Analysis of Quality and Operations Management Systems at Hilton Hotels
VerifiedAdded on 2020/04/07
|42
|7379
|205
Report
AI Summary
This report provides a comprehensive analysis of the quality and operations management systems implemented by Hilton Hotels. It begins with an overview of the Quality Management System (QMS), emphasizing its importance in meeting customer and organizational requirements, and its alignment with ISO 9001 certification. The report explores stakeholder needs, including guests, employees, owners, and the community, and outlines processes to fulfill these needs. A selected process, 'Analyzing Environmental Impacts,' is examined, detailing inputs and outputs. Furthermore, the report discusses the implementation of a continuous improvement program, highlighting elements like the Balanced Score Card, system upgrades, and customer-centric plans. The report also briefly touches upon the Environment Management System (EMS) of Bouygues Construction, covering stakeholders, environmental aspects, and actions. The analysis provides a clear understanding of Hilton's commitment to quality, sustainability, and stakeholder satisfaction, supported by various performance parameters and measurement methods, including surveys and feedback mechanisms.
Contribute Materials
Your contribution can guide someone’s learning journey. Share your
documents today.
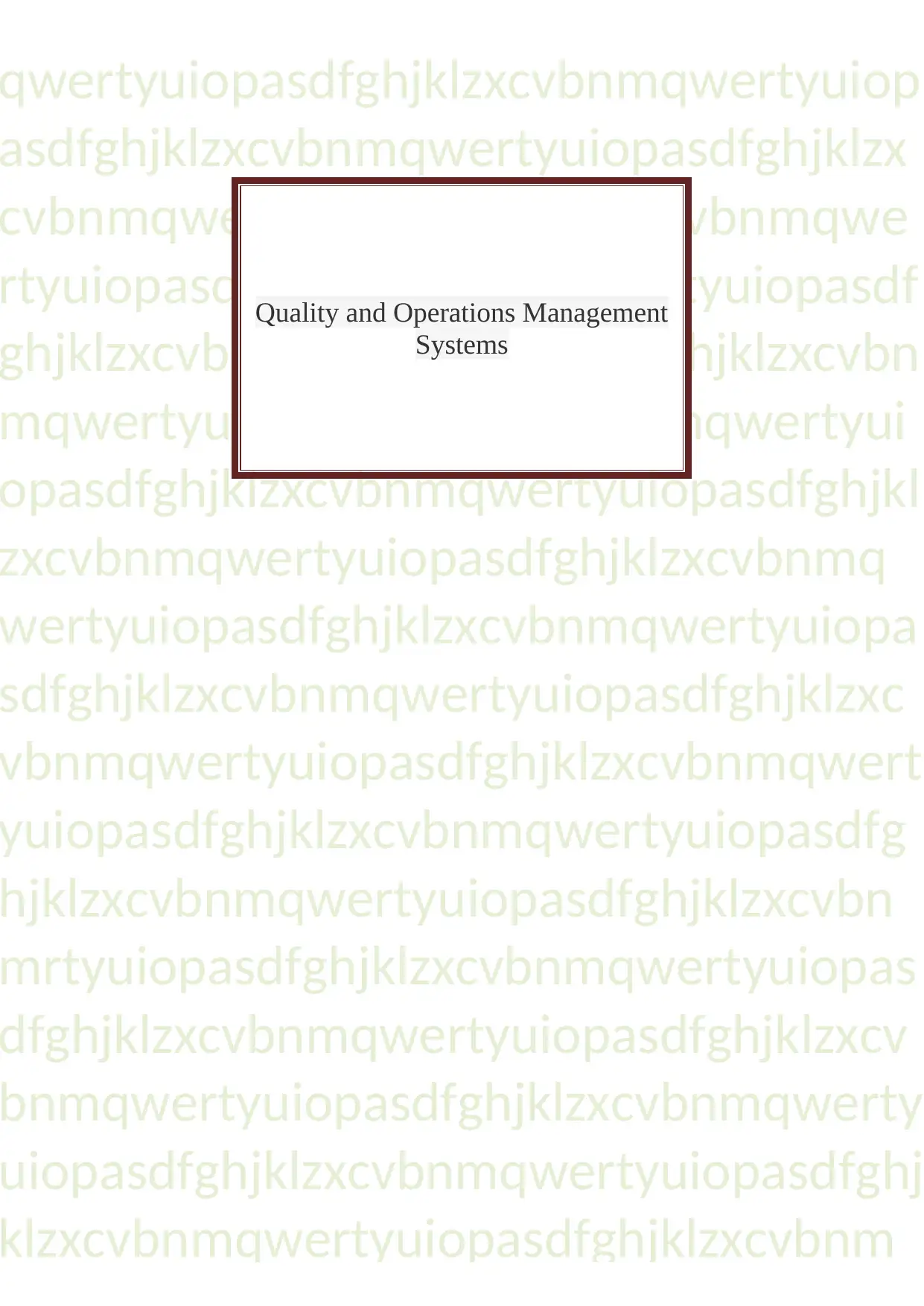
qwertyuiopasdfghjklzxcvbnmqwertyuiop
asdfghjklzxcvbnmqwertyuiopasdfghjklzx
cvbnmqwertyuiopasdfghjklzxcvbnmqwe
rtyuiopasdfghjklzxcvbnmqwertyuiopasdf
ghjklzxcvbnmqwertyuiopasdfghjklzxcvbn
mqwertyuiopasdfghjklzxcvbnmqwertyui
opasdfghjklzxcvbnmqwertyuiopasdfghjkl
zxcvbnmqwertyuiopasdfghjklzxcvbnmq
wertyuiopasdfghjklzxcvbnmqwertyuiopa
sdfghjklzxcvbnmqwertyuiopasdfghjklzxc
vbnmqwertyuiopasdfghjklzxcvbnmqwert
yuiopasdfghjklzxcvbnmqwertyuiopasdfg
hjklzxcvbnmqwertyuiopasdfghjklzxcvbn
mrtyuiopasdfghjklzxcvbnmqwertyuiopas
dfghjklzxcvbnmqwertyuiopasdfghjklzxcv
bnmqwertyuiopasdfghjklzxcvbnmqwerty
uiopasdfghjklzxcvbnmqwertyuiopasdfghj
klzxcvbnmqwertyuiopasdfghjklzxcvbnm
Quality and Operations Management
Systems
asdfghjklzxcvbnmqwertyuiopasdfghjklzx
cvbnmqwertyuiopasdfghjklzxcvbnmqwe
rtyuiopasdfghjklzxcvbnmqwertyuiopasdf
ghjklzxcvbnmqwertyuiopasdfghjklzxcvbn
mqwertyuiopasdfghjklzxcvbnmqwertyui
opasdfghjklzxcvbnmqwertyuiopasdfghjkl
zxcvbnmqwertyuiopasdfghjklzxcvbnmq
wertyuiopasdfghjklzxcvbnmqwertyuiopa
sdfghjklzxcvbnmqwertyuiopasdfghjklzxc
vbnmqwertyuiopasdfghjklzxcvbnmqwert
yuiopasdfghjklzxcvbnmqwertyuiopasdfg
hjklzxcvbnmqwertyuiopasdfghjklzxcvbn
mrtyuiopasdfghjklzxcvbnmqwertyuiopas
dfghjklzxcvbnmqwertyuiopasdfghjklzxcv
bnmqwertyuiopasdfghjklzxcvbnmqwerty
uiopasdfghjklzxcvbnmqwertyuiopasdfghj
klzxcvbnmqwertyuiopasdfghjklzxcvbnm
Quality and Operations Management
Systems
Secure Best Marks with AI Grader
Need help grading? Try our AI Grader for instant feedback on your assignments.
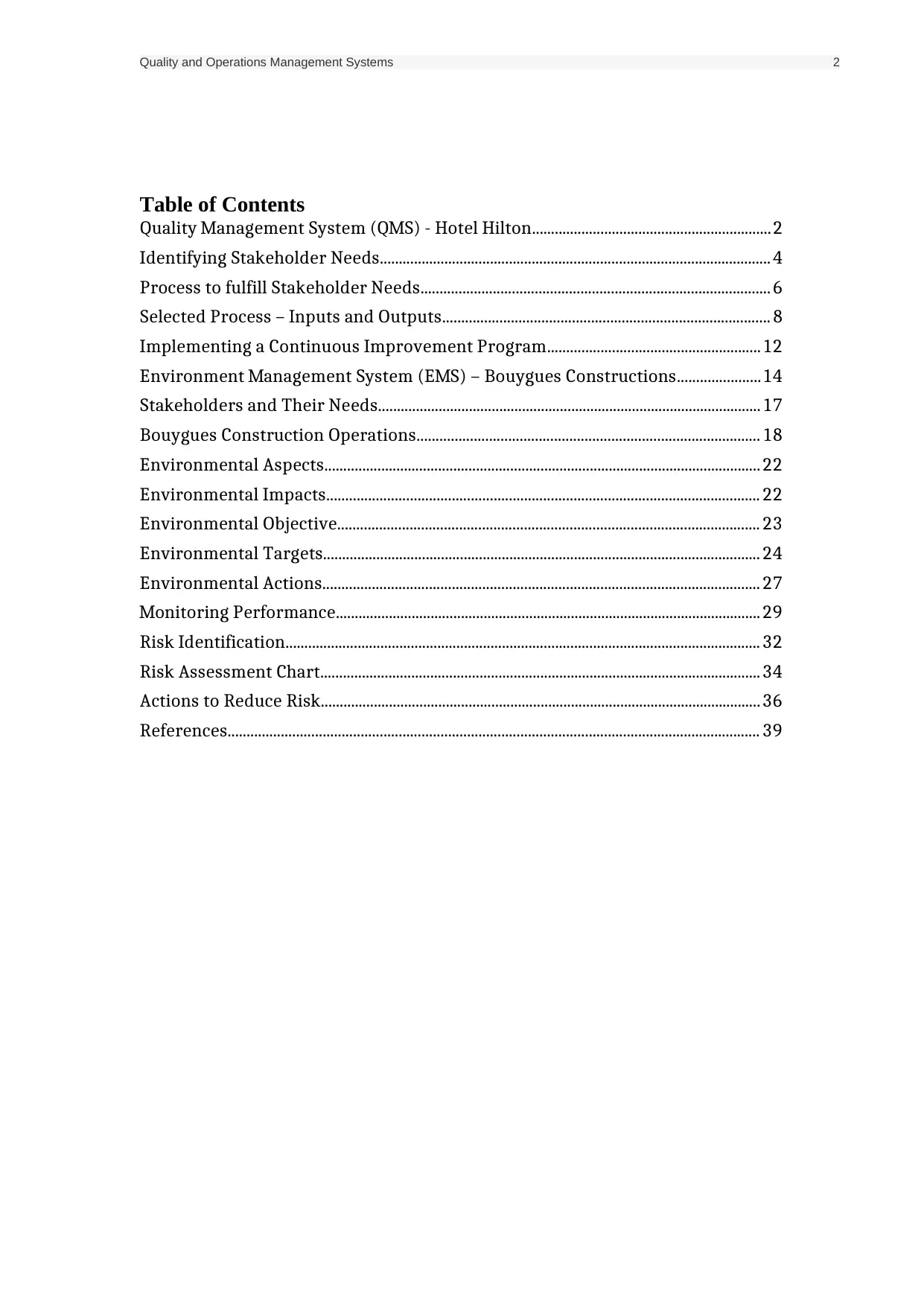
Quality and Operations Management Systems 2
Table of Contents
Quality Management System (QMS) - Hotel Hilton...............................................................2
Identifying Stakeholder Needs.......................................................................................................4
Process to fulfill Stakeholder Needs............................................................................................6
Selected Process – Inputs and Outputs......................................................................................8
Implementing a Continuous Improvement Program........................................................12
Environment Management System (EMS) – Bouygues Constructions......................14
Stakeholders and Their Needs.....................................................................................................17
Bouygues Construction Operations..........................................................................................18
Environmental Aspects...................................................................................................................22
Environmental Impacts.................................................................................................................. 22
Environmental Objective............................................................................................................... 23
Environmental Targets................................................................................................................... 24
Environmental Actions................................................................................................................... 27
Monitoring Performance................................................................................................................29
Risk Identification.............................................................................................................................32
Risk Assessment Chart....................................................................................................................34
Actions to Reduce Risk....................................................................................................................36
References............................................................................................................................................ 39
Table of Contents
Quality Management System (QMS) - Hotel Hilton...............................................................2
Identifying Stakeholder Needs.......................................................................................................4
Process to fulfill Stakeholder Needs............................................................................................6
Selected Process – Inputs and Outputs......................................................................................8
Implementing a Continuous Improvement Program........................................................12
Environment Management System (EMS) – Bouygues Constructions......................14
Stakeholders and Their Needs.....................................................................................................17
Bouygues Construction Operations..........................................................................................18
Environmental Aspects...................................................................................................................22
Environmental Impacts.................................................................................................................. 22
Environmental Objective............................................................................................................... 23
Environmental Targets................................................................................................................... 24
Environmental Actions................................................................................................................... 27
Monitoring Performance................................................................................................................29
Risk Identification.............................................................................................................................32
Risk Assessment Chart....................................................................................................................34
Actions to Reduce Risk....................................................................................................................36
References............................................................................................................................................ 39
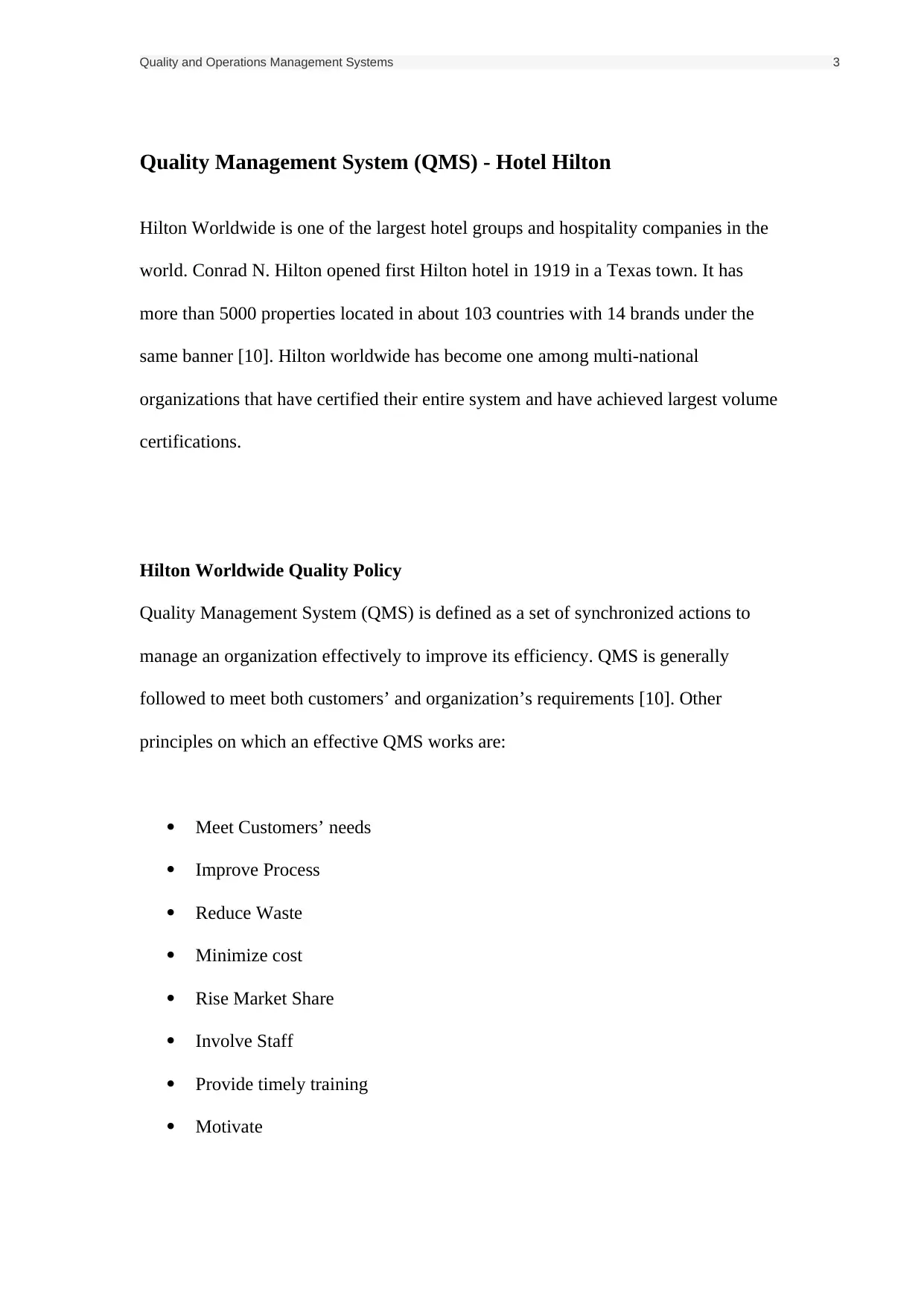
Quality and Operations Management Systems 3
Quality Management System (QMS) - Hotel Hilton
Hilton Worldwide is one of the largest hotel groups and hospitality companies in the
world. Conrad N. Hilton opened first Hilton hotel in 1919 in a Texas town. It has
more than 5000 properties located in about 103 countries with 14 brands under the
same banner [10]. Hilton worldwide has become one among multi-national
organizations that have certified their entire system and have achieved largest volume
certifications.
Hilton Worldwide Quality Policy
Quality Management System (QMS) is defined as a set of synchronized actions to
manage an organization effectively to improve its efficiency. QMS is generally
followed to meet both customers’ and organization’s requirements [10]. Other
principles on which an effective QMS works are:
Meet Customers’ needs
Improve Process
Reduce Waste
Minimize cost
Rise Market Share
Involve Staff
Provide timely training
Motivate
Quality Management System (QMS) - Hotel Hilton
Hilton Worldwide is one of the largest hotel groups and hospitality companies in the
world. Conrad N. Hilton opened first Hilton hotel in 1919 in a Texas town. It has
more than 5000 properties located in about 103 countries with 14 brands under the
same banner [10]. Hilton worldwide has become one among multi-national
organizations that have certified their entire system and have achieved largest volume
certifications.
Hilton Worldwide Quality Policy
Quality Management System (QMS) is defined as a set of synchronized actions to
manage an organization effectively to improve its efficiency. QMS is generally
followed to meet both customers’ and organization’s requirements [10]. Other
principles on which an effective QMS works are:
Meet Customers’ needs
Improve Process
Reduce Waste
Minimize cost
Rise Market Share
Involve Staff
Provide timely training
Motivate
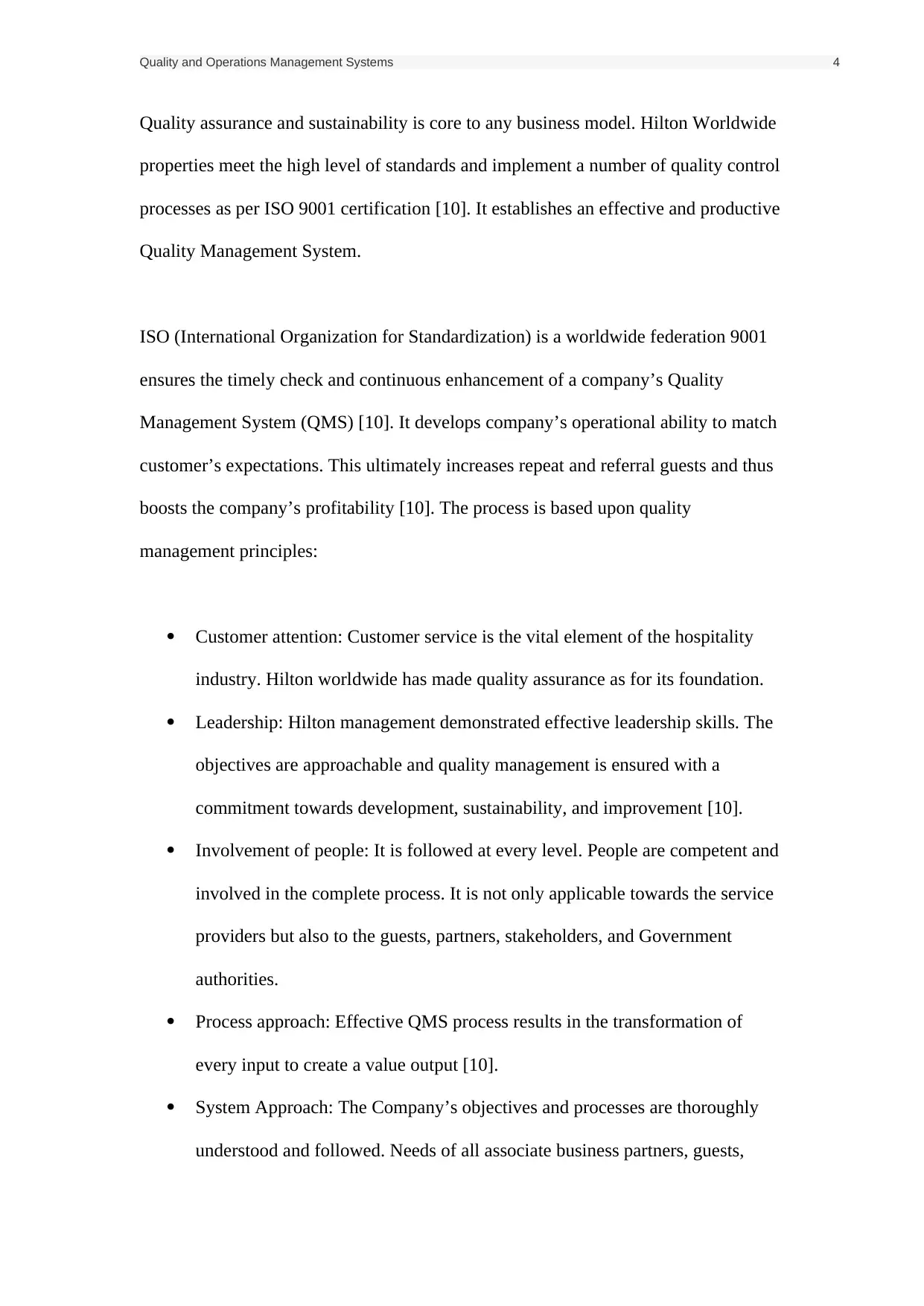
Quality and Operations Management Systems 4
Quality assurance and sustainability is core to any business model. Hilton Worldwide
properties meet the high level of standards and implement a number of quality control
processes as per ISO 9001 certification [10]. It establishes an effective and productive
Quality Management System.
ISO (International Organization for Standardization) is a worldwide federation 9001
ensures the timely check and continuous enhancement of a company’s Quality
Management System (QMS) [10]. It develops company’s operational ability to match
customer’s expectations. This ultimately increases repeat and referral guests and thus
boosts the company’s profitability [10]. The process is based upon quality
management principles:
Customer attention: Customer service is the vital element of the hospitality
industry. Hilton worldwide has made quality assurance as for its foundation.
Leadership: Hilton management demonstrated effective leadership skills. The
objectives are approachable and quality management is ensured with a
commitment towards development, sustainability, and improvement [10].
Involvement of people: It is followed at every level. People are competent and
involved in the complete process. It is not only applicable towards the service
providers but also to the guests, partners, stakeholders, and Government
authorities.
Process approach: Effective QMS process results in the transformation of
every input to create a value output [10].
System Approach: The Company’s objectives and processes are thoroughly
understood and followed. Needs of all associate business partners, guests,
Quality assurance and sustainability is core to any business model. Hilton Worldwide
properties meet the high level of standards and implement a number of quality control
processes as per ISO 9001 certification [10]. It establishes an effective and productive
Quality Management System.
ISO (International Organization for Standardization) is a worldwide federation 9001
ensures the timely check and continuous enhancement of a company’s Quality
Management System (QMS) [10]. It develops company’s operational ability to match
customer’s expectations. This ultimately increases repeat and referral guests and thus
boosts the company’s profitability [10]. The process is based upon quality
management principles:
Customer attention: Customer service is the vital element of the hospitality
industry. Hilton worldwide has made quality assurance as for its foundation.
Leadership: Hilton management demonstrated effective leadership skills. The
objectives are approachable and quality management is ensured with a
commitment towards development, sustainability, and improvement [10].
Involvement of people: It is followed at every level. People are competent and
involved in the complete process. It is not only applicable towards the service
providers but also to the guests, partners, stakeholders, and Government
authorities.
Process approach: Effective QMS process results in the transformation of
every input to create a value output [10].
System Approach: The Company’s objectives and processes are thoroughly
understood and followed. Needs of all associate business partners, guests,
Secure Best Marks with AI Grader
Need help grading? Try our AI Grader for instant feedback on your assignments.
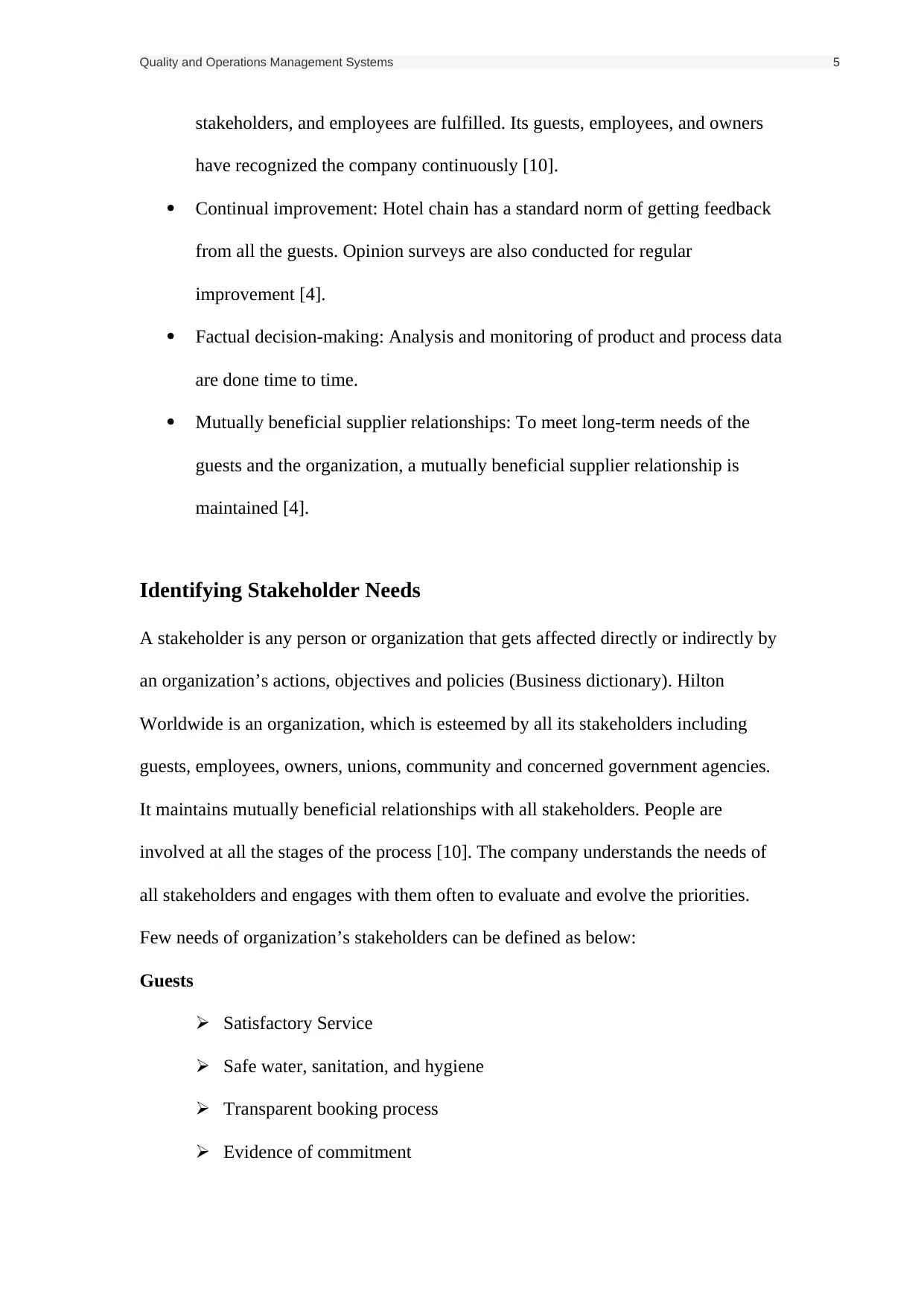
Quality and Operations Management Systems 5
stakeholders, and employees are fulfilled. Its guests, employees, and owners
have recognized the company continuously [10].
Continual improvement: Hotel chain has a standard norm of getting feedback
from all the guests. Opinion surveys are also conducted for regular
improvement [4].
Factual decision-making: Analysis and monitoring of product and process data
are done time to time.
Mutually beneficial supplier relationships: To meet long-term needs of the
guests and the organization, a mutually beneficial supplier relationship is
maintained [4].
Identifying Stakeholder Needs
A stakeholder is any person or organization that gets affected directly or indirectly by
an organization’s actions, objectives and policies (Business dictionary). Hilton
Worldwide is an organization, which is esteemed by all its stakeholders including
guests, employees, owners, unions, community and concerned government agencies.
It maintains mutually beneficial relationships with all stakeholders. People are
involved at all the stages of the process [10]. The company understands the needs of
all stakeholders and engages with them often to evaluate and evolve the priorities.
Few needs of organization’s stakeholders can be defined as below:
Guests
Satisfactory Service
Safe water, sanitation, and hygiene
Transparent booking process
Evidence of commitment
stakeholders, and employees are fulfilled. Its guests, employees, and owners
have recognized the company continuously [10].
Continual improvement: Hotel chain has a standard norm of getting feedback
from all the guests. Opinion surveys are also conducted for regular
improvement [4].
Factual decision-making: Analysis and monitoring of product and process data
are done time to time.
Mutually beneficial supplier relationships: To meet long-term needs of the
guests and the organization, a mutually beneficial supplier relationship is
maintained [4].
Identifying Stakeholder Needs
A stakeholder is any person or organization that gets affected directly or indirectly by
an organization’s actions, objectives and policies (Business dictionary). Hilton
Worldwide is an organization, which is esteemed by all its stakeholders including
guests, employees, owners, unions, community and concerned government agencies.
It maintains mutually beneficial relationships with all stakeholders. People are
involved at all the stages of the process [10]. The company understands the needs of
all stakeholders and engages with them often to evaluate and evolve the priorities.
Few needs of organization’s stakeholders can be defined as below:
Guests
Satisfactory Service
Safe water, sanitation, and hygiene
Transparent booking process
Evidence of commitment
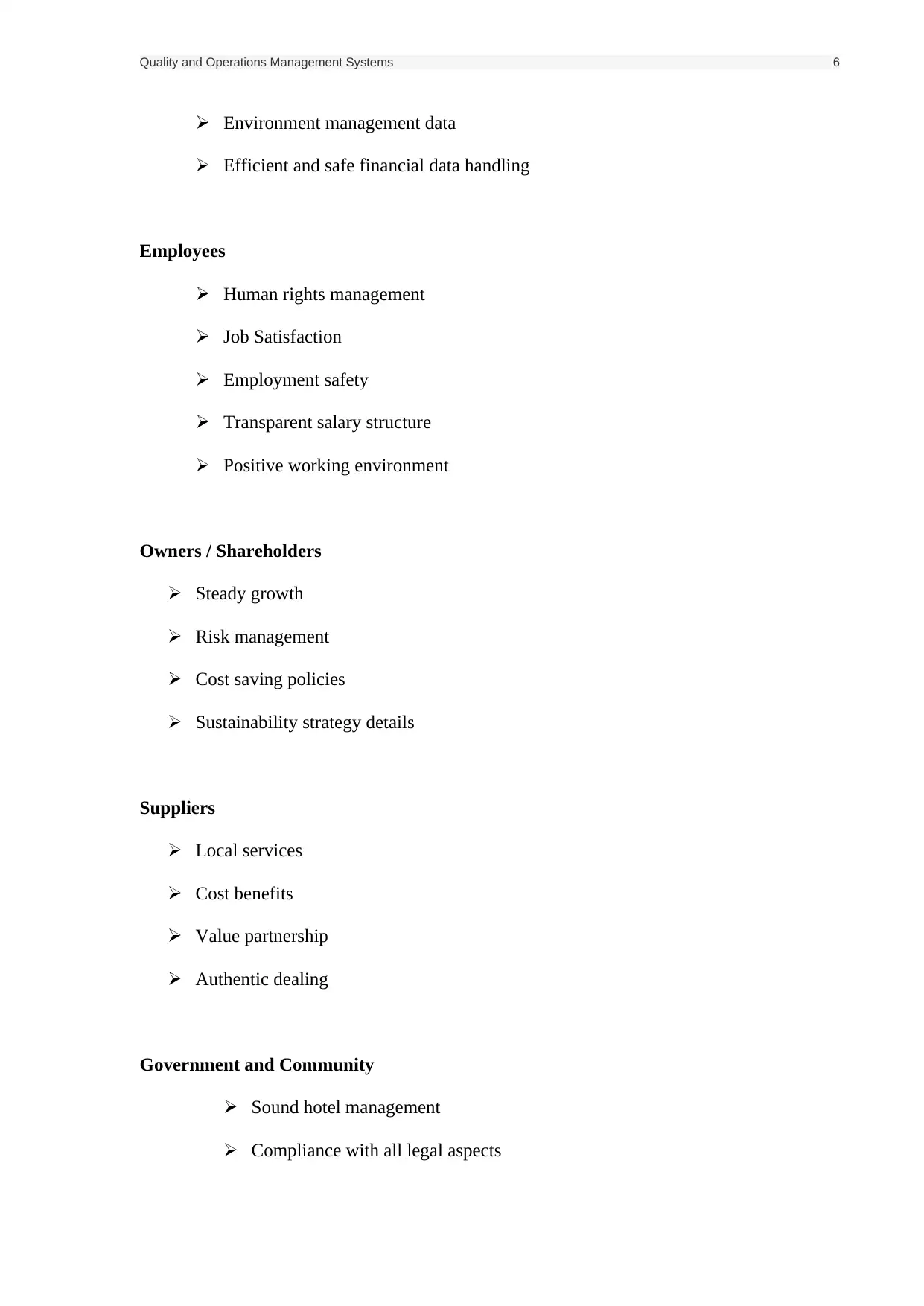
Quality and Operations Management Systems 6
Environment management data
Efficient and safe financial data handling
Employees
Human rights management
Job Satisfaction
Employment safety
Transparent salary structure
Positive working environment
Owners / Shareholders
Steady growth
Risk management
Cost saving policies
Sustainability strategy details
Suppliers
Local services
Cost benefits
Value partnership
Authentic dealing
Government and Community
Sound hotel management
Compliance with all legal aspects
Environment management data
Efficient and safe financial data handling
Employees
Human rights management
Job Satisfaction
Employment safety
Transparent salary structure
Positive working environment
Owners / Shareholders
Steady growth
Risk management
Cost saving policies
Sustainability strategy details
Suppliers
Local services
Cost benefits
Value partnership
Authentic dealing
Government and Community
Sound hotel management
Compliance with all legal aspects
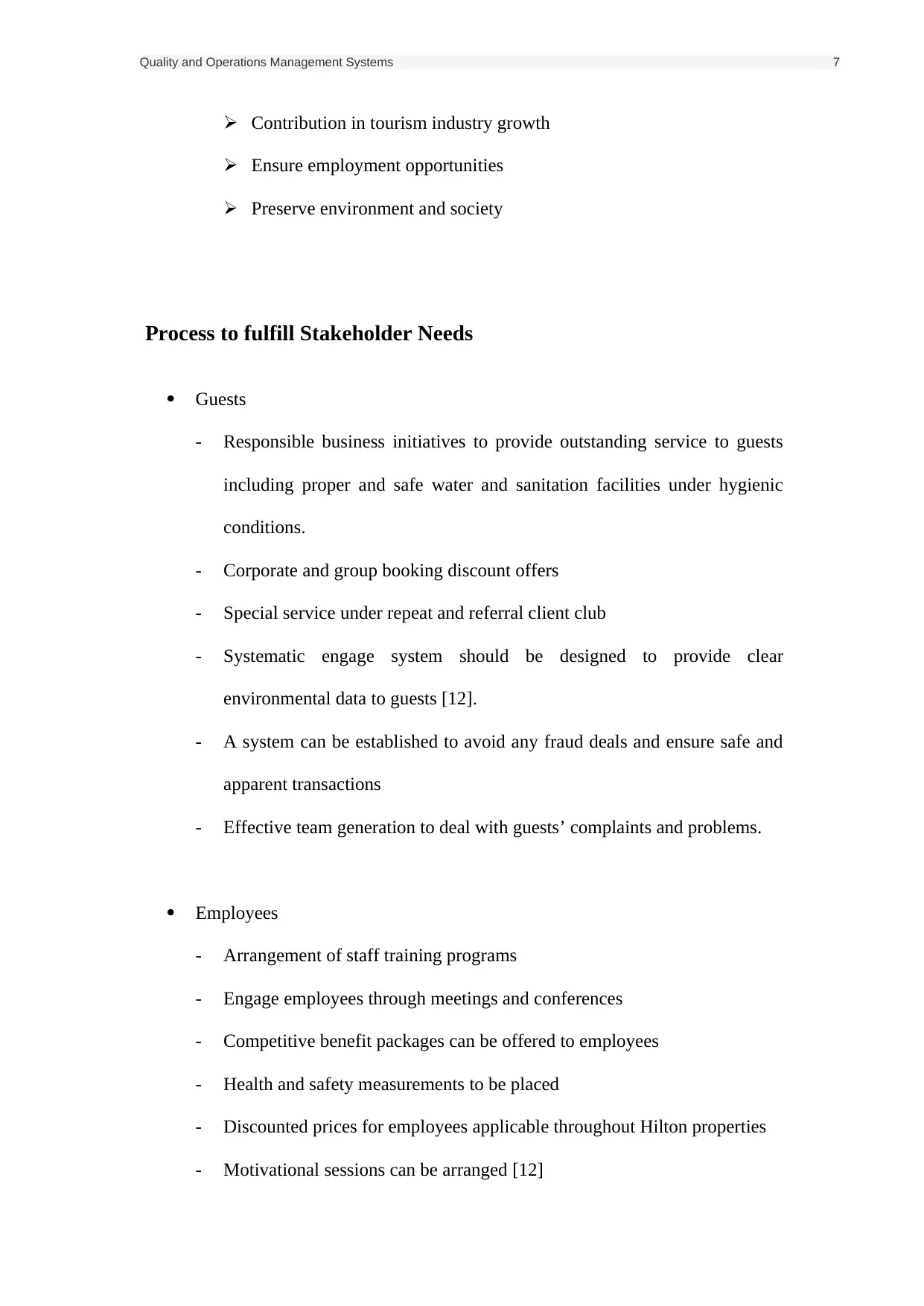
Quality and Operations Management Systems 7
Contribution in tourism industry growth
Ensure employment opportunities
Preserve environment and society
Process to fulfill Stakeholder Needs
Guests
- Responsible business initiatives to provide outstanding service to guests
including proper and safe water and sanitation facilities under hygienic
conditions.
- Corporate and group booking discount offers
- Special service under repeat and referral client club
- Systematic engage system should be designed to provide clear
environmental data to guests [12].
- A system can be established to avoid any fraud deals and ensure safe and
apparent transactions
- Effective team generation to deal with guests’ complaints and problems.
Employees
- Arrangement of staff training programs
- Engage employees through meetings and conferences
- Competitive benefit packages can be offered to employees
- Health and safety measurements to be placed
- Discounted prices for employees applicable throughout Hilton properties
- Motivational sessions can be arranged [12]
Contribution in tourism industry growth
Ensure employment opportunities
Preserve environment and society
Process to fulfill Stakeholder Needs
Guests
- Responsible business initiatives to provide outstanding service to guests
including proper and safe water and sanitation facilities under hygienic
conditions.
- Corporate and group booking discount offers
- Special service under repeat and referral client club
- Systematic engage system should be designed to provide clear
environmental data to guests [12].
- A system can be established to avoid any fraud deals and ensure safe and
apparent transactions
- Effective team generation to deal with guests’ complaints and problems.
Employees
- Arrangement of staff training programs
- Engage employees through meetings and conferences
- Competitive benefit packages can be offered to employees
- Health and safety measurements to be placed
- Discounted prices for employees applicable throughout Hilton properties
- Motivational sessions can be arranged [12]
Paraphrase This Document
Need a fresh take? Get an instant paraphrase of this document with our AI Paraphraser
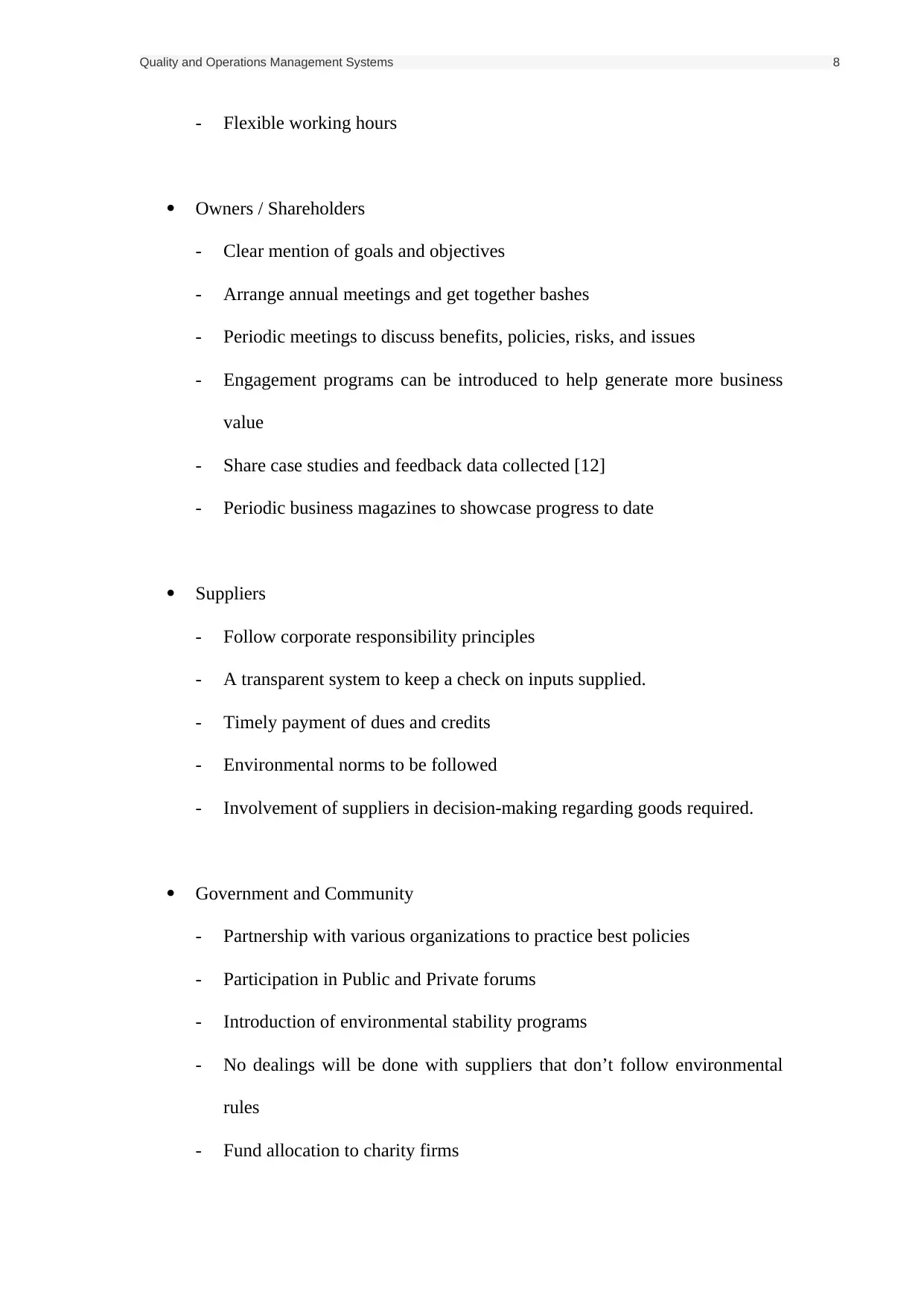
Quality and Operations Management Systems 8
- Flexible working hours
Owners / Shareholders
- Clear mention of goals and objectives
- Arrange annual meetings and get together bashes
- Periodic meetings to discuss benefits, policies, risks, and issues
- Engagement programs can be introduced to help generate more business
value
- Share case studies and feedback data collected [12]
- Periodic business magazines to showcase progress to date
Suppliers
- Follow corporate responsibility principles
- A transparent system to keep a check on inputs supplied.
- Timely payment of dues and credits
- Environmental norms to be followed
- Involvement of suppliers in decision-making regarding goods required.
Government and Community
- Partnership with various organizations to practice best policies
- Participation in Public and Private forums
- Introduction of environmental stability programs
- No dealings will be done with suppliers that don’t follow environmental
rules
- Fund allocation to charity firms
- Flexible working hours
Owners / Shareholders
- Clear mention of goals and objectives
- Arrange annual meetings and get together bashes
- Periodic meetings to discuss benefits, policies, risks, and issues
- Engagement programs can be introduced to help generate more business
value
- Share case studies and feedback data collected [12]
- Periodic business magazines to showcase progress to date
Suppliers
- Follow corporate responsibility principles
- A transparent system to keep a check on inputs supplied.
- Timely payment of dues and credits
- Environmental norms to be followed
- Involvement of suppliers in decision-making regarding goods required.
Government and Community
- Partnership with various organizations to practice best policies
- Participation in Public and Private forums
- Introduction of environmental stability programs
- No dealings will be done with suppliers that don’t follow environmental
rules
- Fund allocation to charity firms
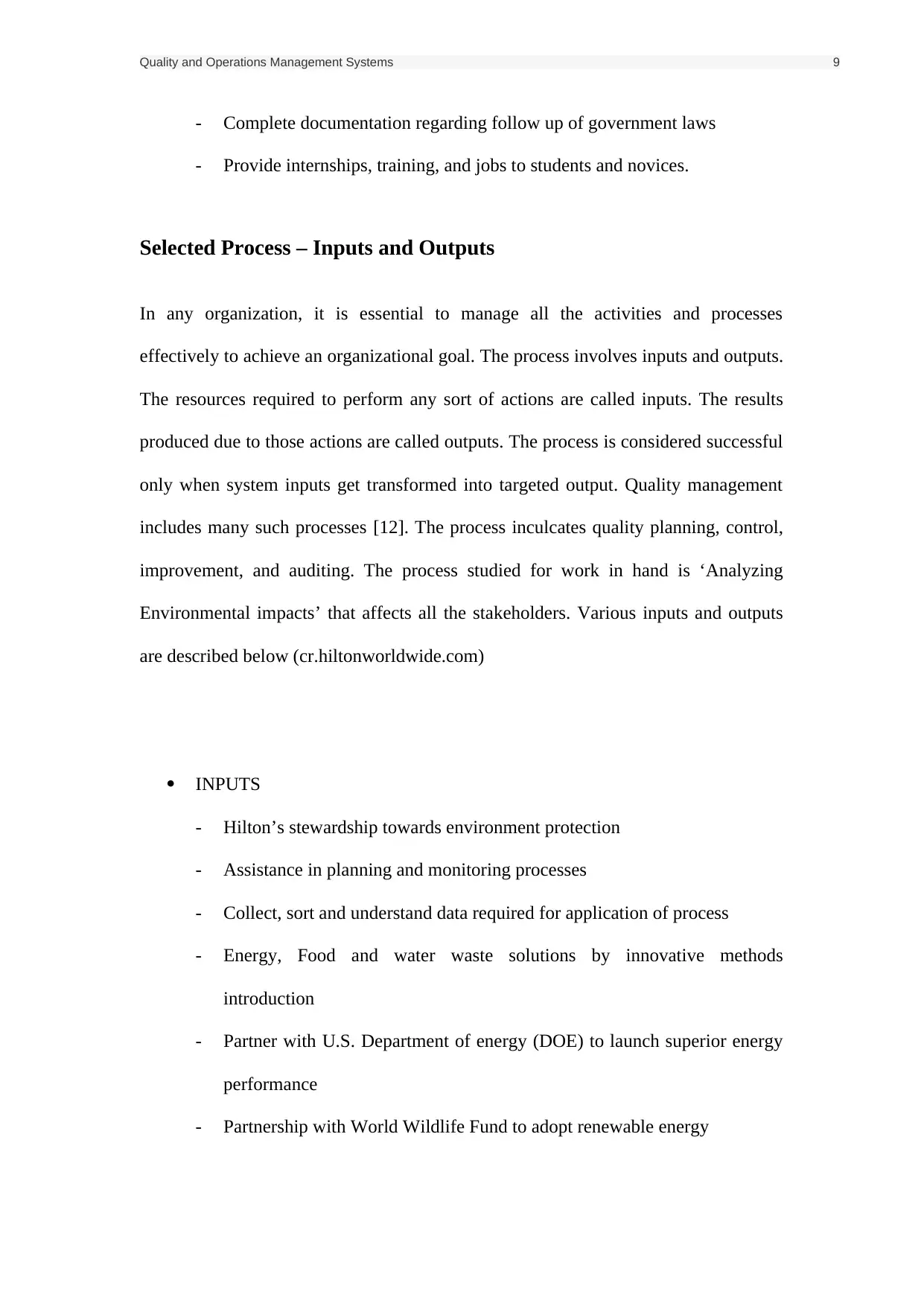
Quality and Operations Management Systems 9
- Complete documentation regarding follow up of government laws
- Provide internships, training, and jobs to students and novices.
Selected Process – Inputs and Outputs
In any organization, it is essential to manage all the activities and processes
effectively to achieve an organizational goal. The process involves inputs and outputs.
The resources required to perform any sort of actions are called inputs. The results
produced due to those actions are called outputs. The process is considered successful
only when system inputs get transformed into targeted output. Quality management
includes many such processes [12]. The process inculcates quality planning, control,
improvement, and auditing. The process studied for work in hand is ‘Analyzing
Environmental impacts’ that affects all the stakeholders. Various inputs and outputs
are described below (cr.hiltonworldwide.com)
INPUTS
- Hilton’s stewardship towards environment protection
- Assistance in planning and monitoring processes
- Collect, sort and understand data required for application of process
- Energy, Food and water waste solutions by innovative methods
introduction
- Partner with U.S. Department of energy (DOE) to launch superior energy
performance
- Partnership with World Wildlife Fund to adopt renewable energy
- Complete documentation regarding follow up of government laws
- Provide internships, training, and jobs to students and novices.
Selected Process – Inputs and Outputs
In any organization, it is essential to manage all the activities and processes
effectively to achieve an organizational goal. The process involves inputs and outputs.
The resources required to perform any sort of actions are called inputs. The results
produced due to those actions are called outputs. The process is considered successful
only when system inputs get transformed into targeted output. Quality management
includes many such processes [12]. The process inculcates quality planning, control,
improvement, and auditing. The process studied for work in hand is ‘Analyzing
Environmental impacts’ that affects all the stakeholders. Various inputs and outputs
are described below (cr.hiltonworldwide.com)
INPUTS
- Hilton’s stewardship towards environment protection
- Assistance in planning and monitoring processes
- Collect, sort and understand data required for application of process
- Energy, Food and water waste solutions by innovative methods
introduction
- Partner with U.S. Department of energy (DOE) to launch superior energy
performance
- Partnership with World Wildlife Fund to adopt renewable energy
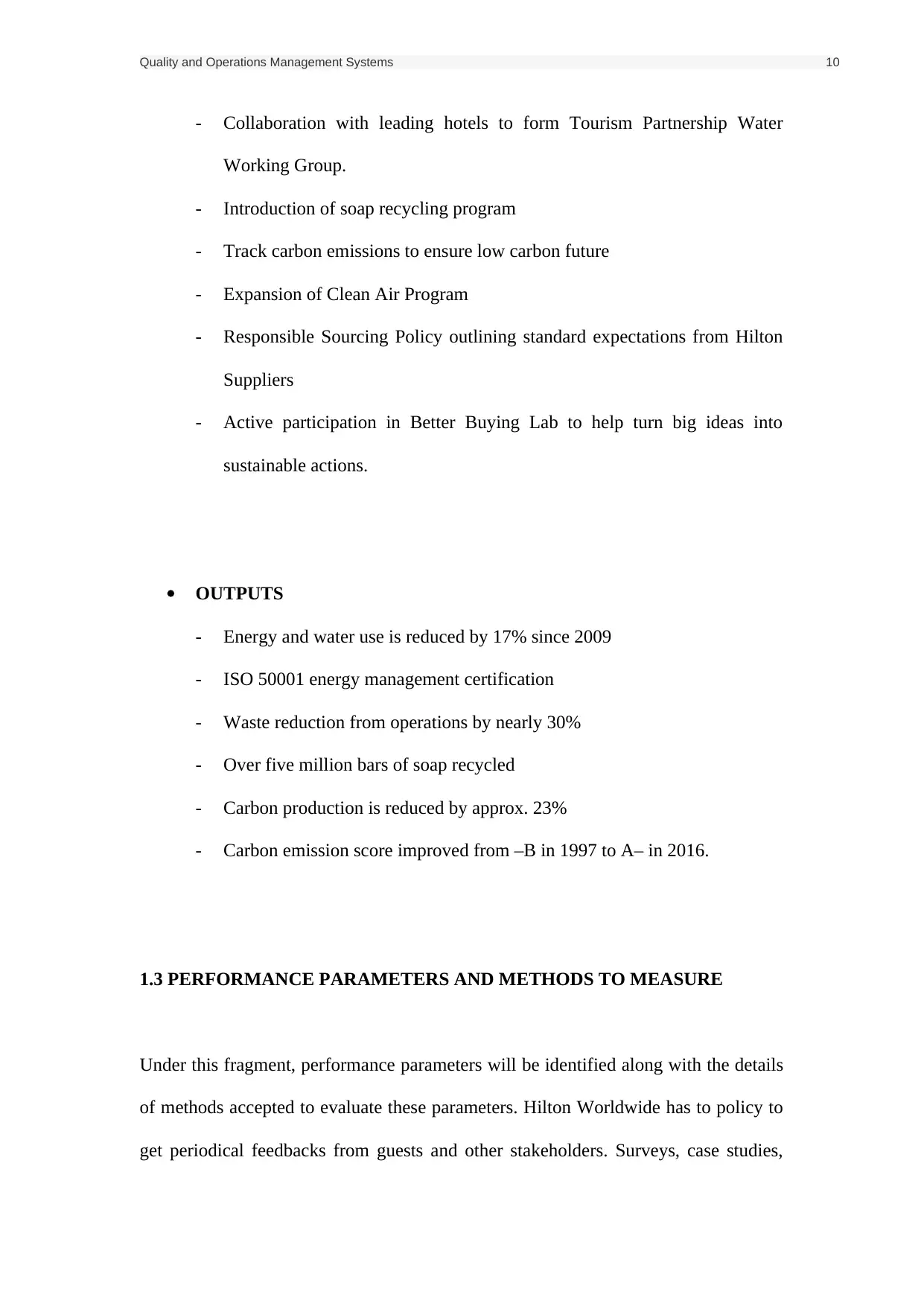
Quality and Operations Management Systems 10
- Collaboration with leading hotels to form Tourism Partnership Water
Working Group.
- Introduction of soap recycling program
- Track carbon emissions to ensure low carbon future
- Expansion of Clean Air Program
- Responsible Sourcing Policy outlining standard expectations from Hilton
Suppliers
- Active participation in Better Buying Lab to help turn big ideas into
sustainable actions.
OUTPUTS
- Energy and water use is reduced by 17% since 2009
- ISO 50001 energy management certification
- Waste reduction from operations by nearly 30%
- Over five million bars of soap recycled
- Carbon production is reduced by approx. 23%
- Carbon emission score improved from –B in 1997 to A– in 2016.
1.3 PERFORMANCE PARAMETERS AND METHODS TO MEASURE
Under this fragment, performance parameters will be identified along with the details
of methods accepted to evaluate these parameters. Hilton Worldwide has to policy to
get periodical feedbacks from guests and other stakeholders. Surveys, case studies,
- Collaboration with leading hotels to form Tourism Partnership Water
Working Group.
- Introduction of soap recycling program
- Track carbon emissions to ensure low carbon future
- Expansion of Clean Air Program
- Responsible Sourcing Policy outlining standard expectations from Hilton
Suppliers
- Active participation in Better Buying Lab to help turn big ideas into
sustainable actions.
OUTPUTS
- Energy and water use is reduced by 17% since 2009
- ISO 50001 energy management certification
- Waste reduction from operations by nearly 30%
- Over five million bars of soap recycled
- Carbon production is reduced by approx. 23%
- Carbon emission score improved from –B in 1997 to A– in 2016.
1.3 PERFORMANCE PARAMETERS AND METHODS TO MEASURE
Under this fragment, performance parameters will be identified along with the details
of methods accepted to evaluate these parameters. Hilton Worldwide has to policy to
get periodical feedbacks from guests and other stakeholders. Surveys, case studies,
Secure Best Marks with AI Grader
Need help grading? Try our AI Grader for instant feedback on your assignments.
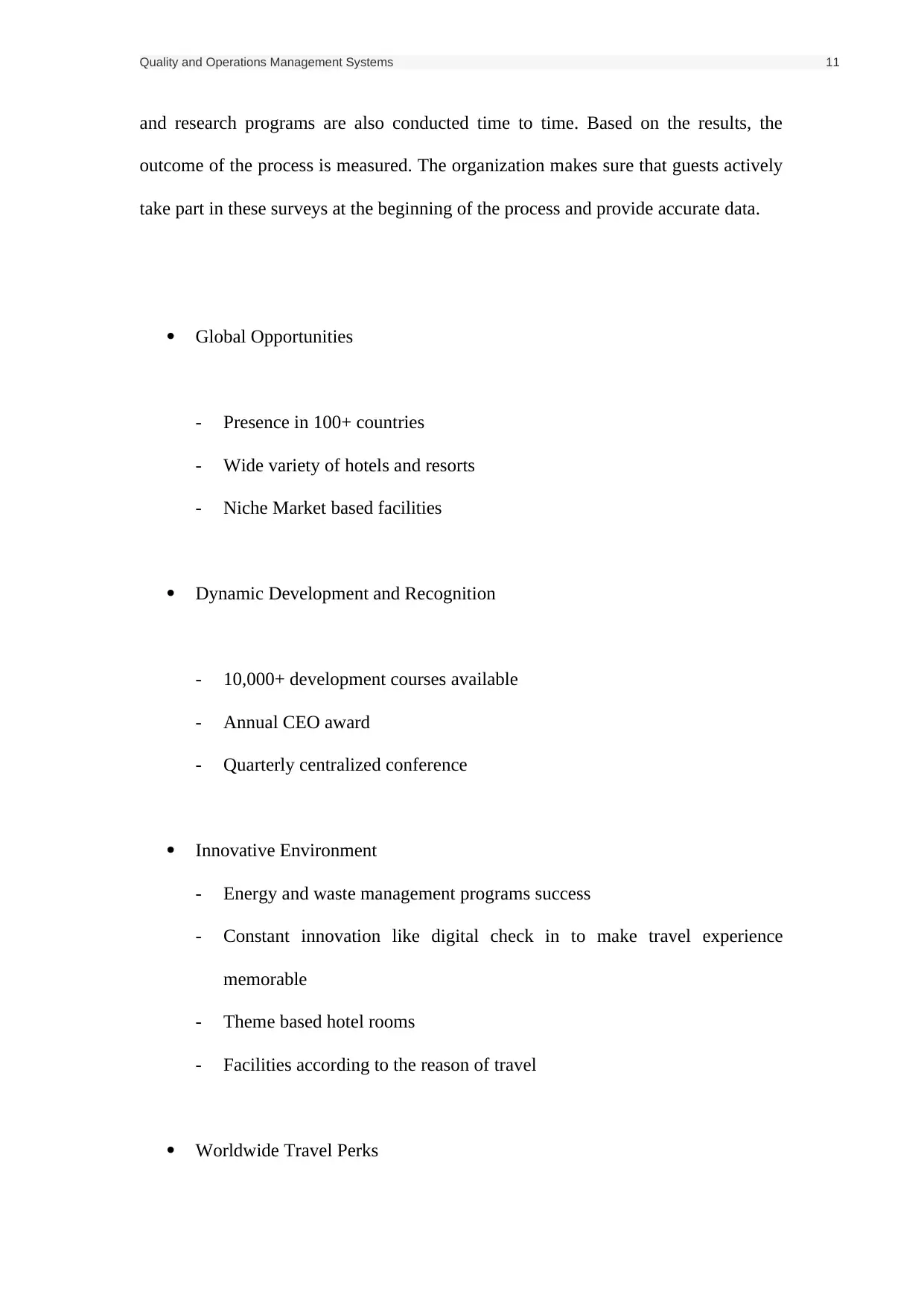
Quality and Operations Management Systems 11
and research programs are also conducted time to time. Based on the results, the
outcome of the process is measured. The organization makes sure that guests actively
take part in these surveys at the beginning of the process and provide accurate data.
Global Opportunities
- Presence in 100+ countries
- Wide variety of hotels and resorts
- Niche Market based facilities
Dynamic Development and Recognition
- 10,000+ development courses available
- Annual CEO award
- Quarterly centralized conference
Innovative Environment
- Energy and waste management programs success
- Constant innovation like digital check in to make travel experience
memorable
- Theme based hotel rooms
- Facilities according to the reason of travel
Worldwide Travel Perks
and research programs are also conducted time to time. Based on the results, the
outcome of the process is measured. The organization makes sure that guests actively
take part in these surveys at the beginning of the process and provide accurate data.
Global Opportunities
- Presence in 100+ countries
- Wide variety of hotels and resorts
- Niche Market based facilities
Dynamic Development and Recognition
- 10,000+ development courses available
- Annual CEO award
- Quarterly centralized conference
Innovative Environment
- Energy and waste management programs success
- Constant innovation like digital check in to make travel experience
memorable
- Theme based hotel rooms
- Facilities according to the reason of travel
Worldwide Travel Perks

Quality and Operations Management Systems 12
- Special passes for employees
- Discounted hotel room tariff for friends and relatives of team members
- Travel points for repeat guests [5]
Industry Leading Benefits
- To support work life benefits
- Entire system certification
Repeat and referral guests
- Customer satisfaction surveys
- Customer policies evaluation
- Guests availing repeat customer special benefits
- Reduced process time
- Communication efficiency
- Easy availability of partner third party service providers
Shareholder Confidence
- Share market price
- Discussion of concerns and comforts in regular meetings
- Timely feedback surveys
Financial sustainability policy
- Internal Auditing
- External Auditing
- Safe and secure transactions
- Special passes for employees
- Discounted hotel room tariff for friends and relatives of team members
- Travel points for repeat guests [5]
Industry Leading Benefits
- To support work life benefits
- Entire system certification
Repeat and referral guests
- Customer satisfaction surveys
- Customer policies evaluation
- Guests availing repeat customer special benefits
- Reduced process time
- Communication efficiency
- Easy availability of partner third party service providers
Shareholder Confidence
- Share market price
- Discussion of concerns and comforts in regular meetings
- Timely feedback surveys
Financial sustainability policy
- Internal Auditing
- External Auditing
- Safe and secure transactions
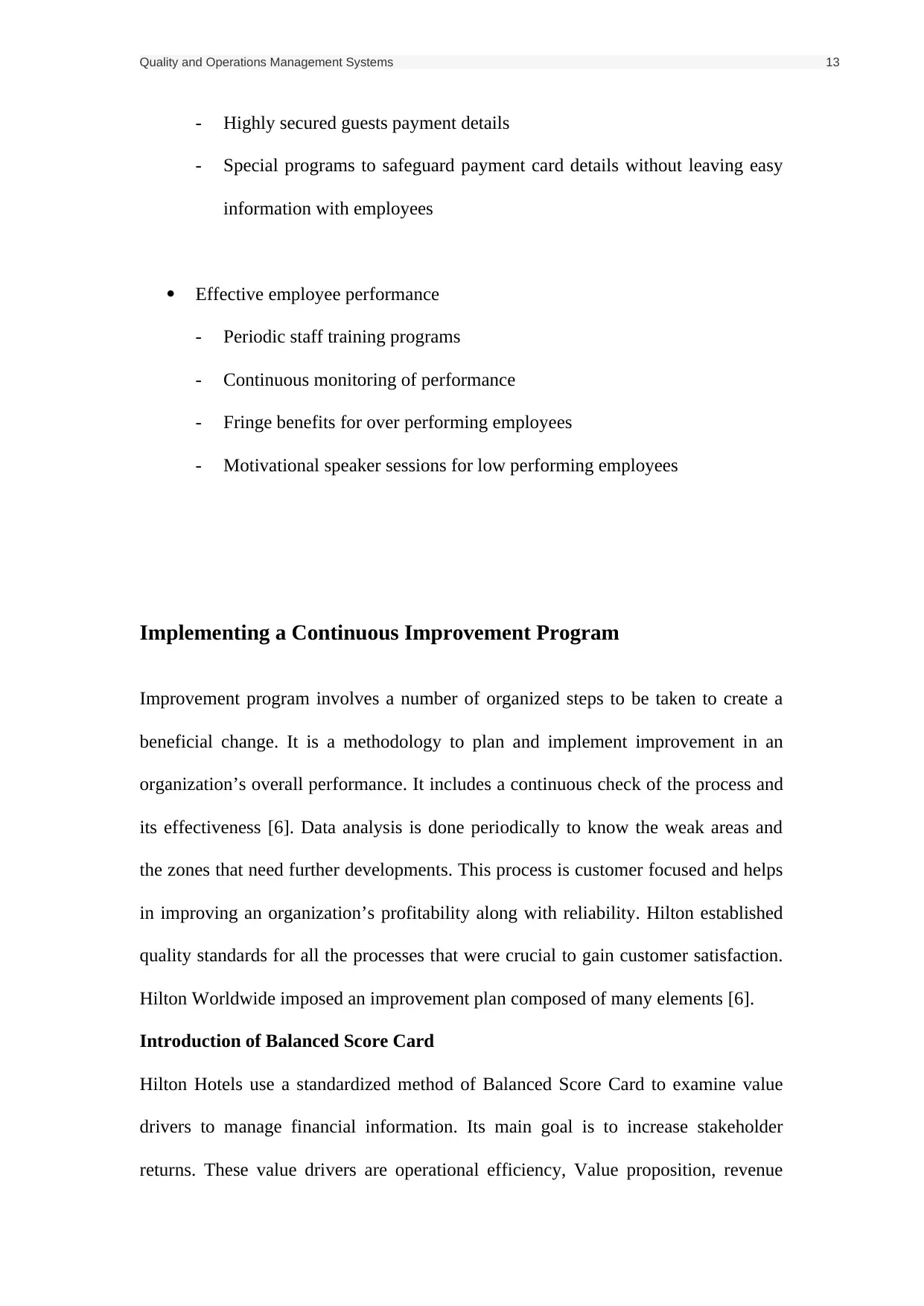
Quality and Operations Management Systems 13
- Highly secured guests payment details
- Special programs to safeguard payment card details without leaving easy
information with employees
Effective employee performance
- Periodic staff training programs
- Continuous monitoring of performance
- Fringe benefits for over performing employees
- Motivational speaker sessions for low performing employees
Implementing a Continuous Improvement Program
Improvement program involves a number of organized steps to be taken to create a
beneficial change. It is a methodology to plan and implement improvement in an
organization’s overall performance. It includes a continuous check of the process and
its effectiveness [6]. Data analysis is done periodically to know the weak areas and
the zones that need further developments. This process is customer focused and helps
in improving an organization’s profitability along with reliability. Hilton established
quality standards for all the processes that were crucial to gain customer satisfaction.
Hilton Worldwide imposed an improvement plan composed of many elements [6].
Introduction of Balanced Score Card
Hilton Hotels use a standardized method of Balanced Score Card to examine value
drivers to manage financial information. Its main goal is to increase stakeholder
returns. These value drivers are operational efficiency, Value proposition, revenue
- Highly secured guests payment details
- Special programs to safeguard payment card details without leaving easy
information with employees
Effective employee performance
- Periodic staff training programs
- Continuous monitoring of performance
- Fringe benefits for over performing employees
- Motivational speaker sessions for low performing employees
Implementing a Continuous Improvement Program
Improvement program involves a number of organized steps to be taken to create a
beneficial change. It is a methodology to plan and implement improvement in an
organization’s overall performance. It includes a continuous check of the process and
its effectiveness [6]. Data analysis is done periodically to know the weak areas and
the zones that need further developments. This process is customer focused and helps
in improving an organization’s profitability along with reliability. Hilton established
quality standards for all the processes that were crucial to gain customer satisfaction.
Hilton Worldwide imposed an improvement plan composed of many elements [6].
Introduction of Balanced Score Card
Hilton Hotels use a standardized method of Balanced Score Card to examine value
drivers to manage financial information. Its main goal is to increase stakeholder
returns. These value drivers are operational efficiency, Value proposition, revenue
Paraphrase This Document
Need a fresh take? Get an instant paraphrase of this document with our AI Paraphraser
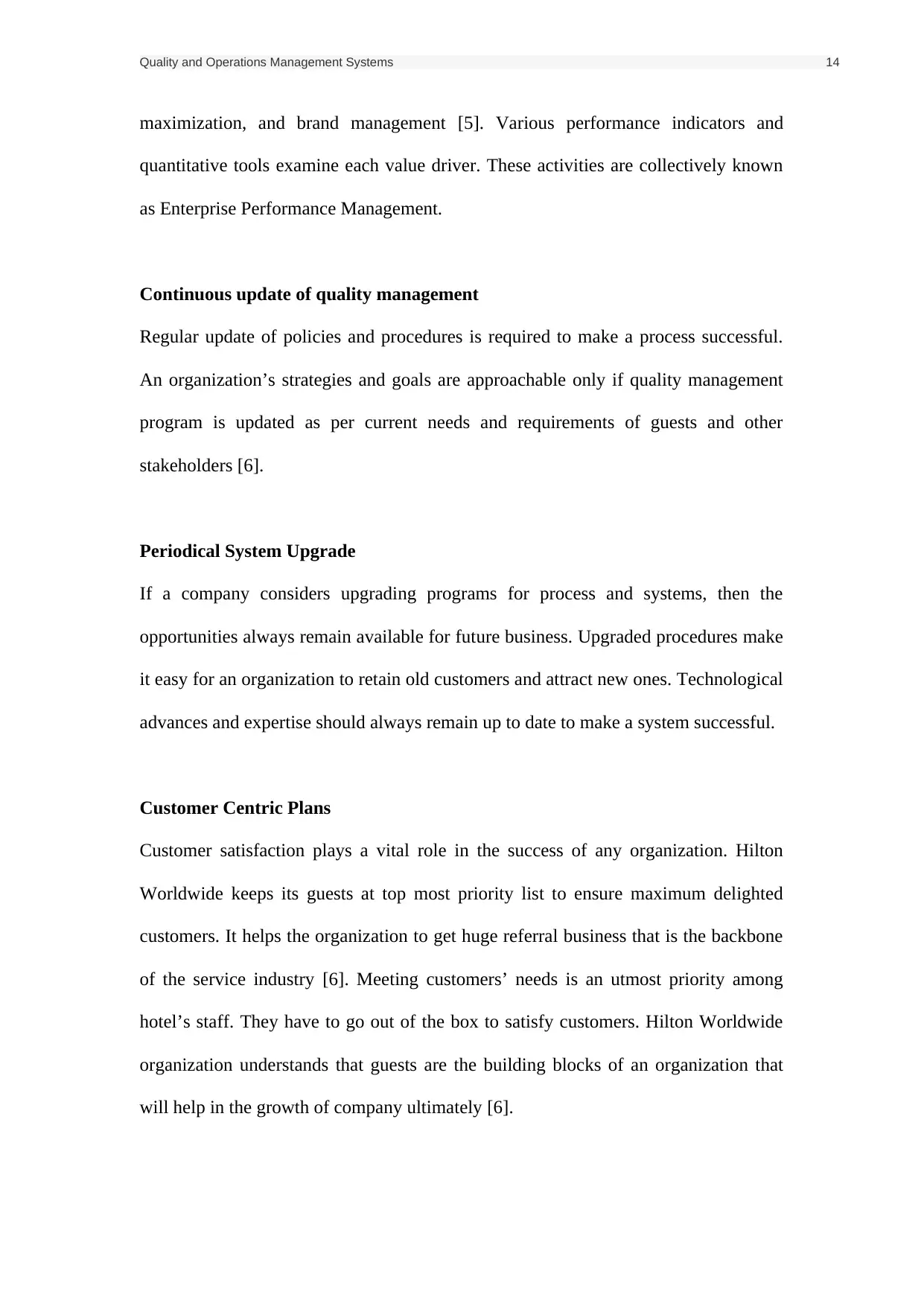
Quality and Operations Management Systems 14
maximization, and brand management [5]. Various performance indicators and
quantitative tools examine each value driver. These activities are collectively known
as Enterprise Performance Management.
Continuous update of quality management
Regular update of policies and procedures is required to make a process successful.
An organization’s strategies and goals are approachable only if quality management
program is updated as per current needs and requirements of guests and other
stakeholders [6].
Periodical System Upgrade
If a company considers upgrading programs for process and systems, then the
opportunities always remain available for future business. Upgraded procedures make
it easy for an organization to retain old customers and attract new ones. Technological
advances and expertise should always remain up to date to make a system successful.
Customer Centric Plans
Customer satisfaction plays a vital role in the success of any organization. Hilton
Worldwide keeps its guests at top most priority list to ensure maximum delighted
customers. It helps the organization to get huge referral business that is the backbone
of the service industry [6]. Meeting customers’ needs is an utmost priority among
hotel’s staff. They have to go out of the box to satisfy customers. Hilton Worldwide
organization understands that guests are the building blocks of an organization that
will help in the growth of company ultimately [6].
maximization, and brand management [5]. Various performance indicators and
quantitative tools examine each value driver. These activities are collectively known
as Enterprise Performance Management.
Continuous update of quality management
Regular update of policies and procedures is required to make a process successful.
An organization’s strategies and goals are approachable only if quality management
program is updated as per current needs and requirements of guests and other
stakeholders [6].
Periodical System Upgrade
If a company considers upgrading programs for process and systems, then the
opportunities always remain available for future business. Upgraded procedures make
it easy for an organization to retain old customers and attract new ones. Technological
advances and expertise should always remain up to date to make a system successful.
Customer Centric Plans
Customer satisfaction plays a vital role in the success of any organization. Hilton
Worldwide keeps its guests at top most priority list to ensure maximum delighted
customers. It helps the organization to get huge referral business that is the backbone
of the service industry [6]. Meeting customers’ needs is an utmost priority among
hotel’s staff. They have to go out of the box to satisfy customers. Hilton Worldwide
organization understands that guests are the building blocks of an organization that
will help in the growth of company ultimately [6].
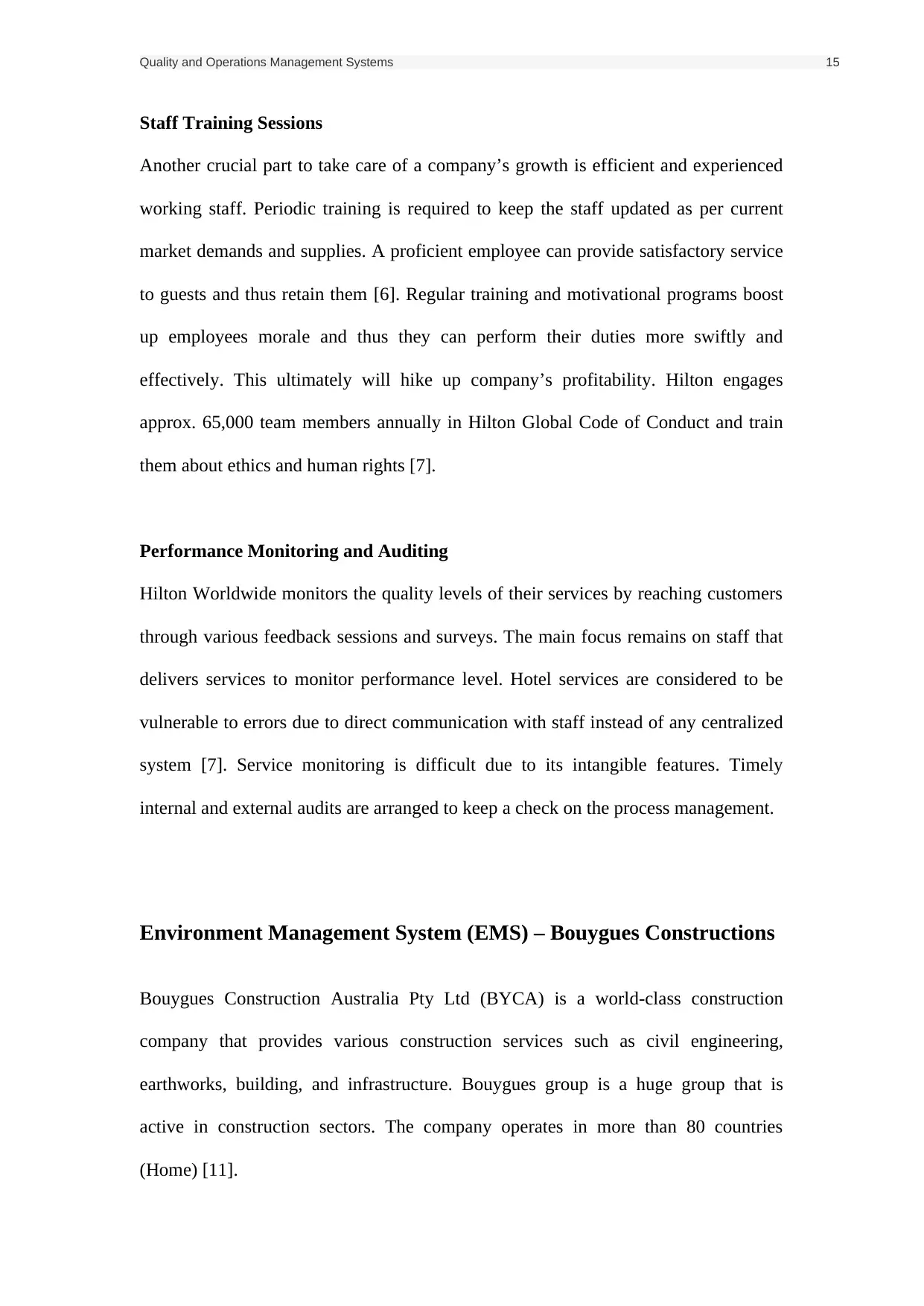
Quality and Operations Management Systems 15
Staff Training Sessions
Another crucial part to take care of a company’s growth is efficient and experienced
working staff. Periodic training is required to keep the staff updated as per current
market demands and supplies. A proficient employee can provide satisfactory service
to guests and thus retain them [6]. Regular training and motivational programs boost
up employees morale and thus they can perform their duties more swiftly and
effectively. This ultimately will hike up company’s profitability. Hilton engages
approx. 65,000 team members annually in Hilton Global Code of Conduct and train
them about ethics and human rights [7].
Performance Monitoring and Auditing
Hilton Worldwide monitors the quality levels of their services by reaching customers
through various feedback sessions and surveys. The main focus remains on staff that
delivers services to monitor performance level. Hotel services are considered to be
vulnerable to errors due to direct communication with staff instead of any centralized
system [7]. Service monitoring is difficult due to its intangible features. Timely
internal and external audits are arranged to keep a check on the process management.
Environment Management System (EMS) – Bouygues Constructions
Bouygues Construction Australia Pty Ltd (BYCA) is a world-class construction
company that provides various construction services such as civil engineering,
earthworks, building, and infrastructure. Bouygues group is a huge group that is
active in construction sectors. The company operates in more than 80 countries
(Home) [11].
Staff Training Sessions
Another crucial part to take care of a company’s growth is efficient and experienced
working staff. Periodic training is required to keep the staff updated as per current
market demands and supplies. A proficient employee can provide satisfactory service
to guests and thus retain them [6]. Regular training and motivational programs boost
up employees morale and thus they can perform their duties more swiftly and
effectively. This ultimately will hike up company’s profitability. Hilton engages
approx. 65,000 team members annually in Hilton Global Code of Conduct and train
them about ethics and human rights [7].
Performance Monitoring and Auditing
Hilton Worldwide monitors the quality levels of their services by reaching customers
through various feedback sessions and surveys. The main focus remains on staff that
delivers services to monitor performance level. Hotel services are considered to be
vulnerable to errors due to direct communication with staff instead of any centralized
system [7]. Service monitoring is difficult due to its intangible features. Timely
internal and external audits are arranged to keep a check on the process management.
Environment Management System (EMS) – Bouygues Constructions
Bouygues Construction Australia Pty Ltd (BYCA) is a world-class construction
company that provides various construction services such as civil engineering,
earthworks, building, and infrastructure. Bouygues group is a huge group that is
active in construction sectors. The company operates in more than 80 countries
(Home) [11].
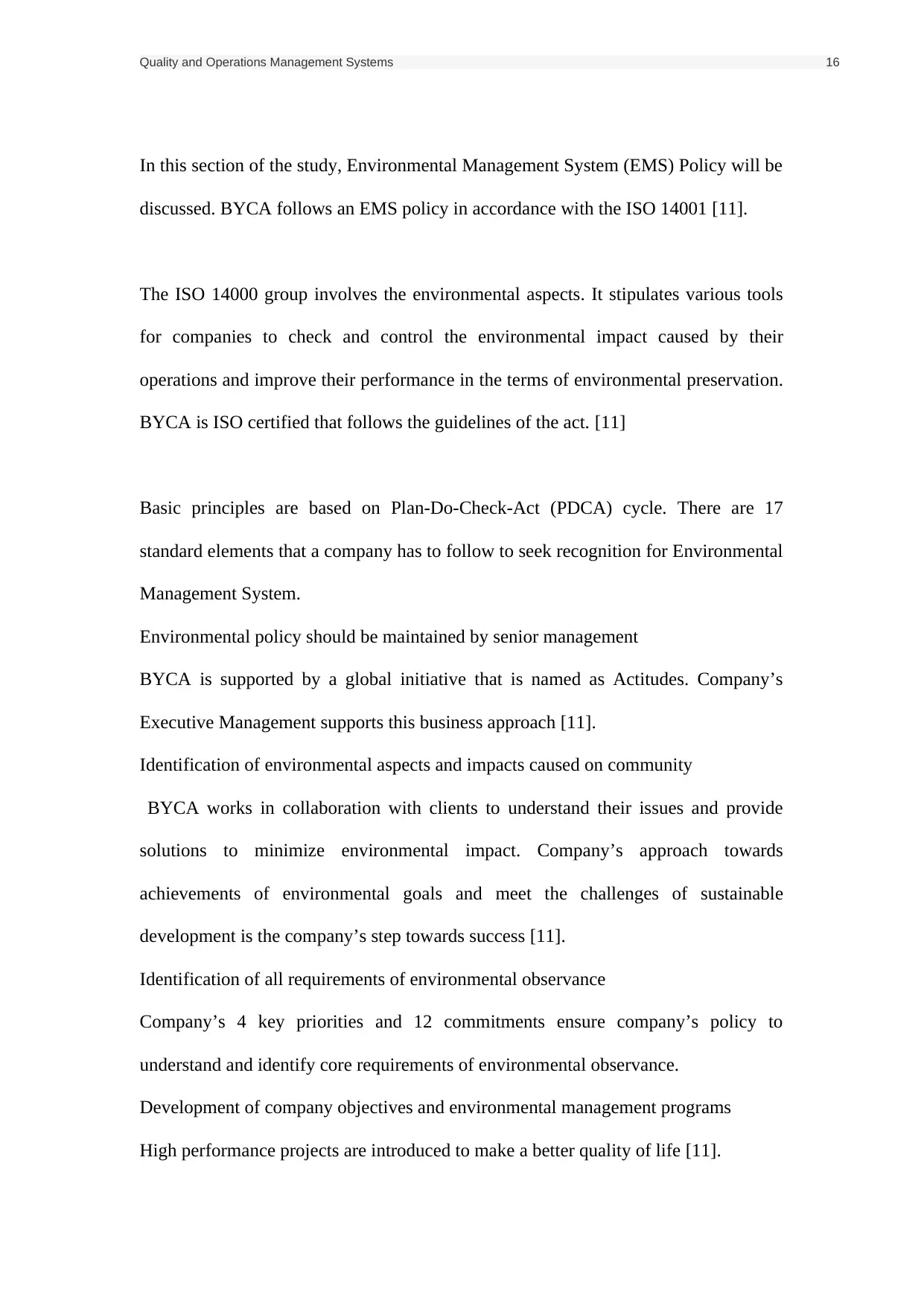
Quality and Operations Management Systems 16
In this section of the study, Environmental Management System (EMS) Policy will be
discussed. BYCA follows an EMS policy in accordance with the ISO 14001 [11].
The ISO 14000 group involves the environmental aspects. It stipulates various tools
for companies to check and control the environmental impact caused by their
operations and improve their performance in the terms of environmental preservation.
BYCA is ISO certified that follows the guidelines of the act. [11]
Basic principles are based on Plan-Do-Check-Act (PDCA) cycle. There are 17
standard elements that a company has to follow to seek recognition for Environmental
Management System.
Environmental policy should be maintained by senior management
BYCA is supported by a global initiative that is named as Actitudes. Company’s
Executive Management supports this business approach [11].
Identification of environmental aspects and impacts caused on community
BYCA works in collaboration with clients to understand their issues and provide
solutions to minimize environmental impact. Company’s approach towards
achievements of environmental goals and meet the challenges of sustainable
development is the company’s step towards success [11].
Identification of all requirements of environmental observance
Company’s 4 key priorities and 12 commitments ensure company’s policy to
understand and identify core requirements of environmental observance.
Development of company objectives and environmental management programs
High performance projects are introduced to make a better quality of life [11].
In this section of the study, Environmental Management System (EMS) Policy will be
discussed. BYCA follows an EMS policy in accordance with the ISO 14001 [11].
The ISO 14000 group involves the environmental aspects. It stipulates various tools
for companies to check and control the environmental impact caused by their
operations and improve their performance in the terms of environmental preservation.
BYCA is ISO certified that follows the guidelines of the act. [11]
Basic principles are based on Plan-Do-Check-Act (PDCA) cycle. There are 17
standard elements that a company has to follow to seek recognition for Environmental
Management System.
Environmental policy should be maintained by senior management
BYCA is supported by a global initiative that is named as Actitudes. Company’s
Executive Management supports this business approach [11].
Identification of environmental aspects and impacts caused on community
BYCA works in collaboration with clients to understand their issues and provide
solutions to minimize environmental impact. Company’s approach towards
achievements of environmental goals and meet the challenges of sustainable
development is the company’s step towards success [11].
Identification of all requirements of environmental observance
Company’s 4 key priorities and 12 commitments ensure company’s policy to
understand and identify core requirements of environmental observance.
Development of company objectives and environmental management programs
High performance projects are introduced to make a better quality of life [11].
Secure Best Marks with AI Grader
Need help grading? Try our AI Grader for instant feedback on your assignments.
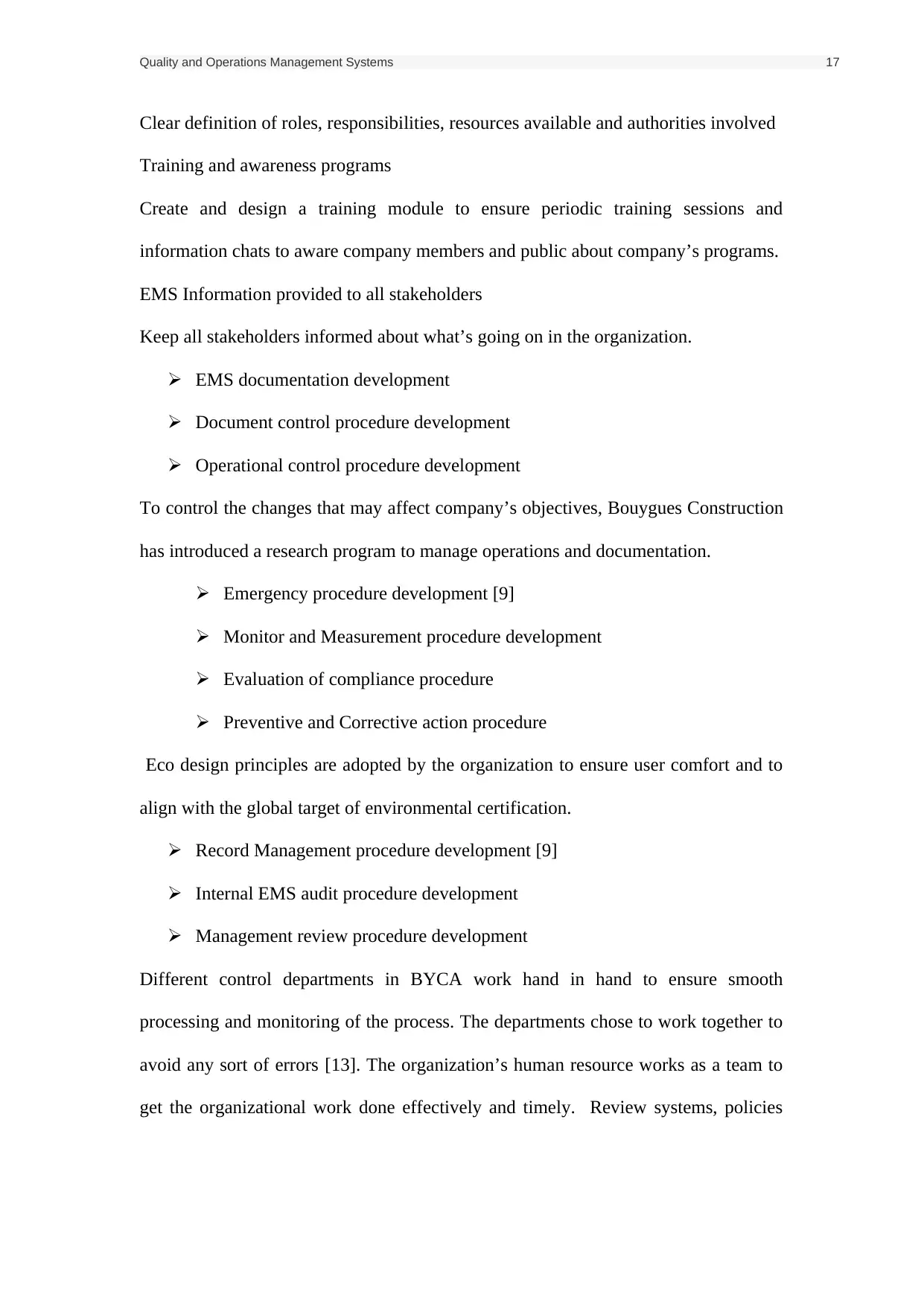
Quality and Operations Management Systems 17
Clear definition of roles, responsibilities, resources available and authorities involved
Training and awareness programs
Create and design a training module to ensure periodic training sessions and
information chats to aware company members and public about company’s programs.
EMS Information provided to all stakeholders
Keep all stakeholders informed about what’s going on in the organization.
EMS documentation development
Document control procedure development
Operational control procedure development
To control the changes that may affect company’s objectives, Bouygues Construction
has introduced a research program to manage operations and documentation.
Emergency procedure development [9]
Monitor and Measurement procedure development
Evaluation of compliance procedure
Preventive and Corrective action procedure
Eco design principles are adopted by the organization to ensure user comfort and to
align with the global target of environmental certification.
Record Management procedure development [9]
Internal EMS audit procedure development
Management review procedure development
Different control departments in BYCA work hand in hand to ensure smooth
processing and monitoring of the process. The departments chose to work together to
avoid any sort of errors [13]. The organization’s human resource works as a team to
get the organizational work done effectively and timely. Review systems, policies
Clear definition of roles, responsibilities, resources available and authorities involved
Training and awareness programs
Create and design a training module to ensure periodic training sessions and
information chats to aware company members and public about company’s programs.
EMS Information provided to all stakeholders
Keep all stakeholders informed about what’s going on in the organization.
EMS documentation development
Document control procedure development
Operational control procedure development
To control the changes that may affect company’s objectives, Bouygues Construction
has introduced a research program to manage operations and documentation.
Emergency procedure development [9]
Monitor and Measurement procedure development
Evaluation of compliance procedure
Preventive and Corrective action procedure
Eco design principles are adopted by the organization to ensure user comfort and to
align with the global target of environmental certification.
Record Management procedure development [9]
Internal EMS audit procedure development
Management review procedure development
Different control departments in BYCA work hand in hand to ensure smooth
processing and monitoring of the process. The departments chose to work together to
avoid any sort of errors [13]. The organization’s human resource works as a team to
get the organizational work done effectively and timely. Review systems, policies
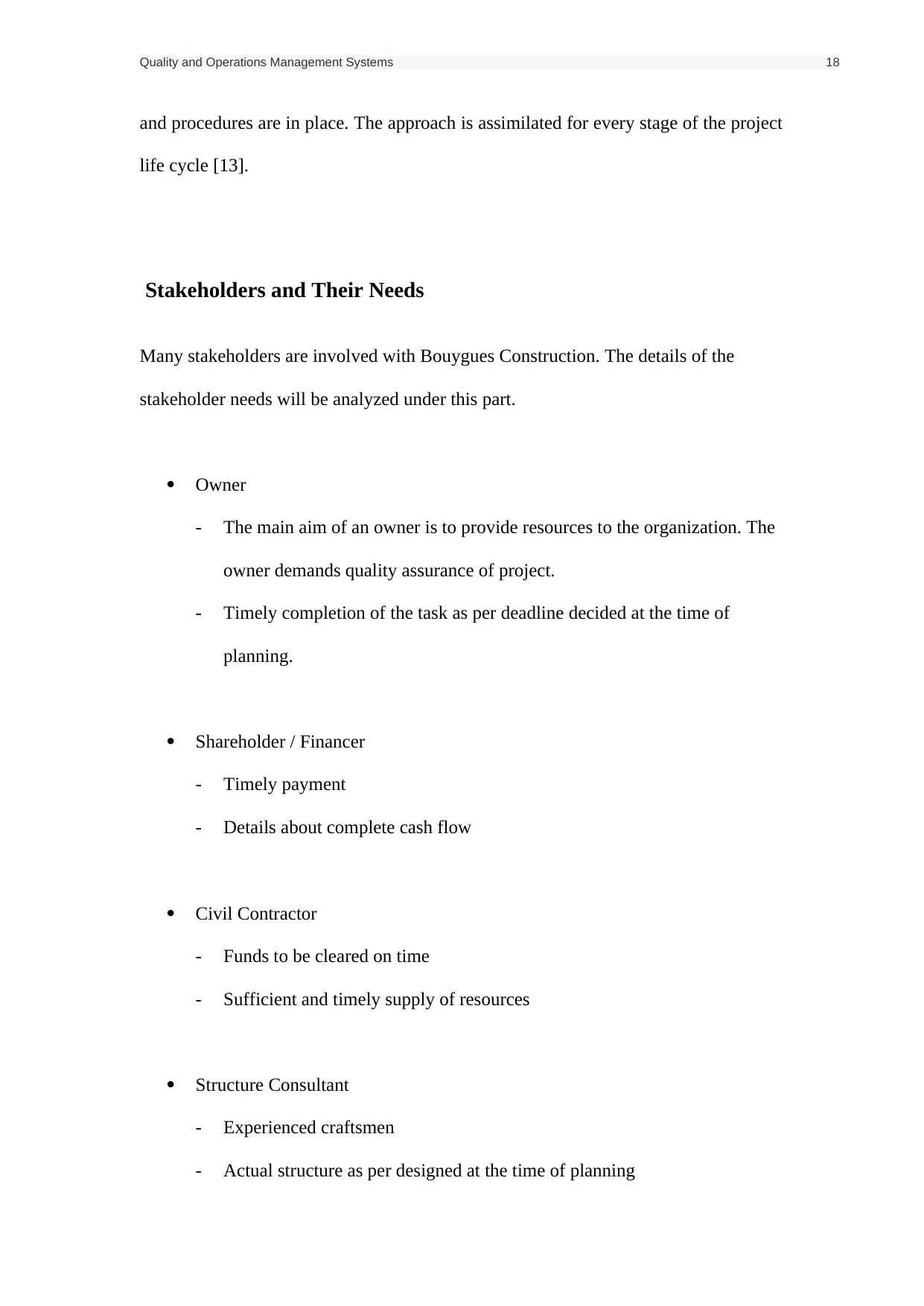
Quality and Operations Management Systems 18
and procedures are in place. The approach is assimilated for every stage of the project
life cycle [13].
Stakeholders and Their Needs
Many stakeholders are involved with Bouygues Construction. The details of the
stakeholder needs will be analyzed under this part.
Owner
- The main aim of an owner is to provide resources to the organization. The
owner demands quality assurance of project.
- Timely completion of the task as per deadline decided at the time of
planning.
Shareholder / Financer
- Timely payment
- Details about complete cash flow
Civil Contractor
- Funds to be cleared on time
- Sufficient and timely supply of resources
Structure Consultant
- Experienced craftsmen
- Actual structure as per designed at the time of planning
and procedures are in place. The approach is assimilated for every stage of the project
life cycle [13].
Stakeholders and Their Needs
Many stakeholders are involved with Bouygues Construction. The details of the
stakeholder needs will be analyzed under this part.
Owner
- The main aim of an owner is to provide resources to the organization. The
owner demands quality assurance of project.
- Timely completion of the task as per deadline decided at the time of
planning.
Shareholder / Financer
- Timely payment
- Details about complete cash flow
Civil Contractor
- Funds to be cleared on time
- Sufficient and timely supply of resources
Structure Consultant
- Experienced craftsmen
- Actual structure as per designed at the time of planning
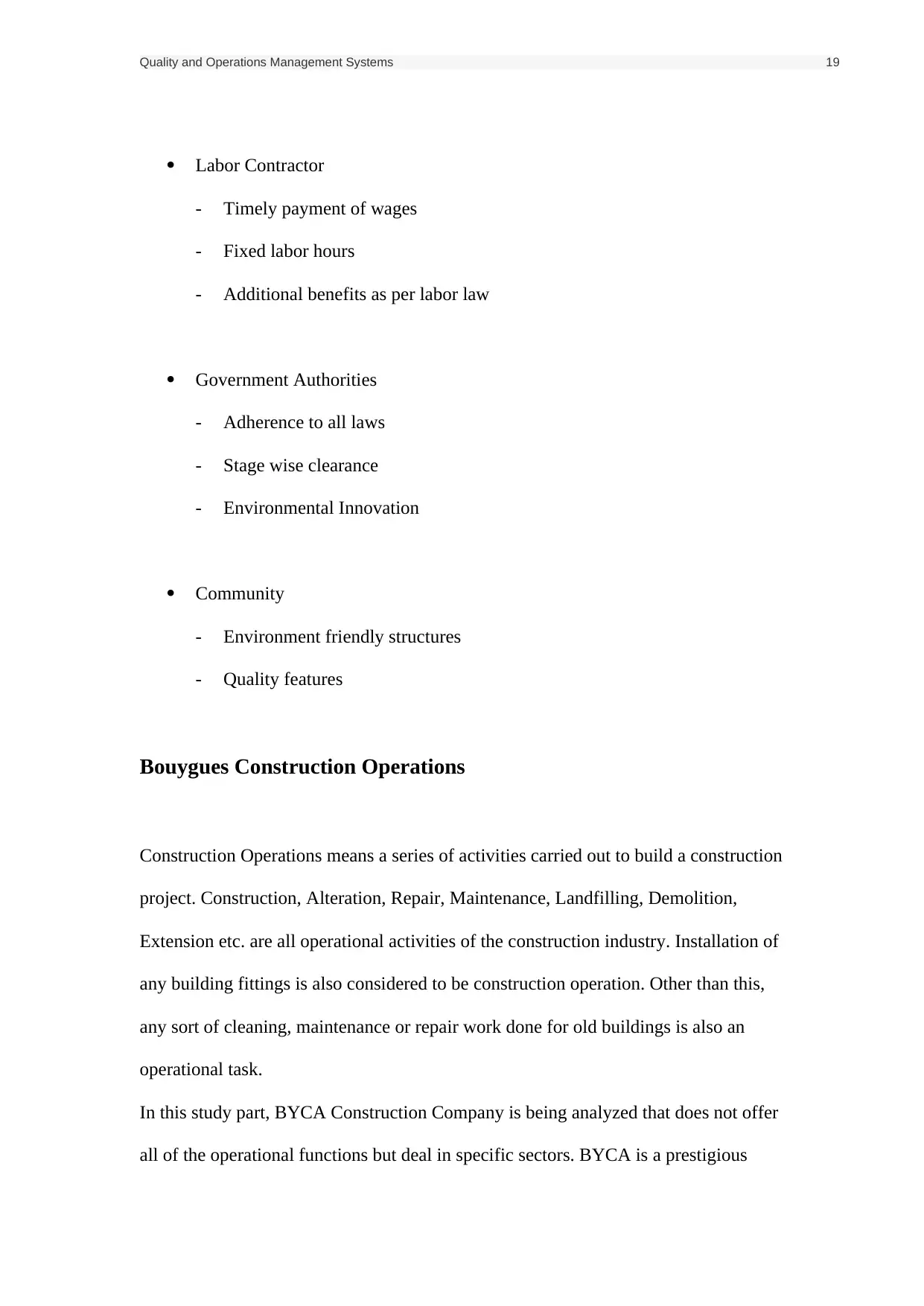
Quality and Operations Management Systems 19
Labor Contractor
- Timely payment of wages
- Fixed labor hours
- Additional benefits as per labor law
Government Authorities
- Adherence to all laws
- Stage wise clearance
- Environmental Innovation
Community
- Environment friendly structures
- Quality features
Bouygues Construction Operations
Construction Operations means a series of activities carried out to build a construction
project. Construction, Alteration, Repair, Maintenance, Landfilling, Demolition,
Extension etc. are all operational activities of the construction industry. Installation of
any building fittings is also considered to be construction operation. Other than this,
any sort of cleaning, maintenance or repair work done for old buildings is also an
operational task.
In this study part, BYCA Construction Company is being analyzed that does not offer
all of the operational functions but deal in specific sectors. BYCA is a prestigious
Labor Contractor
- Timely payment of wages
- Fixed labor hours
- Additional benefits as per labor law
Government Authorities
- Adherence to all laws
- Stage wise clearance
- Environmental Innovation
Community
- Environment friendly structures
- Quality features
Bouygues Construction Operations
Construction Operations means a series of activities carried out to build a construction
project. Construction, Alteration, Repair, Maintenance, Landfilling, Demolition,
Extension etc. are all operational activities of the construction industry. Installation of
any building fittings is also considered to be construction operation. Other than this,
any sort of cleaning, maintenance or repair work done for old buildings is also an
operational task.
In this study part, BYCA Construction Company is being analyzed that does not offer
all of the operational functions but deal in specific sectors. BYCA is a prestigious
Paraphrase This Document
Need a fresh take? Get an instant paraphrase of this document with our AI Paraphraser
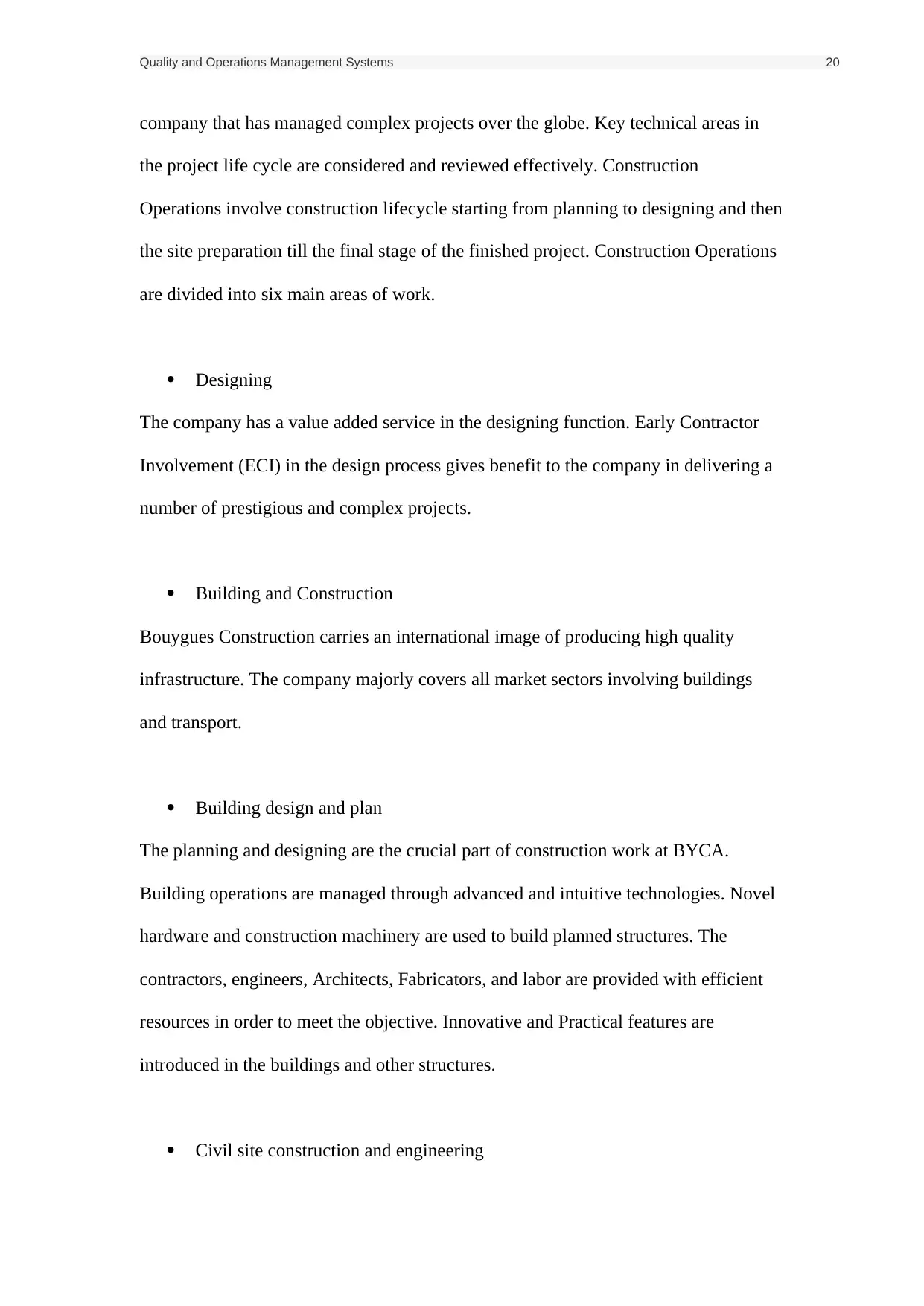
Quality and Operations Management Systems 20
company that has managed complex projects over the globe. Key technical areas in
the project life cycle are considered and reviewed effectively. Construction
Operations involve construction lifecycle starting from planning to designing and then
the site preparation till the final stage of the finished project. Construction Operations
are divided into six main areas of work.
Designing
The company has a value added service in the designing function. Early Contractor
Involvement (ECI) in the design process gives benefit to the company in delivering a
number of prestigious and complex projects.
Building and Construction
Bouygues Construction carries an international image of producing high quality
infrastructure. The company majorly covers all market sectors involving buildings
and transport.
Building design and plan
The planning and designing are the crucial part of construction work at BYCA.
Building operations are managed through advanced and intuitive technologies. Novel
hardware and construction machinery are used to build planned structures. The
contractors, engineers, Architects, Fabricators, and labor are provided with efficient
resources in order to meet the objective. Innovative and Practical features are
introduced in the buildings and other structures.
Civil site construction and engineering
company that has managed complex projects over the globe. Key technical areas in
the project life cycle are considered and reviewed effectively. Construction
Operations involve construction lifecycle starting from planning to designing and then
the site preparation till the final stage of the finished project. Construction Operations
are divided into six main areas of work.
Designing
The company has a value added service in the designing function. Early Contractor
Involvement (ECI) in the design process gives benefit to the company in delivering a
number of prestigious and complex projects.
Building and Construction
Bouygues Construction carries an international image of producing high quality
infrastructure. The company majorly covers all market sectors involving buildings
and transport.
Building design and plan
The planning and designing are the crucial part of construction work at BYCA.
Building operations are managed through advanced and intuitive technologies. Novel
hardware and construction machinery are used to build planned structures. The
contractors, engineers, Architects, Fabricators, and labor are provided with efficient
resources in order to meet the objective. Innovative and Practical features are
introduced in the buildings and other structures.
Civil site construction and engineering
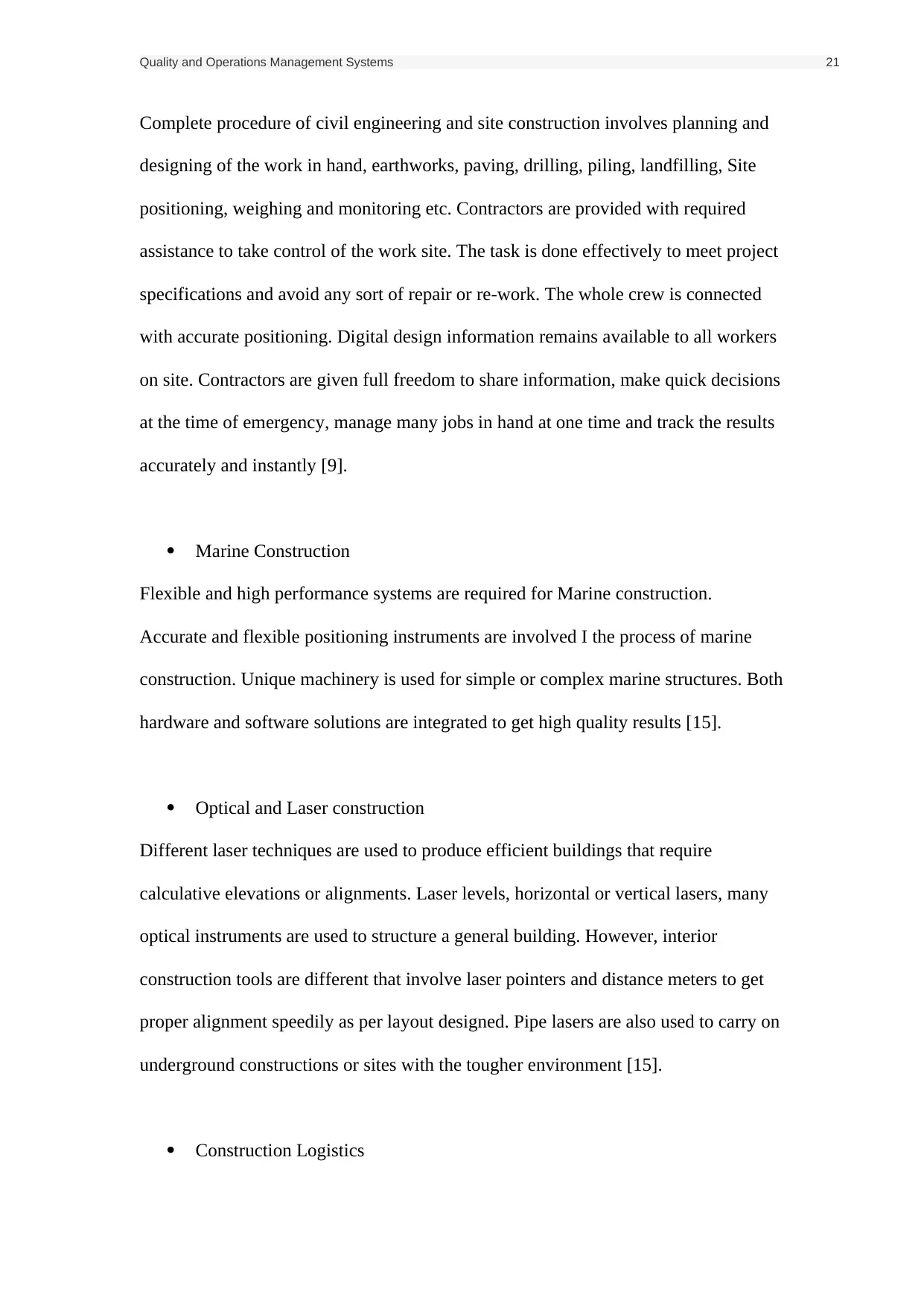
Quality and Operations Management Systems 21
Complete procedure of civil engineering and site construction involves planning and
designing of the work in hand, earthworks, paving, drilling, piling, landfilling, Site
positioning, weighing and monitoring etc. Contractors are provided with required
assistance to take control of the work site. The task is done effectively to meet project
specifications and avoid any sort of repair or re-work. The whole crew is connected
with accurate positioning. Digital design information remains available to all workers
on site. Contractors are given full freedom to share information, make quick decisions
at the time of emergency, manage many jobs in hand at one time and track the results
accurately and instantly [9].
Marine Construction
Flexible and high performance systems are required for Marine construction.
Accurate and flexible positioning instruments are involved I the process of marine
construction. Unique machinery is used for simple or complex marine structures. Both
hardware and software solutions are integrated to get high quality results [15].
Optical and Laser construction
Different laser techniques are used to produce efficient buildings that require
calculative elevations or alignments. Laser levels, horizontal or vertical lasers, many
optical instruments are used to structure a general building. However, interior
construction tools are different that involve laser pointers and distance meters to get
proper alignment speedily as per layout designed. Pipe lasers are also used to carry on
underground constructions or sites with the tougher environment [15].
Construction Logistics
Complete procedure of civil engineering and site construction involves planning and
designing of the work in hand, earthworks, paving, drilling, piling, landfilling, Site
positioning, weighing and monitoring etc. Contractors are provided with required
assistance to take control of the work site. The task is done effectively to meet project
specifications and avoid any sort of repair or re-work. The whole crew is connected
with accurate positioning. Digital design information remains available to all workers
on site. Contractors are given full freedom to share information, make quick decisions
at the time of emergency, manage many jobs in hand at one time and track the results
accurately and instantly [9].
Marine Construction
Flexible and high performance systems are required for Marine construction.
Accurate and flexible positioning instruments are involved I the process of marine
construction. Unique machinery is used for simple or complex marine structures. Both
hardware and software solutions are integrated to get high quality results [15].
Optical and Laser construction
Different laser techniques are used to produce efficient buildings that require
calculative elevations or alignments. Laser levels, horizontal or vertical lasers, many
optical instruments are used to structure a general building. However, interior
construction tools are different that involve laser pointers and distance meters to get
proper alignment speedily as per layout designed. Pipe lasers are also used to carry on
underground constructions or sites with the tougher environment [15].
Construction Logistics
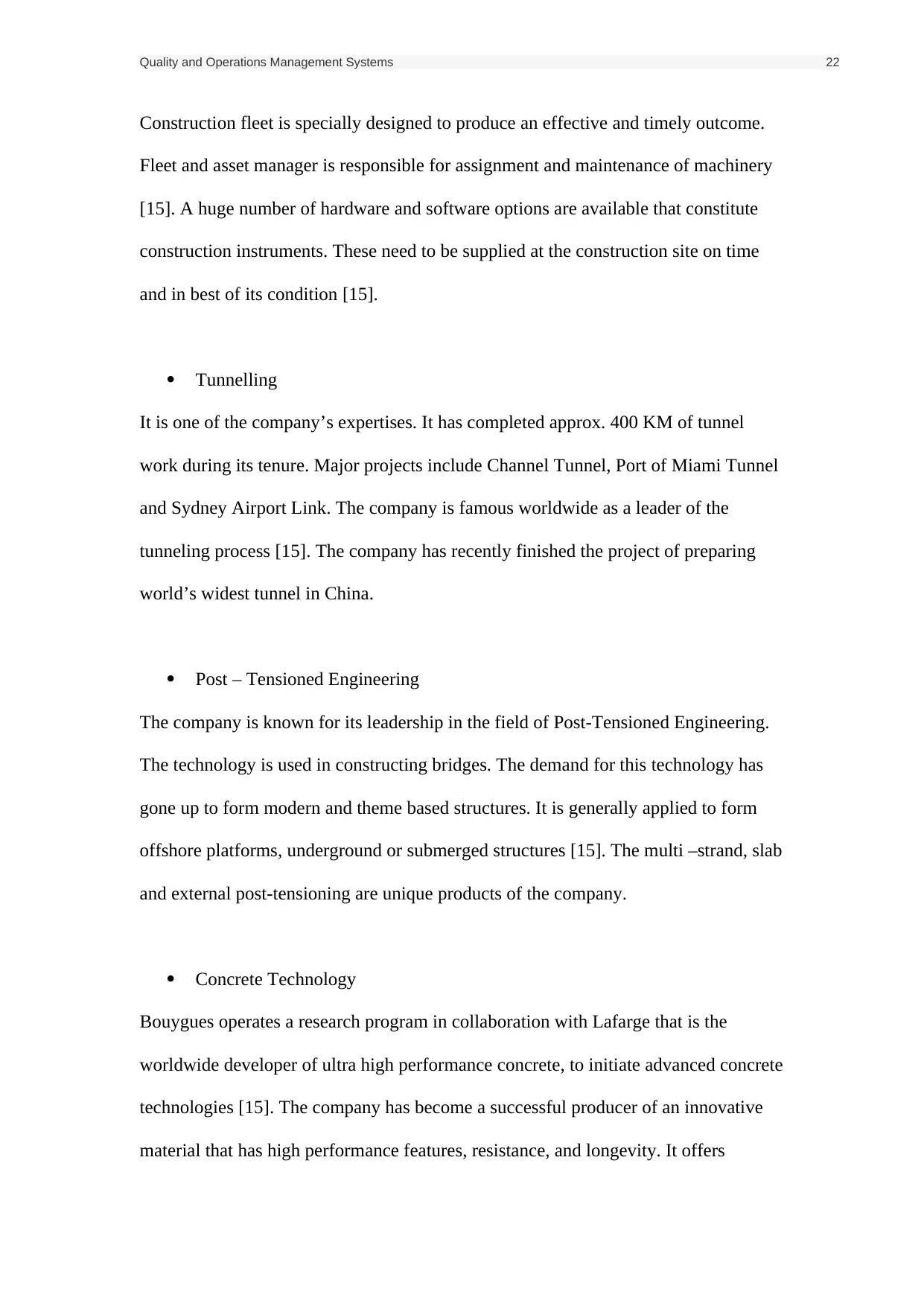
Quality and Operations Management Systems 22
Construction fleet is specially designed to produce an effective and timely outcome.
Fleet and asset manager is responsible for assignment and maintenance of machinery
[15]. A huge number of hardware and software options are available that constitute
construction instruments. These need to be supplied at the construction site on time
and in best of its condition [15].
Tunnelling
It is one of the company’s expertises. It has completed approx. 400 KM of tunnel
work during its tenure. Major projects include Channel Tunnel, Port of Miami Tunnel
and Sydney Airport Link. The company is famous worldwide as a leader of the
tunneling process [15]. The company has recently finished the project of preparing
world’s widest tunnel in China.
Post – Tensioned Engineering
The company is known for its leadership in the field of Post-Tensioned Engineering.
The technology is used in constructing bridges. The demand for this technology has
gone up to form modern and theme based structures. It is generally applied to form
offshore platforms, underground or submerged structures [15]. The multi –strand, slab
and external post-tensioning are unique products of the company.
Concrete Technology
Bouygues operates a research program in collaboration with Lafarge that is the
worldwide developer of ultra high performance concrete, to initiate advanced concrete
technologies [15]. The company has become a successful producer of an innovative
material that has high performance features, resistance, and longevity. It offers
Construction fleet is specially designed to produce an effective and timely outcome.
Fleet and asset manager is responsible for assignment and maintenance of machinery
[15]. A huge number of hardware and software options are available that constitute
construction instruments. These need to be supplied at the construction site on time
and in best of its condition [15].
Tunnelling
It is one of the company’s expertises. It has completed approx. 400 KM of tunnel
work during its tenure. Major projects include Channel Tunnel, Port of Miami Tunnel
and Sydney Airport Link. The company is famous worldwide as a leader of the
tunneling process [15]. The company has recently finished the project of preparing
world’s widest tunnel in China.
Post – Tensioned Engineering
The company is known for its leadership in the field of Post-Tensioned Engineering.
The technology is used in constructing bridges. The demand for this technology has
gone up to form modern and theme based structures. It is generally applied to form
offshore platforms, underground or submerged structures [15]. The multi –strand, slab
and external post-tensioning are unique products of the company.
Concrete Technology
Bouygues operates a research program in collaboration with Lafarge that is the
worldwide developer of ultra high performance concrete, to initiate advanced concrete
technologies [15]. The company has become a successful producer of an innovative
material that has high performance features, resistance, and longevity. It offers
Secure Best Marks with AI Grader
Need help grading? Try our AI Grader for instant feedback on your assignments.
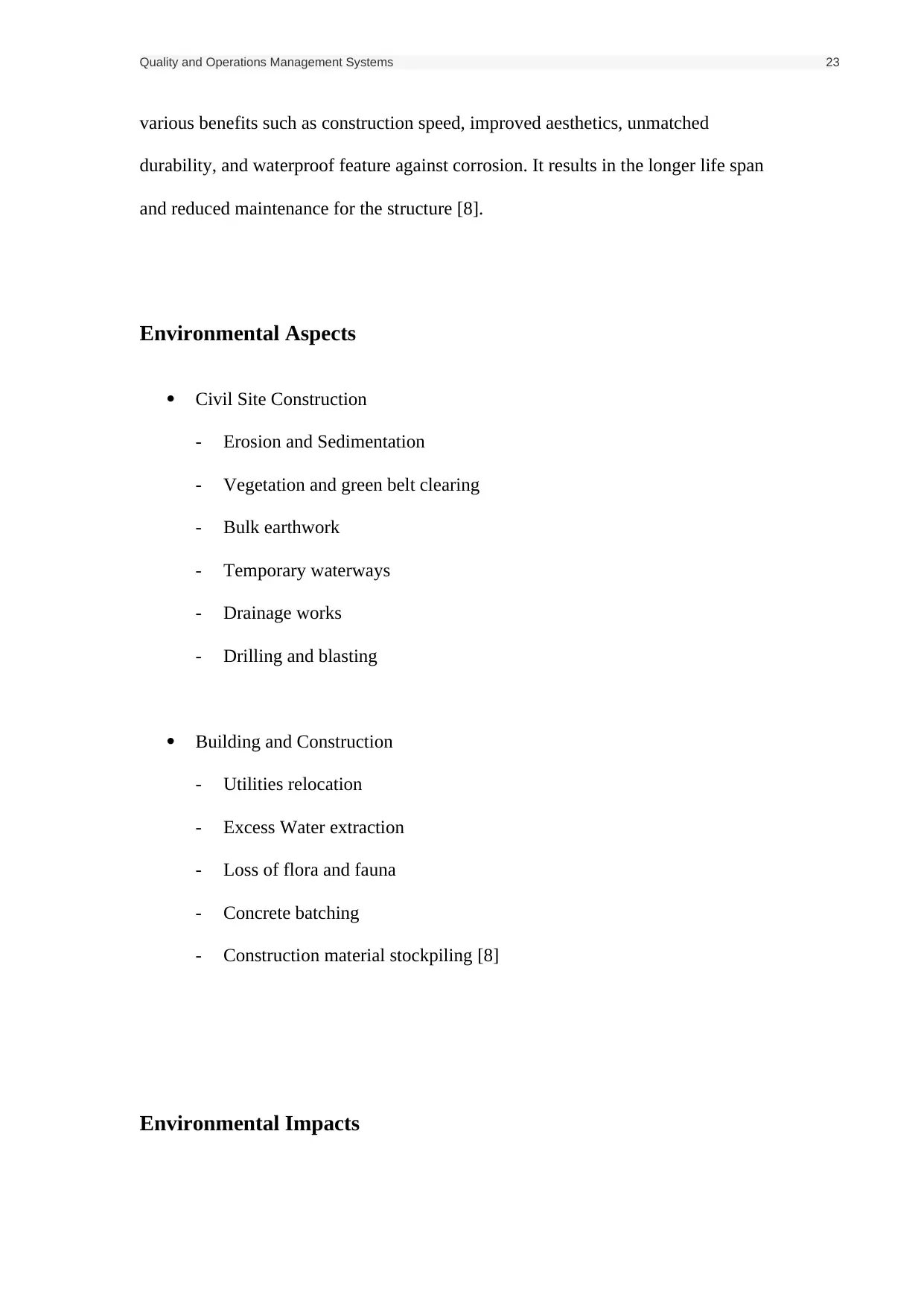
Quality and Operations Management Systems 23
various benefits such as construction speed, improved aesthetics, unmatched
durability, and waterproof feature against corrosion. It results in the longer life span
and reduced maintenance for the structure [8].
Environmental Aspects
Civil Site Construction
- Erosion and Sedimentation
- Vegetation and green belt clearing
- Bulk earthwork
- Temporary waterways
- Drainage works
- Drilling and blasting
Building and Construction
- Utilities relocation
- Excess Water extraction
- Loss of flora and fauna
- Concrete batching
- Construction material stockpiling [8]
Environmental Impacts
various benefits such as construction speed, improved aesthetics, unmatched
durability, and waterproof feature against corrosion. It results in the longer life span
and reduced maintenance for the structure [8].
Environmental Aspects
Civil Site Construction
- Erosion and Sedimentation
- Vegetation and green belt clearing
- Bulk earthwork
- Temporary waterways
- Drainage works
- Drilling and blasting
Building and Construction
- Utilities relocation
- Excess Water extraction
- Loss of flora and fauna
- Concrete batching
- Construction material stockpiling [8]
Environmental Impacts
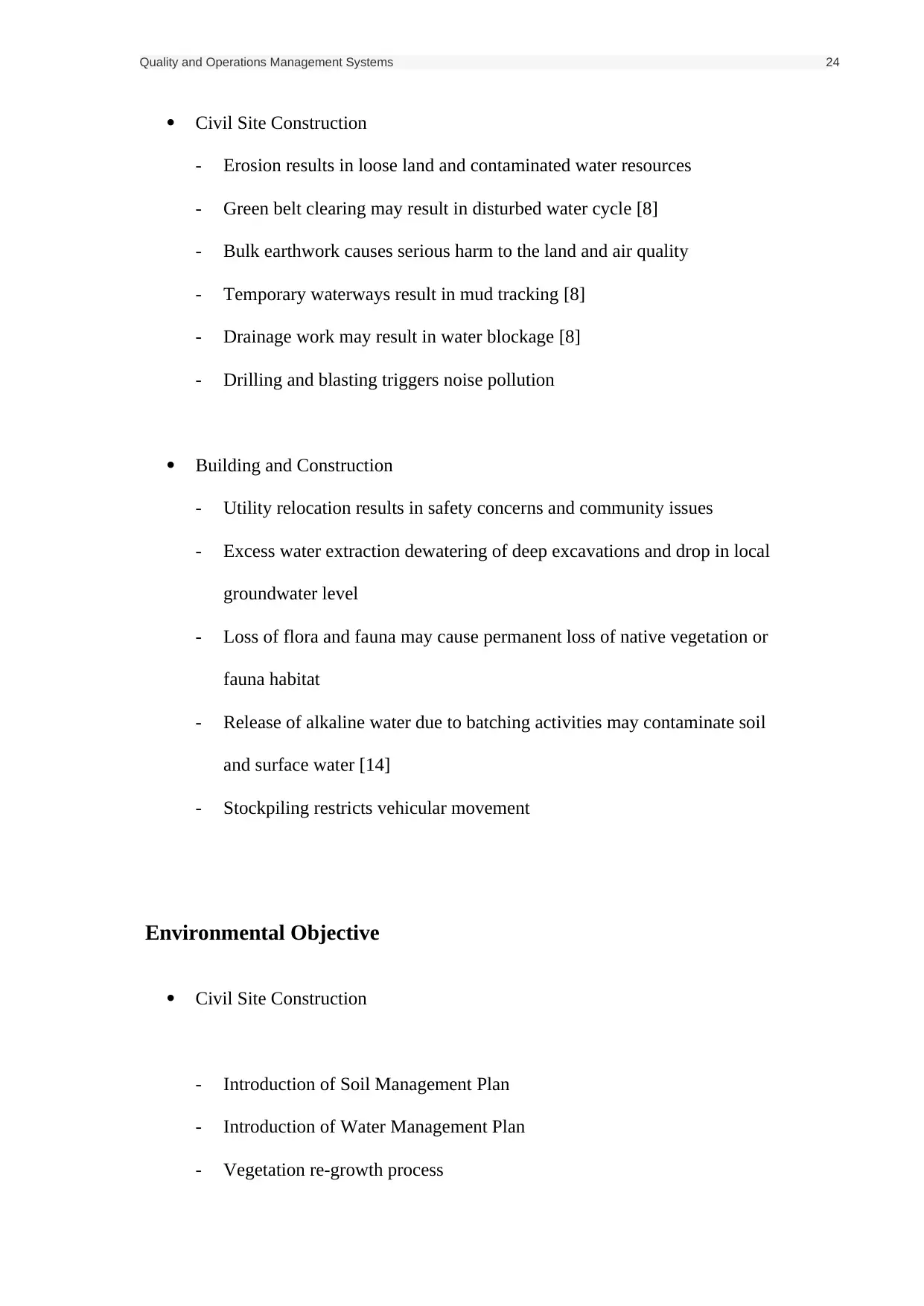
Quality and Operations Management Systems 24
Civil Site Construction
- Erosion results in loose land and contaminated water resources
- Green belt clearing may result in disturbed water cycle [8]
- Bulk earthwork causes serious harm to the land and air quality
- Temporary waterways result in mud tracking [8]
- Drainage work may result in water blockage [8]
- Drilling and blasting triggers noise pollution
Building and Construction
- Utility relocation results in safety concerns and community issues
- Excess water extraction dewatering of deep excavations and drop in local
groundwater level
- Loss of flora and fauna may cause permanent loss of native vegetation or
fauna habitat
- Release of alkaline water due to batching activities may contaminate soil
and surface water [14]
- Stockpiling restricts vehicular movement
Environmental Objective
Civil Site Construction
- Introduction of Soil Management Plan
- Introduction of Water Management Plan
- Vegetation re-growth process
Civil Site Construction
- Erosion results in loose land and contaminated water resources
- Green belt clearing may result in disturbed water cycle [8]
- Bulk earthwork causes serious harm to the land and air quality
- Temporary waterways result in mud tracking [8]
- Drainage work may result in water blockage [8]
- Drilling and blasting triggers noise pollution
Building and Construction
- Utility relocation results in safety concerns and community issues
- Excess water extraction dewatering of deep excavations and drop in local
groundwater level
- Loss of flora and fauna may cause permanent loss of native vegetation or
fauna habitat
- Release of alkaline water due to batching activities may contaminate soil
and surface water [14]
- Stockpiling restricts vehicular movement
Environmental Objective
Civil Site Construction
- Introduction of Soil Management Plan
- Introduction of Water Management Plan
- Vegetation re-growth process
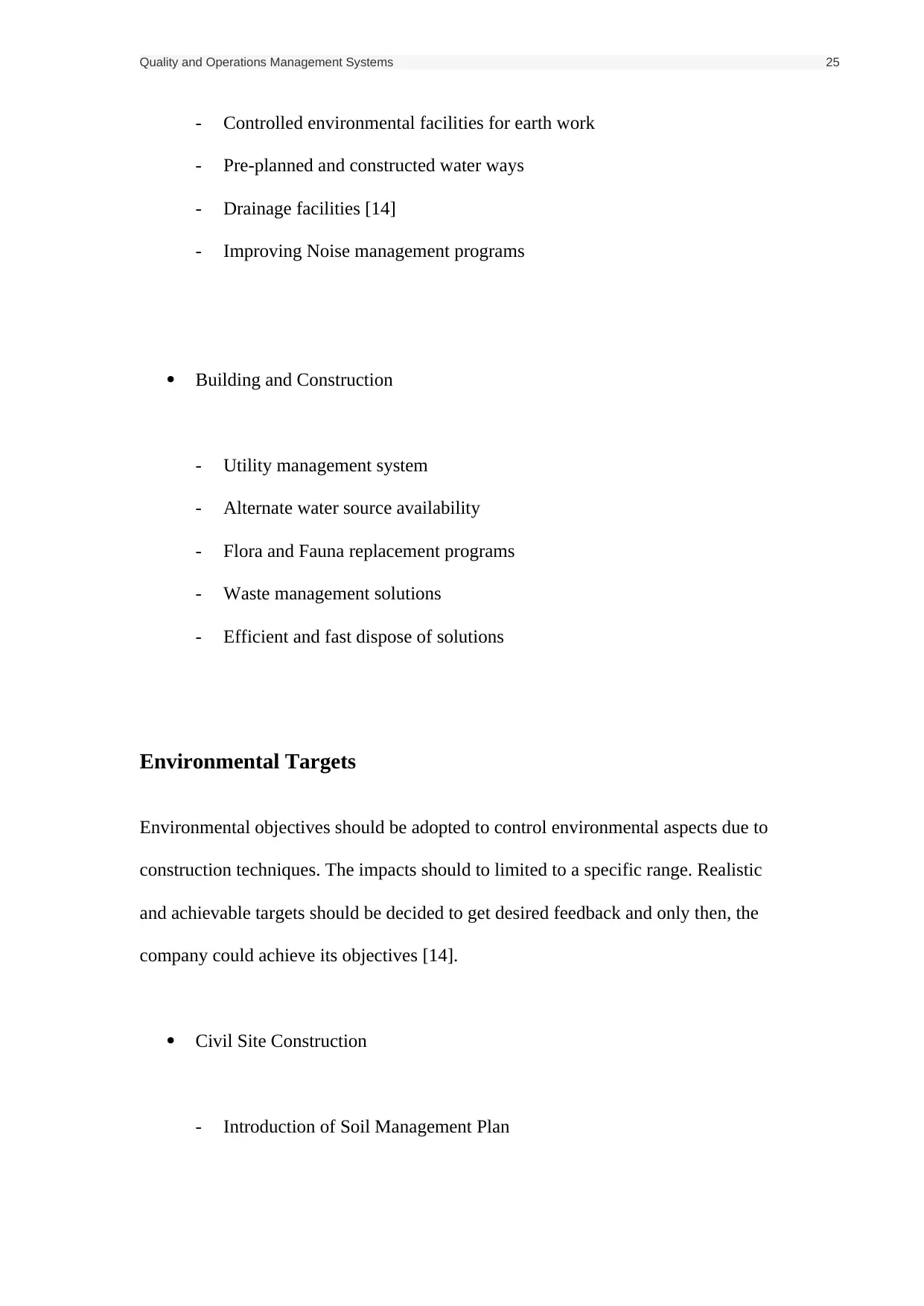
Quality and Operations Management Systems 25
- Controlled environmental facilities for earth work
- Pre-planned and constructed water ways
- Drainage facilities [14]
- Improving Noise management programs
Building and Construction
- Utility management system
- Alternate water source availability
- Flora and Fauna replacement programs
- Waste management solutions
- Efficient and fast dispose of solutions
Environmental Targets
Environmental objectives should be adopted to control environmental aspects due to
construction techniques. The impacts should to limited to a specific range. Realistic
and achievable targets should be decided to get desired feedback and only then, the
company could achieve its objectives [14].
Civil Site Construction
- Introduction of Soil Management Plan
- Controlled environmental facilities for earth work
- Pre-planned and constructed water ways
- Drainage facilities [14]
- Improving Noise management programs
Building and Construction
- Utility management system
- Alternate water source availability
- Flora and Fauna replacement programs
- Waste management solutions
- Efficient and fast dispose of solutions
Environmental Targets
Environmental objectives should be adopted to control environmental aspects due to
construction techniques. The impacts should to limited to a specific range. Realistic
and achievable targets should be decided to get desired feedback and only then, the
company could achieve its objectives [14].
Civil Site Construction
- Introduction of Soil Management Plan
Paraphrase This Document
Need a fresh take? Get an instant paraphrase of this document with our AI Paraphraser
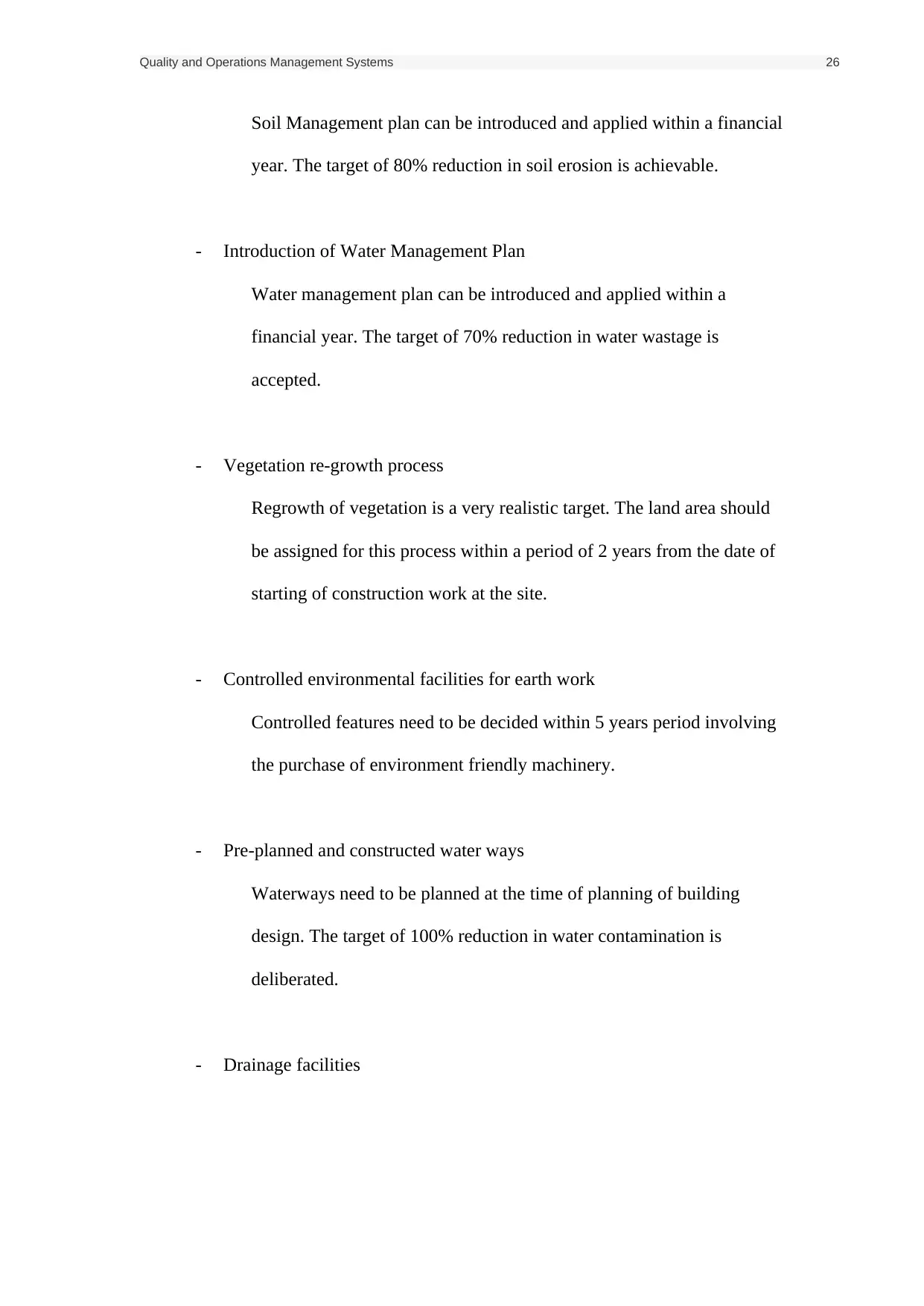
Quality and Operations Management Systems 26
Soil Management plan can be introduced and applied within a financial
year. The target of 80% reduction in soil erosion is achievable.
- Introduction of Water Management Plan
Water management plan can be introduced and applied within a
financial year. The target of 70% reduction in water wastage is
accepted.
- Vegetation re-growth process
Regrowth of vegetation is a very realistic target. The land area should
be assigned for this process within a period of 2 years from the date of
starting of construction work at the site.
- Controlled environmental facilities for earth work
Controlled features need to be decided within 5 years period involving
the purchase of environment friendly machinery.
- Pre-planned and constructed water ways
Waterways need to be planned at the time of planning of building
design. The target of 100% reduction in water contamination is
deliberated.
- Drainage facilities
Soil Management plan can be introduced and applied within a financial
year. The target of 80% reduction in soil erosion is achievable.
- Introduction of Water Management Plan
Water management plan can be introduced and applied within a
financial year. The target of 70% reduction in water wastage is
accepted.
- Vegetation re-growth process
Regrowth of vegetation is a very realistic target. The land area should
be assigned for this process within a period of 2 years from the date of
starting of construction work at the site.
- Controlled environmental facilities for earth work
Controlled features need to be decided within 5 years period involving
the purchase of environment friendly machinery.
- Pre-planned and constructed water ways
Waterways need to be planned at the time of planning of building
design. The target of 100% reduction in water contamination is
deliberated.
- Drainage facilities
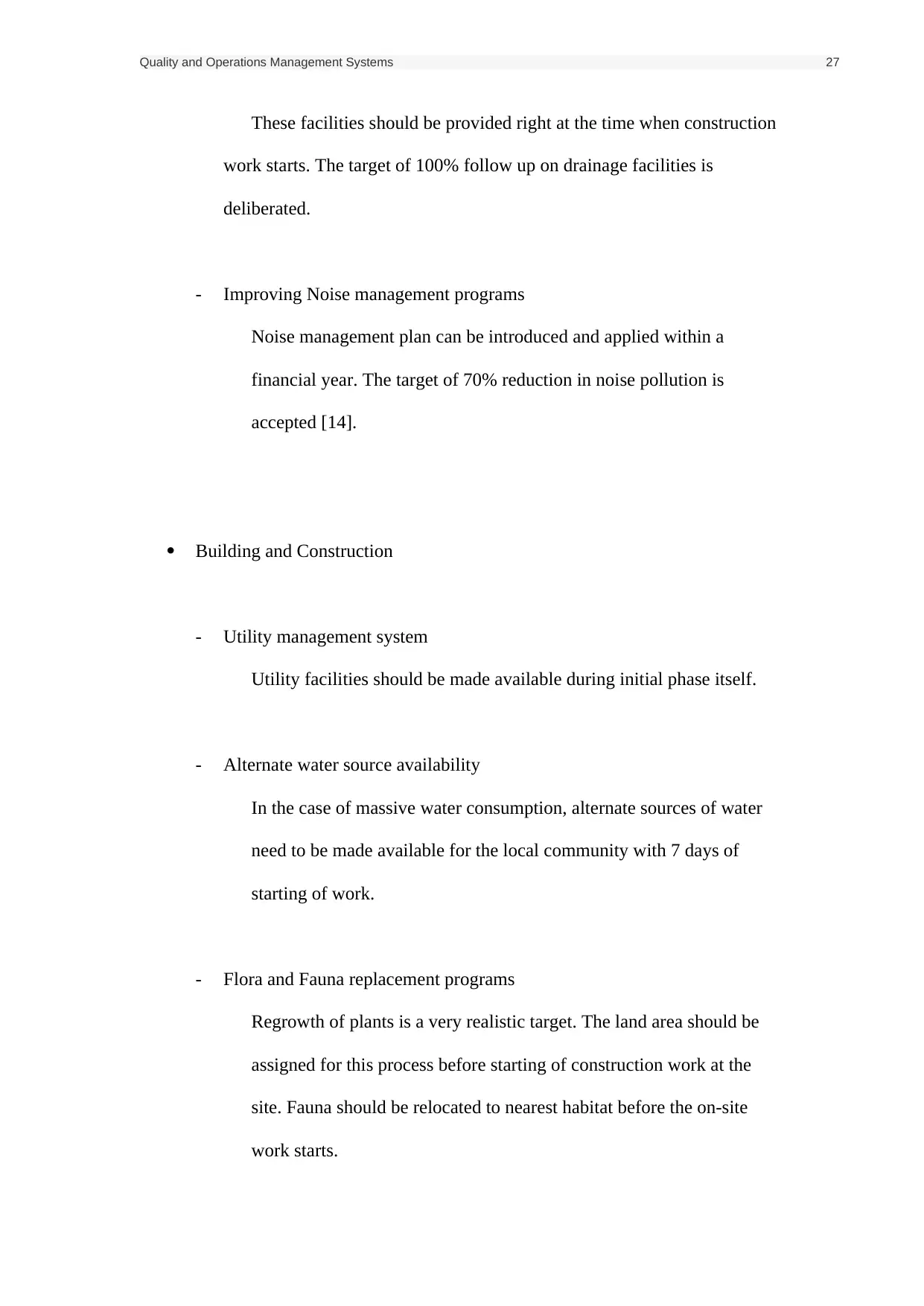
Quality and Operations Management Systems 27
These facilities should be provided right at the time when construction
work starts. The target of 100% follow up on drainage facilities is
deliberated.
- Improving Noise management programs
Noise management plan can be introduced and applied within a
financial year. The target of 70% reduction in noise pollution is
accepted [14].
Building and Construction
- Utility management system
Utility facilities should be made available during initial phase itself.
- Alternate water source availability
In the case of massive water consumption, alternate sources of water
need to be made available for the local community with 7 days of
starting of work.
- Flora and Fauna replacement programs
Regrowth of plants is a very realistic target. The land area should be
assigned for this process before starting of construction work at the
site. Fauna should be relocated to nearest habitat before the on-site
work starts.
These facilities should be provided right at the time when construction
work starts. The target of 100% follow up on drainage facilities is
deliberated.
- Improving Noise management programs
Noise management plan can be introduced and applied within a
financial year. The target of 70% reduction in noise pollution is
accepted [14].
Building and Construction
- Utility management system
Utility facilities should be made available during initial phase itself.
- Alternate water source availability
In the case of massive water consumption, alternate sources of water
need to be made available for the local community with 7 days of
starting of work.
- Flora and Fauna replacement programs
Regrowth of plants is a very realistic target. The land area should be
assigned for this process before starting of construction work at the
site. Fauna should be relocated to nearest habitat before the on-site
work starts.
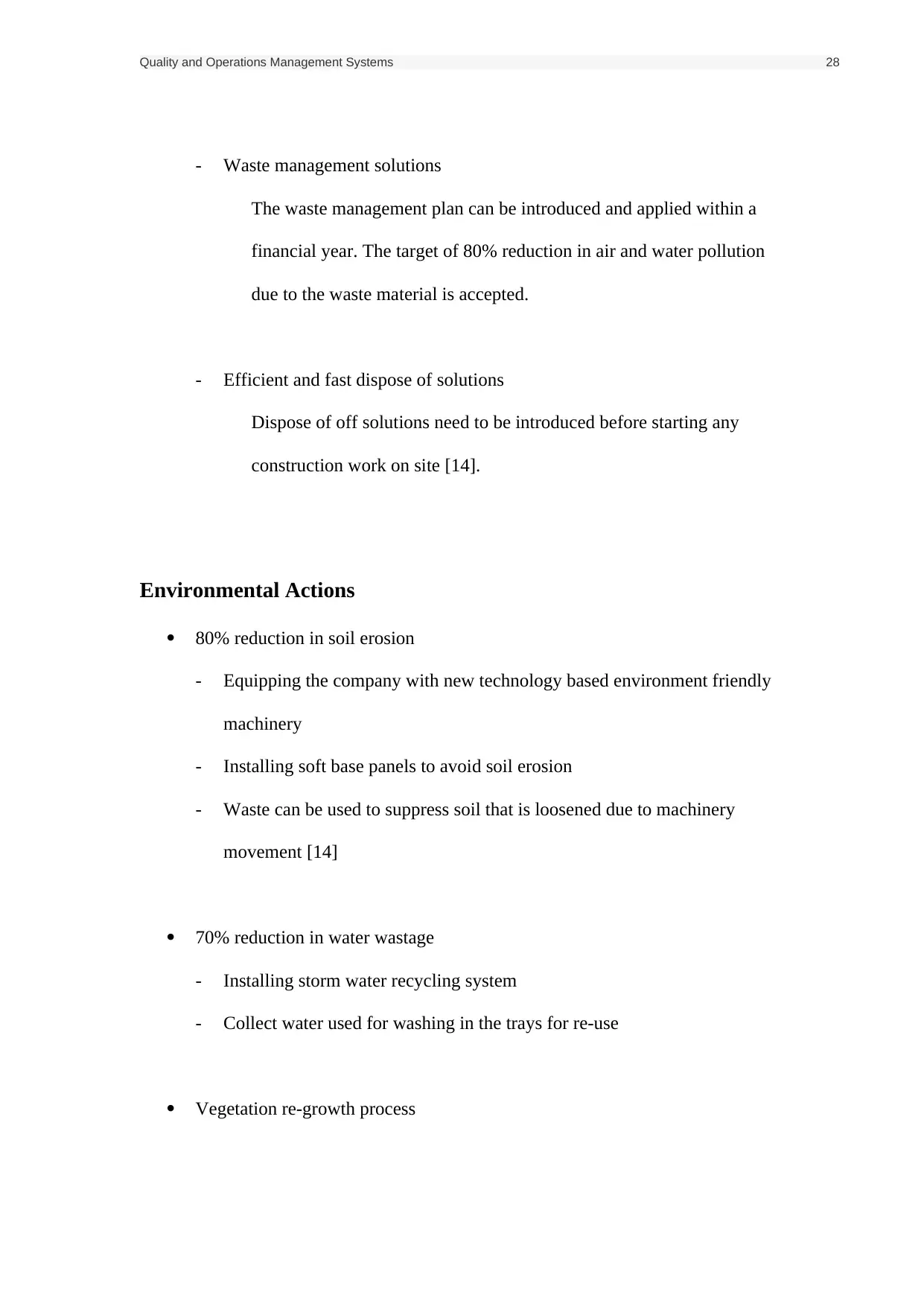
Quality and Operations Management Systems 28
- Waste management solutions
The waste management plan can be introduced and applied within a
financial year. The target of 80% reduction in air and water pollution
due to the waste material is accepted.
- Efficient and fast dispose of solutions
Dispose of off solutions need to be introduced before starting any
construction work on site [14].
Environmental Actions
80% reduction in soil erosion
- Equipping the company with new technology based environment friendly
machinery
- Installing soft base panels to avoid soil erosion
- Waste can be used to suppress soil that is loosened due to machinery
movement [14]
70% reduction in water wastage
- Installing storm water recycling system
- Collect water used for washing in the trays for re-use
Vegetation re-growth process
- Waste management solutions
The waste management plan can be introduced and applied within a
financial year. The target of 80% reduction in air and water pollution
due to the waste material is accepted.
- Efficient and fast dispose of solutions
Dispose of off solutions need to be introduced before starting any
construction work on site [14].
Environmental Actions
80% reduction in soil erosion
- Equipping the company with new technology based environment friendly
machinery
- Installing soft base panels to avoid soil erosion
- Waste can be used to suppress soil that is loosened due to machinery
movement [14]
70% reduction in water wastage
- Installing storm water recycling system
- Collect water used for washing in the trays for re-use
Vegetation re-growth process
Secure Best Marks with AI Grader
Need help grading? Try our AI Grader for instant feedback on your assignments.
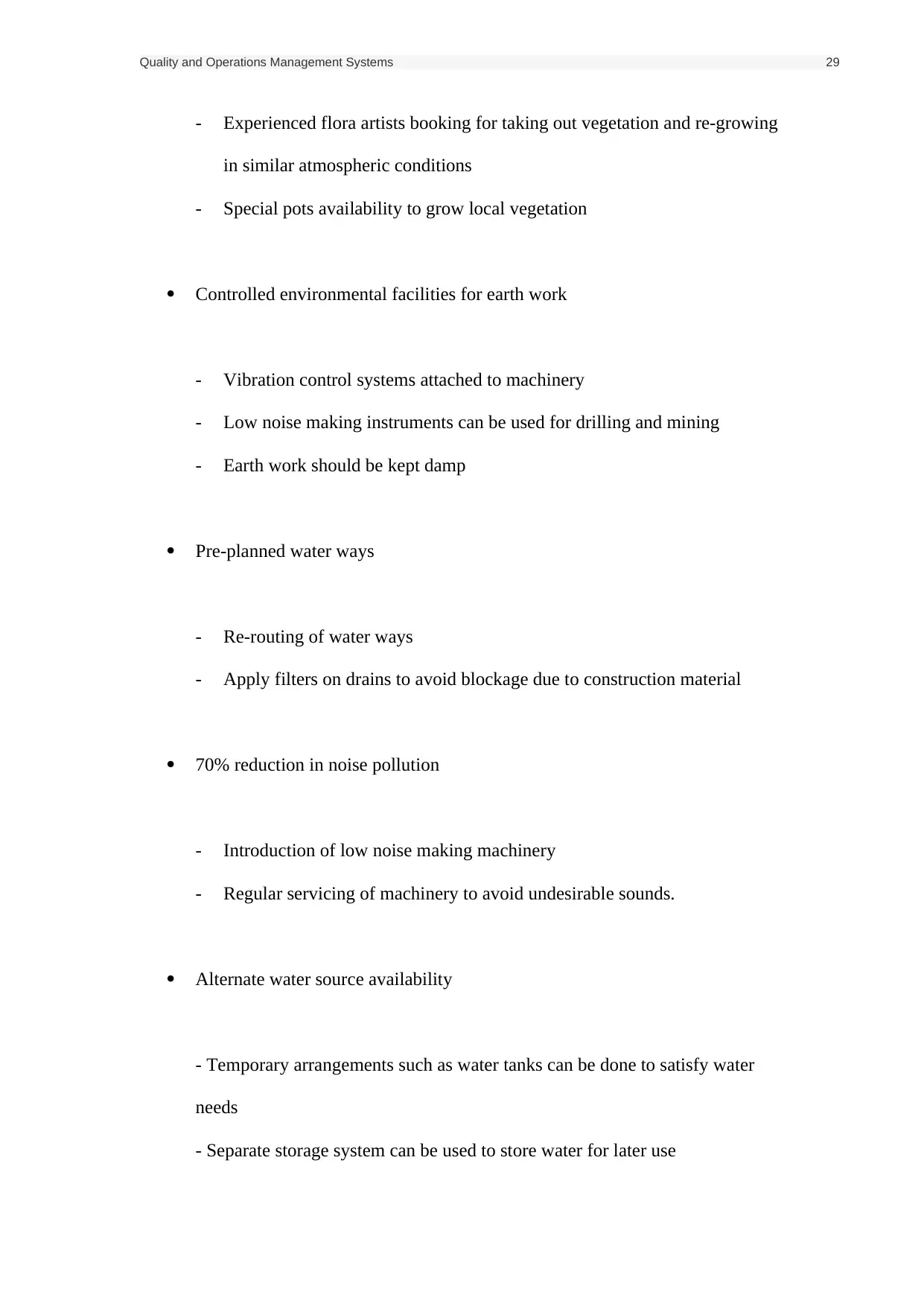
Quality and Operations Management Systems 29
- Experienced flora artists booking for taking out vegetation and re-growing
in similar atmospheric conditions
- Special pots availability to grow local vegetation
Controlled environmental facilities for earth work
- Vibration control systems attached to machinery
- Low noise making instruments can be used for drilling and mining
- Earth work should be kept damp
Pre-planned water ways
- Re-routing of water ways
- Apply filters on drains to avoid blockage due to construction material
70% reduction in noise pollution
- Introduction of low noise making machinery
- Regular servicing of machinery to avoid undesirable sounds.
Alternate water source availability
- Temporary arrangements such as water tanks can be done to satisfy water
needs
- Separate storage system can be used to store water for later use
- Experienced flora artists booking for taking out vegetation and re-growing
in similar atmospheric conditions
- Special pots availability to grow local vegetation
Controlled environmental facilities for earth work
- Vibration control systems attached to machinery
- Low noise making instruments can be used for drilling and mining
- Earth work should be kept damp
Pre-planned water ways
- Re-routing of water ways
- Apply filters on drains to avoid blockage due to construction material
70% reduction in noise pollution
- Introduction of low noise making machinery
- Regular servicing of machinery to avoid undesirable sounds.
Alternate water source availability
- Temporary arrangements such as water tanks can be done to satisfy water
needs
- Separate storage system can be used to store water for later use
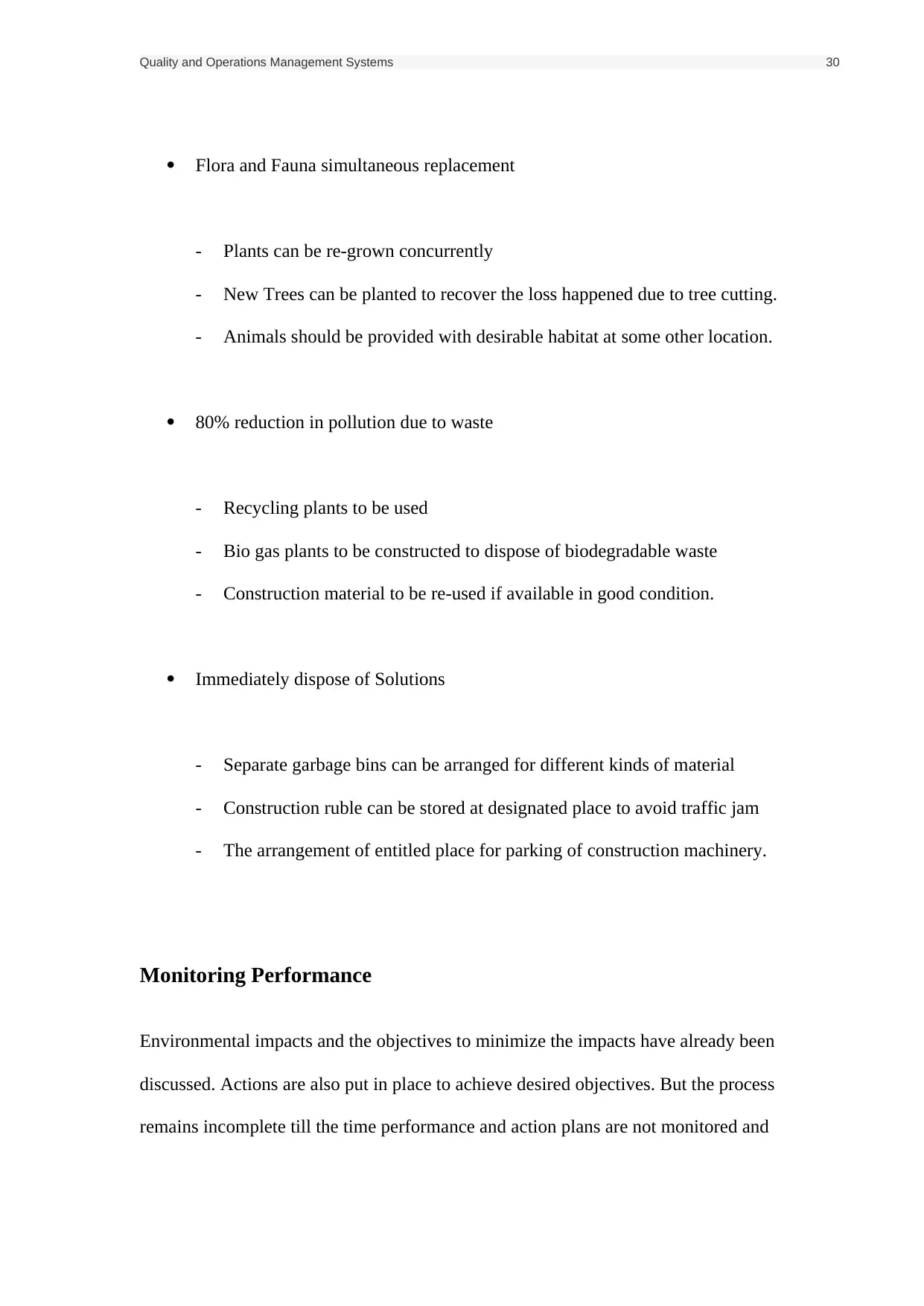
Quality and Operations Management Systems 30
Flora and Fauna simultaneous replacement
- Plants can be re-grown concurrently
- New Trees can be planted to recover the loss happened due to tree cutting.
- Animals should be provided with desirable habitat at some other location.
80% reduction in pollution due to waste
- Recycling plants to be used
- Bio gas plants to be constructed to dispose of biodegradable waste
- Construction material to be re-used if available in good condition.
Immediately dispose of Solutions
- Separate garbage bins can be arranged for different kinds of material
- Construction ruble can be stored at designated place to avoid traffic jam
- The arrangement of entitled place for parking of construction machinery.
Monitoring Performance
Environmental impacts and the objectives to minimize the impacts have already been
discussed. Actions are also put in place to achieve desired objectives. But the process
remains incomplete till the time performance and action plans are not monitored and
Flora and Fauna simultaneous replacement
- Plants can be re-grown concurrently
- New Trees can be planted to recover the loss happened due to tree cutting.
- Animals should be provided with desirable habitat at some other location.
80% reduction in pollution due to waste
- Recycling plants to be used
- Bio gas plants to be constructed to dispose of biodegradable waste
- Construction material to be re-used if available in good condition.
Immediately dispose of Solutions
- Separate garbage bins can be arranged for different kinds of material
- Construction ruble can be stored at designated place to avoid traffic jam
- The arrangement of entitled place for parking of construction machinery.
Monitoring Performance
Environmental impacts and the objectives to minimize the impacts have already been
discussed. Actions are also put in place to achieve desired objectives. But the process
remains incomplete till the time performance and action plans are not monitored and
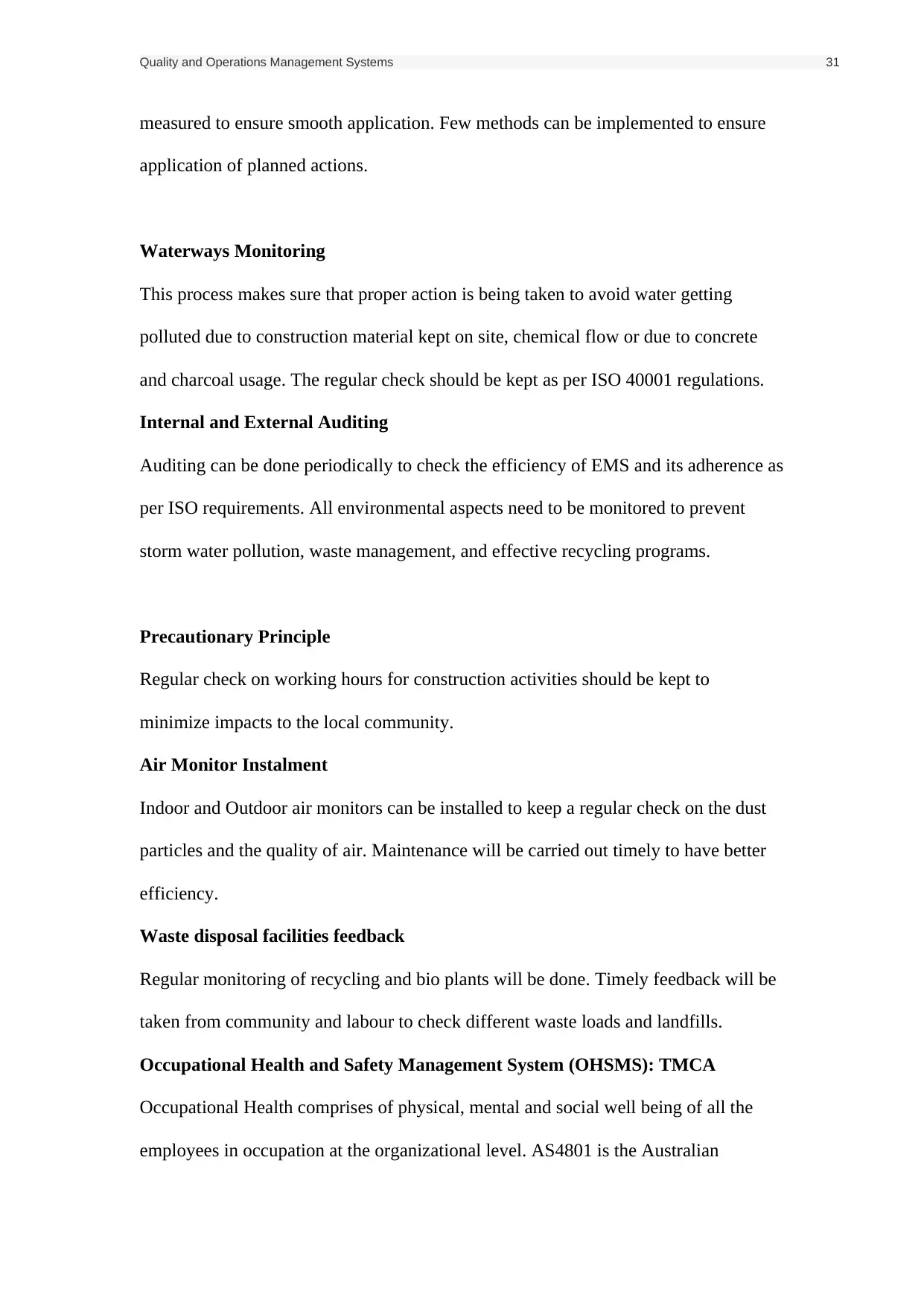
Quality and Operations Management Systems 31
measured to ensure smooth application. Few methods can be implemented to ensure
application of planned actions.
Waterways Monitoring
This process makes sure that proper action is being taken to avoid water getting
polluted due to construction material kept on site, chemical flow or due to concrete
and charcoal usage. The regular check should be kept as per ISO 40001 regulations.
Internal and External Auditing
Auditing can be done periodically to check the efficiency of EMS and its adherence as
per ISO requirements. All environmental aspects need to be monitored to prevent
storm water pollution, waste management, and effective recycling programs.
Precautionary Principle
Regular check on working hours for construction activities should be kept to
minimize impacts to the local community.
Air Monitor Instalment
Indoor and Outdoor air monitors can be installed to keep a regular check on the dust
particles and the quality of air. Maintenance will be carried out timely to have better
efficiency.
Waste disposal facilities feedback
Regular monitoring of recycling and bio plants will be done. Timely feedback will be
taken from community and labour to check different waste loads and landfills.
Occupational Health and Safety Management System (OHSMS): TMCA
Occupational Health comprises of physical, mental and social well being of all the
employees in occupation at the organizational level. AS4801 is the Australian
measured to ensure smooth application. Few methods can be implemented to ensure
application of planned actions.
Waterways Monitoring
This process makes sure that proper action is being taken to avoid water getting
polluted due to construction material kept on site, chemical flow or due to concrete
and charcoal usage. The regular check should be kept as per ISO 40001 regulations.
Internal and External Auditing
Auditing can be done periodically to check the efficiency of EMS and its adherence as
per ISO requirements. All environmental aspects need to be monitored to prevent
storm water pollution, waste management, and effective recycling programs.
Precautionary Principle
Regular check on working hours for construction activities should be kept to
minimize impacts to the local community.
Air Monitor Instalment
Indoor and Outdoor air monitors can be installed to keep a regular check on the dust
particles and the quality of air. Maintenance will be carried out timely to have better
efficiency.
Waste disposal facilities feedback
Regular monitoring of recycling and bio plants will be done. Timely feedback will be
taken from community and labour to check different waste loads and landfills.
Occupational Health and Safety Management System (OHSMS): TMCA
Occupational Health comprises of physical, mental and social well being of all the
employees in occupation at the organizational level. AS4801 is the Australian
Paraphrase This Document
Need a fresh take? Get an instant paraphrase of this document with our AI Paraphraser
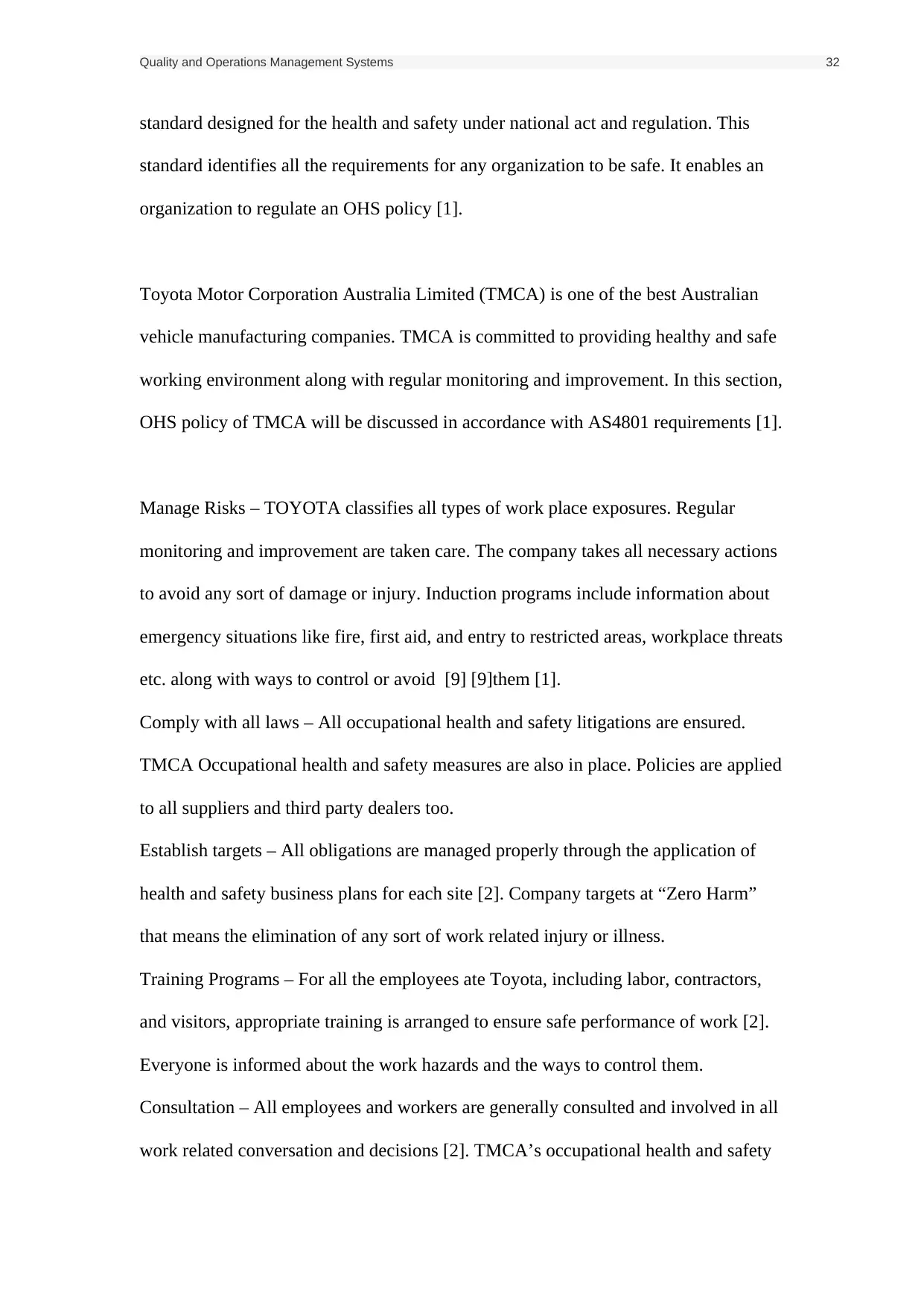
Quality and Operations Management Systems 32
standard designed for the health and safety under national act and regulation. This
standard identifies all the requirements for any organization to be safe. It enables an
organization to regulate an OHS policy [1].
Toyota Motor Corporation Australia Limited (TMCA) is one of the best Australian
vehicle manufacturing companies. TMCA is committed to providing healthy and safe
working environment along with regular monitoring and improvement. In this section,
OHS policy of TMCA will be discussed in accordance with AS4801 requirements [1].
Manage Risks – TOYOTA classifies all types of work place exposures. Regular
monitoring and improvement are taken care. The company takes all necessary actions
to avoid any sort of damage or injury. Induction programs include information about
emergency situations like fire, first aid, and entry to restricted areas, workplace threats
etc. along with ways to control or avoid [9] [9]them [1].
Comply with all laws – All occupational health and safety litigations are ensured.
TMCA Occupational health and safety measures are also in place. Policies are applied
to all suppliers and third party dealers too.
Establish targets – All obligations are managed properly through the application of
health and safety business plans for each site [2]. Company targets at “Zero Harm”
that means the elimination of any sort of work related injury or illness.
Training Programs – For all the employees ate Toyota, including labor, contractors,
and visitors, appropriate training is arranged to ensure safe performance of work [2].
Everyone is informed about the work hazards and the ways to control them.
Consultation – All employees and workers are generally consulted and involved in all
work related conversation and decisions [2]. TMCA’s occupational health and safety
standard designed for the health and safety under national act and regulation. This
standard identifies all the requirements for any organization to be safe. It enables an
organization to regulate an OHS policy [1].
Toyota Motor Corporation Australia Limited (TMCA) is one of the best Australian
vehicle manufacturing companies. TMCA is committed to providing healthy and safe
working environment along with regular monitoring and improvement. In this section,
OHS policy of TMCA will be discussed in accordance with AS4801 requirements [1].
Manage Risks – TOYOTA classifies all types of work place exposures. Regular
monitoring and improvement are taken care. The company takes all necessary actions
to avoid any sort of damage or injury. Induction programs include information about
emergency situations like fire, first aid, and entry to restricted areas, workplace threats
etc. along with ways to control or avoid [9] [9]them [1].
Comply with all laws – All occupational health and safety litigations are ensured.
TMCA Occupational health and safety measures are also in place. Policies are applied
to all suppliers and third party dealers too.
Establish targets – All obligations are managed properly through the application of
health and safety business plans for each site [2]. Company targets at “Zero Harm”
that means the elimination of any sort of work related injury or illness.
Training Programs – For all the employees ate Toyota, including labor, contractors,
and visitors, appropriate training is arranged to ensure safe performance of work [2].
Everyone is informed about the work hazards and the ways to control them.
Consultation – All employees and workers are generally consulted and involved in all
work related conversation and decisions [2]. TMCA’s occupational health and safety
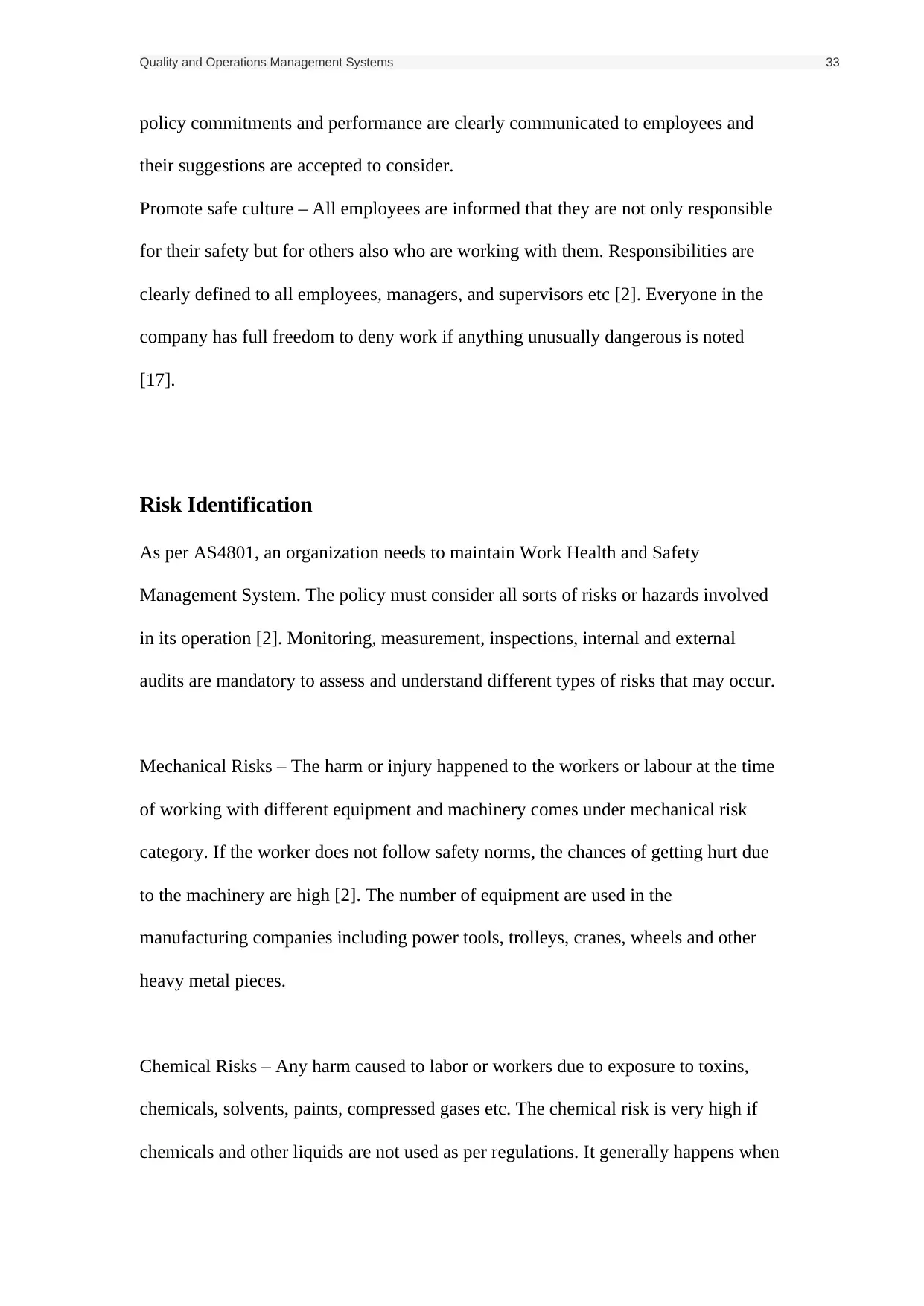
Quality and Operations Management Systems 33
policy commitments and performance are clearly communicated to employees and
their suggestions are accepted to consider.
Promote safe culture – All employees are informed that they are not only responsible
for their safety but for others also who are working with them. Responsibilities are
clearly defined to all employees, managers, and supervisors etc [2]. Everyone in the
company has full freedom to deny work if anything unusually dangerous is noted
[17].
Risk Identification
As per AS4801, an organization needs to maintain Work Health and Safety
Management System. The policy must consider all sorts of risks or hazards involved
in its operation [2]. Monitoring, measurement, inspections, internal and external
audits are mandatory to assess and understand different types of risks that may occur.
Mechanical Risks – The harm or injury happened to the workers or labour at the time
of working with different equipment and machinery comes under mechanical risk
category. If the worker does not follow safety norms, the chances of getting hurt due
to the machinery are high [2]. The number of equipment are used in the
manufacturing companies including power tools, trolleys, cranes, wheels and other
heavy metal pieces.
Chemical Risks – Any harm caused to labor or workers due to exposure to toxins,
chemicals, solvents, paints, compressed gases etc. The chemical risk is very high if
chemicals and other liquids are not used as per regulations. It generally happens when
policy commitments and performance are clearly communicated to employees and
their suggestions are accepted to consider.
Promote safe culture – All employees are informed that they are not only responsible
for their safety but for others also who are working with them. Responsibilities are
clearly defined to all employees, managers, and supervisors etc [2]. Everyone in the
company has full freedom to deny work if anything unusually dangerous is noted
[17].
Risk Identification
As per AS4801, an organization needs to maintain Work Health and Safety
Management System. The policy must consider all sorts of risks or hazards involved
in its operation [2]. Monitoring, measurement, inspections, internal and external
audits are mandatory to assess and understand different types of risks that may occur.
Mechanical Risks – The harm or injury happened to the workers or labour at the time
of working with different equipment and machinery comes under mechanical risk
category. If the worker does not follow safety norms, the chances of getting hurt due
to the machinery are high [2]. The number of equipment are used in the
manufacturing companies including power tools, trolleys, cranes, wheels and other
heavy metal pieces.
Chemical Risks – Any harm caused to labor or workers due to exposure to toxins,
chemicals, solvents, paints, compressed gases etc. The chemical risk is very high if
chemicals and other liquids are not used as per regulations. It generally happens when
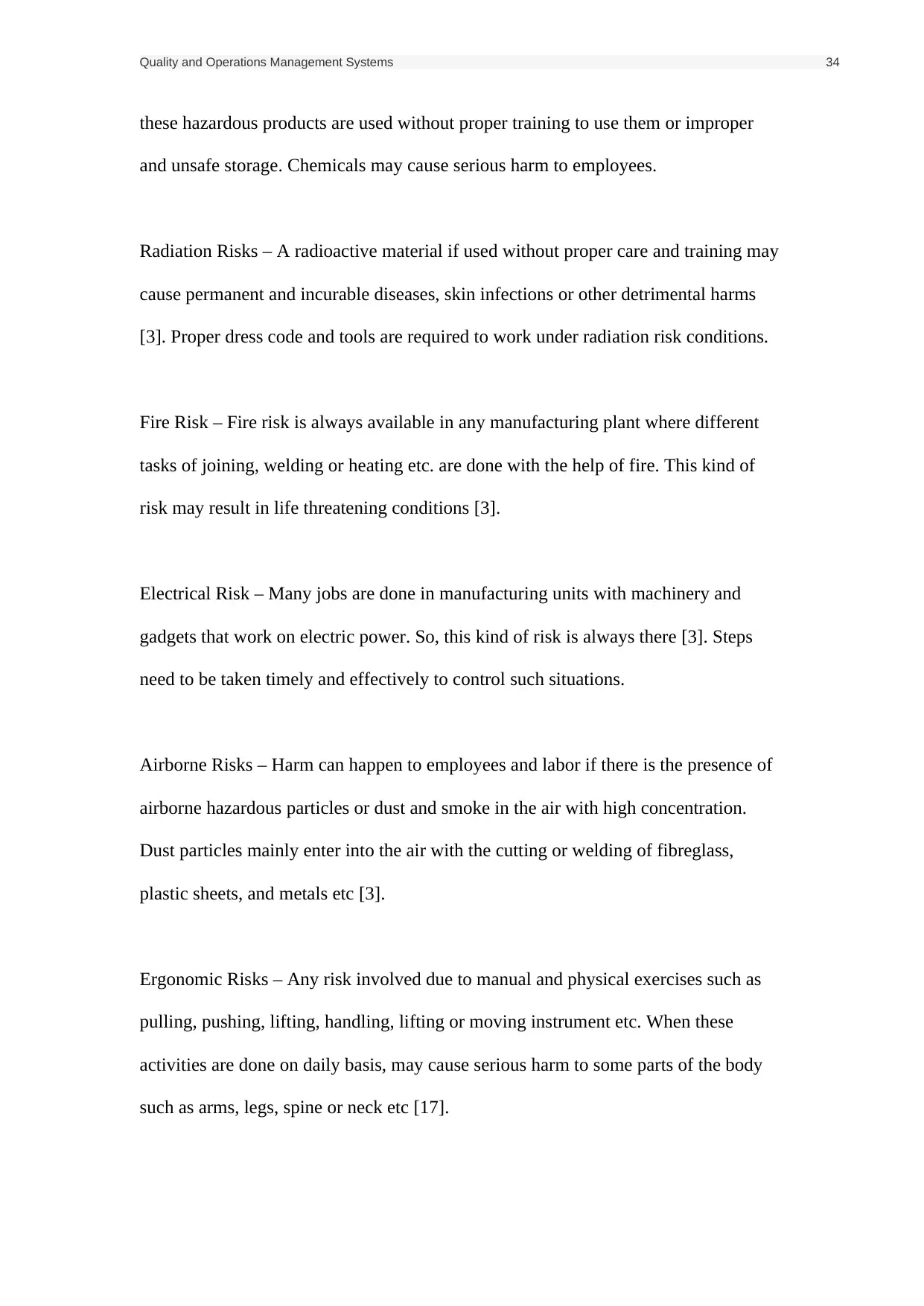
Quality and Operations Management Systems 34
these hazardous products are used without proper training to use them or improper
and unsafe storage. Chemicals may cause serious harm to employees.
Radiation Risks – A radioactive material if used without proper care and training may
cause permanent and incurable diseases, skin infections or other detrimental harms
[3]. Proper dress code and tools are required to work under radiation risk conditions.
Fire Risk – Fire risk is always available in any manufacturing plant where different
tasks of joining, welding or heating etc. are done with the help of fire. This kind of
risk may result in life threatening conditions [3].
Electrical Risk – Many jobs are done in manufacturing units with machinery and
gadgets that work on electric power. So, this kind of risk is always there [3]. Steps
need to be taken timely and effectively to control such situations.
Airborne Risks – Harm can happen to employees and labor if there is the presence of
airborne hazardous particles or dust and smoke in the air with high concentration.
Dust particles mainly enter into the air with the cutting or welding of fibreglass,
plastic sheets, and metals etc [3].
Ergonomic Risks – Any risk involved due to manual and physical exercises such as
pulling, pushing, lifting, handling, lifting or moving instrument etc. When these
activities are done on daily basis, may cause serious harm to some parts of the body
such as arms, legs, spine or neck etc [17].
these hazardous products are used without proper training to use them or improper
and unsafe storage. Chemicals may cause serious harm to employees.
Radiation Risks – A radioactive material if used without proper care and training may
cause permanent and incurable diseases, skin infections or other detrimental harms
[3]. Proper dress code and tools are required to work under radiation risk conditions.
Fire Risk – Fire risk is always available in any manufacturing plant where different
tasks of joining, welding or heating etc. are done with the help of fire. This kind of
risk may result in life threatening conditions [3].
Electrical Risk – Many jobs are done in manufacturing units with machinery and
gadgets that work on electric power. So, this kind of risk is always there [3]. Steps
need to be taken timely and effectively to control such situations.
Airborne Risks – Harm can happen to employees and labor if there is the presence of
airborne hazardous particles or dust and smoke in the air with high concentration.
Dust particles mainly enter into the air with the cutting or welding of fibreglass,
plastic sheets, and metals etc [3].
Ergonomic Risks – Any risk involved due to manual and physical exercises such as
pulling, pushing, lifting, handling, lifting or moving instrument etc. When these
activities are done on daily basis, may cause serious harm to some parts of the body
such as arms, legs, spine or neck etc [17].
Secure Best Marks with AI Grader
Need help grading? Try our AI Grader for instant feedback on your assignments.
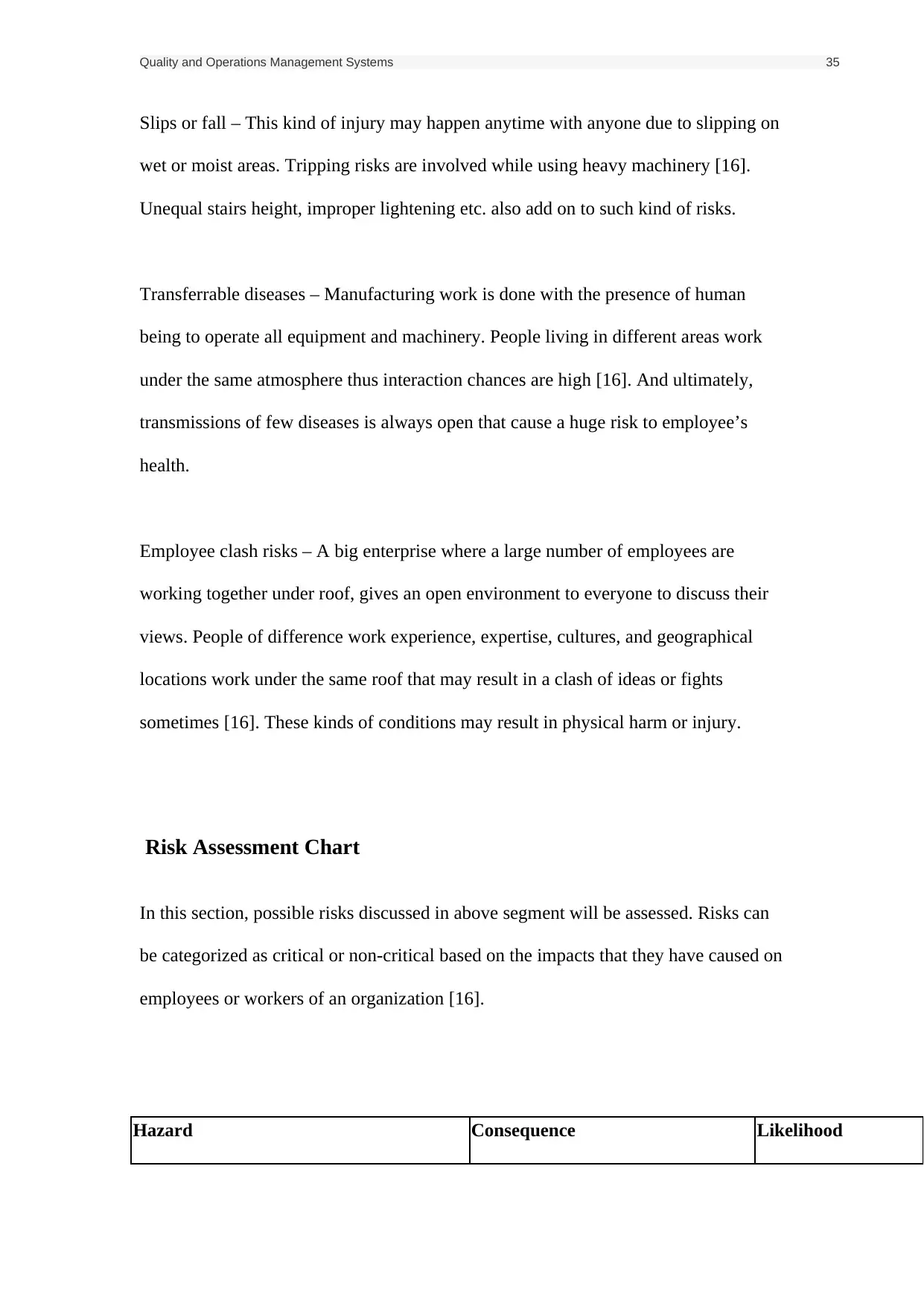
Quality and Operations Management Systems 35
Slips or fall – This kind of injury may happen anytime with anyone due to slipping on
wet or moist areas. Tripping risks are involved while using heavy machinery [16].
Unequal stairs height, improper lightening etc. also add on to such kind of risks.
Transferrable diseases – Manufacturing work is done with the presence of human
being to operate all equipment and machinery. People living in different areas work
under the same atmosphere thus interaction chances are high [16]. And ultimately,
transmissions of few diseases is always open that cause a huge risk to employee’s
health.
Employee clash risks – A big enterprise where a large number of employees are
working together under roof, gives an open environment to everyone to discuss their
views. People of difference work experience, expertise, cultures, and geographical
locations work under the same roof that may result in a clash of ideas or fights
sometimes [16]. These kinds of conditions may result in physical harm or injury.
Risk Assessment Chart
In this section, possible risks discussed in above segment will be assessed. Risks can
be categorized as critical or non-critical based on the impacts that they have caused on
employees or workers of an organization [16].
Hazard Consequence Likelihood
Slips or fall – This kind of injury may happen anytime with anyone due to slipping on
wet or moist areas. Tripping risks are involved while using heavy machinery [16].
Unequal stairs height, improper lightening etc. also add on to such kind of risks.
Transferrable diseases – Manufacturing work is done with the presence of human
being to operate all equipment and machinery. People living in different areas work
under the same atmosphere thus interaction chances are high [16]. And ultimately,
transmissions of few diseases is always open that cause a huge risk to employee’s
health.
Employee clash risks – A big enterprise where a large number of employees are
working together under roof, gives an open environment to everyone to discuss their
views. People of difference work experience, expertise, cultures, and geographical
locations work under the same roof that may result in a clash of ideas or fights
sometimes [16]. These kinds of conditions may result in physical harm or injury.
Risk Assessment Chart
In this section, possible risks discussed in above segment will be assessed. Risks can
be categorized as critical or non-critical based on the impacts that they have caused on
employees or workers of an organization [16].
Hazard Consequence Likelihood
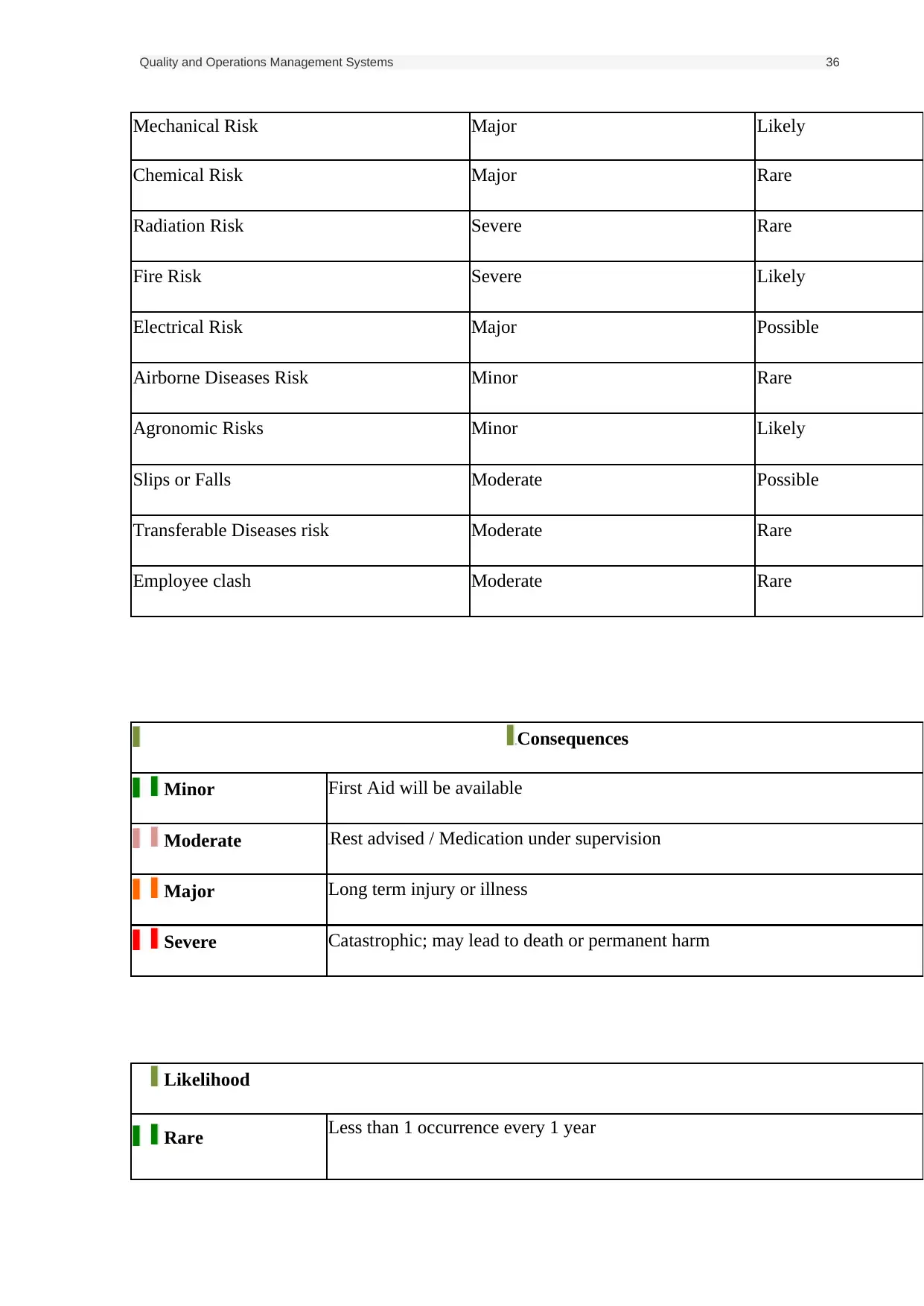
Quality and Operations Management Systems 36
Mechanical Risk Major Likely
Chemical Risk Major Rare
Radiation Risk Severe Rare
Fire Risk Severe Likely
Electrical Risk Major Possible
Airborne Diseases Risk Minor Rare
Agronomic Risks Minor Likely
Slips or Falls Moderate Possible
Transferable Diseases risk Moderate Rare
Employee clash Moderate Rare
Consequences
Minor First Aid will be available
Moderate Rest advised / Medication under supervision
Major Long term injury or illness
Severe Catastrophic; may lead to death or permanent harm
Likelihood
Rare Less than 1 occurrence every 1 year
Mechanical Risk Major Likely
Chemical Risk Major Rare
Radiation Risk Severe Rare
Fire Risk Severe Likely
Electrical Risk Major Possible
Airborne Diseases Risk Minor Rare
Agronomic Risks Minor Likely
Slips or Falls Moderate Possible
Transferable Diseases risk Moderate Rare
Employee clash Moderate Rare
Consequences
Minor First Aid will be available
Moderate Rest advised / Medication under supervision
Major Long term injury or illness
Severe Catastrophic; may lead to death or permanent harm
Likelihood
Rare Less than 1 occurrence every 1 year
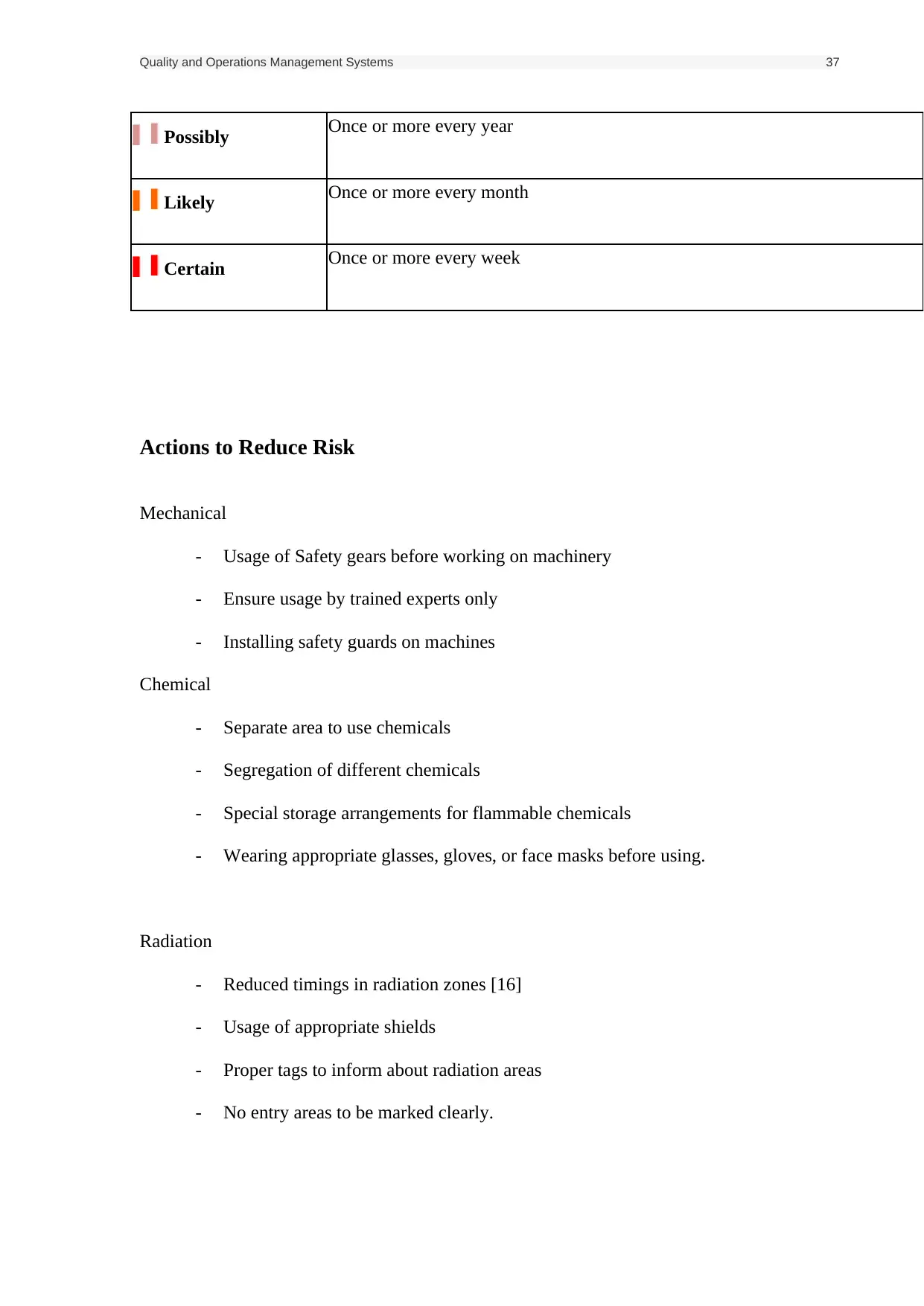
Quality and Operations Management Systems 37
Possibly Once or more every year
Likely Once or more every month
Certain Once or more every week
Actions to Reduce Risk
Mechanical
- Usage of Safety gears before working on machinery
- Ensure usage by trained experts only
- Installing safety guards on machines
Chemical
- Separate area to use chemicals
- Segregation of different chemicals
- Special storage arrangements for flammable chemicals
- Wearing appropriate glasses, gloves, or face masks before using.
Radiation
- Reduced timings in radiation zones [16]
- Usage of appropriate shields
- Proper tags to inform about radiation areas
- No entry areas to be marked clearly.
Possibly Once or more every year
Likely Once or more every month
Certain Once or more every week
Actions to Reduce Risk
Mechanical
- Usage of Safety gears before working on machinery
- Ensure usage by trained experts only
- Installing safety guards on machines
Chemical
- Separate area to use chemicals
- Segregation of different chemicals
- Special storage arrangements for flammable chemicals
- Wearing appropriate glasses, gloves, or face masks before using.
Radiation
- Reduced timings in radiation zones [16]
- Usage of appropriate shields
- Proper tags to inform about radiation areas
- No entry areas to be marked clearly.
Paraphrase This Document
Need a fresh take? Get an instant paraphrase of this document with our AI Paraphraser
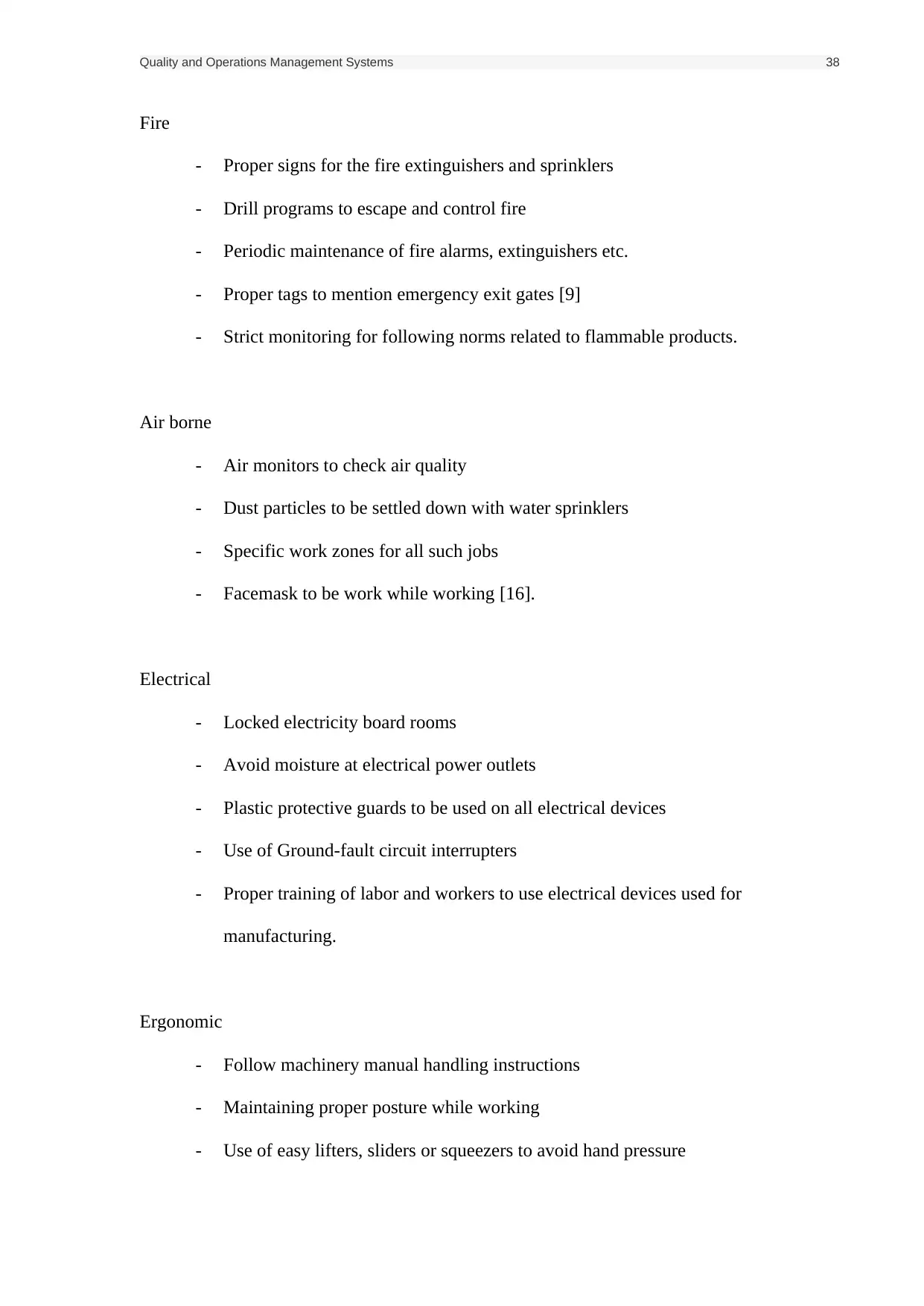
Quality and Operations Management Systems 38
Fire
- Proper signs for the fire extinguishers and sprinklers
- Drill programs to escape and control fire
- Periodic maintenance of fire alarms, extinguishers etc.
- Proper tags to mention emergency exit gates [9]
- Strict monitoring for following norms related to flammable products.
Air borne
- Air monitors to check air quality
- Dust particles to be settled down with water sprinklers
- Specific work zones for all such jobs
- Facemask to be work while working [16].
Electrical
- Locked electricity board rooms
- Avoid moisture at electrical power outlets
- Plastic protective guards to be used on all electrical devices
- Use of Ground-fault circuit interrupters
- Proper training of labor and workers to use electrical devices used for
manufacturing.
Ergonomic
- Follow machinery manual handling instructions
- Maintaining proper posture while working
- Use of easy lifters, sliders or squeezers to avoid hand pressure
Fire
- Proper signs for the fire extinguishers and sprinklers
- Drill programs to escape and control fire
- Periodic maintenance of fire alarms, extinguishers etc.
- Proper tags to mention emergency exit gates [9]
- Strict monitoring for following norms related to flammable products.
Air borne
- Air monitors to check air quality
- Dust particles to be settled down with water sprinklers
- Specific work zones for all such jobs
- Facemask to be work while working [16].
Electrical
- Locked electricity board rooms
- Avoid moisture at electrical power outlets
- Plastic protective guards to be used on all electrical devices
- Use of Ground-fault circuit interrupters
- Proper training of labor and workers to use electrical devices used for
manufacturing.
Ergonomic
- Follow machinery manual handling instructions
- Maintaining proper posture while working
- Use of easy lifters, sliders or squeezers to avoid hand pressure
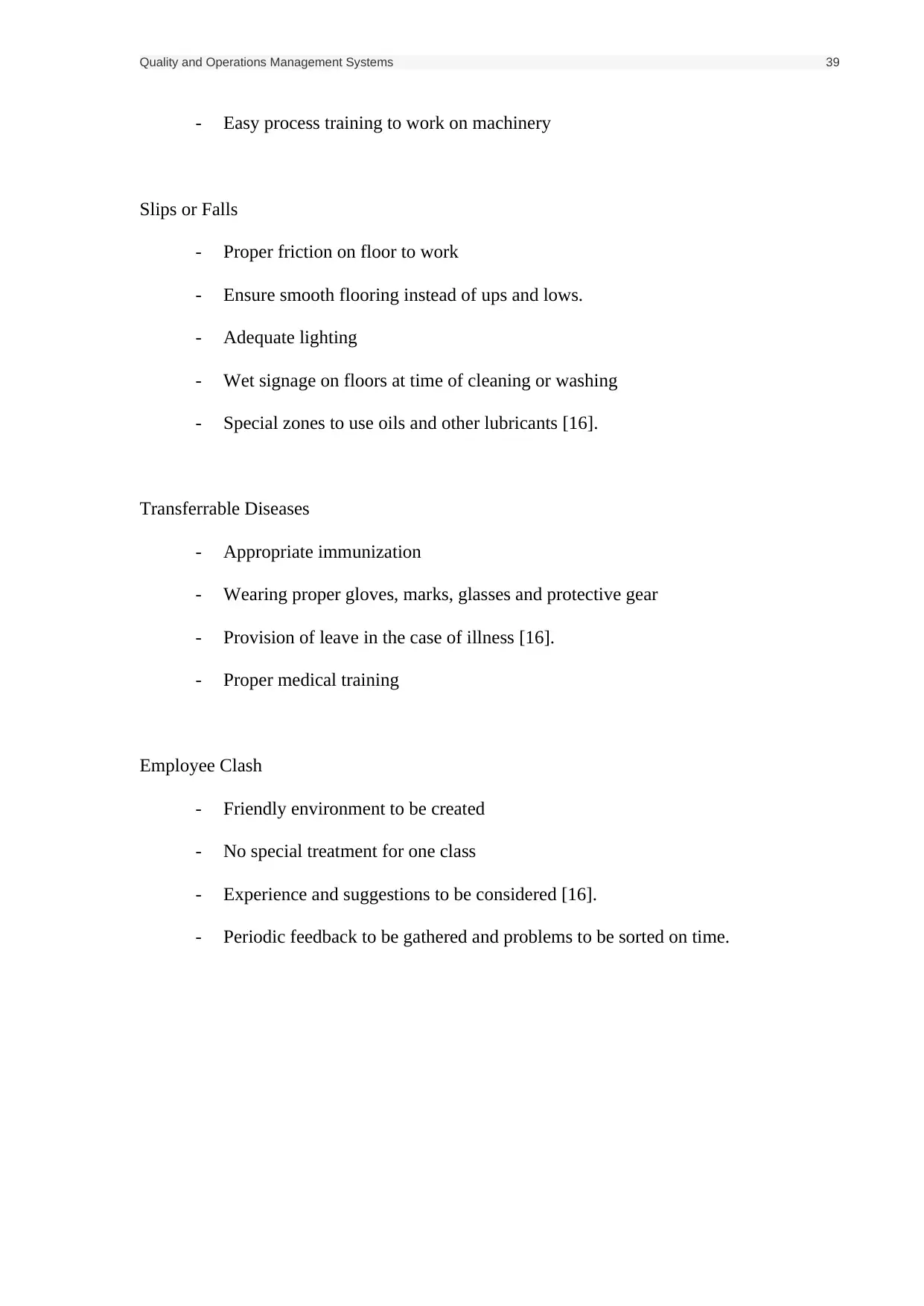
Quality and Operations Management Systems 39
- Easy process training to work on machinery
Slips or Falls
- Proper friction on floor to work
- Ensure smooth flooring instead of ups and lows.
- Adequate lighting
- Wet signage on floors at time of cleaning or washing
- Special zones to use oils and other lubricants [16].
Transferrable Diseases
- Appropriate immunization
- Wearing proper gloves, marks, glasses and protective gear
- Provision of leave in the case of illness [16].
- Proper medical training
Employee Clash
- Friendly environment to be created
- No special treatment for one class
- Experience and suggestions to be considered [16].
- Periodic feedback to be gathered and problems to be sorted on time.
- Easy process training to work on machinery
Slips or Falls
- Proper friction on floor to work
- Ensure smooth flooring instead of ups and lows.
- Adequate lighting
- Wet signage on floors at time of cleaning or washing
- Special zones to use oils and other lubricants [16].
Transferrable Diseases
- Appropriate immunization
- Wearing proper gloves, marks, glasses and protective gear
- Provision of leave in the case of illness [16].
- Proper medical training
Employee Clash
- Friendly environment to be created
- No special treatment for one class
- Experience and suggestions to be considered [16].
- Periodic feedback to be gathered and problems to be sorted on time.
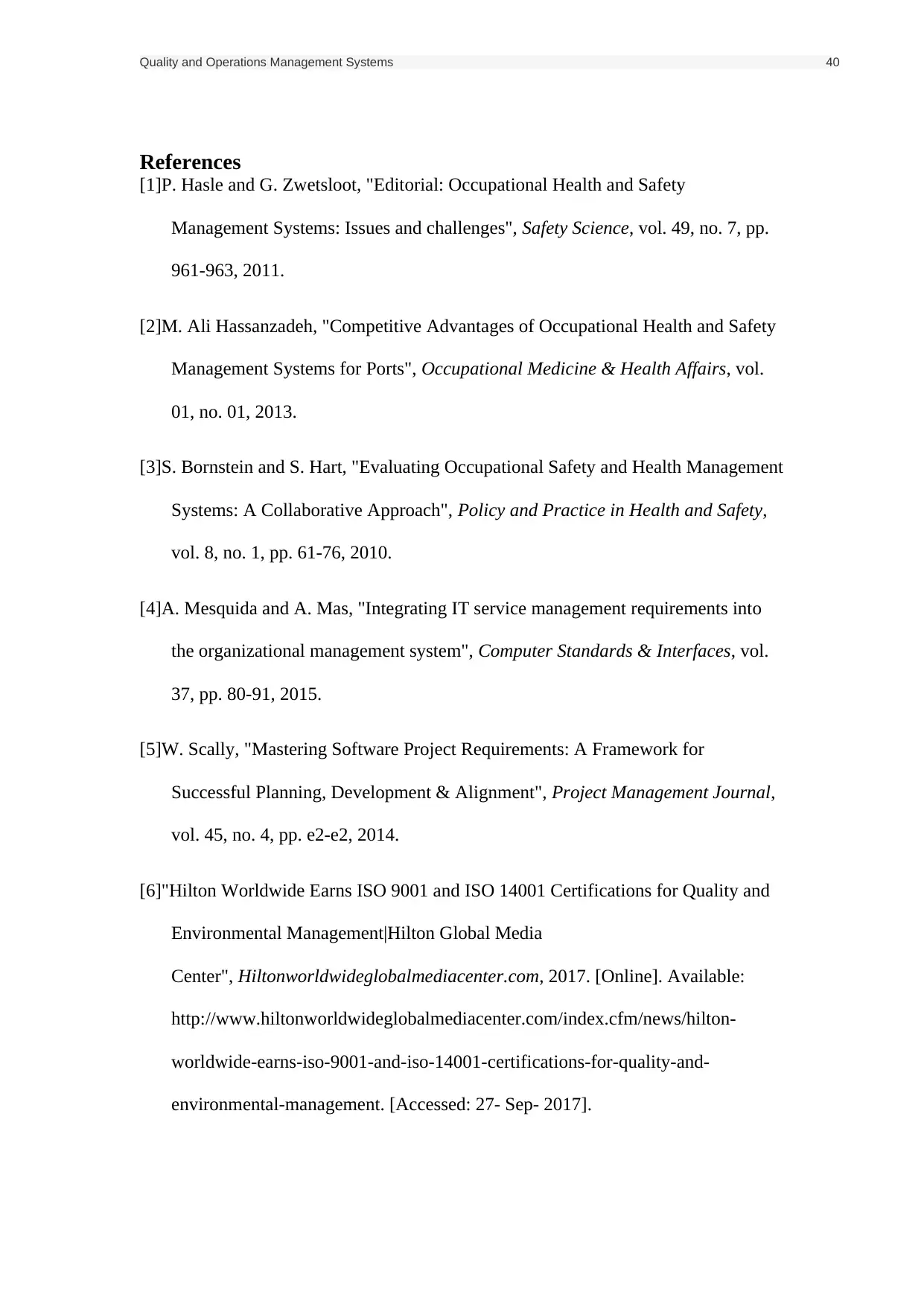
Quality and Operations Management Systems 40
References
[1]P. Hasle and G. Zwetsloot, "Editorial: Occupational Health and Safety
Management Systems: Issues and challenges", Safety Science, vol. 49, no. 7, pp.
961-963, 2011.
[2]M. Ali Hassanzadeh, "Competitive Advantages of Occupational Health and Safety
Management Systems for Ports", Occupational Medicine & Health Affairs, vol.
01, no. 01, 2013.
[3]S. Bornstein and S. Hart, "Evaluating Occupational Safety and Health Management
Systems: A Collaborative Approach", Policy and Practice in Health and Safety,
vol. 8, no. 1, pp. 61-76, 2010.
[4]A. Mesquida and A. Mas, "Integrating IT service management requirements into
the organizational management system", Computer Standards & Interfaces, vol.
37, pp. 80-91, 2015.
[5]W. Scally, "Mastering Software Project Requirements: A Framework for
Successful Planning, Development & Alignment", Project Management Journal,
vol. 45, no. 4, pp. e2-e2, 2014.
[6]"Hilton Worldwide Earns ISO 9001 and ISO 14001 Certifications for Quality and
Environmental Management|Hilton Global Media
Center", Hiltonworldwideglobalmediacenter.com, 2017. [Online]. Available:
http://www.hiltonworldwideglobalmediacenter.com/index.cfm/news/hilton-
worldwide-earns-iso-9001-and-iso-14001-certifications-for-quality-and-
environmental-management. [Accessed: 27- Sep- 2017].
References
[1]P. Hasle and G. Zwetsloot, "Editorial: Occupational Health and Safety
Management Systems: Issues and challenges", Safety Science, vol. 49, no. 7, pp.
961-963, 2011.
[2]M. Ali Hassanzadeh, "Competitive Advantages of Occupational Health and Safety
Management Systems for Ports", Occupational Medicine & Health Affairs, vol.
01, no. 01, 2013.
[3]S. Bornstein and S. Hart, "Evaluating Occupational Safety and Health Management
Systems: A Collaborative Approach", Policy and Practice in Health and Safety,
vol. 8, no. 1, pp. 61-76, 2010.
[4]A. Mesquida and A. Mas, "Integrating IT service management requirements into
the organizational management system", Computer Standards & Interfaces, vol.
37, pp. 80-91, 2015.
[5]W. Scally, "Mastering Software Project Requirements: A Framework for
Successful Planning, Development & Alignment", Project Management Journal,
vol. 45, no. 4, pp. e2-e2, 2014.
[6]"Hilton Worldwide Earns ISO 9001 and ISO 14001 Certifications for Quality and
Environmental Management|Hilton Global Media
Center", Hiltonworldwideglobalmediacenter.com, 2017. [Online]. Available:
http://www.hiltonworldwideglobalmediacenter.com/index.cfm/news/hilton-
worldwide-earns-iso-9001-and-iso-14001-certifications-for-quality-and-
environmental-management. [Accessed: 27- Sep- 2017].
Secure Best Marks with AI Grader
Need help grading? Try our AI Grader for instant feedback on your assignments.
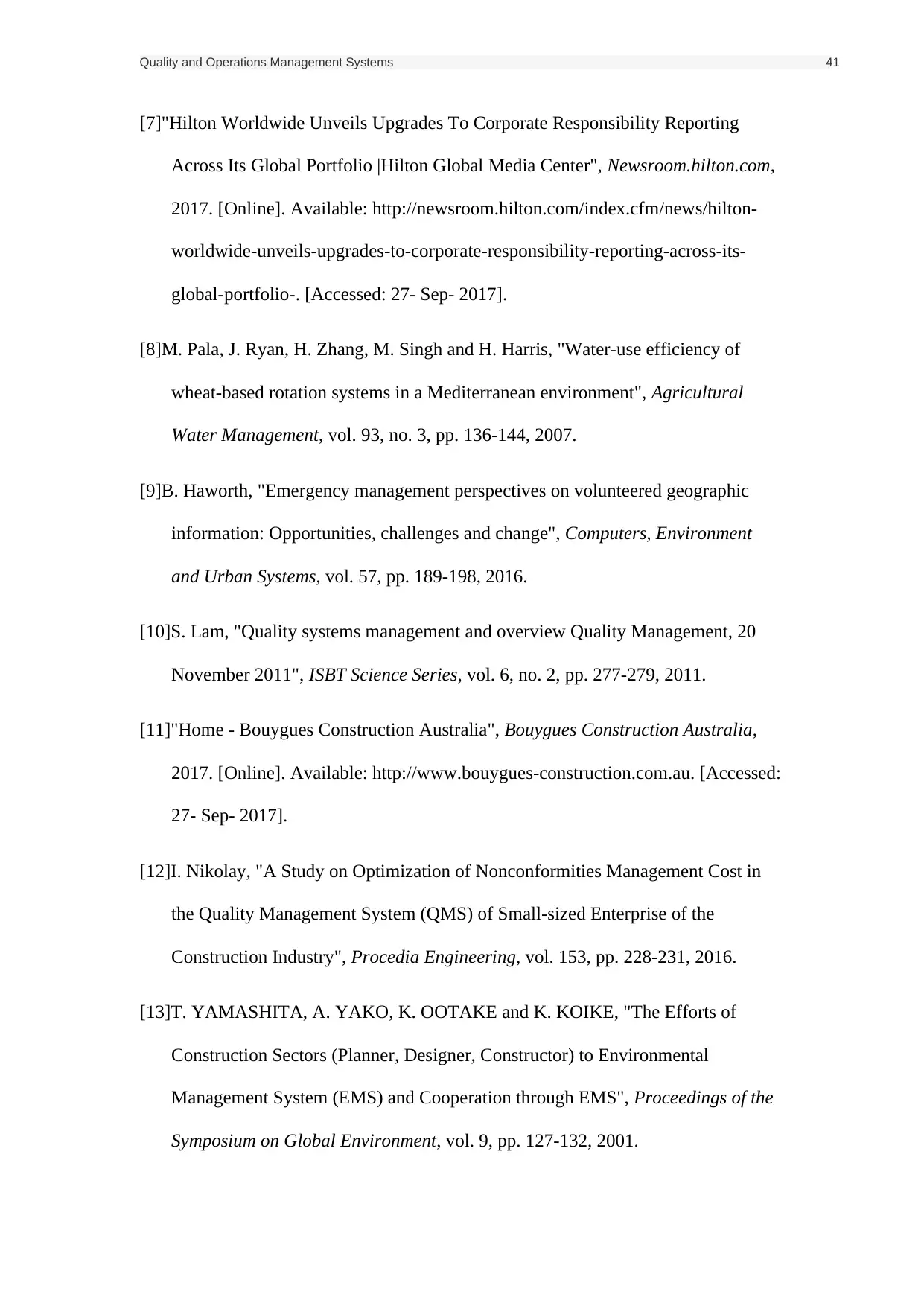
Quality and Operations Management Systems 41
[7]"Hilton Worldwide Unveils Upgrades To Corporate Responsibility Reporting
Across Its Global Portfolio |Hilton Global Media Center", Newsroom.hilton.com,
2017. [Online]. Available: http://newsroom.hilton.com/index.cfm/news/hilton-
worldwide-unveils-upgrades-to-corporate-responsibility-reporting-across-its-
global-portfolio-. [Accessed: 27- Sep- 2017].
[8]M. Pala, J. Ryan, H. Zhang, M. Singh and H. Harris, "Water-use efficiency of
wheat-based rotation systems in a Mediterranean environment", Agricultural
Water Management, vol. 93, no. 3, pp. 136-144, 2007.
[9]B. Haworth, "Emergency management perspectives on volunteered geographic
information: Opportunities, challenges and change", Computers, Environment
and Urban Systems, vol. 57, pp. 189-198, 2016.
[10]S. Lam, "Quality systems management and overview Quality Management, 20
November 2011", ISBT Science Series, vol. 6, no. 2, pp. 277-279, 2011.
[11]"Home - Bouygues Construction Australia", Bouygues Construction Australia,
2017. [Online]. Available: http://www.bouygues-construction.com.au. [Accessed:
27- Sep- 2017].
[12]I. Nikolay, "A Study on Optimization of Nonconformities Management Cost in
the Quality Management System (QMS) of Small-sized Enterprise of the
Construction Industry", Procedia Engineering, vol. 153, pp. 228-231, 2016.
[13]T. YAMASHITA, A. YAKO, K. OOTAKE and K. KOIKE, "The Efforts of
Construction Sectors (Planner, Designer, Constructor) to Environmental
Management System (EMS) and Cooperation through EMS", Proceedings of the
Symposium on Global Environment, vol. 9, pp. 127-132, 2001.
[7]"Hilton Worldwide Unveils Upgrades To Corporate Responsibility Reporting
Across Its Global Portfolio |Hilton Global Media Center", Newsroom.hilton.com,
2017. [Online]. Available: http://newsroom.hilton.com/index.cfm/news/hilton-
worldwide-unveils-upgrades-to-corporate-responsibility-reporting-across-its-
global-portfolio-. [Accessed: 27- Sep- 2017].
[8]M. Pala, J. Ryan, H. Zhang, M. Singh and H. Harris, "Water-use efficiency of
wheat-based rotation systems in a Mediterranean environment", Agricultural
Water Management, vol. 93, no. 3, pp. 136-144, 2007.
[9]B. Haworth, "Emergency management perspectives on volunteered geographic
information: Opportunities, challenges and change", Computers, Environment
and Urban Systems, vol. 57, pp. 189-198, 2016.
[10]S. Lam, "Quality systems management and overview Quality Management, 20
November 2011", ISBT Science Series, vol. 6, no. 2, pp. 277-279, 2011.
[11]"Home - Bouygues Construction Australia", Bouygues Construction Australia,
2017. [Online]. Available: http://www.bouygues-construction.com.au. [Accessed:
27- Sep- 2017].
[12]I. Nikolay, "A Study on Optimization of Nonconformities Management Cost in
the Quality Management System (QMS) of Small-sized Enterprise of the
Construction Industry", Procedia Engineering, vol. 153, pp. 228-231, 2016.
[13]T. YAMASHITA, A. YAKO, K. OOTAKE and K. KOIKE, "The Efforts of
Construction Sectors (Planner, Designer, Constructor) to Environmental
Management System (EMS) and Cooperation through EMS", Proceedings of the
Symposium on Global Environment, vol. 9, pp. 127-132, 2001.
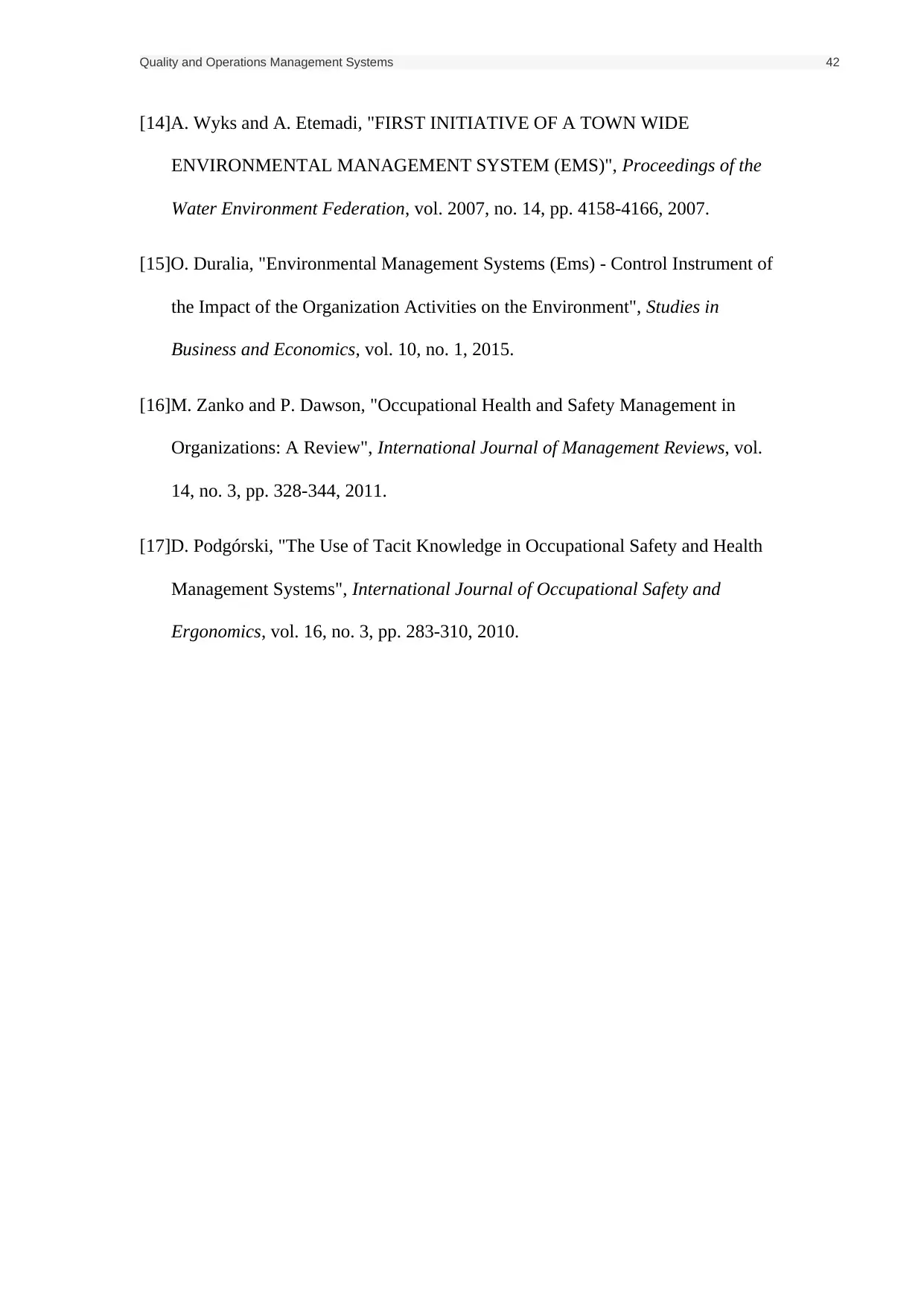
Quality and Operations Management Systems 42
[14]A. Wyks and A. Etemadi, "FIRST INITIATIVE OF A TOWN WIDE
ENVIRONMENTAL MANAGEMENT SYSTEM (EMS)", Proceedings of the
Water Environment Federation, vol. 2007, no. 14, pp. 4158-4166, 2007.
[15]O. Duralia, "Environmental Management Systems (Ems) - Control Instrument of
the Impact of the Organization Activities on the Environment", Studies in
Business and Economics, vol. 10, no. 1, 2015.
[16]M. Zanko and P. Dawson, "Occupational Health and Safety Management in
Organizations: A Review", International Journal of Management Reviews, vol.
14, no. 3, pp. 328-344, 2011.
[17]D. Podgórski, "The Use of Tacit Knowledge in Occupational Safety and Health
Management Systems", International Journal of Occupational Safety and
Ergonomics, vol. 16, no. 3, pp. 283-310, 2010.
[14]A. Wyks and A. Etemadi, "FIRST INITIATIVE OF A TOWN WIDE
ENVIRONMENTAL MANAGEMENT SYSTEM (EMS)", Proceedings of the
Water Environment Federation, vol. 2007, no. 14, pp. 4158-4166, 2007.
[15]O. Duralia, "Environmental Management Systems (Ems) - Control Instrument of
the Impact of the Organization Activities on the Environment", Studies in
Business and Economics, vol. 10, no. 1, 2015.
[16]M. Zanko and P. Dawson, "Occupational Health and Safety Management in
Organizations: A Review", International Journal of Management Reviews, vol.
14, no. 3, pp. 328-344, 2011.
[17]D. Podgórski, "The Use of Tacit Knowledge in Occupational Safety and Health
Management Systems", International Journal of Occupational Safety and
Ergonomics, vol. 16, no. 3, pp. 283-310, 2010.
1 out of 42
Related Documents

Your All-in-One AI-Powered Toolkit for Academic Success.
+13062052269
info@desklib.com
Available 24*7 on WhatsApp / Email
Unlock your academic potential
© 2024 | Zucol Services PVT LTD | All rights reserved.