M.Eng. Progress Report: Machine Maintenance in Paint Industry
VerifiedAdded on 2022/11/14
|36
|7676
|219
Report
AI Summary
This report, submitted by a Master of Engineering student, investigates the crucial role of machine maintenance within the paint industry. It highlights the significance of an optimistic maintenance approach to enhance productivity and minimize downtime, crucial factors in maintaining a competitiv...
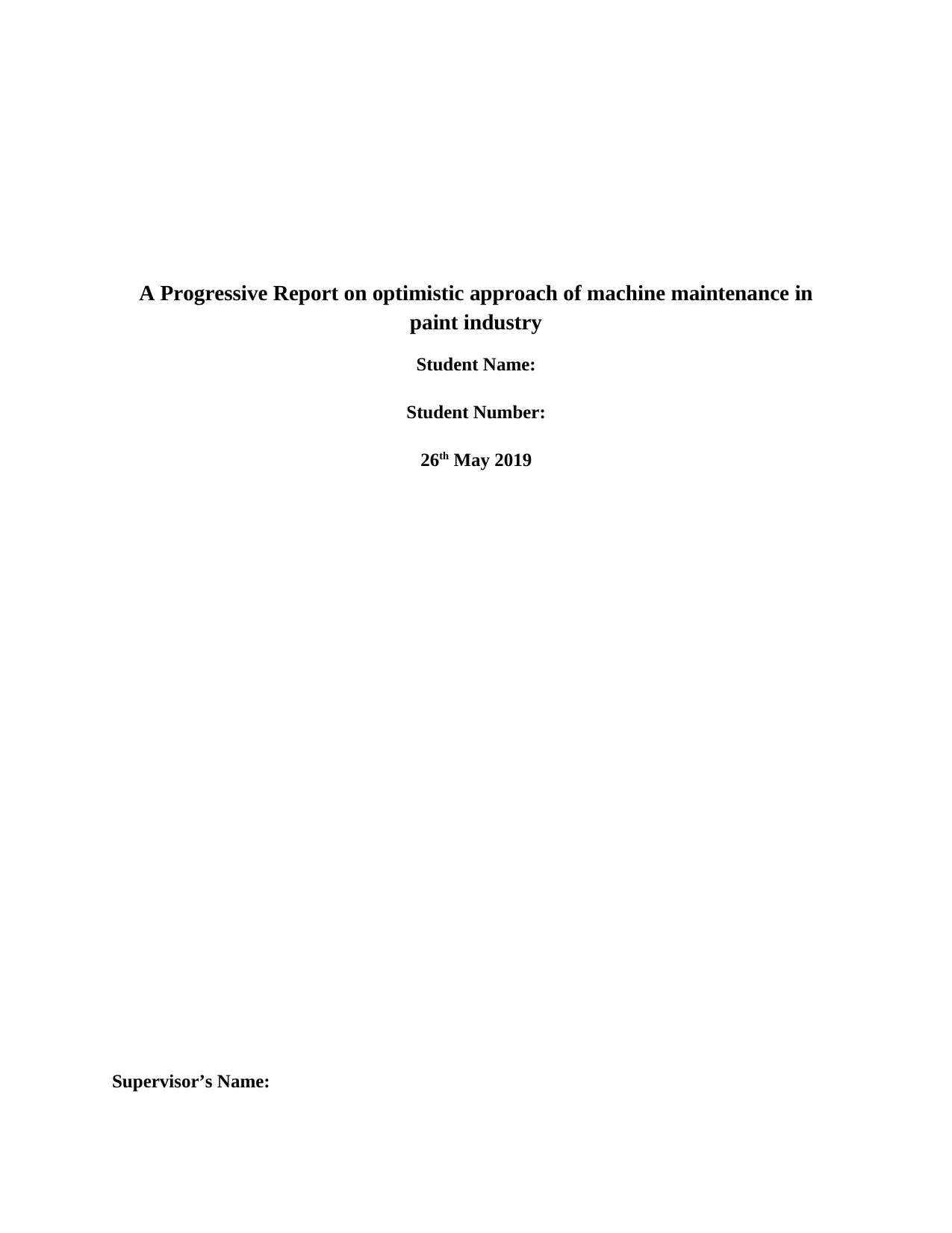
A Progressive Report on optimistic approach of machine maintenance in
paint industry
Student Name:
Student Number:
26th May 2019
Supervisor’s Name:
paint industry
Student Name:
Student Number:
26th May 2019
Supervisor’s Name:
Secure Best Marks with AI Grader
Need help grading? Try our AI Grader for instant feedback on your assignments.
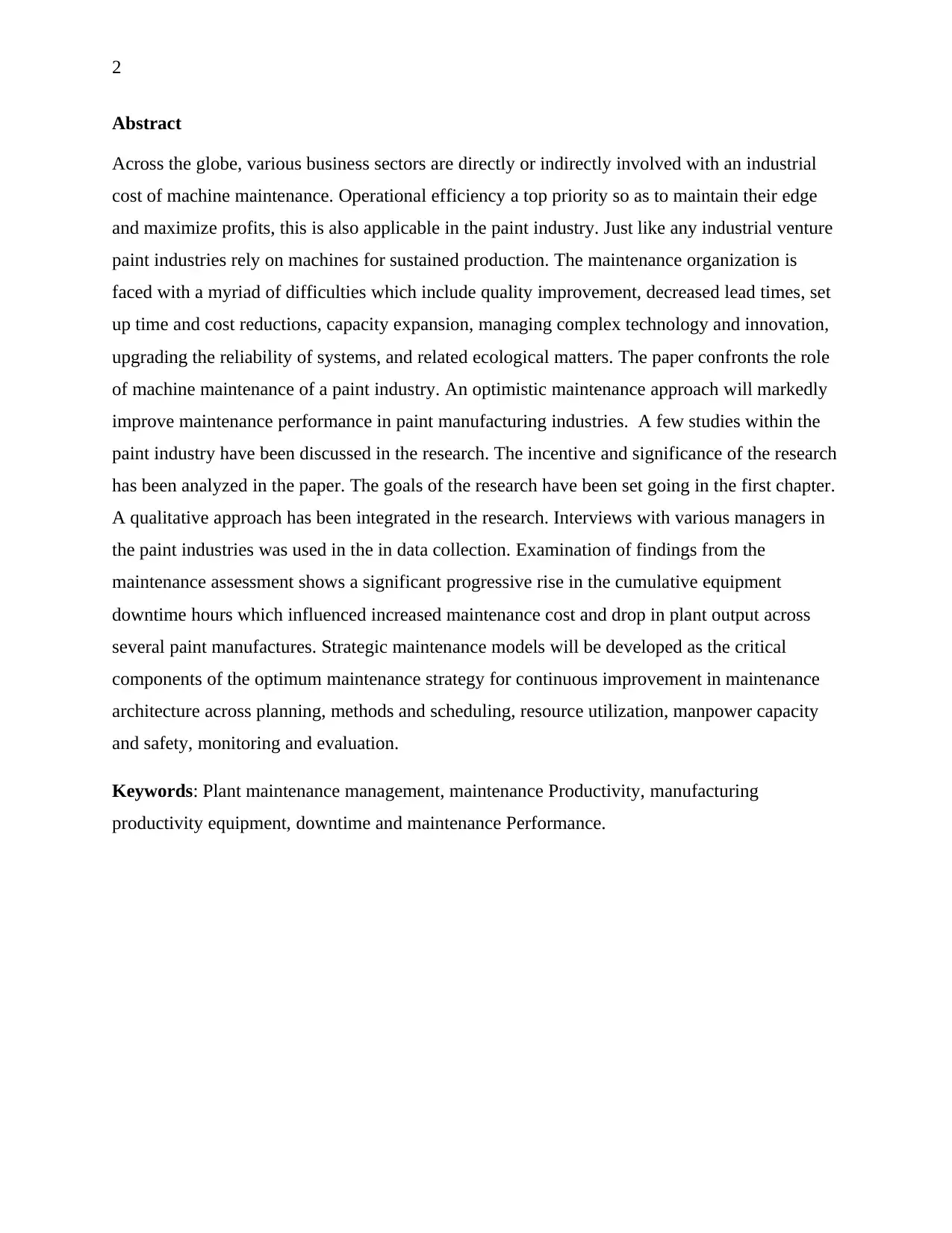
2
Abstract
Across the globe, various business sectors are directly or indirectly involved with an industrial
cost of machine maintenance. Operational efficiency a top priority so as to maintain their edge
and maximize profits, this is also applicable in the paint industry. Just like any industrial venture
paint industries rely on machines for sustained production. The maintenance organization is
faced with a myriad of difficulties which include quality improvement, decreased lead times, set
up time and cost reductions, capacity expansion, managing complex technology and innovation,
upgrading the reliability of systems, and related ecological matters. The paper confronts the role
of machine maintenance of a paint industry. An optimistic maintenance approach will markedly
improve maintenance performance in paint manufacturing industries. A few studies within the
paint industry have been discussed in the research. The incentive and significance of the research
has been analyzed in the paper. The goals of the research have been set going in the first chapter.
A qualitative approach has been integrated in the research. Interviews with various managers in
the paint industries was used in the in data collection. Examination of findings from the
maintenance assessment shows a significant progressive rise in the cumulative equipment
downtime hours which influenced increased maintenance cost and drop in plant output across
several paint manufactures. Strategic maintenance models will be developed as the critical
components of the optimum maintenance strategy for continuous improvement in maintenance
architecture across planning, methods and scheduling, resource utilization, manpower capacity
and safety, monitoring and evaluation.
Keywords: Plant maintenance management, maintenance Productivity, manufacturing
productivity equipment, downtime and maintenance Performance.
Abstract
Across the globe, various business sectors are directly or indirectly involved with an industrial
cost of machine maintenance. Operational efficiency a top priority so as to maintain their edge
and maximize profits, this is also applicable in the paint industry. Just like any industrial venture
paint industries rely on machines for sustained production. The maintenance organization is
faced with a myriad of difficulties which include quality improvement, decreased lead times, set
up time and cost reductions, capacity expansion, managing complex technology and innovation,
upgrading the reliability of systems, and related ecological matters. The paper confronts the role
of machine maintenance of a paint industry. An optimistic maintenance approach will markedly
improve maintenance performance in paint manufacturing industries. A few studies within the
paint industry have been discussed in the research. The incentive and significance of the research
has been analyzed in the paper. The goals of the research have been set going in the first chapter.
A qualitative approach has been integrated in the research. Interviews with various managers in
the paint industries was used in the in data collection. Examination of findings from the
maintenance assessment shows a significant progressive rise in the cumulative equipment
downtime hours which influenced increased maintenance cost and drop in plant output across
several paint manufactures. Strategic maintenance models will be developed as the critical
components of the optimum maintenance strategy for continuous improvement in maintenance
architecture across planning, methods and scheduling, resource utilization, manpower capacity
and safety, monitoring and evaluation.
Keywords: Plant maintenance management, maintenance Productivity, manufacturing
productivity equipment, downtime and maintenance Performance.
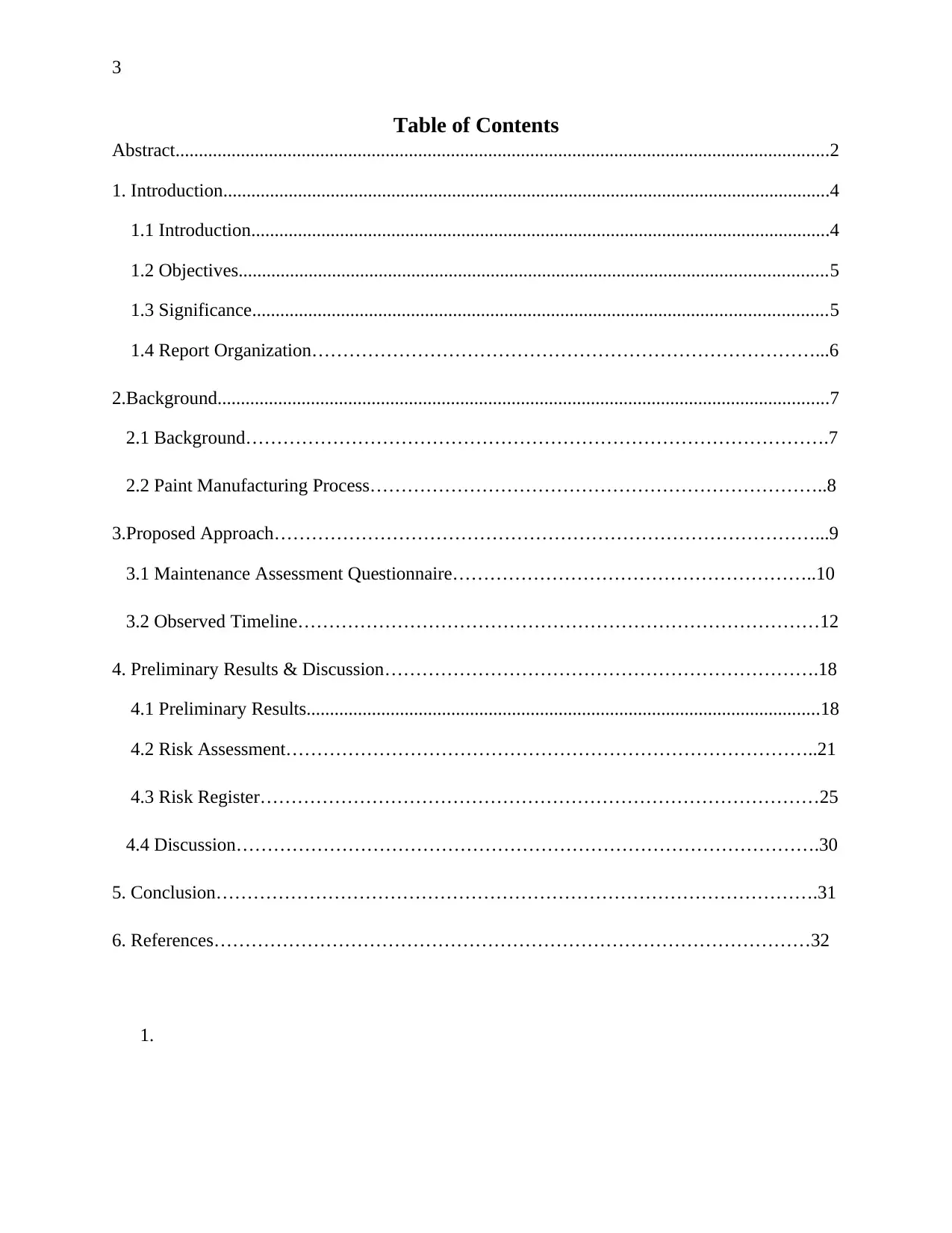
3
Table of Contents
Abstract............................................................................................................................................2
1. Introduction..................................................................................................................................4
1.1 Introduction............................................................................................................................4
1.2 Objectives..............................................................................................................................5
1.3 Significance...........................................................................................................................5
1.4 Report Organization………………………………………………………………………...6
2.Background...................................................................................................................................7
2.1 Background………………………………………………………………………………….7
2.2 Paint Manufacturing Process………………………………………………………………..8
3.Proposed Approach……………………………………………………………………………...9
3.1 Maintenance Assessment Questionnaire…………………………………………………..10
3.2 Observed Timeline…………………………………………………………………………12
4. Preliminary Results & Discussion…………………………………………………………….18
4.1 Preliminary Results..............................................................................................................18
4.2 Risk Assessment…………………………………………………………………………..21
4.3 Risk Register………………………………………………………………………………25
4.4 Discussion………………………………………………………………………………….30
5. Conclusion…………………………………………………………………………………….31
6. References……………………………………………………………………………………32
1.
Table of Contents
Abstract............................................................................................................................................2
1. Introduction..................................................................................................................................4
1.1 Introduction............................................................................................................................4
1.2 Objectives..............................................................................................................................5
1.3 Significance...........................................................................................................................5
1.4 Report Organization………………………………………………………………………...6
2.Background...................................................................................................................................7
2.1 Background………………………………………………………………………………….7
2.2 Paint Manufacturing Process………………………………………………………………..8
3.Proposed Approach……………………………………………………………………………...9
3.1 Maintenance Assessment Questionnaire…………………………………………………..10
3.2 Observed Timeline…………………………………………………………………………12
4. Preliminary Results & Discussion…………………………………………………………….18
4.1 Preliminary Results..............................................................................................................18
4.2 Risk Assessment…………………………………………………………………………..21
4.3 Risk Register………………………………………………………………………………25
4.4 Discussion………………………………………………………………………………….30
5. Conclusion…………………………………………………………………………………….31
6. References……………………………………………………………………………………32
1.
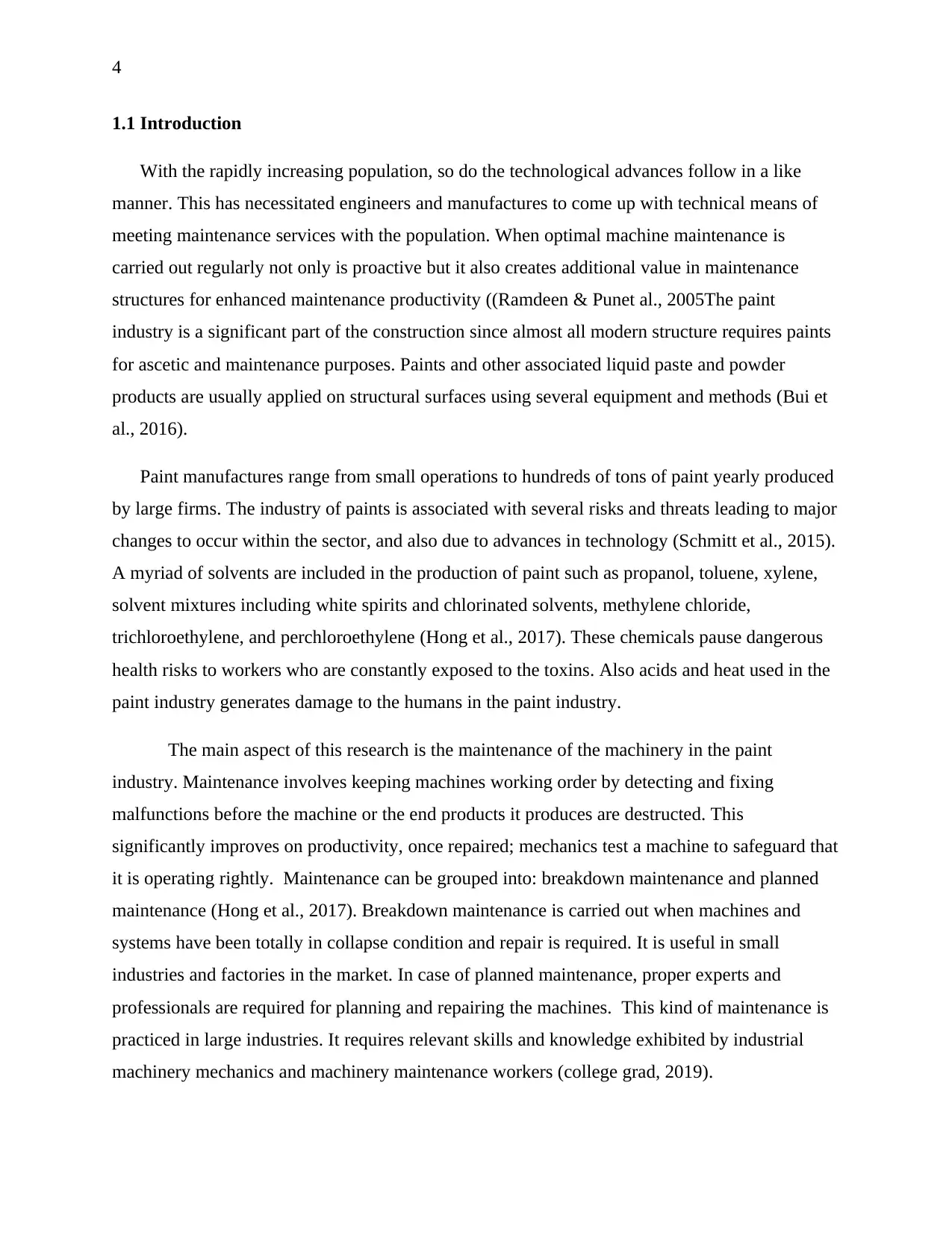
4
1.1 Introduction
With the rapidly increasing population, so do the technological advances follow in a like
manner. This has necessitated engineers and manufactures to come up with technical means of
meeting maintenance services with the population. When optimal machine maintenance is
carried out regularly not only is proactive but it also creates additional value in maintenance
structures for enhanced maintenance productivity ((Ramdeen & Punet al., 2005The paint
industry is a significant part of the construction since almost all modern structure requires paints
for ascetic and maintenance purposes. Paints and other associated liquid paste and powder
products are usually applied on structural surfaces using several equipment and methods (Bui et
al., 2016).
Paint manufactures range from small operations to hundreds of tons of paint yearly produced
by large firms. The industry of paints is associated with several risks and threats leading to major
changes to occur within the sector, and also due to advances in technology (Schmitt et al., 2015).
A myriad of solvents are included in the production of paint such as propanol, toluene, xylene,
solvent mixtures including white spirits and chlorinated solvents, methylene chloride,
trichloroethylene, and perchloroethylene (Hong et al., 2017). These chemicals pause dangerous
health risks to workers who are constantly exposed to the toxins. Also acids and heat used in the
paint industry generates damage to the humans in the paint industry.
The main aspect of this research is the maintenance of the machinery in the paint
industry. Maintenance involves keeping machines working order by detecting and fixing
malfunctions before the machine or the end products it produces are destructed. This
significantly improves on productivity, once repaired; mechanics test a machine to safeguard that
it is operating rightly. Maintenance can be grouped into: breakdown maintenance and planned
maintenance (Hong et al., 2017). Breakdown maintenance is carried out when machines and
systems have been totally in collapse condition and repair is required. It is useful in small
industries and factories in the market. In case of planned maintenance, proper experts and
professionals are required for planning and repairing the machines. This kind of maintenance is
practiced in large industries. It requires relevant skills and knowledge exhibited by industrial
machinery mechanics and machinery maintenance workers (college grad, 2019).
1.1 Introduction
With the rapidly increasing population, so do the technological advances follow in a like
manner. This has necessitated engineers and manufactures to come up with technical means of
meeting maintenance services with the population. When optimal machine maintenance is
carried out regularly not only is proactive but it also creates additional value in maintenance
structures for enhanced maintenance productivity ((Ramdeen & Punet al., 2005The paint
industry is a significant part of the construction since almost all modern structure requires paints
for ascetic and maintenance purposes. Paints and other associated liquid paste and powder
products are usually applied on structural surfaces using several equipment and methods (Bui et
al., 2016).
Paint manufactures range from small operations to hundreds of tons of paint yearly produced
by large firms. The industry of paints is associated with several risks and threats leading to major
changes to occur within the sector, and also due to advances in technology (Schmitt et al., 2015).
A myriad of solvents are included in the production of paint such as propanol, toluene, xylene,
solvent mixtures including white spirits and chlorinated solvents, methylene chloride,
trichloroethylene, and perchloroethylene (Hong et al., 2017). These chemicals pause dangerous
health risks to workers who are constantly exposed to the toxins. Also acids and heat used in the
paint industry generates damage to the humans in the paint industry.
The main aspect of this research is the maintenance of the machinery in the paint
industry. Maintenance involves keeping machines working order by detecting and fixing
malfunctions before the machine or the end products it produces are destructed. This
significantly improves on productivity, once repaired; mechanics test a machine to safeguard that
it is operating rightly. Maintenance can be grouped into: breakdown maintenance and planned
maintenance (Hong et al., 2017). Breakdown maintenance is carried out when machines and
systems have been totally in collapse condition and repair is required. It is useful in small
industries and factories in the market. In case of planned maintenance, proper experts and
professionals are required for planning and repairing the machines. This kind of maintenance is
practiced in large industries. It requires relevant skills and knowledge exhibited by industrial
machinery mechanics and machinery maintenance workers (college grad, 2019).
Secure Best Marks with AI Grader
Need help grading? Try our AI Grader for instant feedback on your assignments.
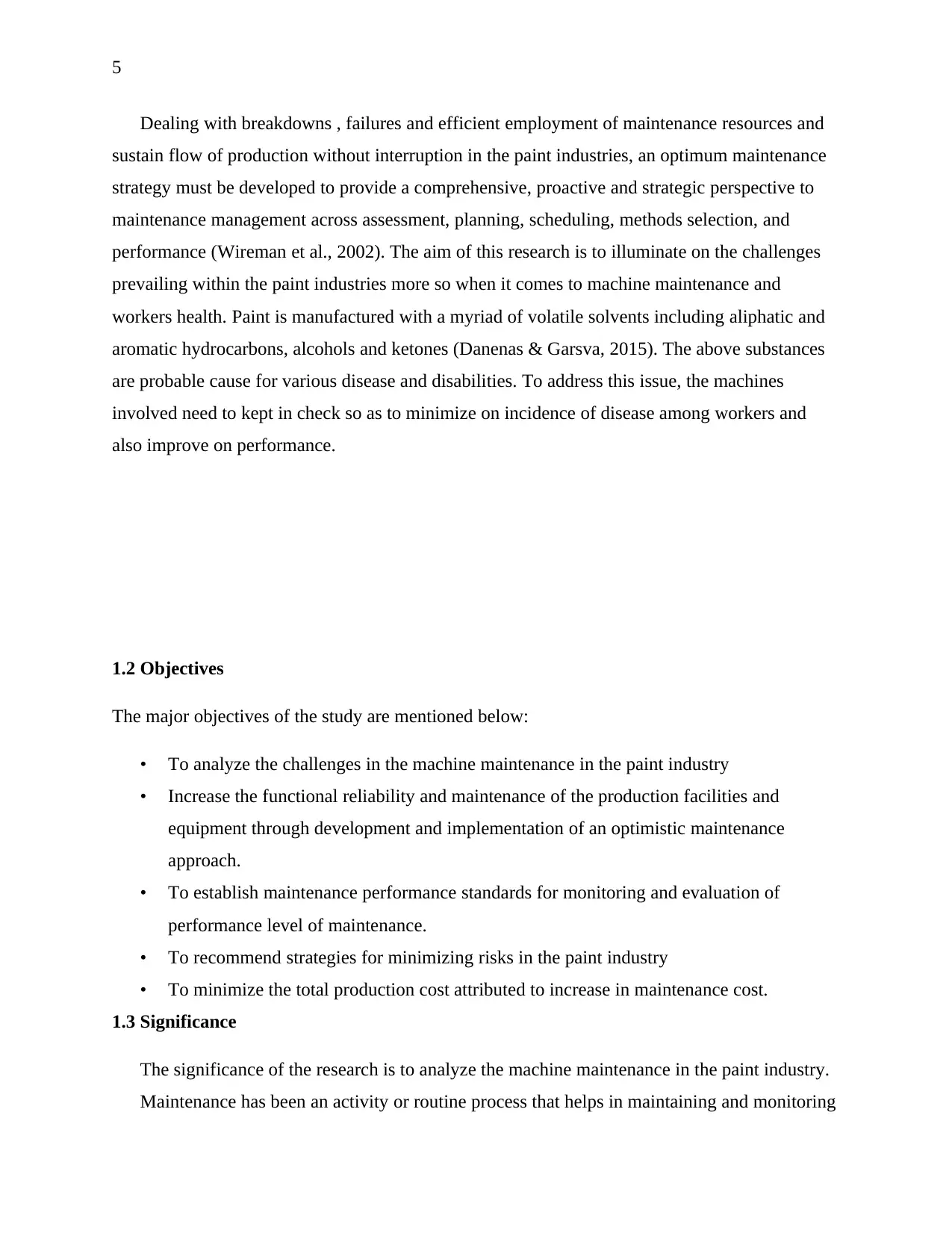
5
Dealing with breakdowns , failures and efficient employment of maintenance resources and
sustain flow of production without interruption in the paint industries, an optimum maintenance
strategy must be developed to provide a comprehensive, proactive and strategic perspective to
maintenance management across assessment, planning, scheduling, methods selection, and
performance (Wireman et al., 2002). The aim of this research is to illuminate on the challenges
prevailing within the paint industries more so when it comes to machine maintenance and
workers health. Paint is manufactured with a myriad of volatile solvents including aliphatic and
aromatic hydrocarbons, alcohols and ketones (Danenas & Garsva, 2015). The above substances
are probable cause for various disease and disabilities. To address this issue, the machines
involved need to kept in check so as to minimize on incidence of disease among workers and
also improve on performance.
1.2 Objectives
The major objectives of the study are mentioned below:
• To analyze the challenges in the machine maintenance in the paint industry
• Increase the functional reliability and maintenance of the production facilities and
equipment through development and implementation of an optimistic maintenance
approach.
• To establish maintenance performance standards for monitoring and evaluation of
performance level of maintenance.
• To recommend strategies for minimizing risks in the paint industry
• To minimize the total production cost attributed to increase in maintenance cost.
1.3 Significance
The significance of the research is to analyze the machine maintenance in the paint industry.
Maintenance has been an activity or routine process that helps in maintaining and monitoring
Dealing with breakdowns , failures and efficient employment of maintenance resources and
sustain flow of production without interruption in the paint industries, an optimum maintenance
strategy must be developed to provide a comprehensive, proactive and strategic perspective to
maintenance management across assessment, planning, scheduling, methods selection, and
performance (Wireman et al., 2002). The aim of this research is to illuminate on the challenges
prevailing within the paint industries more so when it comes to machine maintenance and
workers health. Paint is manufactured with a myriad of volatile solvents including aliphatic and
aromatic hydrocarbons, alcohols and ketones (Danenas & Garsva, 2015). The above substances
are probable cause for various disease and disabilities. To address this issue, the machines
involved need to kept in check so as to minimize on incidence of disease among workers and
also improve on performance.
1.2 Objectives
The major objectives of the study are mentioned below:
• To analyze the challenges in the machine maintenance in the paint industry
• Increase the functional reliability and maintenance of the production facilities and
equipment through development and implementation of an optimistic maintenance
approach.
• To establish maintenance performance standards for monitoring and evaluation of
performance level of maintenance.
• To recommend strategies for minimizing risks in the paint industry
• To minimize the total production cost attributed to increase in maintenance cost.
1.3 Significance
The significance of the research is to analyze the machine maintenance in the paint industry.
Maintenance has been an activity or routine process that helps in maintaining and monitoring
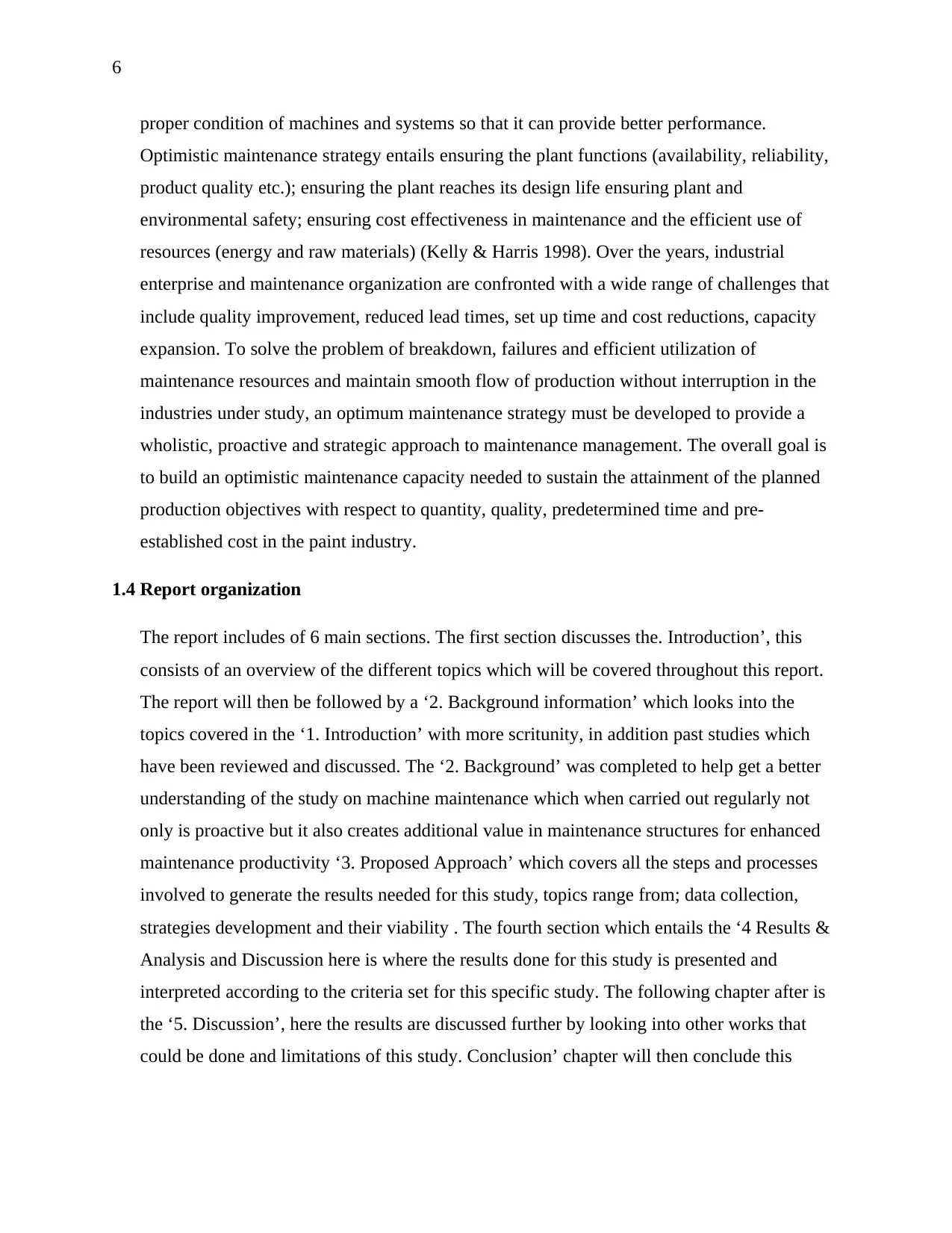
6
proper condition of machines and systems so that it can provide better performance.
Optimistic maintenance strategy entails ensuring the plant functions (availability, reliability,
product quality etc.); ensuring the plant reaches its design life ensuring plant and
environmental safety; ensuring cost effectiveness in maintenance and the efficient use of
resources (energy and raw materials) (Kelly & Harris 1998). Over the years, industrial
enterprise and maintenance organization are confronted with a wide range of challenges that
include quality improvement, reduced lead times, set up time and cost reductions, capacity
expansion. To solve the problem of breakdown, failures and efficient utilization of
maintenance resources and maintain smooth flow of production without interruption in the
industries under study, an optimum maintenance strategy must be developed to provide a
wholistic, proactive and strategic approach to maintenance management. The overall goal is
to build an optimistic maintenance capacity needed to sustain the attainment of the planned
production objectives with respect to quantity, quality, predetermined time and pre-
established cost in the paint industry.
1.4 Report organization
The report includes of 6 main sections. The first section discusses the. Introduction’, this
consists of an overview of the different topics which will be covered throughout this report.
The report will then be followed by a ‘2. Background information’ which looks into the
topics covered in the ‘1. Introduction’ with more scritunity, in addition past studies which
have been reviewed and discussed. The ‘2. Background’ was completed to help get a better
understanding of the study on machine maintenance which when carried out regularly not
only is proactive but it also creates additional value in maintenance structures for enhanced
maintenance productivity ‘3. Proposed Approach’ which covers all the steps and processes
involved to generate the results needed for this study, topics range from; data collection,
strategies development and their viability . The fourth section which entails the ‘4 Results &
Analysis and Discussion here is where the results done for this study is presented and
interpreted according to the criteria set for this specific study. The following chapter after is
the ‘5. Discussion’, here the results are discussed further by looking into other works that
could be done and limitations of this study. Conclusion’ chapter will then conclude this
proper condition of machines and systems so that it can provide better performance.
Optimistic maintenance strategy entails ensuring the plant functions (availability, reliability,
product quality etc.); ensuring the plant reaches its design life ensuring plant and
environmental safety; ensuring cost effectiveness in maintenance and the efficient use of
resources (energy and raw materials) (Kelly & Harris 1998). Over the years, industrial
enterprise and maintenance organization are confronted with a wide range of challenges that
include quality improvement, reduced lead times, set up time and cost reductions, capacity
expansion. To solve the problem of breakdown, failures and efficient utilization of
maintenance resources and maintain smooth flow of production without interruption in the
industries under study, an optimum maintenance strategy must be developed to provide a
wholistic, proactive and strategic approach to maintenance management. The overall goal is
to build an optimistic maintenance capacity needed to sustain the attainment of the planned
production objectives with respect to quantity, quality, predetermined time and pre-
established cost in the paint industry.
1.4 Report organization
The report includes of 6 main sections. The first section discusses the. Introduction’, this
consists of an overview of the different topics which will be covered throughout this report.
The report will then be followed by a ‘2. Background information’ which looks into the
topics covered in the ‘1. Introduction’ with more scritunity, in addition past studies which
have been reviewed and discussed. The ‘2. Background’ was completed to help get a better
understanding of the study on machine maintenance which when carried out regularly not
only is proactive but it also creates additional value in maintenance structures for enhanced
maintenance productivity ‘3. Proposed Approach’ which covers all the steps and processes
involved to generate the results needed for this study, topics range from; data collection,
strategies development and their viability . The fourth section which entails the ‘4 Results &
Analysis and Discussion here is where the results done for this study is presented and
interpreted according to the criteria set for this specific study. The following chapter after is
the ‘5. Discussion’, here the results are discussed further by looking into other works that
could be done and limitations of this study. Conclusion’ chapter will then conclude this
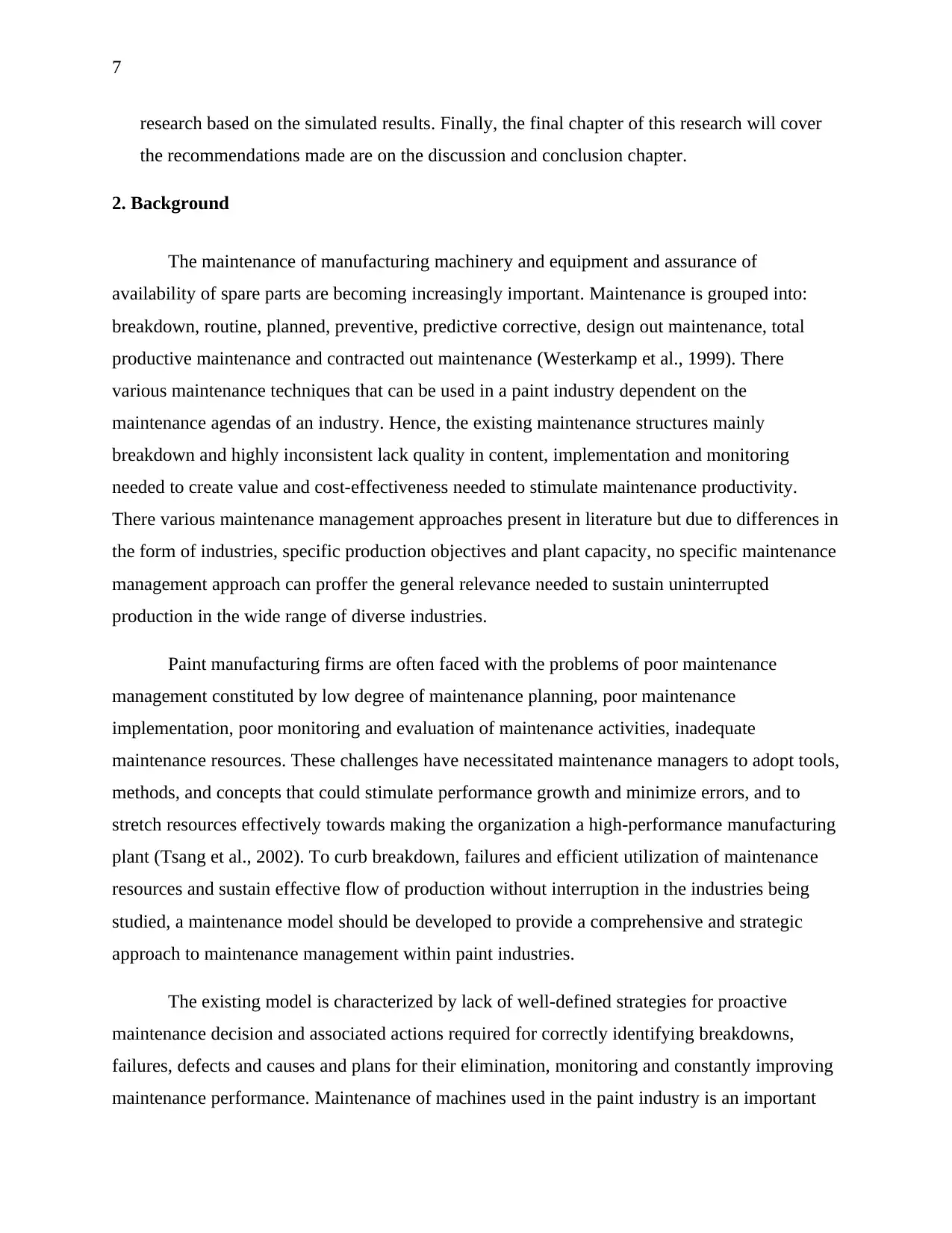
7
research based on the simulated results. Finally, the final chapter of this research will cover
the recommendations made are on the discussion and conclusion chapter.
2. Background
The maintenance of manufacturing machinery and equipment and assurance of
availability of spare parts are becoming increasingly important. Maintenance is grouped into:
breakdown, routine, planned, preventive, predictive corrective, design out maintenance, total
productive maintenance and contracted out maintenance (Westerkamp et al., 1999). There
various maintenance techniques that can be used in a paint industry dependent on the
maintenance agendas of an industry. Hence, the existing maintenance structures mainly
breakdown and highly inconsistent lack quality in content, implementation and monitoring
needed to create value and cost-effectiveness needed to stimulate maintenance productivity.
There various maintenance management approaches present in literature but due to differences in
the form of industries, specific production objectives and plant capacity, no specific maintenance
management approach can proffer the general relevance needed to sustain uninterrupted
production in the wide range of diverse industries.
Paint manufacturing firms are often faced with the problems of poor maintenance
management constituted by low degree of maintenance planning, poor maintenance
implementation, poor monitoring and evaluation of maintenance activities, inadequate
maintenance resources. These challenges have necessitated maintenance managers to adopt tools,
methods, and concepts that could stimulate performance growth and minimize errors, and to
stretch resources effectively towards making the organization a high-performance manufacturing
plant (Tsang et al., 2002). To curb breakdown, failures and efficient utilization of maintenance
resources and sustain effective flow of production without interruption in the industries being
studied, a maintenance model should be developed to provide a comprehensive and strategic
approach to maintenance management within paint industries.
The existing model is characterized by lack of well-defined strategies for proactive
maintenance decision and associated actions required for correctly identifying breakdowns,
failures, defects and causes and plans for their elimination, monitoring and constantly improving
maintenance performance. Maintenance of machines used in the paint industry is an important
research based on the simulated results. Finally, the final chapter of this research will cover
the recommendations made are on the discussion and conclusion chapter.
2. Background
The maintenance of manufacturing machinery and equipment and assurance of
availability of spare parts are becoming increasingly important. Maintenance is grouped into:
breakdown, routine, planned, preventive, predictive corrective, design out maintenance, total
productive maintenance and contracted out maintenance (Westerkamp et al., 1999). There
various maintenance techniques that can be used in a paint industry dependent on the
maintenance agendas of an industry. Hence, the existing maintenance structures mainly
breakdown and highly inconsistent lack quality in content, implementation and monitoring
needed to create value and cost-effectiveness needed to stimulate maintenance productivity.
There various maintenance management approaches present in literature but due to differences in
the form of industries, specific production objectives and plant capacity, no specific maintenance
management approach can proffer the general relevance needed to sustain uninterrupted
production in the wide range of diverse industries.
Paint manufacturing firms are often faced with the problems of poor maintenance
management constituted by low degree of maintenance planning, poor maintenance
implementation, poor monitoring and evaluation of maintenance activities, inadequate
maintenance resources. These challenges have necessitated maintenance managers to adopt tools,
methods, and concepts that could stimulate performance growth and minimize errors, and to
stretch resources effectively towards making the organization a high-performance manufacturing
plant (Tsang et al., 2002). To curb breakdown, failures and efficient utilization of maintenance
resources and sustain effective flow of production without interruption in the industries being
studied, a maintenance model should be developed to provide a comprehensive and strategic
approach to maintenance management within paint industries.
The existing model is characterized by lack of well-defined strategies for proactive
maintenance decision and associated actions required for correctly identifying breakdowns,
failures, defects and causes and plans for their elimination, monitoring and constantly improving
maintenance performance. Maintenance of machines used in the paint industry is an important
Paraphrase This Document
Need a fresh take? Get an instant paraphrase of this document with our AI Paraphraser
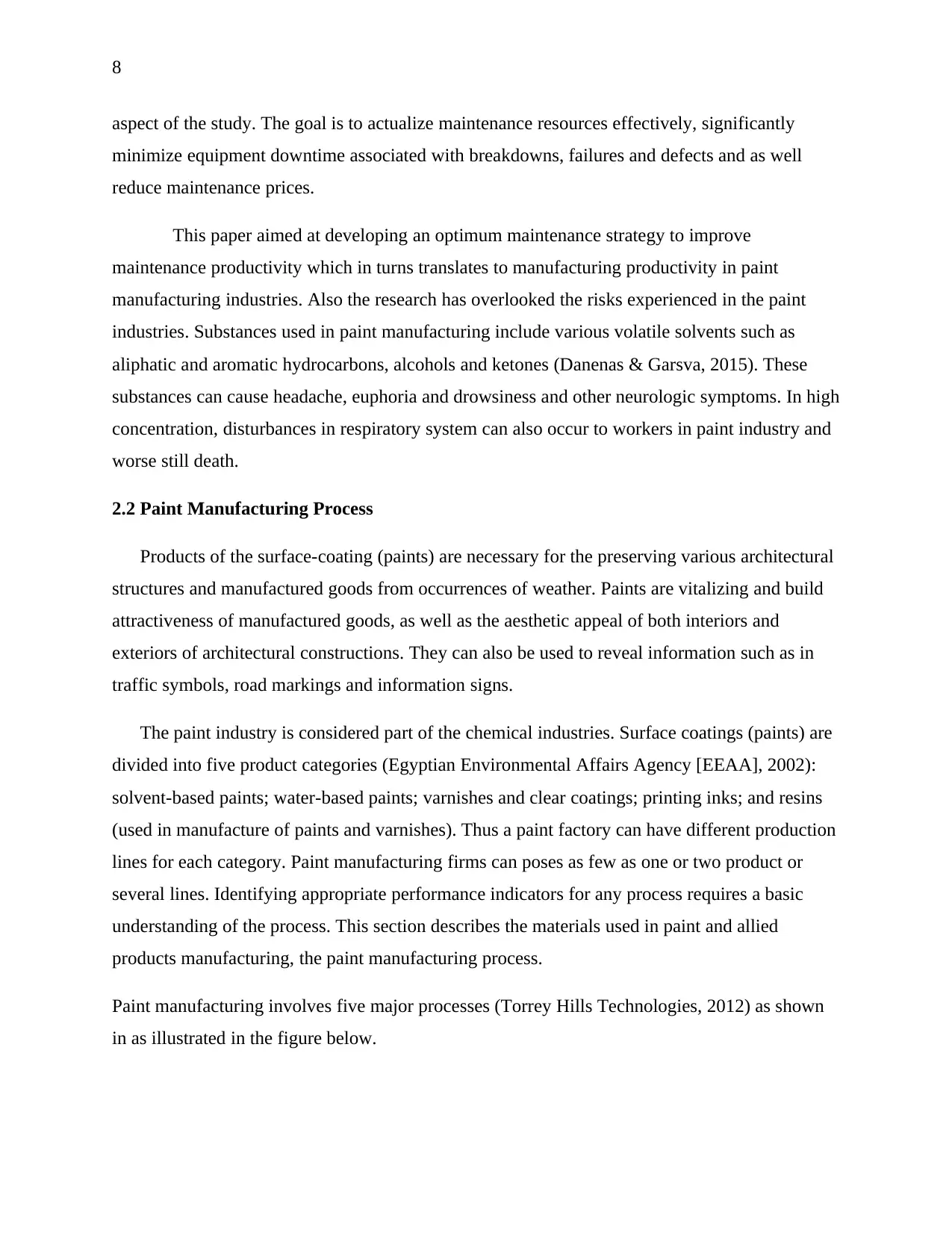
8
aspect of the study. The goal is to actualize maintenance resources effectively, significantly
minimize equipment downtime associated with breakdowns, failures and defects and as well
reduce maintenance prices.
This paper aimed at developing an optimum maintenance strategy to improve
maintenance productivity which in turns translates to manufacturing productivity in paint
manufacturing industries. Also the research has overlooked the risks experienced in the paint
industries. Substances used in paint manufacturing include various volatile solvents such as
aliphatic and aromatic hydrocarbons, alcohols and ketones (Danenas & Garsva, 2015). These
substances can cause headache, euphoria and drowsiness and other neurologic symptoms. In high
concentration, disturbances in respiratory system can also occur to workers in paint industry and
worse still death.
2.2 Paint Manufacturing Process
Products of the surface-coating (paints) are necessary for the preserving various architectural
structures and manufactured goods from occurrences of weather. Paints are vitalizing and build
attractiveness of manufactured goods, as well as the aesthetic appeal of both interiors and
exteriors of architectural constructions. They can also be used to reveal information such as in
traffic symbols, road markings and information signs.
The paint industry is considered part of the chemical industries. Surface coatings (paints) are
divided into five product categories (Egyptian Environmental Affairs Agency [EEAA], 2002):
solvent-based paints; water-based paints; varnishes and clear coatings; printing inks; and resins
(used in manufacture of paints and varnishes). Thus a paint factory can have different production
lines for each category. Paint manufacturing firms can poses as few as one or two product or
several lines. Identifying appropriate performance indicators for any process requires a basic
understanding of the process. This section describes the materials used in paint and allied
products manufacturing, the paint manufacturing process.
Paint manufacturing involves five major processes (Torrey Hills Technologies, 2012) as shown
in as illustrated in the figure below.
aspect of the study. The goal is to actualize maintenance resources effectively, significantly
minimize equipment downtime associated with breakdowns, failures and defects and as well
reduce maintenance prices.
This paper aimed at developing an optimum maintenance strategy to improve
maintenance productivity which in turns translates to manufacturing productivity in paint
manufacturing industries. Also the research has overlooked the risks experienced in the paint
industries. Substances used in paint manufacturing include various volatile solvents such as
aliphatic and aromatic hydrocarbons, alcohols and ketones (Danenas & Garsva, 2015). These
substances can cause headache, euphoria and drowsiness and other neurologic symptoms. In high
concentration, disturbances in respiratory system can also occur to workers in paint industry and
worse still death.
2.2 Paint Manufacturing Process
Products of the surface-coating (paints) are necessary for the preserving various architectural
structures and manufactured goods from occurrences of weather. Paints are vitalizing and build
attractiveness of manufactured goods, as well as the aesthetic appeal of both interiors and
exteriors of architectural constructions. They can also be used to reveal information such as in
traffic symbols, road markings and information signs.
The paint industry is considered part of the chemical industries. Surface coatings (paints) are
divided into five product categories (Egyptian Environmental Affairs Agency [EEAA], 2002):
solvent-based paints; water-based paints; varnishes and clear coatings; printing inks; and resins
(used in manufacture of paints and varnishes). Thus a paint factory can have different production
lines for each category. Paint manufacturing firms can poses as few as one or two product or
several lines. Identifying appropriate performance indicators for any process requires a basic
understanding of the process. This section describes the materials used in paint and allied
products manufacturing, the paint manufacturing process.
Paint manufacturing involves five major processes (Torrey Hills Technologies, 2012) as shown
in as illustrated in the figure below.
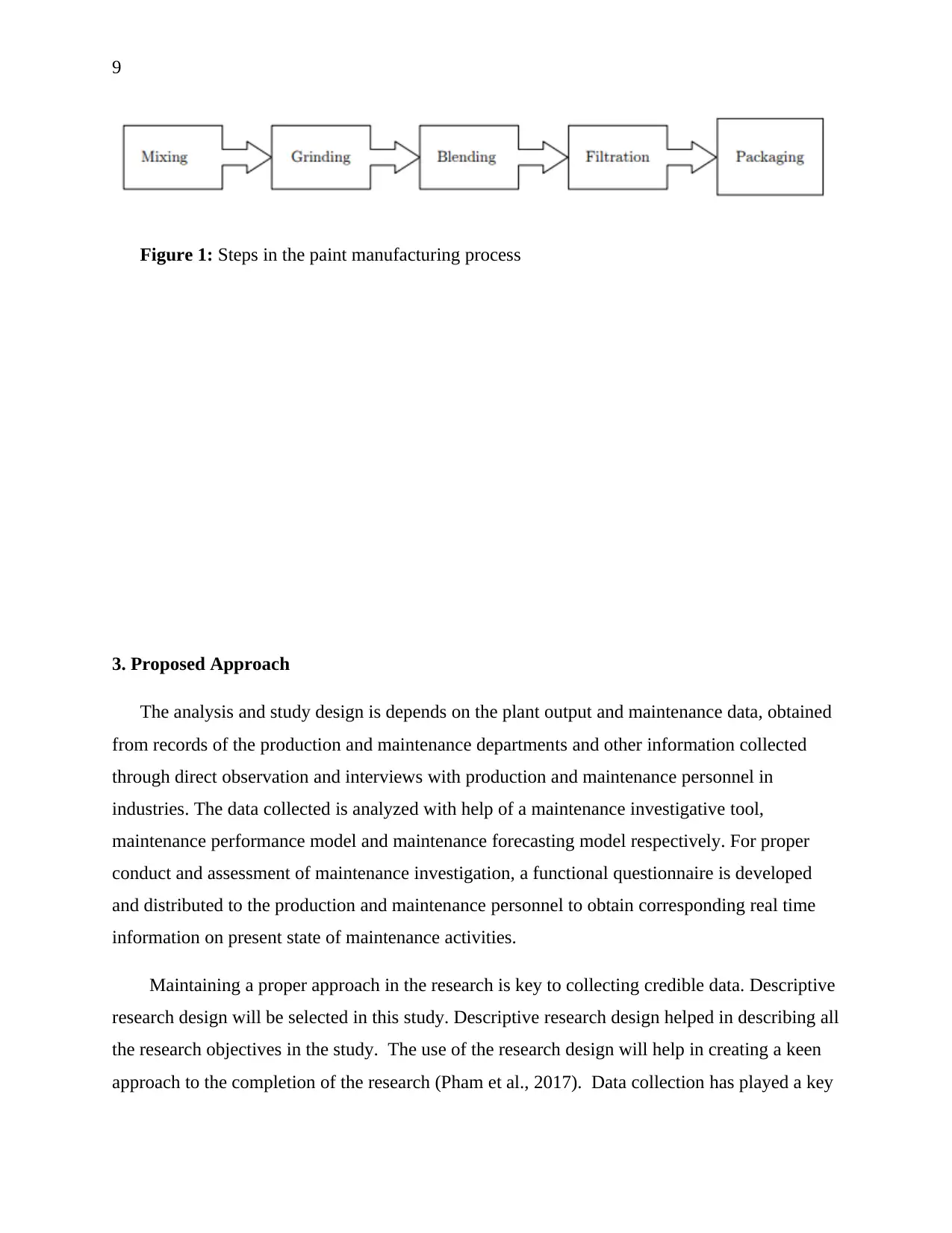
9
Figure 1: Steps in the paint manufacturing process
3. Proposed Approach
The analysis and study design is depends on the plant output and maintenance data, obtained
from records of the production and maintenance departments and other information collected
through direct observation and interviews with production and maintenance personnel in
industries. The data collected is analyzed with help of a maintenance investigative tool,
maintenance performance model and maintenance forecasting model respectively. For proper
conduct and assessment of maintenance investigation, a functional questionnaire is developed
and distributed to the production and maintenance personnel to obtain corresponding real time
information on present state of maintenance activities.
Maintaining a proper approach in the research is key to collecting credible data. Descriptive
research design will be selected in this study. Descriptive research design helped in describing all
the research objectives in the study. The use of the research design will help in creating a keen
approach to the completion of the research (Pham et al., 2017). Data collection has played a key
Figure 1: Steps in the paint manufacturing process
3. Proposed Approach
The analysis and study design is depends on the plant output and maintenance data, obtained
from records of the production and maintenance departments and other information collected
through direct observation and interviews with production and maintenance personnel in
industries. The data collected is analyzed with help of a maintenance investigative tool,
maintenance performance model and maintenance forecasting model respectively. For proper
conduct and assessment of maintenance investigation, a functional questionnaire is developed
and distributed to the production and maintenance personnel to obtain corresponding real time
information on present state of maintenance activities.
Maintaining a proper approach in the research is key to collecting credible data. Descriptive
research design will be selected in this study. Descriptive research design helped in describing all
the research objectives in the study. The use of the research design will help in creating a keen
approach to the completion of the research (Pham et al., 2017). Data collection has played a key
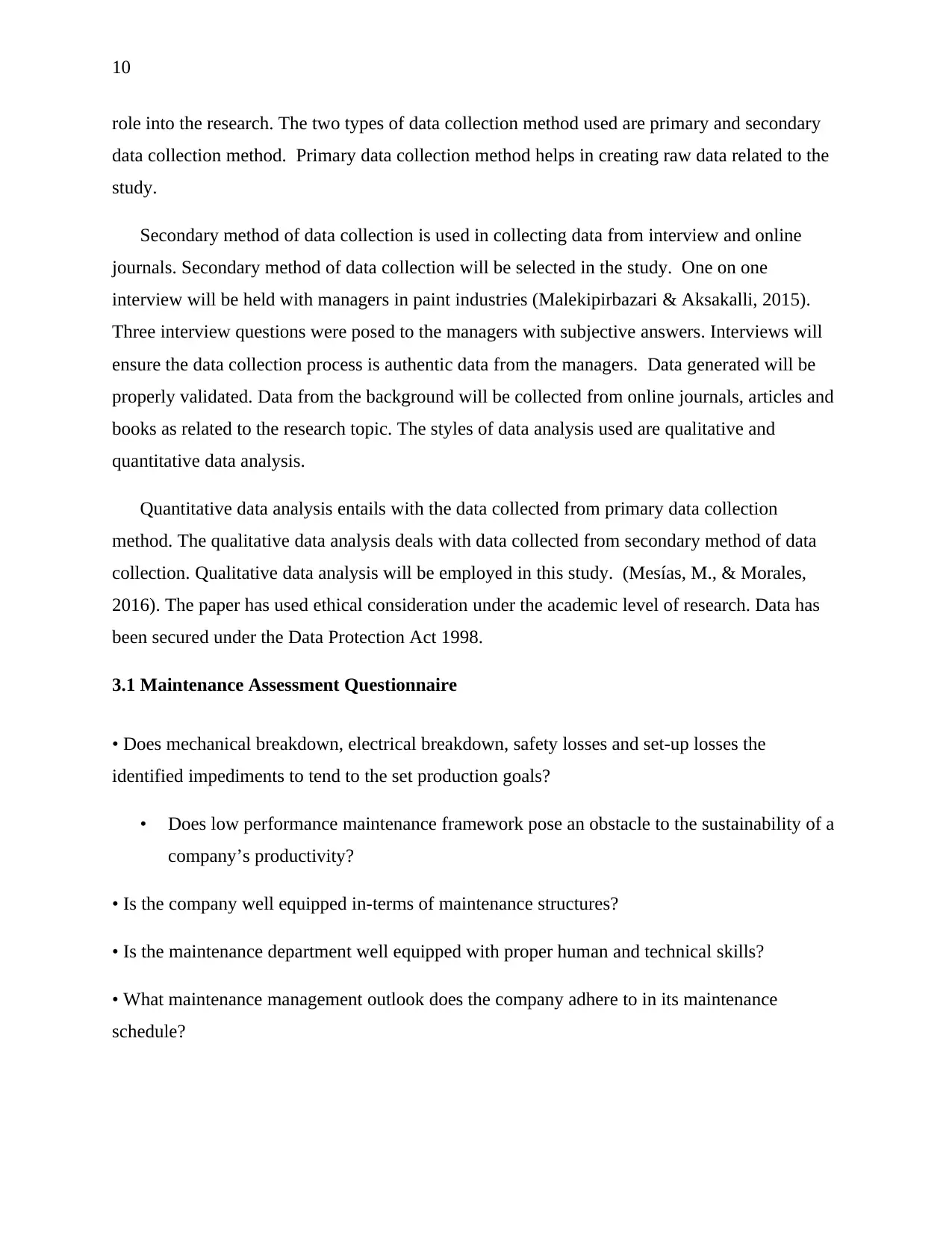
10
role into the research. The two types of data collection method used are primary and secondary
data collection method. Primary data collection method helps in creating raw data related to the
study.
Secondary method of data collection is used in collecting data from interview and online
journals. Secondary method of data collection will be selected in the study. One on one
interview will be held with managers in paint industries (Malekipirbazari & Aksakalli, 2015).
Three interview questions were posed to the managers with subjective answers. Interviews will
ensure the data collection process is authentic data from the managers. Data generated will be
properly validated. Data from the background will be collected from online journals, articles and
books as related to the research topic. The styles of data analysis used are qualitative and
quantitative data analysis.
Quantitative data analysis entails with the data collected from primary data collection
method. The qualitative data analysis deals with data collected from secondary method of data
collection. Qualitative data analysis will be employed in this study. (Mesías, M., & Morales,
2016). The paper has used ethical consideration under the academic level of research. Data has
been secured under the Data Protection Act 1998.
3.1 Maintenance Assessment Questionnaire
• Does mechanical breakdown, electrical breakdown, safety losses and set-up losses the
identified impediments to tend to the set production goals?
• Does low performance maintenance framework pose an obstacle to the sustainability of a
company’s productivity?
• Is the company well equipped in-terms of maintenance structures?
• Is the maintenance department well equipped with proper human and technical skills?
• What maintenance management outlook does the company adhere to in its maintenance
schedule?
role into the research. The two types of data collection method used are primary and secondary
data collection method. Primary data collection method helps in creating raw data related to the
study.
Secondary method of data collection is used in collecting data from interview and online
journals. Secondary method of data collection will be selected in the study. One on one
interview will be held with managers in paint industries (Malekipirbazari & Aksakalli, 2015).
Three interview questions were posed to the managers with subjective answers. Interviews will
ensure the data collection process is authentic data from the managers. Data generated will be
properly validated. Data from the background will be collected from online journals, articles and
books as related to the research topic. The styles of data analysis used are qualitative and
quantitative data analysis.
Quantitative data analysis entails with the data collected from primary data collection
method. The qualitative data analysis deals with data collected from secondary method of data
collection. Qualitative data analysis will be employed in this study. (Mesías, M., & Morales,
2016). The paper has used ethical consideration under the academic level of research. Data has
been secured under the Data Protection Act 1998.
3.1 Maintenance Assessment Questionnaire
• Does mechanical breakdown, electrical breakdown, safety losses and set-up losses the
identified impediments to tend to the set production goals?
• Does low performance maintenance framework pose an obstacle to the sustainability of a
company’s productivity?
• Is the company well equipped in-terms of maintenance structures?
• Is the maintenance department well equipped with proper human and technical skills?
• What maintenance management outlook does the company adhere to in its maintenance
schedule?
Secure Best Marks with AI Grader
Need help grading? Try our AI Grader for instant feedback on your assignments.
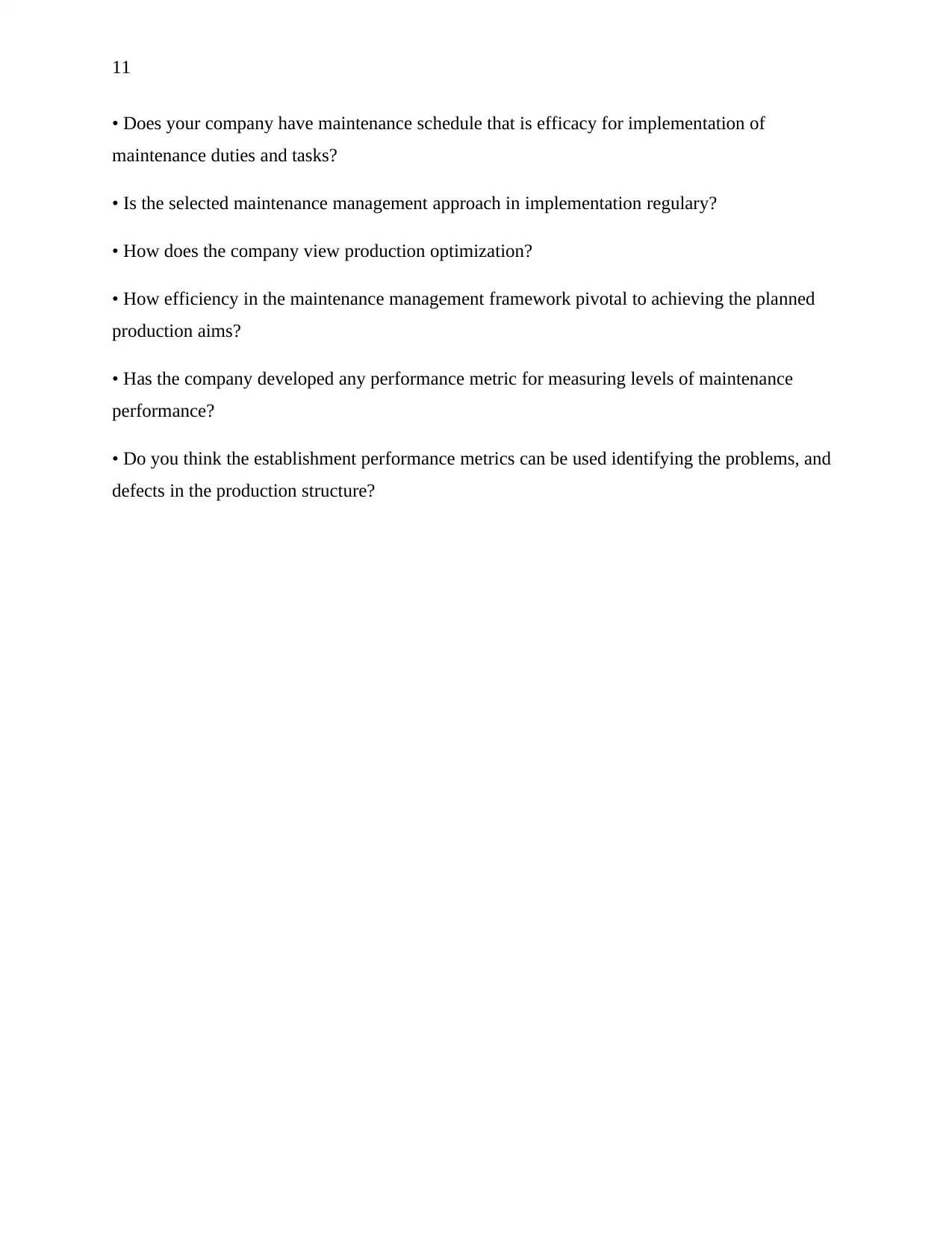
11
• Does your company have maintenance schedule that is efficacy for implementation of
maintenance duties and tasks?
• Is the selected maintenance management approach in implementation regulary?
• How does the company view production optimization?
• How efficiency in the maintenance management framework pivotal to achieving the planned
production aims?
• Has the company developed any performance metric for measuring levels of maintenance
performance?
• Do you think the establishment performance metrics can be used identifying the problems, and
defects in the production structure?
• Does your company have maintenance schedule that is efficacy for implementation of
maintenance duties and tasks?
• Is the selected maintenance management approach in implementation regulary?
• How does the company view production optimization?
• How efficiency in the maintenance management framework pivotal to achieving the planned
production aims?
• Has the company developed any performance metric for measuring levels of maintenance
performance?
• Do you think the establishment performance metrics can be used identifying the problems, and
defects in the production structure?
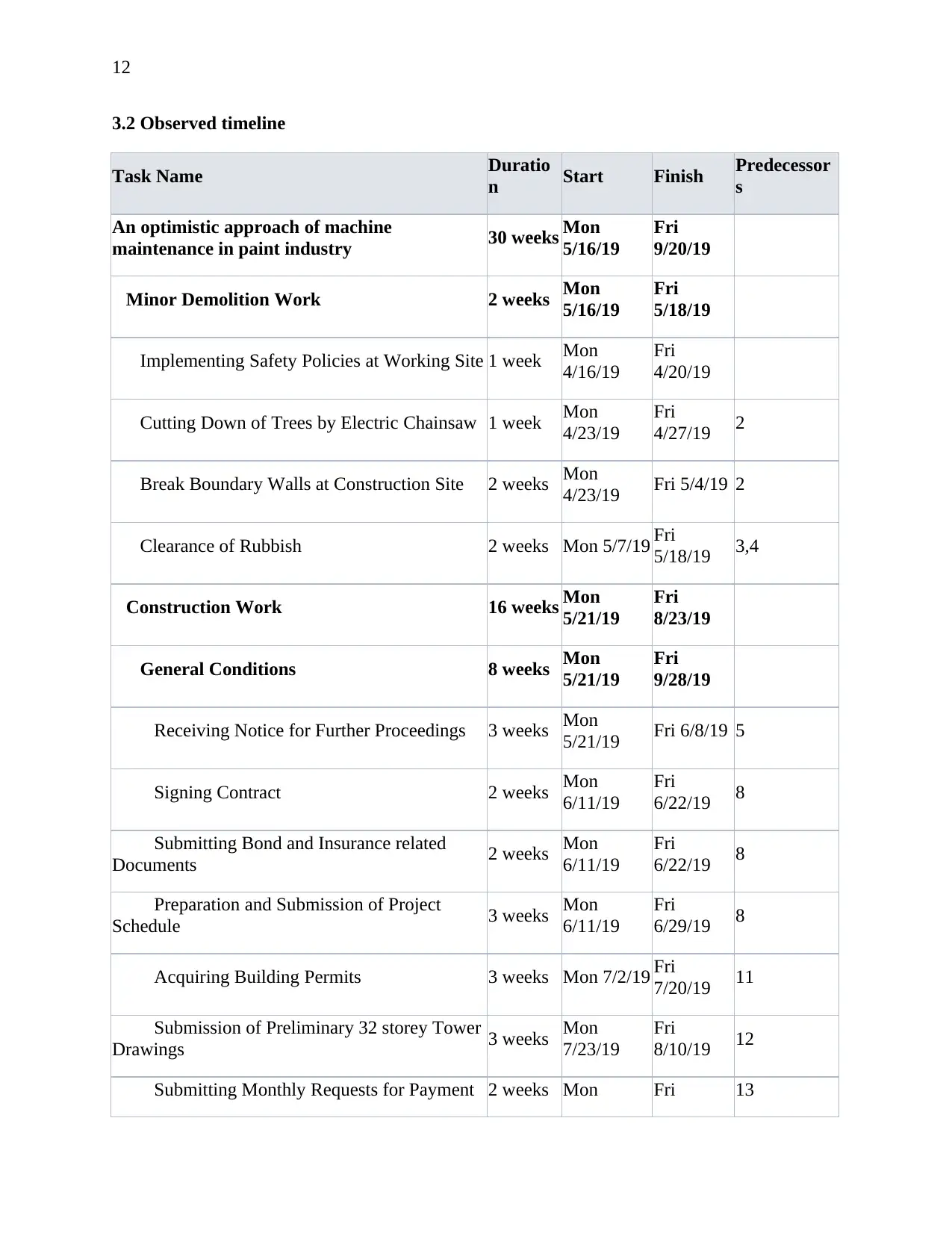
12
3.2 Observed timeline
Task Name Duratio
n Start Finish Predecessor
s
An optimistic approach of machine
maintenance in paint industry 30 weeks Mon
5/16/19
Fri
9/20/19
Minor Demolition Work 2 weeks Mon
5/16/19
Fri
5/18/19
Implementing Safety Policies at Working Site 1 week Mon
4/16/19
Fri
4/20/19
Cutting Down of Trees by Electric Chainsaw 1 week Mon
4/23/19
Fri
4/27/19 2
Break Boundary Walls at Construction Site 2 weeks Mon
4/23/19 Fri 5/4/19 2
Clearance of Rubbish 2 weeks Mon 5/7/19 Fri
5/18/19 3,4
Construction Work 16 weeks Mon
5/21/19
Fri
8/23/19
General Conditions 8 weeks Mon
5/21/19
Fri
9/28/19
Receiving Notice for Further Proceedings 3 weeks Mon
5/21/19 Fri 6/8/19 5
Signing Contract 2 weeks Mon
6/11/19
Fri
6/22/19 8
Submitting Bond and Insurance related
Documents 2 weeks Mon
6/11/19
Fri
6/22/19 8
Preparation and Submission of Project
Schedule 3 weeks Mon
6/11/19
Fri
6/29/19 8
Acquiring Building Permits 3 weeks Mon 7/2/19 Fri
7/20/19 11
Submission of Preliminary 32 storey Tower
Drawings 3 weeks Mon
7/23/19
Fri
8/10/19 12
Submitting Monthly Requests for Payment 2 weeks Mon Fri 13
3.2 Observed timeline
Task Name Duratio
n Start Finish Predecessor
s
An optimistic approach of machine
maintenance in paint industry 30 weeks Mon
5/16/19
Fri
9/20/19
Minor Demolition Work 2 weeks Mon
5/16/19
Fri
5/18/19
Implementing Safety Policies at Working Site 1 week Mon
4/16/19
Fri
4/20/19
Cutting Down of Trees by Electric Chainsaw 1 week Mon
4/23/19
Fri
4/27/19 2
Break Boundary Walls at Construction Site 2 weeks Mon
4/23/19 Fri 5/4/19 2
Clearance of Rubbish 2 weeks Mon 5/7/19 Fri
5/18/19 3,4
Construction Work 16 weeks Mon
5/21/19
Fri
8/23/19
General Conditions 8 weeks Mon
5/21/19
Fri
9/28/19
Receiving Notice for Further Proceedings 3 weeks Mon
5/21/19 Fri 6/8/19 5
Signing Contract 2 weeks Mon
6/11/19
Fri
6/22/19 8
Submitting Bond and Insurance related
Documents 2 weeks Mon
6/11/19
Fri
6/22/19 8
Preparation and Submission of Project
Schedule 3 weeks Mon
6/11/19
Fri
6/29/19 8
Acquiring Building Permits 3 weeks Mon 7/2/19 Fri
7/20/19 11
Submission of Preliminary 32 storey Tower
Drawings 3 weeks Mon
7/23/19
Fri
8/10/19 12
Submitting Monthly Requests for Payment 2 weeks Mon Fri 13
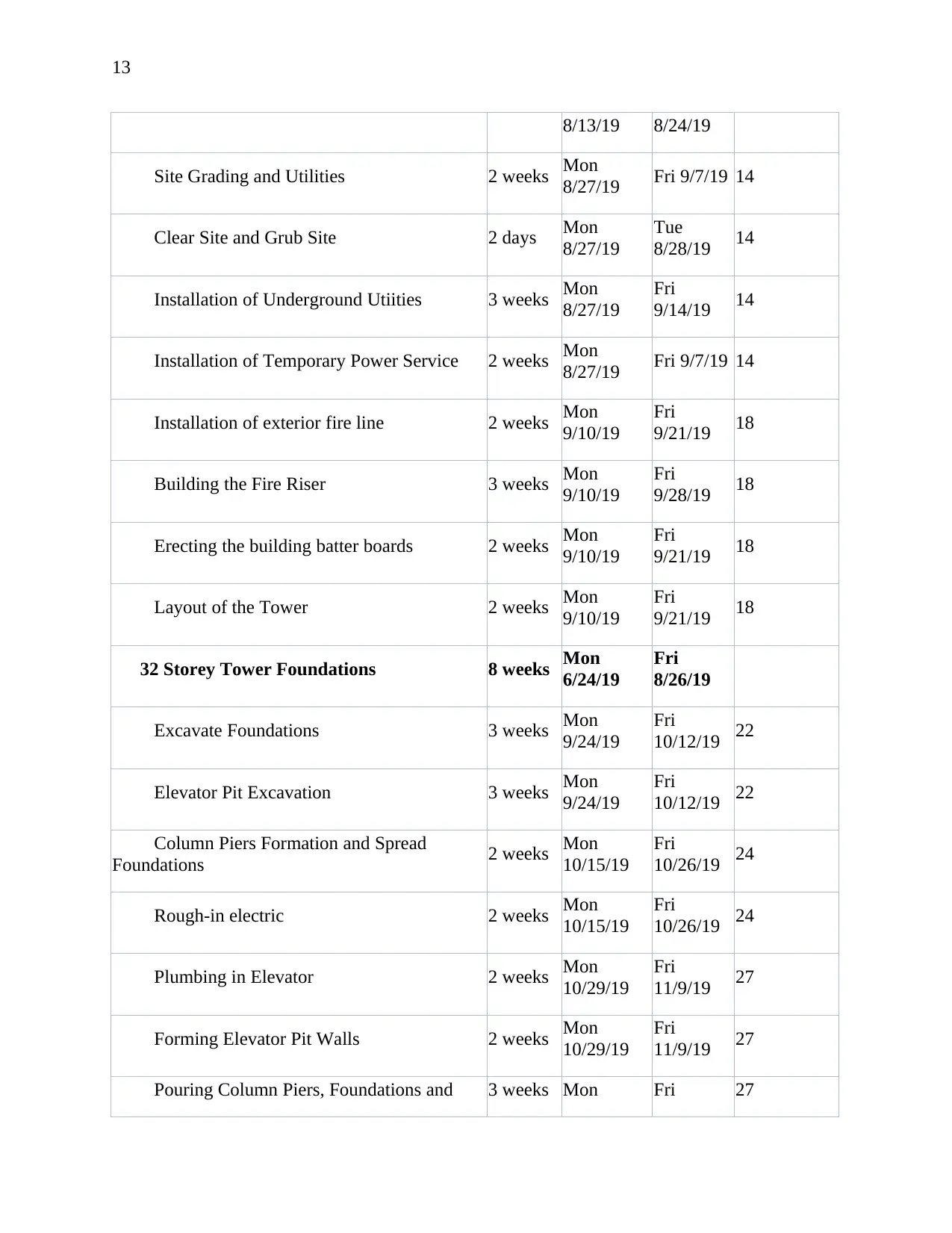
13
8/13/19 8/24/19
Site Grading and Utilities 2 weeks Mon
8/27/19 Fri 9/7/19 14
Clear Site and Grub Site 2 days Mon
8/27/19
Tue
8/28/19 14
Installation of Underground Utiities 3 weeks Mon
8/27/19
Fri
9/14/19 14
Installation of Temporary Power Service 2 weeks Mon
8/27/19 Fri 9/7/19 14
Installation of exterior fire line 2 weeks Mon
9/10/19
Fri
9/21/19 18
Building the Fire Riser 3 weeks Mon
9/10/19
Fri
9/28/19 18
Erecting the building batter boards 2 weeks Mon
9/10/19
Fri
9/21/19 18
Layout of the Tower 2 weeks Mon
9/10/19
Fri
9/21/19 18
32 Storey Tower Foundations 8 weeks Mon
6/24/19
Fri
8/26/19
Excavate Foundations 3 weeks Mon
9/24/19
Fri
10/12/19 22
Elevator Pit Excavation 3 weeks Mon
9/24/19
Fri
10/12/19 22
Column Piers Formation and Spread
Foundations 2 weeks Mon
10/15/19
Fri
10/26/19 24
Rough-in electric 2 weeks Mon
10/15/19
Fri
10/26/19 24
Plumbing in Elevator 2 weeks Mon
10/29/19
Fri
11/9/19 27
Forming Elevator Pit Walls 2 weeks Mon
10/29/19
Fri
11/9/19 27
Pouring Column Piers, Foundations and 3 weeks Mon Fri 27
8/13/19 8/24/19
Site Grading and Utilities 2 weeks Mon
8/27/19 Fri 9/7/19 14
Clear Site and Grub Site 2 days Mon
8/27/19
Tue
8/28/19 14
Installation of Underground Utiities 3 weeks Mon
8/27/19
Fri
9/14/19 14
Installation of Temporary Power Service 2 weeks Mon
8/27/19 Fri 9/7/19 14
Installation of exterior fire line 2 weeks Mon
9/10/19
Fri
9/21/19 18
Building the Fire Riser 3 weeks Mon
9/10/19
Fri
9/28/19 18
Erecting the building batter boards 2 weeks Mon
9/10/19
Fri
9/21/19 18
Layout of the Tower 2 weeks Mon
9/10/19
Fri
9/21/19 18
32 Storey Tower Foundations 8 weeks Mon
6/24/19
Fri
8/26/19
Excavate Foundations 3 weeks Mon
9/24/19
Fri
10/12/19 22
Elevator Pit Excavation 3 weeks Mon
9/24/19
Fri
10/12/19 22
Column Piers Formation and Spread
Foundations 2 weeks Mon
10/15/19
Fri
10/26/19 24
Rough-in electric 2 weeks Mon
10/15/19
Fri
10/26/19 24
Plumbing in Elevator 2 weeks Mon
10/29/19
Fri
11/9/19 27
Forming Elevator Pit Walls 2 weeks Mon
10/29/19
Fri
11/9/19 27
Pouring Column Piers, Foundations and 3 weeks Mon Fri 27
Paraphrase This Document
Need a fresh take? Get an instant paraphrase of this document with our AI Paraphraser
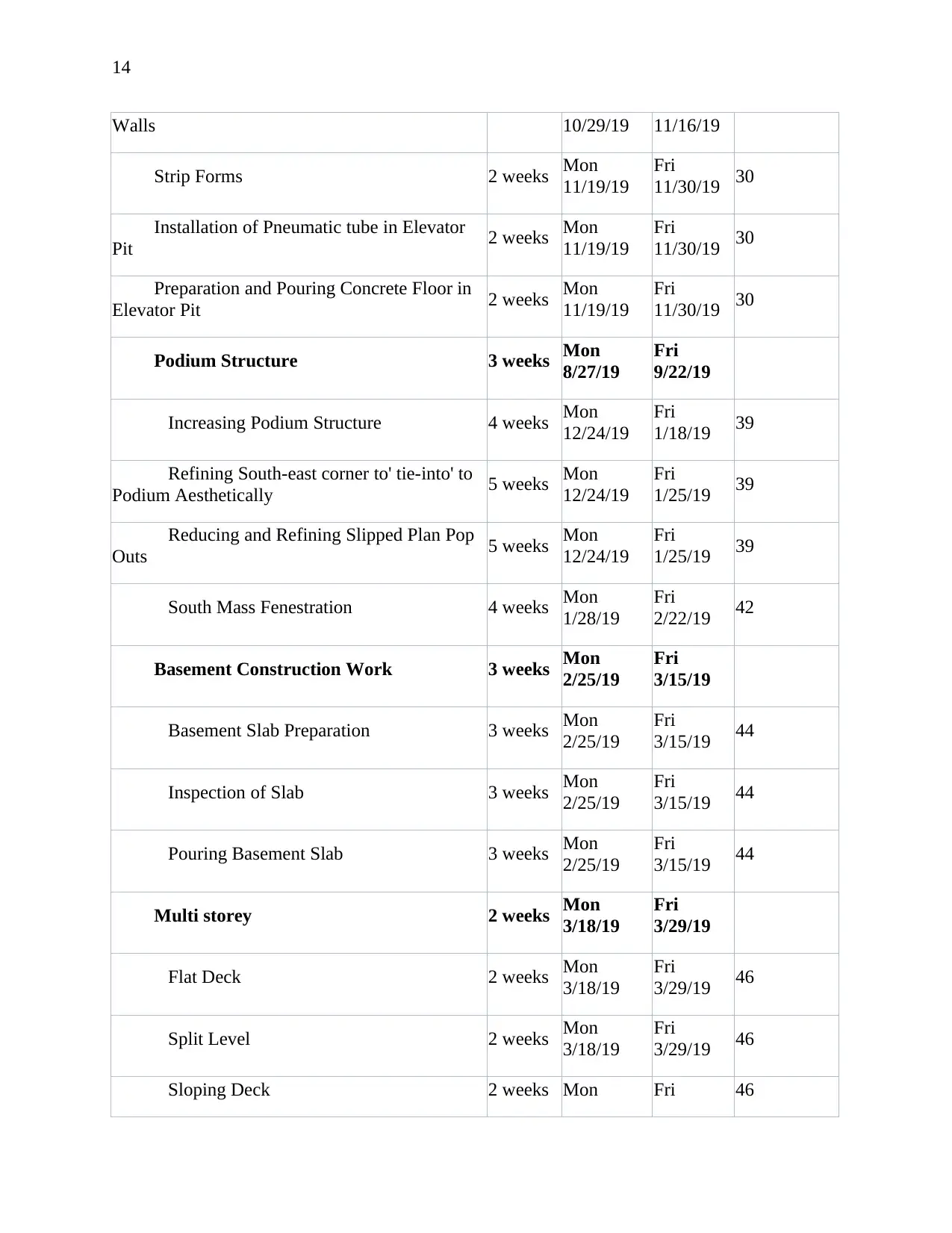
14
Walls 10/29/19 11/16/19
Strip Forms 2 weeks Mon
11/19/19
Fri
11/30/19 30
Installation of Pneumatic tube in Elevator
Pit 2 weeks Mon
11/19/19
Fri
11/30/19 30
Preparation and Pouring Concrete Floor in
Elevator Pit 2 weeks Mon
11/19/19
Fri
11/30/19 30
Podium Structure 3 weeks Mon
8/27/19
Fri
9/22/19
Increasing Podium Structure 4 weeks Mon
12/24/19
Fri
1/18/19 39
Refining South-east corner to' tie-into' to
Podium Aesthetically 5 weeks Mon
12/24/19
Fri
1/25/19 39
Reducing and Refining Slipped Plan Pop
Outs 5 weeks Mon
12/24/19
Fri
1/25/19 39
South Mass Fenestration 4 weeks Mon
1/28/19
Fri
2/22/19 42
Basement Construction Work 3 weeks Mon
2/25/19
Fri
3/15/19
Basement Slab Preparation 3 weeks Mon
2/25/19
Fri
3/15/19 44
Inspection of Slab 3 weeks Mon
2/25/19
Fri
3/15/19 44
Pouring Basement Slab 3 weeks Mon
2/25/19
Fri
3/15/19 44
Multi storey 2 weeks Mon
3/18/19
Fri
3/29/19
Flat Deck 2 weeks Mon
3/18/19
Fri
3/29/19 46
Split Level 2 weeks Mon
3/18/19
Fri
3/29/19 46
Sloping Deck 2 weeks Mon Fri 46
Walls 10/29/19 11/16/19
Strip Forms 2 weeks Mon
11/19/19
Fri
11/30/19 30
Installation of Pneumatic tube in Elevator
Pit 2 weeks Mon
11/19/19
Fri
11/30/19 30
Preparation and Pouring Concrete Floor in
Elevator Pit 2 weeks Mon
11/19/19
Fri
11/30/19 30
Podium Structure 3 weeks Mon
8/27/19
Fri
9/22/19
Increasing Podium Structure 4 weeks Mon
12/24/19
Fri
1/18/19 39
Refining South-east corner to' tie-into' to
Podium Aesthetically 5 weeks Mon
12/24/19
Fri
1/25/19 39
Reducing and Refining Slipped Plan Pop
Outs 5 weeks Mon
12/24/19
Fri
1/25/19 39
South Mass Fenestration 4 weeks Mon
1/28/19
Fri
2/22/19 42
Basement Construction Work 3 weeks Mon
2/25/19
Fri
3/15/19
Basement Slab Preparation 3 weeks Mon
2/25/19
Fri
3/15/19 44
Inspection of Slab 3 weeks Mon
2/25/19
Fri
3/15/19 44
Pouring Basement Slab 3 weeks Mon
2/25/19
Fri
3/15/19 44
Multi storey 2 weeks Mon
3/18/19
Fri
3/29/19
Flat Deck 2 weeks Mon
3/18/19
Fri
3/29/19 46
Split Level 2 weeks Mon
3/18/19
Fri
3/29/19 46
Sloping Deck 2 weeks Mon Fri 46
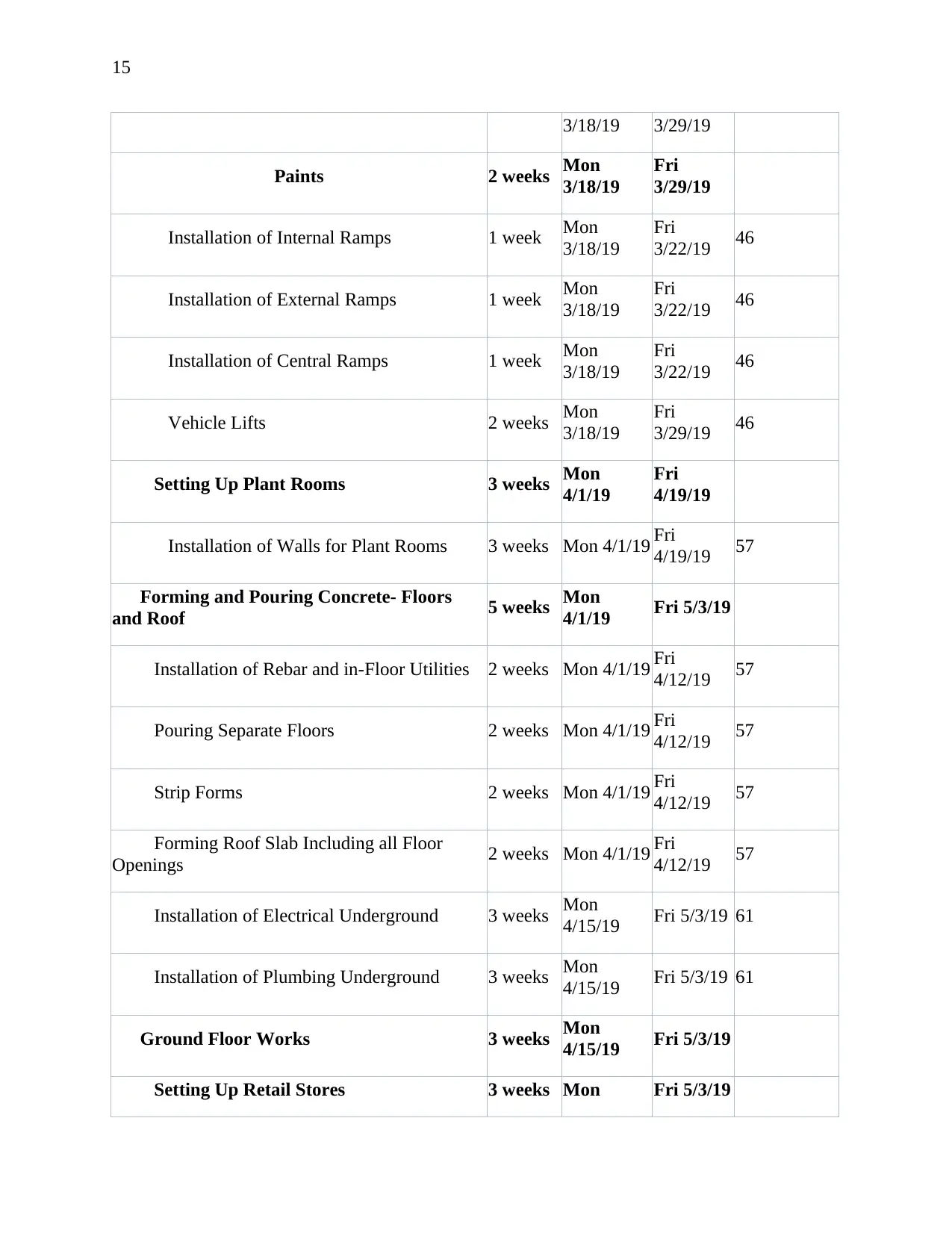
15
3/18/19 3/29/19
Paints 2 weeks Mon
3/18/19
Fri
3/29/19
Installation of Internal Ramps 1 week Mon
3/18/19
Fri
3/22/19 46
Installation of External Ramps 1 week Mon
3/18/19
Fri
3/22/19 46
Installation of Central Ramps 1 week Mon
3/18/19
Fri
3/22/19 46
Vehicle Lifts 2 weeks Mon
3/18/19
Fri
3/29/19 46
Setting Up Plant Rooms 3 weeks Mon
4/1/19
Fri
4/19/19
Installation of Walls for Plant Rooms 3 weeks Mon 4/1/19 Fri
4/19/19 57
Forming and Pouring Concrete- Floors
and Roof 5 weeks Mon
4/1/19 Fri 5/3/19
Installation of Rebar and in-Floor Utilities 2 weeks Mon 4/1/19 Fri
4/12/19 57
Pouring Separate Floors 2 weeks Mon 4/1/19 Fri
4/12/19 57
Strip Forms 2 weeks Mon 4/1/19 Fri
4/12/19 57
Forming Roof Slab Including all Floor
Openings 2 weeks Mon 4/1/19 Fri
4/12/19 57
Installation of Electrical Underground 3 weeks Mon
4/15/19 Fri 5/3/19 61
Installation of Plumbing Underground 3 weeks Mon
4/15/19 Fri 5/3/19 61
Ground Floor Works 3 weeks Mon
4/15/19 Fri 5/3/19
Setting Up Retail Stores 3 weeks Mon Fri 5/3/19
3/18/19 3/29/19
Paints 2 weeks Mon
3/18/19
Fri
3/29/19
Installation of Internal Ramps 1 week Mon
3/18/19
Fri
3/22/19 46
Installation of External Ramps 1 week Mon
3/18/19
Fri
3/22/19 46
Installation of Central Ramps 1 week Mon
3/18/19
Fri
3/22/19 46
Vehicle Lifts 2 weeks Mon
3/18/19
Fri
3/29/19 46
Setting Up Plant Rooms 3 weeks Mon
4/1/19
Fri
4/19/19
Installation of Walls for Plant Rooms 3 weeks Mon 4/1/19 Fri
4/19/19 57
Forming and Pouring Concrete- Floors
and Roof 5 weeks Mon
4/1/19 Fri 5/3/19
Installation of Rebar and in-Floor Utilities 2 weeks Mon 4/1/19 Fri
4/12/19 57
Pouring Separate Floors 2 weeks Mon 4/1/19 Fri
4/12/19 57
Strip Forms 2 weeks Mon 4/1/19 Fri
4/12/19 57
Forming Roof Slab Including all Floor
Openings 2 weeks Mon 4/1/19 Fri
4/12/19 57
Installation of Electrical Underground 3 weeks Mon
4/15/19 Fri 5/3/19 61
Installation of Plumbing Underground 3 weeks Mon
4/15/19 Fri 5/3/19 61
Ground Floor Works 3 weeks Mon
4/15/19 Fri 5/3/19
Setting Up Retail Stores 3 weeks Mon Fri 5/3/19
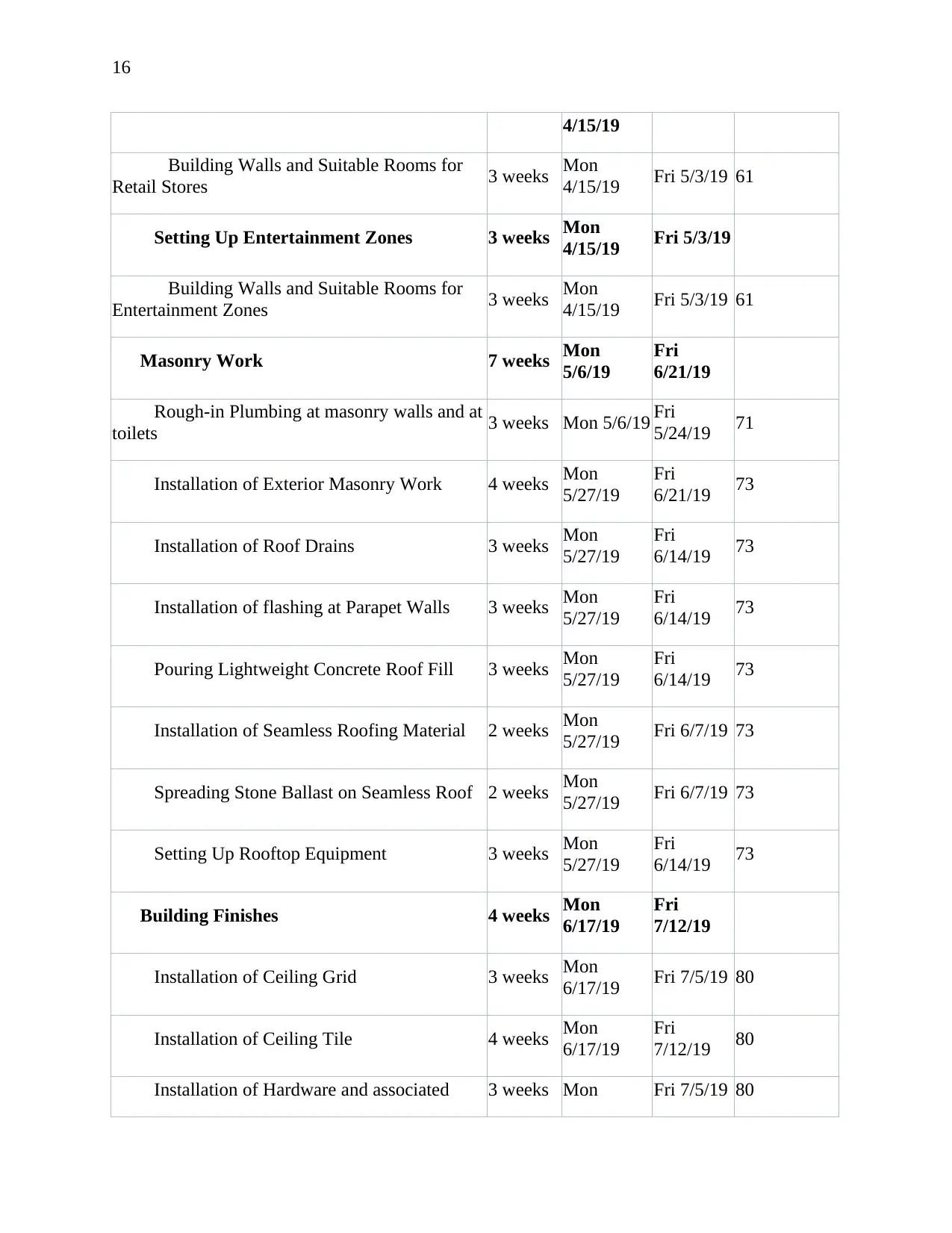
16
4/15/19
Building Walls and Suitable Rooms for
Retail Stores 3 weeks Mon
4/15/19 Fri 5/3/19 61
Setting Up Entertainment Zones 3 weeks Mon
4/15/19 Fri 5/3/19
Building Walls and Suitable Rooms for
Entertainment Zones 3 weeks Mon
4/15/19 Fri 5/3/19 61
Masonry Work 7 weeks Mon
5/6/19
Fri
6/21/19
Rough-in Plumbing at masonry walls and at
toilets 3 weeks Mon 5/6/19 Fri
5/24/19 71
Installation of Exterior Masonry Work 4 weeks Mon
5/27/19
Fri
6/21/19 73
Installation of Roof Drains 3 weeks Mon
5/27/19
Fri
6/14/19 73
Installation of flashing at Parapet Walls 3 weeks Mon
5/27/19
Fri
6/14/19 73
Pouring Lightweight Concrete Roof Fill 3 weeks Mon
5/27/19
Fri
6/14/19 73
Installation of Seamless Roofing Material 2 weeks Mon
5/27/19 Fri 6/7/19 73
Spreading Stone Ballast on Seamless Roof 2 weeks Mon
5/27/19 Fri 6/7/19 73
Setting Up Rooftop Equipment 3 weeks Mon
5/27/19
Fri
6/14/19 73
Building Finishes 4 weeks Mon
6/17/19
Fri
7/12/19
Installation of Ceiling Grid 3 weeks Mon
6/17/19 Fri 7/5/19 80
Installation of Ceiling Tile 4 weeks Mon
6/17/19
Fri
7/12/19 80
Installation of Hardware and associated 3 weeks Mon Fri 7/5/19 80
4/15/19
Building Walls and Suitable Rooms for
Retail Stores 3 weeks Mon
4/15/19 Fri 5/3/19 61
Setting Up Entertainment Zones 3 weeks Mon
4/15/19 Fri 5/3/19
Building Walls and Suitable Rooms for
Entertainment Zones 3 weeks Mon
4/15/19 Fri 5/3/19 61
Masonry Work 7 weeks Mon
5/6/19
Fri
6/21/19
Rough-in Plumbing at masonry walls and at
toilets 3 weeks Mon 5/6/19 Fri
5/24/19 71
Installation of Exterior Masonry Work 4 weeks Mon
5/27/19
Fri
6/21/19 73
Installation of Roof Drains 3 weeks Mon
5/27/19
Fri
6/14/19 73
Installation of flashing at Parapet Walls 3 weeks Mon
5/27/19
Fri
6/14/19 73
Pouring Lightweight Concrete Roof Fill 3 weeks Mon
5/27/19
Fri
6/14/19 73
Installation of Seamless Roofing Material 2 weeks Mon
5/27/19 Fri 6/7/19 73
Spreading Stone Ballast on Seamless Roof 2 weeks Mon
5/27/19 Fri 6/7/19 73
Setting Up Rooftop Equipment 3 weeks Mon
5/27/19
Fri
6/14/19 73
Building Finishes 4 weeks Mon
6/17/19
Fri
7/12/19
Installation of Ceiling Grid 3 weeks Mon
6/17/19 Fri 7/5/19 80
Installation of Ceiling Tile 4 weeks Mon
6/17/19
Fri
7/12/19 80
Installation of Hardware and associated 3 weeks Mon Fri 7/5/19 80
Secure Best Marks with AI Grader
Need help grading? Try our AI Grader for instant feedback on your assignments.
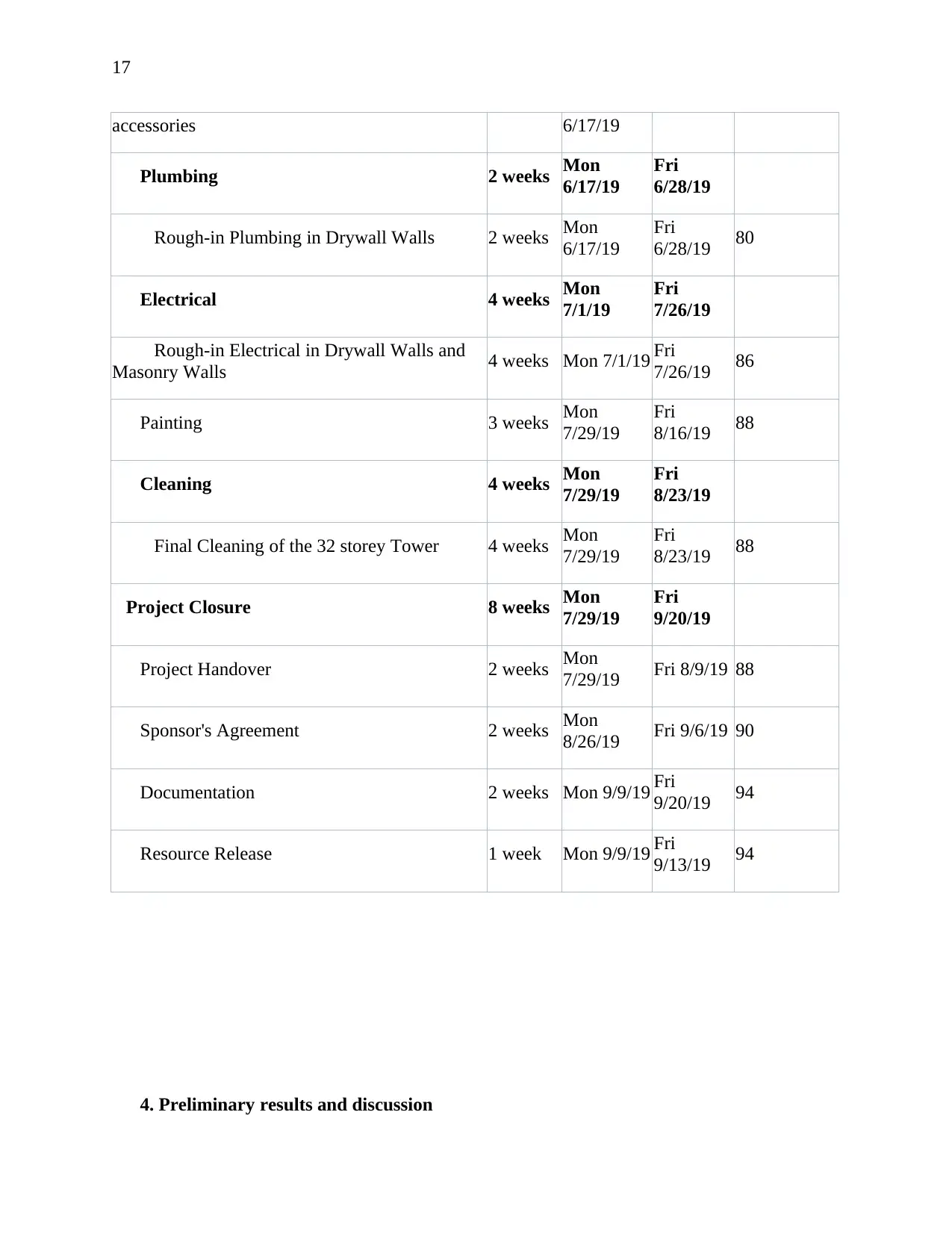
17
accessories 6/17/19
Plumbing 2 weeks Mon
6/17/19
Fri
6/28/19
Rough-in Plumbing in Drywall Walls 2 weeks Mon
6/17/19
Fri
6/28/19 80
Electrical 4 weeks Mon
7/1/19
Fri
7/26/19
Rough-in Electrical in Drywall Walls and
Masonry Walls 4 weeks Mon 7/1/19 Fri
7/26/19 86
Painting 3 weeks Mon
7/29/19
Fri
8/16/19 88
Cleaning 4 weeks Mon
7/29/19
Fri
8/23/19
Final Cleaning of the 32 storey Tower 4 weeks Mon
7/29/19
Fri
8/23/19 88
Project Closure 8 weeks Mon
7/29/19
Fri
9/20/19
Project Handover 2 weeks Mon
7/29/19 Fri 8/9/19 88
Sponsor's Agreement 2 weeks Mon
8/26/19 Fri 9/6/19 90
Documentation 2 weeks Mon 9/9/19 Fri
9/20/19 94
Resource Release 1 week Mon 9/9/19 Fri
9/13/19 94
4. Preliminary results and discussion
accessories 6/17/19
Plumbing 2 weeks Mon
6/17/19
Fri
6/28/19
Rough-in Plumbing in Drywall Walls 2 weeks Mon
6/17/19
Fri
6/28/19 80
Electrical 4 weeks Mon
7/1/19
Fri
7/26/19
Rough-in Electrical in Drywall Walls and
Masonry Walls 4 weeks Mon 7/1/19 Fri
7/26/19 86
Painting 3 weeks Mon
7/29/19
Fri
8/16/19 88
Cleaning 4 weeks Mon
7/29/19
Fri
8/23/19
Final Cleaning of the 32 storey Tower 4 weeks Mon
7/29/19
Fri
8/23/19 88
Project Closure 8 weeks Mon
7/29/19
Fri
9/20/19
Project Handover 2 weeks Mon
7/29/19 Fri 8/9/19 88
Sponsor's Agreement 2 weeks Mon
8/26/19 Fri 9/6/19 90
Documentation 2 weeks Mon 9/9/19 Fri
9/20/19 94
Resource Release 1 week Mon 9/9/19 Fri
9/13/19 94
4. Preliminary results and discussion
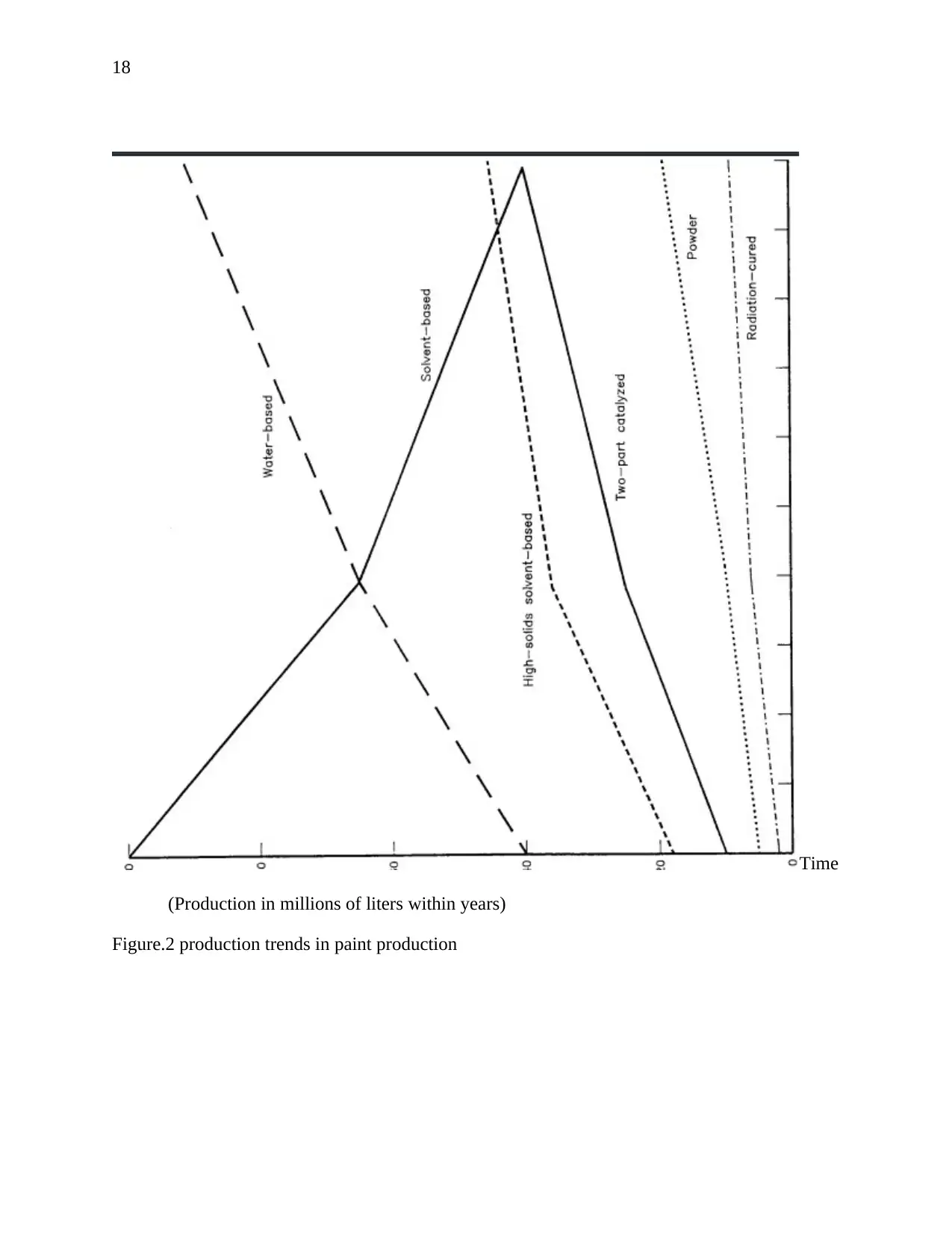
18
Time
(Production in millions of liters within years)
Figure.2 production trends in paint production
Time
(Production in millions of liters within years)
Figure.2 production trends in paint production
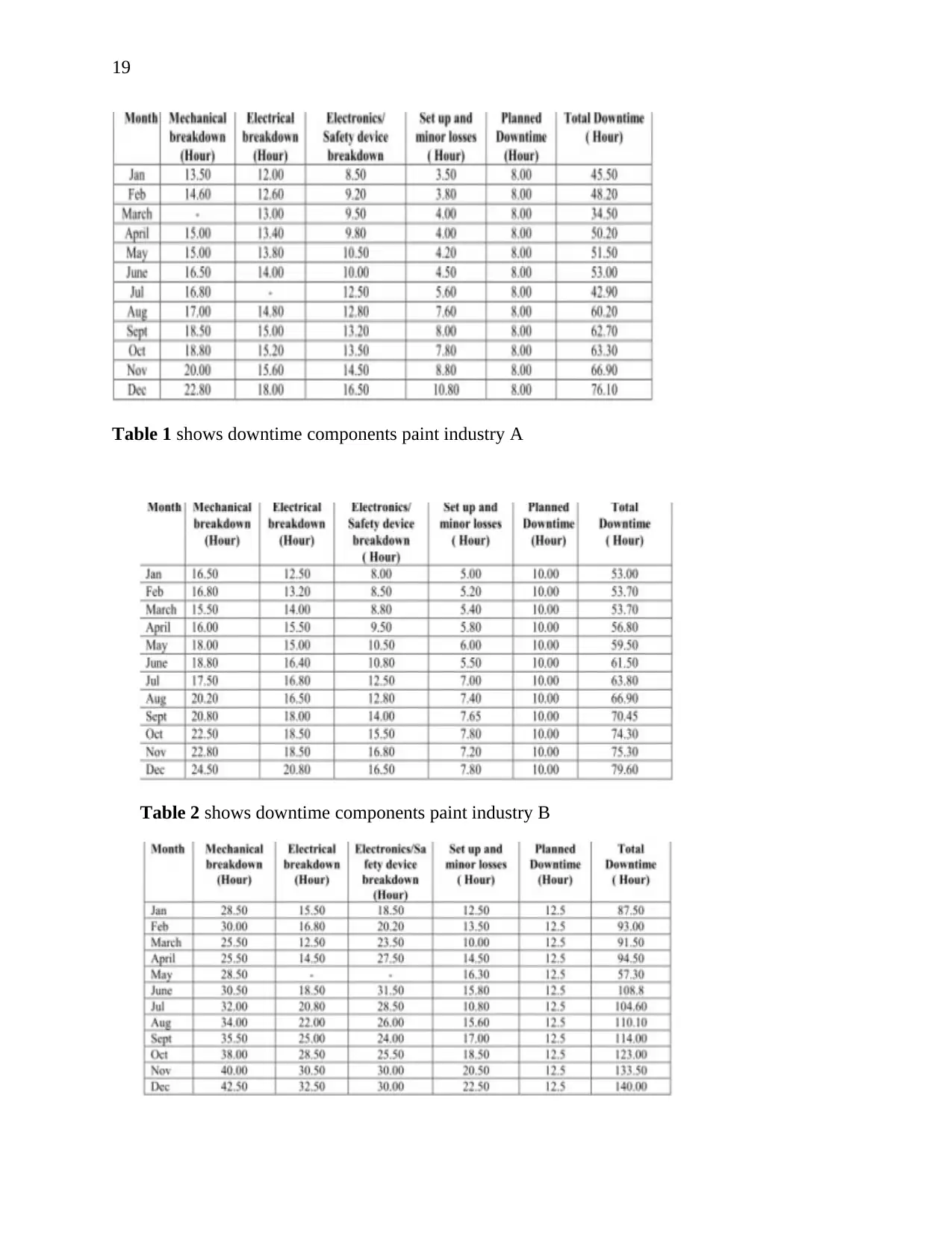
19
Table 1 shows downtime components paint industry A
Table 2 shows downtime components paint industry B
Table 1 shows downtime components paint industry A
Table 2 shows downtime components paint industry B
Paraphrase This Document
Need a fresh take? Get an instant paraphrase of this document with our AI Paraphraser
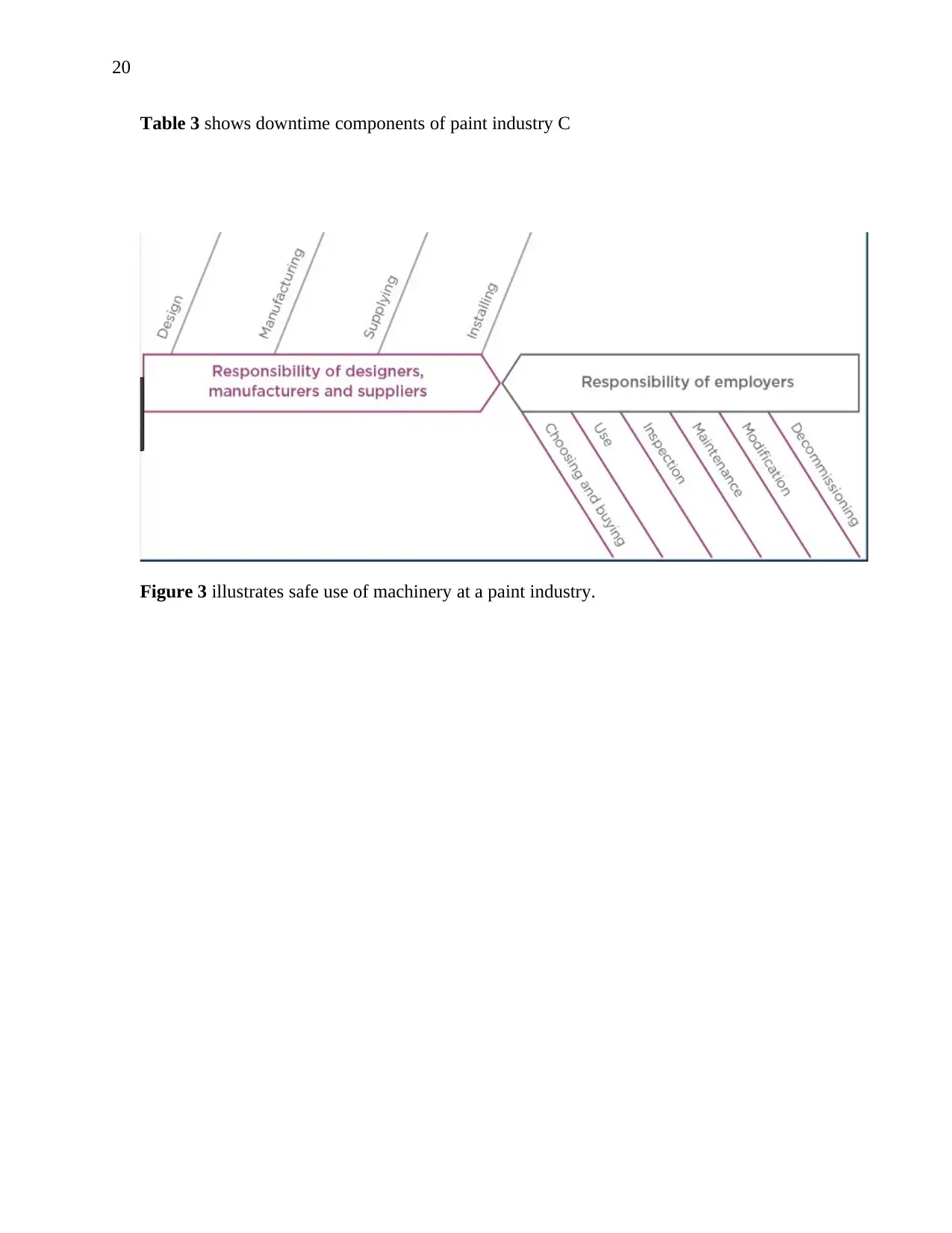
20
Table 3 shows downtime components of paint industry C
Figure 3 illustrates safe use of machinery at a paint industry.
Table 3 shows downtime components of paint industry C
Figure 3 illustrates safe use of machinery at a paint industry.
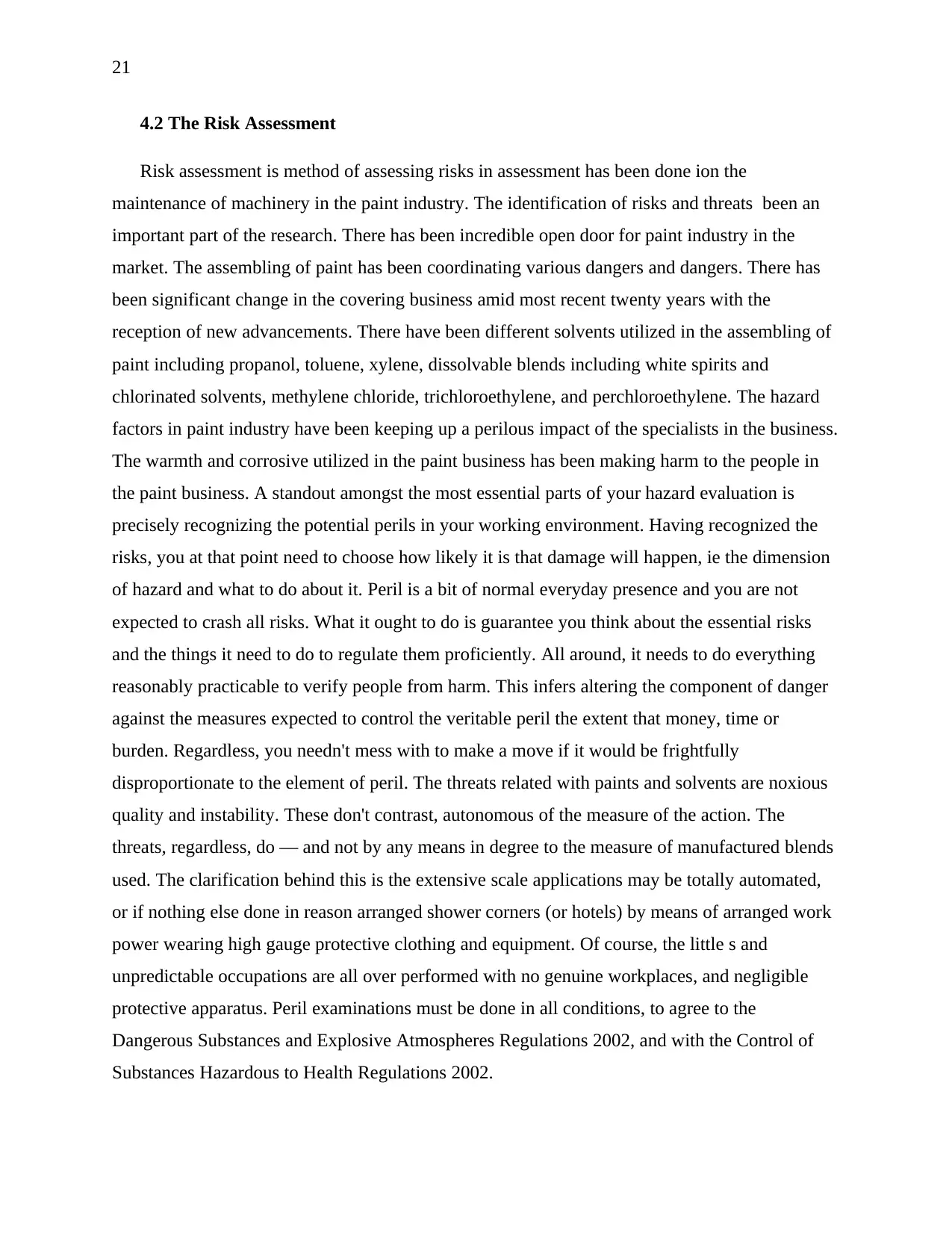
21
4.2 The Risk Assessment
Risk assessment is method of assessing risks in assessment has been done ion the
maintenance of machinery in the paint industry. The identification of risks and threats been an
important part of the research. There has been incredible open door for paint industry in the
market. The assembling of paint has been coordinating various dangers and dangers. There has
been significant change in the covering business amid most recent twenty years with the
reception of new advancements. There have been different solvents utilized in the assembling of
paint including propanol, toluene, xylene, dissolvable blends including white spirits and
chlorinated solvents, methylene chloride, trichloroethylene, and perchloroethylene. The hazard
factors in paint industry have been keeping up a perilous impact of the specialists in the business.
The warmth and corrosive utilized in the paint business has been making harm to the people in
the paint business. A standout amongst the most essential parts of your hazard evaluation is
precisely recognizing the potential perils in your working environment. Having recognized the
risks, you at that point need to choose how likely it is that damage will happen, ie the dimension
of hazard and what to do about it. Peril is a bit of normal everyday presence and you are not
expected to crash all risks. What it ought to do is guarantee you think about the essential risks
and the things it need to do to regulate them proficiently. All around, it needs to do everything
reasonably practicable to verify people from harm. This infers altering the component of danger
against the measures expected to control the veritable peril the extent that money, time or
burden. Regardless, you needn't mess with to make a move if it would be frightfully
disproportionate to the element of peril. The threats related with paints and solvents are noxious
quality and instability. These don't contrast, autonomous of the measure of the action. The
threats, regardless, do ― and not by any means in degree to the measure of manufactured blends
used. The clarification behind this is the extensive scale applications may be totally automated,
or if nothing else done in reason arranged shower corners (or hotels) by means of arranged work
power wearing high gauge protective clothing and equipment. Of course, the little s and
unpredictable occupations are all over performed with no genuine workplaces, and negligible
protective apparatus. Peril examinations must be done in all conditions, to agree to the
Dangerous Substances and Explosive Atmospheres Regulations 2002, and with the Control of
Substances Hazardous to Health Regulations 2002.
4.2 The Risk Assessment
Risk assessment is method of assessing risks in assessment has been done ion the
maintenance of machinery in the paint industry. The identification of risks and threats been an
important part of the research. There has been incredible open door for paint industry in the
market. The assembling of paint has been coordinating various dangers and dangers. There has
been significant change in the covering business amid most recent twenty years with the
reception of new advancements. There have been different solvents utilized in the assembling of
paint including propanol, toluene, xylene, dissolvable blends including white spirits and
chlorinated solvents, methylene chloride, trichloroethylene, and perchloroethylene. The hazard
factors in paint industry have been keeping up a perilous impact of the specialists in the business.
The warmth and corrosive utilized in the paint business has been making harm to the people in
the paint business. A standout amongst the most essential parts of your hazard evaluation is
precisely recognizing the potential perils in your working environment. Having recognized the
risks, you at that point need to choose how likely it is that damage will happen, ie the dimension
of hazard and what to do about it. Peril is a bit of normal everyday presence and you are not
expected to crash all risks. What it ought to do is guarantee you think about the essential risks
and the things it need to do to regulate them proficiently. All around, it needs to do everything
reasonably practicable to verify people from harm. This infers altering the component of danger
against the measures expected to control the veritable peril the extent that money, time or
burden. Regardless, you needn't mess with to make a move if it would be frightfully
disproportionate to the element of peril. The threats related with paints and solvents are noxious
quality and instability. These don't contrast, autonomous of the measure of the action. The
threats, regardless, do ― and not by any means in degree to the measure of manufactured blends
used. The clarification behind this is the extensive scale applications may be totally automated,
or if nothing else done in reason arranged shower corners (or hotels) by means of arranged work
power wearing high gauge protective clothing and equipment. Of course, the little s and
unpredictable occupations are all over performed with no genuine workplaces, and negligible
protective apparatus. Peril examinations must be done in all conditions, to agree to the
Dangerous Substances and Explosive Atmospheres Regulations 2002, and with the Control of
Substances Hazardous to Health Regulations 2002.
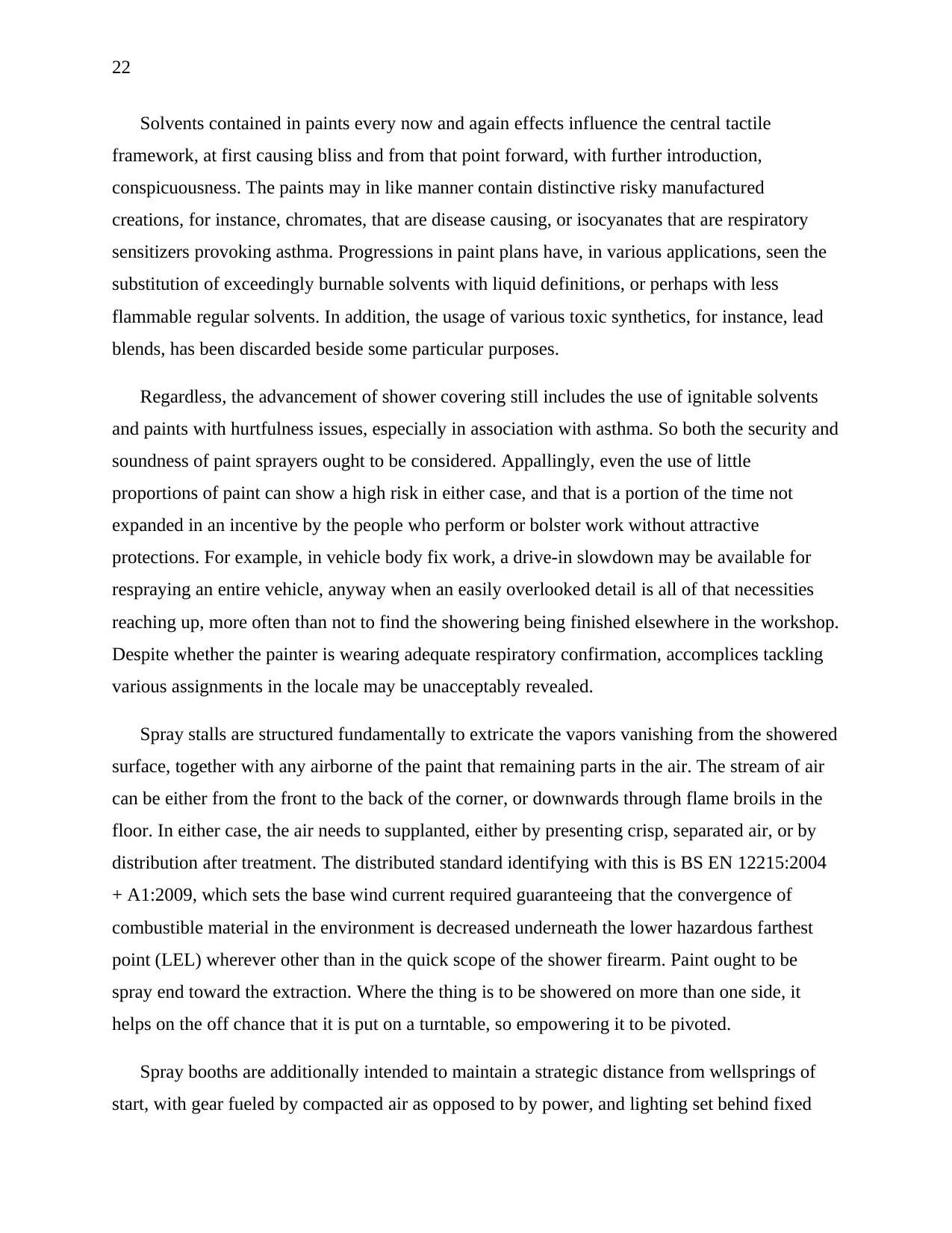
22
Solvents contained in paints every now and again effects influence the central tactile
framework, at first causing bliss and from that point forward, with further introduction,
conspicuousness. The paints may in like manner contain distinctive risky manufactured
creations, for instance, chromates, that are disease causing, or isocyanates that are respiratory
sensitizers provoking asthma. Progressions in paint plans have, in various applications, seen the
substitution of exceedingly burnable solvents with liquid definitions, or perhaps with less
flammable regular solvents. In addition, the usage of various toxic synthetics, for instance, lead
blends, has been discarded beside some particular purposes.
Regardless, the advancement of shower covering still includes the use of ignitable solvents
and paints with hurtfulness issues, especially in association with asthma. So both the security and
soundness of paint sprayers ought to be considered. Appallingly, even the use of little
proportions of paint can show a high risk in either case, and that is a portion of the time not
expanded in an incentive by the people who perform or bolster work without attractive
protections. For example, in vehicle body fix work, a drive-in slowdown may be available for
respraying an entire vehicle, anyway when an easily overlooked detail is all of that necessities
reaching up, more often than not to find the showering being finished elsewhere in the workshop.
Despite whether the painter is wearing adequate respiratory confirmation, accomplices tackling
various assignments in the locale may be unacceptably revealed.
Spray stalls are structured fundamentally to extricate the vapors vanishing from the showered
surface, together with any airborne of the paint that remaining parts in the air. The stream of air
can be either from the front to the back of the corner, or downwards through flame broils in the
floor. In either case, the air needs to supplanted, either by presenting crisp, separated air, or by
distribution after treatment. The distributed standard identifying with this is BS EN 12215:2004
+ A1:2009, which sets the base wind current required guaranteeing that the convergence of
combustible material in the environment is decreased underneath the lower hazardous farthest
point (LEL) wherever other than in the quick scope of the shower firearm. Paint ought to be
spray end toward the extraction. Where the thing is to be showered on more than one side, it
helps on the off chance that it is put on a turntable, so empowering it to be pivoted.
Spray booths are additionally intended to maintain a strategic distance from wellsprings of
start, with gear fueled by compacted air as opposed to by power, and lighting set behind fixed
Solvents contained in paints every now and again effects influence the central tactile
framework, at first causing bliss and from that point forward, with further introduction,
conspicuousness. The paints may in like manner contain distinctive risky manufactured
creations, for instance, chromates, that are disease causing, or isocyanates that are respiratory
sensitizers provoking asthma. Progressions in paint plans have, in various applications, seen the
substitution of exceedingly burnable solvents with liquid definitions, or perhaps with less
flammable regular solvents. In addition, the usage of various toxic synthetics, for instance, lead
blends, has been discarded beside some particular purposes.
Regardless, the advancement of shower covering still includes the use of ignitable solvents
and paints with hurtfulness issues, especially in association with asthma. So both the security and
soundness of paint sprayers ought to be considered. Appallingly, even the use of little
proportions of paint can show a high risk in either case, and that is a portion of the time not
expanded in an incentive by the people who perform or bolster work without attractive
protections. For example, in vehicle body fix work, a drive-in slowdown may be available for
respraying an entire vehicle, anyway when an easily overlooked detail is all of that necessities
reaching up, more often than not to find the showering being finished elsewhere in the workshop.
Despite whether the painter is wearing adequate respiratory confirmation, accomplices tackling
various assignments in the locale may be unacceptably revealed.
Spray stalls are structured fundamentally to extricate the vapors vanishing from the showered
surface, together with any airborne of the paint that remaining parts in the air. The stream of air
can be either from the front to the back of the corner, or downwards through flame broils in the
floor. In either case, the air needs to supplanted, either by presenting crisp, separated air, or by
distribution after treatment. The distributed standard identifying with this is BS EN 12215:2004
+ A1:2009, which sets the base wind current required guaranteeing that the convergence of
combustible material in the environment is decreased underneath the lower hazardous farthest
point (LEL) wherever other than in the quick scope of the shower firearm. Paint ought to be
spray end toward the extraction. Where the thing is to be showered on more than one side, it
helps on the off chance that it is put on a turntable, so empowering it to be pivoted.
Spray booths are additionally intended to maintain a strategic distance from wellsprings of
start, with gear fueled by compacted air as opposed to by power, and lighting set behind fixed
Secure Best Marks with AI Grader
Need help grading? Try our AI Grader for instant feedback on your assignments.
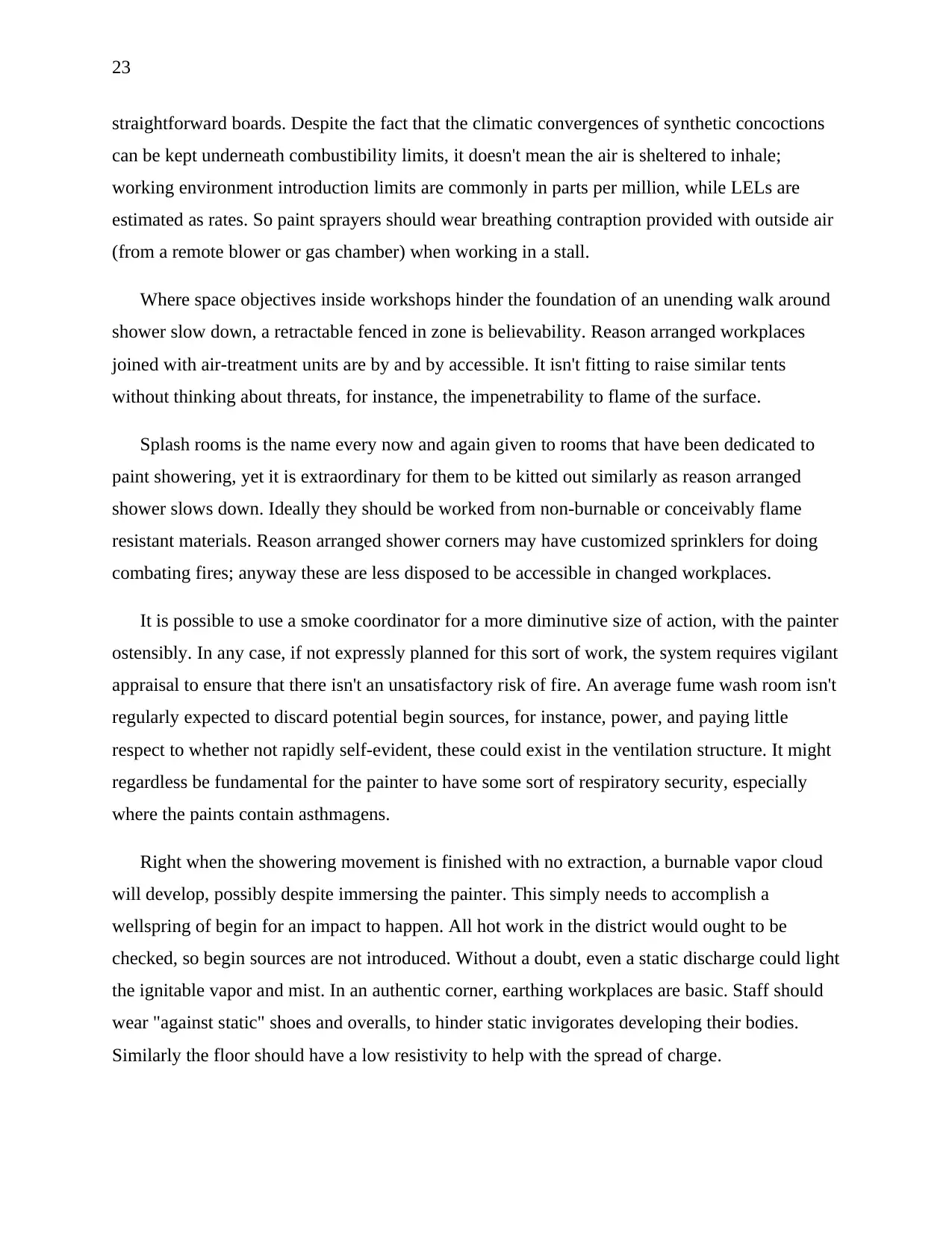
23
straightforward boards. Despite the fact that the climatic convergences of synthetic concoctions
can be kept underneath combustibility limits, it doesn't mean the air is sheltered to inhale;
working environment introduction limits are commonly in parts per million, while LELs are
estimated as rates. So paint sprayers should wear breathing contraption provided with outside air
(from a remote blower or gas chamber) when working in a stall.
Where space objectives inside workshops hinder the foundation of an unending walk around
shower slow down, a retractable fenced in zone is believability. Reason arranged workplaces
joined with air-treatment units are by and by accessible. It isn't fitting to raise similar tents
without thinking about threats, for instance, the impenetrability to flame of the surface.
Splash rooms is the name every now and again given to rooms that have been dedicated to
paint showering, yet it is extraordinary for them to be kitted out similarly as reason arranged
shower slows down. Ideally they should be worked from non-burnable or conceivably flame
resistant materials. Reason arranged shower corners may have customized sprinklers for doing
combating fires; anyway these are less disposed to be accessible in changed workplaces.
It is possible to use a smoke coordinator for a more diminutive size of action, with the painter
ostensibly. In any case, if not expressly planned for this sort of work, the system requires vigilant
appraisal to ensure that there isn't an unsatisfactory risk of fire. An average fume wash room isn't
regularly expected to discard potential begin sources, for instance, power, and paying little
respect to whether not rapidly self-evident, these could exist in the ventilation structure. It might
regardless be fundamental for the painter to have some sort of respiratory security, especially
where the paints contain asthmagens.
Right when the showering movement is finished with no extraction, a burnable vapor cloud
will develop, possibly despite immersing the painter. This simply needs to accomplish a
wellspring of begin for an impact to happen. All hot work in the district would ought to be
checked, so begin sources are not introduced. Without a doubt, even a static discharge could light
the ignitable vapor and mist. In an authentic corner, earthing workplaces are basic. Staff should
wear "against static" shoes and overalls, to hinder static invigorates developing their bodies.
Similarly the floor should have a low resistivity to help with the spread of charge.
straightforward boards. Despite the fact that the climatic convergences of synthetic concoctions
can be kept underneath combustibility limits, it doesn't mean the air is sheltered to inhale;
working environment introduction limits are commonly in parts per million, while LELs are
estimated as rates. So paint sprayers should wear breathing contraption provided with outside air
(from a remote blower or gas chamber) when working in a stall.
Where space objectives inside workshops hinder the foundation of an unending walk around
shower slow down, a retractable fenced in zone is believability. Reason arranged workplaces
joined with air-treatment units are by and by accessible. It isn't fitting to raise similar tents
without thinking about threats, for instance, the impenetrability to flame of the surface.
Splash rooms is the name every now and again given to rooms that have been dedicated to
paint showering, yet it is extraordinary for them to be kitted out similarly as reason arranged
shower slows down. Ideally they should be worked from non-burnable or conceivably flame
resistant materials. Reason arranged shower corners may have customized sprinklers for doing
combating fires; anyway these are less disposed to be accessible in changed workplaces.
It is possible to use a smoke coordinator for a more diminutive size of action, with the painter
ostensibly. In any case, if not expressly planned for this sort of work, the system requires vigilant
appraisal to ensure that there isn't an unsatisfactory risk of fire. An average fume wash room isn't
regularly expected to discard potential begin sources, for instance, power, and paying little
respect to whether not rapidly self-evident, these could exist in the ventilation structure. It might
regardless be fundamental for the painter to have some sort of respiratory security, especially
where the paints contain asthmagens.
Right when the showering movement is finished with no extraction, a burnable vapor cloud
will develop, possibly despite immersing the painter. This simply needs to accomplish a
wellspring of begin for an impact to happen. All hot work in the district would ought to be
checked, so begin sources are not introduced. Without a doubt, even a static discharge could light
the ignitable vapor and mist. In an authentic corner, earthing workplaces are basic. Staff should
wear "against static" shoes and overalls, to hinder static invigorates developing their bodies.
Similarly the floor should have a low resistivity to help with the spread of charge.
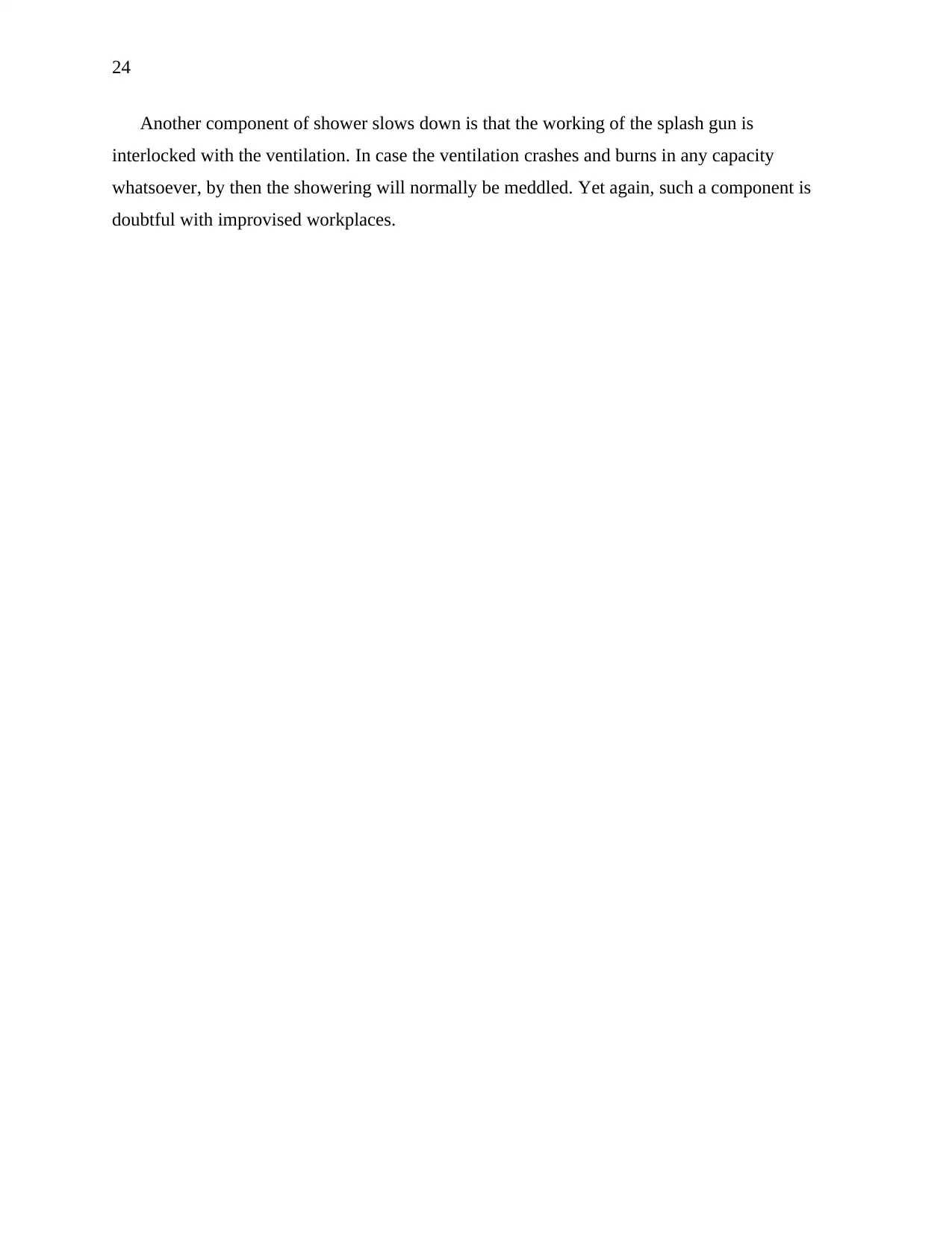
24
Another component of shower slows down is that the working of the splash gun is
interlocked with the ventilation. In case the ventilation crashes and burns in any capacity
whatsoever, by then the showering will normally be meddled. Yet again, such a component is
doubtful with improvised workplaces.
Another component of shower slows down is that the working of the splash gun is
interlocked with the ventilation. In case the ventilation crashes and burns in any capacity
whatsoever, by then the showering will normally be meddled. Yet again, such a component is
doubtful with improvised workplaces.
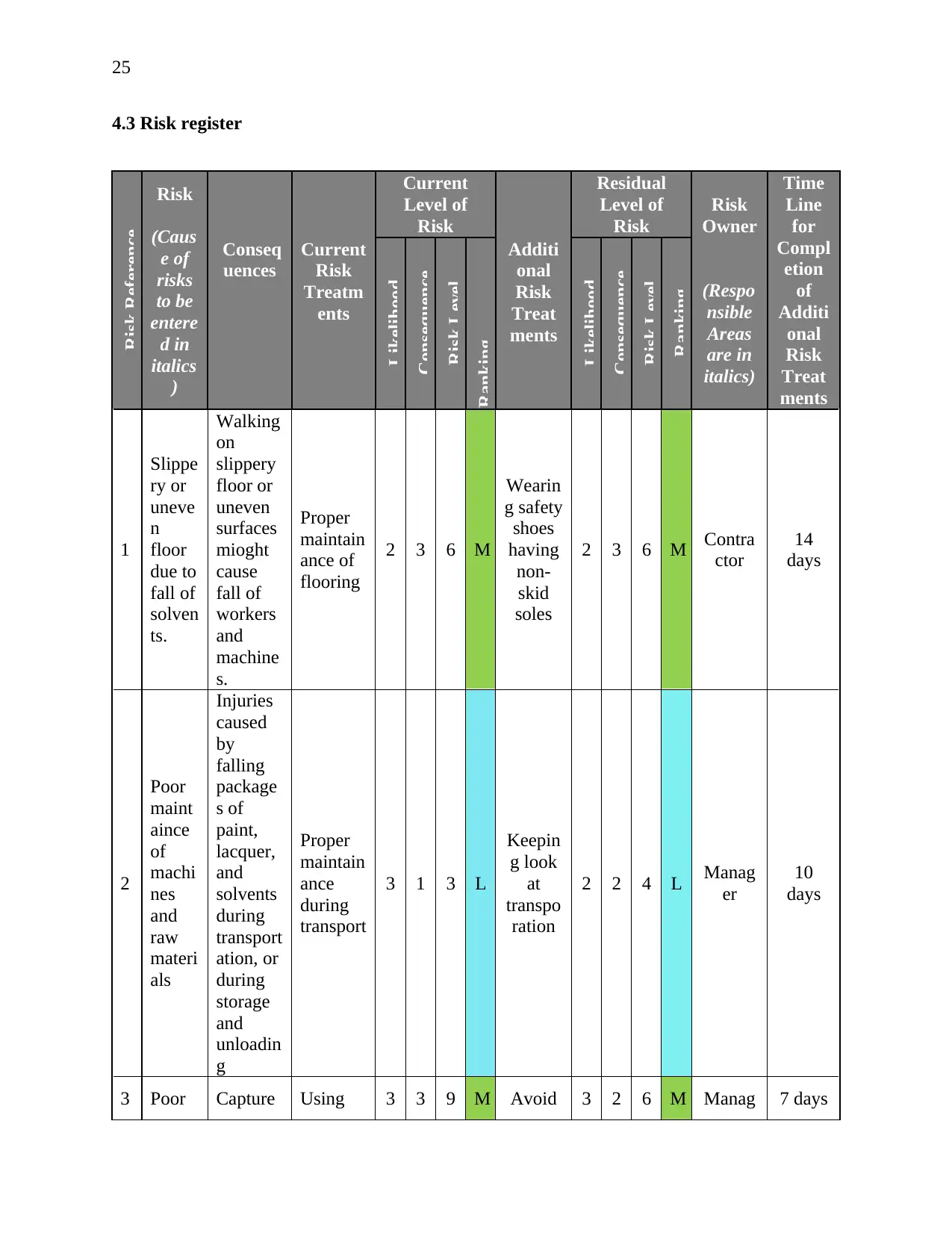
25
4.3 Risk register
Risk Reference
Risk
(Caus
e of
risks
to be
entere
d in
italics
)
Current
Level of
Risk
Residual
Level of
Risk
Risk
Owner
(Respo
nsible
Areas
are in
italics)
Time
Line
for
Compl
etion
of
Additi
onal
Risk
Treat
ments
Conseq
uences
Current
Risk
Treatm
ents
Likelihood
Consequence
Risk Level
Ranking
Additi
onal
Risk
Treat
ments
Likelihood
Consequence
Risk Level
Ranking
1
Slippe
ry or
uneve
n
floor
due to
fall of
solven
ts.
Walking
on
slippery
floor or
uneven
surfaces
mioght
cause
fall of
workers
and
machine
s.
Proper
maintain
ance of
flooring
2 3 6 M
Wearin
g safety
shoes
having
non-
skid
soles
2 3 6 M Contra
ctor
14
days
2
Poor
maint
aince
of
machi
nes
and
raw
materi
als
Injuries
caused
by
falling
package
s of
paint,
lacquer,
and
solvents
during
transport
ation, or
during
storage
and
unloadin
g
Proper
maintain
ance
during
transport
3 1 3 L
Keepin
g look
at
transpo
ration
2 2 4 L Manag
er
10
days
3 Poor Capture Using 3 3 9 M Avoid 3 2 6 M Manag 7 days
4.3 Risk register
Risk Reference
Risk
(Caus
e of
risks
to be
entere
d in
italics
)
Current
Level of
Risk
Residual
Level of
Risk
Risk
Owner
(Respo
nsible
Areas
are in
italics)
Time
Line
for
Compl
etion
of
Additi
onal
Risk
Treat
ments
Conseq
uences
Current
Risk
Treatm
ents
Likelihood
Consequence
Risk Level
Ranking
Additi
onal
Risk
Treat
ments
Likelihood
Consequence
Risk Level
Ranking
1
Slippe
ry or
uneve
n
floor
due to
fall of
solven
ts.
Walking
on
slippery
floor or
uneven
surfaces
mioght
cause
fall of
workers
and
machine
s.
Proper
maintain
ance of
flooring
2 3 6 M
Wearin
g safety
shoes
having
non-
skid
soles
2 3 6 M Contra
ctor
14
days
2
Poor
maint
aince
of
machi
nes
and
raw
materi
als
Injuries
caused
by
falling
package
s of
paint,
lacquer,
and
solvents
during
transport
ation, or
during
storage
and
unloadin
g
Proper
maintain
ance
during
transport
3 1 3 L
Keepin
g look
at
transpo
ration
2 2 4 L Manag
er
10
days
3 Poor Capture Using 3 3 9 M Avoid 3 2 6 M Manag 7 days
Paraphrase This Document
Need a fresh take? Get an instant paraphrase of this document with our AI Paraphraser
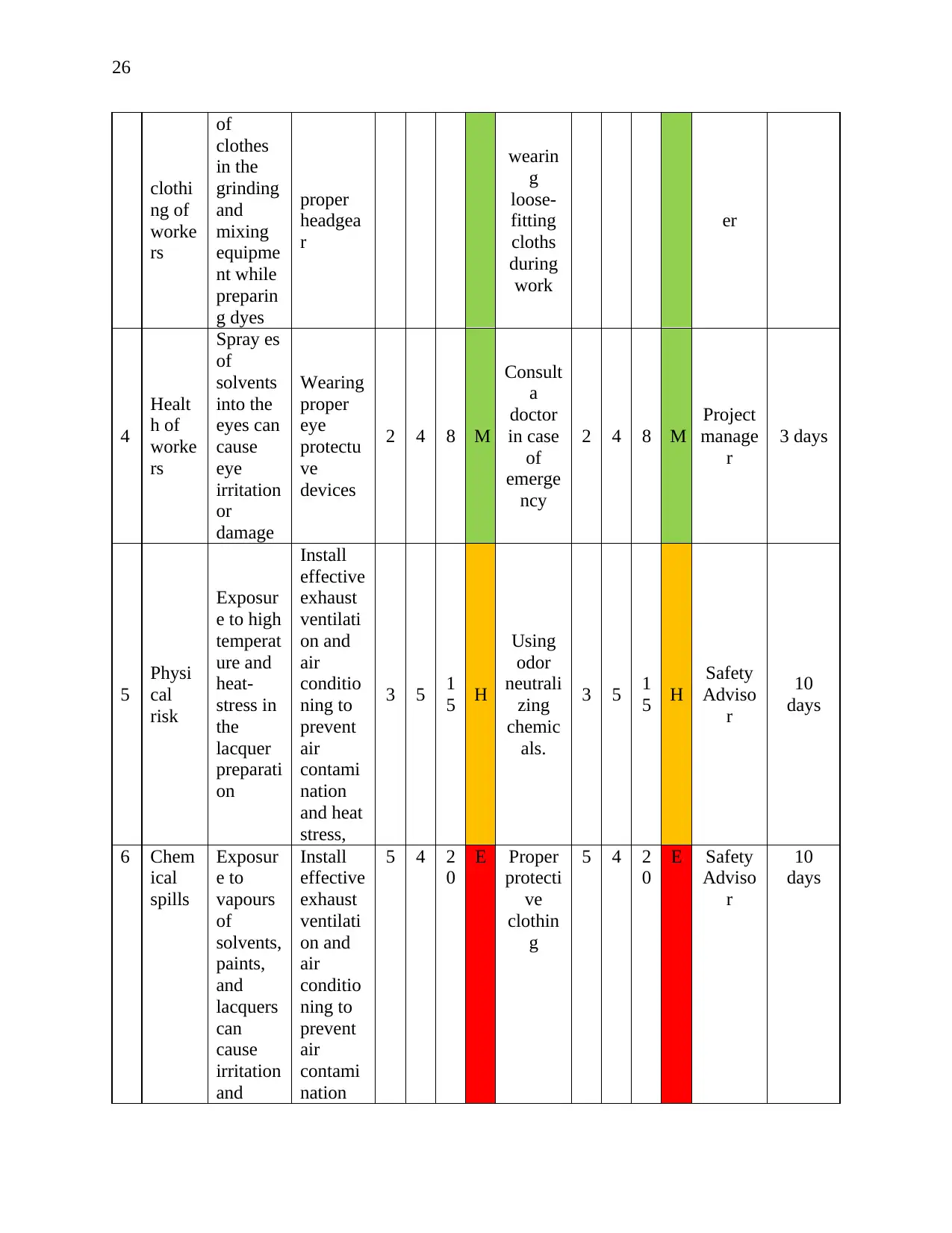
26
clothi
ng of
worke
rs
of
clothes
in the
grinding
and
mixing
equipme
nt while
preparin
g dyes
proper
headgea
r
wearin
g
loose-
fitting
cloths
during
work
er
4
Healt
h of
worke
rs
Spray es
of
solvents
into the
eyes can
cause
eye
irritation
or
damage
Wearing
proper
eye
protectu
ve
devices
2 4 8 M
Consult
a
doctor
in case
of
emerge
ncy
2 4 8 M
Project
manage
r
3 days
5
Physi
cal
risk
Exposur
e to high
temperat
ure and
heat-
stress in
the
lacquer
preparati
on
Install
effective
exhaust
ventilati
on and
air
conditio
ning to
prevent
air
contami
nation
and heat
stress,
3 5 1
5 H
Using
odor
neutrali
zing
chemic
als.
3 5 1
5 H
Safety
Adviso
r
10
days
6 Chem
ical
spills
Exposur
e to
vapours
of
solvents,
paints,
and
lacquers
can
cause
irritation
and
Install
effective
exhaust
ventilati
on and
air
conditio
ning to
prevent
air
contami
nation
5 4 2
0
E Proper
protecti
ve
clothin
g
5 4 2
0
E Safety
Adviso
r
10
days
clothi
ng of
worke
rs
of
clothes
in the
grinding
and
mixing
equipme
nt while
preparin
g dyes
proper
headgea
r
wearin
g
loose-
fitting
cloths
during
work
er
4
Healt
h of
worke
rs
Spray es
of
solvents
into the
eyes can
cause
eye
irritation
or
damage
Wearing
proper
eye
protectu
ve
devices
2 4 8 M
Consult
a
doctor
in case
of
emerge
ncy
2 4 8 M
Project
manage
r
3 days
5
Physi
cal
risk
Exposur
e to high
temperat
ure and
heat-
stress in
the
lacquer
preparati
on
Install
effective
exhaust
ventilati
on and
air
conditio
ning to
prevent
air
contami
nation
and heat
stress,
3 5 1
5 H
Using
odor
neutrali
zing
chemic
als.
3 5 1
5 H
Safety
Adviso
r
10
days
6 Chem
ical
spills
Exposur
e to
vapours
of
solvents,
paints,
and
lacquers
can
cause
irritation
and
Install
effective
exhaust
ventilati
on and
air
conditio
ning to
prevent
air
contami
nation
5 4 2
0
E Proper
protecti
ve
clothin
g
5 4 2
0
E Safety
Adviso
r
10
days
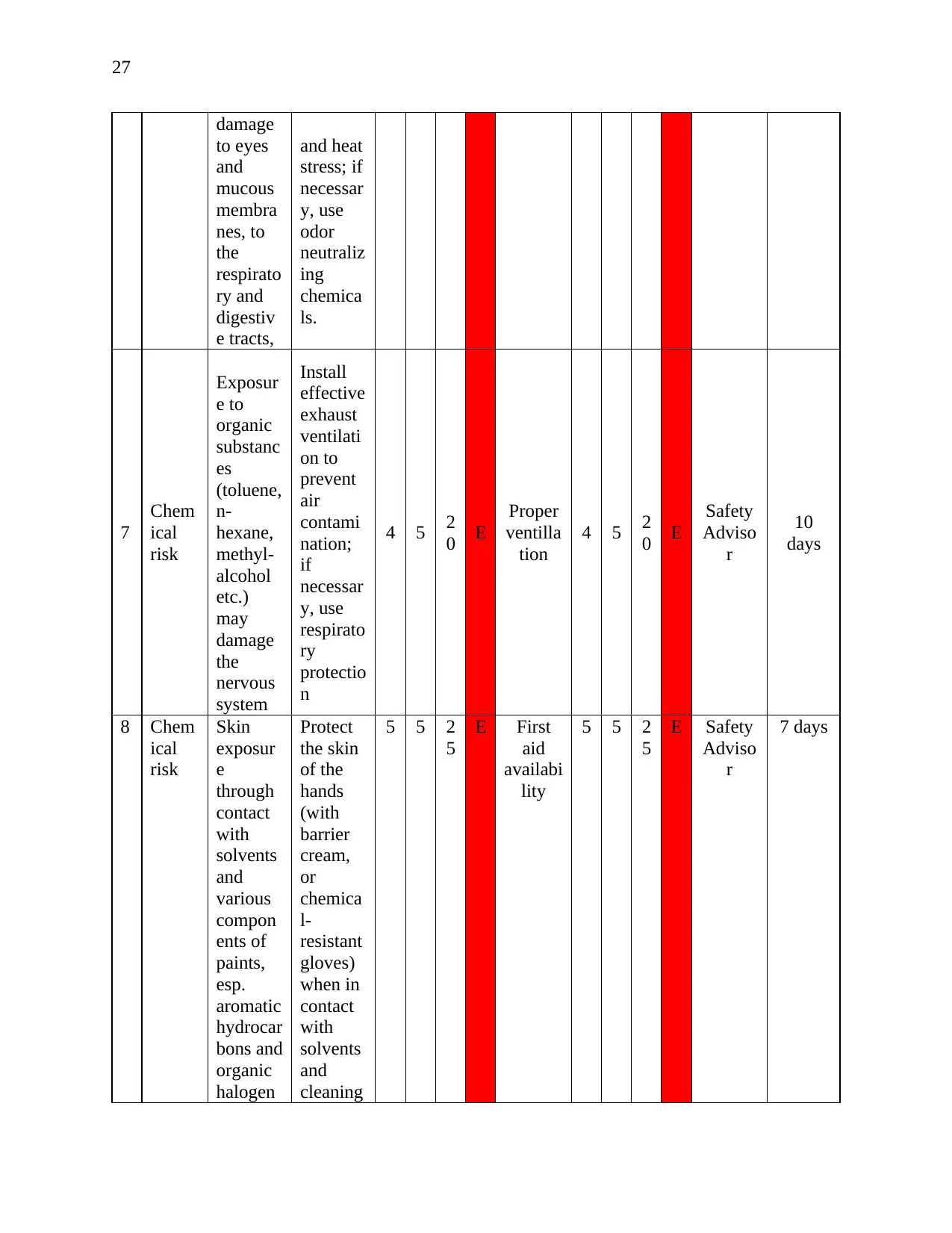
27
damage
to eyes
and
mucous
membra
nes, to
the
respirato
ry and
digestiv
e tracts,
and heat
stress; if
necessar
y, use
odor
neutraliz
ing
chemica
ls.
7
Chem
ical
risk
Exposur
e to
organic
substanc
es
(toluene,
n-
hexane,
methyl-
alcohol
etc.)
may
damage
the
nervous
system
Install
effective
exhaust
ventilati
on to
prevent
air
contami
nation;
if
necessar
y, use
respirato
ry
protectio
n
4 5 2
0 E
Proper
ventilla
tion
4 5 2
0 E
Safety
Adviso
r
10
days
8 Chem
ical
risk
Skin
exposur
e
through
contact
with
solvents
and
various
compon
ents of
paints,
esp.
aromatic
hydrocar
bons and
organic
halogen
Protect
the skin
of the
hands
(with
barrier
cream,
or
chemica
l-
resistant
gloves)
when in
contact
with
solvents
and
cleaning
5 5 2
5
E First
aid
availabi
lity
5 5 2
5
E Safety
Adviso
r
7 days
damage
to eyes
and
mucous
membra
nes, to
the
respirato
ry and
digestiv
e tracts,
and heat
stress; if
necessar
y, use
odor
neutraliz
ing
chemica
ls.
7
Chem
ical
risk
Exposur
e to
organic
substanc
es
(toluene,
n-
hexane,
methyl-
alcohol
etc.)
may
damage
the
nervous
system
Install
effective
exhaust
ventilati
on to
prevent
air
contami
nation;
if
necessar
y, use
respirato
ry
protectio
n
4 5 2
0 E
Proper
ventilla
tion
4 5 2
0 E
Safety
Adviso
r
10
days
8 Chem
ical
risk
Skin
exposur
e
through
contact
with
solvents
and
various
compon
ents of
paints,
esp.
aromatic
hydrocar
bons and
organic
halogen
Protect
the skin
of the
hands
(with
barrier
cream,
or
chemica
l-
resistant
gloves)
when in
contact
with
solvents
and
cleaning
5 5 2
5
E First
aid
availabi
lity
5 5 2
5
E Safety
Adviso
r
7 days
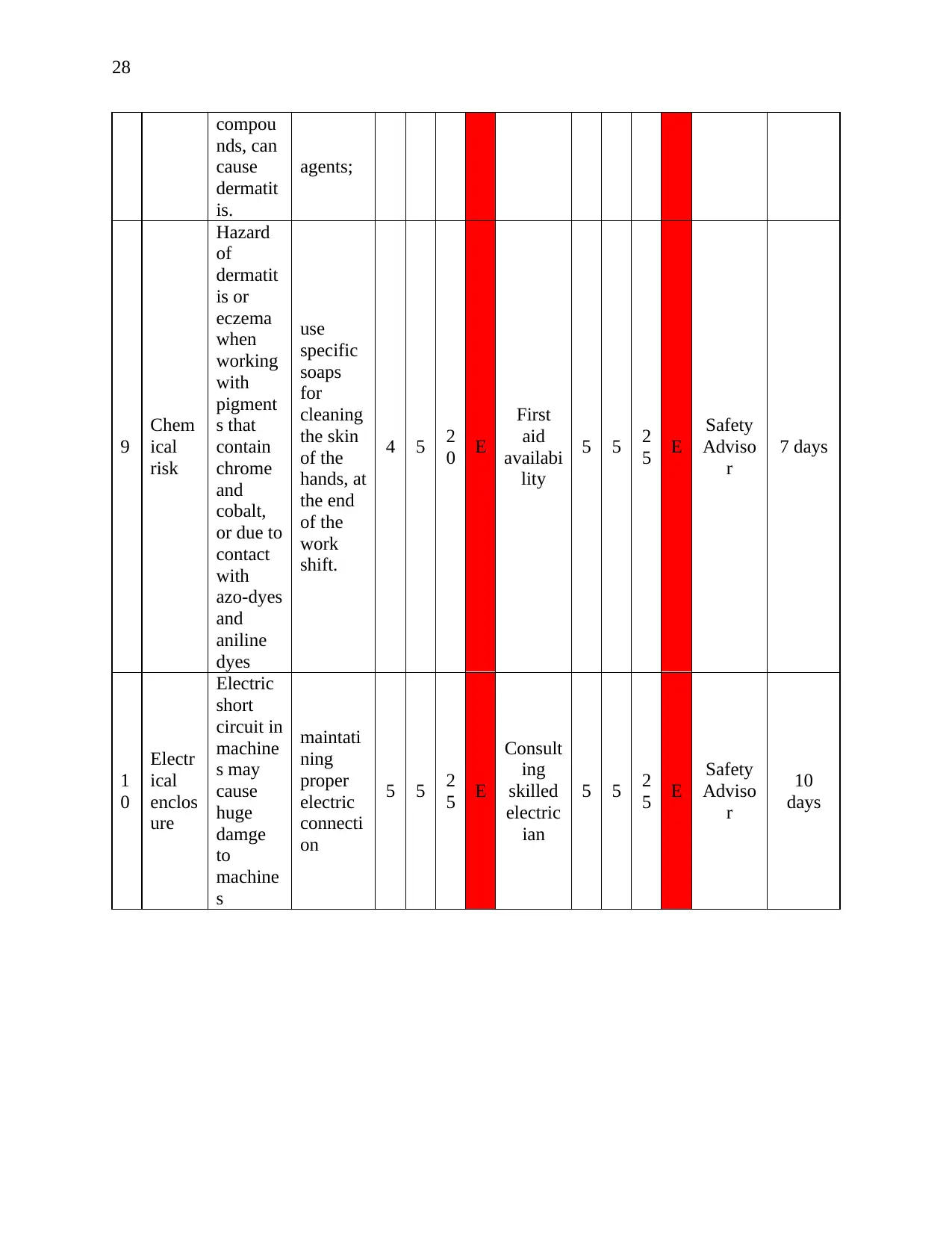
28
compou
nds, can
cause
dermatit
is.
agents;
9
Chem
ical
risk
Hazard
of
dermatit
is or
eczema
when
working
with
pigment
s that
contain
chrome
and
cobalt,
or due to
contact
with
azo-dyes
and
aniline
dyes
use
specific
soaps
for
cleaning
the skin
of the
hands, at
the end
of the
work
shift.
4 5 2
0 E
First
aid
availabi
lity
5 5 2
5 E
Safety
Adviso
r
7 days
1
0
Electr
ical
enclos
ure
Electric
short
circuit in
machine
s may
cause
huge
damge
to
machine
s
maintati
ning
proper
electric
connecti
on
5 5 2
5 E
Consult
ing
skilled
electric
ian
5 5 2
5 E
Safety
Adviso
r
10
days
compou
nds, can
cause
dermatit
is.
agents;
9
Chem
ical
risk
Hazard
of
dermatit
is or
eczema
when
working
with
pigment
s that
contain
chrome
and
cobalt,
or due to
contact
with
azo-dyes
and
aniline
dyes
use
specific
soaps
for
cleaning
the skin
of the
hands, at
the end
of the
work
shift.
4 5 2
0 E
First
aid
availabi
lity
5 5 2
5 E
Safety
Adviso
r
7 days
1
0
Electr
ical
enclos
ure
Electric
short
circuit in
machine
s may
cause
huge
damge
to
machine
s
maintati
ning
proper
electric
connecti
on
5 5 2
5 E
Consult
ing
skilled
electric
ian
5 5 2
5 E
Safety
Adviso
r
10
days
Secure Best Marks with AI Grader
Need help grading? Try our AI Grader for instant feedback on your assignments.
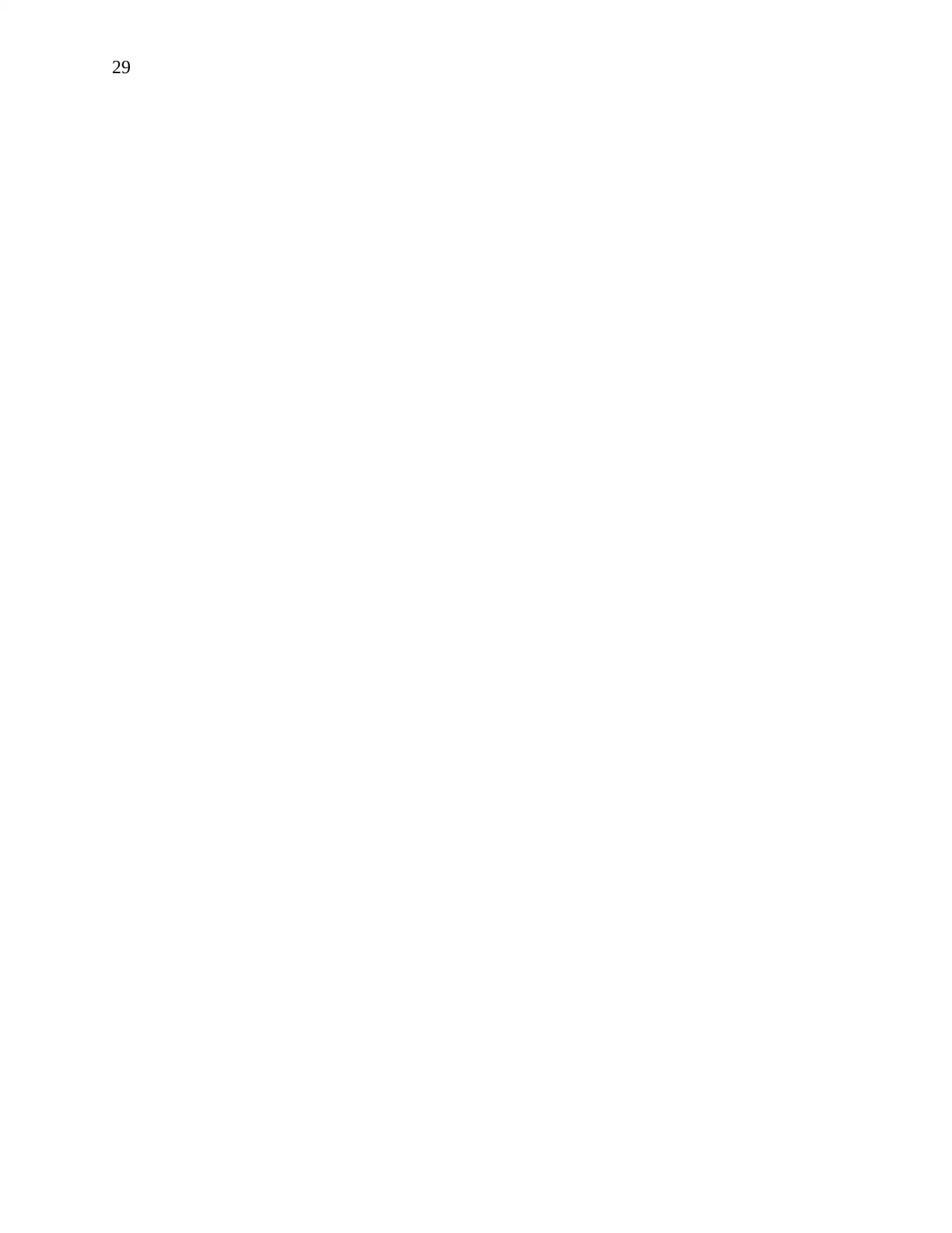
29
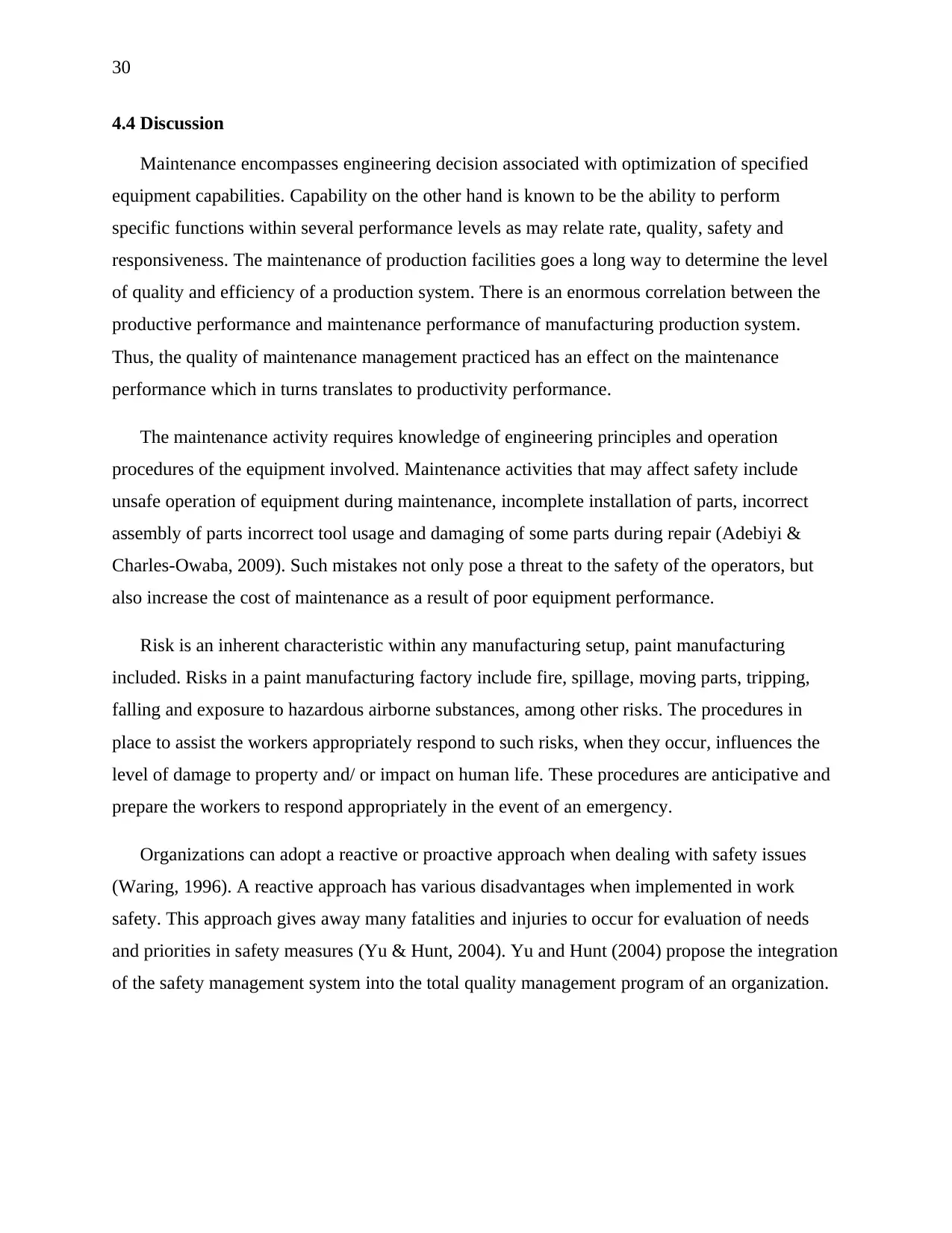
30
4.4 Discussion
Maintenance encompasses engineering decision associated with optimization of specified
equipment capabilities. Capability on the other hand is known to be the ability to perform
specific functions within several performance levels as may relate rate, quality, safety and
responsiveness. The maintenance of production facilities goes a long way to determine the level
of quality and efficiency of a production system. There is an enormous correlation between the
productive performance and maintenance performance of manufacturing production system.
Thus, the quality of maintenance management practiced has an effect on the maintenance
performance which in turns translates to productivity performance.
The maintenance activity requires knowledge of engineering principles and operation
procedures of the equipment involved. Maintenance activities that may affect safety include
unsafe operation of equipment during maintenance, incomplete installation of parts, incorrect
assembly of parts incorrect tool usage and damaging of some parts during repair (Adebiyi &
Charles-Owaba, 2009). Such mistakes not only pose a threat to the safety of the operators, but
also increase the cost of maintenance as a result of poor equipment performance.
Risk is an inherent characteristic within any manufacturing setup, paint manufacturing
included. Risks in a paint manufacturing factory include fire, spillage, moving parts, tripping,
falling and exposure to hazardous airborne substances, among other risks. The procedures in
place to assist the workers appropriately respond to such risks, when they occur, influences the
level of damage to property and/ or impact on human life. These procedures are anticipative and
prepare the workers to respond appropriately in the event of an emergency.
Organizations can adopt a reactive or proactive approach when dealing with safety issues
(Waring, 1996). A reactive approach has various disadvantages when implemented in work
safety. This approach gives away many fatalities and injuries to occur for evaluation of needs
and priorities in safety measures (Yu & Hunt, 2004). Yu and Hunt (2004) propose the integration
of the safety management system into the total quality management program of an organization.
4.4 Discussion
Maintenance encompasses engineering decision associated with optimization of specified
equipment capabilities. Capability on the other hand is known to be the ability to perform
specific functions within several performance levels as may relate rate, quality, safety and
responsiveness. The maintenance of production facilities goes a long way to determine the level
of quality and efficiency of a production system. There is an enormous correlation between the
productive performance and maintenance performance of manufacturing production system.
Thus, the quality of maintenance management practiced has an effect on the maintenance
performance which in turns translates to productivity performance.
The maintenance activity requires knowledge of engineering principles and operation
procedures of the equipment involved. Maintenance activities that may affect safety include
unsafe operation of equipment during maintenance, incomplete installation of parts, incorrect
assembly of parts incorrect tool usage and damaging of some parts during repair (Adebiyi &
Charles-Owaba, 2009). Such mistakes not only pose a threat to the safety of the operators, but
also increase the cost of maintenance as a result of poor equipment performance.
Risk is an inherent characteristic within any manufacturing setup, paint manufacturing
included. Risks in a paint manufacturing factory include fire, spillage, moving parts, tripping,
falling and exposure to hazardous airborne substances, among other risks. The procedures in
place to assist the workers appropriately respond to such risks, when they occur, influences the
level of damage to property and/ or impact on human life. These procedures are anticipative and
prepare the workers to respond appropriately in the event of an emergency.
Organizations can adopt a reactive or proactive approach when dealing with safety issues
(Waring, 1996). A reactive approach has various disadvantages when implemented in work
safety. This approach gives away many fatalities and injuries to occur for evaluation of needs
and priorities in safety measures (Yu & Hunt, 2004). Yu and Hunt (2004) propose the integration
of the safety management system into the total quality management program of an organization.
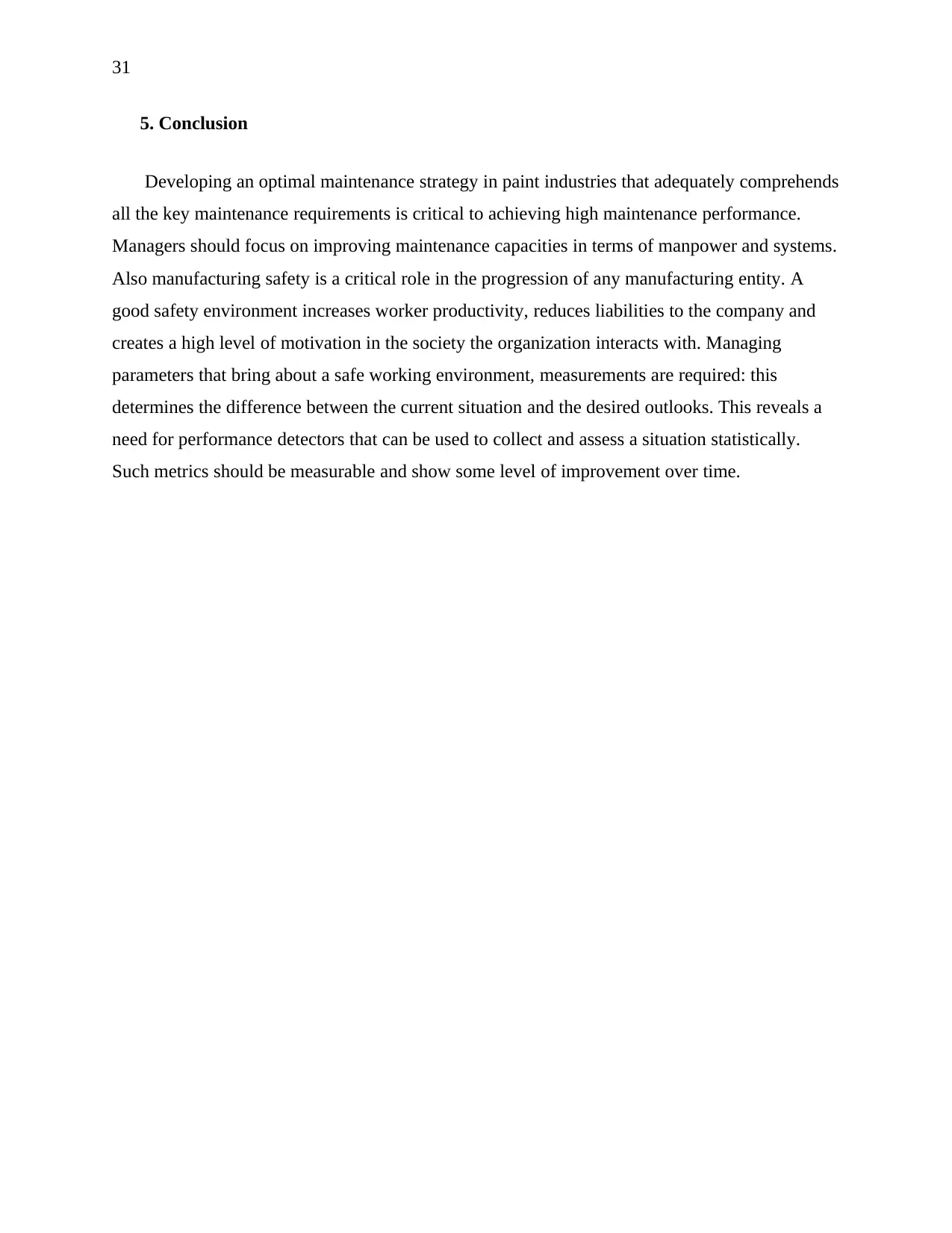
31
5. Conclusion
Developing an optimal maintenance strategy in paint industries that adequately comprehends
all the key maintenance requirements is critical to achieving high maintenance performance.
Managers should focus on improving maintenance capacities in terms of manpower and systems.
Also manufacturing safety is a critical role in the progression of any manufacturing entity. A
good safety environment increases worker productivity, reduces liabilities to the company and
creates a high level of motivation in the society the organization interacts with. Managing
parameters that bring about a safe working environment, measurements are required: this
determines the difference between the current situation and the desired outlooks. This reveals a
need for performance detectors that can be used to collect and assess a situation statistically.
Such metrics should be measurable and show some level of improvement over time.
5. Conclusion
Developing an optimal maintenance strategy in paint industries that adequately comprehends
all the key maintenance requirements is critical to achieving high maintenance performance.
Managers should focus on improving maintenance capacities in terms of manpower and systems.
Also manufacturing safety is a critical role in the progression of any manufacturing entity. A
good safety environment increases worker productivity, reduces liabilities to the company and
creates a high level of motivation in the society the organization interacts with. Managing
parameters that bring about a safe working environment, measurements are required: this
determines the difference between the current situation and the desired outlooks. This reveals a
need for performance detectors that can be used to collect and assess a situation statistically.
Such metrics should be measurable and show some level of improvement over time.
Paraphrase This Document
Need a fresh take? Get an instant paraphrase of this document with our AI Paraphraser
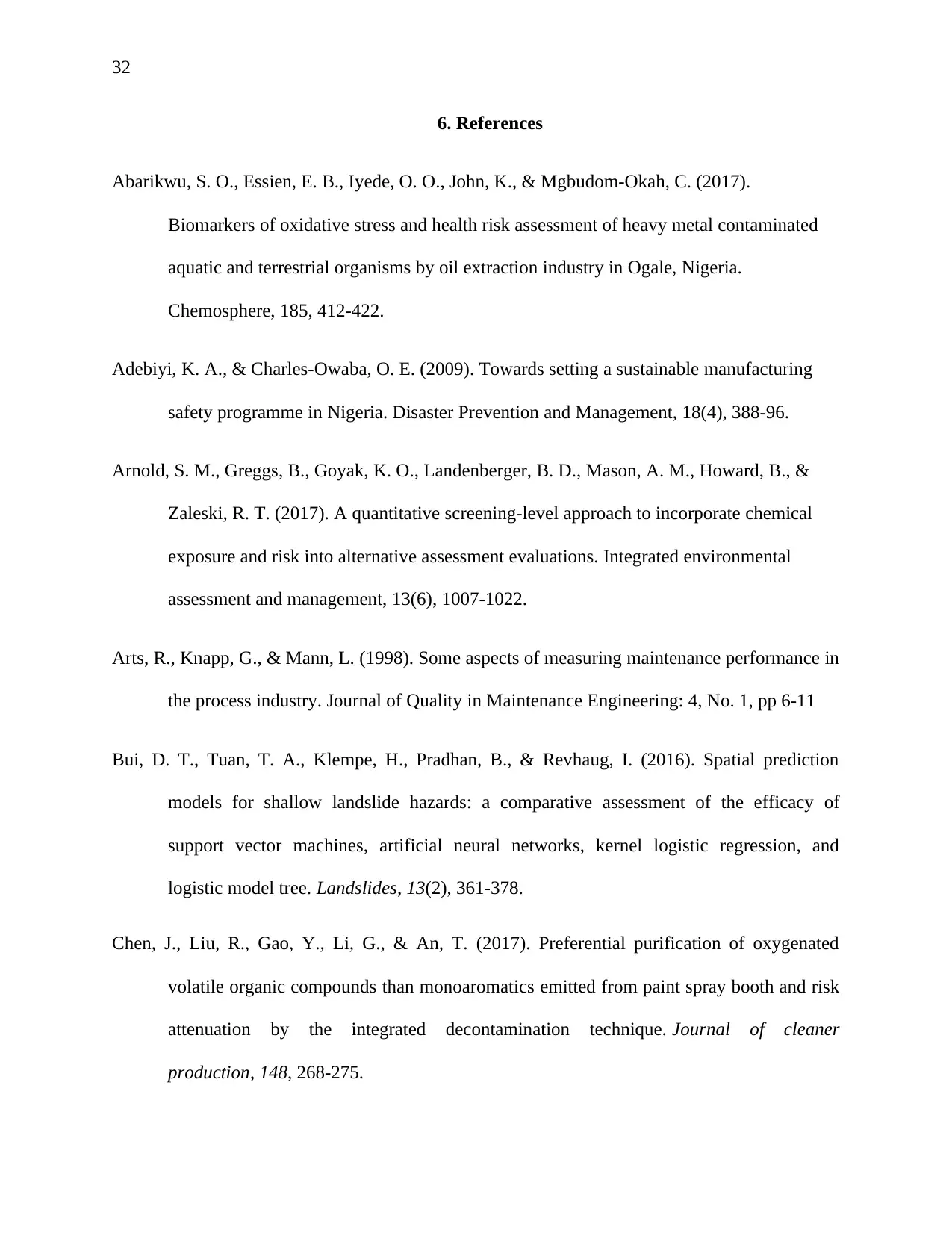
32
6. References
Abarikwu, S. O., Essien, E. B., Iyede, O. O., John, K., & Mgbudom-Okah, C. (2017).
Biomarkers of oxidative stress and health risk assessment of heavy metal contaminated
aquatic and terrestrial organisms by oil extraction industry in Ogale, Nigeria.
Chemosphere, 185, 412-422.
Adebiyi, K. A., & Charles-Owaba, O. E. (2009). Towards setting a sustainable manufacturing
safety programme in Nigeria. Disaster Prevention and Management, 18(4), 388-96.
Arnold, S. M., Greggs, B., Goyak, K. O., Landenberger, B. D., Mason, A. M., Howard, B., &
Zaleski, R. T. (2017). A quantitative screening‐level approach to incorporate chemical
exposure and risk into alternative assessment evaluations. Integrated environmental
assessment and management, 13(6), 1007-1022.
Arts, R., Knapp, G., & Mann, L. (1998). Some aspects of measuring maintenance performance in
the process industry. Journal of Quality in Maintenance Engineering: 4, No. 1, pp 6-11
Bui, D. T., Tuan, T. A., Klempe, H., Pradhan, B., & Revhaug, I. (2016). Spatial prediction
models for shallow landslide hazards: a comparative assessment of the efficacy of
support vector machines, artificial neural networks, kernel logistic regression, and
logistic model tree. Landslides, 13(2), 361-378.
Chen, J., Liu, R., Gao, Y., Li, G., & An, T. (2017). Preferential purification of oxygenated
volatile organic compounds than monoaromatics emitted from paint spray booth and risk
attenuation by the integrated decontamination technique. Journal of cleaner
production, 148, 268-275.
6. References
Abarikwu, S. O., Essien, E. B., Iyede, O. O., John, K., & Mgbudom-Okah, C. (2017).
Biomarkers of oxidative stress and health risk assessment of heavy metal contaminated
aquatic and terrestrial organisms by oil extraction industry in Ogale, Nigeria.
Chemosphere, 185, 412-422.
Adebiyi, K. A., & Charles-Owaba, O. E. (2009). Towards setting a sustainable manufacturing
safety programme in Nigeria. Disaster Prevention and Management, 18(4), 388-96.
Arnold, S. M., Greggs, B., Goyak, K. O., Landenberger, B. D., Mason, A. M., Howard, B., &
Zaleski, R. T. (2017). A quantitative screening‐level approach to incorporate chemical
exposure and risk into alternative assessment evaluations. Integrated environmental
assessment and management, 13(6), 1007-1022.
Arts, R., Knapp, G., & Mann, L. (1998). Some aspects of measuring maintenance performance in
the process industry. Journal of Quality in Maintenance Engineering: 4, No. 1, pp 6-11
Bui, D. T., Tuan, T. A., Klempe, H., Pradhan, B., & Revhaug, I. (2016). Spatial prediction
models for shallow landslide hazards: a comparative assessment of the efficacy of
support vector machines, artificial neural networks, kernel logistic regression, and
logistic model tree. Landslides, 13(2), 361-378.
Chen, J., Liu, R., Gao, Y., Li, G., & An, T. (2017). Preferential purification of oxygenated
volatile organic compounds than monoaromatics emitted from paint spray booth and risk
attenuation by the integrated decontamination technique. Journal of cleaner
production, 148, 268-275.
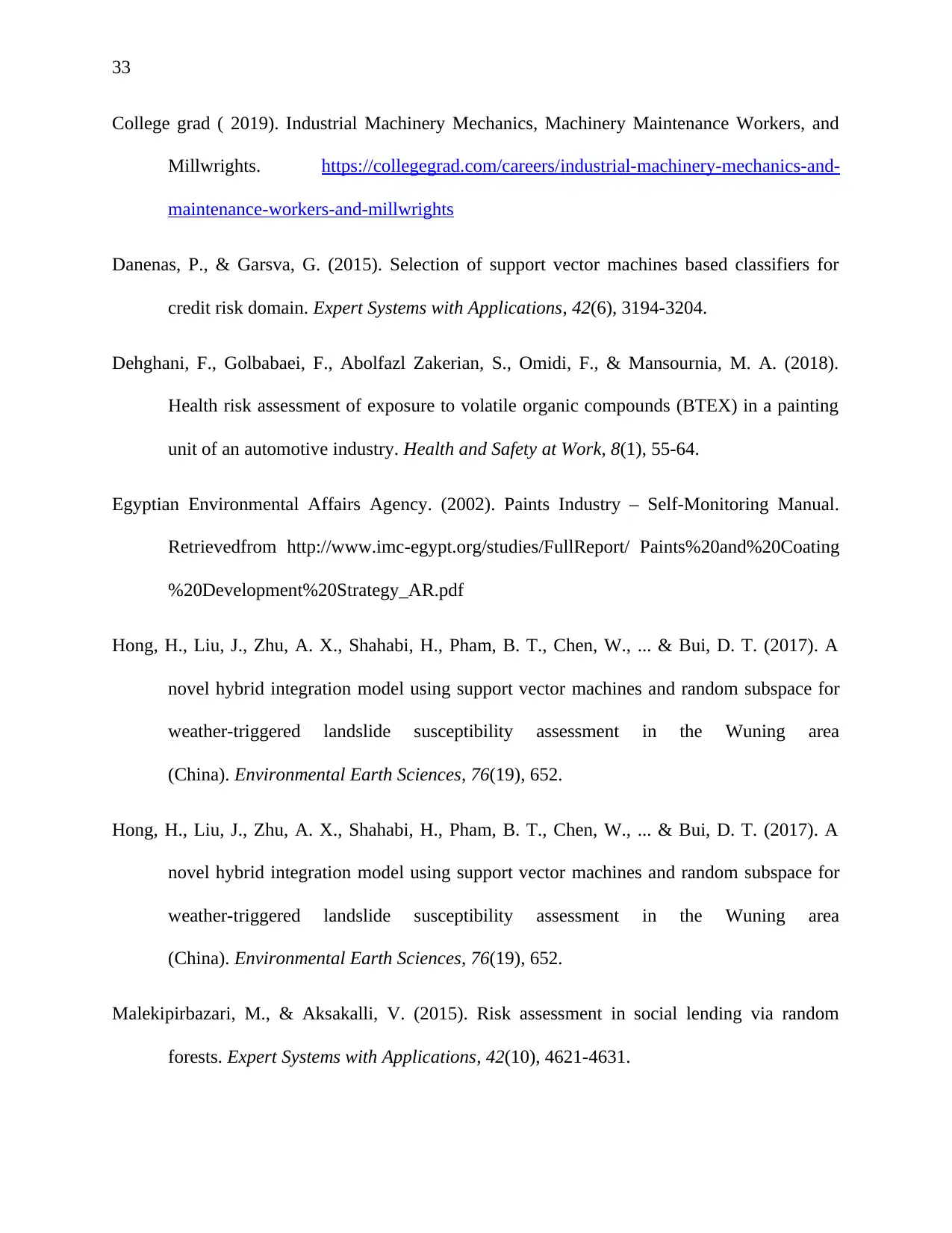
33
College grad ( 2019). Industrial Machinery Mechanics, Machinery Maintenance Workers, and
Millwrights. https://collegegrad.com/careers/industrial-machinery-mechanics-and-
maintenance-workers-and-millwrights
Danenas, P., & Garsva, G. (2015). Selection of support vector machines based classifiers for
credit risk domain. Expert Systems with Applications, 42(6), 3194-3204.
Dehghani, F., Golbabaei, F., Abolfazl Zakerian, S., Omidi, F., & Mansournia, M. A. (2018).
Health risk assessment of exposure to volatile organic compounds (BTEX) in a painting
unit of an automotive industry. Health and Safety at Work, 8(1), 55-64.
Egyptian Environmental Affairs Agency. (2002). Paints Industry – Self-Monitoring Manual.
Retrievedfrom http://www.imc-egypt.org/studies/FullReport/ Paints%20and%20Coating
%20Development%20Strategy_AR.pdf
Hong, H., Liu, J., Zhu, A. X., Shahabi, H., Pham, B. T., Chen, W., ... & Bui, D. T. (2017). A
novel hybrid integration model using support vector machines and random subspace for
weather-triggered landslide susceptibility assessment in the Wuning area
(China). Environmental Earth Sciences, 76(19), 652.
Hong, H., Liu, J., Zhu, A. X., Shahabi, H., Pham, B. T., Chen, W., ... & Bui, D. T. (2017). A
novel hybrid integration model using support vector machines and random subspace for
weather-triggered landslide susceptibility assessment in the Wuning area
(China). Environmental Earth Sciences, 76(19), 652.
Malekipirbazari, M., & Aksakalli, V. (2015). Risk assessment in social lending via random
forests. Expert Systems with Applications, 42(10), 4621-4631.
College grad ( 2019). Industrial Machinery Mechanics, Machinery Maintenance Workers, and
Millwrights. https://collegegrad.com/careers/industrial-machinery-mechanics-and-
maintenance-workers-and-millwrights
Danenas, P., & Garsva, G. (2015). Selection of support vector machines based classifiers for
credit risk domain. Expert Systems with Applications, 42(6), 3194-3204.
Dehghani, F., Golbabaei, F., Abolfazl Zakerian, S., Omidi, F., & Mansournia, M. A. (2018).
Health risk assessment of exposure to volatile organic compounds (BTEX) in a painting
unit of an automotive industry. Health and Safety at Work, 8(1), 55-64.
Egyptian Environmental Affairs Agency. (2002). Paints Industry – Self-Monitoring Manual.
Retrievedfrom http://www.imc-egypt.org/studies/FullReport/ Paints%20and%20Coating
%20Development%20Strategy_AR.pdf
Hong, H., Liu, J., Zhu, A. X., Shahabi, H., Pham, B. T., Chen, W., ... & Bui, D. T. (2017). A
novel hybrid integration model using support vector machines and random subspace for
weather-triggered landslide susceptibility assessment in the Wuning area
(China). Environmental Earth Sciences, 76(19), 652.
Hong, H., Liu, J., Zhu, A. X., Shahabi, H., Pham, B. T., Chen, W., ... & Bui, D. T. (2017). A
novel hybrid integration model using support vector machines and random subspace for
weather-triggered landslide susceptibility assessment in the Wuning area
(China). Environmental Earth Sciences, 76(19), 652.
Malekipirbazari, M., & Aksakalli, V. (2015). Risk assessment in social lending via random
forests. Expert Systems with Applications, 42(10), 4621-4631.
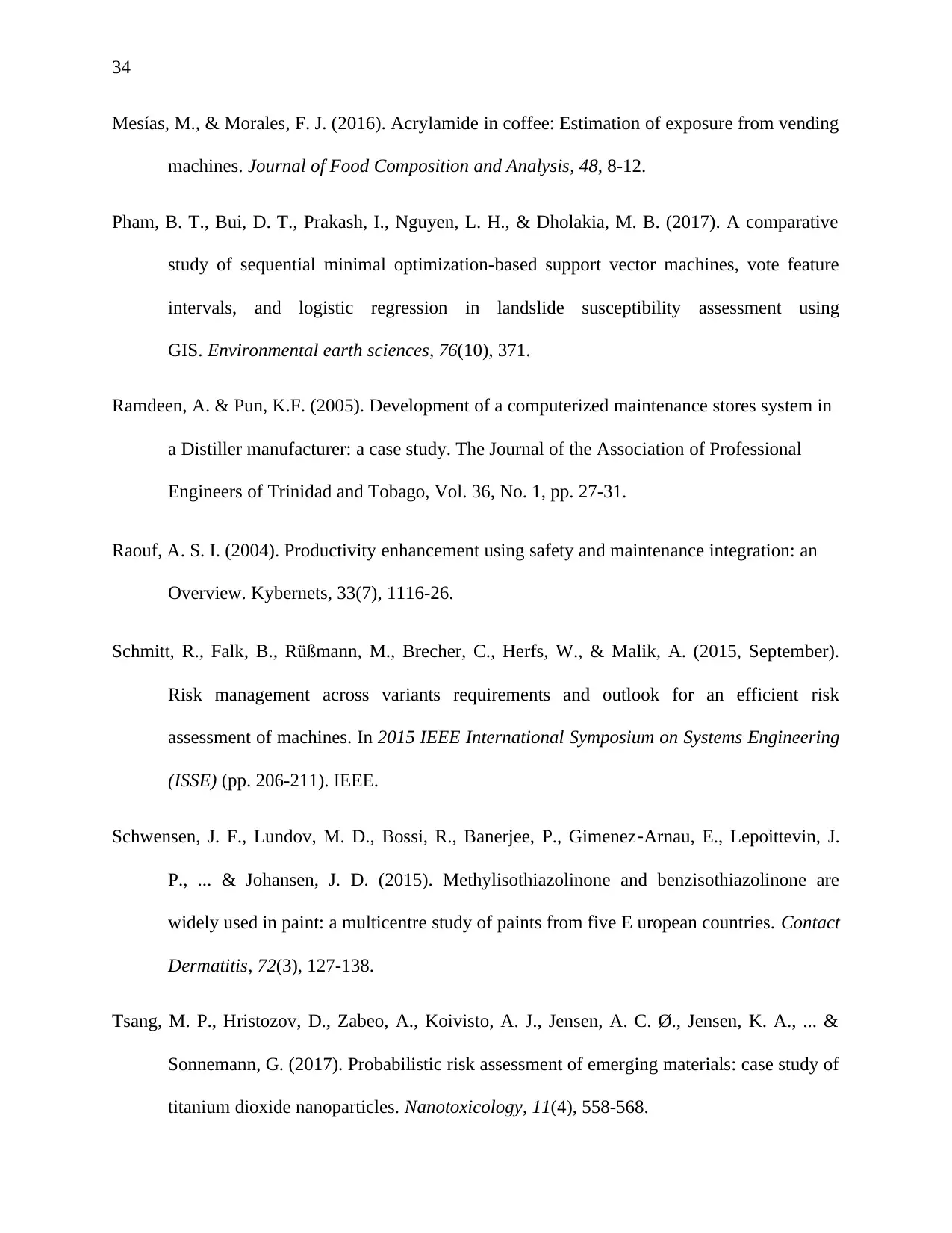
34
Mesías, M., & Morales, F. J. (2016). Acrylamide in coffee: Estimation of exposure from vending
machines. Journal of Food Composition and Analysis, 48, 8-12.
Pham, B. T., Bui, D. T., Prakash, I., Nguyen, L. H., & Dholakia, M. B. (2017). A comparative
study of sequential minimal optimization-based support vector machines, vote feature
intervals, and logistic regression in landslide susceptibility assessment using
GIS. Environmental earth sciences, 76(10), 371.
Ramdeen, A. & Pun, K.F. (2005). Development of a computerized maintenance stores system in
a Distiller manufacturer: a case study. The Journal of the Association of Professional
Engineers of Trinidad and Tobago, Vol. 36, No. 1, pp. 27-31.
Raouf, A. S. I. (2004). Productivity enhancement using safety and maintenance integration: an
Overview. Kybernets, 33(7), 1116-26.
Schmitt, R., Falk, B., Rüßmann, M., Brecher, C., Herfs, W., & Malik, A. (2015, September).
Risk management across variants requirements and outlook for an efficient risk
assessment of machines. In 2015 IEEE International Symposium on Systems Engineering
(ISSE) (pp. 206-211). IEEE.
Schwensen, J. F., Lundov, M. D., Bossi, R., Banerjee, P., Gimenez‐Arnau, E., Lepoittevin, J.
P., ... & Johansen, J. D. (2015). Methylisothiazolinone and benzisothiazolinone are
widely used in paint: a multicentre study of paints from five E uropean countries. Contact
Dermatitis, 72(3), 127-138.
Tsang, M. P., Hristozov, D., Zabeo, A., Koivisto, A. J., Jensen, A. C. Ø., Jensen, K. A., ... &
Sonnemann, G. (2017). Probabilistic risk assessment of emerging materials: case study of
titanium dioxide nanoparticles. Nanotoxicology, 11(4), 558-568.
Mesías, M., & Morales, F. J. (2016). Acrylamide in coffee: Estimation of exposure from vending
machines. Journal of Food Composition and Analysis, 48, 8-12.
Pham, B. T., Bui, D. T., Prakash, I., Nguyen, L. H., & Dholakia, M. B. (2017). A comparative
study of sequential minimal optimization-based support vector machines, vote feature
intervals, and logistic regression in landslide susceptibility assessment using
GIS. Environmental earth sciences, 76(10), 371.
Ramdeen, A. & Pun, K.F. (2005). Development of a computerized maintenance stores system in
a Distiller manufacturer: a case study. The Journal of the Association of Professional
Engineers of Trinidad and Tobago, Vol. 36, No. 1, pp. 27-31.
Raouf, A. S. I. (2004). Productivity enhancement using safety and maintenance integration: an
Overview. Kybernets, 33(7), 1116-26.
Schmitt, R., Falk, B., Rüßmann, M., Brecher, C., Herfs, W., & Malik, A. (2015, September).
Risk management across variants requirements and outlook for an efficient risk
assessment of machines. In 2015 IEEE International Symposium on Systems Engineering
(ISSE) (pp. 206-211). IEEE.
Schwensen, J. F., Lundov, M. D., Bossi, R., Banerjee, P., Gimenez‐Arnau, E., Lepoittevin, J.
P., ... & Johansen, J. D. (2015). Methylisothiazolinone and benzisothiazolinone are
widely used in paint: a multicentre study of paints from five E uropean countries. Contact
Dermatitis, 72(3), 127-138.
Tsang, M. P., Hristozov, D., Zabeo, A., Koivisto, A. J., Jensen, A. C. Ø., Jensen, K. A., ... &
Sonnemann, G. (2017). Probabilistic risk assessment of emerging materials: case study of
titanium dioxide nanoparticles. Nanotoxicology, 11(4), 558-568.
Secure Best Marks with AI Grader
Need help grading? Try our AI Grader for instant feedback on your assignments.
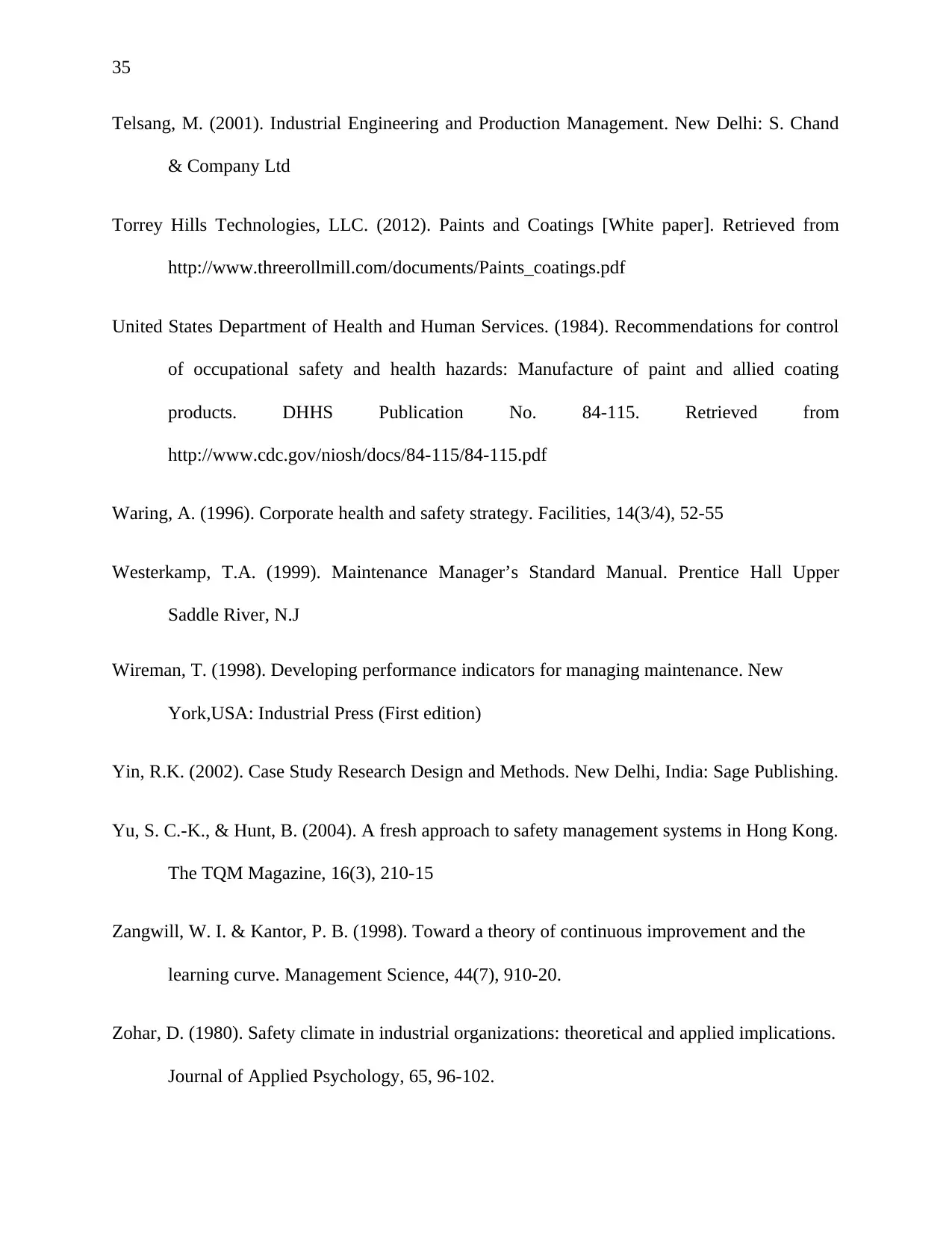
35
Telsang, M. (2001). Industrial Engineering and Production Management. New Delhi: S. Chand
& Company Ltd
Torrey Hills Technologies, LLC. (2012). Paints and Coatings [White paper]. Retrieved from
http://www.threerollmill.com/documents/Paints_coatings.pdf
United States Department of Health and Human Services. (1984). Recommendations for control
of occupational safety and health hazards: Manufacture of paint and allied coating
products. DHHS Publication No. 84-115. Retrieved from
http://www.cdc.gov/niosh/docs/84-115/84-115.pdf
Waring, A. (1996). Corporate health and safety strategy. Facilities, 14(3/4), 52-55
Westerkamp, T.A. (1999). Maintenance Manager’s Standard Manual. Prentice Hall Upper
Saddle River, N.J
Wireman, T. (1998). Developing performance indicators for managing maintenance. New
York,USA: Industrial Press (First edition)
Yin, R.K. (2002). Case Study Research Design and Methods. New Delhi, India: Sage Publishing.
Yu, S. C.-K., & Hunt, B. (2004). A fresh approach to safety management systems in Hong Kong.
The TQM Magazine, 16(3), 210-15
Zangwill, W. I. & Kantor, P. B. (1998). Toward a theory of continuous improvement and the
learning curve. Management Science, 44(7), 910-20.
Zohar, D. (1980). Safety climate in industrial organizations: theoretical and applied implications.
Journal of Applied Psychology, 65, 96-102.
Telsang, M. (2001). Industrial Engineering and Production Management. New Delhi: S. Chand
& Company Ltd
Torrey Hills Technologies, LLC. (2012). Paints and Coatings [White paper]. Retrieved from
http://www.threerollmill.com/documents/Paints_coatings.pdf
United States Department of Health and Human Services. (1984). Recommendations for control
of occupational safety and health hazards: Manufacture of paint and allied coating
products. DHHS Publication No. 84-115. Retrieved from
http://www.cdc.gov/niosh/docs/84-115/84-115.pdf
Waring, A. (1996). Corporate health and safety strategy. Facilities, 14(3/4), 52-55
Westerkamp, T.A. (1999). Maintenance Manager’s Standard Manual. Prentice Hall Upper
Saddle River, N.J
Wireman, T. (1998). Developing performance indicators for managing maintenance. New
York,USA: Industrial Press (First edition)
Yin, R.K. (2002). Case Study Research Design and Methods. New Delhi, India: Sage Publishing.
Yu, S. C.-K., & Hunt, B. (2004). A fresh approach to safety management systems in Hong Kong.
The TQM Magazine, 16(3), 210-15
Zangwill, W. I. & Kantor, P. B. (1998). Toward a theory of continuous improvement and the
learning curve. Management Science, 44(7), 910-20.
Zohar, D. (1980). Safety climate in industrial organizations: theoretical and applied implications.
Journal of Applied Psychology, 65, 96-102.
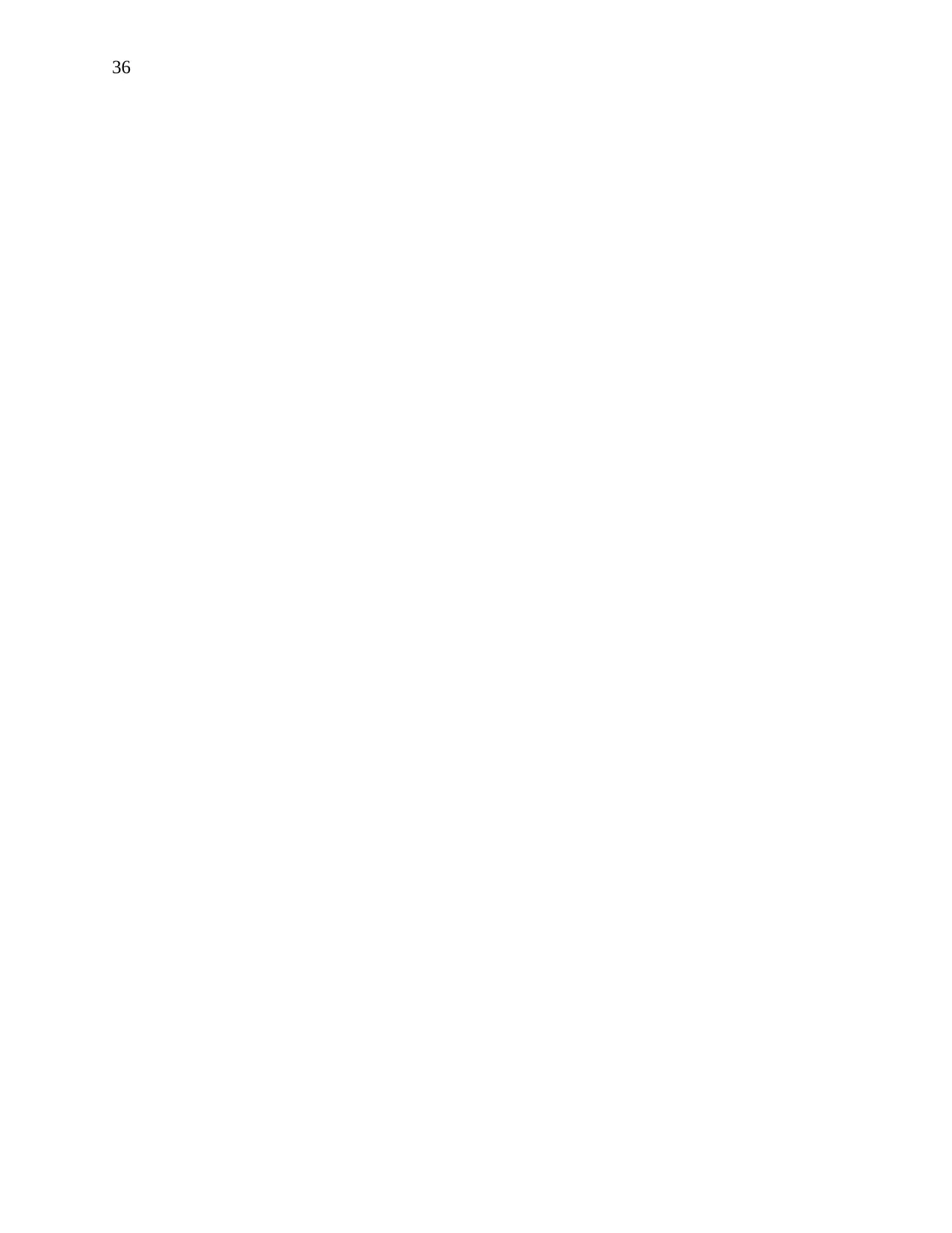
36
1 out of 36
Related Documents

Your All-in-One AI-Powered Toolkit for Academic Success.
+13062052269
info@desklib.com
Available 24*7 on WhatsApp / Email
Unlock your academic potential
© 2024 | Zucol Services PVT LTD | All rights reserved.