Analysis of Operations and Service Management at Marks and Spencer
VerifiedAdded on 2023/01/03
|11
|3310
|3
Report
AI Summary
This report provides a detailed analysis of the operations management practices at Marks and Spencer (M&S), a British multinational retailer. It begins by defining operations management and its importance in enhancing business efficiency. The report identifies and examines key operational practices within M&S, including quality management, supply chain management, and inventory management. It critically analyzes how these practices impact the organization's efficiency, emphasizing the coordination between departments and the optimal use of resources. Furthermore, the report evaluates the integration of technology in these processes, such as the use of CAD, CAM, and various software systems, and assesses their effects on product design, manufacturing, and overall operational efficiency. The report also explores the supporting functions linked to operations management, highlighting their role in ensuring organizational success. The study underscores the importance of operations management in achieving profitability, maintaining a competitive advantage, and adapting to customer requirements within the retail sector. The analysis is enriched with examples of how M&S has implemented these practices and the impact of these practices on the overall business.
Contribute Materials
Your contribution can guide someone’s learning journey. Share your
documents today.
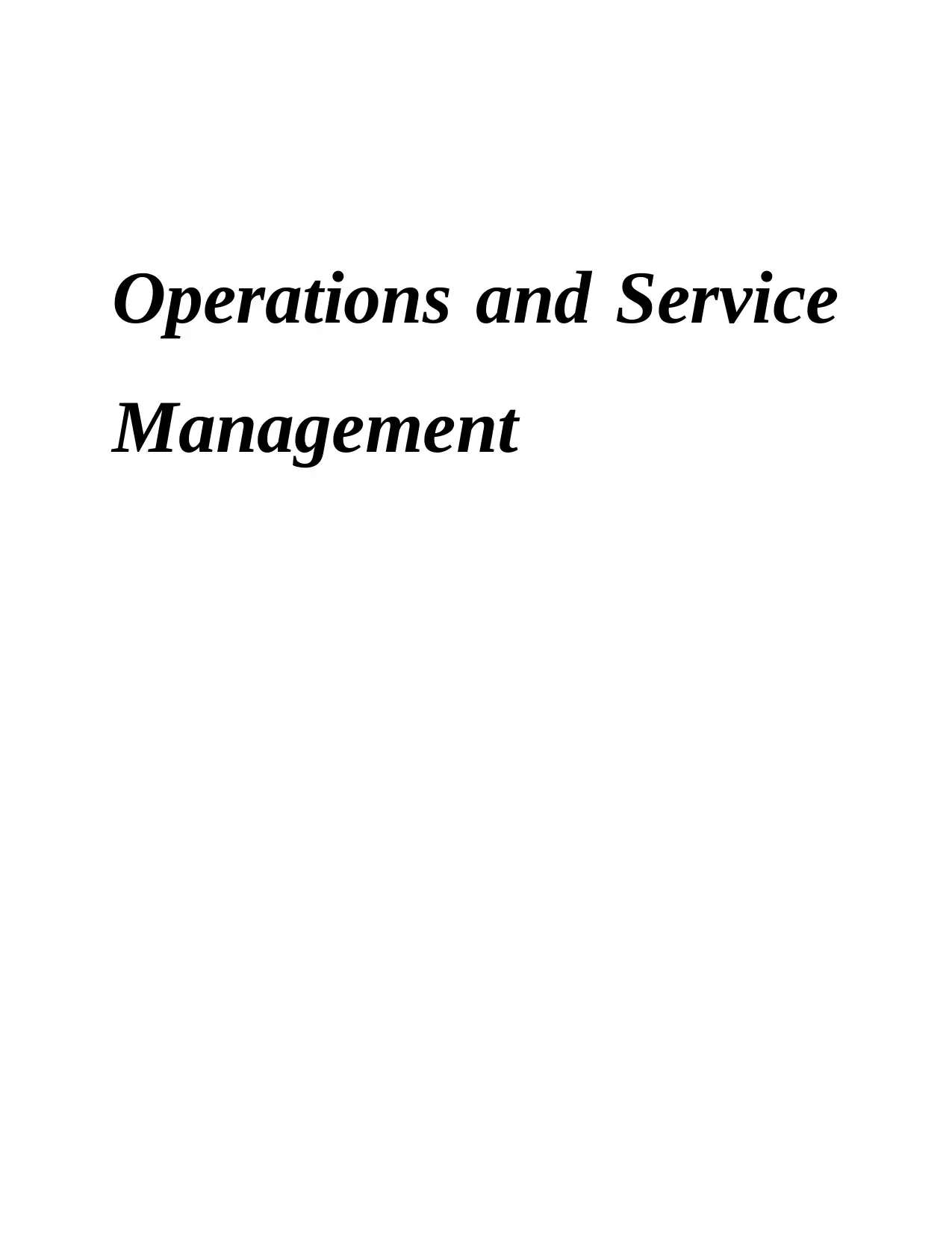
Operations and Service
Management
Management
Secure Best Marks with AI Grader
Need help grading? Try our AI Grader for instant feedback on your assignments.
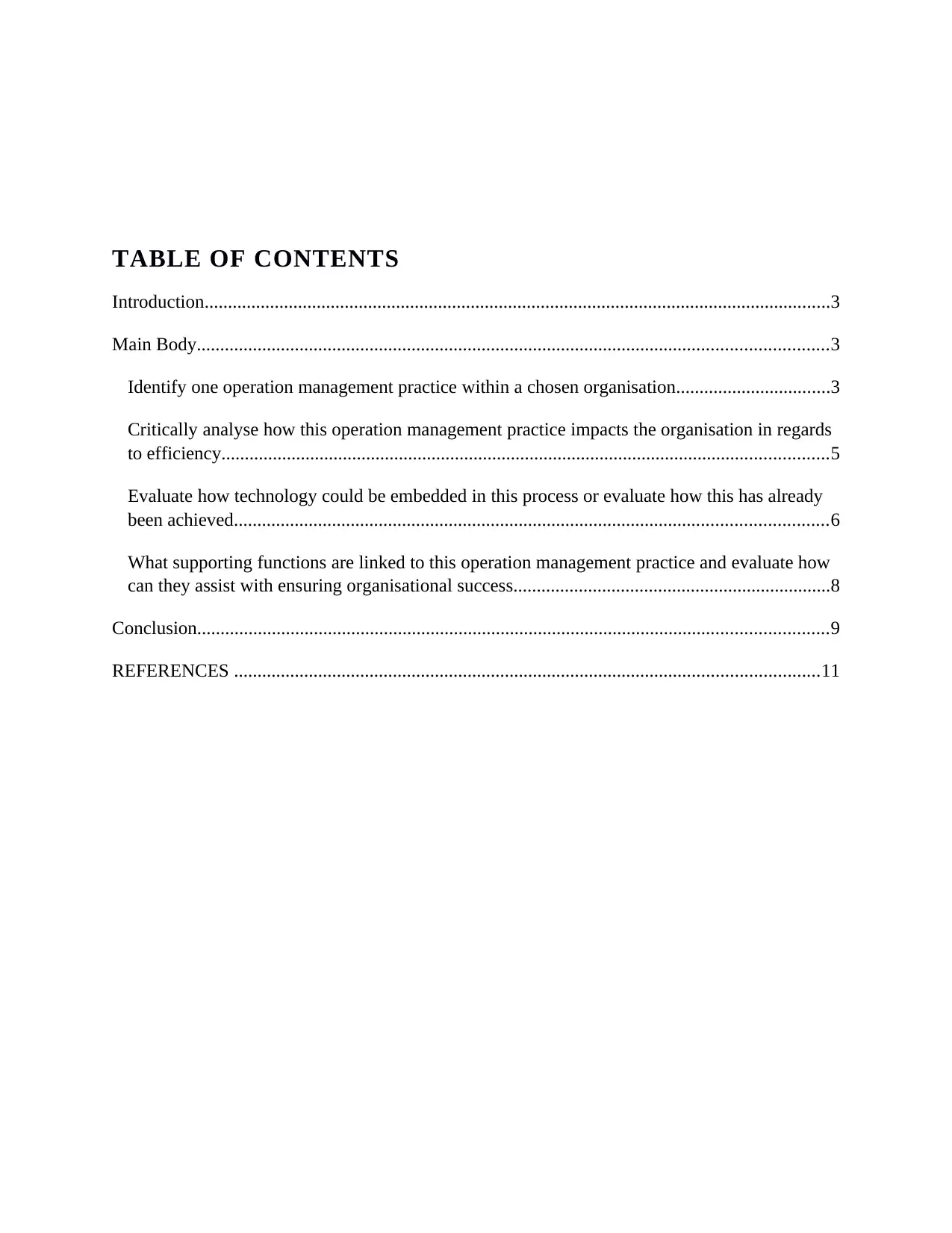
TABLE OF CONTENTS
Introduction......................................................................................................................................3
Main Body.......................................................................................................................................3
Identify one operation management practice within a chosen organisation.................................3
Critically analyse how this operation management practice impacts the organisation in regards
to efficiency..................................................................................................................................5
Evaluate how technology could be embedded in this process or evaluate how this has already
been achieved...............................................................................................................................6
What supporting functions are linked to this operation management practice and evaluate how
can they assist with ensuring organisational success....................................................................8
Conclusion.......................................................................................................................................9
REFERENCES .............................................................................................................................11
Introduction......................................................................................................................................3
Main Body.......................................................................................................................................3
Identify one operation management practice within a chosen organisation.................................3
Critically analyse how this operation management practice impacts the organisation in regards
to efficiency..................................................................................................................................5
Evaluate how technology could be embedded in this process or evaluate how this has already
been achieved...............................................................................................................................6
What supporting functions are linked to this operation management practice and evaluate how
can they assist with ensuring organisational success....................................................................8
Conclusion.......................................................................................................................................9
REFERENCES .............................................................................................................................11
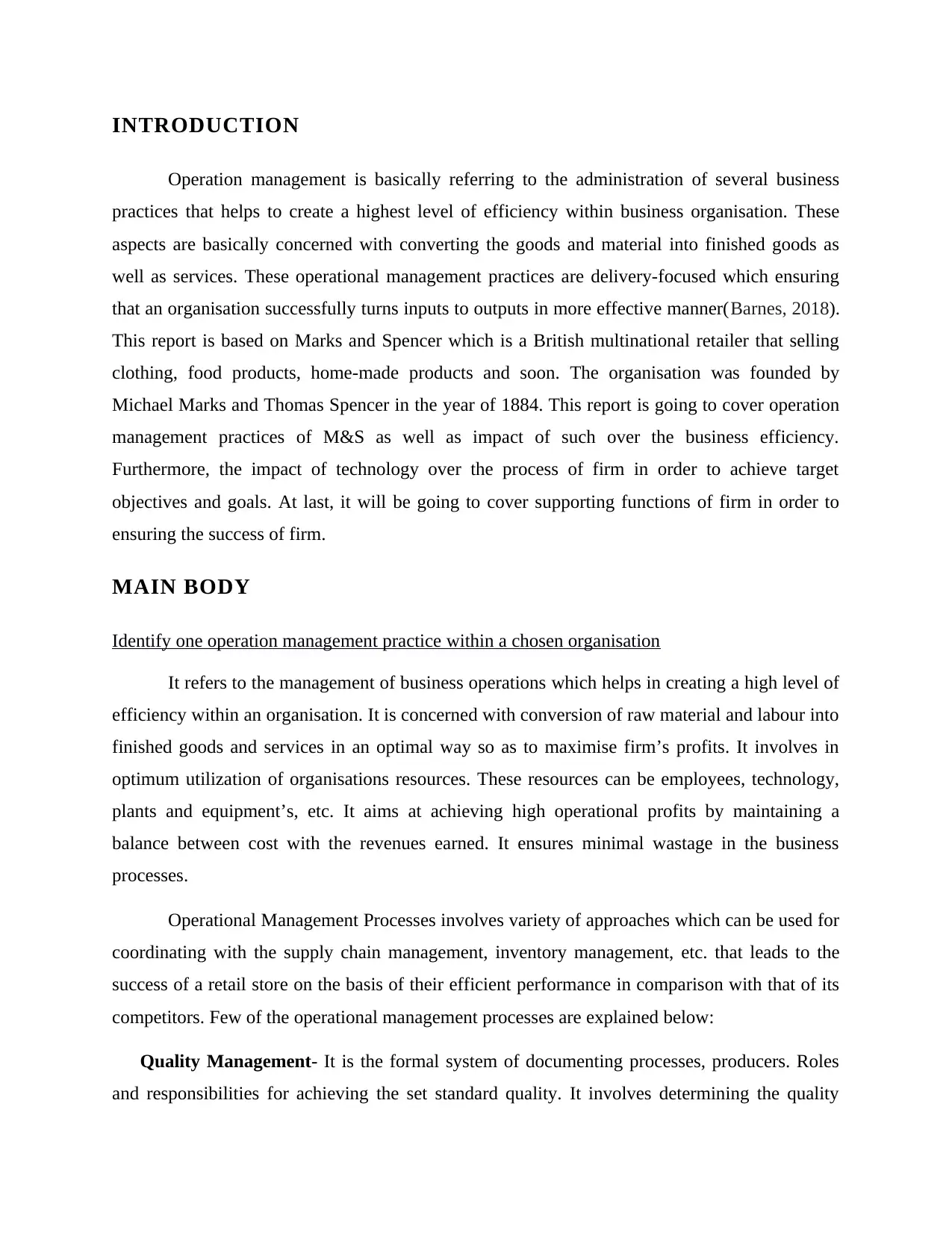
INTRODUCTION
Operation management is basically referring to the administration of several business
practices that helps to create a highest level of efficiency within business organisation. These
aspects are basically concerned with converting the goods and material into finished goods as
well as services. These operational management practices are delivery-focused which ensuring
that an organisation successfully turns inputs to outputs in more effective manner(Barnes, 2018).
This report is based on Marks and Spencer which is a British multinational retailer that selling
clothing, food products, home-made products and soon. The organisation was founded by
Michael Marks and Thomas Spencer in the year of 1884. This report is going to cover operation
management practices of M&S as well as impact of such over the business efficiency.
Furthermore, the impact of technology over the process of firm in order to achieve target
objectives and goals. At last, it will be going to cover supporting functions of firm in order to
ensuring the success of firm.
MAIN BODY
Identify one operation management practice within a chosen organisation
It refers to the management of business operations which helps in creating a high level of
efficiency within an organisation. It is concerned with conversion of raw material and labour into
finished goods and services in an optimal way so as to maximise firm’s profits. It involves in
optimum utilization of organisations resources. These resources can be employees, technology,
plants and equipment’s, etc. It aims at achieving high operational profits by maintaining a
balance between cost with the revenues earned. It ensures minimal wastage in the business
processes.
Operational Management Processes involves variety of approaches which can be used for
coordinating with the supply chain management, inventory management, etc. that leads to the
success of a retail store on the basis of their efficient performance in comparison with that of its
competitors. Few of the operational management processes are explained below:
Quality Management- It is the formal system of documenting processes, producers. Roles
and responsibilities for achieving the set standard quality. It involves determining the quality
Operation management is basically referring to the administration of several business
practices that helps to create a highest level of efficiency within business organisation. These
aspects are basically concerned with converting the goods and material into finished goods as
well as services. These operational management practices are delivery-focused which ensuring
that an organisation successfully turns inputs to outputs in more effective manner(Barnes, 2018).
This report is based on Marks and Spencer which is a British multinational retailer that selling
clothing, food products, home-made products and soon. The organisation was founded by
Michael Marks and Thomas Spencer in the year of 1884. This report is going to cover operation
management practices of M&S as well as impact of such over the business efficiency.
Furthermore, the impact of technology over the process of firm in order to achieve target
objectives and goals. At last, it will be going to cover supporting functions of firm in order to
ensuring the success of firm.
MAIN BODY
Identify one operation management practice within a chosen organisation
It refers to the management of business operations which helps in creating a high level of
efficiency within an organisation. It is concerned with conversion of raw material and labour into
finished goods and services in an optimal way so as to maximise firm’s profits. It involves in
optimum utilization of organisations resources. These resources can be employees, technology,
plants and equipment’s, etc. It aims at achieving high operational profits by maintaining a
balance between cost with the revenues earned. It ensures minimal wastage in the business
processes.
Operational Management Processes involves variety of approaches which can be used for
coordinating with the supply chain management, inventory management, etc. that leads to the
success of a retail store on the basis of their efficient performance in comparison with that of its
competitors. Few of the operational management processes are explained below:
Quality Management- It is the formal system of documenting processes, producers. Roles
and responsibilities for achieving the set standard quality. It involves determining the quality
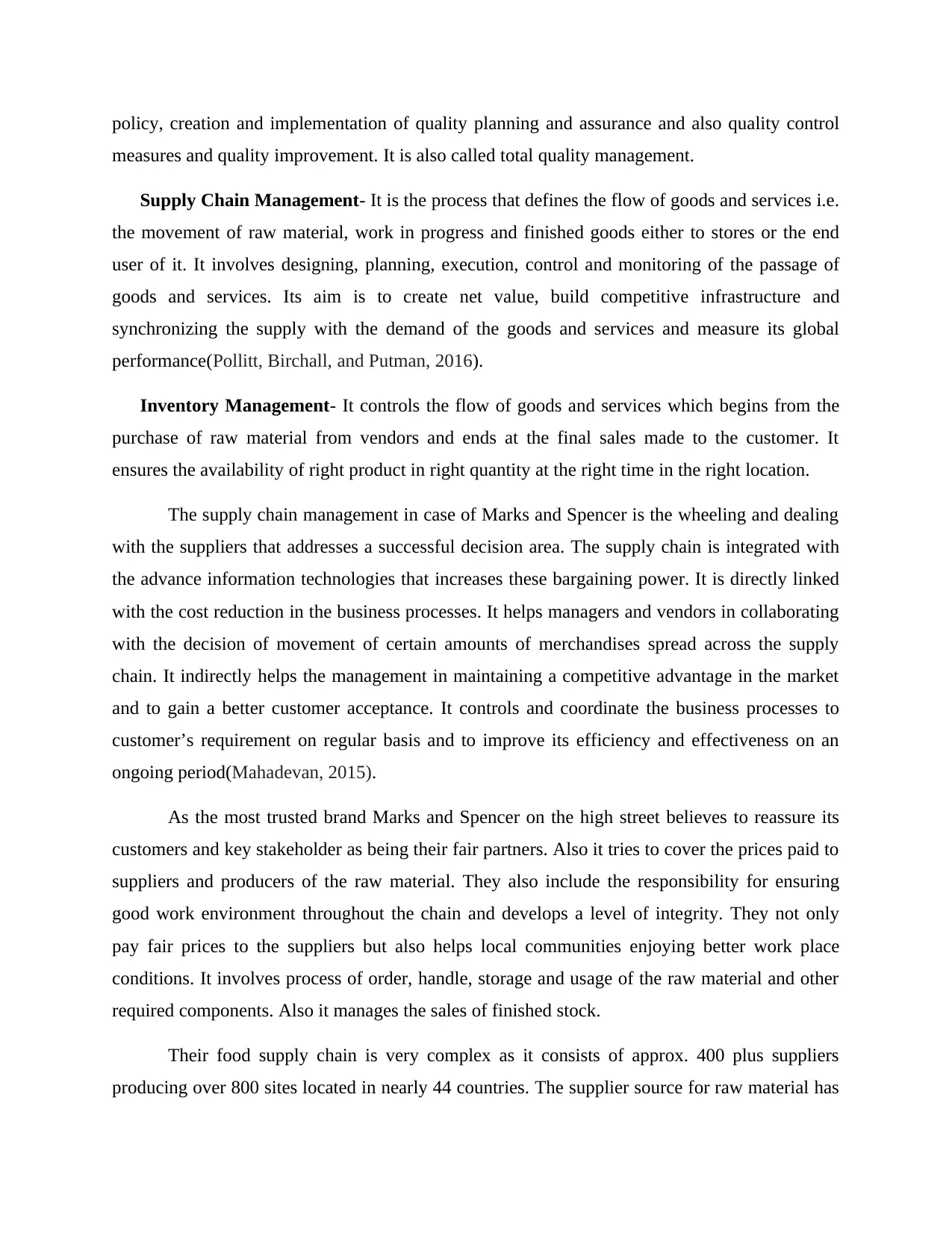
policy, creation and implementation of quality planning and assurance and also quality control
measures and quality improvement. It is also called total quality management.
Supply Chain Management- It is the process that defines the flow of goods and services i.e.
the movement of raw material, work in progress and finished goods either to stores or the end
user of it. It involves designing, planning, execution, control and monitoring of the passage of
goods and services. Its aim is to create net value, build competitive infrastructure and
synchronizing the supply with the demand of the goods and services and measure its global
performance(Pollitt, Birchall, and Putman, 2016).
Inventory Management- It controls the flow of goods and services which begins from the
purchase of raw material from vendors and ends at the final sales made to the customer. It
ensures the availability of right product in right quantity at the right time in the right location.
The supply chain management in case of Marks and Spencer is the wheeling and dealing
with the suppliers that addresses a successful decision area. The supply chain is integrated with
the advance information technologies that increases these bargaining power. It is directly linked
with the cost reduction in the business processes. It helps managers and vendors in collaborating
with the decision of movement of certain amounts of merchandises spread across the supply
chain. It indirectly helps the management in maintaining a competitive advantage in the market
and to gain a better customer acceptance. It controls and coordinate the business processes to
customer’s requirement on regular basis and to improve its efficiency and effectiveness on an
ongoing period(Mahadevan, 2015).
As the most trusted brand Marks and Spencer on the high street believes to reassure its
customers and key stakeholder as being their fair partners. Also it tries to cover the prices paid to
suppliers and producers of the raw material. They also include the responsibility for ensuring
good work environment throughout the chain and develops a level of integrity. They not only
pay fair prices to the suppliers but also helps local communities enjoying better work place
conditions. It involves process of order, handle, storage and usage of the raw material and other
required components. Also it manages the sales of finished stock.
Their food supply chain is very complex as it consists of approx. 400 plus suppliers
producing over 800 sites located in nearly 44 countries. The supplier source for raw material has
measures and quality improvement. It is also called total quality management.
Supply Chain Management- It is the process that defines the flow of goods and services i.e.
the movement of raw material, work in progress and finished goods either to stores or the end
user of it. It involves designing, planning, execution, control and monitoring of the passage of
goods and services. Its aim is to create net value, build competitive infrastructure and
synchronizing the supply with the demand of the goods and services and measure its global
performance(Pollitt, Birchall, and Putman, 2016).
Inventory Management- It controls the flow of goods and services which begins from the
purchase of raw material from vendors and ends at the final sales made to the customer. It
ensures the availability of right product in right quantity at the right time in the right location.
The supply chain management in case of Marks and Spencer is the wheeling and dealing
with the suppliers that addresses a successful decision area. The supply chain is integrated with
the advance information technologies that increases these bargaining power. It is directly linked
with the cost reduction in the business processes. It helps managers and vendors in collaborating
with the decision of movement of certain amounts of merchandises spread across the supply
chain. It indirectly helps the management in maintaining a competitive advantage in the market
and to gain a better customer acceptance. It controls and coordinate the business processes to
customer’s requirement on regular basis and to improve its efficiency and effectiveness on an
ongoing period(Mahadevan, 2015).
As the most trusted brand Marks and Spencer on the high street believes to reassure its
customers and key stakeholder as being their fair partners. Also it tries to cover the prices paid to
suppliers and producers of the raw material. They also include the responsibility for ensuring
good work environment throughout the chain and develops a level of integrity. They not only
pay fair prices to the suppliers but also helps local communities enjoying better work place
conditions. It involves process of order, handle, storage and usage of the raw material and other
required components. Also it manages the sales of finished stock.
Their food supply chain is very complex as it consists of approx. 400 plus suppliers
producing over 800 sites located in nearly 44 countries. The supplier source for raw material has
Secure Best Marks with AI Grader
Need help grading? Try our AI Grader for instant feedback on your assignments.
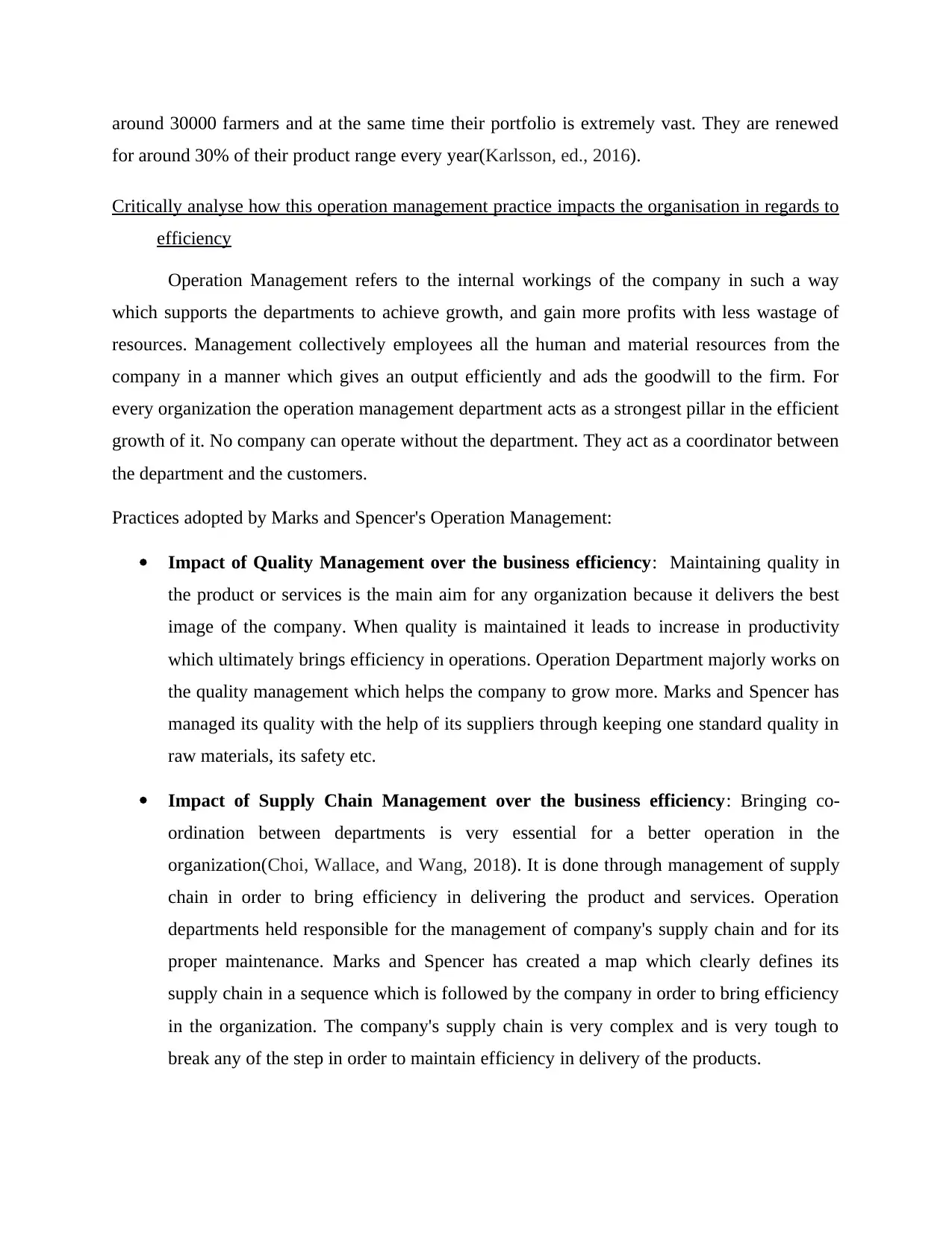
around 30000 farmers and at the same time their portfolio is extremely vast. They are renewed
for around 30% of their product range every year(Karlsson, ed., 2016).
Critically analyse how this operation management practice impacts the organisation in regards to
efficiency
Operation Management refers to the internal workings of the company in such a way
which supports the departments to achieve growth, and gain more profits with less wastage of
resources. Management collectively employees all the human and material resources from the
company in a manner which gives an output efficiently and ads the goodwill to the firm. For
every organization the operation management department acts as a strongest pillar in the efficient
growth of it. No company can operate without the department. They act as a coordinator between
the department and the customers.
Practices adopted by Marks and Spencer's Operation Management:
Impact of Quality Management over the business efficiency: Maintaining quality in
the product or services is the main aim for any organization because it delivers the best
image of the company. When quality is maintained it leads to increase in productivity
which ultimately brings efficiency in operations. Operation Department majorly works on
the quality management which helps the company to grow more. Marks and Spencer has
managed its quality with the help of its suppliers through keeping one standard quality in
raw materials, its safety etc.
Impact of Supply Chain Management over the business efficiency: Bringing co-
ordination between departments is very essential for a better operation in the
organization(Choi, Wallace, and Wang, 2018). It is done through management of supply
chain in order to bring efficiency in delivering the product and services. Operation
departments held responsible for the management of company's supply chain and for its
proper maintenance. Marks and Spencer has created a map which clearly defines its
supply chain in a sequence which is followed by the company in order to bring efficiency
in the organization. The company's supply chain is very complex and is very tough to
break any of the step in order to maintain efficiency in delivery of the products.
for around 30% of their product range every year(Karlsson, ed., 2016).
Critically analyse how this operation management practice impacts the organisation in regards to
efficiency
Operation Management refers to the internal workings of the company in such a way
which supports the departments to achieve growth, and gain more profits with less wastage of
resources. Management collectively employees all the human and material resources from the
company in a manner which gives an output efficiently and ads the goodwill to the firm. For
every organization the operation management department acts as a strongest pillar in the efficient
growth of it. No company can operate without the department. They act as a coordinator between
the department and the customers.
Practices adopted by Marks and Spencer's Operation Management:
Impact of Quality Management over the business efficiency: Maintaining quality in
the product or services is the main aim for any organization because it delivers the best
image of the company. When quality is maintained it leads to increase in productivity
which ultimately brings efficiency in operations. Operation Department majorly works on
the quality management which helps the company to grow more. Marks and Spencer has
managed its quality with the help of its suppliers through keeping one standard quality in
raw materials, its safety etc.
Impact of Supply Chain Management over the business efficiency: Bringing co-
ordination between departments is very essential for a better operation in the
organization(Choi, Wallace, and Wang, 2018). It is done through management of supply
chain in order to bring efficiency in delivering the product and services. Operation
departments held responsible for the management of company's supply chain and for its
proper maintenance. Marks and Spencer has created a map which clearly defines its
supply chain in a sequence which is followed by the company in order to bring efficiency
in the organization. The company's supply chain is very complex and is very tough to
break any of the step in order to maintain efficiency in delivery of the products.
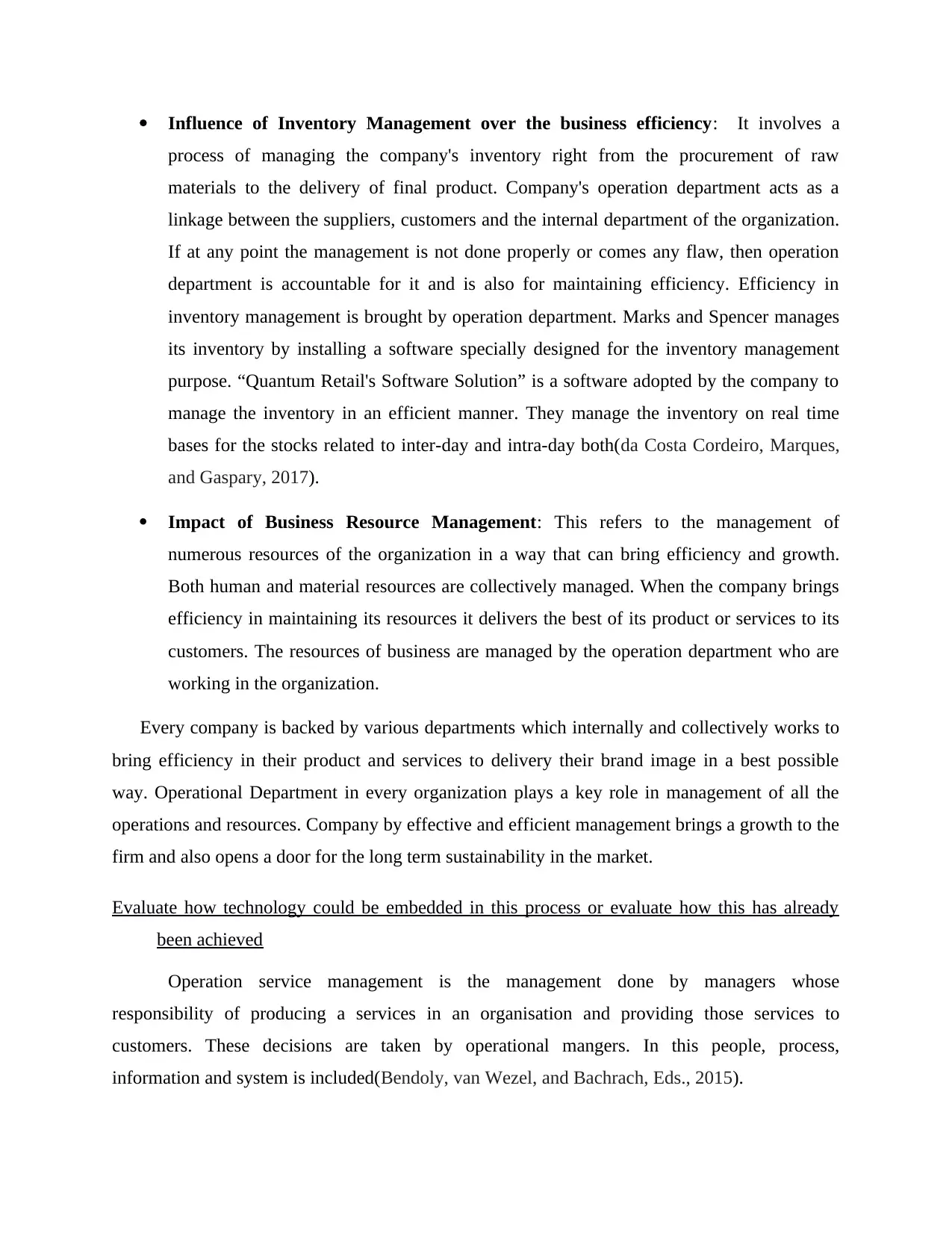
Influence of Inventory Management over the business efficiency: It involves a
process of managing the company's inventory right from the procurement of raw
materials to the delivery of final product. Company's operation department acts as a
linkage between the suppliers, customers and the internal department of the organization.
If at any point the management is not done properly or comes any flaw, then operation
department is accountable for it and is also for maintaining efficiency. Efficiency in
inventory management is brought by operation department. Marks and Spencer manages
its inventory by installing a software specially designed for the inventory management
purpose. “Quantum Retail's Software Solution” is a software adopted by the company to
manage the inventory in an efficient manner. They manage the inventory on real time
bases for the stocks related to inter-day and intra-day both(da Costa Cordeiro, Marques,
and Gaspary, 2017).
Impact of Business Resource Management: This refers to the management of
numerous resources of the organization in a way that can bring efficiency and growth.
Both human and material resources are collectively managed. When the company brings
efficiency in maintaining its resources it delivers the best of its product or services to its
customers. The resources of business are managed by the operation department who are
working in the organization.
Every company is backed by various departments which internally and collectively works to
bring efficiency in their product and services to delivery their brand image in a best possible
way. Operational Department in every organization plays a key role in management of all the
operations and resources. Company by effective and efficient management brings a growth to the
firm and also opens a door for the long term sustainability in the market.
Evaluate how technology could be embedded in this process or evaluate how this has already
been achieved
Operation service management is the management done by managers whose
responsibility of producing a services in an organisation and providing those services to
customers. These decisions are taken by operational mangers. In this people, process,
information and system is included(Bendoly, van Wezel, and Bachrach, Eds., 2015).
process of managing the company's inventory right from the procurement of raw
materials to the delivery of final product. Company's operation department acts as a
linkage between the suppliers, customers and the internal department of the organization.
If at any point the management is not done properly or comes any flaw, then operation
department is accountable for it and is also for maintaining efficiency. Efficiency in
inventory management is brought by operation department. Marks and Spencer manages
its inventory by installing a software specially designed for the inventory management
purpose. “Quantum Retail's Software Solution” is a software adopted by the company to
manage the inventory in an efficient manner. They manage the inventory on real time
bases for the stocks related to inter-day and intra-day both(da Costa Cordeiro, Marques,
and Gaspary, 2017).
Impact of Business Resource Management: This refers to the management of
numerous resources of the organization in a way that can bring efficiency and growth.
Both human and material resources are collectively managed. When the company brings
efficiency in maintaining its resources it delivers the best of its product or services to its
customers. The resources of business are managed by the operation department who are
working in the organization.
Every company is backed by various departments which internally and collectively works to
bring efficiency in their product and services to delivery their brand image in a best possible
way. Operational Department in every organization plays a key role in management of all the
operations and resources. Company by effective and efficient management brings a growth to the
firm and also opens a door for the long term sustainability in the market.
Evaluate how technology could be embedded in this process or evaluate how this has already
been achieved
Operation service management is the management done by managers whose
responsibility of producing a services in an organisation and providing those services to
customers. These decisions are taken by operational mangers. In this people, process,
information and system is included(Bendoly, van Wezel, and Bachrach, Eds., 2015).
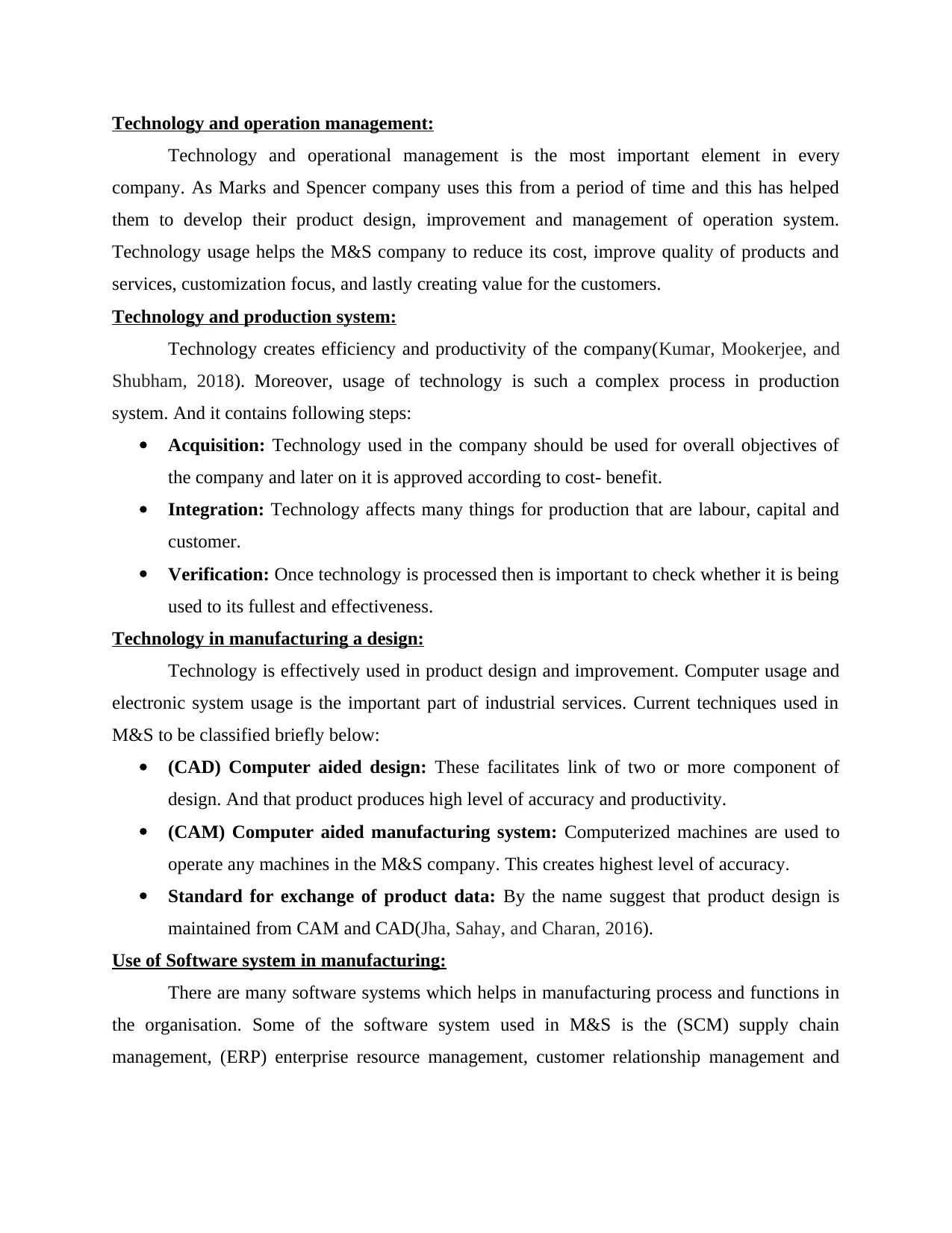
Technology and operation management:
Technology and operational management is the most important element in every
company. As Marks and Spencer company uses this from a period of time and this has helped
them to develop their product design, improvement and management of operation system.
Technology usage helps the M&S company to reduce its cost, improve quality of products and
services, customization focus, and lastly creating value for the customers.
Technology and production system:
Technology creates efficiency and productivity of the company(Kumar, Mookerjee, and
Shubham, 2018). Moreover, usage of technology is such a complex process in production
system. And it contains following steps:
Acquisition: Technology used in the company should be used for overall objectives of
the company and later on it is approved according to cost- benefit.
Integration: Technology affects many things for production that are labour, capital and
customer.
Verification: Once technology is processed then is important to check whether it is being
used to its fullest and effectiveness.
Technology in manufacturing a design:
Technology is effectively used in product design and improvement. Computer usage and
electronic system usage is the important part of industrial services. Current techniques used in
M&S to be classified briefly below:
(CAD) Computer aided design: These facilitates link of two or more component of
design. And that product produces high level of accuracy and productivity.
(CAM) Computer aided manufacturing system: Computerized machines are used to
operate any machines in the M&S company. This creates highest level of accuracy.
Standard for exchange of product data: By the name suggest that product design is
maintained from CAM and CAD(Jha, Sahay, and Charan, 2016).
Use of Software system in manufacturing:
There are many software systems which helps in manufacturing process and functions in
the organisation. Some of the software system used in M&S is the (SCM) supply chain
management, (ERP) enterprise resource management, customer relationship management and
Technology and operational management is the most important element in every
company. As Marks and Spencer company uses this from a period of time and this has helped
them to develop their product design, improvement and management of operation system.
Technology usage helps the M&S company to reduce its cost, improve quality of products and
services, customization focus, and lastly creating value for the customers.
Technology and production system:
Technology creates efficiency and productivity of the company(Kumar, Mookerjee, and
Shubham, 2018). Moreover, usage of technology is such a complex process in production
system. And it contains following steps:
Acquisition: Technology used in the company should be used for overall objectives of
the company and later on it is approved according to cost- benefit.
Integration: Technology affects many things for production that are labour, capital and
customer.
Verification: Once technology is processed then is important to check whether it is being
used to its fullest and effectiveness.
Technology in manufacturing a design:
Technology is effectively used in product design and improvement. Computer usage and
electronic system usage is the important part of industrial services. Current techniques used in
M&S to be classified briefly below:
(CAD) Computer aided design: These facilitates link of two or more component of
design. And that product produces high level of accuracy and productivity.
(CAM) Computer aided manufacturing system: Computerized machines are used to
operate any machines in the M&S company. This creates highest level of accuracy.
Standard for exchange of product data: By the name suggest that product design is
maintained from CAM and CAD(Jha, Sahay, and Charan, 2016).
Use of Software system in manufacturing:
There are many software systems which helps in manufacturing process and functions in
the organisation. Some of the software system used in M&S is the (SCM) supply chain
management, (ERP) enterprise resource management, customer relationship management and
Paraphrase This Document
Need a fresh take? Get an instant paraphrase of this document with our AI Paraphraser
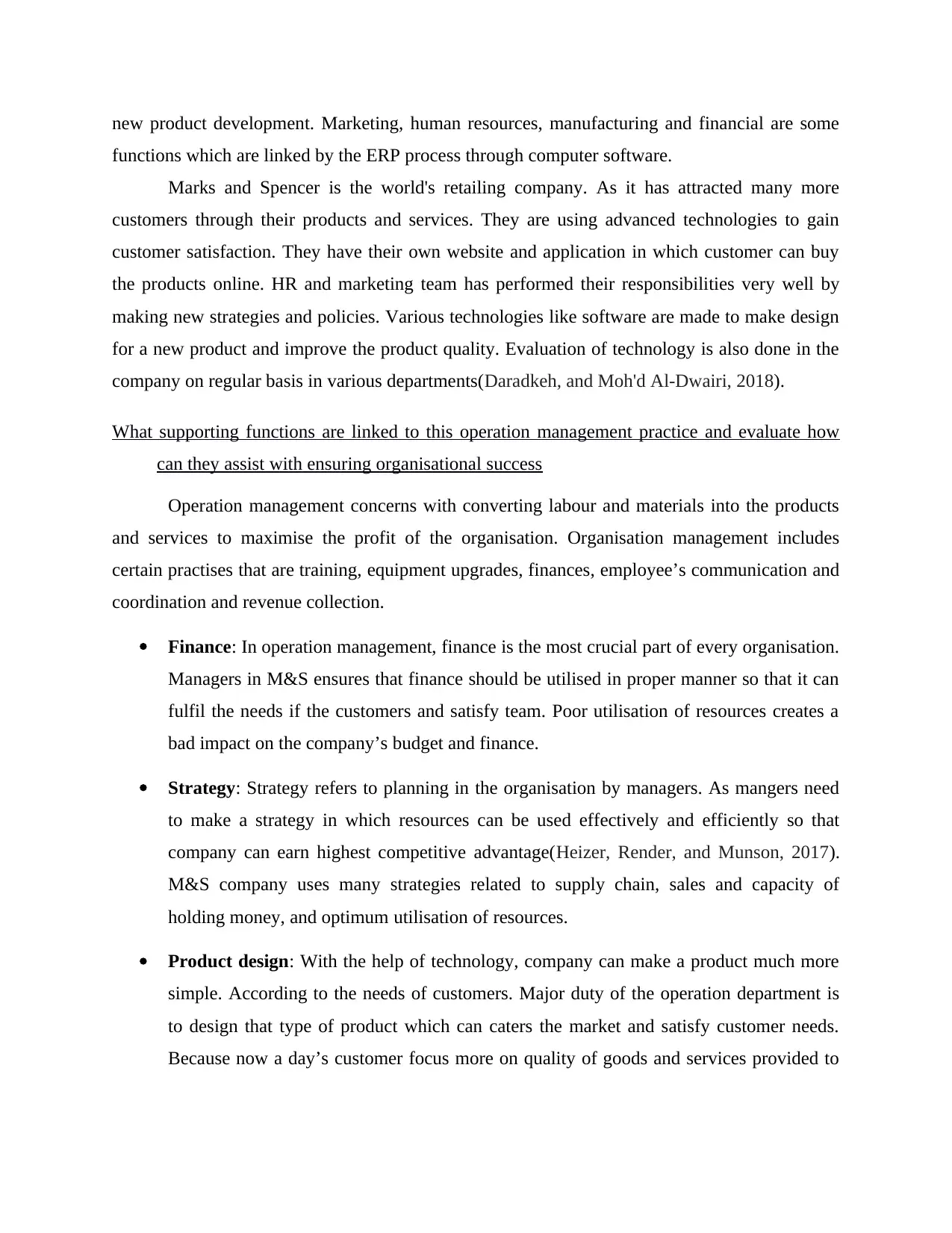
new product development. Marketing, human resources, manufacturing and financial are some
functions which are linked by the ERP process through computer software.
Marks and Spencer is the world's retailing company. As it has attracted many more
customers through their products and services. They are using advanced technologies to gain
customer satisfaction. They have their own website and application in which customer can buy
the products online. HR and marketing team has performed their responsibilities very well by
making new strategies and policies. Various technologies like software are made to make design
for a new product and improve the product quality. Evaluation of technology is also done in the
company on regular basis in various departments(Daradkeh, and Moh'd Al-Dwairi, 2018).
What supporting functions are linked to this operation management practice and evaluate how
can they assist with ensuring organisational success
Operation management concerns with converting labour and materials into the products
and services to maximise the profit of the organisation. Organisation management includes
certain practises that are training, equipment upgrades, finances, employee’s communication and
coordination and revenue collection.
Finance: In operation management, finance is the most crucial part of every organisation.
Managers in M&S ensures that finance should be utilised in proper manner so that it can
fulfil the needs if the customers and satisfy team. Poor utilisation of resources creates a
bad impact on the company’s budget and finance.
Strategy: Strategy refers to planning in the organisation by managers. As mangers need
to make a strategy in which resources can be used effectively and efficiently so that
company can earn highest competitive advantage(Heizer, Render, and Munson, 2017).
M&S company uses many strategies related to supply chain, sales and capacity of
holding money, and optimum utilisation of resources.
Product design: With the help of technology, company can make a product much more
simple. According to the needs of customers. Major duty of the operation department is
to design that type of product which can caters the market and satisfy customer needs.
Because now a day’s customer focus more on quality of goods and services provided to
functions which are linked by the ERP process through computer software.
Marks and Spencer is the world's retailing company. As it has attracted many more
customers through their products and services. They are using advanced technologies to gain
customer satisfaction. They have their own website and application in which customer can buy
the products online. HR and marketing team has performed their responsibilities very well by
making new strategies and policies. Various technologies like software are made to make design
for a new product and improve the product quality. Evaluation of technology is also done in the
company on regular basis in various departments(Daradkeh, and Moh'd Al-Dwairi, 2018).
What supporting functions are linked to this operation management practice and evaluate how
can they assist with ensuring organisational success
Operation management concerns with converting labour and materials into the products
and services to maximise the profit of the organisation. Organisation management includes
certain practises that are training, equipment upgrades, finances, employee’s communication and
coordination and revenue collection.
Finance: In operation management, finance is the most crucial part of every organisation.
Managers in M&S ensures that finance should be utilised in proper manner so that it can
fulfil the needs if the customers and satisfy team. Poor utilisation of resources creates a
bad impact on the company’s budget and finance.
Strategy: Strategy refers to planning in the organisation by managers. As mangers need
to make a strategy in which resources can be used effectively and efficiently so that
company can earn highest competitive advantage(Heizer, Render, and Munson, 2017).
M&S company uses many strategies related to supply chain, sales and capacity of
holding money, and optimum utilisation of resources.
Product design: With the help of technology, company can make a product much more
simple. According to the needs of customers. Major duty of the operation department is
to design that type of product which can caters the market and satisfy customer needs.
Because now a day’s customer focus more on quality of goods and services provided to
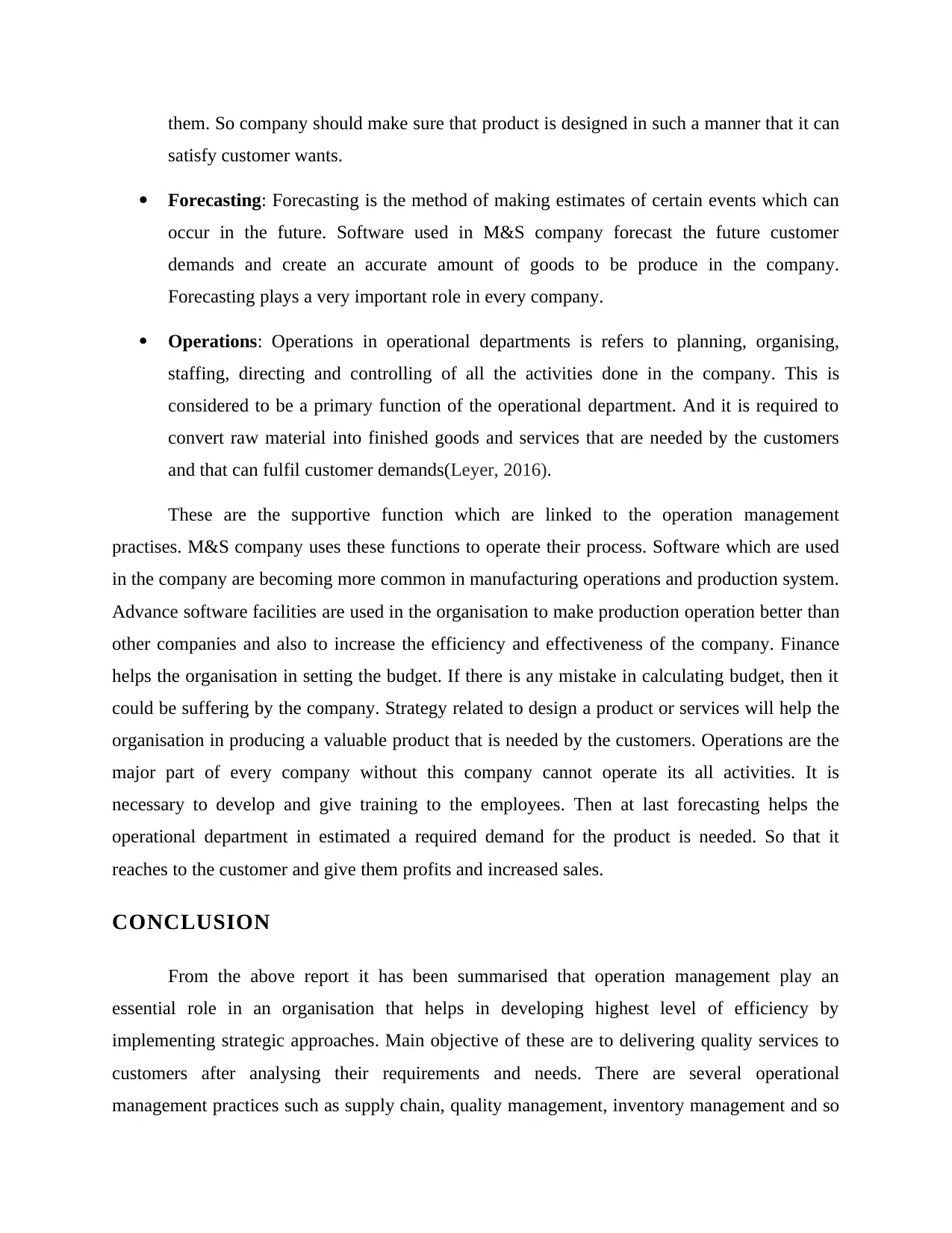
them. So company should make sure that product is designed in such a manner that it can
satisfy customer wants.
Forecasting: Forecasting is the method of making estimates of certain events which can
occur in the future. Software used in M&S company forecast the future customer
demands and create an accurate amount of goods to be produce in the company.
Forecasting plays a very important role in every company.
Operations: Operations in operational departments is refers to planning, organising,
staffing, directing and controlling of all the activities done in the company. This is
considered to be a primary function of the operational department. And it is required to
convert raw material into finished goods and services that are needed by the customers
and that can fulfil customer demands(Leyer, 2016).
These are the supportive function which are linked to the operation management
practises. M&S company uses these functions to operate their process. Software which are used
in the company are becoming more common in manufacturing operations and production system.
Advance software facilities are used in the organisation to make production operation better than
other companies and also to increase the efficiency and effectiveness of the company. Finance
helps the organisation in setting the budget. If there is any mistake in calculating budget, then it
could be suffering by the company. Strategy related to design a product or services will help the
organisation in producing a valuable product that is needed by the customers. Operations are the
major part of every company without this company cannot operate its all activities. It is
necessary to develop and give training to the employees. Then at last forecasting helps the
operational department in estimated a required demand for the product is needed. So that it
reaches to the customer and give them profits and increased sales.
CONCLUSION
From the above report it has been summarised that operation management play an
essential role in an organisation that helps in developing highest level of efficiency by
implementing strategic approaches. Main objective of these are to delivering quality services to
customers after analysing their requirements and needs. There are several operational
management practices such as supply chain, quality management, inventory management and so
satisfy customer wants.
Forecasting: Forecasting is the method of making estimates of certain events which can
occur in the future. Software used in M&S company forecast the future customer
demands and create an accurate amount of goods to be produce in the company.
Forecasting plays a very important role in every company.
Operations: Operations in operational departments is refers to planning, organising,
staffing, directing and controlling of all the activities done in the company. This is
considered to be a primary function of the operational department. And it is required to
convert raw material into finished goods and services that are needed by the customers
and that can fulfil customer demands(Leyer, 2016).
These are the supportive function which are linked to the operation management
practises. M&S company uses these functions to operate their process. Software which are used
in the company are becoming more common in manufacturing operations and production system.
Advance software facilities are used in the organisation to make production operation better than
other companies and also to increase the efficiency and effectiveness of the company. Finance
helps the organisation in setting the budget. If there is any mistake in calculating budget, then it
could be suffering by the company. Strategy related to design a product or services will help the
organisation in producing a valuable product that is needed by the customers. Operations are the
major part of every company without this company cannot operate its all activities. It is
necessary to develop and give training to the employees. Then at last forecasting helps the
operational department in estimated a required demand for the product is needed. So that it
reaches to the customer and give them profits and increased sales.
CONCLUSION
From the above report it has been summarised that operation management play an
essential role in an organisation that helps in developing highest level of efficiency by
implementing strategic approaches. Main objective of these are to delivering quality services to
customers after analysing their requirements and needs. There are several operational
management practices such as supply chain, quality management, inventory management and so
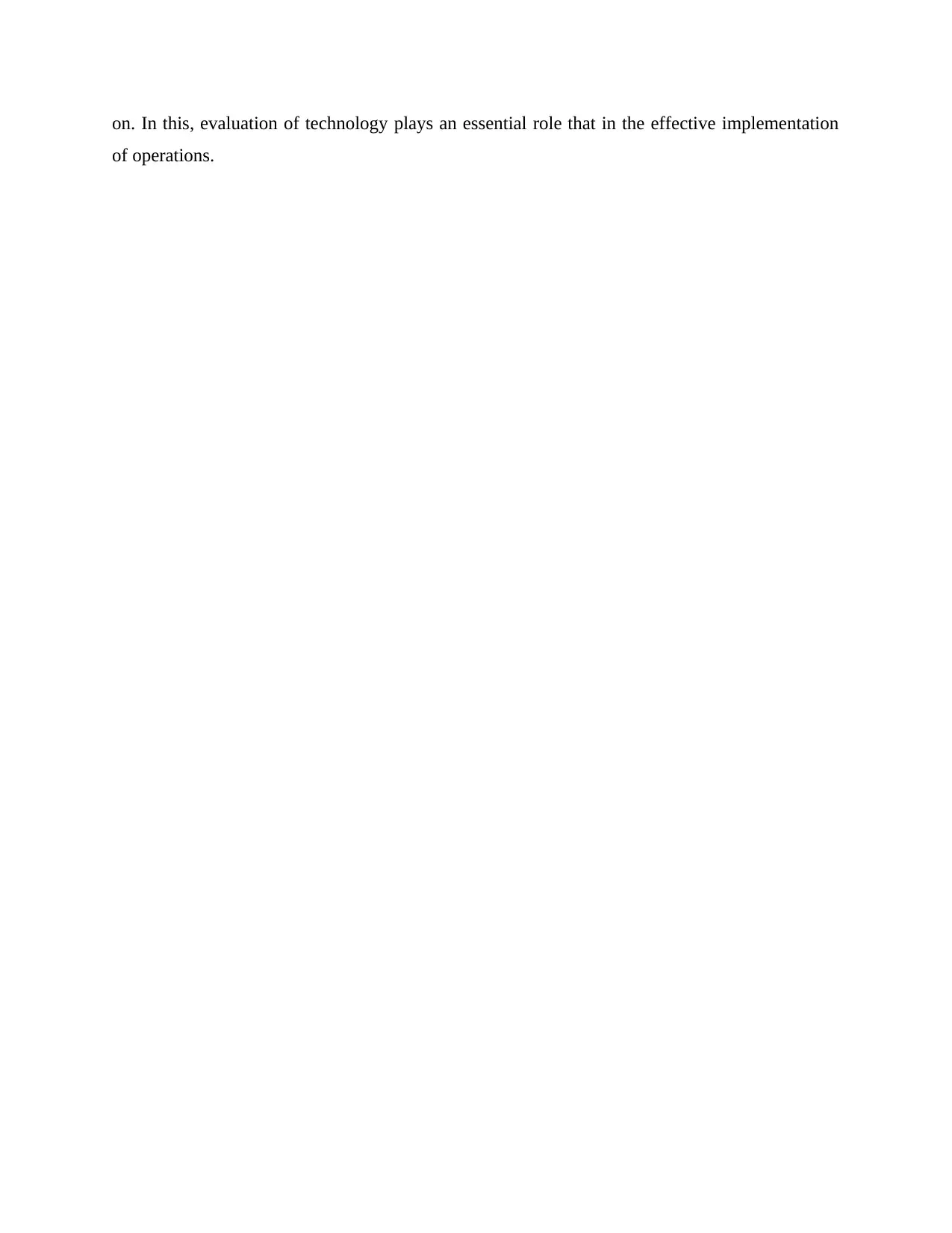
on. In this, evaluation of technology plays an essential role that in the effective implementation
of operations.
of operations.
Secure Best Marks with AI Grader
Need help grading? Try our AI Grader for instant feedback on your assignments.
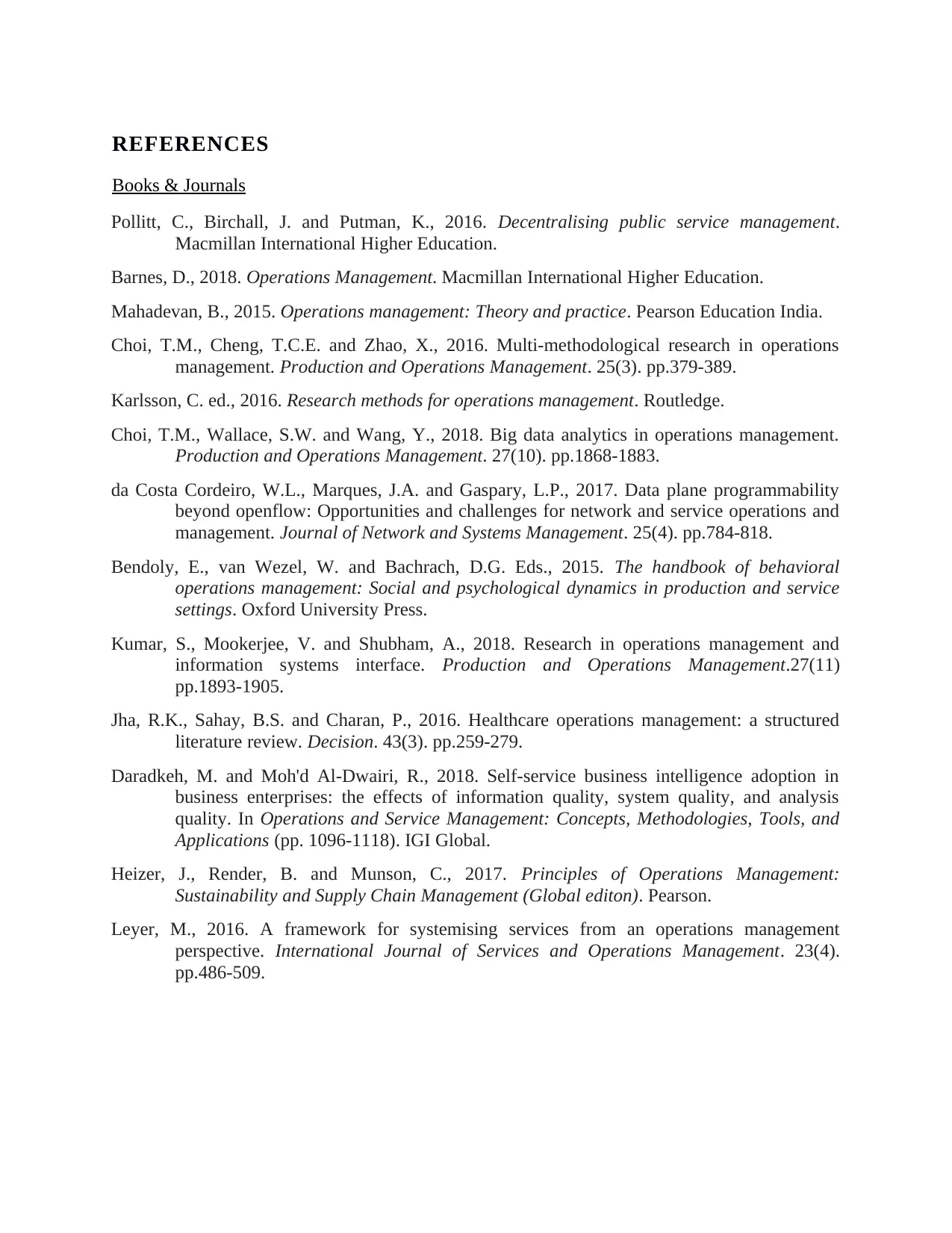
REFERENCES
Books & Journals
Pollitt, C., Birchall, J. and Putman, K., 2016. Decentralising public service management.
Macmillan International Higher Education.
Barnes, D., 2018. Operations Management. Macmillan International Higher Education.
Mahadevan, B., 2015. Operations management: Theory and practice. Pearson Education India.
Choi, T.M., Cheng, T.C.E. and Zhao, X., 2016. Multi‐methodological research in operations
management. Production and Operations Management. 25(3). pp.379-389.
Karlsson, C. ed., 2016. Research methods for operations management. Routledge.
Choi, T.M., Wallace, S.W. and Wang, Y., 2018. Big data analytics in operations management.
Production and Operations Management. 27(10). pp.1868-1883.
da Costa Cordeiro, W.L., Marques, J.A. and Gaspary, L.P., 2017. Data plane programmability
beyond openflow: Opportunities and challenges for network and service operations and
management. Journal of Network and Systems Management. 25(4). pp.784-818.
Bendoly, E., van Wezel, W. and Bachrach, D.G. Eds., 2015. The handbook of behavioral
operations management: Social and psychological dynamics in production and service
settings. Oxford University Press.
Kumar, S., Mookerjee, V. and Shubham, A., 2018. Research in operations management and
information systems interface. Production and Operations Management.27(11)
pp.1893-1905.
Jha, R.K., Sahay, B.S. and Charan, P., 2016. Healthcare operations management: a structured
literature review. Decision. 43(3). pp.259-279.
Daradkeh, M. and Moh'd Al-Dwairi, R., 2018. Self-service business intelligence adoption in
business enterprises: the effects of information quality, system quality, and analysis
quality. In Operations and Service Management: Concepts, Methodologies, Tools, and
Applications (pp. 1096-1118). IGI Global.
Heizer, J., Render, B. and Munson, C., 2017. Principles of Operations Management:
Sustainability and Supply Chain Management (Global editon). Pearson.
Leyer, M., 2016. A framework for systemising services from an operations management
perspective. International Journal of Services and Operations Management. 23(4).
pp.486-509.
Books & Journals
Pollitt, C., Birchall, J. and Putman, K., 2016. Decentralising public service management.
Macmillan International Higher Education.
Barnes, D., 2018. Operations Management. Macmillan International Higher Education.
Mahadevan, B., 2015. Operations management: Theory and practice. Pearson Education India.
Choi, T.M., Cheng, T.C.E. and Zhao, X., 2016. Multi‐methodological research in operations
management. Production and Operations Management. 25(3). pp.379-389.
Karlsson, C. ed., 2016. Research methods for operations management. Routledge.
Choi, T.M., Wallace, S.W. and Wang, Y., 2018. Big data analytics in operations management.
Production and Operations Management. 27(10). pp.1868-1883.
da Costa Cordeiro, W.L., Marques, J.A. and Gaspary, L.P., 2017. Data plane programmability
beyond openflow: Opportunities and challenges for network and service operations and
management. Journal of Network and Systems Management. 25(4). pp.784-818.
Bendoly, E., van Wezel, W. and Bachrach, D.G. Eds., 2015. The handbook of behavioral
operations management: Social and psychological dynamics in production and service
settings. Oxford University Press.
Kumar, S., Mookerjee, V. and Shubham, A., 2018. Research in operations management and
information systems interface. Production and Operations Management.27(11)
pp.1893-1905.
Jha, R.K., Sahay, B.S. and Charan, P., 2016. Healthcare operations management: a structured
literature review. Decision. 43(3). pp.259-279.
Daradkeh, M. and Moh'd Al-Dwairi, R., 2018. Self-service business intelligence adoption in
business enterprises: the effects of information quality, system quality, and analysis
quality. In Operations and Service Management: Concepts, Methodologies, Tools, and
Applications (pp. 1096-1118). IGI Global.
Heizer, J., Render, B. and Munson, C., 2017. Principles of Operations Management:
Sustainability and Supply Chain Management (Global editon). Pearson.
Leyer, M., 2016. A framework for systemising services from an operations management
perspective. International Journal of Services and Operations Management. 23(4).
pp.486-509.
1 out of 11
Related Documents

Your All-in-One AI-Powered Toolkit for Academic Success.
+13062052269
info@desklib.com
Available 24*7 on WhatsApp / Email
Unlock your academic potential
© 2024 | Zucol Services PVT LTD | All rights reserved.