Farm Organic Ltd: Budgeting, Variance Analysis, Costing Solutions
VerifiedAdded on 2022/10/14
|12
|2916
|471
Homework Assignment
AI Summary
This document provides a comprehensive solution to a finance assignment for Farm Organic Ltd. The assignment covers several key areas of financial management, including preparing a cash budget with detailed calculations for budgeted receipts and payments, including purchase and cash collection schedules. It also delves into variance analysis, calculating material price and usage variances, as well as labor rate and efficiency variances. Furthermore, the assignment explores activity-based costing (ABC) through a memorandum, comparing traditional costing methods with ABC and recommending its use. Additionally, the document addresses non-routine decisions, such as make-or-buy analysis, and discusses qualitative factors that influence these decisions. Finally, the assignment includes a discussion on zero-based budgeting (ZBB) explaining its advantages, disadvantages and behavioral implications.
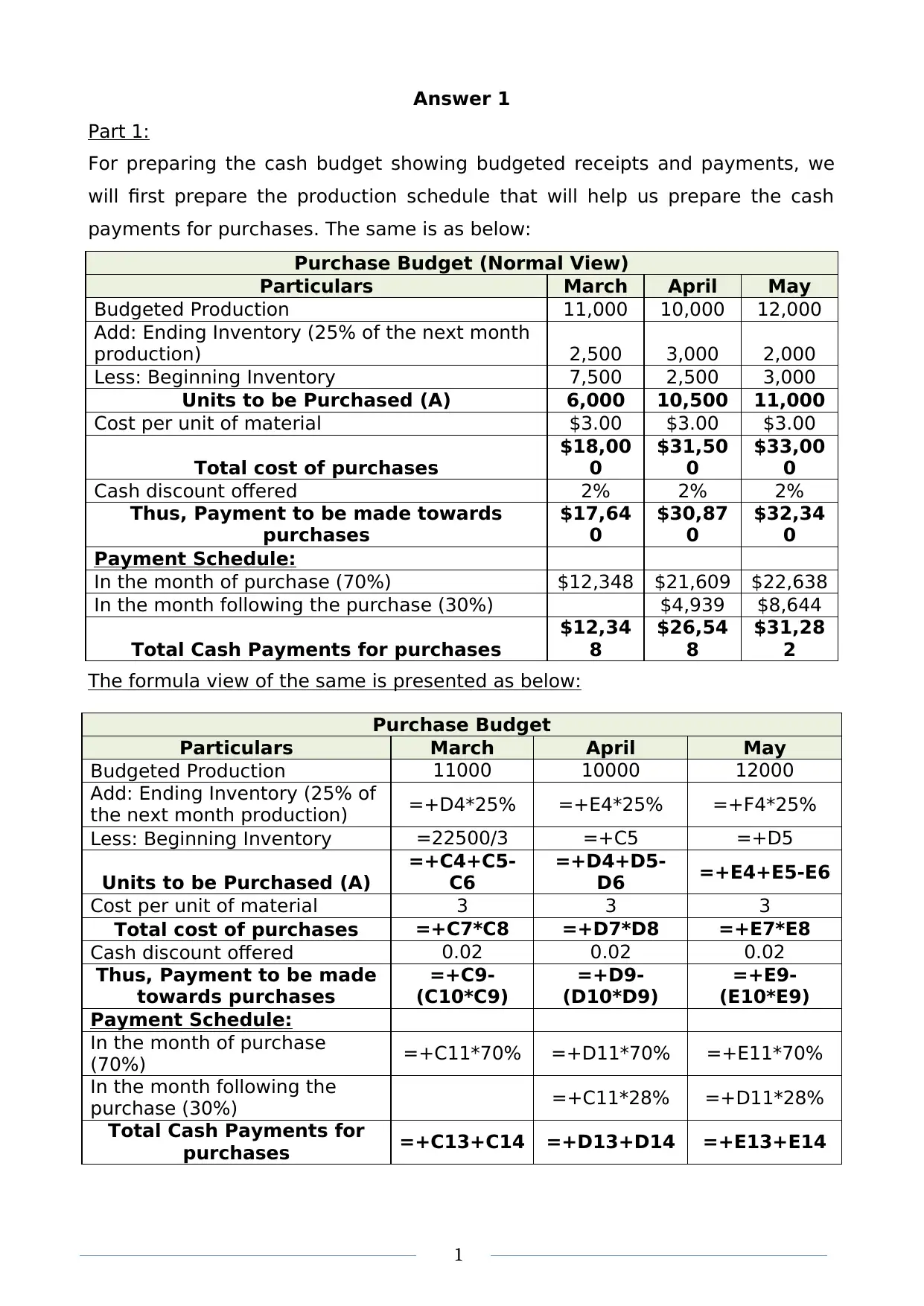
Answer 1
Part 1:
For preparing the cash budget showing budgeted receipts and payments, we
will first prepare the production schedule that will help us prepare the cash
payments for purchases. The same is as below:
Purchase Budget (Normal View)
Particulars March April May
Budgeted Production 11,000 10,000 12,000
Add: Ending Inventory (25% of the next month
production) 2,500 3,000 2,000
Less: Beginning Inventory 7,500 2,500 3,000
Units to be Purchased (A) 6,000 10,500 11,000
Cost per unit of material $3.00 $3.00 $3.00
Total cost of purchases
$18,00
0
$31,50
0
$33,00
0
Cash discount offered 2% 2% 2%
Thus, Payment to be made towards
purchases
$17,64
0
$30,87
0
$32,34
0
Payment Schedule:
In the month of purchase (70%) $12,348 $21,609 $22,638
In the month following the purchase (30%) $4,939 $8,644
Total Cash Payments for purchases
$12,34
8
$26,54
8
$31,28
2
The formula view of the same is presented as below:
Purchase Budget
Particulars March April May
Budgeted Production 11000 10000 12000
Add: Ending Inventory (25% of
the next month production) =+D4*25% =+E4*25% =+F4*25%
Less: Beginning Inventory =22500/3 =+C5 =+D5
Units to be Purchased (A)
=+C4+C5-
C6
=+D4+D5-
D6 =+E4+E5-E6
Cost per unit of material 3 3 3
Total cost of purchases =+C7*C8 =+D7*D8 =+E7*E8
Cash discount offered 0.02 0.02 0.02
Thus, Payment to be made
towards purchases
=+C9-
(C10*C9)
=+D9-
(D10*D9)
=+E9-
(E10*E9)
Payment Schedule:
In the month of purchase
(70%) =+C11*70% =+D11*70% =+E11*70%
In the month following the
purchase (30%) =+C11*28% =+D11*28%
Total Cash Payments for
purchases =+C13+C14 =+D13+D14 =+E13+E14
1
Part 1:
For preparing the cash budget showing budgeted receipts and payments, we
will first prepare the production schedule that will help us prepare the cash
payments for purchases. The same is as below:
Purchase Budget (Normal View)
Particulars March April May
Budgeted Production 11,000 10,000 12,000
Add: Ending Inventory (25% of the next month
production) 2,500 3,000 2,000
Less: Beginning Inventory 7,500 2,500 3,000
Units to be Purchased (A) 6,000 10,500 11,000
Cost per unit of material $3.00 $3.00 $3.00
Total cost of purchases
$18,00
0
$31,50
0
$33,00
0
Cash discount offered 2% 2% 2%
Thus, Payment to be made towards
purchases
$17,64
0
$30,87
0
$32,34
0
Payment Schedule:
In the month of purchase (70%) $12,348 $21,609 $22,638
In the month following the purchase (30%) $4,939 $8,644
Total Cash Payments for purchases
$12,34
8
$26,54
8
$31,28
2
The formula view of the same is presented as below:
Purchase Budget
Particulars March April May
Budgeted Production 11000 10000 12000
Add: Ending Inventory (25% of
the next month production) =+D4*25% =+E4*25% =+F4*25%
Less: Beginning Inventory =22500/3 =+C5 =+D5
Units to be Purchased (A)
=+C4+C5-
C6
=+D4+D5-
D6 =+E4+E5-E6
Cost per unit of material 3 3 3
Total cost of purchases =+C7*C8 =+D7*D8 =+E7*E8
Cash discount offered 0.02 0.02 0.02
Thus, Payment to be made
towards purchases
=+C9-
(C10*C9)
=+D9-
(D10*D9)
=+E9-
(E10*E9)
Payment Schedule:
In the month of purchase
(70%) =+C11*70% =+D11*70% =+E11*70%
In the month following the
purchase (30%) =+C11*28% =+D11*28%
Total Cash Payments for
purchases =+C13+C14 =+D13+D14 =+E13+E14
1
Secure Best Marks with AI Grader
Need help grading? Try our AI Grader for instant feedback on your assignments.
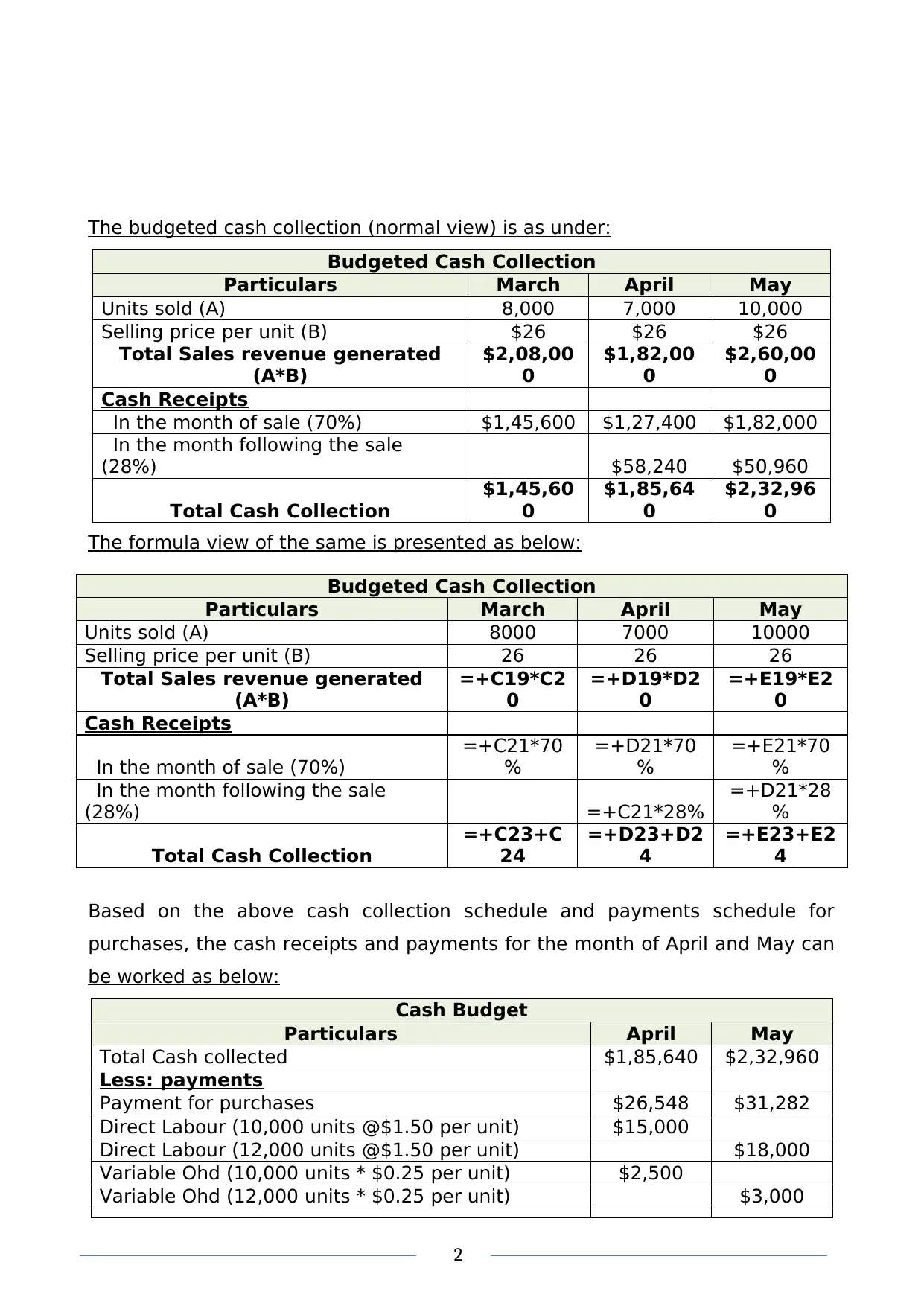
The budgeted cash collection (normal view) is as under:
Budgeted Cash Collection
Particulars March April May
Units sold (A) 8,000 7,000 10,000
Selling price per unit (B) $26 $26 $26
Total Sales revenue generated
(A*B)
$2,08,00
0
$1,82,00
0
$2,60,00
0
Cash Receipts
In the month of sale (70%) $1,45,600 $1,27,400 $1,82,000
In the month following the sale
(28%) $58,240 $50,960
Total Cash Collection
$1,45,60
0
$1,85,64
0
$2,32,96
0
The formula view of the same is presented as below:
Budgeted Cash Collection
Particulars March April May
Units sold (A) 8000 7000 10000
Selling price per unit (B) 26 26 26
Total Sales revenue generated
(A*B)
=+C19*C2
0
=+D19*D2
0
=+E19*E2
0
Cash Receipts
In the month of sale (70%)
=+C21*70
%
=+D21*70
%
=+E21*70
%
In the month following the sale
(28%) =+C21*28%
=+D21*28
%
Total Cash Collection
=+C23+C
24
=+D23+D2
4
=+E23+E2
4
Based on the above cash collection schedule and payments schedule for
purchases, the cash receipts and payments for the month of April and May can
be worked as below:
Cash Budget
Particulars April May
Total Cash collected $1,85,640 $2,32,960
Less: payments
Payment for purchases $26,548 $31,282
Direct Labour (10,000 units @$1.50 per unit) $15,000
Direct Labour (12,000 units @$1.50 per unit) $18,000
Variable Ohd (10,000 units * $0.25 per unit) $2,500
Variable Ohd (12,000 units * $0.25 per unit) $3,000
2
Budgeted Cash Collection
Particulars March April May
Units sold (A) 8,000 7,000 10,000
Selling price per unit (B) $26 $26 $26
Total Sales revenue generated
(A*B)
$2,08,00
0
$1,82,00
0
$2,60,00
0
Cash Receipts
In the month of sale (70%) $1,45,600 $1,27,400 $1,82,000
In the month following the sale
(28%) $58,240 $50,960
Total Cash Collection
$1,45,60
0
$1,85,64
0
$2,32,96
0
The formula view of the same is presented as below:
Budgeted Cash Collection
Particulars March April May
Units sold (A) 8000 7000 10000
Selling price per unit (B) 26 26 26
Total Sales revenue generated
(A*B)
=+C19*C2
0
=+D19*D2
0
=+E19*E2
0
Cash Receipts
In the month of sale (70%)
=+C21*70
%
=+D21*70
%
=+E21*70
%
In the month following the sale
(28%) =+C21*28%
=+D21*28
%
Total Cash Collection
=+C23+C
24
=+D23+D2
4
=+E23+E2
4
Based on the above cash collection schedule and payments schedule for
purchases, the cash receipts and payments for the month of April and May can
be worked as below:
Cash Budget
Particulars April May
Total Cash collected $1,85,640 $2,32,960
Less: payments
Payment for purchases $26,548 $31,282
Direct Labour (10,000 units @$1.50 per unit) $15,000
Direct Labour (12,000 units @$1.50 per unit) $18,000
Variable Ohd (10,000 units * $0.25 per unit) $2,500
Variable Ohd (12,000 units * $0.25 per unit) $3,000
2
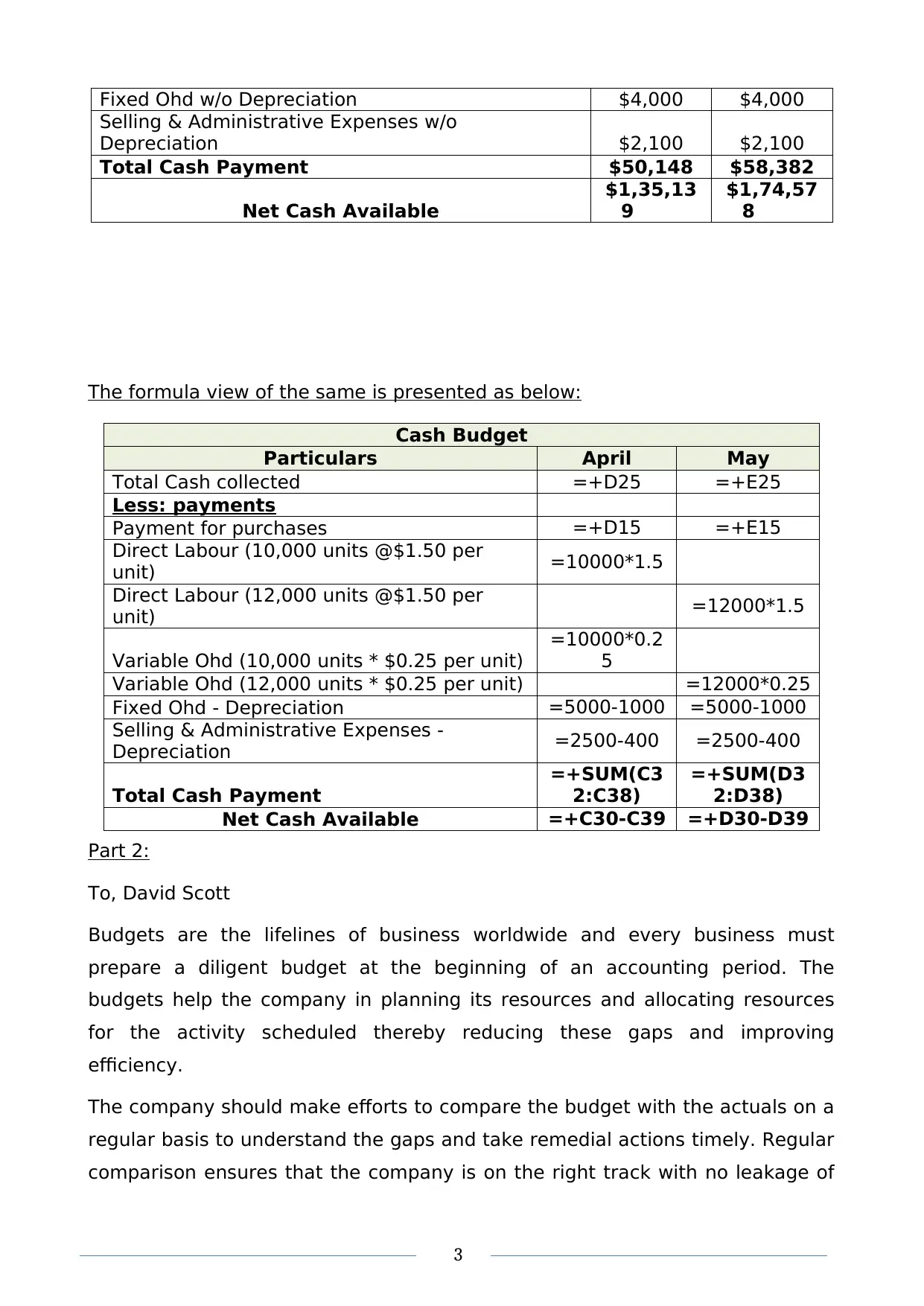
Fixed Ohd w/o Depreciation $4,000 $4,000
Selling & Administrative Expenses w/o
Depreciation $2,100 $2,100
Total Cash Payment $50,148 $58,382
Net Cash Available
$1,35,13
9
$1,74,57
8
The formula view of the same is presented as below:
Cash Budget
Particulars April May
Total Cash collected =+D25 =+E25
Less: payments
Payment for purchases =+D15 =+E15
Direct Labour (10,000 units @$1.50 per
unit) =10000*1.5
Direct Labour (12,000 units @$1.50 per
unit) =12000*1.5
Variable Ohd (10,000 units * $0.25 per unit)
=10000*0.2
5
Variable Ohd (12,000 units * $0.25 per unit) =12000*0.25
Fixed Ohd - Depreciation =5000-1000 =5000-1000
Selling & Administrative Expenses -
Depreciation =2500-400 =2500-400
Total Cash Payment
=+SUM(C3
2:C38)
=+SUM(D3
2:D38)
Net Cash Available =+C30-C39 =+D30-D39
Part 2:
To, David Scott
Budgets are the lifelines of business worldwide and every business must
prepare a diligent budget at the beginning of an accounting period. The
budgets help the company in planning its resources and allocating resources
for the activity scheduled thereby reducing these gaps and improving
efficiency.
The company should make efforts to compare the budget with the actuals on a
regular basis to understand the gaps and take remedial actions timely. Regular
comparison ensures that the company is on the right track with no leakage of
3
Selling & Administrative Expenses w/o
Depreciation $2,100 $2,100
Total Cash Payment $50,148 $58,382
Net Cash Available
$1,35,13
9
$1,74,57
8
The formula view of the same is presented as below:
Cash Budget
Particulars April May
Total Cash collected =+D25 =+E25
Less: payments
Payment for purchases =+D15 =+E15
Direct Labour (10,000 units @$1.50 per
unit) =10000*1.5
Direct Labour (12,000 units @$1.50 per
unit) =12000*1.5
Variable Ohd (10,000 units * $0.25 per unit)
=10000*0.2
5
Variable Ohd (12,000 units * $0.25 per unit) =12000*0.25
Fixed Ohd - Depreciation =5000-1000 =5000-1000
Selling & Administrative Expenses -
Depreciation =2500-400 =2500-400
Total Cash Payment
=+SUM(C3
2:C38)
=+SUM(D3
2:D38)
Net Cash Available =+C30-C39 =+D30-D39
Part 2:
To, David Scott
Budgets are the lifelines of business worldwide and every business must
prepare a diligent budget at the beginning of an accounting period. The
budgets help the company in planning its resources and allocating resources
for the activity scheduled thereby reducing these gaps and improving
efficiency.
The company should make efforts to compare the budget with the actuals on a
regular basis to understand the gaps and take remedial actions timely. Regular
comparison ensures that the company is on the right track with no leakage of
3
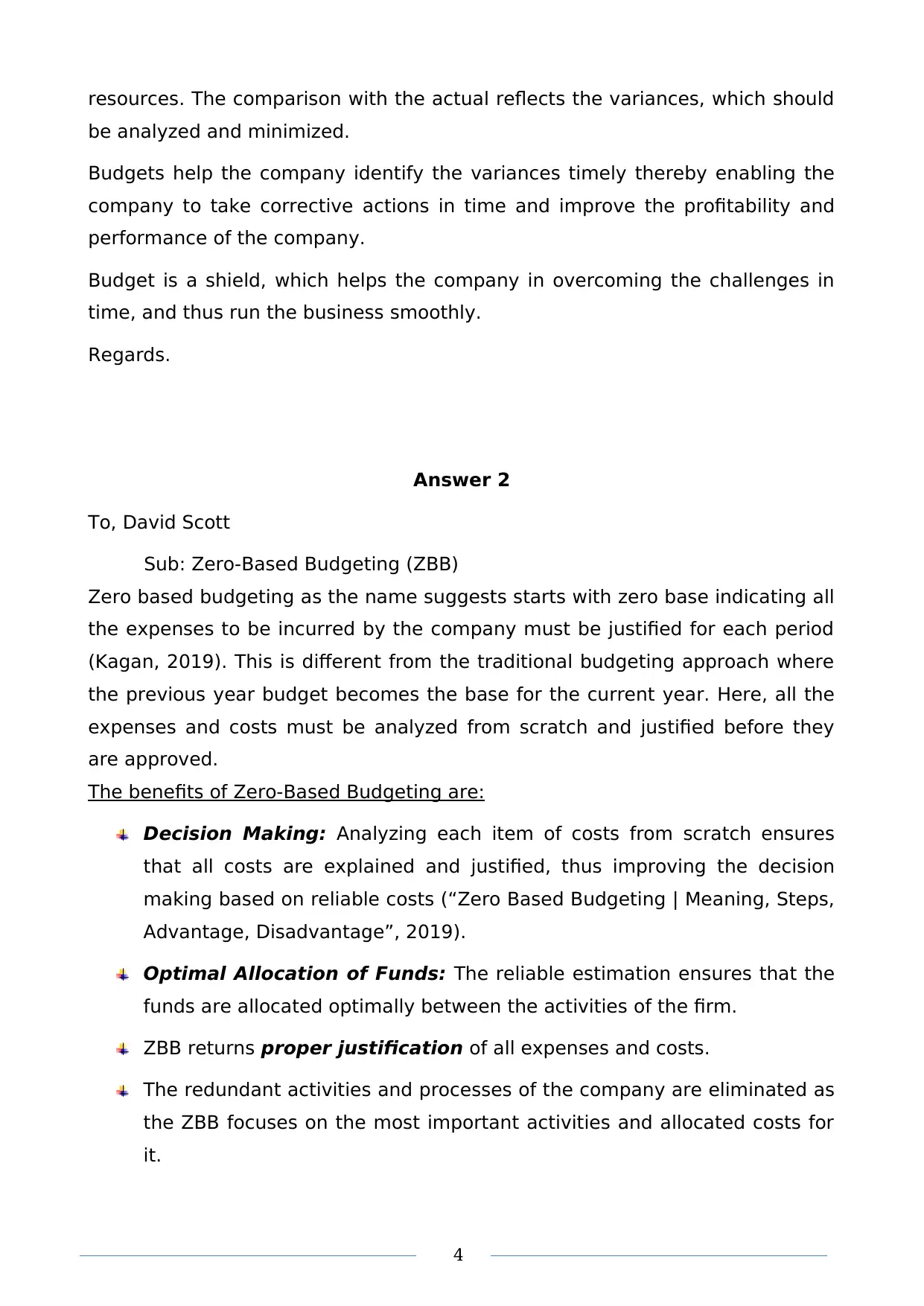
resources. The comparison with the actual reflects the variances, which should
be analyzed and minimized.
Budgets help the company identify the variances timely thereby enabling the
company to take corrective actions in time and improve the profitability and
performance of the company.
Budget is a shield, which helps the company in overcoming the challenges in
time, and thus run the business smoothly.
Regards.
Answer 2
To, David Scott
Sub: Zero-Based Budgeting (ZBB)
Zero based budgeting as the name suggests starts with zero base indicating all
the expenses to be incurred by the company must be justified for each period
(Kagan, 2019). This is different from the traditional budgeting approach where
the previous year budget becomes the base for the current year. Here, all the
expenses and costs must be analyzed from scratch and justified before they
are approved.
The benefits of Zero-Based Budgeting are:
Decision Making: Analyzing each item of costs from scratch ensures
that all costs are explained and justified, thus improving the decision
making based on reliable costs (“Zero Based Budgeting | Meaning, Steps,
Advantage, Disadvantage”, 2019).
Optimal Allocation of Funds: The reliable estimation ensures that the
funds are allocated optimally between the activities of the firm.
ZBB returns proper justification of all expenses and costs.
The redundant activities and processes of the company are eliminated as
the ZBB focuses on the most important activities and allocated costs for
it.
4
be analyzed and minimized.
Budgets help the company identify the variances timely thereby enabling the
company to take corrective actions in time and improve the profitability and
performance of the company.
Budget is a shield, which helps the company in overcoming the challenges in
time, and thus run the business smoothly.
Regards.
Answer 2
To, David Scott
Sub: Zero-Based Budgeting (ZBB)
Zero based budgeting as the name suggests starts with zero base indicating all
the expenses to be incurred by the company must be justified for each period
(Kagan, 2019). This is different from the traditional budgeting approach where
the previous year budget becomes the base for the current year. Here, all the
expenses and costs must be analyzed from scratch and justified before they
are approved.
The benefits of Zero-Based Budgeting are:
Decision Making: Analyzing each item of costs from scratch ensures
that all costs are explained and justified, thus improving the decision
making based on reliable costs (“Zero Based Budgeting | Meaning, Steps,
Advantage, Disadvantage”, 2019).
Optimal Allocation of Funds: The reliable estimation ensures that the
funds are allocated optimally between the activities of the firm.
ZBB returns proper justification of all expenses and costs.
The redundant activities and processes of the company are eliminated as
the ZBB focuses on the most important activities and allocated costs for
it.
4
Secure Best Marks with AI Grader
Need help grading? Try our AI Grader for instant feedback on your assignments.
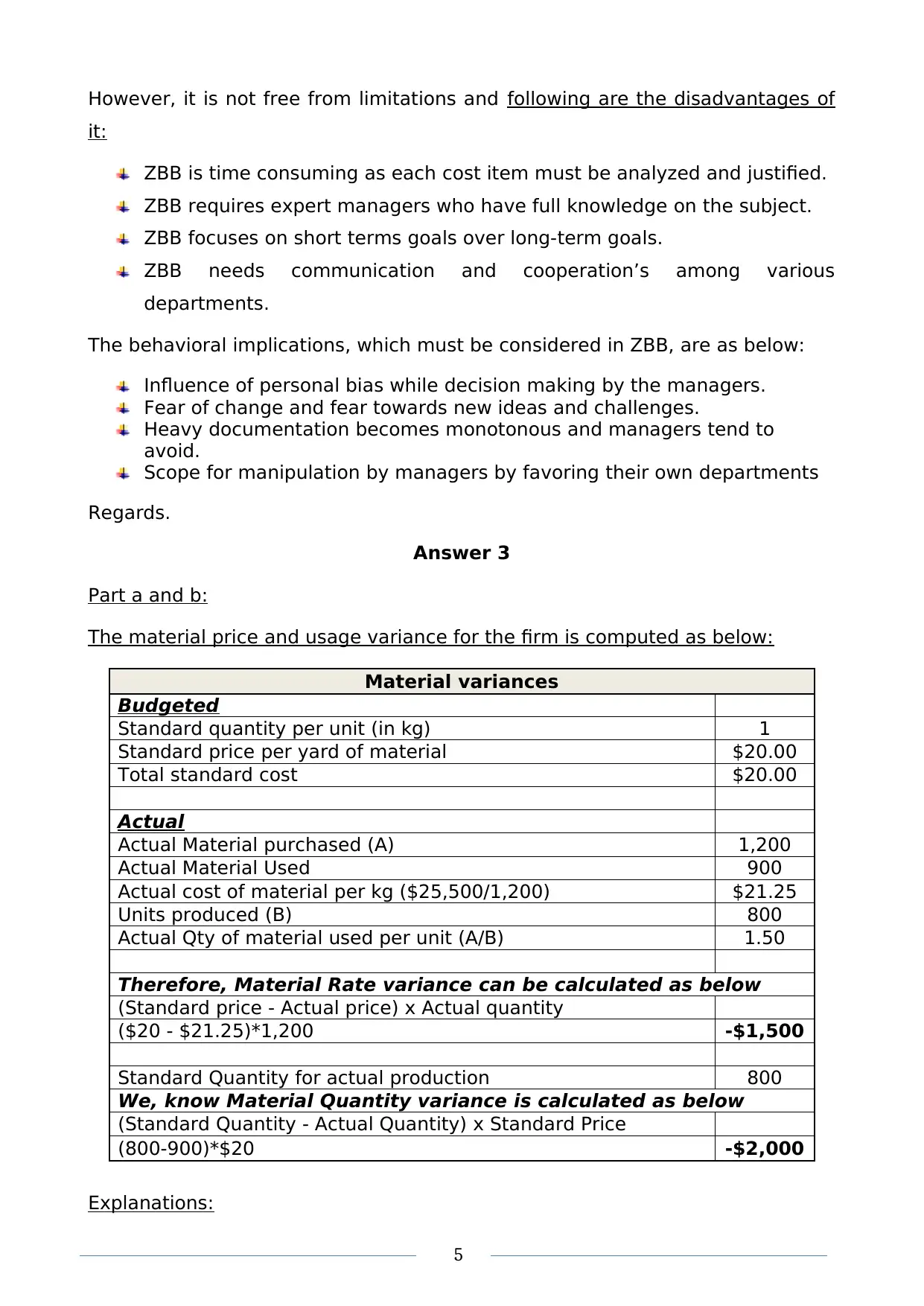
However, it is not free from limitations and following are the disadvantages of
it:
ZBB is time consuming as each cost item must be analyzed and justified.
ZBB requires expert managers who have full knowledge on the subject.
ZBB focuses on short terms goals over long-term goals.
ZBB needs communication and cooperation’s among various
departments.
The behavioral implications, which must be considered in ZBB, are as below:
Influence of personal bias while decision making by the managers.
Fear of change and fear towards new ideas and challenges.
Heavy documentation becomes monotonous and managers tend to
avoid.
Scope for manipulation by managers by favoring their own departments
Regards.
Answer 3
Part a and b:
The material price and usage variance for the firm is computed as below:
Material variances
Budgeted
Standard quantity per unit (in kg) 1
Standard price per yard of material $20.00
Total standard cost $20.00
Actual
Actual Material purchased (A) 1,200
Actual Material Used 900
Actual cost of material per kg ($25,500/1,200) $21.25
Units produced (B) 800
Actual Qty of material used per unit (A/B) 1.50
Therefore, Material Rate variance can be calculated as below
(Standard price - Actual price) x Actual quantity
($20 - $21.25)*1,200 -$1,500
Standard Quantity for actual production 800
We, know Material Quantity variance is calculated as below
(Standard Quantity - Actual Quantity) x Standard Price
(800-900)*$20 -$2,000
Explanations:
5
it:
ZBB is time consuming as each cost item must be analyzed and justified.
ZBB requires expert managers who have full knowledge on the subject.
ZBB focuses on short terms goals over long-term goals.
ZBB needs communication and cooperation’s among various
departments.
The behavioral implications, which must be considered in ZBB, are as below:
Influence of personal bias while decision making by the managers.
Fear of change and fear towards new ideas and challenges.
Heavy documentation becomes monotonous and managers tend to
avoid.
Scope for manipulation by managers by favoring their own departments
Regards.
Answer 3
Part a and b:
The material price and usage variance for the firm is computed as below:
Material variances
Budgeted
Standard quantity per unit (in kg) 1
Standard price per yard of material $20.00
Total standard cost $20.00
Actual
Actual Material purchased (A) 1,200
Actual Material Used 900
Actual cost of material per kg ($25,500/1,200) $21.25
Units produced (B) 800
Actual Qty of material used per unit (A/B) 1.50
Therefore, Material Rate variance can be calculated as below
(Standard price - Actual price) x Actual quantity
($20 - $21.25)*1,200 -$1,500
Standard Quantity for actual production 800
We, know Material Quantity variance is calculated as below
(Standard Quantity - Actual Quantity) x Standard Price
(800-900)*$20 -$2,000
Explanations:
5

Since, the actual material rate per kg is higher than the standard rate per
kg, the variance is unfavorable
Since, the actual quantity used is more than the standard quantity for
actual production, the variance is unfavorable
Answers:
The material price variance is $1,500 unfavorable
The material usage variance is $2,000 unfavorable.
Part c and d:
The direct labour rate and efficiency variance for the firm is computed as
below:
Labour Variances
Budgeted
Standard Labour Hours per unit 0.25
Standard Labour Rate per Hour ($15/0.25) $60.00
Actual
Direct labour hours worked 280
Production (in units) 800
Actual Direct Labour Rate per hour $60.00
From above information, we can calculate the
following:
Actual Labour Rate cost (Labour rate * labor hours) 16,800
Labour Rate variance can be calculated as below
(Standard rate - Actual rate) x Actual hours worked $0
Labour Efficiency variance can be calculated as below
Std hrs for actual production $200
(Standard hours - Actual hours) x Standard rate -$4,800
Explanations:
Since, the actual labour rate per hour is equal to the standard rate per
hour, the variance is NIL
6
kg, the variance is unfavorable
Since, the actual quantity used is more than the standard quantity for
actual production, the variance is unfavorable
Answers:
The material price variance is $1,500 unfavorable
The material usage variance is $2,000 unfavorable.
Part c and d:
The direct labour rate and efficiency variance for the firm is computed as
below:
Labour Variances
Budgeted
Standard Labour Hours per unit 0.25
Standard Labour Rate per Hour ($15/0.25) $60.00
Actual
Direct labour hours worked 280
Production (in units) 800
Actual Direct Labour Rate per hour $60.00
From above information, we can calculate the
following:
Actual Labour Rate cost (Labour rate * labor hours) 16,800
Labour Rate variance can be calculated as below
(Standard rate - Actual rate) x Actual hours worked $0
Labour Efficiency variance can be calculated as below
Std hrs for actual production $200
(Standard hours - Actual hours) x Standard rate -$4,800
Explanations:
Since, the actual labour rate per hour is equal to the standard rate per
hour, the variance is NIL
6

Since, the actual hour is more than the standard hour for actual
production, the variance is unfavorable
Answers:
The direct labour rate variance is 0
The direct labour efficiency variance is $4,800 unfavorable.
Part e:
The total overhead variance for the company will be Actual Overhead less the
standard overhead applied.
Actual Overhead cost = $4,500
Standard overhead applied = 200 units * $3 per unit = $600
Thus, overhead variance = $600 - $4,500 = $3,900 unfavorable.
The journal entries for the cost flow will be as under:
Particulars Debit Credit
Raw Material Inventory $22,500
To Accounts Payable $22,500
(Being raw material purchased on credit)
Work In process Inventory $16,800
To Wages Payable $16,800
(Being wages payable @60 per hour for 280
hours)
Work In process Inventory $4,500
To Manufacturing Overhead $4,500
(Being mfg. ohd. incurred)
7
production, the variance is unfavorable
Answers:
The direct labour rate variance is 0
The direct labour efficiency variance is $4,800 unfavorable.
Part e:
The total overhead variance for the company will be Actual Overhead less the
standard overhead applied.
Actual Overhead cost = $4,500
Standard overhead applied = 200 units * $3 per unit = $600
Thus, overhead variance = $600 - $4,500 = $3,900 unfavorable.
The journal entries for the cost flow will be as under:
Particulars Debit Credit
Raw Material Inventory $22,500
To Accounts Payable $22,500
(Being raw material purchased on credit)
Work In process Inventory $16,800
To Wages Payable $16,800
(Being wages payable @60 per hour for 280
hours)
Work In process Inventory $4,500
To Manufacturing Overhead $4,500
(Being mfg. ohd. incurred)
7
Paraphrase This Document
Need a fresh take? Get an instant paraphrase of this document with our AI Paraphraser
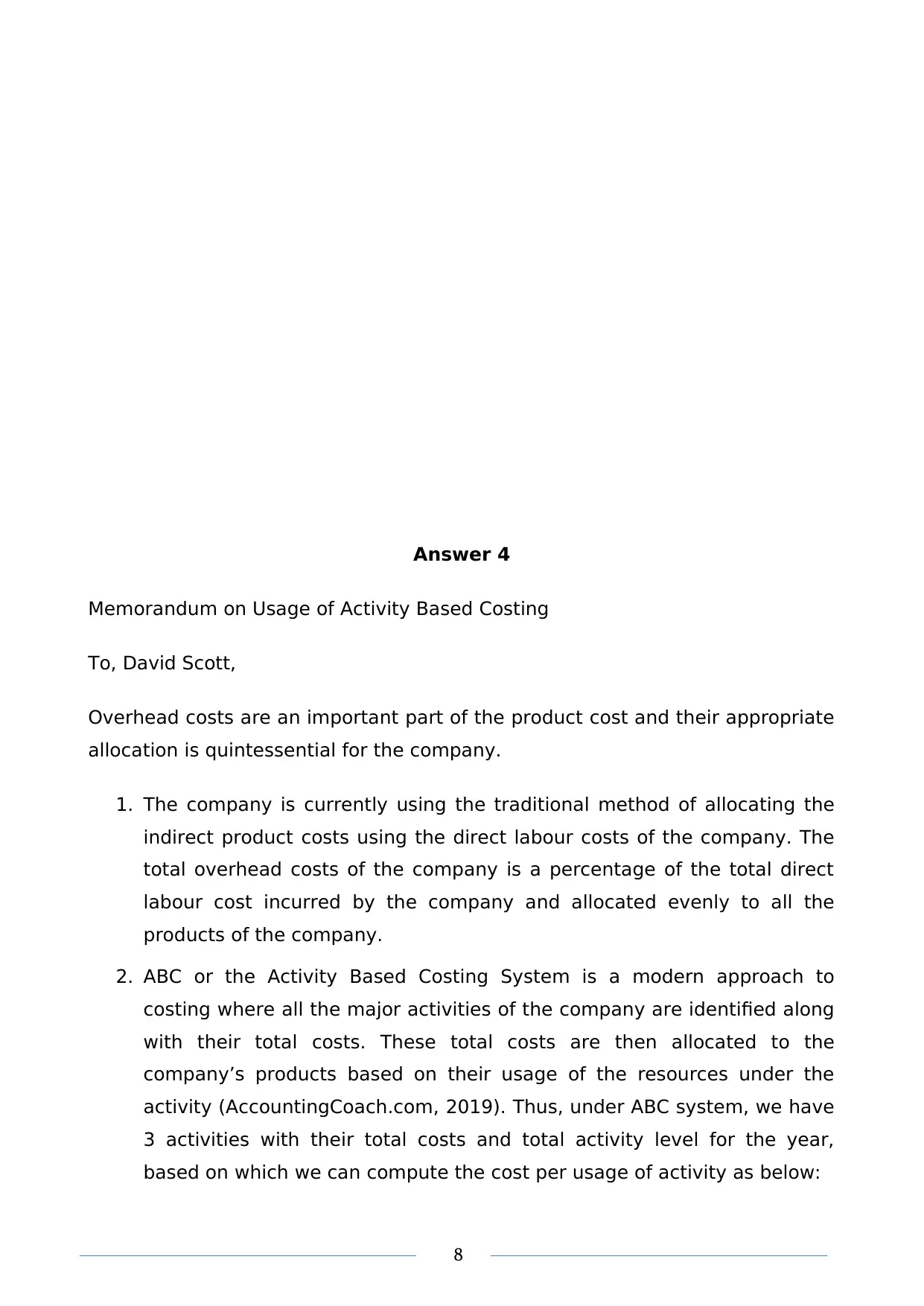
Answer 4
Memorandum on Usage of Activity Based Costing
To, David Scott,
Overhead costs are an important part of the product cost and their appropriate
allocation is quintessential for the company.
1. The company is currently using the traditional method of allocating the
indirect product costs using the direct labour costs of the company. The
total overhead costs of the company is a percentage of the total direct
labour cost incurred by the company and allocated evenly to all the
products of the company.
2. ABC or the Activity Based Costing System is a modern approach to
costing where all the major activities of the company are identified along
with their total costs. These total costs are then allocated to the
company’s products based on their usage of the resources under the
activity (AccountingCoach.com, 2019). Thus, under ABC system, we have
3 activities with their total costs and total activity level for the year,
based on which we can compute the cost per usage of activity as below:
8
Memorandum on Usage of Activity Based Costing
To, David Scott,
Overhead costs are an important part of the product cost and their appropriate
allocation is quintessential for the company.
1. The company is currently using the traditional method of allocating the
indirect product costs using the direct labour costs of the company. The
total overhead costs of the company is a percentage of the total direct
labour cost incurred by the company and allocated evenly to all the
products of the company.
2. ABC or the Activity Based Costing System is a modern approach to
costing where all the major activities of the company are identified along
with their total costs. These total costs are then allocated to the
company’s products based on their usage of the resources under the
activity (AccountingCoach.com, 2019). Thus, under ABC system, we have
3 activities with their total costs and total activity level for the year,
based on which we can compute the cost per usage of activity as below:
8
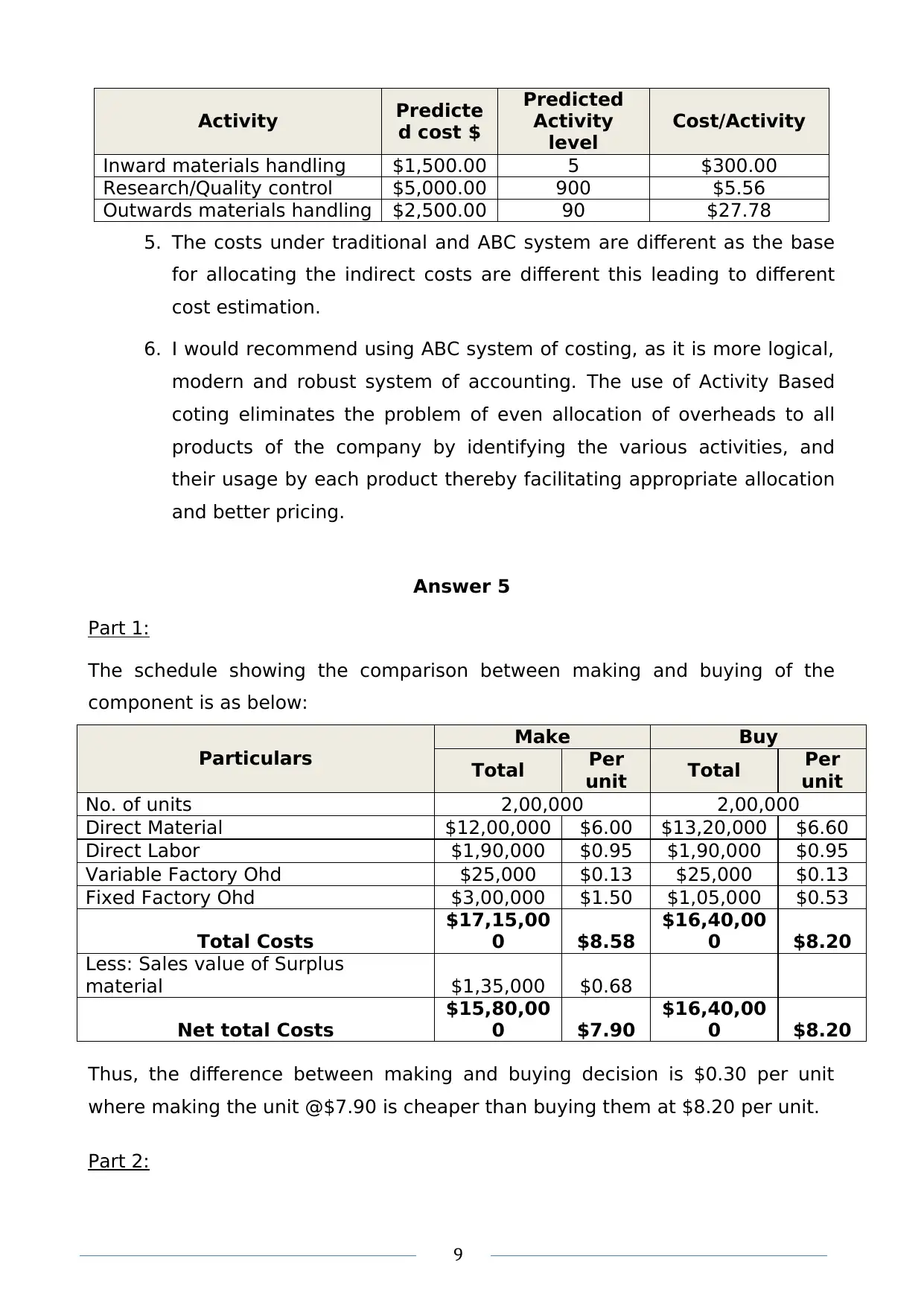
Activity Predicte
d cost $
Predicted
Activity
level
Cost/Activity
Inward materials handling $1,500.00 5 $300.00
Research/Quality control $5,000.00 900 $5.56
Outwards materials handling $2,500.00 90 $27.78
5. The costs under traditional and ABC system are different as the base
for allocating the indirect costs are different this leading to different
cost estimation.
6. I would recommend using ABC system of costing, as it is more logical,
modern and robust system of accounting. The use of Activity Based
coting eliminates the problem of even allocation of overheads to all
products of the company by identifying the various activities, and
their usage by each product thereby facilitating appropriate allocation
and better pricing.
Answer 5
Part 1:
The schedule showing the comparison between making and buying of the
component is as below:
Particulars
Make Buy
Total Per
unit Total Per
unit
No. of units 2,00,000 2,00,000
Direct Material $12,00,000 $6.00 $13,20,000 $6.60
Direct Labor $1,90,000 $0.95 $1,90,000 $0.95
Variable Factory Ohd $25,000 $0.13 $25,000 $0.13
Fixed Factory Ohd $3,00,000 $1.50 $1,05,000 $0.53
Total Costs
$17,15,00
0 $8.58
$16,40,00
0 $8.20
Less: Sales value of Surplus
material $1,35,000 $0.68
Net total Costs
$15,80,00
0 $7.90
$16,40,00
0 $8.20
Thus, the difference between making and buying decision is $0.30 per unit
where making the unit @$7.90 is cheaper than buying them at $8.20 per unit.
Part 2:
9
d cost $
Predicted
Activity
level
Cost/Activity
Inward materials handling $1,500.00 5 $300.00
Research/Quality control $5,000.00 900 $5.56
Outwards materials handling $2,500.00 90 $27.78
5. The costs under traditional and ABC system are different as the base
for allocating the indirect costs are different this leading to different
cost estimation.
6. I would recommend using ABC system of costing, as it is more logical,
modern and robust system of accounting. The use of Activity Based
coting eliminates the problem of even allocation of overheads to all
products of the company by identifying the various activities, and
their usage by each product thereby facilitating appropriate allocation
and better pricing.
Answer 5
Part 1:
The schedule showing the comparison between making and buying of the
component is as below:
Particulars
Make Buy
Total Per
unit Total Per
unit
No. of units 2,00,000 2,00,000
Direct Material $12,00,000 $6.00 $13,20,000 $6.60
Direct Labor $1,90,000 $0.95 $1,90,000 $0.95
Variable Factory Ohd $25,000 $0.13 $25,000 $0.13
Fixed Factory Ohd $3,00,000 $1.50 $1,05,000 $0.53
Total Costs
$17,15,00
0 $8.58
$16,40,00
0 $8.20
Less: Sales value of Surplus
material $1,35,000 $0.68
Net total Costs
$15,80,00
0 $7.90
$16,40,00
0 $8.20
Thus, the difference between making and buying decision is $0.30 per unit
where making the unit @$7.90 is cheaper than buying them at $8.20 per unit.
Part 2:
9
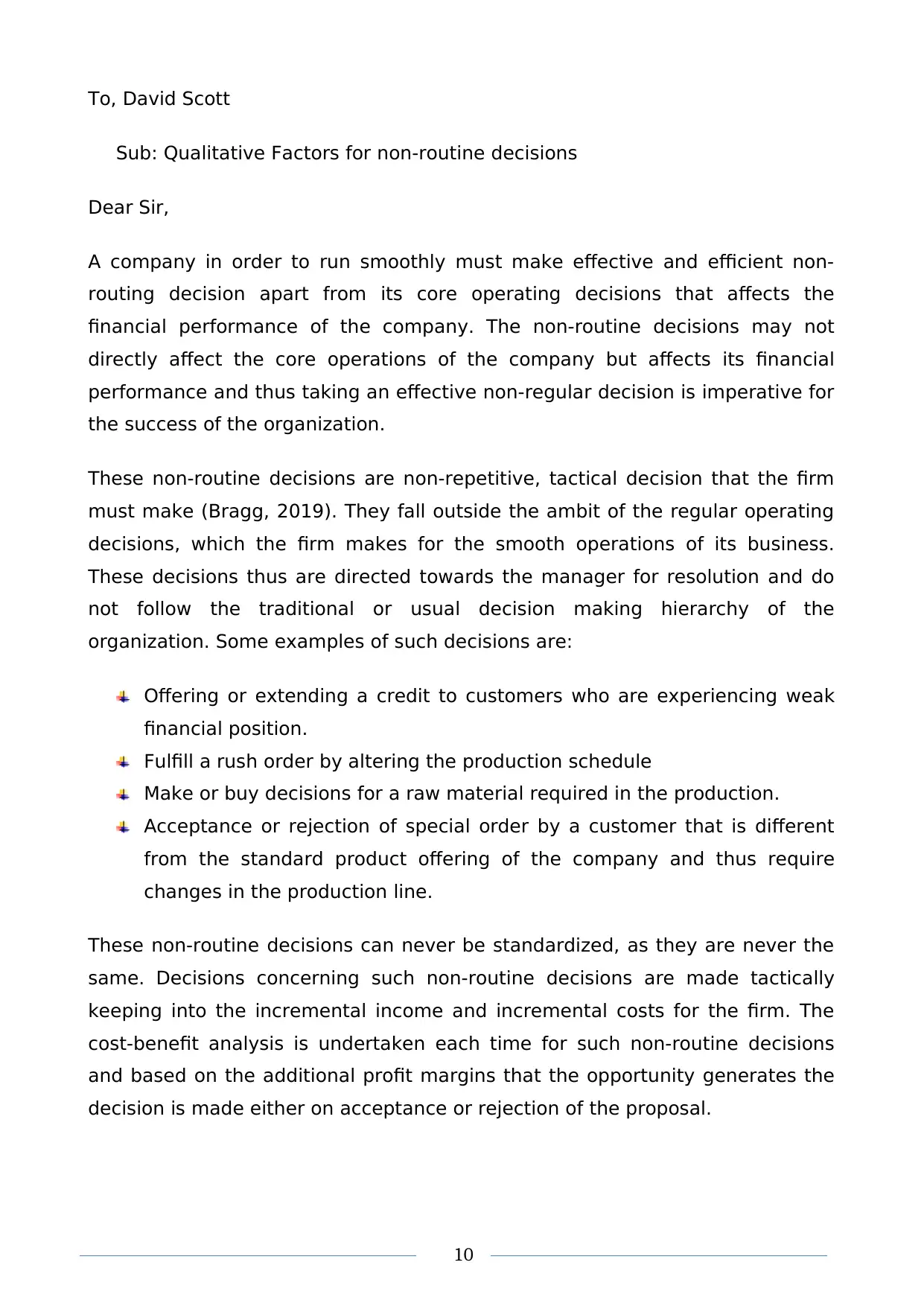
To, David Scott
Sub: Qualitative Factors for non-routine decisions
Dear Sir,
A company in order to run smoothly must make effective and efficient non-
routing decision apart from its core operating decisions that affects the
financial performance of the company. The non-routine decisions may not
directly affect the core operations of the company but affects its financial
performance and thus taking an effective non-regular decision is imperative for
the success of the organization.
These non-routine decisions are non-repetitive, tactical decision that the firm
must make (Bragg, 2019). They fall outside the ambit of the regular operating
decisions, which the firm makes for the smooth operations of its business.
These decisions thus are directed towards the manager for resolution and do
not follow the traditional or usual decision making hierarchy of the
organization. Some examples of such decisions are:
Offering or extending a credit to customers who are experiencing weak
financial position.
Fulfill a rush order by altering the production schedule
Make or buy decisions for a raw material required in the production.
Acceptance or rejection of special order by a customer that is different
from the standard product offering of the company and thus require
changes in the production line.
These non-routine decisions can never be standardized, as they are never the
same. Decisions concerning such non-routine decisions are made tactically
keeping into the incremental income and incremental costs for the firm. The
cost-benefit analysis is undertaken each time for such non-routine decisions
and based on the additional profit margins that the opportunity generates the
decision is made either on acceptance or rejection of the proposal.
10
Sub: Qualitative Factors for non-routine decisions
Dear Sir,
A company in order to run smoothly must make effective and efficient non-
routing decision apart from its core operating decisions that affects the
financial performance of the company. The non-routine decisions may not
directly affect the core operations of the company but affects its financial
performance and thus taking an effective non-regular decision is imperative for
the success of the organization.
These non-routine decisions are non-repetitive, tactical decision that the firm
must make (Bragg, 2019). They fall outside the ambit of the regular operating
decisions, which the firm makes for the smooth operations of its business.
These decisions thus are directed towards the manager for resolution and do
not follow the traditional or usual decision making hierarchy of the
organization. Some examples of such decisions are:
Offering or extending a credit to customers who are experiencing weak
financial position.
Fulfill a rush order by altering the production schedule
Make or buy decisions for a raw material required in the production.
Acceptance or rejection of special order by a customer that is different
from the standard product offering of the company and thus require
changes in the production line.
These non-routine decisions can never be standardized, as they are never the
same. Decisions concerning such non-routine decisions are made tactically
keeping into the incremental income and incremental costs for the firm. The
cost-benefit analysis is undertaken each time for such non-routine decisions
and based on the additional profit margins that the opportunity generates the
decision is made either on acceptance or rejection of the proposal.
10
Secure Best Marks with AI Grader
Need help grading? Try our AI Grader for instant feedback on your assignments.
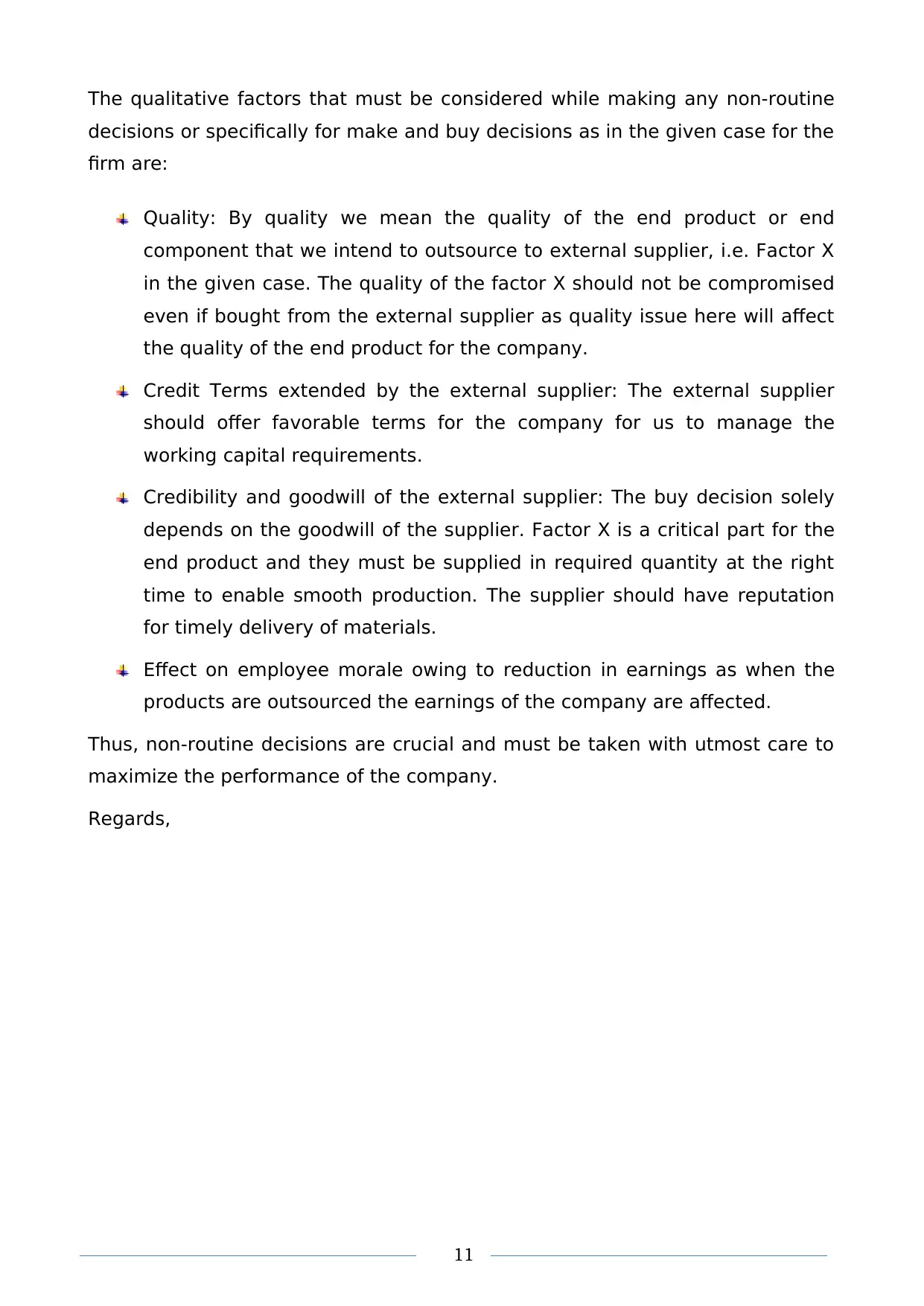
The qualitative factors that must be considered while making any non-routine
decisions or specifically for make and buy decisions as in the given case for the
firm are:
Quality: By quality we mean the quality of the end product or end
component that we intend to outsource to external supplier, i.e. Factor X
in the given case. The quality of the factor X should not be compromised
even if bought from the external supplier as quality issue here will affect
the quality of the end product for the company.
Credit Terms extended by the external supplier: The external supplier
should offer favorable terms for the company for us to manage the
working capital requirements.
Credibility and goodwill of the external supplier: The buy decision solely
depends on the goodwill of the supplier. Factor X is a critical part for the
end product and they must be supplied in required quantity at the right
time to enable smooth production. The supplier should have reputation
for timely delivery of materials.
Effect on employee morale owing to reduction in earnings as when the
products are outsourced the earnings of the company are affected.
Thus, non-routine decisions are crucial and must be taken with utmost care to
maximize the performance of the company.
Regards,
11
decisions or specifically for make and buy decisions as in the given case for the
firm are:
Quality: By quality we mean the quality of the end product or end
component that we intend to outsource to external supplier, i.e. Factor X
in the given case. The quality of the factor X should not be compromised
even if bought from the external supplier as quality issue here will affect
the quality of the end product for the company.
Credit Terms extended by the external supplier: The external supplier
should offer favorable terms for the company for us to manage the
working capital requirements.
Credibility and goodwill of the external supplier: The buy decision solely
depends on the goodwill of the supplier. Factor X is a critical part for the
end product and they must be supplied in required quantity at the right
time to enable smooth production. The supplier should have reputation
for timely delivery of materials.
Effect on employee morale owing to reduction in earnings as when the
products are outsourced the earnings of the company are affected.
Thus, non-routine decisions are crucial and must be taken with utmost care to
maximize the performance of the company.
Regards,
11
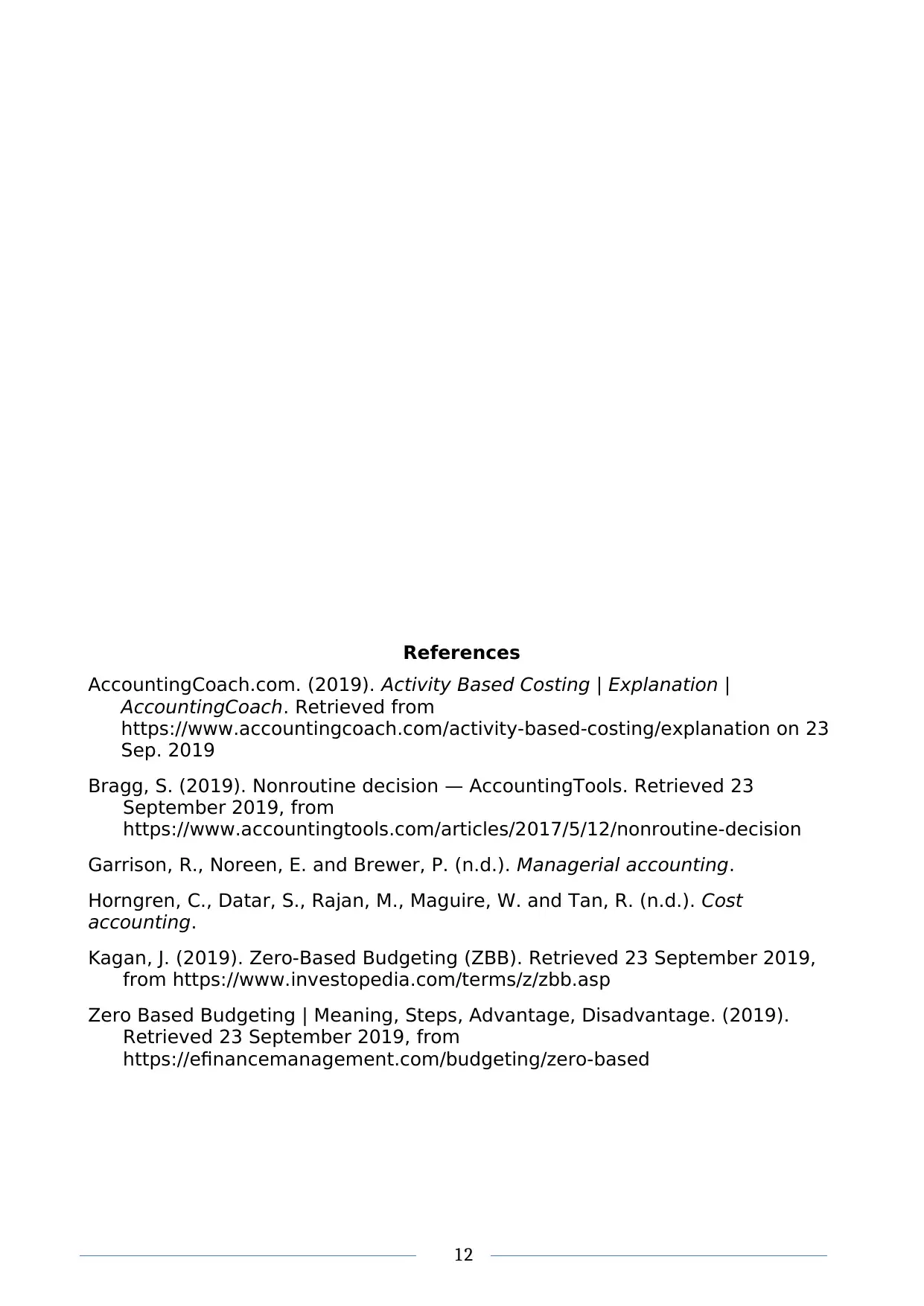
References
AccountingCoach.com. (2019). Activity Based Costing | Explanation |
AccountingCoach. Retrieved from
https://www.accountingcoach.com/activity-based-costing/explanation on 23
Sep. 2019
Bragg, S. (2019). Nonroutine decision — AccountingTools. Retrieved 23
September 2019, from
https://www.accountingtools.com/articles/2017/5/12/nonroutine-decision
Garrison, R., Noreen, E. and Brewer, P. (n.d.). Managerial accounting.
Horngren, C., Datar, S., Rajan, M., Maguire, W. and Tan, R. (n.d.). Cost
accounting.
Kagan, J. (2019). Zero-Based Budgeting (ZBB). Retrieved 23 September 2019,
from https://www.investopedia.com/terms/z/zbb.asp
Zero Based Budgeting | Meaning, Steps, Advantage, Disadvantage. (2019).
Retrieved 23 September 2019, from
https://efinancemanagement.com/budgeting/zero-based
12
AccountingCoach.com. (2019). Activity Based Costing | Explanation |
AccountingCoach. Retrieved from
https://www.accountingcoach.com/activity-based-costing/explanation on 23
Sep. 2019
Bragg, S. (2019). Nonroutine decision — AccountingTools. Retrieved 23
September 2019, from
https://www.accountingtools.com/articles/2017/5/12/nonroutine-decision
Garrison, R., Noreen, E. and Brewer, P. (n.d.). Managerial accounting.
Horngren, C., Datar, S., Rajan, M., Maguire, W. and Tan, R. (n.d.). Cost
accounting.
Kagan, J. (2019). Zero-Based Budgeting (ZBB). Retrieved 23 September 2019,
from https://www.investopedia.com/terms/z/zbb.asp
Zero Based Budgeting | Meaning, Steps, Advantage, Disadvantage. (2019).
Retrieved 23 September 2019, from
https://efinancemanagement.com/budgeting/zero-based
12
1 out of 12
Related Documents

Your All-in-One AI-Powered Toolkit for Academic Success.
+13062052269
info@desklib.com
Available 24*7 on WhatsApp / Email
Unlock your academic potential
© 2024 | Zucol Services PVT LTD | All rights reserved.