Exploring the Links Between Lean Philosophy and Swift Even Flow
VerifiedAdded on 2023/06/08
|6
|1821
|71
Essay
AI Summary
This essay delves into the Lean philosophy, emphasizing waste reduction and value creation, and its integration with the Theory of Swift Even Flow, which focuses on maximizing productivity through swift and even material flow. It discusses the key principles of Lean, including value adding, non-value adding, and value enabling activities, along with the seven wastes. The essay also explains the Theory of Swift Even Flow, highlighting the importance of minimizing non-value-added work, reducing variability, and optimizing production time. Furthermore, it explores how the theory aligns with scientific methods, quality control, and factory concentration to enhance productivity. The essay concludes by illustrating how Lean practices and the Theory of Swift Even Flow can synergistically improve manufacturing processes and service delivery, with examples from cable manufacturing, truck manufacturing, and printing industries.
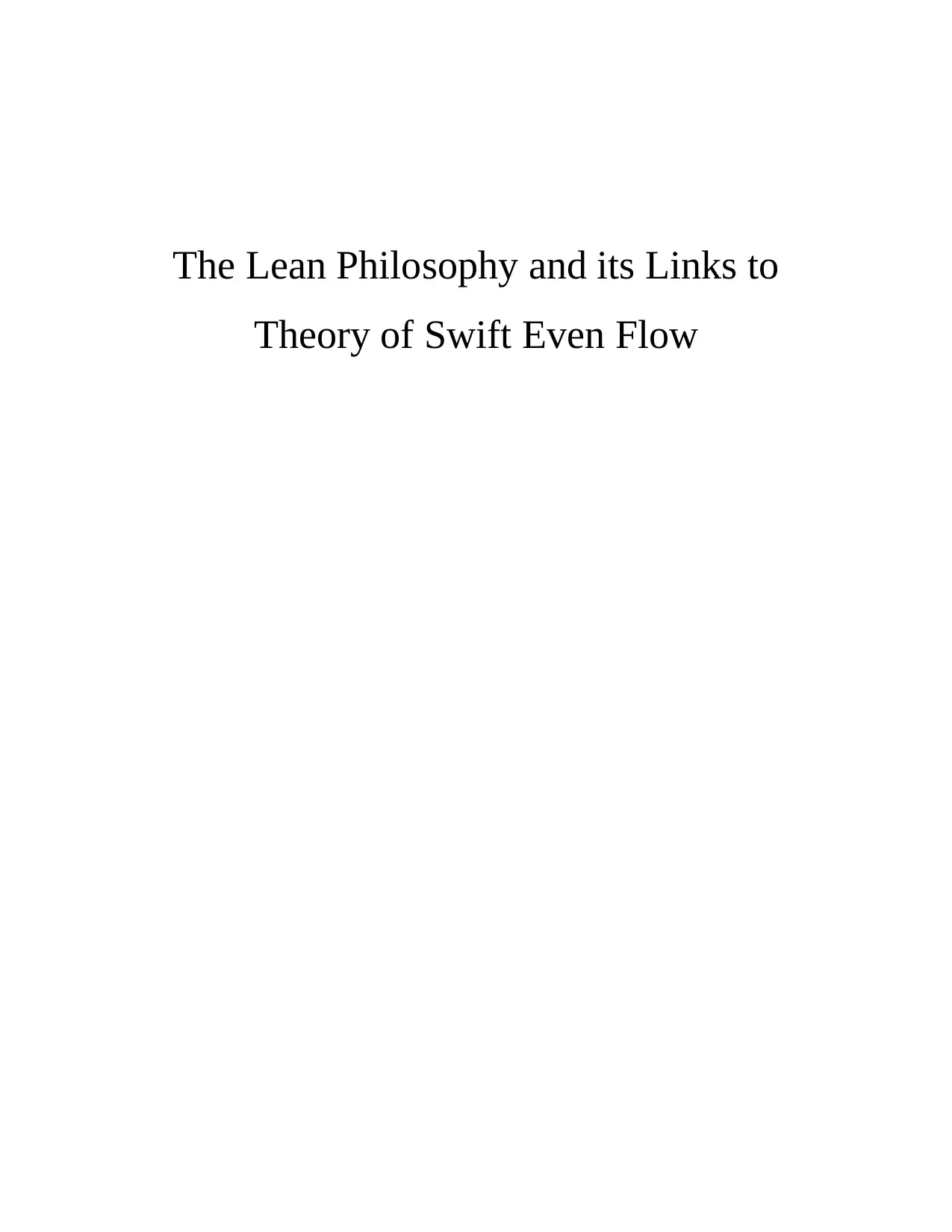
The Lean Philosophy and its Links to
Theory of Swift Even Flow
Theory of Swift Even Flow
Secure Best Marks with AI Grader
Need help grading? Try our AI Grader for instant feedback on your assignments.
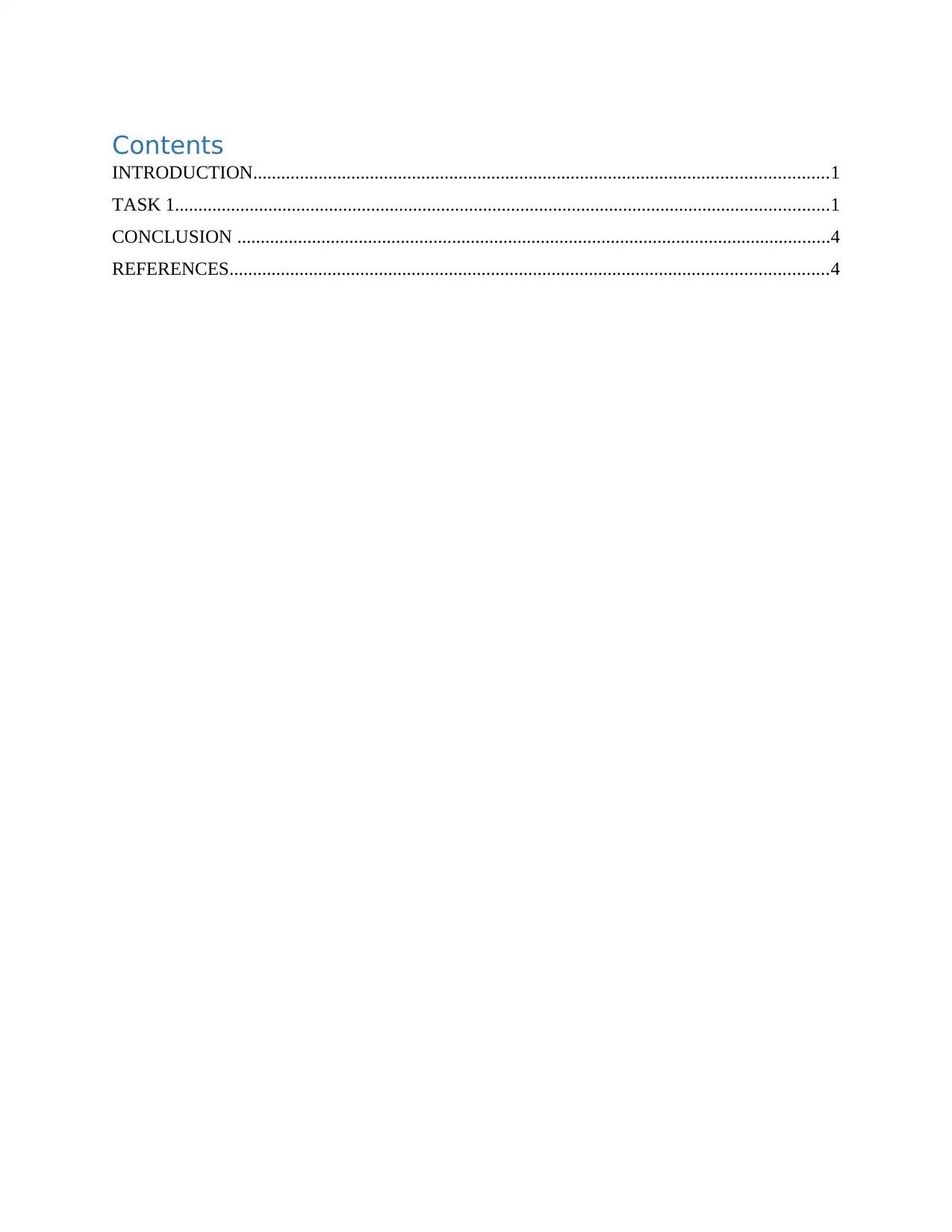
Contents
INTRODUCTION...........................................................................................................................1
TASK 1............................................................................................................................................1
CONCLUSION ...............................................................................................................................4
REFERENCES................................................................................................................................4
INTRODUCTION...........................................................................................................................1
TASK 1............................................................................................................................................1
CONCLUSION ...............................................................................................................................4
REFERENCES................................................................................................................................4
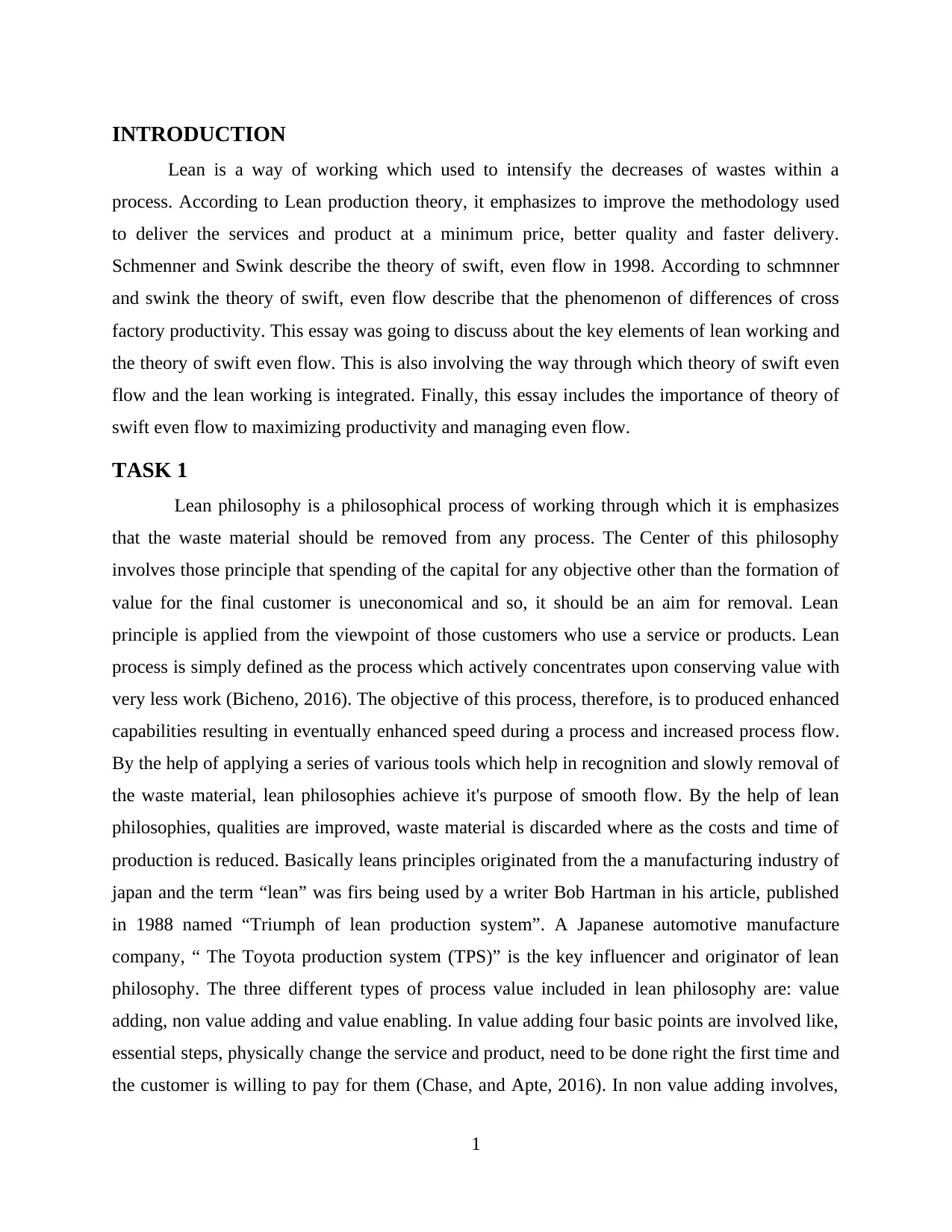
INTRODUCTION
Lean is a way of working which used to intensify the decreases of wastes within a
process. According to Lean production theory, it emphasizes to improve the methodology used
to deliver the services and product at a minimum price, better quality and faster delivery.
Schmenner and Swink describe the theory of swift, even flow in 1998. According to schmnner
and swink the theory of swift, even flow describe that the phenomenon of differences of cross
factory productivity. This essay was going to discuss about the key elements of lean working and
the theory of swift even flow. This is also involving the way through which theory of swift even
flow and the lean working is integrated. Finally, this essay includes the importance of theory of
swift even flow to maximizing productivity and managing even flow.
TASK 1
Lean philosophy is a philosophical process of working through which it is emphasizes
that the waste material should be removed from any process. The Center of this philosophy
involves those principle that spending of the capital for any objective other than the formation of
value for the final customer is uneconomical and so, it should be an aim for removal. Lean
principle is applied from the viewpoint of those customers who use a service or products. Lean
process is simply defined as the process which actively concentrates upon conserving value with
very less work (Bicheno, 2016). The objective of this process, therefore, is to produced enhanced
capabilities resulting in eventually enhanced speed during a process and increased process flow.
By the help of applying a series of various tools which help in recognition and slowly removal of
the waste material, lean philosophies achieve it's purpose of smooth flow. By the help of lean
philosophies, qualities are improved, waste material is discarded where as the costs and time of
production is reduced. Basically leans principles originated from the a manufacturing industry of
japan and the term “lean” was firs being used by a writer Bob Hartman in his article, published
in 1988 named “Triumph of lean production system”. A Japanese automotive manufacture
company, “ The Toyota production system (TPS)” is the key influencer and originator of lean
philosophy. The three different types of process value included in lean philosophy are: value
adding, non value adding and value enabling. In value adding four basic points are involved like,
essential steps, physically change the service and product, need to be done right the first time and
the customer is willing to pay for them (Chase, and Apte, 2016). In non value adding involves,
1
Lean is a way of working which used to intensify the decreases of wastes within a
process. According to Lean production theory, it emphasizes to improve the methodology used
to deliver the services and product at a minimum price, better quality and faster delivery.
Schmenner and Swink describe the theory of swift, even flow in 1998. According to schmnner
and swink the theory of swift, even flow describe that the phenomenon of differences of cross
factory productivity. This essay was going to discuss about the key elements of lean working and
the theory of swift even flow. This is also involving the way through which theory of swift even
flow and the lean working is integrated. Finally, this essay includes the importance of theory of
swift even flow to maximizing productivity and managing even flow.
TASK 1
Lean philosophy is a philosophical process of working through which it is emphasizes
that the waste material should be removed from any process. The Center of this philosophy
involves those principle that spending of the capital for any objective other than the formation of
value for the final customer is uneconomical and so, it should be an aim for removal. Lean
principle is applied from the viewpoint of those customers who use a service or products. Lean
process is simply defined as the process which actively concentrates upon conserving value with
very less work (Bicheno, 2016). The objective of this process, therefore, is to produced enhanced
capabilities resulting in eventually enhanced speed during a process and increased process flow.
By the help of applying a series of various tools which help in recognition and slowly removal of
the waste material, lean philosophies achieve it's purpose of smooth flow. By the help of lean
philosophies, qualities are improved, waste material is discarded where as the costs and time of
production is reduced. Basically leans principles originated from the a manufacturing industry of
japan and the term “lean” was firs being used by a writer Bob Hartman in his article, published
in 1988 named “Triumph of lean production system”. A Japanese automotive manufacture
company, “ The Toyota production system (TPS)” is the key influencer and originator of lean
philosophy. The three different types of process value included in lean philosophy are: value
adding, non value adding and value enabling. In value adding four basic points are involved like,
essential steps, physically change the service and product, need to be done right the first time and
the customer is willing to pay for them (Chase, and Apte, 2016). In non value adding involves,
1
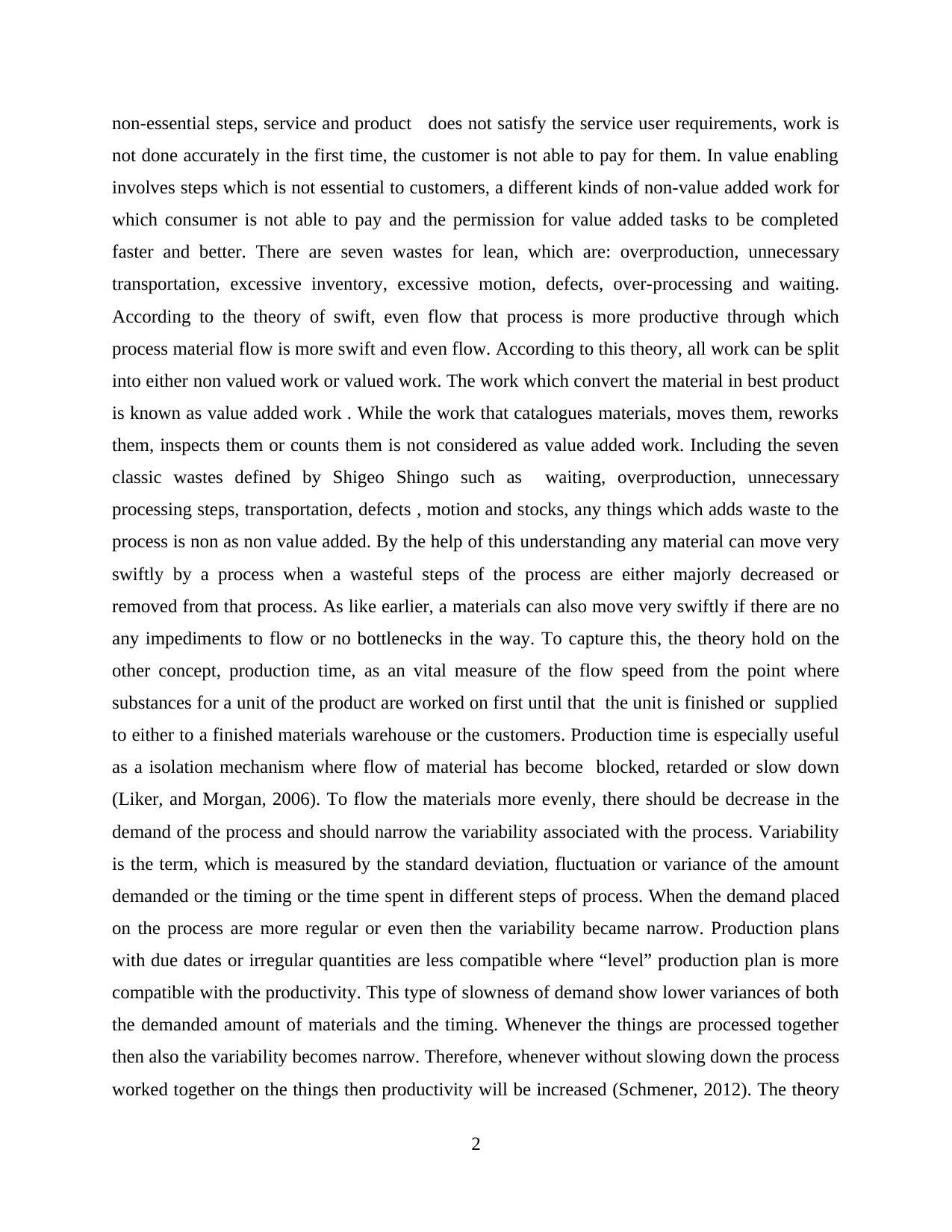
non-essential steps, service and product does not satisfy the service user requirements, work is
not done accurately in the first time, the customer is not able to pay for them. In value enabling
involves steps which is not essential to customers, a different kinds of non-value added work for
which consumer is not able to pay and the permission for value added tasks to be completed
faster and better. There are seven wastes for lean, which are: overproduction, unnecessary
transportation, excessive inventory, excessive motion, defects, over-processing and waiting.
According to the theory of swift, even flow that process is more productive through which
process material flow is more swift and even flow. According to this theory, all work can be split
into either non valued work or valued work. The work which convert the material in best product
is known as value added work . While the work that catalogues materials, moves them, reworks
them, inspects them or counts them is not considered as value added work. Including the seven
classic wastes defined by Shigeo Shingo such as waiting, overproduction, unnecessary
processing steps, transportation, defects , motion and stocks, any things which adds waste to the
process is non as non value added. By the help of this understanding any material can move very
swiftly by a process when a wasteful steps of the process are either majorly decreased or
removed from that process. As like earlier, a materials can also move very swiftly if there are no
any impediments to flow or no bottlenecks in the way. To capture this, the theory hold on the
other concept, production time, as an vital measure of the flow speed from the point where
substances for a unit of the product are worked on first until that the unit is finished or supplied
to either to a finished materials warehouse or the customers. Production time is especially useful
as a isolation mechanism where flow of material has become blocked, retarded or slow down
(Liker, and Morgan, 2006). To flow the materials more evenly, there should be decrease in the
demand of the process and should narrow the variability associated with the process. Variability
is the term, which is measured by the standard deviation, fluctuation or variance of the amount
demanded or the timing or the time spent in different steps of process. When the demand placed
on the process are more regular or even then the variability became narrow. Production plans
with due dates or irregular quantities are less compatible where “level” production plan is more
compatible with the productivity. This type of slowness of demand show lower variances of both
the demanded amount of materials and the timing. Whenever the things are processed together
then also the variability becomes narrow. Therefore, whenever without slowing down the process
worked together on the things then productivity will be increased (Schmener, 2012). The theory
2
not done accurately in the first time, the customer is not able to pay for them. In value enabling
involves steps which is not essential to customers, a different kinds of non-value added work for
which consumer is not able to pay and the permission for value added tasks to be completed
faster and better. There are seven wastes for lean, which are: overproduction, unnecessary
transportation, excessive inventory, excessive motion, defects, over-processing and waiting.
According to the theory of swift, even flow that process is more productive through which
process material flow is more swift and even flow. According to this theory, all work can be split
into either non valued work or valued work. The work which convert the material in best product
is known as value added work . While the work that catalogues materials, moves them, reworks
them, inspects them or counts them is not considered as value added work. Including the seven
classic wastes defined by Shigeo Shingo such as waiting, overproduction, unnecessary
processing steps, transportation, defects , motion and stocks, any things which adds waste to the
process is non as non value added. By the help of this understanding any material can move very
swiftly by a process when a wasteful steps of the process are either majorly decreased or
removed from that process. As like earlier, a materials can also move very swiftly if there are no
any impediments to flow or no bottlenecks in the way. To capture this, the theory hold on the
other concept, production time, as an vital measure of the flow speed from the point where
substances for a unit of the product are worked on first until that the unit is finished or supplied
to either to a finished materials warehouse or the customers. Production time is especially useful
as a isolation mechanism where flow of material has become blocked, retarded or slow down
(Liker, and Morgan, 2006). To flow the materials more evenly, there should be decrease in the
demand of the process and should narrow the variability associated with the process. Variability
is the term, which is measured by the standard deviation, fluctuation or variance of the amount
demanded or the timing or the time spent in different steps of process. When the demand placed
on the process are more regular or even then the variability became narrow. Production plans
with due dates or irregular quantities are less compatible where “level” production plan is more
compatible with the productivity. This type of slowness of demand show lower variances of both
the demanded amount of materials and the timing. Whenever the things are processed together
then also the variability becomes narrow. Therefore, whenever without slowing down the process
worked together on the things then productivity will be increased (Schmener, 2012). The theory
2
Secure Best Marks with AI Grader
Need help grading? Try our AI Grader for instant feedback on your assignments.
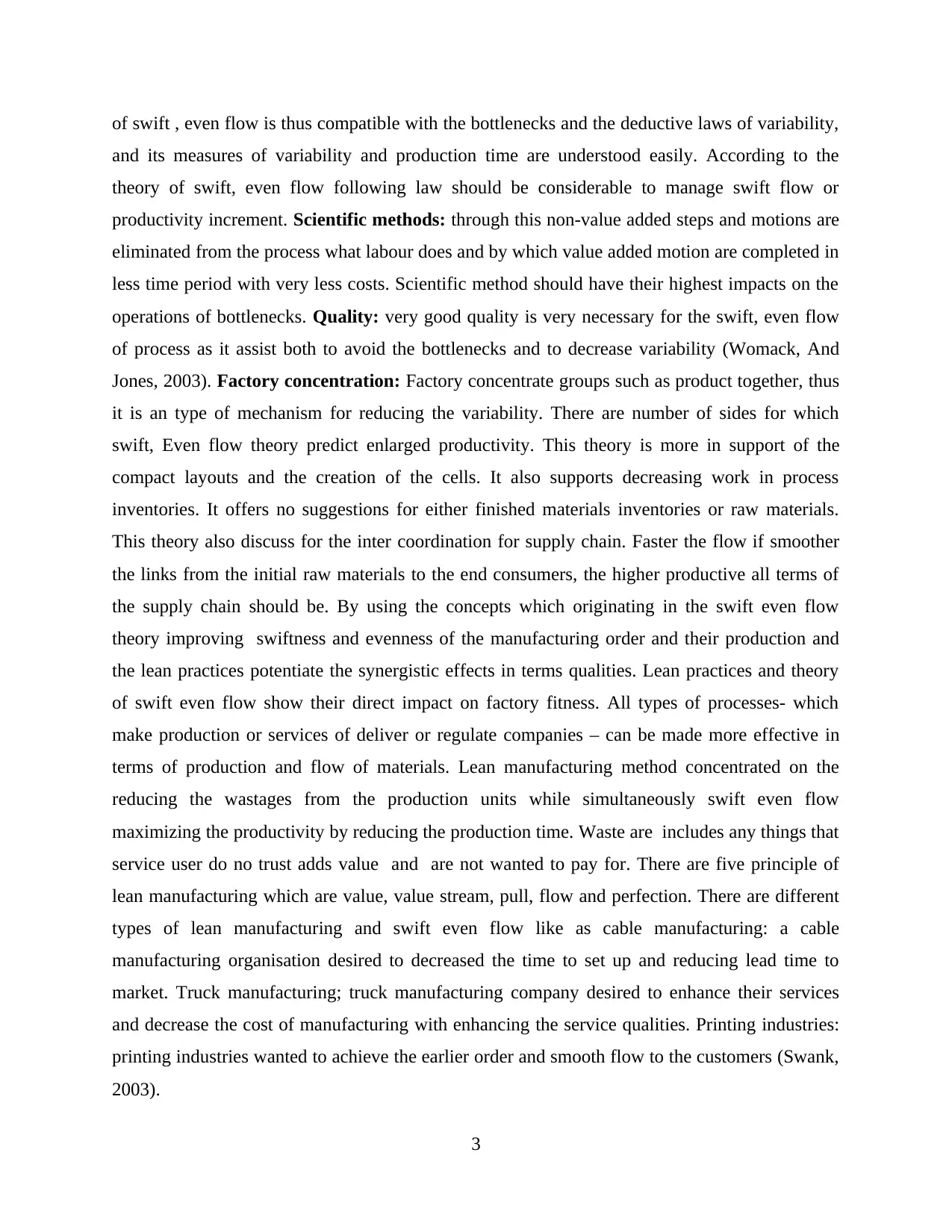
of swift , even flow is thus compatible with the bottlenecks and the deductive laws of variability,
and its measures of variability and production time are understood easily. According to the
theory of swift, even flow following law should be considerable to manage swift flow or
productivity increment. Scientific methods: through this non-value added steps and motions are
eliminated from the process what labour does and by which value added motion are completed in
less time period with very less costs. Scientific method should have their highest impacts on the
operations of bottlenecks. Quality: very good quality is very necessary for the swift, even flow
of process as it assist both to avoid the bottlenecks and to decrease variability (Womack, And
Jones, 2003). Factory concentration: Factory concentrate groups such as product together, thus
it is an type of mechanism for reducing the variability. There are number of sides for which
swift, Even flow theory predict enlarged productivity. This theory is more in support of the
compact layouts and the creation of the cells. It also supports decreasing work in process
inventories. It offers no suggestions for either finished materials inventories or raw materials.
This theory also discuss for the inter coordination for supply chain. Faster the flow if smoother
the links from the initial raw materials to the end consumers, the higher productive all terms of
the supply chain should be. By using the concepts which originating in the swift even flow
theory improving swiftness and evenness of the manufacturing order and their production and
the lean practices potentiate the synergistic effects in terms qualities. Lean practices and theory
of swift even flow show their direct impact on factory fitness. All types of processes- which
make production or services of deliver or regulate companies – can be made more effective in
terms of production and flow of materials. Lean manufacturing method concentrated on the
reducing the wastages from the production units while simultaneously swift even flow
maximizing the productivity by reducing the production time. Waste are includes any things that
service user do no trust adds value and are not wanted to pay for. There are five principle of
lean manufacturing which are value, value stream, pull, flow and perfection. There are different
types of lean manufacturing and swift even flow like as cable manufacturing: a cable
manufacturing organisation desired to decreased the time to set up and reducing lead time to
market. Truck manufacturing; truck manufacturing company desired to enhance their services
and decrease the cost of manufacturing with enhancing the service qualities. Printing industries:
printing industries wanted to achieve the earlier order and smooth flow to the customers (Swank,
2003).
3
and its measures of variability and production time are understood easily. According to the
theory of swift, even flow following law should be considerable to manage swift flow or
productivity increment. Scientific methods: through this non-value added steps and motions are
eliminated from the process what labour does and by which value added motion are completed in
less time period with very less costs. Scientific method should have their highest impacts on the
operations of bottlenecks. Quality: very good quality is very necessary for the swift, even flow
of process as it assist both to avoid the bottlenecks and to decrease variability (Womack, And
Jones, 2003). Factory concentration: Factory concentrate groups such as product together, thus
it is an type of mechanism for reducing the variability. There are number of sides for which
swift, Even flow theory predict enlarged productivity. This theory is more in support of the
compact layouts and the creation of the cells. It also supports decreasing work in process
inventories. It offers no suggestions for either finished materials inventories or raw materials.
This theory also discuss for the inter coordination for supply chain. Faster the flow if smoother
the links from the initial raw materials to the end consumers, the higher productive all terms of
the supply chain should be. By using the concepts which originating in the swift even flow
theory improving swiftness and evenness of the manufacturing order and their production and
the lean practices potentiate the synergistic effects in terms qualities. Lean practices and theory
of swift even flow show their direct impact on factory fitness. All types of processes- which
make production or services of deliver or regulate companies – can be made more effective in
terms of production and flow of materials. Lean manufacturing method concentrated on the
reducing the wastages from the production units while simultaneously swift even flow
maximizing the productivity by reducing the production time. Waste are includes any things that
service user do no trust adds value and are not wanted to pay for. There are five principle of
lean manufacturing which are value, value stream, pull, flow and perfection. There are different
types of lean manufacturing and swift even flow like as cable manufacturing: a cable
manufacturing organisation desired to decreased the time to set up and reducing lead time to
market. Truck manufacturing; truck manufacturing company desired to enhance their services
and decrease the cost of manufacturing with enhancing the service qualities. Printing industries:
printing industries wanted to achieve the earlier order and smooth flow to the customers (Swank,
2003).
3
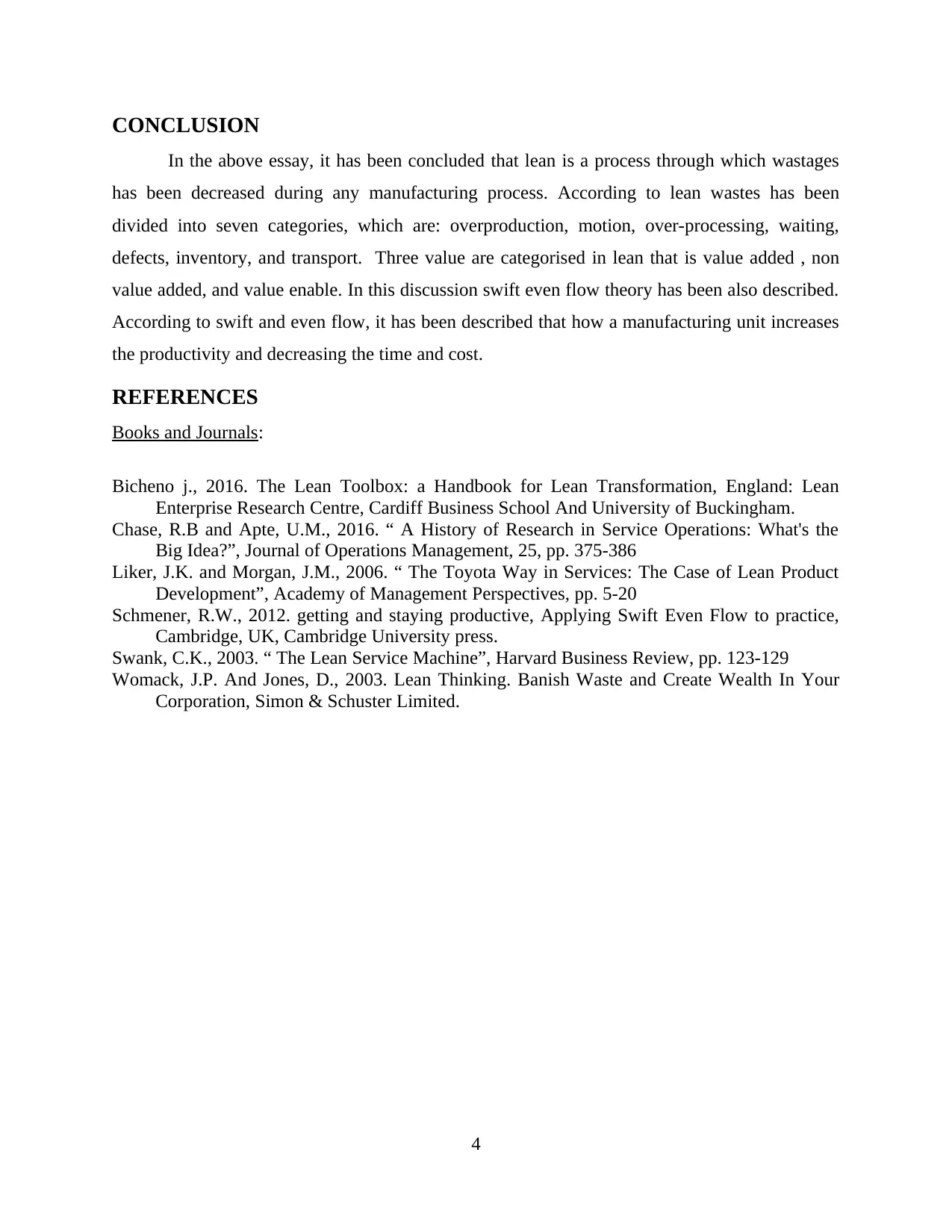
CONCLUSION
In the above essay, it has been concluded that lean is a process through which wastages
has been decreased during any manufacturing process. According to lean wastes has been
divided into seven categories, which are: overproduction, motion, over-processing, waiting,
defects, inventory, and transport. Three value are categorised in lean that is value added , non
value added, and value enable. In this discussion swift even flow theory has been also described.
According to swift and even flow, it has been described that how a manufacturing unit increases
the productivity and decreasing the time and cost.
REFERENCES
Books and Journals:
Bicheno j., 2016. The Lean Toolbox: a Handbook for Lean Transformation, England: Lean
Enterprise Research Centre, Cardiff Business School And University of Buckingham.
Chase, R.B and Apte, U.M., 2016. “ A History of Research in Service Operations: What's the
Big Idea?”, Journal of Operations Management, 25, pp. 375-386
Liker, J.K. and Morgan, J.M., 2006. “ The Toyota Way in Services: The Case of Lean Product
Development”, Academy of Management Perspectives, pp. 5-20
Schmener, R.W., 2012. getting and staying productive, Applying Swift Even Flow to practice,
Cambridge, UK, Cambridge University press.
Swank, C.K., 2003. “ The Lean Service Machine”, Harvard Business Review, pp. 123-129
Womack, J.P. And Jones, D., 2003. Lean Thinking. Banish Waste and Create Wealth In Your
Corporation, Simon & Schuster Limited.
4
In the above essay, it has been concluded that lean is a process through which wastages
has been decreased during any manufacturing process. According to lean wastes has been
divided into seven categories, which are: overproduction, motion, over-processing, waiting,
defects, inventory, and transport. Three value are categorised in lean that is value added , non
value added, and value enable. In this discussion swift even flow theory has been also described.
According to swift and even flow, it has been described that how a manufacturing unit increases
the productivity and decreasing the time and cost.
REFERENCES
Books and Journals:
Bicheno j., 2016. The Lean Toolbox: a Handbook for Lean Transformation, England: Lean
Enterprise Research Centre, Cardiff Business School And University of Buckingham.
Chase, R.B and Apte, U.M., 2016. “ A History of Research in Service Operations: What's the
Big Idea?”, Journal of Operations Management, 25, pp. 375-386
Liker, J.K. and Morgan, J.M., 2006. “ The Toyota Way in Services: The Case of Lean Product
Development”, Academy of Management Perspectives, pp. 5-20
Schmener, R.W., 2012. getting and staying productive, Applying Swift Even Flow to practice,
Cambridge, UK, Cambridge University press.
Swank, C.K., 2003. “ The Lean Service Machine”, Harvard Business Review, pp. 123-129
Womack, J.P. And Jones, D., 2003. Lean Thinking. Banish Waste and Create Wealth In Your
Corporation, Simon & Schuster Limited.
4
1 out of 6
Related Documents

Your All-in-One AI-Powered Toolkit for Academic Success.
+13062052269
info@desklib.com
Available 24*7 on WhatsApp / Email
Unlock your academic potential
© 2024 | Zucol Services PVT LTD | All rights reserved.