Management Accounting Report: Costing, Profitability, and Budgeting
VerifiedAdded on 2023/06/18
|20
|3843
|277
Report
AI Summary
This management accounting report provides a detailed analysis of costing methods, break-even points, and variance analysis. It includes solutions to questions related to Plaistead Plc and Crawford Plc, covering topics such as contribution per unit, break-even sales revenue, margin of safety, profit estimation, and pricing strategies. The report also explores cost allocation methods for different departments, overhead recovery rates, and full job cost calculations. Additionally, it discusses the advantages and disadvantages of absorption costing and provides estimations of budgets and variances for Jayrod Plc. This comprehensive report offers valuable insights into management accounting principles and their practical applications.
Contribute Materials
Your contribution can guide someone’s learning journey. Share your
documents today.
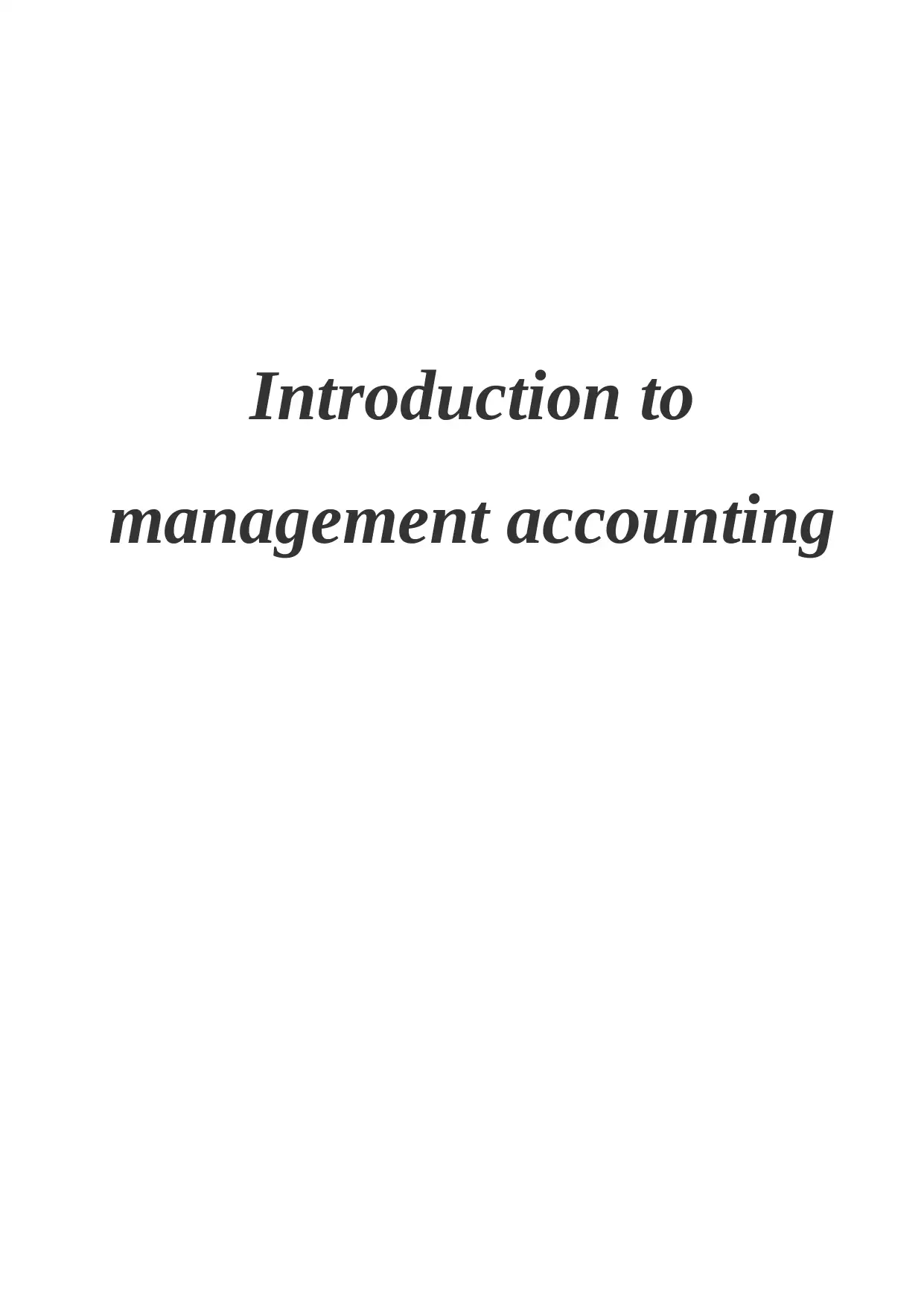
Introduction to
management accounting
management accounting
Secure Best Marks with AI Grader
Need help grading? Try our AI Grader for instant feedback on your assignments.
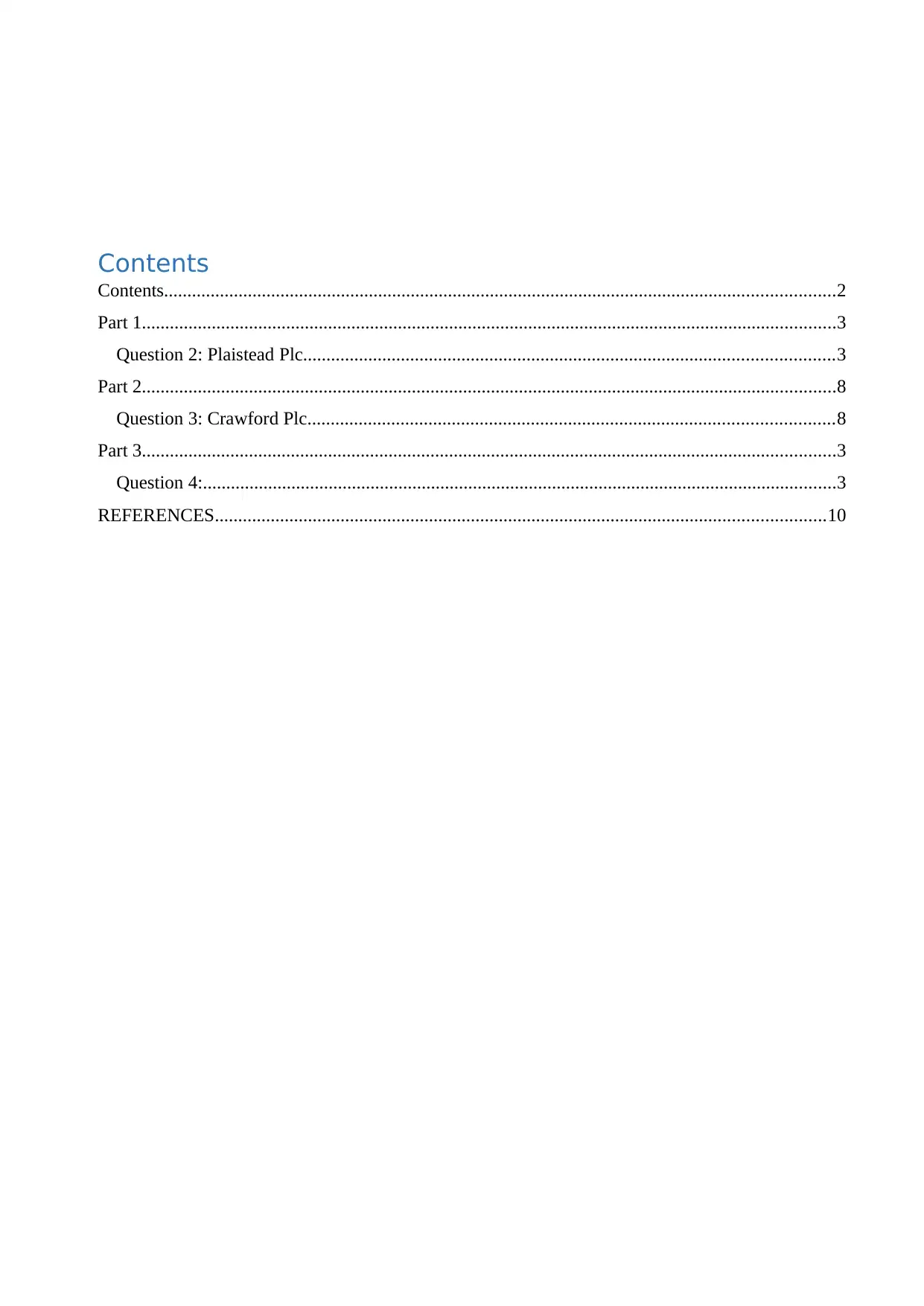
Contents
Contents................................................................................................................................................2
Part 1.....................................................................................................................................................3
Question 2: Plaistead Plc..................................................................................................................3
Part 2.....................................................................................................................................................8
Question 3: Crawford Plc.................................................................................................................8
Part 3.....................................................................................................................................................3
Question 4:........................................................................................................................................3
REFERENCES...................................................................................................................................10
Contents................................................................................................................................................2
Part 1.....................................................................................................................................................3
Question 2: Plaistead Plc..................................................................................................................3
Part 2.....................................................................................................................................................8
Question 3: Crawford Plc.................................................................................................................8
Part 3.....................................................................................................................................................3
Question 4:........................................................................................................................................3
REFERENCES...................................................................................................................................10
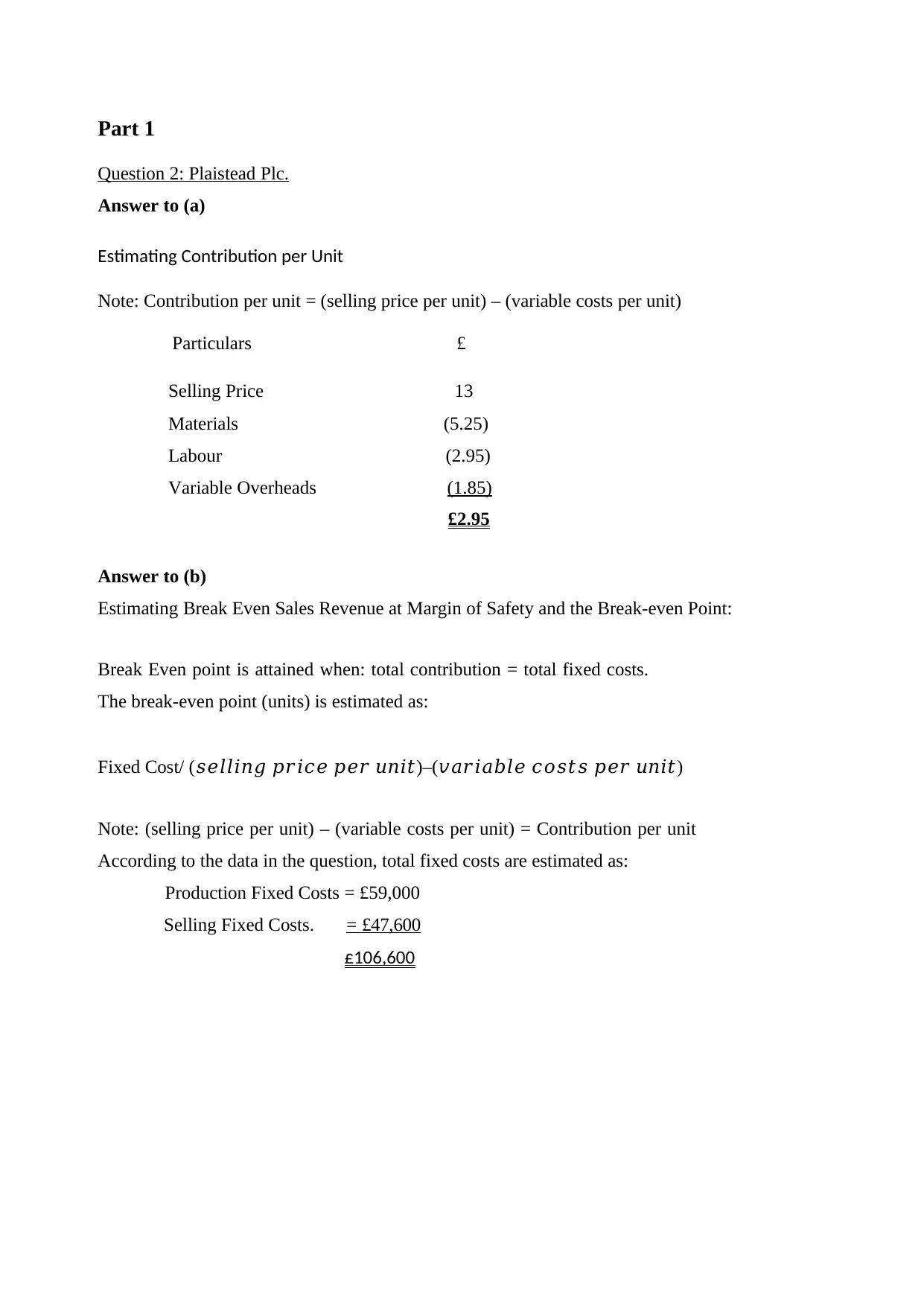
Part 1
Question 2: Plaistead Plc.
Answer to (a)
Estimating Contribution per Unit
Note: Contribution per unit = (selling price per unit) – (variable costs per unit)
Particulars £
Selling Price 13
Materials (5.25)
Labour (2.95)
Variable Overheads (1.85)
£2.95
Answer to (b)
Estimating Break Even Sales Revenue at Margin of Safety and the Break-even Point:
Break Even point is attained when: total contribution = total fixed costs.
The break-even point (units) is estimated as:
Fixed Cost/ (𝑠𝑒𝑙𝑙𝑖𝑛𝑔 𝑝𝑟𝑖𝑐𝑒 𝑝𝑒𝑟 𝑢𝑛𝑖𝑡)–(𝑣𝑎𝑟𝑖𝑎𝑏𝑙𝑒 𝑐𝑜𝑠𝑡𝑠 𝑝𝑒𝑟 𝑢𝑛𝑖𝑡)
Note: (selling price per unit) – (variable costs per unit) = Contribution per unit
According to the data in the question, total fixed costs are estimated as:
Production Fixed Costs = £59,000
Selling Fixed Costs. = £47,600
£106,600
Question 2: Plaistead Plc.
Answer to (a)
Estimating Contribution per Unit
Note: Contribution per unit = (selling price per unit) – (variable costs per unit)
Particulars £
Selling Price 13
Materials (5.25)
Labour (2.95)
Variable Overheads (1.85)
£2.95
Answer to (b)
Estimating Break Even Sales Revenue at Margin of Safety and the Break-even Point:
Break Even point is attained when: total contribution = total fixed costs.
The break-even point (units) is estimated as:
Fixed Cost/ (𝑠𝑒𝑙𝑙𝑖𝑛𝑔 𝑝𝑟𝑖𝑐𝑒 𝑝𝑒𝑟 𝑢𝑛𝑖𝑡)–(𝑣𝑎𝑟𝑖𝑎𝑏𝑙𝑒 𝑐𝑜𝑠𝑡𝑠 𝑝𝑒𝑟 𝑢𝑛𝑖𝑡)
Note: (selling price per unit) – (variable costs per unit) = Contribution per unit
According to the data in the question, total fixed costs are estimated as:
Production Fixed Costs = £59,000
Selling Fixed Costs. = £47,600
£106,600
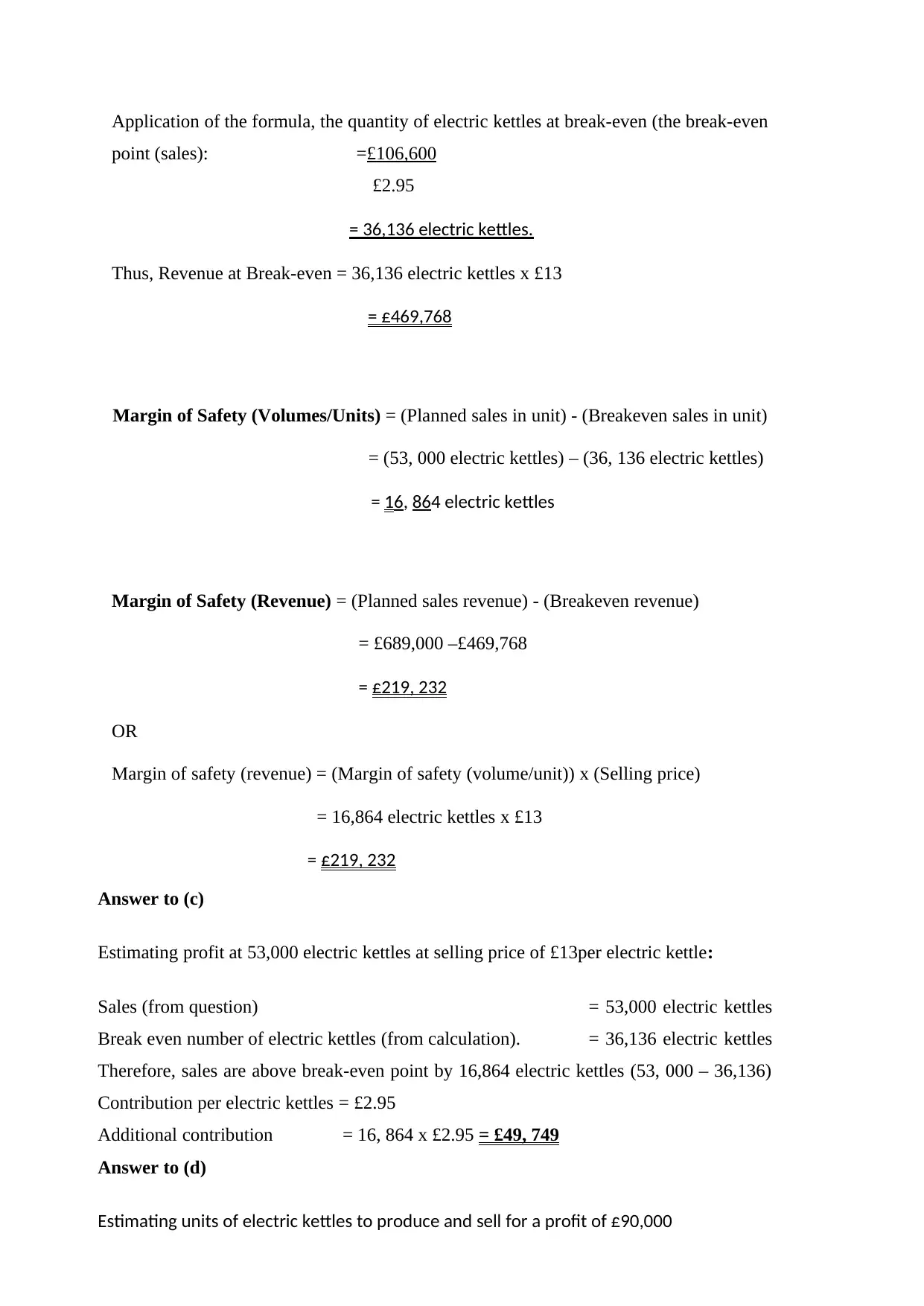
Application of the formula, the quantity of electric kettles at break-even (the break-even
point (sales): =£106,600
£2.95
= 36,136 electric kettles.
Thus, Revenue at Break-even = 36,136 electric kettles x £13
= £469,768
Margin of Safety (Volumes/Units) = (Planned sales in unit) - (Breakeven sales in unit)
= (53, 000 electric kettles) – (36, 136 electric kettles)
= 16, 864 electric kettles
Margin of Safety (Revenue) = (Planned sales revenue) - (Breakeven revenue)
= £689,000 –£469,768
= £219, 232
OR
Margin of safety (revenue) = (Margin of safety (volume/unit)) x (Selling price)
= 16,864 electric kettles x £13
= £219, 232
Answer to (c)
Estimating profit at 53,000 electric kettles at selling price of £13per electric kettle:
Sales (from question) = 53,000 electric kettles
Break even number of electric kettles (from calculation). = 36,136 electric kettles
Therefore, sales are above break-even point by 16,864 electric kettles (53, 000 – 36,136)
Contribution per electric kettles = £2.95
Additional contribution = 16, 864 x £2.95 = £49, 749
Answer to (d)
Estimating units of electric kettles to produce and sell for a profit of £90,000
point (sales): =£106,600
£2.95
= 36,136 electric kettles.
Thus, Revenue at Break-even = 36,136 electric kettles x £13
= £469,768
Margin of Safety (Volumes/Units) = (Planned sales in unit) - (Breakeven sales in unit)
= (53, 000 electric kettles) – (36, 136 electric kettles)
= 16, 864 electric kettles
Margin of Safety (Revenue) = (Planned sales revenue) - (Breakeven revenue)
= £689,000 –£469,768
= £219, 232
OR
Margin of safety (revenue) = (Margin of safety (volume/unit)) x (Selling price)
= 16,864 electric kettles x £13
= £219, 232
Answer to (c)
Estimating profit at 53,000 electric kettles at selling price of £13per electric kettle:
Sales (from question) = 53,000 electric kettles
Break even number of electric kettles (from calculation). = 36,136 electric kettles
Therefore, sales are above break-even point by 16,864 electric kettles (53, 000 – 36,136)
Contribution per electric kettles = £2.95
Additional contribution = 16, 864 x £2.95 = £49, 749
Answer to (d)
Estimating units of electric kettles to produce and sell for a profit of £90,000
Secure Best Marks with AI Grader
Need help grading? Try our AI Grader for instant feedback on your assignments.
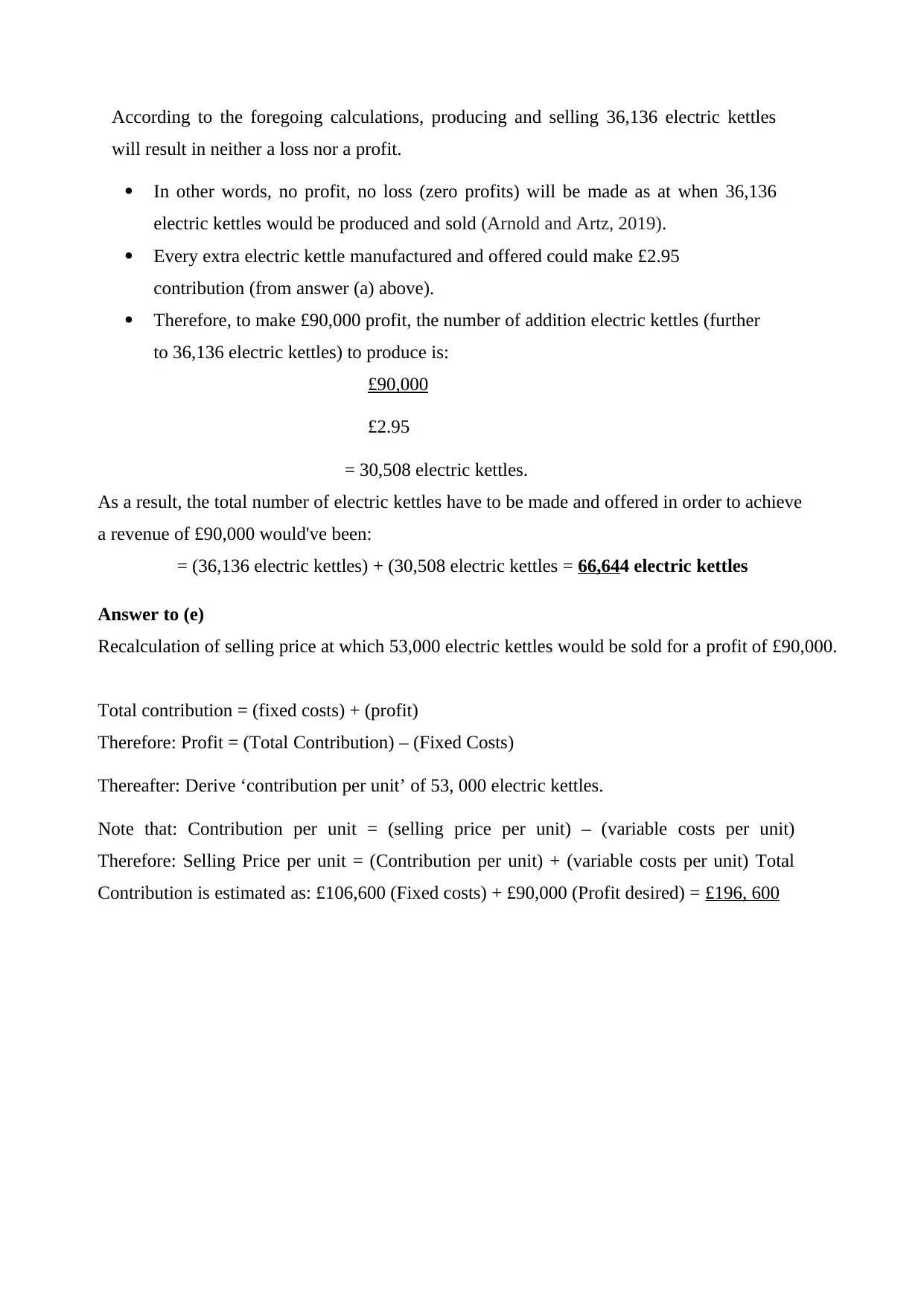
According to the foregoing calculations, producing and selling 36,136 electric kettles
will result in neither a loss nor a profit.
In other words, no profit, no loss (zero profits) will be made as at when 36,136
electric kettles would be produced and sold (Arnold and Artz, 2019).
Every extra electric kettle manufactured and offered could make £2.95
contribution (from answer (a) above).
Therefore, to make £90,000 profit, the number of addition electric kettles (further
to 36,136 electric kettles) to produce is:
£90,000
£2.95
= 30,508 electric kettles.
As a result, the total number of electric kettles have to be made and offered in order to achieve
a revenue of £90,000 would've been:
= (36,136 electric kettles) + (30,508 electric kettles = 66,644 electric kettles
Answer to (e)
Recalculation of selling price at which 53,000 electric kettles would be sold for a profit of £90,000.
Total contribution = (fixed costs) + (profit)
Therefore: Profit = (Total Contribution) – (Fixed Costs)
Thereafter: Derive ‘contribution per unit’ of 53, 000 electric kettles.
Note that: Contribution per unit = (selling price per unit) – (variable costs per unit)
Therefore: Selling Price per unit = (Contribution per unit) + (variable costs per unit) Total
Contribution is estimated as: £106,600 (Fixed costs) + £90,000 (Profit desired) = £196, 600
will result in neither a loss nor a profit.
In other words, no profit, no loss (zero profits) will be made as at when 36,136
electric kettles would be produced and sold (Arnold and Artz, 2019).
Every extra electric kettle manufactured and offered could make £2.95
contribution (from answer (a) above).
Therefore, to make £90,000 profit, the number of addition electric kettles (further
to 36,136 electric kettles) to produce is:
£90,000
£2.95
= 30,508 electric kettles.
As a result, the total number of electric kettles have to be made and offered in order to achieve
a revenue of £90,000 would've been:
= (36,136 electric kettles) + (30,508 electric kettles = 66,644 electric kettles
Answer to (e)
Recalculation of selling price at which 53,000 electric kettles would be sold for a profit of £90,000.
Total contribution = (fixed costs) + (profit)
Therefore: Profit = (Total Contribution) – (Fixed Costs)
Thereafter: Derive ‘contribution per unit’ of 53, 000 electric kettles.
Note that: Contribution per unit = (selling price per unit) – (variable costs per unit)
Therefore: Selling Price per unit = (Contribution per unit) + (variable costs per unit) Total
Contribution is estimated as: £106,600 (Fixed costs) + £90,000 (Profit desired) = £196, 600
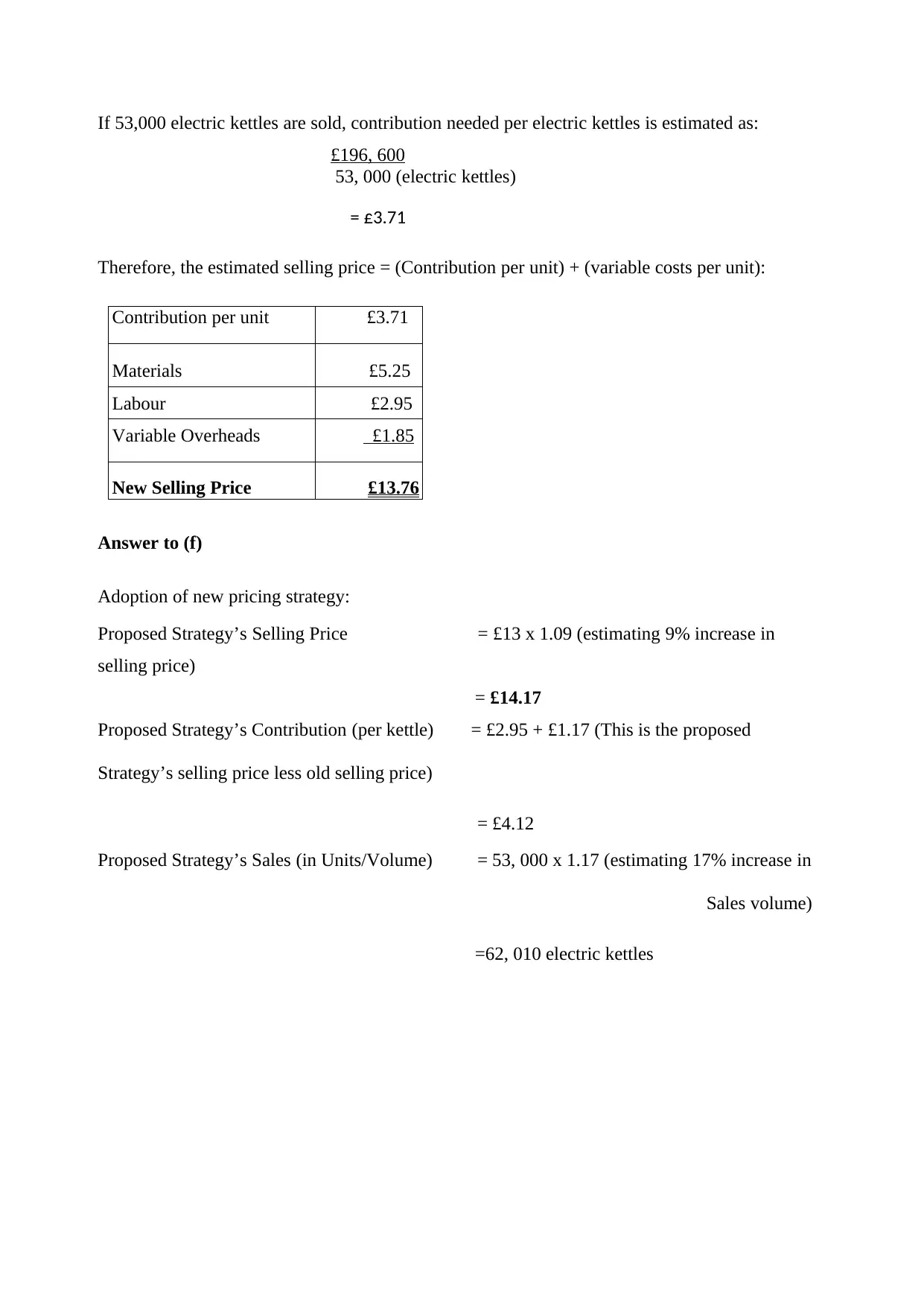
If 53,000 electric kettles are sold, contribution needed per electric kettles is estimated as:
£196, 600
53, 000 (electric kettles)
= £3.71
Therefore, the estimated selling price = (Contribution per unit) + (variable costs per unit):
Contribution per unit £3.71
Materials £5.25
Labour £2.95
Variable Overheads £1.85
New Selling Price £13.76
Answer to (f)
Adoption of new pricing strategy:
Proposed Strategy’s Selling Price = £13 x 1.09 (estimating 9% increase in
selling price)
= £14.17
Proposed Strategy’s Contribution (per kettle) = £2.95 + £1.17 (This is the proposed
Strategy’s selling price less old selling price)
= £4.12
Proposed Strategy’s Sales (in Units/Volume) = 53, 000 x 1.17 (estimating 17% increase in
Sales volume)
=62, 010 electric kettles
£196, 600
53, 000 (electric kettles)
= £3.71
Therefore, the estimated selling price = (Contribution per unit) + (variable costs per unit):
Contribution per unit £3.71
Materials £5.25
Labour £2.95
Variable Overheads £1.85
New Selling Price £13.76
Answer to (f)
Adoption of new pricing strategy:
Proposed Strategy’s Selling Price = £13 x 1.09 (estimating 9% increase in
selling price)
= £14.17
Proposed Strategy’s Contribution (per kettle) = £2.95 + £1.17 (This is the proposed
Strategy’s selling price less old selling price)
= £4.12
Proposed Strategy’s Sales (in Units/Volume) = 53, 000 x 1.17 (estimating 17% increase in
Sales volume)
=62, 010 electric kettles
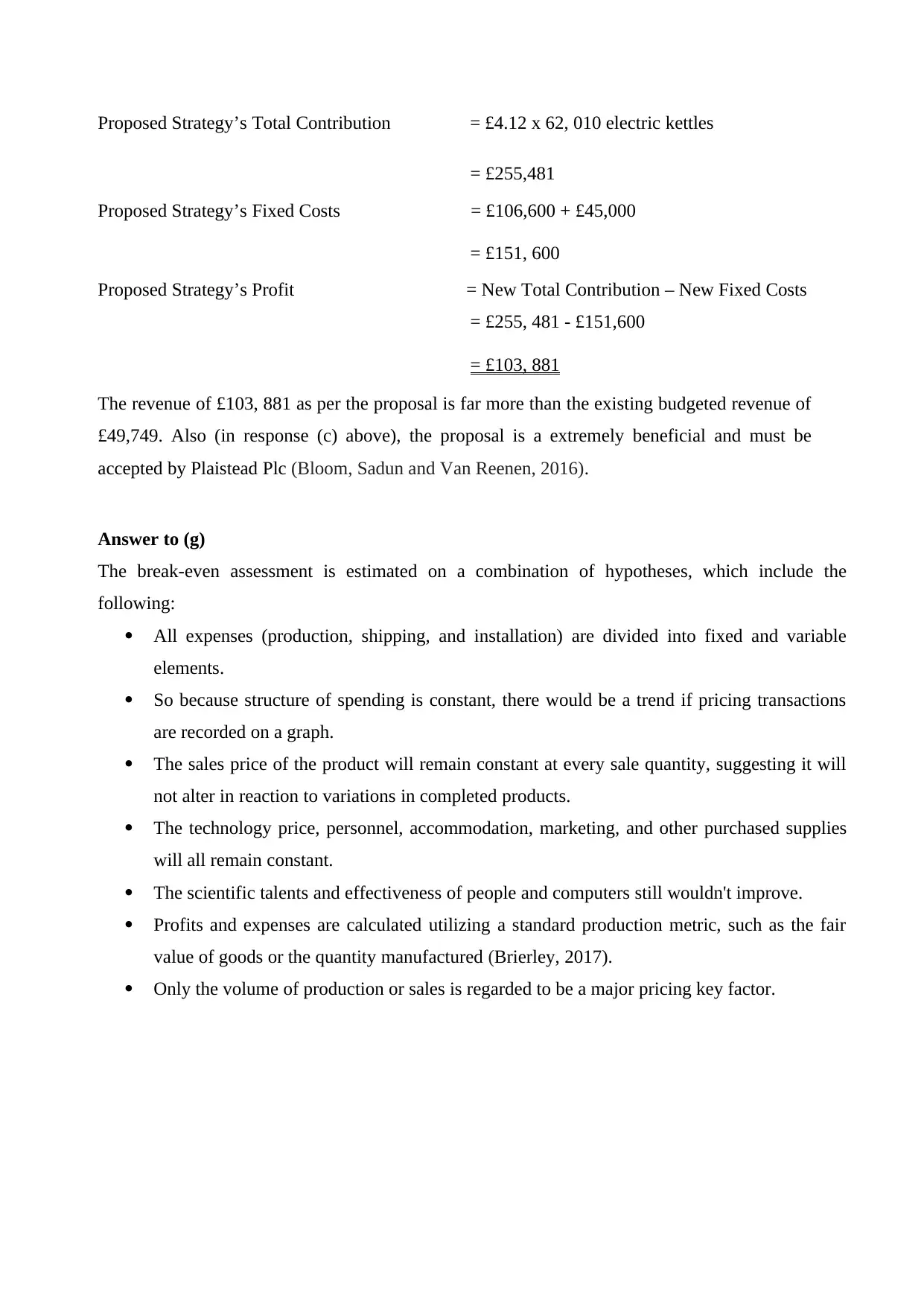
Proposed Strategy’s Total Contribution = £4.12 x 62, 010 electric kettles
= £255,481
Proposed Strategy’s Fixed Costs = £106,600 + £45,000
= £151, 600
Proposed Strategy’s Profit = New Total Contribution – New Fixed Costs
= £255, 481 - £151,600
= £103, 881
The revenue of £103, 881 as per the proposal is far more than the existing budgeted revenue of
£49,749. Also (in response (c) above), the proposal is a extremely beneficial and must be
accepted by Plaistead Plc (Bloom, Sadun and Van Reenen, 2016).
Answer to (g)
The break-even assessment is estimated on a combination of hypotheses, which include the
following:
All expenses (production, shipping, and installation) are divided into fixed and variable
elements.
So because structure of spending is constant, there would be a trend if pricing transactions
are recorded on a graph.
The sales price of the product will remain constant at every sale quantity, suggesting it will
not alter in reaction to variations in completed products.
The technology price, personnel, accommodation, marketing, and other purchased supplies
will all remain constant.
The scientific talents and effectiveness of people and computers still wouldn't improve.
Profits and expenses are calculated utilizing a standard production metric, such as the fair
value of goods or the quantity manufactured (Brierley, 2017).
Only the volume of production or sales is regarded to be a major pricing key factor.
= £255,481
Proposed Strategy’s Fixed Costs = £106,600 + £45,000
= £151, 600
Proposed Strategy’s Profit = New Total Contribution – New Fixed Costs
= £255, 481 - £151,600
= £103, 881
The revenue of £103, 881 as per the proposal is far more than the existing budgeted revenue of
£49,749. Also (in response (c) above), the proposal is a extremely beneficial and must be
accepted by Plaistead Plc (Bloom, Sadun and Van Reenen, 2016).
Answer to (g)
The break-even assessment is estimated on a combination of hypotheses, which include the
following:
All expenses (production, shipping, and installation) are divided into fixed and variable
elements.
So because structure of spending is constant, there would be a trend if pricing transactions
are recorded on a graph.
The sales price of the product will remain constant at every sale quantity, suggesting it will
not alter in reaction to variations in completed products.
The technology price, personnel, accommodation, marketing, and other purchased supplies
will all remain constant.
The scientific talents and effectiveness of people and computers still wouldn't improve.
Profits and expenses are calculated utilizing a standard production metric, such as the fair
value of goods or the quantity manufactured (Brierley, 2017).
Only the volume of production or sales is regarded to be a major pricing key factor.
Paraphrase This Document
Need a fresh take? Get an instant paraphrase of this document with our AI Paraphraser
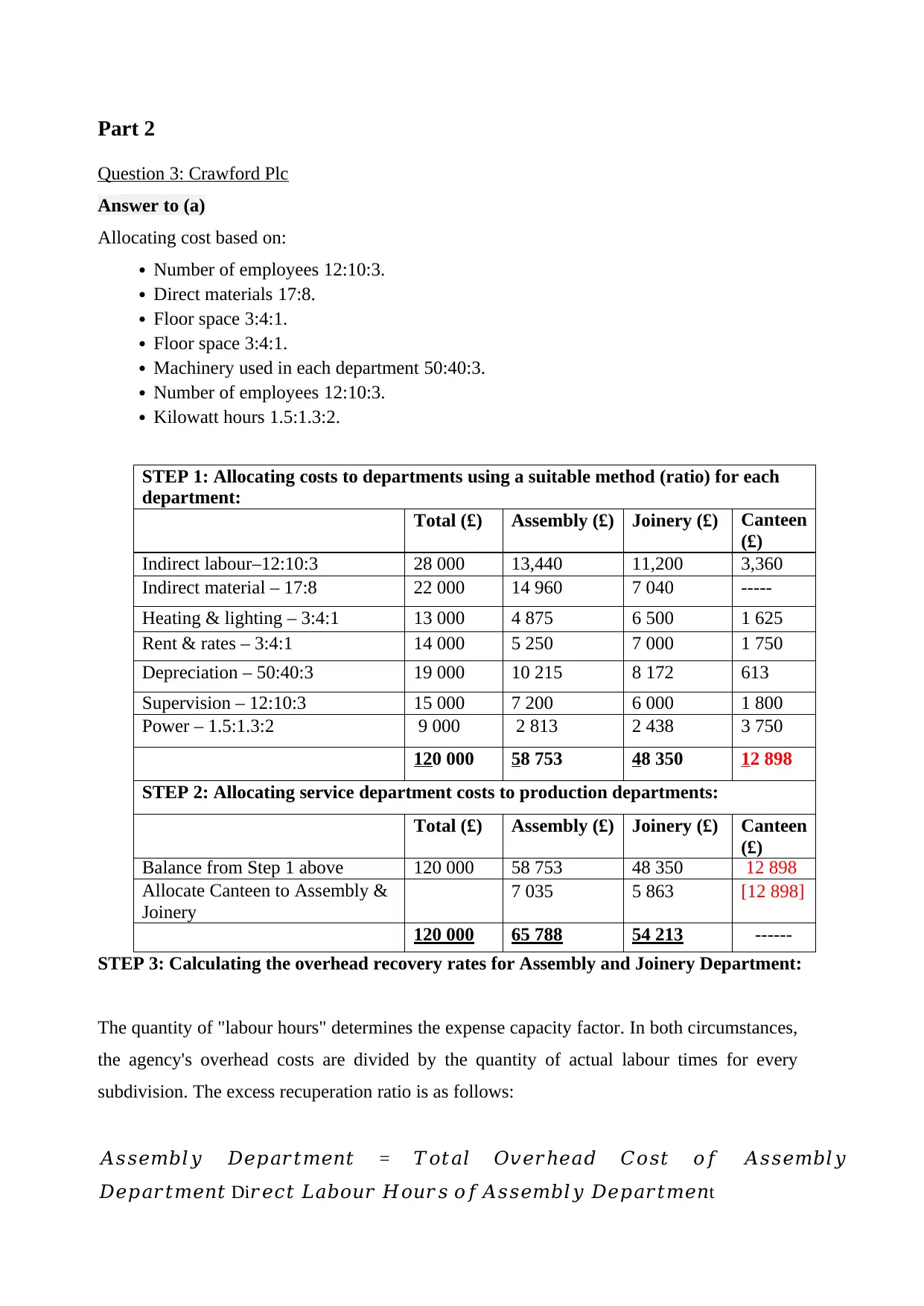
Part 2
Question 3: Crawford Plc
Answer to (a)
Allocating cost based on:
Number of employees 12:10:3.
Direct materials 17:8.
Floor space 3:4:1.
Floor space 3:4:1.
Machinery used in each department 50:40:3.
Number of employees 12:10:3.
Kilowatt hours 1.5:1.3:2.
STEP 1: Allocating costs to departments using a suitable method (ratio) for each
department:
Total (£) Assembly (£) Joinery (£) Canteen
(£)
Indirect labour–12:10:3 28 000 13,440 11,200 3,360
Indirect material – 17:8 22 000 14 960 7 040 -----
Heating & lighting – 3:4:1 13 000 4 875 6 500 1 625
Rent & rates – 3:4:1 14 000 5 250 7 000 1 750
Depreciation – 50:40:3 19 000 10 215 8 172 613
Supervision – 12:10:3 15 000 7 200 6 000 1 800
Power – 1.5:1.3:2 9 000 2 813 2 438 3 750
120 000 58 753 48 350 12 898
STEP 2: Allocating service department costs to production departments:
Total (£) Assembly (£) Joinery (£) Canteen
(£)
Balance from Step 1 above 120 000 58 753 48 350 12 898
Allocate Canteen to Assembly &
Joinery
7 035 5 863 [12 898]
120 000 65 788 54 213 ------
STEP 3: Calculating the overhead recovery rates for Assembly and Joinery Department:
The quantity of "labour hours" determines the expense capacity factor. In both circumstances,
the agency's overhead costs are divided by the quantity of actual labour times for every
subdivision. The excess recuperation ratio is as follows:
𝐴𝑠𝑠𝑒𝑚𝑏𝑙𝑦 𝐷𝑒𝑝𝑎𝑟𝑡𝑚𝑒𝑛𝑡 = 𝑇𝑜𝑡𝑎𝑙 𝑂𝑣𝑒𝑟ℎ𝑒𝑎𝑑 𝐶𝑜𝑠𝑡 𝑜𝑓 𝐴𝑠𝑠𝑒𝑚𝑏𝑙𝑦
𝐷𝑒𝑝𝑎𝑟𝑡𝑚𝑒𝑛𝑡 Di𝑟𝑒𝑐𝑡 𝐿𝑎𝑏𝑜𝑢𝑟 𝐻𝑜𝑢𝑟𝑠 𝑜𝑓𝐴𝑠𝑠𝑒𝑚𝑏𝑙𝑦 𝐷𝑒𝑝𝑎𝑟𝑡𝑚𝑒𝑛t
Question 3: Crawford Plc
Answer to (a)
Allocating cost based on:
Number of employees 12:10:3.
Direct materials 17:8.
Floor space 3:4:1.
Floor space 3:4:1.
Machinery used in each department 50:40:3.
Number of employees 12:10:3.
Kilowatt hours 1.5:1.3:2.
STEP 1: Allocating costs to departments using a suitable method (ratio) for each
department:
Total (£) Assembly (£) Joinery (£) Canteen
(£)
Indirect labour–12:10:3 28 000 13,440 11,200 3,360
Indirect material – 17:8 22 000 14 960 7 040 -----
Heating & lighting – 3:4:1 13 000 4 875 6 500 1 625
Rent & rates – 3:4:1 14 000 5 250 7 000 1 750
Depreciation – 50:40:3 19 000 10 215 8 172 613
Supervision – 12:10:3 15 000 7 200 6 000 1 800
Power – 1.5:1.3:2 9 000 2 813 2 438 3 750
120 000 58 753 48 350 12 898
STEP 2: Allocating service department costs to production departments:
Total (£) Assembly (£) Joinery (£) Canteen
(£)
Balance from Step 1 above 120 000 58 753 48 350 12 898
Allocate Canteen to Assembly &
Joinery
7 035 5 863 [12 898]
120 000 65 788 54 213 ------
STEP 3: Calculating the overhead recovery rates for Assembly and Joinery Department:
The quantity of "labour hours" determines the expense capacity factor. In both circumstances,
the agency's overhead costs are divided by the quantity of actual labour times for every
subdivision. The excess recuperation ratio is as follows:
𝐴𝑠𝑠𝑒𝑚𝑏𝑙𝑦 𝐷𝑒𝑝𝑎𝑟𝑡𝑚𝑒𝑛𝑡 = 𝑇𝑜𝑡𝑎𝑙 𝑂𝑣𝑒𝑟ℎ𝑒𝑎𝑑 𝐶𝑜𝑠𝑡 𝑜𝑓 𝐴𝑠𝑠𝑒𝑚𝑏𝑙𝑦
𝐷𝑒𝑝𝑎𝑟𝑡𝑚𝑒𝑛𝑡 Di𝑟𝑒𝑐𝑡 𝐿𝑎𝑏𝑜𝑢𝑟 𝐻𝑜𝑢𝑟𝑠 𝑜𝑓𝐴𝑠𝑠𝑒𝑚𝑏𝑙𝑦 𝐷𝑒𝑝𝑎𝑟𝑡𝑚𝑒𝑛t
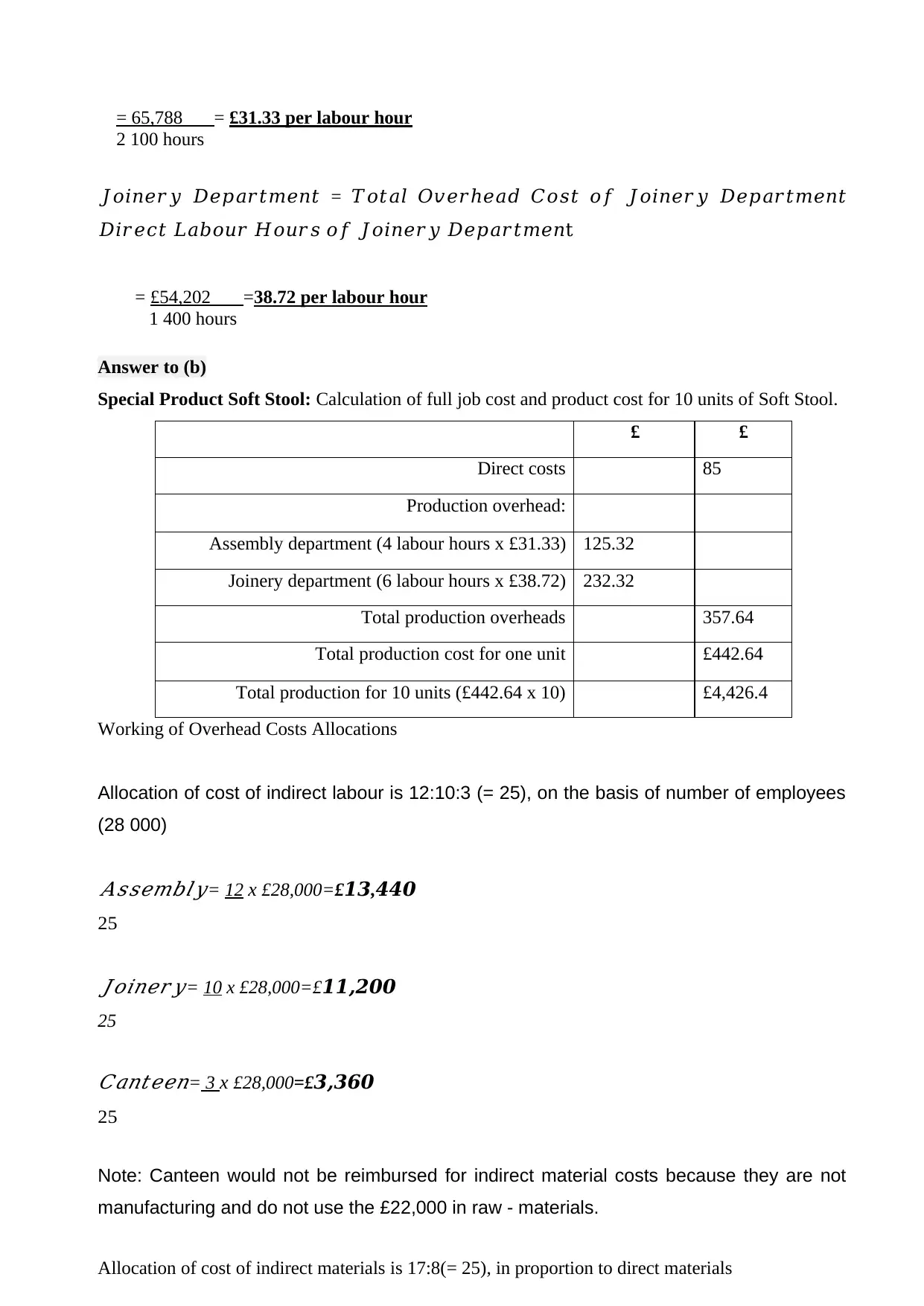
= 65,788 = £31.33 per labour hour
2 100 hours
𝐽𝑜𝑖𝑛𝑒𝑟𝑦 𝐷𝑒𝑝𝑎𝑟𝑡𝑚𝑒𝑛𝑡 = 𝑇𝑜𝑡𝑎𝑙 𝑂𝑣𝑒𝑟ℎ𝑒𝑎𝑑 𝐶𝑜𝑠𝑡 𝑜𝑓 𝐽𝑜𝑖𝑛𝑒𝑟𝑦 𝐷𝑒𝑝𝑎𝑟𝑡𝑚𝑒𝑛𝑡
𝐷𝑖𝑟𝑒𝑐𝑡 𝐿𝑎𝑏𝑜𝑢𝑟 𝐻𝑜𝑢𝑟𝑠 𝑜𝑓 𝐽𝑜𝑖𝑛𝑒𝑟𝑦 𝐷𝑒𝑝𝑎𝑟𝑡𝑚𝑒𝑛t
= £54,202 =38.72 per labour hour
1 400 hours
Answer to (b)
Special Product Soft Stool: Calculation of full job cost and product cost for 10 units of Soft Stool.
£ £
Direct costs 85
Production overhead:
Assembly department (4 labour hours x £31.33) 125.32
Joinery department (6 labour hours x £38.72) 232.32
Total production overheads 357.64
Total production cost for one unit £442.64
Total production for 10 units (£442.64 x 10) £4,426.4
Working of Overhead Costs Allocations
Allocation of cost of indirect labour is 12:10:3 (= 25), on the basis of number of employees
(28 000)
𝐴𝑠𝑠𝑒𝑚𝑏𝑙𝑦= 12 x £28,000=£13,440
25
𝐽𝑜𝑖𝑛𝑒𝑟𝑦= 10 x £28,000=£11,200
25
𝐶𝑎𝑛𝑡𝑒𝑒𝑛= 3 x £28,000=£3,360
25
Note: Canteen would not be reimbursed for indirect material costs because they are not
manufacturing and do not use the £22,000 in raw - materials.
Allocation of cost of indirect materials is 17:8(= 25), in proportion to direct materials
2 100 hours
𝐽𝑜𝑖𝑛𝑒𝑟𝑦 𝐷𝑒𝑝𝑎𝑟𝑡𝑚𝑒𝑛𝑡 = 𝑇𝑜𝑡𝑎𝑙 𝑂𝑣𝑒𝑟ℎ𝑒𝑎𝑑 𝐶𝑜𝑠𝑡 𝑜𝑓 𝐽𝑜𝑖𝑛𝑒𝑟𝑦 𝐷𝑒𝑝𝑎𝑟𝑡𝑚𝑒𝑛𝑡
𝐷𝑖𝑟𝑒𝑐𝑡 𝐿𝑎𝑏𝑜𝑢𝑟 𝐻𝑜𝑢𝑟𝑠 𝑜𝑓 𝐽𝑜𝑖𝑛𝑒𝑟𝑦 𝐷𝑒𝑝𝑎𝑟𝑡𝑚𝑒𝑛t
= £54,202 =38.72 per labour hour
1 400 hours
Answer to (b)
Special Product Soft Stool: Calculation of full job cost and product cost for 10 units of Soft Stool.
£ £
Direct costs 85
Production overhead:
Assembly department (4 labour hours x £31.33) 125.32
Joinery department (6 labour hours x £38.72) 232.32
Total production overheads 357.64
Total production cost for one unit £442.64
Total production for 10 units (£442.64 x 10) £4,426.4
Working of Overhead Costs Allocations
Allocation of cost of indirect labour is 12:10:3 (= 25), on the basis of number of employees
(28 000)
𝐴𝑠𝑠𝑒𝑚𝑏𝑙𝑦= 12 x £28,000=£13,440
25
𝐽𝑜𝑖𝑛𝑒𝑟𝑦= 10 x £28,000=£11,200
25
𝐶𝑎𝑛𝑡𝑒𝑒𝑛= 3 x £28,000=£3,360
25
Note: Canteen would not be reimbursed for indirect material costs because they are not
manufacturing and do not use the £22,000 in raw - materials.
Allocation of cost of indirect materials is 17:8(= 25), in proportion to direct materials
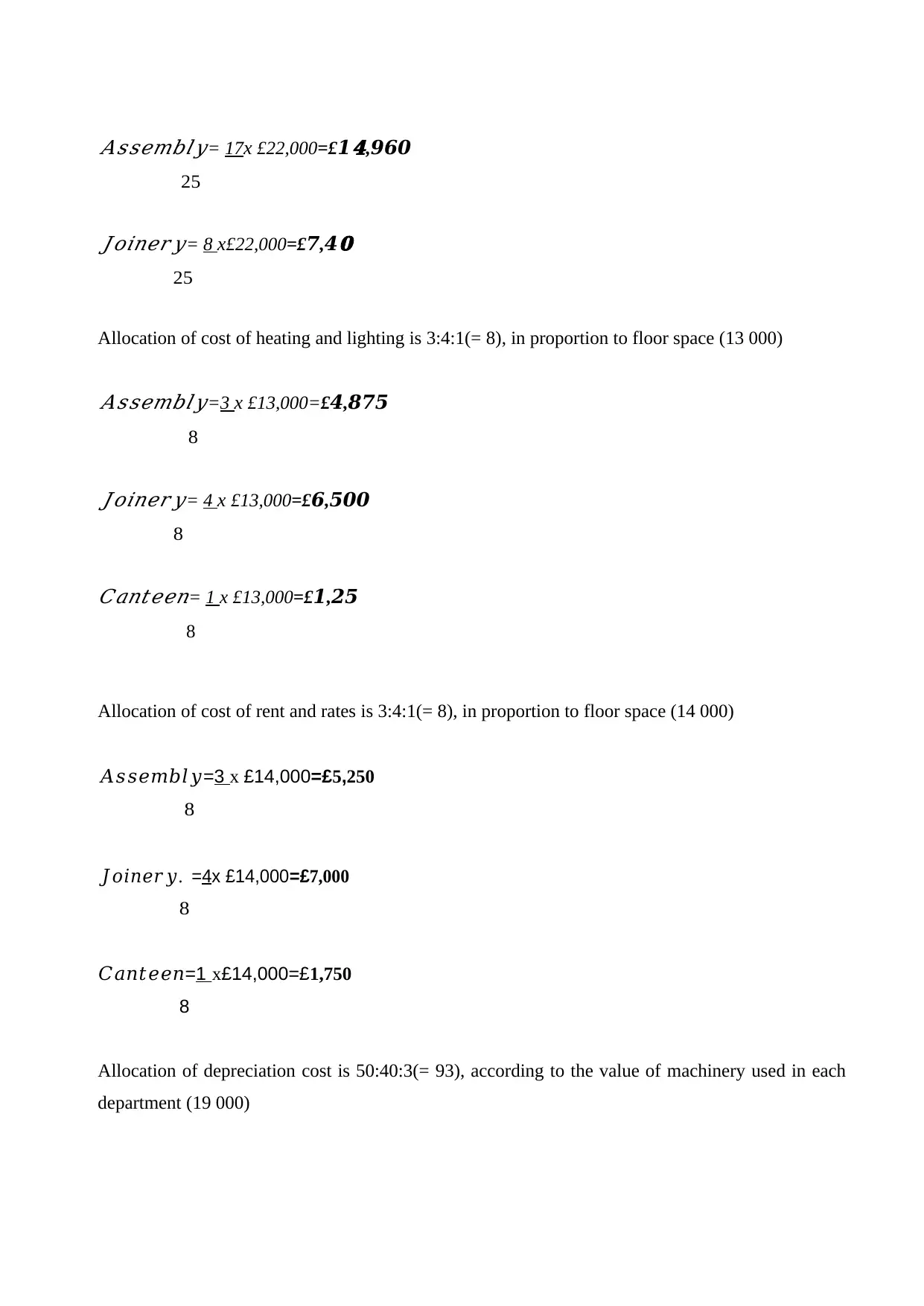
𝐴𝑠𝑠𝑒𝑚𝑏𝑙𝑦= 17x £22,000=£1
𝟒,960
25
𝐽𝑜𝑖𝑛𝑒𝑟𝑦= 8 x£22,000=£7,4
𝟎
25
Allocation of cost of heating and lighting is 3:4:1(= 8), in proportion to floor space (13 000)
𝐴𝑠𝑠𝑒𝑚𝑏𝑙𝑦=3 x £13,000=£4,875
8
𝐽𝑜𝑖𝑛𝑒𝑟𝑦= 4 x £13,000=£6,500
8𝐶𝑎𝑛𝑡𝑒𝑒𝑛= 1 x £13,000=£1,25
8
Allocation of cost of rent and rates is 3:4:1(= 8), in proportion to floor space (14 000)
𝐴𝑠𝑠𝑒𝑚𝑏𝑙𝑦=3 x £14,000=£5,250
8
𝐽𝑜𝑖𝑛𝑒𝑟𝑦. =4x £14,000=£7,000
8
𝐶𝑎𝑛𝑡𝑒𝑒𝑛=1 x£14,000=£1,750
8
Allocation of depreciation cost is 50:40:3(= 93), according to the value of machinery used in each
department (19 000)
𝟒,960
25
𝐽𝑜𝑖𝑛𝑒𝑟𝑦= 8 x£22,000=£7,4
𝟎
25
Allocation of cost of heating and lighting is 3:4:1(= 8), in proportion to floor space (13 000)
𝐴𝑠𝑠𝑒𝑚𝑏𝑙𝑦=3 x £13,000=£4,875
8
𝐽𝑜𝑖𝑛𝑒𝑟𝑦= 4 x £13,000=£6,500
8𝐶𝑎𝑛𝑡𝑒𝑒𝑛= 1 x £13,000=£1,25
8
Allocation of cost of rent and rates is 3:4:1(= 8), in proportion to floor space (14 000)
𝐴𝑠𝑠𝑒𝑚𝑏𝑙𝑦=3 x £14,000=£5,250
8
𝐽𝑜𝑖𝑛𝑒𝑟𝑦. =4x £14,000=£7,000
8
𝐶𝑎𝑛𝑡𝑒𝑒𝑛=1 x£14,000=£1,750
8
Allocation of depreciation cost is 50:40:3(= 93), according to the value of machinery used in each
department (19 000)
Secure Best Marks with AI Grader
Need help grading? Try our AI Grader for instant feedback on your assignments.
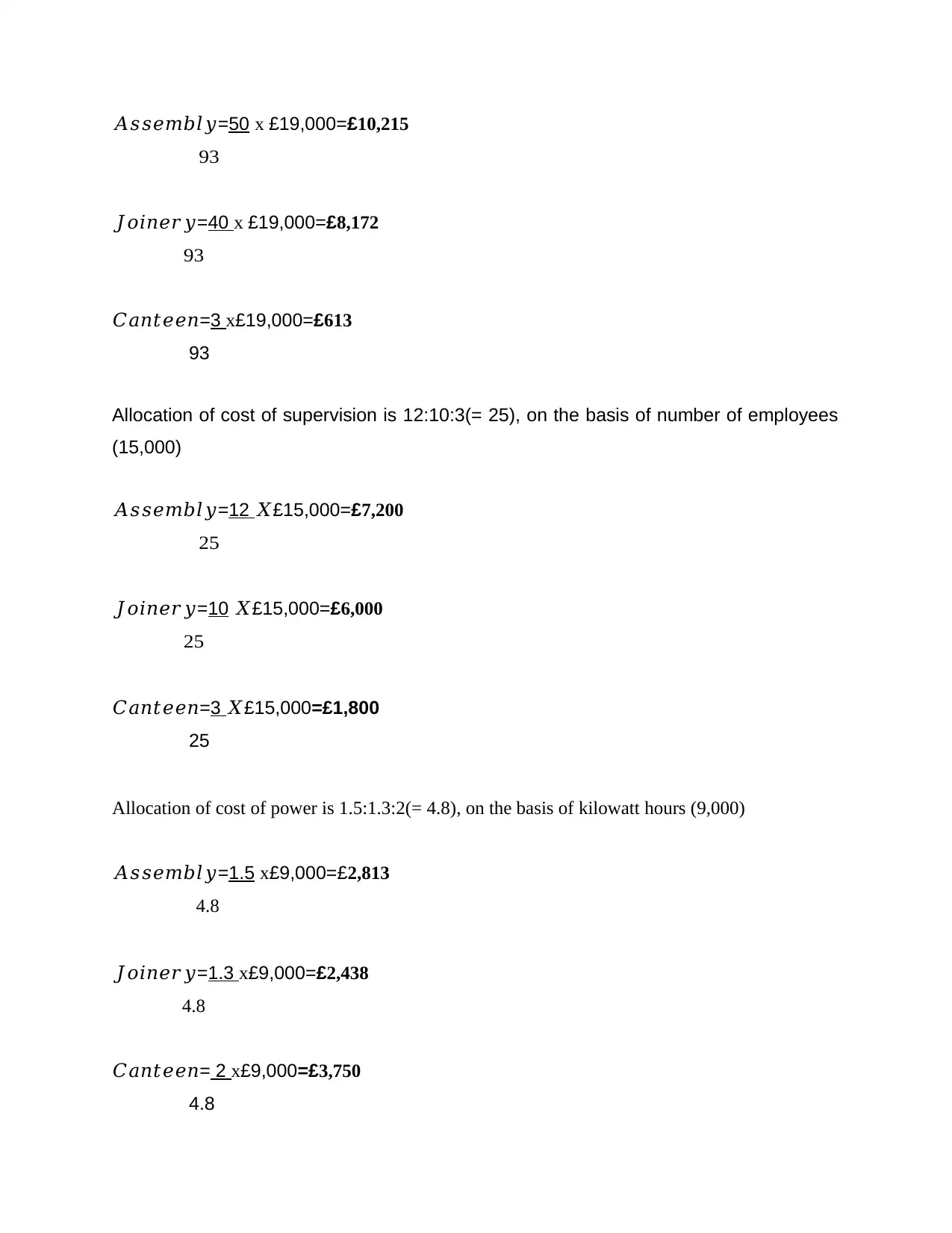
𝐴𝑠𝑠𝑒𝑚𝑏𝑙𝑦=50 x £19,000=£10,215
93
𝐽𝑜𝑖𝑛𝑒𝑟𝑦=40 x £19,000=£8,172
93
𝐶𝑎𝑛𝑡𝑒𝑒𝑛=3 x£19,000=£613
93
Allocation of cost of supervision is 12:10:3(= 25), on the basis of number of employees
(15,000)
𝐴𝑠𝑠𝑒𝑚𝑏𝑙𝑦=12 𝑋£15,000=£7,200
25
𝐽𝑜𝑖𝑛𝑒𝑟𝑦=10 𝑋£15,000=£6,000
25
𝐶𝑎𝑛𝑡𝑒𝑒𝑛=3 𝑋£15,000=£1,800
25
Allocation of cost of power is 1.5:1.3:2(= 4.8), on the basis of kilowatt hours (9,000)
𝐴𝑠𝑠𝑒𝑚𝑏𝑙𝑦=1.5 x£9,000=£2,813
4.8
𝐽𝑜𝑖𝑛𝑒𝑟𝑦=1.3 x£9,000=£2,438
4.8
𝐶𝑎𝑛𝑡𝑒𝑒𝑛= 2 x£9,000=£3,750
4.8
93
𝐽𝑜𝑖𝑛𝑒𝑟𝑦=40 x £19,000=£8,172
93
𝐶𝑎𝑛𝑡𝑒𝑒𝑛=3 x£19,000=£613
93
Allocation of cost of supervision is 12:10:3(= 25), on the basis of number of employees
(15,000)
𝐴𝑠𝑠𝑒𝑚𝑏𝑙𝑦=12 𝑋£15,000=£7,200
25
𝐽𝑜𝑖𝑛𝑒𝑟𝑦=10 𝑋£15,000=£6,000
25
𝐶𝑎𝑛𝑡𝑒𝑒𝑛=3 𝑋£15,000=£1,800
25
Allocation of cost of power is 1.5:1.3:2(= 4.8), on the basis of kilowatt hours (9,000)
𝐴𝑠𝑠𝑒𝑚𝑏𝑙𝑦=1.5 x£9,000=£2,813
4.8
𝐽𝑜𝑖𝑛𝑒𝑟𝑦=1.3 x£9,000=£2,438
4.8
𝐶𝑎𝑛𝑡𝑒𝑒𝑛= 2 x£9,000=£3,750
4.8
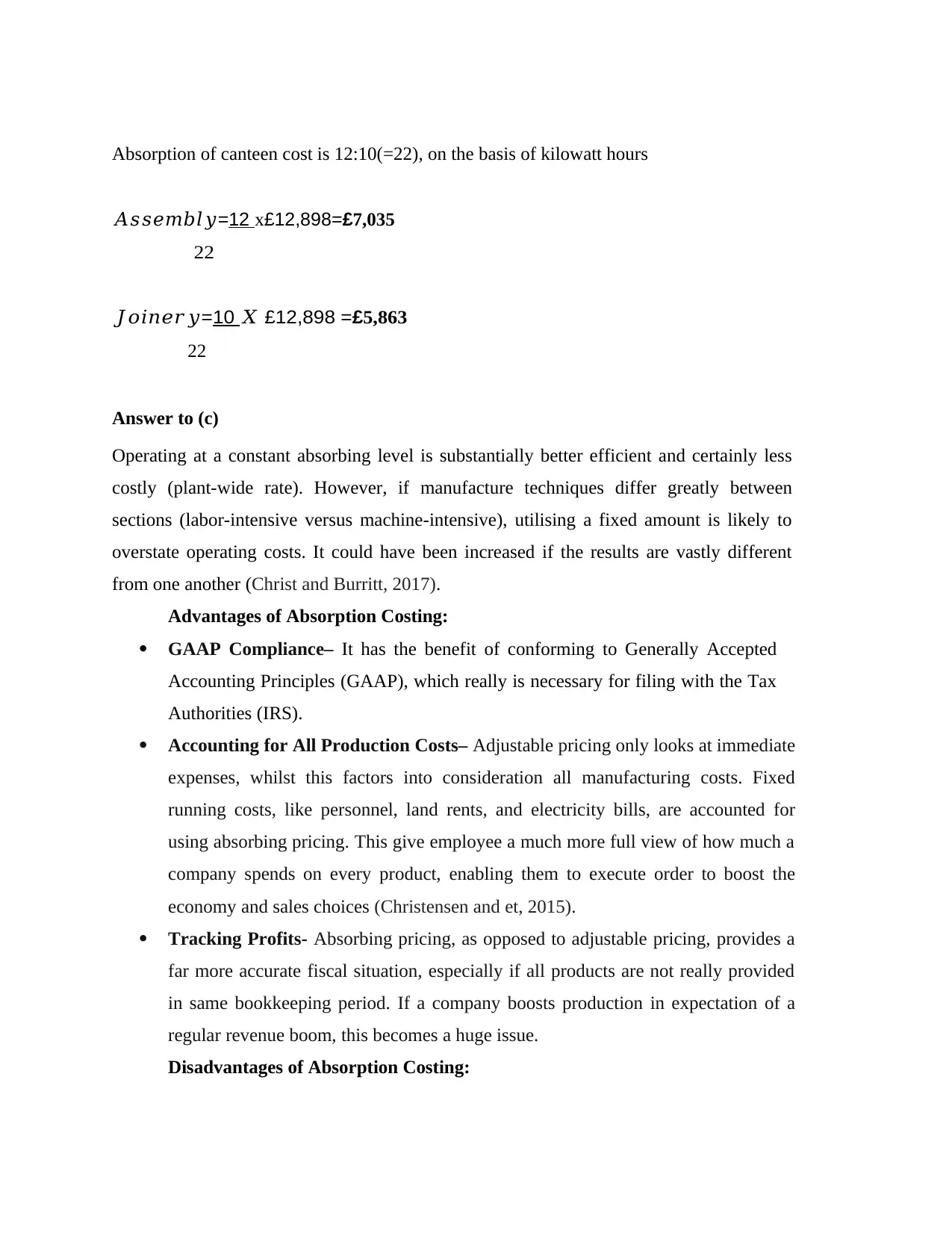
Absorption of canteen cost is 12:10(=22), on the basis of kilowatt hours
𝐴𝑠𝑠𝑒𝑚𝑏𝑙𝑦=12 x£12,898=£7,035
22
𝐽𝑜𝑖𝑛𝑒𝑟𝑦=10 𝑋 £12,898 =£5,863
22
Answer to (c)
Operating at a constant absorbing level is substantially better efficient and certainly less
costly (plant-wide rate). However, if manufacture techniques differ greatly between
sections (labor-intensive versus machine-intensive), utilising a fixed amount is likely to
overstate operating costs. It could have been increased if the results are vastly different
from one another (Christ and Burritt, 2017).
Advantages of Absorption Costing:
GAAP Compliance– It has the benefit of conforming to Generally Accepted
Accounting Principles (GAAP), which really is necessary for filing with the Tax
Authorities (IRS).
Accounting for All Production Costs– Adjustable pricing only looks at immediate
expenses, whilst this factors into consideration all manufacturing costs. Fixed
running costs, like personnel, land rents, and electricity bills, are accounted for
using absorbing pricing. This give employee a much more full view of how much a
company spends on every product, enabling them to execute order to boost the
economy and sales choices (Christensen and et, 2015).
Tracking Profits- Absorbing pricing, as opposed to adjustable pricing, provides a
far more accurate fiscal situation, especially if all products are not really provided
in same bookkeeping period. If a company boosts production in expectation of a
regular revenue boom, this becomes a huge issue.
Disadvantages of Absorption Costing:
𝐴𝑠𝑠𝑒𝑚𝑏𝑙𝑦=12 x£12,898=£7,035
22
𝐽𝑜𝑖𝑛𝑒𝑟𝑦=10 𝑋 £12,898 =£5,863
22
Answer to (c)
Operating at a constant absorbing level is substantially better efficient and certainly less
costly (plant-wide rate). However, if manufacture techniques differ greatly between
sections (labor-intensive versus machine-intensive), utilising a fixed amount is likely to
overstate operating costs. It could have been increased if the results are vastly different
from one another (Christ and Burritt, 2017).
Advantages of Absorption Costing:
GAAP Compliance– It has the benefit of conforming to Generally Accepted
Accounting Principles (GAAP), which really is necessary for filing with the Tax
Authorities (IRS).
Accounting for All Production Costs– Adjustable pricing only looks at immediate
expenses, whilst this factors into consideration all manufacturing costs. Fixed
running costs, like personnel, land rents, and electricity bills, are accounted for
using absorbing pricing. This give employee a much more full view of how much a
company spends on every product, enabling them to execute order to boost the
economy and sales choices (Christensen and et, 2015).
Tracking Profits- Absorbing pricing, as opposed to adjustable pricing, provides a
far more accurate fiscal situation, especially if all products are not really provided
in same bookkeeping period. If a company boosts production in expectation of a
regular revenue boom, this becomes a huge issue.
Disadvantages of Absorption Costing:
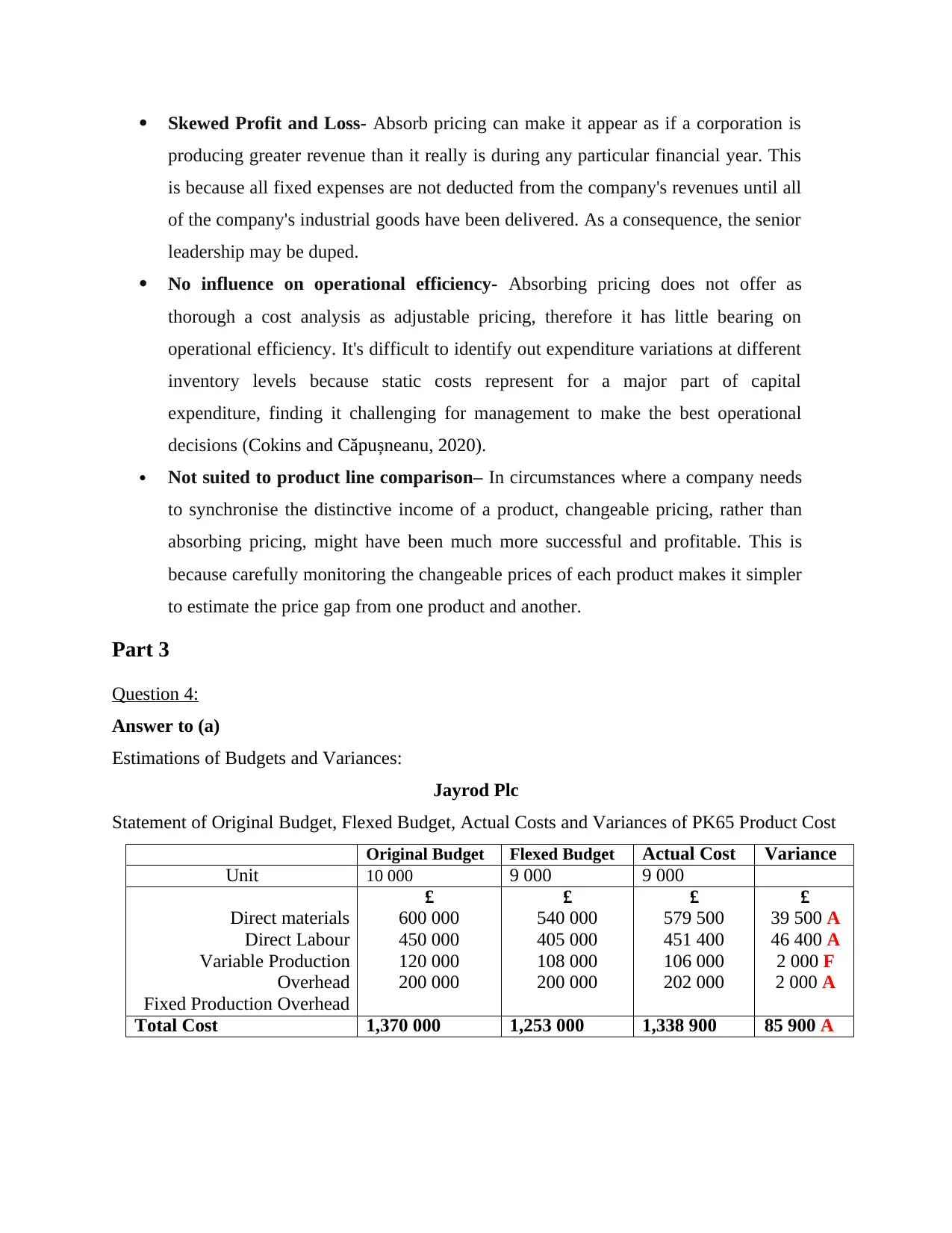
Skewed Profit and Loss- Absorb pricing can make it appear as if a corporation is
producing greater revenue than it really is during any particular financial year. This
is because all fixed expenses are not deducted from the company's revenues until all
of the company's industrial goods have been delivered. As a consequence, the senior
leadership may be duped.
No influence on operational efficiency- Absorbing pricing does not offer as
thorough a cost analysis as adjustable pricing, therefore it has little bearing on
operational efficiency. It's difficult to identify out expenditure variations at different
inventory levels because static costs represent for a major part of capital
expenditure, finding it challenging for management to make the best operational
decisions (Cokins and Căpușneanu, 2020).
Not suited to product line comparison– In circumstances where a company needs
to synchronise the distinctive income of a product, changeable pricing, rather than
absorbing pricing, might have been much more successful and profitable. This is
because carefully monitoring the changeable prices of each product makes it simpler
to estimate the price gap from one product and another.
Part 3
Question 4:
Answer to (a)
Estimations of Budgets and Variances:
Jayrod Plc
Statement of Original Budget, Flexed Budget, Actual Costs and Variances of PK65 Product Cost
Original Budget Flexed Budget Actual Cost Variance
Unit 10 000 9 000 9 000
£ £ £ £
Direct materials 600 000 540 000 579 500 39 500 A
Direct Labour 450 000 405 000 451 400 46 400 A
Variable Production 120 000 108 000 106 000 2 000 F
Overhead 200 000 200 000 202 000 2 000 A
Fixed Production Overhead
Total Cost 1,370 000 1,253 000 1,338 900 85 900 A
producing greater revenue than it really is during any particular financial year. This
is because all fixed expenses are not deducted from the company's revenues until all
of the company's industrial goods have been delivered. As a consequence, the senior
leadership may be duped.
No influence on operational efficiency- Absorbing pricing does not offer as
thorough a cost analysis as adjustable pricing, therefore it has little bearing on
operational efficiency. It's difficult to identify out expenditure variations at different
inventory levels because static costs represent for a major part of capital
expenditure, finding it challenging for management to make the best operational
decisions (Cokins and Căpușneanu, 2020).
Not suited to product line comparison– In circumstances where a company needs
to synchronise the distinctive income of a product, changeable pricing, rather than
absorbing pricing, might have been much more successful and profitable. This is
because carefully monitoring the changeable prices of each product makes it simpler
to estimate the price gap from one product and another.
Part 3
Question 4:
Answer to (a)
Estimations of Budgets and Variances:
Jayrod Plc
Statement of Original Budget, Flexed Budget, Actual Costs and Variances of PK65 Product Cost
Original Budget Flexed Budget Actual Cost Variance
Unit 10 000 9 000 9 000
£ £ £ £
Direct materials 600 000 540 000 579 500 39 500 A
Direct Labour 450 000 405 000 451 400 46 400 A
Variable Production 120 000 108 000 106 000 2 000 F
Overhead 200 000 200 000 202 000 2 000 A
Fixed Production Overhead
Total Cost 1,370 000 1,253 000 1,338 900 85 900 A
Paraphrase This Document
Need a fresh take? Get an instant paraphrase of this document with our AI Paraphraser
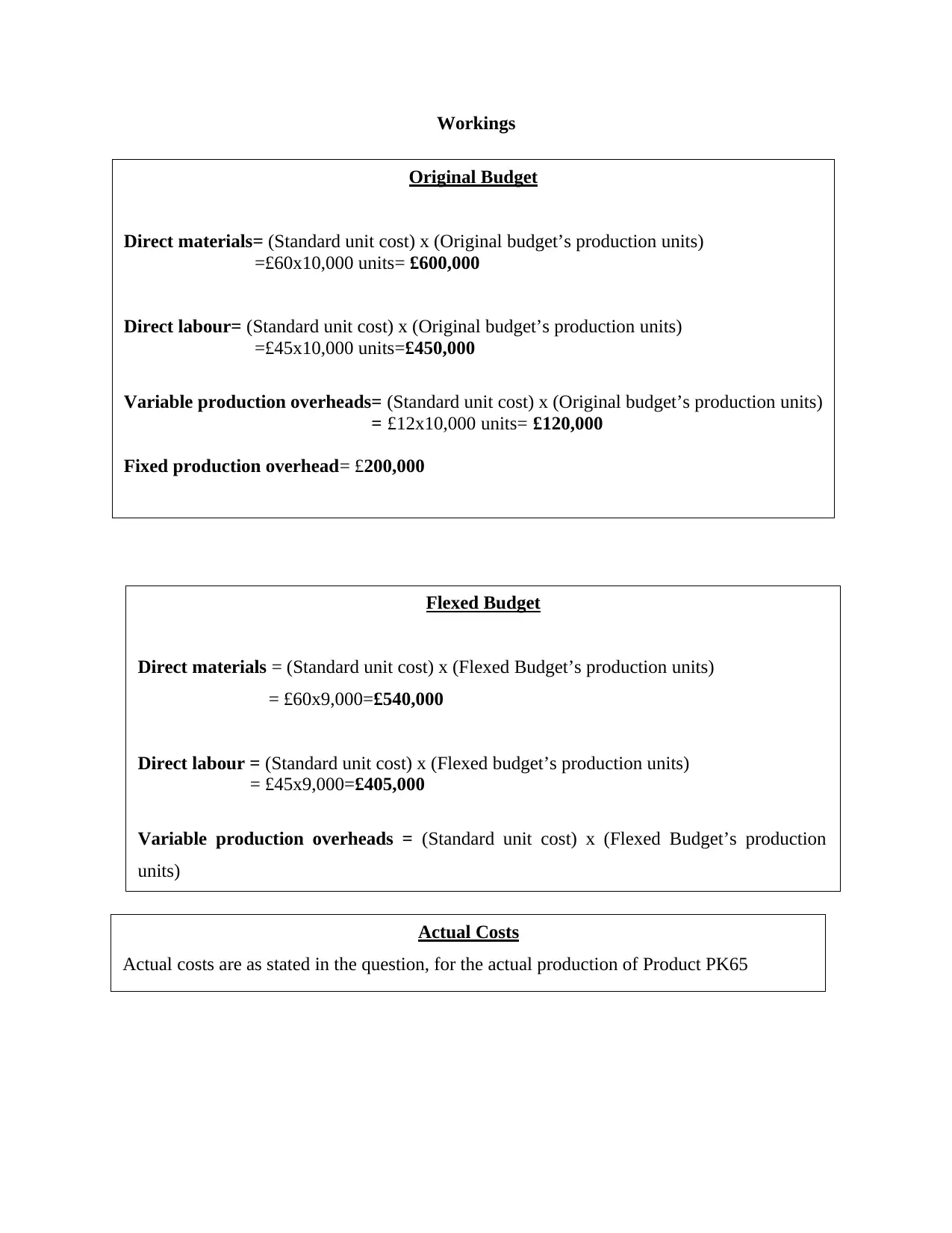
Original Budget
Direct materials= (Standard unit cost) x (Original budget’s production units)
=£60x10,000 units= £600,000
Direct labour= (Standard unit cost) x (Original budget’s production units)
=£45x10,000 units=£450,000
Variable production overheads= (Standard unit cost) x (Original budget’s production units)
= £12x10,000 units= £120,000
Fixed production overhead= £200,000
Actual Costs
Actual costs are as stated in the question, for the actual production of Product PK65
Workings
Flexed Budget
Direct materials = (Standard unit cost) x (Flexed Budget’s production units)
= £60x9,000=£540,000
Direct labour = (Standard unit cost) x (Flexed budget’s production units)
= £45x9,000=£405,000
Variable production overheads = (Standard unit cost) x (Flexed Budget’s production
units)
Direct materials= (Standard unit cost) x (Original budget’s production units)
=£60x10,000 units= £600,000
Direct labour= (Standard unit cost) x (Original budget’s production units)
=£45x10,000 units=£450,000
Variable production overheads= (Standard unit cost) x (Original budget’s production units)
= £12x10,000 units= £120,000
Fixed production overhead= £200,000
Actual Costs
Actual costs are as stated in the question, for the actual production of Product PK65
Workings
Flexed Budget
Direct materials = (Standard unit cost) x (Flexed Budget’s production units)
= £60x9,000=£540,000
Direct labour = (Standard unit cost) x (Flexed budget’s production units)
= £45x9,000=£405,000
Variable production overheads = (Standard unit cost) x (Flexed Budget’s production
units)
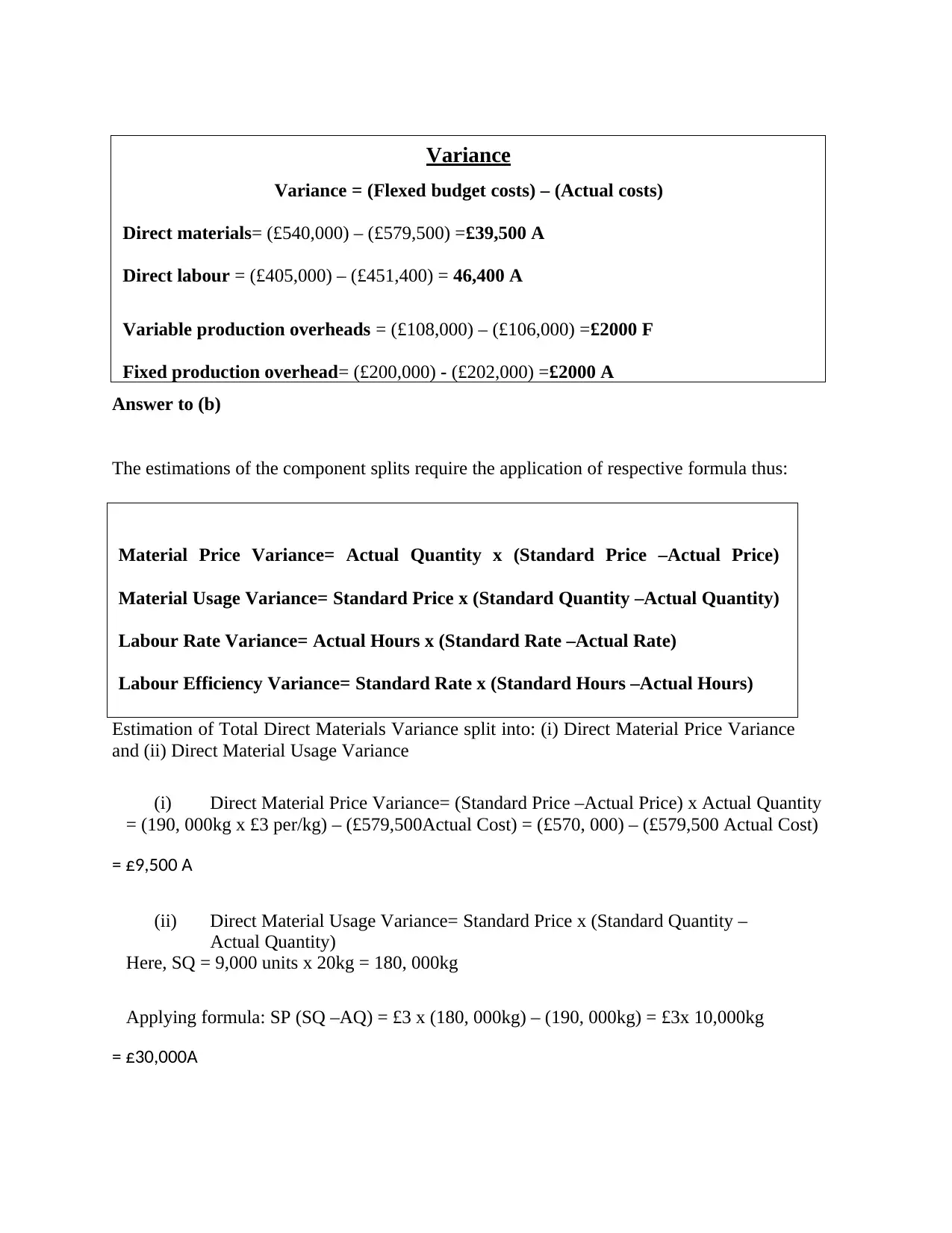
Variance
Variance = (Flexed budget costs) – (Actual costs)
Direct materials= (£540,000) – (£579,500) =£39,500 A
Direct labour = (£405,000) – (£451,400) = 46,400 A
Variable production overheads = (£108,000) – (£106,000) =£2000 F
Fixed production overhead= (£200,000) - (£202,000) =£2000 A
Material Price Variance= Actual Quantity x (Standard Price –Actual Price)
Material Usage Variance= Standard Price x (Standard Quantity –Actual Quantity)
Labour Rate Variance= Actual Hours x (Standard Rate –Actual Rate)
Labour Efficiency Variance= Standard Rate x (Standard Hours –Actual Hours)
Answer to (b)
The estimations of the component splits require the application of respective formula thus:
Estimation of Total Direct Materials Variance split into: (i) Direct Material Price Variance
and (ii) Direct Material Usage Variance
(i) Direct Material Price Variance= (Standard Price –Actual Price) x Actual Quantity
= (190, 000kg x £3 per/kg) – (£579,500Actual Cost) = (£570, 000) – (£579,500 Actual Cost)
= £9,500 A
(ii) Direct Material Usage Variance= Standard Price x (Standard Quantity –
Actual Quantity)
Here, SQ = 9,000 units x 20kg = 180, 000kg
Applying formula: SP (SQ –AQ) = £3 x (180, 000kg) – (190, 000kg) = £3x 10,000kg
= £30,000A
Variance = (Flexed budget costs) – (Actual costs)
Direct materials= (£540,000) – (£579,500) =£39,500 A
Direct labour = (£405,000) – (£451,400) = 46,400 A
Variable production overheads = (£108,000) – (£106,000) =£2000 F
Fixed production overhead= (£200,000) - (£202,000) =£2000 A
Material Price Variance= Actual Quantity x (Standard Price –Actual Price)
Material Usage Variance= Standard Price x (Standard Quantity –Actual Quantity)
Labour Rate Variance= Actual Hours x (Standard Rate –Actual Rate)
Labour Efficiency Variance= Standard Rate x (Standard Hours –Actual Hours)
Answer to (b)
The estimations of the component splits require the application of respective formula thus:
Estimation of Total Direct Materials Variance split into: (i) Direct Material Price Variance
and (ii) Direct Material Usage Variance
(i) Direct Material Price Variance= (Standard Price –Actual Price) x Actual Quantity
= (190, 000kg x £3 per/kg) – (£579,500Actual Cost) = (£570, 000) – (£579,500 Actual Cost)
= £9,500 A
(ii) Direct Material Usage Variance= Standard Price x (Standard Quantity –
Actual Quantity)
Here, SQ = 9,000 units x 20kg = 180, 000kg
Applying formula: SP (SQ –AQ) = £3 x (180, 000kg) – (190, 000kg) = £3x 10,000kg
= £30,000A
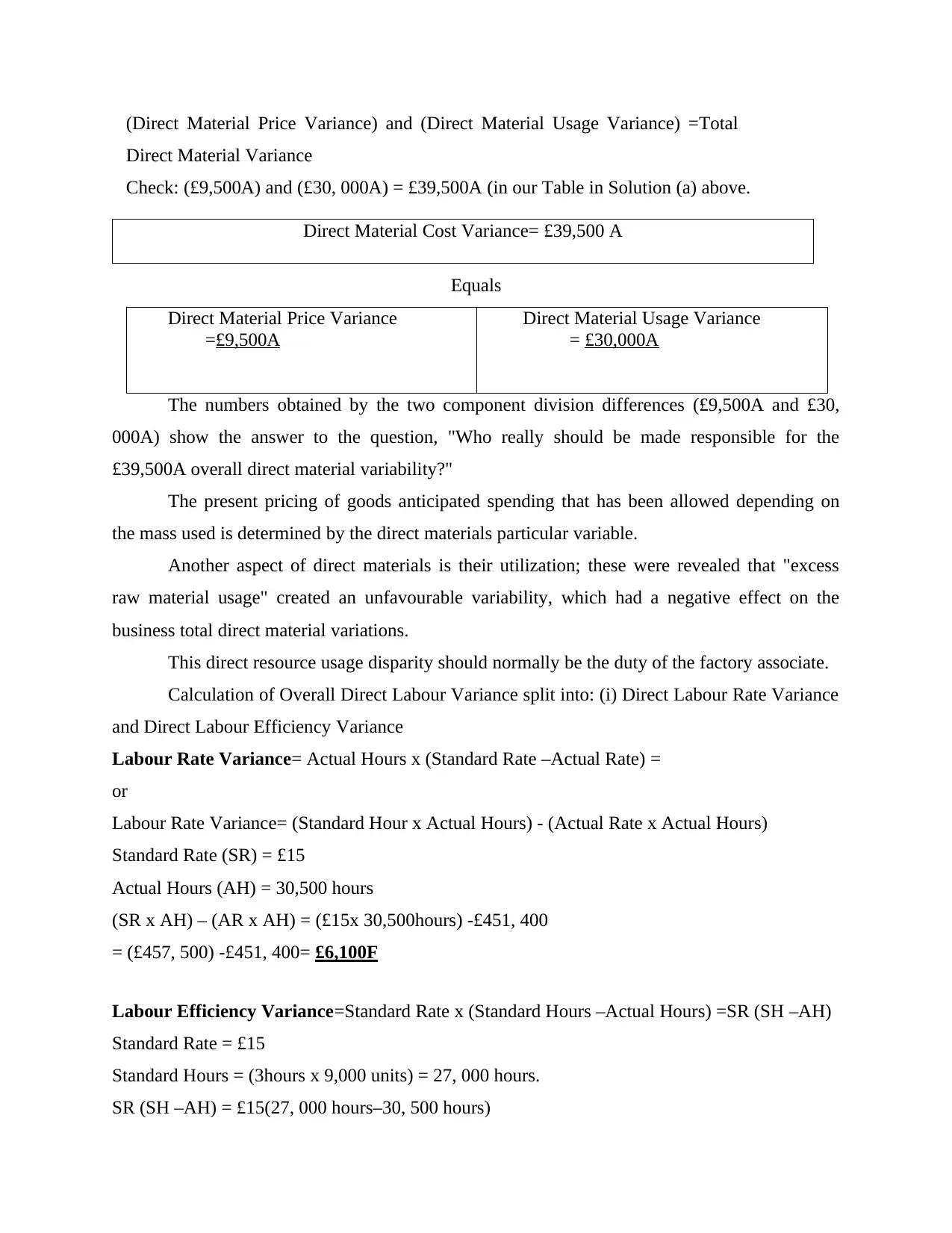
Direct Material Cost Variance= £39,500 A
(Direct Material Price Variance) and (Direct Material Usage Variance) =Total
Direct Material Variance
Check: (£9,500A) and (£30, 000A) = £39,500A (in our Table in Solution (a) above.
Equals
Direct Material Price Variance
=£9,500A
Direct Material Usage Variance
= £30,000A
The numbers obtained by the two component division differences (£9,500A and £30,
000A) show the answer to the question, "Who really should be made responsible for the
£39,500A overall direct material variability?"
The present pricing of goods anticipated spending that has been allowed depending on
the mass used is determined by the direct materials particular variable.
Another aspect of direct materials is their utilization; these were revealed that "excess
raw material usage" created an unfavourable variability, which had a negative effect on the
business total direct material variations.
This direct resource usage disparity should normally be the duty of the factory associate.
Calculation of Overall Direct Labour Variance split into: (i) Direct Labour Rate Variance
and Direct Labour Efficiency Variance
Labour Rate Variance= Actual Hours x (Standard Rate –Actual Rate) =
or
Labour Rate Variance= (Standard Hour x Actual Hours) - (Actual Rate x Actual Hours)
Standard Rate (SR) = £15
Actual Hours (AH) = 30,500 hours
(SR x AH) – (AR x AH) = (£15x 30,500hours) -£451, 400
= (£457, 500) -£451, 400= £6,100F
Labour Efficiency Variance=Standard Rate x (Standard Hours –Actual Hours) =SR (SH –AH)
Standard Rate = £15
Standard Hours = (3hours x 9,000 units) = 27, 000 hours.
SR (SH –AH) = £15(27, 000 hours–30, 500 hours)
(Direct Material Price Variance) and (Direct Material Usage Variance) =Total
Direct Material Variance
Check: (£9,500A) and (£30, 000A) = £39,500A (in our Table in Solution (a) above.
Equals
Direct Material Price Variance
=£9,500A
Direct Material Usage Variance
= £30,000A
The numbers obtained by the two component division differences (£9,500A and £30,
000A) show the answer to the question, "Who really should be made responsible for the
£39,500A overall direct material variability?"
The present pricing of goods anticipated spending that has been allowed depending on
the mass used is determined by the direct materials particular variable.
Another aspect of direct materials is their utilization; these were revealed that "excess
raw material usage" created an unfavourable variability, which had a negative effect on the
business total direct material variations.
This direct resource usage disparity should normally be the duty of the factory associate.
Calculation of Overall Direct Labour Variance split into: (i) Direct Labour Rate Variance
and Direct Labour Efficiency Variance
Labour Rate Variance= Actual Hours x (Standard Rate –Actual Rate) =
or
Labour Rate Variance= (Standard Hour x Actual Hours) - (Actual Rate x Actual Hours)
Standard Rate (SR) = £15
Actual Hours (AH) = 30,500 hours
(SR x AH) – (AR x AH) = (£15x 30,500hours) -£451, 400
= (£457, 500) -£451, 400= £6,100F
Labour Efficiency Variance=Standard Rate x (Standard Hours –Actual Hours) =SR (SH –AH)
Standard Rate = £15
Standard Hours = (3hours x 9,000 units) = 27, 000 hours.
SR (SH –AH) = £15(27, 000 hours–30, 500 hours)
Secure Best Marks with AI Grader
Need help grading? Try our AI Grader for instant feedback on your assignments.
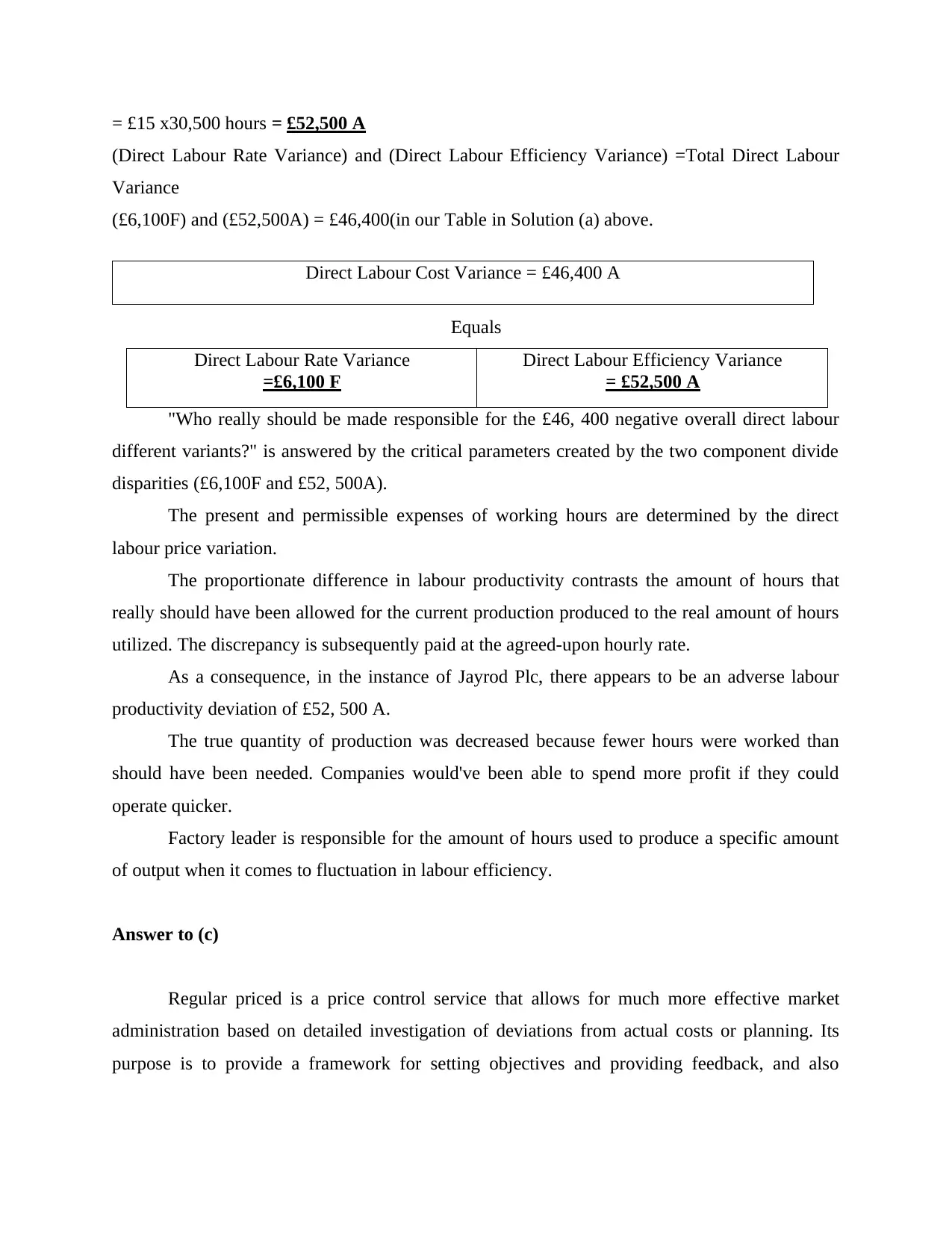
Direct Labour Cost Variance = £46,400 A
= £15 x30,500 hours = £52,500 A
(Direct Labour Rate Variance) and (Direct Labour Efficiency Variance) =Total Direct Labour
Variance
(£6,100F) and (£52,500A) = £46,400(in our Table in Solution (a) above.
Equals
Direct Labour Rate Variance
=£6,100 F
Direct Labour Efficiency Variance
= £52,500 A
"Who really should be made responsible for the £46, 400 negative overall direct labour
different variants?" is answered by the critical parameters created by the two component divide
disparities (£6,100F and £52, 500A).
The present and permissible expenses of working hours are determined by the direct
labour price variation.
The proportionate difference in labour productivity contrasts the amount of hours that
really should have been allowed for the current production produced to the real amount of hours
utilized. The discrepancy is subsequently paid at the agreed-upon hourly rate.
As a consequence, in the instance of Jayrod Plc, there appears to be an adverse labour
productivity deviation of £52, 500 A.
The true quantity of production was decreased because fewer hours were worked than
should have been needed. Companies would've been able to spend more profit if they could
operate quicker.
Factory leader is responsible for the amount of hours used to produce a specific amount
of output when it comes to fluctuation in labour efficiency.
Answer to (c)
Regular priced is a price control service that allows for much more effective market
administration based on detailed investigation of deviations from actual costs or planning. Its
purpose is to provide a framework for setting objectives and providing feedback, and also
= £15 x30,500 hours = £52,500 A
(Direct Labour Rate Variance) and (Direct Labour Efficiency Variance) =Total Direct Labour
Variance
(£6,100F) and (£52,500A) = £46,400(in our Table in Solution (a) above.
Equals
Direct Labour Rate Variance
=£6,100 F
Direct Labour Efficiency Variance
= £52,500 A
"Who really should be made responsible for the £46, 400 negative overall direct labour
different variants?" is answered by the critical parameters created by the two component divide
disparities (£6,100F and £52, 500A).
The present and permissible expenses of working hours are determined by the direct
labour price variation.
The proportionate difference in labour productivity contrasts the amount of hours that
really should have been allowed for the current production produced to the real amount of hours
utilized. The discrepancy is subsequently paid at the agreed-upon hourly rate.
As a consequence, in the instance of Jayrod Plc, there appears to be an adverse labour
productivity deviation of £52, 500 A.
The true quantity of production was decreased because fewer hours were worked than
should have been needed. Companies would've been able to spend more profit if they could
operate quicker.
Factory leader is responsible for the amount of hours used to produce a specific amount
of output when it comes to fluctuation in labour efficiency.
Answer to (c)
Regular priced is a price control service that allows for much more effective market
administration based on detailed investigation of deviations from actual costs or planning. Its
purpose is to provide a framework for setting objectives and providing feedback, and also
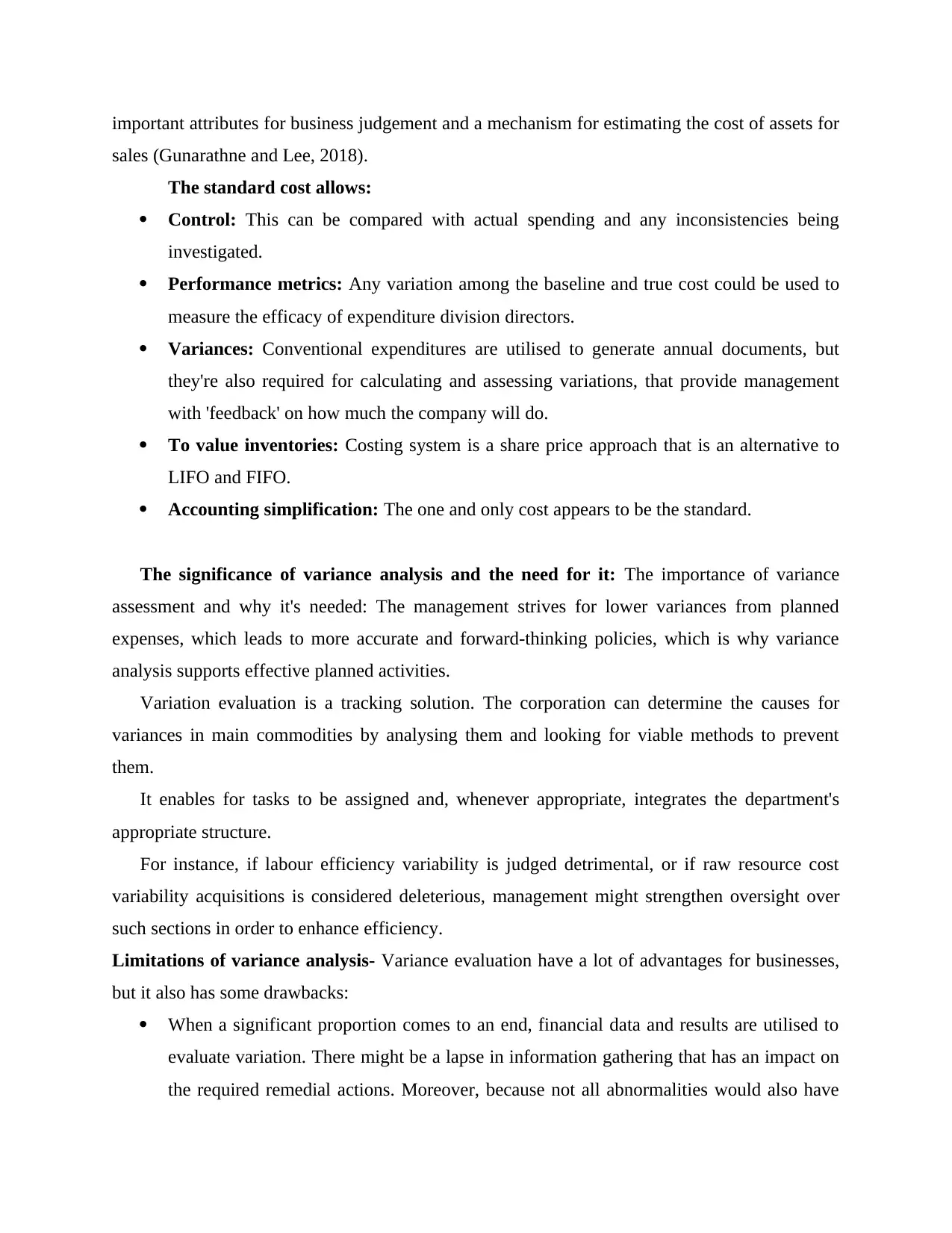
important attributes for business judgement and a mechanism for estimating the cost of assets for
sales (Gunarathne and Lee, 2018).
The standard cost allows:
Control: This can be compared with actual spending and any inconsistencies being
investigated.
Performance metrics: Any variation among the baseline and true cost could be used to
measure the efficacy of expenditure division directors.
Variances: Conventional expenditures are utilised to generate annual documents, but
they're also required for calculating and assessing variations, that provide management
with 'feedback' on how much the company will do.
To value inventories: Costing system is a share price approach that is an alternative to
LIFO and FIFO.
Accounting simplification: The one and only cost appears to be the standard.
The significance of variance analysis and the need for it: The importance of variance
assessment and why it's needed: The management strives for lower variances from planned
expenses, which leads to more accurate and forward-thinking policies, which is why variance
analysis supports effective planned activities.
Variation evaluation is a tracking solution. The corporation can determine the causes for
variances in main commodities by analysing them and looking for viable methods to prevent
them.
It enables for tasks to be assigned and, whenever appropriate, integrates the department's
appropriate structure.
For instance, if labour efficiency variability is judged detrimental, or if raw resource cost
variability acquisitions is considered deleterious, management might strengthen oversight over
such sections in order to enhance efficiency.
Limitations of variance analysis- Variance evaluation have a lot of advantages for businesses,
but it also has some drawbacks:
When a significant proportion comes to an end, financial data and results are utilised to
evaluate variation. There might be a lapse in information gathering that has an impact on
the required remedial actions. Moreover, because not all abnormalities would also have
sales (Gunarathne and Lee, 2018).
The standard cost allows:
Control: This can be compared with actual spending and any inconsistencies being
investigated.
Performance metrics: Any variation among the baseline and true cost could be used to
measure the efficacy of expenditure division directors.
Variances: Conventional expenditures are utilised to generate annual documents, but
they're also required for calculating and assessing variations, that provide management
with 'feedback' on how much the company will do.
To value inventories: Costing system is a share price approach that is an alternative to
LIFO and FIFO.
Accounting simplification: The one and only cost appears to be the standard.
The significance of variance analysis and the need for it: The importance of variance
assessment and why it's needed: The management strives for lower variances from planned
expenses, which leads to more accurate and forward-thinking policies, which is why variance
analysis supports effective planned activities.
Variation evaluation is a tracking solution. The corporation can determine the causes for
variances in main commodities by analysing them and looking for viable methods to prevent
them.
It enables for tasks to be assigned and, whenever appropriate, integrates the department's
appropriate structure.
For instance, if labour efficiency variability is judged detrimental, or if raw resource cost
variability acquisitions is considered deleterious, management might strengthen oversight over
such sections in order to enhance efficiency.
Limitations of variance analysis- Variance evaluation have a lot of advantages for businesses,
but it also has some drawbacks:
When a significant proportion comes to an end, financial data and results are utilised to
evaluate variation. There might be a lapse in information gathering that has an impact on
the required remedial actions. Moreover, because not all abnormalities would also have
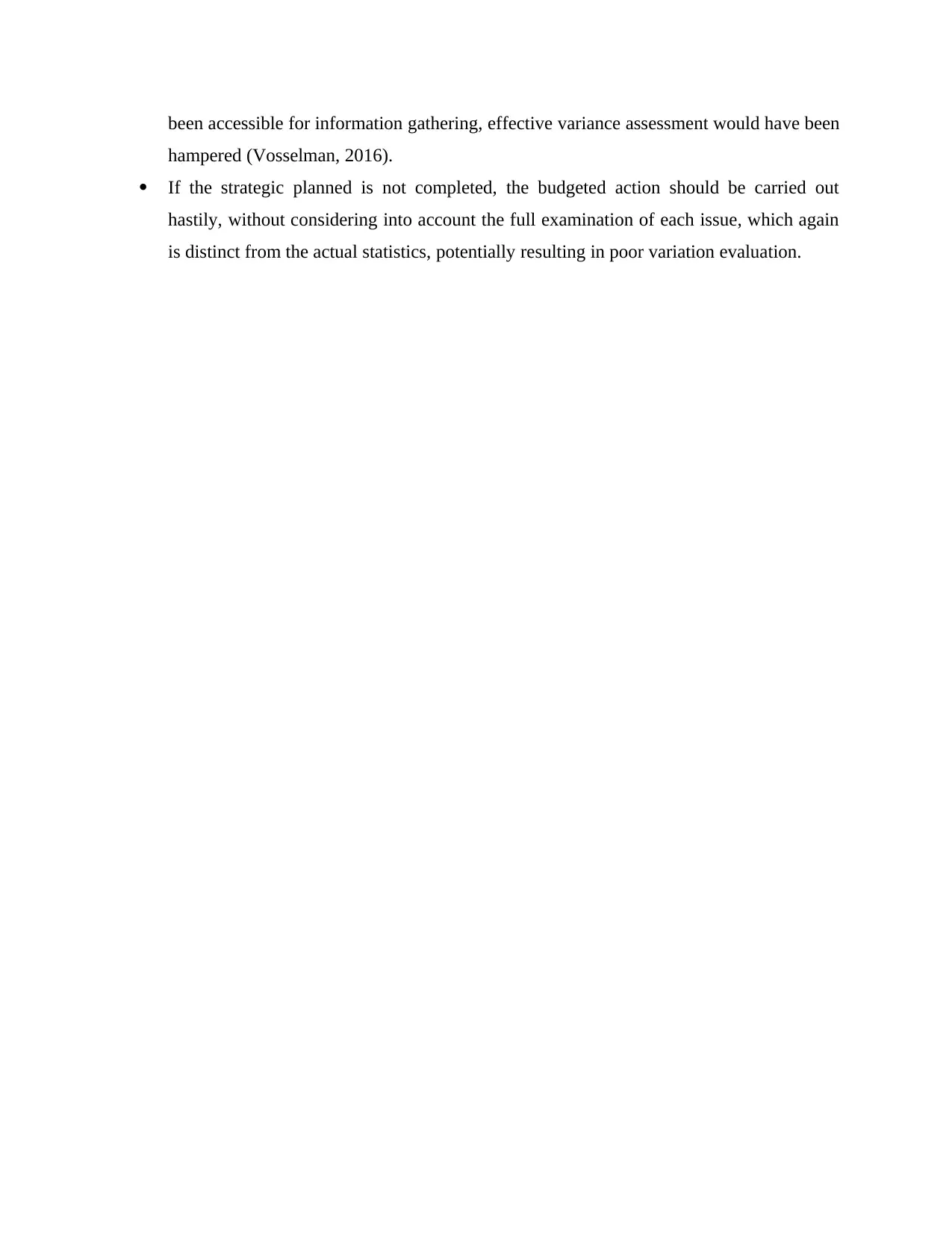
been accessible for information gathering, effective variance assessment would have been
hampered (Vosselman, 2016).
If the strategic planned is not completed, the budgeted action should be carried out
hastily, without considering into account the full examination of each issue, which again
is distinct from the actual statistics, potentially resulting in poor variation evaluation.
hampered (Vosselman, 2016).
If the strategic planned is not completed, the budgeted action should be carried out
hastily, without considering into account the full examination of each issue, which again
is distinct from the actual statistics, potentially resulting in poor variation evaluation.
Paraphrase This Document
Need a fresh take? Get an instant paraphrase of this document with our AI Paraphraser
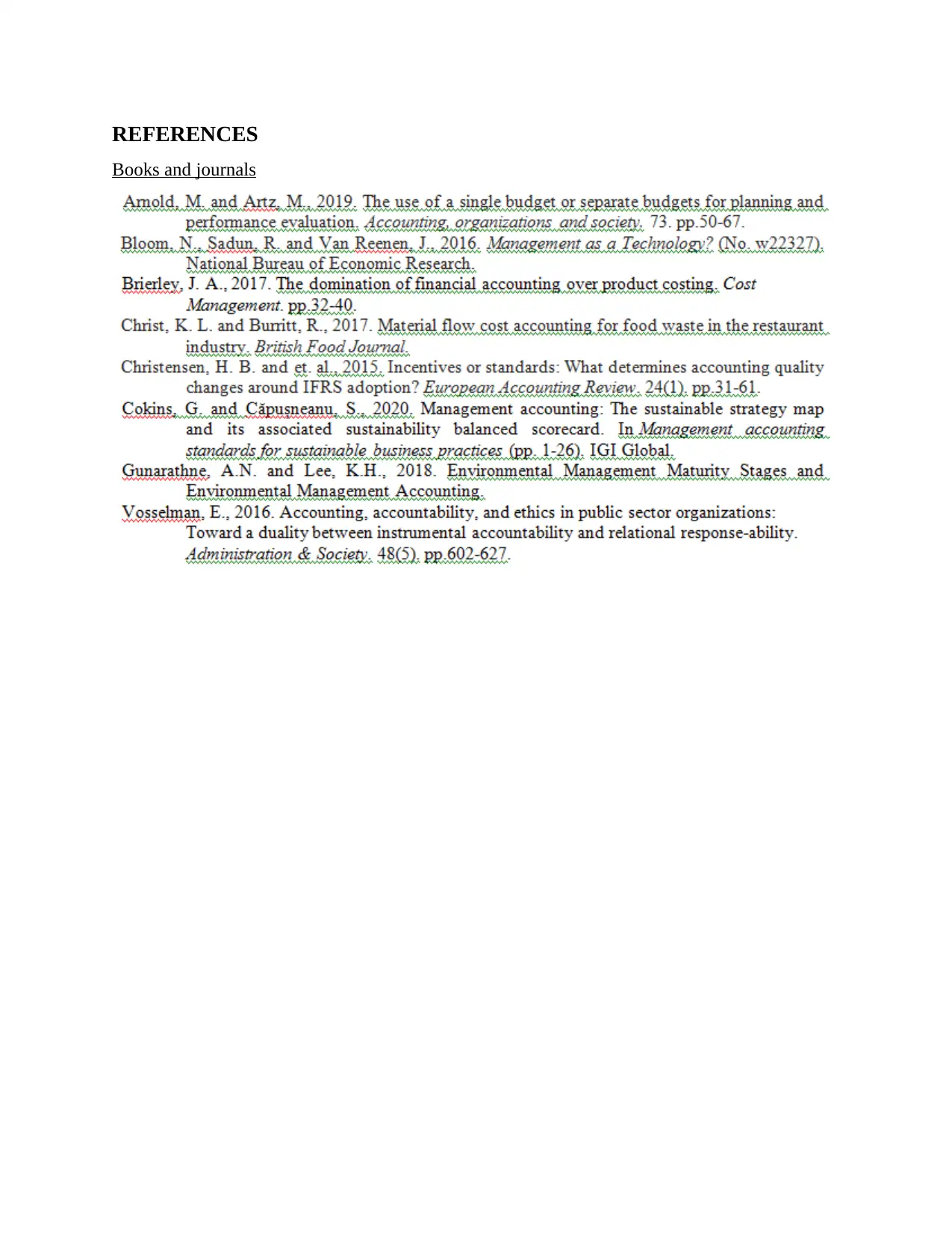
REFERENCES
Books and journals
Books and journals
1 out of 20
Related Documents

Your All-in-One AI-Powered Toolkit for Academic Success.
+13062052269
info@desklib.com
Available 24*7 on WhatsApp / Email
Unlock your academic potential
© 2024 | Zucol Services PVT LTD | All rights reserved.