Fundamentals of Inventory Management: A Detailed Overview
VerifiedAdded on 2019/09/30
|26
|11025
|134
Report
AI Summary
This report provides a comprehensive overview of inventory management, beginning with a definition of inventory and the reasons for maintaining it, such as meeting demand, keeping operations running, managing lead times, hedging against price increases, and taking advantage of quantity discounts. It then delves into inventory control methods, including the ABC approach and cycle counting, which help firms manage large numbers of inventory items efficiently. The report also addresses the critical aspect of balancing inventory levels with costs, detailing the three main types of costs: holding costs, set-up costs, and purchasing costs. Holding costs include storage, personnel, taxes, and obsolescence, while set-up costs involve preparing machines for production or order costs for purchased items. Purchasing costs are simply the cost of the items themselves. By understanding these costs and applying effective control methods, firms can optimize their inventory management strategies to minimize expenses and ensure adequate supply.
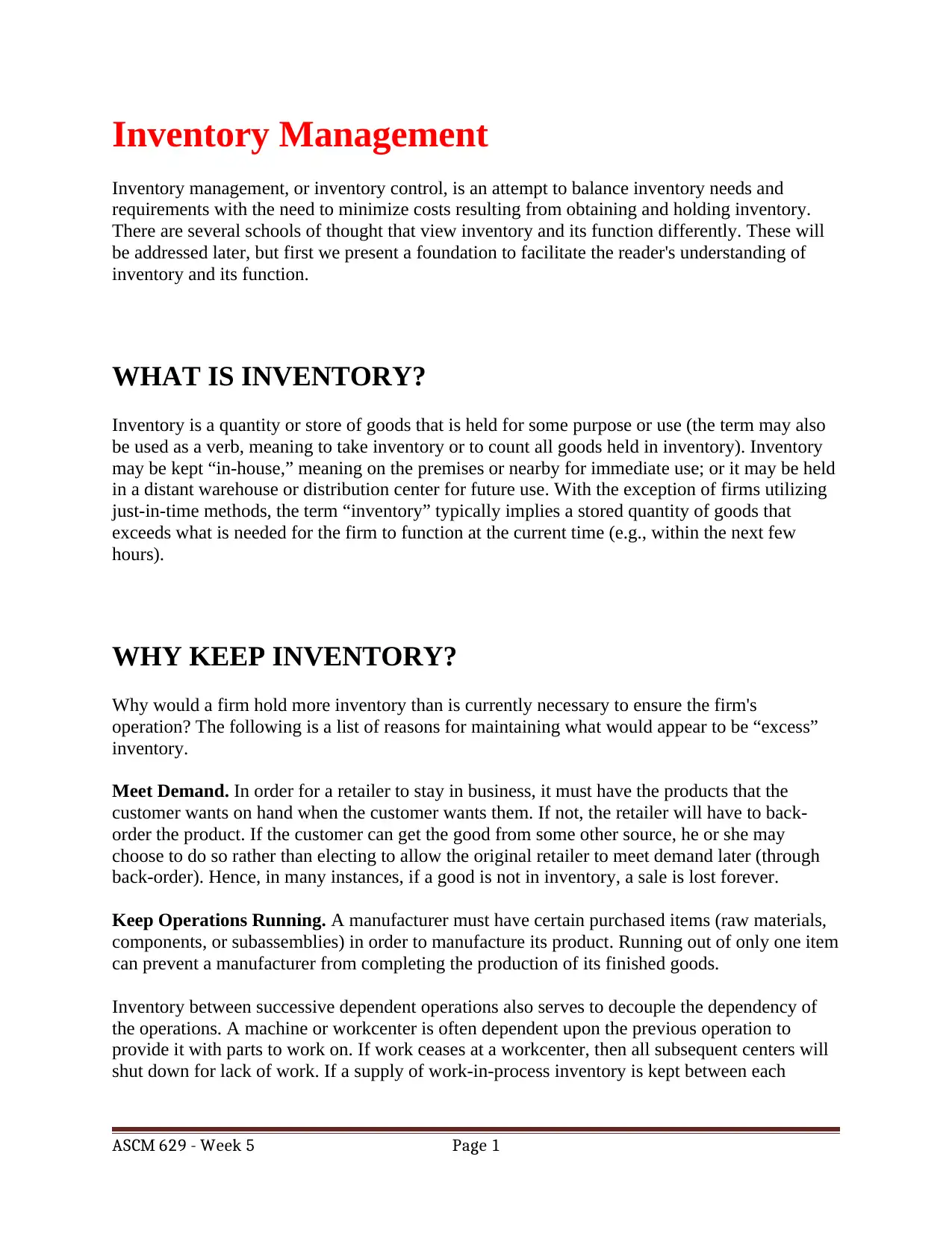
Inventory Management
Inventory management, or inventory control, is an attempt to balance inventory needs and
requirements with the need to minimize costs resulting from obtaining and holding inventory.
There are several schools of thought that view inventory and its function differently. These will
be addressed later, but first we present a foundation to facilitate the reader's understanding of
inventory and its function.
WHAT IS INVENTORY?
Inventory is a quantity or store of goods that is held for some purpose or use (the term may also
be used as a verb, meaning to take inventory or to count all goods held in inventory). Inventory
may be kept “in-house,” meaning on the premises or nearby for immediate use; or it may be held
in a distant warehouse or distribution center for future use. With the exception of firms utilizing
just-in-time methods, the term “inventory” typically implies a stored quantity of goods that
exceeds what is needed for the firm to function at the current time (e.g., within the next few
hours).
WHY KEEP INVENTORY?
Why would a firm hold more inventory than is currently necessary to ensure the firm's
operation? The following is a list of reasons for maintaining what would appear to be “excess”
inventory.
Meet Demand. In order for a retailer to stay in business, it must have the products that the
customer wants on hand when the customer wants them. If not, the retailer will have to back-
order the product. If the customer can get the good from some other source, he or she may
choose to do so rather than electing to allow the original retailer to meet demand later (through
back-order). Hence, in many instances, if a good is not in inventory, a sale is lost forever.
Keep Operations Running. A manufacturer must have certain purchased items (raw materials,
components, or subassemblies) in order to manufacture its product. Running out of only one item
can prevent a manufacturer from completing the production of its finished goods.
Inventory between successive dependent operations also serves to decouple the dependency of
the operations. A machine or workcenter is often dependent upon the previous operation to
provide it with parts to work on. If work ceases at a workcenter, then all subsequent centers will
shut down for lack of work. If a supply of work-in-process inventory is kept between each
ASCM 629 - Week 5 Page 1
Inventory management, or inventory control, is an attempt to balance inventory needs and
requirements with the need to minimize costs resulting from obtaining and holding inventory.
There are several schools of thought that view inventory and its function differently. These will
be addressed later, but first we present a foundation to facilitate the reader's understanding of
inventory and its function.
WHAT IS INVENTORY?
Inventory is a quantity or store of goods that is held for some purpose or use (the term may also
be used as a verb, meaning to take inventory or to count all goods held in inventory). Inventory
may be kept “in-house,” meaning on the premises or nearby for immediate use; or it may be held
in a distant warehouse or distribution center for future use. With the exception of firms utilizing
just-in-time methods, the term “inventory” typically implies a stored quantity of goods that
exceeds what is needed for the firm to function at the current time (e.g., within the next few
hours).
WHY KEEP INVENTORY?
Why would a firm hold more inventory than is currently necessary to ensure the firm's
operation? The following is a list of reasons for maintaining what would appear to be “excess”
inventory.
Meet Demand. In order for a retailer to stay in business, it must have the products that the
customer wants on hand when the customer wants them. If not, the retailer will have to back-
order the product. If the customer can get the good from some other source, he or she may
choose to do so rather than electing to allow the original retailer to meet demand later (through
back-order). Hence, in many instances, if a good is not in inventory, a sale is lost forever.
Keep Operations Running. A manufacturer must have certain purchased items (raw materials,
components, or subassemblies) in order to manufacture its product. Running out of only one item
can prevent a manufacturer from completing the production of its finished goods.
Inventory between successive dependent operations also serves to decouple the dependency of
the operations. A machine or workcenter is often dependent upon the previous operation to
provide it with parts to work on. If work ceases at a workcenter, then all subsequent centers will
shut down for lack of work. If a supply of work-in-process inventory is kept between each
ASCM 629 - Week 5 Page 1
Secure Best Marks with AI Grader
Need help grading? Try our AI Grader for instant feedback on your assignments.
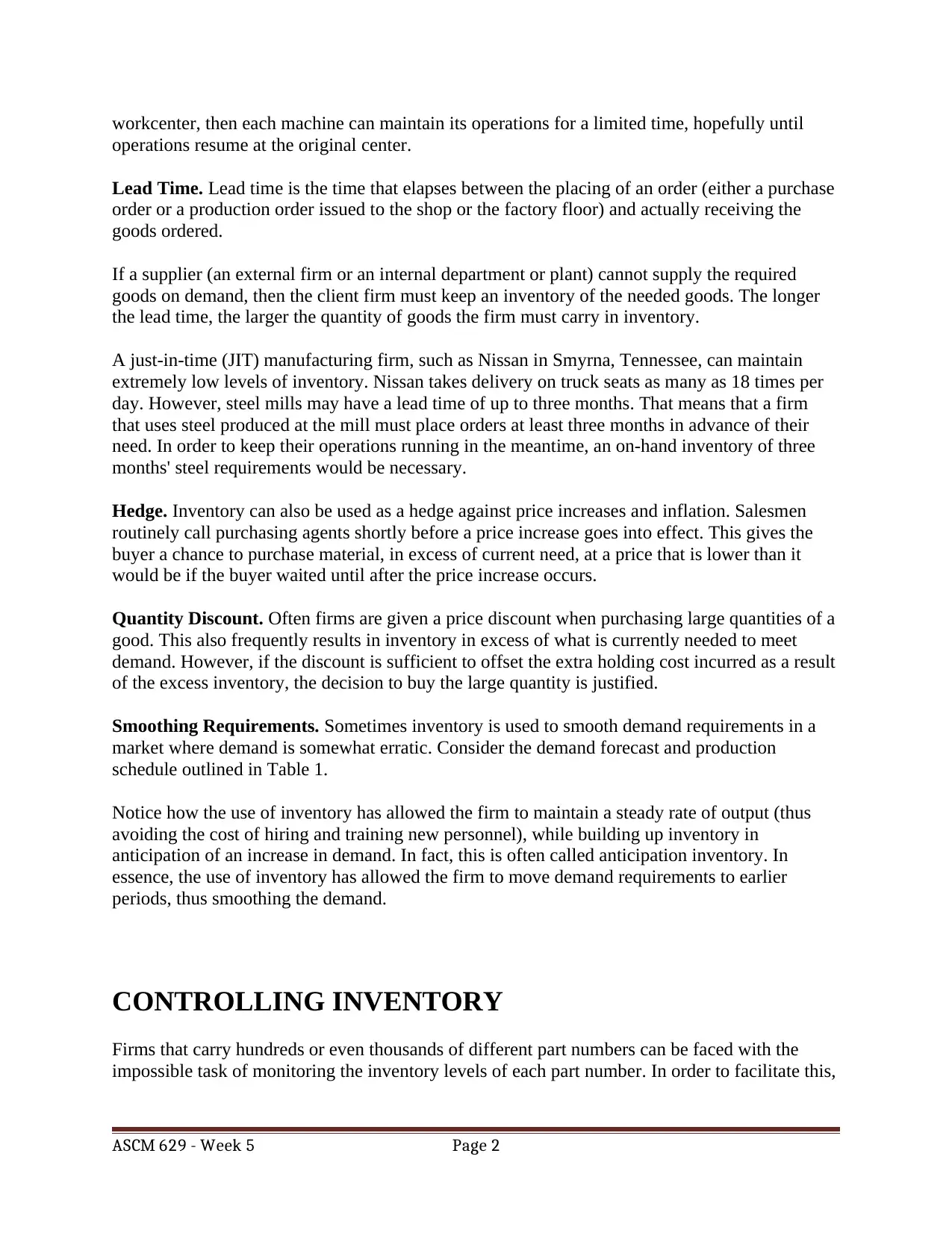
workcenter, then each machine can maintain its operations for a limited time, hopefully until
operations resume at the original center.
Lead Time. Lead time is the time that elapses between the placing of an order (either a purchase
order or a production order issued to the shop or the factory floor) and actually receiving the
goods ordered.
If a supplier (an external firm or an internal department or plant) cannot supply the required
goods on demand, then the client firm must keep an inventory of the needed goods. The longer
the lead time, the larger the quantity of goods the firm must carry in inventory.
A just-in-time (JIT) manufacturing firm, such as Nissan in Smyrna, Tennessee, can maintain
extremely low levels of inventory. Nissan takes delivery on truck seats as many as 18 times per
day. However, steel mills may have a lead time of up to three months. That means that a firm
that uses steel produced at the mill must place orders at least three months in advance of their
need. In order to keep their operations running in the meantime, an on-hand inventory of three
months' steel requirements would be necessary.
Hedge. Inventory can also be used as a hedge against price increases and inflation. Salesmen
routinely call purchasing agents shortly before a price increase goes into effect. This gives the
buyer a chance to purchase material, in excess of current need, at a price that is lower than it
would be if the buyer waited until after the price increase occurs.
Quantity Discount. Often firms are given a price discount when purchasing large quantities of a
good. This also frequently results in inventory in excess of what is currently needed to meet
demand. However, if the discount is sufficient to offset the extra holding cost incurred as a result
of the excess inventory, the decision to buy the large quantity is justified.
Smoothing Requirements. Sometimes inventory is used to smooth demand requirements in a
market where demand is somewhat erratic. Consider the demand forecast and production
schedule outlined in Table 1.
Notice how the use of inventory has allowed the firm to maintain a steady rate of output (thus
avoiding the cost of hiring and training new personnel), while building up inventory in
anticipation of an increase in demand. In fact, this is often called anticipation inventory. In
essence, the use of inventory has allowed the firm to move demand requirements to earlier
periods, thus smoothing the demand.
CONTROLLING INVENTORY
Firms that carry hundreds or even thousands of different part numbers can be faced with the
impossible task of monitoring the inventory levels of each part number. In order to facilitate this,
ASCM 629 - Week 5 Page 2
operations resume at the original center.
Lead Time. Lead time is the time that elapses between the placing of an order (either a purchase
order or a production order issued to the shop or the factory floor) and actually receiving the
goods ordered.
If a supplier (an external firm or an internal department or plant) cannot supply the required
goods on demand, then the client firm must keep an inventory of the needed goods. The longer
the lead time, the larger the quantity of goods the firm must carry in inventory.
A just-in-time (JIT) manufacturing firm, such as Nissan in Smyrna, Tennessee, can maintain
extremely low levels of inventory. Nissan takes delivery on truck seats as many as 18 times per
day. However, steel mills may have a lead time of up to three months. That means that a firm
that uses steel produced at the mill must place orders at least three months in advance of their
need. In order to keep their operations running in the meantime, an on-hand inventory of three
months' steel requirements would be necessary.
Hedge. Inventory can also be used as a hedge against price increases and inflation. Salesmen
routinely call purchasing agents shortly before a price increase goes into effect. This gives the
buyer a chance to purchase material, in excess of current need, at a price that is lower than it
would be if the buyer waited until after the price increase occurs.
Quantity Discount. Often firms are given a price discount when purchasing large quantities of a
good. This also frequently results in inventory in excess of what is currently needed to meet
demand. However, if the discount is sufficient to offset the extra holding cost incurred as a result
of the excess inventory, the decision to buy the large quantity is justified.
Smoothing Requirements. Sometimes inventory is used to smooth demand requirements in a
market where demand is somewhat erratic. Consider the demand forecast and production
schedule outlined in Table 1.
Notice how the use of inventory has allowed the firm to maintain a steady rate of output (thus
avoiding the cost of hiring and training new personnel), while building up inventory in
anticipation of an increase in demand. In fact, this is often called anticipation inventory. In
essence, the use of inventory has allowed the firm to move demand requirements to earlier
periods, thus smoothing the demand.
CONTROLLING INVENTORY
Firms that carry hundreds or even thousands of different part numbers can be faced with the
impossible task of monitoring the inventory levels of each part number. In order to facilitate this,
ASCM 629 - Week 5 Page 2
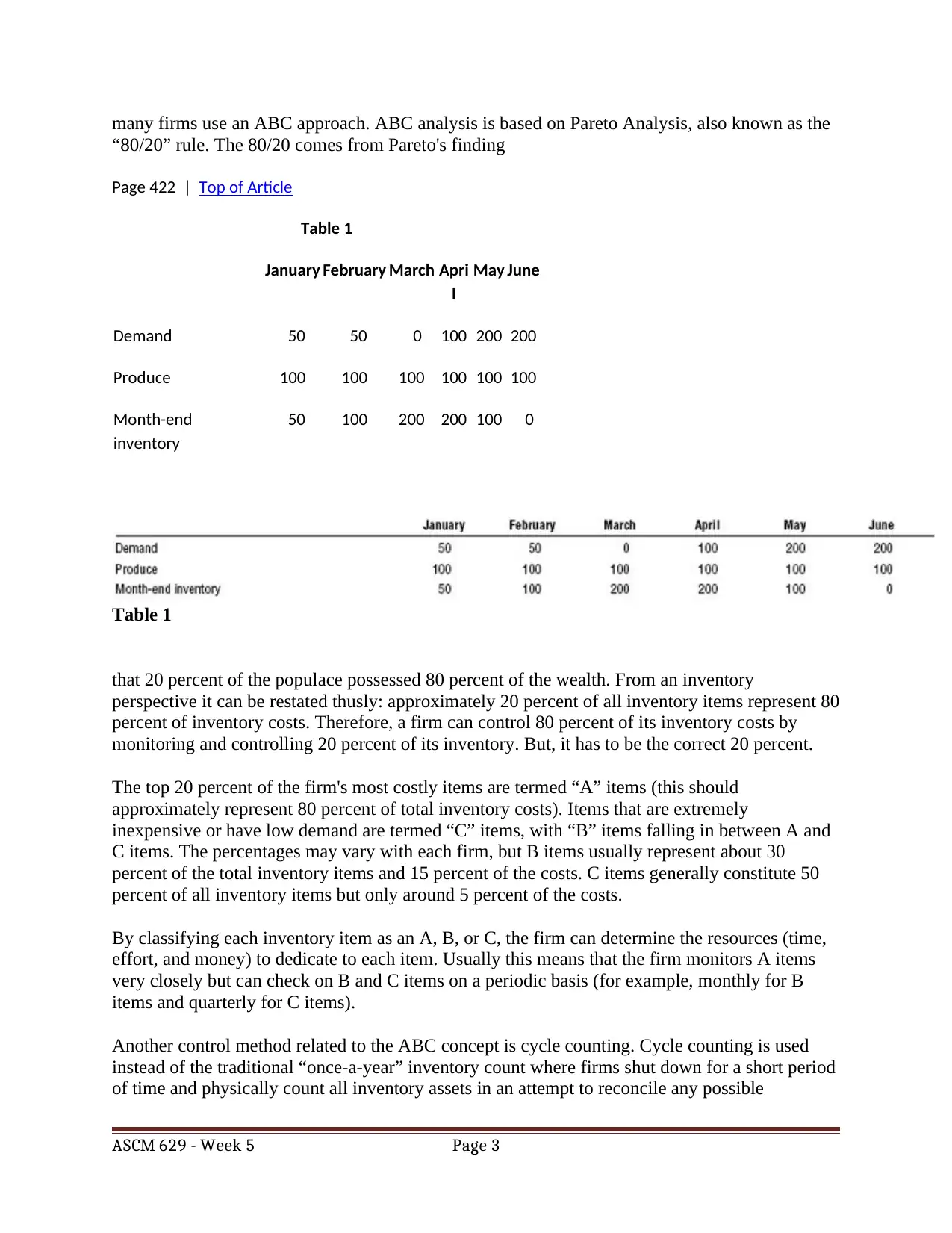
many firms use an ABC approach. ABC analysis is based on Pareto Analysis, also known as the
“80/20” rule. The 80/20 comes from Pareto's finding
Page 422 | Top of Article
Table 1
January February March Apri
l
May June
Demand 50 50 0 100 200 200
Produce 100 100 100 100 100 100
Month-end
inventory
50 100 200 200 100 0
Table 1
that 20 percent of the populace possessed 80 percent of the wealth. From an inventory
perspective it can be restated thusly: approximately 20 percent of all inventory items represent 80
percent of inventory costs. Therefore, a firm can control 80 percent of its inventory costs by
monitoring and controlling 20 percent of its inventory. But, it has to be the correct 20 percent.
The top 20 percent of the firm's most costly items are termed “A” items (this should
approximately represent 80 percent of total inventory costs). Items that are extremely
inexpensive or have low demand are termed “C” items, with “B” items falling in between A and
C items. The percentages may vary with each firm, but B items usually represent about 30
percent of the total inventory items and 15 percent of the costs. C items generally constitute 50
percent of all inventory items but only around 5 percent of the costs.
By classifying each inventory item as an A, B, or C, the firm can determine the resources (time,
effort, and money) to dedicate to each item. Usually this means that the firm monitors A items
very closely but can check on B and C items on a periodic basis (for example, monthly for B
items and quarterly for C items).
Another control method related to the ABC concept is cycle counting. Cycle counting is used
instead of the traditional “once-a-year” inventory count where firms shut down for a short period
of time and physically count all inventory assets in an attempt to reconcile any possible
ASCM 629 - Week 5 Page 3
“80/20” rule. The 80/20 comes from Pareto's finding
Page 422 | Top of Article
Table 1
January February March Apri
l
May June
Demand 50 50 0 100 200 200
Produce 100 100 100 100 100 100
Month-end
inventory
50 100 200 200 100 0
Table 1
that 20 percent of the populace possessed 80 percent of the wealth. From an inventory
perspective it can be restated thusly: approximately 20 percent of all inventory items represent 80
percent of inventory costs. Therefore, a firm can control 80 percent of its inventory costs by
monitoring and controlling 20 percent of its inventory. But, it has to be the correct 20 percent.
The top 20 percent of the firm's most costly items are termed “A” items (this should
approximately represent 80 percent of total inventory costs). Items that are extremely
inexpensive or have low demand are termed “C” items, with “B” items falling in between A and
C items. The percentages may vary with each firm, but B items usually represent about 30
percent of the total inventory items and 15 percent of the costs. C items generally constitute 50
percent of all inventory items but only around 5 percent of the costs.
By classifying each inventory item as an A, B, or C, the firm can determine the resources (time,
effort, and money) to dedicate to each item. Usually this means that the firm monitors A items
very closely but can check on B and C items on a periodic basis (for example, monthly for B
items and quarterly for C items).
Another control method related to the ABC concept is cycle counting. Cycle counting is used
instead of the traditional “once-a-year” inventory count where firms shut down for a short period
of time and physically count all inventory assets in an attempt to reconcile any possible
ASCM 629 - Week 5 Page 3
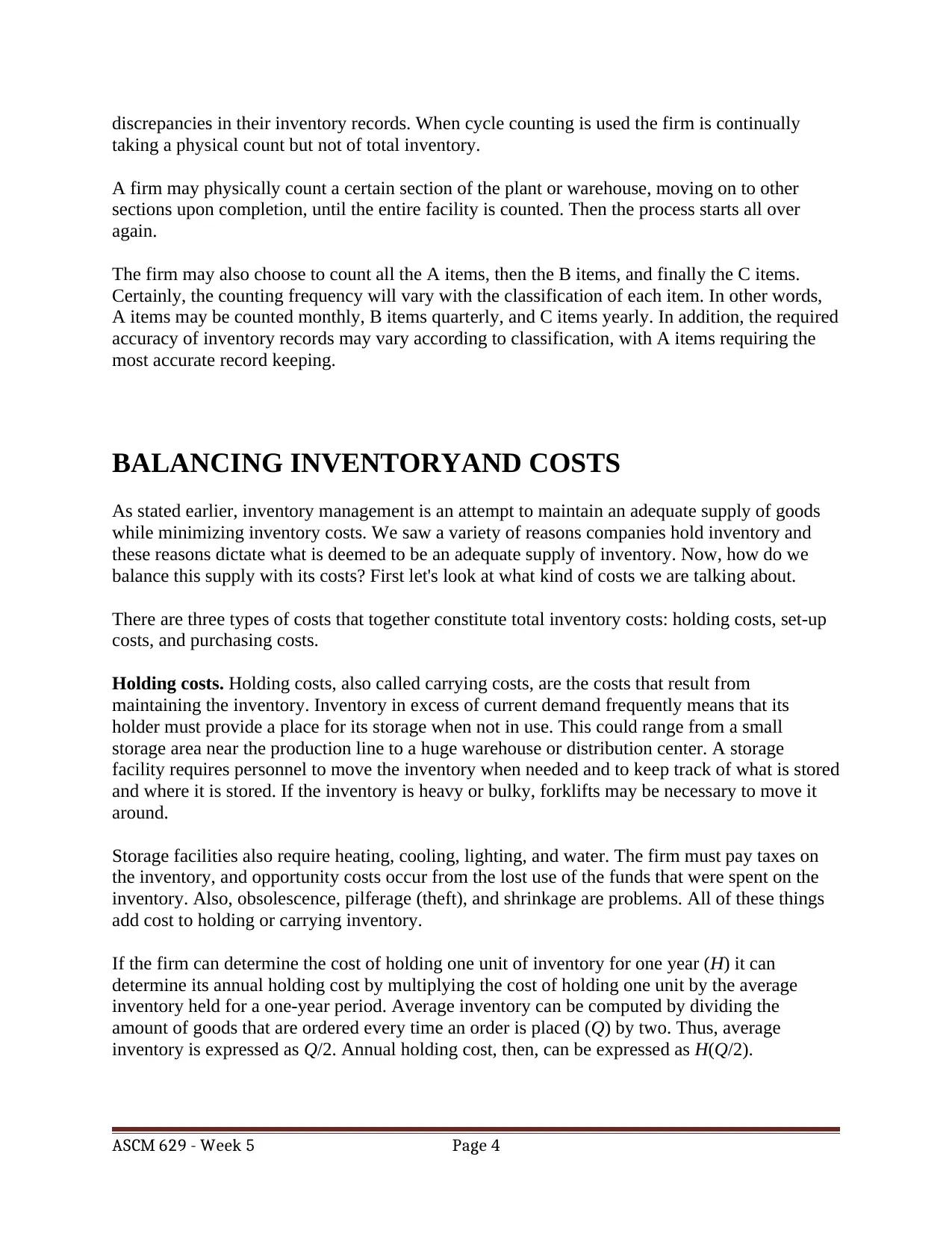
discrepancies in their inventory records. When cycle counting is used the firm is continually
taking a physical count but not of total inventory.
A firm may physically count a certain section of the plant or warehouse, moving on to other
sections upon completion, until the entire facility is counted. Then the process starts all over
again.
The firm may also choose to count all the A items, then the B items, and finally the C items.
Certainly, the counting frequency will vary with the classification of each item. In other words,
A items may be counted monthly, B items quarterly, and C items yearly. In addition, the required
accuracy of inventory records may vary according to classification, with A items requiring the
most accurate record keeping.
BALANCING INVENTORYAND COSTS
As stated earlier, inventory management is an attempt to maintain an adequate supply of goods
while minimizing inventory costs. We saw a variety of reasons companies hold inventory and
these reasons dictate what is deemed to be an adequate supply of inventory. Now, how do we
balance this supply with its costs? First let's look at what kind of costs we are talking about.
There are three types of costs that together constitute total inventory costs: holding costs, set-up
costs, and purchasing costs.
Holding costs. Holding costs, also called carrying costs, are the costs that result from
maintaining the inventory. Inventory in excess of current demand frequently means that its
holder must provide a place for its storage when not in use. This could range from a small
storage area near the production line to a huge warehouse or distribution center. A storage
facility requires personnel to move the inventory when needed and to keep track of what is stored
and where it is stored. If the inventory is heavy or bulky, forklifts may be necessary to move it
around.
Storage facilities also require heating, cooling, lighting, and water. The firm must pay taxes on
the inventory, and opportunity costs occur from the lost use of the funds that were spent on the
inventory. Also, obsolescence, pilferage (theft), and shrinkage are problems. All of these things
add cost to holding or carrying inventory.
If the firm can determine the cost of holding one unit of inventory for one year (H) it can
determine its annual holding cost by multiplying the cost of holding one unit by the average
inventory held for a one-year period. Average inventory can be computed by dividing the
amount of goods that are ordered every time an order is placed (Q) by two. Thus, average
inventory is expressed as Q/2. Annual holding cost, then, can be expressed as H(Q/2).
ASCM 629 - Week 5 Page 4
taking a physical count but not of total inventory.
A firm may physically count a certain section of the plant or warehouse, moving on to other
sections upon completion, until the entire facility is counted. Then the process starts all over
again.
The firm may also choose to count all the A items, then the B items, and finally the C items.
Certainly, the counting frequency will vary with the classification of each item. In other words,
A items may be counted monthly, B items quarterly, and C items yearly. In addition, the required
accuracy of inventory records may vary according to classification, with A items requiring the
most accurate record keeping.
BALANCING INVENTORYAND COSTS
As stated earlier, inventory management is an attempt to maintain an adequate supply of goods
while minimizing inventory costs. We saw a variety of reasons companies hold inventory and
these reasons dictate what is deemed to be an adequate supply of inventory. Now, how do we
balance this supply with its costs? First let's look at what kind of costs we are talking about.
There are three types of costs that together constitute total inventory costs: holding costs, set-up
costs, and purchasing costs.
Holding costs. Holding costs, also called carrying costs, are the costs that result from
maintaining the inventory. Inventory in excess of current demand frequently means that its
holder must provide a place for its storage when not in use. This could range from a small
storage area near the production line to a huge warehouse or distribution center. A storage
facility requires personnel to move the inventory when needed and to keep track of what is stored
and where it is stored. If the inventory is heavy or bulky, forklifts may be necessary to move it
around.
Storage facilities also require heating, cooling, lighting, and water. The firm must pay taxes on
the inventory, and opportunity costs occur from the lost use of the funds that were spent on the
inventory. Also, obsolescence, pilferage (theft), and shrinkage are problems. All of these things
add cost to holding or carrying inventory.
If the firm can determine the cost of holding one unit of inventory for one year (H) it can
determine its annual holding cost by multiplying the cost of holding one unit by the average
inventory held for a one-year period. Average inventory can be computed by dividing the
amount of goods that are ordered every time an order is placed (Q) by two. Thus, average
inventory is expressed as Q/2. Annual holding cost, then, can be expressed as H(Q/2).
ASCM 629 - Week 5 Page 4
Secure Best Marks with AI Grader
Need help grading? Try our AI Grader for instant feedback on your assignments.
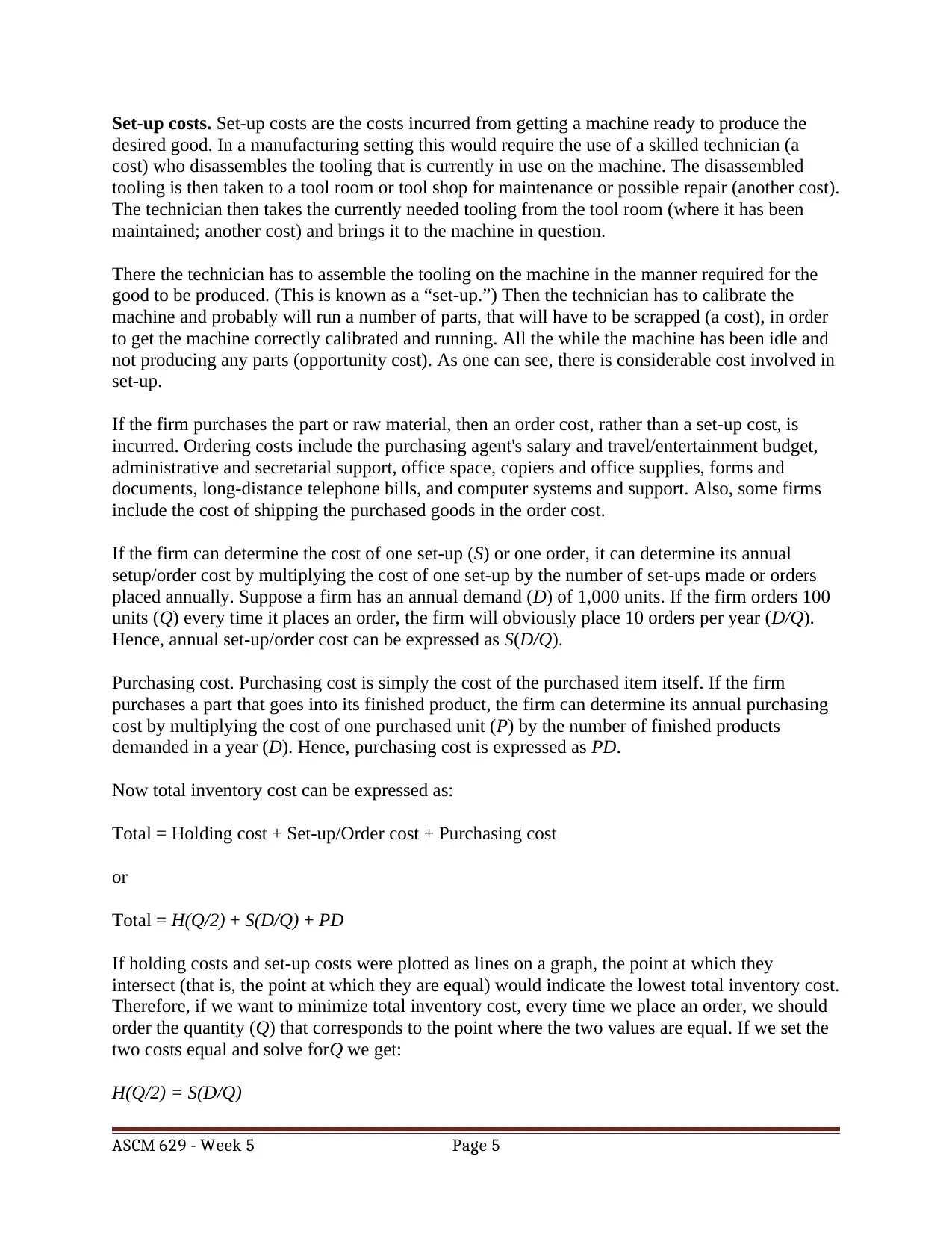
Set-up costs. Set-up costs are the costs incurred from getting a machine ready to produce the
desired good. In a manufacturing setting this would require the use of a skilled technician (a
cost) who disassembles the tooling that is currently in use on the machine. The disassembled
tooling is then taken to a tool room or tool shop for maintenance or possible repair (another cost).
The technician then takes the currently needed tooling from the tool room (where it has been
maintained; another cost) and brings it to the machine in question.
There the technician has to assemble the tooling on the machine in the manner required for the
good to be produced. (This is known as a “set-up.”) Then the technician has to calibrate the
machine and probably will run a number of parts, that will have to be scrapped (a cost), in order
to get the machine correctly calibrated and running. All the while the machine has been idle and
not producing any parts (opportunity cost). As one can see, there is considerable cost involved in
set-up.
If the firm purchases the part or raw material, then an order cost, rather than a set-up cost, is
incurred. Ordering costs include the purchasing agent's salary and travel/entertainment budget,
administrative and secretarial support, office space, copiers and office supplies, forms and
documents, long-distance telephone bills, and computer systems and support. Also, some firms
include the cost of shipping the purchased goods in the order cost.
If the firm can determine the cost of one set-up (S) or one order, it can determine its annual
setup/order cost by multiplying the cost of one set-up by the number of set-ups made or orders
placed annually. Suppose a firm has an annual demand (D) of 1,000 units. If the firm orders 100
units (Q) every time it places an order, the firm will obviously place 10 orders per year (D/Q).
Hence, annual set-up/order cost can be expressed as S(D/Q).
Purchasing cost. Purchasing cost is simply the cost of the purchased item itself. If the firm
purchases a part that goes into its finished product, the firm can determine its annual purchasing
cost by multiplying the cost of one purchased unit (P) by the number of finished products
demanded in a year (D). Hence, purchasing cost is expressed as PD.
Now total inventory cost can be expressed as:
Total = Holding cost + Set-up/Order cost + Purchasing cost
or
Total = H(Q/2) + S(D/Q) + PD
If holding costs and set-up costs were plotted as lines on a graph, the point at which they
intersect (that is, the point at which they are equal) would indicate the lowest total inventory cost.
Therefore, if we want to minimize total inventory cost, every time we place an order, we should
order the quantity (Q) that corresponds to the point where the two values are equal. If we set the
two costs equal and solve forQ we get:
H(Q/2) = S(D/Q)
ASCM 629 - Week 5 Page 5
desired good. In a manufacturing setting this would require the use of a skilled technician (a
cost) who disassembles the tooling that is currently in use on the machine. The disassembled
tooling is then taken to a tool room or tool shop for maintenance or possible repair (another cost).
The technician then takes the currently needed tooling from the tool room (where it has been
maintained; another cost) and brings it to the machine in question.
There the technician has to assemble the tooling on the machine in the manner required for the
good to be produced. (This is known as a “set-up.”) Then the technician has to calibrate the
machine and probably will run a number of parts, that will have to be scrapped (a cost), in order
to get the machine correctly calibrated and running. All the while the machine has been idle and
not producing any parts (opportunity cost). As one can see, there is considerable cost involved in
set-up.
If the firm purchases the part or raw material, then an order cost, rather than a set-up cost, is
incurred. Ordering costs include the purchasing agent's salary and travel/entertainment budget,
administrative and secretarial support, office space, copiers and office supplies, forms and
documents, long-distance telephone bills, and computer systems and support. Also, some firms
include the cost of shipping the purchased goods in the order cost.
If the firm can determine the cost of one set-up (S) or one order, it can determine its annual
setup/order cost by multiplying the cost of one set-up by the number of set-ups made or orders
placed annually. Suppose a firm has an annual demand (D) of 1,000 units. If the firm orders 100
units (Q) every time it places an order, the firm will obviously place 10 orders per year (D/Q).
Hence, annual set-up/order cost can be expressed as S(D/Q).
Purchasing cost. Purchasing cost is simply the cost of the purchased item itself. If the firm
purchases a part that goes into its finished product, the firm can determine its annual purchasing
cost by multiplying the cost of one purchased unit (P) by the number of finished products
demanded in a year (D). Hence, purchasing cost is expressed as PD.
Now total inventory cost can be expressed as:
Total = Holding cost + Set-up/Order cost + Purchasing cost
or
Total = H(Q/2) + S(D/Q) + PD
If holding costs and set-up costs were plotted as lines on a graph, the point at which they
intersect (that is, the point at which they are equal) would indicate the lowest total inventory cost.
Therefore, if we want to minimize total inventory cost, every time we place an order, we should
order the quantity (Q) that corresponds to the point where the two values are equal. If we set the
two costs equal and solve forQ we get:
H(Q/2) = S(D/Q)
ASCM 629 - Week 5 Page 5
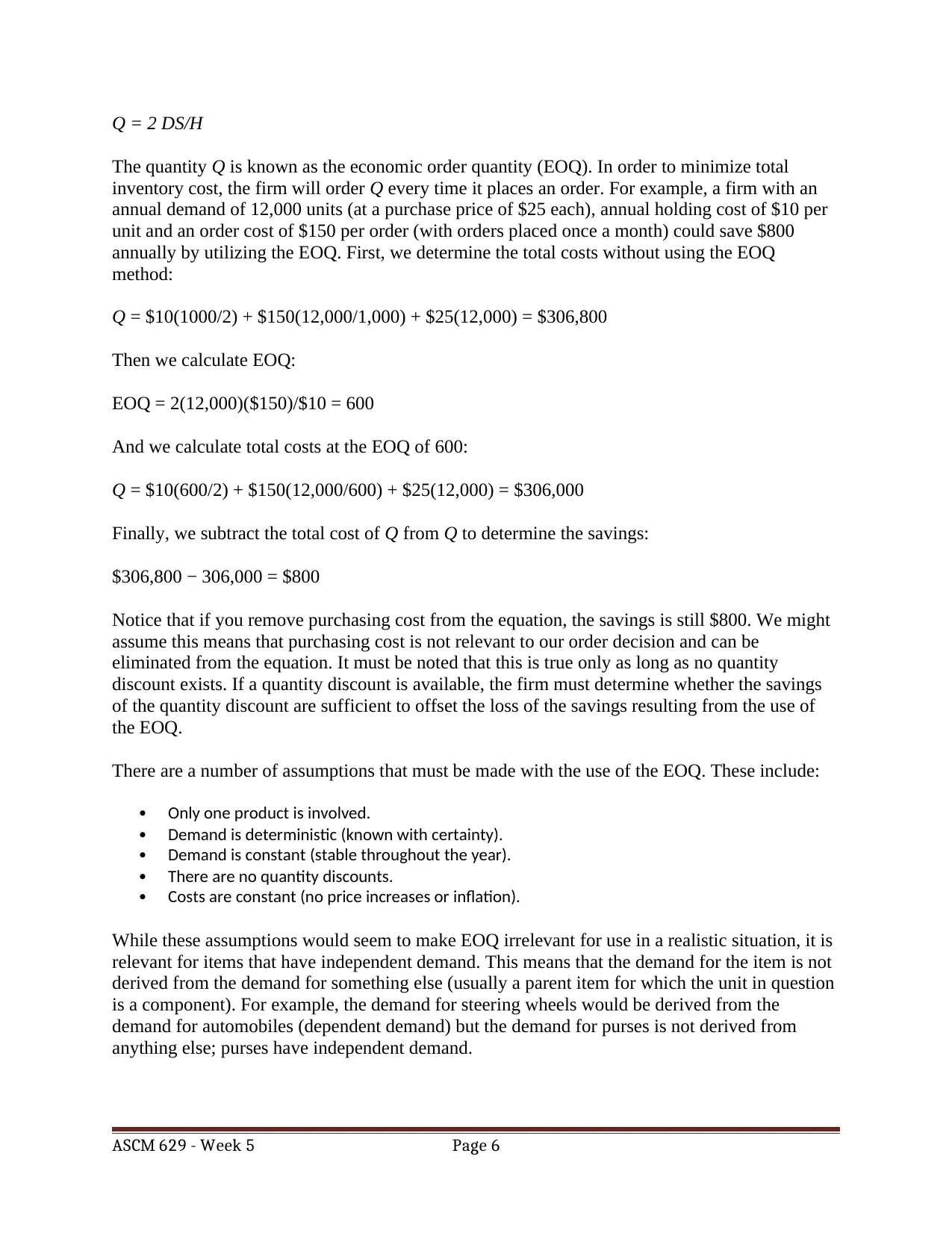
Q = 2 DS/H
The quantity Q is known as the economic order quantity (EOQ). In order to minimize total
inventory cost, the firm will order Q every time it places an order. For example, a firm with an
annual demand of 12,000 units (at a purchase price of $25 each), annual holding cost of $10 per
unit and an order cost of $150 per order (with orders placed once a month) could save $800
annually by utilizing the EOQ. First, we determine the total costs without using the EOQ
method:
Q = $10(1000/2) + $150(12,000/1,000) + $25(12,000) = $306,800
Then we calculate EOQ:
EOQ = 2(12,000)($150)/$10 = 600
And we calculate total costs at the EOQ of 600:
Q = $10(600/2) + $150(12,000/600) + $25(12,000) = $306,000
Finally, we subtract the total cost of Q from Q to determine the savings:
$306,800 − 306,000 = $800
Notice that if you remove purchasing cost from the equation, the savings is still $800. We might
assume this means that purchasing cost is not relevant to our order decision and can be
eliminated from the equation. It must be noted that this is true only as long as no quantity
discount exists. If a quantity discount is available, the firm must determine whether the savings
of the quantity discount are sufficient to offset the loss of the savings resulting from the use of
the EOQ.
There are a number of assumptions that must be made with the use of the EOQ. These include:
Only one product is involved.
Demand is deterministic (known with certainty).
Demand is constant (stable throughout the year).
There are no quantity discounts.
Costs are constant (no price increases or inflation).
While these assumptions would seem to make EOQ irrelevant for use in a realistic situation, it is
relevant for items that have independent demand. This means that the demand for the item is not
derived from the demand for something else (usually a parent item for which the unit in question
is a component). For example, the demand for steering wheels would be derived from the
demand for automobiles (dependent demand) but the demand for purses is not derived from
anything else; purses have independent demand.
ASCM 629 - Week 5 Page 6
The quantity Q is known as the economic order quantity (EOQ). In order to minimize total
inventory cost, the firm will order Q every time it places an order. For example, a firm with an
annual demand of 12,000 units (at a purchase price of $25 each), annual holding cost of $10 per
unit and an order cost of $150 per order (with orders placed once a month) could save $800
annually by utilizing the EOQ. First, we determine the total costs without using the EOQ
method:
Q = $10(1000/2) + $150(12,000/1,000) + $25(12,000) = $306,800
Then we calculate EOQ:
EOQ = 2(12,000)($150)/$10 = 600
And we calculate total costs at the EOQ of 600:
Q = $10(600/2) + $150(12,000/600) + $25(12,000) = $306,000
Finally, we subtract the total cost of Q from Q to determine the savings:
$306,800 − 306,000 = $800
Notice that if you remove purchasing cost from the equation, the savings is still $800. We might
assume this means that purchasing cost is not relevant to our order decision and can be
eliminated from the equation. It must be noted that this is true only as long as no quantity
discount exists. If a quantity discount is available, the firm must determine whether the savings
of the quantity discount are sufficient to offset the loss of the savings resulting from the use of
the EOQ.
There are a number of assumptions that must be made with the use of the EOQ. These include:
Only one product is involved.
Demand is deterministic (known with certainty).
Demand is constant (stable throughout the year).
There are no quantity discounts.
Costs are constant (no price increases or inflation).
While these assumptions would seem to make EOQ irrelevant for use in a realistic situation, it is
relevant for items that have independent demand. This means that the demand for the item is not
derived from the demand for something else (usually a parent item for which the unit in question
is a component). For example, the demand for steering wheels would be derived from the
demand for automobiles (dependent demand) but the demand for purses is not derived from
anything else; purses have independent demand.
ASCM 629 - Week 5 Page 6
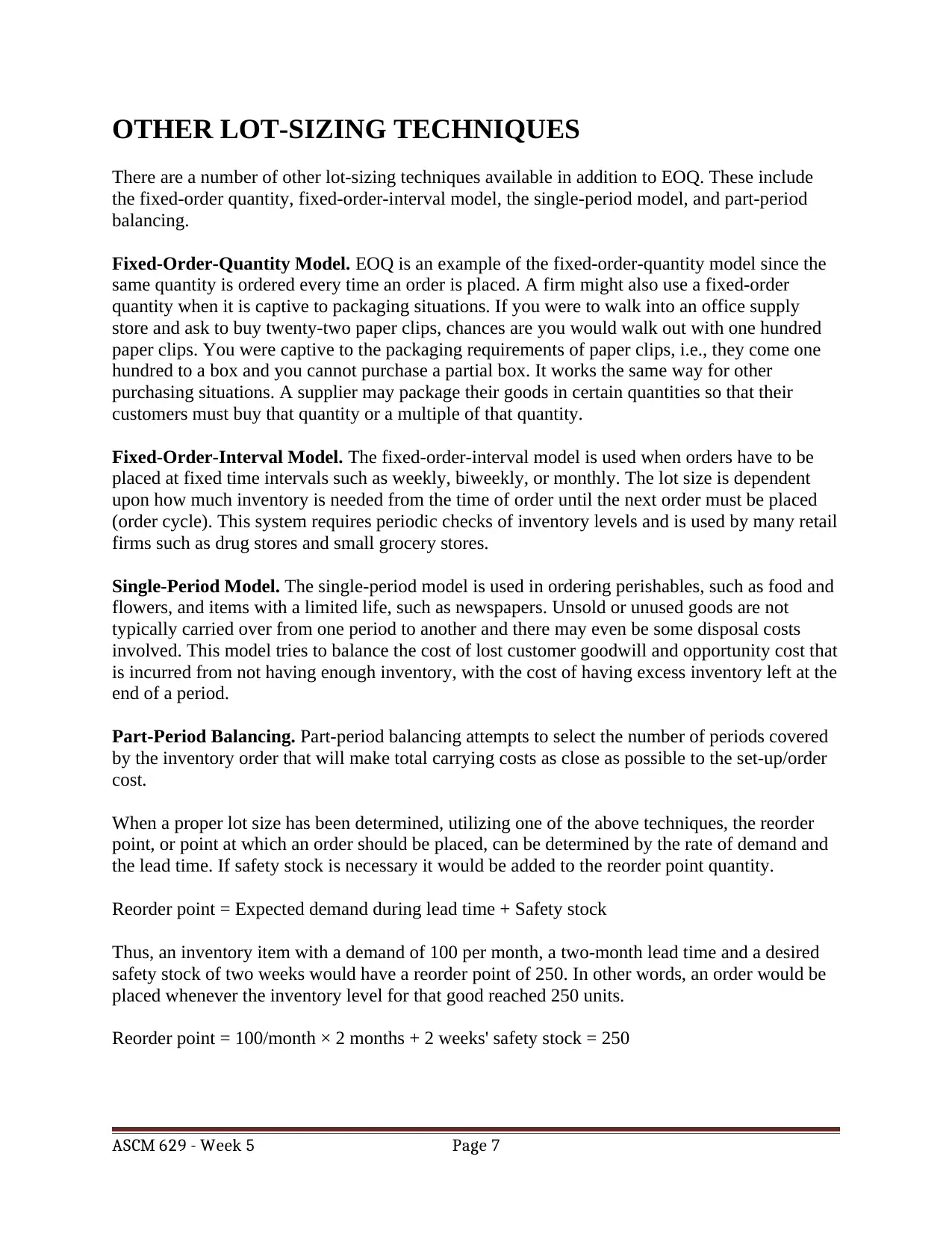
OTHER LOT-SIZING TECHNIQUES
There are a number of other lot-sizing techniques available in addition to EOQ. These include
the fixed-order quantity, fixed-order-interval model, the single-period model, and part-period
balancing.
Fixed-Order-Quantity Model. EOQ is an example of the fixed-order-quantity model since the
same quantity is ordered every time an order is placed. A firm might also use a fixed-order
quantity when it is captive to packaging situations. If you were to walk into an office supply
store and ask to buy twenty-two paper clips, chances are you would walk out with one hundred
paper clips. You were captive to the packaging requirements of paper clips, i.e., they come one
hundred to a box and you cannot purchase a partial box. It works the same way for other
purchasing situations. A supplier may package their goods in certain quantities so that their
customers must buy that quantity or a multiple of that quantity.
Fixed-Order-Interval Model. The fixed-order-interval model is used when orders have to be
placed at fixed time intervals such as weekly, biweekly, or monthly. The lot size is dependent
upon how much inventory is needed from the time of order until the next order must be placed
(order cycle). This system requires periodic checks of inventory levels and is used by many retail
firms such as drug stores and small grocery stores.
Single-Period Model. The single-period model is used in ordering perishables, such as food and
flowers, and items with a limited life, such as newspapers. Unsold or unused goods are not
typically carried over from one period to another and there may even be some disposal costs
involved. This model tries to balance the cost of lost customer goodwill and opportunity cost that
is incurred from not having enough inventory, with the cost of having excess inventory left at the
end of a period.
Part-Period Balancing. Part-period balancing attempts to select the number of periods covered
by the inventory order that will make total carrying costs as close as possible to the set-up/order
cost.
When a proper lot size has been determined, utilizing one of the above techniques, the reorder
point, or point at which an order should be placed, can be determined by the rate of demand and
the lead time. If safety stock is necessary it would be added to the reorder point quantity.
Reorder point = Expected demand during lead time + Safety stock
Thus, an inventory item with a demand of 100 per month, a two-month lead time and a desired
safety stock of two weeks would have a reorder point of 250. In other words, an order would be
placed whenever the inventory level for that good reached 250 units.
Reorder point = 100/month × 2 months + 2 weeks' safety stock = 250
ASCM 629 - Week 5 Page 7
There are a number of other lot-sizing techniques available in addition to EOQ. These include
the fixed-order quantity, fixed-order-interval model, the single-period model, and part-period
balancing.
Fixed-Order-Quantity Model. EOQ is an example of the fixed-order-quantity model since the
same quantity is ordered every time an order is placed. A firm might also use a fixed-order
quantity when it is captive to packaging situations. If you were to walk into an office supply
store and ask to buy twenty-two paper clips, chances are you would walk out with one hundred
paper clips. You were captive to the packaging requirements of paper clips, i.e., they come one
hundred to a box and you cannot purchase a partial box. It works the same way for other
purchasing situations. A supplier may package their goods in certain quantities so that their
customers must buy that quantity or a multiple of that quantity.
Fixed-Order-Interval Model. The fixed-order-interval model is used when orders have to be
placed at fixed time intervals such as weekly, biweekly, or monthly. The lot size is dependent
upon how much inventory is needed from the time of order until the next order must be placed
(order cycle). This system requires periodic checks of inventory levels and is used by many retail
firms such as drug stores and small grocery stores.
Single-Period Model. The single-period model is used in ordering perishables, such as food and
flowers, and items with a limited life, such as newspapers. Unsold or unused goods are not
typically carried over from one period to another and there may even be some disposal costs
involved. This model tries to balance the cost of lost customer goodwill and opportunity cost that
is incurred from not having enough inventory, with the cost of having excess inventory left at the
end of a period.
Part-Period Balancing. Part-period balancing attempts to select the number of periods covered
by the inventory order that will make total carrying costs as close as possible to the set-up/order
cost.
When a proper lot size has been determined, utilizing one of the above techniques, the reorder
point, or point at which an order should be placed, can be determined by the rate of demand and
the lead time. If safety stock is necessary it would be added to the reorder point quantity.
Reorder point = Expected demand during lead time + Safety stock
Thus, an inventory item with a demand of 100 per month, a two-month lead time and a desired
safety stock of two weeks would have a reorder point of 250. In other words, an order would be
placed whenever the inventory level for that good reached 250 units.
Reorder point = 100/month × 2 months + 2 weeks' safety stock = 250
ASCM 629 - Week 5 Page 7
Paraphrase This Document
Need a fresh take? Get an instant paraphrase of this document with our AI Paraphraser
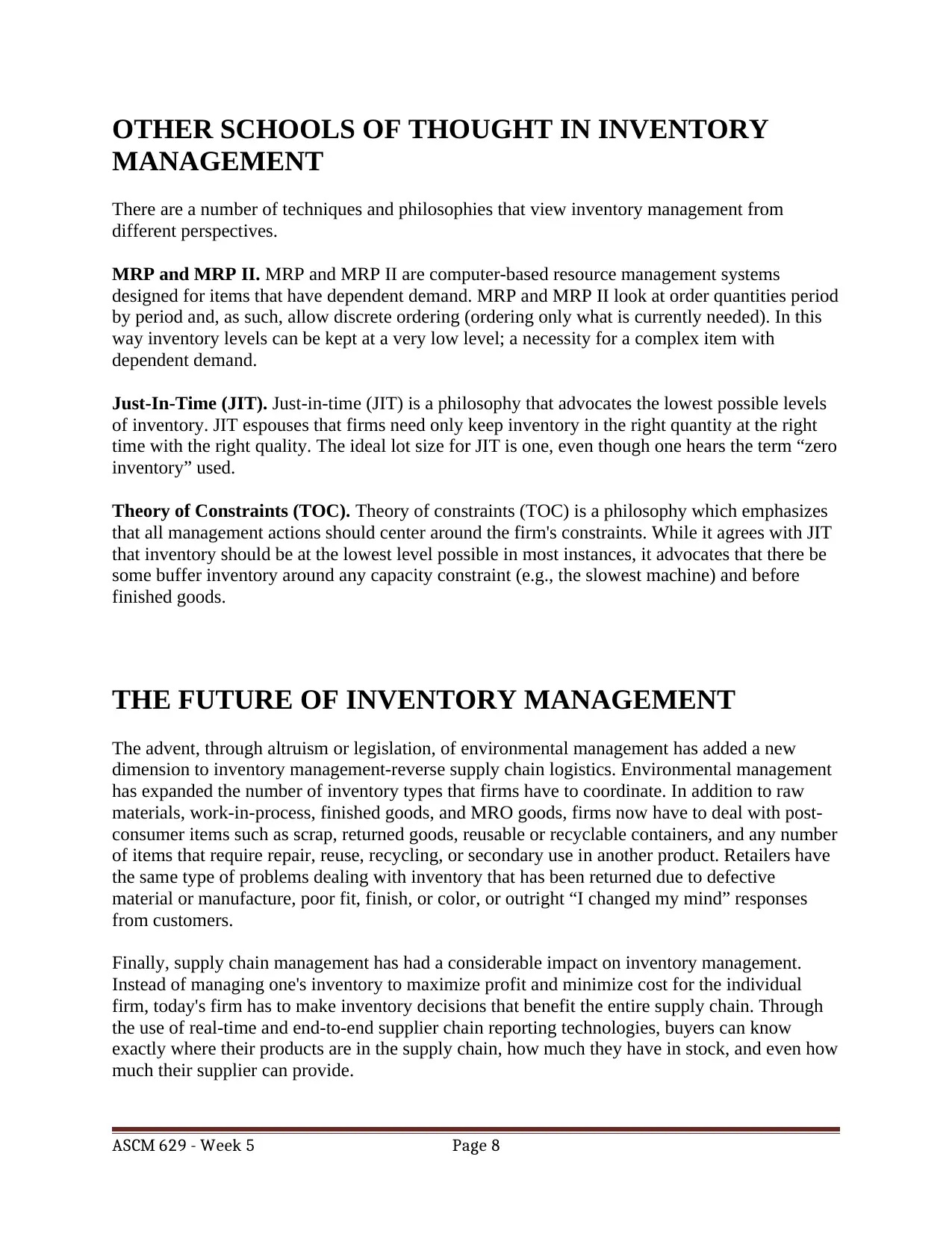
OTHER SCHOOLS OF THOUGHT IN INVENTORY
MANAGEMENT
There are a number of techniques and philosophies that view inventory management from
different perspectives.
MRP and MRP II. MRP and MRP II are computer-based resource management systems
designed for items that have dependent demand. MRP and MRP II look at order quantities period
by period and, as such, allow discrete ordering (ordering only what is currently needed). In this
way inventory levels can be kept at a very low level; a necessity for a complex item with
dependent demand.
Just-In-Time (JIT). Just-in-time (JIT) is a philosophy that advocates the lowest possible levels
of inventory. JIT espouses that firms need only keep inventory in the right quantity at the right
time with the right quality. The ideal lot size for JIT is one, even though one hears the term “zero
inventory” used.
Theory of Constraints (TOC). Theory of constraints (TOC) is a philosophy which emphasizes
that all management actions should center around the firm's constraints. While it agrees with JIT
that inventory should be at the lowest level possible in most instances, it advocates that there be
some buffer inventory around any capacity constraint (e.g., the slowest machine) and before
finished goods.
THE FUTURE OF INVENTORY MANAGEMENT
The advent, through altruism or legislation, of environmental management has added a new
dimension to inventory management-reverse supply chain logistics. Environmental management
has expanded the number of inventory types that firms have to coordinate. In addition to raw
materials, work-in-process, finished goods, and MRO goods, firms now have to deal with post-
consumer items such as scrap, returned goods, reusable or recyclable containers, and any number
of items that require repair, reuse, recycling, or secondary use in another product. Retailers have
the same type of problems dealing with inventory that has been returned due to defective
material or manufacture, poor fit, finish, or color, or outright “I changed my mind” responses
from customers.
Finally, supply chain management has had a considerable impact on inventory management.
Instead of managing one's inventory to maximize profit and minimize cost for the individual
firm, today's firm has to make inventory decisions that benefit the entire supply chain. Through
the use of real-time and end-to-end supplier chain reporting technologies, buyers can know
exactly where their products are in the supply chain, how much they have in stock, and even how
much their supplier can provide.
ASCM 629 - Week 5 Page 8
MANAGEMENT
There are a number of techniques and philosophies that view inventory management from
different perspectives.
MRP and MRP II. MRP and MRP II are computer-based resource management systems
designed for items that have dependent demand. MRP and MRP II look at order quantities period
by period and, as such, allow discrete ordering (ordering only what is currently needed). In this
way inventory levels can be kept at a very low level; a necessity for a complex item with
dependent demand.
Just-In-Time (JIT). Just-in-time (JIT) is a philosophy that advocates the lowest possible levels
of inventory. JIT espouses that firms need only keep inventory in the right quantity at the right
time with the right quality. The ideal lot size for JIT is one, even though one hears the term “zero
inventory” used.
Theory of Constraints (TOC). Theory of constraints (TOC) is a philosophy which emphasizes
that all management actions should center around the firm's constraints. While it agrees with JIT
that inventory should be at the lowest level possible in most instances, it advocates that there be
some buffer inventory around any capacity constraint (e.g., the slowest machine) and before
finished goods.
THE FUTURE OF INVENTORY MANAGEMENT
The advent, through altruism or legislation, of environmental management has added a new
dimension to inventory management-reverse supply chain logistics. Environmental management
has expanded the number of inventory types that firms have to coordinate. In addition to raw
materials, work-in-process, finished goods, and MRO goods, firms now have to deal with post-
consumer items such as scrap, returned goods, reusable or recyclable containers, and any number
of items that require repair, reuse, recycling, or secondary use in another product. Retailers have
the same type of problems dealing with inventory that has been returned due to defective
material or manufacture, poor fit, finish, or color, or outright “I changed my mind” responses
from customers.
Finally, supply chain management has had a considerable impact on inventory management.
Instead of managing one's inventory to maximize profit and minimize cost for the individual
firm, today's firm has to make inventory decisions that benefit the entire supply chain. Through
the use of real-time and end-to-end supplier chain reporting technologies, buyers can know
exactly where their products are in the supply chain, how much they have in stock, and even how
much their supplier can provide.
ASCM 629 - Week 5 Page 8
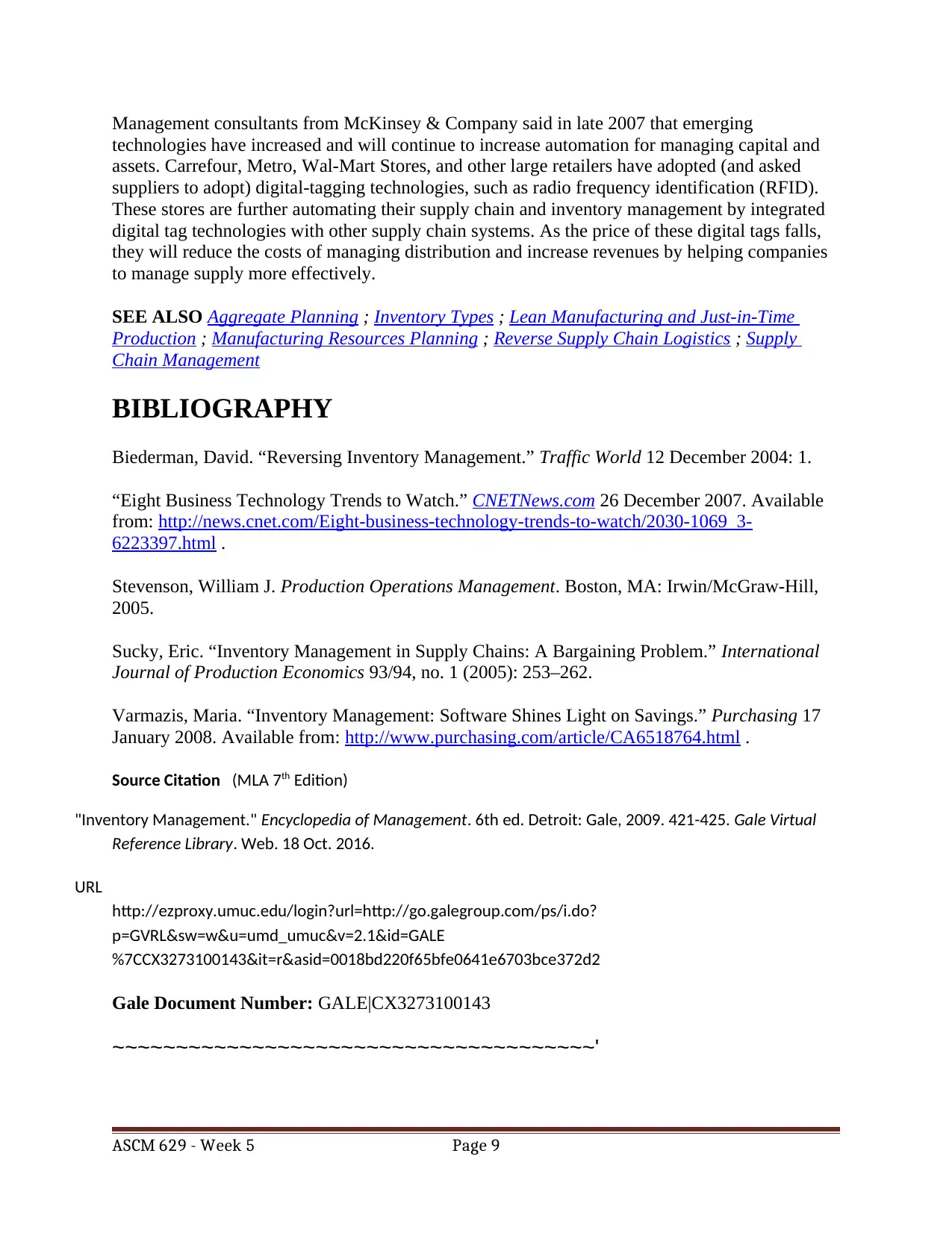
Management consultants from McKinsey & Company said in late 2007 that emerging
technologies have increased and will continue to increase automation for managing capital and
assets. Carrefour, Metro, Wal-Mart Stores, and other large retailers have adopted (and asked
suppliers to adopt) digital-tagging technologies, such as radio frequency identification (RFID).
These stores are further automating their supply chain and inventory management by integrated
digital tag technologies with other supply chain systems. As the price of these digital tags falls,
they will reduce the costs of managing distribution and increase revenues by helping companies
to manage supply more effectively.
SEE ALSO Aggregate Planning ; Inventory Types ; Lean Manufacturing and Just-in-Time
Production ; Manufacturing Resources Planning ; Reverse Supply Chain Logistics ; Supply
Chain Management
BIBLIOGRAPHY
Biederman, David. “Reversing Inventory Management.” Traffic World 12 December 2004: 1.
“Eight Business Technology Trends to Watch.” CNETNews.com 26 December 2007. Available
from: http://news.cnet.com/Eight-business-technology-trends-to-watch/2030-1069_3-
6223397.html .
Stevenson, William J. Production Operations Management. Boston, MA: Irwin/McGraw-Hill,
2005.
Sucky, Eric. “Inventory Management in Supply Chains: A Bargaining Problem.” International
Journal of Production Economics 93/94, no. 1 (2005): 253–262.
Varmazis, Maria. “Inventory Management: Software Shines Light on Savings.” Purchasing 17
January 2008. Available from: http://www.purchasing.com/article/CA6518764.html .
Source Citation (MLA 7th Edition)
"Inventory Management." Encyclopedia of Management. 6th ed. Detroit: Gale, 2009. 421-425. Gale Virtual
Reference Library. Web. 18 Oct. 2016.
URL
http://ezproxy.umuc.edu/login?url=http://go.galegroup.com/ps/i.do?
p=GVRL&sw=w&u=umd_umuc&v=2.1&id=GALE
%7CCX3273100143&it=r&asid=0018bd220f65bfe0641e6703bce372d2
Gale Document Number: GALE|CX3273100143
~~~~~~~~~~~~~~~~~~~~~~~~~~~~~~~~~~~~~~'
ASCM 629 - Week 5 Page 9
technologies have increased and will continue to increase automation for managing capital and
assets. Carrefour, Metro, Wal-Mart Stores, and other large retailers have adopted (and asked
suppliers to adopt) digital-tagging technologies, such as radio frequency identification (RFID).
These stores are further automating their supply chain and inventory management by integrated
digital tag technologies with other supply chain systems. As the price of these digital tags falls,
they will reduce the costs of managing distribution and increase revenues by helping companies
to manage supply more effectively.
SEE ALSO Aggregate Planning ; Inventory Types ; Lean Manufacturing and Just-in-Time
Production ; Manufacturing Resources Planning ; Reverse Supply Chain Logistics ; Supply
Chain Management
BIBLIOGRAPHY
Biederman, David. “Reversing Inventory Management.” Traffic World 12 December 2004: 1.
“Eight Business Technology Trends to Watch.” CNETNews.com 26 December 2007. Available
from: http://news.cnet.com/Eight-business-technology-trends-to-watch/2030-1069_3-
6223397.html .
Stevenson, William J. Production Operations Management. Boston, MA: Irwin/McGraw-Hill,
2005.
Sucky, Eric. “Inventory Management in Supply Chains: A Bargaining Problem.” International
Journal of Production Economics 93/94, no. 1 (2005): 253–262.
Varmazis, Maria. “Inventory Management: Software Shines Light on Savings.” Purchasing 17
January 2008. Available from: http://www.purchasing.com/article/CA6518764.html .
Source Citation (MLA 7th Edition)
"Inventory Management." Encyclopedia of Management. 6th ed. Detroit: Gale, 2009. 421-425. Gale Virtual
Reference Library. Web. 18 Oct. 2016.
URL
http://ezproxy.umuc.edu/login?url=http://go.galegroup.com/ps/i.do?
p=GVRL&sw=w&u=umd_umuc&v=2.1&id=GALE
%7CCX3273100143&it=r&asid=0018bd220f65bfe0641e6703bce372d2
Gale Document Number: GALE|CX3273100143
~~~~~~~~~~~~~~~~~~~~~~~~~~~~~~~~~~~~~~'
ASCM 629 - Week 5 Page 9
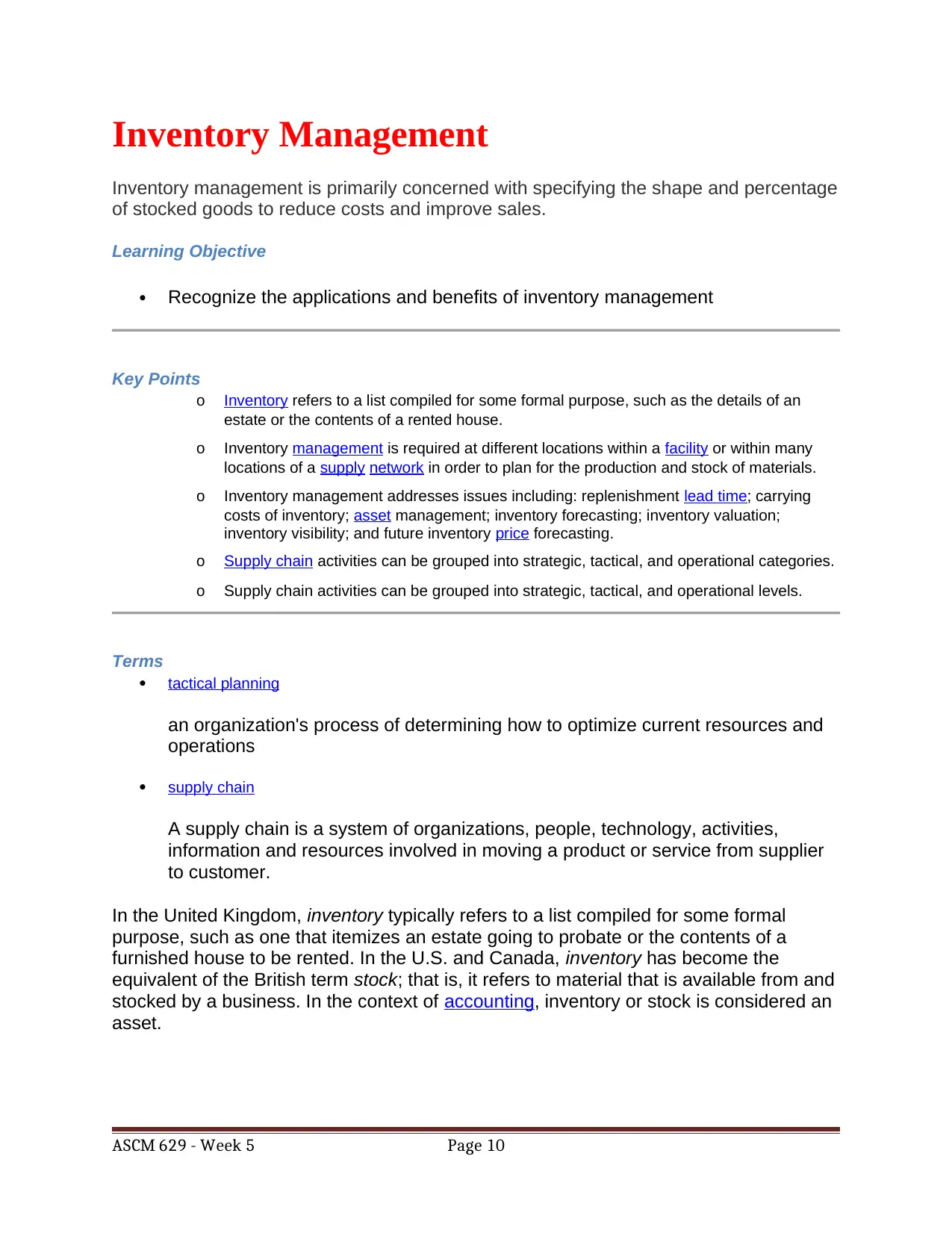
Inventory Management
Inventory management is primarily concerned with specifying the shape and percentage
of stocked goods to reduce costs and improve sales.
Learning Objective
Recognize the applications and benefits of inventory management
Key Points
o Inventory refers to a list compiled for some formal purpose, such as the details of an
estate or the contents of a rented house.
o Inventory management is required at different locations within a facility or within many
locations of a supply network in order to plan for the production and stock of materials.
o Inventory management addresses issues including: replenishment lead time; carrying
costs of inventory; asset management; inventory forecasting; inventory valuation;
inventory visibility; and future inventory price forecasting.
o Supply chain activities can be grouped into strategic, tactical, and operational categories.
o Supply chain activities can be grouped into strategic, tactical, and operational levels.
Terms
tactical planning
an organization's process of determining how to optimize current resources and
operations
supply chain
A supply chain is a system of organizations, people, technology, activities,
information and resources involved in moving a product or service from supplier
to customer.
In the United Kingdom, inventory typically refers to a list compiled for some formal
purpose, such as one that itemizes an estate going to probate or the contents of a
furnished house to be rented. In the U.S. and Canada, inventory has become the
equivalent of the British term stock; that is, it refers to material that is available from and
stocked by a business. In the context of accounting, inventory or stock is considered an
asset.
ASCM 629 - Week 5 Page 10
Inventory management is primarily concerned with specifying the shape and percentage
of stocked goods to reduce costs and improve sales.
Learning Objective
Recognize the applications and benefits of inventory management
Key Points
o Inventory refers to a list compiled for some formal purpose, such as the details of an
estate or the contents of a rented house.
o Inventory management is required at different locations within a facility or within many
locations of a supply network in order to plan for the production and stock of materials.
o Inventory management addresses issues including: replenishment lead time; carrying
costs of inventory; asset management; inventory forecasting; inventory valuation;
inventory visibility; and future inventory price forecasting.
o Supply chain activities can be grouped into strategic, tactical, and operational categories.
o Supply chain activities can be grouped into strategic, tactical, and operational levels.
Terms
tactical planning
an organization's process of determining how to optimize current resources and
operations
supply chain
A supply chain is a system of organizations, people, technology, activities,
information and resources involved in moving a product or service from supplier
to customer.
In the United Kingdom, inventory typically refers to a list compiled for some formal
purpose, such as one that itemizes an estate going to probate or the contents of a
furnished house to be rented. In the U.S. and Canada, inventory has become the
equivalent of the British term stock; that is, it refers to material that is available from and
stocked by a business. In the context of accounting, inventory or stock is considered an
asset.
ASCM 629 - Week 5 Page 10
Secure Best Marks with AI Grader
Need help grading? Try our AI Grader for instant feedback on your assignments.
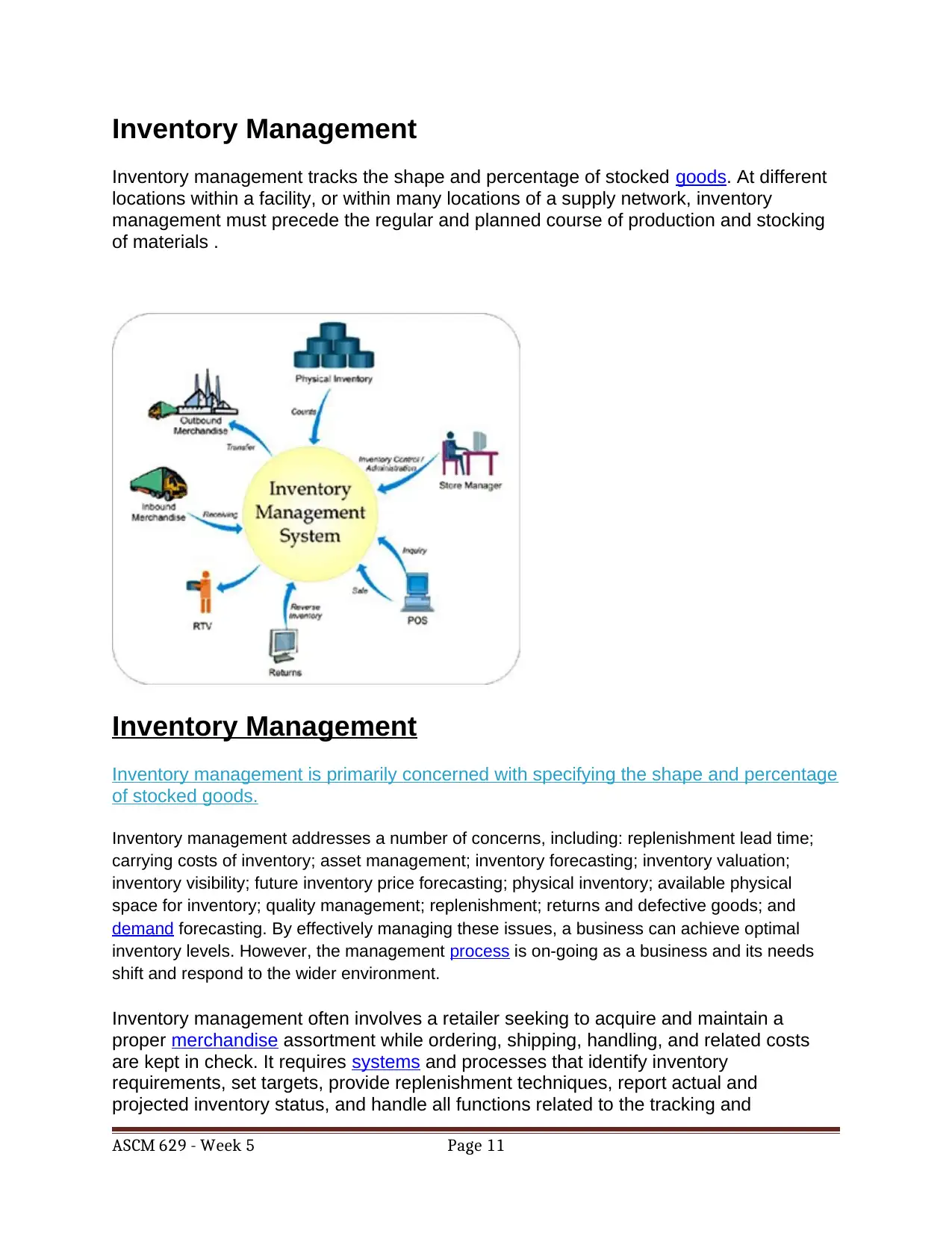
Inventory Management
Inventory management tracks the shape and percentage of stocked goods. At different
locations within a facility, or within many locations of a supply network, inventory
management must precede the regular and planned course of production and stocking
of materials .
Inventory Management
Inventory management is primarily concerned with specifying the shape and percentage
of stocked goods.
Inventory management addresses a number of concerns, including: replenishment lead time;
carrying costs of inventory; asset management; inventory forecasting; inventory valuation;
inventory visibility; future inventory price forecasting; physical inventory; available physical
space for inventory; quality management; replenishment; returns and defective goods; and
demand forecasting. By effectively managing these issues, a business can achieve optimal
inventory levels. However, the management process is on-going as a business and its needs
shift and respond to the wider environment.
Inventory management often involves a retailer seeking to acquire and maintain a
proper merchandise assortment while ordering, shipping, handling, and related costs
are kept in check. It requires systems and processes that identify inventory
requirements, set targets, provide replenishment techniques, report actual and
projected inventory status, and handle all functions related to the tracking and
ASCM 629 - Week 5 Page 11
Inventory management tracks the shape and percentage of stocked goods. At different
locations within a facility, or within many locations of a supply network, inventory
management must precede the regular and planned course of production and stocking
of materials .
Inventory Management
Inventory management is primarily concerned with specifying the shape and percentage
of stocked goods.
Inventory management addresses a number of concerns, including: replenishment lead time;
carrying costs of inventory; asset management; inventory forecasting; inventory valuation;
inventory visibility; future inventory price forecasting; physical inventory; available physical
space for inventory; quality management; replenishment; returns and defective goods; and
demand forecasting. By effectively managing these issues, a business can achieve optimal
inventory levels. However, the management process is on-going as a business and its needs
shift and respond to the wider environment.
Inventory management often involves a retailer seeking to acquire and maintain a
proper merchandise assortment while ordering, shipping, handling, and related costs
are kept in check. It requires systems and processes that identify inventory
requirements, set targets, provide replenishment techniques, report actual and
projected inventory status, and handle all functions related to the tracking and
ASCM 629 - Week 5 Page 11
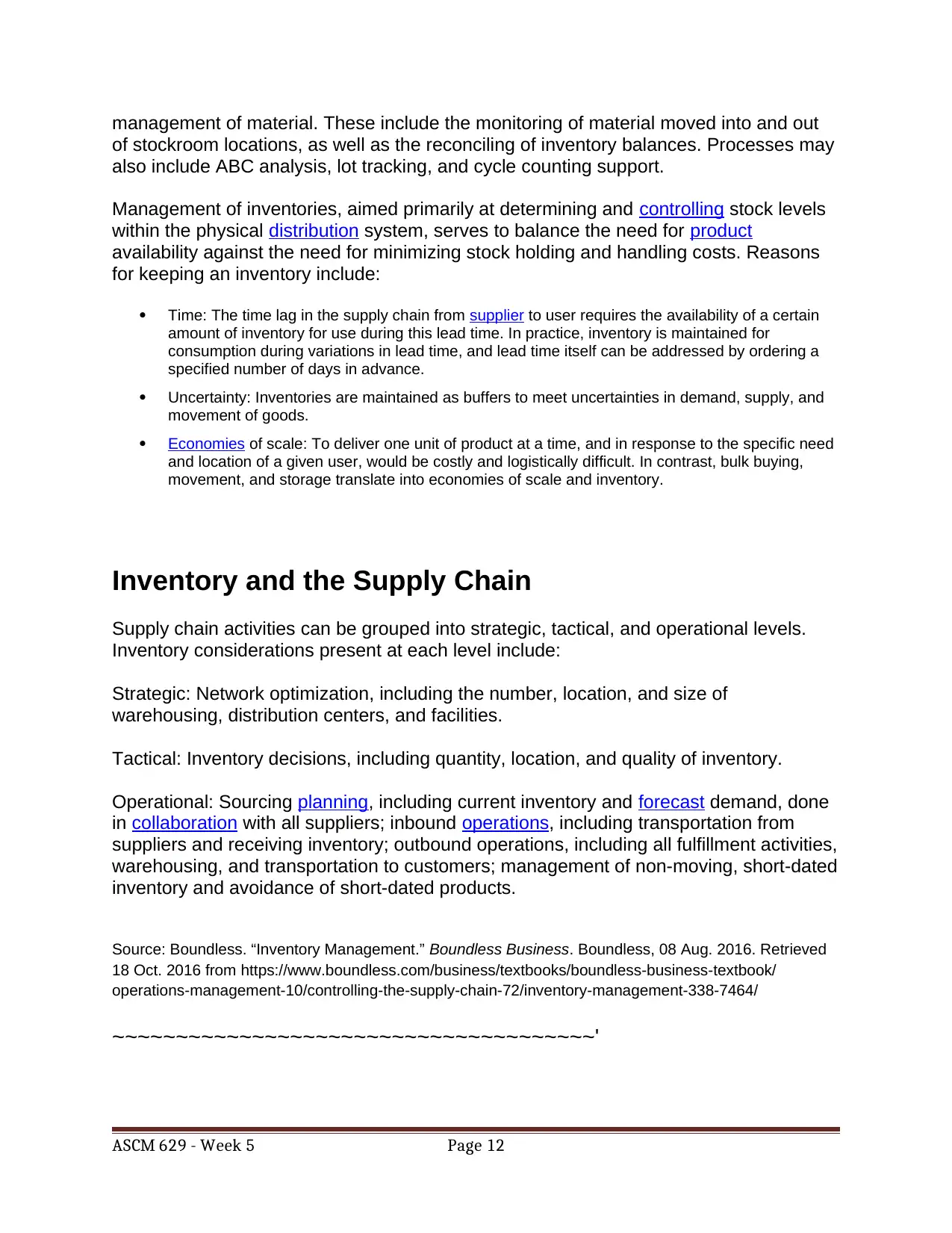
management of material. These include the monitoring of material moved into and out
of stockroom locations, as well as the reconciling of inventory balances. Processes may
also include ABC analysis, lot tracking, and cycle counting support.
Management of inventories, aimed primarily at determining and controlling stock levels
within the physical distribution system, serves to balance the need for product
availability against the need for minimizing stock holding and handling costs. Reasons
for keeping an inventory include:
Time: The time lag in the supply chain from supplier to user requires the availability of a certain
amount of inventory for use during this lead time. In practice, inventory is maintained for
consumption during variations in lead time, and lead time itself can be addressed by ordering a
specified number of days in advance.
Uncertainty: Inventories are maintained as buffers to meet uncertainties in demand, supply, and
movement of goods.
Economies of scale: To deliver one unit of product at a time, and in response to the specific need
and location of a given user, would be costly and logistically difficult. In contrast, bulk buying,
movement, and storage translate into economies of scale and inventory.
Inventory and the Supply Chain
Supply chain activities can be grouped into strategic, tactical, and operational levels.
Inventory considerations present at each level include:
Strategic: Network optimization, including the number, location, and size of
warehousing, distribution centers, and facilities.
Tactical: Inventory decisions, including quantity, location, and quality of inventory.
Operational: Sourcing planning, including current inventory and forecast demand, done
in collaboration with all suppliers; inbound operations, including transportation from
suppliers and receiving inventory; outbound operations, including all fulfillment activities,
warehousing, and transportation to customers; management of non-moving, short-dated
inventory and avoidance of short-dated products.
Source: Boundless. “Inventory Management.” Boundless Business. Boundless, 08 Aug. 2016. Retrieved
18 Oct. 2016 from https://www.boundless.com/business/textbooks/boundless-business-textbook/
operations-management-10/controlling-the-supply-chain-72/inventory-management-338-7464/
~~~~~~~~~~~~~~~~~~~~~~~~~~~~~~~~~~~~~~'
ASCM 629 - Week 5 Page 12
of stockroom locations, as well as the reconciling of inventory balances. Processes may
also include ABC analysis, lot tracking, and cycle counting support.
Management of inventories, aimed primarily at determining and controlling stock levels
within the physical distribution system, serves to balance the need for product
availability against the need for minimizing stock holding and handling costs. Reasons
for keeping an inventory include:
Time: The time lag in the supply chain from supplier to user requires the availability of a certain
amount of inventory for use during this lead time. In practice, inventory is maintained for
consumption during variations in lead time, and lead time itself can be addressed by ordering a
specified number of days in advance.
Uncertainty: Inventories are maintained as buffers to meet uncertainties in demand, supply, and
movement of goods.
Economies of scale: To deliver one unit of product at a time, and in response to the specific need
and location of a given user, would be costly and logistically difficult. In contrast, bulk buying,
movement, and storage translate into economies of scale and inventory.
Inventory and the Supply Chain
Supply chain activities can be grouped into strategic, tactical, and operational levels.
Inventory considerations present at each level include:
Strategic: Network optimization, including the number, location, and size of
warehousing, distribution centers, and facilities.
Tactical: Inventory decisions, including quantity, location, and quality of inventory.
Operational: Sourcing planning, including current inventory and forecast demand, done
in collaboration with all suppliers; inbound operations, including transportation from
suppliers and receiving inventory; outbound operations, including all fulfillment activities,
warehousing, and transportation to customers; management of non-moving, short-dated
inventory and avoidance of short-dated products.
Source: Boundless. “Inventory Management.” Boundless Business. Boundless, 08 Aug. 2016. Retrieved
18 Oct. 2016 from https://www.boundless.com/business/textbooks/boundless-business-textbook/
operations-management-10/controlling-the-supply-chain-72/inventory-management-338-7464/
~~~~~~~~~~~~~~~~~~~~~~~~~~~~~~~~~~~~~~'
ASCM 629 - Week 5 Page 12
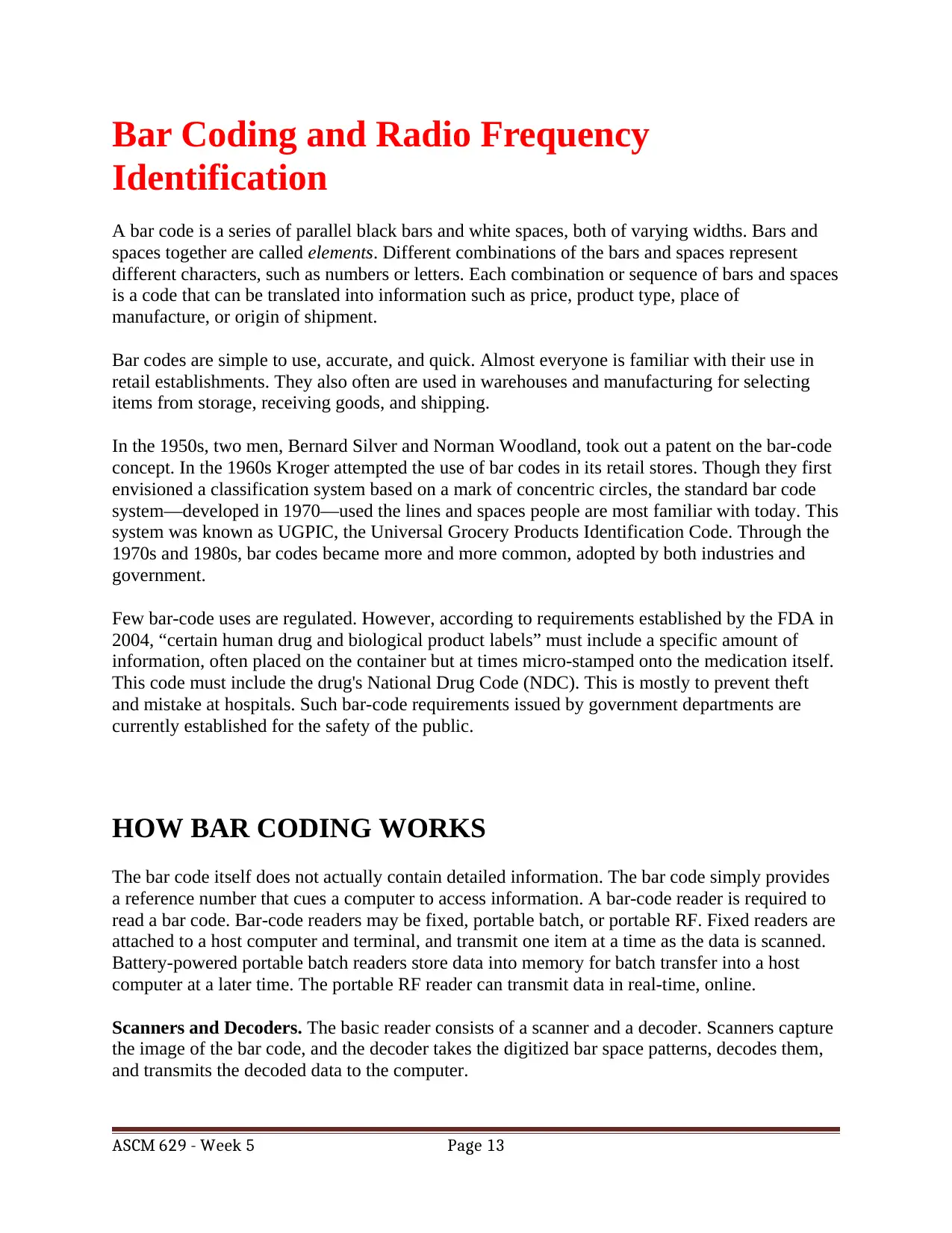
Bar Coding and Radio Frequency
Identification
A bar code is a series of parallel black bars and white spaces, both of varying widths. Bars and
spaces together are called elements. Different combinations of the bars and spaces represent
different characters, such as numbers or letters. Each combination or sequence of bars and spaces
is a code that can be translated into information such as price, product type, place of
manufacture, or origin of shipment.
Bar codes are simple to use, accurate, and quick. Almost everyone is familiar with their use in
retail establishments. They also often are used in warehouses and manufacturing for selecting
items from storage, receiving goods, and shipping.
In the 1950s, two men, Bernard Silver and Norman Woodland, took out a patent on the bar-code
concept. In the 1960s Kroger attempted the use of bar codes in its retail stores. Though they first
envisioned a classification system based on a mark of concentric circles, the standard bar code
system—developed in 1970—used the lines and spaces people are most familiar with today. This
system was known as UGPIC, the Universal Grocery Products Identification Code. Through the
1970s and 1980s, bar codes became more and more common, adopted by both industries and
government.
Few bar-code uses are regulated. However, according to requirements established by the FDA in
2004, “certain human drug and biological product labels” must include a specific amount of
information, often placed on the container but at times micro-stamped onto the medication itself.
This code must include the drug's National Drug Code (NDC). This is mostly to prevent theft
and mistake at hospitals. Such bar-code requirements issued by government departments are
currently established for the safety of the public.
HOW BAR CODING WORKS
The bar code itself does not actually contain detailed information. The bar code simply provides
a reference number that cues a computer to access information. A bar-code reader is required to
read a bar code. Bar-code readers may be fixed, portable batch, or portable RF. Fixed readers are
attached to a host computer and terminal, and transmit one item at a time as the data is scanned.
Battery-powered portable batch readers store data into memory for batch transfer into a host
computer at a later time. The portable RF reader can transmit data in real-time, online.
Scanners and Decoders. The basic reader consists of a scanner and a decoder. Scanners capture
the image of the bar code, and the decoder takes the digitized bar space patterns, decodes them,
and transmits the decoded data to the computer.
ASCM 629 - Week 5 Page 13
Identification
A bar code is a series of parallel black bars and white spaces, both of varying widths. Bars and
spaces together are called elements. Different combinations of the bars and spaces represent
different characters, such as numbers or letters. Each combination or sequence of bars and spaces
is a code that can be translated into information such as price, product type, place of
manufacture, or origin of shipment.
Bar codes are simple to use, accurate, and quick. Almost everyone is familiar with their use in
retail establishments. They also often are used in warehouses and manufacturing for selecting
items from storage, receiving goods, and shipping.
In the 1950s, two men, Bernard Silver and Norman Woodland, took out a patent on the bar-code
concept. In the 1960s Kroger attempted the use of bar codes in its retail stores. Though they first
envisioned a classification system based on a mark of concentric circles, the standard bar code
system—developed in 1970—used the lines and spaces people are most familiar with today. This
system was known as UGPIC, the Universal Grocery Products Identification Code. Through the
1970s and 1980s, bar codes became more and more common, adopted by both industries and
government.
Few bar-code uses are regulated. However, according to requirements established by the FDA in
2004, “certain human drug and biological product labels” must include a specific amount of
information, often placed on the container but at times micro-stamped onto the medication itself.
This code must include the drug's National Drug Code (NDC). This is mostly to prevent theft
and mistake at hospitals. Such bar-code requirements issued by government departments are
currently established for the safety of the public.
HOW BAR CODING WORKS
The bar code itself does not actually contain detailed information. The bar code simply provides
a reference number that cues a computer to access information. A bar-code reader is required to
read a bar code. Bar-code readers may be fixed, portable batch, or portable RF. Fixed readers are
attached to a host computer and terminal, and transmit one item at a time as the data is scanned.
Battery-powered portable batch readers store data into memory for batch transfer into a host
computer at a later time. The portable RF reader can transmit data in real-time, online.
Scanners and Decoders. The basic reader consists of a scanner and a decoder. Scanners capture
the image of the bar code, and the decoder takes the digitized bar space patterns, decodes them,
and transmits the decoded data to the computer.
ASCM 629 - Week 5 Page 13
Paraphrase This Document
Need a fresh take? Get an instant paraphrase of this document with our AI Paraphraser
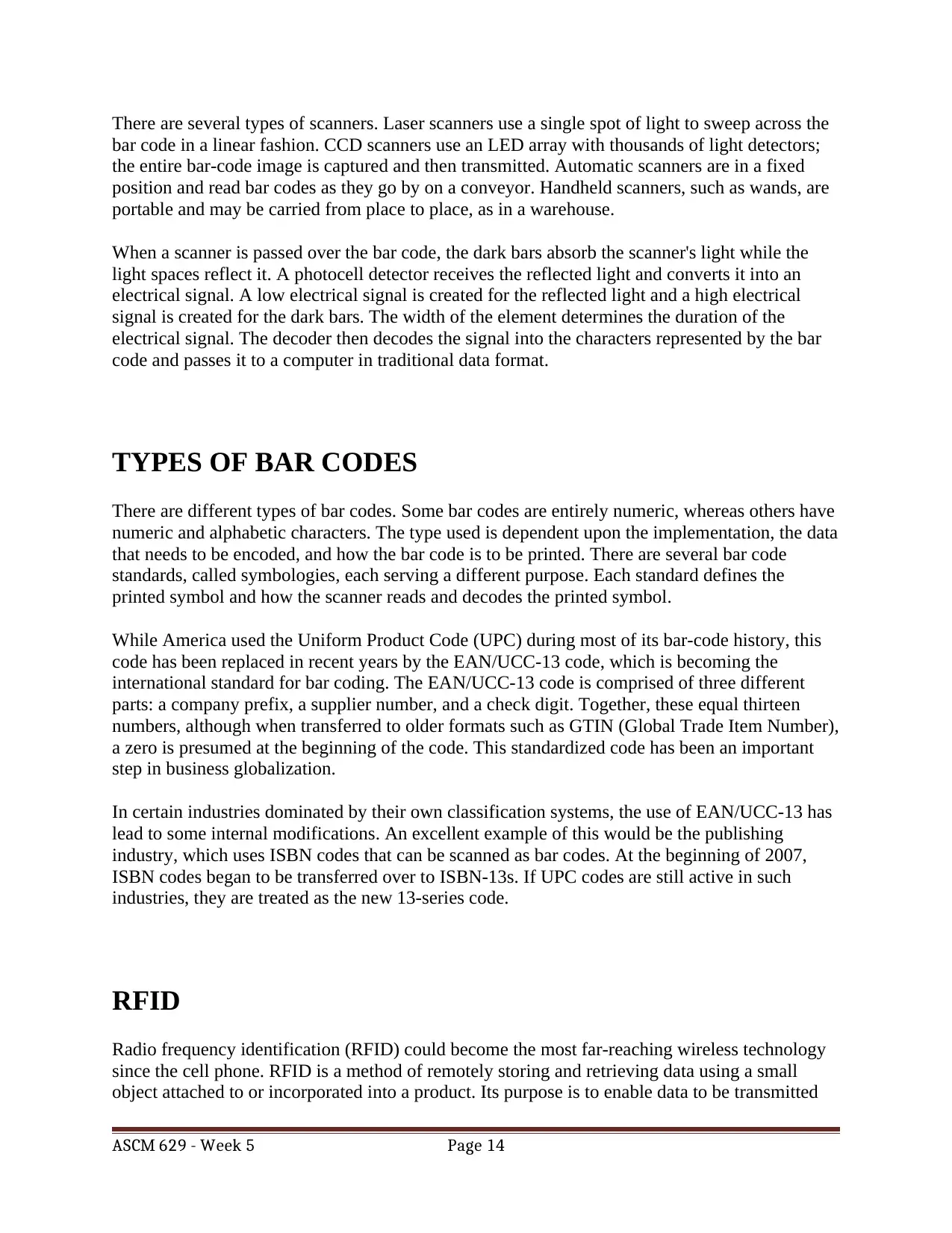
There are several types of scanners. Laser scanners use a single spot of light to sweep across the
bar code in a linear fashion. CCD scanners use an LED array with thousands of light detectors;
the entire bar-code image is captured and then transmitted. Automatic scanners are in a fixed
position and read bar codes as they go by on a conveyor. Handheld scanners, such as wands, are
portable and may be carried from place to place, as in a warehouse.
When a scanner is passed over the bar code, the dark bars absorb the scanner's light while the
light spaces reflect it. A photocell detector receives the reflected light and converts it into an
electrical signal. A low electrical signal is created for the reflected light and a high electrical
signal is created for the dark bars. The width of the element determines the duration of the
electrical signal. The decoder then decodes the signal into the characters represented by the bar
code and passes it to a computer in traditional data format.
TYPES OF BAR CODES
There are different types of bar codes. Some bar codes are entirely numeric, whereas others have
numeric and alphabetic characters. The type used is dependent upon the implementation, the data
that needs to be encoded, and how the bar code is to be printed. There are several bar code
standards, called symbologies, each serving a different purpose. Each standard defines the
printed symbol and how the scanner reads and decodes the printed symbol.
While America used the Uniform Product Code (UPC) during most of its bar-code history, this
code has been replaced in recent years by the EAN/UCC-13 code, which is becoming the
international standard for bar coding. The EAN/UCC-13 code is comprised of three different
parts: a company prefix, a supplier number, and a check digit. Together, these equal thirteen
numbers, although when transferred to older formats such as GTIN (Global Trade Item Number),
a zero is presumed at the beginning of the code. This standardized code has been an important
step in business globalization.
In certain industries dominated by their own classification systems, the use of EAN/UCC-13 has
lead to some internal modifications. An excellent example of this would be the publishing
industry, which uses ISBN codes that can be scanned as bar codes. At the beginning of 2007,
ISBN codes began to be transferred over to ISBN-13s. If UPC codes are still active in such
industries, they are treated as the new 13-series code.
RFID
Radio frequency identification (RFID) could become the most far-reaching wireless technology
since the cell phone. RFID is a method of remotely storing and retrieving data using a small
object attached to or incorporated into a product. Its purpose is to enable data to be transmitted
ASCM 629 - Week 5 Page 14
bar code in a linear fashion. CCD scanners use an LED array with thousands of light detectors;
the entire bar-code image is captured and then transmitted. Automatic scanners are in a fixed
position and read bar codes as they go by on a conveyor. Handheld scanners, such as wands, are
portable and may be carried from place to place, as in a warehouse.
When a scanner is passed over the bar code, the dark bars absorb the scanner's light while the
light spaces reflect it. A photocell detector receives the reflected light and converts it into an
electrical signal. A low electrical signal is created for the reflected light and a high electrical
signal is created for the dark bars. The width of the element determines the duration of the
electrical signal. The decoder then decodes the signal into the characters represented by the bar
code and passes it to a computer in traditional data format.
TYPES OF BAR CODES
There are different types of bar codes. Some bar codes are entirely numeric, whereas others have
numeric and alphabetic characters. The type used is dependent upon the implementation, the data
that needs to be encoded, and how the bar code is to be printed. There are several bar code
standards, called symbologies, each serving a different purpose. Each standard defines the
printed symbol and how the scanner reads and decodes the printed symbol.
While America used the Uniform Product Code (UPC) during most of its bar-code history, this
code has been replaced in recent years by the EAN/UCC-13 code, which is becoming the
international standard for bar coding. The EAN/UCC-13 code is comprised of three different
parts: a company prefix, a supplier number, and a check digit. Together, these equal thirteen
numbers, although when transferred to older formats such as GTIN (Global Trade Item Number),
a zero is presumed at the beginning of the code. This standardized code has been an important
step in business globalization.
In certain industries dominated by their own classification systems, the use of EAN/UCC-13 has
lead to some internal modifications. An excellent example of this would be the publishing
industry, which uses ISBN codes that can be scanned as bar codes. At the beginning of 2007,
ISBN codes began to be transferred over to ISBN-13s. If UPC codes are still active in such
industries, they are treated as the new 13-series code.
RFID
Radio frequency identification (RFID) could become the most far-reaching wireless technology
since the cell phone. RFID is a method of remotely storing and retrieving data using a small
object attached to or incorporated into a product. Its purpose is to enable data to be transmitted
ASCM 629 - Week 5 Page 14
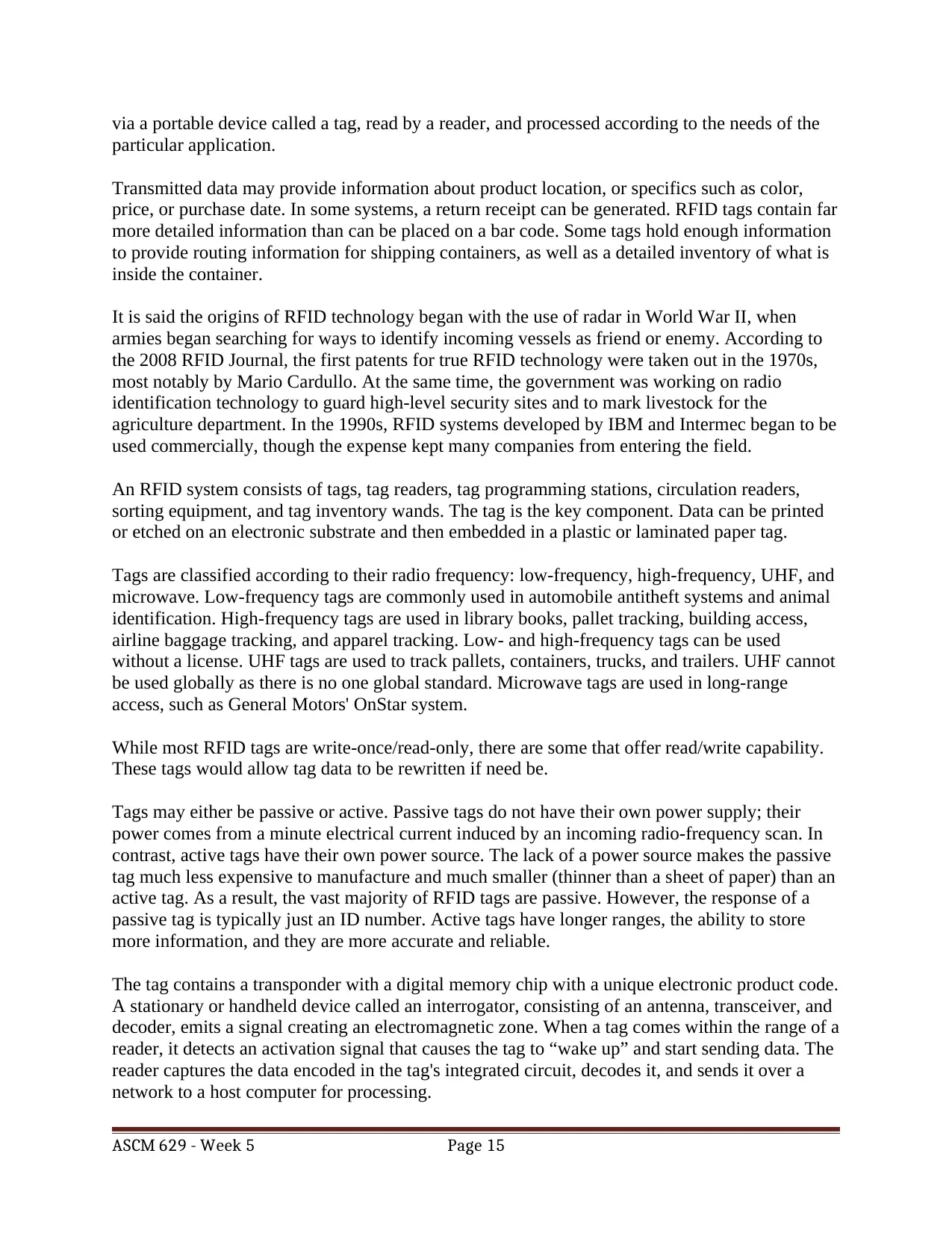
via a portable device called a tag, read by a reader, and processed according to the needs of the
particular application.
Transmitted data may provide information about product location, or specifics such as color,
price, or purchase date. In some systems, a return receipt can be generated. RFID tags contain far
more detailed information than can be placed on a bar code. Some tags hold enough information
to provide routing information for shipping containers, as well as a detailed inventory of what is
inside the container.
It is said the origins of RFID technology began with the use of radar in World War II, when
armies began searching for ways to identify incoming vessels as friend or enemy. According to
the 2008 RFID Journal, the first patents for true RFID technology were taken out in the 1970s,
most notably by Mario Cardullo. At the same time, the government was working on radio
identification technology to guard high-level security sites and to mark livestock for the
agriculture department. In the 1990s, RFID systems developed by IBM and Intermec began to be
used commercially, though the expense kept many companies from entering the field.
An RFID system consists of tags, tag readers, tag programming stations, circulation readers,
sorting equipment, and tag inventory wands. The tag is the key component. Data can be printed
or etched on an electronic substrate and then embedded in a plastic or laminated paper tag.
Tags are classified according to their radio frequency: low-frequency, high-frequency, UHF, and
microwave. Low-frequency tags are commonly used in automobile antitheft systems and animal
identification. High-frequency tags are used in library books, pallet tracking, building access,
airline baggage tracking, and apparel tracking. Low- and high-frequency tags can be used
without a license. UHF tags are used to track pallets, containers, trucks, and trailers. UHF cannot
be used globally as there is no one global standard. Microwave tags are used in long-range
access, such as General Motors' OnStar system.
While most RFID tags are write-once/read-only, there are some that offer read/write capability.
These tags would allow tag data to be rewritten if need be.
Tags may either be passive or active. Passive tags do not have their own power supply; their
power comes from a minute electrical current induced by an incoming radio-frequency scan. In
contrast, active tags have their own power source. The lack of a power source makes the passive
tag much less expensive to manufacture and much smaller (thinner than a sheet of paper) than an
active tag. As a result, the vast majority of RFID tags are passive. However, the response of a
passive tag is typically just an ID number. Active tags have longer ranges, the ability to store
more information, and they are more accurate and reliable.
The tag contains a transponder with a digital memory chip with a unique electronic product code.
A stationary or handheld device called an interrogator, consisting of an antenna, transceiver, and
decoder, emits a signal creating an electromagnetic zone. When a tag comes within the range of a
reader, it detects an activation signal that causes the tag to “wake up” and start sending data. The
reader captures the data encoded in the tag's integrated circuit, decodes it, and sends it over a
network to a host computer for processing.
ASCM 629 - Week 5 Page 15
particular application.
Transmitted data may provide information about product location, or specifics such as color,
price, or purchase date. In some systems, a return receipt can be generated. RFID tags contain far
more detailed information than can be placed on a bar code. Some tags hold enough information
to provide routing information for shipping containers, as well as a detailed inventory of what is
inside the container.
It is said the origins of RFID technology began with the use of radar in World War II, when
armies began searching for ways to identify incoming vessels as friend or enemy. According to
the 2008 RFID Journal, the first patents for true RFID technology were taken out in the 1970s,
most notably by Mario Cardullo. At the same time, the government was working on radio
identification technology to guard high-level security sites and to mark livestock for the
agriculture department. In the 1990s, RFID systems developed by IBM and Intermec began to be
used commercially, though the expense kept many companies from entering the field.
An RFID system consists of tags, tag readers, tag programming stations, circulation readers,
sorting equipment, and tag inventory wands. The tag is the key component. Data can be printed
or etched on an electronic substrate and then embedded in a plastic or laminated paper tag.
Tags are classified according to their radio frequency: low-frequency, high-frequency, UHF, and
microwave. Low-frequency tags are commonly used in automobile antitheft systems and animal
identification. High-frequency tags are used in library books, pallet tracking, building access,
airline baggage tracking, and apparel tracking. Low- and high-frequency tags can be used
without a license. UHF tags are used to track pallets, containers, trucks, and trailers. UHF cannot
be used globally as there is no one global standard. Microwave tags are used in long-range
access, such as General Motors' OnStar system.
While most RFID tags are write-once/read-only, there are some that offer read/write capability.
These tags would allow tag data to be rewritten if need be.
Tags may either be passive or active. Passive tags do not have their own power supply; their
power comes from a minute electrical current induced by an incoming radio-frequency scan. In
contrast, active tags have their own power source. The lack of a power source makes the passive
tag much less expensive to manufacture and much smaller (thinner than a sheet of paper) than an
active tag. As a result, the vast majority of RFID tags are passive. However, the response of a
passive tag is typically just an ID number. Active tags have longer ranges, the ability to store
more information, and they are more accurate and reliable.
The tag contains a transponder with a digital memory chip with a unique electronic product code.
A stationary or handheld device called an interrogator, consisting of an antenna, transceiver, and
decoder, emits a signal creating an electromagnetic zone. When a tag comes within the range of a
reader, it detects an activation signal that causes the tag to “wake up” and start sending data. The
reader captures the data encoded in the tag's integrated circuit, decodes it, and sends it over a
network to a host computer for processing.
ASCM 629 - Week 5 Page 15
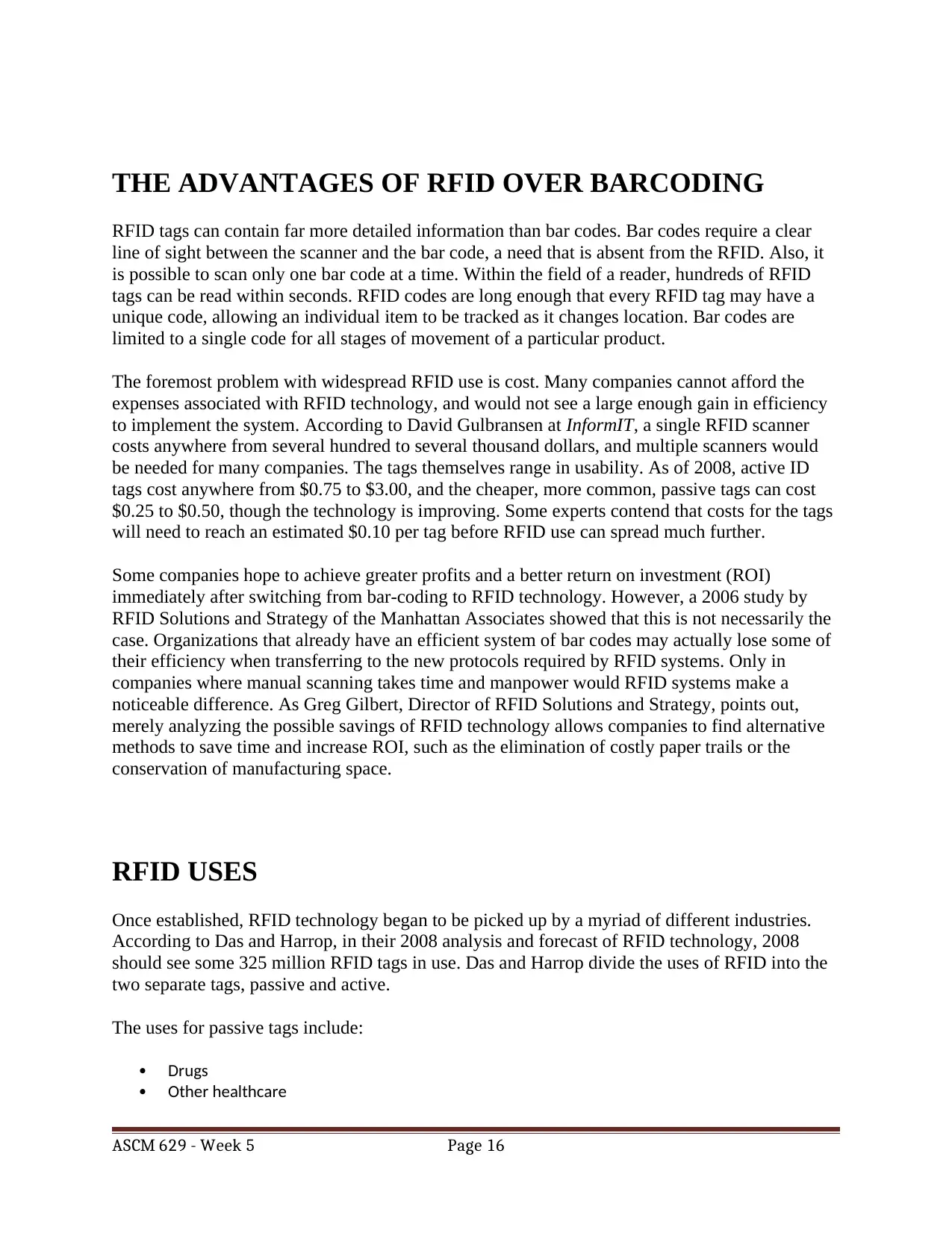
THE ADVANTAGES OF RFID OVER BARCODING
RFID tags can contain far more detailed information than bar codes. Bar codes require a clear
line of sight between the scanner and the bar code, a need that is absent from the RFID. Also, it
is possible to scan only one bar code at a time. Within the field of a reader, hundreds of RFID
tags can be read within seconds. RFID codes are long enough that every RFID tag may have a
unique code, allowing an individual item to be tracked as it changes location. Bar codes are
limited to a single code for all stages of movement of a particular product.
The foremost problem with widespread RFID use is cost. Many companies cannot afford the
expenses associated with RFID technology, and would not see a large enough gain in efficiency
to implement the system. According to David Gulbransen at InformIT, a single RFID scanner
costs anywhere from several hundred to several thousand dollars, and multiple scanners would
be needed for many companies. The tags themselves range in usability. As of 2008, active ID
tags cost anywhere from $0.75 to $3.00, and the cheaper, more common, passive tags can cost
$0.25 to $0.50, though the technology is improving. Some experts contend that costs for the tags
will need to reach an estimated $0.10 per tag before RFID use can spread much further.
Some companies hope to achieve greater profits and a better return on investment (ROI)
immediately after switching from bar-coding to RFID technology. However, a 2006 study by
RFID Solutions and Strategy of the Manhattan Associates showed that this is not necessarily the
case. Organizations that already have an efficient system of bar codes may actually lose some of
their efficiency when transferring to the new protocols required by RFID systems. Only in
companies where manual scanning takes time and manpower would RFID systems make a
noticeable difference. As Greg Gilbert, Director of RFID Solutions and Strategy, points out,
merely analyzing the possible savings of RFID technology allows companies to find alternative
methods to save time and increase ROI, such as the elimination of costly paper trails or the
conservation of manufacturing space.
RFID USES
Once established, RFID technology began to be picked up by a myriad of different industries.
According to Das and Harrop, in their 2008 analysis and forecast of RFID technology, 2008
should see some 325 million RFID tags in use. Das and Harrop divide the uses of RFID into the
two separate tags, passive and active.
The uses for passive tags include:
Drugs
Other healthcare
ASCM 629 - Week 5 Page 16
RFID tags can contain far more detailed information than bar codes. Bar codes require a clear
line of sight between the scanner and the bar code, a need that is absent from the RFID. Also, it
is possible to scan only one bar code at a time. Within the field of a reader, hundreds of RFID
tags can be read within seconds. RFID codes are long enough that every RFID tag may have a
unique code, allowing an individual item to be tracked as it changes location. Bar codes are
limited to a single code for all stages of movement of a particular product.
The foremost problem with widespread RFID use is cost. Many companies cannot afford the
expenses associated with RFID technology, and would not see a large enough gain in efficiency
to implement the system. According to David Gulbransen at InformIT, a single RFID scanner
costs anywhere from several hundred to several thousand dollars, and multiple scanners would
be needed for many companies. The tags themselves range in usability. As of 2008, active ID
tags cost anywhere from $0.75 to $3.00, and the cheaper, more common, passive tags can cost
$0.25 to $0.50, though the technology is improving. Some experts contend that costs for the tags
will need to reach an estimated $0.10 per tag before RFID use can spread much further.
Some companies hope to achieve greater profits and a better return on investment (ROI)
immediately after switching from bar-coding to RFID technology. However, a 2006 study by
RFID Solutions and Strategy of the Manhattan Associates showed that this is not necessarily the
case. Organizations that already have an efficient system of bar codes may actually lose some of
their efficiency when transferring to the new protocols required by RFID systems. Only in
companies where manual scanning takes time and manpower would RFID systems make a
noticeable difference. As Greg Gilbert, Director of RFID Solutions and Strategy, points out,
merely analyzing the possible savings of RFID technology allows companies to find alternative
methods to save time and increase ROI, such as the elimination of costly paper trails or the
conservation of manufacturing space.
RFID USES
Once established, RFID technology began to be picked up by a myriad of different industries.
According to Das and Harrop, in their 2008 analysis and forecast of RFID technology, 2008
should see some 325 million RFID tags in use. Das and Harrop divide the uses of RFID into the
two separate tags, passive and active.
The uses for passive tags include:
Drugs
Other healthcare
ASCM 629 - Week 5 Page 16
Secure Best Marks with AI Grader
Need help grading? Try our AI Grader for instant feedback on your assignments.
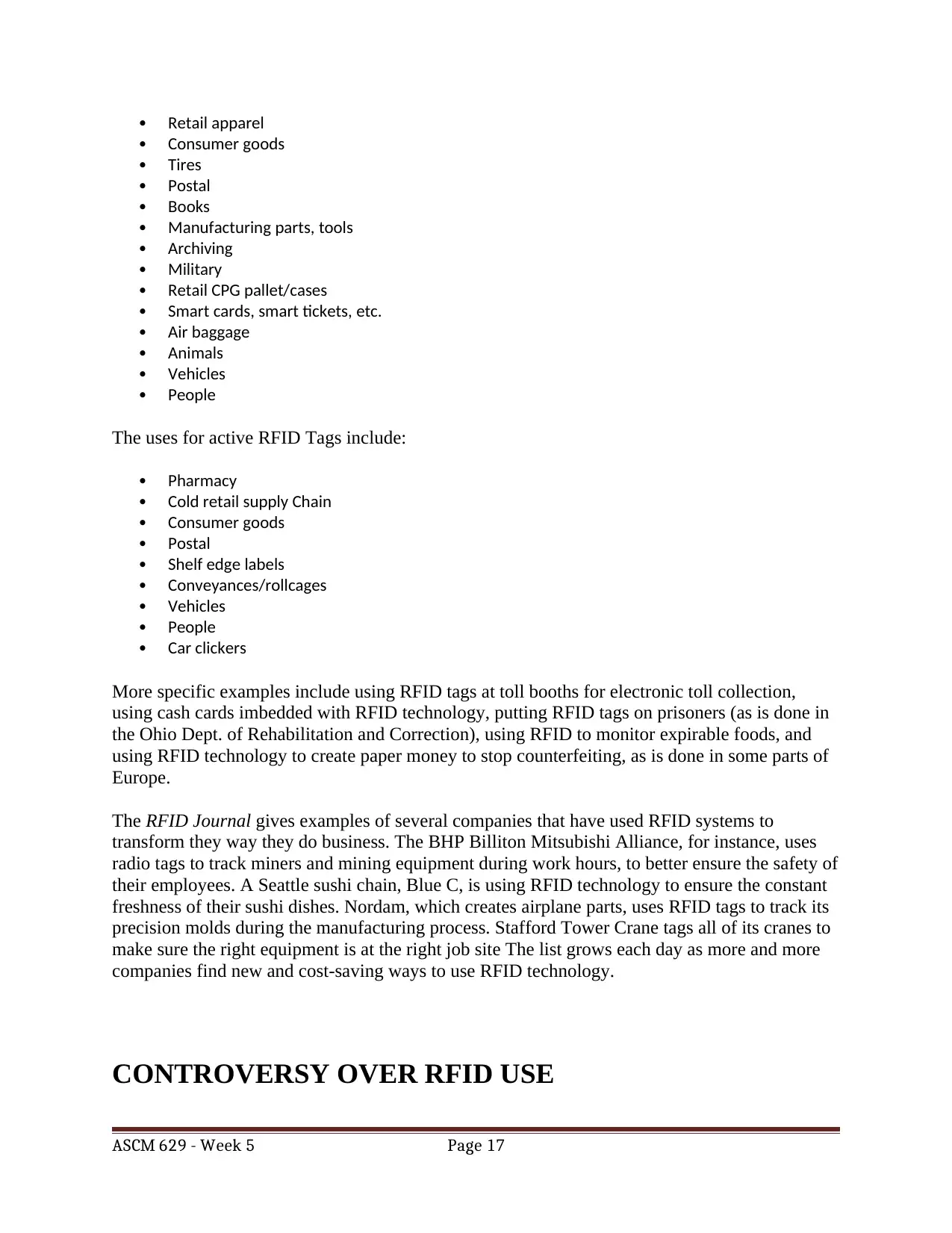
Retail apparel
Consumer goods
Tires
Postal
Books
Manufacturing parts, tools
Archiving
Military
Retail CPG pallet/cases
Smart cards, smart tickets, etc.
Air baggage
Animals
Vehicles
People
The uses for active RFID Tags include:
Pharmacy
Cold retail supply Chain
Consumer goods
Postal
Shelf edge labels
Conveyances/rollcages
Vehicles
People
Car clickers
More specific examples include using RFID tags at toll booths for electronic toll collection,
using cash cards imbedded with RFID technology, putting RFID tags on prisoners (as is done in
the Ohio Dept. of Rehabilitation and Correction), using RFID to monitor expirable foods, and
using RFID technology to create paper money to stop counterfeiting, as is done in some parts of
Europe.
The RFID Journal gives examples of several companies that have used RFID systems to
transform they way they do business. The BHP Billiton Mitsubishi Alliance, for instance, uses
radio tags to track miners and mining equipment during work hours, to better ensure the safety of
their employees. A Seattle sushi chain, Blue C, is using RFID technology to ensure the constant
freshness of their sushi dishes. Nordam, which creates airplane parts, uses RFID tags to track its
precision molds during the manufacturing process. Stafford Tower Crane tags all of its cranes to
make sure the right equipment is at the right job site The list grows each day as more and more
companies find new and cost-saving ways to use RFID technology.
CONTROVERSY OVER RFID USE
ASCM 629 - Week 5 Page 17
Consumer goods
Tires
Postal
Books
Manufacturing parts, tools
Archiving
Military
Retail CPG pallet/cases
Smart cards, smart tickets, etc.
Air baggage
Animals
Vehicles
People
The uses for active RFID Tags include:
Pharmacy
Cold retail supply Chain
Consumer goods
Postal
Shelf edge labels
Conveyances/rollcages
Vehicles
People
Car clickers
More specific examples include using RFID tags at toll booths for electronic toll collection,
using cash cards imbedded with RFID technology, putting RFID tags on prisoners (as is done in
the Ohio Dept. of Rehabilitation and Correction), using RFID to monitor expirable foods, and
using RFID technology to create paper money to stop counterfeiting, as is done in some parts of
Europe.
The RFID Journal gives examples of several companies that have used RFID systems to
transform they way they do business. The BHP Billiton Mitsubishi Alliance, for instance, uses
radio tags to track miners and mining equipment during work hours, to better ensure the safety of
their employees. A Seattle sushi chain, Blue C, is using RFID technology to ensure the constant
freshness of their sushi dishes. Nordam, which creates airplane parts, uses RFID tags to track its
precision molds during the manufacturing process. Stafford Tower Crane tags all of its cranes to
make sure the right equipment is at the right job site The list grows each day as more and more
companies find new and cost-saving ways to use RFID technology.
CONTROVERSY OVER RFID USE
ASCM 629 - Week 5 Page 17
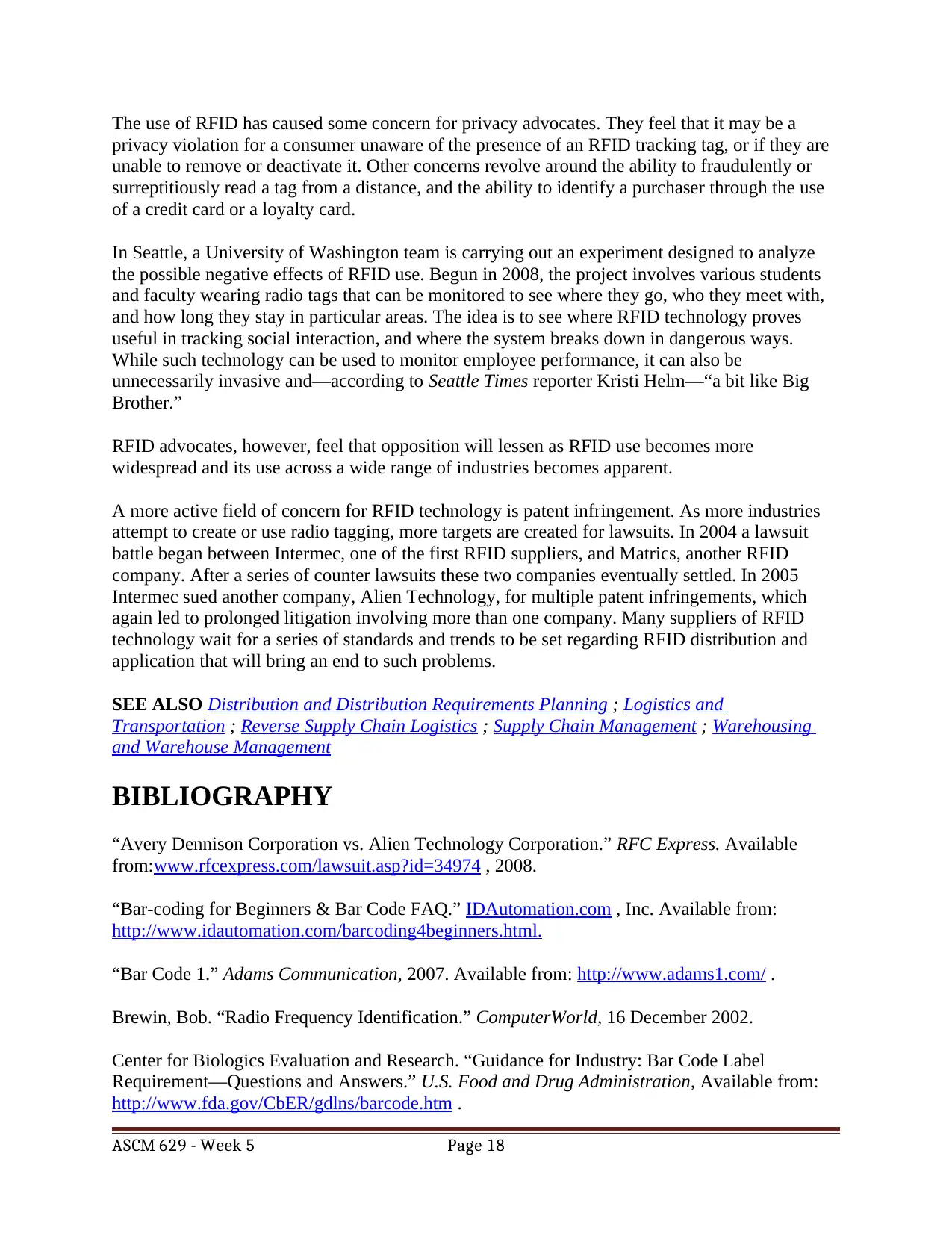
The use of RFID has caused some concern for privacy advocates. They feel that it may be a
privacy violation for a consumer unaware of the presence of an RFID tracking tag, or if they are
unable to remove or deactivate it. Other concerns revolve around the ability to fraudulently or
surreptitiously read a tag from a distance, and the ability to identify a purchaser through the use
of a credit card or a loyalty card.
In Seattle, a University of Washington team is carrying out an experiment designed to analyze
the possible negative effects of RFID use. Begun in 2008, the project involves various students
and faculty wearing radio tags that can be monitored to see where they go, who they meet with,
and how long they stay in particular areas. The idea is to see where RFID technology proves
useful in tracking social interaction, and where the system breaks down in dangerous ways.
While such technology can be used to monitor employee performance, it can also be
unnecessarily invasive and—according to Seattle Times reporter Kristi Helm—“a bit like Big
Brother.”
RFID advocates, however, feel that opposition will lessen as RFID use becomes more
widespread and its use across a wide range of industries becomes apparent.
A more active field of concern for RFID technology is patent infringement. As more industries
attempt to create or use radio tagging, more targets are created for lawsuits. In 2004 a lawsuit
battle began between Intermec, one of the first RFID suppliers, and Matrics, another RFID
company. After a series of counter lawsuits these two companies eventually settled. In 2005
Intermec sued another company, Alien Technology, for multiple patent infringements, which
again led to prolonged litigation involving more than one company. Many suppliers of RFID
technology wait for a series of standards and trends to be set regarding RFID distribution and
application that will bring an end to such problems.
SEE ALSO Distribution and Distribution Requirements Planning ; Logistics and
Transportation ; Reverse Supply Chain Logistics ; Supply Chain Management ; Warehousing
and Warehouse Management
BIBLIOGRAPHY
“Avery Dennison Corporation vs. Alien Technology Corporation.” RFC Express. Available
from:www.rfcexpress.com/lawsuit.asp?id=34974 , 2008.
“Bar-coding for Beginners & Bar Code FAQ.” IDAutomation.com , Inc. Available from:
http://www.idautomation.com/barcoding4beginners.html.
“Bar Code 1.” Adams Communication, 2007. Available from: http://www.adams1.com/ .
Brewin, Bob. “Radio Frequency Identification.” ComputerWorld, 16 December 2002.
Center for Biologics Evaluation and Research. “Guidance for Industry: Bar Code Label
Requirement—Questions and Answers.” U.S. Food and Drug Administration, Available from:
http://www.fda.gov/CbER/gdlns/barcode.htm .
ASCM 629 - Week 5 Page 18
privacy violation for a consumer unaware of the presence of an RFID tracking tag, or if they are
unable to remove or deactivate it. Other concerns revolve around the ability to fraudulently or
surreptitiously read a tag from a distance, and the ability to identify a purchaser through the use
of a credit card or a loyalty card.
In Seattle, a University of Washington team is carrying out an experiment designed to analyze
the possible negative effects of RFID use. Begun in 2008, the project involves various students
and faculty wearing radio tags that can be monitored to see where they go, who they meet with,
and how long they stay in particular areas. The idea is to see where RFID technology proves
useful in tracking social interaction, and where the system breaks down in dangerous ways.
While such technology can be used to monitor employee performance, it can also be
unnecessarily invasive and—according to Seattle Times reporter Kristi Helm—“a bit like Big
Brother.”
RFID advocates, however, feel that opposition will lessen as RFID use becomes more
widespread and its use across a wide range of industries becomes apparent.
A more active field of concern for RFID technology is patent infringement. As more industries
attempt to create or use radio tagging, more targets are created for lawsuits. In 2004 a lawsuit
battle began between Intermec, one of the first RFID suppliers, and Matrics, another RFID
company. After a series of counter lawsuits these two companies eventually settled. In 2005
Intermec sued another company, Alien Technology, for multiple patent infringements, which
again led to prolonged litigation involving more than one company. Many suppliers of RFID
technology wait for a series of standards and trends to be set regarding RFID distribution and
application that will bring an end to such problems.
SEE ALSO Distribution and Distribution Requirements Planning ; Logistics and
Transportation ; Reverse Supply Chain Logistics ; Supply Chain Management ; Warehousing
and Warehouse Management
BIBLIOGRAPHY
“Avery Dennison Corporation vs. Alien Technology Corporation.” RFC Express. Available
from:www.rfcexpress.com/lawsuit.asp?id=34974 , 2008.
“Bar-coding for Beginners & Bar Code FAQ.” IDAutomation.com , Inc. Available from:
http://www.idautomation.com/barcoding4beginners.html.
“Bar Code 1.” Adams Communication, 2007. Available from: http://www.adams1.com/ .
Brewin, Bob. “Radio Frequency Identification.” ComputerWorld, 16 December 2002.
Center for Biologics Evaluation and Research. “Guidance for Industry: Bar Code Label
Requirement—Questions and Answers.” U.S. Food and Drug Administration, Available from:
http://www.fda.gov/CbER/gdlns/barcode.htm .
ASCM 629 - Week 5 Page 18
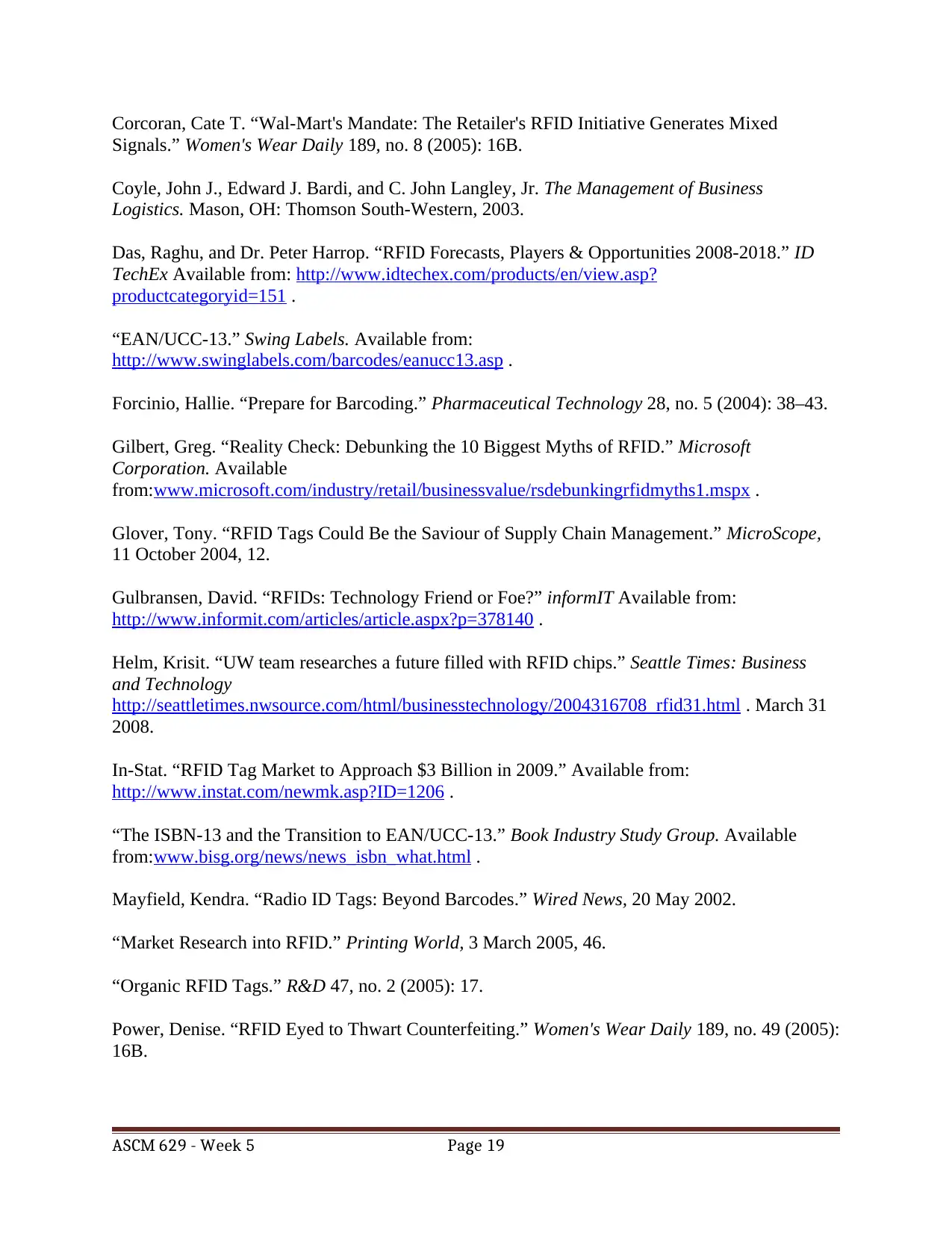
Corcoran, Cate T. “Wal-Mart's Mandate: The Retailer's RFID Initiative Generates Mixed
Signals.” Women's Wear Daily 189, no. 8 (2005): 16B.
Coyle, John J., Edward J. Bardi, and C. John Langley, Jr. The Management of Business
Logistics. Mason, OH: Thomson South-Western, 2003.
Das, Raghu, and Dr. Peter Harrop. “RFID Forecasts, Players & Opportunities 2008-2018.” ID
TechEx Available from: http://www.idtechex.com/products/en/view.asp?
productcategoryid=151 .
“EAN/UCC-13.” Swing Labels. Available from:
http://www.swinglabels.com/barcodes/eanucc13.asp .
Forcinio, Hallie. “Prepare for Barcoding.” Pharmaceutical Technology 28, no. 5 (2004): 38–43.
Gilbert, Greg. “Reality Check: Debunking the 10 Biggest Myths of RFID.” Microsoft
Corporation. Available
from:www.microsoft.com/industry/retail/businessvalue/rsdebunkingrfidmyths1.mspx .
Glover, Tony. “RFID Tags Could Be the Saviour of Supply Chain Management.” MicroScope,
11 October 2004, 12.
Gulbransen, David. “RFIDs: Technology Friend or Foe?” informIT Available from:
http://www.informit.com/articles/article.aspx?p=378140 .
Helm, Krisit. “UW team researches a future filled with RFID chips.” Seattle Times: Business
and Technology
http://seattletimes.nwsource.com/html/businesstechnology/2004316708_rfid31.html . March 31
2008.
In-Stat. “RFID Tag Market to Approach $3 Billion in 2009.” Available from:
http://www.instat.com/newmk.asp?ID=1206 .
“The ISBN-13 and the Transition to EAN/UCC-13.” Book Industry Study Group. Available
from:www.bisg.org/news/news_isbn_what.html .
Mayfield, Kendra. “Radio ID Tags: Beyond Barcodes.” Wired News, 20 May 2002.
“Market Research into RFID.” Printing World, 3 March 2005, 46.
“Organic RFID Tags.” R&D 47, no. 2 (2005): 17.
Power, Denise. “RFID Eyed to Thwart Counterfeiting.” Women's Wear Daily 189, no. 49 (2005):
16B.
ASCM 629 - Week 5 Page 19
Signals.” Women's Wear Daily 189, no. 8 (2005): 16B.
Coyle, John J., Edward J. Bardi, and C. John Langley, Jr. The Management of Business
Logistics. Mason, OH: Thomson South-Western, 2003.
Das, Raghu, and Dr. Peter Harrop. “RFID Forecasts, Players & Opportunities 2008-2018.” ID
TechEx Available from: http://www.idtechex.com/products/en/view.asp?
productcategoryid=151 .
“EAN/UCC-13.” Swing Labels. Available from:
http://www.swinglabels.com/barcodes/eanucc13.asp .
Forcinio, Hallie. “Prepare for Barcoding.” Pharmaceutical Technology 28, no. 5 (2004): 38–43.
Gilbert, Greg. “Reality Check: Debunking the 10 Biggest Myths of RFID.” Microsoft
Corporation. Available
from:www.microsoft.com/industry/retail/businessvalue/rsdebunkingrfidmyths1.mspx .
Glover, Tony. “RFID Tags Could Be the Saviour of Supply Chain Management.” MicroScope,
11 October 2004, 12.
Gulbransen, David. “RFIDs: Technology Friend or Foe?” informIT Available from:
http://www.informit.com/articles/article.aspx?p=378140 .
Helm, Krisit. “UW team researches a future filled with RFID chips.” Seattle Times: Business
and Technology
http://seattletimes.nwsource.com/html/businesstechnology/2004316708_rfid31.html . March 31
2008.
In-Stat. “RFID Tag Market to Approach $3 Billion in 2009.” Available from:
http://www.instat.com/newmk.asp?ID=1206 .
“The ISBN-13 and the Transition to EAN/UCC-13.” Book Industry Study Group. Available
from:www.bisg.org/news/news_isbn_what.html .
Mayfield, Kendra. “Radio ID Tags: Beyond Barcodes.” Wired News, 20 May 2002.
“Market Research into RFID.” Printing World, 3 March 2005, 46.
“Organic RFID Tags.” R&D 47, no. 2 (2005): 17.
Power, Denise. “RFID Eyed to Thwart Counterfeiting.” Women's Wear Daily 189, no. 49 (2005):
16B.
ASCM 629 - Week 5 Page 19
Paraphrase This Document
Need a fresh take? Get an instant paraphrase of this document with our AI Paraphraser
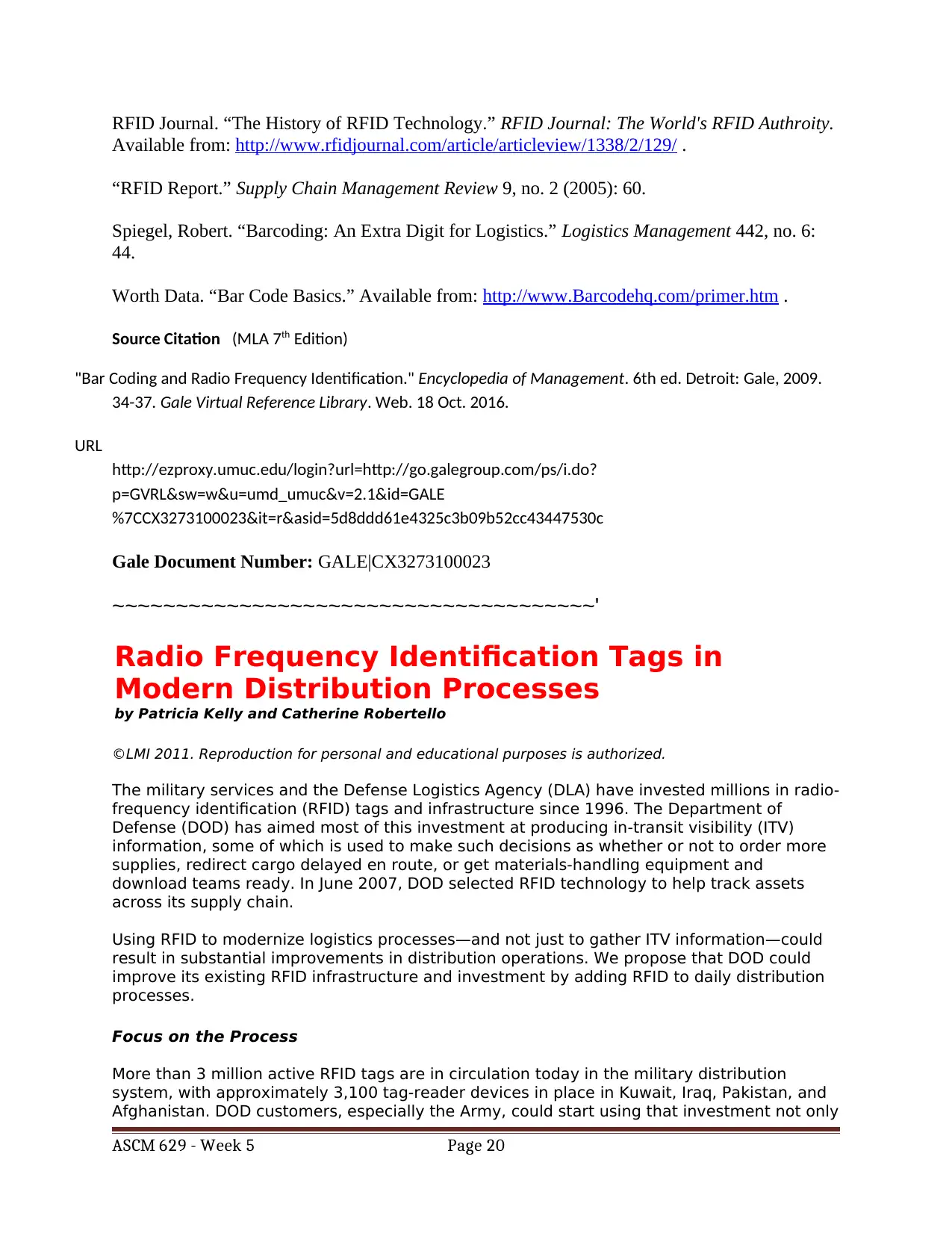
RFID Journal. “The History of RFID Technology.” RFID Journal: The World's RFID Authroity.
Available from: http://www.rfidjournal.com/article/articleview/1338/2/129/ .
“RFID Report.” Supply Chain Management Review 9, no. 2 (2005): 60.
Spiegel, Robert. “Barcoding: An Extra Digit for Logistics.” Logistics Management 442, no. 6:
44.
Worth Data. “Bar Code Basics.” Available from: http://www.Barcodehq.com/primer.htm .
Source Citation (MLA 7th Edition)
"Bar Coding and Radio Frequency Identification." Encyclopedia of Management. 6th ed. Detroit: Gale, 2009.
34-37. Gale Virtual Reference Library. Web. 18 Oct. 2016.
URL
http://ezproxy.umuc.edu/login?url=http://go.galegroup.com/ps/i.do?
p=GVRL&sw=w&u=umd_umuc&v=2.1&id=GALE
%7CCX3273100023&it=r&asid=5d8ddd61e4325c3b09b52cc43447530c
Gale Document Number: GALE|CX3273100023
~~~~~~~~~~~~~~~~~~~~~~~~~~~~~~~~~~~~~~'
Radio Frequency Identification Tags in
Modern Distribution Processes
by Patricia Kelly and Catherine Robertello
©LMI 2011. Reproduction for personal and educational purposes is authorized.
The military services and the Defense Logistics Agency (DLA) have invested millions in radio-
frequency identification (RFID) tags and infrastructure since 1996. The Department of
Defense (DOD) has aimed most of this investment at producing in-transit visibility (ITV)
information, some of which is used to make such decisions as whether or not to order more
supplies, redirect cargo delayed en route, or get materials-handling equipment and
download teams ready. In June 2007, DOD selected RFID technology to help track assets
across its supply chain.
Using RFID to modernize logistics processes—and not just to gather ITV information—could
result in substantial improvements in distribution operations. We propose that DOD could
improve its existing RFID infrastructure and investment by adding RFID to daily distribution
processes.
Focus on the Process
More than 3 million active RFID tags are in circulation today in the military distribution
system, with approximately 3,100 tag-reader devices in place in Kuwait, Iraq, Pakistan, and
Afghanistan. DOD customers, especially the Army, could start using that investment not only
ASCM 629 - Week 5 Page 20
Available from: http://www.rfidjournal.com/article/articleview/1338/2/129/ .
“RFID Report.” Supply Chain Management Review 9, no. 2 (2005): 60.
Spiegel, Robert. “Barcoding: An Extra Digit for Logistics.” Logistics Management 442, no. 6:
44.
Worth Data. “Bar Code Basics.” Available from: http://www.Barcodehq.com/primer.htm .
Source Citation (MLA 7th Edition)
"Bar Coding and Radio Frequency Identification." Encyclopedia of Management. 6th ed. Detroit: Gale, 2009.
34-37. Gale Virtual Reference Library. Web. 18 Oct. 2016.
URL
http://ezproxy.umuc.edu/login?url=http://go.galegroup.com/ps/i.do?
p=GVRL&sw=w&u=umd_umuc&v=2.1&id=GALE
%7CCX3273100023&it=r&asid=5d8ddd61e4325c3b09b52cc43447530c
Gale Document Number: GALE|CX3273100023
~~~~~~~~~~~~~~~~~~~~~~~~~~~~~~~~~~~~~~'
Radio Frequency Identification Tags in
Modern Distribution Processes
by Patricia Kelly and Catherine Robertello
©LMI 2011. Reproduction for personal and educational purposes is authorized.
The military services and the Defense Logistics Agency (DLA) have invested millions in radio-
frequency identification (RFID) tags and infrastructure since 1996. The Department of
Defense (DOD) has aimed most of this investment at producing in-transit visibility (ITV)
information, some of which is used to make such decisions as whether or not to order more
supplies, redirect cargo delayed en route, or get materials-handling equipment and
download teams ready. In June 2007, DOD selected RFID technology to help track assets
across its supply chain.
Using RFID to modernize logistics processes—and not just to gather ITV information—could
result in substantial improvements in distribution operations. We propose that DOD could
improve its existing RFID infrastructure and investment by adding RFID to daily distribution
processes.
Focus on the Process
More than 3 million active RFID tags are in circulation today in the military distribution
system, with approximately 3,100 tag-reader devices in place in Kuwait, Iraq, Pakistan, and
Afghanistan. DOD customers, especially the Army, could start using that investment not only
ASCM 629 - Week 5 Page 20
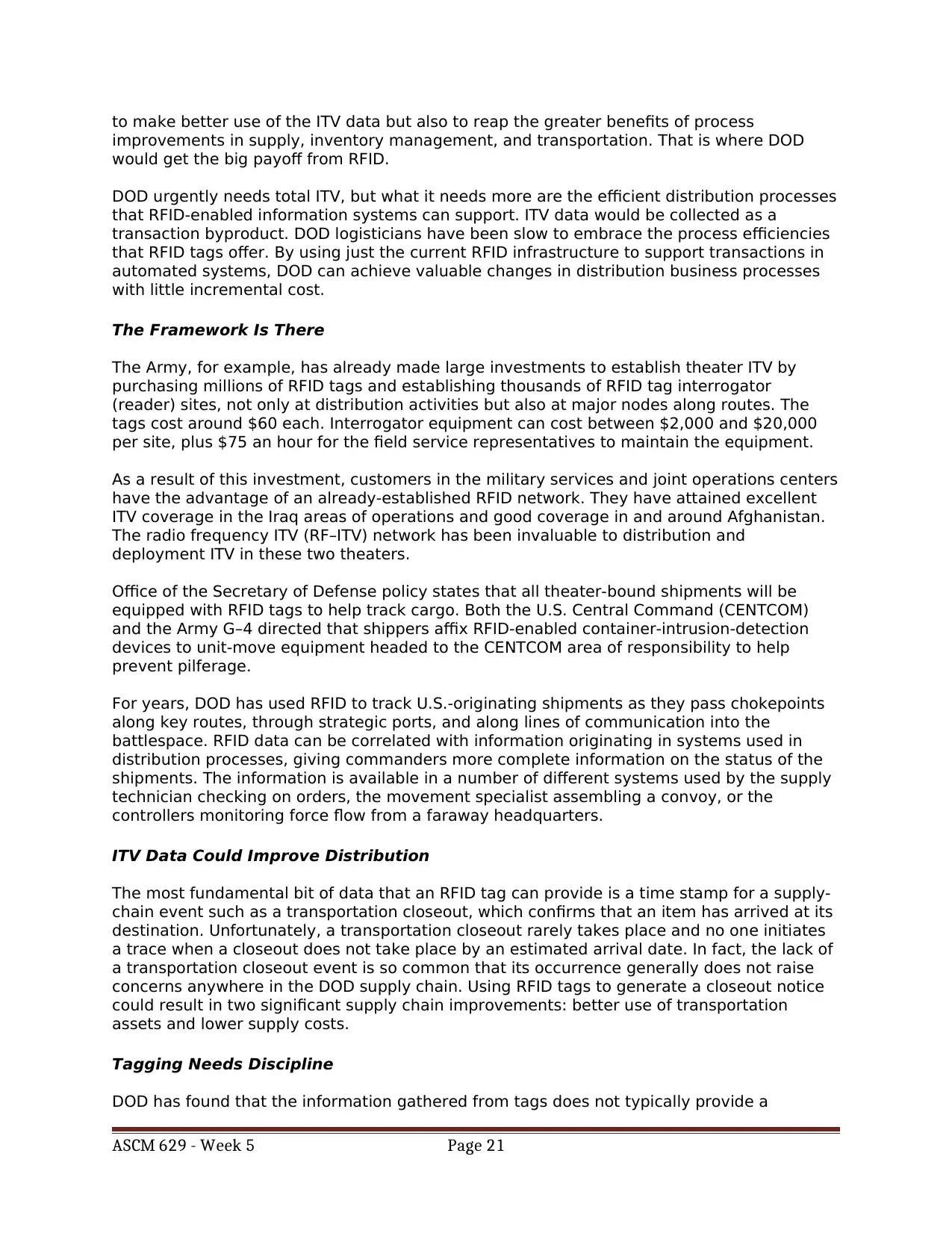
to make better use of the ITV data but also to reap the greater benefits of process
improvements in supply, inventory management, and transportation. That is where DOD
would get the big payoff from RFID.
DOD urgently needs total ITV, but what it needs more are the efficient distribution processes
that RFID-enabled information systems can support. ITV data would be collected as a
transaction byproduct. DOD logisticians have been slow to embrace the process efficiencies
that RFID tags offer. By using just the current RFID infrastructure to support transactions in
automated systems, DOD can achieve valuable changes in distribution business processes
with little incremental cost.
The Framework Is There
The Army, for example, has already made large investments to establish theater ITV by
purchasing millions of RFID tags and establishing thousands of RFID tag interrogator
(reader) sites, not only at distribution activities but also at major nodes along routes. The
tags cost around $60 each. Interrogator equipment can cost between $2,000 and $20,000
per site, plus $75 an hour for the field service representatives to maintain the equipment.
As a result of this investment, customers in the military services and joint operations centers
have the advantage of an already-established RFID network. They have attained excellent
ITV coverage in the Iraq areas of operations and good coverage in and around Afghanistan.
The radio frequency ITV (RF–ITV) network has been invaluable to distribution and
deployment ITV in these two theaters.
Office of the Secretary of Defense policy states that all theater-bound shipments will be
equipped with RFID tags to help track cargo. Both the U.S. Central Command (CENTCOM)
and the Army G–4 directed that shippers affix RFID-enabled container-intrusion-detection
devices to unit-move equipment headed to the CENTCOM area of responsibility to help
prevent pilferage.
For years, DOD has used RFID to track U.S.-originating shipments as they pass chokepoints
along key routes, through strategic ports, and along lines of communication into the
battlespace. RFID data can be correlated with information originating in systems used in
distribution processes, giving commanders more complete information on the status of the
shipments. The information is available in a number of different systems used by the supply
technician checking on orders, the movement specialist assembling a convoy, or the
controllers monitoring force flow from a faraway headquarters.
ITV Data Could Improve Distribution
The most fundamental bit of data that an RFID tag can provide is a time stamp for a supply-
chain event such as a transportation closeout, which confirms that an item has arrived at its
destination. Unfortunately, a transportation closeout rarely takes place and no one initiates
a trace when a closeout does not take place by an estimated arrival date. In fact, the lack of
a transportation closeout event is so common that its occurrence generally does not raise
concerns anywhere in the DOD supply chain. Using RFID tags to generate a closeout notice
could result in two significant supply chain improvements: better use of transportation
assets and lower supply costs.
Tagging Needs Discipline
DOD has found that the information gathered from tags does not typically provide a
ASCM 629 - Week 5 Page 21
improvements in supply, inventory management, and transportation. That is where DOD
would get the big payoff from RFID.
DOD urgently needs total ITV, but what it needs more are the efficient distribution processes
that RFID-enabled information systems can support. ITV data would be collected as a
transaction byproduct. DOD logisticians have been slow to embrace the process efficiencies
that RFID tags offer. By using just the current RFID infrastructure to support transactions in
automated systems, DOD can achieve valuable changes in distribution business processes
with little incremental cost.
The Framework Is There
The Army, for example, has already made large investments to establish theater ITV by
purchasing millions of RFID tags and establishing thousands of RFID tag interrogator
(reader) sites, not only at distribution activities but also at major nodes along routes. The
tags cost around $60 each. Interrogator equipment can cost between $2,000 and $20,000
per site, plus $75 an hour for the field service representatives to maintain the equipment.
As a result of this investment, customers in the military services and joint operations centers
have the advantage of an already-established RFID network. They have attained excellent
ITV coverage in the Iraq areas of operations and good coverage in and around Afghanistan.
The radio frequency ITV (RF–ITV) network has been invaluable to distribution and
deployment ITV in these two theaters.
Office of the Secretary of Defense policy states that all theater-bound shipments will be
equipped with RFID tags to help track cargo. Both the U.S. Central Command (CENTCOM)
and the Army G–4 directed that shippers affix RFID-enabled container-intrusion-detection
devices to unit-move equipment headed to the CENTCOM area of responsibility to help
prevent pilferage.
For years, DOD has used RFID to track U.S.-originating shipments as they pass chokepoints
along key routes, through strategic ports, and along lines of communication into the
battlespace. RFID data can be correlated with information originating in systems used in
distribution processes, giving commanders more complete information on the status of the
shipments. The information is available in a number of different systems used by the supply
technician checking on orders, the movement specialist assembling a convoy, or the
controllers monitoring force flow from a faraway headquarters.
ITV Data Could Improve Distribution
The most fundamental bit of data that an RFID tag can provide is a time stamp for a supply-
chain event such as a transportation closeout, which confirms that an item has arrived at its
destination. Unfortunately, a transportation closeout rarely takes place and no one initiates
a trace when a closeout does not take place by an estimated arrival date. In fact, the lack of
a transportation closeout event is so common that its occurrence generally does not raise
concerns anywhere in the DOD supply chain. Using RFID tags to generate a closeout notice
could result in two significant supply chain improvements: better use of transportation
assets and lower supply costs.
Tagging Needs Discipline
DOD has found that the information gathered from tags does not typically provide a
ASCM 629 - Week 5 Page 21
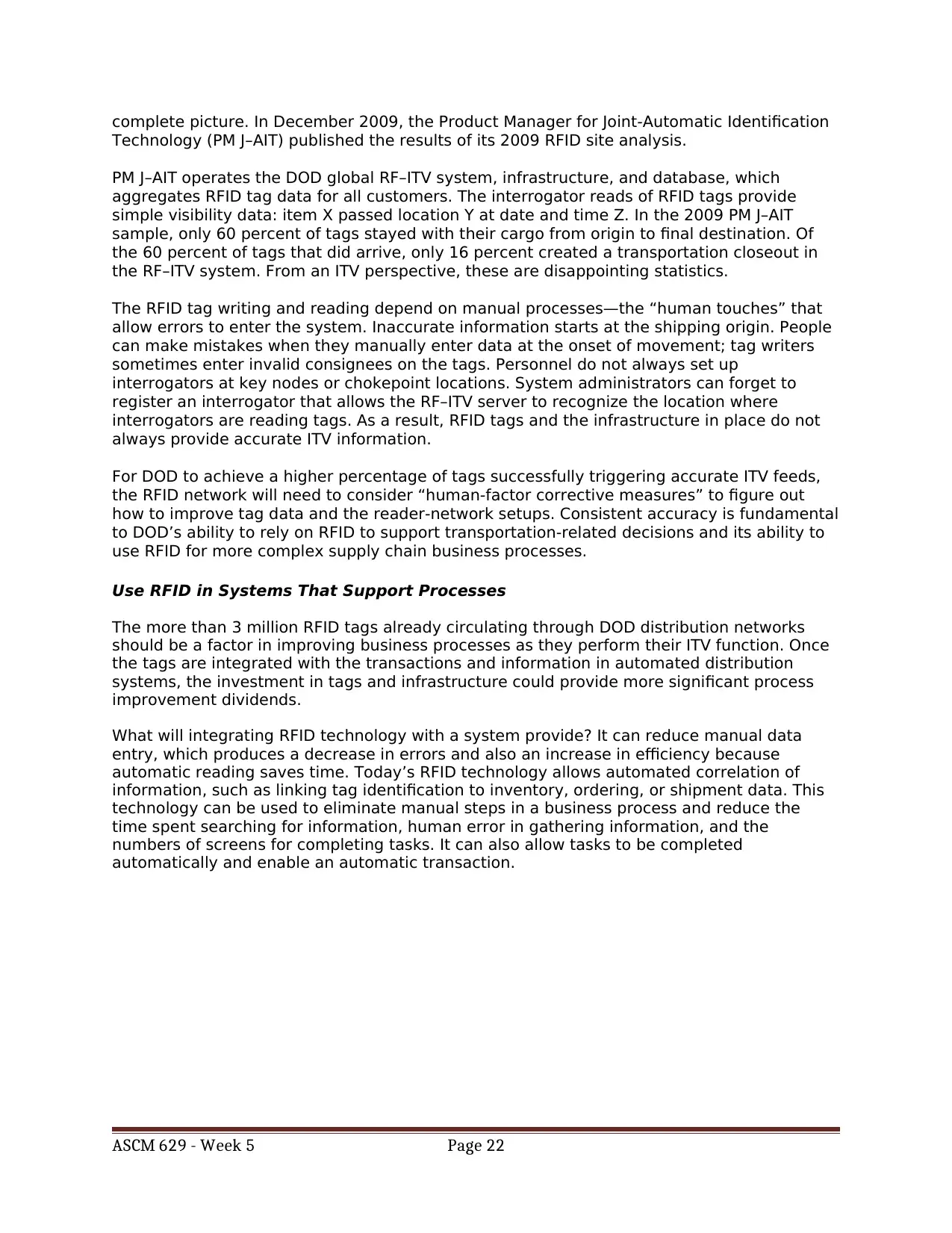
complete picture. In December 2009, the Product Manager for Joint-Automatic Identification
Technology (PM J–AIT) published the results of its 2009 RFID site analysis.
PM J–AIT operates the DOD global RF–ITV system, infrastructure, and database, which
aggregates RFID tag data for all customers. The interrogator reads of RFID tags provide
simple visibility data: item X passed location Y at date and time Z. In the 2009 PM J–AIT
sample, only 60 percent of tags stayed with their cargo from origin to final destination. Of
the 60 percent of tags that did arrive, only 16 percent created a transportation closeout in
the RF–ITV system. From an ITV perspective, these are disappointing statistics.
The RFID tag writing and reading depend on manual processes—the “human touches” that
allow errors to enter the system. Inaccurate information starts at the shipping origin. People
can make mistakes when they manually enter data at the onset of movement; tag writers
sometimes enter invalid consignees on the tags. Personnel do not always set up
interrogators at key nodes or chokepoint locations. System administrators can forget to
register an interrogator that allows the RF–ITV server to recognize the location where
interrogators are reading tags. As a result, RFID tags and the infrastructure in place do not
always provide accurate ITV information.
For DOD to achieve a higher percentage of tags successfully triggering accurate ITV feeds,
the RFID network will need to consider “human-factor corrective measures” to figure out
how to improve tag data and the reader-network setups. Consistent accuracy is fundamental
to DOD’s ability to rely on RFID to support transportation-related decisions and its ability to
use RFID for more complex supply chain business processes.
Use RFID in Systems That Support Processes
The more than 3 million RFID tags already circulating through DOD distribution networks
should be a factor in improving business processes as they perform their ITV function. Once
the tags are integrated with the transactions and information in automated distribution
systems, the investment in tags and infrastructure could provide more significant process
improvement dividends.
What will integrating RFID technology with a system provide? It can reduce manual data
entry, which produces a decrease in errors and also an increase in efficiency because
automatic reading saves time. Today’s RFID technology allows automated correlation of
information, such as linking tag identification to inventory, ordering, or shipment data. This
technology can be used to eliminate manual steps in a business process and reduce the
time spent searching for information, human error in gathering information, and the
numbers of screens for completing tasks. It can also allow tasks to be completed
automatically and enable an automatic transaction.
ASCM 629 - Week 5 Page 22
Technology (PM J–AIT) published the results of its 2009 RFID site analysis.
PM J–AIT operates the DOD global RF–ITV system, infrastructure, and database, which
aggregates RFID tag data for all customers. The interrogator reads of RFID tags provide
simple visibility data: item X passed location Y at date and time Z. In the 2009 PM J–AIT
sample, only 60 percent of tags stayed with their cargo from origin to final destination. Of
the 60 percent of tags that did arrive, only 16 percent created a transportation closeout in
the RF–ITV system. From an ITV perspective, these are disappointing statistics.
The RFID tag writing and reading depend on manual processes—the “human touches” that
allow errors to enter the system. Inaccurate information starts at the shipping origin. People
can make mistakes when they manually enter data at the onset of movement; tag writers
sometimes enter invalid consignees on the tags. Personnel do not always set up
interrogators at key nodes or chokepoint locations. System administrators can forget to
register an interrogator that allows the RF–ITV server to recognize the location where
interrogators are reading tags. As a result, RFID tags and the infrastructure in place do not
always provide accurate ITV information.
For DOD to achieve a higher percentage of tags successfully triggering accurate ITV feeds,
the RFID network will need to consider “human-factor corrective measures” to figure out
how to improve tag data and the reader-network setups. Consistent accuracy is fundamental
to DOD’s ability to rely on RFID to support transportation-related decisions and its ability to
use RFID for more complex supply chain business processes.
Use RFID in Systems That Support Processes
The more than 3 million RFID tags already circulating through DOD distribution networks
should be a factor in improving business processes as they perform their ITV function. Once
the tags are integrated with the transactions and information in automated distribution
systems, the investment in tags and infrastructure could provide more significant process
improvement dividends.
What will integrating RFID technology with a system provide? It can reduce manual data
entry, which produces a decrease in errors and also an increase in efficiency because
automatic reading saves time. Today’s RFID technology allows automated correlation of
information, such as linking tag identification to inventory, ordering, or shipment data. This
technology can be used to eliminate manual steps in a business process and reduce the
time spent searching for information, human error in gathering information, and the
numbers of screens for completing tasks. It can also allow tasks to be completed
automatically and enable an automatic transaction.
ASCM 629 - Week 5 Page 22
Secure Best Marks with AI Grader
Need help grading? Try our AI Grader for instant feedback on your assignments.
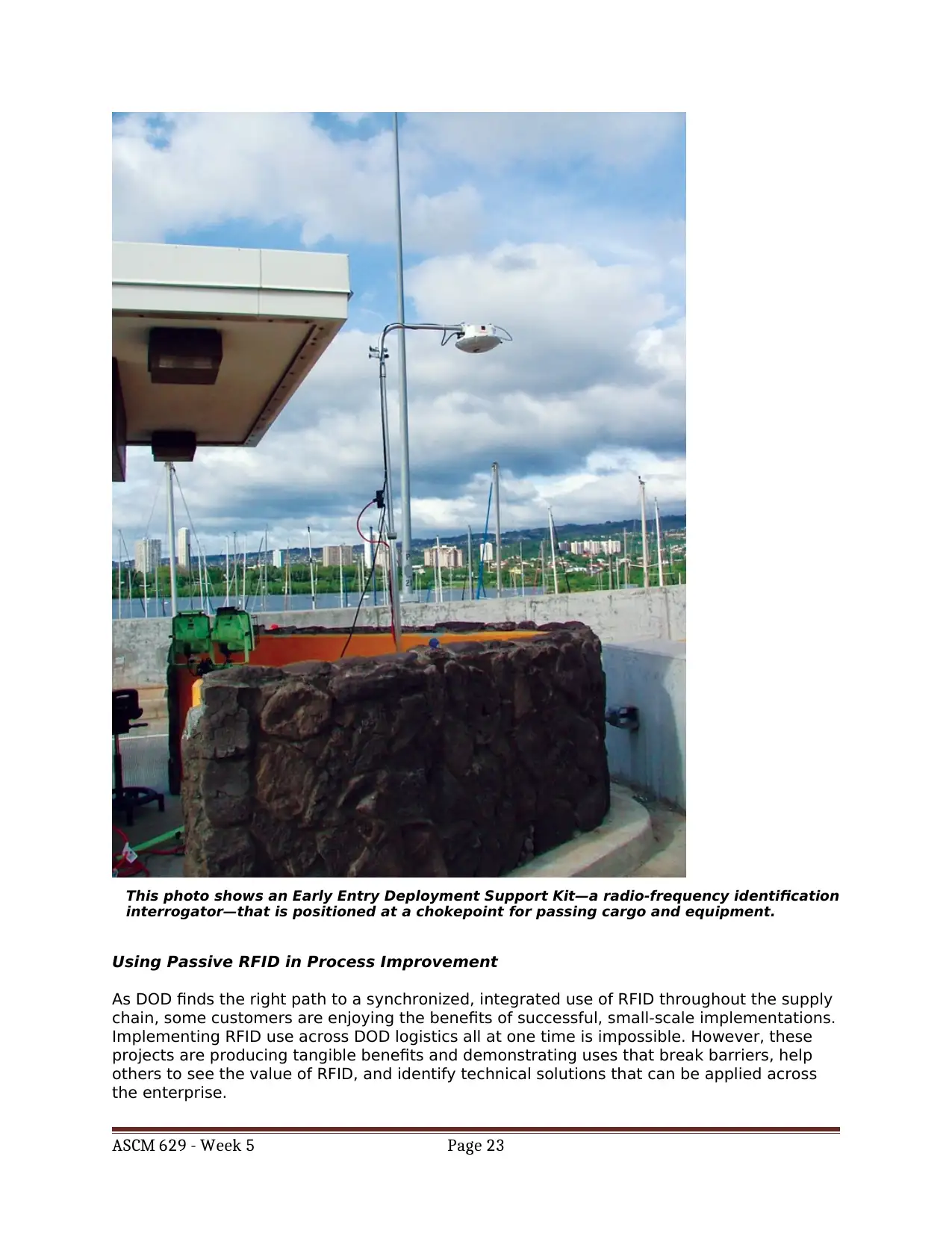
This photo shows an Early Entry Deployment Support Kit—a radio-frequency identification
interrogator—that is positioned at a chokepoint for passing cargo and equipment.
Using Passive RFID in Process Improvement
As DOD finds the right path to a synchronized, integrated use of RFID throughout the supply
chain, some customers are enjoying the benefits of successful, small-scale implementations.
Implementing RFID use across DOD logistics all at one time is impossible. However, these
projects are producing tangible benefits and demonstrating uses that break barriers, help
others to see the value of RFID, and identify technical solutions that can be applied across
the enterprise.
ASCM 629 - Week 5 Page 23
interrogator—that is positioned at a chokepoint for passing cargo and equipment.
Using Passive RFID in Process Improvement
As DOD finds the right path to a synchronized, integrated use of RFID throughout the supply
chain, some customers are enjoying the benefits of successful, small-scale implementations.
Implementing RFID use across DOD logistics all at one time is impossible. However, these
projects are producing tangible benefits and demonstrating uses that break barriers, help
others to see the value of RFID, and identify technical solutions that can be applied across
the enterprise.
ASCM 629 - Week 5 Page 23
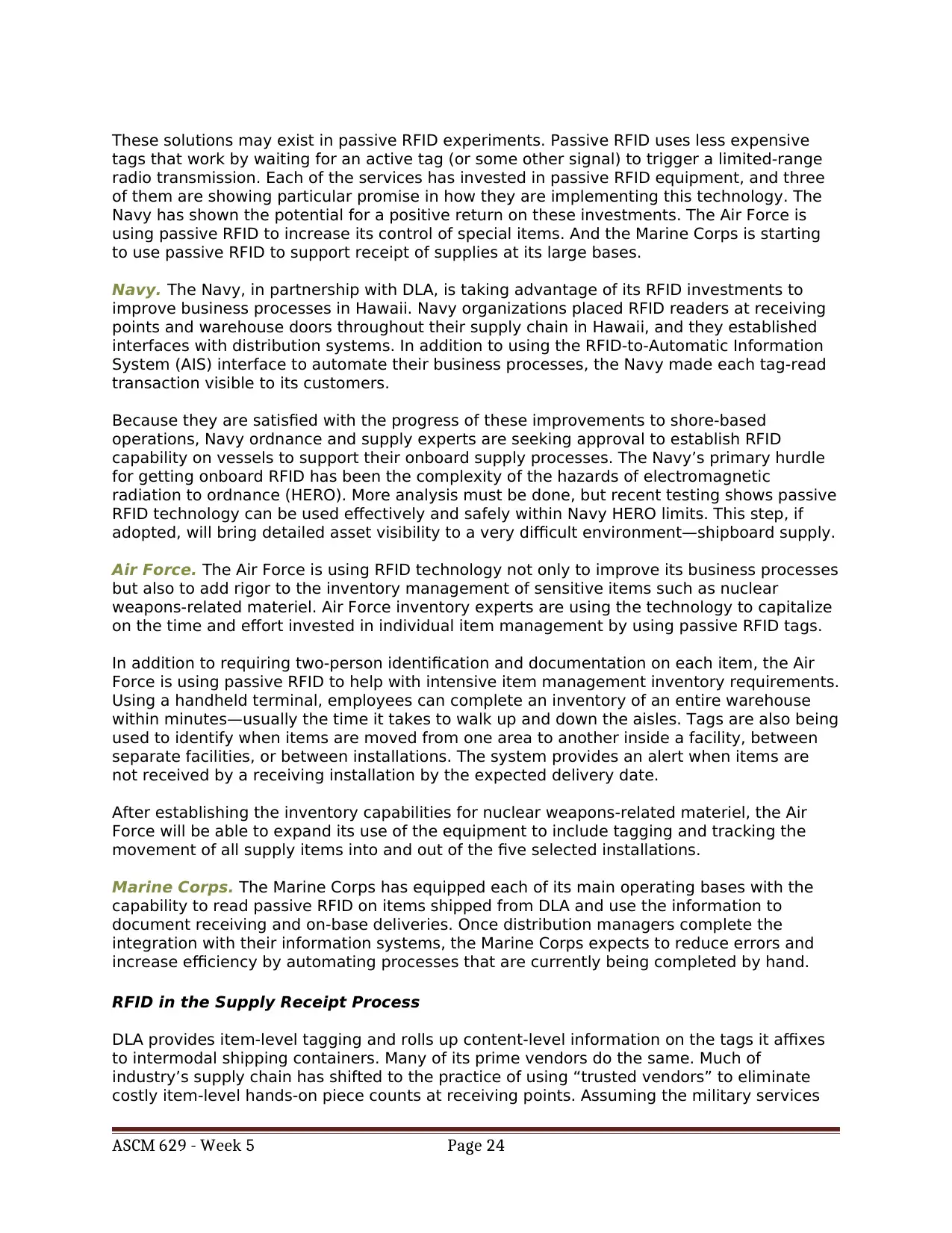
These solutions may exist in passive RFID experiments. Passive RFID uses less expensive
tags that work by waiting for an active tag (or some other signal) to trigger a limited-range
radio transmission. Each of the services has invested in passive RFID equipment, and three
of them are showing particular promise in how they are implementing this technology. The
Navy has shown the potential for a positive return on these investments. The Air Force is
using passive RFID to increase its control of special items. And the Marine Corps is starting
to use passive RFID to support receipt of supplies at its large bases.
Navy. The Navy, in partnership with DLA, is taking advantage of its RFID investments to
improve business processes in Hawaii. Navy organizations placed RFID readers at receiving
points and warehouse doors throughout their supply chain in Hawaii, and they established
interfaces with distribution systems. In addition to using the RFID-to-Automatic Information
System (AIS) interface to automate their business processes, the Navy made each tag-read
transaction visible to its customers.
Because they are satisfied with the progress of these improvements to shore-based
operations, Navy ordnance and supply experts are seeking approval to establish RFID
capability on vessels to support their onboard supply processes. The Navy’s primary hurdle
for getting onboard RFID has been the complexity of the hazards of electromagnetic
radiation to ordnance (HERO). More analysis must be done, but recent testing shows passive
RFID technology can be used effectively and safely within Navy HERO limits. This step, if
adopted, will bring detailed asset visibility to a very difficult environment—shipboard supply.
Air Force. The Air Force is using RFID technology not only to improve its business processes
but also to add rigor to the inventory management of sensitive items such as nuclear
weapons-related materiel. Air Force inventory experts are using the technology to capitalize
on the time and effort invested in individual item management by using passive RFID tags.
In addition to requiring two-person identification and documentation on each item, the Air
Force is using passive RFID to help with intensive item management inventory requirements.
Using a handheld terminal, employees can complete an inventory of an entire warehouse
within minutes—usually the time it takes to walk up and down the aisles. Tags are also being
used to identify when items are moved from one area to another inside a facility, between
separate facilities, or between installations. The system provides an alert when items are
not received by a receiving installation by the expected delivery date.
After establishing the inventory capabilities for nuclear weapons-related materiel, the Air
Force will be able to expand its use of the equipment to include tagging and tracking the
movement of all supply items into and out of the five selected installations.
Marine Corps. The Marine Corps has equipped each of its main operating bases with the
capability to read passive RFID on items shipped from DLA and use the information to
document receiving and on-base deliveries. Once distribution managers complete the
integration with their information systems, the Marine Corps expects to reduce errors and
increase efficiency by automating processes that are currently being completed by hand.
RFID in the Supply Receipt Process
DLA provides item-level tagging and rolls up content-level information on the tags it affixes
to intermodal shipping containers. Many of its prime vendors do the same. Much of
industry’s supply chain has shifted to the practice of using “trusted vendors” to eliminate
costly item-level hands-on piece counts at receiving points. Assuming the military services
ASCM 629 - Week 5 Page 24
tags that work by waiting for an active tag (or some other signal) to trigger a limited-range
radio transmission. Each of the services has invested in passive RFID equipment, and three
of them are showing particular promise in how they are implementing this technology. The
Navy has shown the potential for a positive return on these investments. The Air Force is
using passive RFID to increase its control of special items. And the Marine Corps is starting
to use passive RFID to support receipt of supplies at its large bases.
Navy. The Navy, in partnership with DLA, is taking advantage of its RFID investments to
improve business processes in Hawaii. Navy organizations placed RFID readers at receiving
points and warehouse doors throughout their supply chain in Hawaii, and they established
interfaces with distribution systems. In addition to using the RFID-to-Automatic Information
System (AIS) interface to automate their business processes, the Navy made each tag-read
transaction visible to its customers.
Because they are satisfied with the progress of these improvements to shore-based
operations, Navy ordnance and supply experts are seeking approval to establish RFID
capability on vessels to support their onboard supply processes. The Navy’s primary hurdle
for getting onboard RFID has been the complexity of the hazards of electromagnetic
radiation to ordnance (HERO). More analysis must be done, but recent testing shows passive
RFID technology can be used effectively and safely within Navy HERO limits. This step, if
adopted, will bring detailed asset visibility to a very difficult environment—shipboard supply.
Air Force. The Air Force is using RFID technology not only to improve its business processes
but also to add rigor to the inventory management of sensitive items such as nuclear
weapons-related materiel. Air Force inventory experts are using the technology to capitalize
on the time and effort invested in individual item management by using passive RFID tags.
In addition to requiring two-person identification and documentation on each item, the Air
Force is using passive RFID to help with intensive item management inventory requirements.
Using a handheld terminal, employees can complete an inventory of an entire warehouse
within minutes—usually the time it takes to walk up and down the aisles. Tags are also being
used to identify when items are moved from one area to another inside a facility, between
separate facilities, or between installations. The system provides an alert when items are
not received by a receiving installation by the expected delivery date.
After establishing the inventory capabilities for nuclear weapons-related materiel, the Air
Force will be able to expand its use of the equipment to include tagging and tracking the
movement of all supply items into and out of the five selected installations.
Marine Corps. The Marine Corps has equipped each of its main operating bases with the
capability to read passive RFID on items shipped from DLA and use the information to
document receiving and on-base deliveries. Once distribution managers complete the
integration with their information systems, the Marine Corps expects to reduce errors and
increase efficiency by automating processes that are currently being completed by hand.
RFID in the Supply Receipt Process
DLA provides item-level tagging and rolls up content-level information on the tags it affixes
to intermodal shipping containers. Many of its prime vendors do the same. Much of
industry’s supply chain has shifted to the practice of using “trusted vendors” to eliminate
costly item-level hands-on piece counts at receiving points. Assuming the military services
ASCM 629 - Week 5 Page 24
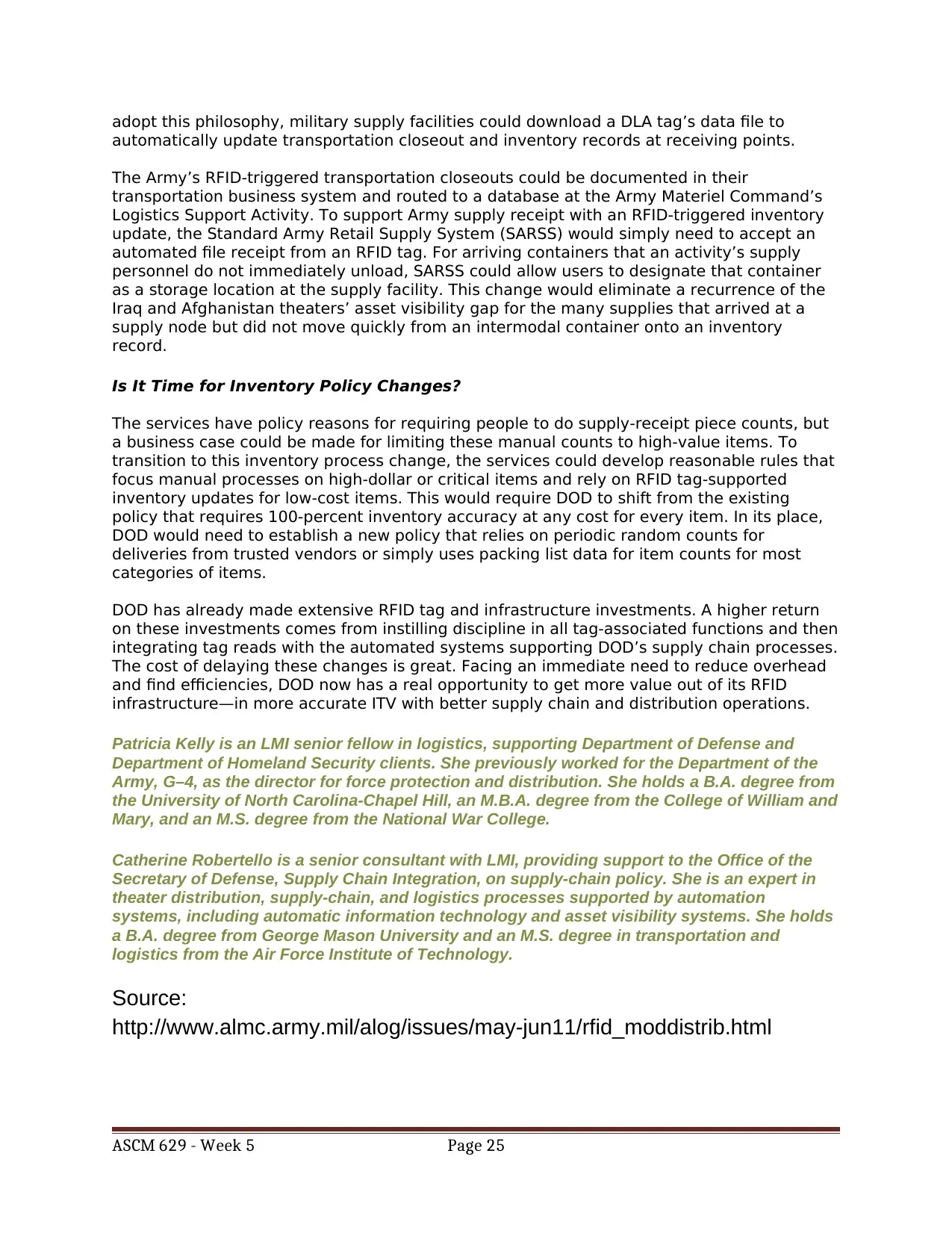
adopt this philosophy, military supply facilities could download a DLA tag’s data file to
automatically update transportation closeout and inventory records at receiving points.
The Army’s RFID-triggered transportation closeouts could be documented in their
transportation business system and routed to a database at the Army Materiel Command’s
Logistics Support Activity. To support Army supply receipt with an RFID-triggered inventory
update, the Standard Army Retail Supply System (SARSS) would simply need to accept an
automated file receipt from an RFID tag. For arriving containers that an activity’s supply
personnel do not immediately unload, SARSS could allow users to designate that container
as a storage location at the supply facility. This change would eliminate a recurrence of the
Iraq and Afghanistan theaters’ asset visibility gap for the many supplies that arrived at a
supply node but did not move quickly from an intermodal container onto an inventory
record.
Is It Time for Inventory Policy Changes?
The services have policy reasons for requiring people to do supply-receipt piece counts, but
a business case could be made for limiting these manual counts to high-value items. To
transition to this inventory process change, the services could develop reasonable rules that
focus manual processes on high-dollar or critical items and rely on RFID tag-supported
inventory updates for low-cost items. This would require DOD to shift from the existing
policy that requires 100-percent inventory accuracy at any cost for every item. In its place,
DOD would need to establish a new policy that relies on periodic random counts for
deliveries from trusted vendors or simply uses packing list data for item counts for most
categories of items.
DOD has already made extensive RFID tag and infrastructure investments. A higher return
on these investments comes from instilling discipline in all tag-associated functions and then
integrating tag reads with the automated systems supporting DOD’s supply chain processes.
The cost of delaying these changes is great. Facing an immediate need to reduce overhead
and find efficiencies, DOD now has a real opportunity to get more value out of its RFID
infrastructure—in more accurate ITV with better supply chain and distribution operations.
Patricia Kelly is an LMI senior fellow in logistics, supporting Department of Defense and
Department of Homeland Security clients. She previously worked for the Department of the
Army, G–4, as the director for force protection and distribution. She holds a B.A. degree from
the University of North Carolina-Chapel Hill, an M.B.A. degree from the College of William and
Mary, and an M.S. degree from the National War College.
Catherine Robertello is a senior consultant with LMI, providing support to the Office of the
Secretary of Defense, Supply Chain Integration, on supply-chain policy. She is an expert in
theater distribution, supply-chain, and logistics processes supported by automation
systems, including automatic information technology and asset visibility systems. She holds
a B.A. degree from George Mason University and an M.S. degree in transportation and
logistics from the Air Force Institute of Technology.
Source:
http://www.almc.army.mil/alog/issues/may-jun11/rfid_moddistrib.html
ASCM 629 - Week 5 Page 25
automatically update transportation closeout and inventory records at receiving points.
The Army’s RFID-triggered transportation closeouts could be documented in their
transportation business system and routed to a database at the Army Materiel Command’s
Logistics Support Activity. To support Army supply receipt with an RFID-triggered inventory
update, the Standard Army Retail Supply System (SARSS) would simply need to accept an
automated file receipt from an RFID tag. For arriving containers that an activity’s supply
personnel do not immediately unload, SARSS could allow users to designate that container
as a storage location at the supply facility. This change would eliminate a recurrence of the
Iraq and Afghanistan theaters’ asset visibility gap for the many supplies that arrived at a
supply node but did not move quickly from an intermodal container onto an inventory
record.
Is It Time for Inventory Policy Changes?
The services have policy reasons for requiring people to do supply-receipt piece counts, but
a business case could be made for limiting these manual counts to high-value items. To
transition to this inventory process change, the services could develop reasonable rules that
focus manual processes on high-dollar or critical items and rely on RFID tag-supported
inventory updates for low-cost items. This would require DOD to shift from the existing
policy that requires 100-percent inventory accuracy at any cost for every item. In its place,
DOD would need to establish a new policy that relies on periodic random counts for
deliveries from trusted vendors or simply uses packing list data for item counts for most
categories of items.
DOD has already made extensive RFID tag and infrastructure investments. A higher return
on these investments comes from instilling discipline in all tag-associated functions and then
integrating tag reads with the automated systems supporting DOD’s supply chain processes.
The cost of delaying these changes is great. Facing an immediate need to reduce overhead
and find efficiencies, DOD now has a real opportunity to get more value out of its RFID
infrastructure—in more accurate ITV with better supply chain and distribution operations.
Patricia Kelly is an LMI senior fellow in logistics, supporting Department of Defense and
Department of Homeland Security clients. She previously worked for the Department of the
Army, G–4, as the director for force protection and distribution. She holds a B.A. degree from
the University of North Carolina-Chapel Hill, an M.B.A. degree from the College of William and
Mary, and an M.S. degree from the National War College.
Catherine Robertello is a senior consultant with LMI, providing support to the Office of the
Secretary of Defense, Supply Chain Integration, on supply-chain policy. She is an expert in
theater distribution, supply-chain, and logistics processes supported by automation
systems, including automatic information technology and asset visibility systems. She holds
a B.A. degree from George Mason University and an M.S. degree in transportation and
logistics from the Air Force Institute of Technology.
Source:
http://www.almc.army.mil/alog/issues/may-jun11/rfid_moddistrib.html
ASCM 629 - Week 5 Page 25
Paraphrase This Document
Need a fresh take? Get an instant paraphrase of this document with our AI Paraphraser
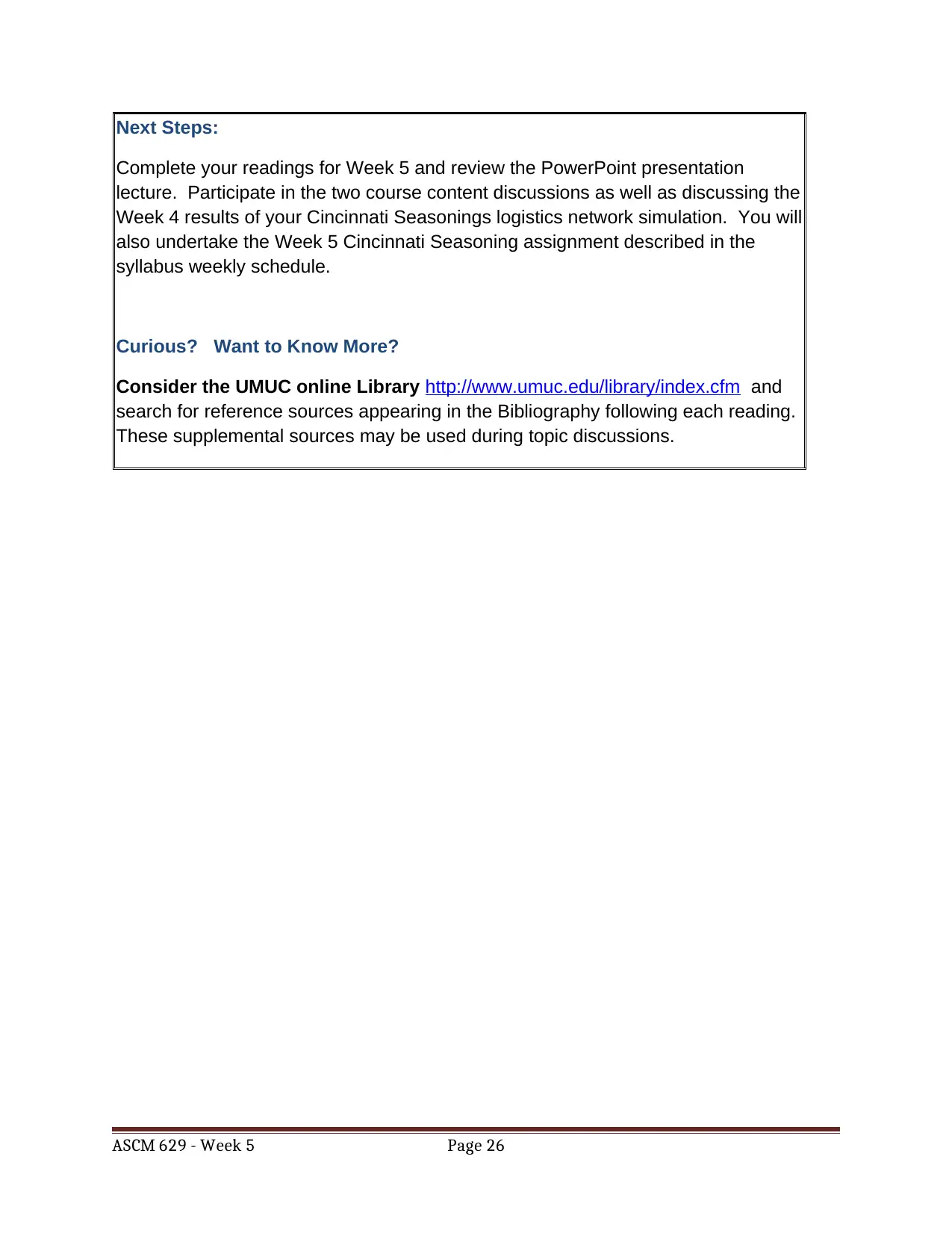
Next Steps:
Complete your readings for Week 5 and review the PowerPoint presentation
lecture. Participate in the two course content discussions as well as discussing the
Week 4 results of your Cincinnati Seasonings logistics network simulation. You will
also undertake the Week 5 Cincinnati Seasoning assignment described in the
syllabus weekly schedule.
Curious? Want to Know More?
Consider the UMUC online Library http://www.umuc.edu/library/index.cfm and
search for reference sources appearing in the Bibliography following each reading.
These supplemental sources may be used during topic discussions.
ASCM 629 - Week 5 Page 26
Complete your readings for Week 5 and review the PowerPoint presentation
lecture. Participate in the two course content discussions as well as discussing the
Week 4 results of your Cincinnati Seasonings logistics network simulation. You will
also undertake the Week 5 Cincinnati Seasoning assignment described in the
syllabus weekly schedule.
Curious? Want to Know More?
Consider the UMUC online Library http://www.umuc.edu/library/index.cfm and
search for reference sources appearing in the Bibliography following each reading.
These supplemental sources may be used during topic discussions.
ASCM 629 - Week 5 Page 26
1 out of 26
Related Documents

Your All-in-One AI-Powered Toolkit for Academic Success.
+13062052269
info@desklib.com
Available 24*7 on WhatsApp / Email
Unlock your academic potential
© 2024 | Zucol Services PVT LTD | All rights reserved.