Dissertation Chapter 1: Introduction to Metal Cutting Process Analysis
VerifiedAdded on 2020/06/06
|5
|781
|97
Thesis and Dissertation
AI Summary
This dissertation chapter provides an introduction to the metal cutting process, with a specific focus on milling. It begins with an overview of metal cutting's significance in manufacturing and the advancements in technology, emphasizing CNC control. The chapter then delves into the background of th...
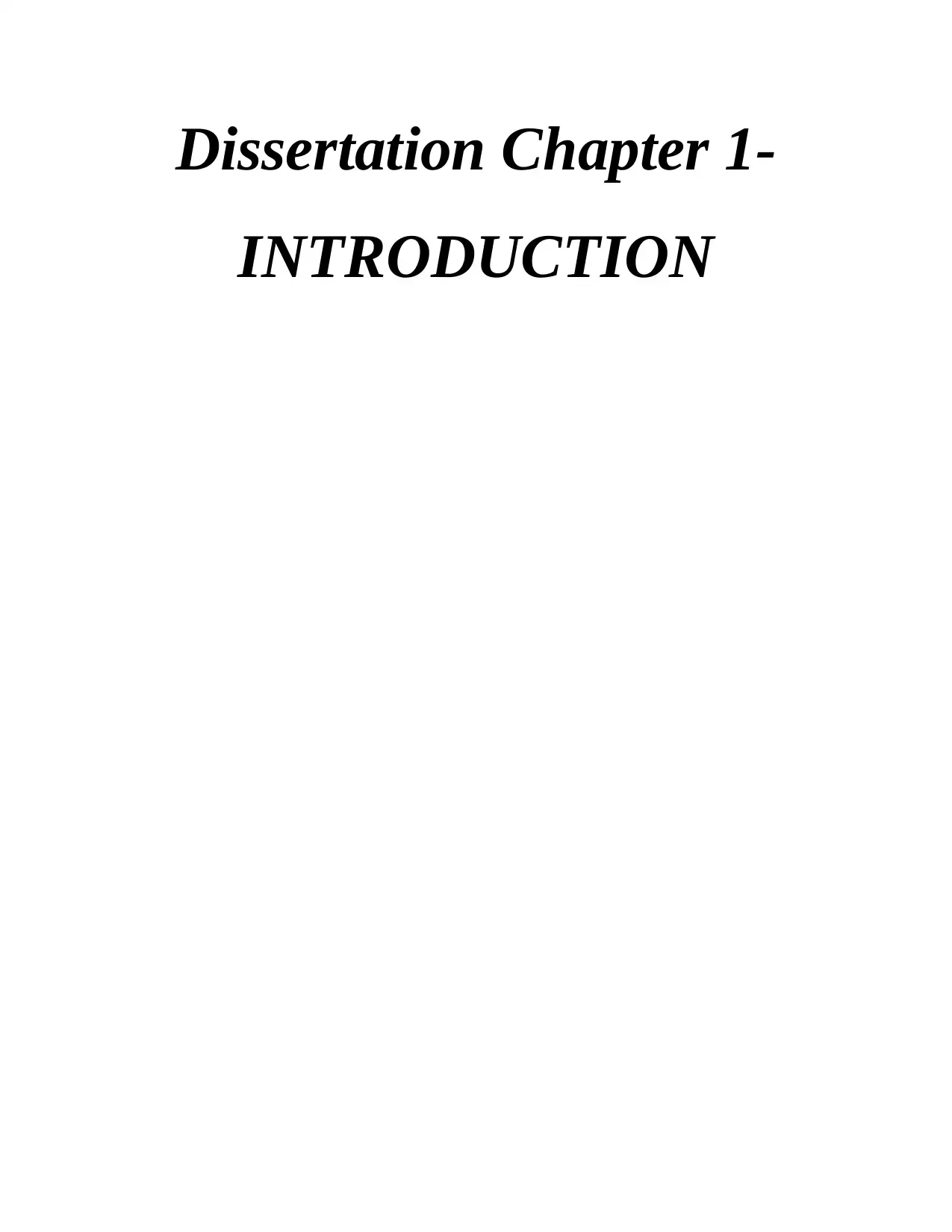
Dissertation Chapter 1-
INTRODUCTION
INTRODUCTION
Paraphrase This Document
Need a fresh take? Get an instant paraphrase of this document with our AI Paraphraser
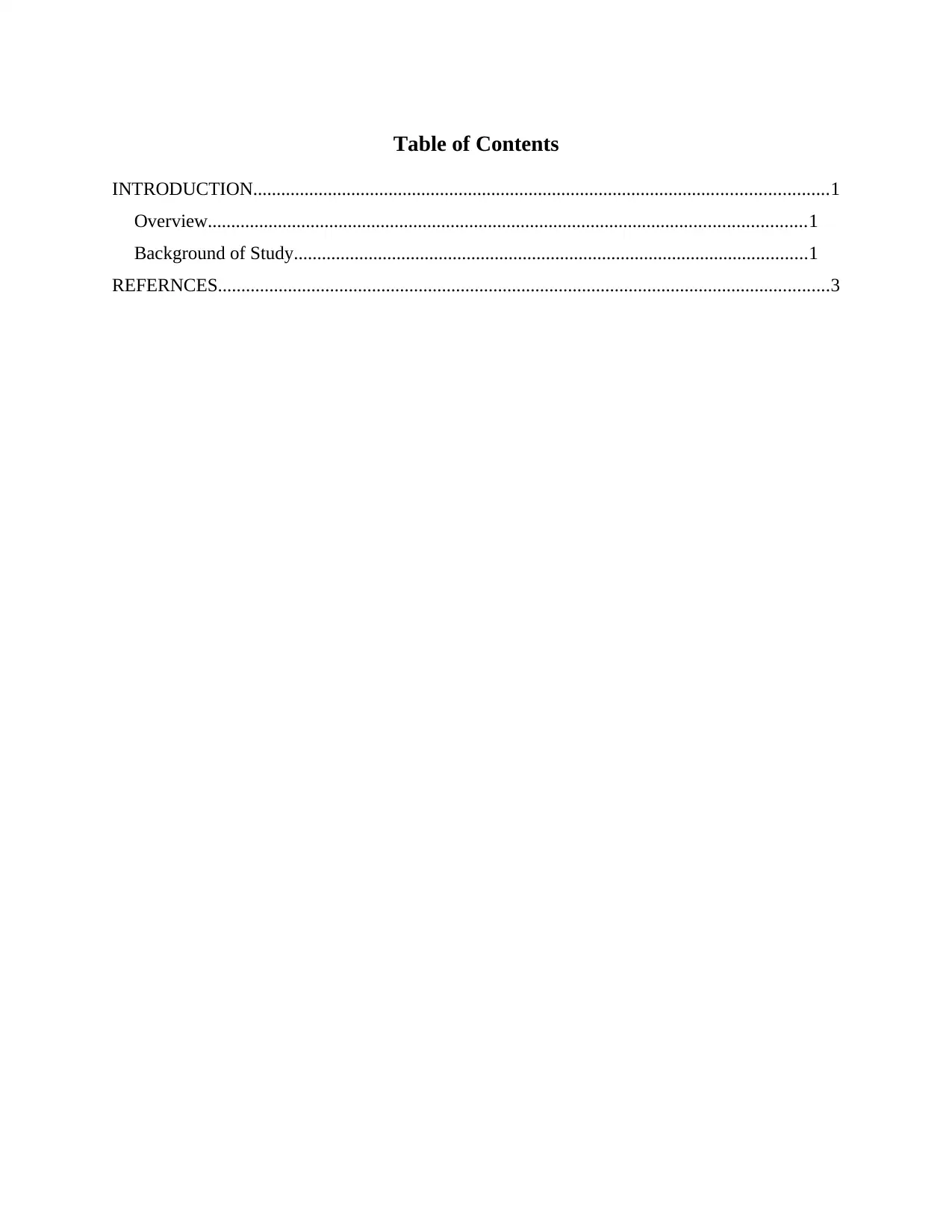
Table of Contents
INTRODUCTION...........................................................................................................................1
Overview................................................................................................................................1
Background of Study..............................................................................................................1
REFERNCES...................................................................................................................................3
INTRODUCTION...........................................................................................................................1
Overview................................................................................................................................1
Background of Study..............................................................................................................1
REFERNCES...................................................................................................................................3
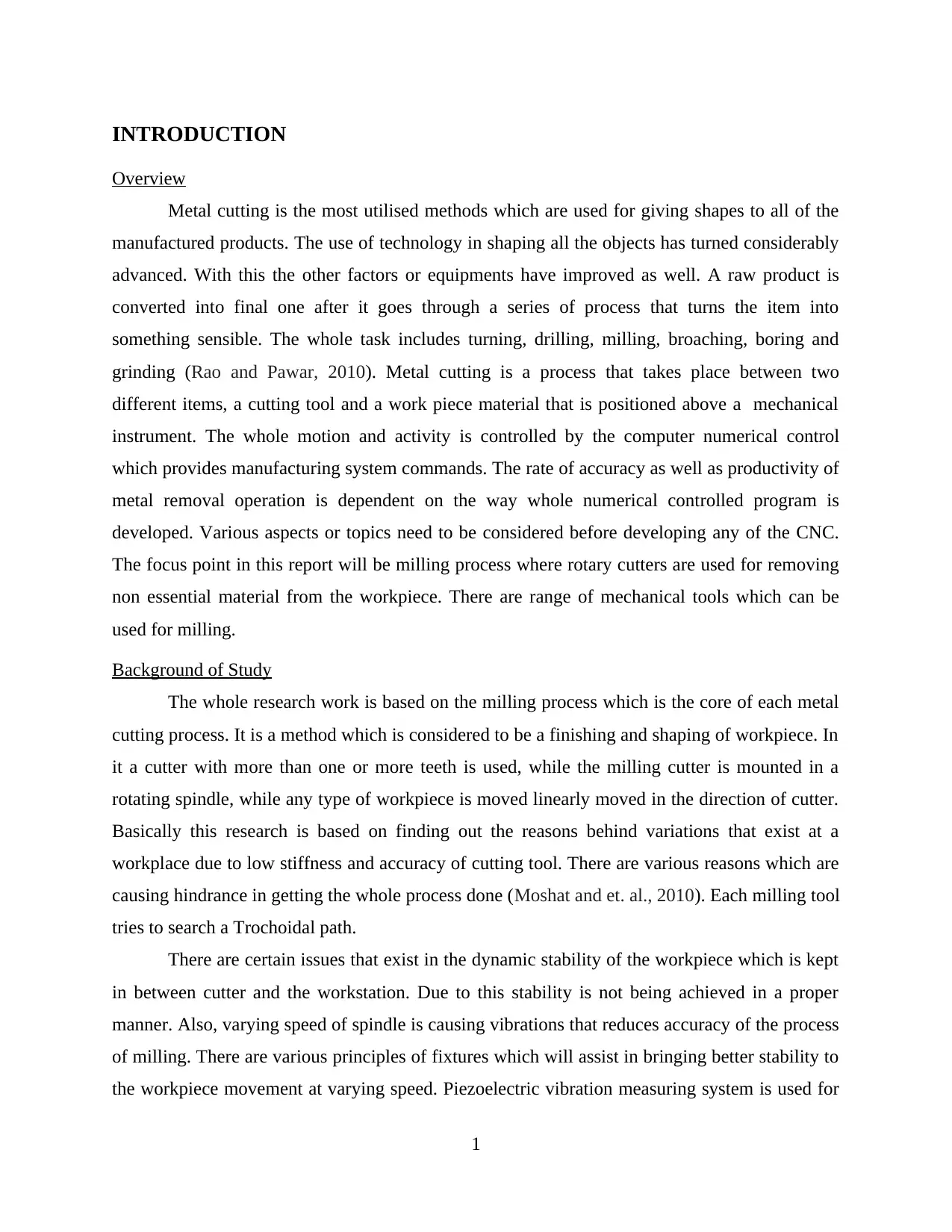
INTRODUCTION
Overview
Metal cutting is the most utilised methods which are used for giving shapes to all of the
manufactured products. The use of technology in shaping all the objects has turned considerably
advanced. With this the other factors or equipments have improved as well. A raw product is
converted into final one after it goes through a series of process that turns the item into
something sensible. The whole task includes turning, drilling, milling, broaching, boring and
grinding (Rao and Pawar, 2010). Metal cutting is a process that takes place between two
different items, a cutting tool and a work piece material that is positioned above a mechanical
instrument. The whole motion and activity is controlled by the computer numerical control
which provides manufacturing system commands. The rate of accuracy as well as productivity of
metal removal operation is dependent on the way whole numerical controlled program is
developed. Various aspects or topics need to be considered before developing any of the CNC.
The focus point in this report will be milling process where rotary cutters are used for removing
non essential material from the workpiece. There are range of mechanical tools which can be
used for milling.
Background of Study
The whole research work is based on the milling process which is the core of each metal
cutting process. It is a method which is considered to be a finishing and shaping of workpiece. In
it a cutter with more than one or more teeth is used, while the milling cutter is mounted in a
rotating spindle, while any type of workpiece is moved linearly moved in the direction of cutter.
Basically this research is based on finding out the reasons behind variations that exist at a
workplace due to low stiffness and accuracy of cutting tool. There are various reasons which are
causing hindrance in getting the whole process done (Moshat and et. al., 2010). Each milling tool
tries to search a Trochoidal path.
There are certain issues that exist in the dynamic stability of the workpiece which is kept
in between cutter and the workstation. Due to this stability is not being achieved in a proper
manner. Also, varying speed of spindle is causing vibrations that reduces accuracy of the process
of milling. There are various principles of fixtures which will assist in bringing better stability to
the workpiece movement at varying speed. Piezoelectric vibration measuring system is used for
1
Overview
Metal cutting is the most utilised methods which are used for giving shapes to all of the
manufactured products. The use of technology in shaping all the objects has turned considerably
advanced. With this the other factors or equipments have improved as well. A raw product is
converted into final one after it goes through a series of process that turns the item into
something sensible. The whole task includes turning, drilling, milling, broaching, boring and
grinding (Rao and Pawar, 2010). Metal cutting is a process that takes place between two
different items, a cutting tool and a work piece material that is positioned above a mechanical
instrument. The whole motion and activity is controlled by the computer numerical control
which provides manufacturing system commands. The rate of accuracy as well as productivity of
metal removal operation is dependent on the way whole numerical controlled program is
developed. Various aspects or topics need to be considered before developing any of the CNC.
The focus point in this report will be milling process where rotary cutters are used for removing
non essential material from the workpiece. There are range of mechanical tools which can be
used for milling.
Background of Study
The whole research work is based on the milling process which is the core of each metal
cutting process. It is a method which is considered to be a finishing and shaping of workpiece. In
it a cutter with more than one or more teeth is used, while the milling cutter is mounted in a
rotating spindle, while any type of workpiece is moved linearly moved in the direction of cutter.
Basically this research is based on finding out the reasons behind variations that exist at a
workplace due to low stiffness and accuracy of cutting tool. There are various reasons which are
causing hindrance in getting the whole process done (Moshat and et. al., 2010). Each milling tool
tries to search a Trochoidal path.
There are certain issues that exist in the dynamic stability of the workpiece which is kept
in between cutter and the workstation. Due to this stability is not being achieved in a proper
manner. Also, varying speed of spindle is causing vibrations that reduces accuracy of the process
of milling. There are various principles of fixtures which will assist in bringing better stability to
the workpiece movement at varying speed. Piezoelectric vibration measuring system is used for
1
⊘ This is a preview!⊘
Do you want full access?
Subscribe today to unlock all pages.

Trusted by 1+ million students worldwide
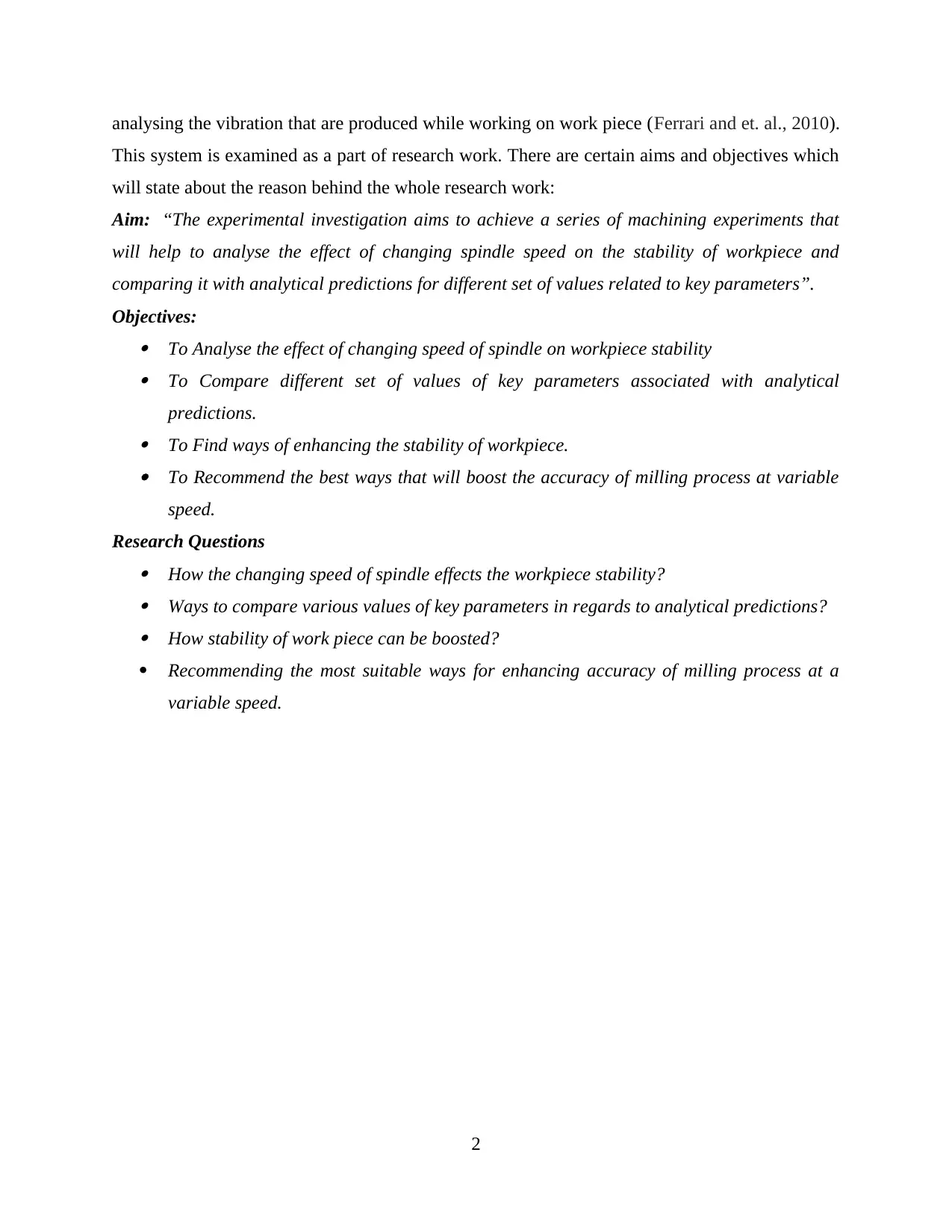
analysing the vibration that are produced while working on work piece (Ferrari and et. al., 2010).
This system is examined as a part of research work. There are certain aims and objectives which
will state about the reason behind the whole research work:
Aim: “The experimental investigation aims to achieve a series of machining experiments that
will help to analyse the effect of changing spindle speed on the stability of workpiece and
comparing it with analytical predictions for different set of values related to key parameters”.
Objectives: To Analyse the effect of changing speed of spindle on workpiece stability To Compare different set of values of key parameters associated with analytical
predictions. To Find ways of enhancing the stability of workpiece. To Recommend the best ways that will boost the accuracy of milling process at variable
speed.
Research Questions How the changing speed of spindle effects the workpiece stability? Ways to compare various values of key parameters in regards to analytical predictions? How stability of work piece can be boosted?
Recommending the most suitable ways for enhancing accuracy of milling process at a
variable speed.
2
This system is examined as a part of research work. There are certain aims and objectives which
will state about the reason behind the whole research work:
Aim: “The experimental investigation aims to achieve a series of machining experiments that
will help to analyse the effect of changing spindle speed on the stability of workpiece and
comparing it with analytical predictions for different set of values related to key parameters”.
Objectives: To Analyse the effect of changing speed of spindle on workpiece stability To Compare different set of values of key parameters associated with analytical
predictions. To Find ways of enhancing the stability of workpiece. To Recommend the best ways that will boost the accuracy of milling process at variable
speed.
Research Questions How the changing speed of spindle effects the workpiece stability? Ways to compare various values of key parameters in regards to analytical predictions? How stability of work piece can be boosted?
Recommending the most suitable ways for enhancing accuracy of milling process at a
variable speed.
2
Paraphrase This Document
Need a fresh take? Get an instant paraphrase of this document with our AI Paraphraser
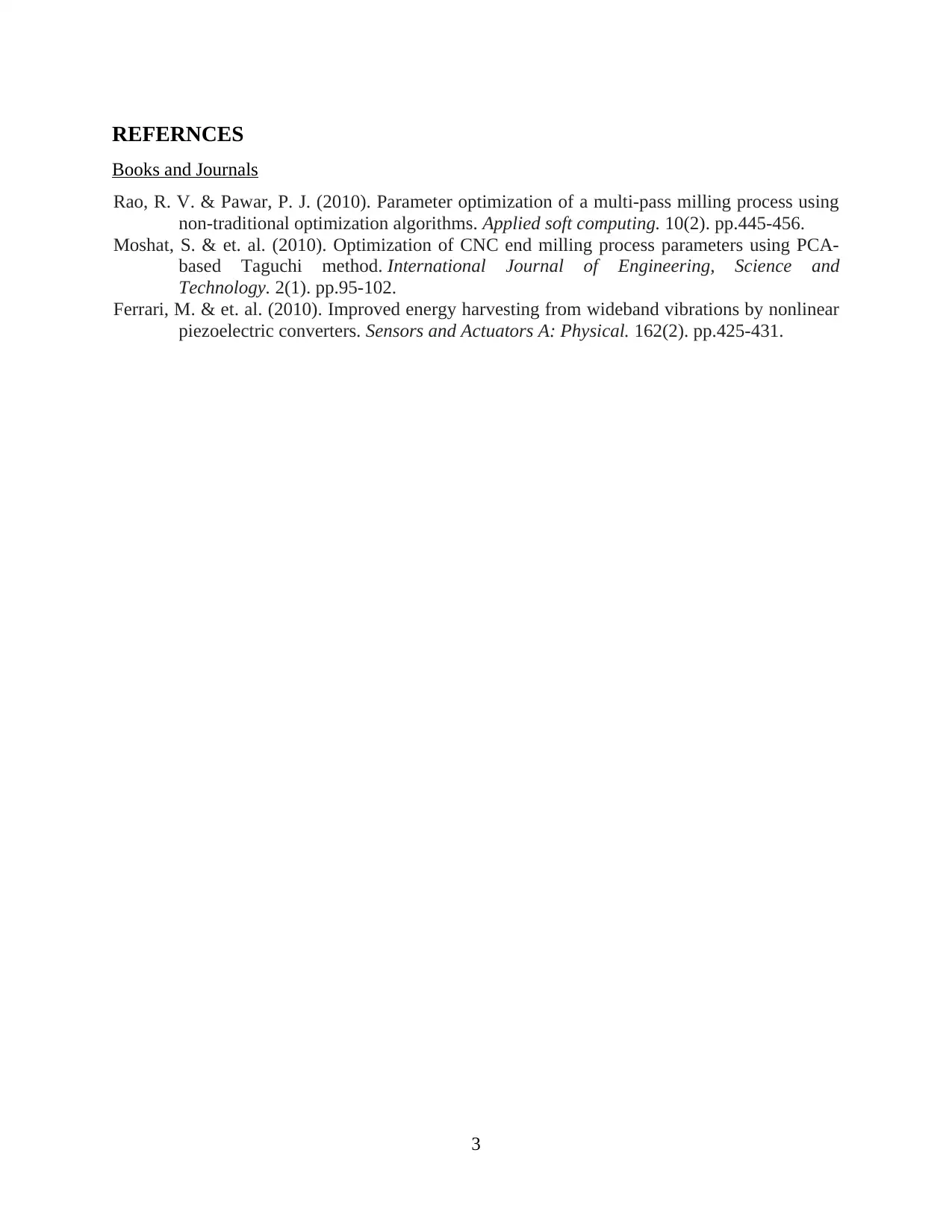
REFERNCES
Books and Journals
Rao, R. V. & Pawar, P. J. (2010). Parameter optimization of a multi-pass milling process using
non-traditional optimization algorithms. Applied soft computing. 10(2). pp.445-456.
Moshat, S. & et. al. (2010). Optimization of CNC end milling process parameters using PCA-
based Taguchi method. International Journal of Engineering, Science and
Technology. 2(1). pp.95-102.
Ferrari, M. & et. al. (2010). Improved energy harvesting from wideband vibrations by nonlinear
piezoelectric converters. Sensors and Actuators A: Physical. 162(2). pp.425-431.
3
Books and Journals
Rao, R. V. & Pawar, P. J. (2010). Parameter optimization of a multi-pass milling process using
non-traditional optimization algorithms. Applied soft computing. 10(2). pp.445-456.
Moshat, S. & et. al. (2010). Optimization of CNC end milling process parameters using PCA-
based Taguchi method. International Journal of Engineering, Science and
Technology. 2(1). pp.95-102.
Ferrari, M. & et. al. (2010). Improved energy harvesting from wideband vibrations by nonlinear
piezoelectric converters. Sensors and Actuators A: Physical. 162(2). pp.425-431.
3
1 out of 5
Related Documents

Your All-in-One AI-Powered Toolkit for Academic Success.
+13062052269
info@desklib.com
Available 24*7 on WhatsApp / Email
Unlock your academic potential
© 2024 | Zucol Services PVT LTD | All rights reserved.