Industrial Systems (Unit 45) Assignment 3: Measuring Systems Report
VerifiedAdded on 2021/02/22
|9
|1741
|441
Report
AI Summary
This report examines industrial measuring systems and closed-loop systems, crucial components in many applications. It delves into practical measurement systems, detailing an AC-to-DC conversion setup with a motor control unit, a tachogenerator for feedback, and the role of a PID controller in mai...
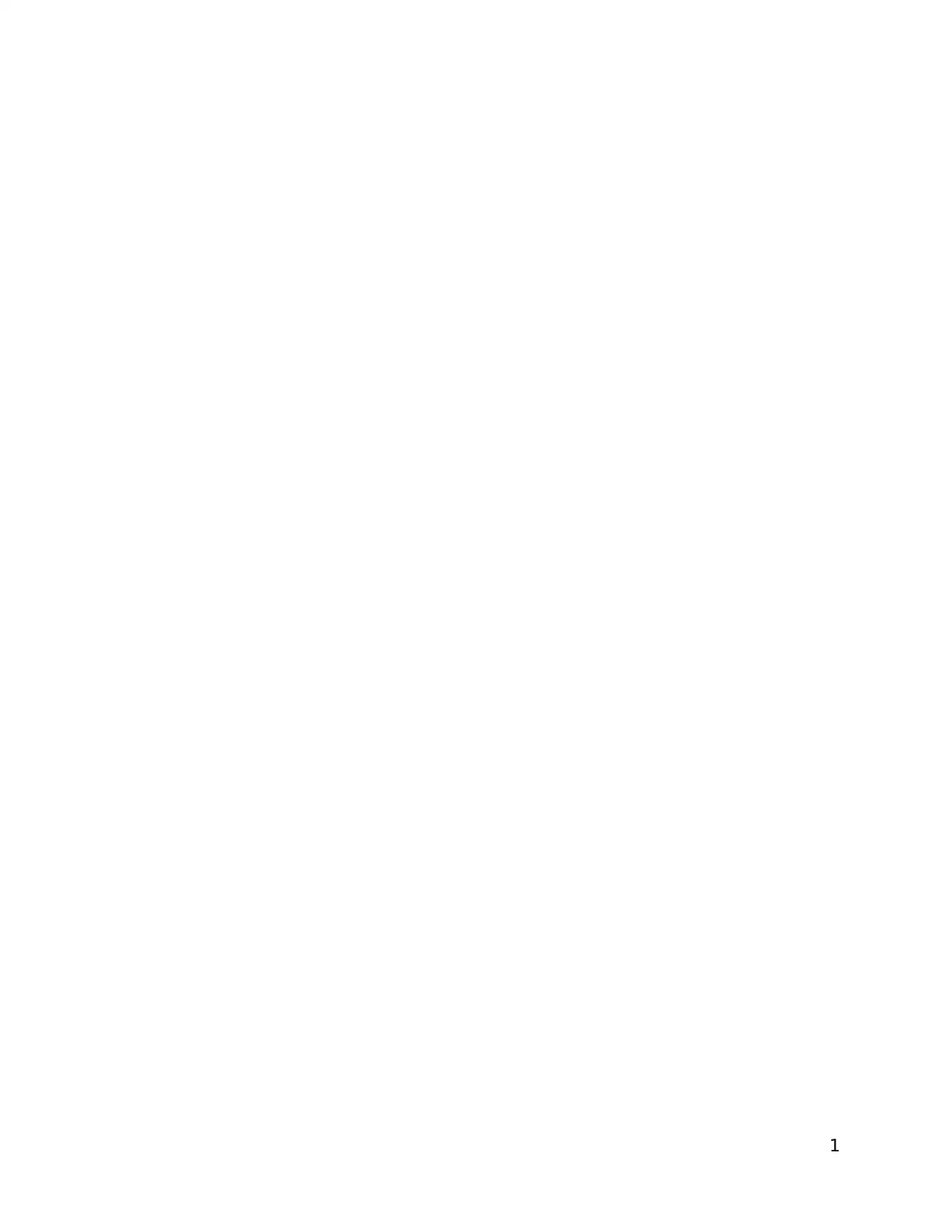
1
Secure Best Marks with AI Grader
Need help grading? Try our AI Grader for instant feedback on your assignments.
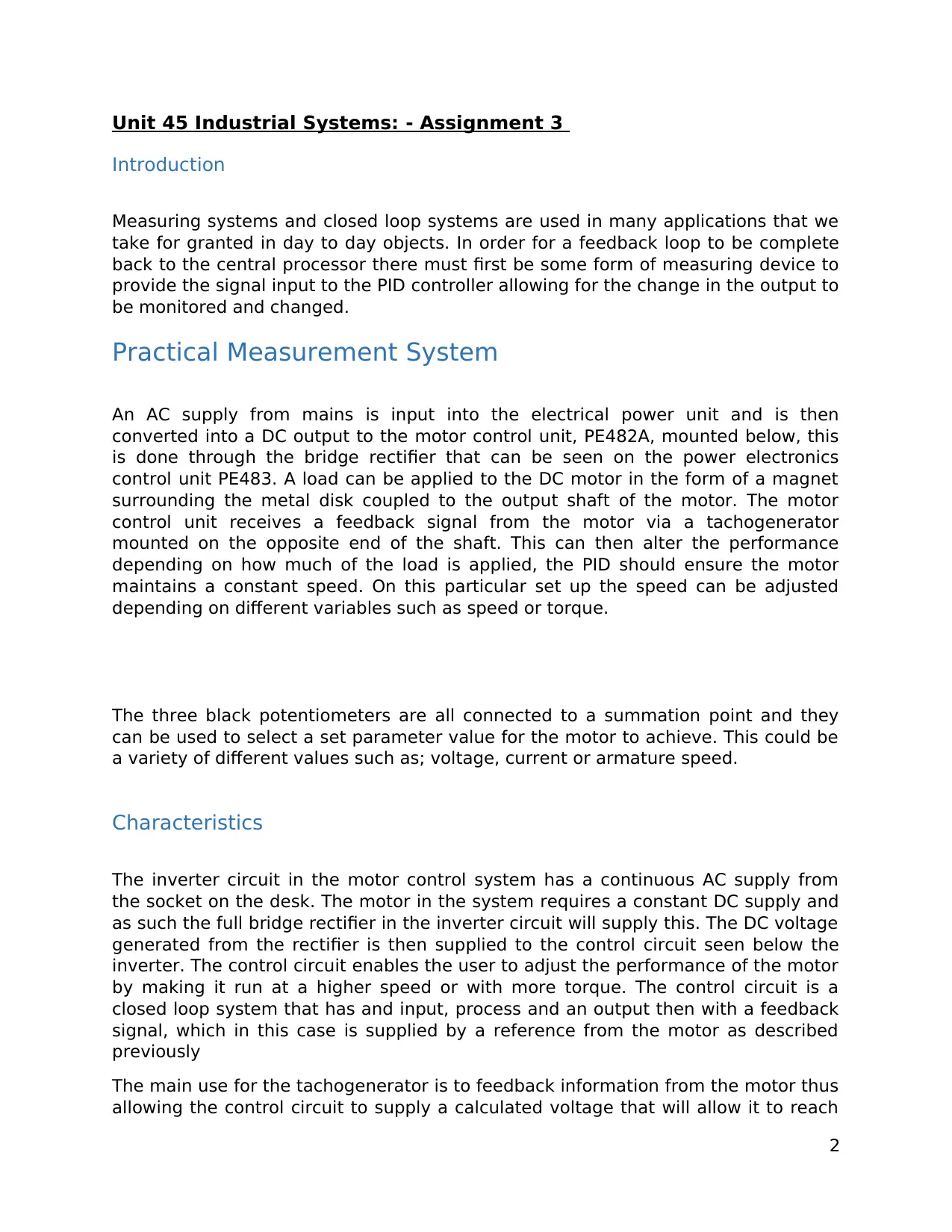
Unit 45 Industrial Systems: - Assignment 3
Introduction
Measuring systems and closed loop systems are used in many applications that we
take for granted in day to day objects. In order for a feedback loop to be complete
back to the central processor there must first be some form of measuring device to
provide the signal input to the PID controller allowing for the change in the output to
be monitored and changed.
Practical Measurement System
An AC supply from mains is input into the electrical power unit and is then
converted into a DC output to the motor control unit, PE482A, mounted below, this
is done through the bridge rectifier that can be seen on the power electronics
control unit PE483. A load can be applied to the DC motor in the form of a magnet
surrounding the metal disk coupled to the output shaft of the motor. The motor
control unit receives a feedback signal from the motor via a tachogenerator
mounted on the opposite end of the shaft. This can then alter the performance
depending on how much of the load is applied, the PID should ensure the motor
maintains a constant speed. On this particular set up the speed can be adjusted
depending on different variables such as speed or torque.
The three black potentiometers are all connected to a summation point and they
can be used to select a set parameter value for the motor to achieve. This could be
a variety of different values such as; voltage, current or armature speed.
Characteristics
The inverter circuit in the motor control system has a continuous AC supply from
the socket on the desk. The motor in the system requires a constant DC supply and
as such the full bridge rectifier in the inverter circuit will supply this. The DC voltage
generated from the rectifier is then supplied to the control circuit seen below the
inverter. The control circuit enables the user to adjust the performance of the motor
by making it run at a higher speed or with more torque. The control circuit is a
closed loop system that has and input, process and an output then with a feedback
signal, which in this case is supplied by a reference from the motor as described
previously
The main use for the tachogenerator is to feedback information from the motor thus
allowing the control circuit to supply a calculated voltage that will allow it to reach
2
Introduction
Measuring systems and closed loop systems are used in many applications that we
take for granted in day to day objects. In order for a feedback loop to be complete
back to the central processor there must first be some form of measuring device to
provide the signal input to the PID controller allowing for the change in the output to
be monitored and changed.
Practical Measurement System
An AC supply from mains is input into the electrical power unit and is then
converted into a DC output to the motor control unit, PE482A, mounted below, this
is done through the bridge rectifier that can be seen on the power electronics
control unit PE483. A load can be applied to the DC motor in the form of a magnet
surrounding the metal disk coupled to the output shaft of the motor. The motor
control unit receives a feedback signal from the motor via a tachogenerator
mounted on the opposite end of the shaft. This can then alter the performance
depending on how much of the load is applied, the PID should ensure the motor
maintains a constant speed. On this particular set up the speed can be adjusted
depending on different variables such as speed or torque.
The three black potentiometers are all connected to a summation point and they
can be used to select a set parameter value for the motor to achieve. This could be
a variety of different values such as; voltage, current or armature speed.
Characteristics
The inverter circuit in the motor control system has a continuous AC supply from
the socket on the desk. The motor in the system requires a constant DC supply and
as such the full bridge rectifier in the inverter circuit will supply this. The DC voltage
generated from the rectifier is then supplied to the control circuit seen below the
inverter. The control circuit enables the user to adjust the performance of the motor
by making it run at a higher speed or with more torque. The control circuit is a
closed loop system that has and input, process and an output then with a feedback
signal, which in this case is supplied by a reference from the motor as described
previously
The main use for the tachogenerator is to feedback information from the motor thus
allowing the control circuit to supply a calculated voltage that will allow it to reach
2
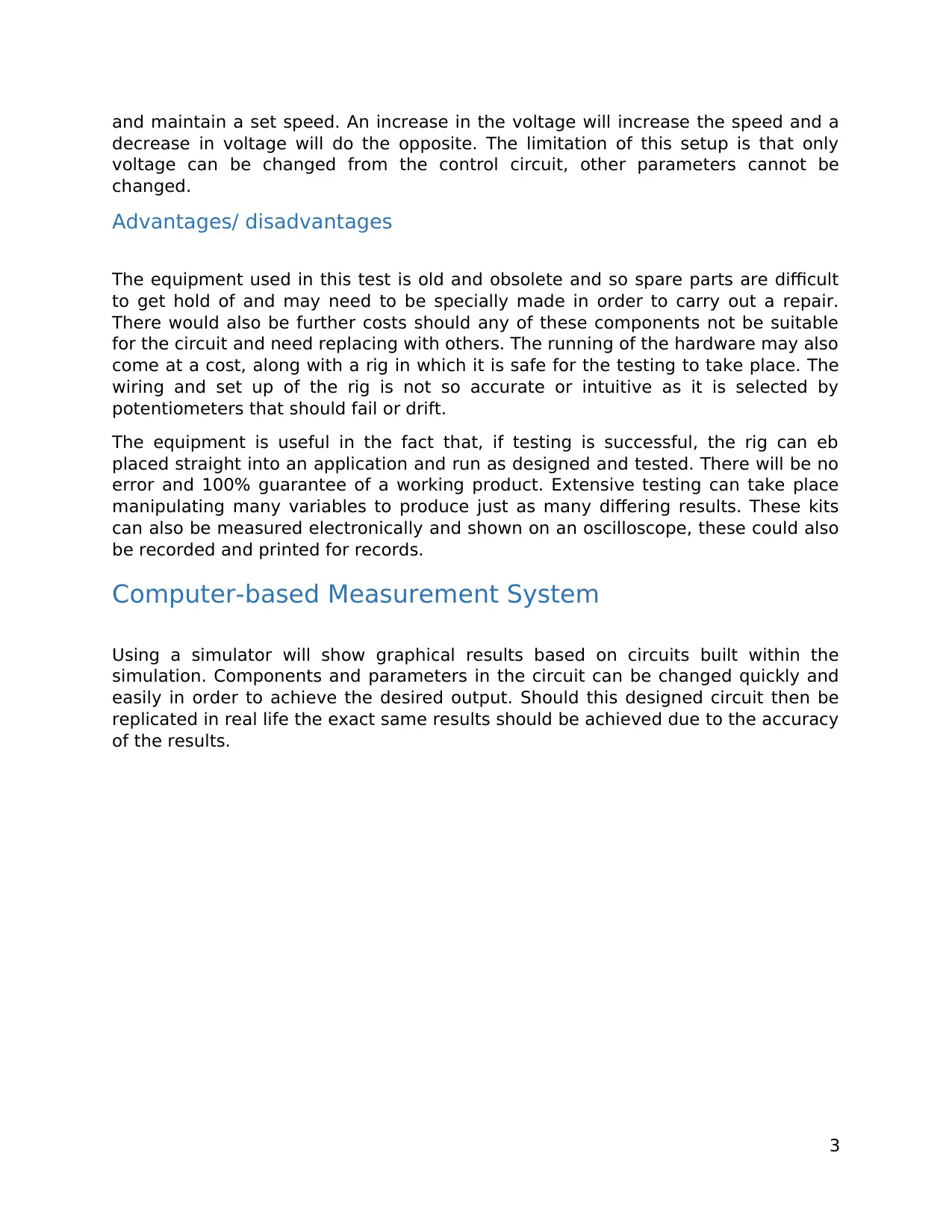
and maintain a set speed. An increase in the voltage will increase the speed and a
decrease in voltage will do the opposite. The limitation of this setup is that only
voltage can be changed from the control circuit, other parameters cannot be
changed.
Advantages/ disadvantages
The equipment used in this test is old and obsolete and so spare parts are difficult
to get hold of and may need to be specially made in order to carry out a repair.
There would also be further costs should any of these components not be suitable
for the circuit and need replacing with others. The running of the hardware may also
come at a cost, along with a rig in which it is safe for the testing to take place. The
wiring and set up of the rig is not so accurate or intuitive as it is selected by
potentiometers that should fail or drift.
The equipment is useful in the fact that, if testing is successful, the rig can eb
placed straight into an application and run as designed and tested. There will be no
error and 100% guarantee of a working product. Extensive testing can take place
manipulating many variables to produce just as many differing results. These kits
can also be measured electronically and shown on an oscilloscope, these could also
be recorded and printed for records.
Computer-based Measurement System
Using a simulator will show graphical results based on circuits built within the
simulation. Components and parameters in the circuit can be changed quickly and
easily in order to achieve the desired output. Should this designed circuit then be
replicated in real life the exact same results should be achieved due to the accuracy
of the results.
3
decrease in voltage will do the opposite. The limitation of this setup is that only
voltage can be changed from the control circuit, other parameters cannot be
changed.
Advantages/ disadvantages
The equipment used in this test is old and obsolete and so spare parts are difficult
to get hold of and may need to be specially made in order to carry out a repair.
There would also be further costs should any of these components not be suitable
for the circuit and need replacing with others. The running of the hardware may also
come at a cost, along with a rig in which it is safe for the testing to take place. The
wiring and set up of the rig is not so accurate or intuitive as it is selected by
potentiometers that should fail or drift.
The equipment is useful in the fact that, if testing is successful, the rig can eb
placed straight into an application and run as designed and tested. There will be no
error and 100% guarantee of a working product. Extensive testing can take place
manipulating many variables to produce just as many differing results. These kits
can also be measured electronically and shown on an oscilloscope, these could also
be recorded and printed for records.
Computer-based Measurement System
Using a simulator will show graphical results based on circuits built within the
simulation. Components and parameters in the circuit can be changed quickly and
easily in order to achieve the desired output. Should this designed circuit then be
replicated in real life the exact same results should be achieved due to the accuracy
of the results.
3
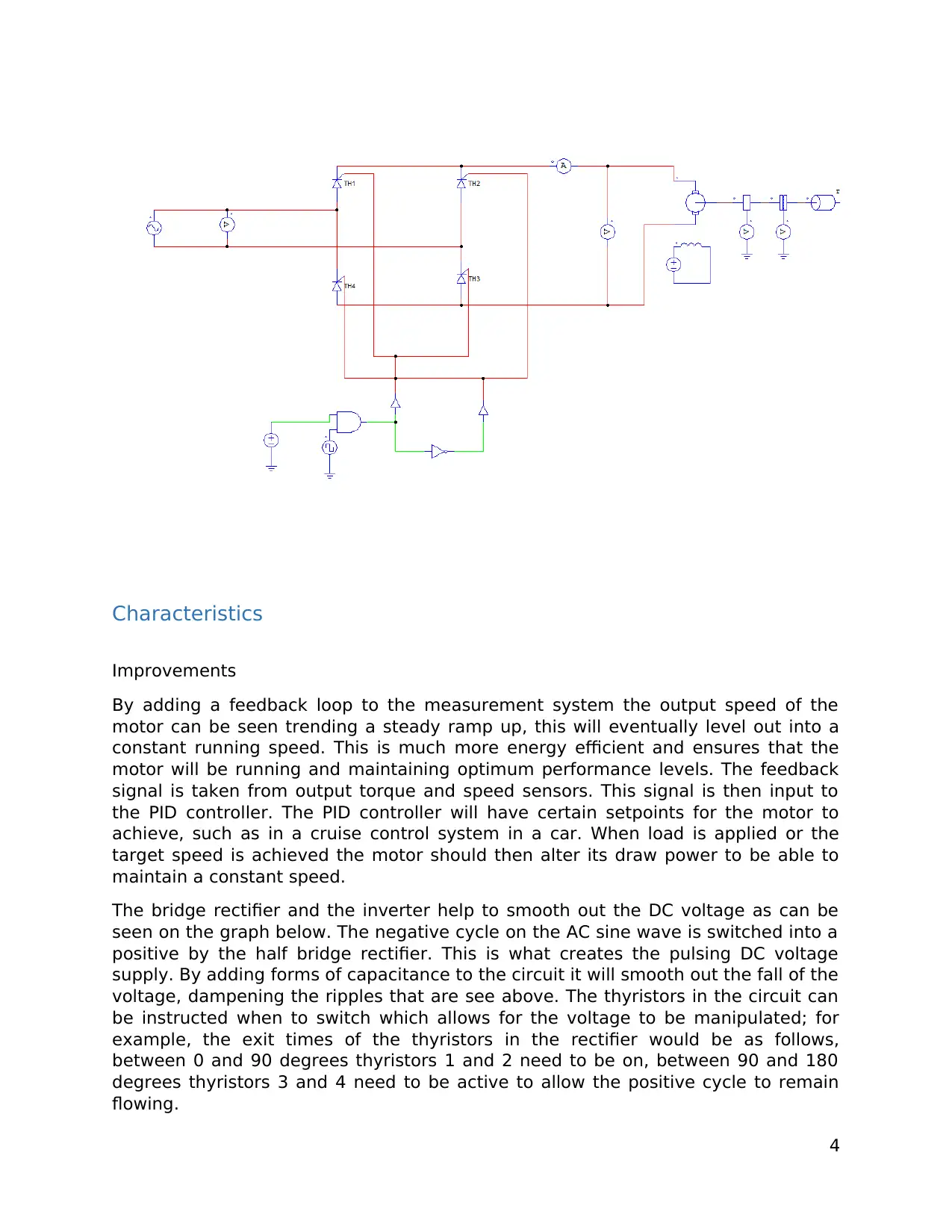
Characteristics
Improvements
By adding a feedback loop to the measurement system the output speed of the
motor can be seen trending a steady ramp up, this will eventually level out into a
constant running speed. This is much more energy efficient and ensures that the
motor will be running and maintaining optimum performance levels. The feedback
signal is taken from output torque and speed sensors. This signal is then input to
the PID controller. The PID controller will have certain setpoints for the motor to
achieve, such as in a cruise control system in a car. When load is applied or the
target speed is achieved the motor should then alter its draw power to be able to
maintain a constant speed.
The bridge rectifier and the inverter help to smooth out the DC voltage as can be
seen on the graph below. The negative cycle on the AC sine wave is switched into a
positive by the half bridge rectifier. This is what creates the pulsing DC voltage
supply. By adding forms of capacitance to the circuit it will smooth out the fall of the
voltage, dampening the ripples that are see above. The thyristors in the circuit can
be instructed when to switch which allows for the voltage to be manipulated; for
example, the exit times of the thyristors in the rectifier would be as follows,
between 0 and 90 degrees thyristors 1 and 2 need to be on, between 90 and 180
degrees thyristors 3 and 4 need to be active to allow the positive cycle to remain
flowing.
4
Improvements
By adding a feedback loop to the measurement system the output speed of the
motor can be seen trending a steady ramp up, this will eventually level out into a
constant running speed. This is much more energy efficient and ensures that the
motor will be running and maintaining optimum performance levels. The feedback
signal is taken from output torque and speed sensors. This signal is then input to
the PID controller. The PID controller will have certain setpoints for the motor to
achieve, such as in a cruise control system in a car. When load is applied or the
target speed is achieved the motor should then alter its draw power to be able to
maintain a constant speed.
The bridge rectifier and the inverter help to smooth out the DC voltage as can be
seen on the graph below. The negative cycle on the AC sine wave is switched into a
positive by the half bridge rectifier. This is what creates the pulsing DC voltage
supply. By adding forms of capacitance to the circuit it will smooth out the fall of the
voltage, dampening the ripples that are see above. The thyristors in the circuit can
be instructed when to switch which allows for the voltage to be manipulated; for
example, the exit times of the thyristors in the rectifier would be as follows,
between 0 and 90 degrees thyristors 1 and 2 need to be on, between 90 and 180
degrees thyristors 3 and 4 need to be active to allow the positive cycle to remain
flowing.
4
Secure Best Marks with AI Grader
Need help grading? Try our AI Grader for instant feedback on your assignments.
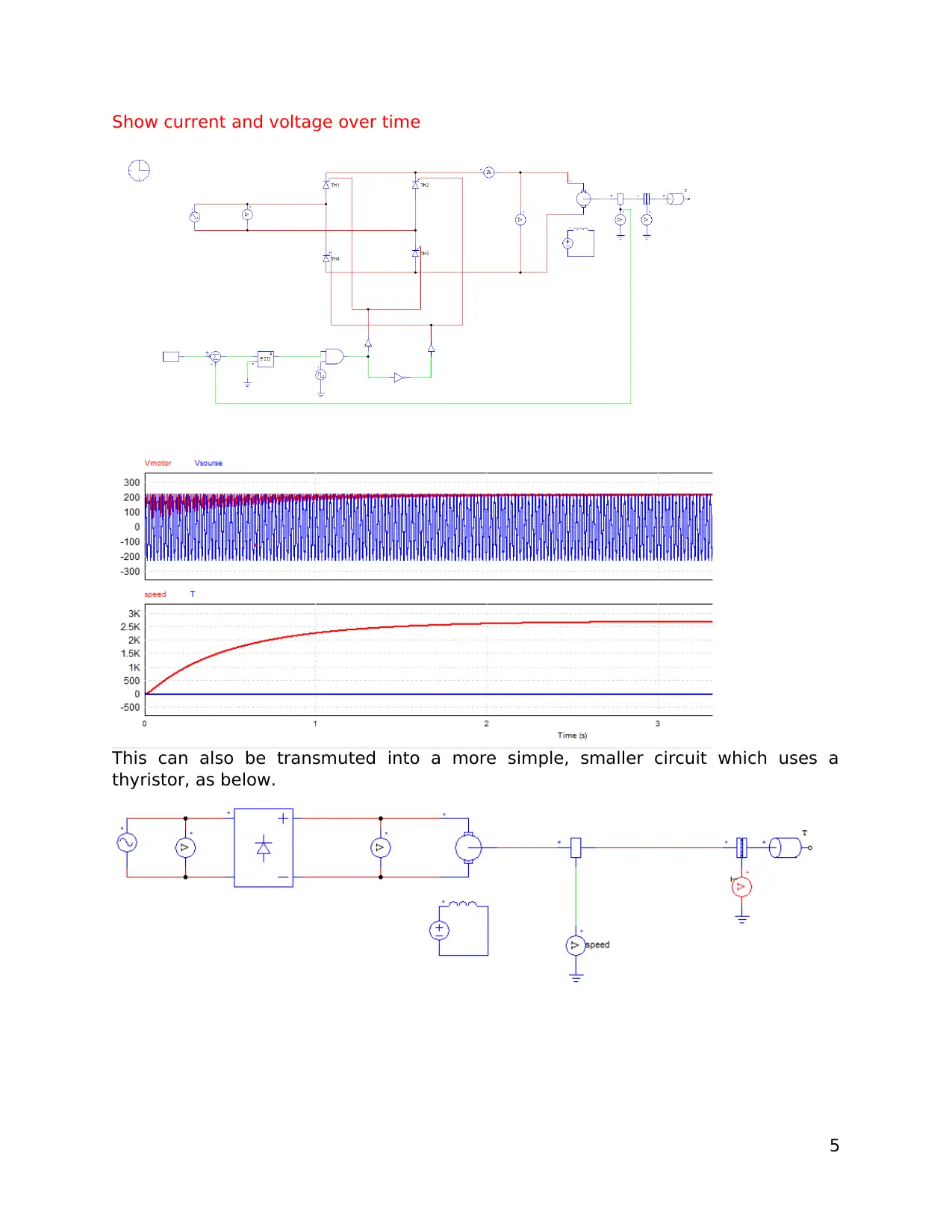
Show current and voltage over time
This can also be transmuted into a more simple, smaller circuit which uses a
thyristor, as below.
5
This can also be transmuted into a more simple, smaller circuit which uses a
thyristor, as below.
5
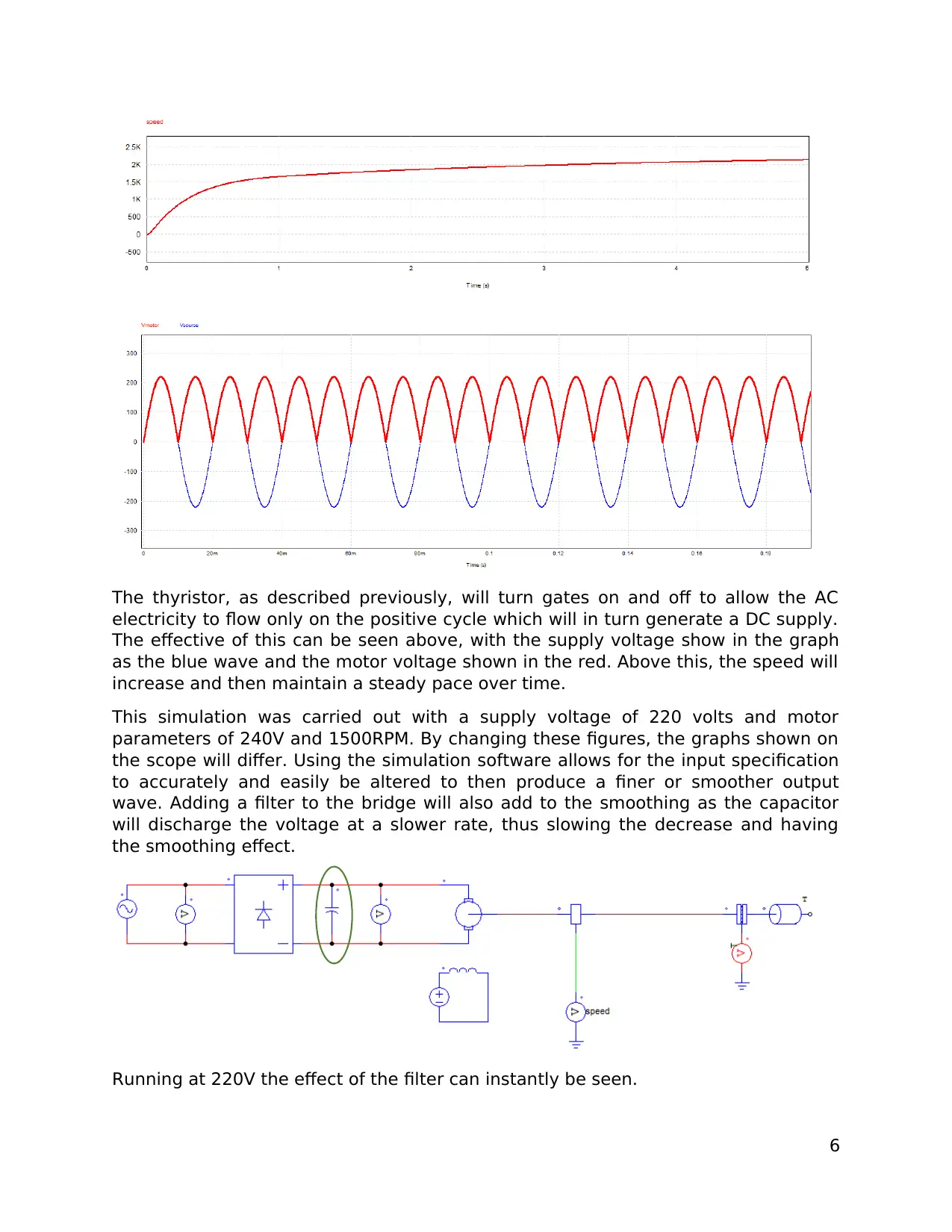
The thyristor, as described previously, will turn gates on and off to allow the AC
electricity to flow only on the positive cycle which will in turn generate a DC supply.
The effective of this can be seen above, with the supply voltage show in the graph
as the blue wave and the motor voltage shown in the red. Above this, the speed will
increase and then maintain a steady pace over time.
This simulation was carried out with a supply voltage of 220 volts and motor
parameters of 240V and 1500RPM. By changing these figures, the graphs shown on
the scope will differ. Using the simulation software allows for the input specification
to accurately and easily be altered to then produce a finer or smoother output
wave. Adding a filter to the bridge will also add to the smoothing as the capacitor
will discharge the voltage at a slower rate, thus slowing the decrease and having
the smoothing effect.
Running at 220V the effect of the filter can instantly be seen.
6
electricity to flow only on the positive cycle which will in turn generate a DC supply.
The effective of this can be seen above, with the supply voltage show in the graph
as the blue wave and the motor voltage shown in the red. Above this, the speed will
increase and then maintain a steady pace over time.
This simulation was carried out with a supply voltage of 220 volts and motor
parameters of 240V and 1500RPM. By changing these figures, the graphs shown on
the scope will differ. Using the simulation software allows for the input specification
to accurately and easily be altered to then produce a finer or smoother output
wave. Adding a filter to the bridge will also add to the smoothing as the capacitor
will discharge the voltage at a slower rate, thus slowing the decrease and having
the smoothing effect.
Running at 220V the effect of the filter can instantly be seen.
6
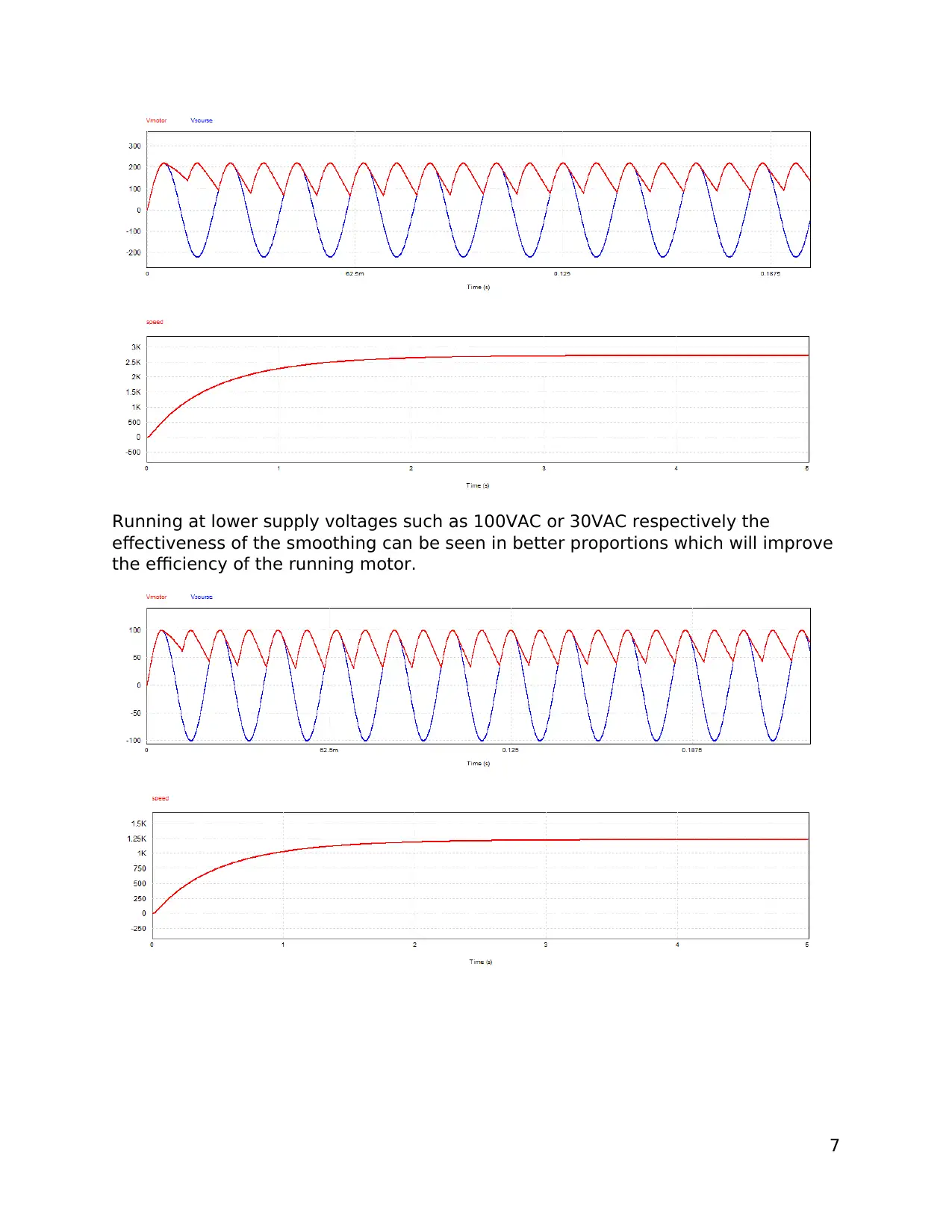
Running at lower supply voltages such as 100VAC or 30VAC respectively the
effectiveness of the smoothing can be seen in better proportions which will improve
the efficiency of the running motor.
7
effectiveness of the smoothing can be seen in better proportions which will improve
the efficiency of the running motor.
7
Paraphrase This Document
Need a fresh take? Get an instant paraphrase of this document with our AI Paraphraser
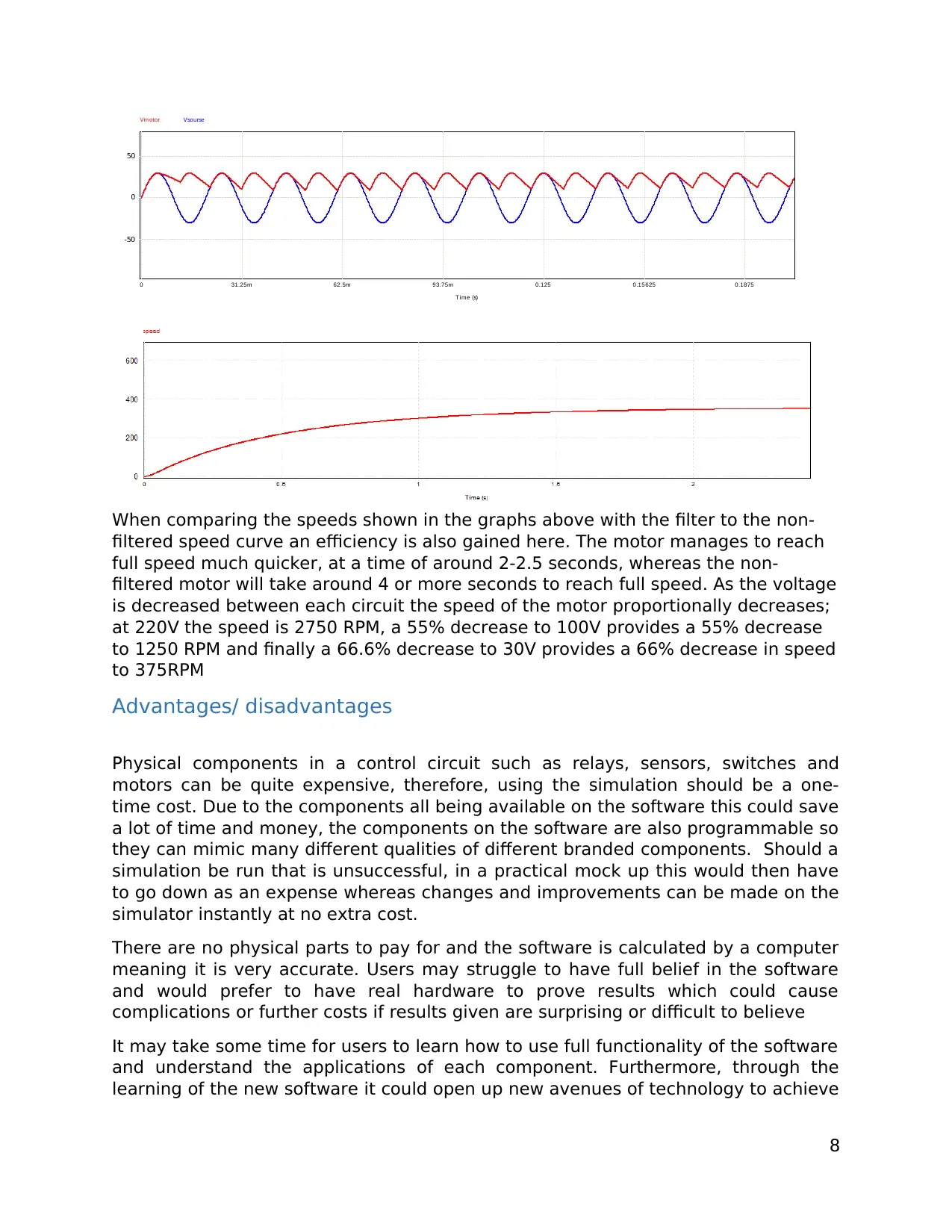
0 31.25m 62.5m 93.75m 0.125 0.15625 0.1875
Time (s)
-50
0
50
Vm otor Vsourse
When comparing the speeds shown in the graphs above with the filter to the non-
filtered speed curve an efficiency is also gained here. The motor manages to reach
full speed much quicker, at a time of around 2-2.5 seconds, whereas the non-
filtered motor will take around 4 or more seconds to reach full speed. As the voltage
is decreased between each circuit the speed of the motor proportionally decreases;
at 220V the speed is 2750 RPM, a 55% decrease to 100V provides a 55% decrease
to 1250 RPM and finally a 66.6% decrease to 30V provides a 66% decrease in speed
to 375RPM
Advantages/ disadvantages
Physical components in a control circuit such as relays, sensors, switches and
motors can be quite expensive, therefore, using the simulation should be a one-
time cost. Due to the components all being available on the software this could save
a lot of time and money, the components on the software are also programmable so
they can mimic many different qualities of different branded components. Should a
simulation be run that is unsuccessful, in a practical mock up this would then have
to go down as an expense whereas changes and improvements can be made on the
simulator instantly at no extra cost.
There are no physical parts to pay for and the software is calculated by a computer
meaning it is very accurate. Users may struggle to have full belief in the software
and would prefer to have real hardware to prove results which could cause
complications or further costs if results given are surprising or difficult to believe
It may take some time for users to learn how to use full functionality of the software
and understand the applications of each component. Furthermore, through the
learning of the new software it could open up new avenues of technology to achieve
8
Time (s)
-50
0
50
Vm otor Vsourse
When comparing the speeds shown in the graphs above with the filter to the non-
filtered speed curve an efficiency is also gained here. The motor manages to reach
full speed much quicker, at a time of around 2-2.5 seconds, whereas the non-
filtered motor will take around 4 or more seconds to reach full speed. As the voltage
is decreased between each circuit the speed of the motor proportionally decreases;
at 220V the speed is 2750 RPM, a 55% decrease to 100V provides a 55% decrease
to 1250 RPM and finally a 66.6% decrease to 30V provides a 66% decrease in speed
to 375RPM
Advantages/ disadvantages
Physical components in a control circuit such as relays, sensors, switches and
motors can be quite expensive, therefore, using the simulation should be a one-
time cost. Due to the components all being available on the software this could save
a lot of time and money, the components on the software are also programmable so
they can mimic many different qualities of different branded components. Should a
simulation be run that is unsuccessful, in a practical mock up this would then have
to go down as an expense whereas changes and improvements can be made on the
simulator instantly at no extra cost.
There are no physical parts to pay for and the software is calculated by a computer
meaning it is very accurate. Users may struggle to have full belief in the software
and would prefer to have real hardware to prove results which could cause
complications or further costs if results given are surprising or difficult to believe
It may take some time for users to learn how to use full functionality of the software
and understand the applications of each component. Furthermore, through the
learning of the new software it could open up new avenues of technology to achieve
8
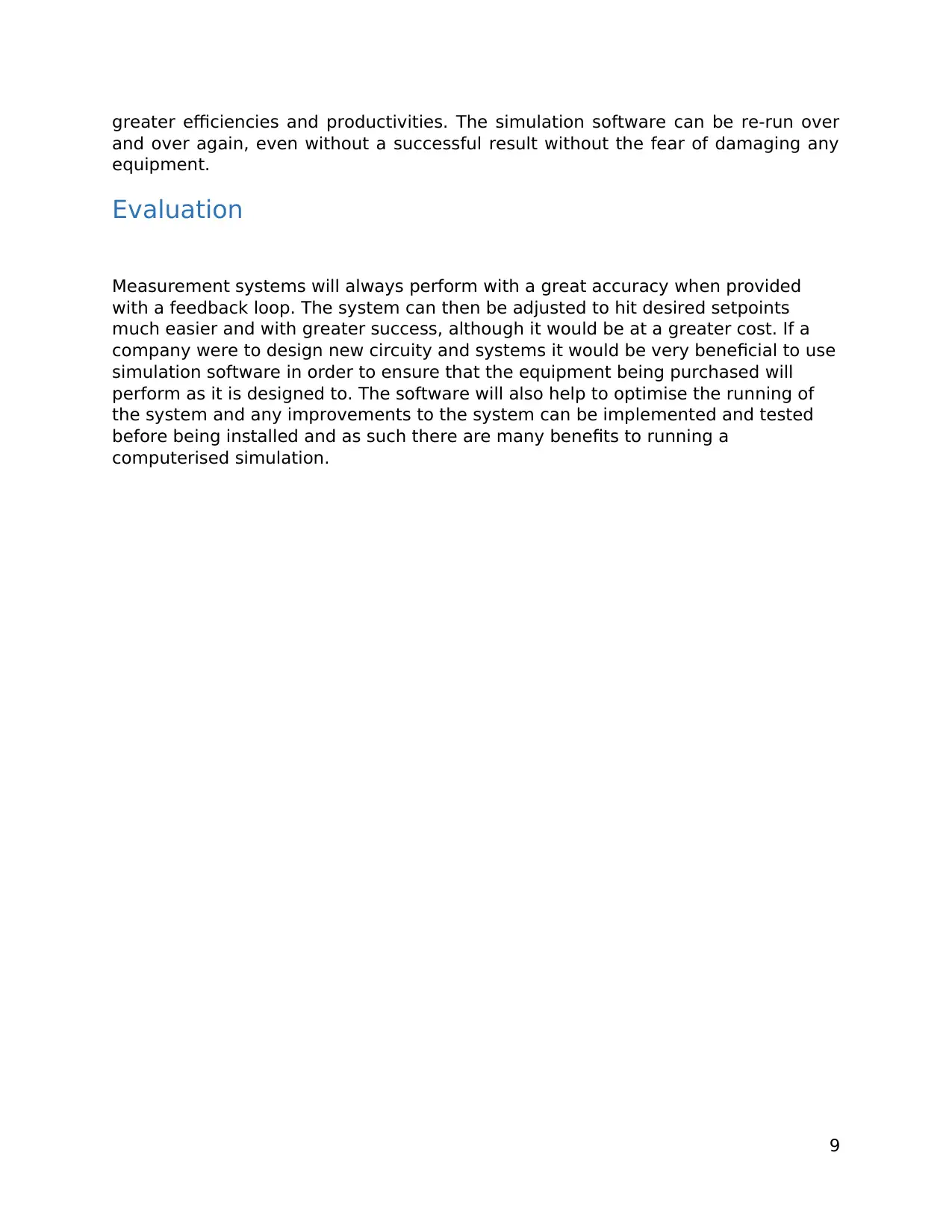
greater efficiencies and productivities. The simulation software can be re-run over
and over again, even without a successful result without the fear of damaging any
equipment.
Evaluation
Measurement systems will always perform with a great accuracy when provided
with a feedback loop. The system can then be adjusted to hit desired setpoints
much easier and with greater success, although it would be at a greater cost. If a
company were to design new circuity and systems it would be very beneficial to use
simulation software in order to ensure that the equipment being purchased will
perform as it is designed to. The software will also help to optimise the running of
the system and any improvements to the system can be implemented and tested
before being installed and as such there are many benefits to running a
computerised simulation.
9
and over again, even without a successful result without the fear of damaging any
equipment.
Evaluation
Measurement systems will always perform with a great accuracy when provided
with a feedback loop. The system can then be adjusted to hit desired setpoints
much easier and with greater success, although it would be at a greater cost. If a
company were to design new circuity and systems it would be very beneficial to use
simulation software in order to ensure that the equipment being purchased will
perform as it is designed to. The software will also help to optimise the running of
the system and any improvements to the system can be implemented and tested
before being installed and as such there are many benefits to running a
computerised simulation.
9
1 out of 9
Related Documents

Your All-in-One AI-Powered Toolkit for Academic Success.
+13062052269
info@desklib.com
Available 24*7 on WhatsApp / Email
Unlock your academic potential
© 2024 | Zucol Services PVT LTD | All rights reserved.