How Kaizen and JIT Strategies Improve Work Processes: Post-Pandemic
VerifiedAdded on 2022/02/23
|13
|4782
|66
Report
AI Summary
This report examines the transformative impact of Kaizen and Just-In-Time (JIT) strategies on organizational work processes, particularly in the wake of the COVID-19 pandemic. It begins by outlining the significant disruptions caused by the pandemic, including supply chain shocks, demand fluctuations, and increased transportation costs, using Mapletree as a case study. The analysis then delves into the core principles of Kaizen, emphasizing continuous improvement and employee involvement, and how these principles can be applied to enhance productivity and adaptability. The report further explores the benefits of JIT, such as inventory reduction and streamlined operations, in mitigating the challenges of the post-pandemic business environment. The discussion includes practical examples like remote working opportunities, and creative problem-solving, highlighting how organizations can leverage these strategies to build more resilient and efficient operations. The report concludes by emphasizing the importance of proactive measures and flexible approaches in navigating the evolving landscape of global business and supply chains, as well as how Kaizen and JIT strategies can improve work processes.
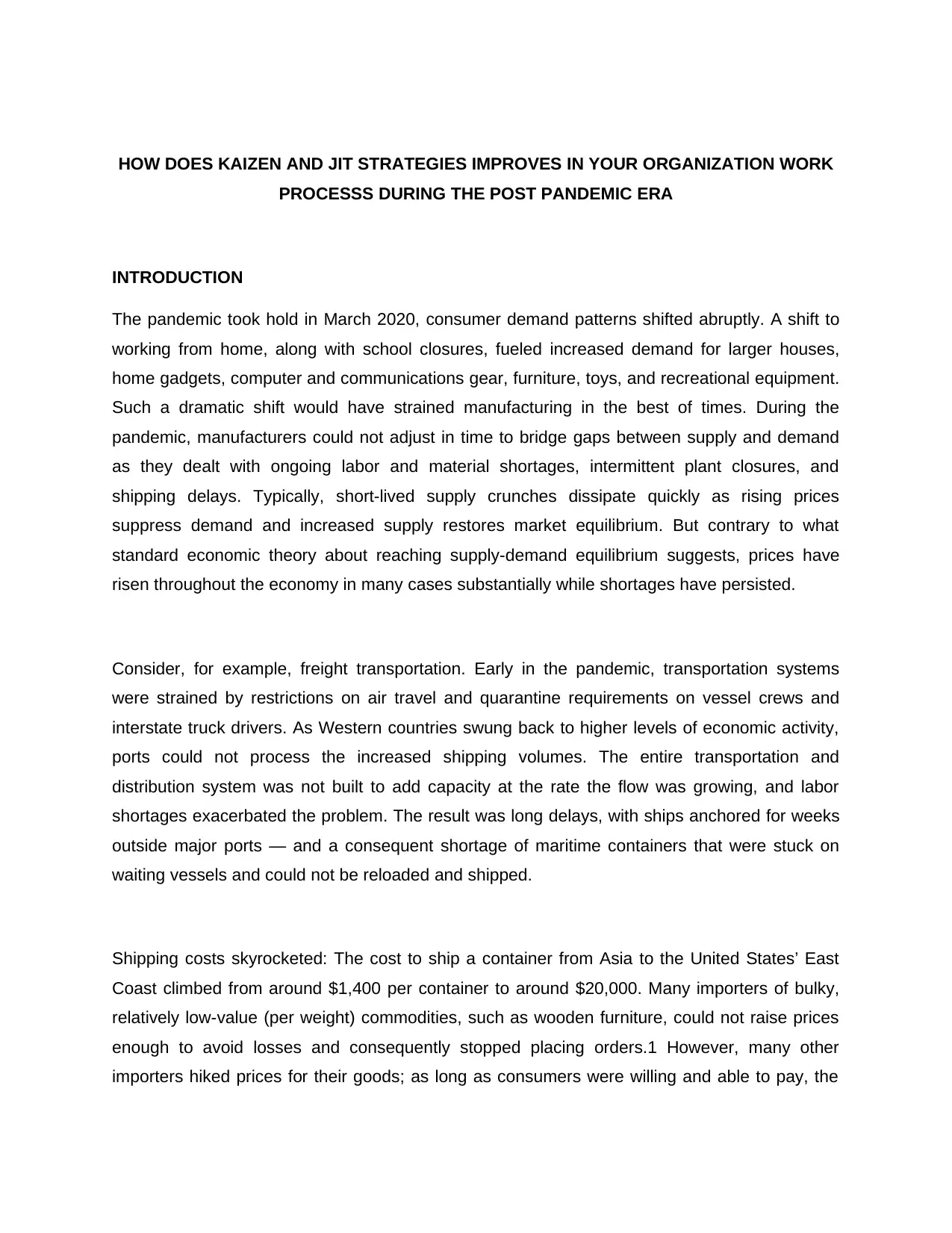
HOW DOES KAIZEN AND JIT STRATEGIES IMPROVES IN YOUR ORGANIZATION WORK
PROCESSS DURING THE POST PANDEMIC ERA
INTRODUCTION
The pandemic took hold in March 2020, consumer demand patterns shifted abruptly. A shift to
working from home, along with school closures, fueled increased demand for larger houses,
home gadgets, computer and communications gear, furniture, toys, and recreational equipment.
Such a dramatic shift would have strained manufacturing in the best of times. During the
pandemic, manufacturers could not adjust in time to bridge gaps between supply and demand
as they dealt with ongoing labor and material shortages, intermittent plant closures, and
shipping delays. Typically, short-lived supply crunches dissipate quickly as rising prices
suppress demand and increased supply restores market equilibrium. But contrary to what
standard economic theory about reaching supply-demand equilibrium suggests, prices have
risen throughout the economy in many cases substantially while shortages have persisted.
Consider, for example, freight transportation. Early in the pandemic, transportation systems
were strained by restrictions on air travel and quarantine requirements on vessel crews and
interstate truck drivers. As Western countries swung back to higher levels of economic activity,
ports could not process the increased shipping volumes. The entire transportation and
distribution system was not built to add capacity at the rate the flow was growing, and labor
shortages exacerbated the problem. The result was long delays, with ships anchored for weeks
outside major ports — and a consequent shortage of maritime containers that were stuck on
waiting vessels and could not be reloaded and shipped.
Shipping costs skyrocketed: The cost to ship a container from Asia to the United States’ East
Coast climbed from around $1,400 per container to around $20,000. Many importers of bulky,
relatively low-value (per weight) commodities, such as wooden furniture, could not raise prices
enough to avoid losses and consequently stopped placing orders.1 However, many other
importers hiked prices for their goods; as long as consumers were willing and able to pay, the
PROCESSS DURING THE POST PANDEMIC ERA
INTRODUCTION
The pandemic took hold in March 2020, consumer demand patterns shifted abruptly. A shift to
working from home, along with school closures, fueled increased demand for larger houses,
home gadgets, computer and communications gear, furniture, toys, and recreational equipment.
Such a dramatic shift would have strained manufacturing in the best of times. During the
pandemic, manufacturers could not adjust in time to bridge gaps between supply and demand
as they dealt with ongoing labor and material shortages, intermittent plant closures, and
shipping delays. Typically, short-lived supply crunches dissipate quickly as rising prices
suppress demand and increased supply restores market equilibrium. But contrary to what
standard economic theory about reaching supply-demand equilibrium suggests, prices have
risen throughout the economy in many cases substantially while shortages have persisted.
Consider, for example, freight transportation. Early in the pandemic, transportation systems
were strained by restrictions on air travel and quarantine requirements on vessel crews and
interstate truck drivers. As Western countries swung back to higher levels of economic activity,
ports could not process the increased shipping volumes. The entire transportation and
distribution system was not built to add capacity at the rate the flow was growing, and labor
shortages exacerbated the problem. The result was long delays, with ships anchored for weeks
outside major ports — and a consequent shortage of maritime containers that were stuck on
waiting vessels and could not be reloaded and shipped.
Shipping costs skyrocketed: The cost to ship a container from Asia to the United States’ East
Coast climbed from around $1,400 per container to around $20,000. Many importers of bulky,
relatively low-value (per weight) commodities, such as wooden furniture, could not raise prices
enough to avoid losses and consequently stopped placing orders.1 However, many other
importers hiked prices for their goods; as long as consumers were willing and able to pay, the
Paraphrase This Document
Need a fresh take? Get an instant paraphrase of this document with our AI Paraphraser
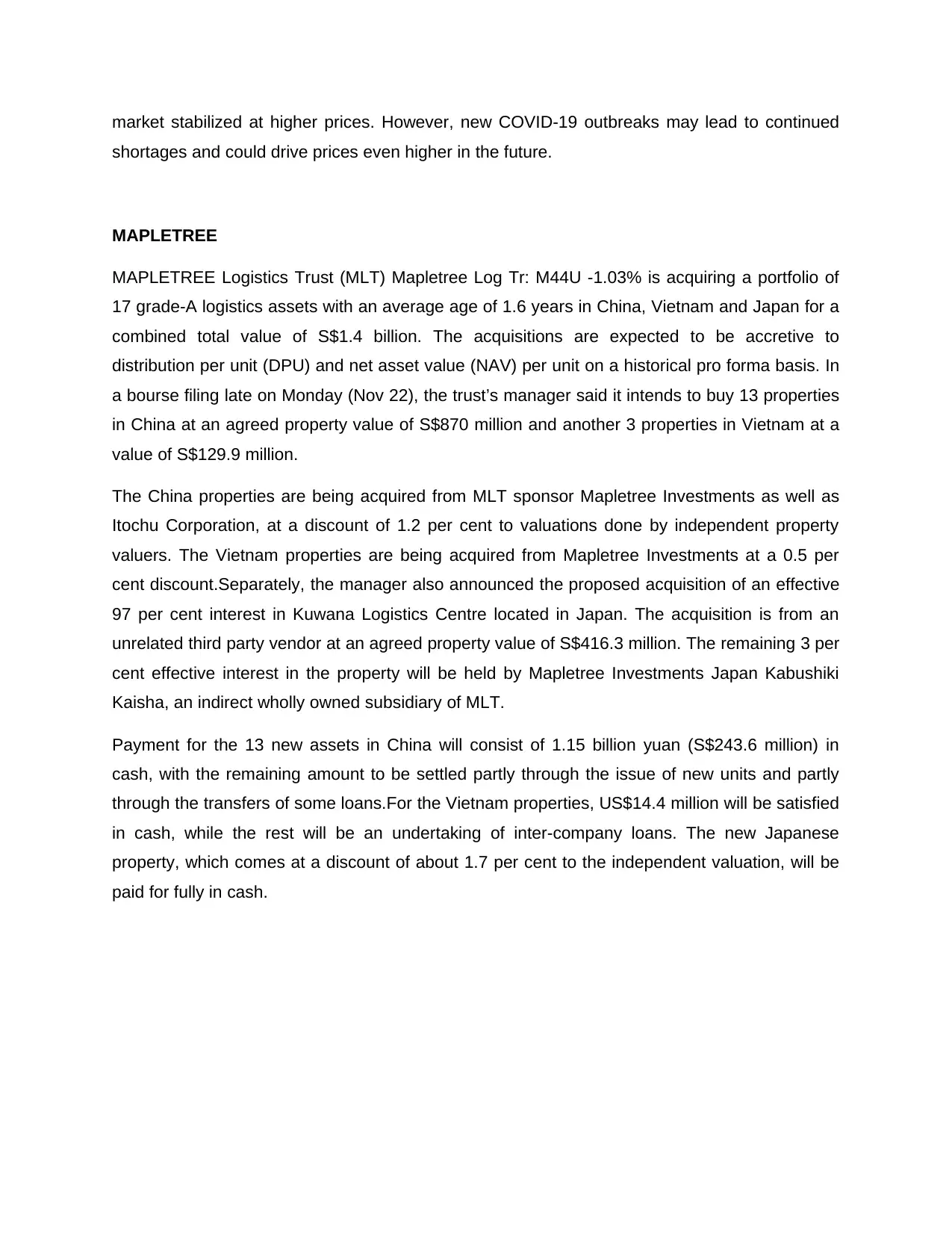
market stabilized at higher prices. However, new COVID-19 outbreaks may lead to continued
shortages and could drive prices even higher in the future.
MAPLETREE
MAPLETREE Logistics Trust (MLT) Mapletree Log Tr: M44U -1.03% is acquiring a portfolio of
17 grade-A logistics assets with an average age of 1.6 years in China, Vietnam and Japan for a
combined total value of S$1.4 billion. The acquisitions are expected to be accretive to
distribution per unit (DPU) and net asset value (NAV) per unit on a historical pro forma basis. In
a bourse filing late on Monday (Nov 22), the trust’s manager said it intends to buy 13 properties
in China at an agreed property value of S$870 million and another 3 properties in Vietnam at a
value of S$129.9 million.
The China properties are being acquired from MLT sponsor Mapletree Investments as well as
Itochu Corporation, at a discount of 1.2 per cent to valuations done by independent property
valuers. The Vietnam properties are being acquired from Mapletree Investments at a 0.5 per
cent discount.Separately, the manager also announced the proposed acquisition of an effective
97 per cent interest in Kuwana Logistics Centre located in Japan. The acquisition is from an
unrelated third party vendor at an agreed property value of S$416.3 million. The remaining 3 per
cent effective interest in the property will be held by Mapletree Investments Japan Kabushiki
Kaisha, an indirect wholly owned subsidiary of MLT.
Payment for the 13 new assets in China will consist of 1.15 billion yuan (S$243.6 million) in
cash, with the remaining amount to be settled partly through the issue of new units and partly
through the transfers of some loans.For the Vietnam properties, US$14.4 million will be satisfied
in cash, while the rest will be an undertaking of inter-company loans. The new Japanese
property, which comes at a discount of about 1.7 per cent to the independent valuation, will be
paid for fully in cash.
shortages and could drive prices even higher in the future.
MAPLETREE
MAPLETREE Logistics Trust (MLT) Mapletree Log Tr: M44U -1.03% is acquiring a portfolio of
17 grade-A logistics assets with an average age of 1.6 years in China, Vietnam and Japan for a
combined total value of S$1.4 billion. The acquisitions are expected to be accretive to
distribution per unit (DPU) and net asset value (NAV) per unit on a historical pro forma basis. In
a bourse filing late on Monday (Nov 22), the trust’s manager said it intends to buy 13 properties
in China at an agreed property value of S$870 million and another 3 properties in Vietnam at a
value of S$129.9 million.
The China properties are being acquired from MLT sponsor Mapletree Investments as well as
Itochu Corporation, at a discount of 1.2 per cent to valuations done by independent property
valuers. The Vietnam properties are being acquired from Mapletree Investments at a 0.5 per
cent discount.Separately, the manager also announced the proposed acquisition of an effective
97 per cent interest in Kuwana Logistics Centre located in Japan. The acquisition is from an
unrelated third party vendor at an agreed property value of S$416.3 million. The remaining 3 per
cent effective interest in the property will be held by Mapletree Investments Japan Kabushiki
Kaisha, an indirect wholly owned subsidiary of MLT.
Payment for the 13 new assets in China will consist of 1.15 billion yuan (S$243.6 million) in
cash, with the remaining amount to be settled partly through the issue of new units and partly
through the transfers of some loans.For the Vietnam properties, US$14.4 million will be satisfied
in cash, while the rest will be an undertaking of inter-company loans. The new Japanese
property, which comes at a discount of about 1.7 per cent to the independent valuation, will be
paid for fully in cash.
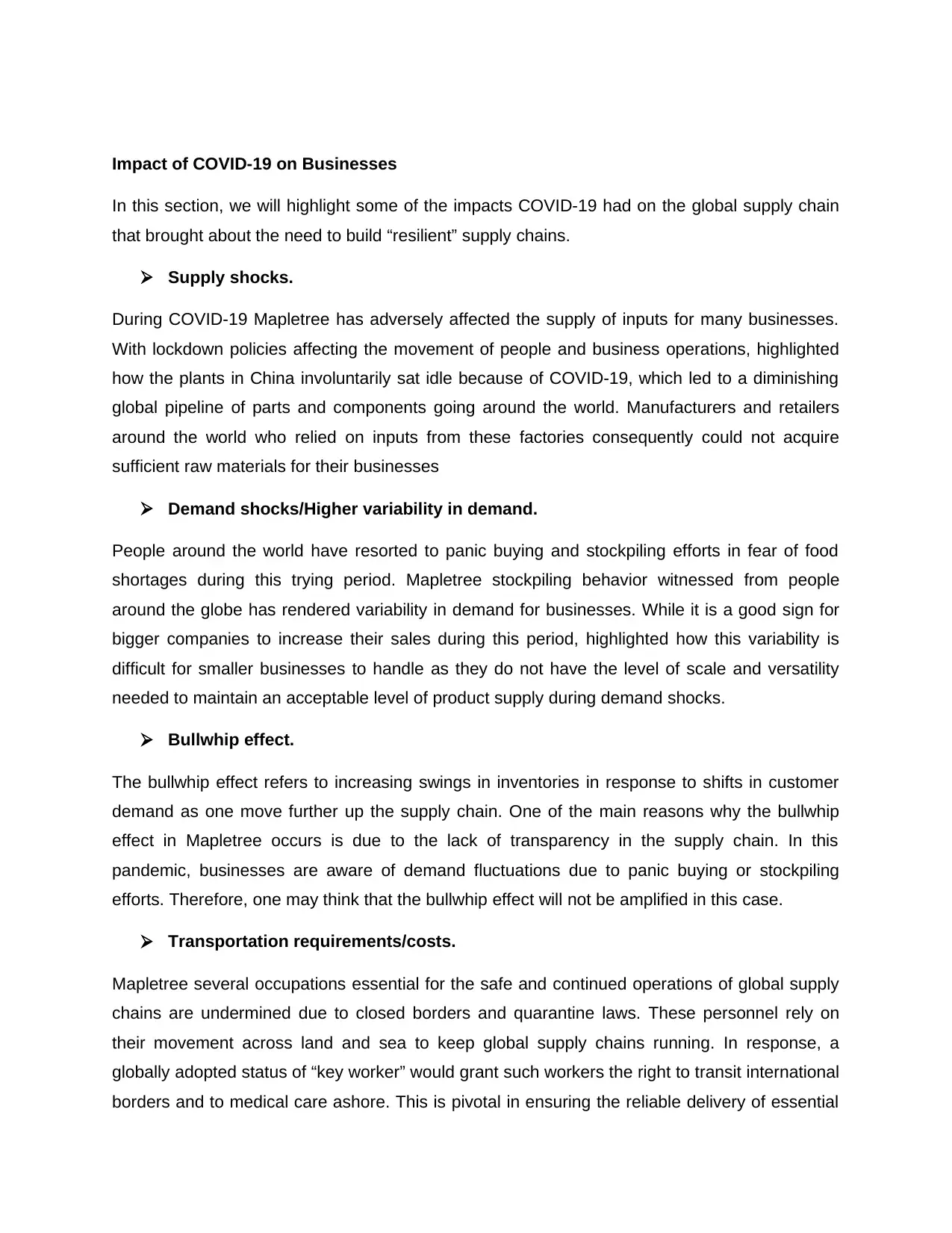
Impact of COVID-19 on Businesses
In this section, we will highlight some of the impacts COVID-19 had on the global supply chain
that brought about the need to build “resilient” supply chains.
Supply shocks.
During COVID-19 Mapletree has adversely affected the supply of inputs for many businesses.
With lockdown policies affecting the movement of people and business operations, highlighted
how the plants in China involuntarily sat idle because of COVID-19, which led to a diminishing
global pipeline of parts and components going around the world. Manufacturers and retailers
around the world who relied on inputs from these factories consequently could not acquire
sufficient raw materials for their businesses
Demand shocks/Higher variability in demand.
People around the world have resorted to panic buying and stockpiling efforts in fear of food
shortages during this trying period. Mapletree stockpiling behavior witnessed from people
around the globe has rendered variability in demand for businesses. While it is a good sign for
bigger companies to increase their sales during this period, highlighted how this variability is
difficult for smaller businesses to handle as they do not have the level of scale and versatility
needed to maintain an acceptable level of product supply during demand shocks.
Bullwhip effect.
The bullwhip effect refers to increasing swings in inventories in response to shifts in customer
demand as one move further up the supply chain. One of the main reasons why the bullwhip
effect in Mapletree occurs is due to the lack of transparency in the supply chain. In this
pandemic, businesses are aware of demand fluctuations due to panic buying or stockpiling
efforts. Therefore, one may think that the bullwhip effect will not be amplified in this case.
Transportation requirements/costs.
Mapletree several occupations essential for the safe and continued operations of global supply
chains are undermined due to closed borders and quarantine laws. These personnel rely on
their movement across land and sea to keep global supply chains running. In response, a
globally adopted status of “key worker” would grant such workers the right to transit international
borders and to medical care ashore. This is pivotal in ensuring the reliable delivery of essential
In this section, we will highlight some of the impacts COVID-19 had on the global supply chain
that brought about the need to build “resilient” supply chains.
Supply shocks.
During COVID-19 Mapletree has adversely affected the supply of inputs for many businesses.
With lockdown policies affecting the movement of people and business operations, highlighted
how the plants in China involuntarily sat idle because of COVID-19, which led to a diminishing
global pipeline of parts and components going around the world. Manufacturers and retailers
around the world who relied on inputs from these factories consequently could not acquire
sufficient raw materials for their businesses
Demand shocks/Higher variability in demand.
People around the world have resorted to panic buying and stockpiling efforts in fear of food
shortages during this trying period. Mapletree stockpiling behavior witnessed from people
around the globe has rendered variability in demand for businesses. While it is a good sign for
bigger companies to increase their sales during this period, highlighted how this variability is
difficult for smaller businesses to handle as they do not have the level of scale and versatility
needed to maintain an acceptable level of product supply during demand shocks.
Bullwhip effect.
The bullwhip effect refers to increasing swings in inventories in response to shifts in customer
demand as one move further up the supply chain. One of the main reasons why the bullwhip
effect in Mapletree occurs is due to the lack of transparency in the supply chain. In this
pandemic, businesses are aware of demand fluctuations due to panic buying or stockpiling
efforts. Therefore, one may think that the bullwhip effect will not be amplified in this case.
Transportation requirements/costs.
Mapletree several occupations essential for the safe and continued operations of global supply
chains are undermined due to closed borders and quarantine laws. These personnel rely on
their movement across land and sea to keep global supply chains running. In response, a
globally adopted status of “key worker” would grant such workers the right to transit international
borders and to medical care ashore. This is pivotal in ensuring the reliable delivery of essential
You're viewing a preview
Unlock full access by subscribing today!
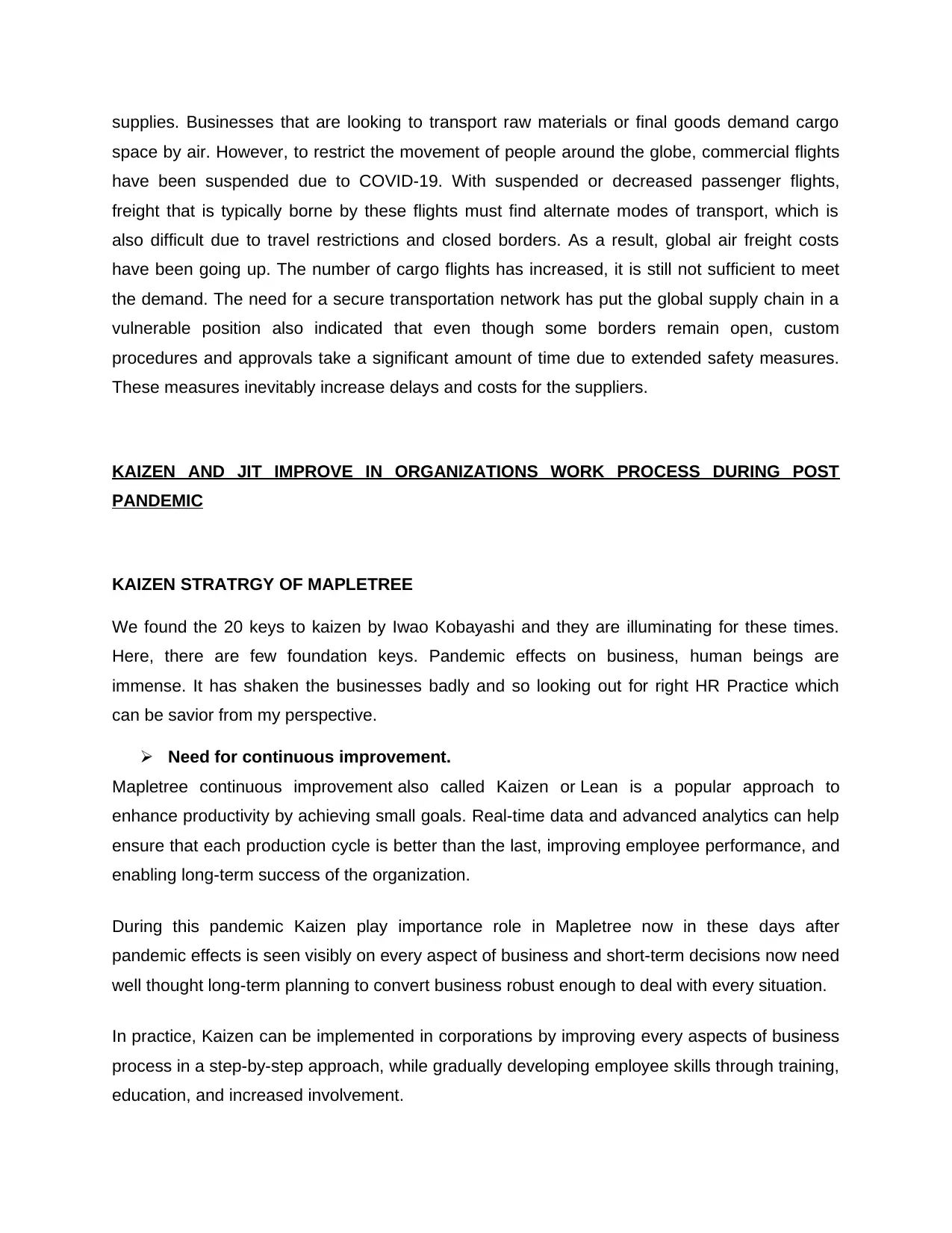
supplies. Businesses that are looking to transport raw materials or final goods demand cargo
space by air. However, to restrict the movement of people around the globe, commercial flights
have been suspended due to COVID-19. With suspended or decreased passenger flights,
freight that is typically borne by these flights must find alternate modes of transport, which is
also difficult due to travel restrictions and closed borders. As a result, global air freight costs
have been going up. The number of cargo flights has increased, it is still not sufficient to meet
the demand. The need for a secure transportation network has put the global supply chain in a
vulnerable position also indicated that even though some borders remain open, custom
procedures and approvals take a significant amount of time due to extended safety measures.
These measures inevitably increase delays and costs for the suppliers.
KAIZEN AND JIT IMPROVE IN ORGANIZATIONS WORK PROCESS DURING POST
PANDEMIC
KAIZEN STRATRGY OF MAPLETREE
We found the 20 keys to kaizen by Iwao Kobayashi and they are illuminating for these times.
Here, there are few foundation keys. Pandemic effects on business, human beings are
immense. It has shaken the businesses badly and so looking out for right HR Practice which
can be savior from my perspective.
Need for continuous improvement.
Mapletree continuous improvement also called Kaizen or Lean is a popular approach to
enhance productivity by achieving small goals. Real-time data and advanced analytics can help
ensure that each production cycle is better than the last, improving employee performance, and
enabling long-term success of the organization.
During this pandemic Kaizen play importance role in Mapletree now in these days after
pandemic effects is seen visibly on every aspect of business and short-term decisions now need
well thought long-term planning to convert business robust enough to deal with every situation.
In practice, Kaizen can be implemented in corporations by improving every aspects of business
process in a step-by-step approach, while gradually developing employee skills through training,
education, and increased involvement.
space by air. However, to restrict the movement of people around the globe, commercial flights
have been suspended due to COVID-19. With suspended or decreased passenger flights,
freight that is typically borne by these flights must find alternate modes of transport, which is
also difficult due to travel restrictions and closed borders. As a result, global air freight costs
have been going up. The number of cargo flights has increased, it is still not sufficient to meet
the demand. The need for a secure transportation network has put the global supply chain in a
vulnerable position also indicated that even though some borders remain open, custom
procedures and approvals take a significant amount of time due to extended safety measures.
These measures inevitably increase delays and costs for the suppliers.
KAIZEN AND JIT IMPROVE IN ORGANIZATIONS WORK PROCESS DURING POST
PANDEMIC
KAIZEN STRATRGY OF MAPLETREE
We found the 20 keys to kaizen by Iwao Kobayashi and they are illuminating for these times.
Here, there are few foundation keys. Pandemic effects on business, human beings are
immense. It has shaken the businesses badly and so looking out for right HR Practice which
can be savior from my perspective.
Need for continuous improvement.
Mapletree continuous improvement also called Kaizen or Lean is a popular approach to
enhance productivity by achieving small goals. Real-time data and advanced analytics can help
ensure that each production cycle is better than the last, improving employee performance, and
enabling long-term success of the organization.
During this pandemic Kaizen play importance role in Mapletree now in these days after
pandemic effects is seen visibly on every aspect of business and short-term decisions now need
well thought long-term planning to convert business robust enough to deal with every situation.
In practice, Kaizen can be implemented in corporations by improving every aspects of business
process in a step-by-step approach, while gradually developing employee skills through training,
education, and increased involvement.
Paraphrase This Document
Need a fresh take? Get an instant paraphrase of this document with our AI Paraphraser
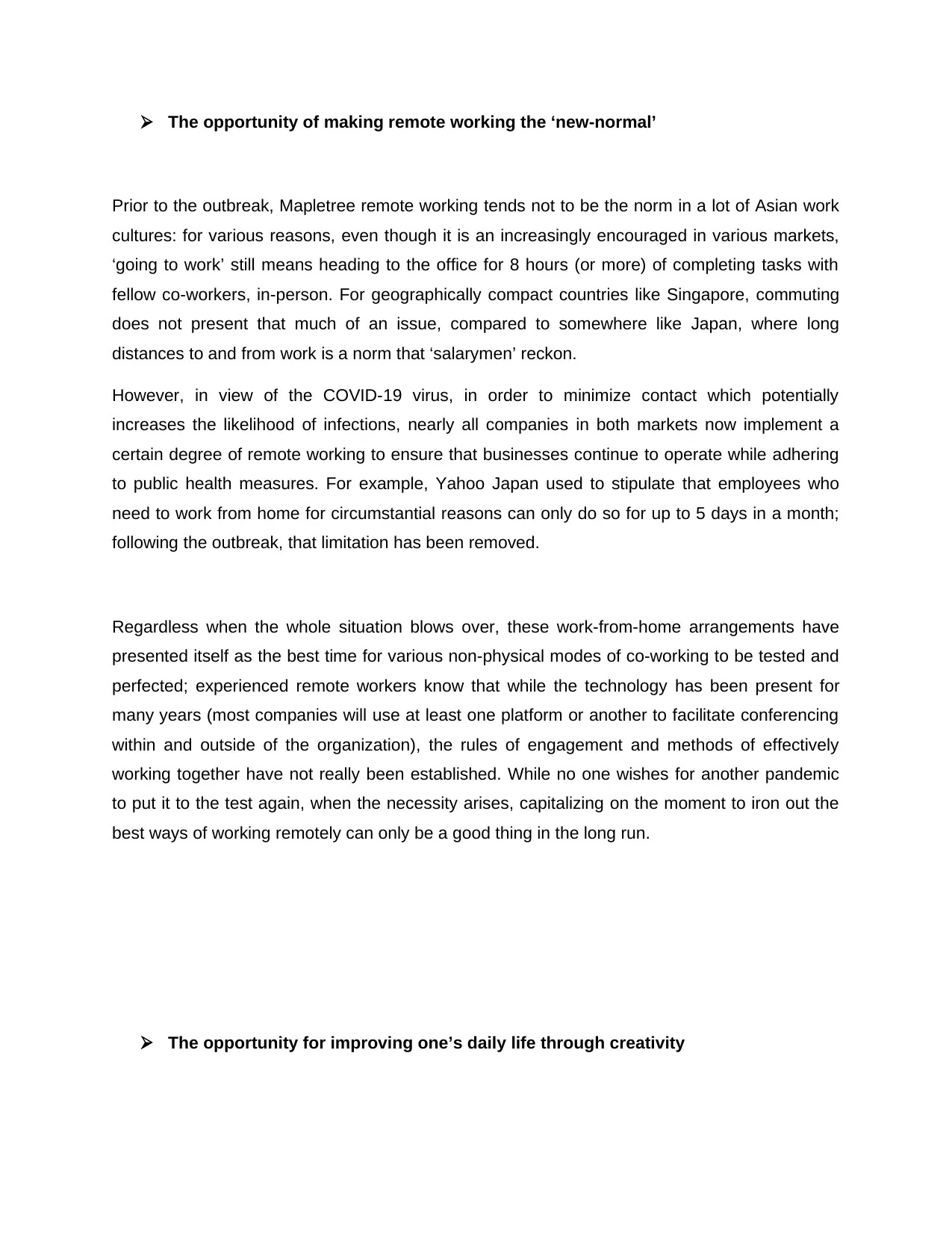
The opportunity of making remote working the ‘new-normal’
Prior to the outbreak, Mapletree remote working tends not to be the norm in a lot of Asian work
cultures: for various reasons, even though it is an increasingly encouraged in various markets,
‘going to work’ still means heading to the office for 8 hours (or more) of completing tasks with
fellow co-workers, in-person. For geographically compact countries like Singapore, commuting
does not present that much of an issue, compared to somewhere like Japan, where long
distances to and from work is a norm that ‘salarymen’ reckon.
However, in view of the COVID-19 virus, in order to minimize contact which potentially
increases the likelihood of infections, nearly all companies in both markets now implement a
certain degree of remote working to ensure that businesses continue to operate while adhering
to public health measures. For example, Yahoo Japan used to stipulate that employees who
need to work from home for circumstantial reasons can only do so for up to 5 days in a month;
following the outbreak, that limitation has been removed.
Regardless when the whole situation blows over, these work-from-home arrangements have
presented itself as the best time for various non-physical modes of co-working to be tested and
perfected; experienced remote workers know that while the technology has been present for
many years (most companies will use at least one platform or another to facilitate conferencing
within and outside of the organization), the rules of engagement and methods of effectively
working together have not really been established. While no one wishes for another pandemic
to put it to the test again, when the necessity arises, capitalizing on the moment to iron out the
best ways of working remotely can only be a good thing in the long run.
The opportunity for improving one’s daily life through creativity
Prior to the outbreak, Mapletree remote working tends not to be the norm in a lot of Asian work
cultures: for various reasons, even though it is an increasingly encouraged in various markets,
‘going to work’ still means heading to the office for 8 hours (or more) of completing tasks with
fellow co-workers, in-person. For geographically compact countries like Singapore, commuting
does not present that much of an issue, compared to somewhere like Japan, where long
distances to and from work is a norm that ‘salarymen’ reckon.
However, in view of the COVID-19 virus, in order to minimize contact which potentially
increases the likelihood of infections, nearly all companies in both markets now implement a
certain degree of remote working to ensure that businesses continue to operate while adhering
to public health measures. For example, Yahoo Japan used to stipulate that employees who
need to work from home for circumstantial reasons can only do so for up to 5 days in a month;
following the outbreak, that limitation has been removed.
Regardless when the whole situation blows over, these work-from-home arrangements have
presented itself as the best time for various non-physical modes of co-working to be tested and
perfected; experienced remote workers know that while the technology has been present for
many years (most companies will use at least one platform or another to facilitate conferencing
within and outside of the organization), the rules of engagement and methods of effectively
working together have not really been established. While no one wishes for another pandemic
to put it to the test again, when the necessity arises, capitalizing on the moment to iron out the
best ways of working remotely can only be a good thing in the long run.
The opportunity for improving one’s daily life through creativity
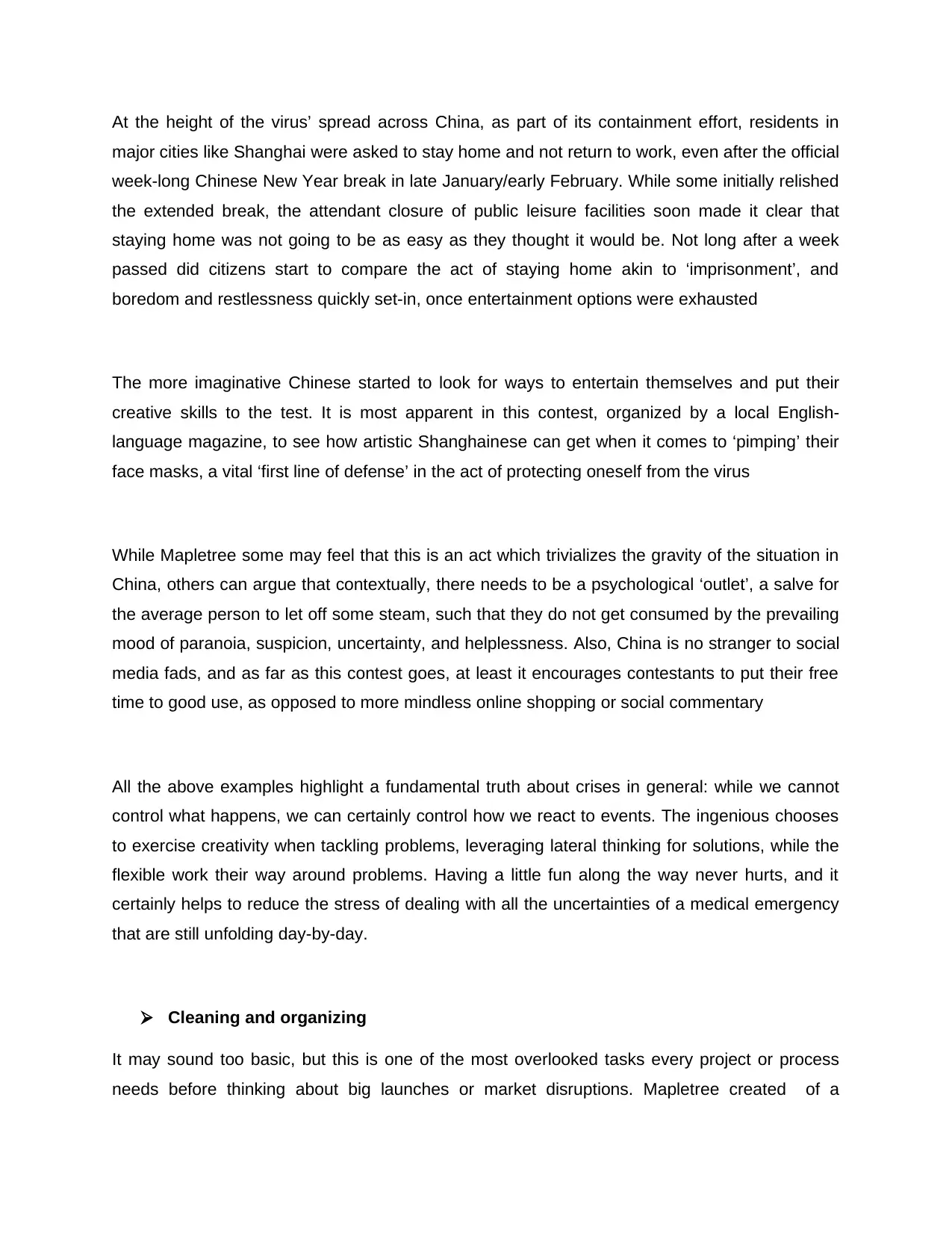
At the height of the virus’ spread across China, as part of its containment effort, residents in
major cities like Shanghai were asked to stay home and not return to work, even after the official
week-long Chinese New Year break in late January/early February. While some initially relished
the extended break, the attendant closure of public leisure facilities soon made it clear that
staying home was not going to be as easy as they thought it would be. Not long after a week
passed did citizens start to compare the act of staying home akin to ‘imprisonment’, and
boredom and restlessness quickly set-in, once entertainment options were exhausted
The more imaginative Chinese started to look for ways to entertain themselves and put their
creative skills to the test. It is most apparent in this contest, organized by a local English-
language magazine, to see how artistic Shanghainese can get when it comes to ‘pimping’ their
face masks, a vital ‘first line of defense’ in the act of protecting oneself from the virus
While Mapletree some may feel that this is an act which trivializes the gravity of the situation in
China, others can argue that contextually, there needs to be a psychological ‘outlet’, a salve for
the average person to let off some steam, such that they do not get consumed by the prevailing
mood of paranoia, suspicion, uncertainty, and helplessness. Also, China is no stranger to social
media fads, and as far as this contest goes, at least it encourages contestants to put their free
time to good use, as opposed to more mindless online shopping or social commentary
All the above examples highlight a fundamental truth about crises in general: while we cannot
control what happens, we can certainly control how we react to events. The ingenious chooses
to exercise creativity when tackling problems, leveraging lateral thinking for solutions, while the
flexible work their way around problems. Having a little fun along the way never hurts, and it
certainly helps to reduce the stress of dealing with all the uncertainties of a medical emergency
that are still unfolding day-by-day.
Cleaning and organizing
It may sound too basic, but this is one of the most overlooked tasks every project or process
needs before thinking about big launches or market disruptions. Mapletree created of a
major cities like Shanghai were asked to stay home and not return to work, even after the official
week-long Chinese New Year break in late January/early February. While some initially relished
the extended break, the attendant closure of public leisure facilities soon made it clear that
staying home was not going to be as easy as they thought it would be. Not long after a week
passed did citizens start to compare the act of staying home akin to ‘imprisonment’, and
boredom and restlessness quickly set-in, once entertainment options were exhausted
The more imaginative Chinese started to look for ways to entertain themselves and put their
creative skills to the test. It is most apparent in this contest, organized by a local English-
language magazine, to see how artistic Shanghainese can get when it comes to ‘pimping’ their
face masks, a vital ‘first line of defense’ in the act of protecting oneself from the virus
While Mapletree some may feel that this is an act which trivializes the gravity of the situation in
China, others can argue that contextually, there needs to be a psychological ‘outlet’, a salve for
the average person to let off some steam, such that they do not get consumed by the prevailing
mood of paranoia, suspicion, uncertainty, and helplessness. Also, China is no stranger to social
media fads, and as far as this contest goes, at least it encourages contestants to put their free
time to good use, as opposed to more mindless online shopping or social commentary
All the above examples highlight a fundamental truth about crises in general: while we cannot
control what happens, we can certainly control how we react to events. The ingenious chooses
to exercise creativity when tackling problems, leveraging lateral thinking for solutions, while the
flexible work their way around problems. Having a little fun along the way never hurts, and it
certainly helps to reduce the stress of dealing with all the uncertainties of a medical emergency
that are still unfolding day-by-day.
Cleaning and organizing
It may sound too basic, but this is one of the most overlooked tasks every project or process
needs before thinking about big launches or market disruptions. Mapletree created of a
You're viewing a preview
Unlock full access by subscribing today!
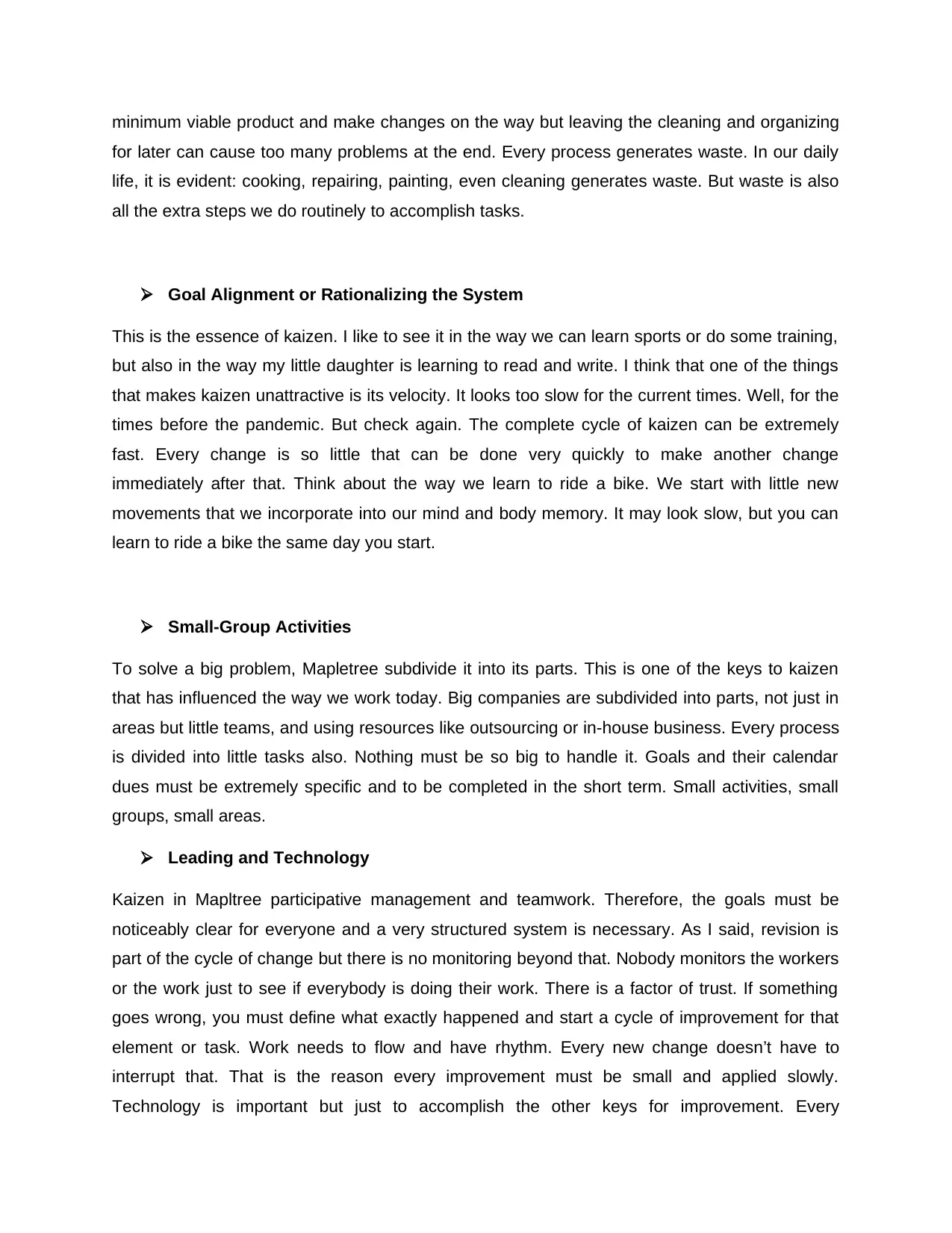
minimum viable product and make changes on the way but leaving the cleaning and organizing
for later can cause too many problems at the end. Every process generates waste. In our daily
life, it is evident: cooking, repairing, painting, even cleaning generates waste. But waste is also
all the extra steps we do routinely to accomplish tasks.
Goal Alignment or Rationalizing the System
This is the essence of kaizen. I like to see it in the way we can learn sports or do some training,
but also in the way my little daughter is learning to read and write. I think that one of the things
that makes kaizen unattractive is its velocity. It looks too slow for the current times. Well, for the
times before the pandemic. But check again. The complete cycle of kaizen can be extremely
fast. Every change is so little that can be done very quickly to make another change
immediately after that. Think about the way we learn to ride a bike. We start with little new
movements that we incorporate into our mind and body memory. It may look slow, but you can
learn to ride a bike the same day you start.
Small-Group Activities
To solve a big problem, Mapletree subdivide it into its parts. This is one of the keys to kaizen
that has influenced the way we work today. Big companies are subdivided into parts, not just in
areas but little teams, and using resources like outsourcing or in-house business. Every process
is divided into little tasks also. Nothing must be so big to handle it. Goals and their calendar
dues must be extremely specific and to be completed in the short term. Small activities, small
groups, small areas.
Leading and Technology
Kaizen in Mapltree participative management and teamwork. Therefore, the goals must be
noticeably clear for everyone and a very structured system is necessary. As I said, revision is
part of the cycle of change but there is no monitoring beyond that. Nobody monitors the workers
or the work just to see if everybody is doing their work. There is a factor of trust. If something
goes wrong, you must define what exactly happened and start a cycle of improvement for that
element or task. Work needs to flow and have rhythm. Every new change doesn’t have to
interrupt that. That is the reason every improvement must be small and applied slowly.
Technology is important but just to accomplish the other keys for improvement. Every
for later can cause too many problems at the end. Every process generates waste. In our daily
life, it is evident: cooking, repairing, painting, even cleaning generates waste. But waste is also
all the extra steps we do routinely to accomplish tasks.
Goal Alignment or Rationalizing the System
This is the essence of kaizen. I like to see it in the way we can learn sports or do some training,
but also in the way my little daughter is learning to read and write. I think that one of the things
that makes kaizen unattractive is its velocity. It looks too slow for the current times. Well, for the
times before the pandemic. But check again. The complete cycle of kaizen can be extremely
fast. Every change is so little that can be done very quickly to make another change
immediately after that. Think about the way we learn to ride a bike. We start with little new
movements that we incorporate into our mind and body memory. It may look slow, but you can
learn to ride a bike the same day you start.
Small-Group Activities
To solve a big problem, Mapletree subdivide it into its parts. This is one of the keys to kaizen
that has influenced the way we work today. Big companies are subdivided into parts, not just in
areas but little teams, and using resources like outsourcing or in-house business. Every process
is divided into little tasks also. Nothing must be so big to handle it. Goals and their calendar
dues must be extremely specific and to be completed in the short term. Small activities, small
groups, small areas.
Leading and Technology
Kaizen in Mapltree participative management and teamwork. Therefore, the goals must be
noticeably clear for everyone and a very structured system is necessary. As I said, revision is
part of the cycle of change but there is no monitoring beyond that. Nobody monitors the workers
or the work just to see if everybody is doing their work. There is a factor of trust. If something
goes wrong, you must define what exactly happened and start a cycle of improvement for that
element or task. Work needs to flow and have rhythm. Every new change doesn’t have to
interrupt that. That is the reason every improvement must be small and applied slowly.
Technology is important but just to accomplish the other keys for improvement. Every
Paraphrase This Document
Need a fresh take? Get an instant paraphrase of this document with our AI Paraphraser
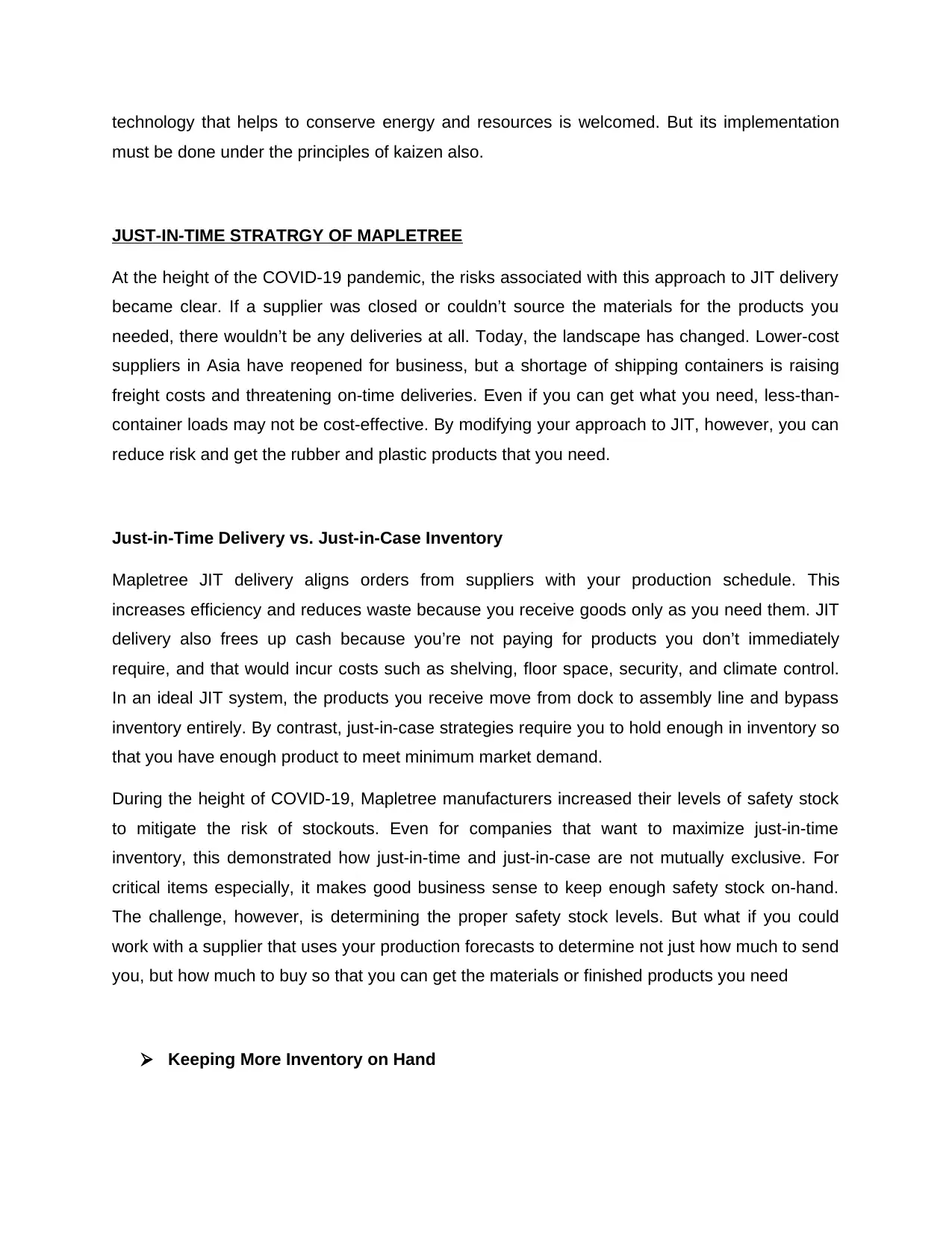
technology that helps to conserve energy and resources is welcomed. But its implementation
must be done under the principles of kaizen also.
JUST-IN-TIME STRATRGY OF MAPLETREE
At the height of the COVID-19 pandemic, the risks associated with this approach to JIT delivery
became clear. If a supplier was closed or couldn’t source the materials for the products you
needed, there wouldn’t be any deliveries at all. Today, the landscape has changed. Lower-cost
suppliers in Asia have reopened for business, but a shortage of shipping containers is raising
freight costs and threatening on-time deliveries. Even if you can get what you need, less-than-
container loads may not be cost-effective. By modifying your approach to JIT, however, you can
reduce risk and get the rubber and plastic products that you need.
Just-in-Time Delivery vs. Just-in-Case Inventory
Mapletree JIT delivery aligns orders from suppliers with your production schedule. This
increases efficiency and reduces waste because you receive goods only as you need them. JIT
delivery also frees up cash because you’re not paying for products you don’t immediately
require, and that would incur costs such as shelving, floor space, security, and climate control.
In an ideal JIT system, the products you receive move from dock to assembly line and bypass
inventory entirely. By contrast, just-in-case strategies require you to hold enough in inventory so
that you have enough product to meet minimum market demand.
During the height of COVID-19, Mapletree manufacturers increased their levels of safety stock
to mitigate the risk of stockouts. Even for companies that want to maximize just-in-time
inventory, this demonstrated how just-in-time and just-in-case are not mutually exclusive. For
critical items especially, it makes good business sense to keep enough safety stock on-hand.
The challenge, however, is determining the proper safety stock levels. But what if you could
work with a supplier that uses your production forecasts to determine not just how much to send
you, but how much to buy so that you can get the materials or finished products you need
Keeping More Inventory on Hand
must be done under the principles of kaizen also.
JUST-IN-TIME STRATRGY OF MAPLETREE
At the height of the COVID-19 pandemic, the risks associated with this approach to JIT delivery
became clear. If a supplier was closed or couldn’t source the materials for the products you
needed, there wouldn’t be any deliveries at all. Today, the landscape has changed. Lower-cost
suppliers in Asia have reopened for business, but a shortage of shipping containers is raising
freight costs and threatening on-time deliveries. Even if you can get what you need, less-than-
container loads may not be cost-effective. By modifying your approach to JIT, however, you can
reduce risk and get the rubber and plastic products that you need.
Just-in-Time Delivery vs. Just-in-Case Inventory
Mapletree JIT delivery aligns orders from suppliers with your production schedule. This
increases efficiency and reduces waste because you receive goods only as you need them. JIT
delivery also frees up cash because you’re not paying for products you don’t immediately
require, and that would incur costs such as shelving, floor space, security, and climate control.
In an ideal JIT system, the products you receive move from dock to assembly line and bypass
inventory entirely. By contrast, just-in-case strategies require you to hold enough in inventory so
that you have enough product to meet minimum market demand.
During the height of COVID-19, Mapletree manufacturers increased their levels of safety stock
to mitigate the risk of stockouts. Even for companies that want to maximize just-in-time
inventory, this demonstrated how just-in-time and just-in-case are not mutually exclusive. For
critical items especially, it makes good business sense to keep enough safety stock on-hand.
The challenge, however, is determining the proper safety stock levels. But what if you could
work with a supplier that uses your production forecasts to determine not just how much to send
you, but how much to buy so that you can get the materials or finished products you need
Keeping More Inventory on Hand
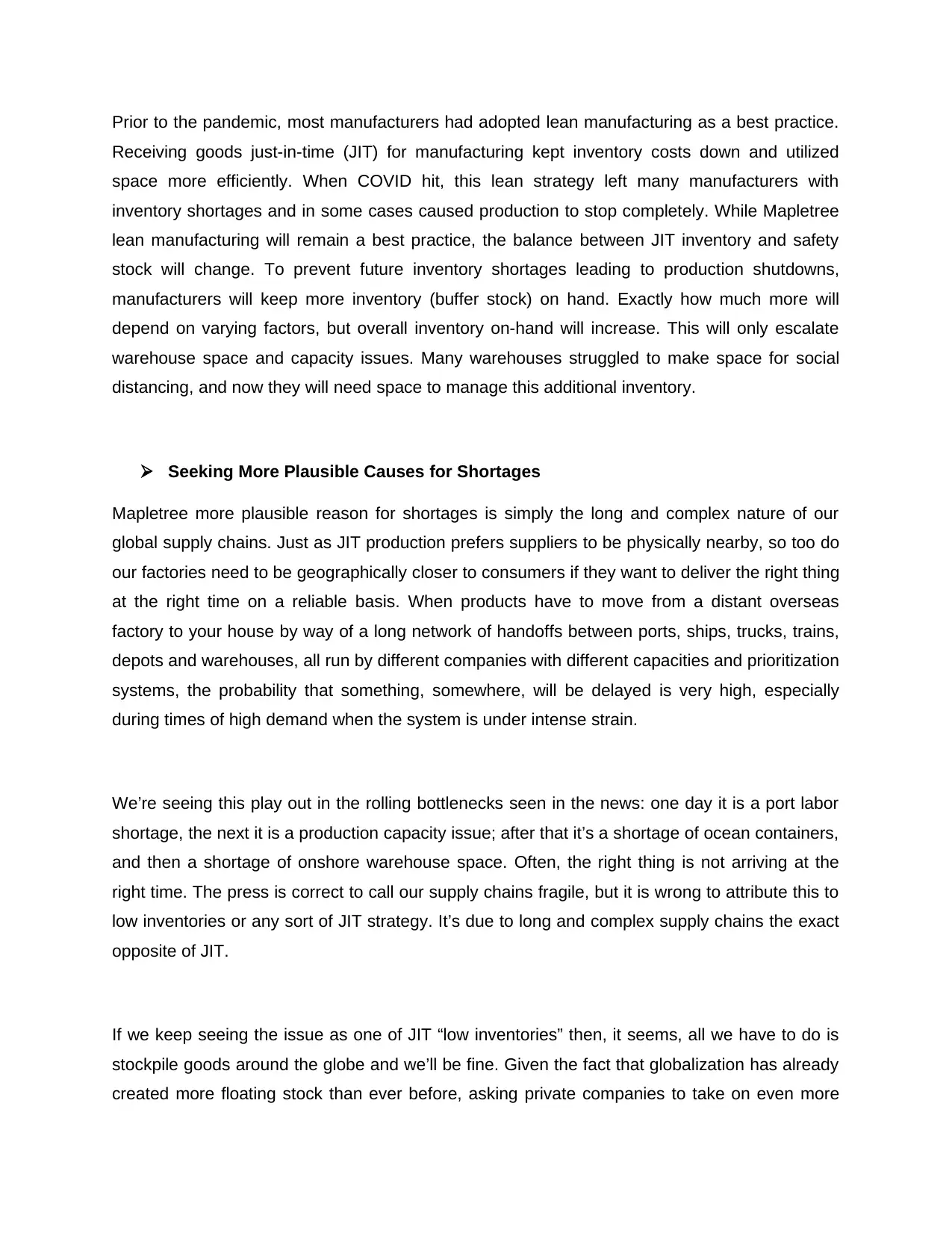
Prior to the pandemic, most manufacturers had adopted lean manufacturing as a best practice.
Receiving goods just-in-time (JIT) for manufacturing kept inventory costs down and utilized
space more efficiently. When COVID hit, this lean strategy left many manufacturers with
inventory shortages and in some cases caused production to stop completely. While Mapletree
lean manufacturing will remain a best practice, the balance between JIT inventory and safety
stock will change. To prevent future inventory shortages leading to production shutdowns,
manufacturers will keep more inventory (buffer stock) on hand. Exactly how much more will
depend on varying factors, but overall inventory on-hand will increase. This will only escalate
warehouse space and capacity issues. Many warehouses struggled to make space for social
distancing, and now they will need space to manage this additional inventory.
Seeking More Plausible Causes for Shortages
Mapletree more plausible reason for shortages is simply the long and complex nature of our
global supply chains. Just as JIT production prefers suppliers to be physically nearby, so too do
our factories need to be geographically closer to consumers if they want to deliver the right thing
at the right time on a reliable basis. When products have to move from a distant overseas
factory to your house by way of a long network of handoffs between ports, ships, trucks, trains,
depots and warehouses, all run by different companies with different capacities and prioritization
systems, the probability that something, somewhere, will be delayed is very high, especially
during times of high demand when the system is under intense strain.
We’re seeing this play out in the rolling bottlenecks seen in the news: one day it is a port labor
shortage, the next it is a production capacity issue; after that it’s a shortage of ocean containers,
and then a shortage of onshore warehouse space. Often, the right thing is not arriving at the
right time. The press is correct to call our supply chains fragile, but it is wrong to attribute this to
low inventories or any sort of JIT strategy. It’s due to long and complex supply chains the exact
opposite of JIT.
If we keep seeing the issue as one of JIT “low inventories” then, it seems, all we have to do is
stockpile goods around the globe and we’ll be fine. Given the fact that globalization has already
created more floating stock than ever before, asking private companies to take on even more
Receiving goods just-in-time (JIT) for manufacturing kept inventory costs down and utilized
space more efficiently. When COVID hit, this lean strategy left many manufacturers with
inventory shortages and in some cases caused production to stop completely. While Mapletree
lean manufacturing will remain a best practice, the balance between JIT inventory and safety
stock will change. To prevent future inventory shortages leading to production shutdowns,
manufacturers will keep more inventory (buffer stock) on hand. Exactly how much more will
depend on varying factors, but overall inventory on-hand will increase. This will only escalate
warehouse space and capacity issues. Many warehouses struggled to make space for social
distancing, and now they will need space to manage this additional inventory.
Seeking More Plausible Causes for Shortages
Mapletree more plausible reason for shortages is simply the long and complex nature of our
global supply chains. Just as JIT production prefers suppliers to be physically nearby, so too do
our factories need to be geographically closer to consumers if they want to deliver the right thing
at the right time on a reliable basis. When products have to move from a distant overseas
factory to your house by way of a long network of handoffs between ports, ships, trucks, trains,
depots and warehouses, all run by different companies with different capacities and prioritization
systems, the probability that something, somewhere, will be delayed is very high, especially
during times of high demand when the system is under intense strain.
We’re seeing this play out in the rolling bottlenecks seen in the news: one day it is a port labor
shortage, the next it is a production capacity issue; after that it’s a shortage of ocean containers,
and then a shortage of onshore warehouse space. Often, the right thing is not arriving at the
right time. The press is correct to call our supply chains fragile, but it is wrong to attribute this to
low inventories or any sort of JIT strategy. It’s due to long and complex supply chains the exact
opposite of JIT.
If we keep seeing the issue as one of JIT “low inventories” then, it seems, all we have to do is
stockpile goods around the globe and we’ll be fine. Given the fact that globalization has already
created more floating stock than ever before, asking private companies to take on even more
You're viewing a preview
Unlock full access by subscribing today!
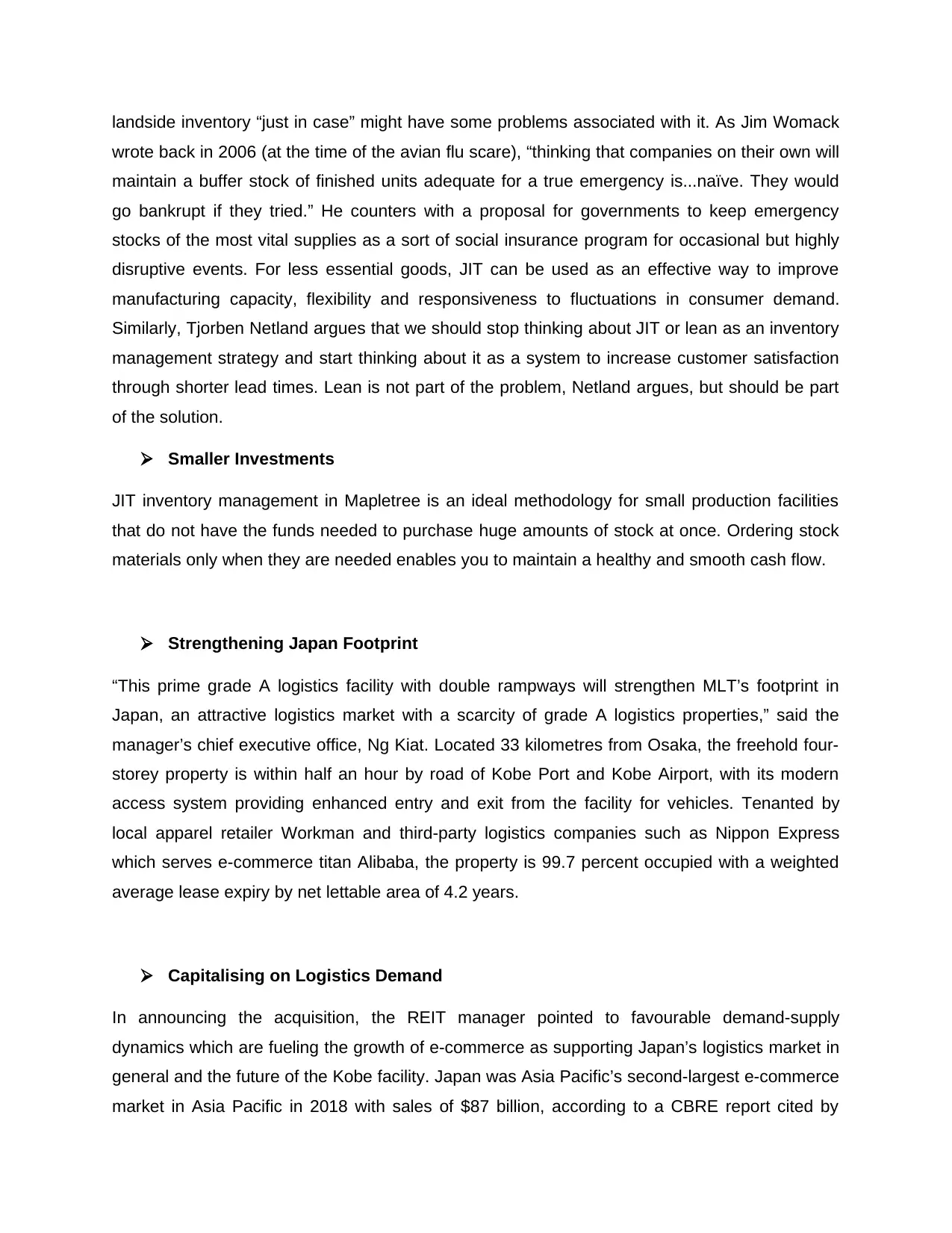
landside inventory “just in case” might have some problems associated with it. As Jim Womack
wrote back in 2006 (at the time of the avian flu scare), “thinking that companies on their own will
maintain a buffer stock of finished units adequate for a true emergency is...naïve. They would
go bankrupt if they tried.” He counters with a proposal for governments to keep emergency
stocks of the most vital supplies as a sort of social insurance program for occasional but highly
disruptive events. For less essential goods, JIT can be used as an effective way to improve
manufacturing capacity, flexibility and responsiveness to fluctuations in consumer demand.
Similarly, Tjorben Netland argues that we should stop thinking about JIT or lean as an inventory
management strategy and start thinking about it as a system to increase customer satisfaction
through shorter lead times. Lean is not part of the problem, Netland argues, but should be part
of the solution.
Smaller Investments
JIT inventory management in Mapletree is an ideal methodology for small production facilities
that do not have the funds needed to purchase huge amounts of stock at once. Ordering stock
materials only when they are needed enables you to maintain a healthy and smooth cash flow.
Strengthening Japan Footprint
“This prime grade A logistics facility with double rampways will strengthen MLT’s footprint in
Japan, an attractive logistics market with a scarcity of grade A logistics properties,” said the
manager’s chief executive office, Ng Kiat. Located 33 kilometres from Osaka, the freehold four-
storey property is within half an hour by road of Kobe Port and Kobe Airport, with its modern
access system providing enhanced entry and exit from the facility for vehicles. Tenanted by
local apparel retailer Workman and third-party logistics companies such as Nippon Express
which serves e-commerce titan Alibaba, the property is 99.7 percent occupied with a weighted
average lease expiry by net lettable area of 4.2 years.
Capitalising on Logistics Demand
In announcing the acquisition, the REIT manager pointed to favourable demand-supply
dynamics which are fueling the growth of e-commerce as supporting Japan’s logistics market in
general and the future of the Kobe facility. Japan was Asia Pacific’s second-largest e-commerce
market in Asia Pacific in 2018 with sales of $87 billion, according to a CBRE report cited by
wrote back in 2006 (at the time of the avian flu scare), “thinking that companies on their own will
maintain a buffer stock of finished units adequate for a true emergency is...naïve. They would
go bankrupt if they tried.” He counters with a proposal for governments to keep emergency
stocks of the most vital supplies as a sort of social insurance program for occasional but highly
disruptive events. For less essential goods, JIT can be used as an effective way to improve
manufacturing capacity, flexibility and responsiveness to fluctuations in consumer demand.
Similarly, Tjorben Netland argues that we should stop thinking about JIT or lean as an inventory
management strategy and start thinking about it as a system to increase customer satisfaction
through shorter lead times. Lean is not part of the problem, Netland argues, but should be part
of the solution.
Smaller Investments
JIT inventory management in Mapletree is an ideal methodology for small production facilities
that do not have the funds needed to purchase huge amounts of stock at once. Ordering stock
materials only when they are needed enables you to maintain a healthy and smooth cash flow.
Strengthening Japan Footprint
“This prime grade A logistics facility with double rampways will strengthen MLT’s footprint in
Japan, an attractive logistics market with a scarcity of grade A logistics properties,” said the
manager’s chief executive office, Ng Kiat. Located 33 kilometres from Osaka, the freehold four-
storey property is within half an hour by road of Kobe Port and Kobe Airport, with its modern
access system providing enhanced entry and exit from the facility for vehicles. Tenanted by
local apparel retailer Workman and third-party logistics companies such as Nippon Express
which serves e-commerce titan Alibaba, the property is 99.7 percent occupied with a weighted
average lease expiry by net lettable area of 4.2 years.
Capitalising on Logistics Demand
In announcing the acquisition, the REIT manager pointed to favourable demand-supply
dynamics which are fueling the growth of e-commerce as supporting Japan’s logistics market in
general and the future of the Kobe facility. Japan was Asia Pacific’s second-largest e-commerce
market in Asia Pacific in 2018 with sales of $87 billion, according to a CBRE report cited by
Paraphrase This Document
Need a fresh take? Get an instant paraphrase of this document with our AI Paraphraser
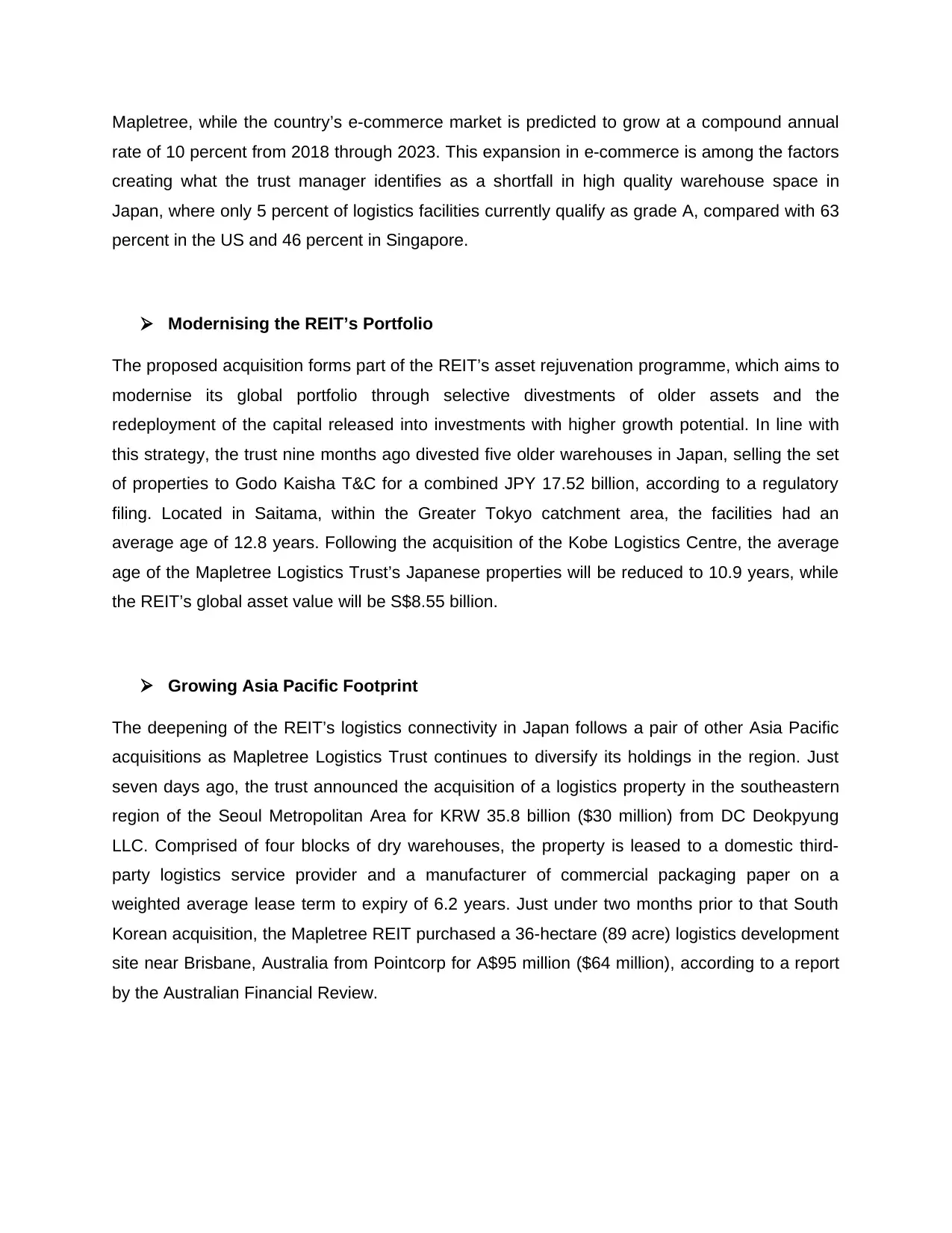
Mapletree, while the country’s e-commerce market is predicted to grow at a compound annual
rate of 10 percent from 2018 through 2023. This expansion in e-commerce is among the factors
creating what the trust manager identifies as a shortfall in high quality warehouse space in
Japan, where only 5 percent of logistics facilities currently qualify as grade A, compared with 63
percent in the US and 46 percent in Singapore.
Modernising the REIT’s Portfolio
The proposed acquisition forms part of the REIT’s asset rejuvenation programme, which aims to
modernise its global portfolio through selective divestments of older assets and the
redeployment of the capital released into investments with higher growth potential. In line with
this strategy, the trust nine months ago divested five older warehouses in Japan, selling the set
of properties to Godo Kaisha T&C for a combined JPY 17.52 billion, according to a regulatory
filing. Located in Saitama, within the Greater Tokyo catchment area, the facilities had an
average age of 12.8 years. Following the acquisition of the Kobe Logistics Centre, the average
age of the Mapletree Logistics Trust’s Japanese properties will be reduced to 10.9 years, while
the REIT’s global asset value will be S$8.55 billion.
Growing Asia Pacific Footprint
The deepening of the REIT’s logistics connectivity in Japan follows a pair of other Asia Pacific
acquisitions as Mapletree Logistics Trust continues to diversify its holdings in the region. Just
seven days ago, the trust announced the acquisition of a logistics property in the southeastern
region of the Seoul Metropolitan Area for KRW 35.8 billion ($30 million) from DC Deokpyung
LLC. Comprised of four blocks of dry warehouses, the property is leased to a domestic third-
party logistics service provider and a manufacturer of commercial packaging paper on a
weighted average lease term to expiry of 6.2 years. Just under two months prior to that South
Korean acquisition, the Mapletree REIT purchased a 36-hectare (89 acre) logistics development
site near Brisbane, Australia from Pointcorp for A$95 million ($64 million), according to a report
by the Australian Financial Review.
rate of 10 percent from 2018 through 2023. This expansion in e-commerce is among the factors
creating what the trust manager identifies as a shortfall in high quality warehouse space in
Japan, where only 5 percent of logistics facilities currently qualify as grade A, compared with 63
percent in the US and 46 percent in Singapore.
Modernising the REIT’s Portfolio
The proposed acquisition forms part of the REIT’s asset rejuvenation programme, which aims to
modernise its global portfolio through selective divestments of older assets and the
redeployment of the capital released into investments with higher growth potential. In line with
this strategy, the trust nine months ago divested five older warehouses in Japan, selling the set
of properties to Godo Kaisha T&C for a combined JPY 17.52 billion, according to a regulatory
filing. Located in Saitama, within the Greater Tokyo catchment area, the facilities had an
average age of 12.8 years. Following the acquisition of the Kobe Logistics Centre, the average
age of the Mapletree Logistics Trust’s Japanese properties will be reduced to 10.9 years, while
the REIT’s global asset value will be S$8.55 billion.
Growing Asia Pacific Footprint
The deepening of the REIT’s logistics connectivity in Japan follows a pair of other Asia Pacific
acquisitions as Mapletree Logistics Trust continues to diversify its holdings in the region. Just
seven days ago, the trust announced the acquisition of a logistics property in the southeastern
region of the Seoul Metropolitan Area for KRW 35.8 billion ($30 million) from DC Deokpyung
LLC. Comprised of four blocks of dry warehouses, the property is leased to a domestic third-
party logistics service provider and a manufacturer of commercial packaging paper on a
weighted average lease term to expiry of 6.2 years. Just under two months prior to that South
Korean acquisition, the Mapletree REIT purchased a 36-hectare (89 acre) logistics development
site near Brisbane, Australia from Pointcorp for A$95 million ($64 million), according to a report
by the Australian Financial Review.
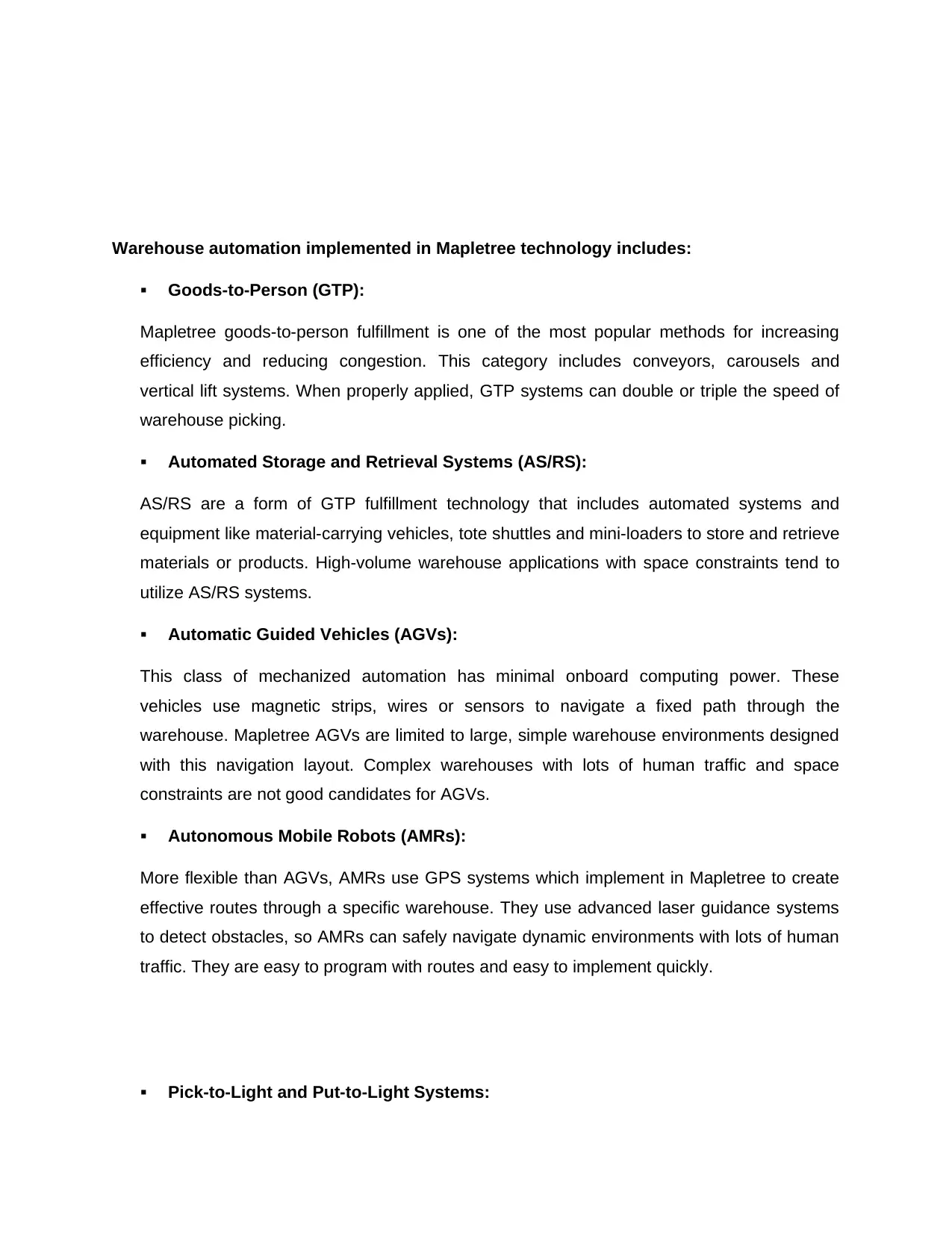
Warehouse automation implemented in Mapletree technology includes:
Goods-to-Person (GTP):
Mapletree goods-to-person fulfillment is one of the most popular methods for increasing
efficiency and reducing congestion. This category includes conveyors, carousels and
vertical lift systems. When properly applied, GTP systems can double or triple the speed of
warehouse picking.
Automated Storage and Retrieval Systems (AS/RS):
AS/RS are a form of GTP fulfillment technology that includes automated systems and
equipment like material-carrying vehicles, tote shuttles and mini-loaders to store and retrieve
materials or products. High-volume warehouse applications with space constraints tend to
utilize AS/RS systems.
Automatic Guided Vehicles (AGVs):
This class of mechanized automation has minimal onboard computing power. These
vehicles use magnetic strips, wires or sensors to navigate a fixed path through the
warehouse. Mapletree AGVs are limited to large, simple warehouse environments designed
with this navigation layout. Complex warehouses with lots of human traffic and space
constraints are not good candidates for AGVs.
Autonomous Mobile Robots (AMRs):
More flexible than AGVs, AMRs use GPS systems which implement in Mapletree to create
effective routes through a specific warehouse. They use advanced laser guidance systems
to detect obstacles, so AMRs can safely navigate dynamic environments with lots of human
traffic. They are easy to program with routes and easy to implement quickly.
Pick-to-Light and Put-to-Light Systems:
Goods-to-Person (GTP):
Mapletree goods-to-person fulfillment is one of the most popular methods for increasing
efficiency and reducing congestion. This category includes conveyors, carousels and
vertical lift systems. When properly applied, GTP systems can double or triple the speed of
warehouse picking.
Automated Storage and Retrieval Systems (AS/RS):
AS/RS are a form of GTP fulfillment technology that includes automated systems and
equipment like material-carrying vehicles, tote shuttles and mini-loaders to store and retrieve
materials or products. High-volume warehouse applications with space constraints tend to
utilize AS/RS systems.
Automatic Guided Vehicles (AGVs):
This class of mechanized automation has minimal onboard computing power. These
vehicles use magnetic strips, wires or sensors to navigate a fixed path through the
warehouse. Mapletree AGVs are limited to large, simple warehouse environments designed
with this navigation layout. Complex warehouses with lots of human traffic and space
constraints are not good candidates for AGVs.
Autonomous Mobile Robots (AMRs):
More flexible than AGVs, AMRs use GPS systems which implement in Mapletree to create
effective routes through a specific warehouse. They use advanced laser guidance systems
to detect obstacles, so AMRs can safely navigate dynamic environments with lots of human
traffic. They are easy to program with routes and easy to implement quickly.
Pick-to-Light and Put-to-Light Systems:
You're viewing a preview
Unlock full access by subscribing today!
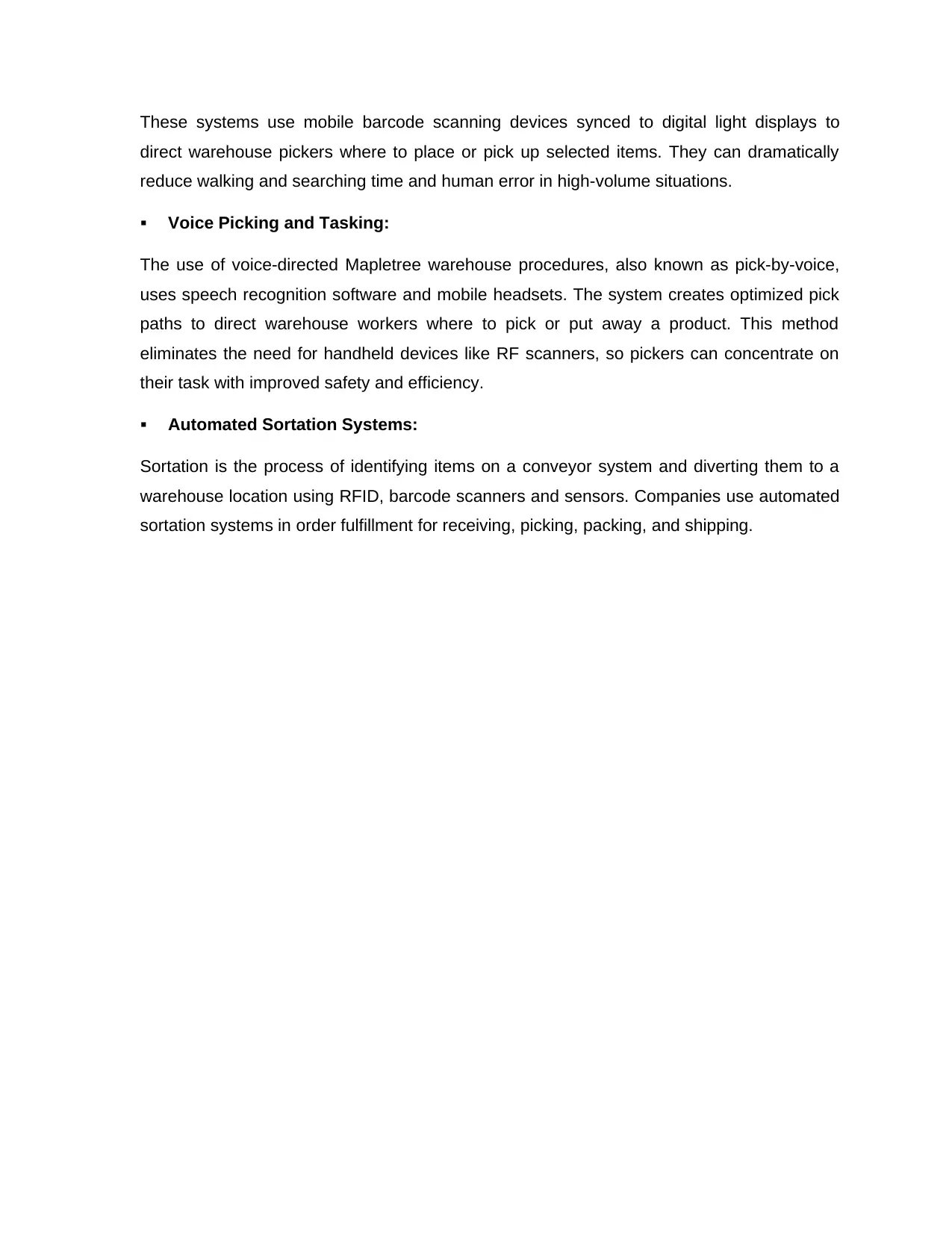
These systems use mobile barcode scanning devices synced to digital light displays to
direct warehouse pickers where to place or pick up selected items. They can dramatically
reduce walking and searching time and human error in high-volume situations.
Voice Picking and Tasking:
The use of voice-directed Mapletree warehouse procedures, also known as pick-by-voice,
uses speech recognition software and mobile headsets. The system creates optimized pick
paths to direct warehouse workers where to pick or put away a product. This method
eliminates the need for handheld devices like RF scanners, so pickers can concentrate on
their task with improved safety and efficiency.
Automated Sortation Systems:
Sortation is the process of identifying items on a conveyor system and diverting them to a
warehouse location using RFID, barcode scanners and sensors. Companies use automated
sortation systems in order fulfillment for receiving, picking, packing, and shipping.
direct warehouse pickers where to place or pick up selected items. They can dramatically
reduce walking and searching time and human error in high-volume situations.
Voice Picking and Tasking:
The use of voice-directed Mapletree warehouse procedures, also known as pick-by-voice,
uses speech recognition software and mobile headsets. The system creates optimized pick
paths to direct warehouse workers where to pick or put away a product. This method
eliminates the need for handheld devices like RF scanners, so pickers can concentrate on
their task with improved safety and efficiency.
Automated Sortation Systems:
Sortation is the process of identifying items on a conveyor system and diverting them to a
warehouse location using RFID, barcode scanners and sensors. Companies use automated
sortation systems in order fulfillment for receiving, picking, packing, and shipping.
1 out of 13

Your All-in-One AI-Powered Toolkit for Academic Success.
+13062052269
info@desklib.com
Available 24*7 on WhatsApp / Email
Unlock your academic potential
© 2024 | Zucol Services PVT LTD | All rights reserved.