Executive Holloware: Operations Improvement and Sustainability
VerifiedAdded on 2023/06/10
|14
|4800
|366
Case Study
AI Summary
This case study examines the challenges faced by Executive Holloware, a company specializing in handmade tea sets, in relation to sustainability and growth. The report identifies issues such as maintaining product quality, inefficient production processes, and a lack of collaboration between departments. A company-wide operations improvement strategy is proposed, emphasizing Total Quality Management (TQM) to enhance product quality, employee performance, and customer service. The strategy includes principles such as customer focus, leadership, process approach, and continuous improvement. Implementing TQM aims to improve overall performance, productivity, and the organizational environment, leading to increased brand value, sales, and customer base. Recommendations focus on collaborative practices, efficient production processes, and sustainable practices to enhance brand awareness and optimize operational costs, ultimately improving the company's reputation and viability.
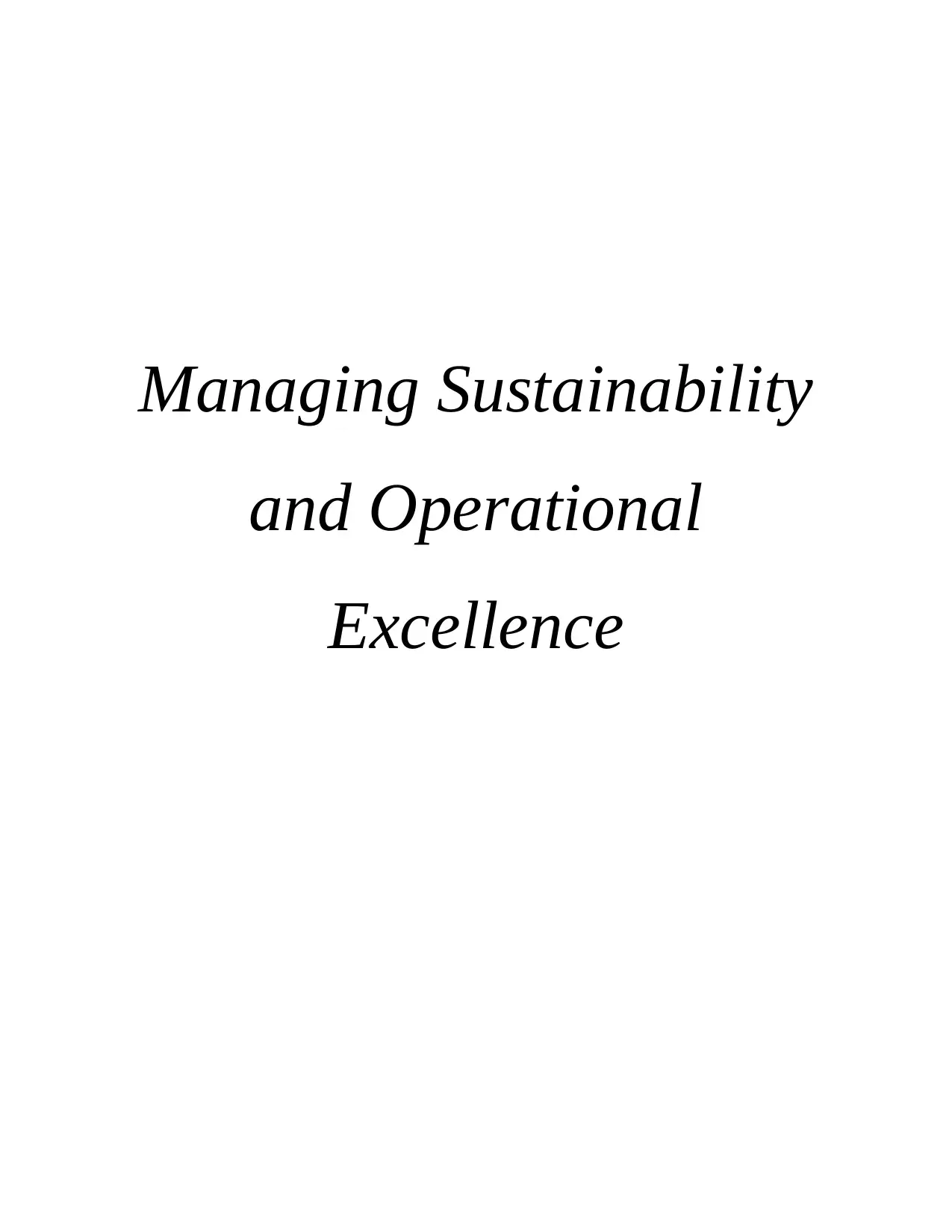
Managing Sustainability
and Operational
Excellence
and Operational
Excellence
Secure Best Marks with AI Grader
Need help grading? Try our AI Grader for instant feedback on your assignments.
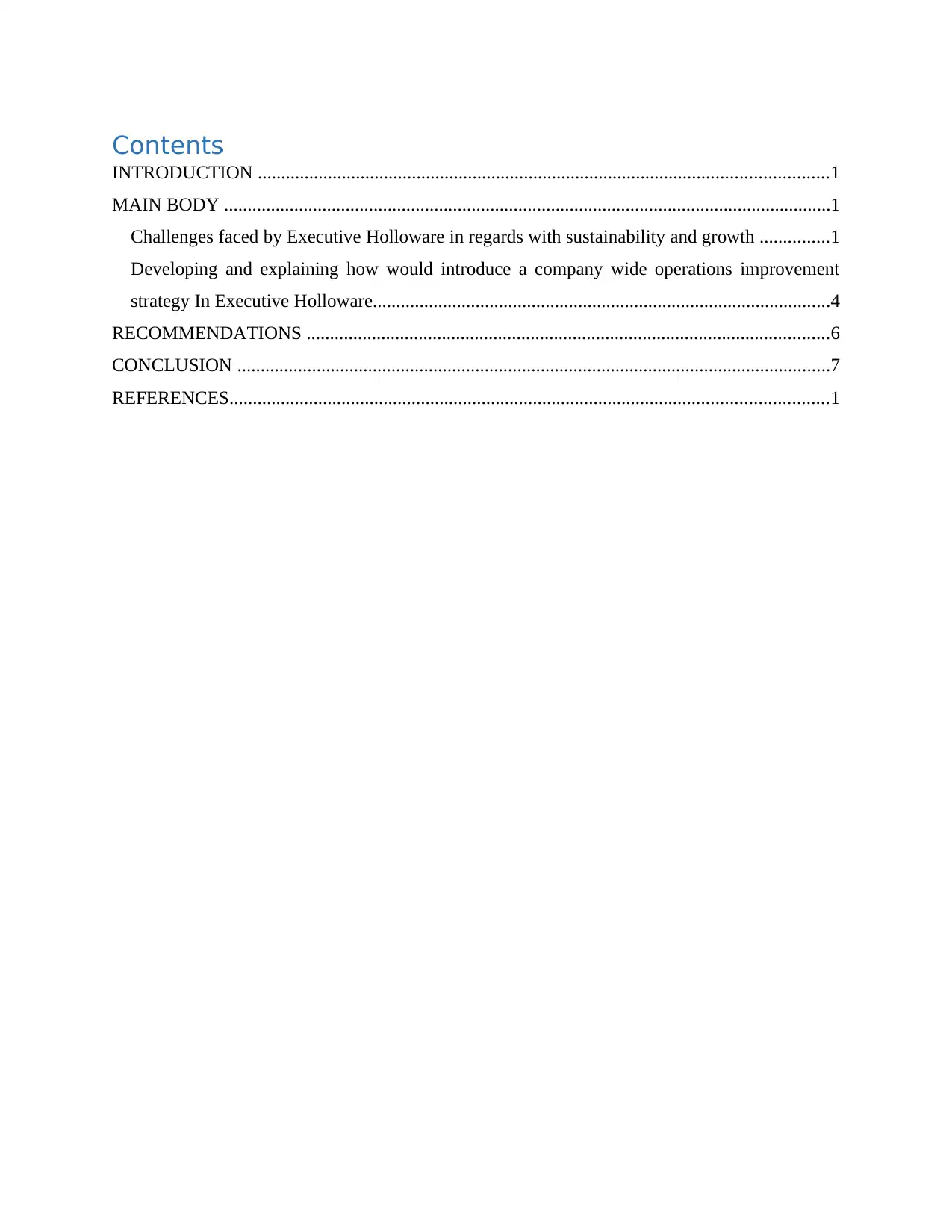
Contents
INTRODUCTION ..........................................................................................................................1
MAIN BODY ..................................................................................................................................1
Challenges faced by Executive Holloware in regards with sustainability and growth ...............1
Developing and explaining how would introduce a company wide operations improvement
strategy In Executive Holloware..................................................................................................4
RECOMMENDATIONS ................................................................................................................6
CONCLUSION ...............................................................................................................................7
REFERENCES................................................................................................................................1
INTRODUCTION ..........................................................................................................................1
MAIN BODY ..................................................................................................................................1
Challenges faced by Executive Holloware in regards with sustainability and growth ...............1
Developing and explaining how would introduce a company wide operations improvement
strategy In Executive Holloware..................................................................................................4
RECOMMENDATIONS ................................................................................................................6
CONCLUSION ...............................................................................................................................7
REFERENCES................................................................................................................................1
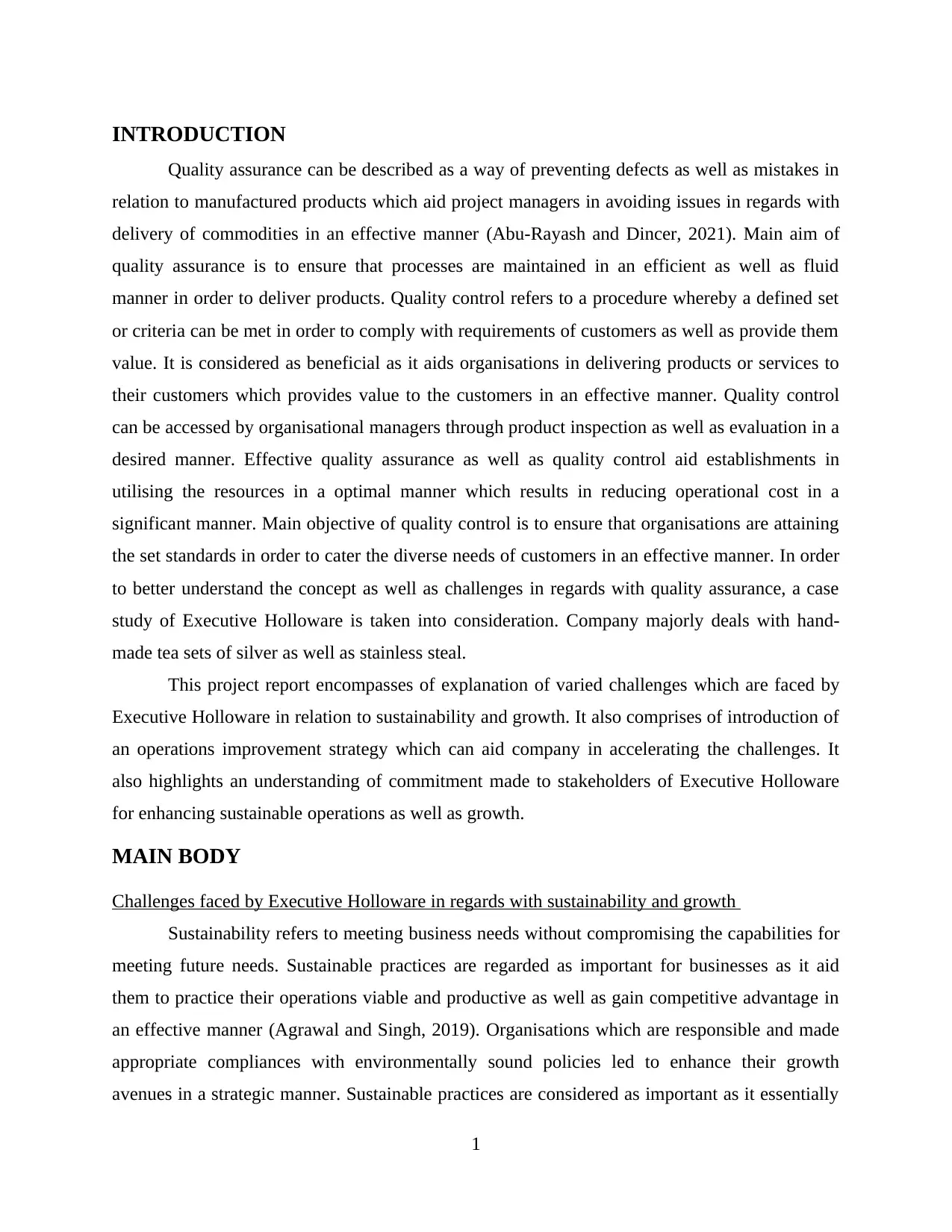
INTRODUCTION
Quality assurance can be described as a way of preventing defects as well as mistakes in
relation to manufactured products which aid project managers in avoiding issues in regards with
delivery of commodities in an effective manner (Abu-Rayash and Dincer, 2021). Main aim of
quality assurance is to ensure that processes are maintained in an efficient as well as fluid
manner in order to deliver products. Quality control refers to a procedure whereby a defined set
or criteria can be met in order to comply with requirements of customers as well as provide them
value. It is considered as beneficial as it aids organisations in delivering products or services to
their customers which provides value to the customers in an effective manner. Quality control
can be accessed by organisational managers through product inspection as well as evaluation in a
desired manner. Effective quality assurance as well as quality control aid establishments in
utilising the resources in a optimal manner which results in reducing operational cost in a
significant manner. Main objective of quality control is to ensure that organisations are attaining
the set standards in order to cater the diverse needs of customers in an effective manner. In order
to better understand the concept as well as challenges in regards with quality assurance, a case
study of Executive Holloware is taken into consideration. Company majorly deals with hand-
made tea sets of silver as well as stainless steal.
This project report encompasses of explanation of varied challenges which are faced by
Executive Holloware in relation to sustainability and growth. It also comprises of introduction of
an operations improvement strategy which can aid company in accelerating the challenges. It
also highlights an understanding of commitment made to stakeholders of Executive Holloware
for enhancing sustainable operations as well as growth.
MAIN BODY
Challenges faced by Executive Holloware in regards with sustainability and growth
Sustainability refers to meeting business needs without compromising the capabilities for
meeting future needs. Sustainable practices are regarded as important for businesses as it aid
them to practice their operations viable and productive as well as gain competitive advantage in
an effective manner (Agrawal and Singh, 2019). Organisations which are responsible and made
appropriate compliances with environmentally sound policies led to enhance their growth
avenues in a strategic manner. Sustainable practices are considered as important as it essentially
1
Quality assurance can be described as a way of preventing defects as well as mistakes in
relation to manufactured products which aid project managers in avoiding issues in regards with
delivery of commodities in an effective manner (Abu-Rayash and Dincer, 2021). Main aim of
quality assurance is to ensure that processes are maintained in an efficient as well as fluid
manner in order to deliver products. Quality control refers to a procedure whereby a defined set
or criteria can be met in order to comply with requirements of customers as well as provide them
value. It is considered as beneficial as it aids organisations in delivering products or services to
their customers which provides value to the customers in an effective manner. Quality control
can be accessed by organisational managers through product inspection as well as evaluation in a
desired manner. Effective quality assurance as well as quality control aid establishments in
utilising the resources in a optimal manner which results in reducing operational cost in a
significant manner. Main objective of quality control is to ensure that organisations are attaining
the set standards in order to cater the diverse needs of customers in an effective manner. In order
to better understand the concept as well as challenges in regards with quality assurance, a case
study of Executive Holloware is taken into consideration. Company majorly deals with hand-
made tea sets of silver as well as stainless steal.
This project report encompasses of explanation of varied challenges which are faced by
Executive Holloware in relation to sustainability and growth. It also comprises of introduction of
an operations improvement strategy which can aid company in accelerating the challenges. It
also highlights an understanding of commitment made to stakeholders of Executive Holloware
for enhancing sustainable operations as well as growth.
MAIN BODY
Challenges faced by Executive Holloware in regards with sustainability and growth
Sustainability refers to meeting business needs without compromising the capabilities for
meeting future needs. Sustainable practices are regarded as important for businesses as it aid
them to practice their operations viable and productive as well as gain competitive advantage in
an effective manner (Agrawal and Singh, 2019). Organisations which are responsible and made
appropriate compliances with environmentally sound policies led to enhance their growth
avenues in a strategic manner. Sustainable practices are considered as important as it essentially
1
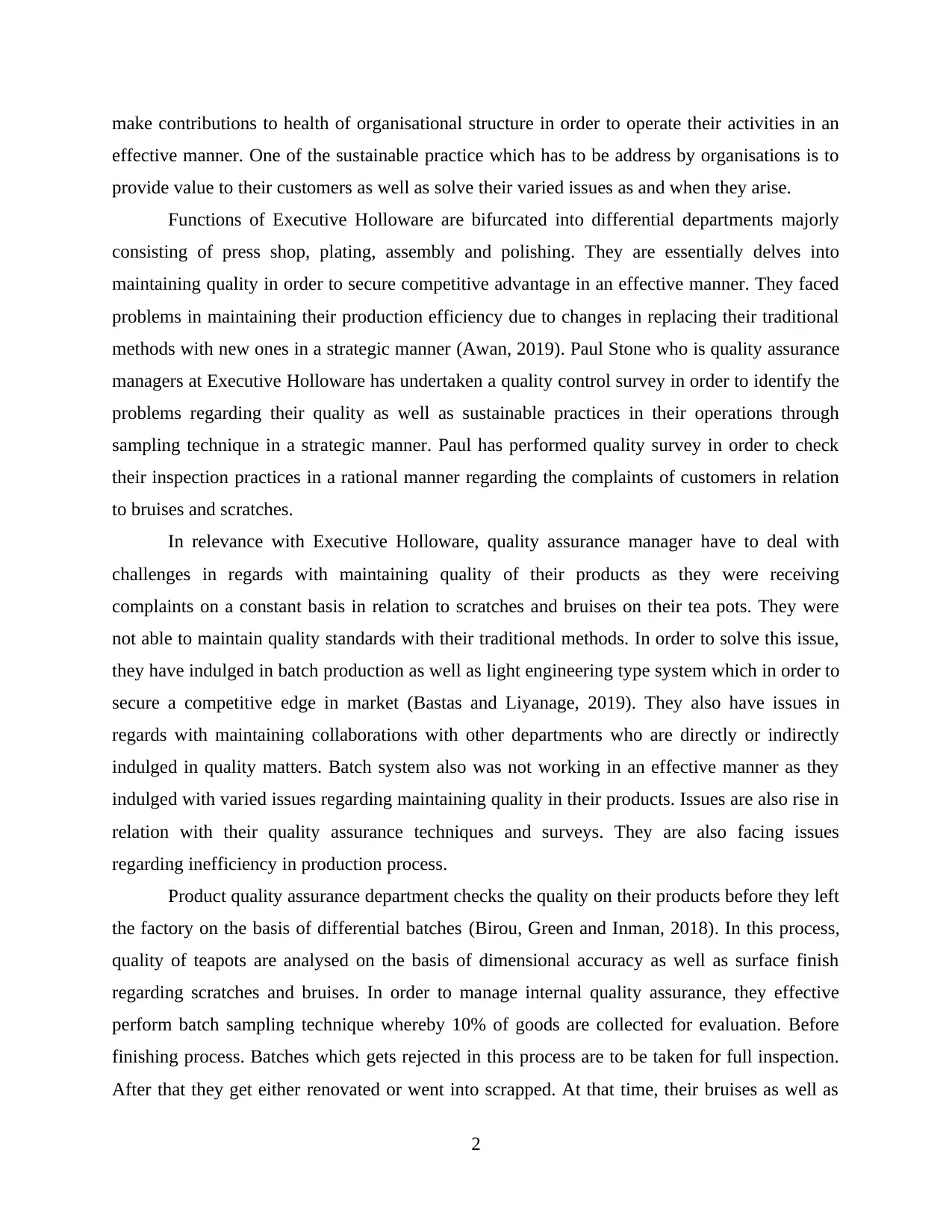
make contributions to health of organisational structure in order to operate their activities in an
effective manner. One of the sustainable practice which has to be address by organisations is to
provide value to their customers as well as solve their varied issues as and when they arise.
Functions of Executive Holloware are bifurcated into differential departments majorly
consisting of press shop, plating, assembly and polishing. They are essentially delves into
maintaining quality in order to secure competitive advantage in an effective manner. They faced
problems in maintaining their production efficiency due to changes in replacing their traditional
methods with new ones in a strategic manner (Awan, 2019). Paul Stone who is quality assurance
managers at Executive Holloware has undertaken a quality control survey in order to identify the
problems regarding their quality as well as sustainable practices in their operations through
sampling technique in a strategic manner. Paul has performed quality survey in order to check
their inspection practices in a rational manner regarding the complaints of customers in relation
to bruises and scratches.
In relevance with Executive Holloware, quality assurance manager have to deal with
challenges in regards with maintaining quality of their products as they were receiving
complaints on a constant basis in relation to scratches and bruises on their tea pots. They were
not able to maintain quality standards with their traditional methods. In order to solve this issue,
they have indulged in batch production as well as light engineering type system which in order to
secure a competitive edge in market (Bastas and Liyanage, 2019). They also have issues in
regards with maintaining collaborations with other departments who are directly or indirectly
indulged in quality matters. Batch system also was not working in an effective manner as they
indulged with varied issues regarding maintaining quality in their products. Issues are also rise in
relation with their quality assurance techniques and surveys. They are also facing issues
regarding inefficiency in production process.
Product quality assurance department checks the quality on their products before they left
the factory on the basis of differential batches (Birou, Green and Inman, 2018). In this process,
quality of teapots are analysed on the basis of dimensional accuracy as well as surface finish
regarding scratches and bruises. In order to manage internal quality assurance, they effective
perform batch sampling technique whereby 10% of goods are collected for evaluation. Before
finishing process. Batches which gets rejected in this process are to be taken for full inspection.
After that they get either renovated or went into scrapped. At that time, their bruises as well as
2
effective manner. One of the sustainable practice which has to be address by organisations is to
provide value to their customers as well as solve their varied issues as and when they arise.
Functions of Executive Holloware are bifurcated into differential departments majorly
consisting of press shop, plating, assembly and polishing. They are essentially delves into
maintaining quality in order to secure competitive advantage in an effective manner. They faced
problems in maintaining their production efficiency due to changes in replacing their traditional
methods with new ones in a strategic manner (Awan, 2019). Paul Stone who is quality assurance
managers at Executive Holloware has undertaken a quality control survey in order to identify the
problems regarding their quality as well as sustainable practices in their operations through
sampling technique in a strategic manner. Paul has performed quality survey in order to check
their inspection practices in a rational manner regarding the complaints of customers in relation
to bruises and scratches.
In relevance with Executive Holloware, quality assurance manager have to deal with
challenges in regards with maintaining quality of their products as they were receiving
complaints on a constant basis in relation to scratches and bruises on their tea pots. They were
not able to maintain quality standards with their traditional methods. In order to solve this issue,
they have indulged in batch production as well as light engineering type system which in order to
secure a competitive edge in market (Bastas and Liyanage, 2019). They also have issues in
regards with maintaining collaborations with other departments who are directly or indirectly
indulged in quality matters. Batch system also was not working in an effective manner as they
indulged with varied issues regarding maintaining quality in their products. Issues are also rise in
relation with their quality assurance techniques and surveys. They are also facing issues
regarding inefficiency in production process.
Product quality assurance department checks the quality on their products before they left
the factory on the basis of differential batches (Birou, Green and Inman, 2018). In this process,
quality of teapots are analysed on the basis of dimensional accuracy as well as surface finish
regarding scratches and bruises. In order to manage internal quality assurance, they effective
perform batch sampling technique whereby 10% of goods are collected for evaluation. Before
finishing process. Batches which gets rejected in this process are to be taken for full inspection.
After that they get either renovated or went into scrapped. At that time, their bruises as well as
2
Secure Best Marks with AI Grader
Need help grading? Try our AI Grader for instant feedback on your assignments.
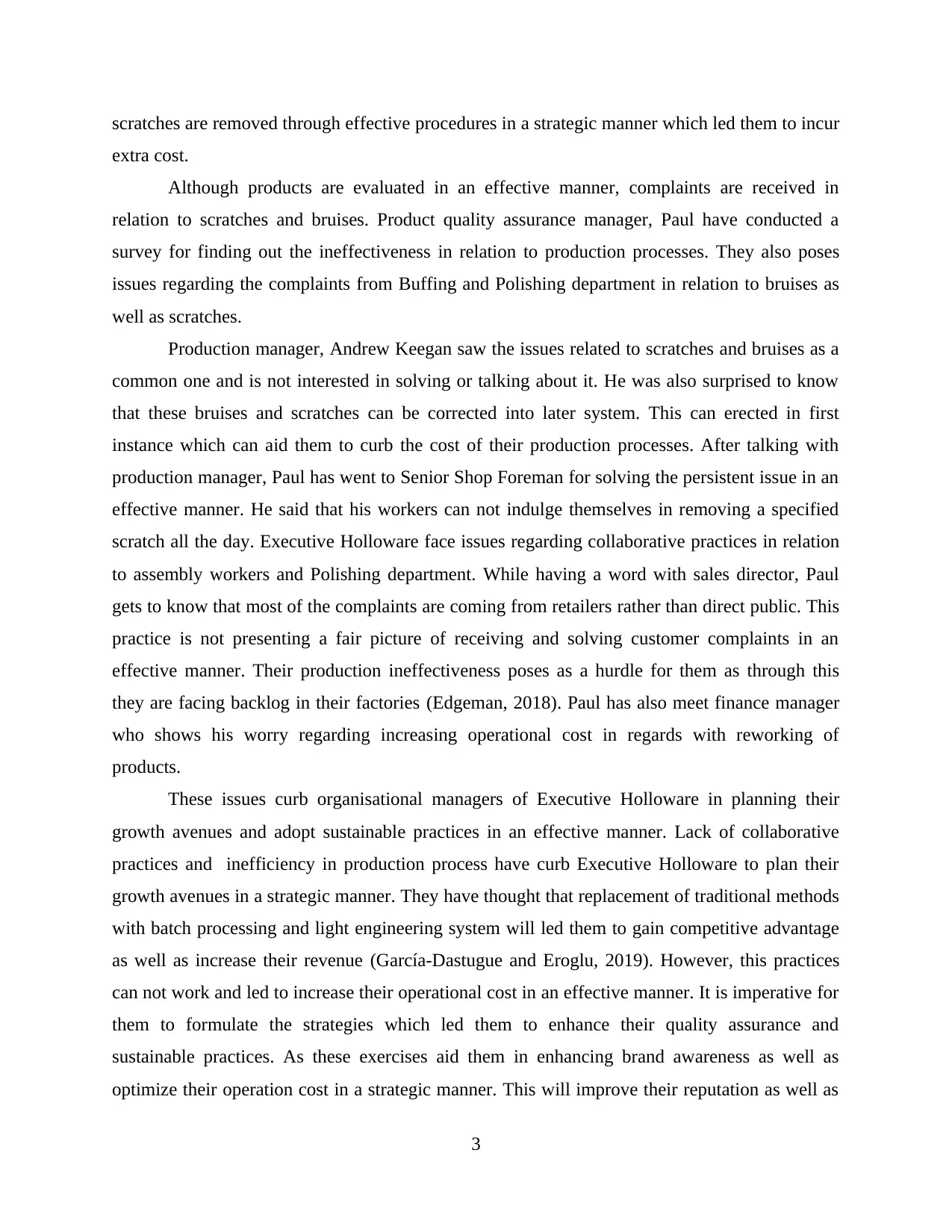
scratches are removed through effective procedures in a strategic manner which led them to incur
extra cost.
Although products are evaluated in an effective manner, complaints are received in
relation to scratches and bruises. Product quality assurance manager, Paul have conducted a
survey for finding out the ineffectiveness in relation to production processes. They also poses
issues regarding the complaints from Buffing and Polishing department in relation to bruises as
well as scratches.
Production manager, Andrew Keegan saw the issues related to scratches and bruises as a
common one and is not interested in solving or talking about it. He was also surprised to know
that these bruises and scratches can be corrected into later system. This can erected in first
instance which can aid them to curb the cost of their production processes. After talking with
production manager, Paul has went to Senior Shop Foreman for solving the persistent issue in an
effective manner. He said that his workers can not indulge themselves in removing a specified
scratch all the day. Executive Holloware face issues regarding collaborative practices in relation
to assembly workers and Polishing department. While having a word with sales director, Paul
gets to know that most of the complaints are coming from retailers rather than direct public. This
practice is not presenting a fair picture of receiving and solving customer complaints in an
effective manner. Their production ineffectiveness poses as a hurdle for them as through this
they are facing backlog in their factories (Edgeman, 2018). Paul has also meet finance manager
who shows his worry regarding increasing operational cost in regards with reworking of
products.
These issues curb organisational managers of Executive Holloware in planning their
growth avenues and adopt sustainable practices in an effective manner. Lack of collaborative
practices and inefficiency in production process have curb Executive Holloware to plan their
growth avenues in a strategic manner. They have thought that replacement of traditional methods
with batch processing and light engineering system will led them to gain competitive advantage
as well as increase their revenue (García‐Dastugue and Eroglu, 2019). However, this practices
can not work and led to increase their operational cost in an effective manner. It is imperative for
them to formulate the strategies which led them to enhance their quality assurance and
sustainable practices. As these exercises aid them in enhancing brand awareness as well as
optimize their operation cost in a strategic manner. This will improve their reputation as well as
3
extra cost.
Although products are evaluated in an effective manner, complaints are received in
relation to scratches and bruises. Product quality assurance manager, Paul have conducted a
survey for finding out the ineffectiveness in relation to production processes. They also poses
issues regarding the complaints from Buffing and Polishing department in relation to bruises as
well as scratches.
Production manager, Andrew Keegan saw the issues related to scratches and bruises as a
common one and is not interested in solving or talking about it. He was also surprised to know
that these bruises and scratches can be corrected into later system. This can erected in first
instance which can aid them to curb the cost of their production processes. After talking with
production manager, Paul has went to Senior Shop Foreman for solving the persistent issue in an
effective manner. He said that his workers can not indulge themselves in removing a specified
scratch all the day. Executive Holloware face issues regarding collaborative practices in relation
to assembly workers and Polishing department. While having a word with sales director, Paul
gets to know that most of the complaints are coming from retailers rather than direct public. This
practice is not presenting a fair picture of receiving and solving customer complaints in an
effective manner. Their production ineffectiveness poses as a hurdle for them as through this
they are facing backlog in their factories (Edgeman, 2018). Paul has also meet finance manager
who shows his worry regarding increasing operational cost in regards with reworking of
products.
These issues curb organisational managers of Executive Holloware in planning their
growth avenues and adopt sustainable practices in an effective manner. Lack of collaborative
practices and inefficiency in production process have curb Executive Holloware to plan their
growth avenues in a strategic manner. They have thought that replacement of traditional methods
with batch processing and light engineering system will led them to gain competitive advantage
as well as increase their revenue (García‐Dastugue and Eroglu, 2019). However, this practices
can not work and led to increase their operational cost in an effective manner. It is imperative for
them to formulate the strategies which led them to enhance their quality assurance and
sustainable practices. As these exercises aid them in enhancing brand awareness as well as
optimize their operation cost in a strategic manner. This will improve their reputation as well as
3
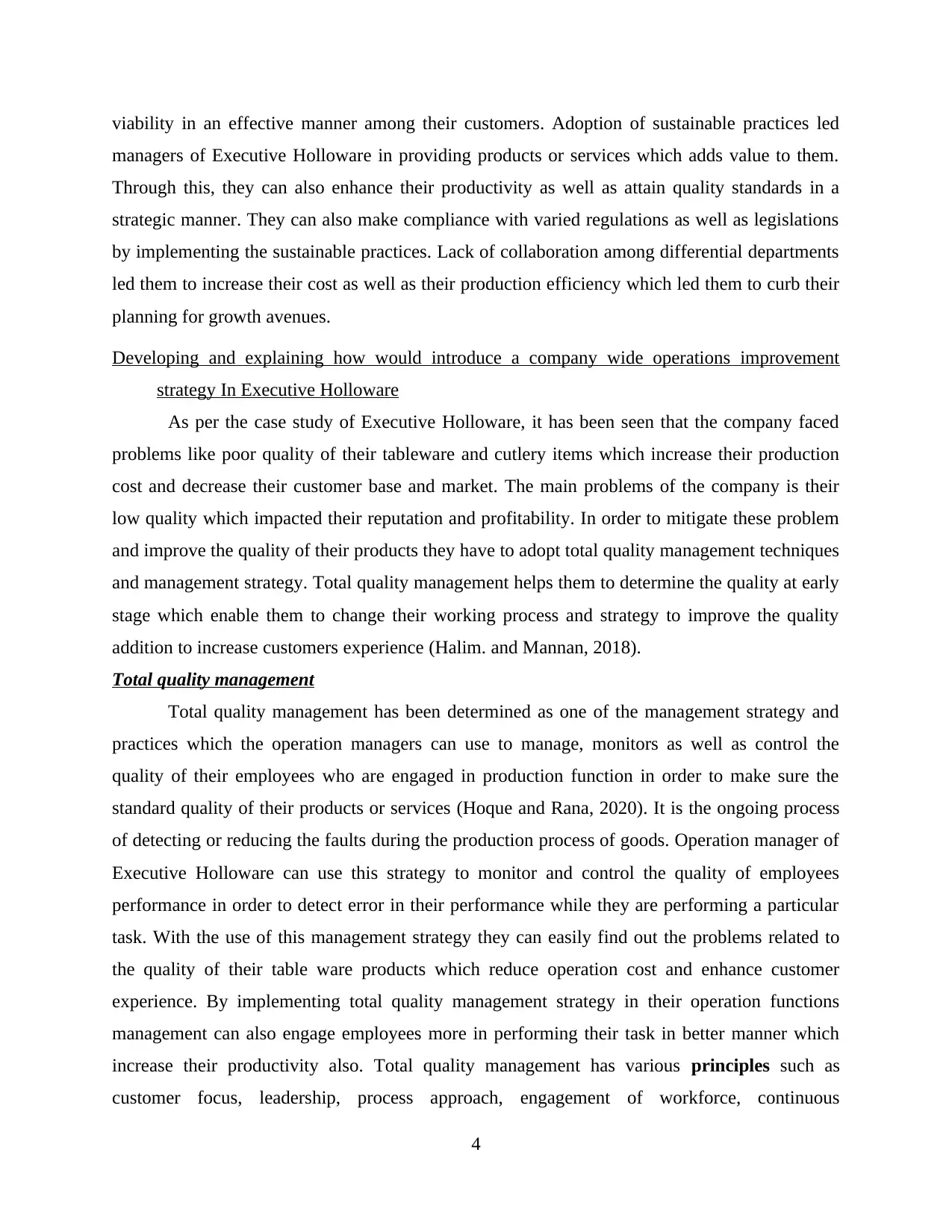
viability in an effective manner among their customers. Adoption of sustainable practices led
managers of Executive Holloware in providing products or services which adds value to them.
Through this, they can also enhance their productivity as well as attain quality standards in a
strategic manner. They can also make compliance with varied regulations as well as legislations
by implementing the sustainable practices. Lack of collaboration among differential departments
led them to increase their cost as well as their production efficiency which led them to curb their
planning for growth avenues.
Developing and explaining how would introduce a company wide operations improvement
strategy In Executive Holloware
As per the case study of Executive Holloware, it has been seen that the company faced
problems like poor quality of their tableware and cutlery items which increase their production
cost and decrease their customer base and market. The main problems of the company is their
low quality which impacted their reputation and profitability. In order to mitigate these problem
and improve the quality of their products they have to adopt total quality management techniques
and management strategy. Total quality management helps them to determine the quality at early
stage which enable them to change their working process and strategy to improve the quality
addition to increase customers experience (Halim. and Mannan, 2018).
Total quality management
Total quality management has been determined as one of the management strategy and
practices which the operation managers can use to manage, monitors as well as control the
quality of their employees who are engaged in production function in order to make sure the
standard quality of their products or services (Hoque and Rana, 2020). It is the ongoing process
of detecting or reducing the faults during the production process of goods. Operation manager of
Executive Holloware can use this strategy to monitor and control the quality of employees
performance in order to detect error in their performance while they are performing a particular
task. With the use of this management strategy they can easily find out the problems related to
the quality of their table ware products which reduce operation cost and enhance customer
experience. By implementing total quality management strategy in their operation functions
management can also engage employees more in performing their task in better manner which
increase their productivity also. Total quality management has various principles such as
customer focus, leadership, process approach, engagement of workforce, continuous
4
managers of Executive Holloware in providing products or services which adds value to them.
Through this, they can also enhance their productivity as well as attain quality standards in a
strategic manner. They can also make compliance with varied regulations as well as legislations
by implementing the sustainable practices. Lack of collaboration among differential departments
led them to increase their cost as well as their production efficiency which led them to curb their
planning for growth avenues.
Developing and explaining how would introduce a company wide operations improvement
strategy In Executive Holloware
As per the case study of Executive Holloware, it has been seen that the company faced
problems like poor quality of their tableware and cutlery items which increase their production
cost and decrease their customer base and market. The main problems of the company is their
low quality which impacted their reputation and profitability. In order to mitigate these problem
and improve the quality of their products they have to adopt total quality management techniques
and management strategy. Total quality management helps them to determine the quality at early
stage which enable them to change their working process and strategy to improve the quality
addition to increase customers experience (Halim. and Mannan, 2018).
Total quality management
Total quality management has been determined as one of the management strategy and
practices which the operation managers can use to manage, monitors as well as control the
quality of their employees who are engaged in production function in order to make sure the
standard quality of their products or services (Hoque and Rana, 2020). It is the ongoing process
of detecting or reducing the faults during the production process of goods. Operation manager of
Executive Holloware can use this strategy to monitor and control the quality of employees
performance in order to detect error in their performance while they are performing a particular
task. With the use of this management strategy they can easily find out the problems related to
the quality of their table ware products which reduce operation cost and enhance customer
experience. By implementing total quality management strategy in their operation functions
management can also engage employees more in performing their task in better manner which
increase their productivity also. Total quality management has various principles such as
customer focus, leadership, process approach, engagement of workforce, continuous
4
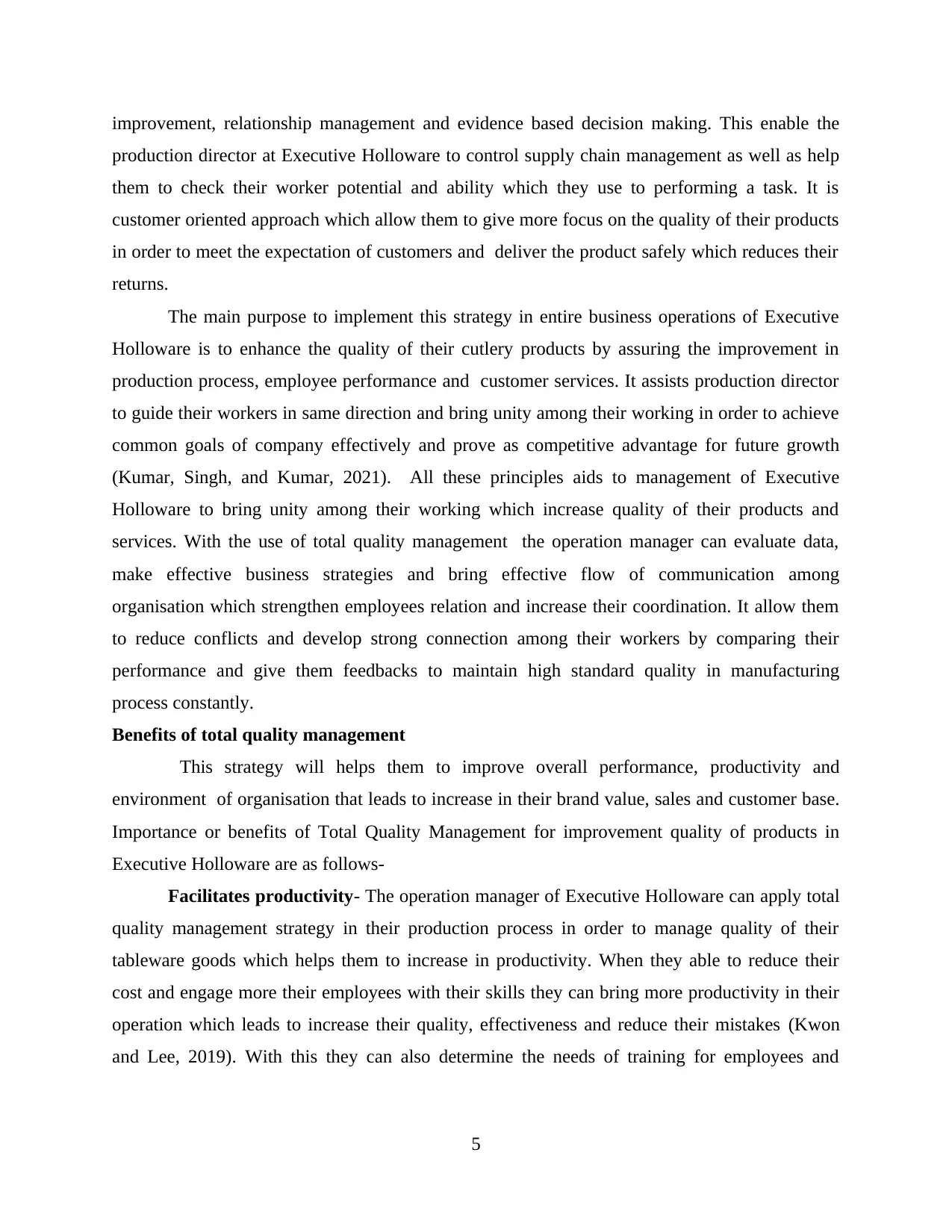
improvement, relationship management and evidence based decision making. This enable the
production director at Executive Holloware to control supply chain management as well as help
them to check their worker potential and ability which they use to performing a task. It is
customer oriented approach which allow them to give more focus on the quality of their products
in order to meet the expectation of customers and deliver the product safely which reduces their
returns.
The main purpose to implement this strategy in entire business operations of Executive
Holloware is to enhance the quality of their cutlery products by assuring the improvement in
production process, employee performance and customer services. It assists production director
to guide their workers in same direction and bring unity among their working in order to achieve
common goals of company effectively and prove as competitive advantage for future growth
(Kumar, Singh, and Kumar, 2021). All these principles aids to management of Executive
Holloware to bring unity among their working which increase quality of their products and
services. With the use of total quality management the operation manager can evaluate data,
make effective business strategies and bring effective flow of communication among
organisation which strengthen employees relation and increase their coordination. It allow them
to reduce conflicts and develop strong connection among their workers by comparing their
performance and give them feedbacks to maintain high standard quality in manufacturing
process constantly.
Benefits of total quality management
This strategy will helps them to improve overall performance, productivity and
environment of organisation that leads to increase in their brand value, sales and customer base.
Importance or benefits of Total Quality Management for improvement quality of products in
Executive Holloware are as follows-
Facilitates productivity- The operation manager of Executive Holloware can apply total
quality management strategy in their production process in order to manage quality of their
tableware goods which helps them to increase in productivity. When they able to reduce their
cost and engage more their employees with their skills they can bring more productivity in their
operation which leads to increase their quality, effectiveness and reduce their mistakes (Kwon
and Lee, 2019). With this they can also determine the needs of training for employees and
5
production director at Executive Holloware to control supply chain management as well as help
them to check their worker potential and ability which they use to performing a task. It is
customer oriented approach which allow them to give more focus on the quality of their products
in order to meet the expectation of customers and deliver the product safely which reduces their
returns.
The main purpose to implement this strategy in entire business operations of Executive
Holloware is to enhance the quality of their cutlery products by assuring the improvement in
production process, employee performance and customer services. It assists production director
to guide their workers in same direction and bring unity among their working in order to achieve
common goals of company effectively and prove as competitive advantage for future growth
(Kumar, Singh, and Kumar, 2021). All these principles aids to management of Executive
Holloware to bring unity among their working which increase quality of their products and
services. With the use of total quality management the operation manager can evaluate data,
make effective business strategies and bring effective flow of communication among
organisation which strengthen employees relation and increase their coordination. It allow them
to reduce conflicts and develop strong connection among their workers by comparing their
performance and give them feedbacks to maintain high standard quality in manufacturing
process constantly.
Benefits of total quality management
This strategy will helps them to improve overall performance, productivity and
environment of organisation that leads to increase in their brand value, sales and customer base.
Importance or benefits of Total Quality Management for improvement quality of products in
Executive Holloware are as follows-
Facilitates productivity- The operation manager of Executive Holloware can apply total
quality management strategy in their production process in order to manage quality of their
tableware goods which helps them to increase in productivity. When they able to reduce their
cost and engage more their employees with their skills they can bring more productivity in their
operation which leads to increase their quality, effectiveness and reduce their mistakes (Kwon
and Lee, 2019). With this they can also determine the needs of training for employees and
5
Paraphrase This Document
Need a fresh take? Get an instant paraphrase of this document with our AI Paraphraser
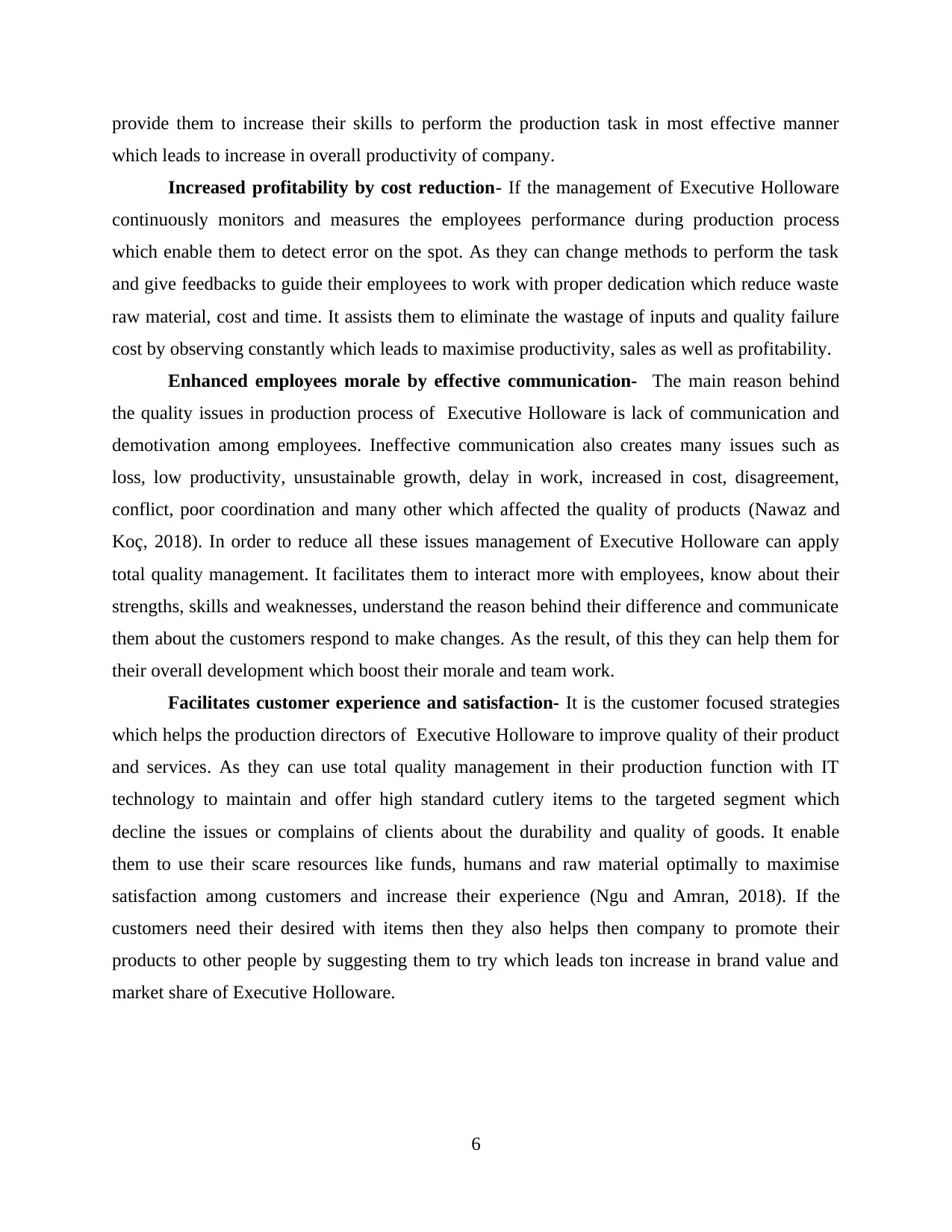
provide them to increase their skills to perform the production task in most effective manner
which leads to increase in overall productivity of company.
Increased profitability by cost reduction- If the management of Executive Holloware
continuously monitors and measures the employees performance during production process
which enable them to detect error on the spot. As they can change methods to perform the task
and give feedbacks to guide their employees to work with proper dedication which reduce waste
raw material, cost and time. It assists them to eliminate the wastage of inputs and quality failure
cost by observing constantly which leads to maximise productivity, sales as well as profitability.
Enhanced employees morale by effective communication- The main reason behind
the quality issues in production process of Executive Holloware is lack of communication and
demotivation among employees. Ineffective communication also creates many issues such as
loss, low productivity, unsustainable growth, delay in work, increased in cost, disagreement,
conflict, poor coordination and many other which affected the quality of products (Nawaz and
Koç, 2018). In order to reduce all these issues management of Executive Holloware can apply
total quality management. It facilitates them to interact more with employees, know about their
strengths, skills and weaknesses, understand the reason behind their difference and communicate
them about the customers respond to make changes. As the result, of this they can help them for
their overall development which boost their morale and team work.
Facilitates customer experience and satisfaction- It is the customer focused strategies
which helps the production directors of Executive Holloware to improve quality of their product
and services. As they can use total quality management in their production function with IT
technology to maintain and offer high standard cutlery items to the targeted segment which
decline the issues or complains of clients about the durability and quality of goods. It enable
them to use their scare resources like funds, humans and raw material optimally to maximise
satisfaction among customers and increase their experience (Ngu and Amran, 2018). If the
customers need their desired with items then they also helps then company to promote their
products to other people by suggesting them to try which leads ton increase in brand value and
market share of Executive Holloware.
6
which leads to increase in overall productivity of company.
Increased profitability by cost reduction- If the management of Executive Holloware
continuously monitors and measures the employees performance during production process
which enable them to detect error on the spot. As they can change methods to perform the task
and give feedbacks to guide their employees to work with proper dedication which reduce waste
raw material, cost and time. It assists them to eliminate the wastage of inputs and quality failure
cost by observing constantly which leads to maximise productivity, sales as well as profitability.
Enhanced employees morale by effective communication- The main reason behind
the quality issues in production process of Executive Holloware is lack of communication and
demotivation among employees. Ineffective communication also creates many issues such as
loss, low productivity, unsustainable growth, delay in work, increased in cost, disagreement,
conflict, poor coordination and many other which affected the quality of products (Nawaz and
Koç, 2018). In order to reduce all these issues management of Executive Holloware can apply
total quality management. It facilitates them to interact more with employees, know about their
strengths, skills and weaknesses, understand the reason behind their difference and communicate
them about the customers respond to make changes. As the result, of this they can help them for
their overall development which boost their morale and team work.
Facilitates customer experience and satisfaction- It is the customer focused strategies
which helps the production directors of Executive Holloware to improve quality of their product
and services. As they can use total quality management in their production function with IT
technology to maintain and offer high standard cutlery items to the targeted segment which
decline the issues or complains of clients about the durability and quality of goods. It enable
them to use their scare resources like funds, humans and raw material optimally to maximise
satisfaction among customers and increase their experience (Ngu and Amran, 2018). If the
customers need their desired with items then they also helps then company to promote their
products to other people by suggesting them to try which leads ton increase in brand value and
market share of Executive Holloware.
6
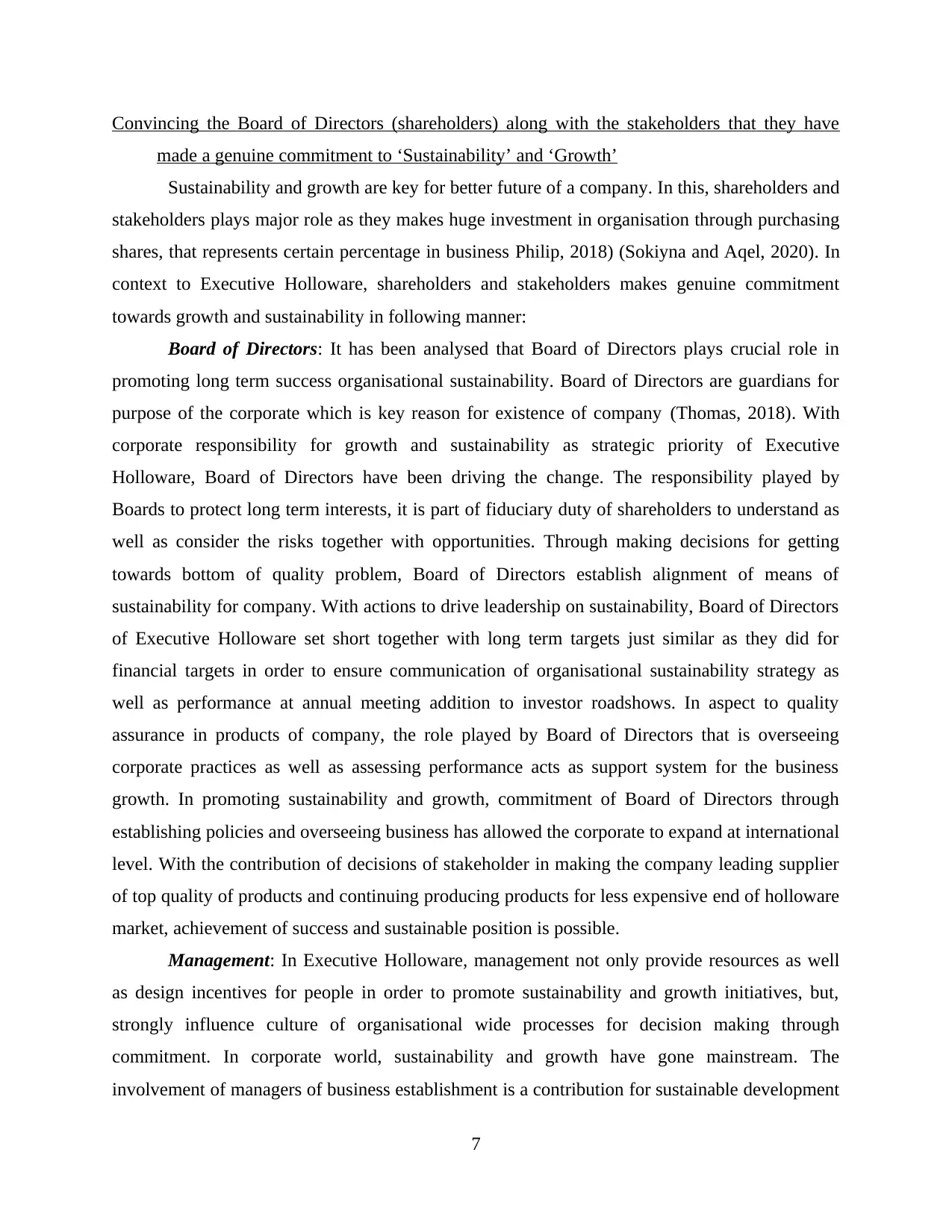
Convincing the Board of Directors (shareholders) along with the stakeholders that they have
made a genuine commitment to ‘Sustainability’ and ‘Growth’
Sustainability and growth are key for better future of a company. In this, shareholders and
stakeholders plays major role as they makes huge investment in organisation through purchasing
shares, that represents certain percentage in business Philip, 2018) (Sokiyna and Aqel, 2020). In
context to Executive Holloware, shareholders and stakeholders makes genuine commitment
towards growth and sustainability in following manner:
Board of Directors: It has been analysed that Board of Directors plays crucial role in
promoting long term success organisational sustainability. Board of Directors are guardians for
purpose of the corporate which is key reason for existence of company (Thomas, 2018). With
corporate responsibility for growth and sustainability as strategic priority of Executive
Holloware, Board of Directors have been driving the change. The responsibility played by
Boards to protect long term interests, it is part of fiduciary duty of shareholders to understand as
well as consider the risks together with opportunities. Through making decisions for getting
towards bottom of quality problem, Board of Directors establish alignment of means of
sustainability for company. With actions to drive leadership on sustainability, Board of Directors
of Executive Holloware set short together with long term targets just similar as they did for
financial targets in order to ensure communication of organisational sustainability strategy as
well as performance at annual meeting addition to investor roadshows. In aspect to quality
assurance in products of company, the role played by Board of Directors that is overseeing
corporate practices as well as assessing performance acts as support system for the business
growth. In promoting sustainability and growth, commitment of Board of Directors through
establishing policies and overseeing business has allowed the corporate to expand at international
level. With the contribution of decisions of stakeholder in making the company leading supplier
of top quality of products and continuing producing products for less expensive end of holloware
market, achievement of success and sustainable position is possible.
Management: In Executive Holloware, management not only provide resources as well
as design incentives for people in order to promote sustainability and growth initiatives, but,
strongly influence culture of organisational wide processes for decision making through
commitment. In corporate world, sustainability and growth have gone mainstream. The
involvement of managers of business establishment is a contribution for sustainable development
7
made a genuine commitment to ‘Sustainability’ and ‘Growth’
Sustainability and growth are key for better future of a company. In this, shareholders and
stakeholders plays major role as they makes huge investment in organisation through purchasing
shares, that represents certain percentage in business Philip, 2018) (Sokiyna and Aqel, 2020). In
context to Executive Holloware, shareholders and stakeholders makes genuine commitment
towards growth and sustainability in following manner:
Board of Directors: It has been analysed that Board of Directors plays crucial role in
promoting long term success organisational sustainability. Board of Directors are guardians for
purpose of the corporate which is key reason for existence of company (Thomas, 2018). With
corporate responsibility for growth and sustainability as strategic priority of Executive
Holloware, Board of Directors have been driving the change. The responsibility played by
Boards to protect long term interests, it is part of fiduciary duty of shareholders to understand as
well as consider the risks together with opportunities. Through making decisions for getting
towards bottom of quality problem, Board of Directors establish alignment of means of
sustainability for company. With actions to drive leadership on sustainability, Board of Directors
of Executive Holloware set short together with long term targets just similar as they did for
financial targets in order to ensure communication of organisational sustainability strategy as
well as performance at annual meeting addition to investor roadshows. In aspect to quality
assurance in products of company, the role played by Board of Directors that is overseeing
corporate practices as well as assessing performance acts as support system for the business
growth. In promoting sustainability and growth, commitment of Board of Directors through
establishing policies and overseeing business has allowed the corporate to expand at international
level. With the contribution of decisions of stakeholder in making the company leading supplier
of top quality of products and continuing producing products for less expensive end of holloware
market, achievement of success and sustainable position is possible.
Management: In Executive Holloware, management not only provide resources as well
as design incentives for people in order to promote sustainability and growth initiatives, but,
strongly influence culture of organisational wide processes for decision making through
commitment. In corporate world, sustainability and growth have gone mainstream. The
involvement of managers of business establishment is a contribution for sustainable development
7
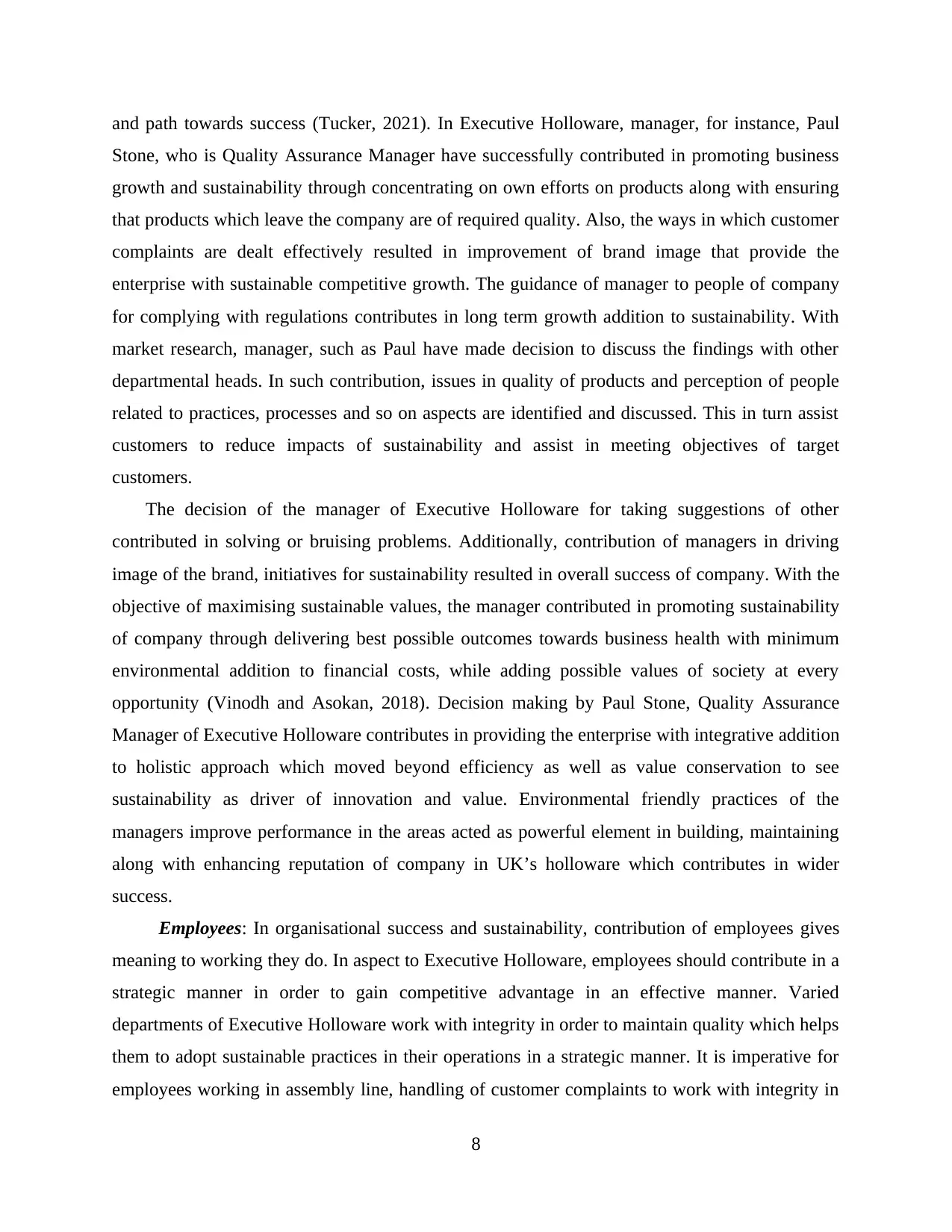
and path towards success (Tucker, 2021). In Executive Holloware, manager, for instance, Paul
Stone, who is Quality Assurance Manager have successfully contributed in promoting business
growth and sustainability through concentrating on own efforts on products along with ensuring
that products which leave the company are of required quality. Also, the ways in which customer
complaints are dealt effectively resulted in improvement of brand image that provide the
enterprise with sustainable competitive growth. The guidance of manager to people of company
for complying with regulations contributes in long term growth addition to sustainability. With
market research, manager, such as Paul have made decision to discuss the findings with other
departmental heads. In such contribution, issues in quality of products and perception of people
related to practices, processes and so on aspects are identified and discussed. This in turn assist
customers to reduce impacts of sustainability and assist in meeting objectives of target
customers.
The decision of the manager of Executive Holloware for taking suggestions of other
contributed in solving or bruising problems. Additionally, contribution of managers in driving
image of the brand, initiatives for sustainability resulted in overall success of company. With the
objective of maximising sustainable values, the manager contributed in promoting sustainability
of company through delivering best possible outcomes towards business health with minimum
environmental addition to financial costs, while adding possible values of society at every
opportunity (Vinodh and Asokan, 2018). Decision making by Paul Stone, Quality Assurance
Manager of Executive Holloware contributes in providing the enterprise with integrative addition
to holistic approach which moved beyond efficiency as well as value conservation to see
sustainability as driver of innovation and value. Environmental friendly practices of the
managers improve performance in the areas acted as powerful element in building, maintaining
along with enhancing reputation of company in UK’s holloware which contributes in wider
success.
Employees: In organisational success and sustainability, contribution of employees gives
meaning to working they do. In aspect to Executive Holloware, employees should contribute in a
strategic manner in order to gain competitive advantage in an effective manner. Varied
departments of Executive Holloware work with integrity in order to maintain quality which helps
them to adopt sustainable practices in their operations in a strategic manner. It is imperative for
employees working in assembly line, handling of customer complaints to work with integrity in
8
Stone, who is Quality Assurance Manager have successfully contributed in promoting business
growth and sustainability through concentrating on own efforts on products along with ensuring
that products which leave the company are of required quality. Also, the ways in which customer
complaints are dealt effectively resulted in improvement of brand image that provide the
enterprise with sustainable competitive growth. The guidance of manager to people of company
for complying with regulations contributes in long term growth addition to sustainability. With
market research, manager, such as Paul have made decision to discuss the findings with other
departmental heads. In such contribution, issues in quality of products and perception of people
related to practices, processes and so on aspects are identified and discussed. This in turn assist
customers to reduce impacts of sustainability and assist in meeting objectives of target
customers.
The decision of the manager of Executive Holloware for taking suggestions of other
contributed in solving or bruising problems. Additionally, contribution of managers in driving
image of the brand, initiatives for sustainability resulted in overall success of company. With the
objective of maximising sustainable values, the manager contributed in promoting sustainability
of company through delivering best possible outcomes towards business health with minimum
environmental addition to financial costs, while adding possible values of society at every
opportunity (Vinodh and Asokan, 2018). Decision making by Paul Stone, Quality Assurance
Manager of Executive Holloware contributes in providing the enterprise with integrative addition
to holistic approach which moved beyond efficiency as well as value conservation to see
sustainability as driver of innovation and value. Environmental friendly practices of the
managers improve performance in the areas acted as powerful element in building, maintaining
along with enhancing reputation of company in UK’s holloware which contributes in wider
success.
Employees: In organisational success and sustainability, contribution of employees gives
meaning to working they do. In aspect to Executive Holloware, employees should contribute in a
strategic manner in order to gain competitive advantage in an effective manner. Varied
departments of Executive Holloware work with integrity in order to maintain quality which helps
them to adopt sustainable practices in their operations in a strategic manner. It is imperative for
employees working in assembly line, handling of customer complaints to work with integrity in
8
Secure Best Marks with AI Grader
Need help grading? Try our AI Grader for instant feedback on your assignments.
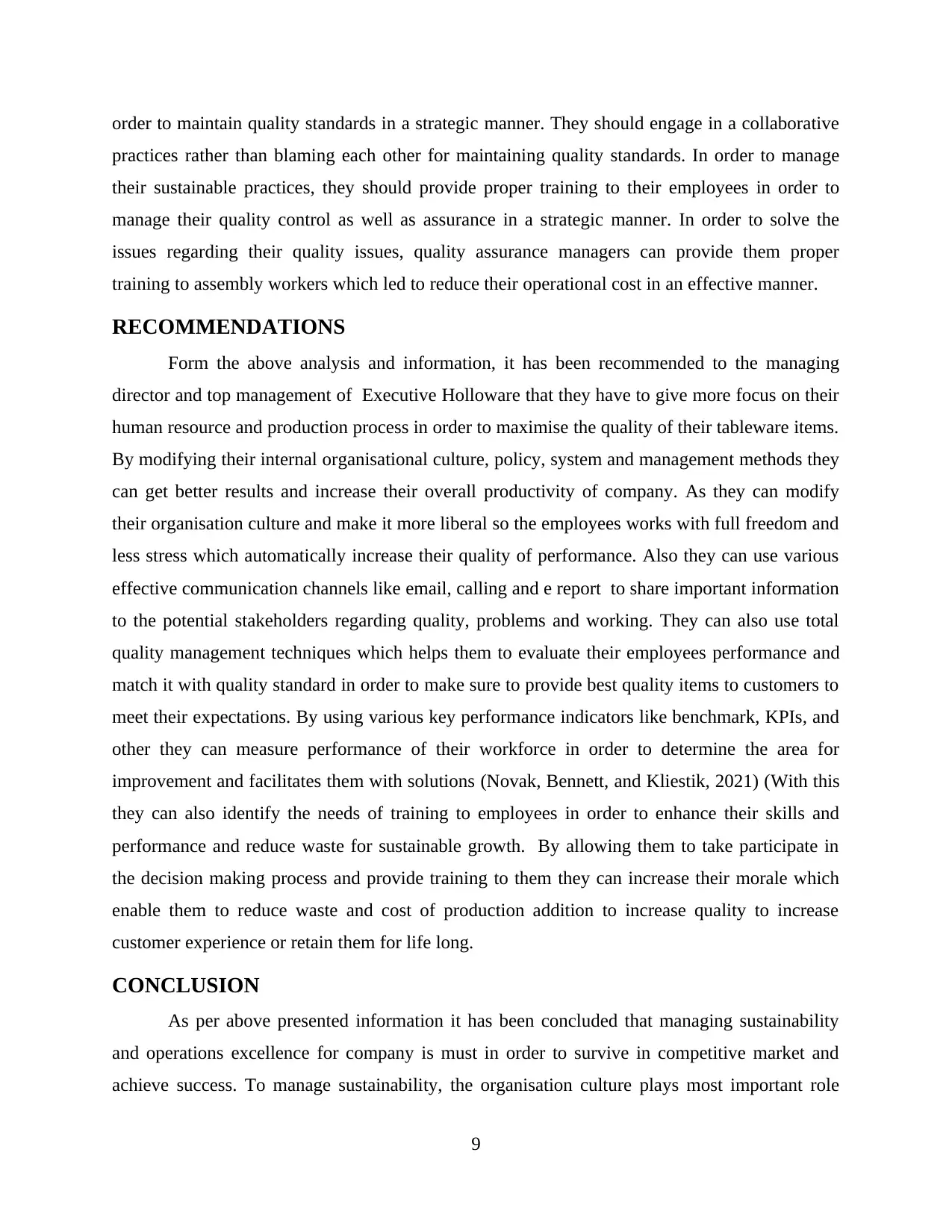
order to maintain quality standards in a strategic manner. They should engage in a collaborative
practices rather than blaming each other for maintaining quality standards. In order to manage
their sustainable practices, they should provide proper training to their employees in order to
manage their quality control as well as assurance in a strategic manner. In order to solve the
issues regarding their quality issues, quality assurance managers can provide them proper
training to assembly workers which led to reduce their operational cost in an effective manner.
RECOMMENDATIONS
Form the above analysis and information, it has been recommended to the managing
director and top management of Executive Holloware that they have to give more focus on their
human resource and production process in order to maximise the quality of their tableware items.
By modifying their internal organisational culture, policy, system and management methods they
can get better results and increase their overall productivity of company. As they can modify
their organisation culture and make it more liberal so the employees works with full freedom and
less stress which automatically increase their quality of performance. Also they can use various
effective communication channels like email, calling and e report to share important information
to the potential stakeholders regarding quality, problems and working. They can also use total
quality management techniques which helps them to evaluate their employees performance and
match it with quality standard in order to make sure to provide best quality items to customers to
meet their expectations. By using various key performance indicators like benchmark, KPIs, and
other they can measure performance of their workforce in order to determine the area for
improvement and facilitates them with solutions (Novak, Bennett, and Kliestik, 2021) (With this
they can also identify the needs of training to employees in order to enhance their skills and
performance and reduce waste for sustainable growth. By allowing them to take participate in
the decision making process and provide training to them they can increase their morale which
enable them to reduce waste and cost of production addition to increase quality to increase
customer experience or retain them for life long.
CONCLUSION
As per above presented information it has been concluded that managing sustainability
and operations excellence for company is must in order to survive in competitive market and
achieve success. To manage sustainability, the organisation culture plays most important role
9
practices rather than blaming each other for maintaining quality standards. In order to manage
their sustainable practices, they should provide proper training to their employees in order to
manage their quality control as well as assurance in a strategic manner. In order to solve the
issues regarding their quality issues, quality assurance managers can provide them proper
training to assembly workers which led to reduce their operational cost in an effective manner.
RECOMMENDATIONS
Form the above analysis and information, it has been recommended to the managing
director and top management of Executive Holloware that they have to give more focus on their
human resource and production process in order to maximise the quality of their tableware items.
By modifying their internal organisational culture, policy, system and management methods they
can get better results and increase their overall productivity of company. As they can modify
their organisation culture and make it more liberal so the employees works with full freedom and
less stress which automatically increase their quality of performance. Also they can use various
effective communication channels like email, calling and e report to share important information
to the potential stakeholders regarding quality, problems and working. They can also use total
quality management techniques which helps them to evaluate their employees performance and
match it with quality standard in order to make sure to provide best quality items to customers to
meet their expectations. By using various key performance indicators like benchmark, KPIs, and
other they can measure performance of their workforce in order to determine the area for
improvement and facilitates them with solutions (Novak, Bennett, and Kliestik, 2021) (With this
they can also identify the needs of training to employees in order to enhance their skills and
performance and reduce waste for sustainable growth. By allowing them to take participate in
the decision making process and provide training to them they can increase their morale which
enable them to reduce waste and cost of production addition to increase quality to increase
customer experience or retain them for life long.
CONCLUSION
As per above presented information it has been concluded that managing sustainability
and operations excellence for company is must in order to survive in competitive market and
achieve success. To manage sustainability, the organisation culture plays most important role
9
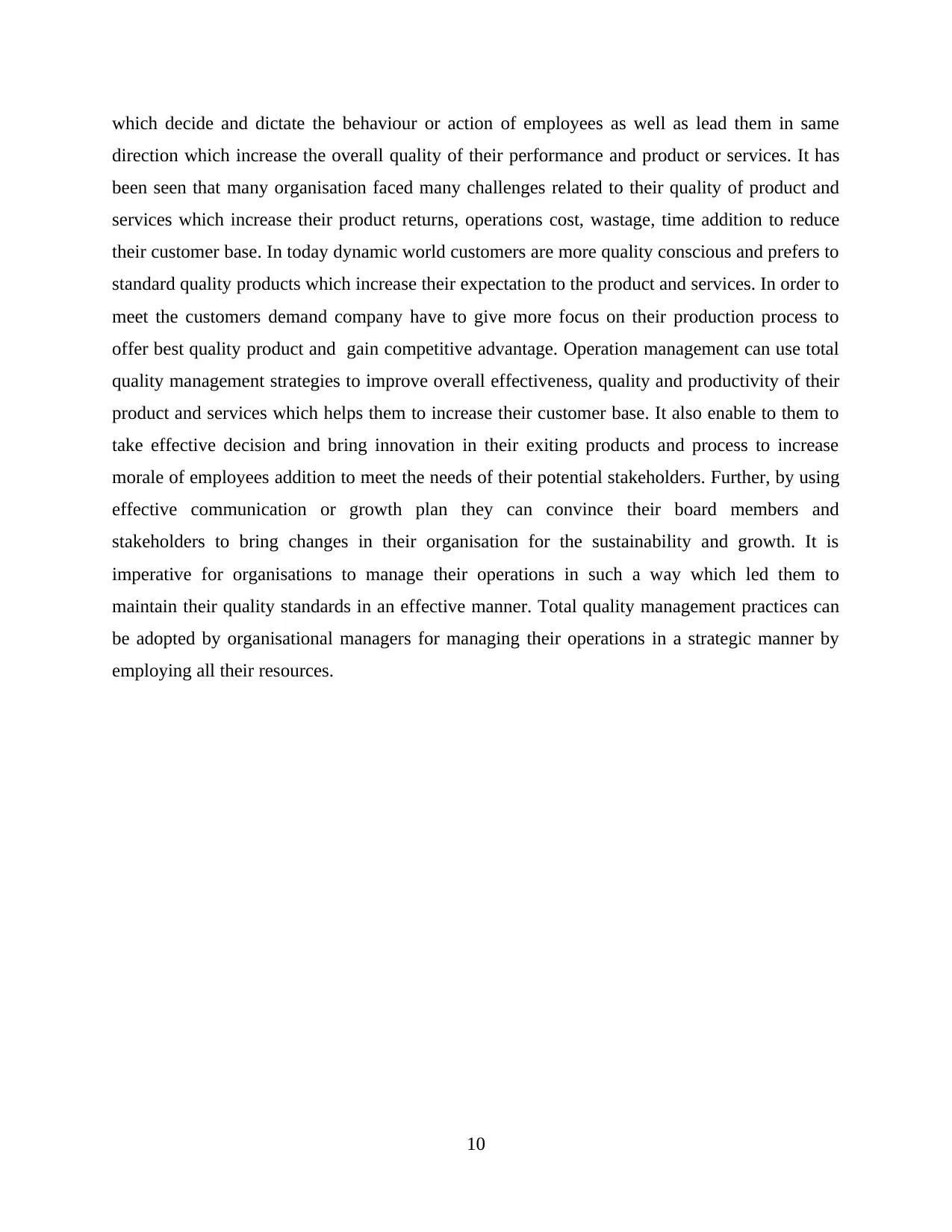
which decide and dictate the behaviour or action of employees as well as lead them in same
direction which increase the overall quality of their performance and product or services. It has
been seen that many organisation faced many challenges related to their quality of product and
services which increase their product returns, operations cost, wastage, time addition to reduce
their customer base. In today dynamic world customers are more quality conscious and prefers to
standard quality products which increase their expectation to the product and services. In order to
meet the customers demand company have to give more focus on their production process to
offer best quality product and gain competitive advantage. Operation management can use total
quality management strategies to improve overall effectiveness, quality and productivity of their
product and services which helps them to increase their customer base. It also enable to them to
take effective decision and bring innovation in their exiting products and process to increase
morale of employees addition to meet the needs of their potential stakeholders. Further, by using
effective communication or growth plan they can convince their board members and
stakeholders to bring changes in their organisation for the sustainability and growth. It is
imperative for organisations to manage their operations in such a way which led them to
maintain their quality standards in an effective manner. Total quality management practices can
be adopted by organisational managers for managing their operations in a strategic manner by
employing all their resources.
10
direction which increase the overall quality of their performance and product or services. It has
been seen that many organisation faced many challenges related to their quality of product and
services which increase their product returns, operations cost, wastage, time addition to reduce
their customer base. In today dynamic world customers are more quality conscious and prefers to
standard quality products which increase their expectation to the product and services. In order to
meet the customers demand company have to give more focus on their production process to
offer best quality product and gain competitive advantage. Operation management can use total
quality management strategies to improve overall effectiveness, quality and productivity of their
product and services which helps them to increase their customer base. It also enable to them to
take effective decision and bring innovation in their exiting products and process to increase
morale of employees addition to meet the needs of their potential stakeholders. Further, by using
effective communication or growth plan they can convince their board members and
stakeholders to bring changes in their organisation for the sustainability and growth. It is
imperative for organisations to manage their operations in such a way which led them to
maintain their quality standards in an effective manner. Total quality management practices can
be adopted by organisational managers for managing their operations in a strategic manner by
employing all their resources.
10
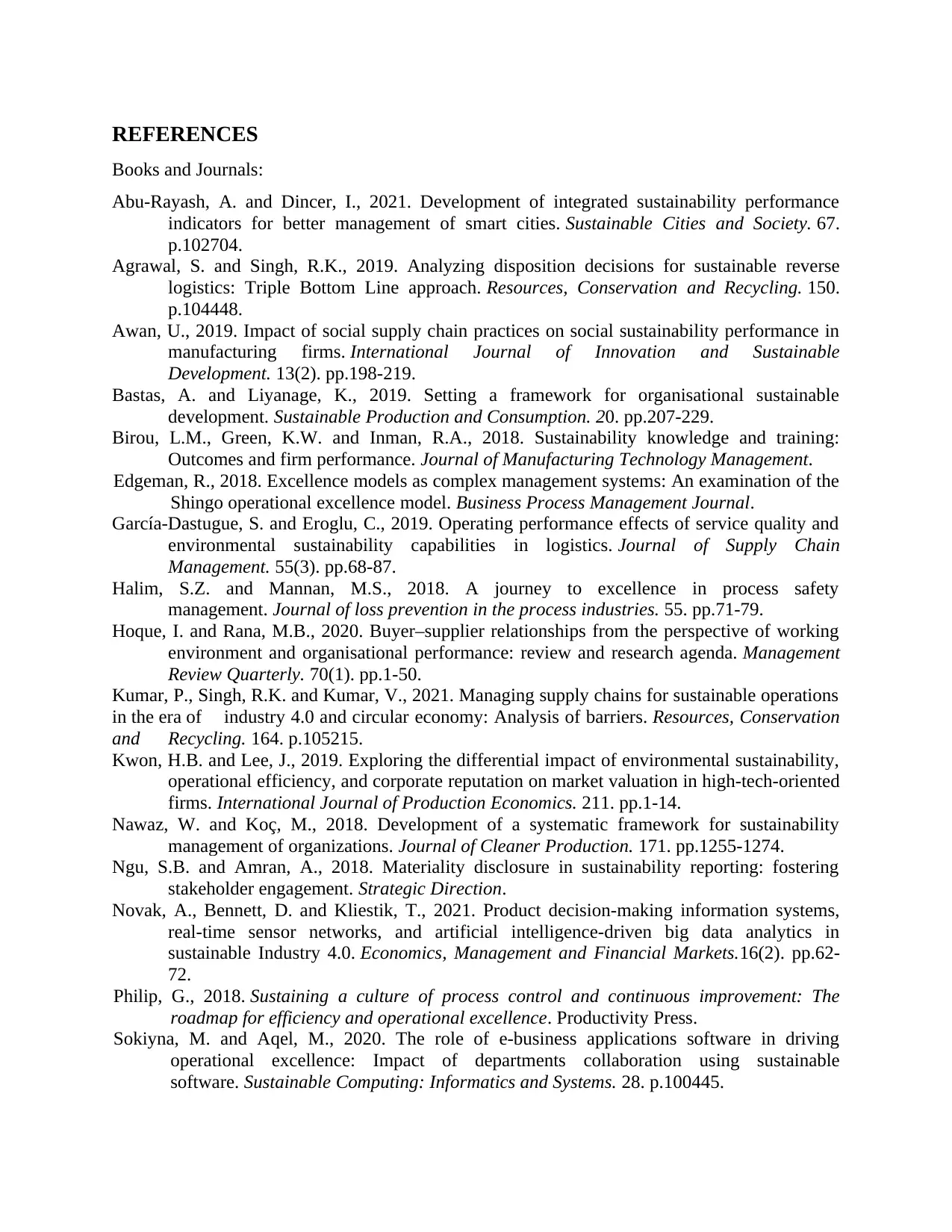
REFERENCES
Books and Journals:
Abu-Rayash, A. and Dincer, I., 2021. Development of integrated sustainability performance
indicators for better management of smart cities. Sustainable Cities and Society. 67.
p.102704.
Agrawal, S. and Singh, R.K., 2019. Analyzing disposition decisions for sustainable reverse
logistics: Triple Bottom Line approach. Resources, Conservation and Recycling. 150.
p.104448.
Awan, U., 2019. Impact of social supply chain practices on social sustainability performance in
manufacturing firms. International Journal of Innovation and Sustainable
Development. 13(2). pp.198-219.
Bastas, A. and Liyanage, K., 2019. Setting a framework for organisational sustainable
development. Sustainable Production and Consumption. 20. pp.207-229.
Birou, L.M., Green, K.W. and Inman, R.A., 2018. Sustainability knowledge and training:
Outcomes and firm performance. Journal of Manufacturing Technology Management.
Edgeman, R., 2018. Excellence models as complex management systems: An examination of the
Shingo operational excellence model. Business Process Management Journal.
García‐Dastugue, S. and Eroglu, C., 2019. Operating performance effects of service quality and
environmental sustainability capabilities in logistics. Journal of Supply Chain
Management. 55(3). pp.68-87.
Halim, S.Z. and Mannan, M.S., 2018. A journey to excellence in process safety
management. Journal of loss prevention in the process industries. 55. pp.71-79.
Hoque, I. and Rana, M.B., 2020. Buyer–supplier relationships from the perspective of working
environment and organisational performance: review and research agenda. Management
Review Quarterly. 70(1). pp.1-50.
Kumar, P., Singh, R.K. and Kumar, V., 2021. Managing supply chains for sustainable operations
in the era of industry 4.0 and circular economy: Analysis of barriers. Resources, Conservation
and Recycling. 164. p.105215.
Kwon, H.B. and Lee, J., 2019. Exploring the differential impact of environmental sustainability,
operational efficiency, and corporate reputation on market valuation in high-tech-oriented
firms. International Journal of Production Economics. 211. pp.1-14.
Nawaz, W. and Koç, M., 2018. Development of a systematic framework for sustainability
management of organizations. Journal of Cleaner Production. 171. pp.1255-1274.
Ngu, S.B. and Amran, A., 2018. Materiality disclosure in sustainability reporting: fostering
stakeholder engagement. Strategic Direction.
Novak, A., Bennett, D. and Kliestik, T., 2021. Product decision-making information systems,
real-time sensor networks, and artificial intelligence-driven big data analytics in
sustainable Industry 4.0. Economics, Management and Financial Markets.16(2). pp.62-
72.
Philip, G., 2018. Sustaining a culture of process control and continuous improvement: The
roadmap for efficiency and operational excellence. Productivity Press.
Sokiyna, M. and Aqel, M., 2020. The role of e-business applications software in driving
operational excellence: Impact of departments collaboration using sustainable
software. Sustainable Computing: Informatics and Systems. 28. p.100445.
Books and Journals:
Abu-Rayash, A. and Dincer, I., 2021. Development of integrated sustainability performance
indicators for better management of smart cities. Sustainable Cities and Society. 67.
p.102704.
Agrawal, S. and Singh, R.K., 2019. Analyzing disposition decisions for sustainable reverse
logistics: Triple Bottom Line approach. Resources, Conservation and Recycling. 150.
p.104448.
Awan, U., 2019. Impact of social supply chain practices on social sustainability performance in
manufacturing firms. International Journal of Innovation and Sustainable
Development. 13(2). pp.198-219.
Bastas, A. and Liyanage, K., 2019. Setting a framework for organisational sustainable
development. Sustainable Production and Consumption. 20. pp.207-229.
Birou, L.M., Green, K.W. and Inman, R.A., 2018. Sustainability knowledge and training:
Outcomes and firm performance. Journal of Manufacturing Technology Management.
Edgeman, R., 2018. Excellence models as complex management systems: An examination of the
Shingo operational excellence model. Business Process Management Journal.
García‐Dastugue, S. and Eroglu, C., 2019. Operating performance effects of service quality and
environmental sustainability capabilities in logistics. Journal of Supply Chain
Management. 55(3). pp.68-87.
Halim, S.Z. and Mannan, M.S., 2018. A journey to excellence in process safety
management. Journal of loss prevention in the process industries. 55. pp.71-79.
Hoque, I. and Rana, M.B., 2020. Buyer–supplier relationships from the perspective of working
environment and organisational performance: review and research agenda. Management
Review Quarterly. 70(1). pp.1-50.
Kumar, P., Singh, R.K. and Kumar, V., 2021. Managing supply chains for sustainable operations
in the era of industry 4.0 and circular economy: Analysis of barriers. Resources, Conservation
and Recycling. 164. p.105215.
Kwon, H.B. and Lee, J., 2019. Exploring the differential impact of environmental sustainability,
operational efficiency, and corporate reputation on market valuation in high-tech-oriented
firms. International Journal of Production Economics. 211. pp.1-14.
Nawaz, W. and Koç, M., 2018. Development of a systematic framework for sustainability
management of organizations. Journal of Cleaner Production. 171. pp.1255-1274.
Ngu, S.B. and Amran, A., 2018. Materiality disclosure in sustainability reporting: fostering
stakeholder engagement. Strategic Direction.
Novak, A., Bennett, D. and Kliestik, T., 2021. Product decision-making information systems,
real-time sensor networks, and artificial intelligence-driven big data analytics in
sustainable Industry 4.0. Economics, Management and Financial Markets.16(2). pp.62-
72.
Philip, G., 2018. Sustaining a culture of process control and continuous improvement: The
roadmap for efficiency and operational excellence. Productivity Press.
Sokiyna, M. and Aqel, M., 2020. The role of e-business applications software in driving
operational excellence: Impact of departments collaboration using sustainable
software. Sustainable Computing: Informatics and Systems. 28. p.100445.
Paraphrase This Document
Need a fresh take? Get an instant paraphrase of this document with our AI Paraphraser
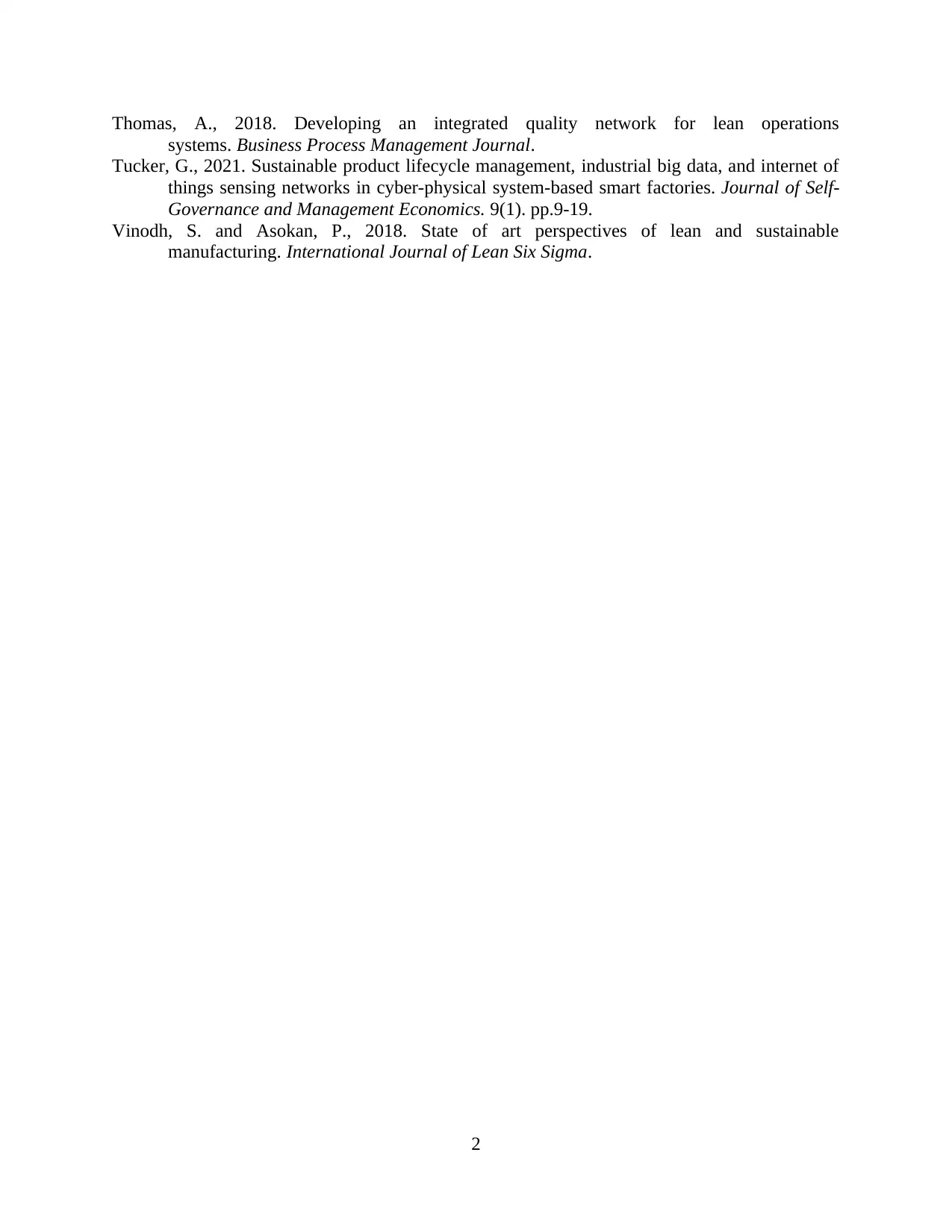
Thomas, A., 2018. Developing an integrated quality network for lean operations
systems. Business Process Management Journal.
Tucker, G., 2021. Sustainable product lifecycle management, industrial big data, and internet of
things sensing networks in cyber-physical system-based smart factories. Journal of Self-
Governance and Management Economics. 9(1). pp.9-19.
Vinodh, S. and Asokan, P., 2018. State of art perspectives of lean and sustainable
manufacturing. International Journal of Lean Six Sigma.
2
systems. Business Process Management Journal.
Tucker, G., 2021. Sustainable product lifecycle management, industrial big data, and internet of
things sensing networks in cyber-physical system-based smart factories. Journal of Self-
Governance and Management Economics. 9(1). pp.9-19.
Vinodh, S. and Asokan, P., 2018. State of art perspectives of lean and sustainable
manufacturing. International Journal of Lean Six Sigma.
2
1 out of 14
Related Documents

Your All-in-One AI-Powered Toolkit for Academic Success.
+13062052269
info@desklib.com
Available 24*7 on WhatsApp / Email
Unlock your academic potential
© 2024 | Zucol Services PVT LTD | All rights reserved.