Analysis of Maraging Steels for Aircraft Landing Gear Applications
VerifiedAdded on 2022/09/27
|17
|6144
|29
Report
AI Summary
This report provides a comprehensive analysis of maraging steels, focusing on their application in aircraft landing gear. It begins with an introduction to maraging steels, defining their composition, typical microstructures, and mechanical properties, including yield and ultimate strength, toughness...
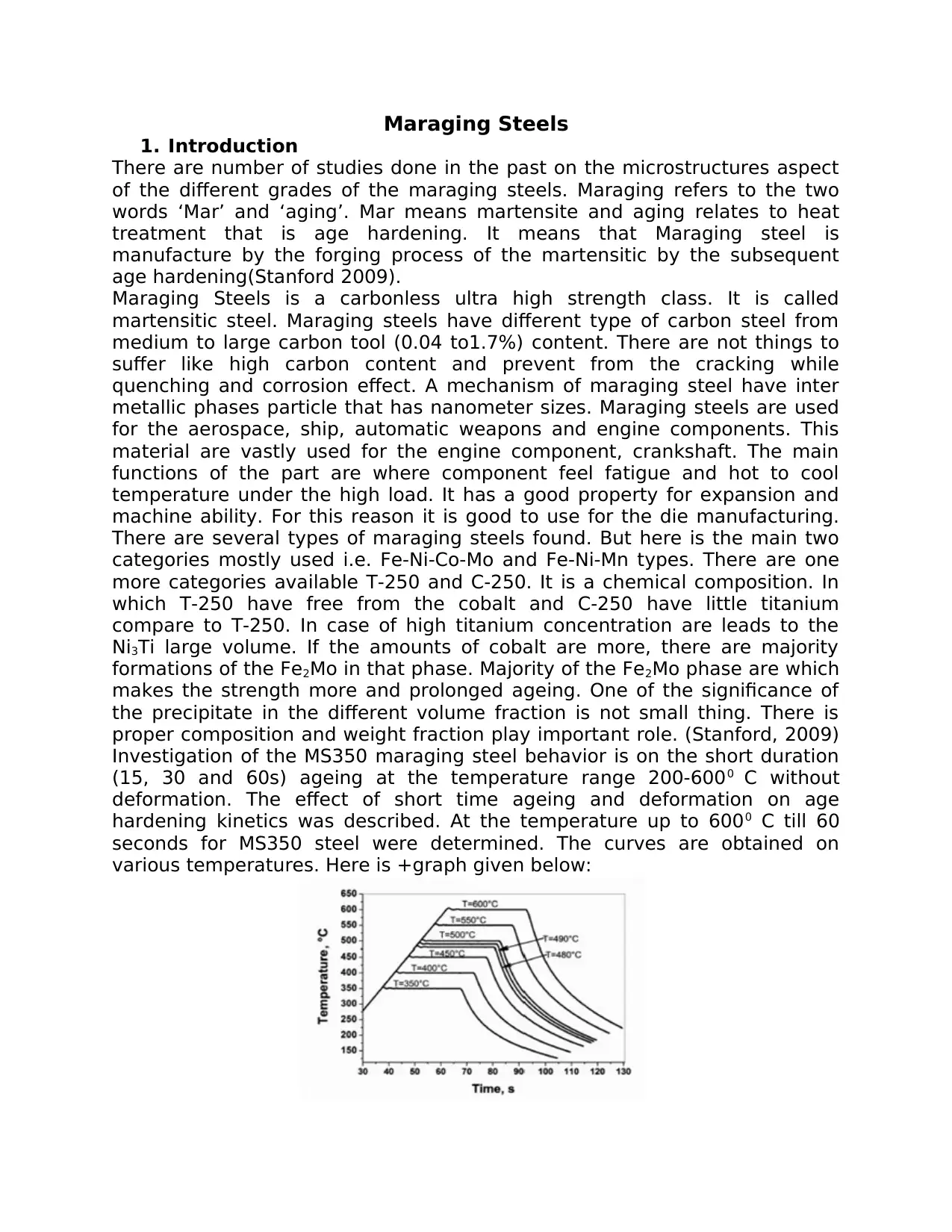
Maraging Steels
1. Introduction
There are number of studies done in the past on the microstructures aspect
of the different grades of the maraging steels. Maraging refers to the two
words ‘Mar’ and ‘aging’. Mar means martensite and aging relates to heat
treatment that is age hardening. It means that Maraging steel is
manufacture by the forging process of the martensitic by the subsequent
age hardening(Stanford 2009).
Maraging Steels is a carbonless ultra high strength class. It is called
martensitic steel. Maraging steels have different type of carbon steel from
medium to large carbon tool (0.04 to1.7%) content. There are not things to
suffer like high carbon content and prevent from the cracking while
quenching and corrosion effect. A mechanism of maraging steel have inter
metallic phases particle that has nanometer sizes. Maraging steels are used
for the aerospace, ship, automatic weapons and engine components. This
material are vastly used for the engine component, crankshaft. The main
functions of the part are where component feel fatigue and hot to cool
temperature under the high load. It has a good property for expansion and
machine ability. For this reason it is good to use for the die manufacturing.
There are several types of maraging steels found. But here is the main two
categories mostly used i.e. Fe-Ni-Co-Mo and Fe-Ni-Mn types. There are one
more categories available T-250 and C-250. It is a chemical composition. In
which T-250 have free from the cobalt and C-250 have little titanium
compare to T-250. In case of high titanium concentration are leads to the
Ni3Ti large volume. If the amounts of cobalt are more, there are majority
formations of the Fe2Mo in that phase. Majority of the Fe2Mo phase are which
makes the strength more and prolonged ageing. One of the significance of
the precipitate in the different volume fraction is not small thing. There is
proper composition and weight fraction play important role. (Stanford, 2009)
Investigation of the MS350 maraging steel behavior is on the short duration
(15, 30 and 60s) ageing at the temperature range 200-6000 C without
deformation. The effect of short time ageing and deformation on age
hardening kinetics was described. At the temperature up to 6000 C till 60
seconds for MS350 steel were determined. The curves are obtained on
various temperatures. Here is +graph given below:
1. Introduction
There are number of studies done in the past on the microstructures aspect
of the different grades of the maraging steels. Maraging refers to the two
words ‘Mar’ and ‘aging’. Mar means martensite and aging relates to heat
treatment that is age hardening. It means that Maraging steel is
manufacture by the forging process of the martensitic by the subsequent
age hardening(Stanford 2009).
Maraging Steels is a carbonless ultra high strength class. It is called
martensitic steel. Maraging steels have different type of carbon steel from
medium to large carbon tool (0.04 to1.7%) content. There are not things to
suffer like high carbon content and prevent from the cracking while
quenching and corrosion effect. A mechanism of maraging steel have inter
metallic phases particle that has nanometer sizes. Maraging steels are used
for the aerospace, ship, automatic weapons and engine components. This
material are vastly used for the engine component, crankshaft. The main
functions of the part are where component feel fatigue and hot to cool
temperature under the high load. It has a good property for expansion and
machine ability. For this reason it is good to use for the die manufacturing.
There are several types of maraging steels found. But here is the main two
categories mostly used i.e. Fe-Ni-Co-Mo and Fe-Ni-Mn types. There are one
more categories available T-250 and C-250. It is a chemical composition. In
which T-250 have free from the cobalt and C-250 have little titanium
compare to T-250. In case of high titanium concentration are leads to the
Ni3Ti large volume. If the amounts of cobalt are more, there are majority
formations of the Fe2Mo in that phase. Majority of the Fe2Mo phase are which
makes the strength more and prolonged ageing. One of the significance of
the precipitate in the different volume fraction is not small thing. There is
proper composition and weight fraction play important role. (Stanford, 2009)
Investigation of the MS350 maraging steel behavior is on the short duration
(15, 30 and 60s) ageing at the temperature range 200-6000 C without
deformation. The effect of short time ageing and deformation on age
hardening kinetics was described. At the temperature up to 6000 C till 60
seconds for MS350 steel were determined. The curves are obtained on
various temperatures. Here is +graph given below:
Secure Best Marks with AI Grader
Need help grading? Try our AI Grader for instant feedback on your assignments.
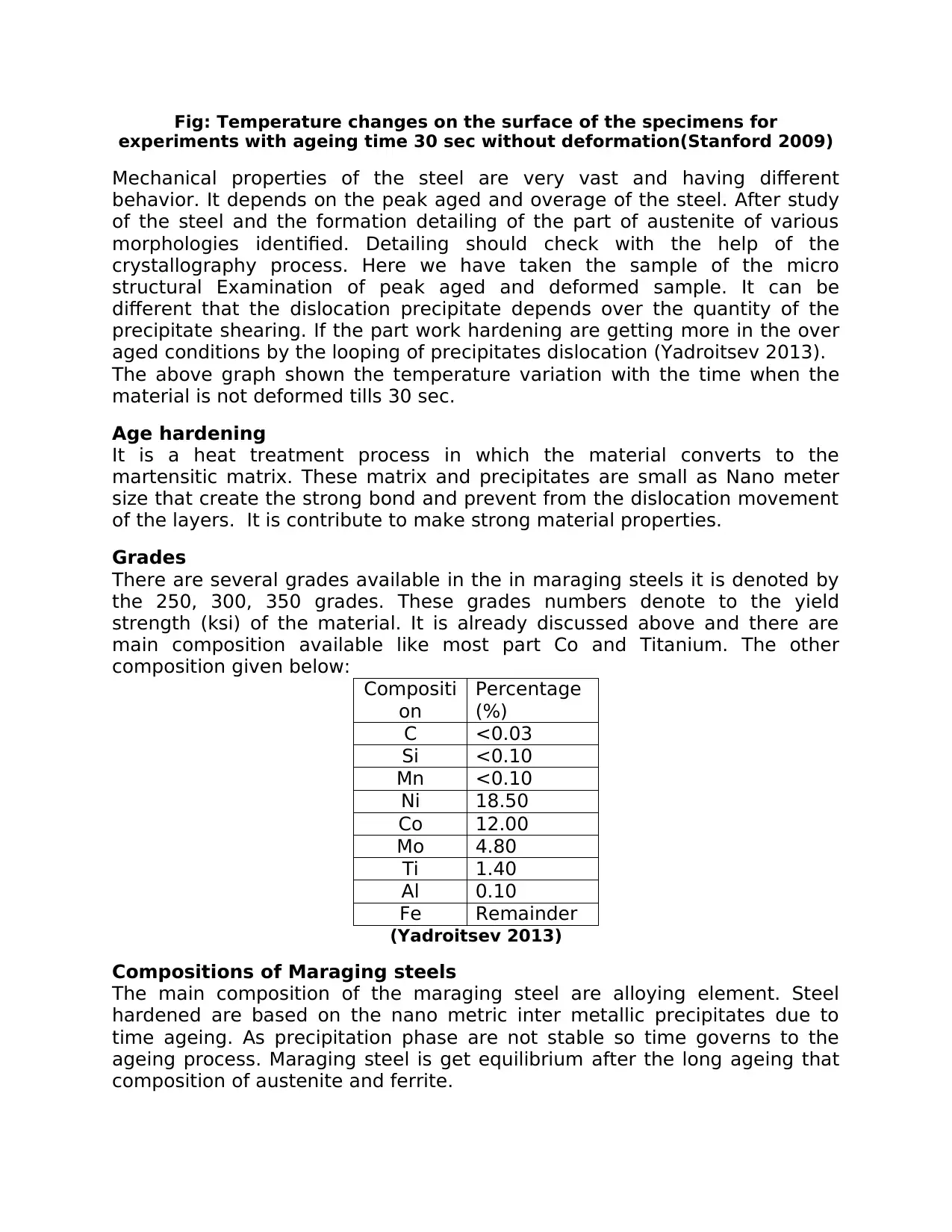
Fig: Temperature changes on the surface of the specimens for
experiments with ageing time 30 sec without deformation(Stanford 2009)
Mechanical properties of the steel are very vast and having different
behavior. It depends on the peak aged and overage of the steel. After study
of the steel and the formation detailing of the part of austenite of various
morphologies identified. Detailing should check with the help of the
crystallography process. Here we have taken the sample of the micro
structural Examination of peak aged and deformed sample. It can be
different that the dislocation precipitate depends over the quantity of the
precipitate shearing. If the part work hardening are getting more in the over
aged conditions by the looping of precipitates dislocation (Yadroitsev 2013).
The above graph shown the temperature variation with the time when the
material is not deformed tills 30 sec.
Age hardening
It is a heat treatment process in which the material converts to the
martensitic matrix. These matrix and precipitates are small as Nano meter
size that create the strong bond and prevent from the dislocation movement
of the layers. It is contribute to make strong material properties.
Grades
There are several grades available in the in maraging steels it is denoted by
the 250, 300, 350 grades. These grades numbers denote to the yield
strength (ksi) of the material. It is already discussed above and there are
main composition available like most part Co and Titanium. The other
composition given below:
Compositi
on
Percentage
(%)
C <0.03
Si <0.10
Mn <0.10
Ni 18.50
Co 12.00
Mo 4.80
Ti 1.40
Al 0.10
Fe Remainder
(Yadroitsev 2013)
Compositions of Maraging steels
The main composition of the maraging steel are alloying element. Steel
hardened are based on the nano metric inter metallic precipitates due to
time ageing. As precipitation phase are not stable so time governs to the
ageing process. Maraging steel is get equilibrium after the long ageing that
composition of austenite and ferrite.
experiments with ageing time 30 sec without deformation(Stanford 2009)
Mechanical properties of the steel are very vast and having different
behavior. It depends on the peak aged and overage of the steel. After study
of the steel and the formation detailing of the part of austenite of various
morphologies identified. Detailing should check with the help of the
crystallography process. Here we have taken the sample of the micro
structural Examination of peak aged and deformed sample. It can be
different that the dislocation precipitate depends over the quantity of the
precipitate shearing. If the part work hardening are getting more in the over
aged conditions by the looping of precipitates dislocation (Yadroitsev 2013).
The above graph shown the temperature variation with the time when the
material is not deformed tills 30 sec.
Age hardening
It is a heat treatment process in which the material converts to the
martensitic matrix. These matrix and precipitates are small as Nano meter
size that create the strong bond and prevent from the dislocation movement
of the layers. It is contribute to make strong material properties.
Grades
There are several grades available in the in maraging steels it is denoted by
the 250, 300, 350 grades. These grades numbers denote to the yield
strength (ksi) of the material. It is already discussed above and there are
main composition available like most part Co and Titanium. The other
composition given below:
Compositi
on
Percentage
(%)
C <0.03
Si <0.10
Mn <0.10
Ni 18.50
Co 12.00
Mo 4.80
Ti 1.40
Al 0.10
Fe Remainder
(Yadroitsev 2013)
Compositions of Maraging steels
The main composition of the maraging steel are alloying element. Steel
hardened are based on the nano metric inter metallic precipitates due to
time ageing. As precipitation phase are not stable so time governs to the
ageing process. Maraging steel is get equilibrium after the long ageing that
composition of austenite and ferrite.
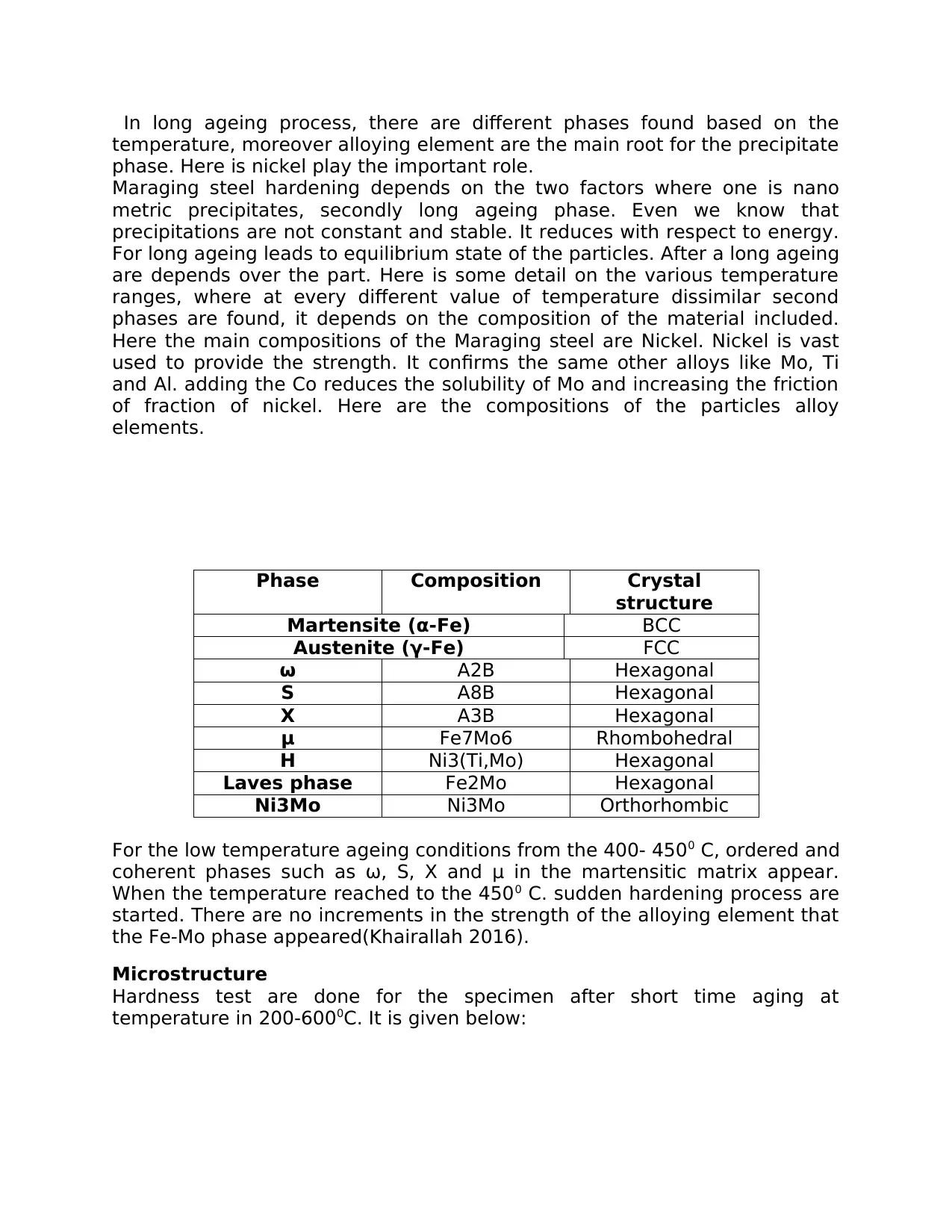
In long ageing process, there are different phases found based on the
temperature, moreover alloying element are the main root for the precipitate
phase. Here is nickel play the important role.
Maraging steel hardening depends on the two factors where one is nano
metric precipitates, secondly long ageing phase. Even we know that
precipitations are not constant and stable. It reduces with respect to energy.
For long ageing leads to equilibrium state of the particles. After a long ageing
are depends over the part. Here is some detail on the various temperature
ranges, where at every different value of temperature dissimilar second
phases are found, it depends on the composition of the material included.
Here the main compositions of the Maraging steel are Nickel. Nickel is vast
used to provide the strength. It confirms the same other alloys like Mo, Ti
and Al. adding the Co reduces the solubility of Mo and increasing the friction
of fraction of nickel. Here are the compositions of the particles alloy
elements.
Phase Composition Crystal
structure
Martensite (α-Fe) BCC
Austenite (γ-Fe) FCC
ω A2B Hexagonal
S A8B Hexagonal
X A3B Hexagonal
μ Fe7Mo6 Rhombohedral
Η Ni3(Ti,Mo) Hexagonal
Laves phase Fe2Mo Hexagonal
Ni3Mo Ni3Mo Orthorhombic
For the low temperature ageing conditions from the 400- 4500 C, ordered and
coherent phases such as ω, S, X and μ in the martensitic matrix appear.
When the temperature reached to the 4500 C. sudden hardening process are
started. There are no increments in the strength of the alloying element that
the Fe-Mo phase appeared(Khairallah 2016).
Microstructure
Hardness test are done for the specimen after short time aging at
temperature in 200-6000C. It is given below:
temperature, moreover alloying element are the main root for the precipitate
phase. Here is nickel play the important role.
Maraging steel hardening depends on the two factors where one is nano
metric precipitates, secondly long ageing phase. Even we know that
precipitations are not constant and stable. It reduces with respect to energy.
For long ageing leads to equilibrium state of the particles. After a long ageing
are depends over the part. Here is some detail on the various temperature
ranges, where at every different value of temperature dissimilar second
phases are found, it depends on the composition of the material included.
Here the main compositions of the Maraging steel are Nickel. Nickel is vast
used to provide the strength. It confirms the same other alloys like Mo, Ti
and Al. adding the Co reduces the solubility of Mo and increasing the friction
of fraction of nickel. Here are the compositions of the particles alloy
elements.
Phase Composition Crystal
structure
Martensite (α-Fe) BCC
Austenite (γ-Fe) FCC
ω A2B Hexagonal
S A8B Hexagonal
X A3B Hexagonal
μ Fe7Mo6 Rhombohedral
Η Ni3(Ti,Mo) Hexagonal
Laves phase Fe2Mo Hexagonal
Ni3Mo Ni3Mo Orthorhombic
For the low temperature ageing conditions from the 400- 4500 C, ordered and
coherent phases such as ω, S, X and μ in the martensitic matrix appear.
When the temperature reached to the 4500 C. sudden hardening process are
started. There are no increments in the strength of the alloying element that
the Fe-Mo phase appeared(Khairallah 2016).
Microstructure
Hardness test are done for the specimen after short time aging at
temperature in 200-6000C. It is given below:
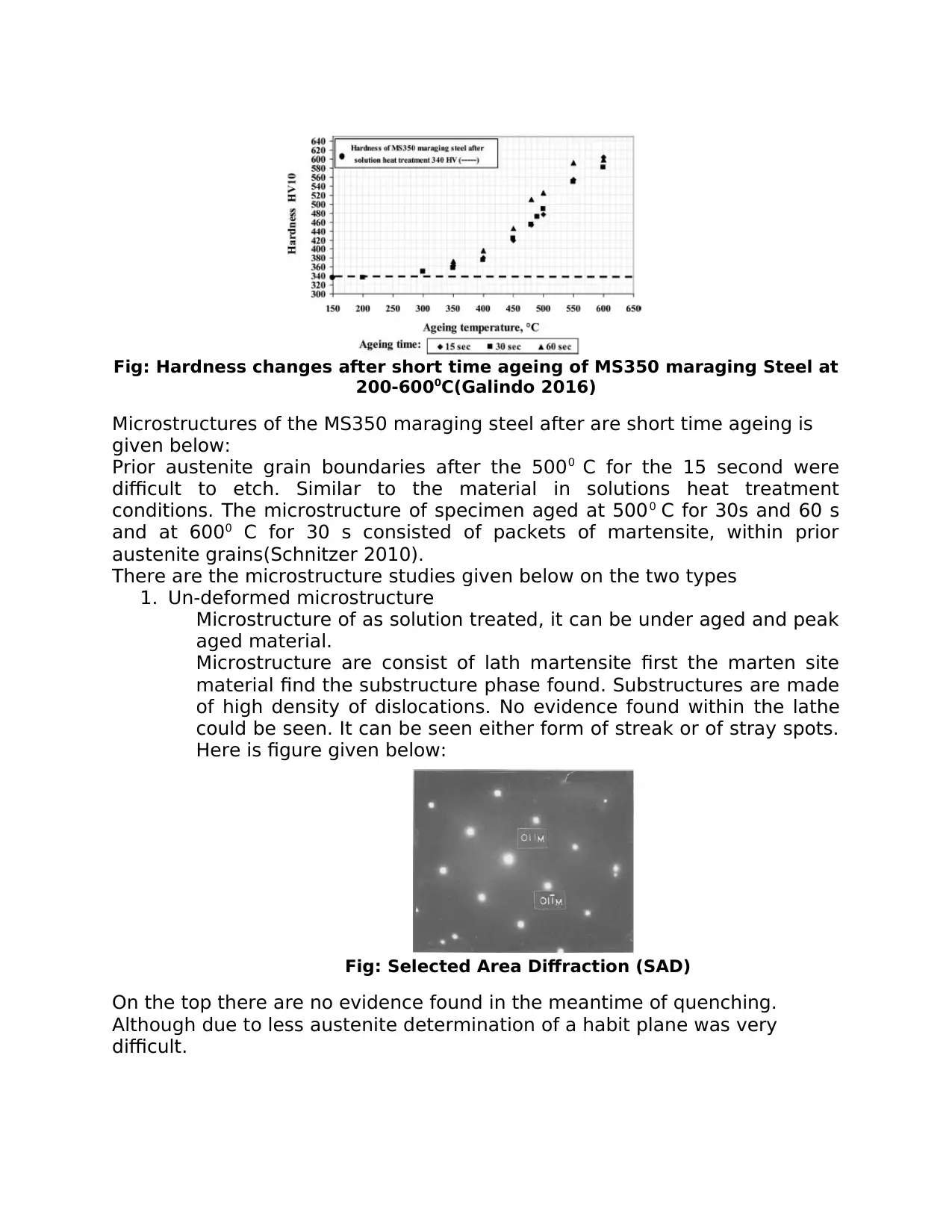
Fig: Hardness changes after short time ageing of MS350 maraging Steel at
200-6000C(Galindo 2016)
Microstructures of the MS350 maraging steel after are short time ageing is
given below:
Prior austenite grain boundaries after the 5000 C for the 15 second were
difficult to etch. Similar to the material in solutions heat treatment
conditions. The microstructure of specimen aged at 5000 C for 30s and 60 s
and at 6000 C for 30 s consisted of packets of martensite, within prior
austenite grains(Schnitzer 2010).
There are the microstructure studies given below on the two types
1. Un-deformed microstructure
Microstructure of as solution treated, it can be under aged and peak
aged material.
Microstructure are consist of lath martensite first the marten site
material find the substructure phase found. Substructures are made
of high density of dislocations. No evidence found within the lathe
could be seen. It can be seen either form of streak or of stray spots.
Here is figure given below:
Fig: Selected Area Diffraction (SAD)
On the top there are no evidence found in the meantime of quenching.
Although due to less austenite determination of a habit plane was very
difficult.
200-6000C(Galindo 2016)
Microstructures of the MS350 maraging steel after are short time ageing is
given below:
Prior austenite grain boundaries after the 5000 C for the 15 second were
difficult to etch. Similar to the material in solutions heat treatment
conditions. The microstructure of specimen aged at 5000 C for 30s and 60 s
and at 6000 C for 30 s consisted of packets of martensite, within prior
austenite grains(Schnitzer 2010).
There are the microstructure studies given below on the two types
1. Un-deformed microstructure
Microstructure of as solution treated, it can be under aged and peak
aged material.
Microstructure are consist of lath martensite first the marten site
material find the substructure phase found. Substructures are made
of high density of dislocations. No evidence found within the lathe
could be seen. It can be seen either form of streak or of stray spots.
Here is figure given below:
Fig: Selected Area Diffraction (SAD)
On the top there are no evidence found in the meantime of quenching.
Although due to less austenite determination of a habit plane was very
difficult.
Secure Best Marks with AI Grader
Need help grading? Try our AI Grader for instant feedback on your assignments.

Fig. Microstructure of specimens after ageing and without following
deformation(Leitner 2011):
a) at 5000 C for 15 seconds; b) at 5000 C for 30 seconds;
c) at 5000 C for 60 seconds; d) at 6000 C for 30 seconds
2. Deformed Microstructure
Basis on the hardness, there is a description about the micro structure.
Result for the different temperature hardness measurement of specimens
short time aged and compressed. Here hardness analyzed till 30 sec.
Fig: Graph between hardness changes and deformation at the
temperature 20-5500 C
And without temperature at 200-600 0 C till 30 sec(Moshka, 2015)
The graph is shown the below for the temperature variation with the
hardness strength. At the temperature range of ageing and specimen
hardness increases from 390 to 500 HV for the strain rate. The full graph and
more detail are given below for the microstructure of the maraging steel.
(Stanford 2009).
deformation(Leitner 2011):
a) at 5000 C for 15 seconds; b) at 5000 C for 30 seconds;
c) at 5000 C for 60 seconds; d) at 6000 C for 30 seconds
2. Deformed Microstructure
Basis on the hardness, there is a description about the micro structure.
Result for the different temperature hardness measurement of specimens
short time aged and compressed. Here hardness analyzed till 30 sec.
Fig: Graph between hardness changes and deformation at the
temperature 20-5500 C
And without temperature at 200-600 0 C till 30 sec(Moshka, 2015)
The graph is shown the below for the temperature variation with the
hardness strength. At the temperature range of ageing and specimen
hardness increases from 390 to 500 HV for the strain rate. The full graph and
more detail are given below for the microstructure of the maraging steel.
(Stanford 2009).
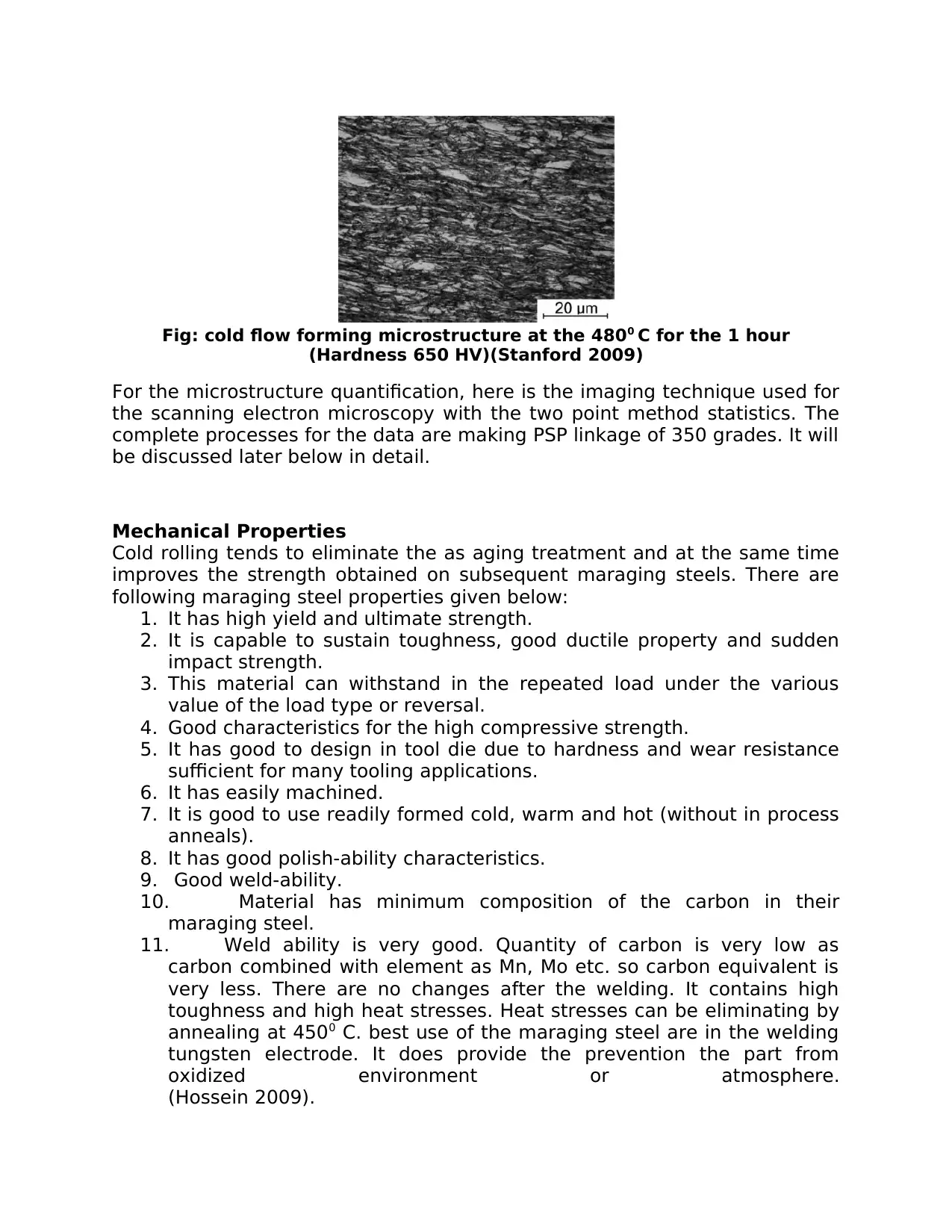
Fig: cold flow forming microstructure at the 4800 C for the 1 hour
(Hardness 650 HV)(Stanford 2009)
For the microstructure quantification, here is the imaging technique used for
the scanning electron microscopy with the two point method statistics. The
complete processes for the data are making PSP linkage of 350 grades. It will
be discussed later below in detail.
Mechanical Properties
Cold rolling tends to eliminate the as aging treatment and at the same time
improves the strength obtained on subsequent maraging steels. There are
following maraging steel properties given below:
1. It has high yield and ultimate strength.
2. It is capable to sustain toughness, good ductile property and sudden
impact strength.
3. This material can withstand in the repeated load under the various
value of the load type or reversal.
4. Good characteristics for the high compressive strength.
5. It has good to design in tool die due to hardness and wear resistance
sufficient for many tooling applications.
6. It has easily machined.
7. It is good to use readily formed cold, warm and hot (without in process
anneals).
8. It has good polish-ability characteristics.
9. Good weld-ability.
10. Material has minimum composition of the carbon in their
maraging steel.
11. Weld ability is very good. Quantity of carbon is very low as
carbon combined with element as Mn, Mo etc. so carbon equivalent is
very less. There are no changes after the welding. It contains high
toughness and high heat stresses. Heat stresses can be eliminating by
annealing at 4500 C. best use of the maraging steel are in the welding
tungsten electrode. It does provide the prevention the part from
oxidized environment or atmosphere.
(Hossein 2009).
(Hardness 650 HV)(Stanford 2009)
For the microstructure quantification, here is the imaging technique used for
the scanning electron microscopy with the two point method statistics. The
complete processes for the data are making PSP linkage of 350 grades. It will
be discussed later below in detail.
Mechanical Properties
Cold rolling tends to eliminate the as aging treatment and at the same time
improves the strength obtained on subsequent maraging steels. There are
following maraging steel properties given below:
1. It has high yield and ultimate strength.
2. It is capable to sustain toughness, good ductile property and sudden
impact strength.
3. This material can withstand in the repeated load under the various
value of the load type or reversal.
4. Good characteristics for the high compressive strength.
5. It has good to design in tool die due to hardness and wear resistance
sufficient for many tooling applications.
6. It has easily machined.
7. It is good to use readily formed cold, warm and hot (without in process
anneals).
8. It has good polish-ability characteristics.
9. Good weld-ability.
10. Material has minimum composition of the carbon in their
maraging steel.
11. Weld ability is very good. Quantity of carbon is very low as
carbon combined with element as Mn, Mo etc. so carbon equivalent is
very less. There are no changes after the welding. It contains high
toughness and high heat stresses. Heat stresses can be eliminating by
annealing at 4500 C. best use of the maraging steel are in the welding
tungsten electrode. It does provide the prevention the part from
oxidized environment or atmosphere.
(Hossein 2009).
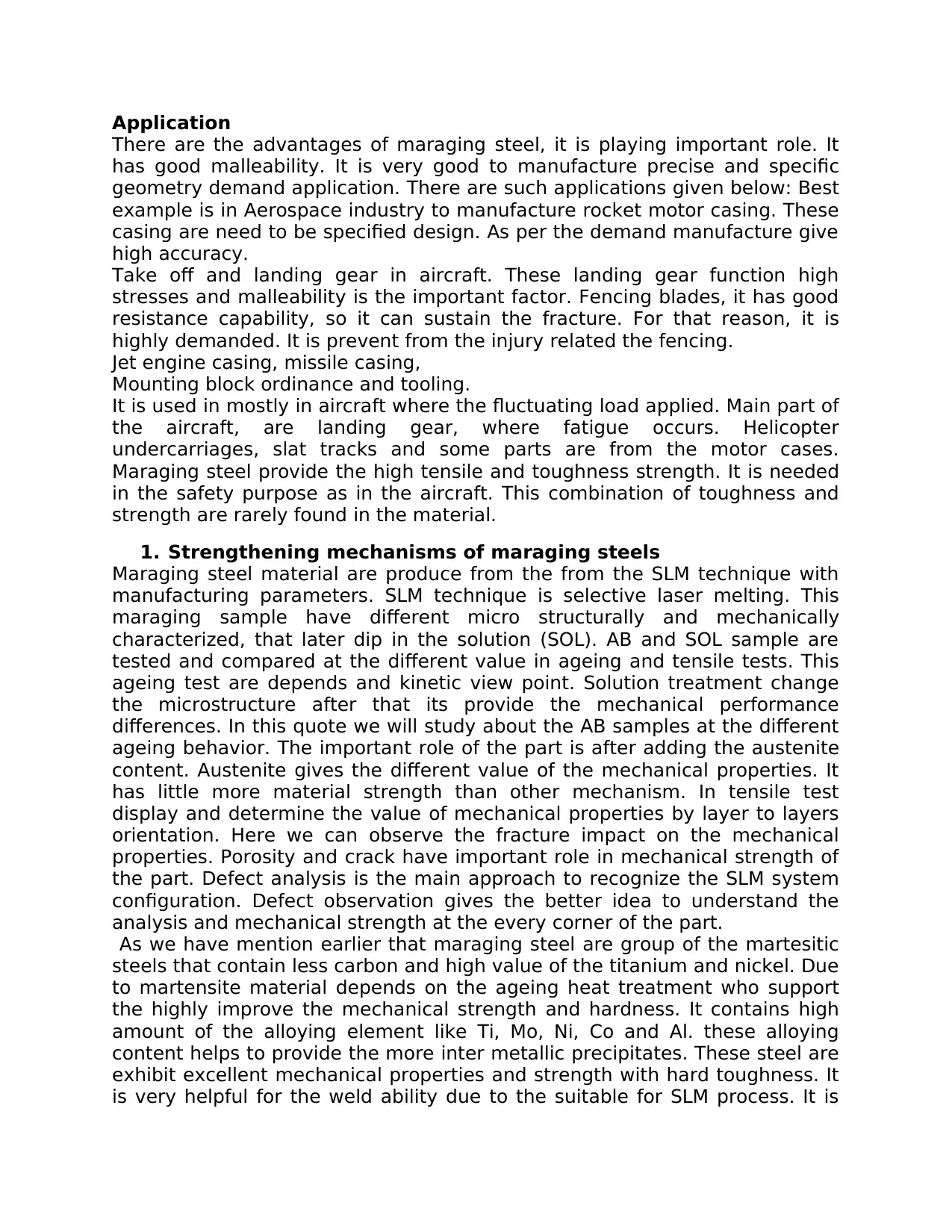
Application
There are the advantages of maraging steel, it is playing important role. It
has good malleability. It is very good to manufacture precise and specific
geometry demand application. There are such applications given below: Best
example is in Aerospace industry to manufacture rocket motor casing. These
casing are need to be specified design. As per the demand manufacture give
high accuracy.
Take off and landing gear in aircraft. These landing gear function high
stresses and malleability is the important factor. Fencing blades, it has good
resistance capability, so it can sustain the fracture. For that reason, it is
highly demanded. It is prevent from the injury related the fencing.
Jet engine casing, missile casing,
Mounting block ordinance and tooling.
It is used in mostly in aircraft where the fluctuating load applied. Main part of
the aircraft, are landing gear, where fatigue occurs. Helicopter
undercarriages, slat tracks and some parts are from the motor cases.
Maraging steel provide the high tensile and toughness strength. It is needed
in the safety purpose as in the aircraft. This combination of toughness and
strength are rarely found in the material.
1. Strengthening mechanisms of maraging steels
Maraging steel material are produce from the from the SLM technique with
manufacturing parameters. SLM technique is selective laser melting. This
maraging sample have different micro structurally and mechanically
characterized, that later dip in the solution (SOL). AB and SOL sample are
tested and compared at the different value in ageing and tensile tests. This
ageing test are depends and kinetic view point. Solution treatment change
the microstructure after that its provide the mechanical performance
differences. In this quote we will study about the AB samples at the different
ageing behavior. The important role of the part is after adding the austenite
content. Austenite gives the different value of the mechanical properties. It
has little more material strength than other mechanism. In tensile test
display and determine the value of mechanical properties by layer to layers
orientation. Here we can observe the fracture impact on the mechanical
properties. Porosity and crack have important role in mechanical strength of
the part. Defect analysis is the main approach to recognize the SLM system
configuration. Defect observation gives the better idea to understand the
analysis and mechanical strength at the every corner of the part.
As we have mention earlier that maraging steel are group of the martesitic
steels that contain less carbon and high value of the titanium and nickel. Due
to martensite material depends on the ageing heat treatment who support
the highly improve the mechanical strength and hardness. It contains high
amount of the alloying element like Ti, Mo, Ni, Co and Al. these alloying
content helps to provide the more inter metallic precipitates. These steel are
exhibit excellent mechanical properties and strength with hard toughness. It
is very helpful for the weld ability due to the suitable for SLM process. It is
There are the advantages of maraging steel, it is playing important role. It
has good malleability. It is very good to manufacture precise and specific
geometry demand application. There are such applications given below: Best
example is in Aerospace industry to manufacture rocket motor casing. These
casing are need to be specified design. As per the demand manufacture give
high accuracy.
Take off and landing gear in aircraft. These landing gear function high
stresses and malleability is the important factor. Fencing blades, it has good
resistance capability, so it can sustain the fracture. For that reason, it is
highly demanded. It is prevent from the injury related the fencing.
Jet engine casing, missile casing,
Mounting block ordinance and tooling.
It is used in mostly in aircraft where the fluctuating load applied. Main part of
the aircraft, are landing gear, where fatigue occurs. Helicopter
undercarriages, slat tracks and some parts are from the motor cases.
Maraging steel provide the high tensile and toughness strength. It is needed
in the safety purpose as in the aircraft. This combination of toughness and
strength are rarely found in the material.
1. Strengthening mechanisms of maraging steels
Maraging steel material are produce from the from the SLM technique with
manufacturing parameters. SLM technique is selective laser melting. This
maraging sample have different micro structurally and mechanically
characterized, that later dip in the solution (SOL). AB and SOL sample are
tested and compared at the different value in ageing and tensile tests. This
ageing test are depends and kinetic view point. Solution treatment change
the microstructure after that its provide the mechanical performance
differences. In this quote we will study about the AB samples at the different
ageing behavior. The important role of the part is after adding the austenite
content. Austenite gives the different value of the mechanical properties. It
has little more material strength than other mechanism. In tensile test
display and determine the value of mechanical properties by layer to layers
orientation. Here we can observe the fracture impact on the mechanical
properties. Porosity and crack have important role in mechanical strength of
the part. Defect analysis is the main approach to recognize the SLM system
configuration. Defect observation gives the better idea to understand the
analysis and mechanical strength at the every corner of the part.
As we have mention earlier that maraging steel are group of the martesitic
steels that contain less carbon and high value of the titanium and nickel. Due
to martensite material depends on the ageing heat treatment who support
the highly improve the mechanical strength and hardness. It contains high
amount of the alloying element like Ti, Mo, Ni, Co and Al. these alloying
content helps to provide the more inter metallic precipitates. These steel are
exhibit excellent mechanical properties and strength with hard toughness. It
is very helpful for the weld ability due to the suitable for SLM process. It is
Paraphrase This Document
Need a fresh take? Get an instant paraphrase of this document with our AI Paraphraser
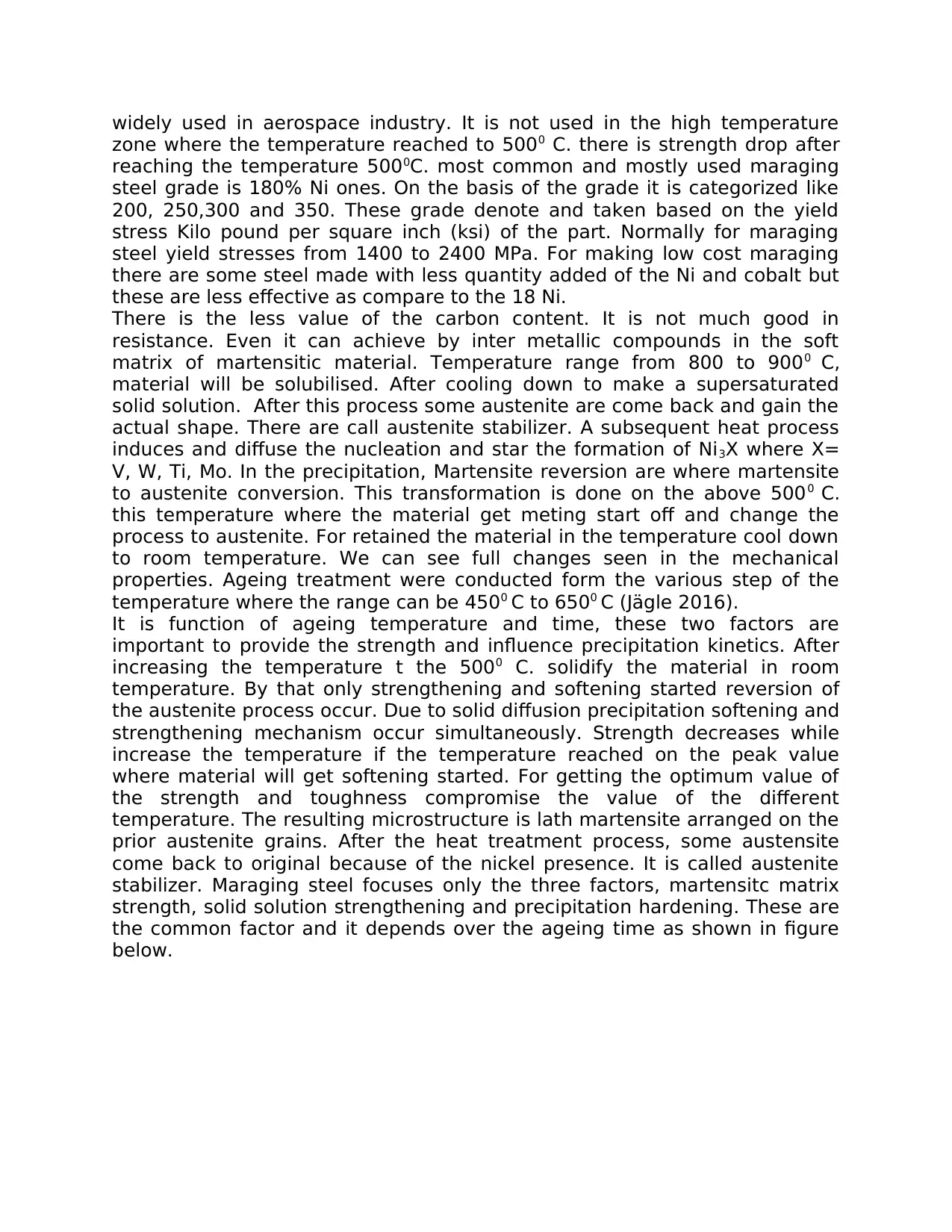
widely used in aerospace industry. It is not used in the high temperature
zone where the temperature reached to 5000 C. there is strength drop after
reaching the temperature 5000C. most common and mostly used maraging
steel grade is 180% Ni ones. On the basis of the grade it is categorized like
200, 250,300 and 350. These grade denote and taken based on the yield
stress Kilo pound per square inch (ksi) of the part. Normally for maraging
steel yield stresses from 1400 to 2400 MPa. For making low cost maraging
there are some steel made with less quantity added of the Ni and cobalt but
these are less effective as compare to the 18 Ni.
There is the less value of the carbon content. It is not much good in
resistance. Even it can achieve by inter metallic compounds in the soft
matrix of martensitic material. Temperature range from 800 to 9000 C,
material will be solubilised. After cooling down to make a supersaturated
solid solution. After this process some austenite are come back and gain the
actual shape. There are call austenite stabilizer. A subsequent heat process
induces and diffuse the nucleation and star the formation of Ni3X where X=
V, W, Ti, Mo. In the precipitation, Martensite reversion are where martensite
to austenite conversion. This transformation is done on the above 5000 C.
this temperature where the material get meting start off and change the
process to austenite. For retained the material in the temperature cool down
to room temperature. We can see full changes seen in the mechanical
properties. Ageing treatment were conducted form the various step of the
temperature where the range can be 4500 C to 6500 C (Jägle 2016).
It is function of ageing temperature and time, these two factors are
important to provide the strength and influence precipitation kinetics. After
increasing the temperature t the 5000 C. solidify the material in room
temperature. By that only strengthening and softening started reversion of
the austenite process occur. Due to solid diffusion precipitation softening and
strengthening mechanism occur simultaneously. Strength decreases while
increase the temperature if the temperature reached on the peak value
where material will get softening started. For getting the optimum value of
the strength and toughness compromise the value of the different
temperature. The resulting microstructure is lath martensite arranged on the
prior austenite grains. After the heat treatment process, some austensite
come back to original because of the nickel presence. It is called austenite
stabilizer. Maraging steel focuses only the three factors, martensitc matrix
strength, solid solution strengthening and precipitation hardening. These are
the common factor and it depends over the ageing time as shown in figure
below.
zone where the temperature reached to 5000 C. there is strength drop after
reaching the temperature 5000C. most common and mostly used maraging
steel grade is 180% Ni ones. On the basis of the grade it is categorized like
200, 250,300 and 350. These grade denote and taken based on the yield
stress Kilo pound per square inch (ksi) of the part. Normally for maraging
steel yield stresses from 1400 to 2400 MPa. For making low cost maraging
there are some steel made with less quantity added of the Ni and cobalt but
these are less effective as compare to the 18 Ni.
There is the less value of the carbon content. It is not much good in
resistance. Even it can achieve by inter metallic compounds in the soft
matrix of martensitic material. Temperature range from 800 to 9000 C,
material will be solubilised. After cooling down to make a supersaturated
solid solution. After this process some austenite are come back and gain the
actual shape. There are call austenite stabilizer. A subsequent heat process
induces and diffuse the nucleation and star the formation of Ni3X where X=
V, W, Ti, Mo. In the precipitation, Martensite reversion are where martensite
to austenite conversion. This transformation is done on the above 5000 C.
this temperature where the material get meting start off and change the
process to austenite. For retained the material in the temperature cool down
to room temperature. We can see full changes seen in the mechanical
properties. Ageing treatment were conducted form the various step of the
temperature where the range can be 4500 C to 6500 C (Jägle 2016).
It is function of ageing temperature and time, these two factors are
important to provide the strength and influence precipitation kinetics. After
increasing the temperature t the 5000 C. solidify the material in room
temperature. By that only strengthening and softening started reversion of
the austenite process occur. Due to solid diffusion precipitation softening and
strengthening mechanism occur simultaneously. Strength decreases while
increase the temperature if the temperature reached on the peak value
where material will get softening started. For getting the optimum value of
the strength and toughness compromise the value of the different
temperature. The resulting microstructure is lath martensite arranged on the
prior austenite grains. After the heat treatment process, some austensite
come back to original because of the nickel presence. It is called austenite
stabilizer. Maraging steel focuses only the three factors, martensitc matrix
strength, solid solution strengthening and precipitation hardening. These are
the common factor and it depends over the ageing time as shown in figure
below.
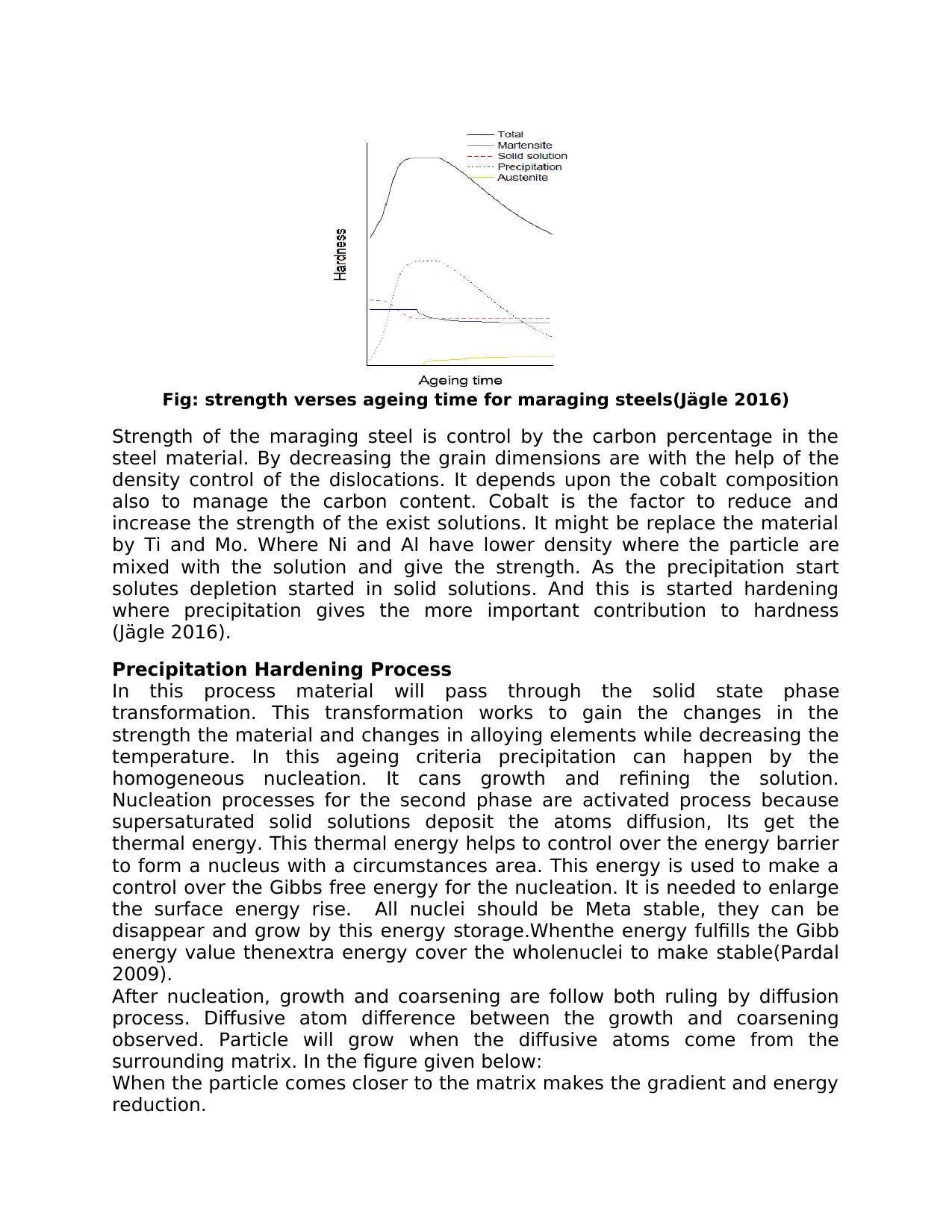
Fig: strength verses ageing time for maraging steels(Jägle 2016)
Strength of the maraging steel is control by the carbon percentage in the
steel material. By decreasing the grain dimensions are with the help of the
density control of the dislocations. It depends upon the cobalt composition
also to manage the carbon content. Cobalt is the factor to reduce and
increase the strength of the exist solutions. It might be replace the material
by Ti and Mo. Where Ni and Al have lower density where the particle are
mixed with the solution and give the strength. As the precipitation start
solutes depletion started in solid solutions. And this is started hardening
where precipitation gives the more important contribution to hardness
(Jägle 2016).
Precipitation Hardening Process
In this process material will pass through the solid state phase
transformation. This transformation works to gain the changes in the
strength the material and changes in alloying elements while decreasing the
temperature. In this ageing criteria precipitation can happen by the
homogeneous nucleation. It cans growth and refining the solution.
Nucleation processes for the second phase are activated process because
supersaturated solid solutions deposit the atoms diffusion, Its get the
thermal energy. This thermal energy helps to control over the energy barrier
to form a nucleus with a circumstances area. This energy is used to make a
control over the Gibbs free energy for the nucleation. It is needed to enlarge
the surface energy rise. All nuclei should be Meta stable, they can be
disappear and grow by this energy storage.Whenthe energy fulfills the Gibb
energy value thenextra energy cover the wholenuclei to make stable(Pardal
2009).
After nucleation, growth and coarsening are follow both ruling by diffusion
process. Diffusive atom difference between the growth and coarsening
observed. Particle will grow when the diffusive atoms come from the
surrounding matrix. In the figure given below:
When the particle comes closer to the matrix makes the gradient and energy
reduction.
Strength of the maraging steel is control by the carbon percentage in the
steel material. By decreasing the grain dimensions are with the help of the
density control of the dislocations. It depends upon the cobalt composition
also to manage the carbon content. Cobalt is the factor to reduce and
increase the strength of the exist solutions. It might be replace the material
by Ti and Mo. Where Ni and Al have lower density where the particle are
mixed with the solution and give the strength. As the precipitation start
solutes depletion started in solid solutions. And this is started hardening
where precipitation gives the more important contribution to hardness
(Jägle 2016).
Precipitation Hardening Process
In this process material will pass through the solid state phase
transformation. This transformation works to gain the changes in the
strength the material and changes in alloying elements while decreasing the
temperature. In this ageing criteria precipitation can happen by the
homogeneous nucleation. It cans growth and refining the solution.
Nucleation processes for the second phase are activated process because
supersaturated solid solutions deposit the atoms diffusion, Its get the
thermal energy. This thermal energy helps to control over the energy barrier
to form a nucleus with a circumstances area. This energy is used to make a
control over the Gibbs free energy for the nucleation. It is needed to enlarge
the surface energy rise. All nuclei should be Meta stable, they can be
disappear and grow by this energy storage.Whenthe energy fulfills the Gibb
energy value thenextra energy cover the wholenuclei to make stable(Pardal
2009).
After nucleation, growth and coarsening are follow both ruling by diffusion
process. Diffusive atom difference between the growth and coarsening
observed. Particle will grow when the diffusive atoms come from the
surrounding matrix. In the figure given below:
When the particle comes closer to the matrix makes the gradient and energy
reduction.
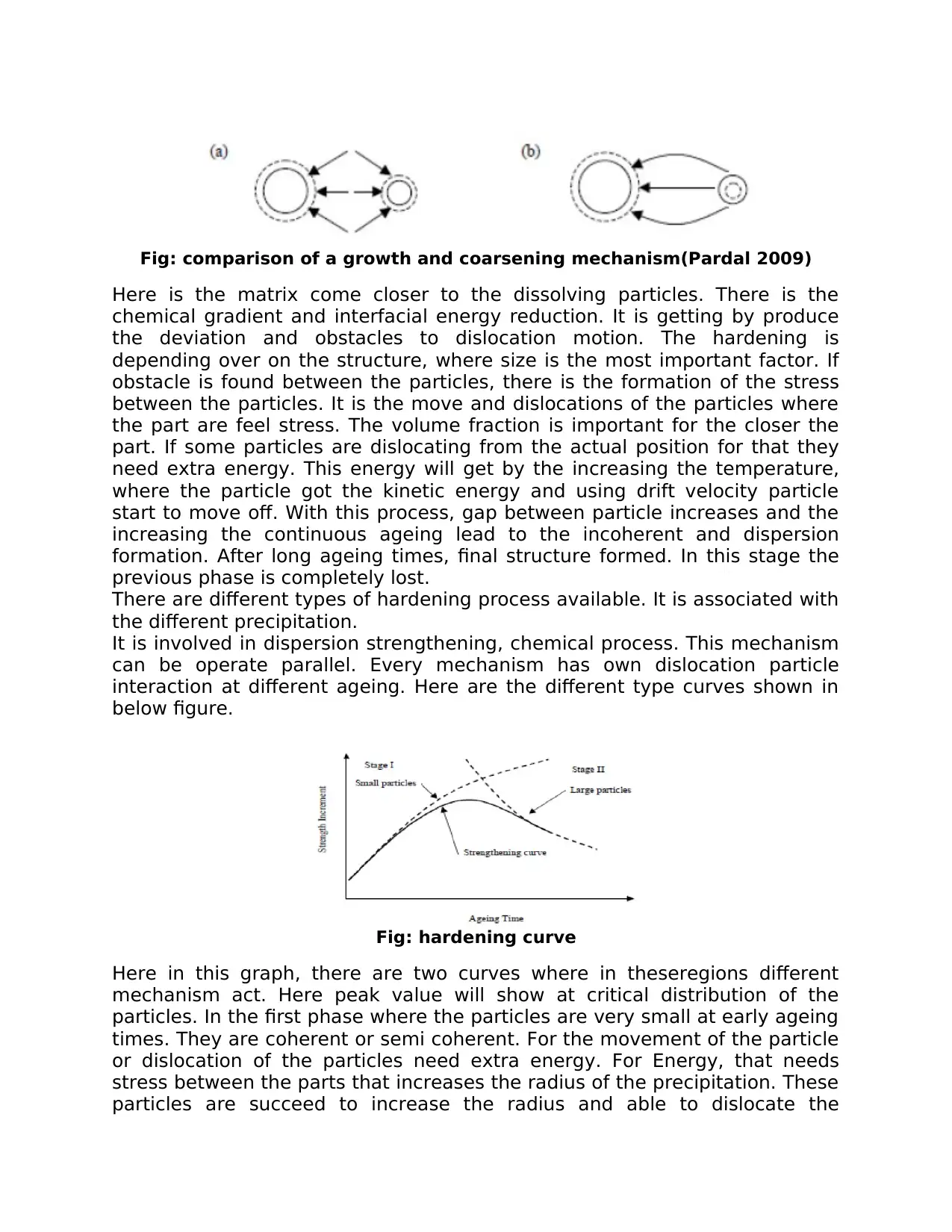
Fig: comparison of a growth and coarsening mechanism(Pardal 2009)
Here is the matrix come closer to the dissolving particles. There is the
chemical gradient and interfacial energy reduction. It is getting by produce
the deviation and obstacles to dislocation motion. The hardening is
depending over on the structure, where size is the most important factor. If
obstacle is found between the particles, there is the formation of the stress
between the particles. It is the move and dislocations of the particles where
the part are feel stress. The volume fraction is important for the closer the
part. If some particles are dislocating from the actual position for that they
need extra energy. This energy will get by the increasing the temperature,
where the particle got the kinetic energy and using drift velocity particle
start to move off. With this process, gap between particle increases and the
increasing the continuous ageing lead to the incoherent and dispersion
formation. After long ageing times, final structure formed. In this stage the
previous phase is completely lost.
There are different types of hardening process available. It is associated with
the different precipitation.
It is involved in dispersion strengthening, chemical process. This mechanism
can be operate parallel. Every mechanism has own dislocation particle
interaction at different ageing. Here are the different type curves shown in
below figure.
Fig: hardening curve
Here in this graph, there are two curves where in theseregions different
mechanism act. Here peak value will show at critical distribution of the
particles. In the first phase where the particles are very small at early ageing
times. They are coherent or semi coherent. For the movement of the particle
or dislocation of the particles need extra energy. For Energy, that needs
stress between the parts that increases the radius of the precipitation. These
particles are succeed to increase the radius and able to dislocate the
Here is the matrix come closer to the dissolving particles. There is the
chemical gradient and interfacial energy reduction. It is getting by produce
the deviation and obstacles to dislocation motion. The hardening is
depending over on the structure, where size is the most important factor. If
obstacle is found between the particles, there is the formation of the stress
between the particles. It is the move and dislocations of the particles where
the part are feel stress. The volume fraction is important for the closer the
part. If some particles are dislocating from the actual position for that they
need extra energy. This energy will get by the increasing the temperature,
where the particle got the kinetic energy and using drift velocity particle
start to move off. With this process, gap between particle increases and the
increasing the continuous ageing lead to the incoherent and dispersion
formation. After long ageing times, final structure formed. In this stage the
previous phase is completely lost.
There are different types of hardening process available. It is associated with
the different precipitation.
It is involved in dispersion strengthening, chemical process. This mechanism
can be operate parallel. Every mechanism has own dislocation particle
interaction at different ageing. Here are the different type curves shown in
below figure.
Fig: hardening curve
Here in this graph, there are two curves where in theseregions different
mechanism act. Here peak value will show at critical distribution of the
particles. In the first phase where the particles are very small at early ageing
times. They are coherent or semi coherent. For the movement of the particle
or dislocation of the particles need extra energy. For Energy, that needs
stress between the parts that increases the radius of the precipitation. These
particles are succeed to increase the radius and able to dislocate the
Secure Best Marks with AI Grader
Need help grading? Try our AI Grader for instant feedback on your assignments.
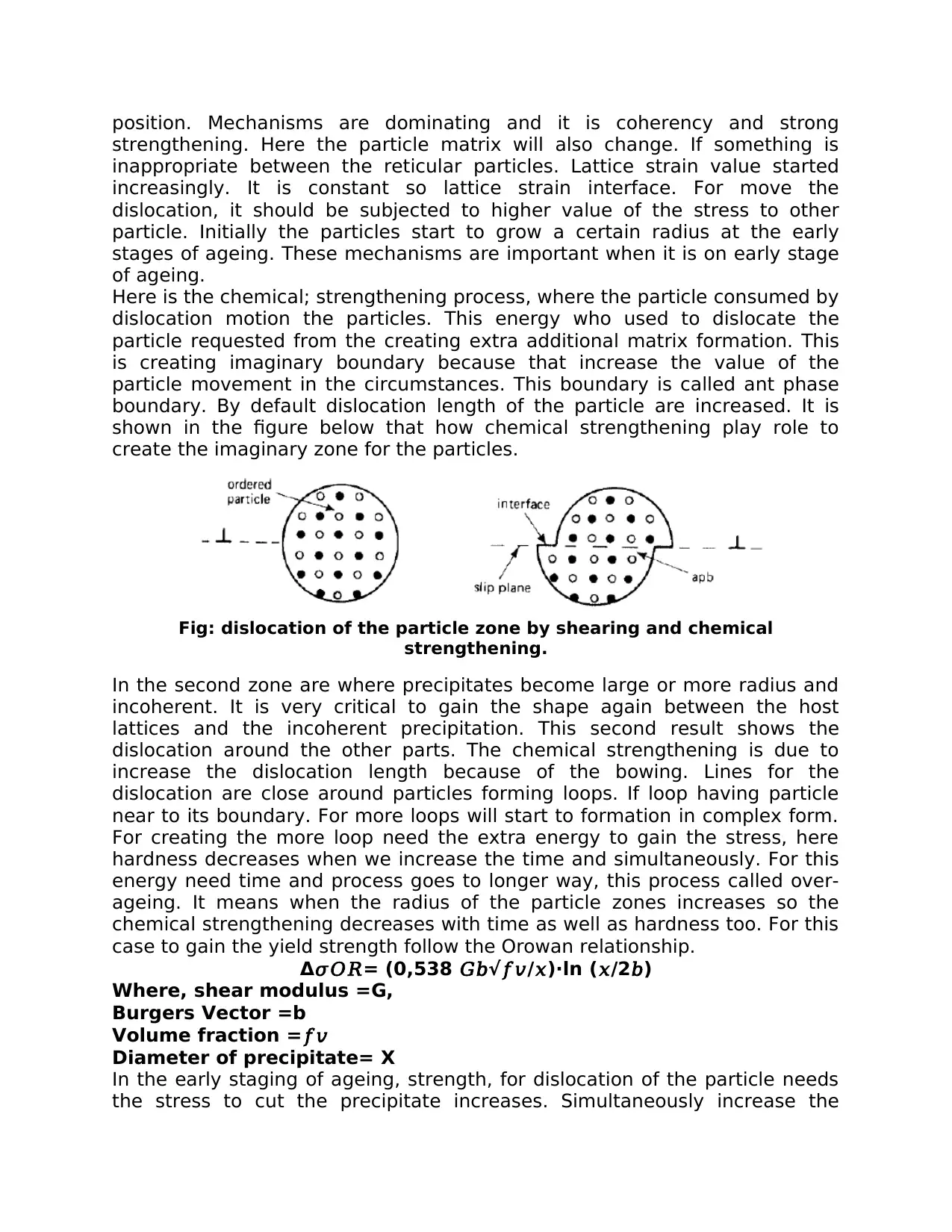
position. Mechanisms are dominating and it is coherency and strong
strengthening. Here the particle matrix will also change. If something is
inappropriate between the reticular particles. Lattice strain value started
increasingly. It is constant so lattice strain interface. For move the
dislocation, it should be subjected to higher value of the stress to other
particle. Initially the particles start to grow a certain radius at the early
stages of ageing. These mechanisms are important when it is on early stage
of ageing.
Here is the chemical; strengthening process, where the particle consumed by
dislocation motion the particles. This energy who used to dislocate the
particle requested from the creating extra additional matrix formation. This
is creating imaginary boundary because that increase the value of the
particle movement in the circumstances. This boundary is called ant phase
boundary. By default dislocation length of the particle are increased. It is
shown in the figure below that how chemical strengthening play role to
create the imaginary zone for the particles.
Fig: dislocation of the particle zone by shearing and chemical
strengthening.
In the second zone are where precipitates become large or more radius and
incoherent. It is very critical to gain the shape again between the host
lattices and the incoherent precipitation. This second result shows the
dislocation around the other parts. The chemical strengthening is due to
increase the dislocation length because of the bowing. Lines for the
dislocation are close around particles forming loops. If loop having particle
near to its boundary. For more loops will start to formation in complex form.
For creating the more loop need the extra energy to gain the stress, here
hardness decreases when we increase the time and simultaneously. For this
energy need time and process goes to longer way, this process called over-
ageing. It means when the radius of the particle zones increases so the
chemical strengthening decreases with time as well as hardness too. For this
case to gain the yield strength follow the Orowan relationship.
Δ𝜎𝑂𝑅= (0,538 𝐺𝑏√𝑓𝑣/𝑥)∙ln (𝑥/2𝑏)
Where, shear modulus =G,
Burgers Vector =b
Volume fraction =𝑓𝑣
Diameter of precipitate= X
In the early staging of ageing, strength, for dislocation of the particle needs
the stress to cut the precipitate increases. Simultaneously increase the
strengthening. Here the particle matrix will also change. If something is
inappropriate between the reticular particles. Lattice strain value started
increasingly. It is constant so lattice strain interface. For move the
dislocation, it should be subjected to higher value of the stress to other
particle. Initially the particles start to grow a certain radius at the early
stages of ageing. These mechanisms are important when it is on early stage
of ageing.
Here is the chemical; strengthening process, where the particle consumed by
dislocation motion the particles. This energy who used to dislocate the
particle requested from the creating extra additional matrix formation. This
is creating imaginary boundary because that increase the value of the
particle movement in the circumstances. This boundary is called ant phase
boundary. By default dislocation length of the particle are increased. It is
shown in the figure below that how chemical strengthening play role to
create the imaginary zone for the particles.
Fig: dislocation of the particle zone by shearing and chemical
strengthening.
In the second zone are where precipitates become large or more radius and
incoherent. It is very critical to gain the shape again between the host
lattices and the incoherent precipitation. This second result shows the
dislocation around the other parts. The chemical strengthening is due to
increase the dislocation length because of the bowing. Lines for the
dislocation are close around particles forming loops. If loop having particle
near to its boundary. For more loops will start to formation in complex form.
For creating the more loop need the extra energy to gain the stress, here
hardness decreases when we increase the time and simultaneously. For this
energy need time and process goes to longer way, this process called over-
ageing. It means when the radius of the particle zones increases so the
chemical strengthening decreases with time as well as hardness too. For this
case to gain the yield strength follow the Orowan relationship.
Δ𝜎𝑂𝑅= (0,538 𝐺𝑏√𝑓𝑣/𝑥)∙ln (𝑥/2𝑏)
Where, shear modulus =G,
Burgers Vector =b
Volume fraction =𝑓𝑣
Diameter of precipitate= X
In the early staging of ageing, strength, for dislocation of the particle needs
the stress to cut the precipitate increases. Simultaneously increase the
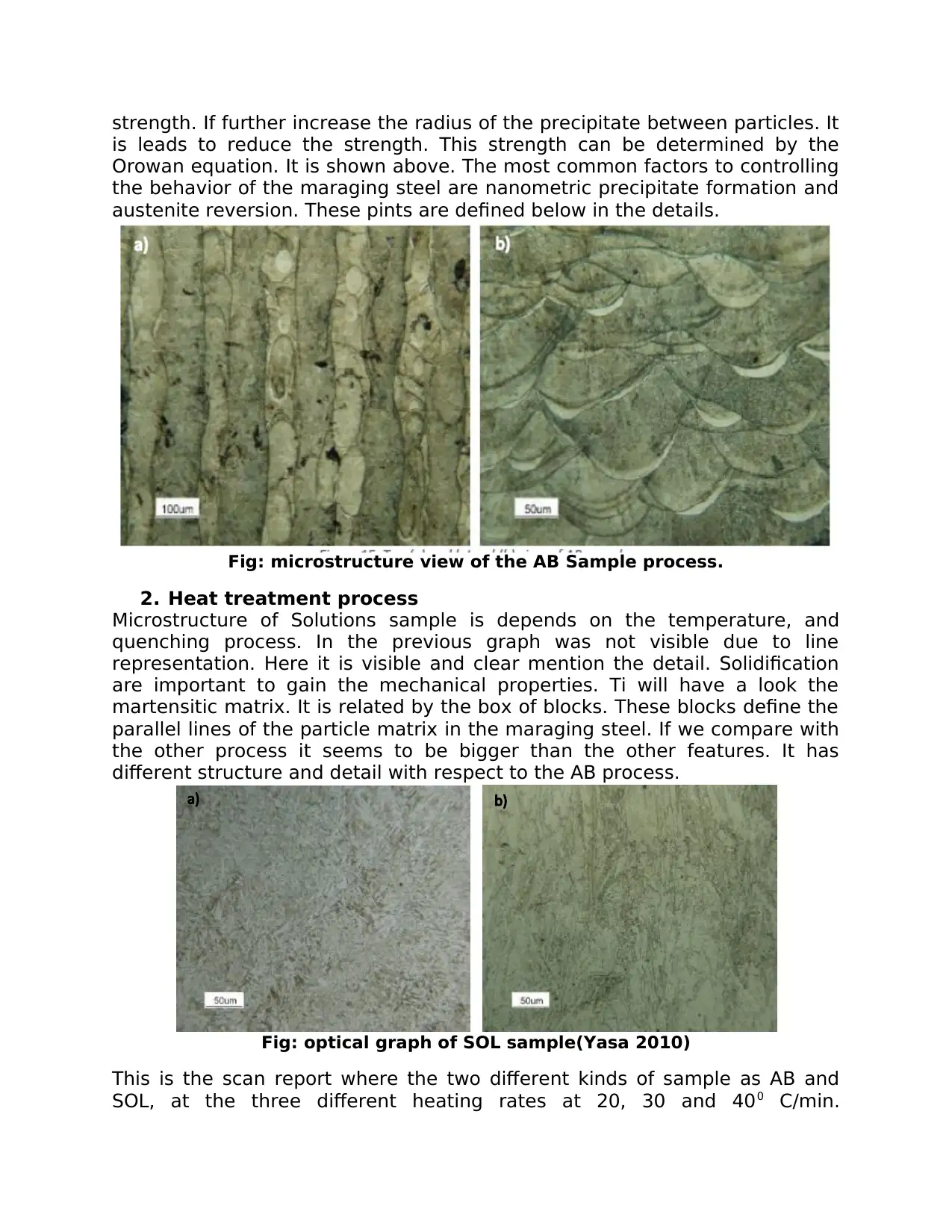
strength. If further increase the radius of the precipitate between particles. It
is leads to reduce the strength. This strength can be determined by the
Orowan equation. It is shown above. The most common factors to controlling
the behavior of the maraging steel are nanometric precipitate formation and
austenite reversion. These pints are defined below in the details.
Fig: microstructure view of the AB Sample process.
2. Heat treatment process
Microstructure of Solutions sample is depends on the temperature, and
quenching process. In the previous graph was not visible due to line
representation. Here it is visible and clear mention the detail. Solidification
are important to gain the mechanical properties. Ti will have a look the
martensitic matrix. It is related by the box of blocks. These blocks define the
parallel lines of the particle matrix in the maraging steel. If we compare with
the other process it seems to be bigger than the other features. It has
different structure and detail with respect to the AB process.
Fig: optical graph of SOL sample(Yasa 2010)
This is the scan report where the two different kinds of sample as AB and
SOL, at the three different heating rates at 20, 30 and 400 C/min.
is leads to reduce the strength. This strength can be determined by the
Orowan equation. It is shown above. The most common factors to controlling
the behavior of the maraging steel are nanometric precipitate formation and
austenite reversion. These pints are defined below in the details.
Fig: microstructure view of the AB Sample process.
2. Heat treatment process
Microstructure of Solutions sample is depends on the temperature, and
quenching process. In the previous graph was not visible due to line
representation. Here it is visible and clear mention the detail. Solidification
are important to gain the mechanical properties. Ti will have a look the
martensitic matrix. It is related by the box of blocks. These blocks define the
parallel lines of the particle matrix in the maraging steel. If we compare with
the other process it seems to be bigger than the other features. It has
different structure and detail with respect to the AB process.
Fig: optical graph of SOL sample(Yasa 2010)
This is the scan report where the two different kinds of sample as AB and
SOL, at the three different heating rates at 20, 30 and 400 C/min.
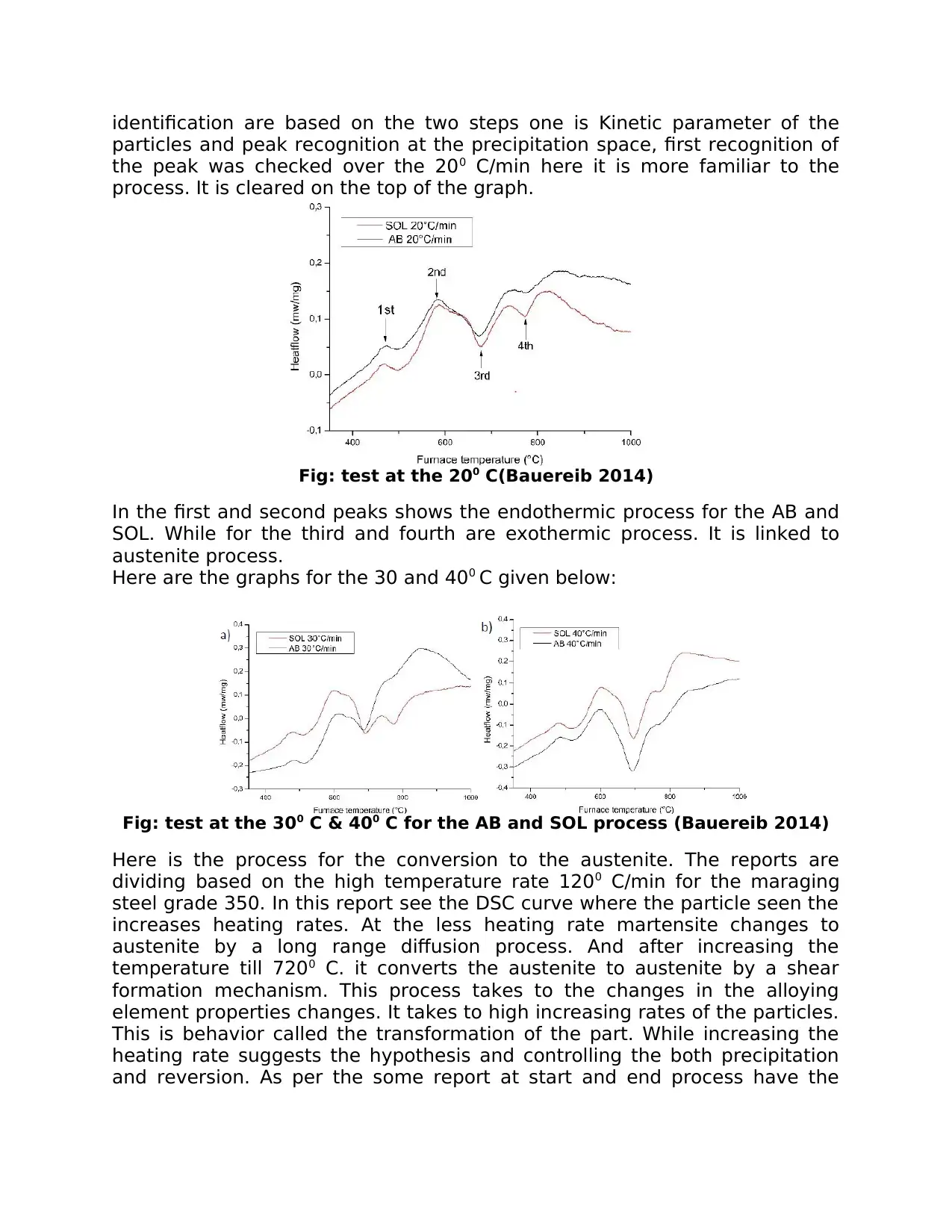
identification are based on the two steps one is Kinetic parameter of the
particles and peak recognition at the precipitation space, first recognition of
the peak was checked over the 200 C/min here it is more familiar to the
process. It is cleared on the top of the graph.
Fig: test at the 200 C(Bauereib 2014)
In the first and second peaks shows the endothermic process for the AB and
SOL. While for the third and fourth are exothermic process. It is linked to
austenite process.
Here are the graphs for the 30 and 400 C given below:
Fig: test at the 300 C & 400 C for the AB and SOL process (Bauereib 2014)
Here is the process for the conversion to the austenite. The reports are
dividing based on the high temperature rate 1200 C/min for the maraging
steel grade 350. In this report see the DSC curve where the particle seen the
increases heating rates. At the less heating rate martensite changes to
austenite by a long range diffusion process. And after increasing the
temperature till 7200 C. it converts the austenite to austenite by a shear
formation mechanism. This process takes to the changes in the alloying
element properties changes. It takes to high increasing rates of the particles.
This is behavior called the transformation of the part. While increasing the
heating rate suggests the hypothesis and controlling the both precipitation
and reversion. As per the some report at start and end process have the
particles and peak recognition at the precipitation space, first recognition of
the peak was checked over the 200 C/min here it is more familiar to the
process. It is cleared on the top of the graph.
Fig: test at the 200 C(Bauereib 2014)
In the first and second peaks shows the endothermic process for the AB and
SOL. While for the third and fourth are exothermic process. It is linked to
austenite process.
Here are the graphs for the 30 and 400 C given below:
Fig: test at the 300 C & 400 C for the AB and SOL process (Bauereib 2014)
Here is the process for the conversion to the austenite. The reports are
dividing based on the high temperature rate 1200 C/min for the maraging
steel grade 350. In this report see the DSC curve where the particle seen the
increases heating rates. At the less heating rate martensite changes to
austenite by a long range diffusion process. And after increasing the
temperature till 7200 C. it converts the austenite to austenite by a shear
formation mechanism. This process takes to the changes in the alloying
element properties changes. It takes to high increasing rates of the particles.
This is behavior called the transformation of the part. While increasing the
heating rate suggests the hypothesis and controlling the both precipitation
and reversion. As per the some report at start and end process have the
Paraphrase This Document
Need a fresh take? Get an instant paraphrase of this document with our AI Paraphraser
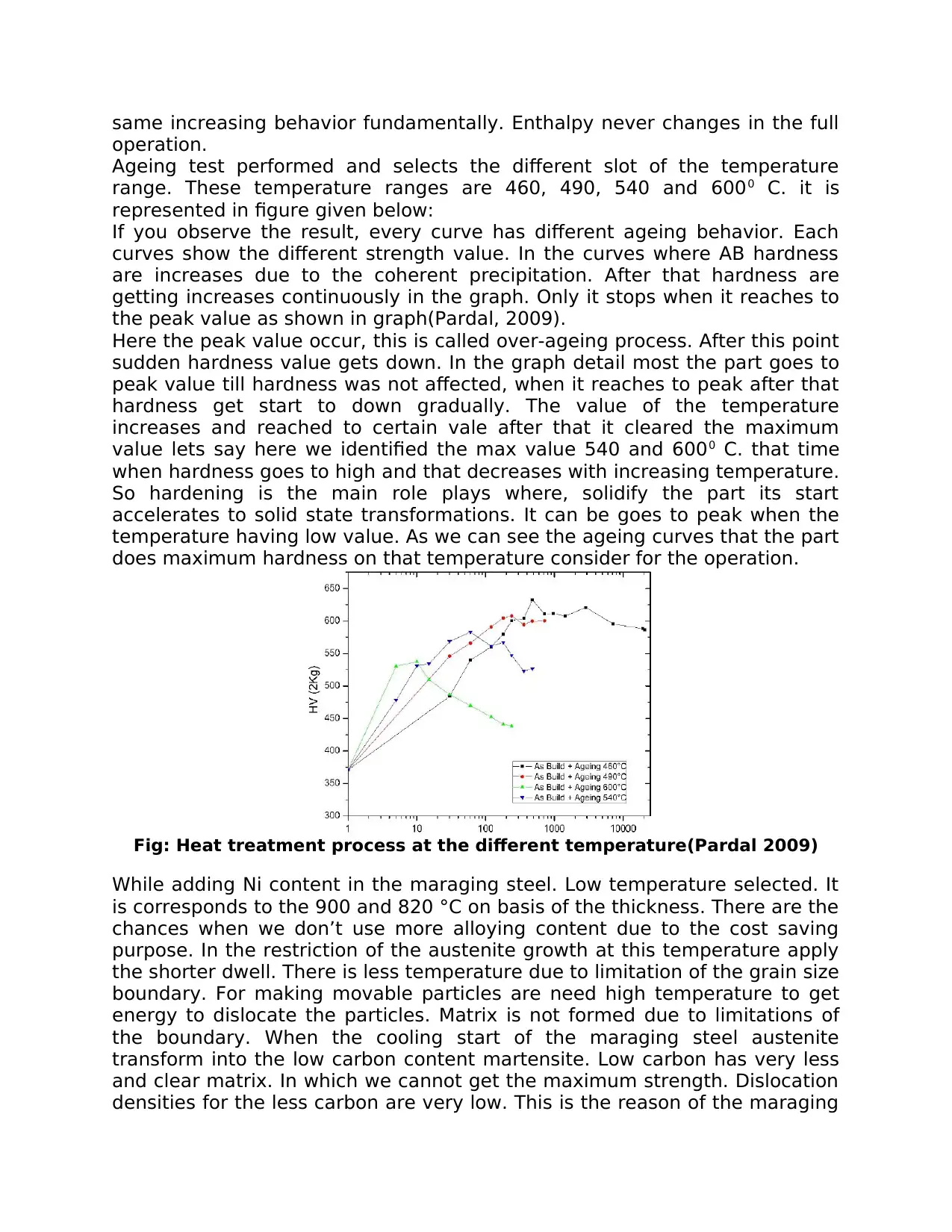
same increasing behavior fundamentally. Enthalpy never changes in the full
operation.
Ageing test performed and selects the different slot of the temperature
range. These temperature ranges are 460, 490, 540 and 6000 C. it is
represented in figure given below:
If you observe the result, every curve has different ageing behavior. Each
curves show the different strength value. In the curves where AB hardness
are increases due to the coherent precipitation. After that hardness are
getting increases continuously in the graph. Only it stops when it reaches to
the peak value as shown in graph(Pardal, 2009).
Here the peak value occur, this is called over-ageing process. After this point
sudden hardness value gets down. In the graph detail most the part goes to
peak value till hardness was not affected, when it reaches to peak after that
hardness get start to down gradually. The value of the temperature
increases and reached to certain vale after that it cleared the maximum
value lets say here we identified the max value 540 and 6000 C. that time
when hardness goes to high and that decreases with increasing temperature.
So hardening is the main role plays where, solidify the part its start
accelerates to solid state transformations. It can be goes to peak when the
temperature having low value. As we can see the ageing curves that the part
does maximum hardness on that temperature consider for the operation.
Fig: Heat treatment process at the different temperature(Pardal 2009)
While adding Ni content in the maraging steel. Low temperature selected. It
is corresponds to the 900 and 820 °C on basis of the thickness. There are the
chances when we don’t use more alloying content due to the cost saving
purpose. In the restriction of the austenite growth at this temperature apply
the shorter dwell. There is less temperature due to limitation of the grain size
boundary. For making movable particles are need high temperature to get
energy to dislocate the particles. Matrix is not formed due to limitations of
the boundary. When the cooling start of the maraging steel austenite
transform into the low carbon content martensite. Low carbon has very less
and clear matrix. In which we cannot get the maximum strength. Dislocation
densities for the less carbon are very low. This is the reason of the maraging
operation.
Ageing test performed and selects the different slot of the temperature
range. These temperature ranges are 460, 490, 540 and 6000 C. it is
represented in figure given below:
If you observe the result, every curve has different ageing behavior. Each
curves show the different strength value. In the curves where AB hardness
are increases due to the coherent precipitation. After that hardness are
getting increases continuously in the graph. Only it stops when it reaches to
the peak value as shown in graph(Pardal, 2009).
Here the peak value occur, this is called over-ageing process. After this point
sudden hardness value gets down. In the graph detail most the part goes to
peak value till hardness was not affected, when it reaches to peak after that
hardness get start to down gradually. The value of the temperature
increases and reached to certain vale after that it cleared the maximum
value lets say here we identified the max value 540 and 6000 C. that time
when hardness goes to high and that decreases with increasing temperature.
So hardening is the main role plays where, solidify the part its start
accelerates to solid state transformations. It can be goes to peak when the
temperature having low value. As we can see the ageing curves that the part
does maximum hardness on that temperature consider for the operation.
Fig: Heat treatment process at the different temperature(Pardal 2009)
While adding Ni content in the maraging steel. Low temperature selected. It
is corresponds to the 900 and 820 °C on basis of the thickness. There are the
chances when we don’t use more alloying content due to the cost saving
purpose. In the restriction of the austenite growth at this temperature apply
the shorter dwell. There is less temperature due to limitation of the grain size
boundary. For making movable particles are need high temperature to get
energy to dislocate the particles. Matrix is not formed due to limitations of
the boundary. When the cooling start of the maraging steel austenite
transform into the low carbon content martensite. Low carbon has very less
and clear matrix. In which we cannot get the maximum strength. Dislocation
densities for the less carbon are very low. This is the reason of the maraging
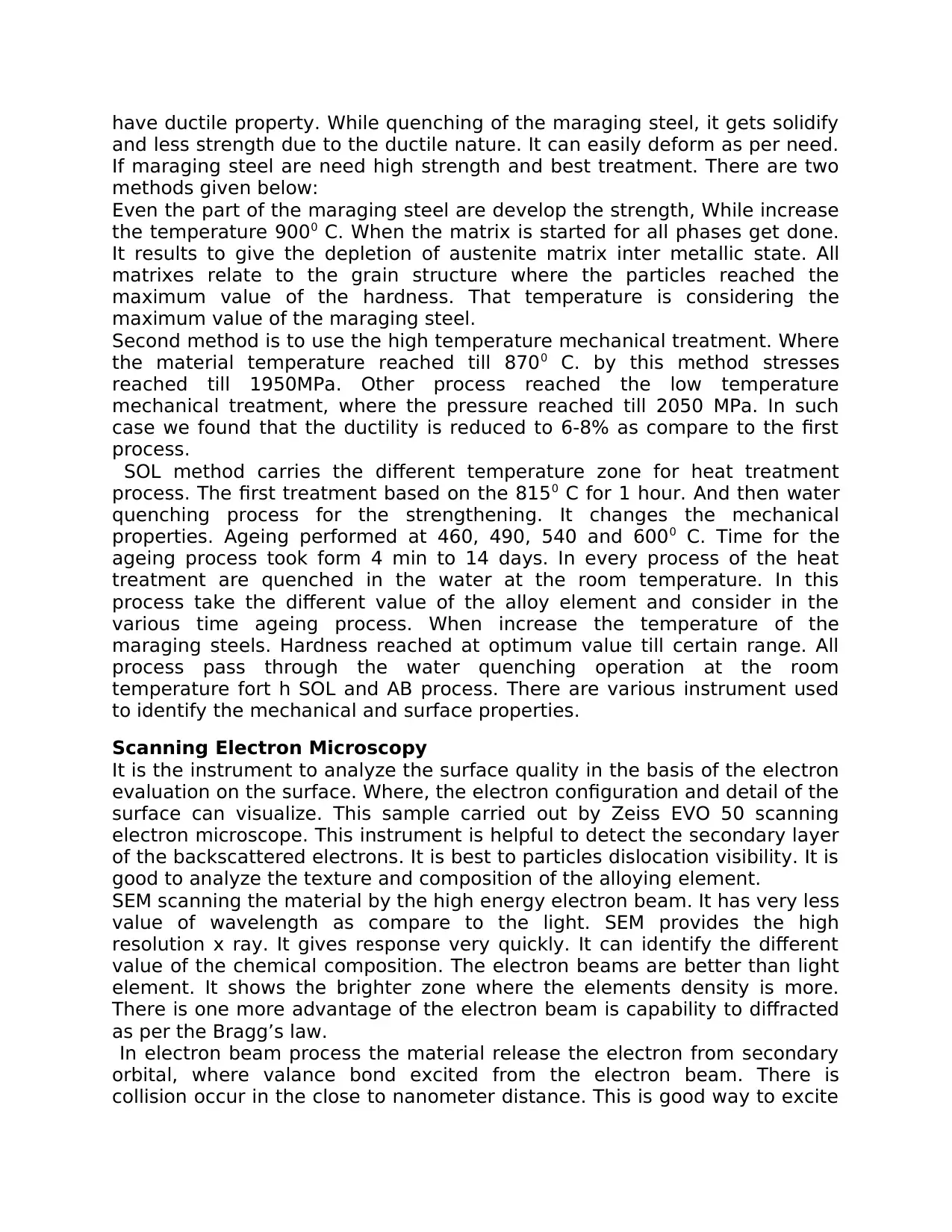
have ductile property. While quenching of the maraging steel, it gets solidify
and less strength due to the ductile nature. It can easily deform as per need.
If maraging steel are need high strength and best treatment. There are two
methods given below:
Even the part of the maraging steel are develop the strength, While increase
the temperature 9000 C. When the matrix is started for all phases get done.
It results to give the depletion of austenite matrix inter metallic state. All
matrixes relate to the grain structure where the particles reached the
maximum value of the hardness. That temperature is considering the
maximum value of the maraging steel.
Second method is to use the high temperature mechanical treatment. Where
the material temperature reached till 8700 C. by this method stresses
reached till 1950MPa. Other process reached the low temperature
mechanical treatment, where the pressure reached till 2050 MPa. In such
case we found that the ductility is reduced to 6-8% as compare to the first
process.
SOL method carries the different temperature zone for heat treatment
process. The first treatment based on the 8150 C for 1 hour. And then water
quenching process for the strengthening. It changes the mechanical
properties. Ageing performed at 460, 490, 540 and 6000 C. Time for the
ageing process took form 4 min to 14 days. In every process of the heat
treatment are quenched in the water at the room temperature. In this
process take the different value of the alloy element and consider in the
various time ageing process. When increase the temperature of the
maraging steels. Hardness reached at optimum value till certain range. All
process pass through the water quenching operation at the room
temperature fort h SOL and AB process. There are various instrument used
to identify the mechanical and surface properties.
Scanning Electron Microscopy
It is the instrument to analyze the surface quality in the basis of the electron
evaluation on the surface. Where, the electron configuration and detail of the
surface can visualize. This sample carried out by Zeiss EVO 50 scanning
electron microscope. This instrument is helpful to detect the secondary layer
of the backscattered electrons. It is best to particles dislocation visibility. It is
good to analyze the texture and composition of the alloying element.
SEM scanning the material by the high energy electron beam. It has very less
value of wavelength as compare to the light. SEM provides the high
resolution x ray. It gives response very quickly. It can identify the different
value of the chemical composition. The electron beams are better than light
element. It shows the brighter zone where the elements density is more.
There is one more advantage of the electron beam is capability to diffracted
as per the Bragg’s law.
In electron beam process the material release the electron from secondary
orbital, where valance bond excited from the electron beam. There is
collision occur in the close to nanometer distance. This is good way to excite
and less strength due to the ductile nature. It can easily deform as per need.
If maraging steel are need high strength and best treatment. There are two
methods given below:
Even the part of the maraging steel are develop the strength, While increase
the temperature 9000 C. When the matrix is started for all phases get done.
It results to give the depletion of austenite matrix inter metallic state. All
matrixes relate to the grain structure where the particles reached the
maximum value of the hardness. That temperature is considering the
maximum value of the maraging steel.
Second method is to use the high temperature mechanical treatment. Where
the material temperature reached till 8700 C. by this method stresses
reached till 1950MPa. Other process reached the low temperature
mechanical treatment, where the pressure reached till 2050 MPa. In such
case we found that the ductility is reduced to 6-8% as compare to the first
process.
SOL method carries the different temperature zone for heat treatment
process. The first treatment based on the 8150 C for 1 hour. And then water
quenching process for the strengthening. It changes the mechanical
properties. Ageing performed at 460, 490, 540 and 6000 C. Time for the
ageing process took form 4 min to 14 days. In every process of the heat
treatment are quenched in the water at the room temperature. In this
process take the different value of the alloy element and consider in the
various time ageing process. When increase the temperature of the
maraging steels. Hardness reached at optimum value till certain range. All
process pass through the water quenching operation at the room
temperature fort h SOL and AB process. There are various instrument used
to identify the mechanical and surface properties.
Scanning Electron Microscopy
It is the instrument to analyze the surface quality in the basis of the electron
evaluation on the surface. Where, the electron configuration and detail of the
surface can visualize. This sample carried out by Zeiss EVO 50 scanning
electron microscope. This instrument is helpful to detect the secondary layer
of the backscattered electrons. It is best to particles dislocation visibility. It is
good to analyze the texture and composition of the alloying element.
SEM scanning the material by the high energy electron beam. It has very less
value of wavelength as compare to the light. SEM provides the high
resolution x ray. It gives response very quickly. It can identify the different
value of the chemical composition. The electron beams are better than light
element. It shows the brighter zone where the elements density is more.
There is one more advantage of the electron beam is capability to diffracted
as per the Bragg’s law.
In electron beam process the material release the electron from secondary
orbital, where valance bond excited from the electron beam. There is
collision occur in the close to nanometer distance. This is good way to excite
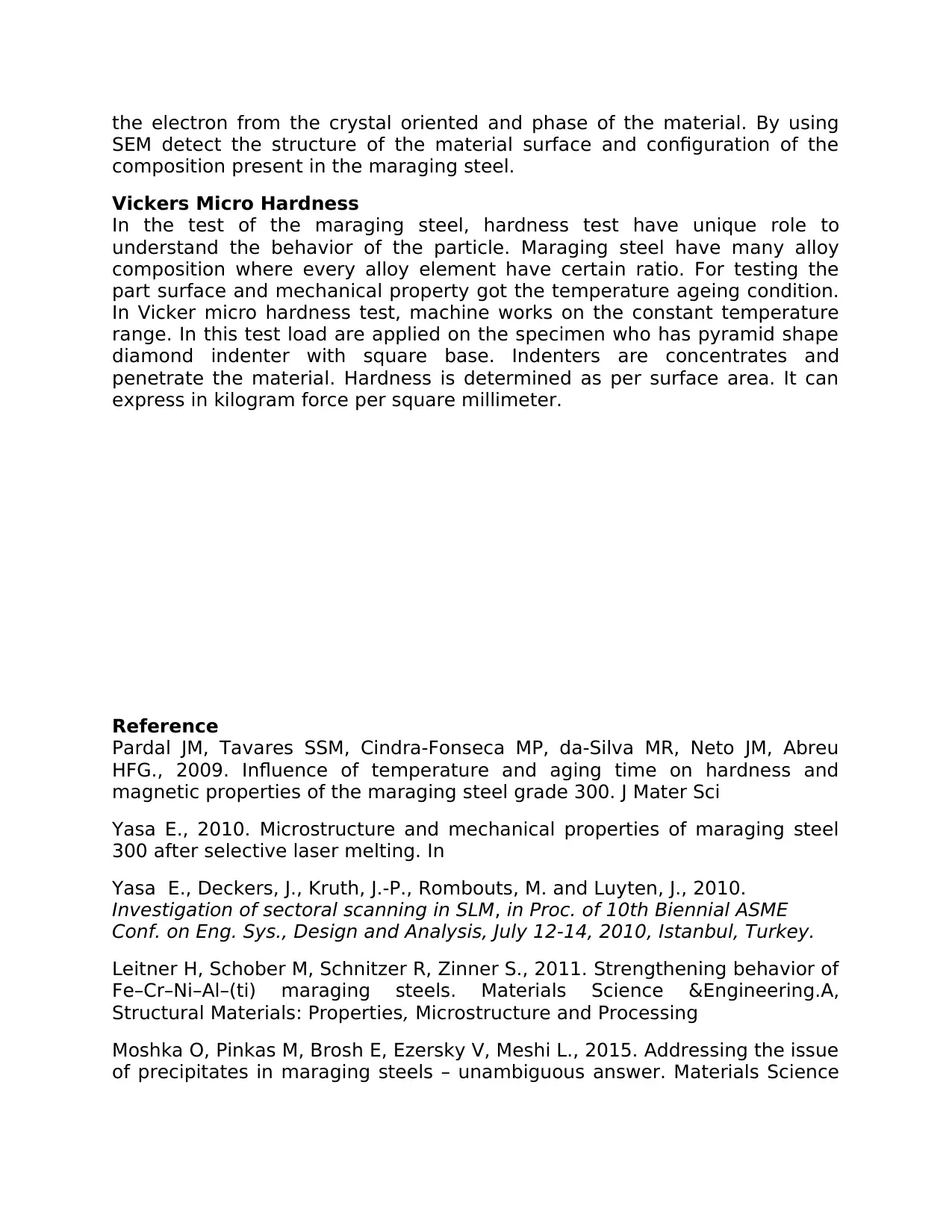
the electron from the crystal oriented and phase of the material. By using
SEM detect the structure of the material surface and configuration of the
composition present in the maraging steel.
Vickers Micro Hardness
In the test of the maraging steel, hardness test have unique role to
understand the behavior of the particle. Maraging steel have many alloy
composition where every alloy element have certain ratio. For testing the
part surface and mechanical property got the temperature ageing condition.
In Vicker micro hardness test, machine works on the constant temperature
range. In this test load are applied on the specimen who has pyramid shape
diamond indenter with square base. Indenters are concentrates and
penetrate the material. Hardness is determined as per surface area. It can
express in kilogram force per square millimeter.
Reference
Pardal JM, Tavares SSM, Cindra-Fonseca MP, da-Silva MR, Neto JM, Abreu
HFG., 2009. Influence of temperature and aging time on hardness and
magnetic properties of the maraging steel grade 300. J Mater Sci
Yasa E., 2010. Microstructure and mechanical properties of maraging steel
300 after selective laser melting. In
Yasa E., Deckers, J., Kruth, J.-P., Rombouts, M. and Luyten, J., 2010.
Investigation of sectoral scanning in SLM, in Proc. of 10th Biennial ASME
Conf. on Eng. Sys., Design and Analysis, July 12-14, 2010, Istanbul, Turkey.
Leitner H, Schober M, Schnitzer R, Zinner S., 2011. Strengthening behavior of
Fe–Cr–Ni–Al–(ti) maraging steels. Materials Science &Engineering.A,
Structural Materials: Properties, Microstructure and Processing
Moshka O, Pinkas M, Brosh E, Ezersky V, Meshi L., 2015. Addressing the issue
of precipitates in maraging steels – unambiguous answer. Materials Science
SEM detect the structure of the material surface and configuration of the
composition present in the maraging steel.
Vickers Micro Hardness
In the test of the maraging steel, hardness test have unique role to
understand the behavior of the particle. Maraging steel have many alloy
composition where every alloy element have certain ratio. For testing the
part surface and mechanical property got the temperature ageing condition.
In Vicker micro hardness test, machine works on the constant temperature
range. In this test load are applied on the specimen who has pyramid shape
diamond indenter with square base. Indenters are concentrates and
penetrate the material. Hardness is determined as per surface area. It can
express in kilogram force per square millimeter.
Reference
Pardal JM, Tavares SSM, Cindra-Fonseca MP, da-Silva MR, Neto JM, Abreu
HFG., 2009. Influence of temperature and aging time on hardness and
magnetic properties of the maraging steel grade 300. J Mater Sci
Yasa E., 2010. Microstructure and mechanical properties of maraging steel
300 after selective laser melting. In
Yasa E., Deckers, J., Kruth, J.-P., Rombouts, M. and Luyten, J., 2010.
Investigation of sectoral scanning in SLM, in Proc. of 10th Biennial ASME
Conf. on Eng. Sys., Design and Analysis, July 12-14, 2010, Istanbul, Turkey.
Leitner H, Schober M, Schnitzer R, Zinner S., 2011. Strengthening behavior of
Fe–Cr–Ni–Al–(ti) maraging steels. Materials Science &Engineering.A,
Structural Materials: Properties, Microstructure and Processing
Moshka O, Pinkas M, Brosh E, Ezersky V, Meshi L., 2015. Addressing the issue
of precipitates in maraging steels – unambiguous answer. Materials Science
Secure Best Marks with AI Grader
Need help grading? Try our AI Grader for instant feedback on your assignments.
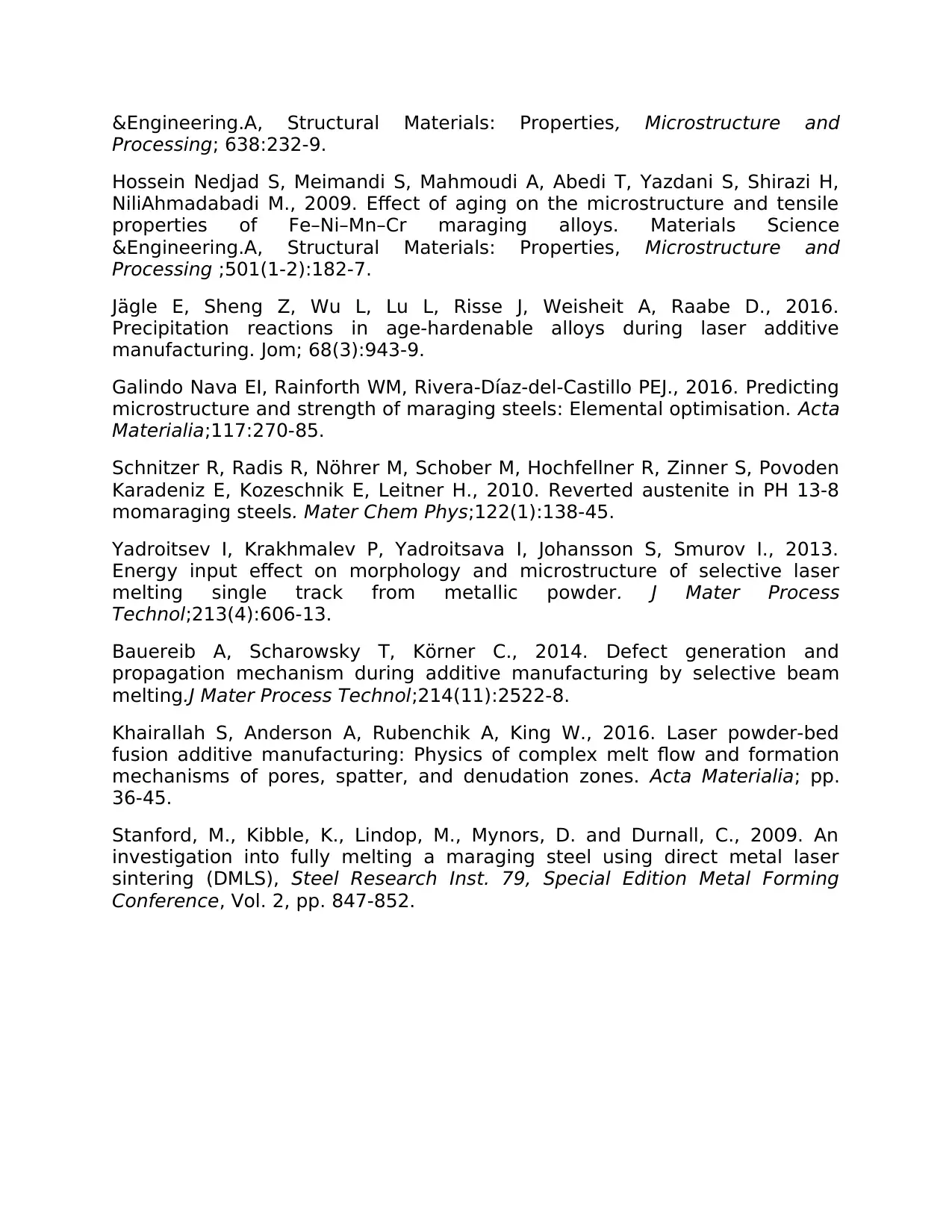
&Engineering.A, Structural Materials: Properties, Microstructure and
Processing; 638:232-9.
Hossein Nedjad S, Meimandi S, Mahmoudi A, Abedi T, Yazdani S, Shirazi H,
NiliAhmadabadi M., 2009. Effect of aging on the microstructure and tensile
properties of Fe–Ni–Mn–Cr maraging alloys. Materials Science
&Engineering.A, Structural Materials: Properties, Microstructure and
Processing ;501(1-2):182-7.
Jägle E, Sheng Z, Wu L, Lu L, Risse J, Weisheit A, Raabe D., 2016.
Precipitation reactions in age-hardenable alloys during laser additive
manufacturing. Jom; 68(3):943-9.
Galindo Nava EI, Rainforth WM, Rivera-Díaz-del-Castillo PEJ., 2016. Predicting
microstructure and strength of maraging steels: Elemental optimisation. Acta
Materialia;117:270-85.
Schnitzer R, Radis R, Nöhrer M, Schober M, Hochfellner R, Zinner S, Povoden
Karadeniz E, Kozeschnik E, Leitner H., 2010. Reverted austenite in PH 13-8
momaraging steels. Mater Chem Phys;122(1):138-45.
Yadroitsev I, Krakhmalev P, Yadroitsava I, Johansson S, Smurov I., 2013.
Energy input effect on morphology and microstructure of selective laser
melting single track from metallic powder. J Mater Process
Technol;213(4):606-13.
Bauereib A, Scharowsky T, Körner C., 2014. Defect generation and
propagation mechanism during additive manufacturing by selective beam
melting.J Mater Process Technol;214(11):2522-8.
Khairallah S, Anderson A, Rubenchik A, King W., 2016. Laser powder-bed
fusion additive manufacturing: Physics of complex melt flow and formation
mechanisms of pores, spatter, and denudation zones. Acta Materialia; pp.
36-45.
Stanford, M., Kibble, K., Lindop, M., Mynors, D. and Durnall, C., 2009. An
investigation into fully melting a maraging steel using direct metal laser
sintering (DMLS), Steel Research Inst. 79, Special Edition Metal Forming
Conference, Vol. 2, pp. 847-852.
Processing; 638:232-9.
Hossein Nedjad S, Meimandi S, Mahmoudi A, Abedi T, Yazdani S, Shirazi H,
NiliAhmadabadi M., 2009. Effect of aging on the microstructure and tensile
properties of Fe–Ni–Mn–Cr maraging alloys. Materials Science
&Engineering.A, Structural Materials: Properties, Microstructure and
Processing ;501(1-2):182-7.
Jägle E, Sheng Z, Wu L, Lu L, Risse J, Weisheit A, Raabe D., 2016.
Precipitation reactions in age-hardenable alloys during laser additive
manufacturing. Jom; 68(3):943-9.
Galindo Nava EI, Rainforth WM, Rivera-Díaz-del-Castillo PEJ., 2016. Predicting
microstructure and strength of maraging steels: Elemental optimisation. Acta
Materialia;117:270-85.
Schnitzer R, Radis R, Nöhrer M, Schober M, Hochfellner R, Zinner S, Povoden
Karadeniz E, Kozeschnik E, Leitner H., 2010. Reverted austenite in PH 13-8
momaraging steels. Mater Chem Phys;122(1):138-45.
Yadroitsev I, Krakhmalev P, Yadroitsava I, Johansson S, Smurov I., 2013.
Energy input effect on morphology and microstructure of selective laser
melting single track from metallic powder. J Mater Process
Technol;213(4):606-13.
Bauereib A, Scharowsky T, Körner C., 2014. Defect generation and
propagation mechanism during additive manufacturing by selective beam
melting.J Mater Process Technol;214(11):2522-8.
Khairallah S, Anderson A, Rubenchik A, King W., 2016. Laser powder-bed
fusion additive manufacturing: Physics of complex melt flow and formation
mechanisms of pores, spatter, and denudation zones. Acta Materialia; pp.
36-45.
Stanford, M., Kibble, K., Lindop, M., Mynors, D. and Durnall, C., 2009. An
investigation into fully melting a maraging steel using direct metal laser
sintering (DMLS), Steel Research Inst. 79, Special Edition Metal Forming
Conference, Vol. 2, pp. 847-852.
1 out of 17

Your All-in-One AI-Powered Toolkit for Academic Success.
+13062052269
info@desklib.com
Available 24*7 on WhatsApp / Email
Unlock your academic potential
© 2024 | Zucol Services PVT LTD | All rights reserved.