International Business: Lean Operations and Sustainability Critique
VerifiedAdded on 2020/02/24
|12
|2950
|94
Report
AI Summary
This report provides a critical analysis of the relationship between lean operations and sustainable operations, focusing on the article by Rich & Piercy (2014). The report begins with an executive summary outlining the intertwined concepts of operations management, emphasizing the importance of sustainability and lean strategies for waste reduction, particularly within the supply chain, workforce, and service industries. The critique delves into the purpose, key questions, and most important aspects of the article, highlighting the connection between lean principles and sustainability. It examines the mutual benefits, challenges, and the integration of both approaches. The report also explores main inferences, assumptions, and the limitations of lean in certain industries, such as oil and plastic manufacturing. The conclusion stresses the need for a comprehensive approach to operations management, integrating lean and sustainability to achieve a competitive edge, meet customer expectations, and ensure long-term value creation. The report offers recommendations for future strategies in global organizations.
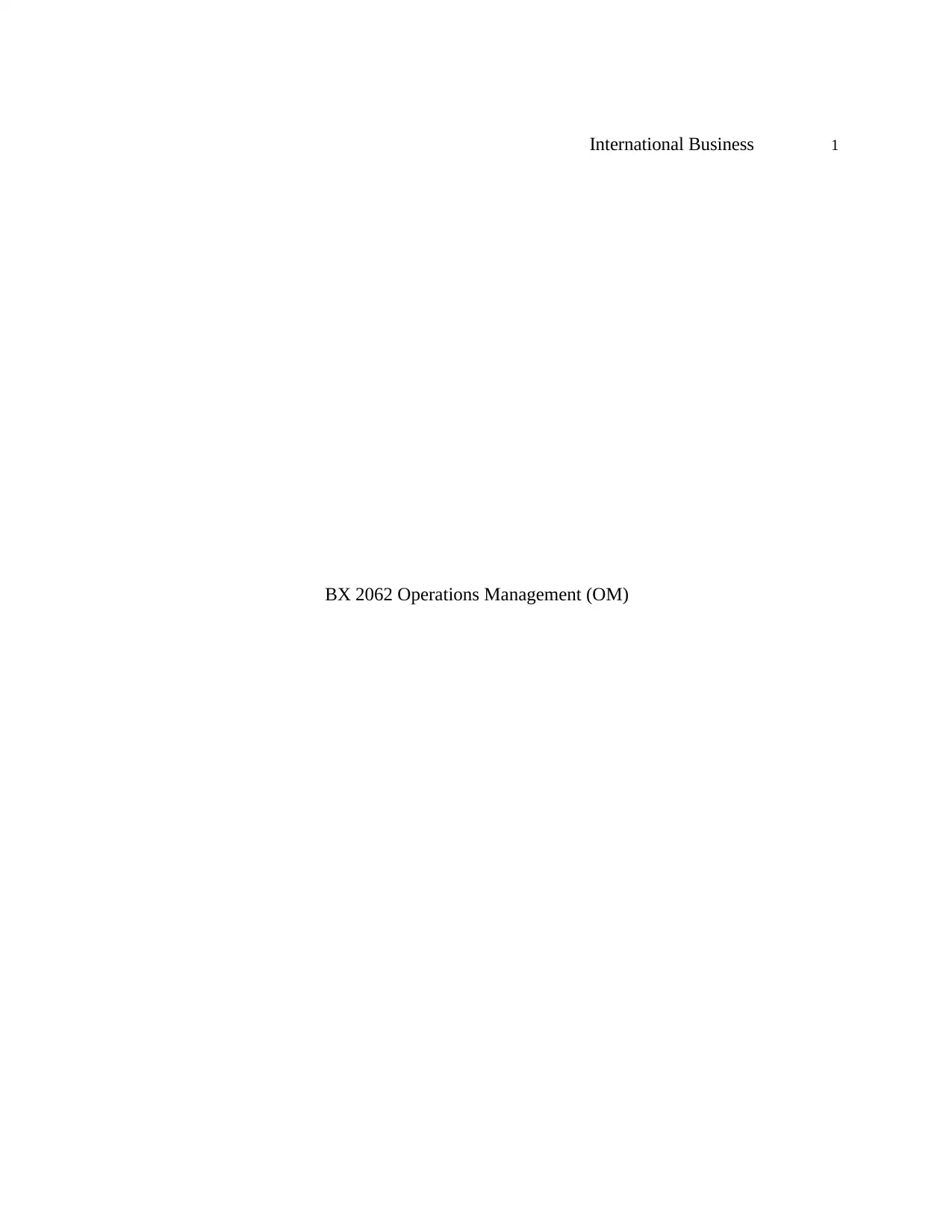
International Business 1
BX 2062 Operations Management (OM)
BX 2062 Operations Management (OM)
Secure Best Marks with AI Grader
Need help grading? Try our AI Grader for instant feedback on your assignments.
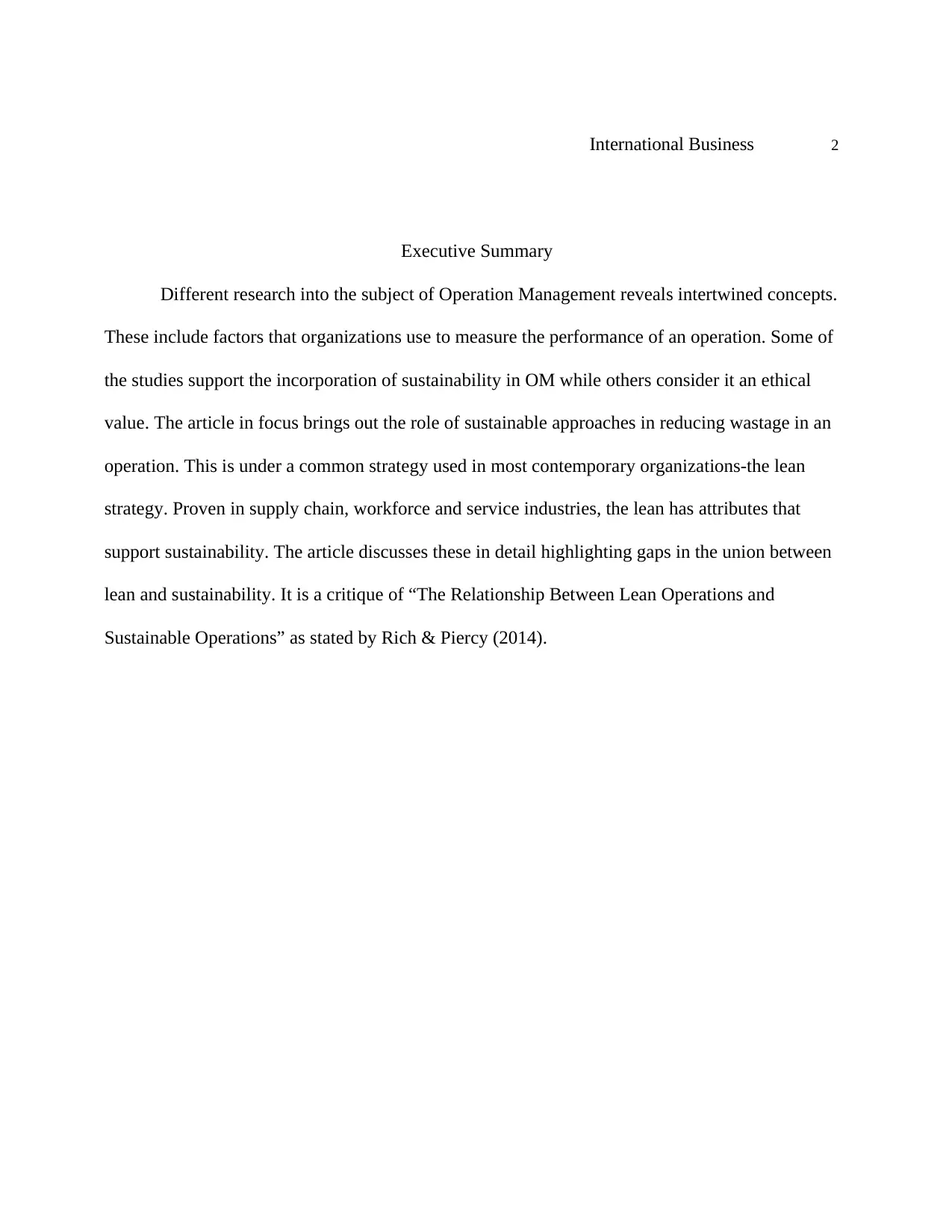
International Business 2
Executive Summary
Different research into the subject of Operation Management reveals intertwined concepts.
These include factors that organizations use to measure the performance of an operation. Some of
the studies support the incorporation of sustainability in OM while others consider it an ethical
value. The article in focus brings out the role of sustainable approaches in reducing wastage in an
operation. This is under a common strategy used in most contemporary organizations-the lean
strategy. Proven in supply chain, workforce and service industries, the lean has attributes that
support sustainability. The article discusses these in detail highlighting gaps in the union between
lean and sustainability. It is a critique of “The Relationship Between Lean Operations and
Sustainable Operations” as stated by Rich & Piercy (2014).
Executive Summary
Different research into the subject of Operation Management reveals intertwined concepts.
These include factors that organizations use to measure the performance of an operation. Some of
the studies support the incorporation of sustainability in OM while others consider it an ethical
value. The article in focus brings out the role of sustainable approaches in reducing wastage in an
operation. This is under a common strategy used in most contemporary organizations-the lean
strategy. Proven in supply chain, workforce and service industries, the lean has attributes that
support sustainability. The article discusses these in detail highlighting gaps in the union between
lean and sustainability. It is a critique of “The Relationship Between Lean Operations and
Sustainable Operations” as stated by Rich & Piercy (2014).
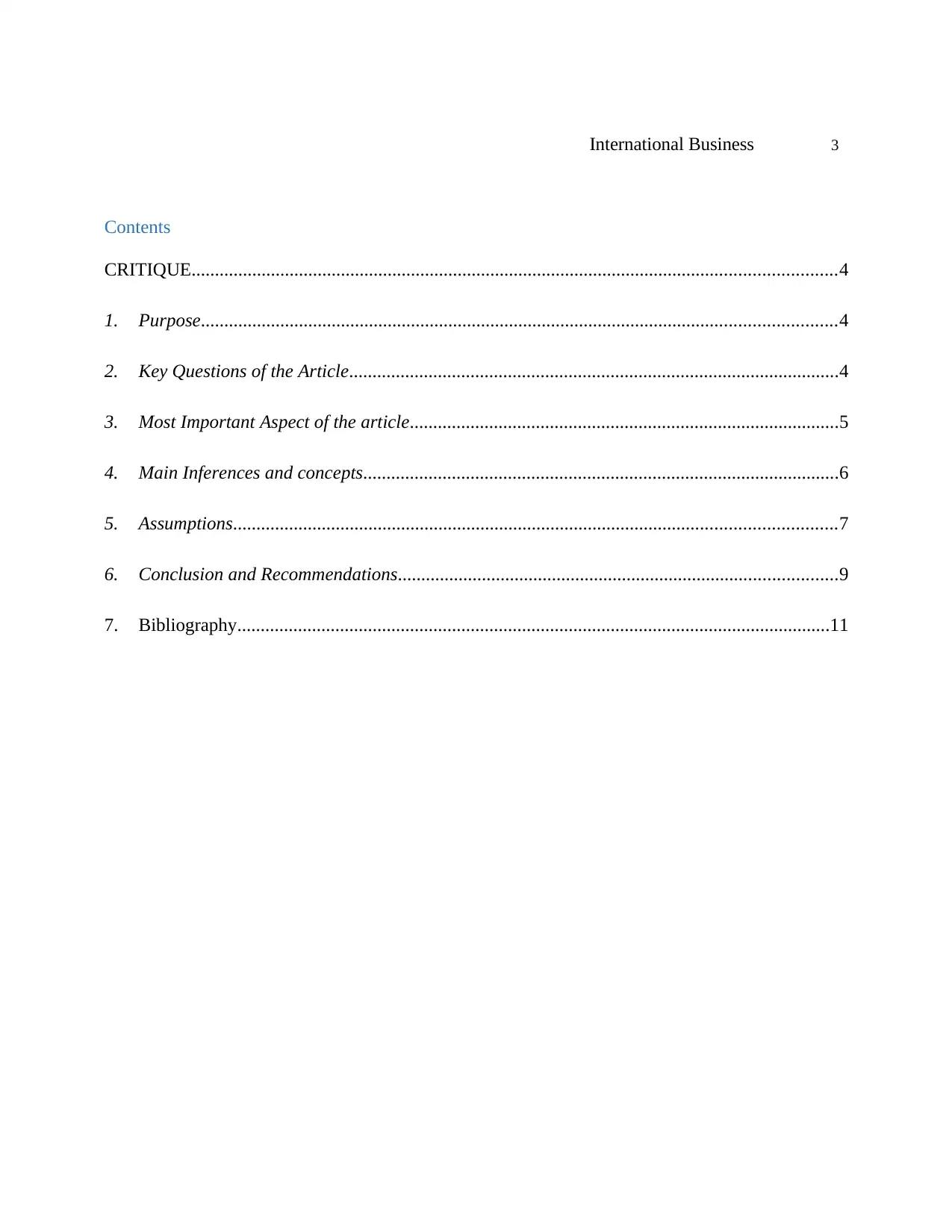
International Business 3
Contents
CRITIQUE..........................................................................................................................................4
1. Purpose........................................................................................................................................4
2. Key Questions of the Article.........................................................................................................4
3. Most Important Aspect of the article............................................................................................5
4. Main Inferences and concepts......................................................................................................6
5. Assumptions.................................................................................................................................7
6. Conclusion and Recommendations..............................................................................................9
7. Bibliography...............................................................................................................................11
Contents
CRITIQUE..........................................................................................................................................4
1. Purpose........................................................................................................................................4
2. Key Questions of the Article.........................................................................................................4
3. Most Important Aspect of the article............................................................................................5
4. Main Inferences and concepts......................................................................................................6
5. Assumptions.................................................................................................................................7
6. Conclusion and Recommendations..............................................................................................9
7. Bibliography...............................................................................................................................11
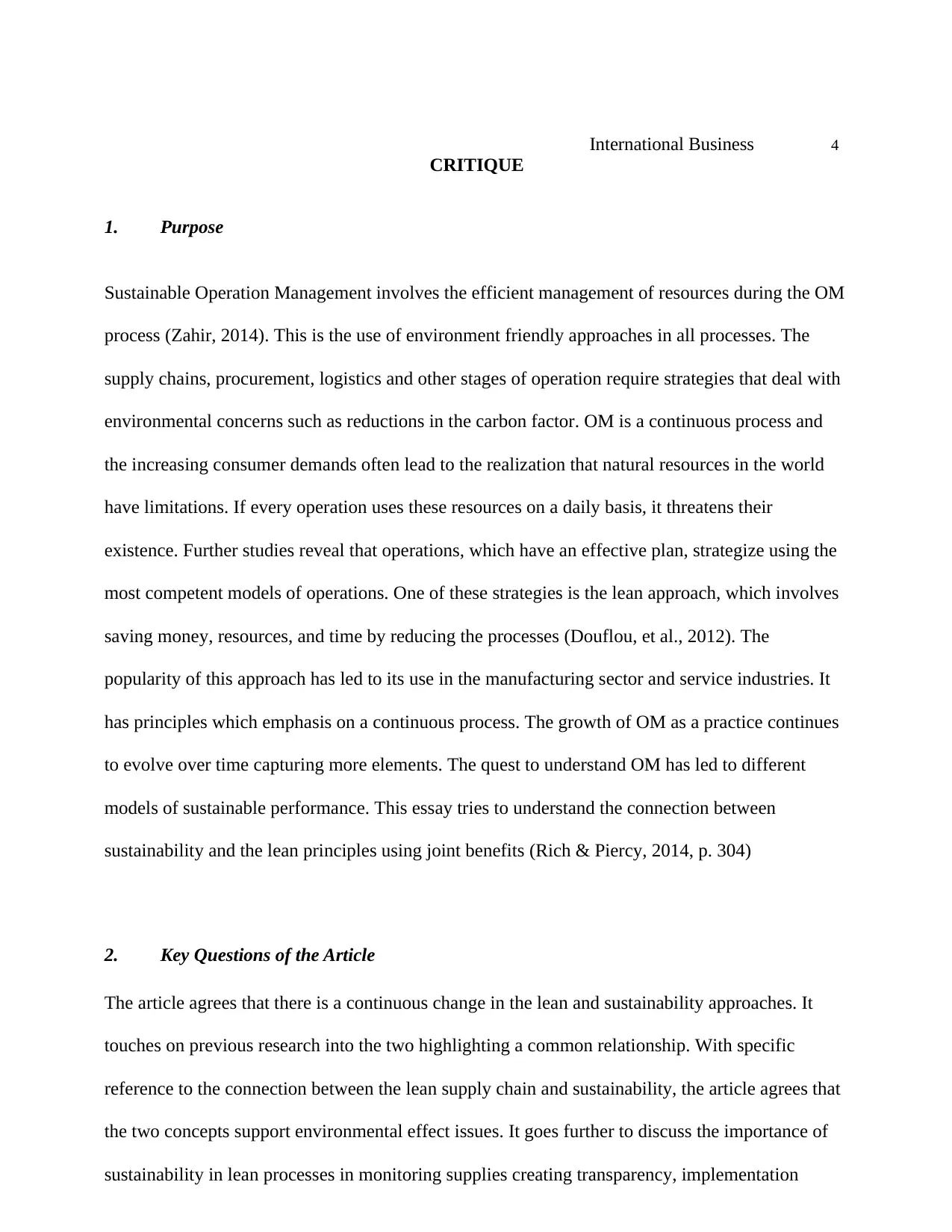
International Business 4
CRITIQUE
1. Purpose
Sustainable Operation Management involves the efficient management of resources during the OM
process (Zahir, 2014). This is the use of environment friendly approaches in all processes. The
supply chains, procurement, logistics and other stages of operation require strategies that deal with
environmental concerns such as reductions in the carbon factor. OM is a continuous process and
the increasing consumer demands often lead to the realization that natural resources in the world
have limitations. If every operation uses these resources on a daily basis, it threatens their
existence. Further studies reveal that operations, which have an effective plan, strategize using the
most competent models of operations. One of these strategies is the lean approach, which involves
saving money, resources, and time by reducing the processes (Douflou, et al., 2012). The
popularity of this approach has led to its use in the manufacturing sector and service industries. It
has principles which emphasis on a continuous process. The growth of OM as a practice continues
to evolve over time capturing more elements. The quest to understand OM has led to different
models of sustainable performance. This essay tries to understand the connection between
sustainability and the lean principles using joint benefits (Rich & Piercy, 2014, p. 304)
2. Key Questions of the Article
The article agrees that there is a continuous change in the lean and sustainability approaches. It
touches on previous research into the two highlighting a common relationship. With specific
reference to the connection between the lean supply chain and sustainability, the article agrees that
the two concepts support environmental effect issues. It goes further to discuss the importance of
sustainability in lean processes in monitoring supplies creating transparency, implementation
CRITIQUE
1. Purpose
Sustainable Operation Management involves the efficient management of resources during the OM
process (Zahir, 2014). This is the use of environment friendly approaches in all processes. The
supply chains, procurement, logistics and other stages of operation require strategies that deal with
environmental concerns such as reductions in the carbon factor. OM is a continuous process and
the increasing consumer demands often lead to the realization that natural resources in the world
have limitations. If every operation uses these resources on a daily basis, it threatens their
existence. Further studies reveal that operations, which have an effective plan, strategize using the
most competent models of operations. One of these strategies is the lean approach, which involves
saving money, resources, and time by reducing the processes (Douflou, et al., 2012). The
popularity of this approach has led to its use in the manufacturing sector and service industries. It
has principles which emphasis on a continuous process. The growth of OM as a practice continues
to evolve over time capturing more elements. The quest to understand OM has led to different
models of sustainable performance. This essay tries to understand the connection between
sustainability and the lean principles using joint benefits (Rich & Piercy, 2014, p. 304)
2. Key Questions of the Article
The article agrees that there is a continuous change in the lean and sustainability approaches. It
touches on previous research into the two highlighting a common relationship. With specific
reference to the connection between the lean supply chain and sustainability, the article agrees that
the two concepts support environmental effect issues. It goes further to discuss the importance of
sustainability in lean processes in monitoring supplies creating transparency, implementation
Secure Best Marks with AI Grader
Need help grading? Try our AI Grader for instant feedback on your assignments.
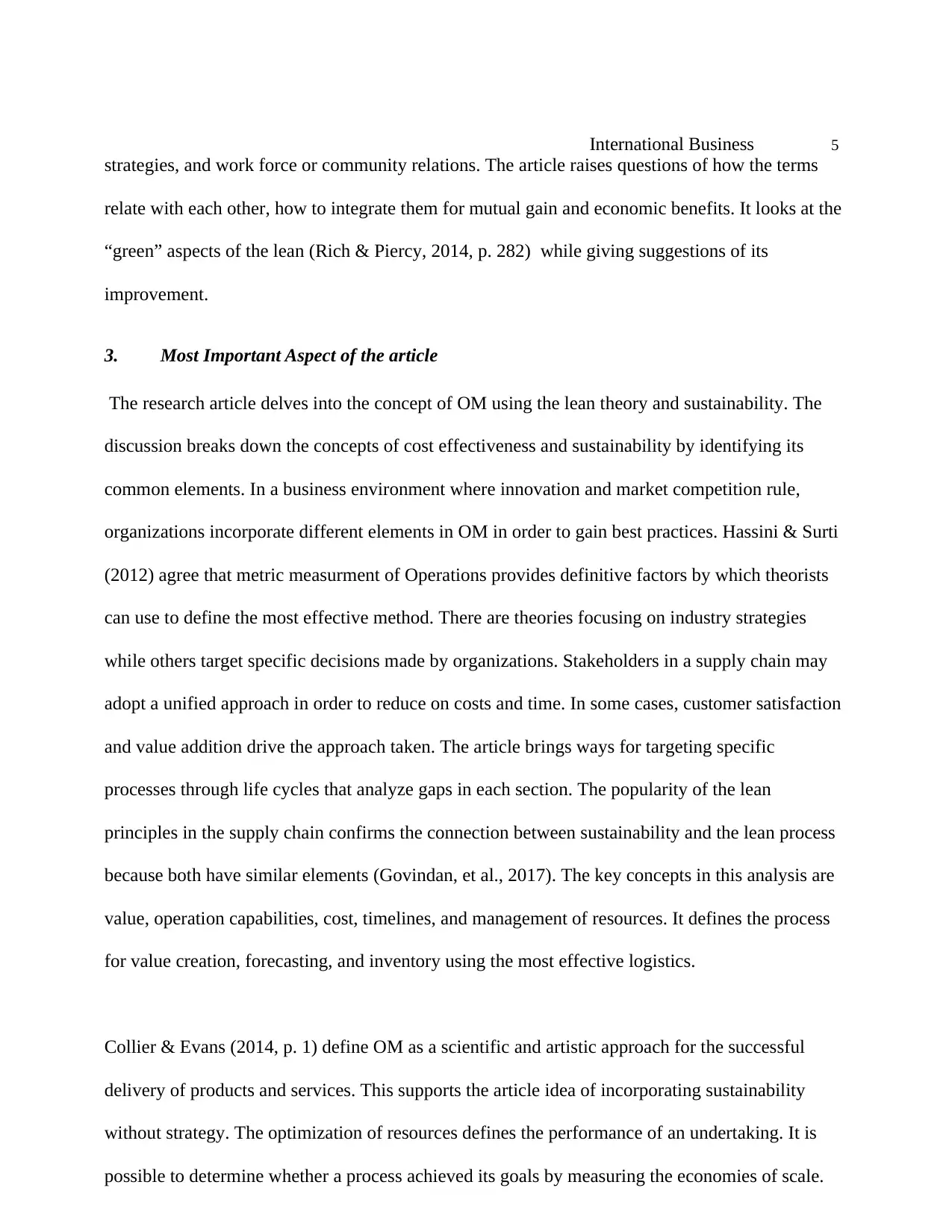
International Business 5
strategies, and work force or community relations. The article raises questions of how the terms
relate with each other, how to integrate them for mutual gain and economic benefits. It looks at the
“green” aspects of the lean (Rich & Piercy, 2014, p. 282) while giving suggestions of its
improvement.
3. Most Important Aspect of the article
The research article delves into the concept of OM using the lean theory and sustainability. The
discussion breaks down the concepts of cost effectiveness and sustainability by identifying its
common elements. In a business environment where innovation and market competition rule,
organizations incorporate different elements in OM in order to gain best practices. Hassini & Surti
(2012) agree that metric measurment of Operations provides definitive factors by which theorists
can use to define the most effective method. There are theories focusing on industry strategies
while others target specific decisions made by organizations. Stakeholders in a supply chain may
adopt a unified approach in order to reduce on costs and time. In some cases, customer satisfaction
and value addition drive the approach taken. The article brings ways for targeting specific
processes through life cycles that analyze gaps in each section. The popularity of the lean
principles in the supply chain confirms the connection between sustainability and the lean process
because both have similar elements (Govindan, et al., 2017). The key concepts in this analysis are
value, operation capabilities, cost, timelines, and management of resources. It defines the process
for value creation, forecasting, and inventory using the most effective logistics.
Collier & Evans (2014, p. 1) define OM as a scientific and artistic approach for the successful
delivery of products and services. This supports the article idea of incorporating sustainability
without strategy. The optimization of resources defines the performance of an undertaking. It is
possible to determine whether a process achieved its goals by measuring the economies of scale.
strategies, and work force or community relations. The article raises questions of how the terms
relate with each other, how to integrate them for mutual gain and economic benefits. It looks at the
“green” aspects of the lean (Rich & Piercy, 2014, p. 282) while giving suggestions of its
improvement.
3. Most Important Aspect of the article
The research article delves into the concept of OM using the lean theory and sustainability. The
discussion breaks down the concepts of cost effectiveness and sustainability by identifying its
common elements. In a business environment where innovation and market competition rule,
organizations incorporate different elements in OM in order to gain best practices. Hassini & Surti
(2012) agree that metric measurment of Operations provides definitive factors by which theorists
can use to define the most effective method. There are theories focusing on industry strategies
while others target specific decisions made by organizations. Stakeholders in a supply chain may
adopt a unified approach in order to reduce on costs and time. In some cases, customer satisfaction
and value addition drive the approach taken. The article brings ways for targeting specific
processes through life cycles that analyze gaps in each section. The popularity of the lean
principles in the supply chain confirms the connection between sustainability and the lean process
because both have similar elements (Govindan, et al., 2017). The key concepts in this analysis are
value, operation capabilities, cost, timelines, and management of resources. It defines the process
for value creation, forecasting, and inventory using the most effective logistics.
Collier & Evans (2014, p. 1) define OM as a scientific and artistic approach for the successful
delivery of products and services. This supports the article idea of incorporating sustainability
without strategy. The optimization of resources defines the performance of an undertaking. It is
possible to determine whether a process achieved its goals by measuring the economies of scale.
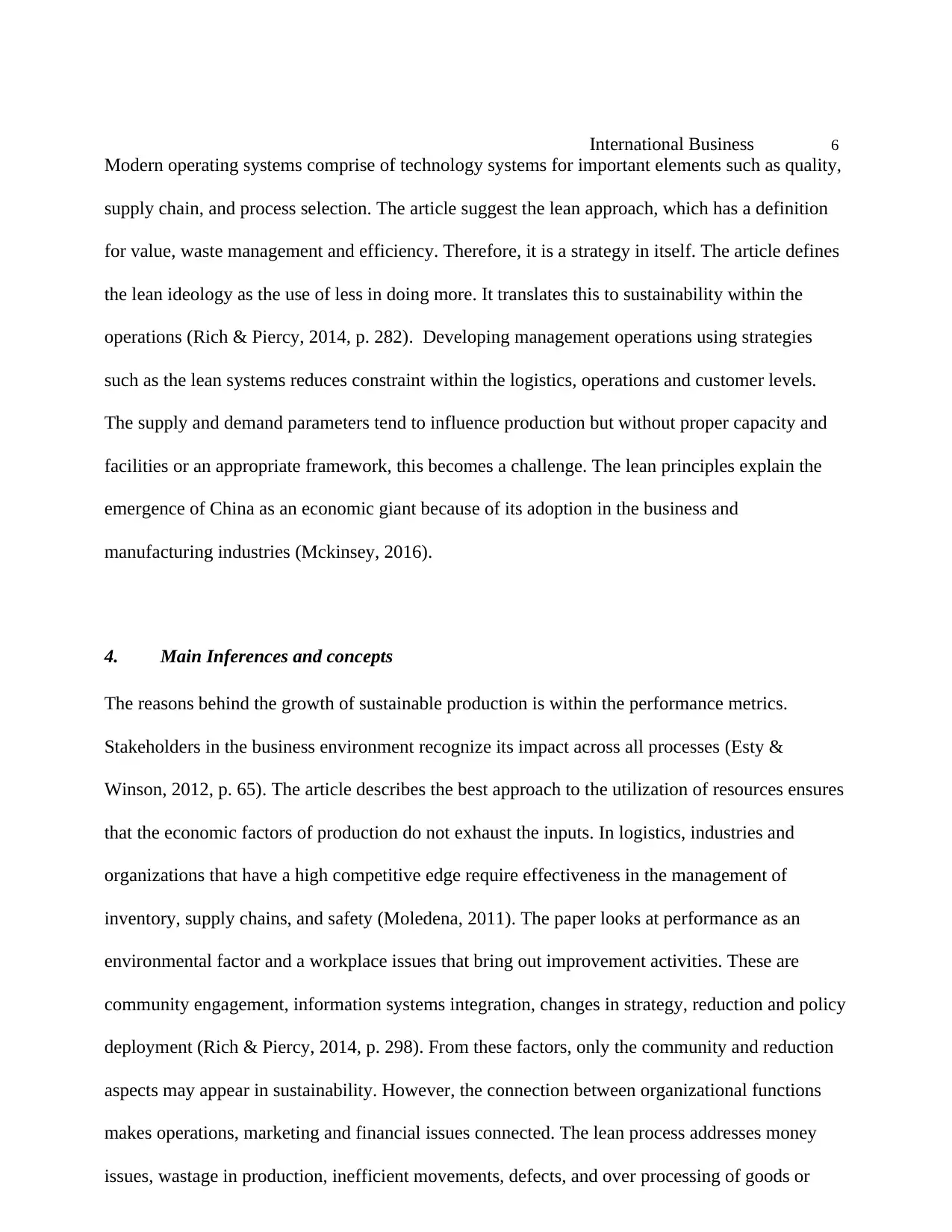
International Business 6
Modern operating systems comprise of technology systems for important elements such as quality,
supply chain, and process selection. The article suggest the lean approach, which has a definition
for value, waste management and efficiency. Therefore, it is a strategy in itself. The article defines
the lean ideology as the use of less in doing more. It translates this to sustainability within the
operations (Rich & Piercy, 2014, p. 282). Developing management operations using strategies
such as the lean systems reduces constraint within the logistics, operations and customer levels.
The supply and demand parameters tend to influence production but without proper capacity and
facilities or an appropriate framework, this becomes a challenge. The lean principles explain the
emergence of China as an economic giant because of its adoption in the business and
manufacturing industries (Mckinsey, 2016).
4. Main Inferences and concepts
The reasons behind the growth of sustainable production is within the performance metrics.
Stakeholders in the business environment recognize its impact across all processes (Esty &
Winson, 2012, p. 65). The article describes the best approach to the utilization of resources ensures
that the economic factors of production do not exhaust the inputs. In logistics, industries and
organizations that have a high competitive edge require effectiveness in the management of
inventory, supply chains, and safety (Moledena, 2011). The paper looks at performance as an
environmental factor and a workplace issues that bring out improvement activities. These are
community engagement, information systems integration, changes in strategy, reduction and policy
deployment (Rich & Piercy, 2014, p. 298). From these factors, only the community and reduction
aspects may appear in sustainability. However, the connection between organizational functions
makes operations, marketing and financial issues connected. The lean process addresses money
issues, wastage in production, inefficient movements, defects, and over processing of goods or
Modern operating systems comprise of technology systems for important elements such as quality,
supply chain, and process selection. The article suggest the lean approach, which has a definition
for value, waste management and efficiency. Therefore, it is a strategy in itself. The article defines
the lean ideology as the use of less in doing more. It translates this to sustainability within the
operations (Rich & Piercy, 2014, p. 282). Developing management operations using strategies
such as the lean systems reduces constraint within the logistics, operations and customer levels.
The supply and demand parameters tend to influence production but without proper capacity and
facilities or an appropriate framework, this becomes a challenge. The lean principles explain the
emergence of China as an economic giant because of its adoption in the business and
manufacturing industries (Mckinsey, 2016).
4. Main Inferences and concepts
The reasons behind the growth of sustainable production is within the performance metrics.
Stakeholders in the business environment recognize its impact across all processes (Esty &
Winson, 2012, p. 65). The article describes the best approach to the utilization of resources ensures
that the economic factors of production do not exhaust the inputs. In logistics, industries and
organizations that have a high competitive edge require effectiveness in the management of
inventory, supply chains, and safety (Moledena, 2011). The paper looks at performance as an
environmental factor and a workplace issues that bring out improvement activities. These are
community engagement, information systems integration, changes in strategy, reduction and policy
deployment (Rich & Piercy, 2014, p. 298). From these factors, only the community and reduction
aspects may appear in sustainability. However, the connection between organizational functions
makes operations, marketing and financial issues connected. The lean process addresses money
issues, wastage in production, inefficient movements, defects, and over processing of goods or
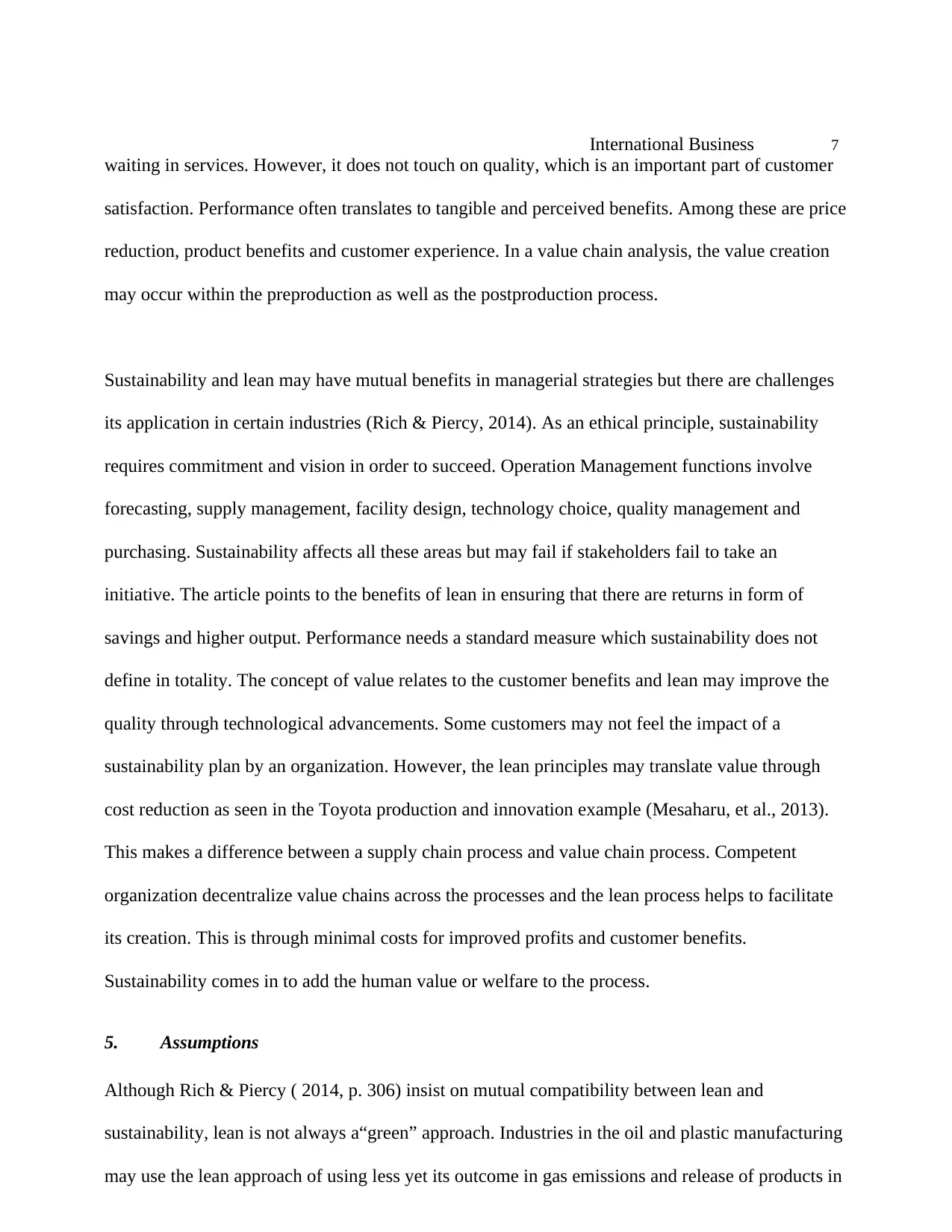
International Business 7
waiting in services. However, it does not touch on quality, which is an important part of customer
satisfaction. Performance often translates to tangible and perceived benefits. Among these are price
reduction, product benefits and customer experience. In a value chain analysis, the value creation
may occur within the preproduction as well as the postproduction process.
Sustainability and lean may have mutual benefits in managerial strategies but there are challenges
its application in certain industries (Rich & Piercy, 2014). As an ethical principle, sustainability
requires commitment and vision in order to succeed. Operation Management functions involve
forecasting, supply management, facility design, technology choice, quality management and
purchasing. Sustainability affects all these areas but may fail if stakeholders fail to take an
initiative. The article points to the benefits of lean in ensuring that there are returns in form of
savings and higher output. Performance needs a standard measure which sustainability does not
define in totality. The concept of value relates to the customer benefits and lean may improve the
quality through technological advancements. Some customers may not feel the impact of a
sustainability plan by an organization. However, the lean principles may translate value through
cost reduction as seen in the Toyota production and innovation example (Mesaharu, et al., 2013).
This makes a difference between a supply chain process and value chain process. Competent
organization decentralize value chains across the processes and the lean process helps to facilitate
its creation. This is through minimal costs for improved profits and customer benefits.
Sustainability comes in to add the human value or welfare to the process.
5. Assumptions
Although Rich & Piercy ( 2014, p. 306) insist on mutual compatibility between lean and
sustainability, lean is not always a“green” approach. Industries in the oil and plastic manufacturing
may use the lean approach of using less yet its outcome in gas emissions and release of products in
waiting in services. However, it does not touch on quality, which is an important part of customer
satisfaction. Performance often translates to tangible and perceived benefits. Among these are price
reduction, product benefits and customer experience. In a value chain analysis, the value creation
may occur within the preproduction as well as the postproduction process.
Sustainability and lean may have mutual benefits in managerial strategies but there are challenges
its application in certain industries (Rich & Piercy, 2014). As an ethical principle, sustainability
requires commitment and vision in order to succeed. Operation Management functions involve
forecasting, supply management, facility design, technology choice, quality management and
purchasing. Sustainability affects all these areas but may fail if stakeholders fail to take an
initiative. The article points to the benefits of lean in ensuring that there are returns in form of
savings and higher output. Performance needs a standard measure which sustainability does not
define in totality. The concept of value relates to the customer benefits and lean may improve the
quality through technological advancements. Some customers may not feel the impact of a
sustainability plan by an organization. However, the lean principles may translate value through
cost reduction as seen in the Toyota production and innovation example (Mesaharu, et al., 2013).
This makes a difference between a supply chain process and value chain process. Competent
organization decentralize value chains across the processes and the lean process helps to facilitate
its creation. This is through minimal costs for improved profits and customer benefits.
Sustainability comes in to add the human value or welfare to the process.
5. Assumptions
Although Rich & Piercy ( 2014, p. 306) insist on mutual compatibility between lean and
sustainability, lean is not always a“green” approach. Industries in the oil and plastic manufacturing
may use the lean approach of using less yet its outcome in gas emissions and release of products in
Paraphrase This Document
Need a fresh take? Get an instant paraphrase of this document with our AI Paraphraser
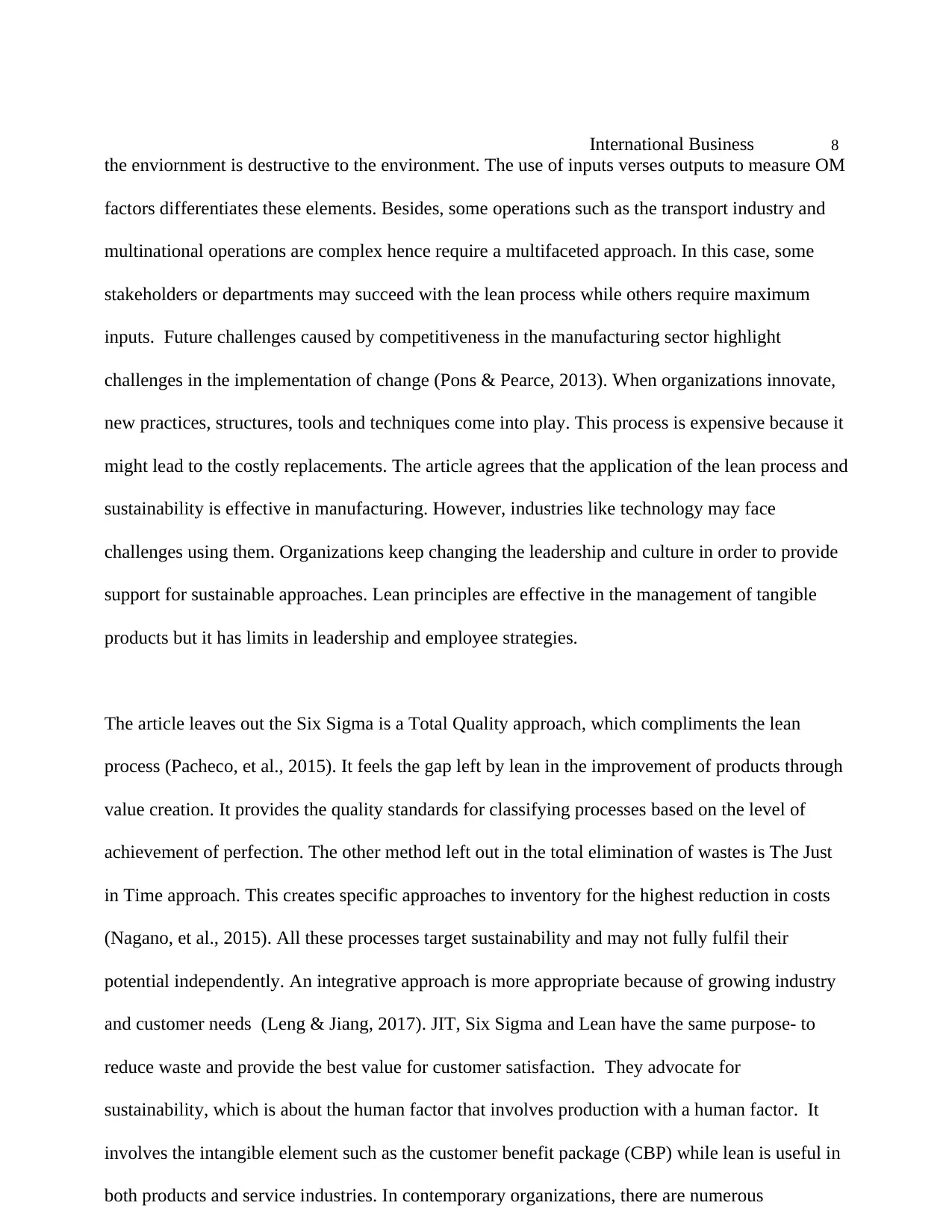
International Business 8
the enviornment is destructive to the environment. The use of inputs verses outputs to measure OM
factors differentiates these elements. Besides, some operations such as the transport industry and
multinational operations are complex hence require a multifaceted approach. In this case, some
stakeholders or departments may succeed with the lean process while others require maximum
inputs. Future challenges caused by competitiveness in the manufacturing sector highlight
challenges in the implementation of change (Pons & Pearce, 2013). When organizations innovate,
new practices, structures, tools and techniques come into play. This process is expensive because it
might lead to the costly replacements. The article agrees that the application of the lean process and
sustainability is effective in manufacturing. However, industries like technology may face
challenges using them. Organizations keep changing the leadership and culture in order to provide
support for sustainable approaches. Lean principles are effective in the management of tangible
products but it has limits in leadership and employee strategies.
The article leaves out the Six Sigma is a Total Quality approach, which compliments the lean
process (Pacheco, et al., 2015). It feels the gap left by lean in the improvement of products through
value creation. It provides the quality standards for classifying processes based on the level of
achievement of perfection. The other method left out in the total elimination of wastes is The Just
in Time approach. This creates specific approaches to inventory for the highest reduction in costs
(Nagano, et al., 2015). All these processes target sustainability and may not fully fulfil their
potential independently. An integrative approach is more appropriate because of growing industry
and customer needs (Leng & Jiang, 2017). JIT, Six Sigma and Lean have the same purpose- to
reduce waste and provide the best value for customer satisfaction. They advocate for
sustainability, which is about the human factor that involves production with a human factor. It
involves the intangible element such as the customer benefit package (CBP) while lean is useful in
both products and service industries. In contemporary organizations, there are numerous
the enviornment is destructive to the environment. The use of inputs verses outputs to measure OM
factors differentiates these elements. Besides, some operations such as the transport industry and
multinational operations are complex hence require a multifaceted approach. In this case, some
stakeholders or departments may succeed with the lean process while others require maximum
inputs. Future challenges caused by competitiveness in the manufacturing sector highlight
challenges in the implementation of change (Pons & Pearce, 2013). When organizations innovate,
new practices, structures, tools and techniques come into play. This process is expensive because it
might lead to the costly replacements. The article agrees that the application of the lean process and
sustainability is effective in manufacturing. However, industries like technology may face
challenges using them. Organizations keep changing the leadership and culture in order to provide
support for sustainable approaches. Lean principles are effective in the management of tangible
products but it has limits in leadership and employee strategies.
The article leaves out the Six Sigma is a Total Quality approach, which compliments the lean
process (Pacheco, et al., 2015). It feels the gap left by lean in the improvement of products through
value creation. It provides the quality standards for classifying processes based on the level of
achievement of perfection. The other method left out in the total elimination of wastes is The Just
in Time approach. This creates specific approaches to inventory for the highest reduction in costs
(Nagano, et al., 2015). All these processes target sustainability and may not fully fulfil their
potential independently. An integrative approach is more appropriate because of growing industry
and customer needs (Leng & Jiang, 2017). JIT, Six Sigma and Lean have the same purpose- to
reduce waste and provide the best value for customer satisfaction. They advocate for
sustainability, which is about the human factor that involves production with a human factor. It
involves the intangible element such as the customer benefit package (CBP) while lean is useful in
both products and service industries. In contemporary organizations, there are numerous
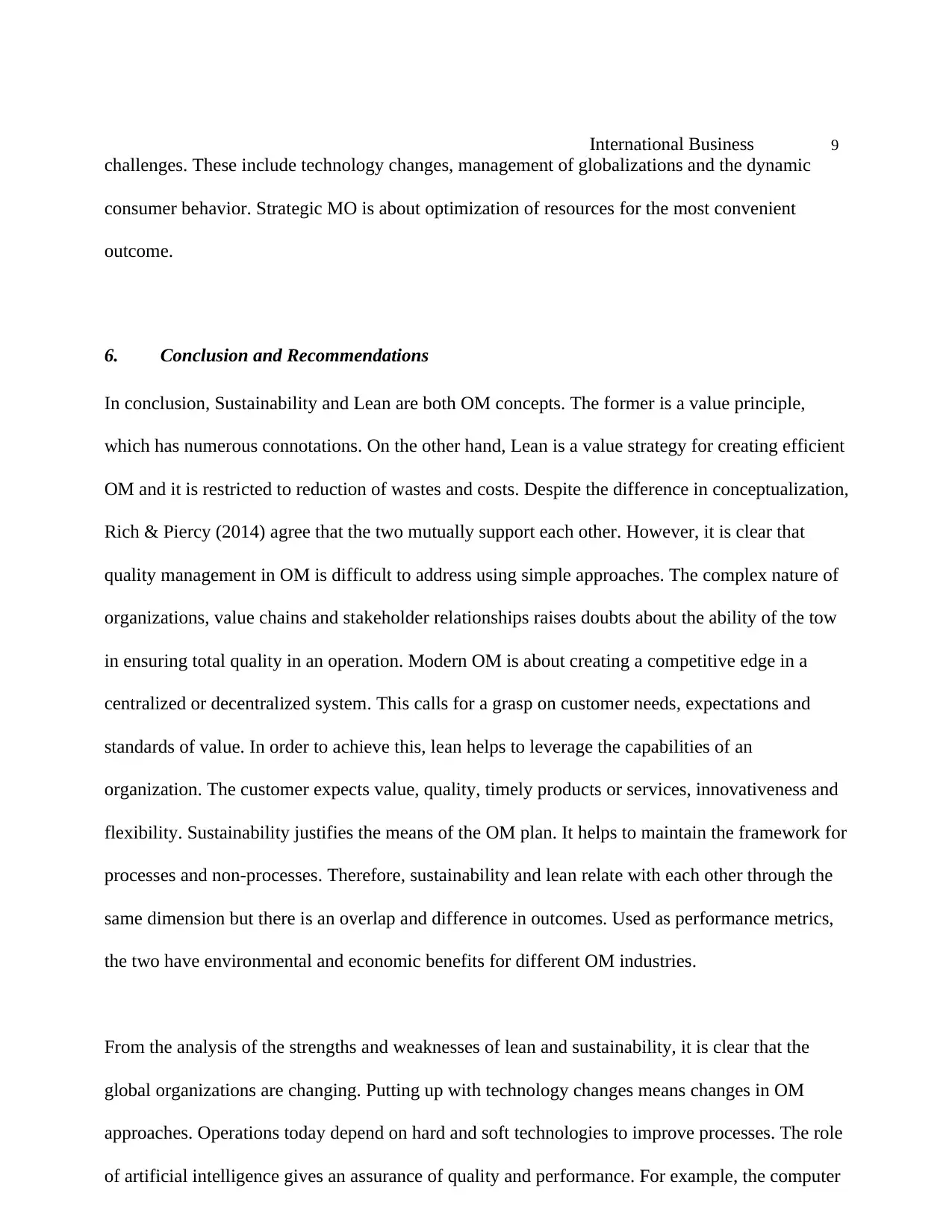
International Business 9
challenges. These include technology changes, management of globalizations and the dynamic
consumer behavior. Strategic MO is about optimization of resources for the most convenient
outcome.
6. Conclusion and Recommendations
In conclusion, Sustainability and Lean are both OM concepts. The former is a value principle,
which has numerous connotations. On the other hand, Lean is a value strategy for creating efficient
OM and it is restricted to reduction of wastes and costs. Despite the difference in conceptualization,
Rich & Piercy (2014) agree that the two mutually support each other. However, it is clear that
quality management in OM is difficult to address using simple approaches. The complex nature of
organizations, value chains and stakeholder relationships raises doubts about the ability of the tow
in ensuring total quality in an operation. Modern OM is about creating a competitive edge in a
centralized or decentralized system. This calls for a grasp on customer needs, expectations and
standards of value. In order to achieve this, lean helps to leverage the capabilities of an
organization. The customer expects value, quality, timely products or services, innovativeness and
flexibility. Sustainability justifies the means of the OM plan. It helps to maintain the framework for
processes and non-processes. Therefore, sustainability and lean relate with each other through the
same dimension but there is an overlap and difference in outcomes. Used as performance metrics,
the two have environmental and economic benefits for different OM industries.
From the analysis of the strengths and weaknesses of lean and sustainability, it is clear that the
global organizations are changing. Putting up with technology changes means changes in OM
approaches. Operations today depend on hard and soft technologies to improve processes. The role
of artificial intelligence gives an assurance of quality and performance. For example, the computer
challenges. These include technology changes, management of globalizations and the dynamic
consumer behavior. Strategic MO is about optimization of resources for the most convenient
outcome.
6. Conclusion and Recommendations
In conclusion, Sustainability and Lean are both OM concepts. The former is a value principle,
which has numerous connotations. On the other hand, Lean is a value strategy for creating efficient
OM and it is restricted to reduction of wastes and costs. Despite the difference in conceptualization,
Rich & Piercy (2014) agree that the two mutually support each other. However, it is clear that
quality management in OM is difficult to address using simple approaches. The complex nature of
organizations, value chains and stakeholder relationships raises doubts about the ability of the tow
in ensuring total quality in an operation. Modern OM is about creating a competitive edge in a
centralized or decentralized system. This calls for a grasp on customer needs, expectations and
standards of value. In order to achieve this, lean helps to leverage the capabilities of an
organization. The customer expects value, quality, timely products or services, innovativeness and
flexibility. Sustainability justifies the means of the OM plan. It helps to maintain the framework for
processes and non-processes. Therefore, sustainability and lean relate with each other through the
same dimension but there is an overlap and difference in outcomes. Used as performance metrics,
the two have environmental and economic benefits for different OM industries.
From the analysis of the strengths and weaknesses of lean and sustainability, it is clear that the
global organizations are changing. Putting up with technology changes means changes in OM
approaches. Operations today depend on hard and soft technologies to improve processes. The role
of artificial intelligence gives an assurance of quality and performance. For example, the computer
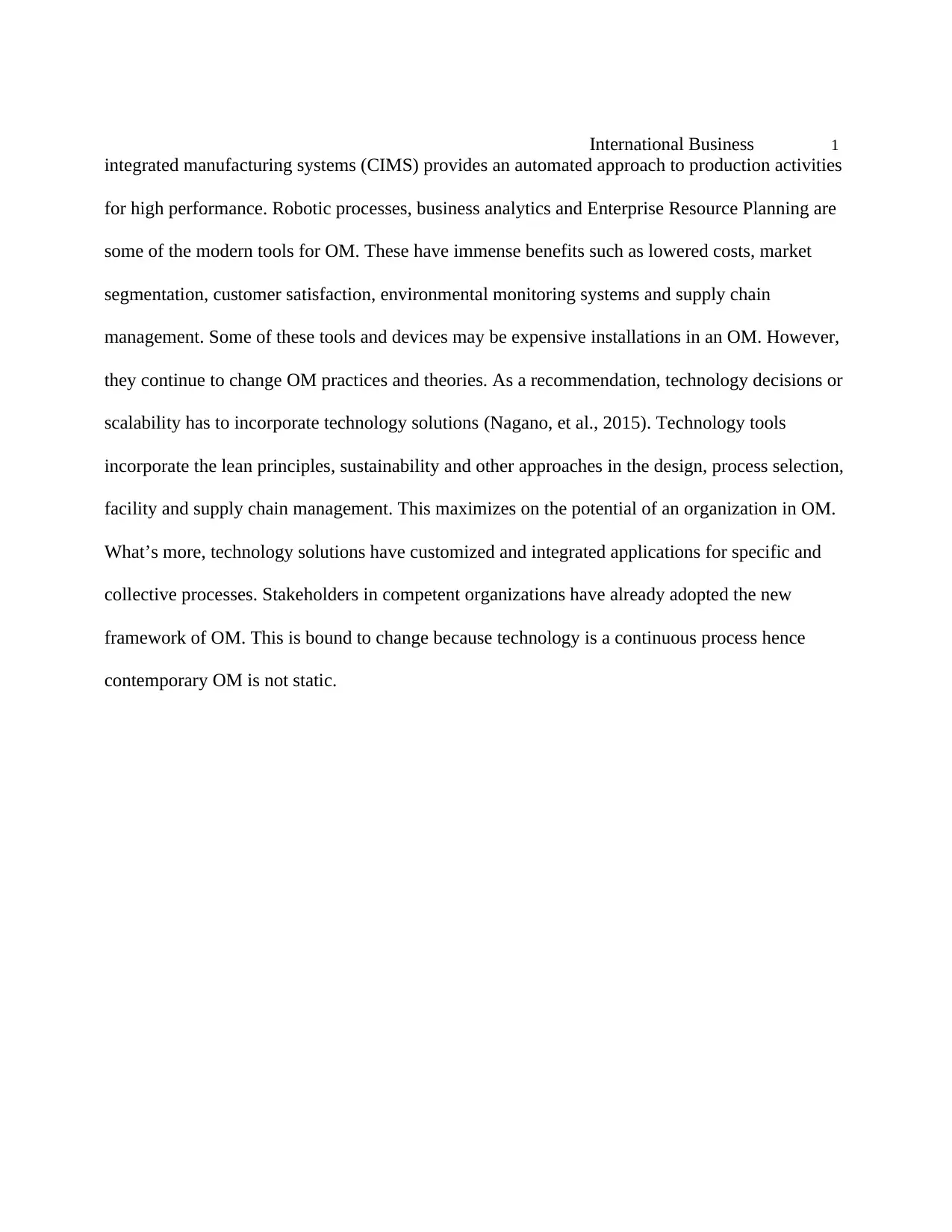
International Business 1
0integrated manufacturing systems (CIMS) provides an automated approach to production activities
for high performance. Robotic processes, business analytics and Enterprise Resource Planning are
some of the modern tools for OM. These have immense benefits such as lowered costs, market
segmentation, customer satisfaction, environmental monitoring systems and supply chain
management. Some of these tools and devices may be expensive installations in an OM. However,
they continue to change OM practices and theories. As a recommendation, technology decisions or
scalability has to incorporate technology solutions (Nagano, et al., 2015). Technology tools
incorporate the lean principles, sustainability and other approaches in the design, process selection,
facility and supply chain management. This maximizes on the potential of an organization in OM.
What’s more, technology solutions have customized and integrated applications for specific and
collective processes. Stakeholders in competent organizations have already adopted the new
framework of OM. This is bound to change because technology is a continuous process hence
contemporary OM is not static.
0integrated manufacturing systems (CIMS) provides an automated approach to production activities
for high performance. Robotic processes, business analytics and Enterprise Resource Planning are
some of the modern tools for OM. These have immense benefits such as lowered costs, market
segmentation, customer satisfaction, environmental monitoring systems and supply chain
management. Some of these tools and devices may be expensive installations in an OM. However,
they continue to change OM practices and theories. As a recommendation, technology decisions or
scalability has to incorporate technology solutions (Nagano, et al., 2015). Technology tools
incorporate the lean principles, sustainability and other approaches in the design, process selection,
facility and supply chain management. This maximizes on the potential of an organization in OM.
What’s more, technology solutions have customized and integrated applications for specific and
collective processes. Stakeholders in competent organizations have already adopted the new
framework of OM. This is bound to change because technology is a continuous process hence
contemporary OM is not static.
Secure Best Marks with AI Grader
Need help grading? Try our AI Grader for instant feedback on your assignments.
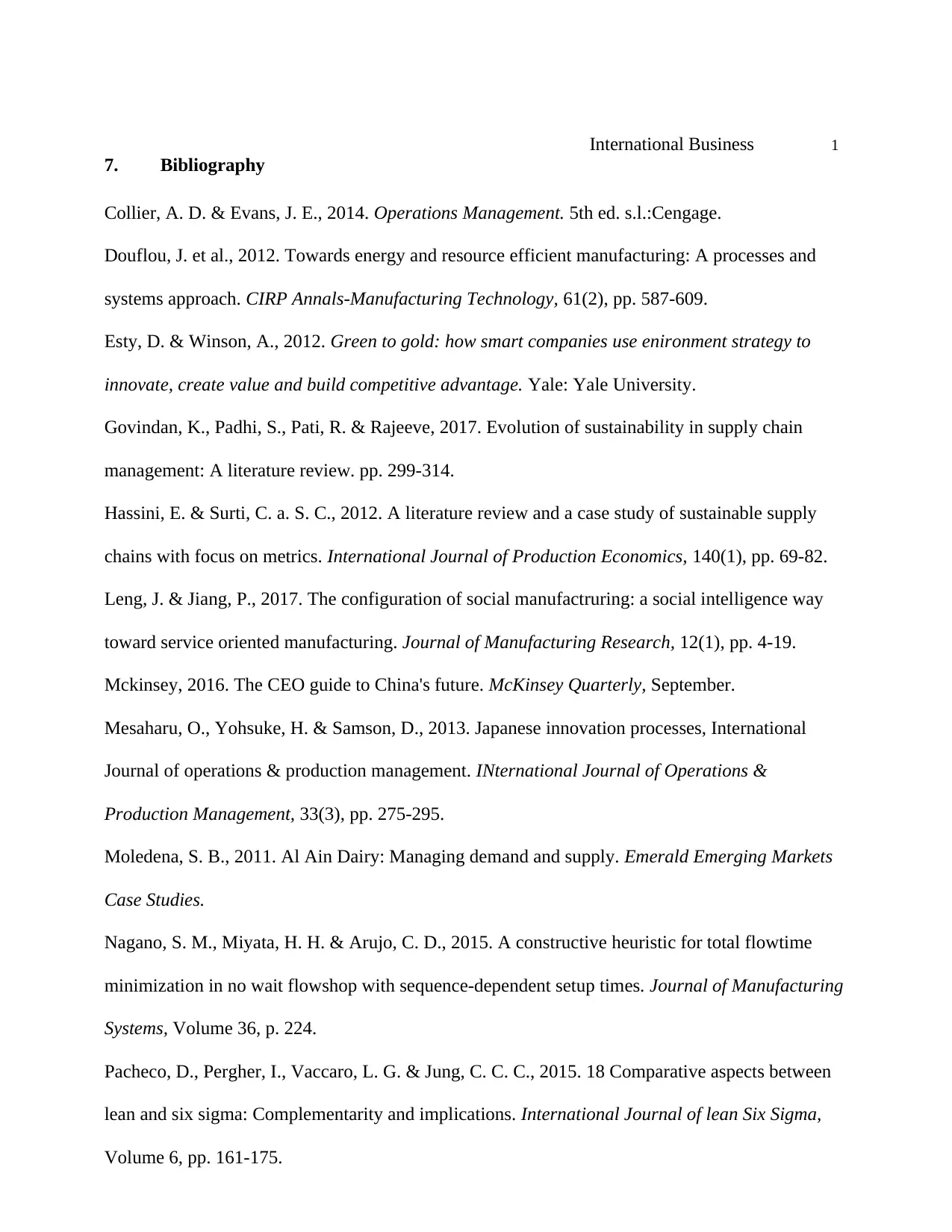
International Business 1
17. Bibliography
Collier, A. D. & Evans, J. E., 2014. Operations Management. 5th ed. s.l.:Cengage.
Douflou, J. et al., 2012. Towards energy and resource efficient manufacturing: A processes and
systems approach. CIRP Annals-Manufacturing Technology, 61(2), pp. 587-609.
Esty, D. & Winson, A., 2012. Green to gold: how smart companies use enironment strategy to
innovate, create value and build competitive advantage. Yale: Yale University.
Govindan, K., Padhi, S., Pati, R. & Rajeeve, 2017. Evolution of sustainability in supply chain
management: A literature review. pp. 299-314.
Hassini, E. & Surti, C. a. S. C., 2012. A literature review and a case study of sustainable supply
chains with focus on metrics. International Journal of Production Economics, 140(1), pp. 69-82.
Leng, J. & Jiang, P., 2017. The configuration of social manufactruring: a social intelligence way
toward service oriented manufacturing. Journal of Manufacturing Research, 12(1), pp. 4-19.
Mckinsey, 2016. The CEO guide to China's future. McKinsey Quarterly, September.
Mesaharu, O., Yohsuke, H. & Samson, D., 2013. Japanese innovation processes, International
Journal of operations & production management. INternational Journal of Operations &
Production Management, 33(3), pp. 275-295.
Moledena, S. B., 2011. Al Ain Dairy: Managing demand and supply. Emerald Emerging Markets
Case Studies.
Nagano, S. M., Miyata, H. H. & Arujo, C. D., 2015. A constructive heuristic for total flowtime
minimization in no wait flowshop with sequence-dependent setup times. Journal of Manufacturing
Systems, Volume 36, p. 224.
Pacheco, D., Pergher, I., Vaccaro, L. G. & Jung, C. C. C., 2015. 18 Comparative aspects between
lean and six sigma: Complementarity and implications. International Journal of lean Six Sigma,
Volume 6, pp. 161-175.
17. Bibliography
Collier, A. D. & Evans, J. E., 2014. Operations Management. 5th ed. s.l.:Cengage.
Douflou, J. et al., 2012. Towards energy and resource efficient manufacturing: A processes and
systems approach. CIRP Annals-Manufacturing Technology, 61(2), pp. 587-609.
Esty, D. & Winson, A., 2012. Green to gold: how smart companies use enironment strategy to
innovate, create value and build competitive advantage. Yale: Yale University.
Govindan, K., Padhi, S., Pati, R. & Rajeeve, 2017. Evolution of sustainability in supply chain
management: A literature review. pp. 299-314.
Hassini, E. & Surti, C. a. S. C., 2012. A literature review and a case study of sustainable supply
chains with focus on metrics. International Journal of Production Economics, 140(1), pp. 69-82.
Leng, J. & Jiang, P., 2017. The configuration of social manufactruring: a social intelligence way
toward service oriented manufacturing. Journal of Manufacturing Research, 12(1), pp. 4-19.
Mckinsey, 2016. The CEO guide to China's future. McKinsey Quarterly, September.
Mesaharu, O., Yohsuke, H. & Samson, D., 2013. Japanese innovation processes, International
Journal of operations & production management. INternational Journal of Operations &
Production Management, 33(3), pp. 275-295.
Moledena, S. B., 2011. Al Ain Dairy: Managing demand and supply. Emerald Emerging Markets
Case Studies.
Nagano, S. M., Miyata, H. H. & Arujo, C. D., 2015. A constructive heuristic for total flowtime
minimization in no wait flowshop with sequence-dependent setup times. Journal of Manufacturing
Systems, Volume 36, p. 224.
Pacheco, D., Pergher, I., Vaccaro, L. G. & Jung, C. C. C., 2015. 18 Comparative aspects between
lean and six sigma: Complementarity and implications. International Journal of lean Six Sigma,
Volume 6, pp. 161-175.
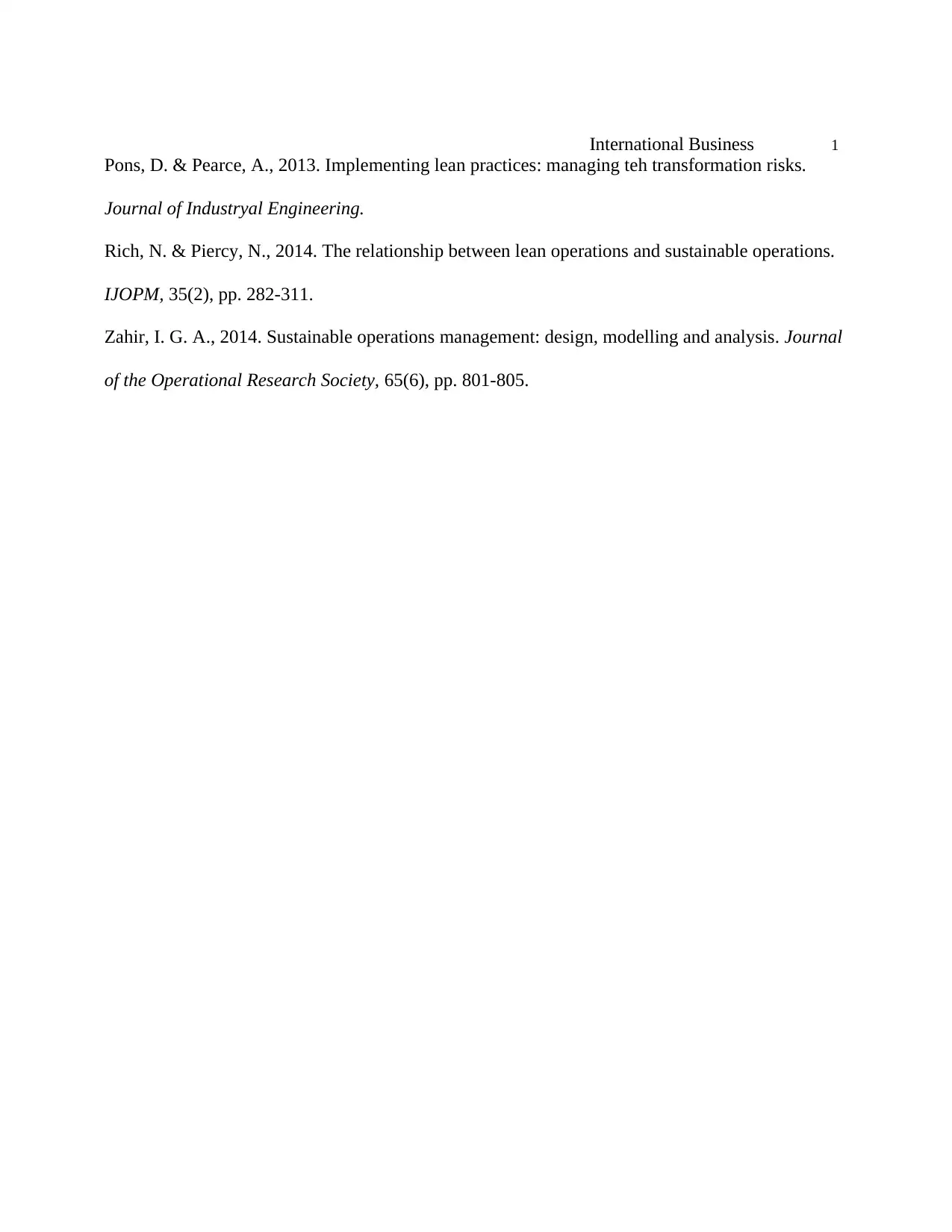
International Business 1
2Pons, D. & Pearce, A., 2013. Implementing lean practices: managing teh transformation risks.
Journal of Industryal Engineering.
Rich, N. & Piercy, N., 2014. The relationship between lean operations and sustainable operations.
IJOPM, 35(2), pp. 282-311.
Zahir, I. G. A., 2014. Sustainable operations management: design, modelling and analysis. Journal
of the Operational Research Society, 65(6), pp. 801-805.
2Pons, D. & Pearce, A., 2013. Implementing lean practices: managing teh transformation risks.
Journal of Industryal Engineering.
Rich, N. & Piercy, N., 2014. The relationship between lean operations and sustainable operations.
IJOPM, 35(2), pp. 282-311.
Zahir, I. G. A., 2014. Sustainable operations management: design, modelling and analysis. Journal
of the Operational Research Society, 65(6), pp. 801-805.
1 out of 12
Related Documents

Your All-in-One AI-Powered Toolkit for Academic Success.
+13062052269
info@desklib.com
Available 24*7 on WhatsApp / Email
Unlock your academic potential
© 2024 | Zucol Services PVT LTD | All rights reserved.