Report: Costing Analysis of Fantori Ltd (ACC200, Term 3 2018)
VerifiedAdded on 2023/04/24
|15
|2322
|142
Report
AI Summary
This report analyzes Fantori Ltd, a sewing machine manufacturer, focusing on its costing methods and the behavior of an overseas buyer. The company currently uses traditional costing, allocating overhead based on machine hours. The report compares this approach to activity-based costing (ABC), demonstrating how different costing methods impact product pricing and profitability. It explores the reasons why the overseas buyer is only interested in the advanced model and not the basic model, suggesting that the traditional costing method may be distorting the perceived costs of the products. The report includes calculations of costs using both traditional and ABC methods, analyzes the impact of under-applied overhead, and provides insights into how Fantori Ltd can improve its costing practices to make informed business decisions, especially regarding pricing and sales strategies. The report also includes statements of profit and loss under both costing methods, calculation of sales prices per unit, and an explanation of overhead expenses and their allocation, along with treatments for under-applied overhead. Finally, the report concludes with a practical example of under-absorption and the various methods to treat it.
Contribute Materials
Your contribution can guide someone’s learning journey. Share your
documents today.
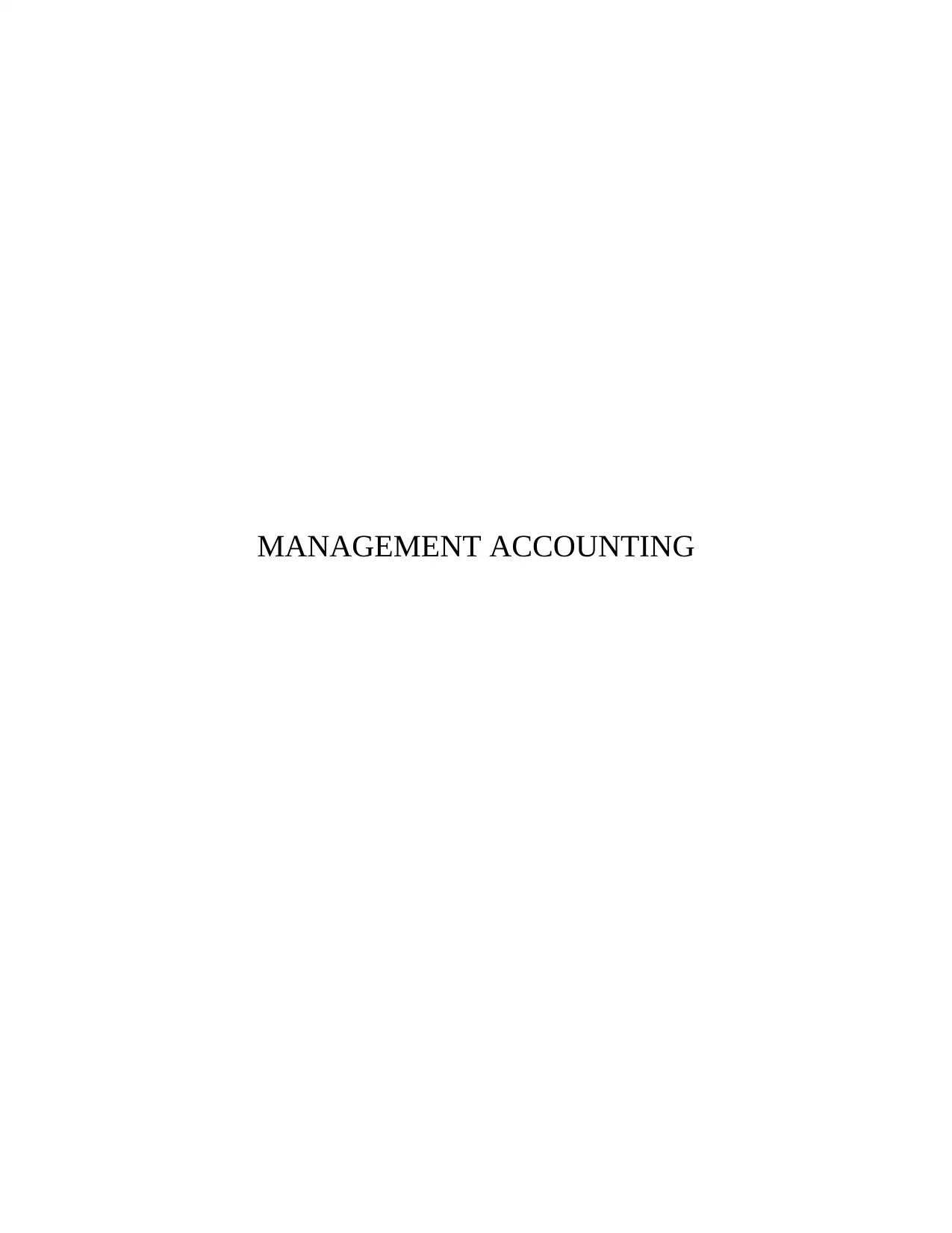
MANAGEMENT ACCOUNTING
Secure Best Marks with AI Grader
Need help grading? Try our AI Grader for instant feedback on your assignments.
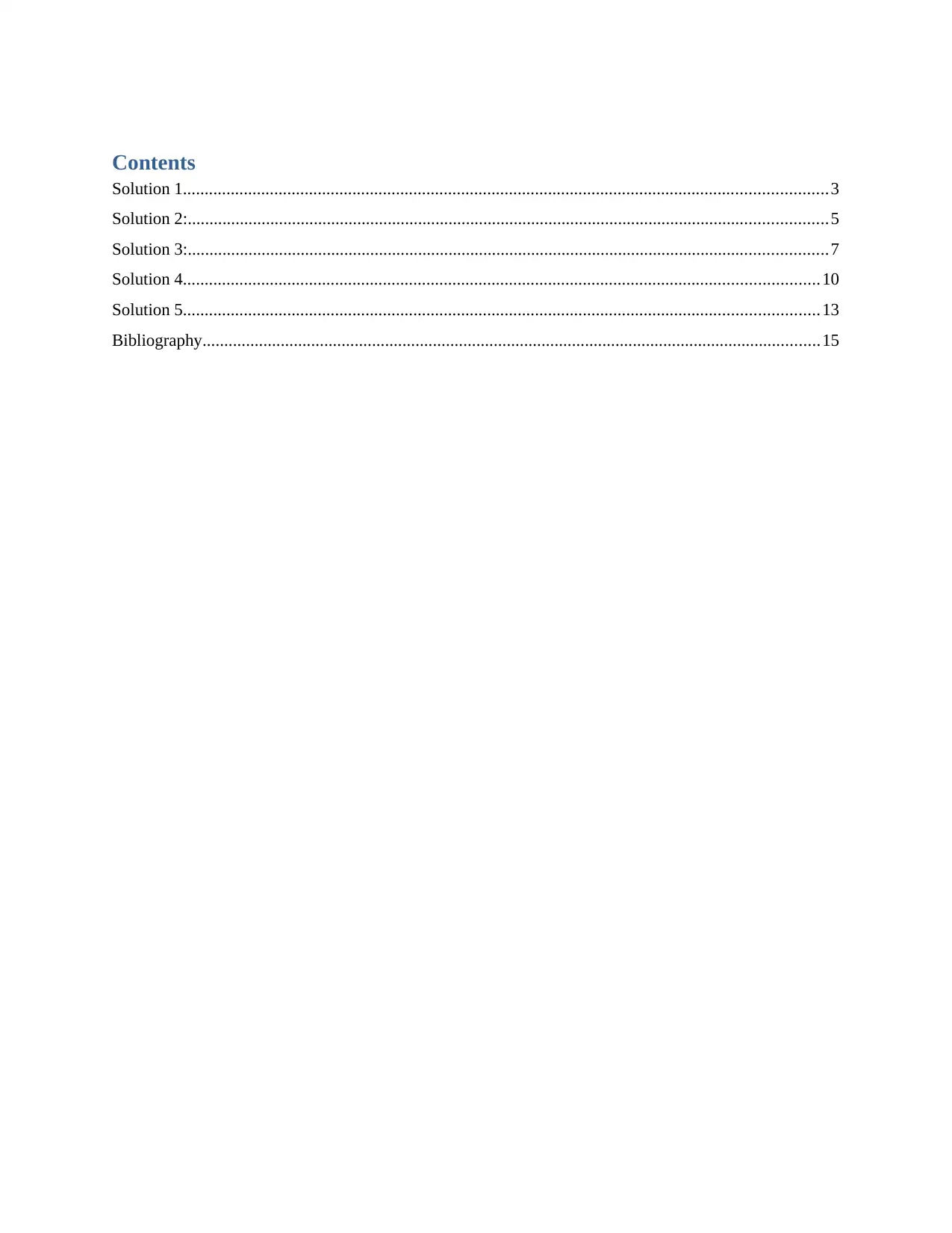
Contents
Solution 1....................................................................................................................................................3
Solution 2:...................................................................................................................................................5
Solution 3:...................................................................................................................................................7
Solution 4..................................................................................................................................................10
Solution 5..................................................................................................................................................13
Bibliography..............................................................................................................................................15
Solution 1....................................................................................................................................................3
Solution 2:...................................................................................................................................................5
Solution 3:...................................................................................................................................................7
Solution 4..................................................................................................................................................10
Solution 5..................................................................................................................................................13
Bibliography..............................................................................................................................................15
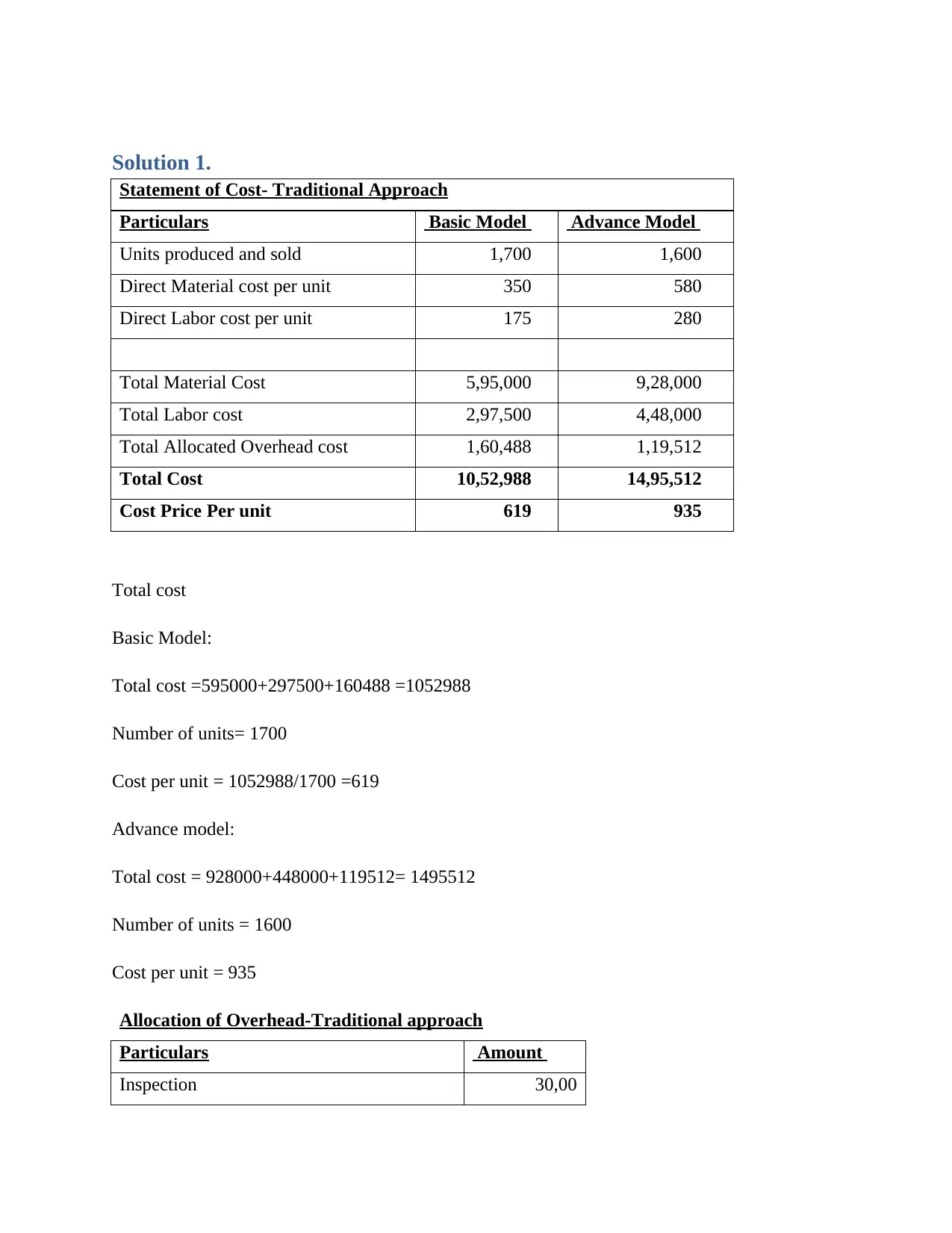
Solution 1.
Statement of Cost- Traditional Approach
Particulars Basic Model Advance Model
Units produced and sold 1,700 1,600
Direct Material cost per unit 350 580
Direct Labor cost per unit 175 280
Total Material Cost 5,95,000 9,28,000
Total Labor cost 2,97,500 4,48,000
Total Allocated Overhead cost 1,60,488 1,19,512
Total Cost 10,52,988 14,95,512
Cost Price Per unit 619 935
Total cost
Basic Model:
Total cost =595000+297500+160488 =1052988
Number of units= 1700
Cost per unit = 1052988/1700 =619
Advance model:
Total cost = 928000+448000+119512= 1495512
Number of units = 1600
Cost per unit = 935
Allocation of Overhead-Traditional approach
Particulars Amount
Inspection 30,00
Statement of Cost- Traditional Approach
Particulars Basic Model Advance Model
Units produced and sold 1,700 1,600
Direct Material cost per unit 350 580
Direct Labor cost per unit 175 280
Total Material Cost 5,95,000 9,28,000
Total Labor cost 2,97,500 4,48,000
Total Allocated Overhead cost 1,60,488 1,19,512
Total Cost 10,52,988 14,95,512
Cost Price Per unit 619 935
Total cost
Basic Model:
Total cost =595000+297500+160488 =1052988
Number of units= 1700
Cost per unit = 1052988/1700 =619
Advance model:
Total cost = 928000+448000+119512= 1495512
Number of units = 1600
Cost per unit = 935
Allocation of Overhead-Traditional approach
Particulars Amount
Inspection 30,00
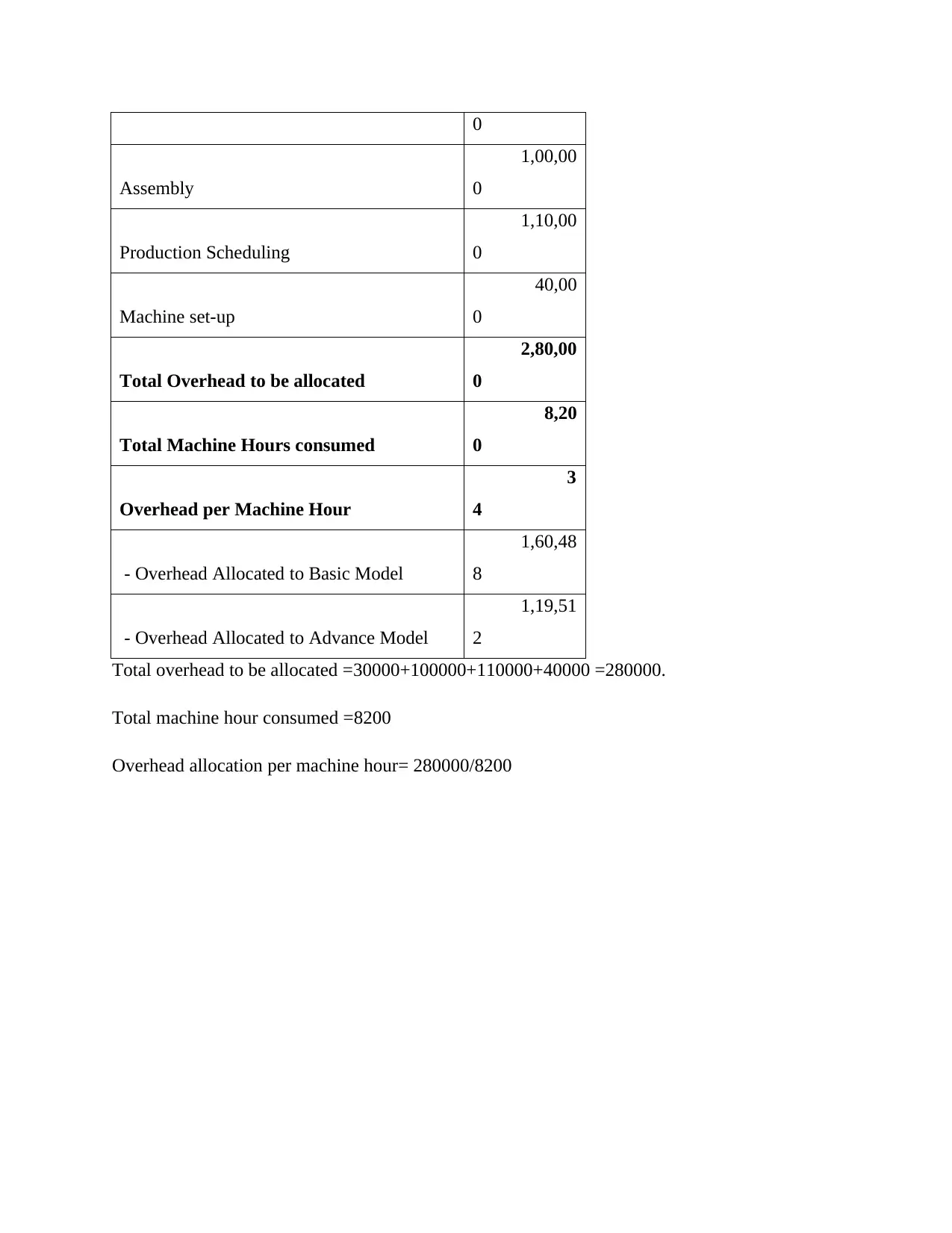
0
Assembly
1,00,00
0
Production Scheduling
1,10,00
0
Machine set-up
40,00
0
Total Overhead to be allocated
2,80,00
0
Total Machine Hours consumed
8,20
0
Overhead per Machine Hour
3
4
- Overhead Allocated to Basic Model
1,60,48
8
- Overhead Allocated to Advance Model
1,19,51
2
Total overhead to be allocated =30000+100000+110000+40000 =280000.
Total machine hour consumed =8200
Overhead allocation per machine hour= 280000/8200
Assembly
1,00,00
0
Production Scheduling
1,10,00
0
Machine set-up
40,00
0
Total Overhead to be allocated
2,80,00
0
Total Machine Hours consumed
8,20
0
Overhead per Machine Hour
3
4
- Overhead Allocated to Basic Model
1,60,48
8
- Overhead Allocated to Advance Model
1,19,51
2
Total overhead to be allocated =30000+100000+110000+40000 =280000.
Total machine hour consumed =8200
Overhead allocation per machine hour= 280000/8200
Secure Best Marks with AI Grader
Need help grading? Try our AI Grader for instant feedback on your assignments.
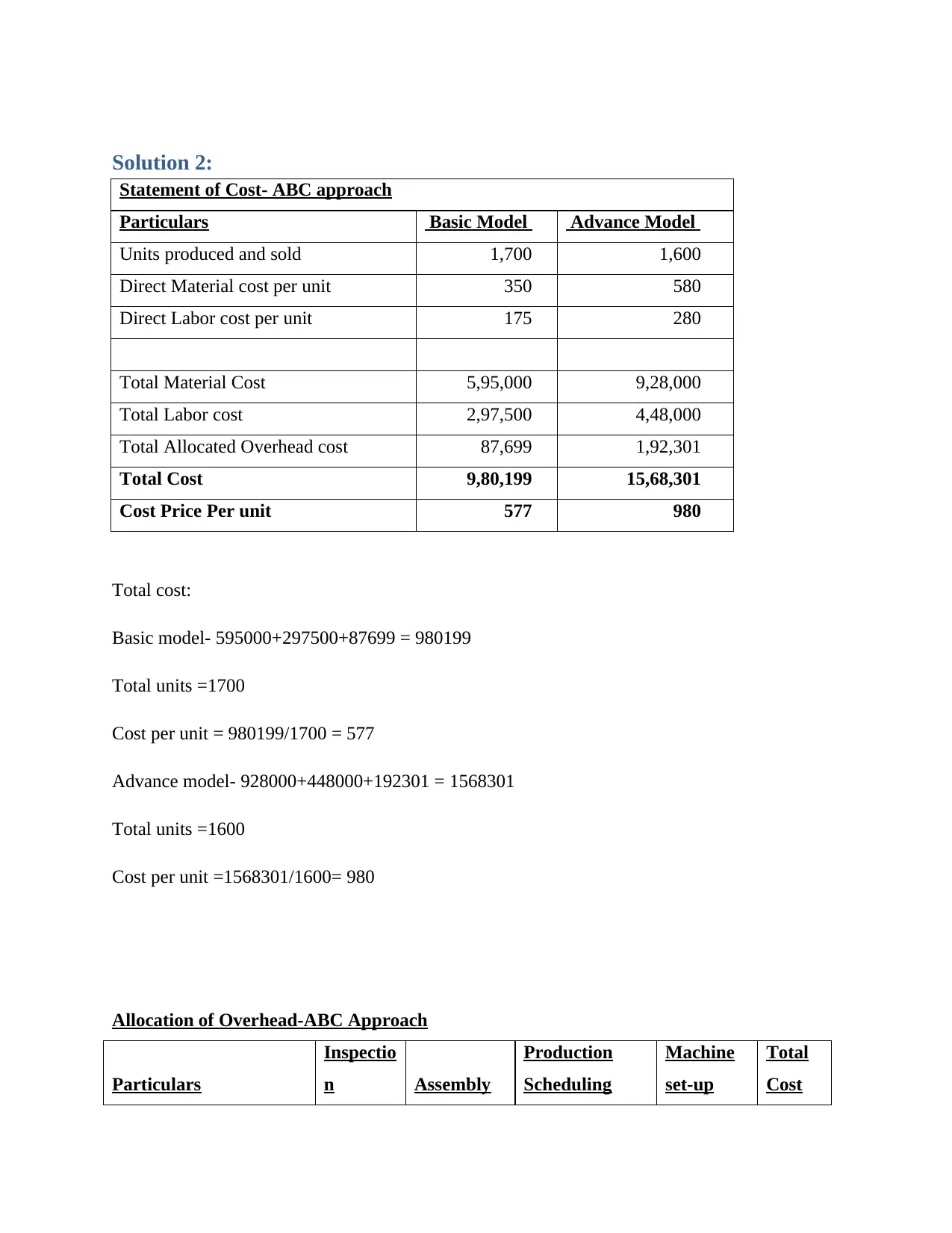
Solution 2:
Statement of Cost- ABC approach
Particulars Basic Model Advance Model
Units produced and sold 1,700 1,600
Direct Material cost per unit 350 580
Direct Labor cost per unit 175 280
Total Material Cost 5,95,000 9,28,000
Total Labor cost 2,97,500 4,48,000
Total Allocated Overhead cost 87,699 1,92,301
Total Cost 9,80,199 15,68,301
Cost Price Per unit 577 980
Total cost:
Basic model- 595000+297500+87699 = 980199
Total units =1700
Cost per unit = 980199/1700 = 577
Advance model- 928000+448000+192301 = 1568301
Total units =1600
Cost per unit =1568301/1600= 980
Allocation of Overhead-ABC Approach
Particulars
Inspectio
n Assembly
Production
Scheduling
Machine
set-up
Total
Cost
Statement of Cost- ABC approach
Particulars Basic Model Advance Model
Units produced and sold 1,700 1,600
Direct Material cost per unit 350 580
Direct Labor cost per unit 175 280
Total Material Cost 5,95,000 9,28,000
Total Labor cost 2,97,500 4,48,000
Total Allocated Overhead cost 87,699 1,92,301
Total Cost 9,80,199 15,68,301
Cost Price Per unit 577 980
Total cost:
Basic model- 595000+297500+87699 = 980199
Total units =1700
Cost per unit = 980199/1700 = 577
Advance model- 928000+448000+192301 = 1568301
Total units =1600
Cost per unit =1568301/1600= 980
Allocation of Overhead-ABC Approach
Particulars
Inspectio
n Assembly
Production
Scheduling
Machine
set-up
Total
Cost
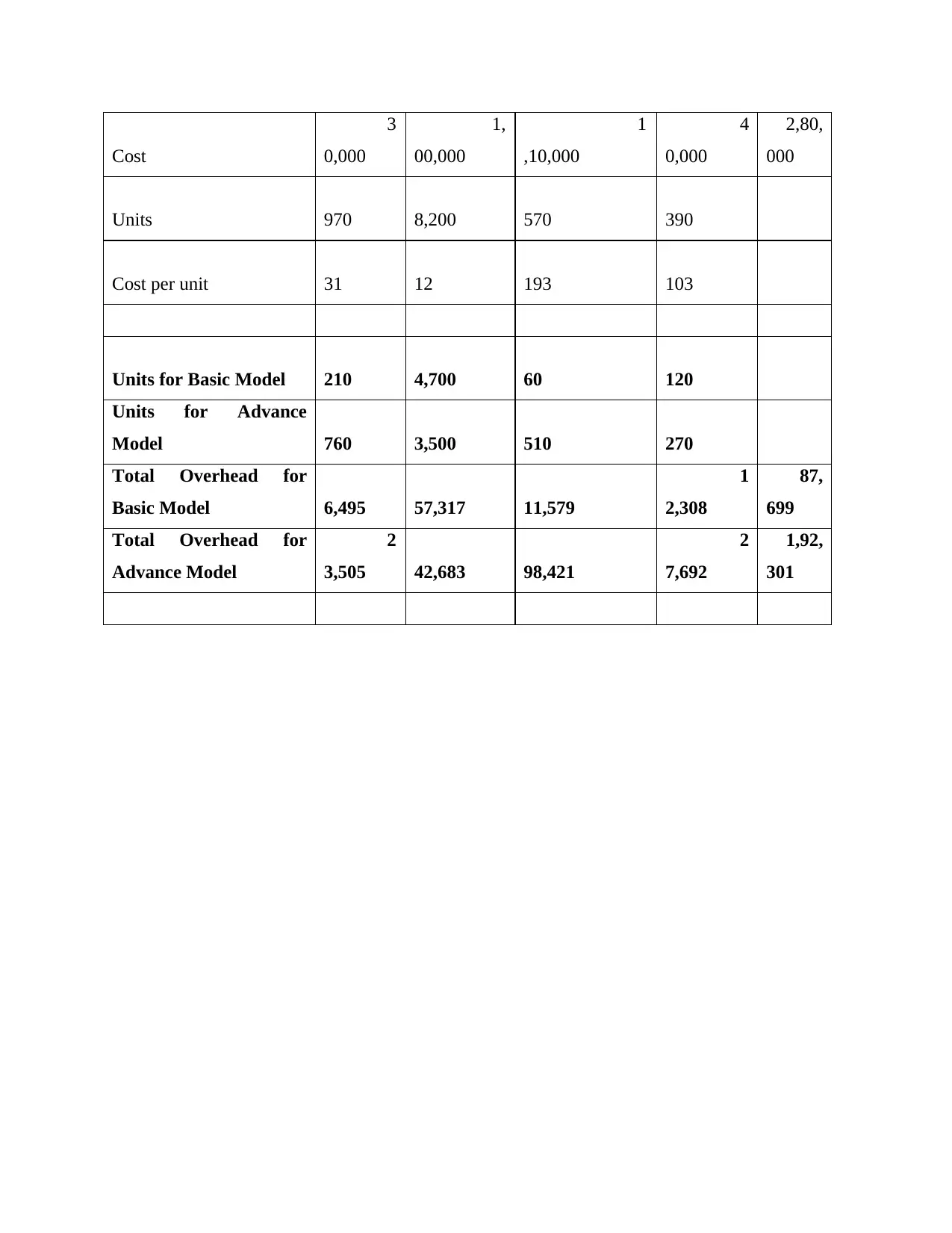
Cost
3
0,000
1,
00,000
1
,10,000
4
0,000
2,80,
000
Units 970 8,200 570 390
Cost per unit 31 12 193 103
Units for Basic Model 210 4,700 60 120
Units for Advance
Model 760 3,500 510 270
Total Overhead for
Basic Model 6,495 57,317 11,579
1
2,308
87,
699
Total Overhead for
Advance Model
2
3,505 42,683 98,421
2
7,692
1,92,
301
3
0,000
1,
00,000
1
,10,000
4
0,000
2,80,
000
Units 970 8,200 570 390
Cost per unit 31 12 193 103
Units for Basic Model 210 4,700 60 120
Units for Advance
Model 760 3,500 510 270
Total Overhead for
Basic Model 6,495 57,317 11,579
1
2,308
87,
699
Total Overhead for
Advance Model
2
3,505 42,683 98,421
2
7,692
1,92,
301
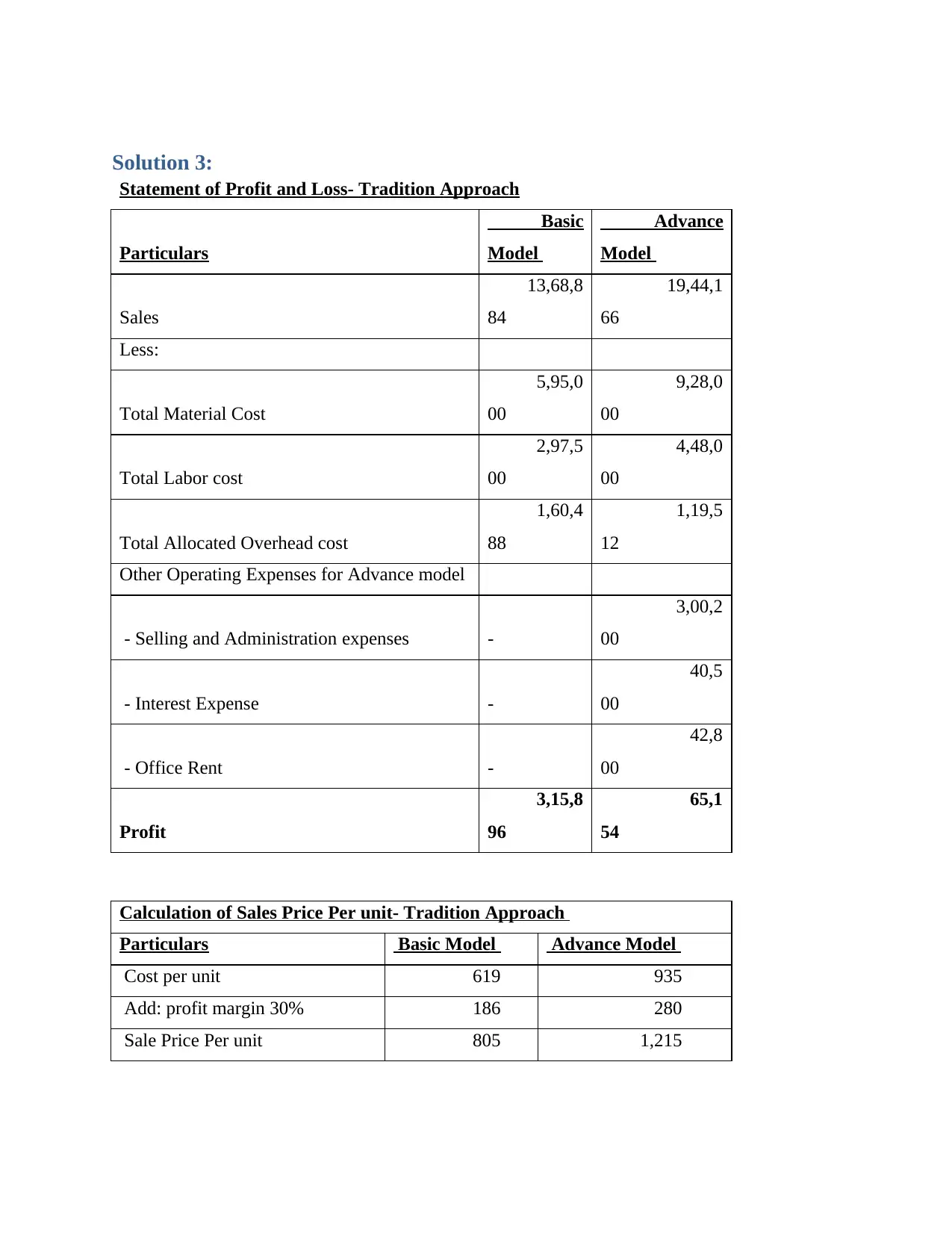
Solution 3:
Statement of Profit and Loss- Tradition Approach
Particulars
Basic
Model
Advance
Model
Sales
13,68,8
84
19,44,1
66
Less:
Total Material Cost
5,95,0
00
9,28,0
00
Total Labor cost
2,97,5
00
4,48,0
00
Total Allocated Overhead cost
1,60,4
88
1,19,5
12
Other Operating Expenses for Advance model
- Selling and Administration expenses -
3,00,2
00
- Interest Expense -
40,5
00
- Office Rent -
42,8
00
Profit
3,15,8
96
65,1
54
Calculation of Sales Price Per unit- Tradition Approach
Particulars Basic Model Advance Model
Cost per unit 619 935
Add: profit margin 30% 186 280
Sale Price Per unit 805 1,215
Statement of Profit and Loss- Tradition Approach
Particulars
Basic
Model
Advance
Model
Sales
13,68,8
84
19,44,1
66
Less:
Total Material Cost
5,95,0
00
9,28,0
00
Total Labor cost
2,97,5
00
4,48,0
00
Total Allocated Overhead cost
1,60,4
88
1,19,5
12
Other Operating Expenses for Advance model
- Selling and Administration expenses -
3,00,2
00
- Interest Expense -
40,5
00
- Office Rent -
42,8
00
Profit
3,15,8
96
65,1
54
Calculation of Sales Price Per unit- Tradition Approach
Particulars Basic Model Advance Model
Cost per unit 619 935
Add: profit margin 30% 186 280
Sale Price Per unit 805 1,215
Paraphrase This Document
Need a fresh take? Get an instant paraphrase of this document with our AI Paraphraser
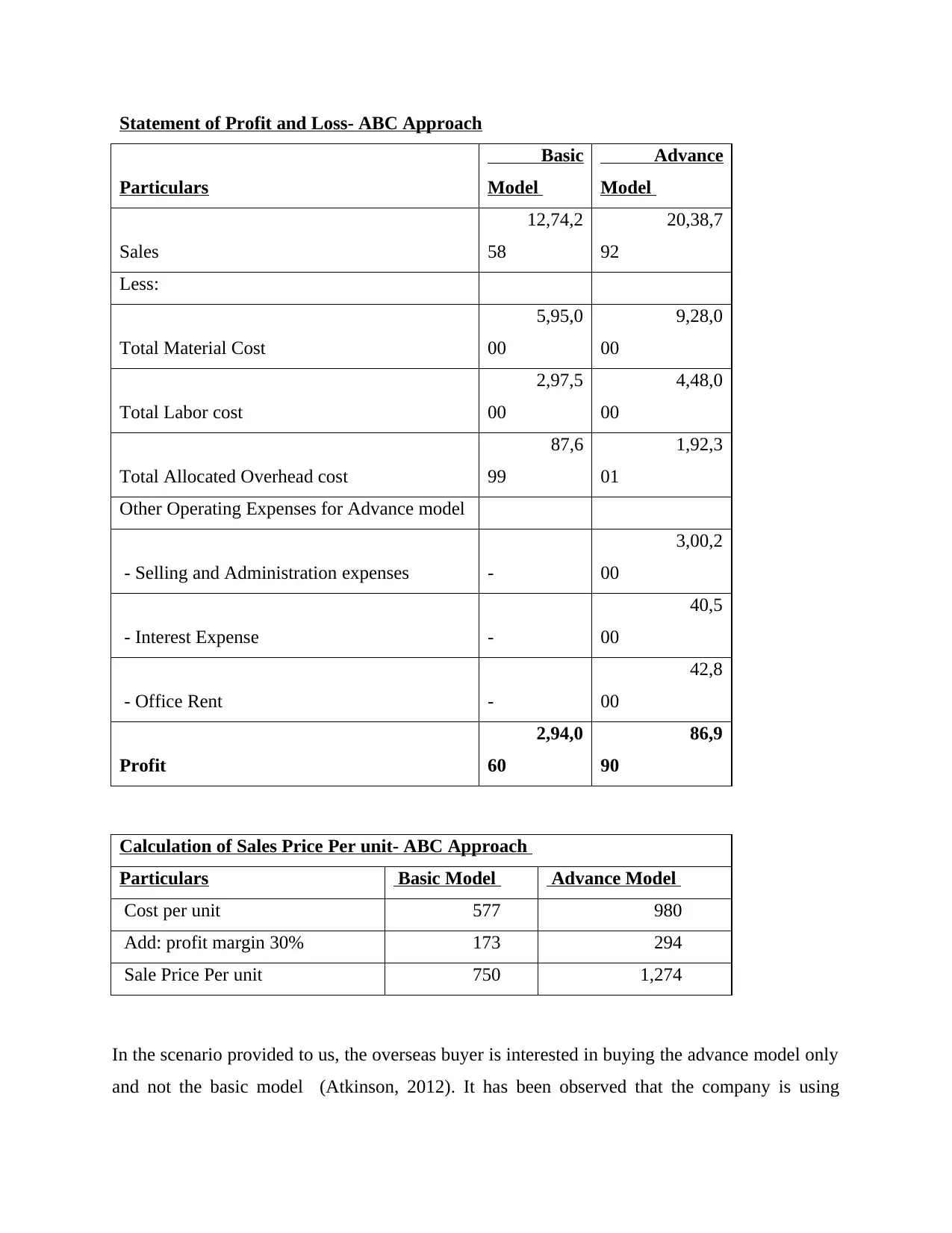
Statement of Profit and Loss- ABC Approach
Particulars
Basic
Model
Advance
Model
Sales
12,74,2
58
20,38,7
92
Less:
Total Material Cost
5,95,0
00
9,28,0
00
Total Labor cost
2,97,5
00
4,48,0
00
Total Allocated Overhead cost
87,6
99
1,92,3
01
Other Operating Expenses for Advance model
- Selling and Administration expenses -
3,00,2
00
- Interest Expense -
40,5
00
- Office Rent -
42,8
00
Profit
2,94,0
60
86,9
90
Calculation of Sales Price Per unit- ABC Approach
Particulars Basic Model Advance Model
Cost per unit 577 980
Add: profit margin 30% 173 294
Sale Price Per unit 750 1,274
In the scenario provided to us, the overseas buyer is interested in buying the advance model only
and not the basic model (Atkinson, 2012). It has been observed that the company is using
Particulars
Basic
Model
Advance
Model
Sales
12,74,2
58
20,38,7
92
Less:
Total Material Cost
5,95,0
00
9,28,0
00
Total Labor cost
2,97,5
00
4,48,0
00
Total Allocated Overhead cost
87,6
99
1,92,3
01
Other Operating Expenses for Advance model
- Selling and Administration expenses -
3,00,2
00
- Interest Expense -
40,5
00
- Office Rent -
42,8
00
Profit
2,94,0
60
86,9
90
Calculation of Sales Price Per unit- ABC Approach
Particulars Basic Model Advance Model
Cost per unit 577 980
Add: profit margin 30% 173 294
Sale Price Per unit 750 1,274
In the scenario provided to us, the overseas buyer is interested in buying the advance model only
and not the basic model (Atkinson, 2012). It has been observed that the company is using
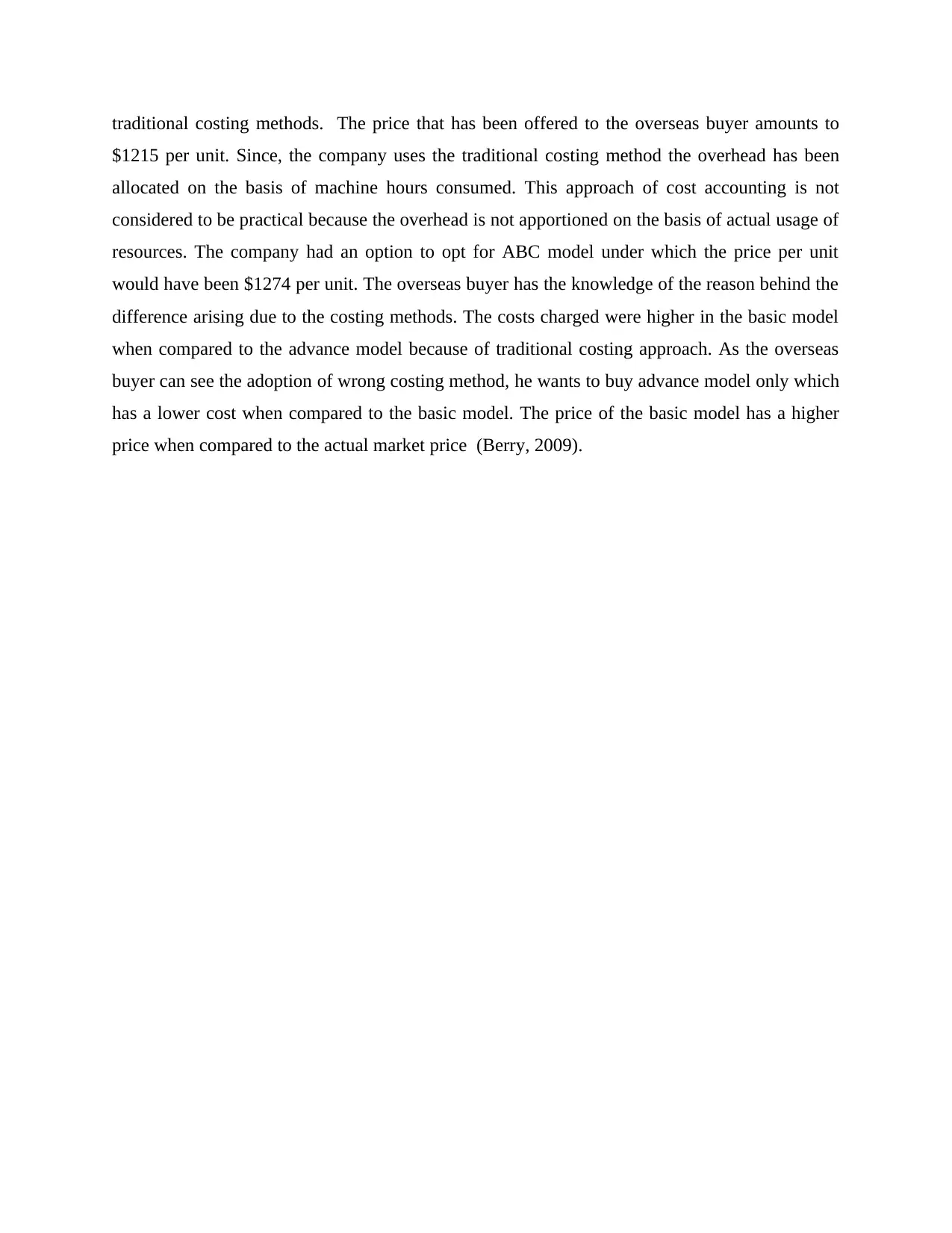
traditional costing methods. The price that has been offered to the overseas buyer amounts to
$1215 per unit. Since, the company uses the traditional costing method the overhead has been
allocated on the basis of machine hours consumed. This approach of cost accounting is not
considered to be practical because the overhead is not apportioned on the basis of actual usage of
resources. The company had an option to opt for ABC model under which the price per unit
would have been $1274 per unit. The overseas buyer has the knowledge of the reason behind the
difference arising due to the costing methods. The costs charged were higher in the basic model
when compared to the advance model because of traditional costing approach. As the overseas
buyer can see the adoption of wrong costing method, he wants to buy advance model only which
has a lower cost when compared to the basic model. The price of the basic model has a higher
price when compared to the actual market price (Berry, 2009).
$1215 per unit. Since, the company uses the traditional costing method the overhead has been
allocated on the basis of machine hours consumed. This approach of cost accounting is not
considered to be practical because the overhead is not apportioned on the basis of actual usage of
resources. The company had an option to opt for ABC model under which the price per unit
would have been $1274 per unit. The overseas buyer has the knowledge of the reason behind the
difference arising due to the costing methods. The costs charged were higher in the basic model
when compared to the advance model because of traditional costing approach. As the overseas
buyer can see the adoption of wrong costing method, he wants to buy advance model only which
has a lower cost when compared to the basic model. The price of the basic model has a higher
price when compared to the actual market price (Berry, 2009).
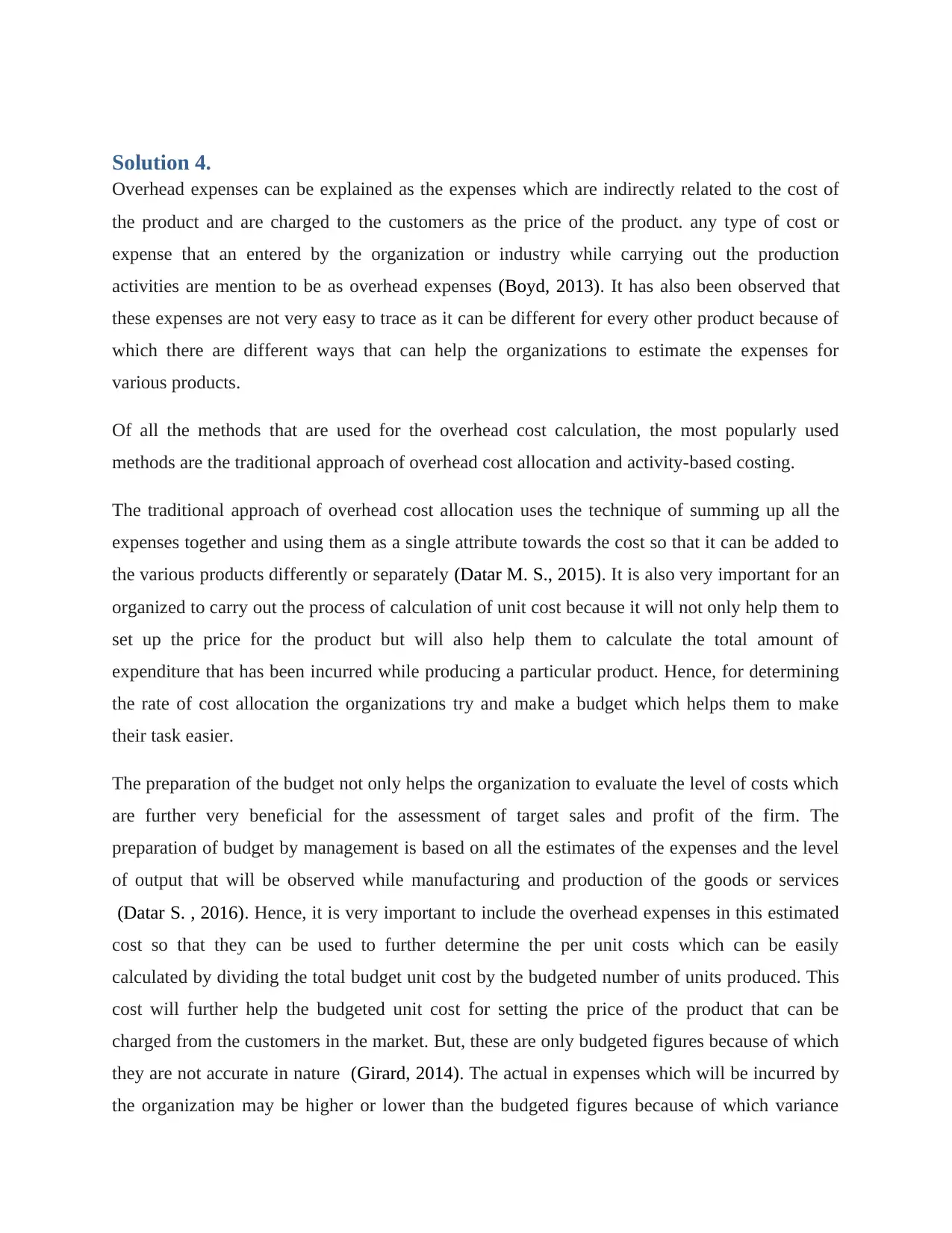
Solution 4.
Overhead expenses can be explained as the expenses which are indirectly related to the cost of
the product and are charged to the customers as the price of the product. any type of cost or
expense that an entered by the organization or industry while carrying out the production
activities are mention to be as overhead expenses (Boyd, 2013). It has also been observed that
these expenses are not very easy to trace as it can be different for every other product because of
which there are different ways that can help the organizations to estimate the expenses for
various products.
Of all the methods that are used for the overhead cost calculation, the most popularly used
methods are the traditional approach of overhead cost allocation and activity-based costing.
The traditional approach of overhead cost allocation uses the technique of summing up all the
expenses together and using them as a single attribute towards the cost so that it can be added to
the various products differently or separately (Datar M. S., 2015). It is also very important for an
organized to carry out the process of calculation of unit cost because it will not only help them to
set up the price for the product but will also help them to calculate the total amount of
expenditure that has been incurred while producing a particular product. Hence, for determining
the rate of cost allocation the organizations try and make a budget which helps them to make
their task easier.
The preparation of the budget not only helps the organization to evaluate the level of costs which
are further very beneficial for the assessment of target sales and profit of the firm. The
preparation of budget by management is based on all the estimates of the expenses and the level
of output that will be observed while manufacturing and production of the goods or services
(Datar S. , 2016). Hence, it is very important to include the overhead expenses in this estimated
cost so that they can be used to further determine the per unit costs which can be easily
calculated by dividing the total budget unit cost by the budgeted number of units produced. This
cost will further help the budgeted unit cost for setting the price of the product that can be
charged from the customers in the market. But, these are only budgeted figures because of which
they are not accurate in nature (Girard, 2014). The actual in expenses which will be incurred by
the organization may be higher or lower than the budgeted figures because of which variance
Overhead expenses can be explained as the expenses which are indirectly related to the cost of
the product and are charged to the customers as the price of the product. any type of cost or
expense that an entered by the organization or industry while carrying out the production
activities are mention to be as overhead expenses (Boyd, 2013). It has also been observed that
these expenses are not very easy to trace as it can be different for every other product because of
which there are different ways that can help the organizations to estimate the expenses for
various products.
Of all the methods that are used for the overhead cost calculation, the most popularly used
methods are the traditional approach of overhead cost allocation and activity-based costing.
The traditional approach of overhead cost allocation uses the technique of summing up all the
expenses together and using them as a single attribute towards the cost so that it can be added to
the various products differently or separately (Datar M. S., 2015). It is also very important for an
organized to carry out the process of calculation of unit cost because it will not only help them to
set up the price for the product but will also help them to calculate the total amount of
expenditure that has been incurred while producing a particular product. Hence, for determining
the rate of cost allocation the organizations try and make a budget which helps them to make
their task easier.
The preparation of the budget not only helps the organization to evaluate the level of costs which
are further very beneficial for the assessment of target sales and profit of the firm. The
preparation of budget by management is based on all the estimates of the expenses and the level
of output that will be observed while manufacturing and production of the goods or services
(Datar S. , 2016). Hence, it is very important to include the overhead expenses in this estimated
cost so that they can be used to further determine the per unit costs which can be easily
calculated by dividing the total budget unit cost by the budgeted number of units produced. This
cost will further help the budgeted unit cost for setting the price of the product that can be
charged from the customers in the market. But, these are only budgeted figures because of which
they are not accurate in nature (Girard, 2014). The actual in expenses which will be incurred by
the organization may be higher or lower than the budgeted figures because of which variance
Secure Best Marks with AI Grader
Need help grading? Try our AI Grader for instant feedback on your assignments.
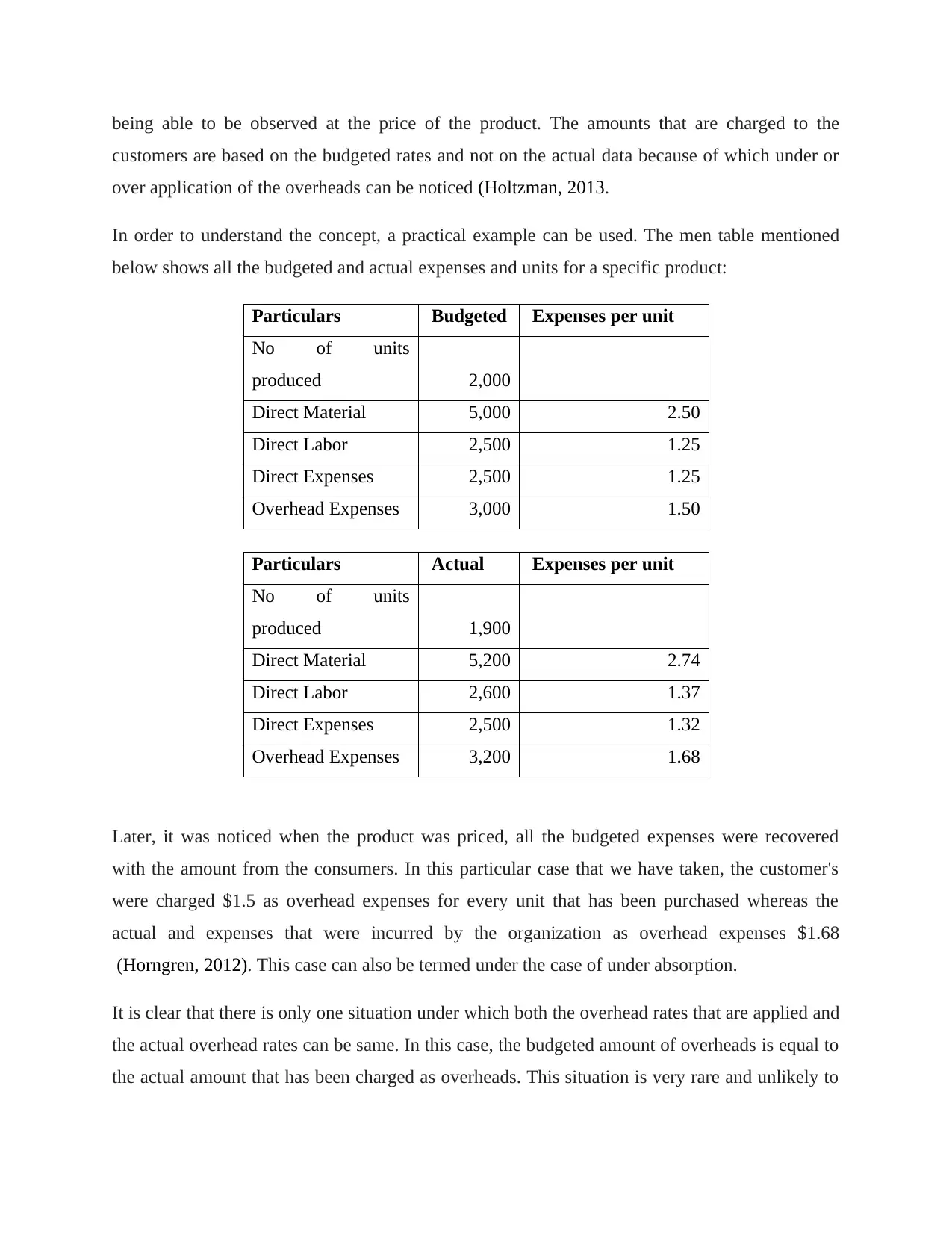
being able to be observed at the price of the product. The amounts that are charged to the
customers are based on the budgeted rates and not on the actual data because of which under or
over application of the overheads can be noticed (Holtzman, 2013.
In order to understand the concept, a practical example can be used. The men table mentioned
below shows all the budgeted and actual expenses and units for a specific product:
Particulars Budgeted Expenses per unit
No of units
produced 2,000
Direct Material 5,000 2.50
Direct Labor 2,500 1.25
Direct Expenses 2,500 1.25
Overhead Expenses 3,000 1.50
Particulars Actual Expenses per unit
No of units
produced 1,900
Direct Material 5,200 2.74
Direct Labor 2,600 1.37
Direct Expenses 2,500 1.32
Overhead Expenses 3,200 1.68
Later, it was noticed when the product was priced, all the budgeted expenses were recovered
with the amount from the consumers. In this particular case that we have taken, the customer's
were charged $1.5 as overhead expenses for every unit that has been purchased whereas the
actual and expenses that were incurred by the organization as overhead expenses $1.68
(Horngren, 2012). This case can also be termed under the case of under absorption.
It is clear that there is only one situation under which both the overhead rates that are applied and
the actual overhead rates can be same. In this case, the budgeted amount of overheads is equal to
the actual amount that has been charged as overheads. This situation is very rare and unlikely to
customers are based on the budgeted rates and not on the actual data because of which under or
over application of the overheads can be noticed (Holtzman, 2013.
In order to understand the concept, a practical example can be used. The men table mentioned
below shows all the budgeted and actual expenses and units for a specific product:
Particulars Budgeted Expenses per unit
No of units
produced 2,000
Direct Material 5,000 2.50
Direct Labor 2,500 1.25
Direct Expenses 2,500 1.25
Overhead Expenses 3,000 1.50
Particulars Actual Expenses per unit
No of units
produced 1,900
Direct Material 5,200 2.74
Direct Labor 2,600 1.37
Direct Expenses 2,500 1.32
Overhead Expenses 3,200 1.68
Later, it was noticed when the product was priced, all the budgeted expenses were recovered
with the amount from the consumers. In this particular case that we have taken, the customer's
were charged $1.5 as overhead expenses for every unit that has been purchased whereas the
actual and expenses that were incurred by the organization as overhead expenses $1.68
(Horngren, 2012). This case can also be termed under the case of under absorption.
It is clear that there is only one situation under which both the overhead rates that are applied and
the actual overhead rates can be same. In this case, the budgeted amount of overheads is equal to
the actual amount that has been charged as overheads. This situation is very rare and unlikely to
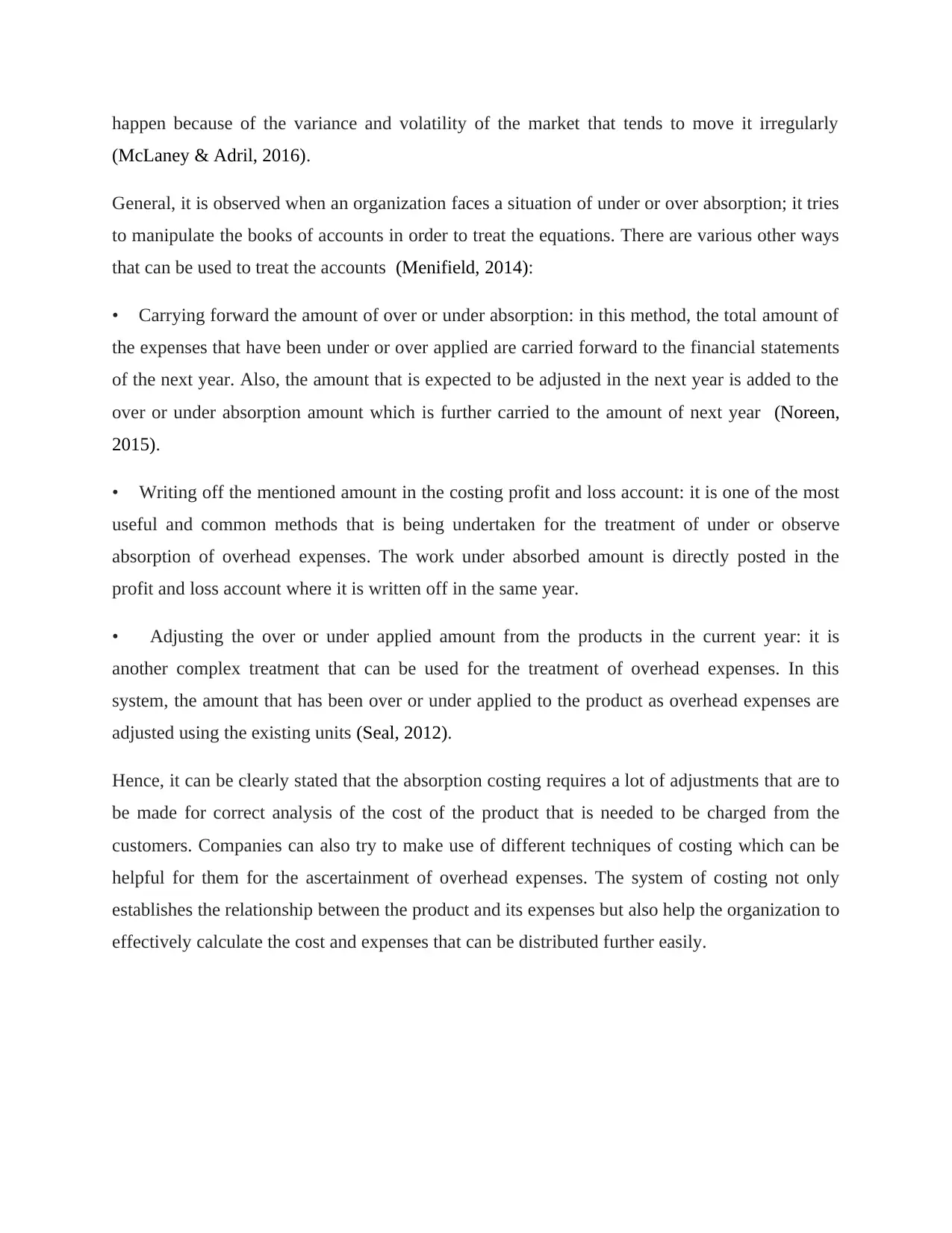
happen because of the variance and volatility of the market that tends to move it irregularly
(McLaney & Adril, 2016).
General, it is observed when an organization faces a situation of under or over absorption; it tries
to manipulate the books of accounts in order to treat the equations. There are various other ways
that can be used to treat the accounts (Menifield, 2014):
• Carrying forward the amount of over or under absorption: in this method, the total amount of
the expenses that have been under or over applied are carried forward to the financial statements
of the next year. Also, the amount that is expected to be adjusted in the next year is added to the
over or under absorption amount which is further carried to the amount of next year (Noreen,
2015).
• Writing off the mentioned amount in the costing profit and loss account: it is one of the most
useful and common methods that is being undertaken for the treatment of under or observe
absorption of overhead expenses. The work under absorbed amount is directly posted in the
profit and loss account where it is written off in the same year.
• Adjusting the over or under applied amount from the products in the current year: it is
another complex treatment that can be used for the treatment of overhead expenses. In this
system, the amount that has been over or under applied to the product as overhead expenses are
adjusted using the existing units (Seal, 2012).
Hence, it can be clearly stated that the absorption costing requires a lot of adjustments that are to
be made for correct analysis of the cost of the product that is needed to be charged from the
customers. Companies can also try to make use of different techniques of costing which can be
helpful for them for the ascertainment of overhead expenses. The system of costing not only
establishes the relationship between the product and its expenses but also help the organization to
effectively calculate the cost and expenses that can be distributed further easily.
(McLaney & Adril, 2016).
General, it is observed when an organization faces a situation of under or over absorption; it tries
to manipulate the books of accounts in order to treat the equations. There are various other ways
that can be used to treat the accounts (Menifield, 2014):
• Carrying forward the amount of over or under absorption: in this method, the total amount of
the expenses that have been under or over applied are carried forward to the financial statements
of the next year. Also, the amount that is expected to be adjusted in the next year is added to the
over or under absorption amount which is further carried to the amount of next year (Noreen,
2015).
• Writing off the mentioned amount in the costing profit and loss account: it is one of the most
useful and common methods that is being undertaken for the treatment of under or observe
absorption of overhead expenses. The work under absorbed amount is directly posted in the
profit and loss account where it is written off in the same year.
• Adjusting the over or under applied amount from the products in the current year: it is
another complex treatment that can be used for the treatment of overhead expenses. In this
system, the amount that has been over or under applied to the product as overhead expenses are
adjusted using the existing units (Seal, 2012).
Hence, it can be clearly stated that the absorption costing requires a lot of adjustments that are to
be made for correct analysis of the cost of the product that is needed to be charged from the
customers. Companies can also try to make use of different techniques of costing which can be
helpful for them for the ascertainment of overhead expenses. The system of costing not only
establishes the relationship between the product and its expenses but also help the organization to
effectively calculate the cost and expenses that can be distributed further easily.
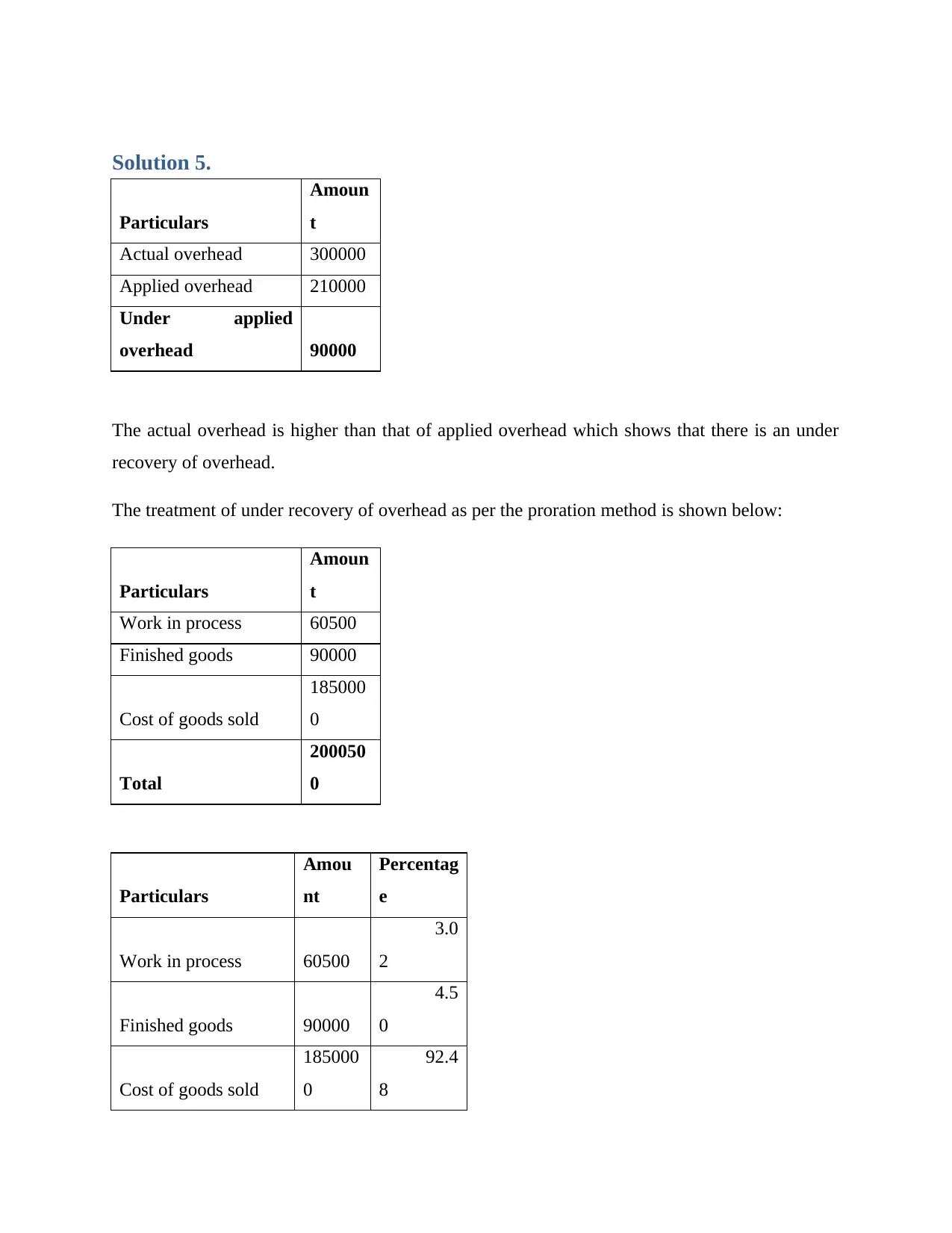
Solution 5.
Particulars
Amoun
t
Actual overhead 300000
Applied overhead 210000
Under applied
overhead 90000
The actual overhead is higher than that of applied overhead which shows that there is an under
recovery of overhead.
The treatment of under recovery of overhead as per the proration method is shown below:
Particulars
Amoun
t
Work in process 60500
Finished goods 90000
Cost of goods sold
185000
0
Total
200050
0
Particulars
Amou
nt
Percentag
e
Work in process 60500
3.0
2
Finished goods 90000
4.5
0
Cost of goods sold
185000
0
92.4
8
Particulars
Amoun
t
Actual overhead 300000
Applied overhead 210000
Under applied
overhead 90000
The actual overhead is higher than that of applied overhead which shows that there is an under
recovery of overhead.
The treatment of under recovery of overhead as per the proration method is shown below:
Particulars
Amoun
t
Work in process 60500
Finished goods 90000
Cost of goods sold
185000
0
Total
200050
0
Particulars
Amou
nt
Percentag
e
Work in process 60500
3.0
2
Finished goods 90000
4.5
0
Cost of goods sold
185000
0
92.4
8
Paraphrase This Document
Need a fresh take? Get an instant paraphrase of this document with our AI Paraphraser
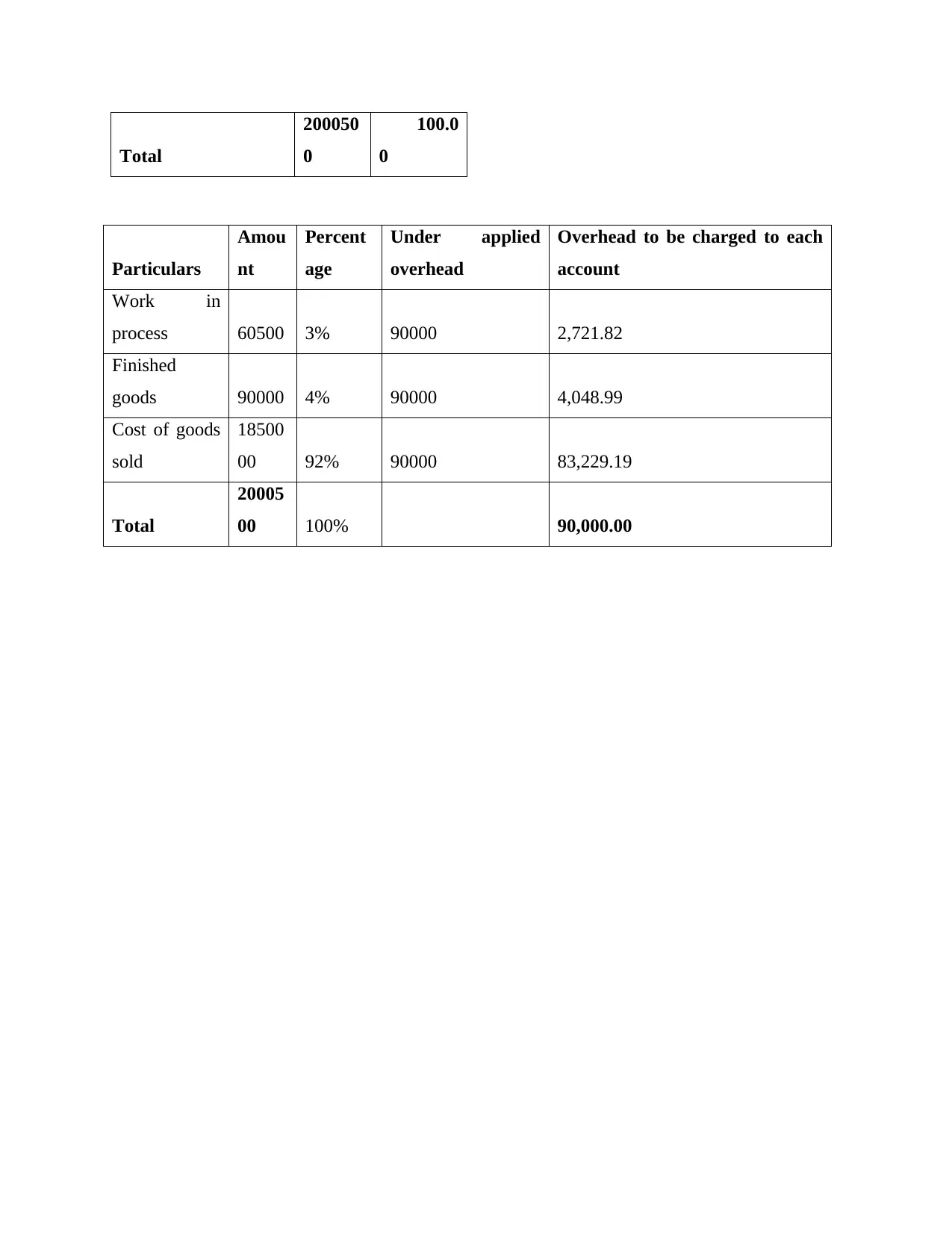
Total
200050
0
100.0
0
Particulars
Amou
nt
Percent
age
Under applied
overhead
Overhead to be charged to each
account
Work in
process 60500 3% 90000 2,721.82
Finished
goods 90000 4% 90000 4,048.99
Cost of goods
sold
18500
00 92% 90000 83,229.19
Total
20005
00 100% 90,000.00
200050
0
100.0
0
Particulars
Amou
nt
Percent
age
Under applied
overhead
Overhead to be charged to each
account
Work in
process 60500 3% 90000 2,721.82
Finished
goods 90000 4% 90000 4,048.99
Cost of goods
sold
18500
00 92% 90000 83,229.19
Total
20005
00 100% 90,000.00
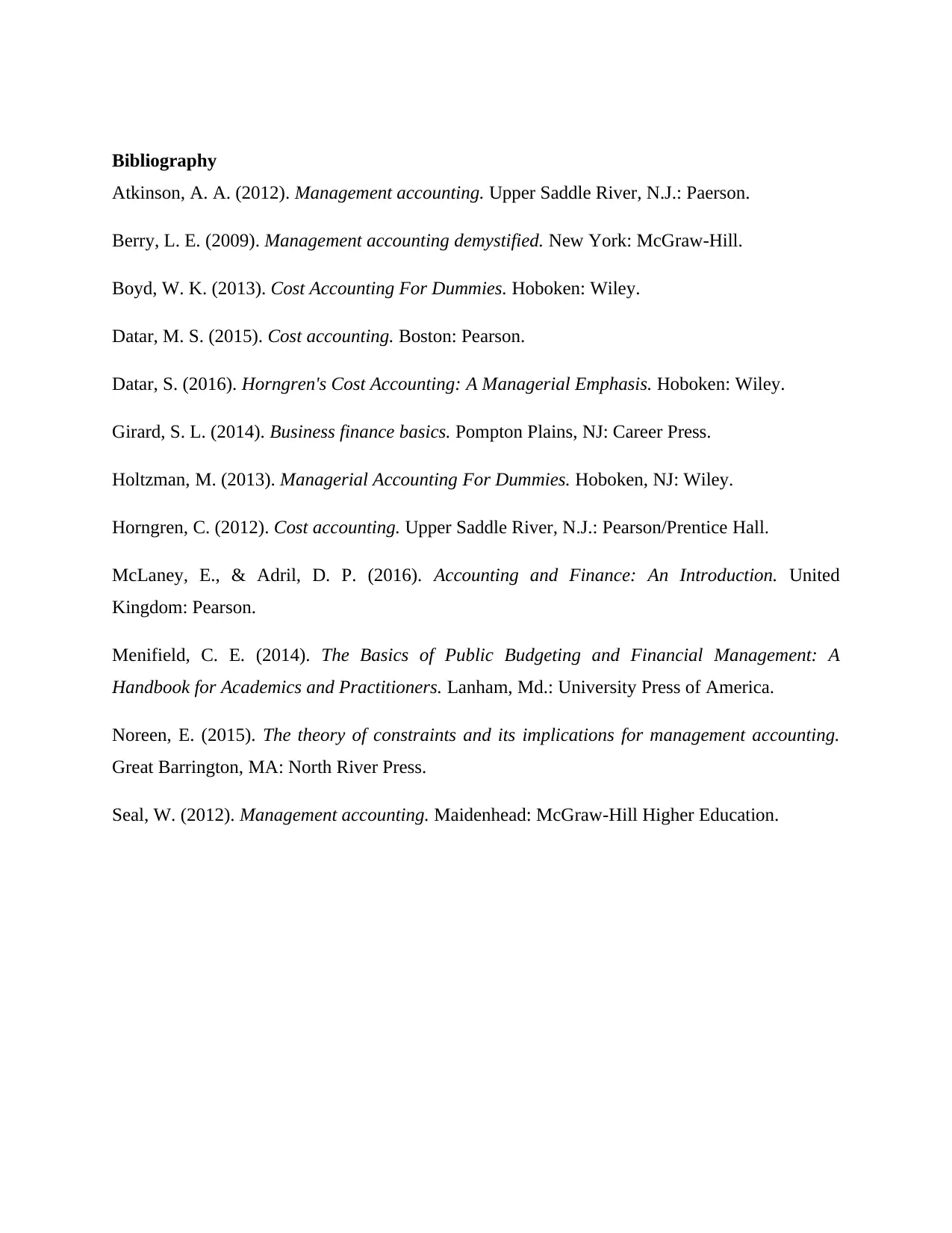
Bibliography
Atkinson, A. A. (2012). Management accounting. Upper Saddle River, N.J.: Paerson.
Berry, L. E. (2009). Management accounting demystified. New York: McGraw-Hill.
Boyd, W. K. (2013). Cost Accounting For Dummies. Hoboken: Wiley.
Datar, M. S. (2015). Cost accounting. Boston: Pearson.
Datar, S. (2016). Horngren's Cost Accounting: A Managerial Emphasis. Hoboken: Wiley.
Girard, S. L. (2014). Business finance basics. Pompton Plains, NJ: Career Press.
Holtzman, M. (2013). Managerial Accounting For Dummies. Hoboken, NJ: Wiley.
Horngren, C. (2012). Cost accounting. Upper Saddle River, N.J.: Pearson/Prentice Hall.
McLaney, E., & Adril, D. P. (2016). Accounting and Finance: An Introduction. United
Kingdom: Pearson.
Menifield, C. E. (2014). The Basics of Public Budgeting and Financial Management: A
Handbook for Academics and Practitioners. Lanham, Md.: University Press of America.
Noreen, E. (2015). The theory of constraints and its implications for management accounting.
Great Barrington, MA: North River Press.
Seal, W. (2012). Management accounting. Maidenhead: McGraw-Hill Higher Education.
Atkinson, A. A. (2012). Management accounting. Upper Saddle River, N.J.: Paerson.
Berry, L. E. (2009). Management accounting demystified. New York: McGraw-Hill.
Boyd, W. K. (2013). Cost Accounting For Dummies. Hoboken: Wiley.
Datar, M. S. (2015). Cost accounting. Boston: Pearson.
Datar, S. (2016). Horngren's Cost Accounting: A Managerial Emphasis. Hoboken: Wiley.
Girard, S. L. (2014). Business finance basics. Pompton Plains, NJ: Career Press.
Holtzman, M. (2013). Managerial Accounting For Dummies. Hoboken, NJ: Wiley.
Horngren, C. (2012). Cost accounting. Upper Saddle River, N.J.: Pearson/Prentice Hall.
McLaney, E., & Adril, D. P. (2016). Accounting and Finance: An Introduction. United
Kingdom: Pearson.
Menifield, C. E. (2014). The Basics of Public Budgeting and Financial Management: A
Handbook for Academics and Practitioners. Lanham, Md.: University Press of America.
Noreen, E. (2015). The theory of constraints and its implications for management accounting.
Great Barrington, MA: North River Press.
Seal, W. (2012). Management accounting. Maidenhead: McGraw-Hill Higher Education.
1 out of 15
Related Documents

Your All-in-One AI-Powered Toolkit for Academic Success.
+13062052269
info@desklib.com
Available 24*7 on WhatsApp / Email
Unlock your academic potential
© 2024 | Zucol Services PVT LTD | All rights reserved.