Surface Engineering Techniques for Enhanced Hot Forging Die Lifespan
VerifiedAdded on 2023/01/20
|9
|1994
|77
Report
AI Summary
This report investigates the application of advanced surface engineering techniques to improve the service life and performance of hot forging dies. It begins by outlining the functions and common failure mechanisms of hot forging dies, including electro-mechanical, thermal, and fatigue loads. The report then discusses enabling surface engineering technologies such as plasma and ion-based deposition systems, diffusion treatments, and electroless coating methods. It emphasizes the importance of lubricant selection and surface treatment methods like ion nitriding and carbon nitriding in mitigating wear, thermal deformation, and fatigue. The study considers factors such as thermal softening, abrasive wear, and material properties, presenting data from FE analysis and tempering curves. The conclusion highlights that surface treatment, combined with appropriate lubricants and heat management, can significantly increase the service life and dimensional accuracy of forging tools, potentially increasing the life of the hot forging die by approximately 15-20%.
Contribute Materials
Your contribution can guide someone’s learning journey. Share your
documents today.
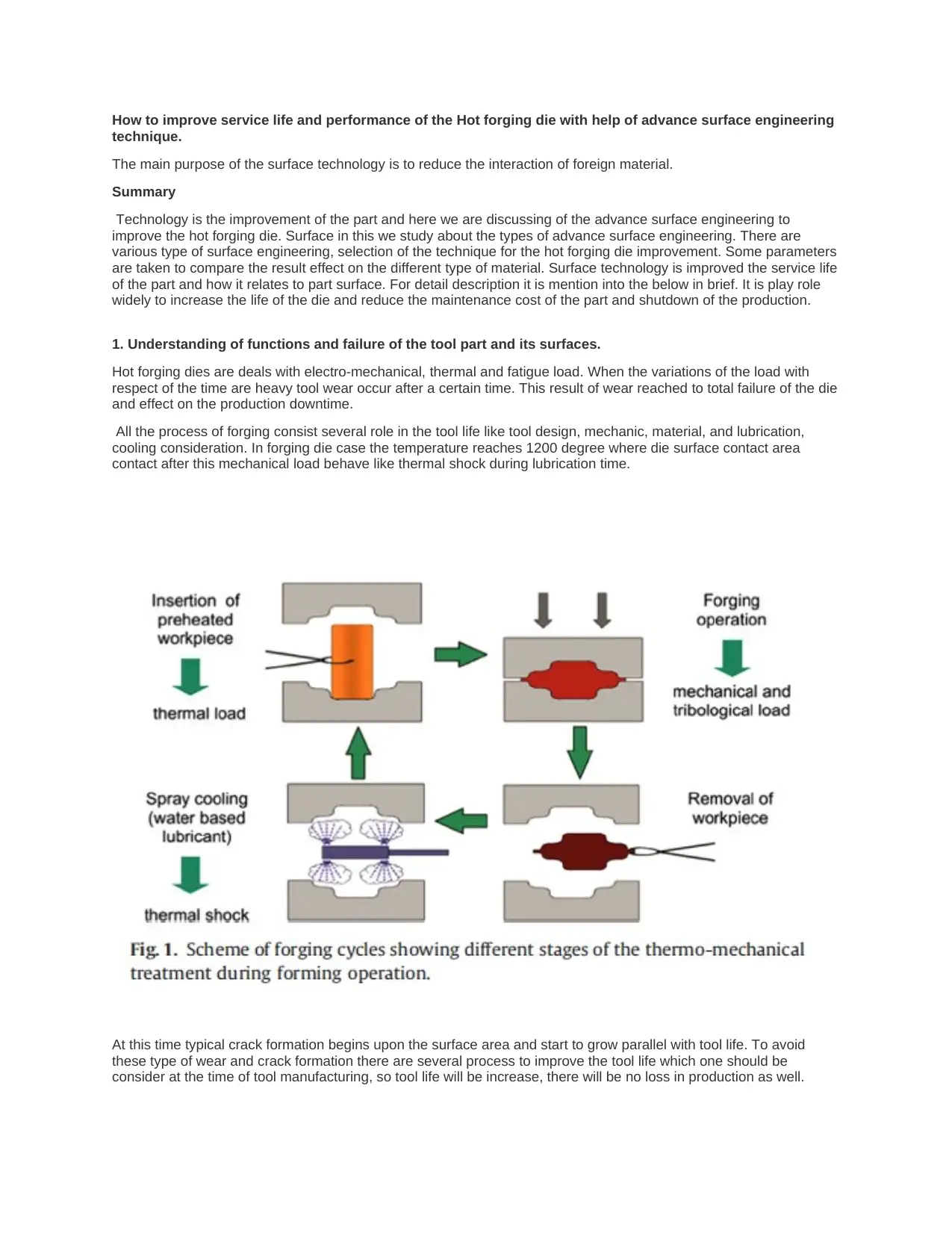
How to improve service life and performance of the Hot forging die with help of advance surface engineering
technique.
The main purpose of the surface technology is to reduce the interaction of foreign material.
Summary
Technology is the improvement of the part and here we are discussing of the advance surface engineering to
improve the hot forging die. Surface in this we study about the types of advance surface engineering. There are
various type of surface engineering, selection of the technique for the hot forging die improvement. Some parameters
are taken to compare the result effect on the different type of material. Surface technology is improved the service life
of the part and how it relates to part surface. For detail description it is mention into the below in brief. It is play role
widely to increase the life of the die and reduce the maintenance cost of the part and shutdown of the production.
1. Understanding of functions and failure of the tool part and its surfaces.
Hot forging dies are deals with electro-mechanical, thermal and fatigue load. When the variations of the load with
respect of the time are heavy tool wear occur after a certain time. This result of wear reached to total failure of the die
and effect on the production downtime.
All the process of forging consist several role in the tool life like tool design, mechanic, material, and lubrication,
cooling consideration. In forging die case the temperature reaches 1200 degree where die surface contact area
contact after this mechanical load behave like thermal shock during lubrication time.
At this time typical crack formation begins upon the surface area and start to grow parallel with tool life. To avoid
these type of wear and crack formation there are several process to improve the tool life which one should be
consider at the time of tool manufacturing, so tool life will be increase, there will be no loss in production as well.
technique.
The main purpose of the surface technology is to reduce the interaction of foreign material.
Summary
Technology is the improvement of the part and here we are discussing of the advance surface engineering to
improve the hot forging die. Surface in this we study about the types of advance surface engineering. There are
various type of surface engineering, selection of the technique for the hot forging die improvement. Some parameters
are taken to compare the result effect on the different type of material. Surface technology is improved the service life
of the part and how it relates to part surface. For detail description it is mention into the below in brief. It is play role
widely to increase the life of the die and reduce the maintenance cost of the part and shutdown of the production.
1. Understanding of functions and failure of the tool part and its surfaces.
Hot forging dies are deals with electro-mechanical, thermal and fatigue load. When the variations of the load with
respect of the time are heavy tool wear occur after a certain time. This result of wear reached to total failure of the die
and effect on the production downtime.
All the process of forging consist several role in the tool life like tool design, mechanic, material, and lubrication,
cooling consideration. In forging die case the temperature reaches 1200 degree where die surface contact area
contact after this mechanical load behave like thermal shock during lubrication time.
At this time typical crack formation begins upon the surface area and start to grow parallel with tool life. To avoid
these type of wear and crack formation there are several process to improve the tool life which one should be
consider at the time of tool manufacturing, so tool life will be increase, there will be no loss in production as well.
Secure Best Marks with AI Grader
Need help grading? Try our AI Grader for instant feedback on your assignments.
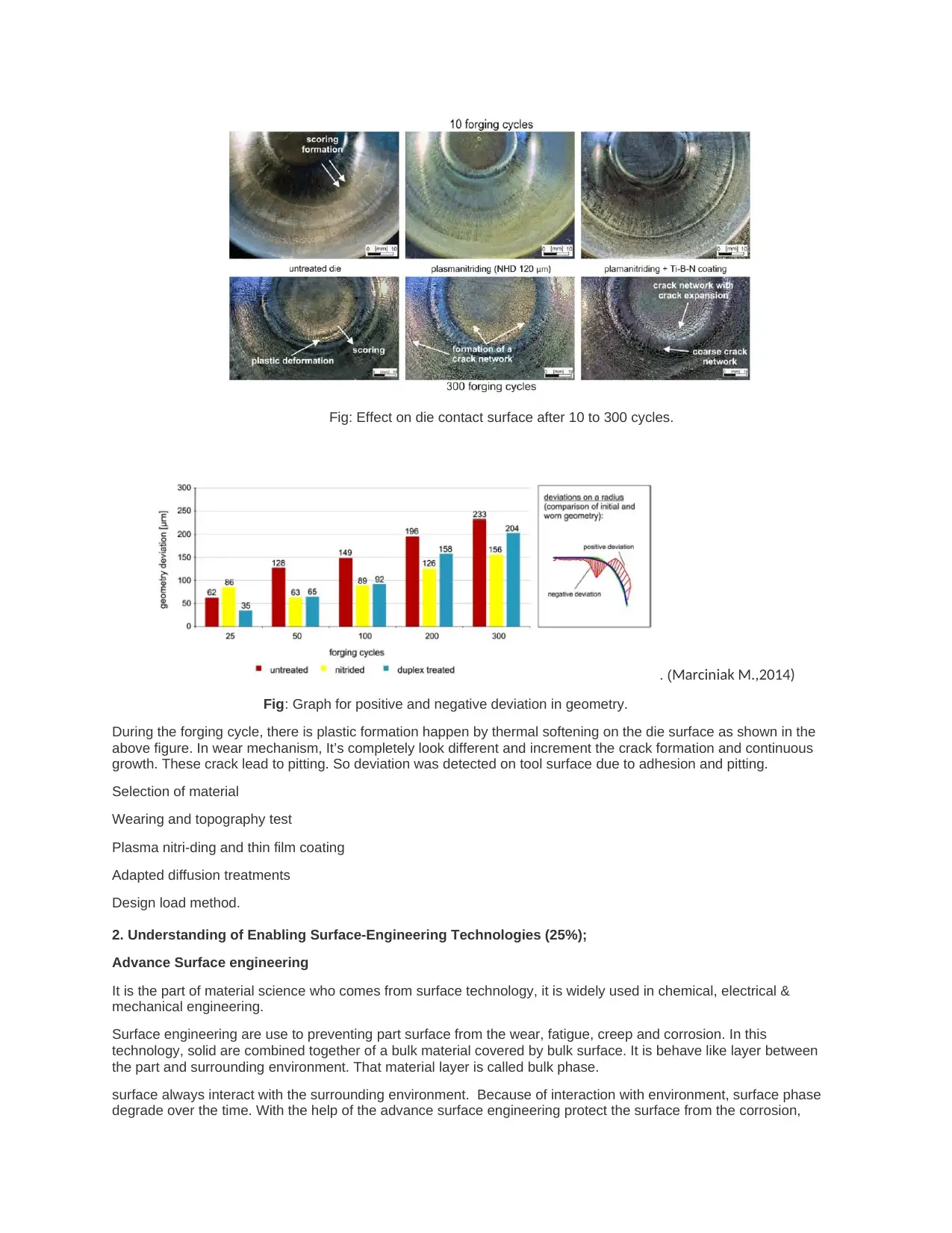
Fig: Effect on die contact surface after 10 to 300 cycles.
. (Marciniak M.,2014)
Fig: Graph for positive and negative deviation in geometry.
During the forging cycle, there is plastic formation happen by thermal softening on the die surface as shown in the
above figure. In wear mechanism, It’s completely look different and increment the crack formation and continuous
growth. These crack lead to pitting. So deviation was detected on tool surface due to adhesion and pitting.
Selection of material
Wearing and topography test
Plasma nitri-ding and thin film coating
Adapted diffusion treatments
Design load method.
2. Understanding of Enabling Surface-Engineering Technologies (25%);
Advance Surface engineering
It is the part of material science who comes from surface technology, it is widely used in chemical, electrical &
mechanical engineering.
Surface engineering are use to preventing part surface from the wear, fatigue, creep and corrosion. In this
technology, solid are combined together of a bulk material covered by bulk surface. It is behave like layer between
the part and surrounding environment. That material layer is called bulk phase.
surface always interact with the surrounding environment. Because of interaction with environment, surface phase
degrade over the time. With the help of the advance surface engineering protect the surface from the corrosion,
. (Marciniak M.,2014)
Fig: Graph for positive and negative deviation in geometry.
During the forging cycle, there is plastic formation happen by thermal softening on the die surface as shown in the
above figure. In wear mechanism, It’s completely look different and increment the crack formation and continuous
growth. These crack lead to pitting. So deviation was detected on tool surface due to adhesion and pitting.
Selection of material
Wearing and topography test
Plasma nitri-ding and thin film coating
Adapted diffusion treatments
Design load method.
2. Understanding of Enabling Surface-Engineering Technologies (25%);
Advance Surface engineering
It is the part of material science who comes from surface technology, it is widely used in chemical, electrical &
mechanical engineering.
Surface engineering are use to preventing part surface from the wear, fatigue, creep and corrosion. In this
technology, solid are combined together of a bulk material covered by bulk surface. It is behave like layer between
the part and surrounding environment. That material layer is called bulk phase.
surface always interact with the surrounding environment. Because of interaction with environment, surface phase
degrade over the time. With the help of the advance surface engineering protect the surface from the corrosion,
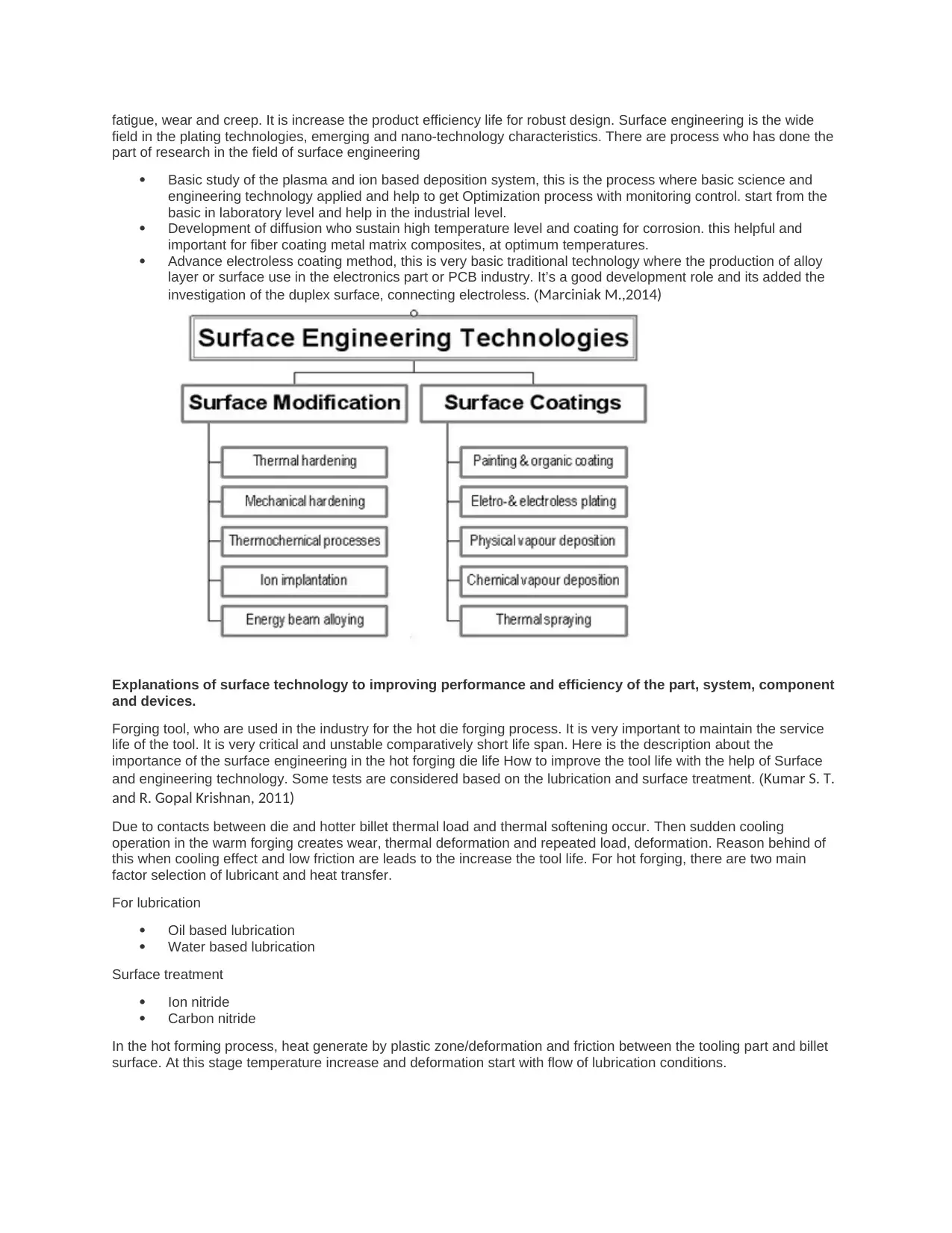
fatigue, wear and creep. It is increase the product efficiency life for robust design. Surface engineering is the wide
field in the plating technologies, emerging and nano-technology characteristics. There are process who has done the
part of research in the field of surface engineering
Basic study of the plasma and ion based deposition system, this is the process where basic science and
engineering technology applied and help to get Optimization process with monitoring control. start from the
basic in laboratory level and help in the industrial level.
Development of diffusion who sustain high temperature level and coating for corrosion. this helpful and
important for fiber coating metal matrix composites, at optimum temperatures.
Advance electroless coating method, this is very basic traditional technology where the production of alloy
layer or surface use in the electronics part or PCB industry. It’s a good development role and its added the
investigation of the duplex surface, connecting electroless. (Marciniak M.,2014)
Explanations of surface technology to improving performance and efficiency of the part, system, component
and devices.
Forging tool, who are used in the industry for the hot die forging process. It is very important to maintain the service
life of the tool. It is very critical and unstable comparatively short life span. Here is the description about the
importance of the surface engineering in the hot forging die life How to improve the tool life with the help of Surface
and engineering technology. Some tests are considered based on the lubrication and surface treatment. (Kumar S. T.
and R. Gopal Krishnan, 2011)
Due to contacts between die and hotter billet thermal load and thermal softening occur. Then sudden cooling
operation in the warm forging creates wear, thermal deformation and repeated load, deformation. Reason behind of
this when cooling effect and low friction are leads to the increase the tool life. For hot forging, there are two main
factor selection of lubricant and heat transfer.
For lubrication
Oil based lubrication
Water based lubrication
Surface treatment
Ion nitride
Carbon nitride
In the hot forming process, heat generate by plastic zone/deformation and friction between the tooling part and billet
surface. At this stage temperature increase and deformation start with flow of lubrication conditions.
field in the plating technologies, emerging and nano-technology characteristics. There are process who has done the
part of research in the field of surface engineering
Basic study of the plasma and ion based deposition system, this is the process where basic science and
engineering technology applied and help to get Optimization process with monitoring control. start from the
basic in laboratory level and help in the industrial level.
Development of diffusion who sustain high temperature level and coating for corrosion. this helpful and
important for fiber coating metal matrix composites, at optimum temperatures.
Advance electroless coating method, this is very basic traditional technology where the production of alloy
layer or surface use in the electronics part or PCB industry. It’s a good development role and its added the
investigation of the duplex surface, connecting electroless. (Marciniak M.,2014)
Explanations of surface technology to improving performance and efficiency of the part, system, component
and devices.
Forging tool, who are used in the industry for the hot die forging process. It is very important to maintain the service
life of the tool. It is very critical and unstable comparatively short life span. Here is the description about the
importance of the surface engineering in the hot forging die life How to improve the tool life with the help of Surface
and engineering technology. Some tests are considered based on the lubrication and surface treatment. (Kumar S. T.
and R. Gopal Krishnan, 2011)
Due to contacts between die and hotter billet thermal load and thermal softening occur. Then sudden cooling
operation in the warm forging creates wear, thermal deformation and repeated load, deformation. Reason behind of
this when cooling effect and low friction are leads to the increase the tool life. For hot forging, there are two main
factor selection of lubricant and heat transfer.
For lubrication
Oil based lubrication
Water based lubrication
Surface treatment
Ion nitride
Carbon nitride
In the hot forming process, heat generate by plastic zone/deformation and friction between the tooling part and billet
surface. At this stage temperature increase and deformation start with flow of lubrication conditions.
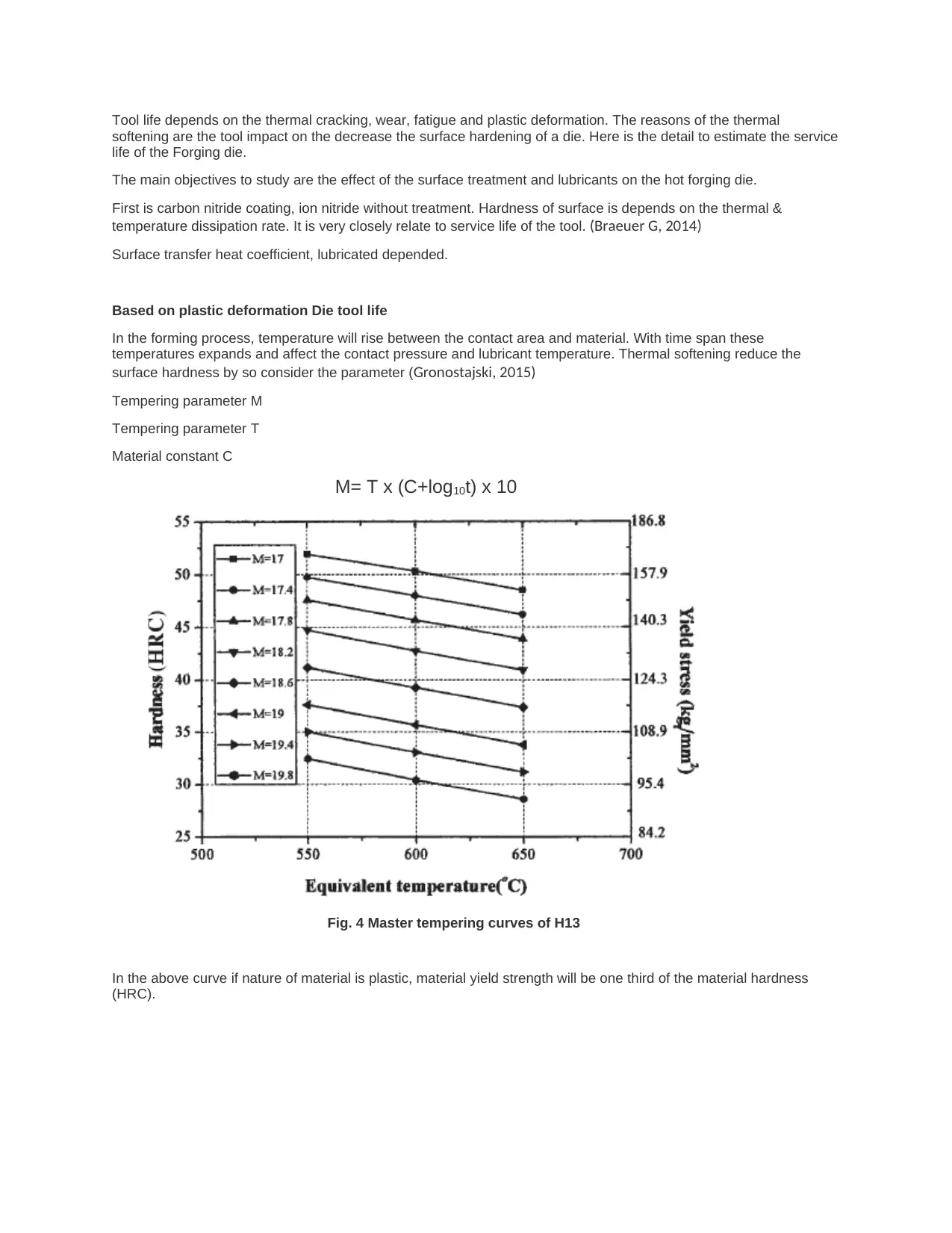
Tool life depends on the thermal cracking, wear, fatigue and plastic deformation. The reasons of the thermal
softening are the tool impact on the decrease the surface hardening of a die. Here is the detail to estimate the service
life of the Forging die.
The main objectives to study are the effect of the surface treatment and lubricants on the hot forging die.
First is carbon nitride coating, ion nitride without treatment. Hardness of surface is depends on the thermal &
temperature dissipation rate. It is very closely relate to service life of the tool. (Braeuer G, 2014)
Surface transfer heat coefficient, lubricated depended.
Based on plastic deformation Die tool life
In the forming process, temperature will rise between the contact area and material. With time span these
temperatures expands and affect the contact pressure and lubricant temperature. Thermal softening reduce the
surface hardness by so consider the parameter (Gronostajski, 2015)
Tempering parameter M
Tempering parameter T
Material constant C
M= T x (C+log10t) x 10
Fig. 4 Master tempering curves of H13
In the above curve if nature of material is plastic, material yield strength will be one third of the material hardness
(HRC).
softening are the tool impact on the decrease the surface hardening of a die. Here is the detail to estimate the service
life of the Forging die.
The main objectives to study are the effect of the surface treatment and lubricants on the hot forging die.
First is carbon nitride coating, ion nitride without treatment. Hardness of surface is depends on the thermal &
temperature dissipation rate. It is very closely relate to service life of the tool. (Braeuer G, 2014)
Surface transfer heat coefficient, lubricated depended.
Based on plastic deformation Die tool life
In the forming process, temperature will rise between the contact area and material. With time span these
temperatures expands and affect the contact pressure and lubricant temperature. Thermal softening reduce the
surface hardness by so consider the parameter (Gronostajski, 2015)
Tempering parameter M
Tempering parameter T
Material constant C
M= T x (C+log10t) x 10
Fig. 4 Master tempering curves of H13
In the above curve if nature of material is plastic, material yield strength will be one third of the material hardness
(HRC).
Secure Best Marks with AI Grader
Need help grading? Try our AI Grader for instant feedback on your assignments.
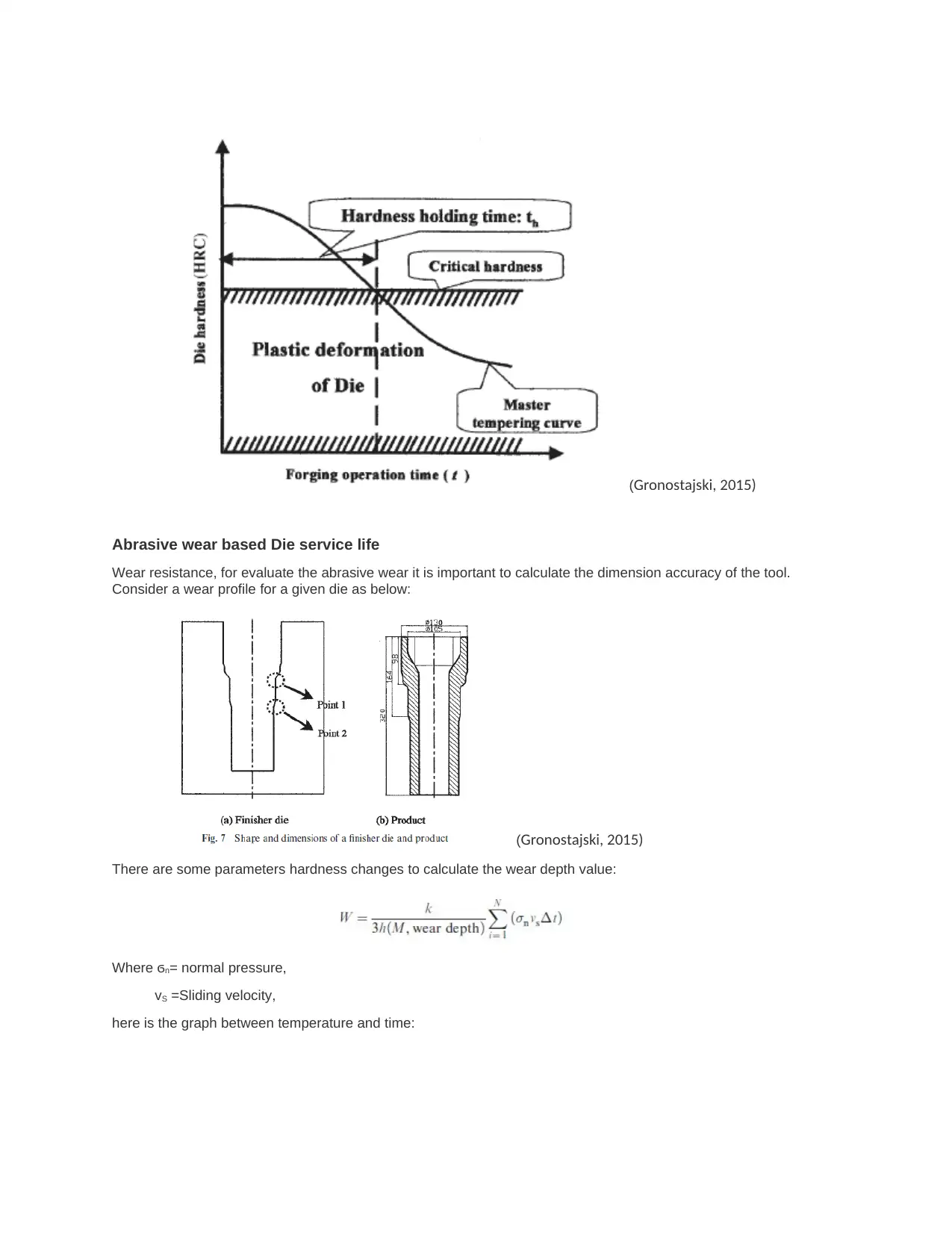
(Gronostajski, 2015)
Abrasive wear based Die service life
Wear resistance, for evaluate the abrasive wear it is important to calculate the dimension accuracy of the tool.
Consider a wear profile for a given die as below:
(Gronostajski, 2015)
There are some parameters hardness changes to calculate the wear depth value:
Where ϭn= normal pressure,
vS =Sliding velocity,
here is the graph between temperature and time:
Abrasive wear based Die service life
Wear resistance, for evaluate the abrasive wear it is important to calculate the dimension accuracy of the tool.
Consider a wear profile for a given die as below:
(Gronostajski, 2015)
There are some parameters hardness changes to calculate the wear depth value:
Where ϭn= normal pressure,
vS =Sliding velocity,
here is the graph between temperature and time:
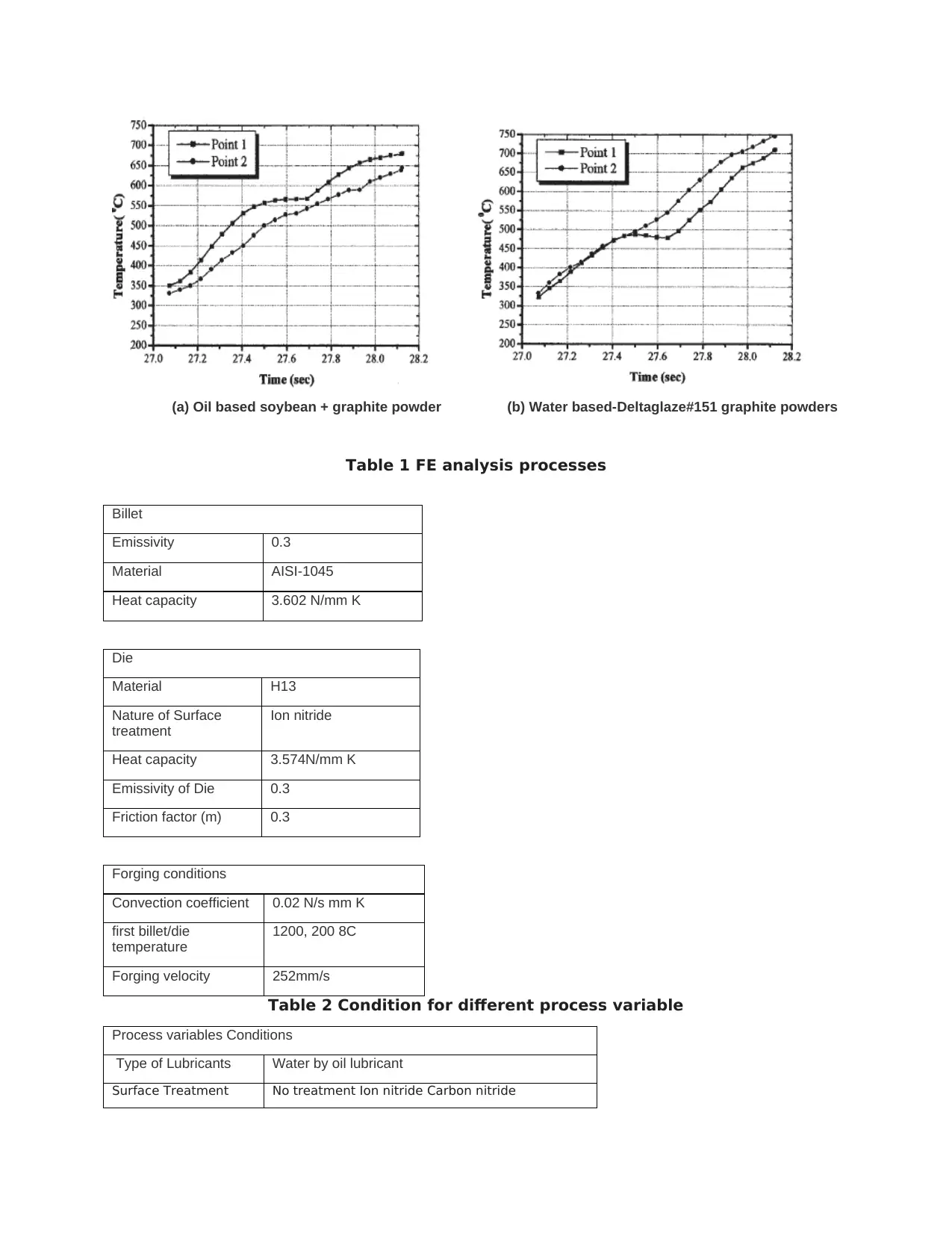
(a) Oil based soybean + graphite powder (b) Water based-Deltaglaze#151 graphite powders
Table 1 FE analysis processes
Billet
Emissivity 0.3
Material AISI-1045
Heat capacity 3.602 N/mm K
Die
Material H13
Nature of Surface
treatment
Ion nitride
Heat capacity 3.574N/mm K
Emissivity of Die 0.3
Friction factor (m) 0.3
Forging conditions
Convection coefficient 0.02 N/s mm K
first billet/die
temperature
1200, 200 8C
Forging velocity 252mm/s
Table 2 Condition for different process variable
Process variables Conditions
Type of Lubricants Water by oil lubricant
Surface Treatment No treatment Ion nitride Carbon nitride
Table 1 FE analysis processes
Billet
Emissivity 0.3
Material AISI-1045
Heat capacity 3.602 N/mm K
Die
Material H13
Nature of Surface
treatment
Ion nitride
Heat capacity 3.574N/mm K
Emissivity of Die 0.3
Friction factor (m) 0.3
Forging conditions
Convection coefficient 0.02 N/s mm K
first billet/die
temperature
1200, 200 8C
Forging velocity 252mm/s
Table 2 Condition for different process variable
Process variables Conditions
Type of Lubricants Water by oil lubricant
Surface Treatment No treatment Ion nitride Carbon nitride
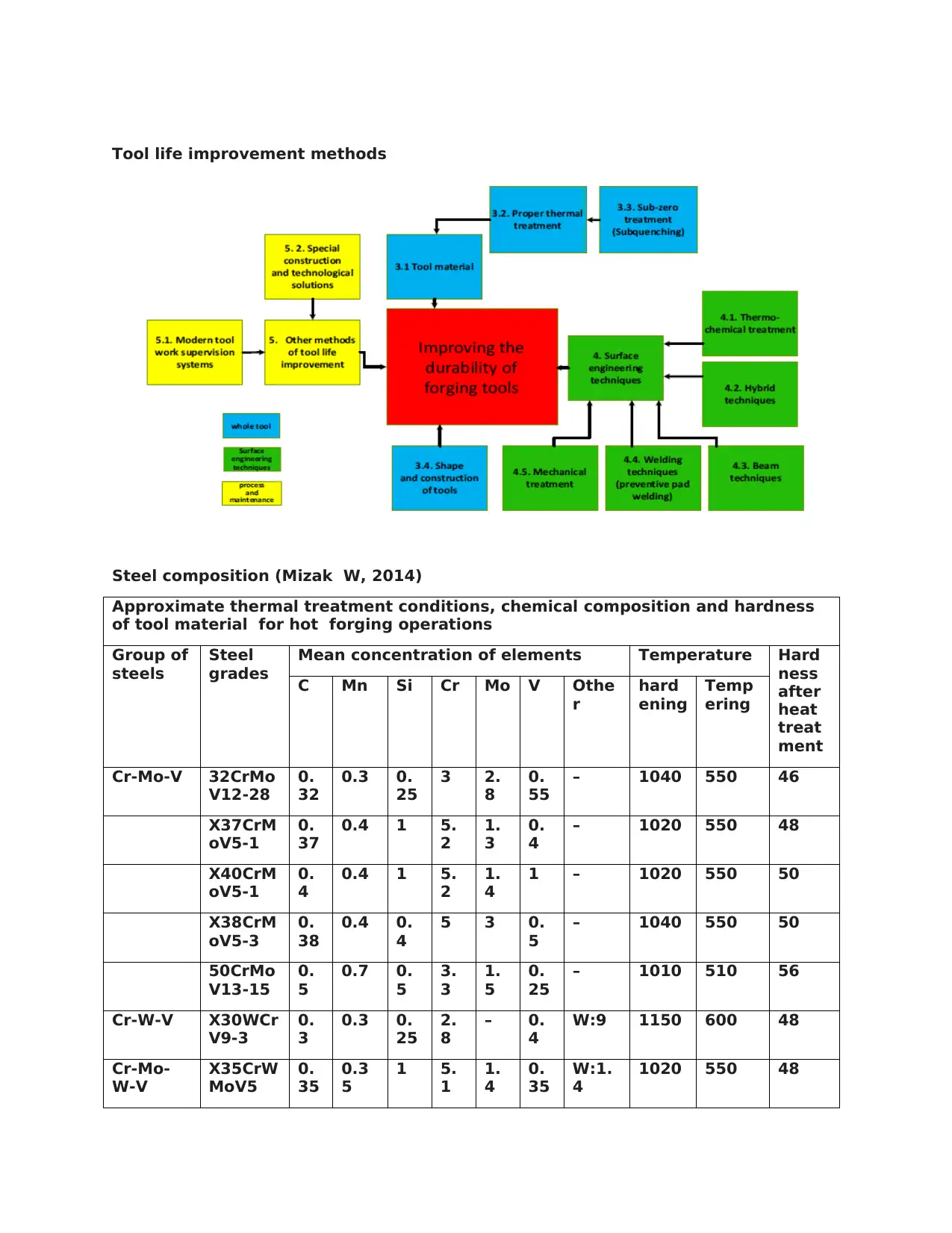
Tool life improvement methods
Steel composition (Mizak W, 2014)
Approximate thermal treatment conditions, chemical composition and hardness
of tool material for hot forging operations
Group of
steels
Steel
grades
Mean concentration of elements Temperature Hard
ness
after
heat
treat
ment
C Mn Si Cr Mo V Othe
r
hard
ening
Temp
ering
Cr-Mo-V 32CrMo
V12-28
0.
32
0.3 0.
25
3 2.
8
0.
55
– 1040 550 46
X37CrM
oV5-1
0.
37
0.4 1 5.
2
1.
3
0.
4
– 1020 550 48
X40CrM
oV5-1
0.
4
0.4 1 5.
2
1.
4
1 – 1020 550 50
X38CrM
oV5-3
0.
38
0.4 0.
4
5 3 0.
5
– 1040 550 50
50CrMo
V13-15
0.
5
0.7 0.
5
3.
3
1.
5
0.
25
– 1010 510 56
Cr-W-V X30WCr
V9-3
0.
3
0.3 0.
25
2.
8
– 0.
4
W:9 1150 600 48
Cr-Mo-
W-V
X35CrW
MoV5
0.
35
0.3
5
1 5.
1
1.
4
0.
35
W:1.
4
1020 550 48
Steel composition (Mizak W, 2014)
Approximate thermal treatment conditions, chemical composition and hardness
of tool material for hot forging operations
Group of
steels
Steel
grades
Mean concentration of elements Temperature Hard
ness
after
heat
treat
ment
C Mn Si Cr Mo V Othe
r
hard
ening
Temp
ering
Cr-Mo-V 32CrMo
V12-28
0.
32
0.3 0.
25
3 2.
8
0.
55
– 1040 550 46
X37CrM
oV5-1
0.
37
0.4 1 5.
2
1.
3
0.
4
– 1020 550 48
X40CrM
oV5-1
0.
4
0.4 1 5.
2
1.
4
1 – 1020 550 50
X38CrM
oV5-3
0.
38
0.4 0.
4
5 3 0.
5
– 1040 550 50
50CrMo
V13-15
0.
5
0.7 0.
5
3.
3
1.
5
0.
25
– 1010 510 56
Cr-W-V X30WCr
V9-3
0.
3
0.3 0.
25
2.
8
– 0.
4
W:9 1150 600 48
Cr-Mo-
W-V
X35CrW
MoV5
0.
35
0.3
5
1 5.
1
1.
4
0.
35
W:1.
4
1020 550 48
Paraphrase This Document
Need a fresh take? Get an instant paraphrase of this document with our AI Paraphraser
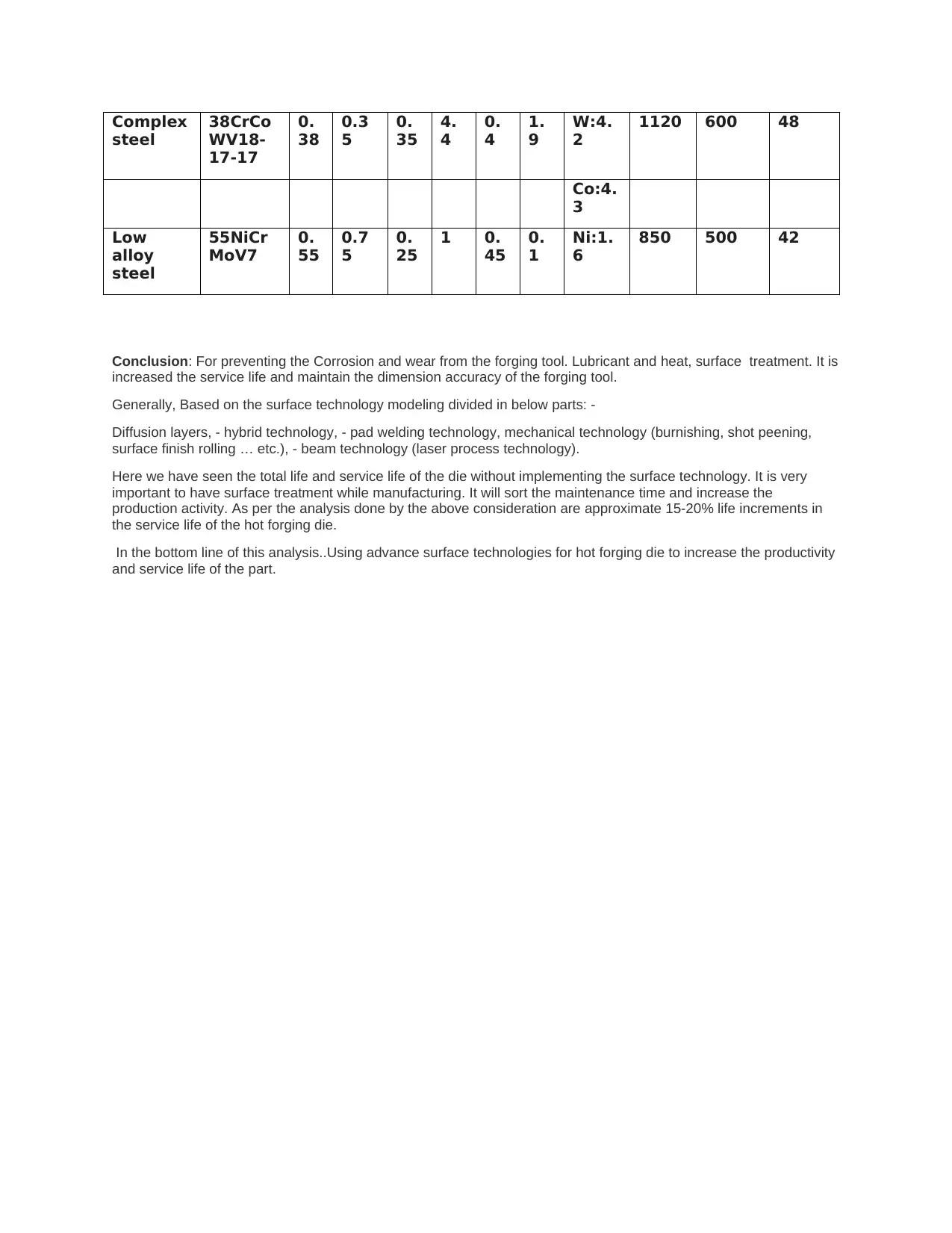
Complex
steel
38CrCo
WV18-
17-17
0.
38
0.3
5
0.
35
4.
4
0.
4
1.
9
W:4.
2
1120 600 48
Co:4.
3
Low
alloy
steel
55NiCr
MoV7
0.
55
0.7
5
0.
25
1 0.
45
0.
1
Ni:1.
6
850 500 42
Conclusion: For preventing the Corrosion and wear from the forging tool. Lubricant and heat, surface treatment. It is
increased the service life and maintain the dimension accuracy of the forging tool.
Generally, Based on the surface technology modeling divided in below parts: -
Diffusion layers, - hybrid technology, - pad welding technology, mechanical technology (burnishing, shot peening,
surface finish rolling … etc.), - beam technology (laser process technology).
Here we have seen the total life and service life of the die without implementing the surface technology. It is very
important to have surface treatment while manufacturing. It will sort the maintenance time and increase the
production activity. As per the analysis done by the above consideration are approximate 15-20% life increments in
the service life of the hot forging die.
In the bottom line of this analysis..Using advance surface technologies for hot forging die to increase the productivity
and service life of the part.
steel
38CrCo
WV18-
17-17
0.
38
0.3
5
0.
35
4.
4
0.
4
1.
9
W:4.
2
1120 600 48
Co:4.
3
Low
alloy
steel
55NiCr
MoV7
0.
55
0.7
5
0.
25
1 0.
45
0.
1
Ni:1.
6
850 500 42
Conclusion: For preventing the Corrosion and wear from the forging tool. Lubricant and heat, surface treatment. It is
increased the service life and maintain the dimension accuracy of the forging tool.
Generally, Based on the surface technology modeling divided in below parts: -
Diffusion layers, - hybrid technology, - pad welding technology, mechanical technology (burnishing, shot peening,
surface finish rolling … etc.), - beam technology (laser process technology).
Here we have seen the total life and service life of the die without implementing the surface technology. It is very
important to have surface treatment while manufacturing. It will sort the maintenance time and increase the
production activity. As per the analysis done by the above consideration are approximate 15-20% life increments in
the service life of the hot forging die.
In the bottom line of this analysis..Using advance surface technologies for hot forging die to increase the productivity
and service life of the part.
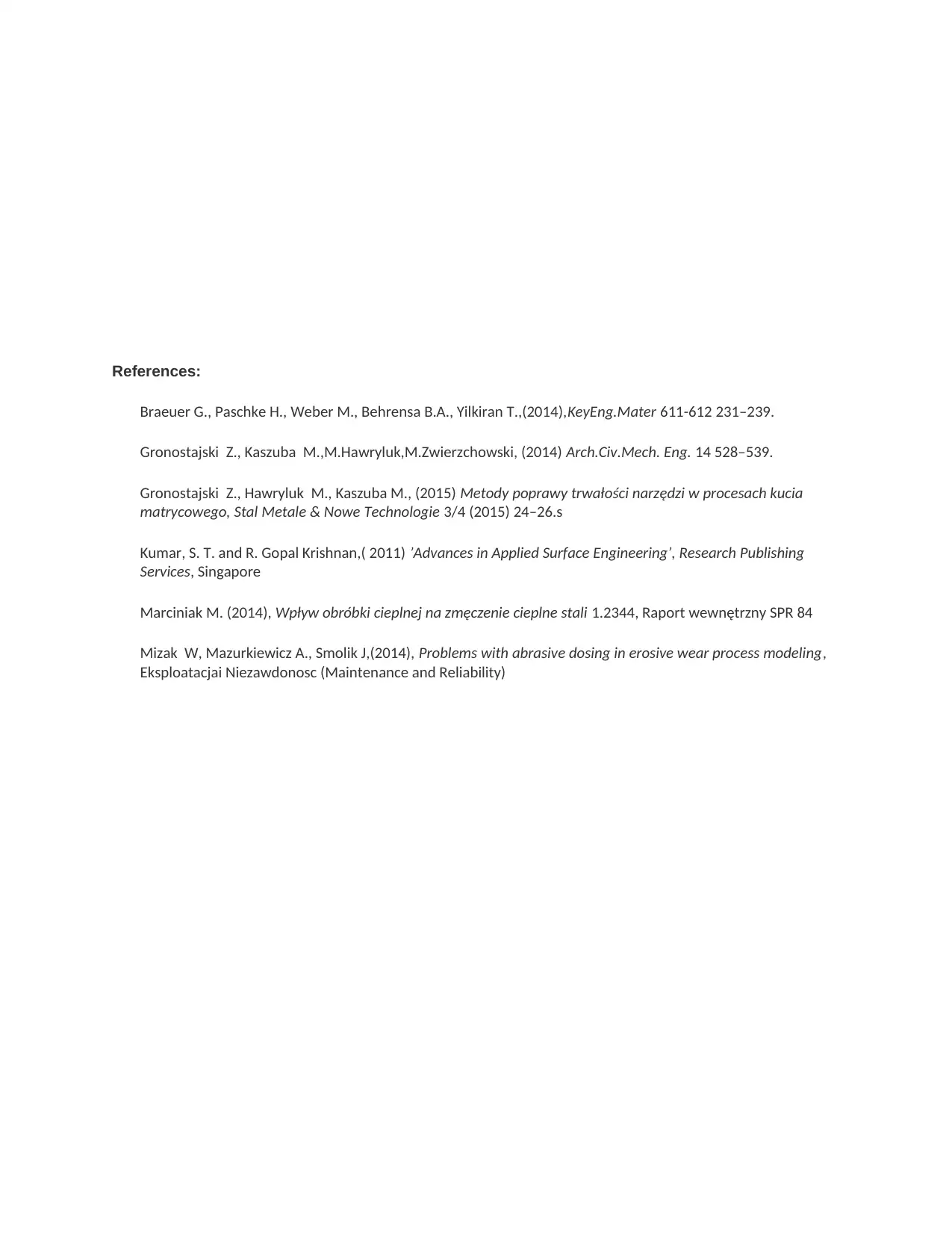
References:
Braeuer G., Paschke H., Weber M., Behrensa B.A., Yilkiran T.,(2014),KeyEng.Mater 611-612 231–239.
Gronostajski Z., Kaszuba M.,M.Hawryluk,M.Zwierzchowski, (2014) Arch.Civ.Mech. Eng. 14 528–539.
Gronostajski Z., Hawryluk M., Kaszuba M., (2015) Metody poprawy trwałości narzędzi w procesach kucia
matrycowego, Stal Metale & Nowe Technologie 3/4 (2015) 24–26.s
Kumar, S. T. and R. Gopal Krishnan,( 2011) ’Advances in Applied Surface Engineering’, Research Publishing
Services, Singapore
Marciniak M. (2014), Wpływ obróbki cieplnej na zmęczenie cieplne stali 1.2344, Raport wewnętrzny SPR 84
Mizak W, Mazurkiewicz A., Smolik J,(2014), Problems with abrasive dosing in erosive wear process modeling,
Eksploatacjai Niezawdonosc (Maintenance and Reliability)
Braeuer G., Paschke H., Weber M., Behrensa B.A., Yilkiran T.,(2014),KeyEng.Mater 611-612 231–239.
Gronostajski Z., Kaszuba M.,M.Hawryluk,M.Zwierzchowski, (2014) Arch.Civ.Mech. Eng. 14 528–539.
Gronostajski Z., Hawryluk M., Kaszuba M., (2015) Metody poprawy trwałości narzędzi w procesach kucia
matrycowego, Stal Metale & Nowe Technologie 3/4 (2015) 24–26.s
Kumar, S. T. and R. Gopal Krishnan,( 2011) ’Advances in Applied Surface Engineering’, Research Publishing
Services, Singapore
Marciniak M. (2014), Wpływ obróbki cieplnej na zmęczenie cieplne stali 1.2344, Raport wewnętrzny SPR 84
Mizak W, Mazurkiewicz A., Smolik J,(2014), Problems with abrasive dosing in erosive wear process modeling,
Eksploatacjai Niezawdonosc (Maintenance and Reliability)
1 out of 9

Your All-in-One AI-Powered Toolkit for Academic Success.
+13062052269
info@desklib.com
Available 24*7 on WhatsApp / Email
Unlock your academic potential
© 2024 | Zucol Services PVT LTD | All rights reserved.