Operations Improvement Strategy for Mercedes-Benz (UGB 165)
VerifiedAdded on 2023/01/05
|12
|3610
|82
Report
AI Summary
This report delves into the operations improvement strategy for Mercedes-Benz, a leading German automotive marque, addressing declining productivity and profitability amidst increasing competition from brands like Audi and BMW. The report begins by explaining the importance of operations management and introduces a company-wide improvement strategy. This strategy involves utilizing tools and techniques such as Cause and Effect Diagrams, Total Quality Management (TQM), Lean Manufacturing, Just in Time (JIT) inventory management, and the Kaizen tool for continuous improvement. The report also analyzes specific operational strategies that Audi and BMW can implement to gain market share from Mercedes-Benz. The analysis covers various aspects, including product quality, design, and the use of advanced manufacturing techniques to enhance overall business performance and customer satisfaction. The report aims to provide insights into how Mercedes-Benz can regain its competitive edge in the automotive industry by focusing on improving its operations.
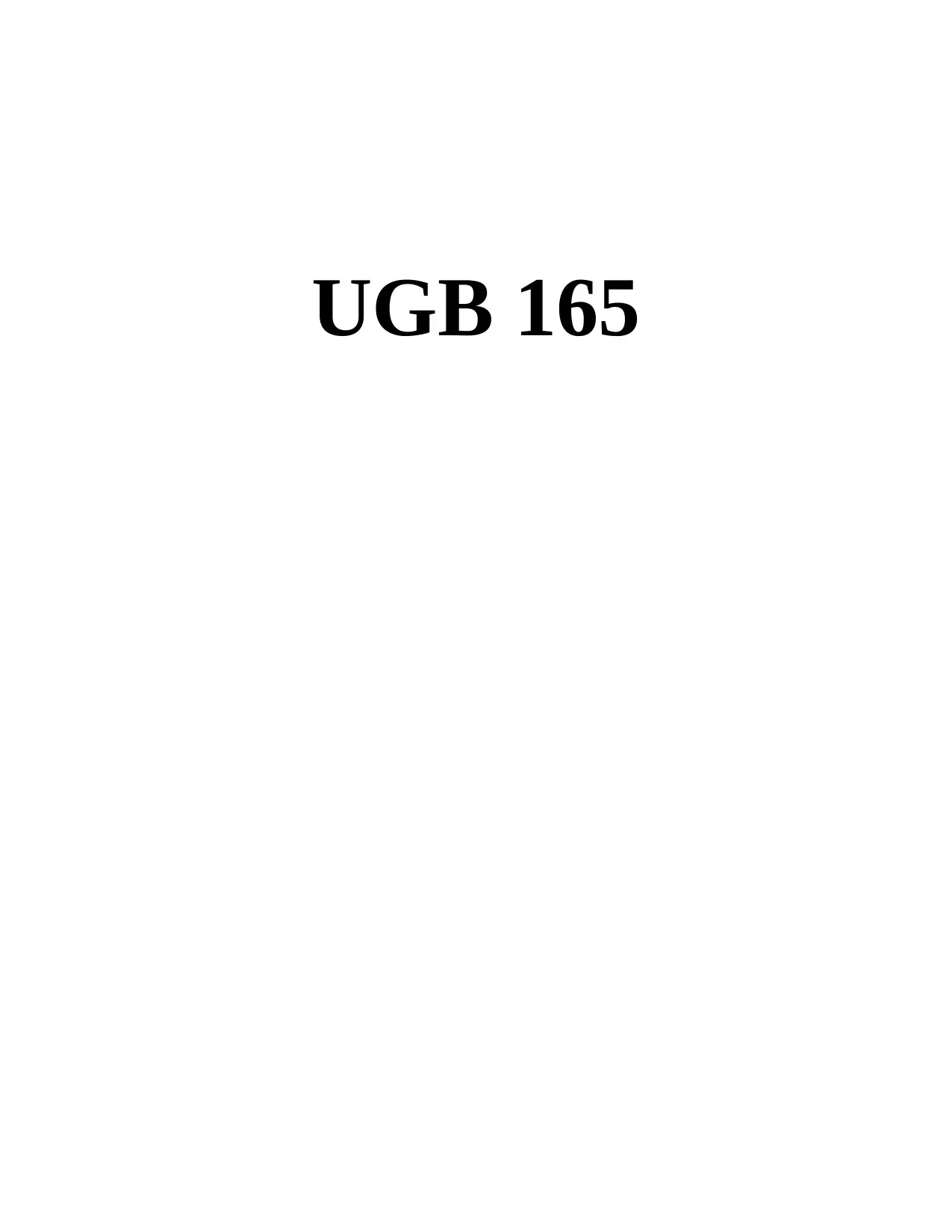
UGB 165
Paraphrase This Document
Need a fresh take? Get an instant paraphrase of this document with our AI Paraphraser
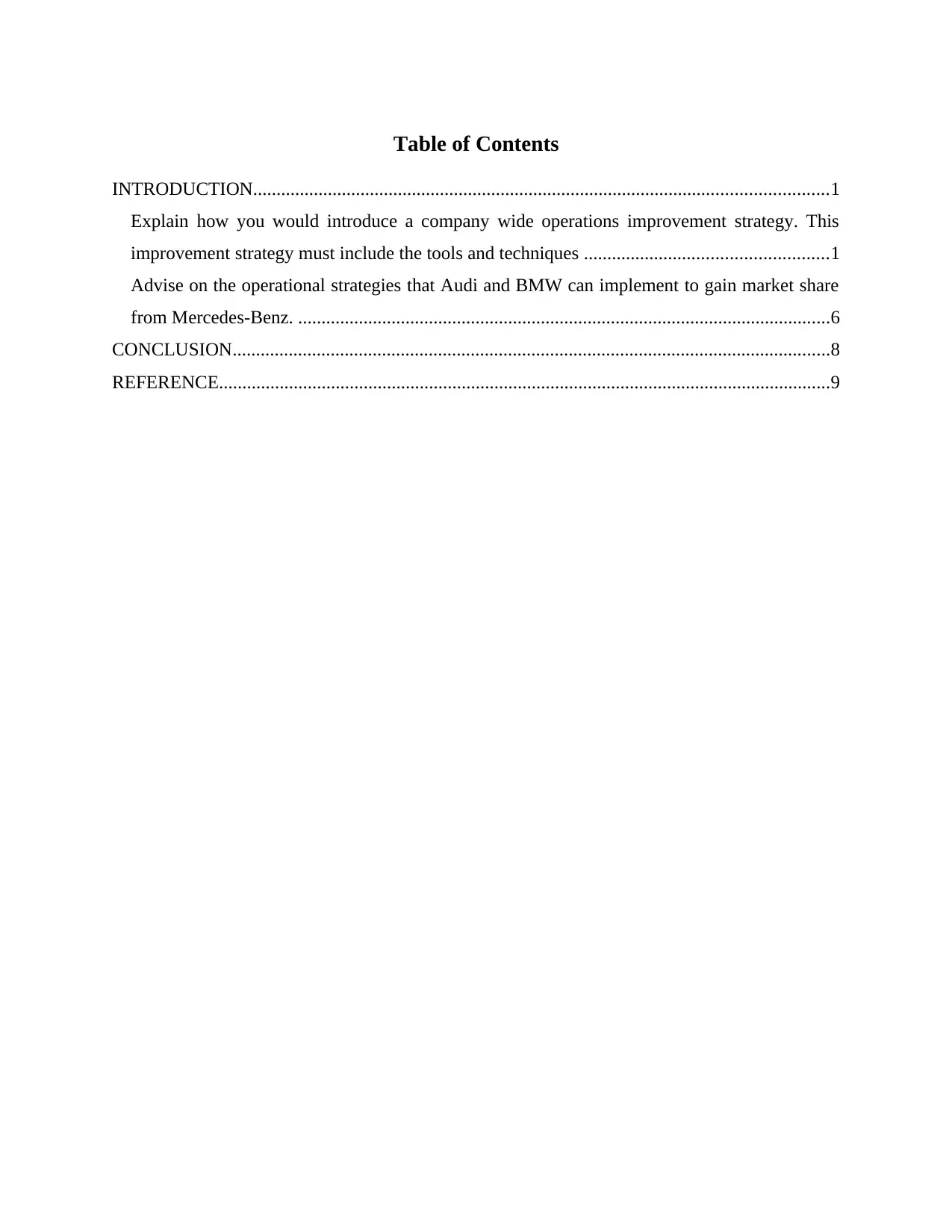
Table of Contents
INTRODUCTION...........................................................................................................................1
Explain how you would introduce a company wide operations improvement strategy. This
improvement strategy must include the tools and techniques ....................................................1
Advise on the operational strategies that Audi and BMW can implement to gain market share
from Mercedes-Benz. ..................................................................................................................6
CONCLUSION................................................................................................................................8
REFERENCE...................................................................................................................................9
INTRODUCTION...........................................................................................................................1
Explain how you would introduce a company wide operations improvement strategy. This
improvement strategy must include the tools and techniques ....................................................1
Advise on the operational strategies that Audi and BMW can implement to gain market share
from Mercedes-Benz. ..................................................................................................................6
CONCLUSION................................................................................................................................8
REFERENCE...................................................................................................................................9
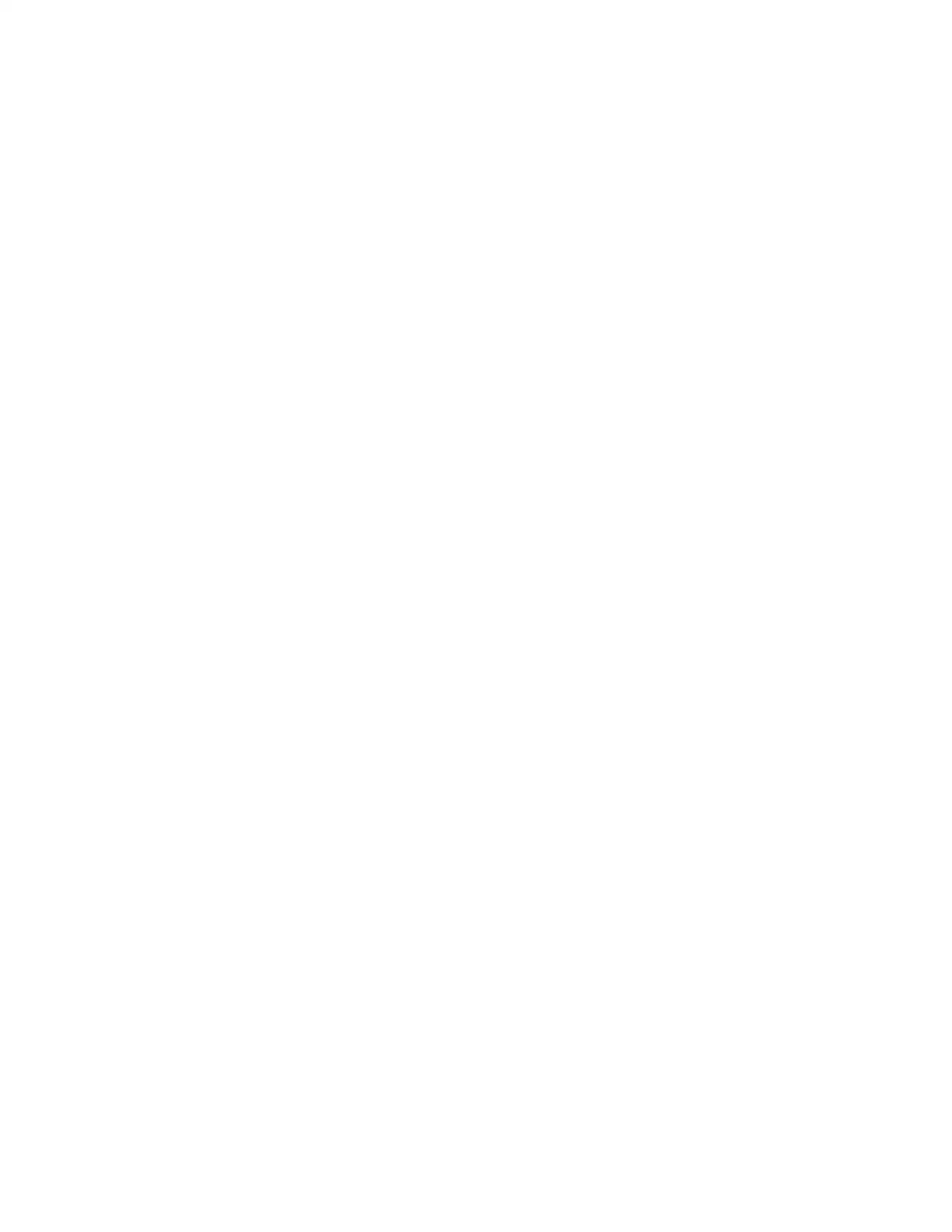
⊘ This is a preview!⊘
Do you want full access?
Subscribe today to unlock all pages.

Trusted by 1+ million students worldwide
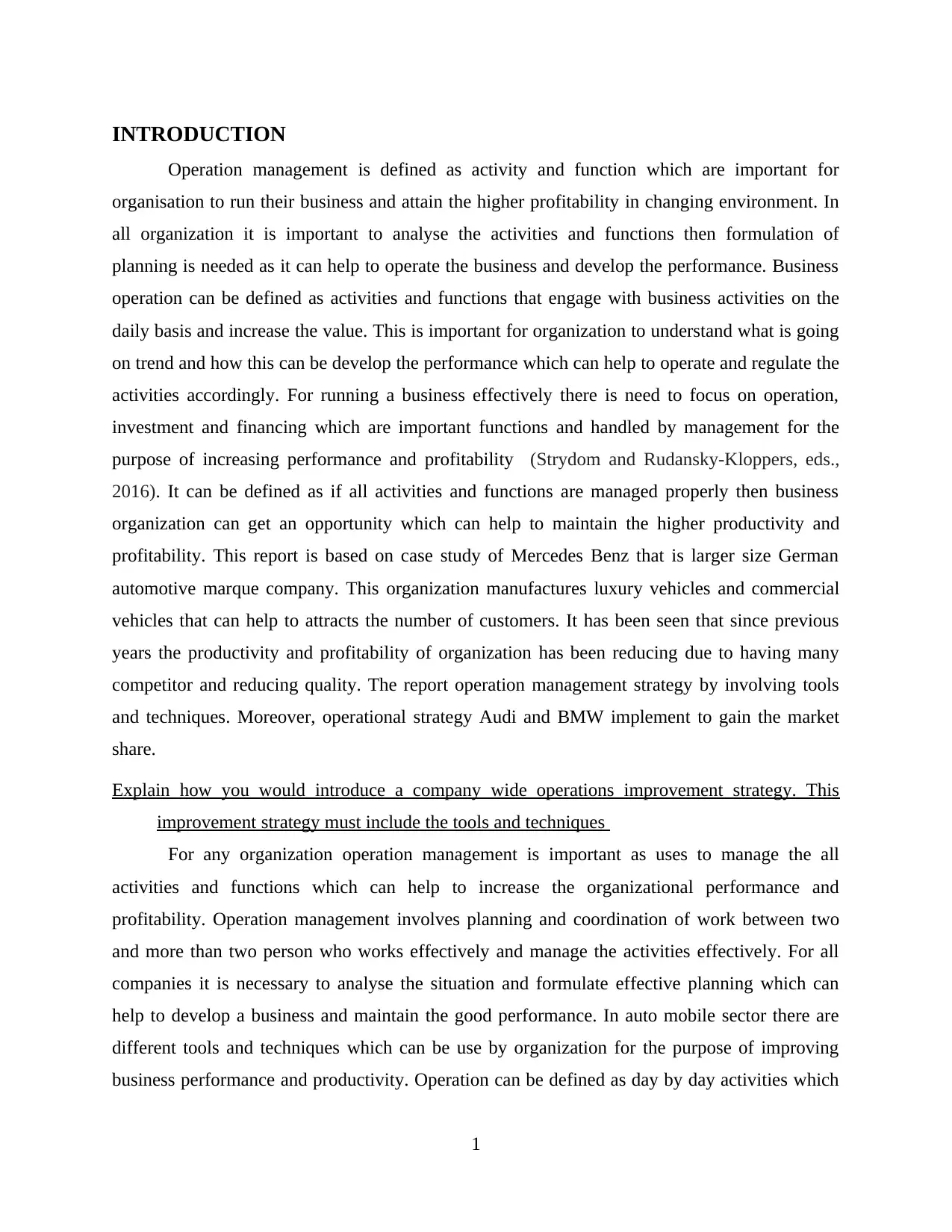
INTRODUCTION
Operation management is defined as activity and function which are important for
organisation to run their business and attain the higher profitability in changing environment. In
all organization it is important to analyse the activities and functions then formulation of
planning is needed as it can help to operate the business and develop the performance. Business
operation can be defined as activities and functions that engage with business activities on the
daily basis and increase the value. This is important for organization to understand what is going
on trend and how this can be develop the performance which can help to operate and regulate the
activities accordingly. For running a business effectively there is need to focus on operation,
investment and financing which are important functions and handled by management for the
purpose of increasing performance and profitability (Strydom and Rudansky-Kloppers, eds.,
2016). It can be defined as if all activities and functions are managed properly then business
organization can get an opportunity which can help to maintain the higher productivity and
profitability. This report is based on case study of Mercedes Benz that is larger size German
automotive marque company. This organization manufactures luxury vehicles and commercial
vehicles that can help to attracts the number of customers. It has been seen that since previous
years the productivity and profitability of organization has been reducing due to having many
competitor and reducing quality. The report operation management strategy by involving tools
and techniques. Moreover, operational strategy Audi and BMW implement to gain the market
share.
Explain how you would introduce a company wide operations improvement strategy. This
improvement strategy must include the tools and techniques
For any organization operation management is important as uses to manage the all
activities and functions which can help to increase the organizational performance and
profitability. Operation management involves planning and coordination of work between two
and more than two person who works effectively and manage the activities effectively. For all
companies it is necessary to analyse the situation and formulate effective planning which can
help to develop a business and maintain the good performance. In auto mobile sector there are
different tools and techniques which can be use by organization for the purpose of improving
business performance and productivity. Operation can be defined as day by day activities which
1
Operation management is defined as activity and function which are important for
organisation to run their business and attain the higher profitability in changing environment. In
all organization it is important to analyse the activities and functions then formulation of
planning is needed as it can help to operate the business and develop the performance. Business
operation can be defined as activities and functions that engage with business activities on the
daily basis and increase the value. This is important for organization to understand what is going
on trend and how this can be develop the performance which can help to operate and regulate the
activities accordingly. For running a business effectively there is need to focus on operation,
investment and financing which are important functions and handled by management for the
purpose of increasing performance and profitability (Strydom and Rudansky-Kloppers, eds.,
2016). It can be defined as if all activities and functions are managed properly then business
organization can get an opportunity which can help to maintain the higher productivity and
profitability. This report is based on case study of Mercedes Benz that is larger size German
automotive marque company. This organization manufactures luxury vehicles and commercial
vehicles that can help to attracts the number of customers. It has been seen that since previous
years the productivity and profitability of organization has been reducing due to having many
competitor and reducing quality. The report operation management strategy by involving tools
and techniques. Moreover, operational strategy Audi and BMW implement to gain the market
share.
Explain how you would introduce a company wide operations improvement strategy. This
improvement strategy must include the tools and techniques
For any organization operation management is important as uses to manage the all
activities and functions which can help to increase the organizational performance and
profitability. Operation management involves planning and coordination of work between two
and more than two person who works effectively and manage the activities effectively. For all
companies it is necessary to analyse the situation and formulate effective planning which can
help to develop a business and maintain the good performance. In auto mobile sector there are
different tools and techniques which can be use by organization for the purpose of improving
business performance and productivity. Operation can be defined as day by day activities which
1
Paraphrase This Document
Need a fresh take? Get an instant paraphrase of this document with our AI Paraphraser
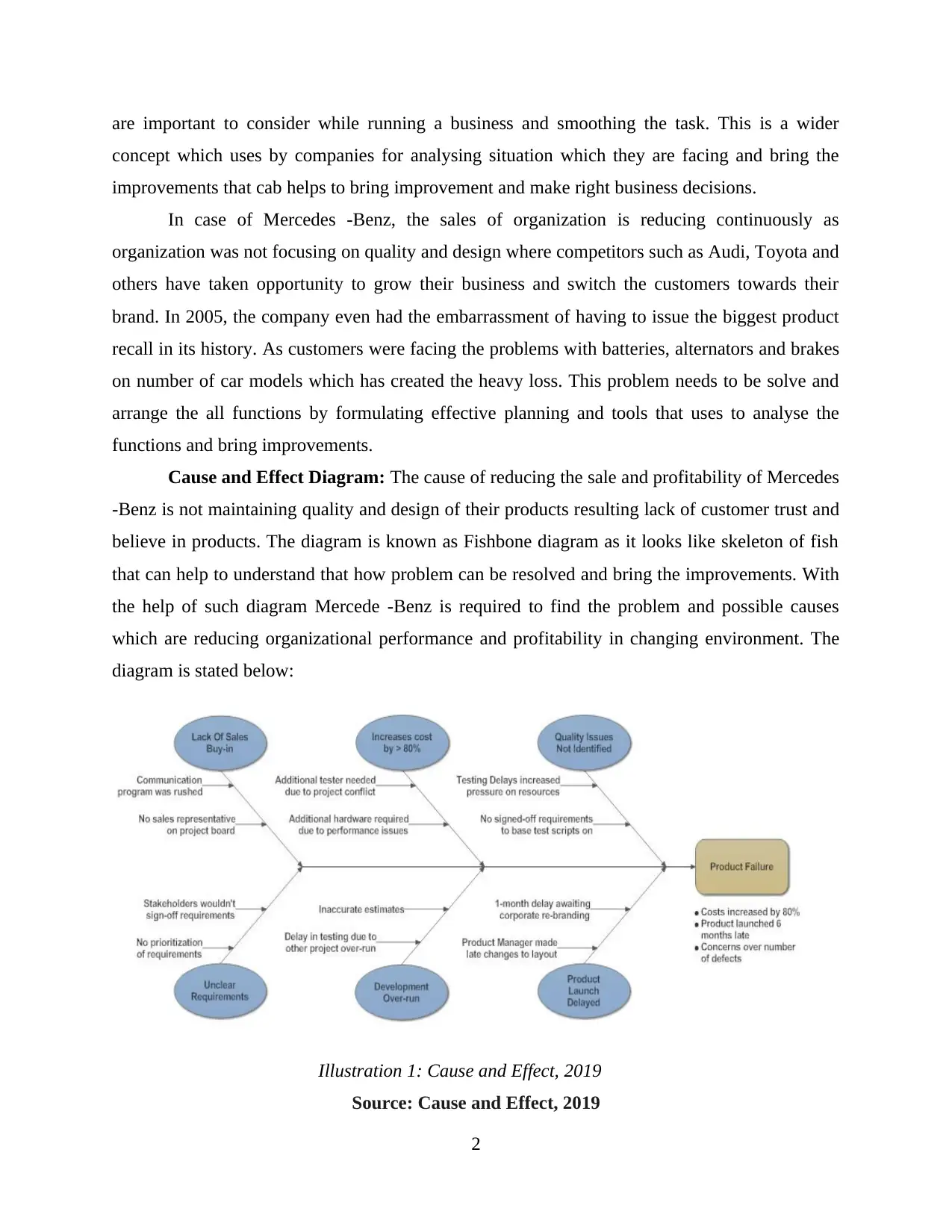
are important to consider while running a business and smoothing the task. This is a wider
concept which uses by companies for analysing situation which they are facing and bring the
improvements that cab helps to bring improvement and make right business decisions.
In case of Mercedes -Benz, the sales of organization is reducing continuously as
organization was not focusing on quality and design where competitors such as Audi, Toyota and
others have taken opportunity to grow their business and switch the customers towards their
brand. In 2005, the company even had the embarrassment of having to issue the biggest product
recall in its history. As customers were facing the problems with batteries, alternators and brakes
on number of car models which has created the heavy loss. This problem needs to be solve and
arrange the all functions by formulating effective planning and tools that uses to analyse the
functions and bring improvements.
Cause and Effect Diagram: The cause of reducing the sale and profitability of Mercedes
-Benz is not maintaining quality and design of their products resulting lack of customer trust and
believe in products. The diagram is known as Fishbone diagram as it looks like skeleton of fish
that can help to understand that how problem can be resolved and bring the improvements. With
the help of such diagram Mercede -Benz is required to find the problem and possible causes
which are reducing organizational performance and profitability in changing environment. The
diagram is stated below:
Illustration 1: Cause and Effect, 2019
Source: Cause and Effect, 2019
2
concept which uses by companies for analysing situation which they are facing and bring the
improvements that cab helps to bring improvement and make right business decisions.
In case of Mercedes -Benz, the sales of organization is reducing continuously as
organization was not focusing on quality and design where competitors such as Audi, Toyota and
others have taken opportunity to grow their business and switch the customers towards their
brand. In 2005, the company even had the embarrassment of having to issue the biggest product
recall in its history. As customers were facing the problems with batteries, alternators and brakes
on number of car models which has created the heavy loss. This problem needs to be solve and
arrange the all functions by formulating effective planning and tools that uses to analyse the
functions and bring improvements.
Cause and Effect Diagram: The cause of reducing the sale and profitability of Mercedes
-Benz is not maintaining quality and design of their products resulting lack of customer trust and
believe in products. The diagram is known as Fishbone diagram as it looks like skeleton of fish
that can help to understand that how problem can be resolved and bring the improvements. With
the help of such diagram Mercede -Benz is required to find the problem and possible causes
which are reducing organizational performance and profitability in changing environment. The
diagram is stated below:
Illustration 1: Cause and Effect, 2019
Source: Cause and Effect, 2019
2
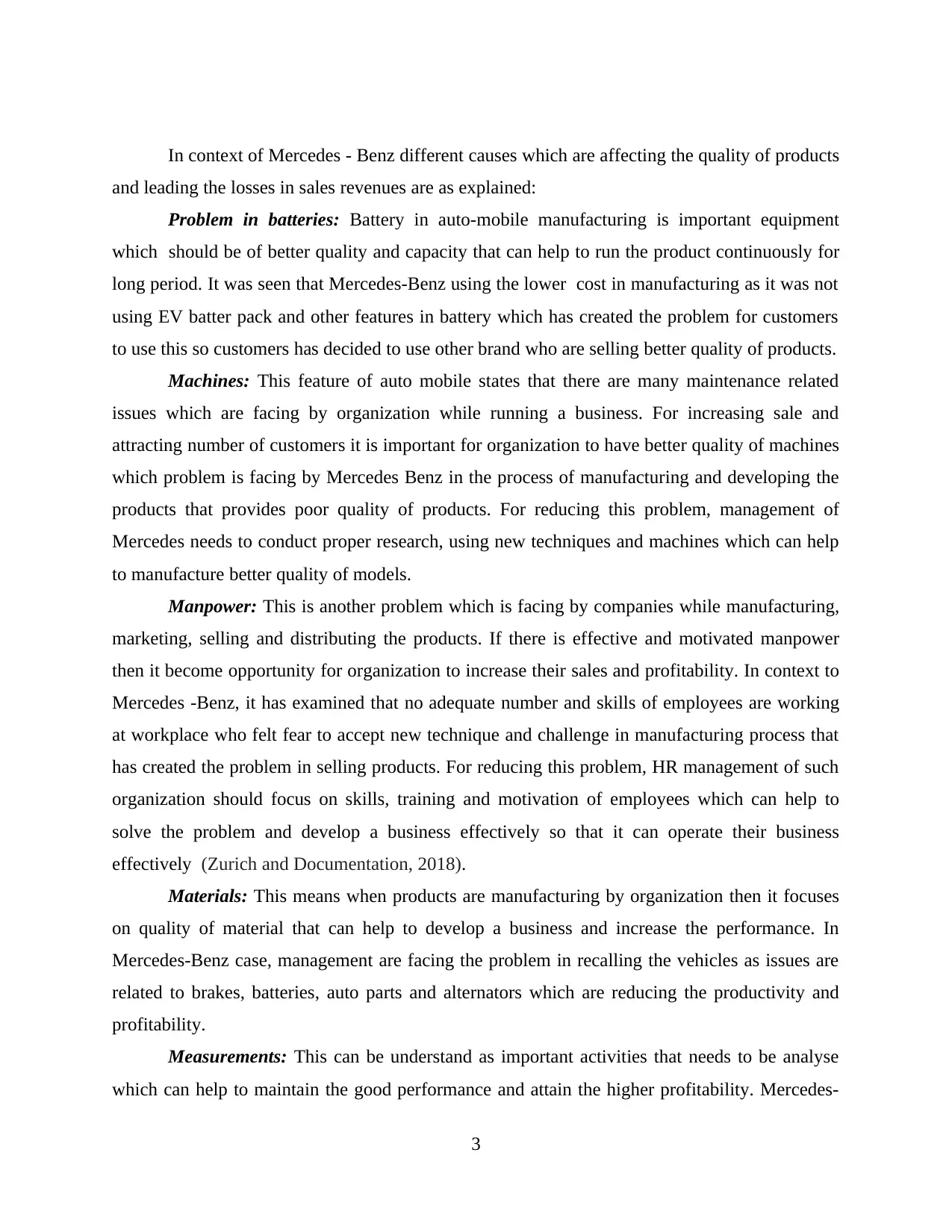
In context of Mercedes - Benz different causes which are affecting the quality of products
and leading the losses in sales revenues are as explained:
Problem in batteries: Battery in auto-mobile manufacturing is important equipment
which should be of better quality and capacity that can help to run the product continuously for
long period. It was seen that Mercedes-Benz using the lower cost in manufacturing as it was not
using EV batter pack and other features in battery which has created the problem for customers
to use this so customers has decided to use other brand who are selling better quality of products.
Machines: This feature of auto mobile states that there are many maintenance related
issues which are facing by organization while running a business. For increasing sale and
attracting number of customers it is important for organization to have better quality of machines
which problem is facing by Mercedes Benz in the process of manufacturing and developing the
products that provides poor quality of products. For reducing this problem, management of
Mercedes needs to conduct proper research, using new techniques and machines which can help
to manufacture better quality of models.
Manpower: This is another problem which is facing by companies while manufacturing,
marketing, selling and distributing the products. If there is effective and motivated manpower
then it become opportunity for organization to increase their sales and profitability. In context to
Mercedes -Benz, it has examined that no adequate number and skills of employees are working
at workplace who felt fear to accept new technique and challenge in manufacturing process that
has created the problem in selling products. For reducing this problem, HR management of such
organization should focus on skills, training and motivation of employees which can help to
solve the problem and develop a business effectively so that it can operate their business
effectively (Zurich and Documentation, 2018).
Materials: This means when products are manufacturing by organization then it focuses
on quality of material that can help to develop a business and increase the performance. In
Mercedes-Benz case, management are facing the problem in recalling the vehicles as issues are
related to brakes, batteries, auto parts and alternators which are reducing the productivity and
profitability.
Measurements: This can be understand as important activities that needs to be analyse
which can help to maintain the good performance and attain the higher profitability. Mercedes-
3
and leading the losses in sales revenues are as explained:
Problem in batteries: Battery in auto-mobile manufacturing is important equipment
which should be of better quality and capacity that can help to run the product continuously for
long period. It was seen that Mercedes-Benz using the lower cost in manufacturing as it was not
using EV batter pack and other features in battery which has created the problem for customers
to use this so customers has decided to use other brand who are selling better quality of products.
Machines: This feature of auto mobile states that there are many maintenance related
issues which are facing by organization while running a business. For increasing sale and
attracting number of customers it is important for organization to have better quality of machines
which problem is facing by Mercedes Benz in the process of manufacturing and developing the
products that provides poor quality of products. For reducing this problem, management of
Mercedes needs to conduct proper research, using new techniques and machines which can help
to manufacture better quality of models.
Manpower: This is another problem which is facing by companies while manufacturing,
marketing, selling and distributing the products. If there is effective and motivated manpower
then it become opportunity for organization to increase their sales and profitability. In context to
Mercedes -Benz, it has examined that no adequate number and skills of employees are working
at workplace who felt fear to accept new technique and challenge in manufacturing process that
has created the problem in selling products. For reducing this problem, HR management of such
organization should focus on skills, training and motivation of employees which can help to
solve the problem and develop a business effectively so that it can operate their business
effectively (Zurich and Documentation, 2018).
Materials: This means when products are manufacturing by organization then it focuses
on quality of material that can help to develop a business and increase the performance. In
Mercedes-Benz case, management are facing the problem in recalling the vehicles as issues are
related to brakes, batteries, auto parts and alternators which are reducing the productivity and
profitability.
Measurements: This can be understand as important activities that needs to be analyse
which can help to maintain the good performance and attain the higher profitability. Mercedes-
3
⊘ This is a preview!⊘
Do you want full access?
Subscribe today to unlock all pages.

Trusted by 1+ million students worldwide
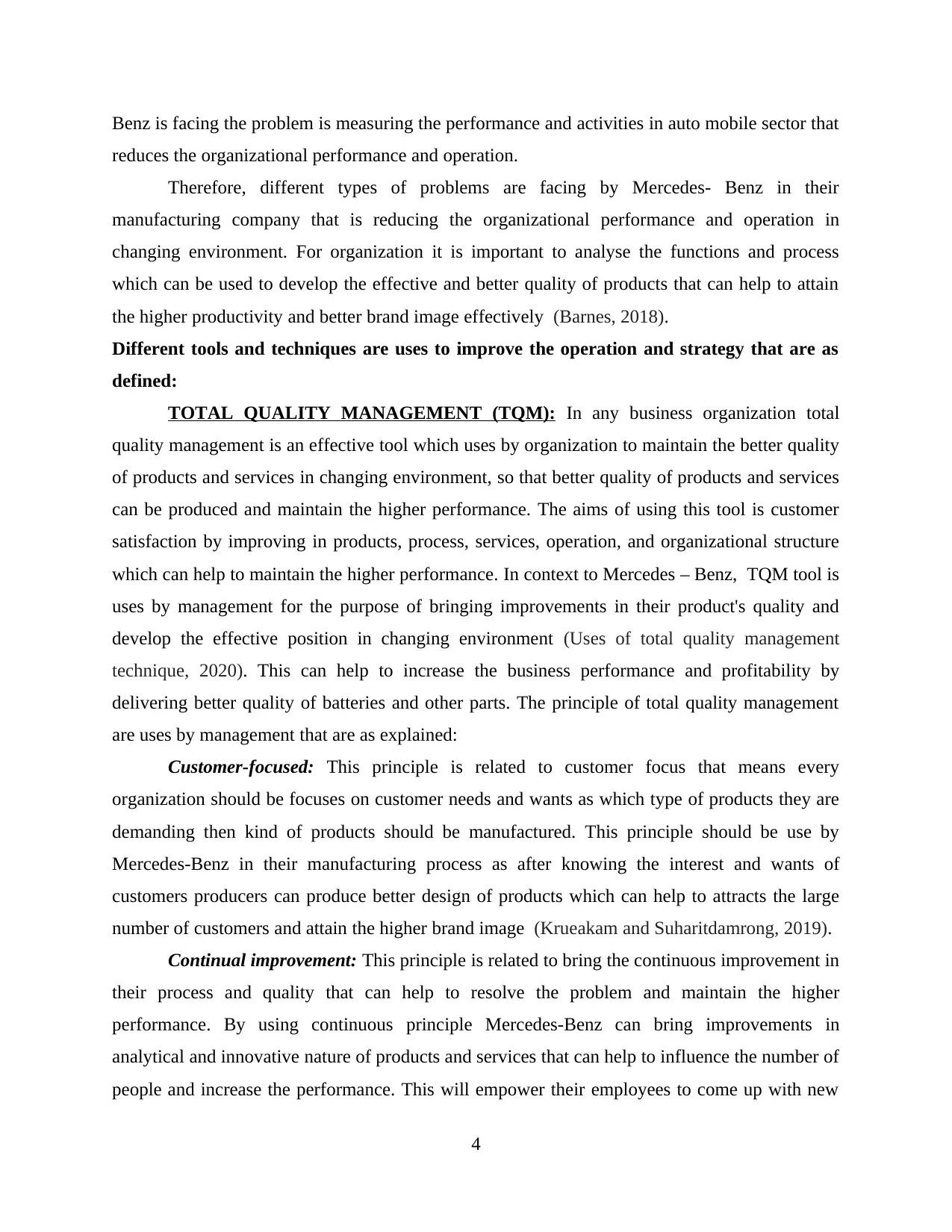
Benz is facing the problem is measuring the performance and activities in auto mobile sector that
reduces the organizational performance and operation.
Therefore, different types of problems are facing by Mercedes- Benz in their
manufacturing company that is reducing the organizational performance and operation in
changing environment. For organization it is important to analyse the functions and process
which can be used to develop the effective and better quality of products that can help to attain
the higher productivity and better brand image effectively (Barnes, 2018).
Different tools and techniques are uses to improve the operation and strategy that are as
defined:
TOTAL QUALITY MANAGEMENT (TQM): In any business organization total
quality management is an effective tool which uses by organization to maintain the better quality
of products and services in changing environment, so that better quality of products and services
can be produced and maintain the higher performance. The aims of using this tool is customer
satisfaction by improving in products, process, services, operation, and organizational structure
which can help to maintain the higher performance. In context to Mercedes – Benz, TQM tool is
uses by management for the purpose of bringing improvements in their product's quality and
develop the effective position in changing environment (Uses of total quality management
technique, 2020). This can help to increase the business performance and profitability by
delivering better quality of batteries and other parts. The principle of total quality management
are uses by management that are as explained:
Customer-focused: This principle is related to customer focus that means every
organization should be focuses on customer needs and wants as which type of products they are
demanding then kind of products should be manufactured. This principle should be use by
Mercedes-Benz in their manufacturing process as after knowing the interest and wants of
customers producers can produce better design of products which can help to attracts the large
number of customers and attain the higher brand image (Krueakam and Suharitdamrong, 2019).
Continual improvement: This principle is related to bring the continuous improvement in
their process and quality that can help to resolve the problem and maintain the higher
performance. By using continuous principle Mercedes-Benz can bring improvements in
analytical and innovative nature of products and services that can help to influence the number of
people and increase the performance. This will empower their employees to come up with new
4
reduces the organizational performance and operation.
Therefore, different types of problems are facing by Mercedes- Benz in their
manufacturing company that is reducing the organizational performance and operation in
changing environment. For organization it is important to analyse the functions and process
which can be used to develop the effective and better quality of products that can help to attain
the higher productivity and better brand image effectively (Barnes, 2018).
Different tools and techniques are uses to improve the operation and strategy that are as
defined:
TOTAL QUALITY MANAGEMENT (TQM): In any business organization total
quality management is an effective tool which uses by organization to maintain the better quality
of products and services in changing environment, so that better quality of products and services
can be produced and maintain the higher performance. The aims of using this tool is customer
satisfaction by improving in products, process, services, operation, and organizational structure
which can help to maintain the higher performance. In context to Mercedes – Benz, TQM tool is
uses by management for the purpose of bringing improvements in their product's quality and
develop the effective position in changing environment (Uses of total quality management
technique, 2020). This can help to increase the business performance and profitability by
delivering better quality of batteries and other parts. The principle of total quality management
are uses by management that are as explained:
Customer-focused: This principle is related to customer focus that means every
organization should be focuses on customer needs and wants as which type of products they are
demanding then kind of products should be manufactured. This principle should be use by
Mercedes-Benz in their manufacturing process as after knowing the interest and wants of
customers producers can produce better design of products which can help to attracts the large
number of customers and attain the higher brand image (Krueakam and Suharitdamrong, 2019).
Continual improvement: This principle is related to bring the continuous improvement in
their process and quality that can help to resolve the problem and maintain the higher
performance. By using continuous principle Mercedes-Benz can bring improvements in
analytical and innovative nature of products and services that can help to influence the number of
people and increase the performance. This will empower their employees to come up with new
4
Paraphrase This Document
Need a fresh take? Get an instant paraphrase of this document with our AI Paraphraser
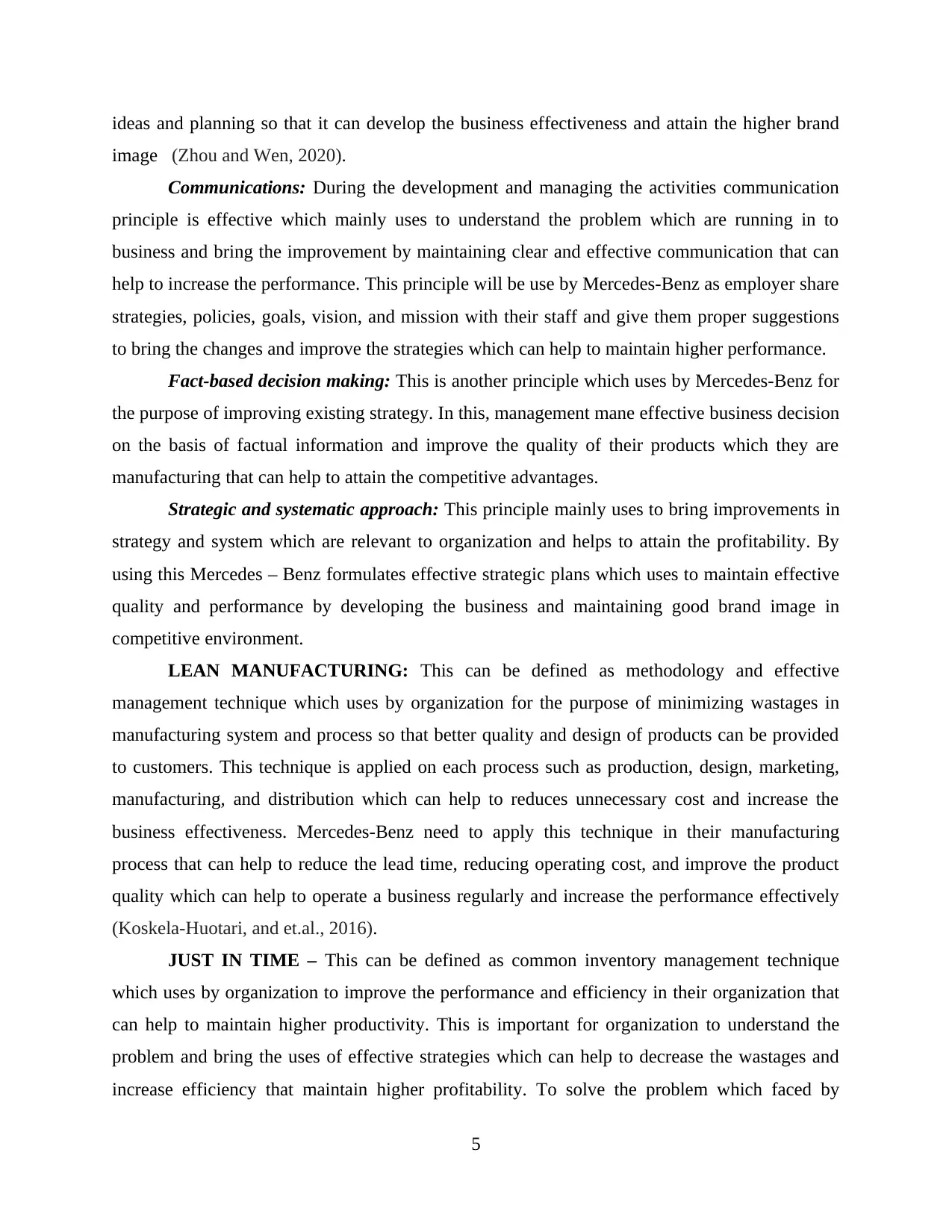
ideas and planning so that it can develop the business effectiveness and attain the higher brand
image (Zhou and Wen, 2020).
Communications: During the development and managing the activities communication
principle is effective which mainly uses to understand the problem which are running in to
business and bring the improvement by maintaining clear and effective communication that can
help to increase the performance. This principle will be use by Mercedes-Benz as employer share
strategies, policies, goals, vision, and mission with their staff and give them proper suggestions
to bring the changes and improve the strategies which can help to maintain higher performance.
Fact-based decision making: This is another principle which uses by Mercedes-Benz for
the purpose of improving existing strategy. In this, management mane effective business decision
on the basis of factual information and improve the quality of their products which they are
manufacturing that can help to attain the competitive advantages.
Strategic and systematic approach: This principle mainly uses to bring improvements in
strategy and system which are relevant to organization and helps to attain the profitability. By
using this Mercedes – Benz formulates effective strategic plans which uses to maintain effective
quality and performance by developing the business and maintaining good brand image in
competitive environment.
LEAN MANUFACTURING: This can be defined as methodology and effective
management technique which uses by organization for the purpose of minimizing wastages in
manufacturing system and process so that better quality and design of products can be provided
to customers. This technique is applied on each process such as production, design, marketing,
manufacturing, and distribution which can help to reduces unnecessary cost and increase the
business effectiveness. Mercedes-Benz need to apply this technique in their manufacturing
process that can help to reduce the lead time, reducing operating cost, and improve the product
quality which can help to operate a business regularly and increase the performance effectively
(Koskela-Huotari, and et.al., 2016).
JUST IN TIME – This can be defined as common inventory management technique
which uses by organization to improve the performance and efficiency in their organization that
can help to maintain higher productivity. This is important for organization to understand the
problem and bring the uses of effective strategies which can help to decrease the wastages and
increase efficiency that maintain higher profitability. To solve the problem which faced by
5
image (Zhou and Wen, 2020).
Communications: During the development and managing the activities communication
principle is effective which mainly uses to understand the problem which are running in to
business and bring the improvement by maintaining clear and effective communication that can
help to increase the performance. This principle will be use by Mercedes-Benz as employer share
strategies, policies, goals, vision, and mission with their staff and give them proper suggestions
to bring the changes and improve the strategies which can help to maintain higher performance.
Fact-based decision making: This is another principle which uses by Mercedes-Benz for
the purpose of improving existing strategy. In this, management mane effective business decision
on the basis of factual information and improve the quality of their products which they are
manufacturing that can help to attain the competitive advantages.
Strategic and systematic approach: This principle mainly uses to bring improvements in
strategy and system which are relevant to organization and helps to attain the profitability. By
using this Mercedes – Benz formulates effective strategic plans which uses to maintain effective
quality and performance by developing the business and maintaining good brand image in
competitive environment.
LEAN MANUFACTURING: This can be defined as methodology and effective
management technique which uses by organization for the purpose of minimizing wastages in
manufacturing system and process so that better quality and design of products can be provided
to customers. This technique is applied on each process such as production, design, marketing,
manufacturing, and distribution which can help to reduces unnecessary cost and increase the
business effectiveness. Mercedes-Benz need to apply this technique in their manufacturing
process that can help to reduce the lead time, reducing operating cost, and improve the product
quality which can help to operate a business regularly and increase the performance effectively
(Koskela-Huotari, and et.al., 2016).
JUST IN TIME – This can be defined as common inventory management technique
which uses by organization to improve the performance and efficiency in their organization that
can help to maintain higher productivity. This is important for organization to understand the
problem and bring the uses of effective strategies which can help to decrease the wastages and
increase efficiency that maintain higher profitability. To solve the problem which faced by
5
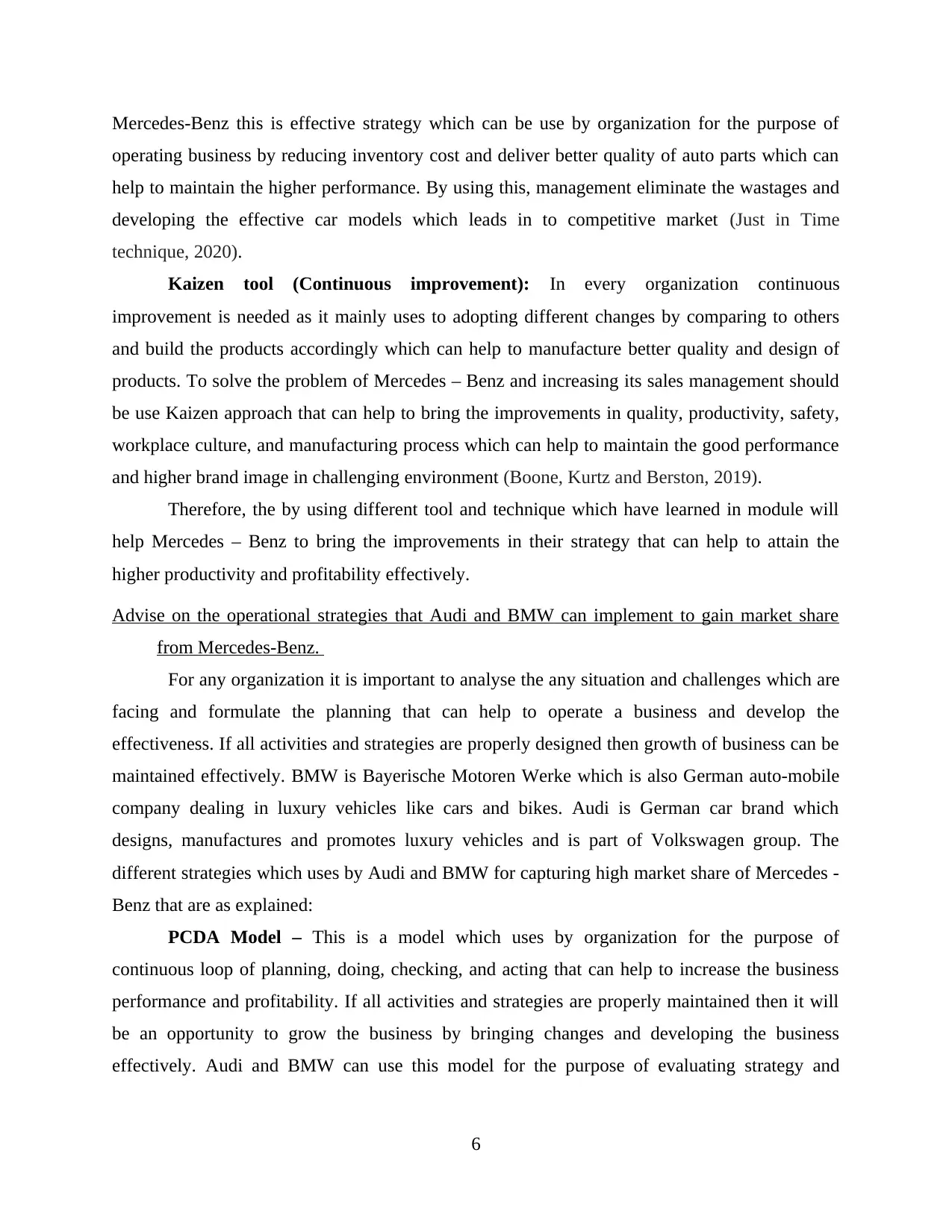
Mercedes-Benz this is effective strategy which can be use by organization for the purpose of
operating business by reducing inventory cost and deliver better quality of auto parts which can
help to maintain the higher performance. By using this, management eliminate the wastages and
developing the effective car models which leads in to competitive market (Just in Time
technique, 2020).
Kaizen tool (Continuous improvement): In every organization continuous
improvement is needed as it mainly uses to adopting different changes by comparing to others
and build the products accordingly which can help to manufacture better quality and design of
products. To solve the problem of Mercedes – Benz and increasing its sales management should
be use Kaizen approach that can help to bring the improvements in quality, productivity, safety,
workplace culture, and manufacturing process which can help to maintain the good performance
and higher brand image in challenging environment (Boone, Kurtz and Berston, 2019).
Therefore, the by using different tool and technique which have learned in module will
help Mercedes – Benz to bring the improvements in their strategy that can help to attain the
higher productivity and profitability effectively.
Advise on the operational strategies that Audi and BMW can implement to gain market share
from Mercedes-Benz.
For any organization it is important to analyse the any situation and challenges which are
facing and formulate the planning that can help to operate a business and develop the
effectiveness. If all activities and strategies are properly designed then growth of business can be
maintained effectively. BMW is Bayerische Motoren Werke which is also German auto-mobile
company dealing in luxury vehicles like cars and bikes. Audi is German car brand which
designs, manufactures and promotes luxury vehicles and is part of Volkswagen group. The
different strategies which uses by Audi and BMW for capturing high market share of Mercedes -
Benz that are as explained:
PCDA Model – This is a model which uses by organization for the purpose of
continuous loop of planning, doing, checking, and acting that can help to increase the business
performance and profitability. If all activities and strategies are properly maintained then it will
be an opportunity to grow the business by bringing changes and developing the business
effectively. Audi and BMW can use this model for the purpose of evaluating strategy and
6
operating business by reducing inventory cost and deliver better quality of auto parts which can
help to maintain the higher performance. By using this, management eliminate the wastages and
developing the effective car models which leads in to competitive market (Just in Time
technique, 2020).
Kaizen tool (Continuous improvement): In every organization continuous
improvement is needed as it mainly uses to adopting different changes by comparing to others
and build the products accordingly which can help to manufacture better quality and design of
products. To solve the problem of Mercedes – Benz and increasing its sales management should
be use Kaizen approach that can help to bring the improvements in quality, productivity, safety,
workplace culture, and manufacturing process which can help to maintain the good performance
and higher brand image in challenging environment (Boone, Kurtz and Berston, 2019).
Therefore, the by using different tool and technique which have learned in module will
help Mercedes – Benz to bring the improvements in their strategy that can help to attain the
higher productivity and profitability effectively.
Advise on the operational strategies that Audi and BMW can implement to gain market share
from Mercedes-Benz.
For any organization it is important to analyse the any situation and challenges which are
facing and formulate the planning that can help to operate a business and develop the
effectiveness. If all activities and strategies are properly designed then growth of business can be
maintained effectively. BMW is Bayerische Motoren Werke which is also German auto-mobile
company dealing in luxury vehicles like cars and bikes. Audi is German car brand which
designs, manufactures and promotes luxury vehicles and is part of Volkswagen group. The
different strategies which uses by Audi and BMW for capturing high market share of Mercedes -
Benz that are as explained:
PCDA Model – This is a model which uses by organization for the purpose of
continuous loop of planning, doing, checking, and acting that can help to increase the business
performance and profitability. If all activities and strategies are properly maintained then it will
be an opportunity to grow the business by bringing changes and developing the business
effectively. Audi and BMW can use this model for the purpose of evaluating strategy and
6
⊘ This is a preview!⊘
Do you want full access?
Subscribe today to unlock all pages.

Trusted by 1+ million students worldwide
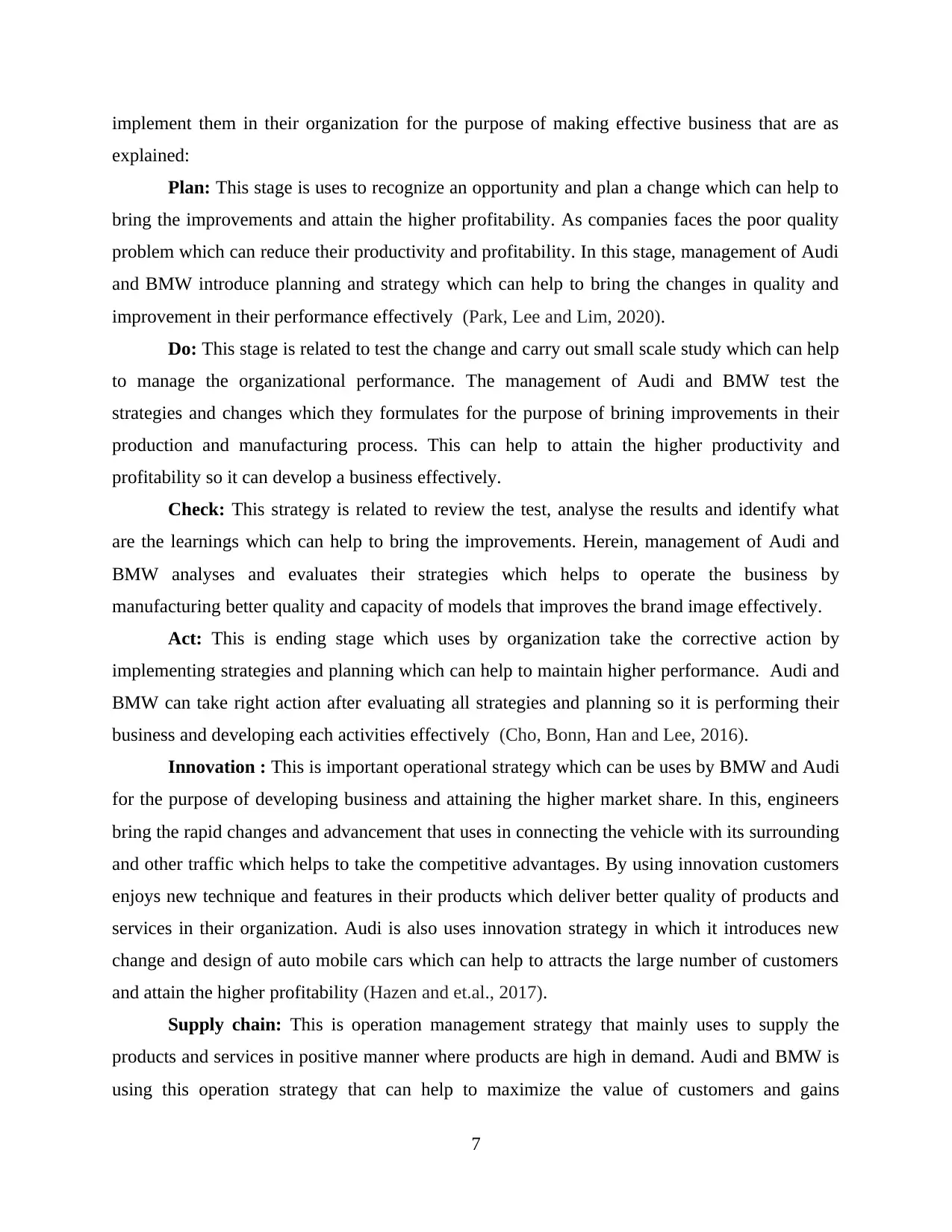
implement them in their organization for the purpose of making effective business that are as
explained:
Plan: This stage is uses to recognize an opportunity and plan a change which can help to
bring the improvements and attain the higher profitability. As companies faces the poor quality
problem which can reduce their productivity and profitability. In this stage, management of Audi
and BMW introduce planning and strategy which can help to bring the changes in quality and
improvement in their performance effectively (Park, Lee and Lim, 2020).
Do: This stage is related to test the change and carry out small scale study which can help
to manage the organizational performance. The management of Audi and BMW test the
strategies and changes which they formulates for the purpose of brining improvements in their
production and manufacturing process. This can help to attain the higher productivity and
profitability so it can develop a business effectively.
Check: This strategy is related to review the test, analyse the results and identify what
are the learnings which can help to bring the improvements. Herein, management of Audi and
BMW analyses and evaluates their strategies which helps to operate the business by
manufacturing better quality and capacity of models that improves the brand image effectively.
Act: This is ending stage which uses by organization take the corrective action by
implementing strategies and planning which can help to maintain higher performance. Audi and
BMW can take right action after evaluating all strategies and planning so it is performing their
business and developing each activities effectively (Cho, Bonn, Han and Lee, 2016).
Innovation : This is important operational strategy which can be uses by BMW and Audi
for the purpose of developing business and attaining the higher market share. In this, engineers
bring the rapid changes and advancement that uses in connecting the vehicle with its surrounding
and other traffic which helps to take the competitive advantages. By using innovation customers
enjoys new technique and features in their products which deliver better quality of products and
services in their organization. Audi is also uses innovation strategy in which it introduces new
change and design of auto mobile cars which can help to attracts the large number of customers
and attain the higher profitability (Hazen and et.al., 2017).
Supply chain: This is operation management strategy that mainly uses to supply the
products and services in positive manner where products are high in demand. Audi and BMW is
using this operation strategy that can help to maximize the value of customers and gains
7
explained:
Plan: This stage is uses to recognize an opportunity and plan a change which can help to
bring the improvements and attain the higher profitability. As companies faces the poor quality
problem which can reduce their productivity and profitability. In this stage, management of Audi
and BMW introduce planning and strategy which can help to bring the changes in quality and
improvement in their performance effectively (Park, Lee and Lim, 2020).
Do: This stage is related to test the change and carry out small scale study which can help
to manage the organizational performance. The management of Audi and BMW test the
strategies and changes which they formulates for the purpose of brining improvements in their
production and manufacturing process. This can help to attain the higher productivity and
profitability so it can develop a business effectively.
Check: This strategy is related to review the test, analyse the results and identify what
are the learnings which can help to bring the improvements. Herein, management of Audi and
BMW analyses and evaluates their strategies which helps to operate the business by
manufacturing better quality and capacity of models that improves the brand image effectively.
Act: This is ending stage which uses by organization take the corrective action by
implementing strategies and planning which can help to maintain higher performance. Audi and
BMW can take right action after evaluating all strategies and planning so it is performing their
business and developing each activities effectively (Cho, Bonn, Han and Lee, 2016).
Innovation : This is important operational strategy which can be uses by BMW and Audi
for the purpose of developing business and attaining the higher market share. In this, engineers
bring the rapid changes and advancement that uses in connecting the vehicle with its surrounding
and other traffic which helps to take the competitive advantages. By using innovation customers
enjoys new technique and features in their products which deliver better quality of products and
services in their organization. Audi is also uses innovation strategy in which it introduces new
change and design of auto mobile cars which can help to attracts the large number of customers
and attain the higher profitability (Hazen and et.al., 2017).
Supply chain: This is operation management strategy that mainly uses to supply the
products and services in positive manner where products are high in demand. Audi and BMW is
using this operation strategy that can help to maximize the value of customers and gains
7
Paraphrase This Document
Need a fresh take? Get an instant paraphrase of this document with our AI Paraphraser
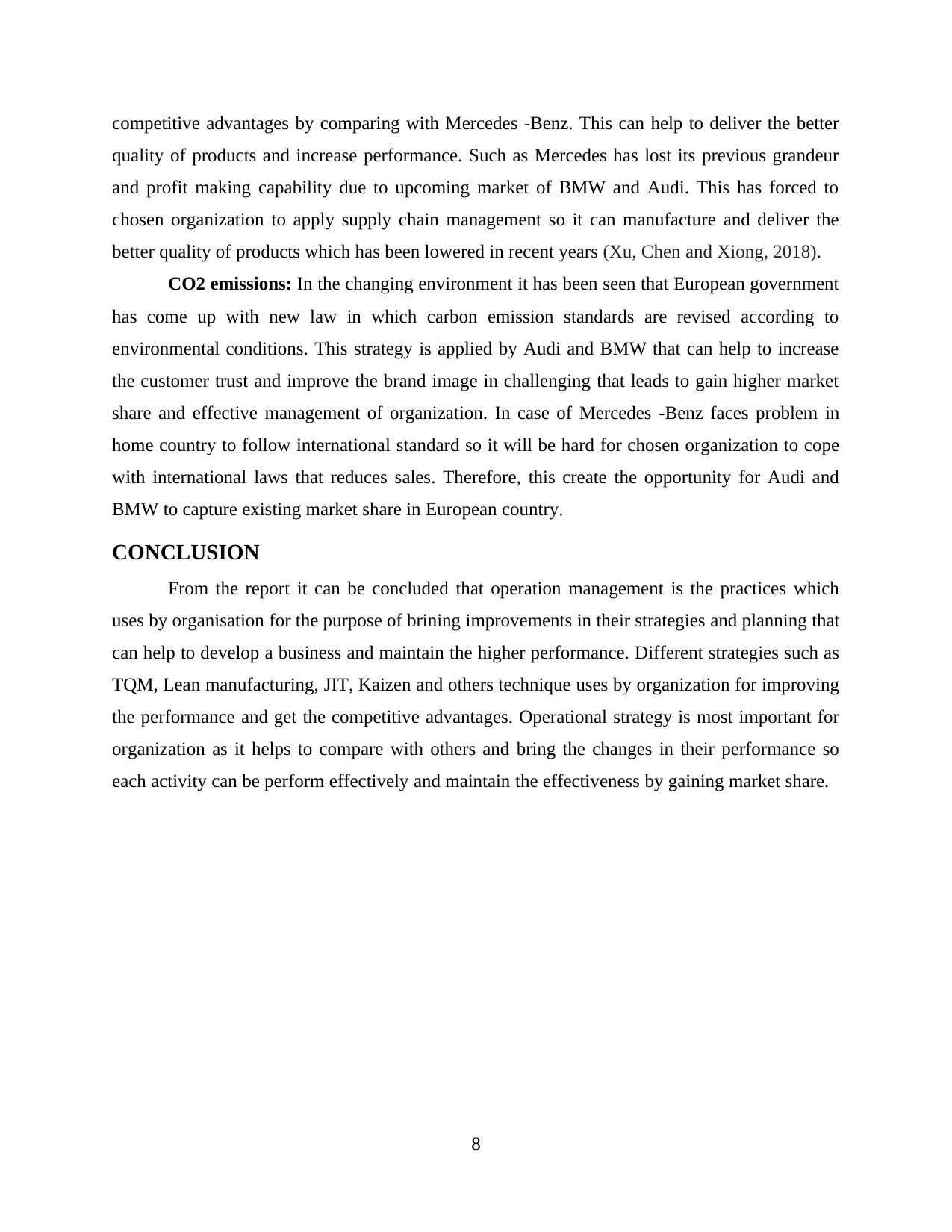
competitive advantages by comparing with Mercedes -Benz. This can help to deliver the better
quality of products and increase performance. Such as Mercedes has lost its previous grandeur
and profit making capability due to upcoming market of BMW and Audi. This has forced to
chosen organization to apply supply chain management so it can manufacture and deliver the
better quality of products which has been lowered in recent years (Xu, Chen and Xiong, 2018).
CO2 emissions: In the changing environment it has been seen that European government
has come up with new law in which carbon emission standards are revised according to
environmental conditions. This strategy is applied by Audi and BMW that can help to increase
the customer trust and improve the brand image in challenging that leads to gain higher market
share and effective management of organization. In case of Mercedes -Benz faces problem in
home country to follow international standard so it will be hard for chosen organization to cope
with international laws that reduces sales. Therefore, this create the opportunity for Audi and
BMW to capture existing market share in European country.
CONCLUSION
From the report it can be concluded that operation management is the practices which
uses by organisation for the purpose of brining improvements in their strategies and planning that
can help to develop a business and maintain the higher performance. Different strategies such as
TQM, Lean manufacturing, JIT, Kaizen and others technique uses by organization for improving
the performance and get the competitive advantages. Operational strategy is most important for
organization as it helps to compare with others and bring the changes in their performance so
each activity can be perform effectively and maintain the effectiveness by gaining market share.
8
quality of products and increase performance. Such as Mercedes has lost its previous grandeur
and profit making capability due to upcoming market of BMW and Audi. This has forced to
chosen organization to apply supply chain management so it can manufacture and deliver the
better quality of products which has been lowered in recent years (Xu, Chen and Xiong, 2018).
CO2 emissions: In the changing environment it has been seen that European government
has come up with new law in which carbon emission standards are revised according to
environmental conditions. This strategy is applied by Audi and BMW that can help to increase
the customer trust and improve the brand image in challenging that leads to gain higher market
share and effective management of organization. In case of Mercedes -Benz faces problem in
home country to follow international standard so it will be hard for chosen organization to cope
with international laws that reduces sales. Therefore, this create the opportunity for Audi and
BMW to capture existing market share in European country.
CONCLUSION
From the report it can be concluded that operation management is the practices which
uses by organisation for the purpose of brining improvements in their strategies and planning that
can help to develop a business and maintain the higher performance. Different strategies such as
TQM, Lean manufacturing, JIT, Kaizen and others technique uses by organization for improving
the performance and get the competitive advantages. Operational strategy is most important for
organization as it helps to compare with others and bring the changes in their performance so
each activity can be perform effectively and maintain the effectiveness by gaining market share.
8
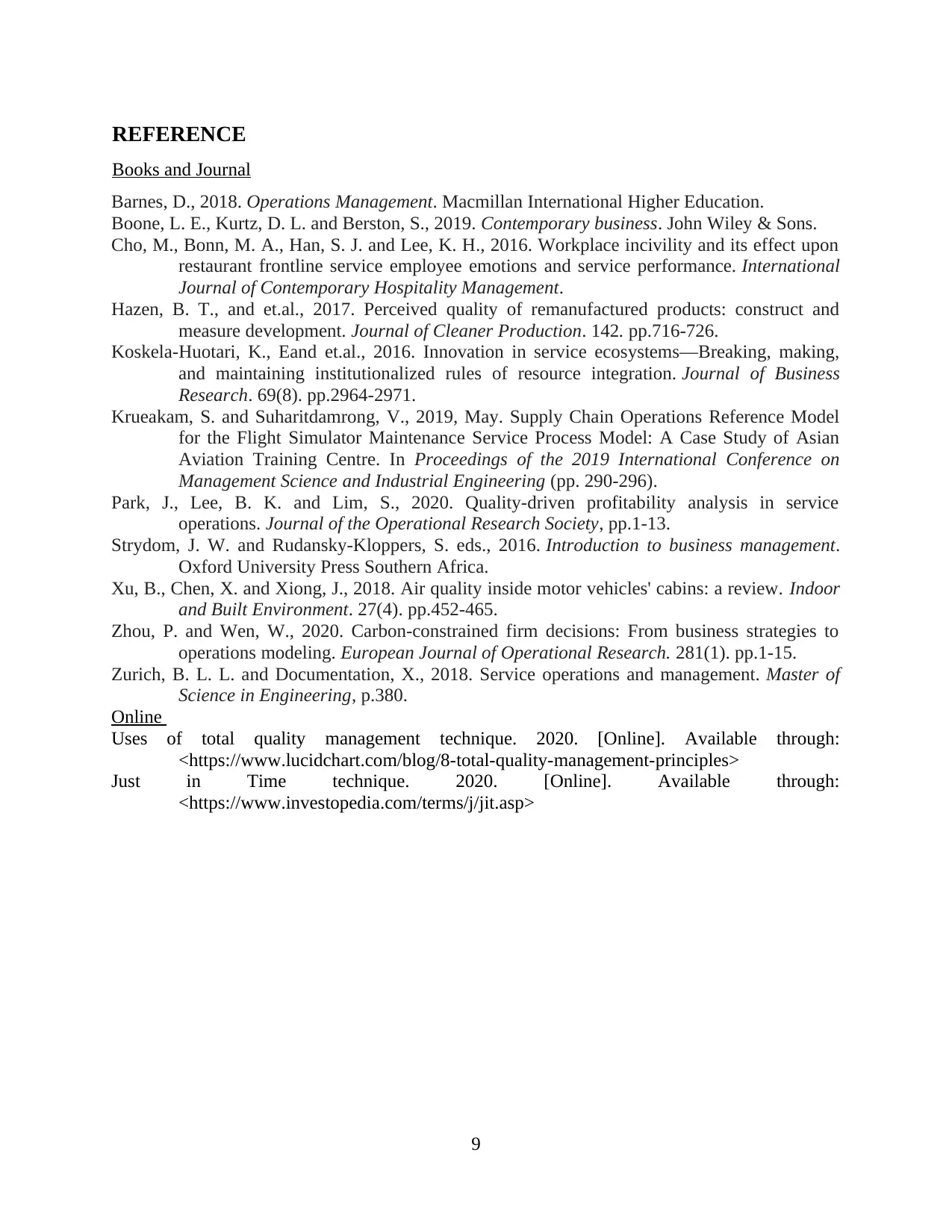
REFERENCE
Books and Journal
Barnes, D., 2018. Operations Management. Macmillan International Higher Education.
Boone, L. E., Kurtz, D. L. and Berston, S., 2019. Contemporary business. John Wiley & Sons.
Cho, M., Bonn, M. A., Han, S. J. and Lee, K. H., 2016. Workplace incivility and its effect upon
restaurant frontline service employee emotions and service performance. International
Journal of Contemporary Hospitality Management.
Hazen, B. T., and et.al., 2017. Perceived quality of remanufactured products: construct and
measure development. Journal of Cleaner Production. 142. pp.716-726.
Koskela-Huotari, K., Eand et.al., 2016. Innovation in service ecosystems—Breaking, making,
and maintaining institutionalized rules of resource integration. Journal of Business
Research. 69(8). pp.2964-2971.
Krueakam, S. and Suharitdamrong, V., 2019, May. Supply Chain Operations Reference Model
for the Flight Simulator Maintenance Service Process Model: A Case Study of Asian
Aviation Training Centre. In Proceedings of the 2019 International Conference on
Management Science and Industrial Engineering (pp. 290-296).
Park, J., Lee, B. K. and Lim, S., 2020. Quality-driven profitability analysis in service
operations. Journal of the Operational Research Society, pp.1-13.
Strydom, J. W. and Rudansky-Kloppers, S. eds., 2016. Introduction to business management.
Oxford University Press Southern Africa.
Xu, B., Chen, X. and Xiong, J., 2018. Air quality inside motor vehicles' cabins: a review. Indoor
and Built Environment. 27(4). pp.452-465.
Zhou, P. and Wen, W., 2020. Carbon-constrained firm decisions: From business strategies to
operations modeling. European Journal of Operational Research. 281(1). pp.1-15.
Zurich, B. L. L. and Documentation, X., 2018. Service operations and management. Master of
Science in Engineering, p.380.
Online
Uses of total quality management technique. 2020. [Online]. Available through:
<https://www.lucidchart.com/blog/8-total-quality-management-principles>
Just in Time technique. 2020. [Online]. Available through:
<https://www.investopedia.com/terms/j/jit.asp>
9
Books and Journal
Barnes, D., 2018. Operations Management. Macmillan International Higher Education.
Boone, L. E., Kurtz, D. L. and Berston, S., 2019. Contemporary business. John Wiley & Sons.
Cho, M., Bonn, M. A., Han, S. J. and Lee, K. H., 2016. Workplace incivility and its effect upon
restaurant frontline service employee emotions and service performance. International
Journal of Contemporary Hospitality Management.
Hazen, B. T., and et.al., 2017. Perceived quality of remanufactured products: construct and
measure development. Journal of Cleaner Production. 142. pp.716-726.
Koskela-Huotari, K., Eand et.al., 2016. Innovation in service ecosystems—Breaking, making,
and maintaining institutionalized rules of resource integration. Journal of Business
Research. 69(8). pp.2964-2971.
Krueakam, S. and Suharitdamrong, V., 2019, May. Supply Chain Operations Reference Model
for the Flight Simulator Maintenance Service Process Model: A Case Study of Asian
Aviation Training Centre. In Proceedings of the 2019 International Conference on
Management Science and Industrial Engineering (pp. 290-296).
Park, J., Lee, B. K. and Lim, S., 2020. Quality-driven profitability analysis in service
operations. Journal of the Operational Research Society, pp.1-13.
Strydom, J. W. and Rudansky-Kloppers, S. eds., 2016. Introduction to business management.
Oxford University Press Southern Africa.
Xu, B., Chen, X. and Xiong, J., 2018. Air quality inside motor vehicles' cabins: a review. Indoor
and Built Environment. 27(4). pp.452-465.
Zhou, P. and Wen, W., 2020. Carbon-constrained firm decisions: From business strategies to
operations modeling. European Journal of Operational Research. 281(1). pp.1-15.
Zurich, B. L. L. and Documentation, X., 2018. Service operations and management. Master of
Science in Engineering, p.380.
Online
Uses of total quality management technique. 2020. [Online]. Available through:
<https://www.lucidchart.com/blog/8-total-quality-management-principles>
Just in Time technique. 2020. [Online]. Available through:
<https://www.investopedia.com/terms/j/jit.asp>
9
⊘ This is a preview!⊘
Do you want full access?
Subscribe today to unlock all pages.

Trusted by 1+ million students worldwide
1 out of 12