XLG Management Accounting Report: Variance Analysis and Decisions
VerifiedAdded on  2022/12/29
|11
|3134
|74
Report
AI Summary
This management accounting report for XLG analyzes sales price variance, sales volume contribution variance, material price planning variance, and material price operational variance. It calculates these variances and discusses their merits and demerits in assessing managerial performance. The report also examines the impact of importing materials from Brazil versus in-house production, considering advantages and disadvantages of each approach. The analysis includes detailed calculations, interpretations of variance results, and strategic recommendations for cost control, performance measurement, and supply chain management, offering insights into decision-making regarding production methods and material sourcing for XLG. The report concludes with a discussion on the importance of strategic decisions in determining the future growth and performance of the organization.
Contribute Materials
Your contribution can guide someone’s learning journey. Share your
documents today.
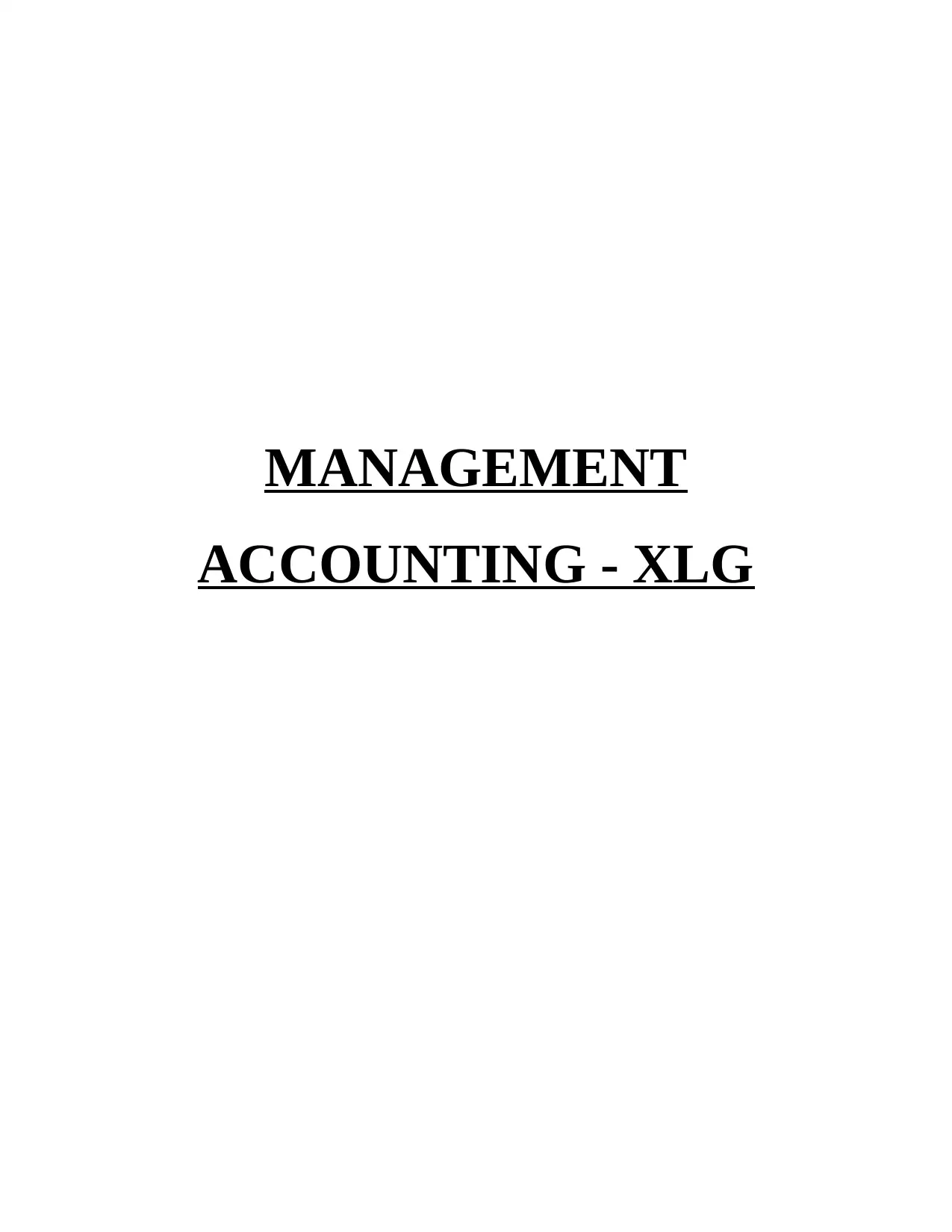
MANAGEMENT
ACCOUNTING - XLG
ACCOUNTING - XLG
Secure Best Marks with AI Grader
Need help grading? Try our AI Grader for instant feedback on your assignments.
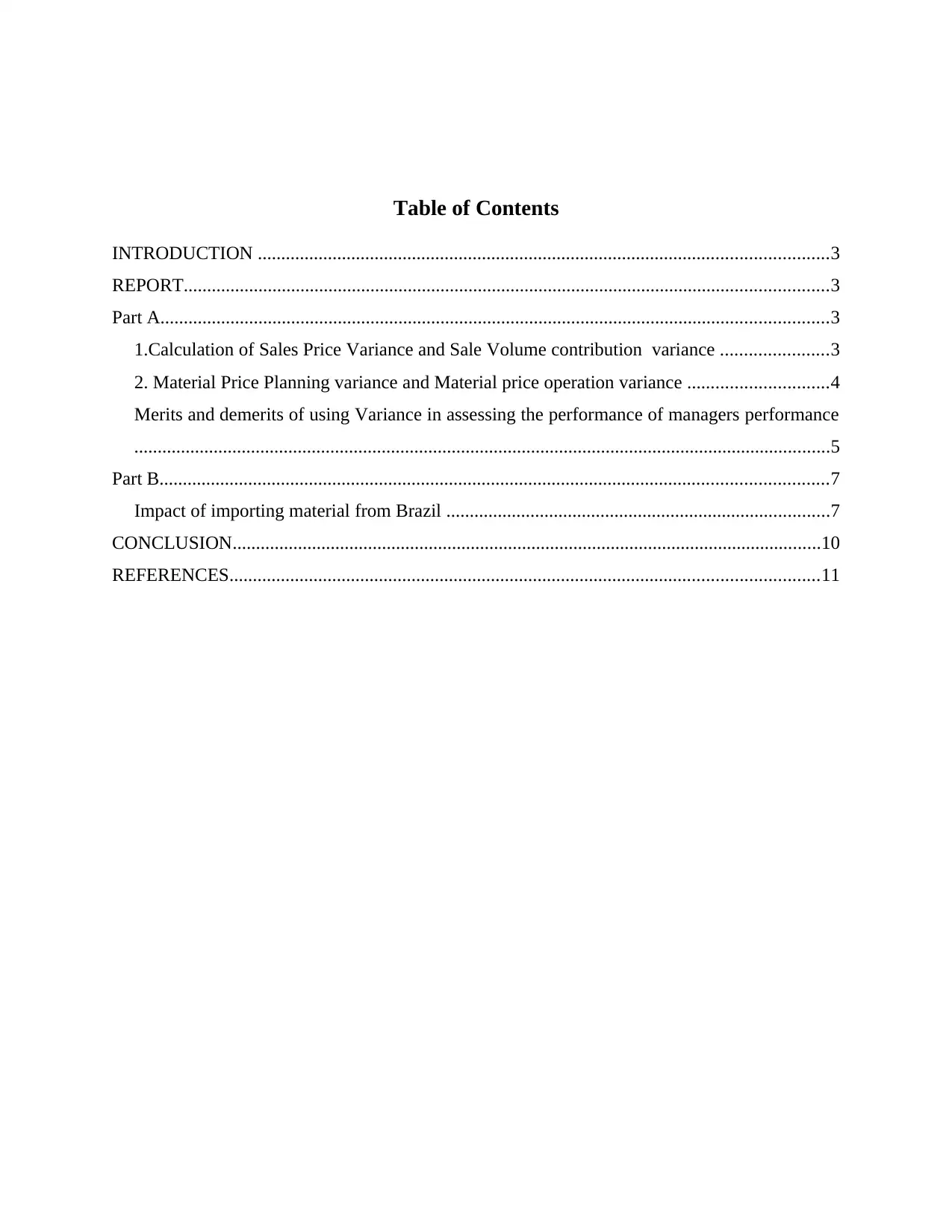
Table of Contents
INTRODUCTION ..........................................................................................................................3
REPORT..........................................................................................................................................3
Part A...............................................................................................................................................3
1.Calculation of Sales Price Variance and Sale Volume contribution variance .......................3
2. Material Price Planning variance and Material price operation variance ..............................4
Merits and demerits of using Variance in assessing the performance of managers performance
.....................................................................................................................................................5
Part B...............................................................................................................................................7
Impact of importing material from Brazil ..................................................................................7
CONCLUSION..............................................................................................................................10
REFERENCES..............................................................................................................................11
INTRODUCTION ..........................................................................................................................3
REPORT..........................................................................................................................................3
Part A...............................................................................................................................................3
1.Calculation of Sales Price Variance and Sale Volume contribution variance .......................3
2. Material Price Planning variance and Material price operation variance ..............................4
Merits and demerits of using Variance in assessing the performance of managers performance
.....................................................................................................................................................5
Part B...............................................................................................................................................7
Impact of importing material from Brazil ..................................................................................7
CONCLUSION..............................................................................................................................10
REFERENCES..............................................................................................................................11
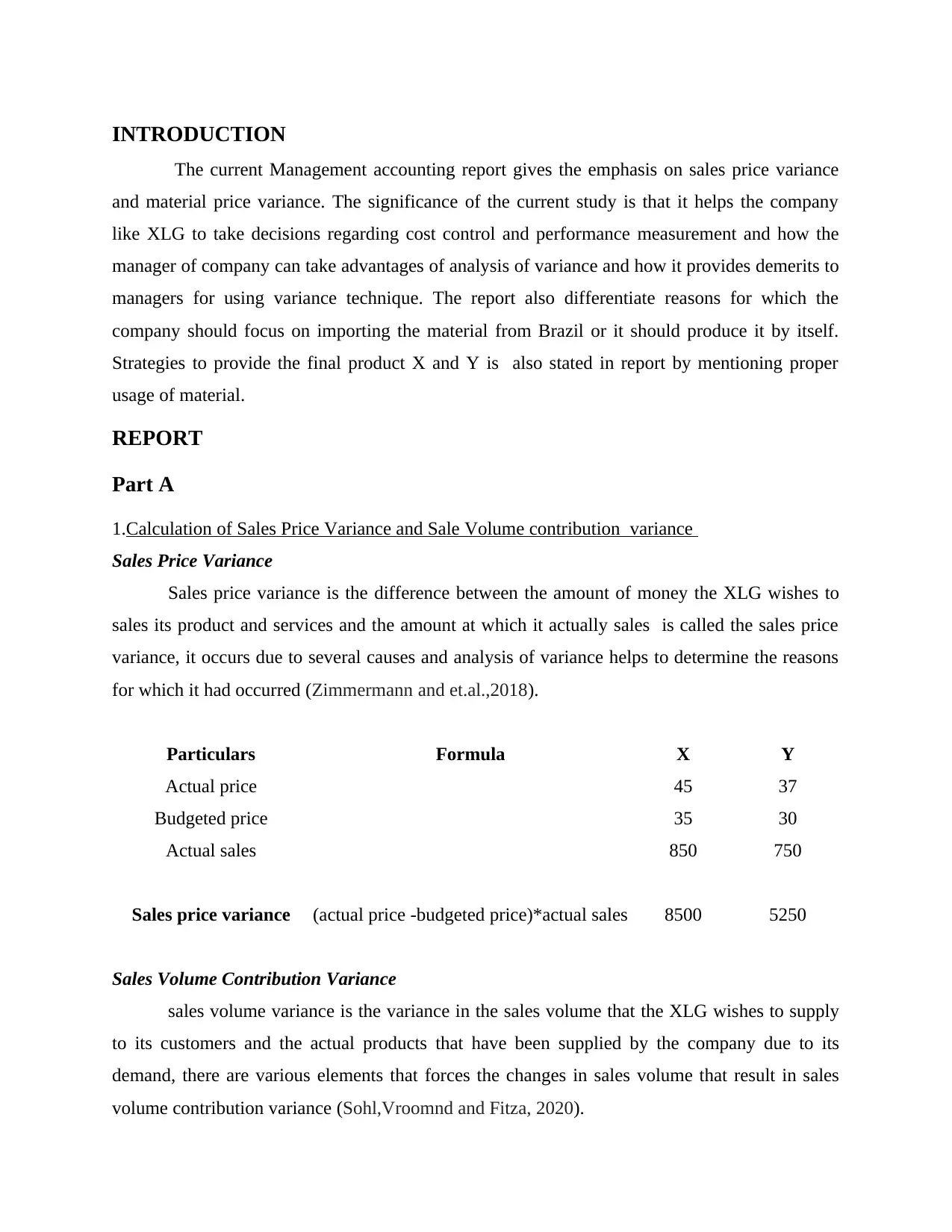
INTRODUCTION
The current Management accounting report gives the emphasis on sales price variance
and material price variance. The significance of the current study is that it helps the company
like XLG to take decisions regarding cost control and performance measurement and how the
manager of company can take advantages of analysis of variance and how it provides demerits to
managers for using variance technique. The report also differentiate reasons for which the
company should focus on importing the material from Brazil or it should produce it by itself.
Strategies to provide the final product X and Y is also stated in report by mentioning proper
usage of material.
REPORT
Part A
1.Calculation of Sales Price Variance and Sale Volume contribution variance
Sales Price Variance
Sales price variance is the difference between the amount of money the XLG wishes to
sales its product and services and the amount at which it actually sales is called the sales price
variance, it occurs due to several causes and analysis of variance helps to determine the reasons
for which it had occurred (Zimmermann and et.al.,2018).
Particulars Formula X Y
Actual price 45 37
Budgeted price 35 30
Actual sales 850 750
Sales price variance (actual price -budgeted price)*actual sales 8500 5250
Sales Volume Contribution Variance
sales volume variance is the variance in the sales volume that the XLG wishes to supply
to its customers and the actual products that have been supplied by the company due to its
demand, there are various elements that forces the changes in sales volume that result in sales
volume contribution variance (Sohl,Vroomnd and Fitza, 2020).
The current Management accounting report gives the emphasis on sales price variance
and material price variance. The significance of the current study is that it helps the company
like XLG to take decisions regarding cost control and performance measurement and how the
manager of company can take advantages of analysis of variance and how it provides demerits to
managers for using variance technique. The report also differentiate reasons for which the
company should focus on importing the material from Brazil or it should produce it by itself.
Strategies to provide the final product X and Y is also stated in report by mentioning proper
usage of material.
REPORT
Part A
1.Calculation of Sales Price Variance and Sale Volume contribution variance
Sales Price Variance
Sales price variance is the difference between the amount of money the XLG wishes to
sales its product and services and the amount at which it actually sales is called the sales price
variance, it occurs due to several causes and analysis of variance helps to determine the reasons
for which it had occurred (Zimmermann and et.al.,2018).
Particulars Formula X Y
Actual price 45 37
Budgeted price 35 30
Actual sales 850 750
Sales price variance (actual price -budgeted price)*actual sales 8500 5250
Sales Volume Contribution Variance
sales volume variance is the variance in the sales volume that the XLG wishes to supply
to its customers and the actual products that have been supplied by the company due to its
demand, there are various elements that forces the changes in sales volume that result in sales
volume contribution variance (Sohl,Vroomnd and Fitza, 2020).
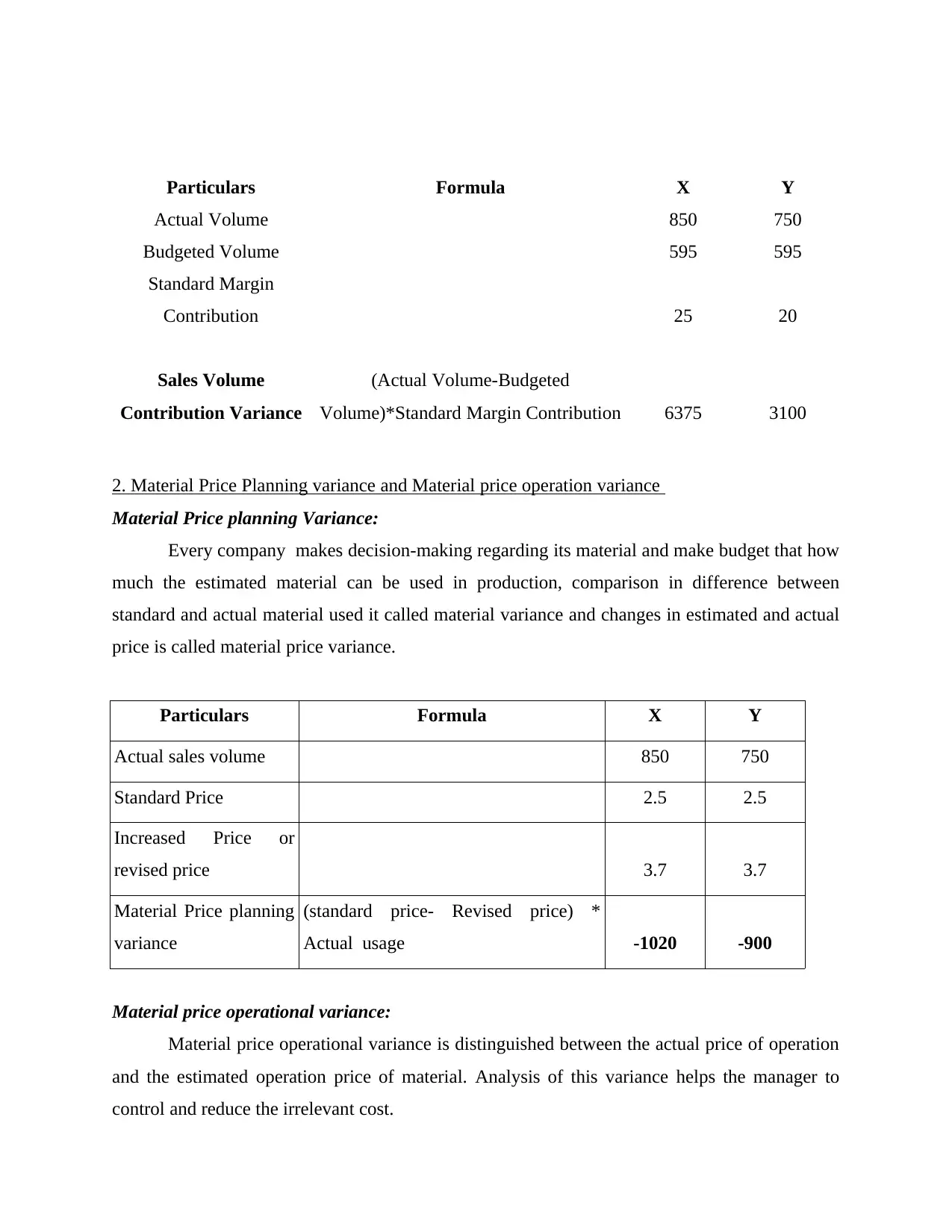
Particulars Formula X Y
Actual Volume 850 750
Budgeted Volume 595 595
Standard Margin
Contribution 25 20
Sales Volume
Contribution Variance
(Actual Volume-Budgeted
Volume)*Standard Margin Contribution 6375 3100
2. Material Price Planning variance and Material price operation variance
Material Price planning Variance:
Every company makes decision-making regarding its material and make budget that how
much the estimated material can be used in production, comparison in difference between
standard and actual material used it called material variance and changes in estimated and actual
price is called material price variance.
Particulars Formula X Y
Actual sales volume 850 750
Standard Price 2.5 2.5
Increased Price or
revised price 3.7 3.7
Material Price planning
variance
(standard price- Revised price) *
Actual usage -1020 -900
Material price operational variance:
Material price operational variance is distinguished between the actual price of operation
and the estimated operation price of material. Analysis of this variance helps the manager to
control and reduce the irrelevant cost.
Actual Volume 850 750
Budgeted Volume 595 595
Standard Margin
Contribution 25 20
Sales Volume
Contribution Variance
(Actual Volume-Budgeted
Volume)*Standard Margin Contribution 6375 3100
2. Material Price Planning variance and Material price operation variance
Material Price planning Variance:
Every company makes decision-making regarding its material and make budget that how
much the estimated material can be used in production, comparison in difference between
standard and actual material used it called material variance and changes in estimated and actual
price is called material price variance.
Particulars Formula X Y
Actual sales volume 850 750
Standard Price 2.5 2.5
Increased Price or
revised price 3.7 3.7
Material Price planning
variance
(standard price- Revised price) *
Actual usage -1020 -900
Material price operational variance:
Material price operational variance is distinguished between the actual price of operation
and the estimated operation price of material. Analysis of this variance helps the manager to
control and reduce the irrelevant cost.
Secure Best Marks with AI Grader
Need help grading? Try our AI Grader for instant feedback on your assignments.
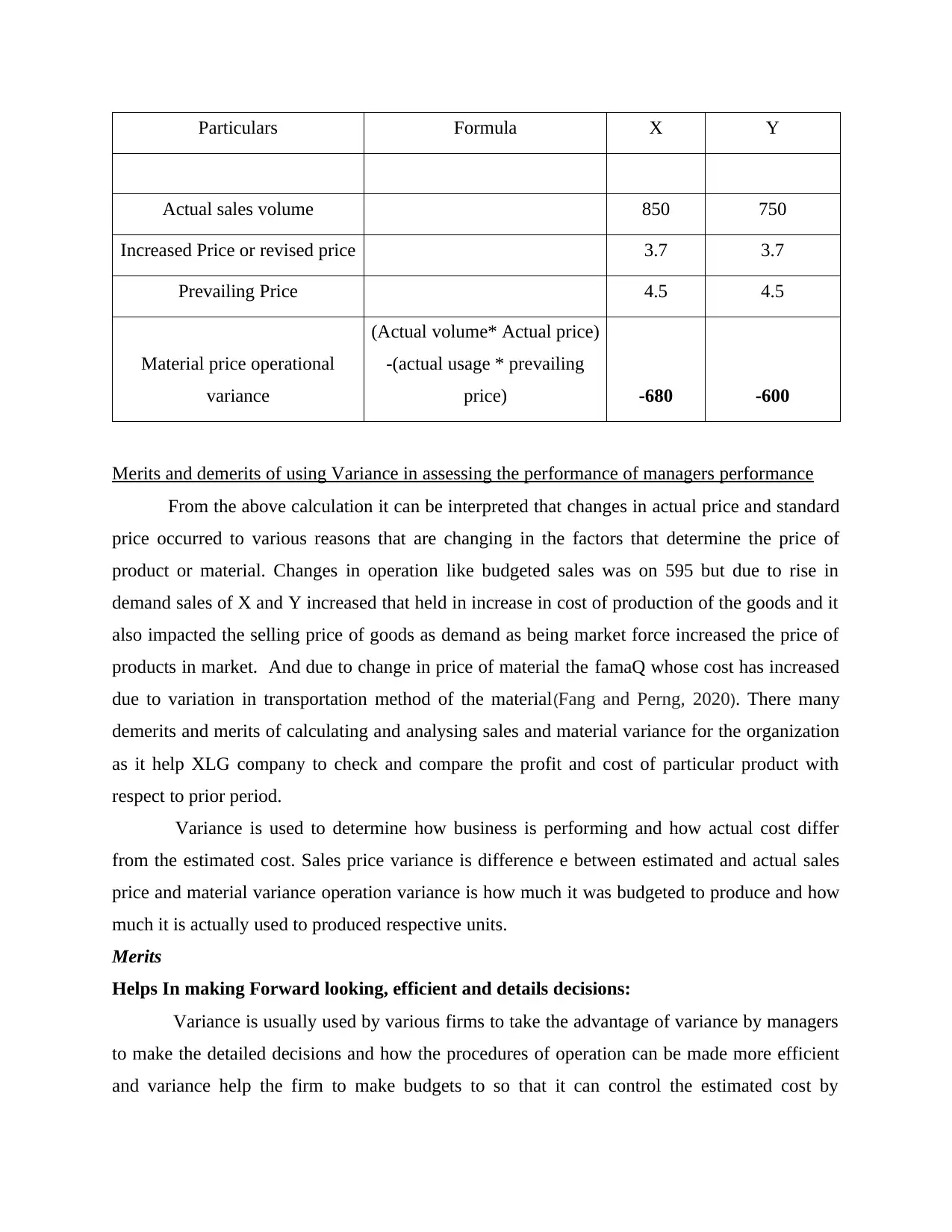
Particulars Formula X Y
Actual sales volume 850 750
Increased Price or revised price 3.7 3.7
Prevailing Price 4.5 4.5
Material price operational
variance
(Actual volume* Actual price)
-(actual usage * prevailing
price) -680 -600
Merits and demerits of using Variance in assessing the performance of managers performance
From the above calculation it can be interpreted that changes in actual price and standard
price occurred to various reasons that are changing in the factors that determine the price of
product or material. Changes in operation like budgeted sales was on 595 but due to rise in
demand sales of X and Y increased that held in increase in cost of production of the goods and it
also impacted the selling price of goods as demand as being market force increased the price of
products in market. And due to change in price of material the famaQ whose cost has increased
due to variation in transportation method of the material(Fang and Perng, 2020). There many
demerits and merits of calculating and analysing sales and material variance for the organization
as it help XLG company to check and compare the profit and cost of particular product with
respect to prior period.
Variance is used to determine how business is performing and how actual cost differ
from the estimated cost. Sales price variance is difference e between estimated and actual sales
price and material variance operation variance is how much it was budgeted to produce and how
much it is actually used to produced respective units.
Merits
Helps In making Forward looking, efficient and details decisions:
Variance is usually used by various firms to take the advantage of variance by managers
to make the detailed decisions and how the procedures of operation can be made more efficient
and variance help the firm to make budgets to so that it can control the estimated cost by
Actual sales volume 850 750
Increased Price or revised price 3.7 3.7
Prevailing Price 4.5 4.5
Material price operational
variance
(Actual volume* Actual price)
-(actual usage * prevailing
price) -680 -600
Merits and demerits of using Variance in assessing the performance of managers performance
From the above calculation it can be interpreted that changes in actual price and standard
price occurred to various reasons that are changing in the factors that determine the price of
product or material. Changes in operation like budgeted sales was on 595 but due to rise in
demand sales of X and Y increased that held in increase in cost of production of the goods and it
also impacted the selling price of goods as demand as being market force increased the price of
products in market. And due to change in price of material the famaQ whose cost has increased
due to variation in transportation method of the material(Fang and Perng, 2020). There many
demerits and merits of calculating and analysing sales and material variance for the organization
as it help XLG company to check and compare the profit and cost of particular product with
respect to prior period.
Variance is used to determine how business is performing and how actual cost differ
from the estimated cost. Sales price variance is difference e between estimated and actual sales
price and material variance operation variance is how much it was budgeted to produce and how
much it is actually used to produced respective units.
Merits
Helps In making Forward looking, efficient and details decisions:
Variance is usually used by various firms to take the advantage of variance by managers
to make the detailed decisions and how the procedures of operation can be made more efficient
and variance help the firm to make budgets to so that it can control the estimated cost by
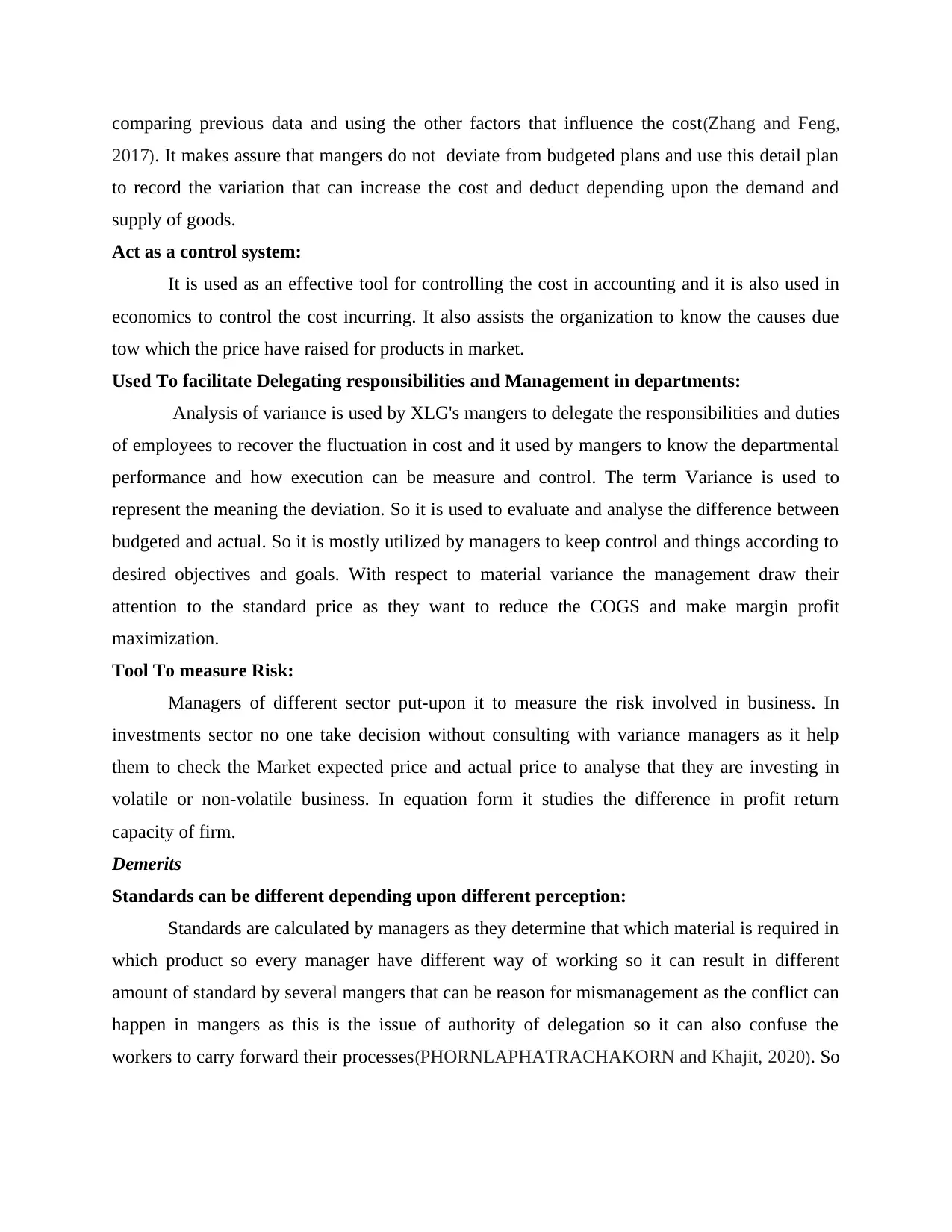
comparing previous data and using the other factors that influence the cost(Zhang and Feng,
2017). It makes assure that mangers do not deviate from budgeted plans and use this detail plan
to record the variation that can increase the cost and deduct depending upon the demand and
supply of goods.
Act as a control system:
It is used as an effective tool for controlling the cost in accounting and it is also used in
economics to control the cost incurring. It also assists the organization to know the causes due
tow which the price have raised for products in market.
Used To facilitate Delegating responsibilities and Management in departments:
Analysis of variance is used by XLG's mangers to delegate the responsibilities and duties
of employees to recover the fluctuation in cost and it used by mangers to know the departmental
performance and how execution can be measure and control. The term Variance is used to
represent the meaning the deviation. So it is used to evaluate and analyse the difference between
budgeted and actual. So it is mostly utilized by managers to keep control and things according to
desired objectives and goals. With respect to material variance the management draw their
attention to the standard price as they want to reduce the COGS and make margin profit
maximization.
Tool To measure Risk:
Managers of different sector put-upon it to measure the risk involved in business. In
investments sector no one take decision without consulting with variance managers as it help
them to check the Market expected price and actual price to analyse that they are investing in
volatile or non-volatile business. In equation form it studies the difference in profit return
capacity of firm.
Demerits
Standards can be different depending upon different perception:
Standards are calculated by managers as they determine that which material is required in
which product so every manager have different way of working so it can result in different
amount of standard by several mangers that can be reason for mismanagement as the conflict can
happen in mangers as this is the issue of authority of delegation so it can also confuse the
workers to carry forward their processes(PHORNLAPHATRACHAKORN and Khajit, 2020). So
2017). It makes assure that mangers do not deviate from budgeted plans and use this detail plan
to record the variation that can increase the cost and deduct depending upon the demand and
supply of goods.
Act as a control system:
It is used as an effective tool for controlling the cost in accounting and it is also used in
economics to control the cost incurring. It also assists the organization to know the causes due
tow which the price have raised for products in market.
Used To facilitate Delegating responsibilities and Management in departments:
Analysis of variance is used by XLG's mangers to delegate the responsibilities and duties
of employees to recover the fluctuation in cost and it used by mangers to know the departmental
performance and how execution can be measure and control. The term Variance is used to
represent the meaning the deviation. So it is used to evaluate and analyse the difference between
budgeted and actual. So it is mostly utilized by managers to keep control and things according to
desired objectives and goals. With respect to material variance the management draw their
attention to the standard price as they want to reduce the COGS and make margin profit
maximization.
Tool To measure Risk:
Managers of different sector put-upon it to measure the risk involved in business. In
investments sector no one take decision without consulting with variance managers as it help
them to check the Market expected price and actual price to analyse that they are investing in
volatile or non-volatile business. In equation form it studies the difference in profit return
capacity of firm.
Demerits
Standards can be different depending upon different perception:
Standards are calculated by managers as they determine that which material is required in
which product so every manager have different way of working so it can result in different
amount of standard by several mangers that can be reason for mismanagement as the conflict can
happen in mangers as this is the issue of authority of delegation so it can also confuse the
workers to carry forward their processes(PHORNLAPHATRACHAKORN and Khajit, 2020). So
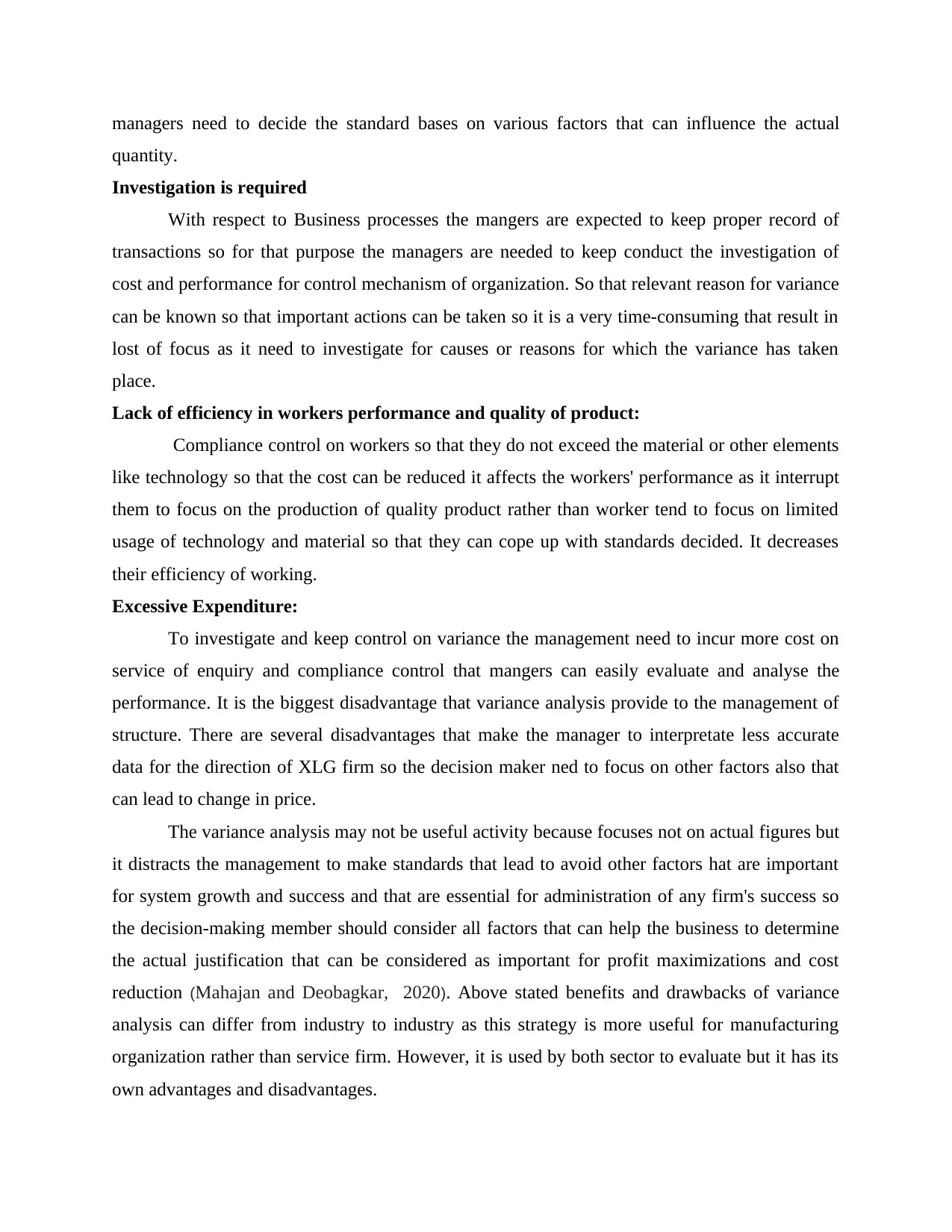
managers need to decide the standard bases on various factors that can influence the actual
quantity.
Investigation is required
With respect to Business processes the mangers are expected to keep proper record of
transactions so for that purpose the managers are needed to keep conduct the investigation of
cost and performance for control mechanism of organization. So that relevant reason for variance
can be known so that important actions can be taken so it is a very time-consuming that result in
lost of focus as it need to investigate for causes or reasons for which the variance has taken
place.
Lack of efficiency in workers performance and quality of product:
Compliance control on workers so that they do not exceed the material or other elements
like technology so that the cost can be reduced it affects the workers' performance as it interrupt
them to focus on the production of quality product rather than worker tend to focus on limited
usage of technology and material so that they can cope up with standards decided. It decreases
their efficiency of working.
Excessive Expenditure:
To investigate and keep control on variance the management need to incur more cost on
service of enquiry and compliance control that mangers can easily evaluate and analyse the
performance. It is the biggest disadvantage that variance analysis provide to the management of
structure. There are several disadvantages that make the manager to interpretate less accurate
data for the direction of XLG firm so the decision maker ned to focus on other factors also that
can lead to change in price.
The variance analysis may not be useful activity because focuses not on actual figures but
it distracts the management to make standards that lead to avoid other factors hat are important
for system growth and success and that are essential for administration of any firm's success so
the decision-making member should consider all factors that can help the business to determine
the actual justification that can be considered as important for profit maximizations and cost
reduction (Mahajan and Deobagkar, 2020). Above stated benefits and drawbacks of variance
analysis can differ from industry to industry as this strategy is more useful for manufacturing
organization rather than service firm. However, it is used by both sector to evaluate but it has its
own advantages and disadvantages.
quantity.
Investigation is required
With respect to Business processes the mangers are expected to keep proper record of
transactions so for that purpose the managers are needed to keep conduct the investigation of
cost and performance for control mechanism of organization. So that relevant reason for variance
can be known so that important actions can be taken so it is a very time-consuming that result in
lost of focus as it need to investigate for causes or reasons for which the variance has taken
place.
Lack of efficiency in workers performance and quality of product:
Compliance control on workers so that they do not exceed the material or other elements
like technology so that the cost can be reduced it affects the workers' performance as it interrupt
them to focus on the production of quality product rather than worker tend to focus on limited
usage of technology and material so that they can cope up with standards decided. It decreases
their efficiency of working.
Excessive Expenditure:
To investigate and keep control on variance the management need to incur more cost on
service of enquiry and compliance control that mangers can easily evaluate and analyse the
performance. It is the biggest disadvantage that variance analysis provide to the management of
structure. There are several disadvantages that make the manager to interpretate less accurate
data for the direction of XLG firm so the decision maker ned to focus on other factors also that
can lead to change in price.
The variance analysis may not be useful activity because focuses not on actual figures but
it distracts the management to make standards that lead to avoid other factors hat are important
for system growth and success and that are essential for administration of any firm's success so
the decision-making member should consider all factors that can help the business to determine
the actual justification that can be considered as important for profit maximizations and cost
reduction (Mahajan and Deobagkar, 2020). Above stated benefits and drawbacks of variance
analysis can differ from industry to industry as this strategy is more useful for manufacturing
organization rather than service firm. However, it is used by both sector to evaluate but it has its
own advantages and disadvantages.
Paraphrase This Document
Need a fresh take? Get an instant paraphrase of this document with our AI Paraphraser
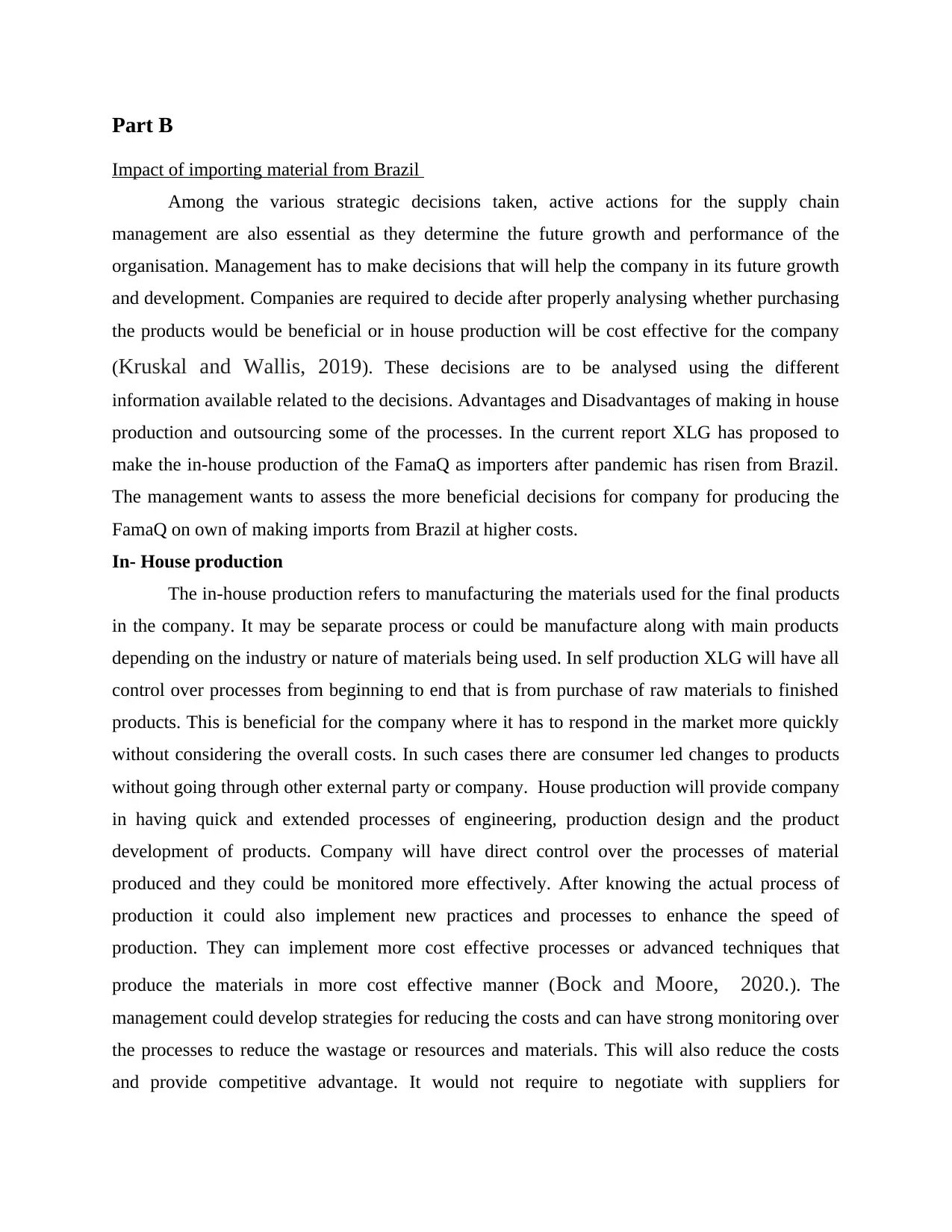
Part B
Impact of importing material from Brazil
Among the various strategic decisions taken, active actions for the supply chain
management are also essential as they determine the future growth and performance of the
organisation. Management has to make decisions that will help the company in its future growth
and development. Companies are required to decide after properly analysing whether purchasing
the products would be beneficial or in house production will be cost effective for the company
(Kruskal and Wallis, 2019). These decisions are to be analysed using the different
information available related to the decisions. Advantages and Disadvantages of making in house
production and outsourcing some of the processes. In the current report XLG has proposed to
make the in-house production of the FamaQ as importers after pandemic has risen from Brazil.
The management wants to assess the more beneficial decisions for company for producing the
FamaQ on own of making imports from Brazil at higher costs.
In- House production
The in-house production refers to manufacturing the materials used for the final products
in the company. It may be separate process or could be manufacture along with main products
depending on the industry or nature of materials being used. In self production XLG will have all
control over processes from beginning to end that is from purchase of raw materials to finished
products. This is beneficial for the company where it has to respond in the market more quickly
without considering the overall costs. In such cases there are consumer led changes to products
without going through other external party or company. House production will provide company
in having quick and extended processes of engineering, production design and the product
development of products. Company will have direct control over the processes of material
produced and they could be monitored more effectively. After knowing the actual process of
production it could also implement new practices and processes to enhance the speed of
production. They can implement more cost effective processes or advanced techniques that
produce the materials in more cost effective manner (Bock and Moore, 2020.). The
management could develop strategies for reducing the costs and can have strong monitoring over
the processes to reduce the wastage or resources and materials. This will also reduce the costs
and provide competitive advantage. It would not require to negotiate with suppliers for
Impact of importing material from Brazil
Among the various strategic decisions taken, active actions for the supply chain
management are also essential as they determine the future growth and performance of the
organisation. Management has to make decisions that will help the company in its future growth
and development. Companies are required to decide after properly analysing whether purchasing
the products would be beneficial or in house production will be cost effective for the company
(Kruskal and Wallis, 2019). These decisions are to be analysed using the different
information available related to the decisions. Advantages and Disadvantages of making in house
production and outsourcing some of the processes. In the current report XLG has proposed to
make the in-house production of the FamaQ as importers after pandemic has risen from Brazil.
The management wants to assess the more beneficial decisions for company for producing the
FamaQ on own of making imports from Brazil at higher costs.
In- House production
The in-house production refers to manufacturing the materials used for the final products
in the company. It may be separate process or could be manufacture along with main products
depending on the industry or nature of materials being used. In self production XLG will have all
control over processes from beginning to end that is from purchase of raw materials to finished
products. This is beneficial for the company where it has to respond in the market more quickly
without considering the overall costs. In such cases there are consumer led changes to products
without going through other external party or company. House production will provide company
in having quick and extended processes of engineering, production design and the product
development of products. Company will have direct control over the processes of material
produced and they could be monitored more effectively. After knowing the actual process of
production it could also implement new practices and processes to enhance the speed of
production. They can implement more cost effective processes or advanced techniques that
produce the materials in more cost effective manner (Bock and Moore, 2020.). The
management could develop strategies for reducing the costs and can have strong monitoring over
the processes to reduce the wastage or resources and materials. This will also reduce the costs
and provide competitive advantage. It would not require to negotiate with suppliers for
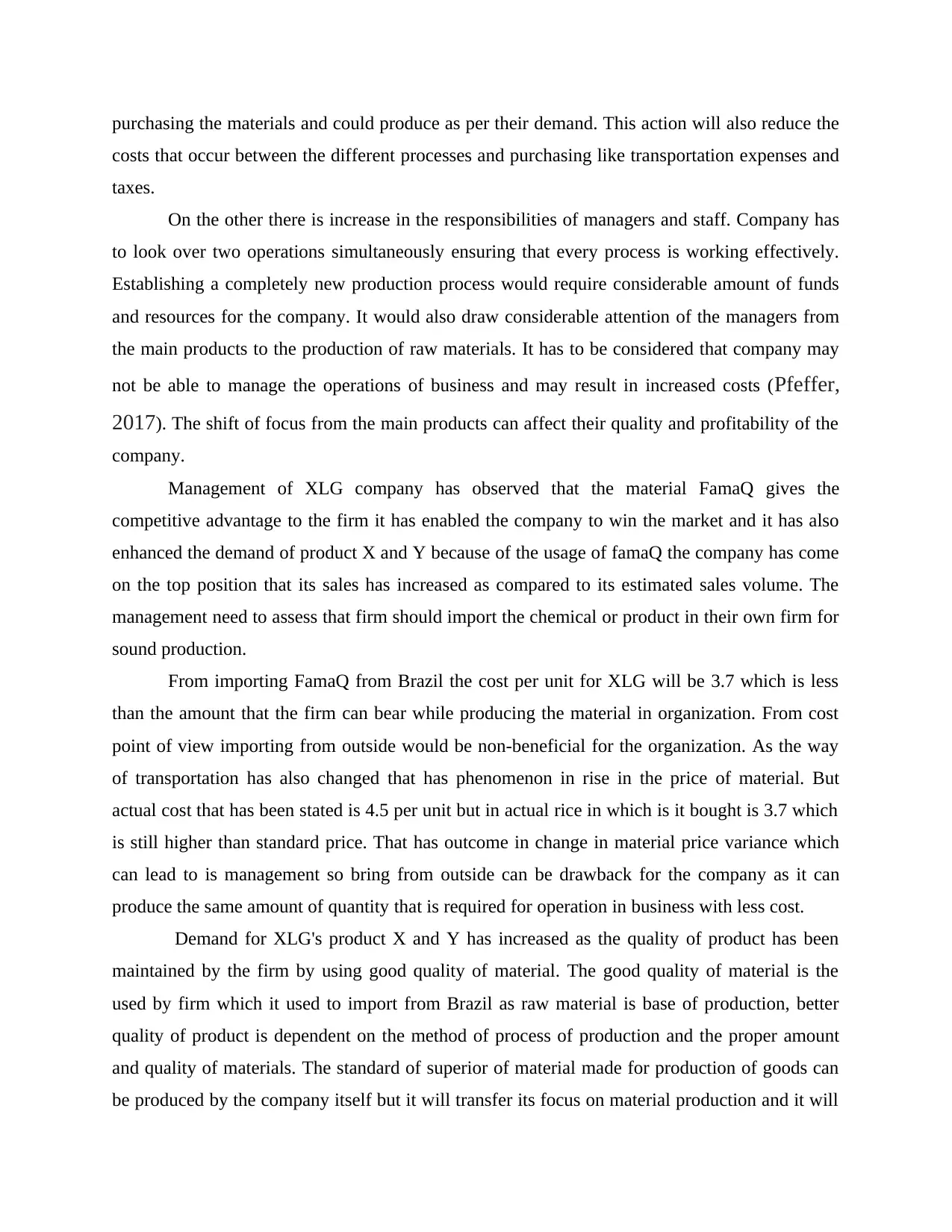
purchasing the materials and could produce as per their demand. This action will also reduce the
costs that occur between the different processes and purchasing like transportation expenses and
taxes.
On the other there is increase in the responsibilities of managers and staff. Company has
to look over two operations simultaneously ensuring that every process is working effectively.
Establishing a completely new production process would require considerable amount of funds
and resources for the company. It would also draw considerable attention of the managers from
the main products to the production of raw materials. It has to be considered that company may
not be able to manage the operations of business and may result in increased costs (Pfeffer,
2017). The shift of focus from the main products can affect their quality and profitability of the
company.
Management of XLG company has observed that the material FamaQ gives the
competitive advantage to the firm it has enabled the company to win the market and it has also
enhanced the demand of product X and Y because of the usage of famaQ the company has come
on the top position that its sales has increased as compared to its estimated sales volume. The
management need to assess that firm should import the chemical or product in their own firm for
sound production.
From importing FamaQ from Brazil the cost per unit for XLG will be 3.7 which is less
than the amount that the firm can bear while producing the material in organization. From cost
point of view importing from outside would be non-beneficial for the organization. As the way
of transportation has also changed that has phenomenon in rise in the price of material. But
actual cost that has been stated is 4.5 per unit but in actual rice in which is it bought is 3.7 which
is still higher than standard price. That has outcome in change in material price variance which
can lead to is management so bring from outside can be drawback for the company as it can
produce the same amount of quantity that is required for operation in business with less cost.
Demand for XLG's product X and Y has increased as the quality of product has been
maintained by the firm by using good quality of material. The good quality of material is the
used by firm which it used to import from Brazil as raw material is base of production, better
quality of product is dependent on the method of process of production and the proper amount
and quality of materials. The standard of superior of material made for production of goods can
be produced by the company itself but it will transfer its focus on material production and it will
costs that occur between the different processes and purchasing like transportation expenses and
taxes.
On the other there is increase in the responsibilities of managers and staff. Company has
to look over two operations simultaneously ensuring that every process is working effectively.
Establishing a completely new production process would require considerable amount of funds
and resources for the company. It would also draw considerable attention of the managers from
the main products to the production of raw materials. It has to be considered that company may
not be able to manage the operations of business and may result in increased costs (Pfeffer,
2017). The shift of focus from the main products can affect their quality and profitability of the
company.
Management of XLG company has observed that the material FamaQ gives the
competitive advantage to the firm it has enabled the company to win the market and it has also
enhanced the demand of product X and Y because of the usage of famaQ the company has come
on the top position that its sales has increased as compared to its estimated sales volume. The
management need to assess that firm should import the chemical or product in their own firm for
sound production.
From importing FamaQ from Brazil the cost per unit for XLG will be 3.7 which is less
than the amount that the firm can bear while producing the material in organization. From cost
point of view importing from outside would be non-beneficial for the organization. As the way
of transportation has also changed that has phenomenon in rise in the price of material. But
actual cost that has been stated is 4.5 per unit but in actual rice in which is it bought is 3.7 which
is still higher than standard price. That has outcome in change in material price variance which
can lead to is management so bring from outside can be drawback for the company as it can
produce the same amount of quantity that is required for operation in business with less cost.
Demand for XLG's product X and Y has increased as the quality of product has been
maintained by the firm by using good quality of material. The good quality of material is the
used by firm which it used to import from Brazil as raw material is base of production, better
quality of product is dependent on the method of process of production and the proper amount
and quality of materials. The standard of superior of material made for production of goods can
be produced by the company itself but it will transfer its focus on material production and it will
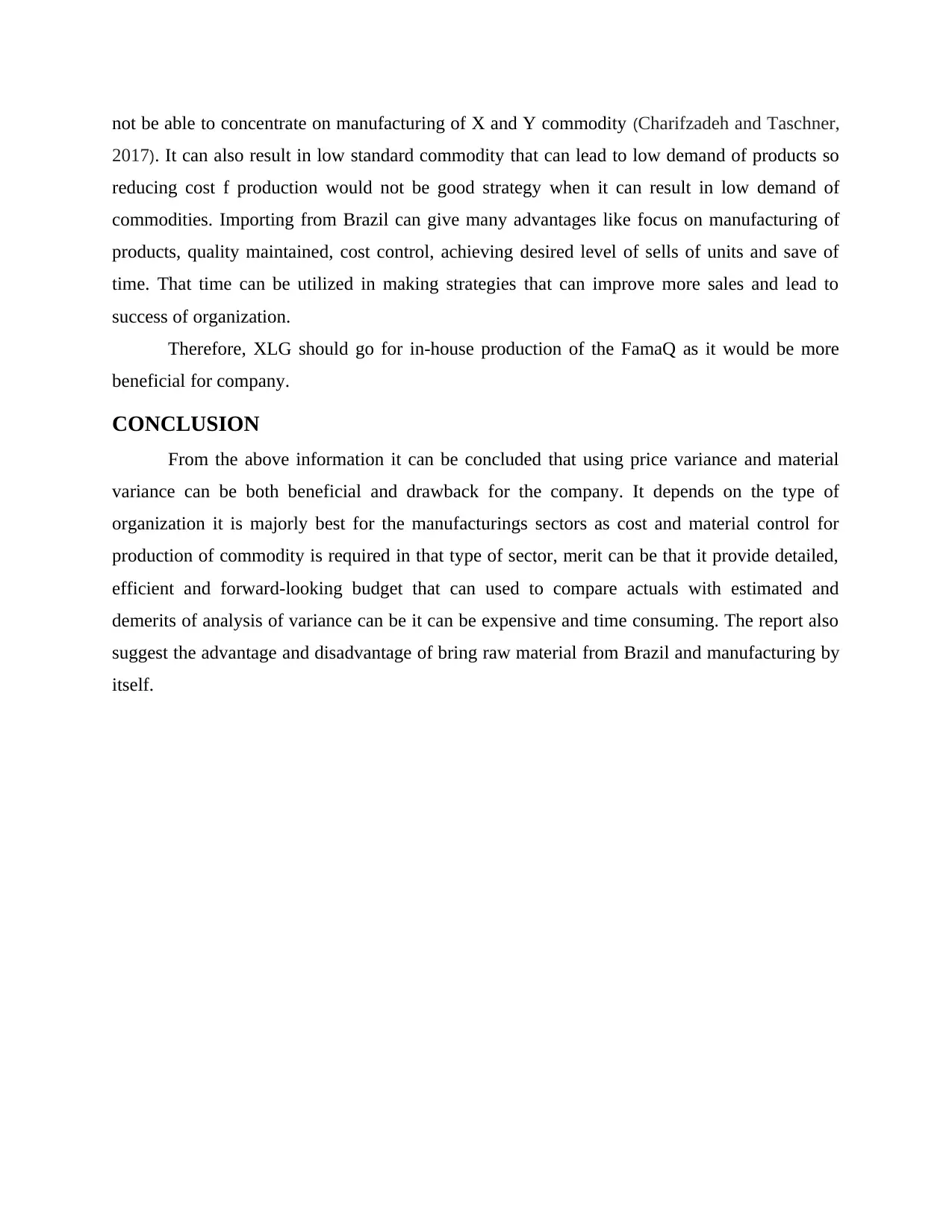
not be able to concentrate on manufacturing of X and Y commodity (Charifzadeh and Taschner,
2017). It can also result in low standard commodity that can lead to low demand of products so
reducing cost f production would not be good strategy when it can result in low demand of
commodities. Importing from Brazil can give many advantages like focus on manufacturing of
products, quality maintained, cost control, achieving desired level of sells of units and save of
time. That time can be utilized in making strategies that can improve more sales and lead to
success of organization.
Therefore, XLG should go for in-house production of the FamaQ as it would be more
beneficial for company.
CONCLUSION
From the above information it can be concluded that using price variance and material
variance can be both beneficial and drawback for the company. It depends on the type of
organization it is majorly best for the manufacturings sectors as cost and material control for
production of commodity is required in that type of sector, merit can be that it provide detailed,
efficient and forward-looking budget that can used to compare actuals with estimated and
demerits of analysis of variance can be it can be expensive and time consuming. The report also
suggest the advantage and disadvantage of bring raw material from Brazil and manufacturing by
itself.
2017). It can also result in low standard commodity that can lead to low demand of products so
reducing cost f production would not be good strategy when it can result in low demand of
commodities. Importing from Brazil can give many advantages like focus on manufacturing of
products, quality maintained, cost control, achieving desired level of sells of units and save of
time. That time can be utilized in making strategies that can improve more sales and lead to
success of organization.
Therefore, XLG should go for in-house production of the FamaQ as it would be more
beneficial for company.
CONCLUSION
From the above information it can be concluded that using price variance and material
variance can be both beneficial and drawback for the company. It depends on the type of
organization it is majorly best for the manufacturings sectors as cost and material control for
production of commodity is required in that type of sector, merit can be that it provide detailed,
efficient and forward-looking budget that can used to compare actuals with estimated and
demerits of analysis of variance can be it can be expensive and time consuming. The report also
suggest the advantage and disadvantage of bring raw material from Brazil and manufacturing by
itself.
Secure Best Marks with AI Grader
Need help grading? Try our AI Grader for instant feedback on your assignments.
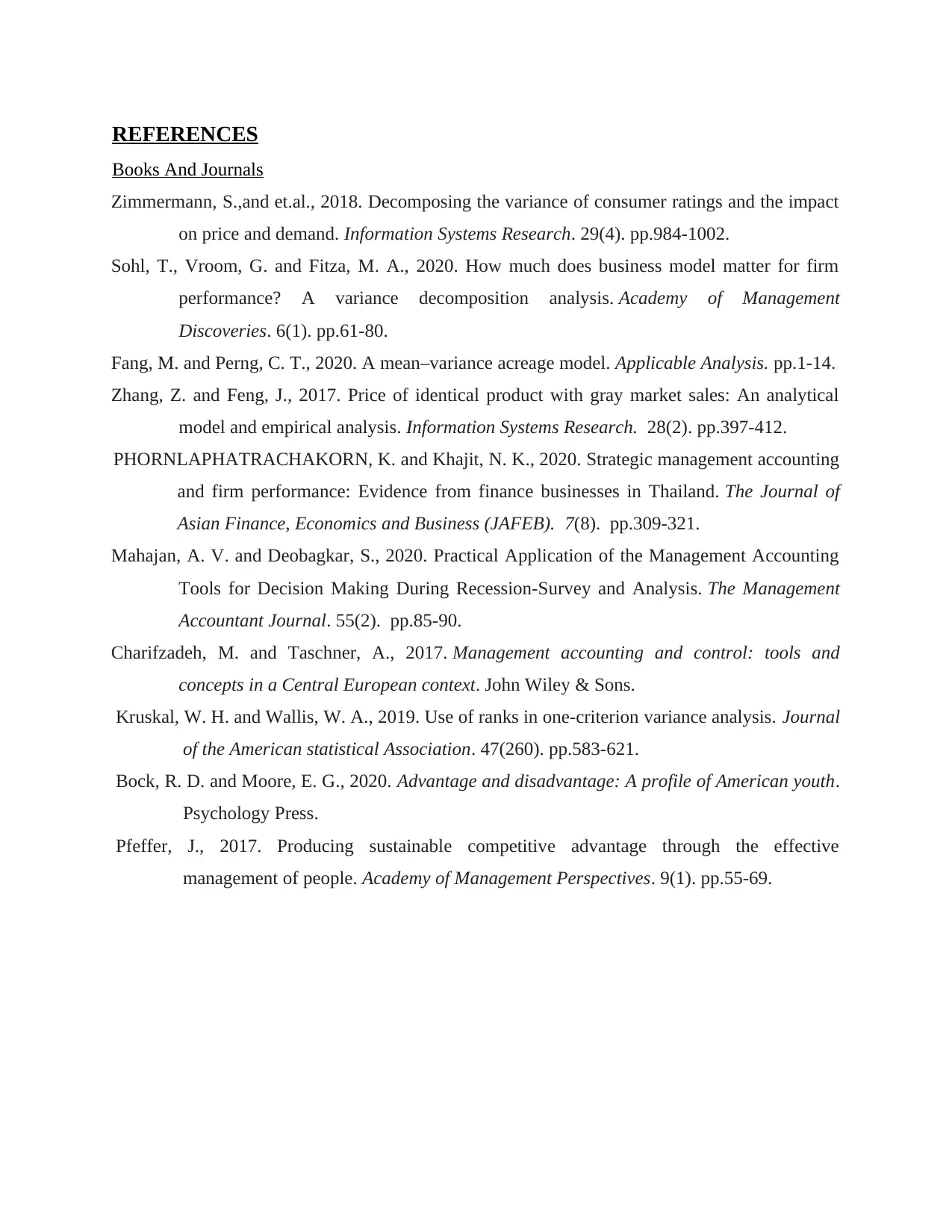
REFERENCES
Books And Journals
Zimmermann, S.,and et.al., 2018. Decomposing the variance of consumer ratings and the impact
on price and demand. Information Systems Research. 29(4). pp.984-1002.
Sohl, T., Vroom, G. and Fitza, M. A., 2020. How much does business model matter for firm
performance? A variance decomposition analysis. Academy of Management
Discoveries. 6(1). pp.61-80.
Fang, M. and Perng, C. T., 2020. A mean–variance acreage model. Applicable Analysis. pp.1-14.
Zhang, Z. and Feng, J., 2017. Price of identical product with gray market sales: An analytical
model and empirical analysis. Information Systems Research. 28(2). pp.397-412.
PHORNLAPHATRACHAKORN, K. and Khajit, N. K., 2020. Strategic management accounting
and firm performance: Evidence from finance businesses in Thailand. The Journal of
Asian Finance, Economics and Business (JAFEB). 7(8). pp.309-321.
Mahajan, A. V. and Deobagkar, S., 2020. Practical Application of the Management Accounting
Tools for Decision Making During Recession-Survey and Analysis. The Management
Accountant Journal. 55(2). pp.85-90.
Charifzadeh, M. and Taschner, A., 2017. Management accounting and control: tools and
concepts in a Central European context. John Wiley & Sons.
Kruskal, W. H. and Wallis, W. A., 2019. Use of ranks in one-criterion variance analysis. Journal
of the American statistical Association. 47(260). pp.583-621.
Bock, R. D. and Moore, E. G., 2020. Advantage and disadvantage: A profile of American youth.
Psychology Press.
Pfeffer, J., 2017. Producing sustainable competitive advantage through the effective
management of people. Academy of Management Perspectives. 9(1). pp.55-69.
Books And Journals
Zimmermann, S.,and et.al., 2018. Decomposing the variance of consumer ratings and the impact
on price and demand. Information Systems Research. 29(4). pp.984-1002.
Sohl, T., Vroom, G. and Fitza, M. A., 2020. How much does business model matter for firm
performance? A variance decomposition analysis. Academy of Management
Discoveries. 6(1). pp.61-80.
Fang, M. and Perng, C. T., 2020. A mean–variance acreage model. Applicable Analysis. pp.1-14.
Zhang, Z. and Feng, J., 2017. Price of identical product with gray market sales: An analytical
model and empirical analysis. Information Systems Research. 28(2). pp.397-412.
PHORNLAPHATRACHAKORN, K. and Khajit, N. K., 2020. Strategic management accounting
and firm performance: Evidence from finance businesses in Thailand. The Journal of
Asian Finance, Economics and Business (JAFEB). 7(8). pp.309-321.
Mahajan, A. V. and Deobagkar, S., 2020. Practical Application of the Management Accounting
Tools for Decision Making During Recession-Survey and Analysis. The Management
Accountant Journal. 55(2). pp.85-90.
Charifzadeh, M. and Taschner, A., 2017. Management accounting and control: tools and
concepts in a Central European context. John Wiley & Sons.
Kruskal, W. H. and Wallis, W. A., 2019. Use of ranks in one-criterion variance analysis. Journal
of the American statistical Association. 47(260). pp.583-621.
Bock, R. D. and Moore, E. G., 2020. Advantage and disadvantage: A profile of American youth.
Psychology Press.
Pfeffer, J., 2017. Producing sustainable competitive advantage through the effective
management of people. Academy of Management Perspectives. 9(1). pp.55-69.
1 out of 11
Related Documents

Your All-in-One AI-Powered Toolkit for Academic Success.
 +13062052269
info@desklib.com
Available 24*7 on WhatsApp / Email
Unlock your academic potential
© 2024  |  Zucol Services PVT LTD  |  All rights reserved.