Study and Performance Analysis of Gas Engine Driven Gas Compressor
VerifiedAdded on 2023/01/03
|33
|8219
|1
Report
AI Summary
This report provides a comprehensive analysis of a reciprocating gas engine driven gas compressor, focusing on the Waukesha model L7044GSI engine driving an Ariel JGK/4 compressor used in gas lift applications. The study investigates various failure modes, including spark plug failures, engine vibration, lubrication and cooling system failures, and bearing failures, detailing their causes and potential solutions. The project aims to evaluate the engine's performance, identify root causes of failures, minimize breakdowns, and explore upgrades using modern techniques such as condition monitoring devices and PLC controllers. The report includes an introduction to reciprocating gas engines and compressors, a literature review covering relevant research, and a detailed discussion of the research methodology, results, and conclusions, offering recommendations for improved engine performance and reliability. The study also emphasizes the importance of understanding the components and systems, and the causes of the failures in the reciprocating gas engine.
Contribute Materials
Your contribution can guide someone’s learning journey. Share your
documents today.
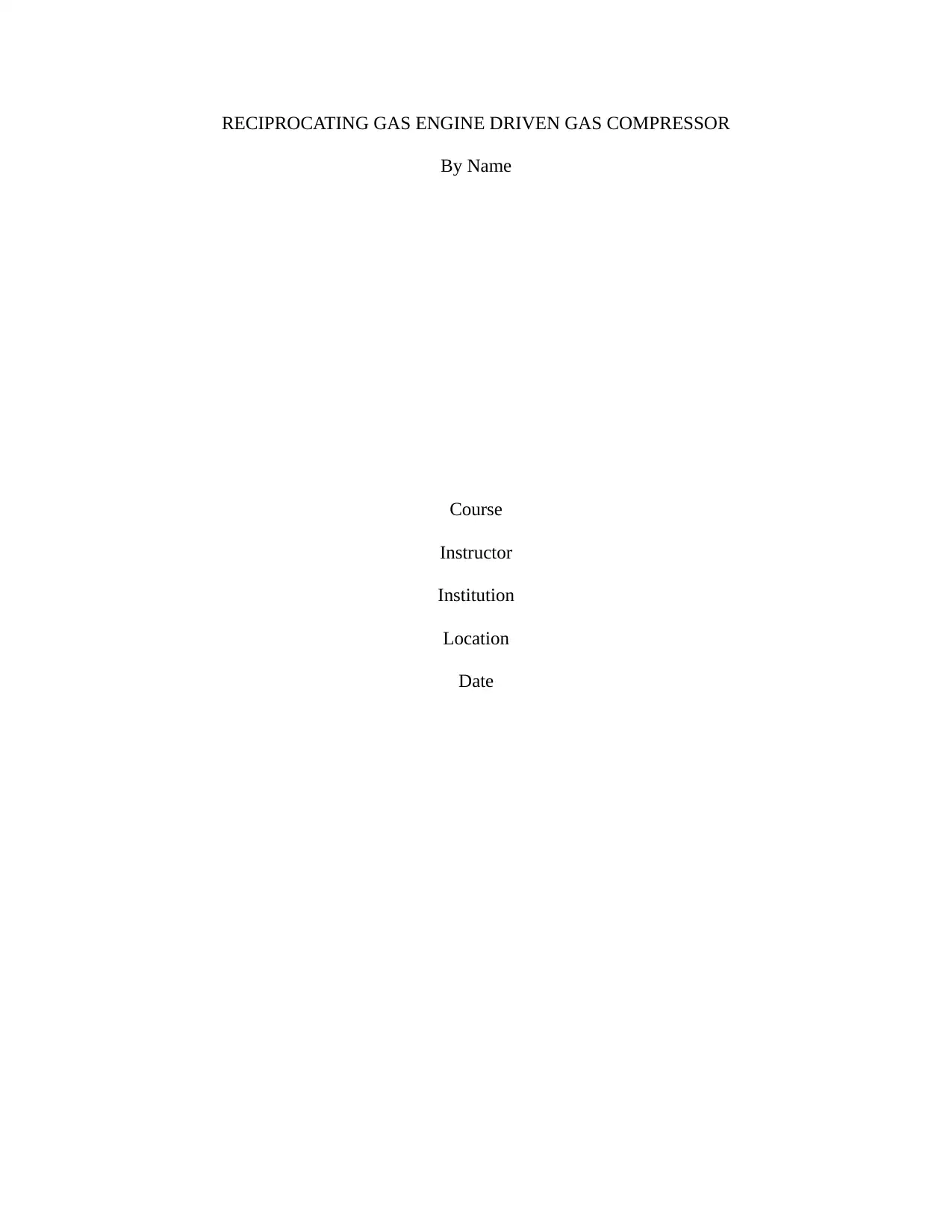
RECIPROCATING GAS ENGINE DRIVEN GAS COMPRESSOR
By Name
Course
Instructor
Institution
Location
Date
By Name
Course
Instructor
Institution
Location
Date
Secure Best Marks with AI Grader
Need help grading? Try our AI Grader for instant feedback on your assignments.

ACKNOWLEDGEMENT
The preparation of this thesis is a demanding task that calls for maximum dedication and
cooperation from various significant people and institutions. Listing all of them might be
impossible. First and foremost I thank the Almighty God for having granted me the life and
energy to enable me get to this far. May power and glory go back to Him who dwells above. I
would like to also thank my supervisor(s) who dedicated a lot of the quality time and
perseverance towards the preparation of this thesis proposal. I am equally humbled to thank them
sincerely for every positive immediate responses, guidance and encouragement that has seen me
get to this level of this task this time. May I also thank the University as well for their faithful
commitment and moral support.
The preparation of this thesis is a demanding task that calls for maximum dedication and
cooperation from various significant people and institutions. Listing all of them might be
impossible. First and foremost I thank the Almighty God for having granted me the life and
energy to enable me get to this far. May power and glory go back to Him who dwells above. I
would like to also thank my supervisor(s) who dedicated a lot of the quality time and
perseverance towards the preparation of this thesis proposal. I am equally humbled to thank them
sincerely for every positive immediate responses, guidance and encouragement that has seen me
get to this level of this task this time. May I also thank the University as well for their faithful
commitment and moral support.

ABSTRACT
The reciprocating compressor is used in the delivery of gases at relatively high pressure. The
reciprocating compressor is likely the best known as well as most widely adopted of all
compressors. The present study gives focus on the on the various modes of failure of
reciprocating engine compressors, failures on the various components, their causes as well as
possible solutions. For this study the focus is on the on the mechanical failure analysis of the
different components and their effects on the performance of the engine. Among the failures
studied failures include: the sparkplug failure (oil contamination, wrong timing, wrong
installation (over tight or loose) as well as fuel gas condensate because the fuel gas was
unprocessed properly), engine vibration analysis (misalignment of couplings between engine and
compressor and looseness), engine lubrication system & cooling system failure analysis (oil seal
leakage, oil pump fail), Bearing failure analysis alongside Gas Compressor Failure analyzes
The reciprocating compressor is used in the delivery of gases at relatively high pressure. The
reciprocating compressor is likely the best known as well as most widely adopted of all
compressors. The present study gives focus on the on the various modes of failure of
reciprocating engine compressors, failures on the various components, their causes as well as
possible solutions. For this study the focus is on the on the mechanical failure analysis of the
different components and their effects on the performance of the engine. Among the failures
studied failures include: the sparkplug failure (oil contamination, wrong timing, wrong
installation (over tight or loose) as well as fuel gas condensate because the fuel gas was
unprocessed properly), engine vibration analysis (misalignment of couplings between engine and
compressor and looseness), engine lubrication system & cooling system failure analysis (oil seal
leakage, oil pump fail), Bearing failure analysis alongside Gas Compressor Failure analyzes

Contents
ACKNOWLEDGEMENT.................................................................................................................................1
ABSTRACT....................................................................................................................................................2
CHAPTER 1: INTRODUCTION........................................................................................................................4
Background..............................................................................................................................................4
Reciprocating gas engines...................................................................................................................4
Reciprocating Compressors.................................................................................................................5
Reasons for compression.....................................................................................................................6
Problems of Internal Combustion Engine................................................................................................7
Project Aims & Objectives.......................................................................................................................9
CHAPTER 2: LITERATURE REVIEW..............................................................................................................10
Reciprocating Process Compressor used in Oil and Gas Industry..........................................................16
CHAPTER 3: RESEARCH METHODOLOGY...................................................................................................19
Advantages of secondary sources of information.................................................................................20
Disadvantages of secondary data sources.............................................................................................20
CHAPTER 4: RESULTS AND DISCUSSION.....................................................................................................21
Spark plugs failures analyze...................................................................................................................21
Causes of spark plug failure...............................................................................................................21
Causes of problems in spark plug......................................................................................................22
Engine vibration.................................................................................................................................23
Engine lubrication systems................................................................................................................24
Bearing failure...................................................................................................................................25
CONCLUSION.............................................................................................................................................28
RECOMMENDATIONS................................................................................................................................28
REFERENCES..............................................................................................................................................29
ACKNOWLEDGEMENT.................................................................................................................................1
ABSTRACT....................................................................................................................................................2
CHAPTER 1: INTRODUCTION........................................................................................................................4
Background..............................................................................................................................................4
Reciprocating gas engines...................................................................................................................4
Reciprocating Compressors.................................................................................................................5
Reasons for compression.....................................................................................................................6
Problems of Internal Combustion Engine................................................................................................7
Project Aims & Objectives.......................................................................................................................9
CHAPTER 2: LITERATURE REVIEW..............................................................................................................10
Reciprocating Process Compressor used in Oil and Gas Industry..........................................................16
CHAPTER 3: RESEARCH METHODOLOGY...................................................................................................19
Advantages of secondary sources of information.................................................................................20
Disadvantages of secondary data sources.............................................................................................20
CHAPTER 4: RESULTS AND DISCUSSION.....................................................................................................21
Spark plugs failures analyze...................................................................................................................21
Causes of spark plug failure...............................................................................................................21
Causes of problems in spark plug......................................................................................................22
Engine vibration.................................................................................................................................23
Engine lubrication systems................................................................................................................24
Bearing failure...................................................................................................................................25
CONCLUSION.............................................................................................................................................28
RECOMMENDATIONS................................................................................................................................28
REFERENCES..............................................................................................................................................29
Secure Best Marks with AI Grader
Need help grading? Try our AI Grader for instant feedback on your assignments.

CHAPTER 1: INTRODUCTION
Background
Reciprocating gas engines
A reciprocating gas engine defines a machine used in the conversion of pressure to rotational
motion and is one of the types of internal combustion engines of a spark ignition that is fuelled
using gas. There are numerous types of gas reciprocating engines that are used in various
industries with the main ones including:
Internal combustion engines which are extensively applied in the motor vehicles
Stem engine which is the majority of industrial revolution; as well as
Niche application as in the case of Stirling engine (Alfares, Falah and Elkholy, 2007)
Internal combustion engines are grouped into two further methods a spark ignition engine in
which the spark plugs starts off the process of combustion and compression ignition engine in
which air is compressed within the cylinder hence resulting in heating it in such a way that the
heated air results in ignition of the injected fuel earlier or then.
This cases study in an evaluation of the most common types of failure analysis experienced in
the gas engine brand called Waukesha model L7044GSI that is used in driving the gas
compressor model Ariel JGK/4 having a capacity of 30 MMSCF cumulatively that was often
applied in the oil and gas production plant (Álvarez-Flórez and Egusquiza, 2015). The machine
is used for gas lift in the oil field. Compressed oil is channelled into the earth force oil to coming
to the surface of the ground in which the gas gets to the surface with the crude oil and thereafter
separation of the components takes place. The reliability of the engine was of great importance
bearing in mind the fact that the station was being perceived to be very critical for the process of
Background
Reciprocating gas engines
A reciprocating gas engine defines a machine used in the conversion of pressure to rotational
motion and is one of the types of internal combustion engines of a spark ignition that is fuelled
using gas. There are numerous types of gas reciprocating engines that are used in various
industries with the main ones including:
Internal combustion engines which are extensively applied in the motor vehicles
Stem engine which is the majority of industrial revolution; as well as
Niche application as in the case of Stirling engine (Alfares, Falah and Elkholy, 2007)
Internal combustion engines are grouped into two further methods a spark ignition engine in
which the spark plugs starts off the process of combustion and compression ignition engine in
which air is compressed within the cylinder hence resulting in heating it in such a way that the
heated air results in ignition of the injected fuel earlier or then.
This cases study in an evaluation of the most common types of failure analysis experienced in
the gas engine brand called Waukesha model L7044GSI that is used in driving the gas
compressor model Ariel JGK/4 having a capacity of 30 MMSCF cumulatively that was often
applied in the oil and gas production plant (Álvarez-Flórez and Egusquiza, 2015). The machine
is used for gas lift in the oil field. Compressed oil is channelled into the earth force oil to coming
to the surface of the ground in which the gas gets to the surface with the crude oil and thereafter
separation of the components takes place. The reliability of the engine was of great importance
bearing in mind the fact that the station was being perceived to be very critical for the process of

production hence frequent monitoring of the state as well as health of the compressor would
serve as an issuance of earlier warning prior to the occurrence of any fault that would otherwise
result in devastating failure. The stability of the machine was quite low as a result of failure of
most of the components as well as the machine trips.
Figure 1: Waukesha model L7044GSI Reciprocating gas engine
Reciprocating Compressors
A reciprocating compressor also known as a piston compressor is a compressor used for positive
displacement that makes use of pistons that are controlled by crankshaft in the delivery of gases
at relatively high pressure (Becerra et al., 2011). The intake gas finds its ways into sanction
manifold and thereafter gets into the compression cylinder in which a piston driven compresses it
in a reciprocating motion through a crankshaft and then released. Among the applications of a
reciprocating compressor include gas pipelines, oil refineries, natural gas processing plants,
chemical plants as well as refrigeration plants. One of the most unique applications is blowing of
plastic bottles that are made using polyethene terephthalate. Numerous seals as well as bearings
in the ionic liquid piston compressor were eliminated in the design since the ionic liquid is
immiscible with the gas (Parulekar, Hudson and Boyd, 2018). The service life of this device is
serve as an issuance of earlier warning prior to the occurrence of any fault that would otherwise
result in devastating failure. The stability of the machine was quite low as a result of failure of
most of the components as well as the machine trips.
Figure 1: Waukesha model L7044GSI Reciprocating gas engine
Reciprocating Compressors
A reciprocating compressor also known as a piston compressor is a compressor used for positive
displacement that makes use of pistons that are controlled by crankshaft in the delivery of gases
at relatively high pressure (Becerra et al., 2011). The intake gas finds its ways into sanction
manifold and thereafter gets into the compression cylinder in which a piston driven compresses it
in a reciprocating motion through a crankshaft and then released. Among the applications of a
reciprocating compressor include gas pipelines, oil refineries, natural gas processing plants,
chemical plants as well as refrigeration plants. One of the most unique applications is blowing of
plastic bottles that are made using polyethene terephthalate. Numerous seals as well as bearings
in the ionic liquid piston compressor were eliminated in the design since the ionic liquid is
immiscible with the gas (Parulekar, Hudson and Boyd, 2018). The service life of this device is

approximately 10 fold as compared to that of a conventional diaphragm compression and has
lower maintenance when being used. The costs of energy are lowered by about 20%. The heat
exchangers used in the conventional piston compressor are eliminated since the heat is removed
in cylinder ion which is the point of its generation. About 100 per cent of energy that goes into
the processes is utilized with very minimal amounts of the energy being wasted in the form of
reject heat.
Figure 2: Reciprocating Compressor
Reasons for compression
Transportation of gas via a pipeline
Reinjection of gas into reservoir
Storage of gas at relatively high pressure
Circulation of gas via process
Gas lift
Gas lift: Compressed gas is as well applicable in gas lift in which the compressed gas is
channel down into the earth to initiate the upward flow of oil to the surface of the ground.
The gas carries with it the crude oil to the ground surface where the separation is conducted
(Rezvani, Javanmardi and Mostaghim, 2018). The specific density is increased by gas
lower maintenance when being used. The costs of energy are lowered by about 20%. The heat
exchangers used in the conventional piston compressor are eliminated since the heat is removed
in cylinder ion which is the point of its generation. About 100 per cent of energy that goes into
the processes is utilized with very minimal amounts of the energy being wasted in the form of
reject heat.
Figure 2: Reciprocating Compressor
Reasons for compression
Transportation of gas via a pipeline
Reinjection of gas into reservoir
Storage of gas at relatively high pressure
Circulation of gas via process
Gas lift
Gas lift: Compressed gas is as well applicable in gas lift in which the compressed gas is
channel down into the earth to initiate the upward flow of oil to the surface of the ground.
The gas carries with it the crude oil to the ground surface where the separation is conducted
(Rezvani, Javanmardi and Mostaghim, 2018). The specific density is increased by gas
Paraphrase This Document
Need a fresh take? Get an instant paraphrase of this document with our AI Paraphraser

injection that enables the movement of the oil to the surface using the same downhole
pressure.
Figure 3: Gas Lift
Problems of Internal Combustion Engine
Compressed gas is as well applicable in gas lift where compressed gas is channel down into earth
to initiate upward flow of oil to the surface of the ground. The gas carries with it the crude oil to
the ground surface where the separation is conducted. The specific density is increased by gas
injection that enables the movement of the oil to the surface using the same downhole pressure
Three main challenges may be faced with regard to internal combustion engine problems:
Bad fuel mix
Lack of spark; and
Lack of compression
There are numerous ways through which bad fuel mix may take place include:
Running out of gas making engine get air with no fuel
Clogging of air intake hence availability of fuel but no air
pressure.
Figure 3: Gas Lift
Problems of Internal Combustion Engine
Compressed gas is as well applicable in gas lift where compressed gas is channel down into earth
to initiate upward flow of oil to the surface of the ground. The gas carries with it the crude oil to
the ground surface where the separation is conducted. The specific density is increased by gas
injection that enables the movement of the oil to the surface using the same downhole pressure
Three main challenges may be faced with regard to internal combustion engine problems:
Bad fuel mix
Lack of spark; and
Lack of compression
There are numerous ways through which bad fuel mix may take place include:
Running out of gas making engine get air with no fuel
Clogging of air intake hence availability of fuel but no air

There might be excess supply or very low supply of fuel to the mix by the fuel system
meaning the combustion does not take place properly (Feese and Kokot, 2016)
The fuel may be containing an impurity for instance water in the gas tank preventing
the fuel from undergoing combustion
Lack of compression
In case the air and fuel charge cannot be properly compressed, the process of combustion
would not work as expected. Among the reasons for lack of proper compression may include:
Wearing out of the piston rings
Lack of proper sealing of the intake or exhaust valves permitting leakage of
compression
Presence of a hole in the cylinder-The most common hole within a cylinder takes
place at the cylinder top where the cylinder is attached. In general terms, the cylinder
head bolt as well as the cylinder along a think gasket pressed between often ensures a
proper seal (Kumar, 2017). Breakage of the gasket results in the development of
small holes between cylinder head and cylinder and such holes results in leakage.
Lack of spark: There may no spark at all or the existing one may be weak as a result of:
Wearing out of the spark or wire leading to the same
Occurrence of spark too soon or too late in the cycle making the fuel not to timely
ignite
Cut or missing of the wire or the system sending a spark down the work not properly
functioning
meaning the combustion does not take place properly (Feese and Kokot, 2016)
The fuel may be containing an impurity for instance water in the gas tank preventing
the fuel from undergoing combustion
Lack of compression
In case the air and fuel charge cannot be properly compressed, the process of combustion
would not work as expected. Among the reasons for lack of proper compression may include:
Wearing out of the piston rings
Lack of proper sealing of the intake or exhaust valves permitting leakage of
compression
Presence of a hole in the cylinder-The most common hole within a cylinder takes
place at the cylinder top where the cylinder is attached. In general terms, the cylinder
head bolt as well as the cylinder along a think gasket pressed between often ensures a
proper seal (Kumar, 2017). Breakage of the gasket results in the development of
small holes between cylinder head and cylinder and such holes results in leakage.
Lack of spark: There may no spark at all or the existing one may be weak as a result of:
Wearing out of the spark or wire leading to the same
Occurrence of spark too soon or too late in the cycle making the fuel not to timely
ignite
Cut or missing of the wire or the system sending a spark down the work not properly
functioning
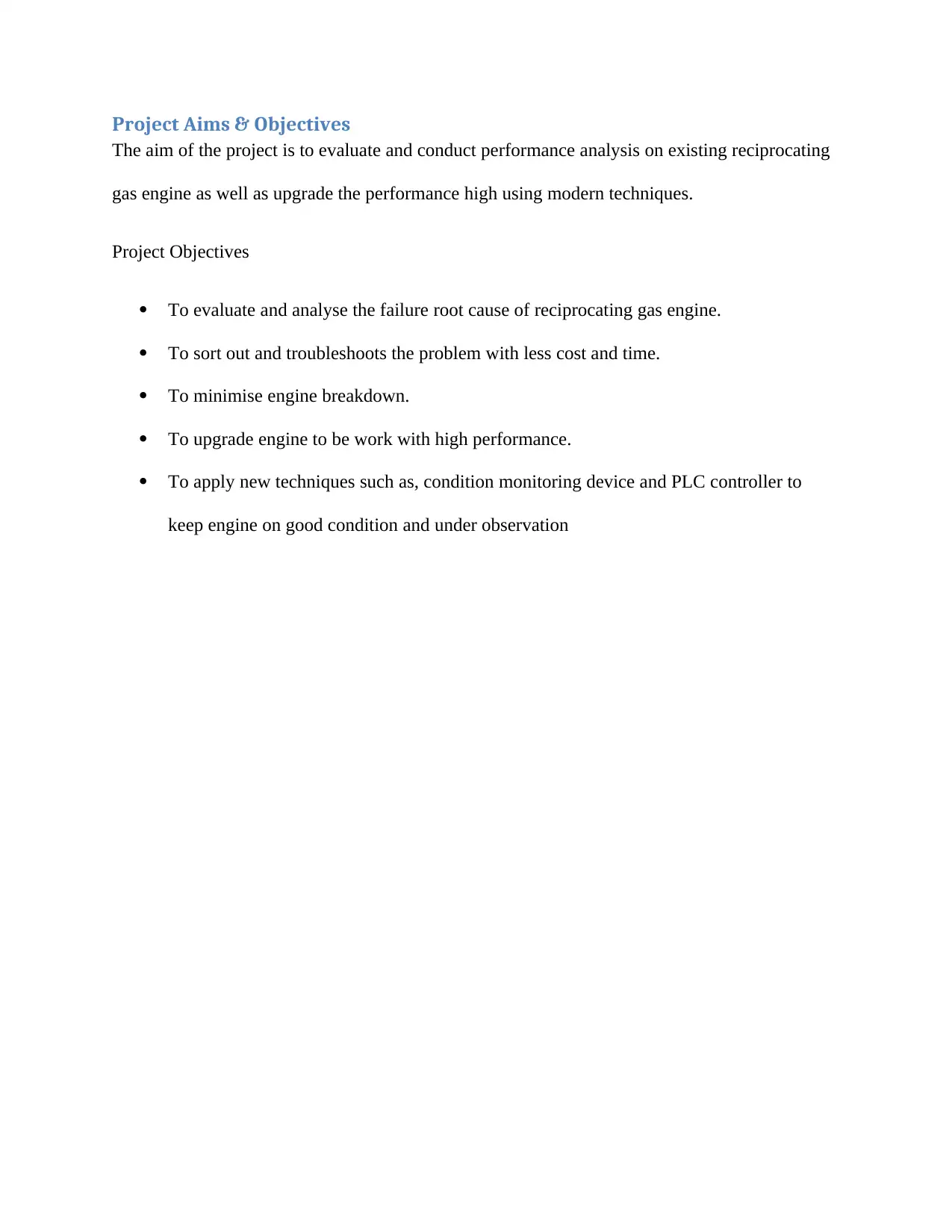
Project Aims & Objectives
The aim of the project is to evaluate and conduct performance analysis on existing reciprocating
gas engine as well as upgrade the performance high using modern techniques.
Project Objectives
To evaluate and analyse the failure root cause of reciprocating gas engine.
To sort out and troubleshoots the problem with less cost and time.
To minimise engine breakdown.
To upgrade engine to be work with high performance.
To apply new techniques such as, condition monitoring device and PLC controller to
keep engine on good condition and under observation
The aim of the project is to evaluate and conduct performance analysis on existing reciprocating
gas engine as well as upgrade the performance high using modern techniques.
Project Objectives
To evaluate and analyse the failure root cause of reciprocating gas engine.
To sort out and troubleshoots the problem with less cost and time.
To minimise engine breakdown.
To upgrade engine to be work with high performance.
To apply new techniques such as, condition monitoring device and PLC controller to
keep engine on good condition and under observation
Secure Best Marks with AI Grader
Need help grading? Try our AI Grader for instant feedback on your assignments.
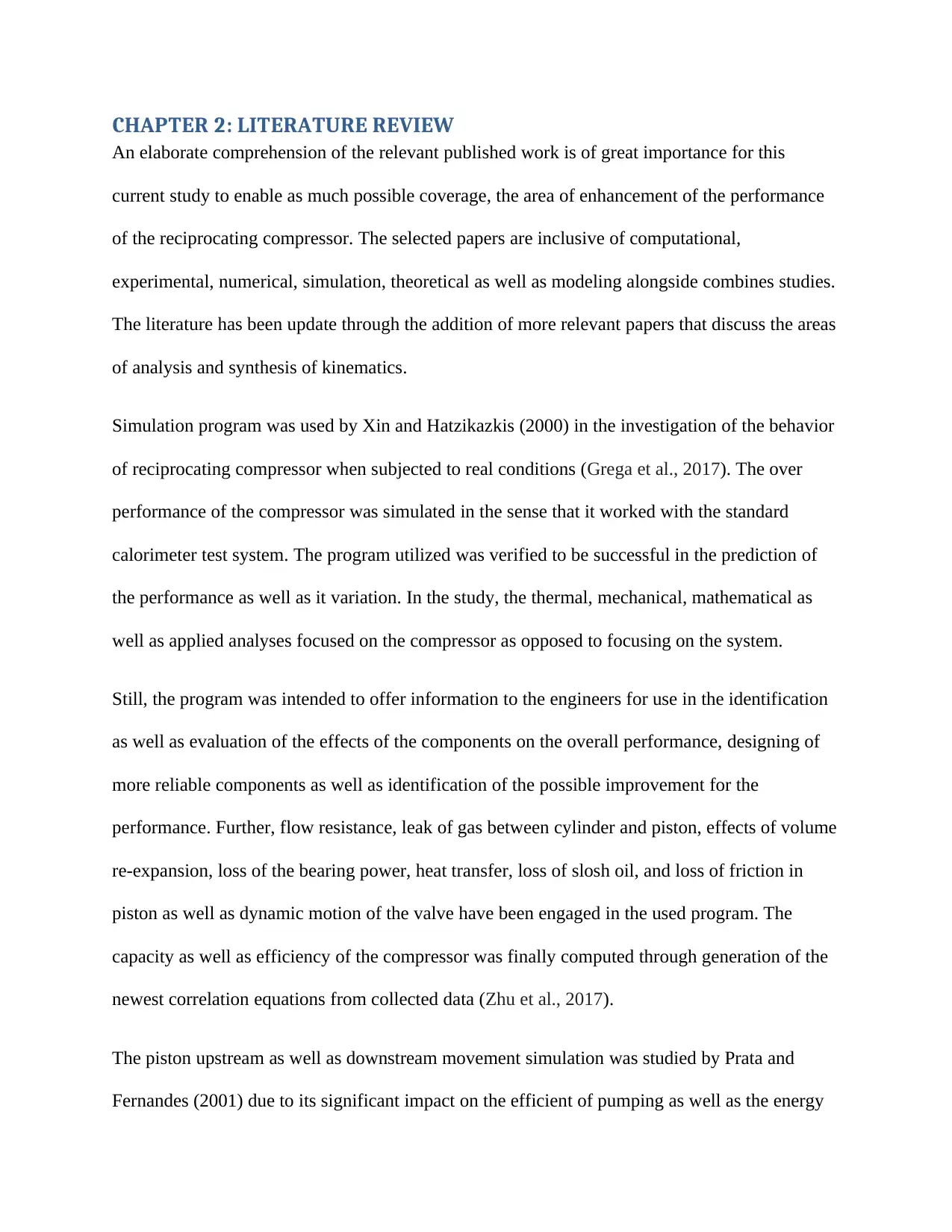
CHAPTER 2: LITERATURE REVIEW
An elaborate comprehension of the relevant published work is of great importance for this
current study to enable as much possible coverage, the area of enhancement of the performance
of the reciprocating compressor. The selected papers are inclusive of computational,
experimental, numerical, simulation, theoretical as well as modeling alongside combines studies.
The literature has been update through the addition of more relevant papers that discuss the areas
of analysis and synthesis of kinematics.
Simulation program was used by Xin and Hatzikazkis (2000) in the investigation of the behavior
of reciprocating compressor when subjected to real conditions (Grega et al., 2017). The over
performance of the compressor was simulated in the sense that it worked with the standard
calorimeter test system. The program utilized was verified to be successful in the prediction of
the performance as well as it variation. In the study, the thermal, mechanical, mathematical as
well as applied analyses focused on the compressor as opposed to focusing on the system.
Still, the program was intended to offer information to the engineers for use in the identification
as well as evaluation of the effects of the components on the overall performance, designing of
more reliable components as well as identification of the possible improvement for the
performance. Further, flow resistance, leak of gas between cylinder and piston, effects of volume
re-expansion, loss of the bearing power, heat transfer, loss of slosh oil, and loss of friction in
piston as well as dynamic motion of the valve have been engaged in the used program. The
capacity as well as efficiency of the compressor was finally computed through generation of the
newest correlation equations from collected data (Zhu et al., 2017).
The piston upstream as well as downstream movement simulation was studied by Prata and
Fernandes (2001) due to its significant impact on the efficient of pumping as well as the energy
An elaborate comprehension of the relevant published work is of great importance for this
current study to enable as much possible coverage, the area of enhancement of the performance
of the reciprocating compressor. The selected papers are inclusive of computational,
experimental, numerical, simulation, theoretical as well as modeling alongside combines studies.
The literature has been update through the addition of more relevant papers that discuss the areas
of analysis and synthesis of kinematics.
Simulation program was used by Xin and Hatzikazkis (2000) in the investigation of the behavior
of reciprocating compressor when subjected to real conditions (Grega et al., 2017). The over
performance of the compressor was simulated in the sense that it worked with the standard
calorimeter test system. The program utilized was verified to be successful in the prediction of
the performance as well as it variation. In the study, the thermal, mechanical, mathematical as
well as applied analyses focused on the compressor as opposed to focusing on the system.
Still, the program was intended to offer information to the engineers for use in the identification
as well as evaluation of the effects of the components on the overall performance, designing of
more reliable components as well as identification of the possible improvement for the
performance. Further, flow resistance, leak of gas between cylinder and piston, effects of volume
re-expansion, loss of the bearing power, heat transfer, loss of slosh oil, and loss of friction in
piston as well as dynamic motion of the valve have been engaged in the used program. The
capacity as well as efficiency of the compressor was finally computed through generation of the
newest correlation equations from collected data (Zhu et al., 2017).
The piston upstream as well as downstream movement simulation was studied by Prata and
Fernandes (2001) due to its significant impact on the efficient of pumping as well as the energy
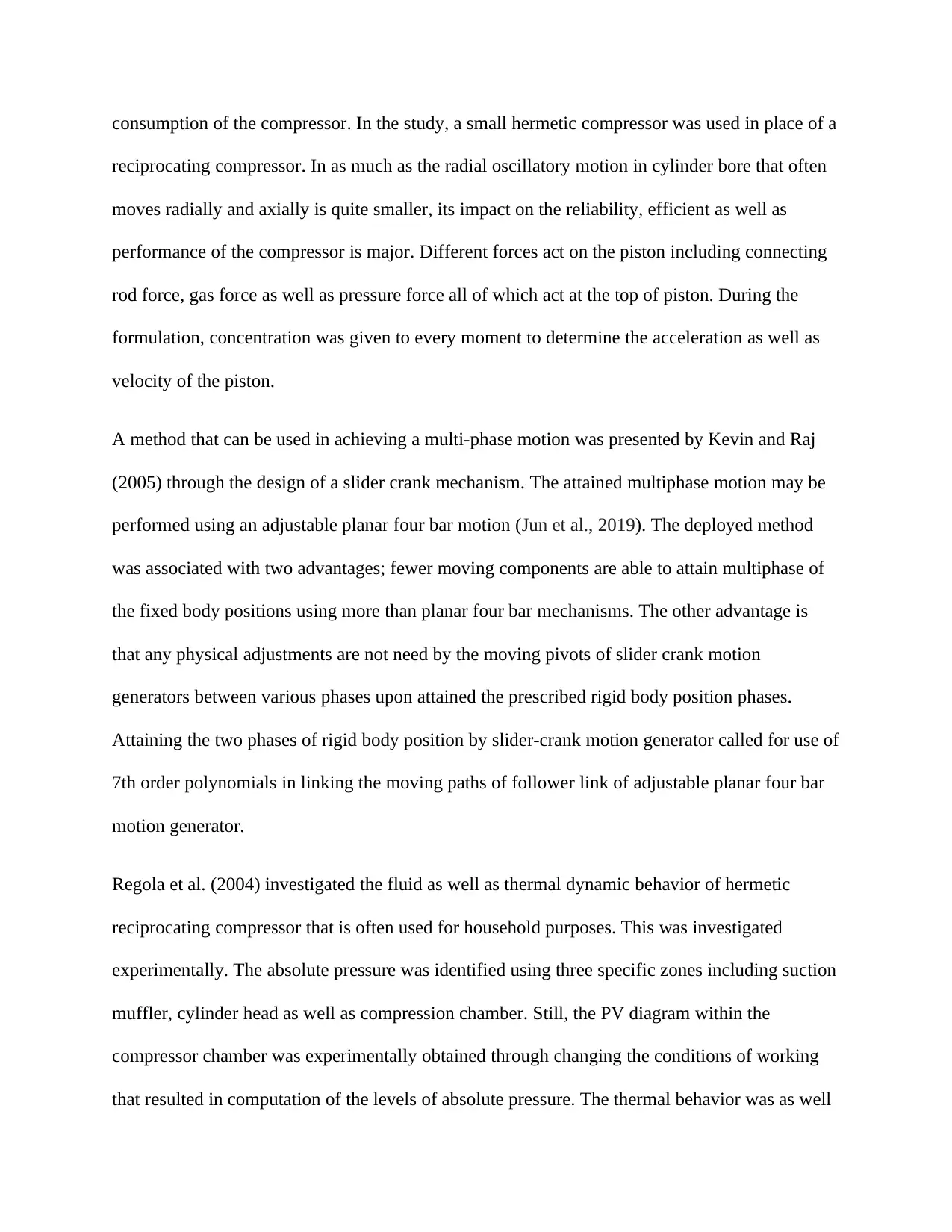
consumption of the compressor. In the study, a small hermetic compressor was used in place of a
reciprocating compressor. In as much as the radial oscillatory motion in cylinder bore that often
moves radially and axially is quite smaller, its impact on the reliability, efficient as well as
performance of the compressor is major. Different forces act on the piston including connecting
rod force, gas force as well as pressure force all of which act at the top of piston. During the
formulation, concentration was given to every moment to determine the acceleration as well as
velocity of the piston.
A method that can be used in achieving a multi-phase motion was presented by Kevin and Raj
(2005) through the design of a slider crank mechanism. The attained multiphase motion may be
performed using an adjustable planar four bar motion (Jun et al., 2019). The deployed method
was associated with two advantages; fewer moving components are able to attain multiphase of
the fixed body positions using more than planar four bar mechanisms. The other advantage is
that any physical adjustments are not need by the moving pivots of slider crank motion
generators between various phases upon attained the prescribed rigid body position phases.
Attaining the two phases of rigid body position by slider-crank motion generator called for use of
7th order polynomials in linking the moving paths of follower link of adjustable planar four bar
motion generator.
Regola et al. (2004) investigated the fluid as well as thermal dynamic behavior of hermetic
reciprocating compressor that is often used for household purposes. This was investigated
experimentally. The absolute pressure was identified using three specific zones including suction
muffler, cylinder head as well as compression chamber. Still, the PV diagram within the
compressor chamber was experimentally obtained through changing the conditions of working
that resulted in computation of the levels of absolute pressure. The thermal behavior was as well
reciprocating compressor. In as much as the radial oscillatory motion in cylinder bore that often
moves radially and axially is quite smaller, its impact on the reliability, efficient as well as
performance of the compressor is major. Different forces act on the piston including connecting
rod force, gas force as well as pressure force all of which act at the top of piston. During the
formulation, concentration was given to every moment to determine the acceleration as well as
velocity of the piston.
A method that can be used in achieving a multi-phase motion was presented by Kevin and Raj
(2005) through the design of a slider crank mechanism. The attained multiphase motion may be
performed using an adjustable planar four bar motion (Jun et al., 2019). The deployed method
was associated with two advantages; fewer moving components are able to attain multiphase of
the fixed body positions using more than planar four bar mechanisms. The other advantage is
that any physical adjustments are not need by the moving pivots of slider crank motion
generators between various phases upon attained the prescribed rigid body position phases.
Attaining the two phases of rigid body position by slider-crank motion generator called for use of
7th order polynomials in linking the moving paths of follower link of adjustable planar four bar
motion generator.
Regola et al. (2004) investigated the fluid as well as thermal dynamic behavior of hermetic
reciprocating compressor that is often used for household purposes. This was investigated
experimentally. The absolute pressure was identified using three specific zones including suction
muffler, cylinder head as well as compression chamber. Still, the PV diagram within the
compressor chamber was experimentally obtained through changing the conditions of working
that resulted in computation of the levels of absolute pressure. The thermal behavior was as well
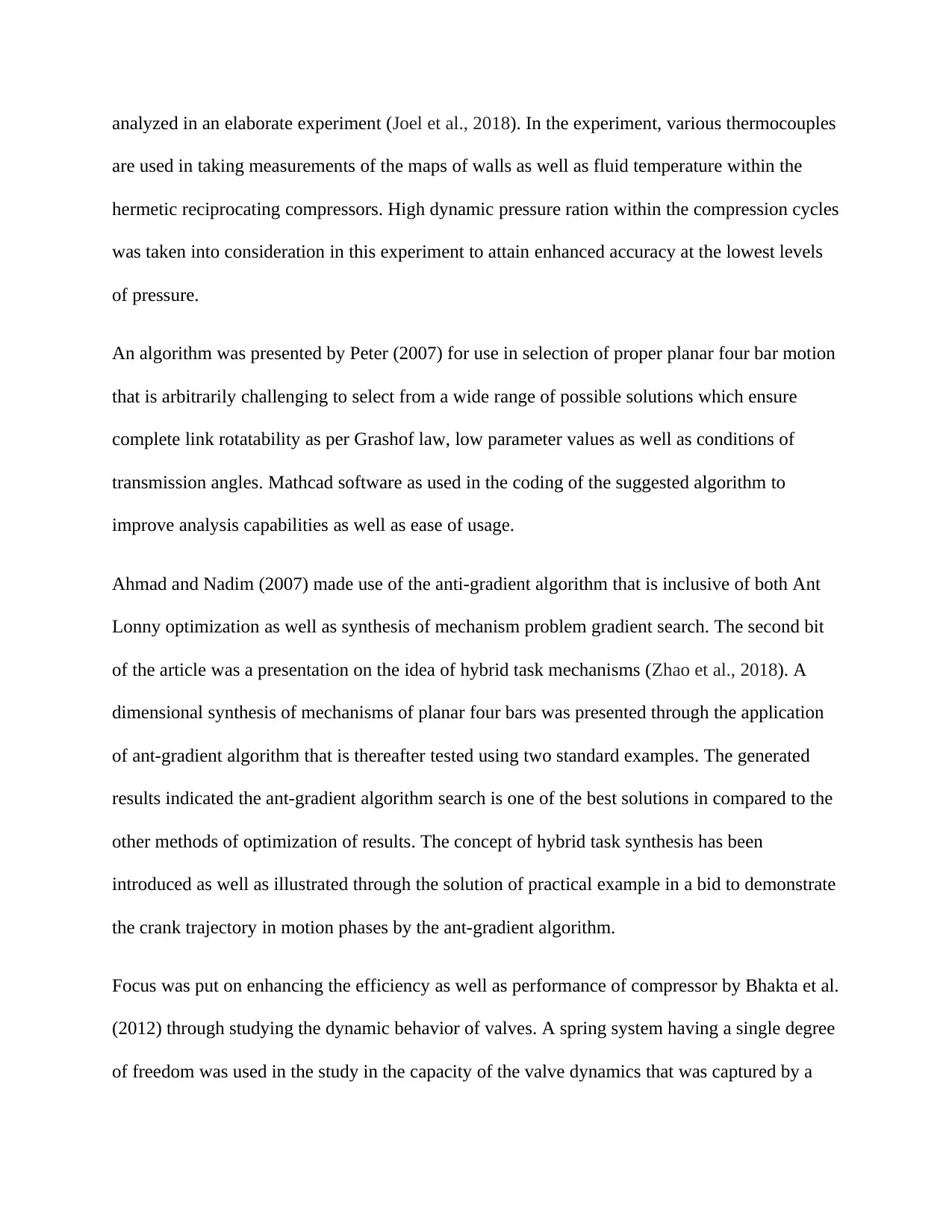
analyzed in an elaborate experiment (Joel et al., 2018). In the experiment, various thermocouples
are used in taking measurements of the maps of walls as well as fluid temperature within the
hermetic reciprocating compressors. High dynamic pressure ration within the compression cycles
was taken into consideration in this experiment to attain enhanced accuracy at the lowest levels
of pressure.
An algorithm was presented by Peter (2007) for use in selection of proper planar four bar motion
that is arbitrarily challenging to select from a wide range of possible solutions which ensure
complete link rotatability as per Grashof law, low parameter values as well as conditions of
transmission angles. Mathcad software as used in the coding of the suggested algorithm to
improve analysis capabilities as well as ease of usage.
Ahmad and Nadim (2007) made use of the anti-gradient algorithm that is inclusive of both Ant
Lonny optimization as well as synthesis of mechanism problem gradient search. The second bit
of the article was a presentation on the idea of hybrid task mechanisms (Zhao et al., 2018). A
dimensional synthesis of mechanisms of planar four bars was presented through the application
of ant-gradient algorithm that is thereafter tested using two standard examples. The generated
results indicated the ant-gradient algorithm search is one of the best solutions in compared to the
other methods of optimization of results. The concept of hybrid task synthesis has been
introduced as well as illustrated through the solution of practical example in a bid to demonstrate
the crank trajectory in motion phases by the ant-gradient algorithm.
Focus was put on enhancing the efficiency as well as performance of compressor by Bhakta et al.
(2012) through studying the dynamic behavior of valves. A spring system having a single degree
of freedom was used in the study in the capacity of the valve dynamics that was captured by a
are used in taking measurements of the maps of walls as well as fluid temperature within the
hermetic reciprocating compressors. High dynamic pressure ration within the compression cycles
was taken into consideration in this experiment to attain enhanced accuracy at the lowest levels
of pressure.
An algorithm was presented by Peter (2007) for use in selection of proper planar four bar motion
that is arbitrarily challenging to select from a wide range of possible solutions which ensure
complete link rotatability as per Grashof law, low parameter values as well as conditions of
transmission angles. Mathcad software as used in the coding of the suggested algorithm to
improve analysis capabilities as well as ease of usage.
Ahmad and Nadim (2007) made use of the anti-gradient algorithm that is inclusive of both Ant
Lonny optimization as well as synthesis of mechanism problem gradient search. The second bit
of the article was a presentation on the idea of hybrid task mechanisms (Zhao et al., 2018). A
dimensional synthesis of mechanisms of planar four bars was presented through the application
of ant-gradient algorithm that is thereafter tested using two standard examples. The generated
results indicated the ant-gradient algorithm search is one of the best solutions in compared to the
other methods of optimization of results. The concept of hybrid task synthesis has been
introduced as well as illustrated through the solution of practical example in a bid to demonstrate
the crank trajectory in motion phases by the ant-gradient algorithm.
Focus was put on enhancing the efficiency as well as performance of compressor by Bhakta et al.
(2012) through studying the dynamic behavior of valves. A spring system having a single degree
of freedom was used in the study in the capacity of the valve dynamics that was captured by a
Paraphrase This Document
Need a fresh take? Get an instant paraphrase of this document with our AI Paraphraser
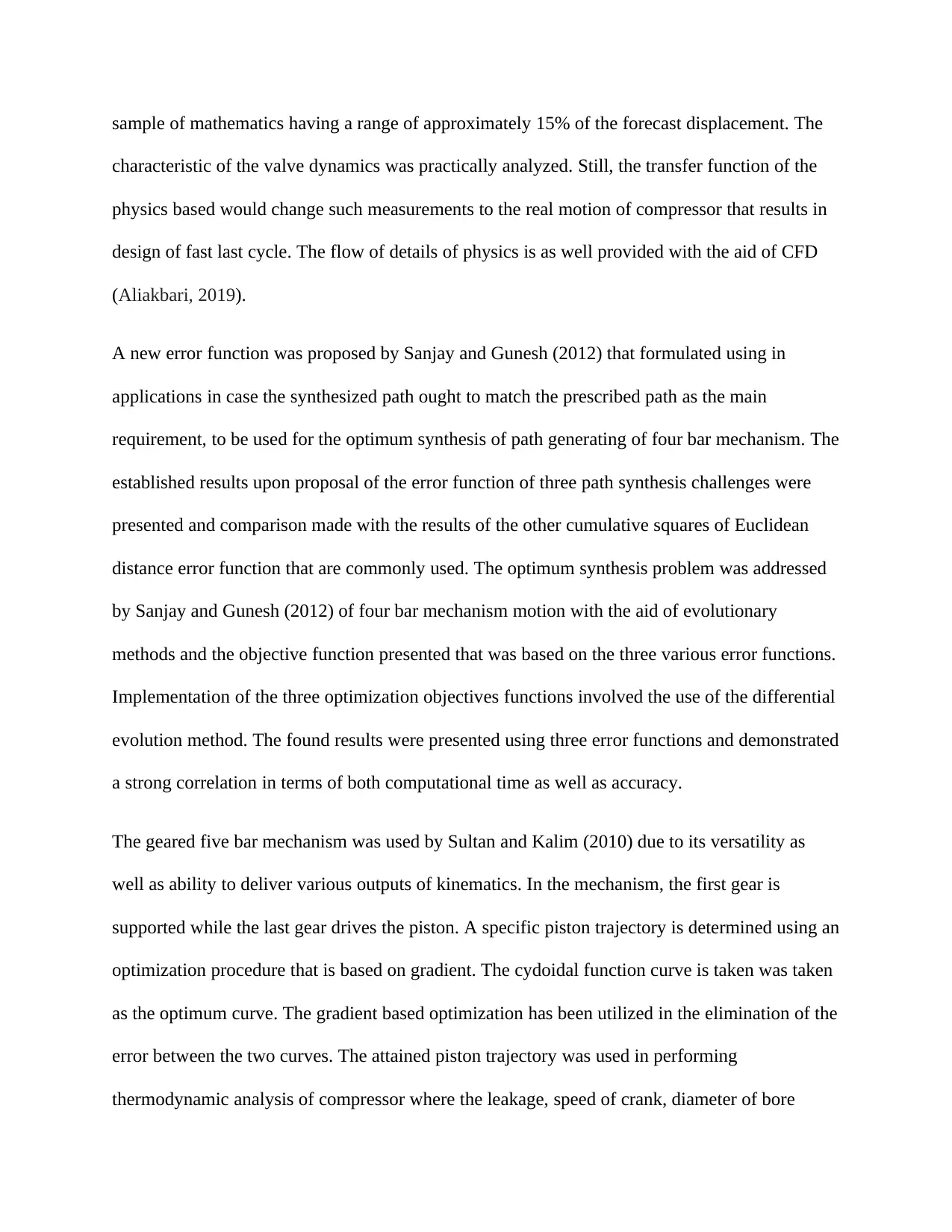
sample of mathematics having a range of approximately 15% of the forecast displacement. The
characteristic of the valve dynamics was practically analyzed. Still, the transfer function of the
physics based would change such measurements to the real motion of compressor that results in
design of fast last cycle. The flow of details of physics is as well provided with the aid of CFD
(Aliakbari, 2019).
A new error function was proposed by Sanjay and Gunesh (2012) that formulated using in
applications in case the synthesized path ought to match the prescribed path as the main
requirement, to be used for the optimum synthesis of path generating of four bar mechanism. The
established results upon proposal of the error function of three path synthesis challenges were
presented and comparison made with the results of the other cumulative squares of Euclidean
distance error function that are commonly used. The optimum synthesis problem was addressed
by Sanjay and Gunesh (2012) of four bar mechanism motion with the aid of evolutionary
methods and the objective function presented that was based on the three various error functions.
Implementation of the three optimization objectives functions involved the use of the differential
evolution method. The found results were presented using three error functions and demonstrated
a strong correlation in terms of both computational time as well as accuracy.
The geared five bar mechanism was used by Sultan and Kalim (2010) due to its versatility as
well as ability to deliver various outputs of kinematics. In the mechanism, the first gear is
supported while the last gear drives the piston. A specific piston trajectory is determined using an
optimization procedure that is based on gradient. The cydoidal function curve is taken was taken
as the optimum curve. The gradient based optimization has been utilized in the elimination of the
error between the two curves. The attained piston trajectory was used in performing
thermodynamic analysis of compressor where the leakage, speed of crank, diameter of bore
characteristic of the valve dynamics was practically analyzed. Still, the transfer function of the
physics based would change such measurements to the real motion of compressor that results in
design of fast last cycle. The flow of details of physics is as well provided with the aid of CFD
(Aliakbari, 2019).
A new error function was proposed by Sanjay and Gunesh (2012) that formulated using in
applications in case the synthesized path ought to match the prescribed path as the main
requirement, to be used for the optimum synthesis of path generating of four bar mechanism. The
established results upon proposal of the error function of three path synthesis challenges were
presented and comparison made with the results of the other cumulative squares of Euclidean
distance error function that are commonly used. The optimum synthesis problem was addressed
by Sanjay and Gunesh (2012) of four bar mechanism motion with the aid of evolutionary
methods and the objective function presented that was based on the three various error functions.
Implementation of the three optimization objectives functions involved the use of the differential
evolution method. The found results were presented using three error functions and demonstrated
a strong correlation in terms of both computational time as well as accuracy.
The geared five bar mechanism was used by Sultan and Kalim (2010) due to its versatility as
well as ability to deliver various outputs of kinematics. In the mechanism, the first gear is
supported while the last gear drives the piston. A specific piston trajectory is determined using an
optimization procedure that is based on gradient. The cydoidal function curve is taken was taken
as the optimum curve. The gradient based optimization has been utilized in the elimination of the
error between the two curves. The attained piston trajectory was used in performing
thermodynamic analysis of compressor where the leakage, speed of crank, diameter of bore
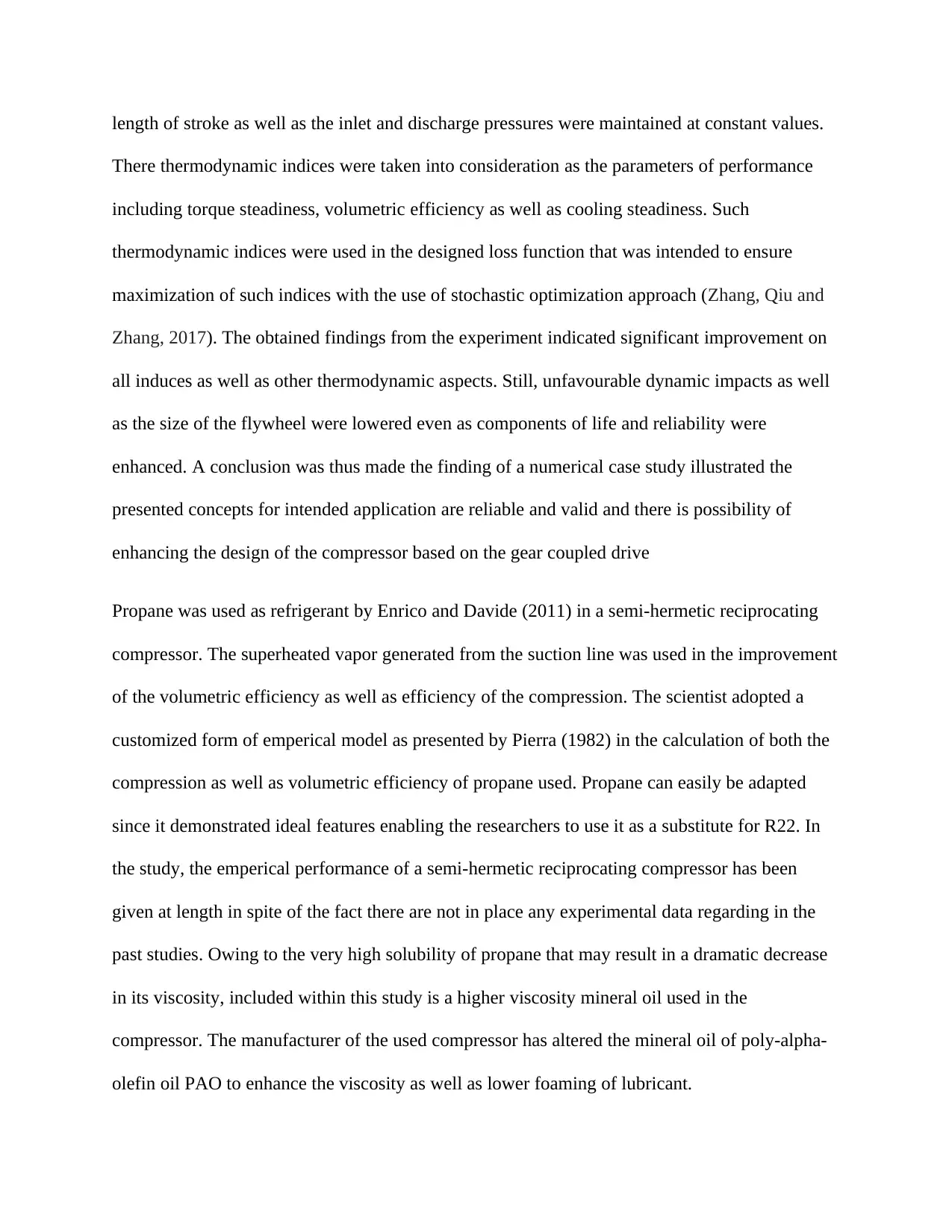
length of stroke as well as the inlet and discharge pressures were maintained at constant values.
There thermodynamic indices were taken into consideration as the parameters of performance
including torque steadiness, volumetric efficiency as well as cooling steadiness. Such
thermodynamic indices were used in the designed loss function that was intended to ensure
maximization of such indices with the use of stochastic optimization approach (Zhang, Qiu and
Zhang, 2017). The obtained findings from the experiment indicated significant improvement on
all induces as well as other thermodynamic aspects. Still, unfavourable dynamic impacts as well
as the size of the flywheel were lowered even as components of life and reliability were
enhanced. A conclusion was thus made the finding of a numerical case study illustrated the
presented concepts for intended application are reliable and valid and there is possibility of
enhancing the design of the compressor based on the gear coupled drive
Propane was used as refrigerant by Enrico and Davide (2011) in a semi-hermetic reciprocating
compressor. The superheated vapor generated from the suction line was used in the improvement
of the volumetric efficiency as well as efficiency of the compression. The scientist adopted a
customized form of emperical model as presented by Pierra (1982) in the calculation of both the
compression as well as volumetric efficiency of propane used. Propane can easily be adapted
since it demonstrated ideal features enabling the researchers to use it as a substitute for R22. In
the study, the emperical performance of a semi-hermetic reciprocating compressor has been
given at length in spite of the fact there are not in place any experimental data regarding in the
past studies. Owing to the very high solubility of propane that may result in a dramatic decrease
in its viscosity, included within this study is a higher viscosity mineral oil used in the
compressor. The manufacturer of the used compressor has altered the mineral oil of poly-alpha-
olefin oil PAO to enhance the viscosity as well as lower foaming of lubricant.
There thermodynamic indices were taken into consideration as the parameters of performance
including torque steadiness, volumetric efficiency as well as cooling steadiness. Such
thermodynamic indices were used in the designed loss function that was intended to ensure
maximization of such indices with the use of stochastic optimization approach (Zhang, Qiu and
Zhang, 2017). The obtained findings from the experiment indicated significant improvement on
all induces as well as other thermodynamic aspects. Still, unfavourable dynamic impacts as well
as the size of the flywheel were lowered even as components of life and reliability were
enhanced. A conclusion was thus made the finding of a numerical case study illustrated the
presented concepts for intended application are reliable and valid and there is possibility of
enhancing the design of the compressor based on the gear coupled drive
Propane was used as refrigerant by Enrico and Davide (2011) in a semi-hermetic reciprocating
compressor. The superheated vapor generated from the suction line was used in the improvement
of the volumetric efficiency as well as efficiency of the compression. The scientist adopted a
customized form of emperical model as presented by Pierra (1982) in the calculation of both the
compression as well as volumetric efficiency of propane used. Propane can easily be adapted
since it demonstrated ideal features enabling the researchers to use it as a substitute for R22. In
the study, the emperical performance of a semi-hermetic reciprocating compressor has been
given at length in spite of the fact there are not in place any experimental data regarding in the
past studies. Owing to the very high solubility of propane that may result in a dramatic decrease
in its viscosity, included within this study is a higher viscosity mineral oil used in the
compressor. The manufacturer of the used compressor has altered the mineral oil of poly-alpha-
olefin oil PAO to enhance the viscosity as well as lower foaming of lubricant.
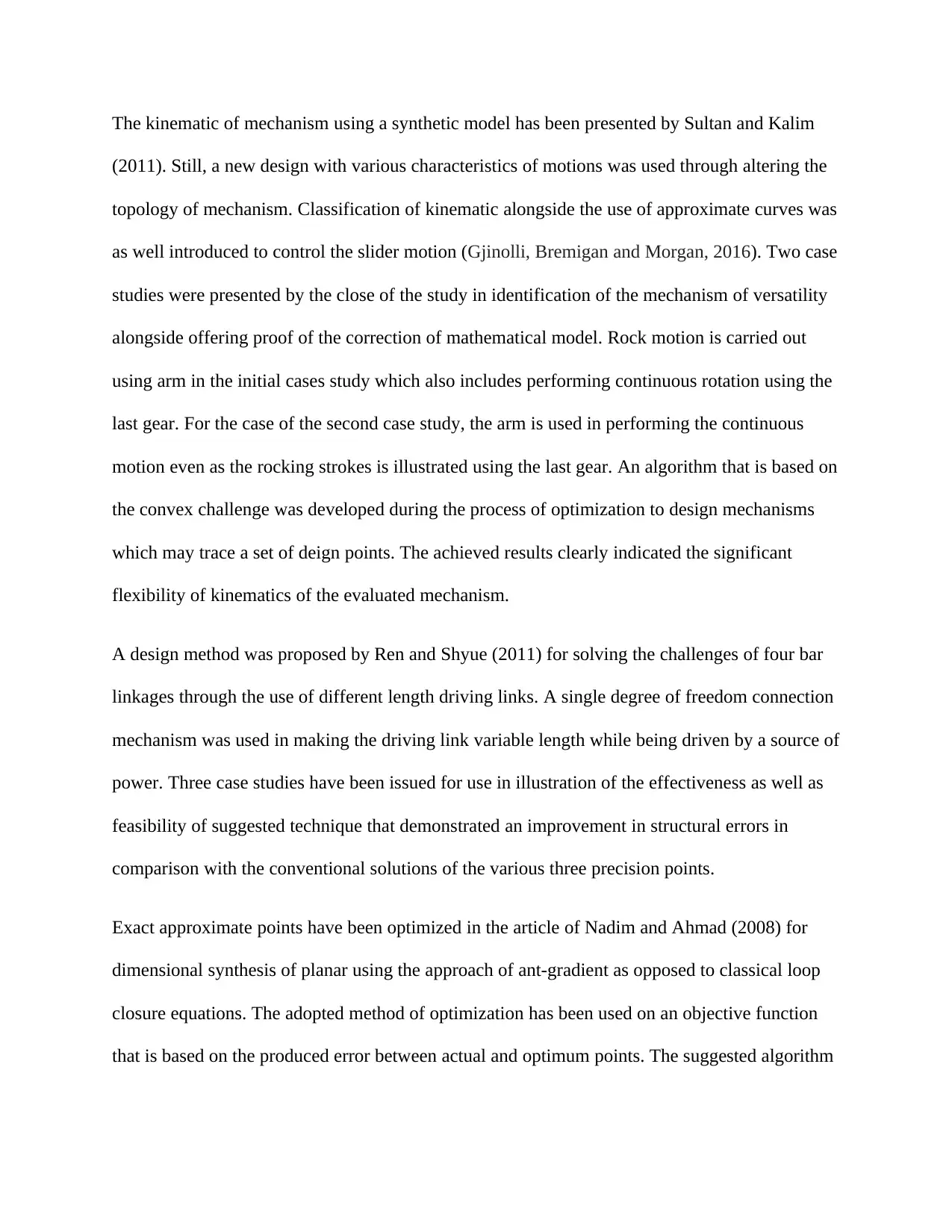
The kinematic of mechanism using a synthetic model has been presented by Sultan and Kalim
(2011). Still, a new design with various characteristics of motions was used through altering the
topology of mechanism. Classification of kinematic alongside the use of approximate curves was
as well introduced to control the slider motion (Gjinolli, Bremigan and Morgan, 2016). Two case
studies were presented by the close of the study in identification of the mechanism of versatility
alongside offering proof of the correction of mathematical model. Rock motion is carried out
using arm in the initial cases study which also includes performing continuous rotation using the
last gear. For the case of the second case study, the arm is used in performing the continuous
motion even as the rocking strokes is illustrated using the last gear. An algorithm that is based on
the convex challenge was developed during the process of optimization to design mechanisms
which may trace a set of deign points. The achieved results clearly indicated the significant
flexibility of kinematics of the evaluated mechanism.
A design method was proposed by Ren and Shyue (2011) for solving the challenges of four bar
linkages through the use of different length driving links. A single degree of freedom connection
mechanism was used in making the driving link variable length while being driven by a source of
power. Three case studies have been issued for use in illustration of the effectiveness as well as
feasibility of suggested technique that demonstrated an improvement in structural errors in
comparison with the conventional solutions of the various three precision points.
Exact approximate points have been optimized in the article of Nadim and Ahmad (2008) for
dimensional synthesis of planar using the approach of ant-gradient as opposed to classical loop
closure equations. The adopted method of optimization has been used on an objective function
that is based on the produced error between actual and optimum points. The suggested algorithm
(2011). Still, a new design with various characteristics of motions was used through altering the
topology of mechanism. Classification of kinematic alongside the use of approximate curves was
as well introduced to control the slider motion (Gjinolli, Bremigan and Morgan, 2016). Two case
studies were presented by the close of the study in identification of the mechanism of versatility
alongside offering proof of the correction of mathematical model. Rock motion is carried out
using arm in the initial cases study which also includes performing continuous rotation using the
last gear. For the case of the second case study, the arm is used in performing the continuous
motion even as the rocking strokes is illustrated using the last gear. An algorithm that is based on
the convex challenge was developed during the process of optimization to design mechanisms
which may trace a set of deign points. The achieved results clearly indicated the significant
flexibility of kinematics of the evaluated mechanism.
A design method was proposed by Ren and Shyue (2011) for solving the challenges of four bar
linkages through the use of different length driving links. A single degree of freedom connection
mechanism was used in making the driving link variable length while being driven by a source of
power. Three case studies have been issued for use in illustration of the effectiveness as well as
feasibility of suggested technique that demonstrated an improvement in structural errors in
comparison with the conventional solutions of the various three precision points.
Exact approximate points have been optimized in the article of Nadim and Ahmad (2008) for
dimensional synthesis of planar using the approach of ant-gradient as opposed to classical loop
closure equations. The adopted method of optimization has been used on an objective function
that is based on the produced error between actual and optimum points. The suggested algorithm
Secure Best Marks with AI Grader
Need help grading? Try our AI Grader for instant feedback on your assignments.
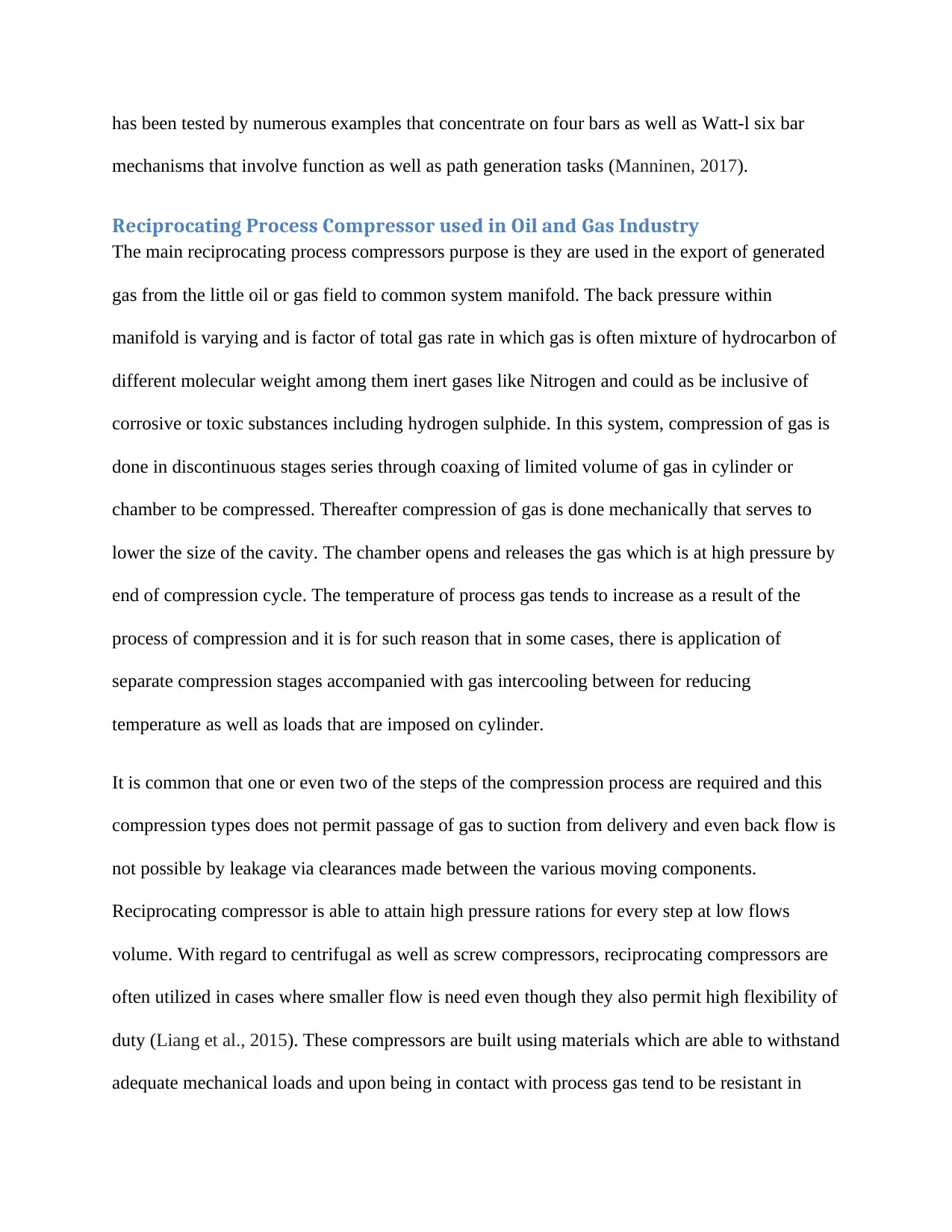
has been tested by numerous examples that concentrate on four bars as well as Watt-l six bar
mechanisms that involve function as well as path generation tasks (Manninen, 2017).
Reciprocating Process Compressor used in Oil and Gas Industry
The main reciprocating process compressors purpose is they are used in the export of generated
gas from the little oil or gas field to common system manifold. The back pressure within
manifold is varying and is factor of total gas rate in which gas is often mixture of hydrocarbon of
different molecular weight among them inert gases like Nitrogen and could as be inclusive of
corrosive or toxic substances including hydrogen sulphide. In this system, compression of gas is
done in discontinuous stages series through coaxing of limited volume of gas in cylinder or
chamber to be compressed. Thereafter compression of gas is done mechanically that serves to
lower the size of the cavity. The chamber opens and releases the gas which is at high pressure by
end of compression cycle. The temperature of process gas tends to increase as a result of the
process of compression and it is for such reason that in some cases, there is application of
separate compression stages accompanied with gas intercooling between for reducing
temperature as well as loads that are imposed on cylinder.
It is common that one or even two of the steps of the compression process are required and this
compression types does not permit passage of gas to suction from delivery and even back flow is
not possible by leakage via clearances made between the various moving components.
Reciprocating compressor is able to attain high pressure rations for every step at low flows
volume. With regard to centrifugal as well as screw compressors, reciprocating compressors are
often utilized in cases where smaller flow is need even though they also permit high flexibility of
duty (Liang et al., 2015). These compressors are built using materials which are able to withstand
adequate mechanical loads and upon being in contact with process gas tend to be resistant in
mechanisms that involve function as well as path generation tasks (Manninen, 2017).
Reciprocating Process Compressor used in Oil and Gas Industry
The main reciprocating process compressors purpose is they are used in the export of generated
gas from the little oil or gas field to common system manifold. The back pressure within
manifold is varying and is factor of total gas rate in which gas is often mixture of hydrocarbon of
different molecular weight among them inert gases like Nitrogen and could as be inclusive of
corrosive or toxic substances including hydrogen sulphide. In this system, compression of gas is
done in discontinuous stages series through coaxing of limited volume of gas in cylinder or
chamber to be compressed. Thereafter compression of gas is done mechanically that serves to
lower the size of the cavity. The chamber opens and releases the gas which is at high pressure by
end of compression cycle. The temperature of process gas tends to increase as a result of the
process of compression and it is for such reason that in some cases, there is application of
separate compression stages accompanied with gas intercooling between for reducing
temperature as well as loads that are imposed on cylinder.
It is common that one or even two of the steps of the compression process are required and this
compression types does not permit passage of gas to suction from delivery and even back flow is
not possible by leakage via clearances made between the various moving components.
Reciprocating compressor is able to attain high pressure rations for every step at low flows
volume. With regard to centrifugal as well as screw compressors, reciprocating compressors are
often utilized in cases where smaller flow is need even though they also permit high flexibility of
duty (Liang et al., 2015). These compressors are built using materials which are able to withstand
adequate mechanical loads and upon being in contact with process gas tend to be resistant in
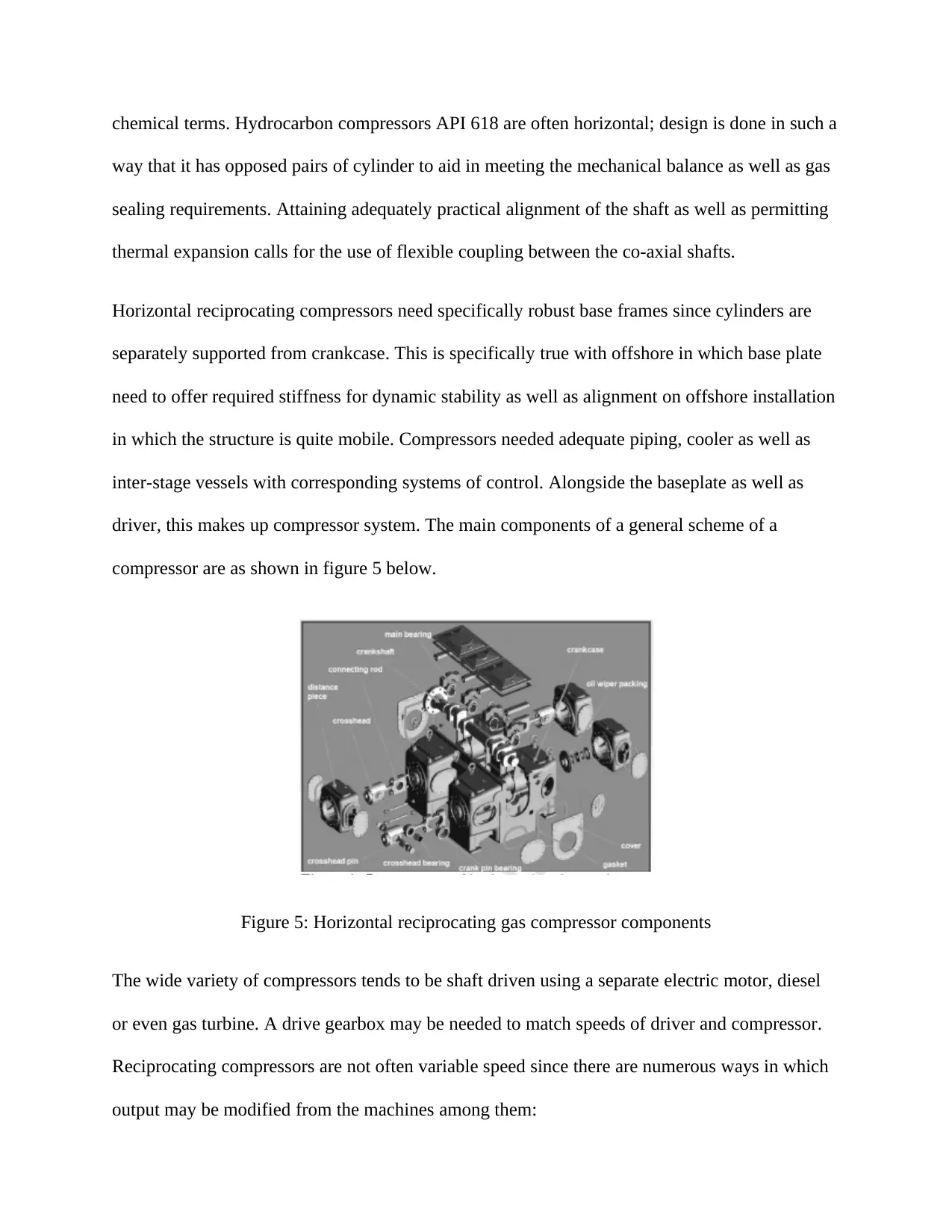
chemical terms. Hydrocarbon compressors API 618 are often horizontal; design is done in such a
way that it has opposed pairs of cylinder to aid in meeting the mechanical balance as well as gas
sealing requirements. Attaining adequately practical alignment of the shaft as well as permitting
thermal expansion calls for the use of flexible coupling between the co-axial shafts.
Horizontal reciprocating compressors need specifically robust base frames since cylinders are
separately supported from crankcase. This is specifically true with offshore in which base plate
need to offer required stiffness for dynamic stability as well as alignment on offshore installation
in which the structure is quite mobile. Compressors needed adequate piping, cooler as well as
inter-stage vessels with corresponding systems of control. Alongside the baseplate as well as
driver, this makes up compressor system. The main components of a general scheme of a
compressor are as shown in figure 5 below.
Figure 5: Horizontal reciprocating gas compressor components
The wide variety of compressors tends to be shaft driven using a separate electric motor, diesel
or even gas turbine. A drive gearbox may be needed to match speeds of driver and compressor.
Reciprocating compressors are not often variable speed since there are numerous ways in which
output may be modified from the machines among them:
way that it has opposed pairs of cylinder to aid in meeting the mechanical balance as well as gas
sealing requirements. Attaining adequately practical alignment of the shaft as well as permitting
thermal expansion calls for the use of flexible coupling between the co-axial shafts.
Horizontal reciprocating compressors need specifically robust base frames since cylinders are
separately supported from crankcase. This is specifically true with offshore in which base plate
need to offer required stiffness for dynamic stability as well as alignment on offshore installation
in which the structure is quite mobile. Compressors needed adequate piping, cooler as well as
inter-stage vessels with corresponding systems of control. Alongside the baseplate as well as
driver, this makes up compressor system. The main components of a general scheme of a
compressor are as shown in figure 5 below.
Figure 5: Horizontal reciprocating gas compressor components
The wide variety of compressors tends to be shaft driven using a separate electric motor, diesel
or even gas turbine. A drive gearbox may be needed to match speeds of driver and compressor.
Reciprocating compressors are not often variable speed since there are numerous ways in which
output may be modified from the machines among them:
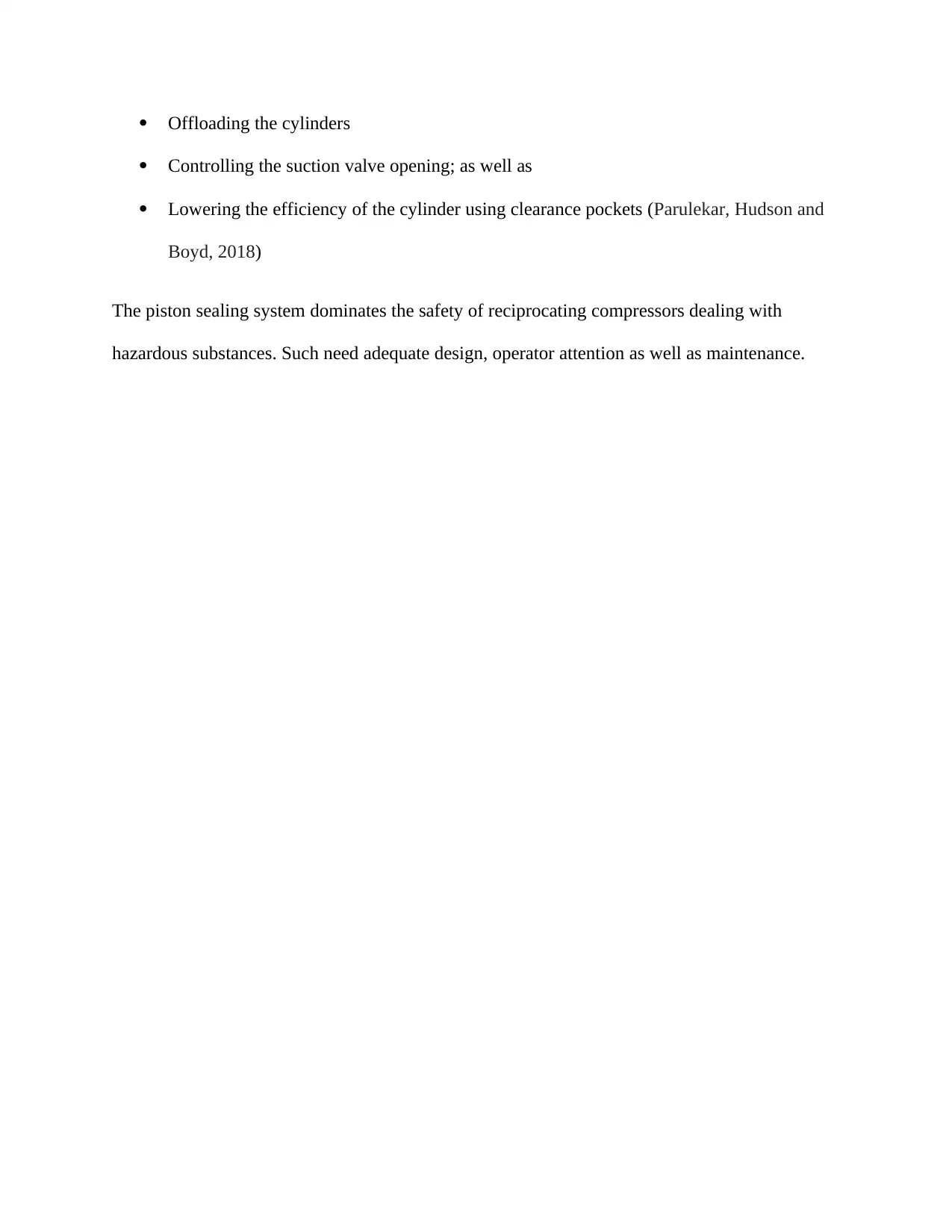
Offloading the cylinders
Controlling the suction valve opening; as well as
Lowering the efficiency of the cylinder using clearance pockets (Parulekar, Hudson and
Boyd, 2018)
The piston sealing system dominates the safety of reciprocating compressors dealing with
hazardous substances. Such need adequate design, operator attention as well as maintenance.
Controlling the suction valve opening; as well as
Lowering the efficiency of the cylinder using clearance pockets (Parulekar, Hudson and
Boyd, 2018)
The piston sealing system dominates the safety of reciprocating compressors dealing with
hazardous substances. Such need adequate design, operator attention as well as maintenance.
Paraphrase This Document
Need a fresh take? Get an instant paraphrase of this document with our AI Paraphraser
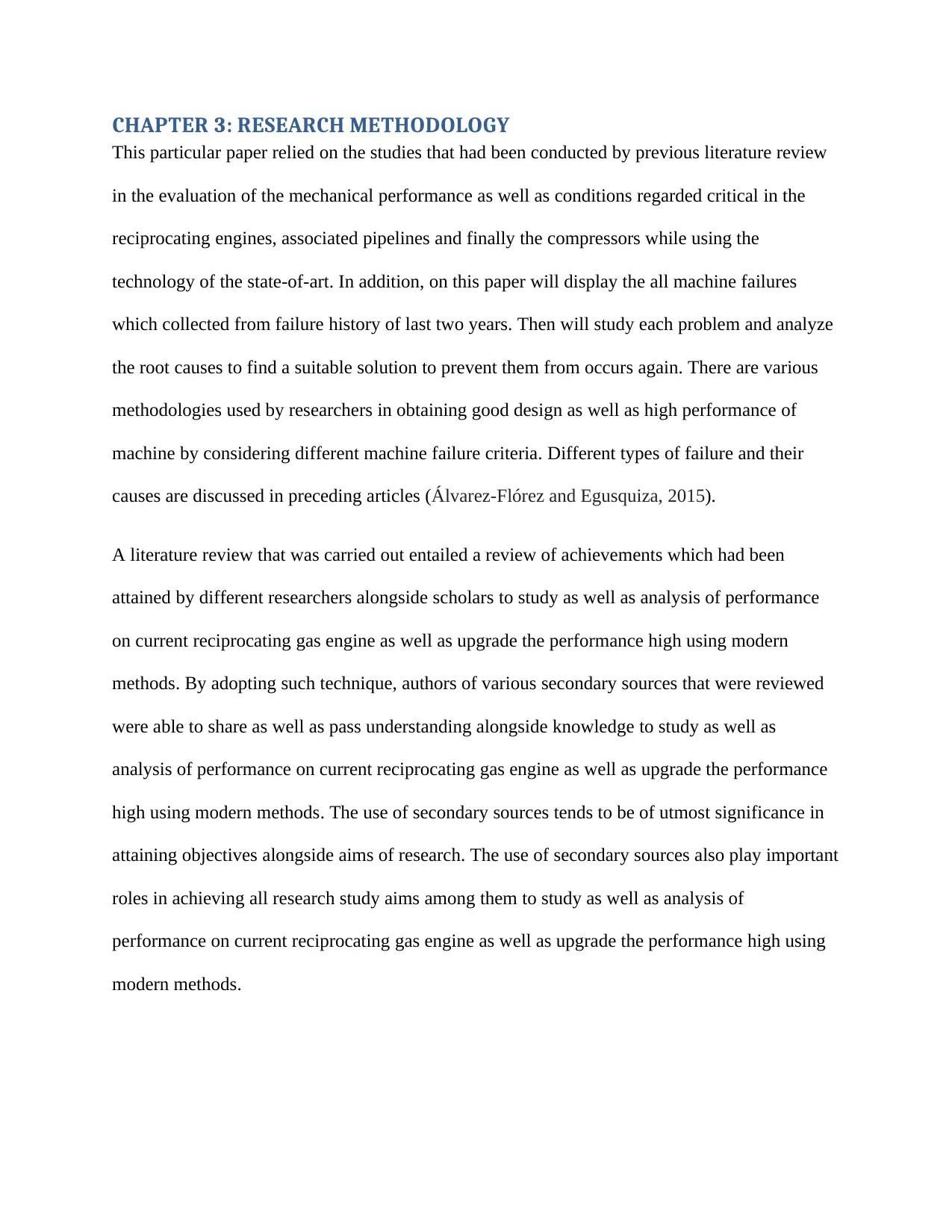
CHAPTER 3: RESEARCH METHODOLOGY
This particular paper relied on the studies that had been conducted by previous literature review
in the evaluation of the mechanical performance as well as conditions regarded critical in the
reciprocating engines, associated pipelines and finally the compressors while using the
technology of the state-of-art. In addition, on this paper will display the all machine failures
which collected from failure history of last two years. Then will study each problem and analyze
the root causes to find a suitable solution to prevent them from occurs again. There are various
methodologies used by researchers in obtaining good design as well as high performance of
machine by considering different machine failure criteria. Different types of failure and their
causes are discussed in preceding articles (Álvarez-Flórez and Egusquiza, 2015).
A literature review that was carried out entailed a review of achievements which had been
attained by different researchers alongside scholars to study as well as analysis of performance
on current reciprocating gas engine as well as upgrade the performance high using modern
methods. By adopting such technique, authors of various secondary sources that were reviewed
were able to share as well as pass understanding alongside knowledge to study as well as
analysis of performance on current reciprocating gas engine as well as upgrade the performance
high using modern methods. The use of secondary sources tends to be of utmost significance in
attaining objectives alongside aims of research. The use of secondary sources also play important
roles in achieving all research study aims among them to study as well as analysis of
performance on current reciprocating gas engine as well as upgrade the performance high using
modern methods.
This particular paper relied on the studies that had been conducted by previous literature review
in the evaluation of the mechanical performance as well as conditions regarded critical in the
reciprocating engines, associated pipelines and finally the compressors while using the
technology of the state-of-art. In addition, on this paper will display the all machine failures
which collected from failure history of last two years. Then will study each problem and analyze
the root causes to find a suitable solution to prevent them from occurs again. There are various
methodologies used by researchers in obtaining good design as well as high performance of
machine by considering different machine failure criteria. Different types of failure and their
causes are discussed in preceding articles (Álvarez-Flórez and Egusquiza, 2015).
A literature review that was carried out entailed a review of achievements which had been
attained by different researchers alongside scholars to study as well as analysis of performance
on current reciprocating gas engine as well as upgrade the performance high using modern
methods. By adopting such technique, authors of various secondary sources that were reviewed
were able to share as well as pass understanding alongside knowledge to study as well as
analysis of performance on current reciprocating gas engine as well as upgrade the performance
high using modern methods. The use of secondary sources tends to be of utmost significance in
attaining objectives alongside aims of research. The use of secondary sources also play important
roles in achieving all research study aims among them to study as well as analysis of
performance on current reciprocating gas engine as well as upgrade the performance high using
modern methods.
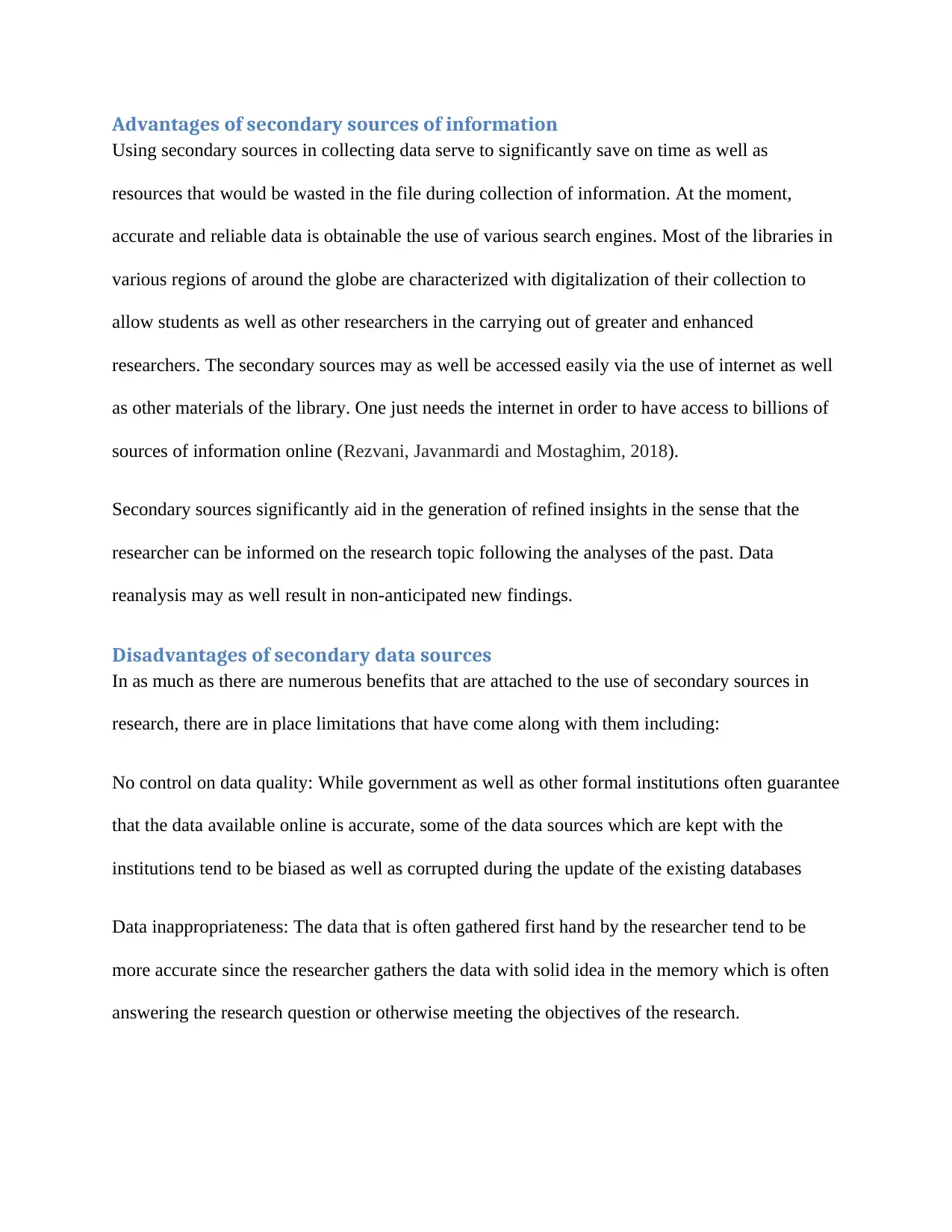
Advantages of secondary sources of information
Using secondary sources in collecting data serve to significantly save on time as well as
resources that would be wasted in the file during collection of information. At the moment,
accurate and reliable data is obtainable the use of various search engines. Most of the libraries in
various regions of around the globe are characterized with digitalization of their collection to
allow students as well as other researchers in the carrying out of greater and enhanced
researchers. The secondary sources may as well be accessed easily via the use of internet as well
as other materials of the library. One just needs the internet in order to have access to billions of
sources of information online (Rezvani, Javanmardi and Mostaghim, 2018).
Secondary sources significantly aid in the generation of refined insights in the sense that the
researcher can be informed on the research topic following the analyses of the past. Data
reanalysis may as well result in non-anticipated new findings.
Disadvantages of secondary data sources
In as much as there are numerous benefits that are attached to the use of secondary sources in
research, there are in place limitations that have come along with them including:
No control on data quality: While government as well as other formal institutions often guarantee
that the data available online is accurate, some of the data sources which are kept with the
institutions tend to be biased as well as corrupted during the update of the existing databases
Data inappropriateness: The data that is often gathered first hand by the researcher tend to be
more accurate since the researcher gathers the data with solid idea in the memory which is often
answering the research question or otherwise meeting the objectives of the research.
Using secondary sources in collecting data serve to significantly save on time as well as
resources that would be wasted in the file during collection of information. At the moment,
accurate and reliable data is obtainable the use of various search engines. Most of the libraries in
various regions of around the globe are characterized with digitalization of their collection to
allow students as well as other researchers in the carrying out of greater and enhanced
researchers. The secondary sources may as well be accessed easily via the use of internet as well
as other materials of the library. One just needs the internet in order to have access to billions of
sources of information online (Rezvani, Javanmardi and Mostaghim, 2018).
Secondary sources significantly aid in the generation of refined insights in the sense that the
researcher can be informed on the research topic following the analyses of the past. Data
reanalysis may as well result in non-anticipated new findings.
Disadvantages of secondary data sources
In as much as there are numerous benefits that are attached to the use of secondary sources in
research, there are in place limitations that have come along with them including:
No control on data quality: While government as well as other formal institutions often guarantee
that the data available online is accurate, some of the data sources which are kept with the
institutions tend to be biased as well as corrupted during the update of the existing databases
Data inappropriateness: The data that is often gathered first hand by the researcher tend to be
more accurate since the researcher gathers the data with solid idea in the memory which is often
answering the research question or otherwise meeting the objectives of the research.
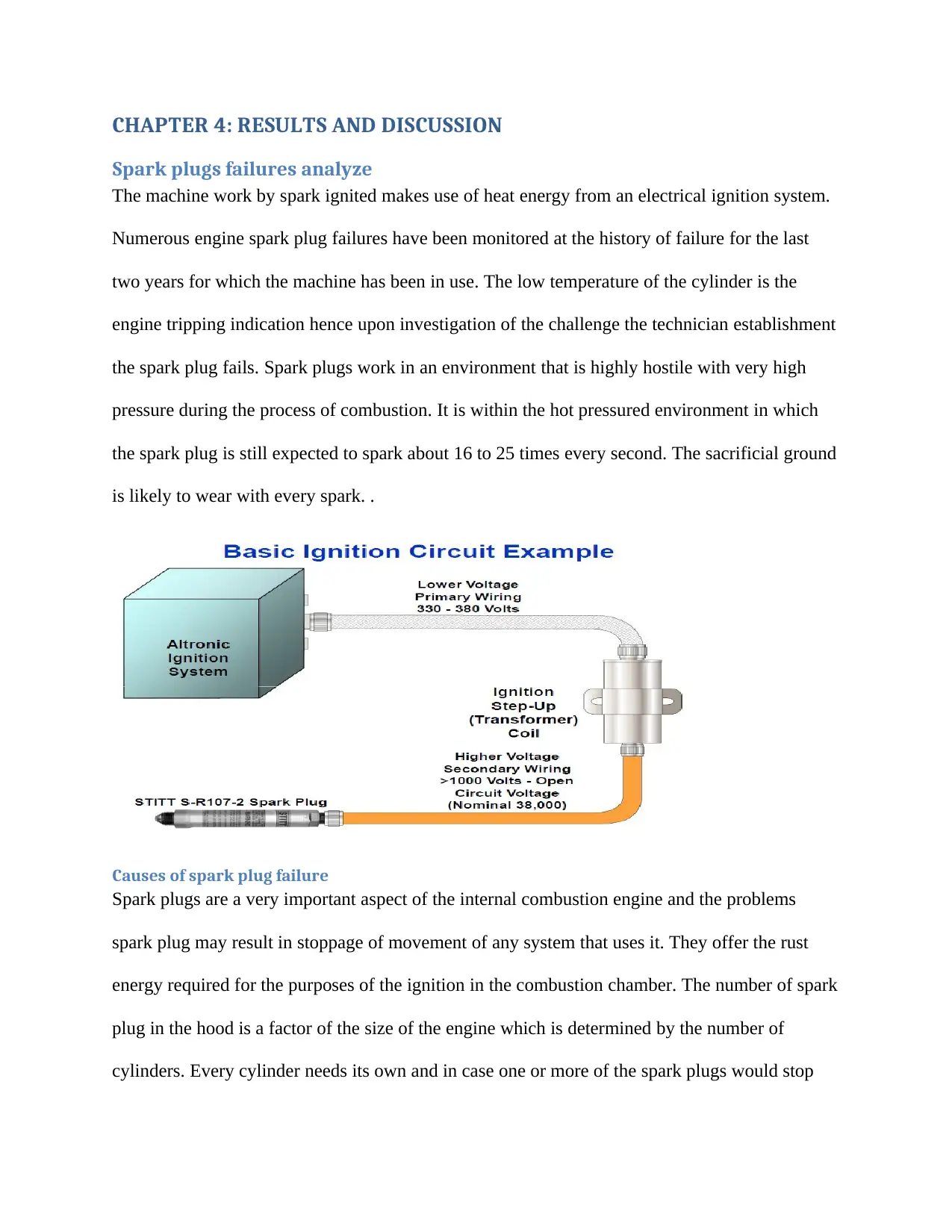
CHAPTER 4: RESULTS AND DISCUSSION
Spark plugs failures analyze
The machine work by spark ignited makes use of heat energy from an electrical ignition system.
Numerous engine spark plug failures have been monitored at the history of failure for the last
two years for which the machine has been in use. The low temperature of the cylinder is the
engine tripping indication hence upon investigation of the challenge the technician establishment
the spark plug fails. Spark plugs work in an environment that is highly hostile with very high
pressure during the process of combustion. It is within the hot pressured environment in which
the spark plug is still expected to spark about 16 to 25 times every second. The sacrificial ground
is likely to wear with every spark. .
Causes of spark plug failure
Spark plugs are a very important aspect of the internal combustion engine and the problems
spark plug may result in stoppage of movement of any system that uses it. They offer the rust
energy required for the purposes of the ignition in the combustion chamber. The number of spark
plug in the hood is a factor of the size of the engine which is determined by the number of
cylinders. Every cylinder needs its own and in case one or more of the spark plugs would stop
Spark plugs failures analyze
The machine work by spark ignited makes use of heat energy from an electrical ignition system.
Numerous engine spark plug failures have been monitored at the history of failure for the last
two years for which the machine has been in use. The low temperature of the cylinder is the
engine tripping indication hence upon investigation of the challenge the technician establishment
the spark plug fails. Spark plugs work in an environment that is highly hostile with very high
pressure during the process of combustion. It is within the hot pressured environment in which
the spark plug is still expected to spark about 16 to 25 times every second. The sacrificial ground
is likely to wear with every spark. .
Causes of spark plug failure
Spark plugs are a very important aspect of the internal combustion engine and the problems
spark plug may result in stoppage of movement of any system that uses it. They offer the rust
energy required for the purposes of the ignition in the combustion chamber. The number of spark
plug in the hood is a factor of the size of the engine which is determined by the number of
cylinders. Every cylinder needs its own and in case one or more of the spark plugs would stop
Secure Best Marks with AI Grader
Need help grading? Try our AI Grader for instant feedback on your assignments.
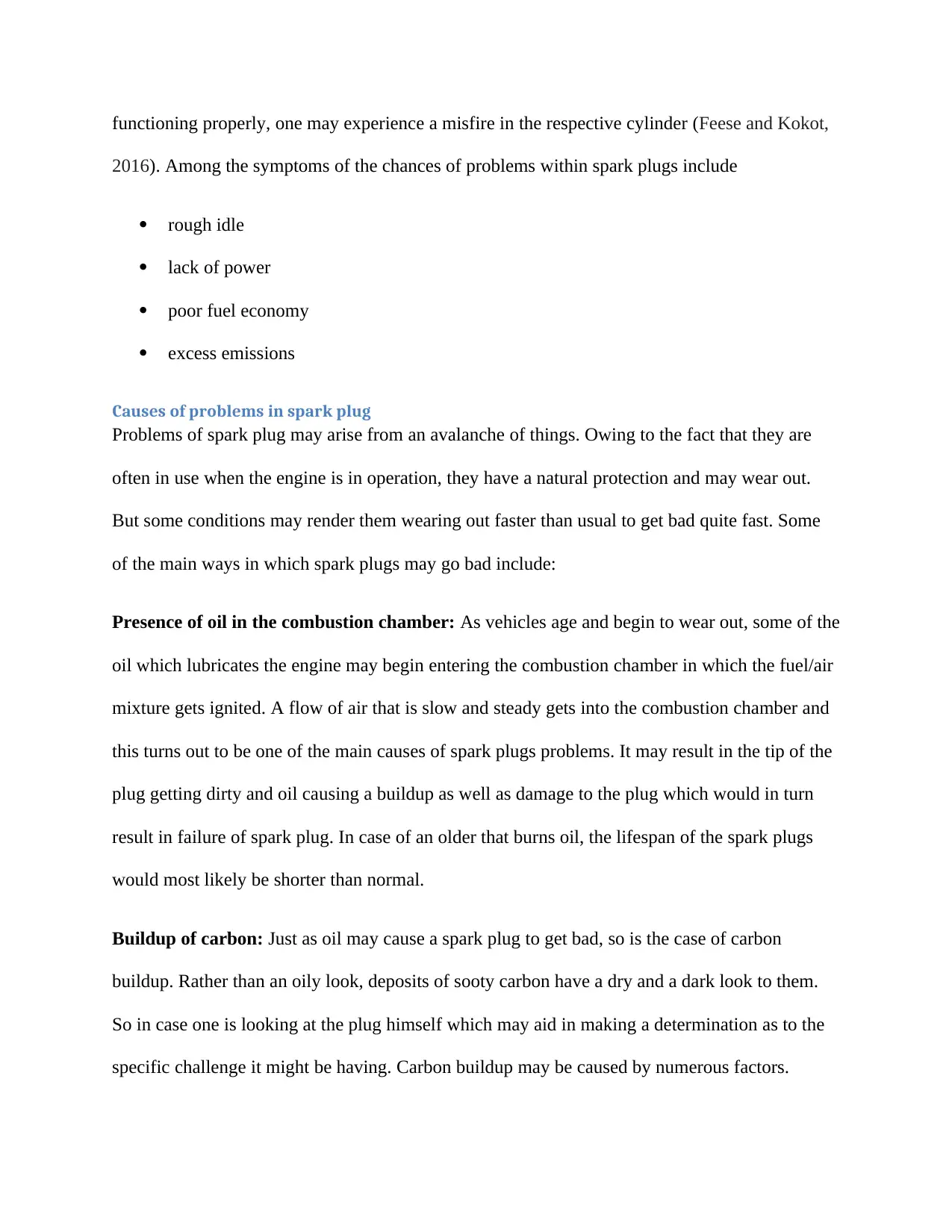
functioning properly, one may experience a misfire in the respective cylinder (Feese and Kokot,
2016). Among the symptoms of the chances of problems within spark plugs include
rough idle
lack of power
poor fuel economy
excess emissions
Causes of problems in spark plug
Problems of spark plug may arise from an avalanche of things. Owing to the fact that they are
often in use when the engine is in operation, they have a natural protection and may wear out.
But some conditions may render them wearing out faster than usual to get bad quite fast. Some
of the main ways in which spark plugs may go bad include:
Presence of oil in the combustion chamber: As vehicles age and begin to wear out, some of the
oil which lubricates the engine may begin entering the combustion chamber in which the fuel/air
mixture gets ignited. A flow of air that is slow and steady gets into the combustion chamber and
this turns out to be one of the main causes of spark plugs problems. It may result in the tip of the
plug getting dirty and oil causing a buildup as well as damage to the plug which would in turn
result in failure of spark plug. In case of an older that burns oil, the lifespan of the spark plugs
would most likely be shorter than normal.
Buildup of carbon: Just as oil may cause a spark plug to get bad, so is the case of carbon
buildup. Rather than an oily look, deposits of sooty carbon have a dry and a dark look to them.
So in case one is looking at the plug himself which may aid in making a determination as to the
specific challenge it might be having. Carbon buildup may be caused by numerous factors.
2016). Among the symptoms of the chances of problems within spark plugs include
rough idle
lack of power
poor fuel economy
excess emissions
Causes of problems in spark plug
Problems of spark plug may arise from an avalanche of things. Owing to the fact that they are
often in use when the engine is in operation, they have a natural protection and may wear out.
But some conditions may render them wearing out faster than usual to get bad quite fast. Some
of the main ways in which spark plugs may go bad include:
Presence of oil in the combustion chamber: As vehicles age and begin to wear out, some of the
oil which lubricates the engine may begin entering the combustion chamber in which the fuel/air
mixture gets ignited. A flow of air that is slow and steady gets into the combustion chamber and
this turns out to be one of the main causes of spark plugs problems. It may result in the tip of the
plug getting dirty and oil causing a buildup as well as damage to the plug which would in turn
result in failure of spark plug. In case of an older that burns oil, the lifespan of the spark plugs
would most likely be shorter than normal.
Buildup of carbon: Just as oil may cause a spark plug to get bad, so is the case of carbon
buildup. Rather than an oily look, deposits of sooty carbon have a dry and a dark look to them.
So in case one is looking at the plug himself which may aid in making a determination as to the
specific challenge it might be having. Carbon buildup may be caused by numerous factors.
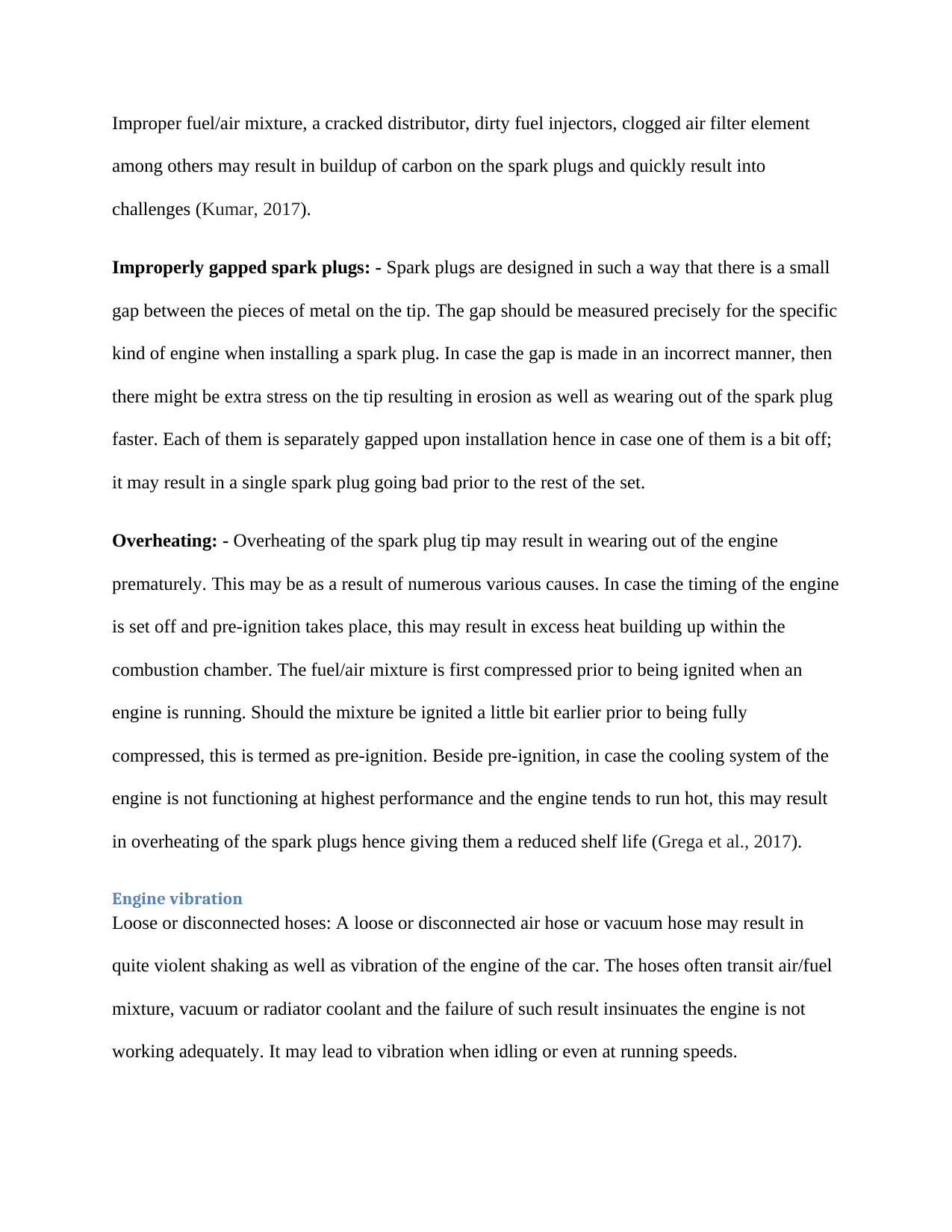
Improper fuel/air mixture, a cracked distributor, dirty fuel injectors, clogged air filter element
among others may result in buildup of carbon on the spark plugs and quickly result into
challenges (Kumar, 2017).
Improperly gapped spark plugs: - Spark plugs are designed in such a way that there is a small
gap between the pieces of metal on the tip. The gap should be measured precisely for the specific
kind of engine when installing a spark plug. In case the gap is made in an incorrect manner, then
there might be extra stress on the tip resulting in erosion as well as wearing out of the spark plug
faster. Each of them is separately gapped upon installation hence in case one of them is a bit off;
it may result in a single spark plug going bad prior to the rest of the set.
Overheating: - Overheating of the spark plug tip may result in wearing out of the engine
prematurely. This may be as a result of numerous various causes. In case the timing of the engine
is set off and pre-ignition takes place, this may result in excess heat building up within the
combustion chamber. The fuel/air mixture is first compressed prior to being ignited when an
engine is running. Should the mixture be ignited a little bit earlier prior to being fully
compressed, this is termed as pre-ignition. Beside pre-ignition, in case the cooling system of the
engine is not functioning at highest performance and the engine tends to run hot, this may result
in overheating of the spark plugs hence giving them a reduced shelf life (Grega et al., 2017).
Engine vibration
Loose or disconnected hoses: A loose or disconnected air hose or vacuum hose may result in
quite violent shaking as well as vibration of the engine of the car. The hoses often transit air/fuel
mixture, vacuum or radiator coolant and the failure of such result insinuates the engine is not
working adequately. It may lead to vibration when idling or even at running speeds.
among others may result in buildup of carbon on the spark plugs and quickly result into
challenges (Kumar, 2017).
Improperly gapped spark plugs: - Spark plugs are designed in such a way that there is a small
gap between the pieces of metal on the tip. The gap should be measured precisely for the specific
kind of engine when installing a spark plug. In case the gap is made in an incorrect manner, then
there might be extra stress on the tip resulting in erosion as well as wearing out of the spark plug
faster. Each of them is separately gapped upon installation hence in case one of them is a bit off;
it may result in a single spark plug going bad prior to the rest of the set.
Overheating: - Overheating of the spark plug tip may result in wearing out of the engine
prematurely. This may be as a result of numerous various causes. In case the timing of the engine
is set off and pre-ignition takes place, this may result in excess heat building up within the
combustion chamber. The fuel/air mixture is first compressed prior to being ignited when an
engine is running. Should the mixture be ignited a little bit earlier prior to being fully
compressed, this is termed as pre-ignition. Beside pre-ignition, in case the cooling system of the
engine is not functioning at highest performance and the engine tends to run hot, this may result
in overheating of the spark plugs hence giving them a reduced shelf life (Grega et al., 2017).
Engine vibration
Loose or disconnected hoses: A loose or disconnected air hose or vacuum hose may result in
quite violent shaking as well as vibration of the engine of the car. The hoses often transit air/fuel
mixture, vacuum or radiator coolant and the failure of such result insinuates the engine is not
working adequately. It may lead to vibration when idling or even at running speeds.
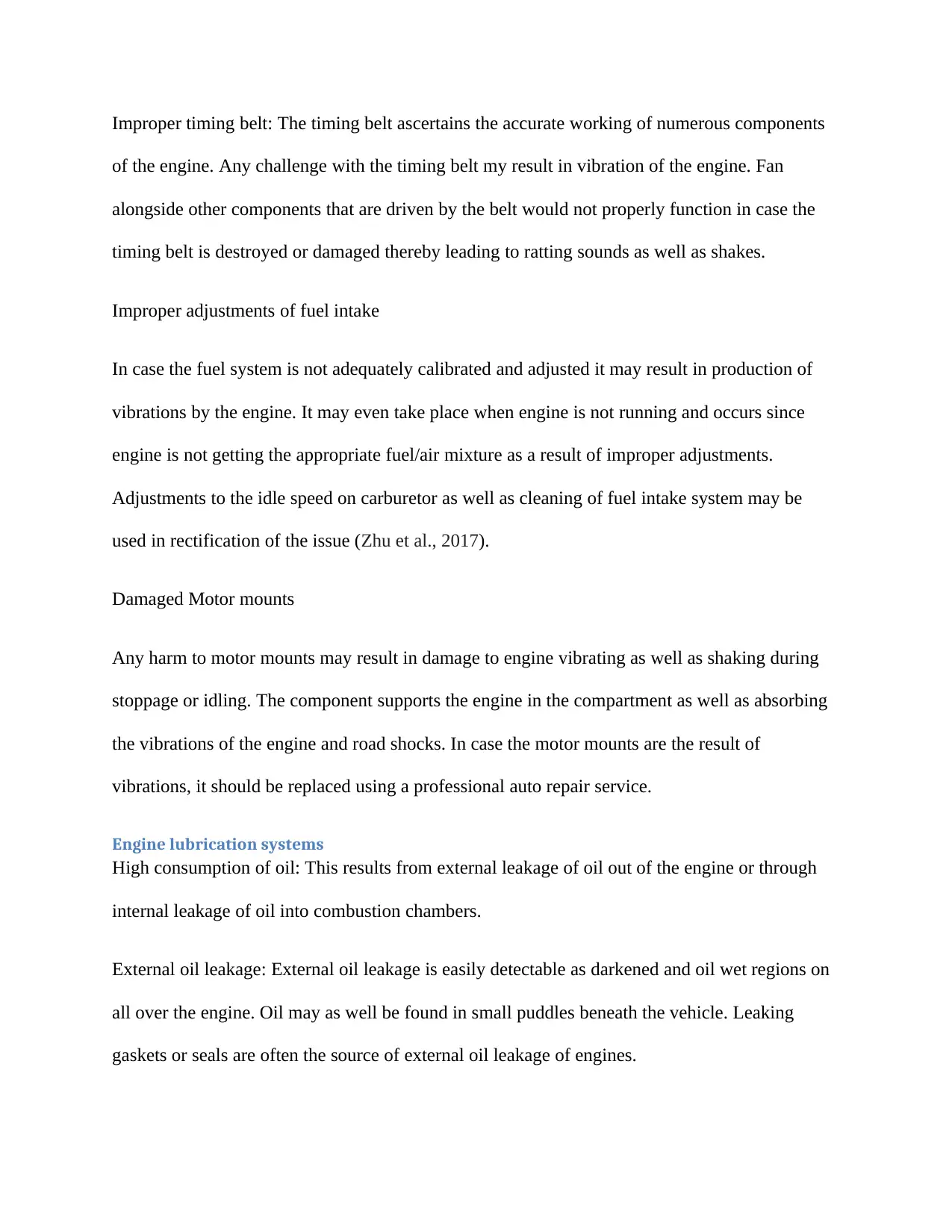
Improper timing belt: The timing belt ascertains the accurate working of numerous components
of the engine. Any challenge with the timing belt my result in vibration of the engine. Fan
alongside other components that are driven by the belt would not properly function in case the
timing belt is destroyed or damaged thereby leading to ratting sounds as well as shakes.
Improper adjustments of fuel intake
In case the fuel system is not adequately calibrated and adjusted it may result in production of
vibrations by the engine. It may even take place when engine is not running and occurs since
engine is not getting the appropriate fuel/air mixture as a result of improper adjustments.
Adjustments to the idle speed on carburetor as well as cleaning of fuel intake system may be
used in rectification of the issue (Zhu et al., 2017).
Damaged Motor mounts
Any harm to motor mounts may result in damage to engine vibrating as well as shaking during
stoppage or idling. The component supports the engine in the compartment as well as absorbing
the vibrations of the engine and road shocks. In case the motor mounts are the result of
vibrations, it should be replaced using a professional auto repair service.
Engine lubrication systems
High consumption of oil: This results from external leakage of oil out of the engine or through
internal leakage of oil into combustion chambers.
External oil leakage: External oil leakage is easily detectable as darkened and oil wet regions on
all over the engine. Oil may as well be found in small puddles beneath the vehicle. Leaking
gaskets or seals are often the source of external oil leakage of engines.
of the engine. Any challenge with the timing belt my result in vibration of the engine. Fan
alongside other components that are driven by the belt would not properly function in case the
timing belt is destroyed or damaged thereby leading to ratting sounds as well as shakes.
Improper adjustments of fuel intake
In case the fuel system is not adequately calibrated and adjusted it may result in production of
vibrations by the engine. It may even take place when engine is not running and occurs since
engine is not getting the appropriate fuel/air mixture as a result of improper adjustments.
Adjustments to the idle speed on carburetor as well as cleaning of fuel intake system may be
used in rectification of the issue (Zhu et al., 2017).
Damaged Motor mounts
Any harm to motor mounts may result in damage to engine vibrating as well as shaking during
stoppage or idling. The component supports the engine in the compartment as well as absorbing
the vibrations of the engine and road shocks. In case the motor mounts are the result of
vibrations, it should be replaced using a professional auto repair service.
Engine lubrication systems
High consumption of oil: This results from external leakage of oil out of the engine or through
internal leakage of oil into combustion chambers.
External oil leakage: External oil leakage is easily detectable as darkened and oil wet regions on
all over the engine. Oil may as well be found in small puddles beneath the vehicle. Leaking
gaskets or seals are often the source of external oil leakage of engines.
Paraphrase This Document
Need a fresh take? Get an instant paraphrase of this document with our AI Paraphraser
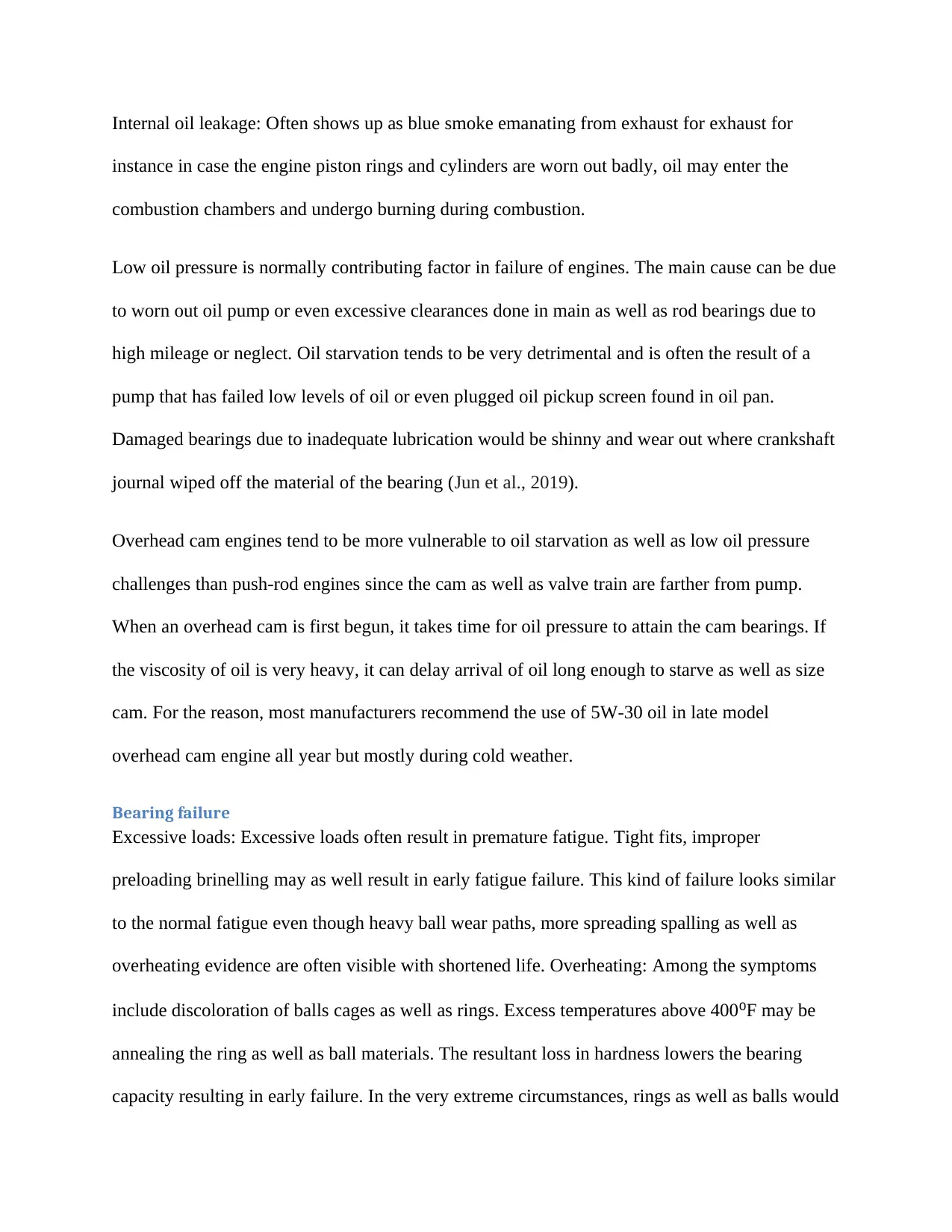
Internal oil leakage: Often shows up as blue smoke emanating from exhaust for exhaust for
instance in case the engine piston rings and cylinders are worn out badly, oil may enter the
combustion chambers and undergo burning during combustion.
Low oil pressure is normally contributing factor in failure of engines. The main cause can be due
to worn out oil pump or even excessive clearances done in main as well as rod bearings due to
high mileage or neglect. Oil starvation tends to be very detrimental and is often the result of a
pump that has failed low levels of oil or even plugged oil pickup screen found in oil pan.
Damaged bearings due to inadequate lubrication would be shinny and wear out where crankshaft
journal wiped off the material of the bearing (Jun et al., 2019).
Overhead cam engines tend to be more vulnerable to oil starvation as well as low oil pressure
challenges than push-rod engines since the cam as well as valve train are farther from pump.
When an overhead cam is first begun, it takes time for oil pressure to attain the cam bearings. If
the viscosity of oil is very heavy, it can delay arrival of oil long enough to starve as well as size
cam. For the reason, most manufacturers recommend the use of 5W-30 oil in late model
overhead cam engine all year but mostly during cold weather.
Bearing failure
Excessive loads: Excessive loads often result in premature fatigue. Tight fits, improper
preloading brinelling may as well result in early fatigue failure. This kind of failure looks similar
to the normal fatigue even though heavy ball wear paths, more spreading spalling as well as
overheating evidence are often visible with shortened life. Overheating: Among the symptoms
include discoloration of balls cages as well as rings. Excess temperatures above 400⁰F may be
annealing the ring as well as ball materials. The resultant loss in hardness lowers the bearing
capacity resulting in early failure. In the very extreme circumstances, rings as well as balls would
instance in case the engine piston rings and cylinders are worn out badly, oil may enter the
combustion chambers and undergo burning during combustion.
Low oil pressure is normally contributing factor in failure of engines. The main cause can be due
to worn out oil pump or even excessive clearances done in main as well as rod bearings due to
high mileage or neglect. Oil starvation tends to be very detrimental and is often the result of a
pump that has failed low levels of oil or even plugged oil pickup screen found in oil pan.
Damaged bearings due to inadequate lubrication would be shinny and wear out where crankshaft
journal wiped off the material of the bearing (Jun et al., 2019).
Overhead cam engines tend to be more vulnerable to oil starvation as well as low oil pressure
challenges than push-rod engines since the cam as well as valve train are farther from pump.
When an overhead cam is first begun, it takes time for oil pressure to attain the cam bearings. If
the viscosity of oil is very heavy, it can delay arrival of oil long enough to starve as well as size
cam. For the reason, most manufacturers recommend the use of 5W-30 oil in late model
overhead cam engine all year but mostly during cold weather.
Bearing failure
Excessive loads: Excessive loads often result in premature fatigue. Tight fits, improper
preloading brinelling may as well result in early fatigue failure. This kind of failure looks similar
to the normal fatigue even though heavy ball wear paths, more spreading spalling as well as
overheating evidence are often visible with shortened life. Overheating: Among the symptoms
include discoloration of balls cages as well as rings. Excess temperatures above 400⁰F may be
annealing the ring as well as ball materials. The resultant loss in hardness lowers the bearing
capacity resulting in early failure. In the very extreme circumstances, rings as well as balls would
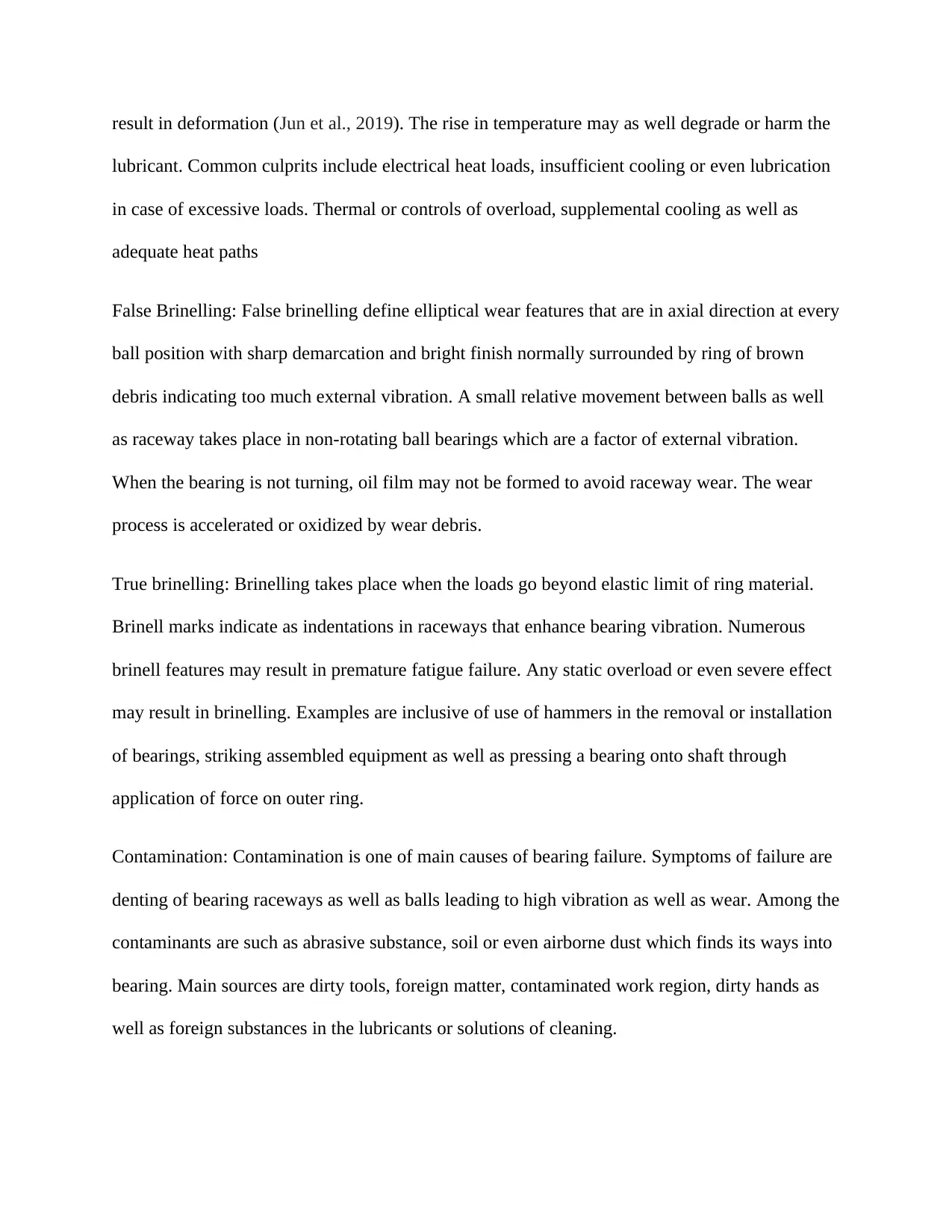
result in deformation (Jun et al., 2019). The rise in temperature may as well degrade or harm the
lubricant. Common culprits include electrical heat loads, insufficient cooling or even lubrication
in case of excessive loads. Thermal or controls of overload, supplemental cooling as well as
adequate heat paths
False Brinelling: False brinelling define elliptical wear features that are in axial direction at every
ball position with sharp demarcation and bright finish normally surrounded by ring of brown
debris indicating too much external vibration. A small relative movement between balls as well
as raceway takes place in non-rotating ball bearings which are a factor of external vibration.
When the bearing is not turning, oil film may not be formed to avoid raceway wear. The wear
process is accelerated or oxidized by wear debris.
True brinelling: Brinelling takes place when the loads go beyond elastic limit of ring material.
Brinell marks indicate as indentations in raceways that enhance bearing vibration. Numerous
brinell features may result in premature fatigue failure. Any static overload or even severe effect
may result in brinelling. Examples are inclusive of use of hammers in the removal or installation
of bearings, striking assembled equipment as well as pressing a bearing onto shaft through
application of force on outer ring.
Contamination: Contamination is one of main causes of bearing failure. Symptoms of failure are
denting of bearing raceways as well as balls leading to high vibration as well as wear. Among the
contaminants are such as abrasive substance, soil or even airborne dust which finds its ways into
bearing. Main sources are dirty tools, foreign matter, contaminated work region, dirty hands as
well as foreign substances in the lubricants or solutions of cleaning.
lubricant. Common culprits include electrical heat loads, insufficient cooling or even lubrication
in case of excessive loads. Thermal or controls of overload, supplemental cooling as well as
adequate heat paths
False Brinelling: False brinelling define elliptical wear features that are in axial direction at every
ball position with sharp demarcation and bright finish normally surrounded by ring of brown
debris indicating too much external vibration. A small relative movement between balls as well
as raceway takes place in non-rotating ball bearings which are a factor of external vibration.
When the bearing is not turning, oil film may not be formed to avoid raceway wear. The wear
process is accelerated or oxidized by wear debris.
True brinelling: Brinelling takes place when the loads go beyond elastic limit of ring material.
Brinell marks indicate as indentations in raceways that enhance bearing vibration. Numerous
brinell features may result in premature fatigue failure. Any static overload or even severe effect
may result in brinelling. Examples are inclusive of use of hammers in the removal or installation
of bearings, striking assembled equipment as well as pressing a bearing onto shaft through
application of force on outer ring.
Contamination: Contamination is one of main causes of bearing failure. Symptoms of failure are
denting of bearing raceways as well as balls leading to high vibration as well as wear. Among the
contaminants are such as abrasive substance, soil or even airborne dust which finds its ways into
bearing. Main sources are dirty tools, foreign matter, contaminated work region, dirty hands as
well as foreign substances in the lubricants or solutions of cleaning.
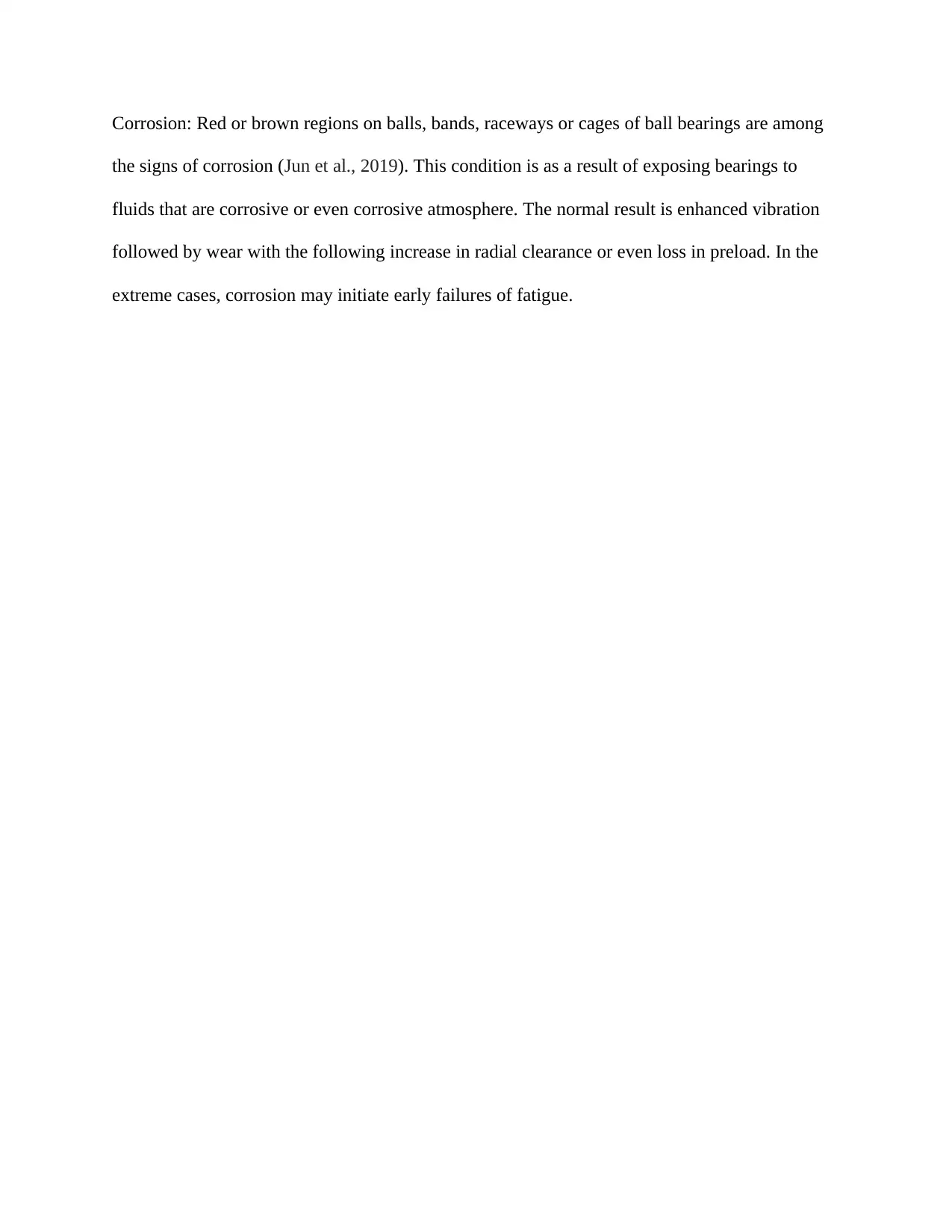
Corrosion: Red or brown regions on balls, bands, raceways or cages of ball bearings are among
the signs of corrosion (Jun et al., 2019). This condition is as a result of exposing bearings to
fluids that are corrosive or even corrosive atmosphere. The normal result is enhanced vibration
followed by wear with the following increase in radial clearance or even loss in preload. In the
extreme cases, corrosion may initiate early failures of fatigue.
the signs of corrosion (Jun et al., 2019). This condition is as a result of exposing bearings to
fluids that are corrosive or even corrosive atmosphere. The normal result is enhanced vibration
followed by wear with the following increase in radial clearance or even loss in preload. In the
extreme cases, corrosion may initiate early failures of fatigue.
Secure Best Marks with AI Grader
Need help grading? Try our AI Grader for instant feedback on your assignments.
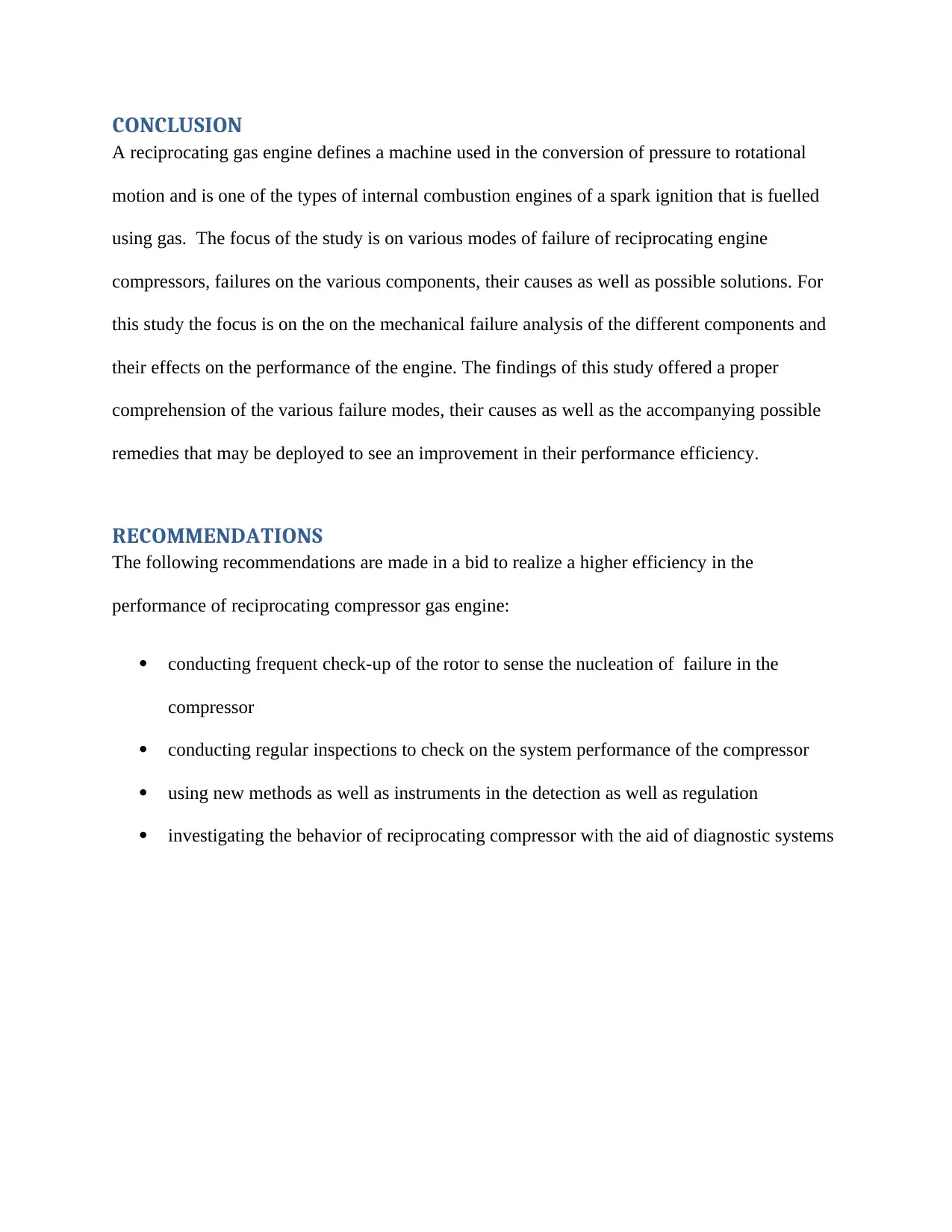
CONCLUSION
A reciprocating gas engine defines a machine used in the conversion of pressure to rotational
motion and is one of the types of internal combustion engines of a spark ignition that is fuelled
using gas. The focus of the study is on various modes of failure of reciprocating engine
compressors, failures on the various components, their causes as well as possible solutions. For
this study the focus is on the on the mechanical failure analysis of the different components and
their effects on the performance of the engine. The findings of this study offered a proper
comprehension of the various failure modes, their causes as well as the accompanying possible
remedies that may be deployed to see an improvement in their performance efficiency.
RECOMMENDATIONS
The following recommendations are made in a bid to realize a higher efficiency in the
performance of reciprocating compressor gas engine:
conducting frequent check-up of the rotor to sense the nucleation of failure in the
compressor
conducting regular inspections to check on the system performance of the compressor
using new methods as well as instruments in the detection as well as regulation
investigating the behavior of reciprocating compressor with the aid of diagnostic systems
A reciprocating gas engine defines a machine used in the conversion of pressure to rotational
motion and is one of the types of internal combustion engines of a spark ignition that is fuelled
using gas. The focus of the study is on various modes of failure of reciprocating engine
compressors, failures on the various components, their causes as well as possible solutions. For
this study the focus is on the on the mechanical failure analysis of the different components and
their effects on the performance of the engine. The findings of this study offered a proper
comprehension of the various failure modes, their causes as well as the accompanying possible
remedies that may be deployed to see an improvement in their performance efficiency.
RECOMMENDATIONS
The following recommendations are made in a bid to realize a higher efficiency in the
performance of reciprocating compressor gas engine:
conducting frequent check-up of the rotor to sense the nucleation of failure in the
compressor
conducting regular inspections to check on the system performance of the compressor
using new methods as well as instruments in the detection as well as regulation
investigating the behavior of reciprocating compressor with the aid of diagnostic systems
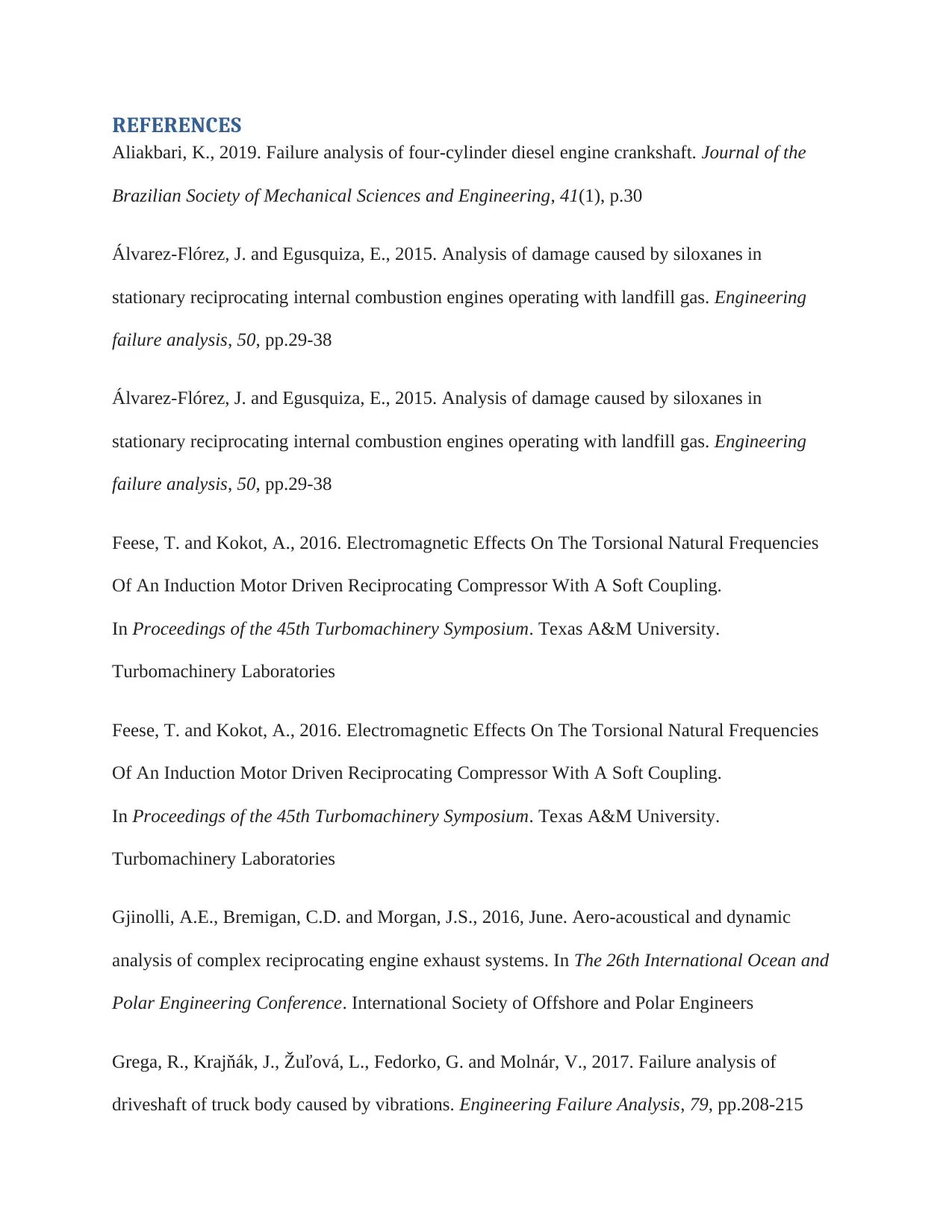
REFERENCES
Aliakbari, K., 2019. Failure analysis of four-cylinder diesel engine crankshaft. Journal of the
Brazilian Society of Mechanical Sciences and Engineering, 41(1), p.30
Álvarez-Flórez, J. and Egusquiza, E., 2015. Analysis of damage caused by siloxanes in
stationary reciprocating internal combustion engines operating with landfill gas. Engineering
failure analysis, 50, pp.29-38
Álvarez-Flórez, J. and Egusquiza, E., 2015. Analysis of damage caused by siloxanes in
stationary reciprocating internal combustion engines operating with landfill gas. Engineering
failure analysis, 50, pp.29-38
Feese, T. and Kokot, A., 2016. Electromagnetic Effects On The Torsional Natural Frequencies
Of An Induction Motor Driven Reciprocating Compressor With A Soft Coupling.
In Proceedings of the 45th Turbomachinery Symposium. Texas A&M University.
Turbomachinery Laboratories
Feese, T. and Kokot, A., 2016. Electromagnetic Effects On The Torsional Natural Frequencies
Of An Induction Motor Driven Reciprocating Compressor With A Soft Coupling.
In Proceedings of the 45th Turbomachinery Symposium. Texas A&M University.
Turbomachinery Laboratories
Gjinolli, A.E., Bremigan, C.D. and Morgan, J.S., 2016, June. Aero-acoustical and dynamic
analysis of complex reciprocating engine exhaust systems. In The 26th International Ocean and
Polar Engineering Conference. International Society of Offshore and Polar Engineers
Grega, R., Krajňák, J., Žuľová, L., Fedorko, G. and Molnár, V., 2017. Failure analysis of
driveshaft of truck body caused by vibrations. Engineering Failure Analysis, 79, pp.208-215
Aliakbari, K., 2019. Failure analysis of four-cylinder diesel engine crankshaft. Journal of the
Brazilian Society of Mechanical Sciences and Engineering, 41(1), p.30
Álvarez-Flórez, J. and Egusquiza, E., 2015. Analysis of damage caused by siloxanes in
stationary reciprocating internal combustion engines operating with landfill gas. Engineering
failure analysis, 50, pp.29-38
Álvarez-Flórez, J. and Egusquiza, E., 2015. Analysis of damage caused by siloxanes in
stationary reciprocating internal combustion engines operating with landfill gas. Engineering
failure analysis, 50, pp.29-38
Feese, T. and Kokot, A., 2016. Electromagnetic Effects On The Torsional Natural Frequencies
Of An Induction Motor Driven Reciprocating Compressor With A Soft Coupling.
In Proceedings of the 45th Turbomachinery Symposium. Texas A&M University.
Turbomachinery Laboratories
Feese, T. and Kokot, A., 2016. Electromagnetic Effects On The Torsional Natural Frequencies
Of An Induction Motor Driven Reciprocating Compressor With A Soft Coupling.
In Proceedings of the 45th Turbomachinery Symposium. Texas A&M University.
Turbomachinery Laboratories
Gjinolli, A.E., Bremigan, C.D. and Morgan, J.S., 2016, June. Aero-acoustical and dynamic
analysis of complex reciprocating engine exhaust systems. In The 26th International Ocean and
Polar Engineering Conference. International Society of Offshore and Polar Engineers
Grega, R., Krajňák, J., Žuľová, L., Fedorko, G. and Molnár, V., 2017. Failure analysis of
driveshaft of truck body caused by vibrations. Engineering Failure Analysis, 79, pp.208-215
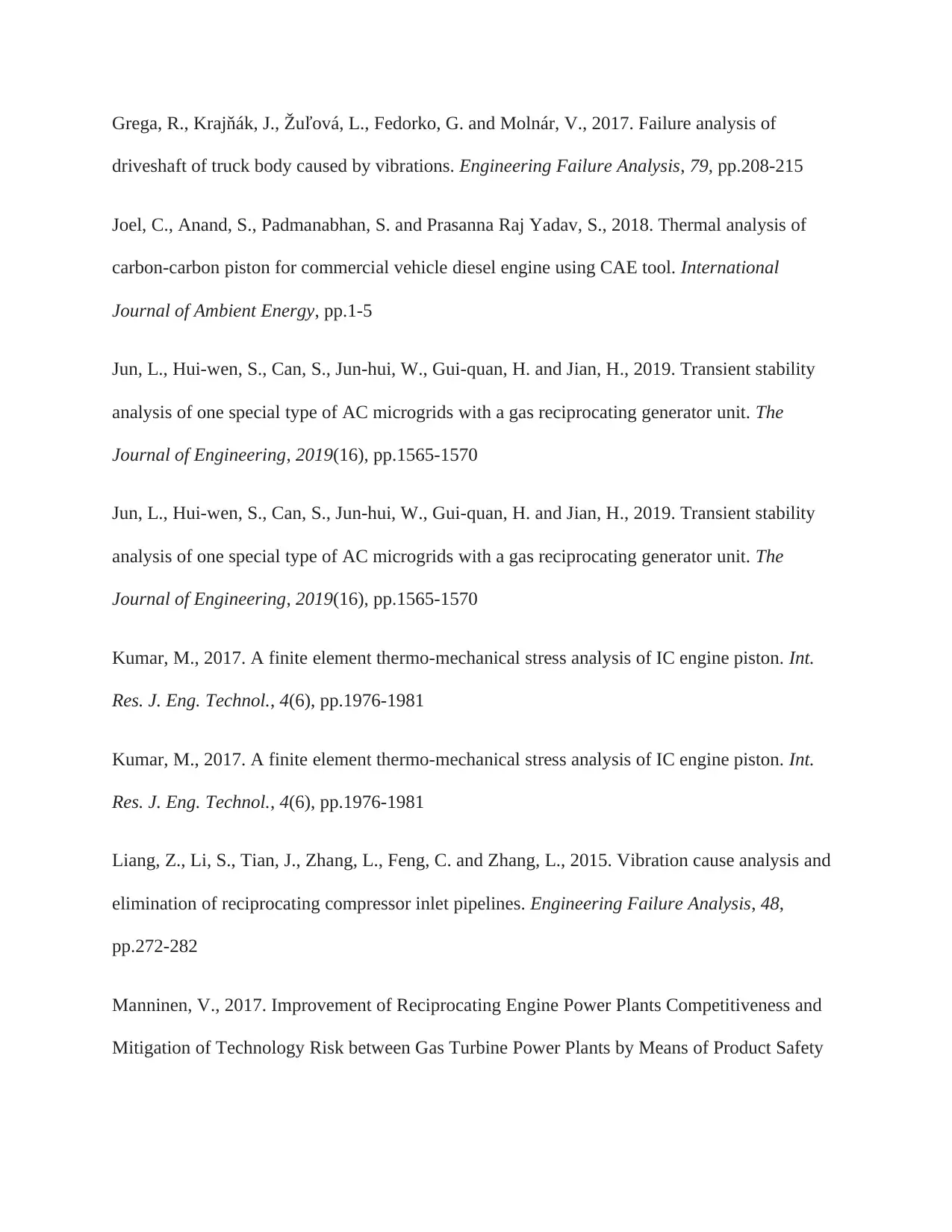
Grega, R., Krajňák, J., Žuľová, L., Fedorko, G. and Molnár, V., 2017. Failure analysis of
driveshaft of truck body caused by vibrations. Engineering Failure Analysis, 79, pp.208-215
Joel, C., Anand, S., Padmanabhan, S. and Prasanna Raj Yadav, S., 2018. Thermal analysis of
carbon-carbon piston for commercial vehicle diesel engine using CAE tool. International
Journal of Ambient Energy, pp.1-5
Jun, L., Hui-wen, S., Can, S., Jun-hui, W., Gui-quan, H. and Jian, H., 2019. Transient stability
analysis of one special type of AC microgrids with a gas reciprocating generator unit. The
Journal of Engineering, 2019(16), pp.1565-1570
Jun, L., Hui-wen, S., Can, S., Jun-hui, W., Gui-quan, H. and Jian, H., 2019. Transient stability
analysis of one special type of AC microgrids with a gas reciprocating generator unit. The
Journal of Engineering, 2019(16), pp.1565-1570
Kumar, M., 2017. A finite element thermo-mechanical stress analysis of IC engine piston. Int.
Res. J. Eng. Technol., 4(6), pp.1976-1981
Kumar, M., 2017. A finite element thermo-mechanical stress analysis of IC engine piston. Int.
Res. J. Eng. Technol., 4(6), pp.1976-1981
Liang, Z., Li, S., Tian, J., Zhang, L., Feng, C. and Zhang, L., 2015. Vibration cause analysis and
elimination of reciprocating compressor inlet pipelines. Engineering Failure Analysis, 48,
pp.272-282
Manninen, V., 2017. Improvement of Reciprocating Engine Power Plants Competitiveness and
Mitigation of Technology Risk between Gas Turbine Power Plants by Means of Product Safety
driveshaft of truck body caused by vibrations. Engineering Failure Analysis, 79, pp.208-215
Joel, C., Anand, S., Padmanabhan, S. and Prasanna Raj Yadav, S., 2018. Thermal analysis of
carbon-carbon piston for commercial vehicle diesel engine using CAE tool. International
Journal of Ambient Energy, pp.1-5
Jun, L., Hui-wen, S., Can, S., Jun-hui, W., Gui-quan, H. and Jian, H., 2019. Transient stability
analysis of one special type of AC microgrids with a gas reciprocating generator unit. The
Journal of Engineering, 2019(16), pp.1565-1570
Jun, L., Hui-wen, S., Can, S., Jun-hui, W., Gui-quan, H. and Jian, H., 2019. Transient stability
analysis of one special type of AC microgrids with a gas reciprocating generator unit. The
Journal of Engineering, 2019(16), pp.1565-1570
Kumar, M., 2017. A finite element thermo-mechanical stress analysis of IC engine piston. Int.
Res. J. Eng. Technol., 4(6), pp.1976-1981
Kumar, M., 2017. A finite element thermo-mechanical stress analysis of IC engine piston. Int.
Res. J. Eng. Technol., 4(6), pp.1976-1981
Liang, Z., Li, S., Tian, J., Zhang, L., Feng, C. and Zhang, L., 2015. Vibration cause analysis and
elimination of reciprocating compressor inlet pipelines. Engineering Failure Analysis, 48,
pp.272-282
Manninen, V., 2017. Improvement of Reciprocating Engine Power Plants Competitiveness and
Mitigation of Technology Risk between Gas Turbine Power Plants by Means of Product Safety
Paraphrase This Document
Need a fresh take? Get an instant paraphrase of this document with our AI Paraphraser
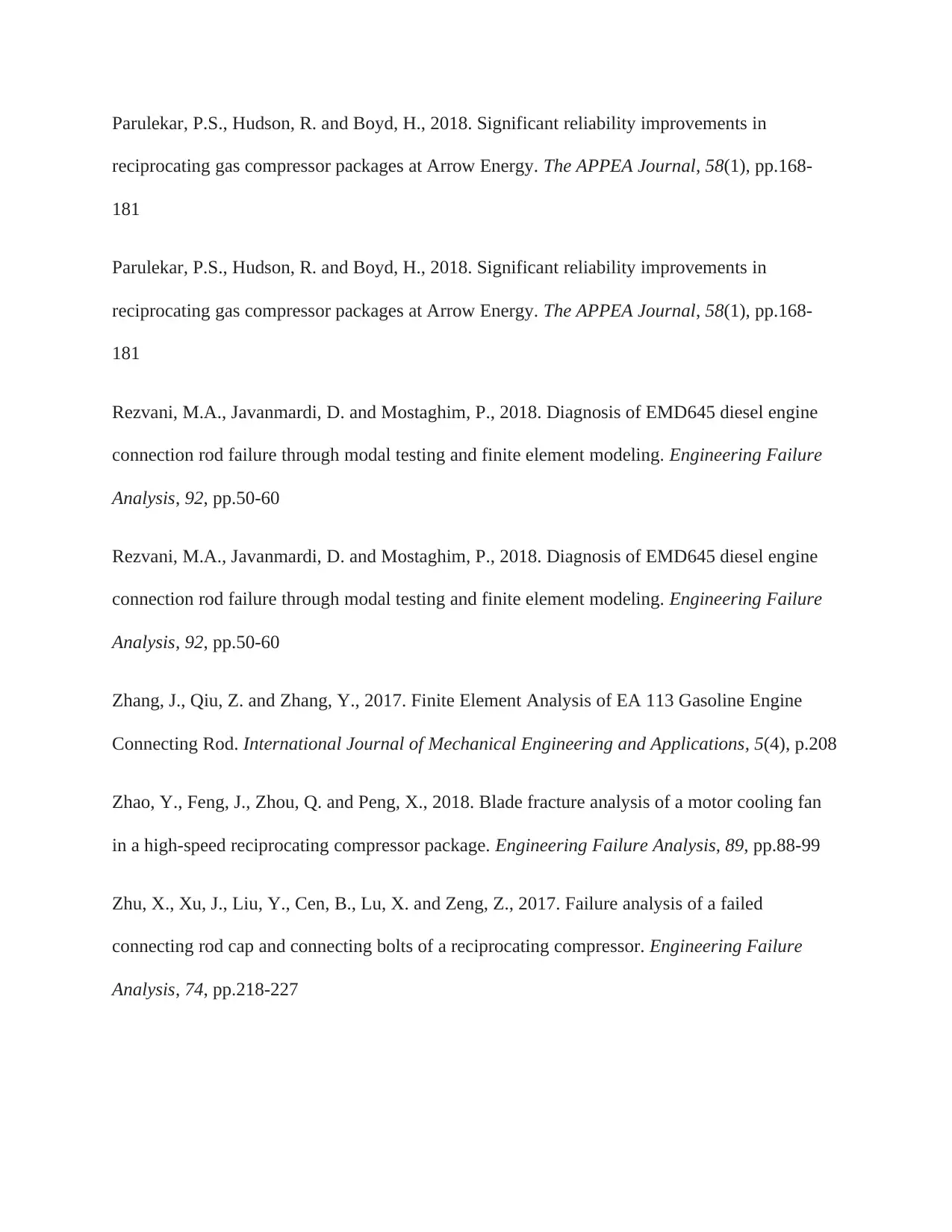
Parulekar, P.S., Hudson, R. and Boyd, H., 2018. Significant reliability improvements in
reciprocating gas compressor packages at Arrow Energy. The APPEA Journal, 58(1), pp.168-
181
Parulekar, P.S., Hudson, R. and Boyd, H., 2018. Significant reliability improvements in
reciprocating gas compressor packages at Arrow Energy. The APPEA Journal, 58(1), pp.168-
181
Rezvani, M.A., Javanmardi, D. and Mostaghim, P., 2018. Diagnosis of EMD645 diesel engine
connection rod failure through modal testing and finite element modeling. Engineering Failure
Analysis, 92, pp.50-60
Rezvani, M.A., Javanmardi, D. and Mostaghim, P., 2018. Diagnosis of EMD645 diesel engine
connection rod failure through modal testing and finite element modeling. Engineering Failure
Analysis, 92, pp.50-60
Zhang, J., Qiu, Z. and Zhang, Y., 2017. Finite Element Analysis of EA 113 Gasoline Engine
Connecting Rod. International Journal of Mechanical Engineering and Applications, 5(4), p.208
Zhao, Y., Feng, J., Zhou, Q. and Peng, X., 2018. Blade fracture analysis of a motor cooling fan
in a high-speed reciprocating compressor package. Engineering Failure Analysis, 89, pp.88-99
Zhu, X., Xu, J., Liu, Y., Cen, B., Lu, X. and Zeng, Z., 2017. Failure analysis of a failed
connecting rod cap and connecting bolts of a reciprocating compressor. Engineering Failure
Analysis, 74, pp.218-227
reciprocating gas compressor packages at Arrow Energy. The APPEA Journal, 58(1), pp.168-
181
Parulekar, P.S., Hudson, R. and Boyd, H., 2018. Significant reliability improvements in
reciprocating gas compressor packages at Arrow Energy. The APPEA Journal, 58(1), pp.168-
181
Rezvani, M.A., Javanmardi, D. and Mostaghim, P., 2018. Diagnosis of EMD645 diesel engine
connection rod failure through modal testing and finite element modeling. Engineering Failure
Analysis, 92, pp.50-60
Rezvani, M.A., Javanmardi, D. and Mostaghim, P., 2018. Diagnosis of EMD645 diesel engine
connection rod failure through modal testing and finite element modeling. Engineering Failure
Analysis, 92, pp.50-60
Zhang, J., Qiu, Z. and Zhang, Y., 2017. Finite Element Analysis of EA 113 Gasoline Engine
Connecting Rod. International Journal of Mechanical Engineering and Applications, 5(4), p.208
Zhao, Y., Feng, J., Zhou, Q. and Peng, X., 2018. Blade fracture analysis of a motor cooling fan
in a high-speed reciprocating compressor package. Engineering Failure Analysis, 89, pp.88-99
Zhu, X., Xu, J., Liu, Y., Cen, B., Lu, X. and Zeng, Z., 2017. Failure analysis of a failed
connecting rod cap and connecting bolts of a reciprocating compressor. Engineering Failure
Analysis, 74, pp.218-227
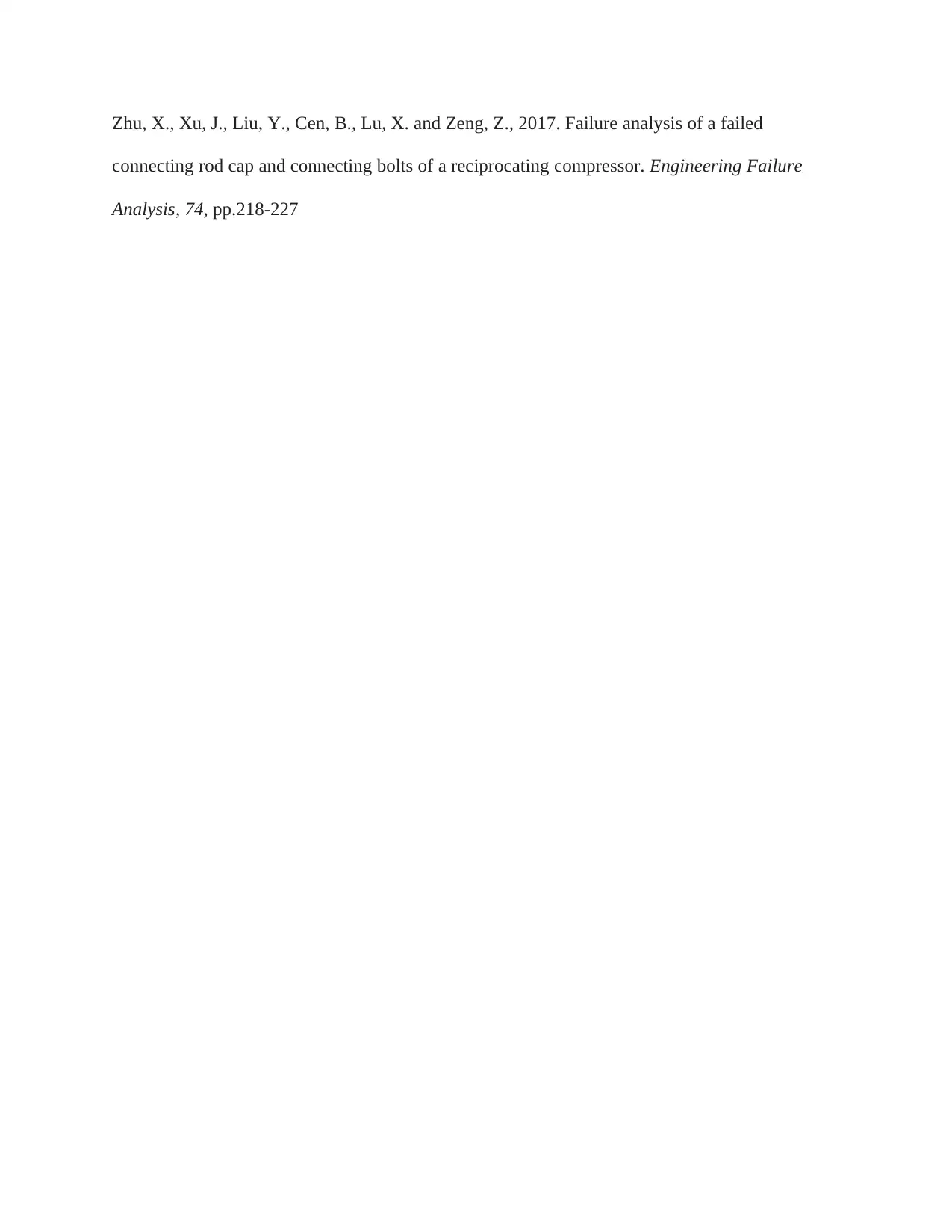
Zhu, X., Xu, J., Liu, Y., Cen, B., Lu, X. and Zeng, Z., 2017. Failure analysis of a failed
connecting rod cap and connecting bolts of a reciprocating compressor. Engineering Failure
Analysis, 74, pp.218-227
connecting rod cap and connecting bolts of a reciprocating compressor. Engineering Failure
Analysis, 74, pp.218-227
1 out of 33

Your All-in-One AI-Powered Toolkit for Academic Success.
+13062052269
info@desklib.com
Available 24*7 on WhatsApp / Email
Unlock your academic potential
© 2024 | Zucol Services PVT LTD | All rights reserved.