Management Accounting Report: Cost Analysis and Budgeting Techniques
VerifiedAdded on 2020/07/22
|17
|4413
|32
Report
AI Summary
This report delves into the core concepts of management accounting, encompassing cost classification, various costing methods, and budgeting processes. It begins with an introduction to accounting and its role in budget estimation and cost control, followed by a detailed examination of cost types, including direct, indirect, manufacturing, and period costs. The report then explores various costing methods such as job costing, batch costing, process costing, and service costing, with a focus on their application. Furthermore, the report analyzes different costing techniques like absorption costing, marginal costing, and activity-based costing, providing calculations and examples. The report also covers the aims, objectives, and methods of the budgeting process, along with a case study demonstrating budget formulation. Finally, it calculates and analyzes variances, providing findings from case studies and offering recommendations.
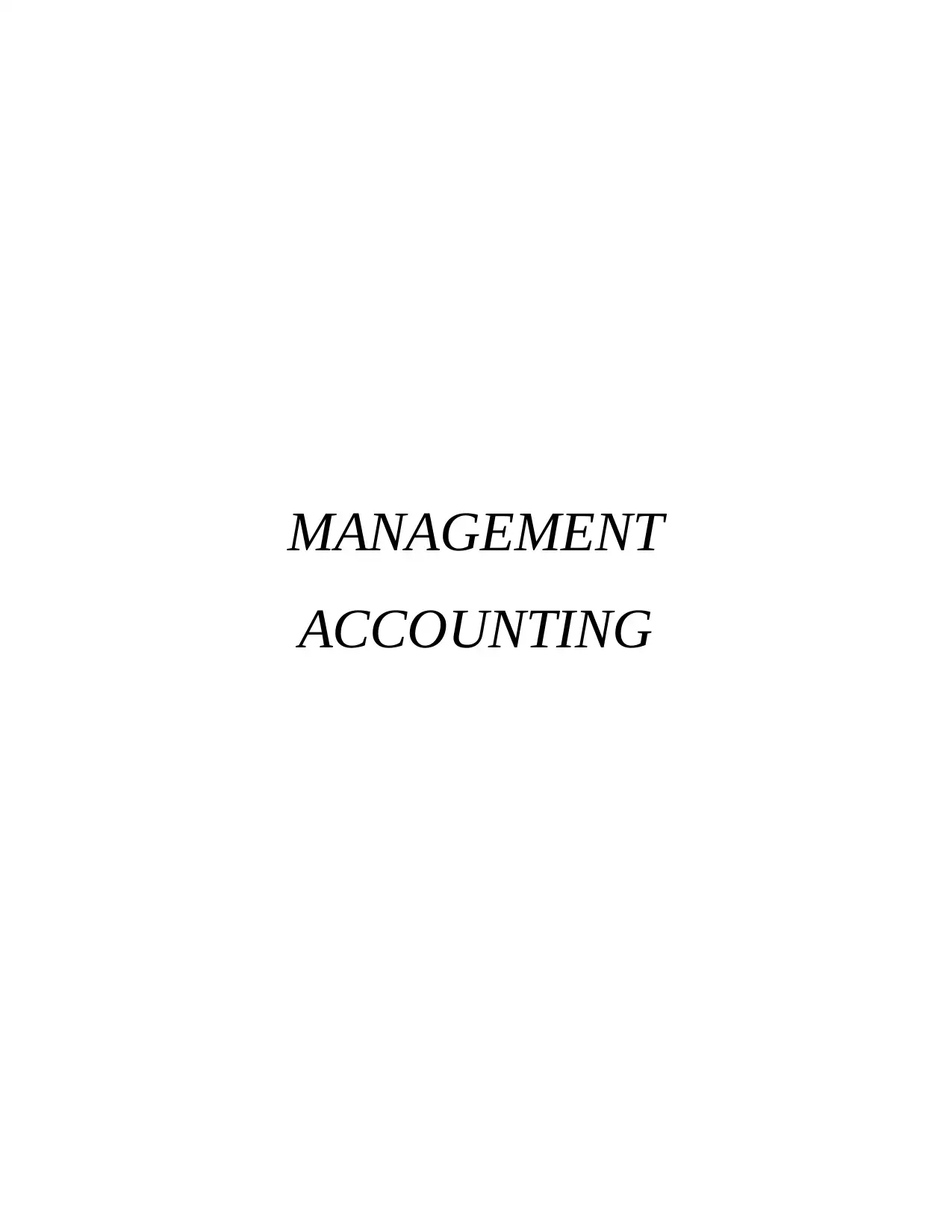
MANAGEMENT
ACCOUNTING
ACCOUNTING
Paraphrase This Document
Need a fresh take? Get an instant paraphrase of this document with our AI Paraphraser
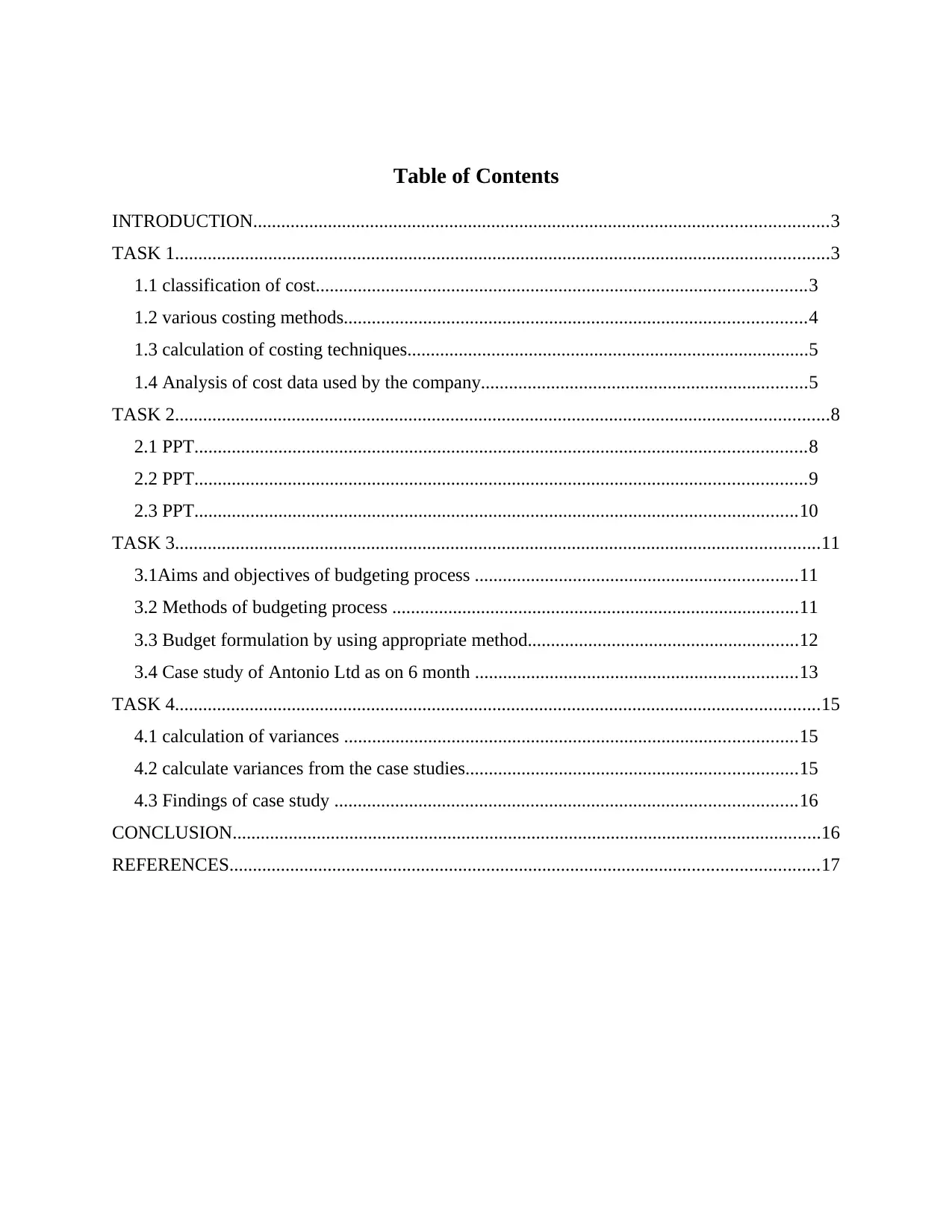
Table of Contents
INTRODUCTION...........................................................................................................................3
TASK 1............................................................................................................................................3
1.1 classification of cost.........................................................................................................3
1.2 various costing methods...................................................................................................4
1.3 calculation of costing techniques......................................................................................5
1.4 Analysis of cost data used by the company......................................................................5
TASK 2............................................................................................................................................8
2.1 PPT...................................................................................................................................8
2.2 PPT...................................................................................................................................9
2.3 PPT.................................................................................................................................10
TASK 3..........................................................................................................................................11
3.1Aims and objectives of budgeting process .....................................................................11
3.2 Methods of budgeting process .......................................................................................11
3.3 Budget formulation by using appropriate method..........................................................12
3.4 Case study of Antonio Ltd as on 6 month .....................................................................13
TASK 4..........................................................................................................................................15
4.1 calculation of variances .................................................................................................15
4.2 calculate variances from the case studies.......................................................................15
4.3 Findings of case study ...................................................................................................16
CONCLUSION..............................................................................................................................16
REFERENCES..............................................................................................................................17
INTRODUCTION...........................................................................................................................3
TASK 1............................................................................................................................................3
1.1 classification of cost.........................................................................................................3
1.2 various costing methods...................................................................................................4
1.3 calculation of costing techniques......................................................................................5
1.4 Analysis of cost data used by the company......................................................................5
TASK 2............................................................................................................................................8
2.1 PPT...................................................................................................................................8
2.2 PPT...................................................................................................................................9
2.3 PPT.................................................................................................................................10
TASK 3..........................................................................................................................................11
3.1Aims and objectives of budgeting process .....................................................................11
3.2 Methods of budgeting process .......................................................................................11
3.3 Budget formulation by using appropriate method..........................................................12
3.4 Case study of Antonio Ltd as on 6 month .....................................................................13
TASK 4..........................................................................................................................................15
4.1 calculation of variances .................................................................................................15
4.2 calculate variances from the case studies.......................................................................15
4.3 Findings of case study ...................................................................................................16
CONCLUSION..............................................................................................................................16
REFERENCES..............................................................................................................................17
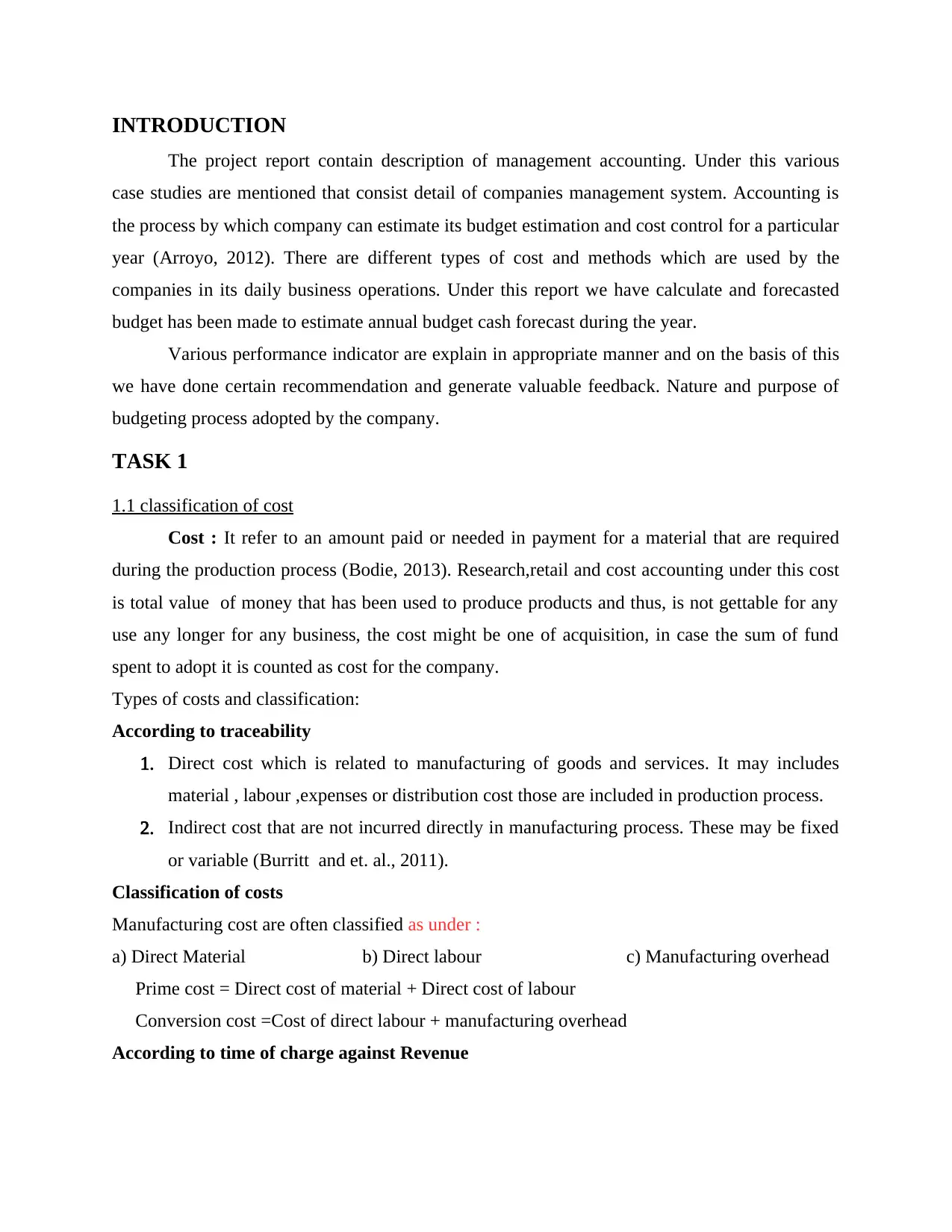
INTRODUCTION
The project report contain description of management accounting. Under this various
case studies are mentioned that consist detail of companies management system. Accounting is
the process by which company can estimate its budget estimation and cost control for a particular
year (Arroyo, 2012). There are different types of cost and methods which are used by the
companies in its daily business operations. Under this report we have calculate and forecasted
budget has been made to estimate annual budget cash forecast during the year.
Various performance indicator are explain in appropriate manner and on the basis of this
we have done certain recommendation and generate valuable feedback. Nature and purpose of
budgeting process adopted by the company.
TASK 1
1.1 classification of cost
Cost : It refer to an amount paid or needed in payment for a material that are required
during the production process (Bodie, 2013). Research,retail and cost accounting under this cost
is total value of money that has been used to produce products and thus, is not gettable for any
use any longer for any business, the cost might be one of acquisition, in case the sum of fund
spent to adopt it is counted as cost for the company.
Types of costs and classification:
According to traceability
1. Direct cost which is related to manufacturing of goods and services. It may includes
material , labour ,expenses or distribution cost those are included in production process.
2. Indirect cost that are not incurred directly in manufacturing process. These may be fixed
or variable (Burritt and et. al., 2011).
Classification of costs
Manufacturing cost are often classified as under :
a) Direct Material b) Direct labour c) Manufacturing overhead
Prime cost = Direct cost of material + Direct cost of labour
Conversion cost =Cost of direct labour + manufacturing overhead
According to time of charge against Revenue
The project report contain description of management accounting. Under this various
case studies are mentioned that consist detail of companies management system. Accounting is
the process by which company can estimate its budget estimation and cost control for a particular
year (Arroyo, 2012). There are different types of cost and methods which are used by the
companies in its daily business operations. Under this report we have calculate and forecasted
budget has been made to estimate annual budget cash forecast during the year.
Various performance indicator are explain in appropriate manner and on the basis of this
we have done certain recommendation and generate valuable feedback. Nature and purpose of
budgeting process adopted by the company.
TASK 1
1.1 classification of cost
Cost : It refer to an amount paid or needed in payment for a material that are required
during the production process (Bodie, 2013). Research,retail and cost accounting under this cost
is total value of money that has been used to produce products and thus, is not gettable for any
use any longer for any business, the cost might be one of acquisition, in case the sum of fund
spent to adopt it is counted as cost for the company.
Types of costs and classification:
According to traceability
1. Direct cost which is related to manufacturing of goods and services. It may includes
material , labour ,expenses or distribution cost those are included in production process.
2. Indirect cost that are not incurred directly in manufacturing process. These may be fixed
or variable (Burritt and et. al., 2011).
Classification of costs
Manufacturing cost are often classified as under :
a) Direct Material b) Direct labour c) Manufacturing overhead
Prime cost = Direct cost of material + Direct cost of labour
Conversion cost =Cost of direct labour + manufacturing overhead
According to time of charge against Revenue
You're viewing a preview
Unlock full access by subscribing today!
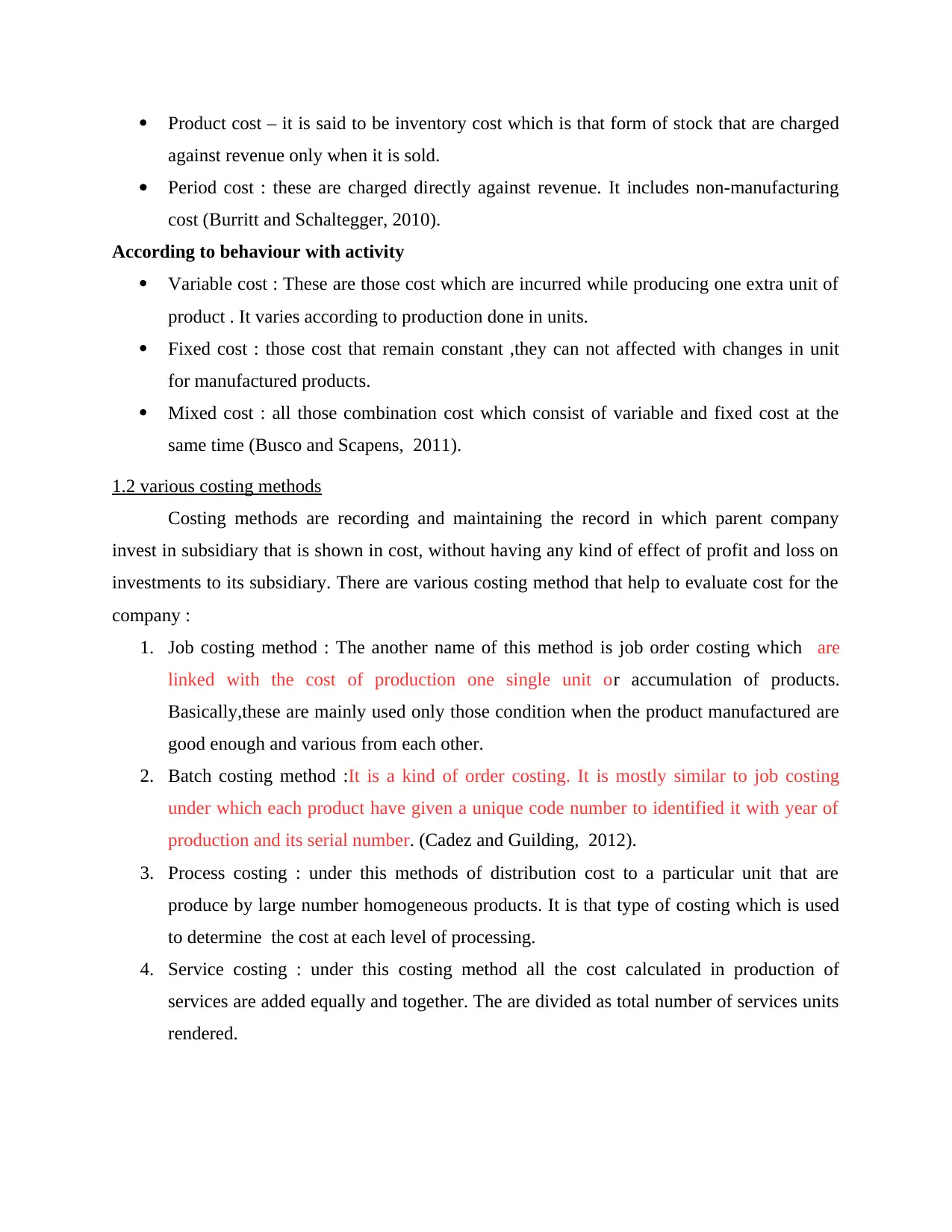
Product cost – it is said to be inventory cost which is that form of stock that are charged
against revenue only when it is sold.
Period cost : these are charged directly against revenue. It includes non-manufacturing
cost (Burritt and Schaltegger, 2010).
According to behaviour with activity
Variable cost : These are those cost which are incurred while producing one extra unit of
product . It varies according to production done in units.
Fixed cost : those cost that remain constant ,they can not affected with changes in unit
for manufactured products.
Mixed cost : all those combination cost which consist of variable and fixed cost at the
same time (Busco and Scapens, 2011).
1.2 various costing methods
Costing methods are recording and maintaining the record in which parent company
invest in subsidiary that is shown in cost, without having any kind of effect of profit and loss on
investments to its subsidiary. There are various costing method that help to evaluate cost for the
company :
1. Job costing method : The another name of this method is job order costing which are
linked with the cost of production one single unit or accumulation of products.
Basically,these are mainly used only those condition when the product manufactured are
good enough and various from each other.
2. Batch costing method :It is a kind of order costing. It is mostly similar to job costing
under which each product have given a unique code number to identified it with year of
production and its serial number. (Cadez and Guilding, 2012).
3. Process costing : under this methods of distribution cost to a particular unit that are
produce by large number homogeneous products. It is that type of costing which is used
to determine the cost at each level of processing.
4. Service costing : under this costing method all the cost calculated in production of
services are added equally and together. The are divided as total number of services units
rendered.
against revenue only when it is sold.
Period cost : these are charged directly against revenue. It includes non-manufacturing
cost (Burritt and Schaltegger, 2010).
According to behaviour with activity
Variable cost : These are those cost which are incurred while producing one extra unit of
product . It varies according to production done in units.
Fixed cost : those cost that remain constant ,they can not affected with changes in unit
for manufactured products.
Mixed cost : all those combination cost which consist of variable and fixed cost at the
same time (Busco and Scapens, 2011).
1.2 various costing methods
Costing methods are recording and maintaining the record in which parent company
invest in subsidiary that is shown in cost, without having any kind of effect of profit and loss on
investments to its subsidiary. There are various costing method that help to evaluate cost for the
company :
1. Job costing method : The another name of this method is job order costing which are
linked with the cost of production one single unit or accumulation of products.
Basically,these are mainly used only those condition when the product manufactured are
good enough and various from each other.
2. Batch costing method :It is a kind of order costing. It is mostly similar to job costing
under which each product have given a unique code number to identified it with year of
production and its serial number. (Cadez and Guilding, 2012).
3. Process costing : under this methods of distribution cost to a particular unit that are
produce by large number homogeneous products. It is that type of costing which is used
to determine the cost at each level of processing.
4. Service costing : under this costing method all the cost calculated in production of
services are added equally and together. The are divided as total number of services units
rendered.
Paraphrase This Document
Need a fresh take? Get an instant paraphrase of this document with our AI Paraphraser
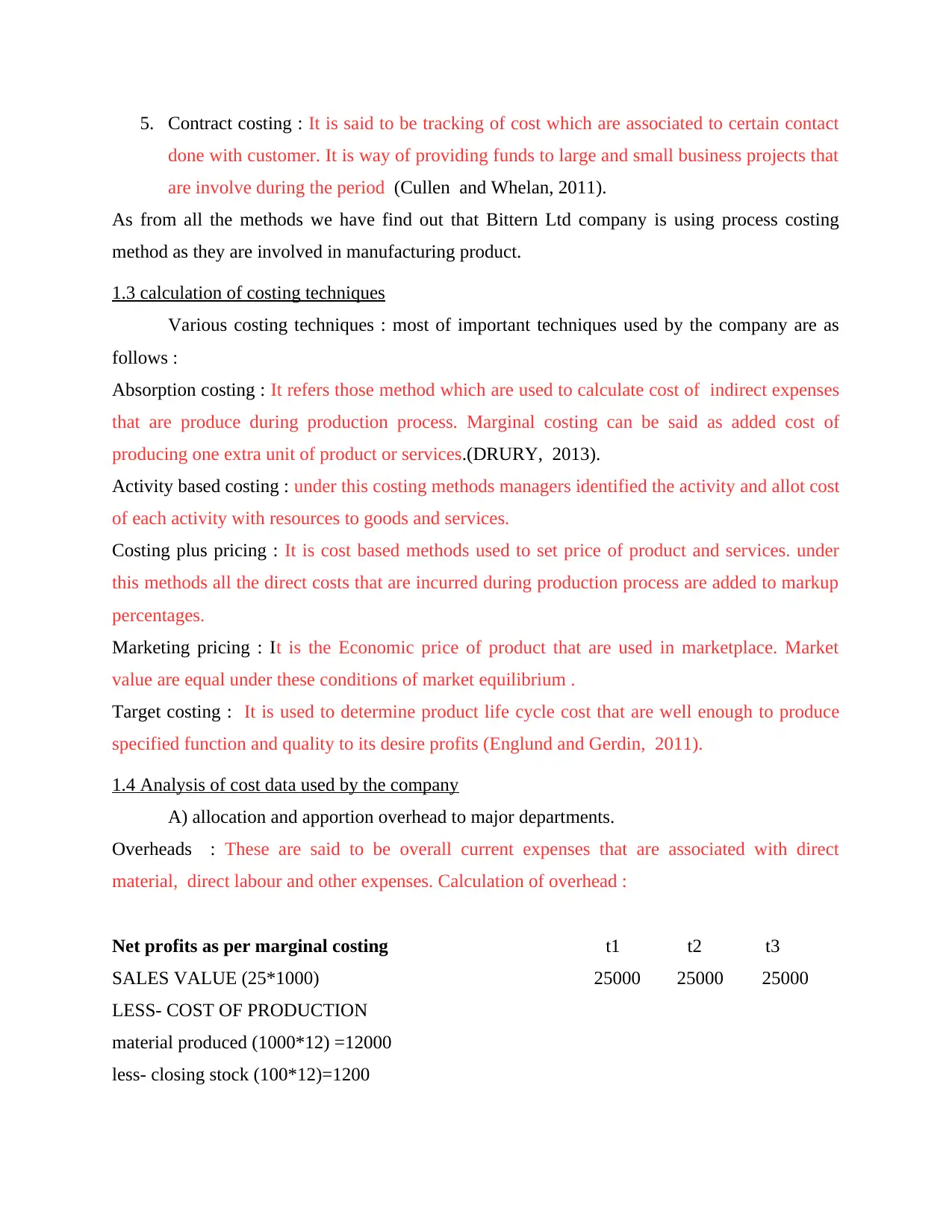
5. Contract costing : It is said to be tracking of cost which are associated to certain contact
done with customer. It is way of providing funds to large and small business projects that
are involve during the period (Cullen and Whelan, 2011).
As from all the methods we have find out that Bittern Ltd company is using process costing
method as they are involved in manufacturing product.
1.3 calculation of costing techniques
Various costing techniques : most of important techniques used by the company are as
follows :
Absorption costing : It refers those method which are used to calculate cost of indirect expenses
that are produce during production process. Marginal costing can be said as added cost of
producing one extra unit of product or services.(DRURY, 2013).
Activity based costing : under this costing methods managers identified the activity and allot cost
of each activity with resources to goods and services.
Costing plus pricing : It is cost based methods used to set price of product and services. under
this methods all the direct costs that are incurred during production process are added to markup
percentages.
Marketing pricing : It is the Economic price of product that are used in marketplace. Market
value are equal under these conditions of market equilibrium .
Target costing : It is used to determine product life cycle cost that are well enough to produce
specified function and quality to its desire profits (Englund and Gerdin, 2011).
1.4 Analysis of cost data used by the company
A) allocation and apportion overhead to major departments.
Overheads : These are said to be overall current expenses that are associated with direct
material, direct labour and other expenses. Calculation of overhead :
Net profits as per marginal costing t1 t2 t3
SALES VALUE (25*1000) 25000 25000 25000
LESS- COST OF PRODUCTION
material produced (1000*12) =12000
less- closing stock (100*12)=1200
done with customer. It is way of providing funds to large and small business projects that
are involve during the period (Cullen and Whelan, 2011).
As from all the methods we have find out that Bittern Ltd company is using process costing
method as they are involved in manufacturing product.
1.3 calculation of costing techniques
Various costing techniques : most of important techniques used by the company are as
follows :
Absorption costing : It refers those method which are used to calculate cost of indirect expenses
that are produce during production process. Marginal costing can be said as added cost of
producing one extra unit of product or services.(DRURY, 2013).
Activity based costing : under this costing methods managers identified the activity and allot cost
of each activity with resources to goods and services.
Costing plus pricing : It is cost based methods used to set price of product and services. under
this methods all the direct costs that are incurred during production process are added to markup
percentages.
Marketing pricing : It is the Economic price of product that are used in marketplace. Market
value are equal under these conditions of market equilibrium .
Target costing : It is used to determine product life cycle cost that are well enough to produce
specified function and quality to its desire profits (Englund and Gerdin, 2011).
1.4 Analysis of cost data used by the company
A) allocation and apportion overhead to major departments.
Overheads : These are said to be overall current expenses that are associated with direct
material, direct labour and other expenses. Calculation of overhead :
Net profits as per marginal costing t1 t2 t3
SALES VALUE (25*1000) 25000 25000 25000
LESS- COST OF PRODUCTION
material produced (1000*12) =12000
less- closing stock (100*12)=1200
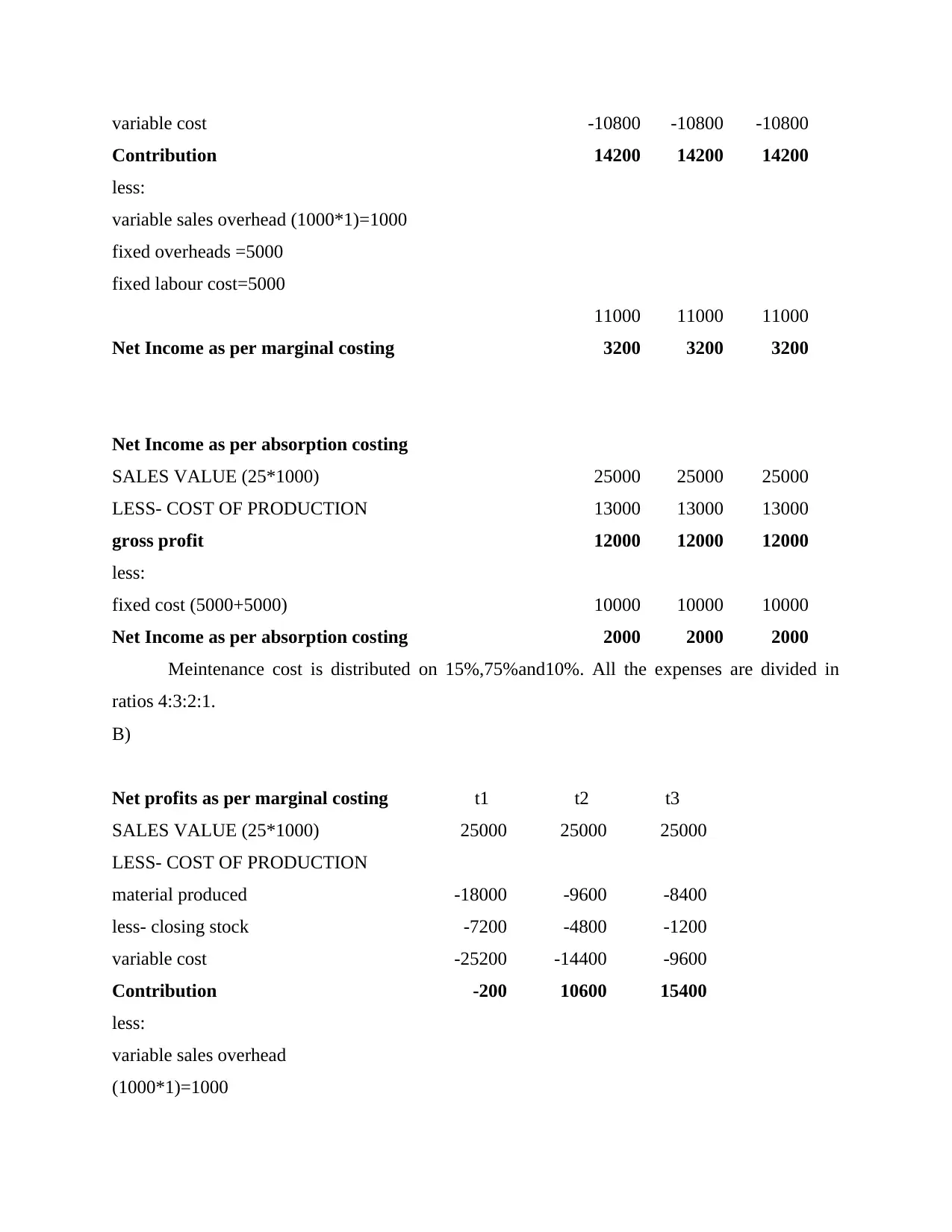
variable cost -10800 -10800 -10800
Contribution 14200 14200 14200
less:
variable sales overhead (1000*1)=1000
fixed overheads =5000
fixed labour cost=5000
11000 11000 11000
Net Income as per marginal costing 3200 3200 3200
Net Income as per absorption costing
SALES VALUE (25*1000) 25000 25000 25000
LESS- COST OF PRODUCTION 13000 13000 13000
gross profit 12000 12000 12000
less:
fixed cost (5000+5000) 10000 10000 10000
Net Income as per absorption costing 2000 2000 2000
Meintenance cost is distributed on 15%,75%and10%. All the expenses are divided in
ratios 4:3:2:1.
B)
Net profits as per marginal costing t1 t2 t3
SALES VALUE (25*1000) 25000 25000 25000
LESS- COST OF PRODUCTION
material produced -18000 -9600 -8400
less- closing stock -7200 -4800 -1200
variable cost -25200 -14400 -9600
Contribution -200 10600 15400
less:
variable sales overhead
(1000*1)=1000
Contribution 14200 14200 14200
less:
variable sales overhead (1000*1)=1000
fixed overheads =5000
fixed labour cost=5000
11000 11000 11000
Net Income as per marginal costing 3200 3200 3200
Net Income as per absorption costing
SALES VALUE (25*1000) 25000 25000 25000
LESS- COST OF PRODUCTION 13000 13000 13000
gross profit 12000 12000 12000
less:
fixed cost (5000+5000) 10000 10000 10000
Net Income as per absorption costing 2000 2000 2000
Meintenance cost is distributed on 15%,75%and10%. All the expenses are divided in
ratios 4:3:2:1.
B)
Net profits as per marginal costing t1 t2 t3
SALES VALUE (25*1000) 25000 25000 25000
LESS- COST OF PRODUCTION
material produced -18000 -9600 -8400
less- closing stock -7200 -4800 -1200
variable cost -25200 -14400 -9600
Contribution -200 10600 15400
less:
variable sales overhead
(1000*1)=1000
You're viewing a preview
Unlock full access by subscribing today!
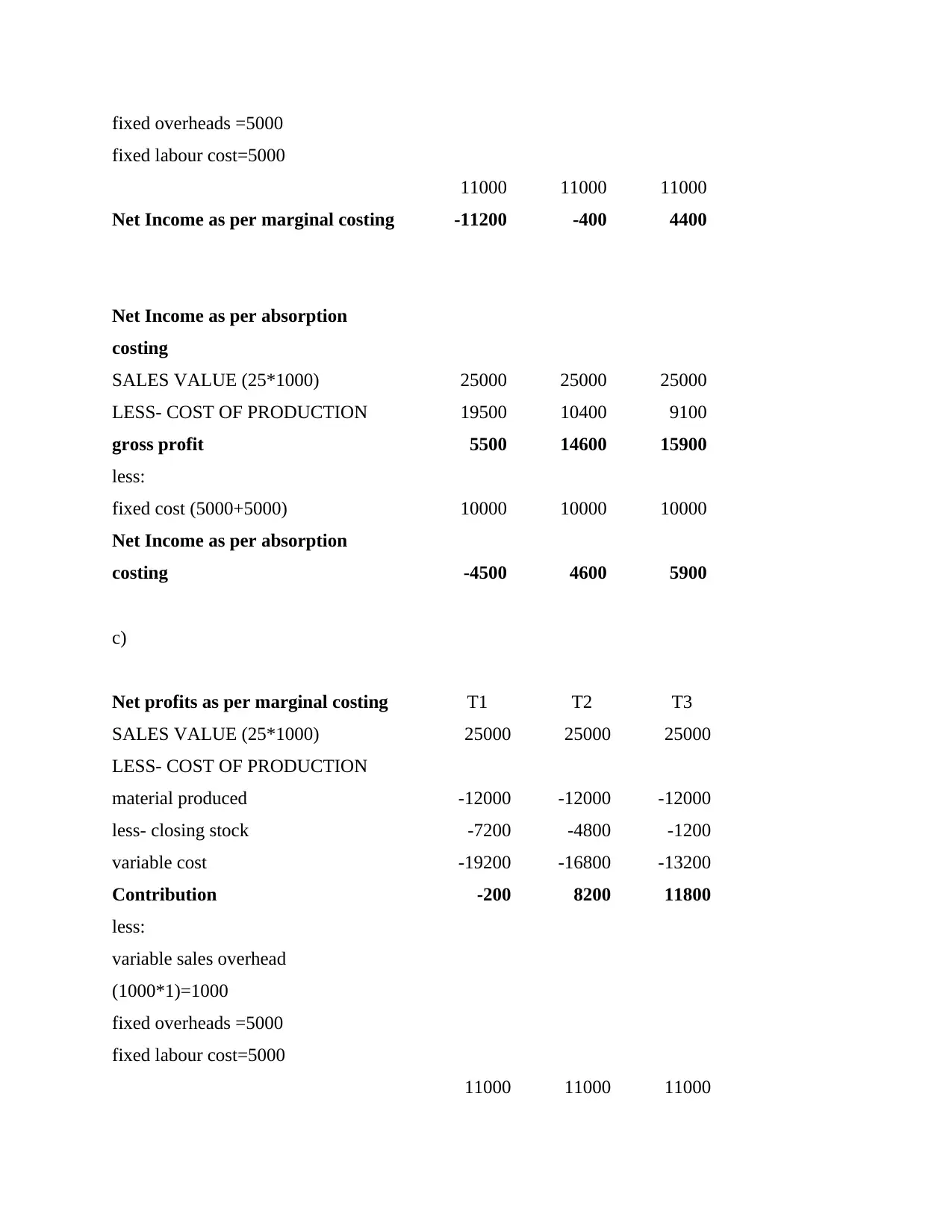
fixed overheads =5000
fixed labour cost=5000
11000 11000 11000
Net Income as per marginal costing -11200 -400 4400
Net Income as per absorption
costing
SALES VALUE (25*1000) 25000 25000 25000
LESS- COST OF PRODUCTION 19500 10400 9100
gross profit 5500 14600 15900
less:
fixed cost (5000+5000) 10000 10000 10000
Net Income as per absorption
costing -4500 4600 5900
c)
Net profits as per marginal costing T1 T2 T3
SALES VALUE (25*1000) 25000 25000 25000
LESS- COST OF PRODUCTION
material produced -12000 -12000 -12000
less- closing stock -7200 -4800 -1200
variable cost -19200 -16800 -13200
Contribution -200 8200 11800
less:
variable sales overhead
(1000*1)=1000
fixed overheads =5000
fixed labour cost=5000
11000 11000 11000
fixed labour cost=5000
11000 11000 11000
Net Income as per marginal costing -11200 -400 4400
Net Income as per absorption
costing
SALES VALUE (25*1000) 25000 25000 25000
LESS- COST OF PRODUCTION 19500 10400 9100
gross profit 5500 14600 15900
less:
fixed cost (5000+5000) 10000 10000 10000
Net Income as per absorption
costing -4500 4600 5900
c)
Net profits as per marginal costing T1 T2 T3
SALES VALUE (25*1000) 25000 25000 25000
LESS- COST OF PRODUCTION
material produced -12000 -12000 -12000
less- closing stock -7200 -4800 -1200
variable cost -19200 -16800 -13200
Contribution -200 8200 11800
less:
variable sales overhead
(1000*1)=1000
fixed overheads =5000
fixed labour cost=5000
11000 11000 11000
Paraphrase This Document
Need a fresh take? Get an instant paraphrase of this document with our AI Paraphraser
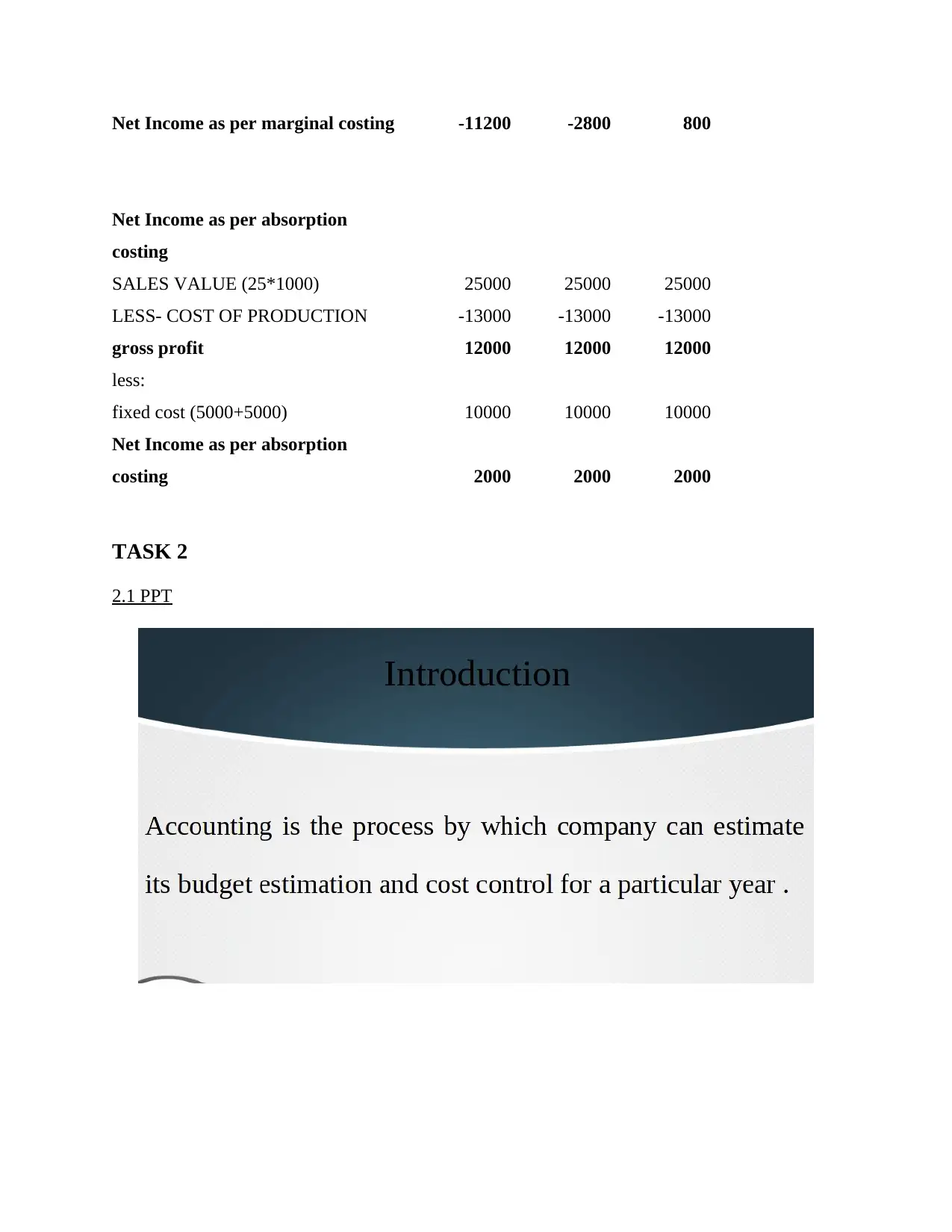
Net Income as per marginal costing -11200 -2800 800
Net Income as per absorption
costing
SALES VALUE (25*1000) 25000 25000 25000
LESS- COST OF PRODUCTION -13000 -13000 -13000
gross profit 12000 12000 12000
less:
fixed cost (5000+5000) 10000 10000 10000
Net Income as per absorption
costing 2000 2000 2000
TASK 2
2.1 PPT
Net Income as per absorption
costing
SALES VALUE (25*1000) 25000 25000 25000
LESS- COST OF PRODUCTION -13000 -13000 -13000
gross profit 12000 12000 12000
less:
fixed cost (5000+5000) 10000 10000 10000
Net Income as per absorption
costing 2000 2000 2000
TASK 2
2.1 PPT
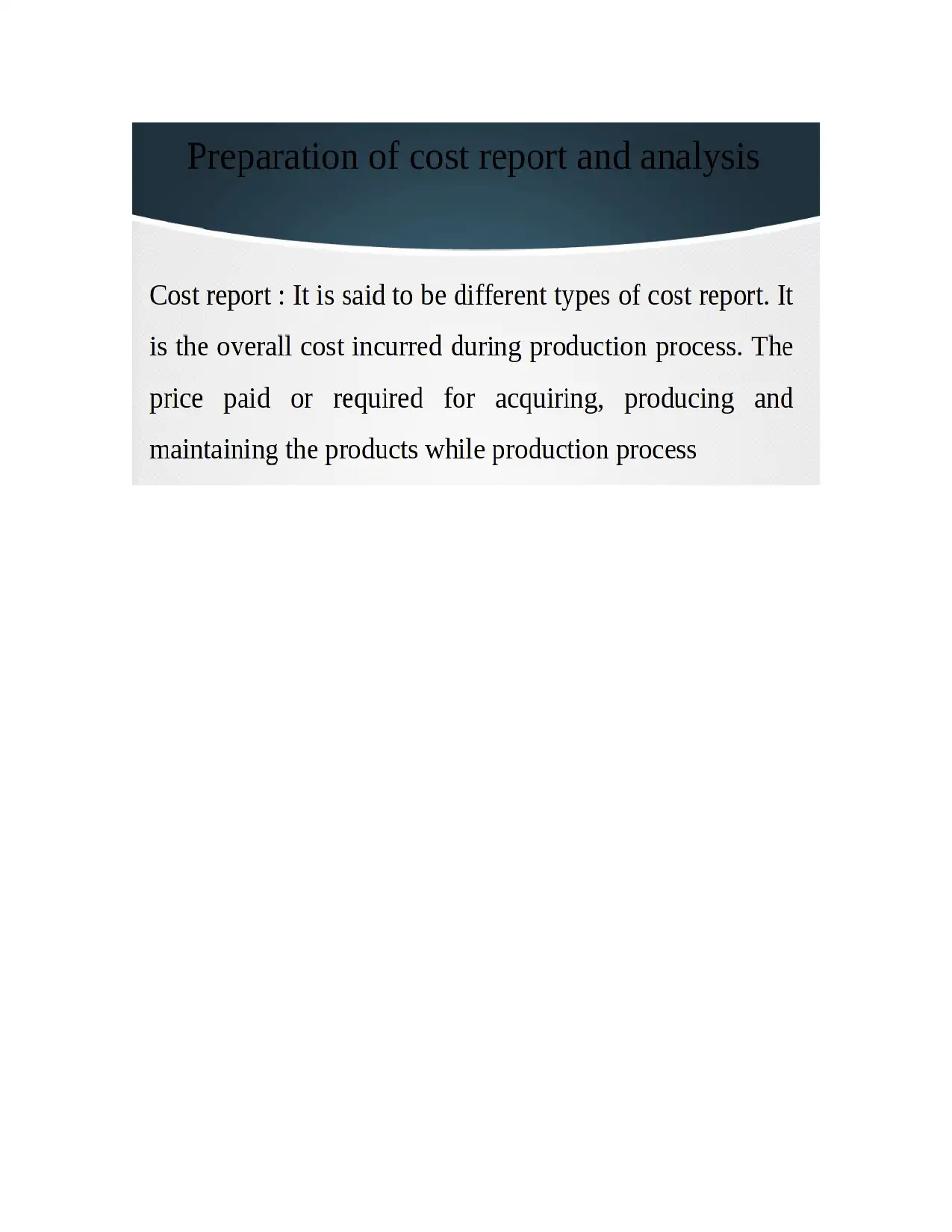
You're viewing a preview
Unlock full access by subscribing today!
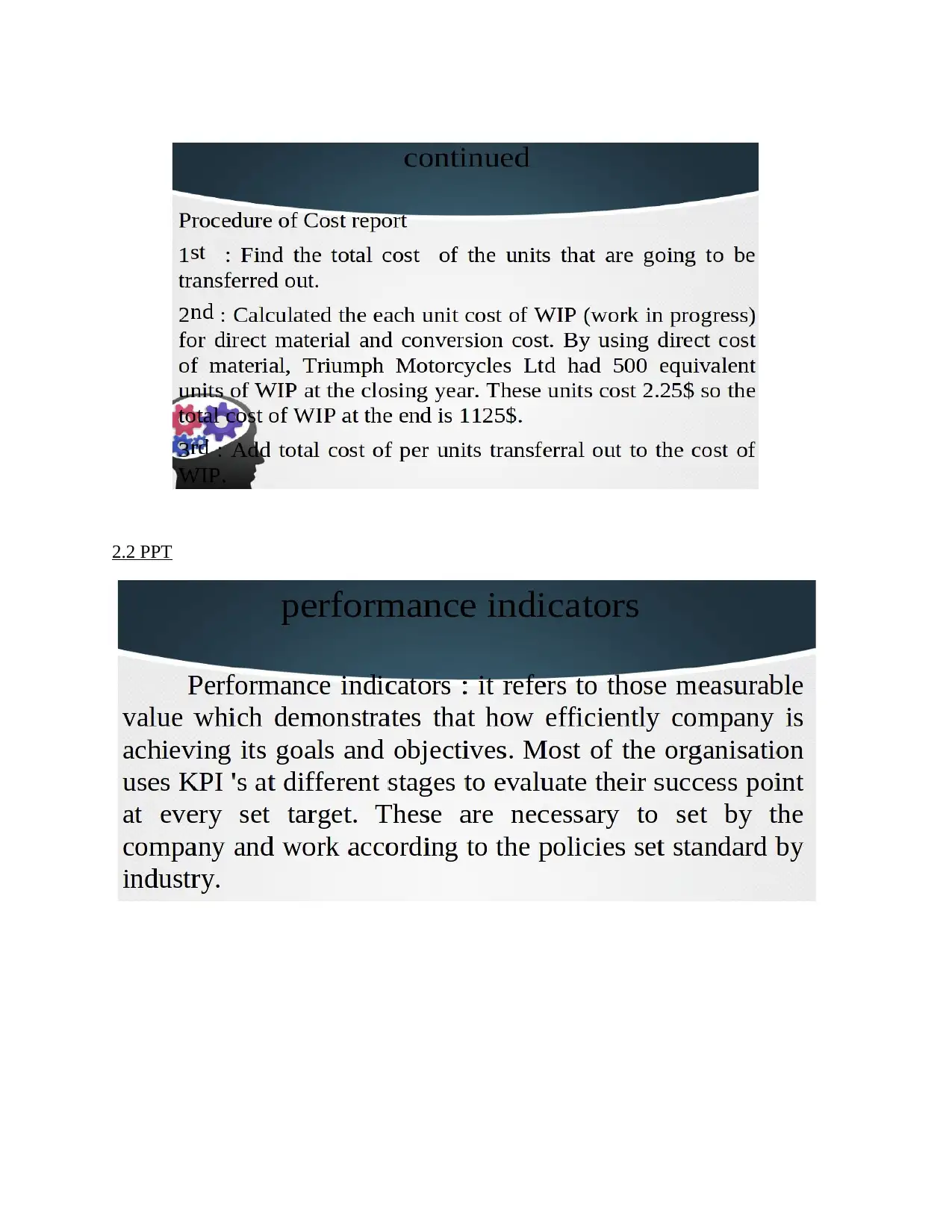
2.2 PPT
Paraphrase This Document
Need a fresh take? Get an instant paraphrase of this document with our AI Paraphraser
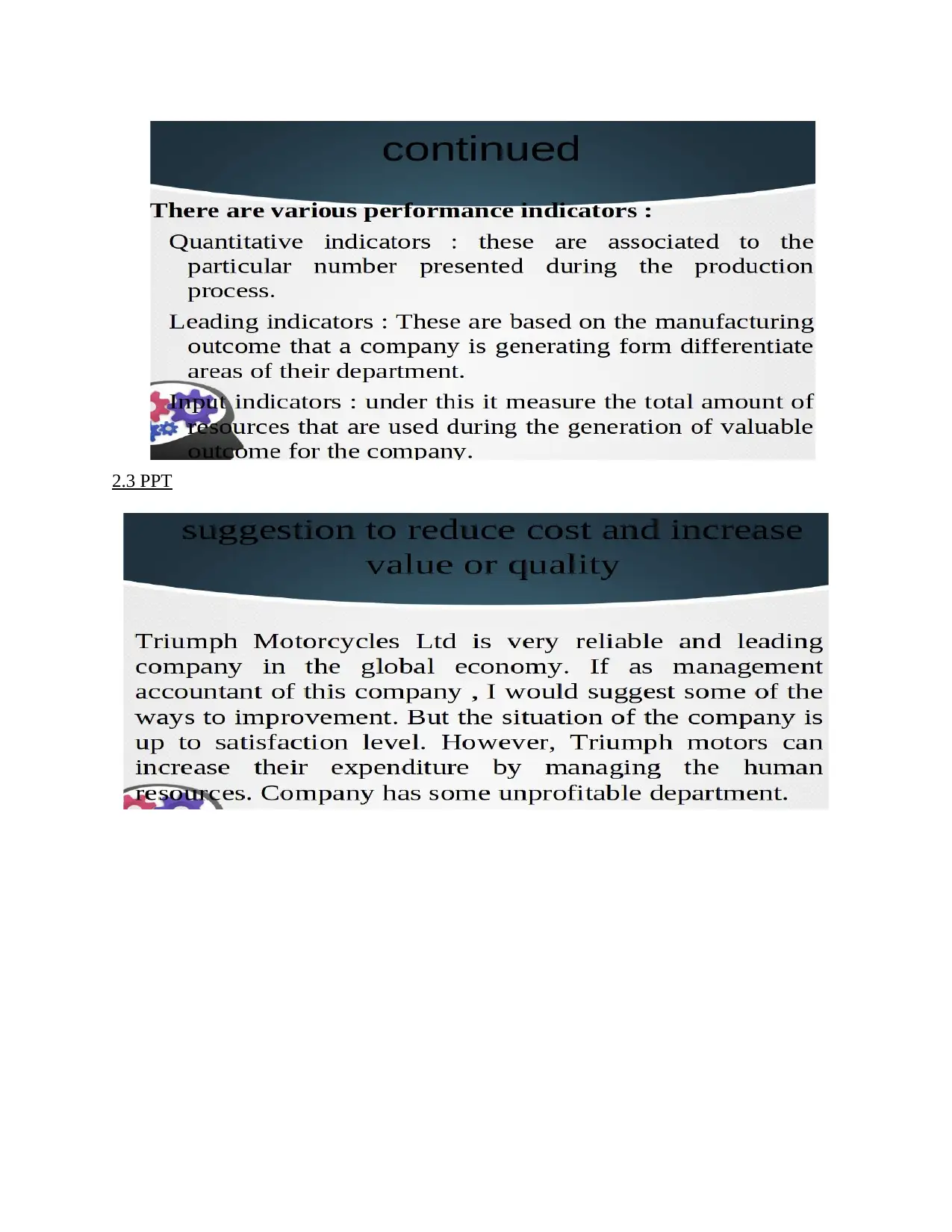
2.3 PPT
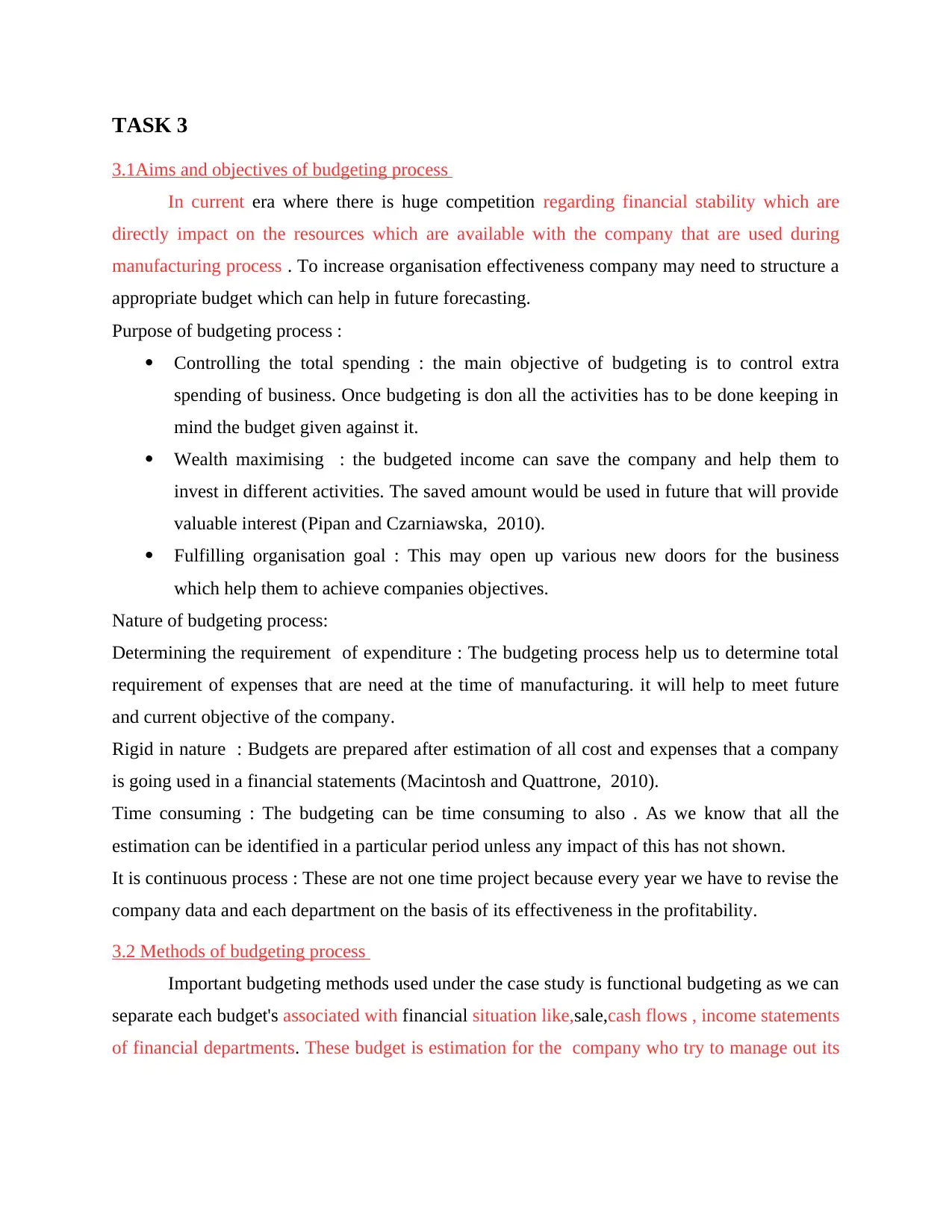
TASK 3
3.1Aims and objectives of budgeting process
In current era where there is huge competition regarding financial stability which are
directly impact on the resources which are available with the company that are used during
manufacturing process . To increase organisation effectiveness company may need to structure a
appropriate budget which can help in future forecasting.
Purpose of budgeting process :
Controlling the total spending : the main objective of budgeting is to control extra
spending of business. Once budgeting is don all the activities has to be done keeping in
mind the budget given against it.
Wealth maximising : the budgeted income can save the company and help them to
invest in different activities. The saved amount would be used in future that will provide
valuable interest (Pipan and Czarniawska, 2010).
Fulfilling organisation goal : This may open up various new doors for the business
which help them to achieve companies objectives.
Nature of budgeting process:
Determining the requirement of expenditure : The budgeting process help us to determine total
requirement of expenses that are need at the time of manufacturing. it will help to meet future
and current objective of the company.
Rigid in nature : Budgets are prepared after estimation of all cost and expenses that a company
is going used in a financial statements (Macintosh and Quattrone, 2010).
Time consuming : The budgeting can be time consuming to also . As we know that all the
estimation can be identified in a particular period unless any impact of this has not shown.
It is continuous process : These are not one time project because every year we have to revise the
company data and each department on the basis of its effectiveness in the profitability.
3.2 Methods of budgeting process
Important budgeting methods used under the case study is functional budgeting as we can
separate each budget's associated with financial situation like,sale,cash flows , income statements
of financial departments. These budget is estimation for the company who try to manage out its
3.1Aims and objectives of budgeting process
In current era where there is huge competition regarding financial stability which are
directly impact on the resources which are available with the company that are used during
manufacturing process . To increase organisation effectiveness company may need to structure a
appropriate budget which can help in future forecasting.
Purpose of budgeting process :
Controlling the total spending : the main objective of budgeting is to control extra
spending of business. Once budgeting is don all the activities has to be done keeping in
mind the budget given against it.
Wealth maximising : the budgeted income can save the company and help them to
invest in different activities. The saved amount would be used in future that will provide
valuable interest (Pipan and Czarniawska, 2010).
Fulfilling organisation goal : This may open up various new doors for the business
which help them to achieve companies objectives.
Nature of budgeting process:
Determining the requirement of expenditure : The budgeting process help us to determine total
requirement of expenses that are need at the time of manufacturing. it will help to meet future
and current objective of the company.
Rigid in nature : Budgets are prepared after estimation of all cost and expenses that a company
is going used in a financial statements (Macintosh and Quattrone, 2010).
Time consuming : The budgeting can be time consuming to also . As we know that all the
estimation can be identified in a particular period unless any impact of this has not shown.
It is continuous process : These are not one time project because every year we have to revise the
company data and each department on the basis of its effectiveness in the profitability.
3.2 Methods of budgeting process
Important budgeting methods used under the case study is functional budgeting as we can
separate each budget's associated with financial situation like,sale,cash flows , income statements
of financial departments. These budget is estimation for the company who try to manage out its
You're viewing a preview
Unlock full access by subscribing today!
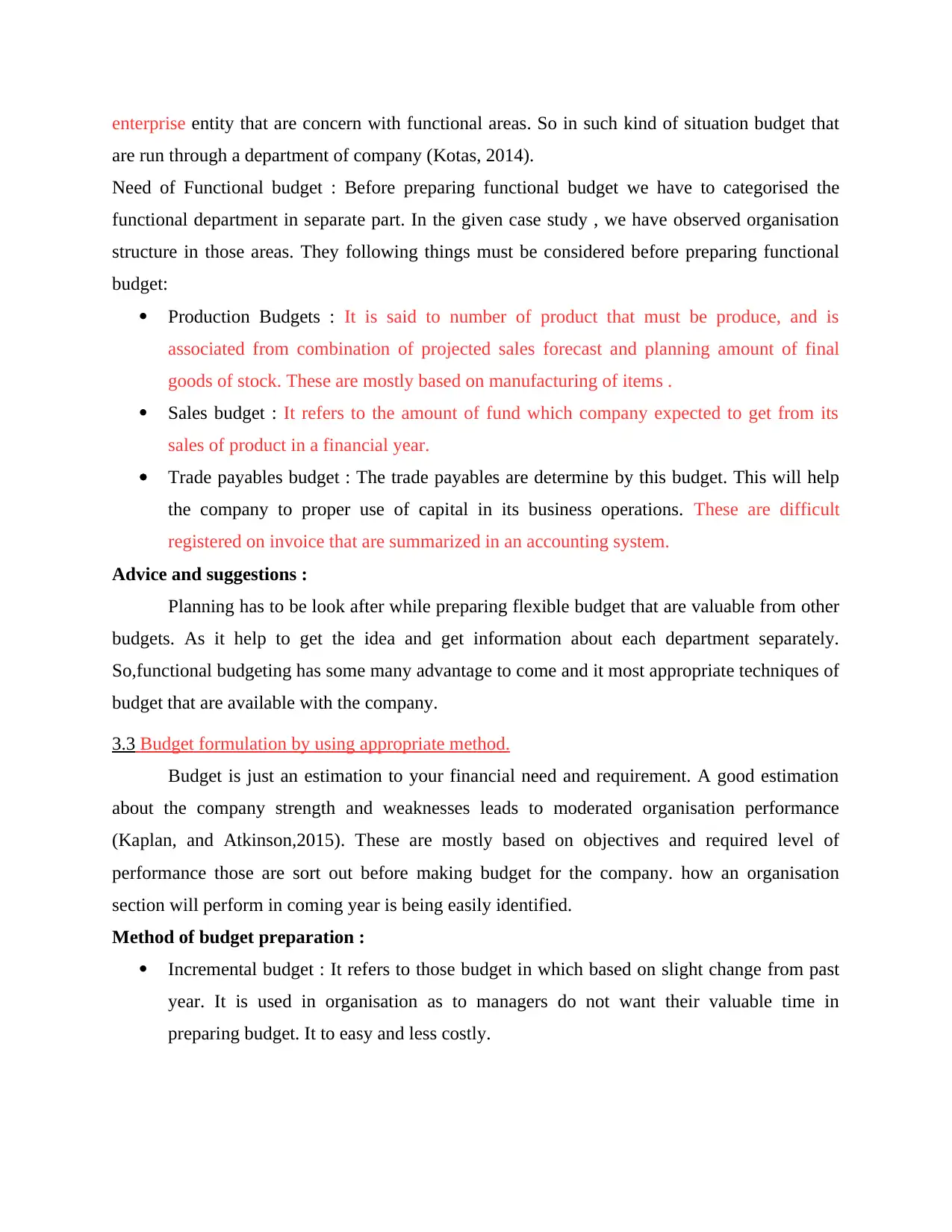
enterprise entity that are concern with functional areas. So in such kind of situation budget that
are run through a department of company (Kotas, 2014).
Need of Functional budget : Before preparing functional budget we have to categorised the
functional department in separate part. In the given case study , we have observed organisation
structure in those areas. They following things must be considered before preparing functional
budget:
Production Budgets : It is said to number of product that must be produce, and is
associated from combination of projected sales forecast and planning amount of final
goods of stock. These are mostly based on manufacturing of items .
Sales budget : It refers to the amount of fund which company expected to get from its
sales of product in a financial year.
Trade payables budget : The trade payables are determine by this budget. This will help
the company to proper use of capital in its business operations. These are difficult
registered on invoice that are summarized in an accounting system.
Advice and suggestions :
Planning has to be look after while preparing flexible budget that are valuable from other
budgets. As it help to get the idea and get information about each department separately.
So,functional budgeting has some many advantage to come and it most appropriate techniques of
budget that are available with the company.
3.3 Budget formulation by using appropriate method.
Budget is just an estimation to your financial need and requirement. A good estimation
about the company strength and weaknesses leads to moderated organisation performance
(Kaplan, and Atkinson,2015). These are mostly based on objectives and required level of
performance those are sort out before making budget for the company. how an organisation
section will perform in coming year is being easily identified.
Method of budget preparation :
Incremental budget : It refers to those budget in which based on slight change from past
year. It is used in organisation as to managers do not want their valuable time in
preparing budget. It to easy and less costly.
are run through a department of company (Kotas, 2014).
Need of Functional budget : Before preparing functional budget we have to categorised the
functional department in separate part. In the given case study , we have observed organisation
structure in those areas. They following things must be considered before preparing functional
budget:
Production Budgets : It is said to number of product that must be produce, and is
associated from combination of projected sales forecast and planning amount of final
goods of stock. These are mostly based on manufacturing of items .
Sales budget : It refers to the amount of fund which company expected to get from its
sales of product in a financial year.
Trade payables budget : The trade payables are determine by this budget. This will help
the company to proper use of capital in its business operations. These are difficult
registered on invoice that are summarized in an accounting system.
Advice and suggestions :
Planning has to be look after while preparing flexible budget that are valuable from other
budgets. As it help to get the idea and get information about each department separately.
So,functional budgeting has some many advantage to come and it most appropriate techniques of
budget that are available with the company.
3.3 Budget formulation by using appropriate method.
Budget is just an estimation to your financial need and requirement. A good estimation
about the company strength and weaknesses leads to moderated organisation performance
(Kaplan, and Atkinson,2015). These are mostly based on objectives and required level of
performance those are sort out before making budget for the company. how an organisation
section will perform in coming year is being easily identified.
Method of budget preparation :
Incremental budget : It refers to those budget in which based on slight change from past
year. It is used in organisation as to managers do not want their valuable time in
preparing budget. It to easy and less costly.
Paraphrase This Document
Need a fresh take? Get an instant paraphrase of this document with our AI Paraphraser
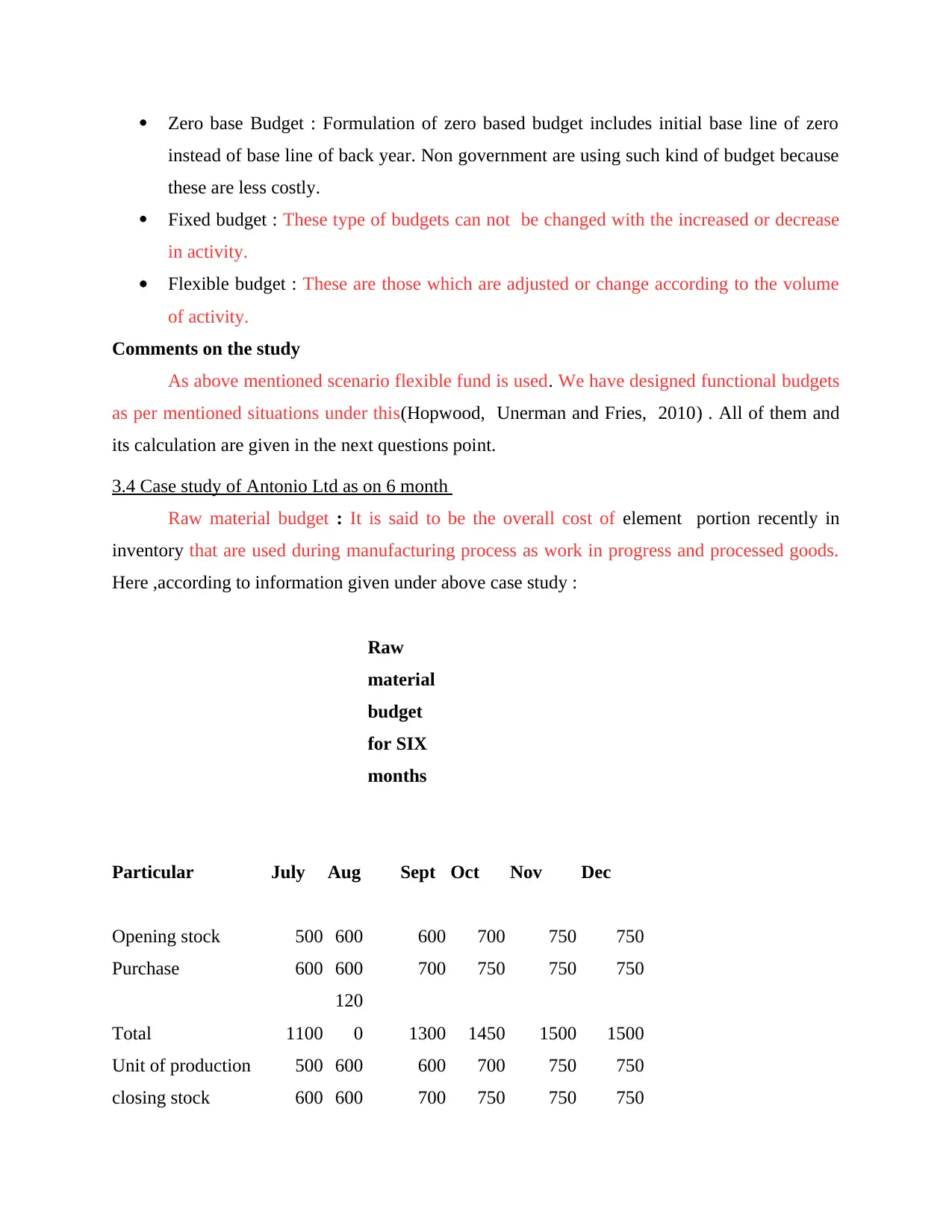
Zero base Budget : Formulation of zero based budget includes initial base line of zero
instead of base line of back year. Non government are using such kind of budget because
these are less costly.
Fixed budget : These type of budgets can not be changed with the increased or decrease
in activity.
Flexible budget : These are those which are adjusted or change according to the volume
of activity.
Comments on the study
As above mentioned scenario flexible fund is used. We have designed functional budgets
as per mentioned situations under this(Hopwood, Unerman and Fries, 2010) . All of them and
its calculation are given in the next questions point.
3.4 Case study of Antonio Ltd as on 6 month
Raw material budget : It is said to be the overall cost of element portion recently in
inventory that are used during manufacturing process as work in progress and processed goods.
Here ,according to information given under above case study :
Raw
material
budget
for SIX
months
Particular July Aug Sept Oct Nov Dec
Opening stock 500 600 600 700 750 750
Purchase 600 600 700 750 750 750
Total 1100
120
0 1300 1450 1500 1500
Unit of production 500 600 600 700 750 750
closing stock 600 600 700 750 750 750
instead of base line of back year. Non government are using such kind of budget because
these are less costly.
Fixed budget : These type of budgets can not be changed with the increased or decrease
in activity.
Flexible budget : These are those which are adjusted or change according to the volume
of activity.
Comments on the study
As above mentioned scenario flexible fund is used. We have designed functional budgets
as per mentioned situations under this(Hopwood, Unerman and Fries, 2010) . All of them and
its calculation are given in the next questions point.
3.4 Case study of Antonio Ltd as on 6 month
Raw material budget : It is said to be the overall cost of element portion recently in
inventory that are used during manufacturing process as work in progress and processed goods.
Here ,according to information given under above case study :
Raw
material
budget
for SIX
months
Particular July Aug Sept Oct Nov Dec
Opening stock 500 600 600 700 750 750
Purchase 600 600 700 750 750 750
Total 1100
120
0 1300 1450 1500 1500
Unit of production 500 600 600 700 750 750
closing stock 600 600 700 750 750 750
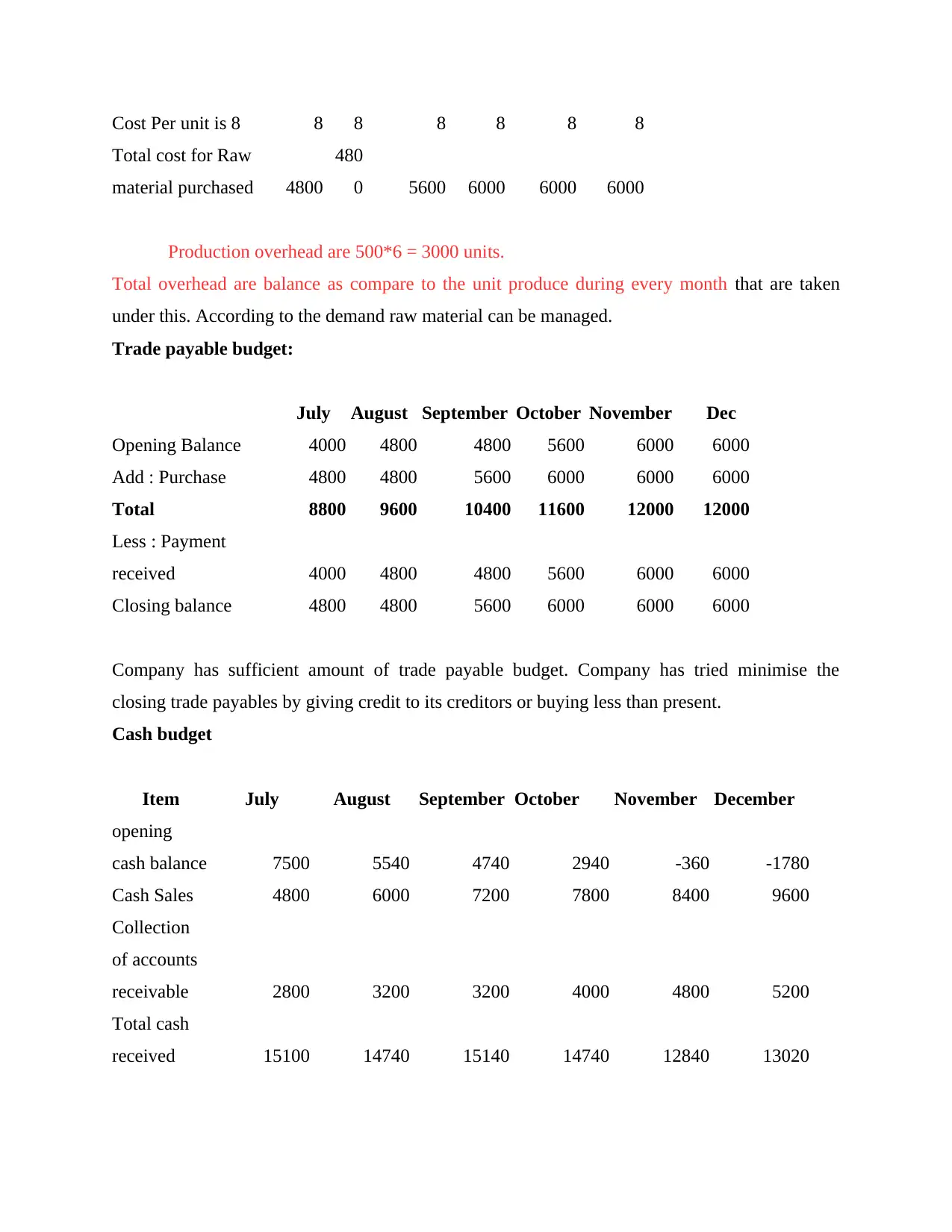
Cost Per unit is 8 8 8 8 8 8 8
Total cost for Raw
material purchased 4800
480
0 5600 6000 6000 6000
Production overhead are 500*6 = 3000 units.
Total overhead are balance as compare to the unit produce during every month that are taken
under this. According to the demand raw material can be managed.
Trade payable budget:
July August September October November Dec
Opening Balance 4000 4800 4800 5600 6000 6000
Add : Purchase 4800 4800 5600 6000 6000 6000
Total 8800 9600 10400 11600 12000 12000
Less : Payment
received 4000 4800 4800 5600 6000 6000
Closing balance 4800 4800 5600 6000 6000 6000
Company has sufficient amount of trade payable budget. Company has tried minimise the
closing trade payables by giving credit to its creditors or buying less than present.
Cash budget
Item July August September October November December
opening
cash balance 7500 5540 4740 2940 -360 -1780
Cash Sales 4800 6000 7200 7800 8400 9600
Collection
of accounts
receivable 2800 3200 3200 4000 4800 5200
Total cash
received 15100 14740 15140 14740 12840 13020
Total cost for Raw
material purchased 4800
480
0 5600 6000 6000 6000
Production overhead are 500*6 = 3000 units.
Total overhead are balance as compare to the unit produce during every month that are taken
under this. According to the demand raw material can be managed.
Trade payable budget:
July August September October November Dec
Opening Balance 4000 4800 4800 5600 6000 6000
Add : Purchase 4800 4800 5600 6000 6000 6000
Total 8800 9600 10400 11600 12000 12000
Less : Payment
received 4000 4800 4800 5600 6000 6000
Closing balance 4800 4800 5600 6000 6000 6000
Company has sufficient amount of trade payable budget. Company has tried minimise the
closing trade payables by giving credit to its creditors or buying less than present.
Cash budget
Item July August September October November December
opening
cash balance 7500 5540 4740 2940 -360 -1780
Cash Sales 4800 6000 7200 7800 8400 9600
Collection
of accounts
receivable 2800 3200 3200 4000 4800 5200
Total cash
received 15100 14740 15140 14740 12840 13020
You're viewing a preview
Unlock full access by subscribing today!
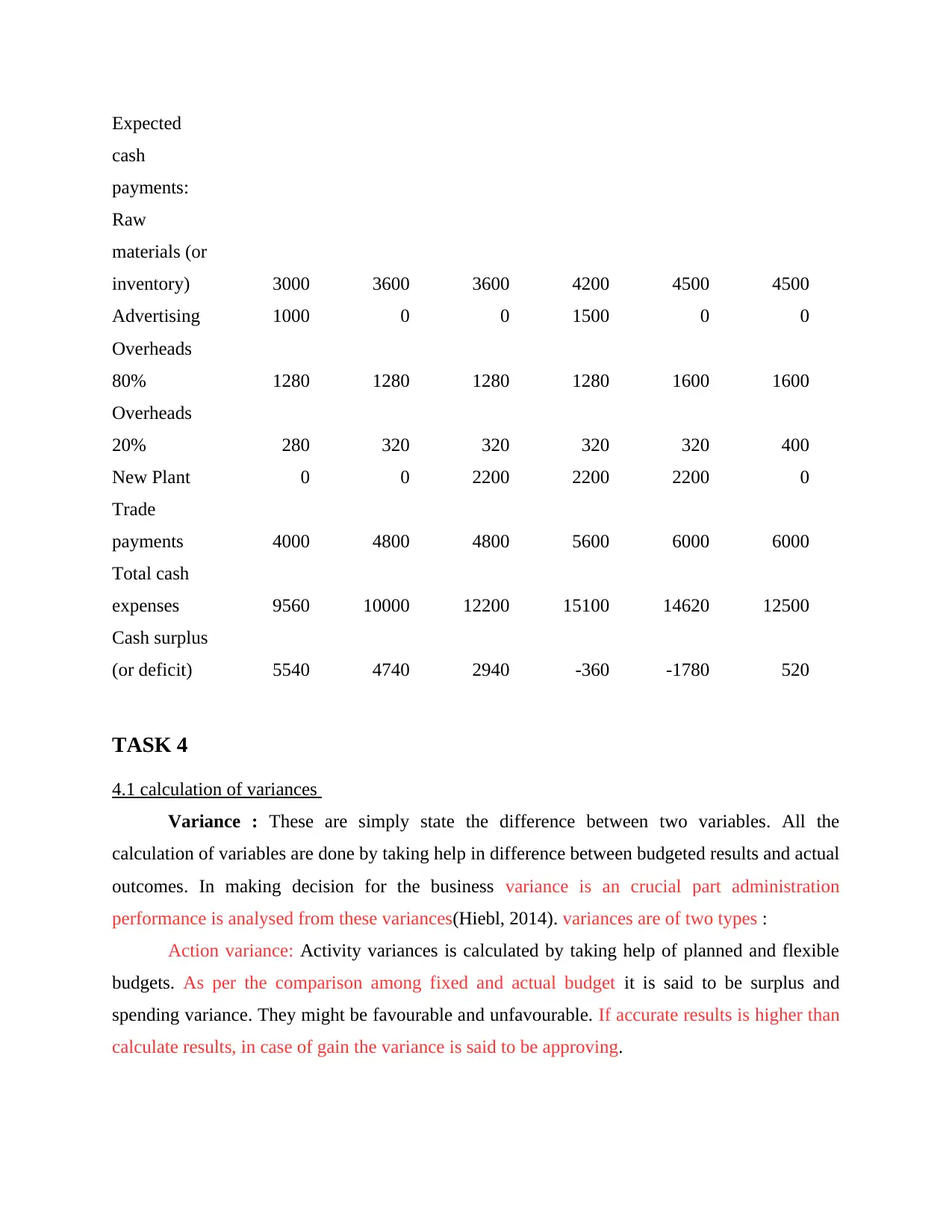
Expected
cash
payments:
Raw
materials (or
inventory) 3000 3600 3600 4200 4500 4500
Advertising 1000 0 0 1500 0 0
Overheads
80% 1280 1280 1280 1280 1600 1600
Overheads
20% 280 320 320 320 320 400
New Plant 0 0 2200 2200 2200 0
Trade
payments 4000 4800 4800 5600 6000 6000
Total cash
expenses 9560 10000 12200 15100 14620 12500
Cash surplus
(or deficit) 5540 4740 2940 -360 -1780 520
TASK 4
4.1 calculation of variances
Variance : These are simply state the difference between two variables. All the
calculation of variables are done by taking help in difference between budgeted results and actual
outcomes. In making decision for the business variance is an crucial part administration
performance is analysed from these variances(Hiebl, 2014). variances are of two types :
Action variance: Activity variances is calculated by taking help of planned and flexible
budgets. As per the comparison among fixed and actual budget it is said to be surplus and
spending variance. They might be favourable and unfavourable. If accurate results is higher than
calculate results, in case of gain the variance is said to be approving.
cash
payments:
Raw
materials (or
inventory) 3000 3600 3600 4200 4500 4500
Advertising 1000 0 0 1500 0 0
Overheads
80% 1280 1280 1280 1280 1600 1600
Overheads
20% 280 320 320 320 320 400
New Plant 0 0 2200 2200 2200 0
Trade
payments 4000 4800 4800 5600 6000 6000
Total cash
expenses 9560 10000 12200 15100 14620 12500
Cash surplus
(or deficit) 5540 4740 2940 -360 -1780 520
TASK 4
4.1 calculation of variances
Variance : These are simply state the difference between two variables. All the
calculation of variables are done by taking help in difference between budgeted results and actual
outcomes. In making decision for the business variance is an crucial part administration
performance is analysed from these variances(Hiebl, 2014). variances are of two types :
Action variance: Activity variances is calculated by taking help of planned and flexible
budgets. As per the comparison among fixed and actual budget it is said to be surplus and
spending variance. They might be favourable and unfavourable. If accurate results is higher than
calculate results, in case of gain the variance is said to be approving.
Paraphrase This Document
Need a fresh take? Get an instant paraphrase of this document with our AI Paraphraser
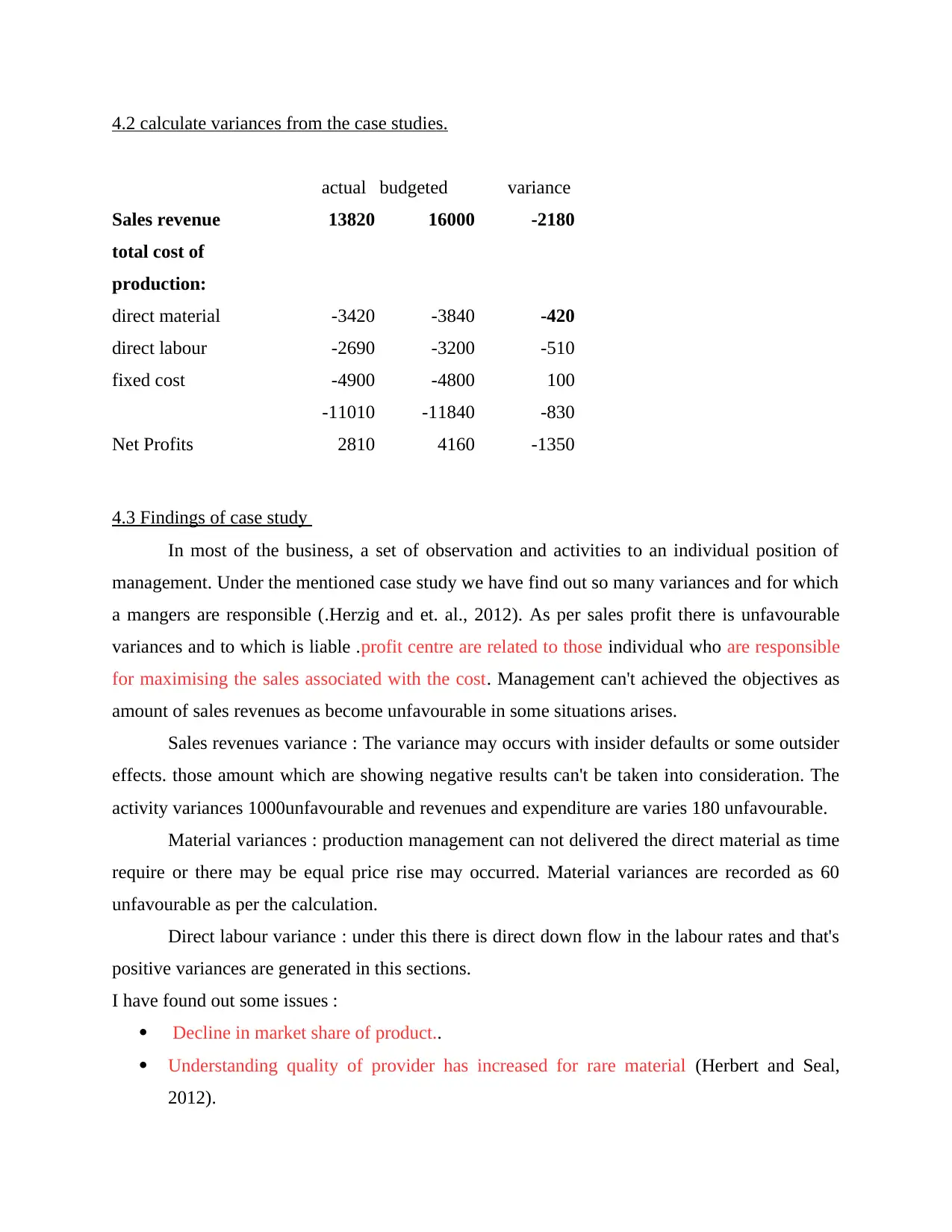
4.2 calculate variances from the case studies.
actual budgeted variance
Sales revenue 13820 16000 -2180
total cost of
production:
direct material -3420 -3840 -420
direct labour -2690 -3200 -510
fixed cost -4900 -4800 100
-11010 -11840 -830
Net Profits 2810 4160 -1350
4.3 Findings of case study
In most of the business, a set of observation and activities to an individual position of
management. Under the mentioned case study we have find out so many variances and for which
a mangers are responsible (.Herzig and et. al., 2012). As per sales profit there is unfavourable
variances and to which is liable .profit centre are related to those individual who are responsible
for maximising the sales associated with the cost. Management can't achieved the objectives as
amount of sales revenues as become unfavourable in some situations arises.
Sales revenues variance : The variance may occurs with insider defaults or some outsider
effects. those amount which are showing negative results can't be taken into consideration. The
activity variances 1000unfavourable and revenues and expenditure are varies 180 unfavourable.
Material variances : production management can not delivered the direct material as time
require or there may be equal price rise may occurred. Material variances are recorded as 60
unfavourable as per the calculation.
Direct labour variance : under this there is direct down flow in the labour rates and that's
positive variances are generated in this sections.
I have found out some issues :
Decline in market share of product..
Understanding quality of provider has increased for rare material (Herbert and Seal,
2012).
actual budgeted variance
Sales revenue 13820 16000 -2180
total cost of
production:
direct material -3420 -3840 -420
direct labour -2690 -3200 -510
fixed cost -4900 -4800 100
-11010 -11840 -830
Net Profits 2810 4160 -1350
4.3 Findings of case study
In most of the business, a set of observation and activities to an individual position of
management. Under the mentioned case study we have find out so many variances and for which
a mangers are responsible (.Herzig and et. al., 2012). As per sales profit there is unfavourable
variances and to which is liable .profit centre are related to those individual who are responsible
for maximising the sales associated with the cost. Management can't achieved the objectives as
amount of sales revenues as become unfavourable in some situations arises.
Sales revenues variance : The variance may occurs with insider defaults or some outsider
effects. those amount which are showing negative results can't be taken into consideration. The
activity variances 1000unfavourable and revenues and expenditure are varies 180 unfavourable.
Material variances : production management can not delivered the direct material as time
require or there may be equal price rise may occurred. Material variances are recorded as 60
unfavourable as per the calculation.
Direct labour variance : under this there is direct down flow in the labour rates and that's
positive variances are generated in this sections.
I have found out some issues :
Decline in market share of product..
Understanding quality of provider has increased for rare material (Herbert and Seal,
2012).
1 out of 17
Related Documents

Your All-in-One AI-Powered Toolkit for Academic Success.
+13062052269
info@desklib.com
Available 24*7 on WhatsApp / Email
Unlock your academic potential
© 2024 | Zucol Services PVT LTD | All rights reserved.