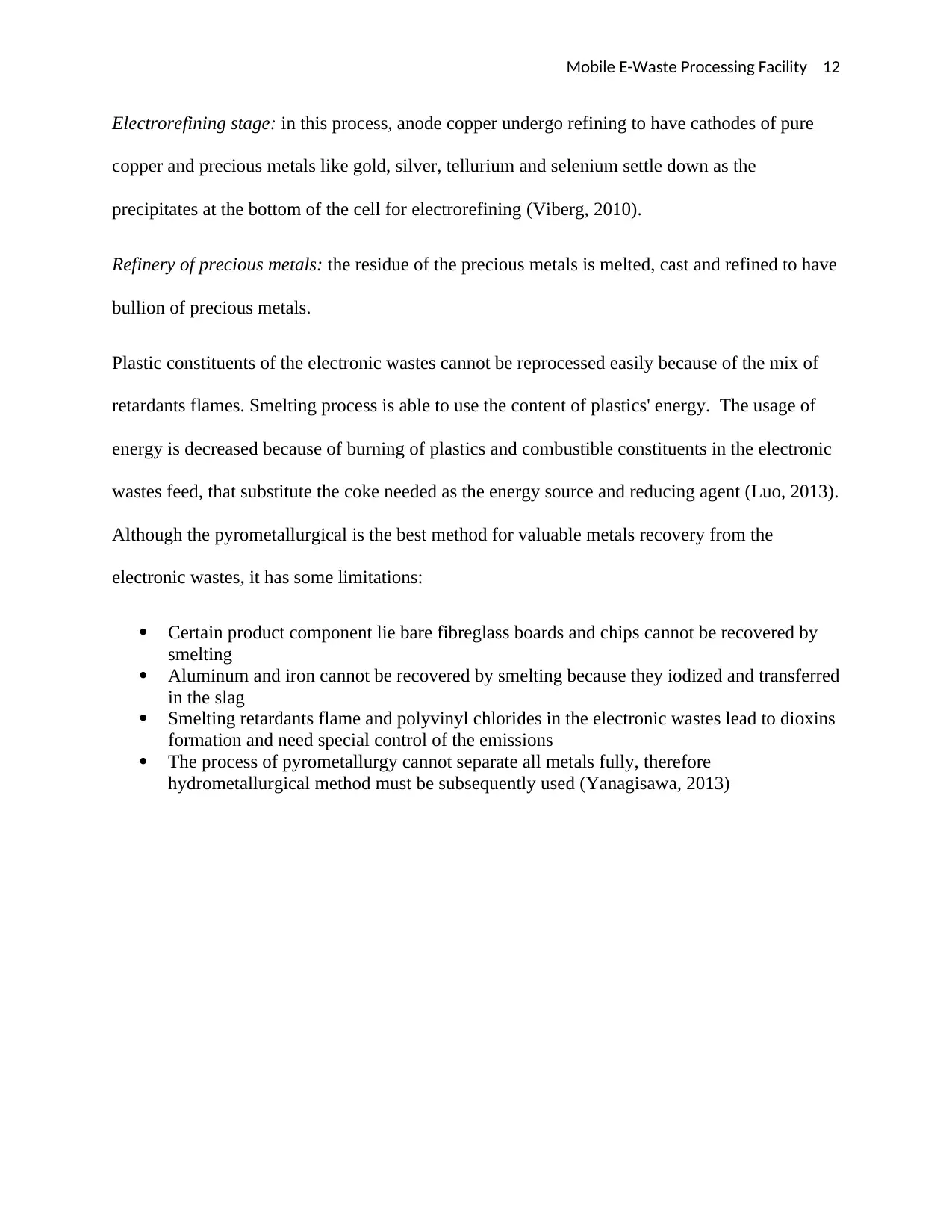
Mobile E-Waste Processing Facility 12
Electrorefining stage: in this process, anode copper undergo refining to have cathodes of pure
copper and precious metals like gold, silver, tellurium and selenium settle down as the
precipitates at the bottom of the cell for electrorefining (Viberg, 2010).
Refinery of precious metals: the residue of the precious metals is melted, cast and refined to have
bullion of precious metals.
Plastic constituents of the electronic wastes cannot be reprocessed easily because of the mix of
retardants flames. Smelting process is able to use the content of plastics' energy. The usage of
energy is decreased because of burning of plastics and combustible constituents in the electronic
wastes feed, that substitute the coke needed as the energy source and reducing agent (Luo, 2013).
Although the pyrometallurgical is the best method for valuable metals recovery from the
electronic wastes, it has some limitations:
Certain product component lie bare fibreglass boards and chips cannot be recovered by
smelting
Aluminum and iron cannot be recovered by smelting because they iodized and transferred
in the slag
Smelting retardants flame and polyvinyl chlorides in the electronic wastes lead to dioxins
formation and need special control of the emissions
The process of pyrometallurgy cannot separate all metals fully, therefore
hydrometallurgical method must be subsequently used (Yanagisawa, 2013)
Electrorefining stage: in this process, anode copper undergo refining to have cathodes of pure
copper and precious metals like gold, silver, tellurium and selenium settle down as the
precipitates at the bottom of the cell for electrorefining (Viberg, 2010).
Refinery of precious metals: the residue of the precious metals is melted, cast and refined to have
bullion of precious metals.
Plastic constituents of the electronic wastes cannot be reprocessed easily because of the mix of
retardants flames. Smelting process is able to use the content of plastics' energy. The usage of
energy is decreased because of burning of plastics and combustible constituents in the electronic
wastes feed, that substitute the coke needed as the energy source and reducing agent (Luo, 2013).
Although the pyrometallurgical is the best method for valuable metals recovery from the
electronic wastes, it has some limitations:
Certain product component lie bare fibreglass boards and chips cannot be recovered by
smelting
Aluminum and iron cannot be recovered by smelting because they iodized and transferred
in the slag
Smelting retardants flame and polyvinyl chlorides in the electronic wastes lead to dioxins
formation and need special control of the emissions
The process of pyrometallurgy cannot separate all metals fully, therefore
hydrometallurgical method must be subsequently used (Yanagisawa, 2013)
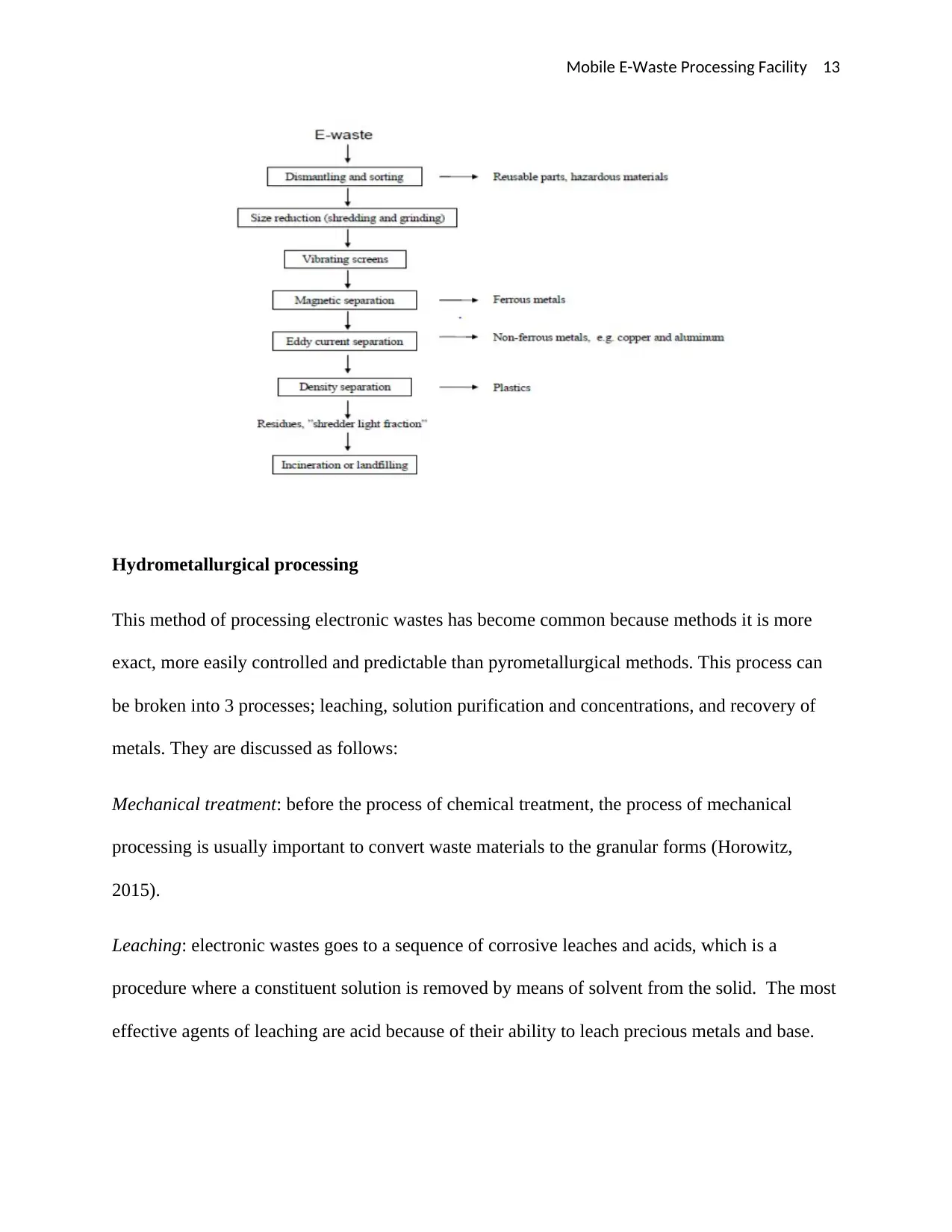
Mobile E-Waste Processing Facility 13
Hydrometallurgical processing
This method of processing electronic wastes has become common because methods it is more
exact, more easily controlled and predictable than pyrometallurgical methods. This process can
be broken into 3 processes; leaching, solution purification and concentrations, and recovery of
metals. They are discussed as follows:
Mechanical treatment: before the process of chemical treatment, the process of mechanical
processing is usually important to convert waste materials to the granular forms (Horowitz,
2015).
Leaching: electronic wastes goes to a sequence of corrosive leaches and acids, which is a
procedure where a constituent solution is removed by means of solvent from the solid. The most
effective agents of leaching are acid because of their ability to leach precious metals and base.
Hydrometallurgical processing
This method of processing electronic wastes has become common because methods it is more
exact, more easily controlled and predictable than pyrometallurgical methods. This process can
be broken into 3 processes; leaching, solution purification and concentrations, and recovery of
metals. They are discussed as follows:
Mechanical treatment: before the process of chemical treatment, the process of mechanical
processing is usually important to convert waste materials to the granular forms (Horowitz,
2015).
Leaching: electronic wastes goes to a sequence of corrosive leaches and acids, which is a
procedure where a constituent solution is removed by means of solvent from the solid. The most
effective agents of leaching are acid because of their ability to leach precious metals and base.
Paraphrase This Document
Need a fresh take? Get an instant paraphrase of this document with our AI Paraphraser
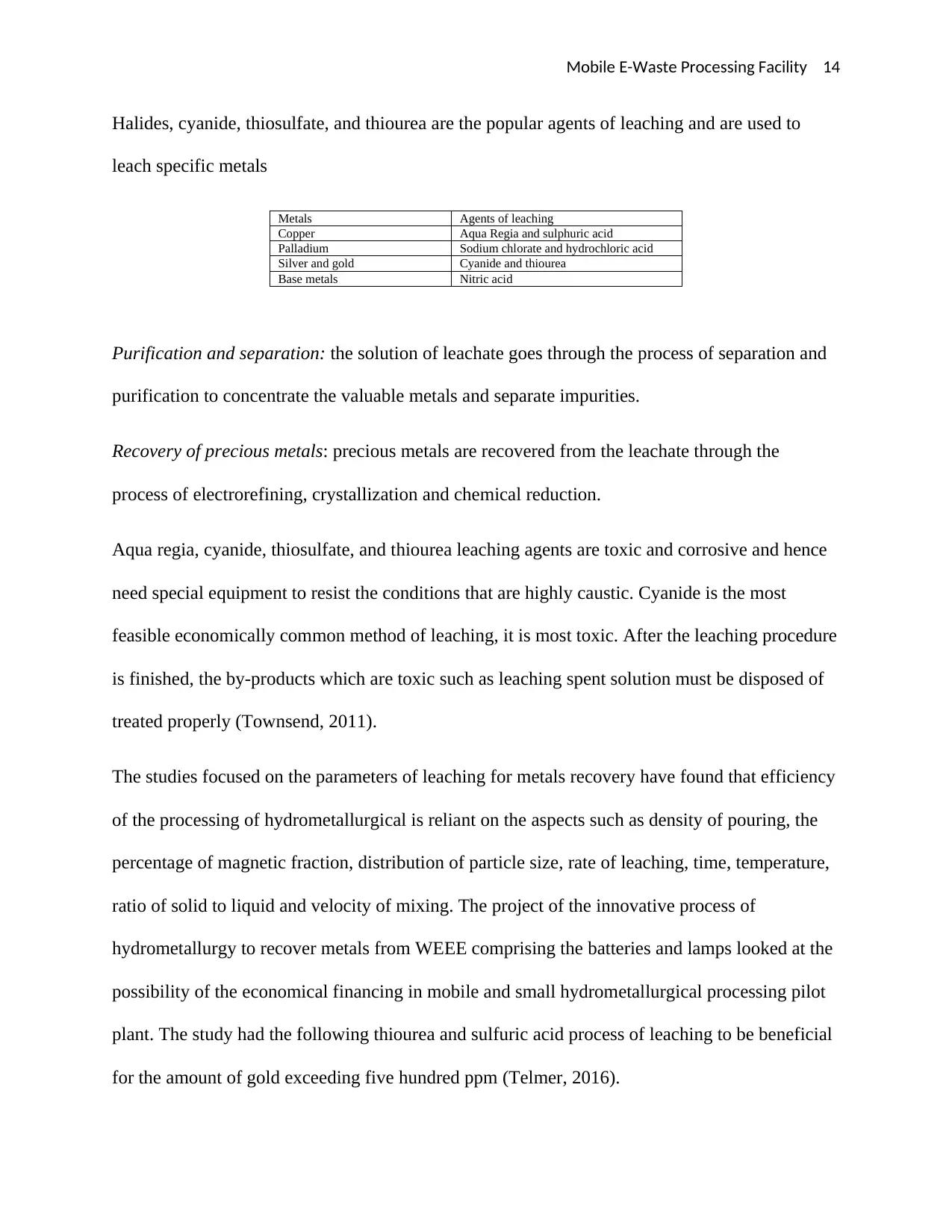
Mobile E-Waste Processing Facility 14
Halides, cyanide, thiosulfate, and thiourea are the popular agents of leaching and are used to
leach specific metals
Metals Agents of leaching
Copper Aqua Regia and sulphuric acid
Palladium Sodium chlorate and hydrochloric acid
Silver and gold Cyanide and thiourea
Base metals Nitric acid
Purification and separation: the solution of leachate goes through the process of separation and
purification to concentrate the valuable metals and separate impurities.
Recovery of precious metals: precious metals are recovered from the leachate through the
process of electrorefining, crystallization and chemical reduction.
Aqua regia, cyanide, thiosulfate, and thiourea leaching agents are toxic and corrosive and hence
need special equipment to resist the conditions that are highly caustic. Cyanide is the most
feasible economically common method of leaching, it is most toxic. After the leaching procedure
is finished, the by-products which are toxic such as leaching spent solution must be disposed of
treated properly (Townsend, 2011).
The studies focused on the parameters of leaching for metals recovery have found that efficiency
of the processing of hydrometallurgical is reliant on the aspects such as density of pouring, the
percentage of magnetic fraction, distribution of particle size, rate of leaching, time, temperature,
ratio of solid to liquid and velocity of mixing. The project of the innovative process of
hydrometallurgy to recover metals from WEEE comprising the batteries and lamps looked at the
possibility of the economical financing in mobile and small hydrometallurgical processing pilot
plant. The study had the following thiourea and sulfuric acid process of leaching to be beneficial
for the amount of gold exceeding five hundred ppm (Telmer, 2016).
Halides, cyanide, thiosulfate, and thiourea are the popular agents of leaching and are used to
leach specific metals
Metals Agents of leaching
Copper Aqua Regia and sulphuric acid
Palladium Sodium chlorate and hydrochloric acid
Silver and gold Cyanide and thiourea
Base metals Nitric acid
Purification and separation: the solution of leachate goes through the process of separation and
purification to concentrate the valuable metals and separate impurities.
Recovery of precious metals: precious metals are recovered from the leachate through the
process of electrorefining, crystallization and chemical reduction.
Aqua regia, cyanide, thiosulfate, and thiourea leaching agents are toxic and corrosive and hence
need special equipment to resist the conditions that are highly caustic. Cyanide is the most
feasible economically common method of leaching, it is most toxic. After the leaching procedure
is finished, the by-products which are toxic such as leaching spent solution must be disposed of
treated properly (Townsend, 2011).
The studies focused on the parameters of leaching for metals recovery have found that efficiency
of the processing of hydrometallurgical is reliant on the aspects such as density of pouring, the
percentage of magnetic fraction, distribution of particle size, rate of leaching, time, temperature,
ratio of solid to liquid and velocity of mixing. The project of the innovative process of
hydrometallurgy to recover metals from WEEE comprising the batteries and lamps looked at the
possibility of the economical financing in mobile and small hydrometallurgical processing pilot
plant. The study had the following thiourea and sulfuric acid process of leaching to be beneficial
for the amount of gold exceeding five hundred ppm (Telmer, 2016).
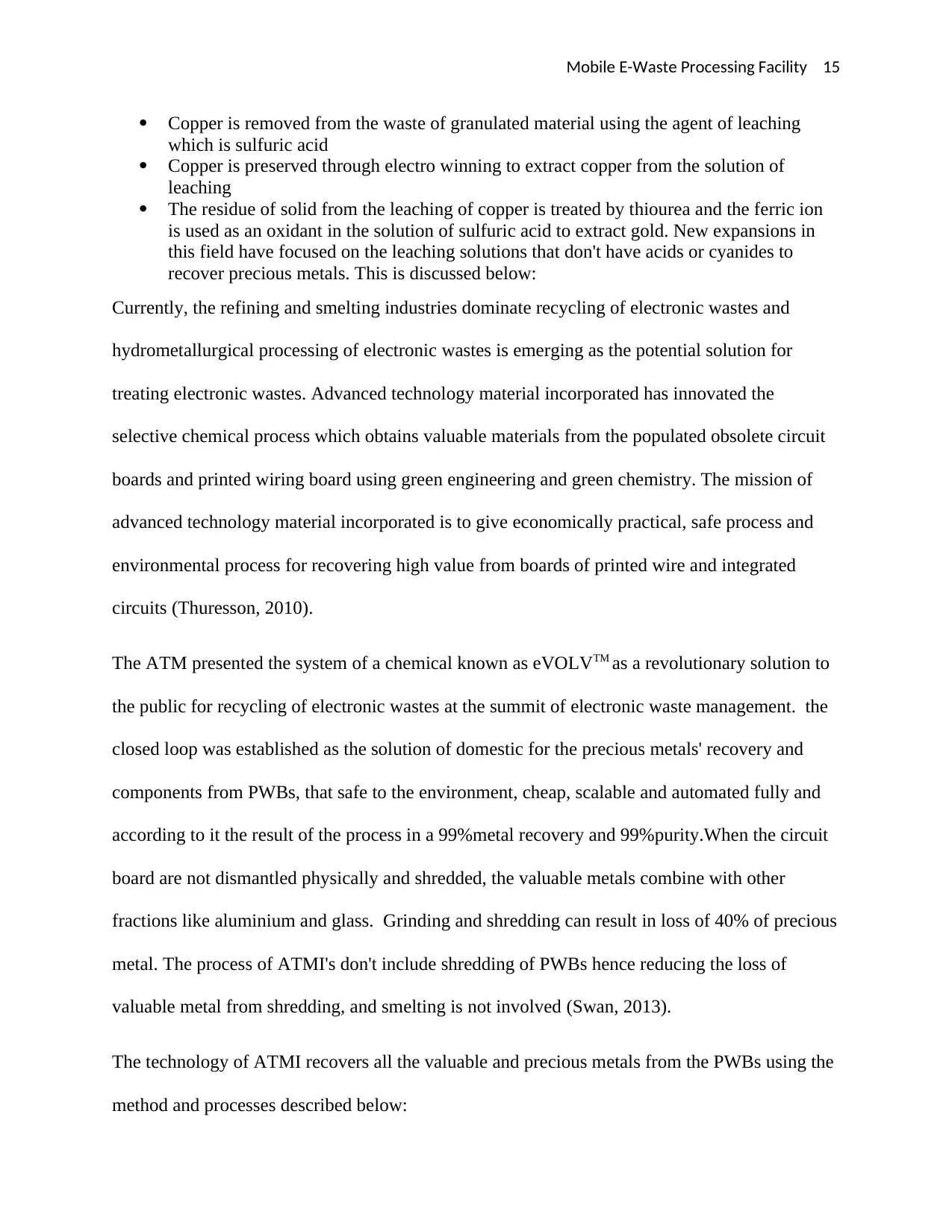
Mobile E-Waste Processing Facility 15
Copper is removed from the waste of granulated material using the agent of leaching
which is sulfuric acid
Copper is preserved through electro winning to extract copper from the solution of
leaching
The residue of solid from the leaching of copper is treated by thiourea and the ferric ion
is used as an oxidant in the solution of sulfuric acid to extract gold. New expansions in
this field have focused on the leaching solutions that don't have acids or cyanides to
recover precious metals. This is discussed below:
Currently, the refining and smelting industries dominate recycling of electronic wastes and
hydrometallurgical processing of electronic wastes is emerging as the potential solution for
treating electronic wastes. Advanced technology material incorporated has innovated the
selective chemical process which obtains valuable materials from the populated obsolete circuit
boards and printed wiring board using green engineering and green chemistry. The mission of
advanced technology material incorporated is to give economically practical, safe process and
environmental process for recovering high value from boards of printed wire and integrated
circuits (Thuresson, 2010).
The ATM presented the system of a chemical known as eVOLVTM as a revolutionary solution to
the public for recycling of electronic wastes at the summit of electronic waste management. the
closed loop was established as the solution of domestic for the precious metals' recovery and
components from PWBs, that safe to the environment, cheap, scalable and automated fully and
according to it the result of the process in a 99%metal recovery and 99%purity.When the circuit
board are not dismantled physically and shredded, the valuable metals combine with other
fractions like aluminium and glass. Grinding and shredding can result in loss of 40% of precious
metal. The process of ATMI's don't include shredding of PWBs hence reducing the loss of
valuable metal from shredding, and smelting is not involved (Swan, 2013).
The technology of ATMI recovers all the valuable and precious metals from the PWBs using the
method and processes described below:
Copper is removed from the waste of granulated material using the agent of leaching
which is sulfuric acid
Copper is preserved through electro winning to extract copper from the solution of
leaching
The residue of solid from the leaching of copper is treated by thiourea and the ferric ion
is used as an oxidant in the solution of sulfuric acid to extract gold. New expansions in
this field have focused on the leaching solutions that don't have acids or cyanides to
recover precious metals. This is discussed below:
Currently, the refining and smelting industries dominate recycling of electronic wastes and
hydrometallurgical processing of electronic wastes is emerging as the potential solution for
treating electronic wastes. Advanced technology material incorporated has innovated the
selective chemical process which obtains valuable materials from the populated obsolete circuit
boards and printed wiring board using green engineering and green chemistry. The mission of
advanced technology material incorporated is to give economically practical, safe process and
environmental process for recovering high value from boards of printed wire and integrated
circuits (Thuresson, 2010).
The ATM presented the system of a chemical known as eVOLVTM as a revolutionary solution to
the public for recycling of electronic wastes at the summit of electronic waste management. the
closed loop was established as the solution of domestic for the precious metals' recovery and
components from PWBs, that safe to the environment, cheap, scalable and automated fully and
according to it the result of the process in a 99%metal recovery and 99%purity.When the circuit
board are not dismantled physically and shredded, the valuable metals combine with other
fractions like aluminium and glass. Grinding and shredding can result in loss of 40% of precious
metal. The process of ATMI's don't include shredding of PWBs hence reducing the loss of
valuable metal from shredding, and smelting is not involved (Swan, 2013).
The technology of ATMI recovers all the valuable and precious metals from the PWBs using the
method and processes described below:
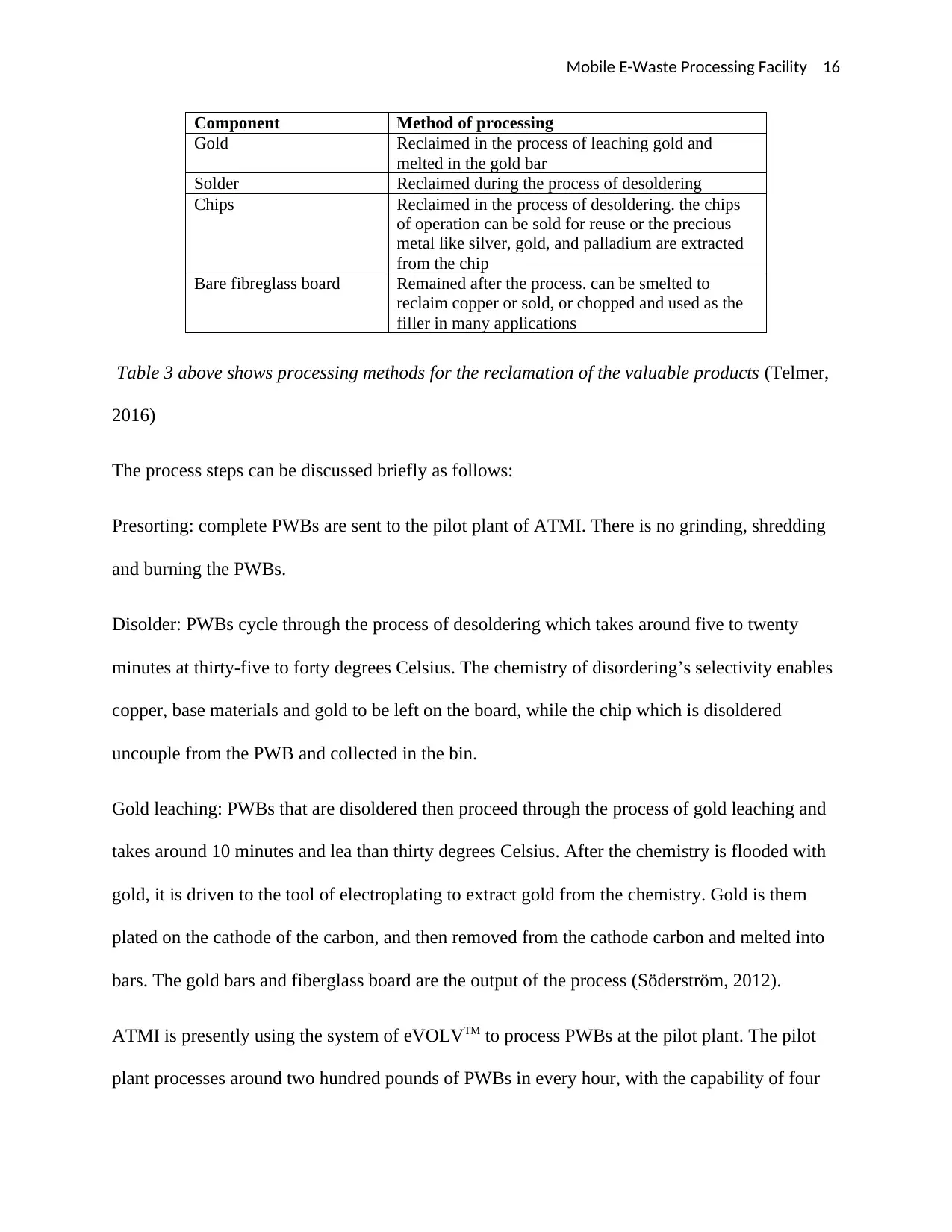
Mobile E-Waste Processing Facility 16
Component Method of processing
Gold Reclaimed in the process of leaching gold and
melted in the gold bar
Solder Reclaimed during the process of desoldering
Chips Reclaimed in the process of desoldering. the chips
of operation can be sold for reuse or the precious
metal like silver, gold, and palladium are extracted
from the chip
Bare fibreglass board Remained after the process. can be smelted to
reclaim copper or sold, or chopped and used as the
filler in many applications
Table 3 above shows processing methods for the reclamation of the valuable products (Telmer,
2016)
The process steps can be discussed briefly as follows:
Presorting: complete PWBs are sent to the pilot plant of ATMI. There is no grinding, shredding
and burning the PWBs.
Disolder: PWBs cycle through the process of desoldering which takes around five to twenty
minutes at thirty-five to forty degrees Celsius. The chemistry of disordering’s selectivity enables
copper, base materials and gold to be left on the board, while the chip which is disoldered
uncouple from the PWB and collected in the bin.
Gold leaching: PWBs that are disoldered then proceed through the process of gold leaching and
takes around 10 minutes and lea than thirty degrees Celsius. After the chemistry is flooded with
gold, it is driven to the tool of electroplating to extract gold from the chemistry. Gold is them
plated on the cathode of the carbon, and then removed from the cathode carbon and melted into
bars. The gold bars and fiberglass board are the output of the process (Söderström, 2012).
ATMI is presently using the system of eVOLVTM to process PWBs at the pilot plant. The pilot
plant processes around two hundred pounds of PWBs in every hour, with the capability of four
Component Method of processing
Gold Reclaimed in the process of leaching gold and
melted in the gold bar
Solder Reclaimed during the process of desoldering
Chips Reclaimed in the process of desoldering. the chips
of operation can be sold for reuse or the precious
metal like silver, gold, and palladium are extracted
from the chip
Bare fibreglass board Remained after the process. can be smelted to
reclaim copper or sold, or chopped and used as the
filler in many applications
Table 3 above shows processing methods for the reclamation of the valuable products (Telmer,
2016)
The process steps can be discussed briefly as follows:
Presorting: complete PWBs are sent to the pilot plant of ATMI. There is no grinding, shredding
and burning the PWBs.
Disolder: PWBs cycle through the process of desoldering which takes around five to twenty
minutes at thirty-five to forty degrees Celsius. The chemistry of disordering’s selectivity enables
copper, base materials and gold to be left on the board, while the chip which is disoldered
uncouple from the PWB and collected in the bin.
Gold leaching: PWBs that are disoldered then proceed through the process of gold leaching and
takes around 10 minutes and lea than thirty degrees Celsius. After the chemistry is flooded with
gold, it is driven to the tool of electroplating to extract gold from the chemistry. Gold is them
plated on the cathode of the carbon, and then removed from the cathode carbon and melted into
bars. The gold bars and fiberglass board are the output of the process (Söderström, 2012).
ATMI is presently using the system of eVOLVTM to process PWBs at the pilot plant. The pilot
plant processes around two hundred pounds of PWBs in every hour, with the capability of four
Secure Best Marks with AI Grader
Need help grading? Try our AI Grader for instant feedback on your assignments.

Mobile E-Waste Processing Facility 17
hundred pounds in every hour. The procedure is automated completely and comprises the system
of the conveyor to move the board through its chemical process. The solitary waste that is
produced in the process is around two hundred gallons of wastewater that are treated every week
and no solid is produced as an outcome of the procedure of e VOLV. The process of leaching
gold is done roughly five hours every day (Swan, 2013).
The license of ATMI model is structured such that the chemistries’’ specifics are not disclosed.
The ATMI supplies the chemistries with the licenses and ATMI personnel to run the process. By
providing the personnel of ATMI, ATMI is able to pledge the effectiveness of the systems and
make sure that technologies are not disclosed and received a royalty based on the percentage of
the recovered component. There are roughly thirty to fifty pounds of chip in one hundred pounds
of RAMs and hence chips recovery is the important component of the process of electronic waste
recycling (Sadiki, 2012)
Detailed designs for the integrated mobile recycling plants
A movable plant for demonstration has been constructed in the container truck and engaged for
the treating of residue of electronic wastes using the process of hydrometallurgy. The
implementation and practices from the field plants to portable plants help in solving the problems
of electronic wastes by recovering resources and improving the environmental ecology. Field
plants normally take a large space available in small cities and countries, to solve the issues, the
integrated mobile plant will be designed (Schüler, 2010).
To meet the functions of treatment and collection, the preceding accomplishments are adapted to
the process of recycling electronic waste and designed an integrated mobile plant of recycling
suitable in mall cities and countries. In the requirement of compactness and mobility, huge
hundred pounds in every hour. The procedure is automated completely and comprises the system
of the conveyor to move the board through its chemical process. The solitary waste that is
produced in the process is around two hundred gallons of wastewater that are treated every week
and no solid is produced as an outcome of the procedure of e VOLV. The process of leaching
gold is done roughly five hours every day (Swan, 2013).
The license of ATMI model is structured such that the chemistries’’ specifics are not disclosed.
The ATMI supplies the chemistries with the licenses and ATMI personnel to run the process. By
providing the personnel of ATMI, ATMI is able to pledge the effectiveness of the systems and
make sure that technologies are not disclosed and received a royalty based on the percentage of
the recovered component. There are roughly thirty to fifty pounds of chip in one hundred pounds
of RAMs and hence chips recovery is the important component of the process of electronic waste
recycling (Sadiki, 2012)
Detailed designs for the integrated mobile recycling plants
A movable plant for demonstration has been constructed in the container truck and engaged for
the treating of residue of electronic wastes using the process of hydrometallurgy. The
implementation and practices from the field plants to portable plants help in solving the problems
of electronic wastes by recovering resources and improving the environmental ecology. Field
plants normally take a large space available in small cities and countries, to solve the issues, the
integrated mobile plant will be designed (Schüler, 2010).
To meet the functions of treatment and collection, the preceding accomplishments are adapted to
the process of recycling electronic waste and designed an integrated mobile plant of recycling
suitable in mall cities and countries. In the requirement of compactness and mobility, huge
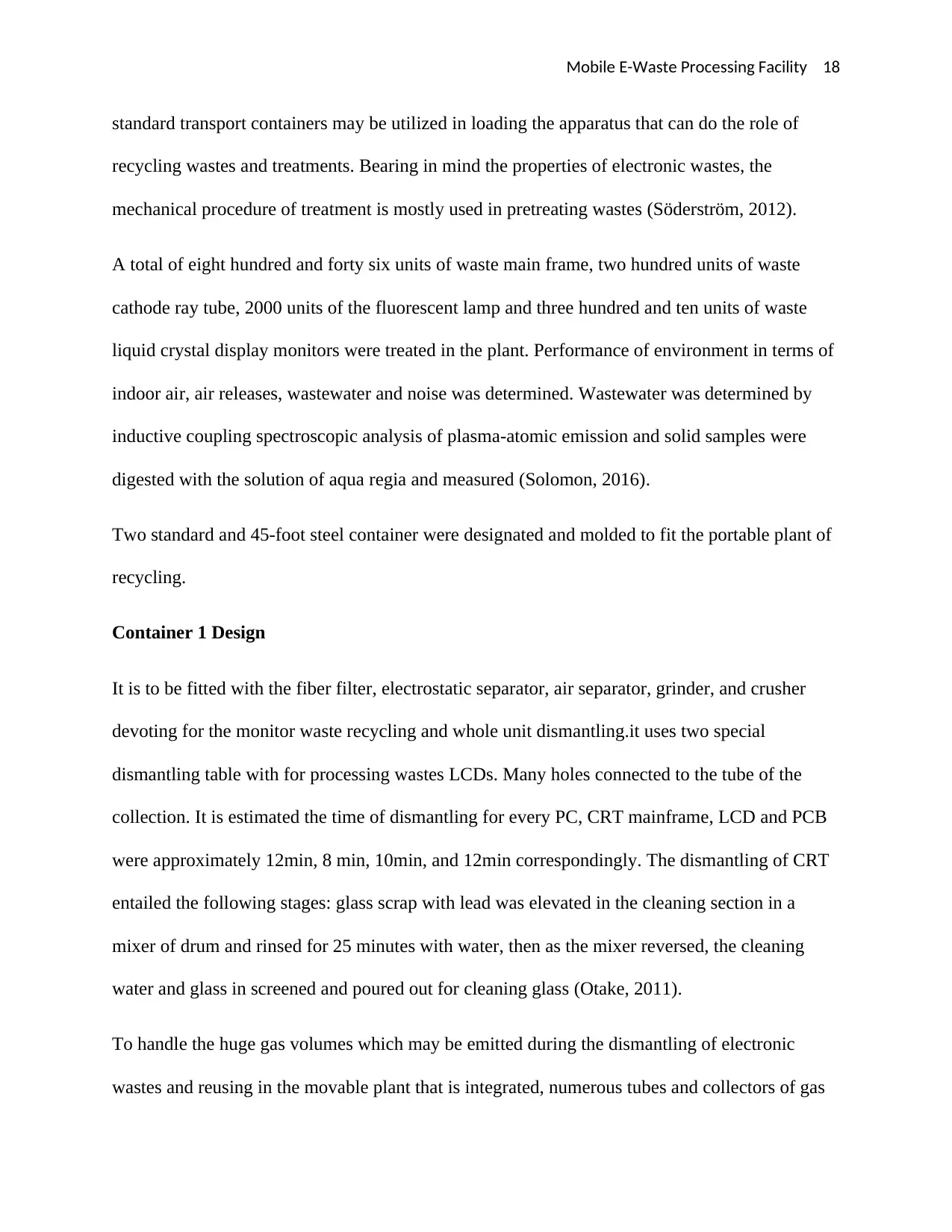
Mobile E-Waste Processing Facility 18
standard transport containers may be utilized in loading the apparatus that can do the role of
recycling wastes and treatments. Bearing in mind the properties of electronic wastes, the
mechanical procedure of treatment is mostly used in pretreating wastes (Söderström, 2012).
A total of eight hundred and forty six units of waste main frame, two hundred units of waste
cathode ray tube, 2000 units of the fluorescent lamp and three hundred and ten units of waste
liquid crystal display monitors were treated in the plant. Performance of environment in terms of
indoor air, air releases, wastewater and noise was determined. Wastewater was determined by
inductive coupling spectroscopic analysis of plasma-atomic emission and solid samples were
digested with the solution of aqua regia and measured (Solomon, 2016).
Two standard and 45-foot steel container were designated and molded to fit the portable plant of
recycling.
Container 1 Design
It is to be fitted with the fiber filter, electrostatic separator, air separator, grinder, and crusher
devoting for the monitor waste recycling and whole unit dismantling.it uses two special
dismantling table with for processing wastes LCDs. Many holes connected to the tube of the
collection. It is estimated the time of dismantling for every PC, CRT mainframe, LCD and PCB
were approximately 12min, 8 min, 10min, and 12min correspondingly. The dismantling of CRT
entailed the following stages: glass scrap with lead was elevated in the cleaning section in a
mixer of drum and rinsed for 25 minutes with water, then as the mixer reversed, the cleaning
water and glass in screened and poured out for cleaning glass (Otake, 2011).
To handle the huge gas volumes which may be emitted during the dismantling of electronic
wastes and reusing in the movable plant that is integrated, numerous tubes and collectors of gas
standard transport containers may be utilized in loading the apparatus that can do the role of
recycling wastes and treatments. Bearing in mind the properties of electronic wastes, the
mechanical procedure of treatment is mostly used in pretreating wastes (Söderström, 2012).
A total of eight hundred and forty six units of waste main frame, two hundred units of waste
cathode ray tube, 2000 units of the fluorescent lamp and three hundred and ten units of waste
liquid crystal display monitors were treated in the plant. Performance of environment in terms of
indoor air, air releases, wastewater and noise was determined. Wastewater was determined by
inductive coupling spectroscopic analysis of plasma-atomic emission and solid samples were
digested with the solution of aqua regia and measured (Solomon, 2016).
Two standard and 45-foot steel container were designated and molded to fit the portable plant of
recycling.
Container 1 Design
It is to be fitted with the fiber filter, electrostatic separator, air separator, grinder, and crusher
devoting for the monitor waste recycling and whole unit dismantling.it uses two special
dismantling table with for processing wastes LCDs. Many holes connected to the tube of the
collection. It is estimated the time of dismantling for every PC, CRT mainframe, LCD and PCB
were approximately 12min, 8 min, 10min, and 12min correspondingly. The dismantling of CRT
entailed the following stages: glass scrap with lead was elevated in the cleaning section in a
mixer of drum and rinsed for 25 minutes with water, then as the mixer reversed, the cleaning
water and glass in screened and poured out for cleaning glass (Otake, 2011).
To handle the huge gas volumes which may be emitted during the dismantling of electronic
wastes and reusing in the movable plant that is integrated, numerous tubes and collectors of gas
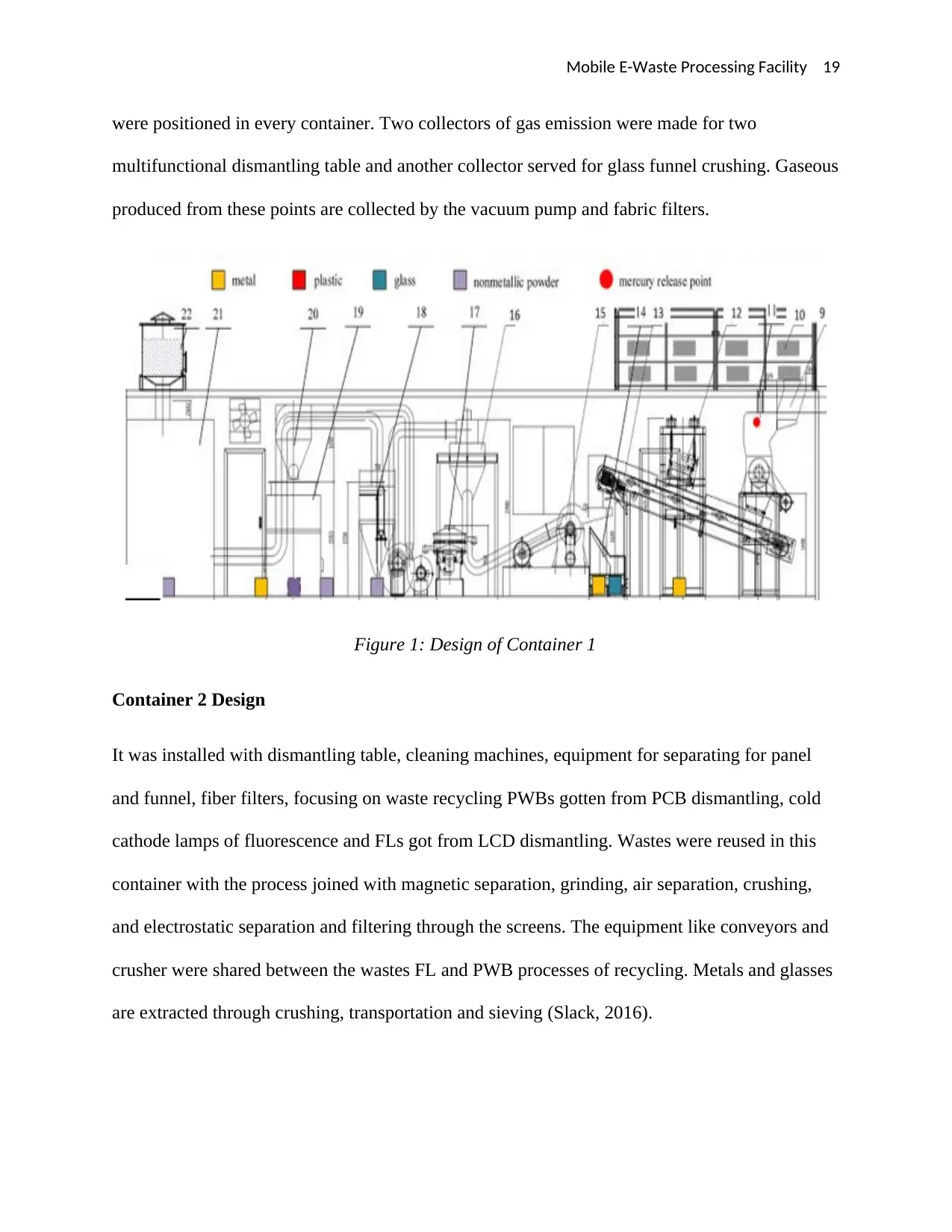
Mobile E-Waste Processing Facility 19
were positioned in every container. Two collectors of gas emission were made for two
multifunctional dismantling table and another collector served for glass funnel crushing. Gaseous
produced from these points are collected by the vacuum pump and fabric filters.
Figure 1: Design of Container 1
Container 2 Design
It was installed with dismantling table, cleaning machines, equipment for separating for panel
and funnel, fiber filters, focusing on waste recycling PWBs gotten from PCB dismantling, cold
cathode lamps of fluorescence and FLs got from LCD dismantling. Wastes were reused in this
container with the process joined with magnetic separation, grinding, air separation, crushing,
and electrostatic separation and filtering through the screens. The equipment like conveyors and
crusher were shared between the wastes FL and PWB processes of recycling. Metals and glasses
are extracted through crushing, transportation and sieving (Slack, 2016).
were positioned in every container. Two collectors of gas emission were made for two
multifunctional dismantling table and another collector served for glass funnel crushing. Gaseous
produced from these points are collected by the vacuum pump and fabric filters.
Figure 1: Design of Container 1
Container 2 Design
It was installed with dismantling table, cleaning machines, equipment for separating for panel
and funnel, fiber filters, focusing on waste recycling PWBs gotten from PCB dismantling, cold
cathode lamps of fluorescence and FLs got from LCD dismantling. Wastes were reused in this
container with the process joined with magnetic separation, grinding, air separation, crushing,
and electrostatic separation and filtering through the screens. The equipment like conveyors and
crusher were shared between the wastes FL and PWB processes of recycling. Metals and glasses
are extracted through crushing, transportation and sieving (Slack, 2016).
Paraphrase This Document
Need a fresh take? Get an instant paraphrase of this document with our AI Paraphraser
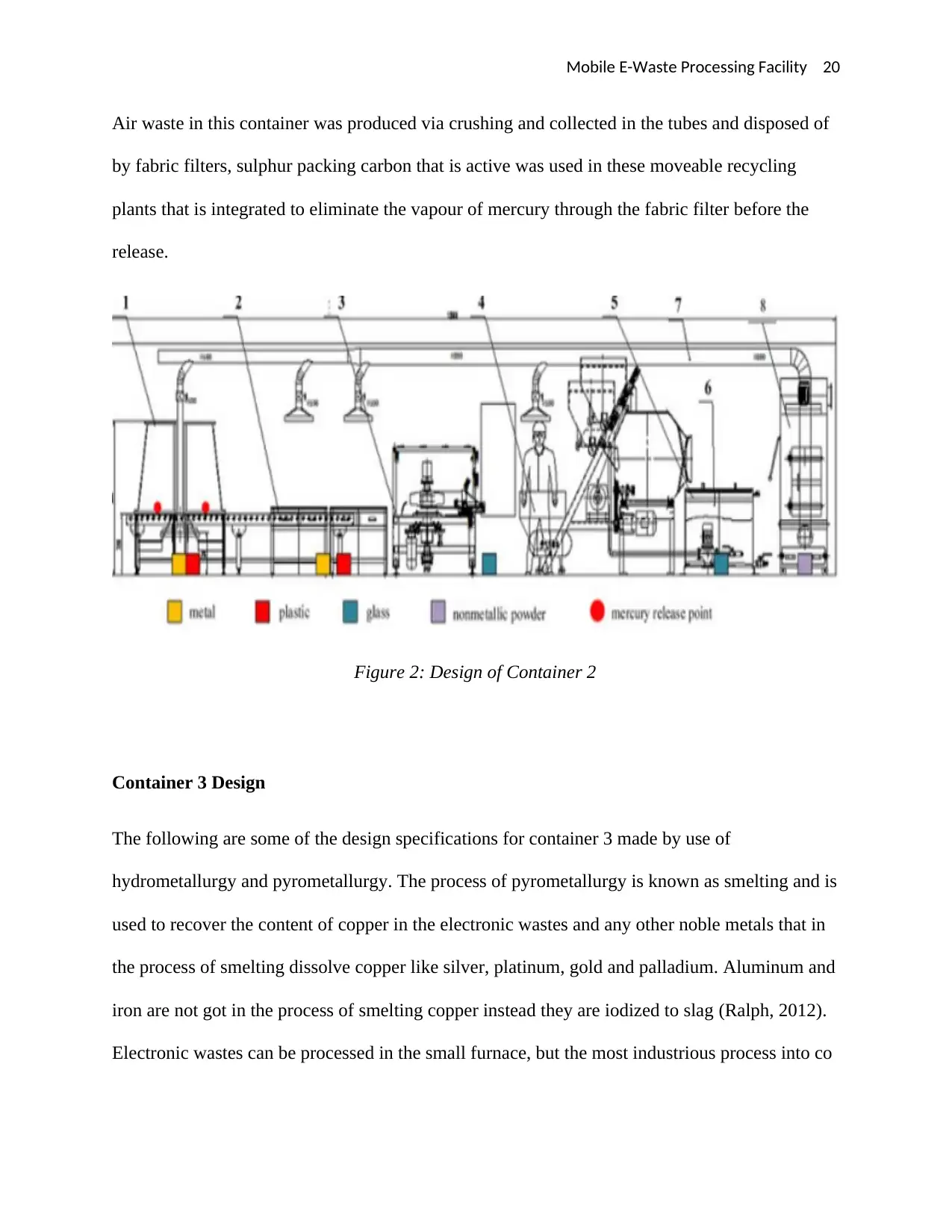
Mobile E-Waste Processing Facility 20
Air waste in this container was produced via crushing and collected in the tubes and disposed of
by fabric filters, sulphur packing carbon that is active was used in these moveable recycling
plants that is integrated to eliminate the vapour of mercury through the fabric filter before the
release.
Figure 2: Design of Container 2
Container 3 Design
The following are some of the design specifications for container 3 made by use of
hydrometallurgy and pyrometallurgy. The process of pyrometallurgy is known as smelting and is
used to recover the content of copper in the electronic wastes and any other noble metals that in
the process of smelting dissolve copper like silver, platinum, gold and palladium. Aluminum and
iron are not got in the process of smelting copper instead they are iodized to slag (Ralph, 2012).
Electronic wastes can be processed in the small furnace, but the most industrious process into co
Air waste in this container was produced via crushing and collected in the tubes and disposed of
by fabric filters, sulphur packing carbon that is active was used in these moveable recycling
plants that is integrated to eliminate the vapour of mercury through the fabric filter before the
release.
Figure 2: Design of Container 2
Container 3 Design
The following are some of the design specifications for container 3 made by use of
hydrometallurgy and pyrometallurgy. The process of pyrometallurgy is known as smelting and is
used to recover the content of copper in the electronic wastes and any other noble metals that in
the process of smelting dissolve copper like silver, platinum, gold and palladium. Aluminum and
iron are not got in the process of smelting copper instead they are iodized to slag (Ralph, 2012).
Electronic wastes can be processed in the small furnace, but the most industrious process into co
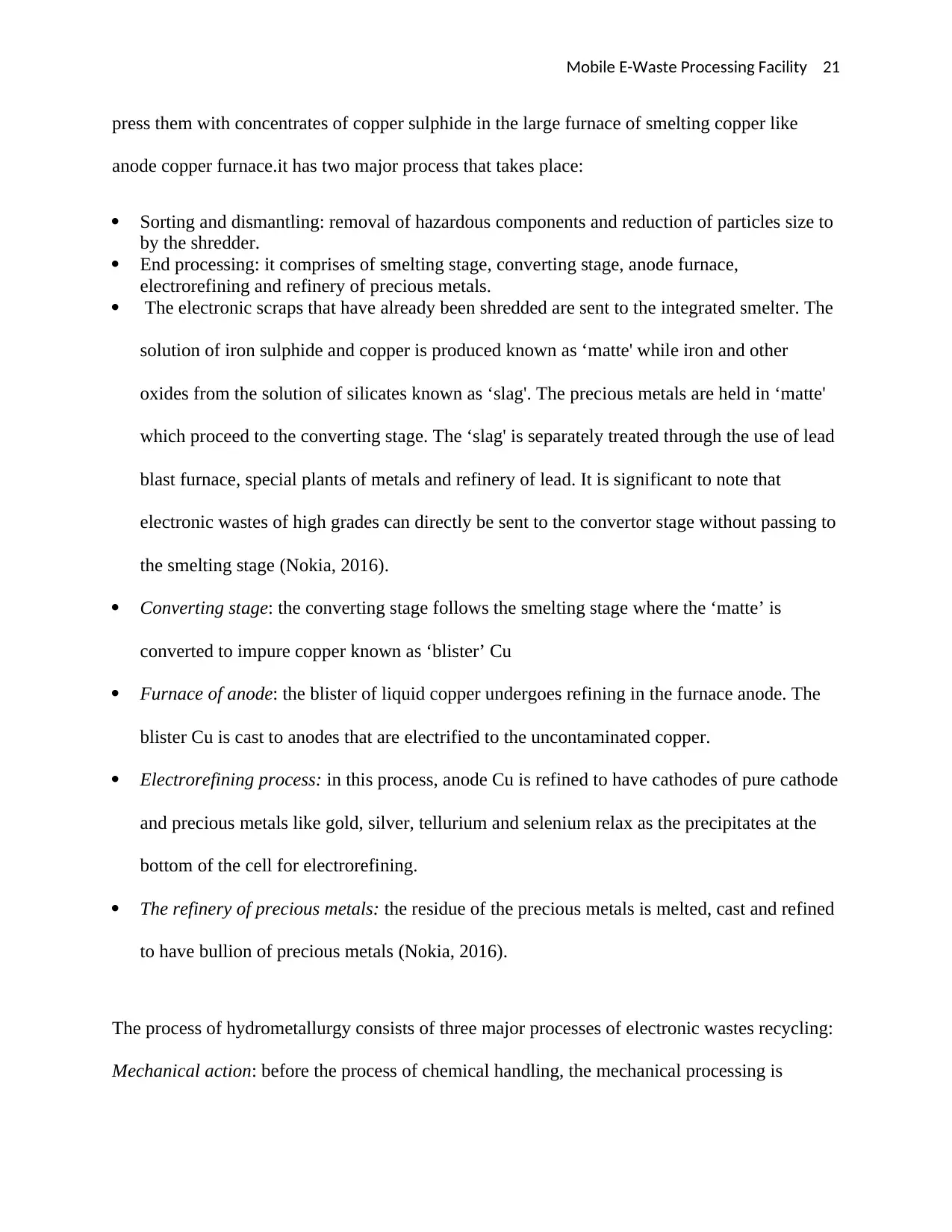
Mobile E-Waste Processing Facility 21
press them with concentrates of copper sulphide in the large furnace of smelting copper like
anode copper furnace.it has two major process that takes place:
Sorting and dismantling: removal of hazardous components and reduction of particles size to
by the shredder.
End processing: it comprises of smelting stage, converting stage, anode furnace,
electrorefining and refinery of precious metals.
The electronic scraps that have already been shredded are sent to the integrated smelter. The
solution of iron sulphide and copper is produced known as ‘matte' while iron and other
oxides from the solution of silicates known as ‘slag'. The precious metals are held in ‘matte'
which proceed to the converting stage. The ‘slag' is separately treated through the use of lead
blast furnace, special plants of metals and refinery of lead. It is significant to note that
electronic wastes of high grades can directly be sent to the convertor stage without passing to
the smelting stage (Nokia, 2016).
Converting stage: the converting stage follows the smelting stage where the ‘matte’ is
converted to impure copper known as ‘blister’ Cu
Furnace of anode: the blister of liquid copper undergoes refining in the furnace anode. The
blister Cu is cast to anodes that are electrified to the uncontaminated copper.
Electrorefining process: in this process, anode Cu is refined to have cathodes of pure cathode
and precious metals like gold, silver, tellurium and selenium relax as the precipitates at the
bottom of the cell for electrorefining.
The refinery of precious metals: the residue of the precious metals is melted, cast and refined
to have bullion of precious metals (Nokia, 2016).
The process of hydrometallurgy consists of three major processes of electronic wastes recycling:
Mechanical action: before the process of chemical handling, the mechanical processing is
press them with concentrates of copper sulphide in the large furnace of smelting copper like
anode copper furnace.it has two major process that takes place:
Sorting and dismantling: removal of hazardous components and reduction of particles size to
by the shredder.
End processing: it comprises of smelting stage, converting stage, anode furnace,
electrorefining and refinery of precious metals.
The electronic scraps that have already been shredded are sent to the integrated smelter. The
solution of iron sulphide and copper is produced known as ‘matte' while iron and other
oxides from the solution of silicates known as ‘slag'. The precious metals are held in ‘matte'
which proceed to the converting stage. The ‘slag' is separately treated through the use of lead
blast furnace, special plants of metals and refinery of lead. It is significant to note that
electronic wastes of high grades can directly be sent to the convertor stage without passing to
the smelting stage (Nokia, 2016).
Converting stage: the converting stage follows the smelting stage where the ‘matte’ is
converted to impure copper known as ‘blister’ Cu
Furnace of anode: the blister of liquid copper undergoes refining in the furnace anode. The
blister Cu is cast to anodes that are electrified to the uncontaminated copper.
Electrorefining process: in this process, anode Cu is refined to have cathodes of pure cathode
and precious metals like gold, silver, tellurium and selenium relax as the precipitates at the
bottom of the cell for electrorefining.
The refinery of precious metals: the residue of the precious metals is melted, cast and refined
to have bullion of precious metals (Nokia, 2016).
The process of hydrometallurgy consists of three major processes of electronic wastes recycling:
Mechanical action: before the process of chemical handling, the mechanical processing is
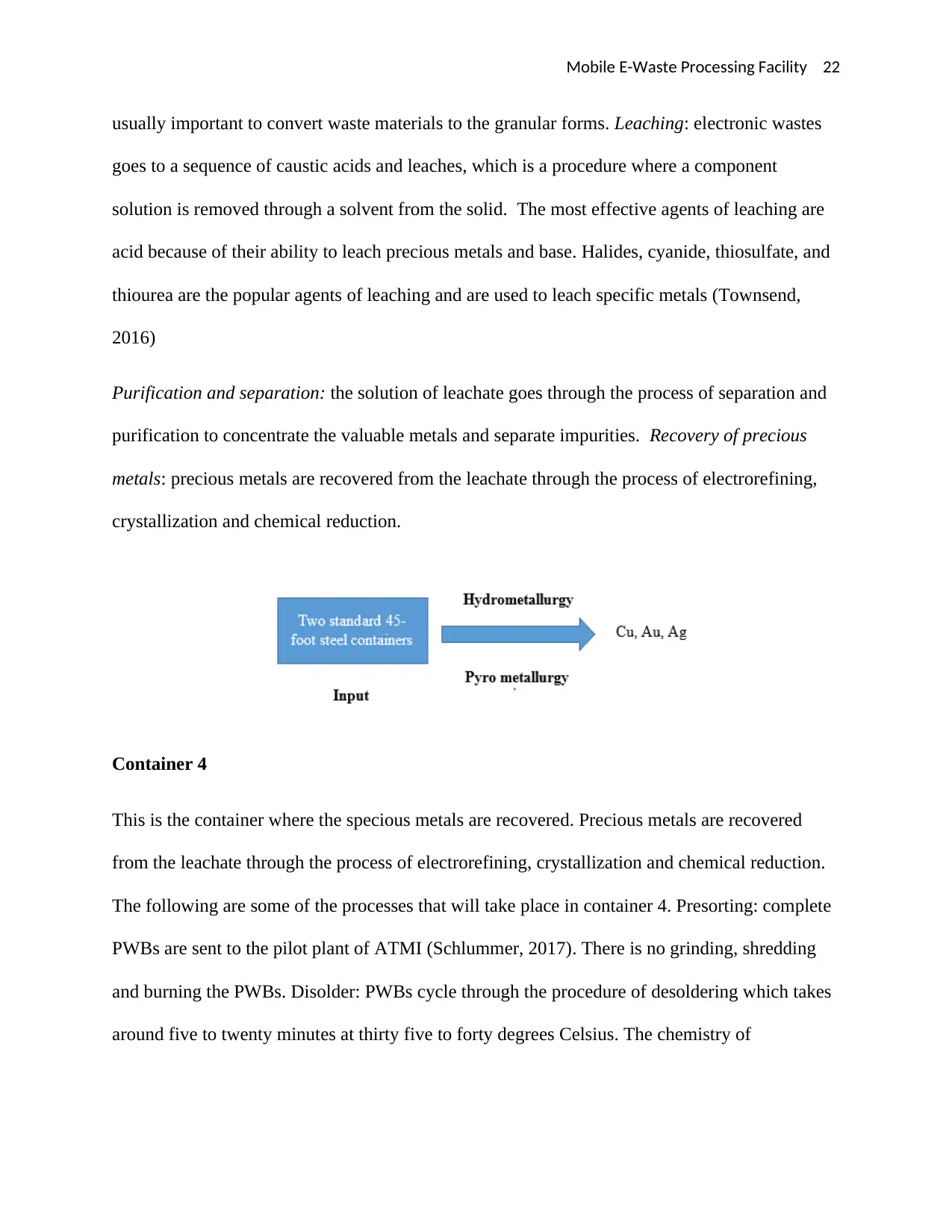
Mobile E-Waste Processing Facility 22
usually important to convert waste materials to the granular forms. Leaching: electronic wastes
goes to a sequence of caustic acids and leaches, which is a procedure where a component
solution is removed through a solvent from the solid. The most effective agents of leaching are
acid because of their ability to leach precious metals and base. Halides, cyanide, thiosulfate, and
thiourea are the popular agents of leaching and are used to leach specific metals (Townsend,
2016)
Purification and separation: the solution of leachate goes through the process of separation and
purification to concentrate the valuable metals and separate impurities. Recovery of precious
metals: precious metals are recovered from the leachate through the process of electrorefining,
crystallization and chemical reduction.
Container 4
This is the container where the specious metals are recovered. Precious metals are recovered
from the leachate through the process of electrorefining, crystallization and chemical reduction.
The following are some of the processes that will take place in container 4. Presorting: complete
PWBs are sent to the pilot plant of ATMI (Schlummer, 2017). There is no grinding, shredding
and burning the PWBs. Disolder: PWBs cycle through the procedure of desoldering which takes
around five to twenty minutes at thirty five to forty degrees Celsius. The chemistry of
usually important to convert waste materials to the granular forms. Leaching: electronic wastes
goes to a sequence of caustic acids and leaches, which is a procedure where a component
solution is removed through a solvent from the solid. The most effective agents of leaching are
acid because of their ability to leach precious metals and base. Halides, cyanide, thiosulfate, and
thiourea are the popular agents of leaching and are used to leach specific metals (Townsend,
2016)
Purification and separation: the solution of leachate goes through the process of separation and
purification to concentrate the valuable metals and separate impurities. Recovery of precious
metals: precious metals are recovered from the leachate through the process of electrorefining,
crystallization and chemical reduction.
Container 4
This is the container where the specious metals are recovered. Precious metals are recovered
from the leachate through the process of electrorefining, crystallization and chemical reduction.
The following are some of the processes that will take place in container 4. Presorting: complete
PWBs are sent to the pilot plant of ATMI (Schlummer, 2017). There is no grinding, shredding
and burning the PWBs. Disolder: PWBs cycle through the procedure of desoldering which takes
around five to twenty minutes at thirty five to forty degrees Celsius. The chemistry of
Secure Best Marks with AI Grader
Need help grading? Try our AI Grader for instant feedback on your assignments.
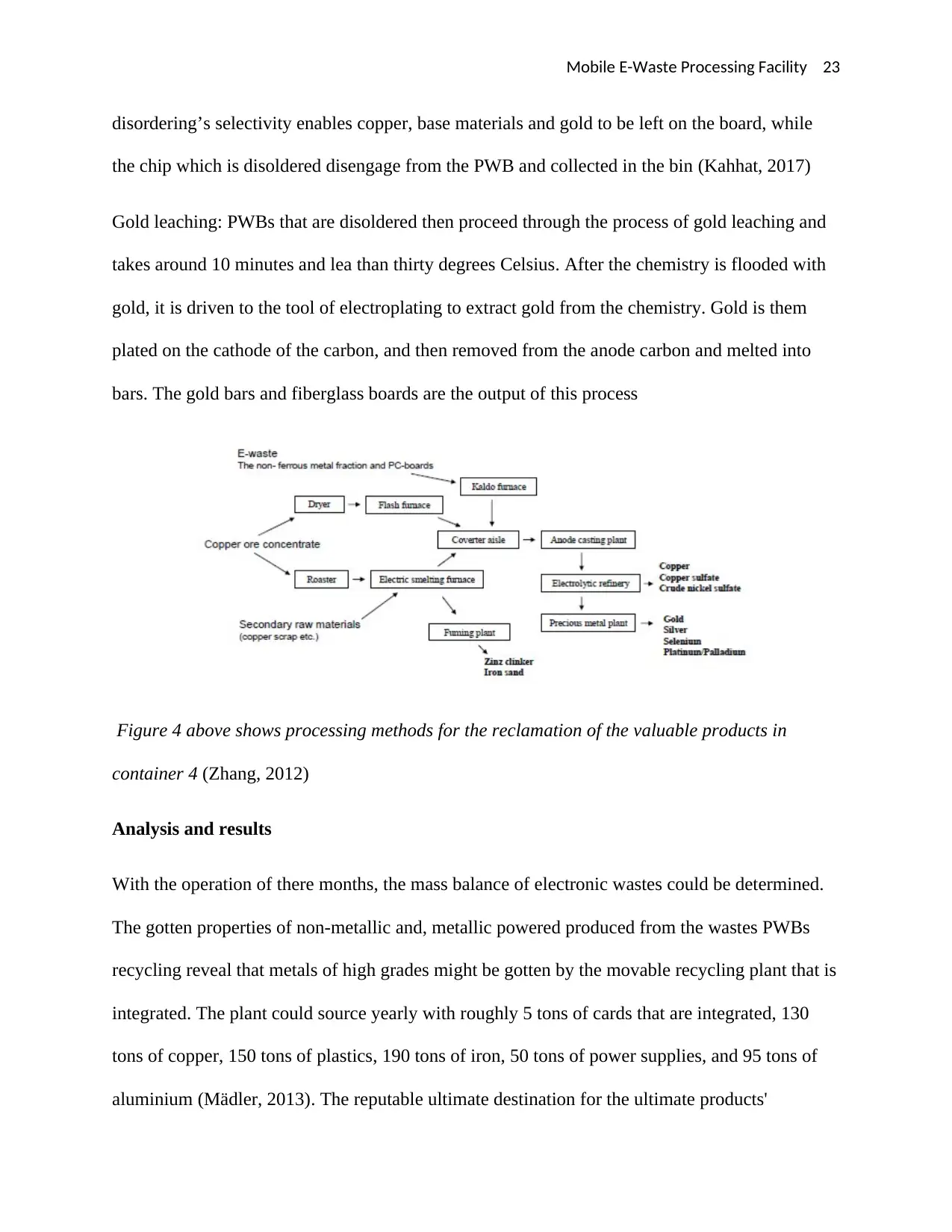
Mobile E-Waste Processing Facility 23
disordering’s selectivity enables copper, base materials and gold to be left on the board, while
the chip which is disoldered disengage from the PWB and collected in the bin (Kahhat, 2017)
Gold leaching: PWBs that are disoldered then proceed through the process of gold leaching and
takes around 10 minutes and lea than thirty degrees Celsius. After the chemistry is flooded with
gold, it is driven to the tool of electroplating to extract gold from the chemistry. Gold is them
plated on the cathode of the carbon, and then removed from the anode carbon and melted into
bars. The gold bars and fiberglass boards are the output of this process
Figure 4 above shows processing methods for the reclamation of the valuable products in
container 4 (Zhang, 2012)
Analysis and results
With the operation of there months, the mass balance of electronic wastes could be determined.
The gotten properties of non-metallic and, metallic powered produced from the wastes PWBs
recycling reveal that metals of high grades might be gotten by the movable recycling plant that is
integrated. The plant could source yearly with roughly 5 tons of cards that are integrated, 130
tons of copper, 150 tons of plastics, 190 tons of iron, 50 tons of power supplies, and 95 tons of
aluminium (Mädler, 2013). The reputable ultimate destination for the ultimate products'
disordering’s selectivity enables copper, base materials and gold to be left on the board, while
the chip which is disoldered disengage from the PWB and collected in the bin (Kahhat, 2017)
Gold leaching: PWBs that are disoldered then proceed through the process of gold leaching and
takes around 10 minutes and lea than thirty degrees Celsius. After the chemistry is flooded with
gold, it is driven to the tool of electroplating to extract gold from the chemistry. Gold is them
plated on the cathode of the carbon, and then removed from the anode carbon and melted into
bars. The gold bars and fiberglass boards are the output of this process
Figure 4 above shows processing methods for the reclamation of the valuable products in
container 4 (Zhang, 2012)
Analysis and results
With the operation of there months, the mass balance of electronic wastes could be determined.
The gotten properties of non-metallic and, metallic powered produced from the wastes PWBs
recycling reveal that metals of high grades might be gotten by the movable recycling plant that is
integrated. The plant could source yearly with roughly 5 tons of cards that are integrated, 130
tons of copper, 150 tons of plastics, 190 tons of iron, 50 tons of power supplies, and 95 tons of
aluminium (Mädler, 2013). The reputable ultimate destination for the ultimate products'
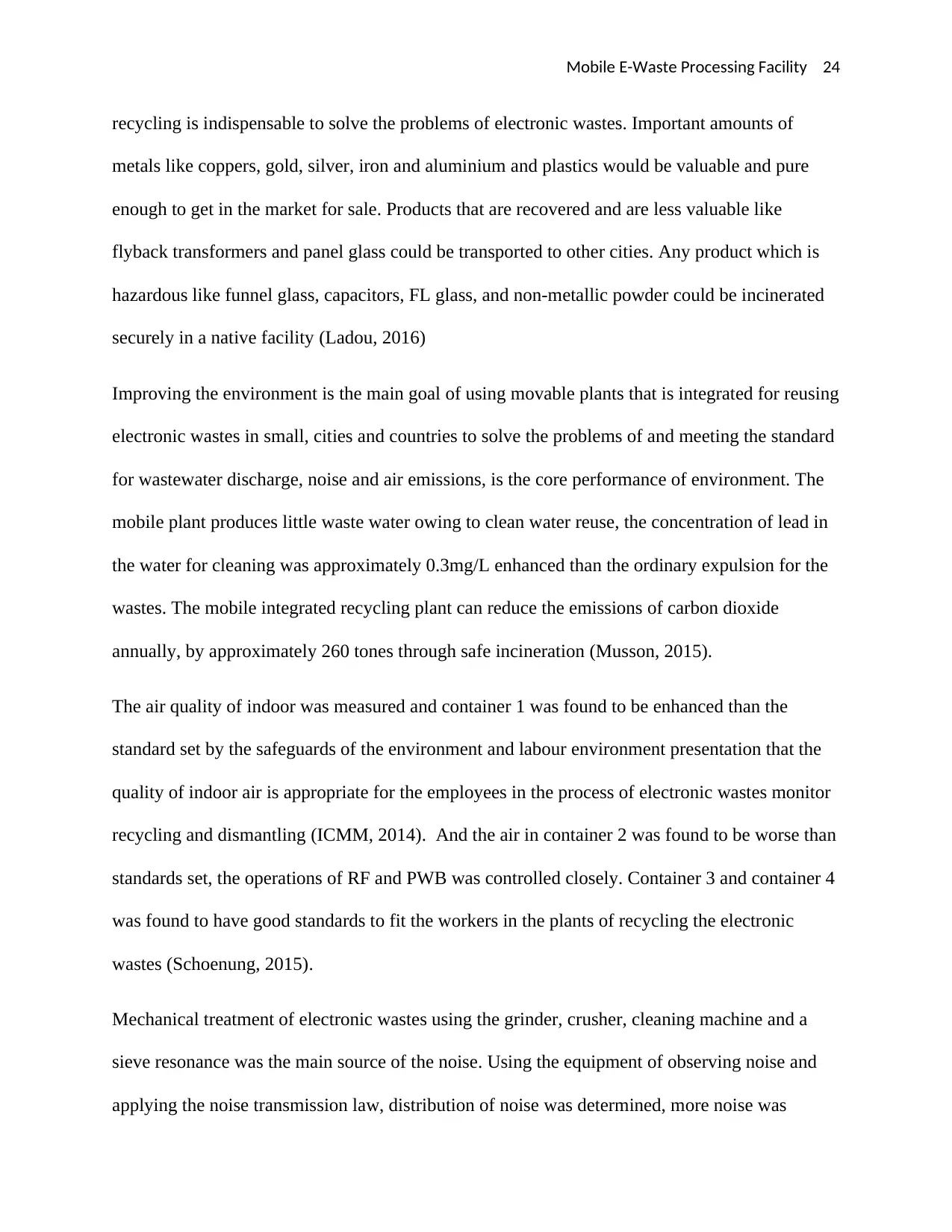
Mobile E-Waste Processing Facility 24
recycling is indispensable to solve the problems of electronic wastes. Important amounts of
metals like coppers, gold, silver, iron and aluminium and plastics would be valuable and pure
enough to get in the market for sale. Products that are recovered and are less valuable like
flyback transformers and panel glass could be transported to other cities. Any product which is
hazardous like funnel glass, capacitors, FL glass, and non-metallic powder could be incinerated
securely in a native facility (Ladou, 2016)
Improving the environment is the main goal of using movable plants that is integrated for reusing
electronic wastes in small, cities and countries to solve the problems of and meeting the standard
for wastewater discharge, noise and air emissions, is the core performance of environment. The
mobile plant produces little waste water owing to clean water reuse, the concentration of lead in
the water for cleaning was approximately 0.3mg/L enhanced than the ordinary expulsion for the
wastes. The mobile integrated recycling plant can reduce the emissions of carbon dioxide
annually, by approximately 260 tones through safe incineration (Musson, 2015).
The air quality of indoor was measured and container 1 was found to be enhanced than the
standard set by the safeguards of the environment and labour environment presentation that the
quality of indoor air is appropriate for the employees in the process of electronic wastes monitor
recycling and dismantling (ICMM, 2014). And the air in container 2 was found to be worse than
standards set, the operations of RF and PWB was controlled closely. Container 3 and container 4
was found to have good standards to fit the workers in the plants of recycling the electronic
wastes (Schoenung, 2015).
Mechanical treatment of electronic wastes using the grinder, crusher, cleaning machine and a
sieve resonance was the main source of the noise. Using the equipment of observing noise and
applying the noise transmission law, distribution of noise was determined, more noise was
recycling is indispensable to solve the problems of electronic wastes. Important amounts of
metals like coppers, gold, silver, iron and aluminium and plastics would be valuable and pure
enough to get in the market for sale. Products that are recovered and are less valuable like
flyback transformers and panel glass could be transported to other cities. Any product which is
hazardous like funnel glass, capacitors, FL glass, and non-metallic powder could be incinerated
securely in a native facility (Ladou, 2016)
Improving the environment is the main goal of using movable plants that is integrated for reusing
electronic wastes in small, cities and countries to solve the problems of and meeting the standard
for wastewater discharge, noise and air emissions, is the core performance of environment. The
mobile plant produces little waste water owing to clean water reuse, the concentration of lead in
the water for cleaning was approximately 0.3mg/L enhanced than the ordinary expulsion for the
wastes. The mobile integrated recycling plant can reduce the emissions of carbon dioxide
annually, by approximately 260 tones through safe incineration (Musson, 2015).
The air quality of indoor was measured and container 1 was found to be enhanced than the
standard set by the safeguards of the environment and labour environment presentation that the
quality of indoor air is appropriate for the employees in the process of electronic wastes monitor
recycling and dismantling (ICMM, 2014). And the air in container 2 was found to be worse than
standards set, the operations of RF and PWB was controlled closely. Container 3 and container 4
was found to have good standards to fit the workers in the plants of recycling the electronic
wastes (Schoenung, 2015).
Mechanical treatment of electronic wastes using the grinder, crusher, cleaning machine and a
sieve resonance was the main source of the noise. Using the equipment of observing noise and
applying the noise transmission law, distribution of noise was determined, more noise was
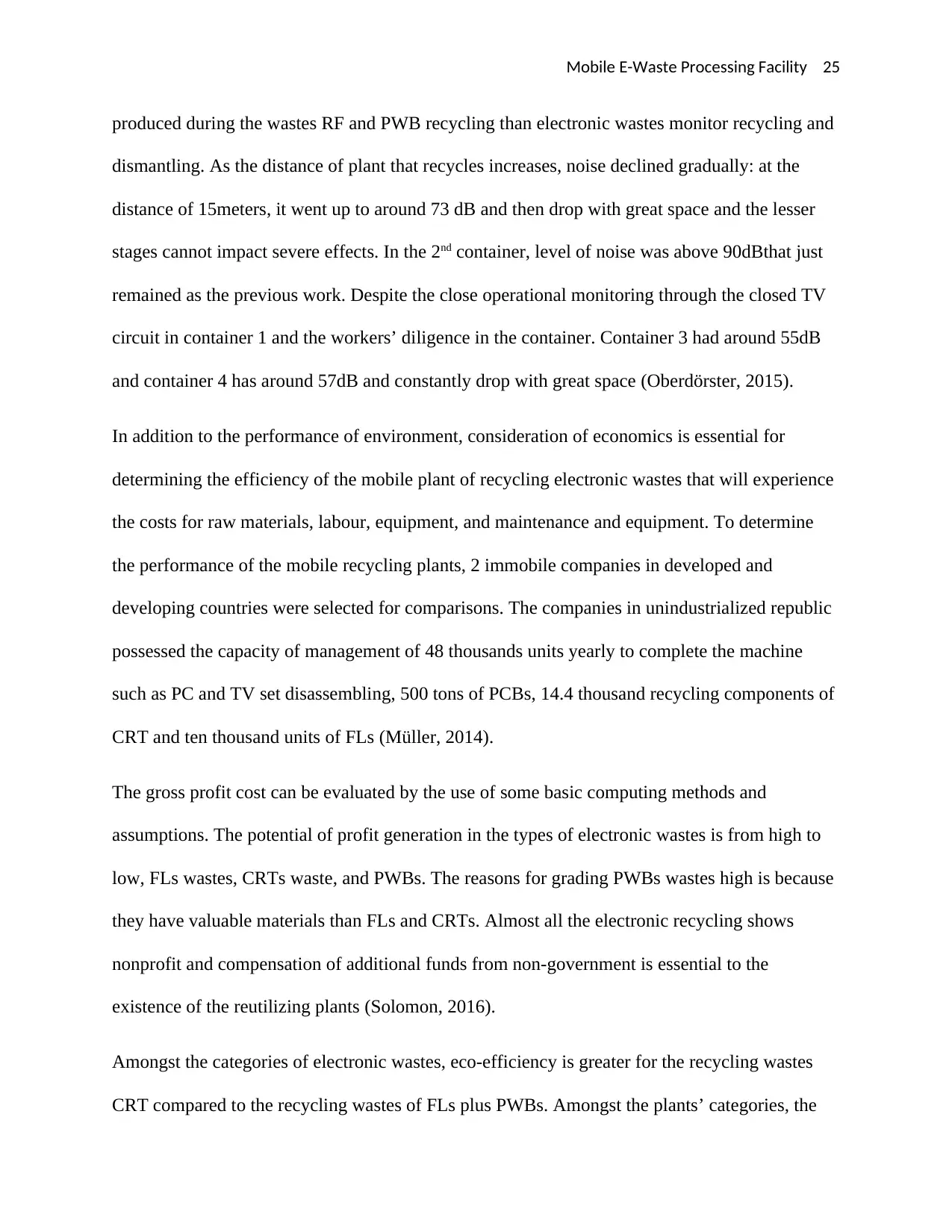
Mobile E-Waste Processing Facility 25
produced during the wastes RF and PWB recycling than electronic wastes monitor recycling and
dismantling. As the distance of plant that recycles increases, noise declined gradually: at the
distance of 15meters, it went up to around 73 dB and then drop with great space and the lesser
stages cannot impact severe effects. In the 2nd container, level of noise was above 90dBthat just
remained as the previous work. Despite the close operational monitoring through the closed TV
circuit in container 1 and the workers’ diligence in the container. Container 3 had around 55dB
and container 4 has around 57dB and constantly drop with great space (Oberdörster, 2015).
In addition to the performance of environment, consideration of economics is essential for
determining the efficiency of the mobile plant of recycling electronic wastes that will experience
the costs for raw materials, labour, equipment, and maintenance and equipment. To determine
the performance of the mobile recycling plants, 2 immobile companies in developed and
developing countries were selected for comparisons. The companies in unindustrialized republic
possessed the capacity of management of 48 thousands units yearly to complete the machine
such as PC and TV set disassembling, 500 tons of PCBs, 14.4 thousand recycling components of
CRT and ten thousand units of FLs (Müller, 2014).
The gross profit cost can be evaluated by the use of some basic computing methods and
assumptions. The potential of profit generation in the types of electronic wastes is from high to
low, FLs wastes, CRTs waste, and PWBs. The reasons for grading PWBs wastes high is because
they have valuable materials than FLs and CRTs. Almost all the electronic recycling shows
nonprofit and compensation of additional funds from non-government is essential to the
existence of the reutilizing plants (Solomon, 2016).
Amongst the categories of electronic wastes, eco-efficiency is greater for the recycling wastes
CRT compared to the recycling wastes of FLs plus PWBs. Amongst the plants’ categories, the
produced during the wastes RF and PWB recycling than electronic wastes monitor recycling and
dismantling. As the distance of plant that recycles increases, noise declined gradually: at the
distance of 15meters, it went up to around 73 dB and then drop with great space and the lesser
stages cannot impact severe effects. In the 2nd container, level of noise was above 90dBthat just
remained as the previous work. Despite the close operational monitoring through the closed TV
circuit in container 1 and the workers’ diligence in the container. Container 3 had around 55dB
and container 4 has around 57dB and constantly drop with great space (Oberdörster, 2015).
In addition to the performance of environment, consideration of economics is essential for
determining the efficiency of the mobile plant of recycling electronic wastes that will experience
the costs for raw materials, labour, equipment, and maintenance and equipment. To determine
the performance of the mobile recycling plants, 2 immobile companies in developed and
developing countries were selected for comparisons. The companies in unindustrialized republic
possessed the capacity of management of 48 thousands units yearly to complete the machine
such as PC and TV set disassembling, 500 tons of PCBs, 14.4 thousand recycling components of
CRT and ten thousand units of FLs (Müller, 2014).
The gross profit cost can be evaluated by the use of some basic computing methods and
assumptions. The potential of profit generation in the types of electronic wastes is from high to
low, FLs wastes, CRTs waste, and PWBs. The reasons for grading PWBs wastes high is because
they have valuable materials than FLs and CRTs. Almost all the electronic recycling shows
nonprofit and compensation of additional funds from non-government is essential to the
existence of the reutilizing plants (Solomon, 2016).
Amongst the categories of electronic wastes, eco-efficiency is greater for the recycling wastes
CRT compared to the recycling wastes of FLs plus PWBs. Amongst the plants’ categories, the
Paraphrase This Document
Need a fresh take? Get an instant paraphrase of this document with our AI Paraphraser
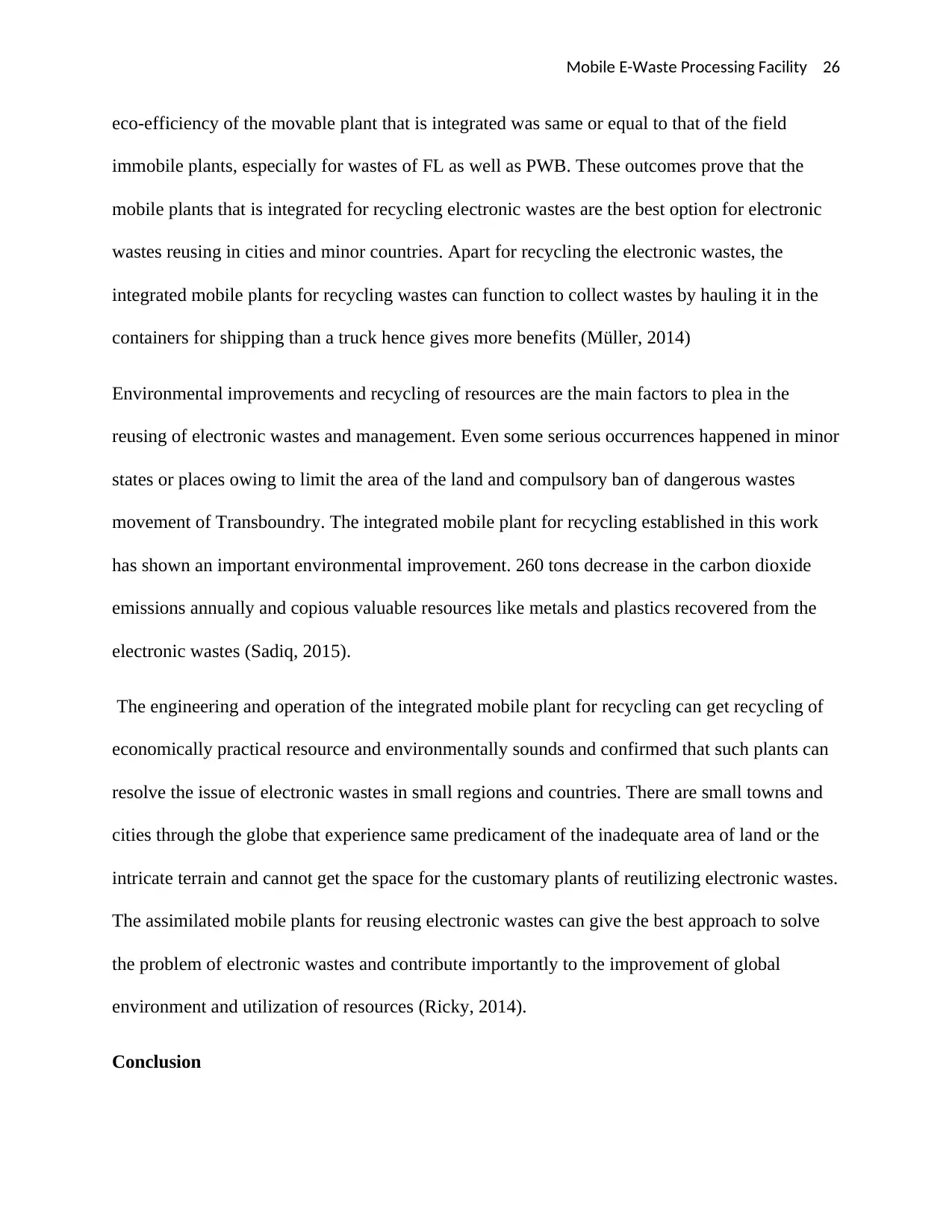
Mobile E-Waste Processing Facility 26
eco-efficiency of the movable plant that is integrated was same or equal to that of the field
immobile plants, especially for wastes of FL as well as PWB. These outcomes prove that the
mobile plants that is integrated for recycling electronic wastes are the best option for electronic
wastes reusing in cities and minor countries. Apart for recycling the electronic wastes, the
integrated mobile plants for recycling wastes can function to collect wastes by hauling it in the
containers for shipping than a truck hence gives more benefits (Müller, 2014)
Environmental improvements and recycling of resources are the main factors to plea in the
reusing of electronic wastes and management. Even some serious occurrences happened in minor
states or places owing to limit the area of the land and compulsory ban of dangerous wastes
movement of Transboundry. The integrated mobile plant for recycling established in this work
has shown an important environmental improvement. 260 tons decrease in the carbon dioxide
emissions annually and copious valuable resources like metals and plastics recovered from the
electronic wastes (Sadiq, 2015).
The engineering and operation of the integrated mobile plant for recycling can get recycling of
economically practical resource and environmentally sounds and confirmed that such plants can
resolve the issue of electronic wastes in small regions and countries. There are small towns and
cities through the globe that experience same predicament of the inadequate area of land or the
intricate terrain and cannot get the space for the customary plants of reutilizing electronic wastes.
The assimilated mobile plants for reusing electronic wastes can give the best approach to solve
the problem of electronic wastes and contribute importantly to the improvement of global
environment and utilization of resources (Ricky, 2014).
Conclusion
eco-efficiency of the movable plant that is integrated was same or equal to that of the field
immobile plants, especially for wastes of FL as well as PWB. These outcomes prove that the
mobile plants that is integrated for recycling electronic wastes are the best option for electronic
wastes reusing in cities and minor countries. Apart for recycling the electronic wastes, the
integrated mobile plants for recycling wastes can function to collect wastes by hauling it in the
containers for shipping than a truck hence gives more benefits (Müller, 2014)
Environmental improvements and recycling of resources are the main factors to plea in the
reusing of electronic wastes and management. Even some serious occurrences happened in minor
states or places owing to limit the area of the land and compulsory ban of dangerous wastes
movement of Transboundry. The integrated mobile plant for recycling established in this work
has shown an important environmental improvement. 260 tons decrease in the carbon dioxide
emissions annually and copious valuable resources like metals and plastics recovered from the
electronic wastes (Sadiq, 2015).
The engineering and operation of the integrated mobile plant for recycling can get recycling of
economically practical resource and environmentally sounds and confirmed that such plants can
resolve the issue of electronic wastes in small regions and countries. There are small towns and
cities through the globe that experience same predicament of the inadequate area of land or the
intricate terrain and cannot get the space for the customary plants of reutilizing electronic wastes.
The assimilated mobile plants for reusing electronic wastes can give the best approach to solve
the problem of electronic wastes and contribute importantly to the improvement of global
environment and utilization of resources (Ricky, 2014).
Conclusion
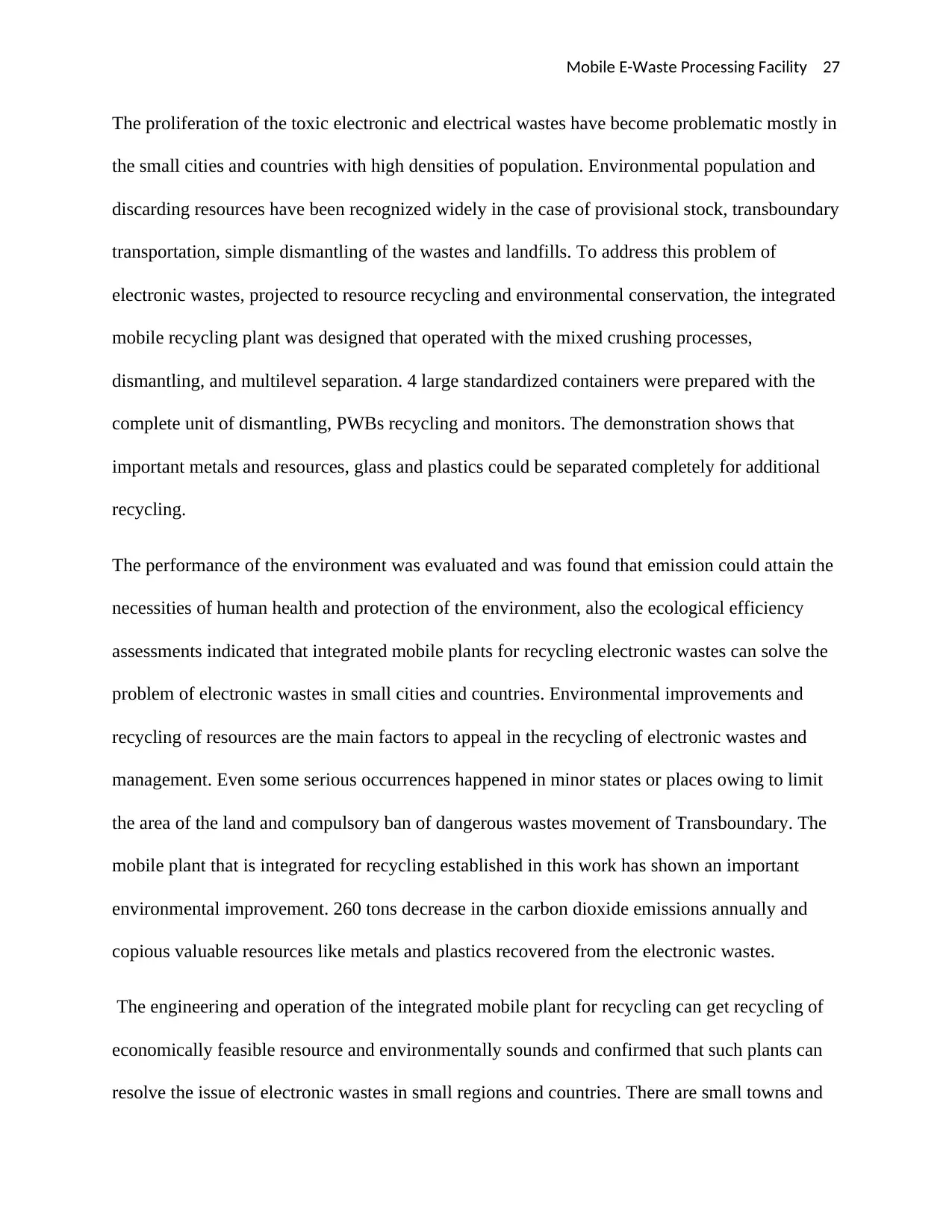
Mobile E-Waste Processing Facility 27
The proliferation of the toxic electronic and electrical wastes have become problematic mostly in
the small cities and countries with high densities of population. Environmental population and
discarding resources have been recognized widely in the case of provisional stock, transboundary
transportation, simple dismantling of the wastes and landfills. To address this problem of
electronic wastes, projected to resource recycling and environmental conservation, the integrated
mobile recycling plant was designed that operated with the mixed crushing processes,
dismantling, and multilevel separation. 4 large standardized containers were prepared with the
complete unit of dismantling, PWBs recycling and monitors. The demonstration shows that
important metals and resources, glass and plastics could be separated completely for additional
recycling.
The performance of the environment was evaluated and was found that emission could attain the
necessities of human health and protection of the environment, also the ecological efficiency
assessments indicated that integrated mobile plants for recycling electronic wastes can solve the
problem of electronic wastes in small cities and countries. Environmental improvements and
recycling of resources are the main factors to appeal in the recycling of electronic wastes and
management. Even some serious occurrences happened in minor states or places owing to limit
the area of the land and compulsory ban of dangerous wastes movement of Transboundary. The
mobile plant that is integrated for recycling established in this work has shown an important
environmental improvement. 260 tons decrease in the carbon dioxide emissions annually and
copious valuable resources like metals and plastics recovered from the electronic wastes.
The engineering and operation of the integrated mobile plant for recycling can get recycling of
economically feasible resource and environmentally sounds and confirmed that such plants can
resolve the issue of electronic wastes in small regions and countries. There are small towns and
The proliferation of the toxic electronic and electrical wastes have become problematic mostly in
the small cities and countries with high densities of population. Environmental population and
discarding resources have been recognized widely in the case of provisional stock, transboundary
transportation, simple dismantling of the wastes and landfills. To address this problem of
electronic wastes, projected to resource recycling and environmental conservation, the integrated
mobile recycling plant was designed that operated with the mixed crushing processes,
dismantling, and multilevel separation. 4 large standardized containers were prepared with the
complete unit of dismantling, PWBs recycling and monitors. The demonstration shows that
important metals and resources, glass and plastics could be separated completely for additional
recycling.
The performance of the environment was evaluated and was found that emission could attain the
necessities of human health and protection of the environment, also the ecological efficiency
assessments indicated that integrated mobile plants for recycling electronic wastes can solve the
problem of electronic wastes in small cities and countries. Environmental improvements and
recycling of resources are the main factors to appeal in the recycling of electronic wastes and
management. Even some serious occurrences happened in minor states or places owing to limit
the area of the land and compulsory ban of dangerous wastes movement of Transboundary. The
mobile plant that is integrated for recycling established in this work has shown an important
environmental improvement. 260 tons decrease in the carbon dioxide emissions annually and
copious valuable resources like metals and plastics recovered from the electronic wastes.
The engineering and operation of the integrated mobile plant for recycling can get recycling of
economically feasible resource and environmentally sounds and confirmed that such plants can
resolve the issue of electronic wastes in small regions and countries. There are small towns and
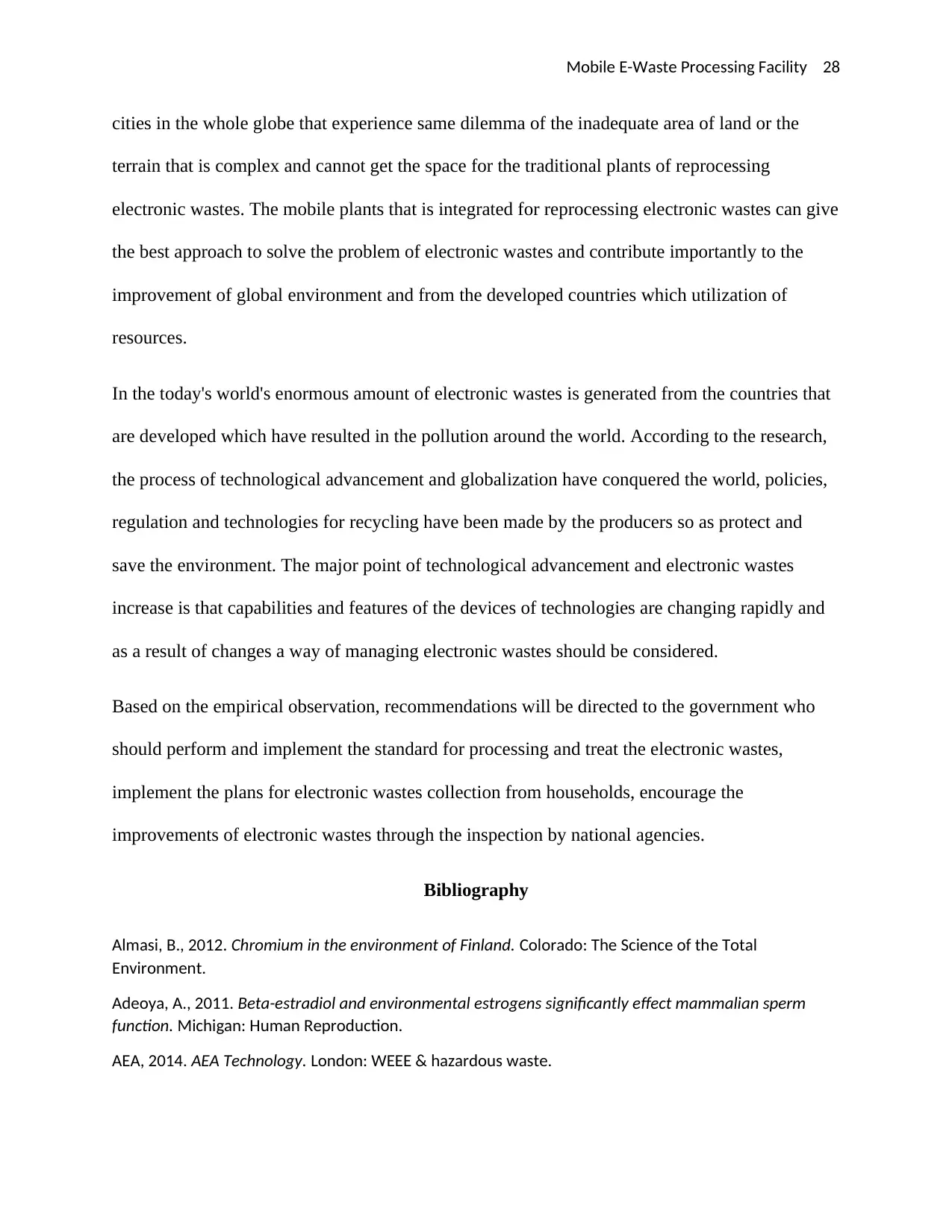
Mobile E-Waste Processing Facility 28
cities in the whole globe that experience same dilemma of the inadequate area of land or the
terrain that is complex and cannot get the space for the traditional plants of reprocessing
electronic wastes. The mobile plants that is integrated for reprocessing electronic wastes can give
the best approach to solve the problem of electronic wastes and contribute importantly to the
improvement of global environment and from the developed countries which utilization of
resources.
In the today's world's enormous amount of electronic wastes is generated from the countries that
are developed which have resulted in the pollution around the world. According to the research,
the process of technological advancement and globalization have conquered the world, policies,
regulation and technologies for recycling have been made by the producers so as protect and
save the environment. The major point of technological advancement and electronic wastes
increase is that capabilities and features of the devices of technologies are changing rapidly and
as a result of changes a way of managing electronic wastes should be considered.
Based on the empirical observation, recommendations will be directed to the government who
should perform and implement the standard for processing and treat the electronic wastes,
implement the plans for electronic wastes collection from households, encourage the
improvements of electronic wastes through the inspection by national agencies.
Bibliography
Almasi, B., 2012. Chromium in the environment of Finland. Colorado: The Science of the Total
Environment.
Adeoya, A., 2011. Beta-estradiol and environmental estrogens significantly effect mammalian sperm
function. Michigan: Human Reproduction.
AEA, 2014. AEA Technology. London: WEEE & hazardous waste.
cities in the whole globe that experience same dilemma of the inadequate area of land or the
terrain that is complex and cannot get the space for the traditional plants of reprocessing
electronic wastes. The mobile plants that is integrated for reprocessing electronic wastes can give
the best approach to solve the problem of electronic wastes and contribute importantly to the
improvement of global environment and from the developed countries which utilization of
resources.
In the today's world's enormous amount of electronic wastes is generated from the countries that
are developed which have resulted in the pollution around the world. According to the research,
the process of technological advancement and globalization have conquered the world, policies,
regulation and technologies for recycling have been made by the producers so as protect and
save the environment. The major point of technological advancement and electronic wastes
increase is that capabilities and features of the devices of technologies are changing rapidly and
as a result of changes a way of managing electronic wastes should be considered.
Based on the empirical observation, recommendations will be directed to the government who
should perform and implement the standard for processing and treat the electronic wastes,
implement the plans for electronic wastes collection from households, encourage the
improvements of electronic wastes through the inspection by national agencies.
Bibliography
Almasi, B., 2012. Chromium in the environment of Finland. Colorado: The Science of the Total
Environment.
Adeoya, A., 2011. Beta-estradiol and environmental estrogens significantly effect mammalian sperm
function. Michigan: Human Reproduction.
AEA, 2014. AEA Technology. London: WEEE & hazardous waste.
Secure Best Marks with AI Grader
Need help grading? Try our AI Grader for instant feedback on your assignments.

Mobile E-Waste Processing Facility 29
Alaee, M., 2017. An overview of commercially used brominated flame retardants, their applications,
their use patterns in different countries. Moscow: Environment International.
Apache, R., 2016. Review on Waste Electrical Electronic Equipment (WEEE). Colorado: United Nations
University.
Allsopp, M., 2010. A review of persistent organic pollutants. Toledo: POPs in the Baltic:.
Allsopp, M., 2013. Disaster: A review of persistent organic pollutants in food. Toledo: Greenpeace.
Allsopp, M., 2015. Environmental and Human Health Concerns in the Processing of Electrical and
Electronic Waste. Paris: Research Laboratories.
Allsopp, M., 2014. State of knowledge of persistent organic pollutants in Europe and the Arctic. Toledo:
Greenpeace.
Andrewes, P., 2012. Plasmid DNA damage caused by stibine and trimethylstibine. Chicago: Toxicology
and Applied Pharmacology.
Antrekowitsch, P., 2010. Metallurgical recycling of electronic scrap. San Antonio: Proceedings of the SPD
congress.
Rasingwa, B., 2012. The formation of dioxins in combustion systems. London: Combustion and flame.
Sampao, R., 2015. Toxicology of selenium. London: Clinical Toxicology.
Canada, R., 2015. Environmentally sound recycling of electronics. Canada: Guidance document from
Electronics Product Stewardship Canada.
Chancerel, P., 2012. Substance flow analysis of the recycling of small waste electrical and electronic
equipment. Berlin: Technische Universität Berlin.
Chancerel, P., 2011. Recycling oriented characterization of small waste electrical and electronic
equipment. Michigan: Waste Management.
Cui, J., 2012. Metallurgical recovery of metals from electronic waste. Mumbai: Journal of Hazardous
Materials.
Cui, J., 2016. Mechanical recycling of waste electrical and electronic equipment. Moscow: Journal of
Hazardous Materials.
Deng, W., 2017. Atmospheric levels and cytotoxicity of PAHs and heavy metals in TSP and PM2.5 at an
electronic waste recycling site in southeast China. China: Atmospheric Environment.
EPA, S., 2011. Persistent Organic Pollutants. Sweeden: A Swedish view of an International Problem.
EPA, S., 2014. Evaluation of human health risks related to the suggested 15 ppb Low POP Content Limit
for PCDD/Fs. Michigan: Low POP Content Limit for PCDD/Fs.
EPA, U., 2011. Approach for addressing dioxin in soil at CERCLA and RCRA sites. Washington: The United
States Environmental Protection Agency.
Alaee, M., 2017. An overview of commercially used brominated flame retardants, their applications,
their use patterns in different countries. Moscow: Environment International.
Apache, R., 2016. Review on Waste Electrical Electronic Equipment (WEEE). Colorado: United Nations
University.
Allsopp, M., 2010. A review of persistent organic pollutants. Toledo: POPs in the Baltic:.
Allsopp, M., 2013. Disaster: A review of persistent organic pollutants in food. Toledo: Greenpeace.
Allsopp, M., 2015. Environmental and Human Health Concerns in the Processing of Electrical and
Electronic Waste. Paris: Research Laboratories.
Allsopp, M., 2014. State of knowledge of persistent organic pollutants in Europe and the Arctic. Toledo:
Greenpeace.
Andrewes, P., 2012. Plasmid DNA damage caused by stibine and trimethylstibine. Chicago: Toxicology
and Applied Pharmacology.
Antrekowitsch, P., 2010. Metallurgical recycling of electronic scrap. San Antonio: Proceedings of the SPD
congress.
Rasingwa, B., 2012. The formation of dioxins in combustion systems. London: Combustion and flame.
Sampao, R., 2015. Toxicology of selenium. London: Clinical Toxicology.
Canada, R., 2015. Environmentally sound recycling of electronics. Canada: Guidance document from
Electronics Product Stewardship Canada.
Chancerel, P., 2012. Substance flow analysis of the recycling of small waste electrical and electronic
equipment. Berlin: Technische Universität Berlin.
Chancerel, P., 2011. Recycling oriented characterization of small waste electrical and electronic
equipment. Michigan: Waste Management.
Cui, J., 2012. Metallurgical recovery of metals from electronic waste. Mumbai: Journal of Hazardous
Materials.
Cui, J., 2016. Mechanical recycling of waste electrical and electronic equipment. Moscow: Journal of
Hazardous Materials.
Deng, W., 2017. Atmospheric levels and cytotoxicity of PAHs and heavy metals in TSP and PM2.5 at an
electronic waste recycling site in southeast China. China: Atmospheric Environment.
EPA, S., 2011. Persistent Organic Pollutants. Sweeden: A Swedish view of an International Problem.
EPA, S., 2014. Evaluation of human health risks related to the suggested 15 ppb Low POP Content Limit
for PCDD/Fs. Michigan: Low POP Content Limit for PCDD/Fs.
EPA, U., 2011. Approach for addressing dioxin in soil at CERCLA and RCRA sites. Washington: The United
States Environmental Protection Agency.
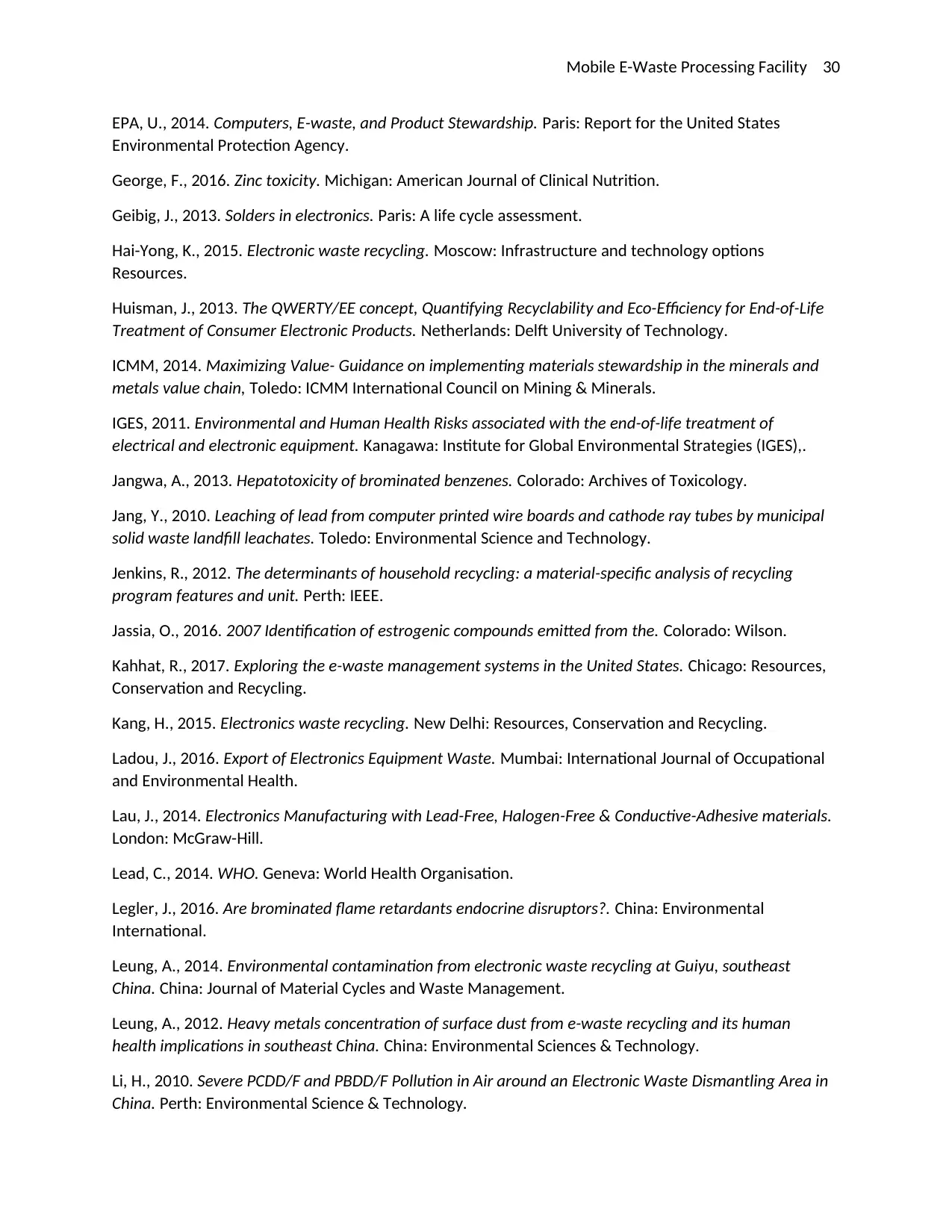
Mobile E-Waste Processing Facility 30
EPA, U., 2014. Computers, E-waste, and Product Stewardship. Paris: Report for the United States
Environmental Protection Agency.
George, F., 2016. Zinc toxicity. Michigan: American Journal of Clinical Nutrition.
Geibig, J., 2013. Solders in electronics. Paris: A life cycle assessment.
Hai-Yong, K., 2015. Electronic waste recycling. Moscow: Infrastructure and technology options
Resources.
Huisman, J., 2013. The QWERTY/EE concept, Quantifying Recyclability and Eco-Efficiency for End-of-Life
Treatment of Consumer Electronic Products. Netherlands: Delft University of Technology.
ICMM, 2014. Maximizing Value- Guidance on implementing materials stewardship in the minerals and
metals value chain, Toledo: ICMM International Council on Mining & Minerals.
IGES, 2011. Environmental and Human Health Risks associated with the end-of-life treatment of
electrical and electronic equipment. Kanagawa: Institute for Global Environmental Strategies (IGES),.
Jangwa, A., 2013. Hepatotoxicity of brominated benzenes. Colorado: Archives of Toxicology.
Jang, Y., 2010. Leaching of lead from computer printed wire boards and cathode ray tubes by municipal
solid waste landfill leachates. Toledo: Environmental Science and Technology.
Jenkins, R., 2012. The determinants of household recycling: a material-specific analysis of recycling
program features and unit. Perth: IEEE.
Jassia, O., 2016. 2007 Identification of estrogenic compounds emitted from the. Colorado: Wilson.
Kahhat, R., 2017. Exploring the e-waste management systems in the United States. Chicago: Resources,
Conservation and Recycling.
Kang, H., 2015. Electronics waste recycling. New Delhi: Resources, Conservation and Recycling.
Ladou, J., 2016. Export of Electronics Equipment Waste. Mumbai: International Journal of Occupational
and Environmental Health.
Lau, J., 2014. Electronics Manufacturing with Lead-Free, Halogen-Free & Conductive-Adhesive materials.
London: McGraw-Hill.
Lead, C., 2014. WHO. Geneva: World Health Organisation.
Legler, J., 2016. Are brominated flame retardants endocrine disruptors?. China: Environmental
International.
Leung, A., 2014. Environmental contamination from electronic waste recycling at Guiyu, southeast
China. China: Journal of Material Cycles and Waste Management.
Leung, A., 2012. Heavy metals concentration of surface dust from e-waste recycling and its human
health implications in southeast China. China: Environmental Sciences & Technology.
Li, H., 2010. Severe PCDD/F and PBDD/F Pollution in Air around an Electronic Waste Dismantling Area in
China. Perth: Environmental Science & Technology.
EPA, U., 2014. Computers, E-waste, and Product Stewardship. Paris: Report for the United States
Environmental Protection Agency.
George, F., 2016. Zinc toxicity. Michigan: American Journal of Clinical Nutrition.
Geibig, J., 2013. Solders in electronics. Paris: A life cycle assessment.
Hai-Yong, K., 2015. Electronic waste recycling. Moscow: Infrastructure and technology options
Resources.
Huisman, J., 2013. The QWERTY/EE concept, Quantifying Recyclability and Eco-Efficiency for End-of-Life
Treatment of Consumer Electronic Products. Netherlands: Delft University of Technology.
ICMM, 2014. Maximizing Value- Guidance on implementing materials stewardship in the minerals and
metals value chain, Toledo: ICMM International Council on Mining & Minerals.
IGES, 2011. Environmental and Human Health Risks associated with the end-of-life treatment of
electrical and electronic equipment. Kanagawa: Institute for Global Environmental Strategies (IGES),.
Jangwa, A., 2013. Hepatotoxicity of brominated benzenes. Colorado: Archives of Toxicology.
Jang, Y., 2010. Leaching of lead from computer printed wire boards and cathode ray tubes by municipal
solid waste landfill leachates. Toledo: Environmental Science and Technology.
Jenkins, R., 2012. The determinants of household recycling: a material-specific analysis of recycling
program features and unit. Perth: IEEE.
Jassia, O., 2016. 2007 Identification of estrogenic compounds emitted from the. Colorado: Wilson.
Kahhat, R., 2017. Exploring the e-waste management systems in the United States. Chicago: Resources,
Conservation and Recycling.
Kang, H., 2015. Electronics waste recycling. New Delhi: Resources, Conservation and Recycling.
Ladou, J., 2016. Export of Electronics Equipment Waste. Mumbai: International Journal of Occupational
and Environmental Health.
Lau, J., 2014. Electronics Manufacturing with Lead-Free, Halogen-Free & Conductive-Adhesive materials.
London: McGraw-Hill.
Lead, C., 2014. WHO. Geneva: World Health Organisation.
Legler, J., 2016. Are brominated flame retardants endocrine disruptors?. China: Environmental
International.
Leung, A., 2014. Environmental contamination from electronic waste recycling at Guiyu, southeast
China. China: Journal of Material Cycles and Waste Management.
Leung, A., 2012. Heavy metals concentration of surface dust from e-waste recycling and its human
health implications in southeast China. China: Environmental Sciences & Technology.
Li, H., 2010. Severe PCDD/F and PBDD/F Pollution in Air around an Electronic Waste Dismantling Area in
China. Perth: Environmental Science & Technology.
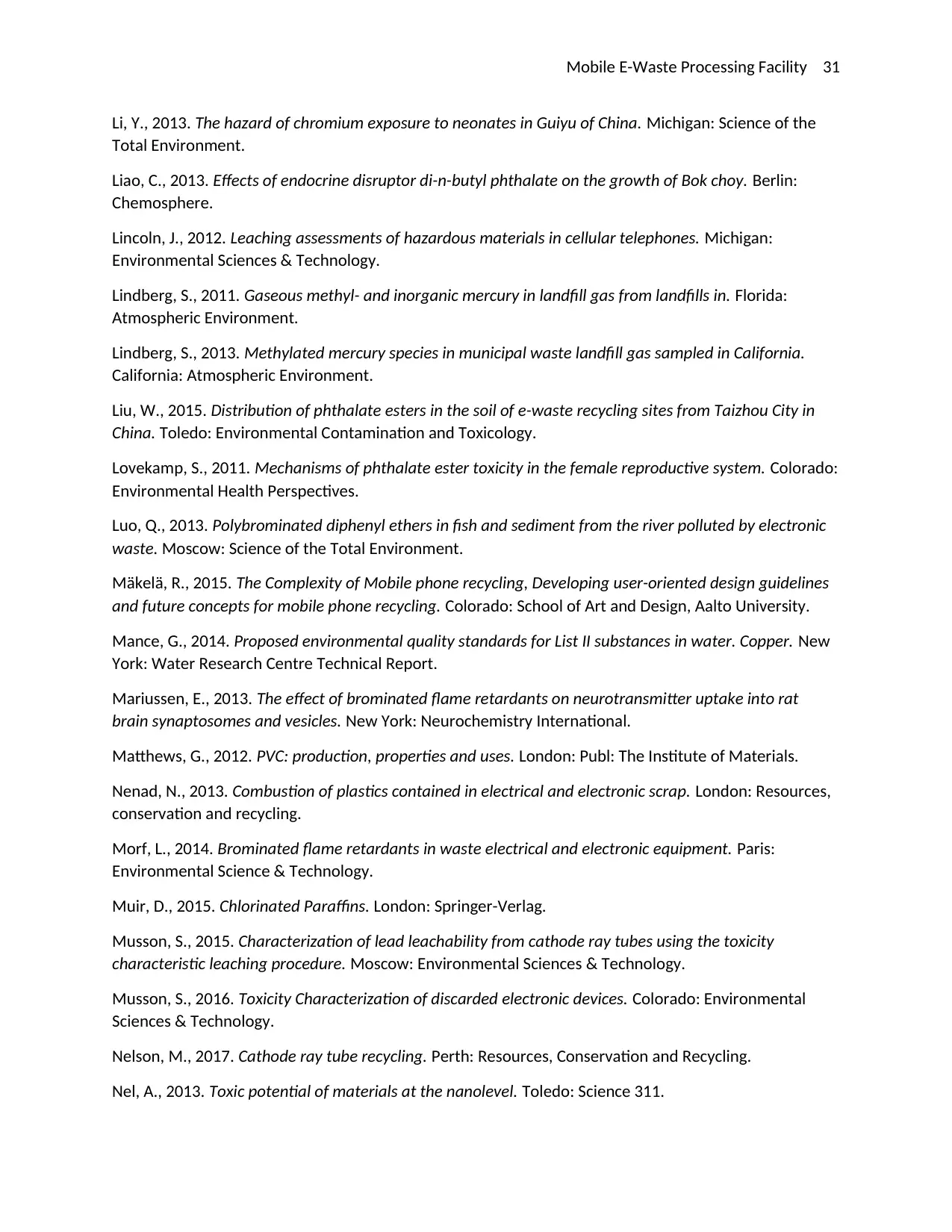
Mobile E-Waste Processing Facility 31
Li, Y., 2013. The hazard of chromium exposure to neonates in Guiyu of China. Michigan: Science of the
Total Environment.
Liao, C., 2013. Effects of endocrine disruptor di-n-butyl phthalate on the growth of Bok choy. Berlin:
Chemosphere.
Lincoln, J., 2012. Leaching assessments of hazardous materials in cellular telephones. Michigan:
Environmental Sciences & Technology.
Lindberg, S., 2011. Gaseous methyl- and inorganic mercury in landfill gas from landfills in. Florida:
Atmospheric Environment.
Lindberg, S., 2013. Methylated mercury species in municipal waste landfill gas sampled in California.
California: Atmospheric Environment.
Liu, W., 2015. Distribution of phthalate esters in the soil of e-waste recycling sites from Taizhou City in
China. Toledo: Environmental Contamination and Toxicology.
Lovekamp, S., 2011. Mechanisms of phthalate ester toxicity in the female reproductive system. Colorado:
Environmental Health Perspectives.
Luo, Q., 2013. Polybrominated diphenyl ethers in fish and sediment from the river polluted by electronic
waste. Moscow: Science of the Total Environment.
Mäkelä, R., 2015. The Complexity of Mobile phone recycling, Developing user-oriented design guidelines
and future concepts for mobile phone recycling. Colorado: School of Art and Design, Aalto University.
Mance, G., 2014. Proposed environmental quality standards for List II substances in water. Copper. New
York: Water Research Centre Technical Report.
Mariussen, E., 2013. The effect of brominated flame retardants on neurotransmitter uptake into rat
brain synaptosomes and vesicles. New York: Neurochemistry International.
Matthews, G., 2012. PVC: production, properties and uses. London: Publ: The Institute of Materials.
Nenad, N., 2013. Combustion of plastics contained in electrical and electronic scrap. London: Resources,
conservation and recycling.
Morf, L., 2014. Brominated flame retardants in waste electrical and electronic equipment. Paris:
Environmental Science & Technology.
Muir, D., 2015. Chlorinated Paraffins. London: Springer-Verlag.
Musson, S., 2015. Characterization of lead leachability from cathode ray tubes using the toxicity
characteristic leaching procedure. Moscow: Environmental Sciences & Technology.
Musson, S., 2016. Toxicity Characterization of discarded electronic devices. Colorado: Environmental
Sciences & Technology.
Nelson, M., 2017. Cathode ray tube recycling. Perth: Resources, Conservation and Recycling.
Nel, A., 2013. Toxic potential of materials at the nanolevel. Toledo: Science 311.
Li, Y., 2013. The hazard of chromium exposure to neonates in Guiyu of China. Michigan: Science of the
Total Environment.
Liao, C., 2013. Effects of endocrine disruptor di-n-butyl phthalate on the growth of Bok choy. Berlin:
Chemosphere.
Lincoln, J., 2012. Leaching assessments of hazardous materials in cellular telephones. Michigan:
Environmental Sciences & Technology.
Lindberg, S., 2011. Gaseous methyl- and inorganic mercury in landfill gas from landfills in. Florida:
Atmospheric Environment.
Lindberg, S., 2013. Methylated mercury species in municipal waste landfill gas sampled in California.
California: Atmospheric Environment.
Liu, W., 2015. Distribution of phthalate esters in the soil of e-waste recycling sites from Taizhou City in
China. Toledo: Environmental Contamination and Toxicology.
Lovekamp, S., 2011. Mechanisms of phthalate ester toxicity in the female reproductive system. Colorado:
Environmental Health Perspectives.
Luo, Q., 2013. Polybrominated diphenyl ethers in fish and sediment from the river polluted by electronic
waste. Moscow: Science of the Total Environment.
Mäkelä, R., 2015. The Complexity of Mobile phone recycling, Developing user-oriented design guidelines
and future concepts for mobile phone recycling. Colorado: School of Art and Design, Aalto University.
Mance, G., 2014. Proposed environmental quality standards for List II substances in water. Copper. New
York: Water Research Centre Technical Report.
Mariussen, E., 2013. The effect of brominated flame retardants on neurotransmitter uptake into rat
brain synaptosomes and vesicles. New York: Neurochemistry International.
Matthews, G., 2012. PVC: production, properties and uses. London: Publ: The Institute of Materials.
Nenad, N., 2013. Combustion of plastics contained in electrical and electronic scrap. London: Resources,
conservation and recycling.
Morf, L., 2014. Brominated flame retardants in waste electrical and electronic equipment. Paris:
Environmental Science & Technology.
Muir, D., 2015. Chlorinated Paraffins. London: Springer-Verlag.
Musson, S., 2015. Characterization of lead leachability from cathode ray tubes using the toxicity
characteristic leaching procedure. Moscow: Environmental Sciences & Technology.
Musson, S., 2016. Toxicity Characterization of discarded electronic devices. Colorado: Environmental
Sciences & Technology.
Nelson, M., 2017. Cathode ray tube recycling. Perth: Resources, Conservation and Recycling.
Nel, A., 2013. Toxic potential of materials at the nanolevel. Toledo: Science 311.
Paraphrase This Document
Need a fresh take? Get an instant paraphrase of this document with our AI Paraphraser
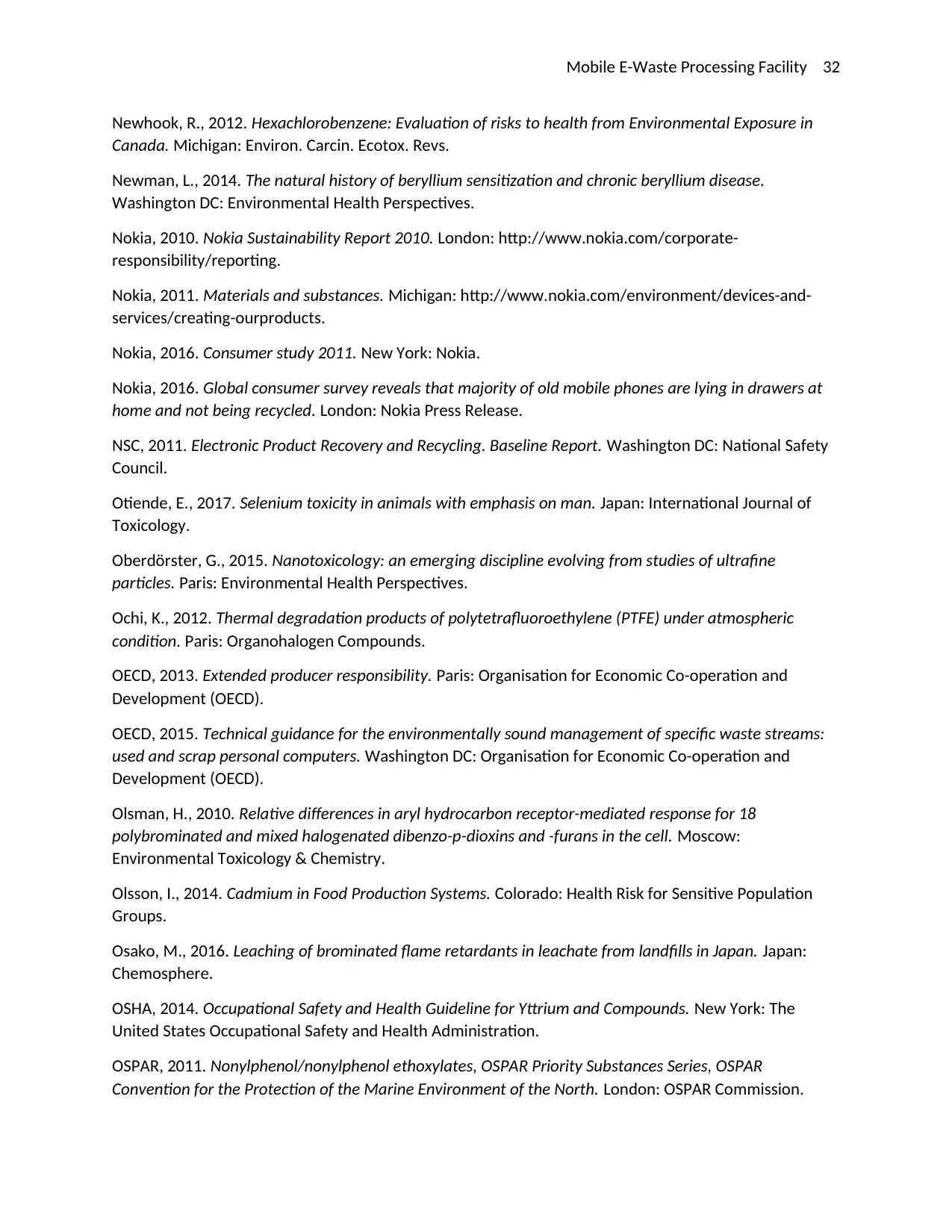
Mobile E-Waste Processing Facility 32
Newhook, R., 2012. Hexachlorobenzene: Evaluation of risks to health from Environmental Exposure in
Canada. Michigan: Environ. Carcin. Ecotox. Revs.
Newman, L., 2014. The natural history of beryllium sensitization and chronic beryllium disease.
Washington DC: Environmental Health Perspectives.
Nokia, 2010. Nokia Sustainability Report 2010. London: http://www.nokia.com/corporate-
responsibility/reporting.
Nokia, 2011. Materials and substances. Michigan: http://www.nokia.com/environment/devices-and-
services/creating-ourproducts.
Nokia, 2016. Consumer study 2011. New York: Nokia.
Nokia, 2016. Global consumer survey reveals that majority of old mobile phones are lying in drawers at
home and not being recycled. London: Nokia Press Release.
NSC, 2011. Electronic Product Recovery and Recycling. Baseline Report. Washington DC: National Safety
Council.
Otiende, E., 2017. Selenium toxicity in animals with emphasis on man. Japan: International Journal of
Toxicology.
Oberdörster, G., 2015. Nanotoxicology: an emerging discipline evolving from studies of ultrafine
particles. Paris: Environmental Health Perspectives.
Ochi, K., 2012. Thermal degradation products of polytetrafluoroethylene (PTFE) under atmospheric
condition. Paris: Organohalogen Compounds.
OECD, 2013. Extended producer responsibility. Paris: Organisation for Economic Co-operation and
Development (OECD).
OECD, 2015. Technical guidance for the environmentally sound management of specific waste streams:
used and scrap personal computers. Washington DC: Organisation for Economic Co-operation and
Development (OECD).
Olsman, H., 2010. Relative differences in aryl hydrocarbon receptor-mediated response for 18
polybrominated and mixed halogenated dibenzo-p-dioxins and -furans in the cell. Moscow:
Environmental Toxicology & Chemistry.
Olsson, I., 2014. Cadmium in Food Production Systems. Colorado: Health Risk for Sensitive Population
Groups.
Osako, M., 2016. Leaching of brominated flame retardants in leachate from landfills in Japan. Japan:
Chemosphere.
OSHA, 2014. Occupational Safety and Health Guideline for Yttrium and Compounds. New York: The
United States Occupational Safety and Health Administration.
OSPAR, 2011. Nonylphenol/nonylphenol ethoxylates, OSPAR Priority Substances Series, OSPAR
Convention for the Protection of the Marine Environment of the North. London: OSPAR Commission.
Newhook, R., 2012. Hexachlorobenzene: Evaluation of risks to health from Environmental Exposure in
Canada. Michigan: Environ. Carcin. Ecotox. Revs.
Newman, L., 2014. The natural history of beryllium sensitization and chronic beryllium disease.
Washington DC: Environmental Health Perspectives.
Nokia, 2010. Nokia Sustainability Report 2010. London: http://www.nokia.com/corporate-
responsibility/reporting.
Nokia, 2011. Materials and substances. Michigan: http://www.nokia.com/environment/devices-and-
services/creating-ourproducts.
Nokia, 2016. Consumer study 2011. New York: Nokia.
Nokia, 2016. Global consumer survey reveals that majority of old mobile phones are lying in drawers at
home and not being recycled. London: Nokia Press Release.
NSC, 2011. Electronic Product Recovery and Recycling. Baseline Report. Washington DC: National Safety
Council.
Otiende, E., 2017. Selenium toxicity in animals with emphasis on man. Japan: International Journal of
Toxicology.
Oberdörster, G., 2015. Nanotoxicology: an emerging discipline evolving from studies of ultrafine
particles. Paris: Environmental Health Perspectives.
Ochi, K., 2012. Thermal degradation products of polytetrafluoroethylene (PTFE) under atmospheric
condition. Paris: Organohalogen Compounds.
OECD, 2013. Extended producer responsibility. Paris: Organisation for Economic Co-operation and
Development (OECD).
OECD, 2015. Technical guidance for the environmentally sound management of specific waste streams:
used and scrap personal computers. Washington DC: Organisation for Economic Co-operation and
Development (OECD).
Olsman, H., 2010. Relative differences in aryl hydrocarbon receptor-mediated response for 18
polybrominated and mixed halogenated dibenzo-p-dioxins and -furans in the cell. Moscow:
Environmental Toxicology & Chemistry.
Olsson, I., 2014. Cadmium in Food Production Systems. Colorado: Health Risk for Sensitive Population
Groups.
Osako, M., 2016. Leaching of brominated flame retardants in leachate from landfills in Japan. Japan:
Chemosphere.
OSHA, 2014. Occupational Safety and Health Guideline for Yttrium and Compounds. New York: The
United States Occupational Safety and Health Administration.
OSPAR, 2011. Nonylphenol/nonylphenol ethoxylates, OSPAR Priority Substances Series, OSPAR
Convention for the Protection of the Marine Environment of the North. London: OSPAR Commission.
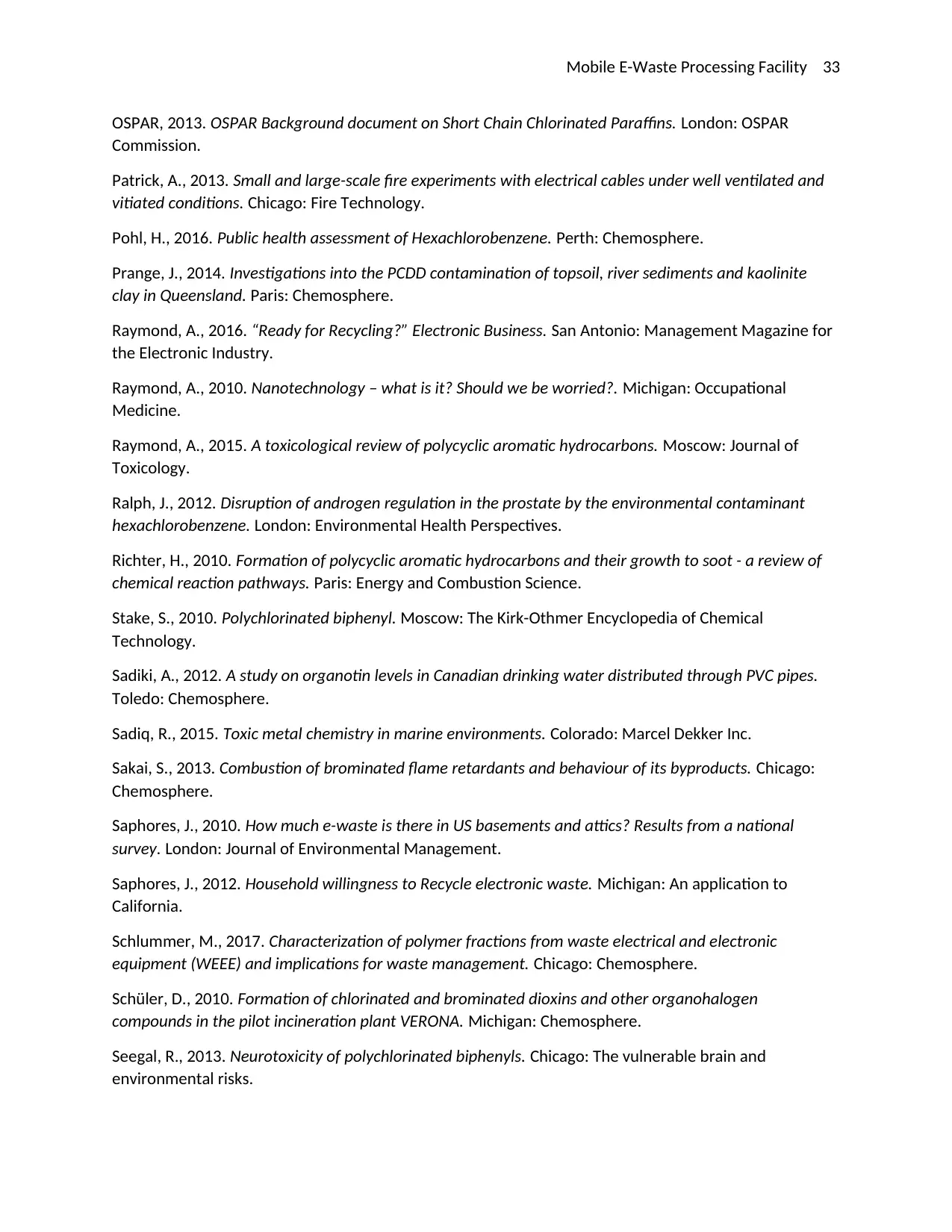
Mobile E-Waste Processing Facility 33
OSPAR, 2013. OSPAR Background document on Short Chain Chlorinated Paraffins. London: OSPAR
Commission.
Patrick, A., 2013. Small and large-scale fire experiments with electrical cables under well ventilated and
vitiated conditions. Chicago: Fire Technology.
Pohl, H., 2016. Public health assessment of Hexachlorobenzene. Perth: Chemosphere.
Prange, J., 2014. Investigations into the PCDD contamination of topsoil, river sediments and kaolinite
clay in Queensland. Paris: Chemosphere.
Raymond, A., 2016. “Ready for Recycling?” Electronic Business. San Antonio: Management Magazine for
the Electronic Industry.
Raymond, A., 2010. Nanotechnology – what is it? Should we be worried?. Michigan: Occupational
Medicine.
Raymond, A., 2015. A toxicological review of polycyclic aromatic hydrocarbons. Moscow: Journal of
Toxicology.
Ralph, J., 2012. Disruption of androgen regulation in the prostate by the environmental contaminant
hexachlorobenzene. London: Environmental Health Perspectives.
Richter, H., 2010. Formation of polycyclic aromatic hydrocarbons and their growth to soot - a review of
chemical reaction pathways. Paris: Energy and Combustion Science.
Stake, S., 2010. Polychlorinated biphenyl. Moscow: The Kirk-Othmer Encyclopedia of Chemical
Technology.
Sadiki, A., 2012. A study on organotin levels in Canadian drinking water distributed through PVC pipes.
Toledo: Chemosphere.
Sadiq, R., 2015. Toxic metal chemistry in marine environments. Colorado: Marcel Dekker Inc.
Sakai, S., 2013. Combustion of brominated flame retardants and behaviour of its byproducts. Chicago:
Chemosphere.
Saphores, J., 2010. How much e-waste is there in US basements and attics? Results from a national
survey. London: Journal of Environmental Management.
Saphores, J., 2012. Household willingness to Recycle electronic waste. Michigan: An application to
California.
Schlummer, M., 2017. Characterization of polymer fractions from waste electrical and electronic
equipment (WEEE) and implications for waste management. Chicago: Chemosphere.
Schüler, D., 2010. Formation of chlorinated and brominated dioxins and other organohalogen
compounds in the pilot incineration plant VERONA. Michigan: Chemosphere.
Seegal, R., 2013. Neurotoxicity of polychlorinated biphenyls. Chicago: The vulnerable brain and
environmental risks.
OSPAR, 2013. OSPAR Background document on Short Chain Chlorinated Paraffins. London: OSPAR
Commission.
Patrick, A., 2013. Small and large-scale fire experiments with electrical cables under well ventilated and
vitiated conditions. Chicago: Fire Technology.
Pohl, H., 2016. Public health assessment of Hexachlorobenzene. Perth: Chemosphere.
Prange, J., 2014. Investigations into the PCDD contamination of topsoil, river sediments and kaolinite
clay in Queensland. Paris: Chemosphere.
Raymond, A., 2016. “Ready for Recycling?” Electronic Business. San Antonio: Management Magazine for
the Electronic Industry.
Raymond, A., 2010. Nanotechnology – what is it? Should we be worried?. Michigan: Occupational
Medicine.
Raymond, A., 2015. A toxicological review of polycyclic aromatic hydrocarbons. Moscow: Journal of
Toxicology.
Ralph, J., 2012. Disruption of androgen regulation in the prostate by the environmental contaminant
hexachlorobenzene. London: Environmental Health Perspectives.
Richter, H., 2010. Formation of polycyclic aromatic hydrocarbons and their growth to soot - a review of
chemical reaction pathways. Paris: Energy and Combustion Science.
Stake, S., 2010. Polychlorinated biphenyl. Moscow: The Kirk-Othmer Encyclopedia of Chemical
Technology.
Sadiki, A., 2012. A study on organotin levels in Canadian drinking water distributed through PVC pipes.
Toledo: Chemosphere.
Sadiq, R., 2015. Toxic metal chemistry in marine environments. Colorado: Marcel Dekker Inc.
Sakai, S., 2013. Combustion of brominated flame retardants and behaviour of its byproducts. Chicago:
Chemosphere.
Saphores, J., 2010. How much e-waste is there in US basements and attics? Results from a national
survey. London: Journal of Environmental Management.
Saphores, J., 2012. Household willingness to Recycle electronic waste. Michigan: An application to
California.
Schlummer, M., 2017. Characterization of polymer fractions from waste electrical and electronic
equipment (WEEE) and implications for waste management. Chicago: Chemosphere.
Schüler, D., 2010. Formation of chlorinated and brominated dioxins and other organohalogen
compounds in the pilot incineration plant VERONA. Michigan: Chemosphere.
Seegal, R., 2013. Neurotoxicity of polychlorinated biphenyls. Chicago: The vulnerable brain and
environmental risks.
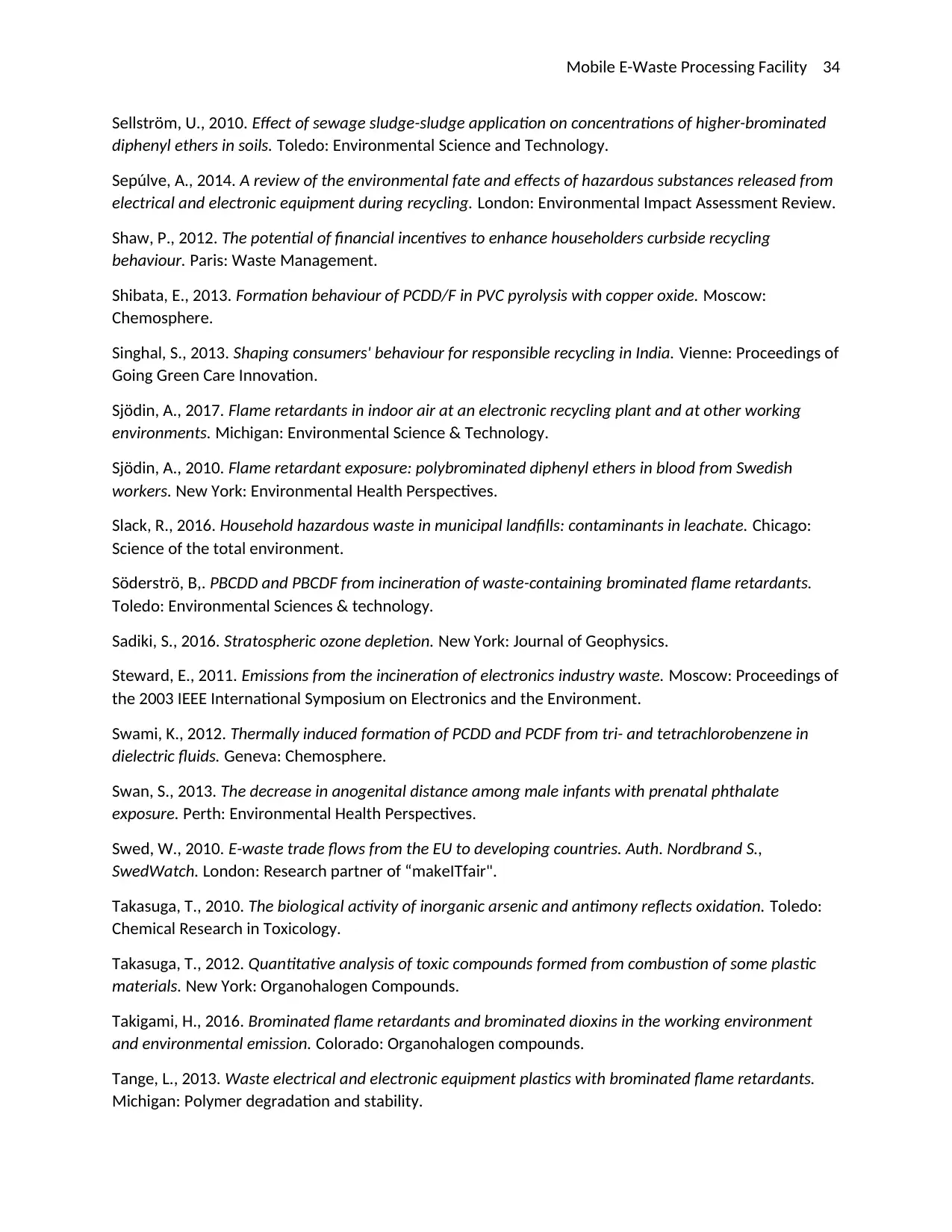
Mobile E-Waste Processing Facility 34
Sellström, U., 2010. Effect of sewage sludge-sludge application on concentrations of higher-brominated
diphenyl ethers in soils. Toledo: Environmental Science and Technology.
Sepúlve, A., 2014. A review of the environmental fate and effects of hazardous substances released from
electrical and electronic equipment during recycling. London: Environmental Impact Assessment Review.
Shaw, P., 2012. The potential of financial incentives to enhance householders curbside recycling
behaviour. Paris: Waste Management.
Shibata, E., 2013. Formation behaviour of PCDD/F in PVC pyrolysis with copper oxide. Moscow:
Chemosphere.
Singhal, S., 2013. Shaping consumers' behaviour for responsible recycling in India. Vienne: Proceedings of
Going Green Care Innovation.
Sjödin, A., 2017. Flame retardants in indoor air at an electronic recycling plant and at other working
environments. Michigan: Environmental Science & Technology.
Sjödin, A., 2010. Flame retardant exposure: polybrominated diphenyl ethers in blood from Swedish
workers. New York: Environmental Health Perspectives.
Slack, R., 2016. Household hazardous waste in municipal landfills: contaminants in leachate. Chicago:
Science of the total environment.
Söderströ, B,. PBCDD and PBCDF from incineration of waste-containing brominated flame retardants.
Toledo: Environmental Sciences & technology.
Sadiki, S., 2016. Stratospheric ozone depletion. New York: Journal of Geophysics.
Steward, E., 2011. Emissions from the incineration of electronics industry waste. Moscow: Proceedings of
the 2003 IEEE International Symposium on Electronics and the Environment.
Swami, K., 2012. Thermally induced formation of PCDD and PCDF from tri- and tetrachlorobenzene in
dielectric fluids. Geneva: Chemosphere.
Swan, S., 2013. The decrease in anogenital distance among male infants with prenatal phthalate
exposure. Perth: Environmental Health Perspectives.
Swed, W., 2010. E-waste trade flows from the EU to developing countries. Auth. Nordbrand S.,
SwedWatch. London: Research partner of “makeITfair".
Takasuga, T., 2010. The biological activity of inorganic arsenic and antimony reflects oxidation. Toledo:
Chemical Research in Toxicology.
Takasuga, T., 2012. Quantitative analysis of toxic compounds formed from combustion of some plastic
materials. New York: Organohalogen Compounds.
Takigami, H., 2016. Brominated flame retardants and brominated dioxins in the working environment
and environmental emission. Colorado: Organohalogen compounds.
Tange, L., 2013. Waste electrical and electronic equipment plastics with brominated flame retardants.
Michigan: Polymer degradation and stability.
Sellström, U., 2010. Effect of sewage sludge-sludge application on concentrations of higher-brominated
diphenyl ethers in soils. Toledo: Environmental Science and Technology.
Sepúlve, A., 2014. A review of the environmental fate and effects of hazardous substances released from
electrical and electronic equipment during recycling. London: Environmental Impact Assessment Review.
Shaw, P., 2012. The potential of financial incentives to enhance householders curbside recycling
behaviour. Paris: Waste Management.
Shibata, E., 2013. Formation behaviour of PCDD/F in PVC pyrolysis with copper oxide. Moscow:
Chemosphere.
Singhal, S., 2013. Shaping consumers' behaviour for responsible recycling in India. Vienne: Proceedings of
Going Green Care Innovation.
Sjödin, A., 2017. Flame retardants in indoor air at an electronic recycling plant and at other working
environments. Michigan: Environmental Science & Technology.
Sjödin, A., 2010. Flame retardant exposure: polybrominated diphenyl ethers in blood from Swedish
workers. New York: Environmental Health Perspectives.
Slack, R., 2016. Household hazardous waste in municipal landfills: contaminants in leachate. Chicago:
Science of the total environment.
Söderströ, B,. PBCDD and PBCDF from incineration of waste-containing brominated flame retardants.
Toledo: Environmental Sciences & technology.
Sadiki, S., 2016. Stratospheric ozone depletion. New York: Journal of Geophysics.
Steward, E., 2011. Emissions from the incineration of electronics industry waste. Moscow: Proceedings of
the 2003 IEEE International Symposium on Electronics and the Environment.
Swami, K., 2012. Thermally induced formation of PCDD and PCDF from tri- and tetrachlorobenzene in
dielectric fluids. Geneva: Chemosphere.
Swan, S., 2013. The decrease in anogenital distance among male infants with prenatal phthalate
exposure. Perth: Environmental Health Perspectives.
Swed, W., 2010. E-waste trade flows from the EU to developing countries. Auth. Nordbrand S.,
SwedWatch. London: Research partner of “makeITfair".
Takasuga, T., 2010. The biological activity of inorganic arsenic and antimony reflects oxidation. Toledo:
Chemical Research in Toxicology.
Takasuga, T., 2012. Quantitative analysis of toxic compounds formed from combustion of some plastic
materials. New York: Organohalogen Compounds.
Takigami, H., 2016. Brominated flame retardants and brominated dioxins in the working environment
and environmental emission. Colorado: Organohalogen compounds.
Tange, L., 2013. Waste electrical and electronic equipment plastics with brominated flame retardants.
Michigan: Polymer degradation and stability.
Secure Best Marks with AI Grader
Need help grading? Try our AI Grader for instant feedback on your assignments.
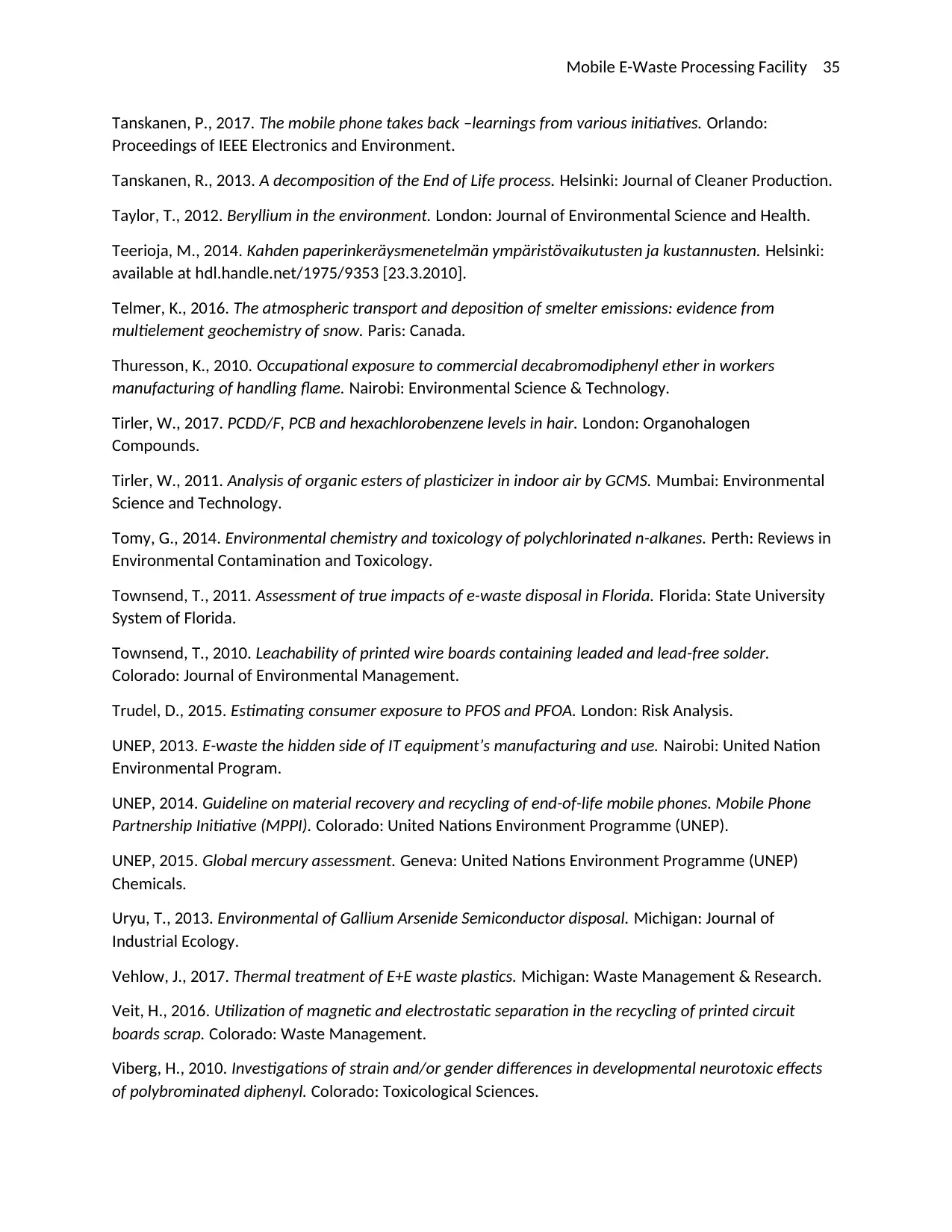
Mobile E-Waste Processing Facility 35
Tanskanen, P., 2017. The mobile phone takes back –learnings from various initiatives. Orlando:
Proceedings of IEEE Electronics and Environment.
Tanskanen, R., 2013. A decomposition of the End of Life process. Helsinki: Journal of Cleaner Production.
Taylor, T., 2012. Beryllium in the environment. London: Journal of Environmental Science and Health.
Teerioja, M., 2014. Kahden paperinkeräysmenetelmän ympäristövaikutusten ja kustannusten. Helsinki:
available at hdl.handle.net/1975/9353 [23.3.2010].
Telmer, K., 2016. The atmospheric transport and deposition of smelter emissions: evidence from
multielement geochemistry of snow. Paris: Canada.
Thuresson, K., 2010. Occupational exposure to commercial decabromodiphenyl ether in workers
manufacturing of handling flame. Nairobi: Environmental Science & Technology.
Tirler, W., 2017. PCDD/F, PCB and hexachlorobenzene levels in hair. London: Organohalogen
Compounds.
Tirler, W., 2011. Analysis of organic esters of plasticizer in indoor air by GCMS. Mumbai: Environmental
Science and Technology.
Tomy, G., 2014. Environmental chemistry and toxicology of polychlorinated n-alkanes. Perth: Reviews in
Environmental Contamination and Toxicology.
Townsend, T., 2011. Assessment of true impacts of e-waste disposal in Florida. Florida: State University
System of Florida.
Townsend, T., 2010. Leachability of printed wire boards containing leaded and lead-free solder.
Colorado: Journal of Environmental Management.
Trudel, D., 2015. Estimating consumer exposure to PFOS and PFOA. London: Risk Analysis.
UNEP, 2013. E-waste the hidden side of IT equipment’s manufacturing and use. Nairobi: United Nation
Environmental Program.
UNEP, 2014. Guideline on material recovery and recycling of end-of-life mobile phones. Mobile Phone
Partnership Initiative (MPPI). Colorado: United Nations Environment Programme (UNEP).
UNEP, 2015. Global mercury assessment. Geneva: United Nations Environment Programme (UNEP)
Chemicals.
Uryu, T., 2013. Environmental of Gallium Arsenide Semiconductor disposal. Michigan: Journal of
Industrial Ecology.
Vehlow, J., 2017. Thermal treatment of E+E waste plastics. Michigan: Waste Management & Research.
Veit, H., 2016. Utilization of magnetic and electrostatic separation in the recycling of printed circuit
boards scrap. Colorado: Waste Management.
Viberg, H., 2010. Investigations of strain and/or gender differences in developmental neurotoxic effects
of polybrominated diphenyl. Colorado: Toxicological Sciences.
Tanskanen, P., 2017. The mobile phone takes back –learnings from various initiatives. Orlando:
Proceedings of IEEE Electronics and Environment.
Tanskanen, R., 2013. A decomposition of the End of Life process. Helsinki: Journal of Cleaner Production.
Taylor, T., 2012. Beryllium in the environment. London: Journal of Environmental Science and Health.
Teerioja, M., 2014. Kahden paperinkeräysmenetelmän ympäristövaikutusten ja kustannusten. Helsinki:
available at hdl.handle.net/1975/9353 [23.3.2010].
Telmer, K., 2016. The atmospheric transport and deposition of smelter emissions: evidence from
multielement geochemistry of snow. Paris: Canada.
Thuresson, K., 2010. Occupational exposure to commercial decabromodiphenyl ether in workers
manufacturing of handling flame. Nairobi: Environmental Science & Technology.
Tirler, W., 2017. PCDD/F, PCB and hexachlorobenzene levels in hair. London: Organohalogen
Compounds.
Tirler, W., 2011. Analysis of organic esters of plasticizer in indoor air by GCMS. Mumbai: Environmental
Science and Technology.
Tomy, G., 2014. Environmental chemistry and toxicology of polychlorinated n-alkanes. Perth: Reviews in
Environmental Contamination and Toxicology.
Townsend, T., 2011. Assessment of true impacts of e-waste disposal in Florida. Florida: State University
System of Florida.
Townsend, T., 2010. Leachability of printed wire boards containing leaded and lead-free solder.
Colorado: Journal of Environmental Management.
Trudel, D., 2015. Estimating consumer exposure to PFOS and PFOA. London: Risk Analysis.
UNEP, 2013. E-waste the hidden side of IT equipment’s manufacturing and use. Nairobi: United Nation
Environmental Program.
UNEP, 2014. Guideline on material recovery and recycling of end-of-life mobile phones. Mobile Phone
Partnership Initiative (MPPI). Colorado: United Nations Environment Programme (UNEP).
UNEP, 2015. Global mercury assessment. Geneva: United Nations Environment Programme (UNEP)
Chemicals.
Uryu, T., 2013. Environmental of Gallium Arsenide Semiconductor disposal. Michigan: Journal of
Industrial Ecology.
Vehlow, J., 2017. Thermal treatment of E+E waste plastics. Michigan: Waste Management & Research.
Veit, H., 2016. Utilization of magnetic and electrostatic separation in the recycling of printed circuit
boards scrap. Colorado: Waste Management.
Viberg, H., 2010. Investigations of strain and/or gender differences in developmental neurotoxic effects
of polybrominated diphenyl. Colorado: Toxicological Sciences.
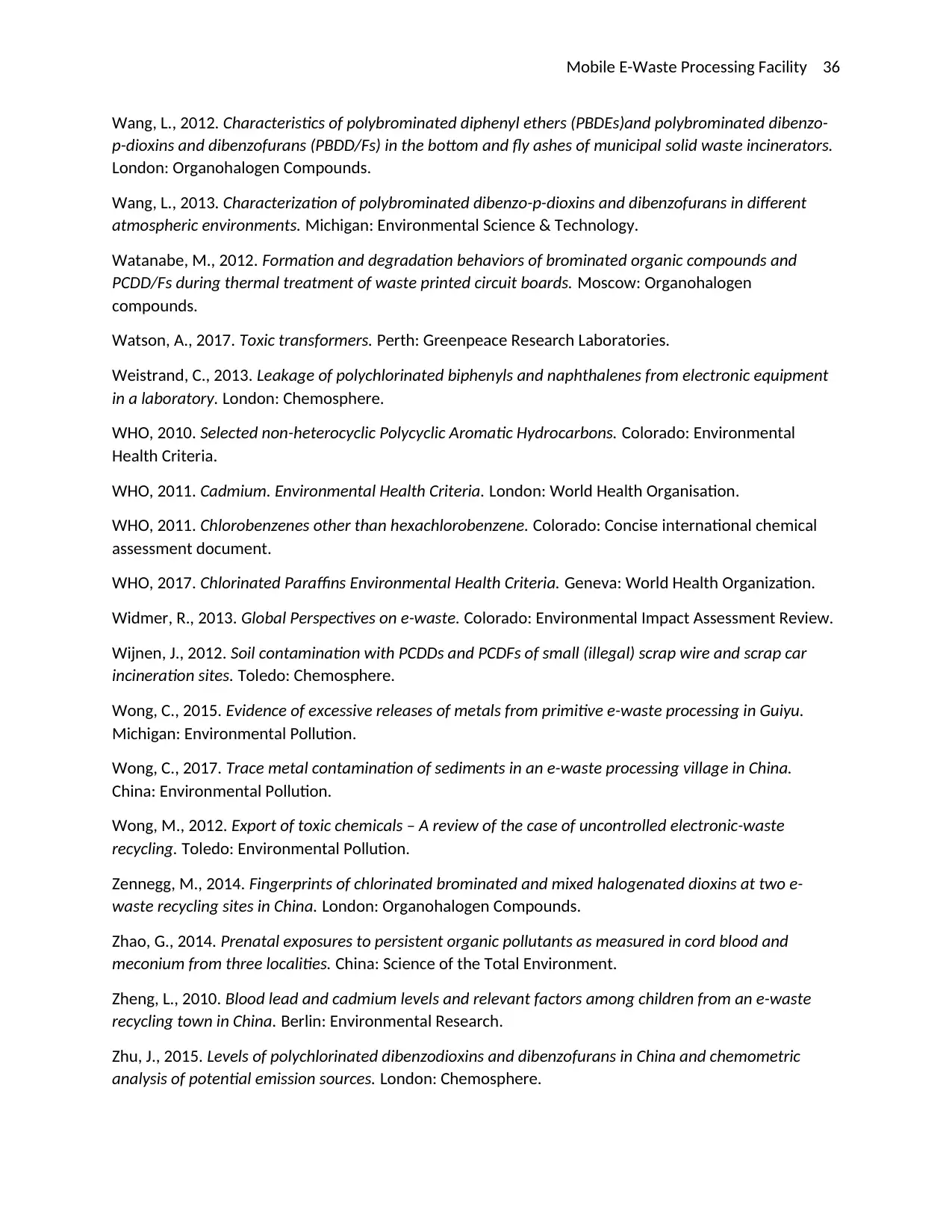
Mobile E-Waste Processing Facility 36
Wang, L., 2012. Characteristics of polybrominated diphenyl ethers (PBDEs)and polybrominated dibenzo-
p-dioxins and dibenzofurans (PBDD/Fs) in the bottom and fly ashes of municipal solid waste incinerators.
London: Organohalogen Compounds.
Wang, L., 2013. Characterization of polybrominated dibenzo-p-dioxins and dibenzofurans in different
atmospheric environments. Michigan: Environmental Science & Technology.
Watanabe, M., 2012. Formation and degradation behaviors of brominated organic compounds and
PCDD/Fs during thermal treatment of waste printed circuit boards. Moscow: Organohalogen
compounds.
Watson, A., 2017. Toxic transformers. Perth: Greenpeace Research Laboratories.
Weistrand, C., 2013. Leakage of polychlorinated biphenyls and naphthalenes from electronic equipment
in a laboratory. London: Chemosphere.
WHO, 2010. Selected non-heterocyclic Polycyclic Aromatic Hydrocarbons. Colorado: Environmental
Health Criteria.
WHO, 2011. Cadmium. Environmental Health Criteria. London: World Health Organisation.
WHO, 2011. Chlorobenzenes other than hexachlorobenzene. Colorado: Concise international chemical
assessment document.
WHO, 2017. Chlorinated Paraffins Environmental Health Criteria. Geneva: World Health Organization.
Widmer, R., 2013. Global Perspectives on e-waste. Colorado: Environmental Impact Assessment Review.
Wijnen, J., 2012. Soil contamination with PCDDs and PCDFs of small (illegal) scrap wire and scrap car
incineration sites. Toledo: Chemosphere.
Wong, C., 2015. Evidence of excessive releases of metals from primitive e-waste processing in Guiyu.
Michigan: Environmental Pollution.
Wong, C., 2017. Trace metal contamination of sediments in an e-waste processing village in China.
China: Environmental Pollution.
Wong, M., 2012. Export of toxic chemicals – A review of the case of uncontrolled electronic-waste
recycling. Toledo: Environmental Pollution.
Zennegg, M., 2014. Fingerprints of chlorinated brominated and mixed halogenated dioxins at two e-
waste recycling sites in China. London: Organohalogen Compounds.
Zhao, G., 2014. Prenatal exposures to persistent organic pollutants as measured in cord blood and
meconium from three localities. China: Science of the Total Environment.
Zheng, L., 2010. Blood lead and cadmium levels and relevant factors among children from an e-waste
recycling town in China. Berlin: Environmental Research.
Zhu, J., 2015. Levels of polychlorinated dibenzodioxins and dibenzofurans in China and chemometric
analysis of potential emission sources. London: Chemosphere.
Wang, L., 2012. Characteristics of polybrominated diphenyl ethers (PBDEs)and polybrominated dibenzo-
p-dioxins and dibenzofurans (PBDD/Fs) in the bottom and fly ashes of municipal solid waste incinerators.
London: Organohalogen Compounds.
Wang, L., 2013. Characterization of polybrominated dibenzo-p-dioxins and dibenzofurans in different
atmospheric environments. Michigan: Environmental Science & Technology.
Watanabe, M., 2012. Formation and degradation behaviors of brominated organic compounds and
PCDD/Fs during thermal treatment of waste printed circuit boards. Moscow: Organohalogen
compounds.
Watson, A., 2017. Toxic transformers. Perth: Greenpeace Research Laboratories.
Weistrand, C., 2013. Leakage of polychlorinated biphenyls and naphthalenes from electronic equipment
in a laboratory. London: Chemosphere.
WHO, 2010. Selected non-heterocyclic Polycyclic Aromatic Hydrocarbons. Colorado: Environmental
Health Criteria.
WHO, 2011. Cadmium. Environmental Health Criteria. London: World Health Organisation.
WHO, 2011. Chlorobenzenes other than hexachlorobenzene. Colorado: Concise international chemical
assessment document.
WHO, 2017. Chlorinated Paraffins Environmental Health Criteria. Geneva: World Health Organization.
Widmer, R., 2013. Global Perspectives on e-waste. Colorado: Environmental Impact Assessment Review.
Wijnen, J., 2012. Soil contamination with PCDDs and PCDFs of small (illegal) scrap wire and scrap car
incineration sites. Toledo: Chemosphere.
Wong, C., 2015. Evidence of excessive releases of metals from primitive e-waste processing in Guiyu.
Michigan: Environmental Pollution.
Wong, C., 2017. Trace metal contamination of sediments in an e-waste processing village in China.
China: Environmental Pollution.
Wong, M., 2012. Export of toxic chemicals – A review of the case of uncontrolled electronic-waste
recycling. Toledo: Environmental Pollution.
Zennegg, M., 2014. Fingerprints of chlorinated brominated and mixed halogenated dioxins at two e-
waste recycling sites in China. London: Organohalogen Compounds.
Zhao, G., 2014. Prenatal exposures to persistent organic pollutants as measured in cord blood and
meconium from three localities. China: Science of the Total Environment.
Zheng, L., 2010. Blood lead and cadmium levels and relevant factors among children from an e-waste
recycling town in China. Berlin: Environmental Research.
Zhu, J., 2015. Levels of polychlorinated dibenzodioxins and dibenzofurans in China and chemometric
analysis of potential emission sources. London: Chemosphere.
1 out of 36
Related Documents

Your All-in-One AI-Powered Toolkit for Academic Success.
+13062052269
info@desklib.com
Available 24*7 on WhatsApp / Email
Unlock your academic potential
© 2024 | Zucol Services PVT LTD | All rights reserved.