Modern Construction Projects 301159: Hickory Group Case Study Analysis
VerifiedAdded on 2019/09/22
|11
|2798
|407
Case Study
AI Summary
This case study examines Hickory Group's innovative integrated high-rise build systems (HBS), a modern construction approach. Founded in 1991, Hickory Group has grown significantly, employing over 550 workers. HBS consolidates various building components, such as bathrooms and facades, into prefabricated units, improving efficiency, safety, and reducing waste. The case study highlights the advantages of HBS over conventional methods, including design flexibility, reduced construction time, and enhanced sustainability, as exemplified by the La Trobe Tower project. HBS utilizes lean construction techniques, Enterprise Resource Planning (ERP), and Building Information Modelling (BIM). It also emphasizes worker safety and environmental responsibility. The system minimizes traffic congestion, reduces waste by 90%, and offers a safer construction environment. The case study concludes by emphasizing the future of construction, particularly for high-rise buildings. This case study, contributed by a student, is available on Desklib, a platform offering AI-based study tools.
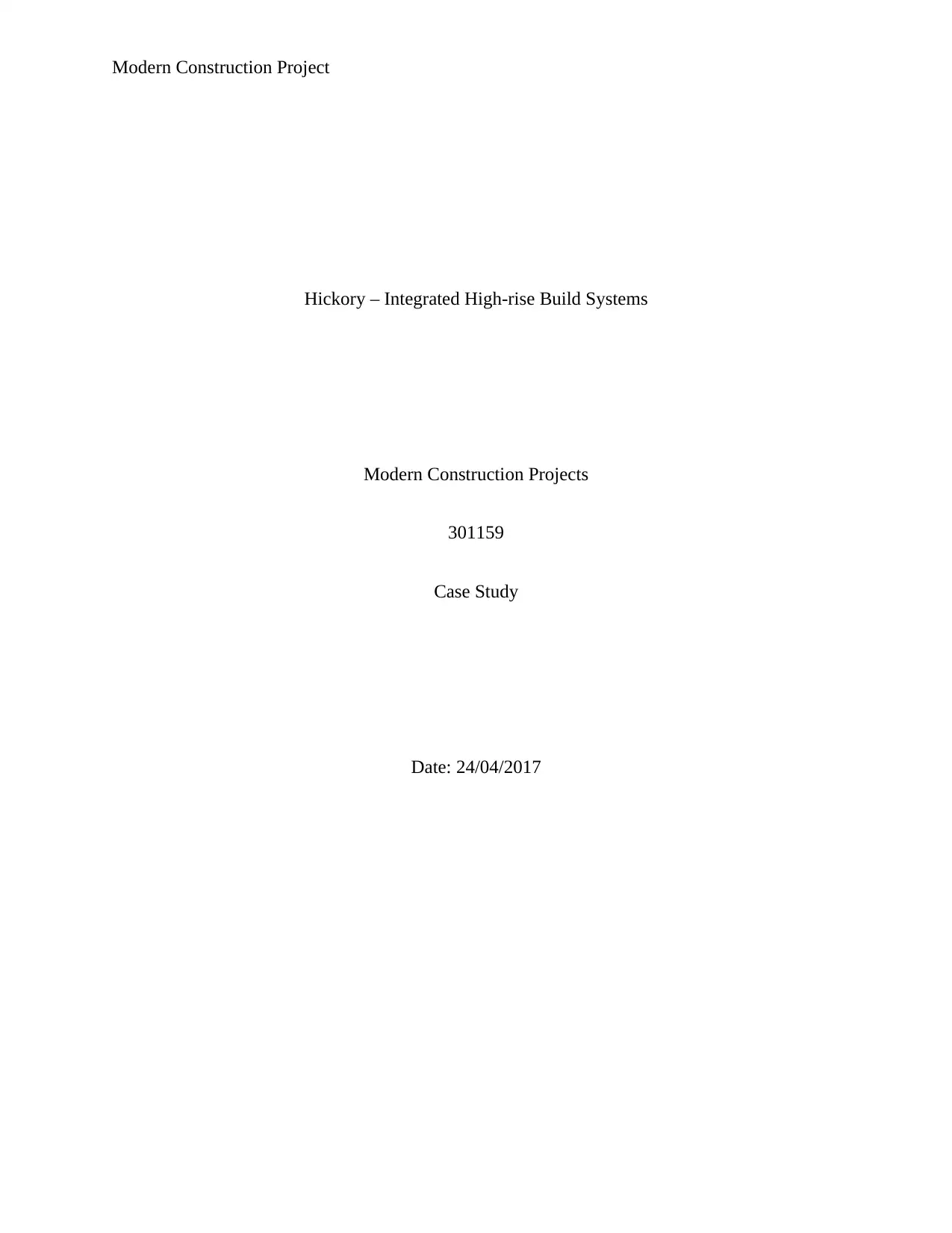
Modern Construction Project
Hickory – Integrated High-rise Build Systems
Modern Construction Projects
301159
Case Study
Date: 24/04/2017
Hickory – Integrated High-rise Build Systems
Modern Construction Projects
301159
Case Study
Date: 24/04/2017
Secure Best Marks with AI Grader
Need help grading? Try our AI Grader for instant feedback on your assignments.
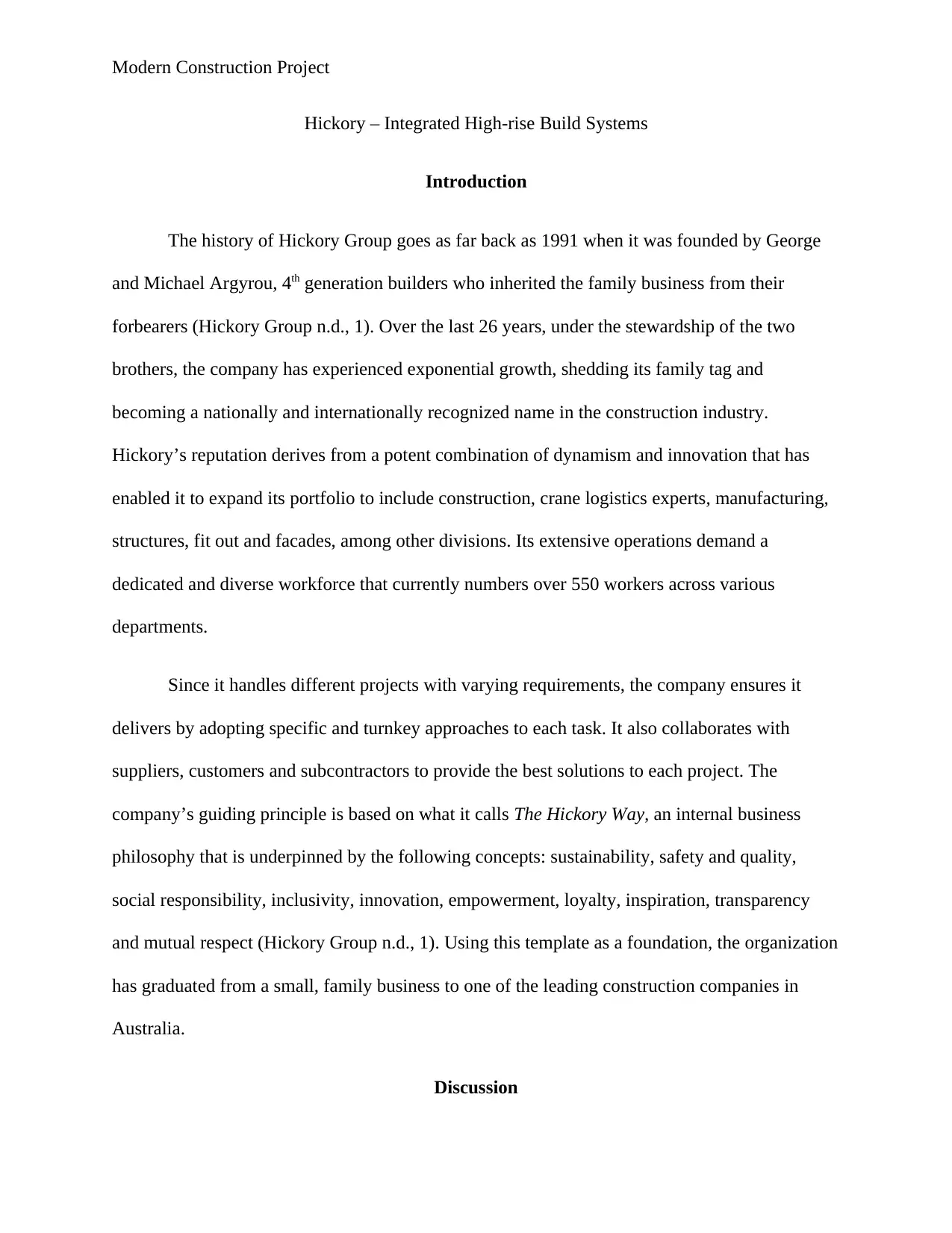
Modern Construction Project
Hickory – Integrated High-rise Build Systems
Introduction
The history of Hickory Group goes as far back as 1991 when it was founded by George
and Michael Argyrou, 4th generation builders who inherited the family business from their
forbearers (Hickory Group n.d., 1). Over the last 26 years, under the stewardship of the two
brothers, the company has experienced exponential growth, shedding its family tag and
becoming a nationally and internationally recognized name in the construction industry.
Hickory’s reputation derives from a potent combination of dynamism and innovation that has
enabled it to expand its portfolio to include construction, crane logistics experts, manufacturing,
structures, fit out and facades, among other divisions. Its extensive operations demand a
dedicated and diverse workforce that currently numbers over 550 workers across various
departments.
Since it handles different projects with varying requirements, the company ensures it
delivers by adopting specific and turnkey approaches to each task. It also collaborates with
suppliers, customers and subcontractors to provide the best solutions to each project. The
company’s guiding principle is based on what it calls The Hickory Way, an internal business
philosophy that is underpinned by the following concepts: sustainability, safety and quality,
social responsibility, inclusivity, innovation, empowerment, loyalty, inspiration, transparency
and mutual respect (Hickory Group n.d., 1). Using this template as a foundation, the organization
has graduated from a small, family business to one of the leading construction companies in
Australia.
Discussion
Hickory – Integrated High-rise Build Systems
Introduction
The history of Hickory Group goes as far back as 1991 when it was founded by George
and Michael Argyrou, 4th generation builders who inherited the family business from their
forbearers (Hickory Group n.d., 1). Over the last 26 years, under the stewardship of the two
brothers, the company has experienced exponential growth, shedding its family tag and
becoming a nationally and internationally recognized name in the construction industry.
Hickory’s reputation derives from a potent combination of dynamism and innovation that has
enabled it to expand its portfolio to include construction, crane logistics experts, manufacturing,
structures, fit out and facades, among other divisions. Its extensive operations demand a
dedicated and diverse workforce that currently numbers over 550 workers across various
departments.
Since it handles different projects with varying requirements, the company ensures it
delivers by adopting specific and turnkey approaches to each task. It also collaborates with
suppliers, customers and subcontractors to provide the best solutions to each project. The
company’s guiding principle is based on what it calls The Hickory Way, an internal business
philosophy that is underpinned by the following concepts: sustainability, safety and quality,
social responsibility, inclusivity, innovation, empowerment, loyalty, inspiration, transparency
and mutual respect (Hickory Group n.d., 1). Using this template as a foundation, the organization
has graduated from a small, family business to one of the leading construction companies in
Australia.
Discussion
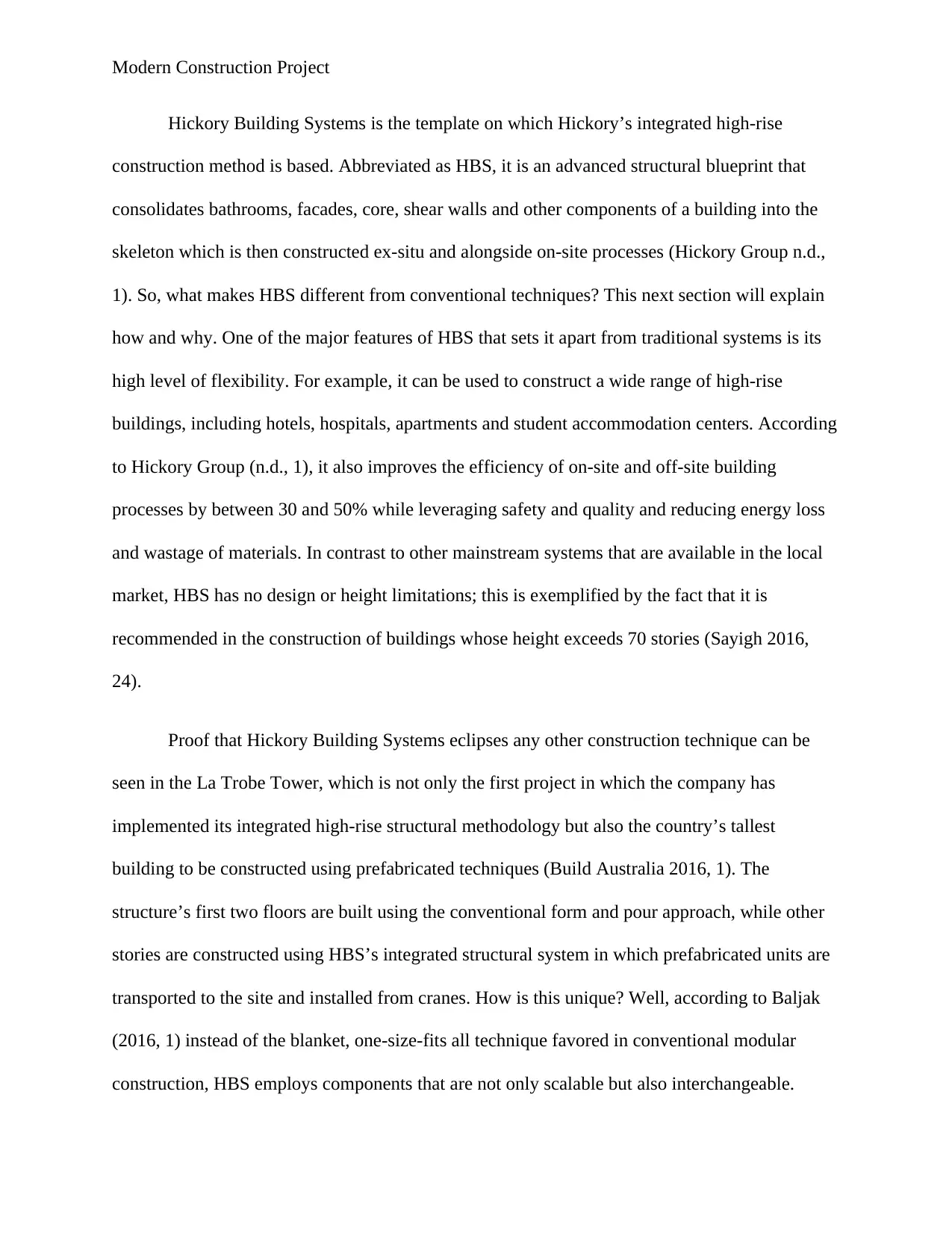
Modern Construction Project
Hickory Building Systems is the template on which Hickory’s integrated high-rise
construction method is based. Abbreviated as HBS, it is an advanced structural blueprint that
consolidates bathrooms, facades, core, shear walls and other components of a building into the
skeleton which is then constructed ex-situ and alongside on-site processes (Hickory Group n.d.,
1). So, what makes HBS different from conventional techniques? This next section will explain
how and why. One of the major features of HBS that sets it apart from traditional systems is its
high level of flexibility. For example, it can be used to construct a wide range of high-rise
buildings, including hotels, hospitals, apartments and student accommodation centers. According
to Hickory Group (n.d., 1), it also improves the efficiency of on-site and off-site building
processes by between 30 and 50% while leveraging safety and quality and reducing energy loss
and wastage of materials. In contrast to other mainstream systems that are available in the local
market, HBS has no design or height limitations; this is exemplified by the fact that it is
recommended in the construction of buildings whose height exceeds 70 stories (Sayigh 2016,
24).
Proof that Hickory Building Systems eclipses any other construction technique can be
seen in the La Trobe Tower, which is not only the first project in which the company has
implemented its integrated high-rise structural methodology but also the country’s tallest
building to be constructed using prefabricated techniques (Build Australia 2016, 1). The
structure’s first two floors are built using the conventional form and pour approach, while other
stories are constructed using HBS’s integrated structural system in which prefabricated units are
transported to the site and installed from cranes. How is this unique? Well, according to Baljak
(2016, 1) instead of the blanket, one-size-fits all technique favored in conventional modular
construction, HBS employs components that are not only scalable but also interchangeable.
Hickory Building Systems is the template on which Hickory’s integrated high-rise
construction method is based. Abbreviated as HBS, it is an advanced structural blueprint that
consolidates bathrooms, facades, core, shear walls and other components of a building into the
skeleton which is then constructed ex-situ and alongside on-site processes (Hickory Group n.d.,
1). So, what makes HBS different from conventional techniques? This next section will explain
how and why. One of the major features of HBS that sets it apart from traditional systems is its
high level of flexibility. For example, it can be used to construct a wide range of high-rise
buildings, including hotels, hospitals, apartments and student accommodation centers. According
to Hickory Group (n.d., 1), it also improves the efficiency of on-site and off-site building
processes by between 30 and 50% while leveraging safety and quality and reducing energy loss
and wastage of materials. In contrast to other mainstream systems that are available in the local
market, HBS has no design or height limitations; this is exemplified by the fact that it is
recommended in the construction of buildings whose height exceeds 70 stories (Sayigh 2016,
24).
Proof that Hickory Building Systems eclipses any other construction technique can be
seen in the La Trobe Tower, which is not only the first project in which the company has
implemented its integrated high-rise structural methodology but also the country’s tallest
building to be constructed using prefabricated techniques (Build Australia 2016, 1). The
structure’s first two floors are built using the conventional form and pour approach, while other
stories are constructed using HBS’s integrated structural system in which prefabricated units are
transported to the site and installed from cranes. How is this unique? Well, according to Baljak
(2016, 1) instead of the blanket, one-size-fits all technique favored in conventional modular
construction, HBS employs components that are not only scalable but also interchangeable.
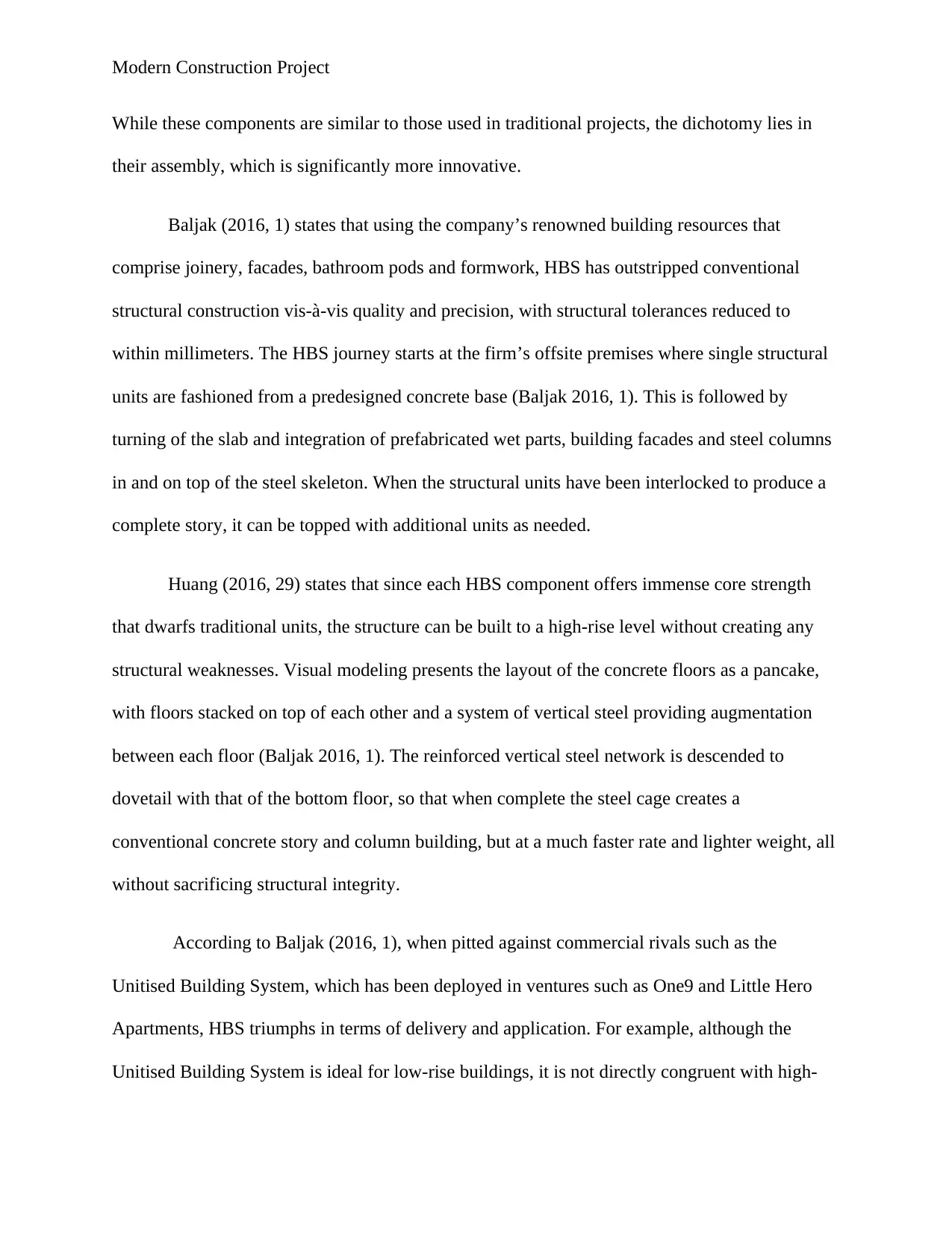
Modern Construction Project
While these components are similar to those used in traditional projects, the dichotomy lies in
their assembly, which is significantly more innovative.
Baljak (2016, 1) states that using the company’s renowned building resources that
comprise joinery, facades, bathroom pods and formwork, HBS has outstripped conventional
structural construction vis-à-vis quality and precision, with structural tolerances reduced to
within millimeters. The HBS journey starts at the firm’s offsite premises where single structural
units are fashioned from a predesigned concrete base (Baljak 2016, 1). This is followed by
turning of the slab and integration of prefabricated wet parts, building facades and steel columns
in and on top of the steel skeleton. When the structural units have been interlocked to produce a
complete story, it can be topped with additional units as needed.
Huang (2016, 29) states that since each HBS component offers immense core strength
that dwarfs traditional units, the structure can be built to a high-rise level without creating any
structural weaknesses. Visual modeling presents the layout of the concrete floors as a pancake,
with floors stacked on top of each other and a system of vertical steel providing augmentation
between each floor (Baljak 2016, 1). The reinforced vertical steel network is descended to
dovetail with that of the bottom floor, so that when complete the steel cage creates a
conventional concrete story and column building, but at a much faster rate and lighter weight, all
without sacrificing structural integrity.
According to Baljak (2016, 1), when pitted against commercial rivals such as the
Unitised Building System, which has been deployed in ventures such as One9 and Little Hero
Apartments, HBS triumphs in terms of delivery and application. For example, although the
Unitised Building System is ideal for low-rise buildings, it is not directly congruent with high-
While these components are similar to those used in traditional projects, the dichotomy lies in
their assembly, which is significantly more innovative.
Baljak (2016, 1) states that using the company’s renowned building resources that
comprise joinery, facades, bathroom pods and formwork, HBS has outstripped conventional
structural construction vis-à-vis quality and precision, with structural tolerances reduced to
within millimeters. The HBS journey starts at the firm’s offsite premises where single structural
units are fashioned from a predesigned concrete base (Baljak 2016, 1). This is followed by
turning of the slab and integration of prefabricated wet parts, building facades and steel columns
in and on top of the steel skeleton. When the structural units have been interlocked to produce a
complete story, it can be topped with additional units as needed.
Huang (2016, 29) states that since each HBS component offers immense core strength
that dwarfs traditional units, the structure can be built to a high-rise level without creating any
structural weaknesses. Visual modeling presents the layout of the concrete floors as a pancake,
with floors stacked on top of each other and a system of vertical steel providing augmentation
between each floor (Baljak 2016, 1). The reinforced vertical steel network is descended to
dovetail with that of the bottom floor, so that when complete the steel cage creates a
conventional concrete story and column building, but at a much faster rate and lighter weight, all
without sacrificing structural integrity.
According to Baljak (2016, 1), when pitted against commercial rivals such as the
Unitised Building System, which has been deployed in ventures such as One9 and Little Hero
Apartments, HBS triumphs in terms of delivery and application. For example, although the
Unitised Building System is ideal for low-rise buildings, it is not directly congruent with high-
Secure Best Marks with AI Grader
Need help grading? Try our AI Grader for instant feedback on your assignments.
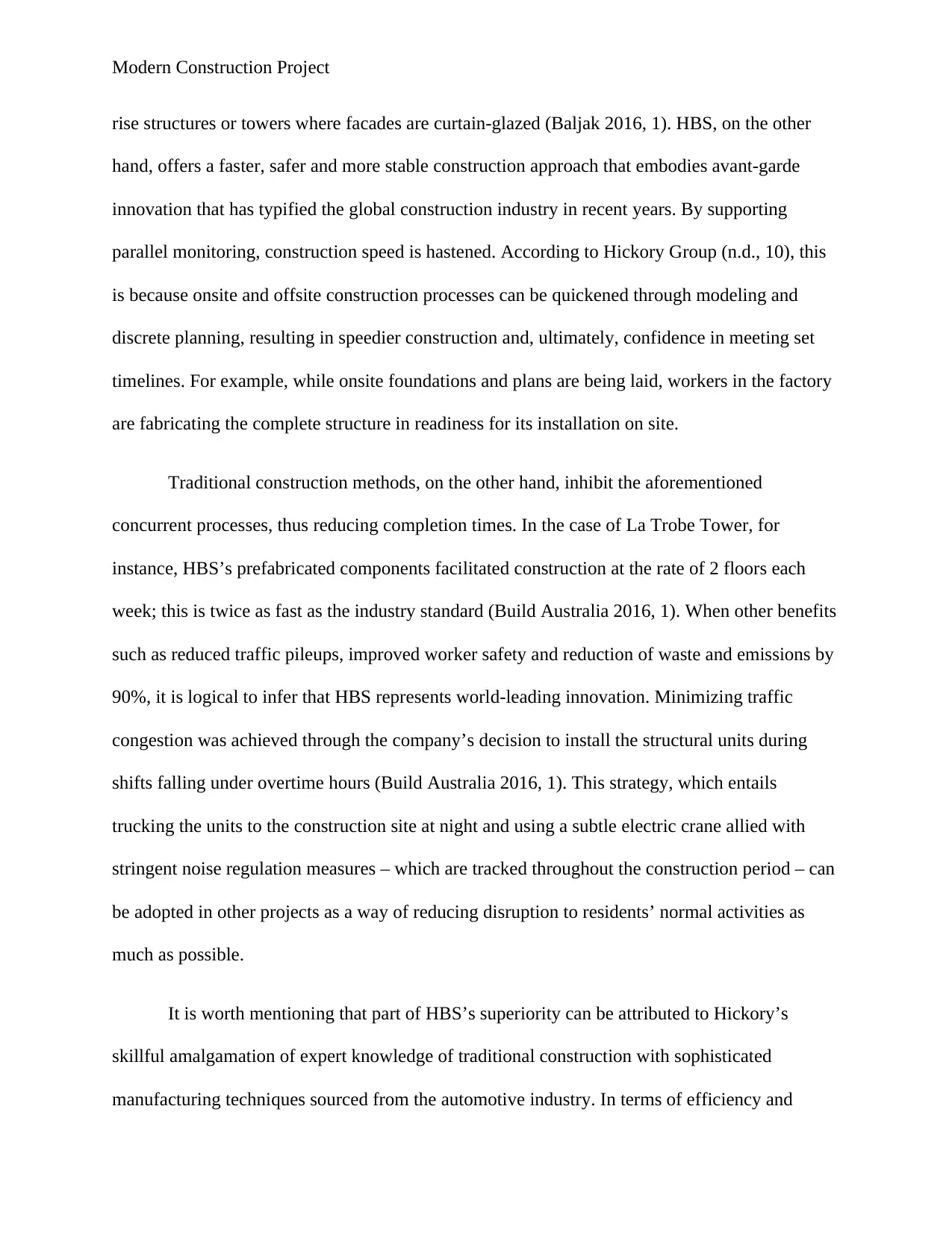
Modern Construction Project
rise structures or towers where facades are curtain-glazed (Baljak 2016, 1). HBS, on the other
hand, offers a faster, safer and more stable construction approach that embodies avant-garde
innovation that has typified the global construction industry in recent years. By supporting
parallel monitoring, construction speed is hastened. According to Hickory Group (n.d., 10), this
is because onsite and offsite construction processes can be quickened through modeling and
discrete planning, resulting in speedier construction and, ultimately, confidence in meeting set
timelines. For example, while onsite foundations and plans are being laid, workers in the factory
are fabricating the complete structure in readiness for its installation on site.
Traditional construction methods, on the other hand, inhibit the aforementioned
concurrent processes, thus reducing completion times. In the case of La Trobe Tower, for
instance, HBS’s prefabricated components facilitated construction at the rate of 2 floors each
week; this is twice as fast as the industry standard (Build Australia 2016, 1). When other benefits
such as reduced traffic pileups, improved worker safety and reduction of waste and emissions by
90%, it is logical to infer that HBS represents world-leading innovation. Minimizing traffic
congestion was achieved through the company’s decision to install the structural units during
shifts falling under overtime hours (Build Australia 2016, 1). This strategy, which entails
trucking the units to the construction site at night and using a subtle electric crane allied with
stringent noise regulation measures – which are tracked throughout the construction period – can
be adopted in other projects as a way of reducing disruption to residents’ normal activities as
much as possible.
It is worth mentioning that part of HBS’s superiority can be attributed to Hickory’s
skillful amalgamation of expert knowledge of traditional construction with sophisticated
manufacturing techniques sourced from the automotive industry. In terms of efficiency and
rise structures or towers where facades are curtain-glazed (Baljak 2016, 1). HBS, on the other
hand, offers a faster, safer and more stable construction approach that embodies avant-garde
innovation that has typified the global construction industry in recent years. By supporting
parallel monitoring, construction speed is hastened. According to Hickory Group (n.d., 10), this
is because onsite and offsite construction processes can be quickened through modeling and
discrete planning, resulting in speedier construction and, ultimately, confidence in meeting set
timelines. For example, while onsite foundations and plans are being laid, workers in the factory
are fabricating the complete structure in readiness for its installation on site.
Traditional construction methods, on the other hand, inhibit the aforementioned
concurrent processes, thus reducing completion times. In the case of La Trobe Tower, for
instance, HBS’s prefabricated components facilitated construction at the rate of 2 floors each
week; this is twice as fast as the industry standard (Build Australia 2016, 1). When other benefits
such as reduced traffic pileups, improved worker safety and reduction of waste and emissions by
90%, it is logical to infer that HBS represents world-leading innovation. Minimizing traffic
congestion was achieved through the company’s decision to install the structural units during
shifts falling under overtime hours (Build Australia 2016, 1). This strategy, which entails
trucking the units to the construction site at night and using a subtle electric crane allied with
stringent noise regulation measures – which are tracked throughout the construction period – can
be adopted in other projects as a way of reducing disruption to residents’ normal activities as
much as possible.
It is worth mentioning that part of HBS’s superiority can be attributed to Hickory’s
skillful amalgamation of expert knowledge of traditional construction with sophisticated
manufacturing techniques sourced from the automotive industry. In terms of efficiency and
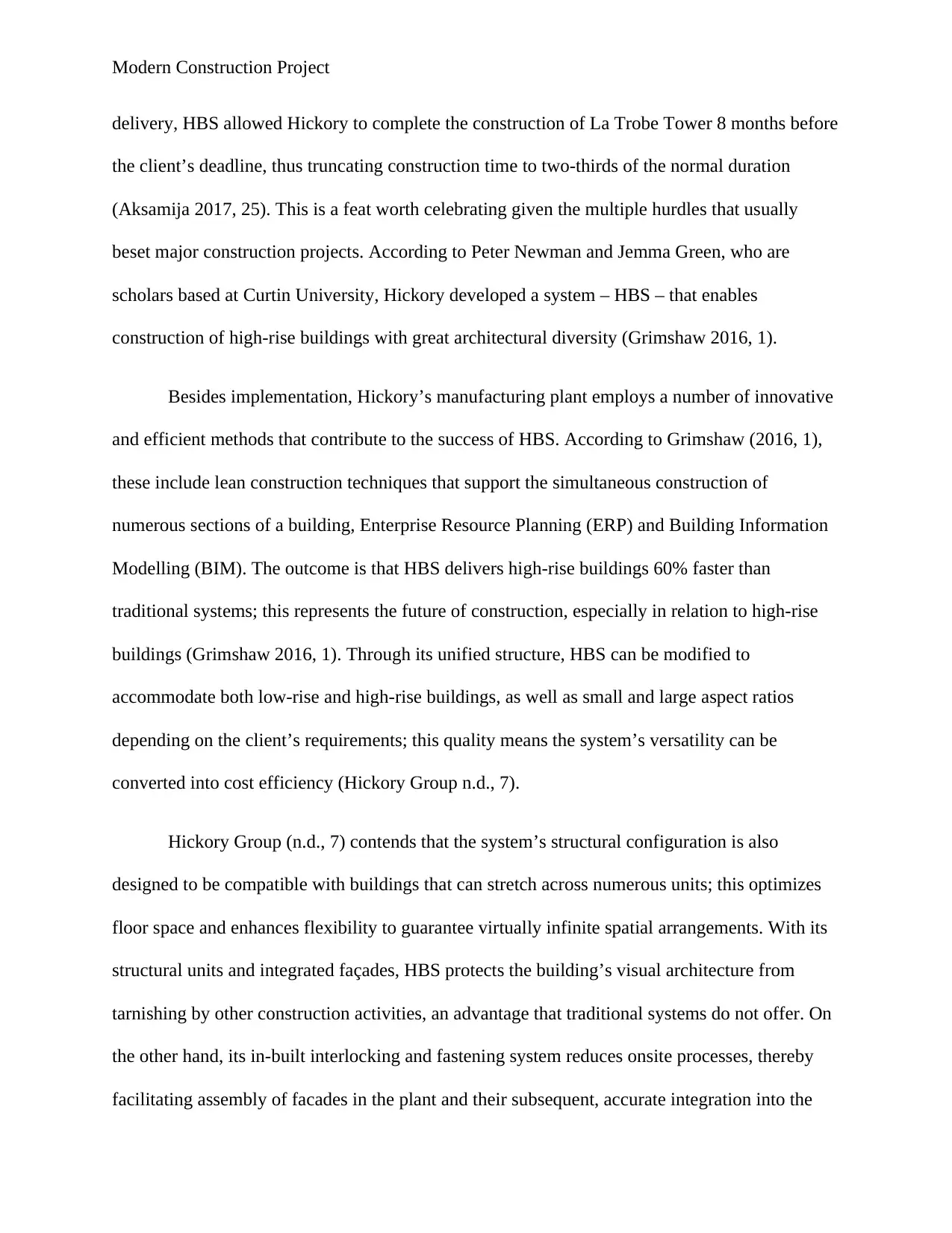
Modern Construction Project
delivery, HBS allowed Hickory to complete the construction of La Trobe Tower 8 months before
the client’s deadline, thus truncating construction time to two-thirds of the normal duration
(Aksamija 2017, 25). This is a feat worth celebrating given the multiple hurdles that usually
beset major construction projects. According to Peter Newman and Jemma Green, who are
scholars based at Curtin University, Hickory developed a system – HBS – that enables
construction of high-rise buildings with great architectural diversity (Grimshaw 2016, 1).
Besides implementation, Hickory’s manufacturing plant employs a number of innovative
and efficient methods that contribute to the success of HBS. According to Grimshaw (2016, 1),
these include lean construction techniques that support the simultaneous construction of
numerous sections of a building, Enterprise Resource Planning (ERP) and Building Information
Modelling (BIM). The outcome is that HBS delivers high-rise buildings 60% faster than
traditional systems; this represents the future of construction, especially in relation to high-rise
buildings (Grimshaw 2016, 1). Through its unified structure, HBS can be modified to
accommodate both low-rise and high-rise buildings, as well as small and large aspect ratios
depending on the client’s requirements; this quality means the system’s versatility can be
converted into cost efficiency (Hickory Group n.d., 7).
Hickory Group (n.d., 7) contends that the system’s structural configuration is also
designed to be compatible with buildings that can stretch across numerous units; this optimizes
floor space and enhances flexibility to guarantee virtually infinite spatial arrangements. With its
structural units and integrated façades, HBS protects the building’s visual architecture from
tarnishing by other construction activities, an advantage that traditional systems do not offer. On
the other hand, its in-built interlocking and fastening system reduces onsite processes, thereby
facilitating assembly of facades in the plant and their subsequent, accurate integration into the
delivery, HBS allowed Hickory to complete the construction of La Trobe Tower 8 months before
the client’s deadline, thus truncating construction time to two-thirds of the normal duration
(Aksamija 2017, 25). This is a feat worth celebrating given the multiple hurdles that usually
beset major construction projects. According to Peter Newman and Jemma Green, who are
scholars based at Curtin University, Hickory developed a system – HBS – that enables
construction of high-rise buildings with great architectural diversity (Grimshaw 2016, 1).
Besides implementation, Hickory’s manufacturing plant employs a number of innovative
and efficient methods that contribute to the success of HBS. According to Grimshaw (2016, 1),
these include lean construction techniques that support the simultaneous construction of
numerous sections of a building, Enterprise Resource Planning (ERP) and Building Information
Modelling (BIM). The outcome is that HBS delivers high-rise buildings 60% faster than
traditional systems; this represents the future of construction, especially in relation to high-rise
buildings (Grimshaw 2016, 1). Through its unified structure, HBS can be modified to
accommodate both low-rise and high-rise buildings, as well as small and large aspect ratios
depending on the client’s requirements; this quality means the system’s versatility can be
converted into cost efficiency (Hickory Group n.d., 7).
Hickory Group (n.d., 7) contends that the system’s structural configuration is also
designed to be compatible with buildings that can stretch across numerous units; this optimizes
floor space and enhances flexibility to guarantee virtually infinite spatial arrangements. With its
structural units and integrated façades, HBS protects the building’s visual architecture from
tarnishing by other construction activities, an advantage that traditional systems do not offer. On
the other hand, its in-built interlocking and fastening system reduces onsite processes, thereby
facilitating assembly of facades in the plant and their subsequent, accurate integration into the
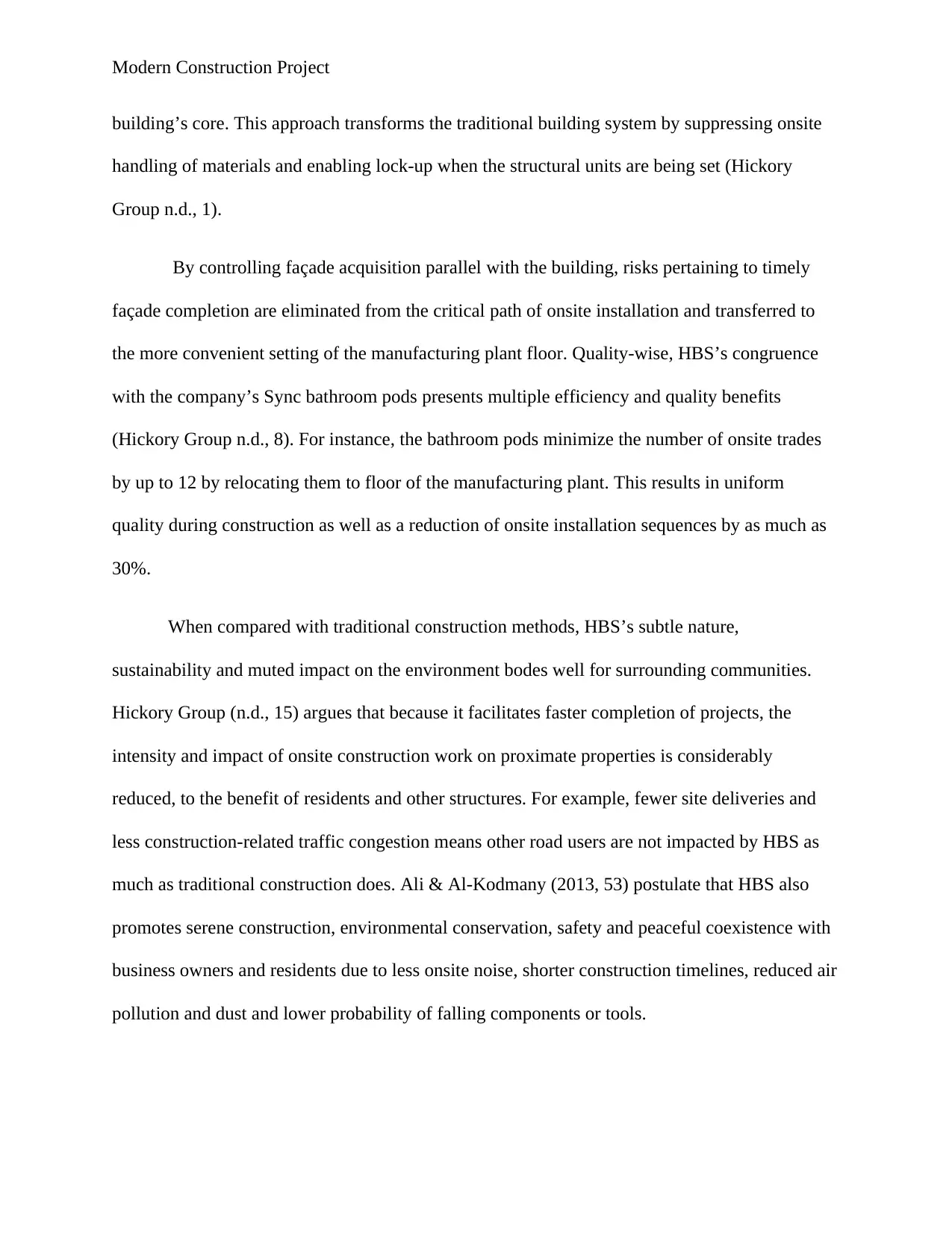
Modern Construction Project
building’s core. This approach transforms the traditional building system by suppressing onsite
handling of materials and enabling lock-up when the structural units are being set (Hickory
Group n.d., 1).
By controlling façade acquisition parallel with the building, risks pertaining to timely
façade completion are eliminated from the critical path of onsite installation and transferred to
the more convenient setting of the manufacturing plant floor. Quality-wise, HBS’s congruence
with the company’s Sync bathroom pods presents multiple efficiency and quality benefits
(Hickory Group n.d., 8). For instance, the bathroom pods minimize the number of onsite trades
by up to 12 by relocating them to floor of the manufacturing plant. This results in uniform
quality during construction as well as a reduction of onsite installation sequences by as much as
30%.
When compared with traditional construction methods, HBS’s subtle nature,
sustainability and muted impact on the environment bodes well for surrounding communities.
Hickory Group (n.d., 15) argues that because it facilitates faster completion of projects, the
intensity and impact of onsite construction work on proximate properties is considerably
reduced, to the benefit of residents and other structures. For example, fewer site deliveries and
less construction-related traffic congestion means other road users are not impacted by HBS as
much as traditional construction does. Ali & Al-Kodmany (2013, 53) postulate that HBS also
promotes serene construction, environmental conservation, safety and peaceful coexistence with
business owners and residents due to less onsite noise, shorter construction timelines, reduced air
pollution and dust and lower probability of falling components or tools.
building’s core. This approach transforms the traditional building system by suppressing onsite
handling of materials and enabling lock-up when the structural units are being set (Hickory
Group n.d., 1).
By controlling façade acquisition parallel with the building, risks pertaining to timely
façade completion are eliminated from the critical path of onsite installation and transferred to
the more convenient setting of the manufacturing plant floor. Quality-wise, HBS’s congruence
with the company’s Sync bathroom pods presents multiple efficiency and quality benefits
(Hickory Group n.d., 8). For instance, the bathroom pods minimize the number of onsite trades
by up to 12 by relocating them to floor of the manufacturing plant. This results in uniform
quality during construction as well as a reduction of onsite installation sequences by as much as
30%.
When compared with traditional construction methods, HBS’s subtle nature,
sustainability and muted impact on the environment bodes well for surrounding communities.
Hickory Group (n.d., 15) argues that because it facilitates faster completion of projects, the
intensity and impact of onsite construction work on proximate properties is considerably
reduced, to the benefit of residents and other structures. For example, fewer site deliveries and
less construction-related traffic congestion means other road users are not impacted by HBS as
much as traditional construction does. Ali & Al-Kodmany (2013, 53) postulate that HBS also
promotes serene construction, environmental conservation, safety and peaceful coexistence with
business owners and residents due to less onsite noise, shorter construction timelines, reduced air
pollution and dust and lower probability of falling components or tools.
Paraphrase This Document
Need a fresh take? Get an instant paraphrase of this document with our AI Paraphraser
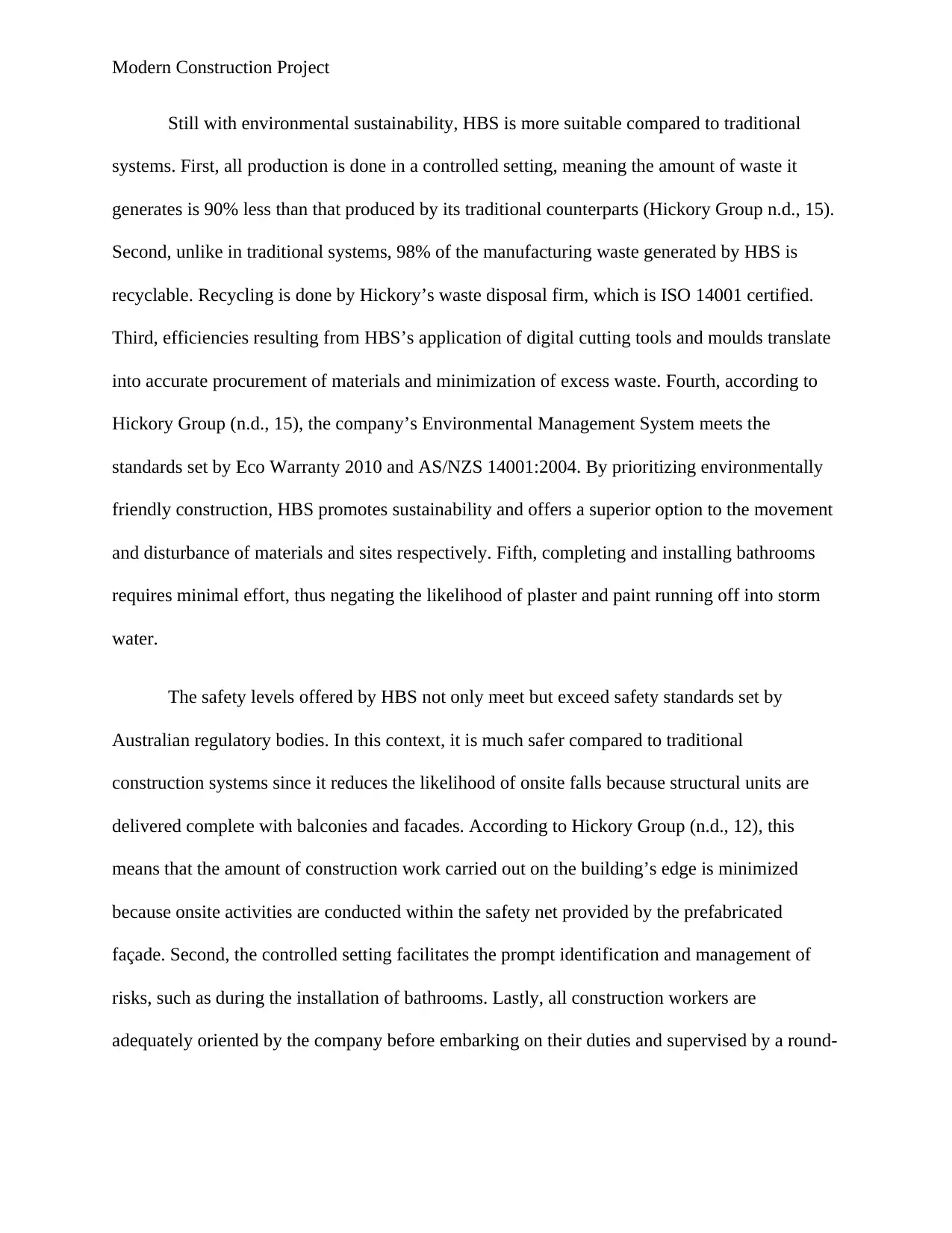
Modern Construction Project
Still with environmental sustainability, HBS is more suitable compared to traditional
systems. First, all production is done in a controlled setting, meaning the amount of waste it
generates is 90% less than that produced by its traditional counterparts (Hickory Group n.d., 15).
Second, unlike in traditional systems, 98% of the manufacturing waste generated by HBS is
recyclable. Recycling is done by Hickory’s waste disposal firm, which is ISO 14001 certified.
Third, efficiencies resulting from HBS’s application of digital cutting tools and moulds translate
into accurate procurement of materials and minimization of excess waste. Fourth, according to
Hickory Group (n.d., 15), the company’s Environmental Management System meets the
standards set by Eco Warranty 2010 and AS/NZS 14001:2004. By prioritizing environmentally
friendly construction, HBS promotes sustainability and offers a superior option to the movement
and disturbance of materials and sites respectively. Fifth, completing and installing bathrooms
requires minimal effort, thus negating the likelihood of plaster and paint running off into storm
water.
The safety levels offered by HBS not only meet but exceed safety standards set by
Australian regulatory bodies. In this context, it is much safer compared to traditional
construction systems since it reduces the likelihood of onsite falls because structural units are
delivered complete with balconies and facades. According to Hickory Group (n.d., 12), this
means that the amount of construction work carried out on the building’s edge is minimized
because onsite activities are conducted within the safety net provided by the prefabricated
façade. Second, the controlled setting facilitates the prompt identification and management of
risks, such as during the installation of bathrooms. Lastly, all construction workers are
adequately oriented by the company before embarking on their duties and supervised by a round-
Still with environmental sustainability, HBS is more suitable compared to traditional
systems. First, all production is done in a controlled setting, meaning the amount of waste it
generates is 90% less than that produced by its traditional counterparts (Hickory Group n.d., 15).
Second, unlike in traditional systems, 98% of the manufacturing waste generated by HBS is
recyclable. Recycling is done by Hickory’s waste disposal firm, which is ISO 14001 certified.
Third, efficiencies resulting from HBS’s application of digital cutting tools and moulds translate
into accurate procurement of materials and minimization of excess waste. Fourth, according to
Hickory Group (n.d., 15), the company’s Environmental Management System meets the
standards set by Eco Warranty 2010 and AS/NZS 14001:2004. By prioritizing environmentally
friendly construction, HBS promotes sustainability and offers a superior option to the movement
and disturbance of materials and sites respectively. Fifth, completing and installing bathrooms
requires minimal effort, thus negating the likelihood of plaster and paint running off into storm
water.
The safety levels offered by HBS not only meet but exceed safety standards set by
Australian regulatory bodies. In this context, it is much safer compared to traditional
construction systems since it reduces the likelihood of onsite falls because structural units are
delivered complete with balconies and facades. According to Hickory Group (n.d., 12), this
means that the amount of construction work carried out on the building’s edge is minimized
because onsite activities are conducted within the safety net provided by the prefabricated
façade. Second, the controlled setting facilitates the prompt identification and management of
risks, such as during the installation of bathrooms. Lastly, all construction workers are
adequately oriented by the company before embarking on their duties and supervised by a round-
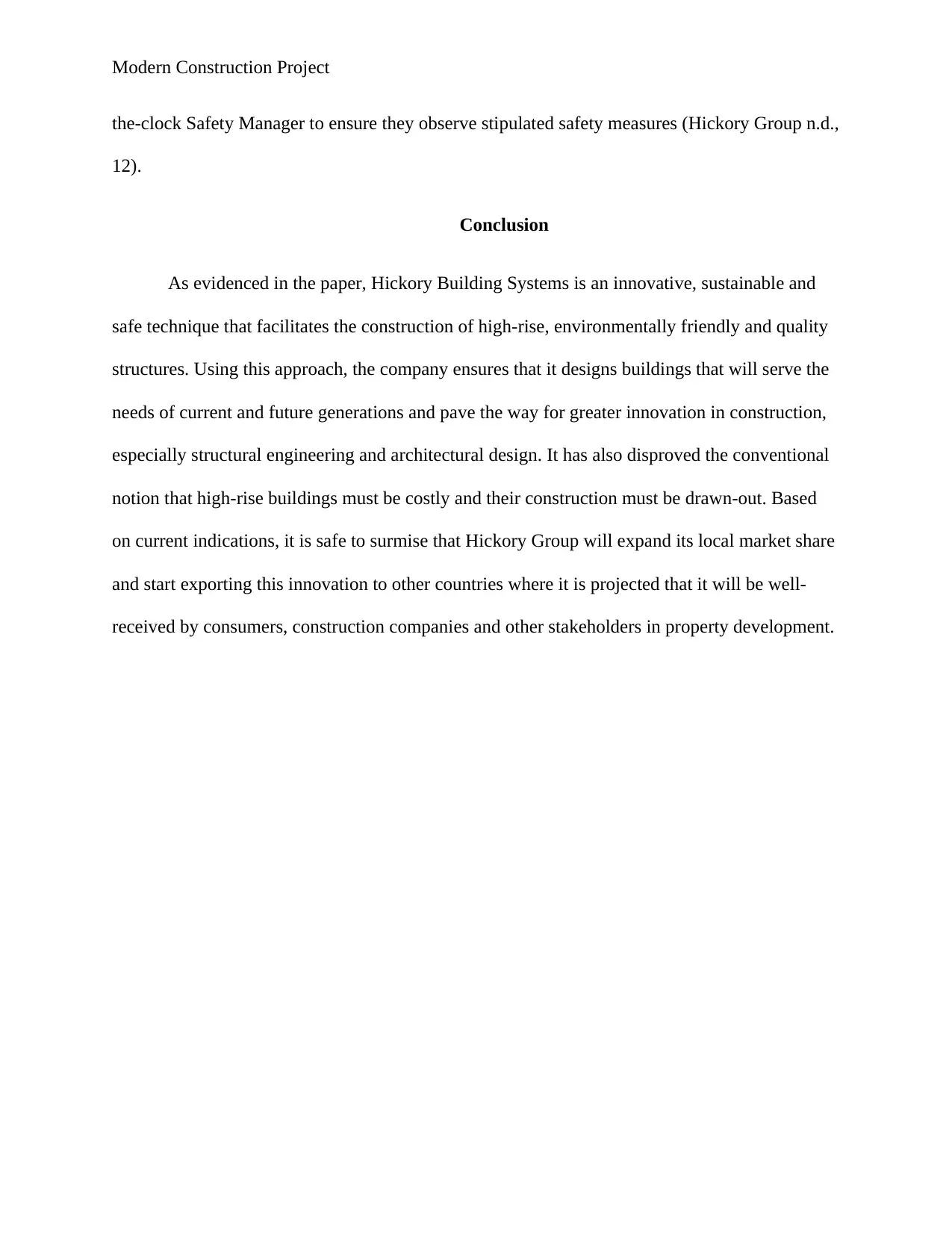
Modern Construction Project
the-clock Safety Manager to ensure they observe stipulated safety measures (Hickory Group n.d.,
12).
Conclusion
As evidenced in the paper, Hickory Building Systems is an innovative, sustainable and
safe technique that facilitates the construction of high-rise, environmentally friendly and quality
structures. Using this approach, the company ensures that it designs buildings that will serve the
needs of current and future generations and pave the way for greater innovation in construction,
especially structural engineering and architectural design. It has also disproved the conventional
notion that high-rise buildings must be costly and their construction must be drawn-out. Based
on current indications, it is safe to surmise that Hickory Group will expand its local market share
and start exporting this innovation to other countries where it is projected that it will be well-
received by consumers, construction companies and other stakeholders in property development.
the-clock Safety Manager to ensure they observe stipulated safety measures (Hickory Group n.d.,
12).
Conclusion
As evidenced in the paper, Hickory Building Systems is an innovative, sustainable and
safe technique that facilitates the construction of high-rise, environmentally friendly and quality
structures. Using this approach, the company ensures that it designs buildings that will serve the
needs of current and future generations and pave the way for greater innovation in construction,
especially structural engineering and architectural design. It has also disproved the conventional
notion that high-rise buildings must be costly and their construction must be drawn-out. Based
on current indications, it is safe to surmise that Hickory Group will expand its local market share
and start exporting this innovation to other countries where it is projected that it will be well-
received by consumers, construction companies and other stakeholders in property development.
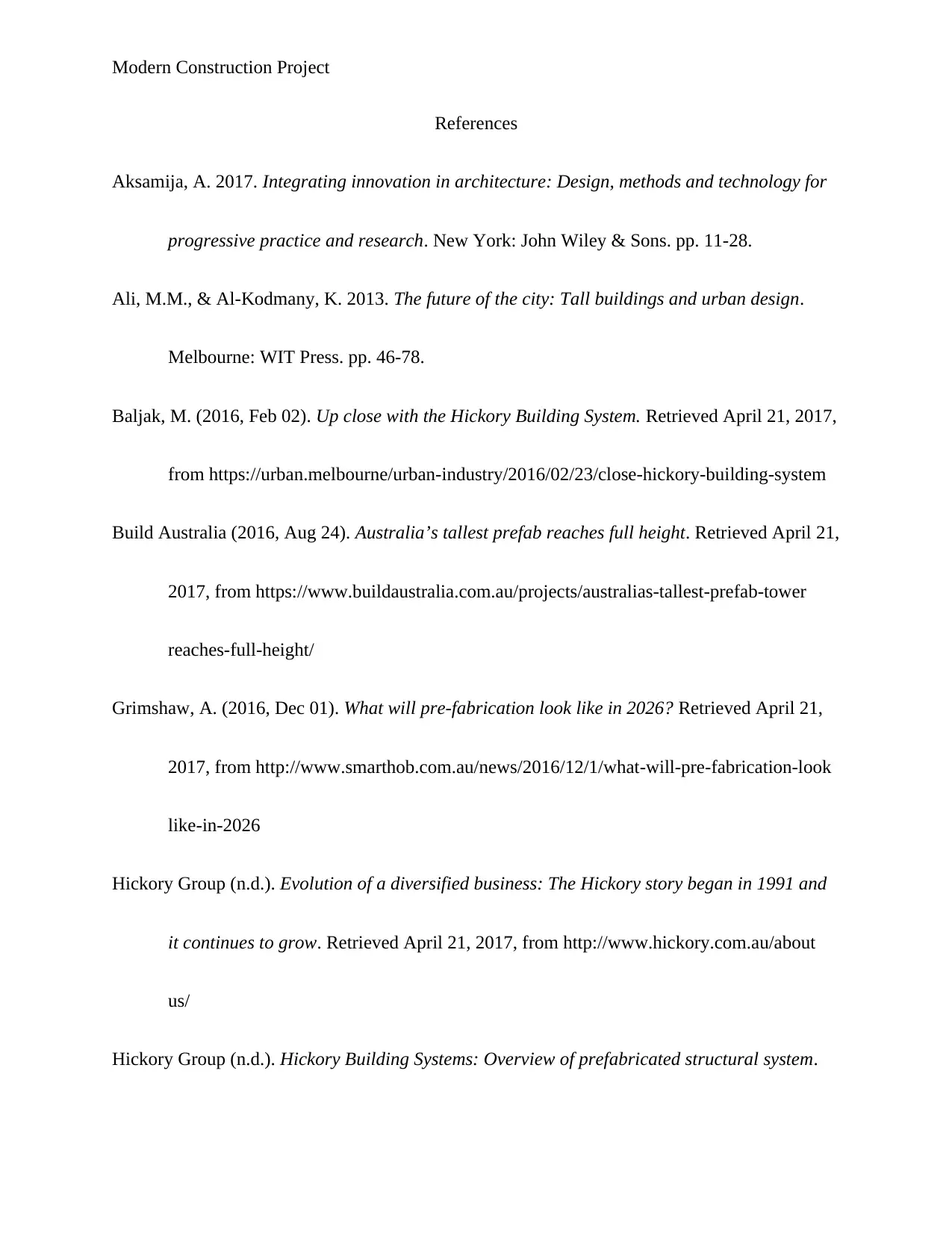
Modern Construction Project
References
Aksamija, A. 2017. Integrating innovation in architecture: Design, methods and technology for
progressive practice and research. New York: John Wiley & Sons. pp. 11-28.
Ali, M.M., & Al-Kodmany, K. 2013. The future of the city: Tall buildings and urban design.
Melbourne: WIT Press. pp. 46-78.
Baljak, M. (2016, Feb 02). Up close with the Hickory Building System. Retrieved April 21, 2017,
from https://urban.melbourne/urban-industry/2016/02/23/close-hickory-building-system
Build Australia (2016, Aug 24). Australia’s tallest prefab reaches full height. Retrieved April 21,
2017, from https://www.buildaustralia.com.au/projects/australias-tallest-prefab-tower
reaches-full-height/
Grimshaw, A. (2016, Dec 01). What will pre-fabrication look like in 2026? Retrieved April 21,
2017, from http://www.smarthob.com.au/news/2016/12/1/what-will-pre-fabrication-look
like-in-2026
Hickory Group (n.d.). Evolution of a diversified business: The Hickory story began in 1991 and
it continues to grow. Retrieved April 21, 2017, from http://www.hickory.com.au/about
us/
Hickory Group (n.d.). Hickory Building Systems: Overview of prefabricated structural system.
References
Aksamija, A. 2017. Integrating innovation in architecture: Design, methods and technology for
progressive practice and research. New York: John Wiley & Sons. pp. 11-28.
Ali, M.M., & Al-Kodmany, K. 2013. The future of the city: Tall buildings and urban design.
Melbourne: WIT Press. pp. 46-78.
Baljak, M. (2016, Feb 02). Up close with the Hickory Building System. Retrieved April 21, 2017,
from https://urban.melbourne/urban-industry/2016/02/23/close-hickory-building-system
Build Australia (2016, Aug 24). Australia’s tallest prefab reaches full height. Retrieved April 21,
2017, from https://www.buildaustralia.com.au/projects/australias-tallest-prefab-tower
reaches-full-height/
Grimshaw, A. (2016, Dec 01). What will pre-fabrication look like in 2026? Retrieved April 21,
2017, from http://www.smarthob.com.au/news/2016/12/1/what-will-pre-fabrication-look
like-in-2026
Hickory Group (n.d.). Evolution of a diversified business: The Hickory story began in 1991 and
it continues to grow. Retrieved April 21, 2017, from http://www.hickory.com.au/about
us/
Hickory Group (n.d.). Hickory Building Systems: Overview of prefabricated structural system.
Secure Best Marks with AI Grader
Need help grading? Try our AI Grader for instant feedback on your assignments.
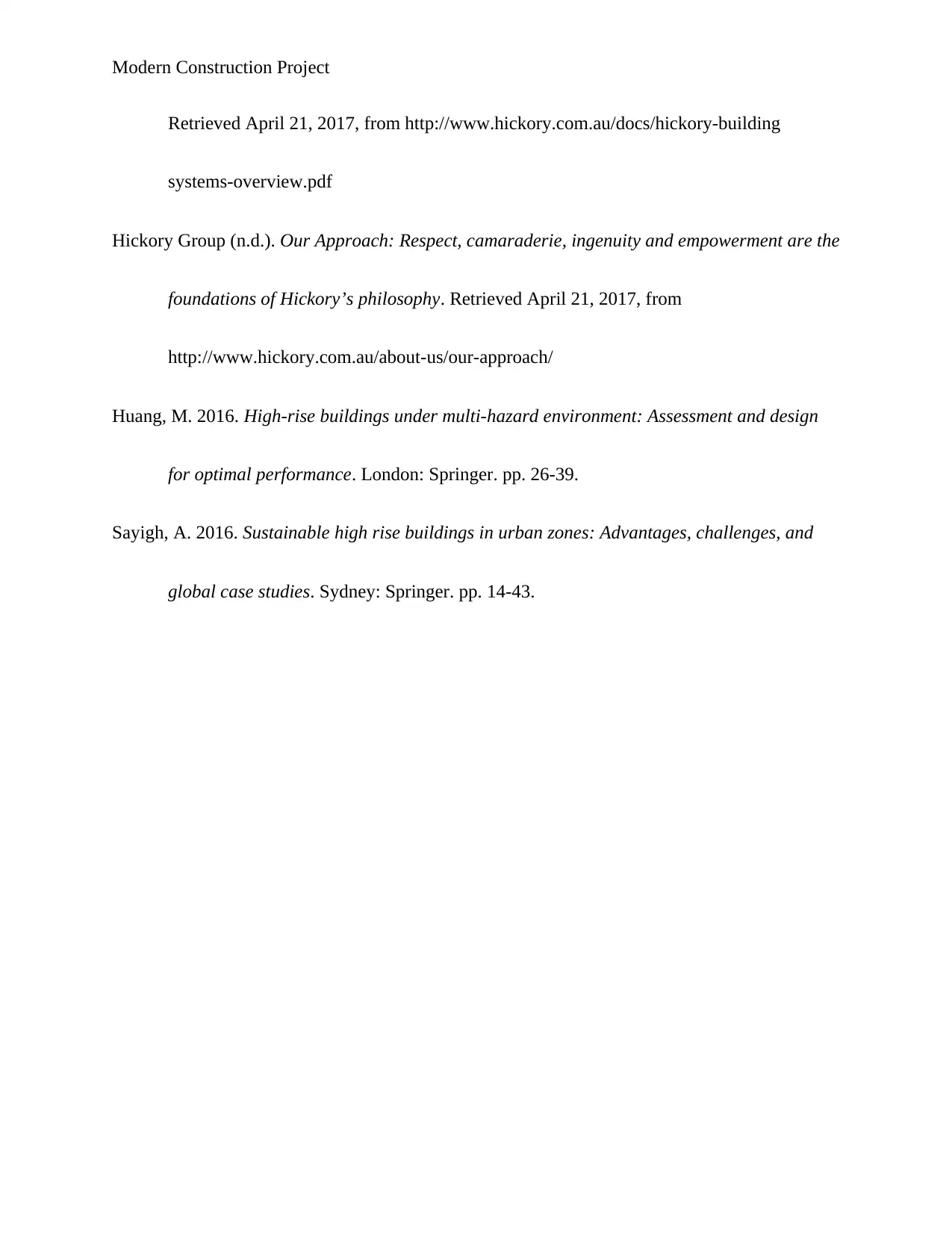
Modern Construction Project
Retrieved April 21, 2017, from http://www.hickory.com.au/docs/hickory-building
systems-overview.pdf
Hickory Group (n.d.). Our Approach: Respect, camaraderie, ingenuity and empowerment are the
foundations of Hickory’s philosophy. Retrieved April 21, 2017, from
http://www.hickory.com.au/about-us/our-approach/
Huang, M. 2016. High-rise buildings under multi-hazard environment: Assessment and design
for optimal performance. London: Springer. pp. 26-39.
Sayigh, A. 2016. Sustainable high rise buildings in urban zones: Advantages, challenges, and
global case studies. Sydney: Springer. pp. 14-43.
Retrieved April 21, 2017, from http://www.hickory.com.au/docs/hickory-building
systems-overview.pdf
Hickory Group (n.d.). Our Approach: Respect, camaraderie, ingenuity and empowerment are the
foundations of Hickory’s philosophy. Retrieved April 21, 2017, from
http://www.hickory.com.au/about-us/our-approach/
Huang, M. 2016. High-rise buildings under multi-hazard environment: Assessment and design
for optimal performance. London: Springer. pp. 26-39.
Sayigh, A. 2016. Sustainable high rise buildings in urban zones: Advantages, challenges, and
global case studies. Sydney: Springer. pp. 14-43.
1 out of 11
Related Documents

Your All-in-One AI-Powered Toolkit for Academic Success.
+13062052269
info@desklib.com
Available 24*7 on WhatsApp / Email
Unlock your academic potential
© 2024 | Zucol Services PVT LTD | All rights reserved.