Improving Inventory Management at Beacon Lighting: A Report
VerifiedAdded on 2019/09/26
|11
|2604
|220
Report
AI Summary
This report examines the inventory management challenges faced by Beacon Lighting Group Limited, a leading lighting solutions company in Australia. The analysis identifies issues such as low inventory turnover, high storage costs, and obsolete inventory, which negatively impact profitability. The report proposes several solutions, including categorizing inventory using ABC analysis, implementing par levels, adopting the First-In, First-Out (FIFO) method, establishing key performance indicators (KPIs) for inventory, and optimizing the inventory turnover rate. The evaluation table assesses each solution based on investment, expected return, time, cost, potential risks, and success rates. The report concludes with a Gantt chart illustrating the implementation plan, emphasizing the importance of effective inventory management for sustainable growth and profit maximization. The suggested solutions are aimed at helping Beacon Lighting streamline operations, reduce costs, and improve customer satisfaction.

Running Head: Managerial Decision Making
MANAGERIAL DECISION MAKING
MANAGERIAL DECISION MAKING
Secure Best Marks with AI Grader
Need help grading? Try our AI Grader for instant feedback on your assignments.
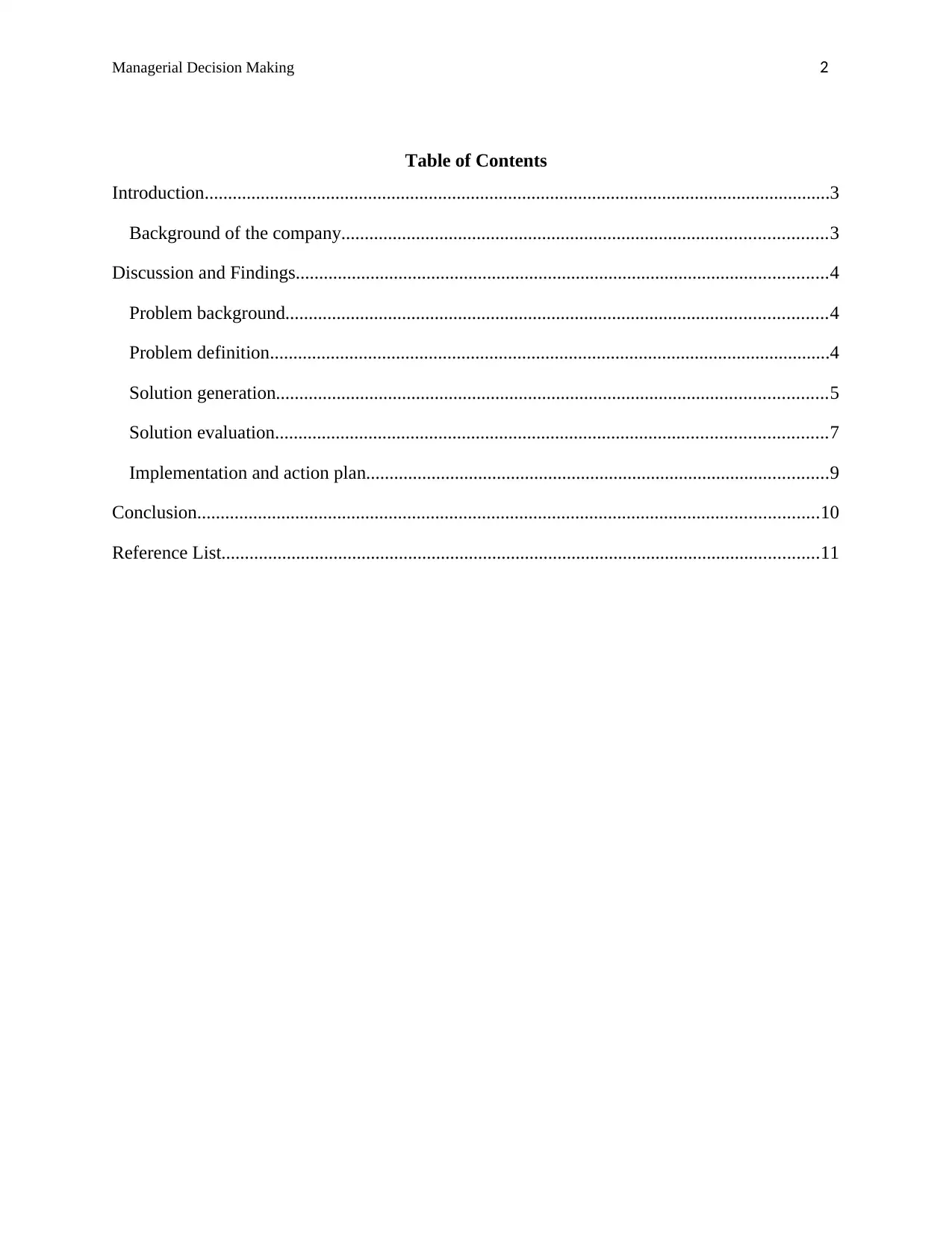
Managerial Decision Making 2
Table of Contents
Introduction......................................................................................................................................3
Background of the company........................................................................................................3
Discussion and Findings..................................................................................................................4
Problem background....................................................................................................................4
Problem definition........................................................................................................................4
Solution generation......................................................................................................................5
Solution evaluation......................................................................................................................7
Implementation and action plan...................................................................................................9
Conclusion.....................................................................................................................................10
Reference List................................................................................................................................11
Table of Contents
Introduction......................................................................................................................................3
Background of the company........................................................................................................3
Discussion and Findings..................................................................................................................4
Problem background....................................................................................................................4
Problem definition........................................................................................................................4
Solution generation......................................................................................................................5
Solution evaluation......................................................................................................................7
Implementation and action plan...................................................................................................9
Conclusion.....................................................................................................................................10
Reference List................................................................................................................................11
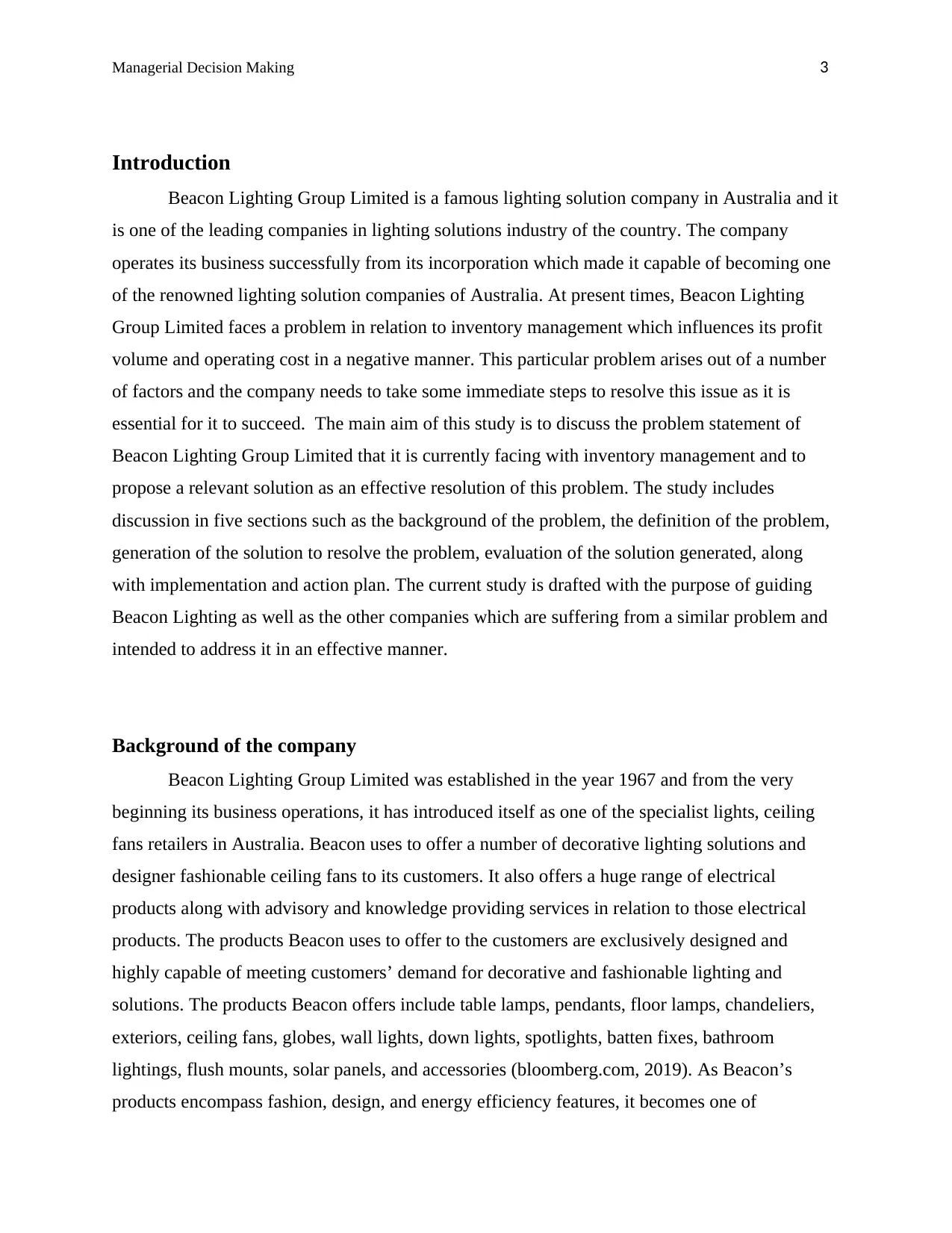
Managerial Decision Making 3
Introduction
Beacon Lighting Group Limited is a famous lighting solution company in Australia and it
is one of the leading companies in lighting solutions industry of the country. The company
operates its business successfully from its incorporation which made it capable of becoming one
of the renowned lighting solution companies of Australia. At present times, Beacon Lighting
Group Limited faces a problem in relation to inventory management which influences its profit
volume and operating cost in a negative manner. This particular problem arises out of a number
of factors and the company needs to take some immediate steps to resolve this issue as it is
essential for it to succeed. The main aim of this study is to discuss the problem statement of
Beacon Lighting Group Limited that it is currently facing with inventory management and to
propose a relevant solution as an effective resolution of this problem. The study includes
discussion in five sections such as the background of the problem, the definition of the problem,
generation of the solution to resolve the problem, evaluation of the solution generated, along
with implementation and action plan. The current study is drafted with the purpose of guiding
Beacon Lighting as well as the other companies which are suffering from a similar problem and
intended to address it in an effective manner.
Background of the company
Beacon Lighting Group Limited was established in the year 1967 and from the very
beginning its business operations, it has introduced itself as one of the specialist lights, ceiling
fans retailers in Australia. Beacon uses to offer a number of decorative lighting solutions and
designer fashionable ceiling fans to its customers. It also offers a huge range of electrical
products along with advisory and knowledge providing services in relation to those electrical
products. The products Beacon uses to offer to the customers are exclusively designed and
highly capable of meeting customers’ demand for decorative and fashionable lighting and
solutions. The products Beacon offers include table lamps, pendants, floor lamps, chandeliers,
exteriors, ceiling fans, globes, wall lights, down lights, spotlights, batten fixes, bathroom
lightings, flush mounts, solar panels, and accessories (bloomberg.com, 2019). As Beacon’s
products encompass fashion, design, and energy efficiency features, it becomes one of
Introduction
Beacon Lighting Group Limited is a famous lighting solution company in Australia and it
is one of the leading companies in lighting solutions industry of the country. The company
operates its business successfully from its incorporation which made it capable of becoming one
of the renowned lighting solution companies of Australia. At present times, Beacon Lighting
Group Limited faces a problem in relation to inventory management which influences its profit
volume and operating cost in a negative manner. This particular problem arises out of a number
of factors and the company needs to take some immediate steps to resolve this issue as it is
essential for it to succeed. The main aim of this study is to discuss the problem statement of
Beacon Lighting Group Limited that it is currently facing with inventory management and to
propose a relevant solution as an effective resolution of this problem. The study includes
discussion in five sections such as the background of the problem, the definition of the problem,
generation of the solution to resolve the problem, evaluation of the solution generated, along
with implementation and action plan. The current study is drafted with the purpose of guiding
Beacon Lighting as well as the other companies which are suffering from a similar problem and
intended to address it in an effective manner.
Background of the company
Beacon Lighting Group Limited was established in the year 1967 and from the very
beginning its business operations, it has introduced itself as one of the specialist lights, ceiling
fans retailers in Australia. Beacon uses to offer a number of decorative lighting solutions and
designer fashionable ceiling fans to its customers. It also offers a huge range of electrical
products along with advisory and knowledge providing services in relation to those electrical
products. The products Beacon uses to offer to the customers are exclusively designed and
highly capable of meeting customers’ demand for decorative and fashionable lighting and
solutions. The products Beacon offers include table lamps, pendants, floor lamps, chandeliers,
exteriors, ceiling fans, globes, wall lights, down lights, spotlights, batten fixes, bathroom
lightings, flush mounts, solar panels, and accessories (bloomberg.com, 2019). As Beacon’s
products encompass fashion, design, and energy efficiency features, it becomes one of

Managerial Decision Making 4
Australia's favourite lighting solution companies. Beacon is aimed to expand its business in the
national and international market by improving the customer's environment. Beacon Lighting is
committed in order to provide environmentally friendly and fashionable products to the
customers with expertise delivery system and unparalleled service (beaconlightinggroup.com.au,
2019).
Discussion and Findings
Problem background
Management of inventory is one of the most crucial tasks every manufacturing and
retailing company needs to concentrate. Poor inventory management often leads companies to
face frequent stockouts, blockage of cash, and wastage of raw materials as well as finished
products due to their reduced effectiveness and usefulness and more. Lack of proper strategies
and practices in order to manage inventory increases the business cost. At Beacon Lighting
Group Limited, the improper inventory management practices led it to face a number of
problems associated with low inventory turnover rate, increasing the cost of storage, imbalanced
lead times, and a large amount of backdated or obsolete inventory. Beacon Lighting's less focus
on its inventory management will affect its severely in long-run which will accordingly lead the
company to lose customers and reduction in profitability (Lwiki et al. 2013). During the past few
years, Beacon Lighting is facing this issue and it makes the company invest more in channeling
inventory. Ineffective inventory management starts with improper analysis and inventory
handling strategy. The lack of thorough analysis and measurement of inventory led Beacon Light
to face problems related to poor inventory management. Due to the lack of an inventory
management system, Beacon uses to face a lot of hindrances while providing optimum customer
satisfactory products and related services.
Problem definition
The problem Beacon Lighting Group Limited of Australia currently facing is inventory
management. Inventory management is an element of a company’s supply chain management.
The process of inventory management uses to supervise the movement of finished goods from
Australia's favourite lighting solution companies. Beacon is aimed to expand its business in the
national and international market by improving the customer's environment. Beacon Lighting is
committed in order to provide environmentally friendly and fashionable products to the
customers with expertise delivery system and unparalleled service (beaconlightinggroup.com.au,
2019).
Discussion and Findings
Problem background
Management of inventory is one of the most crucial tasks every manufacturing and
retailing company needs to concentrate. Poor inventory management often leads companies to
face frequent stockouts, blockage of cash, and wastage of raw materials as well as finished
products due to their reduced effectiveness and usefulness and more. Lack of proper strategies
and practices in order to manage inventory increases the business cost. At Beacon Lighting
Group Limited, the improper inventory management practices led it to face a number of
problems associated with low inventory turnover rate, increasing the cost of storage, imbalanced
lead times, and a large amount of backdated or obsolete inventory. Beacon Lighting's less focus
on its inventory management will affect its severely in long-run which will accordingly lead the
company to lose customers and reduction in profitability (Lwiki et al. 2013). During the past few
years, Beacon Lighting is facing this issue and it makes the company invest more in channeling
inventory. Ineffective inventory management starts with improper analysis and inventory
handling strategy. The lack of thorough analysis and measurement of inventory led Beacon Light
to face problems related to poor inventory management. Due to the lack of an inventory
management system, Beacon uses to face a lot of hindrances while providing optimum customer
satisfactory products and related services.
Problem definition
The problem Beacon Lighting Group Limited of Australia currently facing is inventory
management. Inventory management is an element of a company’s supply chain management.
The process of inventory management uses to supervise the movement of finished goods from
Secure Best Marks with AI Grader
Need help grading? Try our AI Grader for instant feedback on your assignments.

Managerial Decision Making 5
the manufacturers to their warehouses and after that, from these warehouses to the point of actual
sale (Chen & Simchi-Levi, 2012). For Beacon Lighting and other companies, the key function
associated to inventory management practices is to have a detailed and reliable record of every
newly finished or returned goods as it leaves for the point of sale or enters into a warehouse.
Since the past few years, Beacon Lighting is facing the problem of managing its inventory in a
proper manner which led it to face issues like blockage of cash, increasing wastes, and operating
cost. Due to the lack of inventory management days in inventory at Beacon is high in
comparison to its competitors. This problem makes Beacon to raise a huge amount of capital for
investing in the channel which is expected to impact the company’s long-term growth
(Krajewski, Ritzman & Malhotra, 2013).
Solution generation
In order to guide Beacon Lighting Group Limited in managing inventories and in
resolving the issues, it faces due to improper inventory management, the following solutions are
generated -
1. Categorising inventory by using ABC analysis
ABC analysis refers to a technique that could be used by Beacon Lighting for arranging
its inventory into a hierarchy by considering the most important items in its inventory to the least
important items in its inventory. The company needs to practice ABC analysis in the following
manner -
A-listed items: The highest priority, and best-selling stock which requires reordering at a
regular interval or daily and quality review in a constant manner
B-listed items: The valuable but medium-priority stock which requires reordering on a
monthly basis
C-listed items: The very less-valuable and low-priority stocks which are carried in high
volumes with a minimum number of reordering
the manufacturers to their warehouses and after that, from these warehouses to the point of actual
sale (Chen & Simchi-Levi, 2012). For Beacon Lighting and other companies, the key function
associated to inventory management practices is to have a detailed and reliable record of every
newly finished or returned goods as it leaves for the point of sale or enters into a warehouse.
Since the past few years, Beacon Lighting is facing the problem of managing its inventory in a
proper manner which led it to face issues like blockage of cash, increasing wastes, and operating
cost. Due to the lack of inventory management days in inventory at Beacon is high in
comparison to its competitors. This problem makes Beacon to raise a huge amount of capital for
investing in the channel which is expected to impact the company’s long-term growth
(Krajewski, Ritzman & Malhotra, 2013).
Solution generation
In order to guide Beacon Lighting Group Limited in managing inventories and in
resolving the issues, it faces due to improper inventory management, the following solutions are
generated -
1. Categorising inventory by using ABC analysis
ABC analysis refers to a technique that could be used by Beacon Lighting for arranging
its inventory into a hierarchy by considering the most important items in its inventory to the least
important items in its inventory. The company needs to practice ABC analysis in the following
manner -
A-listed items: The highest priority, and best-selling stock which requires reordering at a
regular interval or daily and quality review in a constant manner
B-listed items: The valuable but medium-priority stock which requires reordering on a
monthly basis
C-listed items: The very less-valuable and low-priority stocks which are carried in high
volumes with a minimum number of reordering

Managerial Decision Making 6
Beacon Lighting needs to organise its stock within its warehouse in accordance with how
they move (sell) and what amount of value these stocks bring into the business. This is required
for optimising storage space as well as streamlines the order fulfillment process (Ravinder &
Misra, 2014).
2. Par Levels
Par levels stand as another solution generated here to support Beacon in managing its
inventory. Par levels refer to the minimum number (in amount) of products need to be kept into
the warehouse shelves throughout the year. At the time, when inventory level declines below
these pre-determined levels, it informs a company that the time has arrived when it needs to
order more. Par levels indicate how fast stocks sell as well as how much time it takes to get it
them back in the stock. Par levels must be checked on a daily basis to make sure that they make
required adjustments while needed and make sense for the company (here, Beacon Lighting)
(score.org, 2019).
3. First-In First-Out Method (FIFO)
In the task of inventory management, FIFO is one of the most important principles
(Muller, 2019). It means, a company (here, Beacon Lighting) needs to sell the stock it gets in
first (first-in), by holding the newest stock. It is mostly applicable for perishable items but also
good to apply for non-perishable items in stock as the rapid technological growth often make a
stock outdated by replacing it with a newer one. This particular inventory solution helps a
company to reduce the wastage of raw materials due to obsolescence (Atieh et al. 2016).
4. Establishment of inventory KPIs
Inventory KPIs help a company to measure its performance during a particular time in a
specific area toward a pre-determined target or an oreganisation which is related to its business
operations. These KPIs help a company to eliminate its guesswork and provide clear milestones
that to be achieved in every week or quarter, or year. Setting up inventory KPIs is a part of a
Beacon Lighting needs to organise its stock within its warehouse in accordance with how
they move (sell) and what amount of value these stocks bring into the business. This is required
for optimising storage space as well as streamlines the order fulfillment process (Ravinder &
Misra, 2014).
2. Par Levels
Par levels stand as another solution generated here to support Beacon in managing its
inventory. Par levels refer to the minimum number (in amount) of products need to be kept into
the warehouse shelves throughout the year. At the time, when inventory level declines below
these pre-determined levels, it informs a company that the time has arrived when it needs to
order more. Par levels indicate how fast stocks sell as well as how much time it takes to get it
them back in the stock. Par levels must be checked on a daily basis to make sure that they make
required adjustments while needed and make sense for the company (here, Beacon Lighting)
(score.org, 2019).
3. First-In First-Out Method (FIFO)
In the task of inventory management, FIFO is one of the most important principles
(Muller, 2019). It means, a company (here, Beacon Lighting) needs to sell the stock it gets in
first (first-in), by holding the newest stock. It is mostly applicable for perishable items but also
good to apply for non-perishable items in stock as the rapid technological growth often make a
stock outdated by replacing it with a newer one. This particular inventory solution helps a
company to reduce the wastage of raw materials due to obsolescence (Atieh et al. 2016).
4. Establishment of inventory KPIs
Inventory KPIs help a company to measure its performance during a particular time in a
specific area toward a pre-determined target or an oreganisation which is related to its business
operations. These KPIs help a company to eliminate its guesswork and provide clear milestones
that to be achieved in every week or quarter, or year. Setting up inventory KPIs is a part of a

Managerial Decision Making 7
company’s strategic decisions making the process (Wild, 2017). The common inventory KPIs a
company (here, Beacon Lighting) needs to focus on are –
Carrying costs of inventory
Inventory turnover rate
Cycle time
Inventory write-off as well as inventory write-down
Status of order and tracking
Fill Rate
5. Optimising the rate of inventory turnover
A company’s inventory turnover rate stands as a measure of how many times its
inventory is used or sold in a particular time period like in a year. By calculating inventory
turnover rate a company could gain better grasp on the prevailing market (customer) demand for
its products, the amount blocked in obsolete stock it currently carrying and the steps required to
be taken to stock inventory or sell the same (Mohammaditabar, Ghodsypour & O'Brien, 2012).
The formula required to be used for calculating the rate of inventory turnover is dividing the
COGS (Cost of Goods Sold) of the company for a particular period by its average inventory
{(opening inventory + closing inventory / 2}.
Beacon Lighting will be able to increase its inventory turnover rate by
Experimenting with pricing
Forecasting Customer Demand
Liquidating obsolete stock
Redistributing inventory among other warehouses
company’s strategic decisions making the process (Wild, 2017). The common inventory KPIs a
company (here, Beacon Lighting) needs to focus on are –
Carrying costs of inventory
Inventory turnover rate
Cycle time
Inventory write-off as well as inventory write-down
Status of order and tracking
Fill Rate
5. Optimising the rate of inventory turnover
A company’s inventory turnover rate stands as a measure of how many times its
inventory is used or sold in a particular time period like in a year. By calculating inventory
turnover rate a company could gain better grasp on the prevailing market (customer) demand for
its products, the amount blocked in obsolete stock it currently carrying and the steps required to
be taken to stock inventory or sell the same (Mohammaditabar, Ghodsypour & O'Brien, 2012).
The formula required to be used for calculating the rate of inventory turnover is dividing the
COGS (Cost of Goods Sold) of the company for a particular period by its average inventory
{(opening inventory + closing inventory / 2}.
Beacon Lighting will be able to increase its inventory turnover rate by
Experimenting with pricing
Forecasting Customer Demand
Liquidating obsolete stock
Redistributing inventory among other warehouses
Paraphrase This Document
Need a fresh take? Get an instant paraphrase of this document with our AI Paraphraser

Managerial Decision Making 8
Solution evaluation
In order to evaluate the above discussed solutions to resolve the inventory management
related issues an efficiency evaluation table is provided below considering the factors attached to
the prescribed solutions -
Factors Categorising
inventory by
using ABC
analysis
Par Levels First-In
First-Out
Method
(FIFO)
Establishment
of inventory
KPIs
Optimising
the rate of
inventory
turnover
Investment Medium Medium Medium Low Low
Expected Return
on Investment
High Medium High Medium High
Time required
for
implementation
High Low Moderate Low High
Cost of
implementation
Medium Low Medium Low Medium
Potential Risks Medium Medium High Low Low
Success rates High Medium High Medium High
Table 1: Evaluation Table
(Source: Created by the researcher)
In accordance with the above mentioned solutions, the most suitable solutions that could
help Beacon to sort out its problem with inventory management are
Categorising inventory by using ABC analysis
Solution evaluation
In order to evaluate the above discussed solutions to resolve the inventory management
related issues an efficiency evaluation table is provided below considering the factors attached to
the prescribed solutions -
Factors Categorising
inventory by
using ABC
analysis
Par Levels First-In
First-Out
Method
(FIFO)
Establishment
of inventory
KPIs
Optimising
the rate of
inventory
turnover
Investment Medium Medium Medium Low Low
Expected Return
on Investment
High Medium High Medium High
Time required
for
implementation
High Low Moderate Low High
Cost of
implementation
Medium Low Medium Low Medium
Potential Risks Medium Medium High Low Low
Success rates High Medium High Medium High
Table 1: Evaluation Table
(Source: Created by the researcher)
In accordance with the above mentioned solutions, the most suitable solutions that could
help Beacon to sort out its problem with inventory management are
Categorising inventory by using ABC analysis

Managerial Decision Making 9
First-In First-Out Method (FIFO)
Establishment of inventory KPIs
Optimising the rate of inventory turnover
Benefits of solutions prescribed above in inventory management
The system of categorising inventory by using ABC analysis will help Beacon to
organise its stock within its warehouse accordingly to the volume of their sales. It will also help
Beacon to streamline order fulfillment and optimise storage space. The application of the FIFO
method will assist Beacon to report lower profit which accordingly helps it to pay lower tax. This
particular method will save money and time in managing inventory. Establishment of inventory
KPIs will help Beacon to gauge its performance by comparing it with the pre-fixed criteria of
good inventory management. On the other hand, Optimising the rate of inventory turnover will
help the company to ensure the continuous flow of inventory which will help it to avoid the
threat of cash blockage and wastages of stock. All solutions maintained above will help Beacon
to achieve efficiency as well as productivity in its operations and will help it to maximize sales
volume and profit by minimising production oriented costs and other operating costs required to
maintain or manage inventories (Axsäter, 2015).
Implementation and action plan
Name of the
solution
Week 1 Week 2 Week 3 Week 4
Categorising
inventory by
using ABC
analysis
First-In First-Out
Method (FIFO)
First-In First-Out Method (FIFO)
Establishment of inventory KPIs
Optimising the rate of inventory turnover
Benefits of solutions prescribed above in inventory management
The system of categorising inventory by using ABC analysis will help Beacon to
organise its stock within its warehouse accordingly to the volume of their sales. It will also help
Beacon to streamline order fulfillment and optimise storage space. The application of the FIFO
method will assist Beacon to report lower profit which accordingly helps it to pay lower tax. This
particular method will save money and time in managing inventory. Establishment of inventory
KPIs will help Beacon to gauge its performance by comparing it with the pre-fixed criteria of
good inventory management. On the other hand, Optimising the rate of inventory turnover will
help the company to ensure the continuous flow of inventory which will help it to avoid the
threat of cash blockage and wastages of stock. All solutions maintained above will help Beacon
to achieve efficiency as well as productivity in its operations and will help it to maximize sales
volume and profit by minimising production oriented costs and other operating costs required to
maintain or manage inventories (Axsäter, 2015).
Implementation and action plan
Name of the
solution
Week 1 Week 2 Week 3 Week 4
Categorising
inventory by
using ABC
analysis
First-In First-Out
Method (FIFO)

Managerial Decision Making 10
Establishment of
inventory KPIs
Optimising the
rate of inventory
turnover
Figure 1: Gantt Chart
(Source: Created by the researcher)
Conclusion
Inventory management is highly significant for a company’s sustainability, continuous
growth, and development as it ensures sales and profit maximisation and reduces the cost of
operations. In this study, some of the most effective inventory management systems are
discussed by implementing which a manufacturing company like Beacon Lighting Group
Limited of Australia will be benefitted and enhance its inventory management process. At the
end of this study, it is very relevant to conclude here that Beacon Lighting Group needs to adopt
the above mentioned solutions as soon as they can to reduce or eliminate the problem it is
currently facing due to poor inventory management.
Establishment of
inventory KPIs
Optimising the
rate of inventory
turnover
Figure 1: Gantt Chart
(Source: Created by the researcher)
Conclusion
Inventory management is highly significant for a company’s sustainability, continuous
growth, and development as it ensures sales and profit maximisation and reduces the cost of
operations. In this study, some of the most effective inventory management systems are
discussed by implementing which a manufacturing company like Beacon Lighting Group
Limited of Australia will be benefitted and enhance its inventory management process. At the
end of this study, it is very relevant to conclude here that Beacon Lighting Group needs to adopt
the above mentioned solutions as soon as they can to reduce or eliminate the problem it is
currently facing due to poor inventory management.
Secure Best Marks with AI Grader
Need help grading? Try our AI Grader for instant feedback on your assignments.
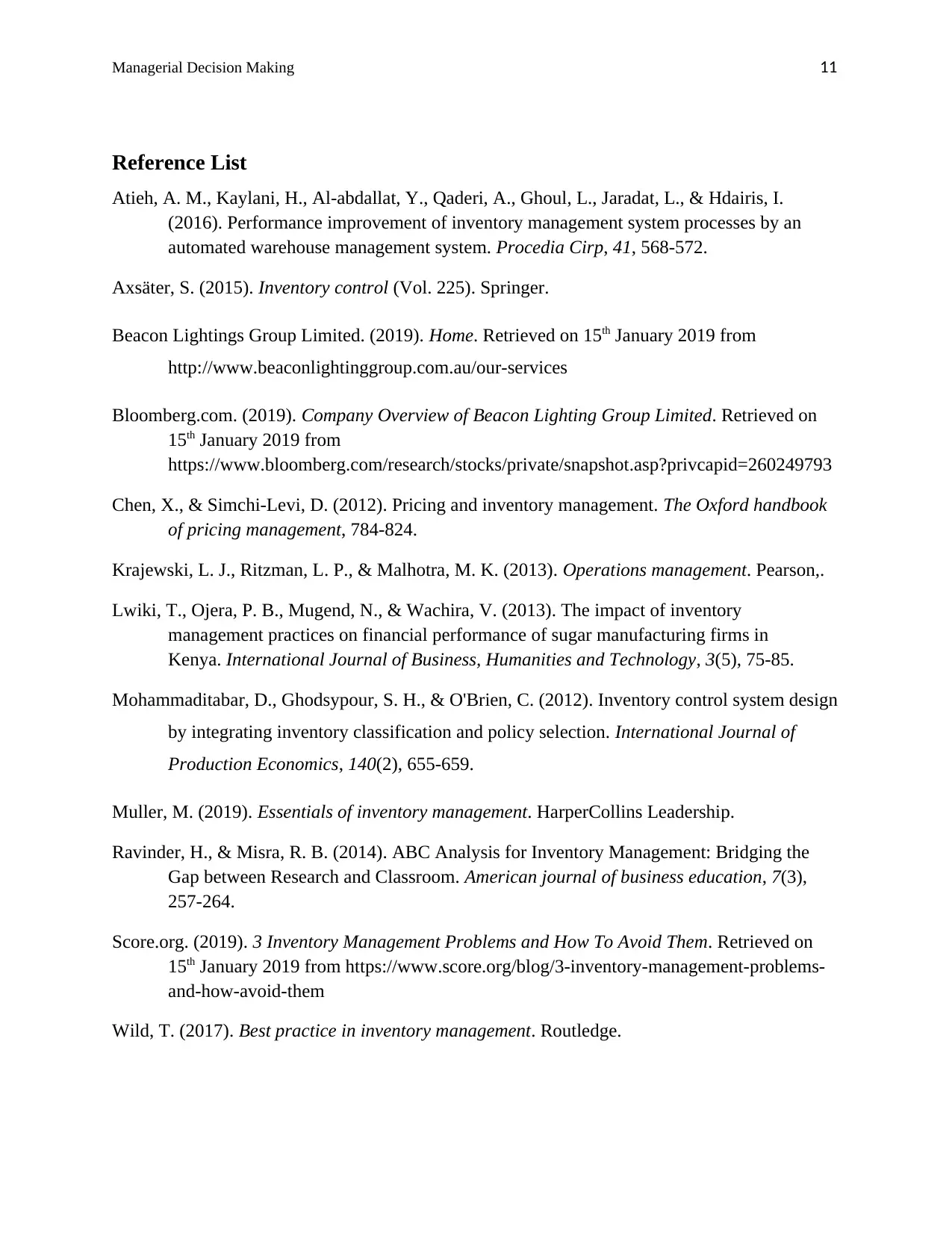
Managerial Decision Making 11
Reference List
Atieh, A. M., Kaylani, H., Al-abdallat, Y., Qaderi, A., Ghoul, L., Jaradat, L., & Hdairis, I.
(2016). Performance improvement of inventory management system processes by an
automated warehouse management system. Procedia Cirp, 41, 568-572.
Axsäter, S. (2015). Inventory control (Vol. 225). Springer.
Beacon Lightings Group Limited. (2019). Home. Retrieved on 15th January 2019 from
http://www.beaconlightinggroup.com.au/our-services
Bloomberg.com. (2019). Company Overview of Beacon Lighting Group Limited. Retrieved on
15th January 2019 from
https://www.bloomberg.com/research/stocks/private/snapshot.asp?privcapid=260249793
Chen, X., & Simchi-Levi, D. (2012). Pricing and inventory management. The Oxford handbook
of pricing management, 784-824.
Krajewski, L. J., Ritzman, L. P., & Malhotra, M. K. (2013). Operations management. Pearson,.
Lwiki, T., Ojera, P. B., Mugend, N., & Wachira, V. (2013). The impact of inventory
management practices on financial performance of sugar manufacturing firms in
Kenya. International Journal of Business, Humanities and Technology, 3(5), 75-85.
Mohammaditabar, D., Ghodsypour, S. H., & O'Brien, C. (2012). Inventory control system design
by integrating inventory classification and policy selection. International Journal of
Production Economics, 140(2), 655-659.
Muller, M. (2019). Essentials of inventory management. HarperCollins Leadership.
Ravinder, H., & Misra, R. B. (2014). ABC Analysis for Inventory Management: Bridging the
Gap between Research and Classroom. American journal of business education, 7(3),
257-264.
Score.org. (2019). 3 Inventory Management Problems and How To Avoid Them. Retrieved on
15th January 2019 from https://www.score.org/blog/3-inventory-management-problems-
and-how-avoid-them
Wild, T. (2017). Best practice in inventory management. Routledge.
Reference List
Atieh, A. M., Kaylani, H., Al-abdallat, Y., Qaderi, A., Ghoul, L., Jaradat, L., & Hdairis, I.
(2016). Performance improvement of inventory management system processes by an
automated warehouse management system. Procedia Cirp, 41, 568-572.
Axsäter, S. (2015). Inventory control (Vol. 225). Springer.
Beacon Lightings Group Limited. (2019). Home. Retrieved on 15th January 2019 from
http://www.beaconlightinggroup.com.au/our-services
Bloomberg.com. (2019). Company Overview of Beacon Lighting Group Limited. Retrieved on
15th January 2019 from
https://www.bloomberg.com/research/stocks/private/snapshot.asp?privcapid=260249793
Chen, X., & Simchi-Levi, D. (2012). Pricing and inventory management. The Oxford handbook
of pricing management, 784-824.
Krajewski, L. J., Ritzman, L. P., & Malhotra, M. K. (2013). Operations management. Pearson,.
Lwiki, T., Ojera, P. B., Mugend, N., & Wachira, V. (2013). The impact of inventory
management practices on financial performance of sugar manufacturing firms in
Kenya. International Journal of Business, Humanities and Technology, 3(5), 75-85.
Mohammaditabar, D., Ghodsypour, S. H., & O'Brien, C. (2012). Inventory control system design
by integrating inventory classification and policy selection. International Journal of
Production Economics, 140(2), 655-659.
Muller, M. (2019). Essentials of inventory management. HarperCollins Leadership.
Ravinder, H., & Misra, R. B. (2014). ABC Analysis for Inventory Management: Bridging the
Gap between Research and Classroom. American journal of business education, 7(3),
257-264.
Score.org. (2019). 3 Inventory Management Problems and How To Avoid Them. Retrieved on
15th January 2019 from https://www.score.org/blog/3-inventory-management-problems-
and-how-avoid-them
Wild, T. (2017). Best practice in inventory management. Routledge.
1 out of 11
Related Documents

Your All-in-One AI-Powered Toolkit for Academic Success.
+13062052269
info@desklib.com
Available 24*7 on WhatsApp / Email
Unlock your academic potential
© 2024 | Zucol Services PVT LTD | All rights reserved.