Lean Six Sigma Assignment: Respect for People and Lean Community
VerifiedAdded on 2022/09/14
|9
|2564
|13
Report
AI Summary
This report provides a comprehensive analysis of the 'Respect for People' principle within the context of Lean Six Sigma, a critical component for successful Lean implementation. The report explores the historical background of the principle, tracing its origins and evolution, particularly highlighting its significance within Toyota's operational model. It examines the concept of respect for people, its impact on employee engagement, teamwork, and stakeholder relationships, and its role in fostering a culture of continuous improvement. The report further investigates the contribution of respect for people to the Lean community, addressing the under-representation of this principle in research and practice. It provides examples and practical insights into how organizations can effectively integrate this principle to drive sustainable improvements and overcome common barriers to adoption. The report also discusses the barriers to the adaptation of respect for people in lean manufacturing and concludes by emphasizing the importance of this principle for long-term success and the creation of a thriving Lean community.
Contribute Materials
Your contribution can guide someone’s learning journey. Share your
documents today.
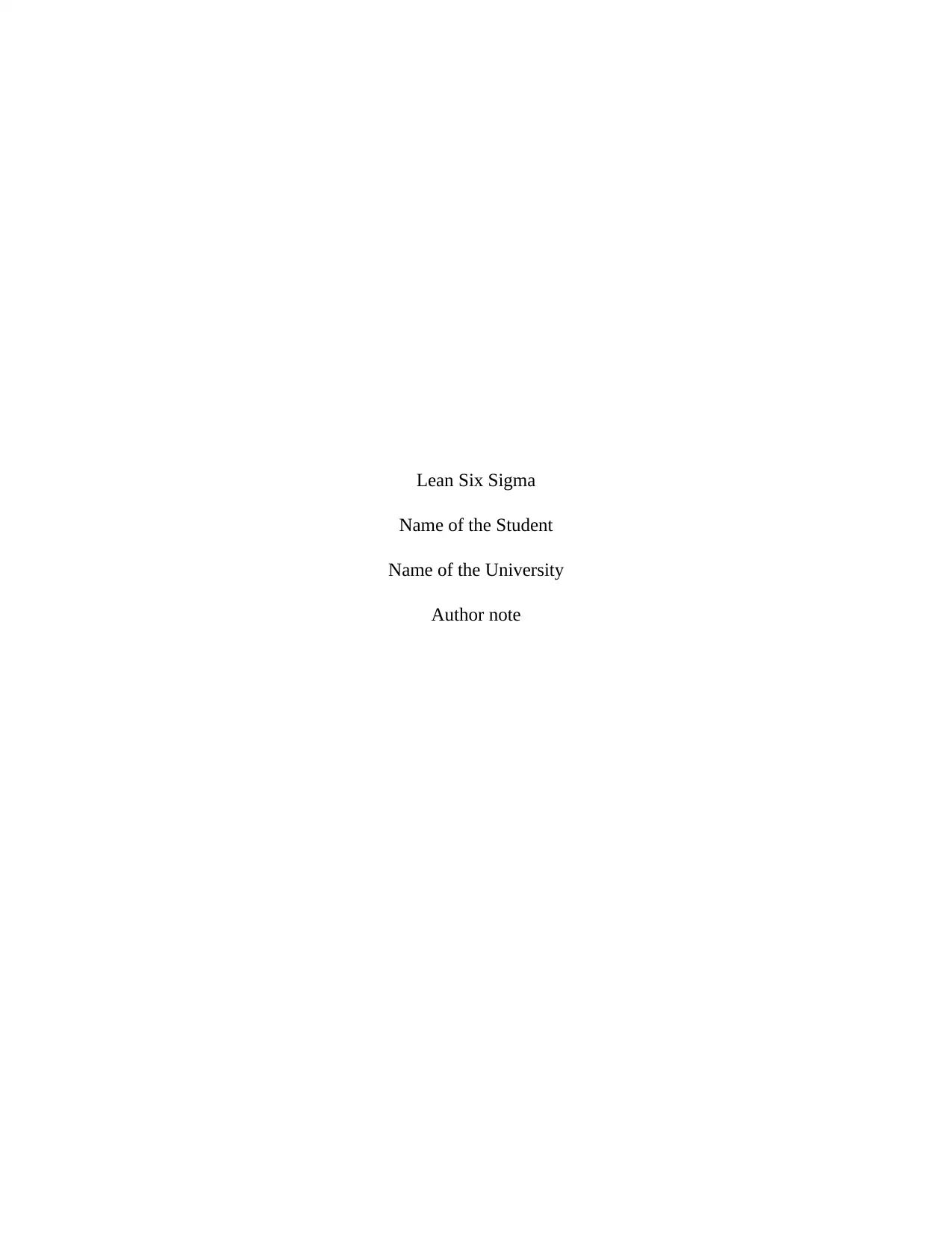
Lean Six Sigma
Name of the Student
Name of the University
Author note
Name of the Student
Name of the University
Author note
Secure Best Marks with AI Grader
Need help grading? Try our AI Grader for instant feedback on your assignments.
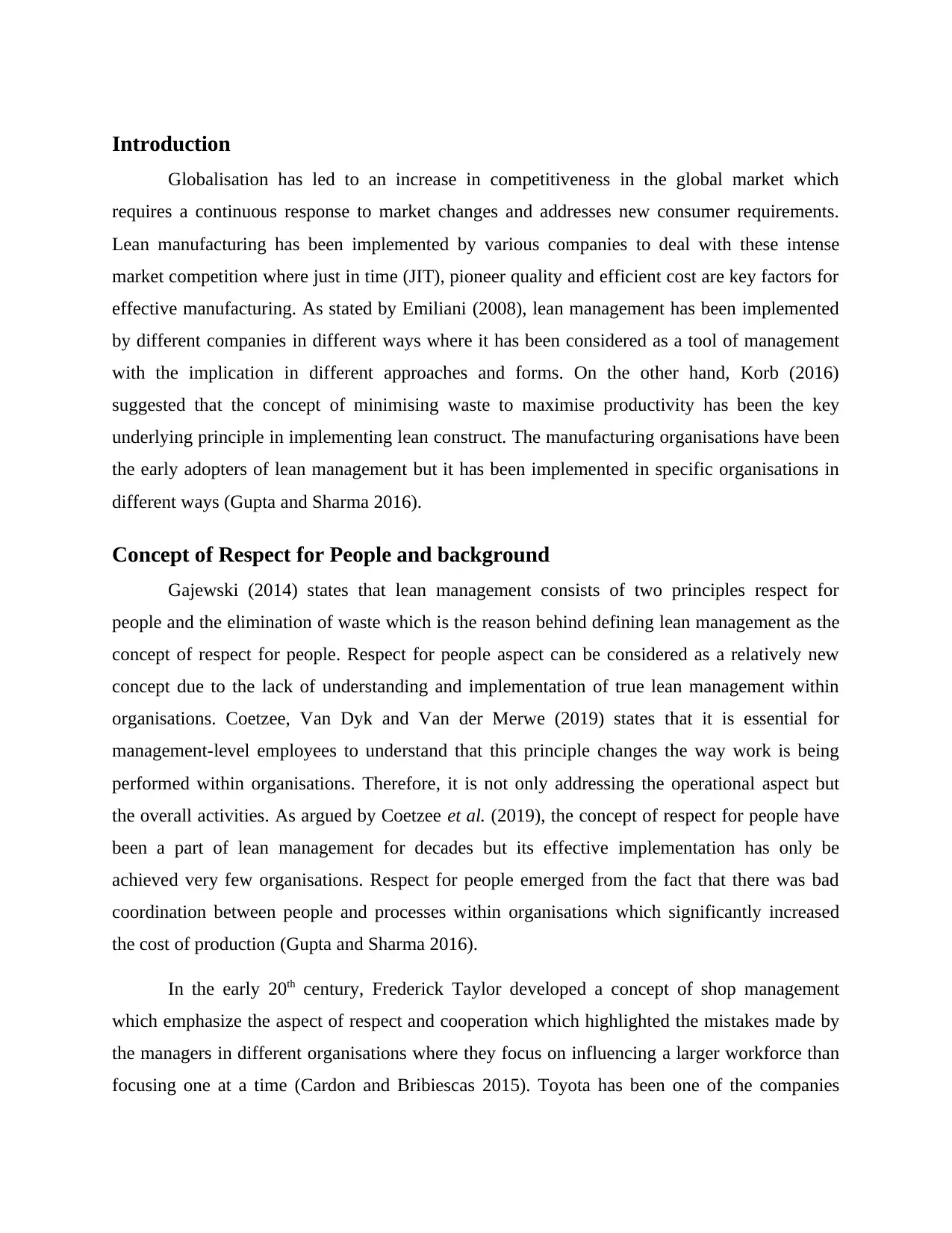
Introduction
Globalisation has led to an increase in competitiveness in the global market which
requires a continuous response to market changes and addresses new consumer requirements.
Lean manufacturing has been implemented by various companies to deal with these intense
market competition where just in time (JIT), pioneer quality and efficient cost are key factors for
effective manufacturing. As stated by Emiliani (2008), lean management has been implemented
by different companies in different ways where it has been considered as a tool of management
with the implication in different approaches and forms. On the other hand, Korb (2016)
suggested that the concept of minimising waste to maximise productivity has been the key
underlying principle in implementing lean construct. The manufacturing organisations have been
the early adopters of lean management but it has been implemented in specific organisations in
different ways (Gupta and Sharma 2016).
Concept of Respect for People and background
Gajewski (2014) states that lean management consists of two principles respect for
people and the elimination of waste which is the reason behind defining lean management as the
concept of respect for people. Respect for people aspect can be considered as a relatively new
concept due to the lack of understanding and implementation of true lean management within
organisations. Coetzee, Van Dyk and Van der Merwe (2019) states that it is essential for
management-level employees to understand that this principle changes the way work is being
performed within organisations. Therefore, it is not only addressing the operational aspect but
the overall activities. As argued by Coetzee et al. (2019), the concept of respect for people have
been a part of lean management for decades but its effective implementation has only be
achieved very few organisations. Respect for people emerged from the fact that there was bad
coordination between people and processes within organisations which significantly increased
the cost of production (Gupta and Sharma 2016).
In the early 20th century, Frederick Taylor developed a concept of shop management
which emphasize the aspect of respect and cooperation which highlighted the mistakes made by
the managers in different organisations where they focus on influencing a larger workforce than
focusing one at a time (Cardon and Bribiescas 2015). Toyota has been one of the companies
Globalisation has led to an increase in competitiveness in the global market which
requires a continuous response to market changes and addresses new consumer requirements.
Lean manufacturing has been implemented by various companies to deal with these intense
market competition where just in time (JIT), pioneer quality and efficient cost are key factors for
effective manufacturing. As stated by Emiliani (2008), lean management has been implemented
by different companies in different ways where it has been considered as a tool of management
with the implication in different approaches and forms. On the other hand, Korb (2016)
suggested that the concept of minimising waste to maximise productivity has been the key
underlying principle in implementing lean construct. The manufacturing organisations have been
the early adopters of lean management but it has been implemented in specific organisations in
different ways (Gupta and Sharma 2016).
Concept of Respect for People and background
Gajewski (2014) states that lean management consists of two principles respect for
people and the elimination of waste which is the reason behind defining lean management as the
concept of respect for people. Respect for people aspect can be considered as a relatively new
concept due to the lack of understanding and implementation of true lean management within
organisations. Coetzee, Van Dyk and Van der Merwe (2019) states that it is essential for
management-level employees to understand that this principle changes the way work is being
performed within organisations. Therefore, it is not only addressing the operational aspect but
the overall activities. As argued by Coetzee et al. (2019), the concept of respect for people have
been a part of lean management for decades but its effective implementation has only be
achieved very few organisations. Respect for people emerged from the fact that there was bad
coordination between people and processes within organisations which significantly increased
the cost of production (Gupta and Sharma 2016).
In the early 20th century, Frederick Taylor developed a concept of shop management
which emphasize the aspect of respect and cooperation which highlighted the mistakes made by
the managers in different organisations where they focus on influencing a larger workforce than
focusing one at a time (Cardon and Bribiescas 2015). Toyota has been one of the companies
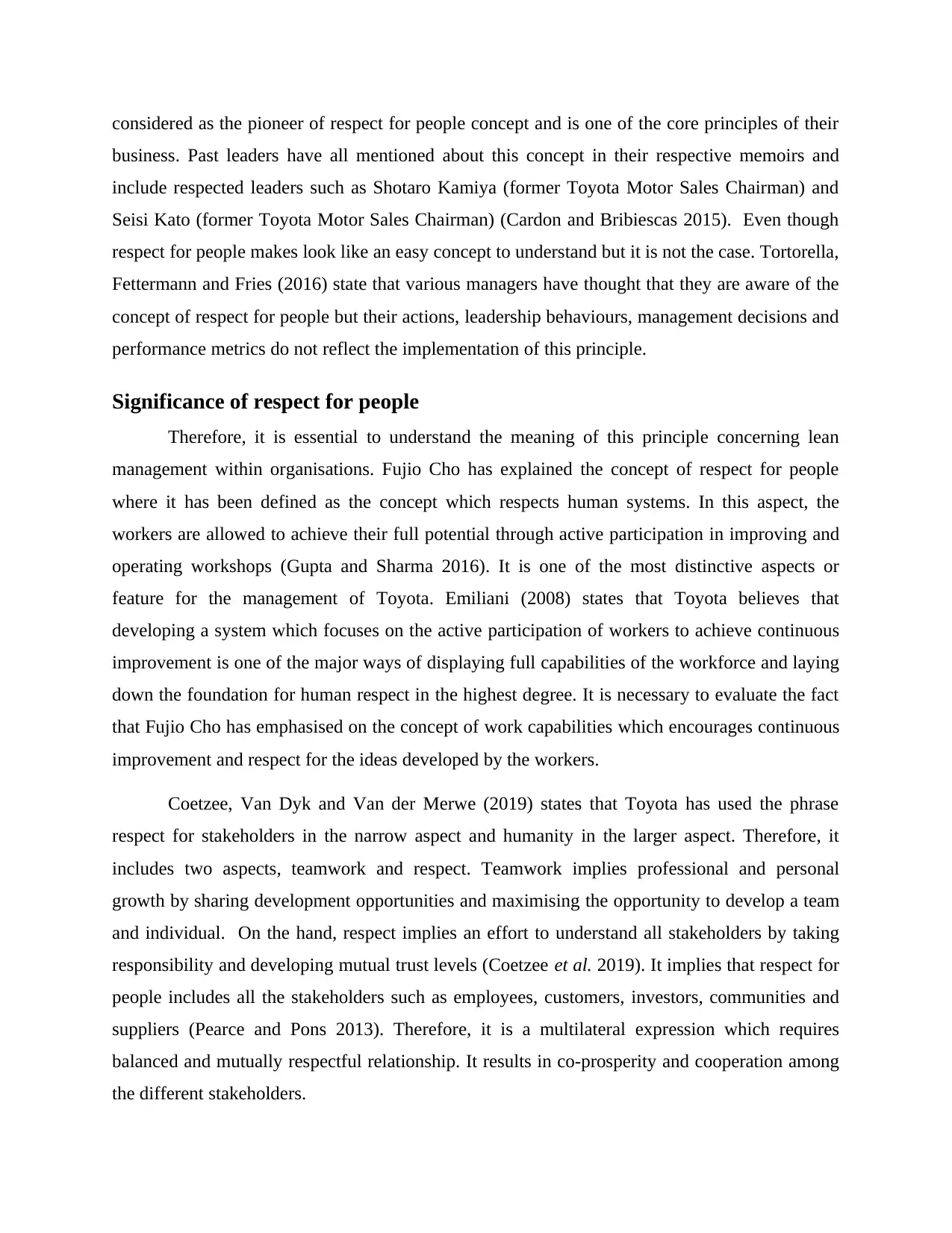
considered as the pioneer of respect for people concept and is one of the core principles of their
business. Past leaders have all mentioned about this concept in their respective memoirs and
include respected leaders such as Shotaro Kamiya (former Toyota Motor Sales Chairman) and
Seisi Kato (former Toyota Motor Sales Chairman) (Cardon and Bribiescas 2015). Even though
respect for people makes look like an easy concept to understand but it is not the case. Tortorella,
Fettermann and Fries (2016) state that various managers have thought that they are aware of the
concept of respect for people but their actions, leadership behaviours, management decisions and
performance metrics do not reflect the implementation of this principle.
Significance of respect for people
Therefore, it is essential to understand the meaning of this principle concerning lean
management within organisations. Fujio Cho has explained the concept of respect for people
where it has been defined as the concept which respects human systems. In this aspect, the
workers are allowed to achieve their full potential through active participation in improving and
operating workshops (Gupta and Sharma 2016). It is one of the most distinctive aspects or
feature for the management of Toyota. Emiliani (2008) states that Toyota believes that
developing a system which focuses on the active participation of workers to achieve continuous
improvement is one of the major ways of displaying full capabilities of the workforce and laying
down the foundation for human respect in the highest degree. It is necessary to evaluate the fact
that Fujio Cho has emphasised on the concept of work capabilities which encourages continuous
improvement and respect for the ideas developed by the workers.
Coetzee, Van Dyk and Van der Merwe (2019) states that Toyota has used the phrase
respect for stakeholders in the narrow aspect and humanity in the larger aspect. Therefore, it
includes two aspects, teamwork and respect. Teamwork implies professional and personal
growth by sharing development opportunities and maximising the opportunity to develop a team
and individual. On the hand, respect implies an effort to understand all stakeholders by taking
responsibility and developing mutual trust levels (Coetzee et al. 2019). It implies that respect for
people includes all the stakeholders such as employees, customers, investors, communities and
suppliers (Pearce and Pons 2013). Therefore, it is a multilateral expression which requires
balanced and mutually respectful relationship. It results in co-prosperity and cooperation among
the different stakeholders.
business. Past leaders have all mentioned about this concept in their respective memoirs and
include respected leaders such as Shotaro Kamiya (former Toyota Motor Sales Chairman) and
Seisi Kato (former Toyota Motor Sales Chairman) (Cardon and Bribiescas 2015). Even though
respect for people makes look like an easy concept to understand but it is not the case. Tortorella,
Fettermann and Fries (2016) state that various managers have thought that they are aware of the
concept of respect for people but their actions, leadership behaviours, management decisions and
performance metrics do not reflect the implementation of this principle.
Significance of respect for people
Therefore, it is essential to understand the meaning of this principle concerning lean
management within organisations. Fujio Cho has explained the concept of respect for people
where it has been defined as the concept which respects human systems. In this aspect, the
workers are allowed to achieve their full potential through active participation in improving and
operating workshops (Gupta and Sharma 2016). It is one of the most distinctive aspects or
feature for the management of Toyota. Emiliani (2008) states that Toyota believes that
developing a system which focuses on the active participation of workers to achieve continuous
improvement is one of the major ways of displaying full capabilities of the workforce and laying
down the foundation for human respect in the highest degree. It is necessary to evaluate the fact
that Fujio Cho has emphasised on the concept of work capabilities which encourages continuous
improvement and respect for the ideas developed by the workers.
Coetzee, Van Dyk and Van der Merwe (2019) states that Toyota has used the phrase
respect for stakeholders in the narrow aspect and humanity in the larger aspect. Therefore, it
includes two aspects, teamwork and respect. Teamwork implies professional and personal
growth by sharing development opportunities and maximising the opportunity to develop a team
and individual. On the hand, respect implies an effort to understand all stakeholders by taking
responsibility and developing mutual trust levels (Coetzee et al. 2019). It implies that respect for
people includes all the stakeholders such as employees, customers, investors, communities and
suppliers (Pearce and Pons 2013). Therefore, it is a multilateral expression which requires
balanced and mutually respectful relationship. It results in co-prosperity and cooperation among
the different stakeholders.
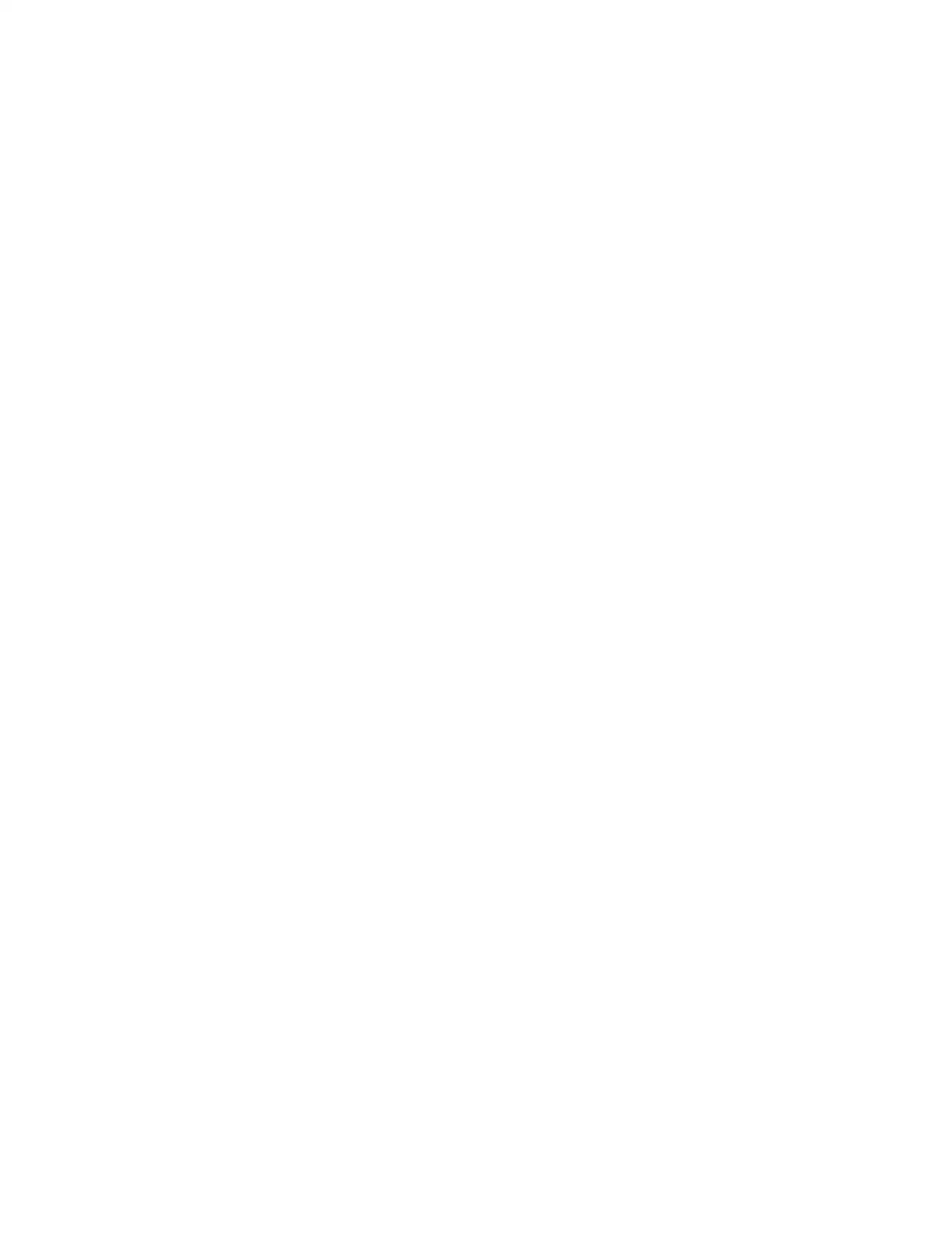
Secure Best Marks with AI Grader
Need help grading? Try our AI Grader for instant feedback on your assignments.
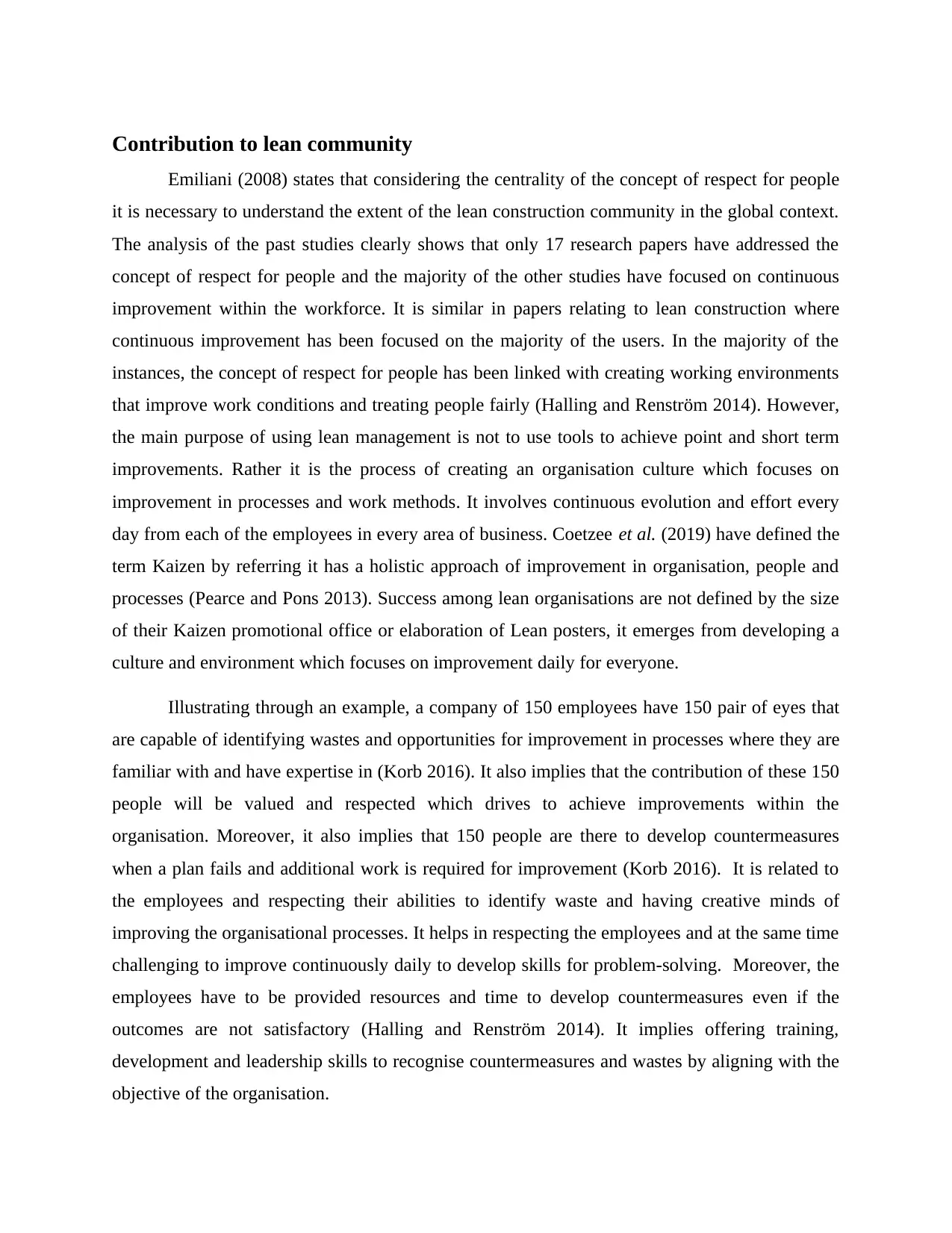
Contribution to lean community
Emiliani (2008) states that considering the centrality of the concept of respect for people
it is necessary to understand the extent of the lean construction community in the global context.
The analysis of the past studies clearly shows that only 17 research papers have addressed the
concept of respect for people and the majority of the other studies have focused on continuous
improvement within the workforce. It is similar in papers relating to lean construction where
continuous improvement has been focused on the majority of the users. In the majority of the
instances, the concept of respect for people has been linked with creating working environments
that improve work conditions and treating people fairly (Halling and Renström 2014). However,
the main purpose of using lean management is not to use tools to achieve point and short term
improvements. Rather it is the process of creating an organisation culture which focuses on
improvement in processes and work methods. It involves continuous evolution and effort every
day from each of the employees in every area of business. Coetzee et al. (2019) have defined the
term Kaizen by referring it has a holistic approach of improvement in organisation, people and
processes (Pearce and Pons 2013). Success among lean organisations are not defined by the size
of their Kaizen promotional office or elaboration of Lean posters, it emerges from developing a
culture and environment which focuses on improvement daily for everyone.
Illustrating through an example, a company of 150 employees have 150 pair of eyes that
are capable of identifying wastes and opportunities for improvement in processes where they are
familiar with and have expertise in (Korb 2016). It also implies that the contribution of these 150
people will be valued and respected which drives to achieve improvements within the
organisation. Moreover, it also implies that 150 people are there to develop countermeasures
when a plan fails and additional work is required for improvement (Korb 2016). It is related to
the employees and respecting their abilities to identify waste and having creative minds of
improving the organisational processes. It helps in respecting the employees and at the same time
challenging to improve continuously daily to develop skills for problem-solving. Moreover, the
employees have to be provided resources and time to develop countermeasures even if the
outcomes are not satisfactory (Halling and Renström 2014). It implies offering training,
development and leadership skills to recognise countermeasures and wastes by aligning with the
objective of the organisation.
Emiliani (2008) states that considering the centrality of the concept of respect for people
it is necessary to understand the extent of the lean construction community in the global context.
The analysis of the past studies clearly shows that only 17 research papers have addressed the
concept of respect for people and the majority of the other studies have focused on continuous
improvement within the workforce. It is similar in papers relating to lean construction where
continuous improvement has been focused on the majority of the users. In the majority of the
instances, the concept of respect for people has been linked with creating working environments
that improve work conditions and treating people fairly (Halling and Renström 2014). However,
the main purpose of using lean management is not to use tools to achieve point and short term
improvements. Rather it is the process of creating an organisation culture which focuses on
improvement in processes and work methods. It involves continuous evolution and effort every
day from each of the employees in every area of business. Coetzee et al. (2019) have defined the
term Kaizen by referring it has a holistic approach of improvement in organisation, people and
processes (Pearce and Pons 2013). Success among lean organisations are not defined by the size
of their Kaizen promotional office or elaboration of Lean posters, it emerges from developing a
culture and environment which focuses on improvement daily for everyone.
Illustrating through an example, a company of 150 employees have 150 pair of eyes that
are capable of identifying wastes and opportunities for improvement in processes where they are
familiar with and have expertise in (Korb 2016). It also implies that the contribution of these 150
people will be valued and respected which drives to achieve improvements within the
organisation. Moreover, it also implies that 150 people are there to develop countermeasures
when a plan fails and additional work is required for improvement (Korb 2016). It is related to
the employees and respecting their abilities to identify waste and having creative minds of
improving the organisational processes. It helps in respecting the employees and at the same time
challenging to improve continuously daily to develop skills for problem-solving. Moreover, the
employees have to be provided resources and time to develop countermeasures even if the
outcomes are not satisfactory (Halling and Renström 2014). It implies offering training,
development and leadership skills to recognise countermeasures and wastes by aligning with the
objective of the organisation.
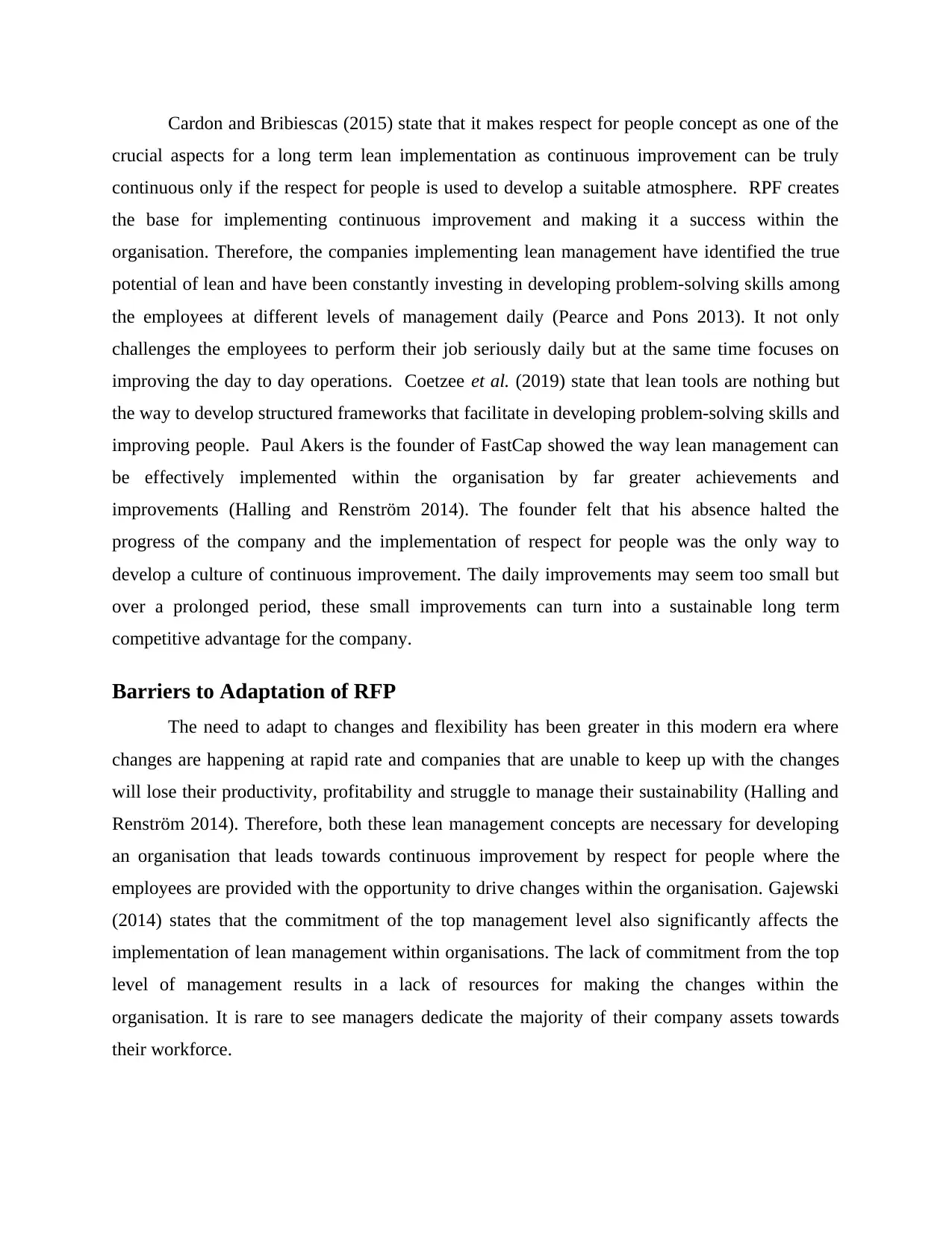
Cardon and Bribiescas (2015) state that it makes respect for people concept as one of the
crucial aspects for a long term lean implementation as continuous improvement can be truly
continuous only if the respect for people is used to develop a suitable atmosphere. RPF creates
the base for implementing continuous improvement and making it a success within the
organisation. Therefore, the companies implementing lean management have identified the true
potential of lean and have been constantly investing in developing problem-solving skills among
the employees at different levels of management daily (Pearce and Pons 2013). It not only
challenges the employees to perform their job seriously daily but at the same time focuses on
improving the day to day operations. Coetzee et al. (2019) state that lean tools are nothing but
the way to develop structured frameworks that facilitate in developing problem-solving skills and
improving people. Paul Akers is the founder of FastCap showed the way lean management can
be effectively implemented within the organisation by far greater achievements and
improvements (Halling and Renström 2014). The founder felt that his absence halted the
progress of the company and the implementation of respect for people was the only way to
develop a culture of continuous improvement. The daily improvements may seem too small but
over a prolonged period, these small improvements can turn into a sustainable long term
competitive advantage for the company.
Barriers to Adaptation of RFP
The need to adapt to changes and flexibility has been greater in this modern era where
changes are happening at rapid rate and companies that are unable to keep up with the changes
will lose their productivity, profitability and struggle to manage their sustainability (Halling and
Renström 2014). Therefore, both these lean management concepts are necessary for developing
an organisation that leads towards continuous improvement by respect for people where the
employees are provided with the opportunity to drive changes within the organisation. Gajewski
(2014) states that the commitment of the top management level also significantly affects the
implementation of lean management within organisations. The lack of commitment from the top
level of management results in a lack of resources for making the changes within the
organisation. It is rare to see managers dedicate the majority of their company assets towards
their workforce.
crucial aspects for a long term lean implementation as continuous improvement can be truly
continuous only if the respect for people is used to develop a suitable atmosphere. RPF creates
the base for implementing continuous improvement and making it a success within the
organisation. Therefore, the companies implementing lean management have identified the true
potential of lean and have been constantly investing in developing problem-solving skills among
the employees at different levels of management daily (Pearce and Pons 2013). It not only
challenges the employees to perform their job seriously daily but at the same time focuses on
improving the day to day operations. Coetzee et al. (2019) state that lean tools are nothing but
the way to develop structured frameworks that facilitate in developing problem-solving skills and
improving people. Paul Akers is the founder of FastCap showed the way lean management can
be effectively implemented within the organisation by far greater achievements and
improvements (Halling and Renström 2014). The founder felt that his absence halted the
progress of the company and the implementation of respect for people was the only way to
develop a culture of continuous improvement. The daily improvements may seem too small but
over a prolonged period, these small improvements can turn into a sustainable long term
competitive advantage for the company.
Barriers to Adaptation of RFP
The need to adapt to changes and flexibility has been greater in this modern era where
changes are happening at rapid rate and companies that are unable to keep up with the changes
will lose their productivity, profitability and struggle to manage their sustainability (Halling and
Renström 2014). Therefore, both these lean management concepts are necessary for developing
an organisation that leads towards continuous improvement by respect for people where the
employees are provided with the opportunity to drive changes within the organisation. Gajewski
(2014) states that the commitment of the top management level also significantly affects the
implementation of lean management within organisations. The lack of commitment from the top
level of management results in a lack of resources for making the changes within the
organisation. It is rare to see managers dedicate the majority of their company assets towards
their workforce.
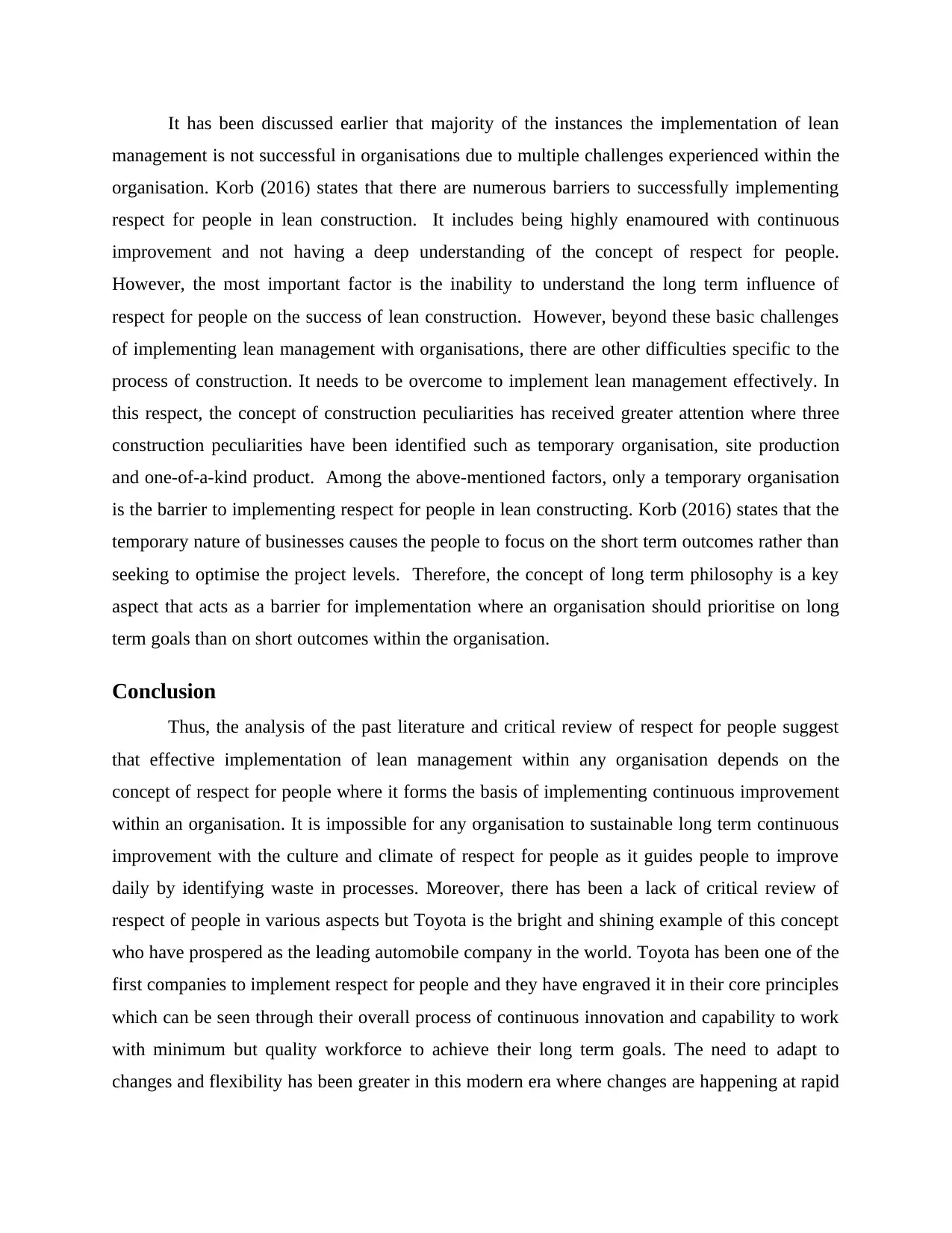
It has been discussed earlier that majority of the instances the implementation of lean
management is not successful in organisations due to multiple challenges experienced within the
organisation. Korb (2016) states that there are numerous barriers to successfully implementing
respect for people in lean construction. It includes being highly enamoured with continuous
improvement and not having a deep understanding of the concept of respect for people.
However, the most important factor is the inability to understand the long term influence of
respect for people on the success of lean construction. However, beyond these basic challenges
of implementing lean management with organisations, there are other difficulties specific to the
process of construction. It needs to be overcome to implement lean management effectively. In
this respect, the concept of construction peculiarities has received greater attention where three
construction peculiarities have been identified such as temporary organisation, site production
and one-of-a-kind product. Among the above-mentioned factors, only a temporary organisation
is the barrier to implementing respect for people in lean constructing. Korb (2016) states that the
temporary nature of businesses causes the people to focus on the short term outcomes rather than
seeking to optimise the project levels. Therefore, the concept of long term philosophy is a key
aspect that acts as a barrier for implementation where an organisation should prioritise on long
term goals than on short outcomes within the organisation.
Conclusion
Thus, the analysis of the past literature and critical review of respect for people suggest
that effective implementation of lean management within any organisation depends on the
concept of respect for people where it forms the basis of implementing continuous improvement
within an organisation. It is impossible for any organisation to sustainable long term continuous
improvement with the culture and climate of respect for people as it guides people to improve
daily by identifying waste in processes. Moreover, there has been a lack of critical review of
respect of people in various aspects but Toyota is the bright and shining example of this concept
who have prospered as the leading automobile company in the world. Toyota has been one of the
first companies to implement respect for people and they have engraved it in their core principles
which can be seen through their overall process of continuous innovation and capability to work
with minimum but quality workforce to achieve their long term goals. The need to adapt to
changes and flexibility has been greater in this modern era where changes are happening at rapid
management is not successful in organisations due to multiple challenges experienced within the
organisation. Korb (2016) states that there are numerous barriers to successfully implementing
respect for people in lean construction. It includes being highly enamoured with continuous
improvement and not having a deep understanding of the concept of respect for people.
However, the most important factor is the inability to understand the long term influence of
respect for people on the success of lean construction. However, beyond these basic challenges
of implementing lean management with organisations, there are other difficulties specific to the
process of construction. It needs to be overcome to implement lean management effectively. In
this respect, the concept of construction peculiarities has received greater attention where three
construction peculiarities have been identified such as temporary organisation, site production
and one-of-a-kind product. Among the above-mentioned factors, only a temporary organisation
is the barrier to implementing respect for people in lean constructing. Korb (2016) states that the
temporary nature of businesses causes the people to focus on the short term outcomes rather than
seeking to optimise the project levels. Therefore, the concept of long term philosophy is a key
aspect that acts as a barrier for implementation where an organisation should prioritise on long
term goals than on short outcomes within the organisation.
Conclusion
Thus, the analysis of the past literature and critical review of respect for people suggest
that effective implementation of lean management within any organisation depends on the
concept of respect for people where it forms the basis of implementing continuous improvement
within an organisation. It is impossible for any organisation to sustainable long term continuous
improvement with the culture and climate of respect for people as it guides people to improve
daily by identifying waste in processes. Moreover, there has been a lack of critical review of
respect of people in various aspects but Toyota is the bright and shining example of this concept
who have prospered as the leading automobile company in the world. Toyota has been one of the
first companies to implement respect for people and they have engraved it in their core principles
which can be seen through their overall process of continuous innovation and capability to work
with minimum but quality workforce to achieve their long term goals. The need to adapt to
changes and flexibility has been greater in this modern era where changes are happening at rapid
Paraphrase This Document
Need a fresh take? Get an instant paraphrase of this document with our AI Paraphraser
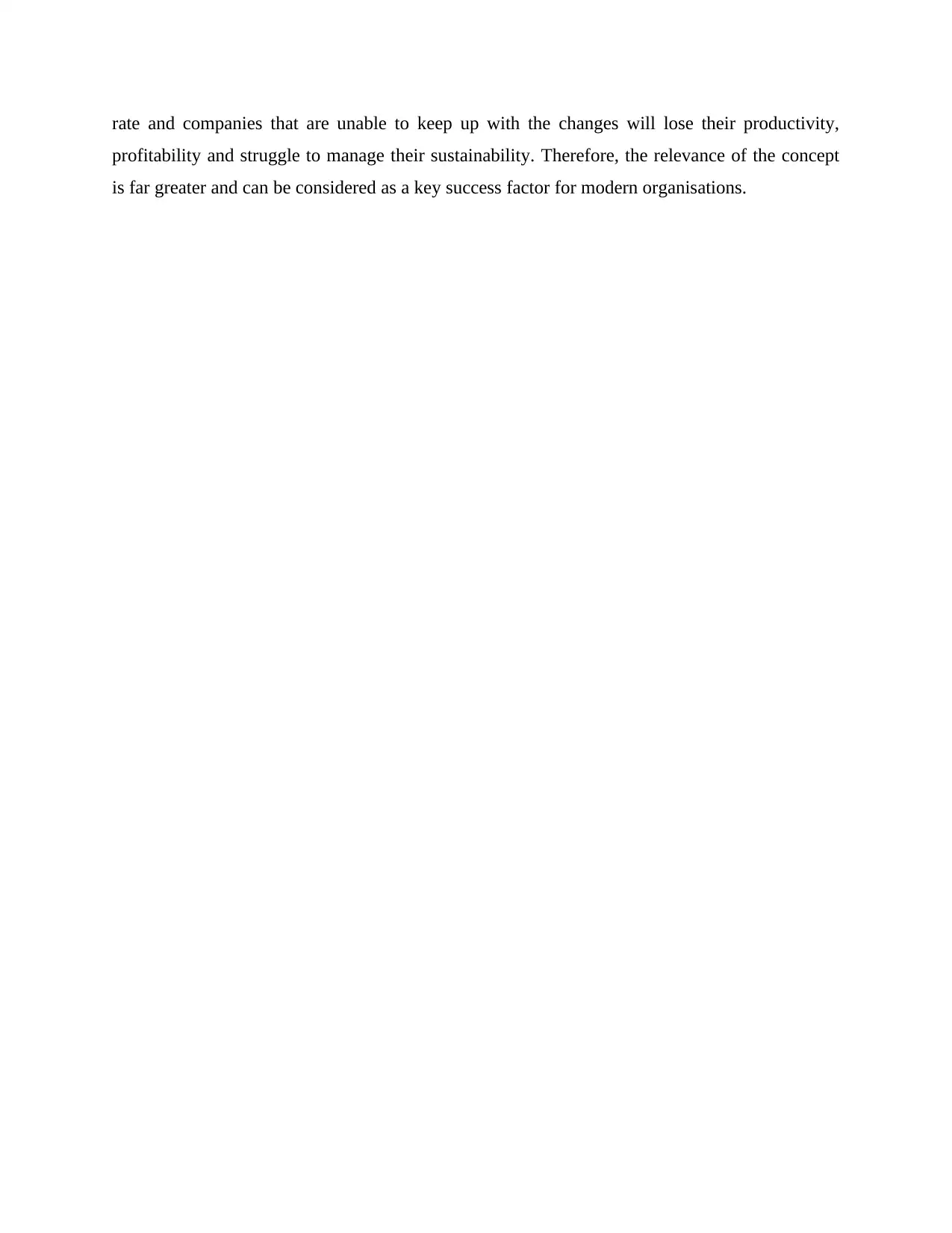
rate and companies that are unable to keep up with the changes will lose their productivity,
profitability and struggle to manage their sustainability. Therefore, the relevance of the concept
is far greater and can be considered as a key success factor for modern organisations.
profitability and struggle to manage their sustainability. Therefore, the relevance of the concept
is far greater and can be considered as a key success factor for modern organisations.
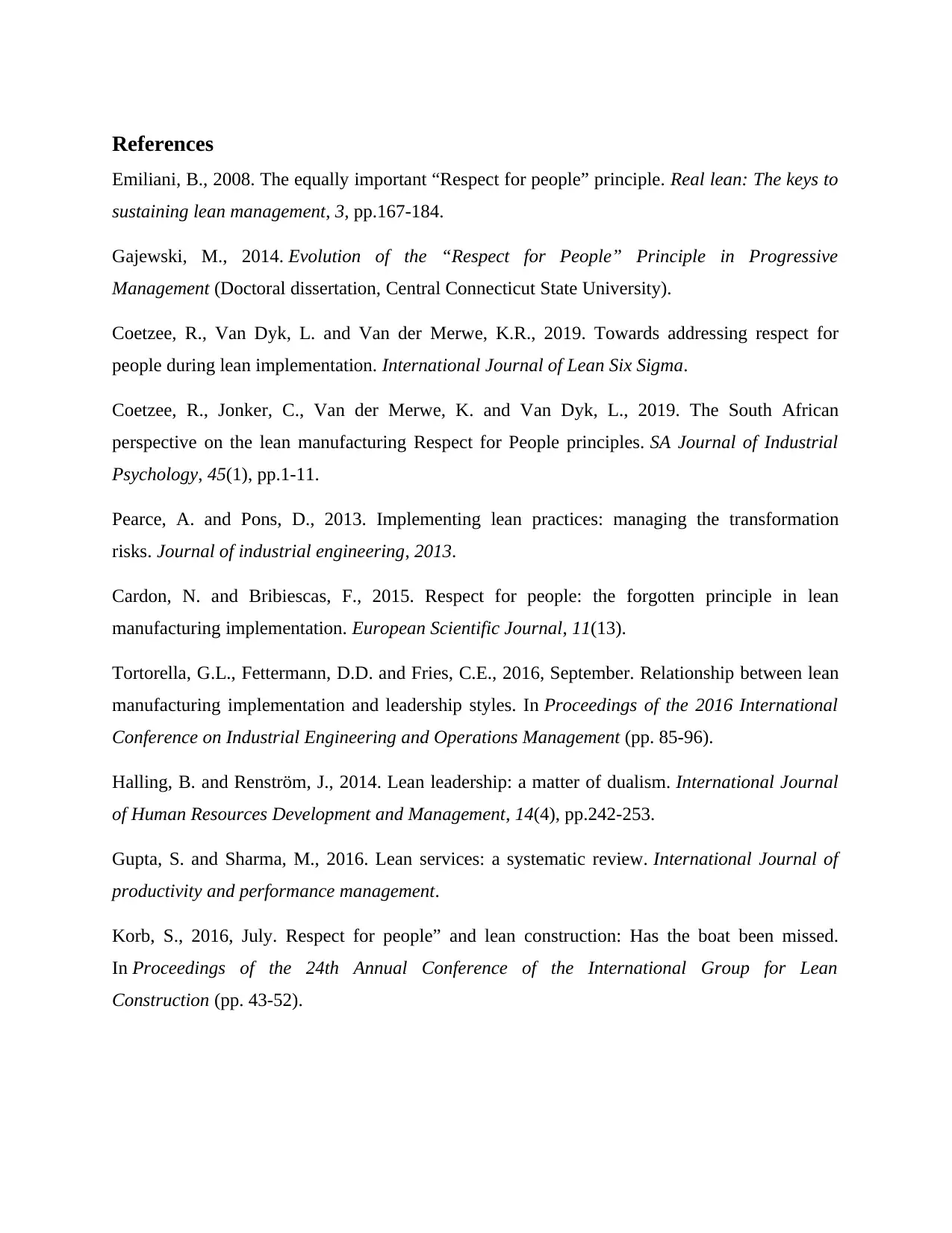
References
Emiliani, B., 2008. The equally important “Respect for people” principle. Real lean: The keys to
sustaining lean management, 3, pp.167-184.
Gajewski, M., 2014. Evolution of the “Respect for People” Principle in Progressive
Management (Doctoral dissertation, Central Connecticut State University).
Coetzee, R., Van Dyk, L. and Van der Merwe, K.R., 2019. Towards addressing respect for
people during lean implementation. International Journal of Lean Six Sigma.
Coetzee, R., Jonker, C., Van der Merwe, K. and Van Dyk, L., 2019. The South African
perspective on the lean manufacturing Respect for People principles. SA Journal of Industrial
Psychology, 45(1), pp.1-11.
Pearce, A. and Pons, D., 2013. Implementing lean practices: managing the transformation
risks. Journal of industrial engineering, 2013.
Cardon, N. and Bribiescas, F., 2015. Respect for people: the forgotten principle in lean
manufacturing implementation. European Scientific Journal, 11(13).
Tortorella, G.L., Fettermann, D.D. and Fries, C.E., 2016, September. Relationship between lean
manufacturing implementation and leadership styles. In Proceedings of the 2016 International
Conference on Industrial Engineering and Operations Management (pp. 85-96).
Halling, B. and Renström, J., 2014. Lean leadership: a matter of dualism. International Journal
of Human Resources Development and Management, 14(4), pp.242-253.
Gupta, S. and Sharma, M., 2016. Lean services: a systematic review. International Journal of
productivity and performance management.
Korb, S., 2016, July. Respect for people” and lean construction: Has the boat been missed.
In Proceedings of the 24th Annual Conference of the International Group for Lean
Construction (pp. 43-52).
Emiliani, B., 2008. The equally important “Respect for people” principle. Real lean: The keys to
sustaining lean management, 3, pp.167-184.
Gajewski, M., 2014. Evolution of the “Respect for People” Principle in Progressive
Management (Doctoral dissertation, Central Connecticut State University).
Coetzee, R., Van Dyk, L. and Van der Merwe, K.R., 2019. Towards addressing respect for
people during lean implementation. International Journal of Lean Six Sigma.
Coetzee, R., Jonker, C., Van der Merwe, K. and Van Dyk, L., 2019. The South African
perspective on the lean manufacturing Respect for People principles. SA Journal of Industrial
Psychology, 45(1), pp.1-11.
Pearce, A. and Pons, D., 2013. Implementing lean practices: managing the transformation
risks. Journal of industrial engineering, 2013.
Cardon, N. and Bribiescas, F., 2015. Respect for people: the forgotten principle in lean
manufacturing implementation. European Scientific Journal, 11(13).
Tortorella, G.L., Fettermann, D.D. and Fries, C.E., 2016, September. Relationship between lean
manufacturing implementation and leadership styles. In Proceedings of the 2016 International
Conference on Industrial Engineering and Operations Management (pp. 85-96).
Halling, B. and Renström, J., 2014. Lean leadership: a matter of dualism. International Journal
of Human Resources Development and Management, 14(4), pp.242-253.
Gupta, S. and Sharma, M., 2016. Lean services: a systematic review. International Journal of
productivity and performance management.
Korb, S., 2016, July. Respect for people” and lean construction: Has the boat been missed.
In Proceedings of the 24th Annual Conference of the International Group for Lean
Construction (pp. 43-52).
1 out of 9
Related Documents

Your All-in-One AI-Powered Toolkit for Academic Success.
+13062052269
info@desklib.com
Available 24*7 on WhatsApp / Email
Unlock your academic potential
© 2024 | Zucol Services PVT LTD | All rights reserved.