ENCORE 4010 Research Project: Friction Welding in Production
VerifiedAdded on  2023/01/17
|32
|6570
|493
Project
AI Summary
This research project, submitted by Karan Saggu for ENCOR 4010, delves into the process of friction welding. It begins with a problem statement emphasizing the growing use of friction welding for joining dissimilar materials and its impact on joint strength and safety. The project includes an abstract summarizing the technique's automation, advantages, and limitations. The introduction provides a background on friction welding, its working principle, and feasibility studies. The document details the advantages and disadvantages of friction welding and explores its industrial applications, including marine, aerospace, and railway industries. Different types of friction welding, such as inertial friction welding and continuous induction methods, are discussed. The project also includes a timeline, proposal metrics, and a conclusion, along with references. The research aims to provide a comprehensive overview of friction welding, its parameters, and its importance in various manufacturing sectors.
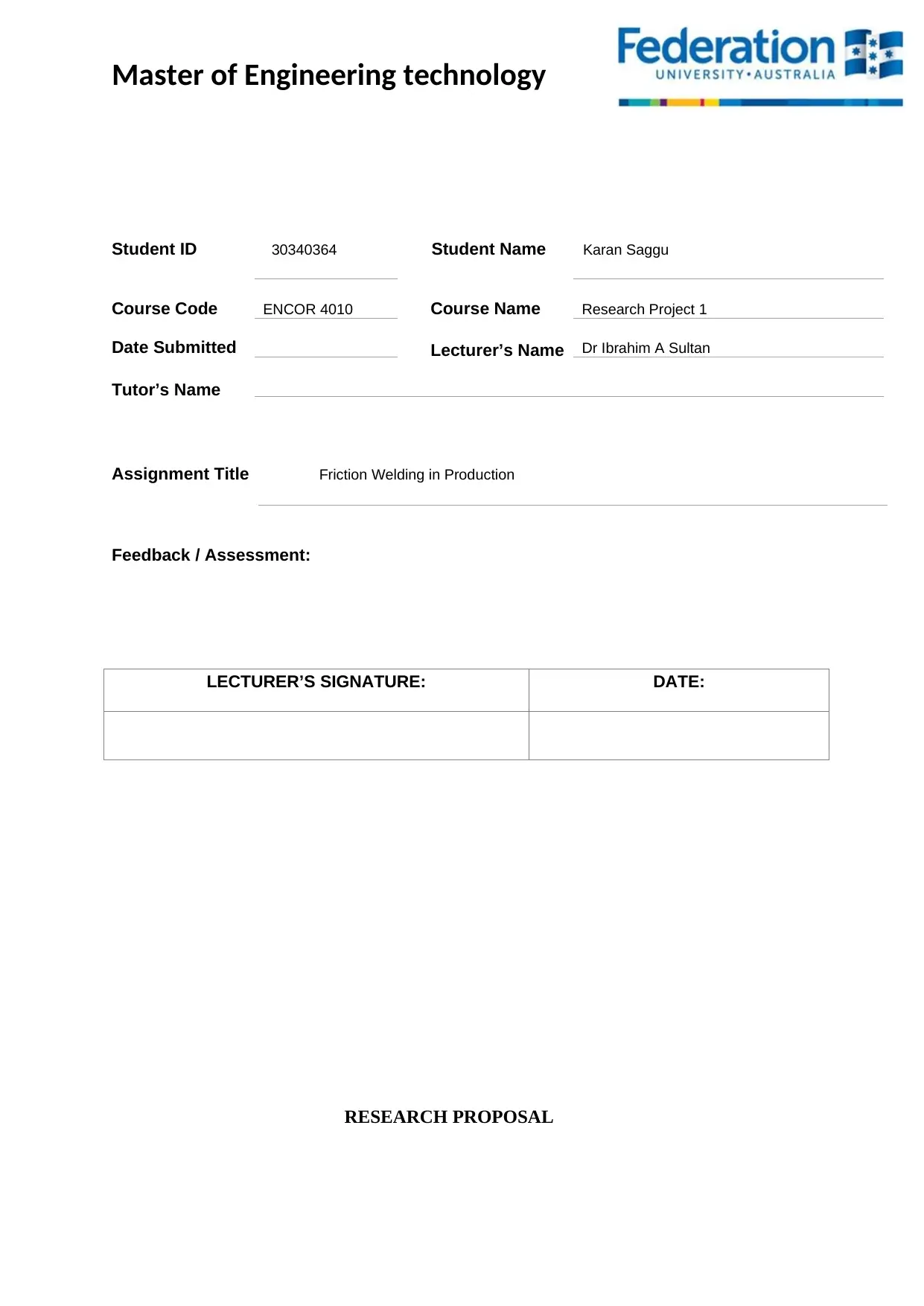
Master of Engineering technology
Student ID 30340364 Student Name Karan Saggu
Assignment Title Friction Welding in Production
Feedback / Assessment:
LECTURER’S SIGNATURE: DATE:
RESEARCH PROPOSAL
Course Code ENCOR 4010 Course Name Research Project 1
Date Submitted Lecturer’s Name Dr Ibrahim A Sultan
Tutor’s Name
Student ID 30340364 Student Name Karan Saggu
Assignment Title Friction Welding in Production
Feedback / Assessment:
LECTURER’S SIGNATURE: DATE:
RESEARCH PROPOSAL
Course Code ENCOR 4010 Course Name Research Project 1
Date Submitted Lecturer’s Name Dr Ibrahim A Sultan
Tutor’s Name
Paraphrase This Document
Need a fresh take? Get an instant paraphrase of this document with our AI Paraphraser
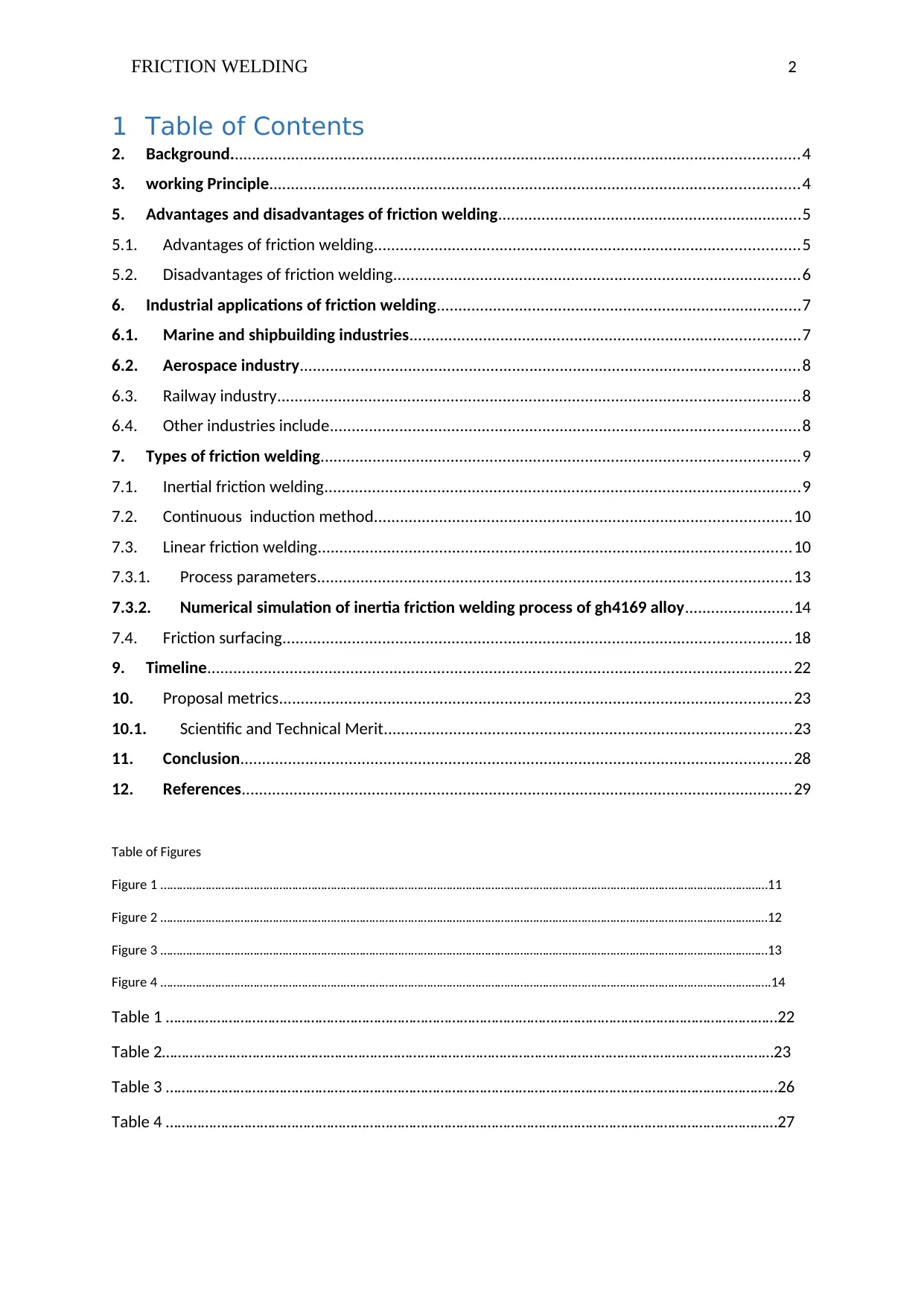
FRICTION WELDING 2
1 Table of Contents
2. Background...................................................................................................................................4
3. working Principle..........................................................................................................................4
5. Advantages and disadvantages of friction welding......................................................................5
5.1. Advantages of friction welding..................................................................................................5
5.2. Disadvantages of friction welding..............................................................................................6
6. Industrial applications of friction welding....................................................................................7
6.1. Marine and shipbuilding industries..........................................................................................7
6.2. Aerospace industry...................................................................................................................8
6.3. Railway industry........................................................................................................................8
6.4. Other industries include............................................................................................................8
7. Types of friction welding..............................................................................................................9
7.1. Inertial friction welding..............................................................................................................9
7.2. Continuous induction method................................................................................................10
7.3. Linear friction welding.............................................................................................................10
7.3.1. Process parameters.............................................................................................................13
7.3.2. Numerical simulation of inertia friction welding process of gh4169 alloy.........................14
7.4. Friction surfacing.....................................................................................................................18
9. Timeline.......................................................................................................................................22
10. Proposal metrics......................................................................................................................23
10.1. Scientific and Technical Merit..............................................................................................23
11. Conclusion...............................................................................................................................28
12. References...............................................................................................................................29
Table of Figures
Figure 1 ………………………………………………………………………………………………………………………………………………………………………11
Figure 2 ………………………………………………………………………………………………………………………………………………………………………12
Figure 3 ………………………………………………………………………………………………………………………………………………………………………13
Figure 4 ……………………………………………………………………………………………………………………………………………………………………….14
Table 1 …………………………………………………………………………………………………………………………………………22
Table 2…………………………………………………………………………………………………………………………………………23
Table 3 …………………………………………………………………………………………………………………………………………26
Table 4 …………………………………………………………………………………………………………………………………………27
1 Table of Contents
2. Background...................................................................................................................................4
3. working Principle..........................................................................................................................4
5. Advantages and disadvantages of friction welding......................................................................5
5.1. Advantages of friction welding..................................................................................................5
5.2. Disadvantages of friction welding..............................................................................................6
6. Industrial applications of friction welding....................................................................................7
6.1. Marine and shipbuilding industries..........................................................................................7
6.2. Aerospace industry...................................................................................................................8
6.3. Railway industry........................................................................................................................8
6.4. Other industries include............................................................................................................8
7. Types of friction welding..............................................................................................................9
7.1. Inertial friction welding..............................................................................................................9
7.2. Continuous induction method................................................................................................10
7.3. Linear friction welding.............................................................................................................10
7.3.1. Process parameters.............................................................................................................13
7.3.2. Numerical simulation of inertia friction welding process of gh4169 alloy.........................14
7.4. Friction surfacing.....................................................................................................................18
9. Timeline.......................................................................................................................................22
10. Proposal metrics......................................................................................................................23
10.1. Scientific and Technical Merit..............................................................................................23
11. Conclusion...............................................................................................................................28
12. References...............................................................................................................................29
Table of Figures
Figure 1 ………………………………………………………………………………………………………………………………………………………………………11
Figure 2 ………………………………………………………………………………………………………………………………………………………………………12
Figure 3 ………………………………………………………………………………………………………………………………………………………………………13
Figure 4 ……………………………………………………………………………………………………………………………………………………………………….14
Table 1 …………………………………………………………………………………………………………………………………………22
Table 2…………………………………………………………………………………………………………………………………………23
Table 3 …………………………………………………………………………………………………………………………………………26
Table 4 …………………………………………………………………………………………………………………………………………27
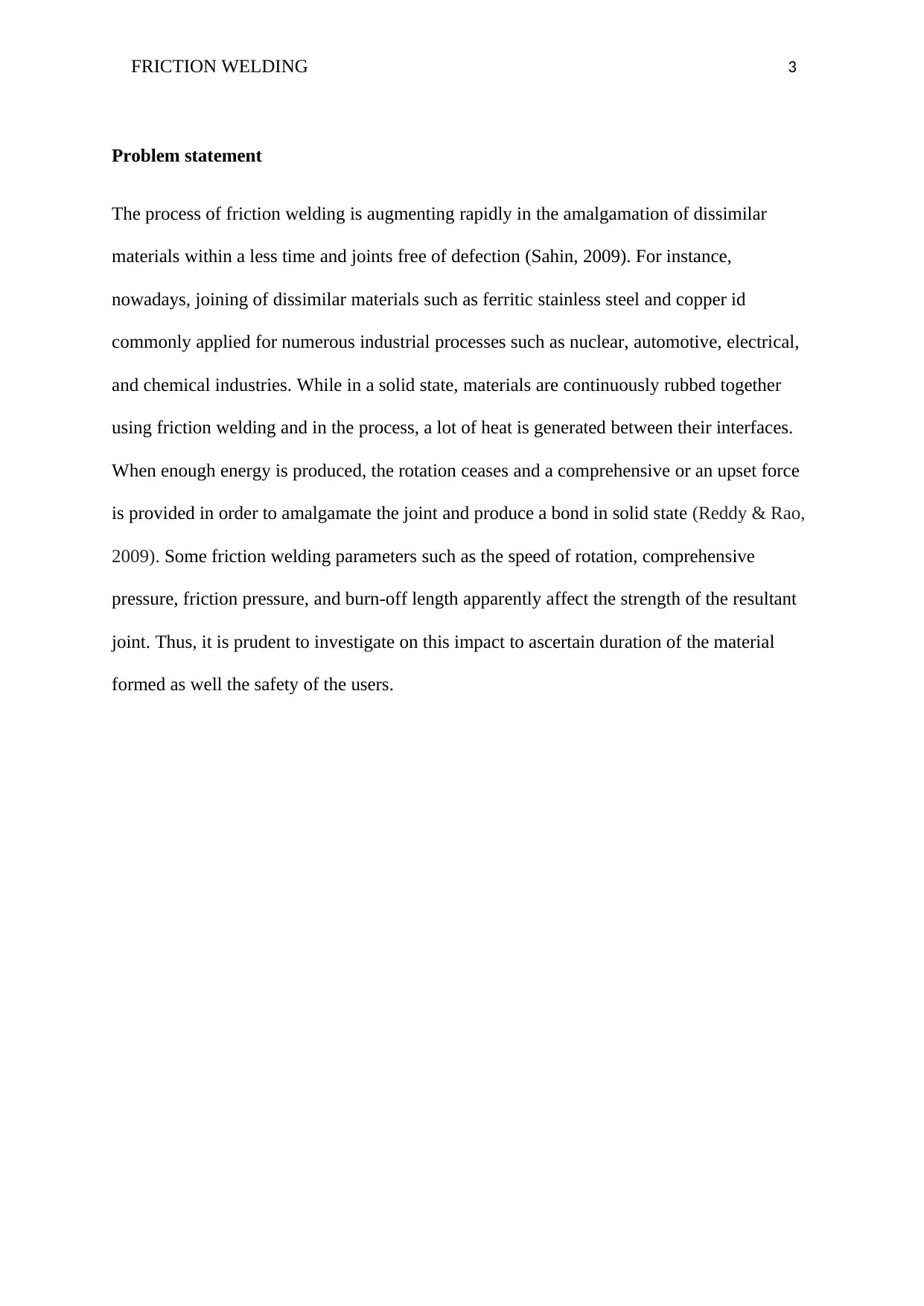
FRICTION WELDING 3
Problem statement
The process of friction welding is augmenting rapidly in the amalgamation of dissimilar
materials within a less time and joints free of defection (Sahin, 2009). For instance,
nowadays, joining of dissimilar materials such as ferritic stainless steel and copper id
commonly applied for numerous industrial processes such as nuclear, automotive, electrical,
and chemical industries. While in a solid state, materials are continuously rubbed together
using friction welding and in the process, a lot of heat is generated between their interfaces.
When enough energy is produced, the rotation ceases and a comprehensive or an upset force
is provided in order to amalgamate the joint and produce a bond in solid state (Reddy & Rao,
2009). Some friction welding parameters such as the speed of rotation, comprehensive
pressure, friction pressure, and burn-off length apparently affect the strength of the resultant
joint. Thus, it is prudent to investigate on this impact to ascertain duration of the material
formed as well the safety of the users.
Problem statement
The process of friction welding is augmenting rapidly in the amalgamation of dissimilar
materials within a less time and joints free of defection (Sahin, 2009). For instance,
nowadays, joining of dissimilar materials such as ferritic stainless steel and copper id
commonly applied for numerous industrial processes such as nuclear, automotive, electrical,
and chemical industries. While in a solid state, materials are continuously rubbed together
using friction welding and in the process, a lot of heat is generated between their interfaces.
When enough energy is produced, the rotation ceases and a comprehensive or an upset force
is provided in order to amalgamate the joint and produce a bond in solid state (Reddy & Rao,
2009). Some friction welding parameters such as the speed of rotation, comprehensive
pressure, friction pressure, and burn-off length apparently affect the strength of the resultant
joint. Thus, it is prudent to investigate on this impact to ascertain duration of the material
formed as well the safety of the users.
You're viewing a preview
Unlock full access by subscribing today!
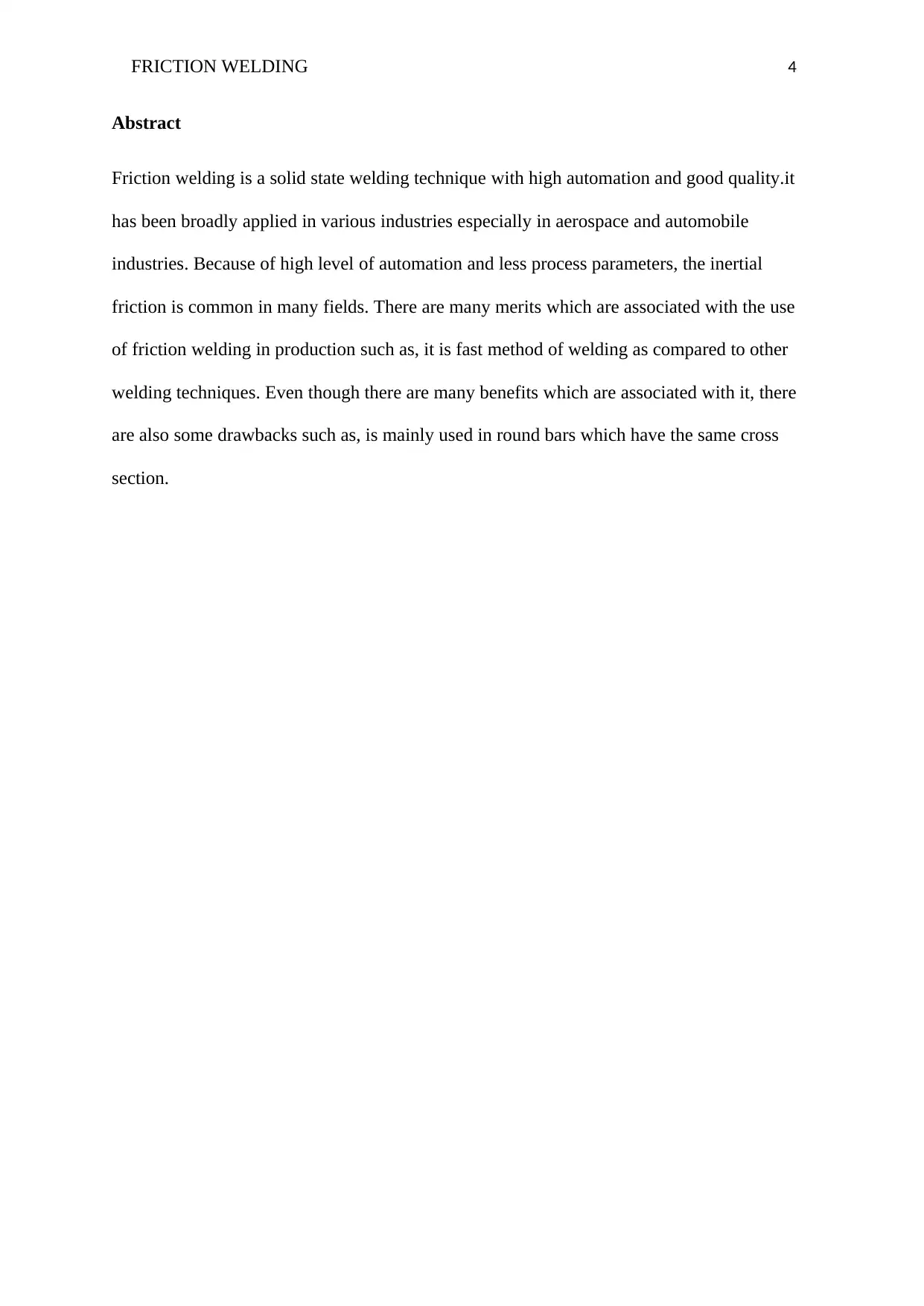
FRICTION WELDING 4
Abstract
Friction welding is a solid state welding technique with high automation and good quality.it
has been broadly applied in various industries especially in aerospace and automobile
industries. Because of high level of automation and less process parameters, the inertial
friction is common in many fields. There are many merits which are associated with the use
of friction welding in production such as, it is fast method of welding as compared to other
welding techniques. Even though there are many benefits which are associated with it, there
are also some drawbacks such as, is mainly used in round bars which have the same cross
section.
Abstract
Friction welding is a solid state welding technique with high automation and good quality.it
has been broadly applied in various industries especially in aerospace and automobile
industries. Because of high level of automation and less process parameters, the inertial
friction is common in many fields. There are many merits which are associated with the use
of friction welding in production such as, it is fast method of welding as compared to other
welding techniques. Even though there are many benefits which are associated with it, there
are also some drawbacks such as, is mainly used in round bars which have the same cross
section.
Paraphrase This Document
Need a fresh take? Get an instant paraphrase of this document with our AI Paraphraser
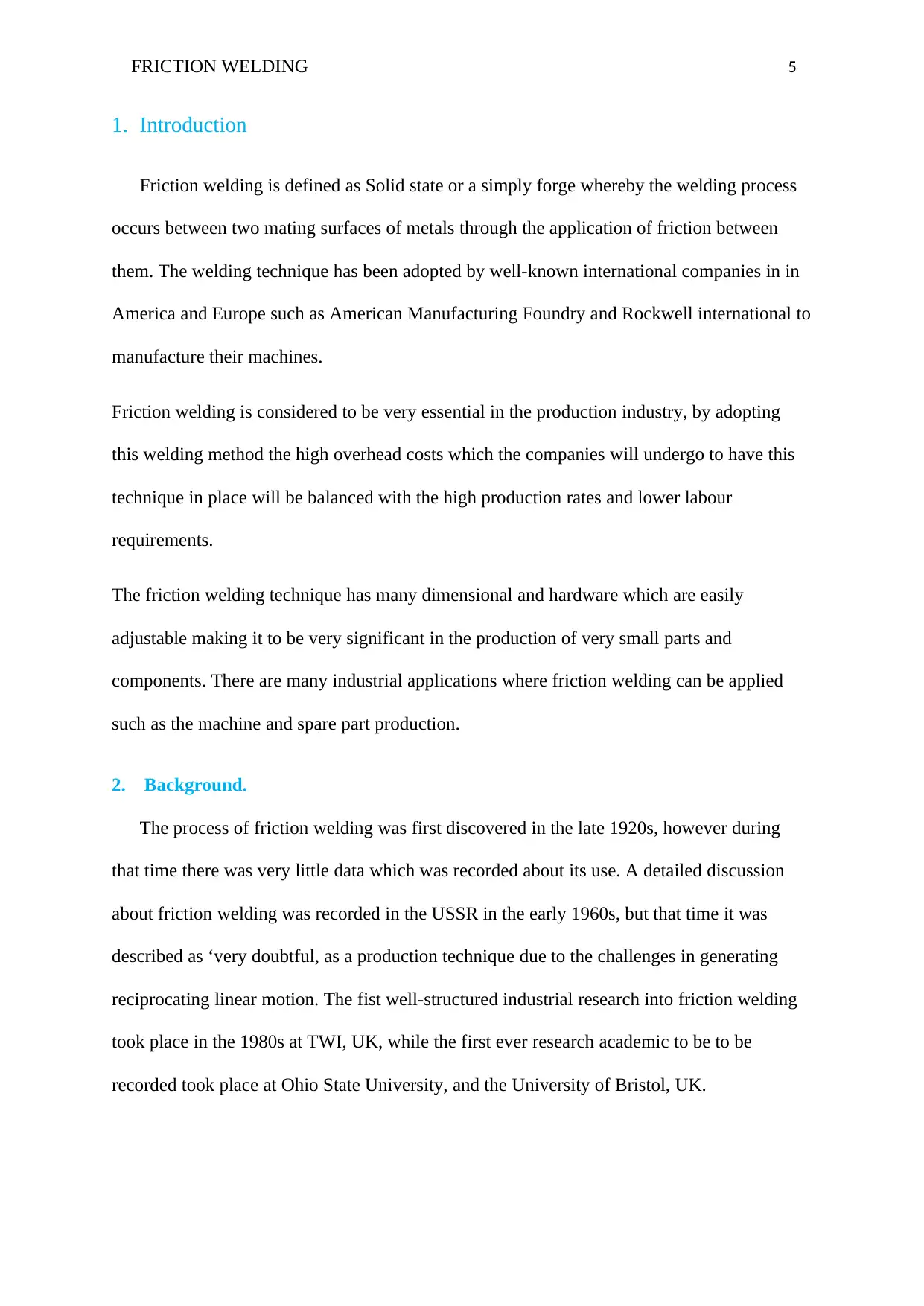
FRICTION WELDING 5
1. Introduction
Friction welding is defined as Solid state or a simply forge whereby the welding process
occurs between two mating surfaces of metals through the application of friction between
them. The welding technique has been adopted by well-known international companies in in
America and Europe such as American Manufacturing Foundry and Rockwell international to
manufacture their machines.
Friction welding is considered to be very essential in the production industry, by adopting
this welding method the high overhead costs which the companies will undergo to have this
technique in place will be balanced with the high production rates and lower labour
requirements.
The friction welding technique has many dimensional and hardware which are easily
adjustable making it to be very significant in the production of very small parts and
components. There are many industrial applications where friction welding can be applied
such as the machine and spare part production.
2. Background.
The process of friction welding was first discovered in the late 1920s, however during
that time there was very little data which was recorded about its use. A detailed discussion
about friction welding was recorded in the USSR in the early 1960s, but that time it was
described as ‘very doubtful, as a production technique due to the challenges in generating
reciprocating linear motion. The fist well-structured industrial research into friction welding
took place in the 1980s at TWI, UK, while the first ever research academic to be to be
recorded took place at Ohio State University, and the University of Bristol, UK.
1. Introduction
Friction welding is defined as Solid state or a simply forge whereby the welding process
occurs between two mating surfaces of metals through the application of friction between
them. The welding technique has been adopted by well-known international companies in in
America and Europe such as American Manufacturing Foundry and Rockwell international to
manufacture their machines.
Friction welding is considered to be very essential in the production industry, by adopting
this welding method the high overhead costs which the companies will undergo to have this
technique in place will be balanced with the high production rates and lower labour
requirements.
The friction welding technique has many dimensional and hardware which are easily
adjustable making it to be very significant in the production of very small parts and
components. There are many industrial applications where friction welding can be applied
such as the machine and spare part production.
2. Background.
The process of friction welding was first discovered in the late 1920s, however during
that time there was very little data which was recorded about its use. A detailed discussion
about friction welding was recorded in the USSR in the early 1960s, but that time it was
described as ‘very doubtful, as a production technique due to the challenges in generating
reciprocating linear motion. The fist well-structured industrial research into friction welding
took place in the 1980s at TWI, UK, while the first ever research academic to be to be
recorded took place at Ohio State University, and the University of Bristol, UK.
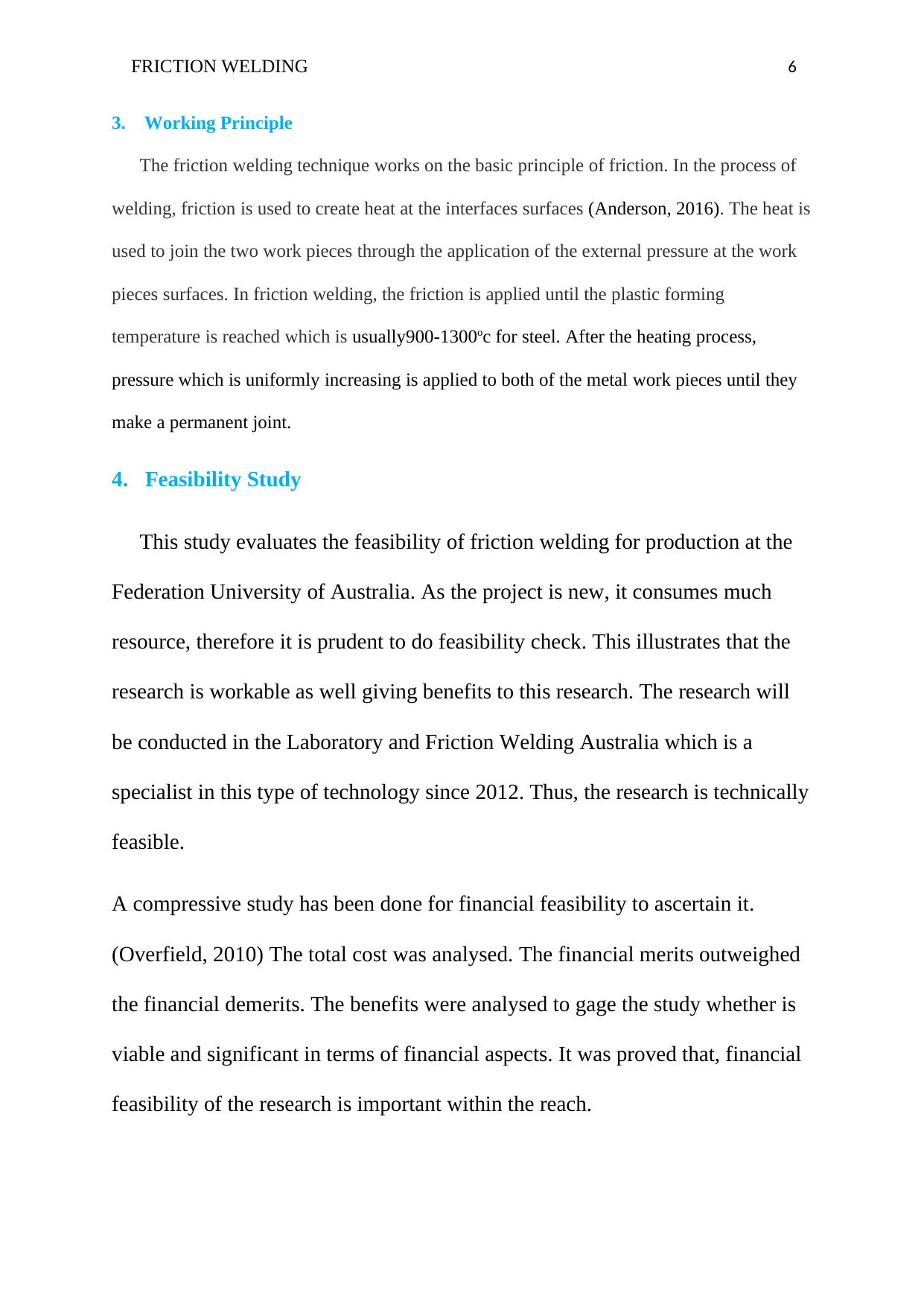
FRICTION WELDING 6
3. Working Principle
The friction welding technique works on the basic principle of friction. In the process of
welding, friction is used to create heat at the interfaces surfaces (Anderson, 2016). The heat is
used to join the two work pieces through the application of the external pressure at the work
pieces surfaces. In friction welding, the friction is applied until the plastic forming
temperature is reached which is usually900-1300oc for steel. After the heating process,
pressure which is uniformly increasing is applied to both of the metal work pieces until they
make a permanent joint.
4. Feasibility Study
This study evaluates the feasibility of friction welding for production at the
Federation University of Australia. As the project is new, it consumes much
resource, therefore it is prudent to do feasibility check. This illustrates that the
research is workable as well giving benefits to this research. The research will
be conducted in the Laboratory and Friction Welding Australia which is a
specialist in this type of technology since 2012. Thus, the research is technically
feasible.
A compressive study has been done for financial feasibility to ascertain it.
(Overfield, 2010) The total cost was analysed. The financial merits outweighed
the financial demerits. The benefits were analysed to gage the study whether is
viable and significant in terms of financial aspects. It was proved that, financial
feasibility of the research is important within the reach.
3. Working Principle
The friction welding technique works on the basic principle of friction. In the process of
welding, friction is used to create heat at the interfaces surfaces (Anderson, 2016). The heat is
used to join the two work pieces through the application of the external pressure at the work
pieces surfaces. In friction welding, the friction is applied until the plastic forming
temperature is reached which is usually900-1300oc for steel. After the heating process,
pressure which is uniformly increasing is applied to both of the metal work pieces until they
make a permanent joint.
4. Feasibility Study
This study evaluates the feasibility of friction welding for production at the
Federation University of Australia. As the project is new, it consumes much
resource, therefore it is prudent to do feasibility check. This illustrates that the
research is workable as well giving benefits to this research. The research will
be conducted in the Laboratory and Friction Welding Australia which is a
specialist in this type of technology since 2012. Thus, the research is technically
feasible.
A compressive study has been done for financial feasibility to ascertain it.
(Overfield, 2010) The total cost was analysed. The financial merits outweighed
the financial demerits. The benefits were analysed to gage the study whether is
viable and significant in terms of financial aspects. It was proved that, financial
feasibility of the research is important within the reach.
You're viewing a preview
Unlock full access by subscribing today!
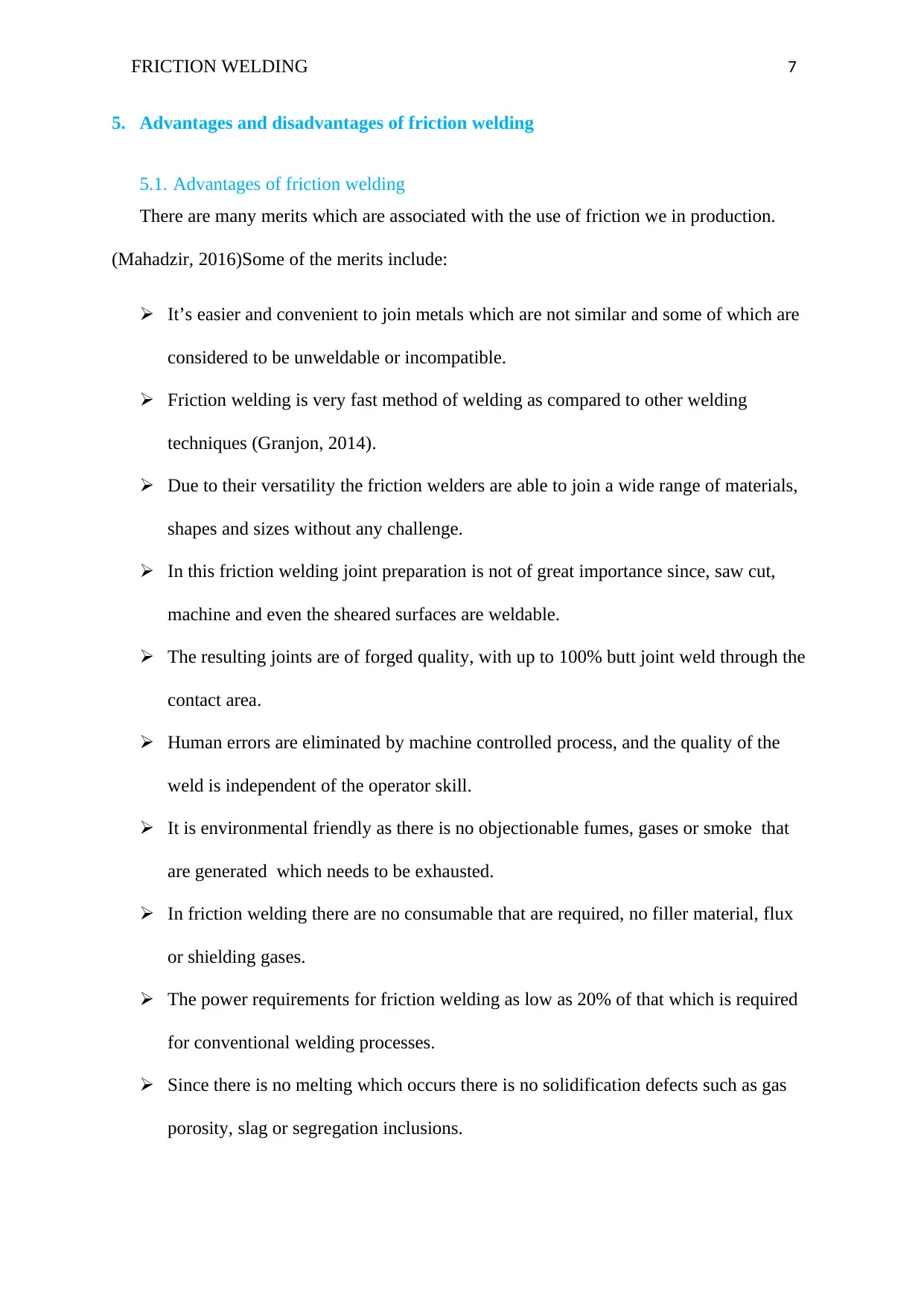
FRICTION WELDING 7
5. Advantages and disadvantages of friction welding
5.1. Advantages of friction welding
There are many merits which are associated with the use of friction we in production.
(Mahadzir, 2016)Some of the merits include:
 It’s easier and convenient to join metals which are not similar and some of which are
considered to be unweldable or incompatible.
 Friction welding is very fast method of welding as compared to other welding
techniques (Granjon, 2014).
 Due to their versatility the friction welders are able to join a wide range of materials,
shapes and sizes without any challenge.
 In this friction welding joint preparation is not of great importance since, saw cut,
machine and even the sheared surfaces are weldable.
 The resulting joints are of forged quality, with up to 100% butt joint weld through the
contact area.
 Human errors are eliminated by machine controlled process, and the quality of the
weld is independent of the operator skill.
 It is environmental friendly as there is no objectionable fumes, gases or smoke that
are generated which needs to be exhausted.
 In friction welding there are no consumable that are required, no filler material, flux
or shielding gases.
 The power requirements for friction welding as low as 20% of that which is required
for conventional welding processes.
 Since there is no melting which occurs there is no solidification defects such as gas
porosity, slag or segregation inclusions.
5. Advantages and disadvantages of friction welding
5.1. Advantages of friction welding
There are many merits which are associated with the use of friction we in production.
(Mahadzir, 2016)Some of the merits include:
 It’s easier and convenient to join metals which are not similar and some of which are
considered to be unweldable or incompatible.
 Friction welding is very fast method of welding as compared to other welding
techniques (Granjon, 2014).
 Due to their versatility the friction welders are able to join a wide range of materials,
shapes and sizes without any challenge.
 In this friction welding joint preparation is not of great importance since, saw cut,
machine and even the sheared surfaces are weldable.
 The resulting joints are of forged quality, with up to 100% butt joint weld through the
contact area.
 Human errors are eliminated by machine controlled process, and the quality of the
weld is independent of the operator skill.
 It is environmental friendly as there is no objectionable fumes, gases or smoke that
are generated which needs to be exhausted.
 In friction welding there are no consumable that are required, no filler material, flux
or shielding gases.
 The power requirements for friction welding as low as 20% of that which is required
for conventional welding processes.
 Since there is no melting which occurs there is no solidification defects such as gas
porosity, slag or segregation inclusions.
Paraphrase This Document
Need a fresh take? Get an instant paraphrase of this document with our AI Paraphraser
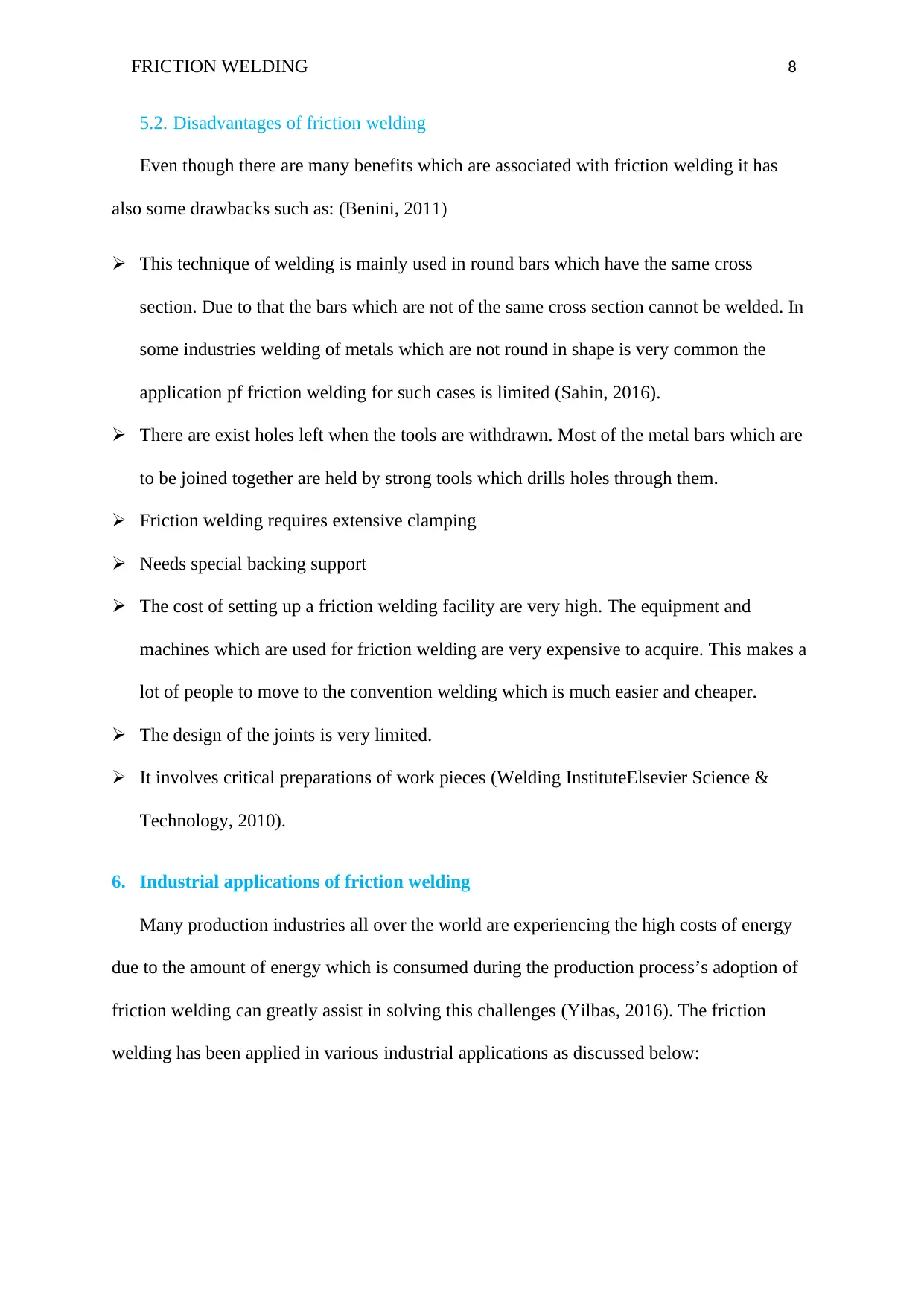
FRICTION WELDING 8
5.2. Disadvantages of friction welding
Even though there are many benefits which are associated with friction welding it has
also some drawbacks such as: (Benini, 2011)
 This technique of welding is mainly used in round bars which have the same cross
section. Due to that the bars which are not of the same cross section cannot be welded. In
some industries welding of metals which are not round in shape is very common the
application pf friction welding for such cases is limited (Sahin, 2016).
 There are exist holes left when the tools are withdrawn. Most of the metal bars which are
to be joined together are held by strong tools which drills holes through them.
 Friction welding requires extensive clamping
 Needs special backing support
 The cost of setting up a friction welding facility are very high. The equipment and
machines which are used for friction welding are very expensive to acquire. This makes a
lot of people to move to the convention welding which is much easier and cheaper.
 The design of the joints is very limited.
 It involves critical preparations of work pieces (Welding InstituteElsevier Science &
Technology, 2010).
6. Industrial applications of friction welding
Many production industries all over the world are experiencing the high costs of energy
due to the amount of energy which is consumed during the production process’s adoption of
friction welding can greatly assist in solving this challenges (Yilbas, 2016). The friction
welding has been applied in various industrial applications as discussed below:
5.2. Disadvantages of friction welding
Even though there are many benefits which are associated with friction welding it has
also some drawbacks such as: (Benini, 2011)
 This technique of welding is mainly used in round bars which have the same cross
section. Due to that the bars which are not of the same cross section cannot be welded. In
some industries welding of metals which are not round in shape is very common the
application pf friction welding for such cases is limited (Sahin, 2016).
 There are exist holes left when the tools are withdrawn. Most of the metal bars which are
to be joined together are held by strong tools which drills holes through them.
 Friction welding requires extensive clamping
 Needs special backing support
 The cost of setting up a friction welding facility are very high. The equipment and
machines which are used for friction welding are very expensive to acquire. This makes a
lot of people to move to the convention welding which is much easier and cheaper.
 The design of the joints is very limited.
 It involves critical preparations of work pieces (Welding InstituteElsevier Science &
Technology, 2010).
6. Industrial applications of friction welding
Many production industries all over the world are experiencing the high costs of energy
due to the amount of energy which is consumed during the production process’s adoption of
friction welding can greatly assist in solving this challenges (Yilbas, 2016). The friction
welding has been applied in various industrial applications as discussed below:
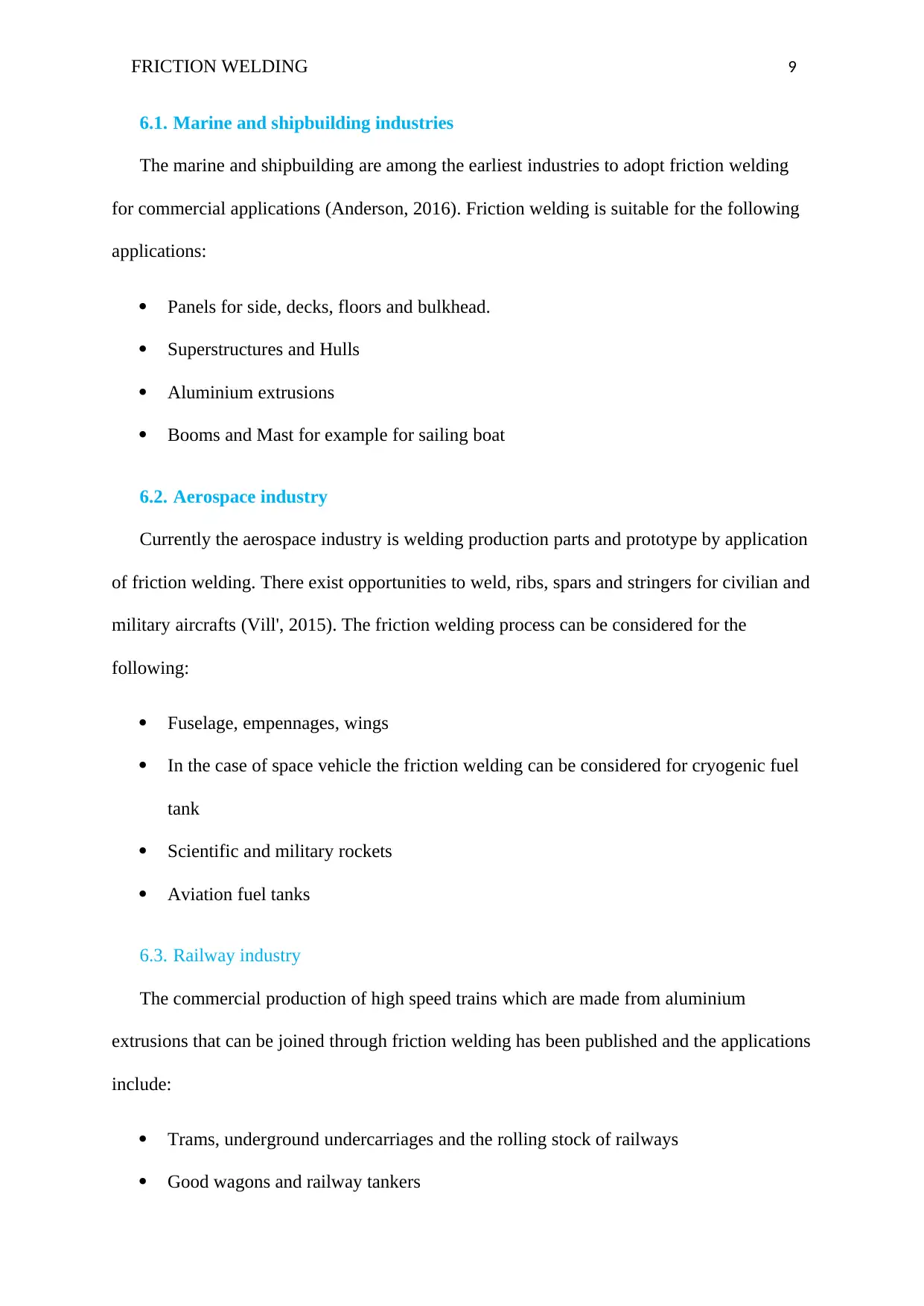
FRICTION WELDING 9
6.1. Marine and shipbuilding industries
The marine and shipbuilding are among the earliest industries to adopt friction welding
for commercial applications (Anderson, 2016). Friction welding is suitable for the following
applications:
ï‚· Panels for side, decks, floors and bulkhead.
ï‚· Superstructures and Hulls
ï‚· Aluminium extrusions
ï‚· Booms and Mast for example for sailing boat
6.2. Aerospace industry
Currently the aerospace industry is welding production parts and prototype by application
of friction welding. There exist opportunities to weld, ribs, spars and stringers for civilian and
military aircrafts (Vill', 2015). The friction welding process can be considered for the
following:
ï‚· Fuselage, empennages, wings
ï‚· In the case of space vehicle the friction welding can be considered for cryogenic fuel
tank
ï‚· Scientific and military rockets
ï‚· Aviation fuel tanks
6.3. Railway industry
The commercial production of high speed trains which are made from aluminium
extrusions that can be joined through friction welding has been published and the applications
include:
ï‚· Trams, underground undercarriages and the rolling stock of railways
ï‚· Good wagons and railway tankers
6.1. Marine and shipbuilding industries
The marine and shipbuilding are among the earliest industries to adopt friction welding
for commercial applications (Anderson, 2016). Friction welding is suitable for the following
applications:
ï‚· Panels for side, decks, floors and bulkhead.
ï‚· Superstructures and Hulls
ï‚· Aluminium extrusions
ï‚· Booms and Mast for example for sailing boat
6.2. Aerospace industry
Currently the aerospace industry is welding production parts and prototype by application
of friction welding. There exist opportunities to weld, ribs, spars and stringers for civilian and
military aircrafts (Vill', 2015). The friction welding process can be considered for the
following:
ï‚· Fuselage, empennages, wings
ï‚· In the case of space vehicle the friction welding can be considered for cryogenic fuel
tank
ï‚· Scientific and military rockets
ï‚· Aviation fuel tanks
6.3. Railway industry
The commercial production of high speed trains which are made from aluminium
extrusions that can be joined through friction welding has been published and the applications
include:
ï‚· Trams, underground undercarriages and the rolling stock of railways
ï‚· Good wagons and railway tankers
You're viewing a preview
Unlock full access by subscribing today!
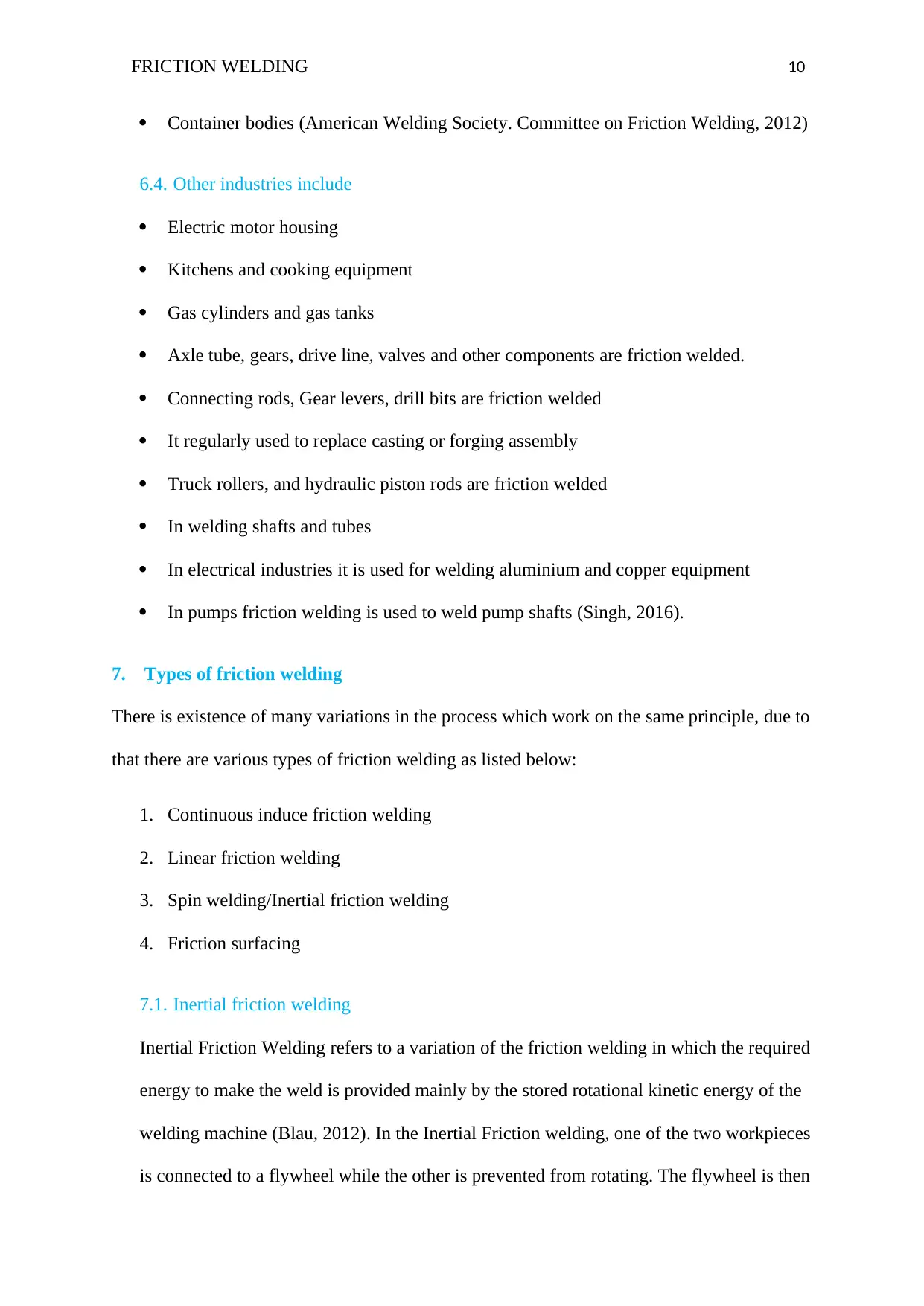
FRICTION WELDING 10
ï‚· Container bodies (American Welding Society. Committee on Friction Welding, 2012)
6.4. Other industries include
ï‚· Electric motor housing
ï‚· Kitchens and cooking equipment
ï‚· Gas cylinders and gas tanks
ï‚· Axle tube, gears, drive line, valves and other components are friction welded.
ï‚· Connecting rods, Gear levers, drill bits are friction welded
ï‚· It regularly used to replace casting or forging assembly
ï‚· Truck rollers, and hydraulic piston rods are friction welded
ï‚· In welding shafts and tubes
ï‚· In electrical industries it is used for welding aluminium and copper equipment
ï‚· In pumps friction welding is used to weld pump shafts (Singh, 2016).
7. Types of friction welding
There is existence of many variations in the process which work on the same principle, due to
that there are various types of friction welding as listed below:
1. Continuous induce friction welding
2. Linear friction welding
3. Spin welding/Inertial friction welding
4. Friction surfacing
7.1. Inertial friction welding
Inertial Friction Welding refers to a variation of the friction welding in which the required
energy to make the weld is provided mainly by the stored rotational kinetic energy of the
welding machine (Blau, 2012). In the Inertial Friction welding, one of the two workpieces
is connected to a flywheel while the other is prevented from rotating. The flywheel is then
ï‚· Container bodies (American Welding Society. Committee on Friction Welding, 2012)
6.4. Other industries include
ï‚· Electric motor housing
ï‚· Kitchens and cooking equipment
ï‚· Gas cylinders and gas tanks
ï‚· Axle tube, gears, drive line, valves and other components are friction welded.
ï‚· Connecting rods, Gear levers, drill bits are friction welded
ï‚· It regularly used to replace casting or forging assembly
ï‚· Truck rollers, and hydraulic piston rods are friction welded
ï‚· In welding shafts and tubes
ï‚· In electrical industries it is used for welding aluminium and copper equipment
ï‚· In pumps friction welding is used to weld pump shafts (Singh, 2016).
7. Types of friction welding
There is existence of many variations in the process which work on the same principle, due to
that there are various types of friction welding as listed below:
1. Continuous induce friction welding
2. Linear friction welding
3. Spin welding/Inertial friction welding
4. Friction surfacing
7.1. Inertial friction welding
Inertial Friction Welding refers to a variation of the friction welding in which the required
energy to make the weld is provided mainly by the stored rotational kinetic energy of the
welding machine (Blau, 2012). In the Inertial Friction welding, one of the two workpieces
is connected to a flywheel while the other is prevented from rotating. The flywheel is then
Paraphrase This Document
Need a fresh take? Get an instant paraphrase of this document with our AI Paraphraser
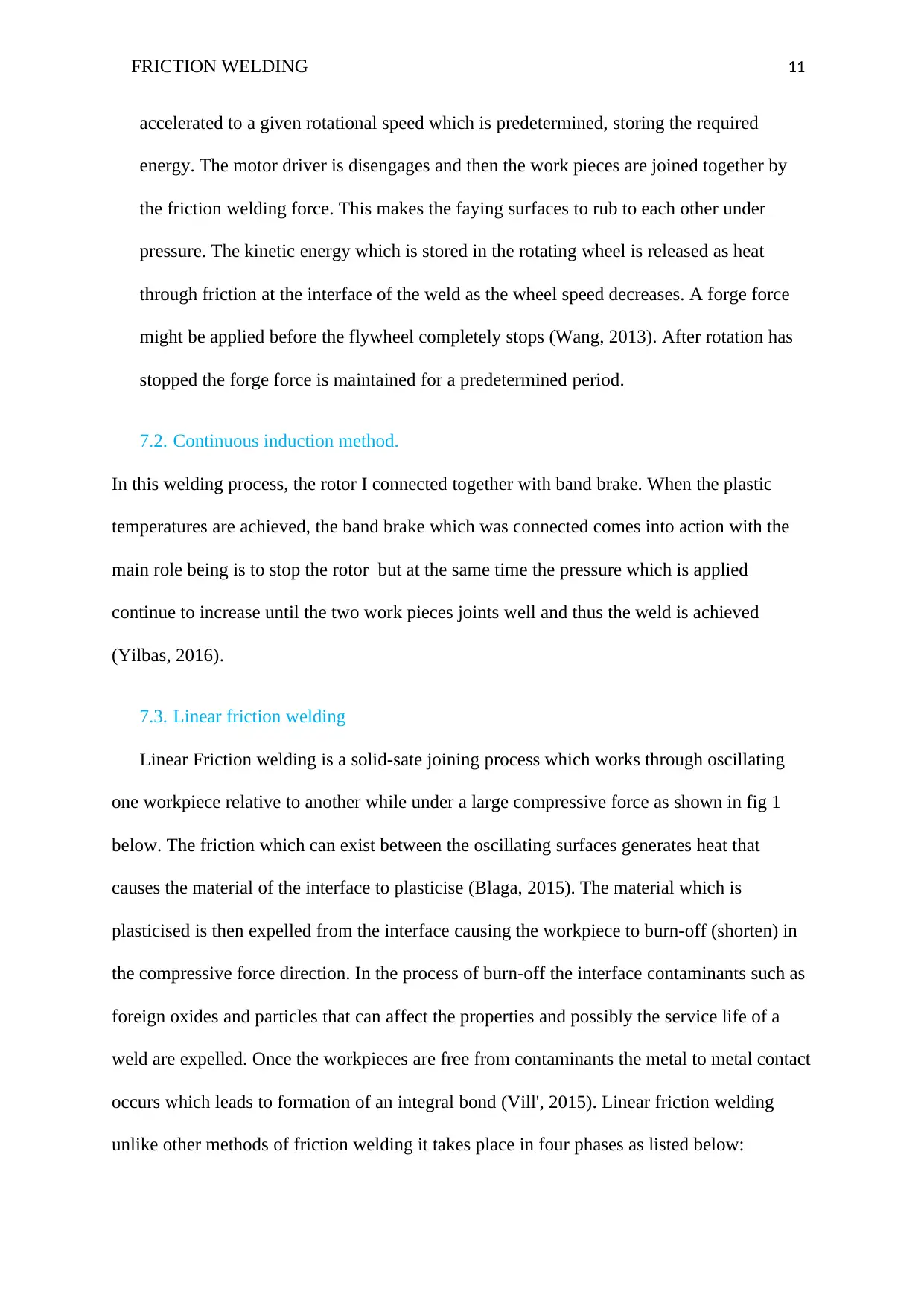
FRICTION WELDING 11
accelerated to a given rotational speed which is predetermined, storing the required
energy. The motor driver is disengages and then the work pieces are joined together by
the friction welding force. This makes the faying surfaces to rub to each other under
pressure. The kinetic energy which is stored in the rotating wheel is released as heat
through friction at the interface of the weld as the wheel speed decreases. A forge force
might be applied before the flywheel completely stops (Wang, 2013). After rotation has
stopped the forge force is maintained for a predetermined period.
7.2. Continuous induction method.
In this welding process, the rotor I connected together with band brake. When the plastic
temperatures are achieved, the band brake which was connected comes into action with the
main role being is to stop the rotor but at the same time the pressure which is applied
continue to increase until the two work pieces joints well and thus the weld is achieved
(Yilbas, 2016).
7.3. Linear friction welding
Linear Friction welding is a solid-sate joining process which works through oscillating
one workpiece relative to another while under a large compressive force as shown in fig 1
below. The friction which can exist between the oscillating surfaces generates heat that
causes the material of the interface to plasticise (Blaga, 2015). The material which is
plasticised is then expelled from the interface causing the workpiece to burn-off (shorten) in
the compressive force direction. In the process of burn-off the interface contaminants such as
foreign oxides and particles that can affect the properties and possibly the service life of a
weld are expelled. Once the workpieces are free from contaminants the metal to metal contact
occurs which leads to formation of an integral bond (Vill', 2015). Linear friction welding
unlike other methods of friction welding it takes place in four phases as listed below:
accelerated to a given rotational speed which is predetermined, storing the required
energy. The motor driver is disengages and then the work pieces are joined together by
the friction welding force. This makes the faying surfaces to rub to each other under
pressure. The kinetic energy which is stored in the rotating wheel is released as heat
through friction at the interface of the weld as the wheel speed decreases. A forge force
might be applied before the flywheel completely stops (Wang, 2013). After rotation has
stopped the forge force is maintained for a predetermined period.
7.2. Continuous induction method.
In this welding process, the rotor I connected together with band brake. When the plastic
temperatures are achieved, the band brake which was connected comes into action with the
main role being is to stop the rotor but at the same time the pressure which is applied
continue to increase until the two work pieces joints well and thus the weld is achieved
(Yilbas, 2016).
7.3. Linear friction welding
Linear Friction welding is a solid-sate joining process which works through oscillating
one workpiece relative to another while under a large compressive force as shown in fig 1
below. The friction which can exist between the oscillating surfaces generates heat that
causes the material of the interface to plasticise (Blaga, 2015). The material which is
plasticised is then expelled from the interface causing the workpiece to burn-off (shorten) in
the compressive force direction. In the process of burn-off the interface contaminants such as
foreign oxides and particles that can affect the properties and possibly the service life of a
weld are expelled. Once the workpieces are free from contaminants the metal to metal contact
occurs which leads to formation of an integral bond (Vill', 2015). Linear friction welding
unlike other methods of friction welding it takes place in four phases as listed below:
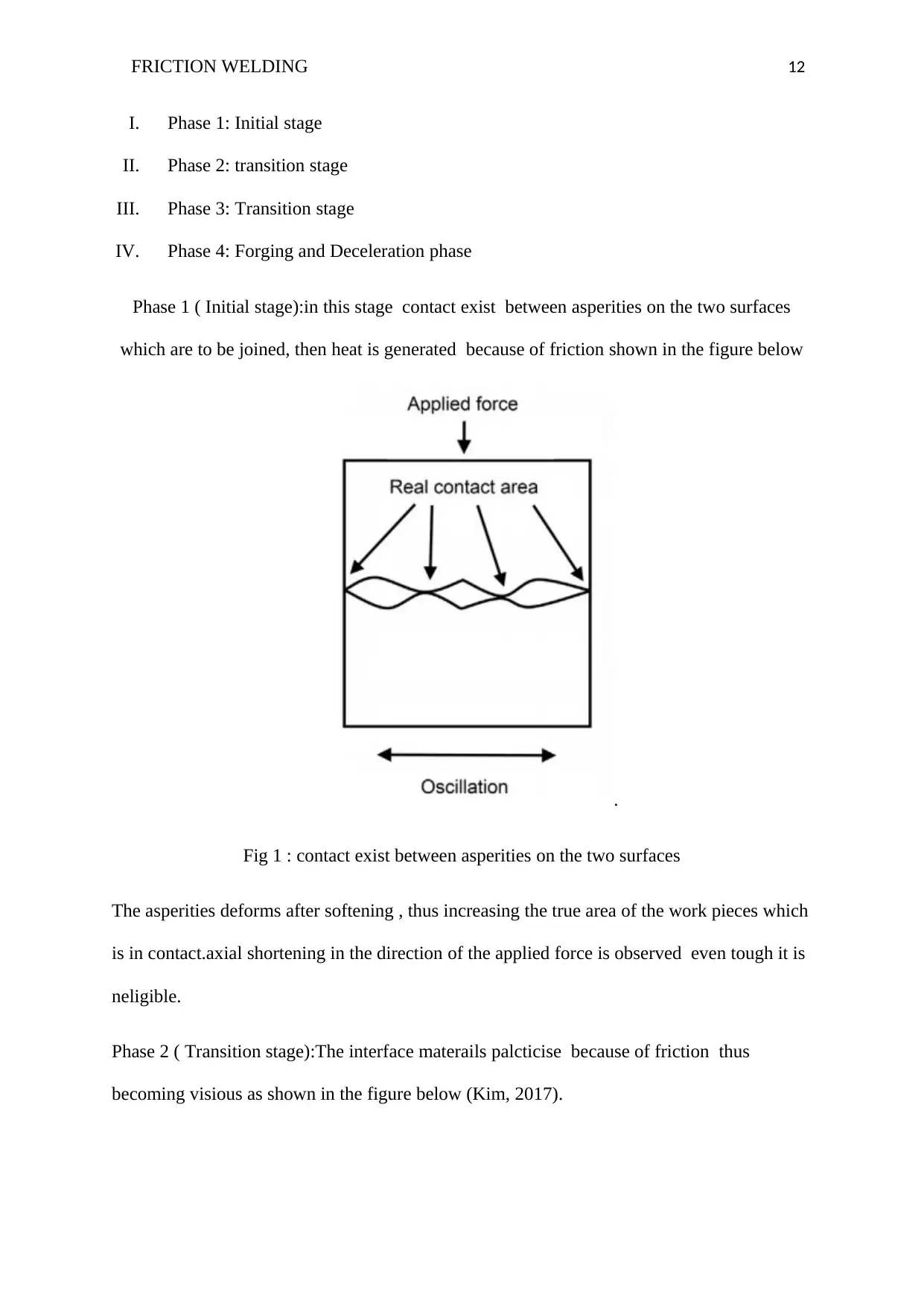
FRICTION WELDING 12
I. Phase 1: Initial stage
II. Phase 2: transition stage
III. Phase 3: Transition stage
IV. Phase 4: Forging and Deceleration phase
Phase 1 ( Initial stage):in this stage contact exist between asperities on the two surfaces
which are to be joined, then heat is generated because of friction shown in the figure below
.
Fig 1 : contact exist between asperities on the two surfaces
The asperities deforms after softening , thus increasing the true area of the work pieces which
is in contact.axial shortening in the direction of the applied force is observed even tough it is
neligible.
Phase 2 ( Transition stage):The interface materails palcticise because of friction thus
becoming visious as shown in the figure below (Kim, 2017).
I. Phase 1: Initial stage
II. Phase 2: transition stage
III. Phase 3: Transition stage
IV. Phase 4: Forging and Deceleration phase
Phase 1 ( Initial stage):in this stage contact exist between asperities on the two surfaces
which are to be joined, then heat is generated because of friction shown in the figure below
.
Fig 1 : contact exist between asperities on the two surfaces
The asperities deforms after softening , thus increasing the true area of the work pieces which
is in contact.axial shortening in the direction of the applied force is observed even tough it is
neligible.
Phase 2 ( Transition stage):The interface materails palcticise because of friction thus
becoming visious as shown in the figure below (Kim, 2017).
You're viewing a preview
Unlock full access by subscribing today!
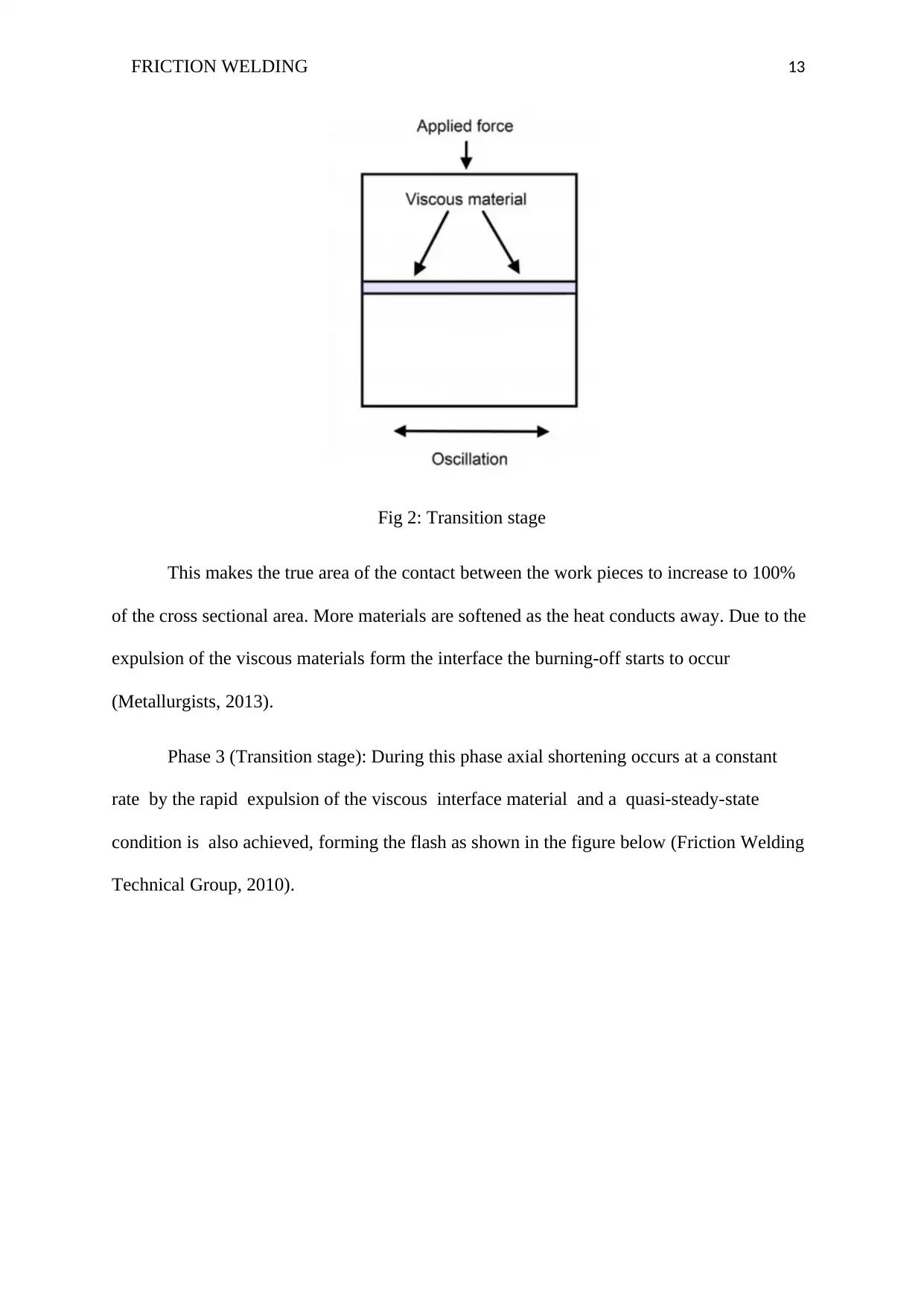
FRICTION WELDING 13
Fig 2: Transition stage
This makes the true area of the contact between the work pieces to increase to 100%
of the cross sectional area. More materials are softened as the heat conducts away. Due to the
expulsion of the viscous materials form the interface the burning-off starts to occur
(Metallurgists, 2013).
Phase 3 (Transition stage): During this phase axial shortening occurs at a constant
rate by the rapid expulsion of the viscous interface material and a quasi-steady-state
condition is also achieved, forming the flash as shown in the figure below (Friction Welding
Technical Group, 2010).
Fig 2: Transition stage
This makes the true area of the contact between the work pieces to increase to 100%
of the cross sectional area. More materials are softened as the heat conducts away. Due to the
expulsion of the viscous materials form the interface the burning-off starts to occur
(Metallurgists, 2013).
Phase 3 (Transition stage): During this phase axial shortening occurs at a constant
rate by the rapid expulsion of the viscous interface material and a quasi-steady-state
condition is also achieved, forming the flash as shown in the figure below (Friction Welding
Technical Group, 2010).
Paraphrase This Document
Need a fresh take? Get an instant paraphrase of this document with our AI Paraphraser
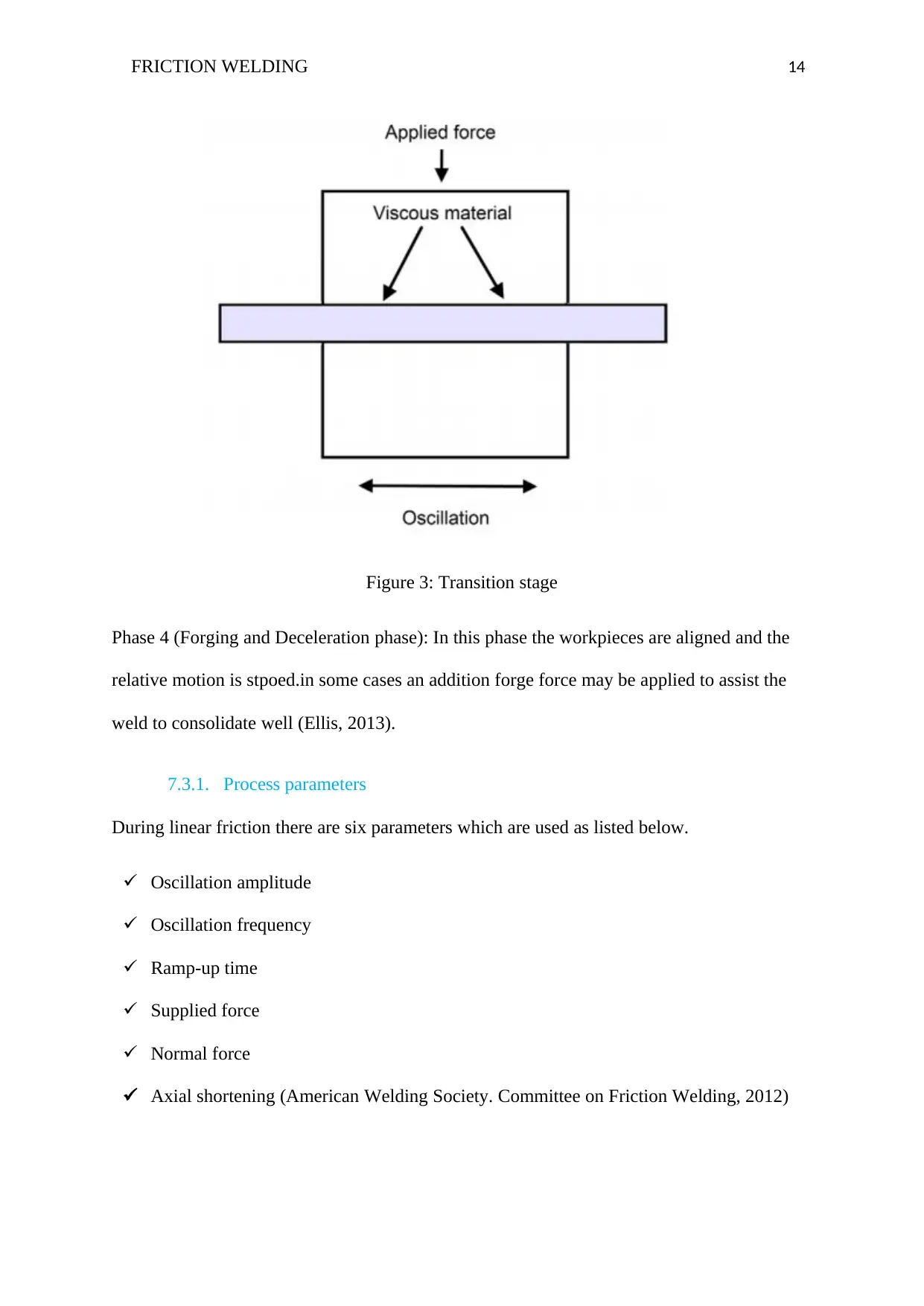
FRICTION WELDING 14
Figure 3: Transition stage
Phase 4 (Forging and Deceleration phase): In this phase the workpieces are aligned and the
relative motion is stpoed.in some cases an addition forge force may be applied to assist the
weld to consolidate well (Ellis, 2013).
7.3.1. Process parameters
During linear friction there are six parameters which are used as listed below.
 Oscillation amplitude
 Oscillation frequency
 Ramp-up time
 Supplied force
 Normal force
 Axial shortening (American Welding Society. Committee on Friction Welding, 2012)
Figure 3: Transition stage
Phase 4 (Forging and Deceleration phase): In this phase the workpieces are aligned and the
relative motion is stpoed.in some cases an addition forge force may be applied to assist the
weld to consolidate well (Ellis, 2013).
7.3.1. Process parameters
During linear friction there are six parameters which are used as listed below.
 Oscillation amplitude
 Oscillation frequency
 Ramp-up time
 Supplied force
 Normal force
 Axial shortening (American Welding Society. Committee on Friction Welding, 2012)
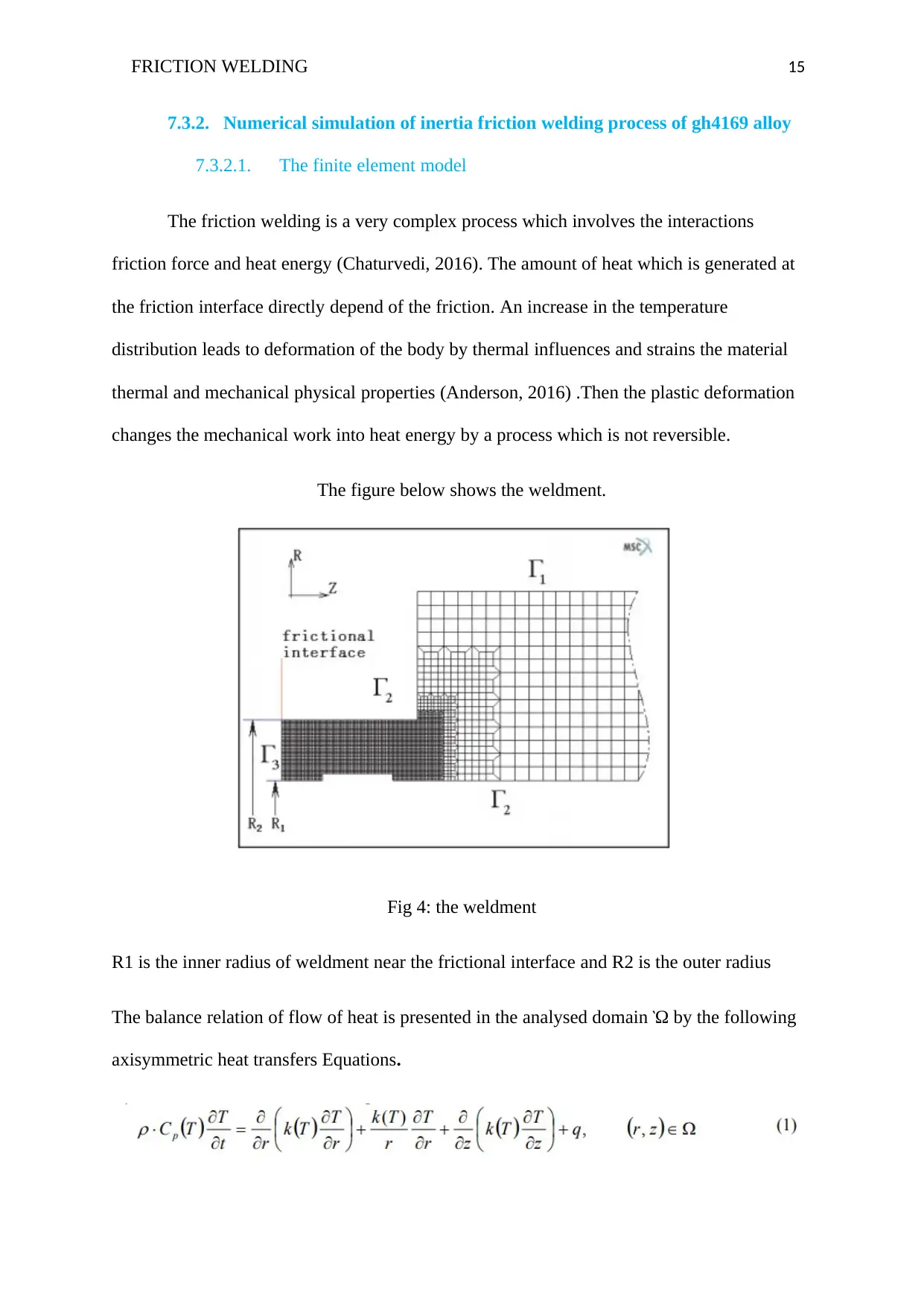
FRICTION WELDING 15
7.3.2. Numerical simulation of inertia friction welding process of gh4169 alloy
7.3.2.1. The finite element model
The friction welding is a very complex process which involves the interactions
friction force and heat energy (Chaturvedi, 2016). The amount of heat which is generated at
the friction interface directly depend of the friction. An increase in the temperature
distribution leads to deformation of the body by thermal influences and strains the material
thermal and mechanical physical properties (Anderson, 2016) .Then the plastic deformation
changes the mechanical work into heat energy by a process which is not reversible.
The figure below shows the weldment.
Fig 4: the weldment
R1 is the inner radius of weldment near the frictional interface and R2 is the outer radius
The balance relation of flow of heat is presented in the analysed domain Ὼ by the following
axisymmetric heat transfers Equations.
7.3.2. Numerical simulation of inertia friction welding process of gh4169 alloy
7.3.2.1. The finite element model
The friction welding is a very complex process which involves the interactions
friction force and heat energy (Chaturvedi, 2016). The amount of heat which is generated at
the friction interface directly depend of the friction. An increase in the temperature
distribution leads to deformation of the body by thermal influences and strains the material
thermal and mechanical physical properties (Anderson, 2016) .Then the plastic deformation
changes the mechanical work into heat energy by a process which is not reversible.
The figure below shows the weldment.
Fig 4: the weldment
R1 is the inner radius of weldment near the frictional interface and R2 is the outer radius
The balance relation of flow of heat is presented in the analysed domain Ὼ by the following
axisymmetric heat transfers Equations.
You're viewing a preview
Unlock full access by subscribing today!
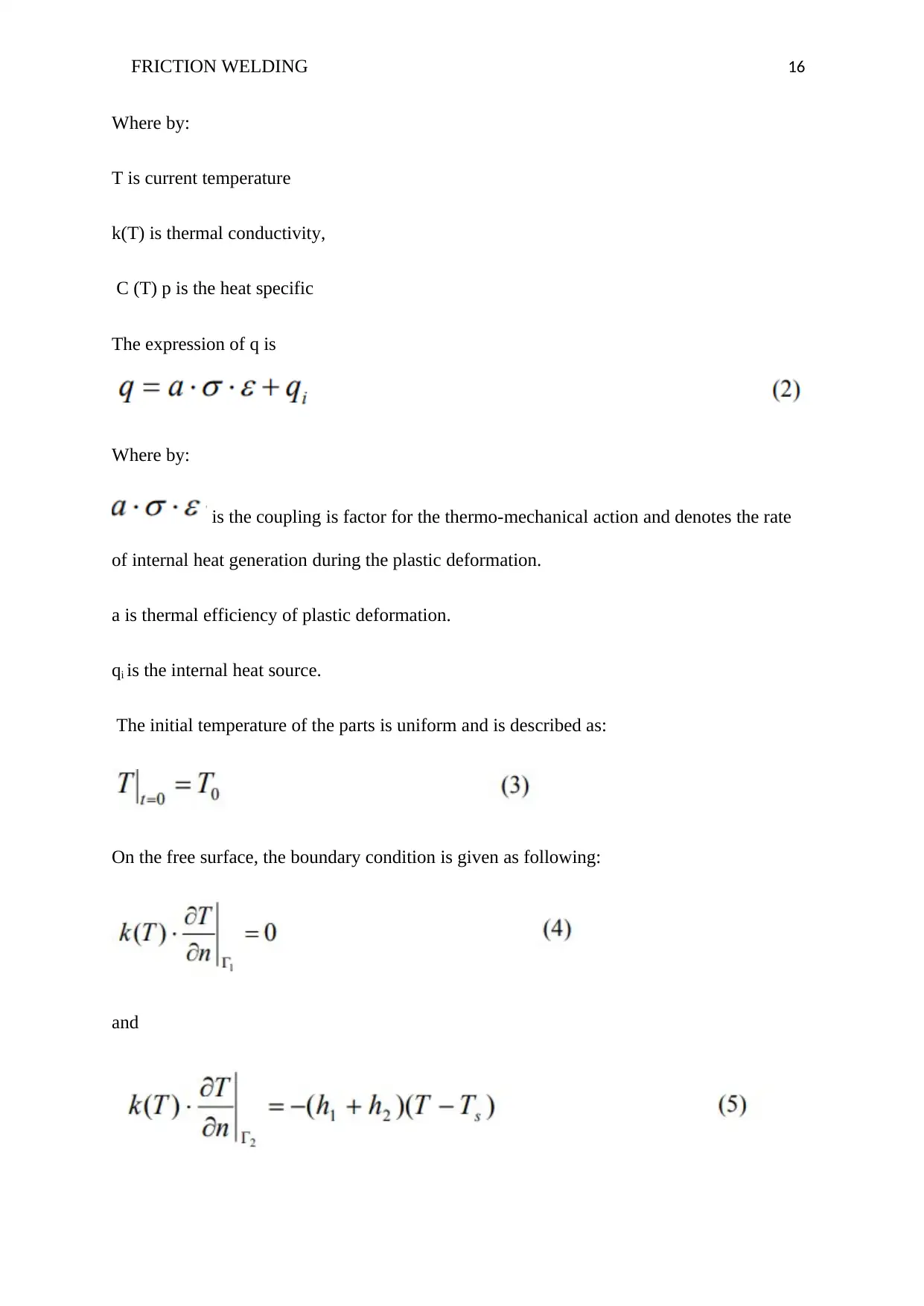
FRICTION WELDING 16
Where by:
T is current temperature
k(T) is thermal conductivity,
C (T) p is the heat specific
The expression of q is
Where by:
is the coupling is factor for the thermo-mechanical action and denotes the rate
of internal heat generation during the plastic deformation.
a is thermal efficiency of plastic deformation.
qi is the internal heat source.
The initial temperature of the parts is uniform and is described as:
On the free surface, the boundary condition is given as following:
and
Where by:
T is current temperature
k(T) is thermal conductivity,
C (T) p is the heat specific
The expression of q is
Where by:
is the coupling is factor for the thermo-mechanical action and denotes the rate
of internal heat generation during the plastic deformation.
a is thermal efficiency of plastic deformation.
qi is the internal heat source.
The initial temperature of the parts is uniform and is described as:
On the free surface, the boundary condition is given as following:
and
Paraphrase This Document
Need a fresh take? Get an instant paraphrase of this document with our AI Paraphraser
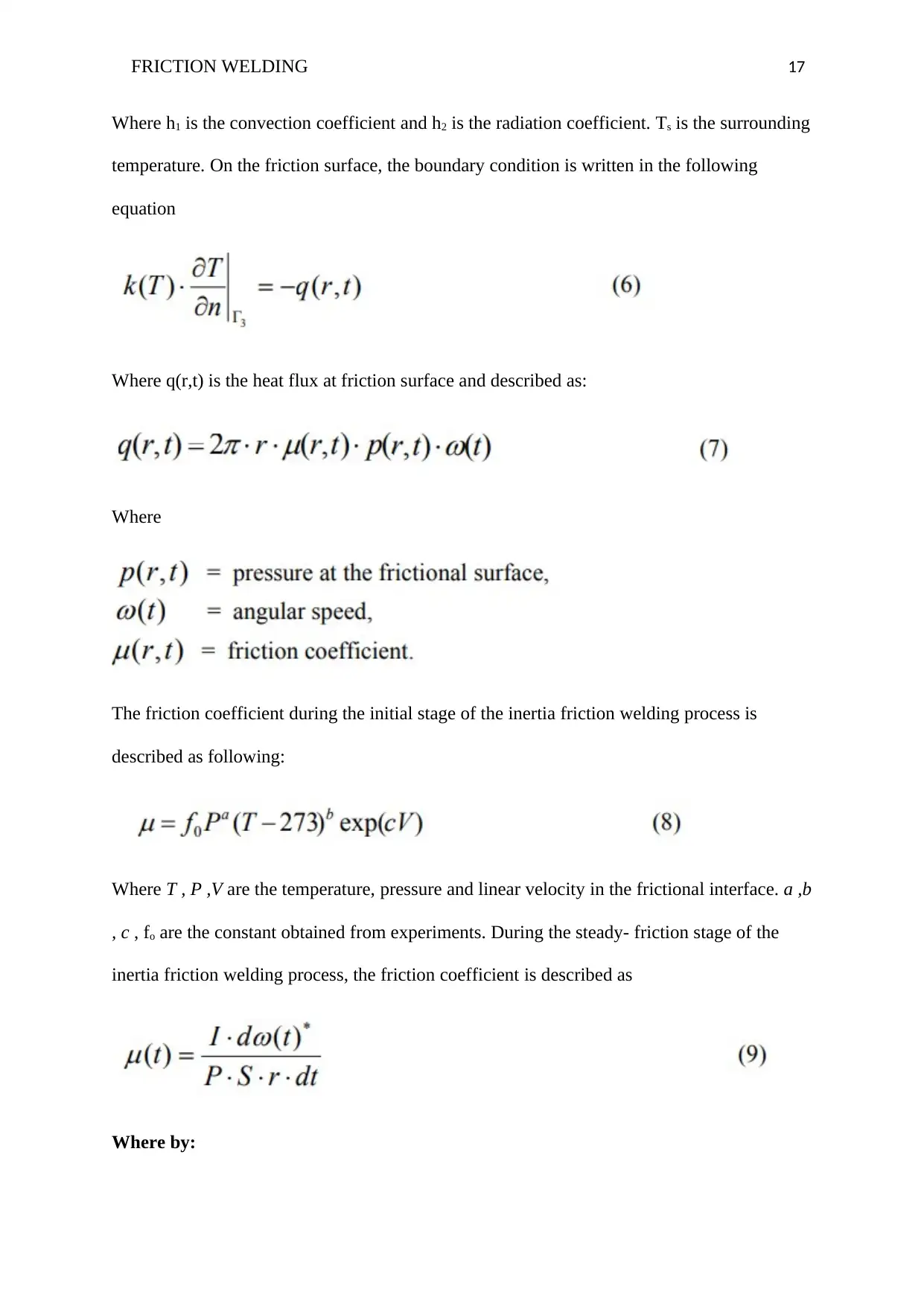
FRICTION WELDING 17
Where h1 is the convection coefficient and h2 is the radiation coefficient. Ts is the surrounding
temperature. On the friction surface, the boundary condition is written in the following
equation
Where q(r,t) is the heat flux at friction surface and described as:
Where
The friction coefficient during the initial stage of the inertia friction welding process is
described as following:
Where T , P ,V are the temperature, pressure and linear velocity in the frictional interface. a ,b
, c , fo are the constant obtained from experiments. During the steady- friction stage of the
inertia friction welding process, the friction coefficient is described as
Where by:
Where h1 is the convection coefficient and h2 is the radiation coefficient. Ts is the surrounding
temperature. On the friction surface, the boundary condition is written in the following
equation
Where q(r,t) is the heat flux at friction surface and described as:
Where
The friction coefficient during the initial stage of the inertia friction welding process is
described as following:
Where T , P ,V are the temperature, pressure and linear velocity in the frictional interface. a ,b
, c , fo are the constant obtained from experiments. During the steady- friction stage of the
inertia friction welding process, the friction coefficient is described as
Where by:
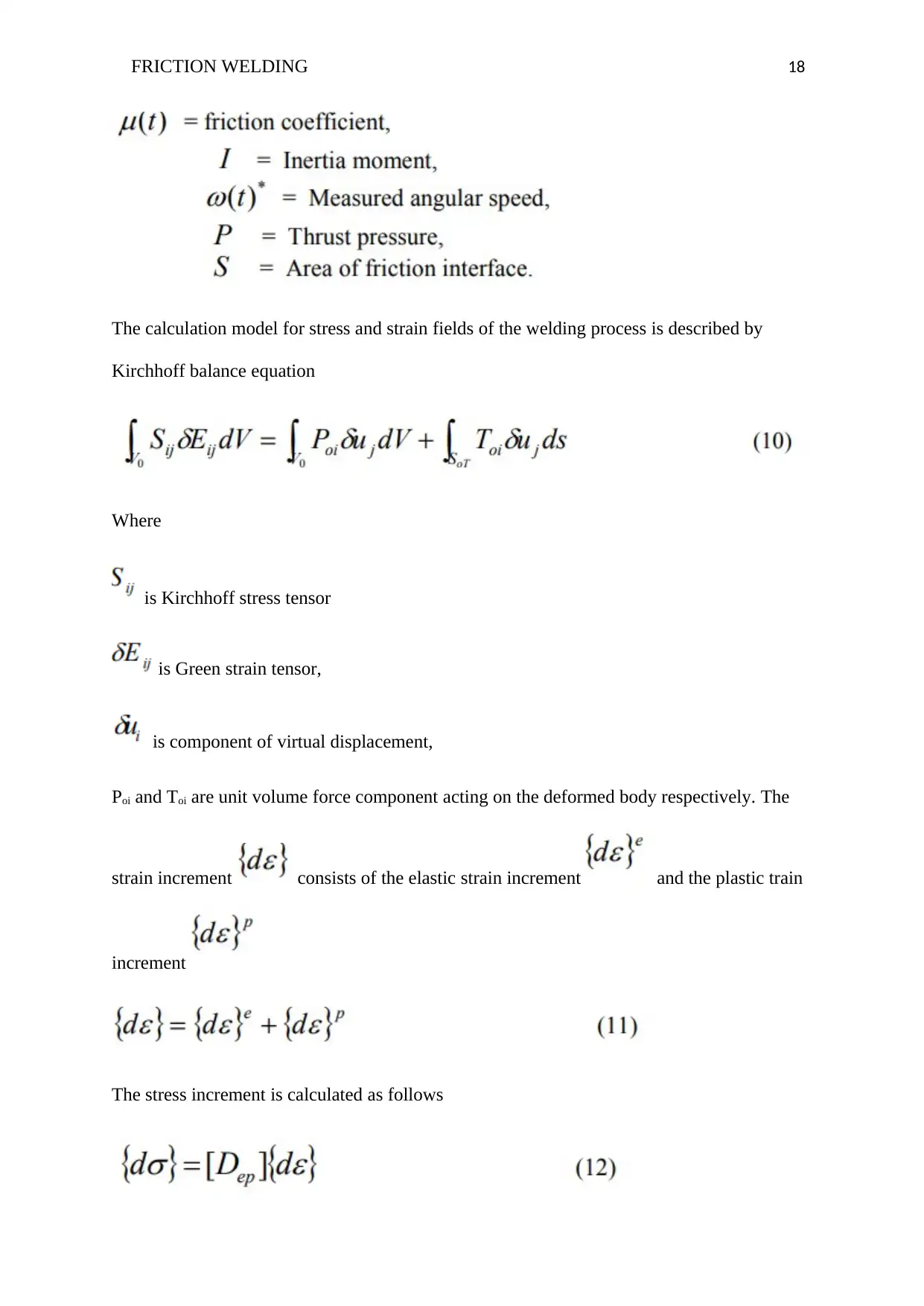
FRICTION WELDING 18
The calculation model for stress and strain fields of the welding process is described by
Kirchhoff balance equation
Where
is Kirchhoff stress tensor
is Green strain tensor,
is component of virtual displacement,
Poi and Toi are unit volume force component acting on the deformed body respectively. The
strain increment consists of the elastic strain increment and the plastic train
increment
The stress increment is calculated as follows
The calculation model for stress and strain fields of the welding process is described by
Kirchhoff balance equation
Where
is Kirchhoff stress tensor
is Green strain tensor,
is component of virtual displacement,
Poi and Toi are unit volume force component acting on the deformed body respectively. The
strain increment consists of the elastic strain increment and the plastic train
increment
The stress increment is calculated as follows
You're viewing a preview
Unlock full access by subscribing today!
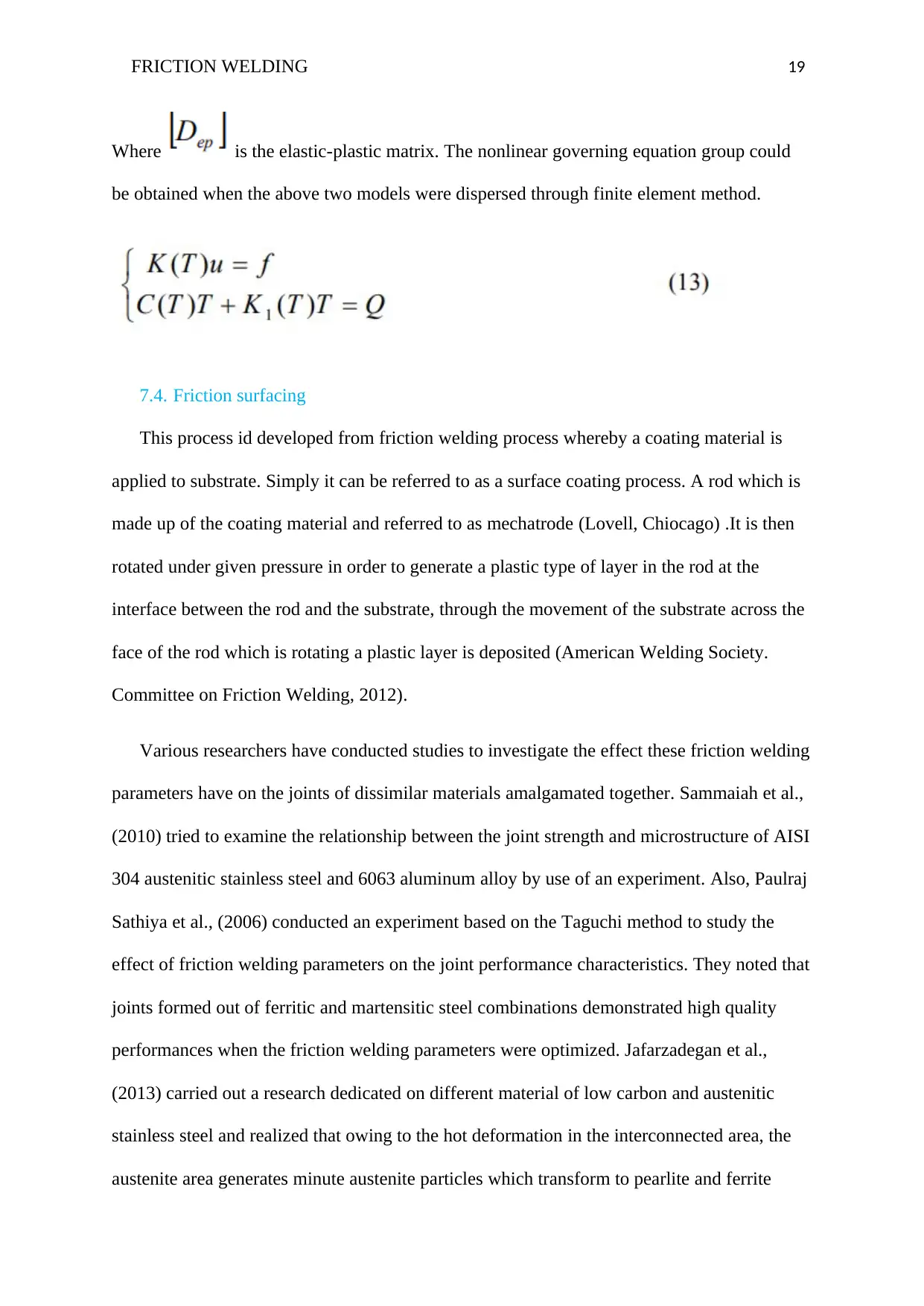
FRICTION WELDING 19
Where is the elastic-plastic matrix. The nonlinear governing equation group could
be obtained when the above two models were dispersed through finite element method.
7.4. Friction surfacing
This process id developed from friction welding process whereby a coating material is
applied to substrate. Simply it can be referred to as a surface coating process. A rod which is
made up of the coating material and referred to as mechatrode (Lovell, Chiocago) .It is then
rotated under given pressure in order to generate a plastic type of layer in the rod at the
interface between the rod and the substrate, through the movement of the substrate across the
face of the rod which is rotating a plastic layer is deposited (American Welding Society.
Committee on Friction Welding, 2012).
Various researchers have conducted studies to investigate the effect these friction welding
parameters have on the joints of dissimilar materials amalgamated together. Sammaiah et al.,
(2010) tried to examine the relationship between the joint strength and microstructure of AISI
304 austenitic stainless steel and 6063 aluminum alloy by use of an experiment. Also, Paulraj
Sathiya et al., (2006) conducted an experiment based on the Taguchi method to study the
effect of friction welding parameters on the joint performance characteristics. They noted that
joints formed out of ferritic and martensitic steel combinations demonstrated high quality
performances when the friction welding parameters were optimized. Jafarzadegan et al.,
(2013) carried out a research dedicated on different material of low carbon and austenitic
stainless steel and realized that owing to the hot deformation in the interconnected area, the
austenite area generates minute austenite particles which transform to pearlite and ferrite
Where is the elastic-plastic matrix. The nonlinear governing equation group could
be obtained when the above two models were dispersed through finite element method.
7.4. Friction surfacing
This process id developed from friction welding process whereby a coating material is
applied to substrate. Simply it can be referred to as a surface coating process. A rod which is
made up of the coating material and referred to as mechatrode (Lovell, Chiocago) .It is then
rotated under given pressure in order to generate a plastic type of layer in the rod at the
interface between the rod and the substrate, through the movement of the substrate across the
face of the rod which is rotating a plastic layer is deposited (American Welding Society.
Committee on Friction Welding, 2012).
Various researchers have conducted studies to investigate the effect these friction welding
parameters have on the joints of dissimilar materials amalgamated together. Sammaiah et al.,
(2010) tried to examine the relationship between the joint strength and microstructure of AISI
304 austenitic stainless steel and 6063 aluminum alloy by use of an experiment. Also, Paulraj
Sathiya et al., (2006) conducted an experiment based on the Taguchi method to study the
effect of friction welding parameters on the joint performance characteristics. They noted that
joints formed out of ferritic and martensitic steel combinations demonstrated high quality
performances when the friction welding parameters were optimized. Jafarzadegan et al.,
(2013) carried out a research dedicated on different material of low carbon and austenitic
stainless steel and realized that owing to the hot deformation in the interconnected area, the
austenite area generates minute austenite particles which transform to pearlite and ferrite
Paraphrase This Document
Need a fresh take? Get an instant paraphrase of this document with our AI Paraphraser
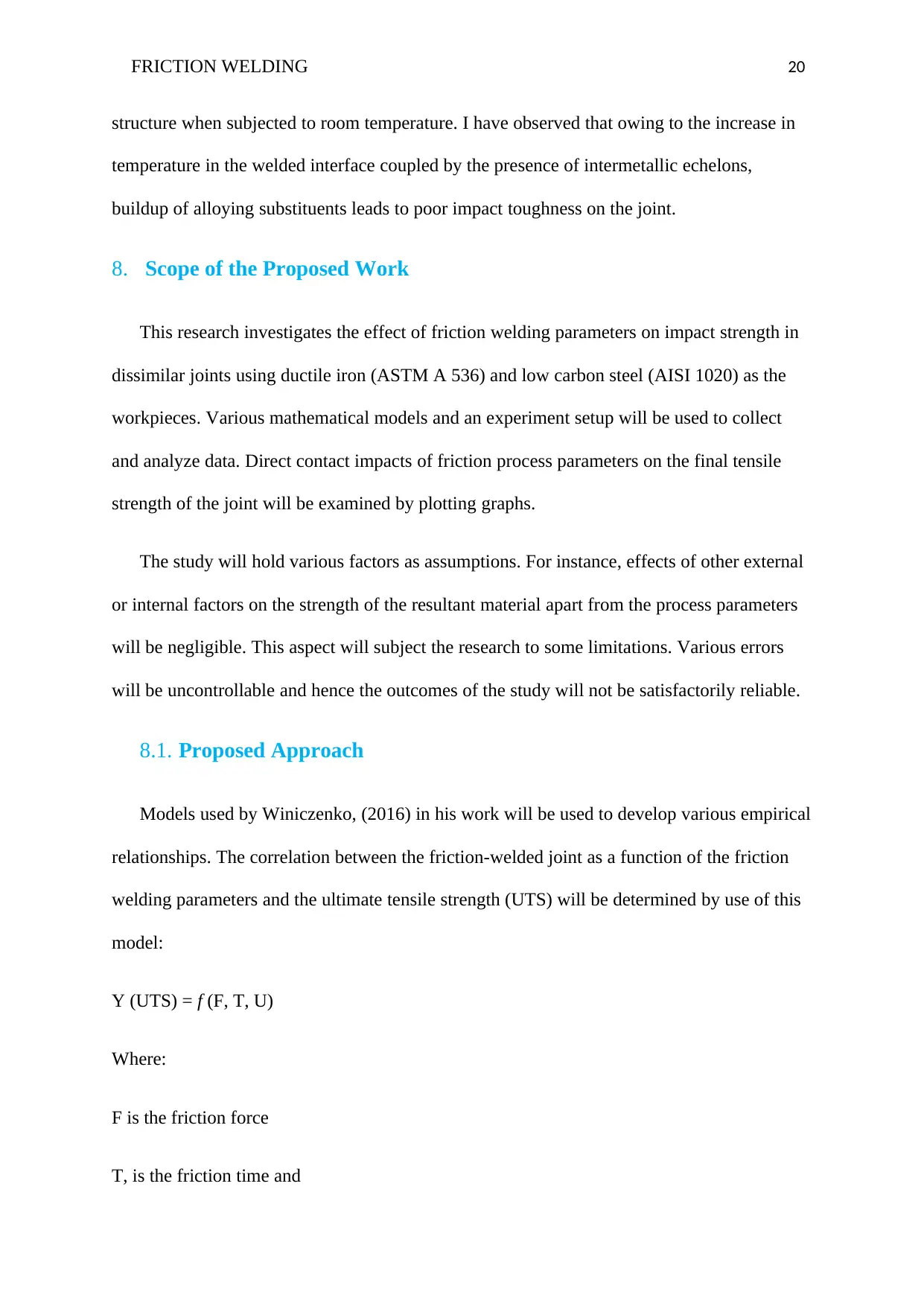
FRICTION WELDING 20
structure when subjected to room temperature. I have observed that owing to the increase in
temperature in the welded interface coupled by the presence of intermetallic echelons,
buildup of alloying substituents leads to poor impact toughness on the joint.
8. Scope of the Proposed Work
This research investigates the effect of friction welding parameters on impact strength in
dissimilar joints using ductile iron (ASTM A 536) and low carbon steel (AISI 1020) as the
workpieces. Various mathematical models and an experiment setup will be used to collect
and analyze data. Direct contact impacts of friction process parameters on the final tensile
strength of the joint will be examined by plotting graphs.
The study will hold various factors as assumptions. For instance, effects of other external
or internal factors on the strength of the resultant material apart from the process parameters
will be negligible. This aspect will subject the research to some limitations. Various errors
will be uncontrollable and hence the outcomes of the study will not be satisfactorily reliable.
8.1. Proposed Approach
Models used by Winiczenko, (2016) in his work will be used to develop various empirical
relationships. The correlation between the friction-welded joint as a function of the friction
welding parameters and the ultimate tensile strength (UTS) will be determined by use of this
model:
Y (UTS) = f (F, T, U)
Where:
F is the friction force
T, is the friction time and
structure when subjected to room temperature. I have observed that owing to the increase in
temperature in the welded interface coupled by the presence of intermetallic echelons,
buildup of alloying substituents leads to poor impact toughness on the joint.
8. Scope of the Proposed Work
This research investigates the effect of friction welding parameters on impact strength in
dissimilar joints using ductile iron (ASTM A 536) and low carbon steel (AISI 1020) as the
workpieces. Various mathematical models and an experiment setup will be used to collect
and analyze data. Direct contact impacts of friction process parameters on the final tensile
strength of the joint will be examined by plotting graphs.
The study will hold various factors as assumptions. For instance, effects of other external
or internal factors on the strength of the resultant material apart from the process parameters
will be negligible. This aspect will subject the research to some limitations. Various errors
will be uncontrollable and hence the outcomes of the study will not be satisfactorily reliable.
8.1. Proposed Approach
Models used by Winiczenko, (2016) in his work will be used to develop various empirical
relationships. The correlation between the friction-welded joint as a function of the friction
welding parameters and the ultimate tensile strength (UTS) will be determined by use of this
model:
Y (UTS) = f (F, T, U)
Where:
F is the friction force
T, is the friction time and
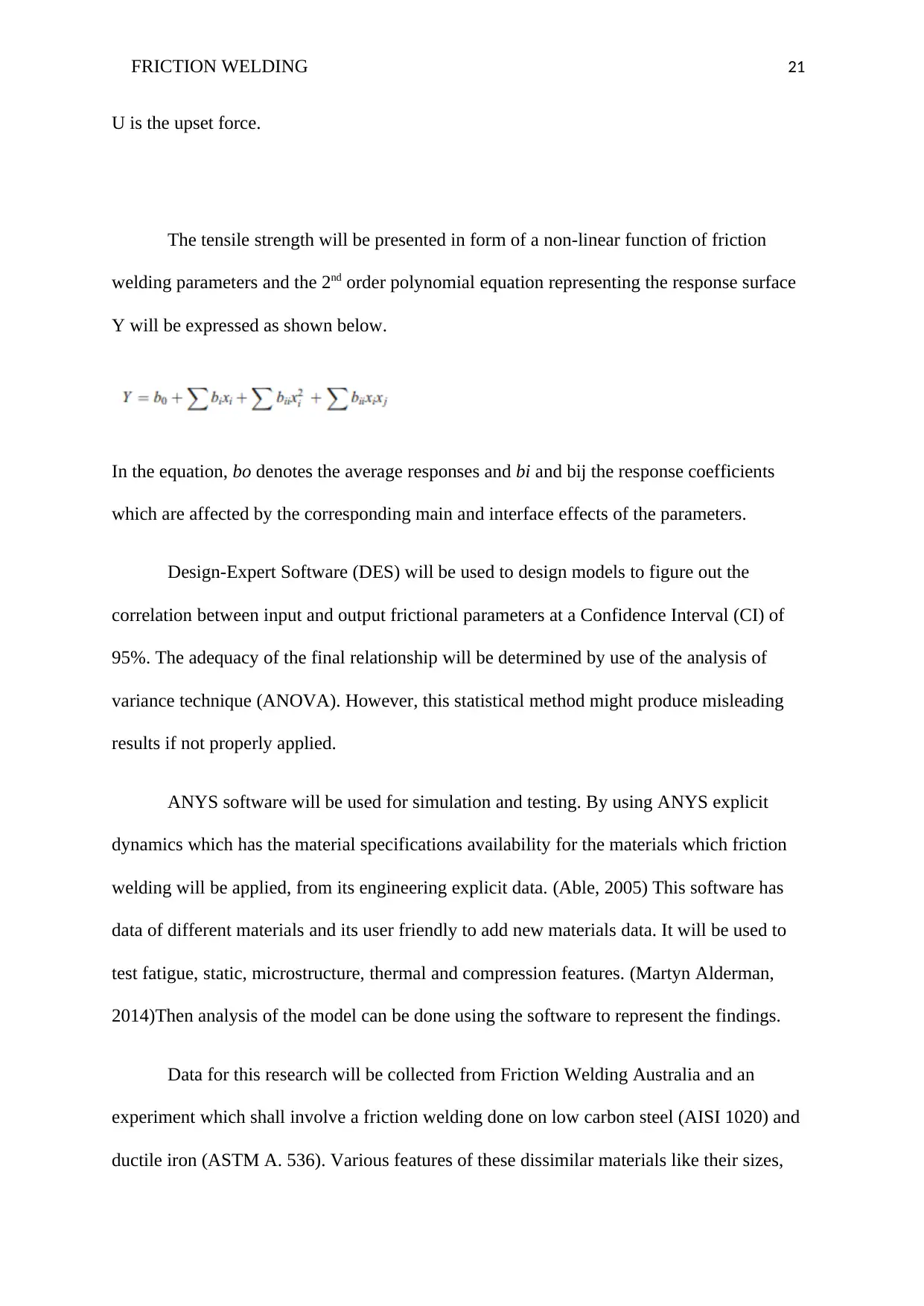
FRICTION WELDING 21
U is the upset force.
The tensile strength will be presented in form of a non-linear function of friction
welding parameters and the 2nd order polynomial equation representing the response surface
Y will be expressed as shown below.
In the equation, bo denotes the average responses and bi and bij the response coefficients
which are affected by the corresponding main and interface effects of the parameters.
Design-Expert Software (DES) will be used to design models to figure out the
correlation between input and output frictional parameters at a Confidence Interval (CI) of
95%. The adequacy of the final relationship will be determined by use of the analysis of
variance technique (ANOVA). However, this statistical method might produce misleading
results if not properly applied.
ANYS software will be used for simulation and testing. By using ANYS explicit
dynamics which has the material specifications availability for the materials which friction
welding will be applied, from its engineering explicit data. (Able, 2005) This software has
data of different materials and its user friendly to add new materials data. It will be used to
test fatigue, static, microstructure, thermal and compression features. (Martyn Alderman,
2014)Then analysis of the model can be done using the software to represent the findings.
Data for this research will be collected from Friction Welding Australia and an
experiment which shall involve a friction welding done on low carbon steel (AISI 1020) and
ductile iron (ASTM A. 536). Various features of these dissimilar materials like their sizes,
U is the upset force.
The tensile strength will be presented in form of a non-linear function of friction
welding parameters and the 2nd order polynomial equation representing the response surface
Y will be expressed as shown below.
In the equation, bo denotes the average responses and bi and bij the response coefficients
which are affected by the corresponding main and interface effects of the parameters.
Design-Expert Software (DES) will be used to design models to figure out the
correlation between input and output frictional parameters at a Confidence Interval (CI) of
95%. The adequacy of the final relationship will be determined by use of the analysis of
variance technique (ANOVA). However, this statistical method might produce misleading
results if not properly applied.
ANYS software will be used for simulation and testing. By using ANYS explicit
dynamics which has the material specifications availability for the materials which friction
welding will be applied, from its engineering explicit data. (Able, 2005) This software has
data of different materials and its user friendly to add new materials data. It will be used to
test fatigue, static, microstructure, thermal and compression features. (Martyn Alderman,
2014)Then analysis of the model can be done using the software to represent the findings.
Data for this research will be collected from Friction Welding Australia and an
experiment which shall involve a friction welding done on low carbon steel (AISI 1020) and
ductile iron (ASTM A. 536). Various features of these dissimilar materials like their sizes,
You're viewing a preview
Unlock full access by subscribing today!
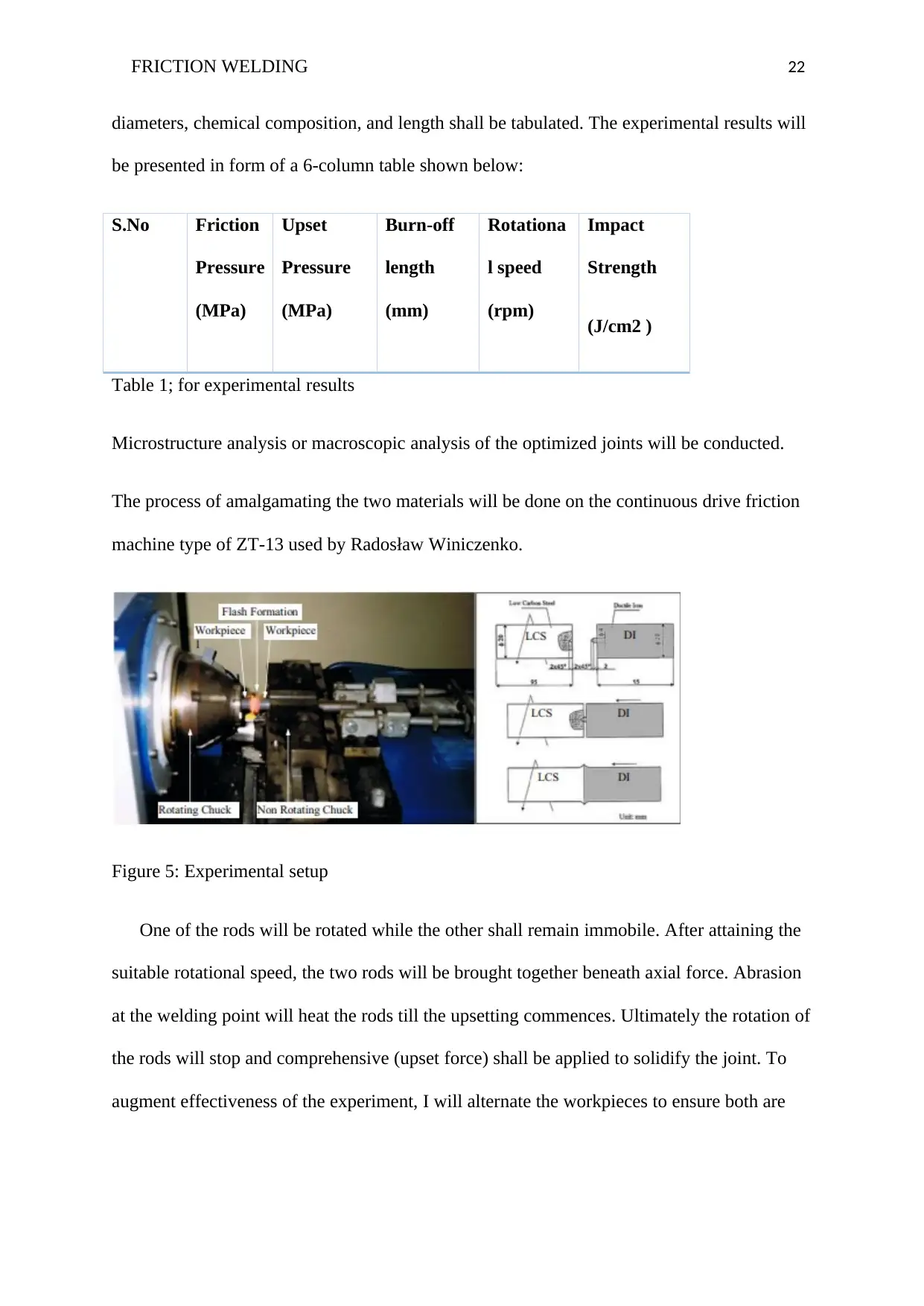
FRICTION WELDING 22
diameters, chemical composition, and length shall be tabulated. The experimental results will
be presented in form of a 6-column table shown below:
S.No Friction
Pressure
(MPa)
Upset
Pressure
(MPa)
Burn-off
length
(mm)
Rotationa
l speed
(rpm)
Impact
Strength
(J/cm2 )
Table 1; for experimental results
Microstructure analysis or macroscopic analysis of the optimized joints will be conducted.
The process of amalgamating the two materials will be done on the continuous drive friction
machine type of ZT-13 used by Radosław Winiczenko.
Figure 5: Experimental setup
One of the rods will be rotated while the other shall remain immobile. After attaining the
suitable rotational speed, the two rods will be brought together beneath axial force. Abrasion
at the welding point will heat the rods till the upsetting commences. Ultimately the rotation of
the rods will stop and comprehensive (upset force) shall be applied to solidify the joint. To
augment effectiveness of the experiment, I will alternate the workpieces to ensure both are
diameters, chemical composition, and length shall be tabulated. The experimental results will
be presented in form of a 6-column table shown below:
S.No Friction
Pressure
(MPa)
Upset
Pressure
(MPa)
Burn-off
length
(mm)
Rotationa
l speed
(rpm)
Impact
Strength
(J/cm2 )
Table 1; for experimental results
Microstructure analysis or macroscopic analysis of the optimized joints will be conducted.
The process of amalgamating the two materials will be done on the continuous drive friction
machine type of ZT-13 used by Radosław Winiczenko.
Figure 5: Experimental setup
One of the rods will be rotated while the other shall remain immobile. After attaining the
suitable rotational speed, the two rods will be brought together beneath axial force. Abrasion
at the welding point will heat the rods till the upsetting commences. Ultimately the rotation of
the rods will stop and comprehensive (upset force) shall be applied to solidify the joint. To
augment effectiveness of the experiment, I will alternate the workpieces to ensure both are
Paraphrase This Document
Need a fresh take? Get an instant paraphrase of this document with our AI Paraphraser
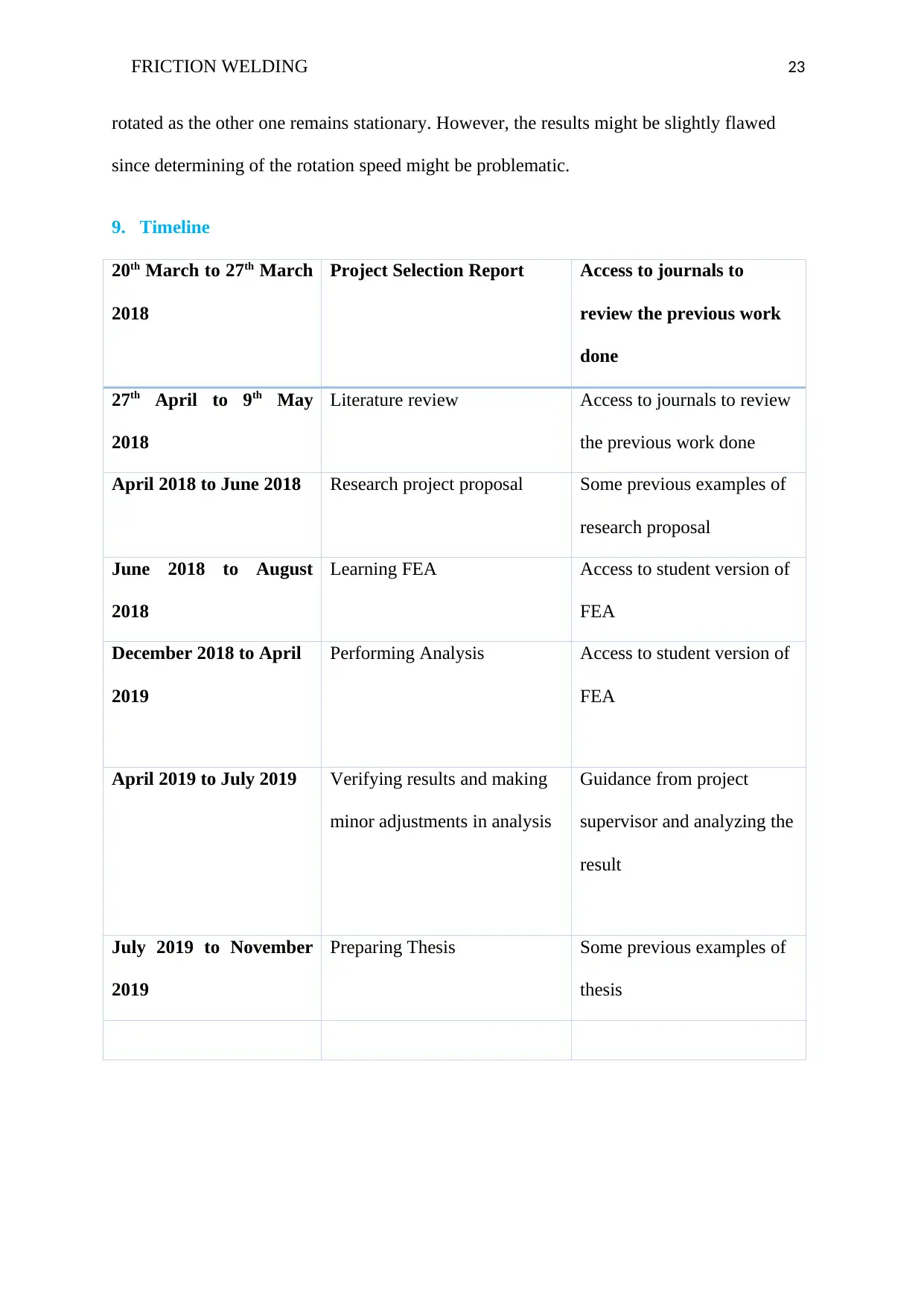
FRICTION WELDING 23
rotated as the other one remains stationary. However, the results might be slightly flawed
since determining of the rotation speed might be problematic.
9. Timeline
20th March to 27th March
2018
Project Selection Report Access to journals to
review the previous work
done
27th April to 9th May
2018
Literature review Access to journals to review
the previous work done
April 2018 to June 2018 Research project proposal Some previous examples of
research proposal
June 2018 to August
2018
Learning FEA Access to student version of
FEA
December 2018 to April
2019
Performing Analysis Access to student version of
FEA
April 2019 to July 2019 Verifying results and making
minor adjustments in analysis
Guidance from project
supervisor and analyzing the
result
July 2019 to November
2019
Preparing Thesis Some previous examples of
thesis
rotated as the other one remains stationary. However, the results might be slightly flawed
since determining of the rotation speed might be problematic.
9. Timeline
20th March to 27th March
2018
Project Selection Report Access to journals to
review the previous work
done
27th April to 9th May
2018
Literature review Access to journals to review
the previous work done
April 2018 to June 2018 Research project proposal Some previous examples of
research proposal
June 2018 to August
2018
Learning FEA Access to student version of
FEA
December 2018 to April
2019
Performing Analysis Access to student version of
FEA
April 2019 to July 2019 Verifying results and making
minor adjustments in analysis
Guidance from project
supervisor and analyzing the
result
July 2019 to November
2019
Preparing Thesis Some previous examples of
thesis
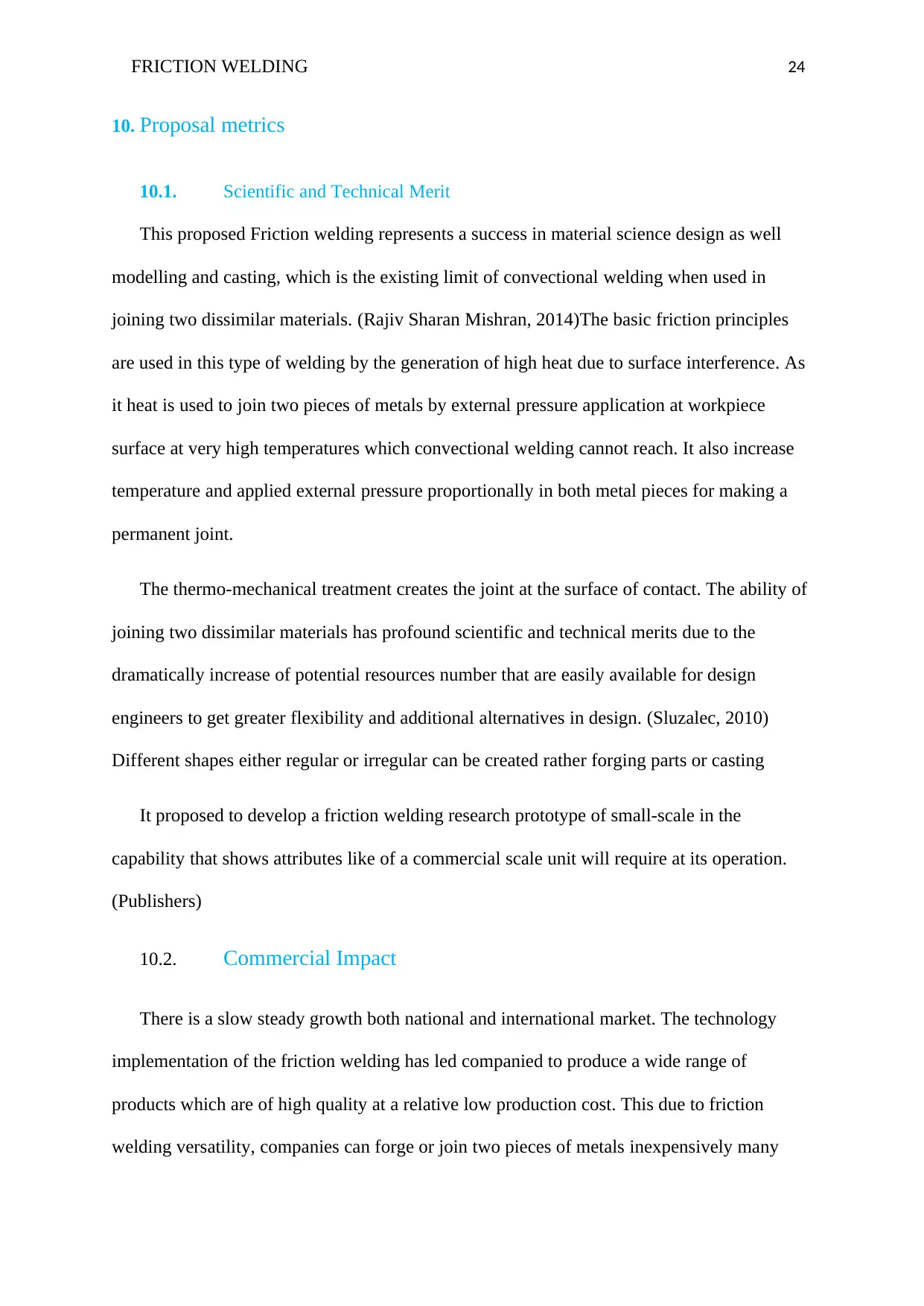
FRICTION WELDING 24
10. Proposal metrics
10.1. Scientific and Technical Merit
This proposed Friction welding represents a success in material science design as well
modelling and casting, which is the existing limit of convectional welding when used in
joining two dissimilar materials. (Rajiv Sharan Mishran, 2014)The basic friction principles
are used in this type of welding by the generation of high heat due to surface interference. As
it heat is used to join two pieces of metals by external pressure application at workpiece
surface at very high temperatures which convectional welding cannot reach. It also increase
temperature and applied external pressure proportionally in both metal pieces for making a
permanent joint.
The thermo-mechanical treatment creates the joint at the surface of contact. The ability of
joining two dissimilar materials has profound scientific and technical merits due to the
dramatically increase of potential resources number that are easily available for design
engineers to get greater flexibility and additional alternatives in design. (Sluzalec, 2010)
Different shapes either regular or irregular can be created rather forging parts or casting
It proposed to develop a friction welding research prototype of small-scale in the
capability that shows attributes like of a commercial scale unit will require at its operation.
(Publishers)
10.2. Commercial Impact
There is a slow steady growth both national and international market. The technology
implementation of the friction welding has led companied to produce a wide range of
products which are of high quality at a relative low production cost. This due to friction
welding versatility, companies can forge or join two pieces of metals inexpensively many
10. Proposal metrics
10.1. Scientific and Technical Merit
This proposed Friction welding represents a success in material science design as well
modelling and casting, which is the existing limit of convectional welding when used in
joining two dissimilar materials. (Rajiv Sharan Mishran, 2014)The basic friction principles
are used in this type of welding by the generation of high heat due to surface interference. As
it heat is used to join two pieces of metals by external pressure application at workpiece
surface at very high temperatures which convectional welding cannot reach. It also increase
temperature and applied external pressure proportionally in both metal pieces for making a
permanent joint.
The thermo-mechanical treatment creates the joint at the surface of contact. The ability of
joining two dissimilar materials has profound scientific and technical merits due to the
dramatically increase of potential resources number that are easily available for design
engineers to get greater flexibility and additional alternatives in design. (Sluzalec, 2010)
Different shapes either regular or irregular can be created rather forging parts or casting
It proposed to develop a friction welding research prototype of small-scale in the
capability that shows attributes like of a commercial scale unit will require at its operation.
(Publishers)
10.2. Commercial Impact
There is a slow steady growth both national and international market. The technology
implementation of the friction welding has led companied to produce a wide range of
products which are of high quality at a relative low production cost. This due to friction
welding versatility, companies can forge or join two pieces of metals inexpensively many
You're viewing a preview
Unlock full access by subscribing today!
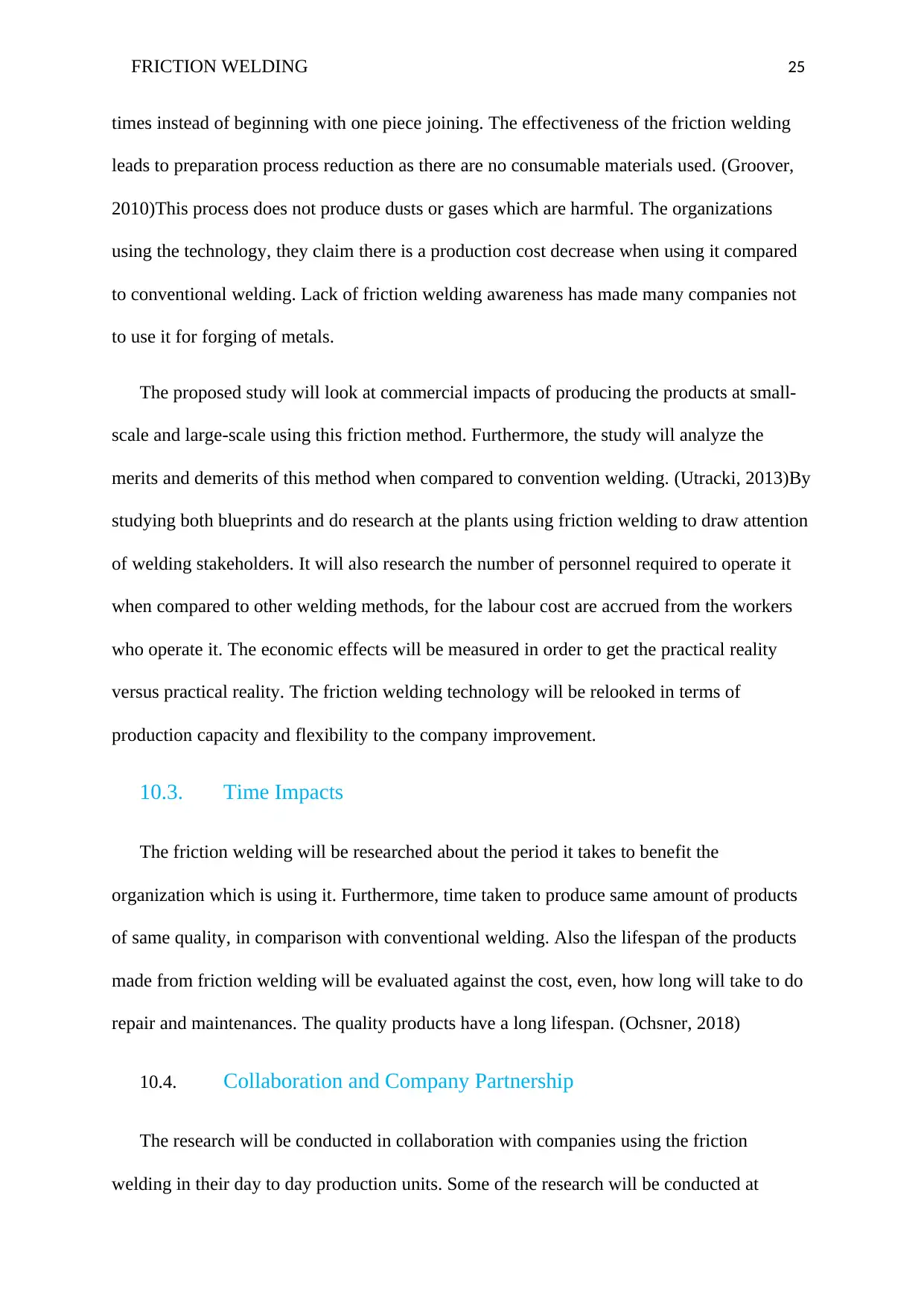
FRICTION WELDING 25
times instead of beginning with one piece joining. The effectiveness of the friction welding
leads to preparation process reduction as there are no consumable materials used. (Groover,
2010)This process does not produce dusts or gases which are harmful. The organizations
using the technology, they claim there is a production cost decrease when using it compared
to conventional welding. Lack of friction welding awareness has made many companies not
to use it for forging of metals.
The proposed study will look at commercial impacts of producing the products at small-
scale and large-scale using this friction method. Furthermore, the study will analyze the
merits and demerits of this method when compared to convention welding. (Utracki, 2013)By
studying both blueprints and do research at the plants using friction welding to draw attention
of welding stakeholders. It will also research the number of personnel required to operate it
when compared to other welding methods, for the labour cost are accrued from the workers
who operate it. The economic effects will be measured in order to get the practical reality
versus practical reality. The friction welding technology will be relooked in terms of
production capacity and flexibility to the company improvement.
10.3. Time Impacts
The friction welding will be researched about the period it takes to benefit the
organization which is using it. Furthermore, time taken to produce same amount of products
of same quality, in comparison with conventional welding. Also the lifespan of the products
made from friction welding will be evaluated against the cost, even, how long will take to do
repair and maintenances. The quality products have a long lifespan. (Ochsner, 2018)
10.4. Collaboration and Company Partnership
The research will be conducted in collaboration with companies using the friction
welding in their day to day production units. Some of the research will be conducted at
times instead of beginning with one piece joining. The effectiveness of the friction welding
leads to preparation process reduction as there are no consumable materials used. (Groover,
2010)This process does not produce dusts or gases which are harmful. The organizations
using the technology, they claim there is a production cost decrease when using it compared
to conventional welding. Lack of friction welding awareness has made many companies not
to use it for forging of metals.
The proposed study will look at commercial impacts of producing the products at small-
scale and large-scale using this friction method. Furthermore, the study will analyze the
merits and demerits of this method when compared to convention welding. (Utracki, 2013)By
studying both blueprints and do research at the plants using friction welding to draw attention
of welding stakeholders. It will also research the number of personnel required to operate it
when compared to other welding methods, for the labour cost are accrued from the workers
who operate it. The economic effects will be measured in order to get the practical reality
versus practical reality. The friction welding technology will be relooked in terms of
production capacity and flexibility to the company improvement.
10.3. Time Impacts
The friction welding will be researched about the period it takes to benefit the
organization which is using it. Furthermore, time taken to produce same amount of products
of same quality, in comparison with conventional welding. Also the lifespan of the products
made from friction welding will be evaluated against the cost, even, how long will take to do
repair and maintenances. The quality products have a long lifespan. (Ochsner, 2018)
10.4. Collaboration and Company Partnership
The research will be conducted in collaboration with companies using the friction
welding in their day to day production units. Some of the research will be conducted at
Paraphrase This Document
Need a fresh take? Get an instant paraphrase of this document with our AI Paraphraser
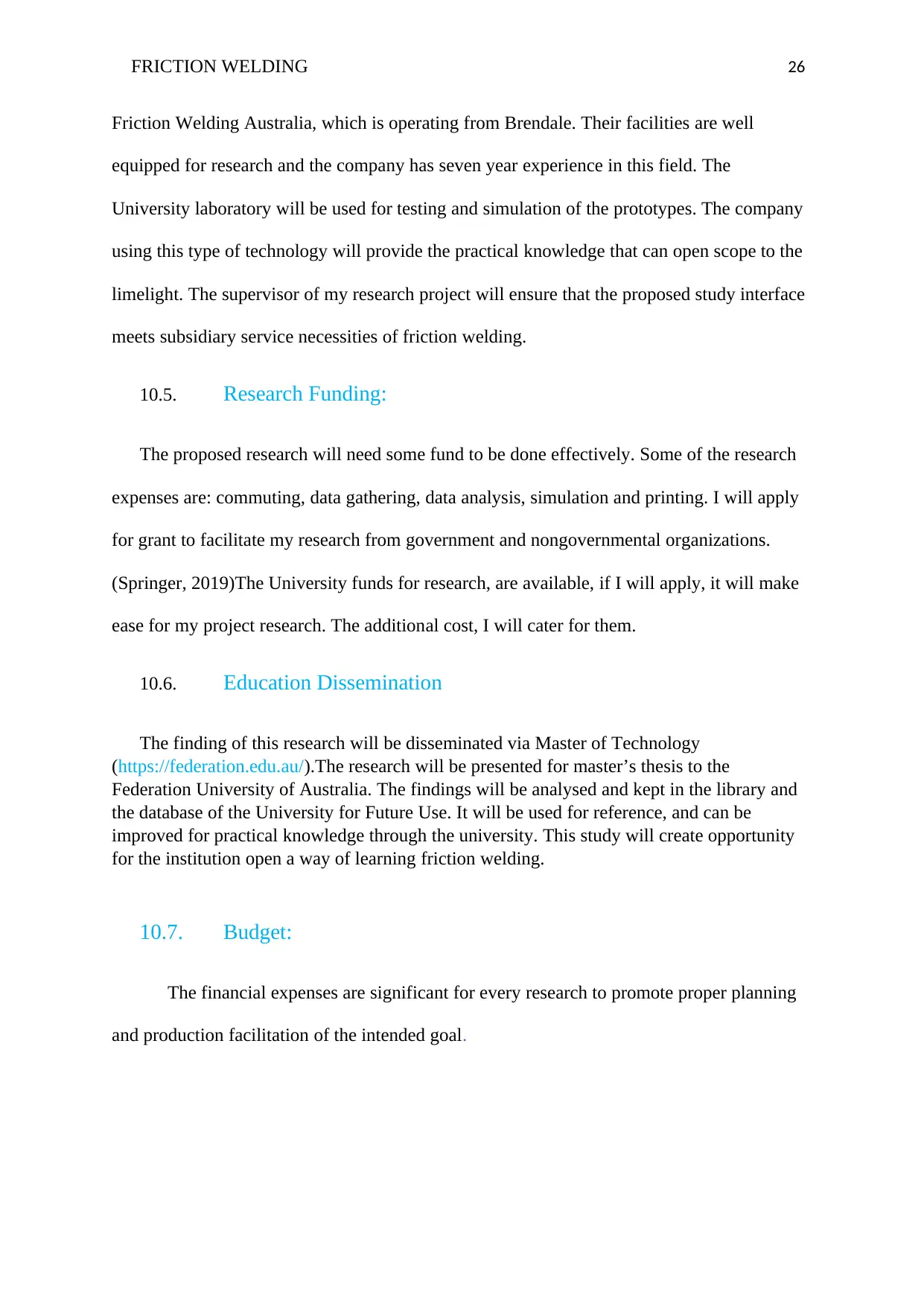
FRICTION WELDING 26
Friction Welding Australia, which is operating from Brendale. Their facilities are well
equipped for research and the company has seven year experience in this field. The
University laboratory will be used for testing and simulation of the prototypes. The company
using this type of technology will provide the practical knowledge that can open scope to the
limelight. The supervisor of my research project will ensure that the proposed study interface
meets subsidiary service necessities of friction welding.
10.5. Research Funding:
The proposed research will need some fund to be done effectively. Some of the research
expenses are: commuting, data gathering, data analysis, simulation and printing. I will apply
for grant to facilitate my research from government and nongovernmental organizations.
(Springer, 2019)The University funds for research, are available, if I will apply, it will make
ease for my project research. The additional cost, I will cater for them.
10.6. Education Dissemination
The finding of this research will be disseminated via Master of Technology
(https://federation.edu.au/).The research will be presented for master’s thesis to the
Federation University of Australia. The findings will be analysed and kept in the library and
the database of the University for Future Use. It will be used for reference, and can be
improved for practical knowledge through the university. This study will create opportunity
for the institution open a way of learning friction welding.
10.7. Budget:
The financial expenses are significant for every research to promote proper planning
and production facilitation of the intended goal.
Friction Welding Australia, which is operating from Brendale. Their facilities are well
equipped for research and the company has seven year experience in this field. The
University laboratory will be used for testing and simulation of the prototypes. The company
using this type of technology will provide the practical knowledge that can open scope to the
limelight. The supervisor of my research project will ensure that the proposed study interface
meets subsidiary service necessities of friction welding.
10.5. Research Funding:
The proposed research will need some fund to be done effectively. Some of the research
expenses are: commuting, data gathering, data analysis, simulation and printing. I will apply
for grant to facilitate my research from government and nongovernmental organizations.
(Springer, 2019)The University funds for research, are available, if I will apply, it will make
ease for my project research. The additional cost, I will cater for them.
10.6. Education Dissemination
The finding of this research will be disseminated via Master of Technology
(https://federation.edu.au/).The research will be presented for master’s thesis to the
Federation University of Australia. The findings will be analysed and kept in the library and
the database of the University for Future Use. It will be used for reference, and can be
improved for practical knowledge through the university. This study will create opportunity
for the institution open a way of learning friction welding.
10.7. Budget:
The financial expenses are significant for every research to promote proper planning
and production facilitation of the intended goal.
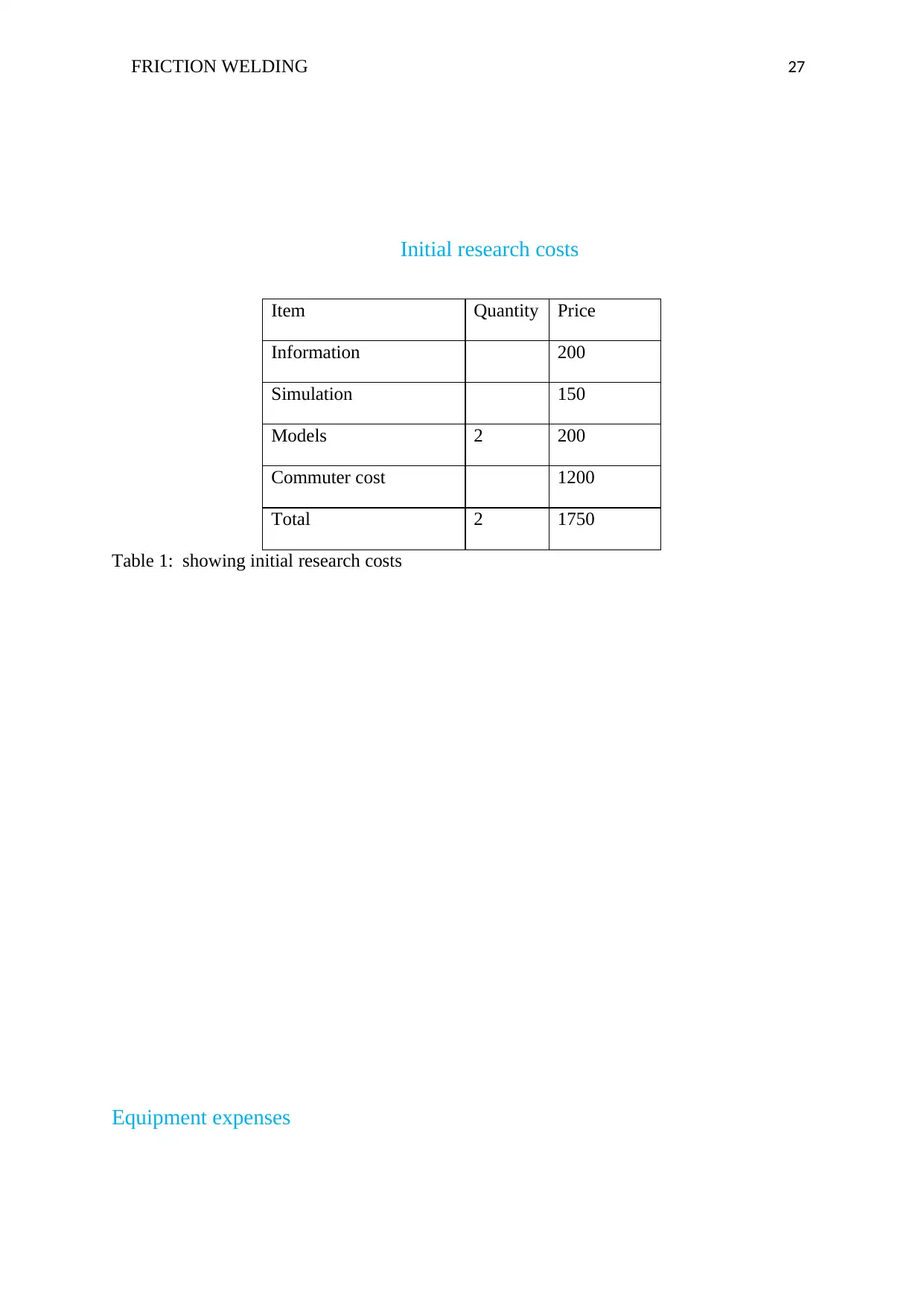
FRICTION WELDING 27
Initial research costs
Item Quantity Price
Information 200
Simulation 150
Models 2 200
Commuter cost 1200
Total 2 1750
Table 1: showing initial research costs
Equipment expenses
Initial research costs
Item Quantity Price
Information 200
Simulation 150
Models 2 200
Commuter cost 1200
Total 2 1750
Table 1: showing initial research costs
Equipment expenses
You're viewing a preview
Unlock full access by subscribing today!
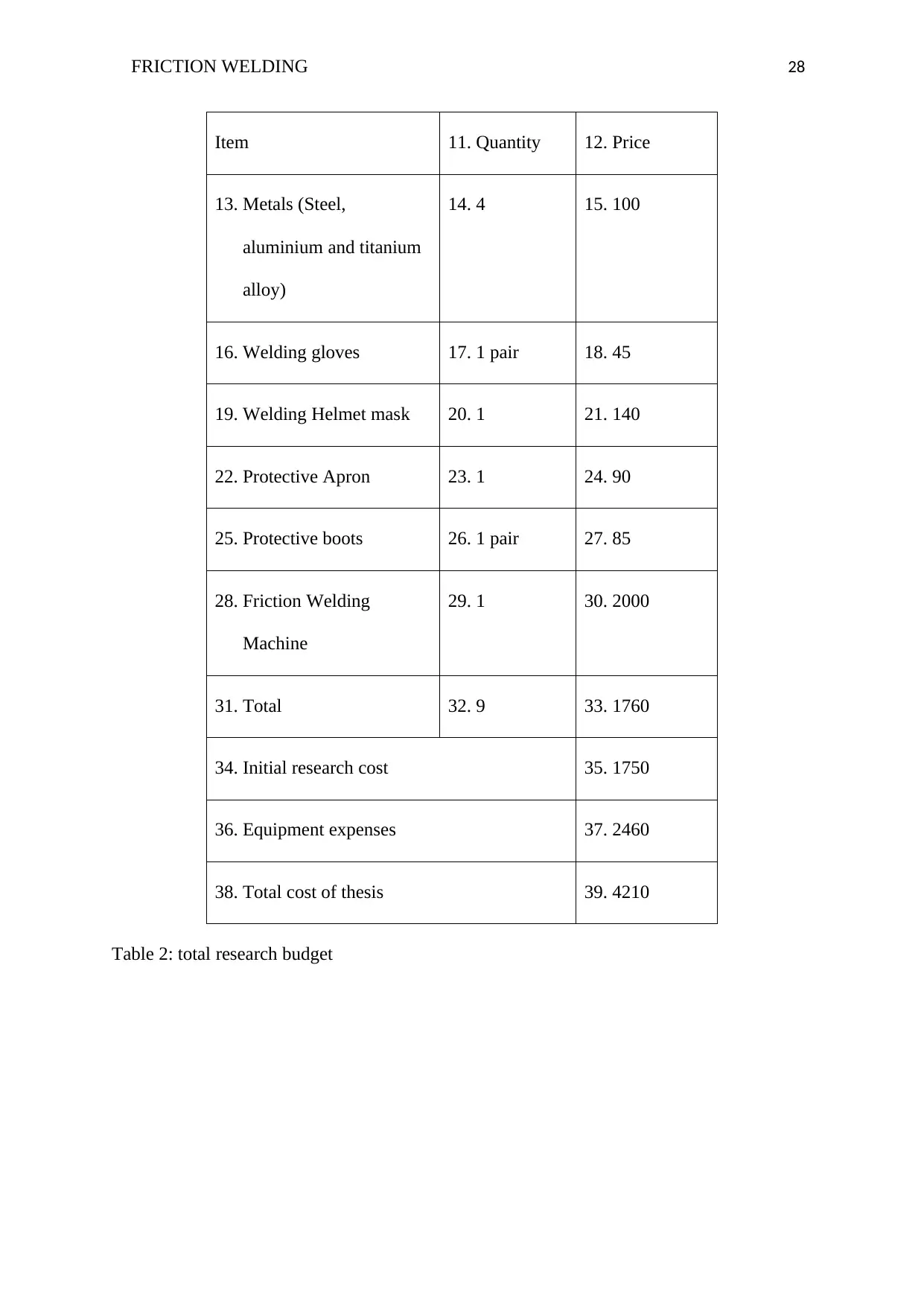
FRICTION WELDING 28
Item 11. Quantity 12. Price
13. Metals (Steel,
aluminium and titanium
alloy)
14. 4 15. 100
16. Welding gloves 17. 1 pair 18. 45
19. Welding Helmet mask 20. 1 21. 140
22. Protective Apron 23. 1 24. 90
25. Protective boots 26. 1 pair 27. 85
28. Friction Welding
Machine
29. 1 30. 2000
31. Total 32. 9 33. 1760
34. Initial research cost 35. 1750
36. Equipment expenses 37. 2460
38. Total cost of thesis 39. 4210
Table 2: total research budget
Item 11. Quantity 12. Price
13. Metals (Steel,
aluminium and titanium
alloy)
14. 4 15. 100
16. Welding gloves 17. 1 pair 18. 45
19. Welding Helmet mask 20. 1 21. 140
22. Protective Apron 23. 1 24. 90
25. Protective boots 26. 1 pair 27. 85
28. Friction Welding
Machine
29. 1 30. 2000
31. Total 32. 9 33. 1760
34. Initial research cost 35. 1750
36. Equipment expenses 37. 2460
38. Total cost of thesis 39. 4210
Table 2: total research budget
Paraphrase This Document
Need a fresh take? Get an instant paraphrase of this document with our AI Paraphraser
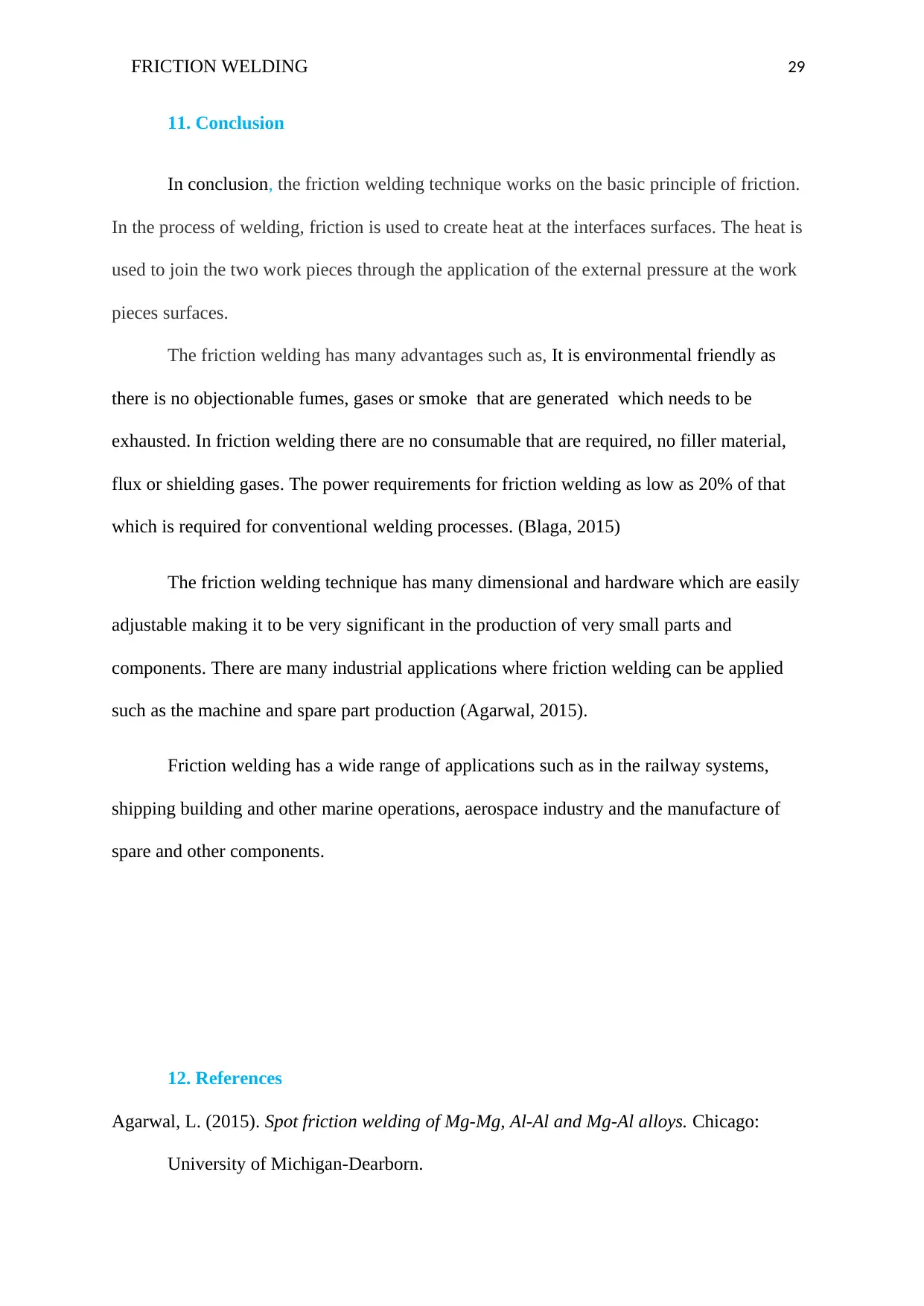
FRICTION WELDING 29
11. Conclusion
In conclusion, the friction welding technique works on the basic principle of friction.
In the process of welding, friction is used to create heat at the interfaces surfaces. The heat is
used to join the two work pieces through the application of the external pressure at the work
pieces surfaces.
The friction welding has many advantages such as, It is environmental friendly as
there is no objectionable fumes, gases or smoke that are generated which needs to be
exhausted. In friction welding there are no consumable that are required, no filler material,
flux or shielding gases. The power requirements for friction welding as low as 20% of that
which is required for conventional welding processes. (Blaga, 2015)
The friction welding technique has many dimensional and hardware which are easily
adjustable making it to be very significant in the production of very small parts and
components. There are many industrial applications where friction welding can be applied
such as the machine and spare part production (Agarwal, 2015).
Friction welding has a wide range of applications such as in the railway systems,
shipping building and other marine operations, aerospace industry and the manufacture of
spare and other components.
12. References
Agarwal, L. (2015). Spot friction welding of Mg-Mg, Al-Al and Mg-Al alloys. Chicago:
University of Michigan-Dearborn.
11. Conclusion
In conclusion, the friction welding technique works on the basic principle of friction.
In the process of welding, friction is used to create heat at the interfaces surfaces. The heat is
used to join the two work pieces through the application of the external pressure at the work
pieces surfaces.
The friction welding has many advantages such as, It is environmental friendly as
there is no objectionable fumes, gases or smoke that are generated which needs to be
exhausted. In friction welding there are no consumable that are required, no filler material,
flux or shielding gases. The power requirements for friction welding as low as 20% of that
which is required for conventional welding processes. (Blaga, 2015)
The friction welding technique has many dimensional and hardware which are easily
adjustable making it to be very significant in the production of very small parts and
components. There are many industrial applications where friction welding can be applied
such as the machine and spare part production (Agarwal, 2015).
Friction welding has a wide range of applications such as in the railway systems,
shipping building and other marine operations, aerospace industry and the manufacture of
spare and other components.
12. References
Agarwal, L. (2015). Spot friction welding of Mg-Mg, Al-Al and Mg-Al alloys. Chicago:
University of Michigan-Dearborn.
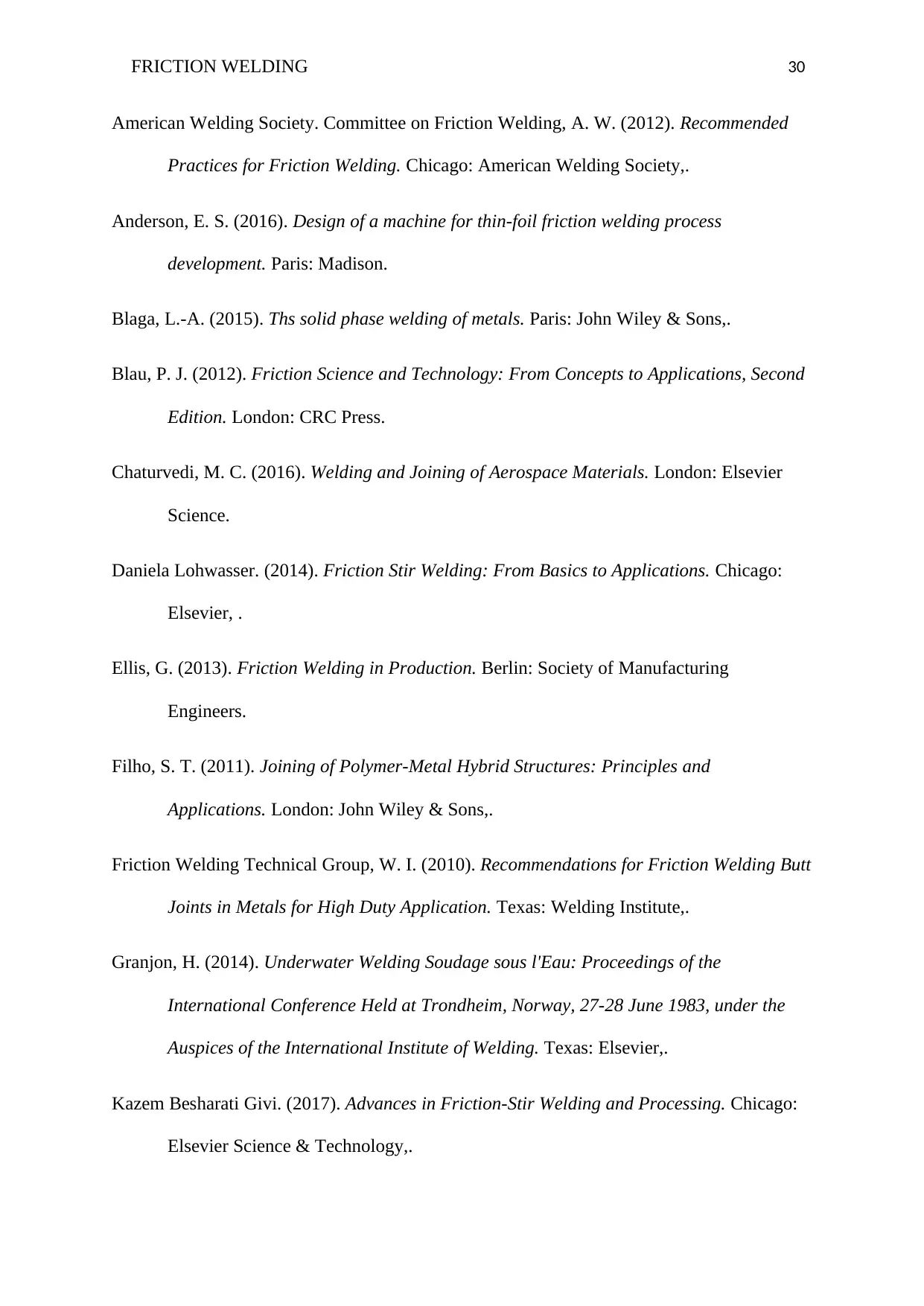
FRICTION WELDING 30
American Welding Society. Committee on Friction Welding, A. W. (2012). Recommended
Practices for Friction Welding. Chicago: American Welding Society,.
Anderson, E. S. (2016). Design of a machine for thin-foil friction welding process
development. Paris: Madison.
Blaga, L.-A. (2015). Ths solid phase welding of metals. Paris: John Wiley & Sons,.
Blau, P. J. (2012). Friction Science and Technology: From Concepts to Applications, Second
Edition. London: CRC Press.
Chaturvedi, M. C. (2016). Welding and Joining of Aerospace Materials. London: Elsevier
Science.
Daniela Lohwasser. (2014). Friction Stir Welding: From Basics to Applications. Chicago:
Elsevier, .
Ellis, G. (2013). Friction Welding in Production. Berlin: Society of Manufacturing
Engineers.
Filho, S. T. (2011). Joining of Polymer-Metal Hybrid Structures: Principles and
Applications. London: John Wiley & Sons,.
Friction Welding Technical Group, W. I. (2010). Recommendations for Friction Welding Butt
Joints in Metals for High Duty Application. Texas: Welding Institute,.
Granjon, H. (2014). Underwater Welding Soudage sous l'Eau: Proceedings of the
International Conference Held at Trondheim, Norway, 27-28 June 1983, under the
Auspices of the International Institute of Welding. Texas: Elsevier,.
Kazem Besharati Givi. (2017). Advances in Friction-Stir Welding and Processing. Chicago:
Elsevier Science & Technology,.
American Welding Society. Committee on Friction Welding, A. W. (2012). Recommended
Practices for Friction Welding. Chicago: American Welding Society,.
Anderson, E. S. (2016). Design of a machine for thin-foil friction welding process
development. Paris: Madison.
Blaga, L.-A. (2015). Ths solid phase welding of metals. Paris: John Wiley & Sons,.
Blau, P. J. (2012). Friction Science and Technology: From Concepts to Applications, Second
Edition. London: CRC Press.
Chaturvedi, M. C. (2016). Welding and Joining of Aerospace Materials. London: Elsevier
Science.
Daniela Lohwasser. (2014). Friction Stir Welding: From Basics to Applications. Chicago:
Elsevier, .
Ellis, G. (2013). Friction Welding in Production. Berlin: Society of Manufacturing
Engineers.
Filho, S. T. (2011). Joining of Polymer-Metal Hybrid Structures: Principles and
Applications. London: John Wiley & Sons,.
Friction Welding Technical Group, W. I. (2010). Recommendations for Friction Welding Butt
Joints in Metals for High Duty Application. Texas: Welding Institute,.
Granjon, H. (2014). Underwater Welding Soudage sous l'Eau: Proceedings of the
International Conference Held at Trondheim, Norway, 27-28 June 1983, under the
Auspices of the International Institute of Welding. Texas: Elsevier,.
Kazem Besharati Givi. (2017). Advances in Friction-Stir Welding and Processing. Chicago:
Elsevier Science & Technology,.
You're viewing a preview
Unlock full access by subscribing today!
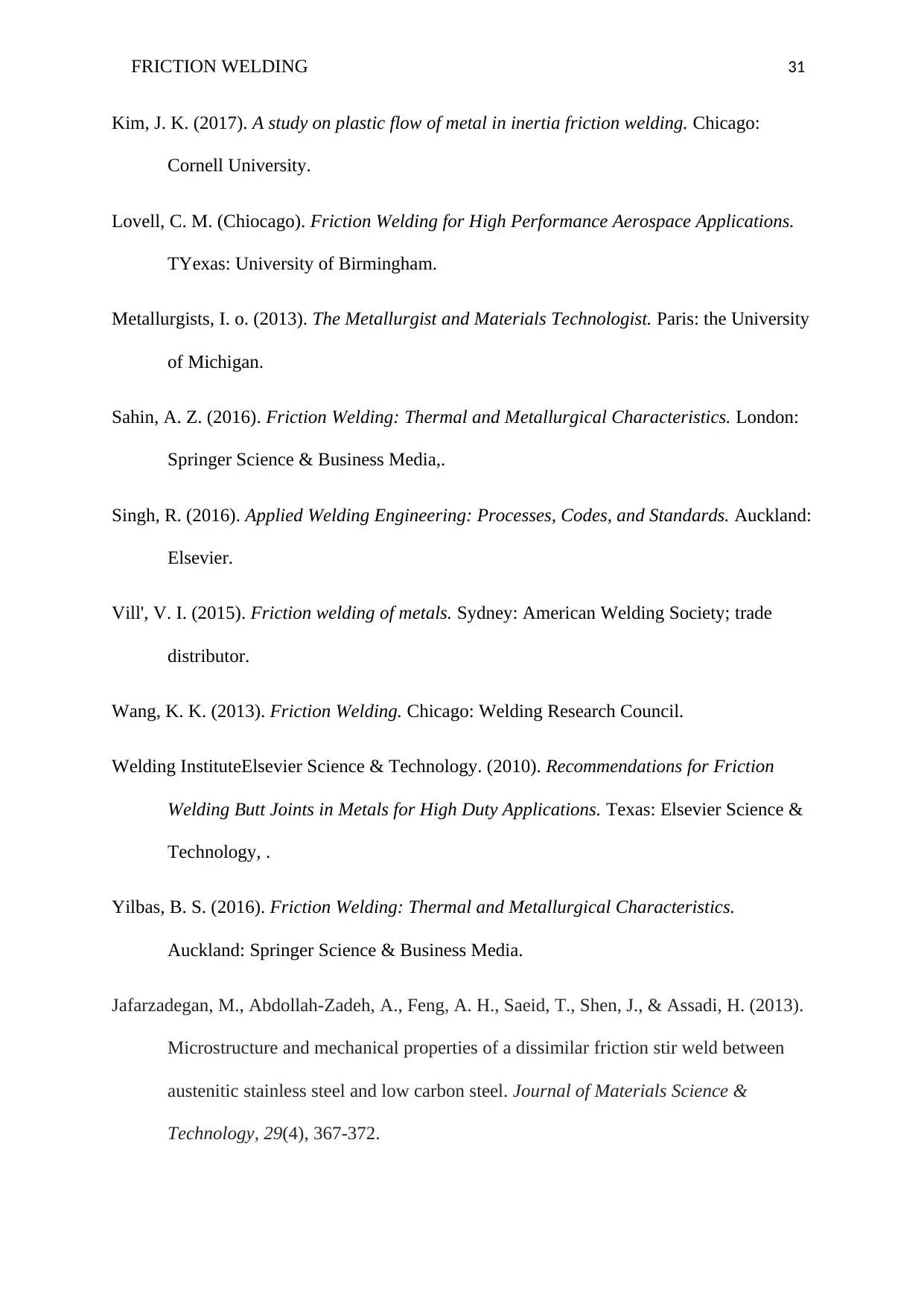
FRICTION WELDING 31
Kim, J. K. (2017). A study on plastic flow of metal in inertia friction welding. Chicago:
Cornell University.
Lovell, C. M. (Chiocago). Friction Welding for High Performance Aerospace Applications.
TYexas: University of Birmingham.
Metallurgists, I. o. (2013). The Metallurgist and Materials Technologist. Paris: the University
of Michigan.
Sahin, A. Z. (2016). Friction Welding: Thermal and Metallurgical Characteristics. London:
Springer Science & Business Media,.
Singh, R. (2016). Applied Welding Engineering: Processes, Codes, and Standards. Auckland:
Elsevier.
Vill', V. I. (2015). Friction welding of metals. Sydney: American Welding Society; trade
distributor.
Wang, K. K. (2013). Friction Welding. Chicago: Welding Research Council.
Welding InstituteElsevier Science & Technology. (2010). Recommendations for Friction
Welding Butt Joints in Metals for High Duty Applications. Texas: Elsevier Science &
Technology, .
Yilbas, B. S. (2016). Friction Welding: Thermal and Metallurgical Characteristics.
Auckland: Springer Science & Business Media.
Jafarzadegan, M., Abdollah-Zadeh, A., Feng, A. H., Saeid, T., Shen, J., & Assadi, H. (2013).
Microstructure and mechanical properties of a dissimilar friction stir weld between
austenitic stainless steel and low carbon steel. Journal of Materials Science &
Technology, 29(4), 367-372.
Kim, J. K. (2017). A study on plastic flow of metal in inertia friction welding. Chicago:
Cornell University.
Lovell, C. M. (Chiocago). Friction Welding for High Performance Aerospace Applications.
TYexas: University of Birmingham.
Metallurgists, I. o. (2013). The Metallurgist and Materials Technologist. Paris: the University
of Michigan.
Sahin, A. Z. (2016). Friction Welding: Thermal and Metallurgical Characteristics. London:
Springer Science & Business Media,.
Singh, R. (2016). Applied Welding Engineering: Processes, Codes, and Standards. Auckland:
Elsevier.
Vill', V. I. (2015). Friction welding of metals. Sydney: American Welding Society; trade
distributor.
Wang, K. K. (2013). Friction Welding. Chicago: Welding Research Council.
Welding InstituteElsevier Science & Technology. (2010). Recommendations for Friction
Welding Butt Joints in Metals for High Duty Applications. Texas: Elsevier Science &
Technology, .
Yilbas, B. S. (2016). Friction Welding: Thermal and Metallurgical Characteristics.
Auckland: Springer Science & Business Media.
Jafarzadegan, M., Abdollah-Zadeh, A., Feng, A. H., Saeid, T., Shen, J., & Assadi, H. (2013).
Microstructure and mechanical properties of a dissimilar friction stir weld between
austenitic stainless steel and low carbon steel. Journal of Materials Science &
Technology, 29(4), 367-372.
Paraphrase This Document
Need a fresh take? Get an instant paraphrase of this document with our AI Paraphraser
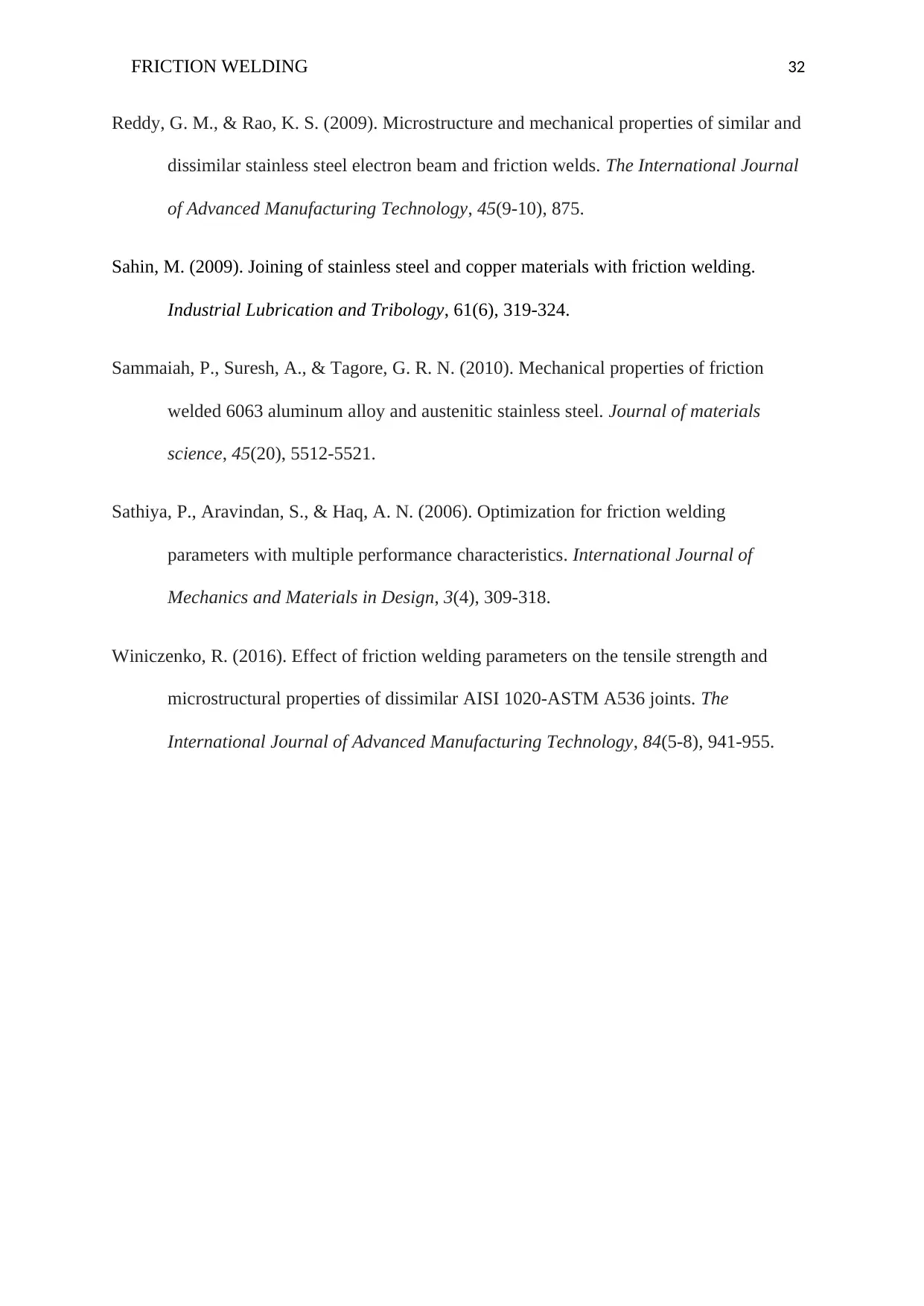
FRICTION WELDING 32
Reddy, G. M., & Rao, K. S. (2009). Microstructure and mechanical properties of similar and
dissimilar stainless steel electron beam and friction welds. The International Journal
of Advanced Manufacturing Technology, 45(9-10), 875.
Sahin, M. (2009). Joining of stainless steel and copper materials with friction welding.
Industrial Lubrication and Tribology, 61(6), 319-324.
Sammaiah, P., Suresh, A., & Tagore, G. R. N. (2010). Mechanical properties of friction
welded 6063 aluminum alloy and austenitic stainless steel. Journal of materials
science, 45(20), 5512-5521.
Sathiya, P., Aravindan, S., & Haq, A. N. (2006). Optimization for friction welding
parameters with multiple performance characteristics. International Journal of
Mechanics and Materials in Design, 3(4), 309-318.
Winiczenko, R. (2016). Effect of friction welding parameters on the tensile strength and
microstructural properties of dissimilar AISI 1020-ASTM A536 joints. The
International Journal of Advanced Manufacturing Technology, 84(5-8), 941-955.
Reddy, G. M., & Rao, K. S. (2009). Microstructure and mechanical properties of similar and
dissimilar stainless steel electron beam and friction welds. The International Journal
of Advanced Manufacturing Technology, 45(9-10), 875.
Sahin, M. (2009). Joining of stainless steel and copper materials with friction welding.
Industrial Lubrication and Tribology, 61(6), 319-324.
Sammaiah, P., Suresh, A., & Tagore, G. R. N. (2010). Mechanical properties of friction
welded 6063 aluminum alloy and austenitic stainless steel. Journal of materials
science, 45(20), 5512-5521.
Sathiya, P., Aravindan, S., & Haq, A. N. (2006). Optimization for friction welding
parameters with multiple performance characteristics. International Journal of
Mechanics and Materials in Design, 3(4), 309-318.
Winiczenko, R. (2016). Effect of friction welding parameters on the tensile strength and
microstructural properties of dissimilar AISI 1020-ASTM A536 joints. The
International Journal of Advanced Manufacturing Technology, 84(5-8), 941-955.
1 out of 32

Your All-in-One AI-Powered Toolkit for Academic Success.
 +13062052269
info@desklib.com
Available 24*7 on WhatsApp / Email
Unlock your academic potential
© 2024  |  Zucol Services PVT LTD  |  All rights reserved.