Report on Hotpoint's Operations and Project Management Strategies
VerifiedAdded on 2020/06/05
|16
|4244
|62
Report
AI Summary
This report provides a comprehensive analysis of Hotpoint's operations and project management strategies within the manufacturing sector. It begins with an introduction to operational management and its principles, focusing on how Hotpoint, a UK-based electronics company, implements these principles in its production of domestic products like televisions. The report then delves into Task 1, offering a critical review of Hotpoint's implementation of operations principles, including reality, organization, fundamentals, accountability, variance, causality, managed passion, humility, and success, along with the application of Six Sigma and Lean principles. Task 2 examines the continuity of improvement plans based on review and analysis, highlighting continuous improvement strategies and their effects on Hotpoint's performance. Furthermore, the report outlines the stages of the Project Life Cycle (PLC), including business cases, project plans, and work breakdown structures (WBS) in Task 3. Finally, Task 4 assesses the effectiveness of PLC in project applications. The report concludes with an overview of the findings and relevant references.
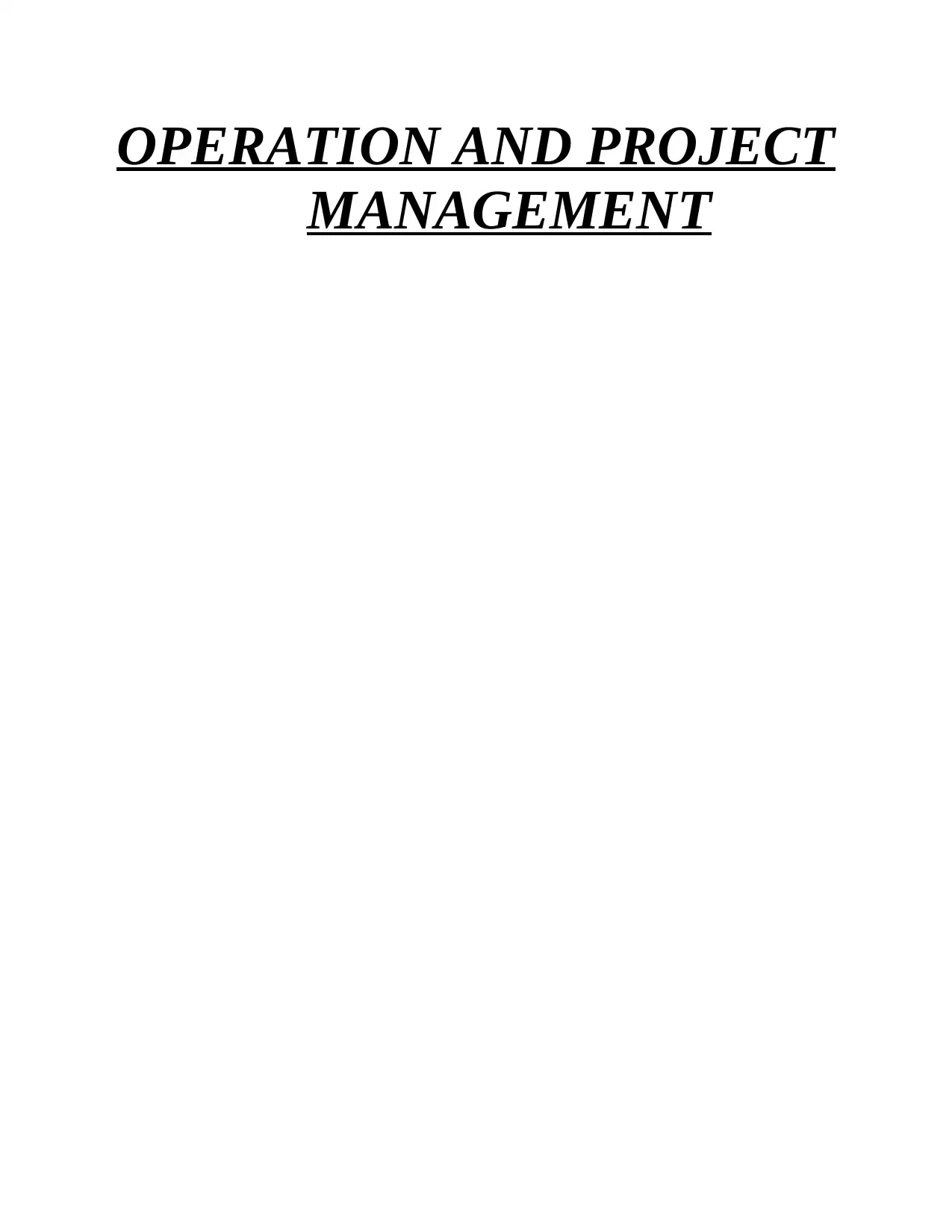
OPERATION AND PROJECT
MANAGEMENT
MANAGEMENT
Secure Best Marks with AI Grader
Need help grading? Try our AI Grader for instant feedback on your assignments.
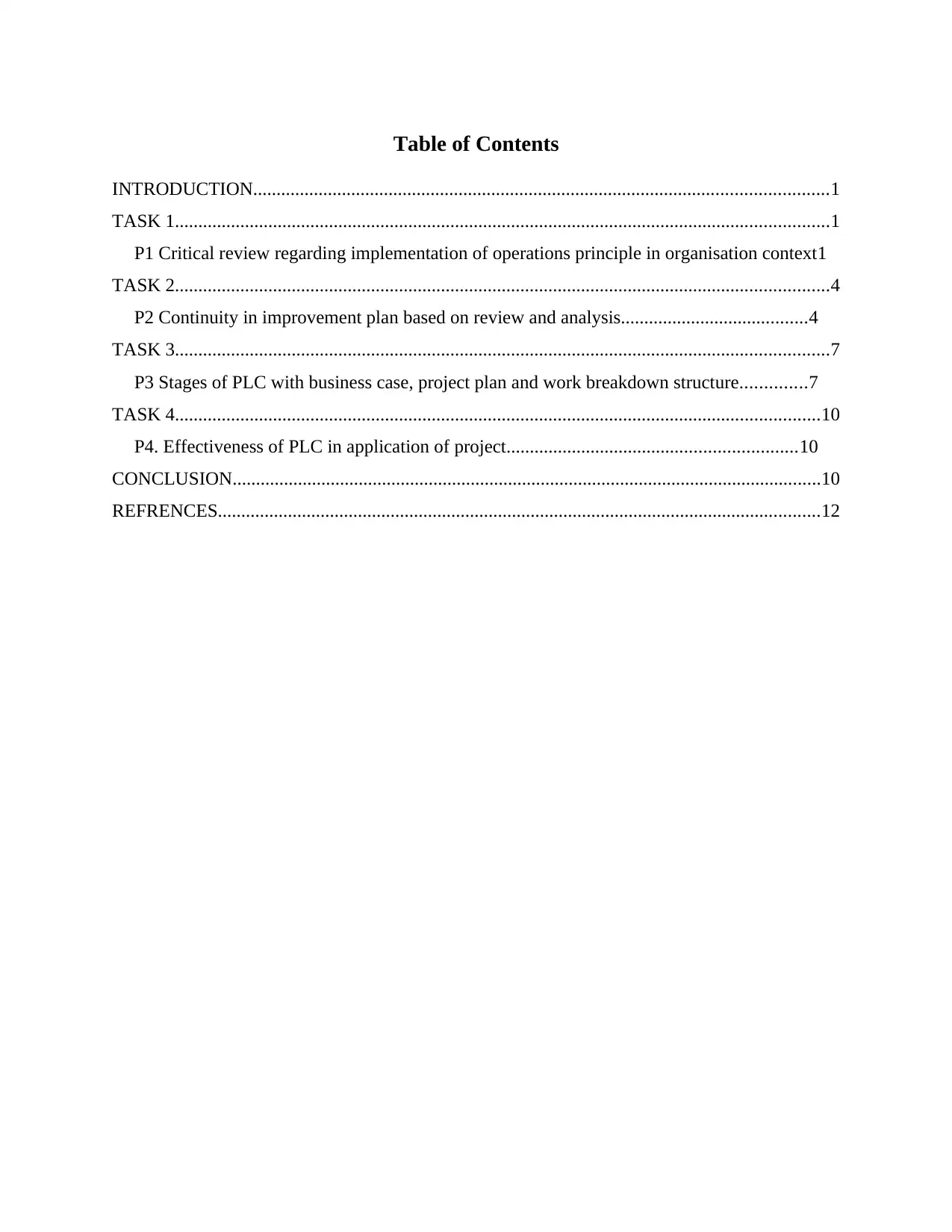
Table of Contents
INTRODUCTION...........................................................................................................................1
TASK 1............................................................................................................................................1
P1 Critical review regarding implementation of operations principle in organisation context1
TASK 2............................................................................................................................................4
P2 Continuity in improvement plan based on review and analysis........................................4
TASK 3............................................................................................................................................7
P3 Stages of PLC with business case, project plan and work breakdown structure..............7
TASK 4..........................................................................................................................................10
P4. Effectiveness of PLC in application of project..............................................................10
CONCLUSION..............................................................................................................................10
REFRENCES.................................................................................................................................12
INTRODUCTION...........................................................................................................................1
TASK 1............................................................................................................................................1
P1 Critical review regarding implementation of operations principle in organisation context1
TASK 2............................................................................................................................................4
P2 Continuity in improvement plan based on review and analysis........................................4
TASK 3............................................................................................................................................7
P3 Stages of PLC with business case, project plan and work breakdown structure..............7
TASK 4..........................................................................................................................................10
P4. Effectiveness of PLC in application of project..............................................................10
CONCLUSION..............................................................................................................................10
REFRENCES.................................................................................................................................12
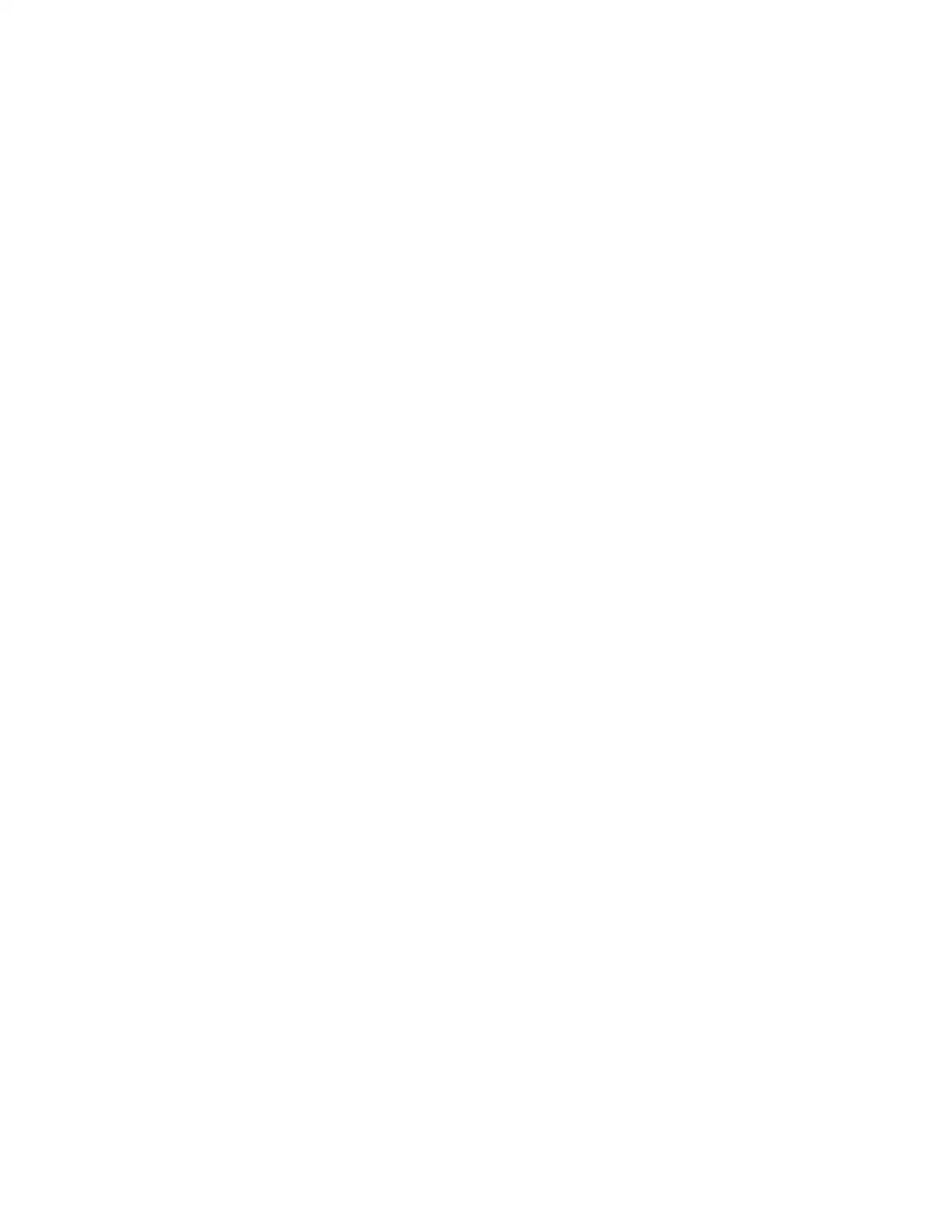
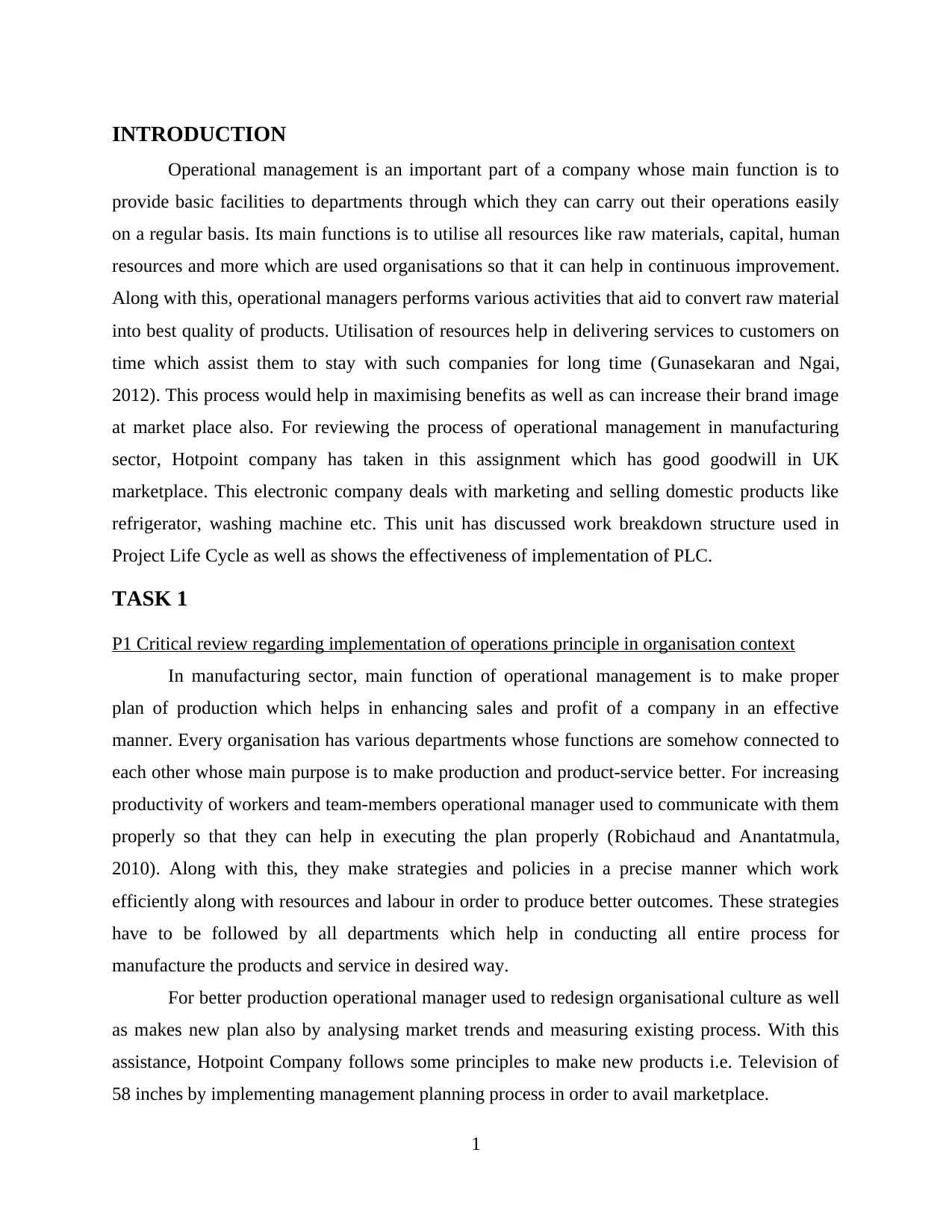
INTRODUCTION
Operational management is an important part of a company whose main function is to
provide basic facilities to departments through which they can carry out their operations easily
on a regular basis. Its main functions is to utilise all resources like raw materials, capital, human
resources and more which are used organisations so that it can help in continuous improvement.
Along with this, operational managers performs various activities that aid to convert raw material
into best quality of products. Utilisation of resources help in delivering services to customers on
time which assist them to stay with such companies for long time (Gunasekaran and Ngai,
2012). This process would help in maximising benefits as well as can increase their brand image
at market place also. For reviewing the process of operational management in manufacturing
sector, Hotpoint company has taken in this assignment which has good goodwill in UK
marketplace. This electronic company deals with marketing and selling domestic products like
refrigerator, washing machine etc. This unit has discussed work breakdown structure used in
Project Life Cycle as well as shows the effectiveness of implementation of PLC.
TASK 1
P1 Critical review regarding implementation of operations principle in organisation context
In manufacturing sector, main function of operational management is to make proper
plan of production which helps in enhancing sales and profit of a company in an effective
manner. Every organisation has various departments whose functions are somehow connected to
each other whose main purpose is to make production and product-service better. For increasing
productivity of workers and team-members operational manager used to communicate with them
properly so that they can help in executing the plan properly (Robichaud and Anantatmula,
2010). Along with this, they make strategies and policies in a precise manner which work
efficiently along with resources and labour in order to produce better outcomes. These strategies
have to be followed by all departments which help in conducting all entire process for
manufacture the products and service in desired way.
For better production operational manager used to redesign organisational culture as well
as makes new plan also by analysing market trends and measuring existing process. With this
assistance, Hotpoint Company follows some principles to make new products i.e. Television of
58 inches by implementing management planning process in order to avail marketplace.
1
Operational management is an important part of a company whose main function is to
provide basic facilities to departments through which they can carry out their operations easily
on a regular basis. Its main functions is to utilise all resources like raw materials, capital, human
resources and more which are used organisations so that it can help in continuous improvement.
Along with this, operational managers performs various activities that aid to convert raw material
into best quality of products. Utilisation of resources help in delivering services to customers on
time which assist them to stay with such companies for long time (Gunasekaran and Ngai,
2012). This process would help in maximising benefits as well as can increase their brand image
at market place also. For reviewing the process of operational management in manufacturing
sector, Hotpoint company has taken in this assignment which has good goodwill in UK
marketplace. This electronic company deals with marketing and selling domestic products like
refrigerator, washing machine etc. This unit has discussed work breakdown structure used in
Project Life Cycle as well as shows the effectiveness of implementation of PLC.
TASK 1
P1 Critical review regarding implementation of operations principle in organisation context
In manufacturing sector, main function of operational management is to make proper
plan of production which helps in enhancing sales and profit of a company in an effective
manner. Every organisation has various departments whose functions are somehow connected to
each other whose main purpose is to make production and product-service better. For increasing
productivity of workers and team-members operational manager used to communicate with them
properly so that they can help in executing the plan properly (Robichaud and Anantatmula,
2010). Along with this, they make strategies and policies in a precise manner which work
efficiently along with resources and labour in order to produce better outcomes. These strategies
have to be followed by all departments which help in conducting all entire process for
manufacture the products and service in desired way.
For better production operational manager used to redesign organisational culture as well
as makes new plan also by analysing market trends and measuring existing process. With this
assistance, Hotpoint Company follows some principles to make new products i.e. Television of
58 inches by implementing management planning process in order to avail marketplace.
1
Secure Best Marks with AI Grader
Need help grading? Try our AI Grader for instant feedback on your assignments.
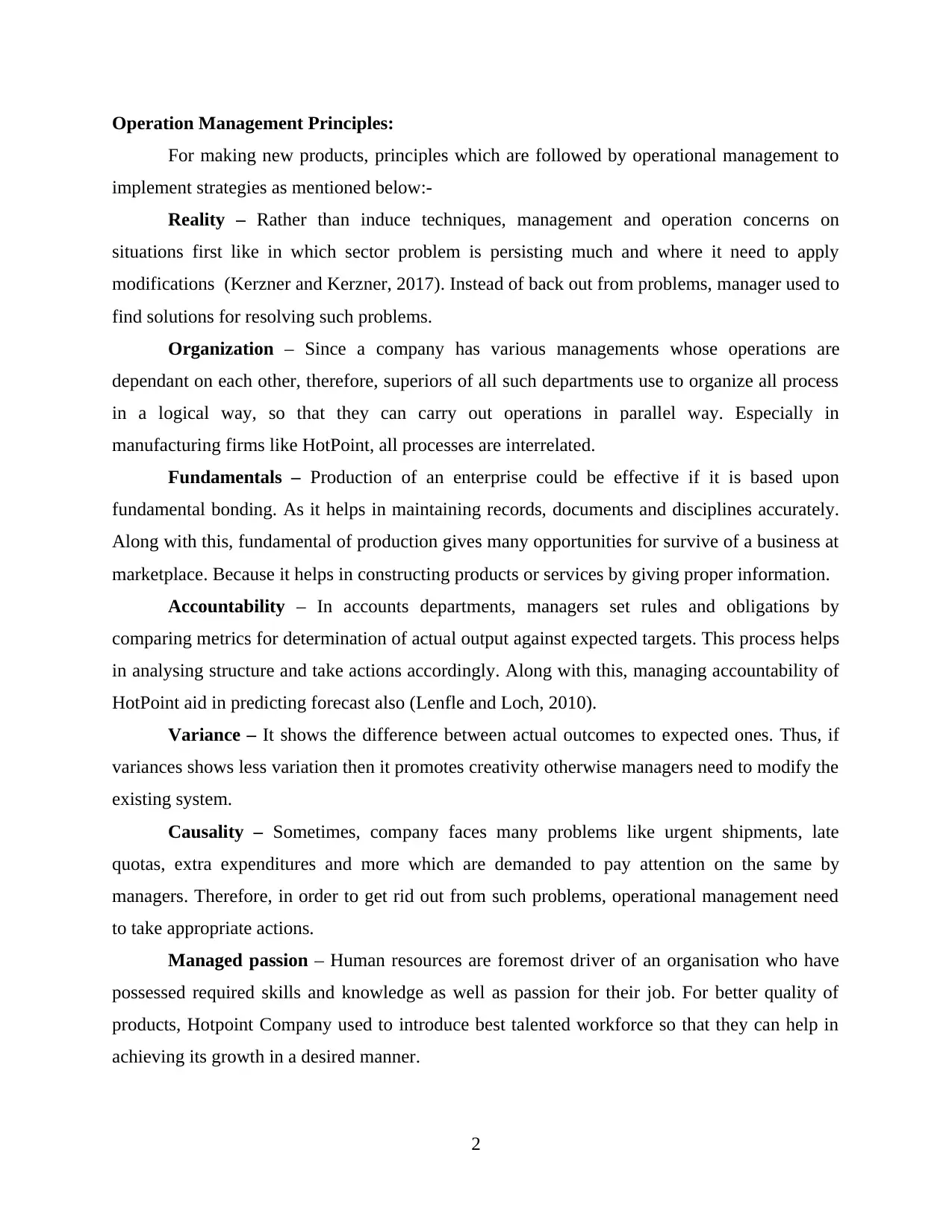
Operation Management Principles:
For making new products, principles which are followed by operational management to
implement strategies as mentioned below:-
Reality – Rather than induce techniques, management and operation concerns on
situations first like in which sector problem is persisting much and where it need to apply
modifications (Kerzner and Kerzner, 2017). Instead of back out from problems, manager used to
find solutions for resolving such problems.
Organization – Since a company has various managements whose operations are
dependant on each other, therefore, superiors of all such departments use to organize all process
in a logical way, so that they can carry out operations in parallel way. Especially in
manufacturing firms like HotPoint, all processes are interrelated.
Fundamentals – Production of an enterprise could be effective if it is based upon
fundamental bonding. As it helps in maintaining records, documents and disciplines accurately.
Along with this, fundamental of production gives many opportunities for survive of a business at
marketplace. Because it helps in constructing products or services by giving proper information.
Accountability – In accounts departments, managers set rules and obligations by
comparing metrics for determination of actual output against expected targets. This process helps
in analysing structure and take actions accordingly. Along with this, managing accountability of
HotPoint aid in predicting forecast also (Lenfle and Loch, 2010).
Variance – It shows the difference between actual outcomes to expected ones. Thus, if
variances shows less variation then it promotes creativity otherwise managers need to modify the
existing system.
Causality – Sometimes, company faces many problems like urgent shipments, late
quotas, extra expenditures and more which are demanded to pay attention on the same by
managers. Therefore, in order to get rid out from such problems, operational management need
to take appropriate actions.
Managed passion – Human resources are foremost driver of an organisation who have
possessed required skills and knowledge as well as passion for their job. For better quality of
products, Hotpoint Company used to introduce best talented workforce so that they can help in
achieving its growth in a desired manner.
2
For making new products, principles which are followed by operational management to
implement strategies as mentioned below:-
Reality – Rather than induce techniques, management and operation concerns on
situations first like in which sector problem is persisting much and where it need to apply
modifications (Kerzner and Kerzner, 2017). Instead of back out from problems, manager used to
find solutions for resolving such problems.
Organization – Since a company has various managements whose operations are
dependant on each other, therefore, superiors of all such departments use to organize all process
in a logical way, so that they can carry out operations in parallel way. Especially in
manufacturing firms like HotPoint, all processes are interrelated.
Fundamentals – Production of an enterprise could be effective if it is based upon
fundamental bonding. As it helps in maintaining records, documents and disciplines accurately.
Along with this, fundamental of production gives many opportunities for survive of a business at
marketplace. Because it helps in constructing products or services by giving proper information.
Accountability – In accounts departments, managers set rules and obligations by
comparing metrics for determination of actual output against expected targets. This process helps
in analysing structure and take actions accordingly. Along with this, managing accountability of
HotPoint aid in predicting forecast also (Lenfle and Loch, 2010).
Variance – It shows the difference between actual outcomes to expected ones. Thus, if
variances shows less variation then it promotes creativity otherwise managers need to modify the
existing system.
Causality – Sometimes, company faces many problems like urgent shipments, late
quotas, extra expenditures and more which are demanded to pay attention on the same by
managers. Therefore, in order to get rid out from such problems, operational management need
to take appropriate actions.
Managed passion – Human resources are foremost driver of an organisation who have
possessed required skills and knowledge as well as passion for their job. For better quality of
products, Hotpoint Company used to introduce best talented workforce so that they can help in
achieving its growth in a desired manner.
2

Humility – Managers are required to manage and maintain positive environment in a
firm which helps people to work well. They should not look at weak points or limitation of
company, but try to get familiar with circumstances, take risks and encourages workers to move.
Therefore, HotPoint always ensures that its organisation is free from discrimination as well as
maintain healthy atmosphere over there (Lindström and et. al. ,2012).
Success – Success of a company depends much on customer who avails it products and
retain with the same for long time. Since, trend of market changes are changing at rapid rate so,
management need to find demand of people and manufacture products accordingly. Along with
this, in order to acquire business objectives successfully managers of HotPoint need to introduce
new technologies in production and operations also.
SIX SIGMA:
SIX SIGMA process is used to identify errors in productions for improving its quality by
eliminating the same. This procedure helps in making products free from defect which aid in
reducing cost as well as saves time (Mir and Pinnington, 2014). Therefore, in high–end
engineering and manufacturing sectors, it is better process. It includes six major tools via Define,
Measure, Analyse, Improve and Control (DMAIC). With this technique, HotPoint becomes able
to make its product free from defects which helps in creating best quality of products.
Define – It defines the demand of people at marketplace and give proper directions
accordingly which helps in accomplishing a certain task successfully.
Measure – This process measures current state of production as well as changes from
beginning to existing state. Along with this, it measure requirement of resources to achieve the
set targets.
Analyse – It identifies basic problems in operations which helps in analysing needs of
modifications so that a firm can meet target on time (Ogunlana, 2010).
Improve – For achievement of desired goals, it looks out at possibilities for changes and
improvisation.
Control – This is the main process which control all activities of entire operations in
order to meet better result.
Lean principle:
Management of Hotpoint Company also follows lean principle which helps in generating
new idea within production. It consists five principles that are- Define Value, Map value stream,
3
firm which helps people to work well. They should not look at weak points or limitation of
company, but try to get familiar with circumstances, take risks and encourages workers to move.
Therefore, HotPoint always ensures that its organisation is free from discrimination as well as
maintain healthy atmosphere over there (Lindström and et. al. ,2012).
Success – Success of a company depends much on customer who avails it products and
retain with the same for long time. Since, trend of market changes are changing at rapid rate so,
management need to find demand of people and manufacture products accordingly. Along with
this, in order to acquire business objectives successfully managers of HotPoint need to introduce
new technologies in production and operations also.
SIX SIGMA:
SIX SIGMA process is used to identify errors in productions for improving its quality by
eliminating the same. This procedure helps in making products free from defect which aid in
reducing cost as well as saves time (Mir and Pinnington, 2014). Therefore, in high–end
engineering and manufacturing sectors, it is better process. It includes six major tools via Define,
Measure, Analyse, Improve and Control (DMAIC). With this technique, HotPoint becomes able
to make its product free from defects which helps in creating best quality of products.
Define – It defines the demand of people at marketplace and give proper directions
accordingly which helps in accomplishing a certain task successfully.
Measure – This process measures current state of production as well as changes from
beginning to existing state. Along with this, it measure requirement of resources to achieve the
set targets.
Analyse – It identifies basic problems in operations which helps in analysing needs of
modifications so that a firm can meet target on time (Ogunlana, 2010).
Improve – For achievement of desired goals, it looks out at possibilities for changes and
improvisation.
Control – This is the main process which control all activities of entire operations in
order to meet better result.
Lean principle:
Management of Hotpoint Company also follows lean principle which helps in generating
new idea within production. It consists five principles that are- Define Value, Map value stream,
3
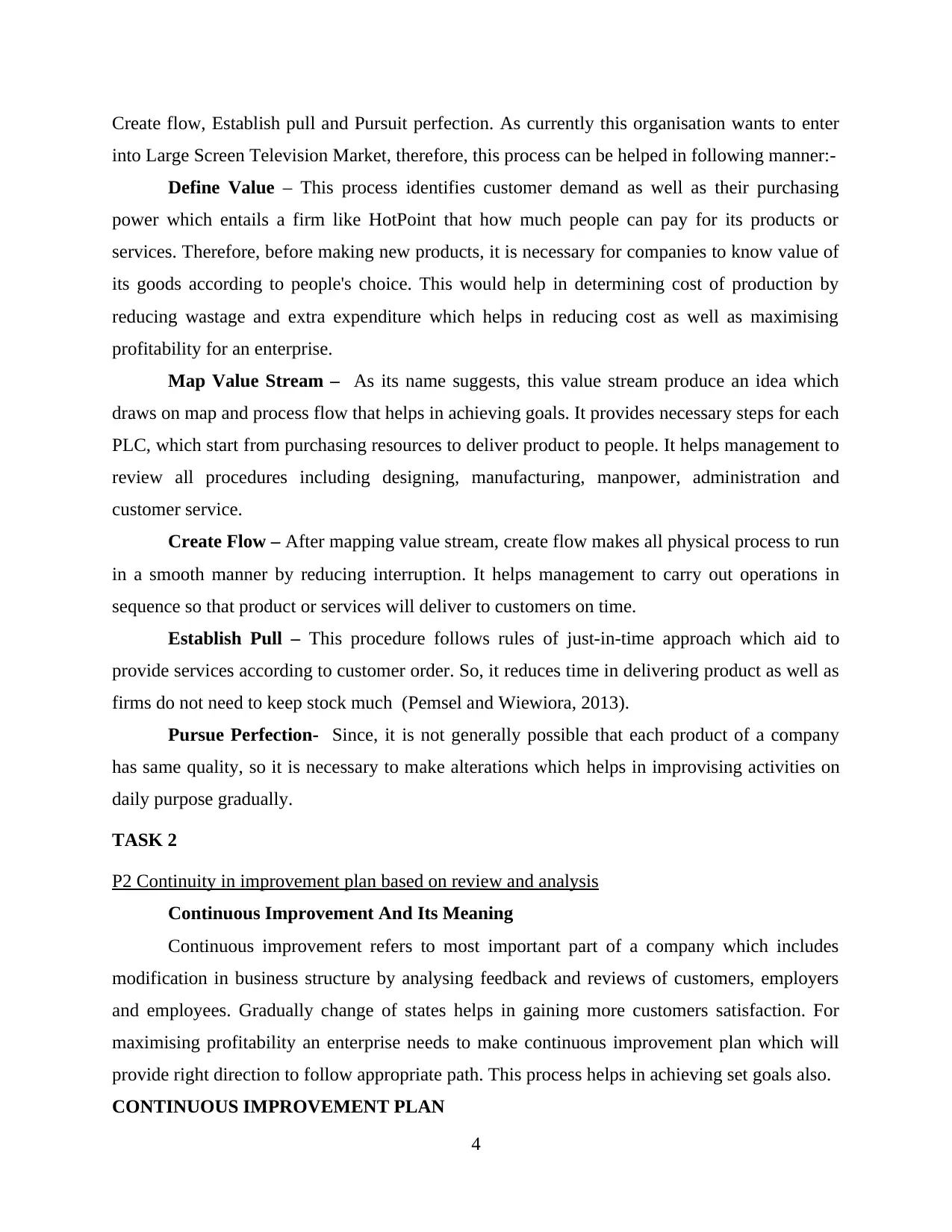
Create flow, Establish pull and Pursuit perfection. As currently this organisation wants to enter
into Large Screen Television Market, therefore, this process can be helped in following manner:-
Define Value – This process identifies customer demand as well as their purchasing
power which entails a firm like HotPoint that how much people can pay for its products or
services. Therefore, before making new products, it is necessary for companies to know value of
its goods according to people's choice. This would help in determining cost of production by
reducing wastage and extra expenditure which helps in reducing cost as well as maximising
profitability for an enterprise.
Map Value Stream – As its name suggests, this value stream produce an idea which
draws on map and process flow that helps in achieving goals. It provides necessary steps for each
PLC, which start from purchasing resources to deliver product to people. It helps management to
review all procedures including designing, manufacturing, manpower, administration and
customer service.
Create Flow – After mapping value stream, create flow makes all physical process to run
in a smooth manner by reducing interruption. It helps management to carry out operations in
sequence so that product or services will deliver to customers on time.
Establish Pull – This procedure follows rules of just-in-time approach which aid to
provide services according to customer order. So, it reduces time in delivering product as well as
firms do not need to keep stock much (Pemsel and Wiewiora, 2013).
Pursue Perfection- Since, it is not generally possible that each product of a company
has same quality, so it is necessary to make alterations which helps in improvising activities on
daily purpose gradually.
TASK 2
P2 Continuity in improvement plan based on review and analysis
Continuous Improvement And Its Meaning
Continuous improvement refers to most important part of a company which includes
modification in business structure by analysing feedback and reviews of customers, employers
and employees. Gradually change of states helps in gaining more customers satisfaction. For
maximising profitability an enterprise needs to make continuous improvement plan which will
provide right direction to follow appropriate path. This process helps in achieving set goals also.
CONTINUOUS IMPROVEMENT PLAN
4
into Large Screen Television Market, therefore, this process can be helped in following manner:-
Define Value – This process identifies customer demand as well as their purchasing
power which entails a firm like HotPoint that how much people can pay for its products or
services. Therefore, before making new products, it is necessary for companies to know value of
its goods according to people's choice. This would help in determining cost of production by
reducing wastage and extra expenditure which helps in reducing cost as well as maximising
profitability for an enterprise.
Map Value Stream – As its name suggests, this value stream produce an idea which
draws on map and process flow that helps in achieving goals. It provides necessary steps for each
PLC, which start from purchasing resources to deliver product to people. It helps management to
review all procedures including designing, manufacturing, manpower, administration and
customer service.
Create Flow – After mapping value stream, create flow makes all physical process to run
in a smooth manner by reducing interruption. It helps management to carry out operations in
sequence so that product or services will deliver to customers on time.
Establish Pull – This procedure follows rules of just-in-time approach which aid to
provide services according to customer order. So, it reduces time in delivering product as well as
firms do not need to keep stock much (Pemsel and Wiewiora, 2013).
Pursue Perfection- Since, it is not generally possible that each product of a company
has same quality, so it is necessary to make alterations which helps in improvising activities on
daily purpose gradually.
TASK 2
P2 Continuity in improvement plan based on review and analysis
Continuous Improvement And Its Meaning
Continuous improvement refers to most important part of a company which includes
modification in business structure by analysing feedback and reviews of customers, employers
and employees. Gradually change of states helps in gaining more customers satisfaction. For
maximising profitability an enterprise needs to make continuous improvement plan which will
provide right direction to follow appropriate path. This process helps in achieving set goals also.
CONTINUOUS IMPROVEMENT PLAN
4
Paraphrase This Document
Need a fresh take? Get an instant paraphrase of this document with our AI Paraphraser
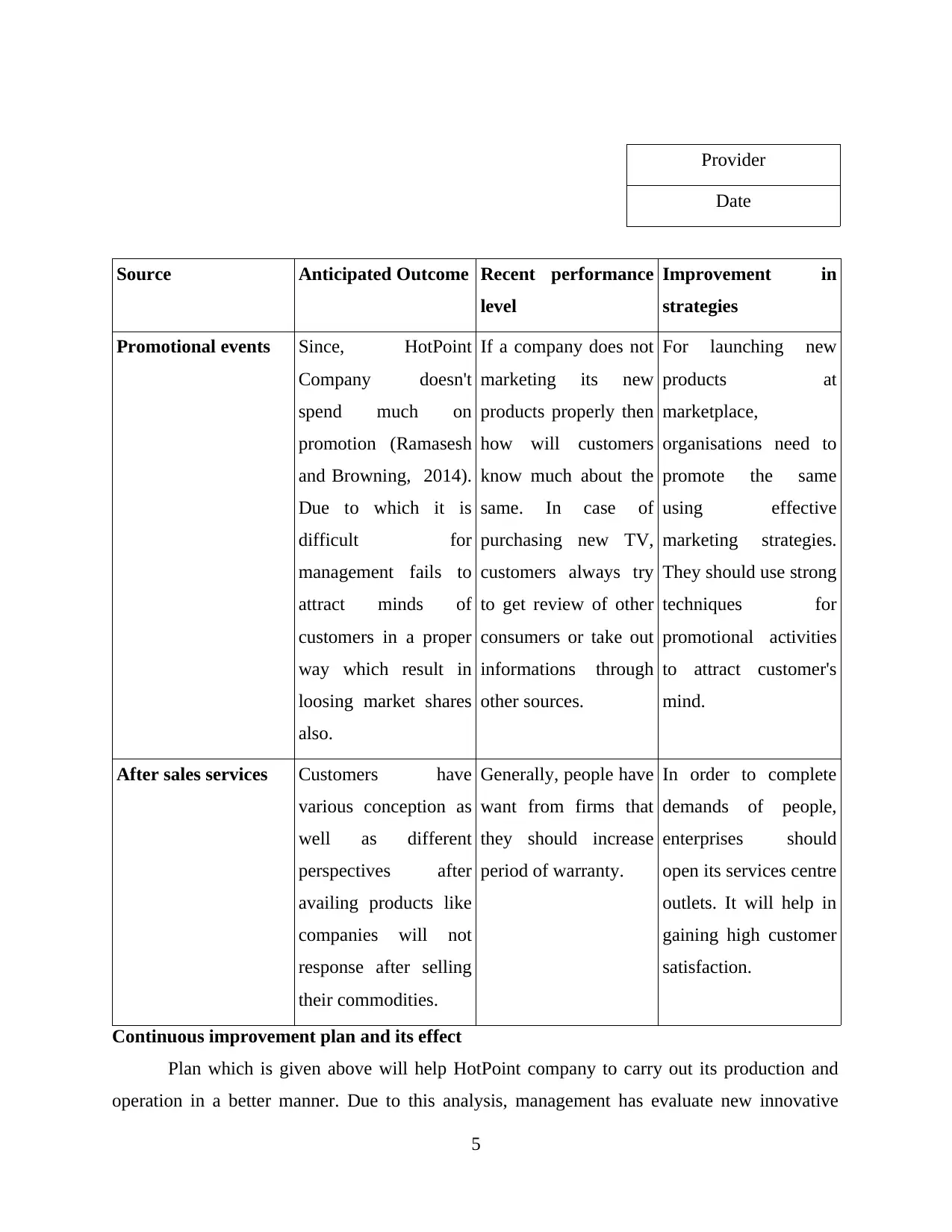
Provider
Date
Source Anticipated Outcome Recent performance
level
Improvement in
strategies
Promotional events Since, HotPoint
Company doesn't
spend much on
promotion (Ramasesh
and Browning, 2014).
Due to which it is
difficult for
management fails to
attract minds of
customers in a proper
way which result in
loosing market shares
also.
If a company does not
marketing its new
products properly then
how will customers
know much about the
same. In case of
purchasing new TV,
customers always try
to get review of other
consumers or take out
informations through
other sources.
For launching new
products at
marketplace,
organisations need to
promote the same
using effective
marketing strategies.
They should use strong
techniques for
promotional activities
to attract customer's
mind.
After sales services Customers have
various conception as
well as different
perspectives after
availing products like
companies will not
response after selling
their commodities.
Generally, people have
want from firms that
they should increase
period of warranty.
In order to complete
demands of people,
enterprises should
open its services centre
outlets. It will help in
gaining high customer
satisfaction.
Continuous improvement plan and its effect
Plan which is given above will help HotPoint company to carry out its production and
operation in a better manner. Due to this analysis, management has evaluate new innovative
5
Date
Source Anticipated Outcome Recent performance
level
Improvement in
strategies
Promotional events Since, HotPoint
Company doesn't
spend much on
promotion (Ramasesh
and Browning, 2014).
Due to which it is
difficult for
management fails to
attract minds of
customers in a proper
way which result in
loosing market shares
also.
If a company does not
marketing its new
products properly then
how will customers
know much about the
same. In case of
purchasing new TV,
customers always try
to get review of other
consumers or take out
informations through
other sources.
For launching new
products at
marketplace,
organisations need to
promote the same
using effective
marketing strategies.
They should use strong
techniques for
promotional activities
to attract customer's
mind.
After sales services Customers have
various conception as
well as different
perspectives after
availing products like
companies will not
response after selling
their commodities.
Generally, people have
want from firms that
they should increase
period of warranty.
In order to complete
demands of people,
enterprises should
open its services centre
outlets. It will help in
gaining high customer
satisfaction.
Continuous improvement plan and its effect
Plan which is given above will help HotPoint company to carry out its production and
operation in a better manner. Due to this analysis, management has evaluate new innovative
5
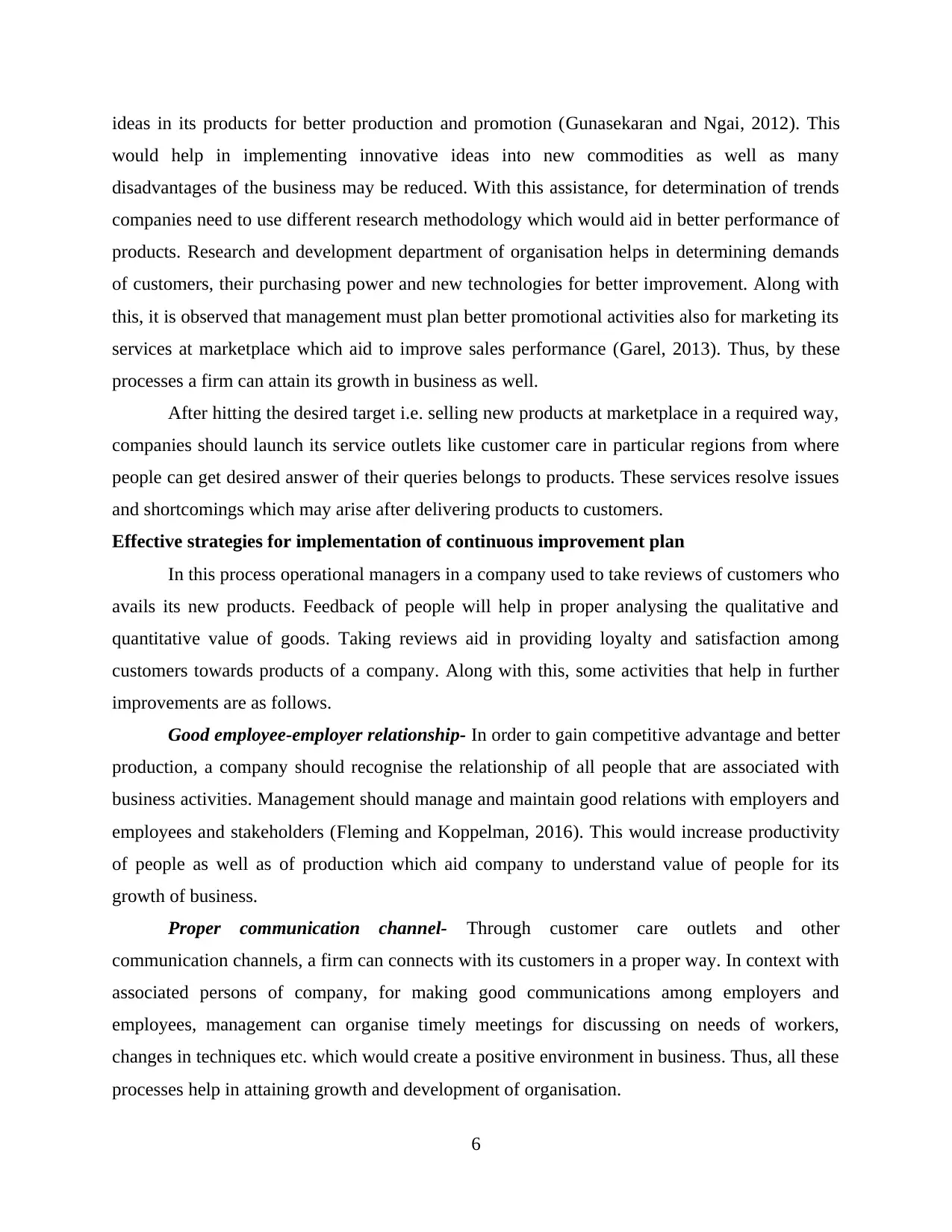
ideas in its products for better production and promotion (Gunasekaran and Ngai, 2012). This
would help in implementing innovative ideas into new commodities as well as many
disadvantages of the business may be reduced. With this assistance, for determination of trends
companies need to use different research methodology which would aid in better performance of
products. Research and development department of organisation helps in determining demands
of customers, their purchasing power and new technologies for better improvement. Along with
this, it is observed that management must plan better promotional activities also for marketing its
services at marketplace which aid to improve sales performance (Garel, 2013). Thus, by these
processes a firm can attain its growth in business as well.
After hitting the desired target i.e. selling new products at marketplace in a required way,
companies should launch its service outlets like customer care in particular regions from where
people can get desired answer of their queries belongs to products. These services resolve issues
and shortcomings which may arise after delivering products to customers.
Effective strategies for implementation of continuous improvement plan
In this process operational managers in a company used to take reviews of customers who
avails its new products. Feedback of people will help in proper analysing the qualitative and
quantitative value of goods. Taking reviews aid in providing loyalty and satisfaction among
customers towards products of a company. Along with this, some activities that help in further
improvements are as follows.
Good employee-employer relationship- In order to gain competitive advantage and better
production, a company should recognise the relationship of all people that are associated with
business activities. Management should manage and maintain good relations with employers and
employees and stakeholders (Fleming and Koppelman, 2016). This would increase productivity
of people as well as of production which aid company to understand value of people for its
growth of business.
Proper communication channel- Through customer care outlets and other
communication channels, a firm can connects with its customers in a proper way. In context with
associated persons of company, for making good communications among employers and
employees, management can organise timely meetings for discussing on needs of workers,
changes in techniques etc. which would create a positive environment in business. Thus, all these
processes help in attaining growth and development of organisation.
6
would help in implementing innovative ideas into new commodities as well as many
disadvantages of the business may be reduced. With this assistance, for determination of trends
companies need to use different research methodology which would aid in better performance of
products. Research and development department of organisation helps in determining demands
of customers, their purchasing power and new technologies for better improvement. Along with
this, it is observed that management must plan better promotional activities also for marketing its
services at marketplace which aid to improve sales performance (Garel, 2013). Thus, by these
processes a firm can attain its growth in business as well.
After hitting the desired target i.e. selling new products at marketplace in a required way,
companies should launch its service outlets like customer care in particular regions from where
people can get desired answer of their queries belongs to products. These services resolve issues
and shortcomings which may arise after delivering products to customers.
Effective strategies for implementation of continuous improvement plan
In this process operational managers in a company used to take reviews of customers who
avails its new products. Feedback of people will help in proper analysing the qualitative and
quantitative value of goods. Taking reviews aid in providing loyalty and satisfaction among
customers towards products of a company. Along with this, some activities that help in further
improvements are as follows.
Good employee-employer relationship- In order to gain competitive advantage and better
production, a company should recognise the relationship of all people that are associated with
business activities. Management should manage and maintain good relations with employers and
employees and stakeholders (Fleming and Koppelman, 2016). This would increase productivity
of people as well as of production which aid company to understand value of people for its
growth of business.
Proper communication channel- Through customer care outlets and other
communication channels, a firm can connects with its customers in a proper way. In context with
associated persons of company, for making good communications among employers and
employees, management can organise timely meetings for discussing on needs of workers,
changes in techniques etc. which would create a positive environment in business. Thus, all these
processes help in attaining growth and development of organisation.
6
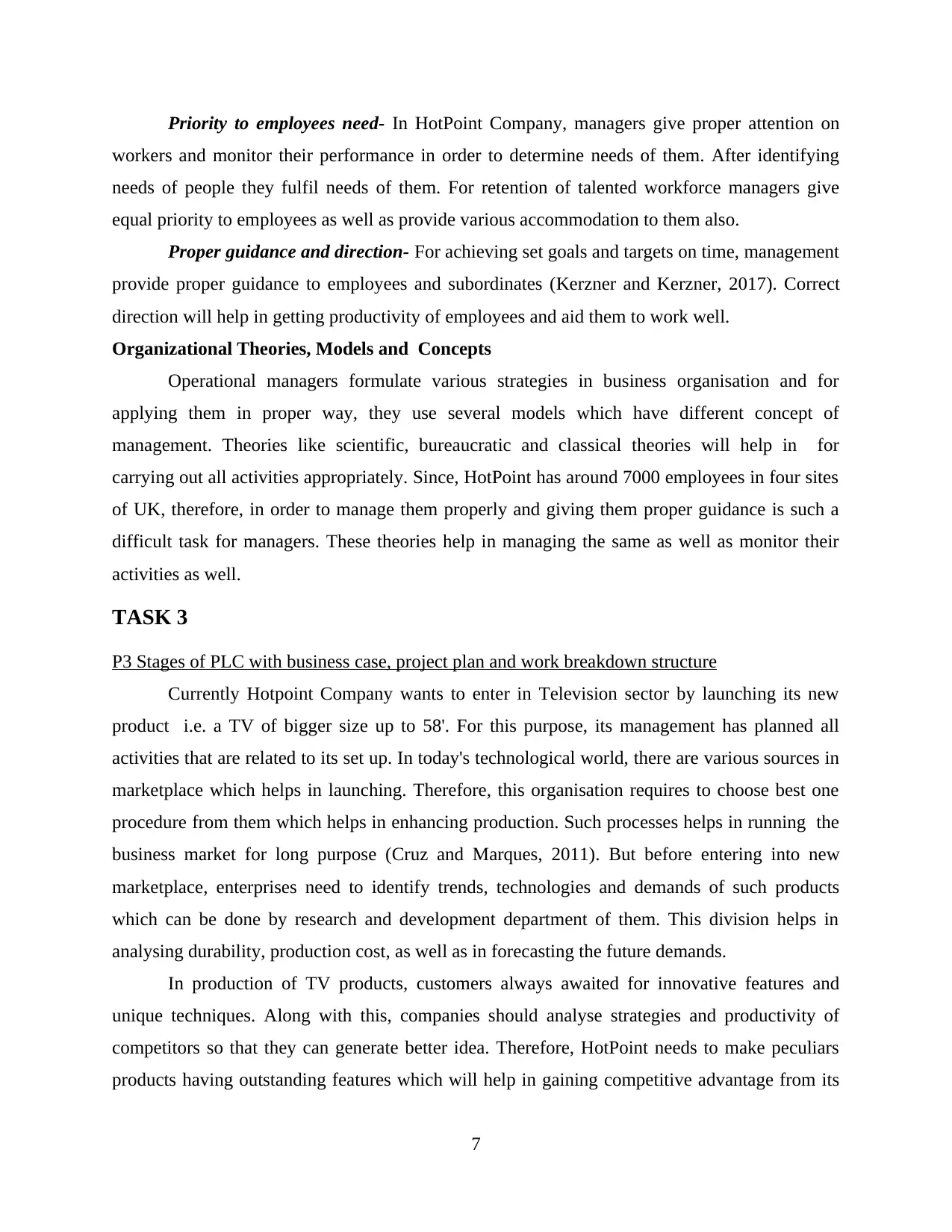
Priority to employees need- In HotPoint Company, managers give proper attention on
workers and monitor their performance in order to determine needs of them. After identifying
needs of people they fulfil needs of them. For retention of talented workforce managers give
equal priority to employees as well as provide various accommodation to them also.
Proper guidance and direction- For achieving set goals and targets on time, management
provide proper guidance to employees and subordinates (Kerzner and Kerzner, 2017). Correct
direction will help in getting productivity of employees and aid them to work well.
Organizational Theories, Models and Concepts
Operational managers formulate various strategies in business organisation and for
applying them in proper way, they use several models which have different concept of
management. Theories like scientific, bureaucratic and classical theories will help in for
carrying out all activities appropriately. Since, HotPoint has around 7000 employees in four sites
of UK, therefore, in order to manage them properly and giving them proper guidance is such a
difficult task for managers. These theories help in managing the same as well as monitor their
activities as well.
TASK 3
P3 Stages of PLC with business case, project plan and work breakdown structure
Currently Hotpoint Company wants to enter in Television sector by launching its new
product i.e. a TV of bigger size up to 58'. For this purpose, its management has planned all
activities that are related to its set up. In today's technological world, there are various sources in
marketplace which helps in launching. Therefore, this organisation requires to choose best one
procedure from them which helps in enhancing production. Such processes helps in running the
business market for long purpose (Cruz and Marques, 2011). But before entering into new
marketplace, enterprises need to identify trends, technologies and demands of such products
which can be done by research and development department of them. This division helps in
analysing durability, production cost, as well as in forecasting the future demands.
In production of TV products, customers always awaited for innovative features and
unique techniques. Along with this, companies should analyse strategies and productivity of
competitors so that they can generate better idea. Therefore, HotPoint needs to make peculiars
products having outstanding features which will help in gaining competitive advantage from its
7
workers and monitor their performance in order to determine needs of them. After identifying
needs of people they fulfil needs of them. For retention of talented workforce managers give
equal priority to employees as well as provide various accommodation to them also.
Proper guidance and direction- For achieving set goals and targets on time, management
provide proper guidance to employees and subordinates (Kerzner and Kerzner, 2017). Correct
direction will help in getting productivity of employees and aid them to work well.
Organizational Theories, Models and Concepts
Operational managers formulate various strategies in business organisation and for
applying them in proper way, they use several models which have different concept of
management. Theories like scientific, bureaucratic and classical theories will help in for
carrying out all activities appropriately. Since, HotPoint has around 7000 employees in four sites
of UK, therefore, in order to manage them properly and giving them proper guidance is such a
difficult task for managers. These theories help in managing the same as well as monitor their
activities as well.
TASK 3
P3 Stages of PLC with business case, project plan and work breakdown structure
Currently Hotpoint Company wants to enter in Television sector by launching its new
product i.e. a TV of bigger size up to 58'. For this purpose, its management has planned all
activities that are related to its set up. In today's technological world, there are various sources in
marketplace which helps in launching. Therefore, this organisation requires to choose best one
procedure from them which helps in enhancing production. Such processes helps in running the
business market for long purpose (Cruz and Marques, 2011). But before entering into new
marketplace, enterprises need to identify trends, technologies and demands of such products
which can be done by research and development department of them. This division helps in
analysing durability, production cost, as well as in forecasting the future demands.
In production of TV products, customers always awaited for innovative features and
unique techniques. Along with this, companies should analyse strategies and productivity of
competitors so that they can generate better idea. Therefore, HotPoint needs to make peculiars
products having outstanding features which will help in gaining competitive advantage from its
7
Secure Best Marks with AI Grader
Need help grading? Try our AI Grader for instant feedback on your assignments.
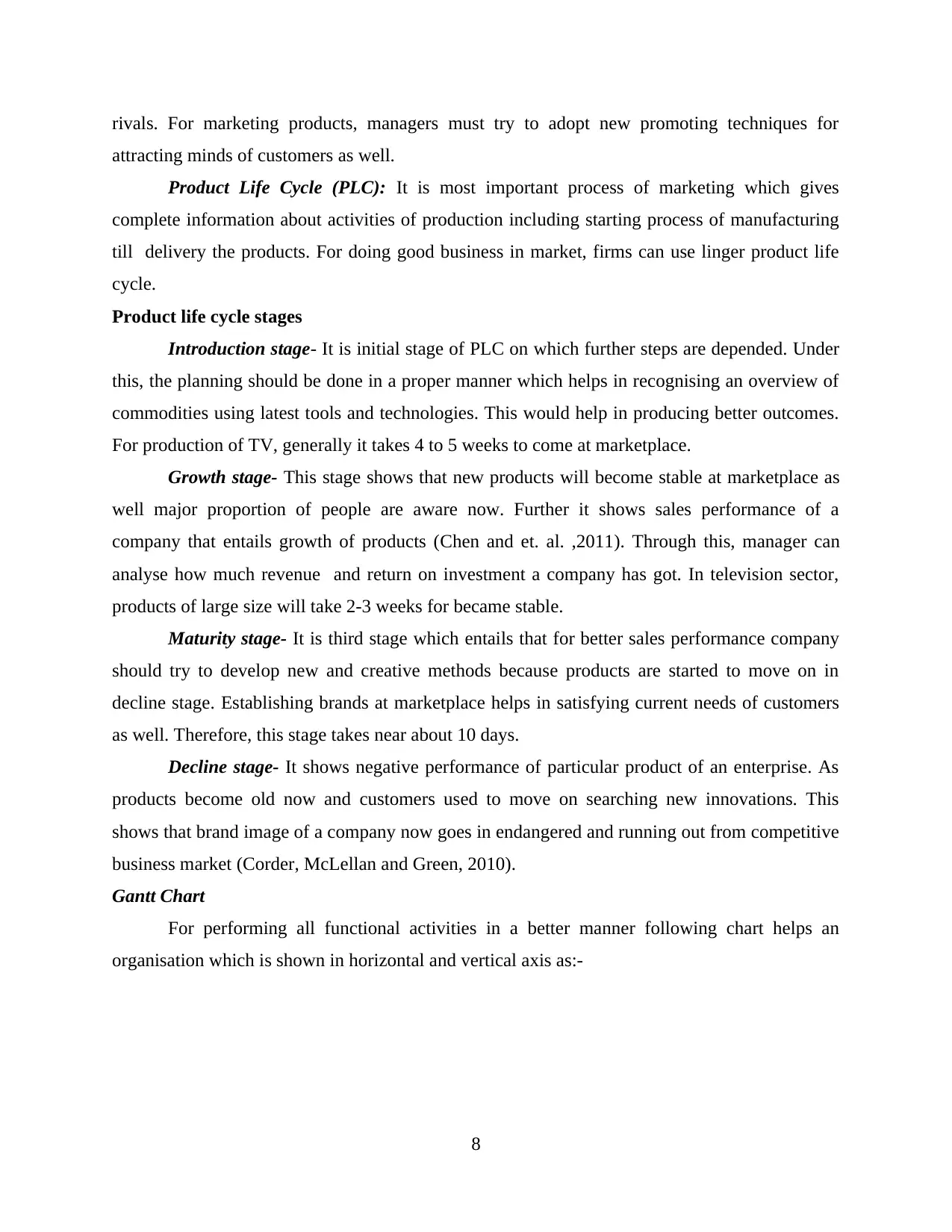
rivals. For marketing products, managers must try to adopt new promoting techniques for
attracting minds of customers as well.
Product Life Cycle (PLC): It is most important process of marketing which gives
complete information about activities of production including starting process of manufacturing
till delivery the products. For doing good business in market, firms can use linger product life
cycle.
Product life cycle stages
Introduction stage- It is initial stage of PLC on which further steps are depended. Under
this, the planning should be done in a proper manner which helps in recognising an overview of
commodities using latest tools and technologies. This would help in producing better outcomes.
For production of TV, generally it takes 4 to 5 weeks to come at marketplace.
Growth stage- This stage shows that new products will become stable at marketplace as
well major proportion of people are aware now. Further it shows sales performance of a
company that entails growth of products (Chen and et. al. ,2011). Through this, manager can
analyse how much revenue and return on investment a company has got. In television sector,
products of large size will take 2-3 weeks for became stable.
Maturity stage- It is third stage which entails that for better sales performance company
should try to develop new and creative methods because products are started to move on in
decline stage. Establishing brands at marketplace helps in satisfying current needs of customers
as well. Therefore, this stage takes near about 10 days.
Decline stage- It shows negative performance of particular product of an enterprise. As
products become old now and customers used to move on searching new innovations. This
shows that brand image of a company now goes in endangered and running out from competitive
business market (Corder, McLellan and Green, 2010).
Gantt Chart
For performing all functional activities in a better manner following chart helps an
organisation which is shown in horizontal and vertical axis as:-
8
attracting minds of customers as well.
Product Life Cycle (PLC): It is most important process of marketing which gives
complete information about activities of production including starting process of manufacturing
till delivery the products. For doing good business in market, firms can use linger product life
cycle.
Product life cycle stages
Introduction stage- It is initial stage of PLC on which further steps are depended. Under
this, the planning should be done in a proper manner which helps in recognising an overview of
commodities using latest tools and technologies. This would help in producing better outcomes.
For production of TV, generally it takes 4 to 5 weeks to come at marketplace.
Growth stage- This stage shows that new products will become stable at marketplace as
well major proportion of people are aware now. Further it shows sales performance of a
company that entails growth of products (Chen and et. al. ,2011). Through this, manager can
analyse how much revenue and return on investment a company has got. In television sector,
products of large size will take 2-3 weeks for became stable.
Maturity stage- It is third stage which entails that for better sales performance company
should try to develop new and creative methods because products are started to move on in
decline stage. Establishing brands at marketplace helps in satisfying current needs of customers
as well. Therefore, this stage takes near about 10 days.
Decline stage- It shows negative performance of particular product of an enterprise. As
products become old now and customers used to move on searching new innovations. This
shows that brand image of a company now goes in endangered and running out from competitive
business market (Corder, McLellan and Green, 2010).
Gantt Chart
For performing all functional activities in a better manner following chart helps an
organisation which is shown in horizontal and vertical axis as:-
8
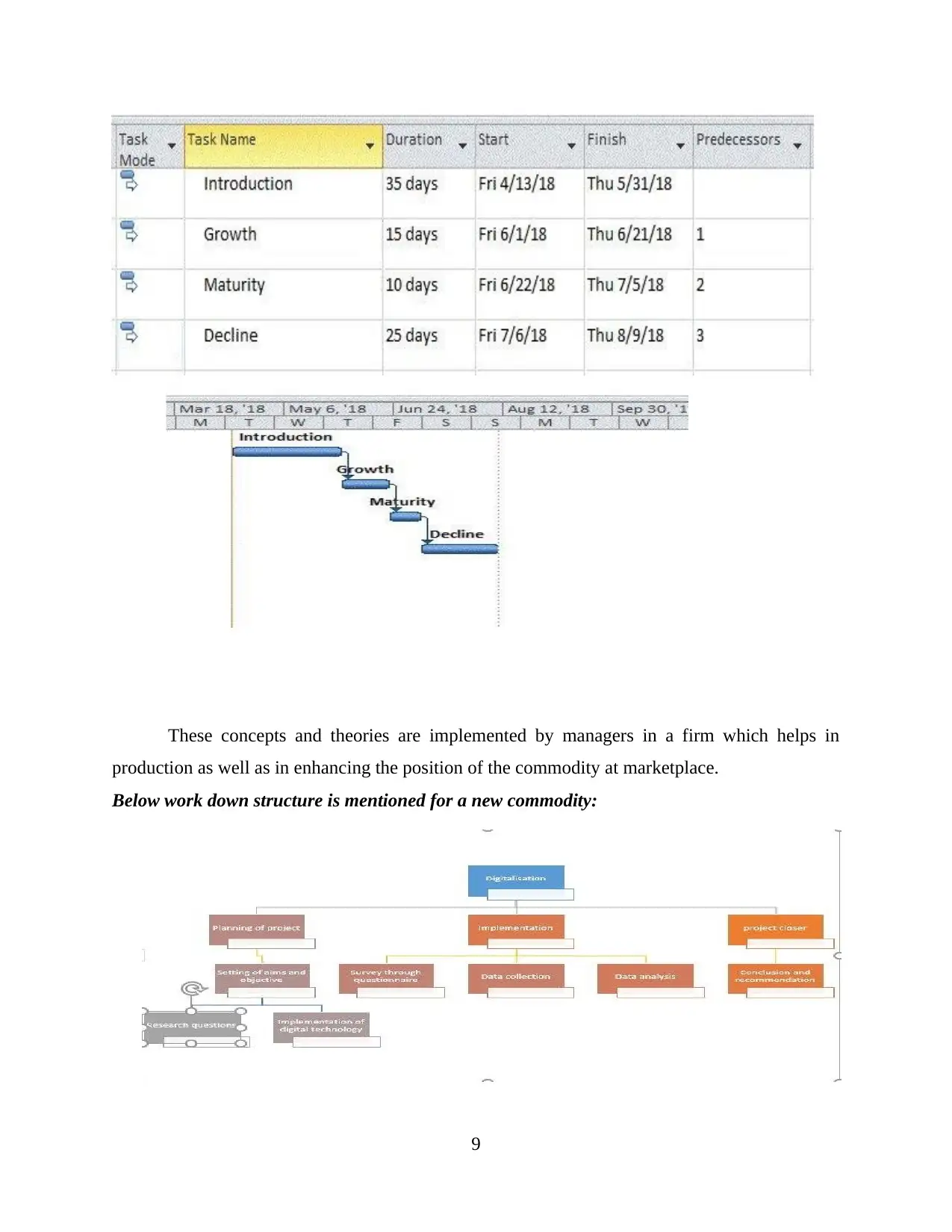
These concepts and theories are implemented by managers in a firm which helps in
production as well as in enhancing the position of the commodity at marketplace.
Below work down structure is mentioned for a new commodity:
9
production as well as in enhancing the position of the commodity at marketplace.
Below work down structure is mentioned for a new commodity:
9
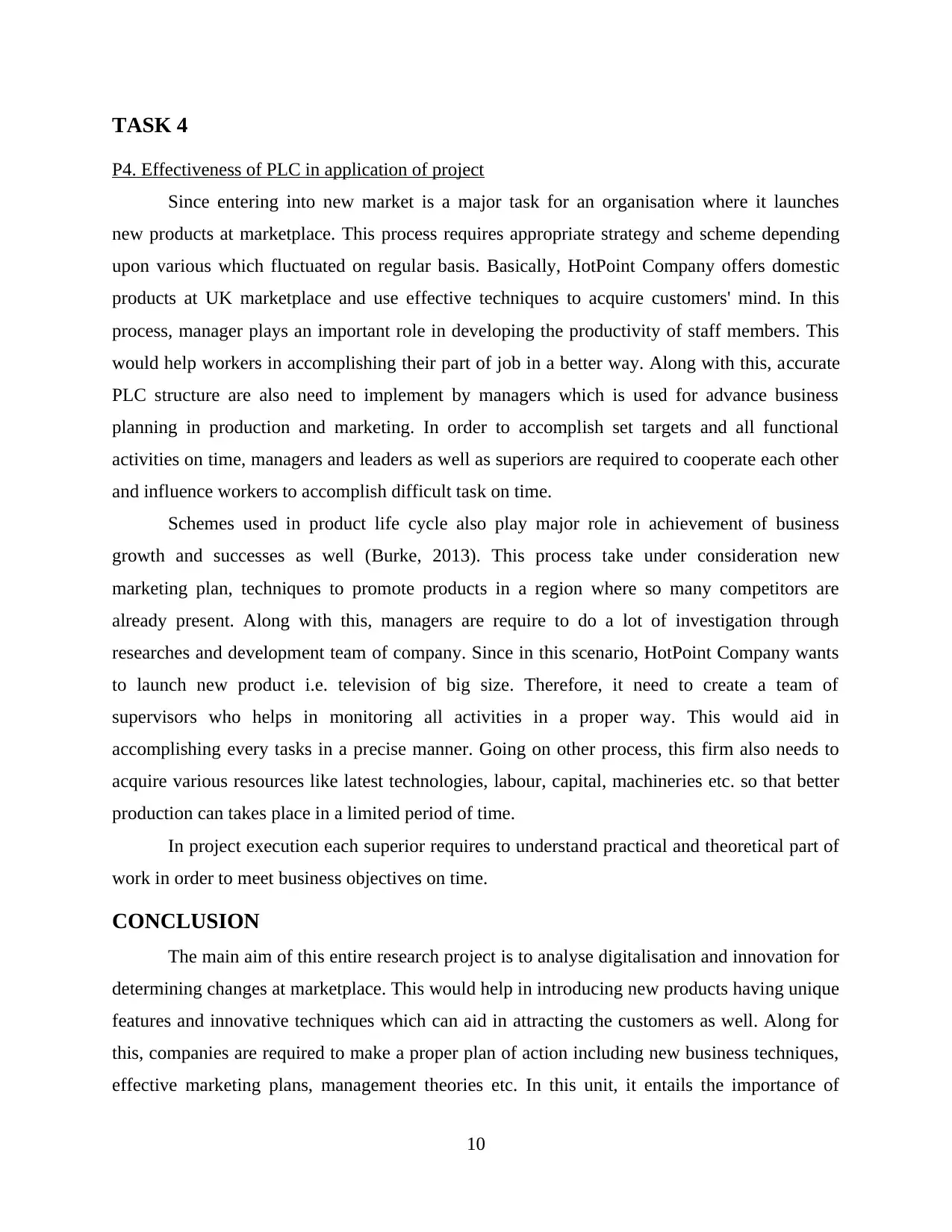
TASK 4
P4. Effectiveness of PLC in application of project
Since entering into new market is a major task for an organisation where it launches
new products at marketplace. This process requires appropriate strategy and scheme depending
upon various which fluctuated on regular basis. Basically, HotPoint Company offers domestic
products at UK marketplace and use effective techniques to acquire customers' mind. In this
process, manager plays an important role in developing the productivity of staff members. This
would help workers in accomplishing their part of job in a better way. Along with this, accurate
PLC structure are also need to implement by managers which is used for advance business
planning in production and marketing. In order to accomplish set targets and all functional
activities on time, managers and leaders as well as superiors are required to cooperate each other
and influence workers to accomplish difficult task on time.
Schemes used in product life cycle also play major role in achievement of business
growth and successes as well (Burke, 2013). This process take under consideration new
marketing plan, techniques to promote products in a region where so many competitors are
already present. Along with this, managers are require to do a lot of investigation through
researches and development team of company. Since in this scenario, HotPoint Company wants
to launch new product i.e. television of big size. Therefore, it need to create a team of
supervisors who helps in monitoring all activities in a proper way. This would aid in
accomplishing every tasks in a precise manner. Going on other process, this firm also needs to
acquire various resources like latest technologies, labour, capital, machineries etc. so that better
production can takes place in a limited period of time.
In project execution each superior requires to understand practical and theoretical part of
work in order to meet business objectives on time.
CONCLUSION
The main aim of this entire research project is to analyse digitalisation and innovation for
determining changes at marketplace. This would help in introducing new products having unique
features and innovative techniques which can aid in attracting the customers as well. Along for
this, companies are required to make a proper plan of action including new business techniques,
effective marketing plans, management theories etc. In this unit, it entails the importance of
10
P4. Effectiveness of PLC in application of project
Since entering into new market is a major task for an organisation where it launches
new products at marketplace. This process requires appropriate strategy and scheme depending
upon various which fluctuated on regular basis. Basically, HotPoint Company offers domestic
products at UK marketplace and use effective techniques to acquire customers' mind. In this
process, manager plays an important role in developing the productivity of staff members. This
would help workers in accomplishing their part of job in a better way. Along with this, accurate
PLC structure are also need to implement by managers which is used for advance business
planning in production and marketing. In order to accomplish set targets and all functional
activities on time, managers and leaders as well as superiors are required to cooperate each other
and influence workers to accomplish difficult task on time.
Schemes used in product life cycle also play major role in achievement of business
growth and successes as well (Burke, 2013). This process take under consideration new
marketing plan, techniques to promote products in a region where so many competitors are
already present. Along with this, managers are require to do a lot of investigation through
researches and development team of company. Since in this scenario, HotPoint Company wants
to launch new product i.e. television of big size. Therefore, it need to create a team of
supervisors who helps in monitoring all activities in a proper way. This would aid in
accomplishing every tasks in a precise manner. Going on other process, this firm also needs to
acquire various resources like latest technologies, labour, capital, machineries etc. so that better
production can takes place in a limited period of time.
In project execution each superior requires to understand practical and theoretical part of
work in order to meet business objectives on time.
CONCLUSION
The main aim of this entire research project is to analyse digitalisation and innovation for
determining changes at marketplace. This would help in introducing new products having unique
features and innovative techniques which can aid in attracting the customers as well. Along for
this, companies are required to make a proper plan of action including new business techniques,
effective marketing plans, management theories etc. In this unit, it entails the importance of
10
Paraphrase This Document
Need a fresh take? Get an instant paraphrase of this document with our AI Paraphraser
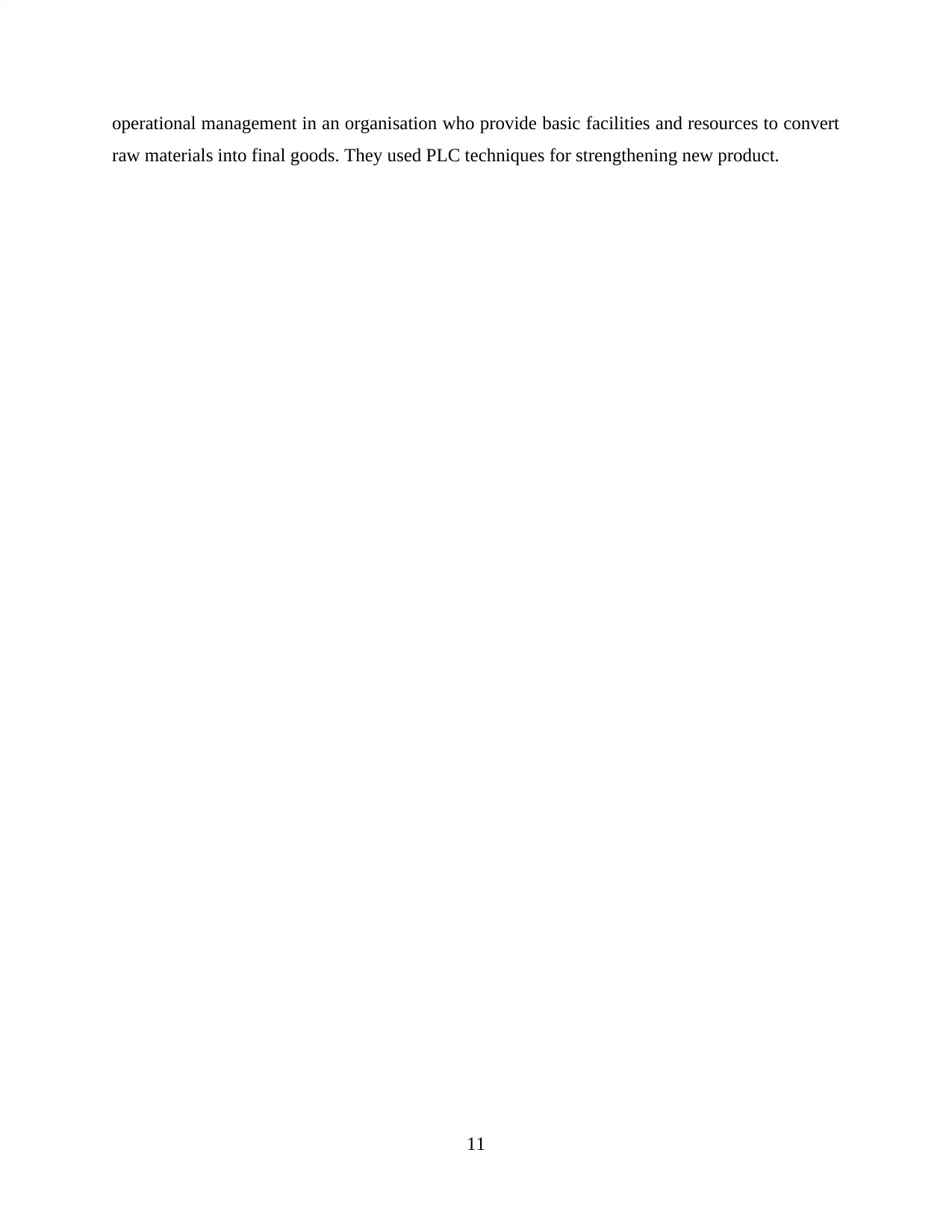
operational management in an organisation who provide basic facilities and resources to convert
raw materials into final goods. They used PLC techniques for strengthening new product.
11
raw materials into final goods. They used PLC techniques for strengthening new product.
11
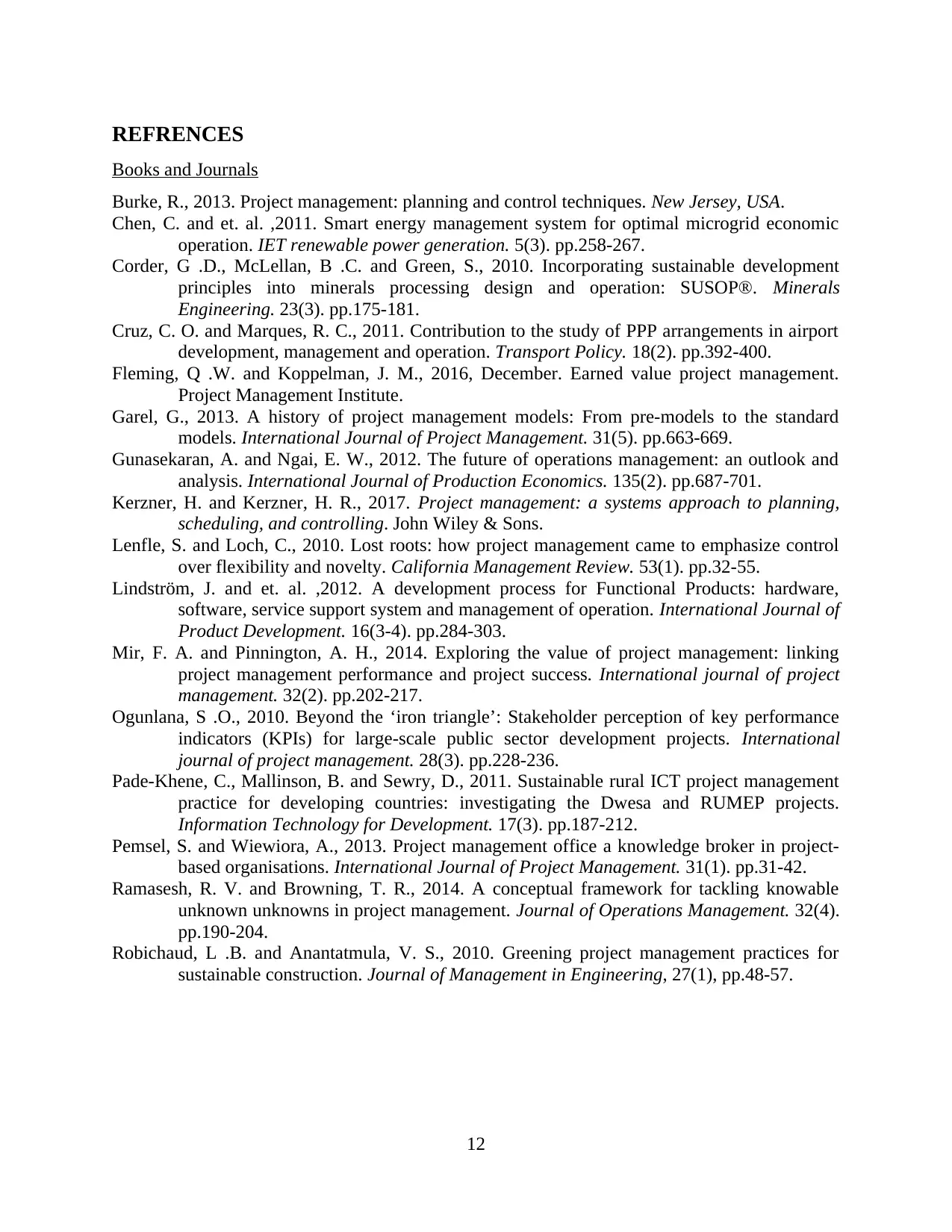
REFRENCES
Books and Journals
Burke, R., 2013. Project management: planning and control techniques. New Jersey, USA.
Chen, C. and et. al. ,2011. Smart energy management system for optimal microgrid economic
operation. IET renewable power generation. 5(3). pp.258-267.
Corder, G .D., McLellan, B .C. and Green, S., 2010. Incorporating sustainable development
principles into minerals processing design and operation: SUSOP®. Minerals
Engineering. 23(3). pp.175-181.
Cruz, C. O. and Marques, R. C., 2011. Contribution to the study of PPP arrangements in airport
development, management and operation. Transport Policy. 18(2). pp.392-400.
Fleming, Q .W. and Koppelman, J. M., 2016, December. Earned value project management.
Project Management Institute.
Garel, G., 2013. A history of project management models: From pre-models to the standard
models. International Journal of Project Management. 31(5). pp.663-669.
Gunasekaran, A. and Ngai, E. W., 2012. The future of operations management: an outlook and
analysis. International Journal of Production Economics. 135(2). pp.687-701.
Kerzner, H. and Kerzner, H. R., 2017. Project management: a systems approach to planning,
scheduling, and controlling. John Wiley & Sons.
Lenfle, S. and Loch, C., 2010. Lost roots: how project management came to emphasize control
over flexibility and novelty. California Management Review. 53(1). pp.32-55.
Lindström, J. and et. al. ,2012. A development process for Functional Products: hardware,
software, service support system and management of operation. International Journal of
Product Development. 16(3-4). pp.284-303.
Mir, F. A. and Pinnington, A. H., 2014. Exploring the value of project management: linking
project management performance and project success. International journal of project
management. 32(2). pp.202-217.
Ogunlana, S .O., 2010. Beyond the ‘iron triangle’: Stakeholder perception of key performance
indicators (KPIs) for large-scale public sector development projects. International
journal of project management. 28(3). pp.228-236.
Pade-Khene, C., Mallinson, B. and Sewry, D., 2011. Sustainable rural ICT project management
practice for developing countries: investigating the Dwesa and RUMEP projects.
Information Technology for Development. 17(3). pp.187-212.
Pemsel, S. and Wiewiora, A., 2013. Project management office a knowledge broker in project-
based organisations. International Journal of Project Management. 31(1). pp.31-42.
Ramasesh, R. V. and Browning, T. R., 2014. A conceptual framework for tackling knowable
unknown unknowns in project management. Journal of Operations Management. 32(4).
pp.190-204.
Robichaud, L .B. and Anantatmula, V. S., 2010. Greening project management practices for
sustainable construction. Journal of Management in Engineering, 27(1), pp.48-57.
12
Books and Journals
Burke, R., 2013. Project management: planning and control techniques. New Jersey, USA.
Chen, C. and et. al. ,2011. Smart energy management system for optimal microgrid economic
operation. IET renewable power generation. 5(3). pp.258-267.
Corder, G .D., McLellan, B .C. and Green, S., 2010. Incorporating sustainable development
principles into minerals processing design and operation: SUSOP®. Minerals
Engineering. 23(3). pp.175-181.
Cruz, C. O. and Marques, R. C., 2011. Contribution to the study of PPP arrangements in airport
development, management and operation. Transport Policy. 18(2). pp.392-400.
Fleming, Q .W. and Koppelman, J. M., 2016, December. Earned value project management.
Project Management Institute.
Garel, G., 2013. A history of project management models: From pre-models to the standard
models. International Journal of Project Management. 31(5). pp.663-669.
Gunasekaran, A. and Ngai, E. W., 2012. The future of operations management: an outlook and
analysis. International Journal of Production Economics. 135(2). pp.687-701.
Kerzner, H. and Kerzner, H. R., 2017. Project management: a systems approach to planning,
scheduling, and controlling. John Wiley & Sons.
Lenfle, S. and Loch, C., 2010. Lost roots: how project management came to emphasize control
over flexibility and novelty. California Management Review. 53(1). pp.32-55.
Lindström, J. and et. al. ,2012. A development process for Functional Products: hardware,
software, service support system and management of operation. International Journal of
Product Development. 16(3-4). pp.284-303.
Mir, F. A. and Pinnington, A. H., 2014. Exploring the value of project management: linking
project management performance and project success. International journal of project
management. 32(2). pp.202-217.
Ogunlana, S .O., 2010. Beyond the ‘iron triangle’: Stakeholder perception of key performance
indicators (KPIs) for large-scale public sector development projects. International
journal of project management. 28(3). pp.228-236.
Pade-Khene, C., Mallinson, B. and Sewry, D., 2011. Sustainable rural ICT project management
practice for developing countries: investigating the Dwesa and RUMEP projects.
Information Technology for Development. 17(3). pp.187-212.
Pemsel, S. and Wiewiora, A., 2013. Project management office a knowledge broker in project-
based organisations. International Journal of Project Management. 31(1). pp.31-42.
Ramasesh, R. V. and Browning, T. R., 2014. A conceptual framework for tackling knowable
unknown unknowns in project management. Journal of Operations Management. 32(4).
pp.190-204.
Robichaud, L .B. and Anantatmula, V. S., 2010. Greening project management practices for
sustainable construction. Journal of Management in Engineering, 27(1), pp.48-57.
12
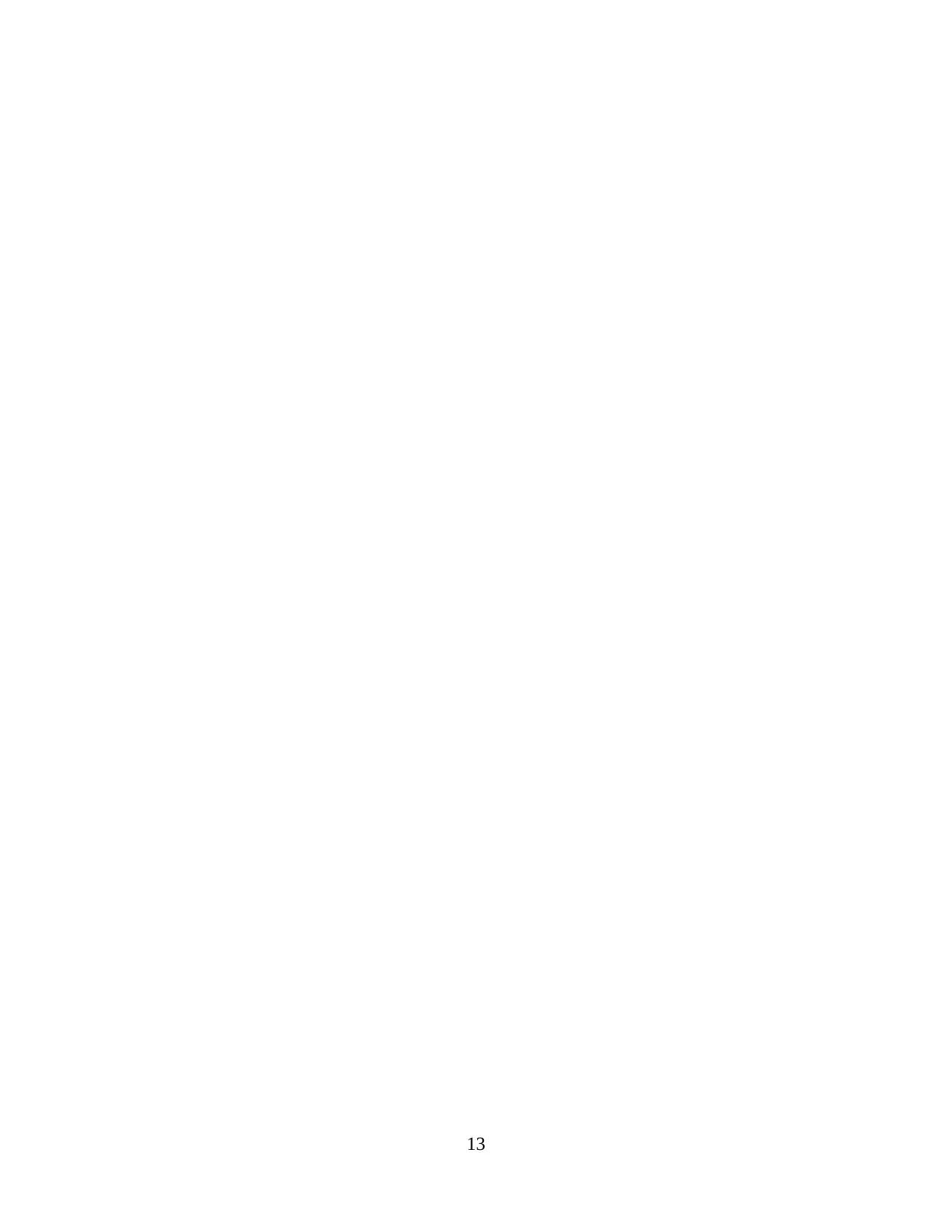
13
1 out of 16
Related Documents

Your All-in-One AI-Powered Toolkit for Academic Success.
+13062052269
info@desklib.com
Available 24*7 on WhatsApp / Email
Unlock your academic potential
© 2024 | Zucol Services PVT LTD | All rights reserved.