Analyzing Jaguar's Operations: Strategy, Process, and Performance
VerifiedAdded on 2023/06/15
|8
|3309
|312
Report
AI Summary
This report evaluates Jaguar's business operation management, focusing on operation strategy, process optimization, and performance improvement. It examines the transformation process, the 4Vs of operations (Volume, Variety, Visibility, Variation), and key performance parameters. The report discusses process maps, layout types, planning, control, and capacity management. It also delves into operations functions such as inventory management, lean production, and supply chain & project management, emphasizing the importance of technology and stakeholder engagement. The analysis aims to provide insights into enhancing Jaguar's operational efficiency and competitiveness in the automotive industry. Desklib offers a platform for students to access this and other solved assignments.
Contribute Materials
Your contribution can guide someone’s learning journey. Share your
documents today.
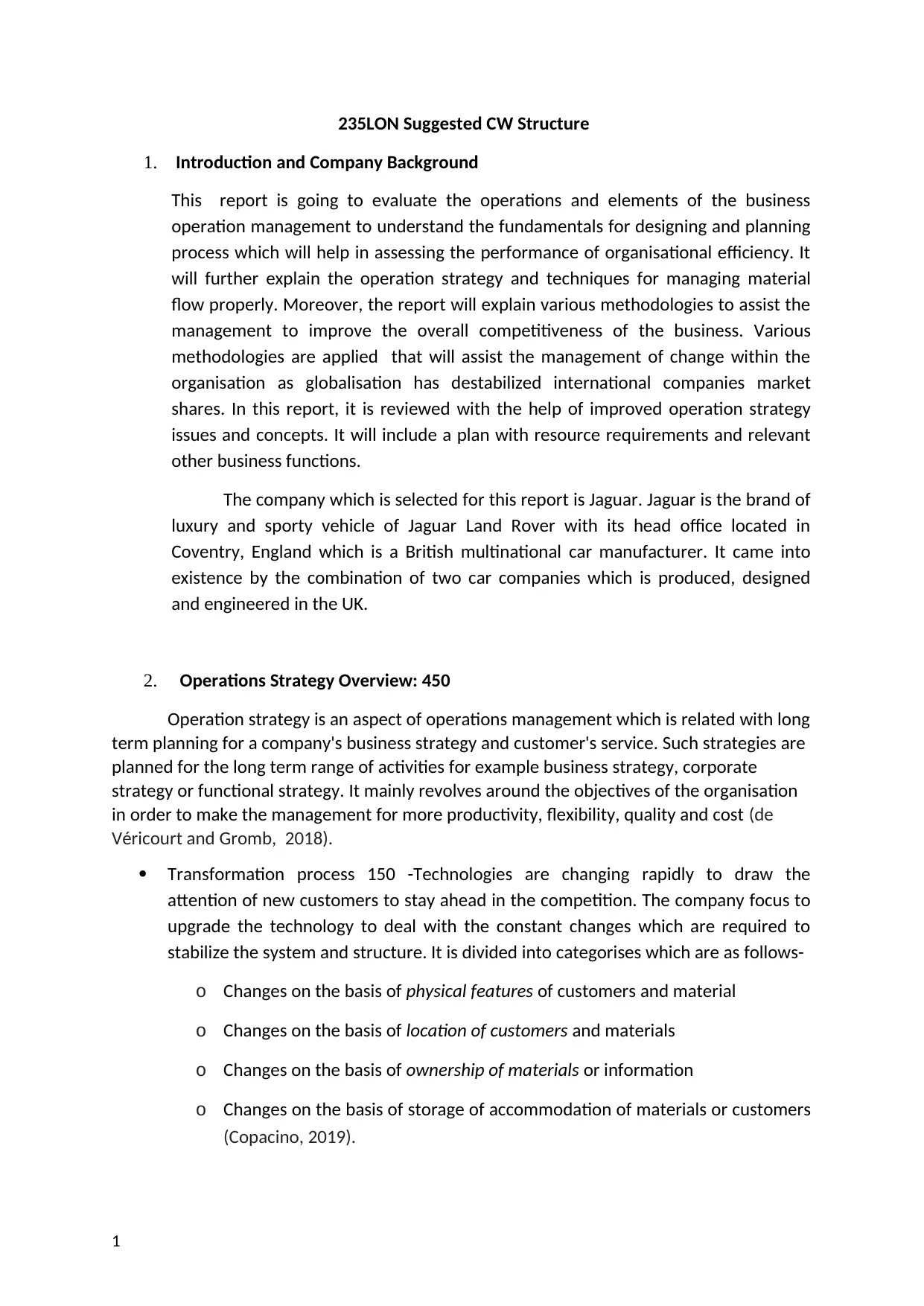
235LON Suggested CW Structure
1. Introduction and Company Background
This report is going to evaluate the operations and elements of the business
operation management to understand the fundamentals for designing and planning
process which will help in assessing the performance of organisational efficiency. It
will further explain the operation strategy and techniques for managing material
flow properly. Moreover, the report will explain various methodologies to assist the
management to improve the overall competitiveness of the business. Various
methodologies are applied that will assist the management of change within the
organisation as globalisation has destabilized international companies market
shares. In this report, it is reviewed with the help of improved operation strategy
issues and concepts. It will include a plan with resource requirements and relevant
other business functions.
The company which is selected for this report is Jaguar. Jaguar is the brand of
luxury and sporty vehicle of Jaguar Land Rover with its head office located in
Coventry, England which is a British multinational car manufacturer. It came into
existence by the combination of two car companies which is produced, designed
and engineered in the UK.
2. Operations Strategy Overview: 450
Operation strategy is an aspect of operations management which is related with long
term planning for a company's business strategy and customer's service. Such strategies are
planned for the long term range of activities for example business strategy, corporate
strategy or functional strategy. It mainly revolves around the objectives of the organisation
in order to make the management for more productivity, flexibility, quality and cost (de
Véricourt and Gromb, 2018).
Transformation process 150 -Technologies are changing rapidly to draw the
attention of new customers to stay ahead in the competition. The company focus to
upgrade the technology to deal with the constant changes which are required to
stabilize the system and structure. It is divided into categorises which are as follows-
o Changes on the basis of physical features of customers and material
o Changes on the basis of location of customers and materials
o Changes on the basis of ownership of materials or information
o Changes on the basis of storage of accommodation of materials or customers
(Copacino, 2019).
1
1. Introduction and Company Background
This report is going to evaluate the operations and elements of the business
operation management to understand the fundamentals for designing and planning
process which will help in assessing the performance of organisational efficiency. It
will further explain the operation strategy and techniques for managing material
flow properly. Moreover, the report will explain various methodologies to assist the
management to improve the overall competitiveness of the business. Various
methodologies are applied that will assist the management of change within the
organisation as globalisation has destabilized international companies market
shares. In this report, it is reviewed with the help of improved operation strategy
issues and concepts. It will include a plan with resource requirements and relevant
other business functions.
The company which is selected for this report is Jaguar. Jaguar is the brand of
luxury and sporty vehicle of Jaguar Land Rover with its head office located in
Coventry, England which is a British multinational car manufacturer. It came into
existence by the combination of two car companies which is produced, designed
and engineered in the UK.
2. Operations Strategy Overview: 450
Operation strategy is an aspect of operations management which is related with long
term planning for a company's business strategy and customer's service. Such strategies are
planned for the long term range of activities for example business strategy, corporate
strategy or functional strategy. It mainly revolves around the objectives of the organisation
in order to make the management for more productivity, flexibility, quality and cost (de
Véricourt and Gromb, 2018).
Transformation process 150 -Technologies are changing rapidly to draw the
attention of new customers to stay ahead in the competition. The company focus to
upgrade the technology to deal with the constant changes which are required to
stabilize the system and structure. It is divided into categorises which are as follows-
o Changes on the basis of physical features of customers and material
o Changes on the basis of location of customers and materials
o Changes on the basis of ownership of materials or information
o Changes on the basis of storage of accommodation of materials or customers
(Copacino, 2019).
1
Secure Best Marks with AI Grader
Need help grading? Try our AI Grader for instant feedback on your assignments.
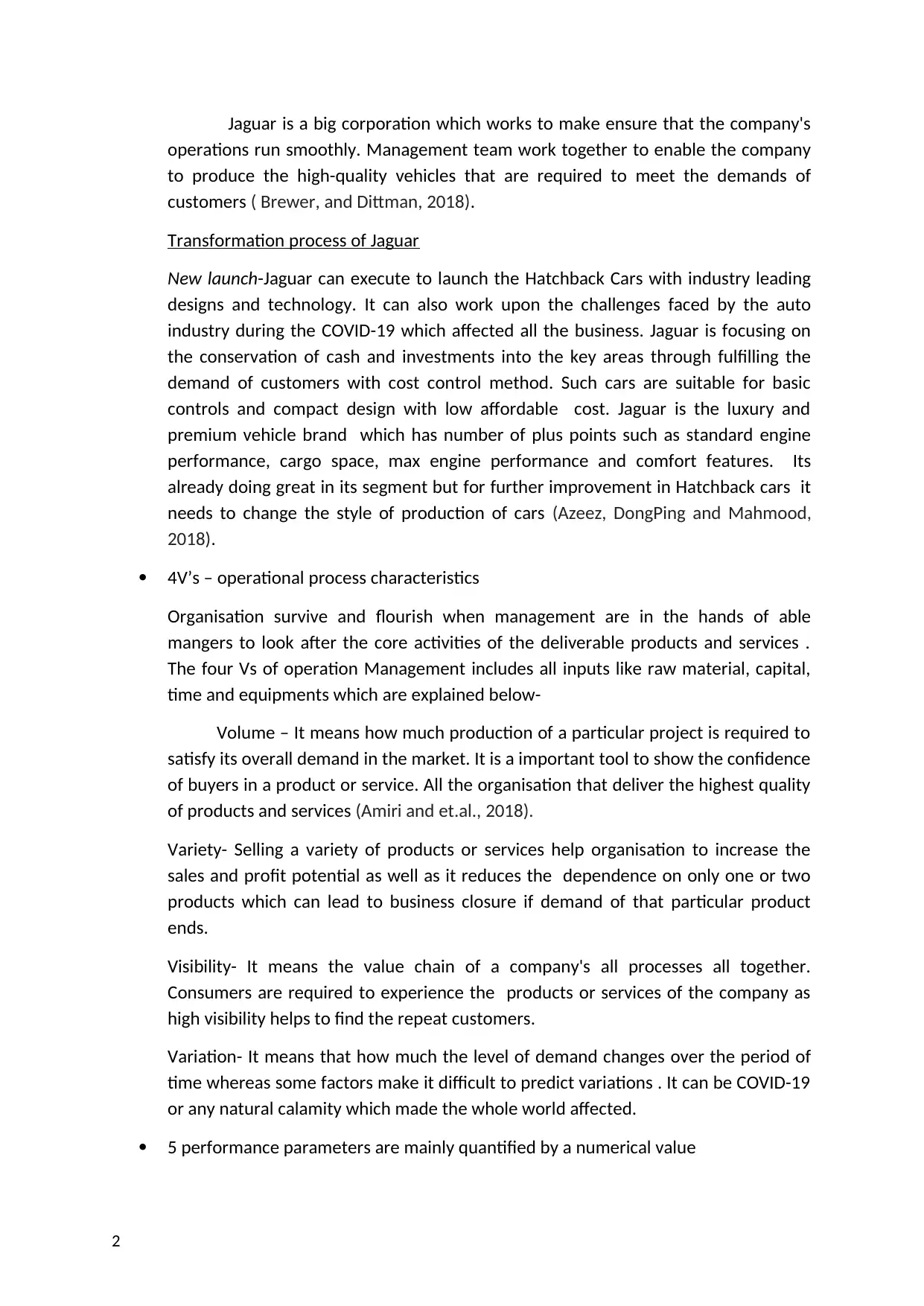
Jaguar is a big corporation which works to make ensure that the company's
operations run smoothly. Management team work together to enable the company
to produce the high-quality vehicles that are required to meet the demands of
customers ( Brewer, and Dittman, 2018).
Transformation process of Jaguar
New launch-Jaguar can execute to launch the Hatchback Cars with industry leading
designs and technology. It can also work upon the challenges faced by the auto
industry during the COVID-19 which affected all the business. Jaguar is focusing on
the conservation of cash and investments into the key areas through fulfilling the
demand of customers with cost control method. Such cars are suitable for basic
controls and compact design with low affordable cost. Jaguar is the luxury and
premium vehicle brand which has number of plus points such as standard engine
performance, cargo space, max engine performance and comfort features. Its
already doing great in its segment but for further improvement in Hatchback cars it
needs to change the style of production of cars (Azeez, DongPing and Mahmood,
2018).
4V’s – operational process characteristics
Organisation survive and flourish when management are in the hands of able
mangers to look after the core activities of the deliverable products and services .
The four Vs of operation Management includes all inputs like raw material, capital,
time and equipments which are explained below-
Volume – It means how much production of a particular project is required to
satisfy its overall demand in the market. It is a important tool to show the confidence
of buyers in a product or service. All the organisation that deliver the highest quality
of products and services (Amiri and et.al., 2018).
Variety- Selling a variety of products or services help organisation to increase the
sales and profit potential as well as it reduces the dependence on only one or two
products which can lead to business closure if demand of that particular product
ends.
Visibility- It means the value chain of a company's all processes all together.
Consumers are required to experience the products or services of the company as
high visibility helps to find the repeat customers.
Variation- It means that how much the level of demand changes over the period of
time whereas some factors make it difficult to predict variations . It can be COVID-19
or any natural calamity which made the whole world affected.
5 performance parameters are mainly quantified by a numerical value
2
operations run smoothly. Management team work together to enable the company
to produce the high-quality vehicles that are required to meet the demands of
customers ( Brewer, and Dittman, 2018).
Transformation process of Jaguar
New launch-Jaguar can execute to launch the Hatchback Cars with industry leading
designs and technology. It can also work upon the challenges faced by the auto
industry during the COVID-19 which affected all the business. Jaguar is focusing on
the conservation of cash and investments into the key areas through fulfilling the
demand of customers with cost control method. Such cars are suitable for basic
controls and compact design with low affordable cost. Jaguar is the luxury and
premium vehicle brand which has number of plus points such as standard engine
performance, cargo space, max engine performance and comfort features. Its
already doing great in its segment but for further improvement in Hatchback cars it
needs to change the style of production of cars (Azeez, DongPing and Mahmood,
2018).
4V’s – operational process characteristics
Organisation survive and flourish when management are in the hands of able
mangers to look after the core activities of the deliverable products and services .
The four Vs of operation Management includes all inputs like raw material, capital,
time and equipments which are explained below-
Volume – It means how much production of a particular project is required to
satisfy its overall demand in the market. It is a important tool to show the confidence
of buyers in a product or service. All the organisation that deliver the highest quality
of products and services (Amiri and et.al., 2018).
Variety- Selling a variety of products or services help organisation to increase the
sales and profit potential as well as it reduces the dependence on only one or two
products which can lead to business closure if demand of that particular product
ends.
Visibility- It means the value chain of a company's all processes all together.
Consumers are required to experience the products or services of the company as
high visibility helps to find the repeat customers.
Variation- It means that how much the level of demand changes over the period of
time whereas some factors make it difficult to predict variations . It can be COVID-19
or any natural calamity which made the whole world affected.
5 performance parameters are mainly quantified by a numerical value
2
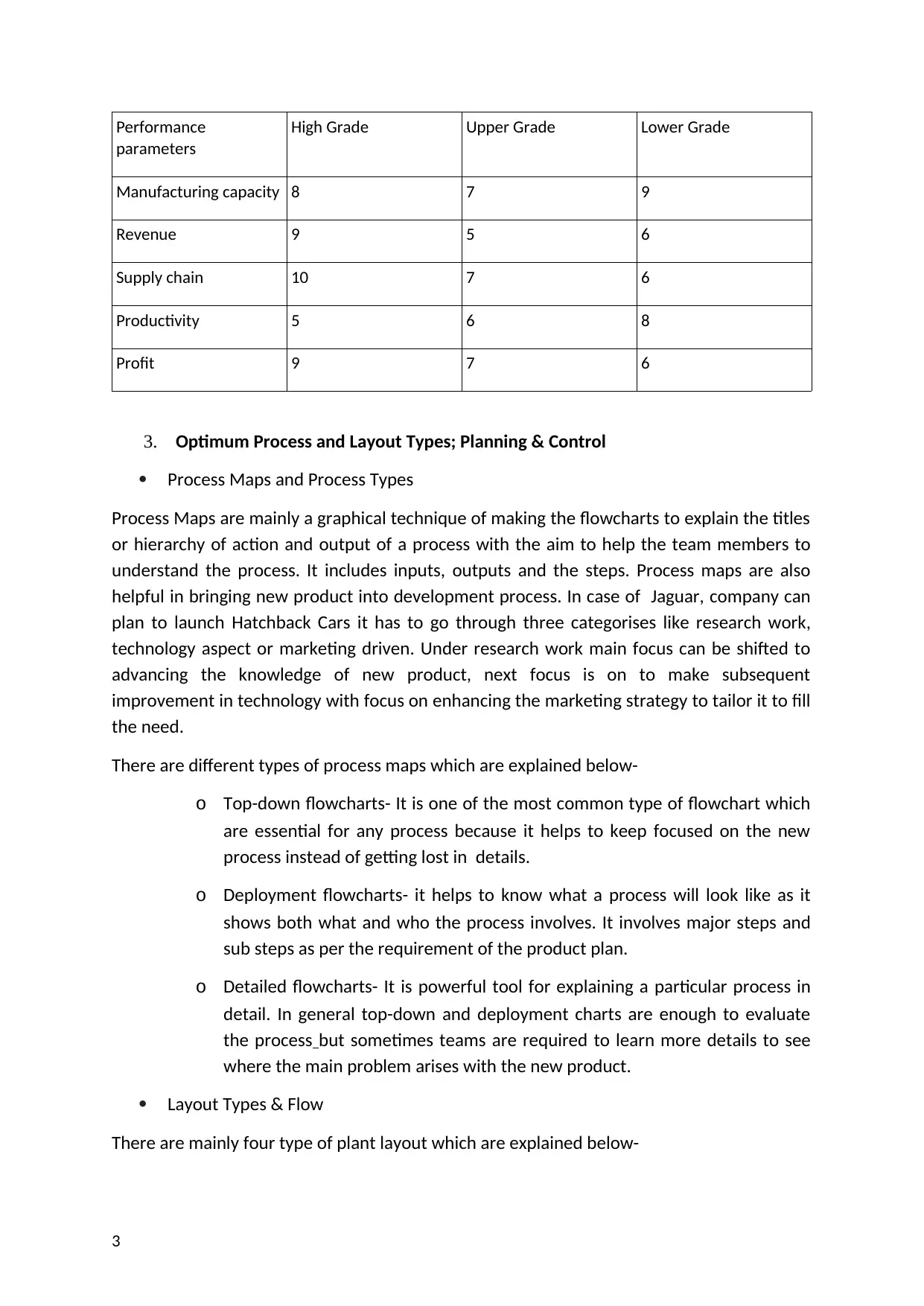
Performance
parameters
High Grade Upper Grade Lower Grade
Manufacturing capacity 8 7 9
Revenue 9 5 6
Supply chain 10 7 6
Productivity 5 6 8
Profit 9 7 6
3. Optimum Process and Layout Types; Planning & Control
Process Maps and Process Types
Process Maps are mainly a graphical technique of making the flowcharts to explain the titles
or hierarchy of action and output of a process with the aim to help the team members to
understand the process. It includes inputs, outputs and the steps. Process maps are also
helpful in bringing new product into development process. In case of Jaguar, company can
plan to launch Hatchback Cars it has to go through three categorises like research work,
technology aspect or marketing driven. Under research work main focus can be shifted to
advancing the knowledge of new product, next focus is on to make subsequent
improvement in technology with focus on enhancing the marketing strategy to tailor it to fill
the need.
There are different types of process maps which are explained below-
o Top-down flowcharts- It is one of the most common type of flowchart which
are essential for any process because it helps to keep focused on the new
process instead of getting lost in details.
o Deployment flowcharts- it helps to know what a process will look like as it
shows both what and who the process involves. It involves major steps and
sub steps as per the requirement of the product plan.
o Detailed flowcharts- It is powerful tool for explaining a particular process in
detail. In general top-down and deployment charts are enough to evaluate
the process but sometimes teams are required to learn more details to see
where the main problem arises with the new product.
Layout Types & Flow
There are mainly four type of plant layout which are explained below-
3
parameters
High Grade Upper Grade Lower Grade
Manufacturing capacity 8 7 9
Revenue 9 5 6
Supply chain 10 7 6
Productivity 5 6 8
Profit 9 7 6
3. Optimum Process and Layout Types; Planning & Control
Process Maps and Process Types
Process Maps are mainly a graphical technique of making the flowcharts to explain the titles
or hierarchy of action and output of a process with the aim to help the team members to
understand the process. It includes inputs, outputs and the steps. Process maps are also
helpful in bringing new product into development process. In case of Jaguar, company can
plan to launch Hatchback Cars it has to go through three categorises like research work,
technology aspect or marketing driven. Under research work main focus can be shifted to
advancing the knowledge of new product, next focus is on to make subsequent
improvement in technology with focus on enhancing the marketing strategy to tailor it to fill
the need.
There are different types of process maps which are explained below-
o Top-down flowcharts- It is one of the most common type of flowchart which
are essential for any process because it helps to keep focused on the new
process instead of getting lost in details.
o Deployment flowcharts- it helps to know what a process will look like as it
shows both what and who the process involves. It involves major steps and
sub steps as per the requirement of the product plan.
o Detailed flowcharts- It is powerful tool for explaining a particular process in
detail. In general top-down and deployment charts are enough to evaluate
the process but sometimes teams are required to learn more details to see
where the main problem arises with the new product.
Layout Types & Flow
There are mainly four type of plant layout which are explained below-
3

o Product or line layout- Under this layout the different materials are grouped
in one sequence. The raw material moves very fast from one workstation to
other stations with proper material handling. It has many benefits such as
low cost of material handling due to short route and continuous operations
o Process layout- Under this layout raw material of a similar type are arranged
together at one place which includes various departments like milling
department, welding department, heating department or painting
department. t has many benefits such as it includes lower initial capital
investment is required and overheads cost are relatively low with greater
flexibility of resources.
o Fixed position layout- It focuses on the movement of machines and man
power it will be applicable to the business where the size of the job is bulky
and heavy. t has many benefits such as the investment over the layout is very
small and adjustments can be made to fulfil the shortage of material.
o Combined layout- Some businesses require all three processes altogether.
Under this resources are arranged in a process layout in a sequence of
manufacture various types and sizes of products. It is to be noted that the
sequence of operations remains same with the various variety of products
and sizes. In this layout involves the fabrication of parts and assembly of
fabrication that tends to employ the process layout. But it has a disadvantage
lack of flexibility which is difficult in supervision and for further extension of
the investment. Equipments which are used in the process layout are
frequently very low because machine usage is dependent upon different
types of output requirements.
Planning, Control and Capacity Management
New product planning is the main task for the company to launch new products . The
automobile industry is adopting new techniques to upgrade new products and
numerous applications in automotive.
Capacity management focuses on the wide variety of planning actions which are
required to ensure that a business infrastructure has sufficient resources to
maximise the potential activities and production output under different situations. It
includes IT monitoring, planning, administration actions which are undertaken to
ensure that IT resources have the capacity to handle data. Main goal is to balance
the cost incurred against the supply and resources required, Develop the capacity
management plan, assist in diagnosing the incidents .
4, Operations Functions450
4
in one sequence. The raw material moves very fast from one workstation to
other stations with proper material handling. It has many benefits such as
low cost of material handling due to short route and continuous operations
o Process layout- Under this layout raw material of a similar type are arranged
together at one place which includes various departments like milling
department, welding department, heating department or painting
department. t has many benefits such as it includes lower initial capital
investment is required and overheads cost are relatively low with greater
flexibility of resources.
o Fixed position layout- It focuses on the movement of machines and man
power it will be applicable to the business where the size of the job is bulky
and heavy. t has many benefits such as the investment over the layout is very
small and adjustments can be made to fulfil the shortage of material.
o Combined layout- Some businesses require all three processes altogether.
Under this resources are arranged in a process layout in a sequence of
manufacture various types and sizes of products. It is to be noted that the
sequence of operations remains same with the various variety of products
and sizes. In this layout involves the fabrication of parts and assembly of
fabrication that tends to employ the process layout. But it has a disadvantage
lack of flexibility which is difficult in supervision and for further extension of
the investment. Equipments which are used in the process layout are
frequently very low because machine usage is dependent upon different
types of output requirements.
Planning, Control and Capacity Management
New product planning is the main task for the company to launch new products . The
automobile industry is adopting new techniques to upgrade new products and
numerous applications in automotive.
Capacity management focuses on the wide variety of planning actions which are
required to ensure that a business infrastructure has sufficient resources to
maximise the potential activities and production output under different situations. It
includes IT monitoring, planning, administration actions which are undertaken to
ensure that IT resources have the capacity to handle data. Main goal is to balance
the cost incurred against the supply and resources required, Develop the capacity
management plan, assist in diagnosing the incidents .
4, Operations Functions450
4
Secure Best Marks with AI Grader
Need help grading? Try our AI Grader for instant feedback on your assignments.
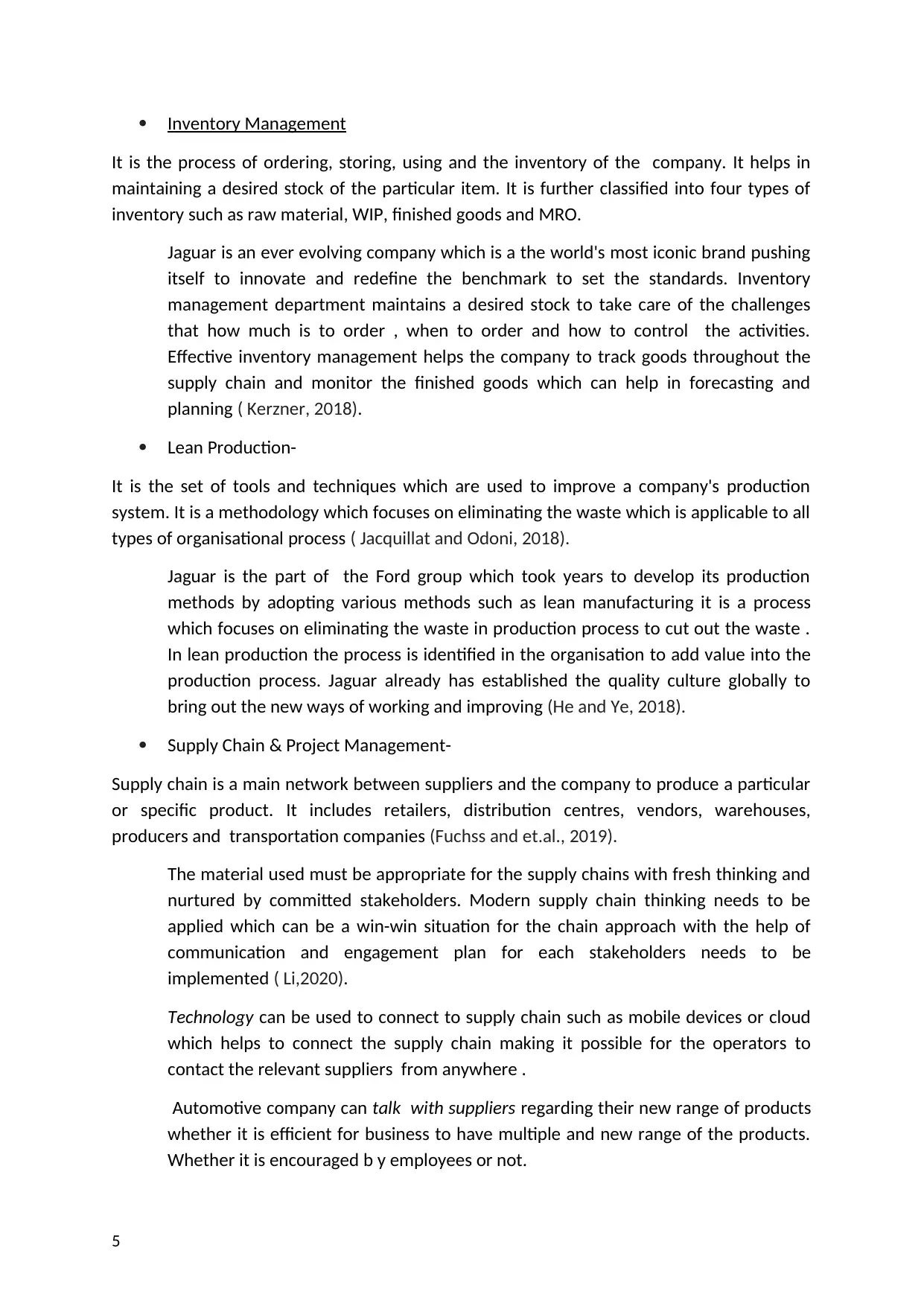
Inventory Management
It is the process of ordering, storing, using and the inventory of the company. It helps in
maintaining a desired stock of the particular item. It is further classified into four types of
inventory such as raw material, WIP, finished goods and MRO.
Jaguar is an ever evolving company which is a the world's most iconic brand pushing
itself to innovate and redefine the benchmark to set the standards. Inventory
management department maintains a desired stock to take care of the challenges
that how much is to order , when to order and how to control the activities.
Effective inventory management helps the company to track goods throughout the
supply chain and monitor the finished goods which can help in forecasting and
planning ( Kerzner, 2018).
Lean Production-
It is the set of tools and techniques which are used to improve a company's production
system. It is a methodology which focuses on eliminating the waste which is applicable to all
types of organisational process ( Jacquillat and Odoni, 2018).
Jaguar is the part of the Ford group which took years to develop its production
methods by adopting various methods such as lean manufacturing it is a process
which focuses on eliminating the waste in production process to cut out the waste .
In lean production the process is identified in the organisation to add value into the
production process. Jaguar already has established the quality culture globally to
bring out the new ways of working and improving (He and Ye, 2018).
Supply Chain & Project Management-
Supply chain is a main network between suppliers and the company to produce a particular
or specific product. It includes retailers, distribution centres, vendors, warehouses,
producers and transportation companies (Fuchss and et.al., 2019).
The material used must be appropriate for the supply chains with fresh thinking and
nurtured by committed stakeholders. Modern supply chain thinking needs to be
applied which can be a win-win situation for the chain approach with the help of
communication and engagement plan for each stakeholders needs to be
implemented ( Li,2020).
Technology can be used to connect to supply chain such as mobile devices or cloud
which helps to connect the supply chain making it possible for the operators to
contact the relevant suppliers from anywhere .
Automotive company can talk with suppliers regarding their new range of products
whether it is efficient for business to have multiple and new range of the products.
Whether it is encouraged b y employees or not.
5
It is the process of ordering, storing, using and the inventory of the company. It helps in
maintaining a desired stock of the particular item. It is further classified into four types of
inventory such as raw material, WIP, finished goods and MRO.
Jaguar is an ever evolving company which is a the world's most iconic brand pushing
itself to innovate and redefine the benchmark to set the standards. Inventory
management department maintains a desired stock to take care of the challenges
that how much is to order , when to order and how to control the activities.
Effective inventory management helps the company to track goods throughout the
supply chain and monitor the finished goods which can help in forecasting and
planning ( Kerzner, 2018).
Lean Production-
It is the set of tools and techniques which are used to improve a company's production
system. It is a methodology which focuses on eliminating the waste which is applicable to all
types of organisational process ( Jacquillat and Odoni, 2018).
Jaguar is the part of the Ford group which took years to develop its production
methods by adopting various methods such as lean manufacturing it is a process
which focuses on eliminating the waste in production process to cut out the waste .
In lean production the process is identified in the organisation to add value into the
production process. Jaguar already has established the quality culture globally to
bring out the new ways of working and improving (He and Ye, 2018).
Supply Chain & Project Management-
Supply chain is a main network between suppliers and the company to produce a particular
or specific product. It includes retailers, distribution centres, vendors, warehouses,
producers and transportation companies (Fuchss and et.al., 2019).
The material used must be appropriate for the supply chains with fresh thinking and
nurtured by committed stakeholders. Modern supply chain thinking needs to be
applied which can be a win-win situation for the chain approach with the help of
communication and engagement plan for each stakeholders needs to be
implemented ( Li,2020).
Technology can be used to connect to supply chain such as mobile devices or cloud
which helps to connect the supply chain making it possible for the operators to
contact the relevant suppliers from anywhere .
Automotive company can talk with suppliers regarding their new range of products
whether it is efficient for business to have multiple and new range of the products.
Whether it is encouraged b y employees or not.
5
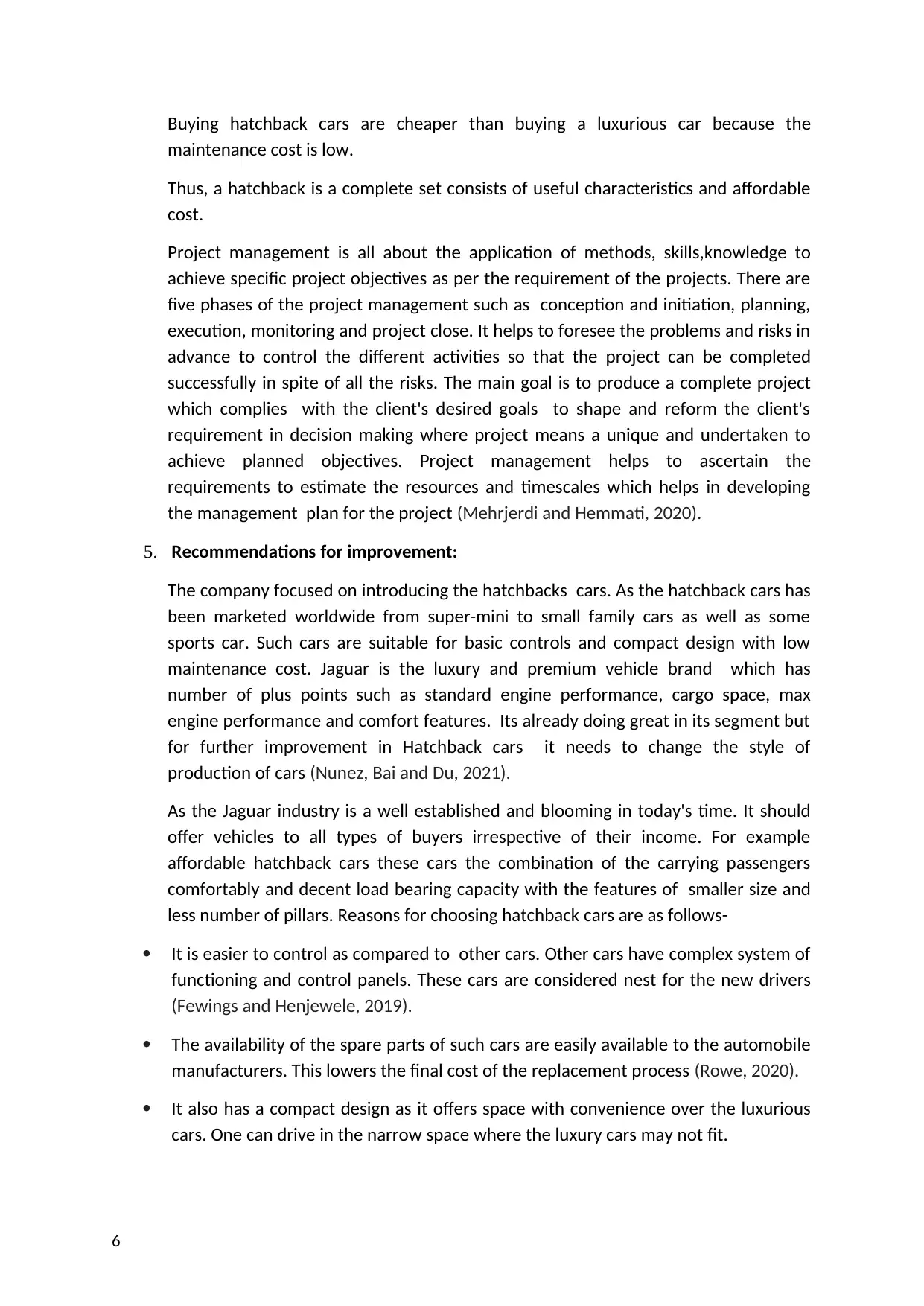
Buying hatchback cars are cheaper than buying a luxurious car because the
maintenance cost is low.
Thus, a hatchback is a complete set consists of useful characteristics and affordable
cost.
Project management is all about the application of methods, skills,knowledge to
achieve specific project objectives as per the requirement of the projects. There are
five phases of the project management such as conception and initiation, planning,
execution, monitoring and project close. It helps to foresee the problems and risks in
advance to control the different activities so that the project can be completed
successfully in spite of all the risks. The main goal is to produce a complete project
which complies with the client's desired goals to shape and reform the client's
requirement in decision making where project means a unique and undertaken to
achieve planned objectives. Project management helps to ascertain the
requirements to estimate the resources and timescales which helps in developing
the management plan for the project (Mehrjerdi and Hemmati, 2020).
5. Recommendations for improvement:
The company focused on introducing the hatchbacks cars. As the hatchback cars has
been marketed worldwide from super-mini to small family cars as well as some
sports car. Such cars are suitable for basic controls and compact design with low
maintenance cost. Jaguar is the luxury and premium vehicle brand which has
number of plus points such as standard engine performance, cargo space, max
engine performance and comfort features. Its already doing great in its segment but
for further improvement in Hatchback cars it needs to change the style of
production of cars (Nunez, Bai and Du, 2021).
As the Jaguar industry is a well established and blooming in today's time. It should
offer vehicles to all types of buyers irrespective of their income. For example
affordable hatchback cars these cars the combination of the carrying passengers
comfortably and decent load bearing capacity with the features of smaller size and
less number of pillars. Reasons for choosing hatchback cars are as follows-
It is easier to control as compared to other cars. Other cars have complex system of
functioning and control panels. These cars are considered nest for the new drivers
(Fewings and Henjewele, 2019).
The availability of the spare parts of such cars are easily available to the automobile
manufacturers. This lowers the final cost of the replacement process (Rowe, 2020).
It also has a compact design as it offers space with convenience over the luxurious
cars. One can drive in the narrow space where the luxury cars may not fit.
6
maintenance cost is low.
Thus, a hatchback is a complete set consists of useful characteristics and affordable
cost.
Project management is all about the application of methods, skills,knowledge to
achieve specific project objectives as per the requirement of the projects. There are
five phases of the project management such as conception and initiation, planning,
execution, monitoring and project close. It helps to foresee the problems and risks in
advance to control the different activities so that the project can be completed
successfully in spite of all the risks. The main goal is to produce a complete project
which complies with the client's desired goals to shape and reform the client's
requirement in decision making where project means a unique and undertaken to
achieve planned objectives. Project management helps to ascertain the
requirements to estimate the resources and timescales which helps in developing
the management plan for the project (Mehrjerdi and Hemmati, 2020).
5. Recommendations for improvement:
The company focused on introducing the hatchbacks cars. As the hatchback cars has
been marketed worldwide from super-mini to small family cars as well as some
sports car. Such cars are suitable for basic controls and compact design with low
maintenance cost. Jaguar is the luxury and premium vehicle brand which has
number of plus points such as standard engine performance, cargo space, max
engine performance and comfort features. Its already doing great in its segment but
for further improvement in Hatchback cars it needs to change the style of
production of cars (Nunez, Bai and Du, 2021).
As the Jaguar industry is a well established and blooming in today's time. It should
offer vehicles to all types of buyers irrespective of their income. For example
affordable hatchback cars these cars the combination of the carrying passengers
comfortably and decent load bearing capacity with the features of smaller size and
less number of pillars. Reasons for choosing hatchback cars are as follows-
It is easier to control as compared to other cars. Other cars have complex system of
functioning and control panels. These cars are considered nest for the new drivers
(Fewings and Henjewele, 2019).
The availability of the spare parts of such cars are easily available to the automobile
manufacturers. This lowers the final cost of the replacement process (Rowe, 2020).
It also has a compact design as it offers space with convenience over the luxurious
cars. One can drive in the narrow space where the luxury cars may not fit.
6
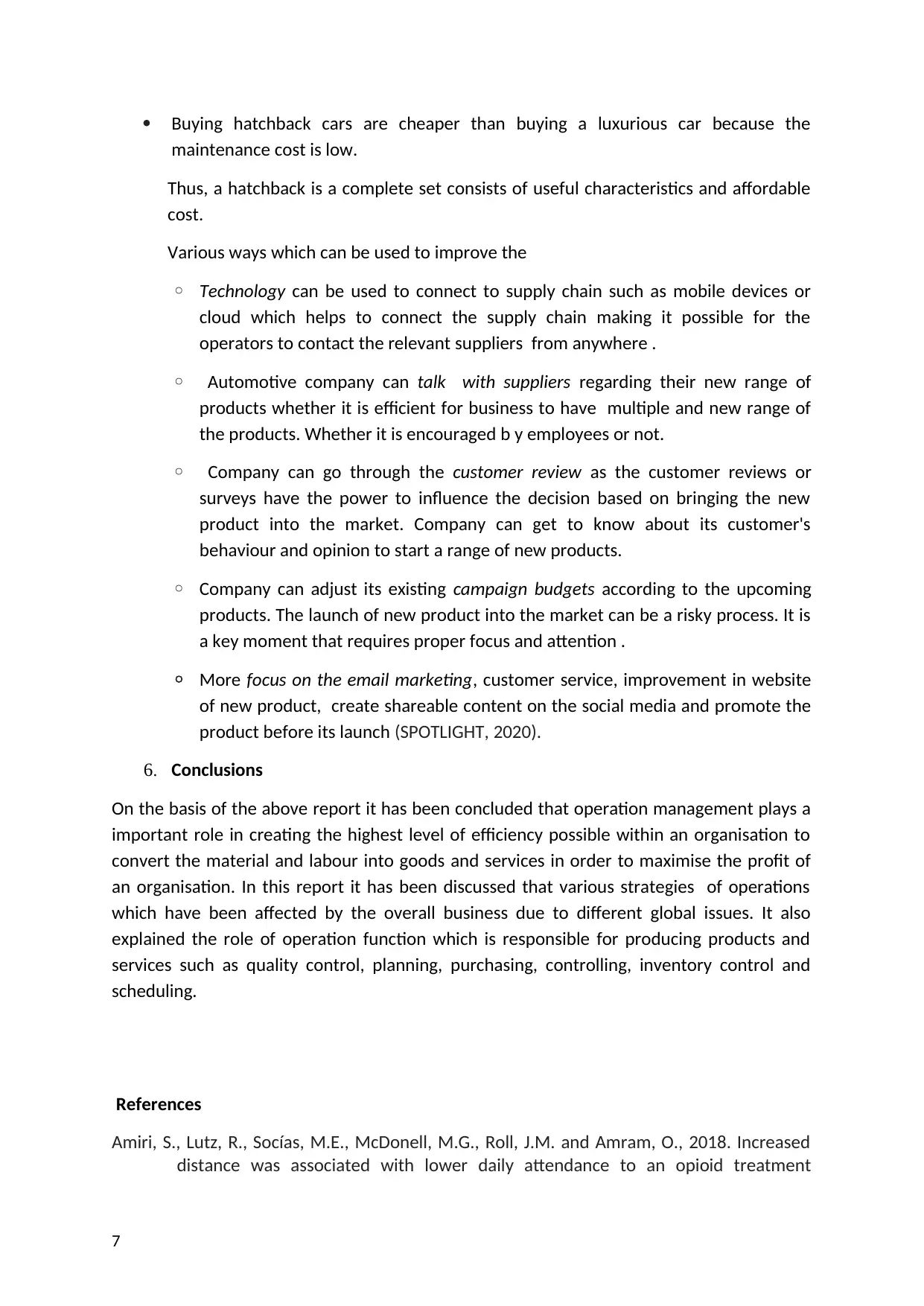
Buying hatchback cars are cheaper than buying a luxurious car because the
maintenance cost is low.
Thus, a hatchback is a complete set consists of useful characteristics and affordable
cost.
Various ways which can be used to improve the
◦ Technology can be used to connect to supply chain such as mobile devices or
cloud which helps to connect the supply chain making it possible for the
operators to contact the relevant suppliers from anywhere .
◦ Automotive company can talk with suppliers regarding their new range of
products whether it is efficient for business to have multiple and new range of
the products. Whether it is encouraged b y employees or not.
◦ Company can go through the customer review as the customer reviews or
surveys have the power to influence the decision based on bringing the new
product into the market. Company can get to know about its customer's
behaviour and opinion to start a range of new products.
◦ Company can adjust its existing campaign budgets according to the upcoming
products. The launch of new product into the market can be a risky process. It is
a key moment that requires proper focus and attention .
◦ More focus on the email marketing, customer service, improvement in website
of new product, create shareable content on the social media and promote the
product before its launch (SPOTLIGHT, 2020).
6. Conclusions
On the basis of the above report it has been concluded that operation management plays a
important role in creating the highest level of efficiency possible within an organisation to
convert the material and labour into goods and services in order to maximise the profit of
an organisation. In this report it has been discussed that various strategies of operations
which have been affected by the overall business due to different global issues. It also
explained the role of operation function which is responsible for producing products and
services such as quality control, planning, purchasing, controlling, inventory control and
scheduling.
References
Amiri, S., Lutz, R., Socías, M.E., McDonell, M.G., Roll, J.M. and Amram, O., 2018. Increased
distance was associated with lower daily attendance to an opioid treatment
7
maintenance cost is low.
Thus, a hatchback is a complete set consists of useful characteristics and affordable
cost.
Various ways which can be used to improve the
◦ Technology can be used to connect to supply chain such as mobile devices or
cloud which helps to connect the supply chain making it possible for the
operators to contact the relevant suppliers from anywhere .
◦ Automotive company can talk with suppliers regarding their new range of
products whether it is efficient for business to have multiple and new range of
the products. Whether it is encouraged b y employees or not.
◦ Company can go through the customer review as the customer reviews or
surveys have the power to influence the decision based on bringing the new
product into the market. Company can get to know about its customer's
behaviour and opinion to start a range of new products.
◦ Company can adjust its existing campaign budgets according to the upcoming
products. The launch of new product into the market can be a risky process. It is
a key moment that requires proper focus and attention .
◦ More focus on the email marketing, customer service, improvement in website
of new product, create shareable content on the social media and promote the
product before its launch (SPOTLIGHT, 2020).
6. Conclusions
On the basis of the above report it has been concluded that operation management plays a
important role in creating the highest level of efficiency possible within an organisation to
convert the material and labour into goods and services in order to maximise the profit of
an organisation. In this report it has been discussed that various strategies of operations
which have been affected by the overall business due to different global issues. It also
explained the role of operation function which is responsible for producing products and
services such as quality control, planning, purchasing, controlling, inventory control and
scheduling.
References
Amiri, S., Lutz, R., Socías, M.E., McDonell, M.G., Roll, J.M. and Amram, O., 2018. Increased
distance was associated with lower daily attendance to an opioid treatment
7
Paraphrase This Document
Need a fresh take? Get an instant paraphrase of this document with our AI Paraphraser
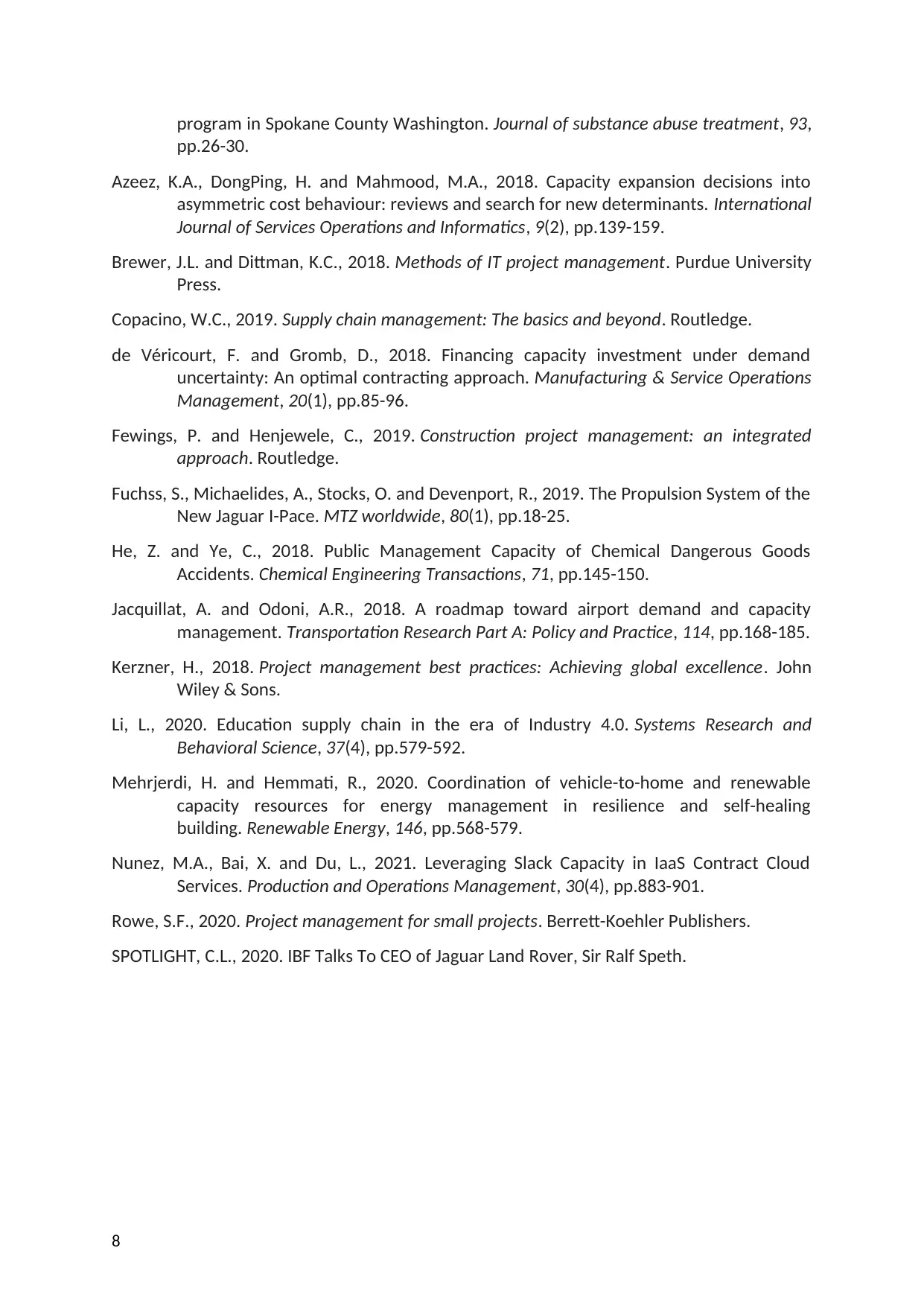
program in Spokane County Washington. Journal of substance abuse treatment, 93,
pp.26-30.
Azeez, K.A., DongPing, H. and Mahmood, M.A., 2018. Capacity expansion decisions into
asymmetric cost behaviour: reviews and search for new determinants. International
Journal of Services Operations and Informatics, 9(2), pp.139-159.
Brewer, J.L. and Dittman, K.C., 2018. Methods of IT project management. Purdue University
Press.
Copacino, W.C., 2019. Supply chain management: The basics and beyond. Routledge.
de Véricourt, F. and Gromb, D., 2018. Financing capacity investment under demand
uncertainty: An optimal contracting approach. Manufacturing & Service Operations
Management, 20(1), pp.85-96.
Fewings, P. and Henjewele, C., 2019. Construction project management: an integrated
approach. Routledge.
Fuchss, S., Michaelides, A., Stocks, O. and Devenport, R., 2019. The Propulsion System of the
New Jaguar I-Pace. MTZ worldwide, 80(1), pp.18-25.
He, Z. and Ye, C., 2018. Public Management Capacity of Chemical Dangerous Goods
Accidents. Chemical Engineering Transactions, 71, pp.145-150.
Jacquillat, A. and Odoni, A.R., 2018. A roadmap toward airport demand and capacity
management. Transportation Research Part A: Policy and Practice, 114, pp.168-185.
Kerzner, H., 2018. Project management best practices: Achieving global excellence. John
Wiley & Sons.
Li, L., 2020. Education supply chain in the era of Industry 4.0. Systems Research and
Behavioral Science, 37(4), pp.579-592.
Mehrjerdi, H. and Hemmati, R., 2020. Coordination of vehicle-to-home and renewable
capacity resources for energy management in resilience and self-healing
building. Renewable Energy, 146, pp.568-579.
Nunez, M.A., Bai, X. and Du, L., 2021. Leveraging Slack Capacity in IaaS Contract Cloud
Services. Production and Operations Management, 30(4), pp.883-901.
Rowe, S.F., 2020. Project management for small projects. Berrett-Koehler Publishers.
SPOTLIGHT, C.L., 2020. IBF Talks To CEO of Jaguar Land Rover, Sir Ralf Speth.
8
pp.26-30.
Azeez, K.A., DongPing, H. and Mahmood, M.A., 2018. Capacity expansion decisions into
asymmetric cost behaviour: reviews and search for new determinants. International
Journal of Services Operations and Informatics, 9(2), pp.139-159.
Brewer, J.L. and Dittman, K.C., 2018. Methods of IT project management. Purdue University
Press.
Copacino, W.C., 2019. Supply chain management: The basics and beyond. Routledge.
de Véricourt, F. and Gromb, D., 2018. Financing capacity investment under demand
uncertainty: An optimal contracting approach. Manufacturing & Service Operations
Management, 20(1), pp.85-96.
Fewings, P. and Henjewele, C., 2019. Construction project management: an integrated
approach. Routledge.
Fuchss, S., Michaelides, A., Stocks, O. and Devenport, R., 2019. The Propulsion System of the
New Jaguar I-Pace. MTZ worldwide, 80(1), pp.18-25.
He, Z. and Ye, C., 2018. Public Management Capacity of Chemical Dangerous Goods
Accidents. Chemical Engineering Transactions, 71, pp.145-150.
Jacquillat, A. and Odoni, A.R., 2018. A roadmap toward airport demand and capacity
management. Transportation Research Part A: Policy and Practice, 114, pp.168-185.
Kerzner, H., 2018. Project management best practices: Achieving global excellence. John
Wiley & Sons.
Li, L., 2020. Education supply chain in the era of Industry 4.0. Systems Research and
Behavioral Science, 37(4), pp.579-592.
Mehrjerdi, H. and Hemmati, R., 2020. Coordination of vehicle-to-home and renewable
capacity resources for energy management in resilience and self-healing
building. Renewable Energy, 146, pp.568-579.
Nunez, M.A., Bai, X. and Du, L., 2021. Leveraging Slack Capacity in IaaS Contract Cloud
Services. Production and Operations Management, 30(4), pp.883-901.
Rowe, S.F., 2020. Project management for small projects. Berrett-Koehler Publishers.
SPOTLIGHT, C.L., 2020. IBF Talks To CEO of Jaguar Land Rover, Sir Ralf Speth.
8
1 out of 8
Related Documents

Your All-in-One AI-Powered Toolkit for Academic Success.
+13062052269
info@desklib.com
Available 24*7 on WhatsApp / Email
Unlock your academic potential
© 2024 | Zucol Services PVT LTD | All rights reserved.