Managing Business Activities: An Operational Plan for Nissan
VerifiedAdded on 2024/05/29
|27
|4955
|318
Report
AI Summary
This report provides a comprehensive overview of managing business activities within Nissan, focusing on key functions, processes, and their interrelationships in achieving organizational goals. It details the methodology used for process mapping, evaluates the output and purpose of quality gateways in operations, and designs plans and SMART objectives for specific areas of responsibility. The report also covers the implementation of systems to achieve objectives efficiently, monitoring and controlling work activities, and designing systems to manage and monitor quality standards. Furthermore, it demonstrates a quality culture for continuous improvement, recommends improvements aligned with organizational objectives, and reports on the wider implications of proposed changes. Finally, the report addresses risk assessments, health and safety regulations, and a systematic review of organizational policies to ensure effectiveness and compliance, concluding with the practical application of these policies in the workplace. Desklib offers more solved assignments and resources for students.
Contribute Materials
Your contribution can guide someone’s learning journey. Share your
documents today.
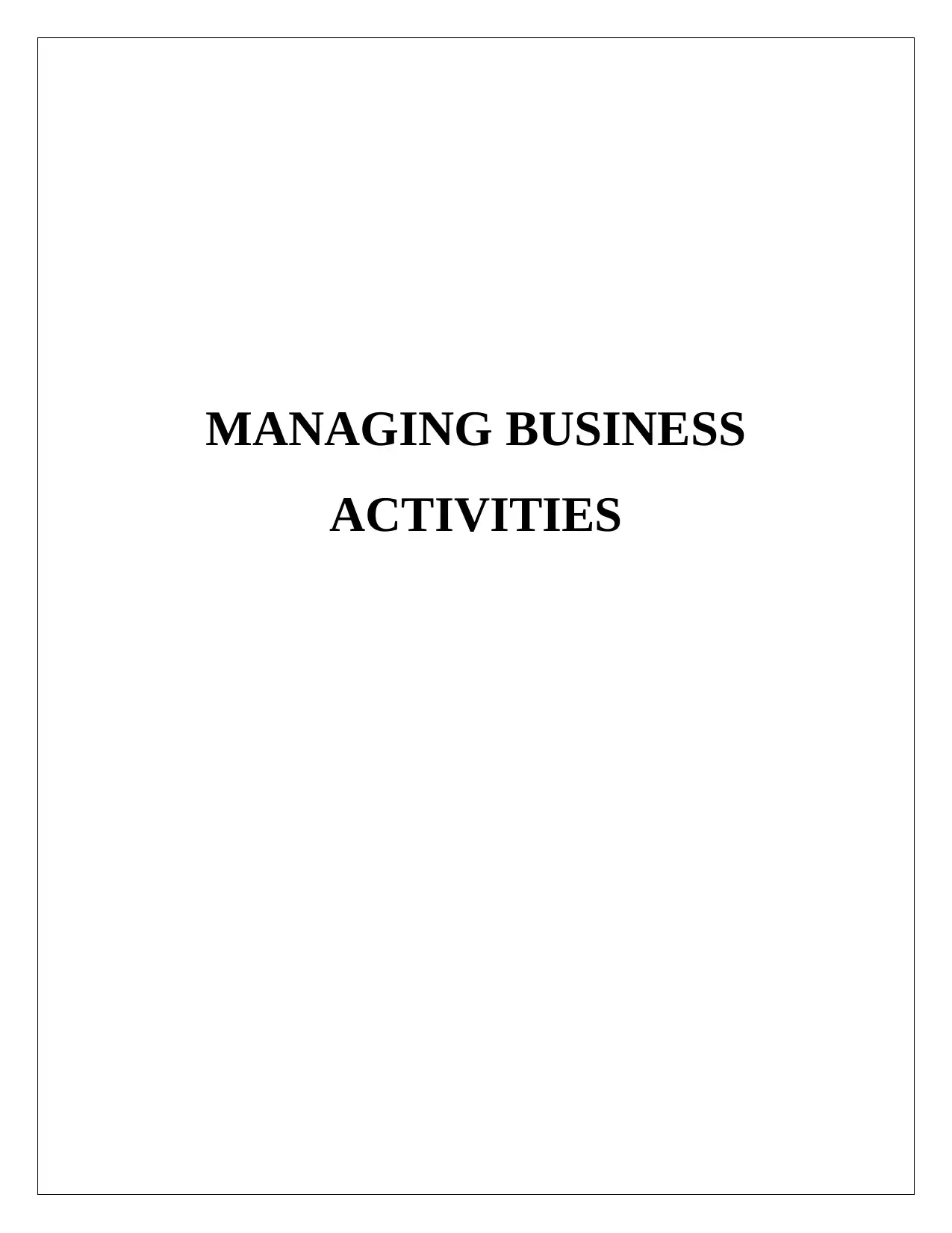
MANAGING BUSINESS
ACTIVITIES
ACTIVITIES
Secure Best Marks with AI Grader
Need help grading? Try our AI Grader for instant feedback on your assignments.
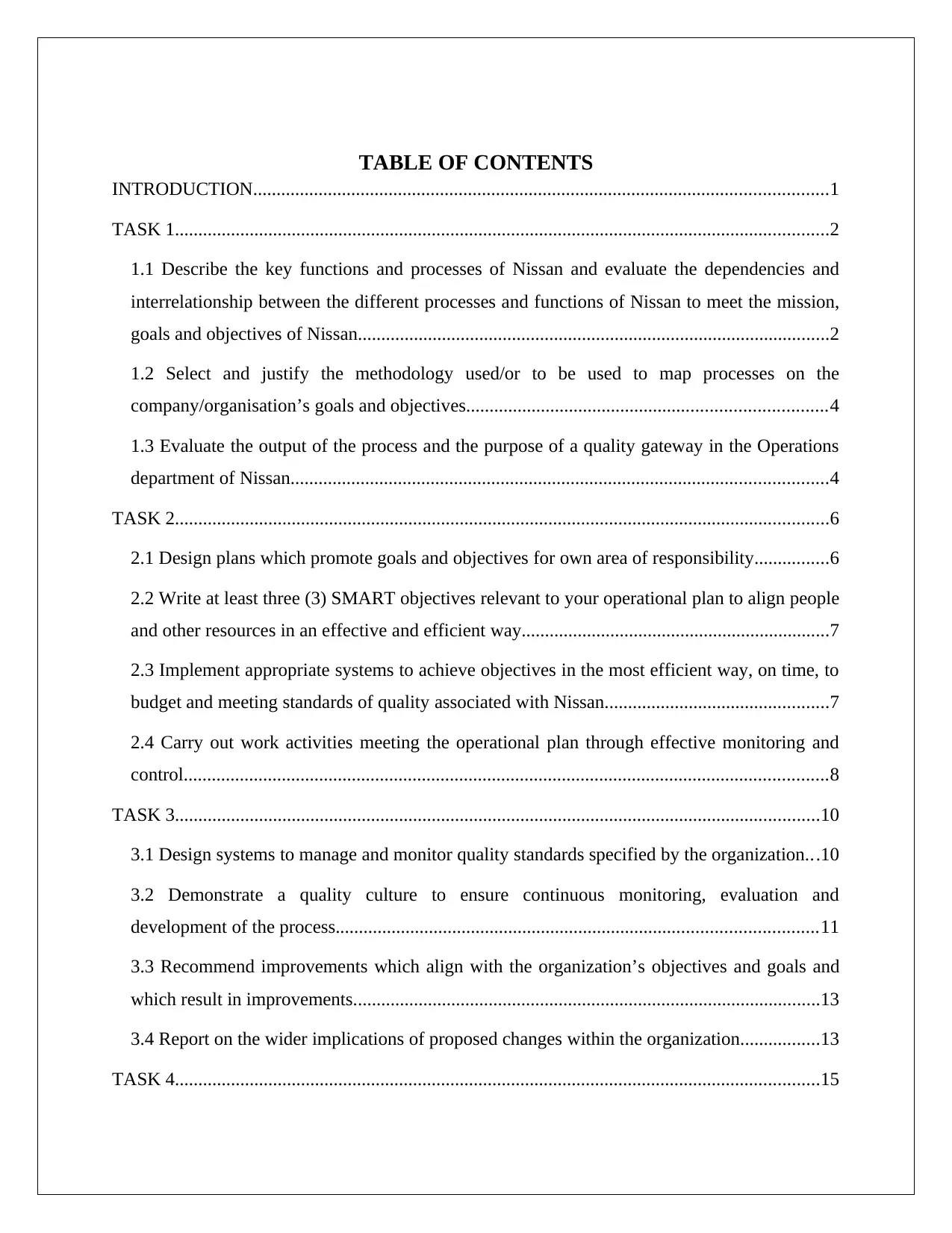
TABLE OF CONTENTS
INTRODUCTION...........................................................................................................................1
TASK 1............................................................................................................................................2
1.1 Describe the key functions and processes of Nissan and evaluate the dependencies and
interrelationship between the different processes and functions of Nissan to meet the mission,
goals and objectives of Nissan.....................................................................................................2
1.2 Select and justify the methodology used/or to be used to map processes on the
company/organisation’s goals and objectives.............................................................................4
1.3 Evaluate the output of the process and the purpose of a quality gateway in the Operations
department of Nissan...................................................................................................................4
TASK 2............................................................................................................................................6
2.1 Design plans which promote goals and objectives for own area of responsibility................6
2.2 Write at least three (3) SMART objectives relevant to your operational plan to align people
and other resources in an effective and efficient way..................................................................7
2.3 Implement appropriate systems to achieve objectives in the most efficient way, on time, to
budget and meeting standards of quality associated with Nissan................................................7
2.4 Carry out work activities meeting the operational plan through effective monitoring and
control..........................................................................................................................................8
TASK 3..........................................................................................................................................10
3.1 Design systems to manage and monitor quality standards specified by the organization...10
3.2 Demonstrate a quality culture to ensure continuous monitoring, evaluation and
development of the process.......................................................................................................11
3.3 Recommend improvements which align with the organization’s objectives and goals and
which result in improvements....................................................................................................13
3.4 Report on the wider implications of proposed changes within the organization.................13
TASK 4..........................................................................................................................................15
INTRODUCTION...........................................................................................................................1
TASK 1............................................................................................................................................2
1.1 Describe the key functions and processes of Nissan and evaluate the dependencies and
interrelationship between the different processes and functions of Nissan to meet the mission,
goals and objectives of Nissan.....................................................................................................2
1.2 Select and justify the methodology used/or to be used to map processes on the
company/organisation’s goals and objectives.............................................................................4
1.3 Evaluate the output of the process and the purpose of a quality gateway in the Operations
department of Nissan...................................................................................................................4
TASK 2............................................................................................................................................6
2.1 Design plans which promote goals and objectives for own area of responsibility................6
2.2 Write at least three (3) SMART objectives relevant to your operational plan to align people
and other resources in an effective and efficient way..................................................................7
2.3 Implement appropriate systems to achieve objectives in the most efficient way, on time, to
budget and meeting standards of quality associated with Nissan................................................7
2.4 Carry out work activities meeting the operational plan through effective monitoring and
control..........................................................................................................................................8
TASK 3..........................................................................................................................................10
3.1 Design systems to manage and monitor quality standards specified by the organization...10
3.2 Demonstrate a quality culture to ensure continuous monitoring, evaluation and
development of the process.......................................................................................................11
3.3 Recommend improvements which align with the organization’s objectives and goals and
which result in improvements....................................................................................................13
3.4 Report on the wider implications of proposed changes within the organization.................13
TASK 4..........................................................................................................................................15
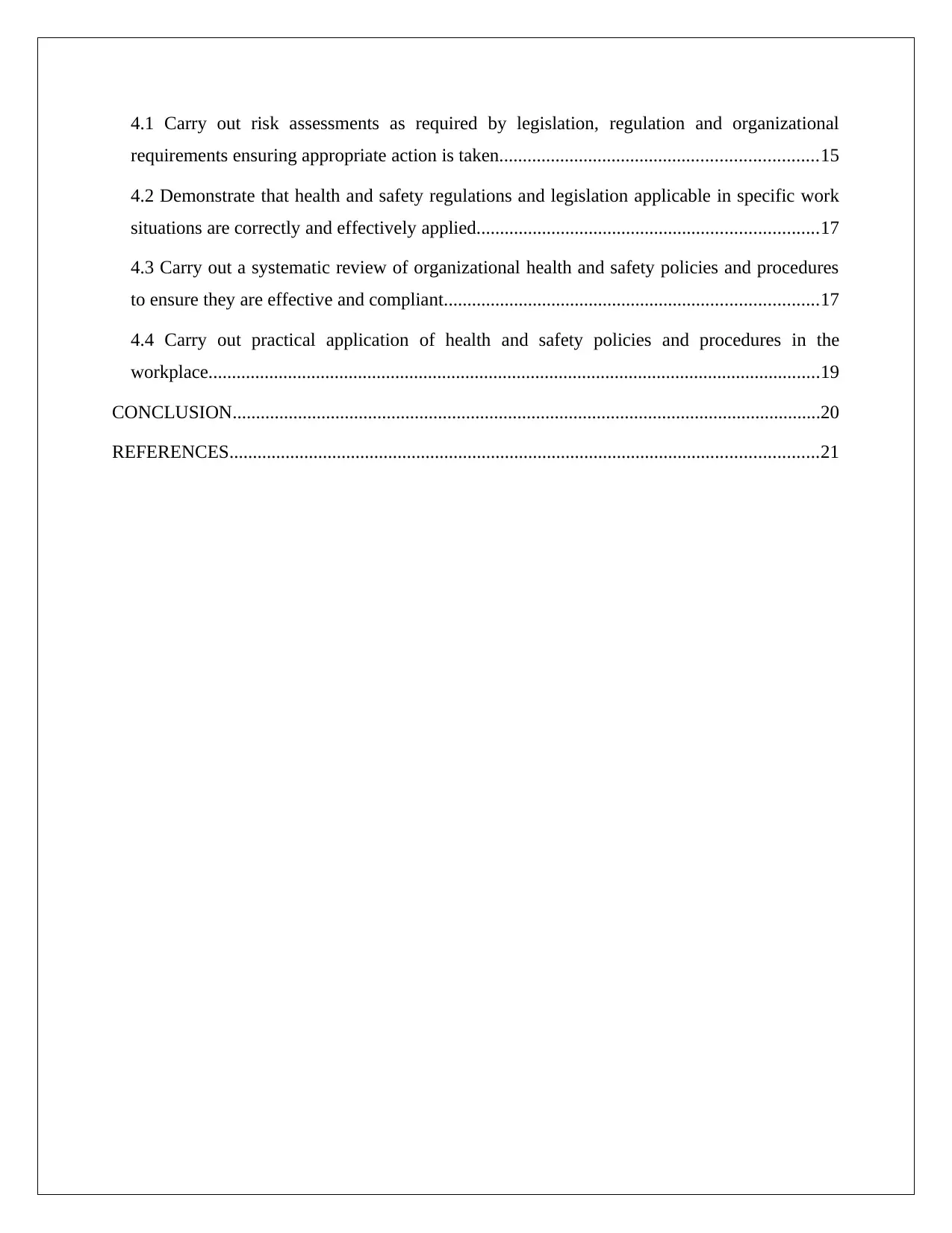
4.1 Carry out risk assessments as required by legislation, regulation and organizational
requirements ensuring appropriate action is taken....................................................................15
4.2 Demonstrate that health and safety regulations and legislation applicable in specific work
situations are correctly and effectively applied.........................................................................17
4.3 Carry out a systematic review of organizational health and safety policies and procedures
to ensure they are effective and compliant................................................................................17
4.4 Carry out practical application of health and safety policies and procedures in the
workplace...................................................................................................................................19
CONCLUSION..............................................................................................................................20
REFERENCES..............................................................................................................................21
requirements ensuring appropriate action is taken....................................................................15
4.2 Demonstrate that health and safety regulations and legislation applicable in specific work
situations are correctly and effectively applied.........................................................................17
4.3 Carry out a systematic review of organizational health and safety policies and procedures
to ensure they are effective and compliant................................................................................17
4.4 Carry out practical application of health and safety policies and procedures in the
workplace...................................................................................................................................19
CONCLUSION..............................................................................................................................20
REFERENCES..............................................................................................................................21
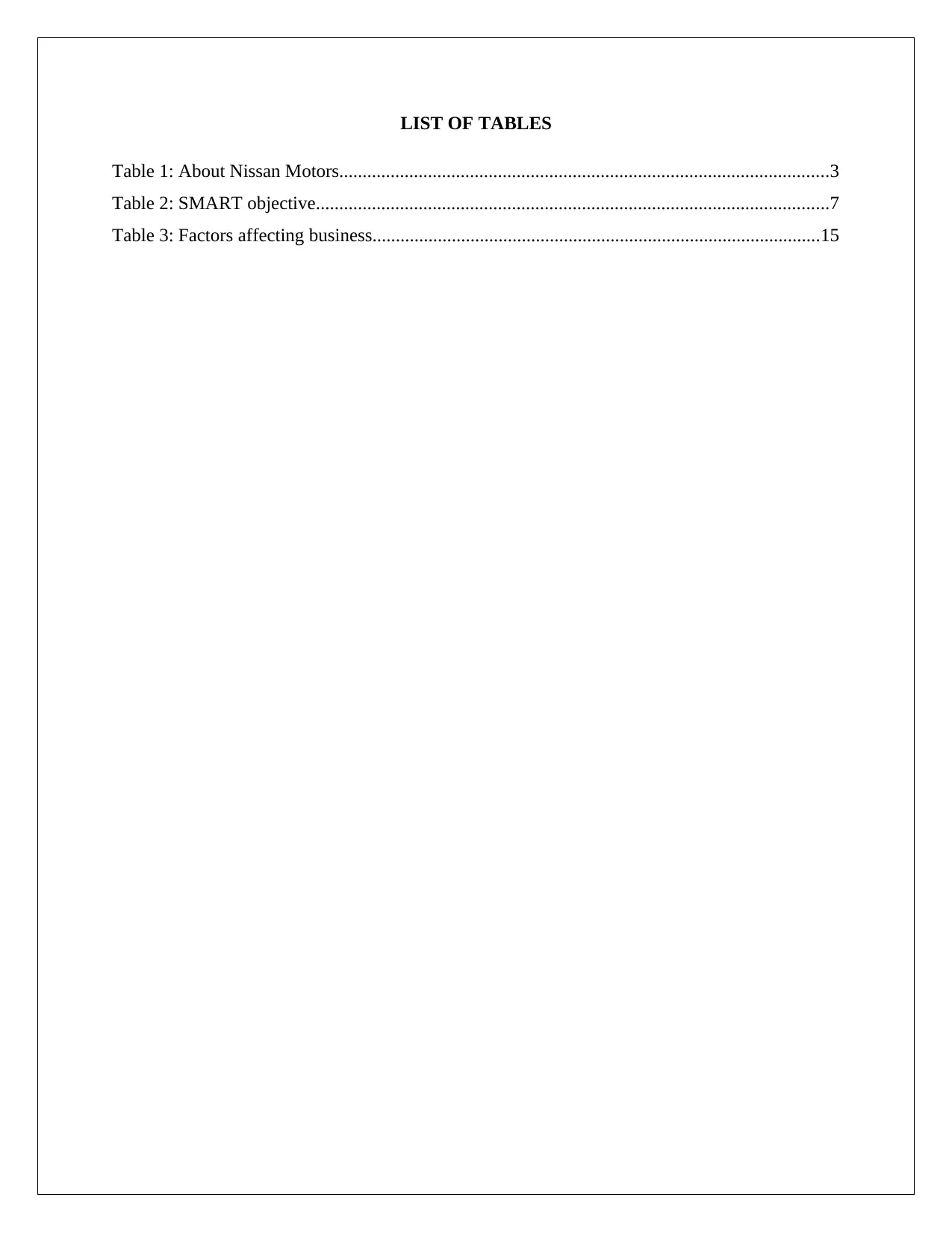
LIST OF TABLES
Table 1: About Nissan Motors.........................................................................................................3
Table 2: SMART objective..............................................................................................................7
Table 3: Factors affecting business................................................................................................15
Table 1: About Nissan Motors.........................................................................................................3
Table 2: SMART objective..............................................................................................................7
Table 3: Factors affecting business................................................................................................15
Secure Best Marks with AI Grader
Need help grading? Try our AI Grader for instant feedback on your assignments.
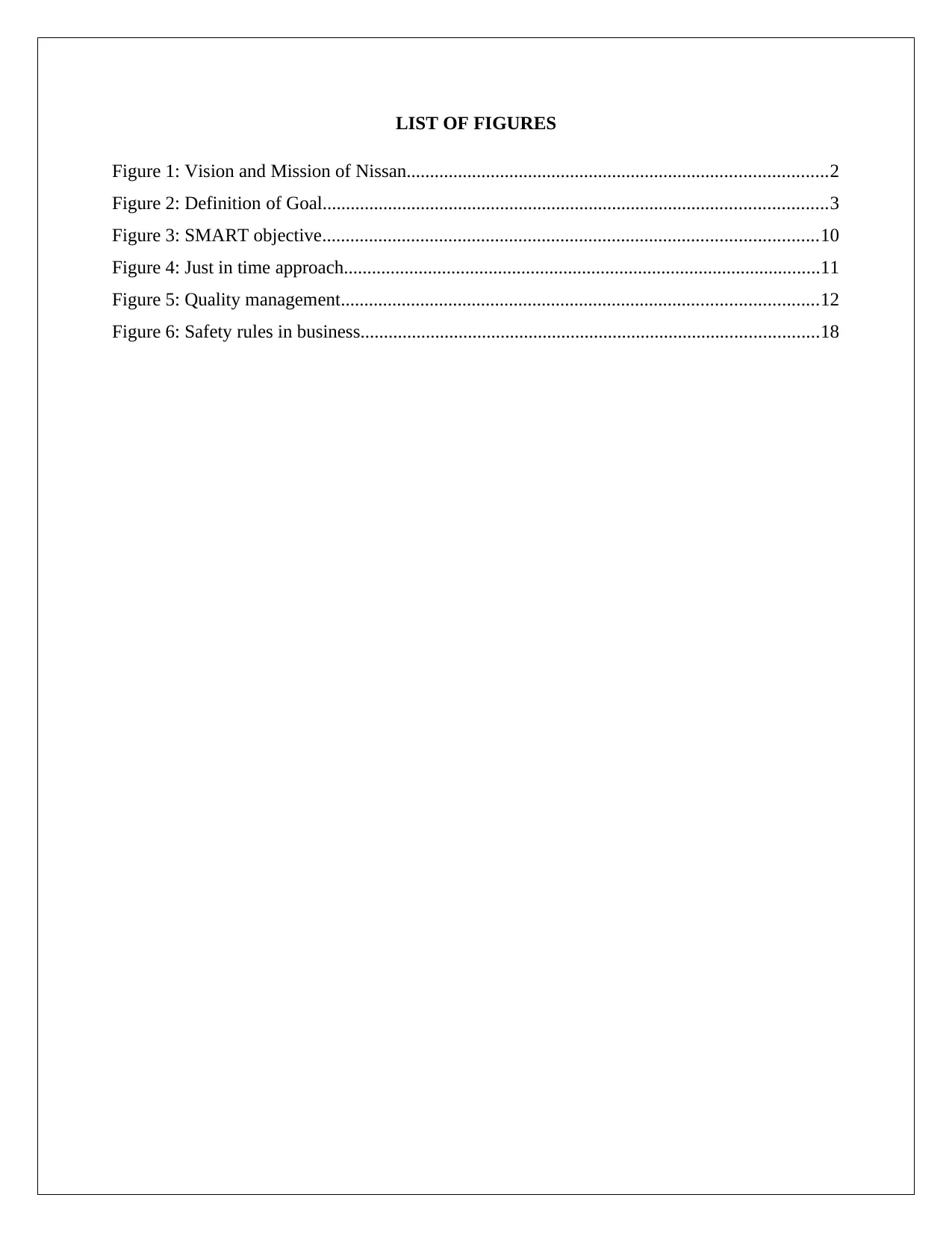
LIST OF FIGURES
Figure 1: Vision and Mission of Nissan..........................................................................................2
Figure 2: Definition of Goal............................................................................................................3
Figure 3: SMART objective..........................................................................................................10
Figure 4: Just in time approach......................................................................................................11
Figure 5: Quality management......................................................................................................12
Figure 6: Safety rules in business..................................................................................................18
Figure 1: Vision and Mission of Nissan..........................................................................................2
Figure 2: Definition of Goal............................................................................................................3
Figure 3: SMART objective..........................................................................................................10
Figure 4: Just in time approach......................................................................................................11
Figure 5: Quality management......................................................................................................12
Figure 6: Safety rules in business..................................................................................................18
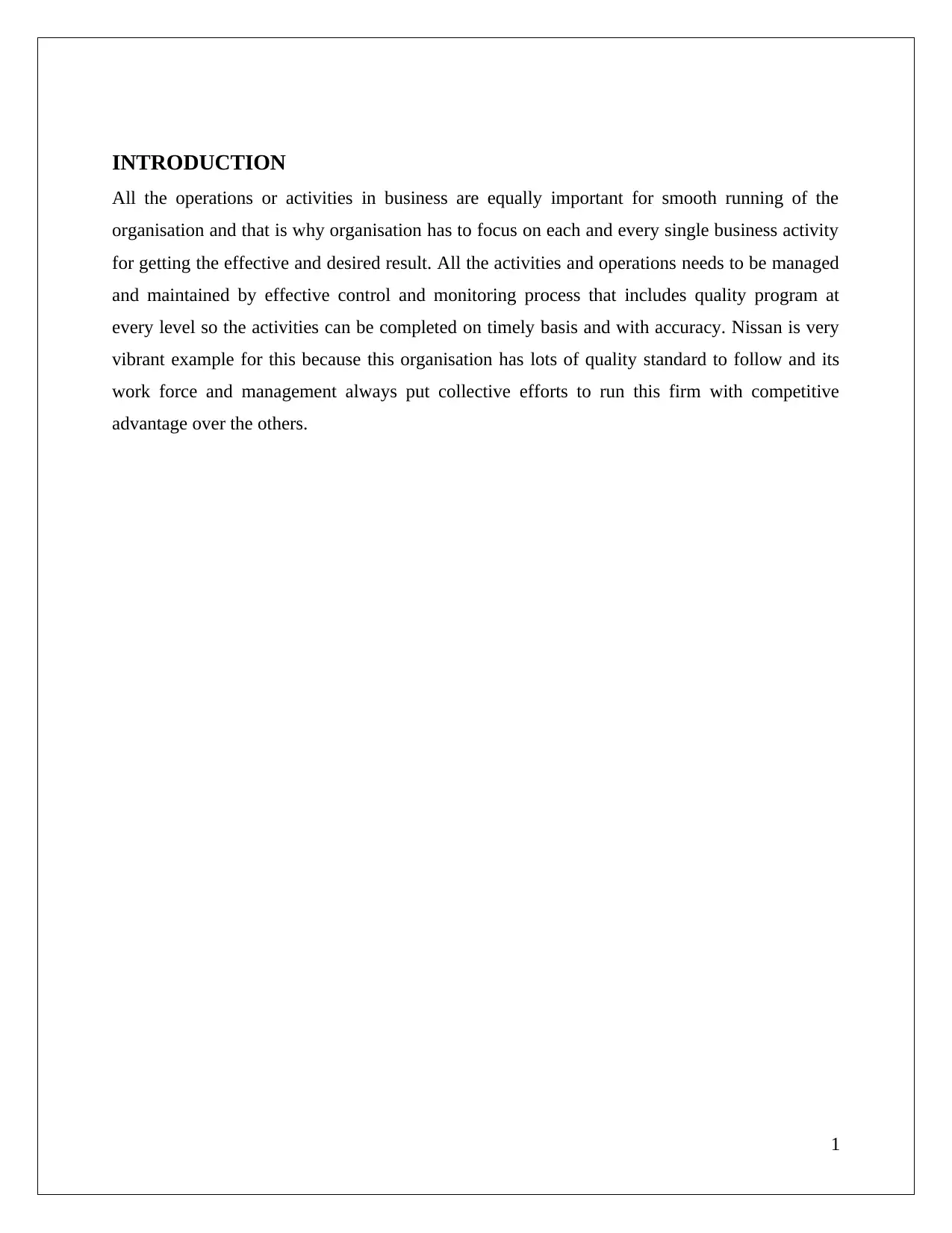
INTRODUCTION
All the operations or activities in business are equally important for smooth running of the
organisation and that is why organisation has to focus on each and every single business activity
for getting the effective and desired result. All the activities and operations needs to be managed
and maintained by effective control and monitoring process that includes quality program at
every level so the activities can be completed on timely basis and with accuracy. Nissan is very
vibrant example for this because this organisation has lots of quality standard to follow and its
work force and management always put collective efforts to run this firm with competitive
advantage over the others.
1
All the operations or activities in business are equally important for smooth running of the
organisation and that is why organisation has to focus on each and every single business activity
for getting the effective and desired result. All the activities and operations needs to be managed
and maintained by effective control and monitoring process that includes quality program at
every level so the activities can be completed on timely basis and with accuracy. Nissan is very
vibrant example for this because this organisation has lots of quality standard to follow and its
work force and management always put collective efforts to run this firm with competitive
advantage over the others.
1
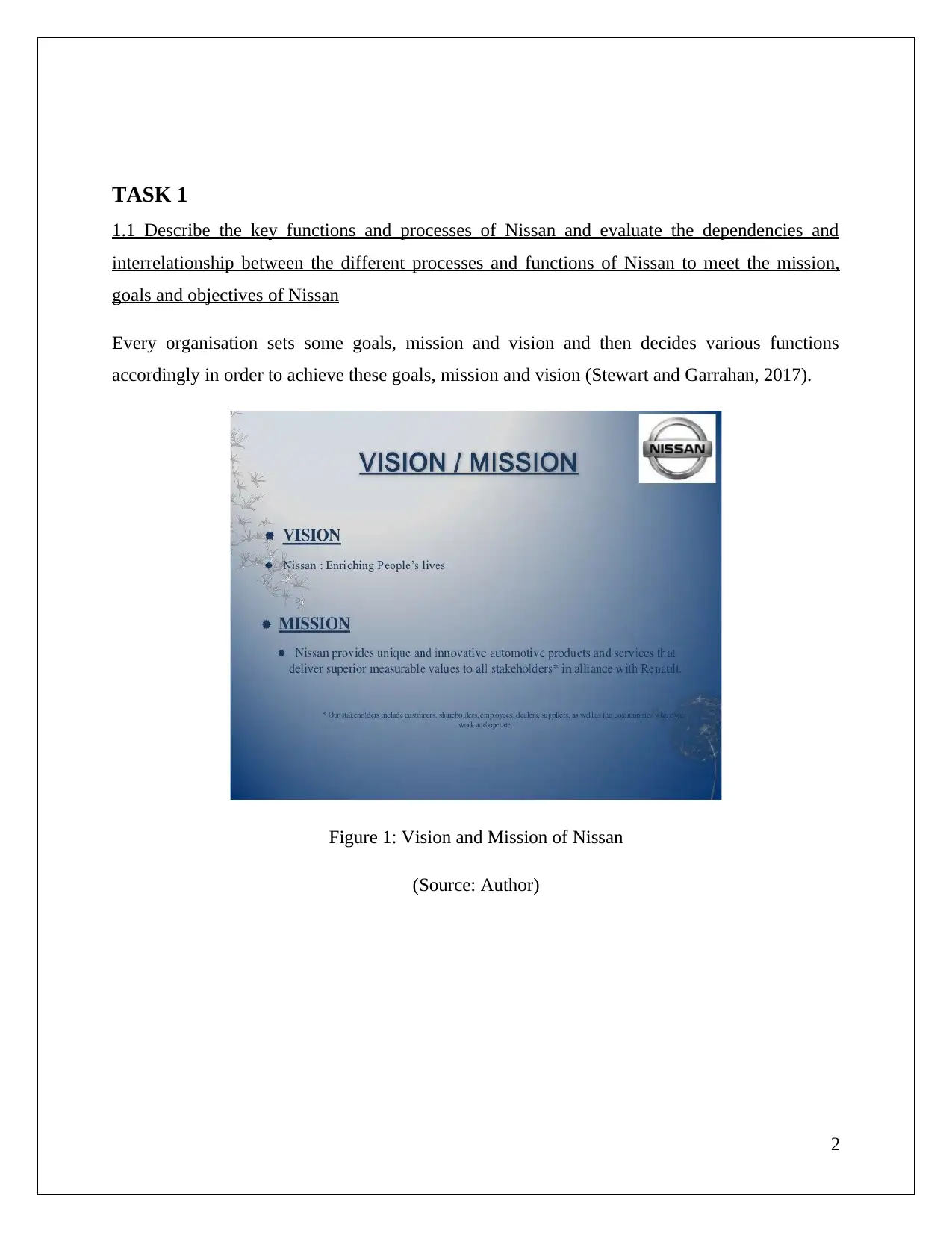
TASK 1
1.1 Describe the key functions and processes of Nissan and evaluate the dependencies and
interrelationship between the different processes and functions of Nissan to meet the mission,
goals and objectives of Nissan
Every organisation sets some goals, mission and vision and then decides various functions
accordingly in order to achieve these goals, mission and vision (Stewart and Garrahan, 2017).
Figure 1: Vision and Mission of Nissan
(Source: Author)
2
1.1 Describe the key functions and processes of Nissan and evaluate the dependencies and
interrelationship between the different processes and functions of Nissan to meet the mission,
goals and objectives of Nissan
Every organisation sets some goals, mission and vision and then decides various functions
accordingly in order to achieve these goals, mission and vision (Stewart and Garrahan, 2017).
Figure 1: Vision and Mission of Nissan
(Source: Author)
2
Paraphrase This Document
Need a fresh take? Get an instant paraphrase of this document with our AI Paraphraser
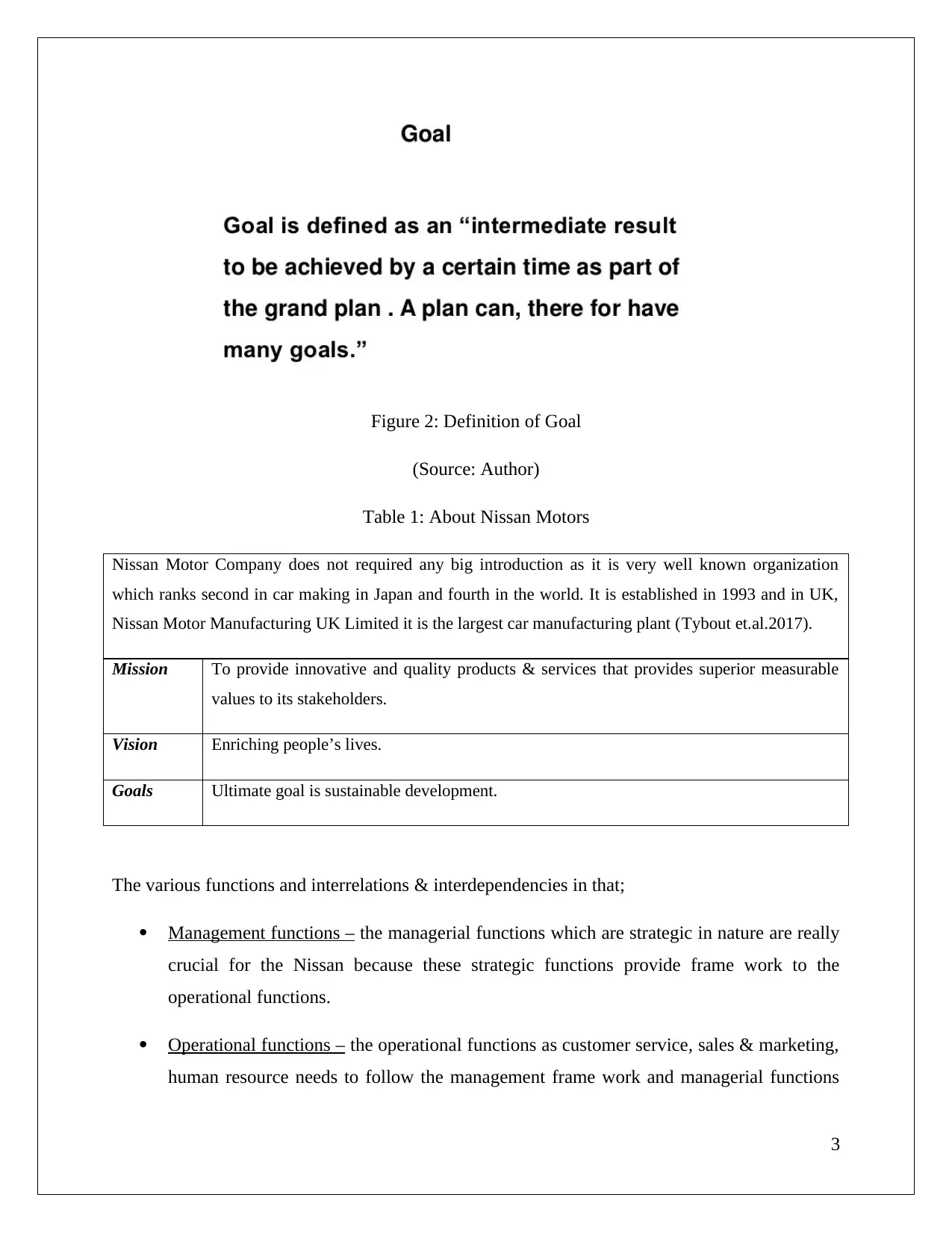
Figure 2: Definition of Goal
(Source: Author)
Table 1: About Nissan Motors
Nissan Motor Company does not required any big introduction as it is very well known organization
which ranks second in car making in Japan and fourth in the world. It is established in 1993 and in UK,
Nissan Motor Manufacturing UK Limited it is the largest car manufacturing plant (Tybout et.al.2017).
Mission To provide innovative and quality products & services that provides superior measurable
values to its stakeholders.
Vision Enriching people’s lives.
Goals Ultimate goal is sustainable development.
The various functions and interrelations & interdependencies in that;
Management functions – the managerial functions which are strategic in nature are really
crucial for the Nissan because these strategic functions provide frame work to the
operational functions.
Operational functions – the operational functions as customer service, sales & marketing,
human resource needs to follow the management frame work and managerial functions
3
(Source: Author)
Table 1: About Nissan Motors
Nissan Motor Company does not required any big introduction as it is very well known organization
which ranks second in car making in Japan and fourth in the world. It is established in 1993 and in UK,
Nissan Motor Manufacturing UK Limited it is the largest car manufacturing plant (Tybout et.al.2017).
Mission To provide innovative and quality products & services that provides superior measurable
values to its stakeholders.
Vision Enriching people’s lives.
Goals Ultimate goal is sustainable development.
The various functions and interrelations & interdependencies in that;
Management functions – the managerial functions which are strategic in nature are really
crucial for the Nissan because these strategic functions provide frame work to the
operational functions.
Operational functions – the operational functions as customer service, sales & marketing,
human resource needs to follow the management frame work and managerial functions
3
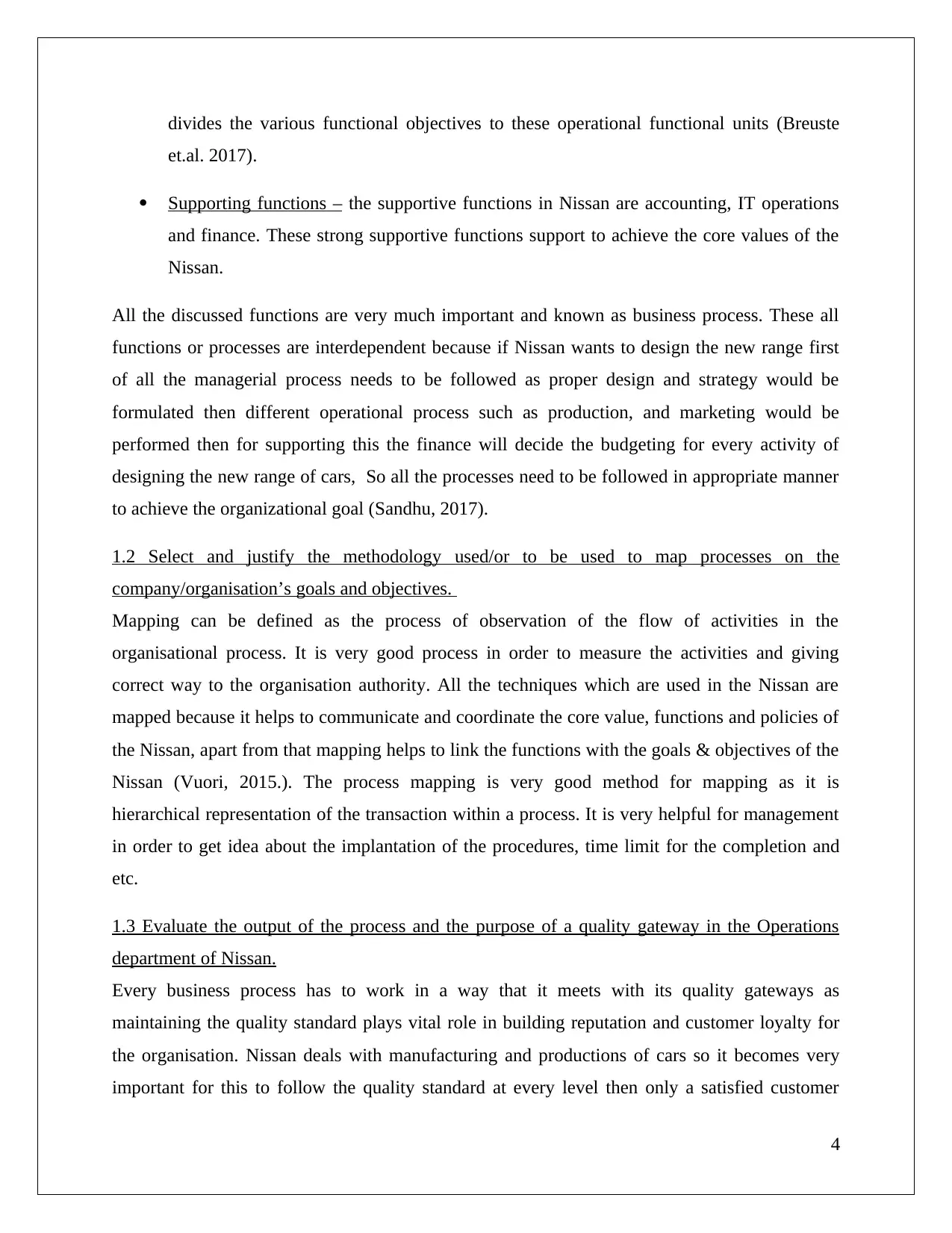
divides the various functional objectives to these operational functional units (Breuste
et.al. 2017).
Supporting functions – the supportive functions in Nissan are accounting, IT operations
and finance. These strong supportive functions support to achieve the core values of the
Nissan.
All the discussed functions are very much important and known as business process. These all
functions or processes are interdependent because if Nissan wants to design the new range first
of all the managerial process needs to be followed as proper design and strategy would be
formulated then different operational process such as production, and marketing would be
performed then for supporting this the finance will decide the budgeting for every activity of
designing the new range of cars, So all the processes need to be followed in appropriate manner
to achieve the organizational goal (Sandhu, 2017).
1.2 Select and justify the methodology used/or to be used to map processes on the
company/organisation’s goals and objectives.
Mapping can be defined as the process of observation of the flow of activities in the
organisational process. It is very good process in order to measure the activities and giving
correct way to the organisation authority. All the techniques which are used in the Nissan are
mapped because it helps to communicate and coordinate the core value, functions and policies of
the Nissan, apart from that mapping helps to link the functions with the goals & objectives of the
Nissan (Vuori, 2015.). The process mapping is very good method for mapping as it is
hierarchical representation of the transaction within a process. It is very helpful for management
in order to get idea about the implantation of the procedures, time limit for the completion and
etc.
1.3 Evaluate the output of the process and the purpose of a quality gateway in the Operations
department of Nissan.
Every business process has to work in a way that it meets with its quality gateways as
maintaining the quality standard plays vital role in building reputation and customer loyalty for
the organisation. Nissan deals with manufacturing and productions of cars so it becomes very
important for this to follow the quality standard at every level then only a satisfied customer
4
et.al. 2017).
Supporting functions – the supportive functions in Nissan are accounting, IT operations
and finance. These strong supportive functions support to achieve the core values of the
Nissan.
All the discussed functions are very much important and known as business process. These all
functions or processes are interdependent because if Nissan wants to design the new range first
of all the managerial process needs to be followed as proper design and strategy would be
formulated then different operational process such as production, and marketing would be
performed then for supporting this the finance will decide the budgeting for every activity of
designing the new range of cars, So all the processes need to be followed in appropriate manner
to achieve the organizational goal (Sandhu, 2017).
1.2 Select and justify the methodology used/or to be used to map processes on the
company/organisation’s goals and objectives.
Mapping can be defined as the process of observation of the flow of activities in the
organisational process. It is very good process in order to measure the activities and giving
correct way to the organisation authority. All the techniques which are used in the Nissan are
mapped because it helps to communicate and coordinate the core value, functions and policies of
the Nissan, apart from that mapping helps to link the functions with the goals & objectives of the
Nissan (Vuori, 2015.). The process mapping is very good method for mapping as it is
hierarchical representation of the transaction within a process. It is very helpful for management
in order to get idea about the implantation of the procedures, time limit for the completion and
etc.
1.3 Evaluate the output of the process and the purpose of a quality gateway in the Operations
department of Nissan.
Every business process has to work in a way that it meets with its quality gateways as
maintaining the quality standard plays vital role in building reputation and customer loyalty for
the organisation. Nissan deals with manufacturing and productions of cars so it becomes very
important for this to follow the quality standard at every level then only a satisfied customer
4
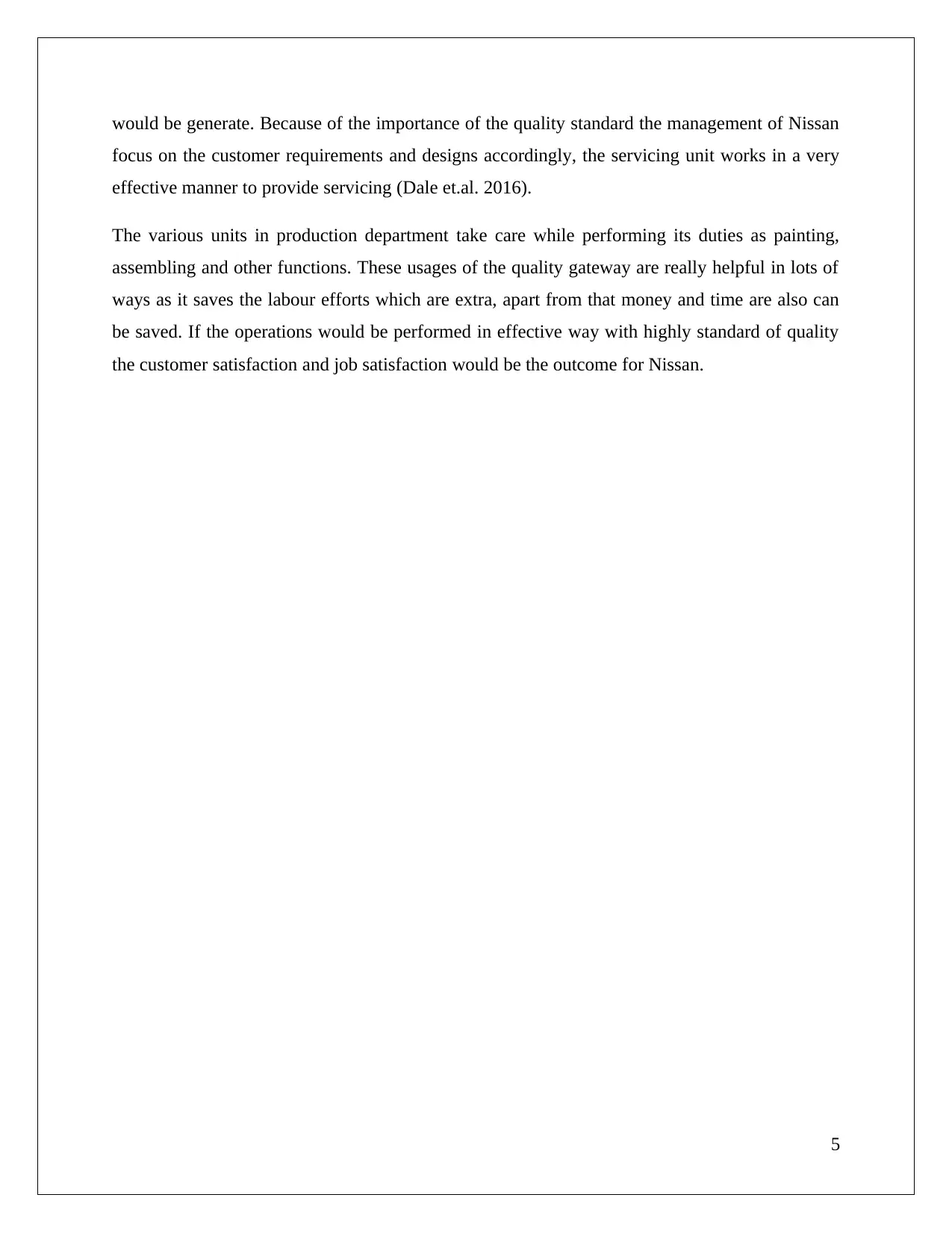
would be generate. Because of the importance of the quality standard the management of Nissan
focus on the customer requirements and designs accordingly, the servicing unit works in a very
effective manner to provide servicing (Dale et.al. 2016).
The various units in production department take care while performing its duties as painting,
assembling and other functions. These usages of the quality gateway are really helpful in lots of
ways as it saves the labour efforts which are extra, apart from that money and time are also can
be saved. If the operations would be performed in effective way with highly standard of quality
the customer satisfaction and job satisfaction would be the outcome for Nissan.
5
focus on the customer requirements and designs accordingly, the servicing unit works in a very
effective manner to provide servicing (Dale et.al. 2016).
The various units in production department take care while performing its duties as painting,
assembling and other functions. These usages of the quality gateway are really helpful in lots of
ways as it saves the labour efforts which are extra, apart from that money and time are also can
be saved. If the operations would be performed in effective way with highly standard of quality
the customer satisfaction and job satisfaction would be the outcome for Nissan.
5
Secure Best Marks with AI Grader
Need help grading? Try our AI Grader for instant feedback on your assignments.
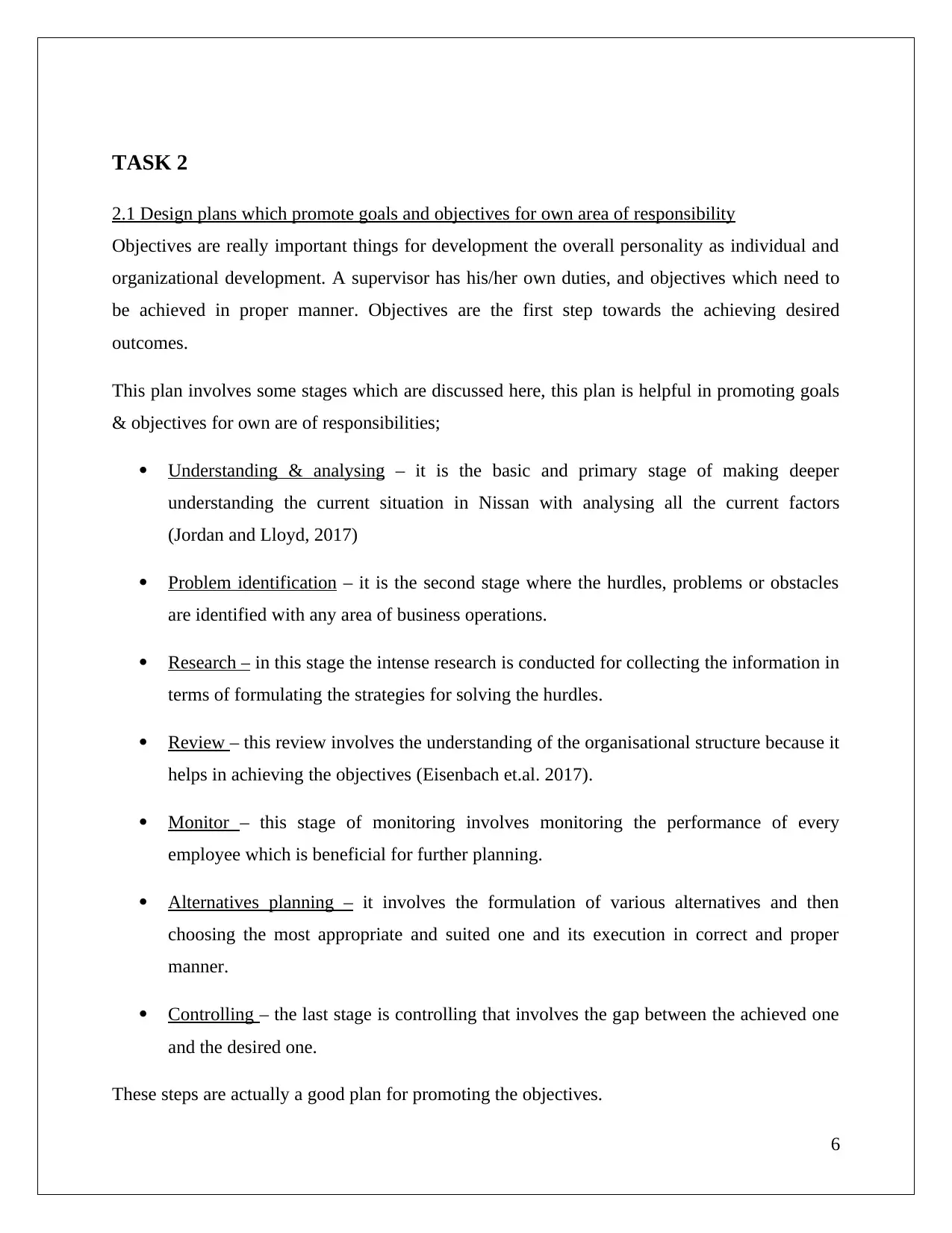
TASK 2
2.1 Design plans which promote goals and objectives for own area of responsibility
Objectives are really important things for development the overall personality as individual and
organizational development. A supervisor has his/her own duties, and objectives which need to
be achieved in proper manner. Objectives are the first step towards the achieving desired
outcomes.
This plan involves some stages which are discussed here, this plan is helpful in promoting goals
& objectives for own are of responsibilities;
Understanding & analysing – it is the basic and primary stage of making deeper
understanding the current situation in Nissan with analysing all the current factors
(Jordan and Lloyd, 2017)
Problem identification – it is the second stage where the hurdles, problems or obstacles
are identified with any area of business operations.
Research – in this stage the intense research is conducted for collecting the information in
terms of formulating the strategies for solving the hurdles.
Review – this review involves the understanding of the organisational structure because it
helps in achieving the objectives (Eisenbach et.al. 2017).
Monitor – this stage of monitoring involves monitoring the performance of every
employee which is beneficial for further planning.
Alternatives planning – it involves the formulation of various alternatives and then
choosing the most appropriate and suited one and its execution in correct and proper
manner.
Controlling – the last stage is controlling that involves the gap between the achieved one
and the desired one.
These steps are actually a good plan for promoting the objectives.
6
2.1 Design plans which promote goals and objectives for own area of responsibility
Objectives are really important things for development the overall personality as individual and
organizational development. A supervisor has his/her own duties, and objectives which need to
be achieved in proper manner. Objectives are the first step towards the achieving desired
outcomes.
This plan involves some stages which are discussed here, this plan is helpful in promoting goals
& objectives for own are of responsibilities;
Understanding & analysing – it is the basic and primary stage of making deeper
understanding the current situation in Nissan with analysing all the current factors
(Jordan and Lloyd, 2017)
Problem identification – it is the second stage where the hurdles, problems or obstacles
are identified with any area of business operations.
Research – in this stage the intense research is conducted for collecting the information in
terms of formulating the strategies for solving the hurdles.
Review – this review involves the understanding of the organisational structure because it
helps in achieving the objectives (Eisenbach et.al. 2017).
Monitor – this stage of monitoring involves monitoring the performance of every
employee which is beneficial for further planning.
Alternatives planning – it involves the formulation of various alternatives and then
choosing the most appropriate and suited one and its execution in correct and proper
manner.
Controlling – the last stage is controlling that involves the gap between the achieved one
and the desired one.
These steps are actually a good plan for promoting the objectives.
6
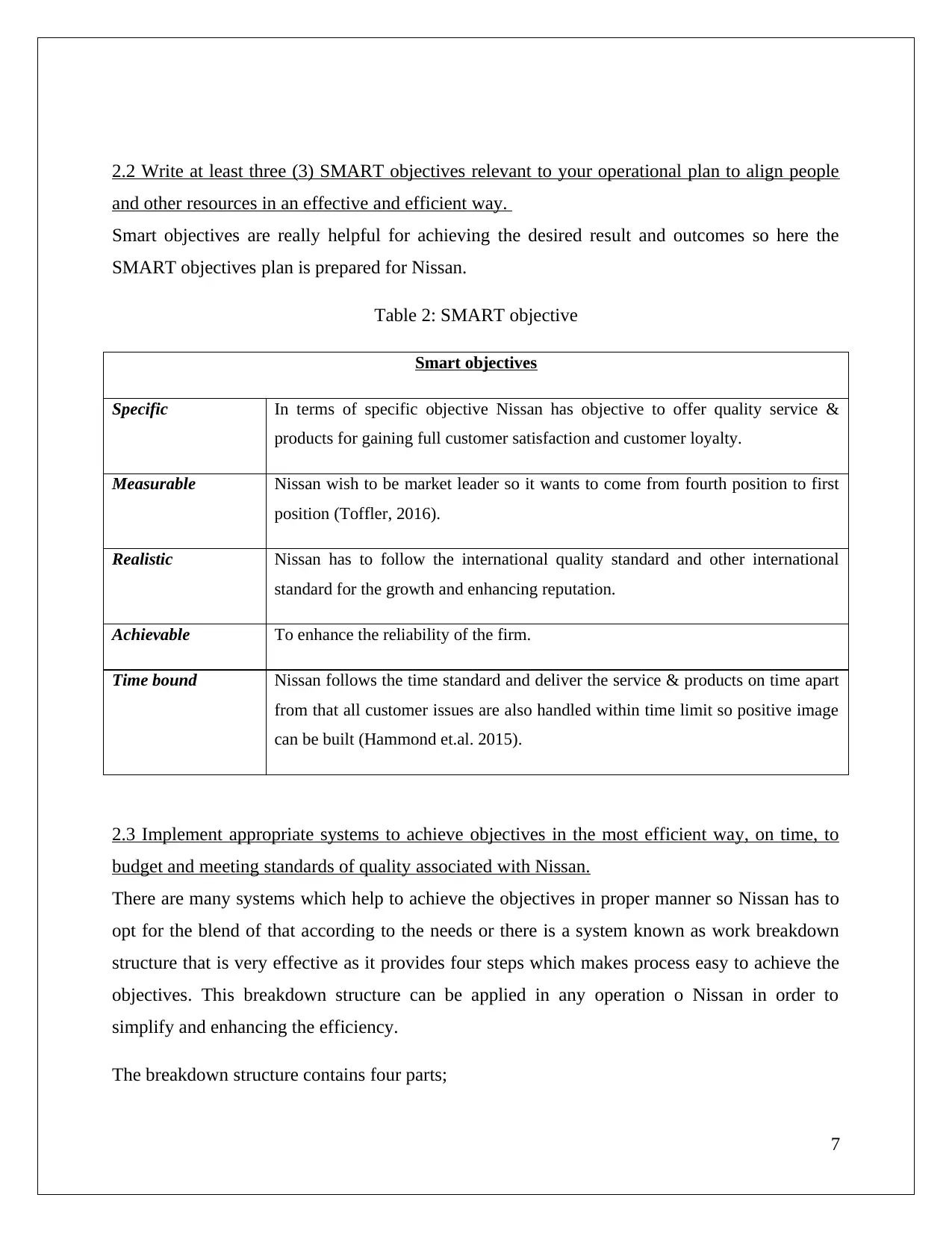
2.2 Write at least three (3) SMART objectives relevant to your operational plan to align people
and other resources in an effective and efficient way.
Smart objectives are really helpful for achieving the desired result and outcomes so here the
SMART objectives plan is prepared for Nissan.
Table 2: SMART objective
Smart objectives
Specific In terms of specific objective Nissan has objective to offer quality service &
products for gaining full customer satisfaction and customer loyalty.
Measurable Nissan wish to be market leader so it wants to come from fourth position to first
position (Toffler, 2016).
Realistic Nissan has to follow the international quality standard and other international
standard for the growth and enhancing reputation.
Achievable To enhance the reliability of the firm.
Time bound Nissan follows the time standard and deliver the service & products on time apart
from that all customer issues are also handled within time limit so positive image
can be built (Hammond et.al. 2015).
2.3 Implement appropriate systems to achieve objectives in the most efficient way, on time, to
budget and meeting standards of quality associated with Nissan.
There are many systems which help to achieve the objectives in proper manner so Nissan has to
opt for the blend of that according to the needs or there is a system known as work breakdown
structure that is very effective as it provides four steps which makes process easy to achieve the
objectives. This breakdown structure can be applied in any operation o Nissan in order to
simplify and enhancing the efficiency.
The breakdown structure contains four parts;
7
and other resources in an effective and efficient way.
Smart objectives are really helpful for achieving the desired result and outcomes so here the
SMART objectives plan is prepared for Nissan.
Table 2: SMART objective
Smart objectives
Specific In terms of specific objective Nissan has objective to offer quality service &
products for gaining full customer satisfaction and customer loyalty.
Measurable Nissan wish to be market leader so it wants to come from fourth position to first
position (Toffler, 2016).
Realistic Nissan has to follow the international quality standard and other international
standard for the growth and enhancing reputation.
Achievable To enhance the reliability of the firm.
Time bound Nissan follows the time standard and deliver the service & products on time apart
from that all customer issues are also handled within time limit so positive image
can be built (Hammond et.al. 2015).
2.3 Implement appropriate systems to achieve objectives in the most efficient way, on time, to
budget and meeting standards of quality associated with Nissan.
There are many systems which help to achieve the objectives in proper manner so Nissan has to
opt for the blend of that according to the needs or there is a system known as work breakdown
structure that is very effective as it provides four steps which makes process easy to achieve the
objectives. This breakdown structure can be applied in any operation o Nissan in order to
simplify and enhancing the efficiency.
The breakdown structure contains four parts;
7
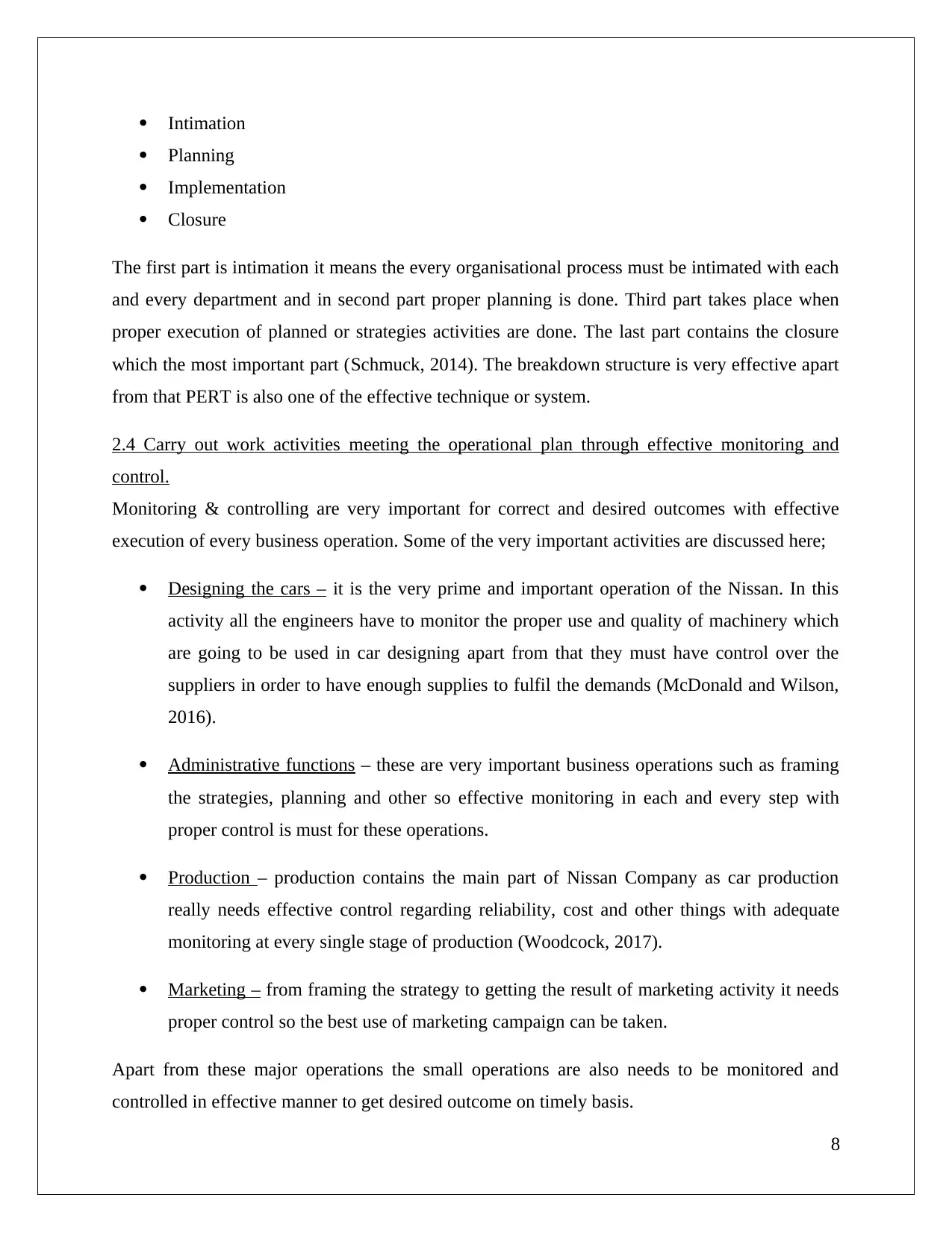
Intimation
Planning
Implementation
Closure
The first part is intimation it means the every organisational process must be intimated with each
and every department and in second part proper planning is done. Third part takes place when
proper execution of planned or strategies activities are done. The last part contains the closure
which the most important part (Schmuck, 2014). The breakdown structure is very effective apart
from that PERT is also one of the effective technique or system.
2.4 Carry out work activities meeting the operational plan through effective monitoring and
control.
Monitoring & controlling are very important for correct and desired outcomes with effective
execution of every business operation. Some of the very important activities are discussed here;
Designing the cars – it is the very prime and important operation of the Nissan. In this
activity all the engineers have to monitor the proper use and quality of machinery which
are going to be used in car designing apart from that they must have control over the
suppliers in order to have enough supplies to fulfil the demands (McDonald and Wilson,
2016).
Administrative functions – these are very important business operations such as framing
the strategies, planning and other so effective monitoring in each and every step with
proper control is must for these operations.
Production – production contains the main part of Nissan Company as car production
really needs effective control regarding reliability, cost and other things with adequate
monitoring at every single stage of production (Woodcock, 2017).
Marketing – from framing the strategy to getting the result of marketing activity it needs
proper control so the best use of marketing campaign can be taken.
Apart from these major operations the small operations are also needs to be monitored and
controlled in effective manner to get desired outcome on timely basis.
8
Planning
Implementation
Closure
The first part is intimation it means the every organisational process must be intimated with each
and every department and in second part proper planning is done. Third part takes place when
proper execution of planned or strategies activities are done. The last part contains the closure
which the most important part (Schmuck, 2014). The breakdown structure is very effective apart
from that PERT is also one of the effective technique or system.
2.4 Carry out work activities meeting the operational plan through effective monitoring and
control.
Monitoring & controlling are very important for correct and desired outcomes with effective
execution of every business operation. Some of the very important activities are discussed here;
Designing the cars – it is the very prime and important operation of the Nissan. In this
activity all the engineers have to monitor the proper use and quality of machinery which
are going to be used in car designing apart from that they must have control over the
suppliers in order to have enough supplies to fulfil the demands (McDonald and Wilson,
2016).
Administrative functions – these are very important business operations such as framing
the strategies, planning and other so effective monitoring in each and every step with
proper control is must for these operations.
Production – production contains the main part of Nissan Company as car production
really needs effective control regarding reliability, cost and other things with adequate
monitoring at every single stage of production (Woodcock, 2017).
Marketing – from framing the strategy to getting the result of marketing activity it needs
proper control so the best use of marketing campaign can be taken.
Apart from these major operations the small operations are also needs to be monitored and
controlled in effective manner to get desired outcome on timely basis.
8
Paraphrase This Document
Need a fresh take? Get an instant paraphrase of this document with our AI Paraphraser
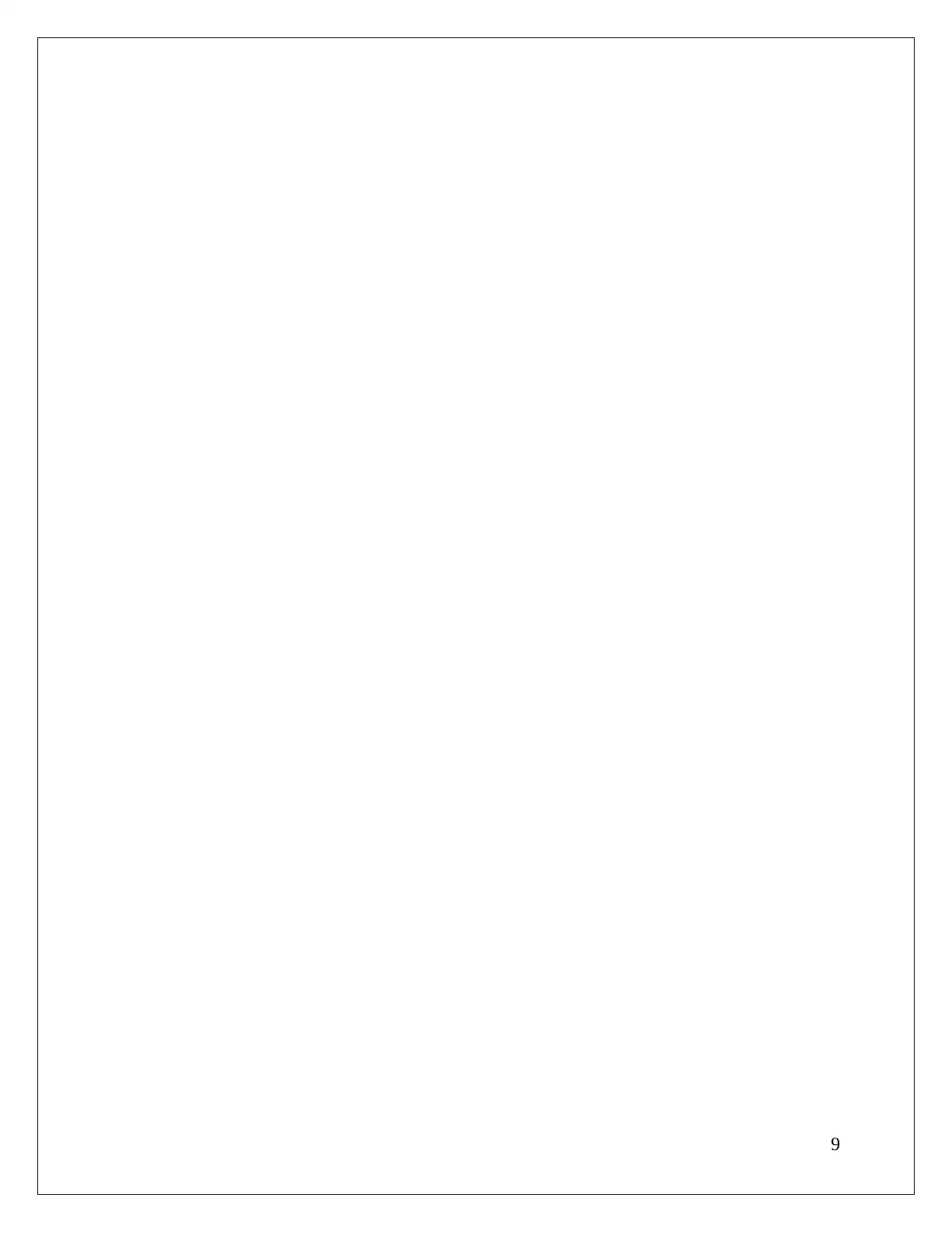
9
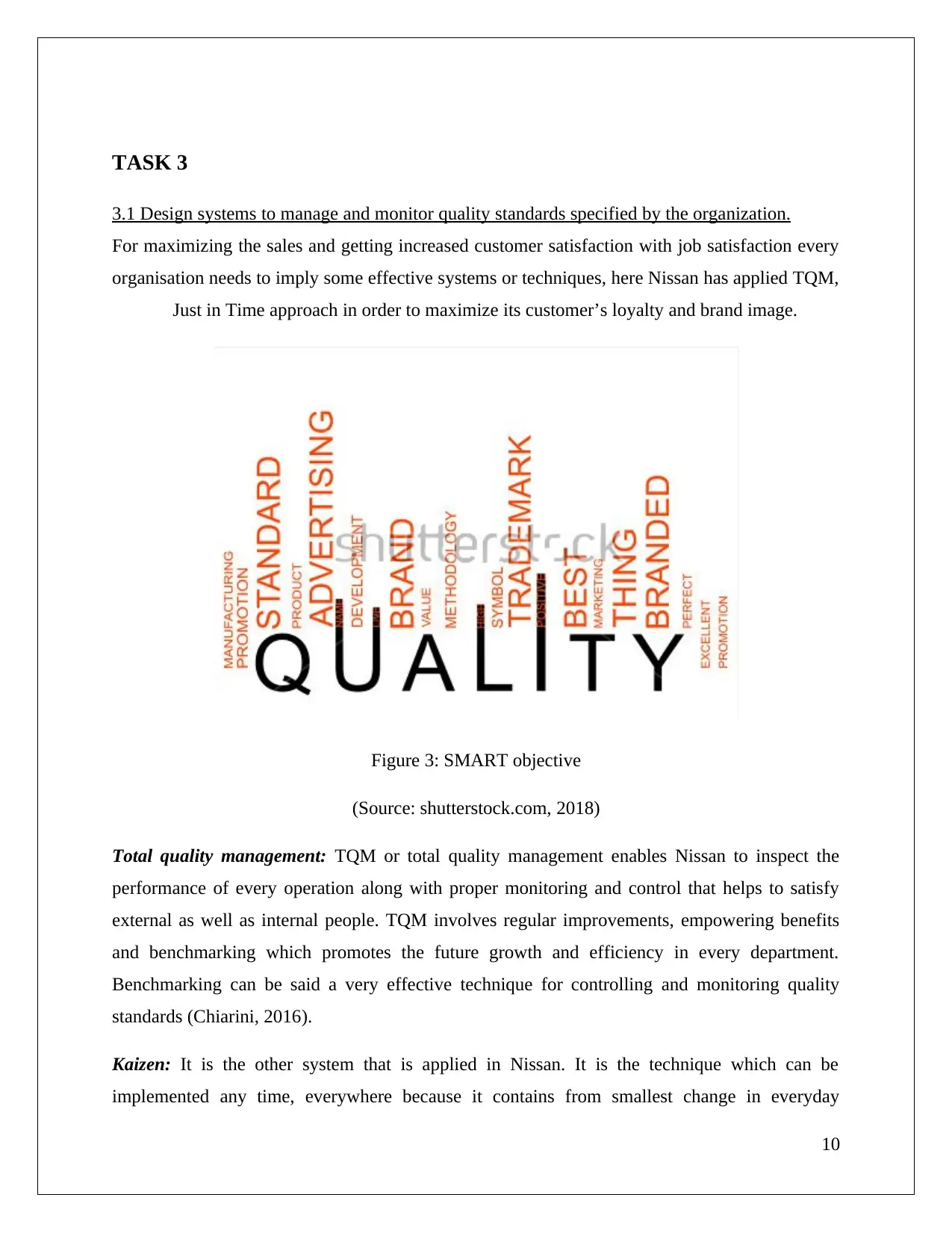
TASK 3
3.1 Design systems to manage and monitor quality standards specified by the organization.
For maximizing the sales and getting increased customer satisfaction with job satisfaction every
organisation needs to imply some effective systems or techniques, here Nissan has applied TQM,
Just in Time approach in order to maximize its customer’s loyalty and brand image.
Figure 3: SMART objective
(Source: shutterstock.com, 2018)
Total quality management: TQM or total quality management enables Nissan to inspect the
performance of every operation along with proper monitoring and control that helps to satisfy
external as well as internal people. TQM involves regular improvements, empowering benefits
and benchmarking which promotes the future growth and efficiency in every department.
Benchmarking can be said a very effective technique for controlling and monitoring quality
standards (Chiarini, 2016).
Kaizen: It is the other system that is applied in Nissan. It is the technique which can be
implemented any time, everywhere because it contains from smallest change in everyday
10
3.1 Design systems to manage and monitor quality standards specified by the organization.
For maximizing the sales and getting increased customer satisfaction with job satisfaction every
organisation needs to imply some effective systems or techniques, here Nissan has applied TQM,
Just in Time approach in order to maximize its customer’s loyalty and brand image.
Figure 3: SMART objective
(Source: shutterstock.com, 2018)
Total quality management: TQM or total quality management enables Nissan to inspect the
performance of every operation along with proper monitoring and control that helps to satisfy
external as well as internal people. TQM involves regular improvements, empowering benefits
and benchmarking which promotes the future growth and efficiency in every department.
Benchmarking can be said a very effective technique for controlling and monitoring quality
standards (Chiarini, 2016).
Kaizen: It is the other system that is applied in Nissan. It is the technique which can be
implemented any time, everywhere because it contains from smallest change in everyday
10
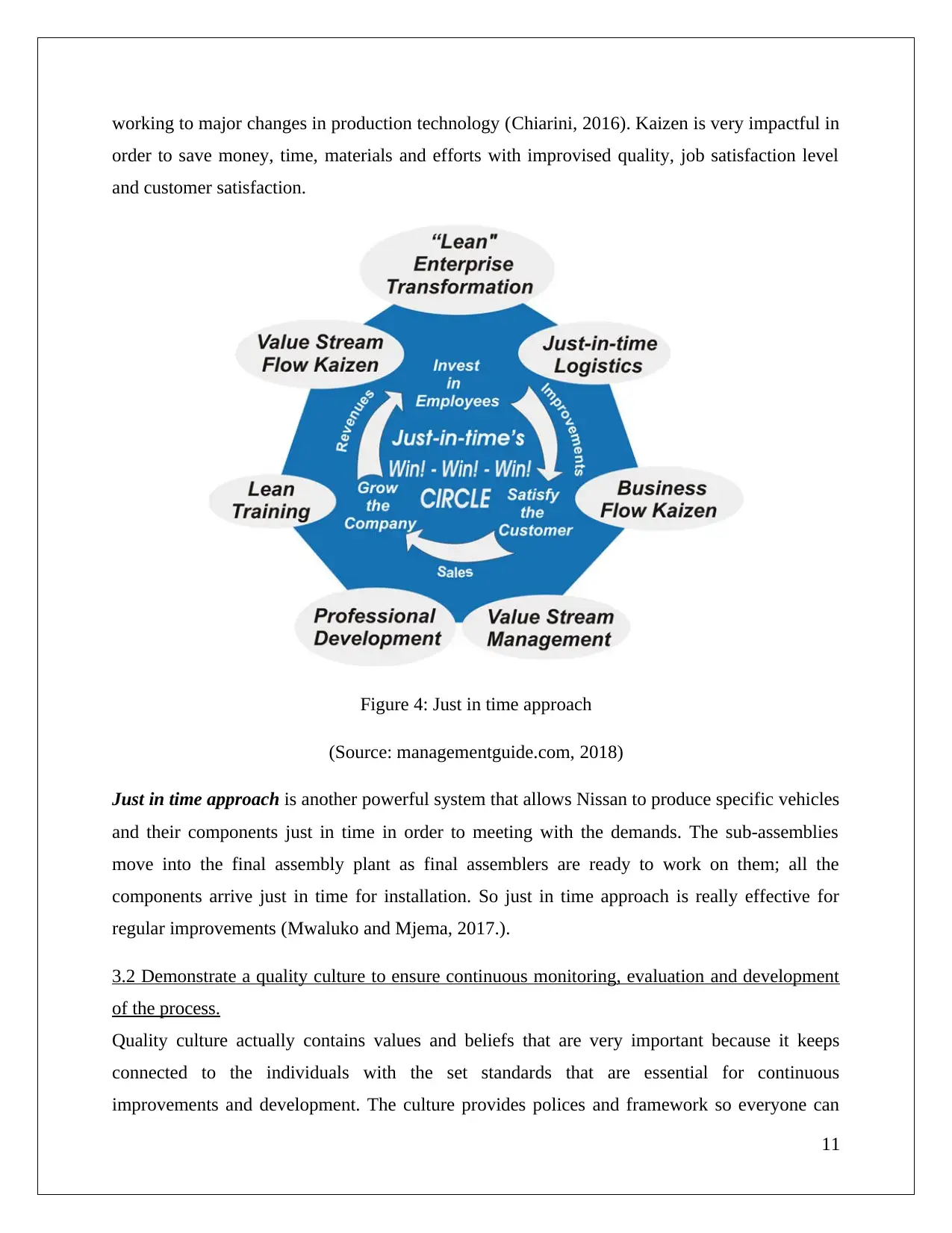
working to major changes in production technology (Chiarini, 2016). Kaizen is very impactful in
order to save money, time, materials and efforts with improvised quality, job satisfaction level
and customer satisfaction.
Figure 4: Just in time approach
(Source: managementguide.com, 2018)
Just in time approach is another powerful system that allows Nissan to produce specific vehicles
and their components just in time in order to meeting with the demands. The sub-assemblies
move into the final assembly plant as final assemblers are ready to work on them; all the
components arrive just in time for installation. So just in time approach is really effective for
regular improvements (Mwaluko and Mjema, 2017.).
3.2 Demonstrate a quality culture to ensure continuous monitoring, evaluation and development
of the process.
Quality culture actually contains values and beliefs that are very important because it keeps
connected to the individuals with the set standards that are essential for continuous
improvements and development. The culture provides polices and framework so everyone can
11
order to save money, time, materials and efforts with improvised quality, job satisfaction level
and customer satisfaction.
Figure 4: Just in time approach
(Source: managementguide.com, 2018)
Just in time approach is another powerful system that allows Nissan to produce specific vehicles
and their components just in time in order to meeting with the demands. The sub-assemblies
move into the final assembly plant as final assemblers are ready to work on them; all the
components arrive just in time for installation. So just in time approach is really effective for
regular improvements (Mwaluko and Mjema, 2017.).
3.2 Demonstrate a quality culture to ensure continuous monitoring, evaluation and development
of the process.
Quality culture actually contains values and beliefs that are very important because it keeps
connected to the individuals with the set standards that are essential for continuous
improvements and development. The culture provides polices and framework so everyone can
11
Secure Best Marks with AI Grader
Need help grading? Try our AI Grader for instant feedback on your assignments.
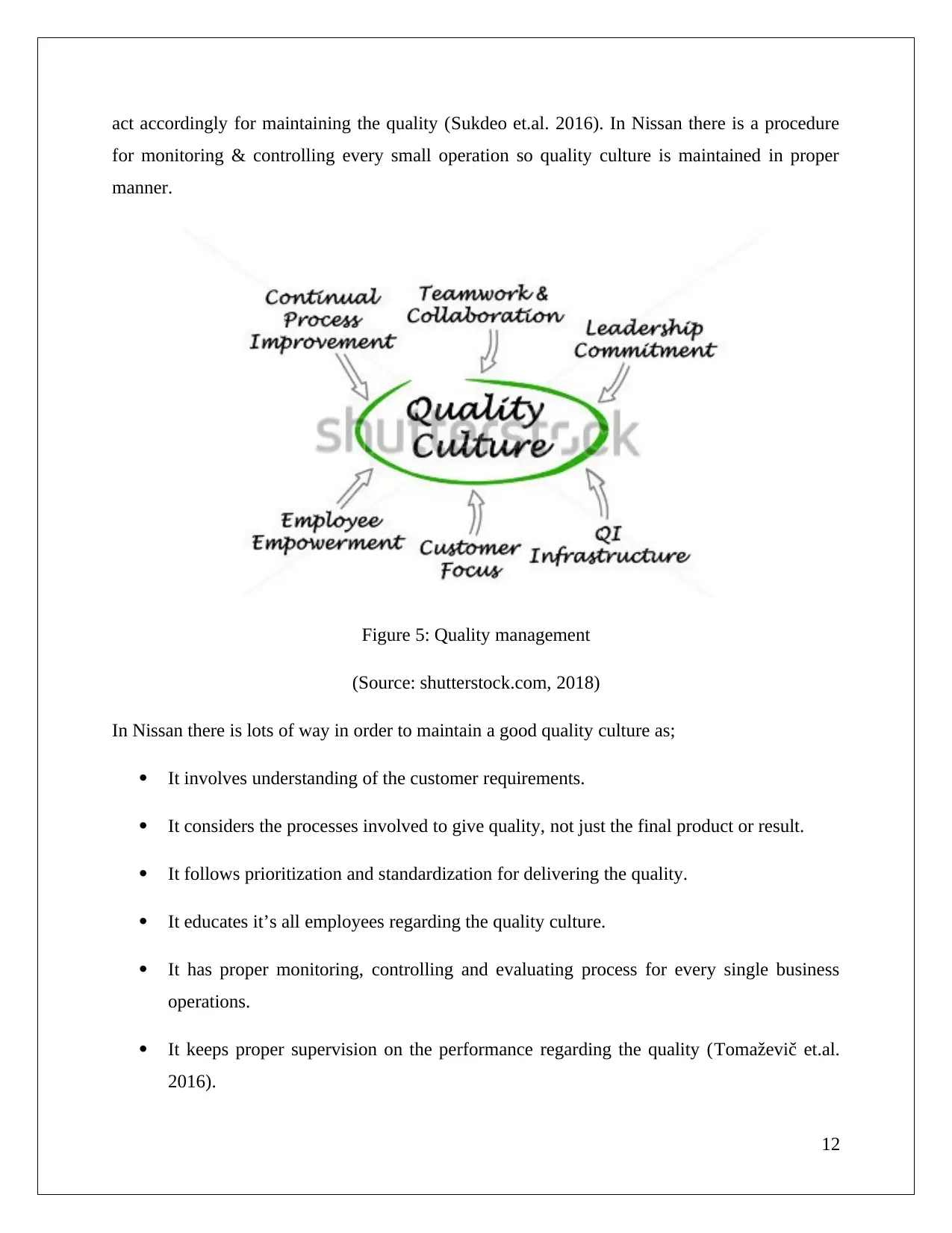
act accordingly for maintaining the quality (Sukdeo et.al. 2016). In Nissan there is a procedure
for monitoring & controlling every small operation so quality culture is maintained in proper
manner.
Figure 5: Quality management
(Source: shutterstock.com, 2018)
In Nissan there is lots of way in order to maintain a good quality culture as;
It involves understanding of the customer requirements.
It considers the processes involved to give quality, not just the final product or result.
It follows prioritization and standardization for delivering the quality.
It educates it’s all employees regarding the quality culture.
It has proper monitoring, controlling and evaluating process for every single business
operations.
It keeps proper supervision on the performance regarding the quality (Tomaževič et.al.
2016).
12
for monitoring & controlling every small operation so quality culture is maintained in proper
manner.
Figure 5: Quality management
(Source: shutterstock.com, 2018)
In Nissan there is lots of way in order to maintain a good quality culture as;
It involves understanding of the customer requirements.
It considers the processes involved to give quality, not just the final product or result.
It follows prioritization and standardization for delivering the quality.
It educates it’s all employees regarding the quality culture.
It has proper monitoring, controlling and evaluating process for every single business
operations.
It keeps proper supervision on the performance regarding the quality (Tomaževič et.al.
2016).
12
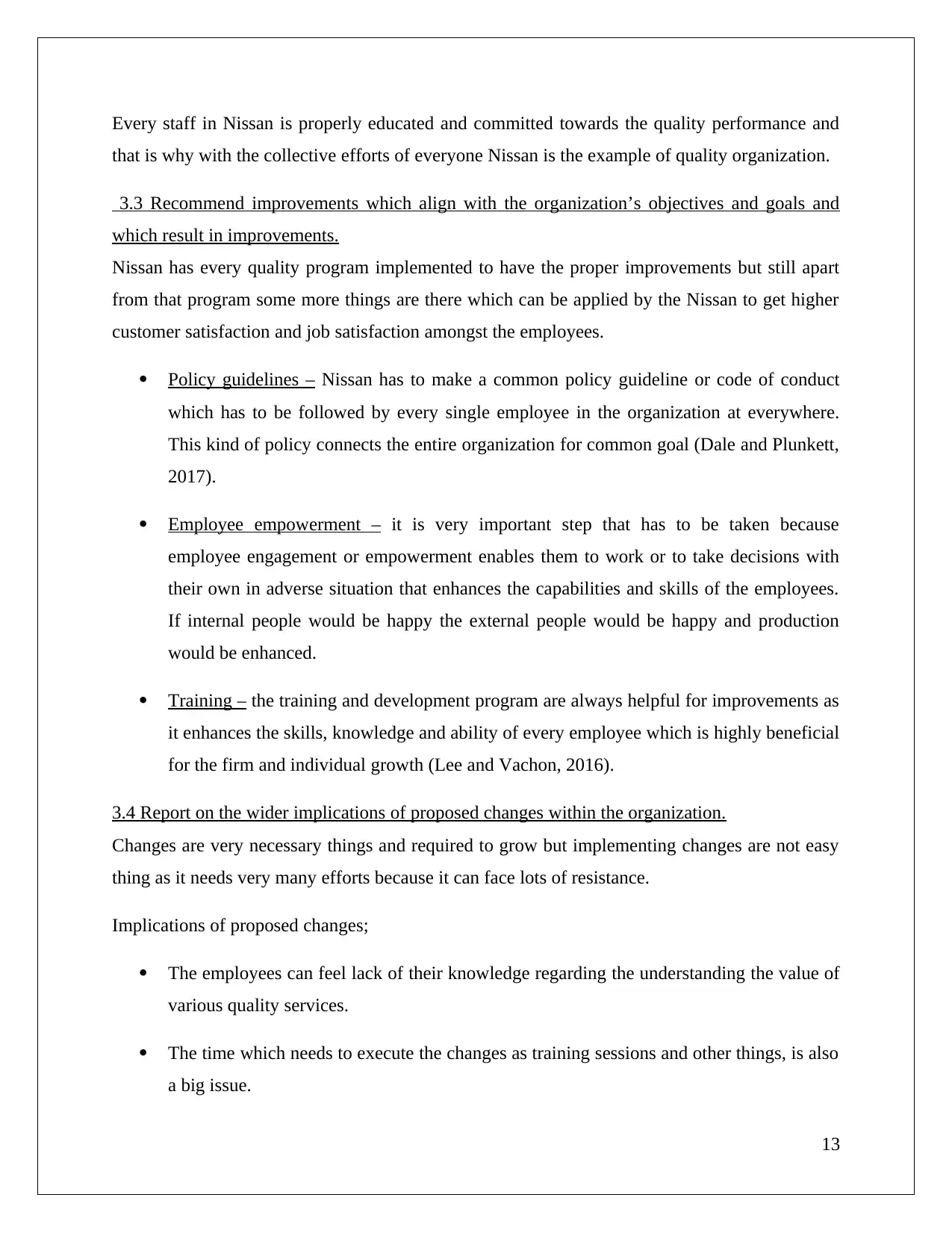
Every staff in Nissan is properly educated and committed towards the quality performance and
that is why with the collective efforts of everyone Nissan is the example of quality organization.
3.3 Recommend improvements which align with the organization’s objectives and goals and
which result in improvements.
Nissan has every quality program implemented to have the proper improvements but still apart
from that program some more things are there which can be applied by the Nissan to get higher
customer satisfaction and job satisfaction amongst the employees.
Policy guidelines – Nissan has to make a common policy guideline or code of conduct
which has to be followed by every single employee in the organization at everywhere.
This kind of policy connects the entire organization for common goal (Dale and Plunkett,
2017).
Employee empowerment – it is very important step that has to be taken because
employee engagement or empowerment enables them to work or to take decisions with
their own in adverse situation that enhances the capabilities and skills of the employees.
If internal people would be happy the external people would be happy and production
would be enhanced.
Training – the training and development program are always helpful for improvements as
it enhances the skills, knowledge and ability of every employee which is highly beneficial
for the firm and individual growth (Lee and Vachon, 2016).
3.4 Report on the wider implications of proposed changes within the organization.
Changes are very necessary things and required to grow but implementing changes are not easy
thing as it needs very many efforts because it can face lots of resistance.
Implications of proposed changes;
The employees can feel lack of their knowledge regarding the understanding the value of
various quality services.
The time which needs to execute the changes as training sessions and other things, is also
a big issue.
13
that is why with the collective efforts of everyone Nissan is the example of quality organization.
3.3 Recommend improvements which align with the organization’s objectives and goals and
which result in improvements.
Nissan has every quality program implemented to have the proper improvements but still apart
from that program some more things are there which can be applied by the Nissan to get higher
customer satisfaction and job satisfaction amongst the employees.
Policy guidelines – Nissan has to make a common policy guideline or code of conduct
which has to be followed by every single employee in the organization at everywhere.
This kind of policy connects the entire organization for common goal (Dale and Plunkett,
2017).
Employee empowerment – it is very important step that has to be taken because
employee engagement or empowerment enables them to work or to take decisions with
their own in adverse situation that enhances the capabilities and skills of the employees.
If internal people would be happy the external people would be happy and production
would be enhanced.
Training – the training and development program are always helpful for improvements as
it enhances the skills, knowledge and ability of every employee which is highly beneficial
for the firm and individual growth (Lee and Vachon, 2016).
3.4 Report on the wider implications of proposed changes within the organization.
Changes are very necessary things and required to grow but implementing changes are not easy
thing as it needs very many efforts because it can face lots of resistance.
Implications of proposed changes;
The employees can feel lack of their knowledge regarding the understanding the value of
various quality services.
The time which needs to execute the changes as training sessions and other things, is also
a big issue.
13
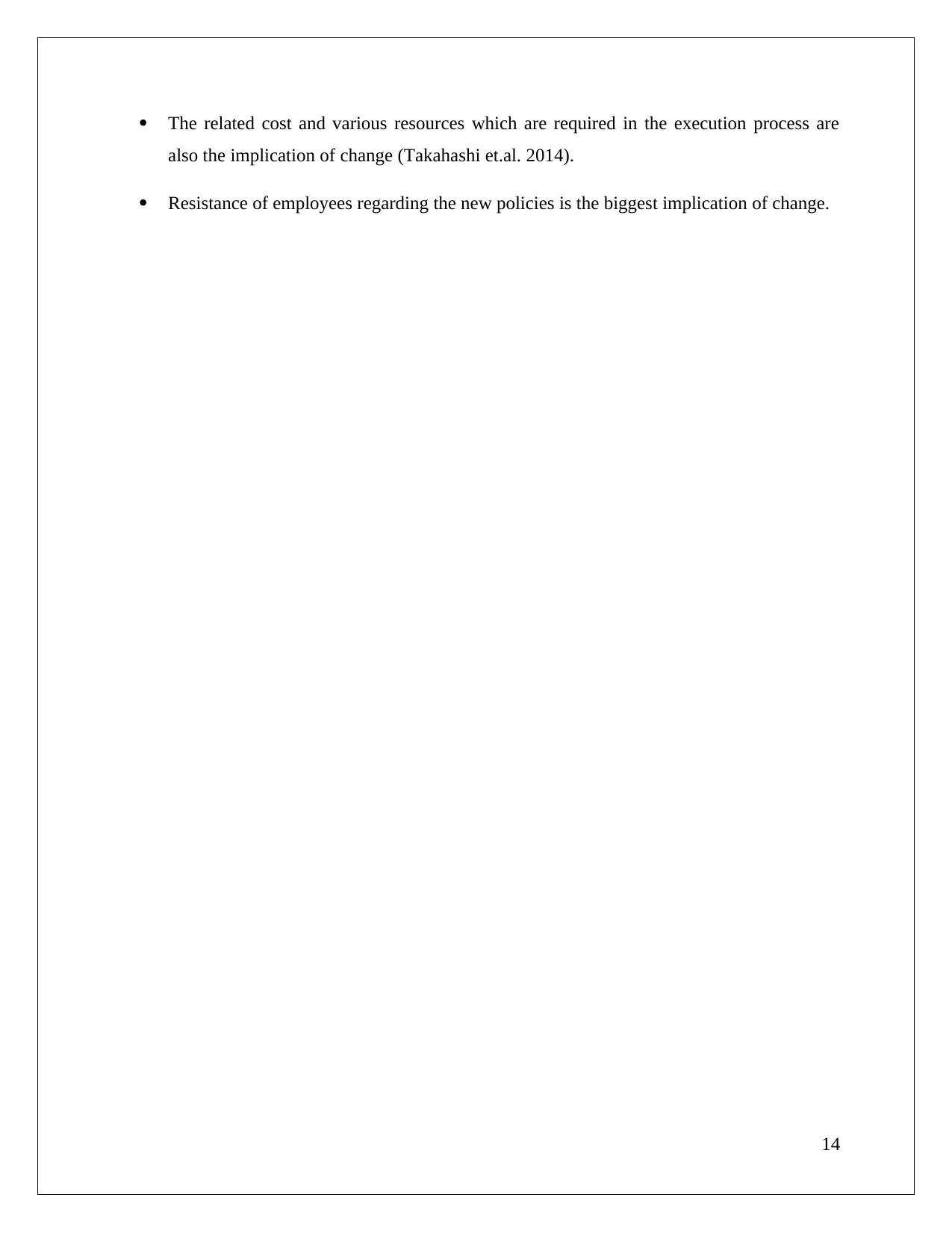
The related cost and various resources which are required in the execution process are
also the implication of change (Takahashi et.al. 2014).
Resistance of employees regarding the new policies is the biggest implication of change.
14
also the implication of change (Takahashi et.al. 2014).
Resistance of employees regarding the new policies is the biggest implication of change.
14
Paraphrase This Document
Need a fresh take? Get an instant paraphrase of this document with our AI Paraphraser
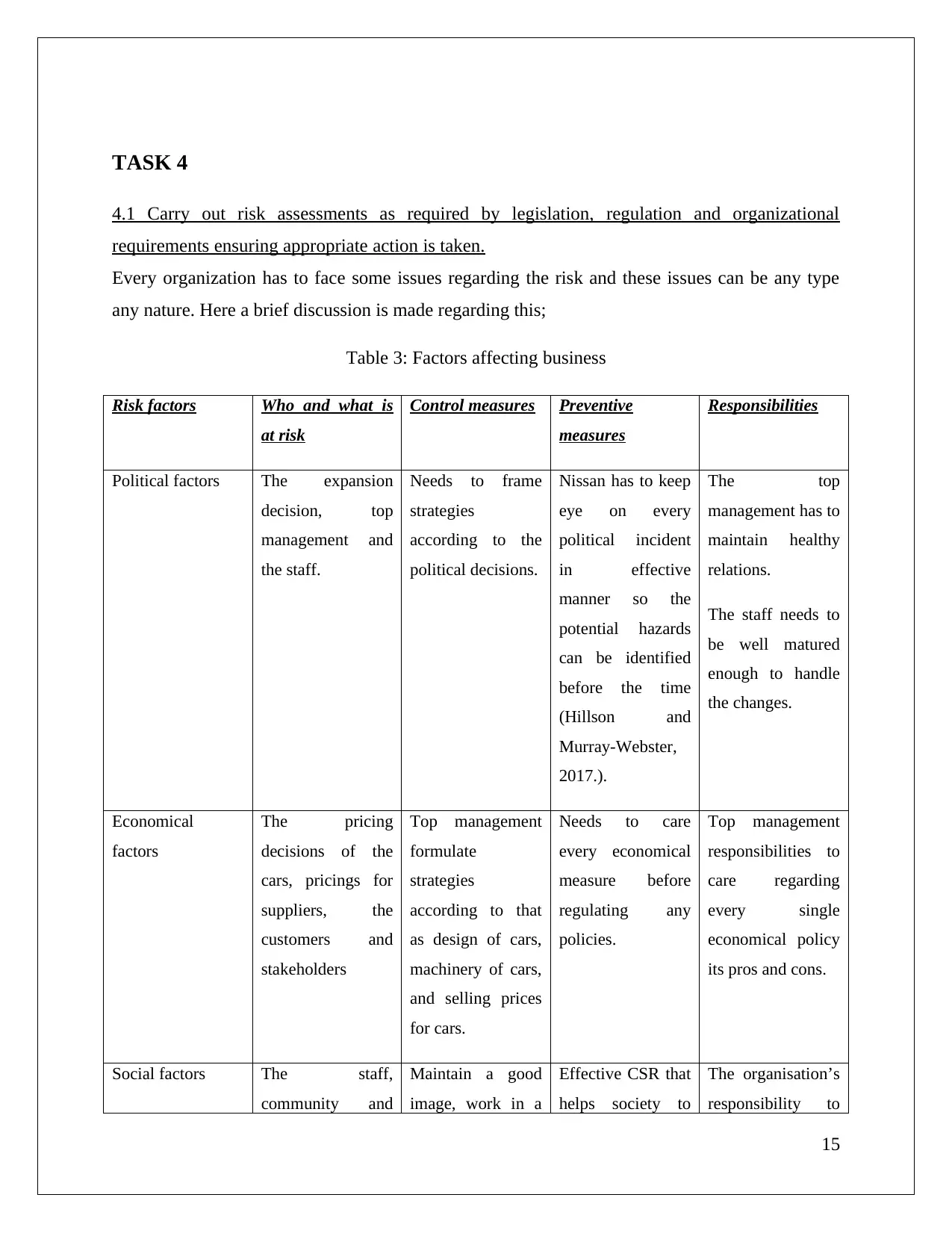
TASK 4
4.1 Carry out risk assessments as required by legislation, regulation and organizational
requirements ensuring appropriate action is taken.
Every organization has to face some issues regarding the risk and these issues can be any type
any nature. Here a brief discussion is made regarding this;
Table 3: Factors affecting business
Risk factors Who and what is
at risk
Control measures Preventive
measures
Responsibilities
Political factors The expansion
decision, top
management and
the staff.
Needs to frame
strategies
according to the
political decisions.
Nissan has to keep
eye on every
political incident
in effective
manner so the
potential hazards
can be identified
before the time
(Hillson and
Murray-Webster,
2017.).
The top
management has to
maintain healthy
relations.
The staff needs to
be well matured
enough to handle
the changes.
Economical
factors
The pricing
decisions of the
cars, pricings for
suppliers, the
customers and
stakeholders
Top management
formulate
strategies
according to that
as design of cars,
machinery of cars,
and selling prices
for cars.
Needs to care
every economical
measure before
regulating any
policies.
Top management
responsibilities to
care regarding
every single
economical policy
its pros and cons.
Social factors The staff,
community and
Maintain a good
image, work in a
Effective CSR that
helps society to
The organisation’s
responsibility to
15
4.1 Carry out risk assessments as required by legislation, regulation and organizational
requirements ensuring appropriate action is taken.
Every organization has to face some issues regarding the risk and these issues can be any type
any nature. Here a brief discussion is made regarding this;
Table 3: Factors affecting business
Risk factors Who and what is
at risk
Control measures Preventive
measures
Responsibilities
Political factors The expansion
decision, top
management and
the staff.
Needs to frame
strategies
according to the
political decisions.
Nissan has to keep
eye on every
political incident
in effective
manner so the
potential hazards
can be identified
before the time
(Hillson and
Murray-Webster,
2017.).
The top
management has to
maintain healthy
relations.
The staff needs to
be well matured
enough to handle
the changes.
Economical
factors
The pricing
decisions of the
cars, pricings for
suppliers, the
customers and
stakeholders
Top management
formulate
strategies
according to that
as design of cars,
machinery of cars,
and selling prices
for cars.
Needs to care
every economical
measure before
regulating any
policies.
Top management
responsibilities to
care regarding
every single
economical policy
its pros and cons.
Social factors The staff,
community and
Maintain a good
image, work in a
Effective CSR that
helps society to
The organisation’s
responsibility to
15
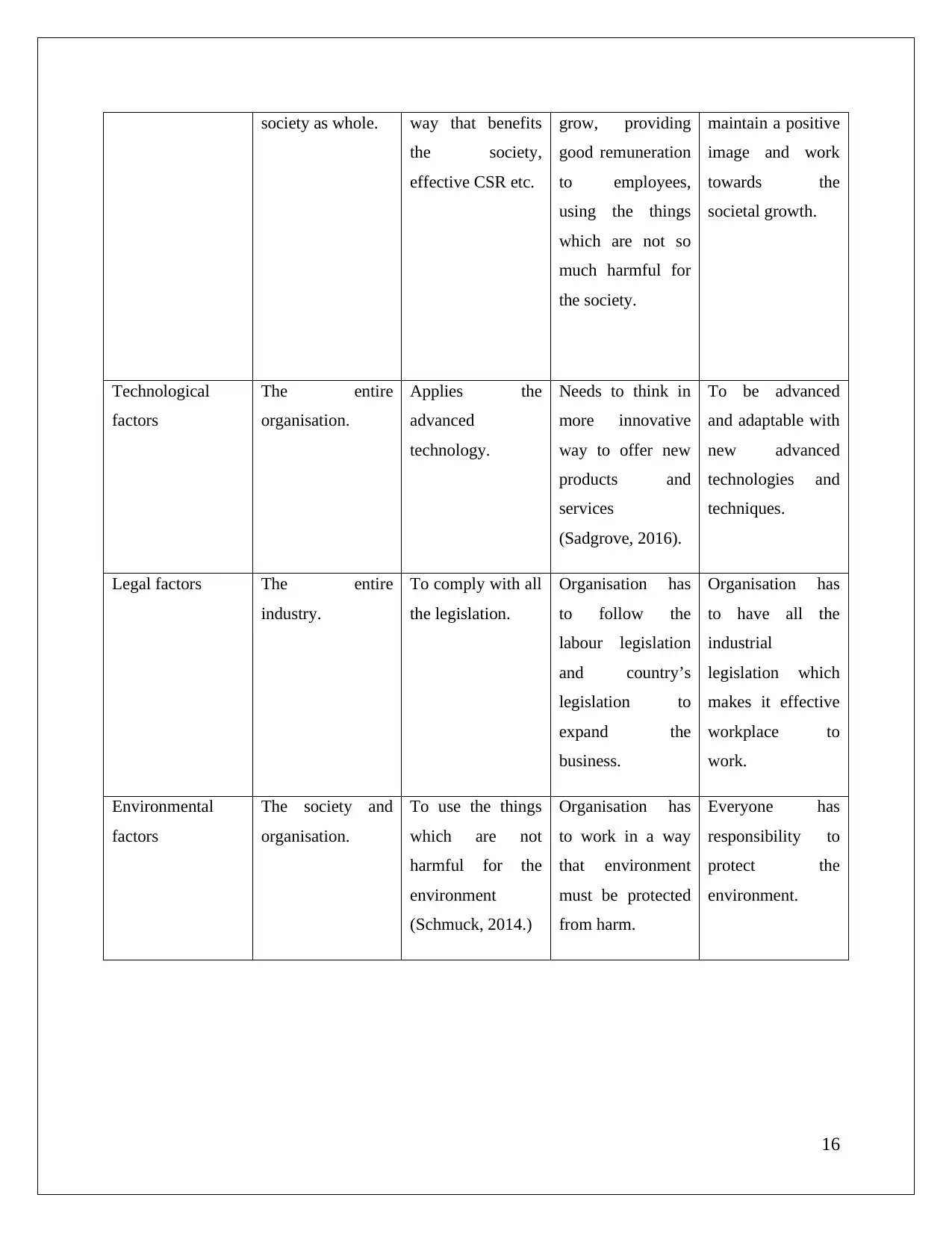
society as whole. way that benefits
the society,
effective CSR etc.
grow, providing
good remuneration
to employees,
using the things
which are not so
much harmful for
the society.
maintain a positive
image and work
towards the
societal growth.
Technological
factors
The entire
organisation.
Applies the
advanced
technology.
Needs to think in
more innovative
way to offer new
products and
services
(Sadgrove, 2016).
To be advanced
and adaptable with
new advanced
technologies and
techniques.
Legal factors The entire
industry.
To comply with all
the legislation.
Organisation has
to follow the
labour legislation
and country’s
legislation to
expand the
business.
Organisation has
to have all the
industrial
legislation which
makes it effective
workplace to
work.
Environmental
factors
The society and
organisation.
To use the things
which are not
harmful for the
environment
(Schmuck, 2014.)
Organisation has
to work in a way
that environment
must be protected
from harm.
Everyone has
responsibility to
protect the
environment.
16
the society,
effective CSR etc.
grow, providing
good remuneration
to employees,
using the things
which are not so
much harmful for
the society.
maintain a positive
image and work
towards the
societal growth.
Technological
factors
The entire
organisation.
Applies the
advanced
technology.
Needs to think in
more innovative
way to offer new
products and
services
(Sadgrove, 2016).
To be advanced
and adaptable with
new advanced
technologies and
techniques.
Legal factors The entire
industry.
To comply with all
the legislation.
Organisation has
to follow the
labour legislation
and country’s
legislation to
expand the
business.
Organisation has
to have all the
industrial
legislation which
makes it effective
workplace to
work.
Environmental
factors
The society and
organisation.
To use the things
which are not
harmful for the
environment
(Schmuck, 2014.)
Organisation has
to work in a way
that environment
must be protected
from harm.
Everyone has
responsibility to
protect the
environment.
16
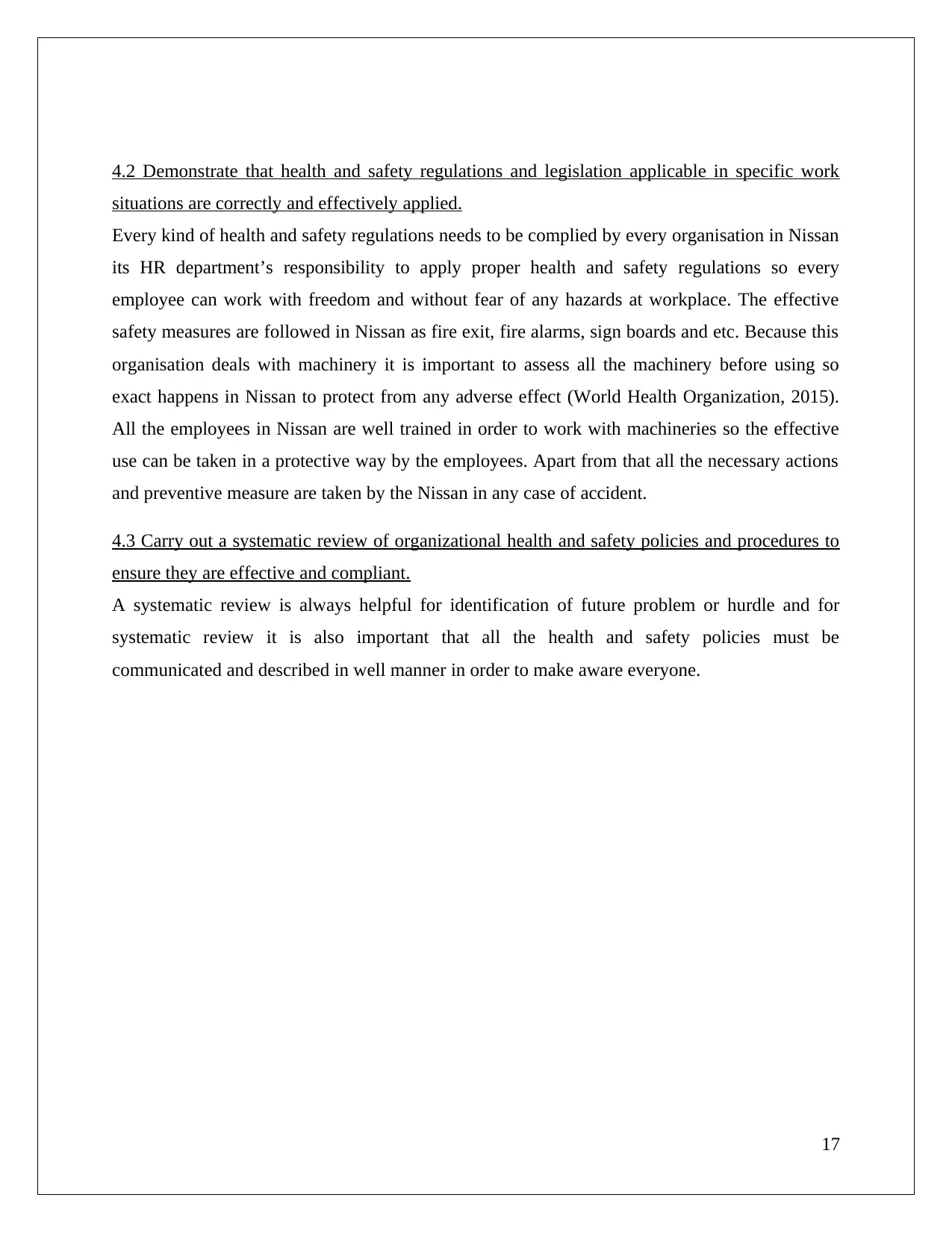
4.2 Demonstrate that health and safety regulations and legislation applicable in specific work
situations are correctly and effectively applied.
Every kind of health and safety regulations needs to be complied by every organisation in Nissan
its HR department’s responsibility to apply proper health and safety regulations so every
employee can work with freedom and without fear of any hazards at workplace. The effective
safety measures are followed in Nissan as fire exit, fire alarms, sign boards and etc. Because this
organisation deals with machinery it is important to assess all the machinery before using so
exact happens in Nissan to protect from any adverse effect (World Health Organization, 2015).
All the employees in Nissan are well trained in order to work with machineries so the effective
use can be taken in a protective way by the employees. Apart from that all the necessary actions
and preventive measure are taken by the Nissan in any case of accident.
4.3 Carry out a systematic review of organizational health and safety policies and procedures to
ensure they are effective and compliant.
A systematic review is always helpful for identification of future problem or hurdle and for
systematic review it is also important that all the health and safety policies must be
communicated and described in well manner in order to make aware everyone.
17
situations are correctly and effectively applied.
Every kind of health and safety regulations needs to be complied by every organisation in Nissan
its HR department’s responsibility to apply proper health and safety regulations so every
employee can work with freedom and without fear of any hazards at workplace. The effective
safety measures are followed in Nissan as fire exit, fire alarms, sign boards and etc. Because this
organisation deals with machinery it is important to assess all the machinery before using so
exact happens in Nissan to protect from any adverse effect (World Health Organization, 2015).
All the employees in Nissan are well trained in order to work with machineries so the effective
use can be taken in a protective way by the employees. Apart from that all the necessary actions
and preventive measure are taken by the Nissan in any case of accident.
4.3 Carry out a systematic review of organizational health and safety policies and procedures to
ensure they are effective and compliant.
A systematic review is always helpful for identification of future problem or hurdle and for
systematic review it is also important that all the health and safety policies must be
communicated and described in well manner in order to make aware everyone.
17
Secure Best Marks with AI Grader
Need help grading? Try our AI Grader for instant feedback on your assignments.
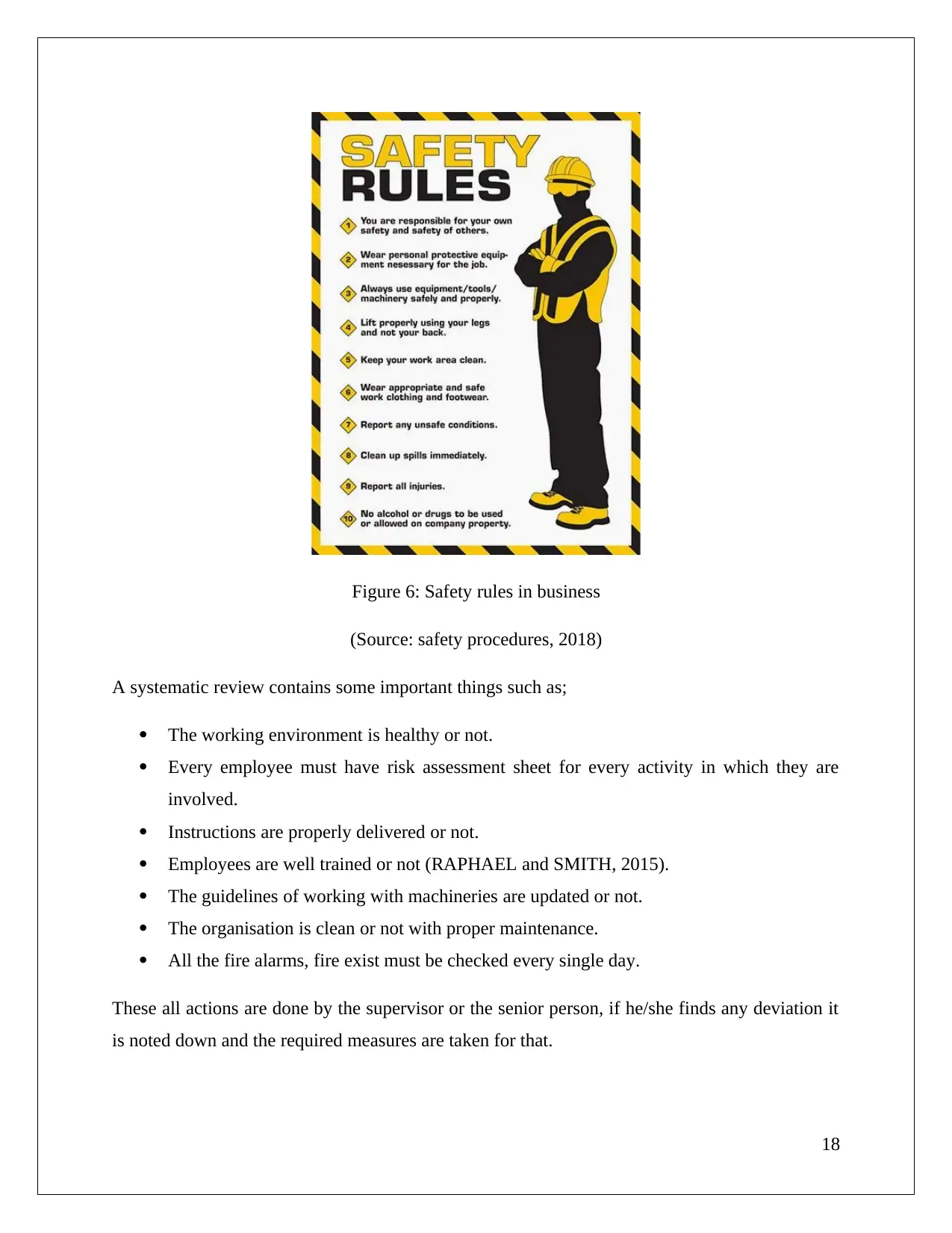
Figure 6: Safety rules in business
(Source: safety procedures, 2018)
A systematic review contains some important things such as;
The working environment is healthy or not.
Every employee must have risk assessment sheet for every activity in which they are
involved.
Instructions are properly delivered or not.
Employees are well trained or not (RAPHAEL and SMITH, 2015).
The guidelines of working with machineries are updated or not.
The organisation is clean or not with proper maintenance.
All the fire alarms, fire exist must be checked every single day.
These all actions are done by the supervisor or the senior person, if he/she finds any deviation it
is noted down and the required measures are taken for that.
18
(Source: safety procedures, 2018)
A systematic review contains some important things such as;
The working environment is healthy or not.
Every employee must have risk assessment sheet for every activity in which they are
involved.
Instructions are properly delivered or not.
Employees are well trained or not (RAPHAEL and SMITH, 2015).
The guidelines of working with machineries are updated or not.
The organisation is clean or not with proper maintenance.
All the fire alarms, fire exist must be checked every single day.
These all actions are done by the supervisor or the senior person, if he/she finds any deviation it
is noted down and the required measures are taken for that.
18
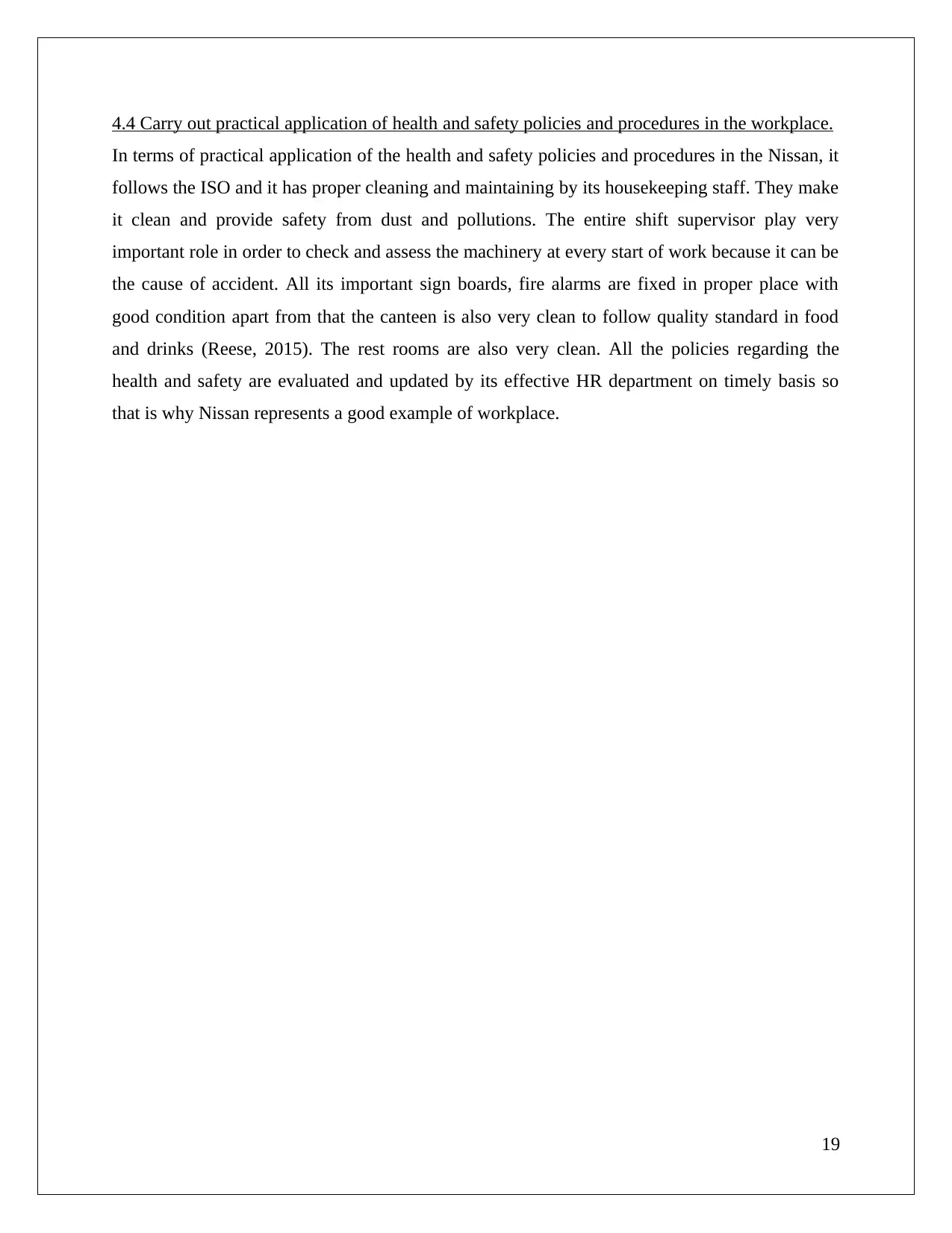
4.4 Carry out practical application of health and safety policies and procedures in the workplace.
In terms of practical application of the health and safety policies and procedures in the Nissan, it
follows the ISO and it has proper cleaning and maintaining by its housekeeping staff. They make
it clean and provide safety from dust and pollutions. The entire shift supervisor play very
important role in order to check and assess the machinery at every start of work because it can be
the cause of accident. All its important sign boards, fire alarms are fixed in proper place with
good condition apart from that the canteen is also very clean to follow quality standard in food
and drinks (Reese, 2015). The rest rooms are also very clean. All the policies regarding the
health and safety are evaluated and updated by its effective HR department on timely basis so
that is why Nissan represents a good example of workplace.
19
In terms of practical application of the health and safety policies and procedures in the Nissan, it
follows the ISO and it has proper cleaning and maintaining by its housekeeping staff. They make
it clean and provide safety from dust and pollutions. The entire shift supervisor play very
important role in order to check and assess the machinery at every start of work because it can be
the cause of accident. All its important sign boards, fire alarms are fixed in proper place with
good condition apart from that the canteen is also very clean to follow quality standard in food
and drinks (Reese, 2015). The rest rooms are also very clean. All the policies regarding the
health and safety are evaluated and updated by its effective HR department on timely basis so
that is why Nissan represents a good example of workplace.
19
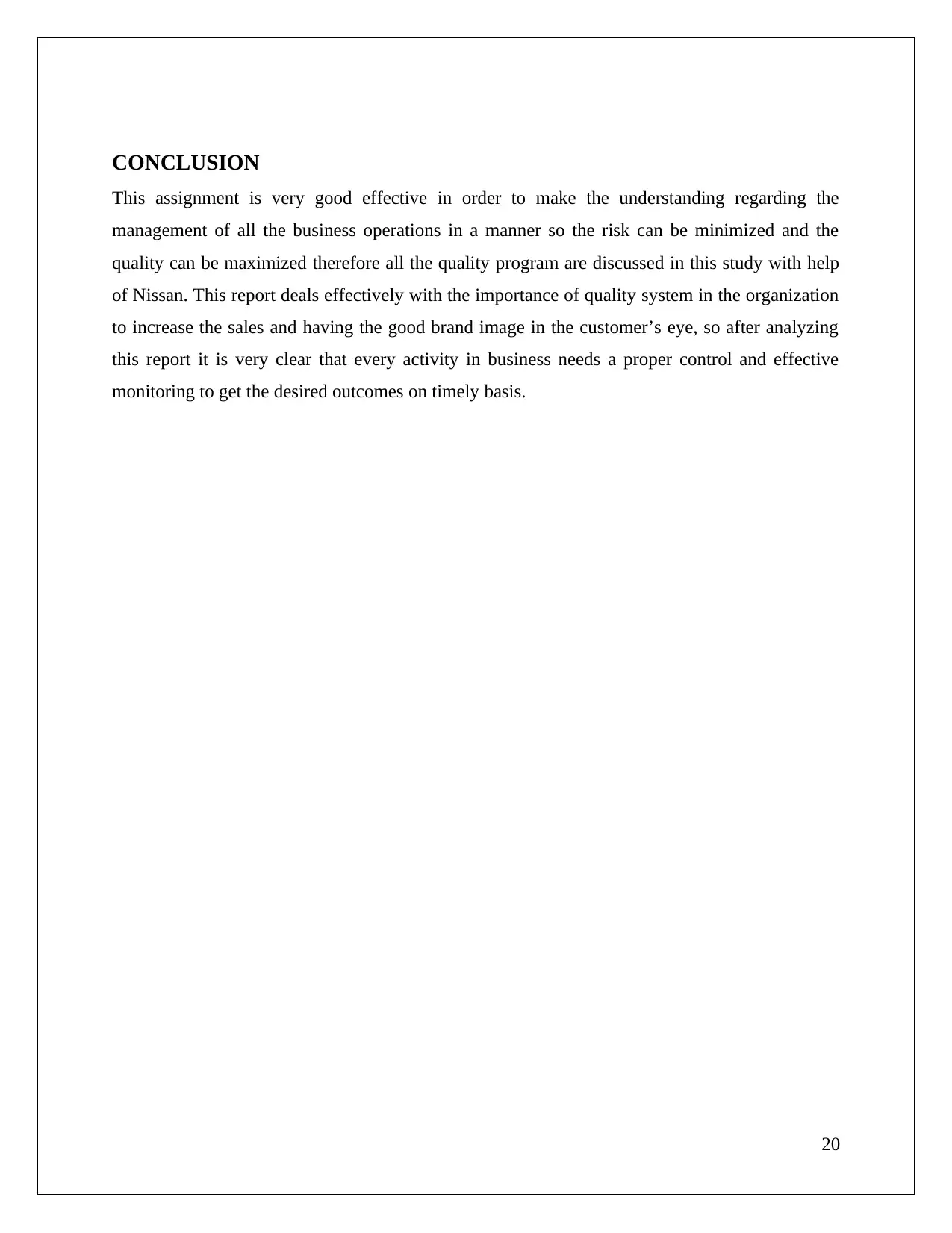
CONCLUSION
This assignment is very good effective in order to make the understanding regarding the
management of all the business operations in a manner so the risk can be minimized and the
quality can be maximized therefore all the quality program are discussed in this study with help
of Nissan. This report deals effectively with the importance of quality system in the organization
to increase the sales and having the good brand image in the customer’s eye, so after analyzing
this report it is very clear that every activity in business needs a proper control and effective
monitoring to get the desired outcomes on timely basis.
20
This assignment is very good effective in order to make the understanding regarding the
management of all the business operations in a manner so the risk can be minimized and the
quality can be maximized therefore all the quality program are discussed in this study with help
of Nissan. This report deals effectively with the importance of quality system in the organization
to increase the sales and having the good brand image in the customer’s eye, so after analyzing
this report it is very clear that every activity in business needs a proper control and effective
monitoring to get the desired outcomes on timely basis.
20
Paraphrase This Document
Need a fresh take? Get an instant paraphrase of this document with our AI Paraphraser
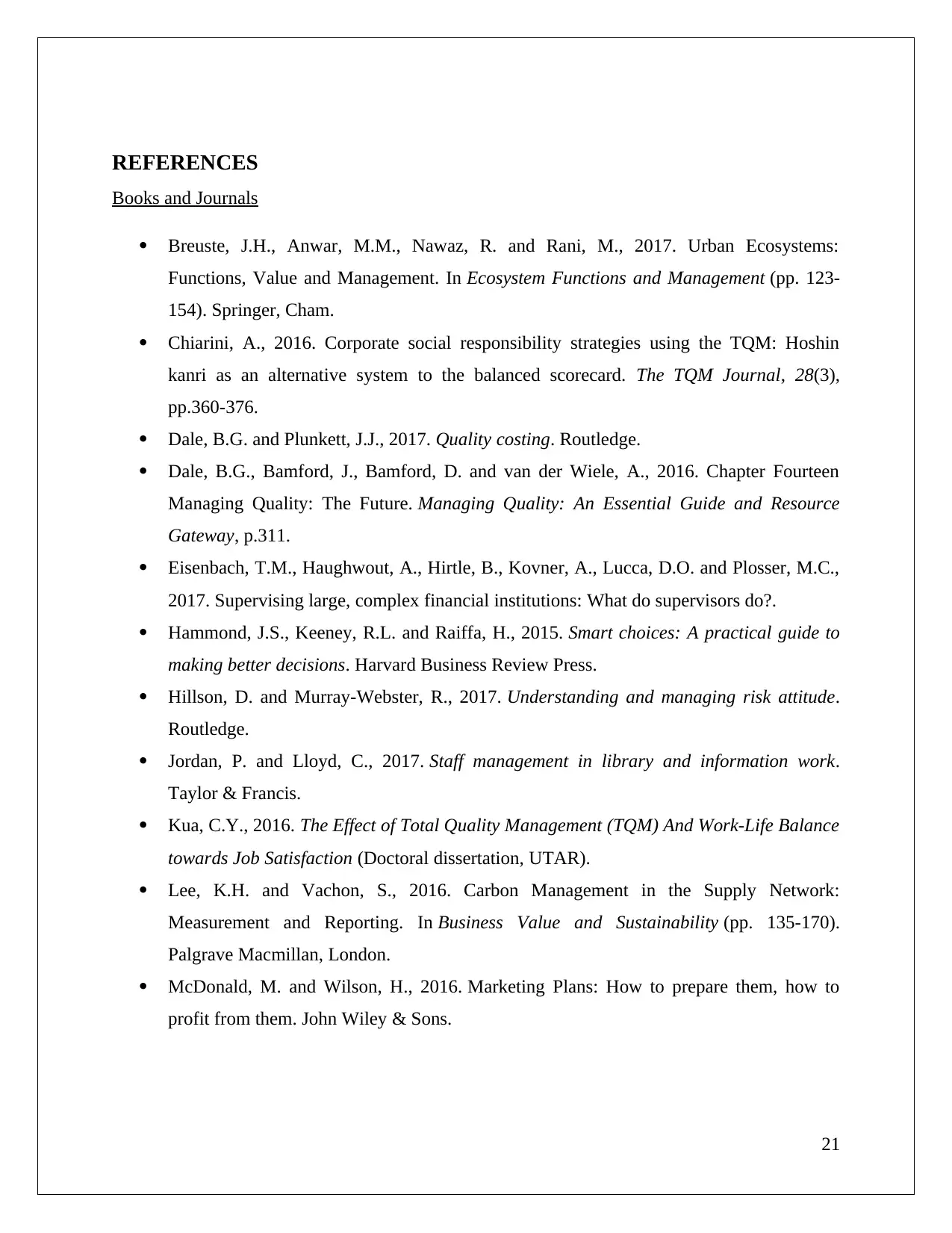
REFERENCES
Books and Journals
Breuste, J.H., Anwar, M.M., Nawaz, R. and Rani, M., 2017. Urban Ecosystems:
Functions, Value and Management. In Ecosystem Functions and Management (pp. 123-
154). Springer, Cham.
Chiarini, A., 2016. Corporate social responsibility strategies using the TQM: Hoshin
kanri as an alternative system to the balanced scorecard. The TQM Journal, 28(3),
pp.360-376.
Dale, B.G. and Plunkett, J.J., 2017. Quality costing. Routledge.
Dale, B.G., Bamford, J., Bamford, D. and van der Wiele, A., 2016. Chapter Fourteen
Managing Quality: The Future. Managing Quality: An Essential Guide and Resource
Gateway, p.311.
Eisenbach, T.M., Haughwout, A., Hirtle, B., Kovner, A., Lucca, D.O. and Plosser, M.C.,
2017. Supervising large, complex financial institutions: What do supervisors do?.
Hammond, J.S., Keeney, R.L. and Raiffa, H., 2015. Smart choices: A practical guide to
making better decisions. Harvard Business Review Press.
Hillson, D. and Murray-Webster, R., 2017. Understanding and managing risk attitude.
Routledge.
Jordan, P. and Lloyd, C., 2017. Staff management in library and information work.
Taylor & Francis.
Kua, C.Y., 2016. The Effect of Total Quality Management (TQM) And Work-Life Balance
towards Job Satisfaction (Doctoral dissertation, UTAR).
Lee, K.H. and Vachon, S., 2016. Carbon Management in the Supply Network:
Measurement and Reporting. In Business Value and Sustainability (pp. 135-170).
Palgrave Macmillan, London.
McDonald, M. and Wilson, H., 2016. Marketing Plans: How to prepare them, how to
profit from them. John Wiley & Sons.
21
Books and Journals
Breuste, J.H., Anwar, M.M., Nawaz, R. and Rani, M., 2017. Urban Ecosystems:
Functions, Value and Management. In Ecosystem Functions and Management (pp. 123-
154). Springer, Cham.
Chiarini, A., 2016. Corporate social responsibility strategies using the TQM: Hoshin
kanri as an alternative system to the balanced scorecard. The TQM Journal, 28(3),
pp.360-376.
Dale, B.G. and Plunkett, J.J., 2017. Quality costing. Routledge.
Dale, B.G., Bamford, J., Bamford, D. and van der Wiele, A., 2016. Chapter Fourteen
Managing Quality: The Future. Managing Quality: An Essential Guide and Resource
Gateway, p.311.
Eisenbach, T.M., Haughwout, A., Hirtle, B., Kovner, A., Lucca, D.O. and Plosser, M.C.,
2017. Supervising large, complex financial institutions: What do supervisors do?.
Hammond, J.S., Keeney, R.L. and Raiffa, H., 2015. Smart choices: A practical guide to
making better decisions. Harvard Business Review Press.
Hillson, D. and Murray-Webster, R., 2017. Understanding and managing risk attitude.
Routledge.
Jordan, P. and Lloyd, C., 2017. Staff management in library and information work.
Taylor & Francis.
Kua, C.Y., 2016. The Effect of Total Quality Management (TQM) And Work-Life Balance
towards Job Satisfaction (Doctoral dissertation, UTAR).
Lee, K.H. and Vachon, S., 2016. Carbon Management in the Supply Network:
Measurement and Reporting. In Business Value and Sustainability (pp. 135-170).
Palgrave Macmillan, London.
McDonald, M. and Wilson, H., 2016. Marketing Plans: How to prepare them, how to
profit from them. John Wiley & Sons.
21
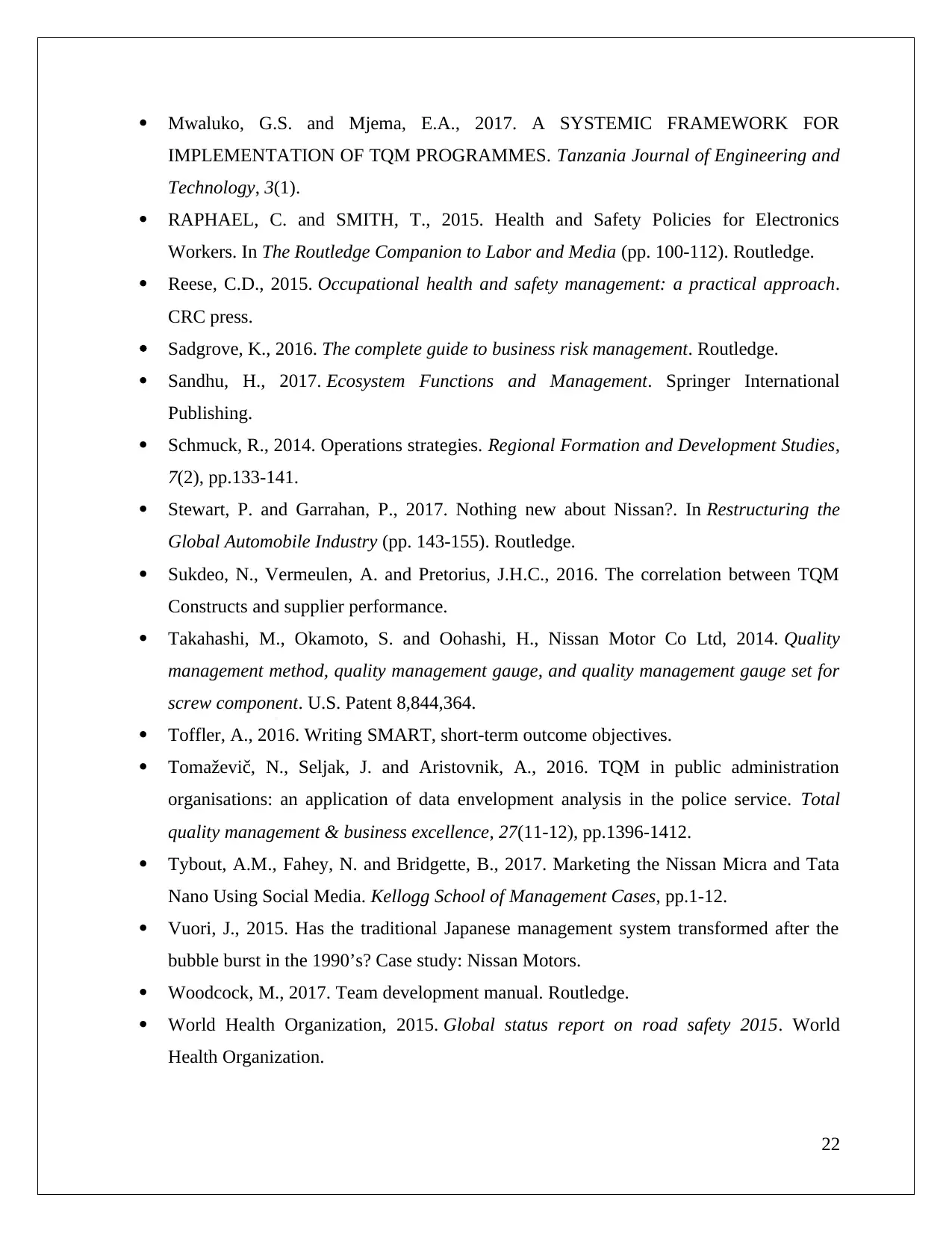
Mwaluko, G.S. and Mjema, E.A., 2017. A SYSTEMIC FRAMEWORK FOR
IMPLEMENTATION OF TQM PROGRAMMES. Tanzania Journal of Engineering and
Technology, 3(1).
RAPHAEL, C. and SMITH, T., 2015. Health and Safety Policies for Electronics
Workers. In The Routledge Companion to Labor and Media (pp. 100-112). Routledge.
Reese, C.D., 2015. Occupational health and safety management: a practical approach.
CRC press.
Sadgrove, K., 2016. The complete guide to business risk management. Routledge.
Sandhu, H., 2017. Ecosystem Functions and Management. Springer International
Publishing.
Schmuck, R., 2014. Operations strategies. Regional Formation and Development Studies,
7(2), pp.133-141.
Stewart, P. and Garrahan, P., 2017. Nothing new about Nissan?. In Restructuring the
Global Automobile Industry (pp. 143-155). Routledge.
Sukdeo, N., Vermeulen, A. and Pretorius, J.H.C., 2016. The correlation between TQM
Constructs and supplier performance.
Takahashi, M., Okamoto, S. and Oohashi, H., Nissan Motor Co Ltd, 2014. Quality
management method, quality management gauge, and quality management gauge set for
screw component. U.S. Patent 8,844,364.
Toffler, A., 2016. Writing SMART, short-term outcome objectives.
Tomaževič, N., Seljak, J. and Aristovnik, A., 2016. TQM in public administration
organisations: an application of data envelopment analysis in the police service. Total
quality management & business excellence, 27(11-12), pp.1396-1412.
Tybout, A.M., Fahey, N. and Bridgette, B., 2017. Marketing the Nissan Micra and Tata
Nano Using Social Media. Kellogg School of Management Cases, pp.1-12.
Vuori, J., 2015. Has the traditional Japanese management system transformed after the
bubble burst in the 1990’s? Case study: Nissan Motors.
Woodcock, M., 2017. Team development manual. Routledge.
World Health Organization, 2015. Global status report on road safety 2015. World
Health Organization.
22
IMPLEMENTATION OF TQM PROGRAMMES. Tanzania Journal of Engineering and
Technology, 3(1).
RAPHAEL, C. and SMITH, T., 2015. Health and Safety Policies for Electronics
Workers. In The Routledge Companion to Labor and Media (pp. 100-112). Routledge.
Reese, C.D., 2015. Occupational health and safety management: a practical approach.
CRC press.
Sadgrove, K., 2016. The complete guide to business risk management. Routledge.
Sandhu, H., 2017. Ecosystem Functions and Management. Springer International
Publishing.
Schmuck, R., 2014. Operations strategies. Regional Formation and Development Studies,
7(2), pp.133-141.
Stewart, P. and Garrahan, P., 2017. Nothing new about Nissan?. In Restructuring the
Global Automobile Industry (pp. 143-155). Routledge.
Sukdeo, N., Vermeulen, A. and Pretorius, J.H.C., 2016. The correlation between TQM
Constructs and supplier performance.
Takahashi, M., Okamoto, S. and Oohashi, H., Nissan Motor Co Ltd, 2014. Quality
management method, quality management gauge, and quality management gauge set for
screw component. U.S. Patent 8,844,364.
Toffler, A., 2016. Writing SMART, short-term outcome objectives.
Tomaževič, N., Seljak, J. and Aristovnik, A., 2016. TQM in public administration
organisations: an application of data envelopment analysis in the police service. Total
quality management & business excellence, 27(11-12), pp.1396-1412.
Tybout, A.M., Fahey, N. and Bridgette, B., 2017. Marketing the Nissan Micra and Tata
Nano Using Social Media. Kellogg School of Management Cases, pp.1-12.
Vuori, J., 2015. Has the traditional Japanese management system transformed after the
bubble burst in the 1990’s? Case study: Nissan Motors.
Woodcock, M., 2017. Team development manual. Routledge.
World Health Organization, 2015. Global status report on road safety 2015. World
Health Organization.
22
1 out of 27
Related Documents

Your All-in-One AI-Powered Toolkit for Academic Success.
+13062052269
info@desklib.com
Available 24*7 on WhatsApp / Email
Unlock your academic potential
© 2024 | Zucol Services PVT LTD | All rights reserved.