BSBMGT608 Manage Continuous Improvement and Innovation Assessment
VerifiedAdded on 2023/06/05
|8
|1705
|80
Homework Assignment
AI Summary
This assignment solution addresses key concepts in continuous improvement and innovation, covering topics such as Kaizen, the Plan-Do-Act cycle, supply chain analysis, and cost-benefit analysis. It explores the characteristics of a learning organization, the importance of a shared vision, and team learning. The solution also delves into Kotter's 8-Step change model, the diffusion of innovation theory, and Total Quality Management. Furthermore, it defines risk, risk management, and risk analysis, including risk mitigation strategies and tools like ISO 9000 standards. Finally, it differentiates between supply chains and value chains, providing a comprehensive overview of the subject matter.

MANAGE CONTINUOUS IMPROVEMENT AND INNOVATION
Manage continuous improvement and innovation
Name of the Student
Name of the University
Author Note:
Manage continuous improvement and innovation
Name of the Student
Name of the University
Author Note:
Paraphrase This Document
Need a fresh take? Get an instant paraphrase of this document with our AI Paraphraser
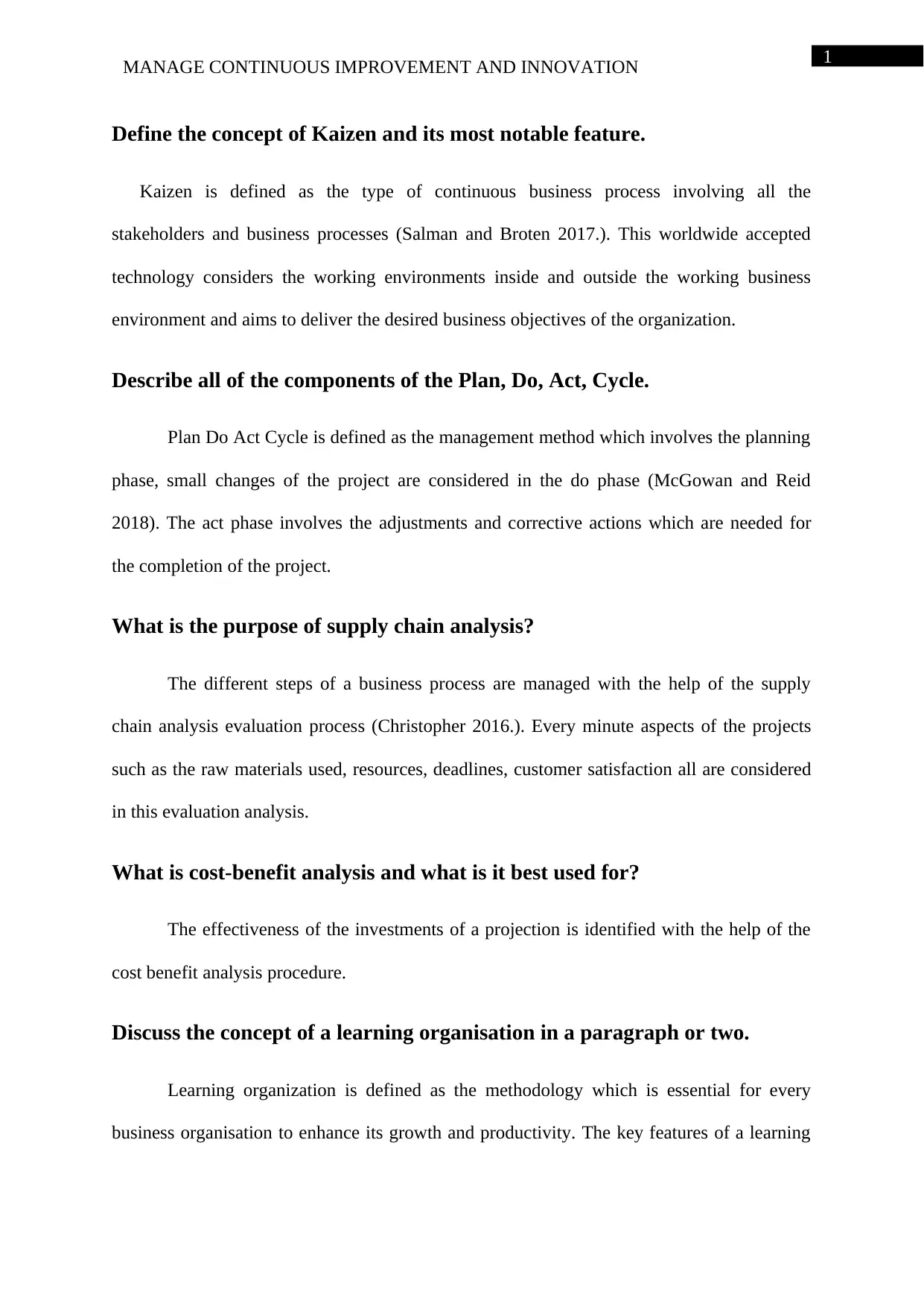
1
MANAGE CONTINUOUS IMPROVEMENT AND INNOVATION
Define the concept of Kaizen and its most notable feature.
Kaizen is defined as the type of continuous business process involving all the
stakeholders and business processes (Salman and Broten 2017.). This worldwide accepted
technology considers the working environments inside and outside the working business
environment and aims to deliver the desired business objectives of the organization.
Describe all of the components of the Plan, Do, Act, Cycle.
Plan Do Act Cycle is defined as the management method which involves the planning
phase, small changes of the project are considered in the do phase (McGowan and Reid
2018). The act phase involves the adjustments and corrective actions which are needed for
the completion of the project.
What is the purpose of supply chain analysis?
The different steps of a business process are managed with the help of the supply
chain analysis evaluation process (Christopher 2016.). Every minute aspects of the projects
such as the raw materials used, resources, deadlines, customer satisfaction all are considered
in this evaluation analysis.
What is cost-benefit analysis and what is it best used for?
The effectiveness of the investments of a projection is identified with the help of the
cost benefit analysis procedure.
Discuss the concept of a learning organisation in a paragraph or two.
Learning organization is defined as the methodology which is essential for every
business organisation to enhance its growth and productivity. The key features of a learning
MANAGE CONTINUOUS IMPROVEMENT AND INNOVATION
Define the concept of Kaizen and its most notable feature.
Kaizen is defined as the type of continuous business process involving all the
stakeholders and business processes (Salman and Broten 2017.). This worldwide accepted
technology considers the working environments inside and outside the working business
environment and aims to deliver the desired business objectives of the organization.
Describe all of the components of the Plan, Do, Act, Cycle.
Plan Do Act Cycle is defined as the management method which involves the planning
phase, small changes of the project are considered in the do phase (McGowan and Reid
2018). The act phase involves the adjustments and corrective actions which are needed for
the completion of the project.
What is the purpose of supply chain analysis?
The different steps of a business process are managed with the help of the supply
chain analysis evaluation process (Christopher 2016.). Every minute aspects of the projects
such as the raw materials used, resources, deadlines, customer satisfaction all are considered
in this evaluation analysis.
What is cost-benefit analysis and what is it best used for?
The effectiveness of the investments of a projection is identified with the help of the
cost benefit analysis procedure.
Discuss the concept of a learning organisation in a paragraph or two.
Learning organization is defined as the methodology which is essential for every
business organisation to enhance its growth and productivity. The key features of a learning
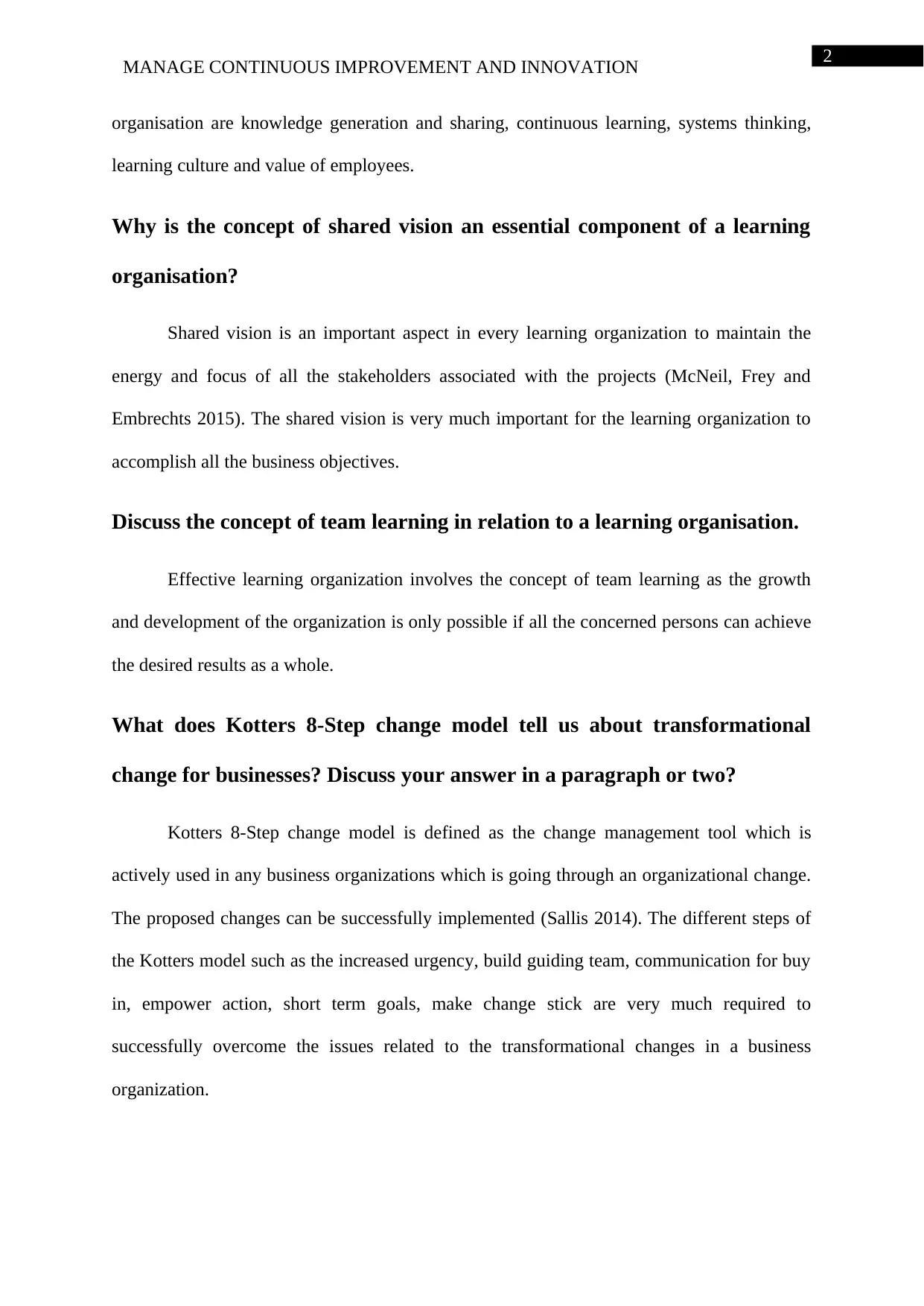
2
MANAGE CONTINUOUS IMPROVEMENT AND INNOVATION
organisation are knowledge generation and sharing, continuous learning, systems thinking,
learning culture and value of employees.
Why is the concept of shared vision an essential component of a learning
organisation?
Shared vision is an important aspect in every learning organization to maintain the
energy and focus of all the stakeholders associated with the projects (McNeil, Frey and
Embrechts 2015). The shared vision is very much important for the learning organization to
accomplish all the business objectives.
Discuss the concept of team learning in relation to a learning organisation.
Effective learning organization involves the concept of team learning as the growth
and development of the organization is only possible if all the concerned persons can achieve
the desired results as a whole.
What does Kotters 8-Step change model tell us about transformational
change for businesses? Discuss your answer in a paragraph or two?
Kotters 8-Step change model is defined as the change management tool which is
actively used in any business organizations which is going through an organizational change.
The proposed changes can be successfully implemented (Sallis 2014). The different steps of
the Kotters model such as the increased urgency, build guiding team, communication for buy
in, empower action, short term goals, make change stick are very much required to
successfully overcome the issues related to the transformational changes in a business
organization.
MANAGE CONTINUOUS IMPROVEMENT AND INNOVATION
organisation are knowledge generation and sharing, continuous learning, systems thinking,
learning culture and value of employees.
Why is the concept of shared vision an essential component of a learning
organisation?
Shared vision is an important aspect in every learning organization to maintain the
energy and focus of all the stakeholders associated with the projects (McNeil, Frey and
Embrechts 2015). The shared vision is very much important for the learning organization to
accomplish all the business objectives.
Discuss the concept of team learning in relation to a learning organisation.
Effective learning organization involves the concept of team learning as the growth
and development of the organization is only possible if all the concerned persons can achieve
the desired results as a whole.
What does Kotters 8-Step change model tell us about transformational
change for businesses? Discuss your answer in a paragraph or two?
Kotters 8-Step change model is defined as the change management tool which is
actively used in any business organizations which is going through an organizational change.
The proposed changes can be successfully implemented (Sallis 2014). The different steps of
the Kotters model such as the increased urgency, build guiding team, communication for buy
in, empower action, short term goals, make change stick are very much required to
successfully overcome the issues related to the transformational changes in a business
organization.
⊘ This is a preview!⊘
Do you want full access?
Subscribe today to unlock all pages.

Trusted by 1+ million students worldwide
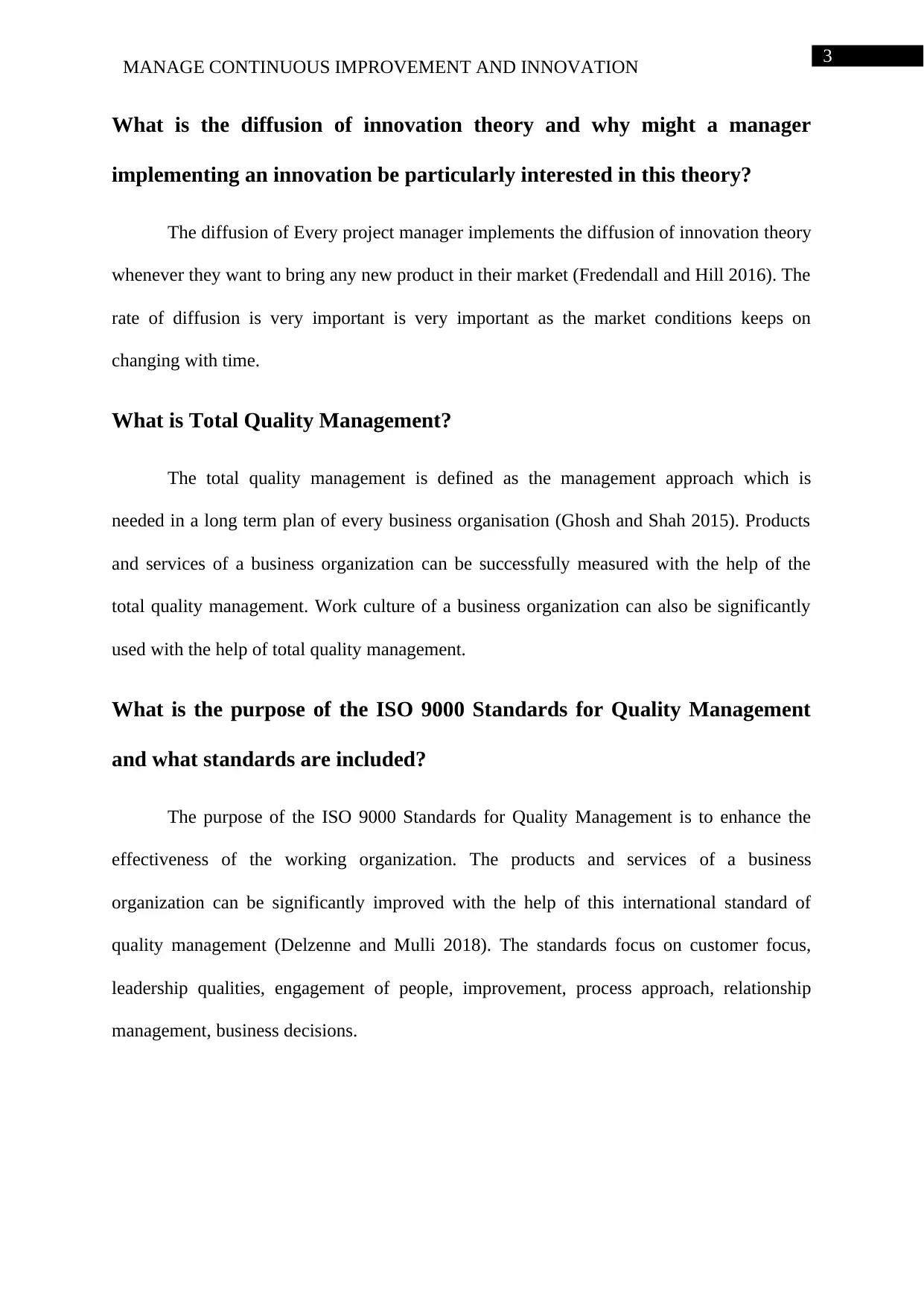
3
MANAGE CONTINUOUS IMPROVEMENT AND INNOVATION
What is the diffusion of innovation theory and why might a manager
implementing an innovation be particularly interested in this theory?
The diffusion of Every project manager implements the diffusion of innovation theory
whenever they want to bring any new product in their market (Fredendall and Hill 2016). The
rate of diffusion is very important is very important as the market conditions keeps on
changing with time.
What is Total Quality Management?
The total quality management is defined as the management approach which is
needed in a long term plan of every business organisation (Ghosh and Shah 2015). Products
and services of a business organization can be successfully measured with the help of the
total quality management. Work culture of a business organization can also be significantly
used with the help of total quality management.
What is the purpose of the ISO 9000 Standards for Quality Management
and what standards are included?
The purpose of the ISO 9000 Standards for Quality Management is to enhance the
effectiveness of the working organization. The products and services of a business
organization can be significantly improved with the help of this international standard of
quality management (Delzenne and Mulli 2018). The standards focus on customer focus,
leadership qualities, engagement of people, improvement, process approach, relationship
management, business decisions.
MANAGE CONTINUOUS IMPROVEMENT AND INNOVATION
What is the diffusion of innovation theory and why might a manager
implementing an innovation be particularly interested in this theory?
The diffusion of Every project manager implements the diffusion of innovation theory
whenever they want to bring any new product in their market (Fredendall and Hill 2016). The
rate of diffusion is very important is very important as the market conditions keeps on
changing with time.
What is Total Quality Management?
The total quality management is defined as the management approach which is
needed in a long term plan of every business organisation (Ghosh and Shah 2015). Products
and services of a business organization can be successfully measured with the help of the
total quality management. Work culture of a business organization can also be significantly
used with the help of total quality management.
What is the purpose of the ISO 9000 Standards for Quality Management
and what standards are included?
The purpose of the ISO 9000 Standards for Quality Management is to enhance the
effectiveness of the working organization. The products and services of a business
organization can be significantly improved with the help of this international standard of
quality management (Delzenne and Mulli 2018). The standards focus on customer focus,
leadership qualities, engagement of people, improvement, process approach, relationship
management, business decisions.
Paraphrase This Document
Need a fresh take? Get an instant paraphrase of this document with our AI Paraphraser
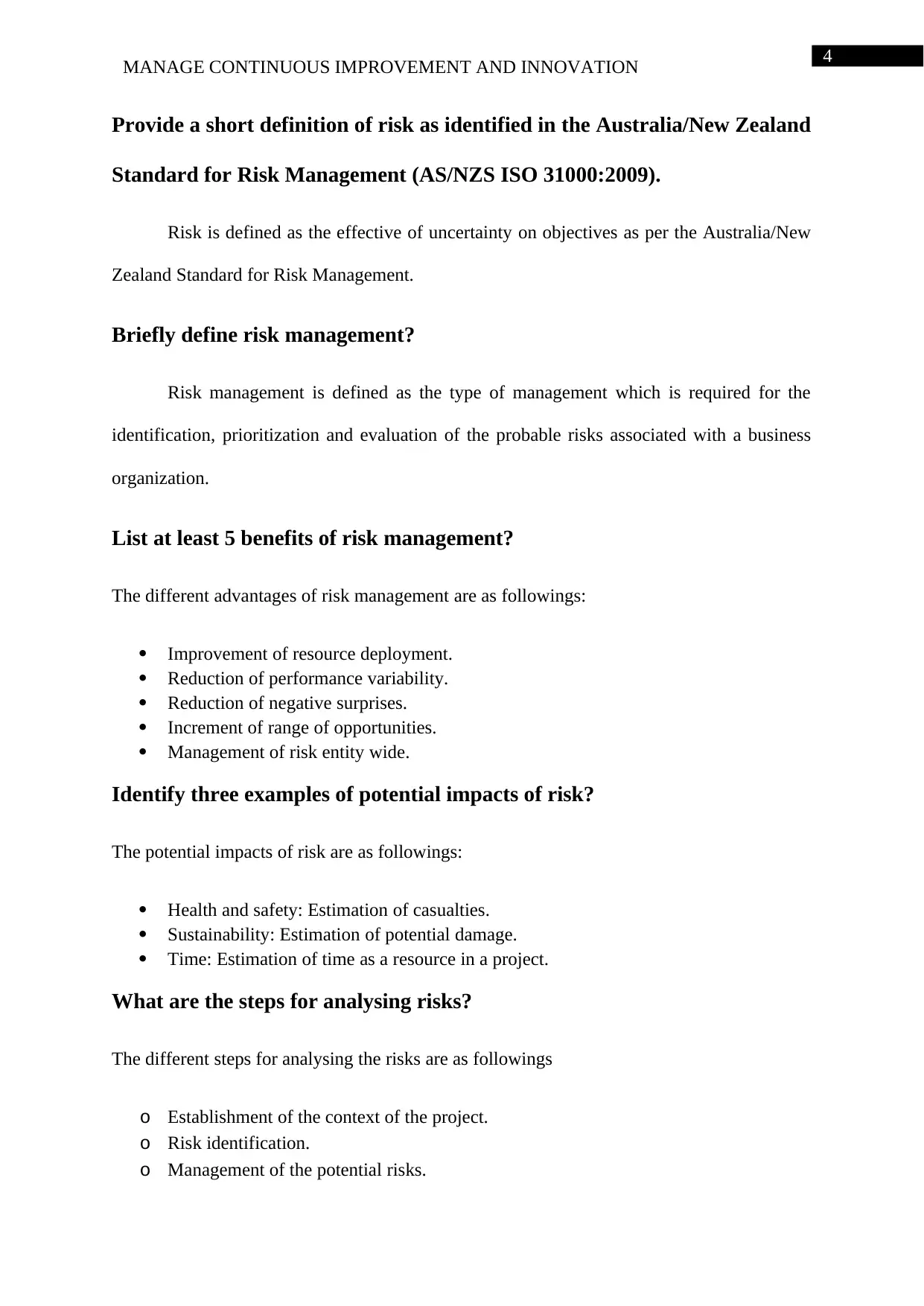
4
MANAGE CONTINUOUS IMPROVEMENT AND INNOVATION
Provide a short definition of risk as identified in the Australia/New Zealand
Standard for Risk Management (AS/NZS ISO 31000:2009).
Risk is defined as the effective of uncertainty on objectives as per the Australia/New
Zealand Standard for Risk Management.
Briefly define risk management?
Risk management is defined as the type of management which is required for the
identification, prioritization and evaluation of the probable risks associated with a business
organization.
List at least 5 benefits of risk management?
The different advantages of risk management are as followings:
Improvement of resource deployment.
Reduction of performance variability.
Reduction of negative surprises.
Increment of range of opportunities.
Management of risk entity wide.
Identify three examples of potential impacts of risk?
The potential impacts of risk are as followings:
Health and safety: Estimation of casualties.
Sustainability: Estimation of potential damage.
Time: Estimation of time as a resource in a project.
What are the steps for analysing risks?
The different steps for analysing the risks are as followings
o Establishment of the context of the project.
o Risk identification.
o Management of the potential risks.
MANAGE CONTINUOUS IMPROVEMENT AND INNOVATION
Provide a short definition of risk as identified in the Australia/New Zealand
Standard for Risk Management (AS/NZS ISO 31000:2009).
Risk is defined as the effective of uncertainty on objectives as per the Australia/New
Zealand Standard for Risk Management.
Briefly define risk management?
Risk management is defined as the type of management which is required for the
identification, prioritization and evaluation of the probable risks associated with a business
organization.
List at least 5 benefits of risk management?
The different advantages of risk management are as followings:
Improvement of resource deployment.
Reduction of performance variability.
Reduction of negative surprises.
Increment of range of opportunities.
Management of risk entity wide.
Identify three examples of potential impacts of risk?
The potential impacts of risk are as followings:
Health and safety: Estimation of casualties.
Sustainability: Estimation of potential damage.
Time: Estimation of time as a resource in a project.
What are the steps for analysing risks?
The different steps for analysing the risks are as followings
o Establishment of the context of the project.
o Risk identification.
o Management of the potential risks.
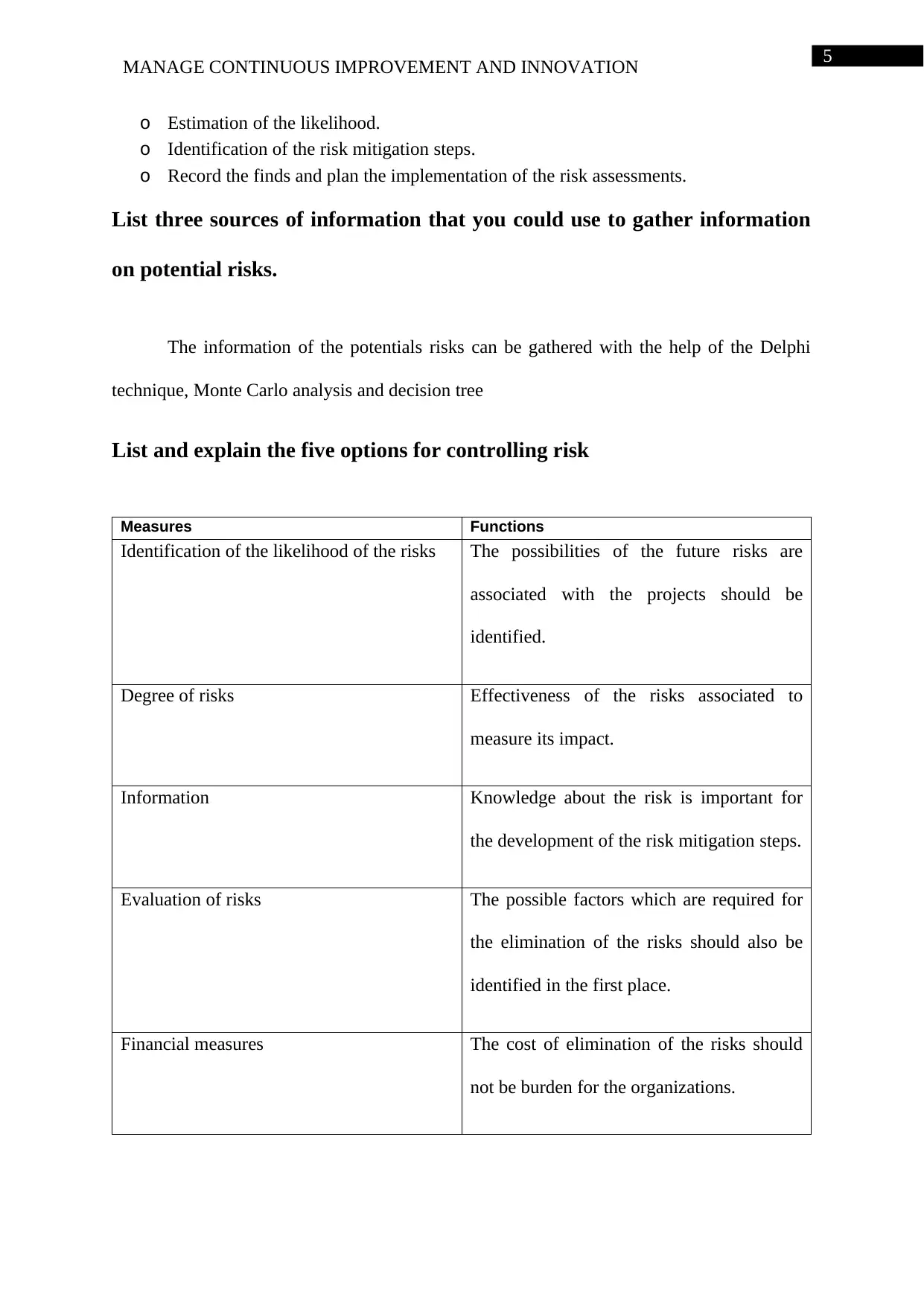
5
MANAGE CONTINUOUS IMPROVEMENT AND INNOVATION
o Estimation of the likelihood.
o Identification of the risk mitigation steps.
o Record the finds and plan the implementation of the risk assessments.
List three sources of information that you could use to gather information
on potential risks.
The information of the potentials risks can be gathered with the help of the Delphi
technique, Monte Carlo analysis and decision tree
List and explain the five options for controlling risk
Measures Functions
Identification of the likelihood of the risks The possibilities of the future risks are
associated with the projects should be
identified.
Degree of risks Effectiveness of the risks associated to
measure its impact.
Information Knowledge about the risk is important for
the development of the risk mitigation steps.
Evaluation of risks The possible factors which are required for
the elimination of the risks should also be
identified in the first place.
Financial measures The cost of elimination of the risks should
not be burden for the organizations.
MANAGE CONTINUOUS IMPROVEMENT AND INNOVATION
o Estimation of the likelihood.
o Identification of the risk mitigation steps.
o Record the finds and plan the implementation of the risk assessments.
List three sources of information that you could use to gather information
on potential risks.
The information of the potentials risks can be gathered with the help of the Delphi
technique, Monte Carlo analysis and decision tree
List and explain the five options for controlling risk
Measures Functions
Identification of the likelihood of the risks The possibilities of the future risks are
associated with the projects should be
identified.
Degree of risks Effectiveness of the risks associated to
measure its impact.
Information Knowledge about the risk is important for
the development of the risk mitigation steps.
Evaluation of risks The possible factors which are required for
the elimination of the risks should also be
identified in the first place.
Financial measures The cost of elimination of the risks should
not be burden for the organizations.
⊘ This is a preview!⊘
Do you want full access?
Subscribe today to unlock all pages.

Trusted by 1+ million students worldwide
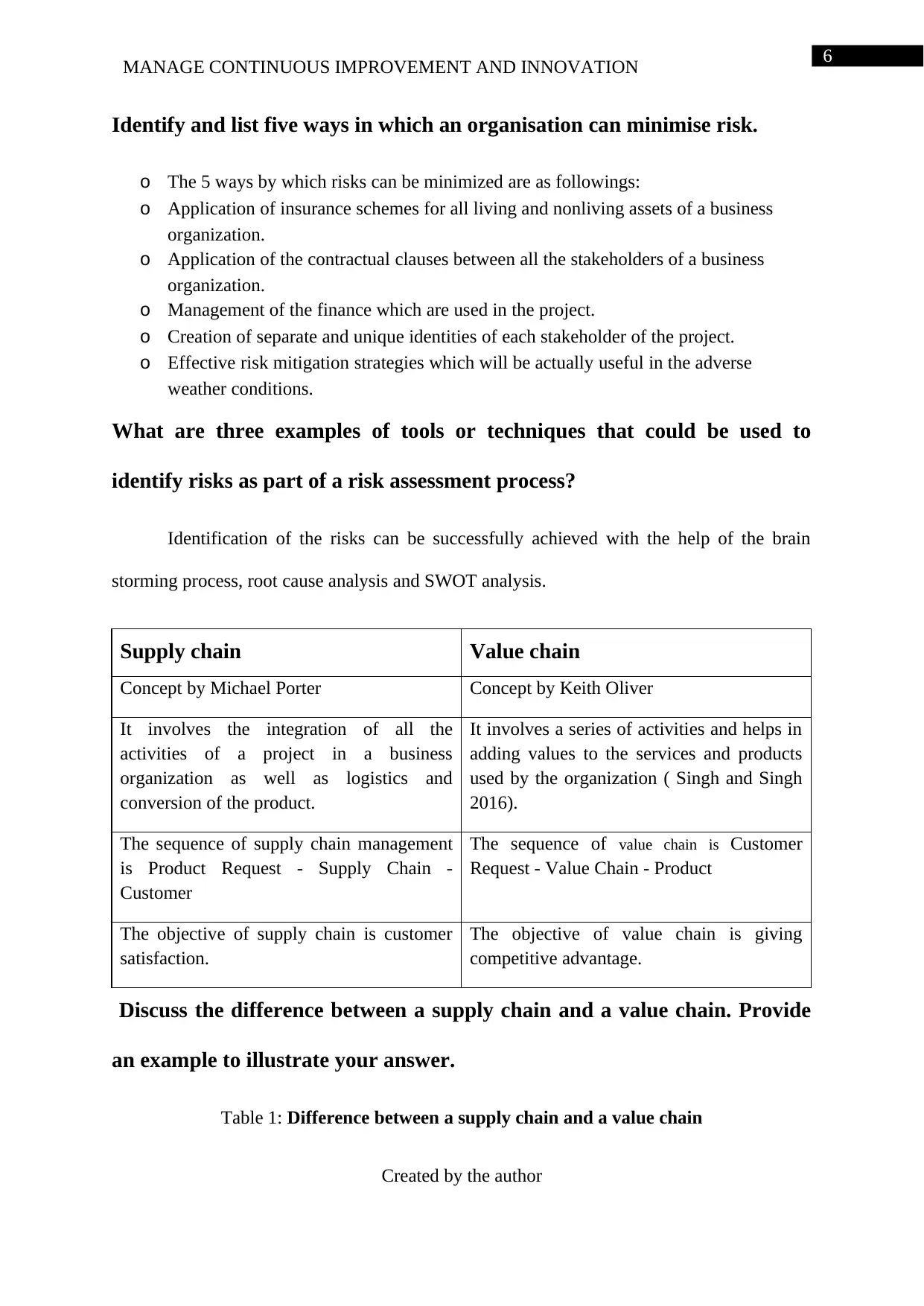
6
MANAGE CONTINUOUS IMPROVEMENT AND INNOVATION
Identify and list five ways in which an organisation can minimise risk.
o The 5 ways by which risks can be minimized are as followings:
o Application of insurance schemes for all living and nonliving assets of a business
organization.
o Application of the contractual clauses between all the stakeholders of a business
organization.
o Management of the finance which are used in the project.
o Creation of separate and unique identities of each stakeholder of the project.
o Effective risk mitigation strategies which will be actually useful in the adverse
weather conditions.
What are three examples of tools or techniques that could be used to
identify risks as part of a risk assessment process?
Identification of the risks can be successfully achieved with the help of the brain
storming process, root cause analysis and SWOT analysis.
Supply chain Value chain
Concept by Michael Porter Concept by Keith Oliver
It involves the integration of all the
activities of a project in a business
organization as well as logistics and
conversion of the product.
It involves a series of activities and helps in
adding values to the services and products
used by the organization ( Singh and Singh
2016).
The sequence of supply chain management
is Product Request - Supply Chain -
Customer
The sequence of value chain is Customer
Request - Value Chain - Product
The objective of supply chain is customer
satisfaction.
The objective of value chain is giving
competitive advantage.
Discuss the difference between a supply chain and a value chain. Provide
an example to illustrate your answer.
Table 1: Difference between a supply chain and a value chain
Created by the author
MANAGE CONTINUOUS IMPROVEMENT AND INNOVATION
Identify and list five ways in which an organisation can minimise risk.
o The 5 ways by which risks can be minimized are as followings:
o Application of insurance schemes for all living and nonliving assets of a business
organization.
o Application of the contractual clauses between all the stakeholders of a business
organization.
o Management of the finance which are used in the project.
o Creation of separate and unique identities of each stakeholder of the project.
o Effective risk mitigation strategies which will be actually useful in the adverse
weather conditions.
What are three examples of tools or techniques that could be used to
identify risks as part of a risk assessment process?
Identification of the risks can be successfully achieved with the help of the brain
storming process, root cause analysis and SWOT analysis.
Supply chain Value chain
Concept by Michael Porter Concept by Keith Oliver
It involves the integration of all the
activities of a project in a business
organization as well as logistics and
conversion of the product.
It involves a series of activities and helps in
adding values to the services and products
used by the organization ( Singh and Singh
2016).
The sequence of supply chain management
is Product Request - Supply Chain -
Customer
The sequence of value chain is Customer
Request - Value Chain - Product
The objective of supply chain is customer
satisfaction.
The objective of value chain is giving
competitive advantage.
Discuss the difference between a supply chain and a value chain. Provide
an example to illustrate your answer.
Table 1: Difference between a supply chain and a value chain
Created by the author
Paraphrase This Document
Need a fresh take? Get an instant paraphrase of this document with our AI Paraphraser
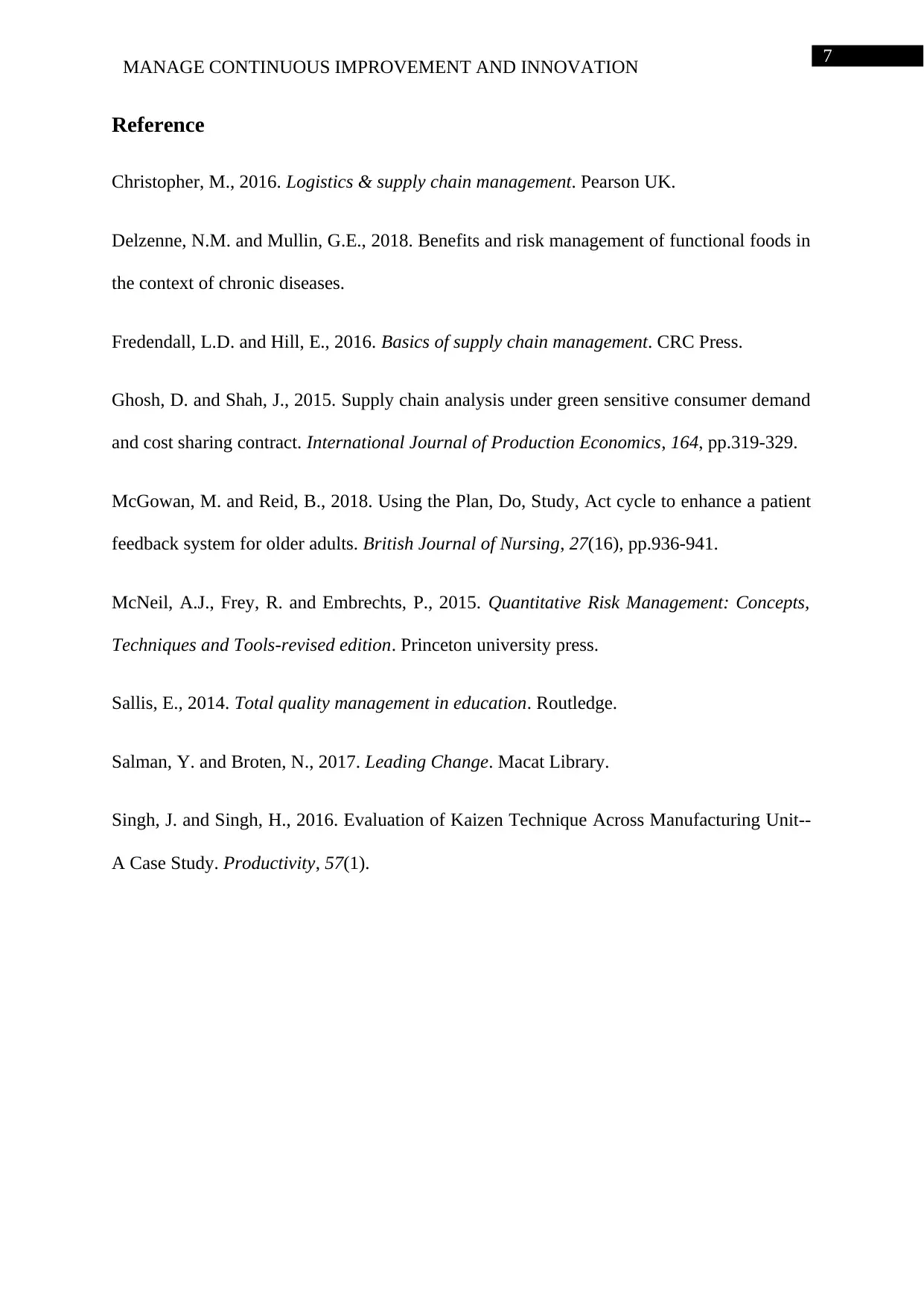
7
MANAGE CONTINUOUS IMPROVEMENT AND INNOVATION
Reference
Christopher, M., 2016. Logistics & supply chain management. Pearson UK.
Delzenne, N.M. and Mullin, G.E., 2018. Benefits and risk management of functional foods in
the context of chronic diseases.
Fredendall, L.D. and Hill, E., 2016. Basics of supply chain management. CRC Press.
Ghosh, D. and Shah, J., 2015. Supply chain analysis under green sensitive consumer demand
and cost sharing contract. International Journal of Production Economics, 164, pp.319-329.
McGowan, M. and Reid, B., 2018. Using the Plan, Do, Study, Act cycle to enhance a patient
feedback system for older adults. British Journal of Nursing, 27(16), pp.936-941.
McNeil, A.J., Frey, R. and Embrechts, P., 2015. Quantitative Risk Management: Concepts,
Techniques and Tools-revised edition. Princeton university press.
Sallis, E., 2014. Total quality management in education. Routledge.
Salman, Y. and Broten, N., 2017. Leading Change. Macat Library.
Singh, J. and Singh, H., 2016. Evaluation of Kaizen Technique Across Manufacturing Unit--
A Case Study. Productivity, 57(1).
MANAGE CONTINUOUS IMPROVEMENT AND INNOVATION
Reference
Christopher, M., 2016. Logistics & supply chain management. Pearson UK.
Delzenne, N.M. and Mullin, G.E., 2018. Benefits and risk management of functional foods in
the context of chronic diseases.
Fredendall, L.D. and Hill, E., 2016. Basics of supply chain management. CRC Press.
Ghosh, D. and Shah, J., 2015. Supply chain analysis under green sensitive consumer demand
and cost sharing contract. International Journal of Production Economics, 164, pp.319-329.
McGowan, M. and Reid, B., 2018. Using the Plan, Do, Study, Act cycle to enhance a patient
feedback system for older adults. British Journal of Nursing, 27(16), pp.936-941.
McNeil, A.J., Frey, R. and Embrechts, P., 2015. Quantitative Risk Management: Concepts,
Techniques and Tools-revised edition. Princeton university press.
Sallis, E., 2014. Total quality management in education. Routledge.
Salman, Y. and Broten, N., 2017. Leading Change. Macat Library.
Singh, J. and Singh, H., 2016. Evaluation of Kaizen Technique Across Manufacturing Unit--
A Case Study. Productivity, 57(1).
1 out of 8
Related Documents

Your All-in-One AI-Powered Toolkit for Academic Success.
+13062052269
info@desklib.com
Available 24*7 on WhatsApp / Email
Unlock your academic potential
© 2024 | Zucol Services PVT LTD | All rights reserved.