Inventory Management: Techniques, Analysis, and Financial Implications
VerifiedAdded on 2020/03/01
|12
|2800
|108
Report
AI Summary
This report provides a comprehensive overview of inventory management, a critical area for supply chain executives. It begins with an introduction to the core concepts, emphasizing the need for balancing supply and demand in the face of unpredictable forecasts. The analysis section delves into various inventory management techniques, including Min-Max ordering, reorder point strategy, economic order quantity (EOQ), and period order quantity (POQ), outlining the advantages and disadvantages of each. The report then explores the importance of inventory accuracy, the hidden costs associated with excessive inventory, and the financial implications of effective inventory management. It highlights how proper inventory control can expose operational inefficiencies and positively impact a company's bottom line, emphasizing the financial benefits of reducing inventory investment and improving inventory turnover. The report concludes by underscoring the significance of optimizing inventory practices to improve overall financial performance in a competitive business environment.
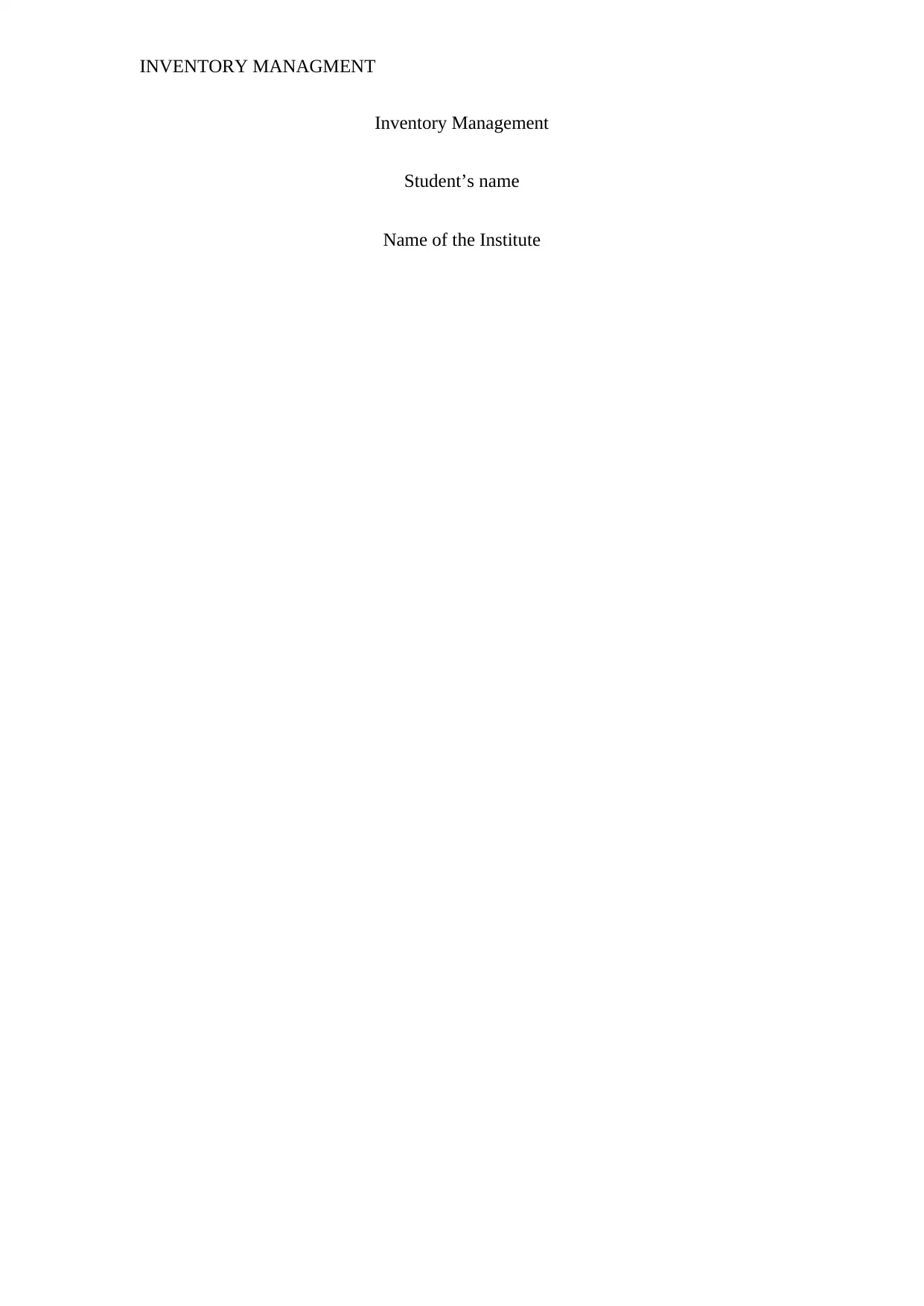
INVENTORY MANAGMENT
Inventory Management
Student’s name
Name of the Institute
Inventory Management
Student’s name
Name of the Institute
Secure Best Marks with AI Grader
Need help grading? Try our AI Grader for instant feedback on your assignments.
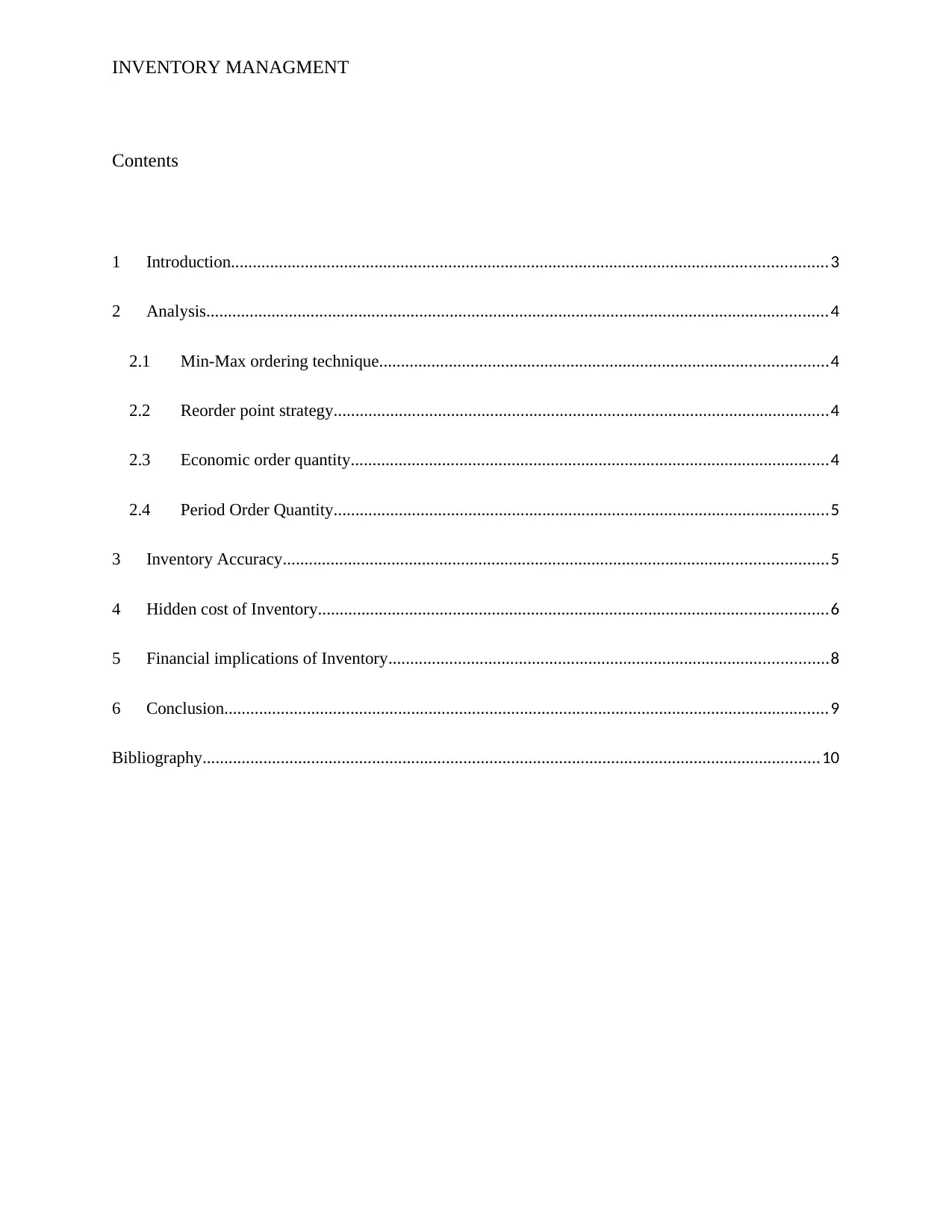
INVENTORY MANAGMENT
Contents
1 Introduction.........................................................................................................................................3
2 Analysis...............................................................................................................................................4
2.1 Min-Max ordering technique.......................................................................................................4
2.2 Reorder point strategy..................................................................................................................4
2.3 Economic order quantity..............................................................................................................4
2.4 Period Order Quantity..................................................................................................................5
3 Inventory Accuracy.............................................................................................................................5
4 Hidden cost of Inventory.....................................................................................................................6
5 Financial implications of Inventory.....................................................................................................8
6 Conclusion...........................................................................................................................................9
Bibliography..............................................................................................................................................10
Contents
1 Introduction.........................................................................................................................................3
2 Analysis...............................................................................................................................................4
2.1 Min-Max ordering technique.......................................................................................................4
2.2 Reorder point strategy..................................................................................................................4
2.3 Economic order quantity..............................................................................................................4
2.4 Period Order Quantity..................................................................................................................5
3 Inventory Accuracy.............................................................................................................................5
4 Hidden cost of Inventory.....................................................................................................................6
5 Financial implications of Inventory.....................................................................................................8
6 Conclusion...........................................................................................................................................9
Bibliography..............................................................................................................................................10
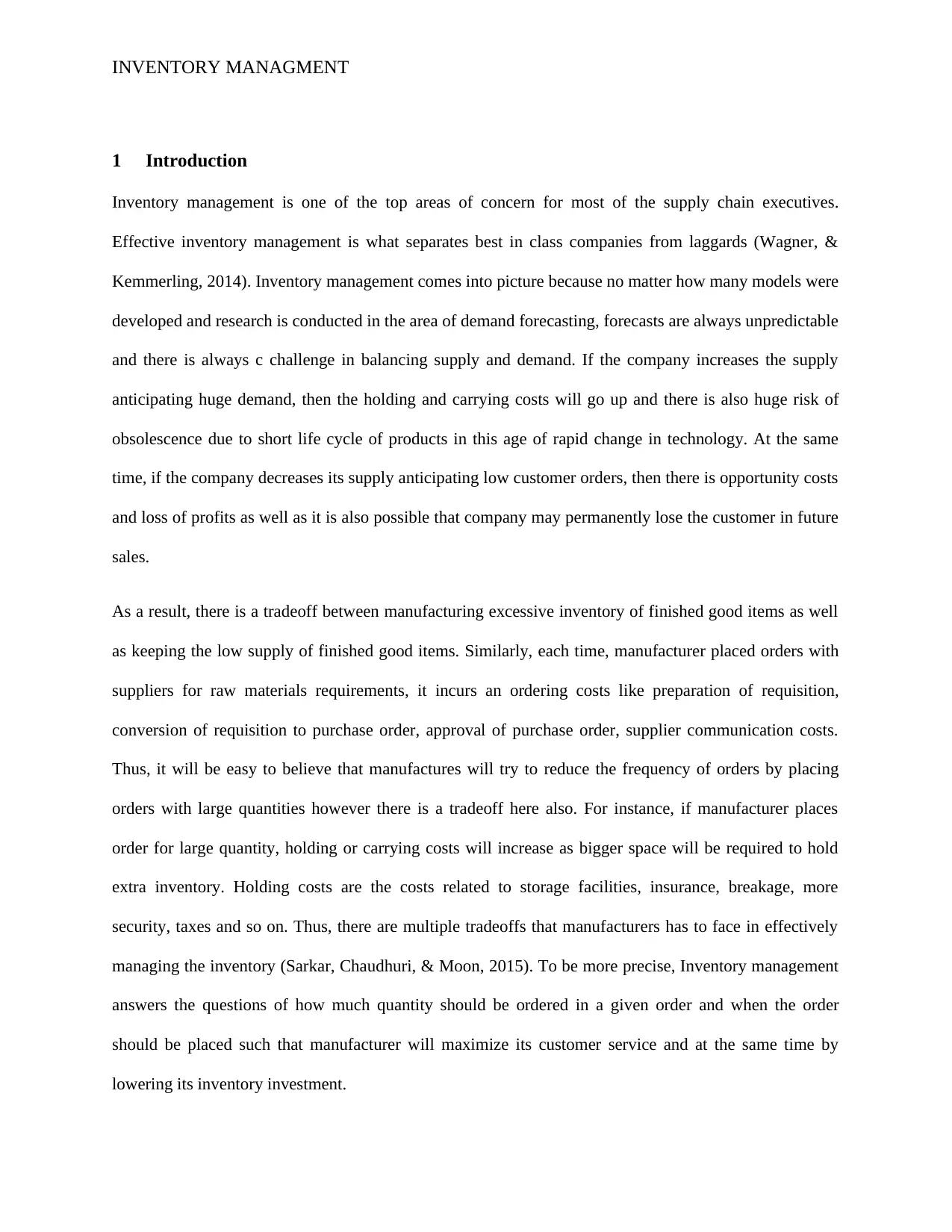
INVENTORY MANAGMENT
1 Introduction
Inventory management is one of the top areas of concern for most of the supply chain executives.
Effective inventory management is what separates best in class companies from laggards (Wagner, &
Kemmerling, 2014). Inventory management comes into picture because no matter how many models were
developed and research is conducted in the area of demand forecasting, forecasts are always unpredictable
and there is always c challenge in balancing supply and demand. If the company increases the supply
anticipating huge demand, then the holding and carrying costs will go up and there is also huge risk of
obsolescence due to short life cycle of products in this age of rapid change in technology. At the same
time, if the company decreases its supply anticipating low customer orders, then there is opportunity costs
and loss of profits as well as it is also possible that company may permanently lose the customer in future
sales.
As a result, there is a tradeoff between manufacturing excessive inventory of finished good items as well
as keeping the low supply of finished good items. Similarly, each time, manufacturer placed orders with
suppliers for raw materials requirements, it incurs an ordering costs like preparation of requisition,
conversion of requisition to purchase order, approval of purchase order, supplier communication costs.
Thus, it will be easy to believe that manufactures will try to reduce the frequency of orders by placing
orders with large quantities however there is a tradeoff here also. For instance, if manufacturer places
order for large quantity, holding or carrying costs will increase as bigger space will be required to hold
extra inventory. Holding costs are the costs related to storage facilities, insurance, breakage, more
security, taxes and so on. Thus, there are multiple tradeoffs that manufacturers has to face in effectively
managing the inventory (Sarkar, Chaudhuri, & Moon, 2015). To be more precise, Inventory management
answers the questions of how much quantity should be ordered in a given order and when the order
should be placed such that manufacturer will maximize its customer service and at the same time by
lowering its inventory investment.
1 Introduction
Inventory management is one of the top areas of concern for most of the supply chain executives.
Effective inventory management is what separates best in class companies from laggards (Wagner, &
Kemmerling, 2014). Inventory management comes into picture because no matter how many models were
developed and research is conducted in the area of demand forecasting, forecasts are always unpredictable
and there is always c challenge in balancing supply and demand. If the company increases the supply
anticipating huge demand, then the holding and carrying costs will go up and there is also huge risk of
obsolescence due to short life cycle of products in this age of rapid change in technology. At the same
time, if the company decreases its supply anticipating low customer orders, then there is opportunity costs
and loss of profits as well as it is also possible that company may permanently lose the customer in future
sales.
As a result, there is a tradeoff between manufacturing excessive inventory of finished good items as well
as keeping the low supply of finished good items. Similarly, each time, manufacturer placed orders with
suppliers for raw materials requirements, it incurs an ordering costs like preparation of requisition,
conversion of requisition to purchase order, approval of purchase order, supplier communication costs.
Thus, it will be easy to believe that manufactures will try to reduce the frequency of orders by placing
orders with large quantities however there is a tradeoff here also. For instance, if manufacturer places
order for large quantity, holding or carrying costs will increase as bigger space will be required to hold
extra inventory. Holding costs are the costs related to storage facilities, insurance, breakage, more
security, taxes and so on. Thus, there are multiple tradeoffs that manufacturers has to face in effectively
managing the inventory (Sarkar, Chaudhuri, & Moon, 2015). To be more precise, Inventory management
answers the questions of how much quantity should be ordered in a given order and when the order
should be placed such that manufacturer will maximize its customer service and at the same time by
lowering its inventory investment.
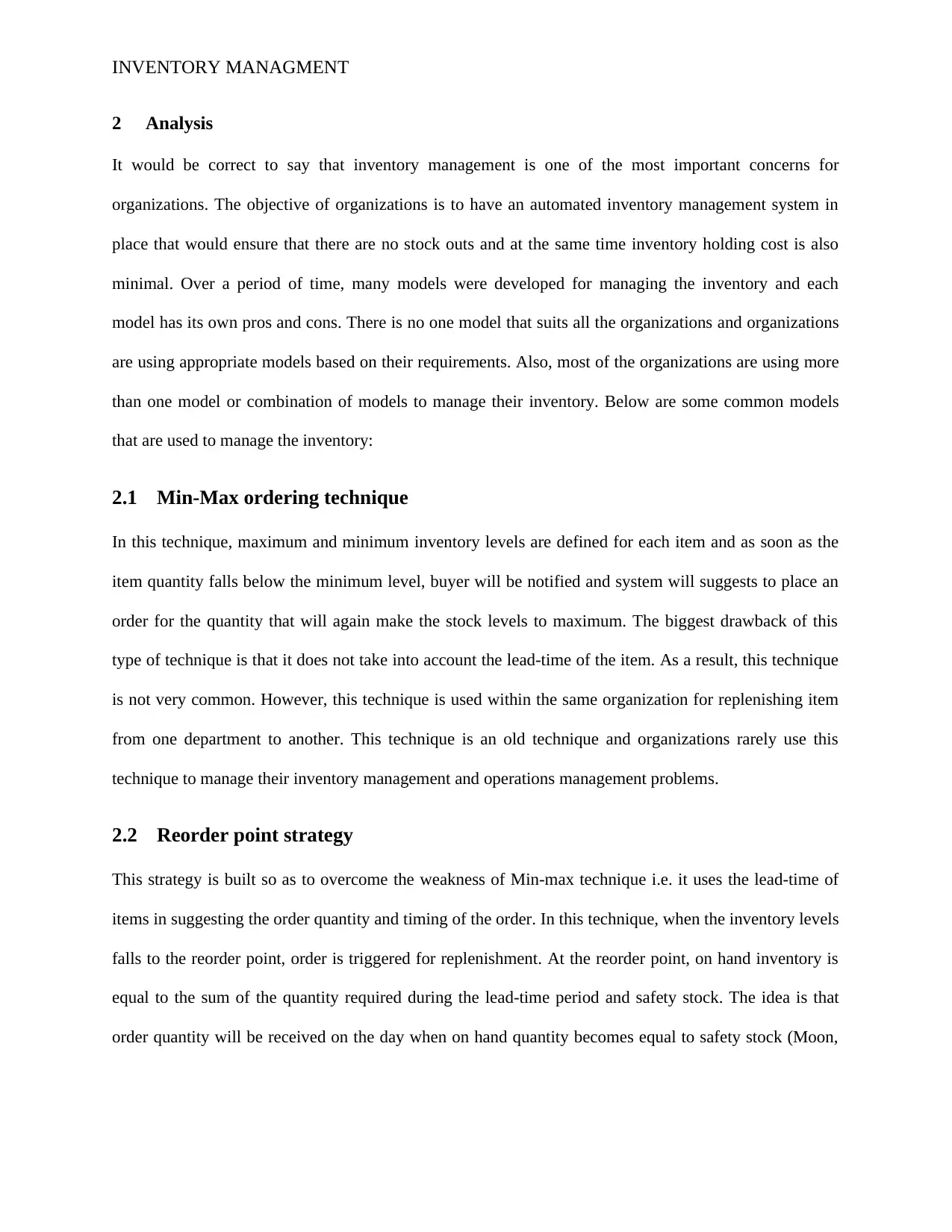
INVENTORY MANAGMENT
2 Analysis
It would be correct to say that inventory management is one of the most important concerns for
organizations. The objective of organizations is to have an automated inventory management system in
place that would ensure that there are no stock outs and at the same time inventory holding cost is also
minimal. Over a period of time, many models were developed for managing the inventory and each
model has its own pros and cons. There is no one model that suits all the organizations and organizations
are using appropriate models based on their requirements. Also, most of the organizations are using more
than one model or combination of models to manage their inventory. Below are some common models
that are used to manage the inventory:
2.1 Min-Max ordering technique
In this technique, maximum and minimum inventory levels are defined for each item and as soon as the
item quantity falls below the minimum level, buyer will be notified and system will suggests to place an
order for the quantity that will again make the stock levels to maximum. The biggest drawback of this
type of technique is that it does not take into account the lead-time of the item. As a result, this technique
is not very common. However, this technique is used within the same organization for replenishing item
from one department to another. This technique is an old technique and organizations rarely use this
technique to manage their inventory management and operations management problems.
2.2 Reorder point strategy
This strategy is built so as to overcome the weakness of Min-max technique i.e. it uses the lead-time of
items in suggesting the order quantity and timing of the order. In this technique, when the inventory levels
falls to the reorder point, order is triggered for replenishment. At the reorder point, on hand inventory is
equal to the sum of the quantity required during the lead-time period and safety stock. The idea is that
order quantity will be received on the day when on hand quantity becomes equal to safety stock (Moon,
2 Analysis
It would be correct to say that inventory management is one of the most important concerns for
organizations. The objective of organizations is to have an automated inventory management system in
place that would ensure that there are no stock outs and at the same time inventory holding cost is also
minimal. Over a period of time, many models were developed for managing the inventory and each
model has its own pros and cons. There is no one model that suits all the organizations and organizations
are using appropriate models based on their requirements. Also, most of the organizations are using more
than one model or combination of models to manage their inventory. Below are some common models
that are used to manage the inventory:
2.1 Min-Max ordering technique
In this technique, maximum and minimum inventory levels are defined for each item and as soon as the
item quantity falls below the minimum level, buyer will be notified and system will suggests to place an
order for the quantity that will again make the stock levels to maximum. The biggest drawback of this
type of technique is that it does not take into account the lead-time of the item. As a result, this technique
is not very common. However, this technique is used within the same organization for replenishing item
from one department to another. This technique is an old technique and organizations rarely use this
technique to manage their inventory management and operations management problems.
2.2 Reorder point strategy
This strategy is built so as to overcome the weakness of Min-max technique i.e. it uses the lead-time of
items in suggesting the order quantity and timing of the order. In this technique, when the inventory levels
falls to the reorder point, order is triggered for replenishment. At the reorder point, on hand inventory is
equal to the sum of the quantity required during the lead-time period and safety stock. The idea is that
order quantity will be received on the day when on hand quantity becomes equal to safety stock (Moon,
Secure Best Marks with AI Grader
Need help grading? Try our AI Grader for instant feedback on your assignments.
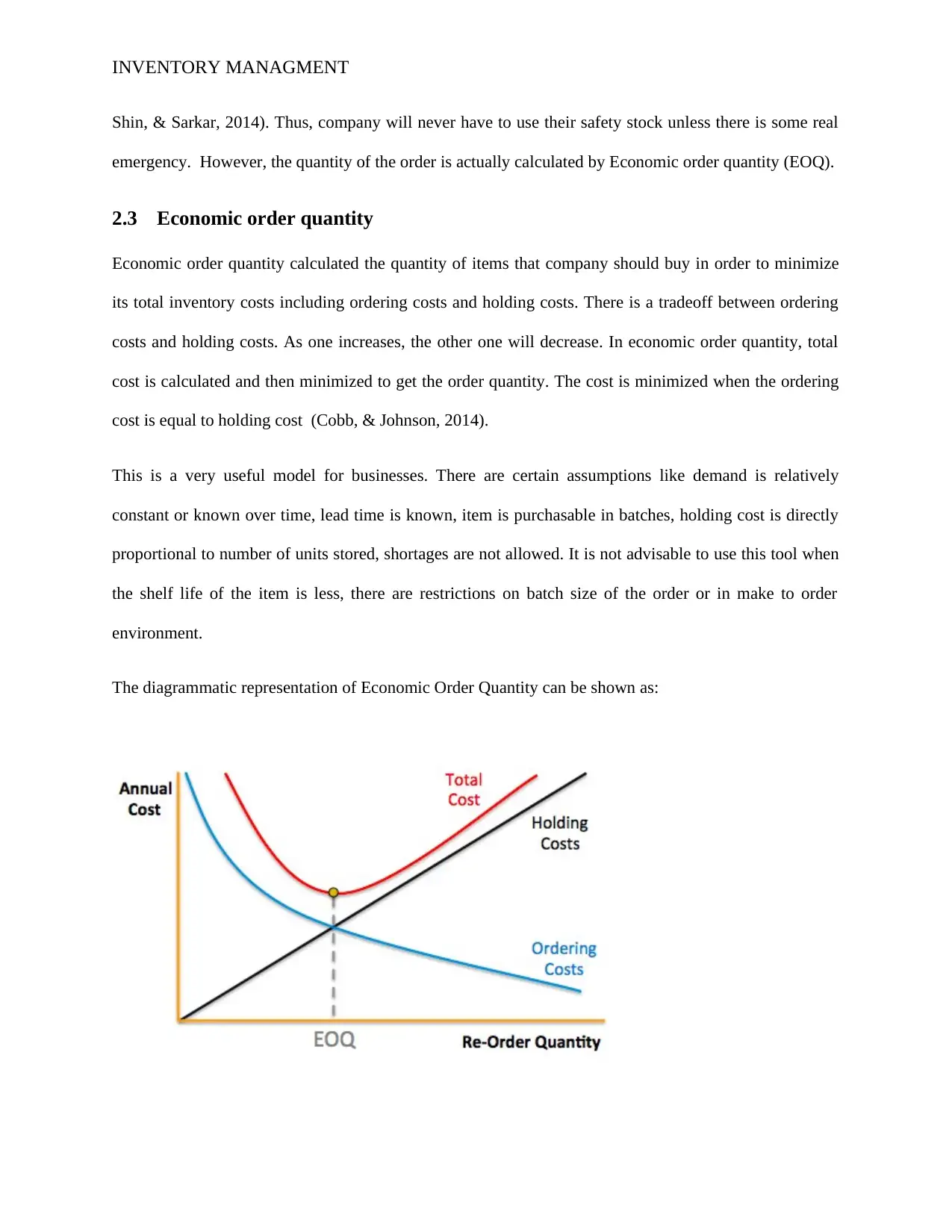
INVENTORY MANAGMENT
Shin, & Sarkar, 2014). Thus, company will never have to use their safety stock unless there is some real
emergency. However, the quantity of the order is actually calculated by Economic order quantity (EOQ).
2.3 Economic order quantity
Economic order quantity calculated the quantity of items that company should buy in order to minimize
its total inventory costs including ordering costs and holding costs. There is a tradeoff between ordering
costs and holding costs. As one increases, the other one will decrease. In economic order quantity, total
cost is calculated and then minimized to get the order quantity. The cost is minimized when the ordering
cost is equal to holding cost (Cobb, & Johnson, 2014).
This is a very useful model for businesses. There are certain assumptions like demand is relatively
constant or known over time, lead time is known, item is purchasable in batches, holding cost is directly
proportional to number of units stored, shortages are not allowed. It is not advisable to use this tool when
the shelf life of the item is less, there are restrictions on batch size of the order or in make to order
environment.
The diagrammatic representation of Economic Order Quantity can be shown as:
Shin, & Sarkar, 2014). Thus, company will never have to use their safety stock unless there is some real
emergency. However, the quantity of the order is actually calculated by Economic order quantity (EOQ).
2.3 Economic order quantity
Economic order quantity calculated the quantity of items that company should buy in order to minimize
its total inventory costs including ordering costs and holding costs. There is a tradeoff between ordering
costs and holding costs. As one increases, the other one will decrease. In economic order quantity, total
cost is calculated and then minimized to get the order quantity. The cost is minimized when the ordering
cost is equal to holding cost (Cobb, & Johnson, 2014).
This is a very useful model for businesses. There are certain assumptions like demand is relatively
constant or known over time, lead time is known, item is purchasable in batches, holding cost is directly
proportional to number of units stored, shortages are not allowed. It is not advisable to use this tool when
the shelf life of the item is less, there are restrictions on batch size of the order or in make to order
environment.
The diagrammatic representation of Economic Order Quantity can be shown as:
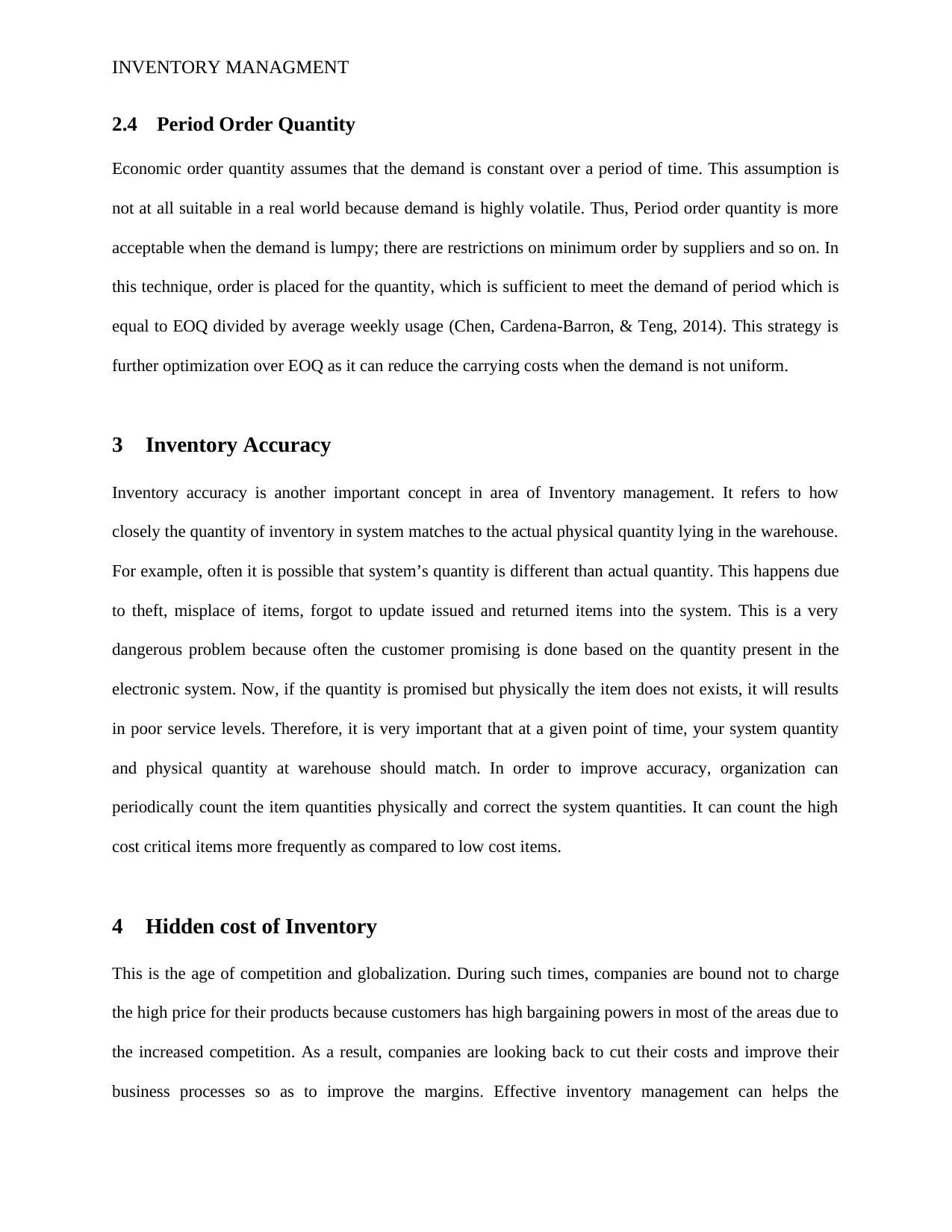
INVENTORY MANAGMENT
2.4 Period Order Quantity
Economic order quantity assumes that the demand is constant over a period of time. This assumption is
not at all suitable in a real world because demand is highly volatile. Thus, Period order quantity is more
acceptable when the demand is lumpy; there are restrictions on minimum order by suppliers and so on. In
this technique, order is placed for the quantity, which is sufficient to meet the demand of period which is
equal to EOQ divided by average weekly usage (Chen, Cardena-Barron, & Teng, 2014). This strategy is
further optimization over EOQ as it can reduce the carrying costs when the demand is not uniform.
3 Inventory Accuracy
Inventory accuracy is another important concept in area of Inventory management. It refers to how
closely the quantity of inventory in system matches to the actual physical quantity lying in the warehouse.
For example, often it is possible that system’s quantity is different than actual quantity. This happens due
to theft, misplace of items, forgot to update issued and returned items into the system. This is a very
dangerous problem because often the customer promising is done based on the quantity present in the
electronic system. Now, if the quantity is promised but physically the item does not exists, it will results
in poor service levels. Therefore, it is very important that at a given point of time, your system quantity
and physical quantity at warehouse should match. In order to improve accuracy, organization can
periodically count the item quantities physically and correct the system quantities. It can count the high
cost critical items more frequently as compared to low cost items.
4 Hidden cost of Inventory
This is the age of competition and globalization. During such times, companies are bound not to charge
the high price for their products because customers has high bargaining powers in most of the areas due to
the increased competition. As a result, companies are looking back to cut their costs and improve their
business processes so as to improve the margins. Effective inventory management can helps the
2.4 Period Order Quantity
Economic order quantity assumes that the demand is constant over a period of time. This assumption is
not at all suitable in a real world because demand is highly volatile. Thus, Period order quantity is more
acceptable when the demand is lumpy; there are restrictions on minimum order by suppliers and so on. In
this technique, order is placed for the quantity, which is sufficient to meet the demand of period which is
equal to EOQ divided by average weekly usage (Chen, Cardena-Barron, & Teng, 2014). This strategy is
further optimization over EOQ as it can reduce the carrying costs when the demand is not uniform.
3 Inventory Accuracy
Inventory accuracy is another important concept in area of Inventory management. It refers to how
closely the quantity of inventory in system matches to the actual physical quantity lying in the warehouse.
For example, often it is possible that system’s quantity is different than actual quantity. This happens due
to theft, misplace of items, forgot to update issued and returned items into the system. This is a very
dangerous problem because often the customer promising is done based on the quantity present in the
electronic system. Now, if the quantity is promised but physically the item does not exists, it will results
in poor service levels. Therefore, it is very important that at a given point of time, your system quantity
and physical quantity at warehouse should match. In order to improve accuracy, organization can
periodically count the item quantities physically and correct the system quantities. It can count the high
cost critical items more frequently as compared to low cost items.
4 Hidden cost of Inventory
This is the age of competition and globalization. During such times, companies are bound not to charge
the high price for their products because customers has high bargaining powers in most of the areas due to
the increased competition. As a result, companies are looking back to cut their costs and improve their
business processes so as to improve the margins. Effective inventory management can helps the
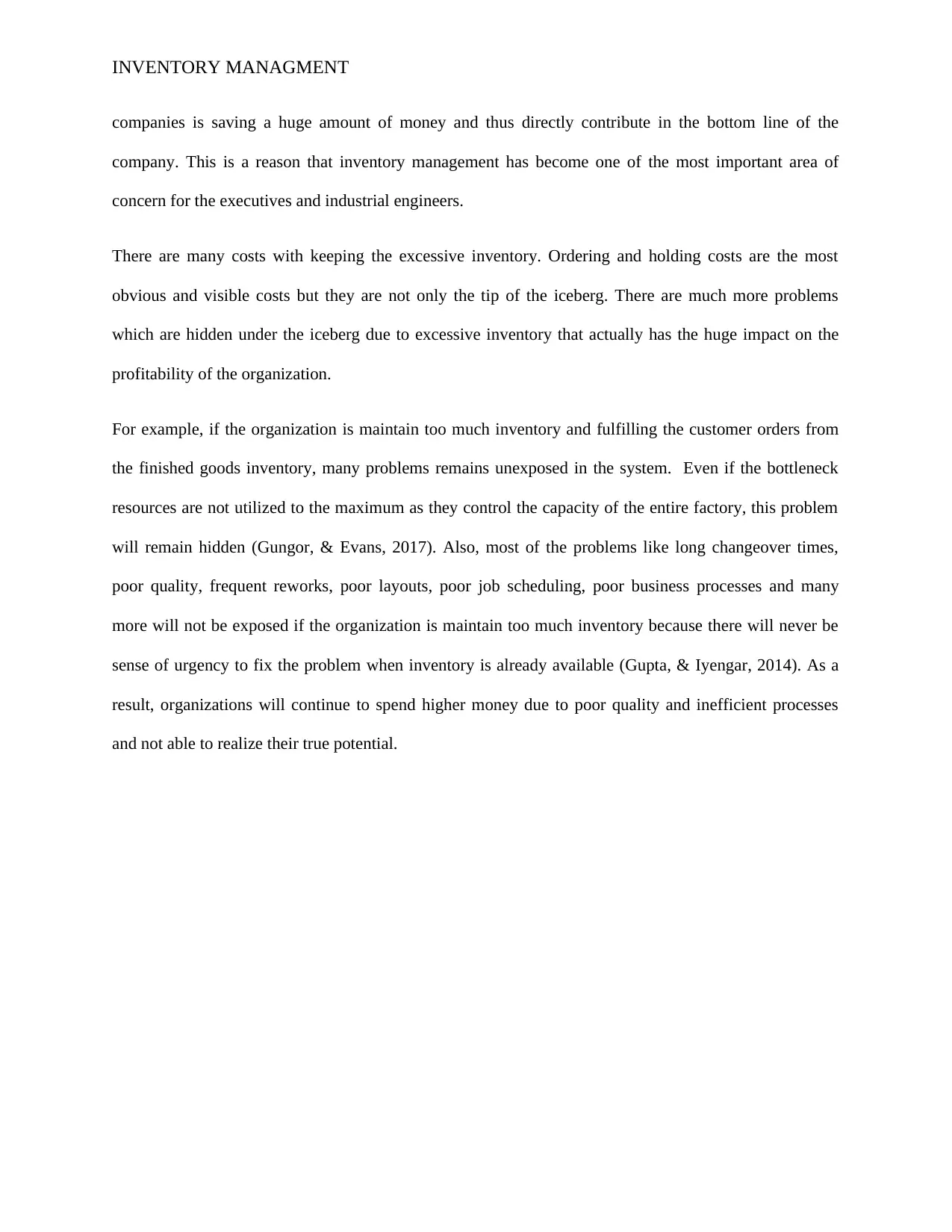
INVENTORY MANAGMENT
companies is saving a huge amount of money and thus directly contribute in the bottom line of the
company. This is a reason that inventory management has become one of the most important area of
concern for the executives and industrial engineers.
There are many costs with keeping the excessive inventory. Ordering and holding costs are the most
obvious and visible costs but they are not only the tip of the iceberg. There are much more problems
which are hidden under the iceberg due to excessive inventory that actually has the huge impact on the
profitability of the organization.
For example, if the organization is maintain too much inventory and fulfilling the customer orders from
the finished goods inventory, many problems remains unexposed in the system. Even if the bottleneck
resources are not utilized to the maximum as they control the capacity of the entire factory, this problem
will remain hidden (Gungor, & Evans, 2017). Also, most of the problems like long changeover times,
poor quality, frequent reworks, poor layouts, poor job scheduling, poor business processes and many
more will not be exposed if the organization is maintain too much inventory because there will never be
sense of urgency to fix the problem when inventory is already available (Gupta, & Iyengar, 2014). As a
result, organizations will continue to spend higher money due to poor quality and inefficient processes
and not able to realize their true potential.
companies is saving a huge amount of money and thus directly contribute in the bottom line of the
company. This is a reason that inventory management has become one of the most important area of
concern for the executives and industrial engineers.
There are many costs with keeping the excessive inventory. Ordering and holding costs are the most
obvious and visible costs but they are not only the tip of the iceberg. There are much more problems
which are hidden under the iceberg due to excessive inventory that actually has the huge impact on the
profitability of the organization.
For example, if the organization is maintain too much inventory and fulfilling the customer orders from
the finished goods inventory, many problems remains unexposed in the system. Even if the bottleneck
resources are not utilized to the maximum as they control the capacity of the entire factory, this problem
will remain hidden (Gungor, & Evans, 2017). Also, most of the problems like long changeover times,
poor quality, frequent reworks, poor layouts, poor job scheduling, poor business processes and many
more will not be exposed if the organization is maintain too much inventory because there will never be
sense of urgency to fix the problem when inventory is already available (Gupta, & Iyengar, 2014). As a
result, organizations will continue to spend higher money due to poor quality and inefficient processes
and not able to realize their true potential.
Paraphrase This Document
Need a fresh take? Get an instant paraphrase of this document with our AI Paraphraser
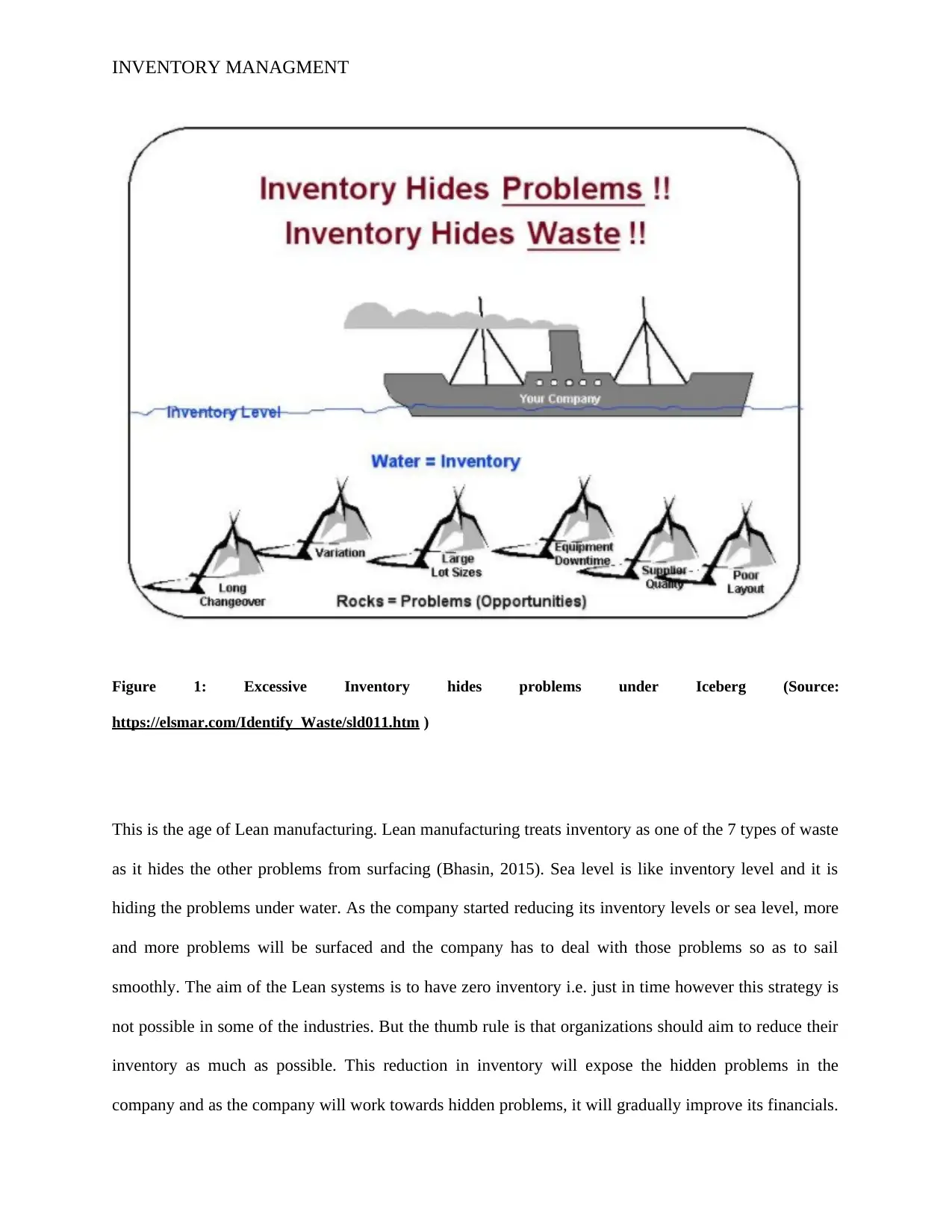
INVENTORY MANAGMENT
Figure 1: Excessive Inventory hides problems under Iceberg (Source:
https://elsmar.com/Identify_Waste/sld011.htm )
This is the age of Lean manufacturing. Lean manufacturing treats inventory as one of the 7 types of waste
as it hides the other problems from surfacing (Bhasin, 2015). Sea level is like inventory level and it is
hiding the problems under water. As the company started reducing its inventory levels or sea level, more
and more problems will be surfaced and the company has to deal with those problems so as to sail
smoothly. The aim of the Lean systems is to have zero inventory i.e. just in time however this strategy is
not possible in some of the industries. But the thumb rule is that organizations should aim to reduce their
inventory as much as possible. This reduction in inventory will expose the hidden problems in the
company and as the company will work towards hidden problems, it will gradually improve its financials.
Figure 1: Excessive Inventory hides problems under Iceberg (Source:
https://elsmar.com/Identify_Waste/sld011.htm )
This is the age of Lean manufacturing. Lean manufacturing treats inventory as one of the 7 types of waste
as it hides the other problems from surfacing (Bhasin, 2015). Sea level is like inventory level and it is
hiding the problems under water. As the company started reducing its inventory levels or sea level, more
and more problems will be surfaced and the company has to deal with those problems so as to sail
smoothly. The aim of the Lean systems is to have zero inventory i.e. just in time however this strategy is
not possible in some of the industries. But the thumb rule is that organizations should aim to reduce their
inventory as much as possible. This reduction in inventory will expose the hidden problems in the
company and as the company will work towards hidden problems, it will gradually improve its financials.
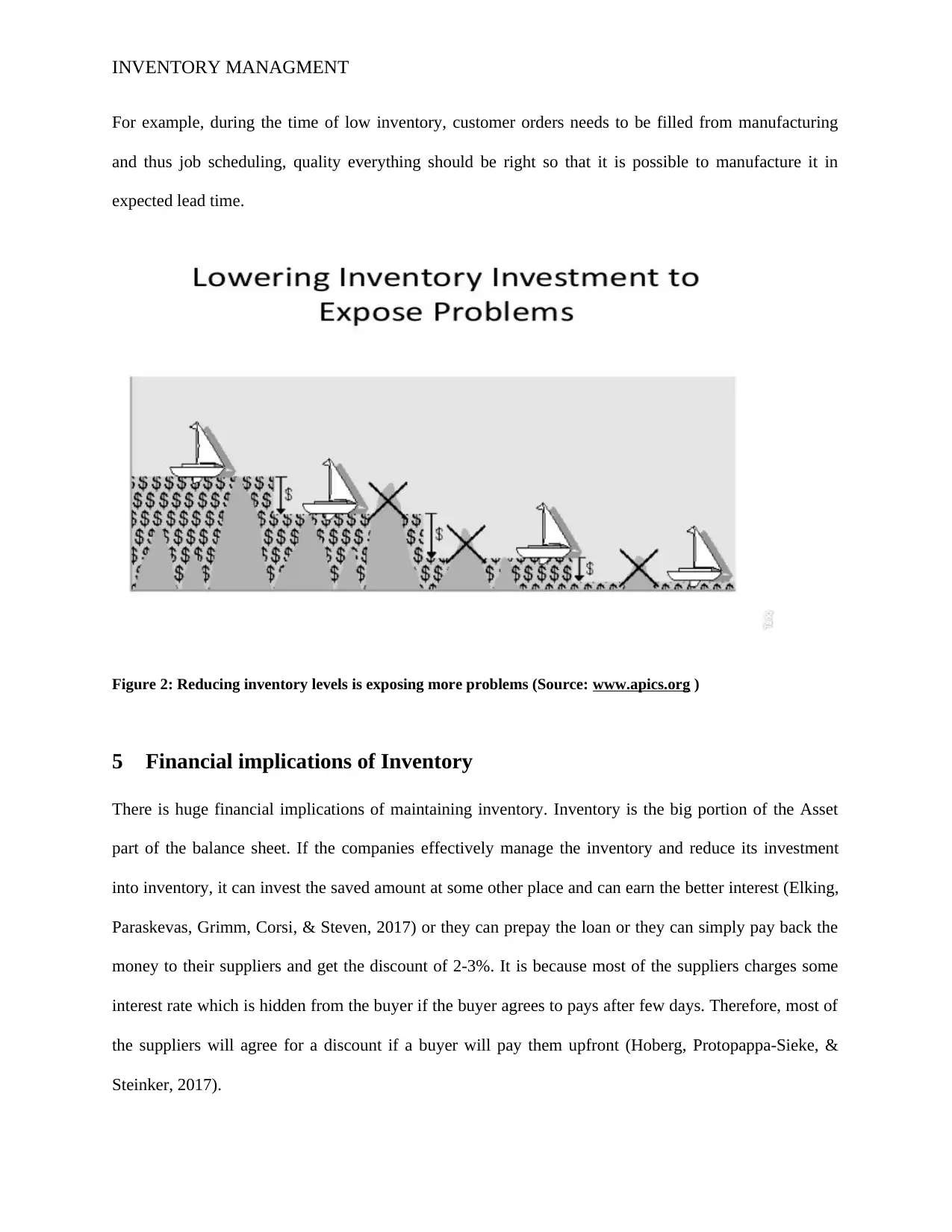
INVENTORY MANAGMENT
For example, during the time of low inventory, customer orders needs to be filled from manufacturing
and thus job scheduling, quality everything should be right so that it is possible to manufacture it in
expected lead time.
Figure 2: Reducing inventory levels is exposing more problems (Source: www.apics.org )
5 Financial implications of Inventory
There is huge financial implications of maintaining inventory. Inventory is the big portion of the Asset
part of the balance sheet. If the companies effectively manage the inventory and reduce its investment
into inventory, it can invest the saved amount at some other place and can earn the better interest (Elking,
Paraskevas, Grimm, Corsi, & Steven, 2017) or they can prepay the loan or they can simply pay back the
money to their suppliers and get the discount of 2-3%. It is because most of the suppliers charges some
interest rate which is hidden from the buyer if the buyer agrees to pays after few days. Therefore, most of
the suppliers will agree for a discount if a buyer will pay them upfront (Hoberg, Protopappa-Sieke, &
Steinker, 2017).
For example, during the time of low inventory, customer orders needs to be filled from manufacturing
and thus job scheduling, quality everything should be right so that it is possible to manufacture it in
expected lead time.
Figure 2: Reducing inventory levels is exposing more problems (Source: www.apics.org )
5 Financial implications of Inventory
There is huge financial implications of maintaining inventory. Inventory is the big portion of the Asset
part of the balance sheet. If the companies effectively manage the inventory and reduce its investment
into inventory, it can invest the saved amount at some other place and can earn the better interest (Elking,
Paraskevas, Grimm, Corsi, & Steven, 2017) or they can prepay the loan or they can simply pay back the
money to their suppliers and get the discount of 2-3%. It is because most of the suppliers charges some
interest rate which is hidden from the buyer if the buyer agrees to pays after few days. Therefore, most of
the suppliers will agree for a discount if a buyer will pay them upfront (Hoberg, Protopappa-Sieke, &
Steinker, 2017).
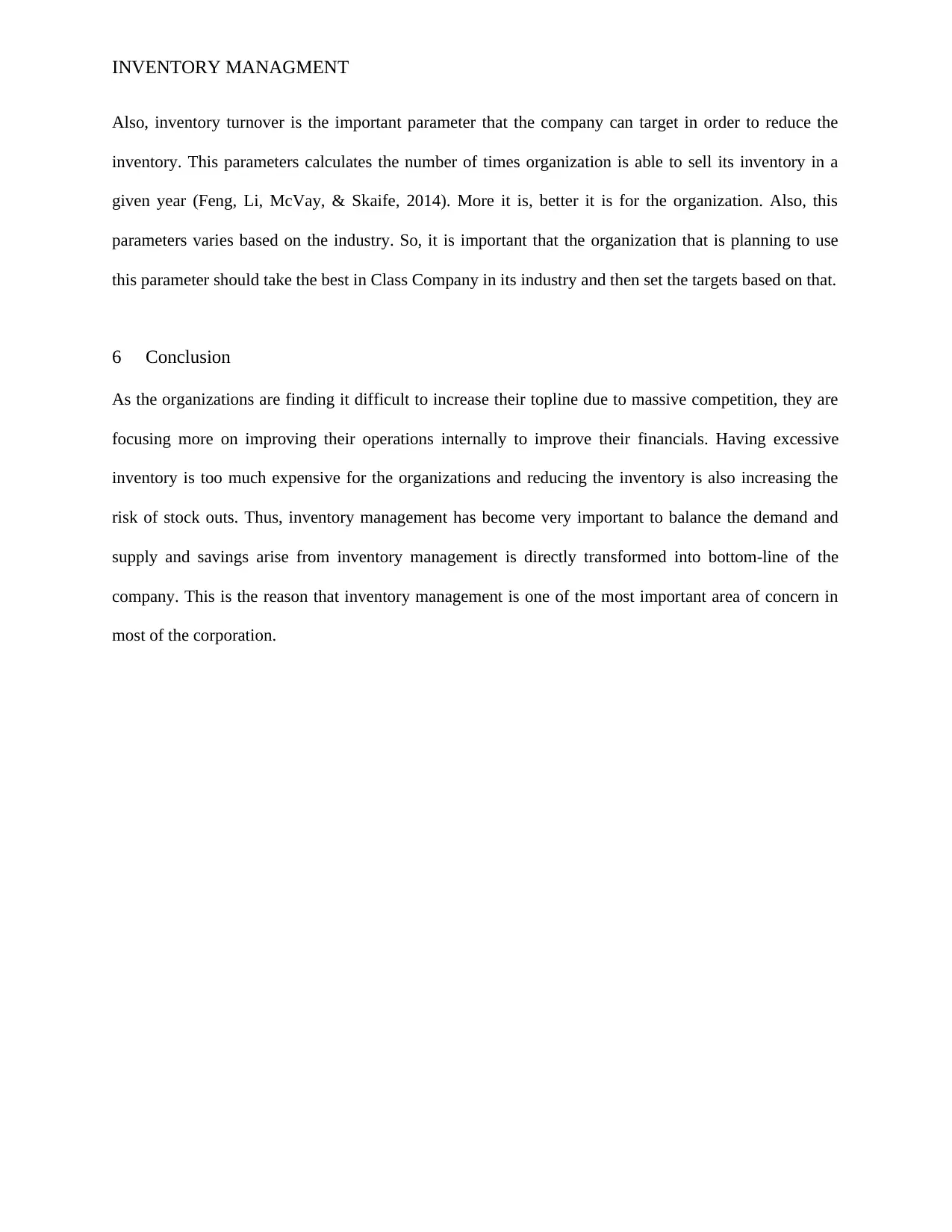
INVENTORY MANAGMENT
Also, inventory turnover is the important parameter that the company can target in order to reduce the
inventory. This parameters calculates the number of times organization is able to sell its inventory in a
given year (Feng, Li, McVay, & Skaife, 2014). More it is, better it is for the organization. Also, this
parameters varies based on the industry. So, it is important that the organization that is planning to use
this parameter should take the best in Class Company in its industry and then set the targets based on that.
6 Conclusion
As the organizations are finding it difficult to increase their topline due to massive competition, they are
focusing more on improving their operations internally to improve their financials. Having excessive
inventory is too much expensive for the organizations and reducing the inventory is also increasing the
risk of stock outs. Thus, inventory management has become very important to balance the demand and
supply and savings arise from inventory management is directly transformed into bottom-line of the
company. This is the reason that inventory management is one of the most important area of concern in
most of the corporation.
Also, inventory turnover is the important parameter that the company can target in order to reduce the
inventory. This parameters calculates the number of times organization is able to sell its inventory in a
given year (Feng, Li, McVay, & Skaife, 2014). More it is, better it is for the organization. Also, this
parameters varies based on the industry. So, it is important that the organization that is planning to use
this parameter should take the best in Class Company in its industry and then set the targets based on that.
6 Conclusion
As the organizations are finding it difficult to increase their topline due to massive competition, they are
focusing more on improving their operations internally to improve their financials. Having excessive
inventory is too much expensive for the organizations and reducing the inventory is also increasing the
risk of stock outs. Thus, inventory management has become very important to balance the demand and
supply and savings arise from inventory management is directly transformed into bottom-line of the
company. This is the reason that inventory management is one of the most important area of concern in
most of the corporation.
Secure Best Marks with AI Grader
Need help grading? Try our AI Grader for instant feedback on your assignments.
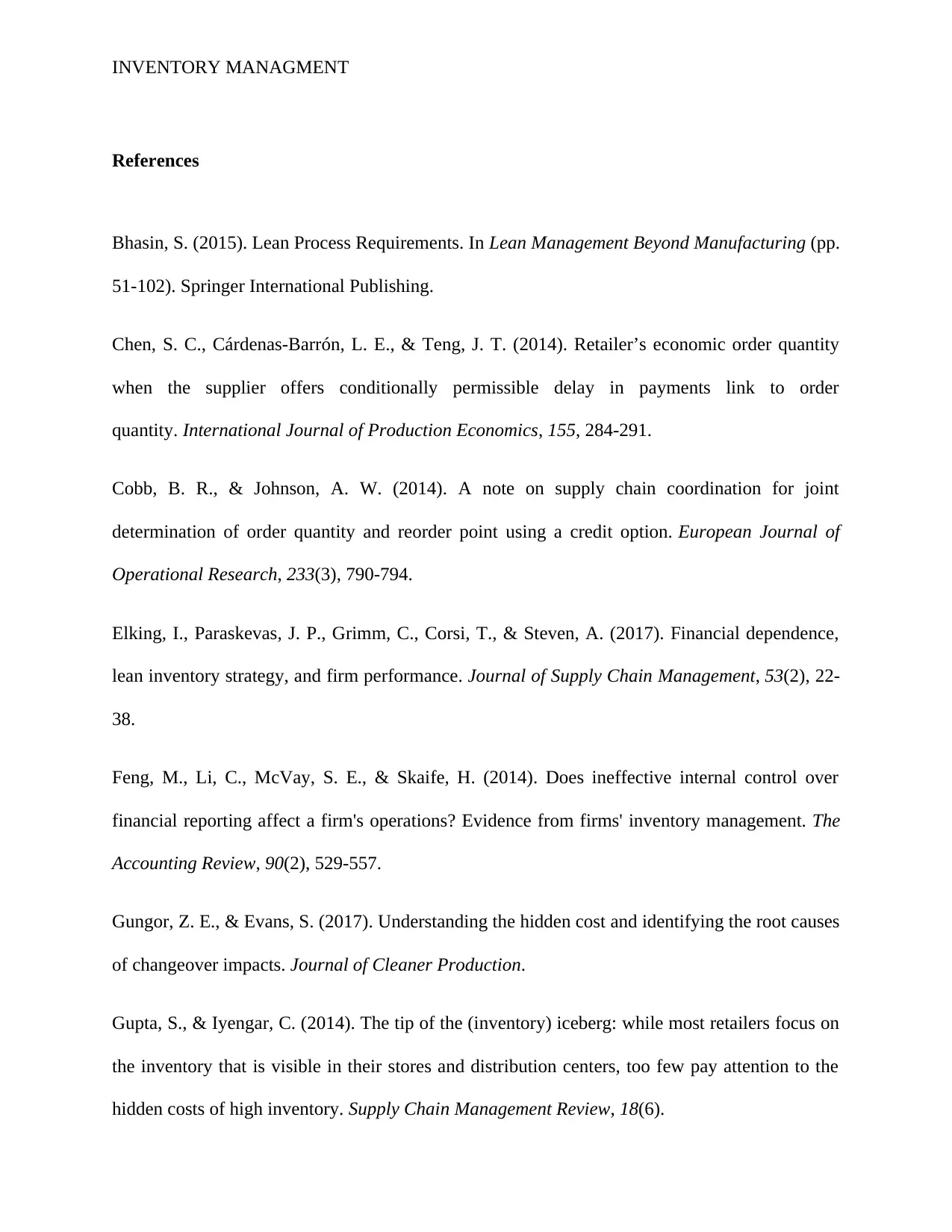
INVENTORY MANAGMENT
References
Bhasin, S. (2015). Lean Process Requirements. In Lean Management Beyond Manufacturing (pp.
51-102). Springer International Publishing.
Chen, S. C., Cárdenas-Barrón, L. E., & Teng, J. T. (2014). Retailer’s economic order quantity
when the supplier offers conditionally permissible delay in payments link to order
quantity. International Journal of Production Economics, 155, 284-291.
Cobb, B. R., & Johnson, A. W. (2014). A note on supply chain coordination for joint
determination of order quantity and reorder point using a credit option. European Journal of
Operational Research, 233(3), 790-794.
Elking, I., Paraskevas, J. P., Grimm, C., Corsi, T., & Steven, A. (2017). Financial dependence,
lean inventory strategy, and firm performance. Journal of Supply Chain Management, 53(2), 22-
38.
Feng, M., Li, C., McVay, S. E., & Skaife, H. (2014). Does ineffective internal control over
financial reporting affect a firm's operations? Evidence from firms' inventory management. The
Accounting Review, 90(2), 529-557.
Gungor, Z. E., & Evans, S. (2017). Understanding the hidden cost and identifying the root causes
of changeover impacts. Journal of Cleaner Production.
Gupta, S., & Iyengar, C. (2014). The tip of the (inventory) iceberg: while most retailers focus on
the inventory that is visible in their stores and distribution centers, too few pay attention to the
hidden costs of high inventory. Supply Chain Management Review, 18(6).
References
Bhasin, S. (2015). Lean Process Requirements. In Lean Management Beyond Manufacturing (pp.
51-102). Springer International Publishing.
Chen, S. C., Cárdenas-Barrón, L. E., & Teng, J. T. (2014). Retailer’s economic order quantity
when the supplier offers conditionally permissible delay in payments link to order
quantity. International Journal of Production Economics, 155, 284-291.
Cobb, B. R., & Johnson, A. W. (2014). A note on supply chain coordination for joint
determination of order quantity and reorder point using a credit option. European Journal of
Operational Research, 233(3), 790-794.
Elking, I., Paraskevas, J. P., Grimm, C., Corsi, T., & Steven, A. (2017). Financial dependence,
lean inventory strategy, and firm performance. Journal of Supply Chain Management, 53(2), 22-
38.
Feng, M., Li, C., McVay, S. E., & Skaife, H. (2014). Does ineffective internal control over
financial reporting affect a firm's operations? Evidence from firms' inventory management. The
Accounting Review, 90(2), 529-557.
Gungor, Z. E., & Evans, S. (2017). Understanding the hidden cost and identifying the root causes
of changeover impacts. Journal of Cleaner Production.
Gupta, S., & Iyengar, C. (2014). The tip of the (inventory) iceberg: while most retailers focus on
the inventory that is visible in their stores and distribution centers, too few pay attention to the
hidden costs of high inventory. Supply Chain Management Review, 18(6).
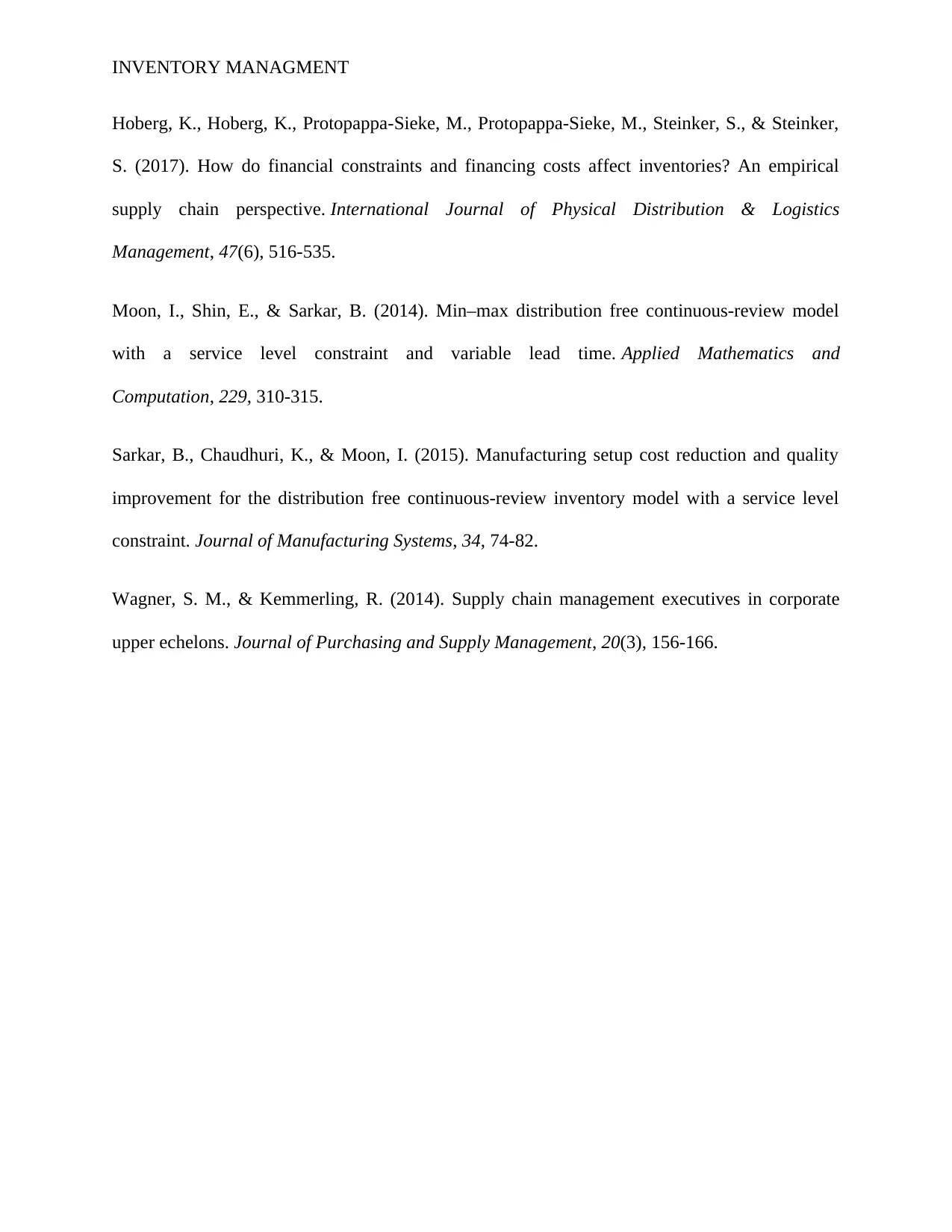
INVENTORY MANAGMENT
Hoberg, K., Hoberg, K., Protopappa-Sieke, M., Protopappa-Sieke, M., Steinker, S., & Steinker,
S. (2017). How do financial constraints and financing costs affect inventories? An empirical
supply chain perspective. International Journal of Physical Distribution & Logistics
Management, 47(6), 516-535.
Moon, I., Shin, E., & Sarkar, B. (2014). Min–max distribution free continuous-review model
with a service level constraint and variable lead time. Applied Mathematics and
Computation, 229, 310-315.
Sarkar, B., Chaudhuri, K., & Moon, I. (2015). Manufacturing setup cost reduction and quality
improvement for the distribution free continuous-review inventory model with a service level
constraint. Journal of Manufacturing Systems, 34, 74-82.
Wagner, S. M., & Kemmerling, R. (2014). Supply chain management executives in corporate
upper echelons. Journal of Purchasing and Supply Management, 20(3), 156-166.
Hoberg, K., Hoberg, K., Protopappa-Sieke, M., Protopappa-Sieke, M., Steinker, S., & Steinker,
S. (2017). How do financial constraints and financing costs affect inventories? An empirical
supply chain perspective. International Journal of Physical Distribution & Logistics
Management, 47(6), 516-535.
Moon, I., Shin, E., & Sarkar, B. (2014). Min–max distribution free continuous-review model
with a service level constraint and variable lead time. Applied Mathematics and
Computation, 229, 310-315.
Sarkar, B., Chaudhuri, K., & Moon, I. (2015). Manufacturing setup cost reduction and quality
improvement for the distribution free continuous-review inventory model with a service level
constraint. Journal of Manufacturing Systems, 34, 74-82.
Wagner, S. M., & Kemmerling, R. (2014). Supply chain management executives in corporate
upper echelons. Journal of Purchasing and Supply Management, 20(3), 156-166.
1 out of 12
Related Documents

Your All-in-One AI-Powered Toolkit for Academic Success.
+13062052269
info@desklib.com
Available 24*7 on WhatsApp / Email
Unlock your academic potential
© 2024 | Zucol Services PVT LTD | All rights reserved.