Instrumentation Assignment: Sensors, Control Systems, and Applications
VerifiedAdded on 2023/06/12
|5
|2184
|296
Homework Assignment
AI Summary
This instrumentation assignment comprehensively explores various aspects of sensors and control systems. It begins by defining key terms like accuracy, sensitivity, error, linearity, span, and hysteresis. The assignment then delves into the construction, operation, and applications of different types of sensors, including pressure sensors (piston type), temperature sensors (bimetallic thermometers), fluid level sensors (differential pressure), and flow rate sensors (ultrasonic flowmeters), providing detailed diagrams and specifications for each. Furthermore, it discusses the importance of signal conditioning in industrial environments, covering amplification, linearization, filtering, and modulation. The assignment also addresses control systems, including two-step control, PID control, and proportional control, explaining concepts like deviation, set point, offset, distance velocity lags, and capacity. It emphasizes the significance of process control in both hazardous and less hostile environments, highlighting its role in ensuring safety, improving production speed, and maintaining product quality. Finally, the assignment concludes with a discussion on closed-loop and open-loop systems, stability, and various parameters affecting control system performance, such as resistance, transfer lag, static gain, dead time, and dynamic gain.
Contribute Materials
Your contribution can guide someone’s learning journey. Share your
documents today.
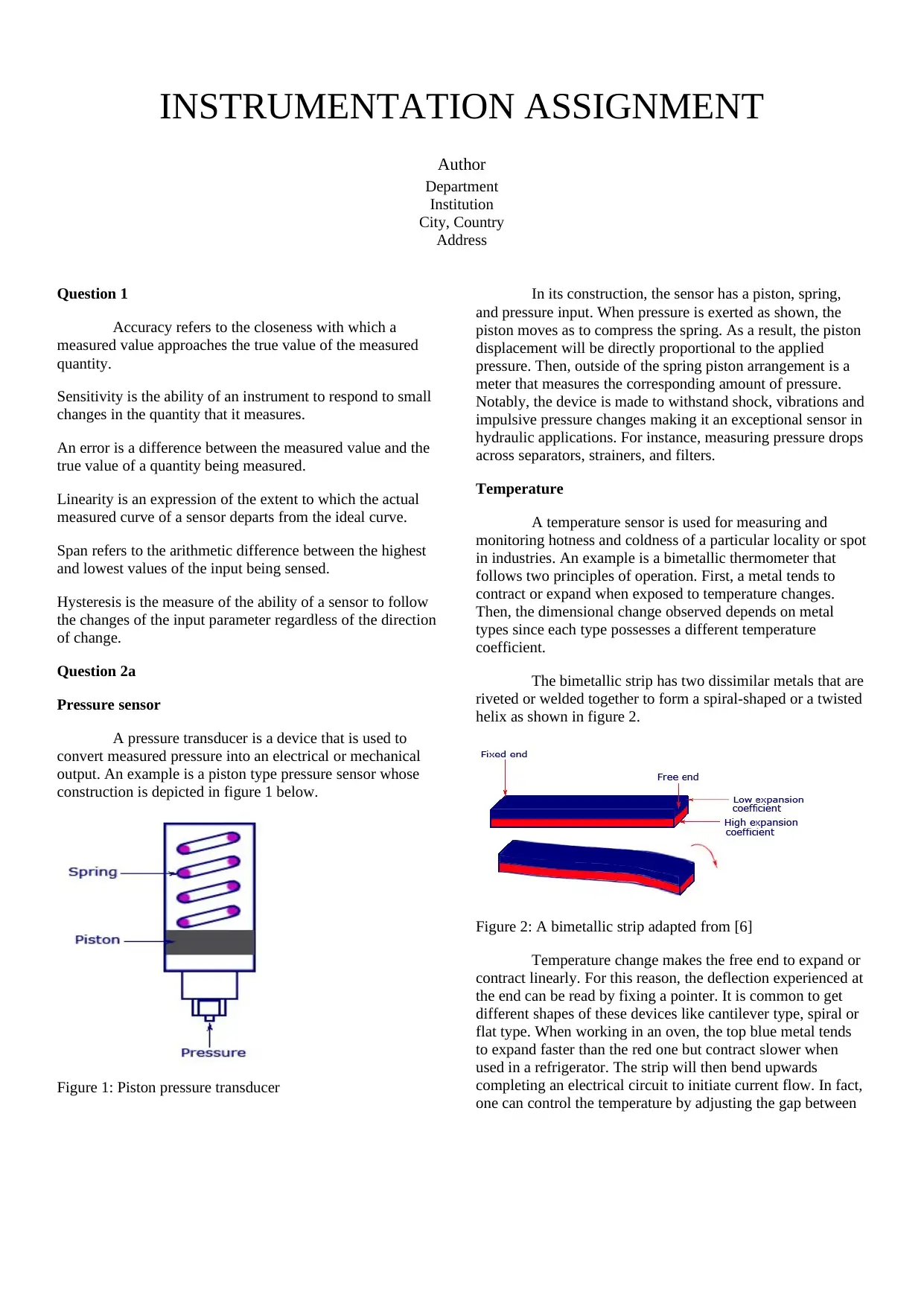
INSTRUMENTATION ASSIGNMENT
Author
Department
Institution
City, Country
Address
Question 1
Accuracy refers to the closeness with which a
measured value approaches the true value of the measured
quantity.
Sensitivity is the ability of an instrument to respond to small
changes in the quantity that it measures.
An error is a difference between the measured value and the
true value of a quantity being measured.
Linearity is an expression of the extent to which the actual
measured curve of a sensor departs from the ideal curve.
Span refers to the arithmetic difference between the highest
and lowest values of the input being sensed.
Hysteresis is the measure of the ability of a sensor to follow
the changes of the input parameter regardless of the direction
of change.
Question 2a
Pressure sensor
A pressure transducer is a device that is used to
convert measured pressure into an electrical or mechanical
output. An example is a piston type pressure sensor whose
construction is depicted in figure 1 below.
Figure 1: Piston pressure transducer
In its construction, the sensor has a piston, spring,
and pressure input. When pressure is exerted as shown, the
piston moves as to compress the spring. As a result, the piston
displacement will be directly proportional to the applied
pressure. Then, outside of the spring piston arrangement is a
meter that measures the corresponding amount of pressure.
Notably, the device is made to withstand shock, vibrations and
impulsive pressure changes making it an exceptional sensor in
hydraulic applications. For instance, measuring pressure drops
across separators, strainers, and filters.
Temperature
A temperature sensor is used for measuring and
monitoring hotness and coldness of a particular locality or spot
in industries. An example is a bimetallic thermometer that
follows two principles of operation. First, a metal tends to
contract or expand when exposed to temperature changes.
Then, the dimensional change observed depends on metal
types since each type possesses a different temperature
coefficient.
The bimetallic strip has two dissimilar metals that are
riveted or welded together to form a spiral-shaped or a twisted
helix as shown in figure 2.
Figure 2: A bimetallic strip adapted from [6]
Temperature change makes the free end to expand or
contract linearly. For this reason, the deflection experienced at
the end can be read by fixing a pointer. It is common to get
different shapes of these devices like cantilever type, spiral or
flat type. When working in an oven, the top blue metal tends
to expand faster than the red one but contract slower when
used in a refrigerator. The strip will then bend upwards
completing an electrical circuit to initiate current flow. In fact,
one can control the temperature by adjusting the gap between
Author
Department
Institution
City, Country
Address
Question 1
Accuracy refers to the closeness with which a
measured value approaches the true value of the measured
quantity.
Sensitivity is the ability of an instrument to respond to small
changes in the quantity that it measures.
An error is a difference between the measured value and the
true value of a quantity being measured.
Linearity is an expression of the extent to which the actual
measured curve of a sensor departs from the ideal curve.
Span refers to the arithmetic difference between the highest
and lowest values of the input being sensed.
Hysteresis is the measure of the ability of a sensor to follow
the changes of the input parameter regardless of the direction
of change.
Question 2a
Pressure sensor
A pressure transducer is a device that is used to
convert measured pressure into an electrical or mechanical
output. An example is a piston type pressure sensor whose
construction is depicted in figure 1 below.
Figure 1: Piston pressure transducer
In its construction, the sensor has a piston, spring,
and pressure input. When pressure is exerted as shown, the
piston moves as to compress the spring. As a result, the piston
displacement will be directly proportional to the applied
pressure. Then, outside of the spring piston arrangement is a
meter that measures the corresponding amount of pressure.
Notably, the device is made to withstand shock, vibrations and
impulsive pressure changes making it an exceptional sensor in
hydraulic applications. For instance, measuring pressure drops
across separators, strainers, and filters.
Temperature
A temperature sensor is used for measuring and
monitoring hotness and coldness of a particular locality or spot
in industries. An example is a bimetallic thermometer that
follows two principles of operation. First, a metal tends to
contract or expand when exposed to temperature changes.
Then, the dimensional change observed depends on metal
types since each type possesses a different temperature
coefficient.
The bimetallic strip has two dissimilar metals that are
riveted or welded together to form a spiral-shaped or a twisted
helix as shown in figure 2.
Figure 2: A bimetallic strip adapted from [6]
Temperature change makes the free end to expand or
contract linearly. For this reason, the deflection experienced at
the end can be read by fixing a pointer. It is common to get
different shapes of these devices like cantilever type, spiral or
flat type. When working in an oven, the top blue metal tends
to expand faster than the red one but contract slower when
used in a refrigerator. The strip will then bend upwards
completing an electrical circuit to initiate current flow. In fact,
one can control the temperature by adjusting the gap between
Secure Best Marks with AI Grader
Need help grading? Try our AI Grader for instant feedback on your assignments.
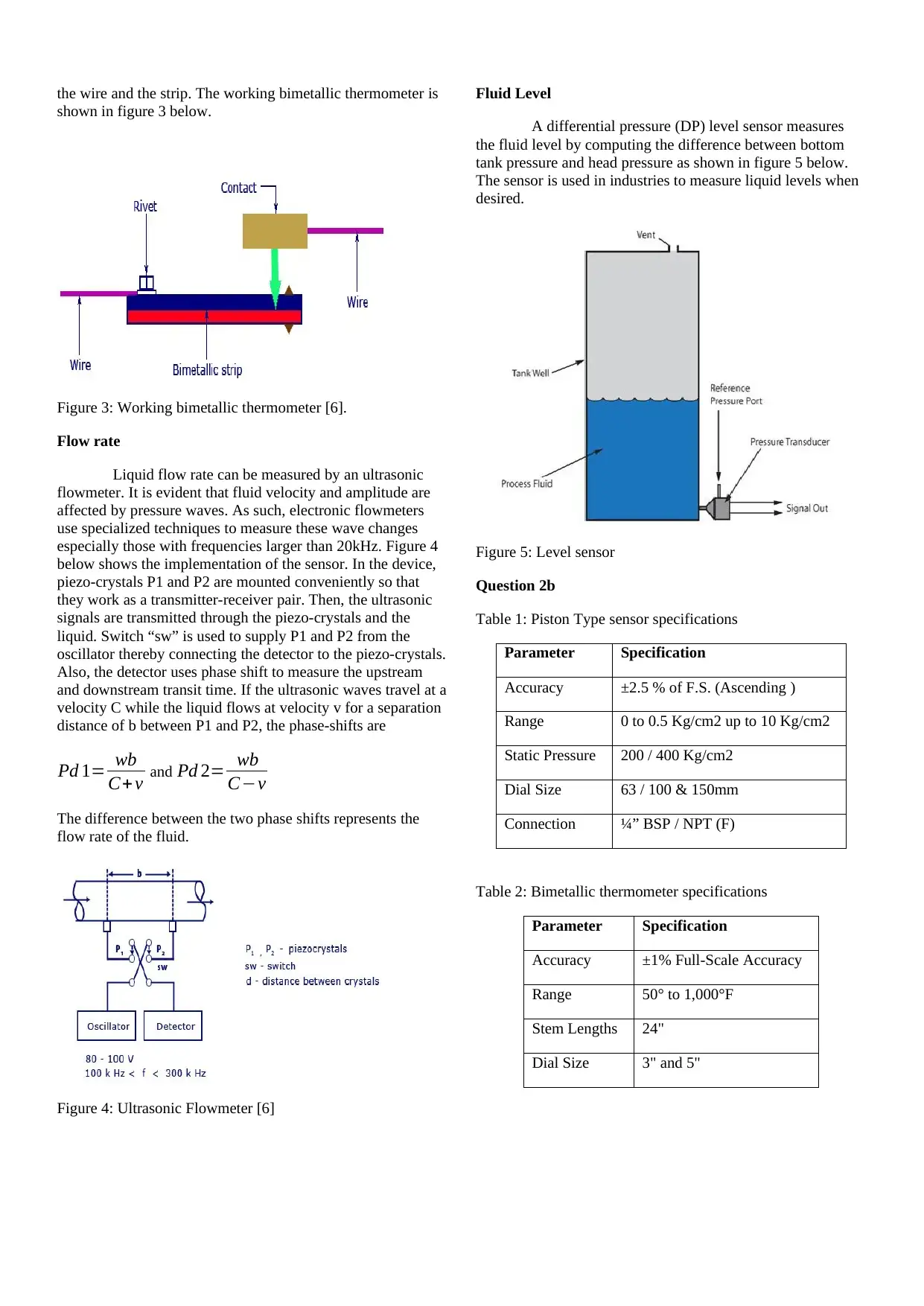
the wire and the strip. The working bimetallic thermometer is
shown in figure 3 below.
Figure 3: Working bimetallic thermometer [6].
Flow rate
Liquid flow rate can be measured by an ultrasonic
flowmeter. It is evident that fluid velocity and amplitude are
affected by pressure waves. As such, electronic flowmeters
use specialized techniques to measure these wave changes
especially those with frequencies larger than 20kHz. Figure 4
below shows the implementation of the sensor. In the device,
piezo-crystals P1 and P2 are mounted conveniently so that
they work as a transmitter-receiver pair. Then, the ultrasonic
signals are transmitted through the piezo-crystals and the
liquid. Switch “sw” is used to supply P1 and P2 from the
oscillator thereby connecting the detector to the piezo-crystals.
Also, the detector uses phase shift to measure the upstream
and downstream transit time. If the ultrasonic waves travel at a
velocity C while the liquid flows at velocity v for a separation
distance of b between P1 and P2, the phase-shifts are
Pd 1= wb
C+ v and Pd 2= wb
C−v
The difference between the two phase shifts represents the
flow rate of the fluid.
Figure 4: Ultrasonic Flowmeter [6]
Fluid Level
A differential pressure (DP) level sensor measures
the fluid level by computing the difference between bottom
tank pressure and head pressure as shown in figure 5 below.
The sensor is used in industries to measure liquid levels when
desired.
Figure 5: Level sensor
Question 2b
Table 1: Piston Type sensor specifications
Parameter Specification
Accuracy ±2.5 % of F.S. (Ascending )
Range 0 to 0.5 Kg/cm2 up to 10 Kg/cm2
Static Pressure 200 / 400 Kg/cm2
Dial Size 63 / 100 & 150mm
Connection ¼” BSP / NPT (F)
Table 2: Bimetallic thermometer specifications
Parameter Specification
Accuracy ±1% Full-Scale Accuracy
Range 50° to 1,000°F
Stem Lengths 24"
Dial Size 3" and 5"
shown in figure 3 below.
Figure 3: Working bimetallic thermometer [6].
Flow rate
Liquid flow rate can be measured by an ultrasonic
flowmeter. It is evident that fluid velocity and amplitude are
affected by pressure waves. As such, electronic flowmeters
use specialized techniques to measure these wave changes
especially those with frequencies larger than 20kHz. Figure 4
below shows the implementation of the sensor. In the device,
piezo-crystals P1 and P2 are mounted conveniently so that
they work as a transmitter-receiver pair. Then, the ultrasonic
signals are transmitted through the piezo-crystals and the
liquid. Switch “sw” is used to supply P1 and P2 from the
oscillator thereby connecting the detector to the piezo-crystals.
Also, the detector uses phase shift to measure the upstream
and downstream transit time. If the ultrasonic waves travel at a
velocity C while the liquid flows at velocity v for a separation
distance of b between P1 and P2, the phase-shifts are
Pd 1= wb
C+ v and Pd 2= wb
C−v
The difference between the two phase shifts represents the
flow rate of the fluid.
Figure 4: Ultrasonic Flowmeter [6]
Fluid Level
A differential pressure (DP) level sensor measures
the fluid level by computing the difference between bottom
tank pressure and head pressure as shown in figure 5 below.
The sensor is used in industries to measure liquid levels when
desired.
Figure 5: Level sensor
Question 2b
Table 1: Piston Type sensor specifications
Parameter Specification
Accuracy ±2.5 % of F.S. (Ascending )
Range 0 to 0.5 Kg/cm2 up to 10 Kg/cm2
Static Pressure 200 / 400 Kg/cm2
Dial Size 63 / 100 & 150mm
Connection ¼” BSP / NPT (F)
Table 2: Bimetallic thermometer specifications
Parameter Specification
Accuracy ±1% Full-Scale Accuracy
Range 50° to 1,000°F
Stem Lengths 24"
Dial Size 3" and 5"
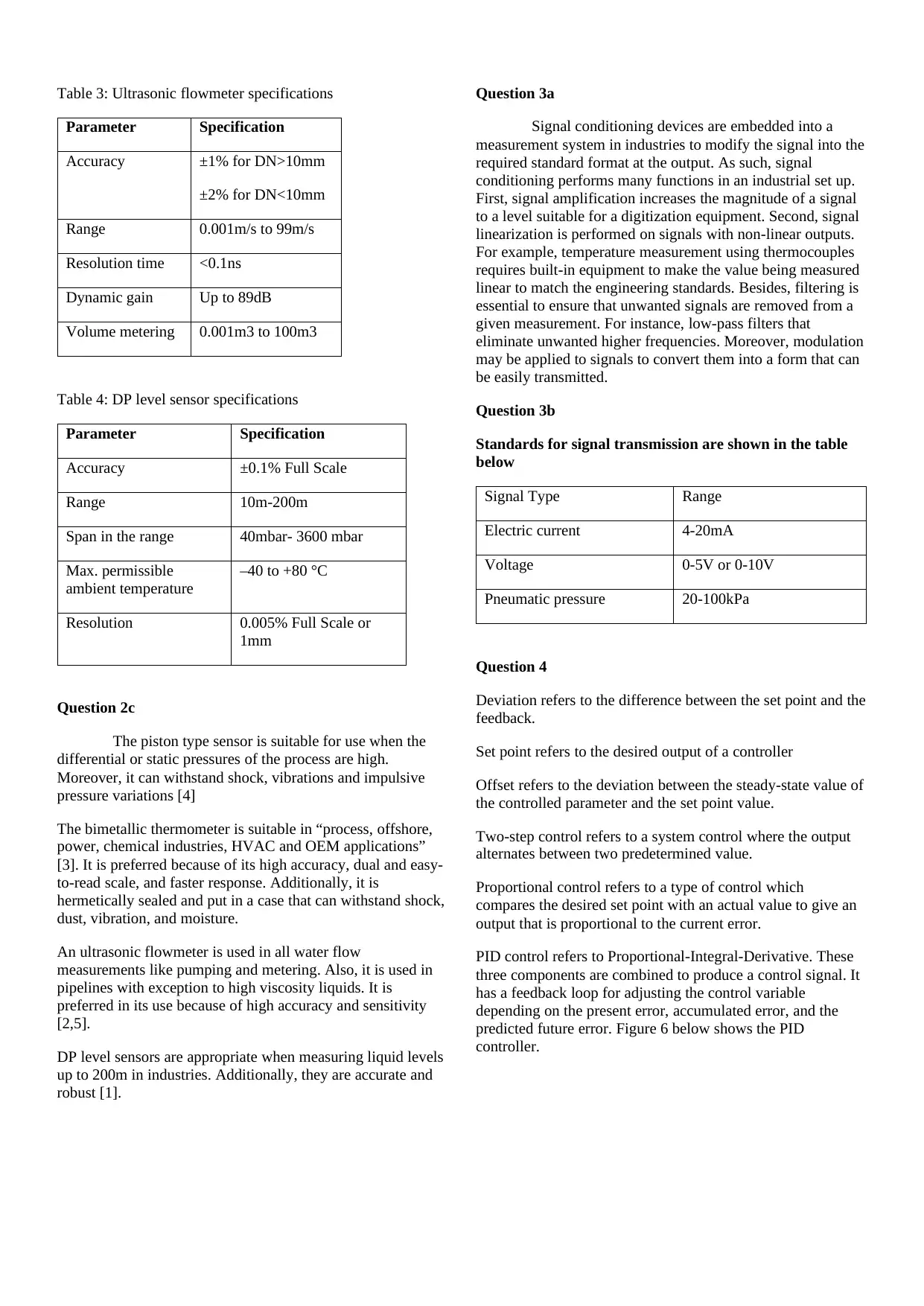
Table 3: Ultrasonic flowmeter specifications
Parameter Specification
Accuracy ±1% for DN>10mm
±2% for DN<10mm
Range 0.001m/s to 99m/s
Resolution time <0.1ns
Dynamic gain Up to 89dB
Volume metering 0.001m3 to 100m3
Table 4: DP level sensor specifications
Parameter Specification
Accuracy ±0.1% Full Scale
Range 10m-200m
Span in the range 40mbar- 3600 mbar
Max. permissible
ambient temperature
–40 to +80 °C
Resolution 0.005% Full Scale or
1mm
Question 2c
The piston type sensor is suitable for use when the
differential or static pressures of the process are high.
Moreover, it can withstand shock, vibrations and impulsive
pressure variations [4]
The bimetallic thermometer is suitable in “process, offshore,
power, chemical industries, HVAC and OEM applications”
[3]. It is preferred because of its high accuracy, dual and easy-
to-read scale, and faster response. Additionally, it is
hermetically sealed and put in a case that can withstand shock,
dust, vibration, and moisture.
An ultrasonic flowmeter is used in all water flow
measurements like pumping and metering. Also, it is used in
pipelines with exception to high viscosity liquids. It is
preferred in its use because of high accuracy and sensitivity
[2,5].
DP level sensors are appropriate when measuring liquid levels
up to 200m in industries. Additionally, they are accurate and
robust [1].
Question 3a
Signal conditioning devices are embedded into a
measurement system in industries to modify the signal into the
required standard format at the output. As such, signal
conditioning performs many functions in an industrial set up.
First, signal amplification increases the magnitude of a signal
to a level suitable for a digitization equipment. Second, signal
linearization is performed on signals with non-linear outputs.
For example, temperature measurement using thermocouples
requires built-in equipment to make the value being measured
linear to match the engineering standards. Besides, filtering is
essential to ensure that unwanted signals are removed from a
given measurement. For instance, low-pass filters that
eliminate unwanted higher frequencies. Moreover, modulation
may be applied to signals to convert them into a form that can
be easily transmitted.
Question 3b
Standards for signal transmission are shown in the table
below
Signal Type Range
Electric current 4-20mA
Voltage 0-5V or 0-10V
Pneumatic pressure 20-100kPa
Question 4
Deviation refers to the difference between the set point and the
feedback.
Set point refers to the desired output of a controller
Offset refers to the deviation between the steady-state value of
the controlled parameter and the set point value.
Two-step control refers to a system control where the output
alternates between two predetermined value.
Proportional control refers to a type of control which
compares the desired set point with an actual value to give an
output that is proportional to the current error.
PID control refers to Proportional-Integral-Derivative. These
three components are combined to produce a control signal. It
has a feedback loop for adjusting the control variable
depending on the present error, accumulated error, and the
predicted future error. Figure 6 below shows the PID
controller.
Parameter Specification
Accuracy ±1% for DN>10mm
±2% for DN<10mm
Range 0.001m/s to 99m/s
Resolution time <0.1ns
Dynamic gain Up to 89dB
Volume metering 0.001m3 to 100m3
Table 4: DP level sensor specifications
Parameter Specification
Accuracy ±0.1% Full Scale
Range 10m-200m
Span in the range 40mbar- 3600 mbar
Max. permissible
ambient temperature
–40 to +80 °C
Resolution 0.005% Full Scale or
1mm
Question 2c
The piston type sensor is suitable for use when the
differential or static pressures of the process are high.
Moreover, it can withstand shock, vibrations and impulsive
pressure variations [4]
The bimetallic thermometer is suitable in “process, offshore,
power, chemical industries, HVAC and OEM applications”
[3]. It is preferred because of its high accuracy, dual and easy-
to-read scale, and faster response. Additionally, it is
hermetically sealed and put in a case that can withstand shock,
dust, vibration, and moisture.
An ultrasonic flowmeter is used in all water flow
measurements like pumping and metering. Also, it is used in
pipelines with exception to high viscosity liquids. It is
preferred in its use because of high accuracy and sensitivity
[2,5].
DP level sensors are appropriate when measuring liquid levels
up to 200m in industries. Additionally, they are accurate and
robust [1].
Question 3a
Signal conditioning devices are embedded into a
measurement system in industries to modify the signal into the
required standard format at the output. As such, signal
conditioning performs many functions in an industrial set up.
First, signal amplification increases the magnitude of a signal
to a level suitable for a digitization equipment. Second, signal
linearization is performed on signals with non-linear outputs.
For example, temperature measurement using thermocouples
requires built-in equipment to make the value being measured
linear to match the engineering standards. Besides, filtering is
essential to ensure that unwanted signals are removed from a
given measurement. For instance, low-pass filters that
eliminate unwanted higher frequencies. Moreover, modulation
may be applied to signals to convert them into a form that can
be easily transmitted.
Question 3b
Standards for signal transmission are shown in the table
below
Signal Type Range
Electric current 4-20mA
Voltage 0-5V or 0-10V
Pneumatic pressure 20-100kPa
Question 4
Deviation refers to the difference between the set point and the
feedback.
Set point refers to the desired output of a controller
Offset refers to the deviation between the steady-state value of
the controlled parameter and the set point value.
Two-step control refers to a system control where the output
alternates between two predetermined value.
Proportional control refers to a type of control which
compares the desired set point with an actual value to give an
output that is proportional to the current error.
PID control refers to Proportional-Integral-Derivative. These
three components are combined to produce a control signal. It
has a feedback loop for adjusting the control variable
depending on the present error, accumulated error, and the
predicted future error. Figure 6 below shows the PID
controller.
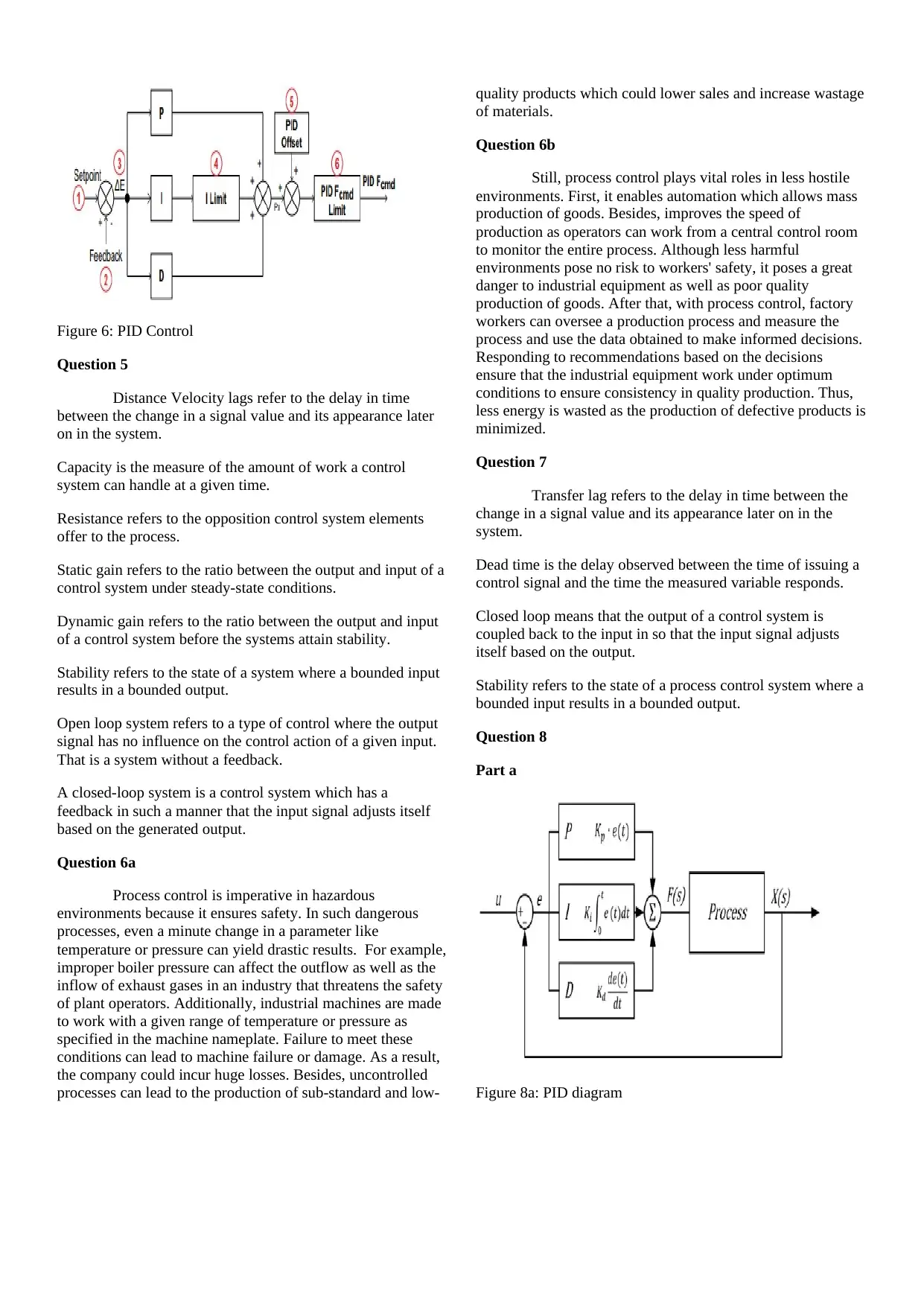
Figure 6: PID Control
Question 5
Distance Velocity lags refer to the delay in time
between the change in a signal value and its appearance later
on in the system.
Capacity is the measure of the amount of work a control
system can handle at a given time.
Resistance refers to the opposition control system elements
offer to the process.
Static gain refers to the ratio between the output and input of a
control system under steady-state conditions.
Dynamic gain refers to the ratio between the output and input
of a control system before the systems attain stability.
Stability refers to the state of a system where a bounded input
results in a bounded output.
Open loop system refers to a type of control where the output
signal has no influence on the control action of a given input.
That is a system without a feedback.
A closed-loop system is a control system which has a
feedback in such a manner that the input signal adjusts itself
based on the generated output.
Question 6a
Process control is imperative in hazardous
environments because it ensures safety. In such dangerous
processes, even a minute change in a parameter like
temperature or pressure can yield drastic results. For example,
improper boiler pressure can affect the outflow as well as the
inflow of exhaust gases in an industry that threatens the safety
of plant operators. Additionally, industrial machines are made
to work with a given range of temperature or pressure as
specified in the machine nameplate. Failure to meet these
conditions can lead to machine failure or damage. As a result,
the company could incur huge losses. Besides, uncontrolled
processes can lead to the production of sub-standard and low-
quality products which could lower sales and increase wastage
of materials.
Question 6b
Still, process control plays vital roles in less hostile
environments. First, it enables automation which allows mass
production of goods. Besides, improves the speed of
production as operators can work from a central control room
to monitor the entire process. Although less harmful
environments pose no risk to workers' safety, it poses a great
danger to industrial equipment as well as poor quality
production of goods. After that, with process control, factory
workers can oversee a production process and measure the
process and use the data obtained to make informed decisions.
Responding to recommendations based on the decisions
ensure that the industrial equipment work under optimum
conditions to ensure consistency in quality production. Thus,
less energy is wasted as the production of defective products is
minimized.
Question 7
Transfer lag refers to the delay in time between the
change in a signal value and its appearance later on in the
system.
Dead time is the delay observed between the time of issuing a
control signal and the time the measured variable responds.
Closed loop means that the output of a control system is
coupled back to the input in so that the input signal adjusts
itself based on the output.
Stability refers to the state of a process control system where a
bounded input results in a bounded output.
Question 8
Part a
Figure 8a: PID diagram
Question 5
Distance Velocity lags refer to the delay in time
between the change in a signal value and its appearance later
on in the system.
Capacity is the measure of the amount of work a control
system can handle at a given time.
Resistance refers to the opposition control system elements
offer to the process.
Static gain refers to the ratio between the output and input of a
control system under steady-state conditions.
Dynamic gain refers to the ratio between the output and input
of a control system before the systems attain stability.
Stability refers to the state of a system where a bounded input
results in a bounded output.
Open loop system refers to a type of control where the output
signal has no influence on the control action of a given input.
That is a system without a feedback.
A closed-loop system is a control system which has a
feedback in such a manner that the input signal adjusts itself
based on the generated output.
Question 6a
Process control is imperative in hazardous
environments because it ensures safety. In such dangerous
processes, even a minute change in a parameter like
temperature or pressure can yield drastic results. For example,
improper boiler pressure can affect the outflow as well as the
inflow of exhaust gases in an industry that threatens the safety
of plant operators. Additionally, industrial machines are made
to work with a given range of temperature or pressure as
specified in the machine nameplate. Failure to meet these
conditions can lead to machine failure or damage. As a result,
the company could incur huge losses. Besides, uncontrolled
processes can lead to the production of sub-standard and low-
quality products which could lower sales and increase wastage
of materials.
Question 6b
Still, process control plays vital roles in less hostile
environments. First, it enables automation which allows mass
production of goods. Besides, improves the speed of
production as operators can work from a central control room
to monitor the entire process. Although less harmful
environments pose no risk to workers' safety, it poses a great
danger to industrial equipment as well as poor quality
production of goods. After that, with process control, factory
workers can oversee a production process and measure the
process and use the data obtained to make informed decisions.
Responding to recommendations based on the decisions
ensure that the industrial equipment work under optimum
conditions to ensure consistency in quality production. Thus,
less energy is wasted as the production of defective products is
minimized.
Question 7
Transfer lag refers to the delay in time between the
change in a signal value and its appearance later on in the
system.
Dead time is the delay observed between the time of issuing a
control signal and the time the measured variable responds.
Closed loop means that the output of a control system is
coupled back to the input in so that the input signal adjusts
itself based on the output.
Stability refers to the state of a process control system where a
bounded input results in a bounded output.
Question 8
Part a
Figure 8a: PID diagram
Secure Best Marks with AI Grader
Need help grading? Try our AI Grader for instant feedback on your assignments.
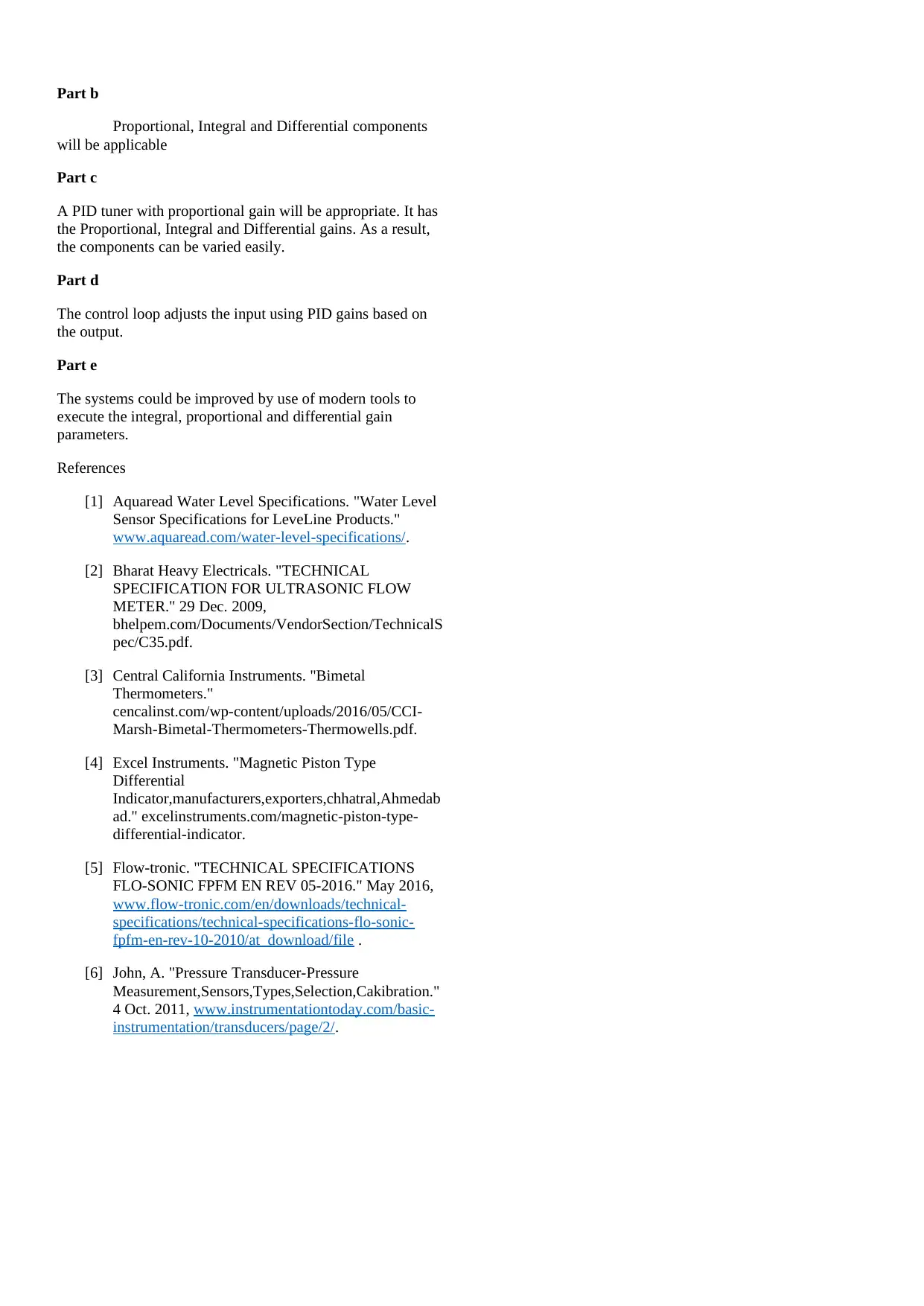
Part b
Proportional, Integral and Differential components
will be applicable
Part c
A PID tuner with proportional gain will be appropriate. It has
the Proportional, Integral and Differential gains. As a result,
the components can be varied easily.
Part d
The control loop adjusts the input using PID gains based on
the output.
Part e
The systems could be improved by use of modern tools to
execute the integral, proportional and differential gain
parameters.
References
[1] Aquaread Water Level Specifications. "Water Level
Sensor Specifications for LeveLine Products."
www.aquaread.com/water-level-specifications/.
[2] Bharat Heavy Electricals. "TECHNICAL
SPECIFICATION FOR ULTRASONIC FLOW
METER." 29 Dec. 2009,
bhelpem.com/Documents/VendorSection/TechnicalS
pec/C35.pdf.
[3] Central California Instruments. "Bimetal
Thermometers."
cencalinst.com/wp-content/uploads/2016/05/CCI-
Marsh-Bimetal-Thermometers-Thermowells.pdf.
[4] Excel Instruments. "Magnetic Piston Type
Differential
Indicator,manufacturers,exporters,chhatral,Ahmedab
ad." excelinstruments.com/magnetic-piston-type-
differential-indicator.
[5] Flow-tronic. "TECHNICAL SPECIFICATIONS
FLO-SONIC FPFM EN REV 05-2016." May 2016,
www.flow-tronic.com/en/downloads/technical-
specifications/technical-specifications-flo-sonic-
fpfm-en-rev-10-2010/at_download/file .
[6] John, A. "Pressure Transducer-Pressure
Measurement,Sensors,Types,Selection,Cakibration."
4 Oct. 2011, www.instrumentationtoday.com/basic-
instrumentation/transducers/page/2/.
Proportional, Integral and Differential components
will be applicable
Part c
A PID tuner with proportional gain will be appropriate. It has
the Proportional, Integral and Differential gains. As a result,
the components can be varied easily.
Part d
The control loop adjusts the input using PID gains based on
the output.
Part e
The systems could be improved by use of modern tools to
execute the integral, proportional and differential gain
parameters.
References
[1] Aquaread Water Level Specifications. "Water Level
Sensor Specifications for LeveLine Products."
www.aquaread.com/water-level-specifications/.
[2] Bharat Heavy Electricals. "TECHNICAL
SPECIFICATION FOR ULTRASONIC FLOW
METER." 29 Dec. 2009,
bhelpem.com/Documents/VendorSection/TechnicalS
pec/C35.pdf.
[3] Central California Instruments. "Bimetal
Thermometers."
cencalinst.com/wp-content/uploads/2016/05/CCI-
Marsh-Bimetal-Thermometers-Thermowells.pdf.
[4] Excel Instruments. "Magnetic Piston Type
Differential
Indicator,manufacturers,exporters,chhatral,Ahmedab
ad." excelinstruments.com/magnetic-piston-type-
differential-indicator.
[5] Flow-tronic. "TECHNICAL SPECIFICATIONS
FLO-SONIC FPFM EN REV 05-2016." May 2016,
www.flow-tronic.com/en/downloads/technical-
specifications/technical-specifications-flo-sonic-
fpfm-en-rev-10-2010/at_download/file .
[6] John, A. "Pressure Transducer-Pressure
Measurement,Sensors,Types,Selection,Cakibration."
4 Oct. 2011, www.instrumentationtoday.com/basic-
instrumentation/transducers/page/2/.
1 out of 5

Your All-in-One AI-Powered Toolkit for Academic Success.
+13062052269
info@desklib.com
Available 24*7 on WhatsApp / Email
Unlock your academic potential
© 2024 | Zucol Services PVT LTD | All rights reserved.