Spring 2019: MECH 0011 Material Manufacturing Report - Belt Sander
VerifiedAdded on 2022/12/23
|16
|3580
|390
Report
AI Summary
This report provides a detailed analysis of the material manufacturing process for a belt sander. It begins with an introduction to belt sanders and their applications, followed by a description of the existent materials used, including sandpaper, Kevlar tape, and the electric motor components. The report then delves into the manufacturing process, outlining the steps involved in making sandpaper, cutting it into strips, applying glue and Kevlar tape, connecting the ends to form a loop, and cutting the belts to the desired widths. A material analysis is presented, comparing the properties of wood, steel, and other materials, along with an assessment of the environmental impact of the manufacturing process, particularly focusing on the advantages of wood. The report also includes a cost analysis for the manufacturing process and concludes with a summary of the findings.
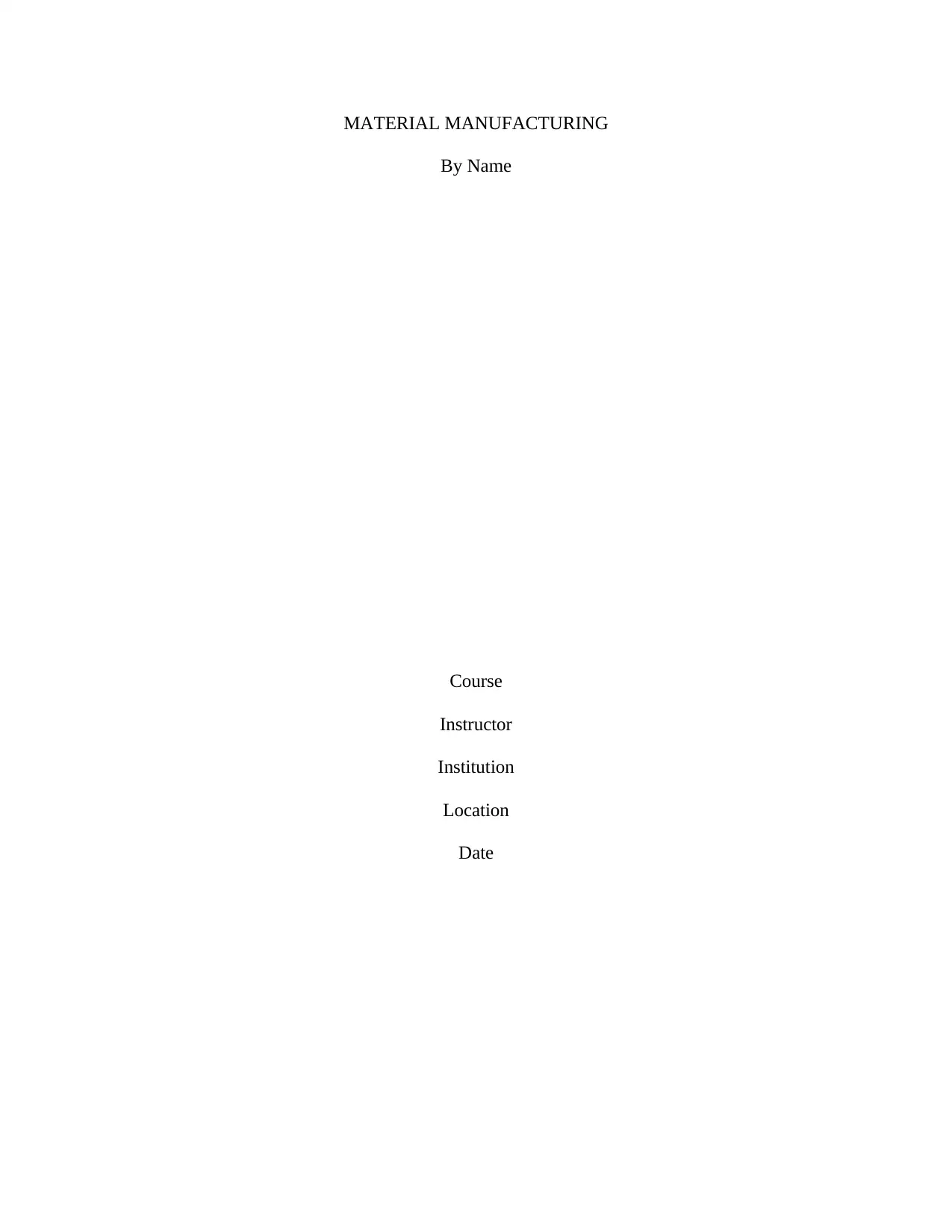
MATERIAL MANUFACTURING
By Name
Course
Instructor
Institution
Location
Date
By Name
Course
Instructor
Institution
Location
Date
Paraphrase This Document
Need a fresh take? Get an instant paraphrase of this document with our AI Paraphraser
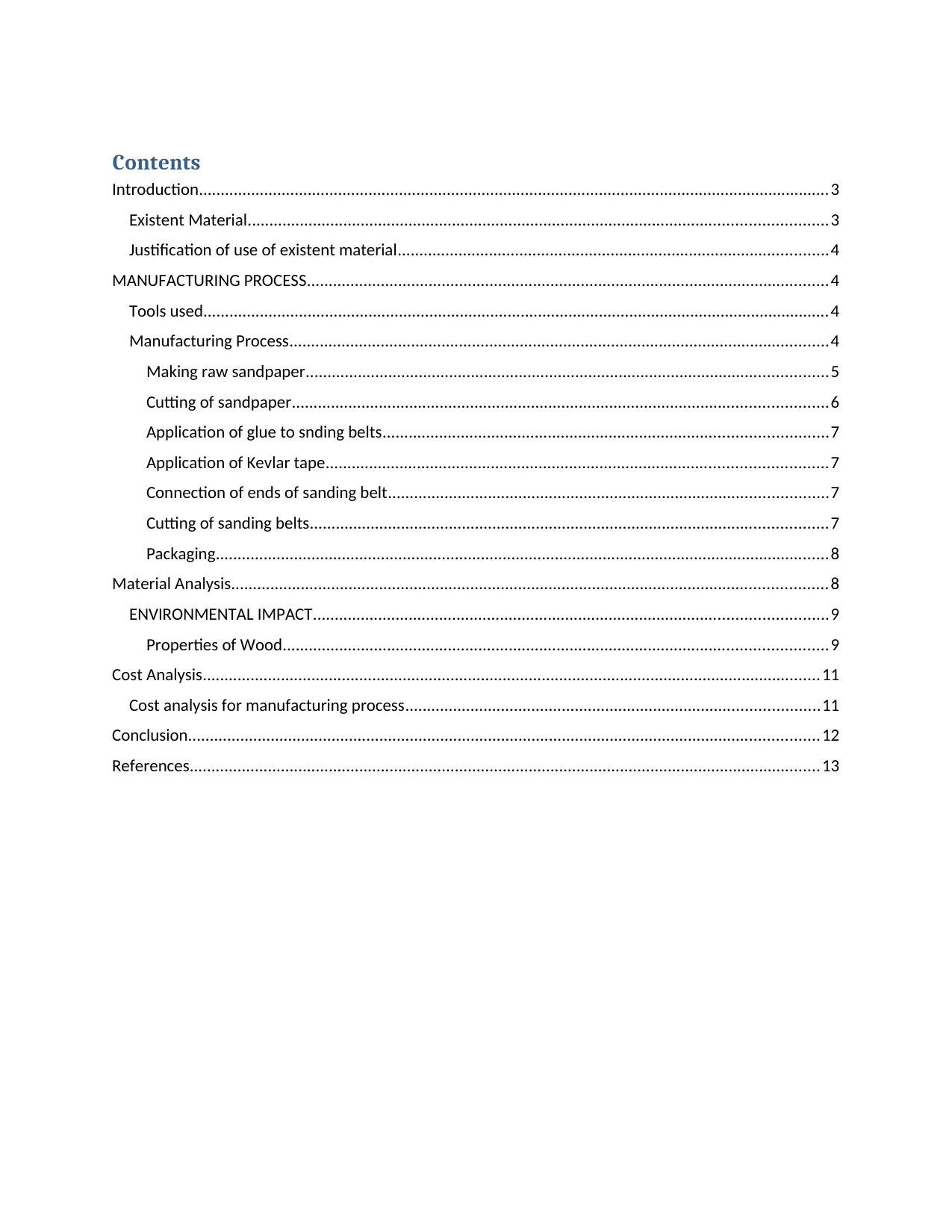
Contents
Introduction.................................................................................................................................................3
Existent Material.....................................................................................................................................3
Justification of use of existent material...................................................................................................4
MANUFACTURING PROCESS........................................................................................................................4
Tools used................................................................................................................................................4
Manufacturing Process............................................................................................................................4
Making raw sandpaper........................................................................................................................5
Cutting of sandpaper...........................................................................................................................6
Application of glue to snding belts......................................................................................................7
Application of Kevlar tape...................................................................................................................7
Connection of ends of sanding belt.....................................................................................................7
Cutting of sanding belts.......................................................................................................................7
Packaging.............................................................................................................................................8
Material Analysis.........................................................................................................................................8
ENVIRONMENTAL IMPACT......................................................................................................................9
Properties of Wood.............................................................................................................................9
Cost Analysis..............................................................................................................................................11
Cost analysis for manufacturing process...............................................................................................11
Conclusion.................................................................................................................................................12
References.................................................................................................................................................13
Introduction.................................................................................................................................................3
Existent Material.....................................................................................................................................3
Justification of use of existent material...................................................................................................4
MANUFACTURING PROCESS........................................................................................................................4
Tools used................................................................................................................................................4
Manufacturing Process............................................................................................................................4
Making raw sandpaper........................................................................................................................5
Cutting of sandpaper...........................................................................................................................6
Application of glue to snding belts......................................................................................................7
Application of Kevlar tape...................................................................................................................7
Connection of ends of sanding belt.....................................................................................................7
Cutting of sanding belts.......................................................................................................................7
Packaging.............................................................................................................................................8
Material Analysis.........................................................................................................................................8
ENVIRONMENTAL IMPACT......................................................................................................................9
Properties of Wood.............................................................................................................................9
Cost Analysis..............................................................................................................................................11
Cost analysis for manufacturing process...............................................................................................11
Conclusion.................................................................................................................................................12
References.................................................................................................................................................13
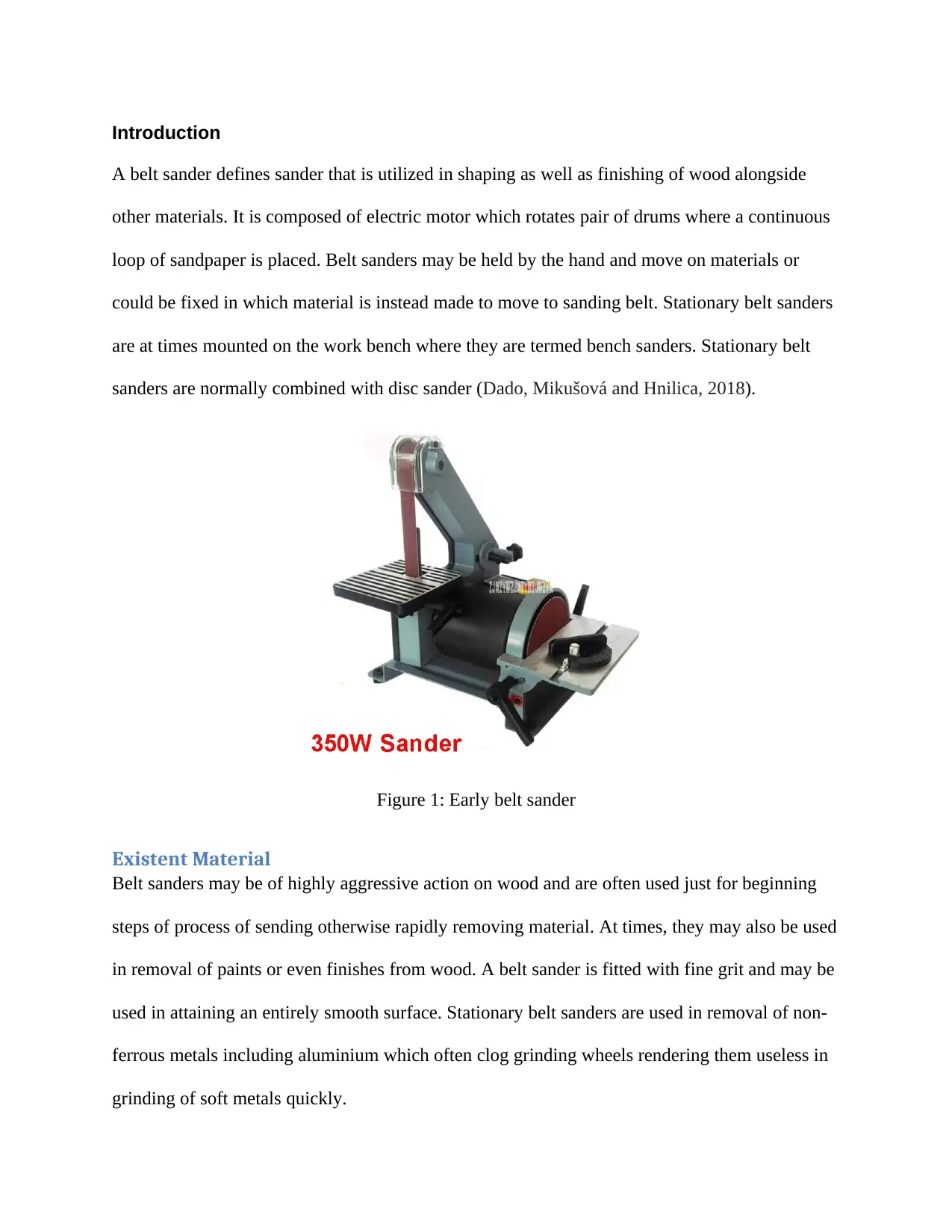
Introduction
A belt sander defines sander that is utilized in shaping as well as finishing of wood alongside
other materials. It is composed of electric motor which rotates pair of drums where a continuous
loop of sandpaper is placed. Belt sanders may be held by the hand and move on materials or
could be fixed in which material is instead made to move to sanding belt. Stationary belt sanders
are at times mounted on the work bench where they are termed bench sanders. Stationary belt
sanders are normally combined with disc sander (Dado, Mikušová and Hnilica, 2018).
Figure 1: Early belt sander
Existent Material
Belt sanders may be of highly aggressive action on wood and are often used just for beginning
steps of process of sending otherwise rapidly removing material. At times, they may also be used
in removal of paints or even finishes from wood. A belt sander is fitted with fine grit and may be
used in attaining an entirely smooth surface. Stationary belt sanders are used in removal of non-
ferrous metals including aluminium which often clog grinding wheels rendering them useless in
grinding of soft metals quickly.
A belt sander defines sander that is utilized in shaping as well as finishing of wood alongside
other materials. It is composed of electric motor which rotates pair of drums where a continuous
loop of sandpaper is placed. Belt sanders may be held by the hand and move on materials or
could be fixed in which material is instead made to move to sanding belt. Stationary belt sanders
are at times mounted on the work bench where they are termed bench sanders. Stationary belt
sanders are normally combined with disc sander (Dado, Mikušová and Hnilica, 2018).
Figure 1: Early belt sander
Existent Material
Belt sanders may be of highly aggressive action on wood and are often used just for beginning
steps of process of sending otherwise rapidly removing material. At times, they may also be used
in removal of paints or even finishes from wood. A belt sander is fitted with fine grit and may be
used in attaining an entirely smooth surface. Stationary belt sanders are used in removal of non-
ferrous metals including aluminium which often clog grinding wheels rendering them useless in
grinding of soft metals quickly.
⊘ This is a preview!⊘
Do you want full access?
Subscribe today to unlock all pages.

Trusted by 1+ million students worldwide
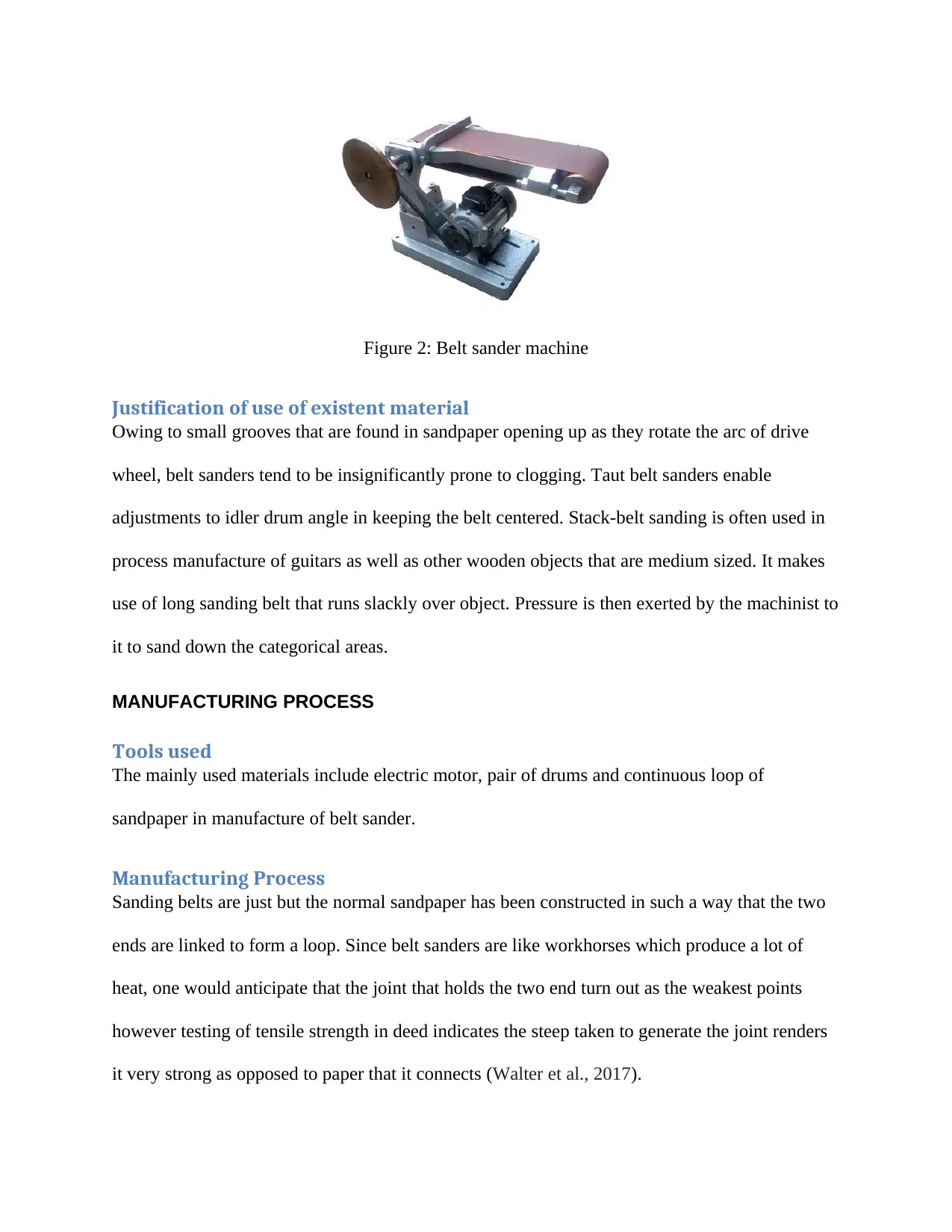
Figure 2: Belt sander machine
Justification of use of existent material
Owing to small grooves that are found in sandpaper opening up as they rotate the arc of drive
wheel, belt sanders tend to be insignificantly prone to clogging. Taut belt sanders enable
adjustments to idler drum angle in keeping the belt centered. Stack-belt sanding is often used in
process manufacture of guitars as well as other wooden objects that are medium sized. It makes
use of long sanding belt that runs slackly over object. Pressure is then exerted by the machinist to
it to sand down the categorical areas.
MANUFACTURING PROCESS
Tools used
The mainly used materials include electric motor, pair of drums and continuous loop of
sandpaper in manufacture of belt sander.
Manufacturing Process
Sanding belts are just but the normal sandpaper has been constructed in such a way that the two
ends are linked to form a loop. Since belt sanders are like workhorses which produce a lot of
heat, one would anticipate that the joint that holds the two end turn out as the weakest points
however testing of tensile strength in deed indicates the steep taken to generate the joint renders
it very strong as opposed to paper that it connects (Walter et al., 2017).
Justification of use of existent material
Owing to small grooves that are found in sandpaper opening up as they rotate the arc of drive
wheel, belt sanders tend to be insignificantly prone to clogging. Taut belt sanders enable
adjustments to idler drum angle in keeping the belt centered. Stack-belt sanding is often used in
process manufacture of guitars as well as other wooden objects that are medium sized. It makes
use of long sanding belt that runs slackly over object. Pressure is then exerted by the machinist to
it to sand down the categorical areas.
MANUFACTURING PROCESS
Tools used
The mainly used materials include electric motor, pair of drums and continuous loop of
sandpaper in manufacture of belt sander.
Manufacturing Process
Sanding belts are just but the normal sandpaper has been constructed in such a way that the two
ends are linked to form a loop. Since belt sanders are like workhorses which produce a lot of
heat, one would anticipate that the joint that holds the two end turn out as the weakest points
however testing of tensile strength in deed indicates the steep taken to generate the joint renders
it very strong as opposed to paper that it connects (Walter et al., 2017).
Paraphrase This Document
Need a fresh take? Get an instant paraphrase of this document with our AI Paraphraser
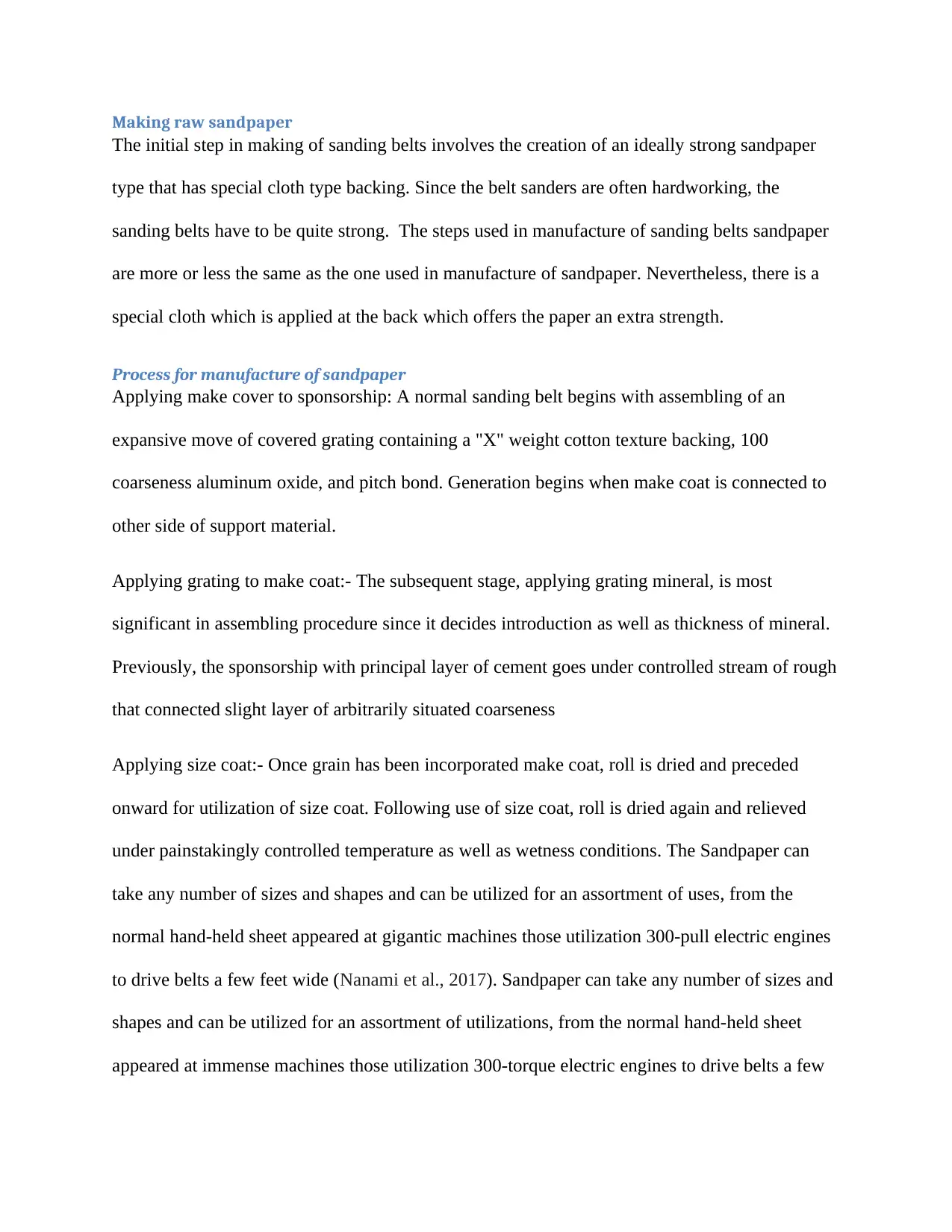
Making raw sandpaper
The initial step in making of sanding belts involves the creation of an ideally strong sandpaper
type that has special cloth type backing. Since the belt sanders are often hardworking, the
sanding belts have to be quite strong. The steps used in manufacture of sanding belts sandpaper
are more or less the same as the one used in manufacture of sandpaper. Nevertheless, there is a
special cloth which is applied at the back which offers the paper an extra strength.
Process for manufacture of sandpaper
Applying make cover to sponsorship: A normal sanding belt begins with assembling of an
expansive move of covered grating containing a "X" weight cotton texture backing, 100
coarseness aluminum oxide, and pitch bond. Generation begins when make coat is connected to
other side of support material.
Applying grating to make coat:- The subsequent stage, applying grating mineral, is most
significant in assembling procedure since it decides introduction as well as thickness of mineral.
Previously, the sponsorship with principal layer of cement goes under controlled stream of rough
that connected slight layer of arbitrarily situated coarseness
Applying size coat:- Once grain has been incorporated make coat, roll is dried and preceded
onward for utilization of size coat. Following use of size coat, roll is dried again and relieved
under painstakingly controlled temperature as well as wetness conditions. The Sandpaper can
take any number of sizes and shapes and can be utilized for an assortment of uses, from the
normal hand-held sheet appeared at gigantic machines those utilization 300-pull electric engines
to drive belts a few feet wide (Nanami et al., 2017). Sandpaper can take any number of sizes and
shapes and can be utilized for an assortment of utilizations, from the normal hand-held sheet
appeared at immense machines those utilization 300-torque electric engines to drive belts a few
The initial step in making of sanding belts involves the creation of an ideally strong sandpaper
type that has special cloth type backing. Since the belt sanders are often hardworking, the
sanding belts have to be quite strong. The steps used in manufacture of sanding belts sandpaper
are more or less the same as the one used in manufacture of sandpaper. Nevertheless, there is a
special cloth which is applied at the back which offers the paper an extra strength.
Process for manufacture of sandpaper
Applying make cover to sponsorship: A normal sanding belt begins with assembling of an
expansive move of covered grating containing a "X" weight cotton texture backing, 100
coarseness aluminum oxide, and pitch bond. Generation begins when make coat is connected to
other side of support material.
Applying grating to make coat:- The subsequent stage, applying grating mineral, is most
significant in assembling procedure since it decides introduction as well as thickness of mineral.
Previously, the sponsorship with principal layer of cement goes under controlled stream of rough
that connected slight layer of arbitrarily situated coarseness
Applying size coat:- Once grain has been incorporated make coat, roll is dried and preceded
onward for utilization of size coat. Following use of size coat, roll is dried again and relieved
under painstakingly controlled temperature as well as wetness conditions. The Sandpaper can
take any number of sizes and shapes and can be utilized for an assortment of uses, from the
normal hand-held sheet appeared at gigantic machines those utilization 300-pull electric engines
to drive belts a few feet wide (Nanami et al., 2017). Sandpaper can take any number of sizes and
shapes and can be utilized for an assortment of utilizations, from the normal hand-held sheet
appeared at immense machines those utilization 300-torque electric engines to drive belts a few
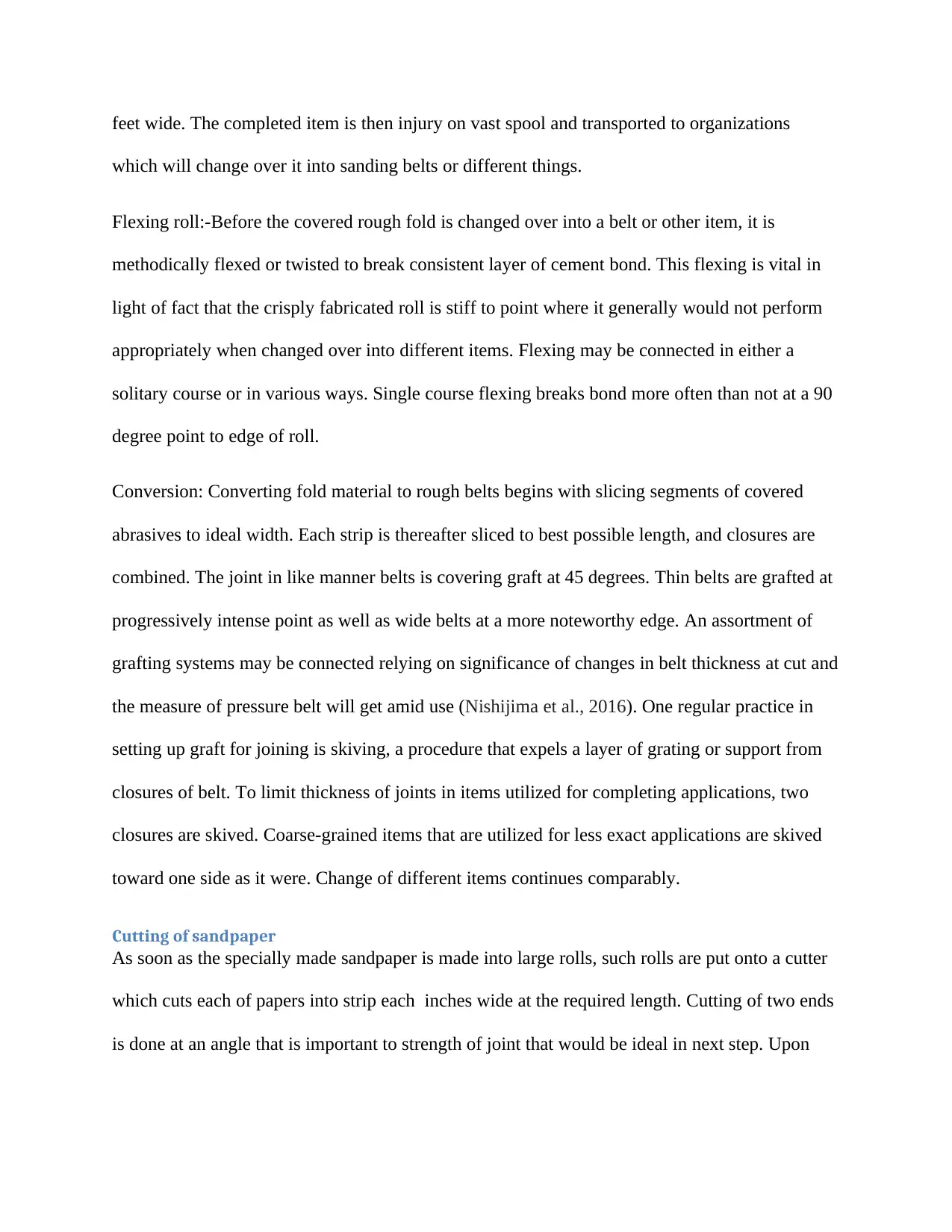
feet wide. The completed item is then injury on vast spool and transported to organizations
which will change over it into sanding belts or different things.
Flexing roll:-Before the covered rough fold is changed over into a belt or other item, it is
methodically flexed or twisted to break consistent layer of cement bond. This flexing is vital in
light of fact that the crisply fabricated roll is stiff to point where it generally would not perform
appropriately when changed over into different items. Flexing may be connected in either a
solitary course or in various ways. Single course flexing breaks bond more often than not at a 90
degree point to edge of roll.
Conversion: Converting fold material to rough belts begins with slicing segments of covered
abrasives to ideal width. Each strip is thereafter sliced to best possible length, and closures are
combined. The joint in like manner belts is covering graft at 45 degrees. Thin belts are grafted at
progressively intense point as well as wide belts at a more noteworthy edge. An assortment of
grafting systems may be connected relying on significance of changes in belt thickness at cut and
the measure of pressure belt will get amid use (Nishijima et al., 2016). One regular practice in
setting up graft for joining is skiving, a procedure that expels a layer of grating or support from
closures of belt. To limit thickness of joints in items utilized for completing applications, two
closures are skived. Coarse-grained items that are utilized for less exact applications are skived
toward one side as it were. Change of different items continues comparably.
Cutting of sandpaper
As soon as the specially made sandpaper is made into large rolls, such rolls are put onto a cutter
which cuts each of papers into strip each inches wide at the required length. Cutting of two ends
is done at an angle that is important to strength of joint that would be ideal in next step. Upon
which will change over it into sanding belts or different things.
Flexing roll:-Before the covered rough fold is changed over into a belt or other item, it is
methodically flexed or twisted to break consistent layer of cement bond. This flexing is vital in
light of fact that the crisply fabricated roll is stiff to point where it generally would not perform
appropriately when changed over into different items. Flexing may be connected in either a
solitary course or in various ways. Single course flexing breaks bond more often than not at a 90
degree point to edge of roll.
Conversion: Converting fold material to rough belts begins with slicing segments of covered
abrasives to ideal width. Each strip is thereafter sliced to best possible length, and closures are
combined. The joint in like manner belts is covering graft at 45 degrees. Thin belts are grafted at
progressively intense point as well as wide belts at a more noteworthy edge. An assortment of
grafting systems may be connected relying on significance of changes in belt thickness at cut and
the measure of pressure belt will get amid use (Nishijima et al., 2016). One regular practice in
setting up graft for joining is skiving, a procedure that expels a layer of grating or support from
closures of belt. To limit thickness of joints in items utilized for completing applications, two
closures are skived. Coarse-grained items that are utilized for less exact applications are skived
toward one side as it were. Change of different items continues comparably.
Cutting of sandpaper
As soon as the specially made sandpaper is made into large rolls, such rolls are put onto a cutter
which cuts each of papers into strip each inches wide at the required length. Cutting of two ends
is done at an angle that is important to strength of joint that would be ideal in next step. Upon
⊘ This is a preview!⊘
Do you want full access?
Subscribe today to unlock all pages.

Trusted by 1+ million students worldwide
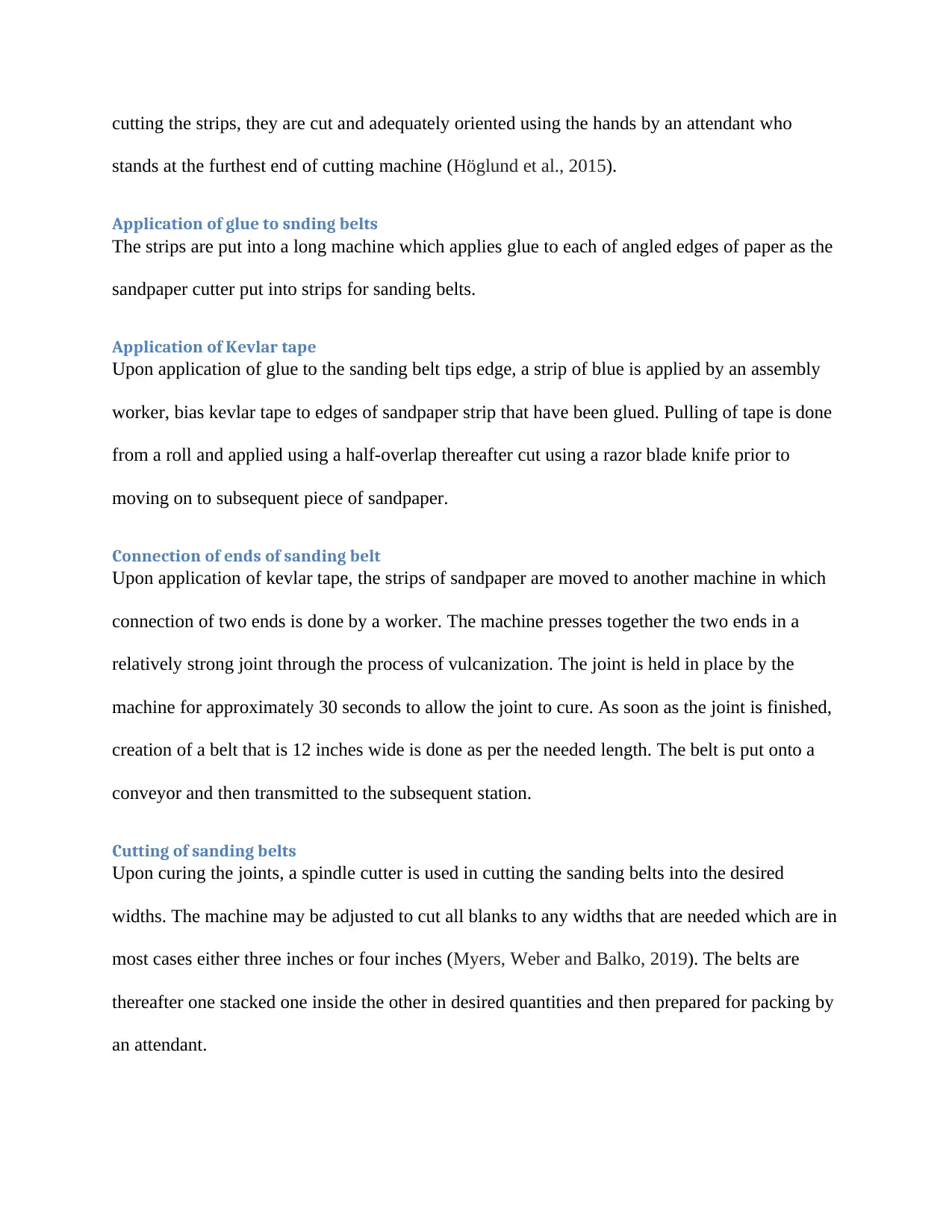
cutting the strips, they are cut and adequately oriented using the hands by an attendant who
stands at the furthest end of cutting machine (Höglund et al., 2015).
Application of glue to snding belts
The strips are put into a long machine which applies glue to each of angled edges of paper as the
sandpaper cutter put into strips for sanding belts.
Application of Kevlar tape
Upon application of glue to the sanding belt tips edge, a strip of blue is applied by an assembly
worker, bias kevlar tape to edges of sandpaper strip that have been glued. Pulling of tape is done
from a roll and applied using a half-overlap thereafter cut using a razor blade knife prior to
moving on to subsequent piece of sandpaper.
Connection of ends of sanding belt
Upon application of kevlar tape, the strips of sandpaper are moved to another machine in which
connection of two ends is done by a worker. The machine presses together the two ends in a
relatively strong joint through the process of vulcanization. The joint is held in place by the
machine for approximately 30 seconds to allow the joint to cure. As soon as the joint is finished,
creation of a belt that is 12 inches wide is done as per the needed length. The belt is put onto a
conveyor and then transmitted to the subsequent station.
Cutting of sanding belts
Upon curing the joints, a spindle cutter is used in cutting the sanding belts into the desired
widths. The machine may be adjusted to cut all blanks to any widths that are needed which are in
most cases either three inches or four inches (Myers, Weber and Balko, 2019). The belts are
thereafter one stacked one inside the other in desired quantities and then prepared for packing by
an attendant.
stands at the furthest end of cutting machine (Höglund et al., 2015).
Application of glue to snding belts
The strips are put into a long machine which applies glue to each of angled edges of paper as the
sandpaper cutter put into strips for sanding belts.
Application of Kevlar tape
Upon application of glue to the sanding belt tips edge, a strip of blue is applied by an assembly
worker, bias kevlar tape to edges of sandpaper strip that have been glued. Pulling of tape is done
from a roll and applied using a half-overlap thereafter cut using a razor blade knife prior to
moving on to subsequent piece of sandpaper.
Connection of ends of sanding belt
Upon application of kevlar tape, the strips of sandpaper are moved to another machine in which
connection of two ends is done by a worker. The machine presses together the two ends in a
relatively strong joint through the process of vulcanization. The joint is held in place by the
machine for approximately 30 seconds to allow the joint to cure. As soon as the joint is finished,
creation of a belt that is 12 inches wide is done as per the needed length. The belt is put onto a
conveyor and then transmitted to the subsequent station.
Cutting of sanding belts
Upon curing the joints, a spindle cutter is used in cutting the sanding belts into the desired
widths. The machine may be adjusted to cut all blanks to any widths that are needed which are in
most cases either three inches or four inches (Myers, Weber and Balko, 2019). The belts are
thereafter one stacked one inside the other in desired quantities and then prepared for packing by
an attendant.
Paraphrase This Document
Need a fresh take? Get an instant paraphrase of this document with our AI Paraphraser
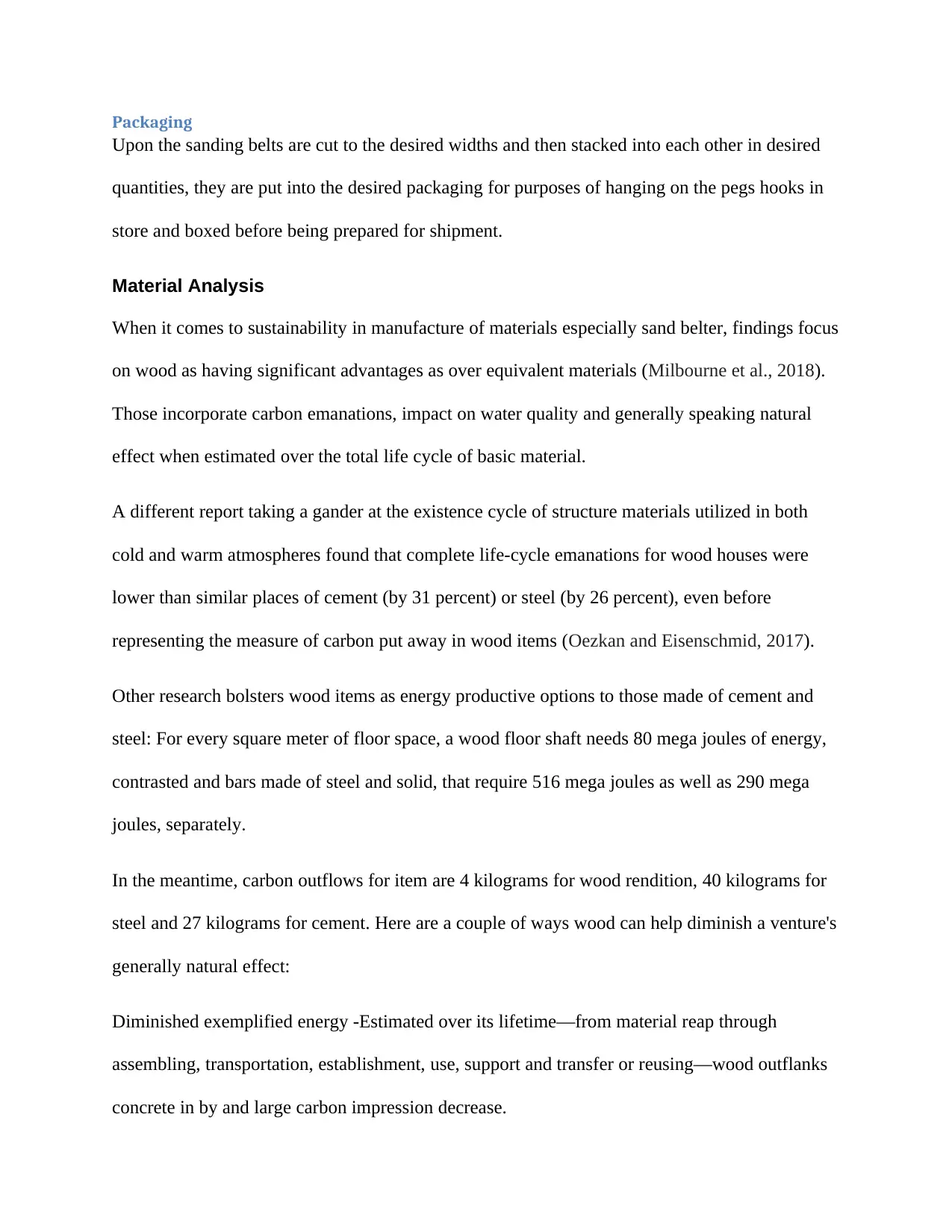
Packaging
Upon the sanding belts are cut to the desired widths and then stacked into each other in desired
quantities, they are put into the desired packaging for purposes of hanging on the pegs hooks in
store and boxed before being prepared for shipment.
Material Analysis
When it comes to sustainability in manufacture of materials especially sand belter, findings focus
on wood as having significant advantages as over equivalent materials (Milbourne et al., 2018).
Those incorporate carbon emanations, impact on water quality and generally speaking natural
effect when estimated over the total life cycle of basic material.
A different report taking a gander at the existence cycle of structure materials utilized in both
cold and warm atmospheres found that complete life-cycle emanations for wood houses were
lower than similar places of cement (by 31 percent) or steel (by 26 percent), even before
representing the measure of carbon put away in wood items (Oezkan and Eisenschmid, 2017).
Other research bolsters wood items as energy productive options to those made of cement and
steel: For every square meter of floor space, a wood floor shaft needs 80 mega joules of energy,
contrasted and bars made of steel and solid, that require 516 mega joules as well as 290 mega
joules, separately.
In the meantime, carbon outflows for item are 4 kilograms for wood rendition, 40 kilograms for
steel and 27 kilograms for cement. Here are a couple of ways wood can help diminish a venture's
generally natural effect:
Diminished exemplified energy -Estimated over its lifetime—from material reap through
assembling, transportation, establishment, use, support and transfer or reusing—wood outflanks
concrete in by and large carbon impression decrease.
Upon the sanding belts are cut to the desired widths and then stacked into each other in desired
quantities, they are put into the desired packaging for purposes of hanging on the pegs hooks in
store and boxed before being prepared for shipment.
Material Analysis
When it comes to sustainability in manufacture of materials especially sand belter, findings focus
on wood as having significant advantages as over equivalent materials (Milbourne et al., 2018).
Those incorporate carbon emanations, impact on water quality and generally speaking natural
effect when estimated over the total life cycle of basic material.
A different report taking a gander at the existence cycle of structure materials utilized in both
cold and warm atmospheres found that complete life-cycle emanations for wood houses were
lower than similar places of cement (by 31 percent) or steel (by 26 percent), even before
representing the measure of carbon put away in wood items (Oezkan and Eisenschmid, 2017).
Other research bolsters wood items as energy productive options to those made of cement and
steel: For every square meter of floor space, a wood floor shaft needs 80 mega joules of energy,
contrasted and bars made of steel and solid, that require 516 mega joules as well as 290 mega
joules, separately.
In the meantime, carbon outflows for item are 4 kilograms for wood rendition, 40 kilograms for
steel and 27 kilograms for cement. Here are a couple of ways wood can help diminish a venture's
generally natural effect:
Diminished exemplified energy -Estimated over its lifetime—from material reap through
assembling, transportation, establishment, use, support and transfer or reusing—wood outflanks
concrete in by and large carbon impression decrease.

Less ozone depleting substance outflows. Worldwide life-cycle evaluation considers have
demonstrated that wood can offer lower ozone harming substance outflows, less air and water
contamination, lower volumes of strong waste and less natural asset use than different materials.
Carbon sequestration-At the point when wood is utilized in a building, the carbon consumed by
the tree as it developed is successfully bolted away, regularly for a considerable length of time
and in some cases much more.
Supportability confirmation-Wood can make it simpler to accomplish outsider affirmation for an
undertaking, improving its esteem and attractiveness.
Table 1: Materials Ranking on scale 1-5
Property Steel Wood
Density 4 3
Yield stress 4 2
Tensile strength 5 2
Corrosion resistance 3 5
Cost per kg 4 2
Fracture toughness 4 4
Young’s modulus 4 2
The main materials rankings as well as alternative materials may be shown below in which the
rankings mean: very poor =1 , poor = 2, average = 3, good = 4, and very good = 5
demonstrated that wood can offer lower ozone harming substance outflows, less air and water
contamination, lower volumes of strong waste and less natural asset use than different materials.
Carbon sequestration-At the point when wood is utilized in a building, the carbon consumed by
the tree as it developed is successfully bolted away, regularly for a considerable length of time
and in some cases much more.
Supportability confirmation-Wood can make it simpler to accomplish outsider affirmation for an
undertaking, improving its esteem and attractiveness.
Table 1: Materials Ranking on scale 1-5
Property Steel Wood
Density 4 3
Yield stress 4 2
Tensile strength 5 2
Corrosion resistance 3 5
Cost per kg 4 2
Fracture toughness 4 4
Young’s modulus 4 2
The main materials rankings as well as alternative materials may be shown below in which the
rankings mean: very poor =1 , poor = 2, average = 3, good = 4, and very good = 5
⊘ This is a preview!⊘
Do you want full access?
Subscribe today to unlock all pages.

Trusted by 1+ million students worldwide
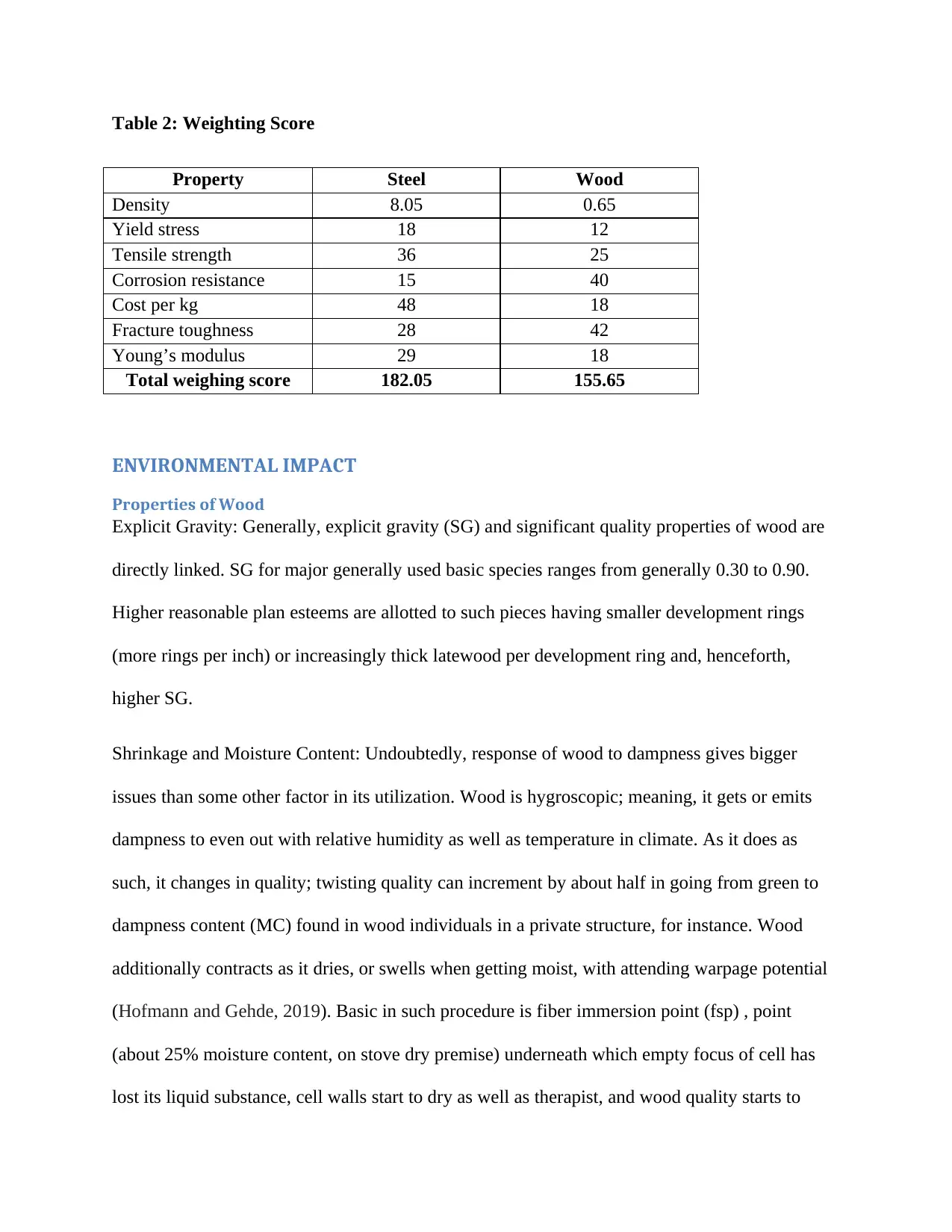
Table 2: Weighting Score
Property Steel Wood
Density 8.05 0.65
Yield stress 18 12
Tensile strength 36 25
Corrosion resistance 15 40
Cost per kg 48 18
Fracture toughness 28 42
Young’s modulus 29 18
Total weighing score 182.05 155.65
ENVIRONMENTAL IMPACT
Properties of Wood
Explicit Gravity: Generally, explicit gravity (SG) and significant quality properties of wood are
directly linked. SG for major generally used basic species ranges from generally 0.30 to 0.90.
Higher reasonable plan esteems are allotted to such pieces having smaller development rings
(more rings per inch) or increasingly thick latewood per development ring and, henceforth,
higher SG.
Shrinkage and Moisture Content: Undoubtedly, response of wood to dampness gives bigger
issues than some other factor in its utilization. Wood is hygroscopic; meaning, it gets or emits
dampness to even out with relative humidity as well as temperature in climate. As it does as
such, it changes in quality; twisting quality can increment by about half in going from green to
dampness content (MC) found in wood individuals in a private structure, for instance. Wood
additionally contracts as it dries, or swells when getting moist, with attending warpage potential
(Hofmann and Gehde, 2019). Basic in such procedure is fiber immersion point (fsp) , point
(about 25% moisture content, on stove dry premise) underneath which empty focus of cell has
lost its liquid substance, cell walls start to dry as well as therapist, and wood quality starts to
Property Steel Wood
Density 8.05 0.65
Yield stress 18 12
Tensile strength 36 25
Corrosion resistance 15 40
Cost per kg 48 18
Fracture toughness 28 42
Young’s modulus 29 18
Total weighing score 182.05 155.65
ENVIRONMENTAL IMPACT
Properties of Wood
Explicit Gravity: Generally, explicit gravity (SG) and significant quality properties of wood are
directly linked. SG for major generally used basic species ranges from generally 0.30 to 0.90.
Higher reasonable plan esteems are allotted to such pieces having smaller development rings
(more rings per inch) or increasingly thick latewood per development ring and, henceforth,
higher SG.
Shrinkage and Moisture Content: Undoubtedly, response of wood to dampness gives bigger
issues than some other factor in its utilization. Wood is hygroscopic; meaning, it gets or emits
dampness to even out with relative humidity as well as temperature in climate. As it does as
such, it changes in quality; twisting quality can increment by about half in going from green to
dampness content (MC) found in wood individuals in a private structure, for instance. Wood
additionally contracts as it dries, or swells when getting moist, with attending warpage potential
(Hofmann and Gehde, 2019). Basic in such procedure is fiber immersion point (fsp) , point
(about 25% moisture content, on stove dry premise) underneath which empty focus of cell has
lost its liquid substance, cell walls start to dry as well as therapist, and wood quality starts to
Paraphrase This Document
Need a fresh take? Get an instant paraphrase of this document with our AI Paraphraser
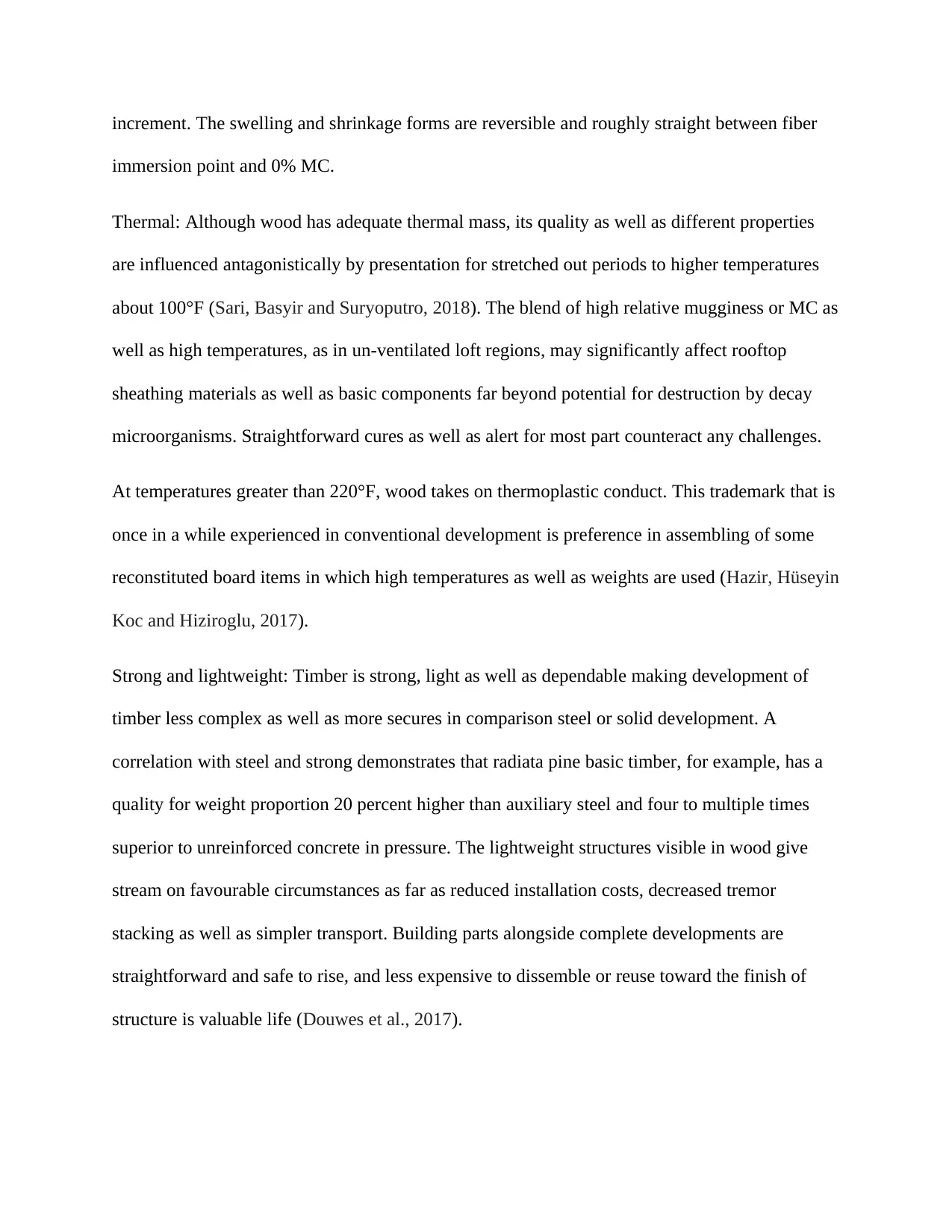
increment. The swelling and shrinkage forms are reversible and roughly straight between fiber
immersion point and 0% MC.
Thermal: Although wood has adequate thermal mass, its quality as well as different properties
are influenced antagonistically by presentation for stretched out periods to higher temperatures
about 100°F (Sari, Basyir and Suryoputro, 2018). The blend of high relative mugginess or MC as
well as high temperatures, as in un-ventilated loft regions, may significantly affect rooftop
sheathing materials as well as basic components far beyond potential for destruction by decay
microorganisms. Straightforward cures as well as alert for most part counteract any challenges.
At temperatures greater than 220°F, wood takes on thermoplastic conduct. This trademark that is
once in a while experienced in conventional development is preference in assembling of some
reconstituted board items in which high temperatures as well as weights are used (Hazir, Hüseyin
Koc and Hiziroglu, 2017).
Strong and lightweight: Timber is strong, light as well as dependable making development of
timber less complex as well as more secures in comparison steel or solid development. A
correlation with steel and strong demonstrates that radiata pine basic timber, for example, has a
quality for weight proportion 20 percent higher than auxiliary steel and four to multiple times
superior to unreinforced concrete in pressure. The lightweight structures visible in wood give
stream on favourable circumstances as far as reduced installation costs, decreased tremor
stacking as well as simpler transport. Building parts alongside complete developments are
straightforward and safe to rise, and less expensive to dissemble or reuse toward the finish of
structure is valuable life (Douwes et al., 2017).
immersion point and 0% MC.
Thermal: Although wood has adequate thermal mass, its quality as well as different properties
are influenced antagonistically by presentation for stretched out periods to higher temperatures
about 100°F (Sari, Basyir and Suryoputro, 2018). The blend of high relative mugginess or MC as
well as high temperatures, as in un-ventilated loft regions, may significantly affect rooftop
sheathing materials as well as basic components far beyond potential for destruction by decay
microorganisms. Straightforward cures as well as alert for most part counteract any challenges.
At temperatures greater than 220°F, wood takes on thermoplastic conduct. This trademark that is
once in a while experienced in conventional development is preference in assembling of some
reconstituted board items in which high temperatures as well as weights are used (Hazir, Hüseyin
Koc and Hiziroglu, 2017).
Strong and lightweight: Timber is strong, light as well as dependable making development of
timber less complex as well as more secures in comparison steel or solid development. A
correlation with steel and strong demonstrates that radiata pine basic timber, for example, has a
quality for weight proportion 20 percent higher than auxiliary steel and four to multiple times
superior to unreinforced concrete in pressure. The lightweight structures visible in wood give
stream on favourable circumstances as far as reduced installation costs, decreased tremor
stacking as well as simpler transport. Building parts alongside complete developments are
straightforward and safe to rise, and less expensive to dissemble or reuse toward the finish of
structure is valuable life (Douwes et al., 2017).
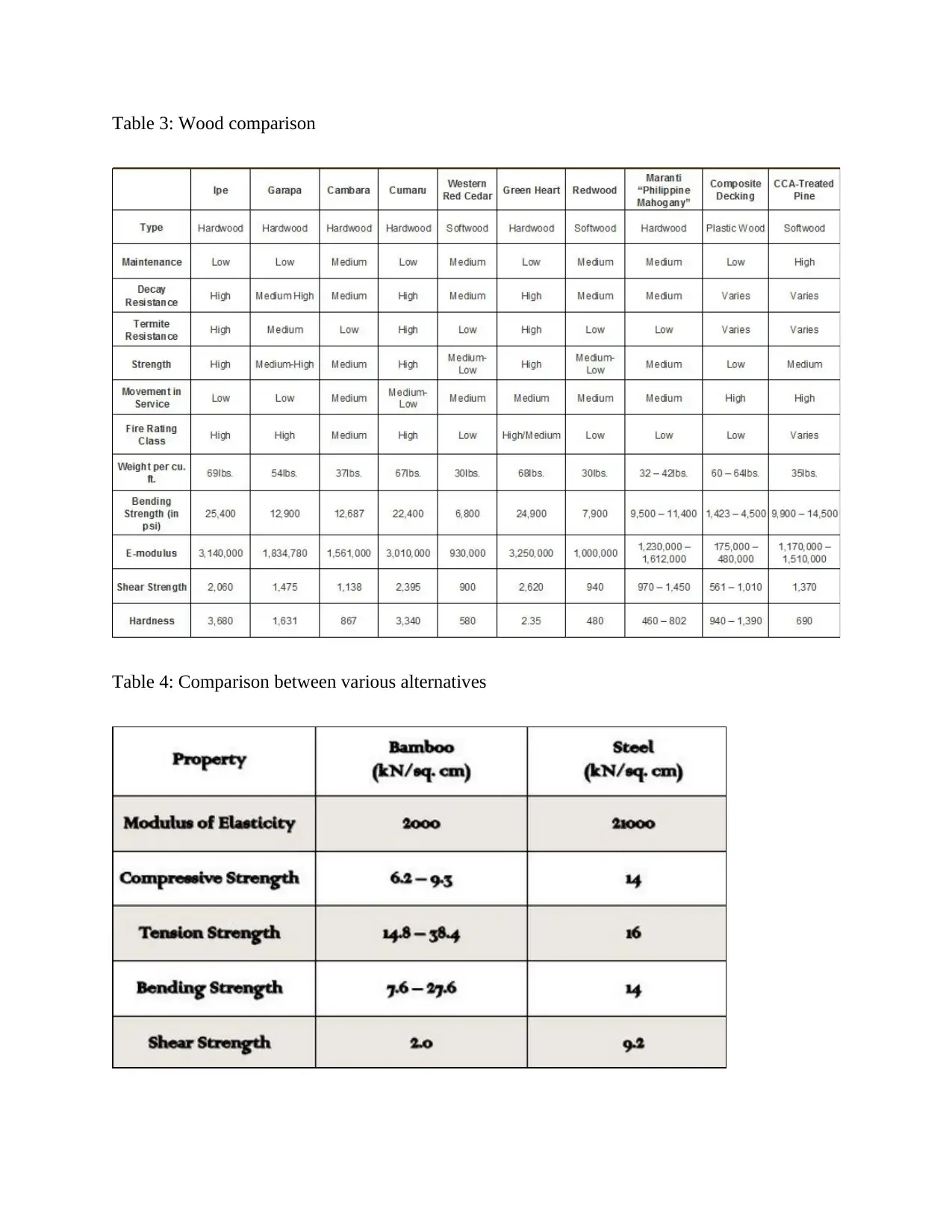
Table 3: Wood comparison
Table 4: Comparison between various alternatives
Table 4: Comparison between various alternatives
⊘ This is a preview!⊘
Do you want full access?
Subscribe today to unlock all pages.

Trusted by 1+ million students worldwide
1 out of 16