Life Cycle Cost Analysis of Coatings for Offshore Steel Pipelines
VerifiedAdded on 2020/02/19
|30
|10027
|187
Report
AI Summary
This report delves into the crucial topic of corrosion protection for offshore steel pipelines, a critical concern in the oil and gas industry. It explores various techniques, including fusion bonded epoxy, polyethylene, and neoprene coatings, designed to extend the operational lifespan of these pipeline...
Read More
Contribute Materials
Your contribution can guide someone’s learning journey. Share your
documents today.
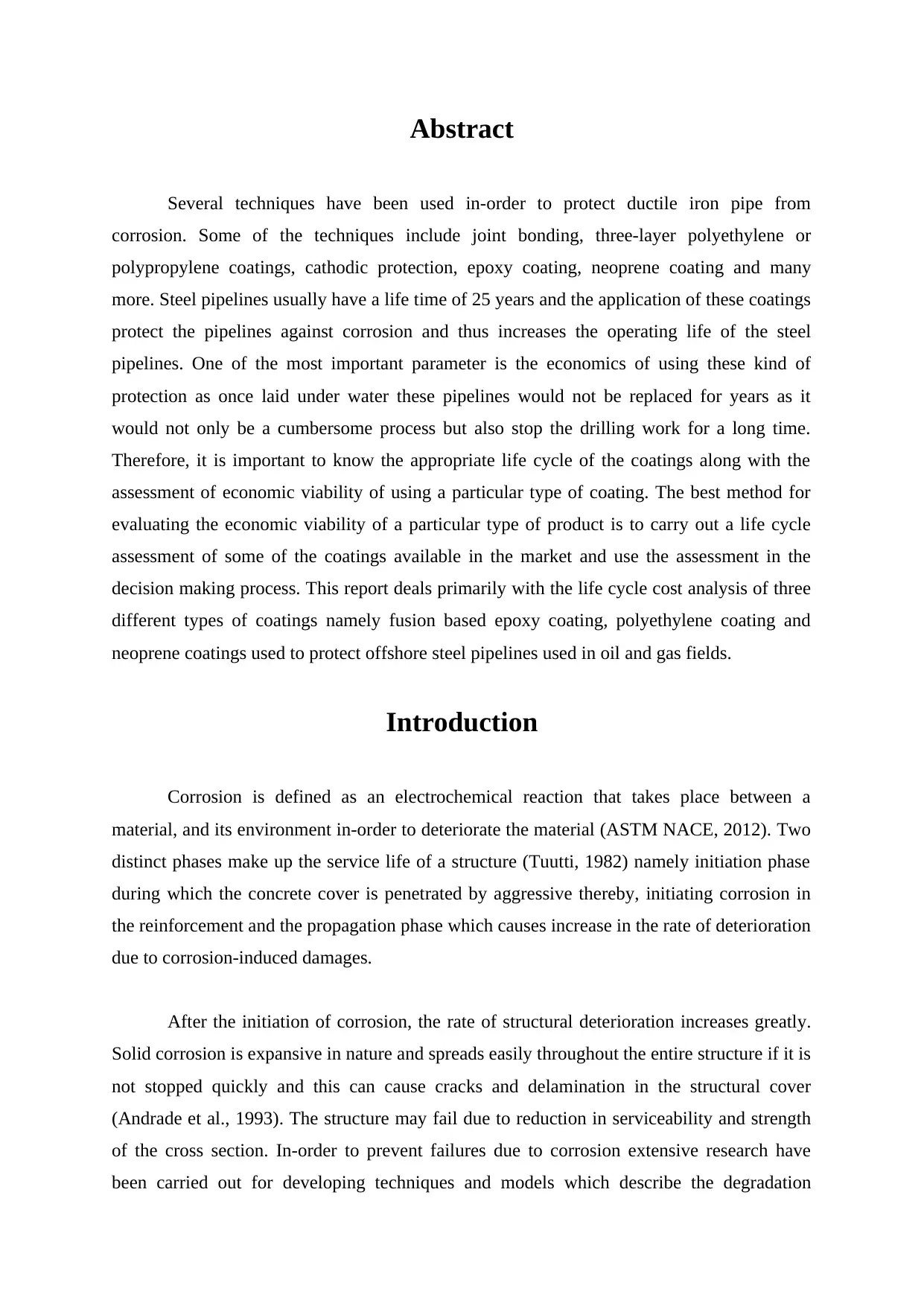
Abstract
Several techniques have been used in-order to protect ductile iron pipe from
corrosion. Some of the techniques include joint bonding, three-layer polyethylene or
polypropylene coatings, cathodic protection, epoxy coating, neoprene coating and many
more. Steel pipelines usually have a life time of 25 years and the application of these coatings
protect the pipelines against corrosion and thus increases the operating life of the steel
pipelines. One of the most important parameter is the economics of using these kind of
protection as once laid under water these pipelines would not be replaced for years as it
would not only be a cumbersome process but also stop the drilling work for a long time.
Therefore, it is important to know the appropriate life cycle of the coatings along with the
assessment of economic viability of using a particular type of coating. The best method for
evaluating the economic viability of a particular type of product is to carry out a life cycle
assessment of some of the coatings available in the market and use the assessment in the
decision making process. This report deals primarily with the life cycle cost analysis of three
different types of coatings namely fusion based epoxy coating, polyethylene coating and
neoprene coatings used to protect offshore steel pipelines used in oil and gas fields.
Introduction
Corrosion is defined as an electrochemical reaction that takes place between a
material, and its environment in-order to deteriorate the material (ASTM NACE, 2012). Two
distinct phases make up the service life of a structure (Tuutti, 1982) namely initiation phase
during which the concrete cover is penetrated by aggressive thereby, initiating corrosion in
the reinforcement and the propagation phase which causes increase in the rate of deterioration
due to corrosion-induced damages.
After the initiation of corrosion, the rate of structural deterioration increases greatly.
Solid corrosion is expansive in nature and spreads easily throughout the entire structure if it is
not stopped quickly and this can cause cracks and delamination in the structural cover
(Andrade et al., 1993). The structure may fail due to reduction in serviceability and strength
of the cross section. In-order to prevent failures due to corrosion extensive research have
been carried out for developing techniques and models which describe the degradation
Several techniques have been used in-order to protect ductile iron pipe from
corrosion. Some of the techniques include joint bonding, three-layer polyethylene or
polypropylene coatings, cathodic protection, epoxy coating, neoprene coating and many
more. Steel pipelines usually have a life time of 25 years and the application of these coatings
protect the pipelines against corrosion and thus increases the operating life of the steel
pipelines. One of the most important parameter is the economics of using these kind of
protection as once laid under water these pipelines would not be replaced for years as it
would not only be a cumbersome process but also stop the drilling work for a long time.
Therefore, it is important to know the appropriate life cycle of the coatings along with the
assessment of economic viability of using a particular type of coating. The best method for
evaluating the economic viability of a particular type of product is to carry out a life cycle
assessment of some of the coatings available in the market and use the assessment in the
decision making process. This report deals primarily with the life cycle cost analysis of three
different types of coatings namely fusion based epoxy coating, polyethylene coating and
neoprene coatings used to protect offshore steel pipelines used in oil and gas fields.
Introduction
Corrosion is defined as an electrochemical reaction that takes place between a
material, and its environment in-order to deteriorate the material (ASTM NACE, 2012). Two
distinct phases make up the service life of a structure (Tuutti, 1982) namely initiation phase
during which the concrete cover is penetrated by aggressive thereby, initiating corrosion in
the reinforcement and the propagation phase which causes increase in the rate of deterioration
due to corrosion-induced damages.
After the initiation of corrosion, the rate of structural deterioration increases greatly.
Solid corrosion is expansive in nature and spreads easily throughout the entire structure if it is
not stopped quickly and this can cause cracks and delamination in the structural cover
(Andrade et al., 1993). The structure may fail due to reduction in serviceability and strength
of the cross section. In-order to prevent failures due to corrosion extensive research have
been carried out for developing techniques and models which describe the degradation
Secure Best Marks with AI Grader
Need help grading? Try our AI Grader for instant feedback on your assignments.
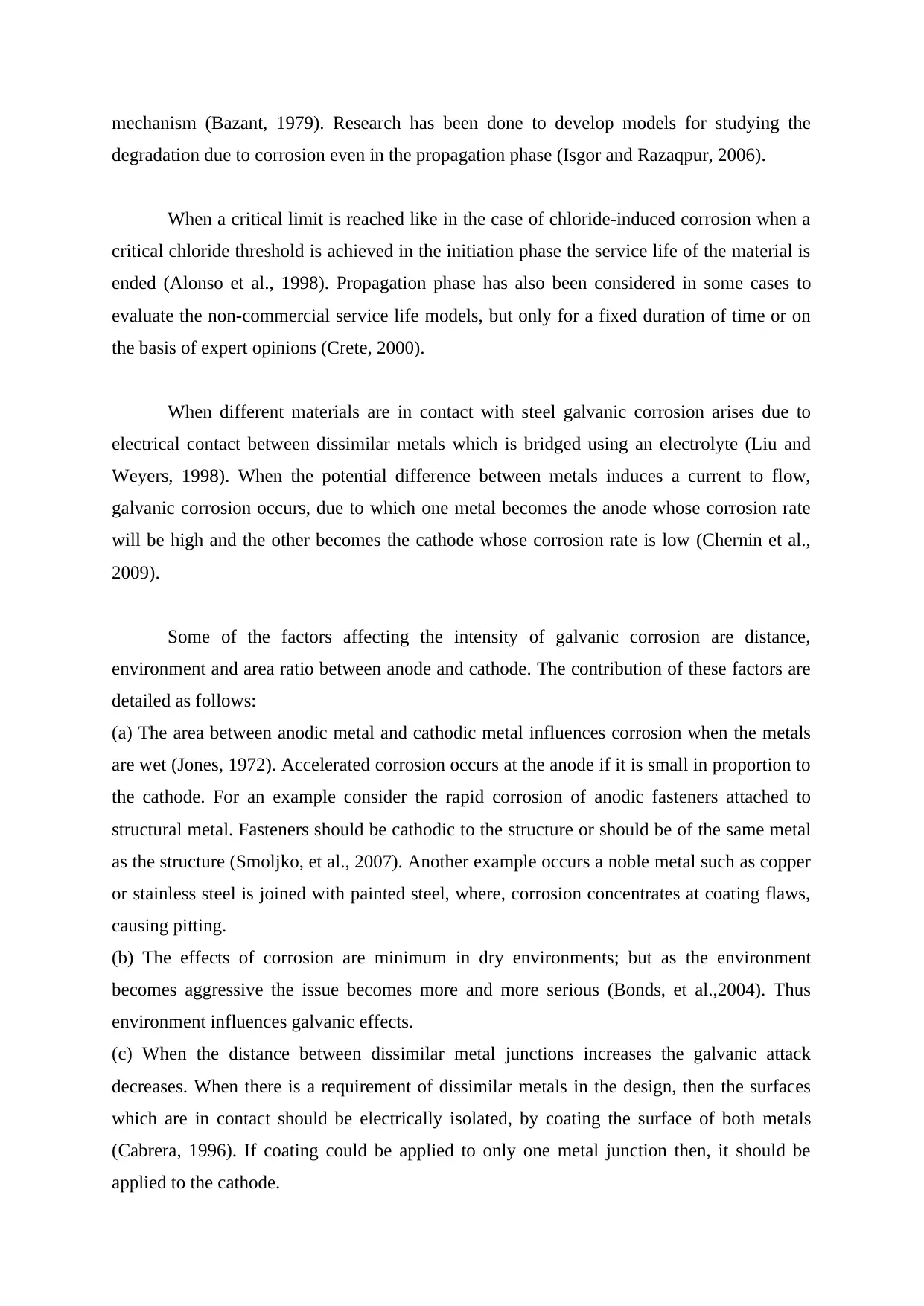
mechanism (Bazant, 1979). Research has been done to develop models for studying the
degradation due to corrosion even in the propagation phase (Isgor and Razaqpur, 2006).
When a critical limit is reached like in the case of chloride-induced corrosion when a
critical chloride threshold is achieved in the initiation phase the service life of the material is
ended (Alonso et al., 1998). Propagation phase has also been considered in some cases to
evaluate the non-commercial service life models, but only for a fixed duration of time or on
the basis of expert opinions (Crete, 2000).
When different materials are in contact with steel galvanic corrosion arises due to
electrical contact between dissimilar metals which is bridged using an electrolyte (Liu and
Weyers, 1998). When the potential difference between metals induces a current to flow,
galvanic corrosion occurs, due to which one metal becomes the anode whose corrosion rate
will be high and the other becomes the cathode whose corrosion rate is low (Chernin et al.,
2009).
Some of the factors affecting the intensity of galvanic corrosion are distance,
environment and area ratio between anode and cathode. The contribution of these factors are
detailed as follows:
(a) The area between anodic metal and cathodic metal influences corrosion when the metals
are wet (Jones, 1972). Accelerated corrosion occurs at the anode if it is small in proportion to
the cathode. For an example consider the rapid corrosion of anodic fasteners attached to
structural metal. Fasteners should be cathodic to the structure or should be of the same metal
as the structure (Smoljko, et al., 2007). Another example occurs a noble metal such as copper
or stainless steel is joined with painted steel, where, corrosion concentrates at coating flaws,
causing pitting.
(b) The effects of corrosion are minimum in dry environments; but as the environment
becomes aggressive the issue becomes more and more serious (Bonds, et al.,2004). Thus
environment influences galvanic effects.
(c) When the distance between dissimilar metal junctions increases the galvanic attack
decreases. When there is a requirement of dissimilar metals in the design, then the surfaces
which are in contact should be electrically isolated, by coating the surface of both metals
(Cabrera, 1996). If coating could be applied to only one metal junction then, it should be
applied to the cathode.
degradation due to corrosion even in the propagation phase (Isgor and Razaqpur, 2006).
When a critical limit is reached like in the case of chloride-induced corrosion when a
critical chloride threshold is achieved in the initiation phase the service life of the material is
ended (Alonso et al., 1998). Propagation phase has also been considered in some cases to
evaluate the non-commercial service life models, but only for a fixed duration of time or on
the basis of expert opinions (Crete, 2000).
When different materials are in contact with steel galvanic corrosion arises due to
electrical contact between dissimilar metals which is bridged using an electrolyte (Liu and
Weyers, 1998). When the potential difference between metals induces a current to flow,
galvanic corrosion occurs, due to which one metal becomes the anode whose corrosion rate
will be high and the other becomes the cathode whose corrosion rate is low (Chernin et al.,
2009).
Some of the factors affecting the intensity of galvanic corrosion are distance,
environment and area ratio between anode and cathode. The contribution of these factors are
detailed as follows:
(a) The area between anodic metal and cathodic metal influences corrosion when the metals
are wet (Jones, 1972). Accelerated corrosion occurs at the anode if it is small in proportion to
the cathode. For an example consider the rapid corrosion of anodic fasteners attached to
structural metal. Fasteners should be cathodic to the structure or should be of the same metal
as the structure (Smoljko, et al., 2007). Another example occurs a noble metal such as copper
or stainless steel is joined with painted steel, where, corrosion concentrates at coating flaws,
causing pitting.
(b) The effects of corrosion are minimum in dry environments; but as the environment
becomes aggressive the issue becomes more and more serious (Bonds, et al.,2004). Thus
environment influences galvanic effects.
(c) When the distance between dissimilar metal junctions increases the galvanic attack
decreases. When there is a requirement of dissimilar metals in the design, then the surfaces
which are in contact should be electrically isolated, by coating the surface of both metals
(Cabrera, 1996). If coating could be applied to only one metal junction then, it should be
applied to the cathode.
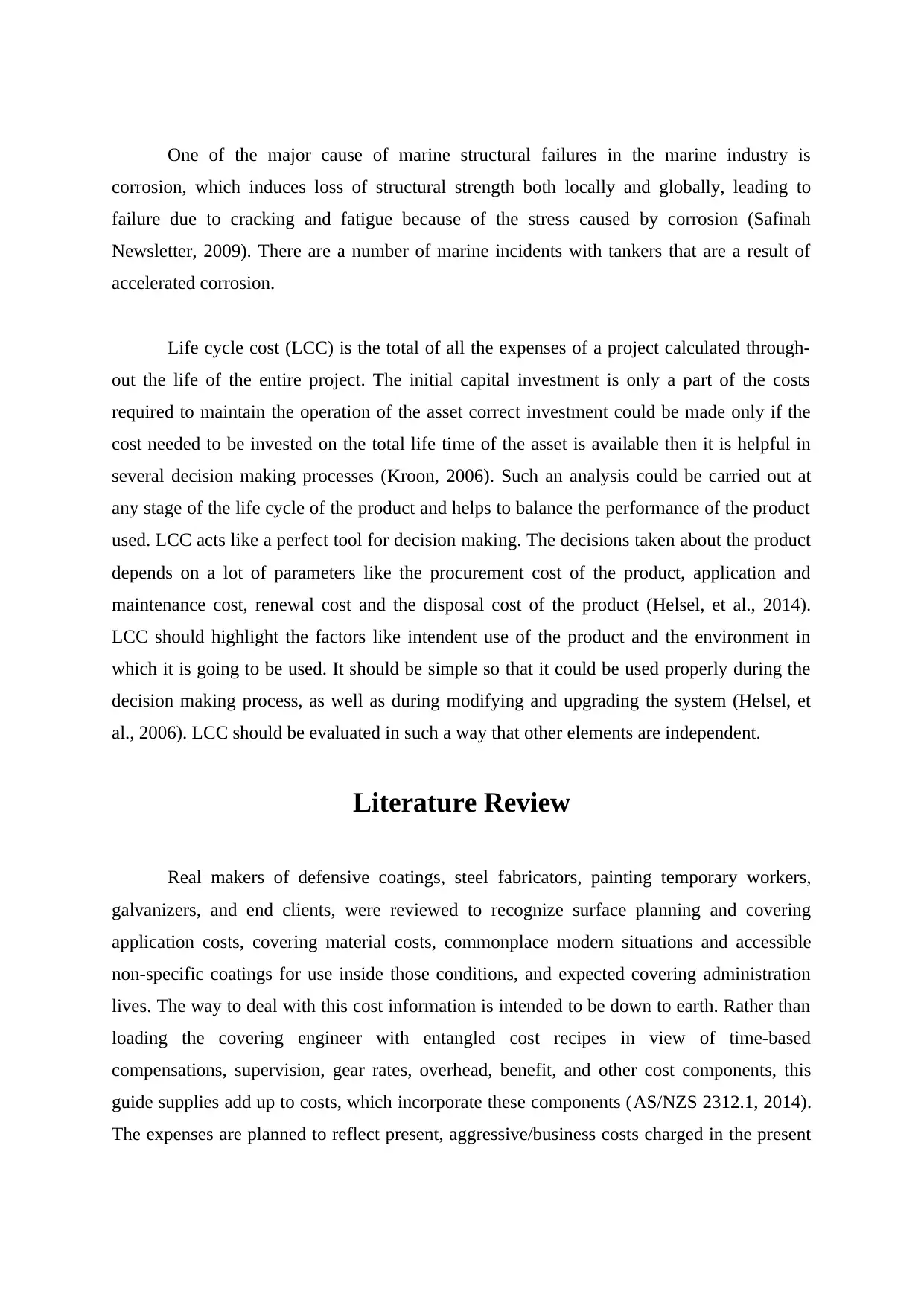
One of the major cause of marine structural failures in the marine industry is
corrosion, which induces loss of structural strength both locally and globally, leading to
failure due to cracking and fatigue because of the stress caused by corrosion (Safinah
Newsletter, 2009). There are a number of marine incidents with tankers that are a result of
accelerated corrosion.
Life cycle cost (LCC) is the total of all the expenses of a project calculated through-
out the life of the entire project. The initial capital investment is only a part of the costs
required to maintain the operation of the asset correct investment could be made only if the
cost needed to be invested on the total life time of the asset is available then it is helpful in
several decision making processes (Kroon, 2006). Such an analysis could be carried out at
any stage of the life cycle of the product and helps to balance the performance of the product
used. LCC acts like a perfect tool for decision making. The decisions taken about the product
depends on a lot of parameters like the procurement cost of the product, application and
maintenance cost, renewal cost and the disposal cost of the product (Helsel, et al., 2014).
LCC should highlight the factors like intendent use of the product and the environment in
which it is going to be used. It should be simple so that it could be used properly during the
decision making process, as well as during modifying and upgrading the system (Helsel, et
al., 2006). LCC should be evaluated in such a way that other elements are independent.
Literature Review
Real makers of defensive coatings, steel fabricators, painting temporary workers,
galvanizers, and end clients, were reviewed to recognize surface planning and covering
application costs, covering material costs, commonplace modern situations and accessible
non-specific coatings for use inside those conditions, and expected covering administration
lives. The way to deal with this cost information is intended to be down to earth. Rather than
loading the covering engineer with entangled cost recipes in view of time-based
compensations, supervision, gear rates, overhead, benefit, and other cost components, this
guide supplies add up to costs, which incorporate these components (AS/NZS 2312.1, 2014).
The expenses are planned to reflect present, aggressive/business costs charged in the present
corrosion, which induces loss of structural strength both locally and globally, leading to
failure due to cracking and fatigue because of the stress caused by corrosion (Safinah
Newsletter, 2009). There are a number of marine incidents with tankers that are a result of
accelerated corrosion.
Life cycle cost (LCC) is the total of all the expenses of a project calculated through-
out the life of the entire project. The initial capital investment is only a part of the costs
required to maintain the operation of the asset correct investment could be made only if the
cost needed to be invested on the total life time of the asset is available then it is helpful in
several decision making processes (Kroon, 2006). Such an analysis could be carried out at
any stage of the life cycle of the product and helps to balance the performance of the product
used. LCC acts like a perfect tool for decision making. The decisions taken about the product
depends on a lot of parameters like the procurement cost of the product, application and
maintenance cost, renewal cost and the disposal cost of the product (Helsel, et al., 2014).
LCC should highlight the factors like intendent use of the product and the environment in
which it is going to be used. It should be simple so that it could be used properly during the
decision making process, as well as during modifying and upgrading the system (Helsel, et
al., 2006). LCC should be evaluated in such a way that other elements are independent.
Literature Review
Real makers of defensive coatings, steel fabricators, painting temporary workers,
galvanizers, and end clients, were reviewed to recognize surface planning and covering
application costs, covering material costs, commonplace modern situations and accessible
non-specific coatings for use inside those conditions, and expected covering administration
lives. The way to deal with this cost information is intended to be down to earth. Rather than
loading the covering engineer with entangled cost recipes in view of time-based
compensations, supervision, gear rates, overhead, benefit, and other cost components, this
guide supplies add up to costs, which incorporate these components (AS/NZS 2312.1, 2014).
The expenses are planned to reflect present, aggressive/business costs charged in the present
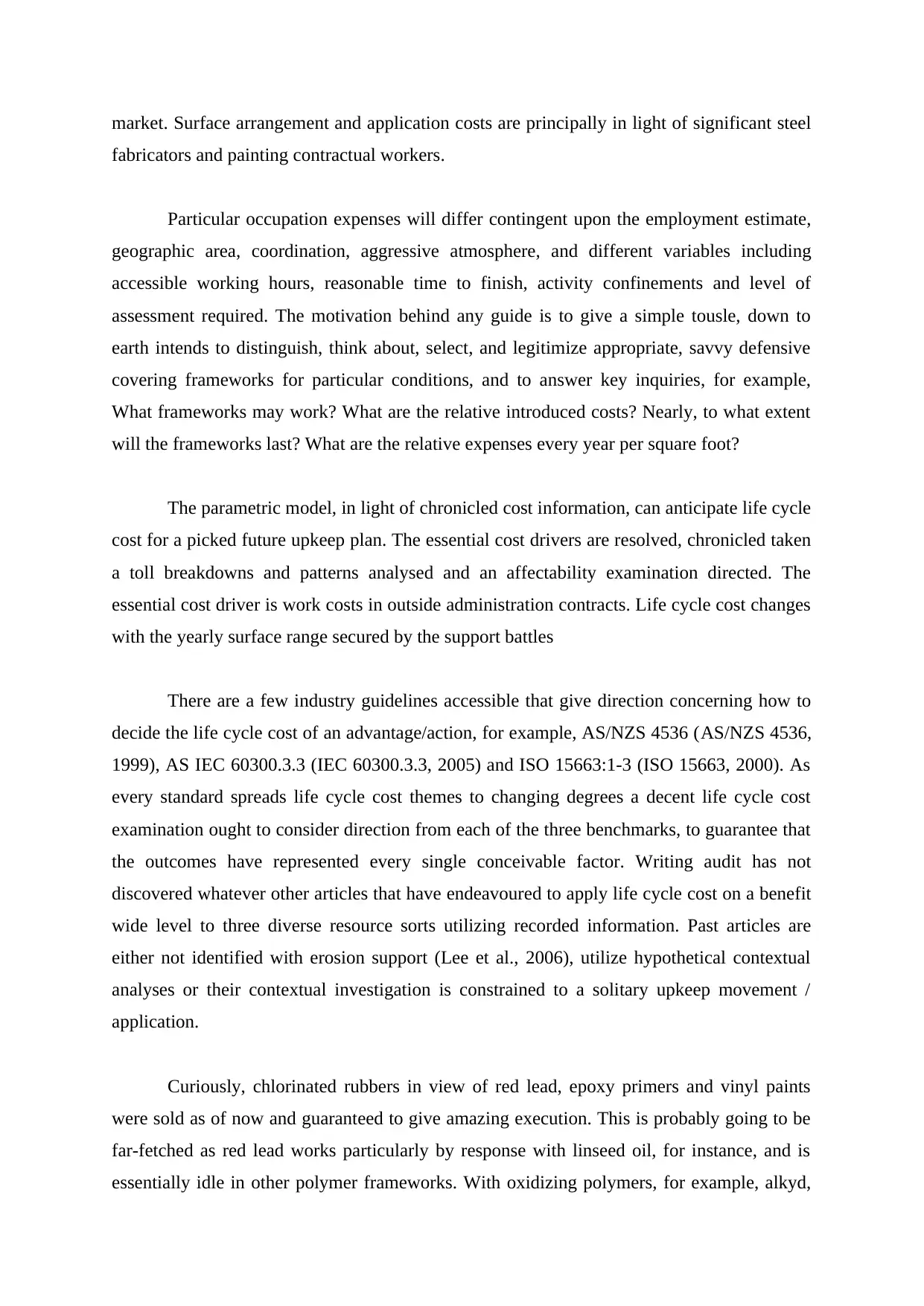
market. Surface arrangement and application costs are principally in light of significant steel
fabricators and painting contractual workers.
Particular occupation expenses will differ contingent upon the employment estimate,
geographic area, coordination, aggressive atmosphere, and different variables including
accessible working hours, reasonable time to finish, activity confinements and level of
assessment required. The motivation behind any guide is to give a simple tousle, down to
earth intends to distinguish, think about, select, and legitimize appropriate, savvy defensive
covering frameworks for particular conditions, and to answer key inquiries, for example,
What frameworks may work? What are the relative introduced costs? Nearly, to what extent
will the frameworks last? What are the relative expenses every year per square foot?
The parametric model, in light of chronicled cost information, can anticipate life cycle
cost for a picked future upkeep plan. The essential cost drivers are resolved, chronicled taken
a toll breakdowns and patterns analysed and an affectability examination directed. The
essential cost driver is work costs in outside administration contracts. Life cycle cost changes
with the yearly surface range secured by the support battles
There are a few industry guidelines accessible that give direction concerning how to
decide the life cycle cost of an advantage/action, for example, AS/NZS 4536 (AS/NZS 4536,
1999), AS IEC 60300.3.3 (IEC 60300.3.3, 2005) and ISO 15663:1-3 (ISO 15663, 2000). As
every standard spreads life cycle cost themes to changing degrees a decent life cycle cost
examination ought to consider direction from each of the three benchmarks, to guarantee that
the outcomes have represented every single conceivable factor. Writing audit has not
discovered whatever other articles that have endeavoured to apply life cycle cost on a benefit
wide level to three diverse resource sorts utilizing recorded information. Past articles are
either not identified with erosion support (Lee et al., 2006), utilize hypothetical contextual
analyses or their contextual investigation is constrained to a solitary upkeep movement /
application.
Curiously, chlorinated rubbers in view of red lead, epoxy primers and vinyl paints
were sold as of now and guaranteed to give amazing execution. This is probably going to be
far-fetched as red lead works particularly by response with linseed oil, for instance, and is
essentially idle in other polymer frameworks. With oxidizing polymers, for example, alkyd,
fabricators and painting contractual workers.
Particular occupation expenses will differ contingent upon the employment estimate,
geographic area, coordination, aggressive atmosphere, and different variables including
accessible working hours, reasonable time to finish, activity confinements and level of
assessment required. The motivation behind any guide is to give a simple tousle, down to
earth intends to distinguish, think about, select, and legitimize appropriate, savvy defensive
covering frameworks for particular conditions, and to answer key inquiries, for example,
What frameworks may work? What are the relative introduced costs? Nearly, to what extent
will the frameworks last? What are the relative expenses every year per square foot?
The parametric model, in light of chronicled cost information, can anticipate life cycle
cost for a picked future upkeep plan. The essential cost drivers are resolved, chronicled taken
a toll breakdowns and patterns analysed and an affectability examination directed. The
essential cost driver is work costs in outside administration contracts. Life cycle cost changes
with the yearly surface range secured by the support battles
There are a few industry guidelines accessible that give direction concerning how to
decide the life cycle cost of an advantage/action, for example, AS/NZS 4536 (AS/NZS 4536,
1999), AS IEC 60300.3.3 (IEC 60300.3.3, 2005) and ISO 15663:1-3 (ISO 15663, 2000). As
every standard spreads life cycle cost themes to changing degrees a decent life cycle cost
examination ought to consider direction from each of the three benchmarks, to guarantee that
the outcomes have represented every single conceivable factor. Writing audit has not
discovered whatever other articles that have endeavoured to apply life cycle cost on a benefit
wide level to three diverse resource sorts utilizing recorded information. Past articles are
either not identified with erosion support (Lee et al., 2006), utilize hypothetical contextual
analyses or their contextual investigation is constrained to a solitary upkeep movement /
application.
Curiously, chlorinated rubbers in view of red lead, epoxy primers and vinyl paints
were sold as of now and guaranteed to give amazing execution. This is probably going to be
far-fetched as red lead works particularly by response with linseed oil, for instance, and is
essentially idle in other polymer frameworks. With oxidizing polymers, for example, alkyd,
Secure Best Marks with AI Grader
Need help grading? Try our AI Grader for instant feedback on your assignments.
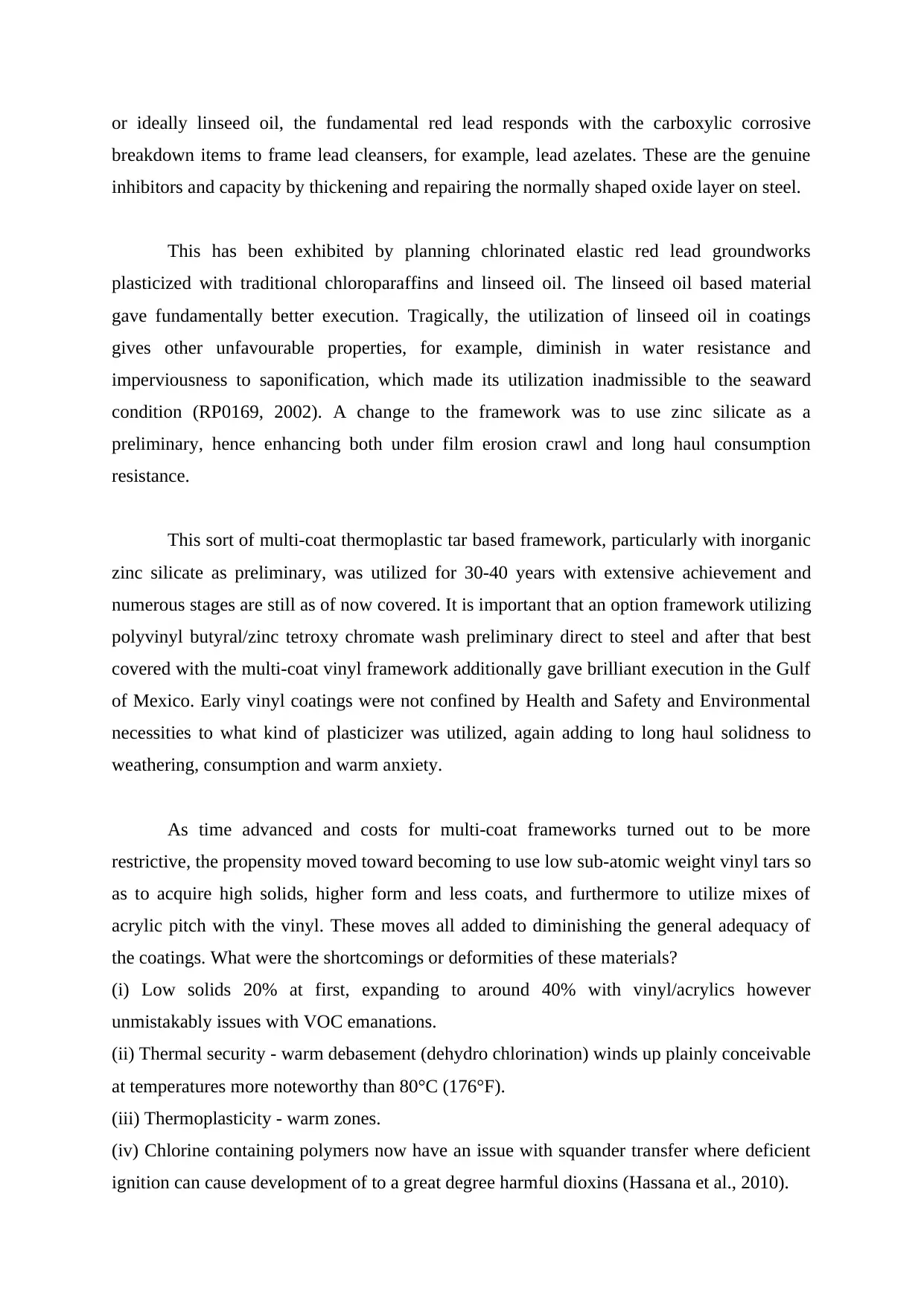
or ideally linseed oil, the fundamental red lead responds with the carboxylic corrosive
breakdown items to frame lead cleansers, for example, lead azelates. These are the genuine
inhibitors and capacity by thickening and repairing the normally shaped oxide layer on steel.
This has been exhibited by planning chlorinated elastic red lead groundworks
plasticized with traditional chloroparaffins and linseed oil. The linseed oil based material
gave fundamentally better execution. Tragically, the utilization of linseed oil in coatings
gives other unfavourable properties, for example, diminish in water resistance and
imperviousness to saponification, which made its utilization inadmissible to the seaward
condition (RP0169, 2002). A change to the framework was to use zinc silicate as a
preliminary, hence enhancing both under film erosion crawl and long haul consumption
resistance.
This sort of multi-coat thermoplastic tar based framework, particularly with inorganic
zinc silicate as preliminary, was utilized for 30-40 years with extensive achievement and
numerous stages are still as of now covered. It is important that an option framework utilizing
polyvinyl butyral/zinc tetroxy chromate wash preliminary direct to steel and after that best
covered with the multi-coat vinyl framework additionally gave brilliant execution in the Gulf
of Mexico. Early vinyl coatings were not confined by Health and Safety and Environmental
necessities to what kind of plasticizer was utilized, again adding to long haul solidness to
weathering, consumption and warm anxiety.
As time advanced and costs for multi-coat frameworks turned out to be more
restrictive, the propensity moved toward becoming to use low sub-atomic weight vinyl tars so
as to acquire high solids, higher form and less coats, and furthermore to utilize mixes of
acrylic pitch with the vinyl. These moves all added to diminishing the general adequacy of
the coatings. What were the shortcomings or deformities of these materials?
(i) Low solids 20% at first, expanding to around 40% with vinyl/acrylics however
unmistakably issues with VOC emanations.
(ii) Thermal security - warm debasement (dehydro chlorination) winds up plainly conceivable
at temperatures more noteworthy than 80°C (176°F).
(iii) Thermoplasticity - warm zones.
(iv) Chlorine containing polymers now have an issue with squander transfer where deficient
ignition can cause development of to a great degree harmful dioxins (Hassana et al., 2010).
breakdown items to frame lead cleansers, for example, lead azelates. These are the genuine
inhibitors and capacity by thickening and repairing the normally shaped oxide layer on steel.
This has been exhibited by planning chlorinated elastic red lead groundworks
plasticized with traditional chloroparaffins and linseed oil. The linseed oil based material
gave fundamentally better execution. Tragically, the utilization of linseed oil in coatings
gives other unfavourable properties, for example, diminish in water resistance and
imperviousness to saponification, which made its utilization inadmissible to the seaward
condition (RP0169, 2002). A change to the framework was to use zinc silicate as a
preliminary, hence enhancing both under film erosion crawl and long haul consumption
resistance.
This sort of multi-coat thermoplastic tar based framework, particularly with inorganic
zinc silicate as preliminary, was utilized for 30-40 years with extensive achievement and
numerous stages are still as of now covered. It is important that an option framework utilizing
polyvinyl butyral/zinc tetroxy chromate wash preliminary direct to steel and after that best
covered with the multi-coat vinyl framework additionally gave brilliant execution in the Gulf
of Mexico. Early vinyl coatings were not confined by Health and Safety and Environmental
necessities to what kind of plasticizer was utilized, again adding to long haul solidness to
weathering, consumption and warm anxiety.
As time advanced and costs for multi-coat frameworks turned out to be more
restrictive, the propensity moved toward becoming to use low sub-atomic weight vinyl tars so
as to acquire high solids, higher form and less coats, and furthermore to utilize mixes of
acrylic pitch with the vinyl. These moves all added to diminishing the general adequacy of
the coatings. What were the shortcomings or deformities of these materials?
(i) Low solids 20% at first, expanding to around 40% with vinyl/acrylics however
unmistakably issues with VOC emanations.
(ii) Thermal security - warm debasement (dehydro chlorination) winds up plainly conceivable
at temperatures more noteworthy than 80°C (176°F).
(iii) Thermoplasticity - warm zones.
(iv) Chlorine containing polymers now have an issue with squander transfer where deficient
ignition can cause development of to a great degree harmful dioxins (Hassana et al., 2010).
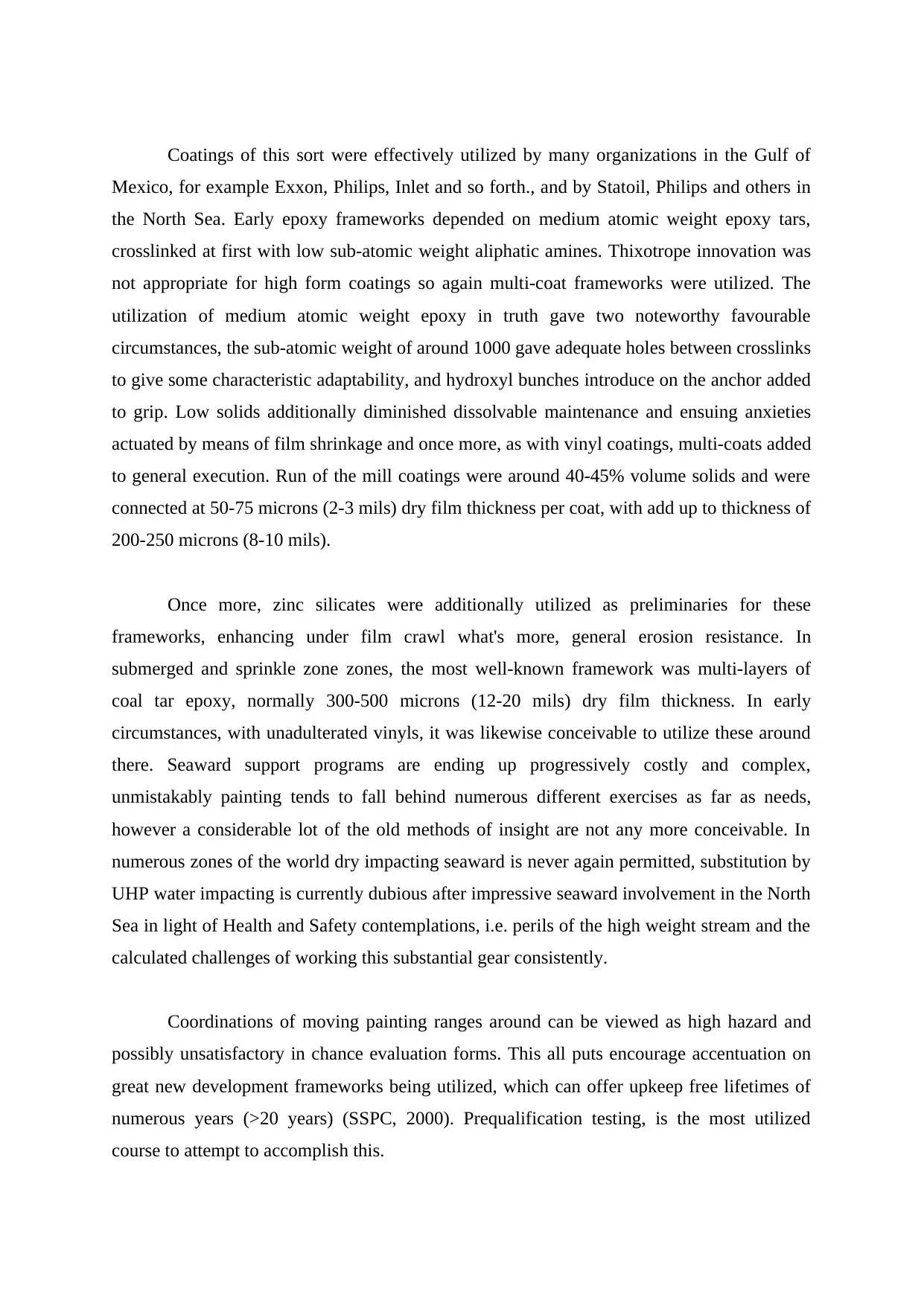
Coatings of this sort were effectively utilized by many organizations in the Gulf of
Mexico, for example Exxon, Philips, Inlet and so forth., and by Statoil, Philips and others in
the North Sea. Early epoxy frameworks depended on medium atomic weight epoxy tars,
crosslinked at first with low sub-atomic weight aliphatic amines. Thixotrope innovation was
not appropriate for high form coatings so again multi-coat frameworks were utilized. The
utilization of medium atomic weight epoxy in truth gave two noteworthy favourable
circumstances, the sub-atomic weight of around 1000 gave adequate holes between crosslinks
to give some characteristic adaptability, and hydroxyl bunches introduce on the anchor added
to grip. Low solids additionally diminished dissolvable maintenance and ensuing anxieties
actuated by means of film shrinkage and once more, as with vinyl coatings, multi-coats added
to general execution. Run of the mill coatings were around 40-45% volume solids and were
connected at 50-75 microns (2-3 mils) dry film thickness per coat, with add up to thickness of
200-250 microns (8-10 mils).
Once more, zinc silicates were additionally utilized as preliminaries for these
frameworks, enhancing under film crawl what's more, general erosion resistance. In
submerged and sprinkle zone zones, the most well-known framework was multi-layers of
coal tar epoxy, normally 300-500 microns (12-20 mils) dry film thickness. In early
circumstances, with unadulterated vinyls, it was likewise conceivable to utilize these around
there. Seaward support programs are ending up progressively costly and complex,
unmistakably painting tends to fall behind numerous different exercises as far as needs,
however a considerable lot of the old methods of insight are not any more conceivable. In
numerous zones of the world dry impacting seaward is never again permitted, substitution by
UHP water impacting is currently dubious after impressive seaward involvement in the North
Sea in light of Health and Safety contemplations, i.e. perils of the high weight stream and the
calculated challenges of working this substantial gear consistently.
Coordinations of moving painting ranges around can be viewed as high hazard and
possibly unsatisfactory in chance evaluation forms. This all puts encourage accentuation on
great new development frameworks being utilized, which can offer upkeep free lifetimes of
numerous years (>20 years) (SSPC, 2000). Prequalification testing, is the most utilized
course to attempt to accomplish this.
Mexico, for example Exxon, Philips, Inlet and so forth., and by Statoil, Philips and others in
the North Sea. Early epoxy frameworks depended on medium atomic weight epoxy tars,
crosslinked at first with low sub-atomic weight aliphatic amines. Thixotrope innovation was
not appropriate for high form coatings so again multi-coat frameworks were utilized. The
utilization of medium atomic weight epoxy in truth gave two noteworthy favourable
circumstances, the sub-atomic weight of around 1000 gave adequate holes between crosslinks
to give some characteristic adaptability, and hydroxyl bunches introduce on the anchor added
to grip. Low solids additionally diminished dissolvable maintenance and ensuing anxieties
actuated by means of film shrinkage and once more, as with vinyl coatings, multi-coats added
to general execution. Run of the mill coatings were around 40-45% volume solids and were
connected at 50-75 microns (2-3 mils) dry film thickness per coat, with add up to thickness of
200-250 microns (8-10 mils).
Once more, zinc silicates were additionally utilized as preliminaries for these
frameworks, enhancing under film crawl what's more, general erosion resistance. In
submerged and sprinkle zone zones, the most well-known framework was multi-layers of
coal tar epoxy, normally 300-500 microns (12-20 mils) dry film thickness. In early
circumstances, with unadulterated vinyls, it was likewise conceivable to utilize these around
there. Seaward support programs are ending up progressively costly and complex,
unmistakably painting tends to fall behind numerous different exercises as far as needs,
however a considerable lot of the old methods of insight are not any more conceivable. In
numerous zones of the world dry impacting seaward is never again permitted, substitution by
UHP water impacting is currently dubious after impressive seaward involvement in the North
Sea in light of Health and Safety contemplations, i.e. perils of the high weight stream and the
calculated challenges of working this substantial gear consistently.
Coordinations of moving painting ranges around can be viewed as high hazard and
possibly unsatisfactory in chance evaluation forms. This all puts encourage accentuation on
great new development frameworks being utilized, which can offer upkeep free lifetimes of
numerous years (>20 years) (SSPC, 2000). Prequalification testing, is the most utilized
course to attempt to accomplish this.
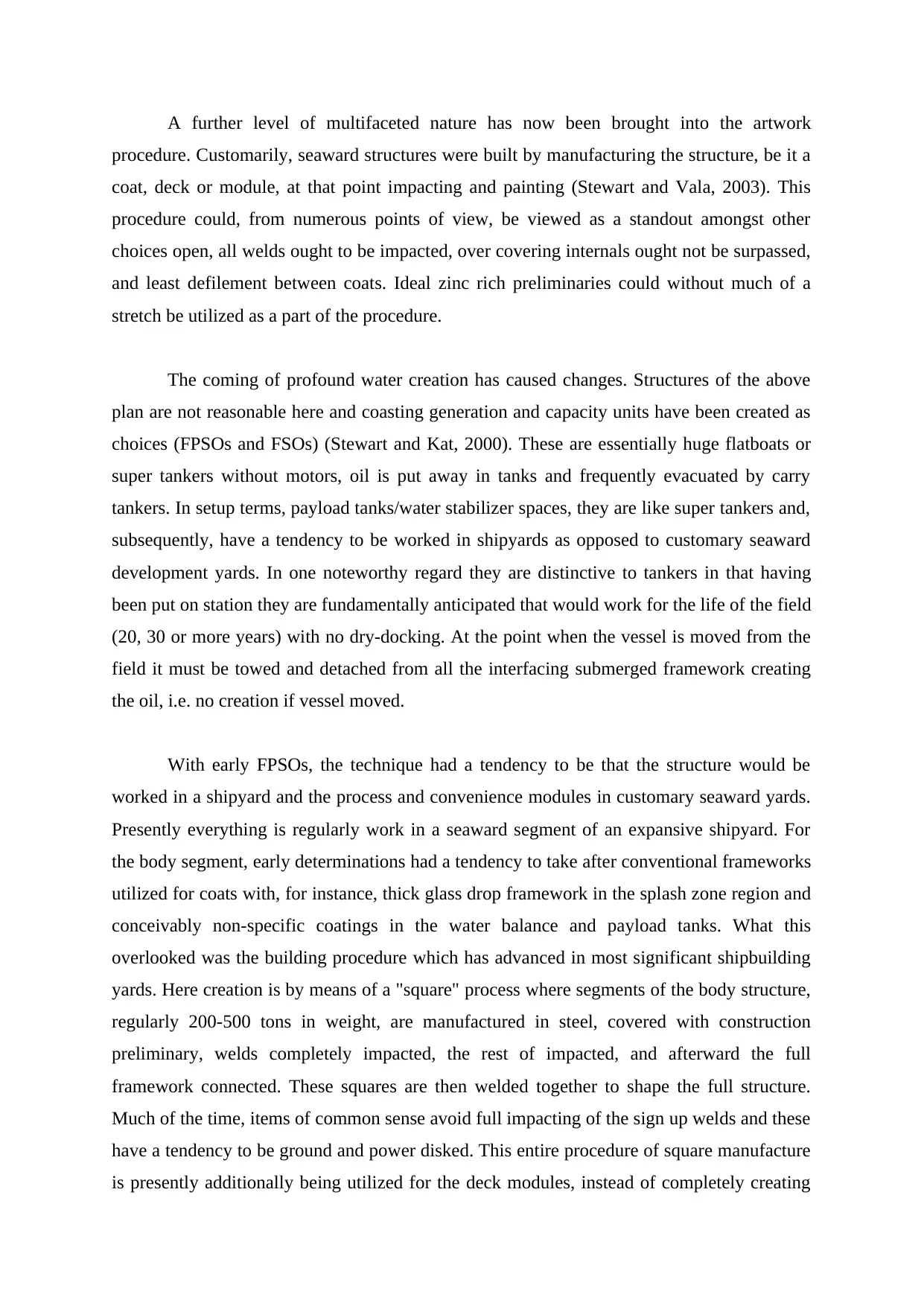
A further level of multifaceted nature has now been brought into the artwork
procedure. Customarily, seaward structures were built by manufacturing the structure, be it a
coat, deck or module, at that point impacting and painting (Stewart and Vala, 2003). This
procedure could, from numerous points of view, be viewed as a standout amongst other
choices open, all welds ought to be impacted, over covering internals ought not be surpassed,
and least defilement between coats. Ideal zinc rich preliminaries could without much of a
stretch be utilized as a part of the procedure.
The coming of profound water creation has caused changes. Structures of the above
plan are not reasonable here and coasting generation and capacity units have been created as
choices (FPSOs and FSOs) (Stewart and Kat, 2000). These are essentially huge flatboats or
super tankers without motors, oil is put away in tanks and frequently evacuated by carry
tankers. In setup terms, payload tanks/water stabilizer spaces, they are like super tankers and,
subsequently, have a tendency to be worked in shipyards as opposed to customary seaward
development yards. In one noteworthy regard they are distinctive to tankers in that having
been put on station they are fundamentally anticipated that would work for the life of the field
(20, 30 or more years) with no dry-docking. At the point when the vessel is moved from the
field it must be towed and detached from all the interfacing submerged framework creating
the oil, i.e. no creation if vessel moved.
With early FPSOs, the technique had a tendency to be that the structure would be
worked in a shipyard and the process and convenience modules in customary seaward yards.
Presently everything is regularly work in a seaward segment of an expansive shipyard. For
the body segment, early determinations had a tendency to take after conventional frameworks
utilized for coats with, for instance, thick glass drop framework in the splash zone region and
conceivably non-specific coatings in the water balance and payload tanks. What this
overlooked was the building procedure which has advanced in most significant shipbuilding
yards. Here creation is by means of a "square" process where segments of the body structure,
regularly 200-500 tons in weight, are manufactured in steel, covered with construction
preliminary, welds completely impacted, the rest of impacted, and afterward the full
framework connected. These squares are then welded together to shape the full structure.
Much of the time, items of common sense avoid full impacting of the sign up welds and these
have a tendency to be ground and power disked. This entire procedure of square manufacture
is presently additionally being utilized for the deck modules, instead of completely creating
procedure. Customarily, seaward structures were built by manufacturing the structure, be it a
coat, deck or module, at that point impacting and painting (Stewart and Vala, 2003). This
procedure could, from numerous points of view, be viewed as a standout amongst other
choices open, all welds ought to be impacted, over covering internals ought not be surpassed,
and least defilement between coats. Ideal zinc rich preliminaries could without much of a
stretch be utilized as a part of the procedure.
The coming of profound water creation has caused changes. Structures of the above
plan are not reasonable here and coasting generation and capacity units have been created as
choices (FPSOs and FSOs) (Stewart and Kat, 2000). These are essentially huge flatboats or
super tankers without motors, oil is put away in tanks and frequently evacuated by carry
tankers. In setup terms, payload tanks/water stabilizer spaces, they are like super tankers and,
subsequently, have a tendency to be worked in shipyards as opposed to customary seaward
development yards. In one noteworthy regard they are distinctive to tankers in that having
been put on station they are fundamentally anticipated that would work for the life of the field
(20, 30 or more years) with no dry-docking. At the point when the vessel is moved from the
field it must be towed and detached from all the interfacing submerged framework creating
the oil, i.e. no creation if vessel moved.
With early FPSOs, the technique had a tendency to be that the structure would be
worked in a shipyard and the process and convenience modules in customary seaward yards.
Presently everything is regularly work in a seaward segment of an expansive shipyard. For
the body segment, early determinations had a tendency to take after conventional frameworks
utilized for coats with, for instance, thick glass drop framework in the splash zone region and
conceivably non-specific coatings in the water balance and payload tanks. What this
overlooked was the building procedure which has advanced in most significant shipbuilding
yards. Here creation is by means of a "square" process where segments of the body structure,
regularly 200-500 tons in weight, are manufactured in steel, covered with construction
preliminary, welds completely impacted, the rest of impacted, and afterward the full
framework connected. These squares are then welded together to shape the full structure.
Much of the time, items of common sense avoid full impacting of the sign up welds and these
have a tendency to be ground and power disked. This entire procedure of square manufacture
is presently additionally being utilized for the deck modules, instead of completely creating
Paraphrase This Document
Need a fresh take? Get an instant paraphrase of this document with our AI Paraphraser
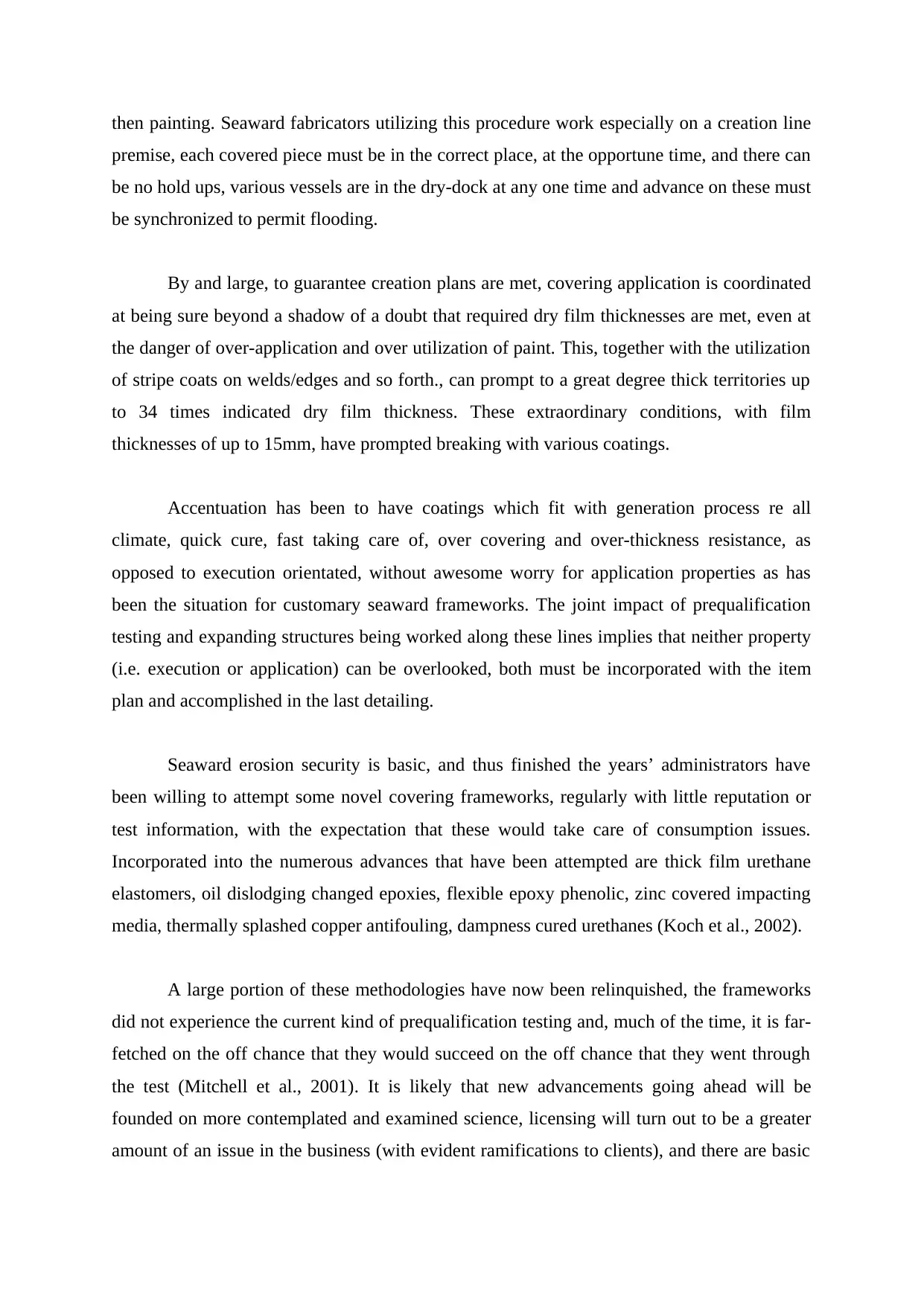
then painting. Seaward fabricators utilizing this procedure work especially on a creation line
premise, each covered piece must be in the correct place, at the opportune time, and there can
be no hold ups, various vessels are in the dry-dock at any one time and advance on these must
be synchronized to permit flooding.
By and large, to guarantee creation plans are met, covering application is coordinated
at being sure beyond a shadow of a doubt that required dry film thicknesses are met, even at
the danger of over-application and over utilization of paint. This, together with the utilization
of stripe coats on welds/edges and so forth., can prompt to a great degree thick territories up
to 34 times indicated dry film thickness. These extraordinary conditions, with film
thicknesses of up to 15mm, have prompted breaking with various coatings.
Accentuation has been to have coatings which fit with generation process re all
climate, quick cure, fast taking care of, over covering and over-thickness resistance, as
opposed to execution orientated, without awesome worry for application properties as has
been the situation for customary seaward frameworks. The joint impact of prequalification
testing and expanding structures being worked along these lines implies that neither property
(i.e. execution or application) can be overlooked, both must be incorporated with the item
plan and accomplished in the last detailing.
Seaward erosion security is basic, and thus finished the years’ administrators have
been willing to attempt some novel covering frameworks, regularly with little reputation or
test information, with the expectation that these would take care of consumption issues.
Incorporated into the numerous advances that have been attempted are thick film urethane
elastomers, oil dislodging changed epoxies, flexible epoxy phenolic, zinc covered impacting
media, thermally splashed copper antifouling, dampness cured urethanes (Koch et al., 2002).
A large portion of these methodologies have now been relinquished, the frameworks
did not experience the current kind of prequalification testing and, much of the time, it is far-
fetched on the off chance that they would succeed on the off chance that they went through
the test (Mitchell et al., 2001). It is likely that new advancements going ahead will be
founded on more contemplated and examined science, licensing will turn out to be a greater
amount of an issue in the business (with evident ramifications to clients), and there are basic
premise, each covered piece must be in the correct place, at the opportune time, and there can
be no hold ups, various vessels are in the dry-dock at any one time and advance on these must
be synchronized to permit flooding.
By and large, to guarantee creation plans are met, covering application is coordinated
at being sure beyond a shadow of a doubt that required dry film thicknesses are met, even at
the danger of over-application and over utilization of paint. This, together with the utilization
of stripe coats on welds/edges and so forth., can prompt to a great degree thick territories up
to 34 times indicated dry film thickness. These extraordinary conditions, with film
thicknesses of up to 15mm, have prompted breaking with various coatings.
Accentuation has been to have coatings which fit with generation process re all
climate, quick cure, fast taking care of, over covering and over-thickness resistance, as
opposed to execution orientated, without awesome worry for application properties as has
been the situation for customary seaward frameworks. The joint impact of prequalification
testing and expanding structures being worked along these lines implies that neither property
(i.e. execution or application) can be overlooked, both must be incorporated with the item
plan and accomplished in the last detailing.
Seaward erosion security is basic, and thus finished the years’ administrators have
been willing to attempt some novel covering frameworks, regularly with little reputation or
test information, with the expectation that these would take care of consumption issues.
Incorporated into the numerous advances that have been attempted are thick film urethane
elastomers, oil dislodging changed epoxies, flexible epoxy phenolic, zinc covered impacting
media, thermally splashed copper antifouling, dampness cured urethanes (Koch et al., 2002).
A large portion of these methodologies have now been relinquished, the frameworks
did not experience the current kind of prequalification testing and, much of the time, it is far-
fetched on the off chance that they would succeed on the off chance that they went through
the test (Mitchell et al., 2001). It is likely that new advancements going ahead will be
founded on more contemplated and examined science, licensing will turn out to be a greater
amount of an issue in the business (with evident ramifications to clients), and there are basic
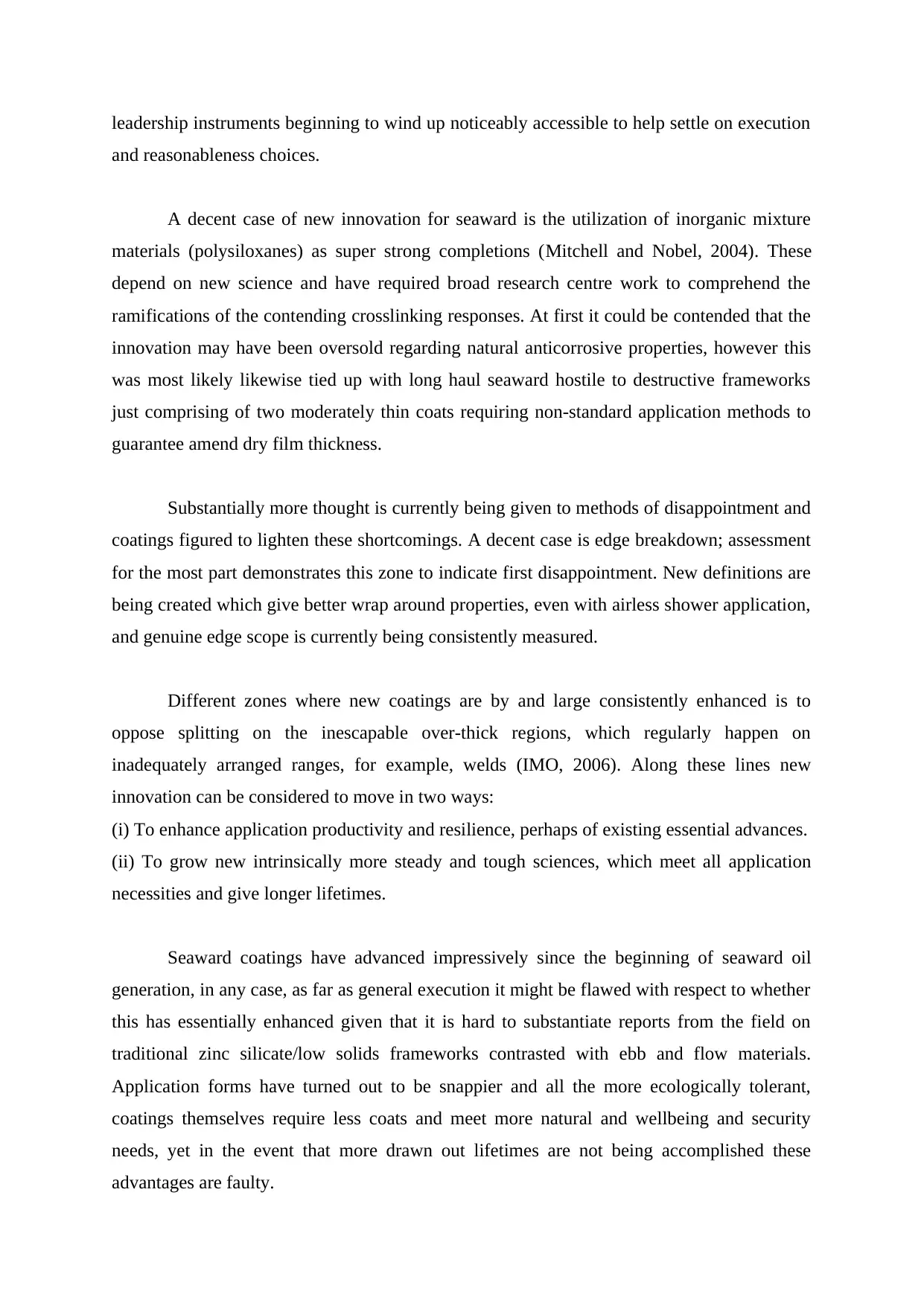
leadership instruments beginning to wind up noticeably accessible to help settle on execution
and reasonableness choices.
A decent case of new innovation for seaward is the utilization of inorganic mixture
materials (polysiloxanes) as super strong completions (Mitchell and Nobel, 2004). These
depend on new science and have required broad research centre work to comprehend the
ramifications of the contending crosslinking responses. At first it could be contended that the
innovation may have been oversold regarding natural anticorrosive properties, however this
was most likely likewise tied up with long haul seaward hostile to destructive frameworks
just comprising of two moderately thin coats requiring non-standard application methods to
guarantee amend dry film thickness.
Substantially more thought is currently being given to methods of disappointment and
coatings figured to lighten these shortcomings. A decent case is edge breakdown; assessment
for the most part demonstrates this zone to indicate first disappointment. New definitions are
being created which give better wrap around properties, even with airless shower application,
and genuine edge scope is currently being consistently measured.
Different zones where new coatings are by and large consistently enhanced is to
oppose splitting on the inescapable over-thick regions, which regularly happen on
inadequately arranged ranges, for example, welds (IMO, 2006). Along these lines new
innovation can be considered to move in two ways:
(i) To enhance application productivity and resilience, perhaps of existing essential advances.
(ii) To grow new intrinsically more steady and tough sciences, which meet all application
necessities and give longer lifetimes.
Seaward coatings have advanced impressively since the beginning of seaward oil
generation, in any case, as far as general execution it might be flawed with respect to whether
this has essentially enhanced given that it is hard to substantiate reports from the field on
traditional zinc silicate/low solids frameworks contrasted with ebb and flow materials.
Application forms have turned out to be snappier and all the more ecologically tolerant,
coatings themselves require less coats and meet more natural and wellbeing and security
needs, yet in the event that more drawn out lifetimes are not being accomplished these
advantages are faulty.
and reasonableness choices.
A decent case of new innovation for seaward is the utilization of inorganic mixture
materials (polysiloxanes) as super strong completions (Mitchell and Nobel, 2004). These
depend on new science and have required broad research centre work to comprehend the
ramifications of the contending crosslinking responses. At first it could be contended that the
innovation may have been oversold regarding natural anticorrosive properties, however this
was most likely likewise tied up with long haul seaward hostile to destructive frameworks
just comprising of two moderately thin coats requiring non-standard application methods to
guarantee amend dry film thickness.
Substantially more thought is currently being given to methods of disappointment and
coatings figured to lighten these shortcomings. A decent case is edge breakdown; assessment
for the most part demonstrates this zone to indicate first disappointment. New definitions are
being created which give better wrap around properties, even with airless shower application,
and genuine edge scope is currently being consistently measured.
Different zones where new coatings are by and large consistently enhanced is to
oppose splitting on the inescapable over-thick regions, which regularly happen on
inadequately arranged ranges, for example, welds (IMO, 2006). Along these lines new
innovation can be considered to move in two ways:
(i) To enhance application productivity and resilience, perhaps of existing essential advances.
(ii) To grow new intrinsically more steady and tough sciences, which meet all application
necessities and give longer lifetimes.
Seaward coatings have advanced impressively since the beginning of seaward oil
generation, in any case, as far as general execution it might be flawed with respect to whether
this has essentially enhanced given that it is hard to substantiate reports from the field on
traditional zinc silicate/low solids frameworks contrasted with ebb and flow materials.
Application forms have turned out to be snappier and all the more ecologically tolerant,
coatings themselves require less coats and meet more natural and wellbeing and security
needs, yet in the event that more drawn out lifetimes are not being accomplished these
advantages are faulty.
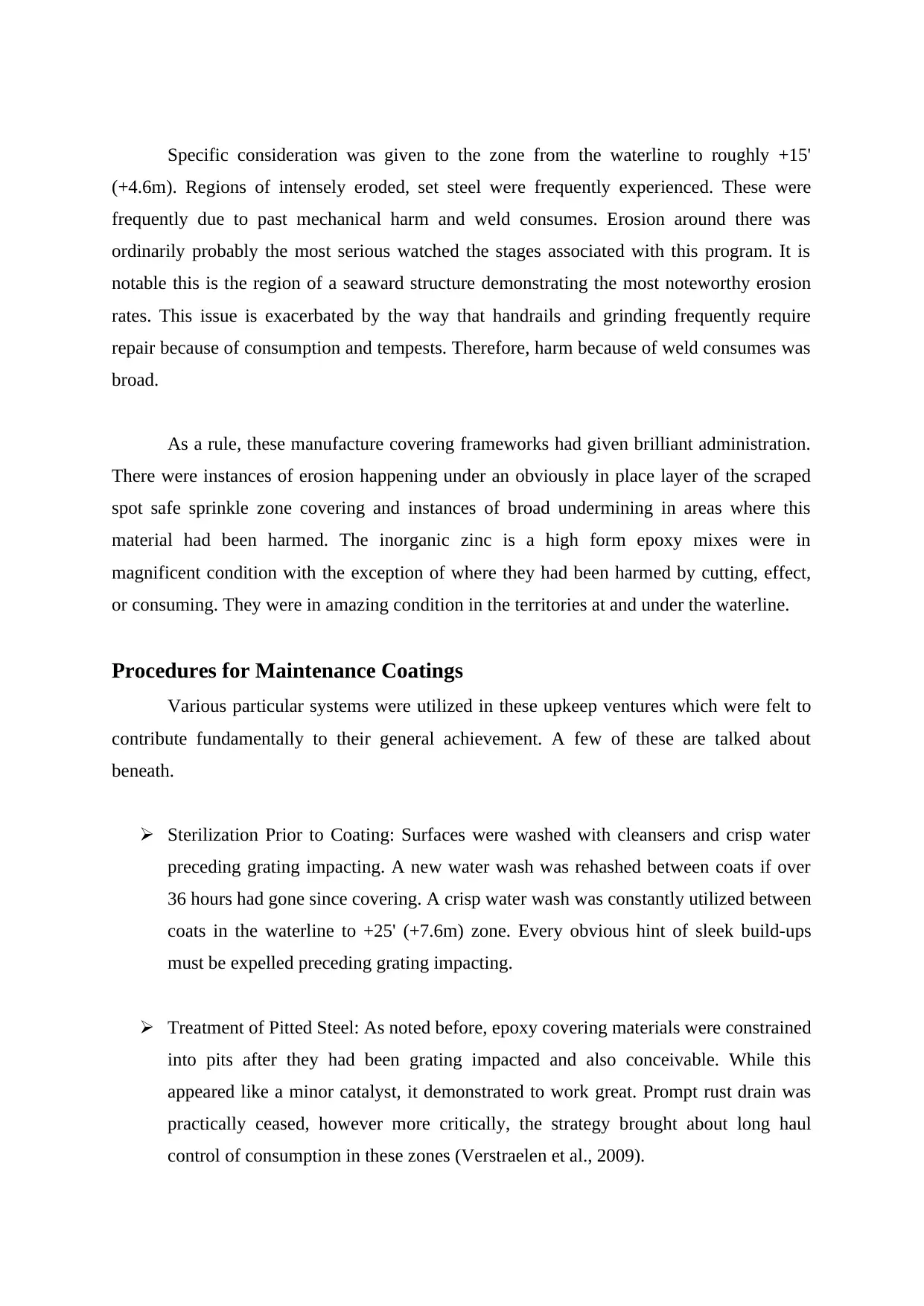
Specific consideration was given to the zone from the waterline to roughly +15'
(+4.6m). Regions of intensely eroded, set steel were frequently experienced. These were
frequently due to past mechanical harm and weld consumes. Erosion around there was
ordinarily probably the most serious watched the stages associated with this program. It is
notable this is the region of a seaward structure demonstrating the most noteworthy erosion
rates. This issue is exacerbated by the way that handrails and grinding frequently require
repair because of consumption and tempests. Therefore, harm because of weld consumes was
broad.
As a rule, these manufacture covering frameworks had given brilliant administration.
There were instances of erosion happening under an obviously in place layer of the scraped
spot safe sprinkle zone covering and instances of broad undermining in areas where this
material had been harmed. The inorganic zinc is a high form epoxy mixes were in
magnificent condition with the exception of where they had been harmed by cutting, effect,
or consuming. They were in amazing condition in the territories at and under the waterline.
Procedures for Maintenance Coatings
Various particular systems were utilized in these upkeep ventures which were felt to
contribute fundamentally to their general achievement. A few of these are talked about
beneath.
Sterilization Prior to Coating: Surfaces were washed with cleansers and crisp water
preceding grating impacting. A new water wash was rehashed between coats if over
36 hours had gone since covering. A crisp water wash was constantly utilized between
coats in the waterline to +25' (+7.6m) zone. Every obvious hint of sleek build-ups
must be expelled preceding grating impacting.
Treatment of Pitted Steel: As noted before, epoxy covering materials were constrained
into pits after they had been grating impacted and also conceivable. While this
appeared like a minor catalyst, it demonstrated to work great. Prompt rust drain was
practically ceased, however more critically, the strategy brought about long haul
control of consumption in these zones (Verstraelen et al., 2009).
(+4.6m). Regions of intensely eroded, set steel were frequently experienced. These were
frequently due to past mechanical harm and weld consumes. Erosion around there was
ordinarily probably the most serious watched the stages associated with this program. It is
notable this is the region of a seaward structure demonstrating the most noteworthy erosion
rates. This issue is exacerbated by the way that handrails and grinding frequently require
repair because of consumption and tempests. Therefore, harm because of weld consumes was
broad.
As a rule, these manufacture covering frameworks had given brilliant administration.
There were instances of erosion happening under an obviously in place layer of the scraped
spot safe sprinkle zone covering and instances of broad undermining in areas where this
material had been harmed. The inorganic zinc is a high form epoxy mixes were in
magnificent condition with the exception of where they had been harmed by cutting, effect,
or consuming. They were in amazing condition in the territories at and under the waterline.
Procedures for Maintenance Coatings
Various particular systems were utilized in these upkeep ventures which were felt to
contribute fundamentally to their general achievement. A few of these are talked about
beneath.
Sterilization Prior to Coating: Surfaces were washed with cleansers and crisp water
preceding grating impacting. A new water wash was rehashed between coats if over
36 hours had gone since covering. A crisp water wash was constantly utilized between
coats in the waterline to +25' (+7.6m) zone. Every obvious hint of sleek build-ups
must be expelled preceding grating impacting.
Treatment of Pitted Steel: As noted before, epoxy covering materials were constrained
into pits after they had been grating impacted and also conceivable. While this
appeared like a minor catalyst, it demonstrated to work great. Prompt rust drain was
practically ceased, however more critically, the strategy brought about long haul
control of consumption in these zones (Verstraelen et al., 2009).
Secure Best Marks with AI Grader
Need help grading? Try our AI Grader for instant feedback on your assignments.
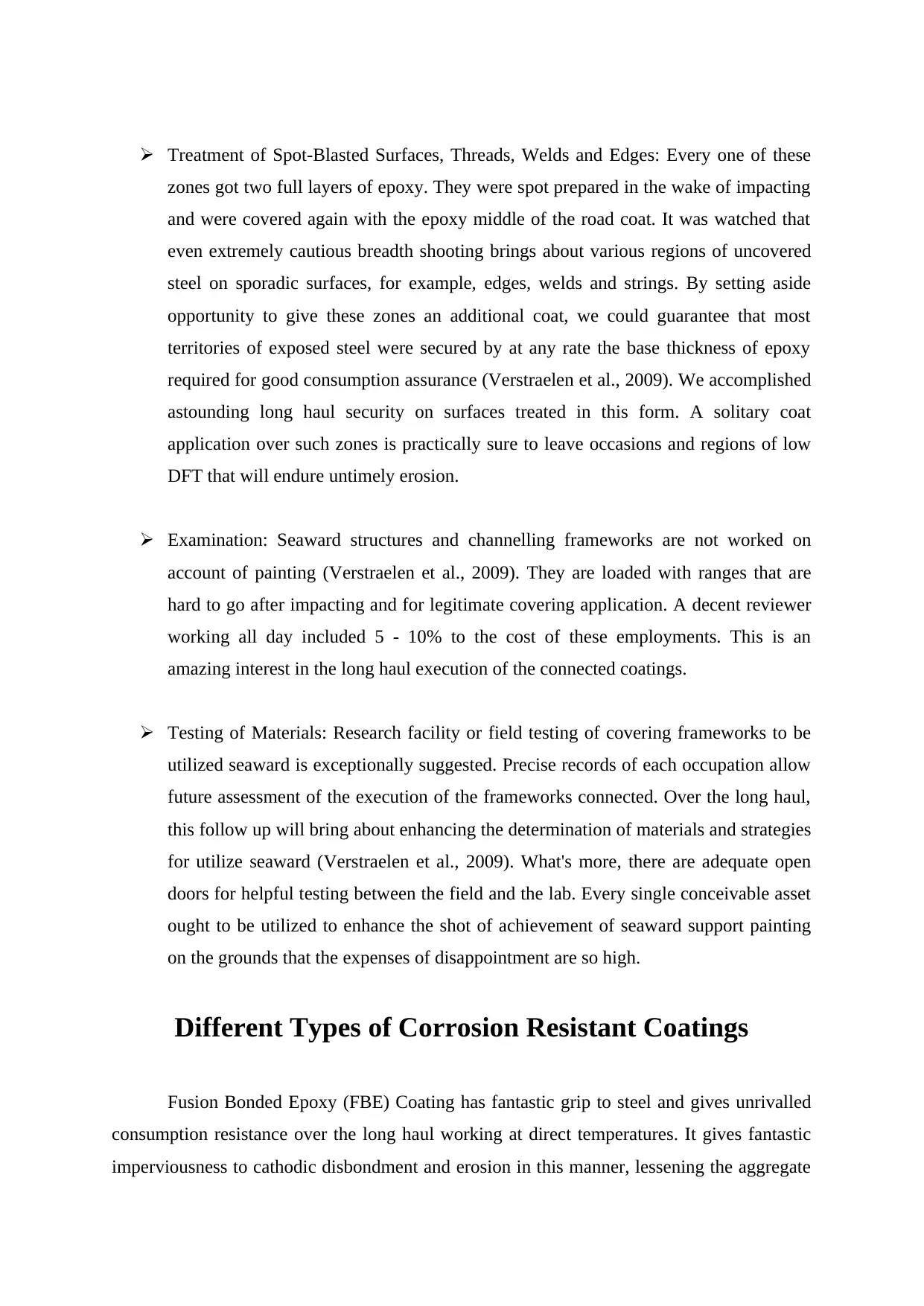
Treatment of Spot-Blasted Surfaces, Threads, Welds and Edges: Every one of these
zones got two full layers of epoxy. They were spot prepared in the wake of impacting
and were covered again with the epoxy middle of the road coat. It was watched that
even extremely cautious breadth shooting brings about various regions of uncovered
steel on sporadic surfaces, for example, edges, welds and strings. By setting aside
opportunity to give these zones an additional coat, we could guarantee that most
territories of exposed steel were secured by at any rate the base thickness of epoxy
required for good consumption assurance (Verstraelen et al., 2009). We accomplished
astounding long haul security on surfaces treated in this form. A solitary coat
application over such zones is practically sure to leave occasions and regions of low
DFT that will endure untimely erosion.
Examination: Seaward structures and channelling frameworks are not worked on
account of painting (Verstraelen et al., 2009). They are loaded with ranges that are
hard to go after impacting and for legitimate covering application. A decent reviewer
working all day included 5 - 10% to the cost of these employments. This is an
amazing interest in the long haul execution of the connected coatings.
Testing of Materials: Research facility or field testing of covering frameworks to be
utilized seaward is exceptionally suggested. Precise records of each occupation allow
future assessment of the execution of the frameworks connected. Over the long haul,
this follow up will bring about enhancing the determination of materials and strategies
for utilize seaward (Verstraelen et al., 2009). What's more, there are adequate open
doors for helpful testing between the field and the lab. Every single conceivable asset
ought to be utilized to enhance the shot of achievement of seaward support painting
on the grounds that the expenses of disappointment are so high.
Different Types of Corrosion Resistant Coatings
Fusion Bonded Epoxy (FBE) Coating has fantastic grip to steel and gives unrivalled
consumption resistance over the long haul working at direct temperatures. It gives fantastic
imperviousness to cathodic disbondment and erosion in this manner, lessening the aggregate
zones got two full layers of epoxy. They were spot prepared in the wake of impacting
and were covered again with the epoxy middle of the road coat. It was watched that
even extremely cautious breadth shooting brings about various regions of uncovered
steel on sporadic surfaces, for example, edges, welds and strings. By setting aside
opportunity to give these zones an additional coat, we could guarantee that most
territories of exposed steel were secured by at any rate the base thickness of epoxy
required for good consumption assurance (Verstraelen et al., 2009). We accomplished
astounding long haul security on surfaces treated in this form. A solitary coat
application over such zones is practically sure to leave occasions and regions of low
DFT that will endure untimely erosion.
Examination: Seaward structures and channelling frameworks are not worked on
account of painting (Verstraelen et al., 2009). They are loaded with ranges that are
hard to go after impacting and for legitimate covering application. A decent reviewer
working all day included 5 - 10% to the cost of these employments. This is an
amazing interest in the long haul execution of the connected coatings.
Testing of Materials: Research facility or field testing of covering frameworks to be
utilized seaward is exceptionally suggested. Precise records of each occupation allow
future assessment of the execution of the frameworks connected. Over the long haul,
this follow up will bring about enhancing the determination of materials and strategies
for utilize seaward (Verstraelen et al., 2009). What's more, there are adequate open
doors for helpful testing between the field and the lab. Every single conceivable asset
ought to be utilized to enhance the shot of achievement of seaward support painting
on the grounds that the expenses of disappointment are so high.
Different Types of Corrosion Resistant Coatings
Fusion Bonded Epoxy (FBE) Coating has fantastic grip to steel and gives unrivalled
consumption resistance over the long haul working at direct temperatures. It gives fantastic
imperviousness to cathodic disbondment and erosion in this manner, lessening the aggregate
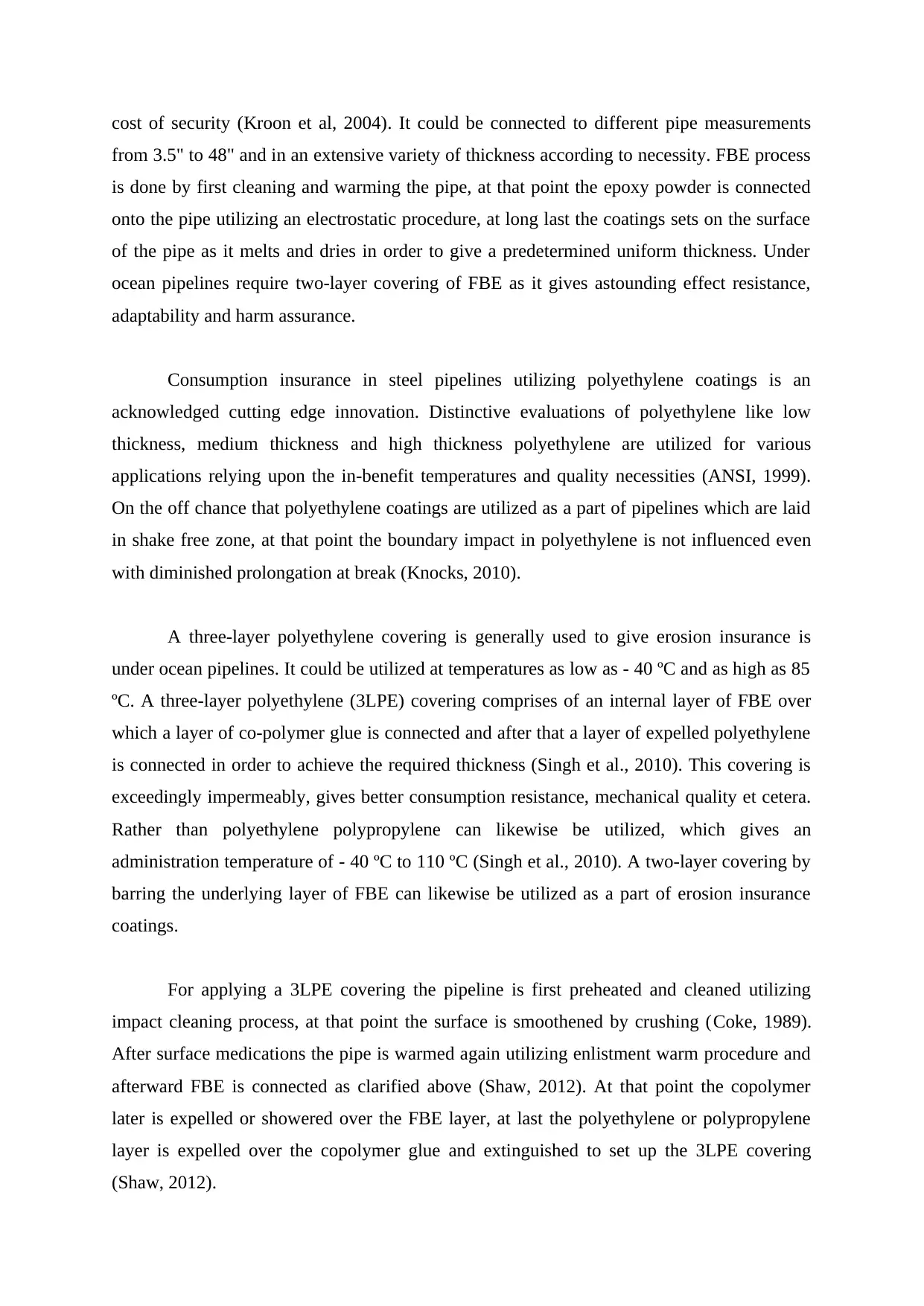
cost of security (Kroon et al, 2004). It could be connected to different pipe measurements
from 3.5" to 48" and in an extensive variety of thickness according to necessity. FBE process
is done by first cleaning and warming the pipe, at that point the epoxy powder is connected
onto the pipe utilizing an electrostatic procedure, at long last the coatings sets on the surface
of the pipe as it melts and dries in order to give a predetermined uniform thickness. Under
ocean pipelines require two-layer covering of FBE as it gives astounding effect resistance,
adaptability and harm assurance.
Consumption insurance in steel pipelines utilizing polyethylene coatings is an
acknowledged cutting edge innovation. Distinctive evaluations of polyethylene like low
thickness, medium thickness and high thickness polyethylene are utilized for various
applications relying upon the in-benefit temperatures and quality necessities (ANSI, 1999).
On the off chance that polyethylene coatings are utilized as a part of pipelines which are laid
in shake free zone, at that point the boundary impact in polyethylene is not influenced even
with diminished prolongation at break (Knocks, 2010).
A three-layer polyethylene covering is generally used to give erosion insurance is
under ocean pipelines. It could be utilized at temperatures as low as - 40 ºC and as high as 85
ºC. A three-layer polyethylene (3LPE) covering comprises of an internal layer of FBE over
which a layer of co-polymer glue is connected and after that a layer of expelled polyethylene
is connected in order to achieve the required thickness (Singh et al., 2010). This covering is
exceedingly impermeably, gives better consumption resistance, mechanical quality et cetera.
Rather than polyethylene polypropylene can likewise be utilized, which gives an
administration temperature of - 40 ºC to 110 ºC (Singh et al., 2010). A two-layer covering by
barring the underlying layer of FBE can likewise be utilized as a part of erosion insurance
coatings.
For applying a 3LPE covering the pipeline is first preheated and cleaned utilizing
impact cleaning process, at that point the surface is smoothened by crushing (Coke, 1989).
After surface medications the pipe is warmed again utilizing enlistment warm procedure and
afterward FBE is connected as clarified above (Shaw, 2012). At that point the copolymer
later is expelled or showered over the FBE layer, at last the polyethylene or polypropylene
layer is expelled over the copolymer glue and extinguished to set up the 3LPE covering
(Shaw, 2012).
from 3.5" to 48" and in an extensive variety of thickness according to necessity. FBE process
is done by first cleaning and warming the pipe, at that point the epoxy powder is connected
onto the pipe utilizing an electrostatic procedure, at long last the coatings sets on the surface
of the pipe as it melts and dries in order to give a predetermined uniform thickness. Under
ocean pipelines require two-layer covering of FBE as it gives astounding effect resistance,
adaptability and harm assurance.
Consumption insurance in steel pipelines utilizing polyethylene coatings is an
acknowledged cutting edge innovation. Distinctive evaluations of polyethylene like low
thickness, medium thickness and high thickness polyethylene are utilized for various
applications relying upon the in-benefit temperatures and quality necessities (ANSI, 1999).
On the off chance that polyethylene coatings are utilized as a part of pipelines which are laid
in shake free zone, at that point the boundary impact in polyethylene is not influenced even
with diminished prolongation at break (Knocks, 2010).
A three-layer polyethylene covering is generally used to give erosion insurance is
under ocean pipelines. It could be utilized at temperatures as low as - 40 ºC and as high as 85
ºC. A three-layer polyethylene (3LPE) covering comprises of an internal layer of FBE over
which a layer of co-polymer glue is connected and after that a layer of expelled polyethylene
is connected in order to achieve the required thickness (Singh et al., 2010). This covering is
exceedingly impermeably, gives better consumption resistance, mechanical quality et cetera.
Rather than polyethylene polypropylene can likewise be utilized, which gives an
administration temperature of - 40 ºC to 110 ºC (Singh et al., 2010). A two-layer covering by
barring the underlying layer of FBE can likewise be utilized as a part of erosion insurance
coatings.
For applying a 3LPE covering the pipeline is first preheated and cleaned utilizing
impact cleaning process, at that point the surface is smoothened by crushing (Coke, 1989).
After surface medications the pipe is warmed again utilizing enlistment warm procedure and
afterward FBE is connected as clarified above (Shaw, 2012). At that point the copolymer
later is expelled or showered over the FBE layer, at last the polyethylene or polypropylene
layer is expelled over the copolymer glue and extinguished to set up the 3LPE covering
(Shaw, 2012).
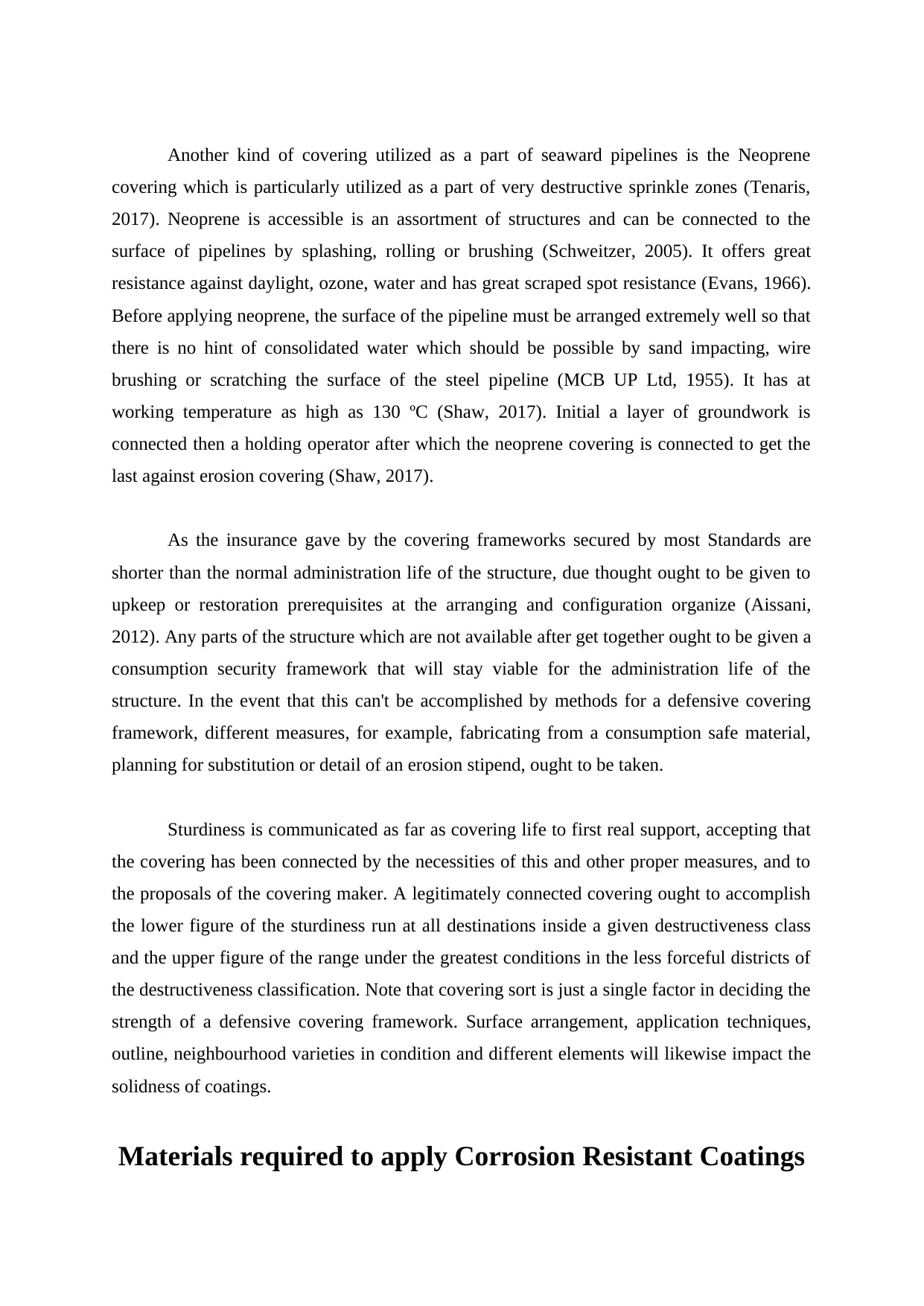
Another kind of covering utilized as a part of seaward pipelines is the Neoprene
covering which is particularly utilized as a part of very destructive sprinkle zones (Tenaris,
2017). Neoprene is accessible is an assortment of structures and can be connected to the
surface of pipelines by splashing, rolling or brushing (Schweitzer, 2005). It offers great
resistance against daylight, ozone, water and has great scraped spot resistance (Evans, 1966).
Before applying neoprene, the surface of the pipeline must be arranged extremely well so that
there is no hint of consolidated water which should be possible by sand impacting, wire
brushing or scratching the surface of the steel pipeline (MCB UP Ltd, 1955). It has at
working temperature as high as 130 ºC (Shaw, 2017). Initial a layer of groundwork is
connected then a holding operator after which the neoprene covering is connected to get the
last against erosion covering (Shaw, 2017).
As the insurance gave by the covering frameworks secured by most Standards are
shorter than the normal administration life of the structure, due thought ought to be given to
upkeep or restoration prerequisites at the arranging and configuration organize (Aissani,
2012). Any parts of the structure which are not available after get together ought to be given a
consumption security framework that will stay viable for the administration life of the
structure. In the event that this can't be accomplished by methods for a defensive covering
framework, different measures, for example, fabricating from a consumption safe material,
planning for substitution or detail of an erosion stipend, ought to be taken.
Sturdiness is communicated as far as covering life to first real support, accepting that
the covering has been connected by the necessities of this and other proper measures, and to
the proposals of the covering maker. A legitimately connected covering ought to accomplish
the lower figure of the sturdiness run at all destinations inside a given destructiveness class
and the upper figure of the range under the greatest conditions in the less forceful districts of
the destructiveness classification. Note that covering sort is just a single factor in deciding the
strength of a defensive covering framework. Surface arrangement, application techniques,
outline, neighbourhood varieties in condition and different elements will likewise impact the
solidness of coatings.
Materials required to apply Corrosion Resistant Coatings
covering which is particularly utilized as a part of very destructive sprinkle zones (Tenaris,
2017). Neoprene is accessible is an assortment of structures and can be connected to the
surface of pipelines by splashing, rolling or brushing (Schweitzer, 2005). It offers great
resistance against daylight, ozone, water and has great scraped spot resistance (Evans, 1966).
Before applying neoprene, the surface of the pipeline must be arranged extremely well so that
there is no hint of consolidated water which should be possible by sand impacting, wire
brushing or scratching the surface of the steel pipeline (MCB UP Ltd, 1955). It has at
working temperature as high as 130 ºC (Shaw, 2017). Initial a layer of groundwork is
connected then a holding operator after which the neoprene covering is connected to get the
last against erosion covering (Shaw, 2017).
As the insurance gave by the covering frameworks secured by most Standards are
shorter than the normal administration life of the structure, due thought ought to be given to
upkeep or restoration prerequisites at the arranging and configuration organize (Aissani,
2012). Any parts of the structure which are not available after get together ought to be given a
consumption security framework that will stay viable for the administration life of the
structure. In the event that this can't be accomplished by methods for a defensive covering
framework, different measures, for example, fabricating from a consumption safe material,
planning for substitution or detail of an erosion stipend, ought to be taken.
Sturdiness is communicated as far as covering life to first real support, accepting that
the covering has been connected by the necessities of this and other proper measures, and to
the proposals of the covering maker. A legitimately connected covering ought to accomplish
the lower figure of the sturdiness run at all destinations inside a given destructiveness class
and the upper figure of the range under the greatest conditions in the less forceful districts of
the destructiveness classification. Note that covering sort is just a single factor in deciding the
strength of a defensive covering framework. Surface arrangement, application techniques,
outline, neighbourhood varieties in condition and different elements will likewise impact the
solidness of coatings.
Materials required to apply Corrosion Resistant Coatings
Paraphrase This Document
Need a fresh take? Get an instant paraphrase of this document with our AI Paraphraser
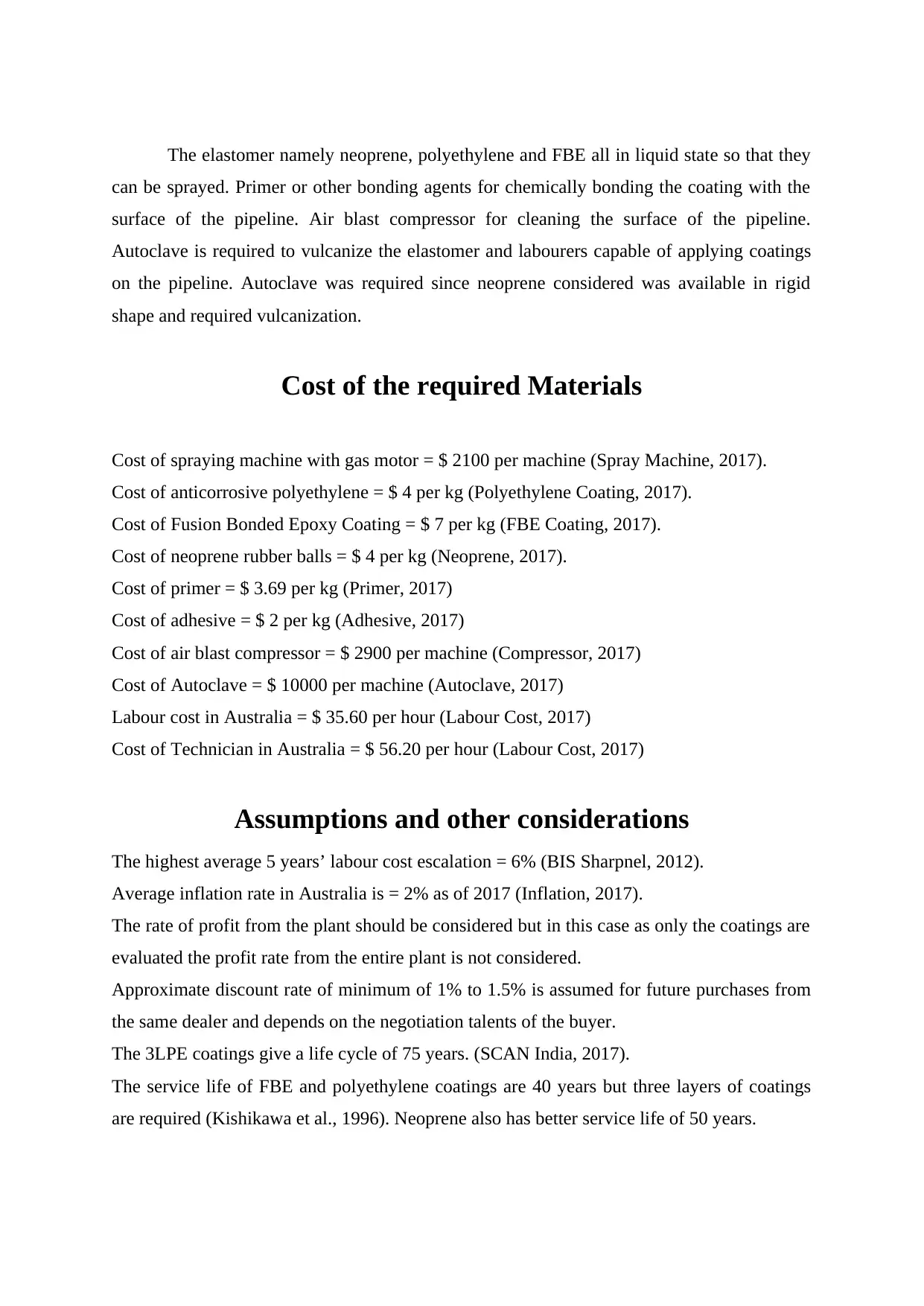
The elastomer namely neoprene, polyethylene and FBE all in liquid state so that they
can be sprayed. Primer or other bonding agents for chemically bonding the coating with the
surface of the pipeline. Air blast compressor for cleaning the surface of the pipeline.
Autoclave is required to vulcanize the elastomer and labourers capable of applying coatings
on the pipeline. Autoclave was required since neoprene considered was available in rigid
shape and required vulcanization.
Cost of the required Materials
Cost of spraying machine with gas motor = $ 2100 per machine (Spray Machine, 2017).
Cost of anticorrosive polyethylene = $ 4 per kg (Polyethylene Coating, 2017).
Cost of Fusion Bonded Epoxy Coating = $ 7 per kg (FBE Coating, 2017).
Cost of neoprene rubber balls = $ 4 per kg (Neoprene, 2017).
Cost of primer = $ 3.69 per kg (Primer, 2017)
Cost of adhesive = $ 2 per kg (Adhesive, 2017)
Cost of air blast compressor = $ 2900 per machine (Compressor, 2017)
Cost of Autoclave = $ 10000 per machine (Autoclave, 2017)
Labour cost in Australia = $ 35.60 per hour (Labour Cost, 2017)
Cost of Technician in Australia = $ 56.20 per hour (Labour Cost, 2017)
Assumptions and other considerations
The highest average 5 years’ labour cost escalation = 6% (BIS Sharpnel, 2012).
Average inflation rate in Australia is = 2% as of 2017 (Inflation, 2017).
The rate of profit from the plant should be considered but in this case as only the coatings are
evaluated the profit rate from the entire plant is not considered.
Approximate discount rate of minimum of 1% to 1.5% is assumed for future purchases from
the same dealer and depends on the negotiation talents of the buyer.
The 3LPE coatings give a life cycle of 75 years. (SCAN India, 2017).
The service life of FBE and polyethylene coatings are 40 years but three layers of coatings
are required (Kishikawa et al., 1996). Neoprene also has better service life of 50 years.
can be sprayed. Primer or other bonding agents for chemically bonding the coating with the
surface of the pipeline. Air blast compressor for cleaning the surface of the pipeline.
Autoclave is required to vulcanize the elastomer and labourers capable of applying coatings
on the pipeline. Autoclave was required since neoprene considered was available in rigid
shape and required vulcanization.
Cost of the required Materials
Cost of spraying machine with gas motor = $ 2100 per machine (Spray Machine, 2017).
Cost of anticorrosive polyethylene = $ 4 per kg (Polyethylene Coating, 2017).
Cost of Fusion Bonded Epoxy Coating = $ 7 per kg (FBE Coating, 2017).
Cost of neoprene rubber balls = $ 4 per kg (Neoprene, 2017).
Cost of primer = $ 3.69 per kg (Primer, 2017)
Cost of adhesive = $ 2 per kg (Adhesive, 2017)
Cost of air blast compressor = $ 2900 per machine (Compressor, 2017)
Cost of Autoclave = $ 10000 per machine (Autoclave, 2017)
Labour cost in Australia = $ 35.60 per hour (Labour Cost, 2017)
Cost of Technician in Australia = $ 56.20 per hour (Labour Cost, 2017)
Assumptions and other considerations
The highest average 5 years’ labour cost escalation = 6% (BIS Sharpnel, 2012).
Average inflation rate in Australia is = 2% as of 2017 (Inflation, 2017).
The rate of profit from the plant should be considered but in this case as only the coatings are
evaluated the profit rate from the entire plant is not considered.
Approximate discount rate of minimum of 1% to 1.5% is assumed for future purchases from
the same dealer and depends on the negotiation talents of the buyer.
The 3LPE coatings give a life cycle of 75 years. (SCAN India, 2017).
The service life of FBE and polyethylene coatings are 40 years but three layers of coatings
are required (Kishikawa et al., 1996). Neoprene also has better service life of 50 years.
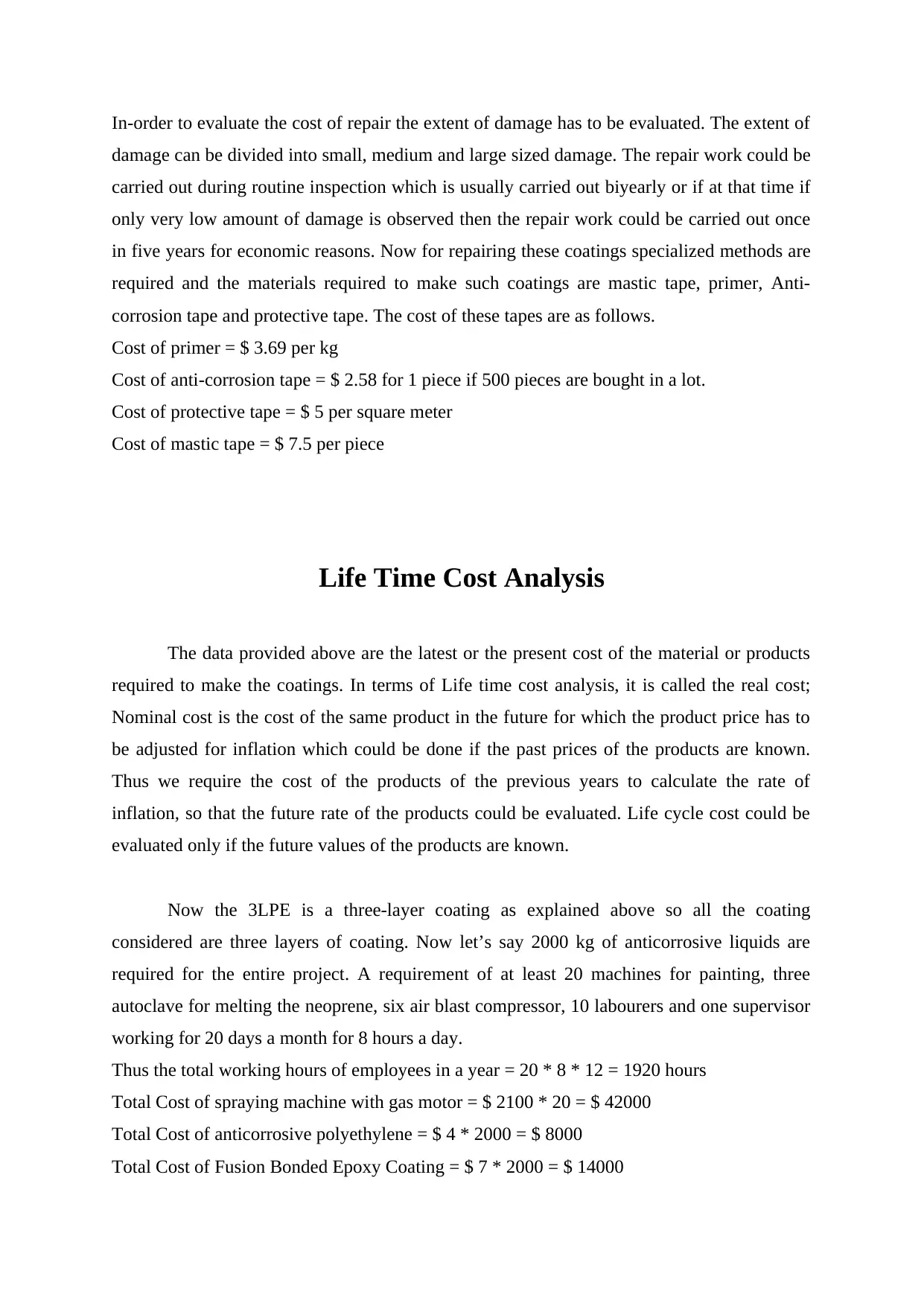
In-order to evaluate the cost of repair the extent of damage has to be evaluated. The extent of
damage can be divided into small, medium and large sized damage. The repair work could be
carried out during routine inspection which is usually carried out biyearly or if at that time if
only very low amount of damage is observed then the repair work could be carried out once
in five years for economic reasons. Now for repairing these coatings specialized methods are
required and the materials required to make such coatings are mastic tape, primer, Anti-
corrosion tape and protective tape. The cost of these tapes are as follows.
Cost of primer = $ 3.69 per kg
Cost of anti-corrosion tape = $ 2.58 for 1 piece if 500 pieces are bought in a lot.
Cost of protective tape = $ 5 per square meter
Cost of mastic tape = $ 7.5 per piece
Life Time Cost Analysis
The data provided above are the latest or the present cost of the material or products
required to make the coatings. In terms of Life time cost analysis, it is called the real cost;
Nominal cost is the cost of the same product in the future for which the product price has to
be adjusted for inflation which could be done if the past prices of the products are known.
Thus we require the cost of the products of the previous years to calculate the rate of
inflation, so that the future rate of the products could be evaluated. Life cycle cost could be
evaluated only if the future values of the products are known.
Now the 3LPE is a three-layer coating as explained above so all the coating
considered are three layers of coating. Now let’s say 2000 kg of anticorrosive liquids are
required for the entire project. A requirement of at least 20 machines for painting, three
autoclave for melting the neoprene, six air blast compressor, 10 labourers and one supervisor
working for 20 days a month for 8 hours a day.
Thus the total working hours of employees in a year = 20 * 8 * 12 = 1920 hours
Total Cost of spraying machine with gas motor = $ 2100 * 20 = $ 42000
Total Cost of anticorrosive polyethylene = $ 4 * 2000 = $ 8000
Total Cost of Fusion Bonded Epoxy Coating = $ 7 * 2000 = $ 14000
damage can be divided into small, medium and large sized damage. The repair work could be
carried out during routine inspection which is usually carried out biyearly or if at that time if
only very low amount of damage is observed then the repair work could be carried out once
in five years for economic reasons. Now for repairing these coatings specialized methods are
required and the materials required to make such coatings are mastic tape, primer, Anti-
corrosion tape and protective tape. The cost of these tapes are as follows.
Cost of primer = $ 3.69 per kg
Cost of anti-corrosion tape = $ 2.58 for 1 piece if 500 pieces are bought in a lot.
Cost of protective tape = $ 5 per square meter
Cost of mastic tape = $ 7.5 per piece
Life Time Cost Analysis
The data provided above are the latest or the present cost of the material or products
required to make the coatings. In terms of Life time cost analysis, it is called the real cost;
Nominal cost is the cost of the same product in the future for which the product price has to
be adjusted for inflation which could be done if the past prices of the products are known.
Thus we require the cost of the products of the previous years to calculate the rate of
inflation, so that the future rate of the products could be evaluated. Life cycle cost could be
evaluated only if the future values of the products are known.
Now the 3LPE is a three-layer coating as explained above so all the coating
considered are three layers of coating. Now let’s say 2000 kg of anticorrosive liquids are
required for the entire project. A requirement of at least 20 machines for painting, three
autoclave for melting the neoprene, six air blast compressor, 10 labourers and one supervisor
working for 20 days a month for 8 hours a day.
Thus the total working hours of employees in a year = 20 * 8 * 12 = 1920 hours
Total Cost of spraying machine with gas motor = $ 2100 * 20 = $ 42000
Total Cost of anticorrosive polyethylene = $ 4 * 2000 = $ 8000
Total Cost of Fusion Bonded Epoxy Coating = $ 7 * 2000 = $ 14000
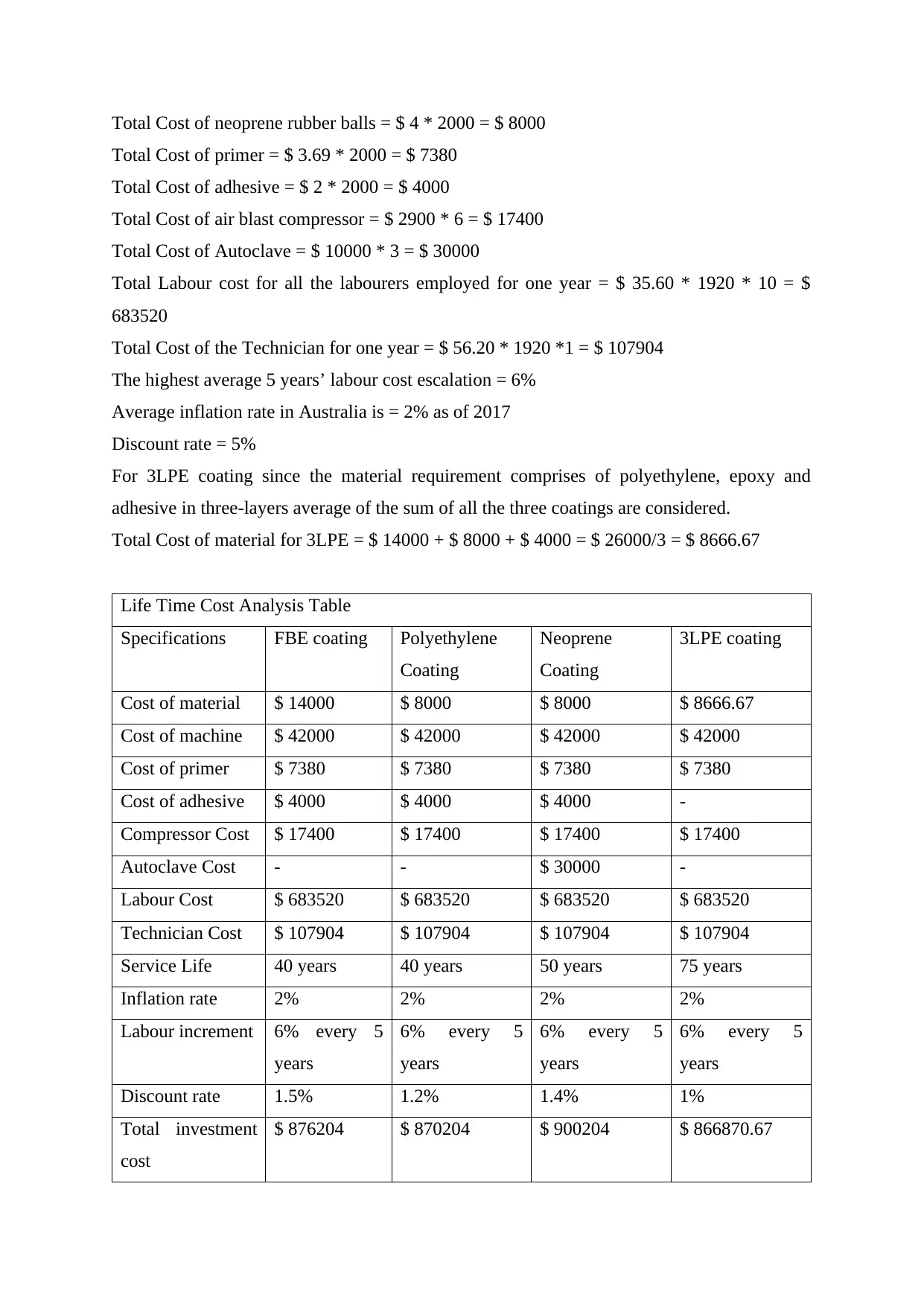
Total Cost of neoprene rubber balls = $ 4 * 2000 = $ 8000
Total Cost of primer = $ 3.69 * 2000 = $ 7380
Total Cost of adhesive = $ 2 * 2000 = $ 4000
Total Cost of air blast compressor = $ 2900 * 6 = $ 17400
Total Cost of Autoclave = $ 10000 * 3 = $ 30000
Total Labour cost for all the labourers employed for one year = $ 35.60 * 1920 * 10 = $
683520
Total Cost of the Technician for one year = $ 56.20 * 1920 *1 = $ 107904
The highest average 5 years’ labour cost escalation = 6%
Average inflation rate in Australia is = 2% as of 2017
Discount rate = 5%
For 3LPE coating since the material requirement comprises of polyethylene, epoxy and
adhesive in three-layers average of the sum of all the three coatings are considered.
Total Cost of material for 3LPE = $ 14000 + $ 8000 + $ 4000 = $ 26000/3 = $ 8666.67
Life Time Cost Analysis Table
Specifications FBE coating Polyethylene
Coating
Neoprene
Coating
3LPE coating
Cost of material $ 14000 $ 8000 $ 8000 $ 8666.67
Cost of machine $ 42000 $ 42000 $ 42000 $ 42000
Cost of primer $ 7380 $ 7380 $ 7380 $ 7380
Cost of adhesive $ 4000 $ 4000 $ 4000 -
Compressor Cost $ 17400 $ 17400 $ 17400 $ 17400
Autoclave Cost - - $ 30000 -
Labour Cost $ 683520 $ 683520 $ 683520 $ 683520
Technician Cost $ 107904 $ 107904 $ 107904 $ 107904
Service Life 40 years 40 years 50 years 75 years
Inflation rate 2% 2% 2% 2%
Labour increment 6% every 5
years
6% every 5
years
6% every 5
years
6% every 5
years
Discount rate 1.5% 1.2% 1.4% 1%
Total investment
cost
$ 876204 $ 870204 $ 900204 $ 866870.67
Total Cost of primer = $ 3.69 * 2000 = $ 7380
Total Cost of adhesive = $ 2 * 2000 = $ 4000
Total Cost of air blast compressor = $ 2900 * 6 = $ 17400
Total Cost of Autoclave = $ 10000 * 3 = $ 30000
Total Labour cost for all the labourers employed for one year = $ 35.60 * 1920 * 10 = $
683520
Total Cost of the Technician for one year = $ 56.20 * 1920 *1 = $ 107904
The highest average 5 years’ labour cost escalation = 6%
Average inflation rate in Australia is = 2% as of 2017
Discount rate = 5%
For 3LPE coating since the material requirement comprises of polyethylene, epoxy and
adhesive in three-layers average of the sum of all the three coatings are considered.
Total Cost of material for 3LPE = $ 14000 + $ 8000 + $ 4000 = $ 26000/3 = $ 8666.67
Life Time Cost Analysis Table
Specifications FBE coating Polyethylene
Coating
Neoprene
Coating
3LPE coating
Cost of material $ 14000 $ 8000 $ 8000 $ 8666.67
Cost of machine $ 42000 $ 42000 $ 42000 $ 42000
Cost of primer $ 7380 $ 7380 $ 7380 $ 7380
Cost of adhesive $ 4000 $ 4000 $ 4000 -
Compressor Cost $ 17400 $ 17400 $ 17400 $ 17400
Autoclave Cost - - $ 30000 -
Labour Cost $ 683520 $ 683520 $ 683520 $ 683520
Technician Cost $ 107904 $ 107904 $ 107904 $ 107904
Service Life 40 years 40 years 50 years 75 years
Inflation rate 2% 2% 2% 2%
Labour increment 6% every 5
years
6% every 5
years
6% every 5
years
6% every 5
years
Discount rate 1.5% 1.2% 1.4% 1%
Total investment
cost
$ 876204 $ 870204 $ 900204 $ 866870.67
Secure Best Marks with AI Grader
Need help grading? Try our AI Grader for instant feedback on your assignments.
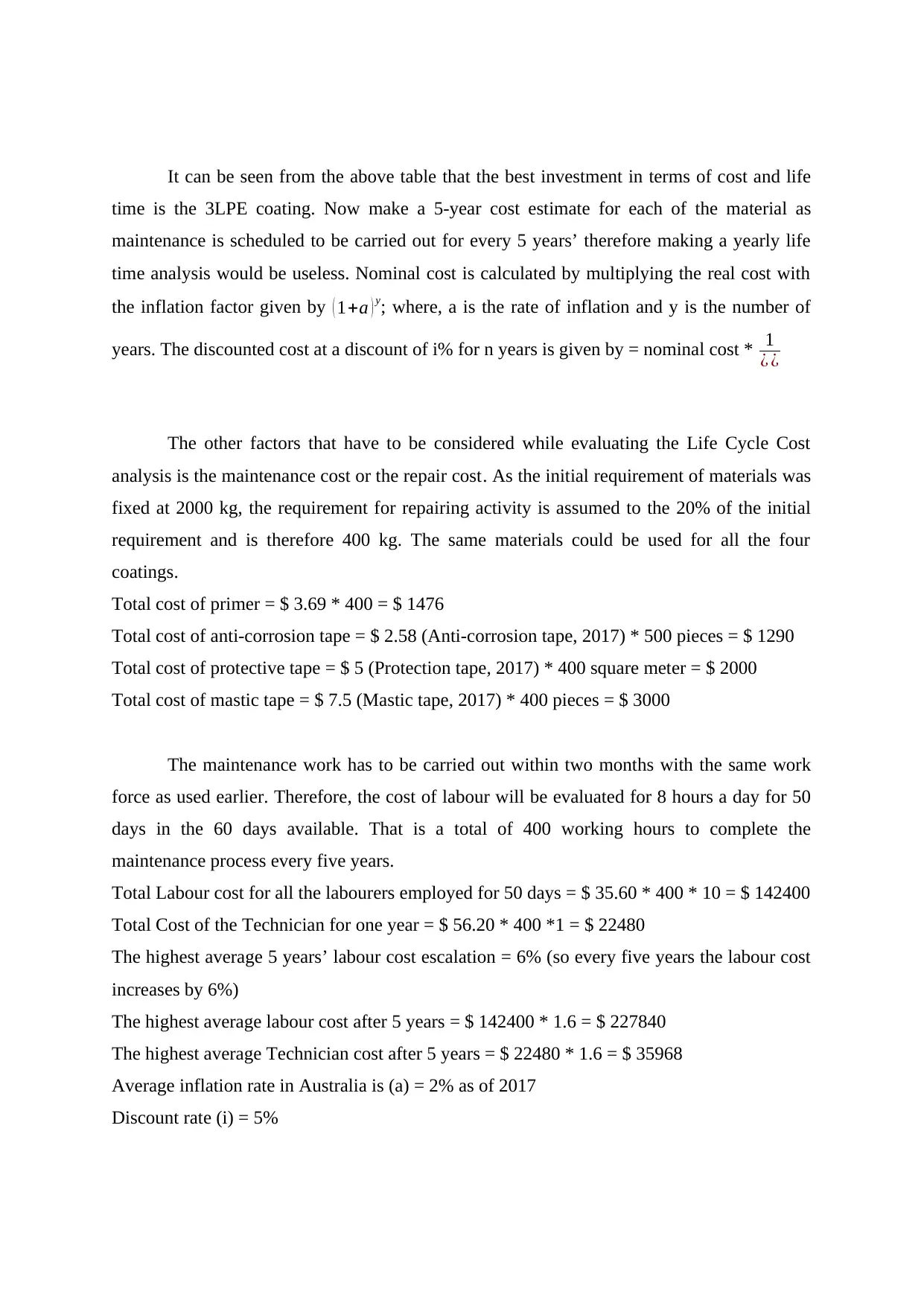
It can be seen from the above table that the best investment in terms of cost and life
time is the 3LPE coating. Now make a 5-year cost estimate for each of the material as
maintenance is scheduled to be carried out for every 5 years’ therefore making a yearly life
time analysis would be useless. Nominal cost is calculated by multiplying the real cost with
the inflation factor given by ( 1+a ) y; where, a is the rate of inflation and y is the number of
years. The discounted cost at a discount of i% for n years is given by = nominal cost * 1
¿ ¿
The other factors that have to be considered while evaluating the Life Cycle Cost
analysis is the maintenance cost or the repair cost. As the initial requirement of materials was
fixed at 2000 kg, the requirement for repairing activity is assumed to the 20% of the initial
requirement and is therefore 400 kg. The same materials could be used for all the four
coatings.
Total cost of primer = $ 3.69 * 400 = $ 1476
Total cost of anti-corrosion tape = $ 2.58 (Anti-corrosion tape, 2017) * 500 pieces = $ 1290
Total cost of protective tape = $ 5 (Protection tape, 2017) * 400 square meter = $ 2000
Total cost of mastic tape = $ 7.5 (Mastic tape, 2017) * 400 pieces = $ 3000
The maintenance work has to be carried out within two months with the same work
force as used earlier. Therefore, the cost of labour will be evaluated for 8 hours a day for 50
days in the 60 days available. That is a total of 400 working hours to complete the
maintenance process every five years.
Total Labour cost for all the labourers employed for 50 days = $ 35.60 * 400 * 10 = $ 142400
Total Cost of the Technician for one year = $ 56.20 * 400 *1 = $ 22480
The highest average 5 years’ labour cost escalation = 6% (so every five years the labour cost
increases by 6%)
The highest average labour cost after 5 years = $ 142400 * 1.6 = $ 227840
The highest average Technician cost after 5 years = $ 22480 * 1.6 = $ 35968
Average inflation rate in Australia is (a) = 2% as of 2017
Discount rate (i) = 5%
time is the 3LPE coating. Now make a 5-year cost estimate for each of the material as
maintenance is scheduled to be carried out for every 5 years’ therefore making a yearly life
time analysis would be useless. Nominal cost is calculated by multiplying the real cost with
the inflation factor given by ( 1+a ) y; where, a is the rate of inflation and y is the number of
years. The discounted cost at a discount of i% for n years is given by = nominal cost * 1
¿ ¿
The other factors that have to be considered while evaluating the Life Cycle Cost
analysis is the maintenance cost or the repair cost. As the initial requirement of materials was
fixed at 2000 kg, the requirement for repairing activity is assumed to the 20% of the initial
requirement and is therefore 400 kg. The same materials could be used for all the four
coatings.
Total cost of primer = $ 3.69 * 400 = $ 1476
Total cost of anti-corrosion tape = $ 2.58 (Anti-corrosion tape, 2017) * 500 pieces = $ 1290
Total cost of protective tape = $ 5 (Protection tape, 2017) * 400 square meter = $ 2000
Total cost of mastic tape = $ 7.5 (Mastic tape, 2017) * 400 pieces = $ 3000
The maintenance work has to be carried out within two months with the same work
force as used earlier. Therefore, the cost of labour will be evaluated for 8 hours a day for 50
days in the 60 days available. That is a total of 400 working hours to complete the
maintenance process every five years.
Total Labour cost for all the labourers employed for 50 days = $ 35.60 * 400 * 10 = $ 142400
Total Cost of the Technician for one year = $ 56.20 * 400 *1 = $ 22480
The highest average 5 years’ labour cost escalation = 6% (so every five years the labour cost
increases by 6%)
The highest average labour cost after 5 years = $ 142400 * 1.6 = $ 227840
The highest average Technician cost after 5 years = $ 22480 * 1.6 = $ 35968
Average inflation rate in Australia is (a) = 2% as of 2017
Discount rate (i) = 5%
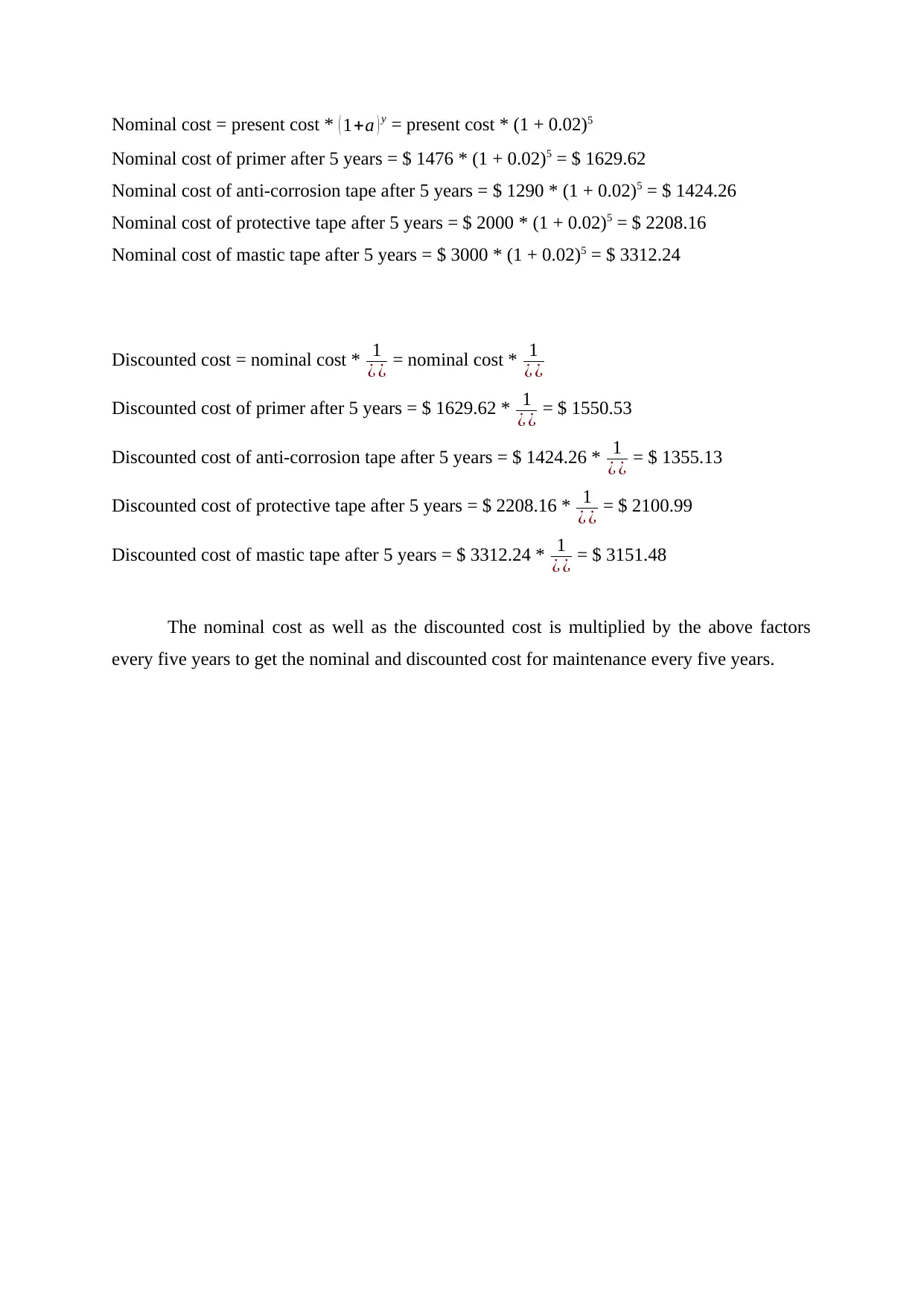
Nominal cost = present cost * ( 1+a ) y = present cost * (1 + 0.02)5
Nominal cost of primer after 5 years = $ 1476 * (1 + 0.02)5 = $ 1629.62
Nominal cost of anti-corrosion tape after 5 years = $ 1290 * (1 + 0.02)5 = $ 1424.26
Nominal cost of protective tape after 5 years = $ 2000 * (1 + 0.02)5 = $ 2208.16
Nominal cost of mastic tape after 5 years = $ 3000 * (1 + 0.02)5 = $ 3312.24
Discounted cost = nominal cost * 1
¿ ¿ = nominal cost * 1
¿ ¿
Discounted cost of primer after 5 years = $ 1629.62 * 1
¿ ¿ = $ 1550.53
Discounted cost of anti-corrosion tape after 5 years = $ 1424.26 * 1
¿ ¿ = $ 1355.13
Discounted cost of protective tape after 5 years = $ 2208.16 * 1
¿ ¿ = $ 2100.99
Discounted cost of mastic tape after 5 years = $ 3312.24 * 1
¿ ¿ = $ 3151.48
The nominal cost as well as the discounted cost is multiplied by the above factors
every five years to get the nominal and discounted cost for maintenance every five years.
Nominal cost of primer after 5 years = $ 1476 * (1 + 0.02)5 = $ 1629.62
Nominal cost of anti-corrosion tape after 5 years = $ 1290 * (1 + 0.02)5 = $ 1424.26
Nominal cost of protective tape after 5 years = $ 2000 * (1 + 0.02)5 = $ 2208.16
Nominal cost of mastic tape after 5 years = $ 3000 * (1 + 0.02)5 = $ 3312.24
Discounted cost = nominal cost * 1
¿ ¿ = nominal cost * 1
¿ ¿
Discounted cost of primer after 5 years = $ 1629.62 * 1
¿ ¿ = $ 1550.53
Discounted cost of anti-corrosion tape after 5 years = $ 1424.26 * 1
¿ ¿ = $ 1355.13
Discounted cost of protective tape after 5 years = $ 2208.16 * 1
¿ ¿ = $ 2100.99
Discounted cost of mastic tape after 5 years = $ 3312.24 * 1
¿ ¿ = $ 3151.48
The nominal cost as well as the discounted cost is multiplied by the above factors
every five years to get the nominal and discounted cost for maintenance every five years.

Life Cycle Cost Analysis of FBE coating
Specifications Year 0 Year 5 Year 10 Year 15 Year 20 Year 25 Year 30 Year 35 Year 40
Investment $
876204.00 - - - - - - - -
Discounted Cost of
Primer - $ 1512.71 $ 1550.34 $ 1588.91 $ 1628.43 $ 1668.94 $ 1710.45 $ 1753.00 $ 1796.60
Discounted Cost of
anti-corrosion tape - $ 1322.09 $ 1354.97 $ 1388.68 $ 1423.22 $ 1458.62 $ 1494.91 $ 1532.09 $ 1570.20
Discounted Cost of
protective tape - $ 2049.75 $ 2100.74 $ 2152.99 $ 2206.54 $ 2261.43 $ 2317.68 $ 2375.33 $ 2434.42
Discounted Cost of
mastic tape - $ 3074.62 $ 3151.10 $ 3229.48 $ 3309.82 $ 3392.15 $ 3476.52 $ 3563.00 $ 3651.63
Total material cost
for repairing - $ 7959.17 $ 8157.15 $ 8360.06 $ 8567.98 $ 8781.14 $ 8999.56 $ 9223.42 $ 9452.85
Labour Cost - $ 227840.00 $ 364544.00 $ 583270.40 $ 933232.64 $ 1493172.22 $ 2389075.56 $ 3822520.89 $ 6116033.43
Supervisor Cost - $ 35968.00 $ 57548.80 $ 92078.08 $ 147324.93 $ 235719.88 $ 377151.82 $ 603442.91 $ 965508.65
Specifications Year 0 Year 5 Year 10 Year 15 Year 20 Year 25 Year 30 Year 35 Year 40
Investment $
876204.00 - - - - - - - -
Discounted Cost of
Primer - $ 1512.71 $ 1550.34 $ 1588.91 $ 1628.43 $ 1668.94 $ 1710.45 $ 1753.00 $ 1796.60
Discounted Cost of
anti-corrosion tape - $ 1322.09 $ 1354.97 $ 1388.68 $ 1423.22 $ 1458.62 $ 1494.91 $ 1532.09 $ 1570.20
Discounted Cost of
protective tape - $ 2049.75 $ 2100.74 $ 2152.99 $ 2206.54 $ 2261.43 $ 2317.68 $ 2375.33 $ 2434.42
Discounted Cost of
mastic tape - $ 3074.62 $ 3151.10 $ 3229.48 $ 3309.82 $ 3392.15 $ 3476.52 $ 3563.00 $ 3651.63
Total material cost
for repairing - $ 7959.17 $ 8157.15 $ 8360.06 $ 8567.98 $ 8781.14 $ 8999.56 $ 9223.42 $ 9452.85
Labour Cost - $ 227840.00 $ 364544.00 $ 583270.40 $ 933232.64 $ 1493172.22 $ 2389075.56 $ 3822520.89 $ 6116033.43
Supervisor Cost - $ 35968.00 $ 57548.80 $ 92078.08 $ 147324.93 $ 235719.88 $ 377151.82 $ 603442.91 $ 965508.65
Paraphrase This Document
Need a fresh take? Get an instant paraphrase of this document with our AI Paraphraser
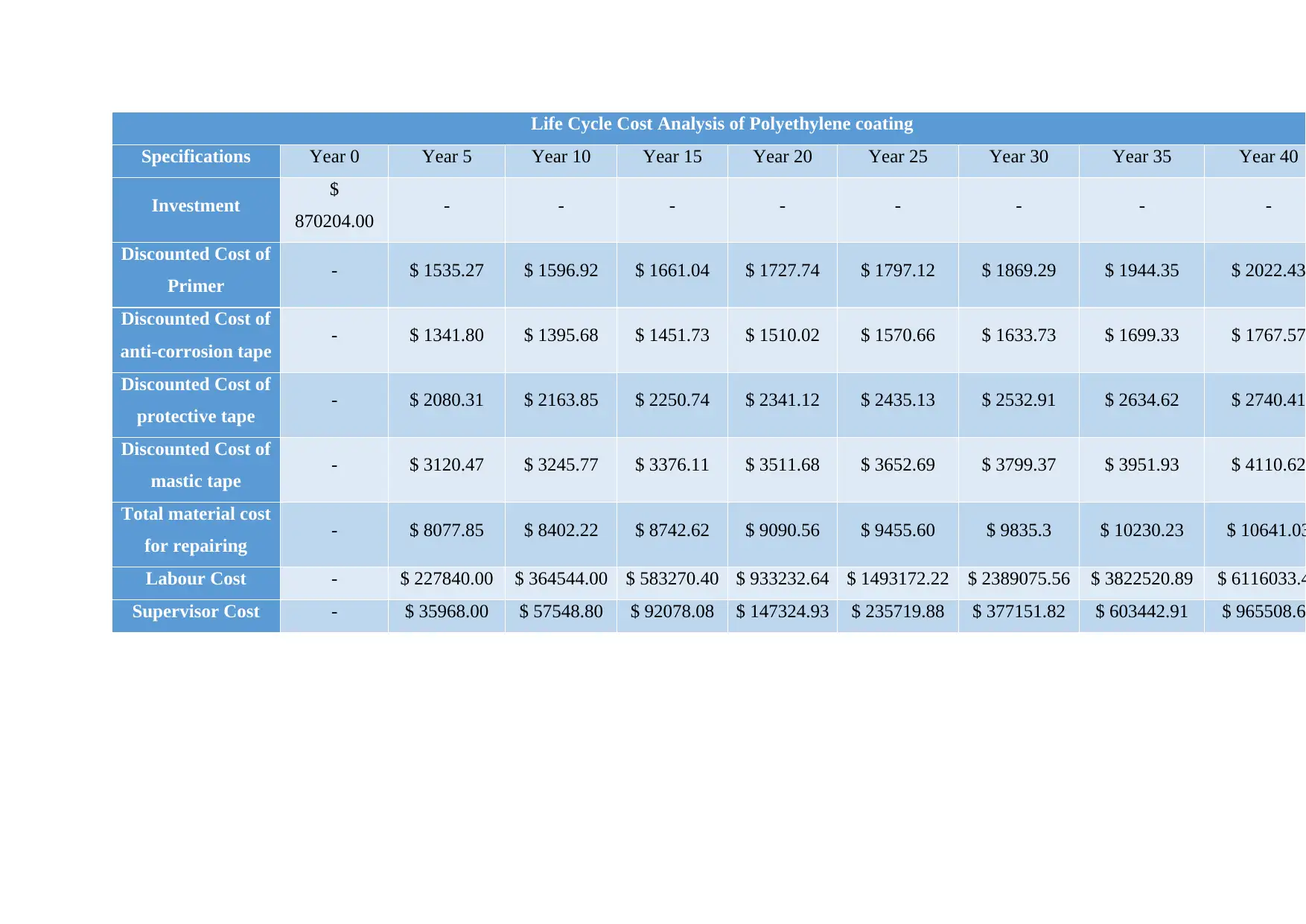
Life Cycle Cost Analysis of Polyethylene coating
Specifications Year 0 Year 5 Year 10 Year 15 Year 20 Year 25 Year 30 Year 35 Year 40
Investment $
870204.00 - - - - - - - -
Discounted Cost of
Primer - $ 1535.27 $ 1596.92 $ 1661.04 $ 1727.74 $ 1797.12 $ 1869.29 $ 1944.35 $ 2022.43
Discounted Cost of
anti-corrosion tape - $ 1341.80 $ 1395.68 $ 1451.73 $ 1510.02 $ 1570.66 $ 1633.73 $ 1699.33 $ 1767.57
Discounted Cost of
protective tape - $ 2080.31 $ 2163.85 $ 2250.74 $ 2341.12 $ 2435.13 $ 2532.91 $ 2634.62 $ 2740.41
Discounted Cost of
mastic tape - $ 3120.47 $ 3245.77 $ 3376.11 $ 3511.68 $ 3652.69 $ 3799.37 $ 3951.93 $ 4110.62
Total material cost
for repairing - $ 8077.85 $ 8402.22 $ 8742.62 $ 9090.56 $ 9455.60 $ 9835.3 $ 10230.23 $ 10641.03
Labour Cost - $ 227840.00 $ 364544.00 $ 583270.40 $ 933232.64 $ 1493172.22 $ 2389075.56 $ 3822520.89 $ 6116033.4
Supervisor Cost - $ 35968.00 $ 57548.80 $ 92078.08 $ 147324.93 $ 235719.88 $ 377151.82 $ 603442.91 $ 965508.6
Specifications Year 0 Year 5 Year 10 Year 15 Year 20 Year 25 Year 30 Year 35 Year 40
Investment $
870204.00 - - - - - - - -
Discounted Cost of
Primer - $ 1535.27 $ 1596.92 $ 1661.04 $ 1727.74 $ 1797.12 $ 1869.29 $ 1944.35 $ 2022.43
Discounted Cost of
anti-corrosion tape - $ 1341.80 $ 1395.68 $ 1451.73 $ 1510.02 $ 1570.66 $ 1633.73 $ 1699.33 $ 1767.57
Discounted Cost of
protective tape - $ 2080.31 $ 2163.85 $ 2250.74 $ 2341.12 $ 2435.13 $ 2532.91 $ 2634.62 $ 2740.41
Discounted Cost of
mastic tape - $ 3120.47 $ 3245.77 $ 3376.11 $ 3511.68 $ 3652.69 $ 3799.37 $ 3951.93 $ 4110.62
Total material cost
for repairing - $ 8077.85 $ 8402.22 $ 8742.62 $ 9090.56 $ 9455.60 $ 9835.3 $ 10230.23 $ 10641.03
Labour Cost - $ 227840.00 $ 364544.00 $ 583270.40 $ 933232.64 $ 1493172.22 $ 2389075.56 $ 3822520.89 $ 6116033.4
Supervisor Cost - $ 35968.00 $ 57548.80 $ 92078.08 $ 147324.93 $ 235719.88 $ 377151.82 $ 603442.91 $ 965508.6
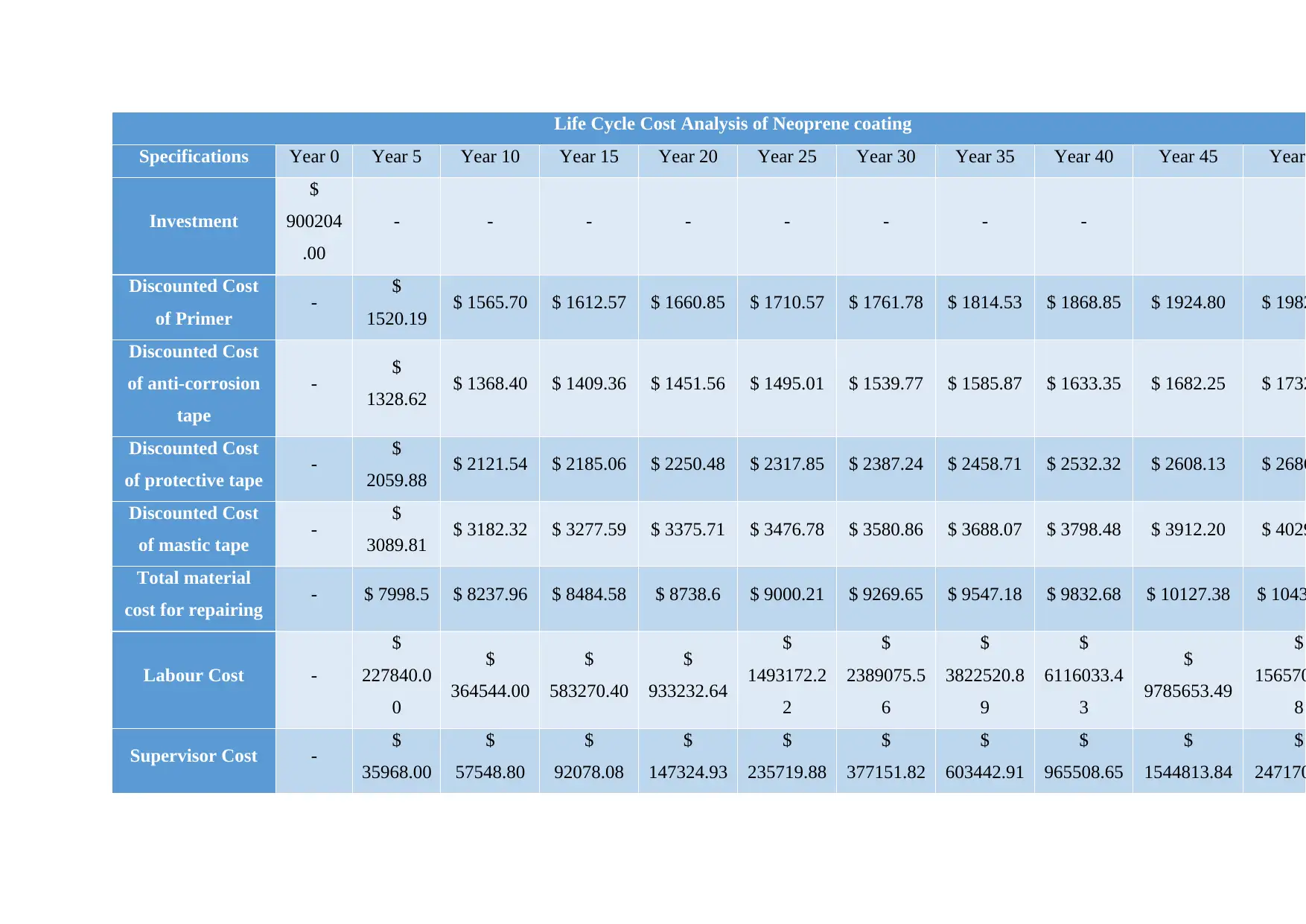
Life Cycle Cost Analysis of Neoprene coating
Specifications Year 0 Year 5 Year 10 Year 15 Year 20 Year 25 Year 30 Year 35 Year 40 Year 45 Year
Investment
$
900204
.00
- - - - - - - -
Discounted Cost
of Primer - $
1520.19 $ 1565.70 $ 1612.57 $ 1660.85 $ 1710.57 $ 1761.78 $ 1814.53 $ 1868.85 $ 1924.80 $ 1982
Discounted Cost
of anti-corrosion
tape
- $
1328.62 $ 1368.40 $ 1409.36 $ 1451.56 $ 1495.01 $ 1539.77 $ 1585.87 $ 1633.35 $ 1682.25 $ 1732
Discounted Cost
of protective tape - $
2059.88 $ 2121.54 $ 2185.06 $ 2250.48 $ 2317.85 $ 2387.24 $ 2458.71 $ 2532.32 $ 2608.13 $ 2686
Discounted Cost
of mastic tape - $
3089.81 $ 3182.32 $ 3277.59 $ 3375.71 $ 3476.78 $ 3580.86 $ 3688.07 $ 3798.48 $ 3912.20 $ 4029
Total material
cost for repairing - $ 7998.5 $ 8237.96 $ 8484.58 $ 8738.6 $ 9000.21 $ 9269.65 $ 9547.18 $ 9832.68 $ 10127.38 $ 1043
Labour Cost -
$
227840.0
0
$
364544.00
$
583270.40
$
933232.64
$
1493172.2
2
$
2389075.5
6
$
3822520.8
9
$
6116033.4
3
$
9785653.49
$
156570
8
Supervisor Cost - $
35968.00
$
57548.80
$
92078.08
$
147324.93
$
235719.88
$
377151.82
$
603442.91
$
965508.65
$
1544813.84
$
247170
Specifications Year 0 Year 5 Year 10 Year 15 Year 20 Year 25 Year 30 Year 35 Year 40 Year 45 Year
Investment
$
900204
.00
- - - - - - - -
Discounted Cost
of Primer - $
1520.19 $ 1565.70 $ 1612.57 $ 1660.85 $ 1710.57 $ 1761.78 $ 1814.53 $ 1868.85 $ 1924.80 $ 1982
Discounted Cost
of anti-corrosion
tape
- $
1328.62 $ 1368.40 $ 1409.36 $ 1451.56 $ 1495.01 $ 1539.77 $ 1585.87 $ 1633.35 $ 1682.25 $ 1732
Discounted Cost
of protective tape - $
2059.88 $ 2121.54 $ 2185.06 $ 2250.48 $ 2317.85 $ 2387.24 $ 2458.71 $ 2532.32 $ 2608.13 $ 2686
Discounted Cost
of mastic tape - $
3089.81 $ 3182.32 $ 3277.59 $ 3375.71 $ 3476.78 $ 3580.86 $ 3688.07 $ 3798.48 $ 3912.20 $ 4029
Total material
cost for repairing - $ 7998.5 $ 8237.96 $ 8484.58 $ 8738.6 $ 9000.21 $ 9269.65 $ 9547.18 $ 9832.68 $ 10127.38 $ 1043
Labour Cost -
$
227840.0
0
$
364544.00
$
583270.40
$
933232.64
$
1493172.2
2
$
2389075.5
6
$
3822520.8
9
$
6116033.4
3
$
9785653.49
$
156570
8
Supervisor Cost - $
35968.00
$
57548.80
$
92078.08
$
147324.93
$
235719.88
$
377151.82
$
603442.91
$
965508.65
$
1544813.84
$
247170
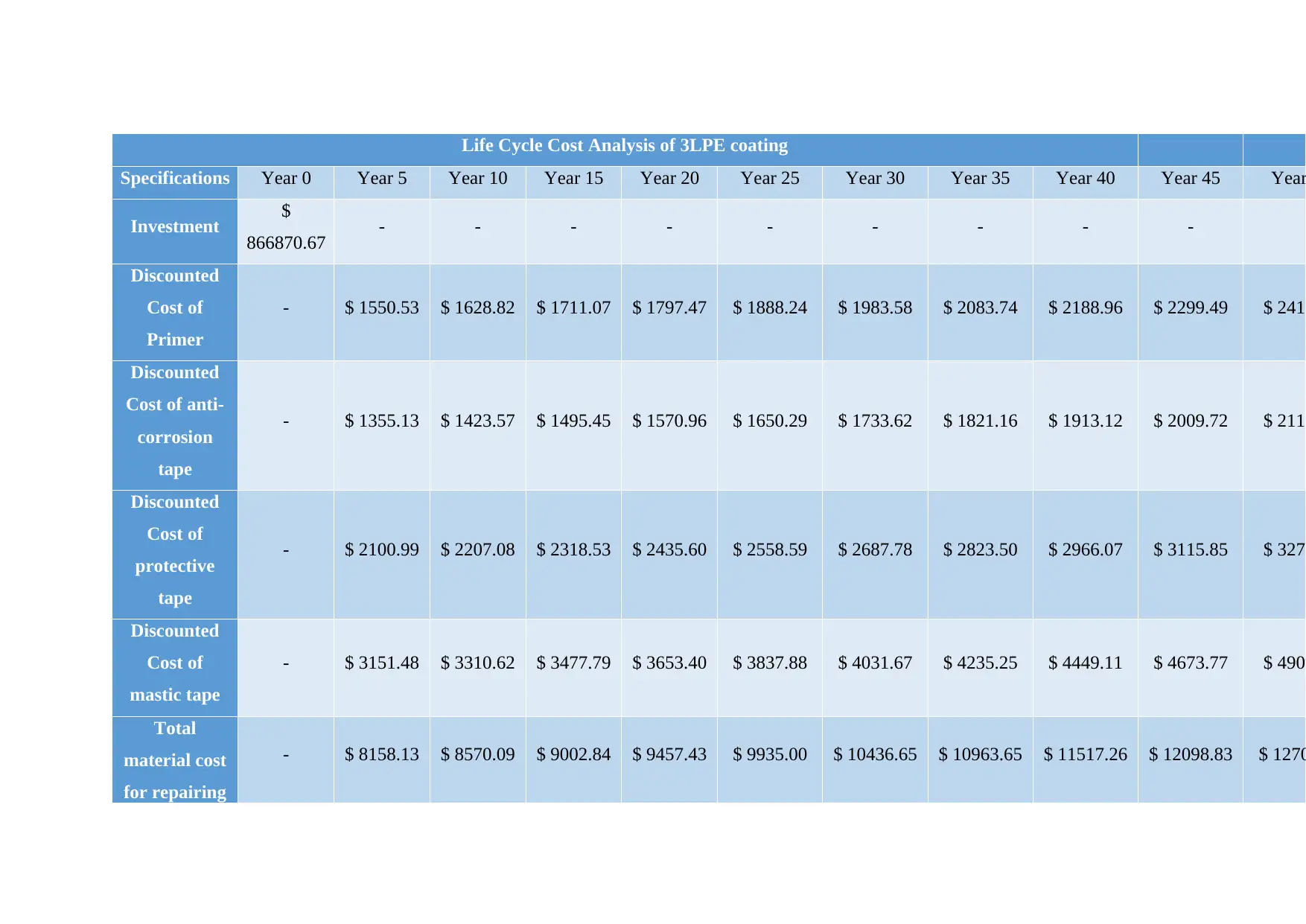
Life Cycle Cost Analysis of 3LPE coating
Specifications Year 0 Year 5 Year 10 Year 15 Year 20 Year 25 Year 30 Year 35 Year 40 Year 45 Year
Investment $
866870.67 - - - - - - - - -
Discounted
Cost of
Primer
- $ 1550.53 $ 1628.82 $ 1711.07 $ 1797.47 $ 1888.24 $ 1983.58 $ 2083.74 $ 2188.96 $ 2299.49 $ 2415
Discounted
Cost of anti-
corrosion
tape
- $ 1355.13 $ 1423.57 $ 1495.45 $ 1570.96 $ 1650.29 $ 1733.62 $ 1821.16 $ 1913.12 $ 2009.72 $ 2111
Discounted
Cost of
protective
tape
- $ 2100.99 $ 2207.08 $ 2318.53 $ 2435.60 $ 2558.59 $ 2687.78 $ 2823.50 $ 2966.07 $ 3115.85 $ 3273
Discounted
Cost of
mastic tape
- $ 3151.48 $ 3310.62 $ 3477.79 $ 3653.40 $ 3837.88 $ 4031.67 $ 4235.25 $ 4449.11 $ 4673.77 $ 4909
Total
material cost
for repairing
- $ 8158.13 $ 8570.09 $ 9002.84 $ 9457.43 $ 9935.00 $ 10436.65 $ 10963.65 $ 11517.26 $ 12098.83 $ 1270
Specifications Year 0 Year 5 Year 10 Year 15 Year 20 Year 25 Year 30 Year 35 Year 40 Year 45 Year
Investment $
866870.67 - - - - - - - - -
Discounted
Cost of
Primer
- $ 1550.53 $ 1628.82 $ 1711.07 $ 1797.47 $ 1888.24 $ 1983.58 $ 2083.74 $ 2188.96 $ 2299.49 $ 2415
Discounted
Cost of anti-
corrosion
tape
- $ 1355.13 $ 1423.57 $ 1495.45 $ 1570.96 $ 1650.29 $ 1733.62 $ 1821.16 $ 1913.12 $ 2009.72 $ 2111
Discounted
Cost of
protective
tape
- $ 2100.99 $ 2207.08 $ 2318.53 $ 2435.60 $ 2558.59 $ 2687.78 $ 2823.50 $ 2966.07 $ 3115.85 $ 3273
Discounted
Cost of
mastic tape
- $ 3151.48 $ 3310.62 $ 3477.79 $ 3653.40 $ 3837.88 $ 4031.67 $ 4235.25 $ 4449.11 $ 4673.77 $ 4909
Total
material cost
for repairing
- $ 8158.13 $ 8570.09 $ 9002.84 $ 9457.43 $ 9935.00 $ 10436.65 $ 10963.65 $ 11517.26 $ 12098.83 $ 1270
Secure Best Marks with AI Grader
Need help grading? Try our AI Grader for instant feedback on your assignments.
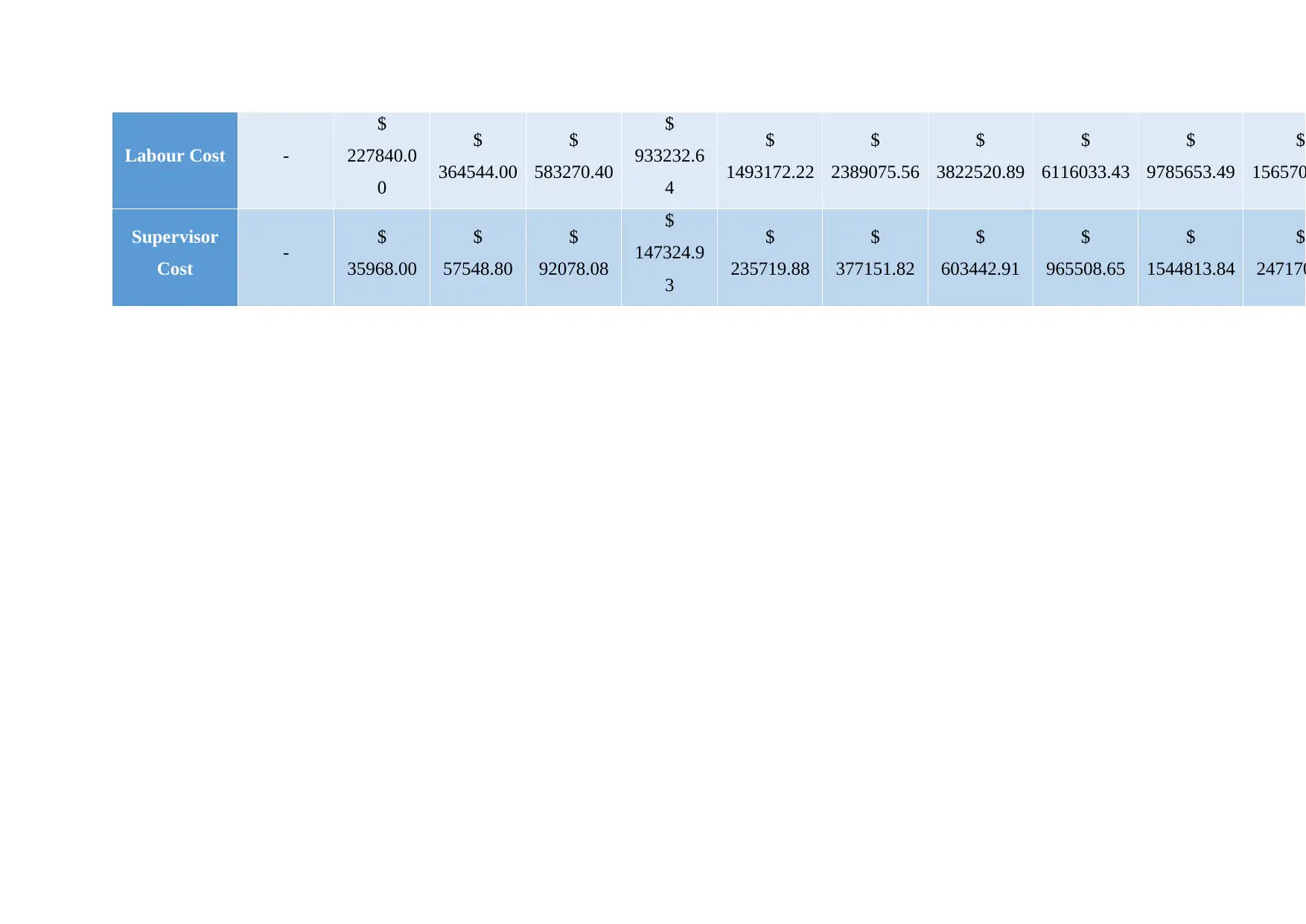
Labour Cost -
$
227840.0
0
$
364544.00
$
583270.40
$
933232.6
4
$
1493172.22
$
2389075.56
$
3822520.89
$
6116033.43
$
9785653.49
$
156570
Supervisor
Cost - $
35968.00
$
57548.80
$
92078.08
$
147324.9
3
$
235719.88
$
377151.82
$
603442.91
$
965508.65
$
1544813.84
$
247170
$
227840.0
0
$
364544.00
$
583270.40
$
933232.6
4
$
1493172.22
$
2389075.56
$
3822520.89
$
6116033.43
$
9785653.49
$
156570
Supervisor
Cost - $
35968.00
$
57548.80
$
92078.08
$
147324.9
3
$
235719.88
$
377151.82
$
603442.91
$
965508.65
$
1544813.84
$
247170
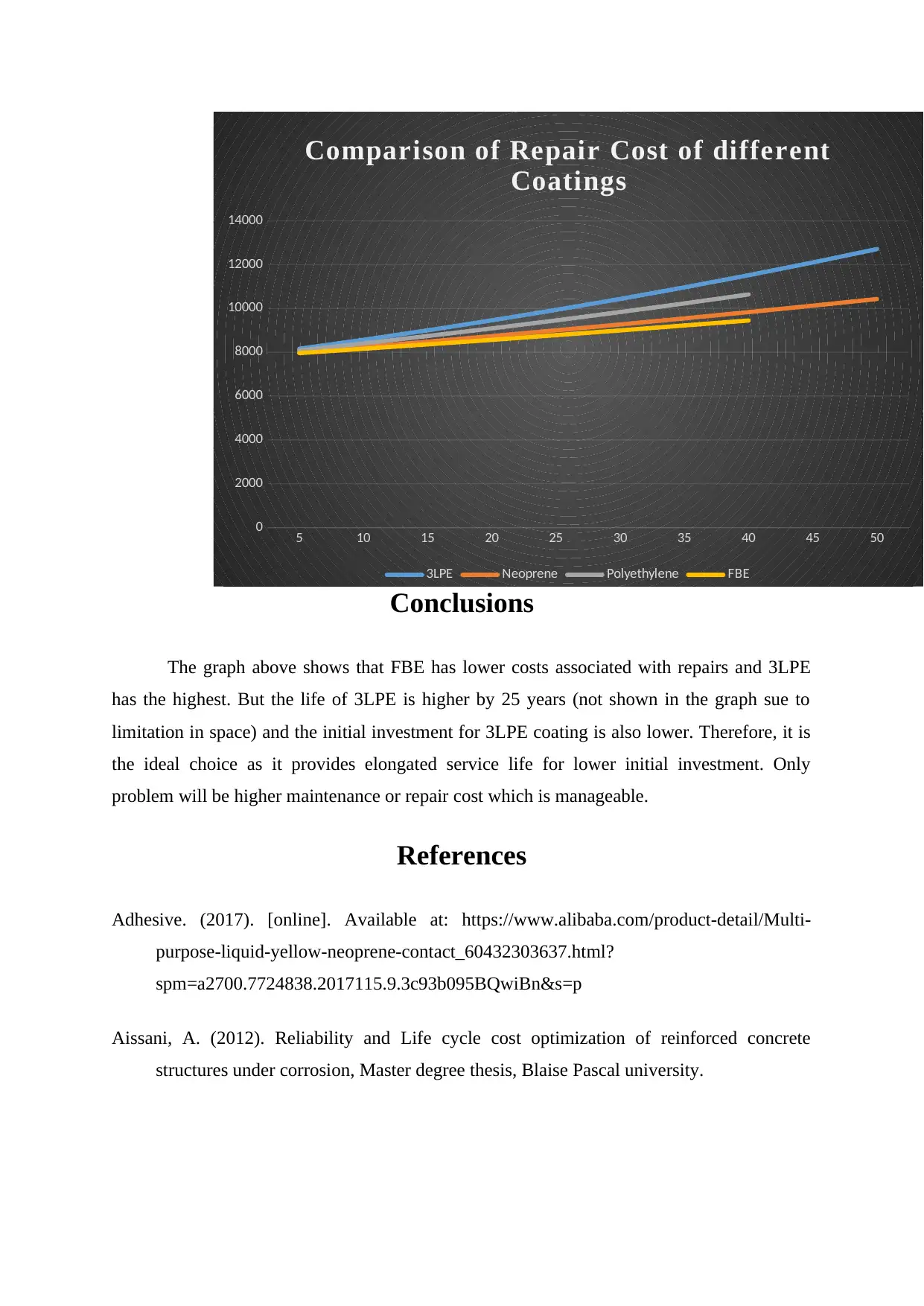
Conclusions
The graph above shows that FBE has lower costs associated with repairs and 3LPE
has the highest. But the life of 3LPE is higher by 25 years (not shown in the graph sue to
limitation in space) and the initial investment for 3LPE coating is also lower. Therefore, it is
the ideal choice as it provides elongated service life for lower initial investment. Only
problem will be higher maintenance or repair cost which is manageable.
References
Adhesive. (2017). [online]. Available at: https://www.alibaba.com/product-detail/Multi-
purpose-liquid-yellow-neoprene-contact_60432303637.html?
spm=a2700.7724838.2017115.9.3c93b095BQwiBn&s=p
Aissani, A. (2012). Reliability and Life cycle cost optimization of reinforced concrete
structures under corrosion, Master degree thesis, Blaise Pascal university.
5 10 15 20 25 30 35 40 45 50
0
2000
4000
6000
8000
10000
12000
14000
Comparison of Repair Cost of different
Coatings
3LPE Neoprene Polyethylene FBE
The graph above shows that FBE has lower costs associated with repairs and 3LPE
has the highest. But the life of 3LPE is higher by 25 years (not shown in the graph sue to
limitation in space) and the initial investment for 3LPE coating is also lower. Therefore, it is
the ideal choice as it provides elongated service life for lower initial investment. Only
problem will be higher maintenance or repair cost which is manageable.
References
Adhesive. (2017). [online]. Available at: https://www.alibaba.com/product-detail/Multi-
purpose-liquid-yellow-neoprene-contact_60432303637.html?
spm=a2700.7724838.2017115.9.3c93b095BQwiBn&s=p
Aissani, A. (2012). Reliability and Life cycle cost optimization of reinforced concrete
structures under corrosion, Master degree thesis, Blaise Pascal university.
5 10 15 20 25 30 35 40 45 50
0
2000
4000
6000
8000
10000
12000
14000
Comparison of Repair Cost of different
Coatings
3LPE Neoprene Polyethylene FBE
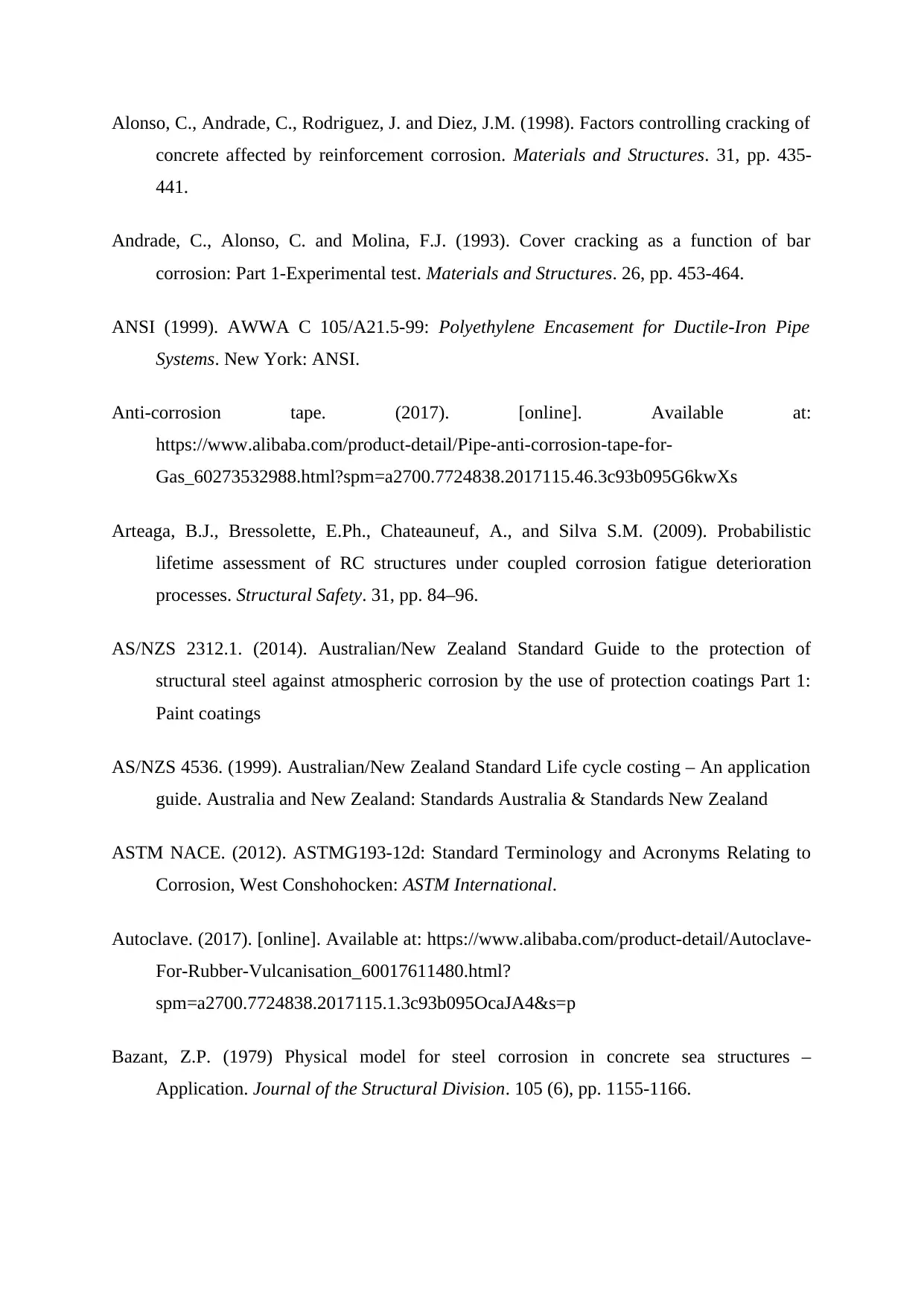
Alonso, C., Andrade, C., Rodriguez, J. and Diez, J.M. (1998). Factors controlling cracking of
concrete affected by reinforcement corrosion. Materials and Structures. 31, pp. 435-
441.
Andrade, C., Alonso, C. and Molina, F.J. (1993). Cover cracking as a function of bar
corrosion: Part 1-Experimental test. Materials and Structures. 26, pp. 453-464.
ANSI (1999). AWWA C 105/A21.5-99: Polyethylene Encasement for Ductile-Iron Pipe
Systems. New York: ANSI.
Anti-corrosion tape. (2017). [online]. Available at:
https://www.alibaba.com/product-detail/Pipe-anti-corrosion-tape-for-
Gas_60273532988.html?spm=a2700.7724838.2017115.46.3c93b095G6kwXs
Arteaga, B.J., Bressolette, E.Ph., Chateauneuf, A., and Silva S.M. (2009). Probabilistic
lifetime assessment of RC structures under coupled corrosion fatigue deterioration
processes. Structural Safety. 31, pp. 84–96.
AS/NZS 2312.1. (2014). Australian/New Zealand Standard Guide to the protection of
structural steel against atmospheric corrosion by the use of protection coatings Part 1:
Paint coatings
AS/NZS 4536. (1999). Australian/New Zealand Standard Life cycle costing – An application
guide. Australia and New Zealand: Standards Australia & Standards New Zealand
ASTM NACE. (2012). ASTMG193-12d: Standard Terminology and Acronyms Relating to
Corrosion, West Conshohocken: ASTM International.
Autoclave. (2017). [online]. Available at: https://www.alibaba.com/product-detail/Autoclave-
For-Rubber-Vulcanisation_60017611480.html?
spm=a2700.7724838.2017115.1.3c93b095OcaJA4&s=p
Bazant, Z.P. (1979) Physical model for steel corrosion in concrete sea structures –
Application. Journal of the Structural Division. 105 (6), pp. 1155-1166.
concrete affected by reinforcement corrosion. Materials and Structures. 31, pp. 435-
441.
Andrade, C., Alonso, C. and Molina, F.J. (1993). Cover cracking as a function of bar
corrosion: Part 1-Experimental test. Materials and Structures. 26, pp. 453-464.
ANSI (1999). AWWA C 105/A21.5-99: Polyethylene Encasement for Ductile-Iron Pipe
Systems. New York: ANSI.
Anti-corrosion tape. (2017). [online]. Available at:
https://www.alibaba.com/product-detail/Pipe-anti-corrosion-tape-for-
Gas_60273532988.html?spm=a2700.7724838.2017115.46.3c93b095G6kwXs
Arteaga, B.J., Bressolette, E.Ph., Chateauneuf, A., and Silva S.M. (2009). Probabilistic
lifetime assessment of RC structures under coupled corrosion fatigue deterioration
processes. Structural Safety. 31, pp. 84–96.
AS/NZS 2312.1. (2014). Australian/New Zealand Standard Guide to the protection of
structural steel against atmospheric corrosion by the use of protection coatings Part 1:
Paint coatings
AS/NZS 4536. (1999). Australian/New Zealand Standard Life cycle costing – An application
guide. Australia and New Zealand: Standards Australia & Standards New Zealand
ASTM NACE. (2012). ASTMG193-12d: Standard Terminology and Acronyms Relating to
Corrosion, West Conshohocken: ASTM International.
Autoclave. (2017). [online]. Available at: https://www.alibaba.com/product-detail/Autoclave-
For-Rubber-Vulcanisation_60017611480.html?
spm=a2700.7724838.2017115.1.3c93b095OcaJA4&s=p
Bazant, Z.P. (1979) Physical model for steel corrosion in concrete sea structures –
Application. Journal of the Structural Division. 105 (6), pp. 1155-1166.
Paraphrase This Document
Need a fresh take? Get an instant paraphrase of this document with our AI Paraphraser
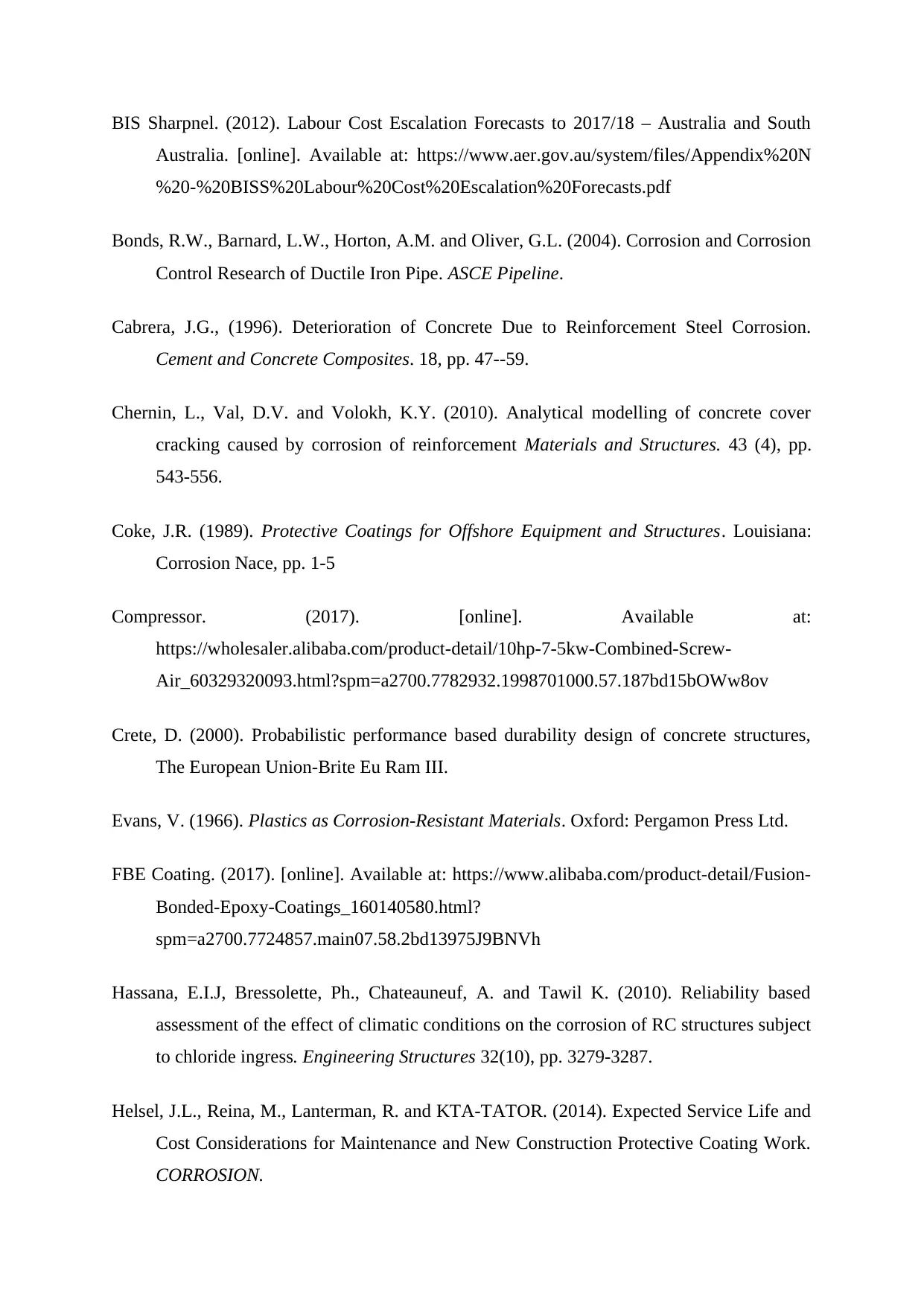
BIS Sharpnel. (2012). Labour Cost Escalation Forecasts to 2017/18 – Australia and South
Australia. [online]. Available at: https://www.aer.gov.au/system/files/Appendix%20N
%20-%20BISS%20Labour%20Cost%20Escalation%20Forecasts.pdf
Bonds, R.W., Barnard, L.W., Horton, A.M. and Oliver, G.L. (2004). Corrosion and Corrosion
Control Research of Ductile Iron Pipe. ASCE Pipeline.
Cabrera, J.G., (1996). Deterioration of Concrete Due to Reinforcement Steel Corrosion.
Cement and Concrete Composites. 18, pp. 47--59.
Chernin, L., Val, D.V. and Volokh, K.Y. (2010). Analytical modelling of concrete cover
cracking caused by corrosion of reinforcement Materials and Structures. 43 (4), pp.
543-556.
Coke, J.R. (1989). Protective Coatings for Offshore Equipment and Structures. Louisiana:
Corrosion Nace, pp. 1-5
Compressor. (2017). [online]. Available at:
https://wholesaler.alibaba.com/product-detail/10hp-7-5kw-Combined-Screw-
Air_60329320093.html?spm=a2700.7782932.1998701000.57.187bd15bOWw8ov
Crete, D. (2000). Probabilistic performance based durability design of concrete structures,
The European Union-Brite Eu Ram III.
Evans, V. (1966). Plastics as Corrosion-Resistant Materials. Oxford: Pergamon Press Ltd.
FBE Coating. (2017). [online]. Available at: https://www.alibaba.com/product-detail/Fusion-
Bonded-Epoxy-Coatings_160140580.html?
spm=a2700.7724857.main07.58.2bd13975J9BNVh
Hassana, E.I.J, Bressolette, Ph., Chateauneuf, A. and Tawil K. (2010). Reliability based
assessment of the effect of climatic conditions on the corrosion of RC structures subject
to chloride ingress. Engineering Structures 32(10), pp. 3279-3287.
Helsel, J.L., Reina, M., Lanterman, R. and KTA-TATOR. (2014). Expected Service Life and
Cost Considerations for Maintenance and New Construction Protective Coating Work.
CORROSION.
Australia. [online]. Available at: https://www.aer.gov.au/system/files/Appendix%20N
%20-%20BISS%20Labour%20Cost%20Escalation%20Forecasts.pdf
Bonds, R.W., Barnard, L.W., Horton, A.M. and Oliver, G.L. (2004). Corrosion and Corrosion
Control Research of Ductile Iron Pipe. ASCE Pipeline.
Cabrera, J.G., (1996). Deterioration of Concrete Due to Reinforcement Steel Corrosion.
Cement and Concrete Composites. 18, pp. 47--59.
Chernin, L., Val, D.V. and Volokh, K.Y. (2010). Analytical modelling of concrete cover
cracking caused by corrosion of reinforcement Materials and Structures. 43 (4), pp.
543-556.
Coke, J.R. (1989). Protective Coatings for Offshore Equipment and Structures. Louisiana:
Corrosion Nace, pp. 1-5
Compressor. (2017). [online]. Available at:
https://wholesaler.alibaba.com/product-detail/10hp-7-5kw-Combined-Screw-
Air_60329320093.html?spm=a2700.7782932.1998701000.57.187bd15bOWw8ov
Crete, D. (2000). Probabilistic performance based durability design of concrete structures,
The European Union-Brite Eu Ram III.
Evans, V. (1966). Plastics as Corrosion-Resistant Materials. Oxford: Pergamon Press Ltd.
FBE Coating. (2017). [online]. Available at: https://www.alibaba.com/product-detail/Fusion-
Bonded-Epoxy-Coatings_160140580.html?
spm=a2700.7724857.main07.58.2bd13975J9BNVh
Hassana, E.I.J, Bressolette, Ph., Chateauneuf, A. and Tawil K. (2010). Reliability based
assessment of the effect of climatic conditions on the corrosion of RC structures subject
to chloride ingress. Engineering Structures 32(10), pp. 3279-3287.
Helsel, J.L., Reina, M., Lanterman, R. and KTA-TATOR. (2014). Expected Service Life and
Cost Considerations for Maintenance and New Construction Protective Coating Work.
CORROSION.
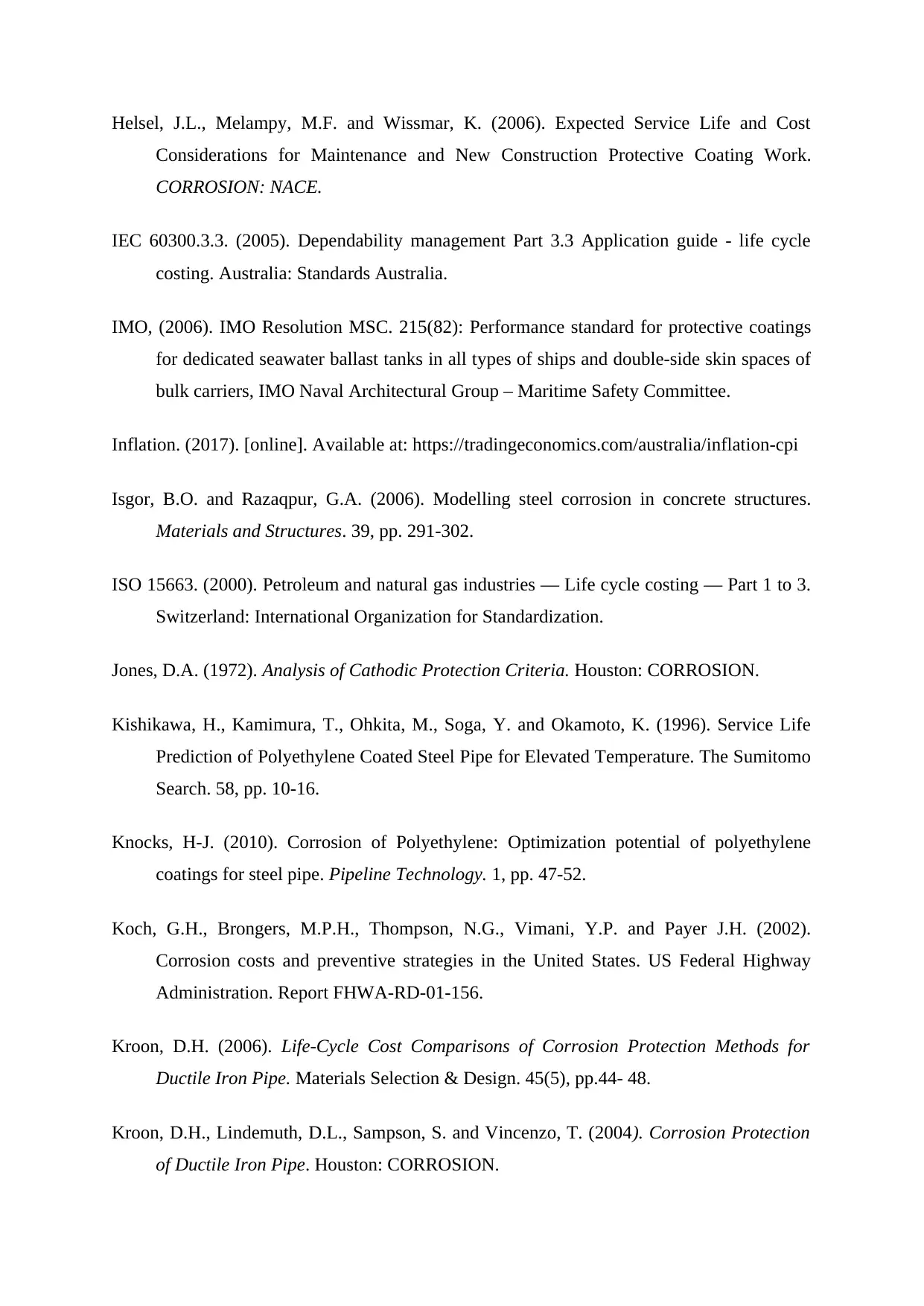
Helsel, J.L., Melampy, M.F. and Wissmar, K. (2006). Expected Service Life and Cost
Considerations for Maintenance and New Construction Protective Coating Work.
CORROSION: NACE.
IEC 60300.3.3. (2005). Dependability management Part 3.3 Application guide - life cycle
costing. Australia: Standards Australia.
IMO, (2006). IMO Resolution MSC. 215(82): Performance standard for protective coatings
for dedicated seawater ballast tanks in all types of ships and double-side skin spaces of
bulk carriers, IMO Naval Architectural Group – Maritime Safety Committee.
Inflation. (2017). [online]. Available at: https://tradingeconomics.com/australia/inflation-cpi
Isgor, B.O. and Razaqpur, G.A. (2006). Modelling steel corrosion in concrete structures.
Materials and Structures. 39, pp. 291-302.
ISO 15663. (2000). Petroleum and natural gas industries — Life cycle costing — Part 1 to 3.
Switzerland: International Organization for Standardization.
Jones, D.A. (1972). Analysis of Cathodic Protection Criteria. Houston: CORROSION.
Kishikawa, H., Kamimura, T., Ohkita, M., Soga, Y. and Okamoto, K. (1996). Service Life
Prediction of Polyethylene Coated Steel Pipe for Elevated Temperature. The Sumitomo
Search. 58, pp. 10-16.
Knocks, H-J. (2010). Corrosion of Polyethylene: Optimization potential of polyethylene
coatings for steel pipe. Pipeline Technology. 1, pp. 47-52.
Koch, G.H., Brongers, M.P.H., Thompson, N.G., Vimani, Y.P. and Payer J.H. (2002).
Corrosion costs and preventive strategies in the United States. US Federal Highway
Administration. Report FHWA-RD-01-156.
Kroon, D.H. (2006). Life-Cycle Cost Comparisons of Corrosion Protection Methods for
Ductile Iron Pipe. Materials Selection & Design. 45(5), pp.44- 48.
Kroon, D.H., Lindemuth, D.L., Sampson, S. and Vincenzo, T. (2004). Corrosion Protection
of Ductile Iron Pipe. Houston: CORROSION.
Considerations for Maintenance and New Construction Protective Coating Work.
CORROSION: NACE.
IEC 60300.3.3. (2005). Dependability management Part 3.3 Application guide - life cycle
costing. Australia: Standards Australia.
IMO, (2006). IMO Resolution MSC. 215(82): Performance standard for protective coatings
for dedicated seawater ballast tanks in all types of ships and double-side skin spaces of
bulk carriers, IMO Naval Architectural Group – Maritime Safety Committee.
Inflation. (2017). [online]. Available at: https://tradingeconomics.com/australia/inflation-cpi
Isgor, B.O. and Razaqpur, G.A. (2006). Modelling steel corrosion in concrete structures.
Materials and Structures. 39, pp. 291-302.
ISO 15663. (2000). Petroleum and natural gas industries — Life cycle costing — Part 1 to 3.
Switzerland: International Organization for Standardization.
Jones, D.A. (1972). Analysis of Cathodic Protection Criteria. Houston: CORROSION.
Kishikawa, H., Kamimura, T., Ohkita, M., Soga, Y. and Okamoto, K. (1996). Service Life
Prediction of Polyethylene Coated Steel Pipe for Elevated Temperature. The Sumitomo
Search. 58, pp. 10-16.
Knocks, H-J. (2010). Corrosion of Polyethylene: Optimization potential of polyethylene
coatings for steel pipe. Pipeline Technology. 1, pp. 47-52.
Koch, G.H., Brongers, M.P.H., Thompson, N.G., Vimani, Y.P. and Payer J.H. (2002).
Corrosion costs and preventive strategies in the United States. US Federal Highway
Administration. Report FHWA-RD-01-156.
Kroon, D.H. (2006). Life-Cycle Cost Comparisons of Corrosion Protection Methods for
Ductile Iron Pipe. Materials Selection & Design. 45(5), pp.44- 48.
Kroon, D.H., Lindemuth, D.L., Sampson, S. and Vincenzo, T. (2004). Corrosion Protection
of Ductile Iron Pipe. Houston: CORROSION.
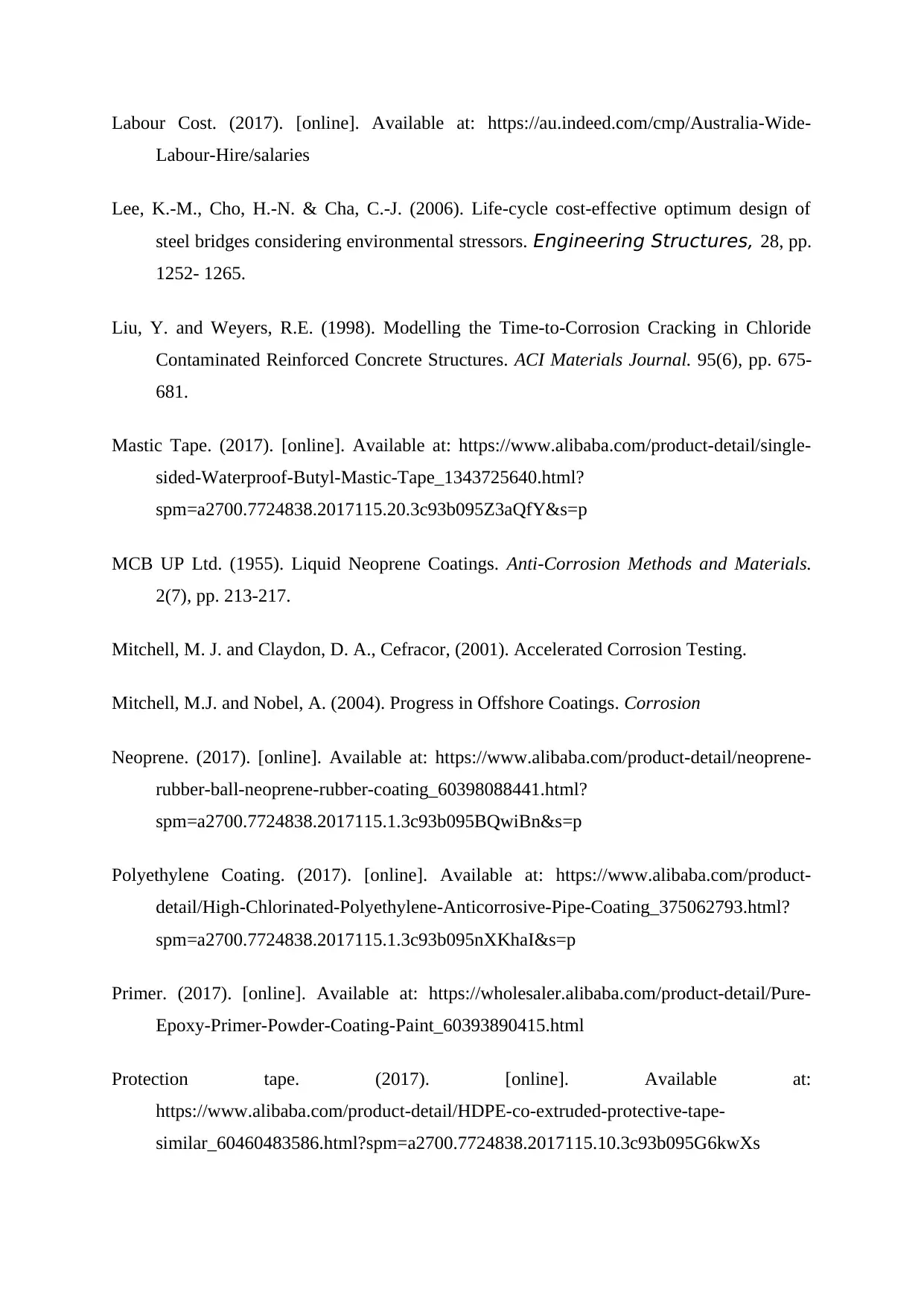
Labour Cost. (2017). [online]. Available at: https://au.indeed.com/cmp/Australia-Wide-
Labour-Hire/salaries
Lee, K.-M., Cho, H.-N. & Cha, C.-J. (2006). Life-cycle cost-effective optimum design of
steel bridges considering environmental stressors. Engineering Structures, 28, pp.
1252- 1265.
Liu, Y. and Weyers, R.E. (1998). Modelling the Time-to-Corrosion Cracking in Chloride
Contaminated Reinforced Concrete Structures. ACI Materials Journal. 95(6), pp. 675-
681.
Mastic Tape. (2017). [online]. Available at: https://www.alibaba.com/product-detail/single-
sided-Waterproof-Butyl-Mastic-Tape_1343725640.html?
spm=a2700.7724838.2017115.20.3c93b095Z3aQfY&s=p
MCB UP Ltd. (1955). Liquid Neoprene Coatings. Anti-Corrosion Methods and Materials.
2(7), pp. 213-217.
Mitchell, M. J. and Claydon, D. A., Cefracor, (2001). Accelerated Corrosion Testing.
Mitchell, M.J. and Nobel, A. (2004). Progress in Offshore Coatings. Corrosion
Neoprene. (2017). [online]. Available at: https://www.alibaba.com/product-detail/neoprene-
rubber-ball-neoprene-rubber-coating_60398088441.html?
spm=a2700.7724838.2017115.1.3c93b095BQwiBn&s=p
Polyethylene Coating. (2017). [online]. Available at: https://www.alibaba.com/product-
detail/High-Chlorinated-Polyethylene-Anticorrosive-Pipe-Coating_375062793.html?
spm=a2700.7724838.2017115.1.3c93b095nXKhaI&s=p
Primer. (2017). [online]. Available at: https://wholesaler.alibaba.com/product-detail/Pure-
Epoxy-Primer-Powder-Coating-Paint_60393890415.html
Protection tape. (2017). [online]. Available at:
https://www.alibaba.com/product-detail/HDPE-co-extruded-protective-tape-
similar_60460483586.html?spm=a2700.7724838.2017115.10.3c93b095G6kwXs
Labour-Hire/salaries
Lee, K.-M., Cho, H.-N. & Cha, C.-J. (2006). Life-cycle cost-effective optimum design of
steel bridges considering environmental stressors. Engineering Structures, 28, pp.
1252- 1265.
Liu, Y. and Weyers, R.E. (1998). Modelling the Time-to-Corrosion Cracking in Chloride
Contaminated Reinforced Concrete Structures. ACI Materials Journal. 95(6), pp. 675-
681.
Mastic Tape. (2017). [online]. Available at: https://www.alibaba.com/product-detail/single-
sided-Waterproof-Butyl-Mastic-Tape_1343725640.html?
spm=a2700.7724838.2017115.20.3c93b095Z3aQfY&s=p
MCB UP Ltd. (1955). Liquid Neoprene Coatings. Anti-Corrosion Methods and Materials.
2(7), pp. 213-217.
Mitchell, M. J. and Claydon, D. A., Cefracor, (2001). Accelerated Corrosion Testing.
Mitchell, M.J. and Nobel, A. (2004). Progress in Offshore Coatings. Corrosion
Neoprene. (2017). [online]. Available at: https://www.alibaba.com/product-detail/neoprene-
rubber-ball-neoprene-rubber-coating_60398088441.html?
spm=a2700.7724838.2017115.1.3c93b095BQwiBn&s=p
Polyethylene Coating. (2017). [online]. Available at: https://www.alibaba.com/product-
detail/High-Chlorinated-Polyethylene-Anticorrosive-Pipe-Coating_375062793.html?
spm=a2700.7724838.2017115.1.3c93b095nXKhaI&s=p
Primer. (2017). [online]. Available at: https://wholesaler.alibaba.com/product-detail/Pure-
Epoxy-Primer-Powder-Coating-Paint_60393890415.html
Protection tape. (2017). [online]. Available at:
https://www.alibaba.com/product-detail/HDPE-co-extruded-protective-tape-
similar_60460483586.html?spm=a2700.7724838.2017115.10.3c93b095G6kwXs
Secure Best Marks with AI Grader
Need help grading? Try our AI Grader for instant feedback on your assignments.
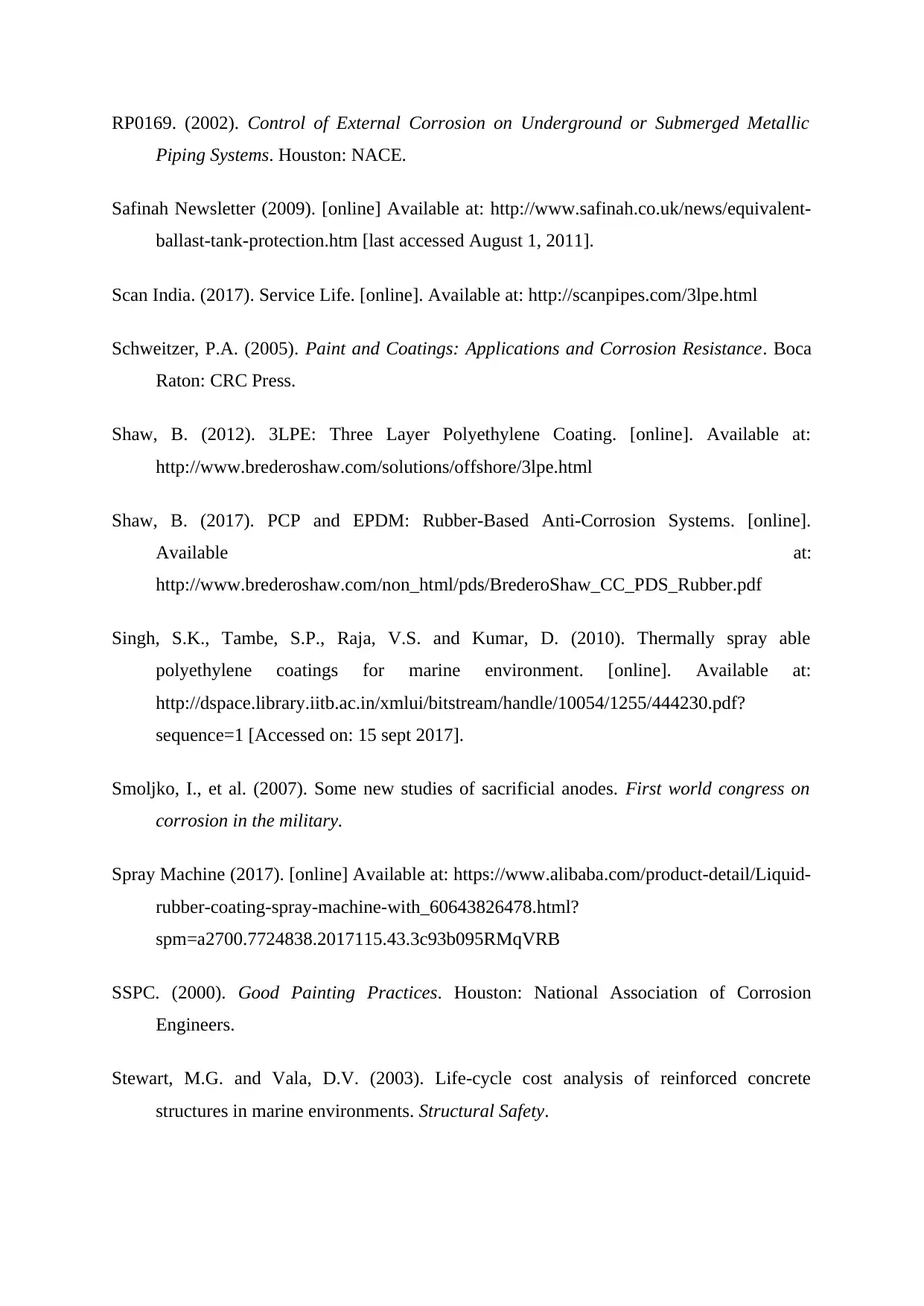
RP0169. (2002). Control of External Corrosion on Underground or Submerged Metallic
Piping Systems. Houston: NACE.
Safinah Newsletter (2009). [online] Available at: http://www.safinah.co.uk/news/equivalent-
ballast-tank-protection.htm [last accessed August 1, 2011].
Scan India. (2017). Service Life. [online]. Available at: http://scanpipes.com/3lpe.html
Schweitzer, P.A. (2005). Paint and Coatings: Applications and Corrosion Resistance. Boca
Raton: CRC Press.
Shaw, B. (2012). 3LPE: Three Layer Polyethylene Coating. [online]. Available at:
http://www.brederoshaw.com/solutions/offshore/3lpe.html
Shaw, B. (2017). PCP and EPDM: Rubber-Based Anti-Corrosion Systems. [online].
Available at:
http://www.brederoshaw.com/non_html/pds/BrederoShaw_CC_PDS_Rubber.pdf
Singh, S.K., Tambe, S.P., Raja, V.S. and Kumar, D. (2010). Thermally spray able
polyethylene coatings for marine environment. [online]. Available at:
http://dspace.library.iitb.ac.in/xmlui/bitstream/handle/10054/1255/444230.pdf?
sequence=1 [Accessed on: 15 sept 2017].
Smoljko, I., et al. (2007). Some new studies of sacrificial anodes. First world congress on
corrosion in the military.
Spray Machine (2017). [online] Available at: https://www.alibaba.com/product-detail/Liquid-
rubber-coating-spray-machine-with_60643826478.html?
spm=a2700.7724838.2017115.43.3c93b095RMqVRB
SSPC. (2000). Good Painting Practices. Houston: National Association of Corrosion
Engineers.
Stewart, M.G. and Vala, D.V. (2003). Life-cycle cost analysis of reinforced concrete
structures in marine environments. Structural Safety.
Piping Systems. Houston: NACE.
Safinah Newsletter (2009). [online] Available at: http://www.safinah.co.uk/news/equivalent-
ballast-tank-protection.htm [last accessed August 1, 2011].
Scan India. (2017). Service Life. [online]. Available at: http://scanpipes.com/3lpe.html
Schweitzer, P.A. (2005). Paint and Coatings: Applications and Corrosion Resistance. Boca
Raton: CRC Press.
Shaw, B. (2012). 3LPE: Three Layer Polyethylene Coating. [online]. Available at:
http://www.brederoshaw.com/solutions/offshore/3lpe.html
Shaw, B. (2017). PCP and EPDM: Rubber-Based Anti-Corrosion Systems. [online].
Available at:
http://www.brederoshaw.com/non_html/pds/BrederoShaw_CC_PDS_Rubber.pdf
Singh, S.K., Tambe, S.P., Raja, V.S. and Kumar, D. (2010). Thermally spray able
polyethylene coatings for marine environment. [online]. Available at:
http://dspace.library.iitb.ac.in/xmlui/bitstream/handle/10054/1255/444230.pdf?
sequence=1 [Accessed on: 15 sept 2017].
Smoljko, I., et al. (2007). Some new studies of sacrificial anodes. First world congress on
corrosion in the military.
Spray Machine (2017). [online] Available at: https://www.alibaba.com/product-detail/Liquid-
rubber-coating-spray-machine-with_60643826478.html?
spm=a2700.7724838.2017115.43.3c93b095RMqVRB
SSPC. (2000). Good Painting Practices. Houston: National Association of Corrosion
Engineers.
Stewart, M.G. and Vala, D.V. (2003). Life-cycle cost analysis of reinforced concrete
structures in marine environments. Structural Safety.
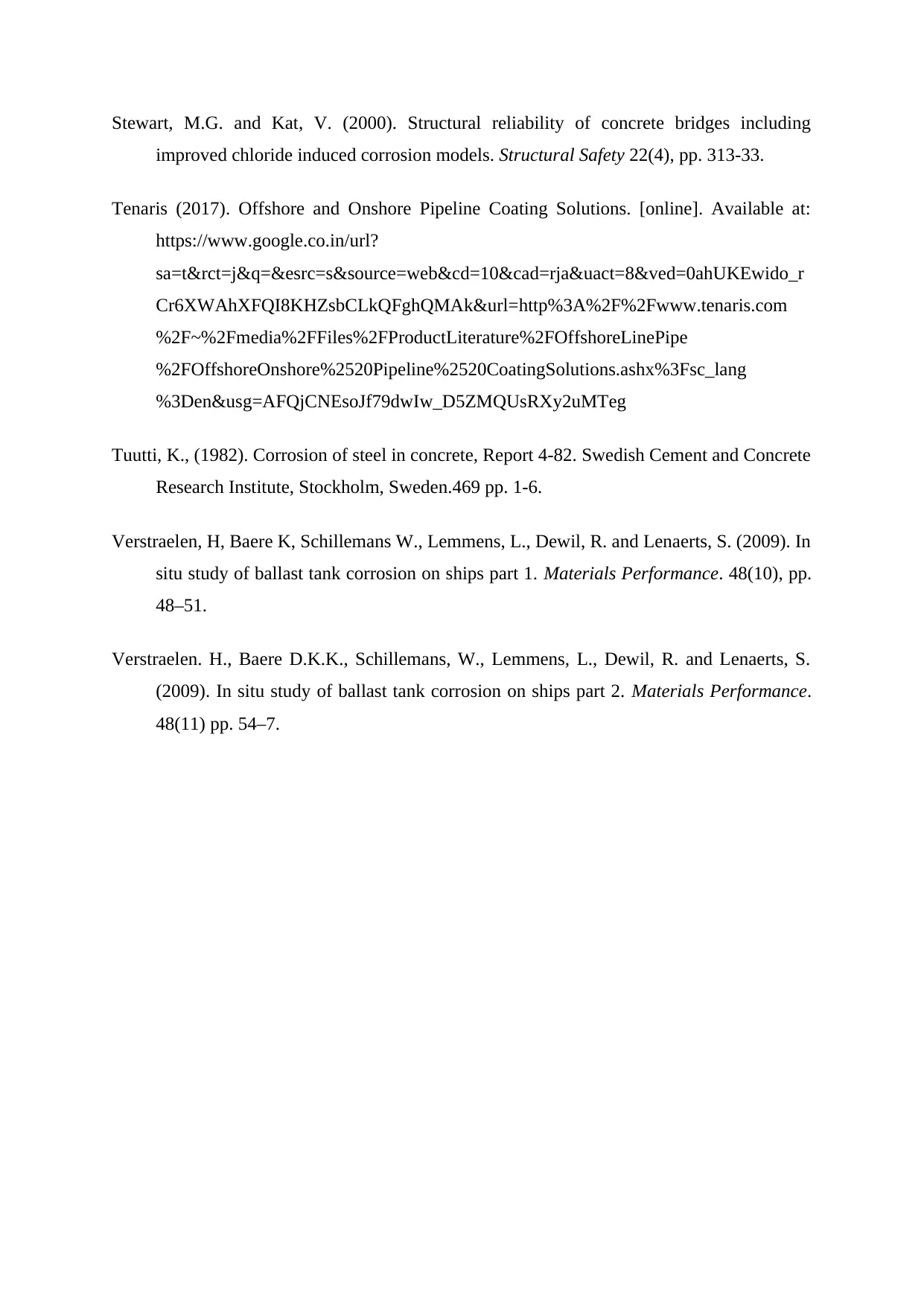
Stewart, M.G. and Kat, V. (2000). Structural reliability of concrete bridges including
improved chloride induced corrosion models. Structural Safety 22(4), pp. 313-33.
Tenaris (2017). Offshore and Onshore Pipeline Coating Solutions. [online]. Available at:
https://www.google.co.in/url?
sa=t&rct=j&q=&esrc=s&source=web&cd=10&cad=rja&uact=8&ved=0ahUKEwido_r
Cr6XWAhXFQI8KHZsbCLkQFghQMAk&url=http%3A%2F%2Fwww.tenaris.com
%2F~%2Fmedia%2FFiles%2FProductLiterature%2FOffshoreLinePipe
%2FOffshoreOnshore%2520Pipeline%2520CoatingSolutions.ashx%3Fsc_lang
%3Den&usg=AFQjCNEsoJf79dwIw_D5ZMQUsRXy2uMTeg
Tuutti, K., (1982). Corrosion of steel in concrete, Report 4-82. Swedish Cement and Concrete
Research Institute, Stockholm, Sweden.469 pp. 1-6.
Verstraelen, H, Baere K, Schillemans W., Lemmens, L., Dewil, R. and Lenaerts, S. (2009). In
situ study of ballast tank corrosion on ships part 1. Materials Performance. 48(10), pp.
48–51.
Verstraelen. H., Baere D.K.K., Schillemans, W., Lemmens, L., Dewil, R. and Lenaerts, S.
(2009). In situ study of ballast tank corrosion on ships part 2. Materials Performance.
48(11) pp. 54–7.
improved chloride induced corrosion models. Structural Safety 22(4), pp. 313-33.
Tenaris (2017). Offshore and Onshore Pipeline Coating Solutions. [online]. Available at:
https://www.google.co.in/url?
sa=t&rct=j&q=&esrc=s&source=web&cd=10&cad=rja&uact=8&ved=0ahUKEwido_r
Cr6XWAhXFQI8KHZsbCLkQFghQMAk&url=http%3A%2F%2Fwww.tenaris.com
%2F~%2Fmedia%2FFiles%2FProductLiterature%2FOffshoreLinePipe
%2FOffshoreOnshore%2520Pipeline%2520CoatingSolutions.ashx%3Fsc_lang
%3Den&usg=AFQjCNEsoJf79dwIw_D5ZMQUsRXy2uMTeg
Tuutti, K., (1982). Corrosion of steel in concrete, Report 4-82. Swedish Cement and Concrete
Research Institute, Stockholm, Sweden.469 pp. 1-6.
Verstraelen, H, Baere K, Schillemans W., Lemmens, L., Dewil, R. and Lenaerts, S. (2009). In
situ study of ballast tank corrosion on ships part 1. Materials Performance. 48(10), pp.
48–51.
Verstraelen. H., Baere D.K.K., Schillemans, W., Lemmens, L., Dewil, R. and Lenaerts, S.
(2009). In situ study of ballast tank corrosion on ships part 2. Materials Performance.
48(11) pp. 54–7.
1 out of 30

Your All-in-One AI-Powered Toolkit for Academic Success.
+13062052269
info@desklib.com
Available 24*7 on WhatsApp / Email
Unlock your academic potential
© 2024 | Zucol Services PVT LTD | All rights reserved.