Manufacturing Systems Report: KPIs, PFA, VSM and Plant Layouts
VerifiedAdded on 2023/04/21
|23
|5885
|375
Report
AI Summary
This report provides a comprehensive overview of manufacturing systems, beginning with a review of key performance indicators (KPIs) and their role in assessing business success. It then explores approaches for establishing performance measures at the shop floor level, focusing on product and batch production, and explains how these measures align with corporate objectives. The report delves into Product Flow Analysis (PFA) and Value Stream Mapping (VSM), illustrating their implementation with examples. It describes different plant layouts, highlighting their benefits in relation to production varieties, volume, and economies of scale. Furthermore, the report critically reviews and compares various tools and techniques used for process improvement within lean manufacturing systems. Finally, the report includes a case study on the performance assessment of a manufacturing plant, providing practical insights and analysis.
Contribute Materials
Your contribution can guide someone’s learning journey. Share your
documents today.

Running head: MANUFACTURING SYSTEMS
Manufacturing Systems
Name of the Student
Name of the University
Author’s note
Manufacturing Systems
Name of the Student
Name of the University
Author’s note
Secure Best Marks with AI Grader
Need help grading? Try our AI Grader for instant feedback on your assignments.

1MANUFACTURING SYSTEMS
Table of Contents
Part A...............................................................................................................................................2
i) Review of Manufacturing Systems and Key Performance Indicators (KPIs)..........................2
ii) Approach for Establishing Performance Measures at Shop Floor Level Production.............3
iii) Product Flow Analysis (PFA) and Value Stream Mapping (VSM).......................................5
iv) Description of Plant Layouts..................................................................................................7
v) Critical Review and Comparison of Various Tools and Techniques......................................8
vi) Definitions of Terms..............................................................................................................9
Part B.............................................................................................................................................10
Case Study: Performance Assessment of Manufacturing Plant................................................10
Part C.............................................................................................................................................14
Question 3..................................................................................................................................14
Question 7..................................................................................................................................15
References......................................................................................................................................17
Table of Contents
Part A...............................................................................................................................................2
i) Review of Manufacturing Systems and Key Performance Indicators (KPIs)..........................2
ii) Approach for Establishing Performance Measures at Shop Floor Level Production.............3
iii) Product Flow Analysis (PFA) and Value Stream Mapping (VSM).......................................5
iv) Description of Plant Layouts..................................................................................................7
v) Critical Review and Comparison of Various Tools and Techniques......................................8
vi) Definitions of Terms..............................................................................................................9
Part B.............................................................................................................................................10
Case Study: Performance Assessment of Manufacturing Plant................................................10
Part C.............................................................................................................................................14
Question 3..................................................................................................................................14
Question 7..................................................................................................................................15
References......................................................................................................................................17
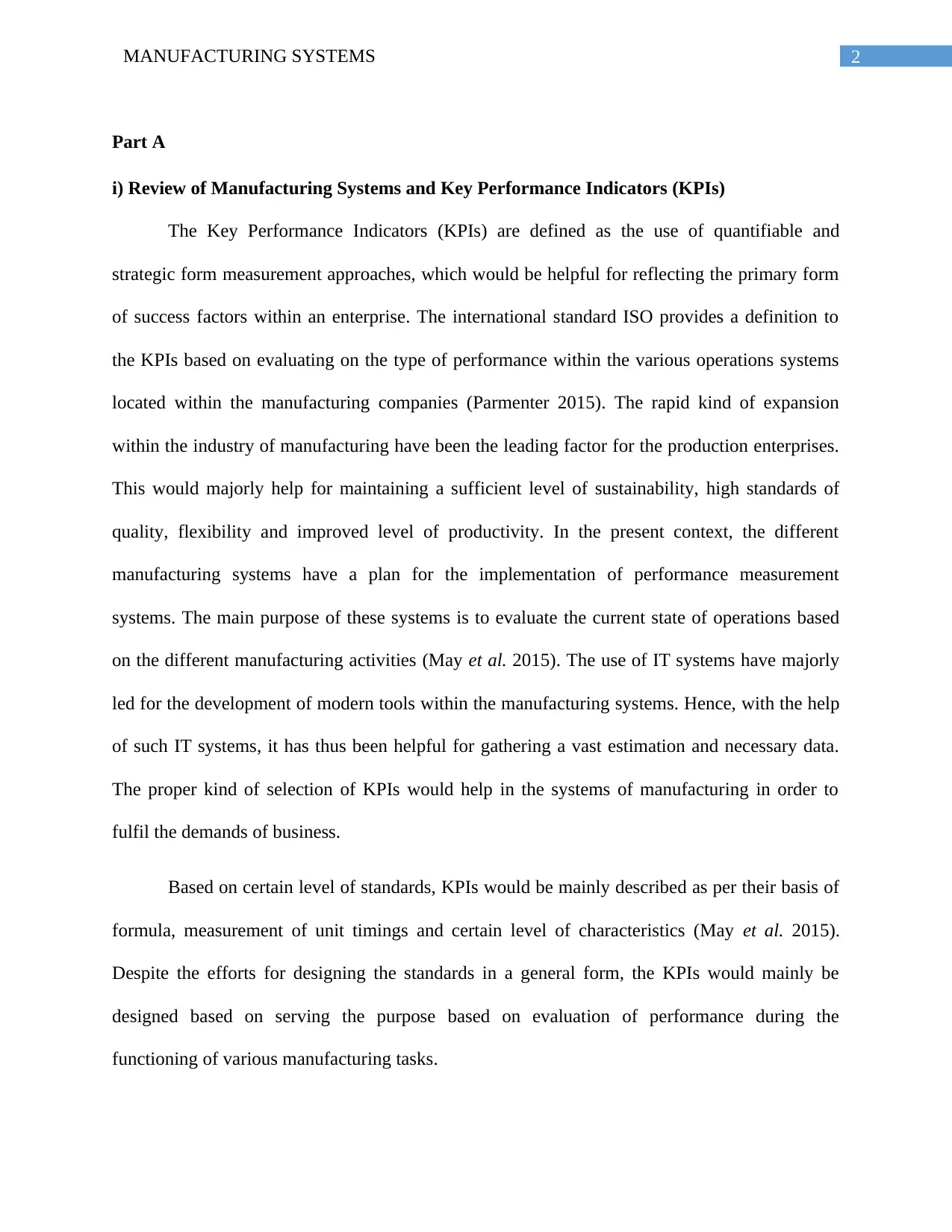
2MANUFACTURING SYSTEMS
Part A
i) Review of Manufacturing Systems and Key Performance Indicators (KPIs)
The Key Performance Indicators (KPIs) are defined as the use of quantifiable and
strategic form measurement approaches, which would be helpful for reflecting the primary form
of success factors within an enterprise. The international standard ISO provides a definition to
the KPIs based on evaluating on the type of performance within the various operations systems
located within the manufacturing companies (Parmenter 2015). The rapid kind of expansion
within the industry of manufacturing have been the leading factor for the production enterprises.
This would majorly help for maintaining a sufficient level of sustainability, high standards of
quality, flexibility and improved level of productivity. In the present context, the different
manufacturing systems have a plan for the implementation of performance measurement
systems. The main purpose of these systems is to evaluate the current state of operations based
on the different manufacturing activities (May et al. 2015). The use of IT systems have majorly
led for the development of modern tools within the manufacturing systems. Hence, with the help
of such IT systems, it has thus been helpful for gathering a vast estimation and necessary data.
The proper kind of selection of KPIs would help in the systems of manufacturing in order to
fulfil the demands of business.
Based on certain level of standards, KPIs would be mainly described as per their basis of
formula, measurement of unit timings and certain level of characteristics (May et al. 2015).
Despite the efforts for designing the standards in a general form, the KPIs would mainly be
designed based on serving the purpose based on evaluation of performance during the
functioning of various manufacturing tasks.
Part A
i) Review of Manufacturing Systems and Key Performance Indicators (KPIs)
The Key Performance Indicators (KPIs) are defined as the use of quantifiable and
strategic form measurement approaches, which would be helpful for reflecting the primary form
of success factors within an enterprise. The international standard ISO provides a definition to
the KPIs based on evaluating on the type of performance within the various operations systems
located within the manufacturing companies (Parmenter 2015). The rapid kind of expansion
within the industry of manufacturing have been the leading factor for the production enterprises.
This would majorly help for maintaining a sufficient level of sustainability, high standards of
quality, flexibility and improved level of productivity. In the present context, the different
manufacturing systems have a plan for the implementation of performance measurement
systems. The main purpose of these systems is to evaluate the current state of operations based
on the different manufacturing activities (May et al. 2015). The use of IT systems have majorly
led for the development of modern tools within the manufacturing systems. Hence, with the help
of such IT systems, it has thus been helpful for gathering a vast estimation and necessary data.
The proper kind of selection of KPIs would help in the systems of manufacturing in order to
fulfil the demands of business.
Based on certain level of standards, KPIs would be mainly described as per their basis of
formula, measurement of unit timings and certain level of characteristics (May et al. 2015).
Despite the efforts for designing the standards in a general form, the KPIs would mainly be
designed based on serving the purpose based on evaluation of performance during the
functioning of various manufacturing tasks.

3MANUFACTURING SYSTEMS
In the present years, there have been major kinds of developments within the
manufacturing systems. There are several kinds of major trends within the manufacturing
systems. Different large executives within the manufacturing industry have to play major roles in
leading the organisation towards much higher concentration and consolidation (Bai and Sarkis
2014). There are various kinds of competitive pressures within the manufacturing industry. The
most common form of development is based on significant restructuring (May et al. 2015). The
various kinds of recommendations based on certain competitive issues would emerge in recent
forms of developments. The creation of a competitive advantage would be helpful for
determining several factors in keeping a competitive advantage within the manufacturing
marketplace. This would help the organisation to realise their potential faults and would thus be
able to take certain proactive measures in order to gain a better position in the global marketplace
(Anand and Grover 2015). Based on the massive kinds of developments, there have been a
massive change within the systems of manufacturing. There are different kinds of new forms of
invention in the field of technology, which have been able to address issues within
competitiveness.
ii) Approach for Establishing Performance Measures at Shop Floor Level Production
Performance measurement is defined as one of the most necessary criteria within a
manufacturing organisation. This technique could thus be applied within the organisation based
on measuring the level of performance made by the organisation. There are several kinds of
indirect methods of measures based within the context of performance. This would also the
measures based on performance, which would include operation costing (Hill 2017). It would
also include the identification of several kinds of problems. There are several kinds of methods
and planning techniques based on scheduling that have been majorly developed for their use in
In the present years, there have been major kinds of developments within the
manufacturing systems. There are several kinds of major trends within the manufacturing
systems. Different large executives within the manufacturing industry have to play major roles in
leading the organisation towards much higher concentration and consolidation (Bai and Sarkis
2014). There are various kinds of competitive pressures within the manufacturing industry. The
most common form of development is based on significant restructuring (May et al. 2015). The
various kinds of recommendations based on certain competitive issues would emerge in recent
forms of developments. The creation of a competitive advantage would be helpful for
determining several factors in keeping a competitive advantage within the manufacturing
marketplace. This would help the organisation to realise their potential faults and would thus be
able to take certain proactive measures in order to gain a better position in the global marketplace
(Anand and Grover 2015). Based on the massive kinds of developments, there have been a
massive change within the systems of manufacturing. There are different kinds of new forms of
invention in the field of technology, which have been able to address issues within
competitiveness.
ii) Approach for Establishing Performance Measures at Shop Floor Level Production
Performance measurement is defined as one of the most necessary criteria within a
manufacturing organisation. This technique could thus be applied within the organisation based
on measuring the level of performance made by the organisation. There are several kinds of
indirect methods of measures based within the context of performance. This would also the
measures based on performance, which would include operation costing (Hill 2017). It would
also include the identification of several kinds of problems. There are several kinds of methods
and planning techniques based on scheduling that have been majorly developed for their use in
Secure Best Marks with AI Grader
Need help grading? Try our AI Grader for instant feedback on your assignments.

4MANUFACTURING SYSTEMS
manufacturing industries. Different kinds of approaches based on modelling would be required
within the manufacturing systems. In the present scenario, the approach that is been used by the
plant management would mostly be able to prioritize the quality of products.
One kind of approach at the shop floor level is the Simple Heuristic approach. This
approach helps in defining the optimal product sequencing based on their due data in a single
machine based on manufacturing (Negahban and Smith 2014). Within this approach, the models
based on linear programming were primarily been developed. This form of approach is mostly
applied based on the major purpose of solving of problems. This form of approach could also be
applicable based on large-scale constraint satisfaction and scheduling problems. This form of
measure have been based on a simple heuristic approach. This approach could be implemented
within several manufacturing companies. This would thus be helpful for different operations of
scheduling based on the exploitation of critical path within a certain network.
Another kind of approach used within the manufacturing systems is also known as linear
programming model (Negahban and Smith 2014). This model would be dependent on
synchronized production planning and scheduling of multi-product batch systems of
manufacturing. There are various scheduling problems that would be able to include the
operational pre-conditions (Fullerton, Kennedy and Widener 2014). It would be important for the
avoidance of comprising for the final delivery product. The different kinds of research within the
activity scheduling based on manufacturing system is also able to include the certain models of
development (Negahban and Smith 2014). The primary objectives of study is based on
scheduling of production within the systems of manufacturing. The study also puts focus on
inventory, planning of horizon costs and production.
manufacturing industries. Different kinds of approaches based on modelling would be required
within the manufacturing systems. In the present scenario, the approach that is been used by the
plant management would mostly be able to prioritize the quality of products.
One kind of approach at the shop floor level is the Simple Heuristic approach. This
approach helps in defining the optimal product sequencing based on their due data in a single
machine based on manufacturing (Negahban and Smith 2014). Within this approach, the models
based on linear programming were primarily been developed. This form of approach is mostly
applied based on the major purpose of solving of problems. This form of approach could also be
applicable based on large-scale constraint satisfaction and scheduling problems. This form of
measure have been based on a simple heuristic approach. This approach could be implemented
within several manufacturing companies. This would thus be helpful for different operations of
scheduling based on the exploitation of critical path within a certain network.
Another kind of approach used within the manufacturing systems is also known as linear
programming model (Negahban and Smith 2014). This model would be dependent on
synchronized production planning and scheduling of multi-product batch systems of
manufacturing. There are various scheduling problems that would be able to include the
operational pre-conditions (Fullerton, Kennedy and Widener 2014). It would be important for the
avoidance of comprising for the final delivery product. The different kinds of research within the
activity scheduling based on manufacturing system is also able to include the certain models of
development (Negahban and Smith 2014). The primary objectives of study is based on
scheduling of production within the systems of manufacturing. The study also puts focus on
inventory, planning of horizon costs and production.
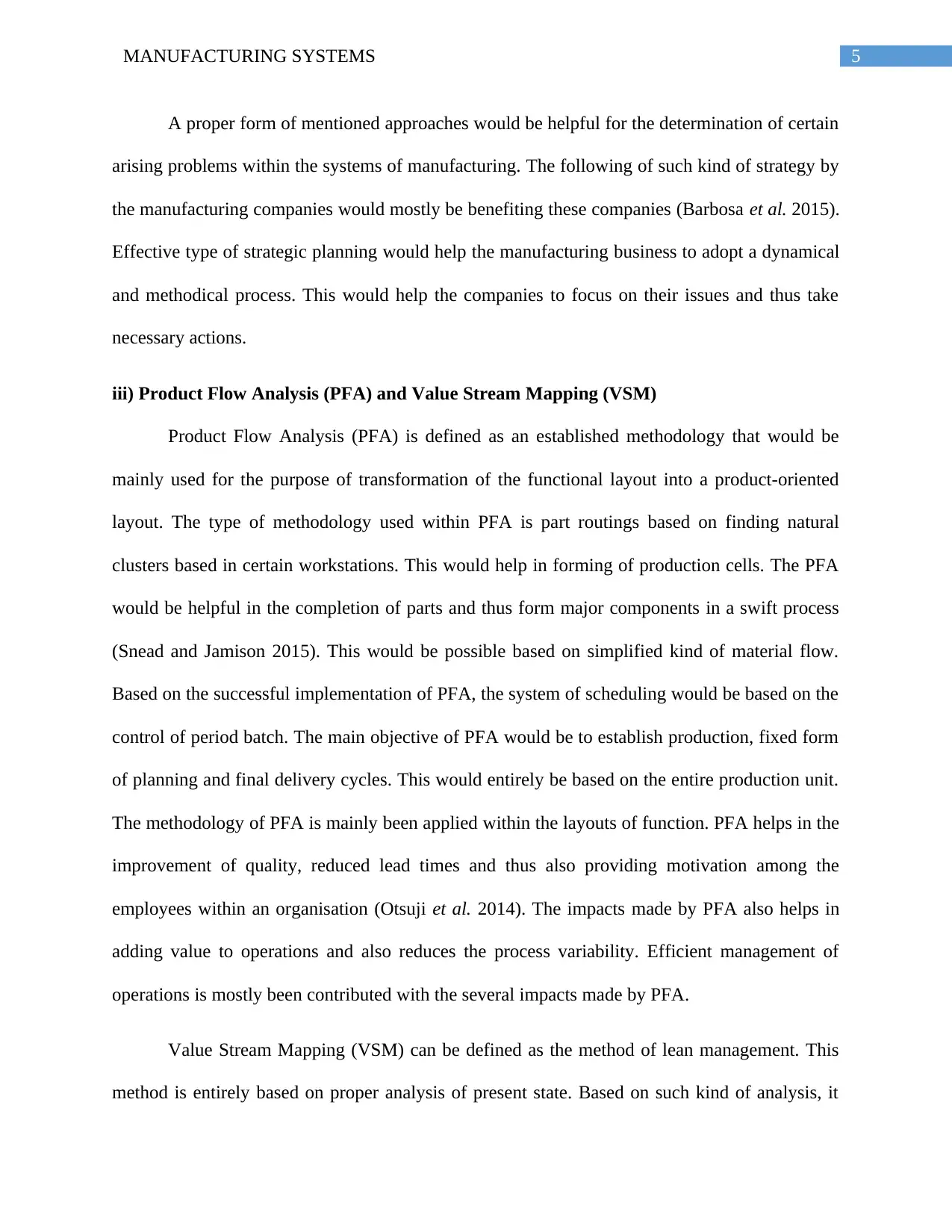
5MANUFACTURING SYSTEMS
A proper form of mentioned approaches would be helpful for the determination of certain
arising problems within the systems of manufacturing. The following of such kind of strategy by
the manufacturing companies would mostly be benefiting these companies (Barbosa et al. 2015).
Effective type of strategic planning would help the manufacturing business to adopt a dynamical
and methodical process. This would help the companies to focus on their issues and thus take
necessary actions.
iii) Product Flow Analysis (PFA) and Value Stream Mapping (VSM)
Product Flow Analysis (PFA) is defined as an established methodology that would be
mainly used for the purpose of transformation of the functional layout into a product-oriented
layout. The type of methodology used within PFA is part routings based on finding natural
clusters based in certain workstations. This would help in forming of production cells. The PFA
would be helpful in the completion of parts and thus form major components in a swift process
(Snead and Jamison 2015). This would be possible based on simplified kind of material flow.
Based on the successful implementation of PFA, the system of scheduling would be based on the
control of period batch. The main objective of PFA would be to establish production, fixed form
of planning and final delivery cycles. This would entirely be based on the entire production unit.
The methodology of PFA is mainly been applied within the layouts of function. PFA helps in the
improvement of quality, reduced lead times and thus also providing motivation among the
employees within an organisation (Otsuji et al. 2014). The impacts made by PFA also helps in
adding value to operations and also reduces the process variability. Efficient management of
operations is mostly been contributed with the several impacts made by PFA.
Value Stream Mapping (VSM) can be defined as the method of lean management. This
method is entirely based on proper analysis of present state. Based on such kind of analysis, it
A proper form of mentioned approaches would be helpful for the determination of certain
arising problems within the systems of manufacturing. The following of such kind of strategy by
the manufacturing companies would mostly be benefiting these companies (Barbosa et al. 2015).
Effective type of strategic planning would help the manufacturing business to adopt a dynamical
and methodical process. This would help the companies to focus on their issues and thus take
necessary actions.
iii) Product Flow Analysis (PFA) and Value Stream Mapping (VSM)
Product Flow Analysis (PFA) is defined as an established methodology that would be
mainly used for the purpose of transformation of the functional layout into a product-oriented
layout. The type of methodology used within PFA is part routings based on finding natural
clusters based in certain workstations. This would help in forming of production cells. The PFA
would be helpful in the completion of parts and thus form major components in a swift process
(Snead and Jamison 2015). This would be possible based on simplified kind of material flow.
Based on the successful implementation of PFA, the system of scheduling would be based on the
control of period batch. The main objective of PFA would be to establish production, fixed form
of planning and final delivery cycles. This would entirely be based on the entire production unit.
The methodology of PFA is mainly been applied within the layouts of function. PFA helps in the
improvement of quality, reduced lead times and thus also providing motivation among the
employees within an organisation (Otsuji et al. 2014). The impacts made by PFA also helps in
adding value to operations and also reduces the process variability. Efficient management of
operations is mostly been contributed with the several impacts made by PFA.
Value Stream Mapping (VSM) can be defined as the method of lean management. This
method is entirely based on proper analysis of present state. Based on such kind of analysis, it

6MANUFACTURING SYSTEMS
would further assist in the design of the future state of mechanisms (Keyte and Locher 2016).
The design based on the various series of events would begin and end with respect to thinking of
the customers. These would further be reduced with the help of lean wastes when compared with
the present map. VSM would majorly focus on such kind of areas within the firm in which there
would be a fundamental requirement of addition of extra services (Snead and Jamison 2015).
Different practitioners of lean methodology have discussed the usage of VSM as an important
tool for identification of waste, reduced process cycle times and also the implementation of
improved processes.
The use of VSM within the manufacturing industry would further help in introspection
and improvement in the present state of processes (Tyagi et al. 2015). The inputs to the VSM
would also include each of the resource based on leveraging of certain produced services or
goods.
would further assist in the design of the future state of mechanisms (Keyte and Locher 2016).
The design based on the various series of events would begin and end with respect to thinking of
the customers. These would further be reduced with the help of lean wastes when compared with
the present map. VSM would majorly focus on such kind of areas within the firm in which there
would be a fundamental requirement of addition of extra services (Snead and Jamison 2015).
Different practitioners of lean methodology have discussed the usage of VSM as an important
tool for identification of waste, reduced process cycle times and also the implementation of
improved processes.
The use of VSM within the manufacturing industry would further help in introspection
and improvement in the present state of processes (Tyagi et al. 2015). The inputs to the VSM
would also include each of the resource based on leveraging of certain produced services or
goods.
Paraphrase This Document
Need a fresh take? Get an instant paraphrase of this document with our AI Paraphraser

7MANUFACTURING SYSTEMS
(Fig 1: The process of VSM in Manufacturing Company)
(Source: Keyte and Locher 2016)
The use of PFA within a particular manufacturing company would be aided by computer
based packaging. This would be made to be possible by forming larger data sets that have to be
analysed. The analysis could be in the form of ‘what-if’ that would be conducted for adapting to
results in certain situations. This kind of performed analysis would thus be repeated within other
manufacturing companies without any kind of requirement based on specially trained people.
iv) Description of Plant Layouts
The different layouts of the plants could be widely considered as follows:
(Fig 1: The process of VSM in Manufacturing Company)
(Source: Keyte and Locher 2016)
The use of PFA within a particular manufacturing company would be aided by computer
based packaging. This would be made to be possible by forming larger data sets that have to be
analysed. The analysis could be in the form of ‘what-if’ that would be conducted for adapting to
results in certain situations. This kind of performed analysis would thus be repeated within other
manufacturing companies without any kind of requirement based on specially trained people.
iv) Description of Plant Layouts
The different layouts of the plants could be widely considered as follows:
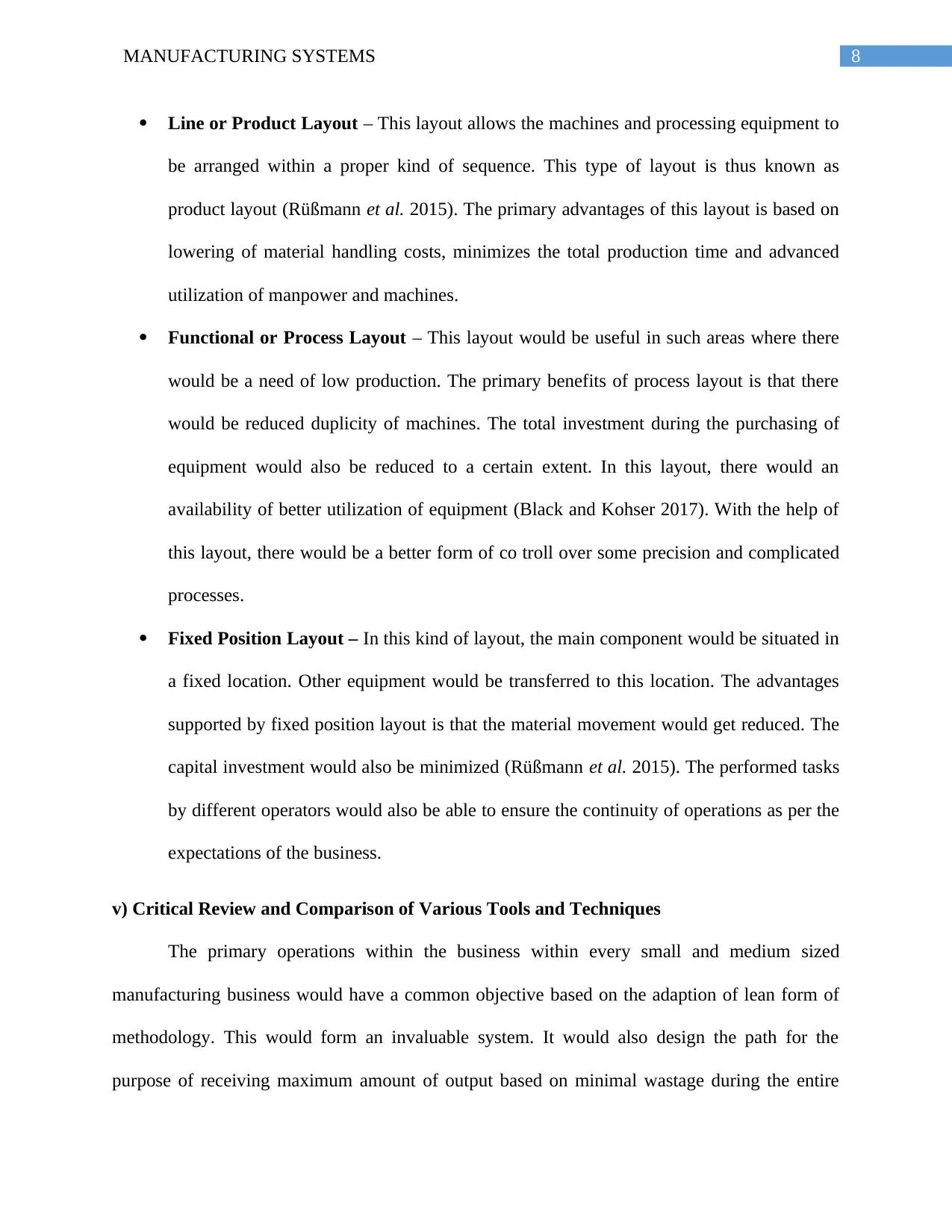
8MANUFACTURING SYSTEMS
Line or Product Layout – This layout allows the machines and processing equipment to
be arranged within a proper kind of sequence. This type of layout is thus known as
product layout (Rüßmann et al. 2015). The primary advantages of this layout is based on
lowering of material handling costs, minimizes the total production time and advanced
utilization of manpower and machines.
Functional or Process Layout – This layout would be useful in such areas where there
would be a need of low production. The primary benefits of process layout is that there
would be reduced duplicity of machines. The total investment during the purchasing of
equipment would also be reduced to a certain extent. In this layout, there would an
availability of better utilization of equipment (Black and Kohser 2017). With the help of
this layout, there would be a better form of co troll over some precision and complicated
processes.
Fixed Position Layout – In this kind of layout, the main component would be situated in
a fixed location. Other equipment would be transferred to this location. The advantages
supported by fixed position layout is that the material movement would get reduced. The
capital investment would also be minimized (Rüßmann et al. 2015). The performed tasks
by different operators would also be able to ensure the continuity of operations as per the
expectations of the business.
v) Critical Review and Comparison of Various Tools and Techniques
The primary operations within the business within every small and medium sized
manufacturing business would have a common objective based on the adaption of lean form of
methodology. This would form an invaluable system. It would also design the path for the
purpose of receiving maximum amount of output based on minimal wastage during the entire
Line or Product Layout – This layout allows the machines and processing equipment to
be arranged within a proper kind of sequence. This type of layout is thus known as
product layout (Rüßmann et al. 2015). The primary advantages of this layout is based on
lowering of material handling costs, minimizes the total production time and advanced
utilization of manpower and machines.
Functional or Process Layout – This layout would be useful in such areas where there
would be a need of low production. The primary benefits of process layout is that there
would be reduced duplicity of machines. The total investment during the purchasing of
equipment would also be reduced to a certain extent. In this layout, there would an
availability of better utilization of equipment (Black and Kohser 2017). With the help of
this layout, there would be a better form of co troll over some precision and complicated
processes.
Fixed Position Layout – In this kind of layout, the main component would be situated in
a fixed location. Other equipment would be transferred to this location. The advantages
supported by fixed position layout is that the material movement would get reduced. The
capital investment would also be minimized (Rüßmann et al. 2015). The performed tasks
by different operators would also be able to ensure the continuity of operations as per the
expectations of the business.
v) Critical Review and Comparison of Various Tools and Techniques
The primary operations within the business within every small and medium sized
manufacturing business would have a common objective based on the adaption of lean form of
methodology. This would form an invaluable system. It would also design the path for the
purpose of receiving maximum amount of output based on minimal wastage during the entire

9MANUFACTURING SYSTEMS
production cycle. The impact of lean methodology would be able to maintain the efficiency of
proper tools. It would also help in providing a critical review of each used tools and techniques
(Bhamu and Singh Sangwan 2014). The use of such kind of techniques would help in improving
the processing and increase the scope for lean systems of manufacturing. The primary idea
behind the lean methodology would be based on eliminating the creation of waste within the
organisation.
Value Stream Mapping – This is defined as a kind of visual tool that would be designed
for the manufacturing business. The use of VSM would define the process of illustration,
analysing and understanding the basic flow of materials from the level of suppliers within the
organisation till the level of customers (Keyte and Locher 2016). The use of VSM would ensure
the appropriate flow of information within the various levels of the organisation.
Kanban – It is also regarded as pull production system. The primary purpose of this
methodology is based on eradication of wastage that would be produced by inventory and
overproduction. The tool helps in the manufacturing process by making use of inventory
(Vinodh, Kumar and Vimal 2014). The process id also required for providing the appropriate
message about the quantity orders.
Total Quality Management – This methodology was primarily implemented within the
Western Electric Company. The TQM is considered as a wide-ranging tool, which would be an
useful approach for the manufacturing organisation. The use of TQM would improve the quality
of products and services. It would also prove to be an enhancement over the organisational
procedures (Ross 2017). The use of TQM would mainly put emphasis on the sustainability over
customer satisfaction. It would also possess capability for the entire streamlining over the
amount of changes that would be made to the functions performed within the organisation.
production cycle. The impact of lean methodology would be able to maintain the efficiency of
proper tools. It would also help in providing a critical review of each used tools and techniques
(Bhamu and Singh Sangwan 2014). The use of such kind of techniques would help in improving
the processing and increase the scope for lean systems of manufacturing. The primary idea
behind the lean methodology would be based on eliminating the creation of waste within the
organisation.
Value Stream Mapping – This is defined as a kind of visual tool that would be designed
for the manufacturing business. The use of VSM would define the process of illustration,
analysing and understanding the basic flow of materials from the level of suppliers within the
organisation till the level of customers (Keyte and Locher 2016). The use of VSM would ensure
the appropriate flow of information within the various levels of the organisation.
Kanban – It is also regarded as pull production system. The primary purpose of this
methodology is based on eradication of wastage that would be produced by inventory and
overproduction. The tool helps in the manufacturing process by making use of inventory
(Vinodh, Kumar and Vimal 2014). The process id also required for providing the appropriate
message about the quantity orders.
Total Quality Management – This methodology was primarily implemented within the
Western Electric Company. The TQM is considered as a wide-ranging tool, which would be an
useful approach for the manufacturing organisation. The use of TQM would improve the quality
of products and services. It would also prove to be an enhancement over the organisational
procedures (Ross 2017). The use of TQM would mainly put emphasis on the sustainability over
customer satisfaction. It would also possess capability for the entire streamlining over the
amount of changes that would be made to the functions performed within the organisation.
Secure Best Marks with AI Grader
Need help grading? Try our AI Grader for instant feedback on your assignments.
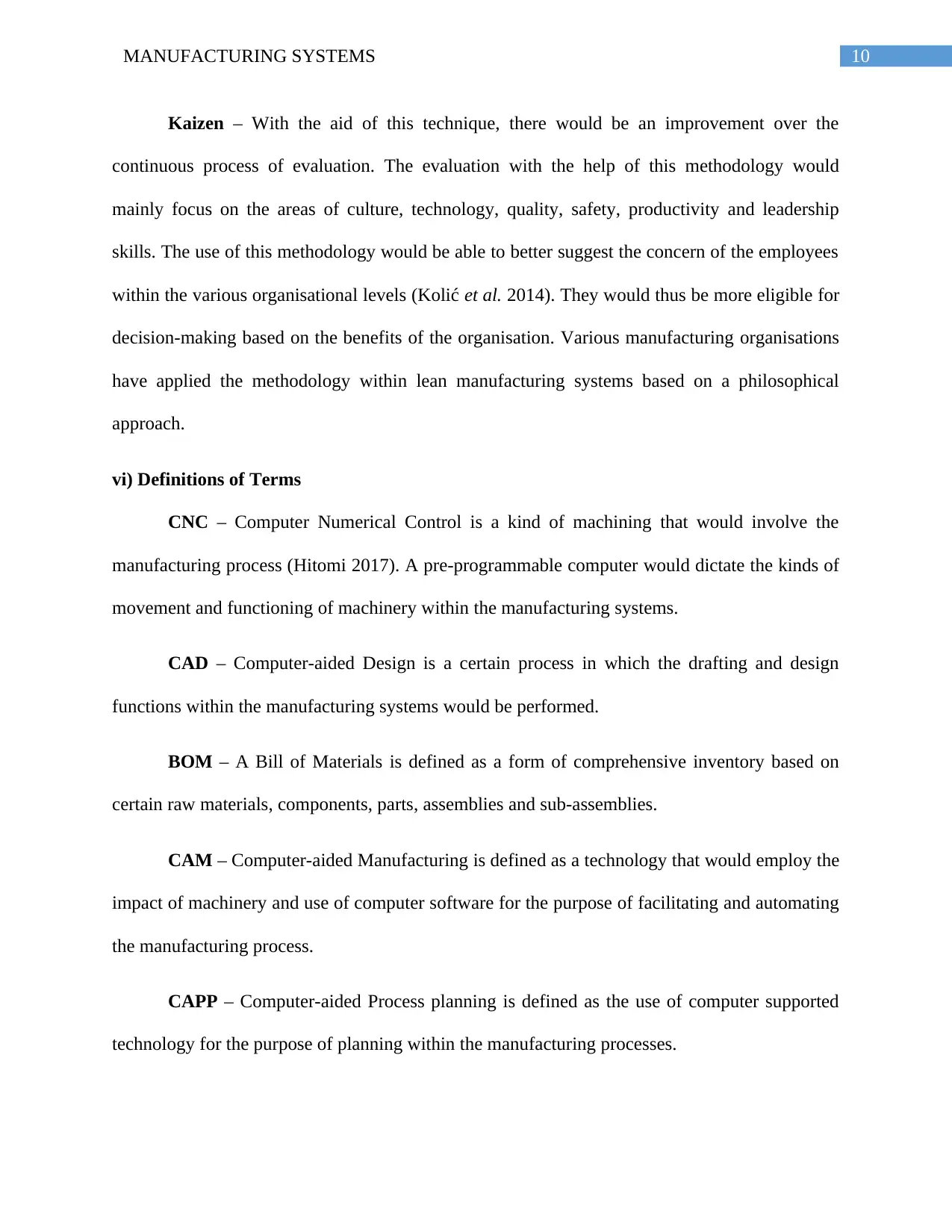
10MANUFACTURING SYSTEMS
Kaizen – With the aid of this technique, there would be an improvement over the
continuous process of evaluation. The evaluation with the help of this methodology would
mainly focus on the areas of culture, technology, quality, safety, productivity and leadership
skills. The use of this methodology would be able to better suggest the concern of the employees
within the various organisational levels (Kolić et al. 2014). They would thus be more eligible for
decision-making based on the benefits of the organisation. Various manufacturing organisations
have applied the methodology within lean manufacturing systems based on a philosophical
approach.
vi) Definitions of Terms
CNC – Computer Numerical Control is a kind of machining that would involve the
manufacturing process (Hitomi 2017). A pre-programmable computer would dictate the kinds of
movement and functioning of machinery within the manufacturing systems.
CAD – Computer-aided Design is a certain process in which the drafting and design
functions within the manufacturing systems would be performed.
BOM – A Bill of Materials is defined as a form of comprehensive inventory based on
certain raw materials, components, parts, assemblies and sub-assemblies.
CAM – Computer-aided Manufacturing is defined as a technology that would employ the
impact of machinery and use of computer software for the purpose of facilitating and automating
the manufacturing process.
CAPP – Computer-aided Process planning is defined as the use of computer supported
technology for the purpose of planning within the manufacturing processes.
Kaizen – With the aid of this technique, there would be an improvement over the
continuous process of evaluation. The evaluation with the help of this methodology would
mainly focus on the areas of culture, technology, quality, safety, productivity and leadership
skills. The use of this methodology would be able to better suggest the concern of the employees
within the various organisational levels (Kolić et al. 2014). They would thus be more eligible for
decision-making based on the benefits of the organisation. Various manufacturing organisations
have applied the methodology within lean manufacturing systems based on a philosophical
approach.
vi) Definitions of Terms
CNC – Computer Numerical Control is a kind of machining that would involve the
manufacturing process (Hitomi 2017). A pre-programmable computer would dictate the kinds of
movement and functioning of machinery within the manufacturing systems.
CAD – Computer-aided Design is a certain process in which the drafting and design
functions within the manufacturing systems would be performed.
BOM – A Bill of Materials is defined as a form of comprehensive inventory based on
certain raw materials, components, parts, assemblies and sub-assemblies.
CAM – Computer-aided Manufacturing is defined as a technology that would employ the
impact of machinery and use of computer software for the purpose of facilitating and automating
the manufacturing process.
CAPP – Computer-aided Process planning is defined as the use of computer supported
technology for the purpose of planning within the manufacturing processes.

11MANUFACTURING SYSTEMS
AGV – Automated Guided Vehicle is a portable robot. This robot has been programmed
for following markers and certain wires attached with the floor.
MPS – Master Production Schedule is a designed plan based on individual commodities
that have to be produced within a certain time period.
MRP – Manufacturing Resource Planning is defined as such kind of systems, which is
responsible for controlling the process of production, purchasing and delivery of products.
FMS – Flexible Manufacturing Systems are different manufacturing systems, which
would show a flexible approach within the manufacturing systems.
CIM – Computer-integrated manufacturing could be defined as the use of automation
systems for product manufacturing.
ERP – Enterprise Resource Planning is a program designed for integrated manufacturing
processes (Ptak and Schragenheim 2016). They help in the information transmission from the
floor of production till the HR department.
Part B
Case Study: Performance Assessment of Manufacturing Plant
Introduction
There is an extreme need for optimising the various kinds of performance within the
manufacturing business. The process of optimisation would be possible based on certain form of
assessment on the overall performance performed within the organisation. This would be
important for meeting with the requirements and needs of different clients and for the business.
Optimising the business performance would pave the way based on assessing the entire
AGV – Automated Guided Vehicle is a portable robot. This robot has been programmed
for following markers and certain wires attached with the floor.
MPS – Master Production Schedule is a designed plan based on individual commodities
that have to be produced within a certain time period.
MRP – Manufacturing Resource Planning is defined as such kind of systems, which is
responsible for controlling the process of production, purchasing and delivery of products.
FMS – Flexible Manufacturing Systems are different manufacturing systems, which
would show a flexible approach within the manufacturing systems.
CIM – Computer-integrated manufacturing could be defined as the use of automation
systems for product manufacturing.
ERP – Enterprise Resource Planning is a program designed for integrated manufacturing
processes (Ptak and Schragenheim 2016). They help in the information transmission from the
floor of production till the HR department.
Part B
Case Study: Performance Assessment of Manufacturing Plant
Introduction
There is an extreme need for optimising the various kinds of performance within the
manufacturing business. The process of optimisation would be possible based on certain form of
assessment on the overall performance performed within the organisation. This would be
important for meeting with the requirements and needs of different clients and for the business.
Optimising the business performance would pave the way based on assessing the entire

12MANUFACTURING SYSTEMS
organisation (Faulkner and Badurdeen 2014). This would be helpful for bringing effectiveness
within the processes of the organisation. This report would put focus on the assessment of
performance within the manufacturing organisation as per the case study provided. The
assessment would primarily include the site and business information, benefits and opportunities,
performance index and the most possible form of options of improvement based on certain Key
Performance Indicators (KPIs).
1. Site and Business Information
Based on providing insights over the business information based on the manufacturing
organisation, it has been discussed that the primary product would include organic chemistry.
Some of the products produced within the manufacturing business would be similar to the final
product. Some of the other products would be still in the stages of further processing. The
maximum number of products is 15 and the product variants are considered as to be none. There
are some demanding customers (Maiga, Nilsson and Jacobs 2014). The primary demands of
customers would be based on the improvement of pharmaceutical quality that would mainly
comprise of 40 percent of the entire manufacturing organisation. The main clients within the
business are BASF, Abott, QA Glaxo Merck and Roche. The next 40 percent of clients would
comprise of agrochemical prices, quality, Novartis, BSF and 20 percent would comprise of
others. The performance of manufacturing would mainly be compared based on the level of
competition with the Sterling Organics Lonza customers located in India and China.
2. Opportunities and Benefits
As per the gathered information from the case study of the organisation, it could thus be
discussed that the output of the plant would be increased based on an estimated potential during
organisation (Faulkner and Badurdeen 2014). This would be helpful for bringing effectiveness
within the processes of the organisation. This report would put focus on the assessment of
performance within the manufacturing organisation as per the case study provided. The
assessment would primarily include the site and business information, benefits and opportunities,
performance index and the most possible form of options of improvement based on certain Key
Performance Indicators (KPIs).
1. Site and Business Information
Based on providing insights over the business information based on the manufacturing
organisation, it has been discussed that the primary product would include organic chemistry.
Some of the products produced within the manufacturing business would be similar to the final
product. Some of the other products would be still in the stages of further processing. The
maximum number of products is 15 and the product variants are considered as to be none. There
are some demanding customers (Maiga, Nilsson and Jacobs 2014). The primary demands of
customers would be based on the improvement of pharmaceutical quality that would mainly
comprise of 40 percent of the entire manufacturing organisation. The main clients within the
business are BASF, Abott, QA Glaxo Merck and Roche. The next 40 percent of clients would
comprise of agrochemical prices, quality, Novartis, BSF and 20 percent would comprise of
others. The performance of manufacturing would mainly be compared based on the level of
competition with the Sterling Organics Lonza customers located in India and China.
2. Opportunities and Benefits
As per the gathered information from the case study of the organisation, it could thus be
discussed that the output of the plant would be increased based on an estimated potential during
Paraphrase This Document
Need a fresh take? Get an instant paraphrase of this document with our AI Paraphraser

13MANUFACTURING SYSTEMS
the annual turnover of the organisation. The annual turnover would reach from 20% to 30%. The
estimated potential benefits would range from 25% to 55% based on the total outcome of the
organisation (Powell et al. 2015). The capacity of plant would thus be improved based on
increasing the efficiency of first pass. This would be entirely based on the consistency of
products that would be improved by 3% to 4%. The uptime would also be improved by 5%.
There is also a frequent changes in the average time for reaching the specialisation of product
changes (Byrn et al. 2015). This could thus be reduced from 3% to 4%. It would be sceptical if
the performance cost of product delivery could be improved and final stock of products could be
reduced. The manufacturing of products is under full scepticism if there would be an addition for
the value of the customers (Zhong et al. 2016). The material and source of good kind of delivery,
reliability and quality could be improved while the reduction of stocks from 2% to 3%. Hence,
the total assessment value for the annual improvement based on manufacturing would be
improved by 25%. This would be entirely based upon the market prices and total outcome. These
would thus be provided based on benefits of about 168.75 million of GBP.
3. Performance Assessment
After a formal assessment of the entire organisation, it could be concluded that the entire
manufacturing process would be able to add some kind of value within the employees. This
could be in terms of 77,640 GBP. The service to the customers would also be increased by 70%
although there has not been a routine wise measurement. The reliability and consistency of the
organisation would also be measured. The absenteeism of the employees that are functioning
within the organisation is also measured. The provided data has shown an increase of 95% within
the rate of products. There has also been a 97% hike in the quality aspects. The maintenance
costs based within the percentage acid value would have been assumed by 50%. The control over
the annual turnover of the organisation. The annual turnover would reach from 20% to 30%. The
estimated potential benefits would range from 25% to 55% based on the total outcome of the
organisation (Powell et al. 2015). The capacity of plant would thus be improved based on
increasing the efficiency of first pass. This would be entirely based on the consistency of
products that would be improved by 3% to 4%. The uptime would also be improved by 5%.
There is also a frequent changes in the average time for reaching the specialisation of product
changes (Byrn et al. 2015). This could thus be reduced from 3% to 4%. It would be sceptical if
the performance cost of product delivery could be improved and final stock of products could be
reduced. The manufacturing of products is under full scepticism if there would be an addition for
the value of the customers (Zhong et al. 2016). The material and source of good kind of delivery,
reliability and quality could be improved while the reduction of stocks from 2% to 3%. Hence,
the total assessment value for the annual improvement based on manufacturing would be
improved by 25%. This would be entirely based upon the market prices and total outcome. These
would thus be provided based on benefits of about 168.75 million of GBP.
3. Performance Assessment
After a formal assessment of the entire organisation, it could be concluded that the entire
manufacturing process would be able to add some kind of value within the employees. This
could be in terms of 77,640 GBP. The service to the customers would also be increased by 70%
although there has not been a routine wise measurement. The reliability and consistency of the
organisation would also be measured. The absenteeism of the employees that are functioning
within the organisation is also measured. The provided data has shown an increase of 95% within
the rate of products. There has also been a 97% hike in the quality aspects. The maintenance
costs based within the percentage acid value would have been assumed by 50%. The control over

14MANUFACTURING SYSTEMS
flexibility within the organisation have not been measured. The routinely change time that has
affected the production includes some kinds of changes and has been measured as 1000. The
overall score has not been measured.
4. Performance Index
The performance index has been calculated on the entire system. They would thus be able
to function in such a way for achieving their goals set by the organisation. The performance
index would thus be measured with the help of the information that would be gained during the
assessment of performance (Garbie 2014). The benefits and opportunities included within the
business would thus be understood. Additionally, it would also be easy to assess the performance
level of the organisation based on achieving of targets within the present position of the
organisation.
5. Possible Improvement Options based on the Key Performance Indicators (KPIs)
On reviewing about the functioning of the systems of manufacturing within the
organisation, it could thus be understood that there are certain troubles within the working of the
organisation (Lindberg et al. 2015). On continuous reviewing of the systems, I have gained a
clear form of understanding about the entire functioning of the overall processes performed
within the organisation. There is high potential within the organisation in order to face the issues
and thus resolve them in an efficient manner. After performing of review of the entire process set
of the organisation, I have been able to counter the different kinds of attacks within the system
occurring within the various levels of the organisation. I have also suggested some kinds of
recommendations to the senior managerial level who have been able to understand the problems
that are occurring within the systems. These problems should be solved on an immediate basis in
flexibility within the organisation have not been measured. The routinely change time that has
affected the production includes some kinds of changes and has been measured as 1000. The
overall score has not been measured.
4. Performance Index
The performance index has been calculated on the entire system. They would thus be able
to function in such a way for achieving their goals set by the organisation. The performance
index would thus be measured with the help of the information that would be gained during the
assessment of performance (Garbie 2014). The benefits and opportunities included within the
business would thus be understood. Additionally, it would also be easy to assess the performance
level of the organisation based on achieving of targets within the present position of the
organisation.
5. Possible Improvement Options based on the Key Performance Indicators (KPIs)
On reviewing about the functioning of the systems of manufacturing within the
organisation, it could thus be understood that there are certain troubles within the working of the
organisation (Lindberg et al. 2015). On continuous reviewing of the systems, I have gained a
clear form of understanding about the entire functioning of the overall processes performed
within the organisation. There is high potential within the organisation in order to face the issues
and thus resolve them in an efficient manner. After performing of review of the entire process set
of the organisation, I have been able to counter the different kinds of attacks within the system
occurring within the various levels of the organisation. I have also suggested some kinds of
recommendations to the senior managerial level who have been able to understand the problems
that are occurring within the systems. These problems should be solved on an immediate basis in
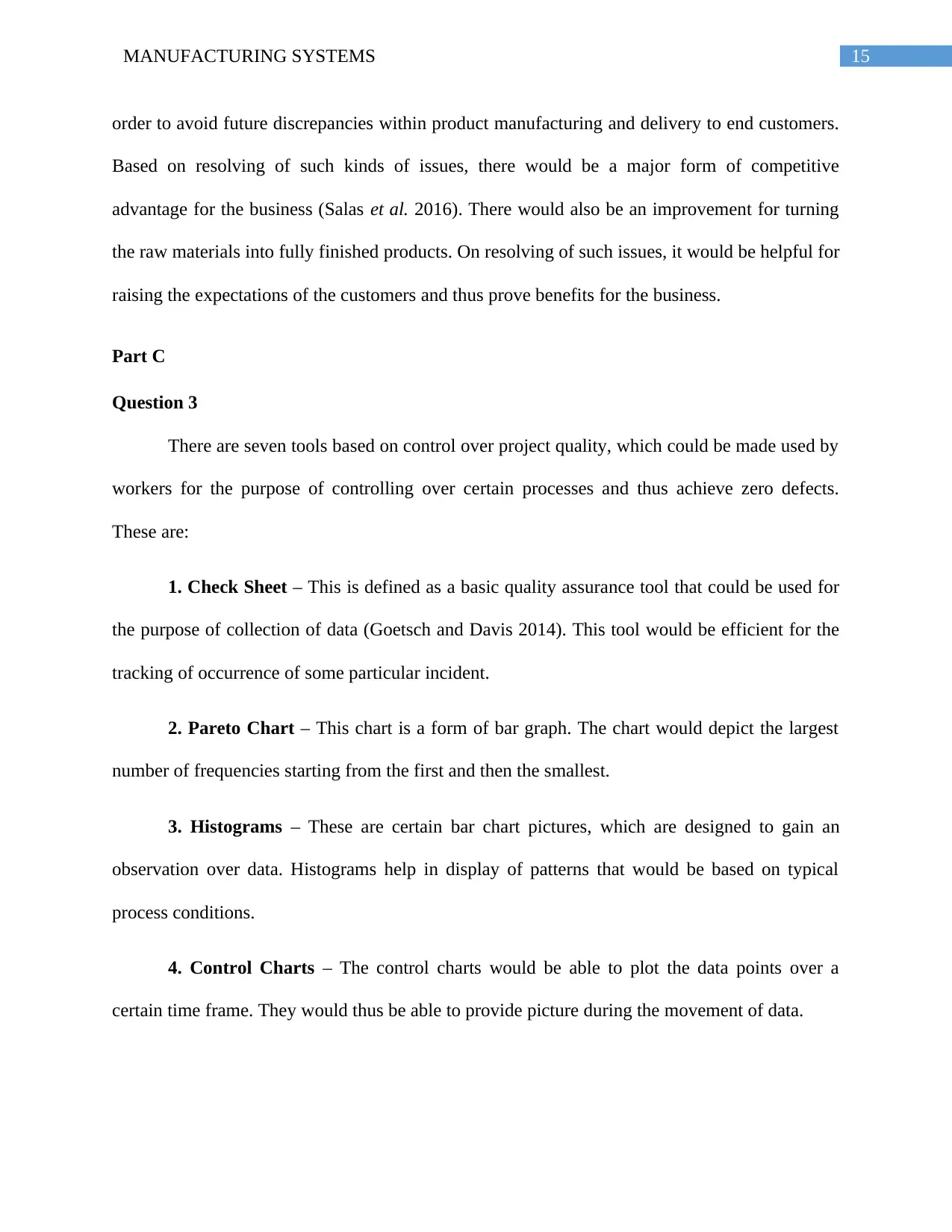
15MANUFACTURING SYSTEMS
order to avoid future discrepancies within product manufacturing and delivery to end customers.
Based on resolving of such kinds of issues, there would be a major form of competitive
advantage for the business (Salas et al. 2016). There would also be an improvement for turning
the raw materials into fully finished products. On resolving of such issues, it would be helpful for
raising the expectations of the customers and thus prove benefits for the business.
Part C
Question 3
There are seven tools based on control over project quality, which could be made used by
workers for the purpose of controlling over certain processes and thus achieve zero defects.
These are:
1. Check Sheet – This is defined as a basic quality assurance tool that could be used for
the purpose of collection of data (Goetsch and Davis 2014). This tool would be efficient for the
tracking of occurrence of some particular incident.
2. Pareto Chart – This chart is a form of bar graph. The chart would depict the largest
number of frequencies starting from the first and then the smallest.
3. Histograms – These are certain bar chart pictures, which are designed to gain an
observation over data. Histograms help in display of patterns that would be based on typical
process conditions.
4. Control Charts – The control charts would be able to plot the data points over a
certain time frame. They would thus be able to provide picture during the movement of data.
order to avoid future discrepancies within product manufacturing and delivery to end customers.
Based on resolving of such kinds of issues, there would be a major form of competitive
advantage for the business (Salas et al. 2016). There would also be an improvement for turning
the raw materials into fully finished products. On resolving of such issues, it would be helpful for
raising the expectations of the customers and thus prove benefits for the business.
Part C
Question 3
There are seven tools based on control over project quality, which could be made used by
workers for the purpose of controlling over certain processes and thus achieve zero defects.
These are:
1. Check Sheet – This is defined as a basic quality assurance tool that could be used for
the purpose of collection of data (Goetsch and Davis 2014). This tool would be efficient for the
tracking of occurrence of some particular incident.
2. Pareto Chart – This chart is a form of bar graph. The chart would depict the largest
number of frequencies starting from the first and then the smallest.
3. Histograms – These are certain bar chart pictures, which are designed to gain an
observation over data. Histograms help in display of patterns that would be based on typical
process conditions.
4. Control Charts – The control charts would be able to plot the data points over a
certain time frame. They would thus be able to provide picture during the movement of data.
Secure Best Marks with AI Grader
Need help grading? Try our AI Grader for instant feedback on your assignments.

16MANUFACTURING SYSTEMS
5. Scatter Diagrams – These are certain graphs, which would be able to depict
relationship among certain variables (Mourtzis and Doukas 2014). The scatter diagrams would
be able to represent the possible kinds of causes and their after effects.
6. Cause and Effect Diagram – This is also known as Fish-bone diagram. This diagram
would help in the depiction of the possible problem causes.
7. Flowchart – This kind of tool would be used by workers for determining the
bottlenecks and breakdowns within the processes of work.
Question 7
Use of flexible form of manufacturing systems would help the manufacturing businesses
to improve their processes. These kind of flexibility approach would be able to produce different
benefits for the business. With the impact of flexibility, the manufacturing business would be
able to adapt to different kinds of changes as per the changing business requirements (Matt,
Rauch and Dallasega 2015). Flexibility within the production processes would also offer two
different kinds of approaches for the manufacturing systems. With the help of such kind of
approaches, it would also be beneficial for ensuring successful business operations within the
manufacturing systems.
Machine flexibility normally refers the way in which a systems would be able to change
their purposes of creating a new type of product. They also describe the ways in which a
particular system would change their operations. Routing flexibility approach is another type of
approach that is used within the business processes. The routing flexibility would also help the
system to adapt to different mode of changes based on volume, capacity or capability (Tao et al.
2017). The main kind of importance these kinds of flexibility approaches is based on ensuring
5. Scatter Diagrams – These are certain graphs, which would be able to depict
relationship among certain variables (Mourtzis and Doukas 2014). The scatter diagrams would
be able to represent the possible kinds of causes and their after effects.
6. Cause and Effect Diagram – This is also known as Fish-bone diagram. This diagram
would help in the depiction of the possible problem causes.
7. Flowchart – This kind of tool would be used by workers for determining the
bottlenecks and breakdowns within the processes of work.
Question 7
Use of flexible form of manufacturing systems would help the manufacturing businesses
to improve their processes. These kind of flexibility approach would be able to produce different
benefits for the business. With the impact of flexibility, the manufacturing business would be
able to adapt to different kinds of changes as per the changing business requirements (Matt,
Rauch and Dallasega 2015). Flexibility within the production processes would also offer two
different kinds of approaches for the manufacturing systems. With the help of such kind of
approaches, it would also be beneficial for ensuring successful business operations within the
manufacturing systems.
Machine flexibility normally refers the way in which a systems would be able to change
their purposes of creating a new type of product. They also describe the ways in which a
particular system would change their operations. Routing flexibility approach is another type of
approach that is used within the business processes. The routing flexibility would also help the
system to adapt to different mode of changes based on volume, capacity or capability (Tao et al.
2017). The main kind of importance these kinds of flexibility approaches is based on ensuring
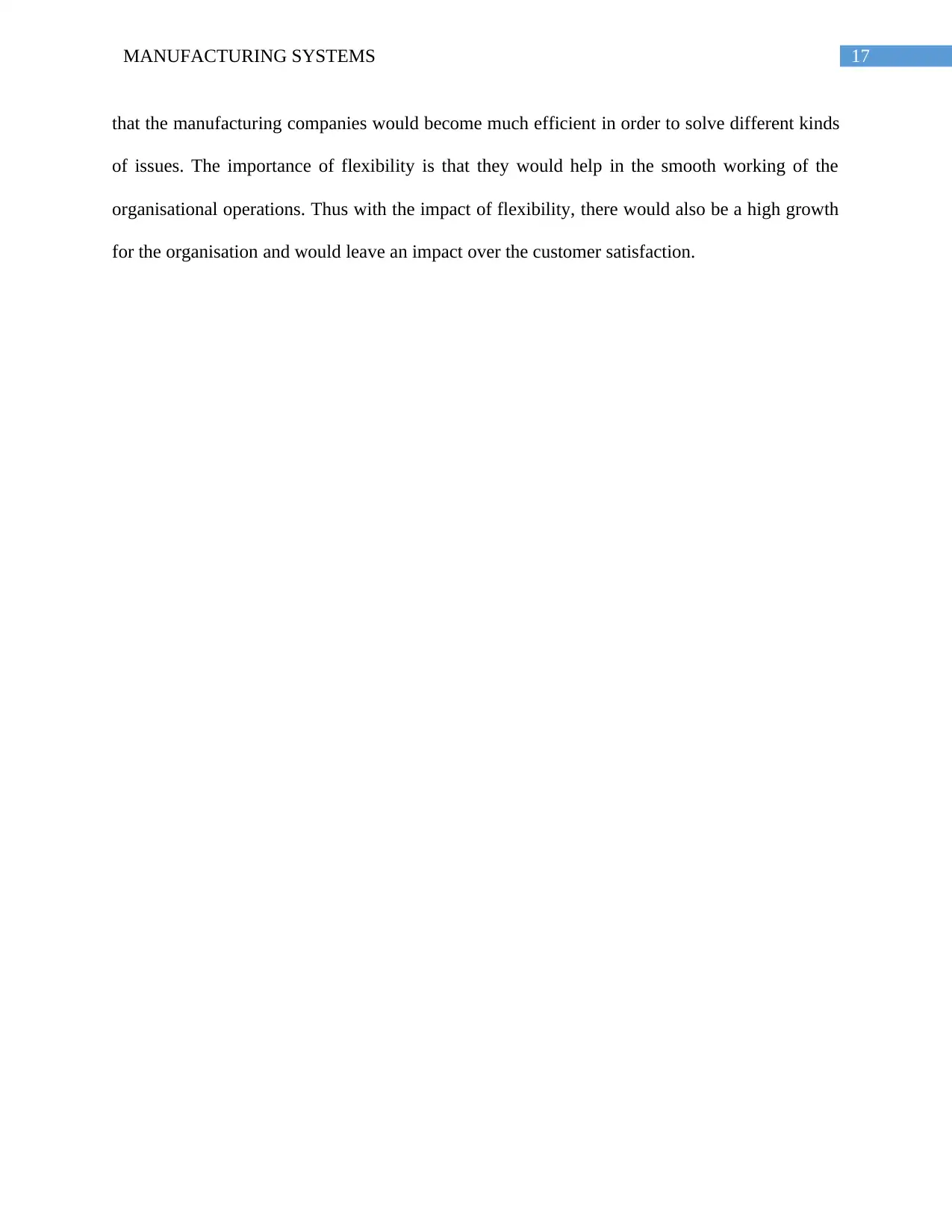
17MANUFACTURING SYSTEMS
that the manufacturing companies would become much efficient in order to solve different kinds
of issues. The importance of flexibility is that they would help in the smooth working of the
organisational operations. Thus with the impact of flexibility, there would also be a high growth
for the organisation and would leave an impact over the customer satisfaction.
that the manufacturing companies would become much efficient in order to solve different kinds
of issues. The importance of flexibility is that they would help in the smooth working of the
organisational operations. Thus with the impact of flexibility, there would also be a high growth
for the organisation and would leave an impact over the customer satisfaction.

18MANUFACTURING SYSTEMS
References
Anand, N. and Grover, N., 2015. Measuring retail supply chain performance: Theoretical model
using key performance indicators (KPIs). Benchmarking: An International Journal, 22(1),
pp.135-166.
Bai, C. and Sarkis, J., 2014. Determining and applying sustainable supplier key performance
indicators. Supply Chain Management: An International Journal, 19(3), pp.275-291.
Barbosa, J., Leitão, P., Adam, E. and Trentesaux, D., 2015. Dynamic self-organization in holonic
multi-agent manufacturing systems: The ADACOR evolution. Computers in Industry, 66, pp.99-
111.
Bhamu, J. and Singh Sangwan, K., 2014. Lean manufacturing: literature review and research
issues. International Journal of Operations & Production Management, 34(7), pp.876-940.
Black, J.T. and Kohser, R.A., 2017. DeGarmo's materials and processes in manufacturing. John
Wiley & Sons.
Byrn, S., Futran, M., Thomas, H., Jayjock, E., Maron, N., Meyer, R.F., Myerson, A.S., Thien,
M.P. and Trout, B.L., 2015. Achieving continuous manufacturing for final dosage formation:
challenges and how to meet them. May 20–21, 2014 continuous manufacturing
symposium. Journal of pharmaceutical sciences, 104(3), pp.792-802.
Faulkner, W. and Badurdeen, F., 2014. Sustainable Value Stream Mapping (Sus-VSM):
methodology to visualize and assess manufacturing sustainability performance. Journal of
cleaner production, 85, pp.8-18.
References
Anand, N. and Grover, N., 2015. Measuring retail supply chain performance: Theoretical model
using key performance indicators (KPIs). Benchmarking: An International Journal, 22(1),
pp.135-166.
Bai, C. and Sarkis, J., 2014. Determining and applying sustainable supplier key performance
indicators. Supply Chain Management: An International Journal, 19(3), pp.275-291.
Barbosa, J., Leitão, P., Adam, E. and Trentesaux, D., 2015. Dynamic self-organization in holonic
multi-agent manufacturing systems: The ADACOR evolution. Computers in Industry, 66, pp.99-
111.
Bhamu, J. and Singh Sangwan, K., 2014. Lean manufacturing: literature review and research
issues. International Journal of Operations & Production Management, 34(7), pp.876-940.
Black, J.T. and Kohser, R.A., 2017. DeGarmo's materials and processes in manufacturing. John
Wiley & Sons.
Byrn, S., Futran, M., Thomas, H., Jayjock, E., Maron, N., Meyer, R.F., Myerson, A.S., Thien,
M.P. and Trout, B.L., 2015. Achieving continuous manufacturing for final dosage formation:
challenges and how to meet them. May 20–21, 2014 continuous manufacturing
symposium. Journal of pharmaceutical sciences, 104(3), pp.792-802.
Faulkner, W. and Badurdeen, F., 2014. Sustainable Value Stream Mapping (Sus-VSM):
methodology to visualize and assess manufacturing sustainability performance. Journal of
cleaner production, 85, pp.8-18.
Paraphrase This Document
Need a fresh take? Get an instant paraphrase of this document with our AI Paraphraser

19MANUFACTURING SYSTEMS
Fullerton, R.R., Kennedy, F.A. and Widener, S.K., 2014. Lean manufacturing and firm
performance: The incremental contribution of lean management accounting practices. Journal of
Operations Management, 32(7-8), pp.414-428.
Garbie, I.H., 2014. An analytical technique to model and assess sustainable development index
in manufacturing enterprises. International Journal of Production Research, 52(16), pp.4876-
4915.
Goetsch, D.L. and Davis, S.B., 2014. Quality management for organizational excellence. Upper
Saddle River, NJ: pearson.
Hill, T., 2017. Manufacturing strategy: the strategic management of the manufacturing function.
Macmillan International Higher Education.
Hitomi, K., 2017. Manufacturing Systems Engineering: A Unified Approach to Manufacturing
Technology, Production Management and Industrial Economics. Routledge.
Keyte, B. and Locher, D.A., 2016. The complete lean enterprise: Value stream mapping for
administrative and office processes. Productivity Press.
Kolić, D., Yao, Y.L., Fafandjel, N. and Hadjina, M., 2014, January. Value stream mapping
micropanel assembly with clustering to improve flow in a shipyard. In International Conference
on Innovative Technologies In-Tech 2014.
Lindberg, C.F., Tan, S., Yan, J. and Starfelt, F., 2015. Key performance indicators improve
industrial performance. Energy procedia, 75, pp.1785-1790.
Fullerton, R.R., Kennedy, F.A. and Widener, S.K., 2014. Lean manufacturing and firm
performance: The incremental contribution of lean management accounting practices. Journal of
Operations Management, 32(7-8), pp.414-428.
Garbie, I.H., 2014. An analytical technique to model and assess sustainable development index
in manufacturing enterprises. International Journal of Production Research, 52(16), pp.4876-
4915.
Goetsch, D.L. and Davis, S.B., 2014. Quality management for organizational excellence. Upper
Saddle River, NJ: pearson.
Hill, T., 2017. Manufacturing strategy: the strategic management of the manufacturing function.
Macmillan International Higher Education.
Hitomi, K., 2017. Manufacturing Systems Engineering: A Unified Approach to Manufacturing
Technology, Production Management and Industrial Economics. Routledge.
Keyte, B. and Locher, D.A., 2016. The complete lean enterprise: Value stream mapping for
administrative and office processes. Productivity Press.
Kolić, D., Yao, Y.L., Fafandjel, N. and Hadjina, M., 2014, January. Value stream mapping
micropanel assembly with clustering to improve flow in a shipyard. In International Conference
on Innovative Technologies In-Tech 2014.
Lindberg, C.F., Tan, S., Yan, J. and Starfelt, F., 2015. Key performance indicators improve
industrial performance. Energy procedia, 75, pp.1785-1790.

20MANUFACTURING SYSTEMS
Maiga, A.S., Nilsson, A. and Jacobs, F.A., 2014. Assessing the interaction effect of cost control
systems and information technology integration on manufacturing plant financial
performance. The British Accounting Review, 46(1), pp.77-90.
Matt, D.T., Rauch, E. and Dallasega, P., 2015. Trends towards Distributed Manufacturing
Systems and modern forms for their design. Procedia CIRP, 33, pp.185-190.
May, G., Barletta, I., Stahl, B. and Taisch, M., 2015. Energy management in production: A novel
method to develop key performance indicators for improving energy efficiency. Applied
Energy, 149, pp.46-61.
Mourtzis, D. and Doukas, M., 2014. The evolution of manufacturing systems: From
craftsmanship to the era of customisation. In Handbook of Research on Design and Management
of Lean Production Systems (pp. 1-29). IGI Global.
Negahban, A. and Smith, J.S., 2014. Simulation for manufacturing system design and operation:
Literature review and analysis. Journal of Manufacturing Systems, 33(2), pp.241-261.
Otsuji, T.G., Bin, J., Yoshimura, A., Tomura, M., Tateyama, D., Minami, I., Yoshikawa, Y.,
Aiba, K., Heuser, J.E., Nishino, T. and Hasegawa, K., 2014. A 3D sphere culture system
containing functional polymers for large-scale human pluripotent stem cell production. Stem cell
reports, 2(5), pp.734-745.
Parmenter, D., 2015. Key performance indicators: developing, implementing, and using winning
KPIs. John Wiley & Sons.
Maiga, A.S., Nilsson, A. and Jacobs, F.A., 2014. Assessing the interaction effect of cost control
systems and information technology integration on manufacturing plant financial
performance. The British Accounting Review, 46(1), pp.77-90.
Matt, D.T., Rauch, E. and Dallasega, P., 2015. Trends towards Distributed Manufacturing
Systems and modern forms for their design. Procedia CIRP, 33, pp.185-190.
May, G., Barletta, I., Stahl, B. and Taisch, M., 2015. Energy management in production: A novel
method to develop key performance indicators for improving energy efficiency. Applied
Energy, 149, pp.46-61.
Mourtzis, D. and Doukas, M., 2014. The evolution of manufacturing systems: From
craftsmanship to the era of customisation. In Handbook of Research on Design and Management
of Lean Production Systems (pp. 1-29). IGI Global.
Negahban, A. and Smith, J.S., 2014. Simulation for manufacturing system design and operation:
Literature review and analysis. Journal of Manufacturing Systems, 33(2), pp.241-261.
Otsuji, T.G., Bin, J., Yoshimura, A., Tomura, M., Tateyama, D., Minami, I., Yoshikawa, Y.,
Aiba, K., Heuser, J.E., Nishino, T. and Hasegawa, K., 2014. A 3D sphere culture system
containing functional polymers for large-scale human pluripotent stem cell production. Stem cell
reports, 2(5), pp.734-745.
Parmenter, D., 2015. Key performance indicators: developing, implementing, and using winning
KPIs. John Wiley & Sons.

21MANUFACTURING SYSTEMS
Powell, D.M., Fu, R., Horowitz, K., Basore, P.A., Woodhouse, M. and Buonassisi, T., 2015. The
capital intensity of photovoltaics manufacturing: barrier to scale and opportunity for
innovation. Energy & Environmental Science, 8(12), pp.3395-3408.
Ptak, C.A. and Schragenheim, E., 2016. ERP: tools, techniques, and applications for integrating
the supply chain. Crc Press.
Ross, J.E., 2017. Total quality management: Text, cases, and readings. Routledge.
Rüßmann, M., Lorenz, M., Gerbert, P., Waldner, M., Justus, J., Engel, P. and Harnisch, M.,
2015. Industry 4.0: The future of productivity and growth in manufacturing industries. Boston
Consulting Group, 9.
Salas, D.A., Ramirez, A.D., Rodríguez, C.R., Petroche, D.M., Boero, A.J. and Duque-Rivera, J.,
2016. Environmental impacts, life cycle assessment and potential improvement measures for
cement production: a literature review. Journal of Cleaner Production, 113, pp.114-122.
Snead, D.R. and Jamison, T.F., 2015. A three‐minute synthesis and purification of ibuprofen:
Pushing the limits of continuous‐flow processing. Angewandte Chemie International
Edition, 54(3), pp.983-987.
Tao, F., Cheng, Y., Zhang, L. and Nee, A.Y., 2017. Advanced manufacturing systems:
socialization characteristics and trends. Journal of Intelligent Manufacturing, 28(5), pp.1079-
1094.
Tyagi, S., Choudhary, A., Cai, X. and Yang, K., 2015. Value stream mapping to reduce the lead-
time of a product development process. International Journal of Production Economics, 160,
pp.202-212.
Powell, D.M., Fu, R., Horowitz, K., Basore, P.A., Woodhouse, M. and Buonassisi, T., 2015. The
capital intensity of photovoltaics manufacturing: barrier to scale and opportunity for
innovation. Energy & Environmental Science, 8(12), pp.3395-3408.
Ptak, C.A. and Schragenheim, E., 2016. ERP: tools, techniques, and applications for integrating
the supply chain. Crc Press.
Ross, J.E., 2017. Total quality management: Text, cases, and readings. Routledge.
Rüßmann, M., Lorenz, M., Gerbert, P., Waldner, M., Justus, J., Engel, P. and Harnisch, M.,
2015. Industry 4.0: The future of productivity and growth in manufacturing industries. Boston
Consulting Group, 9.
Salas, D.A., Ramirez, A.D., Rodríguez, C.R., Petroche, D.M., Boero, A.J. and Duque-Rivera, J.,
2016. Environmental impacts, life cycle assessment and potential improvement measures for
cement production: a literature review. Journal of Cleaner Production, 113, pp.114-122.
Snead, D.R. and Jamison, T.F., 2015. A three‐minute synthesis and purification of ibuprofen:
Pushing the limits of continuous‐flow processing. Angewandte Chemie International
Edition, 54(3), pp.983-987.
Tao, F., Cheng, Y., Zhang, L. and Nee, A.Y., 2017. Advanced manufacturing systems:
socialization characteristics and trends. Journal of Intelligent Manufacturing, 28(5), pp.1079-
1094.
Tyagi, S., Choudhary, A., Cai, X. and Yang, K., 2015. Value stream mapping to reduce the lead-
time of a product development process. International Journal of Production Economics, 160,
pp.202-212.
Secure Best Marks with AI Grader
Need help grading? Try our AI Grader for instant feedback on your assignments.

22MANUFACTURING SYSTEMS
Vinodh, S., Kumar, S.V. and Vimal, K.E.K., 2014. Implementing lean sigma in an Indian rotary
switches manufacturing organisation. Production Planning & Control, 25(4), pp.288-302.
Zhong, R.Y., Newman, S.T., Huang, G.Q. and Lan, S., 2016. Big Data for supply chain
management in the service and manufacturing sectors: Challenges, opportunities, and future
perspectives. Computers & Industrial Engineering, 101, pp.572-591.
Vinodh, S., Kumar, S.V. and Vimal, K.E.K., 2014. Implementing lean sigma in an Indian rotary
switches manufacturing organisation. Production Planning & Control, 25(4), pp.288-302.
Zhong, R.Y., Newman, S.T., Huang, G.Q. and Lan, S., 2016. Big Data for supply chain
management in the service and manufacturing sectors: Challenges, opportunities, and future
perspectives. Computers & Industrial Engineering, 101, pp.572-591.
1 out of 23
Related Documents

Your All-in-One AI-Powered Toolkit for Academic Success.
+13062052269
info@desklib.com
Available 24*7 on WhatsApp / Email
Unlock your academic potential
© 2024 | Zucol Services PVT LTD | All rights reserved.