Operations Management Process Analysis: LKQ Euro Car Parts (BMGT7043)
VerifiedAdded on 2022/07/04
|13
|3628
|32
Report
AI Summary
This report provides a comprehensive analysis of the operations management processes at LKQ Euro Car Parts, a leading UK distributor of vehicle spare parts. It begins by outlining the company's background, including its growth and market position. The report then delves into the Input-Transformation-Output model, detailing the transformed and transforming resources involved in the company's operations. This is followed by an examination of the 4 V's model (Volume, Variety, Variation, and Visibility) as applied to LKQ Euro Car Parts. The report further explores the company's operations objectives, including cost, speed, quality, flexibility, and dependability. Capacity management is also discussed, followed by a section on strengths, weaknesses, and recommendations for improving operational strategies. The report concludes with a summary of key findings and insights into LKQ Euro Car Parts' operations management practices.
Contribute Materials
Your contribution can guide someone’s learning journey. Share your
documents today.
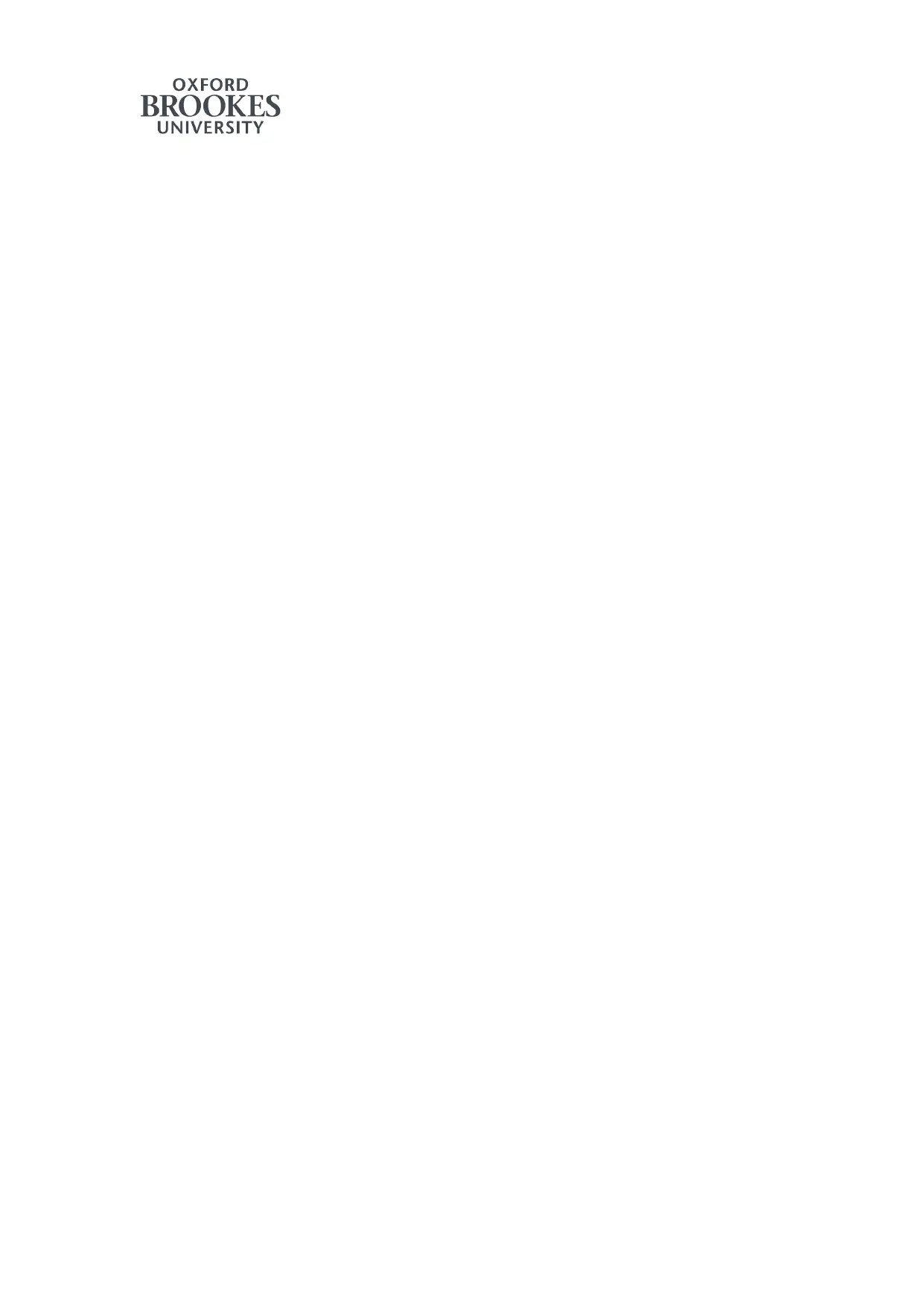
Secure Best Marks with AI Grader
Need help grading? Try our AI Grader for instant feedback on your assignments.
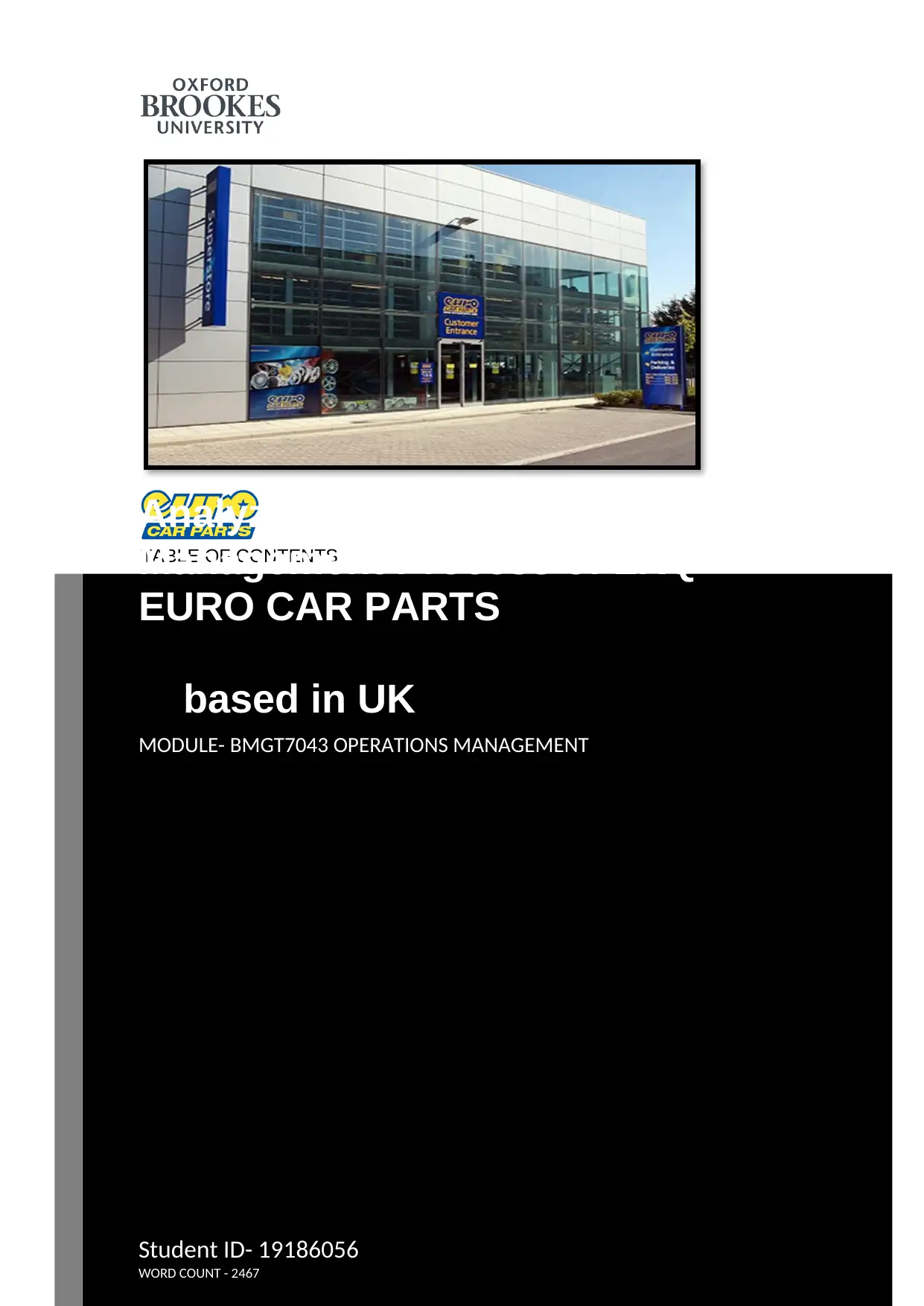
TABLE OF CONTENTS
1. Introduction 2
2. Input-Transformation-Output Model. 3
2.1 Transformed Resources 3
2.2 Transforming Resource 3
2.3 Transformation Process 4
2.4 Output 4
3. The 4 V’s Model 5
3.1 Volume 5
3.2 Variety 5
3.3 Variation 5
3.4 Visibility 6
4. Operations Objectives 6
4.1 Cost 7
4.2 Speed 7
4.3 Quality 7
4.4 Flexibility 7
4.5 Dependability 7
5. Capacity Management 8
6. Strength, Weaknesses, Recommendations & conclusion 9
7. References 11
Table of Figures
Figure 1: Input Transformation Process Model 2
Figure 2: 4 V’s Model 4
Figure 3: Operations Objectives 8
Figure 4: Capacity Management 9
1
Analyzing the Operations
Management Process of LKQ
EURO CAR PARTS
based in UK
MODULE- BMGT7043 OPERATIONS MANAGEMENT
Student ID- 19186056
WORD COUNT - 2467
1. Introduction 2
2. Input-Transformation-Output Model. 3
2.1 Transformed Resources 3
2.2 Transforming Resource 3
2.3 Transformation Process 4
2.4 Output 4
3. The 4 V’s Model 5
3.1 Volume 5
3.2 Variety 5
3.3 Variation 5
3.4 Visibility 6
4. Operations Objectives 6
4.1 Cost 7
4.2 Speed 7
4.3 Quality 7
4.4 Flexibility 7
4.5 Dependability 7
5. Capacity Management 8
6. Strength, Weaknesses, Recommendations & conclusion 9
7. References 11
Table of Figures
Figure 1: Input Transformation Process Model 2
Figure 2: 4 V’s Model 4
Figure 3: Operations Objectives 8
Figure 4: Capacity Management 9
1
Analyzing the Operations
Management Process of LKQ
EURO CAR PARTS
based in UK
MODULE- BMGT7043 OPERATIONS MANAGEMENT
Student ID- 19186056
WORD COUNT - 2467
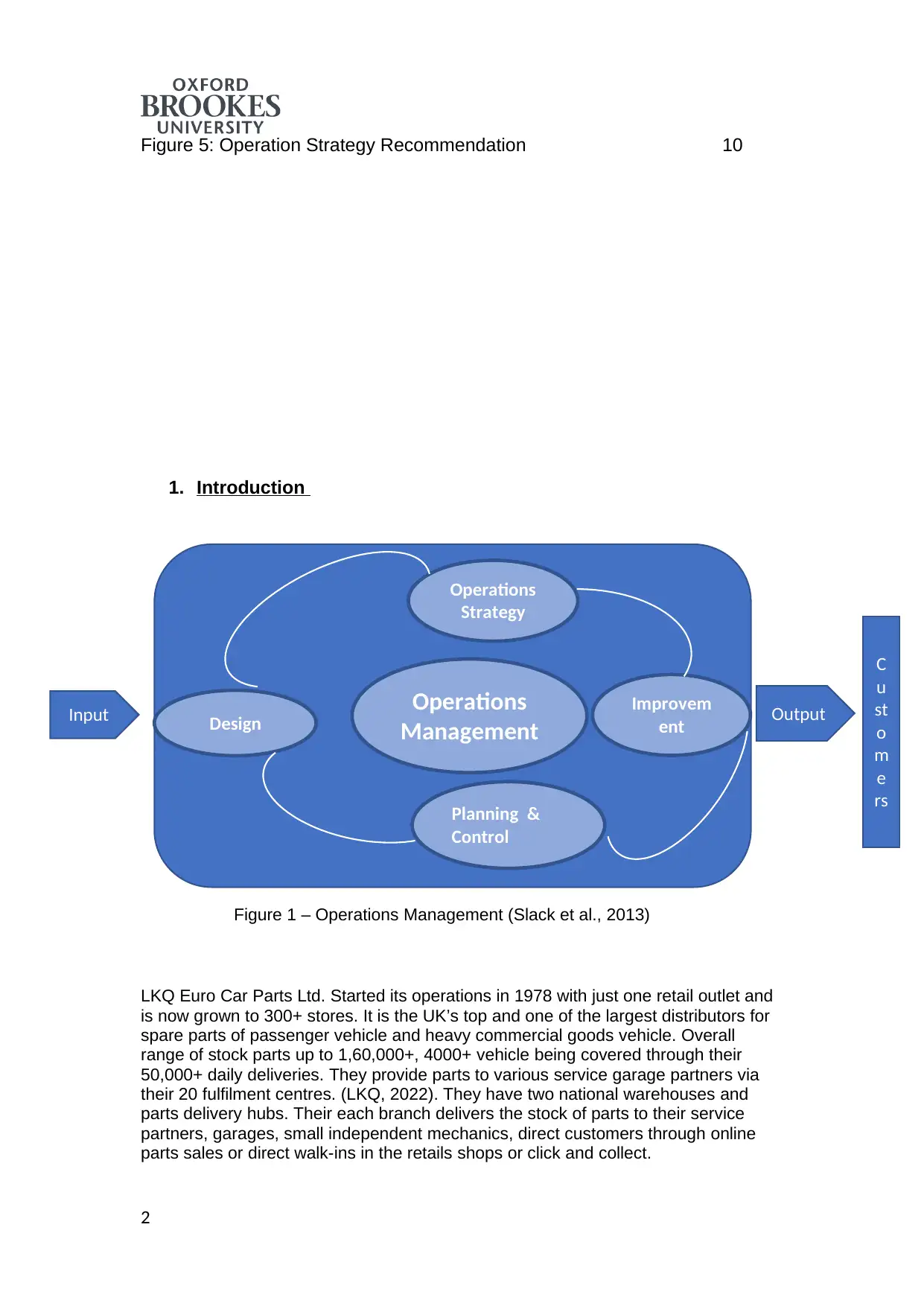
Figure 5: Operation Strategy Recommendation 10
1. Introduction
Figure 1 – Operations Management (Slack et al., 2013)
LKQ Euro Car Parts Ltd. Started its operations in 1978 with just one retail outlet and
is now grown to 300+ stores. It is the UK’s top and one of the largest distributors for
spare parts of passenger vehicle and heavy commercial goods vehicle. Overall
range of stock parts up to 1,60,000+, 4000+ vehicle being covered through their
50,000+ daily deliveries. They provide parts to various service garage partners via
their 20 fulfilment centres. (LKQ, 2022). They have two national warehouses and
parts delivery hubs. Their each branch delivers the stock of parts to their service
partners, garages, small independent mechanics, direct customers through online
parts sales or direct walk-ins in the retails shops or click and collect.
2
Design
Improvem
ent
Operations
Management
Planning &
Control
Operations
Strategy
ment
Input Output
C
u
st
o
m
e
rs
1. Introduction
Figure 1 – Operations Management (Slack et al., 2013)
LKQ Euro Car Parts Ltd. Started its operations in 1978 with just one retail outlet and
is now grown to 300+ stores. It is the UK’s top and one of the largest distributors for
spare parts of passenger vehicle and heavy commercial goods vehicle. Overall
range of stock parts up to 1,60,000+, 4000+ vehicle being covered through their
50,000+ daily deliveries. They provide parts to various service garage partners via
their 20 fulfilment centres. (LKQ, 2022). They have two national warehouses and
parts delivery hubs. Their each branch delivers the stock of parts to their service
partners, garages, small independent mechanics, direct customers through online
parts sales or direct walk-ins in the retails shops or click and collect.
2
Design
Improvem
ent
Operations
Management
Planning &
Control
Operations
Strategy
ment
Input Output
C
u
st
o
m
e
rs
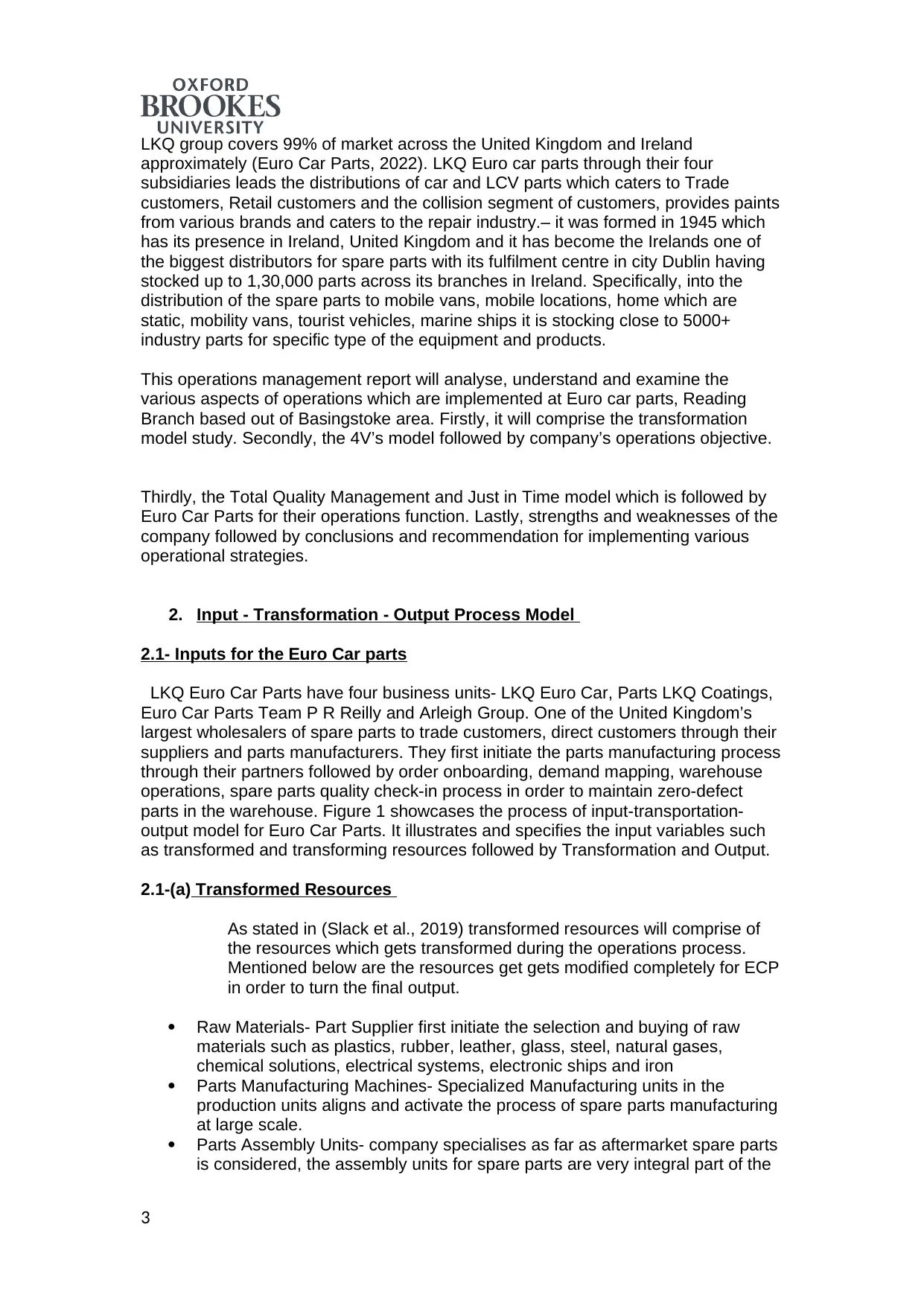
LKQ group covers 99% of market across the United Kingdom and Ireland
approximately (Euro Car Parts, 2022). LKQ Euro car parts through their four
subsidiaries leads the distributions of car and LCV parts which caters to Trade
customers, Retail customers and the collision segment of customers, provides paints
from various brands and caters to the repair industry.– it was formed in 1945 which
has its presence in Ireland, United Kingdom and it has become the Irelands one of
the biggest distributors for spare parts with its fulfilment centre in city Dublin having
stocked up to 1,30,000 parts across its branches in Ireland. Specifically, into the
distribution of the spare parts to mobile vans, mobile locations, home which are
static, mobility vans, tourist vehicles, marine ships it is stocking close to 5000+
industry parts for specific type of the equipment and products.
This operations management report will analyse, understand and examine the
various aspects of operations which are implemented at Euro car parts, Reading
Branch based out of Basingstoke area. Firstly, it will comprise the transformation
model study. Secondly, the 4V’s model followed by company’s operations objective.
Thirdly, the Total Quality Management and Just in Time model which is followed by
Euro Car Parts for their operations function. Lastly, strengths and weaknesses of the
company followed by conclusions and recommendation for implementing various
operational strategies.
2. Input - Transformation - Output Process Model
2.1- Inputs for the Euro Car parts
LKQ Euro Car Parts have four business units- LKQ Euro Car, Parts LKQ Coatings,
Euro Car Parts Team P R Reilly and Arleigh Group. One of the United Kingdom’s
largest wholesalers of spare parts to trade customers, direct customers through their
suppliers and parts manufacturers. They first initiate the parts manufacturing process
through their partners followed by order onboarding, demand mapping, warehouse
operations, spare parts quality check-in process in order to maintain zero-defect
parts in the warehouse. Figure 1 showcases the process of input-transportation-
output model for Euro Car Parts. It illustrates and specifies the input variables such
as transformed and transforming resources followed by Transformation and Output.
2.1-(a) Transformed Resources
As stated in (Slack et al., 2019) transformed resources will comprise of
the resources which gets transformed during the operations process.
Mentioned below are the resources get gets modified completely for ECP
in order to turn the final output.
Raw Materials- Part Supplier first initiate the selection and buying of raw
materials such as plastics, rubber, leather, glass, steel, natural gases,
chemical solutions, electrical systems, electronic ships and iron
Parts Manufacturing Machines- Specialized Manufacturing units in the
production units aligns and activate the process of spare parts manufacturing
at large scale.
Parts Assembly Units- company specialises as far as aftermarket spare parts
is considered, the assembly units for spare parts are very integral part of the
3
approximately (Euro Car Parts, 2022). LKQ Euro car parts through their four
subsidiaries leads the distributions of car and LCV parts which caters to Trade
customers, Retail customers and the collision segment of customers, provides paints
from various brands and caters to the repair industry.– it was formed in 1945 which
has its presence in Ireland, United Kingdom and it has become the Irelands one of
the biggest distributors for spare parts with its fulfilment centre in city Dublin having
stocked up to 1,30,000 parts across its branches in Ireland. Specifically, into the
distribution of the spare parts to mobile vans, mobile locations, home which are
static, mobility vans, tourist vehicles, marine ships it is stocking close to 5000+
industry parts for specific type of the equipment and products.
This operations management report will analyse, understand and examine the
various aspects of operations which are implemented at Euro car parts, Reading
Branch based out of Basingstoke area. Firstly, it will comprise the transformation
model study. Secondly, the 4V’s model followed by company’s operations objective.
Thirdly, the Total Quality Management and Just in Time model which is followed by
Euro Car Parts for their operations function. Lastly, strengths and weaknesses of the
company followed by conclusions and recommendation for implementing various
operational strategies.
2. Input - Transformation - Output Process Model
2.1- Inputs for the Euro Car parts
LKQ Euro Car Parts have four business units- LKQ Euro Car, Parts LKQ Coatings,
Euro Car Parts Team P R Reilly and Arleigh Group. One of the United Kingdom’s
largest wholesalers of spare parts to trade customers, direct customers through their
suppliers and parts manufacturers. They first initiate the parts manufacturing process
through their partners followed by order onboarding, demand mapping, warehouse
operations, spare parts quality check-in process in order to maintain zero-defect
parts in the warehouse. Figure 1 showcases the process of input-transportation-
output model for Euro Car Parts. It illustrates and specifies the input variables such
as transformed and transforming resources followed by Transformation and Output.
2.1-(a) Transformed Resources
As stated in (Slack et al., 2019) transformed resources will comprise of
the resources which gets transformed during the operations process.
Mentioned below are the resources get gets modified completely for ECP
in order to turn the final output.
Raw Materials- Part Supplier first initiate the selection and buying of raw
materials such as plastics, rubber, leather, glass, steel, natural gases,
chemical solutions, electrical systems, electronic ships and iron
Parts Manufacturing Machines- Specialized Manufacturing units in the
production units aligns and activate the process of spare parts manufacturing
at large scale.
Parts Assembly Units- company specialises as far as aftermarket spare parts
is considered, the assembly units for spare parts are very integral part of the
3
Secure Best Marks with AI Grader
Need help grading? Try our AI Grader for instant feedback on your assignments.
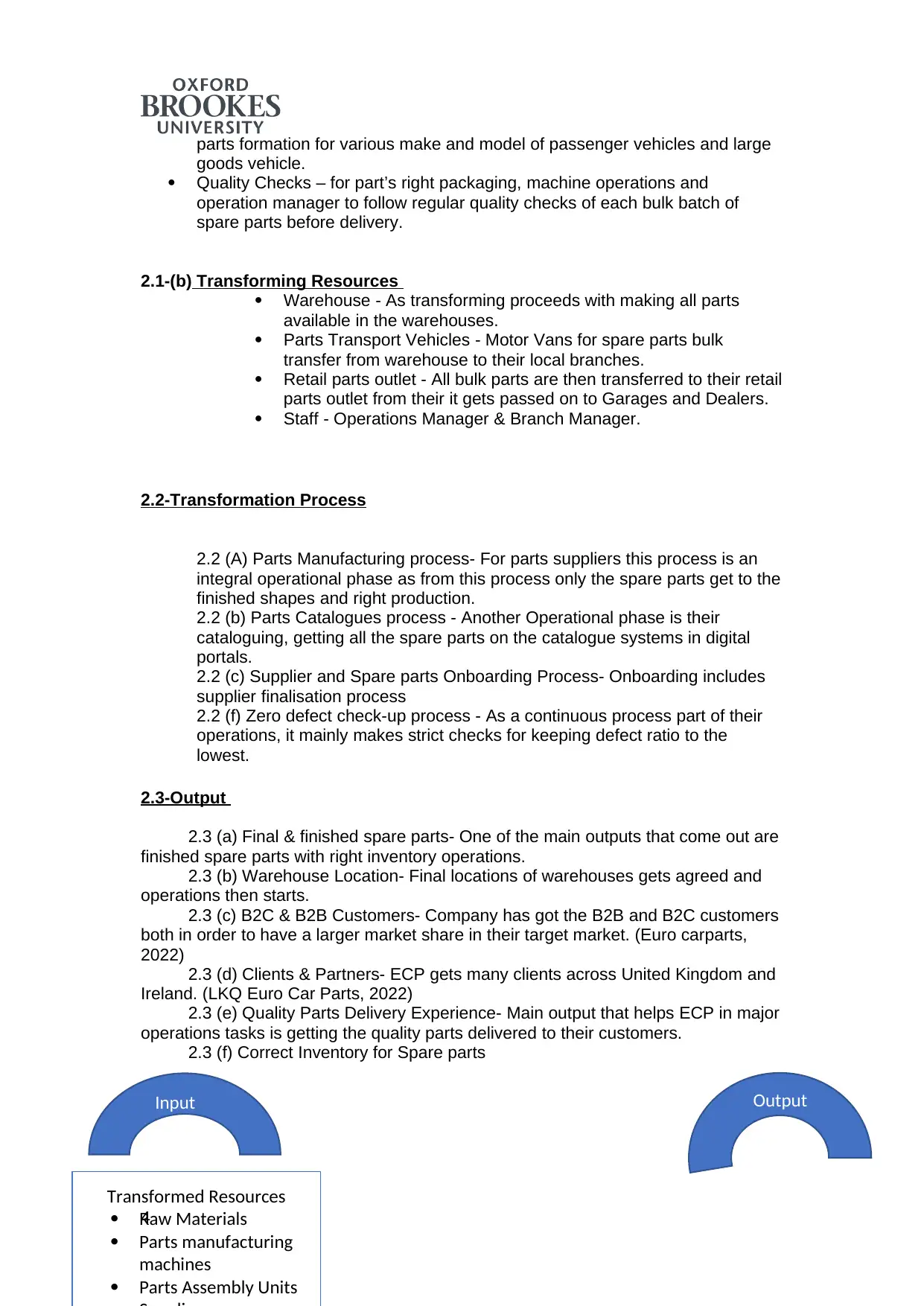
parts formation for various make and model of passenger vehicles and large
goods vehicle.
Quality Checks – for part’s right packaging, machine operations and
operation manager to follow regular quality checks of each bulk batch of
spare parts before delivery.
2.1-(b) Transforming Resources
Warehouse - As transforming proceeds with making all parts
available in the warehouses.
Parts Transport Vehicles - Motor Vans for spare parts bulk
transfer from warehouse to their local branches.
Retail parts outlet - All bulk parts are then transferred to their retail
parts outlet from their it gets passed on to Garages and Dealers.
Staff - Operations Manager & Branch Manager.
2.2-Transformation Process
2.2 (A) Parts Manufacturing process- For parts suppliers this process is an
integral operational phase as from this process only the spare parts get to the
finished shapes and right production.
2.2 (b) Parts Catalogues process - Another Operational phase is their
cataloguing, getting all the spare parts on the catalogue systems in digital
portals.
2.2 (c) Supplier and Spare parts Onboarding Process- Onboarding includes
supplier finalisation process
2.2 (f) Zero defect check-up process - As a continuous process part of their
operations, it mainly makes strict checks for keeping defect ratio to the
lowest.
2.3-Output
2.3 (a) Final & finished spare parts- One of the main outputs that come out are
finished spare parts with right inventory operations.
2.3 (b) Warehouse Location- Final locations of warehouses gets agreed and
operations then starts.
2.3 (c) B2C & B2B Customers- Company has got the B2B and B2C customers
both in order to have a larger market share in their target market. (Euro carparts,
2022)
2.3 (d) Clients & Partners- ECP gets many clients across United Kingdom and
Ireland. (LKQ Euro Car Parts, 2022)
2.3 (e) Quality Parts Delivery Experience- Main output that helps ECP in major
operations tasks is getting the quality parts delivered to their customers.
2.3 (f) Correct Inventory for Spare parts
4
Input Output
Transformed Resources
Raw Materials
Parts manufacturing
machines
Parts Assembly Units
goods vehicle.
Quality Checks – for part’s right packaging, machine operations and
operation manager to follow regular quality checks of each bulk batch of
spare parts before delivery.
2.1-(b) Transforming Resources
Warehouse - As transforming proceeds with making all parts
available in the warehouses.
Parts Transport Vehicles - Motor Vans for spare parts bulk
transfer from warehouse to their local branches.
Retail parts outlet - All bulk parts are then transferred to their retail
parts outlet from their it gets passed on to Garages and Dealers.
Staff - Operations Manager & Branch Manager.
2.2-Transformation Process
2.2 (A) Parts Manufacturing process- For parts suppliers this process is an
integral operational phase as from this process only the spare parts get to the
finished shapes and right production.
2.2 (b) Parts Catalogues process - Another Operational phase is their
cataloguing, getting all the spare parts on the catalogue systems in digital
portals.
2.2 (c) Supplier and Spare parts Onboarding Process- Onboarding includes
supplier finalisation process
2.2 (f) Zero defect check-up process - As a continuous process part of their
operations, it mainly makes strict checks for keeping defect ratio to the
lowest.
2.3-Output
2.3 (a) Final & finished spare parts- One of the main outputs that come out are
finished spare parts with right inventory operations.
2.3 (b) Warehouse Location- Final locations of warehouses gets agreed and
operations then starts.
2.3 (c) B2C & B2B Customers- Company has got the B2B and B2C customers
both in order to have a larger market share in their target market. (Euro carparts,
2022)
2.3 (d) Clients & Partners- ECP gets many clients across United Kingdom and
Ireland. (LKQ Euro Car Parts, 2022)
2.3 (e) Quality Parts Delivery Experience- Main output that helps ECP in major
operations tasks is getting the quality parts delivered to their customers.
2.3 (f) Correct Inventory for Spare parts
4
Input Output
Transformed Resources
Raw Materials
Parts manufacturing
machines
Parts Assembly Units
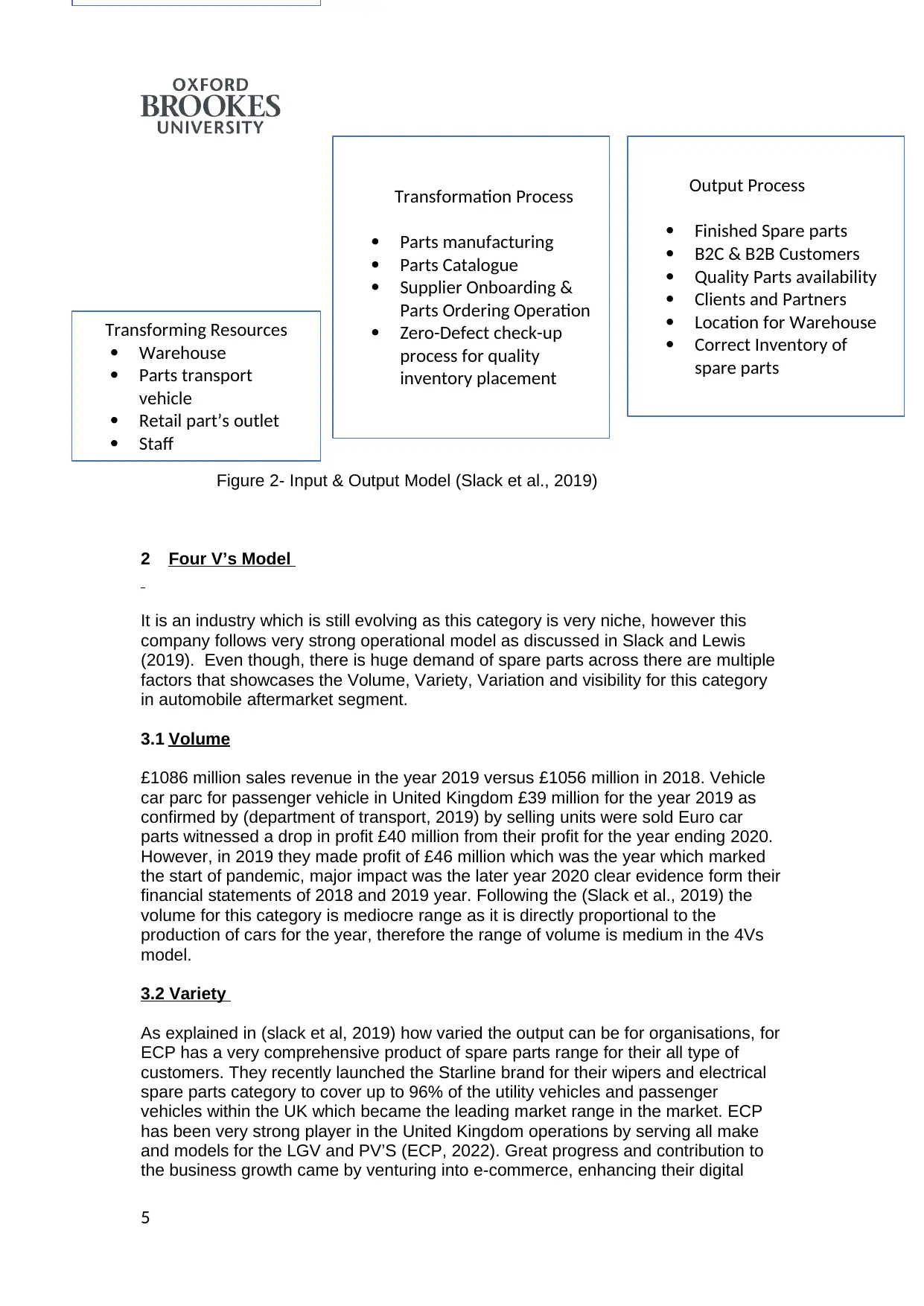
Figure 2- Input & Output Model (Slack et al., 2019)
2 Four V’s Model
It is an industry which is still evolving as this category is very niche, however this
company follows very strong operational model as discussed in Slack and Lewis
(2019). Even though, there is huge demand of spare parts across there are multiple
factors that showcases the Volume, Variety, Variation and visibility for this category
in automobile aftermarket segment.
3.1 Volume
£1086 million sales revenue in the year 2019 versus £1056 million in 2018. Vehicle
car parc for passenger vehicle in United Kingdom £39 million for the year 2019 as
confirmed by (department of transport, 2019) by selling units were sold Euro car
parts witnessed a drop in profit £40 million from their profit for the year ending 2020.
However, in 2019 they made profit of £46 million which was the year which marked
the start of pandemic, major impact was the later year 2020 clear evidence form their
financial statements of 2018 and 2019 year. Following the (Slack et al., 2019) the
volume for this category is mediocre range as it is directly proportional to the
production of cars for the year, therefore the range of volume is medium in the 4Vs
model.
3.2 Variety
As explained in (slack et al, 2019) how varied the output can be for organisations, for
ECP has a very comprehensive product of spare parts range for their all type of
customers. They recently launched the Starline brand for their wipers and electrical
spare parts category to cover up to 96% of the utility vehicles and passenger
vehicles within the UK which became the leading market range in the market. ECP
has been very strong player in the United Kingdom operations by serving all make
and models for the LGV and PV’S (ECP, 2022). Great progress and contribution to
the business growth came by venturing into e-commerce, enhancing their digital
5
Transforming Resources
Warehouse
Parts transport
vehicle
Retail part’s outlet
Staff
Output Process
Finished Spare parts
B2C & B2B Customers
Quality Parts availability
Clients and Partners
Location for Warehouse
Correct Inventory of
spare parts
Transformation Process
Parts manufacturing
Parts Catalogue
Supplier Onboarding &
Parts Ordering Operation
Zero-Defect check-up
process for quality
inventory placement
2 Four V’s Model
It is an industry which is still evolving as this category is very niche, however this
company follows very strong operational model as discussed in Slack and Lewis
(2019). Even though, there is huge demand of spare parts across there are multiple
factors that showcases the Volume, Variety, Variation and visibility for this category
in automobile aftermarket segment.
3.1 Volume
£1086 million sales revenue in the year 2019 versus £1056 million in 2018. Vehicle
car parc for passenger vehicle in United Kingdom £39 million for the year 2019 as
confirmed by (department of transport, 2019) by selling units were sold Euro car
parts witnessed a drop in profit £40 million from their profit for the year ending 2020.
However, in 2019 they made profit of £46 million which was the year which marked
the start of pandemic, major impact was the later year 2020 clear evidence form their
financial statements of 2018 and 2019 year. Following the (Slack et al., 2019) the
volume for this category is mediocre range as it is directly proportional to the
production of cars for the year, therefore the range of volume is medium in the 4Vs
model.
3.2 Variety
As explained in (slack et al, 2019) how varied the output can be for organisations, for
ECP has a very comprehensive product of spare parts range for their all type of
customers. They recently launched the Starline brand for their wipers and electrical
spare parts category to cover up to 96% of the utility vehicles and passenger
vehicles within the UK which became the leading market range in the market. ECP
has been very strong player in the United Kingdom operations by serving all make
and models for the LGV and PV’S (ECP, 2022). Great progress and contribution to
the business growth came by venturing into e-commerce, enhancing their digital
5
Transforming Resources
Warehouse
Parts transport
vehicle
Retail part’s outlet
Staff
Output Process
Finished Spare parts
B2C & B2B Customers
Quality Parts availability
Clients and Partners
Location for Warehouse
Correct Inventory of
spare parts
Transformation Process
Parts manufacturing
Parts Catalogue
Supplier Onboarding &
Parts Ordering Operation
Zero-Defect check-up
process for quality
inventory placement
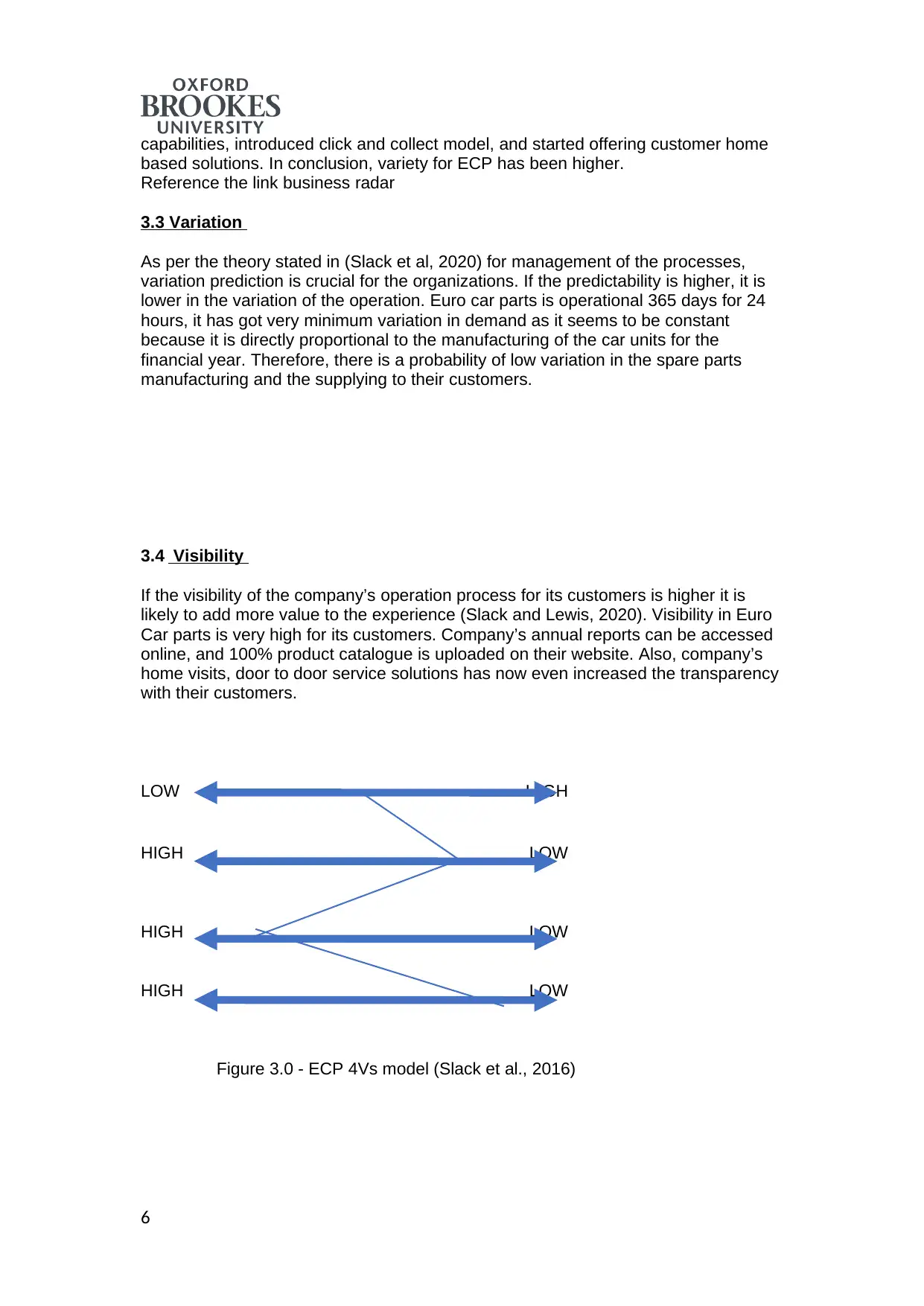
capabilities, introduced click and collect model, and started offering customer home
based solutions. In conclusion, variety for ECP has been higher.
Reference the link business radar
3.3 Variation
As per the theory stated in (Slack et al, 2020) for management of the processes,
variation prediction is crucial for the organizations. If the predictability is higher, it is
lower in the variation of the operation. Euro car parts is operational 365 days for 24
hours, it has got very minimum variation in demand as it seems to be constant
because it is directly proportional to the manufacturing of the car units for the
financial year. Therefore, there is a probability of low variation in the spare parts
manufacturing and the supplying to their customers.
3.4 Visibility
If the visibility of the company’s operation process for its customers is higher it is
likely to add more value to the experience (Slack and Lewis, 2020). Visibility in Euro
Car parts is very high for its customers. Company’s annual reports can be accessed
online, and 100% product catalogue is uploaded on their website. Also, company’s
home visits, door to door service solutions has now even increased the transparency
with their customers.
LOW HIGH
HIGH LOW
HIGH LOW
HIGH LOW
Figure 3.0 - ECP 4Vs model (Slack et al., 2016)
6
based solutions. In conclusion, variety for ECP has been higher.
Reference the link business radar
3.3 Variation
As per the theory stated in (Slack et al, 2020) for management of the processes,
variation prediction is crucial for the organizations. If the predictability is higher, it is
lower in the variation of the operation. Euro car parts is operational 365 days for 24
hours, it has got very minimum variation in demand as it seems to be constant
because it is directly proportional to the manufacturing of the car units for the
financial year. Therefore, there is a probability of low variation in the spare parts
manufacturing and the supplying to their customers.
3.4 Visibility
If the visibility of the company’s operation process for its customers is higher it is
likely to add more value to the experience (Slack and Lewis, 2020). Visibility in Euro
Car parts is very high for its customers. Company’s annual reports can be accessed
online, and 100% product catalogue is uploaded on their website. Also, company’s
home visits, door to door service solutions has now even increased the transparency
with their customers.
LOW HIGH
HIGH LOW
HIGH LOW
HIGH LOW
Figure 3.0 - ECP 4Vs model (Slack et al., 2016)
6
Paraphrase This Document
Need a fresh take? Get an instant paraphrase of this document with our AI Paraphraser
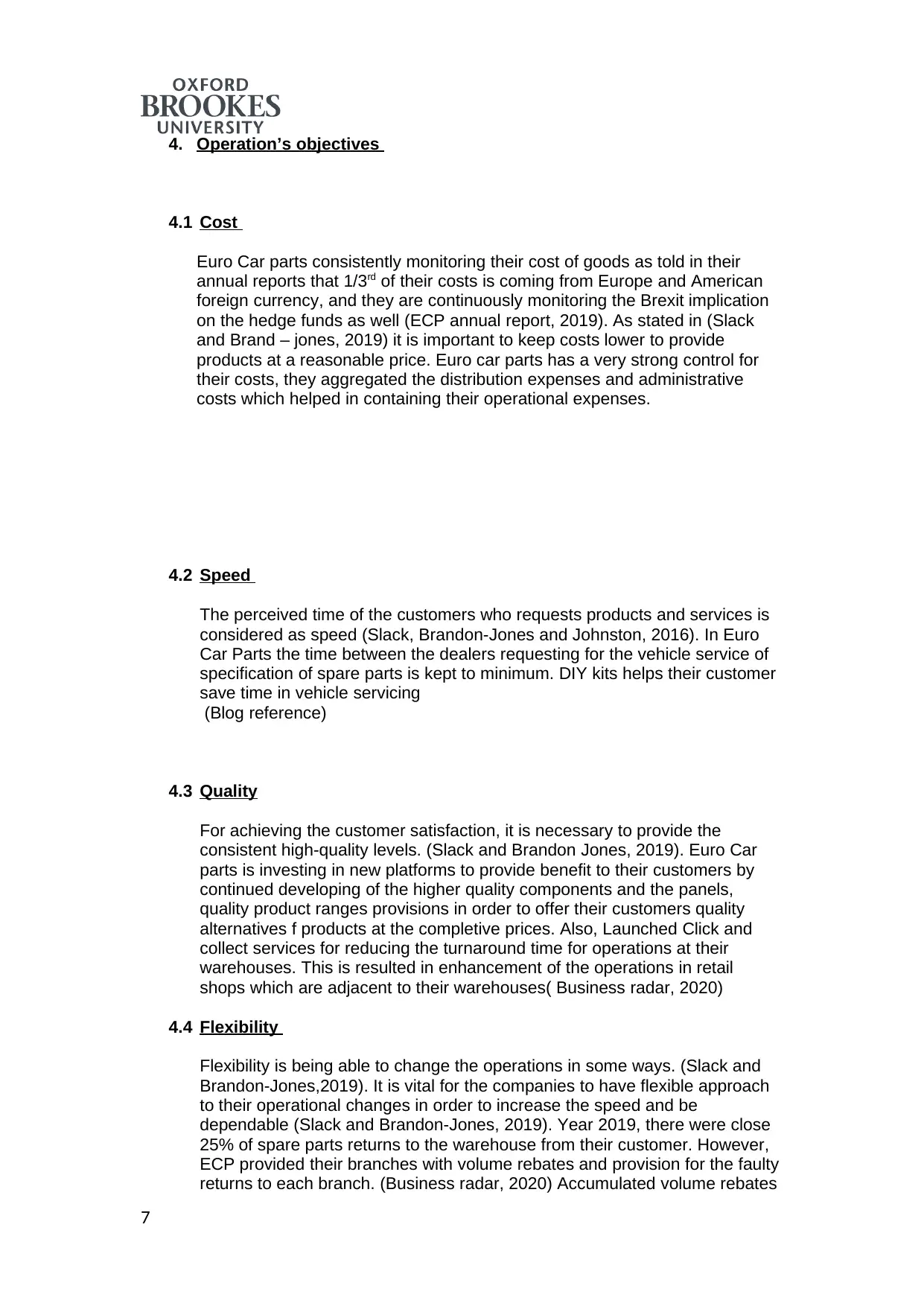
4. Operation’s objectives
4.1 Cost
Euro Car parts consistently monitoring their cost of goods as told in their
annual reports that 1/3rd of their costs is coming from Europe and American
foreign currency, and they are continuously monitoring the Brexit implication
on the hedge funds as well (ECP annual report, 2019). As stated in (Slack
and Brand – jones, 2019) it is important to keep costs lower to provide
products at a reasonable price. Euro car parts has a very strong control for
their costs, they aggregated the distribution expenses and administrative
costs which helped in containing their operational expenses.
4.2 Speed
The perceived time of the customers who requests products and services is
considered as speed (Slack, Brandon-Jones and Johnston, 2016). In Euro
Car Parts the time between the dealers requesting for the vehicle service of
specification of spare parts is kept to minimum. DIY kits helps their customer
save time in vehicle servicing
(Blog reference)
4.3 Quality
For achieving the customer satisfaction, it is necessary to provide the
consistent high-quality levels. (Slack and Brandon Jones, 2019). Euro Car
parts is investing in new platforms to provide benefit to their customers by
continued developing of the higher quality components and the panels,
quality product ranges provisions in order to offer their customers quality
alternatives f products at the completive prices. Also, Launched Click and
collect services for reducing the turnaround time for operations at their
warehouses. This is resulted in enhancement of the operations in retail
shops which are adjacent to their warehouses( Business radar, 2020)
4.4 Flexibility
Flexibility is being able to change the operations in some ways. (Slack and
Brandon-Jones,2019). It is vital for the companies to have flexible approach
to their operational changes in order to increase the speed and be
dependable (Slack and Brandon-Jones, 2019). Year 2019, there were close
25% of spare parts returns to the warehouse from their customer. However,
ECP provided their branches with volume rebates and provision for the faulty
returns to each branch. (Business radar, 2020) Accumulated volume rebates
7
4.1 Cost
Euro Car parts consistently monitoring their cost of goods as told in their
annual reports that 1/3rd of their costs is coming from Europe and American
foreign currency, and they are continuously monitoring the Brexit implication
on the hedge funds as well (ECP annual report, 2019). As stated in (Slack
and Brand – jones, 2019) it is important to keep costs lower to provide
products at a reasonable price. Euro car parts has a very strong control for
their costs, they aggregated the distribution expenses and administrative
costs which helped in containing their operational expenses.
4.2 Speed
The perceived time of the customers who requests products and services is
considered as speed (Slack, Brandon-Jones and Johnston, 2016). In Euro
Car Parts the time between the dealers requesting for the vehicle service of
specification of spare parts is kept to minimum. DIY kits helps their customer
save time in vehicle servicing
(Blog reference)
4.3 Quality
For achieving the customer satisfaction, it is necessary to provide the
consistent high-quality levels. (Slack and Brandon Jones, 2019). Euro Car
parts is investing in new platforms to provide benefit to their customers by
continued developing of the higher quality components and the panels,
quality product ranges provisions in order to offer their customers quality
alternatives f products at the completive prices. Also, Launched Click and
collect services for reducing the turnaround time for operations at their
warehouses. This is resulted in enhancement of the operations in retail
shops which are adjacent to their warehouses( Business radar, 2020)
4.4 Flexibility
Flexibility is being able to change the operations in some ways. (Slack and
Brandon-Jones,2019). It is vital for the companies to have flexible approach
to their operational changes in order to increase the speed and be
dependable (Slack and Brandon-Jones, 2019). Year 2019, there were close
25% of spare parts returns to the warehouse from their customer. However,
ECP provided their branches with volume rebates and provision for the faulty
returns to each branch. (Business radar, 2020) Accumulated volume rebates
7
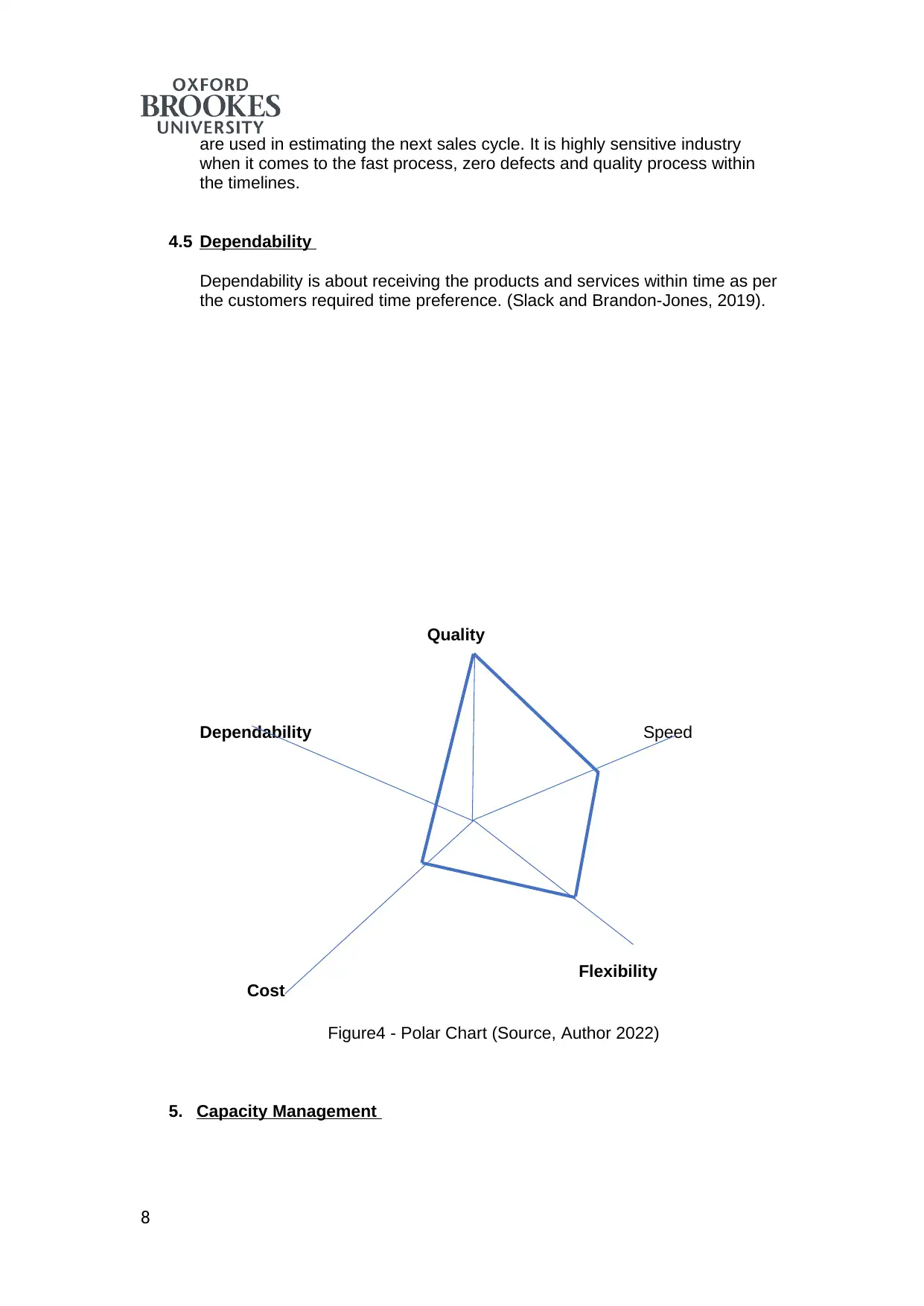
are used in estimating the next sales cycle. It is highly sensitive industry
when it comes to the fast process, zero defects and quality process within
the timelines.
4.5 Dependability
Dependability is about receiving the products and services within time as per
the customers required time preference. (Slack and Brandon-Jones, 2019).
Quality
Dependability Speed
Flexibility
Cost
Figure4 - Polar Chart (Source, Author 2022)
5. Capacity Management
8
when it comes to the fast process, zero defects and quality process within
the timelines.
4.5 Dependability
Dependability is about receiving the products and services within time as per
the customers required time preference. (Slack and Brandon-Jones, 2019).
Quality
Dependability Speed
Flexibility
Cost
Figure4 - Polar Chart (Source, Author 2022)
5. Capacity Management
8
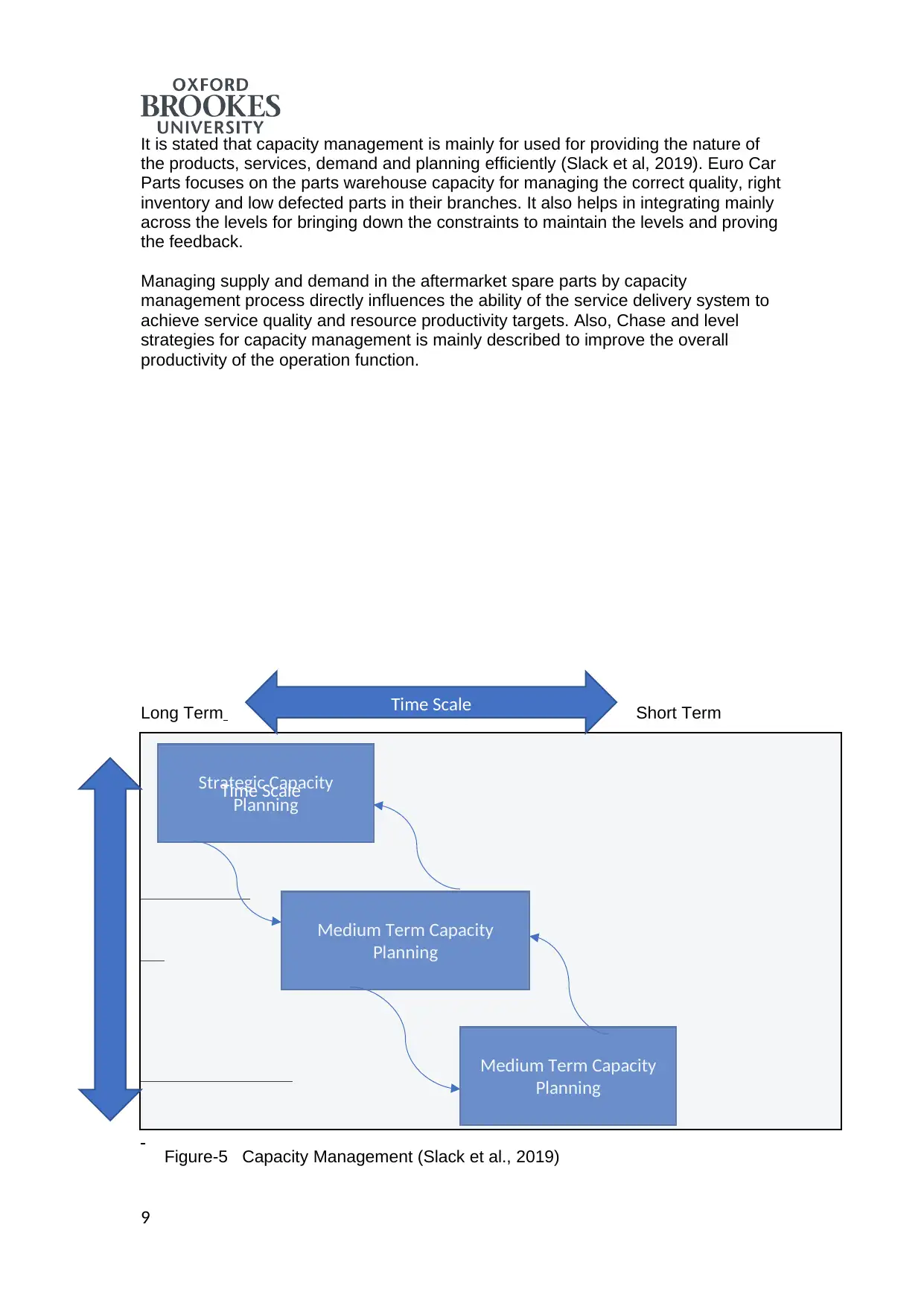
It is stated that capacity management is mainly for used for providing the nature of
the products, services, demand and planning efficiently (Slack et al, 2019). Euro Car
Parts focuses on the parts warehouse capacity for managing the correct quality, right
inventory and low defected parts in their branches. It also helps in integrating mainly
across the levels for bringing down the constraints to maintain the levels and proving
the feedback.
Managing supply and demand in the aftermarket spare parts by capacity
management process directly influences the ability of the service delivery system to
achieve service quality and resource productivity targets. Also, Chase and level
strategies for capacity management is mainly described to improve the overall
productivity of the operation function.
Long Term Short Term
Figure-5 Capacity Management (Slack et al., 2019)
9
Strategic Capacity
Planning
Medium Term Capacity
Planning
Medium Term Capacity
Planning
Time Scale
Time Scale
the products, services, demand and planning efficiently (Slack et al, 2019). Euro Car
Parts focuses on the parts warehouse capacity for managing the correct quality, right
inventory and low defected parts in their branches. It also helps in integrating mainly
across the levels for bringing down the constraints to maintain the levels and proving
the feedback.
Managing supply and demand in the aftermarket spare parts by capacity
management process directly influences the ability of the service delivery system to
achieve service quality and resource productivity targets. Also, Chase and level
strategies for capacity management is mainly described to improve the overall
productivity of the operation function.
Long Term Short Term
Figure-5 Capacity Management (Slack et al., 2019)
9
Strategic Capacity
Planning
Medium Term Capacity
Planning
Medium Term Capacity
Planning
Time Scale
Time Scale
Secure Best Marks with AI Grader
Need help grading? Try our AI Grader for instant feedback on your assignments.
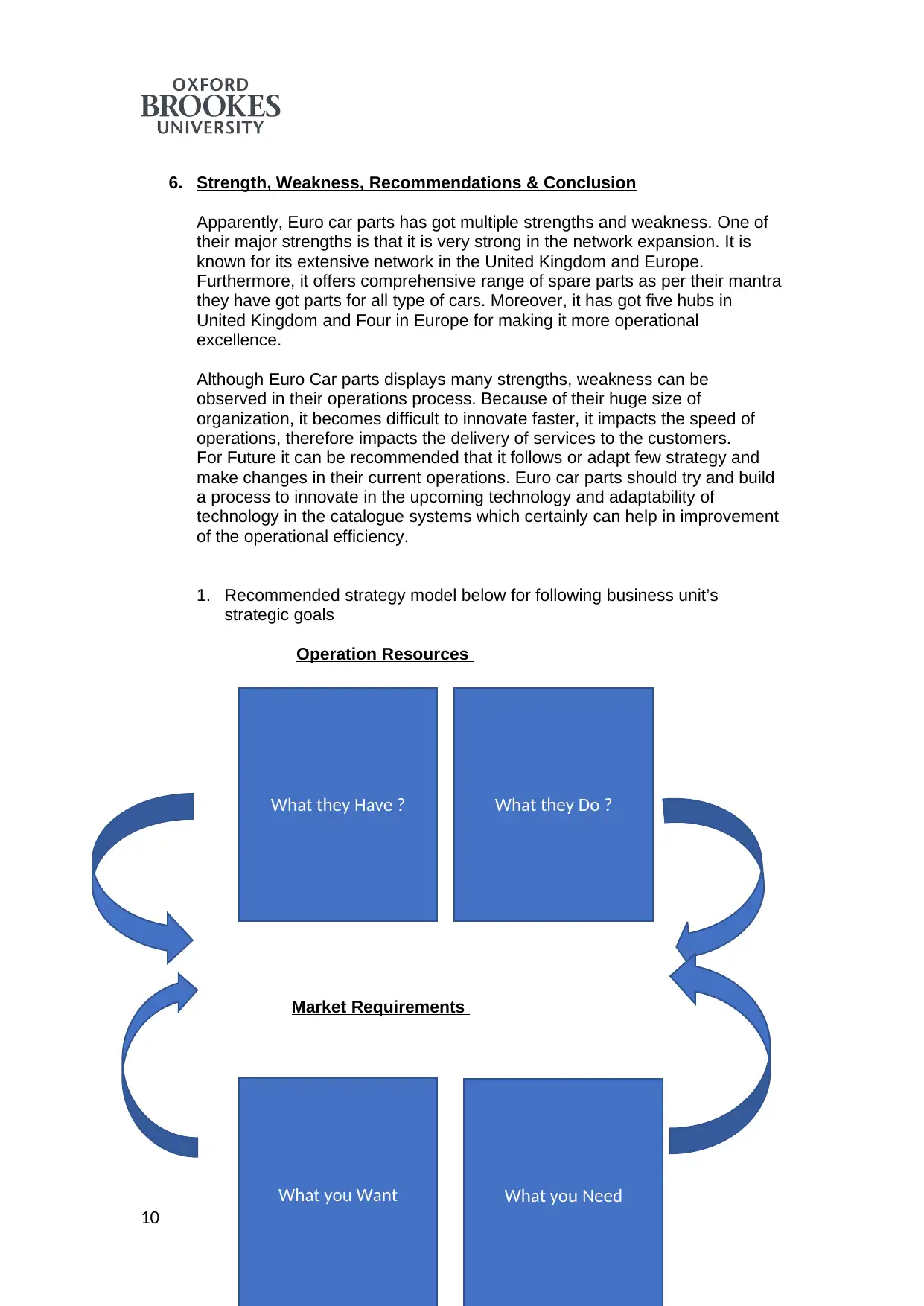
6. Strength, Weakness, Recommendations & Conclusion
Apparently, Euro car parts has got multiple strengths and weakness. One of
their major strengths is that it is very strong in the network expansion. It is
known for its extensive network in the United Kingdom and Europe.
Furthermore, it offers comprehensive range of spare parts as per their mantra
they have got parts for all type of cars. Moreover, it has got five hubs in
United Kingdom and Four in Europe for making it more operational
excellence.
Although Euro Car parts displays many strengths, weakness can be
observed in their operations process. Because of their huge size of
organization, it becomes difficult to innovate faster, it impacts the speed of
operations, therefore impacts the delivery of services to the customers.
For Future it can be recommended that it follows or adapt few strategy and
make changes in their current operations. Euro car parts should try and build
a process to innovate in the upcoming technology and adaptability of
technology in the catalogue systems which certainly can help in improvement
of the operational efficiency.
1. Recommended strategy model below for following business unit’s
strategic goals
Operation Resources
Market Requirements
10
What they Have ? What they Do ?
What you Want What you Need
Apparently, Euro car parts has got multiple strengths and weakness. One of
their major strengths is that it is very strong in the network expansion. It is
known for its extensive network in the United Kingdom and Europe.
Furthermore, it offers comprehensive range of spare parts as per their mantra
they have got parts for all type of cars. Moreover, it has got five hubs in
United Kingdom and Four in Europe for making it more operational
excellence.
Although Euro Car parts displays many strengths, weakness can be
observed in their operations process. Because of their huge size of
organization, it becomes difficult to innovate faster, it impacts the speed of
operations, therefore impacts the delivery of services to the customers.
For Future it can be recommended that it follows or adapt few strategy and
make changes in their current operations. Euro car parts should try and build
a process to innovate in the upcoming technology and adaptability of
technology in the catalogue systems which certainly can help in improvement
of the operational efficiency.
1. Recommended strategy model below for following business unit’s
strategic goals
Operation Resources
Market Requirements
10
What they Have ? What they Do ?
What you Want What you Need
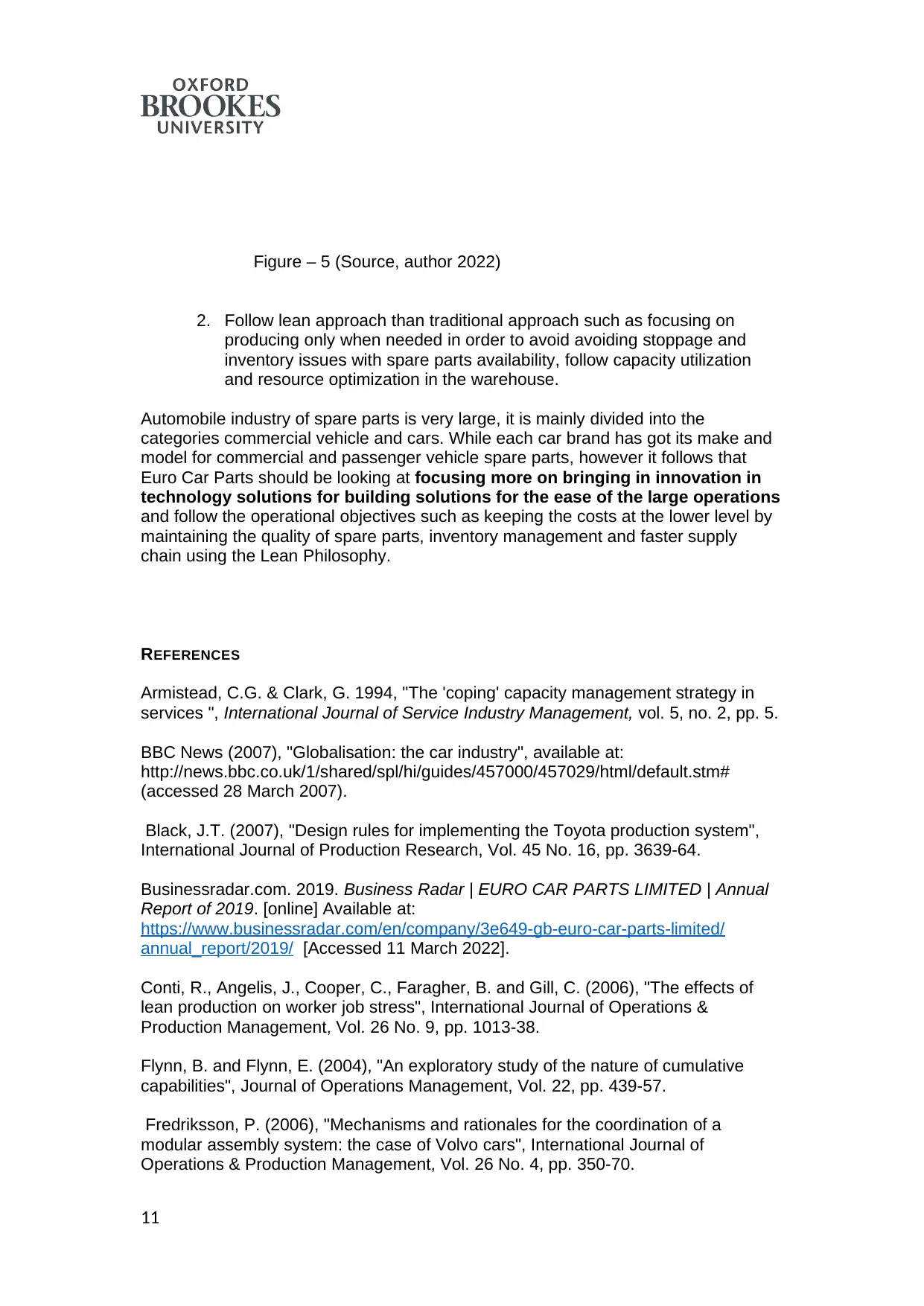
Figure – 5 (Source, author 2022)
2. Follow lean approach than traditional approach such as focusing on
producing only when needed in order to avoid avoiding stoppage and
inventory issues with spare parts availability, follow capacity utilization
and resource optimization in the warehouse.
Automobile industry of spare parts is very large, it is mainly divided into the
categories commercial vehicle and cars. While each car brand has got its make and
model for commercial and passenger vehicle spare parts, however it follows that
Euro Car Parts should be looking at focusing more on bringing in innovation in
technology solutions for building solutions for the ease of the large operations
and follow the operational objectives such as keeping the costs at the lower level by
maintaining the quality of spare parts, inventory management and faster supply
chain using the Lean Philosophy.
REFERENCES
Armistead, C.G. & Clark, G. 1994, "The 'coping' capacity management strategy in
services ", International Journal of Service Industry Management, vol. 5, no. 2, pp. 5.
BBC News (2007), "Globalisation: the car industry", available at:
http://news.bbc.co.uk/1/shared/spl/hi/guides/457000/457029/html/default.stm#
(accessed 28 March 2007).
Black, J.T. (2007), "Design rules for implementing the Toyota production system",
International Journal of Production Research, Vol. 45 No. 16, pp. 3639-64.
Businessradar.com. 2019. Business Radar | EURO CAR PARTS LIMITED | Annual
Report of 2019. [online] Available at:
https://www.businessradar.com/en/company/3e649-gb-euro-car-parts-limited/
annual_report/2019/ [Accessed 11 March 2022].
Conti, R., Angelis, J., Cooper, C., Faragher, B. and Gill, C. (2006), "The effects of
lean production on worker job stress", International Journal of Operations &
Production Management, Vol. 26 No. 9, pp. 1013-38.
Flynn, B. and Flynn, E. (2004), "An exploratory study of the nature of cumulative
capabilities", Journal of Operations Management, Vol. 22, pp. 439-57.
Fredriksson, P. (2006), "Mechanisms and rationales for the coordination of a
modular assembly system: the case of Volvo cars", International Journal of
Operations & Production Management, Vol. 26 No. 4, pp. 350-70.
11
2. Follow lean approach than traditional approach such as focusing on
producing only when needed in order to avoid avoiding stoppage and
inventory issues with spare parts availability, follow capacity utilization
and resource optimization in the warehouse.
Automobile industry of spare parts is very large, it is mainly divided into the
categories commercial vehicle and cars. While each car brand has got its make and
model for commercial and passenger vehicle spare parts, however it follows that
Euro Car Parts should be looking at focusing more on bringing in innovation in
technology solutions for building solutions for the ease of the large operations
and follow the operational objectives such as keeping the costs at the lower level by
maintaining the quality of spare parts, inventory management and faster supply
chain using the Lean Philosophy.
REFERENCES
Armistead, C.G. & Clark, G. 1994, "The 'coping' capacity management strategy in
services ", International Journal of Service Industry Management, vol. 5, no. 2, pp. 5.
BBC News (2007), "Globalisation: the car industry", available at:
http://news.bbc.co.uk/1/shared/spl/hi/guides/457000/457029/html/default.stm#
(accessed 28 March 2007).
Black, J.T. (2007), "Design rules for implementing the Toyota production system",
International Journal of Production Research, Vol. 45 No. 16, pp. 3639-64.
Businessradar.com. 2019. Business Radar | EURO CAR PARTS LIMITED | Annual
Report of 2019. [online] Available at:
https://www.businessradar.com/en/company/3e649-gb-euro-car-parts-limited/
annual_report/2019/ [Accessed 11 March 2022].
Conti, R., Angelis, J., Cooper, C., Faragher, B. and Gill, C. (2006), "The effects of
lean production on worker job stress", International Journal of Operations &
Production Management, Vol. 26 No. 9, pp. 1013-38.
Flynn, B. and Flynn, E. (2004), "An exploratory study of the nature of cumulative
capabilities", Journal of Operations Management, Vol. 22, pp. 439-57.
Fredriksson, P. (2006), "Mechanisms and rationales for the coordination of a
modular assembly system: the case of Volvo cars", International Journal of
Operations & Production Management, Vol. 26 No. 4, pp. 350-70.
11
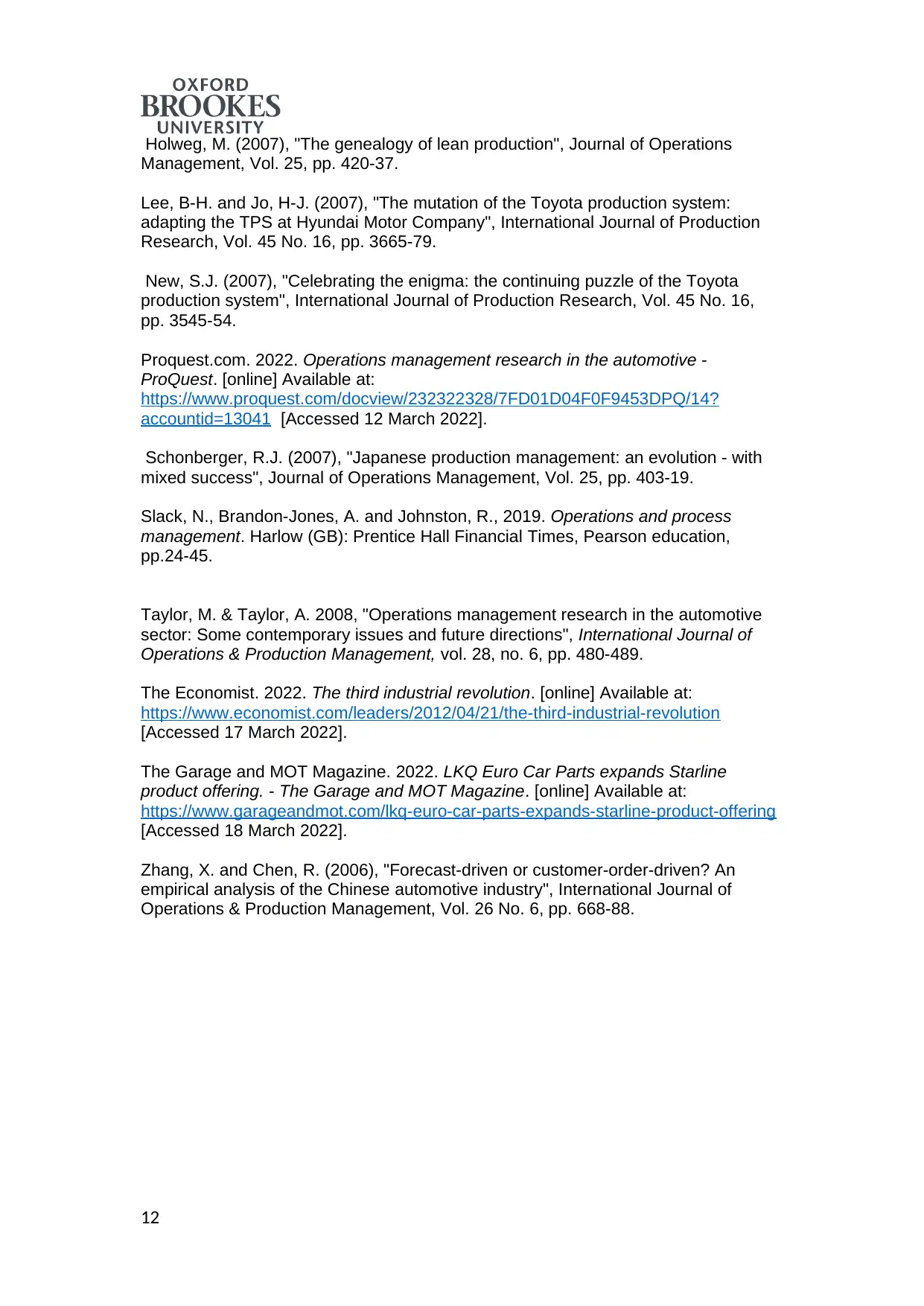
Holweg, M. (2007), "The genealogy of lean production", Journal of Operations
Management, Vol. 25, pp. 420-37.
Lee, B-H. and Jo, H-J. (2007), "The mutation of the Toyota production system:
adapting the TPS at Hyundai Motor Company", International Journal of Production
Research, Vol. 45 No. 16, pp. 3665-79.
New, S.J. (2007), "Celebrating the enigma: the continuing puzzle of the Toyota
production system", International Journal of Production Research, Vol. 45 No. 16,
pp. 3545-54.
Proquest.com. 2022. Operations management research in the automotive -
ProQuest. [online] Available at:
https://www.proquest.com/docview/232322328/7FD01D04F0F9453DPQ/14?
accountid=13041 [Accessed 12 March 2022].
Schonberger, R.J. (2007), "Japanese production management: an evolution - with
mixed success", Journal of Operations Management, Vol. 25, pp. 403-19.
Slack, N., Brandon-Jones, A. and Johnston, R., 2019. Operations and process
management. Harlow (GB): Prentice Hall Financial Times, Pearson education,
pp.24-45.
Taylor, M. & Taylor, A. 2008, "Operations management research in the automotive
sector: Some contemporary issues and future directions", International Journal of
Operations & Production Management, vol. 28, no. 6, pp. 480-489.
The Economist. 2022. The third industrial revolution. [online] Available at:
https://www.economist.com/leaders/2012/04/21/the-third-industrial-revolution
[Accessed 17 March 2022].
The Garage and MOT Magazine. 2022. LKQ Euro Car Parts expands Starline
product offering. - The Garage and MOT Magazine. [online] Available at:
https://www.garageandmot.com/lkq-euro-car-parts-expands-starline-product-offering
[Accessed 18 March 2022].
Zhang, X. and Chen, R. (2006), "Forecast-driven or customer-order-driven? An
empirical analysis of the Chinese automotive industry", International Journal of
Operations & Production Management, Vol. 26 No. 6, pp. 668-88.
12
Management, Vol. 25, pp. 420-37.
Lee, B-H. and Jo, H-J. (2007), "The mutation of the Toyota production system:
adapting the TPS at Hyundai Motor Company", International Journal of Production
Research, Vol. 45 No. 16, pp. 3665-79.
New, S.J. (2007), "Celebrating the enigma: the continuing puzzle of the Toyota
production system", International Journal of Production Research, Vol. 45 No. 16,
pp. 3545-54.
Proquest.com. 2022. Operations management research in the automotive -
ProQuest. [online] Available at:
https://www.proquest.com/docview/232322328/7FD01D04F0F9453DPQ/14?
accountid=13041 [Accessed 12 March 2022].
Schonberger, R.J. (2007), "Japanese production management: an evolution - with
mixed success", Journal of Operations Management, Vol. 25, pp. 403-19.
Slack, N., Brandon-Jones, A. and Johnston, R., 2019. Operations and process
management. Harlow (GB): Prentice Hall Financial Times, Pearson education,
pp.24-45.
Taylor, M. & Taylor, A. 2008, "Operations management research in the automotive
sector: Some contemporary issues and future directions", International Journal of
Operations & Production Management, vol. 28, no. 6, pp. 480-489.
The Economist. 2022. The third industrial revolution. [online] Available at:
https://www.economist.com/leaders/2012/04/21/the-third-industrial-revolution
[Accessed 17 March 2022].
The Garage and MOT Magazine. 2022. LKQ Euro Car Parts expands Starline
product offering. - The Garage and MOT Magazine. [online] Available at:
https://www.garageandmot.com/lkq-euro-car-parts-expands-starline-product-offering
[Accessed 18 March 2022].
Zhang, X. and Chen, R. (2006), "Forecast-driven or customer-order-driven? An
empirical analysis of the Chinese automotive industry", International Journal of
Operations & Production Management, Vol. 26 No. 6, pp. 668-88.
12
1 out of 13

Your All-in-One AI-Powered Toolkit for Academic Success.
+13062052269
info@desklib.com
Available 24*7 on WhatsApp / Email
Unlock your academic potential
© 2024 | Zucol Services PVT LTD | All rights reserved.