Business Research Methodology Report: K Construction, Australia
VerifiedAdded on 2020/04/15
|15
|3593
|360
Report
AI Summary
This report, focusing on K Construction Private Limited, delves into business research methodology, particularly concerning workplace safety and hazard management. Part A addresses the company's background, potential hazards in construction, and relevant regulations like the Work Health and Safety Act 2011. It outlines the implications of physical hazards such as vibration and noise. Part B details a Standard Operating Procedure (SOP) for K Construction, encompassing analysis of existing procedures, identification of objectives, enforcement strategies, and comprehensive worker training. The SOP includes steps for analyzing current safety measures, identifying objectives for new safety protocols, enforcing new SOPs, and training workers on the new SOP. The report also discusses the identification of a workgroup for training, organizational procedures, WHS legislations, and training session plans. The report concludes with follow-up meetings and mentoring sessions to ensure the effectiveness of the new safety measures. The report emphasizes the importance of a structured approach to workplace safety, incorporating legal frameworks, training programs, and ongoing monitoring to mitigate physical hazards and improve worker safety within the construction environment.
Contribute Materials
Your contribution can guide someone’s learning journey. Share your
documents today.
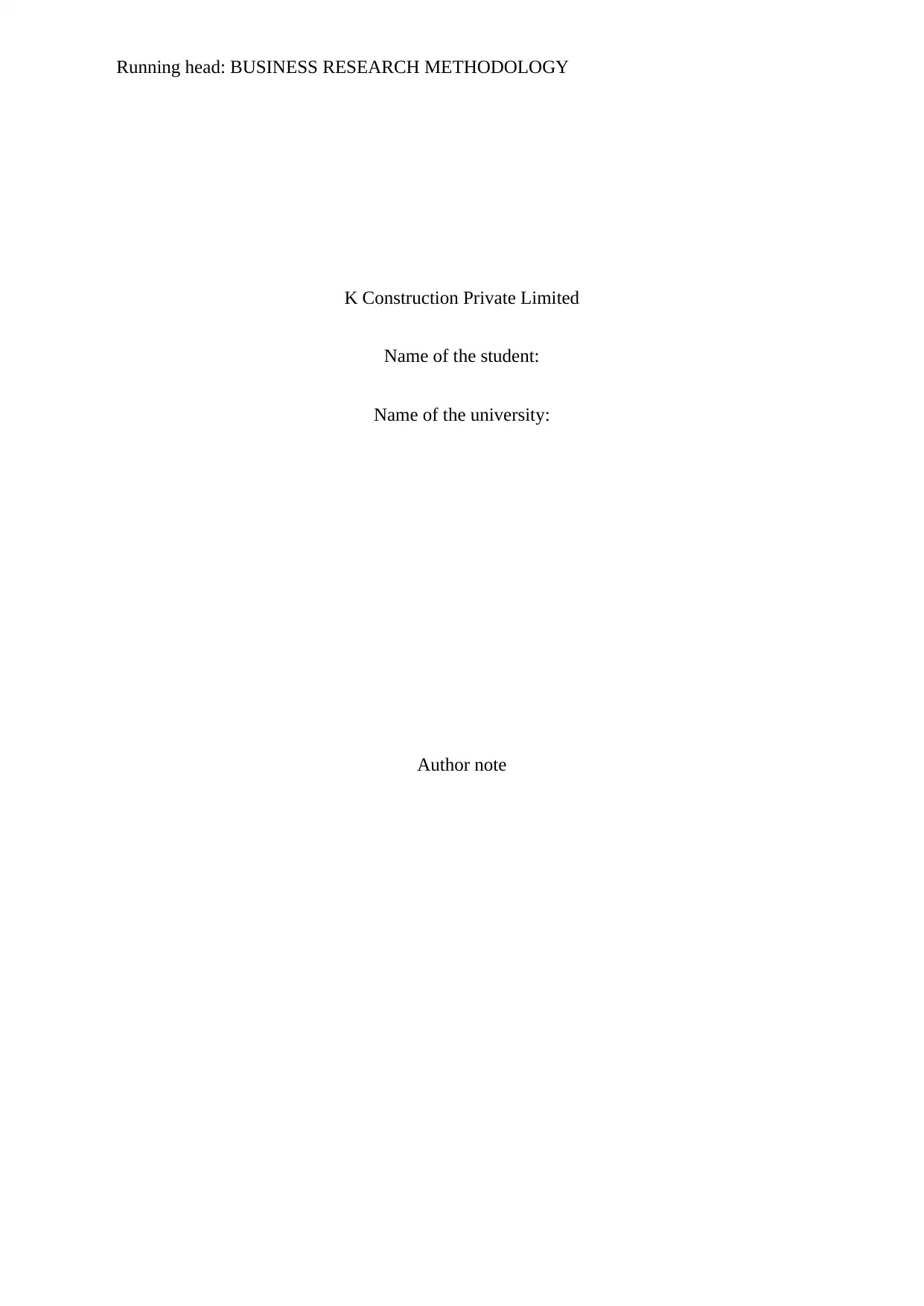
Running head: BUSINESS RESEARCH METHODOLOGY
K Construction Private Limited
Name of the student:
Name of the university:
Author note
K Construction Private Limited
Name of the student:
Name of the university:
Author note
Secure Best Marks with AI Grader
Need help grading? Try our AI Grader for instant feedback on your assignments.
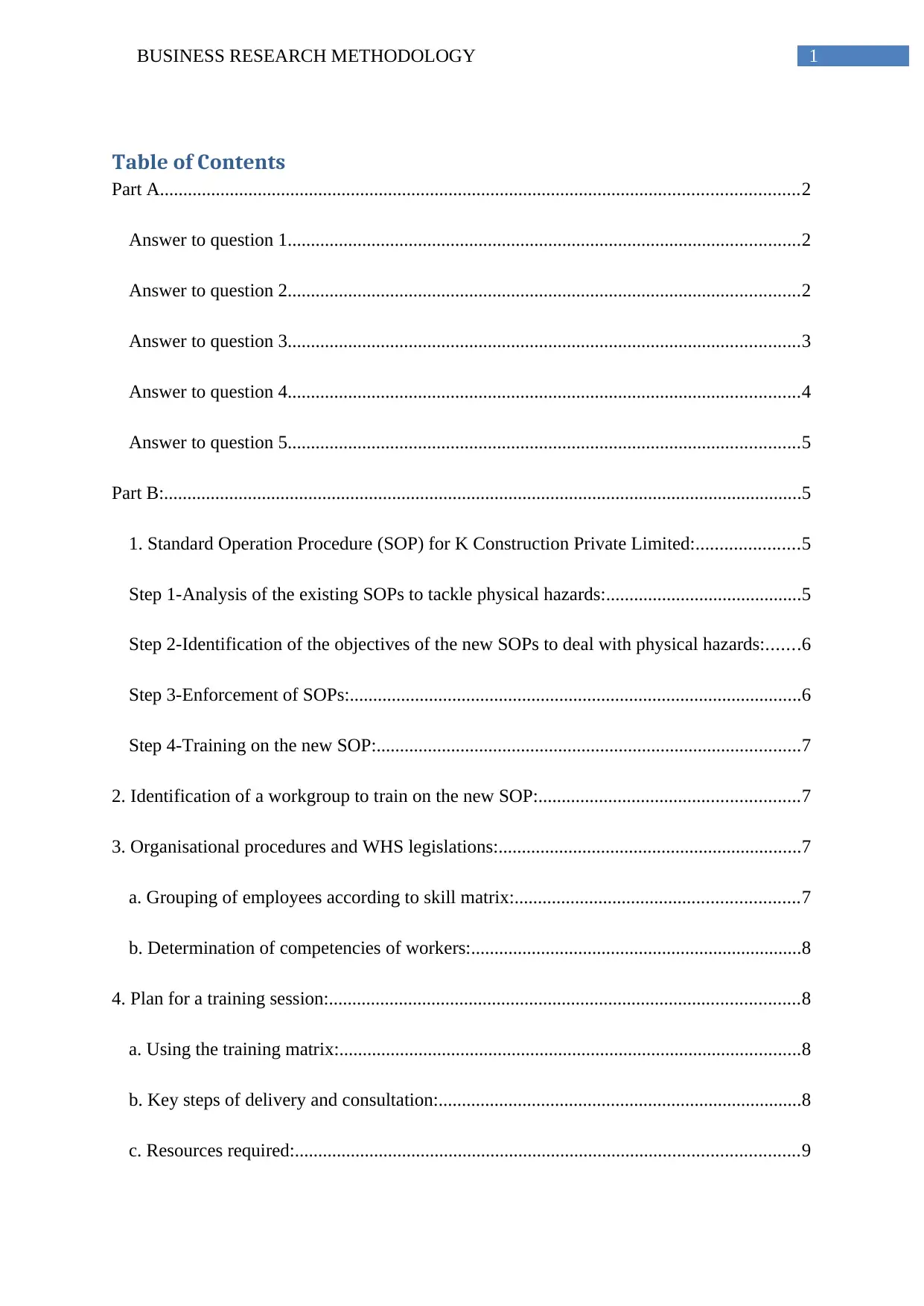
1BUSINESS RESEARCH METHODOLOGY
Table of Contents
Part A.........................................................................................................................................2
Answer to question 1..............................................................................................................2
Answer to question 2..............................................................................................................2
Answer to question 3..............................................................................................................3
Answer to question 4..............................................................................................................4
Answer to question 5..............................................................................................................5
Part B:.........................................................................................................................................5
1. Standard Operation Procedure (SOP) for K Construction Private Limited:......................5
Step 1-Analysis of the existing SOPs to tackle physical hazards:..........................................5
Step 2-Identification of the objectives of the new SOPs to deal with physical hazards:.......6
Step 3-Enforcement of SOPs:.................................................................................................6
Step 4-Training on the new SOP:...........................................................................................7
2. Identification of a workgroup to train on the new SOP:........................................................7
3. Organisational procedures and WHS legislations:.................................................................7
a. Grouping of employees according to skill matrix:.............................................................7
b. Determination of competencies of workers:.......................................................................8
4. Plan for a training session:.....................................................................................................8
a. Using the training matrix:...................................................................................................8
b. Key steps of delivery and consultation:..............................................................................8
c. Resources required:............................................................................................................9
Table of Contents
Part A.........................................................................................................................................2
Answer to question 1..............................................................................................................2
Answer to question 2..............................................................................................................2
Answer to question 3..............................................................................................................3
Answer to question 4..............................................................................................................4
Answer to question 5..............................................................................................................5
Part B:.........................................................................................................................................5
1. Standard Operation Procedure (SOP) for K Construction Private Limited:......................5
Step 1-Analysis of the existing SOPs to tackle physical hazards:..........................................5
Step 2-Identification of the objectives of the new SOPs to deal with physical hazards:.......6
Step 3-Enforcement of SOPs:.................................................................................................6
Step 4-Training on the new SOP:...........................................................................................7
2. Identification of a workgroup to train on the new SOP:........................................................7
3. Organisational procedures and WHS legislations:.................................................................7
a. Grouping of employees according to skill matrix:.............................................................7
b. Determination of competencies of workers:.......................................................................8
4. Plan for a training session:.....................................................................................................8
a. Using the training matrix:...................................................................................................8
b. Key steps of delivery and consultation:..............................................................................8
c. Resources required:............................................................................................................9
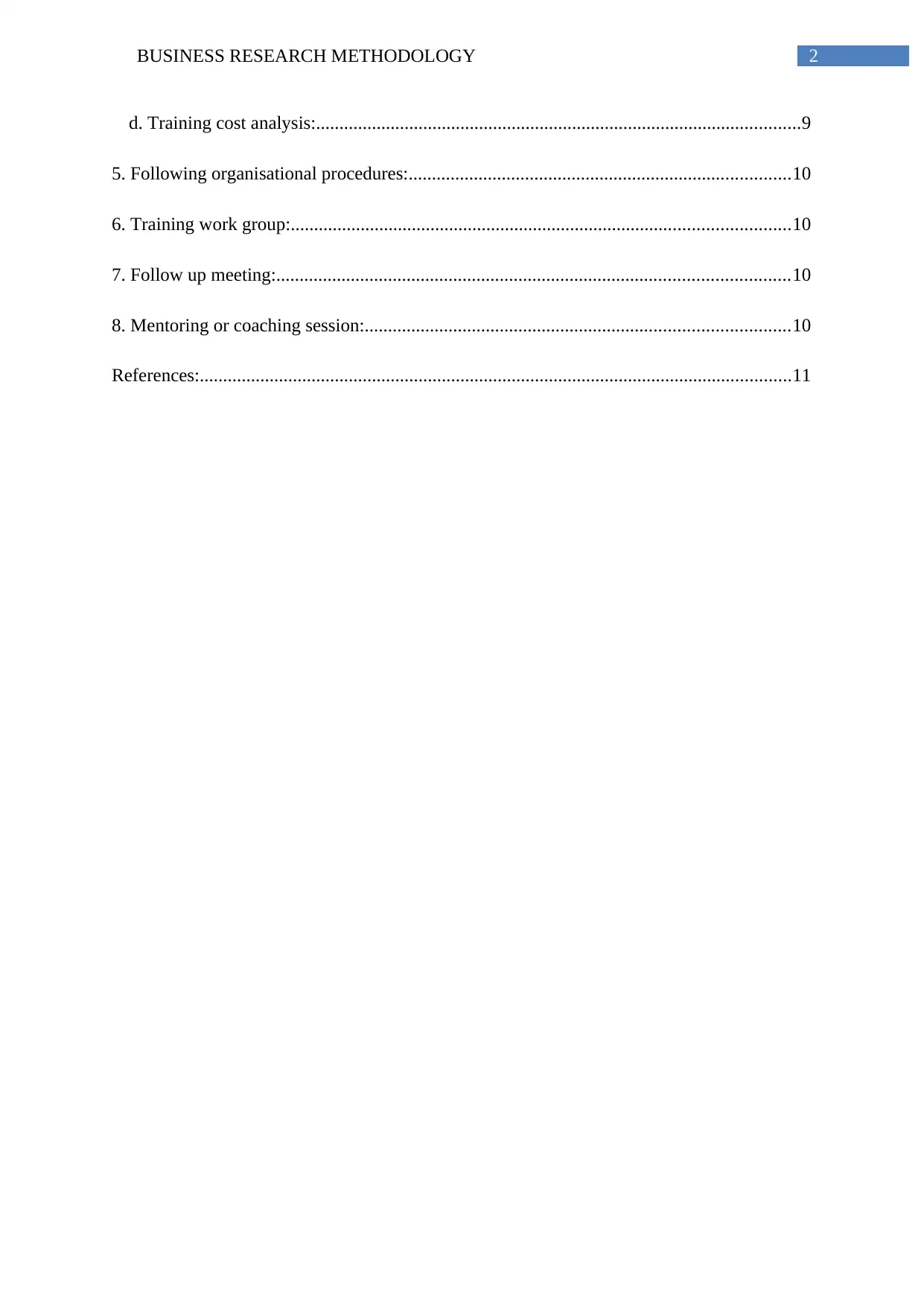
2BUSINESS RESEARCH METHODOLOGY
d. Training cost analysis:........................................................................................................9
5. Following organisational procedures:..................................................................................10
6. Training work group:...........................................................................................................10
7. Follow up meeting:..............................................................................................................10
8. Mentoring or coaching session:...........................................................................................10
References:...............................................................................................................................11
d. Training cost analysis:........................................................................................................9
5. Following organisational procedures:..................................................................................10
6. Training work group:...........................................................................................................10
7. Follow up meeting:..............................................................................................................10
8. Mentoring or coaching session:...........................................................................................10
References:...............................................................................................................................11
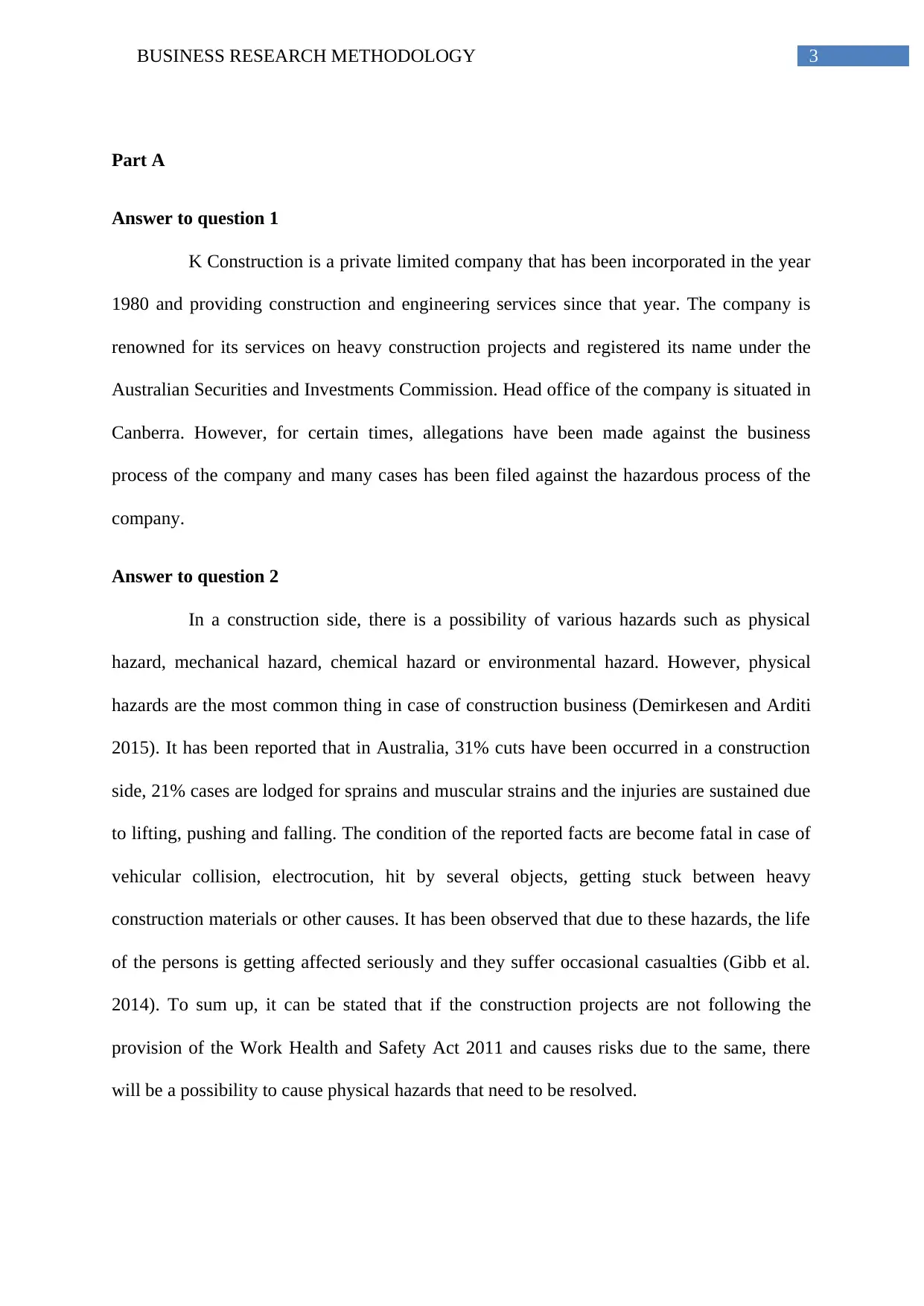
3BUSINESS RESEARCH METHODOLOGY
Part A
Answer to question 1
K Construction is a private limited company that has been incorporated in the year
1980 and providing construction and engineering services since that year. The company is
renowned for its services on heavy construction projects and registered its name under the
Australian Securities and Investments Commission. Head office of the company is situated in
Canberra. However, for certain times, allegations have been made against the business
process of the company and many cases has been filed against the hazardous process of the
company.
Answer to question 2
In a construction side, there is a possibility of various hazards such as physical
hazard, mechanical hazard, chemical hazard or environmental hazard. However, physical
hazards are the most common thing in case of construction business (Demirkesen and Arditi
2015). It has been reported that in Australia, 31% cuts have been occurred in a construction
side, 21% cases are lodged for sprains and muscular strains and the injuries are sustained due
to lifting, pushing and falling. The condition of the reported facts are become fatal in case of
vehicular collision, electrocution, hit by several objects, getting stuck between heavy
construction materials or other causes. It has been observed that due to these hazards, the life
of the persons is getting affected seriously and they suffer occasional casualties (Gibb et al.
2014). To sum up, it can be stated that if the construction projects are not following the
provision of the Work Health and Safety Act 2011 and causes risks due to the same, there
will be a possibility to cause physical hazards that need to be resolved.
Part A
Answer to question 1
K Construction is a private limited company that has been incorporated in the year
1980 and providing construction and engineering services since that year. The company is
renowned for its services on heavy construction projects and registered its name under the
Australian Securities and Investments Commission. Head office of the company is situated in
Canberra. However, for certain times, allegations have been made against the business
process of the company and many cases has been filed against the hazardous process of the
company.
Answer to question 2
In a construction side, there is a possibility of various hazards such as physical
hazard, mechanical hazard, chemical hazard or environmental hazard. However, physical
hazards are the most common thing in case of construction business (Demirkesen and Arditi
2015). It has been reported that in Australia, 31% cuts have been occurred in a construction
side, 21% cases are lodged for sprains and muscular strains and the injuries are sustained due
to lifting, pushing and falling. The condition of the reported facts are become fatal in case of
vehicular collision, electrocution, hit by several objects, getting stuck between heavy
construction materials or other causes. It has been observed that due to these hazards, the life
of the persons is getting affected seriously and they suffer occasional casualties (Gibb et al.
2014). To sum up, it can be stated that if the construction projects are not following the
provision of the Work Health and Safety Act 2011 and causes risks due to the same, there
will be a possibility to cause physical hazards that need to be resolved.
Secure Best Marks with AI Grader
Need help grading? Try our AI Grader for instant feedback on your assignments.
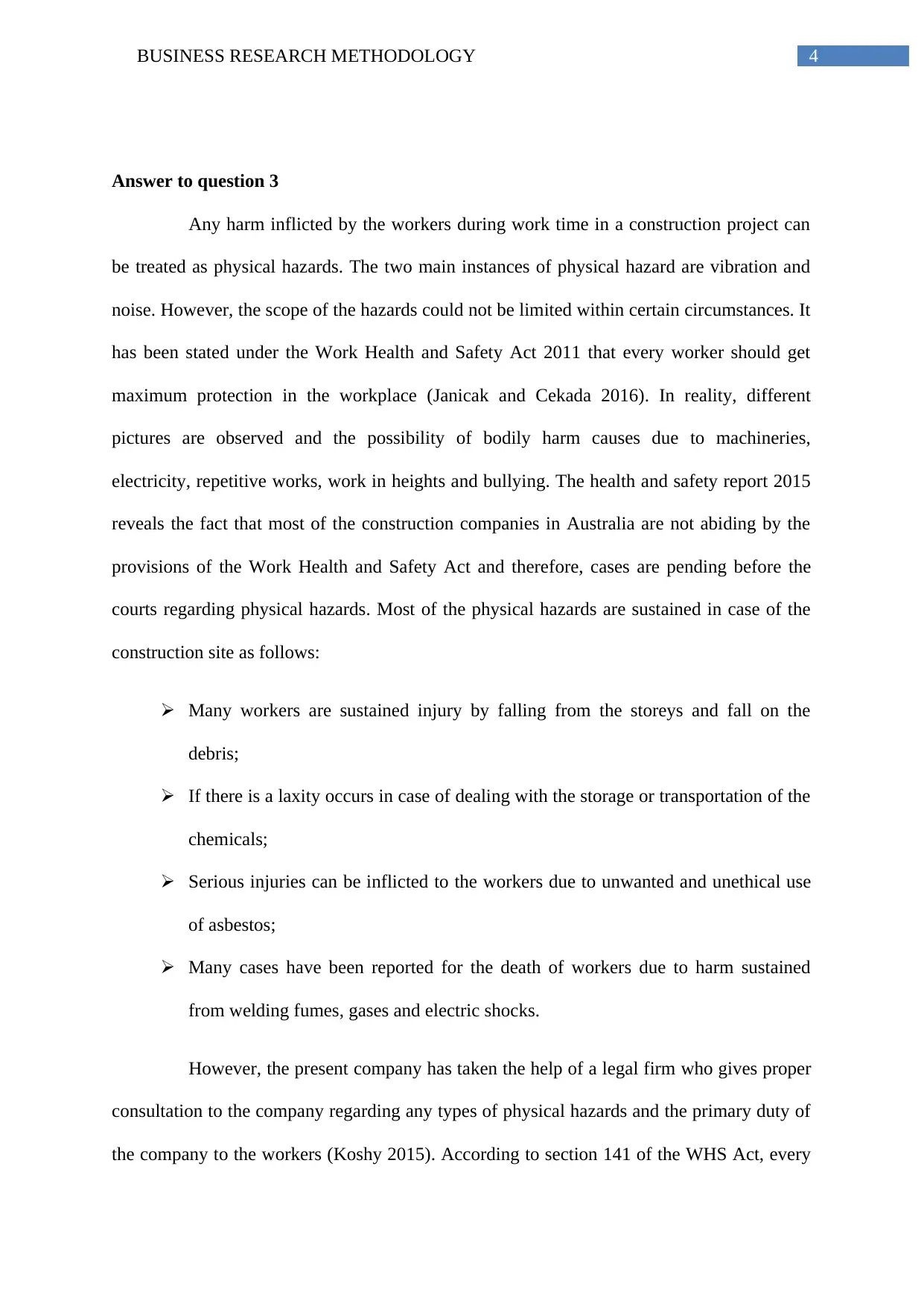
4BUSINESS RESEARCH METHODOLOGY
Answer to question 3
Any harm inflicted by the workers during work time in a construction project can
be treated as physical hazards. The two main instances of physical hazard are vibration and
noise. However, the scope of the hazards could not be limited within certain circumstances. It
has been stated under the Work Health and Safety Act 2011 that every worker should get
maximum protection in the workplace (Janicak and Cekada 2016). In reality, different
pictures are observed and the possibility of bodily harm causes due to machineries,
electricity, repetitive works, work in heights and bullying. The health and safety report 2015
reveals the fact that most of the construction companies in Australia are not abiding by the
provisions of the Work Health and Safety Act and therefore, cases are pending before the
courts regarding physical hazards. Most of the physical hazards are sustained in case of the
construction site as follows:
Many workers are sustained injury by falling from the storeys and fall on the
debris;
If there is a laxity occurs in case of dealing with the storage or transportation of the
chemicals;
Serious injuries can be inflicted to the workers due to unwanted and unethical use
of asbestos;
Many cases have been reported for the death of workers due to harm sustained
from welding fumes, gases and electric shocks.
However, the present company has taken the help of a legal firm who gives proper
consultation to the company regarding any types of physical hazards and the primary duty of
the company to the workers (Koshy 2015). According to section 141 of the WHS Act, every
Answer to question 3
Any harm inflicted by the workers during work time in a construction project can
be treated as physical hazards. The two main instances of physical hazard are vibration and
noise. However, the scope of the hazards could not be limited within certain circumstances. It
has been stated under the Work Health and Safety Act 2011 that every worker should get
maximum protection in the workplace (Janicak and Cekada 2016). In reality, different
pictures are observed and the possibility of bodily harm causes due to machineries,
electricity, repetitive works, work in heights and bullying. The health and safety report 2015
reveals the fact that most of the construction companies in Australia are not abiding by the
provisions of the Work Health and Safety Act and therefore, cases are pending before the
courts regarding physical hazards. Most of the physical hazards are sustained in case of the
construction site as follows:
Many workers are sustained injury by falling from the storeys and fall on the
debris;
If there is a laxity occurs in case of dealing with the storage or transportation of the
chemicals;
Serious injuries can be inflicted to the workers due to unwanted and unethical use
of asbestos;
Many cases have been reported for the death of workers due to harm sustained
from welding fumes, gases and electric shocks.
However, the present company has taken the help of a legal firm who gives proper
consultation to the company regarding any types of physical hazards and the primary duty of
the company to the workers (Koshy 2015). According to section 141 of the WHS Act, every
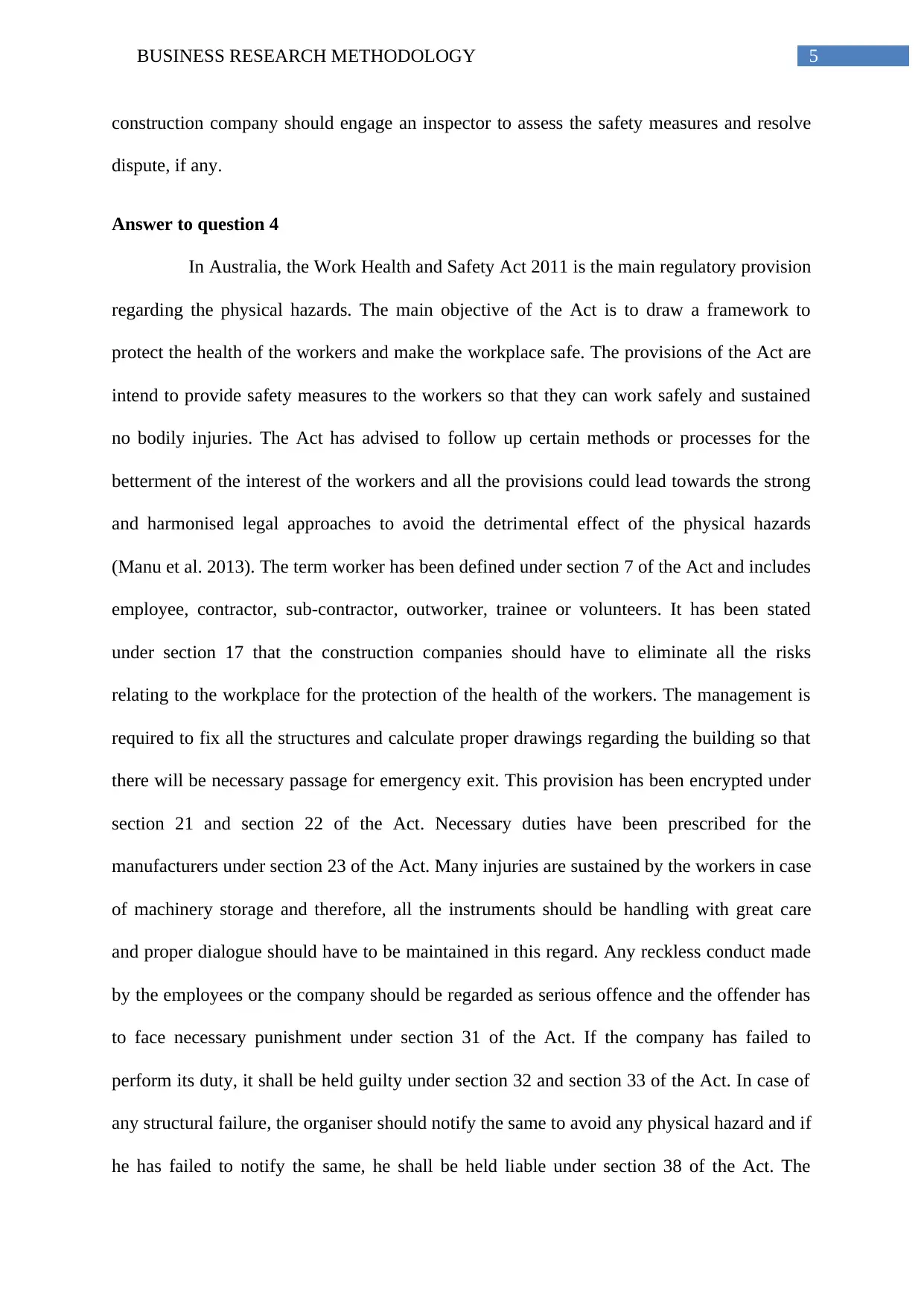
5BUSINESS RESEARCH METHODOLOGY
construction company should engage an inspector to assess the safety measures and resolve
dispute, if any.
Answer to question 4
In Australia, the Work Health and Safety Act 2011 is the main regulatory provision
regarding the physical hazards. The main objective of the Act is to draw a framework to
protect the health of the workers and make the workplace safe. The provisions of the Act are
intend to provide safety measures to the workers so that they can work safely and sustained
no bodily injuries. The Act has advised to follow up certain methods or processes for the
betterment of the interest of the workers and all the provisions could lead towards the strong
and harmonised legal approaches to avoid the detrimental effect of the physical hazards
(Manu et al. 2013). The term worker has been defined under section 7 of the Act and includes
employee, contractor, sub-contractor, outworker, trainee or volunteers. It has been stated
under section 17 that the construction companies should have to eliminate all the risks
relating to the workplace for the protection of the health of the workers. The management is
required to fix all the structures and calculate proper drawings regarding the building so that
there will be necessary passage for emergency exit. This provision has been encrypted under
section 21 and section 22 of the Act. Necessary duties have been prescribed for the
manufacturers under section 23 of the Act. Many injuries are sustained by the workers in case
of machinery storage and therefore, all the instruments should be handling with great care
and proper dialogue should have to be maintained in this regard. Any reckless conduct made
by the employees or the company should be regarded as serious offence and the offender has
to face necessary punishment under section 31 of the Act. If the company has failed to
perform its duty, it shall be held guilty under section 32 and section 33 of the Act. In case of
any structural failure, the organiser should notify the same to avoid any physical hazard and if
he has failed to notify the same, he shall be held liable under section 38 of the Act. The
construction company should engage an inspector to assess the safety measures and resolve
dispute, if any.
Answer to question 4
In Australia, the Work Health and Safety Act 2011 is the main regulatory provision
regarding the physical hazards. The main objective of the Act is to draw a framework to
protect the health of the workers and make the workplace safe. The provisions of the Act are
intend to provide safety measures to the workers so that they can work safely and sustained
no bodily injuries. The Act has advised to follow up certain methods or processes for the
betterment of the interest of the workers and all the provisions could lead towards the strong
and harmonised legal approaches to avoid the detrimental effect of the physical hazards
(Manu et al. 2013). The term worker has been defined under section 7 of the Act and includes
employee, contractor, sub-contractor, outworker, trainee or volunteers. It has been stated
under section 17 that the construction companies should have to eliminate all the risks
relating to the workplace for the protection of the health of the workers. The management is
required to fix all the structures and calculate proper drawings regarding the building so that
there will be necessary passage for emergency exit. This provision has been encrypted under
section 21 and section 22 of the Act. Necessary duties have been prescribed for the
manufacturers under section 23 of the Act. Many injuries are sustained by the workers in case
of machinery storage and therefore, all the instruments should be handling with great care
and proper dialogue should have to be maintained in this regard. Any reckless conduct made
by the employees or the company should be regarded as serious offence and the offender has
to face necessary punishment under section 31 of the Act. If the company has failed to
perform its duty, it shall be held guilty under section 32 and section 33 of the Act. In case of
any structural failure, the organiser should notify the same to avoid any physical hazard and if
he has failed to notify the same, he shall be held liable under section 38 of the Act. The
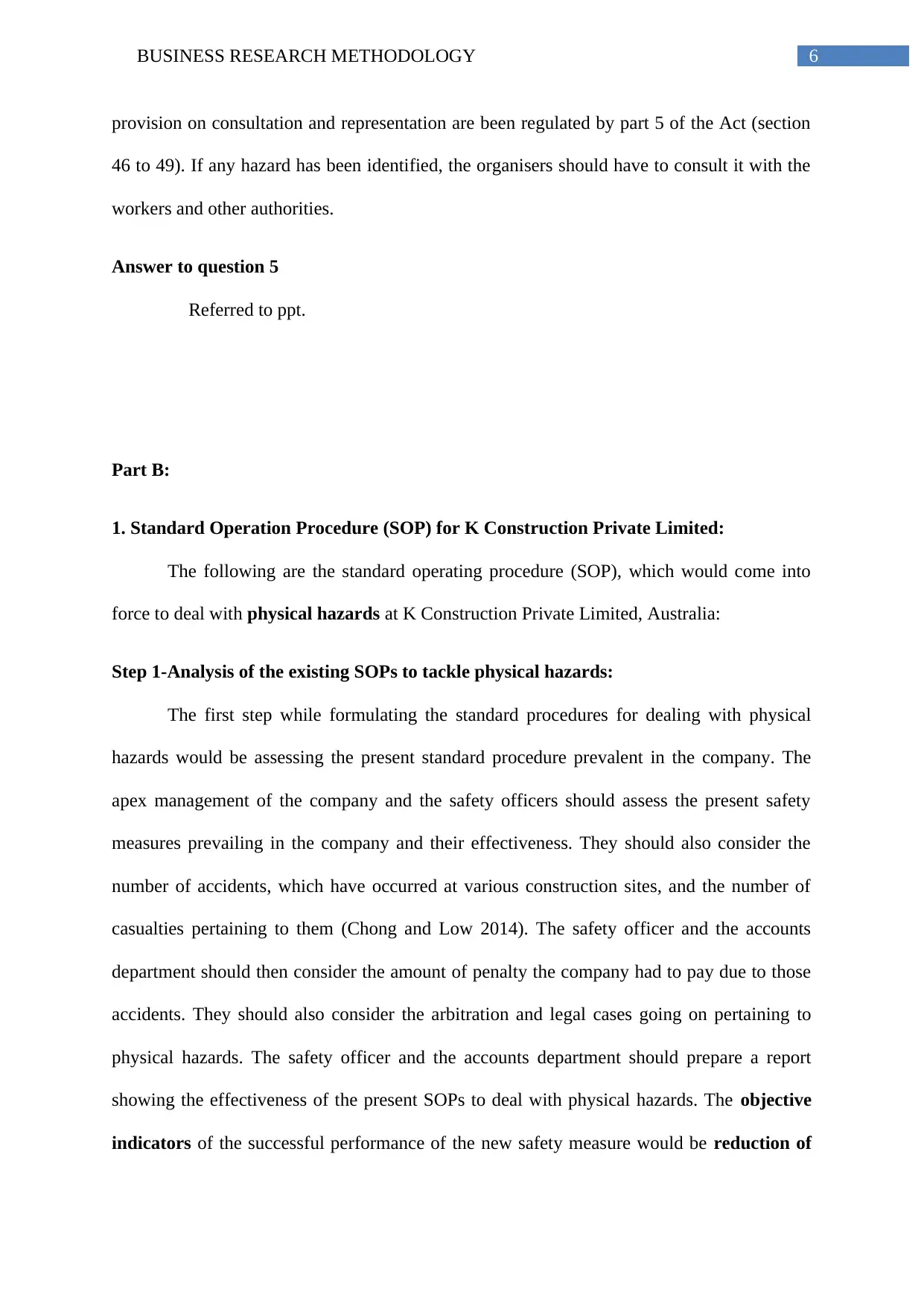
6BUSINESS RESEARCH METHODOLOGY
provision on consultation and representation are been regulated by part 5 of the Act (section
46 to 49). If any hazard has been identified, the organisers should have to consult it with the
workers and other authorities.
Answer to question 5
Referred to ppt.
Part B:
1. Standard Operation Procedure (SOP) for K Construction Private Limited:
The following are the standard operating procedure (SOP), which would come into
force to deal with physical hazards at K Construction Private Limited, Australia:
Step 1-Analysis of the existing SOPs to tackle physical hazards:
The first step while formulating the standard procedures for dealing with physical
hazards would be assessing the present standard procedure prevalent in the company. The
apex management of the company and the safety officers should assess the present safety
measures prevailing in the company and their effectiveness. They should also consider the
number of accidents, which have occurred at various construction sites, and the number of
casualties pertaining to them (Chong and Low 2014). The safety officer and the accounts
department should then consider the amount of penalty the company had to pay due to those
accidents. They should also consider the arbitration and legal cases going on pertaining to
physical hazards. The safety officer and the accounts department should prepare a report
showing the effectiveness of the present SOPs to deal with physical hazards. The objective
indicators of the successful performance of the new safety measure would be reduction of
provision on consultation and representation are been regulated by part 5 of the Act (section
46 to 49). If any hazard has been identified, the organisers should have to consult it with the
workers and other authorities.
Answer to question 5
Referred to ppt.
Part B:
1. Standard Operation Procedure (SOP) for K Construction Private Limited:
The following are the standard operating procedure (SOP), which would come into
force to deal with physical hazards at K Construction Private Limited, Australia:
Step 1-Analysis of the existing SOPs to tackle physical hazards:
The first step while formulating the standard procedures for dealing with physical
hazards would be assessing the present standard procedure prevalent in the company. The
apex management of the company and the safety officers should assess the present safety
measures prevailing in the company and their effectiveness. They should also consider the
number of accidents, which have occurred at various construction sites, and the number of
casualties pertaining to them (Chong and Low 2014). The safety officer and the accounts
department should then consider the amount of penalty the company had to pay due to those
accidents. They should also consider the arbitration and legal cases going on pertaining to
physical hazards. The safety officer and the accounts department should prepare a report
showing the effectiveness of the present SOPs to deal with physical hazards. The objective
indicators of the successful performance of the new safety measure would be reduction of
Paraphrase This Document
Need a fresh take? Get an instant paraphrase of this document with our AI Paraphraser
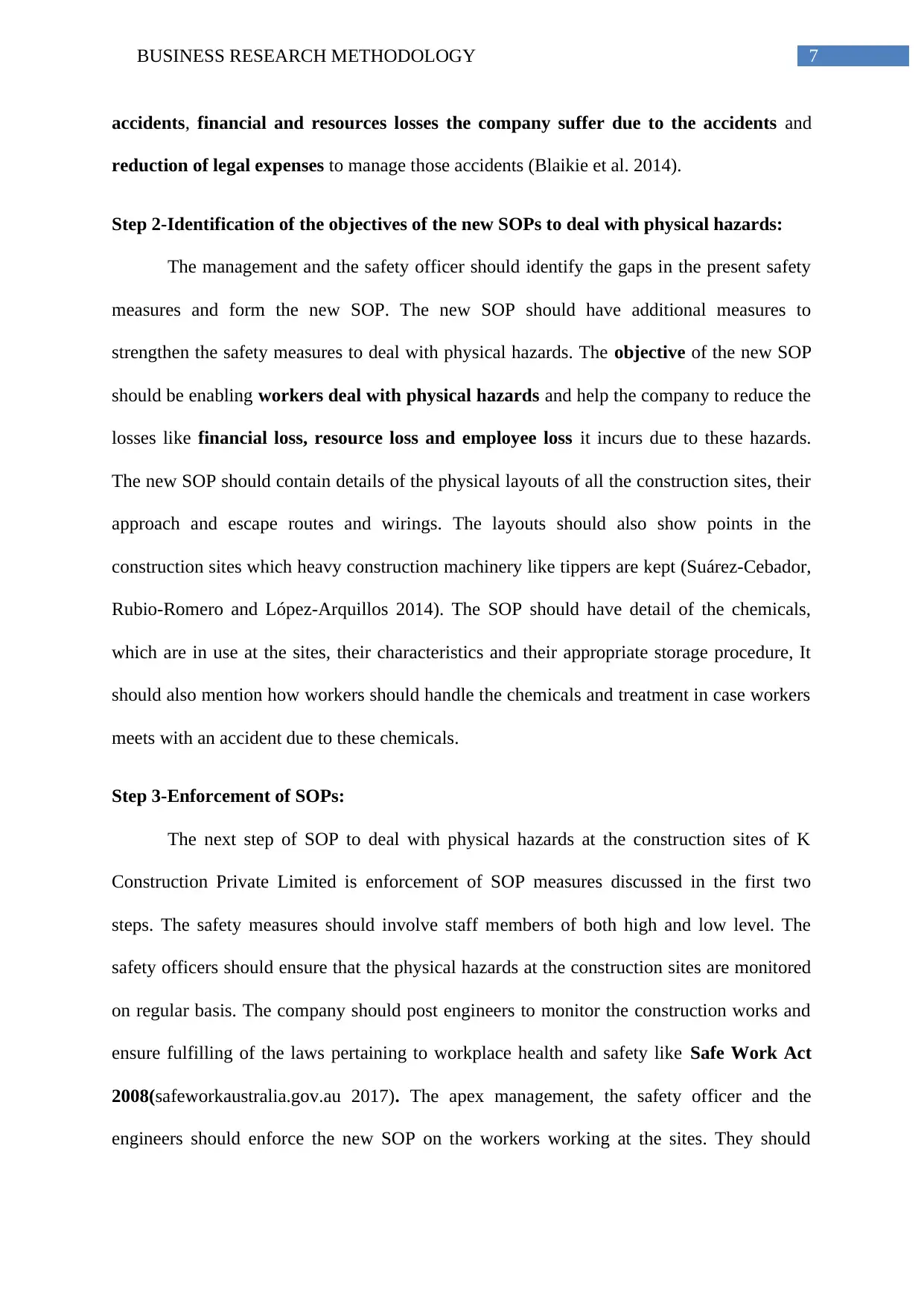
7BUSINESS RESEARCH METHODOLOGY
accidents, financial and resources losses the company suffer due to the accidents and
reduction of legal expenses to manage those accidents (Blaikie et al. 2014).
Step 2-Identification of the objectives of the new SOPs to deal with physical hazards:
The management and the safety officer should identify the gaps in the present safety
measures and form the new SOP. The new SOP should have additional measures to
strengthen the safety measures to deal with physical hazards. The objective of the new SOP
should be enabling workers deal with physical hazards and help the company to reduce the
losses like financial loss, resource loss and employee loss it incurs due to these hazards.
The new SOP should contain details of the physical layouts of all the construction sites, their
approach and escape routes and wirings. The layouts should also show points in the
construction sites which heavy construction machinery like tippers are kept (Suárez-Cebador,
Rubio-Romero and López-Arquillos 2014). The SOP should have detail of the chemicals,
which are in use at the sites, their characteristics and their appropriate storage procedure, It
should also mention how workers should handle the chemicals and treatment in case workers
meets with an accident due to these chemicals.
Step 3-Enforcement of SOPs:
The next step of SOP to deal with physical hazards at the construction sites of K
Construction Private Limited is enforcement of SOP measures discussed in the first two
steps. The safety measures should involve staff members of both high and low level. The
safety officers should ensure that the physical hazards at the construction sites are monitored
on regular basis. The company should post engineers to monitor the construction works and
ensure fulfilling of the laws pertaining to workplace health and safety like Safe Work Act
2008(safeworkaustralia.gov.au 2017). The apex management, the safety officer and the
engineers should enforce the new SOP on the workers working at the sites. They should
accidents, financial and resources losses the company suffer due to the accidents and
reduction of legal expenses to manage those accidents (Blaikie et al. 2014).
Step 2-Identification of the objectives of the new SOPs to deal with physical hazards:
The management and the safety officer should identify the gaps in the present safety
measures and form the new SOP. The new SOP should have additional measures to
strengthen the safety measures to deal with physical hazards. The objective of the new SOP
should be enabling workers deal with physical hazards and help the company to reduce the
losses like financial loss, resource loss and employee loss it incurs due to these hazards.
The new SOP should contain details of the physical layouts of all the construction sites, their
approach and escape routes and wirings. The layouts should also show points in the
construction sites which heavy construction machinery like tippers are kept (Suárez-Cebador,
Rubio-Romero and López-Arquillos 2014). The SOP should have detail of the chemicals,
which are in use at the sites, their characteristics and their appropriate storage procedure, It
should also mention how workers should handle the chemicals and treatment in case workers
meets with an accident due to these chemicals.
Step 3-Enforcement of SOPs:
The next step of SOP to deal with physical hazards at the construction sites of K
Construction Private Limited is enforcement of SOP measures discussed in the first two
steps. The safety measures should involve staff members of both high and low level. The
safety officers should ensure that the physical hazards at the construction sites are monitored
on regular basis. The company should post engineers to monitor the construction works and
ensure fulfilling of the laws pertaining to workplace health and safety like Safe Work Act
2008(safeworkaustralia.gov.au 2017). The apex management, the safety officer and the
engineers should enforce the new SOP on the workers working at the sites. They should
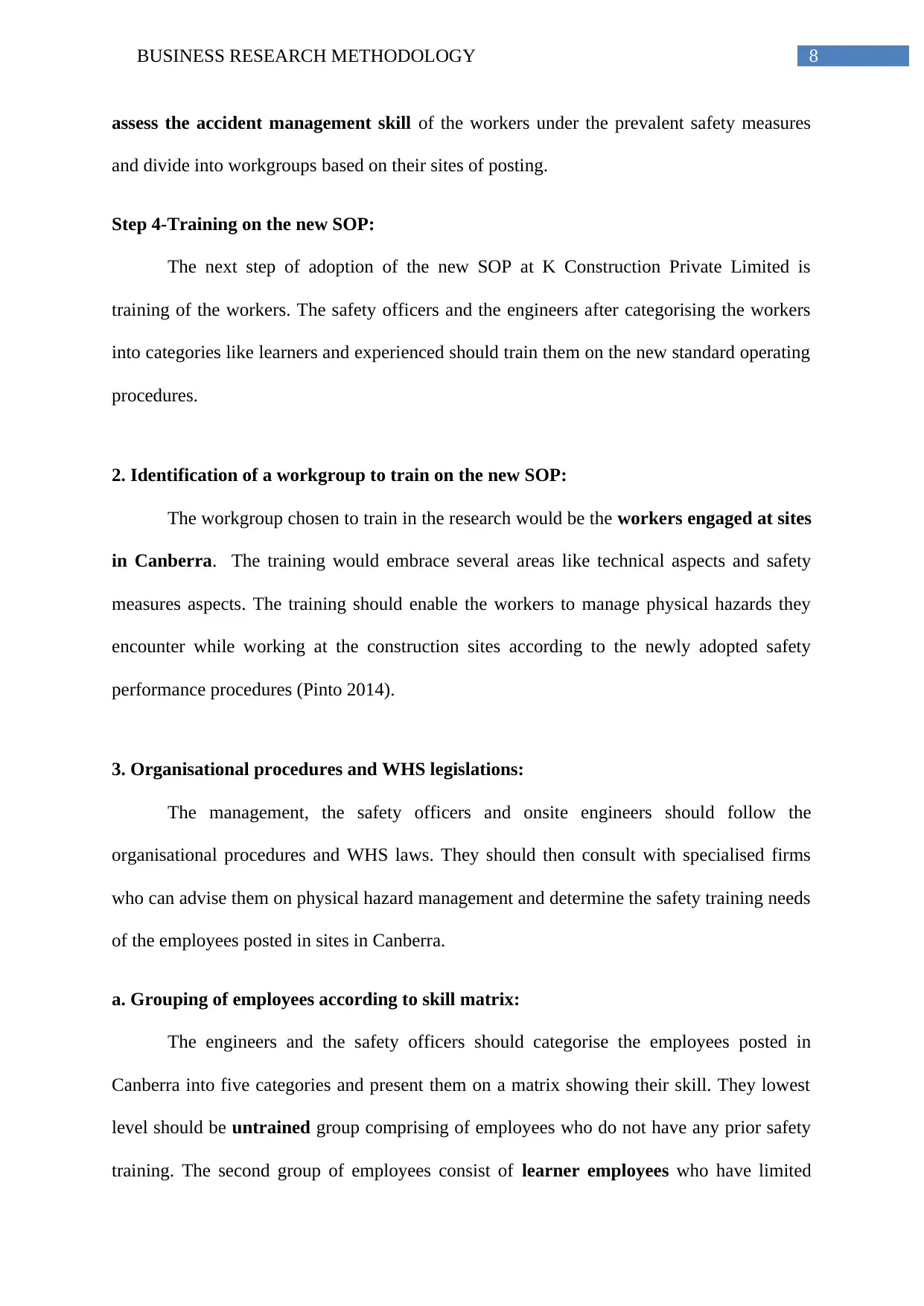
8BUSINESS RESEARCH METHODOLOGY
assess the accident management skill of the workers under the prevalent safety measures
and divide into workgroups based on their sites of posting.
Step 4-Training on the new SOP:
The next step of adoption of the new SOP at K Construction Private Limited is
training of the workers. The safety officers and the engineers after categorising the workers
into categories like learners and experienced should train them on the new standard operating
procedures.
2. Identification of a workgroup to train on the new SOP:
The workgroup chosen to train in the research would be the workers engaged at sites
in Canberra. The training would embrace several areas like technical aspects and safety
measures aspects. The training should enable the workers to manage physical hazards they
encounter while working at the construction sites according to the newly adopted safety
performance procedures (Pinto 2014).
3. Organisational procedures and WHS legislations:
The management, the safety officers and onsite engineers should follow the
organisational procedures and WHS laws. They should then consult with specialised firms
who can advise them on physical hazard management and determine the safety training needs
of the employees posted in sites in Canberra.
a. Grouping of employees according to skill matrix:
The engineers and the safety officers should categorise the employees posted in
Canberra into five categories and present them on a matrix showing their skill. They lowest
level should be untrained group comprising of employees who do not have any prior safety
training. The second group of employees consist of learner employees who have limited
assess the accident management skill of the workers under the prevalent safety measures
and divide into workgroups based on their sites of posting.
Step 4-Training on the new SOP:
The next step of adoption of the new SOP at K Construction Private Limited is
training of the workers. The safety officers and the engineers after categorising the workers
into categories like learners and experienced should train them on the new standard operating
procedures.
2. Identification of a workgroup to train on the new SOP:
The workgroup chosen to train in the research would be the workers engaged at sites
in Canberra. The training would embrace several areas like technical aspects and safety
measures aspects. The training should enable the workers to manage physical hazards they
encounter while working at the construction sites according to the newly adopted safety
performance procedures (Pinto 2014).
3. Organisational procedures and WHS legislations:
The management, the safety officers and onsite engineers should follow the
organisational procedures and WHS laws. They should then consult with specialised firms
who can advise them on physical hazard management and determine the safety training needs
of the employees posted in sites in Canberra.
a. Grouping of employees according to skill matrix:
The engineers and the safety officers should categorise the employees posted in
Canberra into five categories and present them on a matrix showing their skill. They lowest
level should be untrained group comprising of employees who do not have any prior safety
training. The second group of employees consist of learner employees who have limited
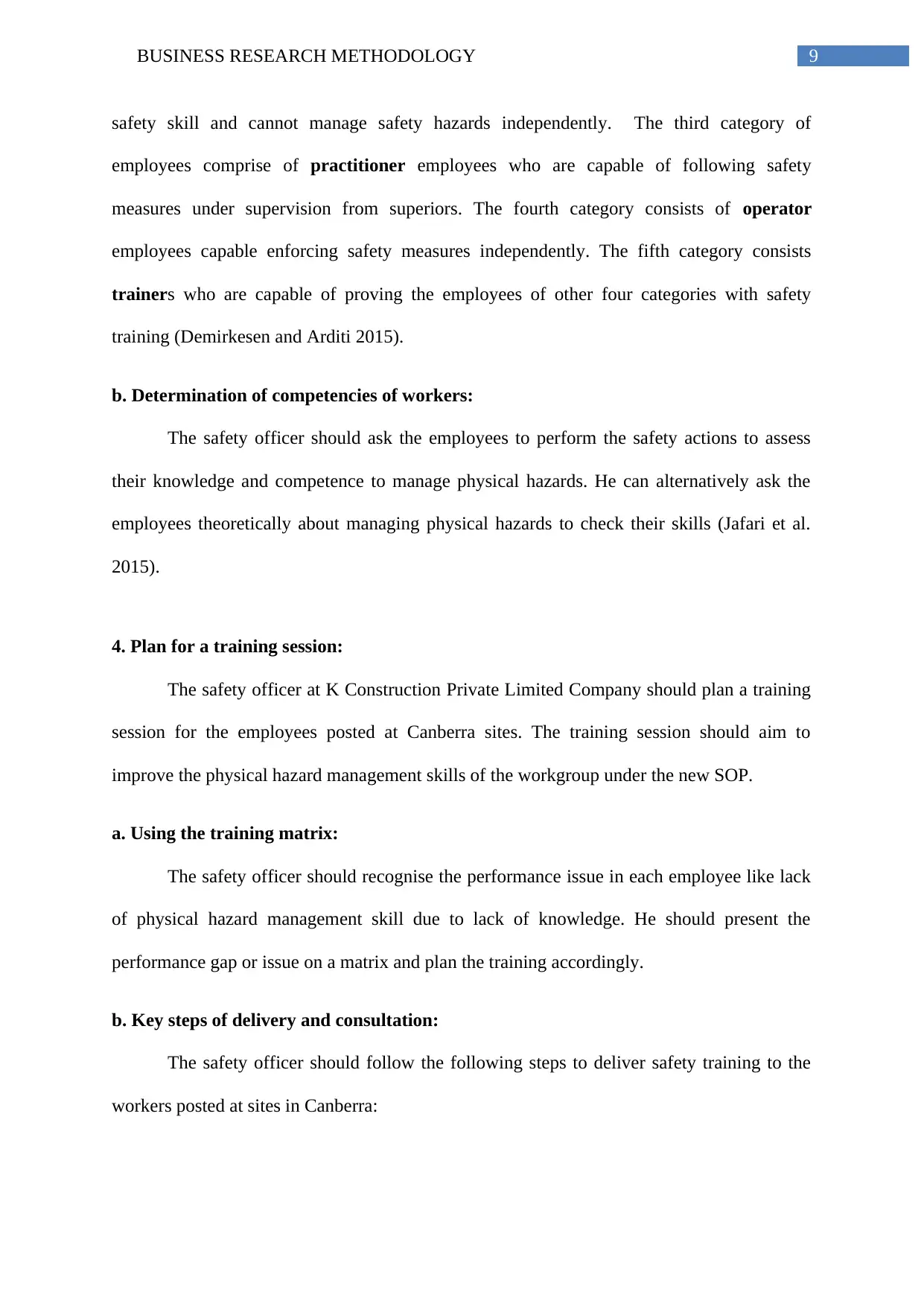
9BUSINESS RESEARCH METHODOLOGY
safety skill and cannot manage safety hazards independently. The third category of
employees comprise of practitioner employees who are capable of following safety
measures under supervision from superiors. The fourth category consists of operator
employees capable enforcing safety measures independently. The fifth category consists
trainers who are capable of proving the employees of other four categories with safety
training (Demirkesen and Arditi 2015).
b. Determination of competencies of workers:
The safety officer should ask the employees to perform the safety actions to assess
their knowledge and competence to manage physical hazards. He can alternatively ask the
employees theoretically about managing physical hazards to check their skills (Jafari et al.
2015).
4. Plan for a training session:
The safety officer at K Construction Private Limited Company should plan a training
session for the employees posted at Canberra sites. The training session should aim to
improve the physical hazard management skills of the workgroup under the new SOP.
a. Using the training matrix:
The safety officer should recognise the performance issue in each employee like lack
of physical hazard management skill due to lack of knowledge. He should present the
performance gap or issue on a matrix and plan the training accordingly.
b. Key steps of delivery and consultation:
The safety officer should follow the following steps to deliver safety training to the
workers posted at sites in Canberra:
safety skill and cannot manage safety hazards independently. The third category of
employees comprise of practitioner employees who are capable of following safety
measures under supervision from superiors. The fourth category consists of operator
employees capable enforcing safety measures independently. The fifth category consists
trainers who are capable of proving the employees of other four categories with safety
training (Demirkesen and Arditi 2015).
b. Determination of competencies of workers:
The safety officer should ask the employees to perform the safety actions to assess
their knowledge and competence to manage physical hazards. He can alternatively ask the
employees theoretically about managing physical hazards to check their skills (Jafari et al.
2015).
4. Plan for a training session:
The safety officer at K Construction Private Limited Company should plan a training
session for the employees posted at Canberra sites. The training session should aim to
improve the physical hazard management skills of the workgroup under the new SOP.
a. Using the training matrix:
The safety officer should recognise the performance issue in each employee like lack
of physical hazard management skill due to lack of knowledge. He should present the
performance gap or issue on a matrix and plan the training accordingly.
b. Key steps of delivery and consultation:
The safety officer should follow the following steps to deliver safety training to the
workers posted at sites in Canberra:
Secure Best Marks with AI Grader
Need help grading? Try our AI Grader for instant feedback on your assignments.
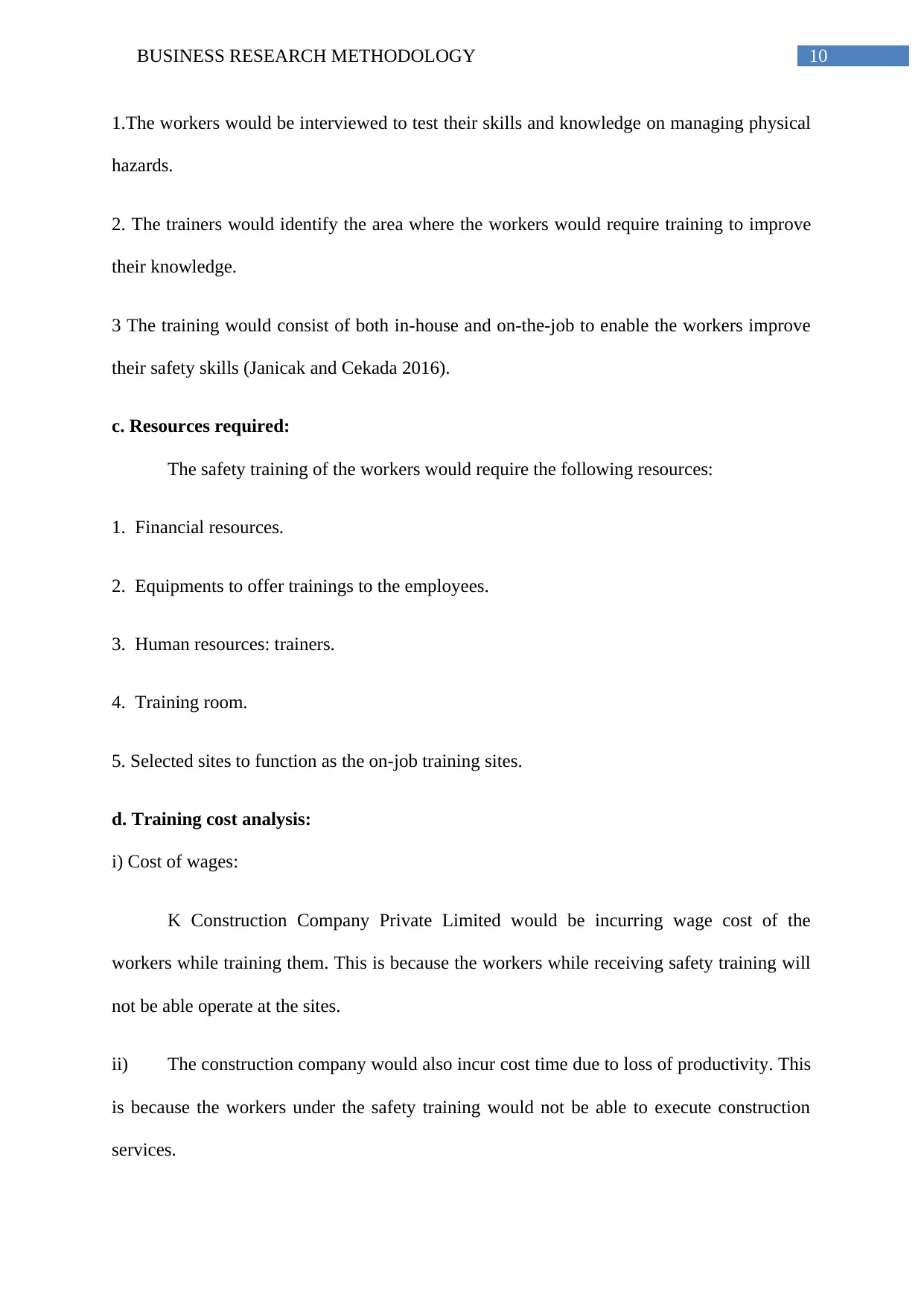
10BUSINESS RESEARCH METHODOLOGY
1.The workers would be interviewed to test their skills and knowledge on managing physical
hazards.
2. The trainers would identify the area where the workers would require training to improve
their knowledge.
3 The training would consist of both in-house and on-the-job to enable the workers improve
their safety skills (Janicak and Cekada 2016).
c. Resources required:
The safety training of the workers would require the following resources:
1. Financial resources.
2. Equipments to offer trainings to the employees.
3. Human resources: trainers.
4. Training room.
5. Selected sites to function as the on-job training sites.
d. Training cost analysis:
i) Cost of wages:
K Construction Company Private Limited would be incurring wage cost of the
workers while training them. This is because the workers while receiving safety training will
not be able operate at the sites.
ii) The construction company would also incur cost time due to loss of productivity. This
is because the workers under the safety training would not be able to execute construction
services.
1.The workers would be interviewed to test their skills and knowledge on managing physical
hazards.
2. The trainers would identify the area where the workers would require training to improve
their knowledge.
3 The training would consist of both in-house and on-the-job to enable the workers improve
their safety skills (Janicak and Cekada 2016).
c. Resources required:
The safety training of the workers would require the following resources:
1. Financial resources.
2. Equipments to offer trainings to the employees.
3. Human resources: trainers.
4. Training room.
5. Selected sites to function as the on-job training sites.
d. Training cost analysis:
i) Cost of wages:
K Construction Company Private Limited would be incurring wage cost of the
workers while training them. This is because the workers while receiving safety training will
not be able operate at the sites.
ii) The construction company would also incur cost time due to loss of productivity. This
is because the workers under the safety training would not be able to execute construction
services.
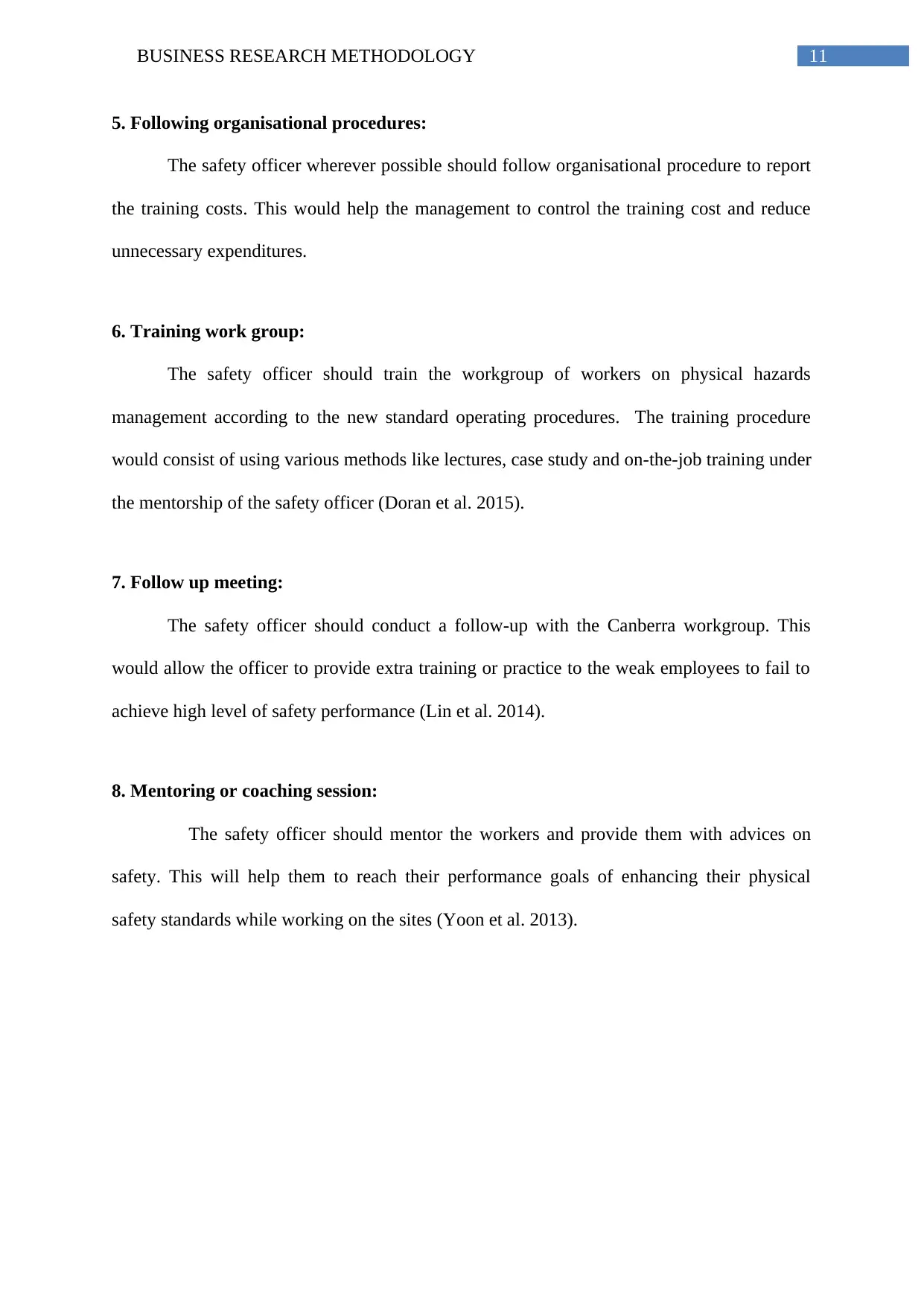
11BUSINESS RESEARCH METHODOLOGY
5. Following organisational procedures:
The safety officer wherever possible should follow organisational procedure to report
the training costs. This would help the management to control the training cost and reduce
unnecessary expenditures.
6. Training work group:
The safety officer should train the workgroup of workers on physical hazards
management according to the new standard operating procedures. The training procedure
would consist of using various methods like lectures, case study and on-the-job training under
the mentorship of the safety officer (Doran et al. 2015).
7. Follow up meeting:
The safety officer should conduct a follow-up with the Canberra workgroup. This
would allow the officer to provide extra training or practice to the weak employees to fail to
achieve high level of safety performance (Lin et al. 2014).
8. Mentoring or coaching session:
The safety officer should mentor the workers and provide them with advices on
safety. This will help them to reach their performance goals of enhancing their physical
safety standards while working on the sites (Yoon et al. 2013).
5. Following organisational procedures:
The safety officer wherever possible should follow organisational procedure to report
the training costs. This would help the management to control the training cost and reduce
unnecessary expenditures.
6. Training work group:
The safety officer should train the workgroup of workers on physical hazards
management according to the new standard operating procedures. The training procedure
would consist of using various methods like lectures, case study and on-the-job training under
the mentorship of the safety officer (Doran et al. 2015).
7. Follow up meeting:
The safety officer should conduct a follow-up with the Canberra workgroup. This
would allow the officer to provide extra training or practice to the weak employees to fail to
achieve high level of safety performance (Lin et al. 2014).
8. Mentoring or coaching session:
The safety officer should mentor the workers and provide them with advices on
safety. This will help them to reach their performance goals of enhancing their physical
safety standards while working on the sites (Yoon et al. 2013).
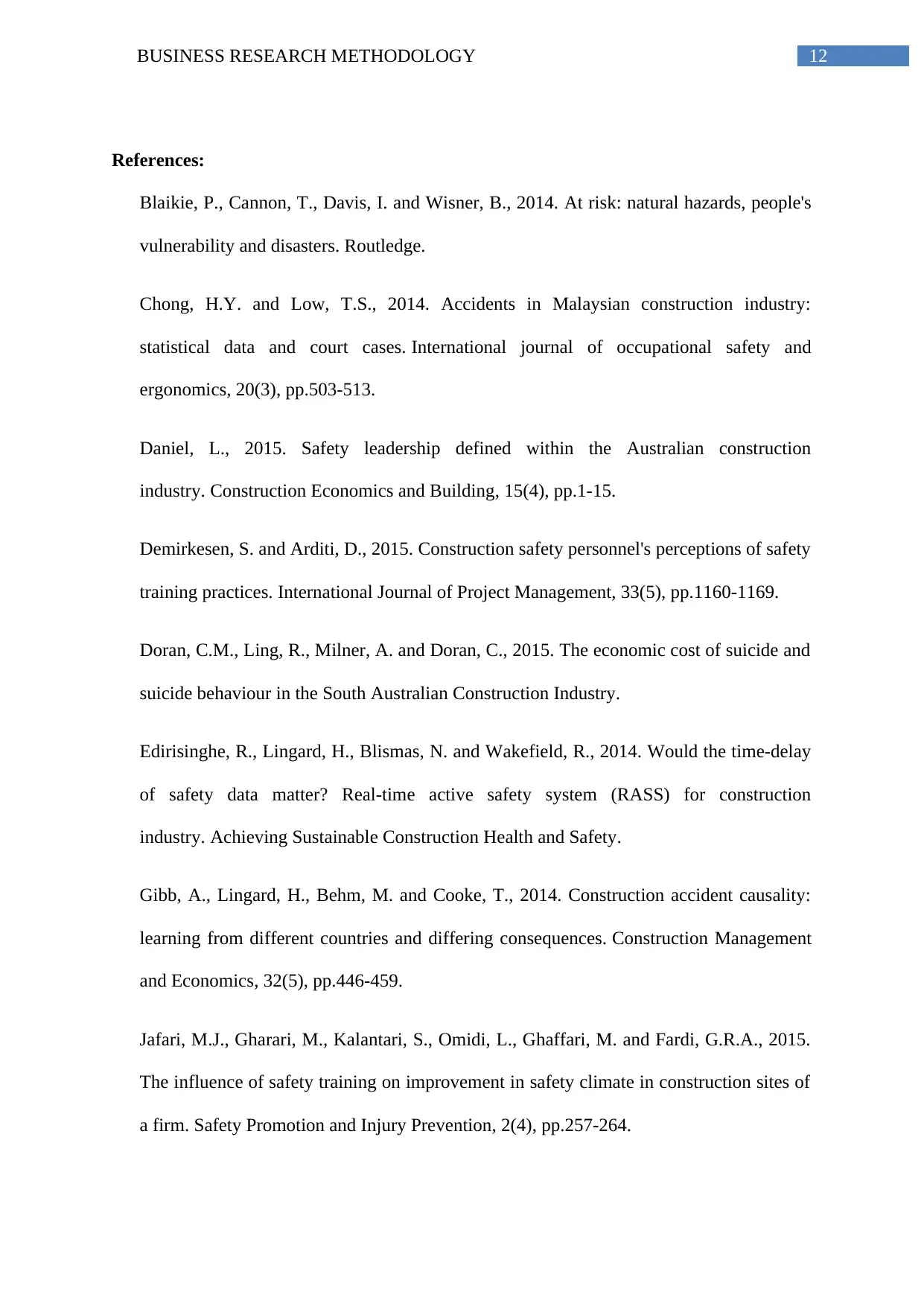
12BUSINESS RESEARCH METHODOLOGY
References:
Blaikie, P., Cannon, T., Davis, I. and Wisner, B., 2014. At risk: natural hazards, people's
vulnerability and disasters. Routledge.
Chong, H.Y. and Low, T.S., 2014. Accidents in Malaysian construction industry:
statistical data and court cases. International journal of occupational safety and
ergonomics, 20(3), pp.503-513.
Daniel, L., 2015. Safety leadership defined within the Australian construction
industry. Construction Economics and Building, 15(4), pp.1-15.
Demirkesen, S. and Arditi, D., 2015. Construction safety personnel's perceptions of safety
training practices. International Journal of Project Management, 33(5), pp.1160-1169.
Doran, C.M., Ling, R., Milner, A. and Doran, C., 2015. The economic cost of suicide and
suicide behaviour in the South Australian Construction Industry.
Edirisinghe, R., Lingard, H., Blismas, N. and Wakefield, R., 2014. Would the time-delay
of safety data matter? Real-time active safety system (RASS) for construction
industry. Achieving Sustainable Construction Health and Safety.
Gibb, A., Lingard, H., Behm, M. and Cooke, T., 2014. Construction accident causality:
learning from different countries and differing consequences. Construction Management
and Economics, 32(5), pp.446-459.
Jafari, M.J., Gharari, M., Kalantari, S., Omidi, L., Ghaffari, M. and Fardi, G.R.A., 2015.
The influence of safety training on improvement in safety climate in construction sites of
a firm. Safety Promotion and Injury Prevention, 2(4), pp.257-264.
References:
Blaikie, P., Cannon, T., Davis, I. and Wisner, B., 2014. At risk: natural hazards, people's
vulnerability and disasters. Routledge.
Chong, H.Y. and Low, T.S., 2014. Accidents in Malaysian construction industry:
statistical data and court cases. International journal of occupational safety and
ergonomics, 20(3), pp.503-513.
Daniel, L., 2015. Safety leadership defined within the Australian construction
industry. Construction Economics and Building, 15(4), pp.1-15.
Demirkesen, S. and Arditi, D., 2015. Construction safety personnel's perceptions of safety
training practices. International Journal of Project Management, 33(5), pp.1160-1169.
Doran, C.M., Ling, R., Milner, A. and Doran, C., 2015. The economic cost of suicide and
suicide behaviour in the South Australian Construction Industry.
Edirisinghe, R., Lingard, H., Blismas, N. and Wakefield, R., 2014. Would the time-delay
of safety data matter? Real-time active safety system (RASS) for construction
industry. Achieving Sustainable Construction Health and Safety.
Gibb, A., Lingard, H., Behm, M. and Cooke, T., 2014. Construction accident causality:
learning from different countries and differing consequences. Construction Management
and Economics, 32(5), pp.446-459.
Jafari, M.J., Gharari, M., Kalantari, S., Omidi, L., Ghaffari, M. and Fardi, G.R.A., 2015.
The influence of safety training on improvement in safety climate in construction sites of
a firm. Safety Promotion and Injury Prevention, 2(4), pp.257-264.
Paraphrase This Document
Need a fresh take? Get an instant paraphrase of this document with our AI Paraphraser
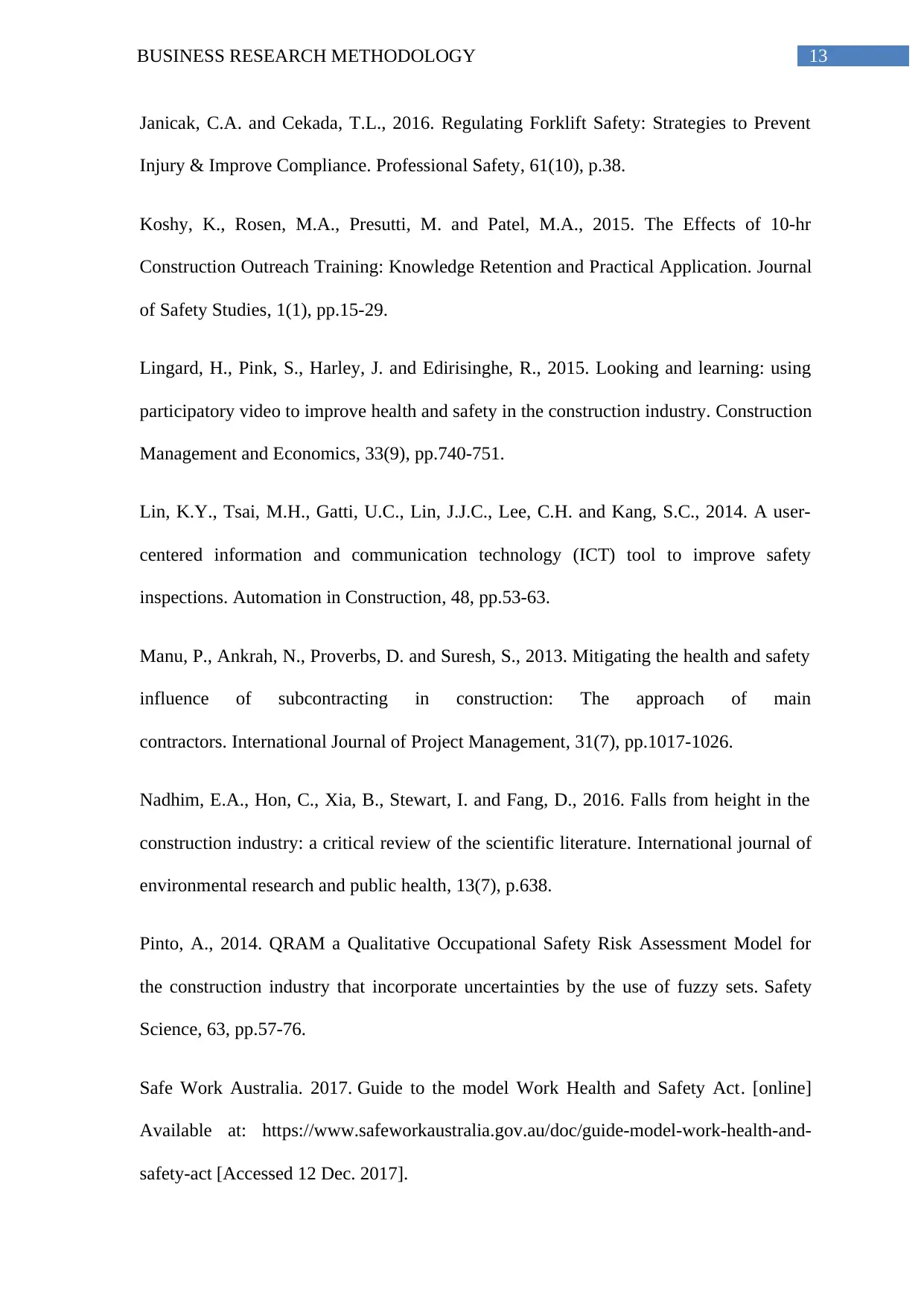
13BUSINESS RESEARCH METHODOLOGY
Janicak, C.A. and Cekada, T.L., 2016. Regulating Forklift Safety: Strategies to Prevent
Injury & Improve Compliance. Professional Safety, 61(10), p.38.
Koshy, K., Rosen, M.A., Presutti, M. and Patel, M.A., 2015. The Effects of 10-hr
Construction Outreach Training: Knowledge Retention and Practical Application. Journal
of Safety Studies, 1(1), pp.15-29.
Lingard, H., Pink, S., Harley, J. and Edirisinghe, R., 2015. Looking and learning: using
participatory video to improve health and safety in the construction industry. Construction
Management and Economics, 33(9), pp.740-751.
Lin, K.Y., Tsai, M.H., Gatti, U.C., Lin, J.J.C., Lee, C.H. and Kang, S.C., 2014. A user-
centered information and communication technology (ICT) tool to improve safety
inspections. Automation in Construction, 48, pp.53-63.
Manu, P., Ankrah, N., Proverbs, D. and Suresh, S., 2013. Mitigating the health and safety
influence of subcontracting in construction: The approach of main
contractors. International Journal of Project Management, 31(7), pp.1017-1026.
Nadhim, E.A., Hon, C., Xia, B., Stewart, I. and Fang, D., 2016. Falls from height in the
construction industry: a critical review of the scientific literature. International journal of
environmental research and public health, 13(7), p.638.
Pinto, A., 2014. QRAM a Qualitative Occupational Safety Risk Assessment Model for
the construction industry that incorporate uncertainties by the use of fuzzy sets. Safety
Science, 63, pp.57-76.
Safe Work Australia. 2017. Guide to the model Work Health and Safety Act. [online]
Available at: https://www.safeworkaustralia.gov.au/doc/guide-model-work-health-and-
safety-act [Accessed 12 Dec. 2017].
Janicak, C.A. and Cekada, T.L., 2016. Regulating Forklift Safety: Strategies to Prevent
Injury & Improve Compliance. Professional Safety, 61(10), p.38.
Koshy, K., Rosen, M.A., Presutti, M. and Patel, M.A., 2015. The Effects of 10-hr
Construction Outreach Training: Knowledge Retention and Practical Application. Journal
of Safety Studies, 1(1), pp.15-29.
Lingard, H., Pink, S., Harley, J. and Edirisinghe, R., 2015. Looking and learning: using
participatory video to improve health and safety in the construction industry. Construction
Management and Economics, 33(9), pp.740-751.
Lin, K.Y., Tsai, M.H., Gatti, U.C., Lin, J.J.C., Lee, C.H. and Kang, S.C., 2014. A user-
centered information and communication technology (ICT) tool to improve safety
inspections. Automation in Construction, 48, pp.53-63.
Manu, P., Ankrah, N., Proverbs, D. and Suresh, S., 2013. Mitigating the health and safety
influence of subcontracting in construction: The approach of main
contractors. International Journal of Project Management, 31(7), pp.1017-1026.
Nadhim, E.A., Hon, C., Xia, B., Stewart, I. and Fang, D., 2016. Falls from height in the
construction industry: a critical review of the scientific literature. International journal of
environmental research and public health, 13(7), p.638.
Pinto, A., 2014. QRAM a Qualitative Occupational Safety Risk Assessment Model for
the construction industry that incorporate uncertainties by the use of fuzzy sets. Safety
Science, 63, pp.57-76.
Safe Work Australia. 2017. Guide to the model Work Health and Safety Act. [online]
Available at: https://www.safeworkaustralia.gov.au/doc/guide-model-work-health-and-
safety-act [Accessed 12 Dec. 2017].
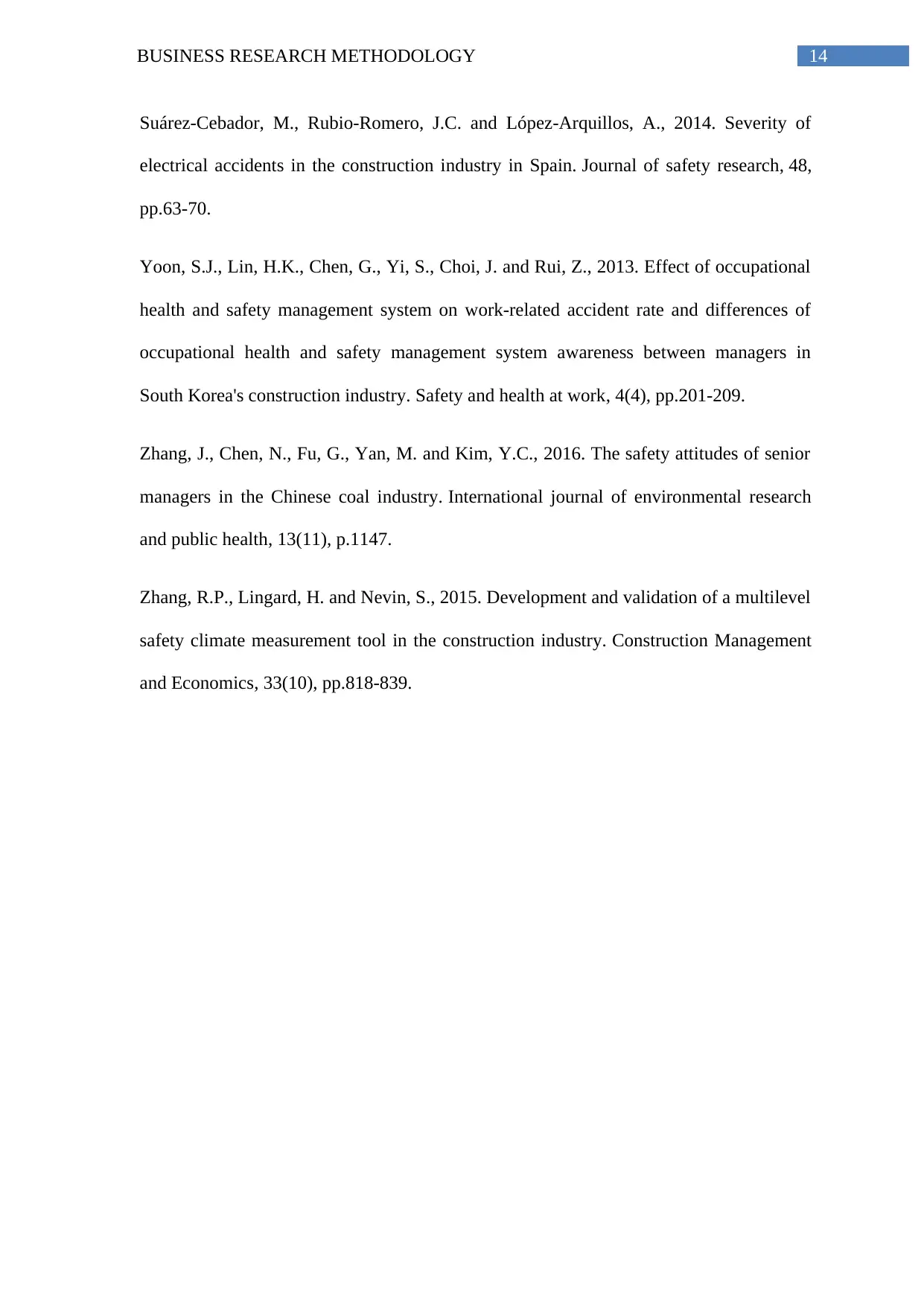
14BUSINESS RESEARCH METHODOLOGY
Suárez-Cebador, M., Rubio-Romero, J.C. and López-Arquillos, A., 2014. Severity of
electrical accidents in the construction industry in Spain. Journal of safety research, 48,
pp.63-70.
Yoon, S.J., Lin, H.K., Chen, G., Yi, S., Choi, J. and Rui, Z., 2013. Effect of occupational
health and safety management system on work-related accident rate and differences of
occupational health and safety management system awareness between managers in
South Korea's construction industry. Safety and health at work, 4(4), pp.201-209.
Zhang, J., Chen, N., Fu, G., Yan, M. and Kim, Y.C., 2016. The safety attitudes of senior
managers in the Chinese coal industry. International journal of environmental research
and public health, 13(11), p.1147.
Zhang, R.P., Lingard, H. and Nevin, S., 2015. Development and validation of a multilevel
safety climate measurement tool in the construction industry. Construction Management
and Economics, 33(10), pp.818-839.
Suárez-Cebador, M., Rubio-Romero, J.C. and López-Arquillos, A., 2014. Severity of
electrical accidents in the construction industry in Spain. Journal of safety research, 48,
pp.63-70.
Yoon, S.J., Lin, H.K., Chen, G., Yi, S., Choi, J. and Rui, Z., 2013. Effect of occupational
health and safety management system on work-related accident rate and differences of
occupational health and safety management system awareness between managers in
South Korea's construction industry. Safety and health at work, 4(4), pp.201-209.
Zhang, J., Chen, N., Fu, G., Yan, M. and Kim, Y.C., 2016. The safety attitudes of senior
managers in the Chinese coal industry. International journal of environmental research
and public health, 13(11), p.1147.
Zhang, R.P., Lingard, H. and Nevin, S., 2015. Development and validation of a multilevel
safety climate measurement tool in the construction industry. Construction Management
and Economics, 33(10), pp.818-839.
1 out of 15
Related Documents

Your All-in-One AI-Powered Toolkit for Academic Success.
+13062052269
info@desklib.com
Available 24*7 on WhatsApp / Email
Unlock your academic potential
© 2024 | Zucol Services PVT LTD | All rights reserved.