Management Accounting Report: Cost Analysis for Jeffrey and Sons
VerifiedAdded on 2020/01/15
|25
|7192
|76
Report
AI Summary
This report provides a comprehensive analysis of management accounting principles applied to a case study involving Jeffrey and Sons, a company manufacturing branded products. The report begins with an introduction to management accounting and its significance in cost control and decision-making. Task 1 delves into cost classification, job costing, and absorption costing techniques, including detailed calculations of unit costs and total job costs for specific jobs. Task 2 focuses on preparing and analyzing cost reports, including variance analysis and performance indicators to identify areas for improvement. Task 3 explores the budgeting process, examining different budgeting methods and the preparation of various budget types, including a cash budget. Finally, Task 4 involves the calculation of variances, the preparation of a reconciliation operating statement, and providing findings to management based on identified responsibility centers. The report concludes with a summary of key findings and recommendations.
Contribute Materials
Your contribution can guide someone’s learning journey. Share your
documents today.
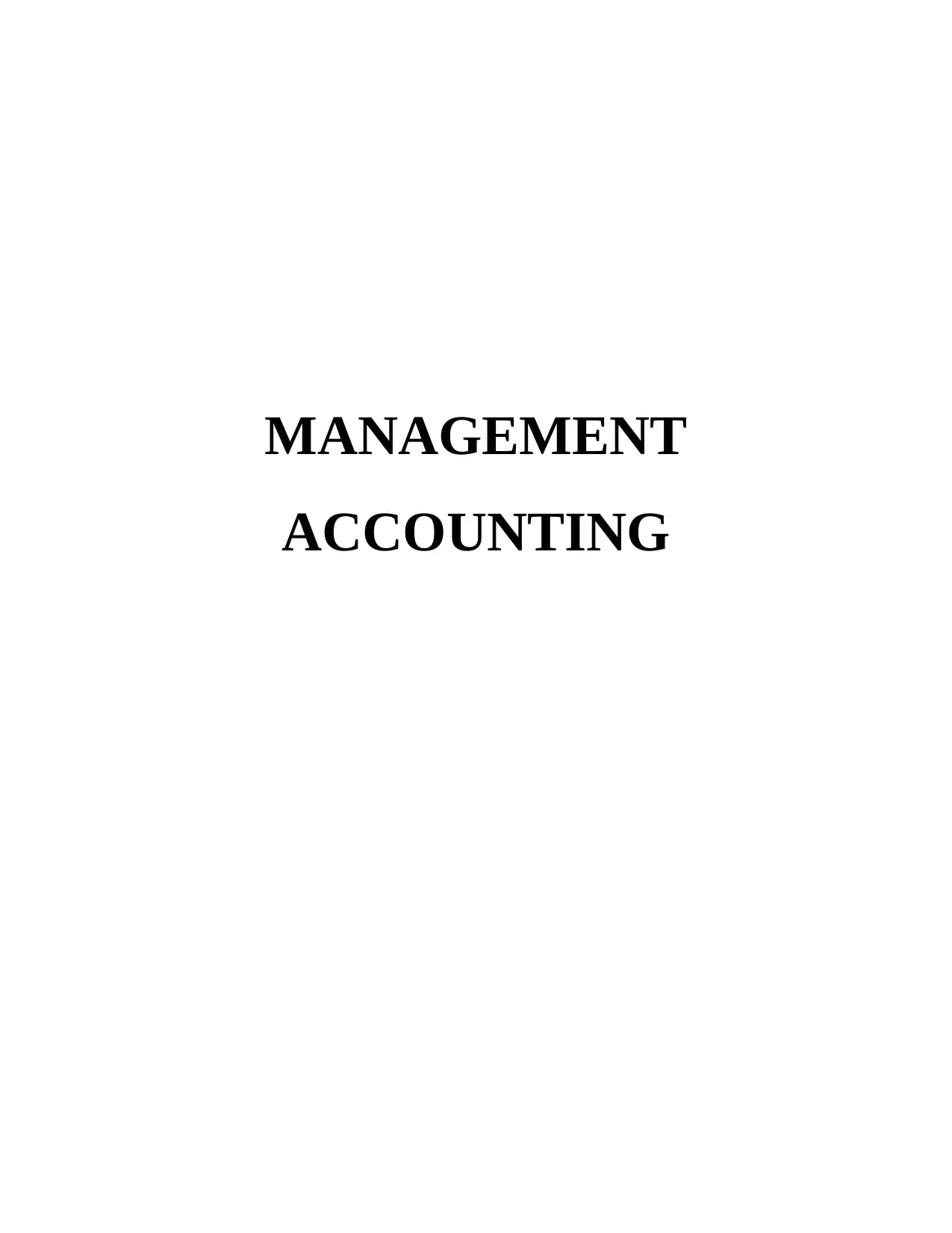
MANAGEMENT
ACCOUNTING
ACCOUNTING
Secure Best Marks with AI Grader
Need help grading? Try our AI Grader for instant feedback on your assignments.
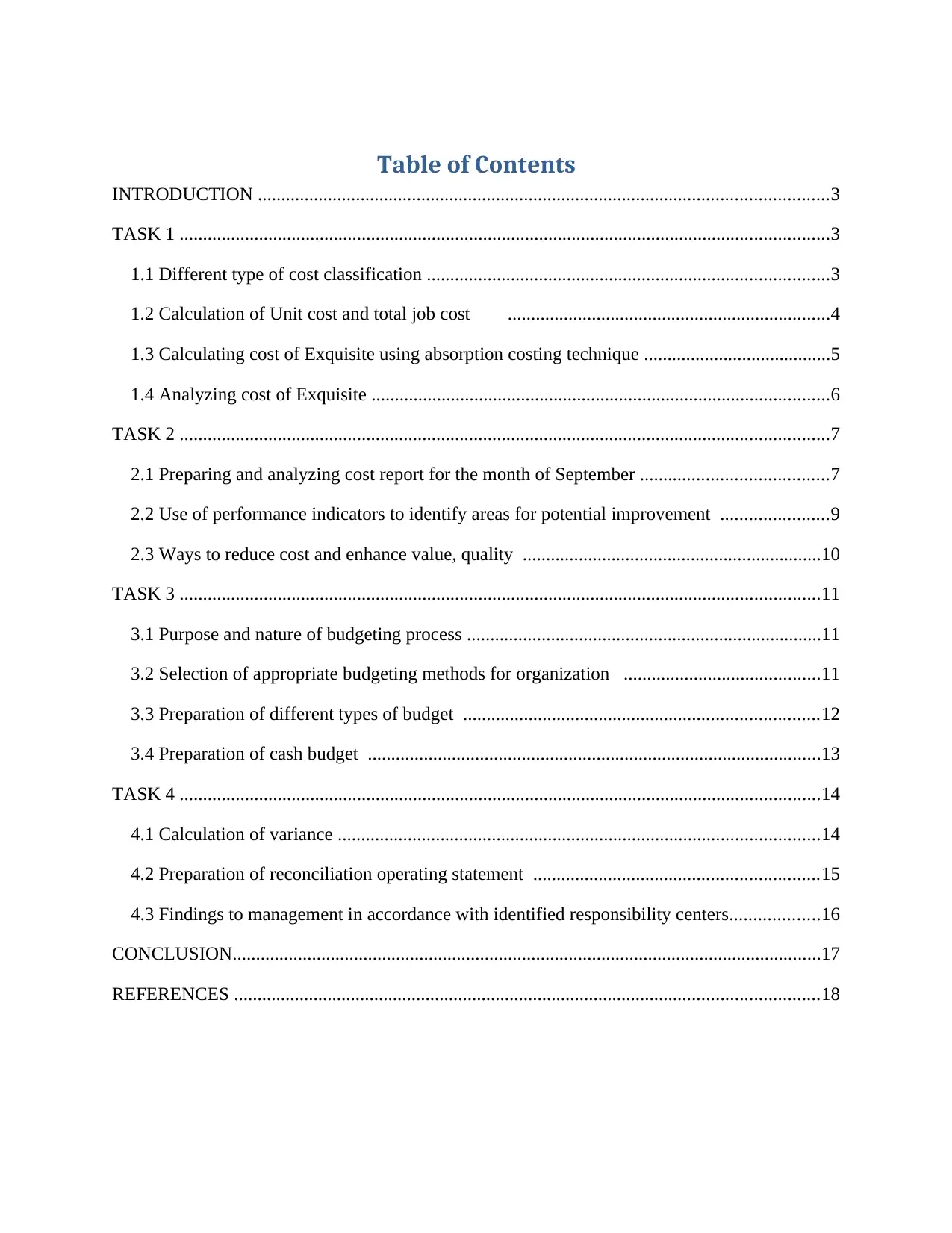
Table of Contents
INTRODUCTION ..........................................................................................................................3
TASK 1 ...........................................................................................................................................3
1.1 Different type of cost classification ......................................................................................3
1.2 Calculation of Unit cost and total job cost .....................................................................4
1.3 Calculating cost of Exquisite using absorption costing technique ........................................5
1.4 Analyzing cost of Exquisite ..................................................................................................6
TASK 2 ...........................................................................................................................................7
2.1 Preparing and analyzing cost report for the month of September ........................................7
2.2 Use of performance indicators to identify areas for potential improvement .......................9
2.3 Ways to reduce cost and enhance value, quality ................................................................10
TASK 3 .........................................................................................................................................11
3.1 Purpose and nature of budgeting process ............................................................................11
3.2 Selection of appropriate budgeting methods for organization ..........................................11
3.3 Preparation of different types of budget ............................................................................12
3.4 Preparation of cash budget .................................................................................................13
TASK 4 .........................................................................................................................................14
4.1 Calculation of variance .......................................................................................................14
4.2 Preparation of reconciliation operating statement .............................................................15
4.3 Findings to management in accordance with identified responsibility centers...................16
CONCLUSION..............................................................................................................................17
REFERENCES .............................................................................................................................18
INTRODUCTION ..........................................................................................................................3
TASK 1 ...........................................................................................................................................3
1.1 Different type of cost classification ......................................................................................3
1.2 Calculation of Unit cost and total job cost .....................................................................4
1.3 Calculating cost of Exquisite using absorption costing technique ........................................5
1.4 Analyzing cost of Exquisite ..................................................................................................6
TASK 2 ...........................................................................................................................................7
2.1 Preparing and analyzing cost report for the month of September ........................................7
2.2 Use of performance indicators to identify areas for potential improvement .......................9
2.3 Ways to reduce cost and enhance value, quality ................................................................10
TASK 3 .........................................................................................................................................11
3.1 Purpose and nature of budgeting process ............................................................................11
3.2 Selection of appropriate budgeting methods for organization ..........................................11
3.3 Preparation of different types of budget ............................................................................12
3.4 Preparation of cash budget .................................................................................................13
TASK 4 .........................................................................................................................................14
4.1 Calculation of variance .......................................................................................................14
4.2 Preparation of reconciliation operating statement .............................................................15
4.3 Findings to management in accordance with identified responsibility centers...................16
CONCLUSION..............................................................................................................................17
REFERENCES .............................................................................................................................18
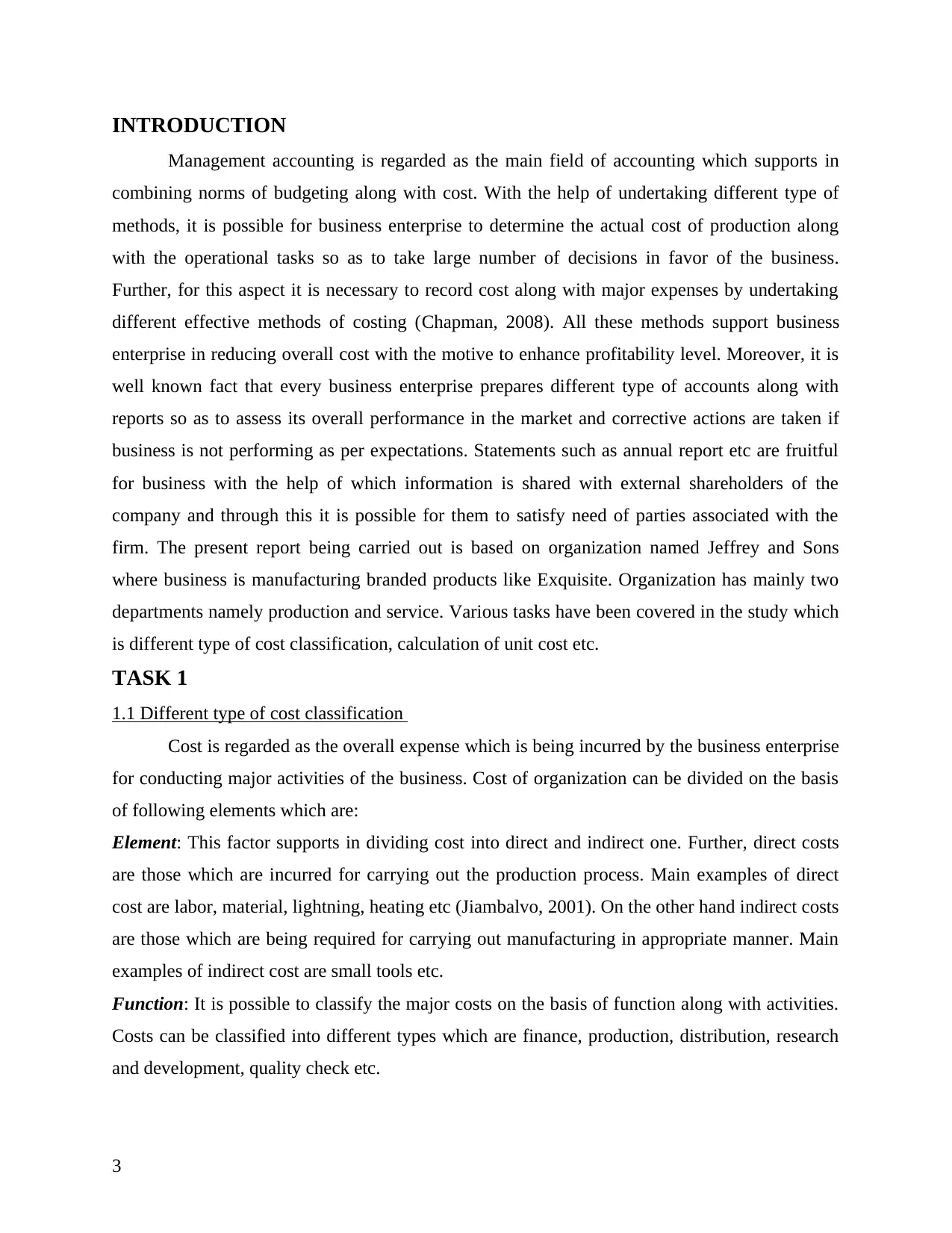
INTRODUCTION
Management accounting is regarded as the main field of accounting which supports in
combining norms of budgeting along with cost. With the help of undertaking different type of
methods, it is possible for business enterprise to determine the actual cost of production along
with the operational tasks so as to take large number of decisions in favor of the business.
Further, for this aspect it is necessary to record cost along with major expenses by undertaking
different effective methods of costing (Chapman, 2008). All these methods support business
enterprise in reducing overall cost with the motive to enhance profitability level. Moreover, it is
well known fact that every business enterprise prepares different type of accounts along with
reports so as to assess its overall performance in the market and corrective actions are taken if
business is not performing as per expectations. Statements such as annual report etc are fruitful
for business with the help of which information is shared with external shareholders of the
company and through this it is possible for them to satisfy need of parties associated with the
firm. The present report being carried out is based on organization named Jeffrey and Sons
where business is manufacturing branded products like Exquisite. Organization has mainly two
departments namely production and service. Various tasks have been covered in the study which
is different type of cost classification, calculation of unit cost etc.
TASK 1
1.1 Different type of cost classification
Cost is regarded as the overall expense which is being incurred by the business enterprise
for conducting major activities of the business. Cost of organization can be divided on the basis
of following elements which are:
Element: This factor supports in dividing cost into direct and indirect one. Further, direct costs
are those which are incurred for carrying out the production process. Main examples of direct
cost are labor, material, lightning, heating etc (Jiambalvo, 2001). On the other hand indirect costs
are those which are being required for carrying out manufacturing in appropriate manner. Main
examples of indirect cost are small tools etc.
Function: It is possible to classify the major costs on the basis of function along with activities.
Costs can be classified into different types which are finance, production, distribution, research
and development, quality check etc.
3
Management accounting is regarded as the main field of accounting which supports in
combining norms of budgeting along with cost. With the help of undertaking different type of
methods, it is possible for business enterprise to determine the actual cost of production along
with the operational tasks so as to take large number of decisions in favor of the business.
Further, for this aspect it is necessary to record cost along with major expenses by undertaking
different effective methods of costing (Chapman, 2008). All these methods support business
enterprise in reducing overall cost with the motive to enhance profitability level. Moreover, it is
well known fact that every business enterprise prepares different type of accounts along with
reports so as to assess its overall performance in the market and corrective actions are taken if
business is not performing as per expectations. Statements such as annual report etc are fruitful
for business with the help of which information is shared with external shareholders of the
company and through this it is possible for them to satisfy need of parties associated with the
firm. The present report being carried out is based on organization named Jeffrey and Sons
where business is manufacturing branded products like Exquisite. Organization has mainly two
departments namely production and service. Various tasks have been covered in the study which
is different type of cost classification, calculation of unit cost etc.
TASK 1
1.1 Different type of cost classification
Cost is regarded as the overall expense which is being incurred by the business enterprise
for conducting major activities of the business. Cost of organization can be divided on the basis
of following elements which are:
Element: This factor supports in dividing cost into direct and indirect one. Further, direct costs
are those which are incurred for carrying out the production process. Main examples of direct
cost are labor, material, lightning, heating etc (Jiambalvo, 2001). On the other hand indirect costs
are those which are being required for carrying out manufacturing in appropriate manner. Main
examples of indirect cost are small tools etc.
Function: It is possible to classify the major costs on the basis of function along with activities.
Costs can be classified into different types which are finance, production, distribution, research
and development, quality check etc.
3
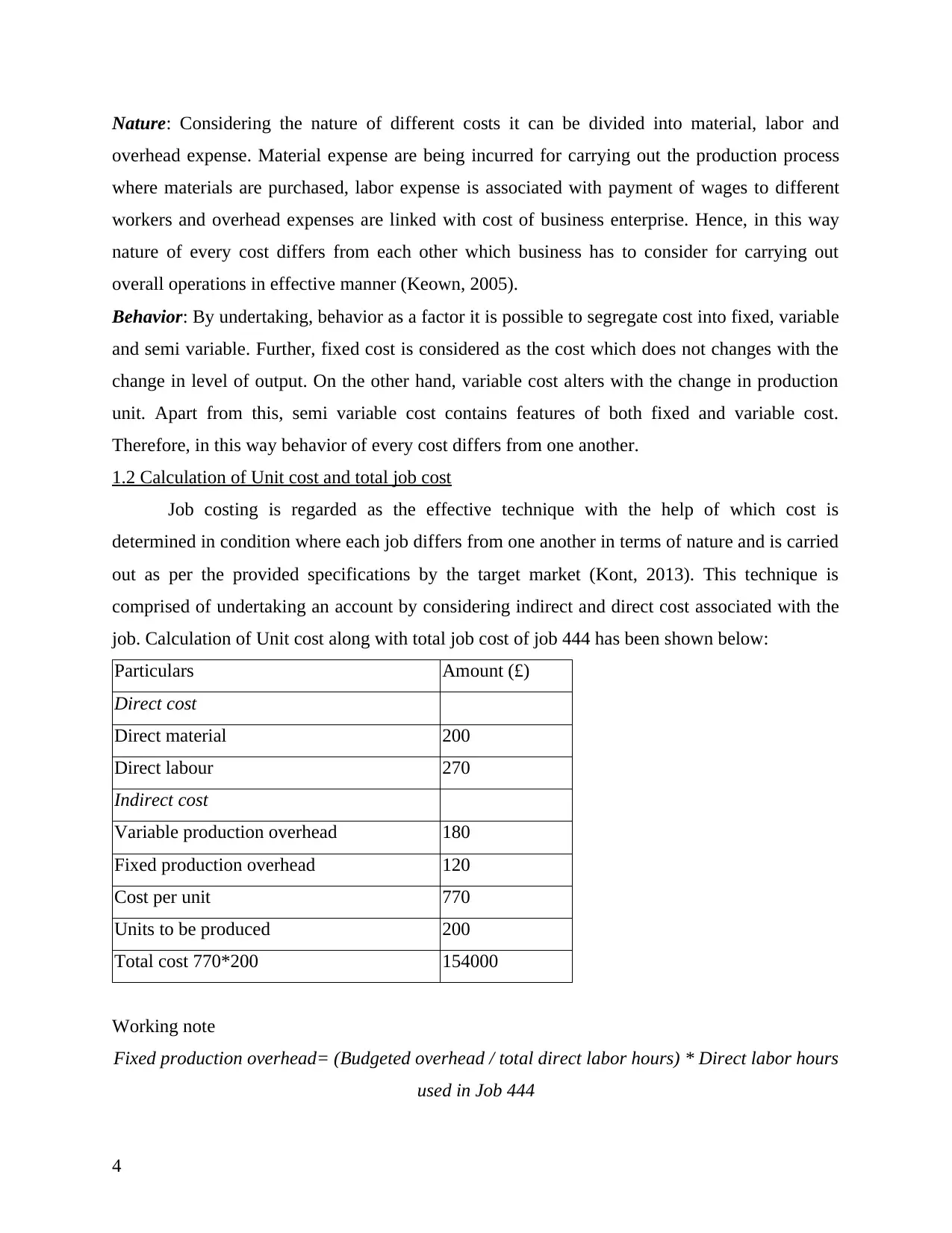
Nature: Considering the nature of different costs it can be divided into material, labor and
overhead expense. Material expense are being incurred for carrying out the production process
where materials are purchased, labor expense is associated with payment of wages to different
workers and overhead expenses are linked with cost of business enterprise. Hence, in this way
nature of every cost differs from each other which business has to consider for carrying out
overall operations in effective manner (Keown, 2005).
Behavior: By undertaking, behavior as a factor it is possible to segregate cost into fixed, variable
and semi variable. Further, fixed cost is considered as the cost which does not changes with the
change in level of output. On the other hand, variable cost alters with the change in production
unit. Apart from this, semi variable cost contains features of both fixed and variable cost.
Therefore, in this way behavior of every cost differs from one another.
1.2 Calculation of Unit cost and total job cost
Job costing is regarded as the effective technique with the help of which cost is
determined in condition where each job differs from one another in terms of nature and is carried
out as per the provided specifications by the target market (Kont, 2013). This technique is
comprised of undertaking an account by considering indirect and direct cost associated with the
job. Calculation of Unit cost along with total job cost of job 444 has been shown below:
Particulars Amount (£)
Direct cost
Direct material 200
Direct labour 270
Indirect cost
Variable production overhead 180
Fixed production overhead 120
Cost per unit 770
Units to be produced 200
Total cost 770*200 154000
Working note
Fixed production overhead= (Budgeted overhead / total direct labor hours) * Direct labor hours
used in Job 444
4
overhead expense. Material expense are being incurred for carrying out the production process
where materials are purchased, labor expense is associated with payment of wages to different
workers and overhead expenses are linked with cost of business enterprise. Hence, in this way
nature of every cost differs from each other which business has to consider for carrying out
overall operations in effective manner (Keown, 2005).
Behavior: By undertaking, behavior as a factor it is possible to segregate cost into fixed, variable
and semi variable. Further, fixed cost is considered as the cost which does not changes with the
change in level of output. On the other hand, variable cost alters with the change in production
unit. Apart from this, semi variable cost contains features of both fixed and variable cost.
Therefore, in this way behavior of every cost differs from one another.
1.2 Calculation of Unit cost and total job cost
Job costing is regarded as the effective technique with the help of which cost is
determined in condition where each job differs from one another in terms of nature and is carried
out as per the provided specifications by the target market (Kont, 2013). This technique is
comprised of undertaking an account by considering indirect and direct cost associated with the
job. Calculation of Unit cost along with total job cost of job 444 has been shown below:
Particulars Amount (£)
Direct cost
Direct material 200
Direct labour 270
Indirect cost
Variable production overhead 180
Fixed production overhead 120
Cost per unit 770
Units to be produced 200
Total cost 770*200 154000
Working note
Fixed production overhead= (Budgeted overhead / total direct labor hours) * Direct labor hours
used in Job 444
4
Secure Best Marks with AI Grader
Need help grading? Try our AI Grader for instant feedback on your assignments.
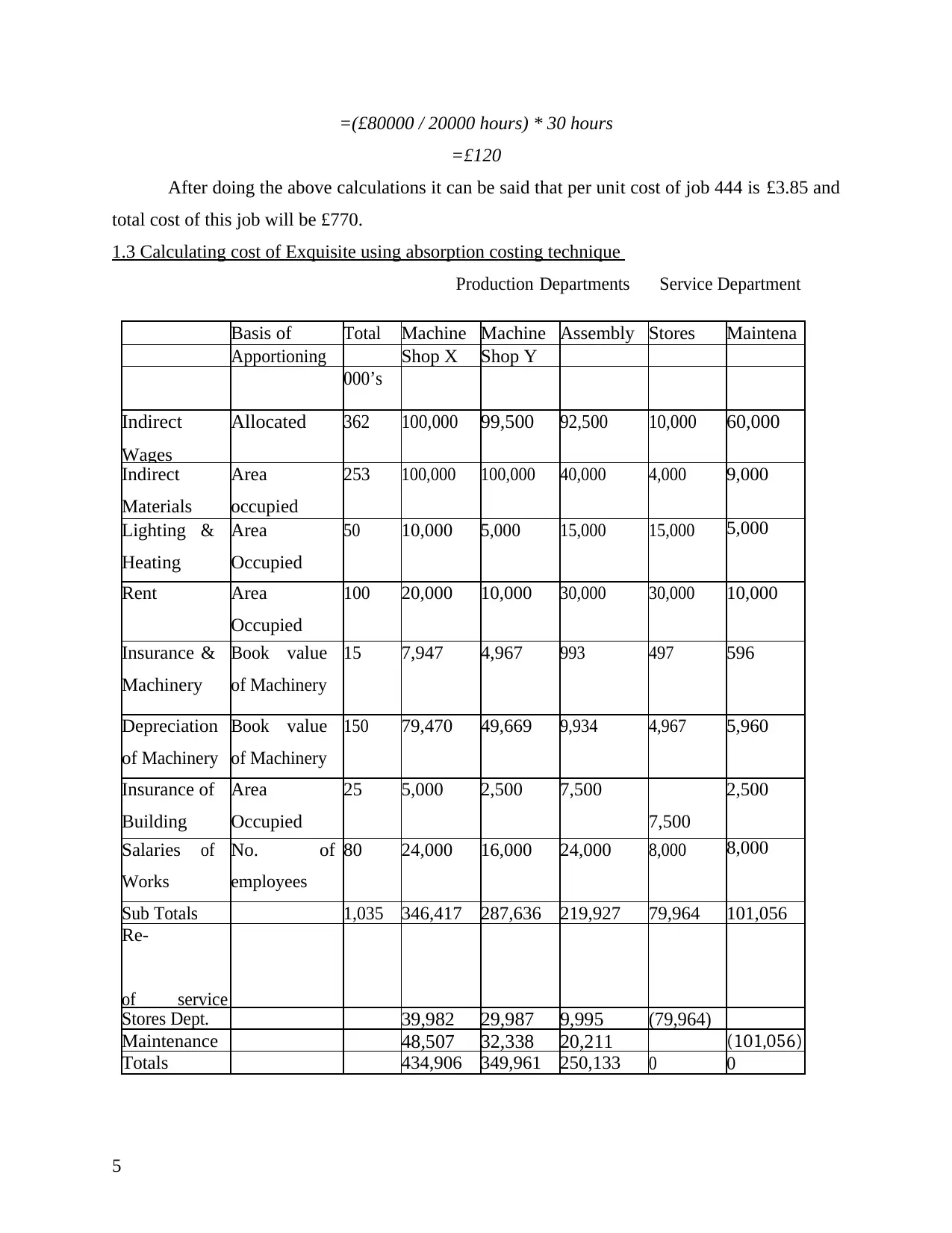
=(£80000 / 20000 hours) * 30 hours
=£120
After doing the above calculations it can be said that per unit cost of job 444 is £3.85 and
total cost of this job will be £770.
1.3 Calculating cost of Exquisite using absorption costing technique
Production Departments Service Department
Basis of Total Machine Machine Assembly Stores Maintena
nceApportioning Shop X Shop Y
000’s
Indirect
Wages
Allocated 362 100,000 99,500 92,500 10,000 60,000
Indirect
Materials
Area
occupied
253 100,000 100,000 40,000 4,000 9,000
Lighting
Heating
& Area
Occupied
50 10,000 5,000 15,000 15,000 5,000
Rent Area
Occupied
100 20,000 10,000 30,000 30,000 10,000
Insurance &
Machinery
Book value
of Machinery
15 7,947 4,967 993 497 596
Depreciation
of Machinery
Book value
of Machinery
150 79,470 49,669 9,934 4,967 5,960
Insurance of
Building
Area
Occupied
25 5,000 2,500 7,500
7,500
2,500
Salaries
Works
of No.
employees
of 80 24,000 16,000 24,000 8,000 8,000
Sub Totals 1,035 346,417 287,636 219,927 79,964 101,056
Re-
of service
Stores Dept. 39,982 29,987 9,995 (79,964)
Maintenance 48,507 32,338 20,211 (101,056)
Totals 434,906 349,961 250,133 0 0
5
=£120
After doing the above calculations it can be said that per unit cost of job 444 is £3.85 and
total cost of this job will be £770.
1.3 Calculating cost of Exquisite using absorption costing technique
Production Departments Service Department
Basis of Total Machine Machine Assembly Stores Maintena
nceApportioning Shop X Shop Y
000’s
Indirect
Wages
Allocated 362 100,000 99,500 92,500 10,000 60,000
Indirect
Materials
Area
occupied
253 100,000 100,000 40,000 4,000 9,000
Lighting
Heating
& Area
Occupied
50 10,000 5,000 15,000 15,000 5,000
Rent Area
Occupied
100 20,000 10,000 30,000 30,000 10,000
Insurance &
Machinery
Book value
of Machinery
15 7,947 4,967 993 497 596
Depreciation
of Machinery
Book value
of Machinery
150 79,470 49,669 9,934 4,967 5,960
Insurance of
Building
Area
Occupied
25 5,000 2,500 7,500
7,500
2,500
Salaries
Works
of No.
employees
of 80 24,000 16,000 24,000 8,000 8,000
Sub Totals 1,035 346,417 287,636 219,927 79,964 101,056
Re-
of service
Stores Dept. 39,982 29,987 9,995 (79,964)
Maintenance 48,507 32,338 20,211 (101,056)
Totals 434,906 349,961 250,133 0 0
5
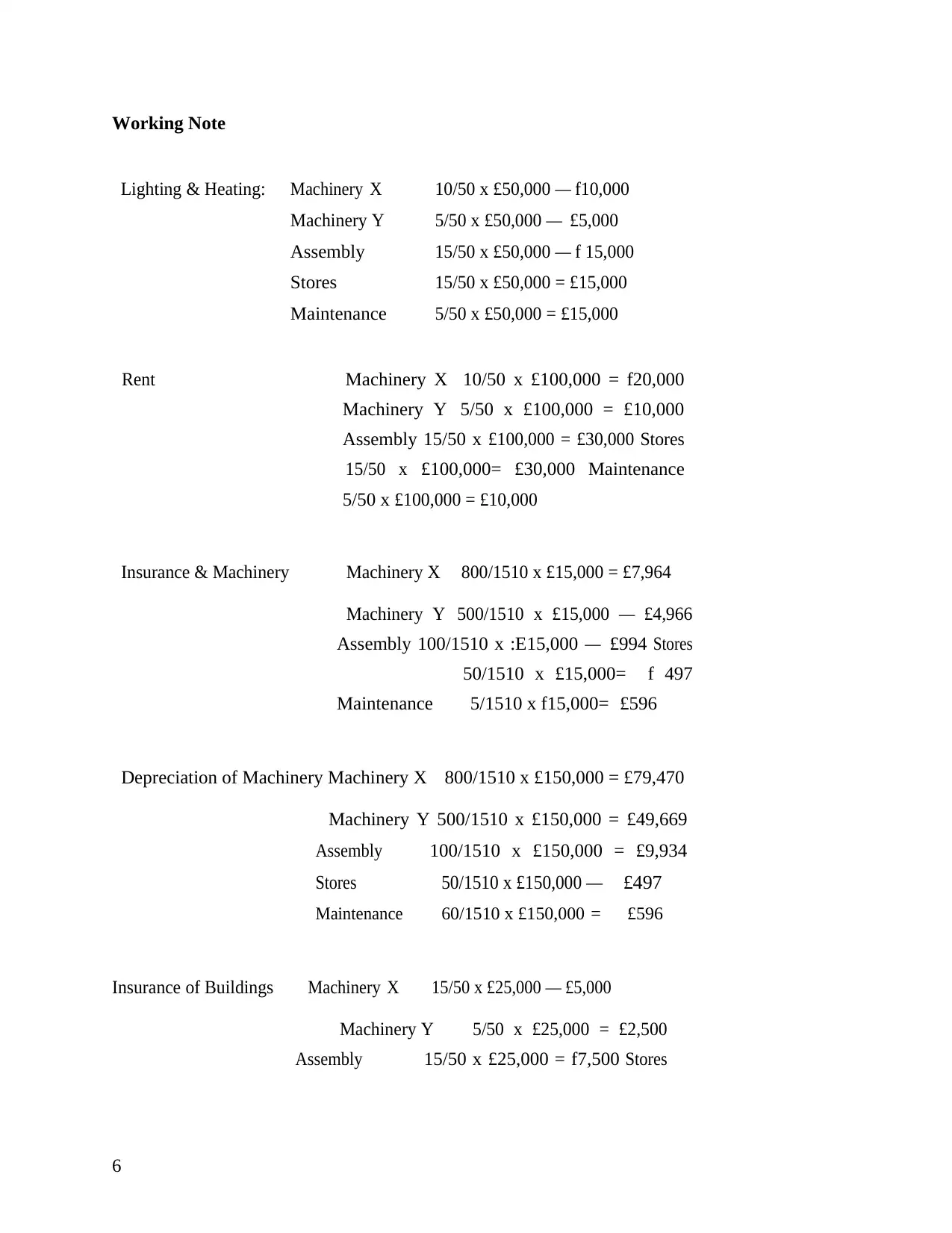
Working Note
Lighting & Heating: Machinery X 10/50 x £50,000 — f10,000
Machinery Y 5/50 x £50,000 — £5,000
Assembly 15/50 x £50,000 — f 15,000
Stores 15/50 x £50,000 = £15,000
Maintenance 5/50 x £50,000 = £15,000
Rent Machinery X 10/50 x £100,000 = f20,000
Machinery Y 5/50 x £100,000 = £10,000
Assembly 15/50 x £100,000 = £30,000 Stores
15/50 x £100,000= £30,000 Maintenance
5/50 x £100,000 = £10,000
Insurance & Machinery Machinery X 800/1510 x £15,000 = £7,964
Machinery Y 500/1510 x £15,000 — £4,966
Assembly 100/1510 x :E15,000 — £994 Stores
50/1510 x £15,000= f 497
Maintenance 5/1510 x f15,000= £596
Depreciation of Machinery Machinery X 800/1510 x £150,000 = £79,470
Machinery Y 500/1510 x £150,000 = £49,669
Assembly 100/1510 x £150,000 = £9,934
Stores 50/1510 x £150,000 — £497
Maintenance 60/1510 x £150,000 = £596
Insurance of Buildings Machinery X 15/50 x £25,000 — £5,000
Machinery Y 5/50 x £25,000 = £2,500
Assembly 15/50 x £25,000 = f7,500 Stores
6
Lighting & Heating: Machinery X 10/50 x £50,000 — f10,000
Machinery Y 5/50 x £50,000 — £5,000
Assembly 15/50 x £50,000 — f 15,000
Stores 15/50 x £50,000 = £15,000
Maintenance 5/50 x £50,000 = £15,000
Rent Machinery X 10/50 x £100,000 = f20,000
Machinery Y 5/50 x £100,000 = £10,000
Assembly 15/50 x £100,000 = £30,000 Stores
15/50 x £100,000= £30,000 Maintenance
5/50 x £100,000 = £10,000
Insurance & Machinery Machinery X 800/1510 x £15,000 = £7,964
Machinery Y 500/1510 x £15,000 — £4,966
Assembly 100/1510 x :E15,000 — £994 Stores
50/1510 x £15,000= f 497
Maintenance 5/1510 x f15,000= £596
Depreciation of Machinery Machinery X 800/1510 x £150,000 = £79,470
Machinery Y 500/1510 x £150,000 = £49,669
Assembly 100/1510 x £150,000 = £9,934
Stores 50/1510 x £150,000 — £497
Maintenance 60/1510 x £150,000 = £596
Insurance of Buildings Machinery X 15/50 x £25,000 — £5,000
Machinery Y 5/50 x £25,000 = £2,500
Assembly 15/50 x £25,000 = f7,500 Stores
6
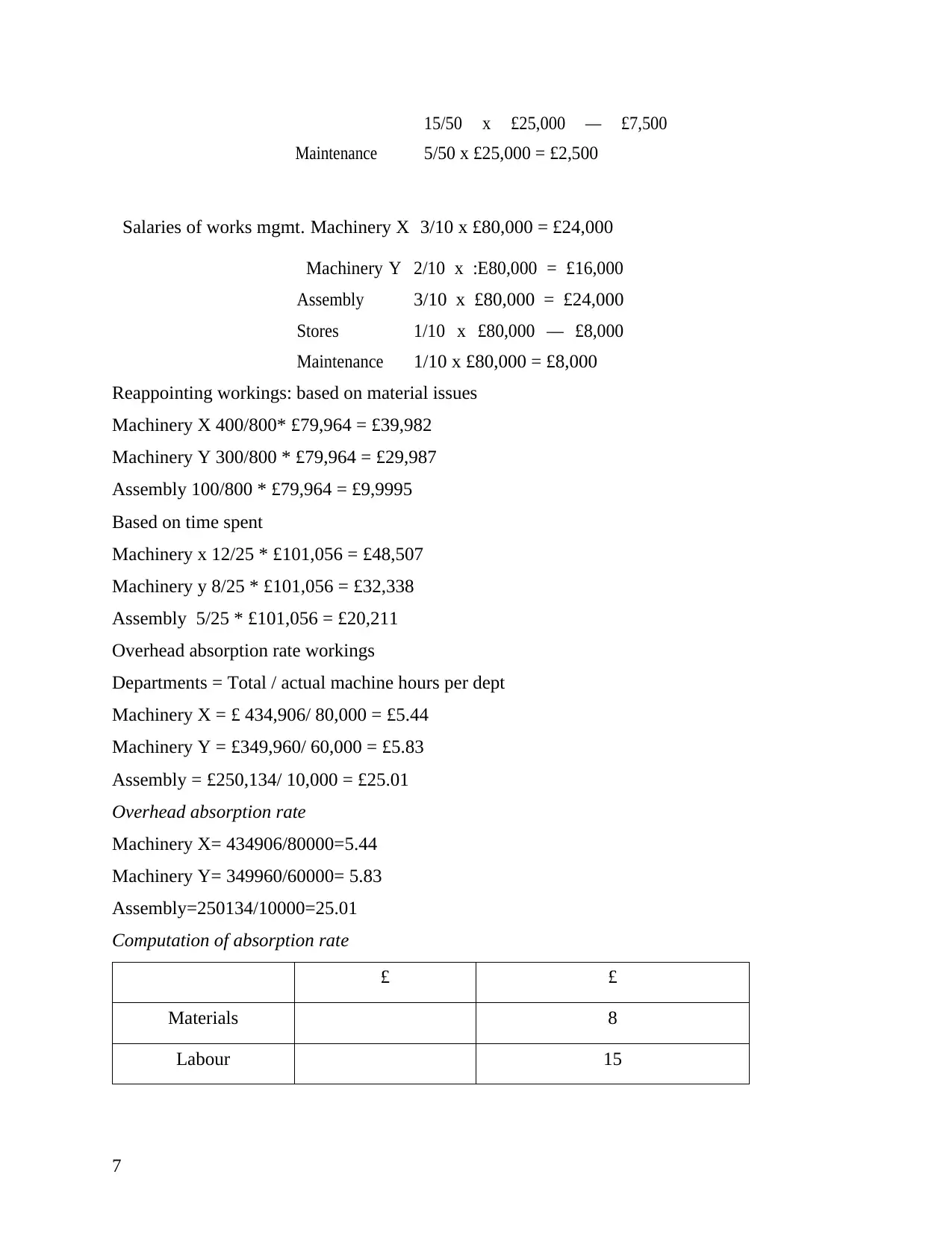
15/50 x £25,000 — £7,500
Maintenance 5/50 x £25,000 = £2,500
Salaries of works mgmt. Machinery X 3/10 x £80,000 = £24,000
Machinery Y 2/10 x :E80,000 = £16,000
Assembly 3/10 x £80,000 = £24,000
Stores 1/10 x £80,000 — £8,000
Maintenance 1/10 x £80,000 = £8,000
Reappointing workings: based on material issues
Machinery X 400/800* £79,964 = £39,982
Machinery Y 300/800 * £79,964 = £29,987
Assembly 100/800 * £79,964 = £9,9995
Based on time spent
Machinery x 12/25 * £101,056 = £48,507
Machinery y 8/25 * £101,056 = £32,338
Assembly 5/25 * £101,056 = £20,211
Overhead absorption rate workings
Departments = Total / actual machine hours per dept
Machinery X = £ 434,906/ 80,000 = £5.44
Machinery Y = £349,960/ 60,000 = £5.83
Assembly = £250,134/ 10,000 = £25.01
Overhead absorption rate
Machinery X= 434906/80000=5.44
Machinery Y= 349960/60000= 5.83
Assembly=250134/10000=25.01
Computation of absorption rate
£ £
Materials 8
Labour 15
7
Maintenance 5/50 x £25,000 = £2,500
Salaries of works mgmt. Machinery X 3/10 x £80,000 = £24,000
Machinery Y 2/10 x :E80,000 = £16,000
Assembly 3/10 x £80,000 = £24,000
Stores 1/10 x £80,000 — £8,000
Maintenance 1/10 x £80,000 = £8,000
Reappointing workings: based on material issues
Machinery X 400/800* £79,964 = £39,982
Machinery Y 300/800 * £79,964 = £29,987
Assembly 100/800 * £79,964 = £9,9995
Based on time spent
Machinery x 12/25 * £101,056 = £48,507
Machinery y 8/25 * £101,056 = £32,338
Assembly 5/25 * £101,056 = £20,211
Overhead absorption rate workings
Departments = Total / actual machine hours per dept
Machinery X = £ 434,906/ 80,000 = £5.44
Machinery Y = £349,960/ 60,000 = £5.83
Assembly = £250,134/ 10,000 = £25.01
Overhead absorption rate
Machinery X= 434906/80000=5.44
Machinery Y= 349960/60000= 5.83
Assembly=250134/10000=25.01
Computation of absorption rate
£ £
Materials 8
Labour 15
7
Paraphrase This Document
Need a fresh take? Get an instant paraphrase of this document with our AI Paraphraser
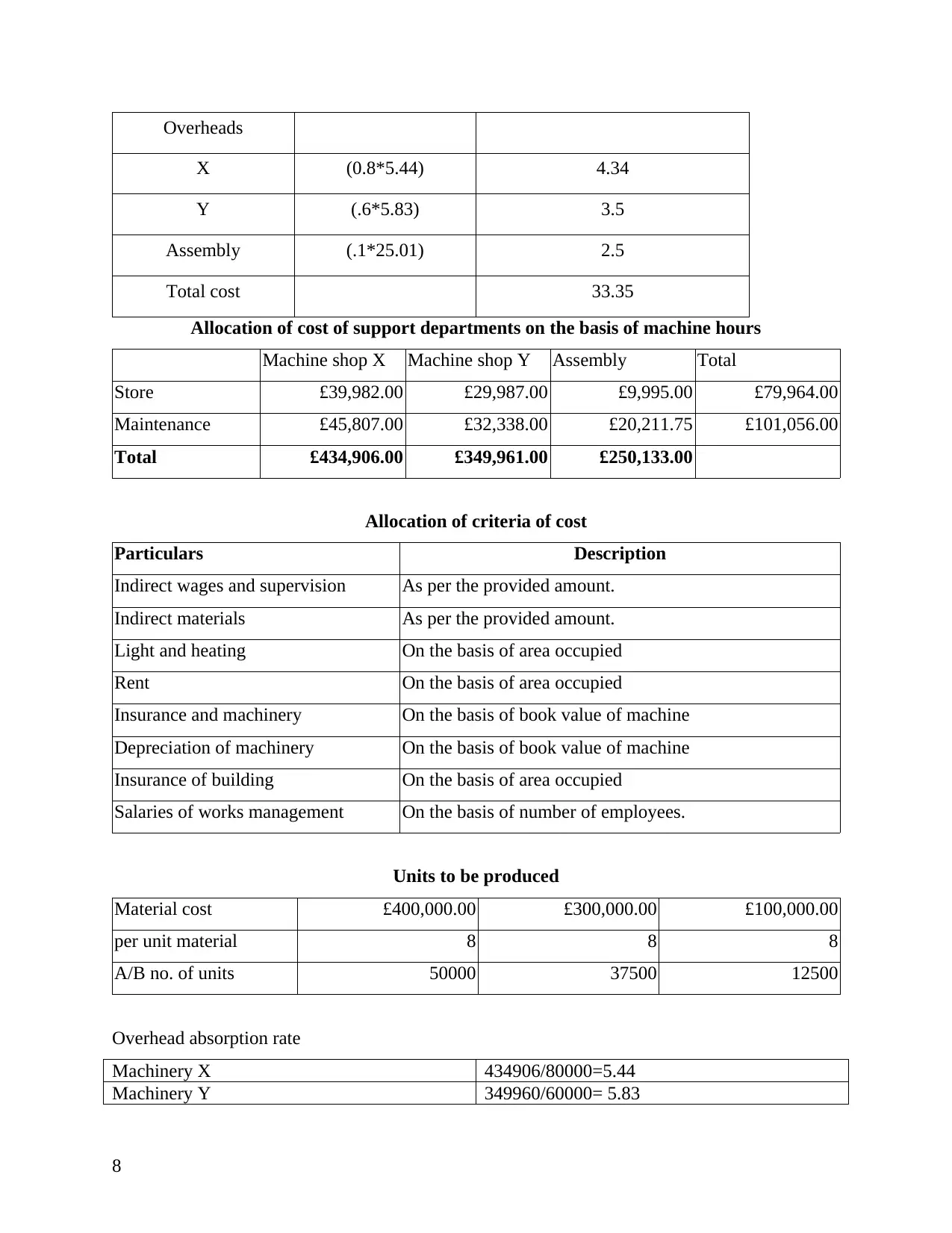
Overheads
X (0.8*5.44) 4.34
Y (.6*5.83) 3.5
Assembly (.1*25.01) 2.5
Total cost 33.35
Allocation of cost of support departments on the basis of machine hours
Machine shop X Machine shop Y Assembly Total
Store £39,982.00 £29,987.00 £9,995.00 £79,964.00
Maintenance £45,807.00 £32,338.00 £20,211.75 £101,056.00
Total £434,906.00 £349,961.00 £250,133.00
Allocation of criteria of cost
Particulars Description
Indirect wages and supervision As per the provided amount.
Indirect materials As per the provided amount.
Light and heating On the basis of area occupied
Rent On the basis of area occupied
Insurance and machinery On the basis of book value of machine
Depreciation of machinery On the basis of book value of machine
Insurance of building On the basis of area occupied
Salaries of works management On the basis of number of employees.
Units to be produced
Material cost £400,000.00 £300,000.00 £100,000.00
per unit material 8 8 8
A/B no. of units 50000 37500 12500
Overhead absorption rate
Machinery X 434906/80000=5.44
Machinery Y 349960/60000= 5.83
8
X (0.8*5.44) 4.34
Y (.6*5.83) 3.5
Assembly (.1*25.01) 2.5
Total cost 33.35
Allocation of cost of support departments on the basis of machine hours
Machine shop X Machine shop Y Assembly Total
Store £39,982.00 £29,987.00 £9,995.00 £79,964.00
Maintenance £45,807.00 £32,338.00 £20,211.75 £101,056.00
Total £434,906.00 £349,961.00 £250,133.00
Allocation of criteria of cost
Particulars Description
Indirect wages and supervision As per the provided amount.
Indirect materials As per the provided amount.
Light and heating On the basis of area occupied
Rent On the basis of area occupied
Insurance and machinery On the basis of book value of machine
Depreciation of machinery On the basis of book value of machine
Insurance of building On the basis of area occupied
Salaries of works management On the basis of number of employees.
Units to be produced
Material cost £400,000.00 £300,000.00 £100,000.00
per unit material 8 8 8
A/B no. of units 50000 37500 12500
Overhead absorption rate
Machinery X 434906/80000=5.44
Machinery Y 349960/60000= 5.83
8
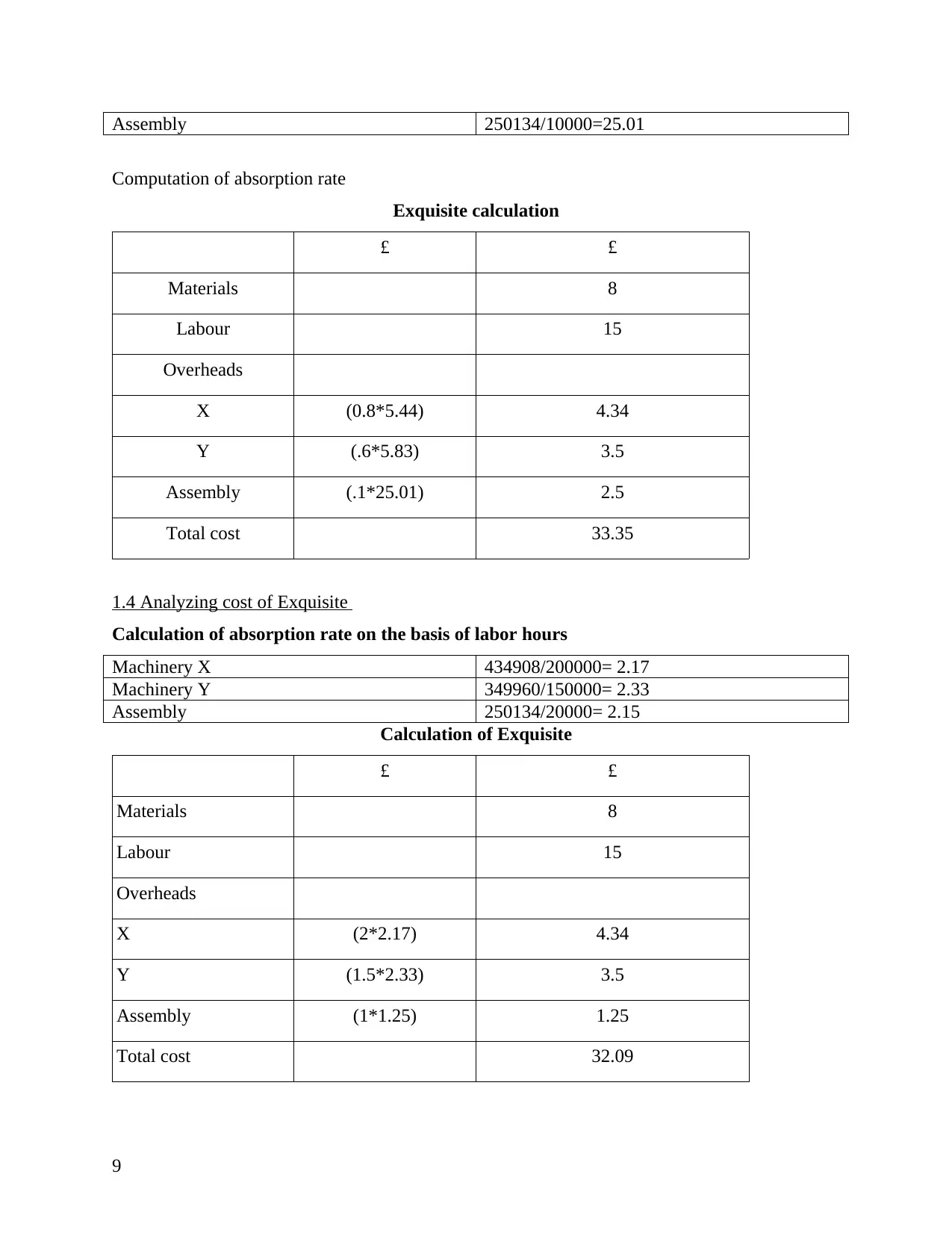
Assembly 250134/10000=25.01
Computation of absorption rate
Exquisite calculation
£ £
Materials 8
Labour 15
Overheads
X (0.8*5.44) 4.34
Y (.6*5.83) 3.5
Assembly (.1*25.01) 2.5
Total cost 33.35
1.4 Analyzing cost of Exquisite
Calculation of absorption rate on the basis of labor hours
Machinery X 434908/200000= 2.17
Machinery Y 349960/150000= 2.33
Assembly 250134/20000= 2.15
Calculation of Exquisite
£ £
Materials 8
Labour 15
Overheads
X (2*2.17) 4.34
Y (1.5*2.33) 3.5
Assembly (1*1.25) 1.25
Total cost 32.09
9
Computation of absorption rate
Exquisite calculation
£ £
Materials 8
Labour 15
Overheads
X (0.8*5.44) 4.34
Y (.6*5.83) 3.5
Assembly (.1*25.01) 2.5
Total cost 33.35
1.4 Analyzing cost of Exquisite
Calculation of absorption rate on the basis of labor hours
Machinery X 434908/200000= 2.17
Machinery Y 349960/150000= 2.33
Assembly 250134/20000= 2.15
Calculation of Exquisite
£ £
Materials 8
Labour 15
Overheads
X (2*2.17) 4.34
Y (1.5*2.33) 3.5
Assembly (1*1.25) 1.25
Total cost 32.09
9
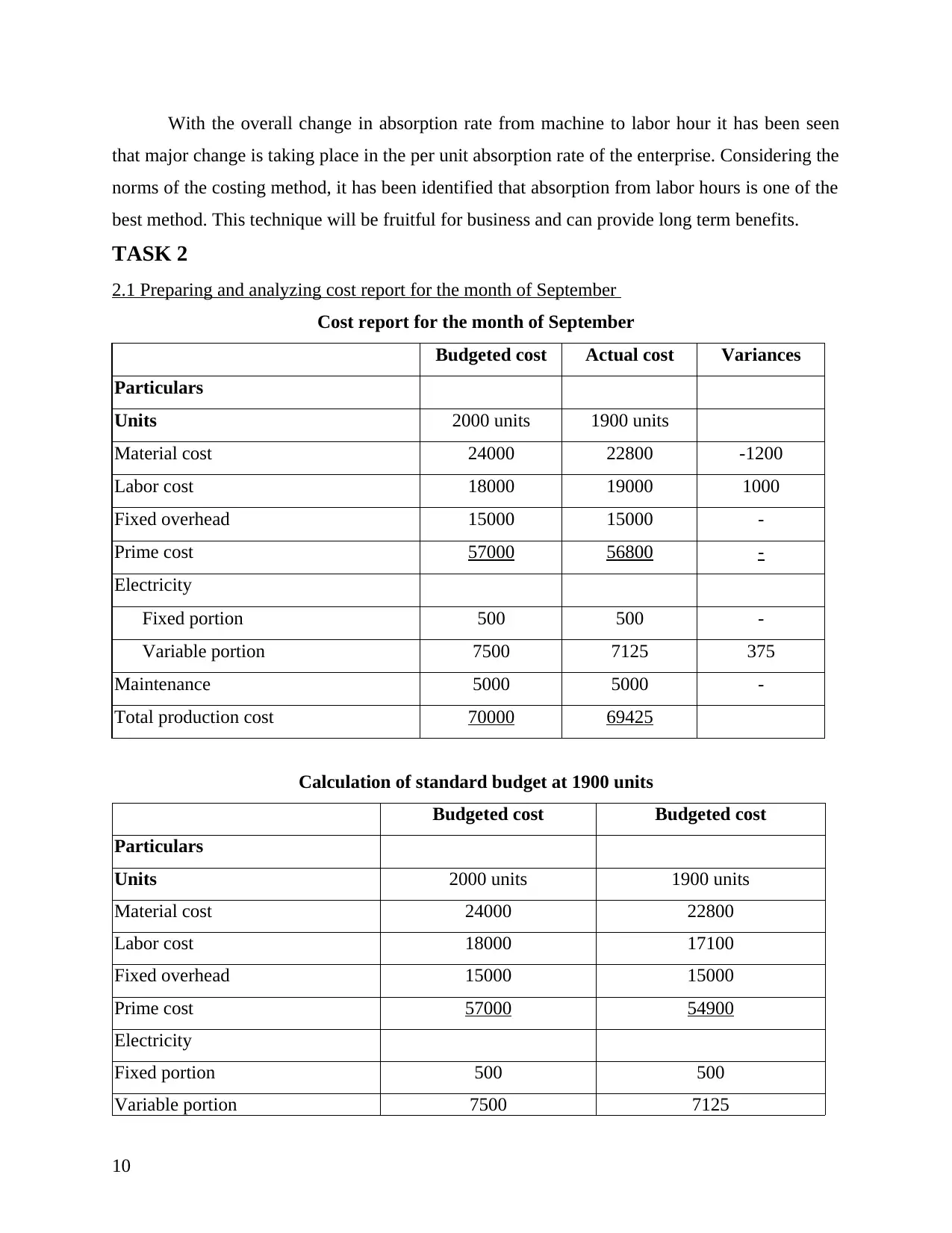
With the overall change in absorption rate from machine to labor hour it has been seen
that major change is taking place in the per unit absorption rate of the enterprise. Considering the
norms of the costing method, it has been identified that absorption from labor hours is one of the
best method. This technique will be fruitful for business and can provide long term benefits.
TASK 2
2.1 Preparing and analyzing cost report for the month of September
Cost report for the month of September
Budgeted cost Actual cost Variances
Particulars
Units 2000 units 1900 units
Material cost 24000 22800 -1200
Labor cost 18000 19000 1000
Fixed overhead 15000 15000 -
Prime cost 57000 56800 -
Electricity
Fixed portion 500 500 -
Variable portion 7500 7125 375
Maintenance 5000 5000 -
Total production cost 70000 69425
Calculation of standard budget at 1900 units
Budgeted cost Budgeted cost
Particulars
Units 2000 units 1900 units
Material cost 24000 22800
Labor cost 18000 17100
Fixed overhead 15000 15000
Prime cost 57000 54900
Electricity
Fixed portion 500 500
Variable portion 7500 7125
10
that major change is taking place in the per unit absorption rate of the enterprise. Considering the
norms of the costing method, it has been identified that absorption from labor hours is one of the
best method. This technique will be fruitful for business and can provide long term benefits.
TASK 2
2.1 Preparing and analyzing cost report for the month of September
Cost report for the month of September
Budgeted cost Actual cost Variances
Particulars
Units 2000 units 1900 units
Material cost 24000 22800 -1200
Labor cost 18000 19000 1000
Fixed overhead 15000 15000 -
Prime cost 57000 56800 -
Electricity
Fixed portion 500 500 -
Variable portion 7500 7125 375
Maintenance 5000 5000 -
Total production cost 70000 69425
Calculation of standard budget at 1900 units
Budgeted cost Budgeted cost
Particulars
Units 2000 units 1900 units
Material cost 24000 22800
Labor cost 18000 17100
Fixed overhead 15000 15000
Prime cost 57000 54900
Electricity
Fixed portion 500 500
Variable portion 7500 7125
10
Secure Best Marks with AI Grader
Need help grading? Try our AI Grader for instant feedback on your assignments.
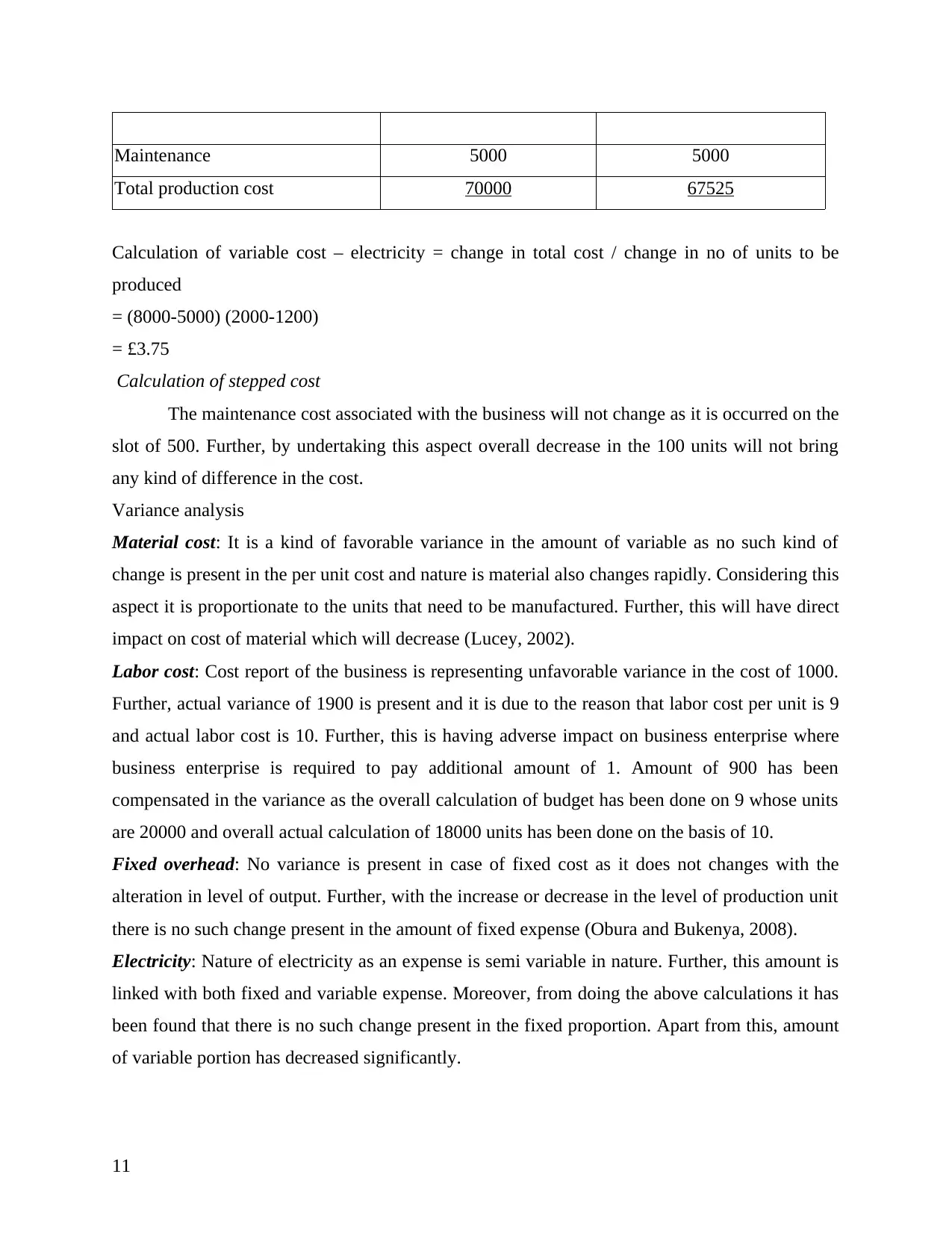
Maintenance 5000 5000
Total production cost 70000 67525
Calculation of variable cost – electricity = change in total cost / change in no of units to be
produced
= (8000-5000) (2000-1200)
= £3.75
Calculation of stepped cost
The maintenance cost associated with the business will not change as it is occurred on the
slot of 500. Further, by undertaking this aspect overall decrease in the 100 units will not bring
any kind of difference in the cost.
Variance analysis
Material cost: It is a kind of favorable variance in the amount of variable as no such kind of
change is present in the per unit cost and nature is material also changes rapidly. Considering this
aspect it is proportionate to the units that need to be manufactured. Further, this will have direct
impact on cost of material which will decrease (Lucey, 2002).
Labor cost: Cost report of the business is representing unfavorable variance in the cost of 1000.
Further, actual variance of 1900 is present and it is due to the reason that labor cost per unit is 9
and actual labor cost is 10. Further, this is having adverse impact on business enterprise where
business enterprise is required to pay additional amount of 1. Amount of 900 has been
compensated in the variance as the overall calculation of budget has been done on 9 whose units
are 20000 and overall actual calculation of 18000 units has been done on the basis of 10.
Fixed overhead: No variance is present in case of fixed cost as it does not changes with the
alteration in level of output. Further, with the increase or decrease in the level of production unit
there is no such change present in the amount of fixed expense (Obura and Bukenya, 2008).
Electricity: Nature of electricity as an expense is semi variable in nature. Further, this amount is
linked with both fixed and variable expense. Moreover, from doing the above calculations it has
been found that there is no such change present in the fixed proportion. Apart from this, amount
of variable portion has decreased significantly.
11
Total production cost 70000 67525
Calculation of variable cost – electricity = change in total cost / change in no of units to be
produced
= (8000-5000) (2000-1200)
= £3.75
Calculation of stepped cost
The maintenance cost associated with the business will not change as it is occurred on the
slot of 500. Further, by undertaking this aspect overall decrease in the 100 units will not bring
any kind of difference in the cost.
Variance analysis
Material cost: It is a kind of favorable variance in the amount of variable as no such kind of
change is present in the per unit cost and nature is material also changes rapidly. Considering this
aspect it is proportionate to the units that need to be manufactured. Further, this will have direct
impact on cost of material which will decrease (Lucey, 2002).
Labor cost: Cost report of the business is representing unfavorable variance in the cost of 1000.
Further, actual variance of 1900 is present and it is due to the reason that labor cost per unit is 9
and actual labor cost is 10. Further, this is having adverse impact on business enterprise where
business enterprise is required to pay additional amount of 1. Amount of 900 has been
compensated in the variance as the overall calculation of budget has been done on 9 whose units
are 20000 and overall actual calculation of 18000 units has been done on the basis of 10.
Fixed overhead: No variance is present in case of fixed cost as it does not changes with the
alteration in level of output. Further, with the increase or decrease in the level of production unit
there is no such change present in the amount of fixed expense (Obura and Bukenya, 2008).
Electricity: Nature of electricity as an expense is semi variable in nature. Further, this amount is
linked with both fixed and variable expense. Moreover, from doing the above calculations it has
been found that there is no such change present in the fixed proportion. Apart from this, amount
of variable portion has decreased significantly.
11
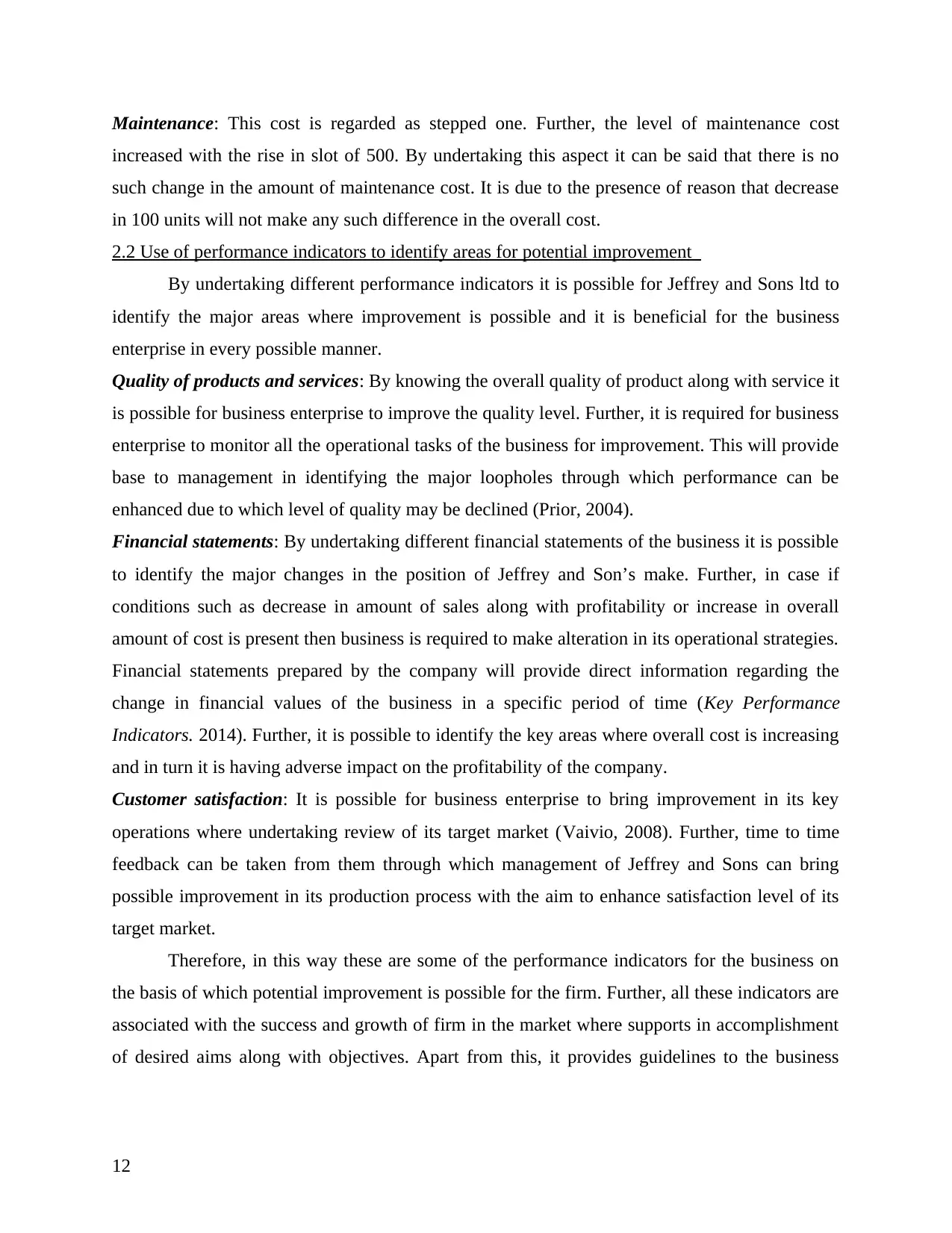
Maintenance: This cost is regarded as stepped one. Further, the level of maintenance cost
increased with the rise in slot of 500. By undertaking this aspect it can be said that there is no
such change in the amount of maintenance cost. It is due to the presence of reason that decrease
in 100 units will not make any such difference in the overall cost.
2.2 Use of performance indicators to identify areas for potential improvement
By undertaking different performance indicators it is possible for Jeffrey and Sons ltd to
identify the major areas where improvement is possible and it is beneficial for the business
enterprise in every possible manner.
Quality of products and services: By knowing the overall quality of product along with service it
is possible for business enterprise to improve the quality level. Further, it is required for business
enterprise to monitor all the operational tasks of the business for improvement. This will provide
base to management in identifying the major loopholes through which performance can be
enhanced due to which level of quality may be declined (Prior, 2004).
Financial statements: By undertaking different financial statements of the business it is possible
to identify the major changes in the position of Jeffrey and Son’s make. Further, in case if
conditions such as decrease in amount of sales along with profitability or increase in overall
amount of cost is present then business is required to make alteration in its operational strategies.
Financial statements prepared by the company will provide direct information regarding the
change in financial values of the business in a specific period of time (Key Performance
Indicators. 2014). Further, it is possible to identify the key areas where overall cost is increasing
and in turn it is having adverse impact on the profitability of the company.
Customer satisfaction: It is possible for business enterprise to bring improvement in its key
operations where undertaking review of its target market (Vaivio, 2008). Further, time to time
feedback can be taken from them through which management of Jeffrey and Sons can bring
possible improvement in its production process with the aim to enhance satisfaction level of its
target market.
Therefore, in this way these are some of the performance indicators for the business on
the basis of which potential improvement is possible for the firm. Further, all these indicators are
associated with the success and growth of firm in the market where supports in accomplishment
of desired aims along with objectives. Apart from this, it provides guidelines to the business
12
increased with the rise in slot of 500. By undertaking this aspect it can be said that there is no
such change in the amount of maintenance cost. It is due to the presence of reason that decrease
in 100 units will not make any such difference in the overall cost.
2.2 Use of performance indicators to identify areas for potential improvement
By undertaking different performance indicators it is possible for Jeffrey and Sons ltd to
identify the major areas where improvement is possible and it is beneficial for the business
enterprise in every possible manner.
Quality of products and services: By knowing the overall quality of product along with service it
is possible for business enterprise to improve the quality level. Further, it is required for business
enterprise to monitor all the operational tasks of the business for improvement. This will provide
base to management in identifying the major loopholes through which performance can be
enhanced due to which level of quality may be declined (Prior, 2004).
Financial statements: By undertaking different financial statements of the business it is possible
to identify the major changes in the position of Jeffrey and Son’s make. Further, in case if
conditions such as decrease in amount of sales along with profitability or increase in overall
amount of cost is present then business is required to make alteration in its operational strategies.
Financial statements prepared by the company will provide direct information regarding the
change in financial values of the business in a specific period of time (Key Performance
Indicators. 2014). Further, it is possible to identify the key areas where overall cost is increasing
and in turn it is having adverse impact on the profitability of the company.
Customer satisfaction: It is possible for business enterprise to bring improvement in its key
operations where undertaking review of its target market (Vaivio, 2008). Further, time to time
feedback can be taken from them through which management of Jeffrey and Sons can bring
possible improvement in its production process with the aim to enhance satisfaction level of its
target market.
Therefore, in this way these are some of the performance indicators for the business on
the basis of which potential improvement is possible for the firm. Further, all these indicators are
associated with the success and growth of firm in the market where supports in accomplishment
of desired aims along with objectives. Apart from this, it provides guidelines to the business
12
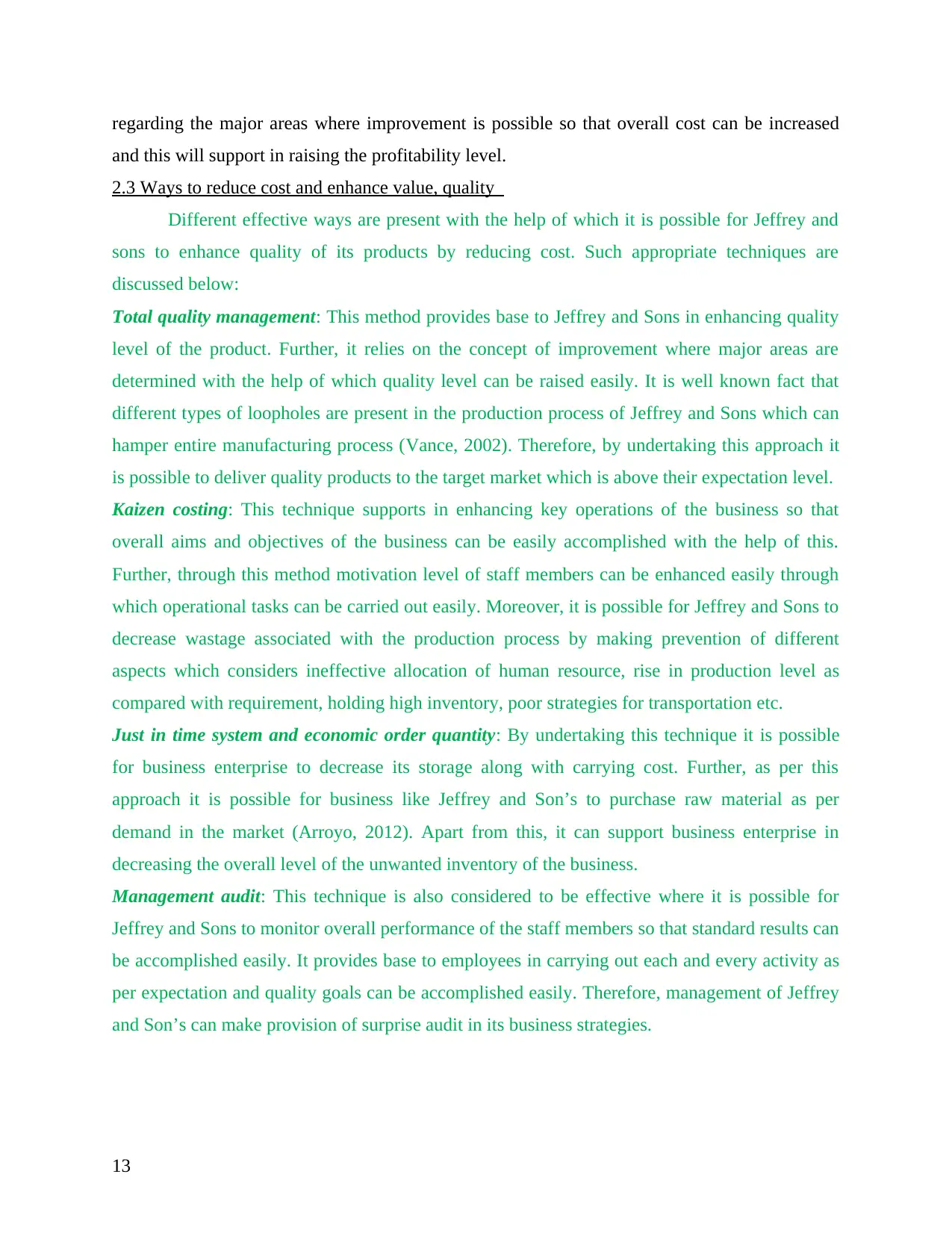
regarding the major areas where improvement is possible so that overall cost can be increased
and this will support in raising the profitability level.
2.3 Ways to reduce cost and enhance value, quality
Different effective ways are present with the help of which it is possible for Jeffrey and
sons to enhance quality of its products by reducing cost. Such appropriate techniques are
discussed below:
Total quality management: This method provides base to Jeffrey and Sons in enhancing quality
level of the product. Further, it relies on the concept of improvement where major areas are
determined with the help of which quality level can be raised easily. It is well known fact that
different types of loopholes are present in the production process of Jeffrey and Sons which can
hamper entire manufacturing process (Vance, 2002). Therefore, by undertaking this approach it
is possible to deliver quality products to the target market which is above their expectation level.
Kaizen costing: This technique supports in enhancing key operations of the business so that
overall aims and objectives of the business can be easily accomplished with the help of this.
Further, through this method motivation level of staff members can be enhanced easily through
which operational tasks can be carried out easily. Moreover, it is possible for Jeffrey and Sons to
decrease wastage associated with the production process by making prevention of different
aspects which considers ineffective allocation of human resource, rise in production level as
compared with requirement, holding high inventory, poor strategies for transportation etc.
Just in time system and economic order quantity: By undertaking this technique it is possible
for business enterprise to decrease its storage along with carrying cost. Further, as per this
approach it is possible for business like Jeffrey and Son’s to purchase raw material as per
demand in the market (Arroyo, 2012). Apart from this, it can support business enterprise in
decreasing the overall level of the unwanted inventory of the business.
Management audit: This technique is also considered to be effective where it is possible for
Jeffrey and Sons to monitor overall performance of the staff members so that standard results can
be accomplished easily. It provides base to employees in carrying out each and every activity as
per expectation and quality goals can be accomplished easily. Therefore, management of Jeffrey
and Son’s can make provision of surprise audit in its business strategies.
13
and this will support in raising the profitability level.
2.3 Ways to reduce cost and enhance value, quality
Different effective ways are present with the help of which it is possible for Jeffrey and
sons to enhance quality of its products by reducing cost. Such appropriate techniques are
discussed below:
Total quality management: This method provides base to Jeffrey and Sons in enhancing quality
level of the product. Further, it relies on the concept of improvement where major areas are
determined with the help of which quality level can be raised easily. It is well known fact that
different types of loopholes are present in the production process of Jeffrey and Sons which can
hamper entire manufacturing process (Vance, 2002). Therefore, by undertaking this approach it
is possible to deliver quality products to the target market which is above their expectation level.
Kaizen costing: This technique supports in enhancing key operations of the business so that
overall aims and objectives of the business can be easily accomplished with the help of this.
Further, through this method motivation level of staff members can be enhanced easily through
which operational tasks can be carried out easily. Moreover, it is possible for Jeffrey and Sons to
decrease wastage associated with the production process by making prevention of different
aspects which considers ineffective allocation of human resource, rise in production level as
compared with requirement, holding high inventory, poor strategies for transportation etc.
Just in time system and economic order quantity: By undertaking this technique it is possible
for business enterprise to decrease its storage along with carrying cost. Further, as per this
approach it is possible for business like Jeffrey and Son’s to purchase raw material as per
demand in the market (Arroyo, 2012). Apart from this, it can support business enterprise in
decreasing the overall level of the unwanted inventory of the business.
Management audit: This technique is also considered to be effective where it is possible for
Jeffrey and Sons to monitor overall performance of the staff members so that standard results can
be accomplished easily. It provides base to employees in carrying out each and every activity as
per expectation and quality goals can be accomplished easily. Therefore, management of Jeffrey
and Son’s can make provision of surprise audit in its business strategies.
13
Paraphrase This Document
Need a fresh take? Get an instant paraphrase of this document with our AI Paraphraser
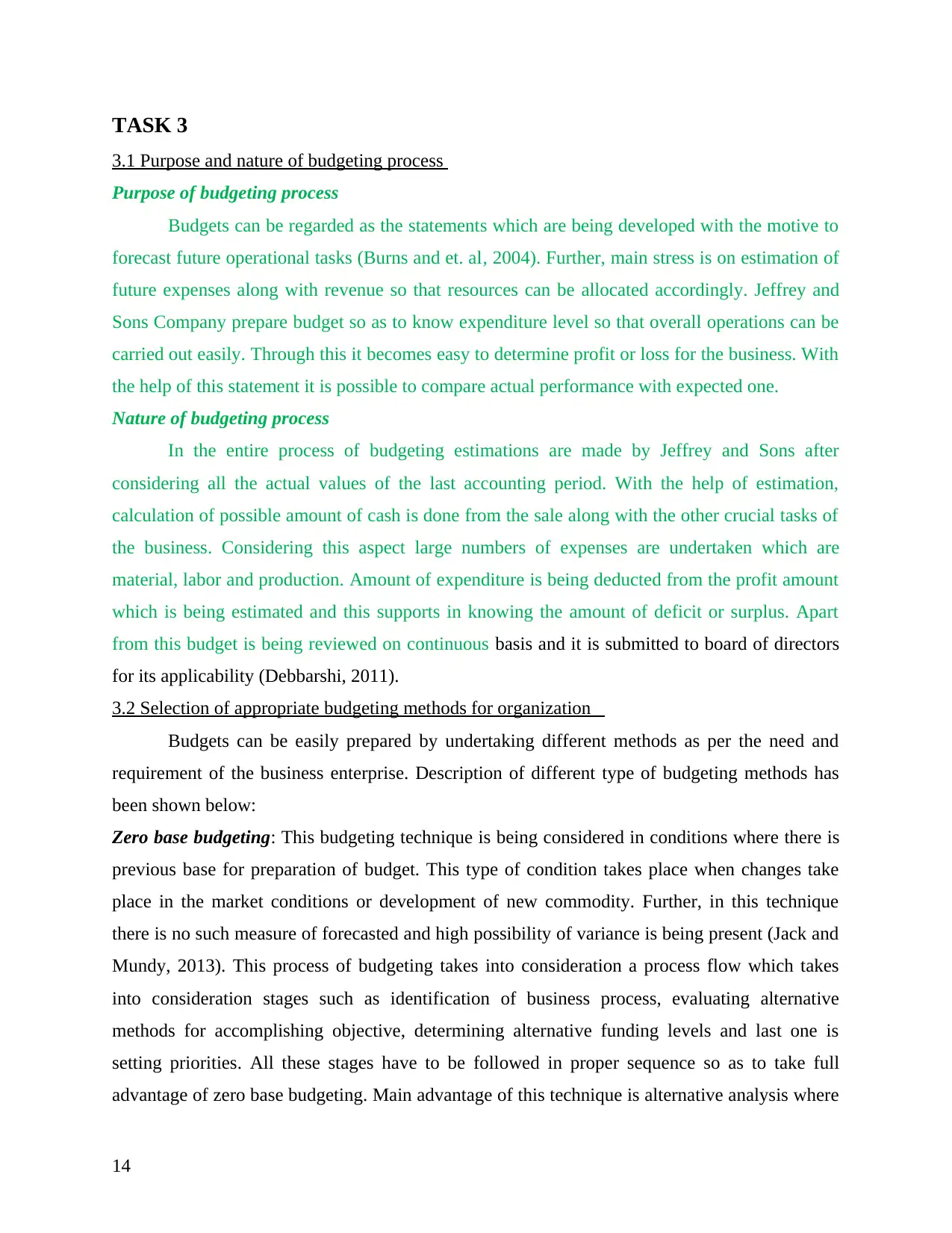
TASK 3
3.1 Purpose and nature of budgeting process
Purpose of budgeting process
Budgets can be regarded as the statements which are being developed with the motive to
forecast future operational tasks (Burns and et. al, 2004). Further, main stress is on estimation of
future expenses along with revenue so that resources can be allocated accordingly. Jeffrey and
Sons Company prepare budget so as to know expenditure level so that overall operations can be
carried out easily. Through this it becomes easy to determine profit or loss for the business. With
the help of this statement it is possible to compare actual performance with expected one.
Nature of budgeting process
In the entire process of budgeting estimations are made by Jeffrey and Sons after
considering all the actual values of the last accounting period. With the help of estimation,
calculation of possible amount of cash is done from the sale along with the other crucial tasks of
the business. Considering this aspect large numbers of expenses are undertaken which are
material, labor and production. Amount of expenditure is being deducted from the profit amount
which is being estimated and this supports in knowing the amount of deficit or surplus. Apart
from this budget is being reviewed on continuous basis and it is submitted to board of directors
for its applicability (Debbarshi, 2011).
3.2 Selection of appropriate budgeting methods for organization
Budgets can be easily prepared by undertaking different methods as per the need and
requirement of the business enterprise. Description of different type of budgeting methods has
been shown below:
Zero base budgeting: This budgeting technique is being considered in conditions where there is
previous base for preparation of budget. This type of condition takes place when changes take
place in the market conditions or development of new commodity. Further, in this technique
there is no such measure of forecasted and high possibility of variance is being present (Jack and
Mundy, 2013). This process of budgeting takes into consideration a process flow which takes
into consideration stages such as identification of business process, evaluating alternative
methods for accomplishing objective, determining alternative funding levels and last one is
setting priorities. All these stages have to be followed in proper sequence so as to take full
advantage of zero base budgeting. Main advantage of this technique is alternative analysis where
14
3.1 Purpose and nature of budgeting process
Purpose of budgeting process
Budgets can be regarded as the statements which are being developed with the motive to
forecast future operational tasks (Burns and et. al, 2004). Further, main stress is on estimation of
future expenses along with revenue so that resources can be allocated accordingly. Jeffrey and
Sons Company prepare budget so as to know expenditure level so that overall operations can be
carried out easily. Through this it becomes easy to determine profit or loss for the business. With
the help of this statement it is possible to compare actual performance with expected one.
Nature of budgeting process
In the entire process of budgeting estimations are made by Jeffrey and Sons after
considering all the actual values of the last accounting period. With the help of estimation,
calculation of possible amount of cash is done from the sale along with the other crucial tasks of
the business. Considering this aspect large numbers of expenses are undertaken which are
material, labor and production. Amount of expenditure is being deducted from the profit amount
which is being estimated and this supports in knowing the amount of deficit or surplus. Apart
from this budget is being reviewed on continuous basis and it is submitted to board of directors
for its applicability (Debbarshi, 2011).
3.2 Selection of appropriate budgeting methods for organization
Budgets can be easily prepared by undertaking different methods as per the need and
requirement of the business enterprise. Description of different type of budgeting methods has
been shown below:
Zero base budgeting: This budgeting technique is being considered in conditions where there is
previous base for preparation of budget. This type of condition takes place when changes take
place in the market conditions or development of new commodity. Further, in this technique
there is no such measure of forecasted and high possibility of variance is being present (Jack and
Mundy, 2013). This process of budgeting takes into consideration a process flow which takes
into consideration stages such as identification of business process, evaluating alternative
methods for accomplishing objective, determining alternative funding levels and last one is
setting priorities. All these stages have to be followed in proper sequence so as to take full
advantage of zero base budgeting. Main advantage of this technique is alternative analysis where
14
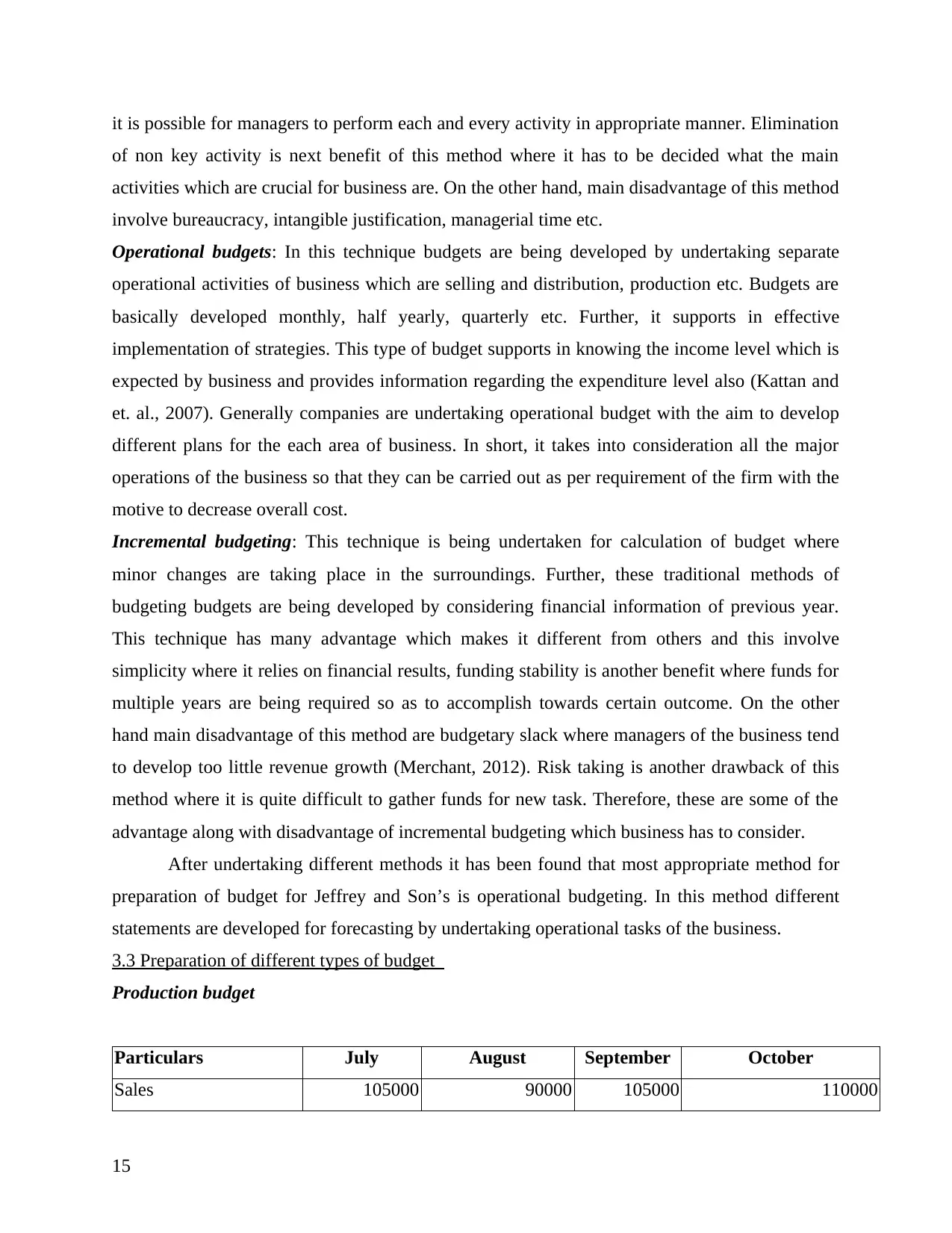
it is possible for managers to perform each and every activity in appropriate manner. Elimination
of non key activity is next benefit of this method where it has to be decided what the main
activities which are crucial for business are. On the other hand, main disadvantage of this method
involve bureaucracy, intangible justification, managerial time etc.
Operational budgets: In this technique budgets are being developed by undertaking separate
operational activities of business which are selling and distribution, production etc. Budgets are
basically developed monthly, half yearly, quarterly etc. Further, it supports in effective
implementation of strategies. This type of budget supports in knowing the income level which is
expected by business and provides information regarding the expenditure level also (Kattan and
et. al., 2007). Generally companies are undertaking operational budget with the aim to develop
different plans for the each area of business. In short, it takes into consideration all the major
operations of the business so that they can be carried out as per requirement of the firm with the
motive to decrease overall cost.
Incremental budgeting: This technique is being undertaken for calculation of budget where
minor changes are taking place in the surroundings. Further, these traditional methods of
budgeting budgets are being developed by considering financial information of previous year.
This technique has many advantage which makes it different from others and this involve
simplicity where it relies on financial results, funding stability is another benefit where funds for
multiple years are being required so as to accomplish towards certain outcome. On the other
hand main disadvantage of this method are budgetary slack where managers of the business tend
to develop too little revenue growth (Merchant, 2012). Risk taking is another drawback of this
method where it is quite difficult to gather funds for new task. Therefore, these are some of the
advantage along with disadvantage of incremental budgeting which business has to consider.
After undertaking different methods it has been found that most appropriate method for
preparation of budget for Jeffrey and Son’s is operational budgeting. In this method different
statements are developed for forecasting by undertaking operational tasks of the business.
3.3 Preparation of different types of budget
Production budget
Particulars July August September October
Sales 105000 90000 105000 110000
15
of non key activity is next benefit of this method where it has to be decided what the main
activities which are crucial for business are. On the other hand, main disadvantage of this method
involve bureaucracy, intangible justification, managerial time etc.
Operational budgets: In this technique budgets are being developed by undertaking separate
operational activities of business which are selling and distribution, production etc. Budgets are
basically developed monthly, half yearly, quarterly etc. Further, it supports in effective
implementation of strategies. This type of budget supports in knowing the income level which is
expected by business and provides information regarding the expenditure level also (Kattan and
et. al., 2007). Generally companies are undertaking operational budget with the aim to develop
different plans for the each area of business. In short, it takes into consideration all the major
operations of the business so that they can be carried out as per requirement of the firm with the
motive to decrease overall cost.
Incremental budgeting: This technique is being undertaken for calculation of budget where
minor changes are taking place in the surroundings. Further, these traditional methods of
budgeting budgets are being developed by considering financial information of previous year.
This technique has many advantage which makes it different from others and this involve
simplicity where it relies on financial results, funding stability is another benefit where funds for
multiple years are being required so as to accomplish towards certain outcome. On the other
hand main disadvantage of this method are budgetary slack where managers of the business tend
to develop too little revenue growth (Merchant, 2012). Risk taking is another drawback of this
method where it is quite difficult to gather funds for new task. Therefore, these are some of the
advantage along with disadvantage of incremental budgeting which business has to consider.
After undertaking different methods it has been found that most appropriate method for
preparation of budget for Jeffrey and Son’s is operational budgeting. In this method different
statements are developed for forecasting by undertaking operational tasks of the business.
3.3 Preparation of different types of budget
Production budget
Particulars July August September October
Sales 105000 90000 105000 110000
15
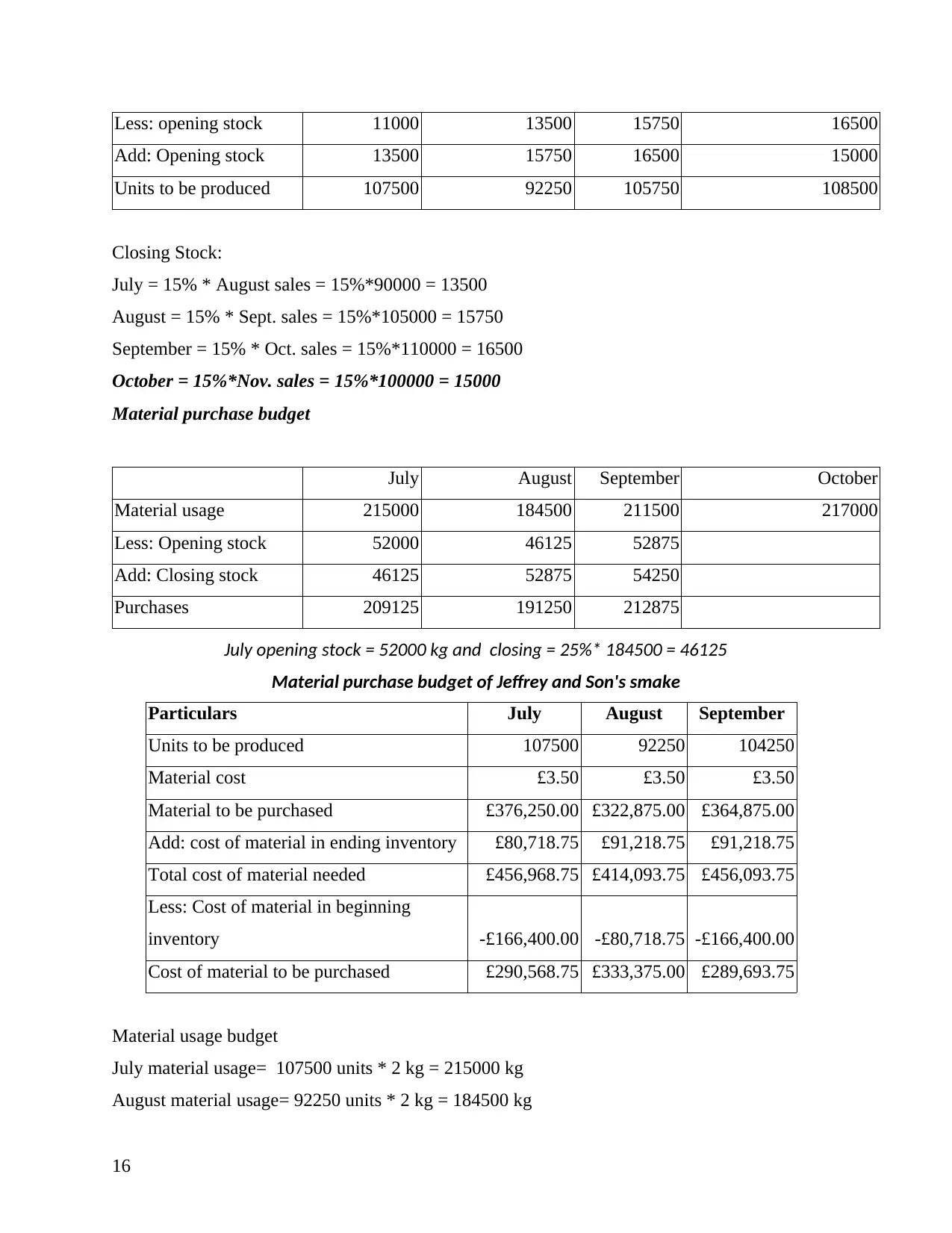
Less: opening stock 11000 13500 15750 16500
Add: Opening stock 13500 15750 16500 15000
Units to be produced 107500 92250 105750 108500
Closing Stock:
July = 15% * August sales = 15%*90000 = 13500
August = 15% * Sept. sales = 15%*105000 = 15750
September = 15% * Oct. sales = 15%*110000 = 16500
October = 15%*Nov. sales = 15%*100000 = 15000
Material purchase budget
July August September October
Material usage 215000 184500 211500 217000
Less: Opening stock 52000 46125 52875
Add: Closing stock 46125 52875 54250
Purchases 209125 191250 212875
July opening stock = 52000 kg and closing = 25%* 184500 = 46125
Material purchase budget of Jeffrey and Son's smake
Particulars July August September
Units to be produced 107500 92250 104250
Material cost £3.50 £3.50 £3.50
Material to be purchased £376,250.00 £322,875.00 £364,875.00
Add: cost of material in ending inventory £80,718.75 £91,218.75 £91,218.75
Total cost of material needed £456,968.75 £414,093.75 £456,093.75
Less: Cost of material in beginning
inventory -£166,400.00 -£80,718.75 -£166,400.00
Cost of material to be purchased £290,568.75 £333,375.00 £289,693.75
Material usage budget
July material usage= 107500 units * 2 kg = 215000 kg
August material usage= 92250 units * 2 kg = 184500 kg
16
Add: Opening stock 13500 15750 16500 15000
Units to be produced 107500 92250 105750 108500
Closing Stock:
July = 15% * August sales = 15%*90000 = 13500
August = 15% * Sept. sales = 15%*105000 = 15750
September = 15% * Oct. sales = 15%*110000 = 16500
October = 15%*Nov. sales = 15%*100000 = 15000
Material purchase budget
July August September October
Material usage 215000 184500 211500 217000
Less: Opening stock 52000 46125 52875
Add: Closing stock 46125 52875 54250
Purchases 209125 191250 212875
July opening stock = 52000 kg and closing = 25%* 184500 = 46125
Material purchase budget of Jeffrey and Son's smake
Particulars July August September
Units to be produced 107500 92250 104250
Material cost £3.50 £3.50 £3.50
Material to be purchased £376,250.00 £322,875.00 £364,875.00
Add: cost of material in ending inventory £80,718.75 £91,218.75 £91,218.75
Total cost of material needed £456,968.75 £414,093.75 £456,093.75
Less: Cost of material in beginning
inventory -£166,400.00 -£80,718.75 -£166,400.00
Cost of material to be purchased £290,568.75 £333,375.00 £289,693.75
Material usage budget
July material usage= 107500 units * 2 kg = 215000 kg
August material usage= 92250 units * 2 kg = 184500 kg
16
Secure Best Marks with AI Grader
Need help grading? Try our AI Grader for instant feedback on your assignments.
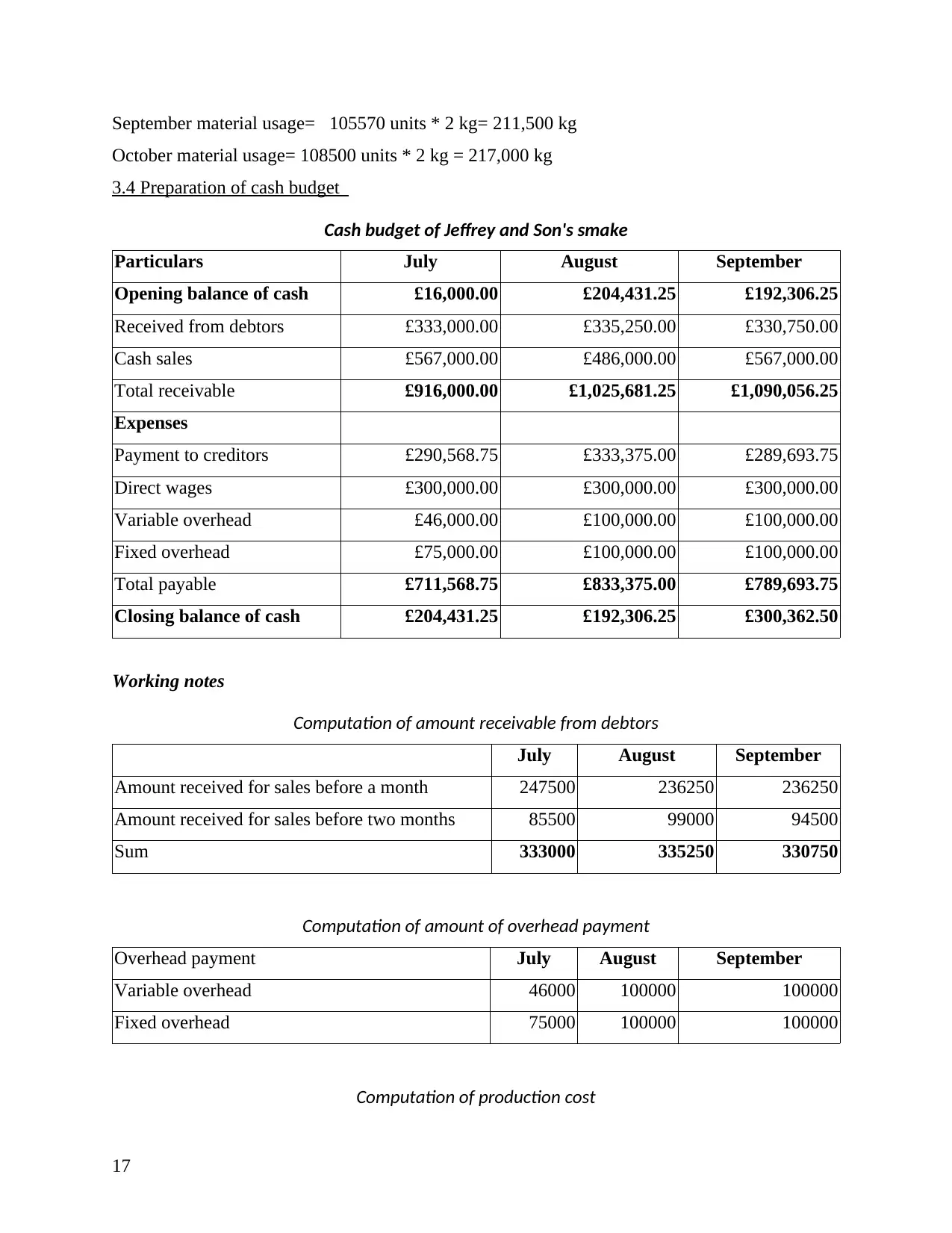
September material usage= 105570 units * 2 kg= 211,500 kg
October material usage= 108500 units * 2 kg = 217,000 kg
3.4 Preparation of cash budget
Cash budget of Jeffrey and Son's smake
Particulars July August September
Opening balance of cash £16,000.00 £204,431.25 £192,306.25
Received from debtors £333,000.00 £335,250.00 £330,750.00
Cash sales £567,000.00 £486,000.00 £567,000.00
Total receivable £916,000.00 £1,025,681.25 £1,090,056.25
Expenses
Payment to creditors £290,568.75 £333,375.00 £289,693.75
Direct wages £300,000.00 £300,000.00 £300,000.00
Variable overhead £46,000.00 £100,000.00 £100,000.00
Fixed overhead £75,000.00 £100,000.00 £100,000.00
Total payable £711,568.75 £833,375.00 £789,693.75
Closing balance of cash £204,431.25 £192,306.25 £300,362.50
Working notes
Computation of amount receivable from debtors
July August September
Amount received for sales before a month 247500 236250 236250
Amount received for sales before two months 85500 99000 94500
Sum 333000 335250 330750
Computation of amount of overhead payment
Overhead payment July August September
Variable overhead 46000 100000 100000
Fixed overhead 75000 100000 100000
Computation of production cost
17
October material usage= 108500 units * 2 kg = 217,000 kg
3.4 Preparation of cash budget
Cash budget of Jeffrey and Son's smake
Particulars July August September
Opening balance of cash £16,000.00 £204,431.25 £192,306.25
Received from debtors £333,000.00 £335,250.00 £330,750.00
Cash sales £567,000.00 £486,000.00 £567,000.00
Total receivable £916,000.00 £1,025,681.25 £1,090,056.25
Expenses
Payment to creditors £290,568.75 £333,375.00 £289,693.75
Direct wages £300,000.00 £300,000.00 £300,000.00
Variable overhead £46,000.00 £100,000.00 £100,000.00
Fixed overhead £75,000.00 £100,000.00 £100,000.00
Total payable £711,568.75 £833,375.00 £789,693.75
Closing balance of cash £204,431.25 £192,306.25 £300,362.50
Working notes
Computation of amount receivable from debtors
July August September
Amount received for sales before a month 247500 236250 236250
Amount received for sales before two months 85500 99000 94500
Sum 333000 335250 330750
Computation of amount of overhead payment
Overhead payment July August September
Variable overhead 46000 100000 100000
Fixed overhead 75000 100000 100000
Computation of production cost
17
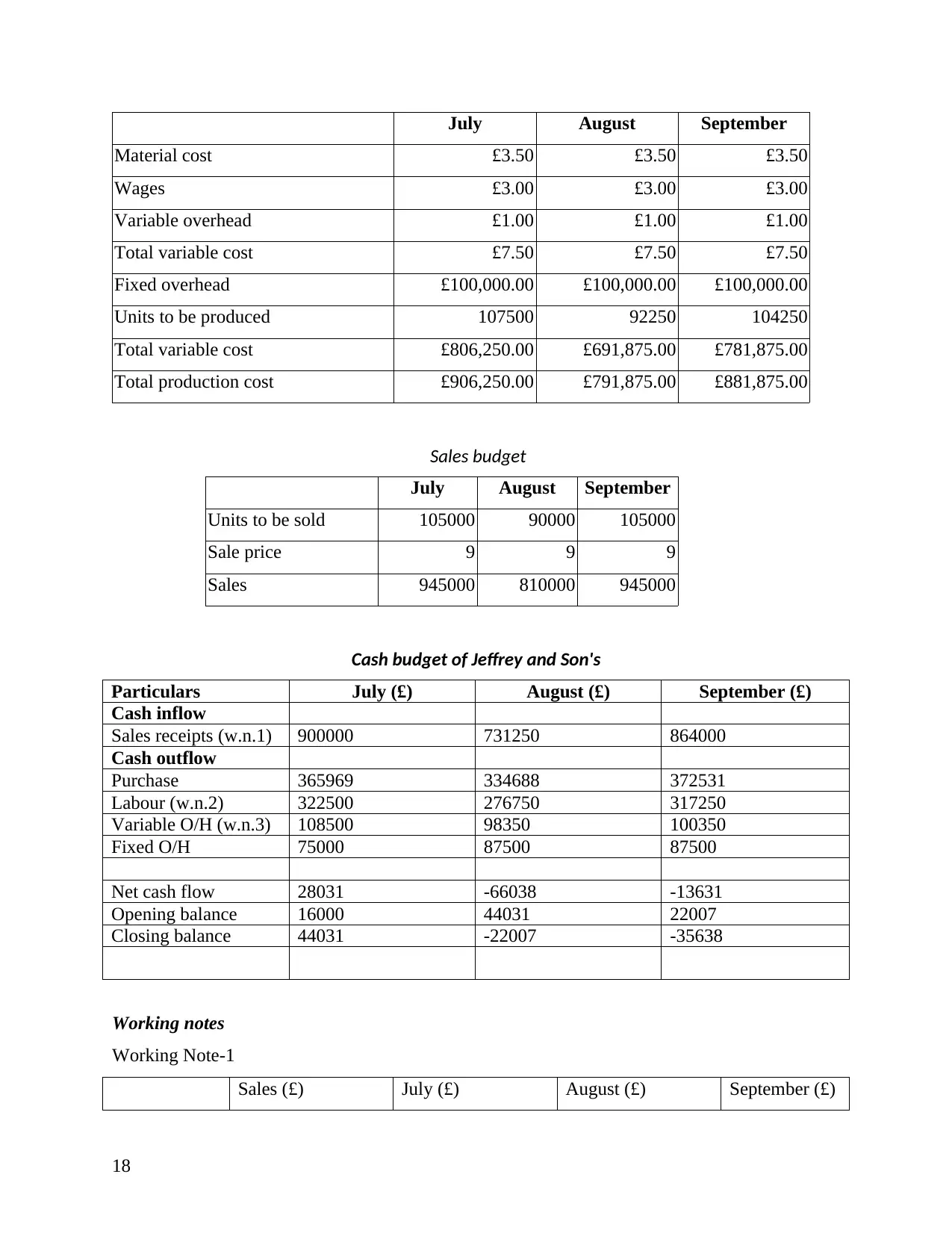
July August September
Material cost £3.50 £3.50 £3.50
Wages £3.00 £3.00 £3.00
Variable overhead £1.00 £1.00 £1.00
Total variable cost £7.50 £7.50 £7.50
Fixed overhead £100,000.00 £100,000.00 £100,000.00
Units to be produced 107500 92250 104250
Total variable cost £806,250.00 £691,875.00 £781,875.00
Total production cost £906,250.00 £791,875.00 £881,875.00
Sales budget
July August September
Units to be sold 105000 90000 105000
Sale price 9 9 9
Sales 945000 810000 945000
Cash budget of Jeffrey and Son's
Particulars July (£) August (£) September (£)
Cash inflow
Sales receipts (w.n.1) 900000 731250 864000
Cash outflow
Purchase 365969 334688 372531
Labour (w.n.2) 322500 276750 317250
Variable O/H (w.n.3) 108500 98350 100350
Fixed O/H 75000 87500 87500
Net cash flow 28031 -66038 -13631
Opening balance 16000 44031 22007
Closing balance 44031 -22007 -35638
Working notes
Working Note-1
Sales (£) July (£) August (£) September (£)
18
Material cost £3.50 £3.50 £3.50
Wages £3.00 £3.00 £3.00
Variable overhead £1.00 £1.00 £1.00
Total variable cost £7.50 £7.50 £7.50
Fixed overhead £100,000.00 £100,000.00 £100,000.00
Units to be produced 107500 92250 104250
Total variable cost £806,250.00 £691,875.00 £781,875.00
Total production cost £906,250.00 £791,875.00 £881,875.00
Sales budget
July August September
Units to be sold 105000 90000 105000
Sale price 9 9 9
Sales 945000 810000 945000
Cash budget of Jeffrey and Son's
Particulars July (£) August (£) September (£)
Cash inflow
Sales receipts (w.n.1) 900000 731250 864000
Cash outflow
Purchase 365969 334688 372531
Labour (w.n.2) 322500 276750 317250
Variable O/H (w.n.3) 108500 98350 100350
Fixed O/H 75000 87500 87500
Net cash flow 28031 -66038 -13631
Opening balance 16000 44031 22007
Closing balance 44031 -22007 -35638
Working notes
Working Note-1
Sales (£) July (£) August (£) September (£)
18
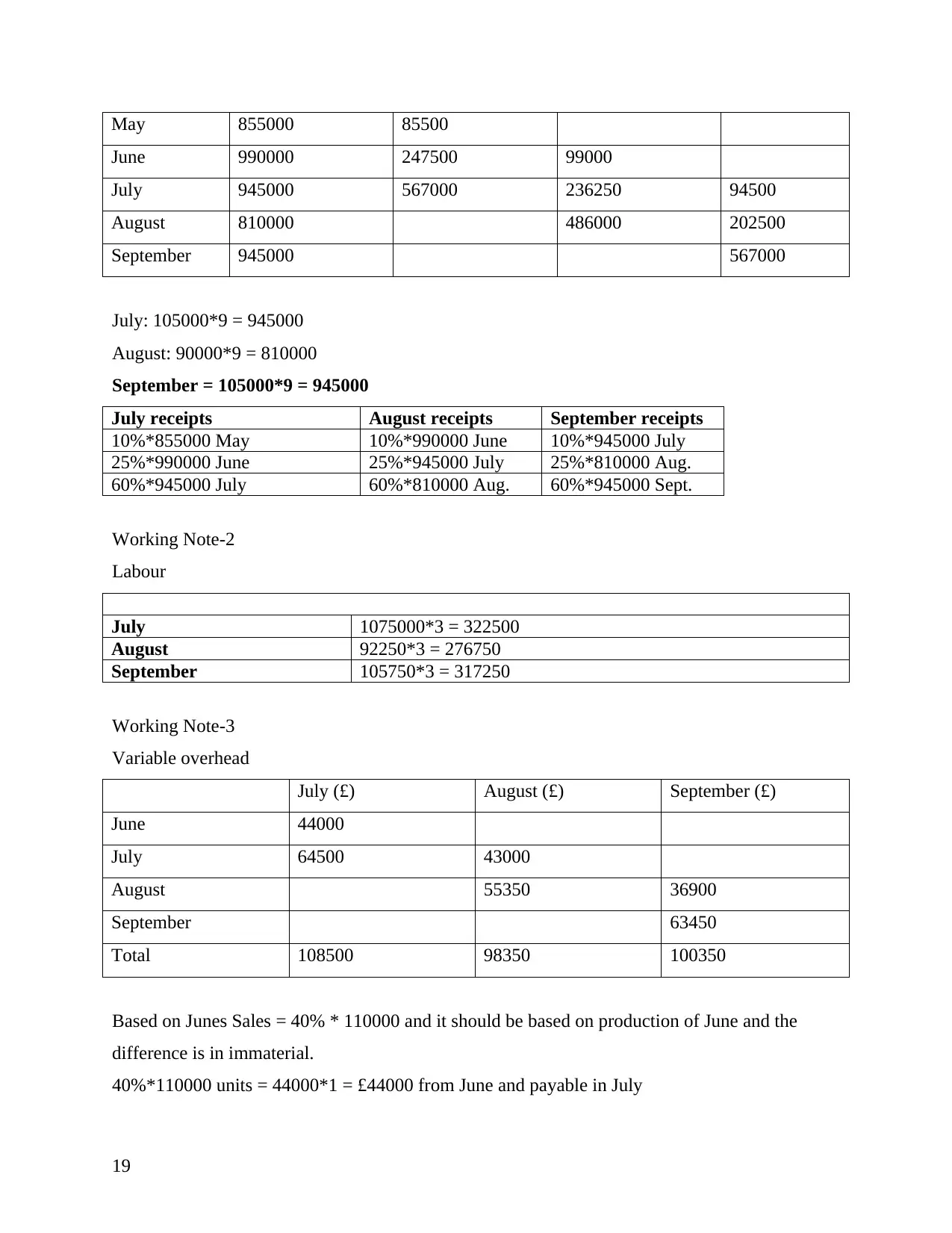
May 855000 85500
June 990000 247500 99000
July 945000 567000 236250 94500
August 810000 486000 202500
September 945000 567000
July: 105000*9 = 945000
August: 90000*9 = 810000
September = 105000*9 = 945000
July receipts August receipts September receipts
10%*855000 May 10%*990000 June 10%*945000 July
25%*990000 June 25%*945000 July 25%*810000 Aug.
60%*945000 July 60%*810000 Aug. 60%*945000 Sept.
Working Note-2
Labour
July 1075000*3 = 322500
August 92250*3 = 276750
September 105750*3 = 317250
Working Note-3
Variable overhead
July (£) August (£) September (£)
June 44000
July 64500 43000
August 55350 36900
September 63450
Total 108500 98350 100350
Based on Junes Sales = 40% * 110000 and it should be based on production of June and the
difference is in immaterial.
40%*110000 units = 44000*1 = £44000 from June and payable in July
19
June 990000 247500 99000
July 945000 567000 236250 94500
August 810000 486000 202500
September 945000 567000
July: 105000*9 = 945000
August: 90000*9 = 810000
September = 105000*9 = 945000
July receipts August receipts September receipts
10%*855000 May 10%*990000 June 10%*945000 July
25%*990000 June 25%*945000 July 25%*810000 Aug.
60%*945000 July 60%*810000 Aug. 60%*945000 Sept.
Working Note-2
Labour
July 1075000*3 = 322500
August 92250*3 = 276750
September 105750*3 = 317250
Working Note-3
Variable overhead
July (£) August (£) September (£)
June 44000
July 64500 43000
August 55350 36900
September 63450
Total 108500 98350 100350
Based on Junes Sales = 40% * 110000 and it should be based on production of June and the
difference is in immaterial.
40%*110000 units = 44000*1 = £44000 from June and payable in July
19
Paraphrase This Document
Need a fresh take? Get an instant paraphrase of this document with our AI Paraphraser
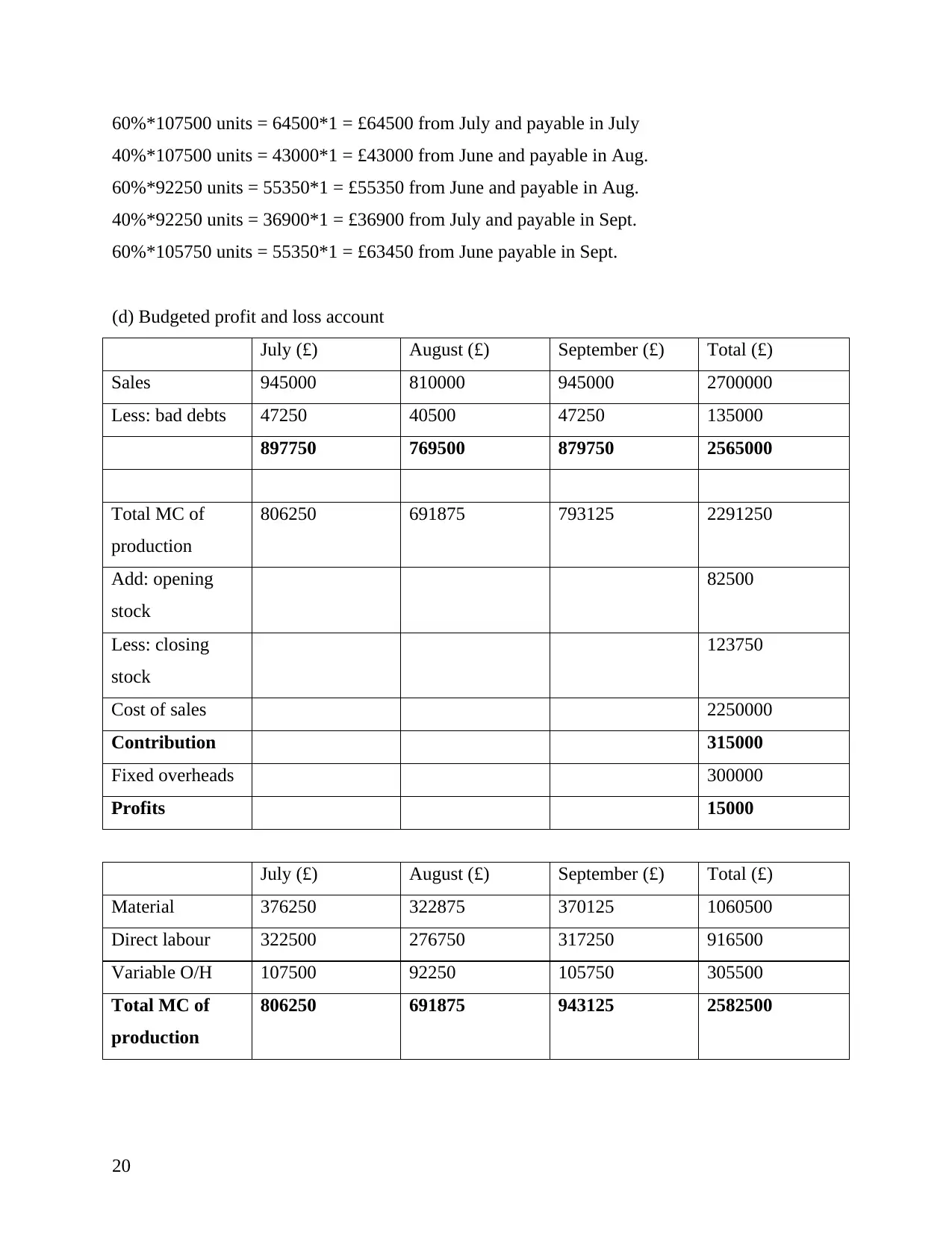
60%*107500 units = 64500*1 = £64500 from July and payable in July
40%*107500 units = 43000*1 = £43000 from June and payable in Aug.
60%*92250 units = 55350*1 = £55350 from June and payable in Aug.
40%*92250 units = 36900*1 = £36900 from July and payable in Sept.
60%*105750 units = 55350*1 = £63450 from June payable in Sept.
(d) Budgeted profit and loss account
July (£) August (£) September (£) Total (£)
Sales 945000 810000 945000 2700000
Less: bad debts 47250 40500 47250 135000
897750 769500 879750 2565000
Total MC of
production
806250 691875 793125 2291250
Add: opening
stock
82500
Less: closing
stock
123750
Cost of sales 2250000
Contribution 315000
Fixed overheads 300000
Profits 15000
July (£) August (£) September (£) Total (£)
Material 376250 322875 370125 1060500
Direct labour 322500 276750 317250 916500
Variable O/H 107500 92250 105750 305500
Total MC of
production
806250 691875 943125 2582500
20
40%*107500 units = 43000*1 = £43000 from June and payable in Aug.
60%*92250 units = 55350*1 = £55350 from June and payable in Aug.
40%*92250 units = 36900*1 = £36900 from July and payable in Sept.
60%*105750 units = 55350*1 = £63450 from June payable in Sept.
(d) Budgeted profit and loss account
July (£) August (£) September (£) Total (£)
Sales 945000 810000 945000 2700000
Less: bad debts 47250 40500 47250 135000
897750 769500 879750 2565000
Total MC of
production
806250 691875 793125 2291250
Add: opening
stock
82500
Less: closing
stock
123750
Cost of sales 2250000
Contribution 315000
Fixed overheads 300000
Profits 15000
July (£) August (£) September (£) Total (£)
Material 376250 322875 370125 1060500
Direct labour 322500 276750 317250 916500
Variable O/H 107500 92250 105750 305500
Total MC of
production
806250 691875 943125 2582500
20
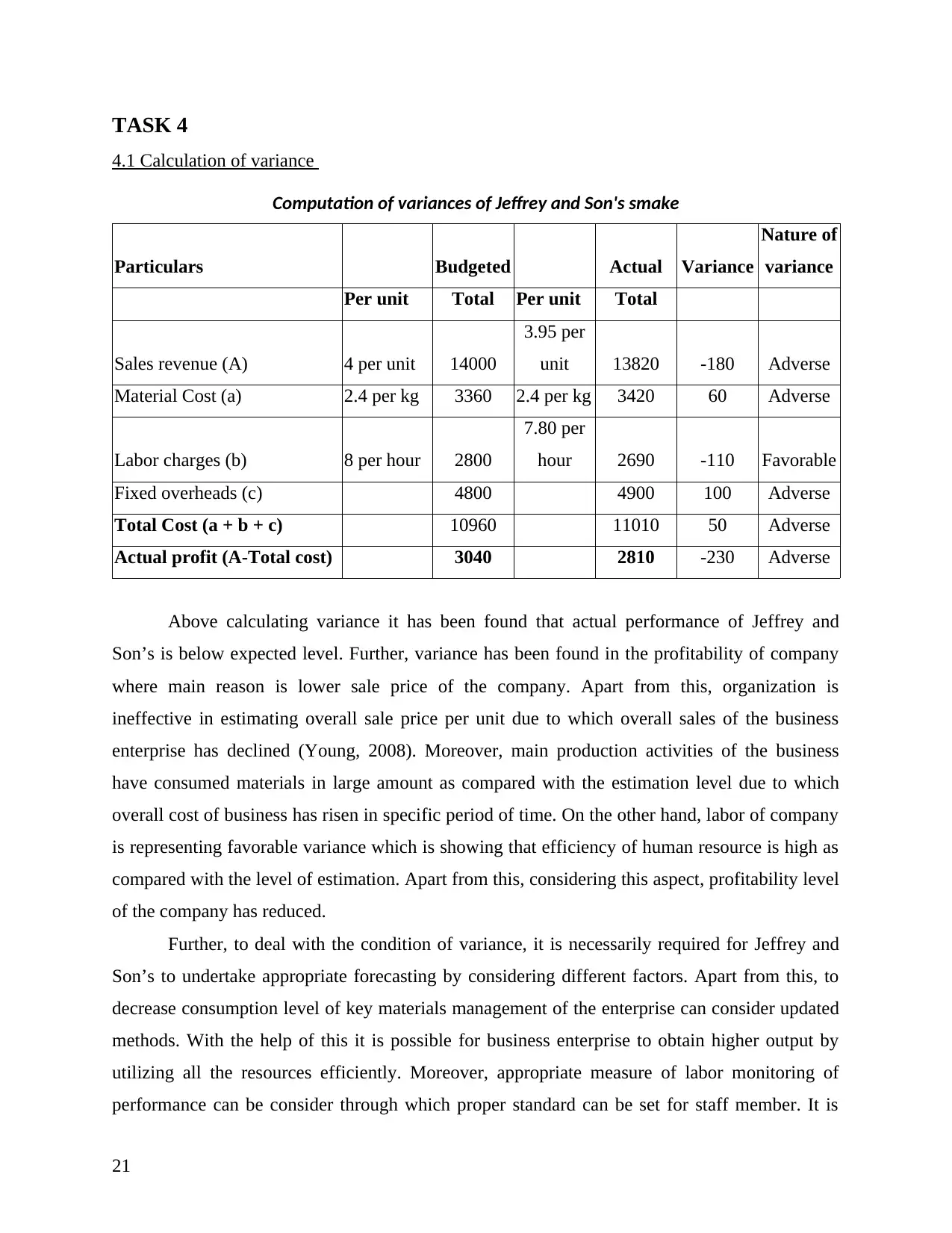
TASK 4
4.1 Calculation of variance
Computation of variances of Jeffrey and Son's smake
Particulars Budgeted Actual Variance
Nature of
variance
Per unit Total Per unit Total
Sales revenue (A) 4 per unit 14000
3.95 per
unit 13820 -180 Adverse
Material Cost (a) 2.4 per kg 3360 2.4 per kg 3420 60 Adverse
Labor charges (b) 8 per hour 2800
7.80 per
hour 2690 -110 Favorable
Fixed overheads (c) 4800 4900 100 Adverse
Total Cost (a + b + c) 10960 11010 50 Adverse
Actual profit (A-Total cost) 3040 2810 -230 Adverse
Above calculating variance it has been found that actual performance of Jeffrey and
Son’s is below expected level. Further, variance has been found in the profitability of company
where main reason is lower sale price of the company. Apart from this, organization is
ineffective in estimating overall sale price per unit due to which overall sales of the business
enterprise has declined (Young, 2008). Moreover, main production activities of the business
have consumed materials in large amount as compared with the estimation level due to which
overall cost of business has risen in specific period of time. On the other hand, labor of company
is representing favorable variance which is showing that efficiency of human resource is high as
compared with the level of estimation. Apart from this, considering this aspect, profitability level
of the company has reduced.
Further, to deal with the condition of variance, it is necessarily required for Jeffrey and
Son’s to undertake appropriate forecasting by considering different factors. Apart from this, to
decrease consumption level of key materials management of the enterprise can consider updated
methods. With the help of this it is possible for business enterprise to obtain higher output by
utilizing all the resources efficiently. Moreover, appropriate measure of labor monitoring of
performance can be consider through which proper standard can be set for staff member. It is
21
4.1 Calculation of variance
Computation of variances of Jeffrey and Son's smake
Particulars Budgeted Actual Variance
Nature of
variance
Per unit Total Per unit Total
Sales revenue (A) 4 per unit 14000
3.95 per
unit 13820 -180 Adverse
Material Cost (a) 2.4 per kg 3360 2.4 per kg 3420 60 Adverse
Labor charges (b) 8 per hour 2800
7.80 per
hour 2690 -110 Favorable
Fixed overheads (c) 4800 4900 100 Adverse
Total Cost (a + b + c) 10960 11010 50 Adverse
Actual profit (A-Total cost) 3040 2810 -230 Adverse
Above calculating variance it has been found that actual performance of Jeffrey and
Son’s is below expected level. Further, variance has been found in the profitability of company
where main reason is lower sale price of the company. Apart from this, organization is
ineffective in estimating overall sale price per unit due to which overall sales of the business
enterprise has declined (Young, 2008). Moreover, main production activities of the business
have consumed materials in large amount as compared with the estimation level due to which
overall cost of business has risen in specific period of time. On the other hand, labor of company
is representing favorable variance which is showing that efficiency of human resource is high as
compared with the level of estimation. Apart from this, considering this aspect, profitability level
of the company has reduced.
Further, to deal with the condition of variance, it is necessarily required for Jeffrey and
Son’s to undertake appropriate forecasting by considering different factors. Apart from this, to
decrease consumption level of key materials management of the enterprise can consider updated
methods. With the help of this it is possible for business enterprise to obtain higher output by
utilizing all the resources efficiently. Moreover, appropriate measure of labor monitoring of
performance can be consider through which proper standard can be set for staff member. It is
21
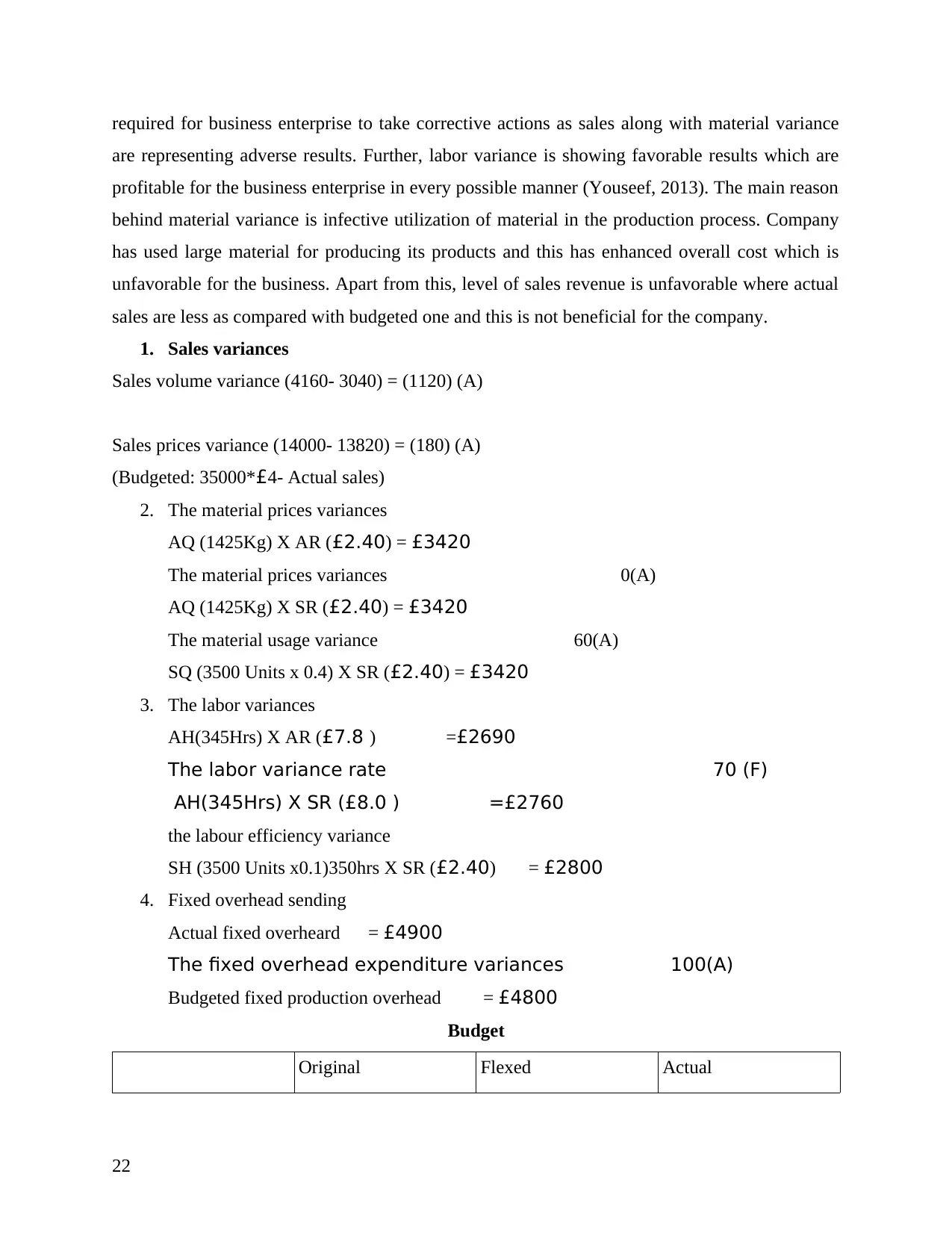
required for business enterprise to take corrective actions as sales along with material variance
are representing adverse results. Further, labor variance is showing favorable results which are
profitable for the business enterprise in every possible manner (Youseef, 2013). The main reason
behind material variance is infective utilization of material in the production process. Company
has used large material for producing its products and this has enhanced overall cost which is
unfavorable for the business. Apart from this, level of sales revenue is unfavorable where actual
sales are less as compared with budgeted one and this is not beneficial for the company.
1. Sales variances
Sales volume variance (4160- 3040) = (1120) (A)
Sales prices variance (14000- 13820) = (180) (A)
(Budgeted: 35000*£4- Actual sales)
2. The material prices variances
AQ (1425Kg) X AR (£2.40) = £3420
The material prices variances 0(A)
AQ (1425Kg) X SR (£2.40) = £3420
The material usage variance 60(A)
SQ (3500 Units x 0.4) X SR (£2.40) = £3420
3. The labor variances
AH(345Hrs) X AR (£7.8 ) =£2690
The labor variance rate 70 (F)
AH(345Hrs) X SR (£8.0 ) =£2760
the labour efficiency variance
SH (3500 Units x0.1)350hrs X SR (£2.40) = £2800
4. Fixed overhead sending
Actual fixed overheard = £4900
The fixed overhead expenditure variances 100(A)
Budgeted fixed production overhead = £4800
Budget
Original Flexed Actual
22
are representing adverse results. Further, labor variance is showing favorable results which are
profitable for the business enterprise in every possible manner (Youseef, 2013). The main reason
behind material variance is infective utilization of material in the production process. Company
has used large material for producing its products and this has enhanced overall cost which is
unfavorable for the business. Apart from this, level of sales revenue is unfavorable where actual
sales are less as compared with budgeted one and this is not beneficial for the company.
1. Sales variances
Sales volume variance (4160- 3040) = (1120) (A)
Sales prices variance (14000- 13820) = (180) (A)
(Budgeted: 35000*£4- Actual sales)
2. The material prices variances
AQ (1425Kg) X AR (£2.40) = £3420
The material prices variances 0(A)
AQ (1425Kg) X SR (£2.40) = £3420
The material usage variance 60(A)
SQ (3500 Units x 0.4) X SR (£2.40) = £3420
3. The labor variances
AH(345Hrs) X AR (£7.8 ) =£2690
The labor variance rate 70 (F)
AH(345Hrs) X SR (£8.0 ) =£2760
the labour efficiency variance
SH (3500 Units x0.1)350hrs X SR (£2.40) = £2800
4. Fixed overhead sending
Actual fixed overheard = £4900
The fixed overhead expenditure variances 100(A)
Budgeted fixed production overhead = £4800
Budget
Original Flexed Actual
22
Secure Best Marks with AI Grader
Need help grading? Try our AI Grader for instant feedback on your assignments.
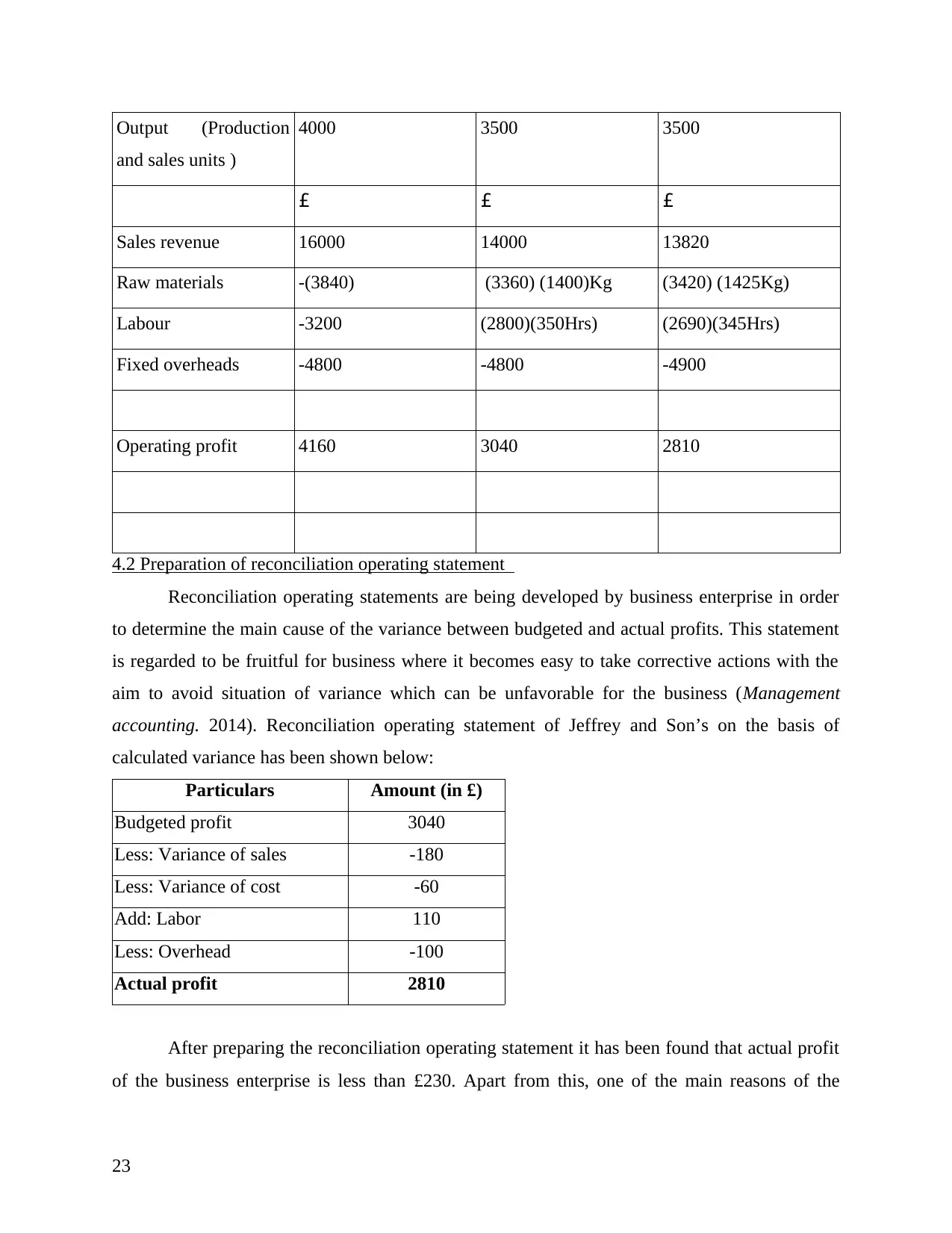
Output (Production
and sales units )
4000 3500 3500
£ £ £
Sales revenue 16000 14000 13820
Raw materials -(3840) (3360) (1400)Kg (3420) (1425Kg)
Labour -3200 (2800)(350Hrs) (2690)(345Hrs)
Fixed overheads -4800 -4800 -4900
Operating profit 4160 3040 2810
4.2 Preparation of reconciliation operating statement
Reconciliation operating statements are being developed by business enterprise in order
to determine the main cause of the variance between budgeted and actual profits. This statement
is regarded to be fruitful for business where it becomes easy to take corrective actions with the
aim to avoid situation of variance which can be unfavorable for the business (Management
accounting. 2014). Reconciliation operating statement of Jeffrey and Son’s on the basis of
calculated variance has been shown below:
Particulars Amount (in £)
Budgeted profit 3040
Less: Variance of sales -180
Less: Variance of cost -60
Add: Labor 110
Less: Overhead -100
Actual profit 2810
After preparing the reconciliation operating statement it has been found that actual profit
of the business enterprise is less than £230. Apart from this, one of the main reasons of the
23
and sales units )
4000 3500 3500
£ £ £
Sales revenue 16000 14000 13820
Raw materials -(3840) (3360) (1400)Kg (3420) (1425Kg)
Labour -3200 (2800)(350Hrs) (2690)(345Hrs)
Fixed overheads -4800 -4800 -4900
Operating profit 4160 3040 2810
4.2 Preparation of reconciliation operating statement
Reconciliation operating statements are being developed by business enterprise in order
to determine the main cause of the variance between budgeted and actual profits. This statement
is regarded to be fruitful for business where it becomes easy to take corrective actions with the
aim to avoid situation of variance which can be unfavorable for the business (Management
accounting. 2014). Reconciliation operating statement of Jeffrey and Son’s on the basis of
calculated variance has been shown below:
Particulars Amount (in £)
Budgeted profit 3040
Less: Variance of sales -180
Less: Variance of cost -60
Add: Labor 110
Less: Overhead -100
Actual profit 2810
After preparing the reconciliation operating statement it has been found that actual profit
of the business enterprise is less than £230. Apart from this, one of the main reasons of the
23
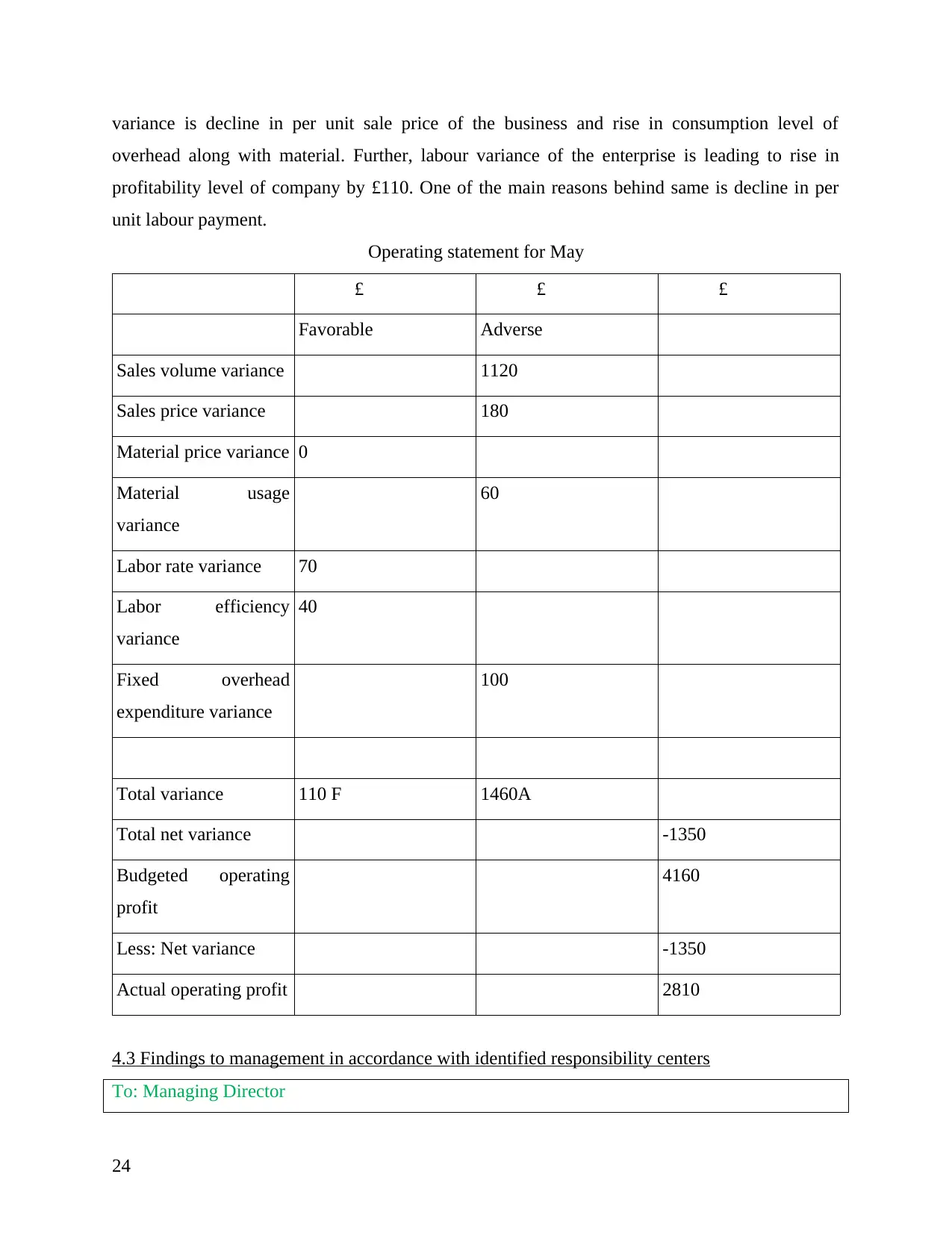
variance is decline in per unit sale price of the business and rise in consumption level of
overhead along with material. Further, labour variance of the enterprise is leading to rise in
profitability level of company by £110. One of the main reasons behind same is decline in per
unit labour payment.
Operating statement for May
£ £ £
Favorable Adverse
Sales volume variance 1120
Sales price variance 180
Material price variance 0
Material usage
variance
60
Labor rate variance 70
Labor efficiency
variance
40
Fixed overhead
expenditure variance
100
Total variance 110 F 1460A
Total net variance -1350
Budgeted operating
profit
4160
Less: Net variance -1350
Actual operating profit 2810
4.3 Findings to management in accordance with identified responsibility centers
To: Managing Director
24
overhead along with material. Further, labour variance of the enterprise is leading to rise in
profitability level of company by £110. One of the main reasons behind same is decline in per
unit labour payment.
Operating statement for May
£ £ £
Favorable Adverse
Sales volume variance 1120
Sales price variance 180
Material price variance 0
Material usage
variance
60
Labor rate variance 70
Labor efficiency
variance
40
Fixed overhead
expenditure variance
100
Total variance 110 F 1460A
Total net variance -1350
Budgeted operating
profit
4160
Less: Net variance -1350
Actual operating profit 2810
4.3 Findings to management in accordance with identified responsibility centers
To: Managing Director
24
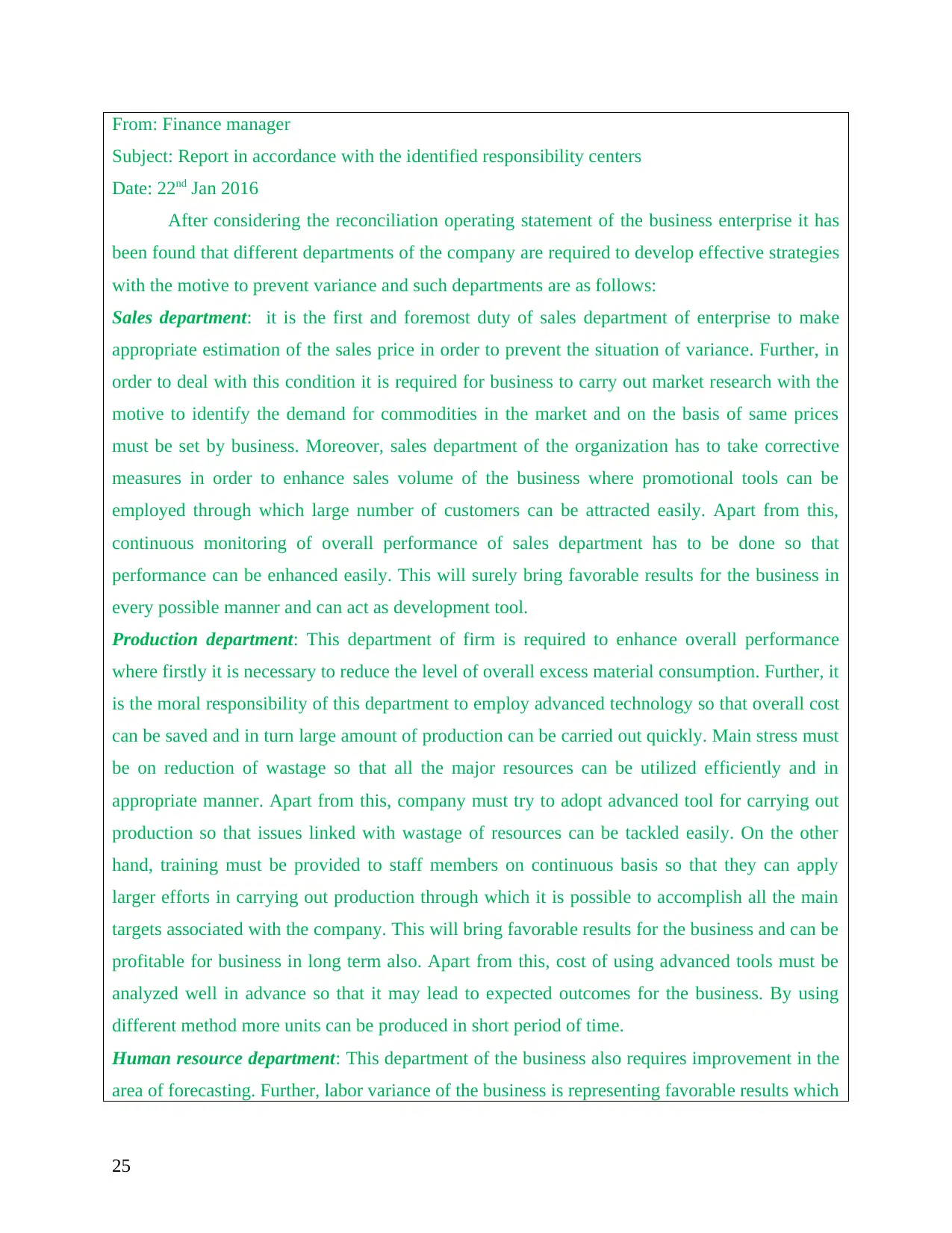
From: Finance manager
Subject: Report in accordance with the identified responsibility centers
Date: 22nd Jan 2016
After considering the reconciliation operating statement of the business enterprise it has
been found that different departments of the company are required to develop effective strategies
with the motive to prevent variance and such departments are as follows:
Sales department: it is the first and foremost duty of sales department of enterprise to make
appropriate estimation of the sales price in order to prevent the situation of variance. Further, in
order to deal with this condition it is required for business to carry out market research with the
motive to identify the demand for commodities in the market and on the basis of same prices
must be set by business. Moreover, sales department of the organization has to take corrective
measures in order to enhance sales volume of the business where promotional tools can be
employed through which large number of customers can be attracted easily. Apart from this,
continuous monitoring of overall performance of sales department has to be done so that
performance can be enhanced easily. This will surely bring favorable results for the business in
every possible manner and can act as development tool.
Production department: This department of firm is required to enhance overall performance
where firstly it is necessary to reduce the level of overall excess material consumption. Further, it
is the moral responsibility of this department to employ advanced technology so that overall cost
can be saved and in turn large amount of production can be carried out quickly. Main stress must
be on reduction of wastage so that all the major resources can be utilized efficiently and in
appropriate manner. Apart from this, company must try to adopt advanced tool for carrying out
production so that issues linked with wastage of resources can be tackled easily. On the other
hand, training must be provided to staff members on continuous basis so that they can apply
larger efforts in carrying out production through which it is possible to accomplish all the main
targets associated with the company. This will bring favorable results for the business and can be
profitable for business in long term also. Apart from this, cost of using advanced tools must be
analyzed well in advance so that it may lead to expected outcomes for the business. By using
different method more units can be produced in short period of time.
Human resource department: This department of the business also requires improvement in the
area of forecasting. Further, labor variance of the business is representing favorable results which
25
Subject: Report in accordance with the identified responsibility centers
Date: 22nd Jan 2016
After considering the reconciliation operating statement of the business enterprise it has
been found that different departments of the company are required to develop effective strategies
with the motive to prevent variance and such departments are as follows:
Sales department: it is the first and foremost duty of sales department of enterprise to make
appropriate estimation of the sales price in order to prevent the situation of variance. Further, in
order to deal with this condition it is required for business to carry out market research with the
motive to identify the demand for commodities in the market and on the basis of same prices
must be set by business. Moreover, sales department of the organization has to take corrective
measures in order to enhance sales volume of the business where promotional tools can be
employed through which large number of customers can be attracted easily. Apart from this,
continuous monitoring of overall performance of sales department has to be done so that
performance can be enhanced easily. This will surely bring favorable results for the business in
every possible manner and can act as development tool.
Production department: This department of firm is required to enhance overall performance
where firstly it is necessary to reduce the level of overall excess material consumption. Further, it
is the moral responsibility of this department to employ advanced technology so that overall cost
can be saved and in turn large amount of production can be carried out quickly. Main stress must
be on reduction of wastage so that all the major resources can be utilized efficiently and in
appropriate manner. Apart from this, company must try to adopt advanced tool for carrying out
production so that issues linked with wastage of resources can be tackled easily. On the other
hand, training must be provided to staff members on continuous basis so that they can apply
larger efforts in carrying out production through which it is possible to accomplish all the main
targets associated with the company. This will bring favorable results for the business and can be
profitable for business in long term also. Apart from this, cost of using advanced tools must be
analyzed well in advance so that it may lead to expected outcomes for the business. By using
different method more units can be produced in short period of time.
Human resource department: This department of the business also requires improvement in the
area of forecasting. Further, labor variance of the business is representing favorable results which
25
1 out of 25
Related Documents

Your All-in-One AI-Powered Toolkit for Academic Success.
+13062052269
info@desklib.com
Available 24*7 on WhatsApp / Email
Unlock your academic potential
© 2024 | Zucol Services PVT LTD | All rights reserved.