ACC200 Project: Connectta Ltd Job Costing System and Overhead Analysis
VerifiedAdded on 2020/10/05
|9
|2463
|188
Project
AI Summary
This project, focusing on ACC200, provides a comprehensive analysis of job costing systems, using Connectta Ltd as a case study. The assignment begins by explaining the appropriateness of job costing for the company, which manufactures computer workstations. It then calculates the work-in-process inventory, determines the cost of finished chairs, and calculates over/under applied overheads. The project delves into the alternative accounting treatments for over-applied and under-applied overhead balances, and finally, explains the importance of activity-based costing in overcoming the limitations of traditional costing systems. The project covers key aspects of cost accounting, including inventory valuation, overhead allocation, and the application of different costing methodologies.
Contribute Materials
Your contribution can guide someone’s learning journey. Share your
documents today.
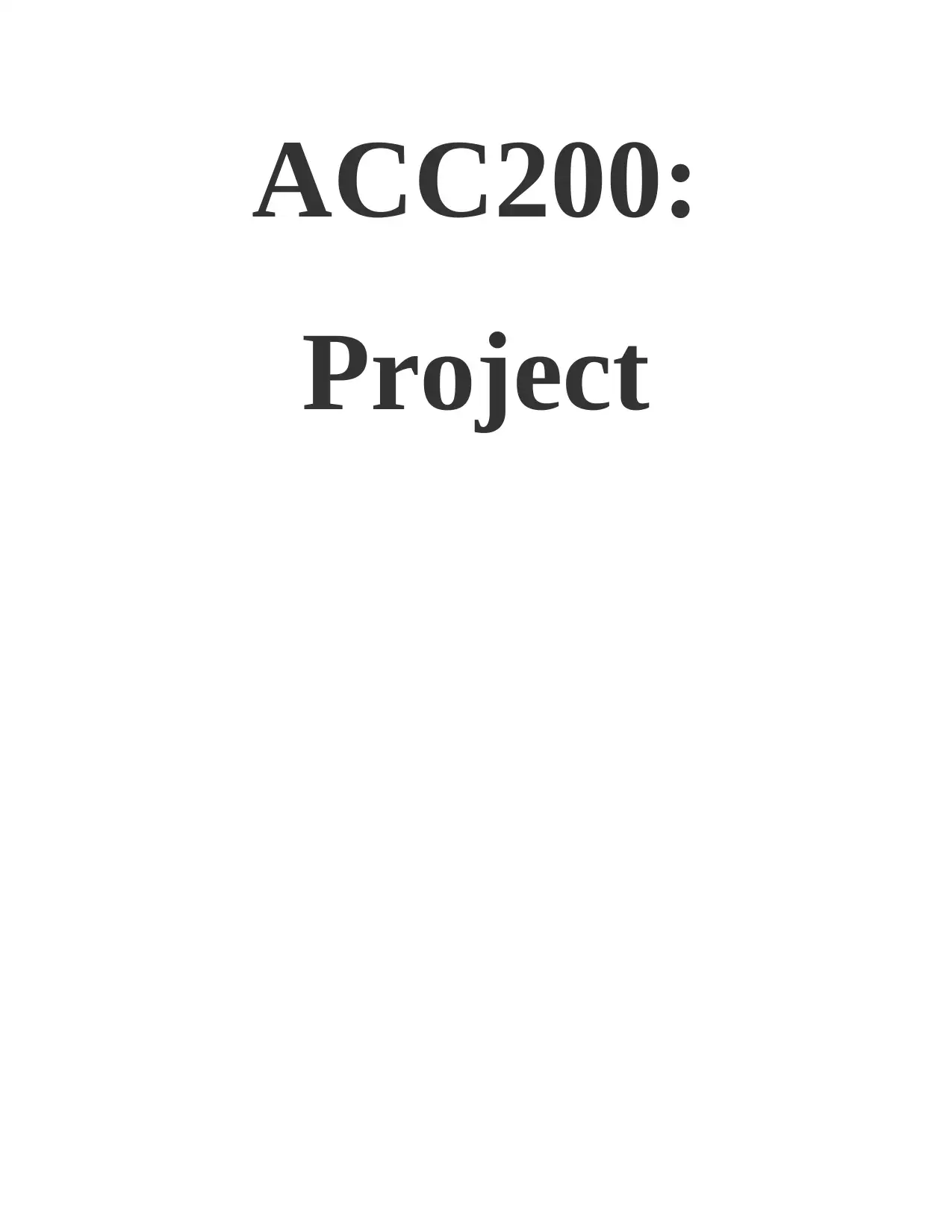
ACC200:
Project
Project
Secure Best Marks with AI Grader
Need help grading? Try our AI Grader for instant feedback on your assignments.
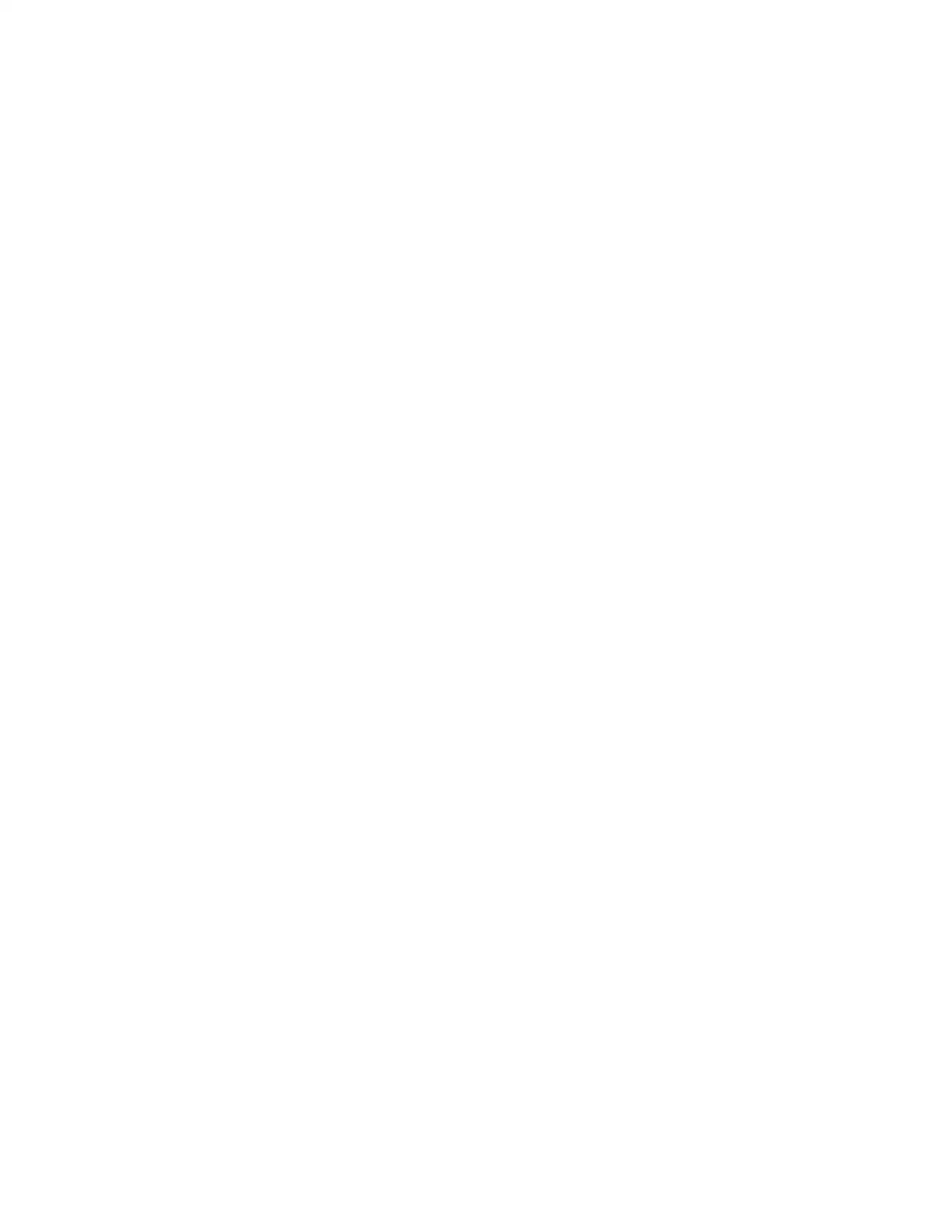
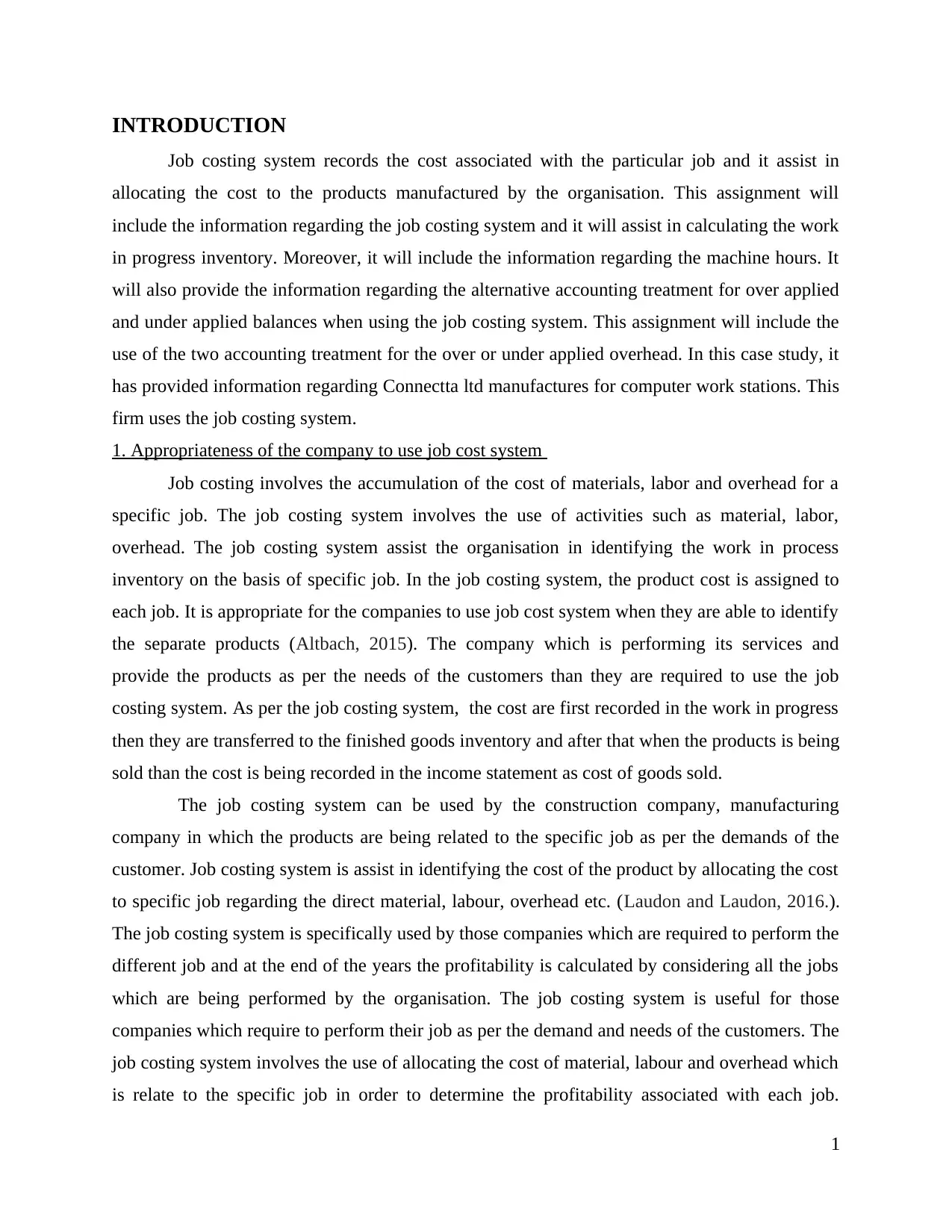
INTRODUCTION
Job costing system records the cost associated with the particular job and it assist in
allocating the cost to the products manufactured by the organisation. This assignment will
include the information regarding the job costing system and it will assist in calculating the work
in progress inventory. Moreover, it will include the information regarding the machine hours. It
will also provide the information regarding the alternative accounting treatment for over applied
and under applied balances when using the job costing system. This assignment will include the
use of the two accounting treatment for the over or under applied overhead. In this case study, it
has provided information regarding Connectta ltd manufactures for computer work stations. This
firm uses the job costing system.
1. Appropriateness of the company to use job cost system
Job costing involves the accumulation of the cost of materials, labor and overhead for a
specific job. The job costing system involves the use of activities such as material, labor,
overhead. The job costing system assist the organisation in identifying the work in process
inventory on the basis of specific job. In the job costing system, the product cost is assigned to
each job. It is appropriate for the companies to use job cost system when they are able to identify
the separate products (Altbach, 2015). The company which is performing its services and
provide the products as per the needs of the customers than they are required to use the job
costing system. As per the job costing system, the cost are first recorded in the work in progress
then they are transferred to the finished goods inventory and after that when the products is being
sold than the cost is being recorded in the income statement as cost of goods sold.
The job costing system can be used by the construction company, manufacturing
company in which the products are being related to the specific job as per the demands of the
customer. Job costing system is assist in identifying the cost of the product by allocating the cost
to specific job regarding the direct material, labour, overhead etc. (Laudon and Laudon, 2016.).
The job costing system is specifically used by those companies which are required to perform the
different job and at the end of the years the profitability is calculated by considering all the jobs
which are being performed by the organisation. The job costing system is useful for those
companies which require to perform their job as per the demand and needs of the customers. The
job costing system involves the use of allocating the cost of material, labour and overhead which
is relate to the specific job in order to determine the profitability associated with each job.
1
Job costing system records the cost associated with the particular job and it assist in
allocating the cost to the products manufactured by the organisation. This assignment will
include the information regarding the job costing system and it will assist in calculating the work
in progress inventory. Moreover, it will include the information regarding the machine hours. It
will also provide the information regarding the alternative accounting treatment for over applied
and under applied balances when using the job costing system. This assignment will include the
use of the two accounting treatment for the over or under applied overhead. In this case study, it
has provided information regarding Connectta ltd manufactures for computer work stations. This
firm uses the job costing system.
1. Appropriateness of the company to use job cost system
Job costing involves the accumulation of the cost of materials, labor and overhead for a
specific job. The job costing system involves the use of activities such as material, labor,
overhead. The job costing system assist the organisation in identifying the work in process
inventory on the basis of specific job. In the job costing system, the product cost is assigned to
each job. It is appropriate for the companies to use job cost system when they are able to identify
the separate products (Altbach, 2015). The company which is performing its services and
provide the products as per the needs of the customers than they are required to use the job
costing system. As per the job costing system, the cost are first recorded in the work in progress
then they are transferred to the finished goods inventory and after that when the products is being
sold than the cost is being recorded in the income statement as cost of goods sold.
The job costing system can be used by the construction company, manufacturing
company in which the products are being related to the specific job as per the demands of the
customer. Job costing system is assist in identifying the cost of the product by allocating the cost
to specific job regarding the direct material, labour, overhead etc. (Laudon and Laudon, 2016.).
The job costing system is specifically used by those companies which are required to perform the
different job and at the end of the years the profitability is calculated by considering all the jobs
which are being performed by the organisation. The job costing system is useful for those
companies which require to perform their job as per the demand and needs of the customers. The
job costing system involves the use of allocating the cost of material, labour and overhead which
is relate to the specific job in order to determine the profitability associated with each job.
1
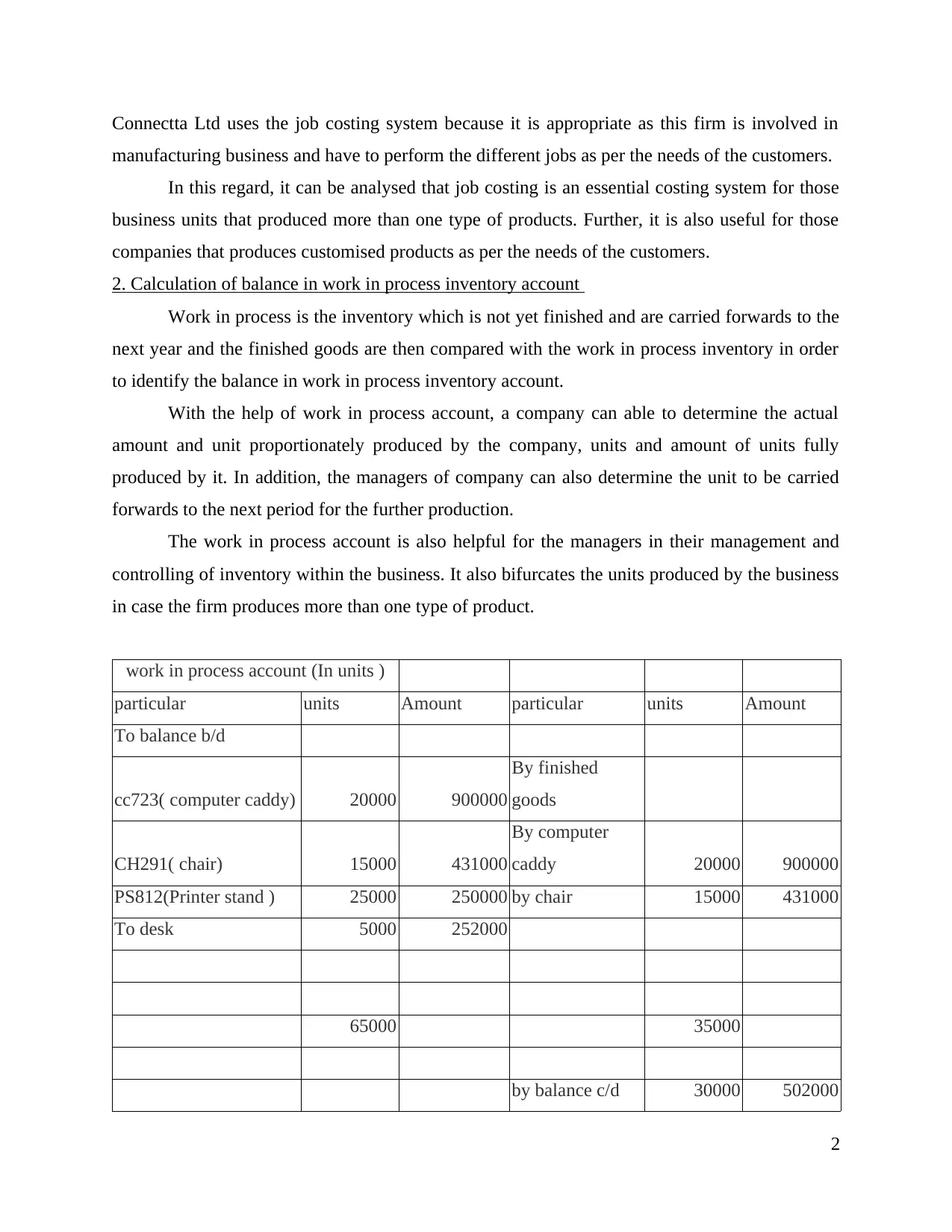
Connectta Ltd uses the job costing system because it is appropriate as this firm is involved in
manufacturing business and have to perform the different jobs as per the needs of the customers.
In this regard, it can be analysed that job costing is an essential costing system for those
business units that produced more than one type of products. Further, it is also useful for those
companies that produces customised products as per the needs of the customers.
2. Calculation of balance in work in process inventory account
Work in process is the inventory which is not yet finished and are carried forwards to the
next year and the finished goods are then compared with the work in process inventory in order
to identify the balance in work in process inventory account.
With the help of work in process account, a company can able to determine the actual
amount and unit proportionately produced by the company, units and amount of units fully
produced by it. In addition, the managers of company can also determine the unit to be carried
forwards to the next period for the further production.
The work in process account is also helpful for the managers in their management and
controlling of inventory within the business. It also bifurcates the units produced by the business
in case the firm produces more than one type of product.
work in process account (In units )
particular units Amount particular units Amount
To balance b/d
cc723( computer caddy) 20000 900000
By finished
goods
CH291( chair) 15000 431000
By computer
caddy 20000 900000
PS812(Printer stand ) 25000 250000 by chair 15000 431000
To desk 5000 252000
65000 35000
by balance c/d 30000 502000
2
manufacturing business and have to perform the different jobs as per the needs of the customers.
In this regard, it can be analysed that job costing is an essential costing system for those
business units that produced more than one type of products. Further, it is also useful for those
companies that produces customised products as per the needs of the customers.
2. Calculation of balance in work in process inventory account
Work in process is the inventory which is not yet finished and are carried forwards to the
next year and the finished goods are then compared with the work in process inventory in order
to identify the balance in work in process inventory account.
With the help of work in process account, a company can able to determine the actual
amount and unit proportionately produced by the company, units and amount of units fully
produced by it. In addition, the managers of company can also determine the unit to be carried
forwards to the next period for the further production.
The work in process account is also helpful for the managers in their management and
controlling of inventory within the business. It also bifurcates the units produced by the business
in case the firm produces more than one type of product.
work in process account (In units )
particular units Amount particular units Amount
To balance b/d
cc723( computer caddy) 20000 900000
By finished
goods
CH291( chair) 15000 431000
By computer
caddy 20000 900000
PS812(Printer stand ) 25000 250000 by chair 15000 431000
To desk 5000 252000
65000 35000
by balance c/d 30000 502000
2
Secure Best Marks with AI Grader
Need help grading? Try our AI Grader for instant feedback on your assignments.
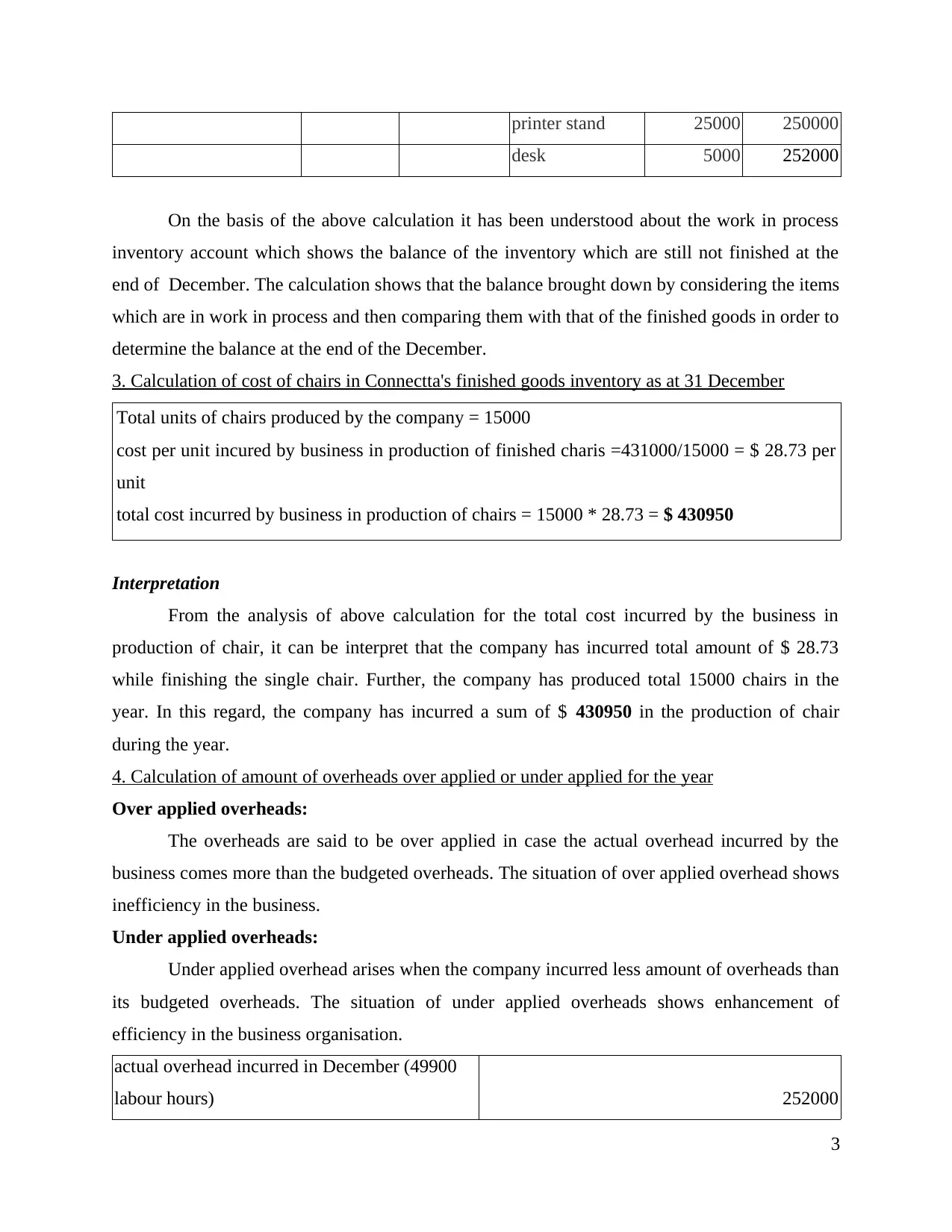
printer stand 25000 250000
desk 5000 252000
On the basis of the above calculation it has been understood about the work in process
inventory account which shows the balance of the inventory which are still not finished at the
end of December. The calculation shows that the balance brought down by considering the items
which are in work in process and then comparing them with that of the finished goods in order to
determine the balance at the end of the December.
3. Calculation of cost of chairs in Connectta's finished goods inventory as at 31 December
Total units of chairs produced by the company = 15000
cost per unit incured by business in production of finished charis =431000/15000 = $ 28.73 per
unit
total cost incurred by business in production of chairs = 15000 * 28.73 = $ 430950
Interpretation
From the analysis of above calculation for the total cost incurred by the business in
production of chair, it can be interpret that the company has incurred total amount of $ 28.73
while finishing the single chair. Further, the company has produced total 15000 chairs in the
year. In this regard, the company has incurred a sum of $ 430950 in the production of chair
during the year.
4. Calculation of amount of overheads over applied or under applied for the year
Over applied overheads:
The overheads are said to be over applied in case the actual overhead incurred by the
business comes more than the budgeted overheads. The situation of over applied overhead shows
inefficiency in the business.
Under applied overheads:
Under applied overhead arises when the company incurred less amount of overheads than
its budgeted overheads. The situation of under applied overheads shows enhancement of
efficiency in the business organisation.
actual overhead incurred in December (49900
labour hours) 252000
3
desk 5000 252000
On the basis of the above calculation it has been understood about the work in process
inventory account which shows the balance of the inventory which are still not finished at the
end of December. The calculation shows that the balance brought down by considering the items
which are in work in process and then comparing them with that of the finished goods in order to
determine the balance at the end of the December.
3. Calculation of cost of chairs in Connectta's finished goods inventory as at 31 December
Total units of chairs produced by the company = 15000
cost per unit incured by business in production of finished charis =431000/15000 = $ 28.73 per
unit
total cost incurred by business in production of chairs = 15000 * 28.73 = $ 430950
Interpretation
From the analysis of above calculation for the total cost incurred by the business in
production of chair, it can be interpret that the company has incurred total amount of $ 28.73
while finishing the single chair. Further, the company has produced total 15000 chairs in the
year. In this regard, the company has incurred a sum of $ 430950 in the production of chair
during the year.
4. Calculation of amount of overheads over applied or under applied for the year
Over applied overheads:
The overheads are said to be over applied in case the actual overhead incurred by the
business comes more than the budgeted overheads. The situation of over applied overhead shows
inefficiency in the business.
Under applied overheads:
Under applied overhead arises when the company incurred less amount of overheads than
its budgeted overheads. The situation of under applied overheads shows enhancement of
efficiency in the business organisation.
actual overhead incurred in December (49900
labour hours) 252000
3
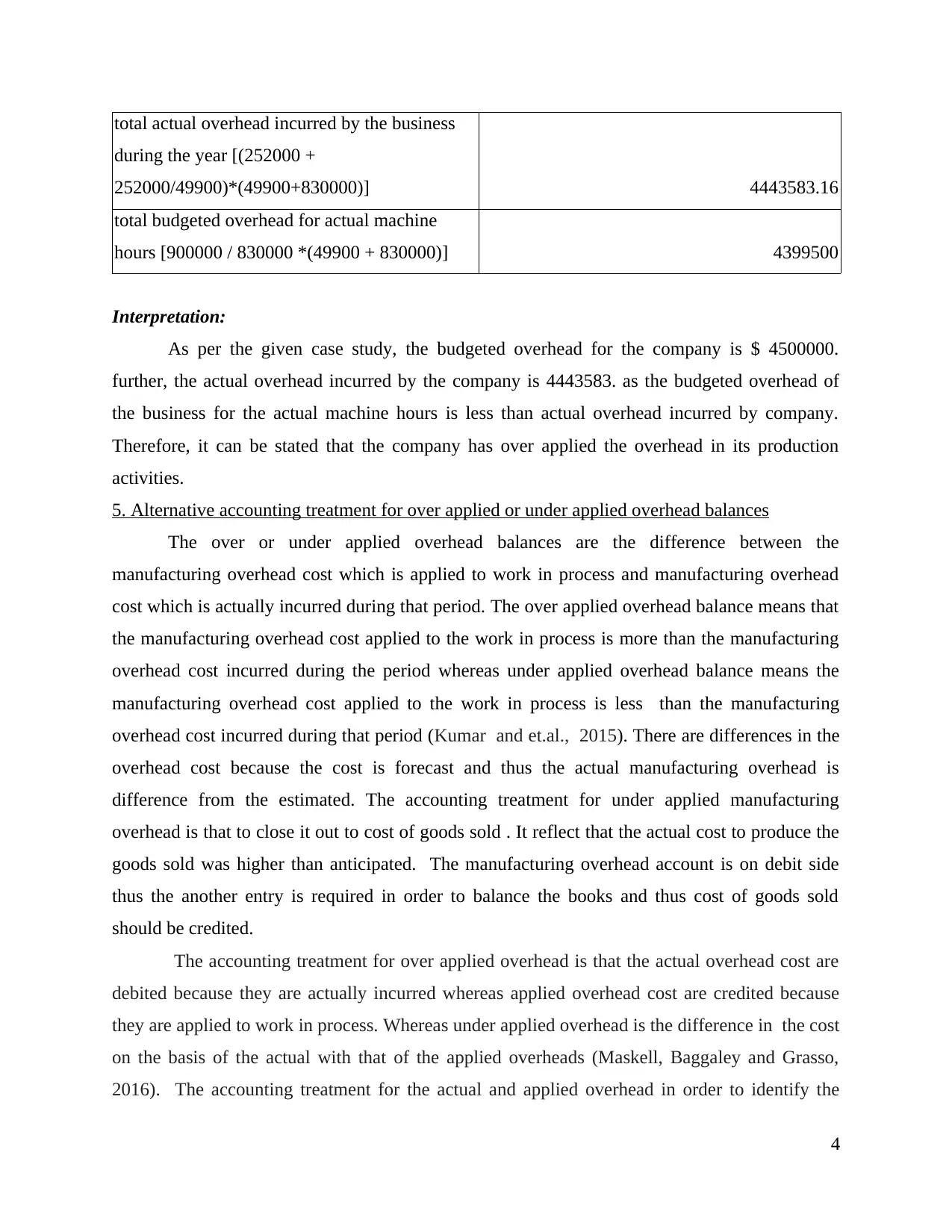
total actual overhead incurred by the business
during the year [(252000 +
252000/49900)*(49900+830000)] 4443583.16
total budgeted overhead for actual machine
hours [900000 / 830000 *(49900 + 830000)] 4399500
Interpretation:
As per the given case study, the budgeted overhead for the company is $ 4500000.
further, the actual overhead incurred by the company is 4443583. as the budgeted overhead of
the business for the actual machine hours is less than actual overhead incurred by company.
Therefore, it can be stated that the company has over applied the overhead in its production
activities.
5. Alternative accounting treatment for over applied or under applied overhead balances
The over or under applied overhead balances are the difference between the
manufacturing overhead cost which is applied to work in process and manufacturing overhead
cost which is actually incurred during that period. The over applied overhead balance means that
the manufacturing overhead cost applied to the work in process is more than the manufacturing
overhead cost incurred during the period whereas under applied overhead balance means the
manufacturing overhead cost applied to the work in process is less than the manufacturing
overhead cost incurred during that period (Kumar and et.al., 2015). There are differences in the
overhead cost because the cost is forecast and thus the actual manufacturing overhead is
difference from the estimated. The accounting treatment for under applied manufacturing
overhead is that to close it out to cost of goods sold . It reflect that the actual cost to produce the
goods sold was higher than anticipated. The manufacturing overhead account is on debit side
thus the another entry is required in order to balance the books and thus cost of goods sold
should be credited.
The accounting treatment for over applied overhead is that the actual overhead cost are
debited because they are actually incurred whereas applied overhead cost are credited because
they are applied to work in process. Whereas under applied overhead is the difference in the cost
on the basis of the actual with that of the applied overheads (Maskell, Baggaley and Grasso,
2016). The accounting treatment for the actual and applied overhead in order to identify the
4
during the year [(252000 +
252000/49900)*(49900+830000)] 4443583.16
total budgeted overhead for actual machine
hours [900000 / 830000 *(49900 + 830000)] 4399500
Interpretation:
As per the given case study, the budgeted overhead for the company is $ 4500000.
further, the actual overhead incurred by the company is 4443583. as the budgeted overhead of
the business for the actual machine hours is less than actual overhead incurred by company.
Therefore, it can be stated that the company has over applied the overhead in its production
activities.
5. Alternative accounting treatment for over applied or under applied overhead balances
The over or under applied overhead balances are the difference between the
manufacturing overhead cost which is applied to work in process and manufacturing overhead
cost which is actually incurred during that period. The over applied overhead balance means that
the manufacturing overhead cost applied to the work in process is more than the manufacturing
overhead cost incurred during the period whereas under applied overhead balance means the
manufacturing overhead cost applied to the work in process is less than the manufacturing
overhead cost incurred during that period (Kumar and et.al., 2015). There are differences in the
overhead cost because the cost is forecast and thus the actual manufacturing overhead is
difference from the estimated. The accounting treatment for under applied manufacturing
overhead is that to close it out to cost of goods sold . It reflect that the actual cost to produce the
goods sold was higher than anticipated. The manufacturing overhead account is on debit side
thus the another entry is required in order to balance the books and thus cost of goods sold
should be credited.
The accounting treatment for over applied overhead is that the actual overhead cost are
debited because they are actually incurred whereas applied overhead cost are credited because
they are applied to work in process. Whereas under applied overhead is the difference in the cost
on the basis of the actual with that of the applied overheads (Maskell, Baggaley and Grasso,
2016). The accounting treatment for the actual and applied overhead in order to identify the
4
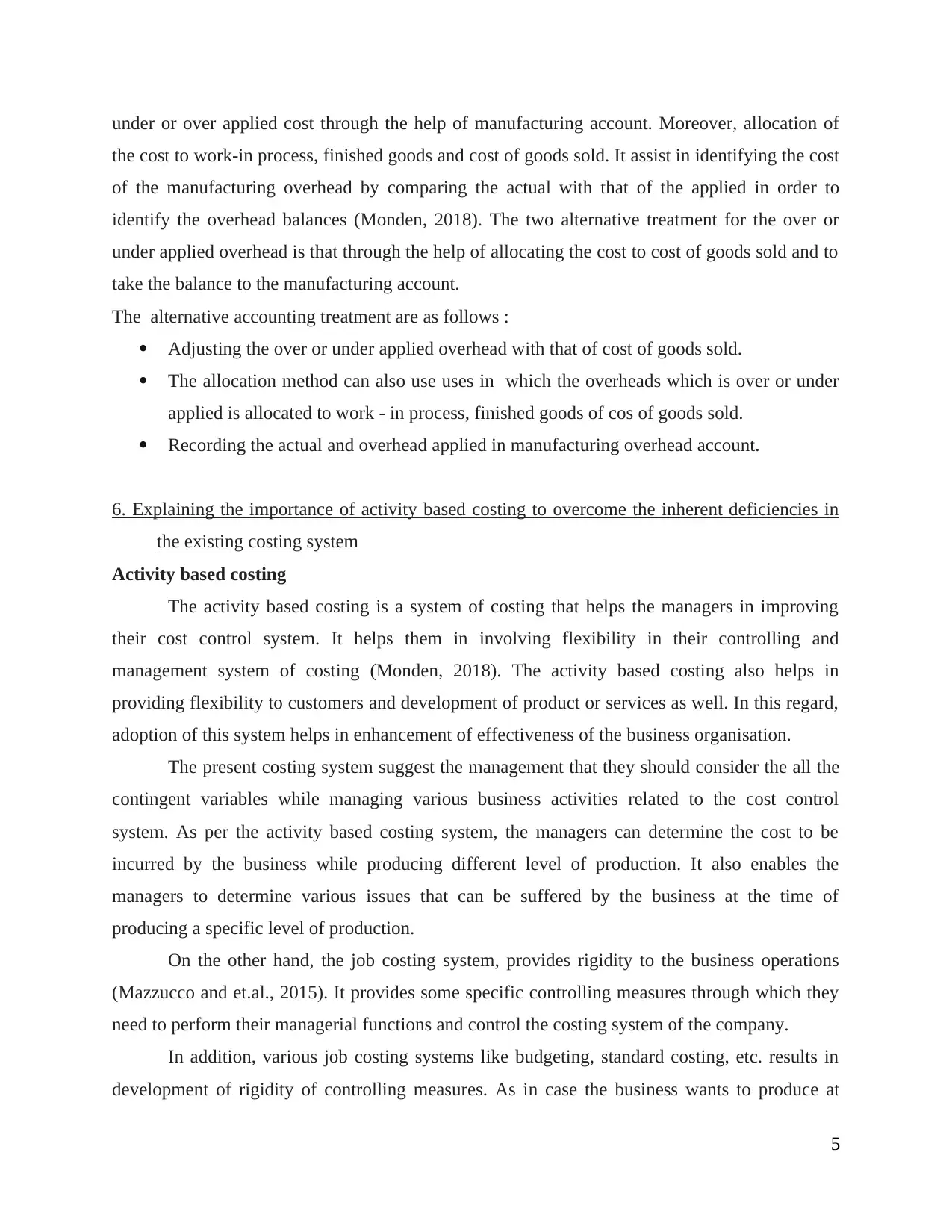
under or over applied cost through the help of manufacturing account. Moreover, allocation of
the cost to work-in process, finished goods and cost of goods sold. It assist in identifying the cost
of the manufacturing overhead by comparing the actual with that of the applied in order to
identify the overhead balances (Monden, 2018). The two alternative treatment for the over or
under applied overhead is that through the help of allocating the cost to cost of goods sold and to
take the balance to the manufacturing account.
The alternative accounting treatment are as follows :
Adjusting the over or under applied overhead with that of cost of goods sold.
The allocation method can also use uses in which the overheads which is over or under
applied is allocated to work - in process, finished goods of cos of goods sold.
Recording the actual and overhead applied in manufacturing overhead account.
6. Explaining the importance of activity based costing to overcome the inherent deficiencies in
the existing costing system
Activity based costing
The activity based costing is a system of costing that helps the managers in improving
their cost control system. It helps them in involving flexibility in their controlling and
management system of costing (Monden, 2018). The activity based costing also helps in
providing flexibility to customers and development of product or services as well. In this regard,
adoption of this system helps in enhancement of effectiveness of the business organisation.
The present costing system suggest the management that they should consider the all the
contingent variables while managing various business activities related to the cost control
system. As per the activity based costing system, the managers can determine the cost to be
incurred by the business while producing different level of production. It also enables the
managers to determine various issues that can be suffered by the business at the time of
producing a specific level of production.
On the other hand, the job costing system, provides rigidity to the business operations
(Mazzucco and et.al., 2015). It provides some specific controlling measures through which they
need to perform their managerial functions and control the costing system of the company.
In addition, various job costing systems like budgeting, standard costing, etc. results in
development of rigidity of controlling measures. As in case the business wants to produce at
5
the cost to work-in process, finished goods and cost of goods sold. It assist in identifying the cost
of the manufacturing overhead by comparing the actual with that of the applied in order to
identify the overhead balances (Monden, 2018). The two alternative treatment for the over or
under applied overhead is that through the help of allocating the cost to cost of goods sold and to
take the balance to the manufacturing account.
The alternative accounting treatment are as follows :
Adjusting the over or under applied overhead with that of cost of goods sold.
The allocation method can also use uses in which the overheads which is over or under
applied is allocated to work - in process, finished goods of cos of goods sold.
Recording the actual and overhead applied in manufacturing overhead account.
6. Explaining the importance of activity based costing to overcome the inherent deficiencies in
the existing costing system
Activity based costing
The activity based costing is a system of costing that helps the managers in improving
their cost control system. It helps them in involving flexibility in their controlling and
management system of costing (Monden, 2018). The activity based costing also helps in
providing flexibility to customers and development of product or services as well. In this regard,
adoption of this system helps in enhancement of effectiveness of the business organisation.
The present costing system suggest the management that they should consider the all the
contingent variables while managing various business activities related to the cost control
system. As per the activity based costing system, the managers can determine the cost to be
incurred by the business while producing different level of production. It also enables the
managers to determine various issues that can be suffered by the business at the time of
producing a specific level of production.
On the other hand, the job costing system, provides rigidity to the business operations
(Mazzucco and et.al., 2015). It provides some specific controlling measures through which they
need to perform their managerial functions and control the costing system of the company.
In addition, various job costing systems like budgeting, standard costing, etc. results in
development of rigidity of controlling measures. As in case the business wants to produce at
5
Paraphrase This Document
Need a fresh take? Get an instant paraphrase of this document with our AI Paraphraser
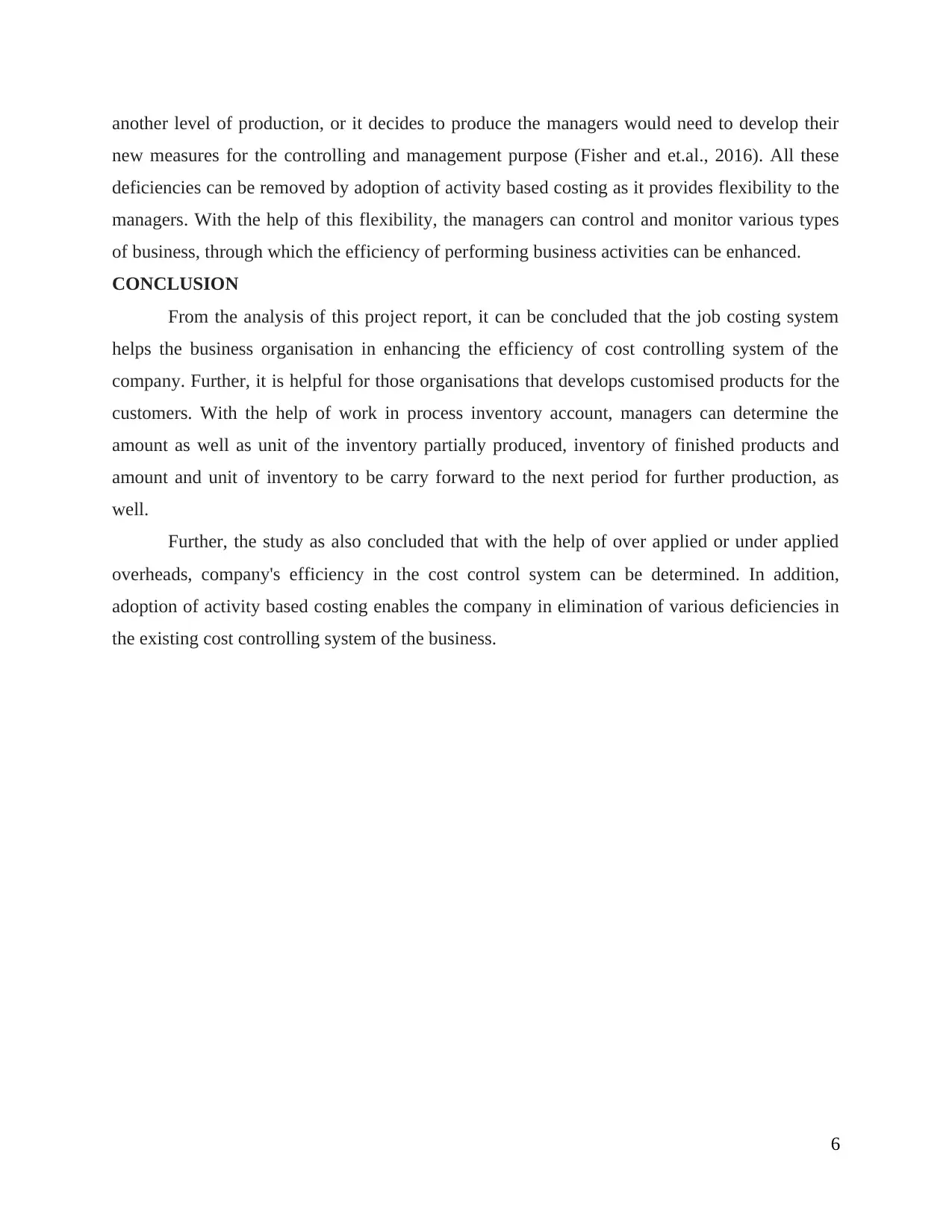
another level of production, or it decides to produce the managers would need to develop their
new measures for the controlling and management purpose (Fisher and et.al., 2016). All these
deficiencies can be removed by adoption of activity based costing as it provides flexibility to the
managers. With the help of this flexibility, the managers can control and monitor various types
of business, through which the efficiency of performing business activities can be enhanced.
CONCLUSION
From the analysis of this project report, it can be concluded that the job costing system
helps the business organisation in enhancing the efficiency of cost controlling system of the
company. Further, it is helpful for those organisations that develops customised products for the
customers. With the help of work in process inventory account, managers can determine the
amount as well as unit of the inventory partially produced, inventory of finished products and
amount and unit of inventory to be carry forward to the next period for further production, as
well.
Further, the study as also concluded that with the help of over applied or under applied
overheads, company's efficiency in the cost control system can be determined. In addition,
adoption of activity based costing enables the company in elimination of various deficiencies in
the existing cost controlling system of the business.
6
new measures for the controlling and management purpose (Fisher and et.al., 2016). All these
deficiencies can be removed by adoption of activity based costing as it provides flexibility to the
managers. With the help of this flexibility, the managers can control and monitor various types
of business, through which the efficiency of performing business activities can be enhanced.
CONCLUSION
From the analysis of this project report, it can be concluded that the job costing system
helps the business organisation in enhancing the efficiency of cost controlling system of the
company. Further, it is helpful for those organisations that develops customised products for the
customers. With the help of work in process inventory account, managers can determine the
amount as well as unit of the inventory partially produced, inventory of finished products and
amount and unit of inventory to be carry forward to the next period for further production, as
well.
Further, the study as also concluded that with the help of over applied or under applied
overheads, company's efficiency in the cost control system can be determined. In addition,
adoption of activity based costing enables the company in elimination of various deficiencies in
the existing cost controlling system of the business.
6
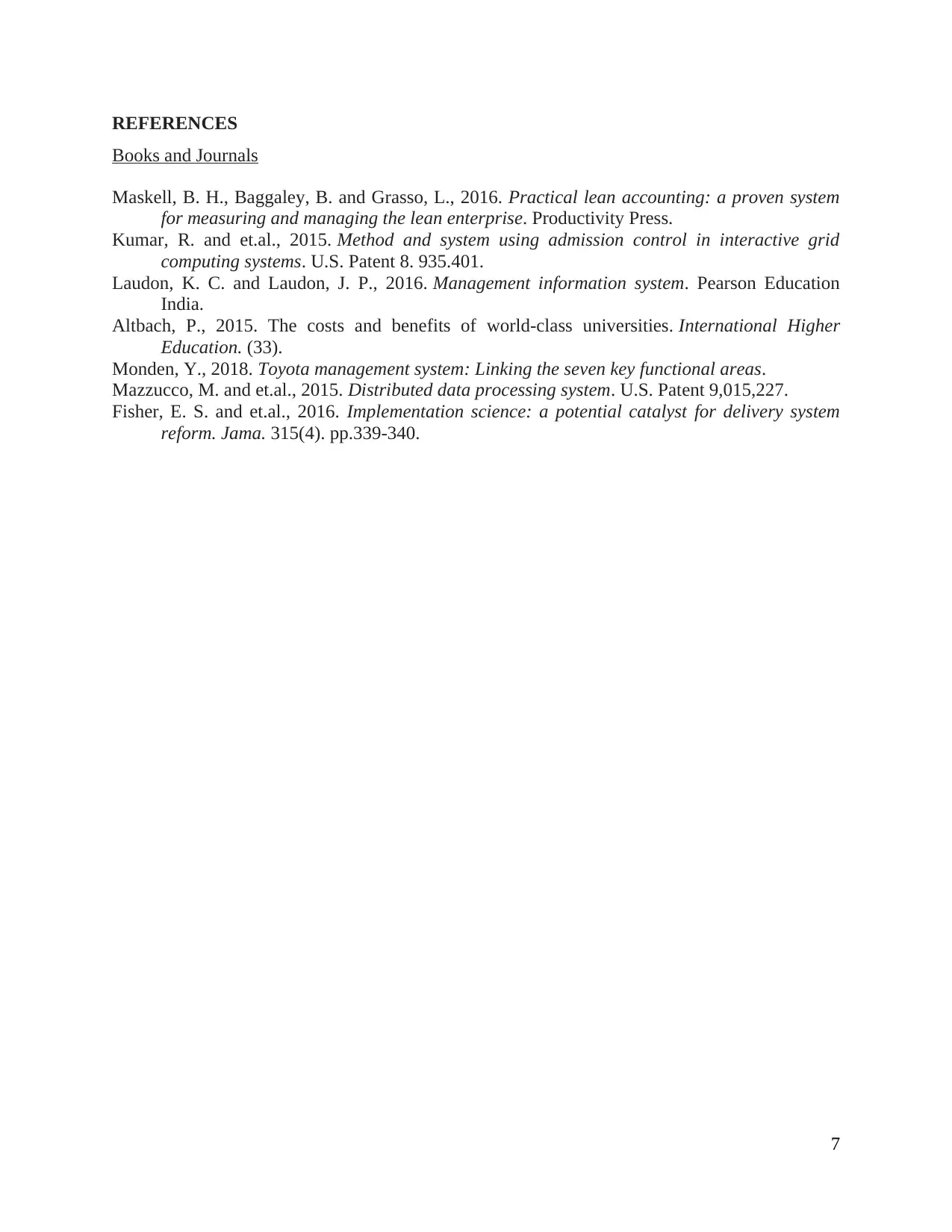
REFERENCES
Books and Journals
Maskell, B. H., Baggaley, B. and Grasso, L., 2016. Practical lean accounting: a proven system
for measuring and managing the lean enterprise. Productivity Press.
Kumar, R. and et.al., 2015. Method and system using admission control in interactive grid
computing systems. U.S. Patent 8. 935.401.
Laudon, K. C. and Laudon, J. P., 2016. Management information system. Pearson Education
India.
Altbach, P., 2015. The costs and benefits of world-class universities. International Higher
Education. (33).
Monden, Y., 2018. Toyota management system: Linking the seven key functional areas.
Mazzucco, M. and et.al., 2015. Distributed data processing system. U.S. Patent 9,015,227.
Fisher, E. S. and et.al., 2016. Implementation science: a potential catalyst for delivery system
reform. Jama. 315(4). pp.339-340.
7
Books and Journals
Maskell, B. H., Baggaley, B. and Grasso, L., 2016. Practical lean accounting: a proven system
for measuring and managing the lean enterprise. Productivity Press.
Kumar, R. and et.al., 2015. Method and system using admission control in interactive grid
computing systems. U.S. Patent 8. 935.401.
Laudon, K. C. and Laudon, J. P., 2016. Management information system. Pearson Education
India.
Altbach, P., 2015. The costs and benefits of world-class universities. International Higher
Education. (33).
Monden, Y., 2018. Toyota management system: Linking the seven key functional areas.
Mazzucco, M. and et.al., 2015. Distributed data processing system. U.S. Patent 9,015,227.
Fisher, E. S. and et.al., 2016. Implementation science: a potential catalyst for delivery system
reform. Jama. 315(4). pp.339-340.
7
1 out of 9
Related Documents

Your All-in-One AI-Powered Toolkit for Academic Success.
+13062052269
info@desklib.com
Available 24*7 on WhatsApp / Email
Unlock your academic potential
© 2024 | Zucol Services PVT LTD | All rights reserved.