GNED 126 - Occupation Health and Safety: Chemical Hazards Report
VerifiedAdded on 2022/10/15
|8
|1927
|23
Report
AI Summary
This report addresses the issue of chemical hazards in the workplace, focusing on the potential health impacts of exposure to various chemical substances in the form of gases, liquids, and solids. It defines chemical hazards, identifies different types such as paints, acids, and cleaning products, and di...
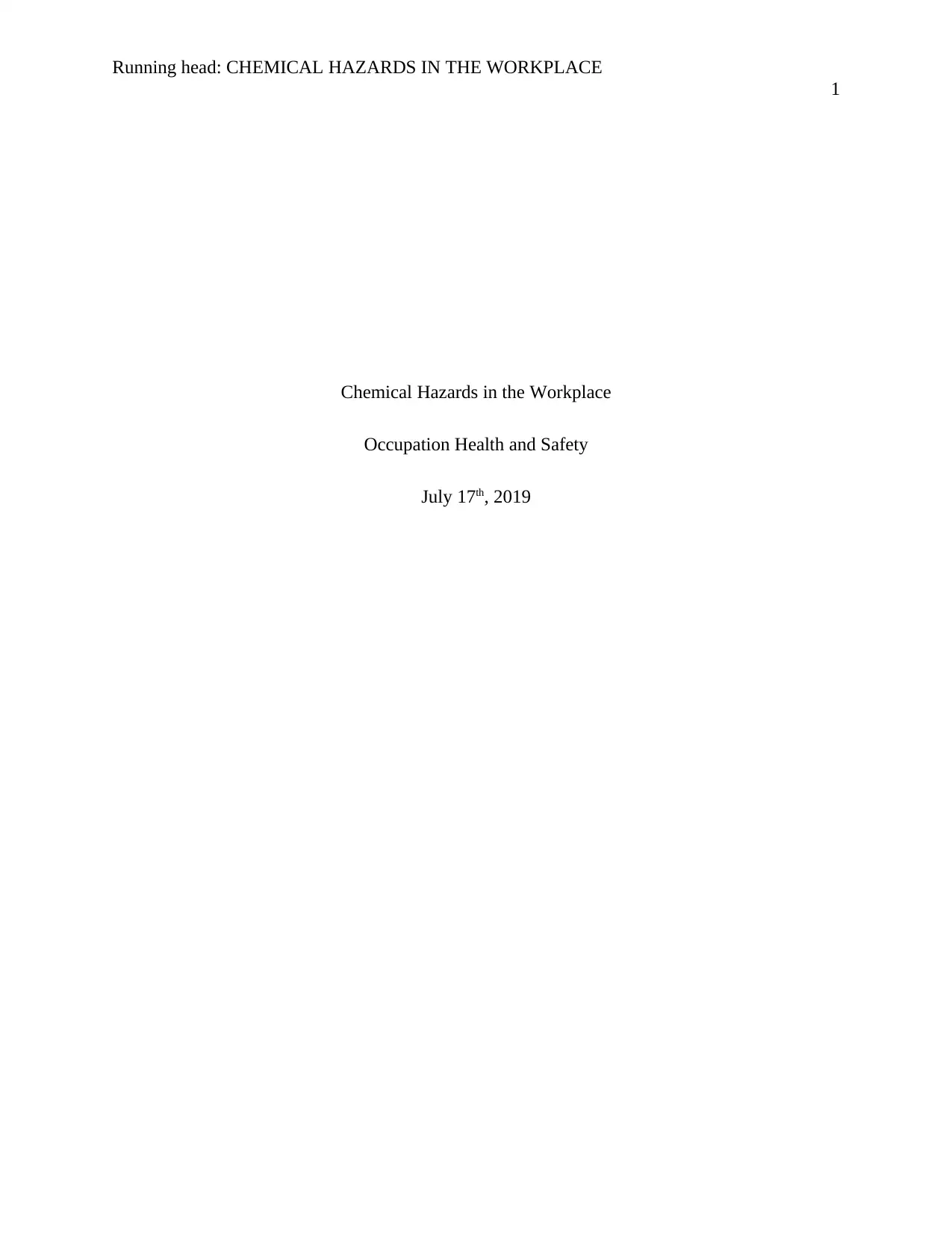
Running head: CHEMICAL HAZARDS IN THE WORKPLACE
1
Chemical Hazards in the Workplace
Occupation Health and Safety
July 17th, 2019
1
Chemical Hazards in the Workplace
Occupation Health and Safety
July 17th, 2019
Paraphrase This Document
Need a fresh take? Get an instant paraphrase of this document with our AI Paraphraser
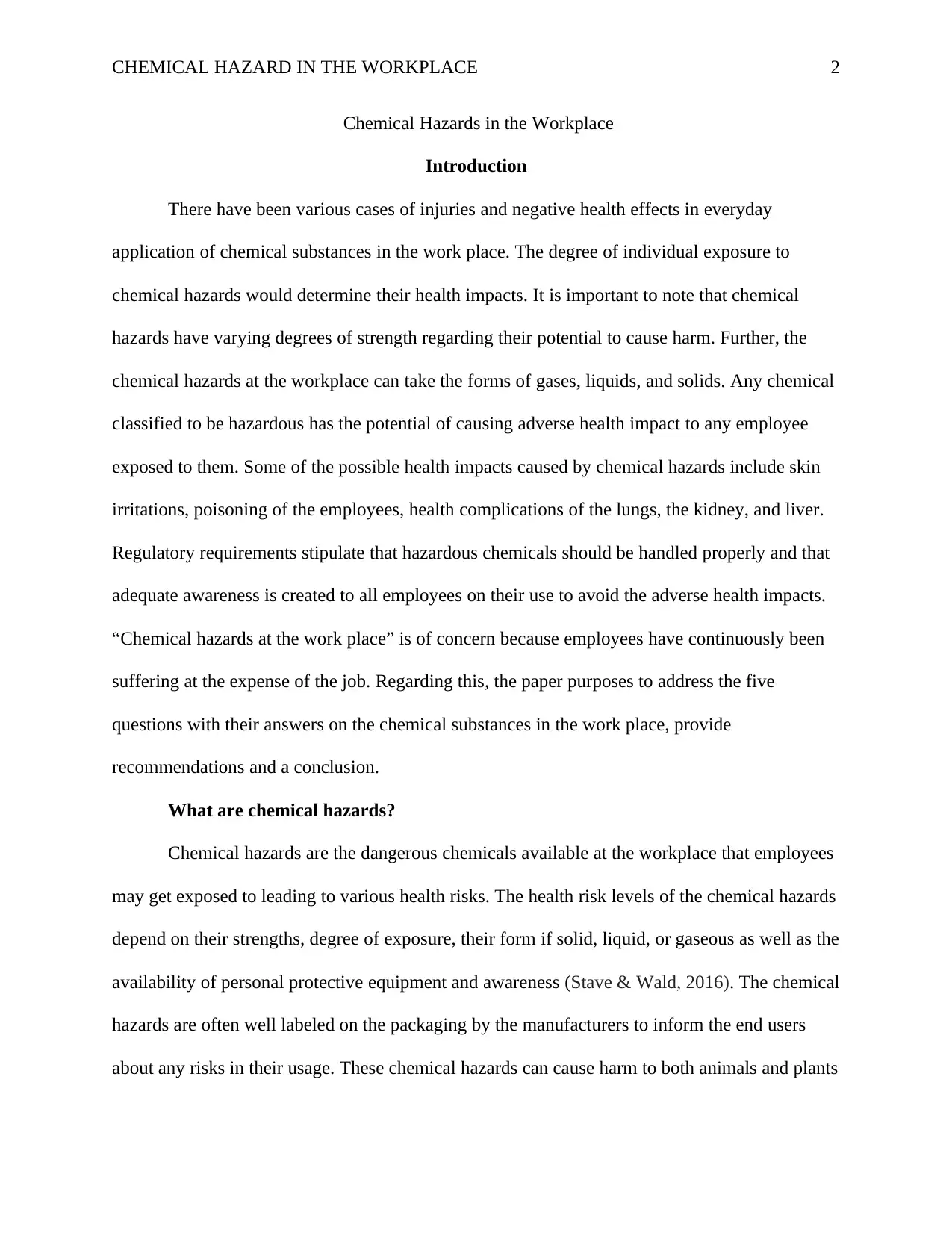
CHEMICAL HAZARD IN THE WORKPLACE 2
Chemical Hazards in the Workplace
Introduction
There have been various cases of injuries and negative health effects in everyday
application of chemical substances in the work place. The degree of individual exposure to
chemical hazards would determine their health impacts. It is important to note that chemical
hazards have varying degrees of strength regarding their potential to cause harm. Further, the
chemical hazards at the workplace can take the forms of gases, liquids, and solids. Any chemical
classified to be hazardous has the potential of causing adverse health impact to any employee
exposed to them. Some of the possible health impacts caused by chemical hazards include skin
irritations, poisoning of the employees, health complications of the lungs, the kidney, and liver.
Regulatory requirements stipulate that hazardous chemicals should be handled properly and that
adequate awareness is created to all employees on their use to avoid the adverse health impacts.
“Chemical hazards at the work place” is of concern because employees have continuously been
suffering at the expense of the job. Regarding this, the paper purposes to address the five
questions with their answers on the chemical substances in the work place, provide
recommendations and a conclusion.
What are chemical hazards?
Chemical hazards are the dangerous chemicals available at the workplace that employees
may get exposed to leading to various health risks. The health risk levels of the chemical hazards
depend on their strengths, degree of exposure, their form if solid, liquid, or gaseous as well as the
availability of personal protective equipment and awareness (Stave & Wald, 2016). The chemical
hazards are often well labeled on the packaging by the manufacturers to inform the end users
about any risks in their usage. These chemical hazards can cause harm to both animals and plants
Chemical Hazards in the Workplace
Introduction
There have been various cases of injuries and negative health effects in everyday
application of chemical substances in the work place. The degree of individual exposure to
chemical hazards would determine their health impacts. It is important to note that chemical
hazards have varying degrees of strength regarding their potential to cause harm. Further, the
chemical hazards at the workplace can take the forms of gases, liquids, and solids. Any chemical
classified to be hazardous has the potential of causing adverse health impact to any employee
exposed to them. Some of the possible health impacts caused by chemical hazards include skin
irritations, poisoning of the employees, health complications of the lungs, the kidney, and liver.
Regulatory requirements stipulate that hazardous chemicals should be handled properly and that
adequate awareness is created to all employees on their use to avoid the adverse health impacts.
“Chemical hazards at the work place” is of concern because employees have continuously been
suffering at the expense of the job. Regarding this, the paper purposes to address the five
questions with their answers on the chemical substances in the work place, provide
recommendations and a conclusion.
What are chemical hazards?
Chemical hazards are the dangerous chemicals available at the workplace that employees
may get exposed to leading to various health risks. The health risk levels of the chemical hazards
depend on their strengths, degree of exposure, their form if solid, liquid, or gaseous as well as the
availability of personal protective equipment and awareness (Stave & Wald, 2016). The chemical
hazards are often well labeled on the packaging by the manufacturers to inform the end users
about any risks in their usage. These chemical hazards can cause harm to both animals and plants
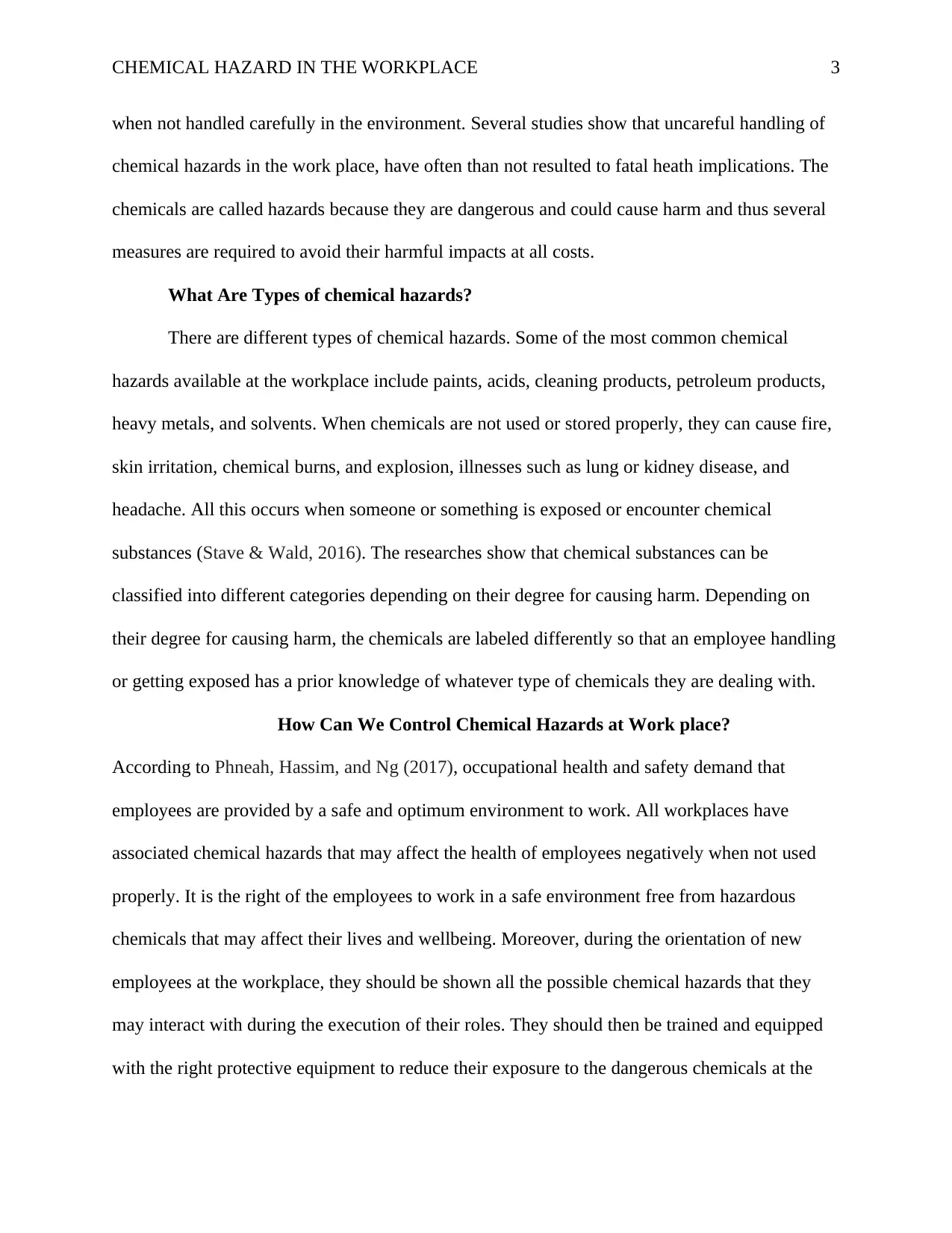
CHEMICAL HAZARD IN THE WORKPLACE 3
when not handled carefully in the environment. Several studies show that uncareful handling of
chemical hazards in the work place, have often than not resulted to fatal heath implications. The
chemicals are called hazards because they are dangerous and could cause harm and thus several
measures are required to avoid their harmful impacts at all costs.
What Are Types of chemical hazards?
There are different types of chemical hazards. Some of the most common chemical
hazards available at the workplace include paints, acids, cleaning products, petroleum products,
heavy metals, and solvents. When chemicals are not used or stored properly, they can cause fire,
skin irritation, chemical burns, and explosion, illnesses such as lung or kidney disease, and
headache. All this occurs when someone or something is exposed or encounter chemical
substances (Stave & Wald, 2016). The researches show that chemical substances can be
classified into different categories depending on their degree for causing harm. Depending on
their degree for causing harm, the chemicals are labeled differently so that an employee handling
or getting exposed has a prior knowledge of whatever type of chemicals they are dealing with.
How Can We Control Chemical Hazards at Work place?
According to Phneah, Hassim, and Ng (2017), occupational health and safety demand that
employees are provided by a safe and optimum environment to work. All workplaces have
associated chemical hazards that may affect the health of employees negatively when not used
properly. It is the right of the employees to work in a safe environment free from hazardous
chemicals that may affect their lives and wellbeing. Moreover, during the orientation of new
employees at the workplace, they should be shown all the possible chemical hazards that they
may interact with during the execution of their roles. They should then be trained and equipped
with the right protective equipment to reduce their exposure to the dangerous chemicals at the
when not handled carefully in the environment. Several studies show that uncareful handling of
chemical hazards in the work place, have often than not resulted to fatal heath implications. The
chemicals are called hazards because they are dangerous and could cause harm and thus several
measures are required to avoid their harmful impacts at all costs.
What Are Types of chemical hazards?
There are different types of chemical hazards. Some of the most common chemical
hazards available at the workplace include paints, acids, cleaning products, petroleum products,
heavy metals, and solvents. When chemicals are not used or stored properly, they can cause fire,
skin irritation, chemical burns, and explosion, illnesses such as lung or kidney disease, and
headache. All this occurs when someone or something is exposed or encounter chemical
substances (Stave & Wald, 2016). The researches show that chemical substances can be
classified into different categories depending on their degree for causing harm. Depending on
their degree for causing harm, the chemicals are labeled differently so that an employee handling
or getting exposed has a prior knowledge of whatever type of chemicals they are dealing with.
How Can We Control Chemical Hazards at Work place?
According to Phneah, Hassim, and Ng (2017), occupational health and safety demand that
employees are provided by a safe and optimum environment to work. All workplaces have
associated chemical hazards that may affect the health of employees negatively when not used
properly. It is the right of the employees to work in a safe environment free from hazardous
chemicals that may affect their lives and wellbeing. Moreover, during the orientation of new
employees at the workplace, they should be shown all the possible chemical hazards that they
may interact with during the execution of their roles. They should then be trained and equipped
with the right protective equipment to reduce their exposure to the dangerous chemicals at the
⊘ This is a preview!⊘
Do you want full access?
Subscribe today to unlock all pages.

Trusted by 1+ million students worldwide
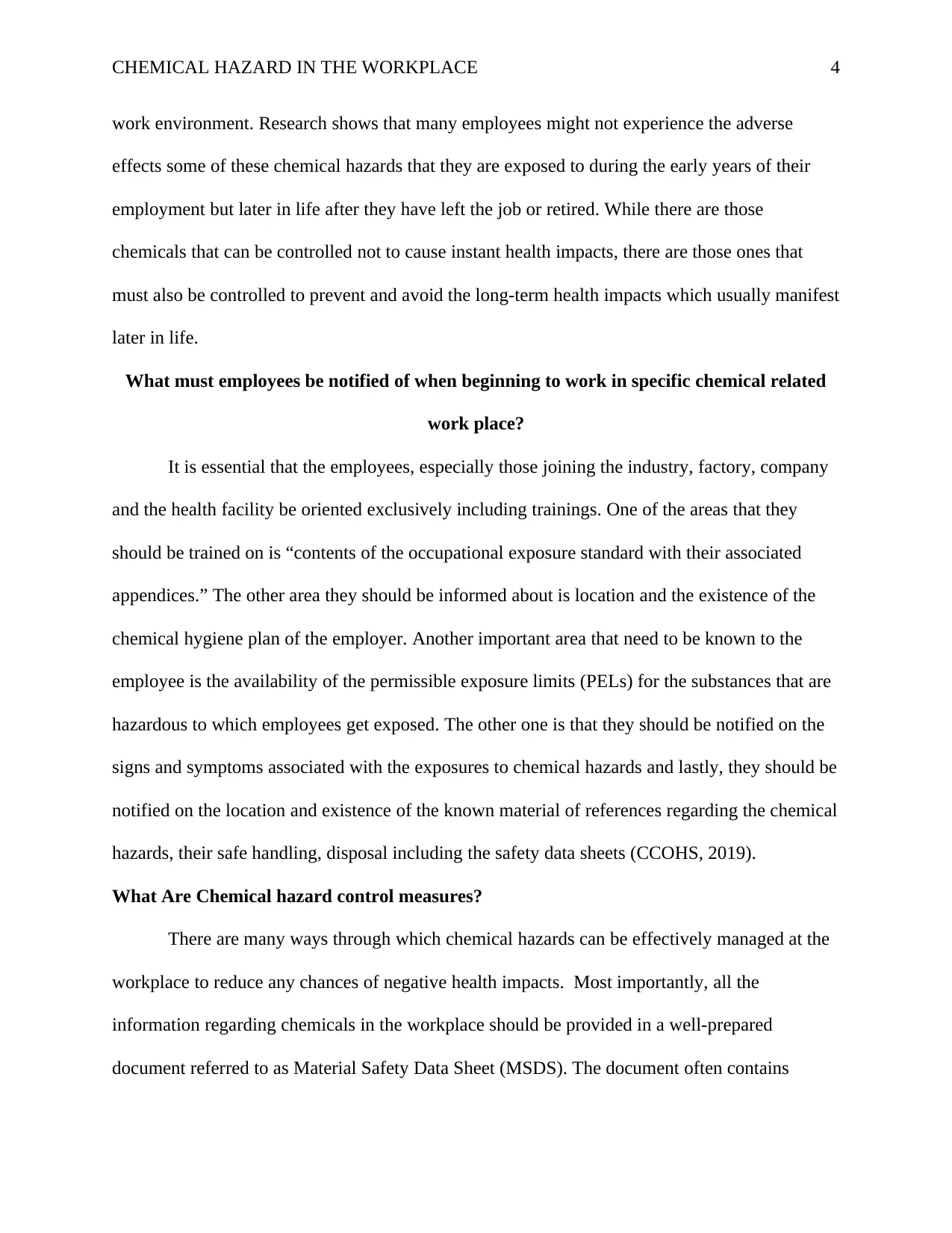
CHEMICAL HAZARD IN THE WORKPLACE 4
work environment. Research shows that many employees might not experience the adverse
effects some of these chemical hazards that they are exposed to during the early years of their
employment but later in life after they have left the job or retired. While there are those
chemicals that can be controlled not to cause instant health impacts, there are those ones that
must also be controlled to prevent and avoid the long-term health impacts which usually manifest
later in life.
What must employees be notified of when beginning to work in specific chemical related
work place?
It is essential that the employees, especially those joining the industry, factory, company
and the health facility be oriented exclusively including trainings. One of the areas that they
should be trained on is “contents of the occupational exposure standard with their associated
appendices.” The other area they should be informed about is location and the existence of the
chemical hygiene plan of the employer. Another important area that need to be known to the
employee is the availability of the permissible exposure limits (PELs) for the substances that are
hazardous to which employees get exposed. The other one is that they should be notified on the
signs and symptoms associated with the exposures to chemical hazards and lastly, they should be
notified on the location and existence of the known material of references regarding the chemical
hazards, their safe handling, disposal including the safety data sheets (CCOHS, 2019).
What Are Chemical hazard control measures?
There are many ways through which chemical hazards can be effectively managed at the
workplace to reduce any chances of negative health impacts. Most importantly, all the
information regarding chemicals in the workplace should be provided in a well-prepared
document referred to as Material Safety Data Sheet (MSDS). The document often contains
work environment. Research shows that many employees might not experience the adverse
effects some of these chemical hazards that they are exposed to during the early years of their
employment but later in life after they have left the job or retired. While there are those
chemicals that can be controlled not to cause instant health impacts, there are those ones that
must also be controlled to prevent and avoid the long-term health impacts which usually manifest
later in life.
What must employees be notified of when beginning to work in specific chemical related
work place?
It is essential that the employees, especially those joining the industry, factory, company
and the health facility be oriented exclusively including trainings. One of the areas that they
should be trained on is “contents of the occupational exposure standard with their associated
appendices.” The other area they should be informed about is location and the existence of the
chemical hygiene plan of the employer. Another important area that need to be known to the
employee is the availability of the permissible exposure limits (PELs) for the substances that are
hazardous to which employees get exposed. The other one is that they should be notified on the
signs and symptoms associated with the exposures to chemical hazards and lastly, they should be
notified on the location and existence of the known material of references regarding the chemical
hazards, their safe handling, disposal including the safety data sheets (CCOHS, 2019).
What Are Chemical hazard control measures?
There are many ways through which chemical hazards can be effectively managed at the
workplace to reduce any chances of negative health impacts. Most importantly, all the
information regarding chemicals in the workplace should be provided in a well-prepared
document referred to as Material Safety Data Sheet (MSDS). The document often contains
Paraphrase This Document
Need a fresh take? Get an instant paraphrase of this document with our AI Paraphraser
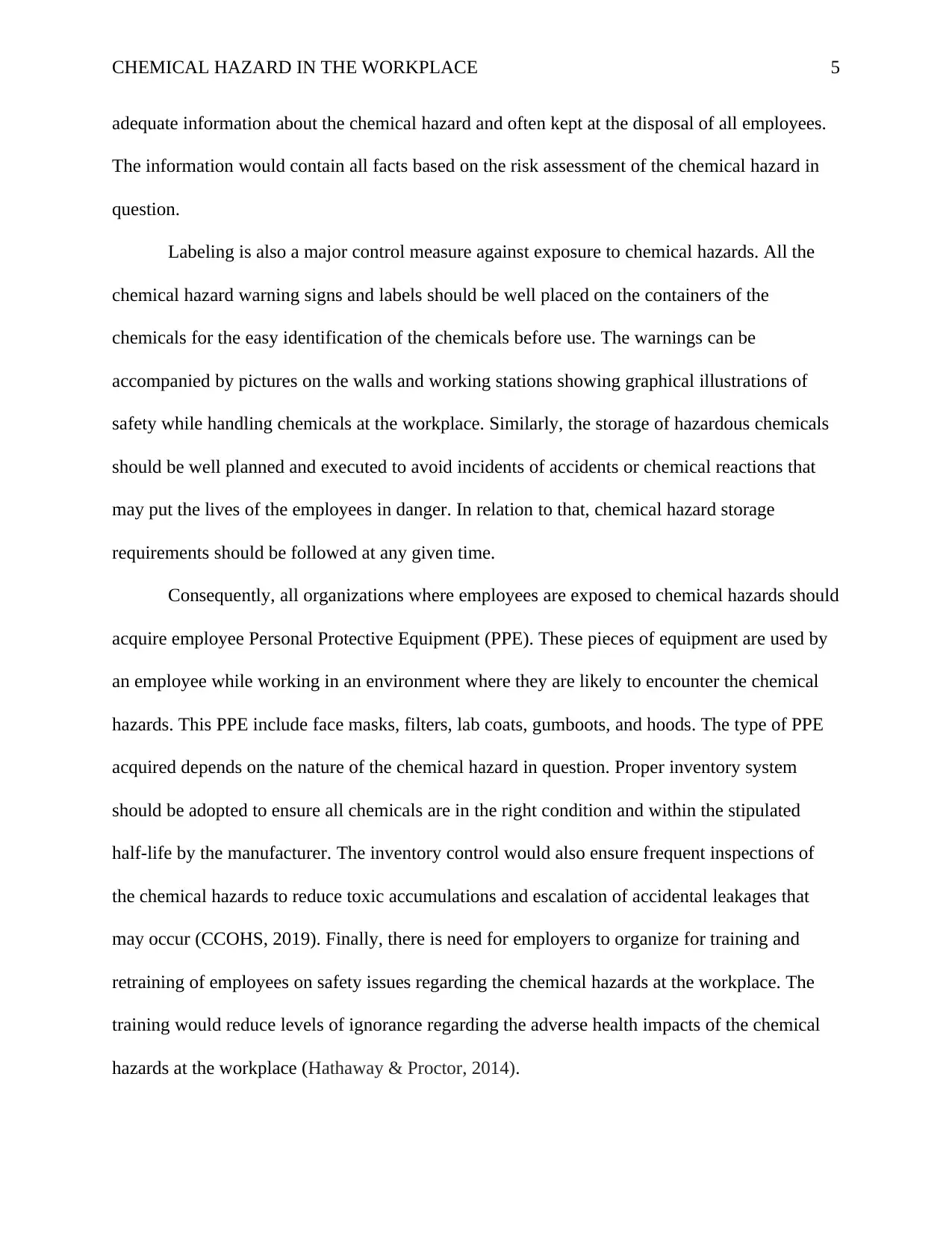
CHEMICAL HAZARD IN THE WORKPLACE 5
adequate information about the chemical hazard and often kept at the disposal of all employees.
The information would contain all facts based on the risk assessment of the chemical hazard in
question.
Labeling is also a major control measure against exposure to chemical hazards. All the
chemical hazard warning signs and labels should be well placed on the containers of the
chemicals for the easy identification of the chemicals before use. The warnings can be
accompanied by pictures on the walls and working stations showing graphical illustrations of
safety while handling chemicals at the workplace. Similarly, the storage of hazardous chemicals
should be well planned and executed to avoid incidents of accidents or chemical reactions that
may put the lives of the employees in danger. In relation to that, chemical hazard storage
requirements should be followed at any given time.
Consequently, all organizations where employees are exposed to chemical hazards should
acquire employee Personal Protective Equipment (PPE). These pieces of equipment are used by
an employee while working in an environment where they are likely to encounter the chemical
hazards. This PPE include face masks, filters, lab coats, gumboots, and hoods. The type of PPE
acquired depends on the nature of the chemical hazard in question. Proper inventory system
should be adopted to ensure all chemicals are in the right condition and within the stipulated
half-life by the manufacturer. The inventory control would also ensure frequent inspections of
the chemical hazards to reduce toxic accumulations and escalation of accidental leakages that
may occur (CCOHS, 2019). Finally, there is need for employers to organize for training and
retraining of employees on safety issues regarding the chemical hazards at the workplace. The
training would reduce levels of ignorance regarding the adverse health impacts of the chemical
hazards at the workplace (Hathaway & Proctor, 2014).
adequate information about the chemical hazard and often kept at the disposal of all employees.
The information would contain all facts based on the risk assessment of the chemical hazard in
question.
Labeling is also a major control measure against exposure to chemical hazards. All the
chemical hazard warning signs and labels should be well placed on the containers of the
chemicals for the easy identification of the chemicals before use. The warnings can be
accompanied by pictures on the walls and working stations showing graphical illustrations of
safety while handling chemicals at the workplace. Similarly, the storage of hazardous chemicals
should be well planned and executed to avoid incidents of accidents or chemical reactions that
may put the lives of the employees in danger. In relation to that, chemical hazard storage
requirements should be followed at any given time.
Consequently, all organizations where employees are exposed to chemical hazards should
acquire employee Personal Protective Equipment (PPE). These pieces of equipment are used by
an employee while working in an environment where they are likely to encounter the chemical
hazards. This PPE include face masks, filters, lab coats, gumboots, and hoods. The type of PPE
acquired depends on the nature of the chemical hazard in question. Proper inventory system
should be adopted to ensure all chemicals are in the right condition and within the stipulated
half-life by the manufacturer. The inventory control would also ensure frequent inspections of
the chemical hazards to reduce toxic accumulations and escalation of accidental leakages that
may occur (CCOHS, 2019). Finally, there is need for employers to organize for training and
retraining of employees on safety issues regarding the chemical hazards at the workplace. The
training would reduce levels of ignorance regarding the adverse health impacts of the chemical
hazards at the workplace (Hathaway & Proctor, 2014).
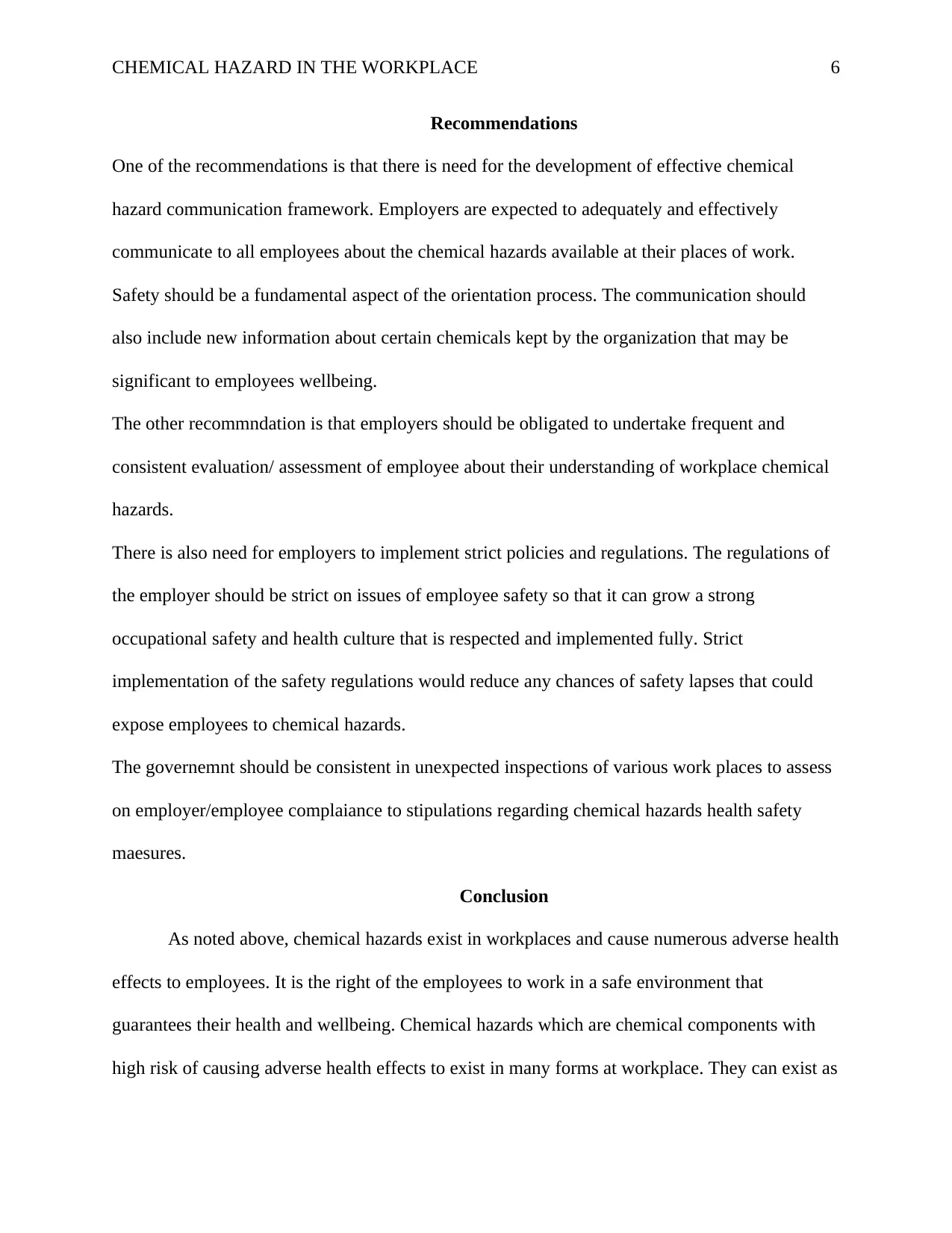
CHEMICAL HAZARD IN THE WORKPLACE 6
Recommendations
One of the recommendations is that there is need for the development of effective chemical
hazard communication framework. Employers are expected to adequately and effectively
communicate to all employees about the chemical hazards available at their places of work.
Safety should be a fundamental aspect of the orientation process. The communication should
also include new information about certain chemicals kept by the organization that may be
significant to employees wellbeing.
The other recommndation is that employers should be obligated to undertake frequent and
consistent evaluation/ assessment of employee about their understanding of workplace chemical
hazards.
There is also need for employers to implement strict policies and regulations. The regulations of
the employer should be strict on issues of employee safety so that it can grow a strong
occupational safety and health culture that is respected and implemented fully. Strict
implementation of the safety regulations would reduce any chances of safety lapses that could
expose employees to chemical hazards.
The governemnt should be consistent in unexpected inspections of various work places to assess
on employer/employee complaiance to stipulations regarding chemical hazards health safety
maesures.
Conclusion
As noted above, chemical hazards exist in workplaces and cause numerous adverse health
effects to employees. It is the right of the employees to work in a safe environment that
guarantees their health and wellbeing. Chemical hazards which are chemical components with
high risk of causing adverse health effects to exist in many forms at workplace. They can exist as
Recommendations
One of the recommendations is that there is need for the development of effective chemical
hazard communication framework. Employers are expected to adequately and effectively
communicate to all employees about the chemical hazards available at their places of work.
Safety should be a fundamental aspect of the orientation process. The communication should
also include new information about certain chemicals kept by the organization that may be
significant to employees wellbeing.
The other recommndation is that employers should be obligated to undertake frequent and
consistent evaluation/ assessment of employee about their understanding of workplace chemical
hazards.
There is also need for employers to implement strict policies and regulations. The regulations of
the employer should be strict on issues of employee safety so that it can grow a strong
occupational safety and health culture that is respected and implemented fully. Strict
implementation of the safety regulations would reduce any chances of safety lapses that could
expose employees to chemical hazards.
The governemnt should be consistent in unexpected inspections of various work places to assess
on employer/employee complaiance to stipulations regarding chemical hazards health safety
maesures.
Conclusion
As noted above, chemical hazards exist in workplaces and cause numerous adverse health
effects to employees. It is the right of the employees to work in a safe environment that
guarantees their health and wellbeing. Chemical hazards which are chemical components with
high risk of causing adverse health effects to exist in many forms at workplace. They can exist as
⊘ This is a preview!⊘
Do you want full access?
Subscribe today to unlock all pages.

Trusted by 1+ million students worldwide
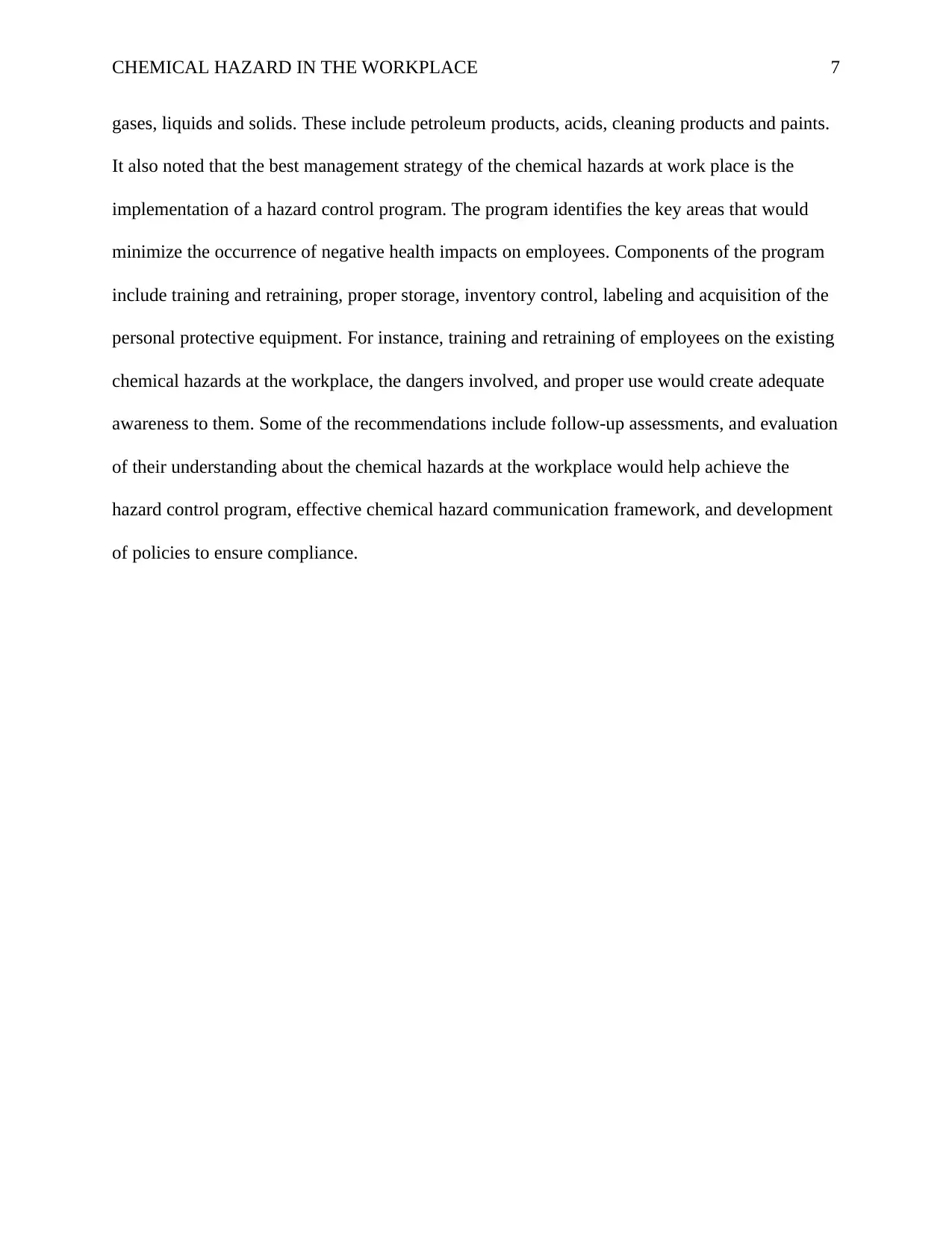
CHEMICAL HAZARD IN THE WORKPLACE 7
gases, liquids and solids. These include petroleum products, acids, cleaning products and paints.
It also noted that the best management strategy of the chemical hazards at work place is the
implementation of a hazard control program. The program identifies the key areas that would
minimize the occurrence of negative health impacts on employees. Components of the program
include training and retraining, proper storage, inventory control, labeling and acquisition of the
personal protective equipment. For instance, training and retraining of employees on the existing
chemical hazards at the workplace, the dangers involved, and proper use would create adequate
awareness to them. Some of the recommendations include follow-up assessments, and evaluation
of their understanding about the chemical hazards at the workplace would help achieve the
hazard control program, effective chemical hazard communication framework, and development
of policies to ensure compliance.
gases, liquids and solids. These include petroleum products, acids, cleaning products and paints.
It also noted that the best management strategy of the chemical hazards at work place is the
implementation of a hazard control program. The program identifies the key areas that would
minimize the occurrence of negative health impacts on employees. Components of the program
include training and retraining, proper storage, inventory control, labeling and acquisition of the
personal protective equipment. For instance, training and retraining of employees on the existing
chemical hazards at the workplace, the dangers involved, and proper use would create adequate
awareness to them. Some of the recommendations include follow-up assessments, and evaluation
of their understanding about the chemical hazards at the workplace would help achieve the
hazard control program, effective chemical hazard communication framework, and development
of policies to ensure compliance.
Paraphrase This Document
Need a fresh take? Get an instant paraphrase of this document with our AI Paraphraser
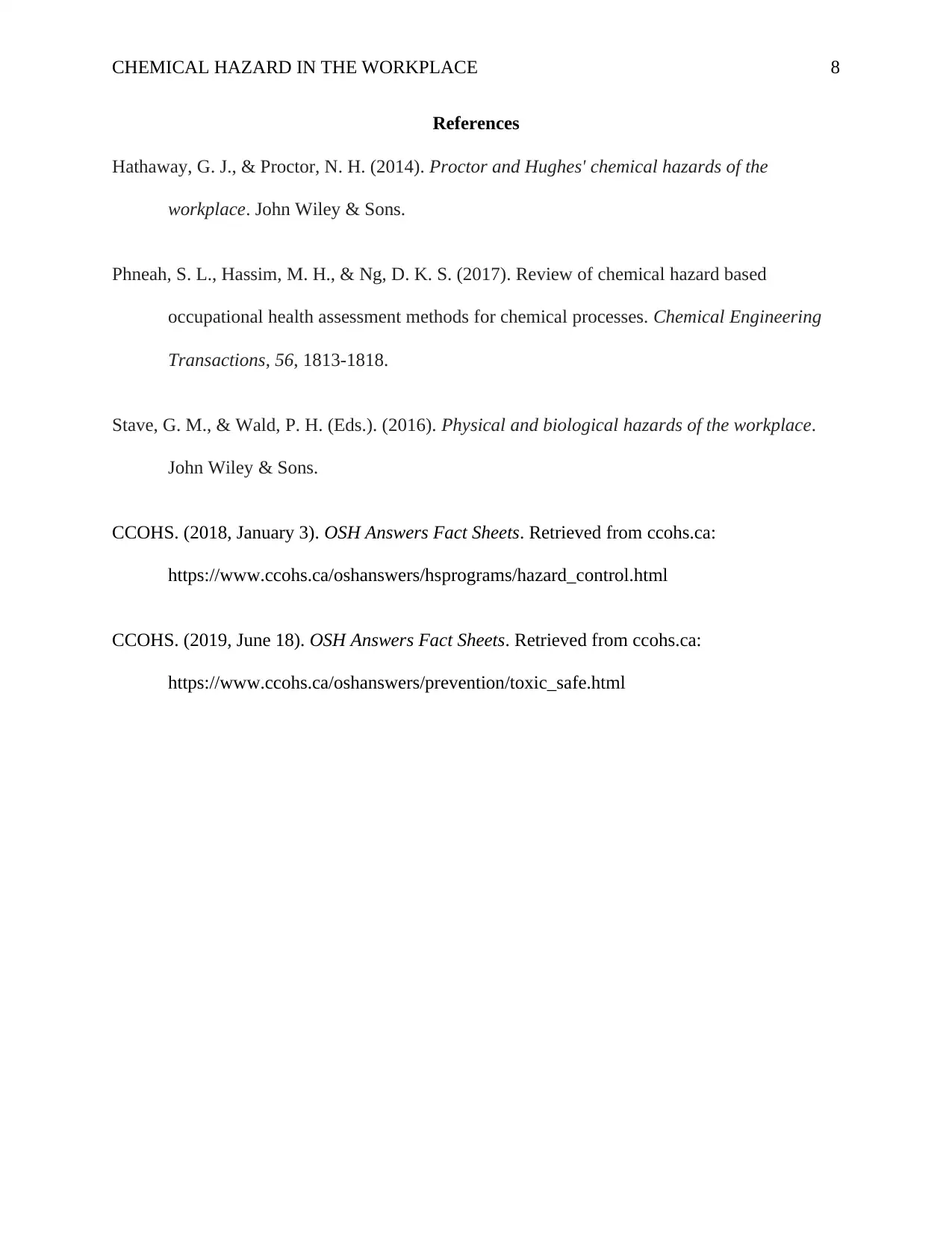
CHEMICAL HAZARD IN THE WORKPLACE 8
References
Hathaway, G. J., & Proctor, N. H. (2014). Proctor and Hughes' chemical hazards of the
workplace. John Wiley & Sons.
Phneah, S. L., Hassim, M. H., & Ng, D. K. S. (2017). Review of chemical hazard based
occupational health assessment methods for chemical processes. Chemical Engineering
Transactions, 56, 1813-1818.
Stave, G. M., & Wald, P. H. (Eds.). (2016). Physical and biological hazards of the workplace.
John Wiley & Sons.
CCOHS. (2018, January 3). OSH Answers Fact Sheets. Retrieved from ccohs.ca:
https://www.ccohs.ca/oshanswers/hsprograms/hazard_control.html
CCOHS. (2019, June 18). OSH Answers Fact Sheets. Retrieved from ccohs.ca:
https://www.ccohs.ca/oshanswers/prevention/toxic_safe.html
References
Hathaway, G. J., & Proctor, N. H. (2014). Proctor and Hughes' chemical hazards of the
workplace. John Wiley & Sons.
Phneah, S. L., Hassim, M. H., & Ng, D. K. S. (2017). Review of chemical hazard based
occupational health assessment methods for chemical processes. Chemical Engineering
Transactions, 56, 1813-1818.
Stave, G. M., & Wald, P. H. (Eds.). (2016). Physical and biological hazards of the workplace.
John Wiley & Sons.
CCOHS. (2018, January 3). OSH Answers Fact Sheets. Retrieved from ccohs.ca:
https://www.ccohs.ca/oshanswers/hsprograms/hazard_control.html
CCOHS. (2019, June 18). OSH Answers Fact Sheets. Retrieved from ccohs.ca:
https://www.ccohs.ca/oshanswers/prevention/toxic_safe.html
1 out of 8
Related Documents

Your All-in-One AI-Powered Toolkit for Academic Success.
+13062052269
info@desklib.com
Available 24*7 on WhatsApp / Email
Unlock your academic potential
© 2024 | Zucol Services PVT LTD | All rights reserved.