Manufacturing Systems Report: Performance, Flow Analysis, and Layouts
VerifiedAdded on 2023/04/21
|23
|6090
|118
Report
AI Summary
This comprehensive report delves into the intricacies of manufacturing systems, commencing with a review of key performance indicators (KPIs) and their significance in evaluating operational efficiency. It explores approaches to establish performance measures at the shop floor level, emphasizing their implementation to achieve corporate objectives. The report elucidates Product Flow Analysis (PFA) and Value Stream Mapping (VSM) methodologies, illustrating their application with practical examples. It then describes various plant layouts, highlighting their benefits in relation to production varieties, volume, and economies of scale. A critical review and comparison of lean manufacturing tools and techniques are provided, followed by definitions of relevant acronyms. Finally, the report includes a case study analyzing the performance of a manufacturing plant, incorporating data analysis and evaluation to assess its operational effectiveness and identify areas for enhancement. The report is a valuable resource for students studying manufacturing systems, providing a detailed overview of key concepts, methodologies, and practical applications.
Contribute Materials
Your contribution can guide someone’s learning journey. Share your
documents today.
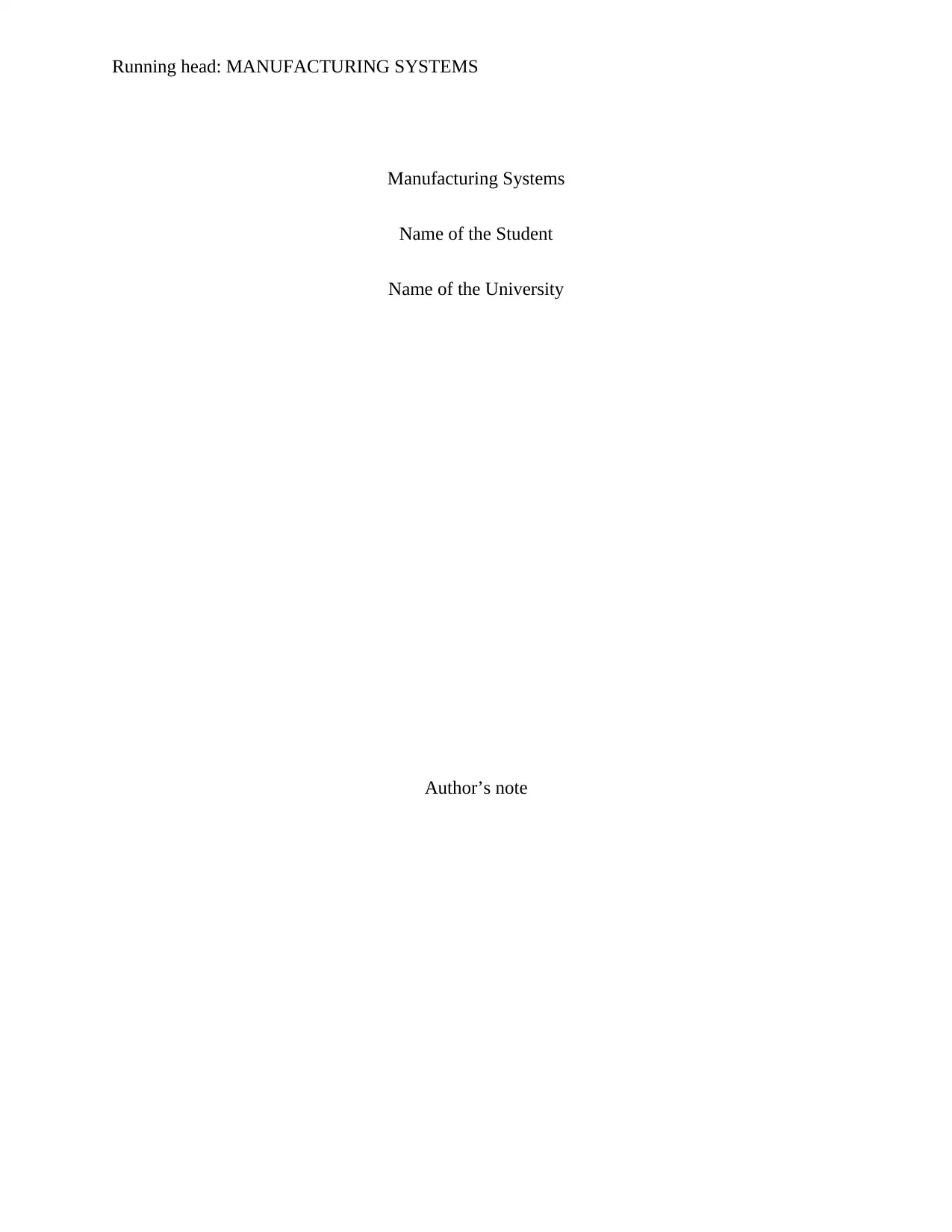
Running head: MANUFACTURING SYSTEMS
Manufacturing Systems
Name of the Student
Name of the University
Author’s note
Manufacturing Systems
Name of the Student
Name of the University
Author’s note
Secure Best Marks with AI Grader
Need help grading? Try our AI Grader for instant feedback on your assignments.
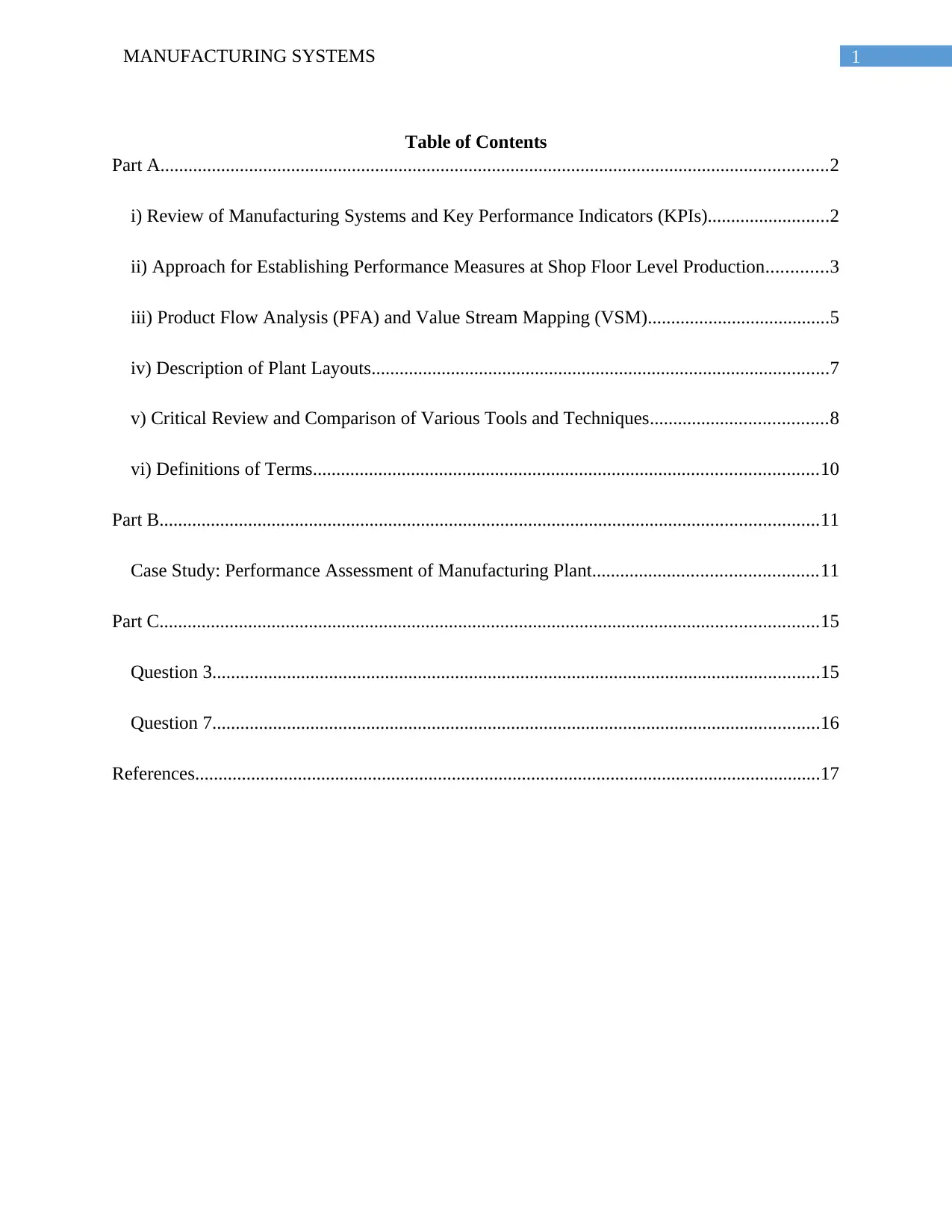
1MANUFACTURING SYSTEMS
Table of Contents
Part A...............................................................................................................................................2
i) Review of Manufacturing Systems and Key Performance Indicators (KPIs)..........................2
ii) Approach for Establishing Performance Measures at Shop Floor Level Production.............3
iii) Product Flow Analysis (PFA) and Value Stream Mapping (VSM).......................................5
iv) Description of Plant Layouts..................................................................................................7
v) Critical Review and Comparison of Various Tools and Techniques......................................8
vi) Definitions of Terms............................................................................................................10
Part B.............................................................................................................................................11
Case Study: Performance Assessment of Manufacturing Plant................................................11
Part C.............................................................................................................................................15
Question 3..................................................................................................................................15
Question 7..................................................................................................................................16
References......................................................................................................................................17
Table of Contents
Part A...............................................................................................................................................2
i) Review of Manufacturing Systems and Key Performance Indicators (KPIs)..........................2
ii) Approach for Establishing Performance Measures at Shop Floor Level Production.............3
iii) Product Flow Analysis (PFA) and Value Stream Mapping (VSM).......................................5
iv) Description of Plant Layouts..................................................................................................7
v) Critical Review and Comparison of Various Tools and Techniques......................................8
vi) Definitions of Terms............................................................................................................10
Part B.............................................................................................................................................11
Case Study: Performance Assessment of Manufacturing Plant................................................11
Part C.............................................................................................................................................15
Question 3..................................................................................................................................15
Question 7..................................................................................................................................16
References......................................................................................................................................17
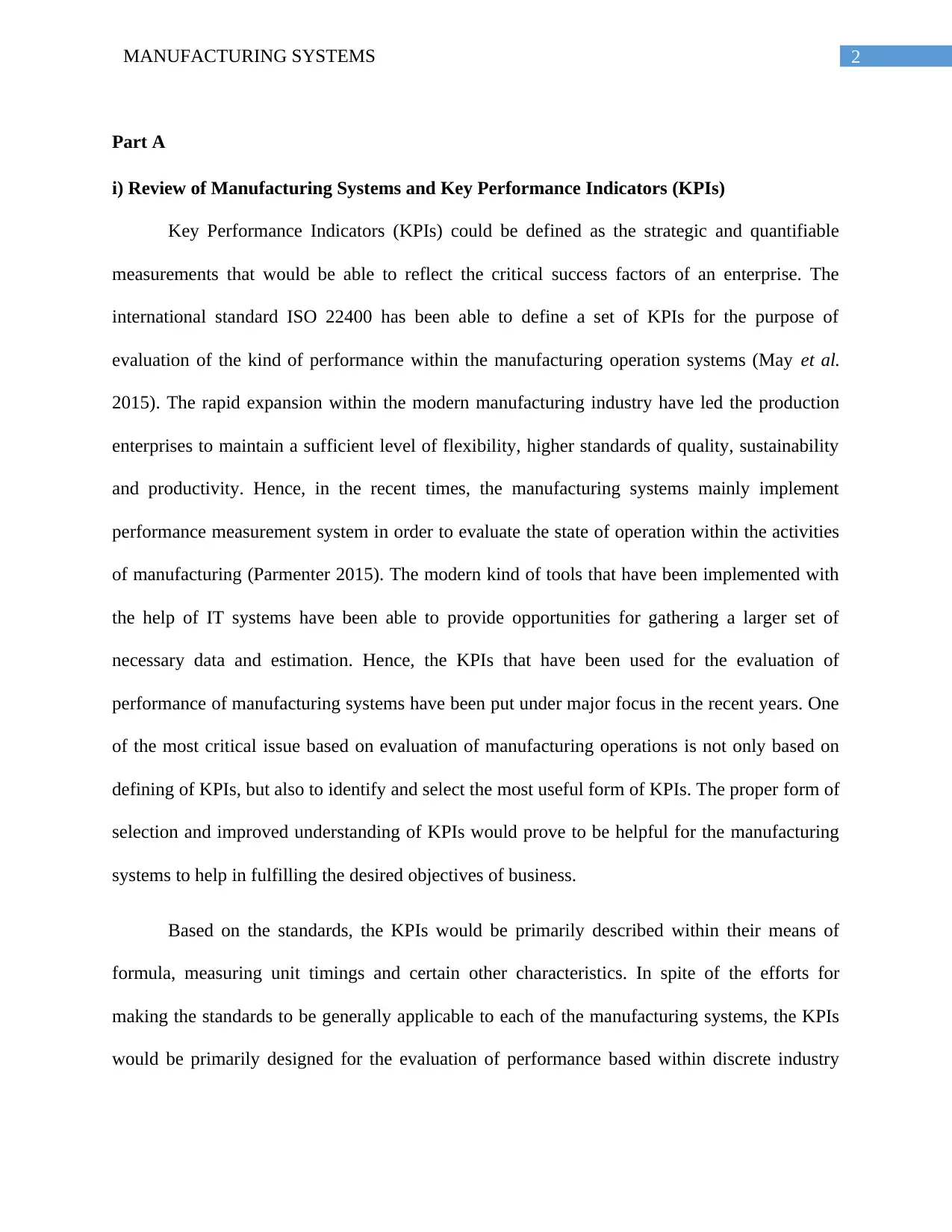
2MANUFACTURING SYSTEMS
Part A
i) Review of Manufacturing Systems and Key Performance Indicators (KPIs)
Key Performance Indicators (KPIs) could be defined as the strategic and quantifiable
measurements that would be able to reflect the critical success factors of an enterprise. The
international standard ISO 22400 has been able to define a set of KPIs for the purpose of
evaluation of the kind of performance within the manufacturing operation systems (May et al.
2015). The rapid expansion within the modern manufacturing industry have led the production
enterprises to maintain a sufficient level of flexibility, higher standards of quality, sustainability
and productivity. Hence, in the recent times, the manufacturing systems mainly implement
performance measurement system in order to evaluate the state of operation within the activities
of manufacturing (Parmenter 2015). The modern kind of tools that have been implemented with
the help of IT systems have been able to provide opportunities for gathering a larger set of
necessary data and estimation. Hence, the KPIs that have been used for the evaluation of
performance of manufacturing systems have been put under major focus in the recent years. One
of the most critical issue based on evaluation of manufacturing operations is not only based on
defining of KPIs, but also to identify and select the most useful form of KPIs. The proper form of
selection and improved understanding of KPIs would prove to be helpful for the manufacturing
systems to help in fulfilling the desired objectives of business.
Based on the standards, the KPIs would be primarily described within their means of
formula, measuring unit timings and certain other characteristics. In spite of the efforts for
making the standards to be generally applicable to each of the manufacturing systems, the KPIs
would be primarily designed for the evaluation of performance based within discrete industry
Part A
i) Review of Manufacturing Systems and Key Performance Indicators (KPIs)
Key Performance Indicators (KPIs) could be defined as the strategic and quantifiable
measurements that would be able to reflect the critical success factors of an enterprise. The
international standard ISO 22400 has been able to define a set of KPIs for the purpose of
evaluation of the kind of performance within the manufacturing operation systems (May et al.
2015). The rapid expansion within the modern manufacturing industry have led the production
enterprises to maintain a sufficient level of flexibility, higher standards of quality, sustainability
and productivity. Hence, in the recent times, the manufacturing systems mainly implement
performance measurement system in order to evaluate the state of operation within the activities
of manufacturing (Parmenter 2015). The modern kind of tools that have been implemented with
the help of IT systems have been able to provide opportunities for gathering a larger set of
necessary data and estimation. Hence, the KPIs that have been used for the evaluation of
performance of manufacturing systems have been put under major focus in the recent years. One
of the most critical issue based on evaluation of manufacturing operations is not only based on
defining of KPIs, but also to identify and select the most useful form of KPIs. The proper form of
selection and improved understanding of KPIs would prove to be helpful for the manufacturing
systems to help in fulfilling the desired objectives of business.
Based on the standards, the KPIs would be primarily described within their means of
formula, measuring unit timings and certain other characteristics. In spite of the efforts for
making the standards to be generally applicable to each of the manufacturing systems, the KPIs
would be primarily designed for the evaluation of performance based within discrete industry
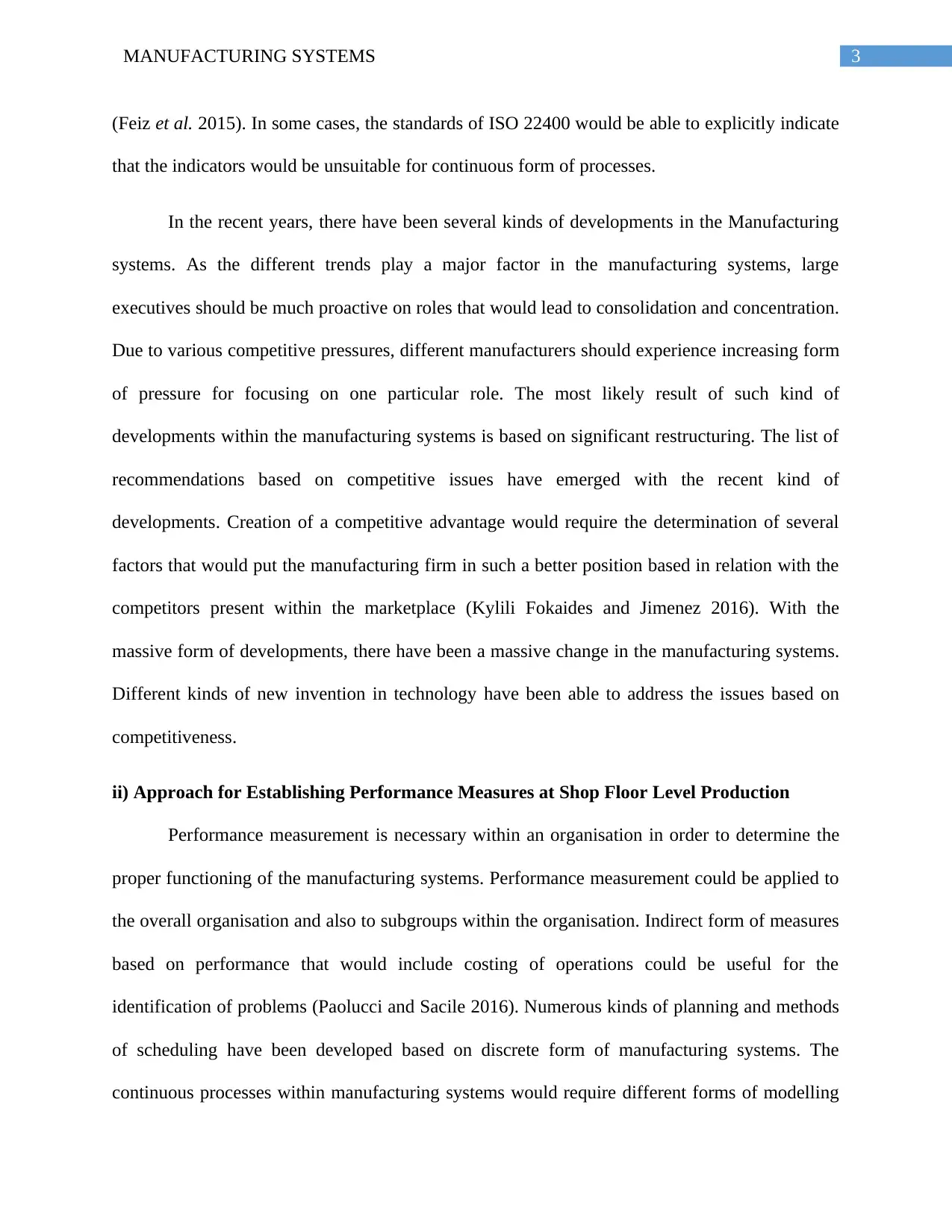
3MANUFACTURING SYSTEMS
(Feiz et al. 2015). In some cases, the standards of ISO 22400 would be able to explicitly indicate
that the indicators would be unsuitable for continuous form of processes.
In the recent years, there have been several kinds of developments in the Manufacturing
systems. As the different trends play a major factor in the manufacturing systems, large
executives should be much proactive on roles that would lead to consolidation and concentration.
Due to various competitive pressures, different manufacturers should experience increasing form
of pressure for focusing on one particular role. The most likely result of such kind of
developments within the manufacturing systems is based on significant restructuring. The list of
recommendations based on competitive issues have emerged with the recent kind of
developments. Creation of a competitive advantage would require the determination of several
factors that would put the manufacturing firm in such a better position based in relation with the
competitors present within the marketplace (Kylili Fokaides and Jimenez 2016). With the
massive form of developments, there have been a massive change in the manufacturing systems.
Different kinds of new invention in technology have been able to address the issues based on
competitiveness.
ii) Approach for Establishing Performance Measures at Shop Floor Level Production
Performance measurement is necessary within an organisation in order to determine the
proper functioning of the manufacturing systems. Performance measurement could be applied to
the overall organisation and also to subgroups within the organisation. Indirect form of measures
based on performance that would include costing of operations could be useful for the
identification of problems (Paolucci and Sacile 2016). Numerous kinds of planning and methods
of scheduling have been developed based on discrete form of manufacturing systems. The
continuous processes within manufacturing systems would require different forms of modelling
(Feiz et al. 2015). In some cases, the standards of ISO 22400 would be able to explicitly indicate
that the indicators would be unsuitable for continuous form of processes.
In the recent years, there have been several kinds of developments in the Manufacturing
systems. As the different trends play a major factor in the manufacturing systems, large
executives should be much proactive on roles that would lead to consolidation and concentration.
Due to various competitive pressures, different manufacturers should experience increasing form
of pressure for focusing on one particular role. The most likely result of such kind of
developments within the manufacturing systems is based on significant restructuring. The list of
recommendations based on competitive issues have emerged with the recent kind of
developments. Creation of a competitive advantage would require the determination of several
factors that would put the manufacturing firm in such a better position based in relation with the
competitors present within the marketplace (Kylili Fokaides and Jimenez 2016). With the
massive form of developments, there have been a massive change in the manufacturing systems.
Different kinds of new invention in technology have been able to address the issues based on
competitiveness.
ii) Approach for Establishing Performance Measures at Shop Floor Level Production
Performance measurement is necessary within an organisation in order to determine the
proper functioning of the manufacturing systems. Performance measurement could be applied to
the overall organisation and also to subgroups within the organisation. Indirect form of measures
based on performance that would include costing of operations could be useful for the
identification of problems (Paolucci and Sacile 2016). Numerous kinds of planning and methods
of scheduling have been developed based on discrete form of manufacturing systems. The
continuous processes within manufacturing systems would require different forms of modelling
Secure Best Marks with AI Grader
Need help grading? Try our AI Grader for instant feedback on your assignments.
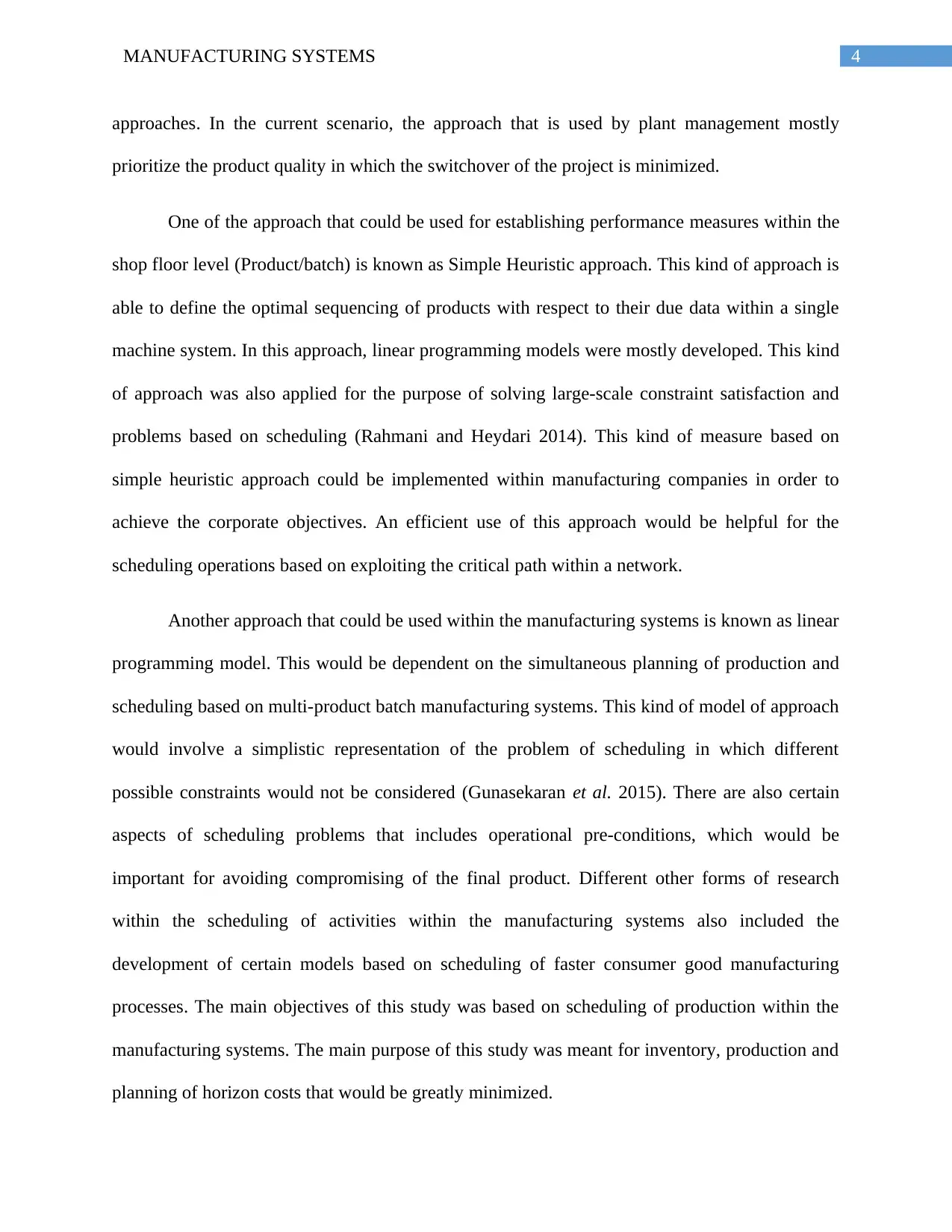
4MANUFACTURING SYSTEMS
approaches. In the current scenario, the approach that is used by plant management mostly
prioritize the product quality in which the switchover of the project is minimized.
One of the approach that could be used for establishing performance measures within the
shop floor level (Product/batch) is known as Simple Heuristic approach. This kind of approach is
able to define the optimal sequencing of products with respect to their due data within a single
machine system. In this approach, linear programming models were mostly developed. This kind
of approach was also applied for the purpose of solving large-scale constraint satisfaction and
problems based on scheduling (Rahmani and Heydari 2014). This kind of measure based on
simple heuristic approach could be implemented within manufacturing companies in order to
achieve the corporate objectives. An efficient use of this approach would be helpful for the
scheduling operations based on exploiting the critical path within a network.
Another approach that could be used within the manufacturing systems is known as linear
programming model. This would be dependent on the simultaneous planning of production and
scheduling based on multi-product batch manufacturing systems. This kind of model of approach
would involve a simplistic representation of the problem of scheduling in which different
possible constraints would not be considered (Gunasekaran et al. 2015). There are also certain
aspects of scheduling problems that includes operational pre-conditions, which would be
important for avoiding compromising of the final product. Different other forms of research
within the scheduling of activities within the manufacturing systems also included the
development of certain models based on scheduling of faster consumer good manufacturing
processes. The main objectives of this study was based on scheduling of production within the
manufacturing systems. The main purpose of this study was meant for inventory, production and
planning of horizon costs that would be greatly minimized.
approaches. In the current scenario, the approach that is used by plant management mostly
prioritize the product quality in which the switchover of the project is minimized.
One of the approach that could be used for establishing performance measures within the
shop floor level (Product/batch) is known as Simple Heuristic approach. This kind of approach is
able to define the optimal sequencing of products with respect to their due data within a single
machine system. In this approach, linear programming models were mostly developed. This kind
of approach was also applied for the purpose of solving large-scale constraint satisfaction and
problems based on scheduling (Rahmani and Heydari 2014). This kind of measure based on
simple heuristic approach could be implemented within manufacturing companies in order to
achieve the corporate objectives. An efficient use of this approach would be helpful for the
scheduling operations based on exploiting the critical path within a network.
Another approach that could be used within the manufacturing systems is known as linear
programming model. This would be dependent on the simultaneous planning of production and
scheduling based on multi-product batch manufacturing systems. This kind of model of approach
would involve a simplistic representation of the problem of scheduling in which different
possible constraints would not be considered (Gunasekaran et al. 2015). There are also certain
aspects of scheduling problems that includes operational pre-conditions, which would be
important for avoiding compromising of the final product. Different other forms of research
within the scheduling of activities within the manufacturing systems also included the
development of certain models based on scheduling of faster consumer good manufacturing
processes. The main objectives of this study was based on scheduling of production within the
manufacturing systems. The main purpose of this study was meant for inventory, production and
planning of horizon costs that would be greatly minimized.
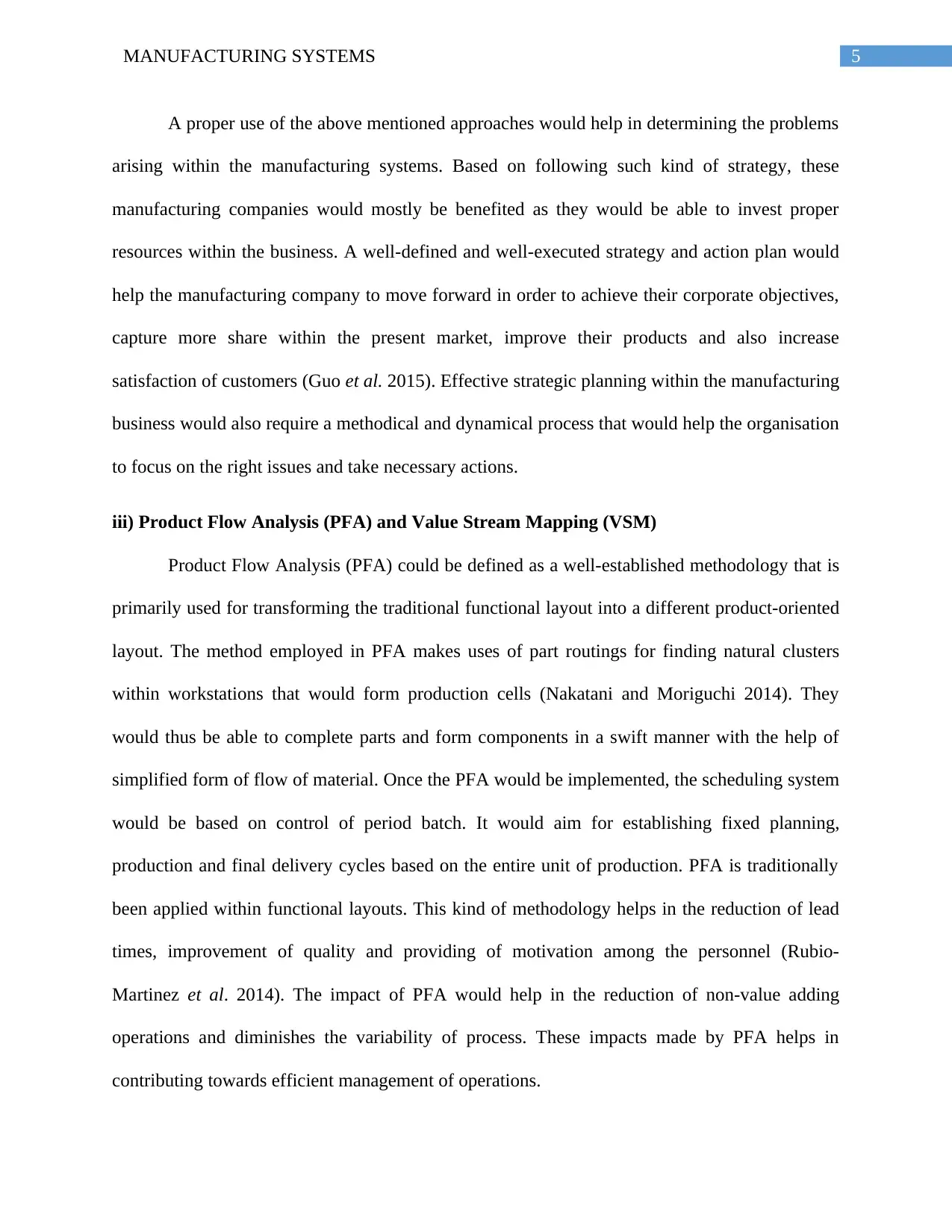
5MANUFACTURING SYSTEMS
A proper use of the above mentioned approaches would help in determining the problems
arising within the manufacturing systems. Based on following such kind of strategy, these
manufacturing companies would mostly be benefited as they would be able to invest proper
resources within the business. A well-defined and well-executed strategy and action plan would
help the manufacturing company to move forward in order to achieve their corporate objectives,
capture more share within the present market, improve their products and also increase
satisfaction of customers (Guo et al. 2015). Effective strategic planning within the manufacturing
business would also require a methodical and dynamical process that would help the organisation
to focus on the right issues and take necessary actions.
iii) Product Flow Analysis (PFA) and Value Stream Mapping (VSM)
Product Flow Analysis (PFA) could be defined as a well-established methodology that is
primarily used for transforming the traditional functional layout into a different product-oriented
layout. The method employed in PFA makes uses of part routings for finding natural clusters
within workstations that would form production cells (Nakatani and Moriguchi 2014). They
would thus be able to complete parts and form components in a swift manner with the help of
simplified form of flow of material. Once the PFA would be implemented, the scheduling system
would be based on control of period batch. It would aim for establishing fixed planning,
production and final delivery cycles based on the entire unit of production. PFA is traditionally
been applied within functional layouts. This kind of methodology helps in the reduction of lead
times, improvement of quality and providing of motivation among the personnel (Rubio-
Martinez et al. 2014). The impact of PFA would help in the reduction of non-value adding
operations and diminishes the variability of process. These impacts made by PFA helps in
contributing towards efficient management of operations.
A proper use of the above mentioned approaches would help in determining the problems
arising within the manufacturing systems. Based on following such kind of strategy, these
manufacturing companies would mostly be benefited as they would be able to invest proper
resources within the business. A well-defined and well-executed strategy and action plan would
help the manufacturing company to move forward in order to achieve their corporate objectives,
capture more share within the present market, improve their products and also increase
satisfaction of customers (Guo et al. 2015). Effective strategic planning within the manufacturing
business would also require a methodical and dynamical process that would help the organisation
to focus on the right issues and take necessary actions.
iii) Product Flow Analysis (PFA) and Value Stream Mapping (VSM)
Product Flow Analysis (PFA) could be defined as a well-established methodology that is
primarily used for transforming the traditional functional layout into a different product-oriented
layout. The method employed in PFA makes uses of part routings for finding natural clusters
within workstations that would form production cells (Nakatani and Moriguchi 2014). They
would thus be able to complete parts and form components in a swift manner with the help of
simplified form of flow of material. Once the PFA would be implemented, the scheduling system
would be based on control of period batch. It would aim for establishing fixed planning,
production and final delivery cycles based on the entire unit of production. PFA is traditionally
been applied within functional layouts. This kind of methodology helps in the reduction of lead
times, improvement of quality and providing of motivation among the personnel (Rubio-
Martinez et al. 2014). The impact of PFA would help in the reduction of non-value adding
operations and diminishes the variability of process. These impacts made by PFA helps in
contributing towards efficient management of operations.
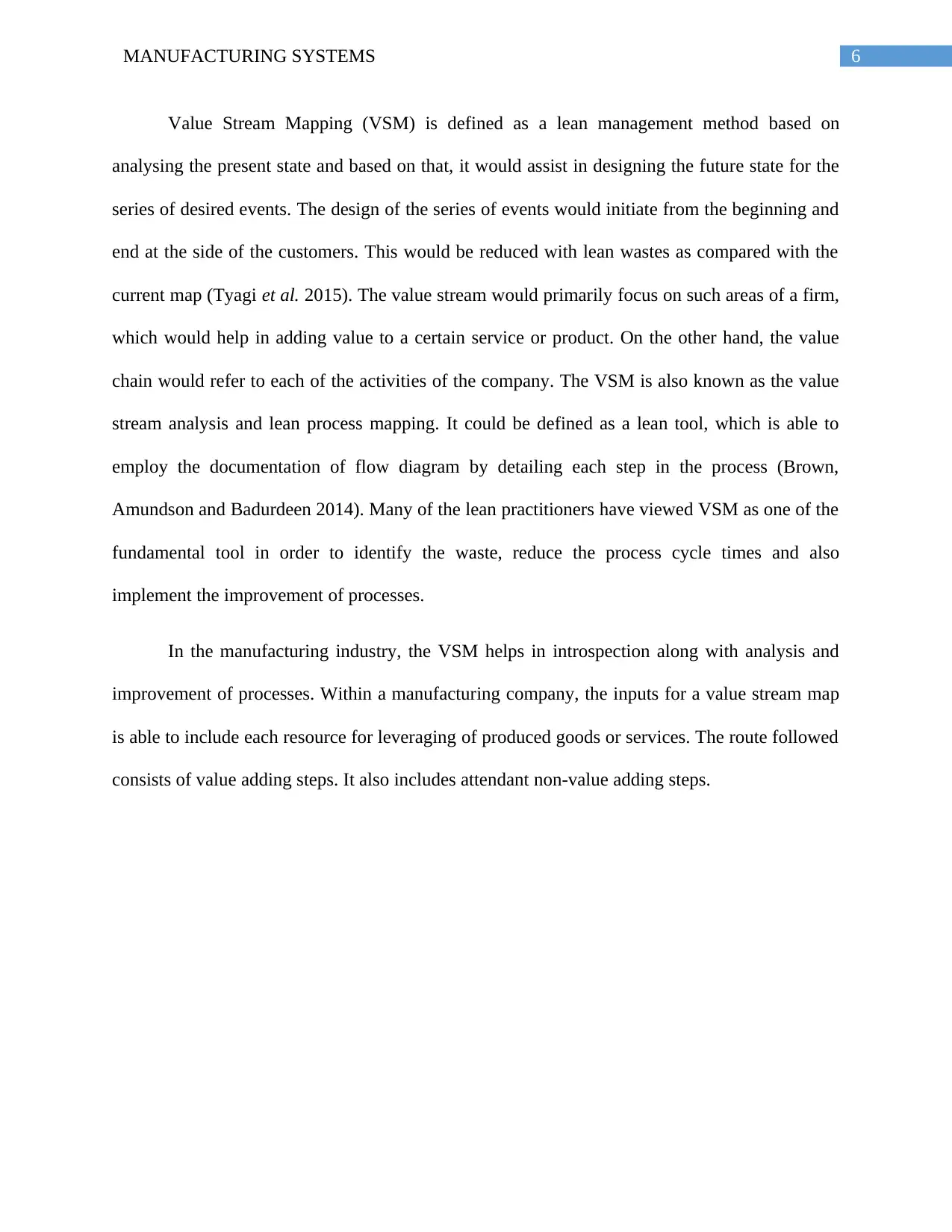
6MANUFACTURING SYSTEMS
Value Stream Mapping (VSM) is defined as a lean management method based on
analysing the present state and based on that, it would assist in designing the future state for the
series of desired events. The design of the series of events would initiate from the beginning and
end at the side of the customers. This would be reduced with lean wastes as compared with the
current map (Tyagi et al. 2015). The value stream would primarily focus on such areas of a firm,
which would help in adding value to a certain service or product. On the other hand, the value
chain would refer to each of the activities of the company. The VSM is also known as the value
stream analysis and lean process mapping. It could be defined as a lean tool, which is able to
employ the documentation of flow diagram by detailing each step in the process (Brown,
Amundson and Badurdeen 2014). Many of the lean practitioners have viewed VSM as one of the
fundamental tool in order to identify the waste, reduce the process cycle times and also
implement the improvement of processes.
In the manufacturing industry, the VSM helps in introspection along with analysis and
improvement of processes. Within a manufacturing company, the inputs for a value stream map
is able to include each resource for leveraging of produced goods or services. The route followed
consists of value adding steps. It also includes attendant non-value adding steps.
Value Stream Mapping (VSM) is defined as a lean management method based on
analysing the present state and based on that, it would assist in designing the future state for the
series of desired events. The design of the series of events would initiate from the beginning and
end at the side of the customers. This would be reduced with lean wastes as compared with the
current map (Tyagi et al. 2015). The value stream would primarily focus on such areas of a firm,
which would help in adding value to a certain service or product. On the other hand, the value
chain would refer to each of the activities of the company. The VSM is also known as the value
stream analysis and lean process mapping. It could be defined as a lean tool, which is able to
employ the documentation of flow diagram by detailing each step in the process (Brown,
Amundson and Badurdeen 2014). Many of the lean practitioners have viewed VSM as one of the
fundamental tool in order to identify the waste, reduce the process cycle times and also
implement the improvement of processes.
In the manufacturing industry, the VSM helps in introspection along with analysis and
improvement of processes. Within a manufacturing company, the inputs for a value stream map
is able to include each resource for leveraging of produced goods or services. The route followed
consists of value adding steps. It also includes attendant non-value adding steps.
Paraphrase This Document
Need a fresh take? Get an instant paraphrase of this document with our AI Paraphraser
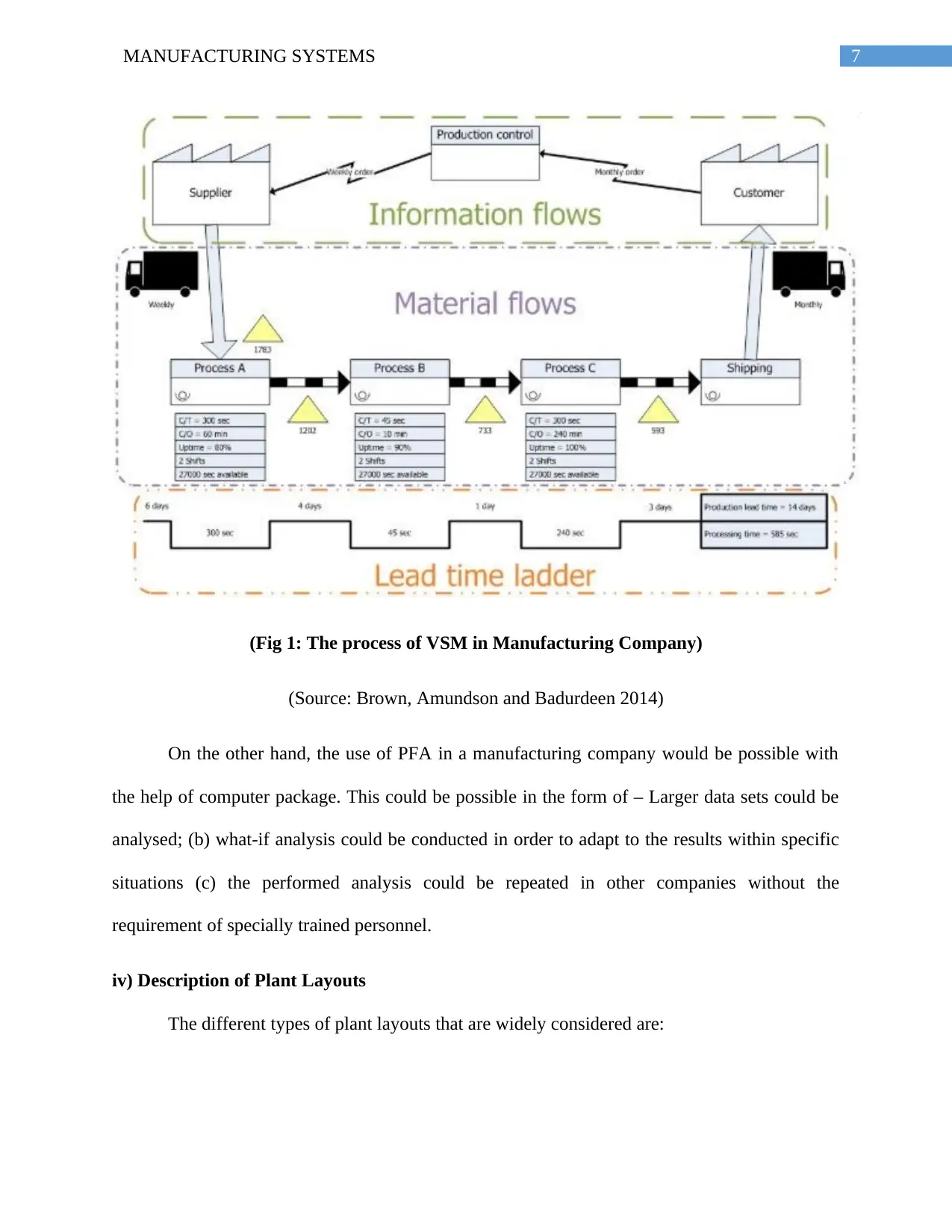
7MANUFACTURING SYSTEMS
(Fig 1: The process of VSM in Manufacturing Company)
(Source: Brown, Amundson and Badurdeen 2014)
On the other hand, the use of PFA in a manufacturing company would be possible with
the help of computer package. This could be possible in the form of – Larger data sets could be
analysed; (b) what-if analysis could be conducted in order to adapt to the results within specific
situations (c) the performed analysis could be repeated in other companies without the
requirement of specially trained personnel.
iv) Description of Plant Layouts
The different types of plant layouts that are widely considered are:
(Fig 1: The process of VSM in Manufacturing Company)
(Source: Brown, Amundson and Badurdeen 2014)
On the other hand, the use of PFA in a manufacturing company would be possible with
the help of computer package. This could be possible in the form of – Larger data sets could be
analysed; (b) what-if analysis could be conducted in order to adapt to the results within specific
situations (c) the performed analysis could be repeated in other companies without the
requirement of specially trained personnel.
iv) Description of Plant Layouts
The different types of plant layouts that are widely considered are:
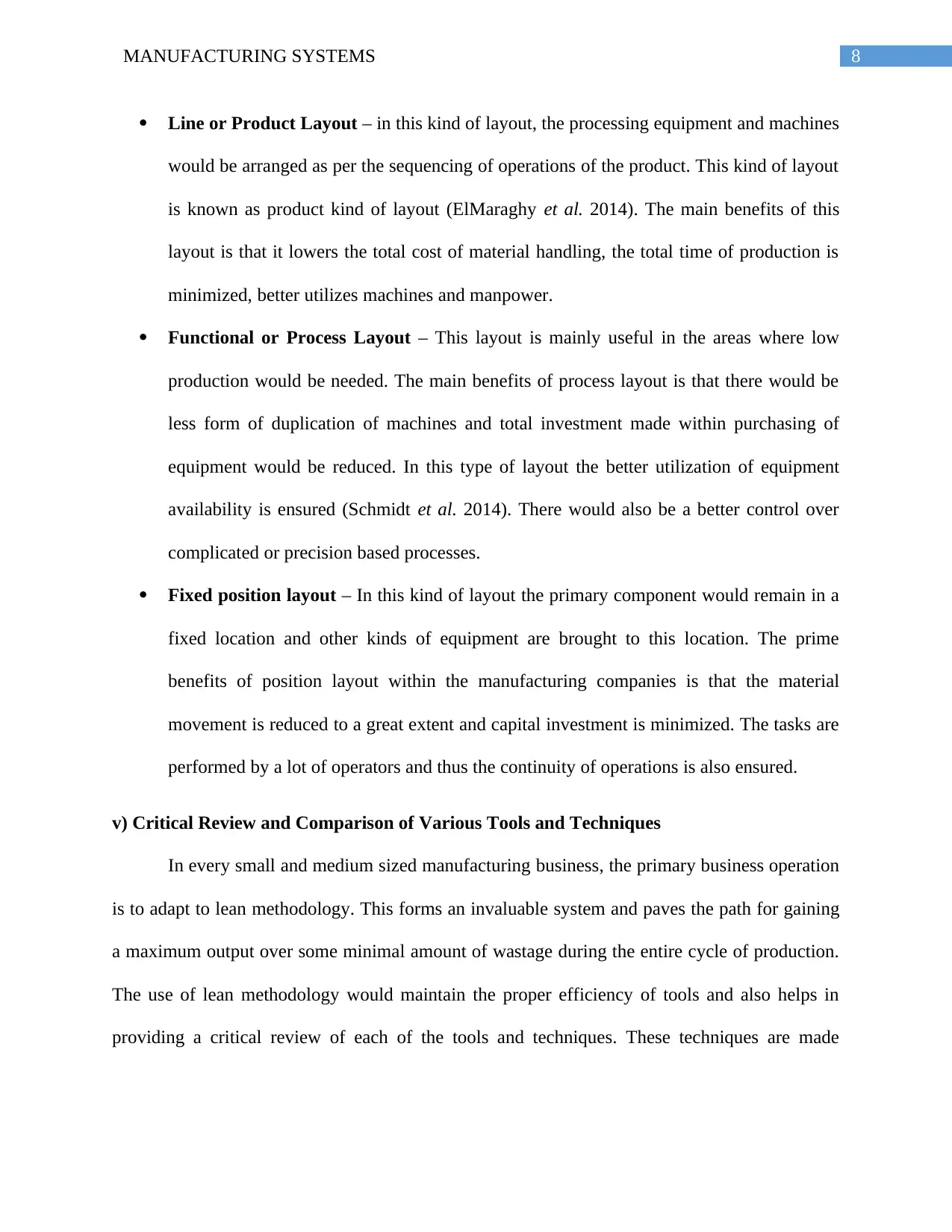
8MANUFACTURING SYSTEMS
Line or Product Layout – in this kind of layout, the processing equipment and machines
would be arranged as per the sequencing of operations of the product. This kind of layout
is known as product kind of layout (ElMaraghy et al. 2014). The main benefits of this
layout is that it lowers the total cost of material handling, the total time of production is
minimized, better utilizes machines and manpower.
Functional or Process Layout – This layout is mainly useful in the areas where low
production would be needed. The main benefits of process layout is that there would be
less form of duplication of machines and total investment made within purchasing of
equipment would be reduced. In this type of layout the better utilization of equipment
availability is ensured (Schmidt et al. 2014). There would also be a better control over
complicated or precision based processes.
Fixed position layout – In this kind of layout the primary component would remain in a
fixed location and other kinds of equipment are brought to this location. The prime
benefits of position layout within the manufacturing companies is that the material
movement is reduced to a great extent and capital investment is minimized. The tasks are
performed by a lot of operators and thus the continuity of operations is also ensured.
v) Critical Review and Comparison of Various Tools and Techniques
In every small and medium sized manufacturing business, the primary business operation
is to adapt to lean methodology. This forms an invaluable system and paves the path for gaining
a maximum output over some minimal amount of wastage during the entire cycle of production.
The use of lean methodology would maintain the proper efficiency of tools and also helps in
providing a critical review of each of the tools and techniques. These techniques are made
Line or Product Layout – in this kind of layout, the processing equipment and machines
would be arranged as per the sequencing of operations of the product. This kind of layout
is known as product kind of layout (ElMaraghy et al. 2014). The main benefits of this
layout is that it lowers the total cost of material handling, the total time of production is
minimized, better utilizes machines and manpower.
Functional or Process Layout – This layout is mainly useful in the areas where low
production would be needed. The main benefits of process layout is that there would be
less form of duplication of machines and total investment made within purchasing of
equipment would be reduced. In this type of layout the better utilization of equipment
availability is ensured (Schmidt et al. 2014). There would also be a better control over
complicated or precision based processes.
Fixed position layout – In this kind of layout the primary component would remain in a
fixed location and other kinds of equipment are brought to this location. The prime
benefits of position layout within the manufacturing companies is that the material
movement is reduced to a great extent and capital investment is minimized. The tasks are
performed by a lot of operators and thus the continuity of operations is also ensured.
v) Critical Review and Comparison of Various Tools and Techniques
In every small and medium sized manufacturing business, the primary business operation
is to adapt to lean methodology. This forms an invaluable system and paves the path for gaining
a maximum output over some minimal amount of wastage during the entire cycle of production.
The use of lean methodology would maintain the proper efficiency of tools and also helps in
providing a critical review of each of the tools and techniques. These techniques are made
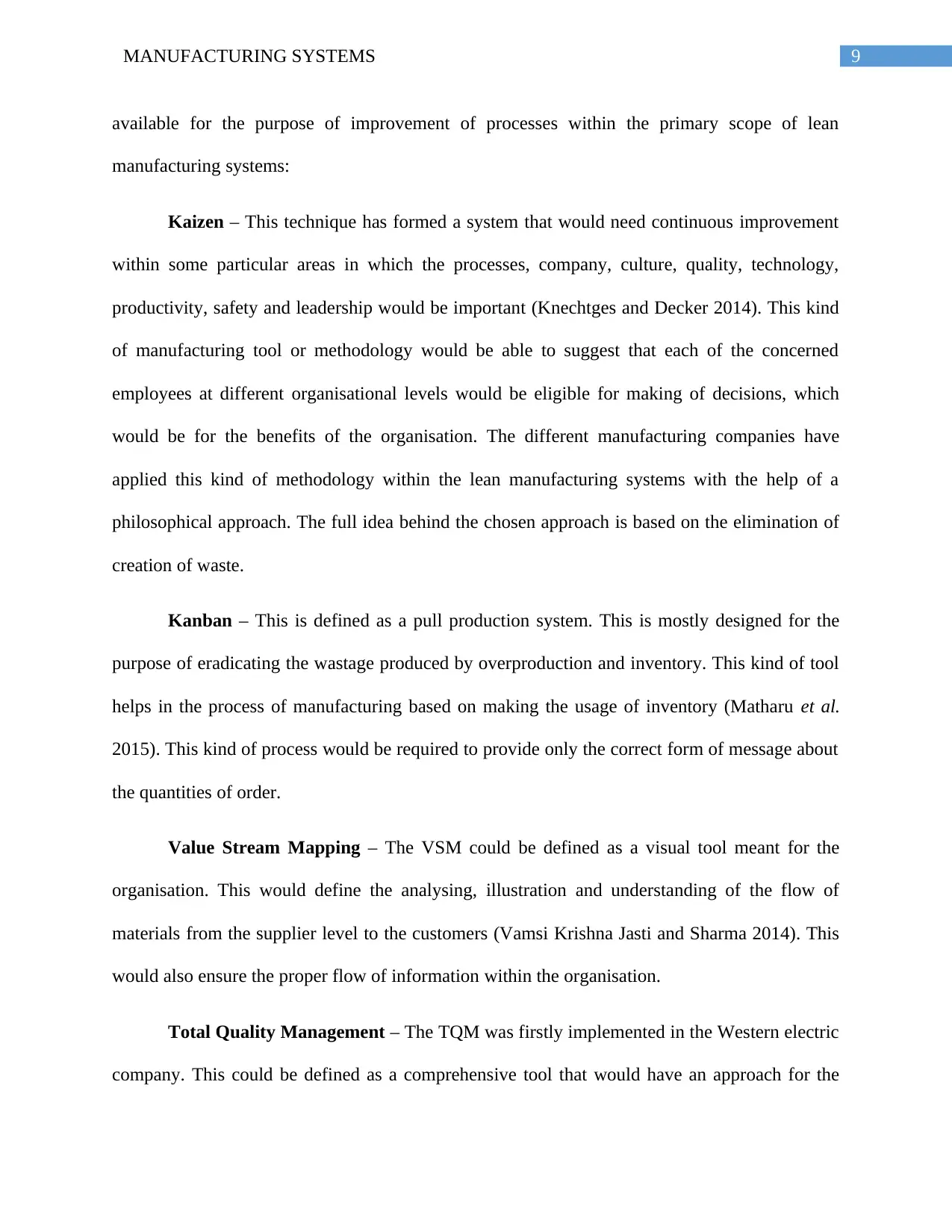
9MANUFACTURING SYSTEMS
available for the purpose of improvement of processes within the primary scope of lean
manufacturing systems:
Kaizen – This technique has formed a system that would need continuous improvement
within some particular areas in which the processes, company, culture, quality, technology,
productivity, safety and leadership would be important (Knechtges and Decker 2014). This kind
of manufacturing tool or methodology would be able to suggest that each of the concerned
employees at different organisational levels would be eligible for making of decisions, which
would be for the benefits of the organisation. The different manufacturing companies have
applied this kind of methodology within the lean manufacturing systems with the help of a
philosophical approach. The full idea behind the chosen approach is based on the elimination of
creation of waste.
Kanban – This is defined as a pull production system. This is mostly designed for the
purpose of eradicating the wastage produced by overproduction and inventory. This kind of tool
helps in the process of manufacturing based on making the usage of inventory (Matharu et al.
2015). This kind of process would be required to provide only the correct form of message about
the quantities of order.
Value Stream Mapping – The VSM could be defined as a visual tool meant for the
organisation. This would define the analysing, illustration and understanding of the flow of
materials from the supplier level to the customers (Vamsi Krishna Jasti and Sharma 2014). This
would also ensure the proper flow of information within the organisation.
Total Quality Management – The TQM was firstly implemented in the Western electric
company. This could be defined as a comprehensive tool that would have an approach for the
available for the purpose of improvement of processes within the primary scope of lean
manufacturing systems:
Kaizen – This technique has formed a system that would need continuous improvement
within some particular areas in which the processes, company, culture, quality, technology,
productivity, safety and leadership would be important (Knechtges and Decker 2014). This kind
of manufacturing tool or methodology would be able to suggest that each of the concerned
employees at different organisational levels would be eligible for making of decisions, which
would be for the benefits of the organisation. The different manufacturing companies have
applied this kind of methodology within the lean manufacturing systems with the help of a
philosophical approach. The full idea behind the chosen approach is based on the elimination of
creation of waste.
Kanban – This is defined as a pull production system. This is mostly designed for the
purpose of eradicating the wastage produced by overproduction and inventory. This kind of tool
helps in the process of manufacturing based on making the usage of inventory (Matharu et al.
2015). This kind of process would be required to provide only the correct form of message about
the quantities of order.
Value Stream Mapping – The VSM could be defined as a visual tool meant for the
organisation. This would define the analysing, illustration and understanding of the flow of
materials from the supplier level to the customers (Vamsi Krishna Jasti and Sharma 2014). This
would also ensure the proper flow of information within the organisation.
Total Quality Management – The TQM was firstly implemented in the Western electric
company. This could be defined as a comprehensive tool that would have an approach for the
Secure Best Marks with AI Grader
Need help grading? Try our AI Grader for instant feedback on your assignments.
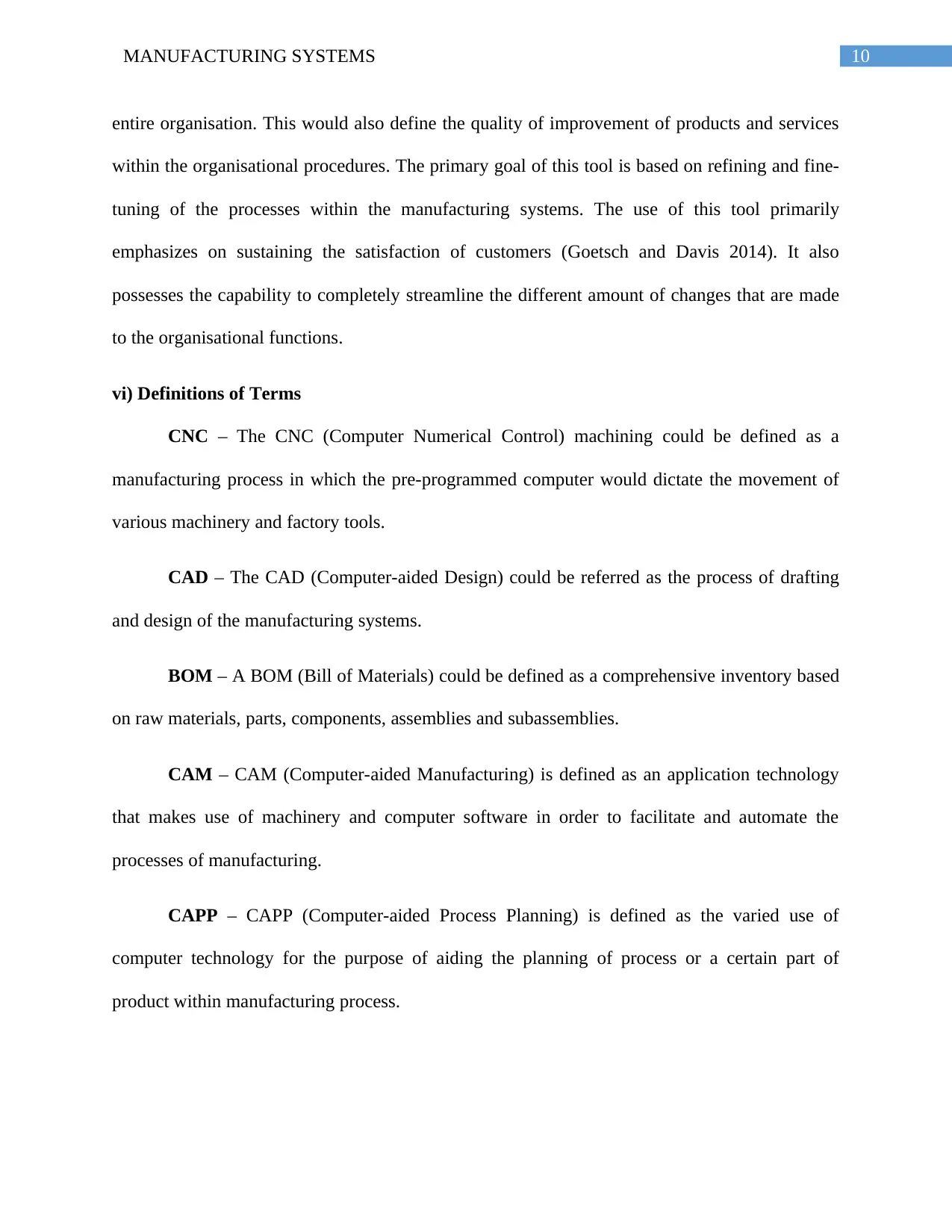
10MANUFACTURING SYSTEMS
entire organisation. This would also define the quality of improvement of products and services
within the organisational procedures. The primary goal of this tool is based on refining and fine-
tuning of the processes within the manufacturing systems. The use of this tool primarily
emphasizes on sustaining the satisfaction of customers (Goetsch and Davis 2014). It also
possesses the capability to completely streamline the different amount of changes that are made
to the organisational functions.
vi) Definitions of Terms
CNC – The CNC (Computer Numerical Control) machining could be defined as a
manufacturing process in which the pre-programmed computer would dictate the movement of
various machinery and factory tools.
CAD – The CAD (Computer-aided Design) could be referred as the process of drafting
and design of the manufacturing systems.
BOM – A BOM (Bill of Materials) could be defined as a comprehensive inventory based
on raw materials, parts, components, assemblies and subassemblies.
CAM – CAM (Computer-aided Manufacturing) is defined as an application technology
that makes use of machinery and computer software in order to facilitate and automate the
processes of manufacturing.
CAPP – CAPP (Computer-aided Process Planning) is defined as the varied use of
computer technology for the purpose of aiding the planning of process or a certain part of
product within manufacturing process.
entire organisation. This would also define the quality of improvement of products and services
within the organisational procedures. The primary goal of this tool is based on refining and fine-
tuning of the processes within the manufacturing systems. The use of this tool primarily
emphasizes on sustaining the satisfaction of customers (Goetsch and Davis 2014). It also
possesses the capability to completely streamline the different amount of changes that are made
to the organisational functions.
vi) Definitions of Terms
CNC – The CNC (Computer Numerical Control) machining could be defined as a
manufacturing process in which the pre-programmed computer would dictate the movement of
various machinery and factory tools.
CAD – The CAD (Computer-aided Design) could be referred as the process of drafting
and design of the manufacturing systems.
BOM – A BOM (Bill of Materials) could be defined as a comprehensive inventory based
on raw materials, parts, components, assemblies and subassemblies.
CAM – CAM (Computer-aided Manufacturing) is defined as an application technology
that makes use of machinery and computer software in order to facilitate and automate the
processes of manufacturing.
CAPP – CAPP (Computer-aided Process Planning) is defined as the varied use of
computer technology for the purpose of aiding the planning of process or a certain part of
product within manufacturing process.
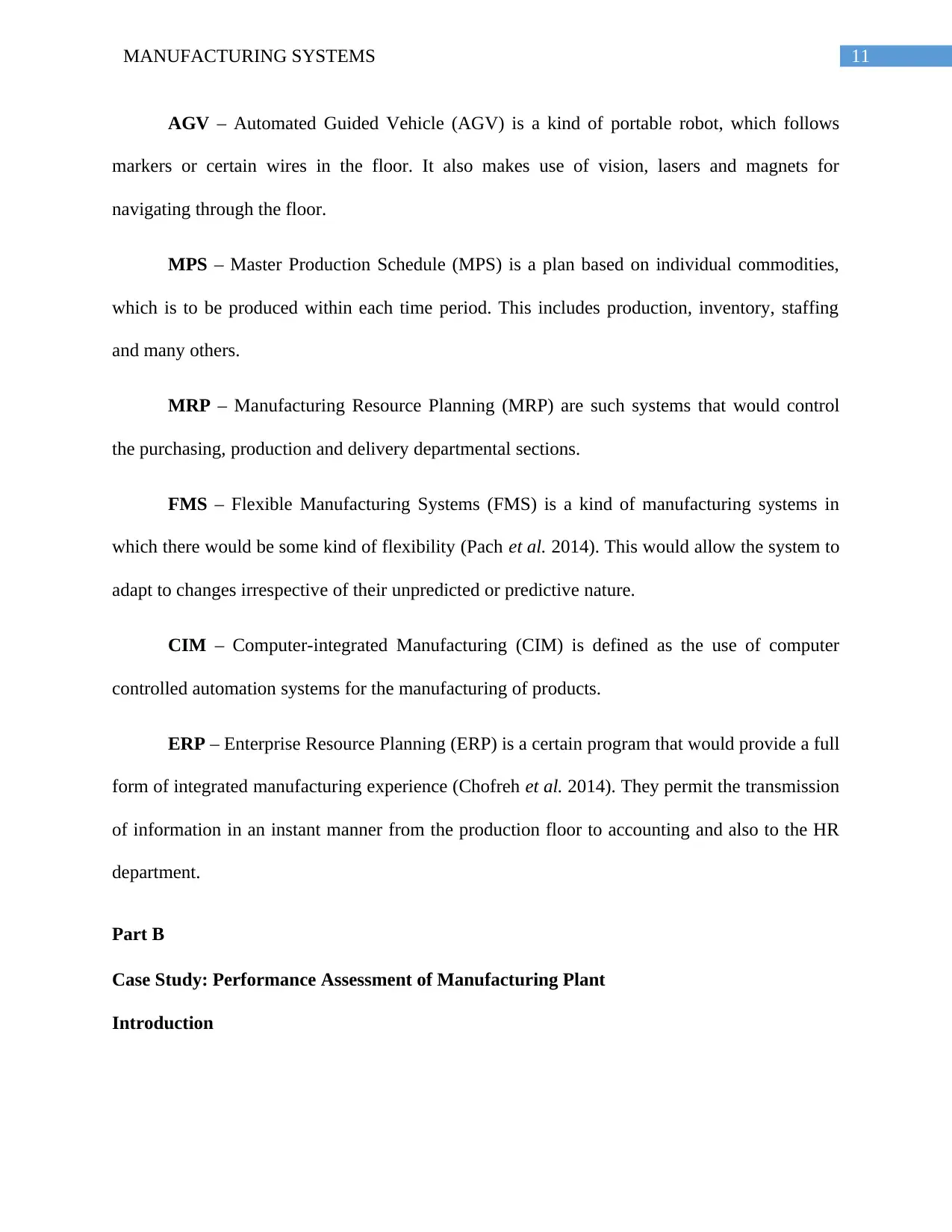
11MANUFACTURING SYSTEMS
AGV – Automated Guided Vehicle (AGV) is a kind of portable robot, which follows
markers or certain wires in the floor. It also makes use of vision, lasers and magnets for
navigating through the floor.
MPS – Master Production Schedule (MPS) is a plan based on individual commodities,
which is to be produced within each time period. This includes production, inventory, staffing
and many others.
MRP – Manufacturing Resource Planning (MRP) are such systems that would control
the purchasing, production and delivery departmental sections.
FMS – Flexible Manufacturing Systems (FMS) is a kind of manufacturing systems in
which there would be some kind of flexibility (Pach et al. 2014). This would allow the system to
adapt to changes irrespective of their unpredicted or predictive nature.
CIM – Computer-integrated Manufacturing (CIM) is defined as the use of computer
controlled automation systems for the manufacturing of products.
ERP – Enterprise Resource Planning (ERP) is a certain program that would provide a full
form of integrated manufacturing experience (Chofreh et al. 2014). They permit the transmission
of information in an instant manner from the production floor to accounting and also to the HR
department.
Part B
Case Study: Performance Assessment of Manufacturing Plant
Introduction
AGV – Automated Guided Vehicle (AGV) is a kind of portable robot, which follows
markers or certain wires in the floor. It also makes use of vision, lasers and magnets for
navigating through the floor.
MPS – Master Production Schedule (MPS) is a plan based on individual commodities,
which is to be produced within each time period. This includes production, inventory, staffing
and many others.
MRP – Manufacturing Resource Planning (MRP) are such systems that would control
the purchasing, production and delivery departmental sections.
FMS – Flexible Manufacturing Systems (FMS) is a kind of manufacturing systems in
which there would be some kind of flexibility (Pach et al. 2014). This would allow the system to
adapt to changes irrespective of their unpredicted or predictive nature.
CIM – Computer-integrated Manufacturing (CIM) is defined as the use of computer
controlled automation systems for the manufacturing of products.
ERP – Enterprise Resource Planning (ERP) is a certain program that would provide a full
form of integrated manufacturing experience (Chofreh et al. 2014). They permit the transmission
of information in an instant manner from the production floor to accounting and also to the HR
department.
Part B
Case Study: Performance Assessment of Manufacturing Plant
Introduction
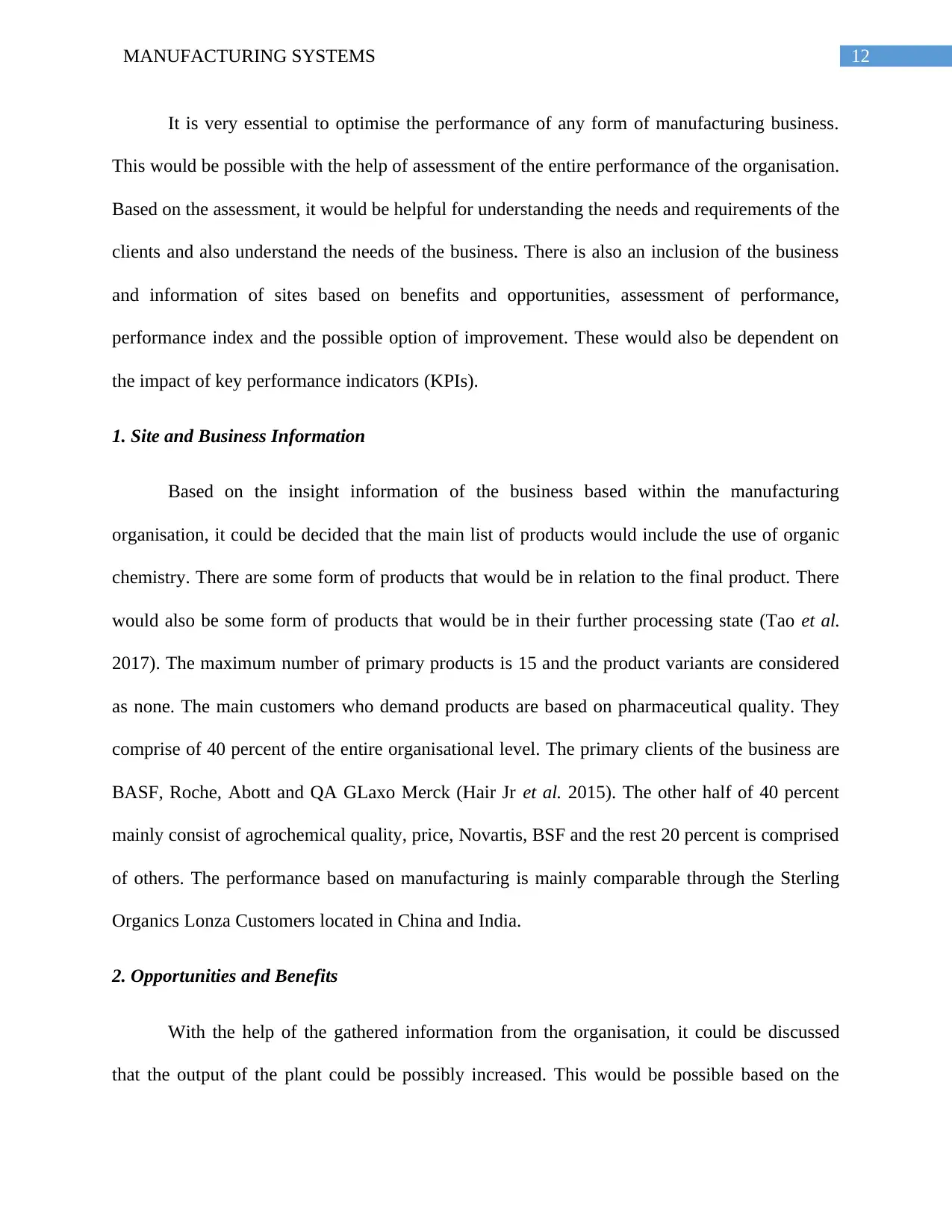
12MANUFACTURING SYSTEMS
It is very essential to optimise the performance of any form of manufacturing business.
This would be possible with the help of assessment of the entire performance of the organisation.
Based on the assessment, it would be helpful for understanding the needs and requirements of the
clients and also understand the needs of the business. There is also an inclusion of the business
and information of sites based on benefits and opportunities, assessment of performance,
performance index and the possible option of improvement. These would also be dependent on
the impact of key performance indicators (KPIs).
1. Site and Business Information
Based on the insight information of the business based within the manufacturing
organisation, it could be decided that the main list of products would include the use of organic
chemistry. There are some form of products that would be in relation to the final product. There
would also be some form of products that would be in their further processing state (Tao et al.
2017). The maximum number of primary products is 15 and the product variants are considered
as none. The main customers who demand products are based on pharmaceutical quality. They
comprise of 40 percent of the entire organisational level. The primary clients of the business are
BASF, Roche, Abott and QA GLaxo Merck (Hair Jr et al. 2015). The other half of 40 percent
mainly consist of agrochemical quality, price, Novartis, BSF and the rest 20 percent is comprised
of others. The performance based on manufacturing is mainly comparable through the Sterling
Organics Lonza Customers located in China and India.
2. Opportunities and Benefits
With the help of the gathered information from the organisation, it could be discussed
that the output of the plant could be possibly increased. This would be possible based on the
It is very essential to optimise the performance of any form of manufacturing business.
This would be possible with the help of assessment of the entire performance of the organisation.
Based on the assessment, it would be helpful for understanding the needs and requirements of the
clients and also understand the needs of the business. There is also an inclusion of the business
and information of sites based on benefits and opportunities, assessment of performance,
performance index and the possible option of improvement. These would also be dependent on
the impact of key performance indicators (KPIs).
1. Site and Business Information
Based on the insight information of the business based within the manufacturing
organisation, it could be decided that the main list of products would include the use of organic
chemistry. There are some form of products that would be in relation to the final product. There
would also be some form of products that would be in their further processing state (Tao et al.
2017). The maximum number of primary products is 15 and the product variants are considered
as none. The main customers who demand products are based on pharmaceutical quality. They
comprise of 40 percent of the entire organisational level. The primary clients of the business are
BASF, Roche, Abott and QA GLaxo Merck (Hair Jr et al. 2015). The other half of 40 percent
mainly consist of agrochemical quality, price, Novartis, BSF and the rest 20 percent is comprised
of others. The performance based on manufacturing is mainly comparable through the Sterling
Organics Lonza Customers located in China and India.
2. Opportunities and Benefits
With the help of the gathered information from the organisation, it could be discussed
that the output of the plant could be possibly increased. This would be possible based on the
Paraphrase This Document
Need a fresh take? Get an instant paraphrase of this document with our AI Paraphraser
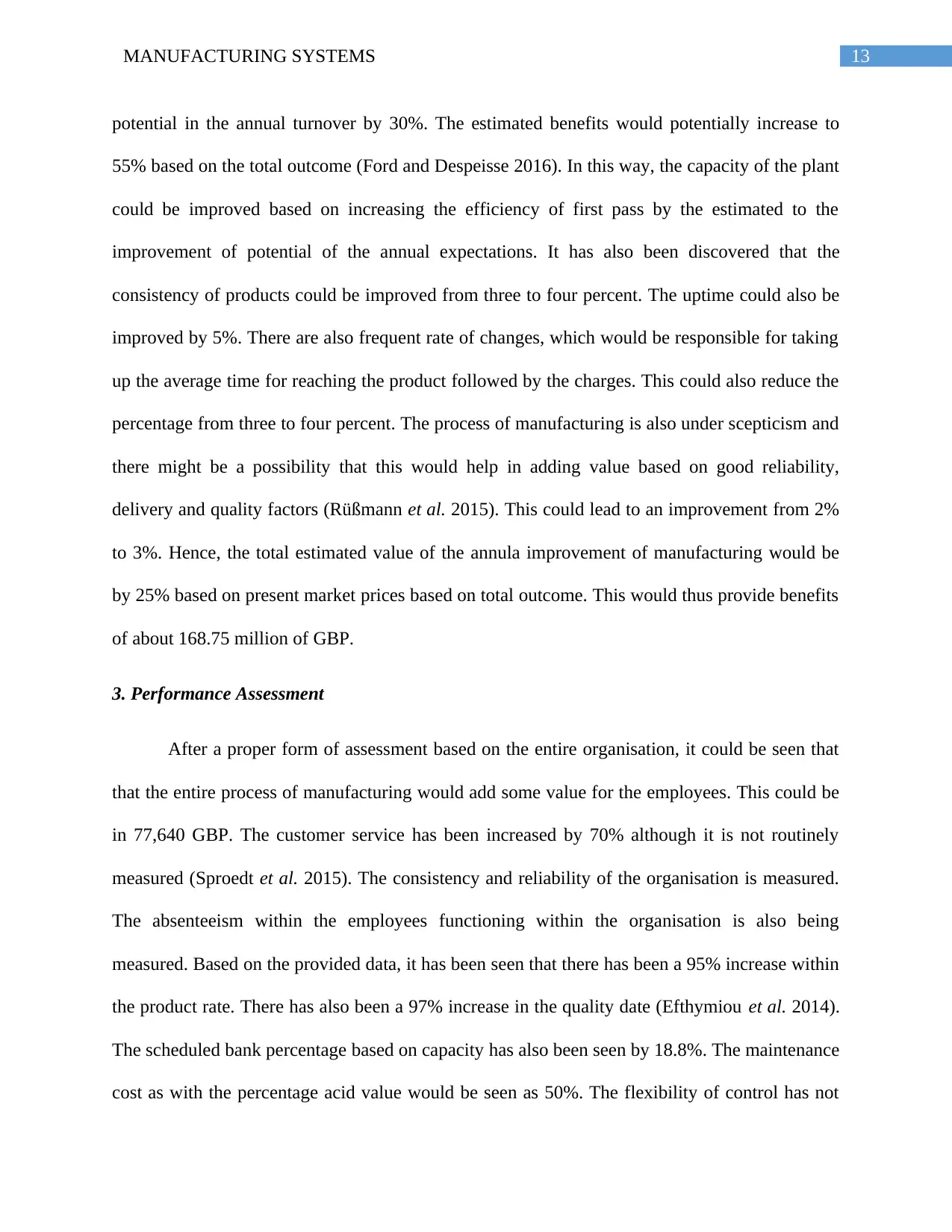
13MANUFACTURING SYSTEMS
potential in the annual turnover by 30%. The estimated benefits would potentially increase to
55% based on the total outcome (Ford and Despeisse 2016). In this way, the capacity of the plant
could be improved based on increasing the efficiency of first pass by the estimated to the
improvement of potential of the annual expectations. It has also been discovered that the
consistency of products could be improved from three to four percent. The uptime could also be
improved by 5%. There are also frequent rate of changes, which would be responsible for taking
up the average time for reaching the product followed by the charges. This could also reduce the
percentage from three to four percent. The process of manufacturing is also under scepticism and
there might be a possibility that this would help in adding value based on good reliability,
delivery and quality factors (Rüßmann et al. 2015). This could lead to an improvement from 2%
to 3%. Hence, the total estimated value of the annula improvement of manufacturing would be
by 25% based on present market prices based on total outcome. This would thus provide benefits
of about 168.75 million of GBP.
3. Performance Assessment
After a proper form of assessment based on the entire organisation, it could be seen that
that the entire process of manufacturing would add some value for the employees. This could be
in 77,640 GBP. The customer service has been increased by 70% although it is not routinely
measured (Sproedt et al. 2015). The consistency and reliability of the organisation is measured.
The absenteeism within the employees functioning within the organisation is also being
measured. Based on the provided data, it has been seen that there has been a 95% increase within
the product rate. There has also been a 97% increase in the quality date (Efthymiou et al. 2014).
The scheduled bank percentage based on capacity has also been seen by 18.8%. The maintenance
cost as with the percentage acid value would be seen as 50%. The flexibility of control has not
potential in the annual turnover by 30%. The estimated benefits would potentially increase to
55% based on the total outcome (Ford and Despeisse 2016). In this way, the capacity of the plant
could be improved based on increasing the efficiency of first pass by the estimated to the
improvement of potential of the annual expectations. It has also been discovered that the
consistency of products could be improved from three to four percent. The uptime could also be
improved by 5%. There are also frequent rate of changes, which would be responsible for taking
up the average time for reaching the product followed by the charges. This could also reduce the
percentage from three to four percent. The process of manufacturing is also under scepticism and
there might be a possibility that this would help in adding value based on good reliability,
delivery and quality factors (Rüßmann et al. 2015). This could lead to an improvement from 2%
to 3%. Hence, the total estimated value of the annula improvement of manufacturing would be
by 25% based on present market prices based on total outcome. This would thus provide benefits
of about 168.75 million of GBP.
3. Performance Assessment
After a proper form of assessment based on the entire organisation, it could be seen that
that the entire process of manufacturing would add some value for the employees. This could be
in 77,640 GBP. The customer service has been increased by 70% although it is not routinely
measured (Sproedt et al. 2015). The consistency and reliability of the organisation is measured.
The absenteeism within the employees functioning within the organisation is also being
measured. Based on the provided data, it has been seen that there has been a 95% increase within
the product rate. There has also been a 97% increase in the quality date (Efthymiou et al. 2014).
The scheduled bank percentage based on capacity has also been seen by 18.8%. The maintenance
cost as with the percentage acid value would be seen as 50%. The flexibility of control has not
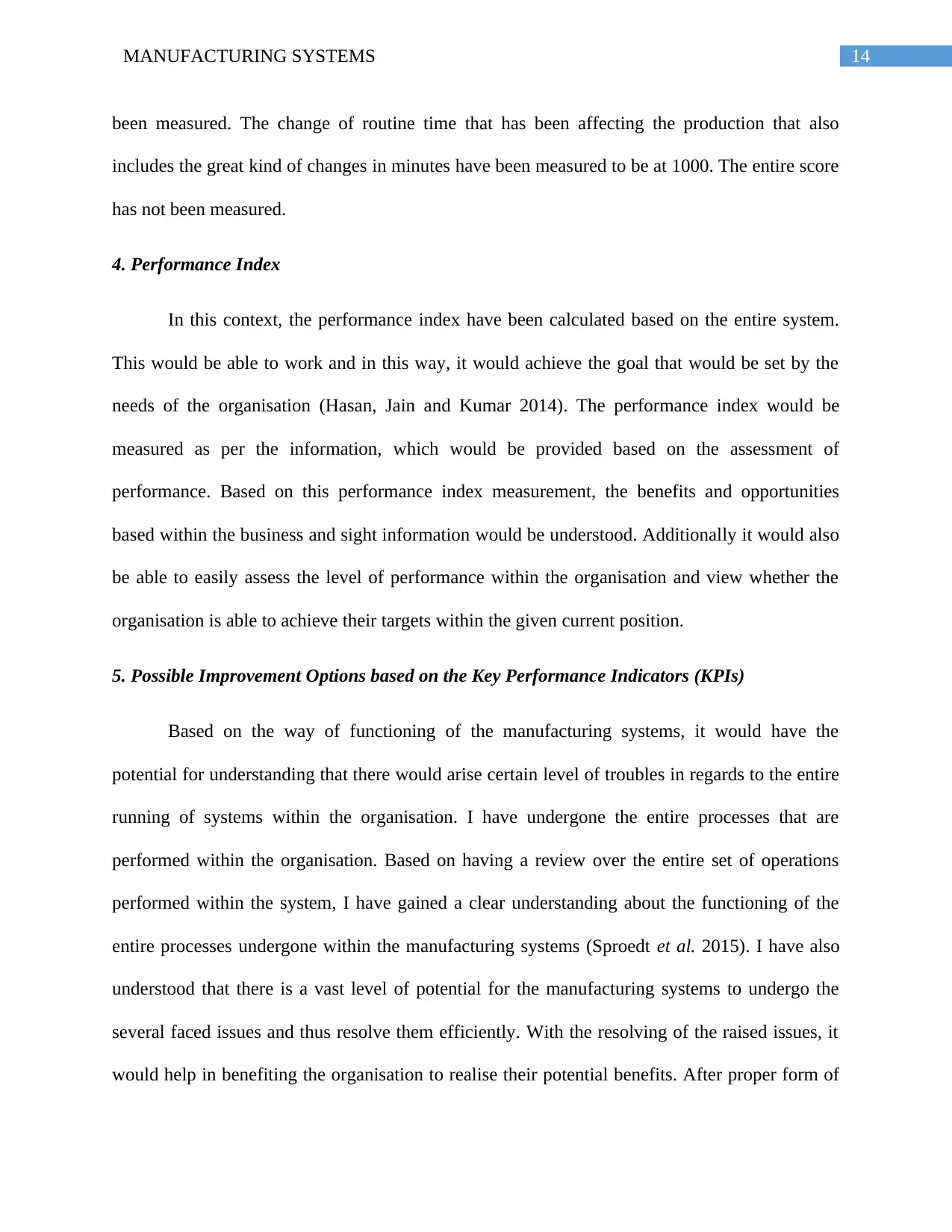
14MANUFACTURING SYSTEMS
been measured. The change of routine time that has been affecting the production that also
includes the great kind of changes in minutes have been measured to be at 1000. The entire score
has not been measured.
4. Performance Index
In this context, the performance index have been calculated based on the entire system.
This would be able to work and in this way, it would achieve the goal that would be set by the
needs of the organisation (Hasan, Jain and Kumar 2014). The performance index would be
measured as per the information, which would be provided based on the assessment of
performance. Based on this performance index measurement, the benefits and opportunities
based within the business and sight information would be understood. Additionally it would also
be able to easily assess the level of performance within the organisation and view whether the
organisation is able to achieve their targets within the given current position.
5. Possible Improvement Options based on the Key Performance Indicators (KPIs)
Based on the way of functioning of the manufacturing systems, it would have the
potential for understanding that there would arise certain level of troubles in regards to the entire
running of systems within the organisation. I have undergone the entire processes that are
performed within the organisation. Based on having a review over the entire set of operations
performed within the system, I have gained a clear understanding about the functioning of the
entire processes undergone within the manufacturing systems (Sproedt et al. 2015). I have also
understood that there is a vast level of potential for the manufacturing systems to undergo the
several faced issues and thus resolve them efficiently. With the resolving of the raised issues, it
would help in benefiting the organisation to realise their potential benefits. After proper form of
been measured. The change of routine time that has been affecting the production that also
includes the great kind of changes in minutes have been measured to be at 1000. The entire score
has not been measured.
4. Performance Index
In this context, the performance index have been calculated based on the entire system.
This would be able to work and in this way, it would achieve the goal that would be set by the
needs of the organisation (Hasan, Jain and Kumar 2014). The performance index would be
measured as per the information, which would be provided based on the assessment of
performance. Based on this performance index measurement, the benefits and opportunities
based within the business and sight information would be understood. Additionally it would also
be able to easily assess the level of performance within the organisation and view whether the
organisation is able to achieve their targets within the given current position.
5. Possible Improvement Options based on the Key Performance Indicators (KPIs)
Based on the way of functioning of the manufacturing systems, it would have the
potential for understanding that there would arise certain level of troubles in regards to the entire
running of systems within the organisation. I have undergone the entire processes that are
performed within the organisation. Based on having a review over the entire set of operations
performed within the system, I have gained a clear understanding about the functioning of the
entire processes undergone within the manufacturing systems (Sproedt et al. 2015). I have also
understood that there is a vast level of potential for the manufacturing systems to undergo the
several faced issues and thus resolve them efficiently. With the resolving of the raised issues, it
would help in benefiting the organisation to realise their potential benefits. After proper form of
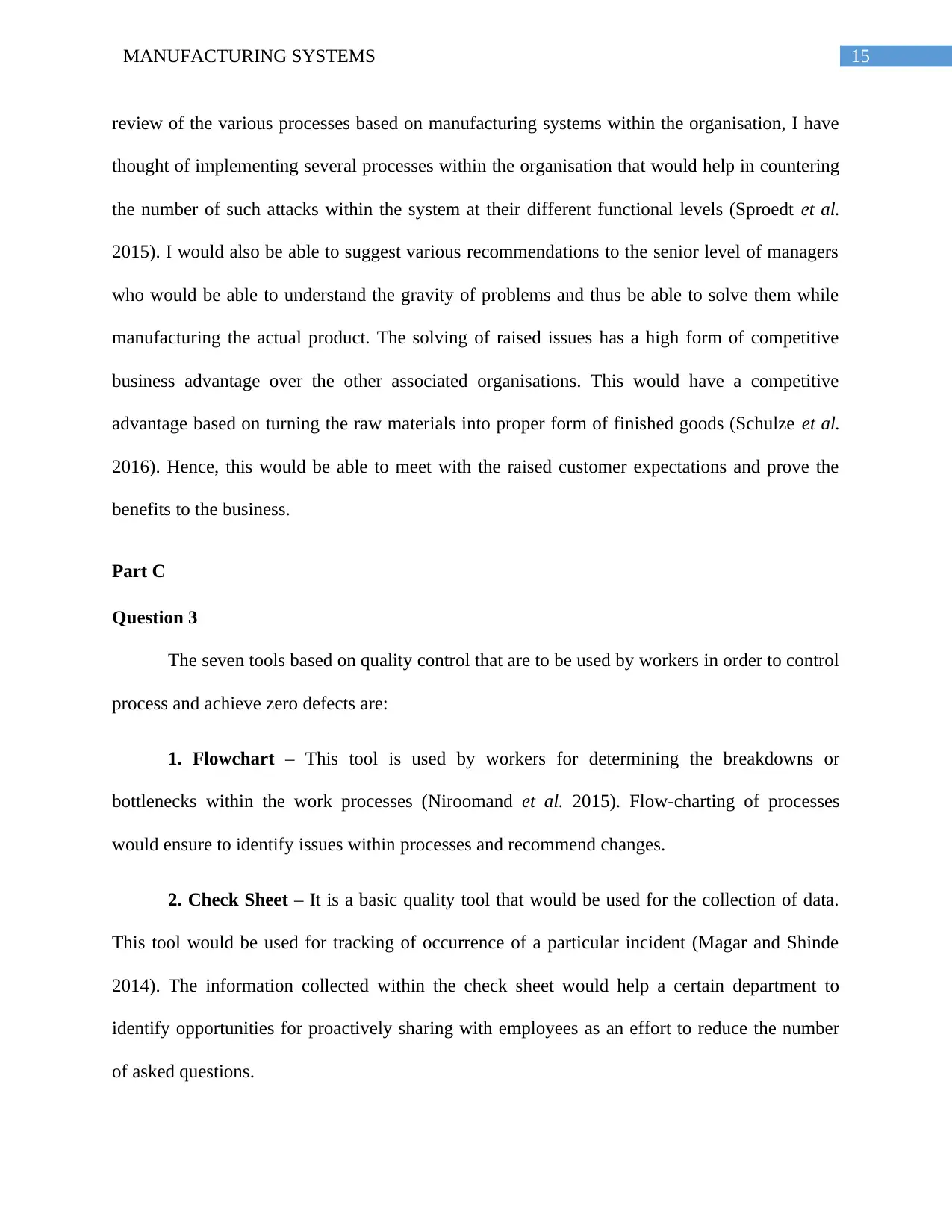
15MANUFACTURING SYSTEMS
review of the various processes based on manufacturing systems within the organisation, I have
thought of implementing several processes within the organisation that would help in countering
the number of such attacks within the system at their different functional levels (Sproedt et al.
2015). I would also be able to suggest various recommendations to the senior level of managers
who would be able to understand the gravity of problems and thus be able to solve them while
manufacturing the actual product. The solving of raised issues has a high form of competitive
business advantage over the other associated organisations. This would have a competitive
advantage based on turning the raw materials into proper form of finished goods (Schulze et al.
2016). Hence, this would be able to meet with the raised customer expectations and prove the
benefits to the business.
Part C
Question 3
The seven tools based on quality control that are to be used by workers in order to control
process and achieve zero defects are:
1. Flowchart – This tool is used by workers for determining the breakdowns or
bottlenecks within the work processes (Niroomand et al. 2015). Flow-charting of processes
would ensure to identify issues within processes and recommend changes.
2. Check Sheet – It is a basic quality tool that would be used for the collection of data.
This tool would be used for tracking of occurrence of a particular incident (Magar and Shinde
2014). The information collected within the check sheet would help a certain department to
identify opportunities for proactively sharing with employees as an effort to reduce the number
of asked questions.
review of the various processes based on manufacturing systems within the organisation, I have
thought of implementing several processes within the organisation that would help in countering
the number of such attacks within the system at their different functional levels (Sproedt et al.
2015). I would also be able to suggest various recommendations to the senior level of managers
who would be able to understand the gravity of problems and thus be able to solve them while
manufacturing the actual product. The solving of raised issues has a high form of competitive
business advantage over the other associated organisations. This would have a competitive
advantage based on turning the raw materials into proper form of finished goods (Schulze et al.
2016). Hence, this would be able to meet with the raised customer expectations and prove the
benefits to the business.
Part C
Question 3
The seven tools based on quality control that are to be used by workers in order to control
process and achieve zero defects are:
1. Flowchart – This tool is used by workers for determining the breakdowns or
bottlenecks within the work processes (Niroomand et al. 2015). Flow-charting of processes
would ensure to identify issues within processes and recommend changes.
2. Check Sheet – It is a basic quality tool that would be used for the collection of data.
This tool would be used for tracking of occurrence of a particular incident (Magar and Shinde
2014). The information collected within the check sheet would help a certain department to
identify opportunities for proactively sharing with employees as an effort to reduce the number
of asked questions.
Secure Best Marks with AI Grader
Need help grading? Try our AI Grader for instant feedback on your assignments.
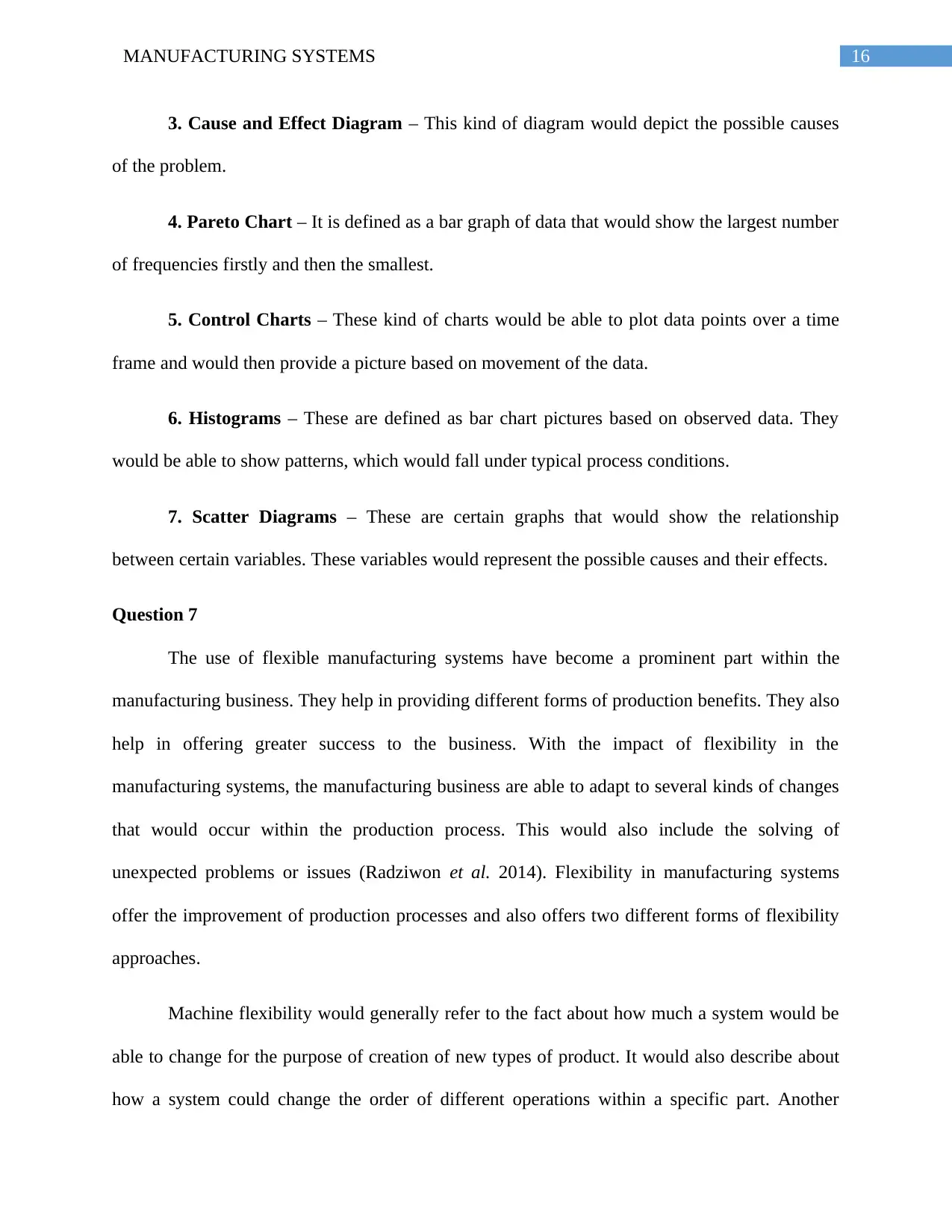
16MANUFACTURING SYSTEMS
3. Cause and Effect Diagram – This kind of diagram would depict the possible causes
of the problem.
4. Pareto Chart – It is defined as a bar graph of data that would show the largest number
of frequencies firstly and then the smallest.
5. Control Charts – These kind of charts would be able to plot data points over a time
frame and would then provide a picture based on movement of the data.
6. Histograms – These are defined as bar chart pictures based on observed data. They
would be able to show patterns, which would fall under typical process conditions.
7. Scatter Diagrams – These are certain graphs that would show the relationship
between certain variables. These variables would represent the possible causes and their effects.
Question 7
The use of flexible manufacturing systems have become a prominent part within the
manufacturing business. They help in providing different forms of production benefits. They also
help in offering greater success to the business. With the impact of flexibility in the
manufacturing systems, the manufacturing business are able to adapt to several kinds of changes
that would occur within the production process. This would also include the solving of
unexpected problems or issues (Radziwon et al. 2014). Flexibility in manufacturing systems
offer the improvement of production processes and also offers two different forms of flexibility
approaches.
Machine flexibility would generally refer to the fact about how much a system would be
able to change for the purpose of creation of new types of product. It would also describe about
how a system could change the order of different operations within a specific part. Another
3. Cause and Effect Diagram – This kind of diagram would depict the possible causes
of the problem.
4. Pareto Chart – It is defined as a bar graph of data that would show the largest number
of frequencies firstly and then the smallest.
5. Control Charts – These kind of charts would be able to plot data points over a time
frame and would then provide a picture based on movement of the data.
6. Histograms – These are defined as bar chart pictures based on observed data. They
would be able to show patterns, which would fall under typical process conditions.
7. Scatter Diagrams – These are certain graphs that would show the relationship
between certain variables. These variables would represent the possible causes and their effects.
Question 7
The use of flexible manufacturing systems have become a prominent part within the
manufacturing business. They help in providing different forms of production benefits. They also
help in offering greater success to the business. With the impact of flexibility in the
manufacturing systems, the manufacturing business are able to adapt to several kinds of changes
that would occur within the production process. This would also include the solving of
unexpected problems or issues (Radziwon et al. 2014). Flexibility in manufacturing systems
offer the improvement of production processes and also offers two different forms of flexibility
approaches.
Machine flexibility would generally refer to the fact about how much a system would be
able to change for the purpose of creation of new types of product. It would also describe about
how a system could change the order of different operations within a specific part. Another
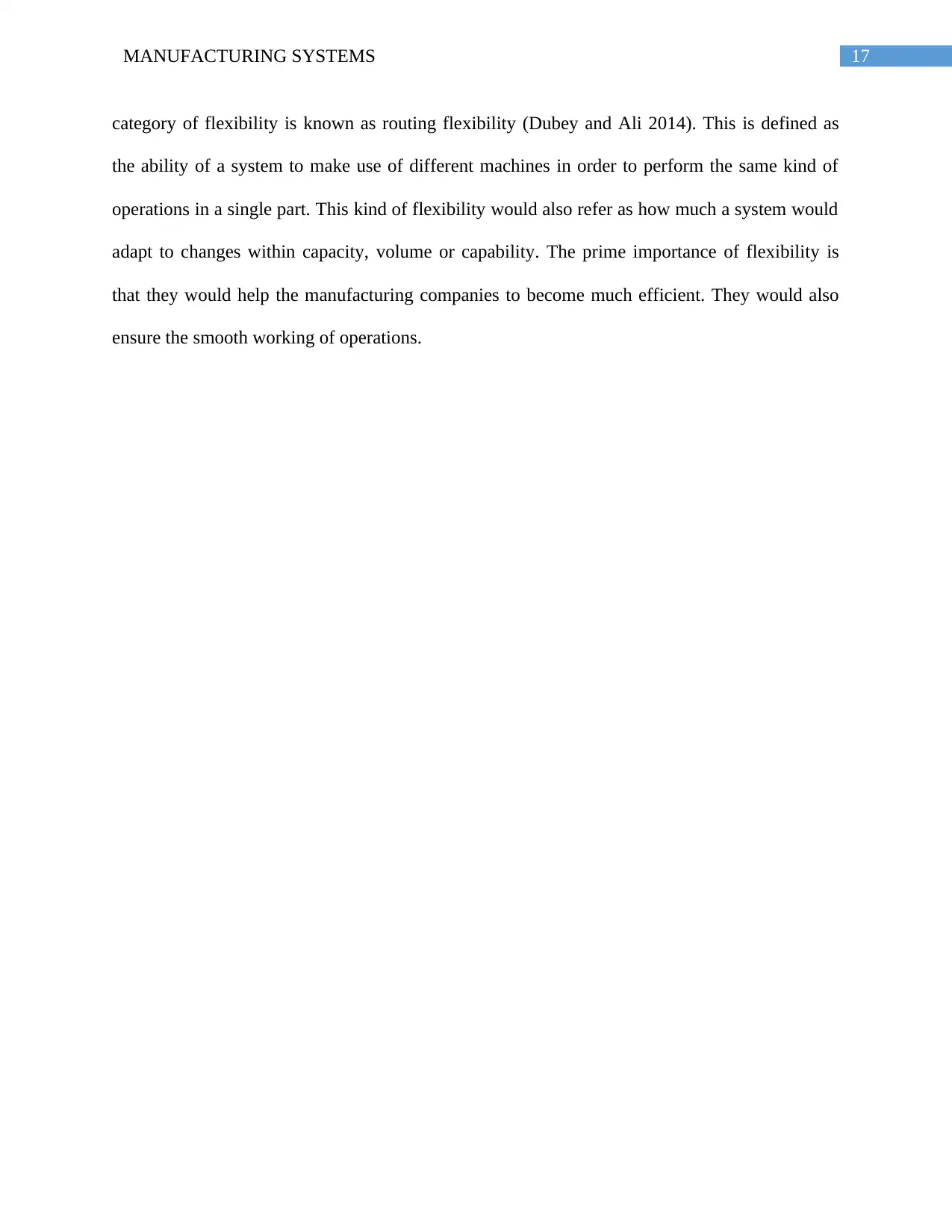
17MANUFACTURING SYSTEMS
category of flexibility is known as routing flexibility (Dubey and Ali 2014). This is defined as
the ability of a system to make use of different machines in order to perform the same kind of
operations in a single part. This kind of flexibility would also refer as how much a system would
adapt to changes within capacity, volume or capability. The prime importance of flexibility is
that they would help the manufacturing companies to become much efficient. They would also
ensure the smooth working of operations.
category of flexibility is known as routing flexibility (Dubey and Ali 2014). This is defined as
the ability of a system to make use of different machines in order to perform the same kind of
operations in a single part. This kind of flexibility would also refer as how much a system would
adapt to changes within capacity, volume or capability. The prime importance of flexibility is
that they would help the manufacturing companies to become much efficient. They would also
ensure the smooth working of operations.
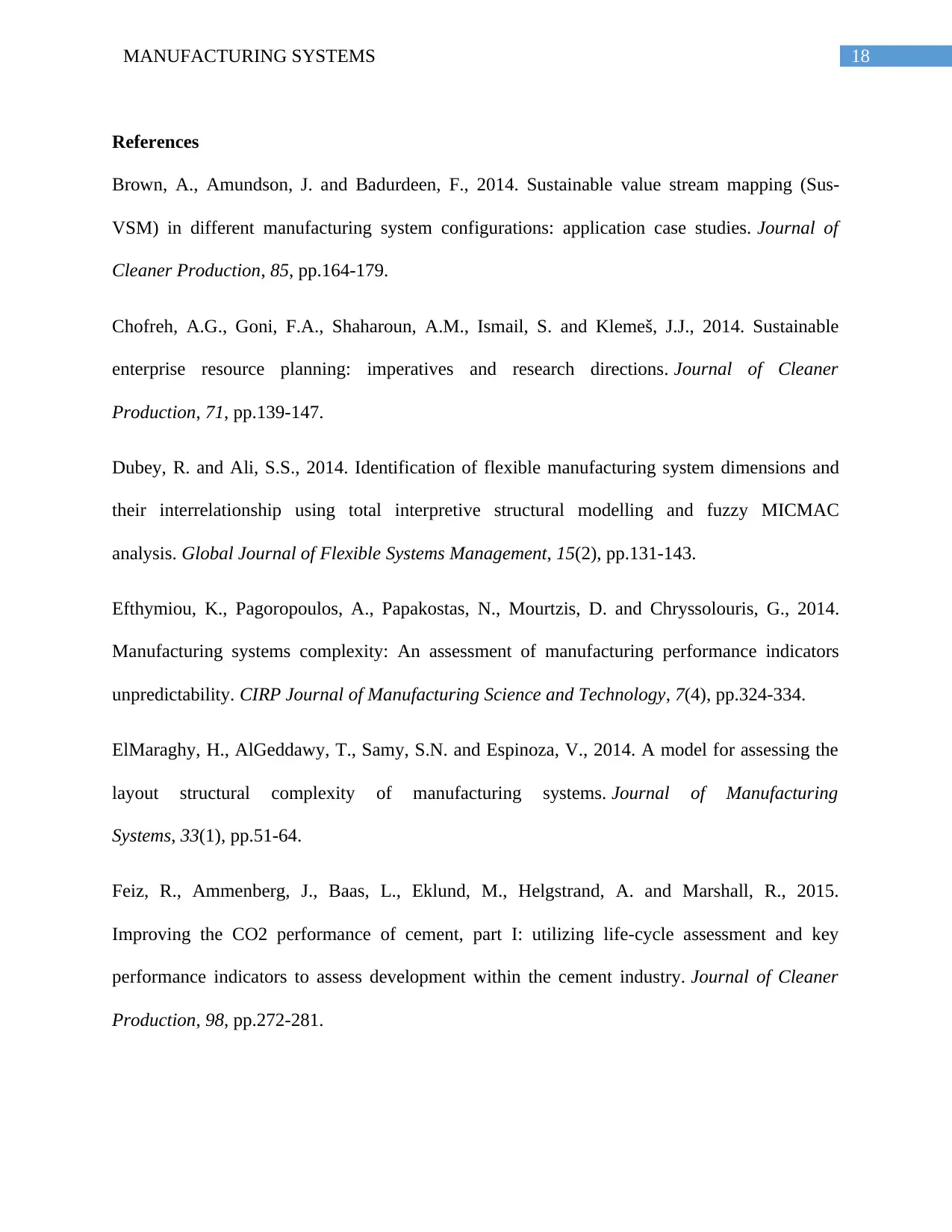
18MANUFACTURING SYSTEMS
References
Brown, A., Amundson, J. and Badurdeen, F., 2014. Sustainable value stream mapping (Sus-
VSM) in different manufacturing system configurations: application case studies. Journal of
Cleaner Production, 85, pp.164-179.
Chofreh, A.G., Goni, F.A., Shaharoun, A.M., Ismail, S. and Klemeš, J.J., 2014. Sustainable
enterprise resource planning: imperatives and research directions. Journal of Cleaner
Production, 71, pp.139-147.
Dubey, R. and Ali, S.S., 2014. Identification of flexible manufacturing system dimensions and
their interrelationship using total interpretive structural modelling and fuzzy MICMAC
analysis. Global Journal of Flexible Systems Management, 15(2), pp.131-143.
Efthymiou, K., Pagoropoulos, A., Papakostas, N., Mourtzis, D. and Chryssolouris, G., 2014.
Manufacturing systems complexity: An assessment of manufacturing performance indicators
unpredictability. CIRP Journal of Manufacturing Science and Technology, 7(4), pp.324-334.
ElMaraghy, H., AlGeddawy, T., Samy, S.N. and Espinoza, V., 2014. A model for assessing the
layout structural complexity of manufacturing systems. Journal of Manufacturing
Systems, 33(1), pp.51-64.
Feiz, R., Ammenberg, J., Baas, L., Eklund, M., Helgstrand, A. and Marshall, R., 2015.
Improving the CO2 performance of cement, part I: utilizing life-cycle assessment and key
performance indicators to assess development within the cement industry. Journal of Cleaner
Production, 98, pp.272-281.
References
Brown, A., Amundson, J. and Badurdeen, F., 2014. Sustainable value stream mapping (Sus-
VSM) in different manufacturing system configurations: application case studies. Journal of
Cleaner Production, 85, pp.164-179.
Chofreh, A.G., Goni, F.A., Shaharoun, A.M., Ismail, S. and Klemeš, J.J., 2014. Sustainable
enterprise resource planning: imperatives and research directions. Journal of Cleaner
Production, 71, pp.139-147.
Dubey, R. and Ali, S.S., 2014. Identification of flexible manufacturing system dimensions and
their interrelationship using total interpretive structural modelling and fuzzy MICMAC
analysis. Global Journal of Flexible Systems Management, 15(2), pp.131-143.
Efthymiou, K., Pagoropoulos, A., Papakostas, N., Mourtzis, D. and Chryssolouris, G., 2014.
Manufacturing systems complexity: An assessment of manufacturing performance indicators
unpredictability. CIRP Journal of Manufacturing Science and Technology, 7(4), pp.324-334.
ElMaraghy, H., AlGeddawy, T., Samy, S.N. and Espinoza, V., 2014. A model for assessing the
layout structural complexity of manufacturing systems. Journal of Manufacturing
Systems, 33(1), pp.51-64.
Feiz, R., Ammenberg, J., Baas, L., Eklund, M., Helgstrand, A. and Marshall, R., 2015.
Improving the CO2 performance of cement, part I: utilizing life-cycle assessment and key
performance indicators to assess development within the cement industry. Journal of Cleaner
Production, 98, pp.272-281.
Paraphrase This Document
Need a fresh take? Get an instant paraphrase of this document with our AI Paraphraser
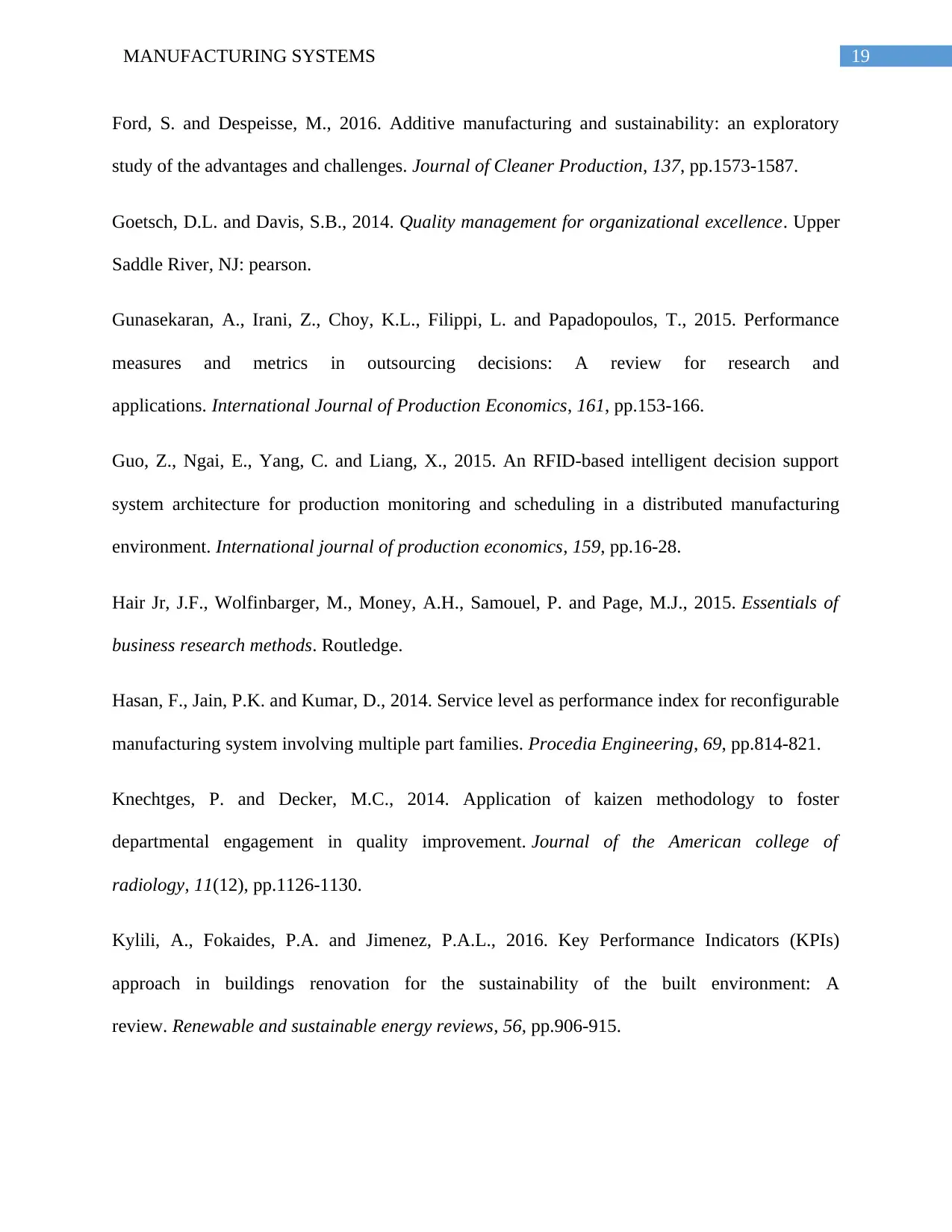
19MANUFACTURING SYSTEMS
Ford, S. and Despeisse, M., 2016. Additive manufacturing and sustainability: an exploratory
study of the advantages and challenges. Journal of Cleaner Production, 137, pp.1573-1587.
Goetsch, D.L. and Davis, S.B., 2014. Quality management for organizational excellence. Upper
Saddle River, NJ: pearson.
Gunasekaran, A., Irani, Z., Choy, K.L., Filippi, L. and Papadopoulos, T., 2015. Performance
measures and metrics in outsourcing decisions: A review for research and
applications. International Journal of Production Economics, 161, pp.153-166.
Guo, Z., Ngai, E., Yang, C. and Liang, X., 2015. An RFID-based intelligent decision support
system architecture for production monitoring and scheduling in a distributed manufacturing
environment. International journal of production economics, 159, pp.16-28.
Hair Jr, J.F., Wolfinbarger, M., Money, A.H., Samouel, P. and Page, M.J., 2015. Essentials of
business research methods. Routledge.
Hasan, F., Jain, P.K. and Kumar, D., 2014. Service level as performance index for reconfigurable
manufacturing system involving multiple part families. Procedia Engineering, 69, pp.814-821.
Knechtges, P. and Decker, M.C., 2014. Application of kaizen methodology to foster
departmental engagement in quality improvement. Journal of the American college of
radiology, 11(12), pp.1126-1130.
Kylili, A., Fokaides, P.A. and Jimenez, P.A.L., 2016. Key Performance Indicators (KPIs)
approach in buildings renovation for the sustainability of the built environment: A
review. Renewable and sustainable energy reviews, 56, pp.906-915.
Ford, S. and Despeisse, M., 2016. Additive manufacturing and sustainability: an exploratory
study of the advantages and challenges. Journal of Cleaner Production, 137, pp.1573-1587.
Goetsch, D.L. and Davis, S.B., 2014. Quality management for organizational excellence. Upper
Saddle River, NJ: pearson.
Gunasekaran, A., Irani, Z., Choy, K.L., Filippi, L. and Papadopoulos, T., 2015. Performance
measures and metrics in outsourcing decisions: A review for research and
applications. International Journal of Production Economics, 161, pp.153-166.
Guo, Z., Ngai, E., Yang, C. and Liang, X., 2015. An RFID-based intelligent decision support
system architecture for production monitoring and scheduling in a distributed manufacturing
environment. International journal of production economics, 159, pp.16-28.
Hair Jr, J.F., Wolfinbarger, M., Money, A.H., Samouel, P. and Page, M.J., 2015. Essentials of
business research methods. Routledge.
Hasan, F., Jain, P.K. and Kumar, D., 2014. Service level as performance index for reconfigurable
manufacturing system involving multiple part families. Procedia Engineering, 69, pp.814-821.
Knechtges, P. and Decker, M.C., 2014. Application of kaizen methodology to foster
departmental engagement in quality improvement. Journal of the American college of
radiology, 11(12), pp.1126-1130.
Kylili, A., Fokaides, P.A. and Jimenez, P.A.L., 2016. Key Performance Indicators (KPIs)
approach in buildings renovation for the sustainability of the built environment: A
review. Renewable and sustainable energy reviews, 56, pp.906-915.
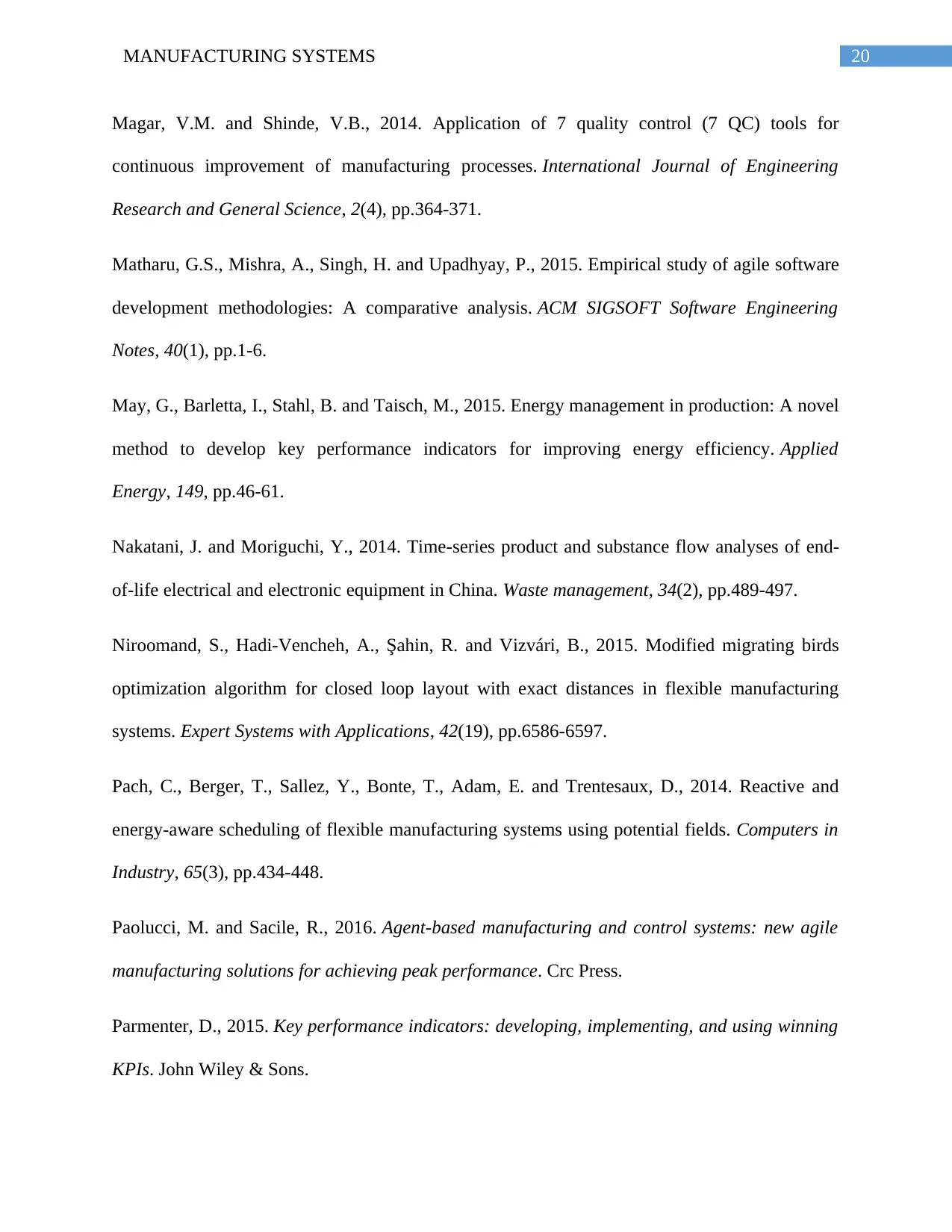
20MANUFACTURING SYSTEMS
Magar, V.M. and Shinde, V.B., 2014. Application of 7 quality control (7 QC) tools for
continuous improvement of manufacturing processes. International Journal of Engineering
Research and General Science, 2(4), pp.364-371.
Matharu, G.S., Mishra, A., Singh, H. and Upadhyay, P., 2015. Empirical study of agile software
development methodologies: A comparative analysis. ACM SIGSOFT Software Engineering
Notes, 40(1), pp.1-6.
May, G., Barletta, I., Stahl, B. and Taisch, M., 2015. Energy management in production: A novel
method to develop key performance indicators for improving energy efficiency. Applied
Energy, 149, pp.46-61.
Nakatani, J. and Moriguchi, Y., 2014. Time-series product and substance flow analyses of end-
of-life electrical and electronic equipment in China. Waste management, 34(2), pp.489-497.
Niroomand, S., Hadi-Vencheh, A., Şahin, R. and Vizvári, B., 2015. Modified migrating birds
optimization algorithm for closed loop layout with exact distances in flexible manufacturing
systems. Expert Systems with Applications, 42(19), pp.6586-6597.
Pach, C., Berger, T., Sallez, Y., Bonte, T., Adam, E. and Trentesaux, D., 2014. Reactive and
energy-aware scheduling of flexible manufacturing systems using potential fields. Computers in
Industry, 65(3), pp.434-448.
Paolucci, M. and Sacile, R., 2016. Agent-based manufacturing and control systems: new agile
manufacturing solutions for achieving peak performance. Crc Press.
Parmenter, D., 2015. Key performance indicators: developing, implementing, and using winning
KPIs. John Wiley & Sons.
Magar, V.M. and Shinde, V.B., 2014. Application of 7 quality control (7 QC) tools for
continuous improvement of manufacturing processes. International Journal of Engineering
Research and General Science, 2(4), pp.364-371.
Matharu, G.S., Mishra, A., Singh, H. and Upadhyay, P., 2015. Empirical study of agile software
development methodologies: A comparative analysis. ACM SIGSOFT Software Engineering
Notes, 40(1), pp.1-6.
May, G., Barletta, I., Stahl, B. and Taisch, M., 2015. Energy management in production: A novel
method to develop key performance indicators for improving energy efficiency. Applied
Energy, 149, pp.46-61.
Nakatani, J. and Moriguchi, Y., 2014. Time-series product and substance flow analyses of end-
of-life electrical and electronic equipment in China. Waste management, 34(2), pp.489-497.
Niroomand, S., Hadi-Vencheh, A., Şahin, R. and Vizvári, B., 2015. Modified migrating birds
optimization algorithm for closed loop layout with exact distances in flexible manufacturing
systems. Expert Systems with Applications, 42(19), pp.6586-6597.
Pach, C., Berger, T., Sallez, Y., Bonte, T., Adam, E. and Trentesaux, D., 2014. Reactive and
energy-aware scheduling of flexible manufacturing systems using potential fields. Computers in
Industry, 65(3), pp.434-448.
Paolucci, M. and Sacile, R., 2016. Agent-based manufacturing and control systems: new agile
manufacturing solutions for achieving peak performance. Crc Press.
Parmenter, D., 2015. Key performance indicators: developing, implementing, and using winning
KPIs. John Wiley & Sons.
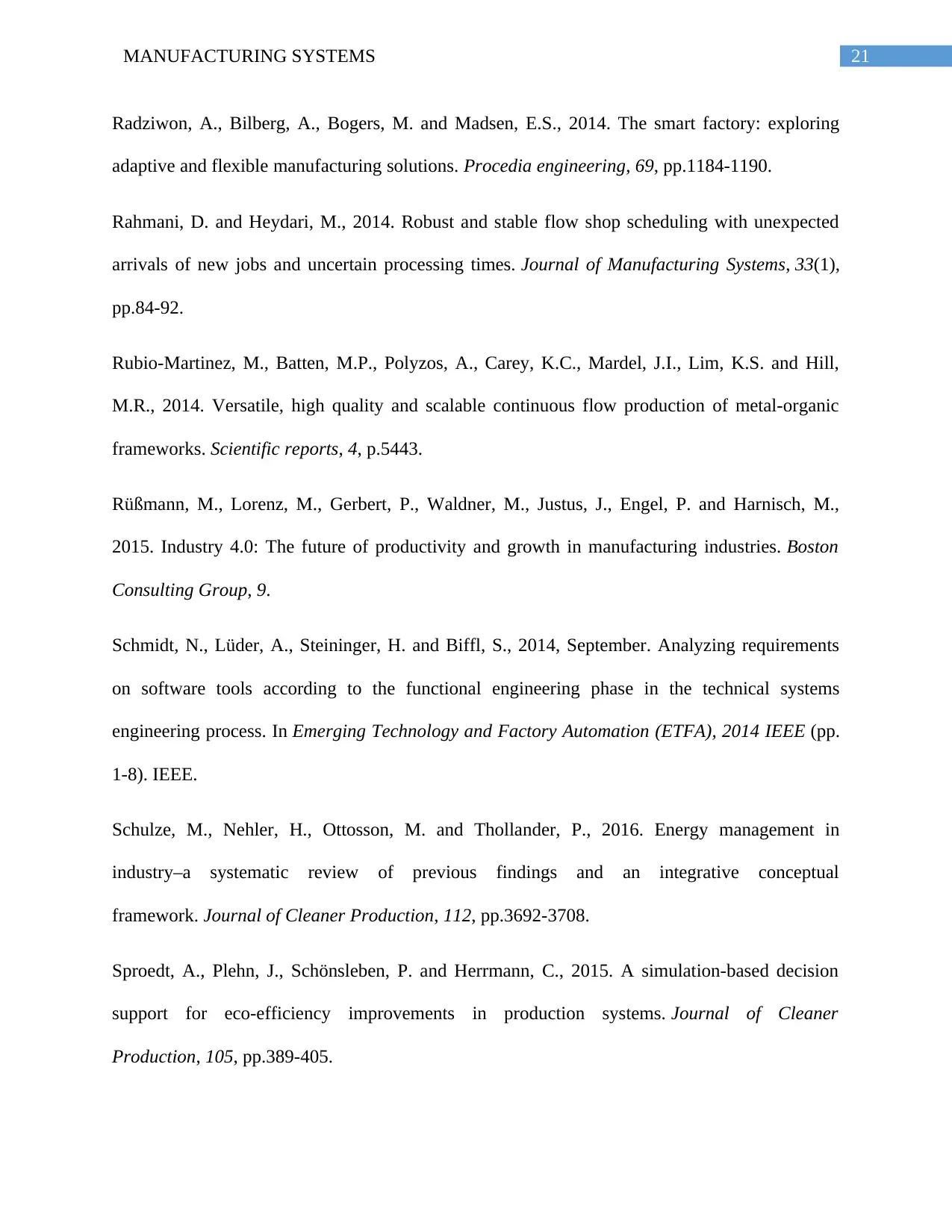
21MANUFACTURING SYSTEMS
Radziwon, A., Bilberg, A., Bogers, M. and Madsen, E.S., 2014. The smart factory: exploring
adaptive and flexible manufacturing solutions. Procedia engineering, 69, pp.1184-1190.
Rahmani, D. and Heydari, M., 2014. Robust and stable flow shop scheduling with unexpected
arrivals of new jobs and uncertain processing times. Journal of Manufacturing Systems, 33(1),
pp.84-92.
Rubio-Martinez, M., Batten, M.P., Polyzos, A., Carey, K.C., Mardel, J.I., Lim, K.S. and Hill,
M.R., 2014. Versatile, high quality and scalable continuous flow production of metal-organic
frameworks. Scientific reports, 4, p.5443.
Rüßmann, M., Lorenz, M., Gerbert, P., Waldner, M., Justus, J., Engel, P. and Harnisch, M.,
2015. Industry 4.0: The future of productivity and growth in manufacturing industries. Boston
Consulting Group, 9.
Schmidt, N., Lüder, A., Steininger, H. and Biffl, S., 2014, September. Analyzing requirements
on software tools according to the functional engineering phase in the technical systems
engineering process. In Emerging Technology and Factory Automation (ETFA), 2014 IEEE (pp.
1-8). IEEE.
Schulze, M., Nehler, H., Ottosson, M. and Thollander, P., 2016. Energy management in
industry–a systematic review of previous findings and an integrative conceptual
framework. Journal of Cleaner Production, 112, pp.3692-3708.
Sproedt, A., Plehn, J., Schönsleben, P. and Herrmann, C., 2015. A simulation-based decision
support for eco-efficiency improvements in production systems. Journal of Cleaner
Production, 105, pp.389-405.
Radziwon, A., Bilberg, A., Bogers, M. and Madsen, E.S., 2014. The smart factory: exploring
adaptive and flexible manufacturing solutions. Procedia engineering, 69, pp.1184-1190.
Rahmani, D. and Heydari, M., 2014. Robust and stable flow shop scheduling with unexpected
arrivals of new jobs and uncertain processing times. Journal of Manufacturing Systems, 33(1),
pp.84-92.
Rubio-Martinez, M., Batten, M.P., Polyzos, A., Carey, K.C., Mardel, J.I., Lim, K.S. and Hill,
M.R., 2014. Versatile, high quality and scalable continuous flow production of metal-organic
frameworks. Scientific reports, 4, p.5443.
Rüßmann, M., Lorenz, M., Gerbert, P., Waldner, M., Justus, J., Engel, P. and Harnisch, M.,
2015. Industry 4.0: The future of productivity and growth in manufacturing industries. Boston
Consulting Group, 9.
Schmidt, N., Lüder, A., Steininger, H. and Biffl, S., 2014, September. Analyzing requirements
on software tools according to the functional engineering phase in the technical systems
engineering process. In Emerging Technology and Factory Automation (ETFA), 2014 IEEE (pp.
1-8). IEEE.
Schulze, M., Nehler, H., Ottosson, M. and Thollander, P., 2016. Energy management in
industry–a systematic review of previous findings and an integrative conceptual
framework. Journal of Cleaner Production, 112, pp.3692-3708.
Sproedt, A., Plehn, J., Schönsleben, P. and Herrmann, C., 2015. A simulation-based decision
support for eco-efficiency improvements in production systems. Journal of Cleaner
Production, 105, pp.389-405.
Secure Best Marks with AI Grader
Need help grading? Try our AI Grader for instant feedback on your assignments.
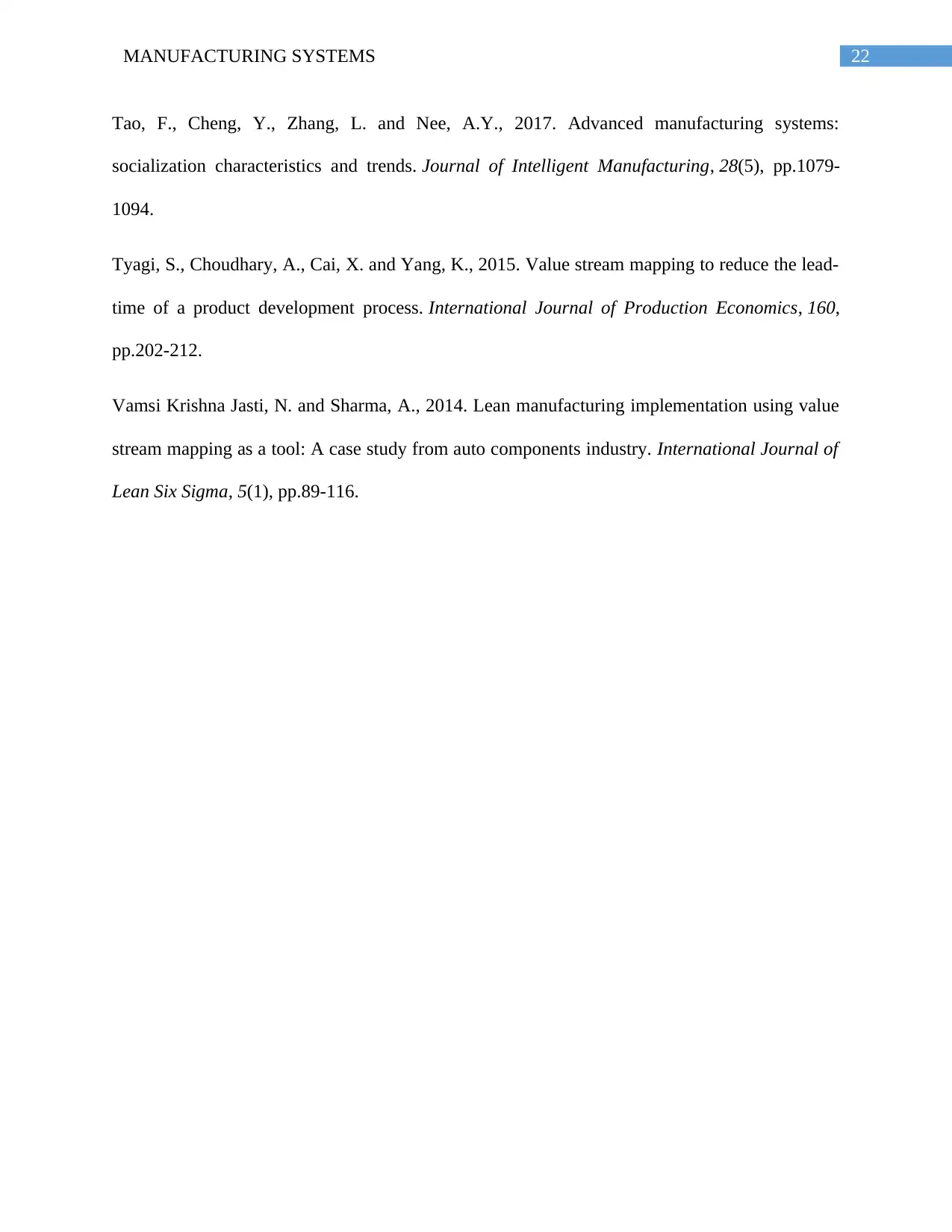
22MANUFACTURING SYSTEMS
Tao, F., Cheng, Y., Zhang, L. and Nee, A.Y., 2017. Advanced manufacturing systems:
socialization characteristics and trends. Journal of Intelligent Manufacturing, 28(5), pp.1079-
1094.
Tyagi, S., Choudhary, A., Cai, X. and Yang, K., 2015. Value stream mapping to reduce the lead-
time of a product development process. International Journal of Production Economics, 160,
pp.202-212.
Vamsi Krishna Jasti, N. and Sharma, A., 2014. Lean manufacturing implementation using value
stream mapping as a tool: A case study from auto components industry. International Journal of
Lean Six Sigma, 5(1), pp.89-116.
Tao, F., Cheng, Y., Zhang, L. and Nee, A.Y., 2017. Advanced manufacturing systems:
socialization characteristics and trends. Journal of Intelligent Manufacturing, 28(5), pp.1079-
1094.
Tyagi, S., Choudhary, A., Cai, X. and Yang, K., 2015. Value stream mapping to reduce the lead-
time of a product development process. International Journal of Production Economics, 160,
pp.202-212.
Vamsi Krishna Jasti, N. and Sharma, A., 2014. Lean manufacturing implementation using value
stream mapping as a tool: A case study from auto components industry. International Journal of
Lean Six Sigma, 5(1), pp.89-116.
1 out of 23
Related Documents

Your All-in-One AI-Powered Toolkit for Academic Success.
+13062052269
info@desklib.com
Available 24*7 on WhatsApp / Email
Unlock your academic potential
© 2024 | Zucol Services PVT LTD | All rights reserved.