JFL Supply Chain Management: Problems, Analysis, and Recommendations
VerifiedAdded on 2022/12/22
|16
|4391
|98
Report
AI Summary
This report provides a critical analysis of the supply chain management issues faced by Jungle Furniture Ltd (JFL). It examines the challenges related to raw material procurement, inventory management, and communication between departments, which impact production and customer service. The r...
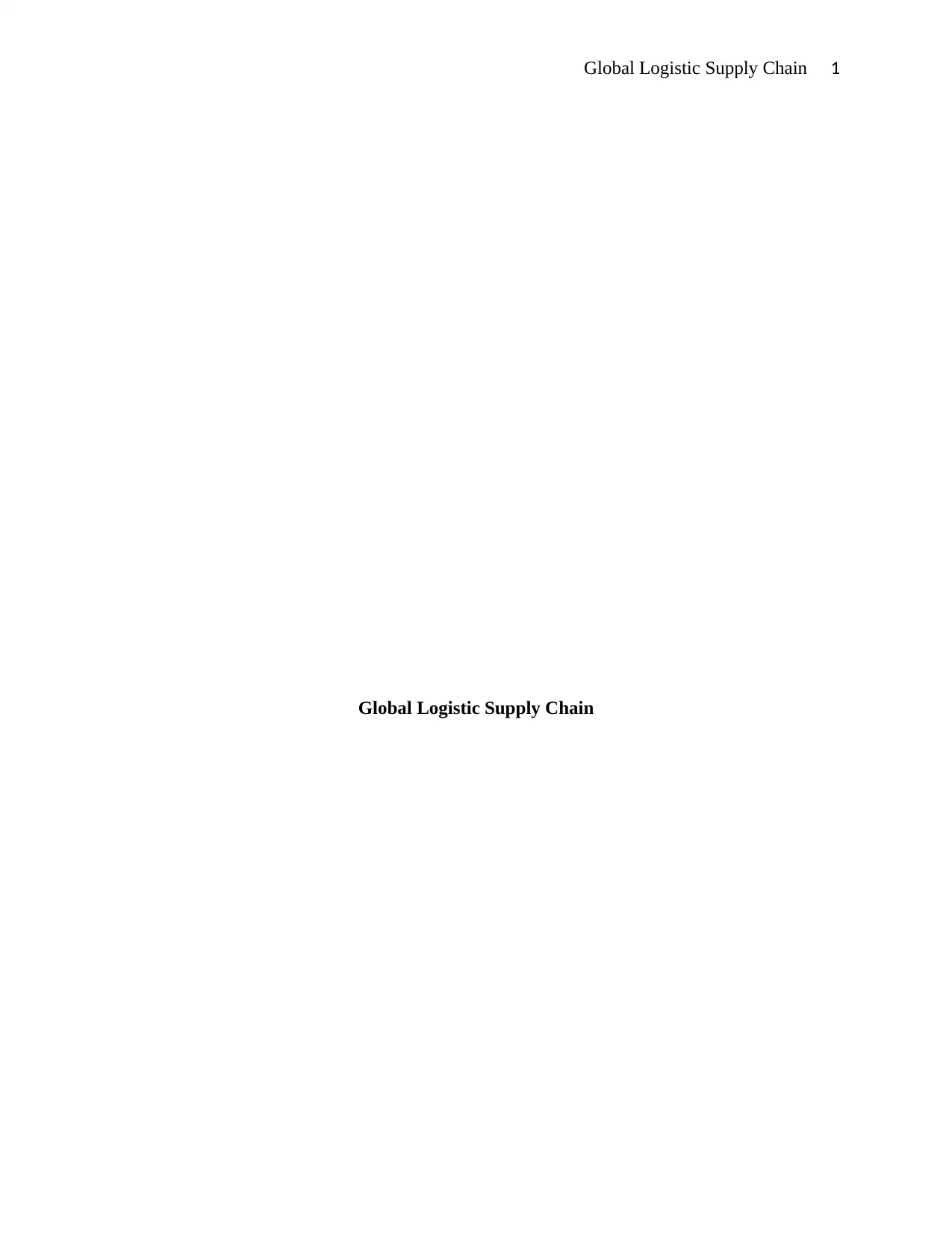
Global Logistic Supply Chain 1
Global Logistic Supply Chain
Global Logistic Supply Chain
Paraphrase This Document
Need a fresh take? Get an instant paraphrase of this document with our AI Paraphraser

Global Logistic Supply Chain 2
Executive summary
The success of an organization depends on effectiveness of supply chain management. It is
essential for the organizations to have an effective operation management to manage the
production procedure as well as manage the supply chain management practices. Jungle
Furniture Ltd (JFL) is facing issues in its supply chain management, which has influenced its
production procedure and productivity. Customer services and resource utilization are two major
objectives of supply chain management that must be considered by the organizations to attain the
organizational objectives in desired manner. In addition, the organizations should make efforts to
improve their supply chain management practices to improve their operational functions in better
manner.
Executive summary
The success of an organization depends on effectiveness of supply chain management. It is
essential for the organizations to have an effective operation management to manage the
production procedure as well as manage the supply chain management practices. Jungle
Furniture Ltd (JFL) is facing issues in its supply chain management, which has influenced its
production procedure and productivity. Customer services and resource utilization are two major
objectives of supply chain management that must be considered by the organizations to attain the
organizational objectives in desired manner. In addition, the organizations should make efforts to
improve their supply chain management practices to improve their operational functions in better
manner.
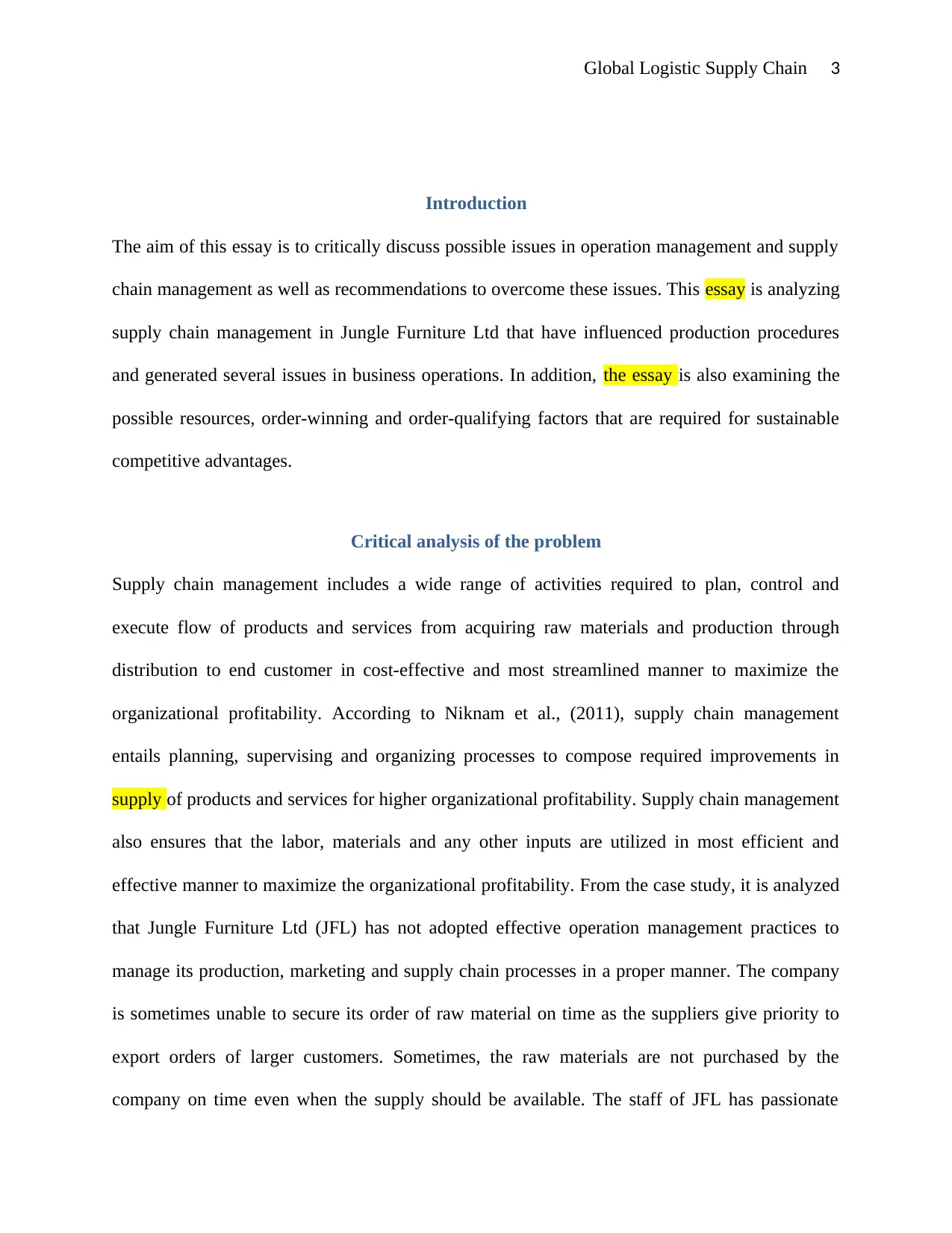
Global Logistic Supply Chain 3
Introduction
The aim of this essay is to critically discuss possible issues in operation management and supply
chain management as well as recommendations to overcome these issues. This essay is analyzing
supply chain management in Jungle Furniture Ltd that have influenced production procedures
and generated several issues in business operations. In addition, the essay is also examining the
possible resources, order-winning and order-qualifying factors that are required for sustainable
competitive advantages.
Critical analysis of the problem
Supply chain management includes a wide range of activities required to plan, control and
execute flow of products and services from acquiring raw materials and production through
distribution to end customer in cost-effective and most streamlined manner to maximize the
organizational profitability. According to Niknam et al., (2011), supply chain management
entails planning, supervising and organizing processes to compose required improvements in
supply of products and services for higher organizational profitability. Supply chain management
also ensures that the labor, materials and any other inputs are utilized in most efficient and
effective manner to maximize the organizational profitability. From the case study, it is analyzed
that Jungle Furniture Ltd (JFL) has not adopted effective operation management practices to
manage its production, marketing and supply chain processes in a proper manner. The company
is sometimes unable to secure its order of raw material on time as the suppliers give priority to
export orders of larger customers. Sometimes, the raw materials are not purchased by the
company on time even when the supply should be available. The staff of JFL has passionate
Introduction
The aim of this essay is to critically discuss possible issues in operation management and supply
chain management as well as recommendations to overcome these issues. This essay is analyzing
supply chain management in Jungle Furniture Ltd that have influenced production procedures
and generated several issues in business operations. In addition, the essay is also examining the
possible resources, order-winning and order-qualifying factors that are required for sustainable
competitive advantages.
Critical analysis of the problem
Supply chain management includes a wide range of activities required to plan, control and
execute flow of products and services from acquiring raw materials and production through
distribution to end customer in cost-effective and most streamlined manner to maximize the
organizational profitability. According to Niknam et al., (2011), supply chain management
entails planning, supervising and organizing processes to compose required improvements in
supply of products and services for higher organizational profitability. Supply chain management
also ensures that the labor, materials and any other inputs are utilized in most efficient and
effective manner to maximize the organizational profitability. From the case study, it is analyzed
that Jungle Furniture Ltd (JFL) has not adopted effective operation management practices to
manage its production, marketing and supply chain processes in a proper manner. The company
is sometimes unable to secure its order of raw material on time as the suppliers give priority to
export orders of larger customers. Sometimes, the raw materials are not purchased by the
company on time even when the supply should be available. The staff of JFL has passionate
⊘ This is a preview!⊘
Do you want full access?
Subscribe today to unlock all pages.

Trusted by 1+ million students worldwide
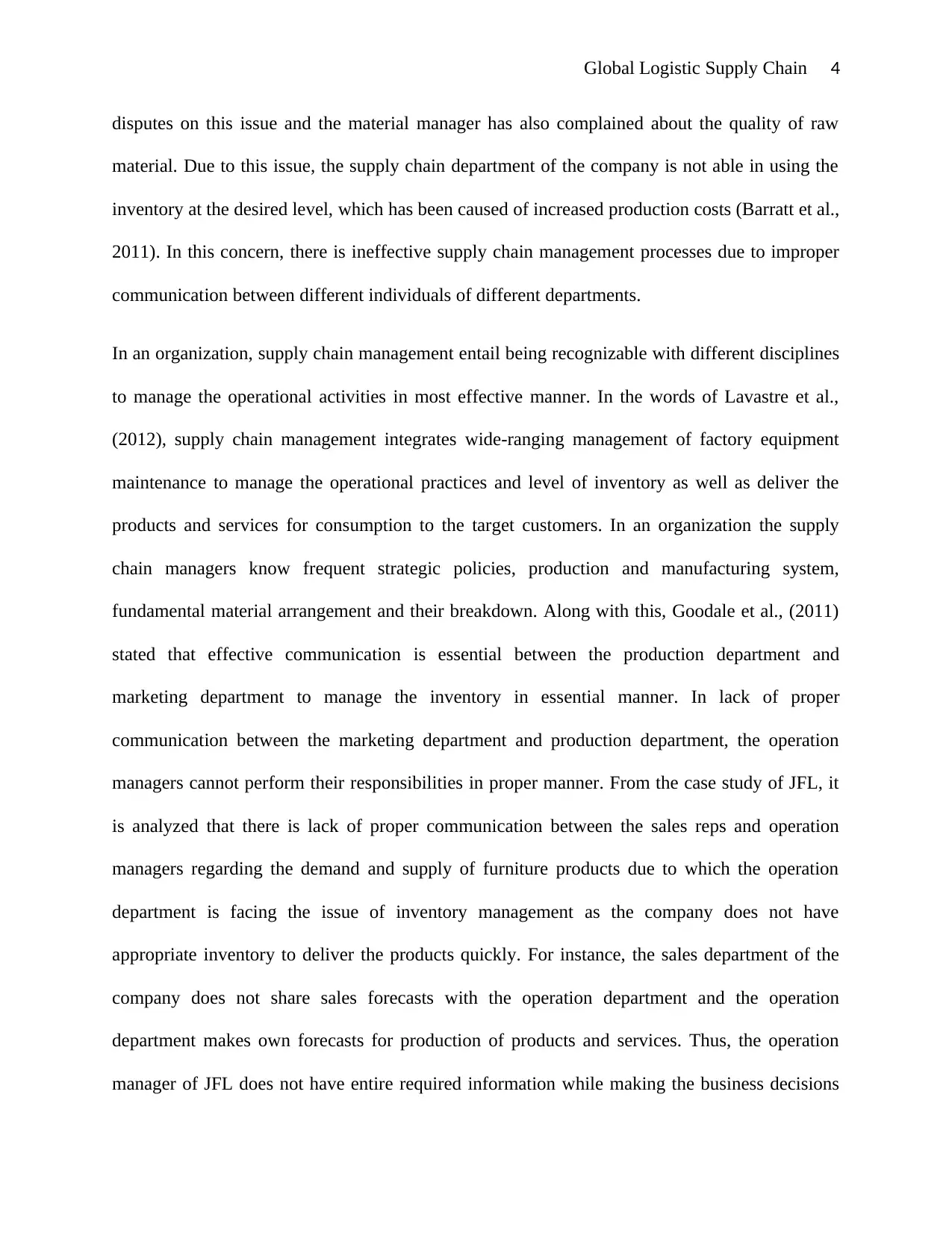
Global Logistic Supply Chain 4
disputes on this issue and the material manager has also complained about the quality of raw
material. Due to this issue, the supply chain department of the company is not able in using the
inventory at the desired level, which has been caused of increased production costs (Barratt et al.,
2011). In this concern, there is ineffective supply chain management processes due to improper
communication between different individuals of different departments.
In an organization, supply chain management entail being recognizable with different disciplines
to manage the operational activities in most effective manner. In the words of Lavastre et al.,
(2012), supply chain management integrates wide-ranging management of factory equipment
maintenance to manage the operational practices and level of inventory as well as deliver the
products and services for consumption to the target customers. In an organization the supply
chain managers know frequent strategic policies, production and manufacturing system,
fundamental material arrangement and their breakdown. Along with this, Goodale et al., (2011)
stated that effective communication is essential between the production department and
marketing department to manage the inventory in essential manner. In lack of proper
communication between the marketing department and production department, the operation
managers cannot perform their responsibilities in proper manner. From the case study of JFL, it
is analyzed that there is lack of proper communication between the sales reps and operation
managers regarding the demand and supply of furniture products due to which the operation
department is facing the issue of inventory management as the company does not have
appropriate inventory to deliver the products quickly. For instance, the sales department of the
company does not share sales forecasts with the operation department and the operation
department makes own forecasts for production of products and services. Thus, the operation
manager of JFL does not have entire required information while making the business decisions
disputes on this issue and the material manager has also complained about the quality of raw
material. Due to this issue, the supply chain department of the company is not able in using the
inventory at the desired level, which has been caused of increased production costs (Barratt et al.,
2011). In this concern, there is ineffective supply chain management processes due to improper
communication between different individuals of different departments.
In an organization, supply chain management entail being recognizable with different disciplines
to manage the operational activities in most effective manner. In the words of Lavastre et al.,
(2012), supply chain management integrates wide-ranging management of factory equipment
maintenance to manage the operational practices and level of inventory as well as deliver the
products and services for consumption to the target customers. In an organization the supply
chain managers know frequent strategic policies, production and manufacturing system,
fundamental material arrangement and their breakdown. Along with this, Goodale et al., (2011)
stated that effective communication is essential between the production department and
marketing department to manage the inventory in essential manner. In lack of proper
communication between the marketing department and production department, the operation
managers cannot perform their responsibilities in proper manner. From the case study of JFL, it
is analyzed that there is lack of proper communication between the sales reps and operation
managers regarding the demand and supply of furniture products due to which the operation
department is facing the issue of inventory management as the company does not have
appropriate inventory to deliver the products quickly. For instance, the sales department of the
company does not share sales forecasts with the operation department and the operation
department makes own forecasts for production of products and services. Thus, the operation
manager of JFL does not have entire required information while making the business decisions
Paraphrase This Document
Need a fresh take? Get an instant paraphrase of this document with our AI Paraphraser
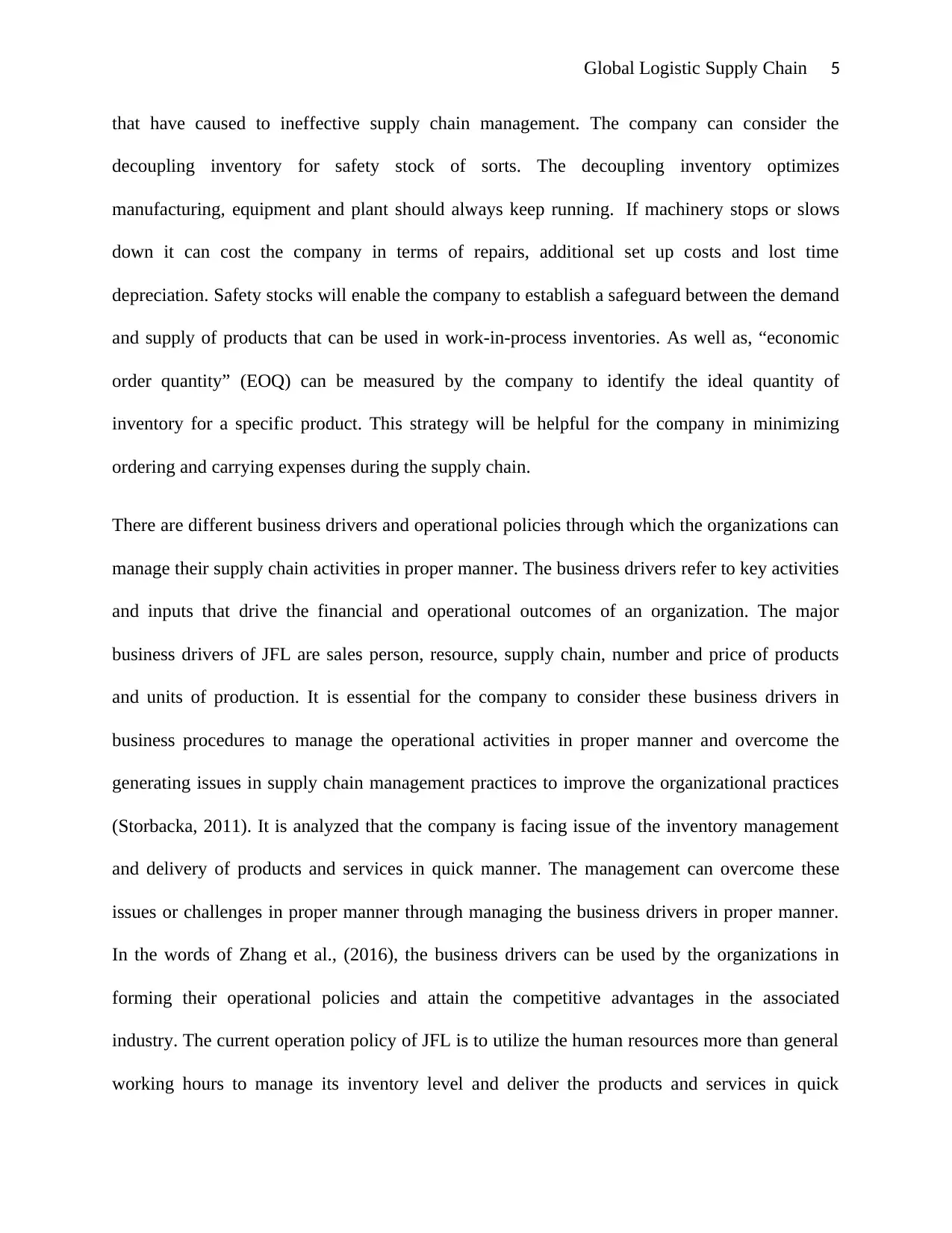
Global Logistic Supply Chain 5
that have caused to ineffective supply chain management. The company can consider the
decoupling inventory for safety stock of sorts. The decoupling inventory optimizes
manufacturing, equipment and plant should always keep running. If machinery stops or slows
down it can cost the company in terms of repairs, additional set up costs and lost time
depreciation. Safety stocks will enable the company to establish a safeguard between the demand
and supply of products that can be used in work-in-process inventories. As well as, “economic
order quantity” (EOQ) can be measured by the company to identify the ideal quantity of
inventory for a specific product. This strategy will be helpful for the company in minimizing
ordering and carrying expenses during the supply chain.
There are different business drivers and operational policies through which the organizations can
manage their supply chain activities in proper manner. The business drivers refer to key activities
and inputs that drive the financial and operational outcomes of an organization. The major
business drivers of JFL are sales person, resource, supply chain, number and price of products
and units of production. It is essential for the company to consider these business drivers in
business procedures to manage the operational activities in proper manner and overcome the
generating issues in supply chain management practices to improve the organizational practices
(Storbacka, 2011). It is analyzed that the company is facing issue of the inventory management
and delivery of products and services in quick manner. The management can overcome these
issues or challenges in proper manner through managing the business drivers in proper manner.
In the words of Zhang et al., (2016), the business drivers can be used by the organizations in
forming their operational policies and attain the competitive advantages in the associated
industry. The current operation policy of JFL is to utilize the human resources more than general
working hours to manage its inventory level and deliver the products and services in quick
that have caused to ineffective supply chain management. The company can consider the
decoupling inventory for safety stock of sorts. The decoupling inventory optimizes
manufacturing, equipment and plant should always keep running. If machinery stops or slows
down it can cost the company in terms of repairs, additional set up costs and lost time
depreciation. Safety stocks will enable the company to establish a safeguard between the demand
and supply of products that can be used in work-in-process inventories. As well as, “economic
order quantity” (EOQ) can be measured by the company to identify the ideal quantity of
inventory for a specific product. This strategy will be helpful for the company in minimizing
ordering and carrying expenses during the supply chain.
There are different business drivers and operational policies through which the organizations can
manage their supply chain activities in proper manner. The business drivers refer to key activities
and inputs that drive the financial and operational outcomes of an organization. The major
business drivers of JFL are sales person, resource, supply chain, number and price of products
and units of production. It is essential for the company to consider these business drivers in
business procedures to manage the operational activities in proper manner and overcome the
generating issues in supply chain management practices to improve the organizational practices
(Storbacka, 2011). It is analyzed that the company is facing issue of the inventory management
and delivery of products and services in quick manner. The management can overcome these
issues or challenges in proper manner through managing the business drivers in proper manner.
In the words of Zhang et al., (2016), the business drivers can be used by the organizations in
forming their operational policies and attain the competitive advantages in the associated
industry. The current operation policy of JFL is to utilize the human resources more than general
working hours to manage its inventory level and deliver the products and services in quick
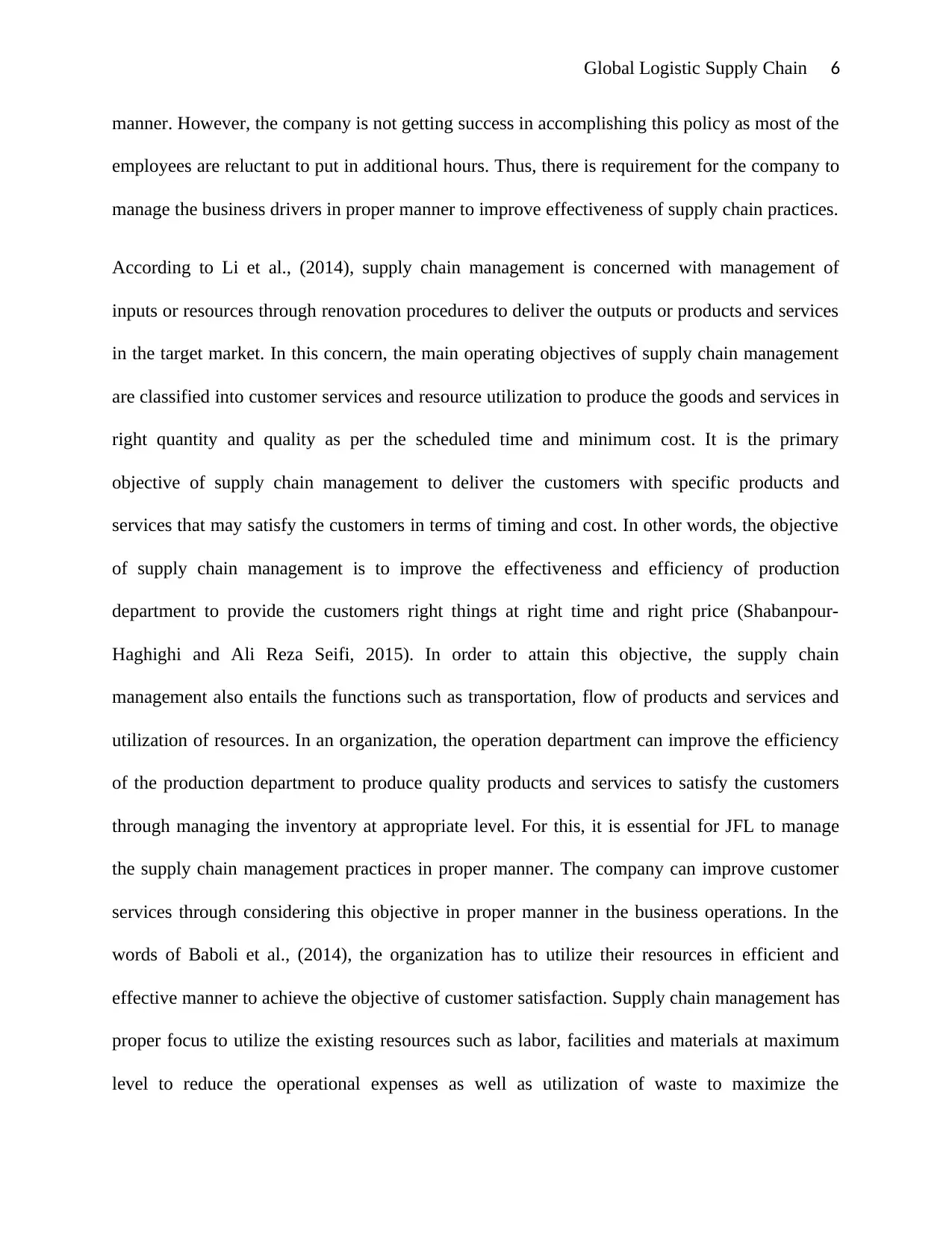
Global Logistic Supply Chain 6
manner. However, the company is not getting success in accomplishing this policy as most of the
employees are reluctant to put in additional hours. Thus, there is requirement for the company to
manage the business drivers in proper manner to improve effectiveness of supply chain practices.
According to Li et al., (2014), supply chain management is concerned with management of
inputs or resources through renovation procedures to deliver the outputs or products and services
in the target market. In this concern, the main operating objectives of supply chain management
are classified into customer services and resource utilization to produce the goods and services in
right quantity and quality as per the scheduled time and minimum cost. It is the primary
objective of supply chain management to deliver the customers with specific products and
services that may satisfy the customers in terms of timing and cost. In other words, the objective
of supply chain management is to improve the effectiveness and efficiency of production
department to provide the customers right things at right time and right price (Shabanpour-
Haghighi and Ali Reza Seifi, 2015). In order to attain this objective, the supply chain
management also entails the functions such as transportation, flow of products and services and
utilization of resources. In an organization, the operation department can improve the efficiency
of the production department to produce quality products and services to satisfy the customers
through managing the inventory at appropriate level. For this, it is essential for JFL to manage
the supply chain management practices in proper manner. The company can improve customer
services through considering this objective in proper manner in the business operations. In the
words of Baboli et al., (2014), the organization has to utilize their resources in efficient and
effective manner to achieve the objective of customer satisfaction. Supply chain management has
proper focus to utilize the existing resources such as labor, facilities and materials at maximum
level to reduce the operational expenses as well as utilization of waste to maximize the
manner. However, the company is not getting success in accomplishing this policy as most of the
employees are reluctant to put in additional hours. Thus, there is requirement for the company to
manage the business drivers in proper manner to improve effectiveness of supply chain practices.
According to Li et al., (2014), supply chain management is concerned with management of
inputs or resources through renovation procedures to deliver the outputs or products and services
in the target market. In this concern, the main operating objectives of supply chain management
are classified into customer services and resource utilization to produce the goods and services in
right quantity and quality as per the scheduled time and minimum cost. It is the primary
objective of supply chain management to deliver the customers with specific products and
services that may satisfy the customers in terms of timing and cost. In other words, the objective
of supply chain management is to improve the effectiveness and efficiency of production
department to provide the customers right things at right time and right price (Shabanpour-
Haghighi and Ali Reza Seifi, 2015). In order to attain this objective, the supply chain
management also entails the functions such as transportation, flow of products and services and
utilization of resources. In an organization, the operation department can improve the efficiency
of the production department to produce quality products and services to satisfy the customers
through managing the inventory at appropriate level. For this, it is essential for JFL to manage
the supply chain management practices in proper manner. The company can improve customer
services through considering this objective in proper manner in the business operations. In the
words of Baboli et al., (2014), the organization has to utilize their resources in efficient and
effective manner to achieve the objective of customer satisfaction. Supply chain management has
proper focus to utilize the existing resources such as labor, facilities and materials at maximum
level to reduce the operational expenses as well as utilization of waste to maximize the
⊘ This is a preview!⊘
Do you want full access?
Subscribe today to unlock all pages.

Trusted by 1+ million students worldwide
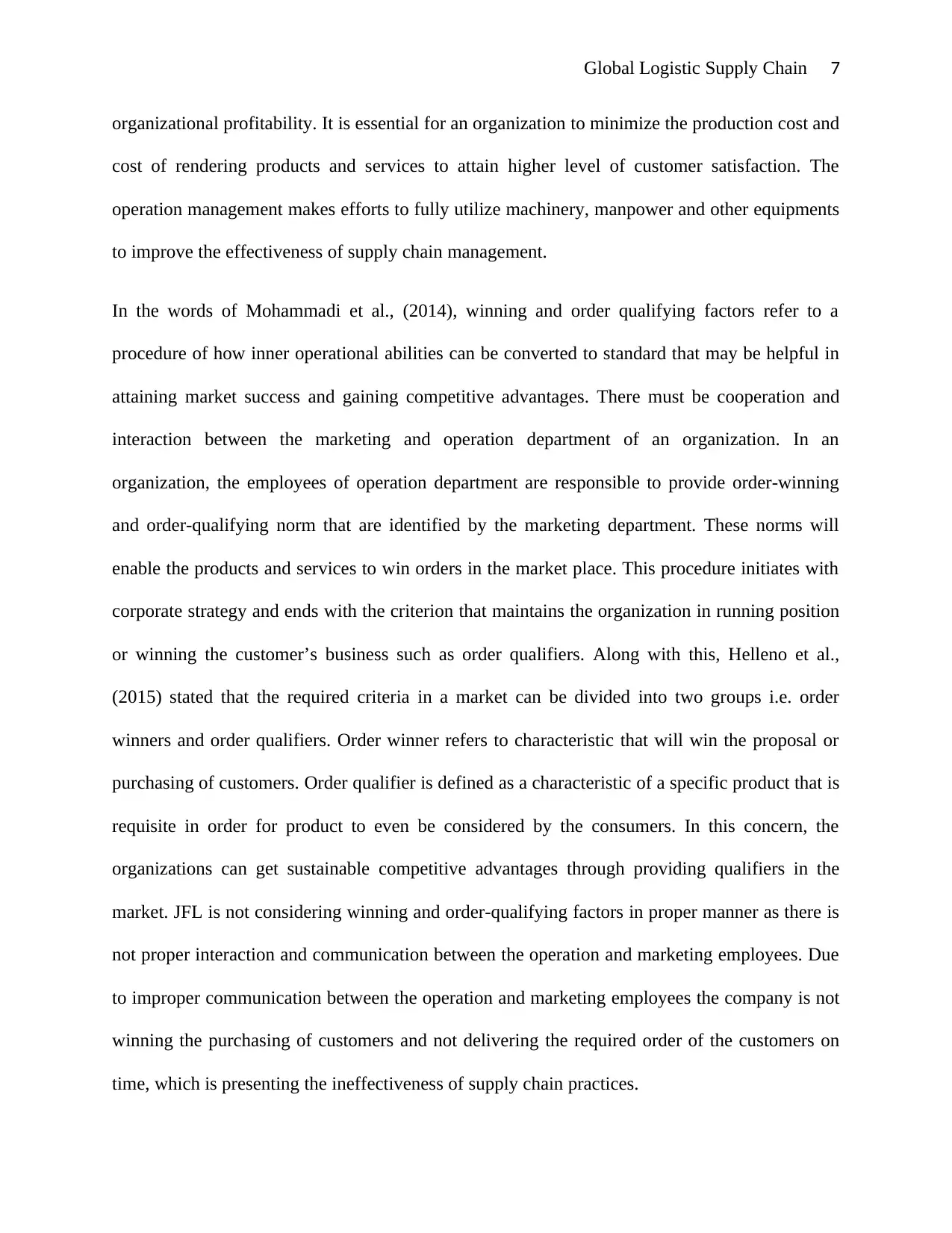
Global Logistic Supply Chain 7
organizational profitability. It is essential for an organization to minimize the production cost and
cost of rendering products and services to attain higher level of customer satisfaction. The
operation management makes efforts to fully utilize machinery, manpower and other equipments
to improve the effectiveness of supply chain management.
In the words of Mohammadi et al., (2014), winning and order qualifying factors refer to a
procedure of how inner operational abilities can be converted to standard that may be helpful in
attaining market success and gaining competitive advantages. There must be cooperation and
interaction between the marketing and operation department of an organization. In an
organization, the employees of operation department are responsible to provide order-winning
and order-qualifying norm that are identified by the marketing department. These norms will
enable the products and services to win orders in the market place. This procedure initiates with
corporate strategy and ends with the criterion that maintains the organization in running position
or winning the customer’s business such as order qualifiers. Along with this, Helleno et al.,
(2015) stated that the required criteria in a market can be divided into two groups i.e. order
winners and order qualifiers. Order winner refers to characteristic that will win the proposal or
purchasing of customers. Order qualifier is defined as a characteristic of a specific product that is
requisite in order for product to even be considered by the consumers. In this concern, the
organizations can get sustainable competitive advantages through providing qualifiers in the
market. JFL is not considering winning and order-qualifying factors in proper manner as there is
not proper interaction and communication between the operation and marketing employees. Due
to improper communication between the operation and marketing employees the company is not
winning the purchasing of customers and not delivering the required order of the customers on
time, which is presenting the ineffectiveness of supply chain practices.
organizational profitability. It is essential for an organization to minimize the production cost and
cost of rendering products and services to attain higher level of customer satisfaction. The
operation management makes efforts to fully utilize machinery, manpower and other equipments
to improve the effectiveness of supply chain management.
In the words of Mohammadi et al., (2014), winning and order qualifying factors refer to a
procedure of how inner operational abilities can be converted to standard that may be helpful in
attaining market success and gaining competitive advantages. There must be cooperation and
interaction between the marketing and operation department of an organization. In an
organization, the employees of operation department are responsible to provide order-winning
and order-qualifying norm that are identified by the marketing department. These norms will
enable the products and services to win orders in the market place. This procedure initiates with
corporate strategy and ends with the criterion that maintains the organization in running position
or winning the customer’s business such as order qualifiers. Along with this, Helleno et al.,
(2015) stated that the required criteria in a market can be divided into two groups i.e. order
winners and order qualifiers. Order winner refers to characteristic that will win the proposal or
purchasing of customers. Order qualifier is defined as a characteristic of a specific product that is
requisite in order for product to even be considered by the consumers. In this concern, the
organizations can get sustainable competitive advantages through providing qualifiers in the
market. JFL is not considering winning and order-qualifying factors in proper manner as there is
not proper interaction and communication between the operation and marketing employees. Due
to improper communication between the operation and marketing employees the company is not
winning the purchasing of customers and not delivering the required order of the customers on
time, which is presenting the ineffectiveness of supply chain practices.
Paraphrase This Document
Need a fresh take? Get an instant paraphrase of this document with our AI Paraphraser
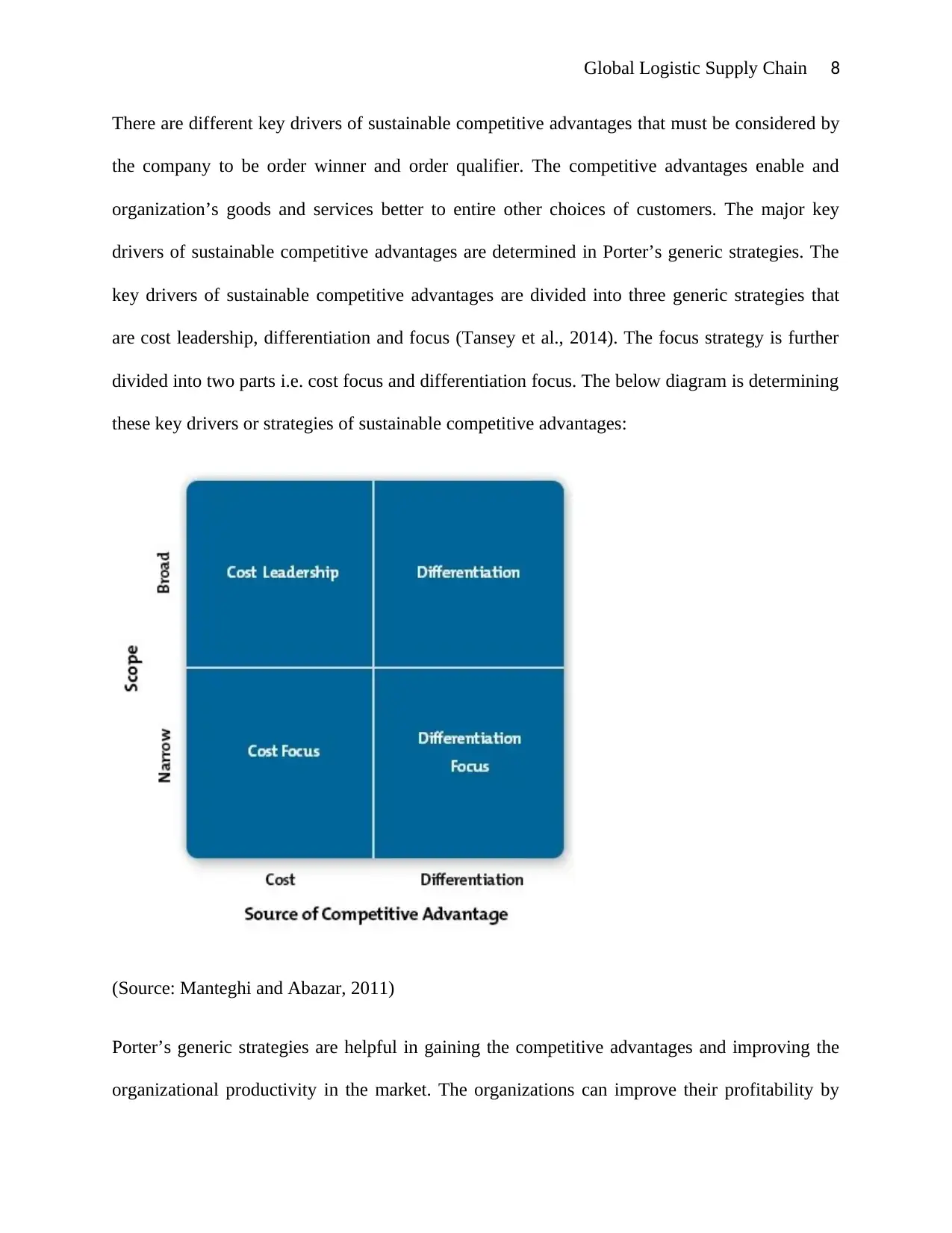
Global Logistic Supply Chain 8
There are different key drivers of sustainable competitive advantages that must be considered by
the company to be order winner and order qualifier. The competitive advantages enable and
organization’s goods and services better to entire other choices of customers. The major key
drivers of sustainable competitive advantages are determined in Porter’s generic strategies. The
key drivers of sustainable competitive advantages are divided into three generic strategies that
are cost leadership, differentiation and focus (Tansey et al., 2014). The focus strategy is further
divided into two parts i.e. cost focus and differentiation focus. The below diagram is determining
these key drivers or strategies of sustainable competitive advantages:
(Source: Manteghi and Abazar, 2011)
Porter’s generic strategies are helpful in gaining the competitive advantages and improving the
organizational productivity in the market. The organizations can improve their profitability by
There are different key drivers of sustainable competitive advantages that must be considered by
the company to be order winner and order qualifier. The competitive advantages enable and
organization’s goods and services better to entire other choices of customers. The major key
drivers of sustainable competitive advantages are determined in Porter’s generic strategies. The
key drivers of sustainable competitive advantages are divided into three generic strategies that
are cost leadership, differentiation and focus (Tansey et al., 2014). The focus strategy is further
divided into two parts i.e. cost focus and differentiation focus. The below diagram is determining
these key drivers or strategies of sustainable competitive advantages:
(Source: Manteghi and Abazar, 2011)
Porter’s generic strategies are helpful in gaining the competitive advantages and improving the
organizational productivity in the market. The organizations can improve their profitability by
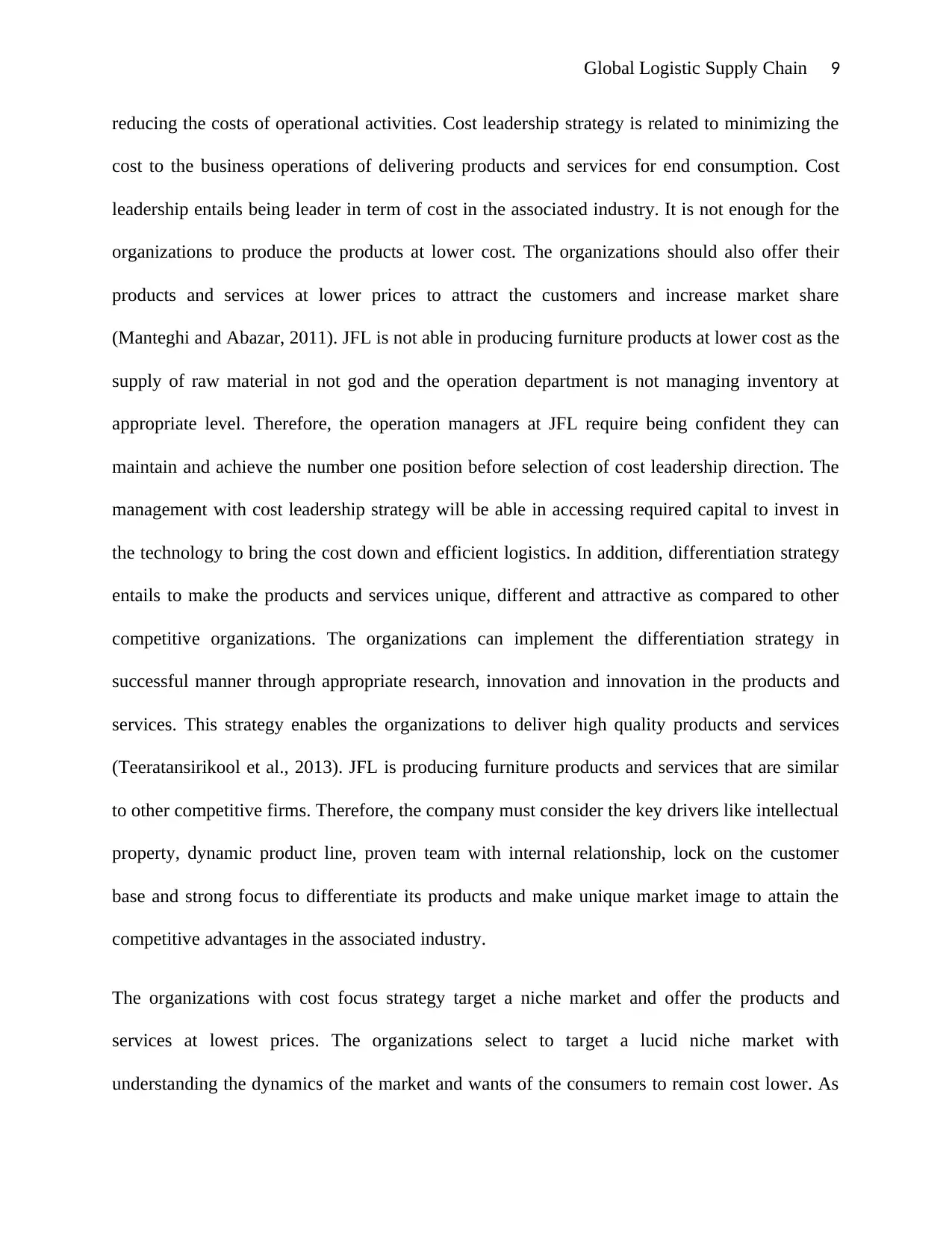
Global Logistic Supply Chain 9
reducing the costs of operational activities. Cost leadership strategy is related to minimizing the
cost to the business operations of delivering products and services for end consumption. Cost
leadership entails being leader in term of cost in the associated industry. It is not enough for the
organizations to produce the products at lower cost. The organizations should also offer their
products and services at lower prices to attract the customers and increase market share
(Manteghi and Abazar, 2011). JFL is not able in producing furniture products at lower cost as the
supply of raw material in not god and the operation department is not managing inventory at
appropriate level. Therefore, the operation managers at JFL require being confident they can
maintain and achieve the number one position before selection of cost leadership direction. The
management with cost leadership strategy will be able in accessing required capital to invest in
the technology to bring the cost down and efficient logistics. In addition, differentiation strategy
entails to make the products and services unique, different and attractive as compared to other
competitive organizations. The organizations can implement the differentiation strategy in
successful manner through appropriate research, innovation and innovation in the products and
services. This strategy enables the organizations to deliver high quality products and services
(Teeratansirikool et al., 2013). JFL is producing furniture products and services that are similar
to other competitive firms. Therefore, the company must consider the key drivers like intellectual
property, dynamic product line, proven team with internal relationship, lock on the customer
base and strong focus to differentiate its products and make unique market image to attain the
competitive advantages in the associated industry.
The organizations with cost focus strategy target a niche market and offer the products and
services at lowest prices. The organizations select to target a lucid niche market with
understanding the dynamics of the market and wants of the consumers to remain cost lower. As
reducing the costs of operational activities. Cost leadership strategy is related to minimizing the
cost to the business operations of delivering products and services for end consumption. Cost
leadership entails being leader in term of cost in the associated industry. It is not enough for the
organizations to produce the products at lower cost. The organizations should also offer their
products and services at lower prices to attract the customers and increase market share
(Manteghi and Abazar, 2011). JFL is not able in producing furniture products at lower cost as the
supply of raw material in not god and the operation department is not managing inventory at
appropriate level. Therefore, the operation managers at JFL require being confident they can
maintain and achieve the number one position before selection of cost leadership direction. The
management with cost leadership strategy will be able in accessing required capital to invest in
the technology to bring the cost down and efficient logistics. In addition, differentiation strategy
entails to make the products and services unique, different and attractive as compared to other
competitive organizations. The organizations can implement the differentiation strategy in
successful manner through appropriate research, innovation and innovation in the products and
services. This strategy enables the organizations to deliver high quality products and services
(Teeratansirikool et al., 2013). JFL is producing furniture products and services that are similar
to other competitive firms. Therefore, the company must consider the key drivers like intellectual
property, dynamic product line, proven team with internal relationship, lock on the customer
base and strong focus to differentiate its products and make unique market image to attain the
competitive advantages in the associated industry.
The organizations with cost focus strategy target a niche market and offer the products and
services at lowest prices. The organizations select to target a lucid niche market with
understanding the dynamics of the market and wants of the consumers to remain cost lower. As
⊘ This is a preview!⊘
Do you want full access?
Subscribe today to unlock all pages.

Trusted by 1+ million students worldwide
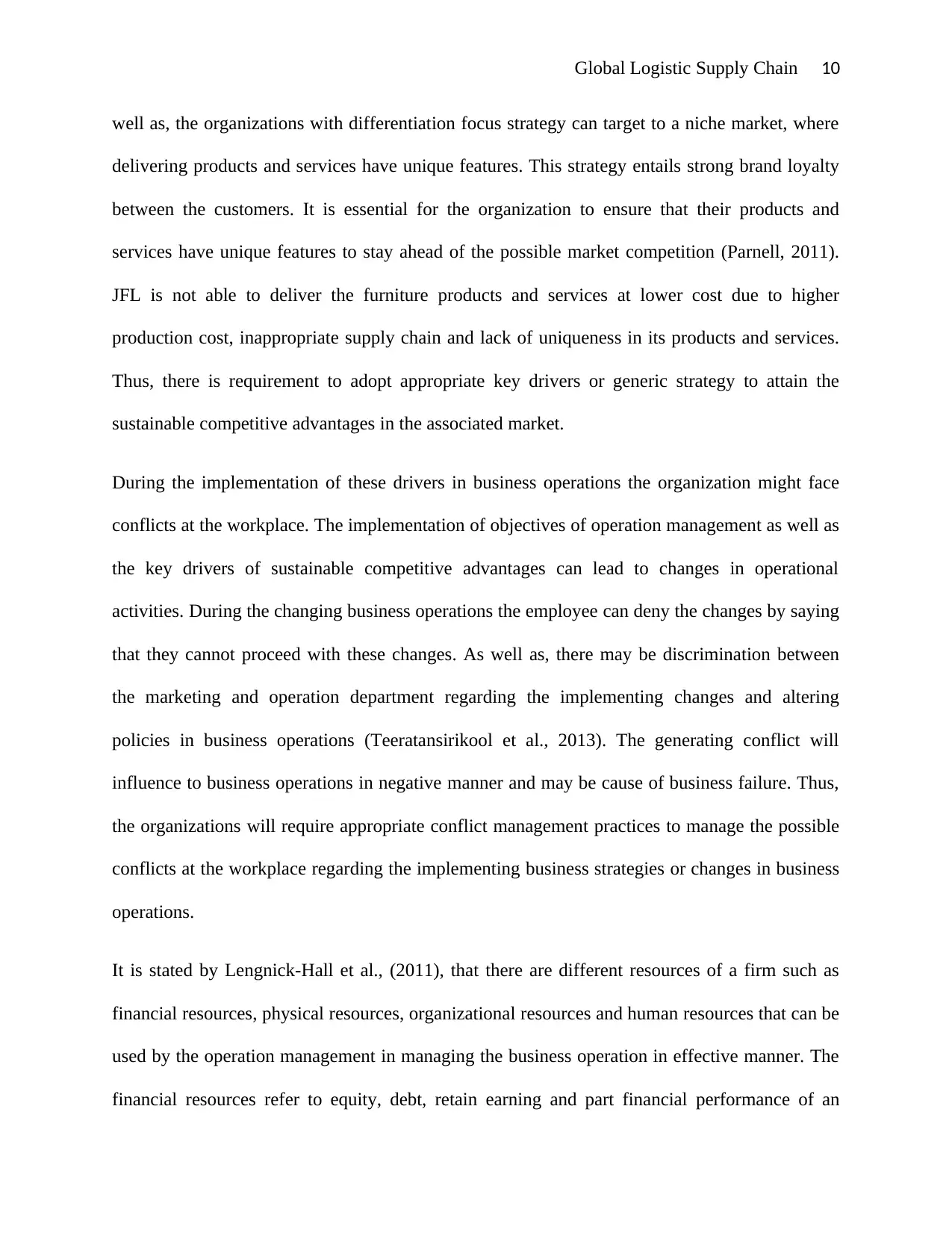
Global Logistic Supply Chain 10
well as, the organizations with differentiation focus strategy can target to a niche market, where
delivering products and services have unique features. This strategy entails strong brand loyalty
between the customers. It is essential for the organization to ensure that their products and
services have unique features to stay ahead of the possible market competition (Parnell, 2011).
JFL is not able to deliver the furniture products and services at lower cost due to higher
production cost, inappropriate supply chain and lack of uniqueness in its products and services.
Thus, there is requirement to adopt appropriate key drivers or generic strategy to attain the
sustainable competitive advantages in the associated market.
During the implementation of these drivers in business operations the organization might face
conflicts at the workplace. The implementation of objectives of operation management as well as
the key drivers of sustainable competitive advantages can lead to changes in operational
activities. During the changing business operations the employee can deny the changes by saying
that they cannot proceed with these changes. As well as, there may be discrimination between
the marketing and operation department regarding the implementing changes and altering
policies in business operations (Teeratansirikool et al., 2013). The generating conflict will
influence to business operations in negative manner and may be cause of business failure. Thus,
the organizations will require appropriate conflict management practices to manage the possible
conflicts at the workplace regarding the implementing business strategies or changes in business
operations.
It is stated by Lengnick-Hall et al., (2011), that there are different resources of a firm such as
financial resources, physical resources, organizational resources and human resources that can be
used by the operation management in managing the business operation in effective manner. The
financial resources refer to equity, debt, retain earning and part financial performance of an
well as, the organizations with differentiation focus strategy can target to a niche market, where
delivering products and services have unique features. This strategy entails strong brand loyalty
between the customers. It is essential for the organization to ensure that their products and
services have unique features to stay ahead of the possible market competition (Parnell, 2011).
JFL is not able to deliver the furniture products and services at lower cost due to higher
production cost, inappropriate supply chain and lack of uniqueness in its products and services.
Thus, there is requirement to adopt appropriate key drivers or generic strategy to attain the
sustainable competitive advantages in the associated market.
During the implementation of these drivers in business operations the organization might face
conflicts at the workplace. The implementation of objectives of operation management as well as
the key drivers of sustainable competitive advantages can lead to changes in operational
activities. During the changing business operations the employee can deny the changes by saying
that they cannot proceed with these changes. As well as, there may be discrimination between
the marketing and operation department regarding the implementing changes and altering
policies in business operations (Teeratansirikool et al., 2013). The generating conflict will
influence to business operations in negative manner and may be cause of business failure. Thus,
the organizations will require appropriate conflict management practices to manage the possible
conflicts at the workplace regarding the implementing business strategies or changes in business
operations.
It is stated by Lengnick-Hall et al., (2011), that there are different resources of a firm such as
financial resources, physical resources, organizational resources and human resources that can be
used by the operation management in managing the business operation in effective manner. The
financial resources refer to equity, debt, retain earning and part financial performance of an
Paraphrase This Document
Need a fresh take? Get an instant paraphrase of this document with our AI Paraphraser
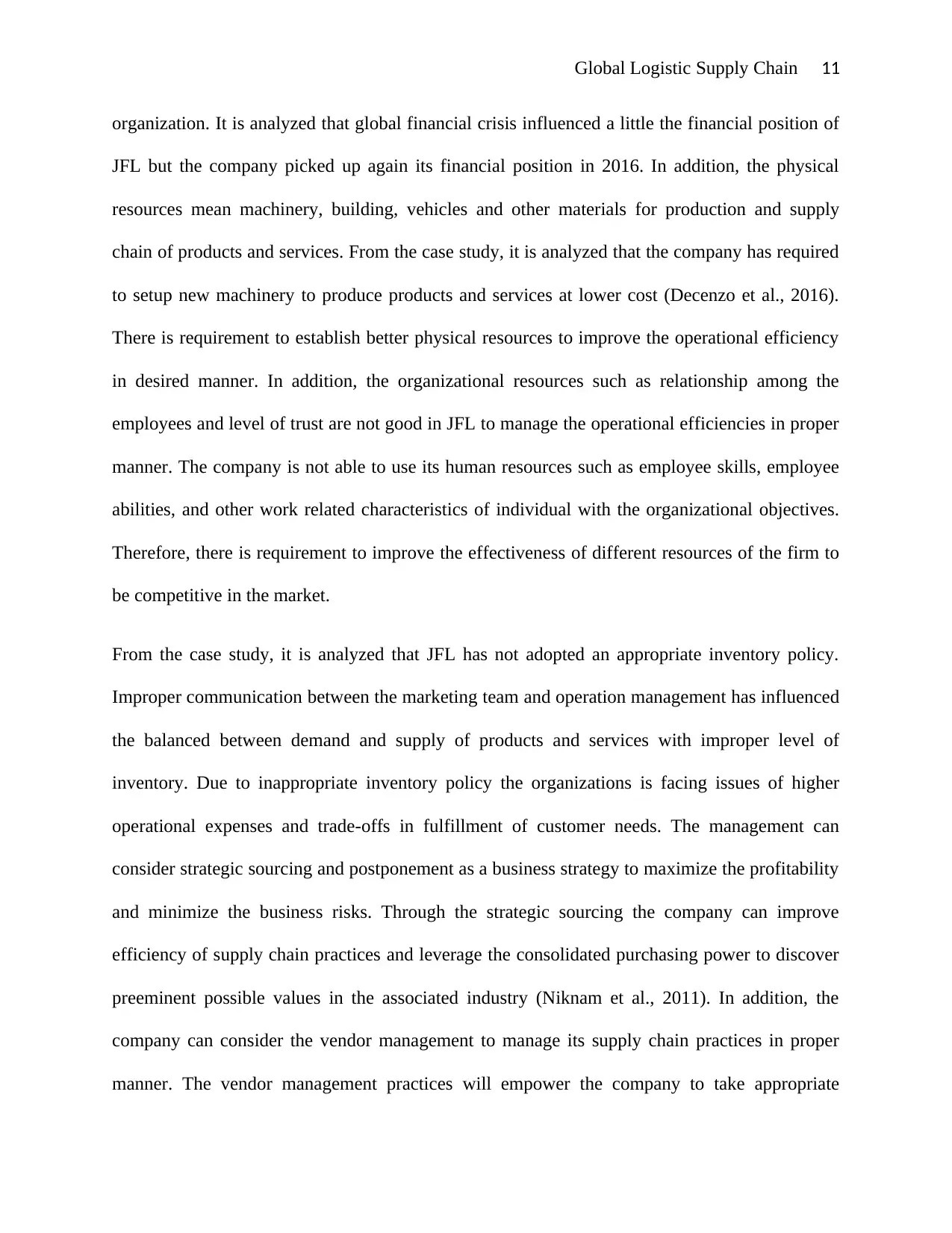
Global Logistic Supply Chain 11
organization. It is analyzed that global financial crisis influenced a little the financial position of
JFL but the company picked up again its financial position in 2016. In addition, the physical
resources mean machinery, building, vehicles and other materials for production and supply
chain of products and services. From the case study, it is analyzed that the company has required
to setup new machinery to produce products and services at lower cost (Decenzo et al., 2016).
There is requirement to establish better physical resources to improve the operational efficiency
in desired manner. In addition, the organizational resources such as relationship among the
employees and level of trust are not good in JFL to manage the operational efficiencies in proper
manner. The company is not able to use its human resources such as employee skills, employee
abilities, and other work related characteristics of individual with the organizational objectives.
Therefore, there is requirement to improve the effectiveness of different resources of the firm to
be competitive in the market.
From the case study, it is analyzed that JFL has not adopted an appropriate inventory policy.
Improper communication between the marketing team and operation management has influenced
the balanced between demand and supply of products and services with improper level of
inventory. Due to inappropriate inventory policy the organizations is facing issues of higher
operational expenses and trade-offs in fulfillment of customer needs. The management can
consider strategic sourcing and postponement as a business strategy to maximize the profitability
and minimize the business risks. Through the strategic sourcing the company can improve
efficiency of supply chain practices and leverage the consolidated purchasing power to discover
preeminent possible values in the associated industry (Niknam et al., 2011). In addition, the
company can consider the vendor management to manage its supply chain practices in proper
manner. The vendor management practices will empower the company to take appropriate
organization. It is analyzed that global financial crisis influenced a little the financial position of
JFL but the company picked up again its financial position in 2016. In addition, the physical
resources mean machinery, building, vehicles and other materials for production and supply
chain of products and services. From the case study, it is analyzed that the company has required
to setup new machinery to produce products and services at lower cost (Decenzo et al., 2016).
There is requirement to establish better physical resources to improve the operational efficiency
in desired manner. In addition, the organizational resources such as relationship among the
employees and level of trust are not good in JFL to manage the operational efficiencies in proper
manner. The company is not able to use its human resources such as employee skills, employee
abilities, and other work related characteristics of individual with the organizational objectives.
Therefore, there is requirement to improve the effectiveness of different resources of the firm to
be competitive in the market.
From the case study, it is analyzed that JFL has not adopted an appropriate inventory policy.
Improper communication between the marketing team and operation management has influenced
the balanced between demand and supply of products and services with improper level of
inventory. Due to inappropriate inventory policy the organizations is facing issues of higher
operational expenses and trade-offs in fulfillment of customer needs. The management can
consider strategic sourcing and postponement as a business strategy to maximize the profitability
and minimize the business risks. Through the strategic sourcing the company can improve
efficiency of supply chain practices and leverage the consolidated purchasing power to discover
preeminent possible values in the associated industry (Niknam et al., 2011). In addition, the
company can consider the vendor management to manage its supply chain practices in proper
manner. The vendor management practices will empower the company to take appropriate
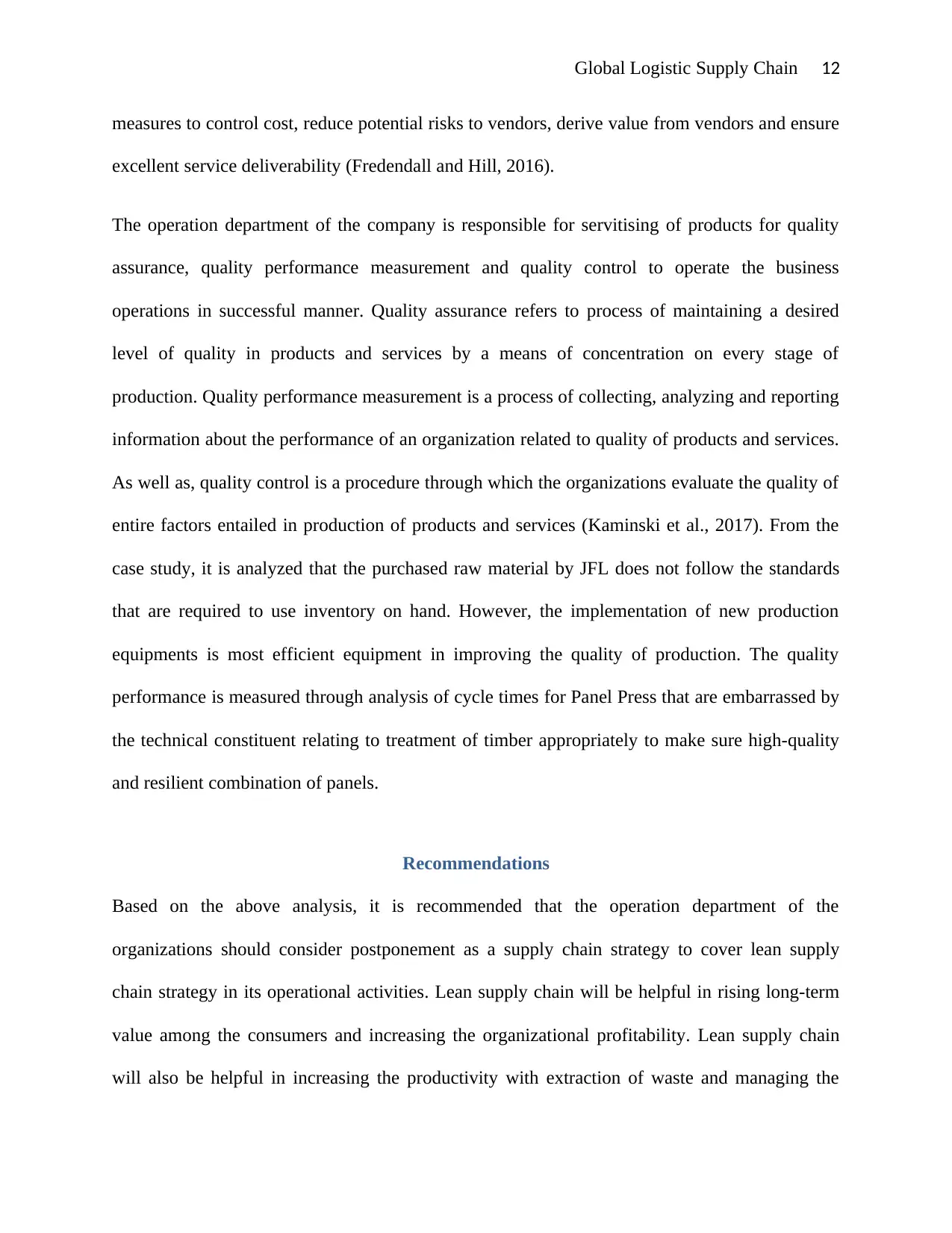
Global Logistic Supply Chain 12
measures to control cost, reduce potential risks to vendors, derive value from vendors and ensure
excellent service deliverability (Fredendall and Hill, 2016).
The operation department of the company is responsible for servitising of products for quality
assurance, quality performance measurement and quality control to operate the business
operations in successful manner. Quality assurance refers to process of maintaining a desired
level of quality in products and services by a means of concentration on every stage of
production. Quality performance measurement is a process of collecting, analyzing and reporting
information about the performance of an organization related to quality of products and services.
As well as, quality control is a procedure through which the organizations evaluate the quality of
entire factors entailed in production of products and services (Kaminski et al., 2017). From the
case study, it is analyzed that the purchased raw material by JFL does not follow the standards
that are required to use inventory on hand. However, the implementation of new production
equipments is most efficient equipment in improving the quality of production. The quality
performance is measured through analysis of cycle times for Panel Press that are embarrassed by
the technical constituent relating to treatment of timber appropriately to make sure high-quality
and resilient combination of panels.
Recommendations
Based on the above analysis, it is recommended that the operation department of the
organizations should consider postponement as a supply chain strategy to cover lean supply
chain strategy in its operational activities. Lean supply chain will be helpful in rising long-term
value among the consumers and increasing the organizational profitability. Lean supply chain
will also be helpful in increasing the productivity with extraction of waste and managing the
measures to control cost, reduce potential risks to vendors, derive value from vendors and ensure
excellent service deliverability (Fredendall and Hill, 2016).
The operation department of the company is responsible for servitising of products for quality
assurance, quality performance measurement and quality control to operate the business
operations in successful manner. Quality assurance refers to process of maintaining a desired
level of quality in products and services by a means of concentration on every stage of
production. Quality performance measurement is a process of collecting, analyzing and reporting
information about the performance of an organization related to quality of products and services.
As well as, quality control is a procedure through which the organizations evaluate the quality of
entire factors entailed in production of products and services (Kaminski et al., 2017). From the
case study, it is analyzed that the purchased raw material by JFL does not follow the standards
that are required to use inventory on hand. However, the implementation of new production
equipments is most efficient equipment in improving the quality of production. The quality
performance is measured through analysis of cycle times for Panel Press that are embarrassed by
the technical constituent relating to treatment of timber appropriately to make sure high-quality
and resilient combination of panels.
Recommendations
Based on the above analysis, it is recommended that the operation department of the
organizations should consider postponement as a supply chain strategy to cover lean supply
chain strategy in its operational activities. Lean supply chain will be helpful in rising long-term
value among the consumers and increasing the organizational profitability. Lean supply chain
will also be helpful in increasing the productivity with extraction of waste and managing the
⊘ This is a preview!⊘
Do you want full access?
Subscribe today to unlock all pages.

Trusted by 1+ million students worldwide
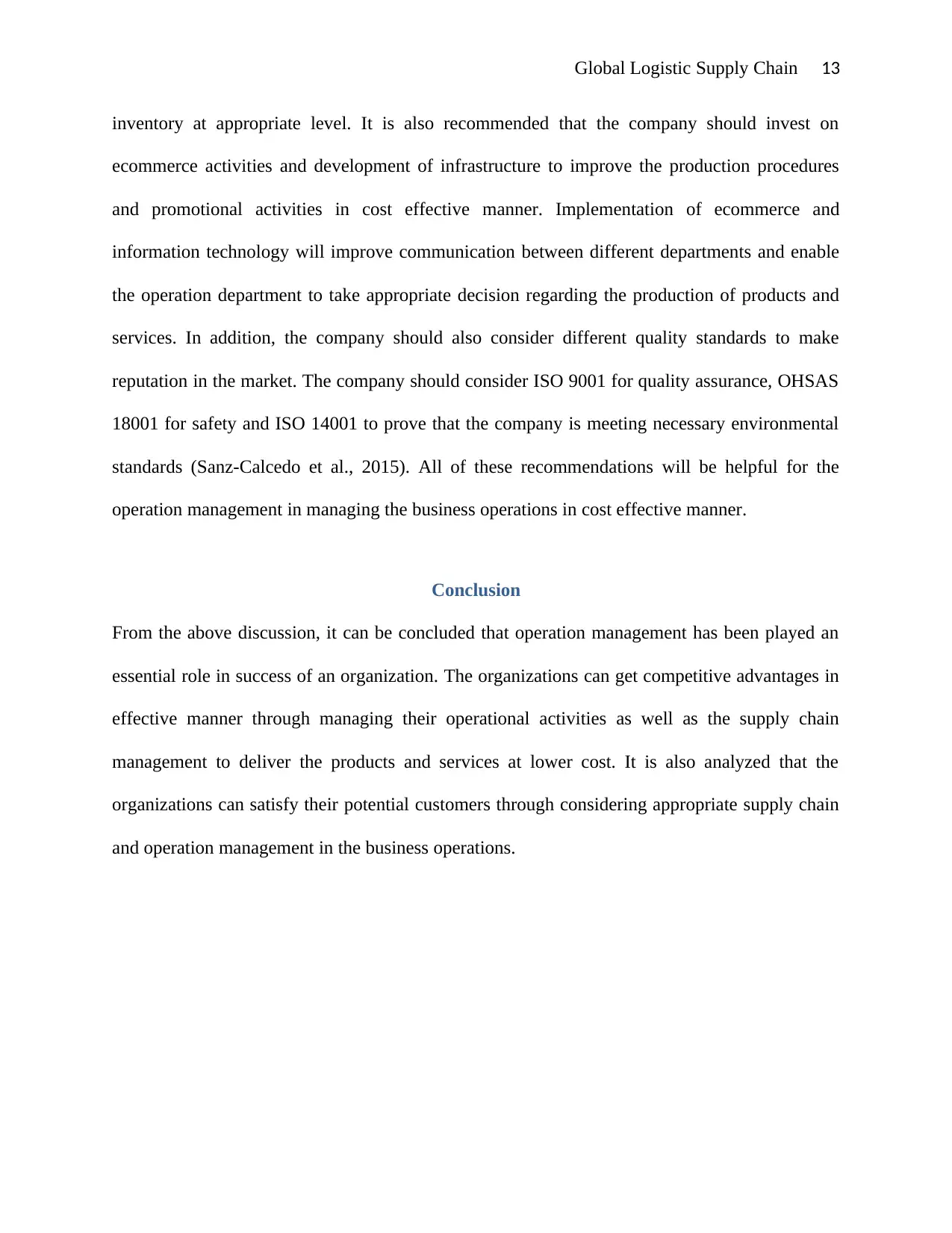
Global Logistic Supply Chain 13
inventory at appropriate level. It is also recommended that the company should invest on
ecommerce activities and development of infrastructure to improve the production procedures
and promotional activities in cost effective manner. Implementation of ecommerce and
information technology will improve communication between different departments and enable
the operation department to take appropriate decision regarding the production of products and
services. In addition, the company should also consider different quality standards to make
reputation in the market. The company should consider ISO 9001 for quality assurance, OHSAS
18001 for safety and ISO 14001 to prove that the company is meeting necessary environmental
standards (Sanz-Calcedo et al., 2015). All of these recommendations will be helpful for the
operation management in managing the business operations in cost effective manner.
Conclusion
From the above discussion, it can be concluded that operation management has been played an
essential role in success of an organization. The organizations can get competitive advantages in
effective manner through managing their operational activities as well as the supply chain
management to deliver the products and services at lower cost. It is also analyzed that the
organizations can satisfy their potential customers through considering appropriate supply chain
and operation management in the business operations.
inventory at appropriate level. It is also recommended that the company should invest on
ecommerce activities and development of infrastructure to improve the production procedures
and promotional activities in cost effective manner. Implementation of ecommerce and
information technology will improve communication between different departments and enable
the operation department to take appropriate decision regarding the production of products and
services. In addition, the company should also consider different quality standards to make
reputation in the market. The company should consider ISO 9001 for quality assurance, OHSAS
18001 for safety and ISO 14001 to prove that the company is meeting necessary environmental
standards (Sanz-Calcedo et al., 2015). All of these recommendations will be helpful for the
operation management in managing the business operations in cost effective manner.
Conclusion
From the above discussion, it can be concluded that operation management has been played an
essential role in success of an organization. The organizations can get competitive advantages in
effective manner through managing their operational activities as well as the supply chain
management to deliver the products and services at lower cost. It is also analyzed that the
organizations can satisfy their potential customers through considering appropriate supply chain
and operation management in the business operations.
Paraphrase This Document
Need a fresh take? Get an instant paraphrase of this document with our AI Paraphraser
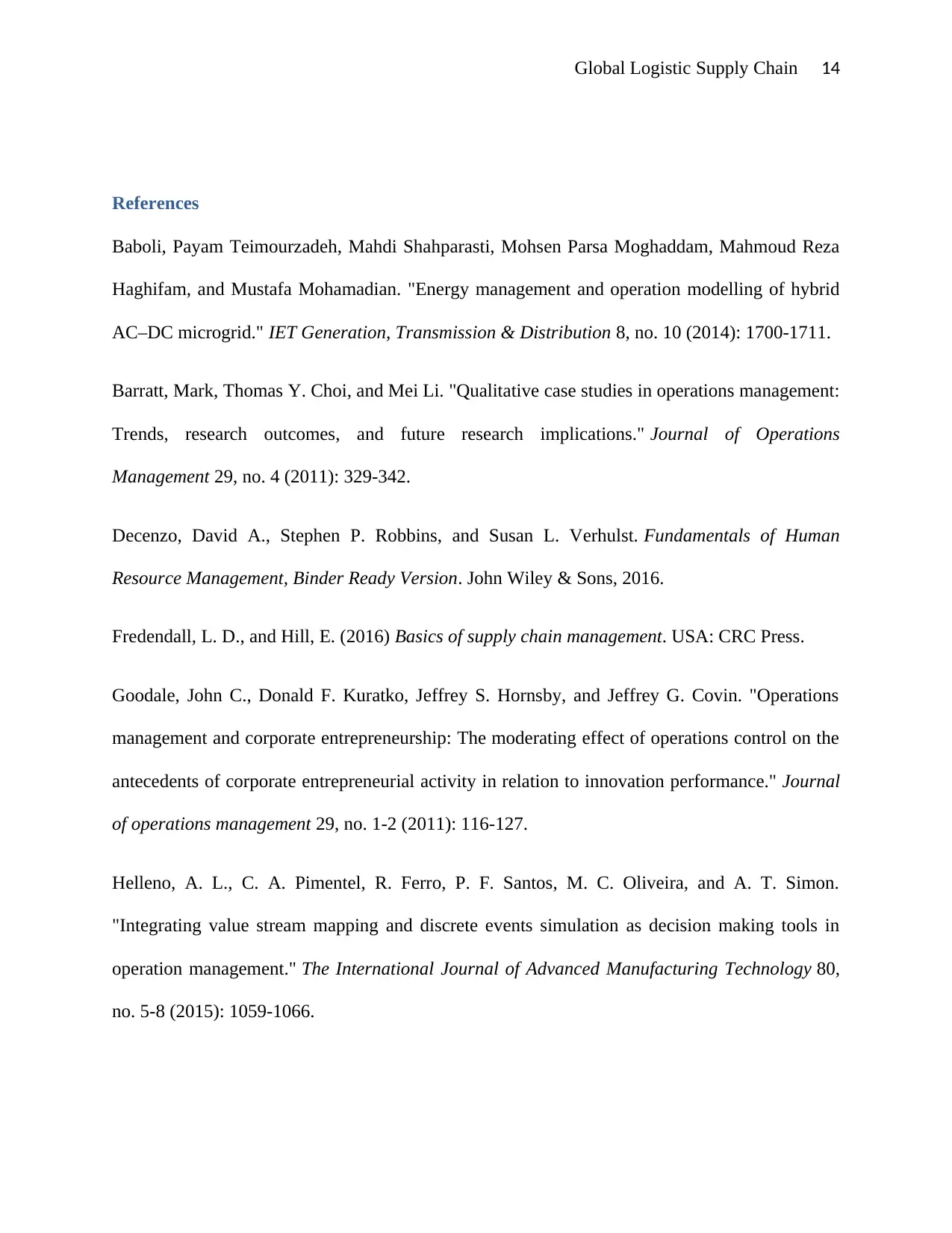
Global Logistic Supply Chain 14
References
Baboli, Payam Teimourzadeh, Mahdi Shahparasti, Mohsen Parsa Moghaddam, Mahmoud Reza
Haghifam, and Mustafa Mohamadian. "Energy management and operation modelling of hybrid
AC–DC microgrid." IET Generation, Transmission & Distribution 8, no. 10 (2014): 1700-1711.
Barratt, Mark, Thomas Y. Choi, and Mei Li. "Qualitative case studies in operations management:
Trends, research outcomes, and future research implications." Journal of Operations
Management 29, no. 4 (2011): 329-342.
Decenzo, David A., Stephen P. Robbins, and Susan L. Verhulst. Fundamentals of Human
Resource Management, Binder Ready Version. John Wiley & Sons, 2016.
Fredendall, L. D., and Hill, E. (2016) Basics of supply chain management. USA: CRC Press.
Goodale, John C., Donald F. Kuratko, Jeffrey S. Hornsby, and Jeffrey G. Covin. "Operations
management and corporate entrepreneurship: The moderating effect of operations control on the
antecedents of corporate entrepreneurial activity in relation to innovation performance." Journal
of operations management 29, no. 1-2 (2011): 116-127.
Helleno, A. L., C. A. Pimentel, R. Ferro, P. F. Santos, M. C. Oliveira, and A. T. Simon.
"Integrating value stream mapping and discrete events simulation as decision making tools in
operation management." The International Journal of Advanced Manufacturing Technology 80,
no. 5-8 (2015): 1059-1066.
References
Baboli, Payam Teimourzadeh, Mahdi Shahparasti, Mohsen Parsa Moghaddam, Mahmoud Reza
Haghifam, and Mustafa Mohamadian. "Energy management and operation modelling of hybrid
AC–DC microgrid." IET Generation, Transmission & Distribution 8, no. 10 (2014): 1700-1711.
Barratt, Mark, Thomas Y. Choi, and Mei Li. "Qualitative case studies in operations management:
Trends, research outcomes, and future research implications." Journal of Operations
Management 29, no. 4 (2011): 329-342.
Decenzo, David A., Stephen P. Robbins, and Susan L. Verhulst. Fundamentals of Human
Resource Management, Binder Ready Version. John Wiley & Sons, 2016.
Fredendall, L. D., and Hill, E. (2016) Basics of supply chain management. USA: CRC Press.
Goodale, John C., Donald F. Kuratko, Jeffrey S. Hornsby, and Jeffrey G. Covin. "Operations
management and corporate entrepreneurship: The moderating effect of operations control on the
antecedents of corporate entrepreneurial activity in relation to innovation performance." Journal
of operations management 29, no. 1-2 (2011): 116-127.
Helleno, A. L., C. A. Pimentel, R. Ferro, P. F. Santos, M. C. Oliveira, and A. T. Simon.
"Integrating value stream mapping and discrete events simulation as decision making tools in
operation management." The International Journal of Advanced Manufacturing Technology 80,
no. 5-8 (2015): 1059-1066.
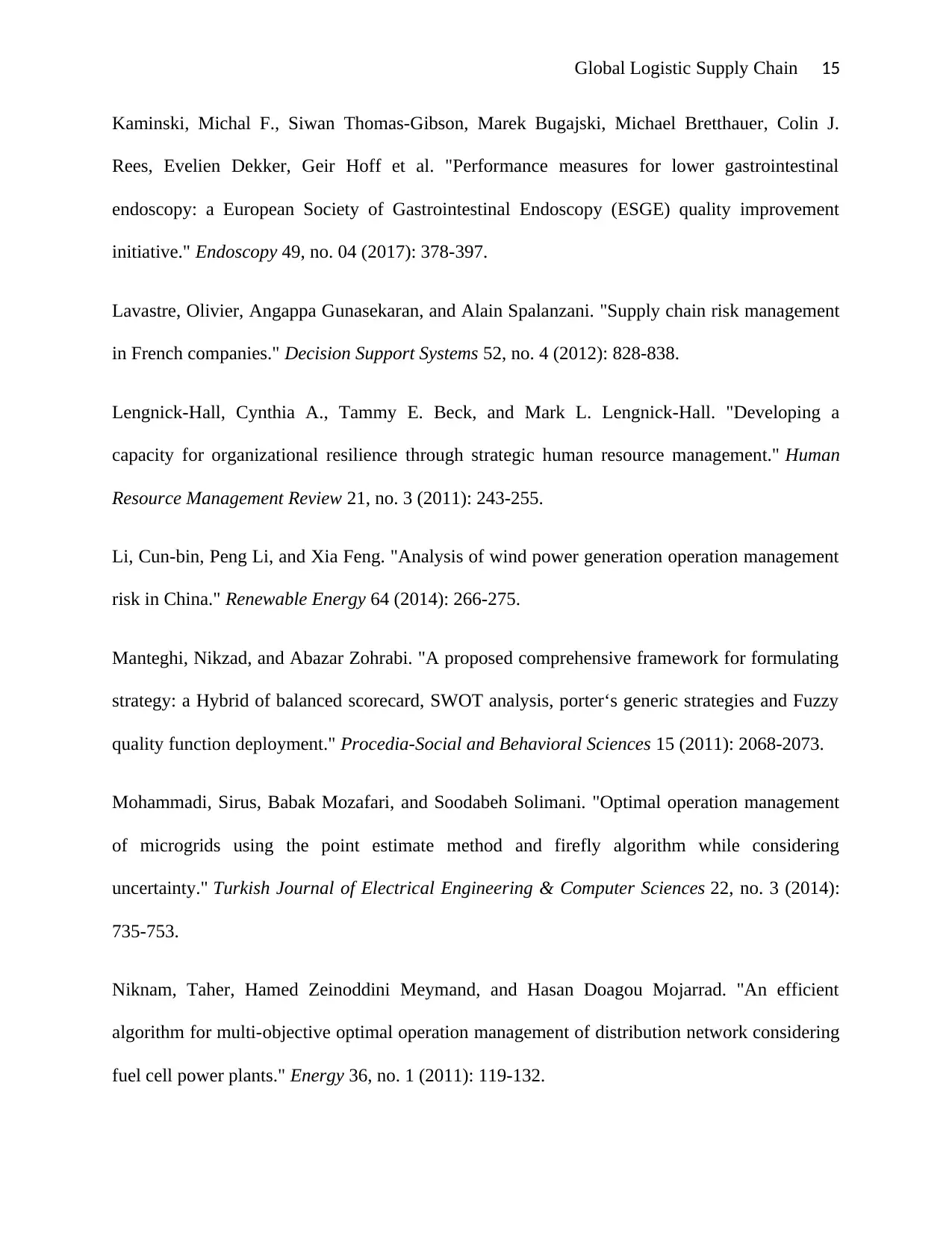
Global Logistic Supply Chain 15
Kaminski, Michal F., Siwan Thomas-Gibson, Marek Bugajski, Michael Bretthauer, Colin J.
Rees, Evelien Dekker, Geir Hoff et al. "Performance measures for lower gastrointestinal
endoscopy: a European Society of Gastrointestinal Endoscopy (ESGE) quality improvement
initiative." Endoscopy 49, no. 04 (2017): 378-397.
Lavastre, Olivier, Angappa Gunasekaran, and Alain Spalanzani. "Supply chain risk management
in French companies." Decision Support Systems 52, no. 4 (2012): 828-838.
Lengnick-Hall, Cynthia A., Tammy E. Beck, and Mark L. Lengnick-Hall. "Developing a
capacity for organizational resilience through strategic human resource management." Human
Resource Management Review 21, no. 3 (2011): 243-255.
Li, Cun-bin, Peng Li, and Xia Feng. "Analysis of wind power generation operation management
risk in China." Renewable Energy 64 (2014): 266-275.
Manteghi, Nikzad, and Abazar Zohrabi. "A proposed comprehensive framework for formulating
strategy: a Hybrid of balanced scorecard, SWOT analysis, porter‘s generic strategies and Fuzzy
quality function deployment." Procedia-Social and Behavioral Sciences 15 (2011): 2068-2073.
Mohammadi, Sirus, Babak Mozafari, and Soodabeh Solimani. "Optimal operation management
of microgrids using the point estimate method and firefly algorithm while considering
uncertainty." Turkish Journal of Electrical Engineering & Computer Sciences 22, no. 3 (2014):
735-753.
Niknam, Taher, Hamed Zeinoddini Meymand, and Hasan Doagou Mojarrad. "An efficient
algorithm for multi-objective optimal operation management of distribution network considering
fuel cell power plants." Energy 36, no. 1 (2011): 119-132.
Kaminski, Michal F., Siwan Thomas-Gibson, Marek Bugajski, Michael Bretthauer, Colin J.
Rees, Evelien Dekker, Geir Hoff et al. "Performance measures for lower gastrointestinal
endoscopy: a European Society of Gastrointestinal Endoscopy (ESGE) quality improvement
initiative." Endoscopy 49, no. 04 (2017): 378-397.
Lavastre, Olivier, Angappa Gunasekaran, and Alain Spalanzani. "Supply chain risk management
in French companies." Decision Support Systems 52, no. 4 (2012): 828-838.
Lengnick-Hall, Cynthia A., Tammy E. Beck, and Mark L. Lengnick-Hall. "Developing a
capacity for organizational resilience through strategic human resource management." Human
Resource Management Review 21, no. 3 (2011): 243-255.
Li, Cun-bin, Peng Li, and Xia Feng. "Analysis of wind power generation operation management
risk in China." Renewable Energy 64 (2014): 266-275.
Manteghi, Nikzad, and Abazar Zohrabi. "A proposed comprehensive framework for formulating
strategy: a Hybrid of balanced scorecard, SWOT analysis, porter‘s generic strategies and Fuzzy
quality function deployment." Procedia-Social and Behavioral Sciences 15 (2011): 2068-2073.
Mohammadi, Sirus, Babak Mozafari, and Soodabeh Solimani. "Optimal operation management
of microgrids using the point estimate method and firefly algorithm while considering
uncertainty." Turkish Journal of Electrical Engineering & Computer Sciences 22, no. 3 (2014):
735-753.
Niknam, Taher, Hamed Zeinoddini Meymand, and Hasan Doagou Mojarrad. "An efficient
algorithm for multi-objective optimal operation management of distribution network considering
fuel cell power plants." Energy 36, no. 1 (2011): 119-132.
⊘ This is a preview!⊘
Do you want full access?
Subscribe today to unlock all pages.

Trusted by 1+ million students worldwide
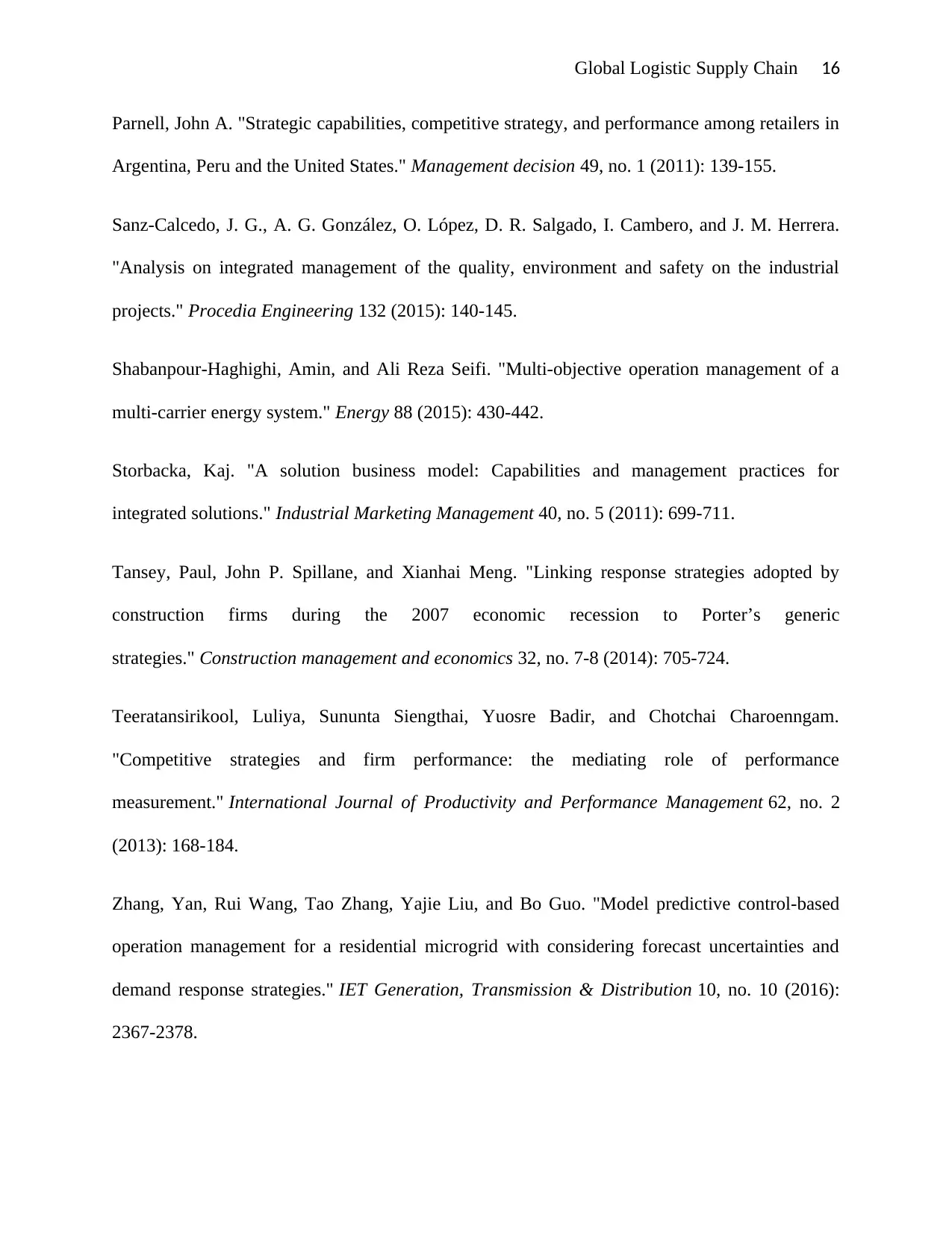
Global Logistic Supply Chain 16
Parnell, John A. "Strategic capabilities, competitive strategy, and performance among retailers in
Argentina, Peru and the United States." Management decision 49, no. 1 (2011): 139-155.
Sanz-Calcedo, J. G., A. G. González, O. López, D. R. Salgado, I. Cambero, and J. M. Herrera.
"Analysis on integrated management of the quality, environment and safety on the industrial
projects." Procedia Engineering 132 (2015): 140-145.
Shabanpour-Haghighi, Amin, and Ali Reza Seifi. "Multi-objective operation management of a
multi-carrier energy system." Energy 88 (2015): 430-442.
Storbacka, Kaj. "A solution business model: Capabilities and management practices for
integrated solutions." Industrial Marketing Management 40, no. 5 (2011): 699-711.
Tansey, Paul, John P. Spillane, and Xianhai Meng. "Linking response strategies adopted by
construction firms during the 2007 economic recession to Porter’s generic
strategies." Construction management and economics 32, no. 7-8 (2014): 705-724.
Teeratansirikool, Luliya, Sununta Siengthai, Yuosre Badir, and Chotchai Charoenngam.
"Competitive strategies and firm performance: the mediating role of performance
measurement." International Journal of Productivity and Performance Management 62, no. 2
(2013): 168-184.
Zhang, Yan, Rui Wang, Tao Zhang, Yajie Liu, and Bo Guo. "Model predictive control-based
operation management for a residential microgrid with considering forecast uncertainties and
demand response strategies." IET Generation, Transmission & Distribution 10, no. 10 (2016):
2367-2378.
Parnell, John A. "Strategic capabilities, competitive strategy, and performance among retailers in
Argentina, Peru and the United States." Management decision 49, no. 1 (2011): 139-155.
Sanz-Calcedo, J. G., A. G. González, O. López, D. R. Salgado, I. Cambero, and J. M. Herrera.
"Analysis on integrated management of the quality, environment and safety on the industrial
projects." Procedia Engineering 132 (2015): 140-145.
Shabanpour-Haghighi, Amin, and Ali Reza Seifi. "Multi-objective operation management of a
multi-carrier energy system." Energy 88 (2015): 430-442.
Storbacka, Kaj. "A solution business model: Capabilities and management practices for
integrated solutions." Industrial Marketing Management 40, no. 5 (2011): 699-711.
Tansey, Paul, John P. Spillane, and Xianhai Meng. "Linking response strategies adopted by
construction firms during the 2007 economic recession to Porter’s generic
strategies." Construction management and economics 32, no. 7-8 (2014): 705-724.
Teeratansirikool, Luliya, Sununta Siengthai, Yuosre Badir, and Chotchai Charoenngam.
"Competitive strategies and firm performance: the mediating role of performance
measurement." International Journal of Productivity and Performance Management 62, no. 2
(2013): 168-184.
Zhang, Yan, Rui Wang, Tao Zhang, Yajie Liu, and Bo Guo. "Model predictive control-based
operation management for a residential microgrid with considering forecast uncertainties and
demand response strategies." IET Generation, Transmission & Distribution 10, no. 10 (2016):
2367-2378.
1 out of 16
Related Documents

Your All-in-One AI-Powered Toolkit for Academic Success.
+13062052269
info@desklib.com
Available 24*7 on WhatsApp / Email
Unlock your academic potential
© 2024 | Zucol Services PVT LTD | All rights reserved.