Analysis of Costing Methods for Management Accounting (ACC200)
VerifiedAdded on 2022/08/27
|10
|2441
|33
Homework Assignment
AI Summary
This assignment analyzes management accounting principles, focusing on the application of traditional costing and activity-based costing (ABC) methods. The student calculates predetermined overhead rates, determines product costs and selling prices for Kona and Malaysian coffee using both methods, and conducts a comparative analysis highlighting the differences between the two costing systems. The assignment includes detailed calculations, cost allocations, and a discussion on the suitability of each method for different business scenarios, with recommendations for pricing structures. The student also provides a clear comparison between Traditional Costing Method and Activity Based Costing Method. The document includes references to support the analysis.
Contribute Materials
Your contribution can guide someone’s learning journey. Share your
documents today.
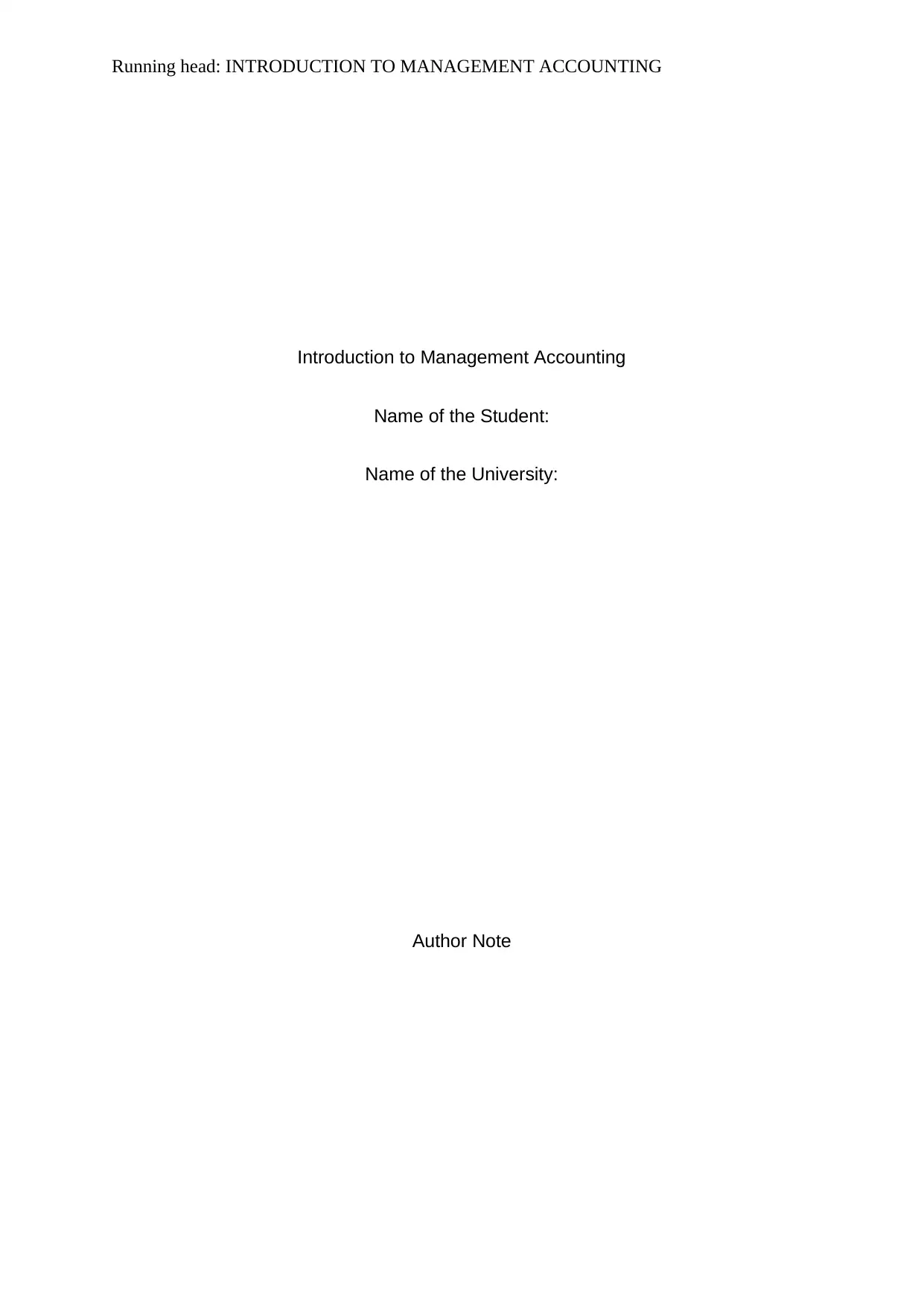
Running head: INTRODUCTION TO MANAGEMENT ACCOUNTING
Introduction to Management Accounting
Name of the Student:
Name of the University:
Author Note
Introduction to Management Accounting
Name of the Student:
Name of the University:
Author Note
Secure Best Marks with AI Grader
Need help grading? Try our AI Grader for instant feedback on your assignments.
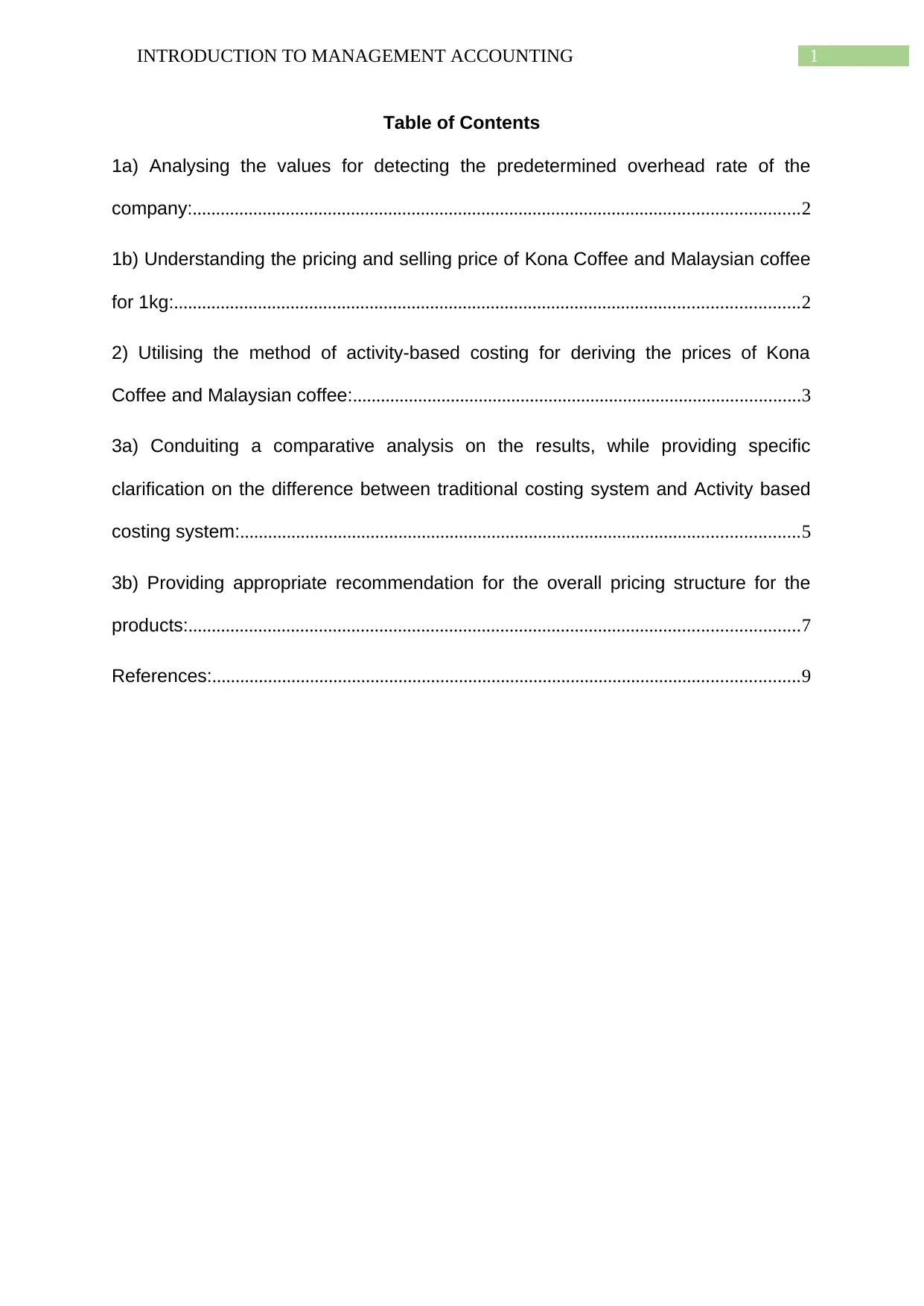
1INTRODUCTION TO MANAGEMENT ACCOUNTING
Table of Contents
1a) Analysing the values for detecting the predetermined overhead rate of the
company:..................................................................................................................................2
1b) Understanding the pricing and selling price of Kona Coffee and Malaysian coffee
for 1kg:......................................................................................................................................2
2) Utilising the method of activity-based costing for deriving the prices of Kona
Coffee and Malaysian coffee:................................................................................................3
3a) Conduiting a comparative analysis on the results, while providing specific
clarification on the difference between traditional costing system and Activity based
costing system:........................................................................................................................5
3b) Providing appropriate recommendation for the overall pricing structure for the
products:...................................................................................................................................7
References:..............................................................................................................................9
Table of Contents
1a) Analysing the values for detecting the predetermined overhead rate of the
company:..................................................................................................................................2
1b) Understanding the pricing and selling price of Kona Coffee and Malaysian coffee
for 1kg:......................................................................................................................................2
2) Utilising the method of activity-based costing for deriving the prices of Kona
Coffee and Malaysian coffee:................................................................................................3
3a) Conduiting a comparative analysis on the results, while providing specific
clarification on the difference between traditional costing system and Activity based
costing system:........................................................................................................................5
3b) Providing appropriate recommendation for the overall pricing structure for the
products:...................................................................................................................................7
References:..............................................................................................................................9
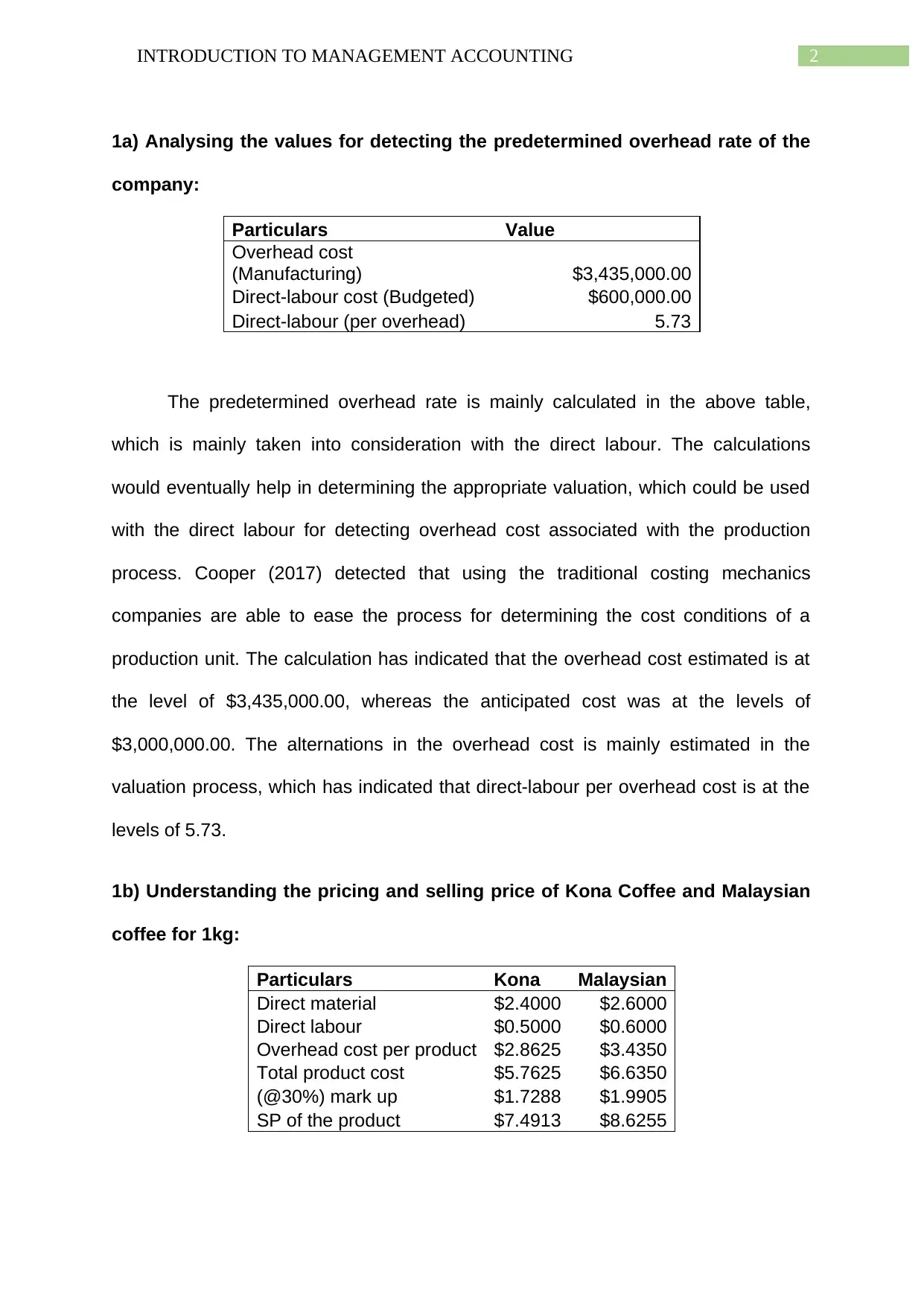
2INTRODUCTION TO MANAGEMENT ACCOUNTING
1a) Analysing the values for detecting the predetermined overhead rate of the
company:
Particulars Value
Overhead cost
(Manufacturing) $3,435,000.00
Direct-labour cost (Budgeted) $600,000.00
Direct-labour (per overhead) 5.73
The predetermined overhead rate is mainly calculated in the above table,
which is mainly taken into consideration with the direct labour. The calculations
would eventually help in determining the appropriate valuation, which could be used
with the direct labour for detecting overhead cost associated with the production
process. Cooper (2017) detected that using the traditional costing mechanics
companies are able to ease the process for determining the cost conditions of a
production unit. The calculation has indicated that the overhead cost estimated is at
the level of $3,435,000.00, whereas the anticipated cost was at the levels of
$3,000,000.00. The alternations in the overhead cost is mainly estimated in the
valuation process, which has indicated that direct-labour per overhead cost is at the
levels of 5.73.
1b) Understanding the pricing and selling price of Kona Coffee and Malaysian
coffee for 1kg:
Particulars Kona Malaysian
Direct material $2.4000 $2.6000
Direct labour $0.5000 $0.6000
Overhead cost per product $2.8625 $3.4350
Total product cost $5.7625 $6.6350
(@30%) mark up $1.7288 $1.9905
SP of the product $7.4913 $8.6255
1a) Analysing the values for detecting the predetermined overhead rate of the
company:
Particulars Value
Overhead cost
(Manufacturing) $3,435,000.00
Direct-labour cost (Budgeted) $600,000.00
Direct-labour (per overhead) 5.73
The predetermined overhead rate is mainly calculated in the above table,
which is mainly taken into consideration with the direct labour. The calculations
would eventually help in determining the appropriate valuation, which could be used
with the direct labour for detecting overhead cost associated with the production
process. Cooper (2017) detected that using the traditional costing mechanics
companies are able to ease the process for determining the cost conditions of a
production unit. The calculation has indicated that the overhead cost estimated is at
the level of $3,435,000.00, whereas the anticipated cost was at the levels of
$3,000,000.00. The alternations in the overhead cost is mainly estimated in the
valuation process, which has indicated that direct-labour per overhead cost is at the
levels of 5.73.
1b) Understanding the pricing and selling price of Kona Coffee and Malaysian
coffee for 1kg:
Particulars Kona Malaysian
Direct material $2.4000 $2.6000
Direct labour $0.5000 $0.6000
Overhead cost per product $2.8625 $3.4350
Total product cost $5.7625 $6.6350
(@30%) mark up $1.7288 $1.9905
SP of the product $7.4913 $8.6255
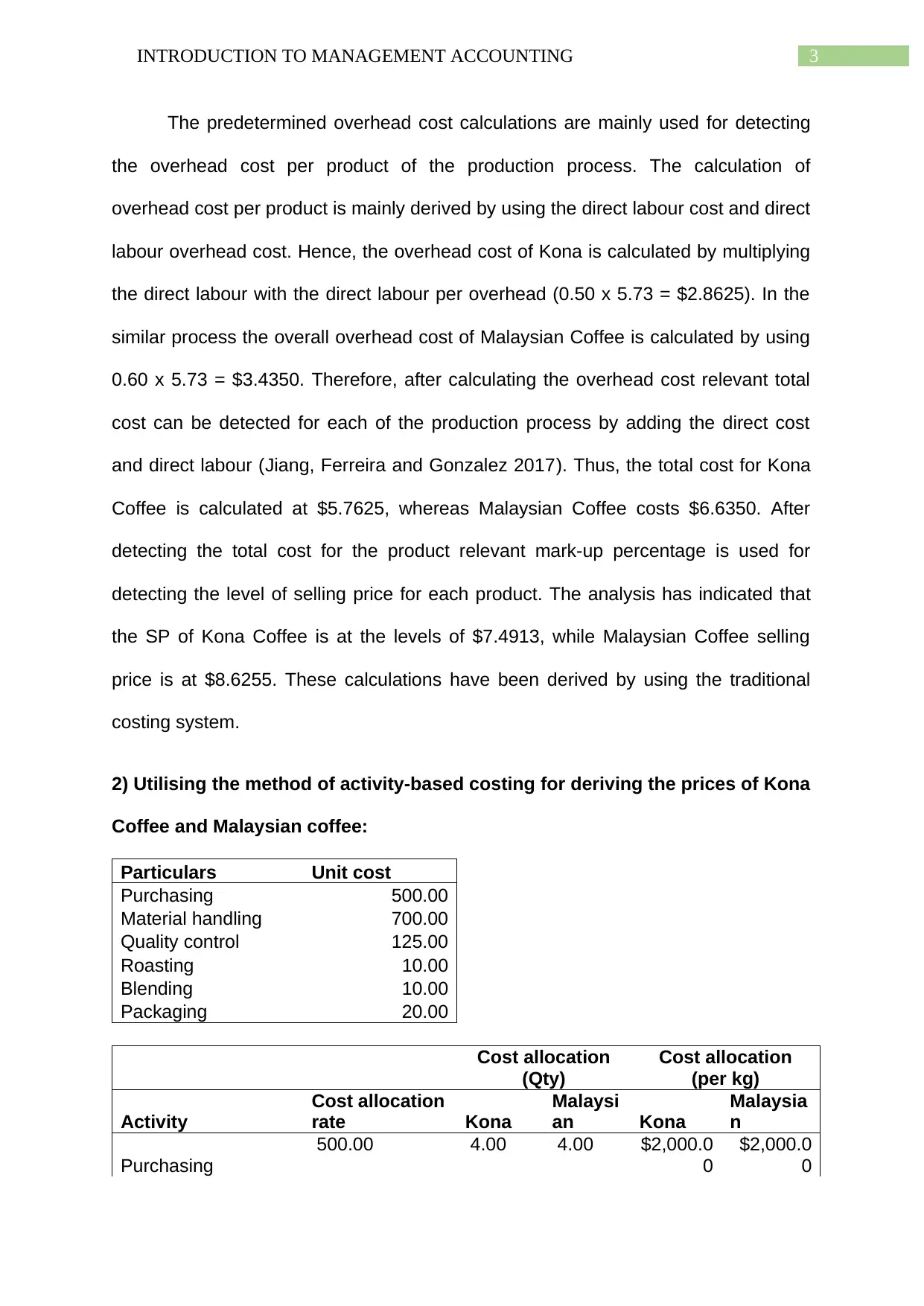
3INTRODUCTION TO MANAGEMENT ACCOUNTING
The predetermined overhead cost calculations are mainly used for detecting
the overhead cost per product of the production process. The calculation of
overhead cost per product is mainly derived by using the direct labour cost and direct
labour overhead cost. Hence, the overhead cost of Kona is calculated by multiplying
the direct labour with the direct labour per overhead (0.50 x 5.73 = $2.8625). In the
similar process the overall overhead cost of Malaysian Coffee is calculated by using
0.60 x 5.73 = $3.4350. Therefore, after calculating the overhead cost relevant total
cost can be detected for each of the production process by adding the direct cost
and direct labour (Jiang, Ferreira and Gonzalez 2017). Thus, the total cost for Kona
Coffee is calculated at $5.7625, whereas Malaysian Coffee costs $6.6350. After
detecting the total cost for the product relevant mark-up percentage is used for
detecting the level of selling price for each product. The analysis has indicated that
the SP of Kona Coffee is at the levels of $7.4913, while Malaysian Coffee selling
price is at $8.6255. These calculations have been derived by using the traditional
costing system.
2) Utilising the method of activity-based costing for deriving the prices of Kona
Coffee and Malaysian coffee:
Particulars Unit cost
Purchasing 500.00
Material handling 700.00
Quality control 125.00
Roasting 10.00
Blending 10.00
Packaging 20.00
Cost allocation
(Qty)
Cost allocation
(per kg)
Activity
Cost allocation
rate Kona
Malaysi
an Kona
Malaysia
n
Purchasing
500.00 4.00 4.00 $2,000.0
0
$2,000.0
0
The predetermined overhead cost calculations are mainly used for detecting
the overhead cost per product of the production process. The calculation of
overhead cost per product is mainly derived by using the direct labour cost and direct
labour overhead cost. Hence, the overhead cost of Kona is calculated by multiplying
the direct labour with the direct labour per overhead (0.50 x 5.73 = $2.8625). In the
similar process the overall overhead cost of Malaysian Coffee is calculated by using
0.60 x 5.73 = $3.4350. Therefore, after calculating the overhead cost relevant total
cost can be detected for each of the production process by adding the direct cost
and direct labour (Jiang, Ferreira and Gonzalez 2017). Thus, the total cost for Kona
Coffee is calculated at $5.7625, whereas Malaysian Coffee costs $6.6350. After
detecting the total cost for the product relevant mark-up percentage is used for
detecting the level of selling price for each product. The analysis has indicated that
the SP of Kona Coffee is at the levels of $7.4913, while Malaysian Coffee selling
price is at $8.6255. These calculations have been derived by using the traditional
costing system.
2) Utilising the method of activity-based costing for deriving the prices of Kona
Coffee and Malaysian coffee:
Particulars Unit cost
Purchasing 500.00
Material handling 700.00
Quality control 125.00
Roasting 10.00
Blending 10.00
Packaging 20.00
Cost allocation
(Qty)
Cost allocation
(per kg)
Activity
Cost allocation
rate Kona
Malaysi
an Kona
Malaysia
n
Purchasing
500.00 4.00 4.00 $2,000.0
0
$2,000.0
0
Secure Best Marks with AI Grader
Need help grading? Try our AI Grader for instant feedback on your assignments.
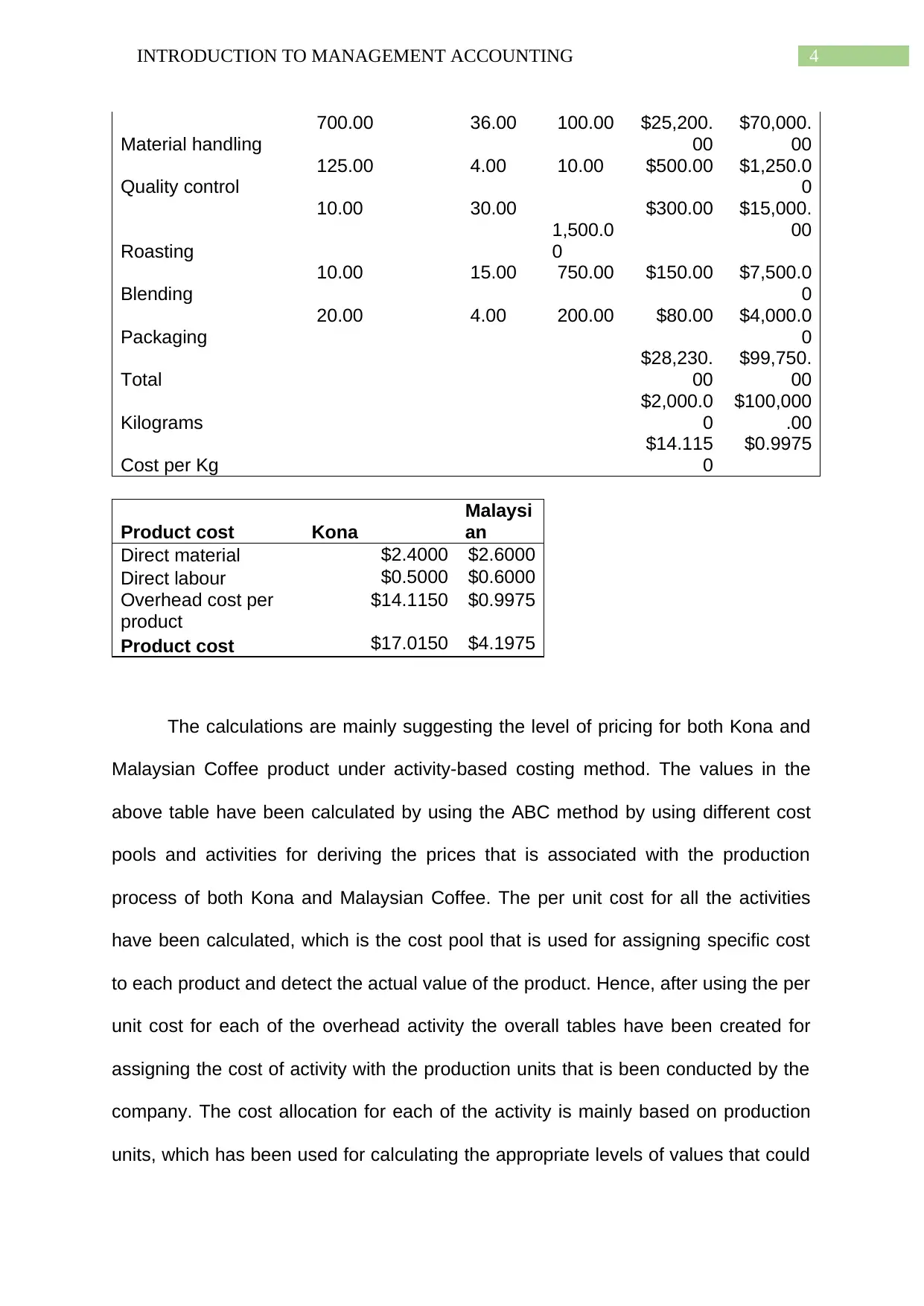
4INTRODUCTION TO MANAGEMENT ACCOUNTING
Material handling
700.00 36.00 100.00 $25,200.
00
$70,000.
00
Quality control
125.00 4.00 10.00 $500.00 $1,250.0
0
Roasting
10.00 30.00
1,500.0
0
$300.00 $15,000.
00
Blending
10.00 15.00 750.00 $150.00 $7,500.0
0
Packaging
20.00 4.00 200.00 $80.00 $4,000.0
0
Total
$28,230.
00
$99,750.
00
Kilograms
$2,000.0
0
$100,000
.00
Cost per Kg
$14.115
0
$0.9975
Product cost Kona
Malaysi
an
Direct material $2.4000 $2.6000
Direct labour $0.5000 $0.6000
Overhead cost per
product
$14.1150 $0.9975
Product cost $17.0150 $4.1975
The calculations are mainly suggesting the level of pricing for both Kona and
Malaysian Coffee product under activity-based costing method. The values in the
above table have been calculated by using the ABC method by using different cost
pools and activities for deriving the prices that is associated with the production
process of both Kona and Malaysian Coffee. The per unit cost for all the activities
have been calculated, which is the cost pool that is used for assigning specific cost
to each product and detect the actual value of the product. Hence, after using the per
unit cost for each of the overhead activity the overall tables have been created for
assigning the cost of activity with the production units that is been conducted by the
company. The cost allocation for each of the activity is mainly based on production
units, which has been used for calculating the appropriate levels of values that could
Material handling
700.00 36.00 100.00 $25,200.
00
$70,000.
00
Quality control
125.00 4.00 10.00 $500.00 $1,250.0
0
Roasting
10.00 30.00
1,500.0
0
$300.00 $15,000.
00
Blending
10.00 15.00 750.00 $150.00 $7,500.0
0
Packaging
20.00 4.00 200.00 $80.00 $4,000.0
0
Total
$28,230.
00
$99,750.
00
Kilograms
$2,000.0
0
$100,000
.00
Cost per Kg
$14.115
0
$0.9975
Product cost Kona
Malaysi
an
Direct material $2.4000 $2.6000
Direct labour $0.5000 $0.6000
Overhead cost per
product
$14.1150 $0.9975
Product cost $17.0150 $4.1975
The calculations are mainly suggesting the level of pricing for both Kona and
Malaysian Coffee product under activity-based costing method. The values in the
above table have been calculated by using the ABC method by using different cost
pools and activities for deriving the prices that is associated with the production
process of both Kona and Malaysian Coffee. The per unit cost for all the activities
have been calculated, which is the cost pool that is used for assigning specific cost
to each product and detect the actual value of the product. Hence, after using the per
unit cost for each of the overhead activity the overall tables have been created for
assigning the cost of activity with the production units that is been conducted by the
company. The cost allocation for each of the activity is mainly based on production
units, which has been used for calculating the appropriate levels of values that could
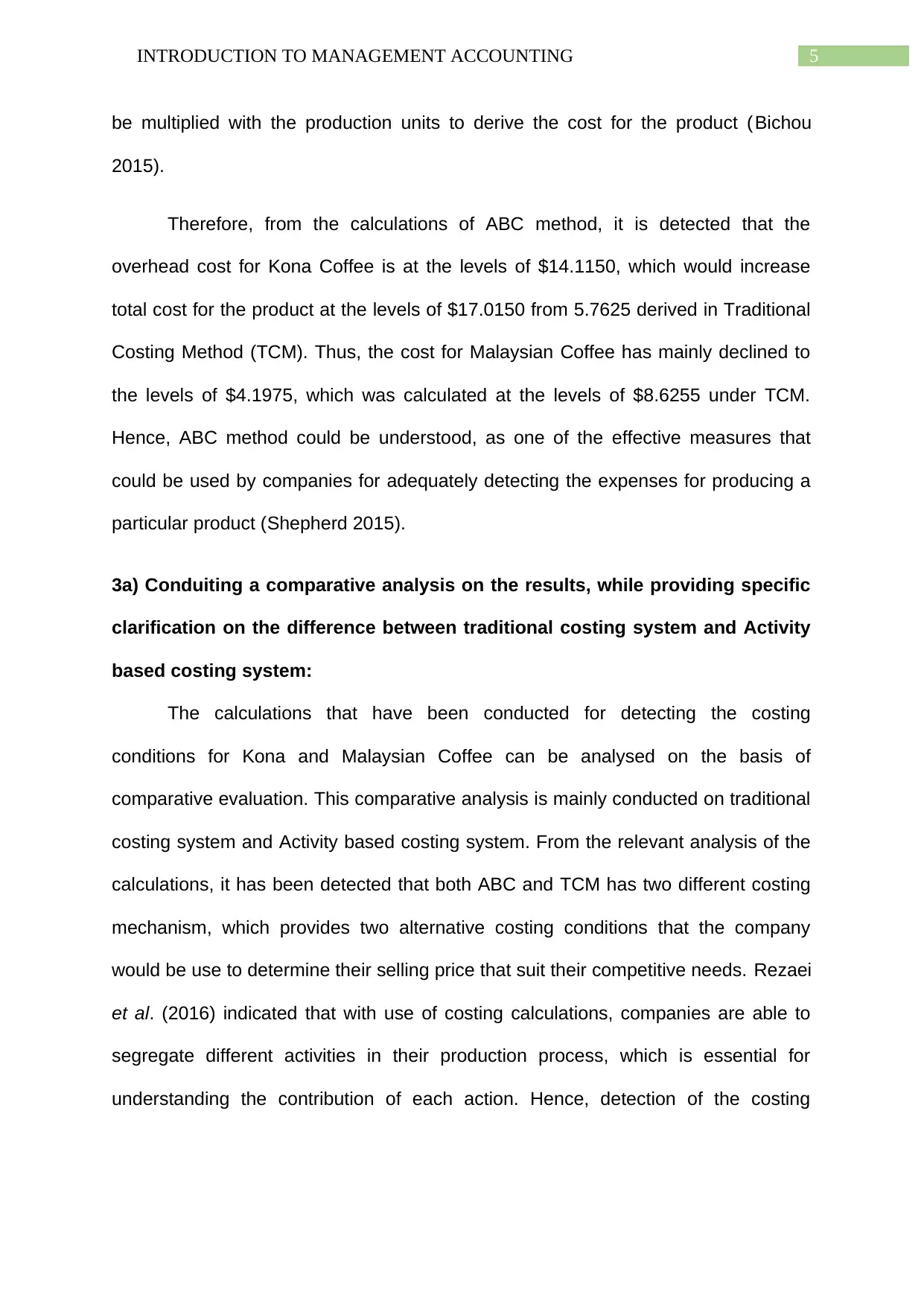
5INTRODUCTION TO MANAGEMENT ACCOUNTING
be multiplied with the production units to derive the cost for the product ( Bichou
2015).
Therefore, from the calculations of ABC method, it is detected that the
overhead cost for Kona Coffee is at the levels of $14.1150, which would increase
total cost for the product at the levels of $17.0150 from 5.7625 derived in Traditional
Costing Method (TCM). Thus, the cost for Malaysian Coffee has mainly declined to
the levels of $4.1975, which was calculated at the levels of $8.6255 under TCM.
Hence, ABC method could be understood, as one of the effective measures that
could be used by companies for adequately detecting the expenses for producing a
particular product (Shepherd 2015).
3a) Conduiting a comparative analysis on the results, while providing specific
clarification on the difference between traditional costing system and Activity
based costing system:
The calculations that have been conducted for detecting the costing
conditions for Kona and Malaysian Coffee can be analysed on the basis of
comparative evaluation. This comparative analysis is mainly conducted on traditional
costing system and Activity based costing system. From the relevant analysis of the
calculations, it has been detected that both ABC and TCM has two different costing
mechanism, which provides two alternative costing conditions that the company
would be use to determine their selling price that suit their competitive needs. Rezaei
et al. (2016) indicated that with use of costing calculations, companies are able to
segregate different activities in their production process, which is essential for
understanding the contribution of each action. Hence, detection of the costing
be multiplied with the production units to derive the cost for the product ( Bichou
2015).
Therefore, from the calculations of ABC method, it is detected that the
overhead cost for Kona Coffee is at the levels of $14.1150, which would increase
total cost for the product at the levels of $17.0150 from 5.7625 derived in Traditional
Costing Method (TCM). Thus, the cost for Malaysian Coffee has mainly declined to
the levels of $4.1975, which was calculated at the levels of $8.6255 under TCM.
Hence, ABC method could be understood, as one of the effective measures that
could be used by companies for adequately detecting the expenses for producing a
particular product (Shepherd 2015).
3a) Conduiting a comparative analysis on the results, while providing specific
clarification on the difference between traditional costing system and Activity
based costing system:
The calculations that have been conducted for detecting the costing
conditions for Kona and Malaysian Coffee can be analysed on the basis of
comparative evaluation. This comparative analysis is mainly conducted on traditional
costing system and Activity based costing system. From the relevant analysis of the
calculations, it has been detected that both ABC and TCM has two different costing
mechanism, which provides two alternative costing conditions that the company
would be use to determine their selling price that suit their competitive needs. Rezaei
et al. (2016) indicated that with use of costing calculations, companies are able to
segregate different activities in their production process, which is essential for
understanding the contribution of each action. Hence, detection of the costing
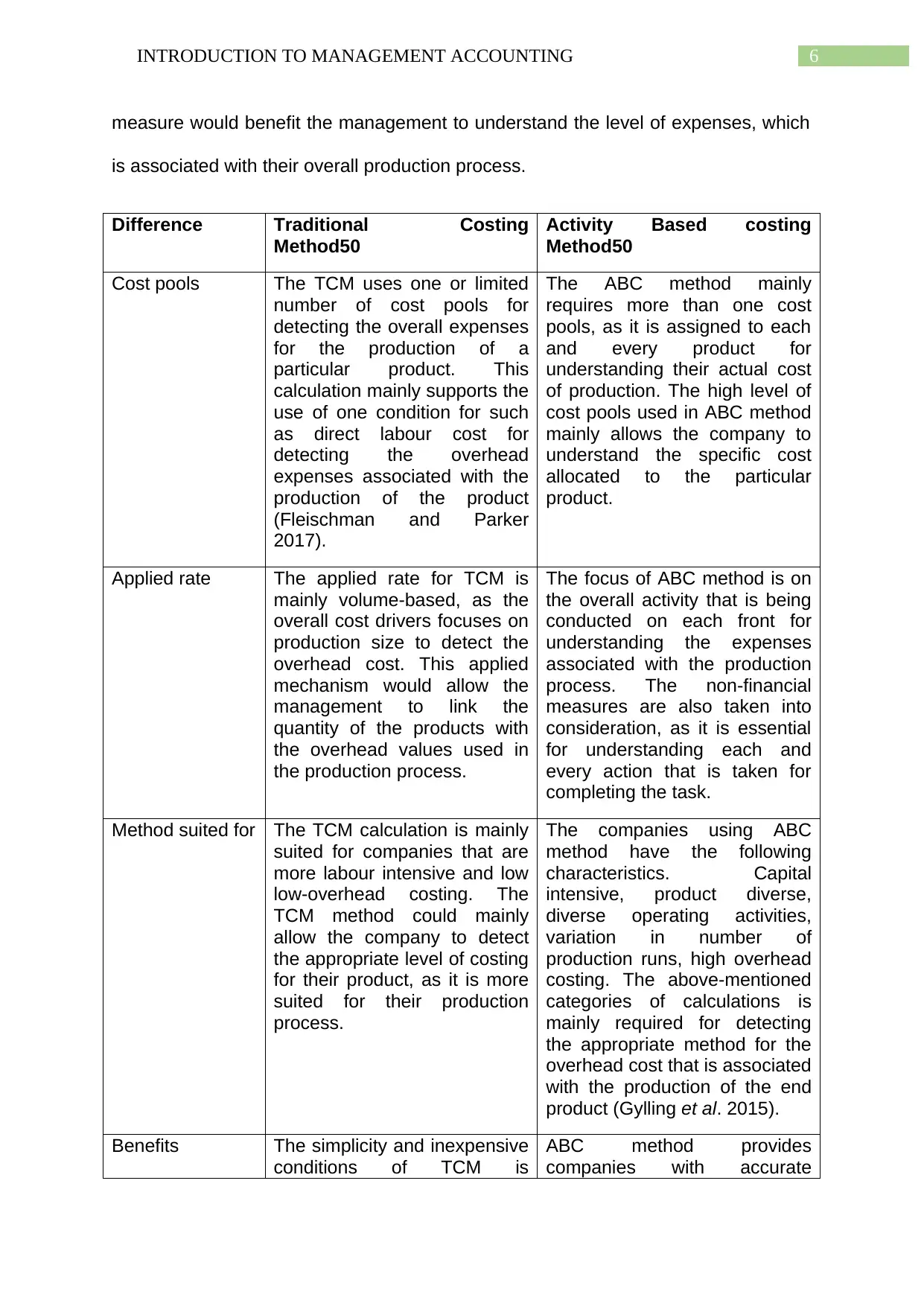
6INTRODUCTION TO MANAGEMENT ACCOUNTING
measure would benefit the management to understand the level of expenses, which
is associated with their overall production process.
Difference Traditional Costing
Method50
Activity Based costing
Method50
Cost pools The TCM uses one or limited
number of cost pools for
detecting the overall expenses
for the production of a
particular product. This
calculation mainly supports the
use of one condition for such
as direct labour cost for
detecting the overhead
expenses associated with the
production of the product
(Fleischman and Parker
2017).
The ABC method mainly
requires more than one cost
pools, as it is assigned to each
and every product for
understanding their actual cost
of production. The high level of
cost pools used in ABC method
mainly allows the company to
understand the specific cost
allocated to the particular
product.
Applied rate The applied rate for TCM is
mainly volume-based, as the
overall cost drivers focuses on
production size to detect the
overhead cost. This applied
mechanism would allow the
management to link the
quantity of the products with
the overhead values used in
the production process.
The focus of ABC method is on
the overall activity that is being
conducted on each front for
understanding the expenses
associated with the production
process. The non-financial
measures are also taken into
consideration, as it is essential
for understanding each and
every action that is taken for
completing the task.
Method suited for The TCM calculation is mainly
suited for companies that are
more labour intensive and low
low-overhead costing. The
TCM method could mainly
allow the company to detect
the appropriate level of costing
for their product, as it is more
suited for their production
process.
The companies using ABC
method have the following
characteristics. Capital
intensive, product diverse,
diverse operating activities,
variation in number of
production runs, high overhead
costing. The above-mentioned
categories of calculations is
mainly required for detecting
the appropriate method for the
overhead cost that is associated
with the production of the end
product (Gylling et al. 2015).
Benefits The simplicity and inexpensive
conditions of TCM is
ABC method provides
companies with accurate
measure would benefit the management to understand the level of expenses, which
is associated with their overall production process.
Difference Traditional Costing
Method50
Activity Based costing
Method50
Cost pools The TCM uses one or limited
number of cost pools for
detecting the overall expenses
for the production of a
particular product. This
calculation mainly supports the
use of one condition for such
as direct labour cost for
detecting the overhead
expenses associated with the
production of the product
(Fleischman and Parker
2017).
The ABC method mainly
requires more than one cost
pools, as it is assigned to each
and every product for
understanding their actual cost
of production. The high level of
cost pools used in ABC method
mainly allows the company to
understand the specific cost
allocated to the particular
product.
Applied rate The applied rate for TCM is
mainly volume-based, as the
overall cost drivers focuses on
production size to detect the
overhead cost. This applied
mechanism would allow the
management to link the
quantity of the products with
the overhead values used in
the production process.
The focus of ABC method is on
the overall activity that is being
conducted on each front for
understanding the expenses
associated with the production
process. The non-financial
measures are also taken into
consideration, as it is essential
for understanding each and
every action that is taken for
completing the task.
Method suited for The TCM calculation is mainly
suited for companies that are
more labour intensive and low
low-overhead costing. The
TCM method could mainly
allow the company to detect
the appropriate level of costing
for their product, as it is more
suited for their production
process.
The companies using ABC
method have the following
characteristics. Capital
intensive, product diverse,
diverse operating activities,
variation in number of
production runs, high overhead
costing. The above-mentioned
categories of calculations is
mainly required for detecting
the appropriate method for the
overhead cost that is associated
with the production of the end
product (Gylling et al. 2015).
Benefits The simplicity and inexpensive
conditions of TCM is
ABC method provides
companies with accurate
Paraphrase This Document
Need a fresh take? Get an instant paraphrase of this document with our AI Paraphraser
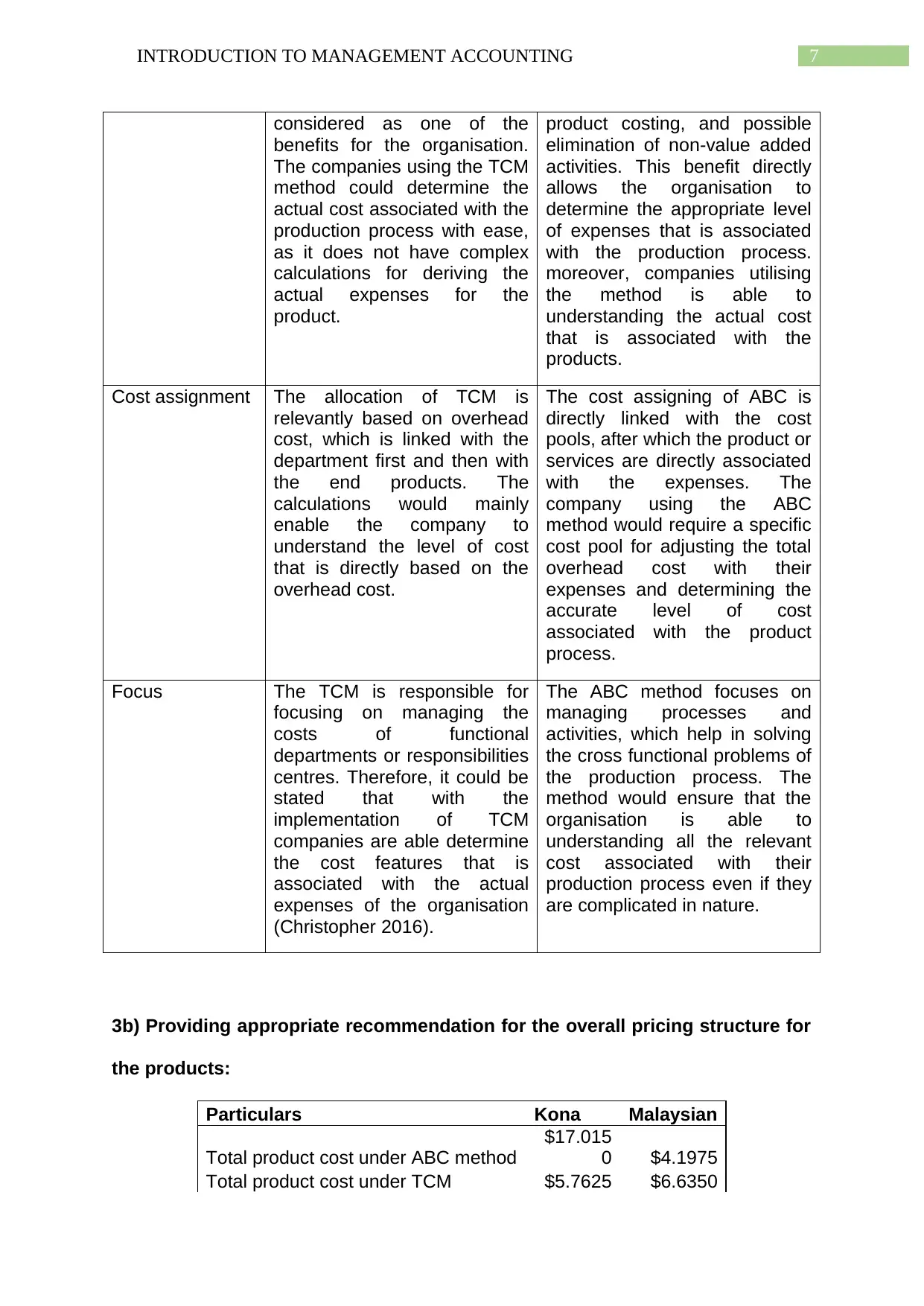
7INTRODUCTION TO MANAGEMENT ACCOUNTING
considered as one of the
benefits for the organisation.
The companies using the TCM
method could determine the
actual cost associated with the
production process with ease,
as it does not have complex
calculations for deriving the
actual expenses for the
product.
product costing, and possible
elimination of non-value added
activities. This benefit directly
allows the organisation to
determine the appropriate level
of expenses that is associated
with the production process.
moreover, companies utilising
the method is able to
understanding the actual cost
that is associated with the
products.
Cost assignment The allocation of TCM is
relevantly based on overhead
cost, which is linked with the
department first and then with
the end products. The
calculations would mainly
enable the company to
understand the level of cost
that is directly based on the
overhead cost.
The cost assigning of ABC is
directly linked with the cost
pools, after which the product or
services are directly associated
with the expenses. The
company using the ABC
method would require a specific
cost pool for adjusting the total
overhead cost with their
expenses and determining the
accurate level of cost
associated with the product
process.
Focus The TCM is responsible for
focusing on managing the
costs of functional
departments or responsibilities
centres. Therefore, it could be
stated that with the
implementation of TCM
companies are able determine
the cost features that is
associated with the actual
expenses of the organisation
(Christopher 2016).
The ABC method focuses on
managing processes and
activities, which help in solving
the cross functional problems of
the production process. The
method would ensure that the
organisation is able to
understanding all the relevant
cost associated with their
production process even if they
are complicated in nature.
3b) Providing appropriate recommendation for the overall pricing structure for
the products:
Particulars Kona Malaysian
Total product cost under ABC method
$17.015
0 $4.1975
Total product cost under TCM $5.7625 $6.6350
considered as one of the
benefits for the organisation.
The companies using the TCM
method could determine the
actual cost associated with the
production process with ease,
as it does not have complex
calculations for deriving the
actual expenses for the
product.
product costing, and possible
elimination of non-value added
activities. This benefit directly
allows the organisation to
determine the appropriate level
of expenses that is associated
with the production process.
moreover, companies utilising
the method is able to
understanding the actual cost
that is associated with the
products.
Cost assignment The allocation of TCM is
relevantly based on overhead
cost, which is linked with the
department first and then with
the end products. The
calculations would mainly
enable the company to
understand the level of cost
that is directly based on the
overhead cost.
The cost assigning of ABC is
directly linked with the cost
pools, after which the product or
services are directly associated
with the expenses. The
company using the ABC
method would require a specific
cost pool for adjusting the total
overhead cost with their
expenses and determining the
accurate level of cost
associated with the product
process.
Focus The TCM is responsible for
focusing on managing the
costs of functional
departments or responsibilities
centres. Therefore, it could be
stated that with the
implementation of TCM
companies are able determine
the cost features that is
associated with the actual
expenses of the organisation
(Christopher 2016).
The ABC method focuses on
managing processes and
activities, which help in solving
the cross functional problems of
the production process. The
method would ensure that the
organisation is able to
understanding all the relevant
cost associated with their
production process even if they
are complicated in nature.
3b) Providing appropriate recommendation for the overall pricing structure for
the products:
Particulars Kona Malaysian
Total product cost under ABC method
$17.015
0 $4.1975
Total product cost under TCM $5.7625 $6.6350
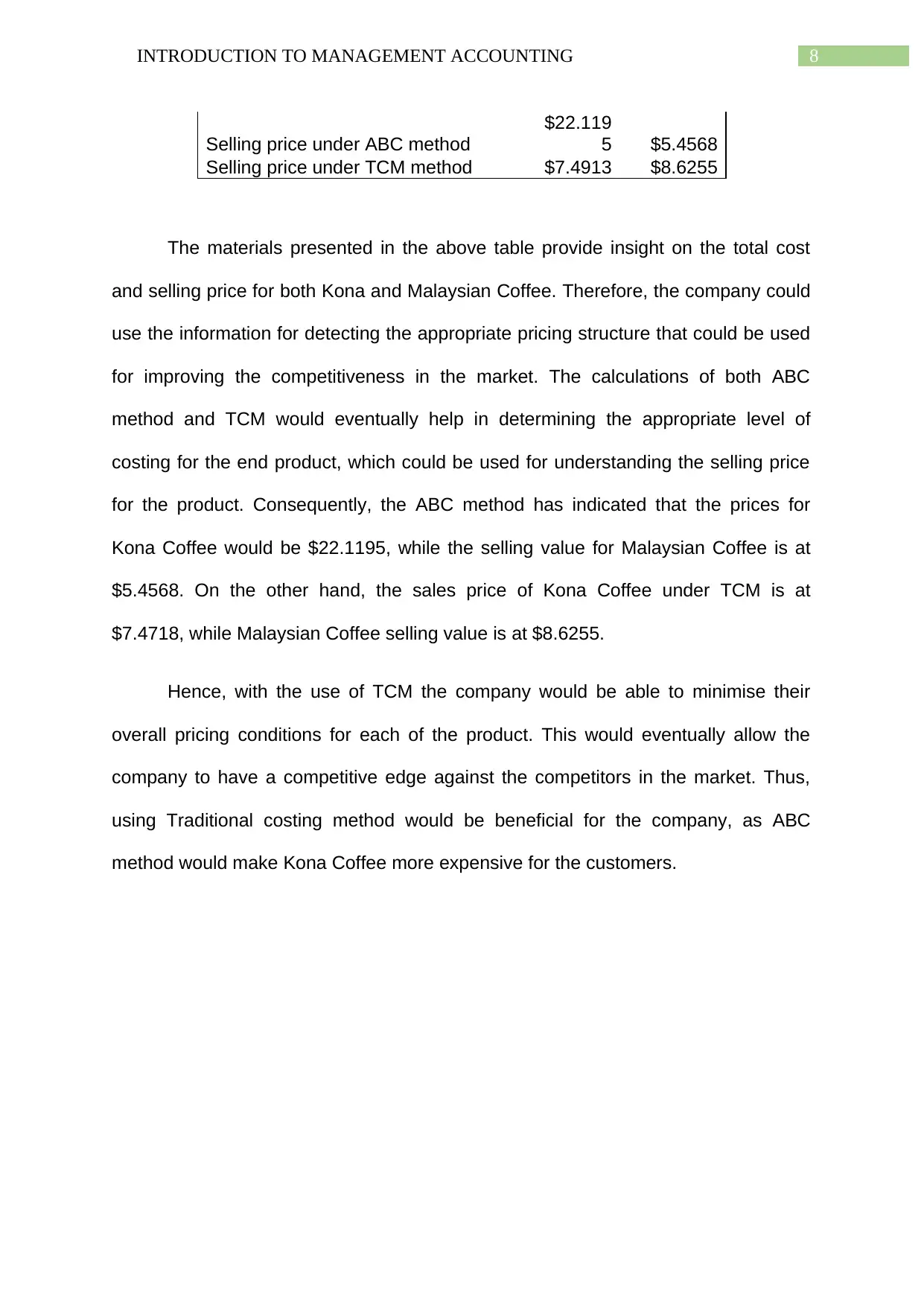
8INTRODUCTION TO MANAGEMENT ACCOUNTING
Selling price under ABC method
$22.119
5 $5.4568
Selling price under TCM method $7.4913 $8.6255
The materials presented in the above table provide insight on the total cost
and selling price for both Kona and Malaysian Coffee. Therefore, the company could
use the information for detecting the appropriate pricing structure that could be used
for improving the competitiveness in the market. The calculations of both ABC
method and TCM would eventually help in determining the appropriate level of
costing for the end product, which could be used for understanding the selling price
for the product. Consequently, the ABC method has indicated that the prices for
Kona Coffee would be $22.1195, while the selling value for Malaysian Coffee is at
$5.4568. On the other hand, the sales price of Kona Coffee under TCM is at
$7.4718, while Malaysian Coffee selling value is at $8.6255.
Hence, with the use of TCM the company would be able to minimise their
overall pricing conditions for each of the product. This would eventually allow the
company to have a competitive edge against the competitors in the market. Thus,
using Traditional costing method would be beneficial for the company, as ABC
method would make Kona Coffee more expensive for the customers.
Selling price under ABC method
$22.119
5 $5.4568
Selling price under TCM method $7.4913 $8.6255
The materials presented in the above table provide insight on the total cost
and selling price for both Kona and Malaysian Coffee. Therefore, the company could
use the information for detecting the appropriate pricing structure that could be used
for improving the competitiveness in the market. The calculations of both ABC
method and TCM would eventually help in determining the appropriate level of
costing for the end product, which could be used for understanding the selling price
for the product. Consequently, the ABC method has indicated that the prices for
Kona Coffee would be $22.1195, while the selling value for Malaysian Coffee is at
$5.4568. On the other hand, the sales price of Kona Coffee under TCM is at
$7.4718, while Malaysian Coffee selling value is at $8.6255.
Hence, with the use of TCM the company would be able to minimise their
overall pricing conditions for each of the product. This would eventually allow the
company to have a competitive edge against the competitors in the market. Thus,
using Traditional costing method would be beneficial for the company, as ABC
method would make Kona Coffee more expensive for the customers.
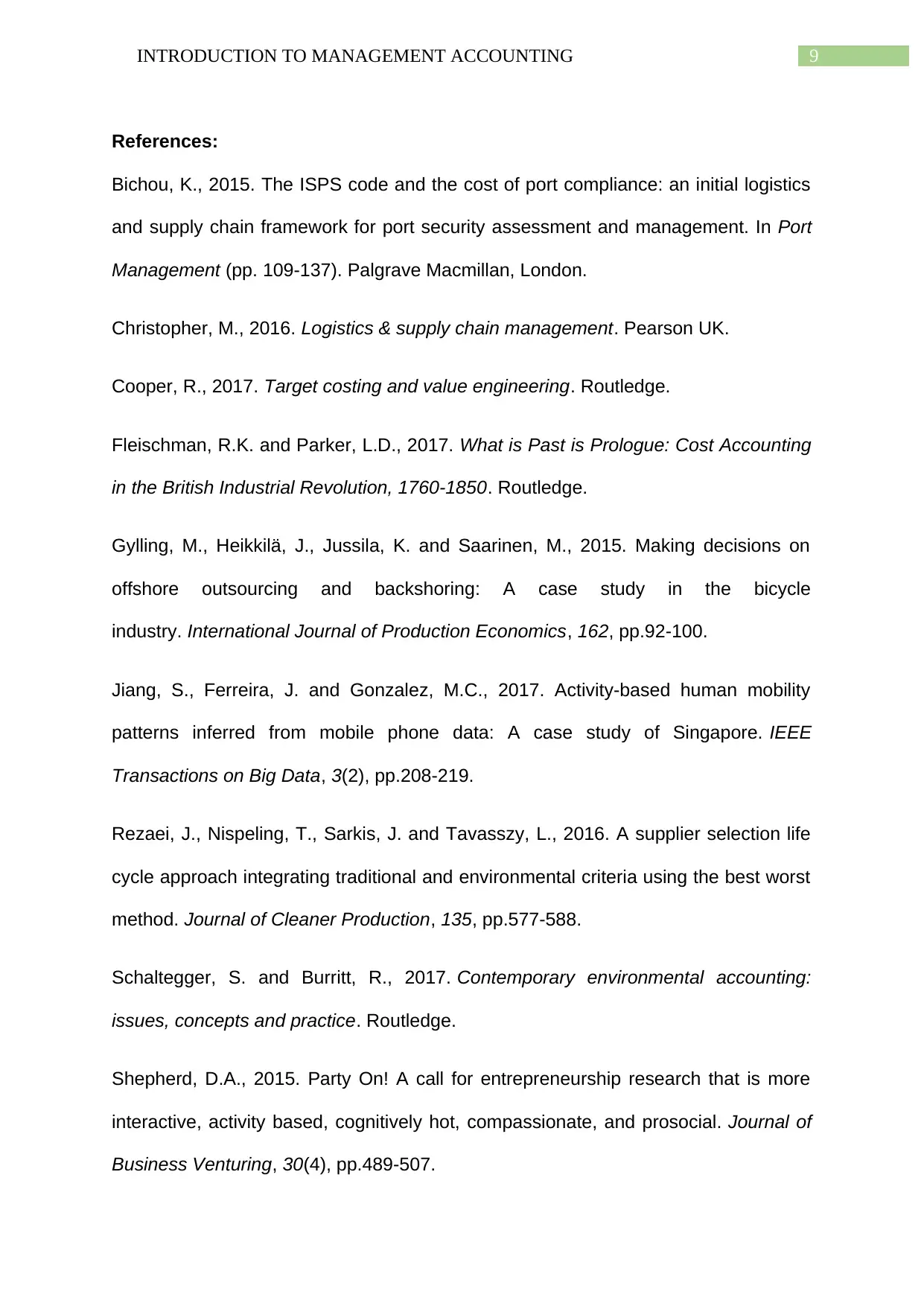
9INTRODUCTION TO MANAGEMENT ACCOUNTING
References:
Bichou, K., 2015. The ISPS code and the cost of port compliance: an initial logistics
and supply chain framework for port security assessment and management. In Port
Management (pp. 109-137). Palgrave Macmillan, London.
Christopher, M., 2016. Logistics & supply chain management. Pearson UK.
Cooper, R., 2017. Target costing and value engineering. Routledge.
Fleischman, R.K. and Parker, L.D., 2017. What is Past is Prologue: Cost Accounting
in the British Industrial Revolution, 1760-1850. Routledge.
Gylling, M., Heikkilä, J., Jussila, K. and Saarinen, M., 2015. Making decisions on
offshore outsourcing and backshoring: A case study in the bicycle
industry. International Journal of Production Economics, 162, pp.92-100.
Jiang, S., Ferreira, J. and Gonzalez, M.C., 2017. Activity-based human mobility
patterns inferred from mobile phone data: A case study of Singapore. IEEE
Transactions on Big Data, 3(2), pp.208-219.
Rezaei, J., Nispeling, T., Sarkis, J. and Tavasszy, L., 2016. A supplier selection life
cycle approach integrating traditional and environmental criteria using the best worst
method. Journal of Cleaner Production, 135, pp.577-588.
Schaltegger, S. and Burritt, R., 2017. Contemporary environmental accounting:
issues, concepts and practice. Routledge.
Shepherd, D.A., 2015. Party On! A call for entrepreneurship research that is more
interactive, activity based, cognitively hot, compassionate, and prosocial. Journal of
Business Venturing, 30(4), pp.489-507.
References:
Bichou, K., 2015. The ISPS code and the cost of port compliance: an initial logistics
and supply chain framework for port security assessment and management. In Port
Management (pp. 109-137). Palgrave Macmillan, London.
Christopher, M., 2016. Logistics & supply chain management. Pearson UK.
Cooper, R., 2017. Target costing and value engineering. Routledge.
Fleischman, R.K. and Parker, L.D., 2017. What is Past is Prologue: Cost Accounting
in the British Industrial Revolution, 1760-1850. Routledge.
Gylling, M., Heikkilä, J., Jussila, K. and Saarinen, M., 2015. Making decisions on
offshore outsourcing and backshoring: A case study in the bicycle
industry. International Journal of Production Economics, 162, pp.92-100.
Jiang, S., Ferreira, J. and Gonzalez, M.C., 2017. Activity-based human mobility
patterns inferred from mobile phone data: A case study of Singapore. IEEE
Transactions on Big Data, 3(2), pp.208-219.
Rezaei, J., Nispeling, T., Sarkis, J. and Tavasszy, L., 2016. A supplier selection life
cycle approach integrating traditional and environmental criteria using the best worst
method. Journal of Cleaner Production, 135, pp.577-588.
Schaltegger, S. and Burritt, R., 2017. Contemporary environmental accounting:
issues, concepts and practice. Routledge.
Shepherd, D.A., 2015. Party On! A call for entrepreneurship research that is more
interactive, activity based, cognitively hot, compassionate, and prosocial. Journal of
Business Venturing, 30(4), pp.489-507.
1 out of 10
Related Documents

Your All-in-One AI-Powered Toolkit for Academic Success.
+13062052269
info@desklib.com
Available 24*7 on WhatsApp / Email
Unlock your academic potential
© 2024 | Zucol Services PVT LTD | All rights reserved.