Mercedes Benz: Comprehensive Report on Operations Improvement Strategy
VerifiedAdded on 2023/01/04
|12
|3726
|25
Report
AI Summary
This report provides a detailed analysis of Mercedes-Benz's operations and services, focusing on improvement strategies to enhance product quality and market expansion. It explores the challenges faced by Mercedes-Benz, including issues stemming from its merger with Chrysler and quality concerns. The report examines the implementation of Total Quality Management (TQM), Just-in-Time (JIT), and lean manufacturing systems to optimize operations. TQM strategies, including repair, refinement, renovation, and reinvention, are discussed in detail. The report also covers the application of JIT and lean manufacturing to reduce waste, improve processes, and increase customer satisfaction. Furthermore, it suggests operational strategies that BMW and Audi could adopt to gain market share. The report emphasizes the importance of continuous improvement, customer focus, and strategic alignment to achieve business goals in the competitive luxury car industry.
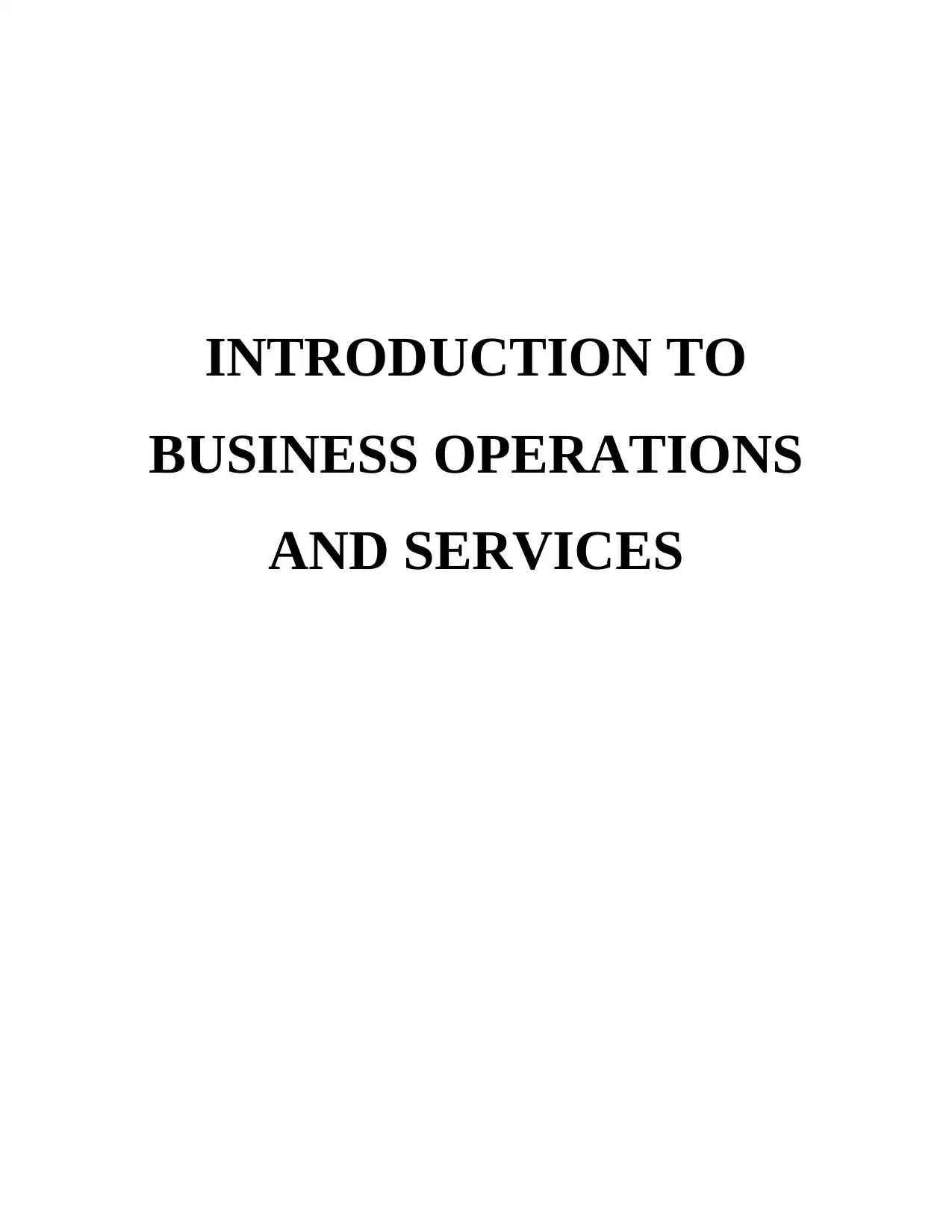
INTRODUCTION TO
BUSINESS OPERATIONS
AND SERVICES
BUSINESS OPERATIONS
AND SERVICES
Paraphrase This Document
Need a fresh take? Get an instant paraphrase of this document with our AI Paraphraser
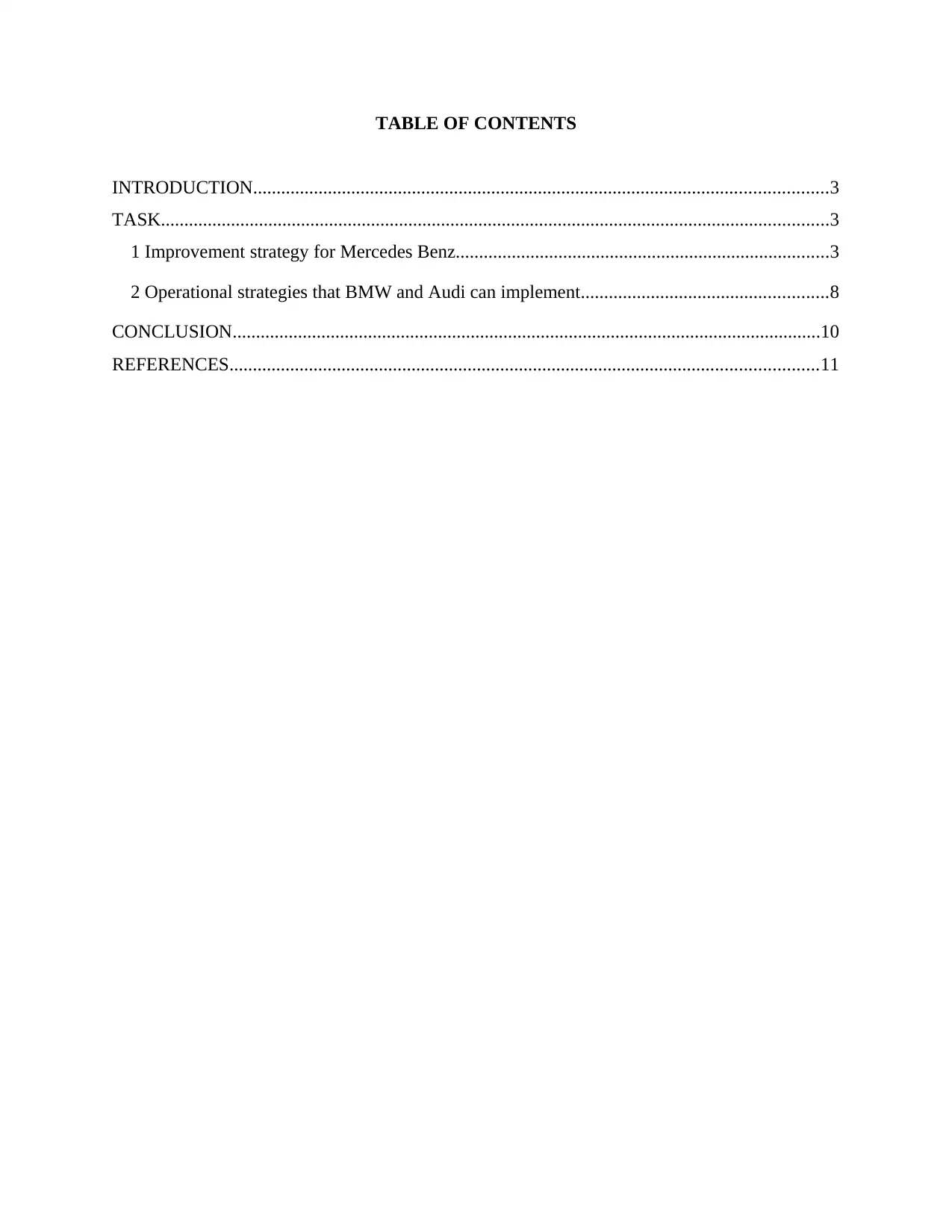
TABLE OF CONTENTS
INTRODUCTION...........................................................................................................................3
TASK...............................................................................................................................................3
1 Improvement strategy for Mercedes Benz................................................................................3
2 Operational strategies that BMW and Audi can implement.....................................................8
CONCLUSION..............................................................................................................................10
REFERENCES..............................................................................................................................11
INTRODUCTION...........................................................................................................................3
TASK...............................................................................................................................................3
1 Improvement strategy for Mercedes Benz................................................................................3
2 Operational strategies that BMW and Audi can implement.....................................................8
CONCLUSION..............................................................................................................................10
REFERENCES..............................................................................................................................11
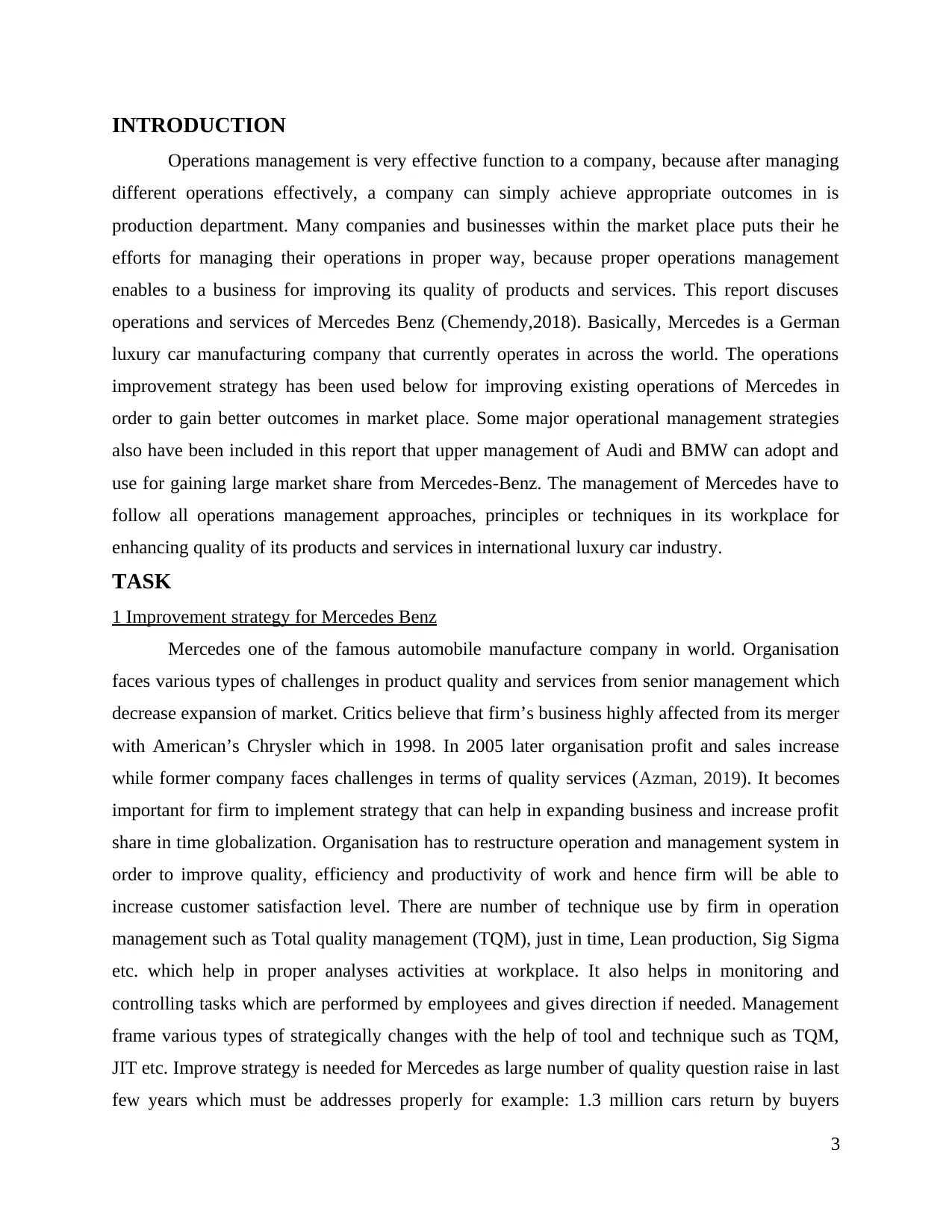
INTRODUCTION
Operations management is very effective function to a company, because after managing
different operations effectively, a company can simply achieve appropriate outcomes in is
production department. Many companies and businesses within the market place puts their he
efforts for managing their operations in proper way, because proper operations management
enables to a business for improving its quality of products and services. This report discuses
operations and services of Mercedes Benz (Chemendy,2018). Basically, Mercedes is a German
luxury car manufacturing company that currently operates in across the world. The operations
improvement strategy has been used below for improving existing operations of Mercedes in
order to gain better outcomes in market place. Some major operational management strategies
also have been included in this report that upper management of Audi and BMW can adopt and
use for gaining large market share from Mercedes-Benz. The management of Mercedes have to
follow all operations management approaches, principles or techniques in its workplace for
enhancing quality of its products and services in international luxury car industry.
TASK
1 Improvement strategy for Mercedes Benz
Mercedes one of the famous automobile manufacture company in world. Organisation
faces various types of challenges in product quality and services from senior management which
decrease expansion of market. Critics believe that firm’s business highly affected from its merger
with American’s Chrysler which in 1998. In 2005 later organisation profit and sales increase
while former company faces challenges in terms of quality services (Azman, 2019). It becomes
important for firm to implement strategy that can help in expanding business and increase profit
share in time globalization. Organisation has to restructure operation and management system in
order to improve quality, efficiency and productivity of work and hence firm will be able to
increase customer satisfaction level. There are number of technique use by firm in operation
management such as Total quality management (TQM), just in time, Lean production, Sig Sigma
etc. which help in proper analyses activities at workplace. It also helps in monitoring and
controlling tasks which are performed by employees and gives direction if needed. Management
frame various types of strategically changes with the help of tool and technique such as TQM,
JIT etc. Improve strategy is needed for Mercedes as large number of quality question raise in last
few years which must be addresses properly for example: 1.3 million cars return by buyers
3
Operations management is very effective function to a company, because after managing
different operations effectively, a company can simply achieve appropriate outcomes in is
production department. Many companies and businesses within the market place puts their he
efforts for managing their operations in proper way, because proper operations management
enables to a business for improving its quality of products and services. This report discuses
operations and services of Mercedes Benz (Chemendy,2018). Basically, Mercedes is a German
luxury car manufacturing company that currently operates in across the world. The operations
improvement strategy has been used below for improving existing operations of Mercedes in
order to gain better outcomes in market place. Some major operational management strategies
also have been included in this report that upper management of Audi and BMW can adopt and
use for gaining large market share from Mercedes-Benz. The management of Mercedes have to
follow all operations management approaches, principles or techniques in its workplace for
enhancing quality of its products and services in international luxury car industry.
TASK
1 Improvement strategy for Mercedes Benz
Mercedes one of the famous automobile manufacture company in world. Organisation
faces various types of challenges in product quality and services from senior management which
decrease expansion of market. Critics believe that firm’s business highly affected from its merger
with American’s Chrysler which in 1998. In 2005 later organisation profit and sales increase
while former company faces challenges in terms of quality services (Azman, 2019). It becomes
important for firm to implement strategy that can help in expanding business and increase profit
share in time globalization. Organisation has to restructure operation and management system in
order to improve quality, efficiency and productivity of work and hence firm will be able to
increase customer satisfaction level. There are number of technique use by firm in operation
management such as Total quality management (TQM), just in time, Lean production, Sig Sigma
etc. which help in proper analyses activities at workplace. It also helps in monitoring and
controlling tasks which are performed by employees and gives direction if needed. Management
frame various types of strategically changes with the help of tool and technique such as TQM,
JIT etc. Improve strategy is needed for Mercedes as large number of quality question raise in last
few years which must be addresses properly for example: 1.3 million cars return by buyers
3
⊘ This is a preview!⊘
Do you want full access?
Subscribe today to unlock all pages.

Trusted by 1+ million students worldwide
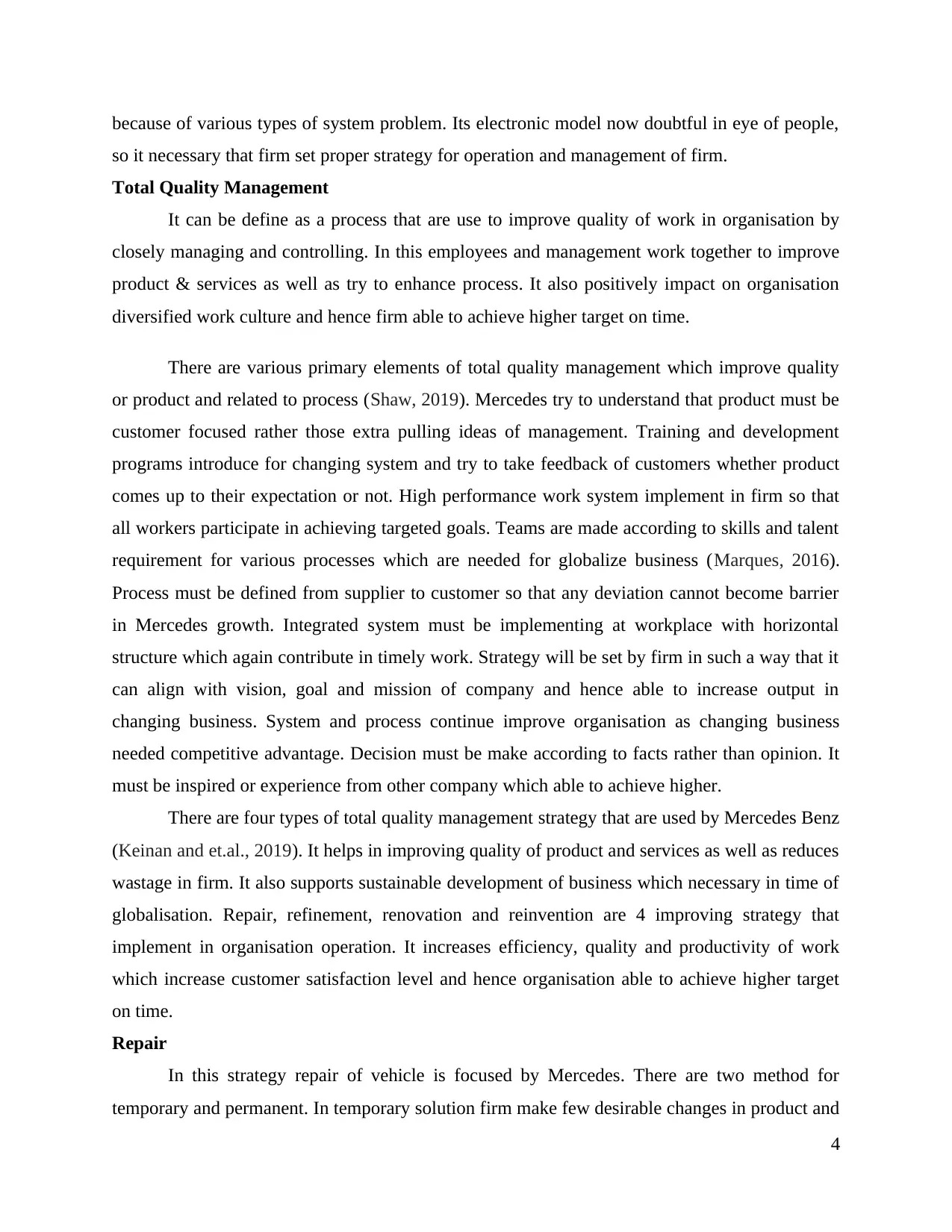
because of various types of system problem. Its electronic model now doubtful in eye of people,
so it necessary that firm set proper strategy for operation and management of firm.
Total Quality Management
It can be define as a process that are use to improve quality of work in organisation by
closely managing and controlling. In this employees and management work together to improve
product & services as well as try to enhance process. It also positively impact on organisation
diversified work culture and hence firm able to achieve higher target on time.
There are various primary elements of total quality management which improve quality
or product and related to process (Shaw, 2019). Mercedes try to understand that product must be
customer focused rather those extra pulling ideas of management. Training and development
programs introduce for changing system and try to take feedback of customers whether product
comes up to their expectation or not. High performance work system implement in firm so that
all workers participate in achieving targeted goals. Teams are made according to skills and talent
requirement for various processes which are needed for globalize business (Marques, 2016).
Process must be defined from supplier to customer so that any deviation cannot become barrier
in Mercedes growth. Integrated system must be implementing at workplace with horizontal
structure which again contribute in timely work. Strategy will be set by firm in such a way that it
can align with vision, goal and mission of company and hence able to increase output in
changing business. System and process continue improve organisation as changing business
needed competitive advantage. Decision must be make according to facts rather than opinion. It
must be inspired or experience from other company which able to achieve higher.
There are four types of total quality management strategy that are used by Mercedes Benz
(Keinan and et.al., 2019). It helps in improving quality of product and services as well as reduces
wastage in firm. It also supports sustainable development of business which necessary in time of
globalisation. Repair, refinement, renovation and reinvention are 4 improving strategy that
implement in organisation operation. It increases efficiency, quality and productivity of work
which increase customer satisfaction level and hence organisation able to achieve higher target
on time.
Repair
In this strategy repair of vehicle is focused by Mercedes. There are two method for
temporary and permanent. In temporary solution firm make few desirable changes in product and
4
so it necessary that firm set proper strategy for operation and management of firm.
Total Quality Management
It can be define as a process that are use to improve quality of work in organisation by
closely managing and controlling. In this employees and management work together to improve
product & services as well as try to enhance process. It also positively impact on organisation
diversified work culture and hence firm able to achieve higher target on time.
There are various primary elements of total quality management which improve quality
or product and related to process (Shaw, 2019). Mercedes try to understand that product must be
customer focused rather those extra pulling ideas of management. Training and development
programs introduce for changing system and try to take feedback of customers whether product
comes up to their expectation or not. High performance work system implement in firm so that
all workers participate in achieving targeted goals. Teams are made according to skills and talent
requirement for various processes which are needed for globalize business (Marques, 2016).
Process must be defined from supplier to customer so that any deviation cannot become barrier
in Mercedes growth. Integrated system must be implementing at workplace with horizontal
structure which again contribute in timely work. Strategy will be set by firm in such a way that it
can align with vision, goal and mission of company and hence able to increase output in
changing business. System and process continue improve organisation as changing business
needed competitive advantage. Decision must be make according to facts rather than opinion. It
must be inspired or experience from other company which able to achieve higher.
There are four types of total quality management strategy that are used by Mercedes Benz
(Keinan and et.al., 2019). It helps in improving quality of product and services as well as reduces
wastage in firm. It also supports sustainable development of business which necessary in time of
globalisation. Repair, refinement, renovation and reinvention are 4 improving strategy that
implement in organisation operation. It increases efficiency, quality and productivity of work
which increase customer satisfaction level and hence organisation able to achieve higher target
on time.
Repair
In this strategy repair of vehicle is focused by Mercedes. There are two method for
temporary and permanent. In temporary solution firm make few desirable changes in product and
4
Paraphrase This Document
Need a fresh take? Get an instant paraphrase of this document with our AI Paraphraser
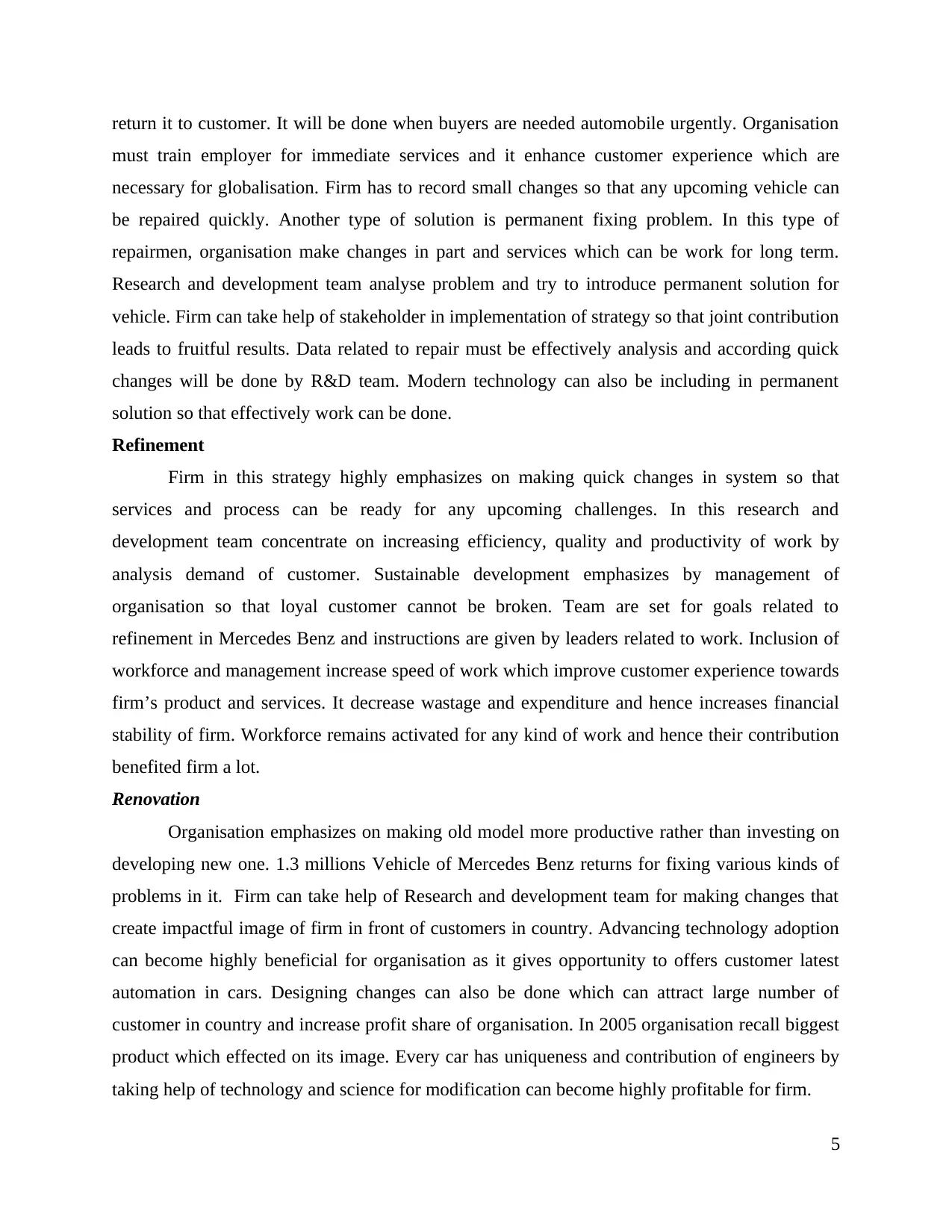
return it to customer. It will be done when buyers are needed automobile urgently. Organisation
must train employer for immediate services and it enhance customer experience which are
necessary for globalisation. Firm has to record small changes so that any upcoming vehicle can
be repaired quickly. Another type of solution is permanent fixing problem. In this type of
repairmen, organisation make changes in part and services which can be work for long term.
Research and development team analyse problem and try to introduce permanent solution for
vehicle. Firm can take help of stakeholder in implementation of strategy so that joint contribution
leads to fruitful results. Data related to repair must be effectively analysis and according quick
changes will be done by R&D team. Modern technology can also be including in permanent
solution so that effectively work can be done.
Refinement
Firm in this strategy highly emphasizes on making quick changes in system so that
services and process can be ready for any upcoming challenges. In this research and
development team concentrate on increasing efficiency, quality and productivity of work by
analysis demand of customer. Sustainable development emphasizes by management of
organisation so that loyal customer cannot be broken. Team are set for goals related to
refinement in Mercedes Benz and instructions are given by leaders related to work. Inclusion of
workforce and management increase speed of work which improve customer experience towards
firm’s product and services. It decrease wastage and expenditure and hence increases financial
stability of firm. Workforce remains activated for any kind of work and hence their contribution
benefited firm a lot.
Renovation
Organisation emphasizes on making old model more productive rather than investing on
developing new one. 1.3 millions Vehicle of Mercedes Benz returns for fixing various kinds of
problems in it. Firm can take help of Research and development team for making changes that
create impactful image of firm in front of customers in country. Advancing technology adoption
can become highly beneficial for organisation as it gives opportunity to offers customer latest
automation in cars. Designing changes can also be done which can attract large number of
customer in country and increase profit share of organisation. In 2005 organisation recall biggest
product which effected on its image. Every car has uniqueness and contribution of engineers by
taking help of technology and science for modification can become highly profitable for firm.
5
must train employer for immediate services and it enhance customer experience which are
necessary for globalisation. Firm has to record small changes so that any upcoming vehicle can
be repaired quickly. Another type of solution is permanent fixing problem. In this type of
repairmen, organisation make changes in part and services which can be work for long term.
Research and development team analyse problem and try to introduce permanent solution for
vehicle. Firm can take help of stakeholder in implementation of strategy so that joint contribution
leads to fruitful results. Data related to repair must be effectively analysis and according quick
changes will be done by R&D team. Modern technology can also be including in permanent
solution so that effectively work can be done.
Refinement
Firm in this strategy highly emphasizes on making quick changes in system so that
services and process can be ready for any upcoming challenges. In this research and
development team concentrate on increasing efficiency, quality and productivity of work by
analysis demand of customer. Sustainable development emphasizes by management of
organisation so that loyal customer cannot be broken. Team are set for goals related to
refinement in Mercedes Benz and instructions are given by leaders related to work. Inclusion of
workforce and management increase speed of work which improve customer experience towards
firm’s product and services. It decrease wastage and expenditure and hence increases financial
stability of firm. Workforce remains activated for any kind of work and hence their contribution
benefited firm a lot.
Renovation
Organisation emphasizes on making old model more productive rather than investing on
developing new one. 1.3 millions Vehicle of Mercedes Benz returns for fixing various kinds of
problems in it. Firm can take help of Research and development team for making changes that
create impactful image of firm in front of customers in country. Advancing technology adoption
can become highly beneficial for organisation as it gives opportunity to offers customer latest
automation in cars. Designing changes can also be done which can attract large number of
customer in country and increase profit share of organisation. In 2005 organisation recall biggest
product which effected on its image. Every car has uniqueness and contribution of engineers by
taking help of technology and science for modification can become highly profitable for firm.
5
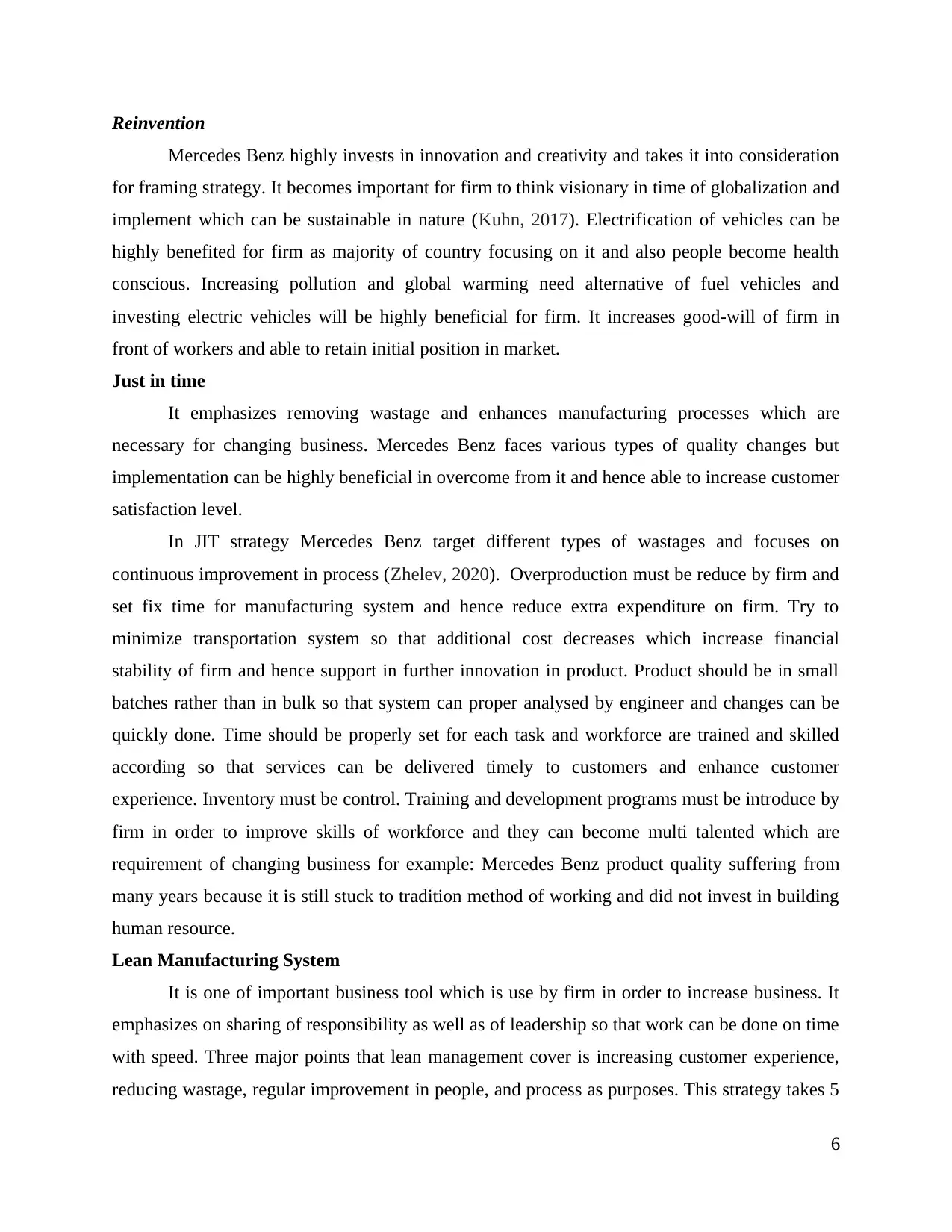
Reinvention
Mercedes Benz highly invests in innovation and creativity and takes it into consideration
for framing strategy. It becomes important for firm to think visionary in time of globalization and
implement which can be sustainable in nature (Kuhn, 2017). Electrification of vehicles can be
highly benefited for firm as majority of country focusing on it and also people become health
conscious. Increasing pollution and global warming need alternative of fuel vehicles and
investing electric vehicles will be highly beneficial for firm. It increases good-will of firm in
front of workers and able to retain initial position in market.
Just in time
It emphasizes removing wastage and enhances manufacturing processes which are
necessary for changing business. Mercedes Benz faces various types of quality changes but
implementation can be highly beneficial in overcome from it and hence able to increase customer
satisfaction level.
In JIT strategy Mercedes Benz target different types of wastages and focuses on
continuous improvement in process (Zhelev, 2020). Overproduction must be reduce by firm and
set fix time for manufacturing system and hence reduce extra expenditure on firm. Try to
minimize transportation system so that additional cost decreases which increase financial
stability of firm and hence support in further innovation in product. Product should be in small
batches rather than in bulk so that system can proper analysed by engineer and changes can be
quickly done. Time should be properly set for each task and workforce are trained and skilled
according so that services can be delivered timely to customers and enhance customer
experience. Inventory must be control. Training and development programs must be introduce by
firm in order to improve skills of workforce and they can become multi talented which are
requirement of changing business for example: Mercedes Benz product quality suffering from
many years because it is still stuck to tradition method of working and did not invest in building
human resource.
Lean Manufacturing System
It is one of important business tool which is use by firm in order to increase business. It
emphasizes on sharing of responsibility as well as of leadership so that work can be done on time
with speed. Three major points that lean management cover is increasing customer experience,
reducing wastage, regular improvement in people, and process as purposes. This strategy takes 5
6
Mercedes Benz highly invests in innovation and creativity and takes it into consideration
for framing strategy. It becomes important for firm to think visionary in time of globalization and
implement which can be sustainable in nature (Kuhn, 2017). Electrification of vehicles can be
highly benefited for firm as majority of country focusing on it and also people become health
conscious. Increasing pollution and global warming need alternative of fuel vehicles and
investing electric vehicles will be highly beneficial for firm. It increases good-will of firm in
front of workers and able to retain initial position in market.
Just in time
It emphasizes removing wastage and enhances manufacturing processes which are
necessary for changing business. Mercedes Benz faces various types of quality changes but
implementation can be highly beneficial in overcome from it and hence able to increase customer
satisfaction level.
In JIT strategy Mercedes Benz target different types of wastages and focuses on
continuous improvement in process (Zhelev, 2020). Overproduction must be reduce by firm and
set fix time for manufacturing system and hence reduce extra expenditure on firm. Try to
minimize transportation system so that additional cost decreases which increase financial
stability of firm and hence support in further innovation in product. Product should be in small
batches rather than in bulk so that system can proper analysed by engineer and changes can be
quickly done. Time should be properly set for each task and workforce are trained and skilled
according so that services can be delivered timely to customers and enhance customer
experience. Inventory must be control. Training and development programs must be introduce by
firm in order to improve skills of workforce and they can become multi talented which are
requirement of changing business for example: Mercedes Benz product quality suffering from
many years because it is still stuck to tradition method of working and did not invest in building
human resource.
Lean Manufacturing System
It is one of important business tool which is use by firm in order to increase business. It
emphasizes on sharing of responsibility as well as of leadership so that work can be done on time
with speed. Three major points that lean management cover is increasing customer experience,
reducing wastage, regular improvement in people, and process as purposes. This strategy takes 5
6
⊘ This is a preview!⊘
Do you want full access?
Subscribe today to unlock all pages.

Trusted by 1+ million students worldwide
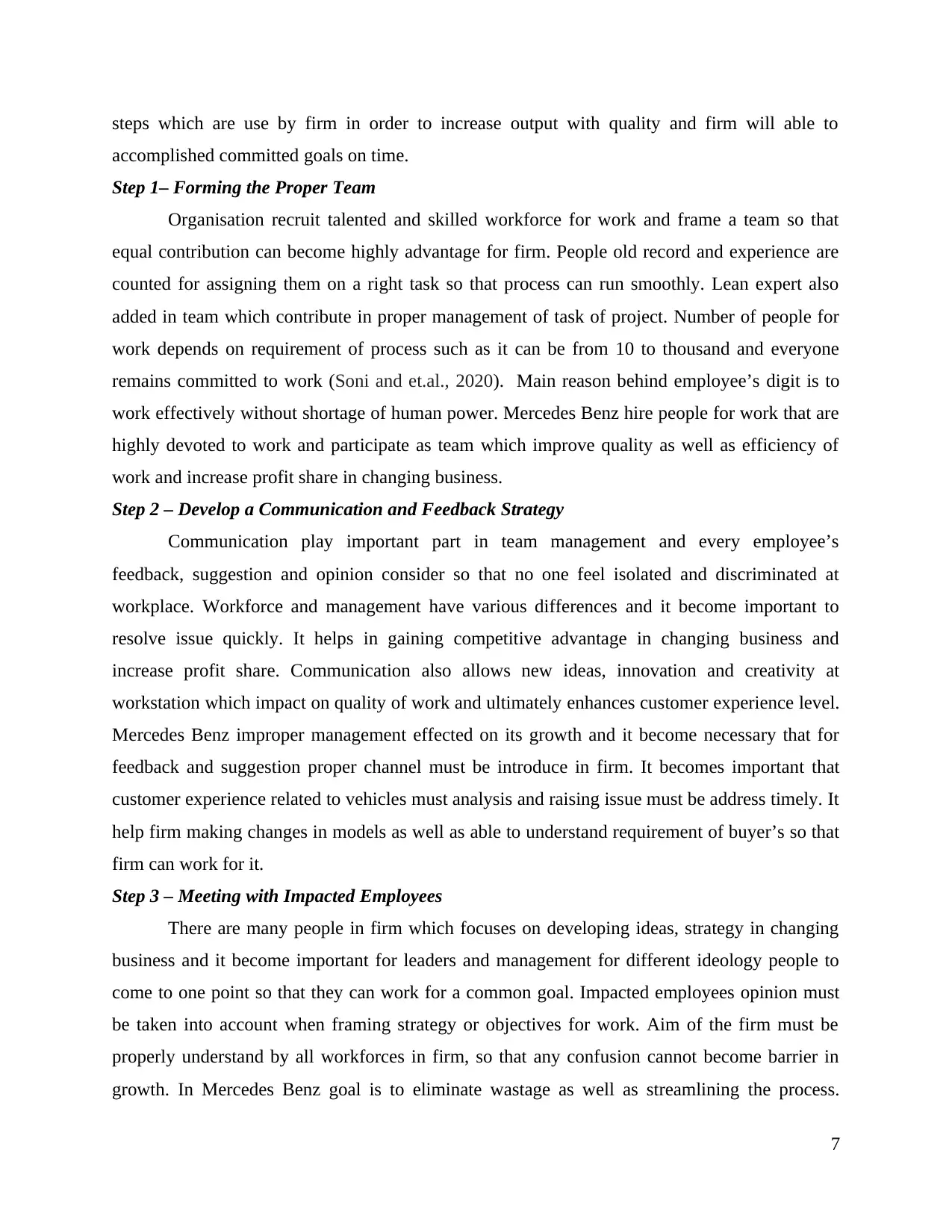
steps which are use by firm in order to increase output with quality and firm will able to
accomplished committed goals on time.
Step 1– Forming the Proper Team
Organisation recruit talented and skilled workforce for work and frame a team so that
equal contribution can become highly advantage for firm. People old record and experience are
counted for assigning them on a right task so that process can run smoothly. Lean expert also
added in team which contribute in proper management of task of project. Number of people for
work depends on requirement of process such as it can be from 10 to thousand and everyone
remains committed to work (Soni and et.al., 2020). Main reason behind employee’s digit is to
work effectively without shortage of human power. Mercedes Benz hire people for work that are
highly devoted to work and participate as team which improve quality as well as efficiency of
work and increase profit share in changing business.
Step 2 – Develop a Communication and Feedback Strategy
Communication play important part in team management and every employee’s
feedback, suggestion and opinion consider so that no one feel isolated and discriminated at
workplace. Workforce and management have various differences and it become important to
resolve issue quickly. It helps in gaining competitive advantage in changing business and
increase profit share. Communication also allows new ideas, innovation and creativity at
workstation which impact on quality of work and ultimately enhances customer experience level.
Mercedes Benz improper management effected on its growth and it become necessary that for
feedback and suggestion proper channel must be introduce in firm. It becomes important that
customer experience related to vehicles must analysis and raising issue must be address timely. It
help firm making changes in models as well as able to understand requirement of buyer’s so that
firm can work for it.
Step 3 – Meeting with Impacted Employees
There are many people in firm which focuses on developing ideas, strategy in changing
business and it become important for leaders and management for different ideology people to
come to one point so that they can work for a common goal. Impacted employees opinion must
be taken into account when framing strategy or objectives for work. Aim of the firm must be
properly understand by all workforces in firm, so that any confusion cannot become barrier in
growth. In Mercedes Benz goal is to eliminate wastage as well as streamlining the process.
7
accomplished committed goals on time.
Step 1– Forming the Proper Team
Organisation recruit talented and skilled workforce for work and frame a team so that
equal contribution can become highly advantage for firm. People old record and experience are
counted for assigning them on a right task so that process can run smoothly. Lean expert also
added in team which contribute in proper management of task of project. Number of people for
work depends on requirement of process such as it can be from 10 to thousand and everyone
remains committed to work (Soni and et.al., 2020). Main reason behind employee’s digit is to
work effectively without shortage of human power. Mercedes Benz hire people for work that are
highly devoted to work and participate as team which improve quality as well as efficiency of
work and increase profit share in changing business.
Step 2 – Develop a Communication and Feedback Strategy
Communication play important part in team management and every employee’s
feedback, suggestion and opinion consider so that no one feel isolated and discriminated at
workplace. Workforce and management have various differences and it become important to
resolve issue quickly. It helps in gaining competitive advantage in changing business and
increase profit share. Communication also allows new ideas, innovation and creativity at
workstation which impact on quality of work and ultimately enhances customer experience level.
Mercedes Benz improper management effected on its growth and it become necessary that for
feedback and suggestion proper channel must be introduce in firm. It becomes important that
customer experience related to vehicles must analysis and raising issue must be address timely. It
help firm making changes in models as well as able to understand requirement of buyer’s so that
firm can work for it.
Step 3 – Meeting with Impacted Employees
There are many people in firm which focuses on developing ideas, strategy in changing
business and it become important for leaders and management for different ideology people to
come to one point so that they can work for a common goal. Impacted employees opinion must
be taken into account when framing strategy or objectives for work. Aim of the firm must be
properly understand by all workforces in firm, so that any confusion cannot become barrier in
growth. In Mercedes Benz goal is to eliminate wastage as well as streamlining the process.
7
Paraphrase This Document
Need a fresh take? Get an instant paraphrase of this document with our AI Paraphraser
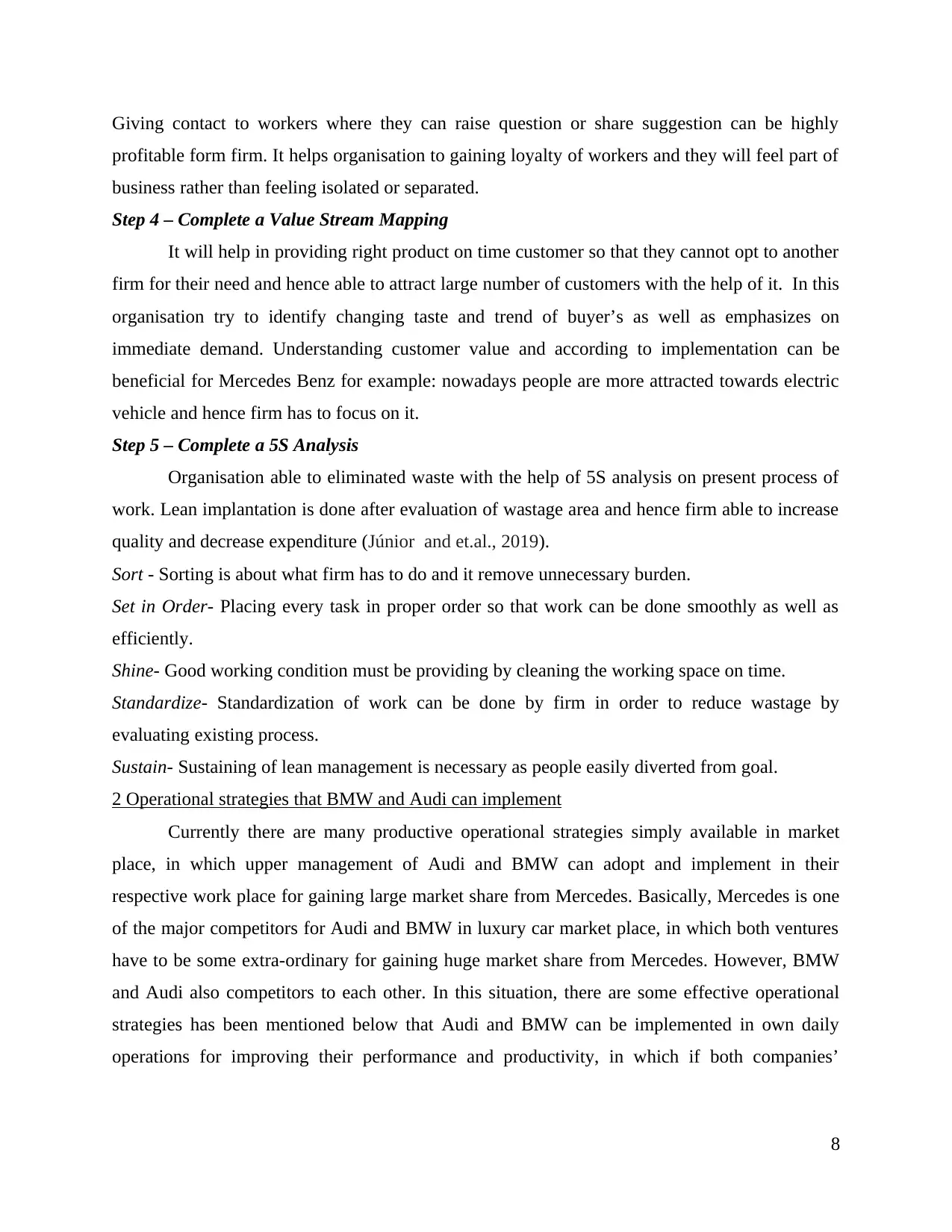
Giving contact to workers where they can raise question or share suggestion can be highly
profitable form firm. It helps organisation to gaining loyalty of workers and they will feel part of
business rather than feeling isolated or separated.
Step 4 – Complete a Value Stream Mapping
It will help in providing right product on time customer so that they cannot opt to another
firm for their need and hence able to attract large number of customers with the help of it. In this
organisation try to identify changing taste and trend of buyer’s as well as emphasizes on
immediate demand. Understanding customer value and according to implementation can be
beneficial for Mercedes Benz for example: nowadays people are more attracted towards electric
vehicle and hence firm has to focus on it.
Step 5 – Complete a 5S Analysis
Organisation able to eliminated waste with the help of 5S analysis on present process of
work. Lean implantation is done after evaluation of wastage area and hence firm able to increase
quality and decrease expenditure (Júnior and et.al., 2019).
Sort - Sorting is about what firm has to do and it remove unnecessary burden.
Set in Order- Placing every task in proper order so that work can be done smoothly as well as
efficiently.
Shine- Good working condition must be providing by cleaning the working space on time.
Standardize- Standardization of work can be done by firm in order to reduce wastage by
evaluating existing process.
Sustain- Sustaining of lean management is necessary as people easily diverted from goal.
2 Operational strategies that BMW and Audi can implement
Currently there are many productive operational strategies simply available in market
place, in which upper management of Audi and BMW can adopt and implement in their
respective work place for gaining large market share from Mercedes. Basically, Mercedes is one
of the major competitors for Audi and BMW in luxury car market place, in which both ventures
have to be some extra-ordinary for gaining huge market share from Mercedes. However, BMW
and Audi also competitors to each other. In this situation, there are some effective operational
strategies has been mentioned below that Audi and BMW can be implemented in own daily
operations for improving their performance and productivity, in which if both companies’
8
profitable form firm. It helps organisation to gaining loyalty of workers and they will feel part of
business rather than feeling isolated or separated.
Step 4 – Complete a Value Stream Mapping
It will help in providing right product on time customer so that they cannot opt to another
firm for their need and hence able to attract large number of customers with the help of it. In this
organisation try to identify changing taste and trend of buyer’s as well as emphasizes on
immediate demand. Understanding customer value and according to implementation can be
beneficial for Mercedes Benz for example: nowadays people are more attracted towards electric
vehicle and hence firm has to focus on it.
Step 5 – Complete a 5S Analysis
Organisation able to eliminated waste with the help of 5S analysis on present process of
work. Lean implantation is done after evaluation of wastage area and hence firm able to increase
quality and decrease expenditure (Júnior and et.al., 2019).
Sort - Sorting is about what firm has to do and it remove unnecessary burden.
Set in Order- Placing every task in proper order so that work can be done smoothly as well as
efficiently.
Shine- Good working condition must be providing by cleaning the working space on time.
Standardize- Standardization of work can be done by firm in order to reduce wastage by
evaluating existing process.
Sustain- Sustaining of lean management is necessary as people easily diverted from goal.
2 Operational strategies that BMW and Audi can implement
Currently there are many productive operational strategies simply available in market
place, in which upper management of Audi and BMW can adopt and implement in their
respective work place for gaining large market share from Mercedes. Basically, Mercedes is one
of the major competitors for Audi and BMW in luxury car market place, in which both ventures
have to be some extra-ordinary for gaining huge market share from Mercedes. However, BMW
and Audi also competitors to each other. In this situation, there are some effective operational
strategies has been mentioned below that Audi and BMW can be implemented in own daily
operations for improving their performance and productivity, in which if both companies’
8
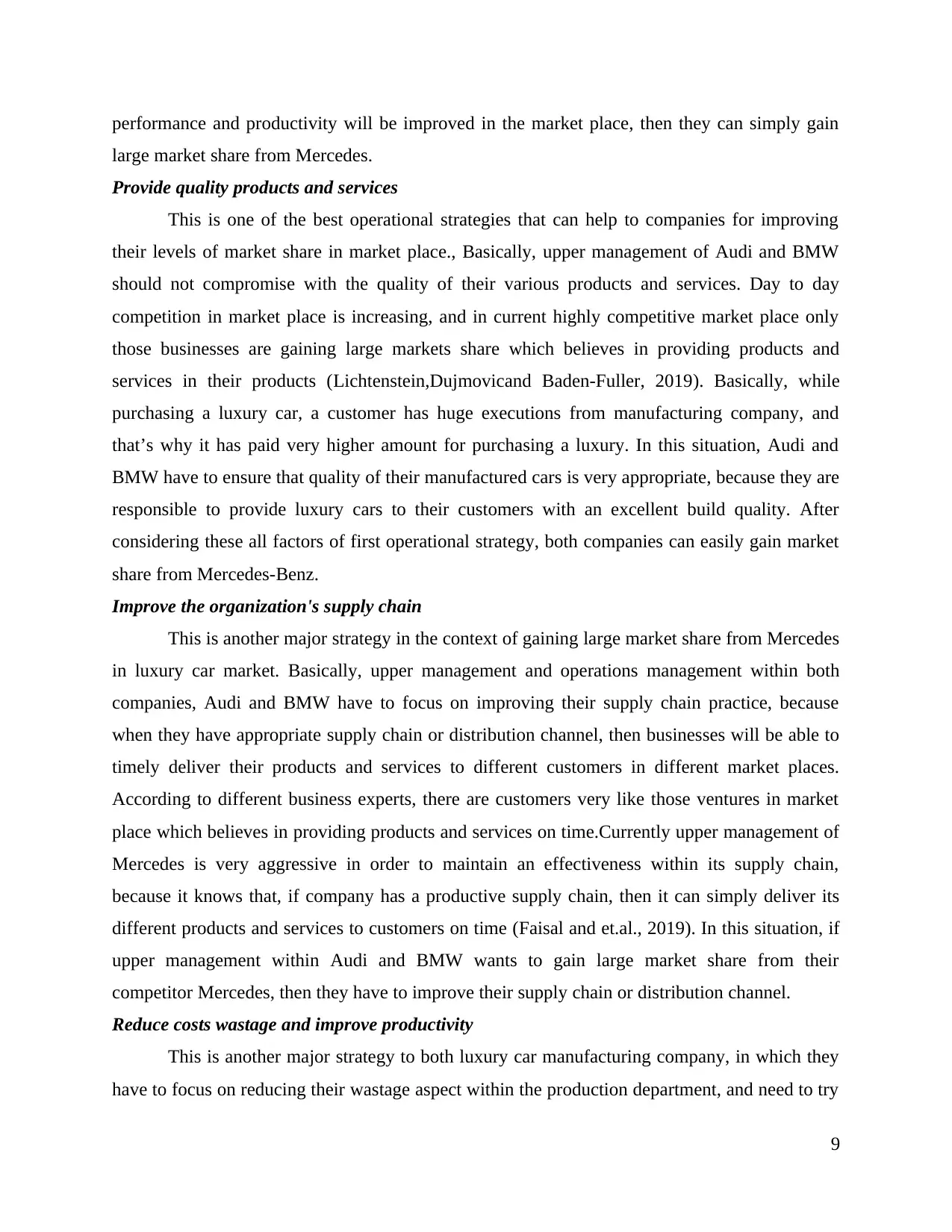
performance and productivity will be improved in the market place, then they can simply gain
large market share from Mercedes.
Provide quality products and services
This is one of the best operational strategies that can help to companies for improving
their levels of market share in market place., Basically, upper management of Audi and BMW
should not compromise with the quality of their various products and services. Day to day
competition in market place is increasing, and in current highly competitive market place only
those businesses are gaining large markets share which believes in providing products and
services in their products (Lichtenstein,Dujmovicand Baden-Fuller, 2019). Basically, while
purchasing a luxury car, a customer has huge executions from manufacturing company, and
that’s why it has paid very higher amount for purchasing a luxury. In this situation, Audi and
BMW have to ensure that quality of their manufactured cars is very appropriate, because they are
responsible to provide luxury cars to their customers with an excellent build quality. After
considering these all factors of first operational strategy, both companies can easily gain market
share from Mercedes-Benz.
Improve the organization's supply chain
This is another major strategy in the context of gaining large market share from Mercedes
in luxury car market. Basically, upper management and operations management within both
companies, Audi and BMW have to focus on improving their supply chain practice, because
when they have appropriate supply chain or distribution channel, then businesses will be able to
timely deliver their products and services to different customers in different market places.
According to different business experts, there are customers very like those ventures in market
place which believes in providing products and services on time.Currently upper management of
Mercedes is very aggressive in order to maintain an effectiveness within its supply chain,
because it knows that, if company has a productive supply chain, then it can simply deliver its
different products and services to customers on time (Faisal and et.al., 2019). In this situation, if
upper management within Audi and BMW wants to gain large market share from their
competitor Mercedes, then they have to improve their supply chain or distribution channel.
Reduce costs wastage and improve productivity
This is another major strategy to both luxury car manufacturing company, in which they
have to focus on reducing their wastage aspect within the production department, and need to try
9
large market share from Mercedes.
Provide quality products and services
This is one of the best operational strategies that can help to companies for improving
their levels of market share in market place., Basically, upper management of Audi and BMW
should not compromise with the quality of their various products and services. Day to day
competition in market place is increasing, and in current highly competitive market place only
those businesses are gaining large markets share which believes in providing products and
services in their products (Lichtenstein,Dujmovicand Baden-Fuller, 2019). Basically, while
purchasing a luxury car, a customer has huge executions from manufacturing company, and
that’s why it has paid very higher amount for purchasing a luxury. In this situation, Audi and
BMW have to ensure that quality of their manufactured cars is very appropriate, because they are
responsible to provide luxury cars to their customers with an excellent build quality. After
considering these all factors of first operational strategy, both companies can easily gain market
share from Mercedes-Benz.
Improve the organization's supply chain
This is another major strategy in the context of gaining large market share from Mercedes
in luxury car market. Basically, upper management and operations management within both
companies, Audi and BMW have to focus on improving their supply chain practice, because
when they have appropriate supply chain or distribution channel, then businesses will be able to
timely deliver their products and services to different customers in different market places.
According to different business experts, there are customers very like those ventures in market
place which believes in providing products and services on time.Currently upper management of
Mercedes is very aggressive in order to maintain an effectiveness within its supply chain,
because it knows that, if company has a productive supply chain, then it can simply deliver its
different products and services to customers on time (Faisal and et.al., 2019). In this situation, if
upper management within Audi and BMW wants to gain large market share from their
competitor Mercedes, then they have to improve their supply chain or distribution channel.
Reduce costs wastage and improve productivity
This is another major strategy to both luxury car manufacturing company, in which they
have to focus on reducing their wastage aspect within the production department, and need to try
9
⊘ This is a preview!⊘
Do you want full access?
Subscribe today to unlock all pages.

Trusted by 1+ million students worldwide
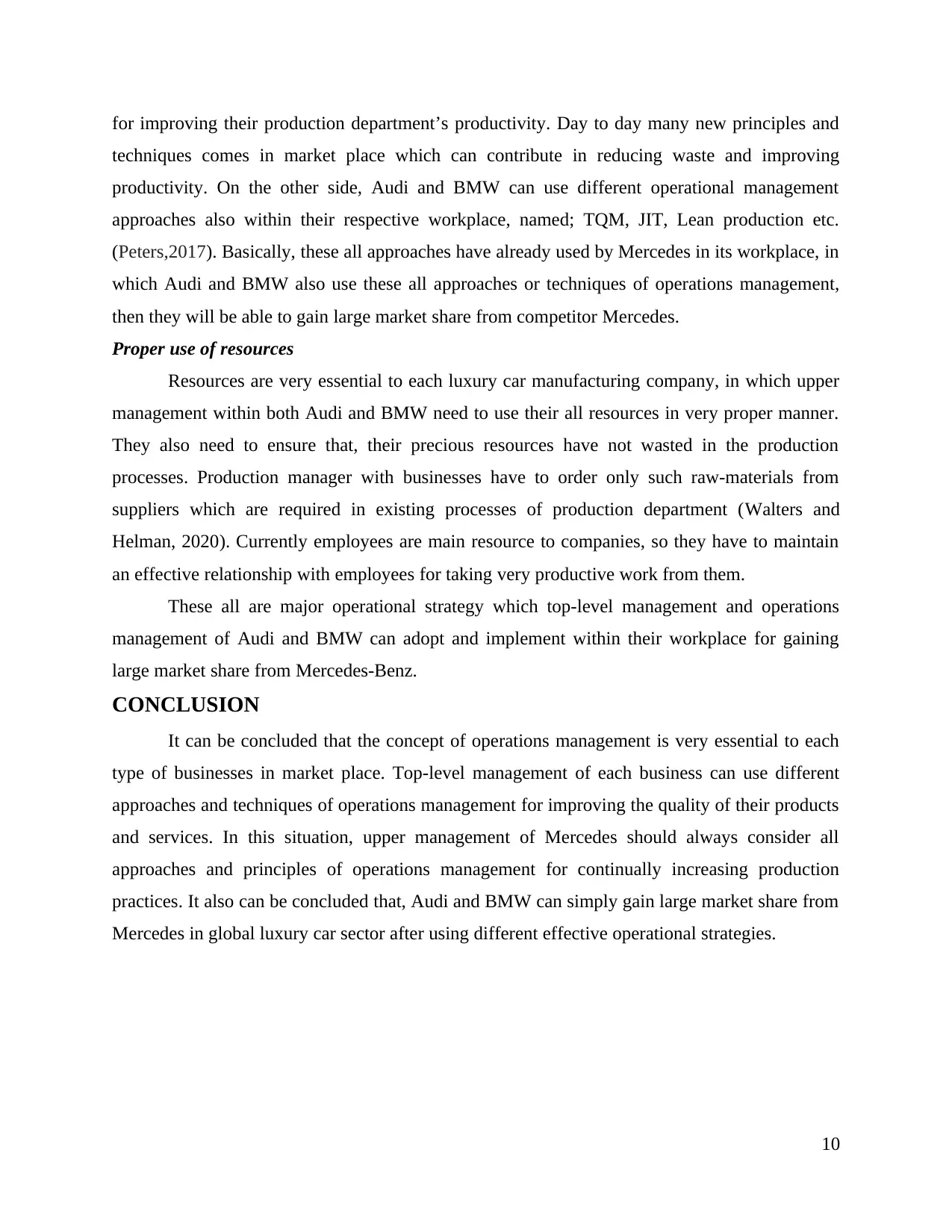
for improving their production department’s productivity. Day to day many new principles and
techniques comes in market place which can contribute in reducing waste and improving
productivity. On the other side, Audi and BMW can use different operational management
approaches also within their respective workplace, named; TQM, JIT, Lean production etc.
(Peters,2017). Basically, these all approaches have already used by Mercedes in its workplace, in
which Audi and BMW also use these all approaches or techniques of operations management,
then they will be able to gain large market share from competitor Mercedes.
Proper use of resources
Resources are very essential to each luxury car manufacturing company, in which upper
management within both Audi and BMW need to use their all resources in very proper manner.
They also need to ensure that, their precious resources have not wasted in the production
processes. Production manager with businesses have to order only such raw-materials from
suppliers which are required in existing processes of production department (Walters and
Helman, 2020). Currently employees are main resource to companies, so they have to maintain
an effective relationship with employees for taking very productive work from them.
These all are major operational strategy which top-level management and operations
management of Audi and BMW can adopt and implement within their workplace for gaining
large market share from Mercedes-Benz.
CONCLUSION
It can be concluded that the concept of operations management is very essential to each
type of businesses in market place. Top-level management of each business can use different
approaches and techniques of operations management for improving the quality of their products
and services. In this situation, upper management of Mercedes should always consider all
approaches and principles of operations management for continually increasing production
practices. It also can be concluded that, Audi and BMW can simply gain large market share from
Mercedes in global luxury car sector after using different effective operational strategies.
10
techniques comes in market place which can contribute in reducing waste and improving
productivity. On the other side, Audi and BMW can use different operational management
approaches also within their respective workplace, named; TQM, JIT, Lean production etc.
(Peters,2017). Basically, these all approaches have already used by Mercedes in its workplace, in
which Audi and BMW also use these all approaches or techniques of operations management,
then they will be able to gain large market share from competitor Mercedes.
Proper use of resources
Resources are very essential to each luxury car manufacturing company, in which upper
management within both Audi and BMW need to use their all resources in very proper manner.
They also need to ensure that, their precious resources have not wasted in the production
processes. Production manager with businesses have to order only such raw-materials from
suppliers which are required in existing processes of production department (Walters and
Helman, 2020). Currently employees are main resource to companies, so they have to maintain
an effective relationship with employees for taking very productive work from them.
These all are major operational strategy which top-level management and operations
management of Audi and BMW can adopt and implement within their workplace for gaining
large market share from Mercedes-Benz.
CONCLUSION
It can be concluded that the concept of operations management is very essential to each
type of businesses in market place. Top-level management of each business can use different
approaches and techniques of operations management for improving the quality of their products
and services. In this situation, upper management of Mercedes should always consider all
approaches and principles of operations management for continually increasing production
practices. It also can be concluded that, Audi and BMW can simply gain large market share from
Mercedes in global luxury car sector after using different effective operational strategies.
10
Paraphrase This Document
Need a fresh take? Get an instant paraphrase of this document with our AI Paraphraser
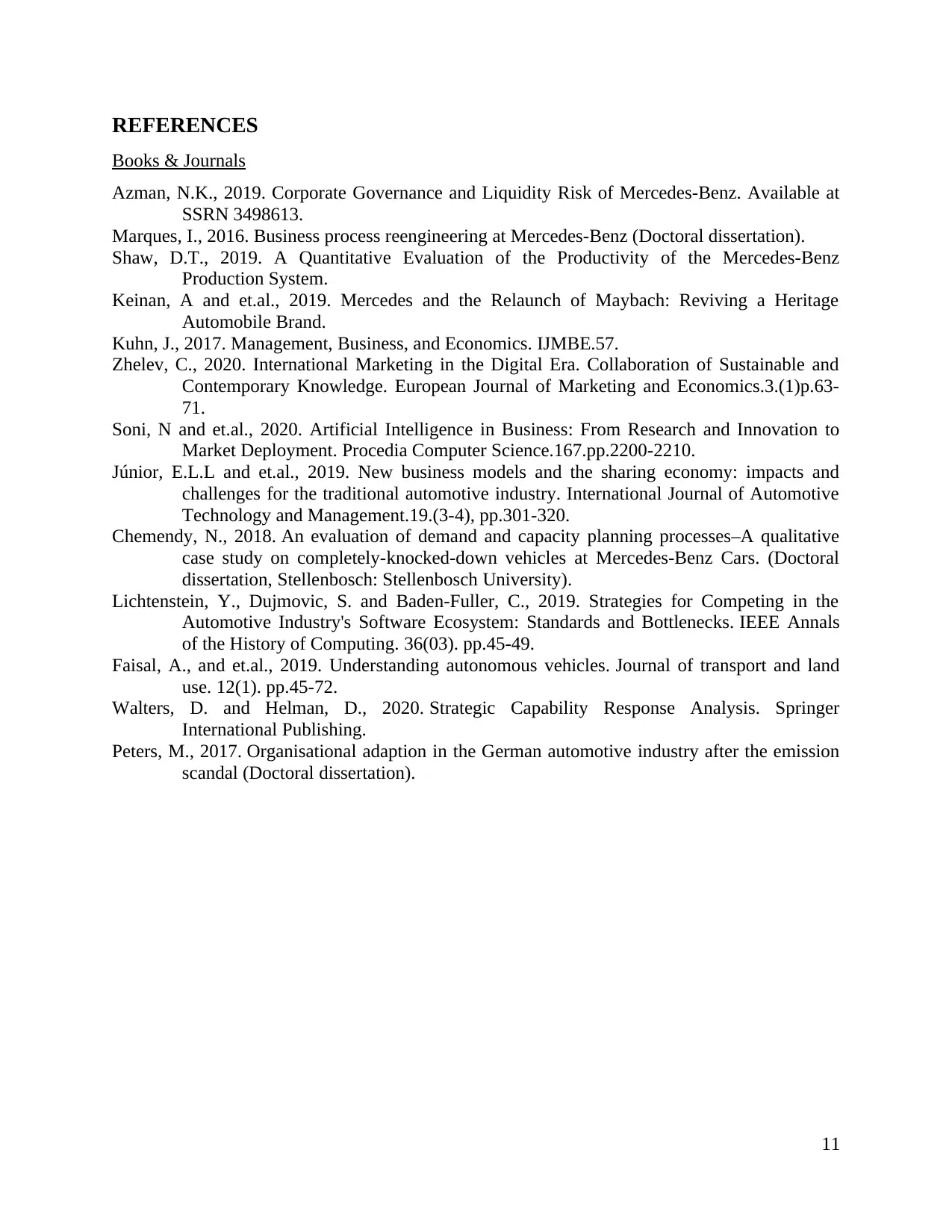
REFERENCES
Books & Journals
Azman, N.K., 2019. Corporate Governance and Liquidity Risk of Mercedes-Benz. Available at
SSRN 3498613.
Marques, I., 2016. Business process reengineering at Mercedes-Benz (Doctoral dissertation).
Shaw, D.T., 2019. A Quantitative Evaluation of the Productivity of the Mercedes-Benz
Production System.
Keinan, A and et.al., 2019. Mercedes and the Relaunch of Maybach: Reviving a Heritage
Automobile Brand.
Kuhn, J., 2017. Management, Business, and Economics. IJMBE.57.
Zhelev, C., 2020. International Marketing in the Digital Era. Collaboration of Sustainable and
Contemporary Knowledge. European Journal of Marketing and Economics.3.(1)p.63-
71.
Soni, N and et.al., 2020. Artificial Intelligence in Business: From Research and Innovation to
Market Deployment. Procedia Computer Science.167.pp.2200-2210.
Júnior, E.L.L and et.al., 2019. New business models and the sharing economy: impacts and
challenges for the traditional automotive industry. International Journal of Automotive
Technology and Management.19.(3-4), pp.301-320.
Chemendy, N., 2018. An evaluation of demand and capacity planning processes–A qualitative
case study on completely-knocked-down vehicles at Mercedes-Benz Cars. (Doctoral
dissertation, Stellenbosch: Stellenbosch University).
Lichtenstein, Y., Dujmovic, S. and Baden-Fuller, C., 2019. Strategies for Competing in the
Automotive Industry's Software Ecosystem: Standards and Bottlenecks. IEEE Annals
of the History of Computing. 36(03). pp.45-49.
Faisal, A., and et.al., 2019. Understanding autonomous vehicles. Journal of transport and land
use. 12(1). pp.45-72.
Walters, D. and Helman, D., 2020. Strategic Capability Response Analysis. Springer
International Publishing.
Peters, M., 2017. Organisational adaption in the German automotive industry after the emission
scandal (Doctoral dissertation).
11
Books & Journals
Azman, N.K., 2019. Corporate Governance and Liquidity Risk of Mercedes-Benz. Available at
SSRN 3498613.
Marques, I., 2016. Business process reengineering at Mercedes-Benz (Doctoral dissertation).
Shaw, D.T., 2019. A Quantitative Evaluation of the Productivity of the Mercedes-Benz
Production System.
Keinan, A and et.al., 2019. Mercedes and the Relaunch of Maybach: Reviving a Heritage
Automobile Brand.
Kuhn, J., 2017. Management, Business, and Economics. IJMBE.57.
Zhelev, C., 2020. International Marketing in the Digital Era. Collaboration of Sustainable and
Contemporary Knowledge. European Journal of Marketing and Economics.3.(1)p.63-
71.
Soni, N and et.al., 2020. Artificial Intelligence in Business: From Research and Innovation to
Market Deployment. Procedia Computer Science.167.pp.2200-2210.
Júnior, E.L.L and et.al., 2019. New business models and the sharing economy: impacts and
challenges for the traditional automotive industry. International Journal of Automotive
Technology and Management.19.(3-4), pp.301-320.
Chemendy, N., 2018. An evaluation of demand and capacity planning processes–A qualitative
case study on completely-knocked-down vehicles at Mercedes-Benz Cars. (Doctoral
dissertation, Stellenbosch: Stellenbosch University).
Lichtenstein, Y., Dujmovic, S. and Baden-Fuller, C., 2019. Strategies for Competing in the
Automotive Industry's Software Ecosystem: Standards and Bottlenecks. IEEE Annals
of the History of Computing. 36(03). pp.45-49.
Faisal, A., and et.al., 2019. Understanding autonomous vehicles. Journal of transport and land
use. 12(1). pp.45-72.
Walters, D. and Helman, D., 2020. Strategic Capability Response Analysis. Springer
International Publishing.
Peters, M., 2017. Organisational adaption in the German automotive industry after the emission
scandal (Doctoral dissertation).
11
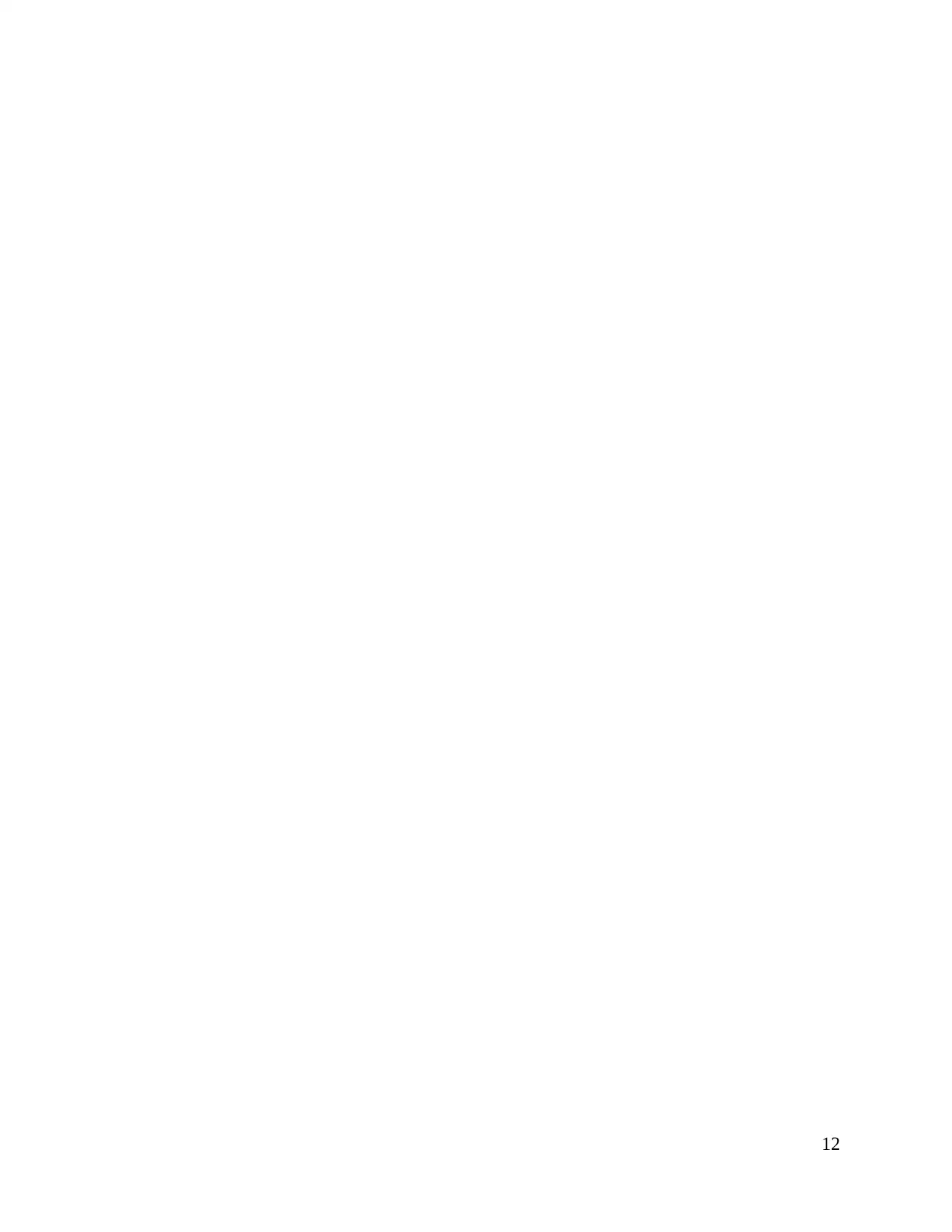
12
⊘ This is a preview!⊘
Do you want full access?
Subscribe today to unlock all pages.

Trusted by 1+ million students worldwide
1 out of 12