A Detailed Report on Lean Management, Six Sigma, and Change Concepts
VerifiedAdded on 2023/01/11
|13
|3448
|84
Report
AI Summary
This report delves into the interconnectedness of lean management, six sigma methodologies, and the crucial aspects of change management within business environments. It begins by defining and differentiating the three key concepts of change: Kaizen (continuous improvement), Kaikaku (radical change), and Kakushin (innovative change), analyzing their individual characteristics, applications, and impacts on organizational processes and performance. The report then explores the relationship between these change concepts and the principles of lean management, emphasizing waste reduction and process optimization, and six sigma, focusing on process improvement and defect reduction. It highlights how these approaches complement each other in driving organizational change and achieving operational excellence. The report underscores the importance of integrating these methodologies to foster a culture of continuous improvement and adaptability in response to both internal and external environmental changes, ultimately aiming to enhance profitability and competitiveness.
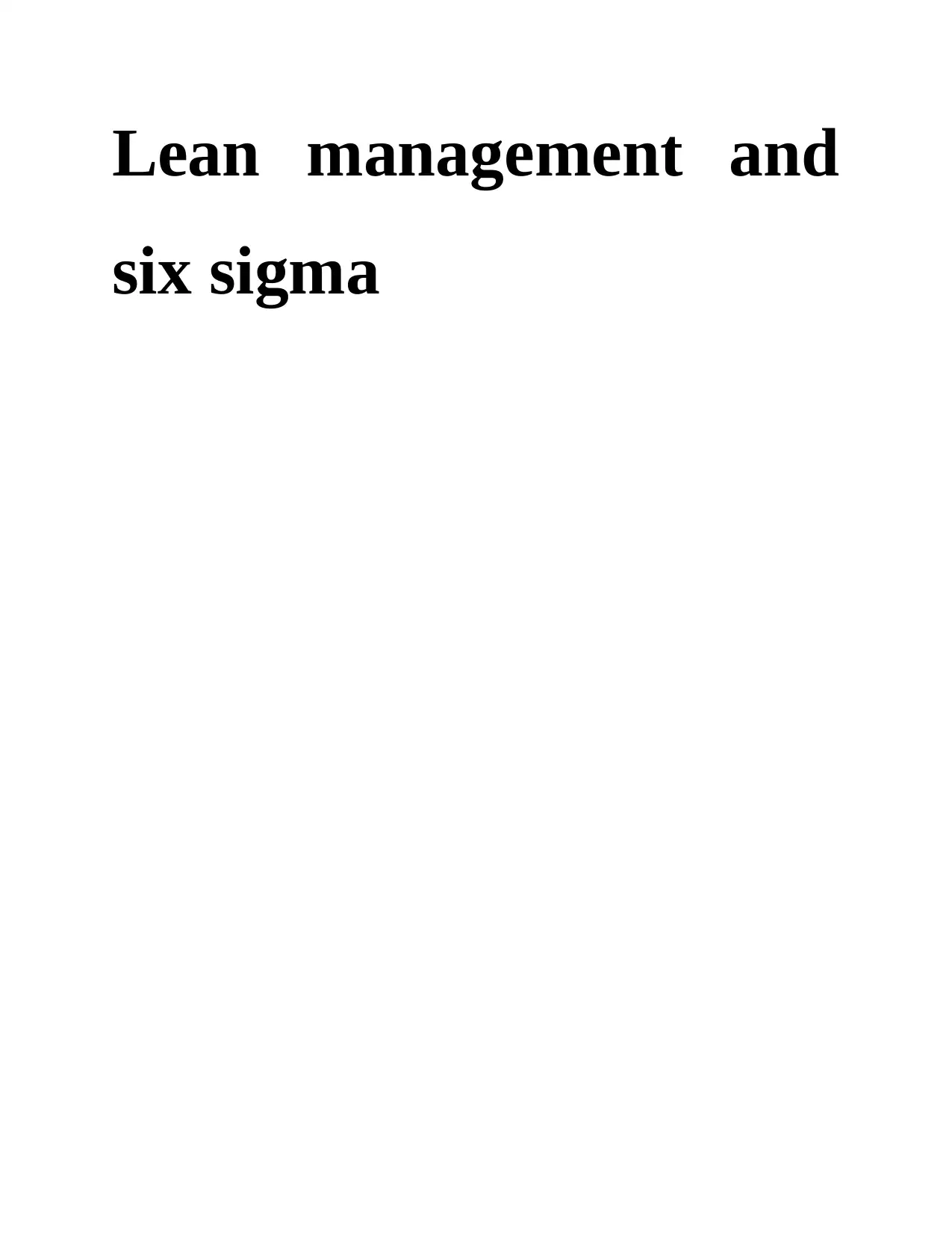
Lean management and
six sigma
six sigma
Secure Best Marks with AI Grader
Need help grading? Try our AI Grader for instant feedback on your assignments.
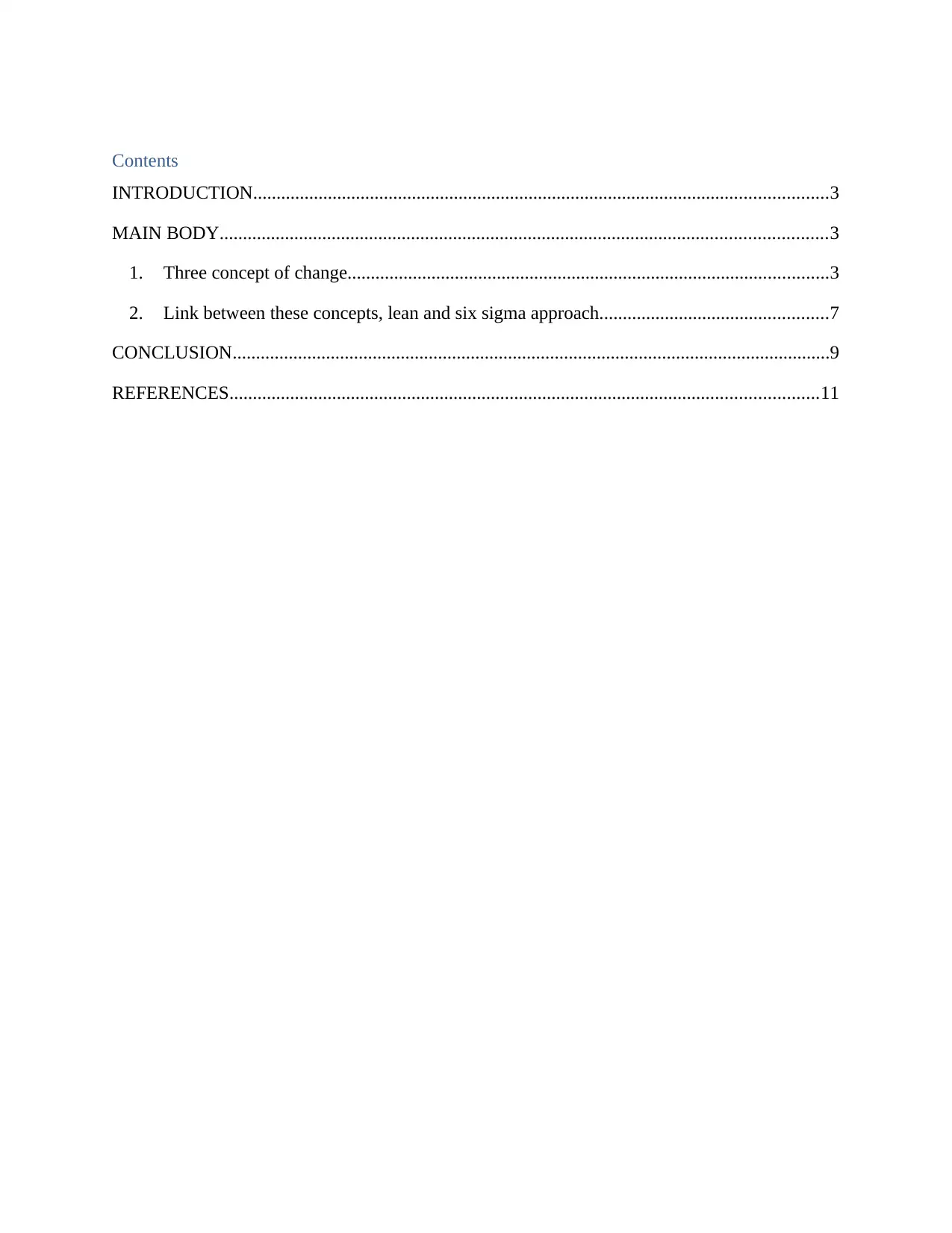
Contents
INTRODUCTION...........................................................................................................................3
MAIN BODY..................................................................................................................................3
1. Three concept of change.......................................................................................................3
2. Link between these concepts, lean and six sigma approach.................................................7
CONCLUSION................................................................................................................................9
REFERENCES..............................................................................................................................11
INTRODUCTION...........................................................................................................................3
MAIN BODY..................................................................................................................................3
1. Three concept of change.......................................................................................................3
2. Link between these concepts, lean and six sigma approach.................................................7
CONCLUSION................................................................................................................................9
REFERENCES..............................................................................................................................11
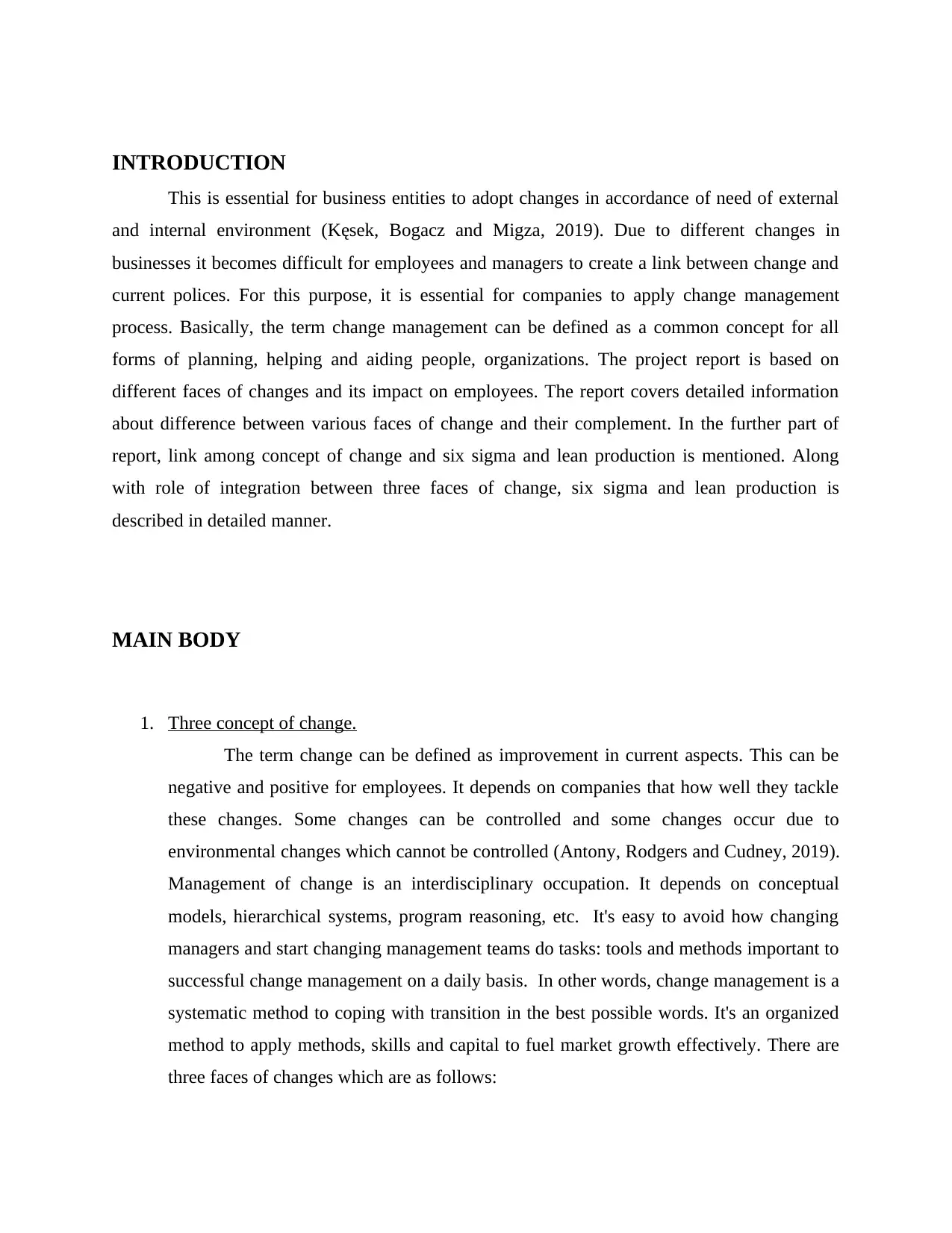
INTRODUCTION
This is essential for business entities to adopt changes in accordance of need of external
and internal environment (Kęsek, Bogacz and Migza, 2019). Due to different changes in
businesses it becomes difficult for employees and managers to create a link between change and
current polices. For this purpose, it is essential for companies to apply change management
process. Basically, the term change management can be defined as a common concept for all
forms of planning, helping and aiding people, organizations. The project report is based on
different faces of changes and its impact on employees. The report covers detailed information
about difference between various faces of change and their complement. In the further part of
report, link among concept of change and six sigma and lean production is mentioned. Along
with role of integration between three faces of change, six sigma and lean production is
described in detailed manner.
MAIN BODY
1. Three concept of change.
The term change can be defined as improvement in current aspects. This can be
negative and positive for employees. It depends on companies that how well they tackle
these changes. Some changes can be controlled and some changes occur due to
environmental changes which cannot be controlled (Antony, Rodgers and Cudney, 2019).
Management of change is an interdisciplinary occupation. It depends on conceptual
models, hierarchical systems, program reasoning, etc. It's easy to avoid how changing
managers and start changing management teams do tasks: tools and methods important to
successful change management on a daily basis. In other words, change management is a
systematic method to coping with transition in the best possible words. It's an organized
method to apply methods, skills and capital to fuel market growth effectively. There are
three faces of changes which are as follows:
This is essential for business entities to adopt changes in accordance of need of external
and internal environment (Kęsek, Bogacz and Migza, 2019). Due to different changes in
businesses it becomes difficult for employees and managers to create a link between change and
current polices. For this purpose, it is essential for companies to apply change management
process. Basically, the term change management can be defined as a common concept for all
forms of planning, helping and aiding people, organizations. The project report is based on
different faces of changes and its impact on employees. The report covers detailed information
about difference between various faces of change and their complement. In the further part of
report, link among concept of change and six sigma and lean production is mentioned. Along
with role of integration between three faces of change, six sigma and lean production is
described in detailed manner.
MAIN BODY
1. Three concept of change.
The term change can be defined as improvement in current aspects. This can be
negative and positive for employees. It depends on companies that how well they tackle
these changes. Some changes can be controlled and some changes occur due to
environmental changes which cannot be controlled (Antony, Rodgers and Cudney, 2019).
Management of change is an interdisciplinary occupation. It depends on conceptual
models, hierarchical systems, program reasoning, etc. It's easy to avoid how changing
managers and start changing management teams do tasks: tools and methods important to
successful change management on a daily basis. In other words, change management is a
systematic method to coping with transition in the best possible words. It's an organized
method to apply methods, skills and capital to fuel market growth effectively. There are
three faces of changes which are as follows:
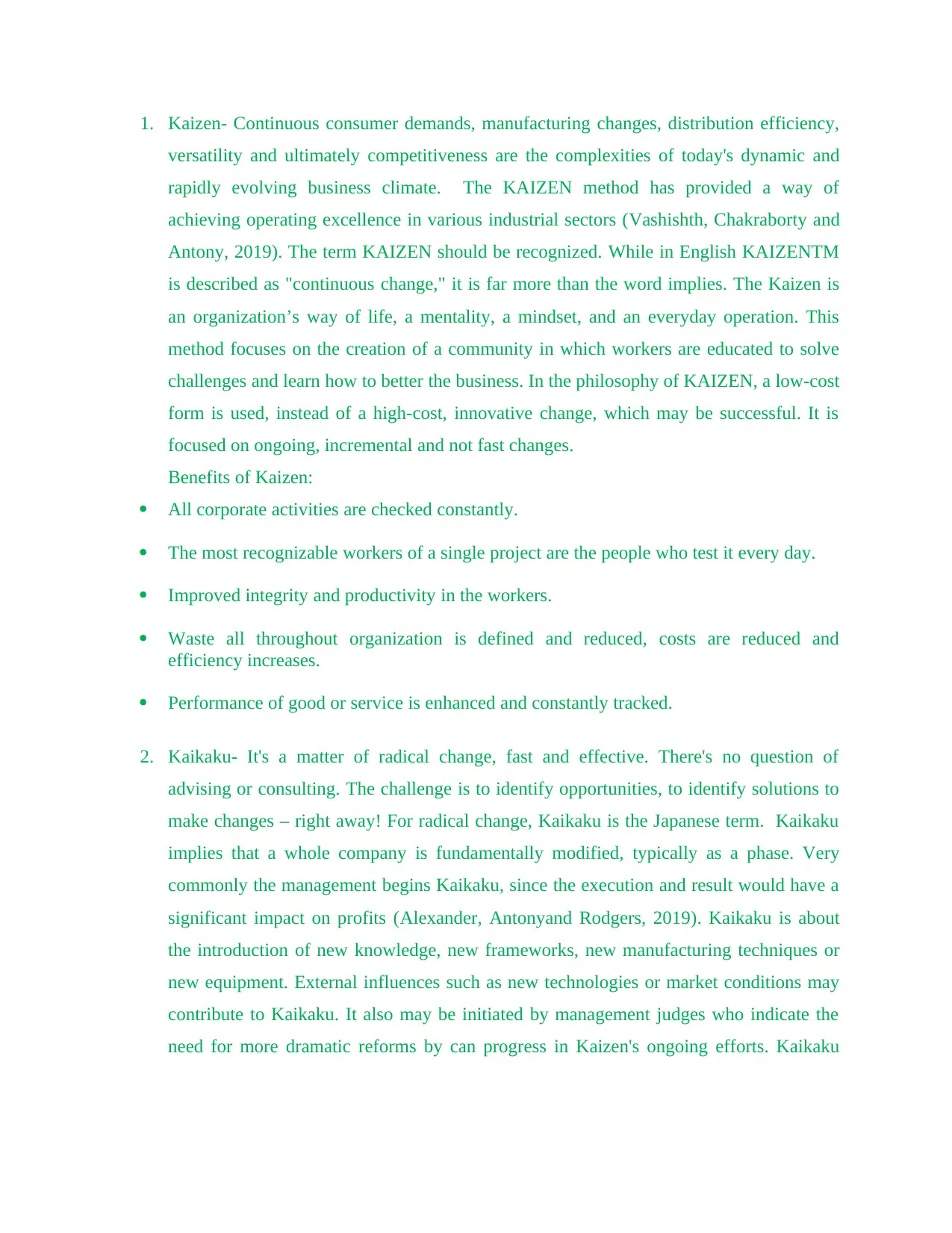
1. Kaizen- Continuous consumer demands, manufacturing changes, distribution efficiency,
versatility and ultimately competitiveness are the complexities of today's dynamic and
rapidly evolving business climate. The KAIZEN method has provided a way of
achieving operating excellence in various industrial sectors (Vashishth, Chakraborty and
Antony, 2019). The term KAIZEN should be recognized. While in English KAIZENTM
is described as "continuous change," it is far more than the word implies. The Kaizen is
an organization’s way of life, a mentality, a mindset, and an everyday operation. This
method focuses on the creation of a community in which workers are educated to solve
challenges and learn how to better the business. In the philosophy of KAIZEN, a low-cost
form is used, instead of a high-cost, innovative change, which may be successful. It is
focused on ongoing, incremental and not fast changes.
Benefits of Kaizen:
All corporate activities are checked constantly.
The most recognizable workers of a single project are the people who test it every day.
Improved integrity and productivity in the workers.
Waste all throughout organization is defined and reduced, costs are reduced and
efficiency increases.
Performance of good or service is enhanced and constantly tracked.
2. Kaikaku- It's a matter of radical change, fast and effective. There's no question of
advising or consulting. The challenge is to identify opportunities, to identify solutions to
make changes – right away! For radical change, Kaikaku is the Japanese term. Kaikaku
implies that a whole company is fundamentally modified, typically as a phase. Very
commonly the management begins Kaikaku, since the execution and result would have a
significant impact on profits (Alexander, Antonyand Rodgers, 2019). Kaikaku is about
the introduction of new knowledge, new frameworks, new manufacturing techniques or
new equipment. External influences such as new technologies or market conditions may
contribute to Kaikaku. It also may be initiated by management judges who indicate the
need for more dramatic reforms by can progress in Kaizen's ongoing efforts. Kaikaku
versatility and ultimately competitiveness are the complexities of today's dynamic and
rapidly evolving business climate. The KAIZEN method has provided a way of
achieving operating excellence in various industrial sectors (Vashishth, Chakraborty and
Antony, 2019). The term KAIZEN should be recognized. While in English KAIZENTM
is described as "continuous change," it is far more than the word implies. The Kaizen is
an organization’s way of life, a mentality, a mindset, and an everyday operation. This
method focuses on the creation of a community in which workers are educated to solve
challenges and learn how to better the business. In the philosophy of KAIZEN, a low-cost
form is used, instead of a high-cost, innovative change, which may be successful. It is
focused on ongoing, incremental and not fast changes.
Benefits of Kaizen:
All corporate activities are checked constantly.
The most recognizable workers of a single project are the people who test it every day.
Improved integrity and productivity in the workers.
Waste all throughout organization is defined and reduced, costs are reduced and
efficiency increases.
Performance of good or service is enhanced and constantly tracked.
2. Kaikaku- It's a matter of radical change, fast and effective. There's no question of
advising or consulting. The challenge is to identify opportunities, to identify solutions to
make changes – right away! For radical change, Kaikaku is the Japanese term. Kaikaku
implies that a whole company is fundamentally modified, typically as a phase. Very
commonly the management begins Kaikaku, since the execution and result would have a
significant impact on profits (Alexander, Antonyand Rodgers, 2019). Kaikaku is about
the introduction of new knowledge, new frameworks, new manufacturing techniques or
new equipment. External influences such as new technologies or market conditions may
contribute to Kaikaku. It also may be initiated by management judges who indicate the
need for more dramatic reforms by can progress in Kaizen's ongoing efforts. Kaikaku
Secure Best Marks with AI Grader
Need help grading? Try our AI Grader for instant feedback on your assignments.
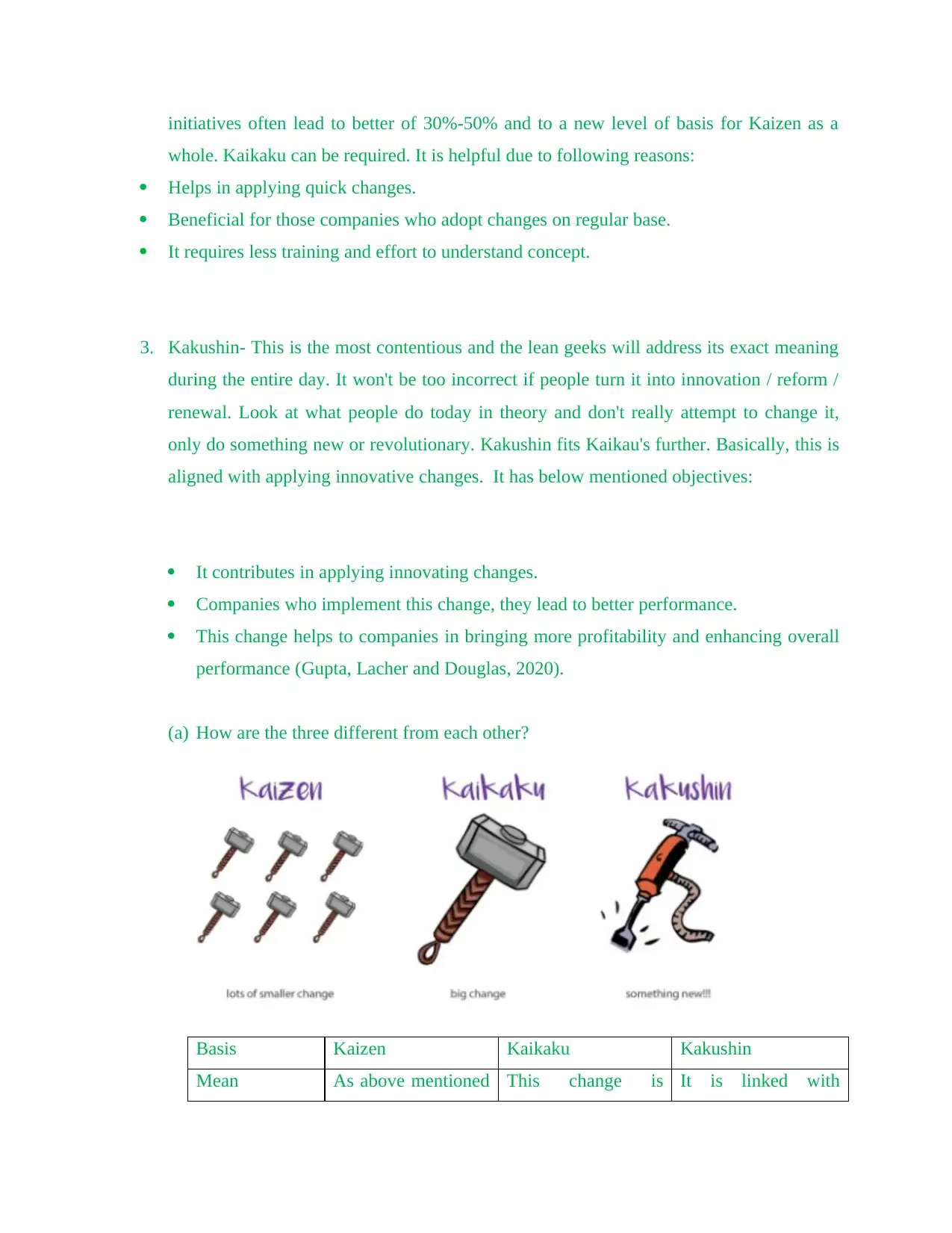
initiatives often lead to better of 30%-50% and to a new level of basis for Kaizen as a
whole. Kaikaku can be required. It is helpful due to following reasons:
Helps in applying quick changes.
Beneficial for those companies who adopt changes on regular base.
It requires less training and effort to understand concept.
3. Kakushin- This is the most contentious and the lean geeks will address its exact meaning
during the entire day. It won't be too incorrect if people turn it into innovation / reform /
renewal. Look at what people do today in theory and don't really attempt to change it,
only do something new or revolutionary. Kakushin fits Kaikau's further. Basically, this is
aligned with applying innovative changes. It has below mentioned objectives:
It contributes in applying innovating changes.
Companies who implement this change, they lead to better performance.
This change helps to companies in bringing more profitability and enhancing overall
performance (Gupta, Lacher and Douglas, 2020).
(a) How are the three different from each other?
Basis Kaizen Kaikaku Kakushin
Mean As above mentioned This change is It is linked with
whole. Kaikaku can be required. It is helpful due to following reasons:
Helps in applying quick changes.
Beneficial for those companies who adopt changes on regular base.
It requires less training and effort to understand concept.
3. Kakushin- This is the most contentious and the lean geeks will address its exact meaning
during the entire day. It won't be too incorrect if people turn it into innovation / reform /
renewal. Look at what people do today in theory and don't really attempt to change it,
only do something new or revolutionary. Kakushin fits Kaikau's further. Basically, this is
aligned with applying innovative changes. It has below mentioned objectives:
It contributes in applying innovating changes.
Companies who implement this change, they lead to better performance.
This change helps to companies in bringing more profitability and enhancing overall
performance (Gupta, Lacher and Douglas, 2020).
(a) How are the three different from each other?
Basis Kaizen Kaikaku Kakushin
Mean As above mentioned This change is It is linked with
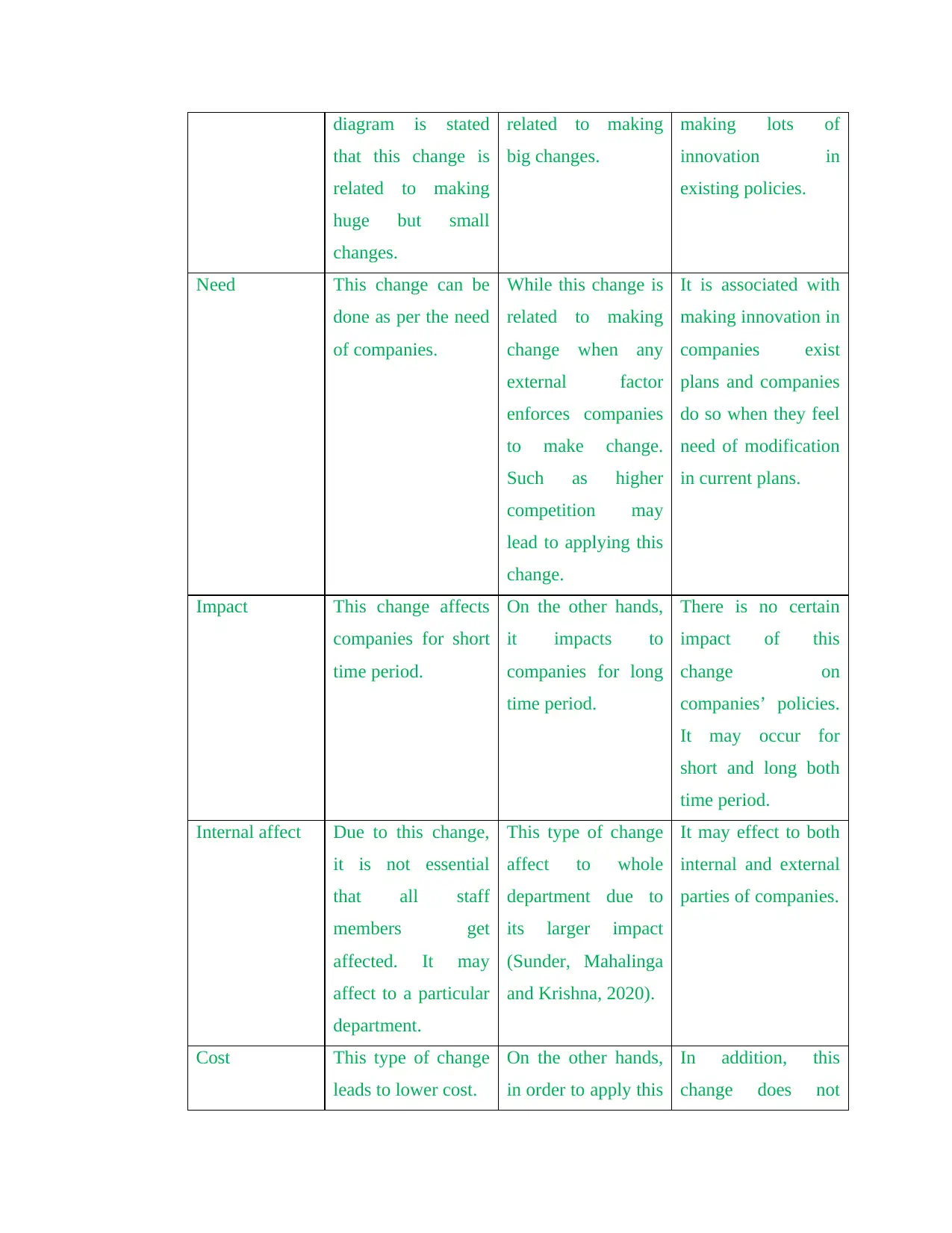
diagram is stated
that this change is
related to making
huge but small
changes.
related to making
big changes.
making lots of
innovation in
existing policies.
Need This change can be
done as per the need
of companies.
While this change is
related to making
change when any
external factor
enforces companies
to make change.
Such as higher
competition may
lead to applying this
change.
It is associated with
making innovation in
companies exist
plans and companies
do so when they feel
need of modification
in current plans.
Impact This change affects
companies for short
time period.
On the other hands,
it impacts to
companies for long
time period.
There is no certain
impact of this
change on
companies’ policies.
It may occur for
short and long both
time period.
Internal affect Due to this change,
it is not essential
that all staff
members get
affected. It may
affect to a particular
department.
This type of change
affect to whole
department due to
its larger impact
(Sunder, Mahalinga
and Krishna, 2020).
It may effect to both
internal and external
parties of companies.
Cost This type of change
leads to lower cost.
On the other hands,
in order to apply this
In addition, this
change does not
that this change is
related to making
huge but small
changes.
related to making
big changes.
making lots of
innovation in
existing policies.
Need This change can be
done as per the need
of companies.
While this change is
related to making
change when any
external factor
enforces companies
to make change.
Such as higher
competition may
lead to applying this
change.
It is associated with
making innovation in
companies exist
plans and companies
do so when they feel
need of modification
in current plans.
Impact This change affects
companies for short
time period.
On the other hands,
it impacts to
companies for long
time period.
There is no certain
impact of this
change on
companies’ policies.
It may occur for
short and long both
time period.
Internal affect Due to this change,
it is not essential
that all staff
members get
affected. It may
affect to a particular
department.
This type of change
affect to whole
department due to
its larger impact
(Sunder, Mahalinga
and Krishna, 2020).
It may effect to both
internal and external
parties of companies.
Cost This type of change
leads to lower cost.
On the other hands,
in order to apply this
In addition, this
change does not
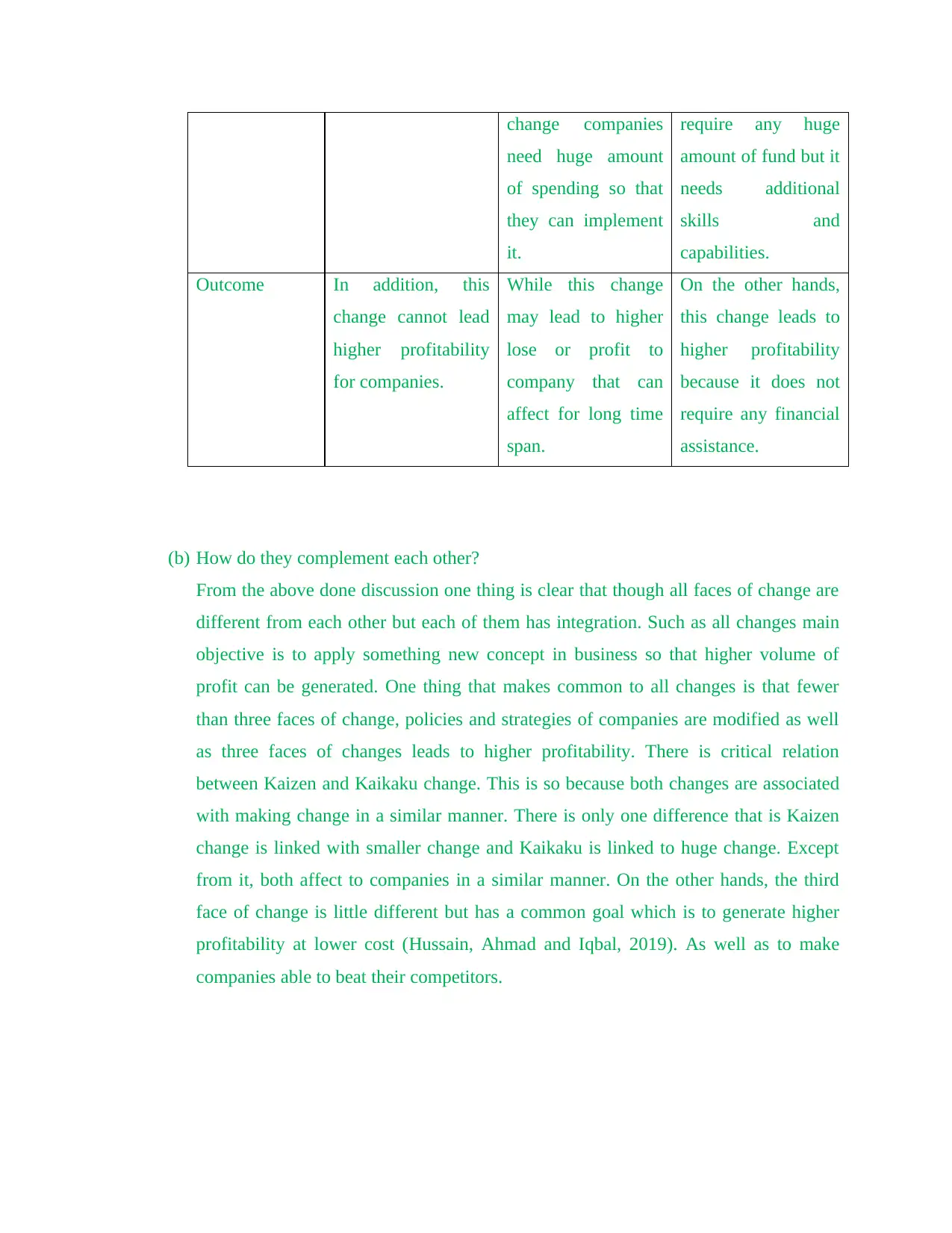
change companies
need huge amount
of spending so that
they can implement
it.
require any huge
amount of fund but it
needs additional
skills and
capabilities.
Outcome In addition, this
change cannot lead
higher profitability
for companies.
While this change
may lead to higher
lose or profit to
company that can
affect for long time
span.
On the other hands,
this change leads to
higher profitability
because it does not
require any financial
assistance.
(b) How do they complement each other?
From the above done discussion one thing is clear that though all faces of change are
different from each other but each of them has integration. Such as all changes main
objective is to apply something new concept in business so that higher volume of
profit can be generated. One thing that makes common to all changes is that fewer
than three faces of change, policies and strategies of companies are modified as well
as three faces of changes leads to higher profitability. There is critical relation
between Kaizen and Kaikaku change. This is so because both changes are associated
with making change in a similar manner. There is only one difference that is Kaizen
change is linked with smaller change and Kaikaku is linked to huge change. Except
from it, both affect to companies in a similar manner. On the other hands, the third
face of change is little different but has a common goal which is to generate higher
profitability at lower cost (Hussain, Ahmad and Iqbal, 2019). As well as to make
companies able to beat their competitors.
need huge amount
of spending so that
they can implement
it.
require any huge
amount of fund but it
needs additional
skills and
capabilities.
Outcome In addition, this
change cannot lead
higher profitability
for companies.
While this change
may lead to higher
lose or profit to
company that can
affect for long time
span.
On the other hands,
this change leads to
higher profitability
because it does not
require any financial
assistance.
(b) How do they complement each other?
From the above done discussion one thing is clear that though all faces of change are
different from each other but each of them has integration. Such as all changes main
objective is to apply something new concept in business so that higher volume of
profit can be generated. One thing that makes common to all changes is that fewer
than three faces of change, policies and strategies of companies are modified as well
as three faces of changes leads to higher profitability. There is critical relation
between Kaizen and Kaikaku change. This is so because both changes are associated
with making change in a similar manner. There is only one difference that is Kaizen
change is linked with smaller change and Kaikaku is linked to huge change. Except
from it, both affect to companies in a similar manner. On the other hands, the third
face of change is little different but has a common goal which is to generate higher
profitability at lower cost (Hussain, Ahmad and Iqbal, 2019). As well as to make
companies able to beat their competitors.
Paraphrase This Document
Need a fresh take? Get an instant paraphrase of this document with our AI Paraphraser
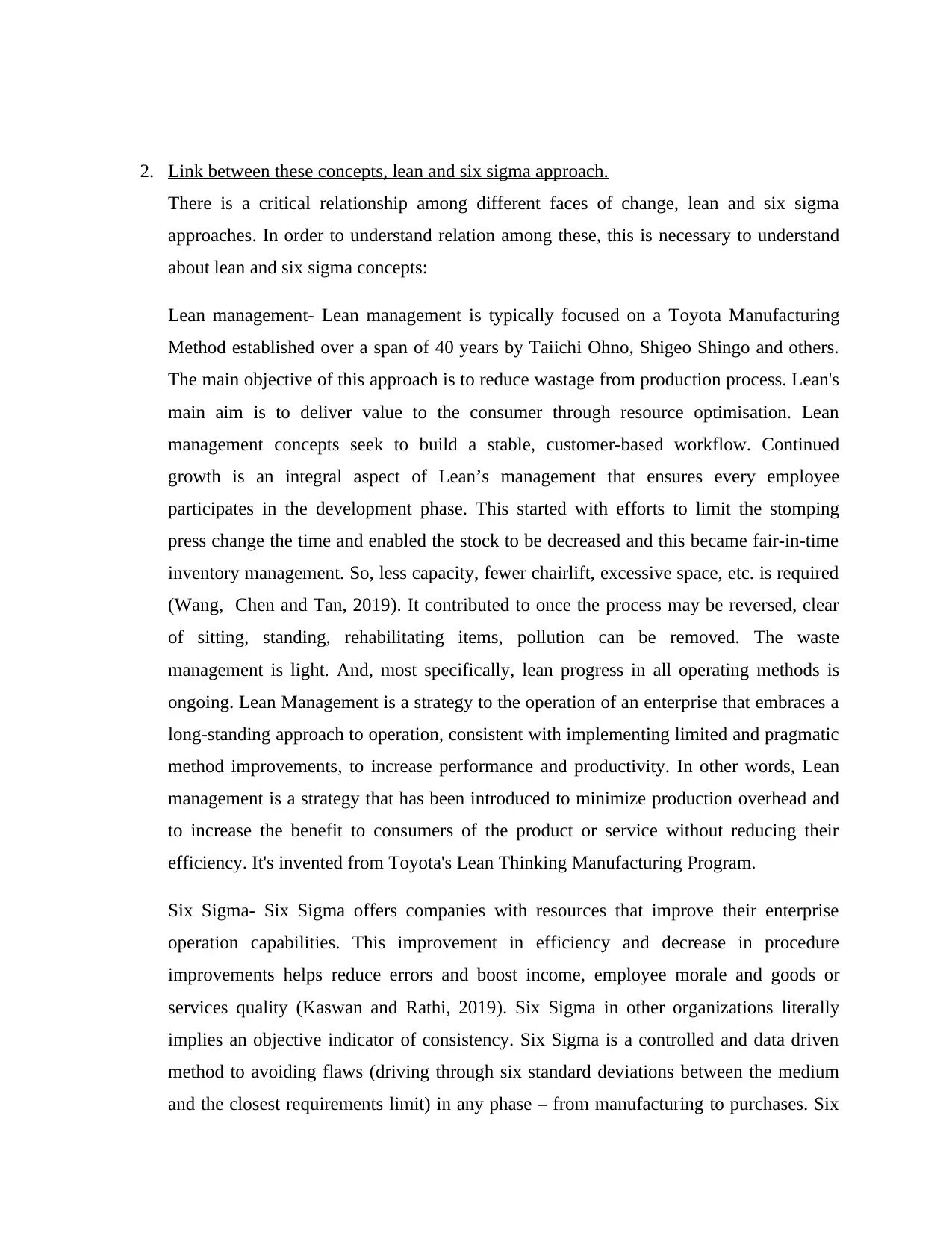
2. Link between these concepts, lean and six sigma approach.
There is a critical relationship among different faces of change, lean and six sigma
approaches. In order to understand relation among these, this is necessary to understand
about lean and six sigma concepts:
Lean management- Lean management is typically focused on a Toyota Manufacturing
Method established over a span of 40 years by Taiichi Ohno, Shigeo Shingo and others.
The main objective of this approach is to reduce wastage from production process. Lean's
main aim is to deliver value to the consumer through resource optimisation. Lean
management concepts seek to build a stable, customer-based workflow. Continued
growth is an integral aspect of Lean’s management that ensures every employee
participates in the development phase. This started with efforts to limit the stomping
press change the time and enabled the stock to be decreased and this became fair-in-time
inventory management. So, less capacity, fewer chairlift, excessive space, etc. is required
(Wang, Chen and Tan, 2019). It contributed to once the process may be reversed, clear
of sitting, standing, rehabilitating items, pollution can be removed. The waste
management is light. And, most specifically, lean progress in all operating methods is
ongoing. Lean Management is a strategy to the operation of an enterprise that embraces a
long-standing approach to operation, consistent with implementing limited and pragmatic
method improvements, to increase performance and productivity. In other words, Lean
management is a strategy that has been introduced to minimize production overhead and
to increase the benefit to consumers of the product or service without reducing their
efficiency. It's invented from Toyota's Lean Thinking Manufacturing Program.
Six Sigma- Six Sigma offers companies with resources that improve their enterprise
operation capabilities. This improvement in efficiency and decrease in procedure
improvements helps reduce errors and boost income, employee morale and goods or
services quality (Kaswan and Rathi, 2019). Six Sigma in other organizations literally
implies an objective indicator of consistency. Six Sigma is a controlled and data driven
method to avoiding flaws (driving through six standard deviations between the medium
and the closest requirements limit) in any phase – from manufacturing to purchases. Six
There is a critical relationship among different faces of change, lean and six sigma
approaches. In order to understand relation among these, this is necessary to understand
about lean and six sigma concepts:
Lean management- Lean management is typically focused on a Toyota Manufacturing
Method established over a span of 40 years by Taiichi Ohno, Shigeo Shingo and others.
The main objective of this approach is to reduce wastage from production process. Lean's
main aim is to deliver value to the consumer through resource optimisation. Lean
management concepts seek to build a stable, customer-based workflow. Continued
growth is an integral aspect of Lean’s management that ensures every employee
participates in the development phase. This started with efforts to limit the stomping
press change the time and enabled the stock to be decreased and this became fair-in-time
inventory management. So, less capacity, fewer chairlift, excessive space, etc. is required
(Wang, Chen and Tan, 2019). It contributed to once the process may be reversed, clear
of sitting, standing, rehabilitating items, pollution can be removed. The waste
management is light. And, most specifically, lean progress in all operating methods is
ongoing. Lean Management is a strategy to the operation of an enterprise that embraces a
long-standing approach to operation, consistent with implementing limited and pragmatic
method improvements, to increase performance and productivity. In other words, Lean
management is a strategy that has been introduced to minimize production overhead and
to increase the benefit to consumers of the product or service without reducing their
efficiency. It's invented from Toyota's Lean Thinking Manufacturing Program.
Six Sigma- Six Sigma offers companies with resources that improve their enterprise
operation capabilities. This improvement in efficiency and decrease in procedure
improvements helps reduce errors and boost income, employee morale and goods or
services quality (Kaswan and Rathi, 2019). Six Sigma in other organizations literally
implies an objective indicator of consistency. Six Sigma is a controlled and data driven
method to avoiding flaws (driving through six standard deviations between the medium
and the closest requirements limit) in any phase – from manufacturing to purchases. Six
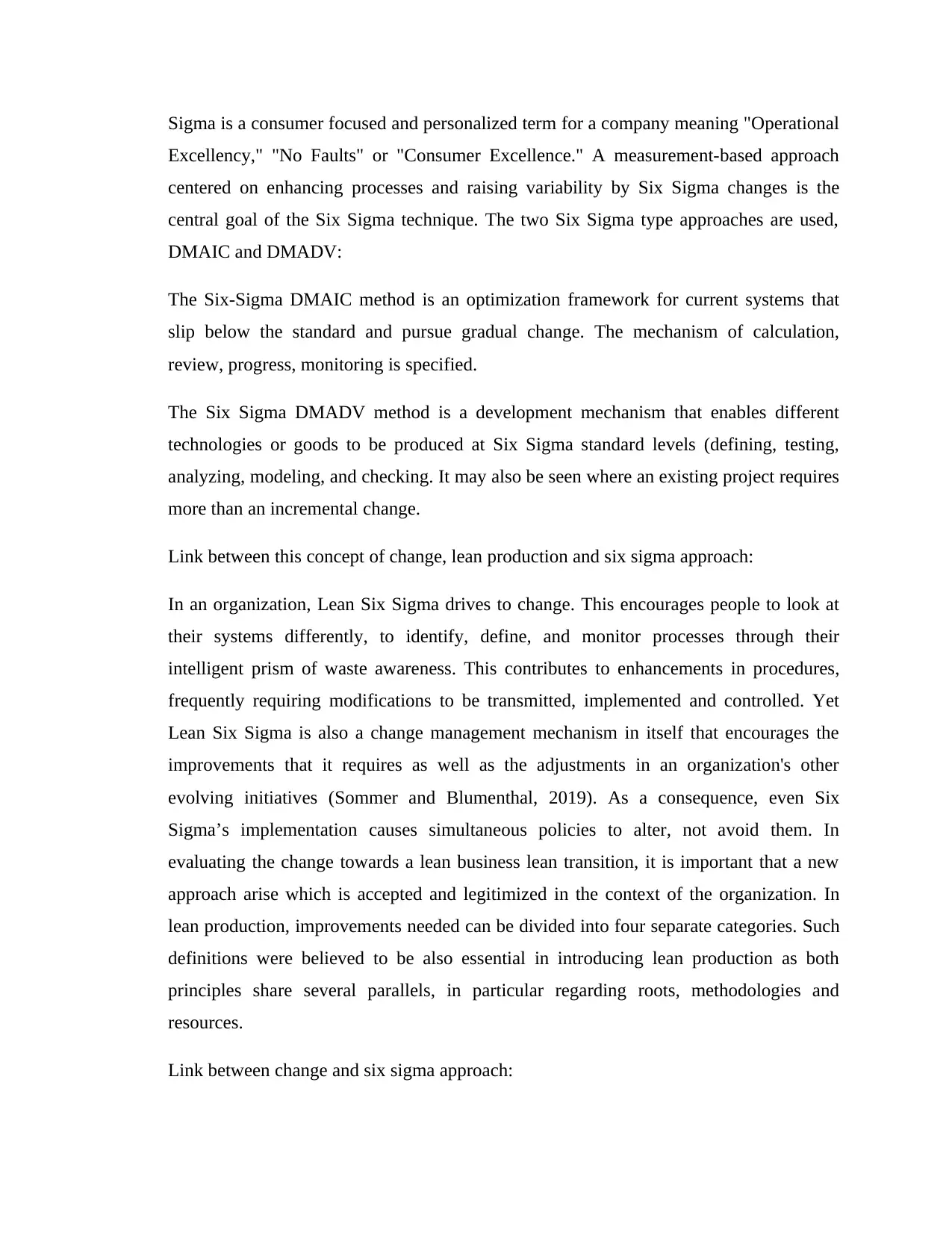
Sigma is a consumer focused and personalized term for a company meaning "Operational
Excellency," "No Faults" or "Consumer Excellence." A measurement-based approach
centered on enhancing processes and raising variability by Six Sigma changes is the
central goal of the Six Sigma technique. The two Six Sigma type approaches are used,
DMAIC and DMADV:
The Six-Sigma DMAIC method is an optimization framework for current systems that
slip below the standard and pursue gradual change. The mechanism of calculation,
review, progress, monitoring is specified.
The Six Sigma DMADV method is a development mechanism that enables different
technologies or goods to be produced at Six Sigma standard levels (defining, testing,
analyzing, modeling, and checking. It may also be seen where an existing project requires
more than an incremental change.
Link between this concept of change, lean production and six sigma approach:
In an organization, Lean Six Sigma drives to change. This encourages people to look at
their systems differently, to identify, define, and monitor processes through their
intelligent prism of waste awareness. This contributes to enhancements in procedures,
frequently requiring modifications to be transmitted, implemented and controlled. Yet
Lean Six Sigma is also a change management mechanism in itself that encourages the
improvements that it requires as well as the adjustments in an organization's other
evolving initiatives (Sommer and Blumenthal, 2019). As a consequence, even Six
Sigma’s implementation causes simultaneous policies to alter, not avoid them. In
evaluating the change towards a lean business lean transition, it is important that a new
approach arise which is accepted and legitimized in the context of the organization. In
lean production, improvements needed can be divided into four separate categories. Such
definitions were believed to be also essential in introducing lean production as both
principles share several parallels, in particular regarding roots, methodologies and
resources.
Link between change and six sigma approach:
Excellency," "No Faults" or "Consumer Excellence." A measurement-based approach
centered on enhancing processes and raising variability by Six Sigma changes is the
central goal of the Six Sigma technique. The two Six Sigma type approaches are used,
DMAIC and DMADV:
The Six-Sigma DMAIC method is an optimization framework for current systems that
slip below the standard and pursue gradual change. The mechanism of calculation,
review, progress, monitoring is specified.
The Six Sigma DMADV method is a development mechanism that enables different
technologies or goods to be produced at Six Sigma standard levels (defining, testing,
analyzing, modeling, and checking. It may also be seen where an existing project requires
more than an incremental change.
Link between this concept of change, lean production and six sigma approach:
In an organization, Lean Six Sigma drives to change. This encourages people to look at
their systems differently, to identify, define, and monitor processes through their
intelligent prism of waste awareness. This contributes to enhancements in procedures,
frequently requiring modifications to be transmitted, implemented and controlled. Yet
Lean Six Sigma is also a change management mechanism in itself that encourages the
improvements that it requires as well as the adjustments in an organization's other
evolving initiatives (Sommer and Blumenthal, 2019). As a consequence, even Six
Sigma’s implementation causes simultaneous policies to alter, not avoid them. In
evaluating the change towards a lean business lean transition, it is important that a new
approach arise which is accepted and legitimized in the context of the organization. In
lean production, improvements needed can be divided into four separate categories. Such
definitions were believed to be also essential in introducing lean production as both
principles share several parallels, in particular regarding roots, methodologies and
resources.
Link between change and six sigma approach:
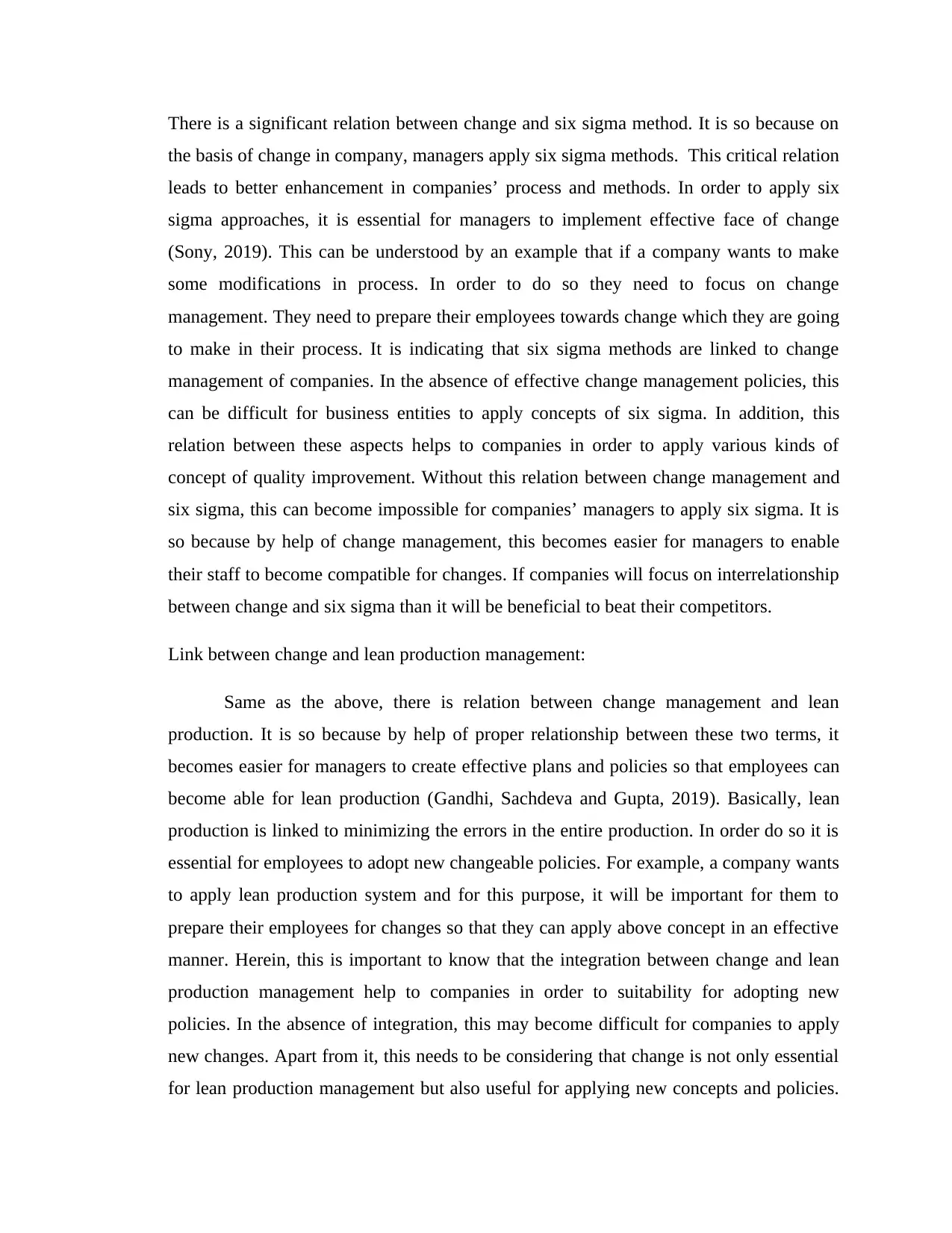
There is a significant relation between change and six sigma method. It is so because on
the basis of change in company, managers apply six sigma methods. This critical relation
leads to better enhancement in companies’ process and methods. In order to apply six
sigma approaches, it is essential for managers to implement effective face of change
(Sony, 2019). This can be understood by an example that if a company wants to make
some modifications in process. In order to do so they need to focus on change
management. They need to prepare their employees towards change which they are going
to make in their process. It is indicating that six sigma methods are linked to change
management of companies. In the absence of effective change management policies, this
can be difficult for business entities to apply concepts of six sigma. In addition, this
relation between these aspects helps to companies in order to apply various kinds of
concept of quality improvement. Without this relation between change management and
six sigma, this can become impossible for companies’ managers to apply six sigma. It is
so because by help of change management, this becomes easier for managers to enable
their staff to become compatible for changes. If companies will focus on interrelationship
between change and six sigma than it will be beneficial to beat their competitors.
Link between change and lean production management:
Same as the above, there is relation between change management and lean
production. It is so because by help of proper relationship between these two terms, it
becomes easier for managers to create effective plans and policies so that employees can
become able for lean production (Gandhi, Sachdeva and Gupta, 2019). Basically, lean
production is linked to minimizing the errors in the entire production. In order do so it is
essential for employees to adopt new changeable policies. For example, a company wants
to apply lean production system and for this purpose, it will be important for them to
prepare their employees for changes so that they can apply above concept in an effective
manner. Herein, this is important to know that the integration between change and lean
production management help to companies in order to suitability for adopting new
policies. In the absence of integration, this may become difficult for companies to apply
new changes. Apart from it, this needs to be considering that change is not only essential
for lean production management but also useful for applying new concepts and policies.
the basis of change in company, managers apply six sigma methods. This critical relation
leads to better enhancement in companies’ process and methods. In order to apply six
sigma approaches, it is essential for managers to implement effective face of change
(Sony, 2019). This can be understood by an example that if a company wants to make
some modifications in process. In order to do so they need to focus on change
management. They need to prepare their employees towards change which they are going
to make in their process. It is indicating that six sigma methods are linked to change
management of companies. In the absence of effective change management policies, this
can be difficult for business entities to apply concepts of six sigma. In addition, this
relation between these aspects helps to companies in order to apply various kinds of
concept of quality improvement. Without this relation between change management and
six sigma, this can become impossible for companies’ managers to apply six sigma. It is
so because by help of change management, this becomes easier for managers to enable
their staff to become compatible for changes. If companies will focus on interrelationship
between change and six sigma than it will be beneficial to beat their competitors.
Link between change and lean production management:
Same as the above, there is relation between change management and lean
production. It is so because by help of proper relationship between these two terms, it
becomes easier for managers to create effective plans and policies so that employees can
become able for lean production (Gandhi, Sachdeva and Gupta, 2019). Basically, lean
production is linked to minimizing the errors in the entire production. In order do so it is
essential for employees to adopt new changeable policies. For example, a company wants
to apply lean production system and for this purpose, it will be important for them to
prepare their employees for changes so that they can apply above concept in an effective
manner. Herein, this is important to know that the integration between change and lean
production management help to companies in order to suitability for adopting new
policies. In the absence of integration, this may become difficult for companies to apply
new changes. Apart from it, this needs to be considering that change is not only essential
for lean production management but also useful for applying new concepts and policies.
Secure Best Marks with AI Grader
Need help grading? Try our AI Grader for instant feedback on your assignments.
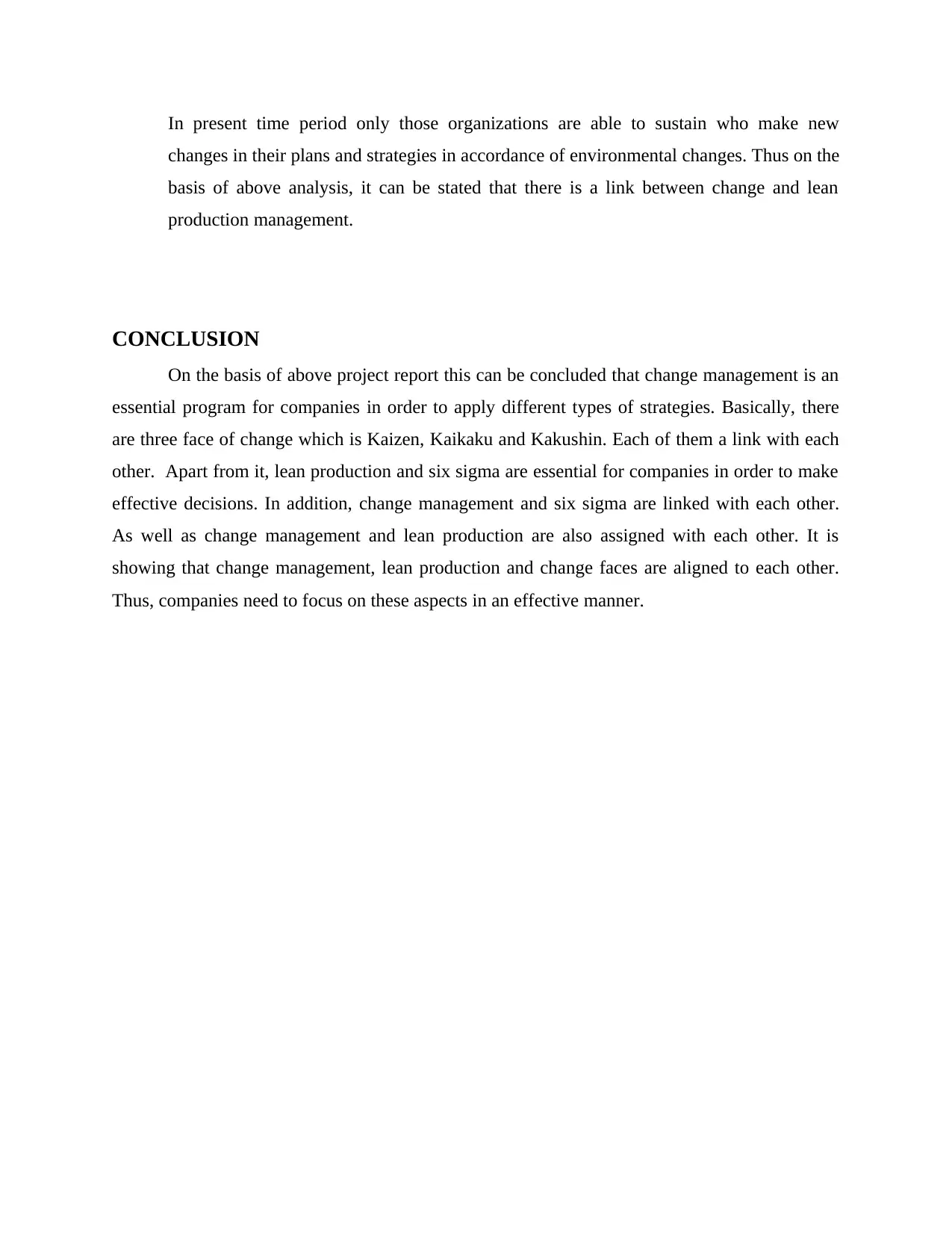
In present time period only those organizations are able to sustain who make new
changes in their plans and strategies in accordance of environmental changes. Thus on the
basis of above analysis, it can be stated that there is a link between change and lean
production management.
CONCLUSION
On the basis of above project report this can be concluded that change management is an
essential program for companies in order to apply different types of strategies. Basically, there
are three face of change which is Kaizen, Kaikaku and Kakushin. Each of them a link with each
other. Apart from it, lean production and six sigma are essential for companies in order to make
effective decisions. In addition, change management and six sigma are linked with each other.
As well as change management and lean production are also assigned with each other. It is
showing that change management, lean production and change faces are aligned to each other.
Thus, companies need to focus on these aspects in an effective manner.
changes in their plans and strategies in accordance of environmental changes. Thus on the
basis of above analysis, it can be stated that there is a link between change and lean
production management.
CONCLUSION
On the basis of above project report this can be concluded that change management is an
essential program for companies in order to apply different types of strategies. Basically, there
are three face of change which is Kaizen, Kaikaku and Kakushin. Each of them a link with each
other. Apart from it, lean production and six sigma are essential for companies in order to make
effective decisions. In addition, change management and six sigma are linked with each other.
As well as change management and lean production are also assigned with each other. It is
showing that change management, lean production and change faces are aligned to each other.
Thus, companies need to focus on these aspects in an effective manner.
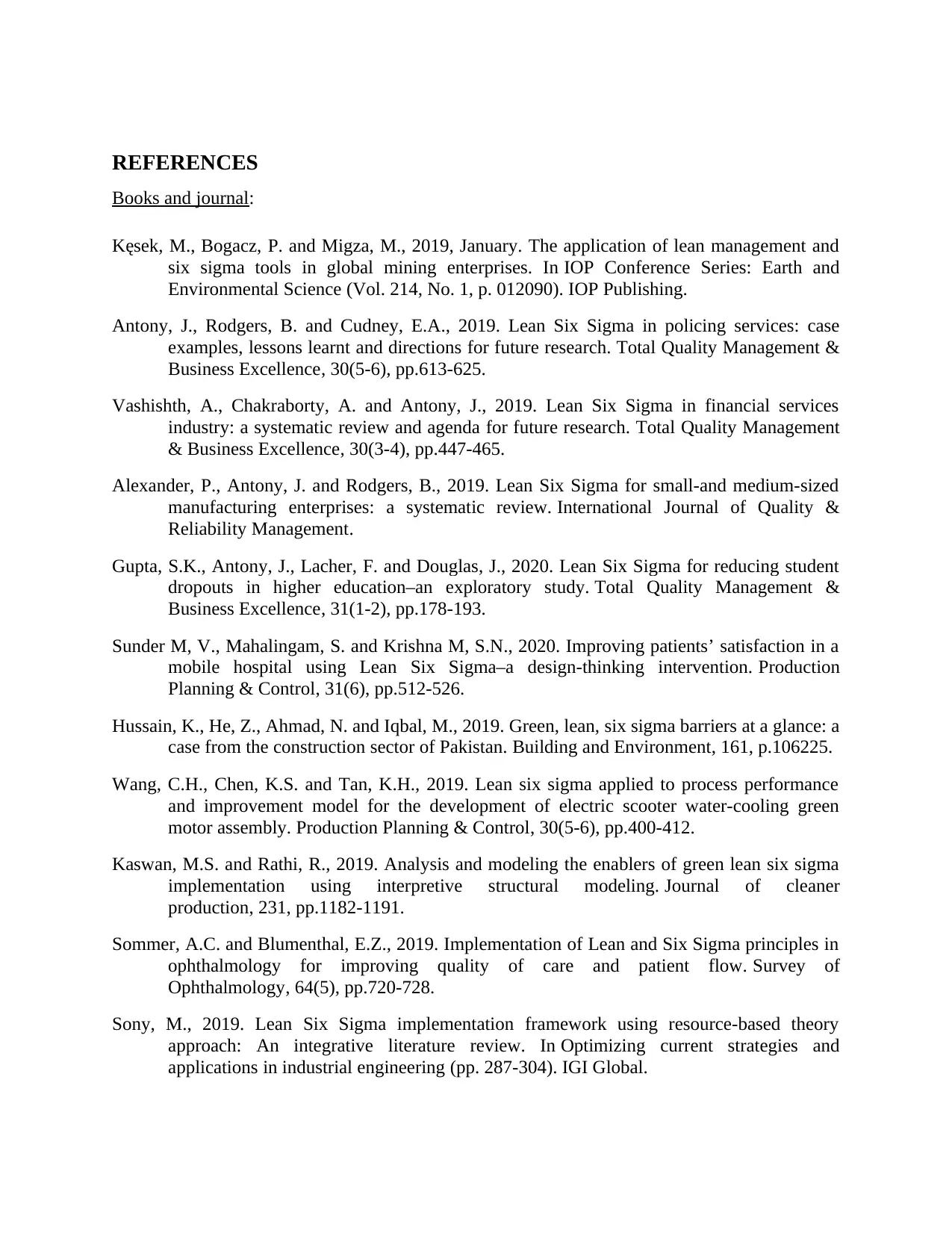
REFERENCES
Books and journal:
Kęsek, M., Bogacz, P. and Migza, M., 2019, January. The application of lean management and
six sigma tools in global mining enterprises. In IOP Conference Series: Earth and
Environmental Science (Vol. 214, No. 1, p. 012090). IOP Publishing.
Antony, J., Rodgers, B. and Cudney, E.A., 2019. Lean Six Sigma in policing services: case
examples, lessons learnt and directions for future research. Total Quality Management &
Business Excellence, 30(5-6), pp.613-625.
Vashishth, A., Chakraborty, A. and Antony, J., 2019. Lean Six Sigma in financial services
industry: a systematic review and agenda for future research. Total Quality Management
& Business Excellence, 30(3-4), pp.447-465.
Alexander, P., Antony, J. and Rodgers, B., 2019. Lean Six Sigma for small-and medium-sized
manufacturing enterprises: a systematic review. International Journal of Quality &
Reliability Management.
Gupta, S.K., Antony, J., Lacher, F. and Douglas, J., 2020. Lean Six Sigma for reducing student
dropouts in higher education–an exploratory study. Total Quality Management &
Business Excellence, 31(1-2), pp.178-193.
Sunder M, V., Mahalingam, S. and Krishna M, S.N., 2020. Improving patients’ satisfaction in a
mobile hospital using Lean Six Sigma–a design-thinking intervention. Production
Planning & Control, 31(6), pp.512-526.
Hussain, K., He, Z., Ahmad, N. and Iqbal, M., 2019. Green, lean, six sigma barriers at a glance: a
case from the construction sector of Pakistan. Building and Environment, 161, p.106225.
Wang, C.H., Chen, K.S. and Tan, K.H., 2019. Lean six sigma applied to process performance
and improvement model for the development of electric scooter water-cooling green
motor assembly. Production Planning & Control, 30(5-6), pp.400-412.
Kaswan, M.S. and Rathi, R., 2019. Analysis and modeling the enablers of green lean six sigma
implementation using interpretive structural modeling. Journal of cleaner
production, 231, pp.1182-1191.
Sommer, A.C. and Blumenthal, E.Z., 2019. Implementation of Lean and Six Sigma principles in
ophthalmology for improving quality of care and patient flow. Survey of
Ophthalmology, 64(5), pp.720-728.
Sony, M., 2019. Lean Six Sigma implementation framework using resource-based theory
approach: An integrative literature review. In Optimizing current strategies and
applications in industrial engineering (pp. 287-304). IGI Global.
Books and journal:
Kęsek, M., Bogacz, P. and Migza, M., 2019, January. The application of lean management and
six sigma tools in global mining enterprises. In IOP Conference Series: Earth and
Environmental Science (Vol. 214, No. 1, p. 012090). IOP Publishing.
Antony, J., Rodgers, B. and Cudney, E.A., 2019. Lean Six Sigma in policing services: case
examples, lessons learnt and directions for future research. Total Quality Management &
Business Excellence, 30(5-6), pp.613-625.
Vashishth, A., Chakraborty, A. and Antony, J., 2019. Lean Six Sigma in financial services
industry: a systematic review and agenda for future research. Total Quality Management
& Business Excellence, 30(3-4), pp.447-465.
Alexander, P., Antony, J. and Rodgers, B., 2019. Lean Six Sigma for small-and medium-sized
manufacturing enterprises: a systematic review. International Journal of Quality &
Reliability Management.
Gupta, S.K., Antony, J., Lacher, F. and Douglas, J., 2020. Lean Six Sigma for reducing student
dropouts in higher education–an exploratory study. Total Quality Management &
Business Excellence, 31(1-2), pp.178-193.
Sunder M, V., Mahalingam, S. and Krishna M, S.N., 2020. Improving patients’ satisfaction in a
mobile hospital using Lean Six Sigma–a design-thinking intervention. Production
Planning & Control, 31(6), pp.512-526.
Hussain, K., He, Z., Ahmad, N. and Iqbal, M., 2019. Green, lean, six sigma barriers at a glance: a
case from the construction sector of Pakistan. Building and Environment, 161, p.106225.
Wang, C.H., Chen, K.S. and Tan, K.H., 2019. Lean six sigma applied to process performance
and improvement model for the development of electric scooter water-cooling green
motor assembly. Production Planning & Control, 30(5-6), pp.400-412.
Kaswan, M.S. and Rathi, R., 2019. Analysis and modeling the enablers of green lean six sigma
implementation using interpretive structural modeling. Journal of cleaner
production, 231, pp.1182-1191.
Sommer, A.C. and Blumenthal, E.Z., 2019. Implementation of Lean and Six Sigma principles in
ophthalmology for improving quality of care and patient flow. Survey of
Ophthalmology, 64(5), pp.720-728.
Sony, M., 2019. Lean Six Sigma implementation framework using resource-based theory
approach: An integrative literature review. In Optimizing current strategies and
applications in industrial engineering (pp. 287-304). IGI Global.
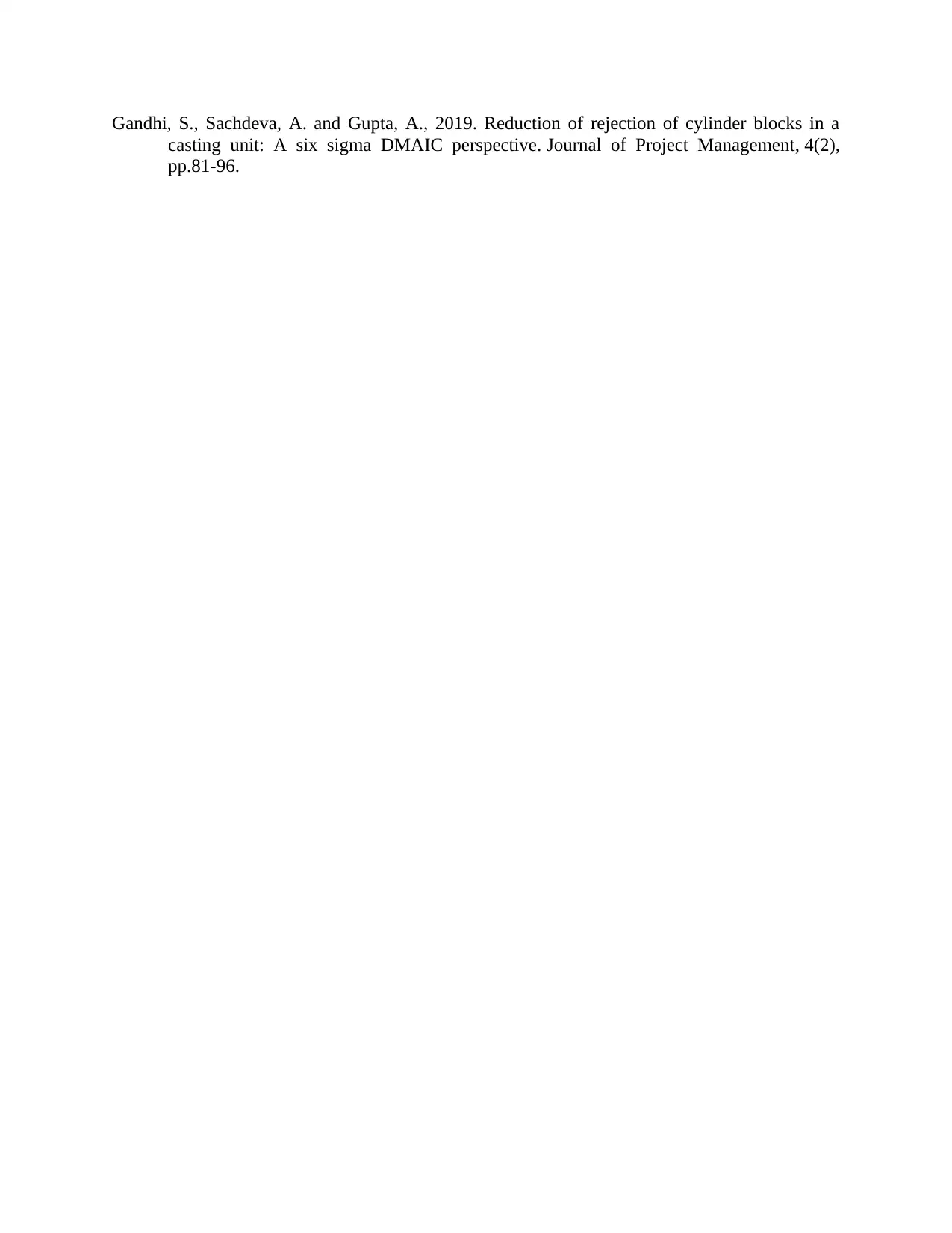
Gandhi, S., Sachdeva, A. and Gupta, A., 2019. Reduction of rejection of cylinder blocks in a
casting unit: A six sigma DMAIC perspective. Journal of Project Management, 4(2),
pp.81-96.
casting unit: A six sigma DMAIC perspective. Journal of Project Management, 4(2),
pp.81-96.
1 out of 13
Related Documents

Your All-in-One AI-Powered Toolkit for Academic Success.
+13062052269
info@desklib.com
Available 24*7 on WhatsApp / Email
Unlock your academic potential
© 2024 | Zucol Services PVT LTD | All rights reserved.