International Construction: Modular Technology in India and Australia
VerifiedAdded on 2020/03/23
|19
|5888
|112
Report
AI Summary
This report provides a comparative analysis of modular construction, examining its adoption and impact in India and Australia. It begins with an executive summary and introduction, highlighting the growing interest in modular construction due to its potential to save costs, reduce construction time, and promote environmental sustainability. The report then presents detailed case studies of India and Australia, exploring the historical context, current trends, and factors influencing the use of modular technology in each country. A comparative analysis identifies similarities and differences, addressing factors like personal attitudes, resistance to change, capital involvement, and economies of scale. The report also discusses the benefits and challenges of modular construction, including reduced construction time, cost savings, consistency, and sustainability. It concludes with recommendations for investors and stakeholders interested in entering the modular construction market, emphasizing the international significance of the trends observed in the two case studies.

RUNNING HEAD: INTERNATIONAL CONSTRUCTION
NAME
UNIT
ASSIGNMENT
ASSESSMENT NUMBER
NAME
UNIT
ASSIGNMENT
ASSESSMENT NUMBER
Secure Best Marks with AI Grader
Need help grading? Try our AI Grader for instant feedback on your assignments.
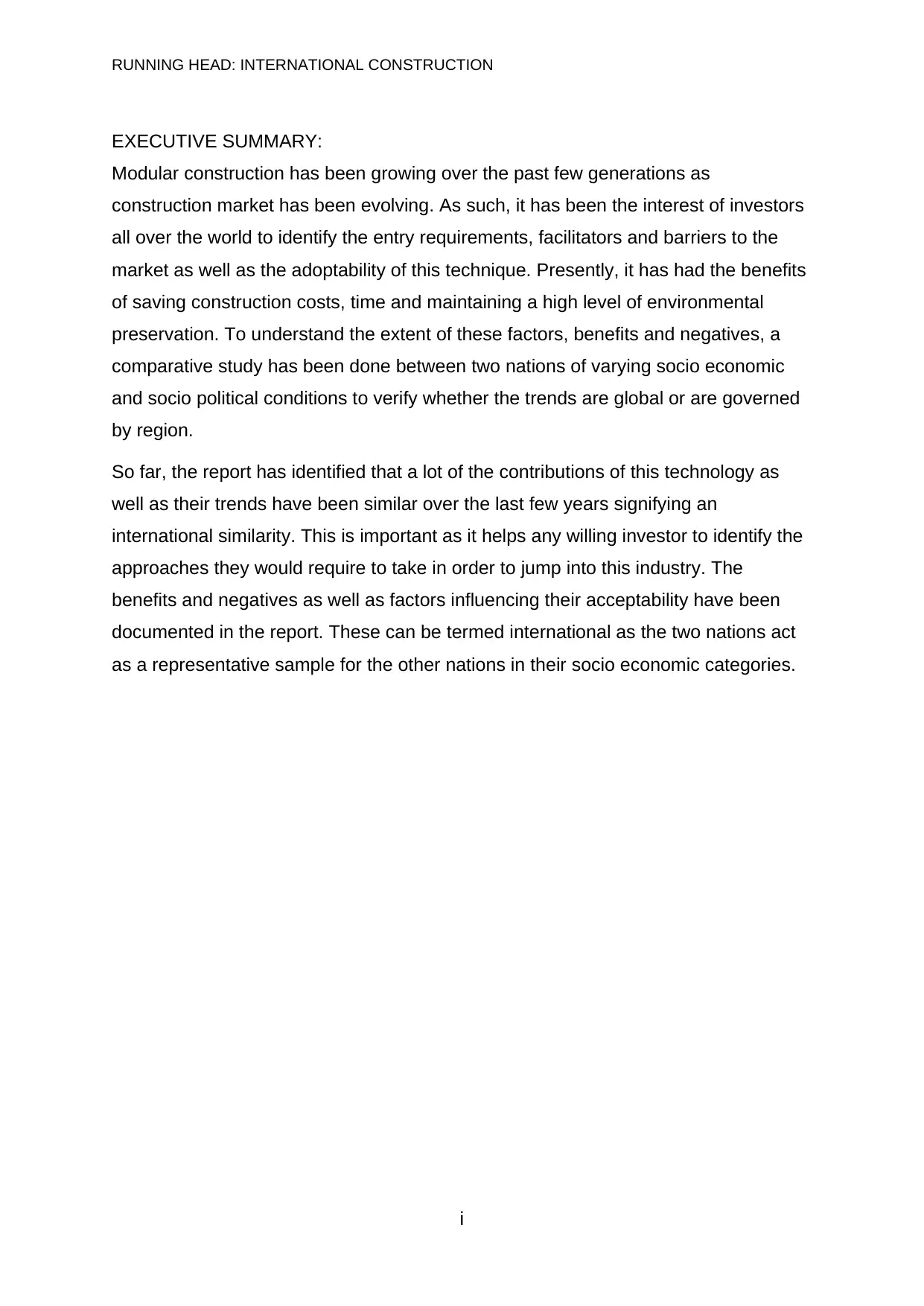
RUNNING HEAD: INTERNATIONAL CONSTRUCTION
EXECUTIVE SUMMARY:
Modular construction has been growing over the past few generations as
construction market has been evolving. As such, it has been the interest of investors
all over the world to identify the entry requirements, facilitators and barriers to the
market as well as the adoptability of this technique. Presently, it has had the benefits
of saving construction costs, time and maintaining a high level of environmental
preservation. To understand the extent of these factors, benefits and negatives, a
comparative study has been done between two nations of varying socio economic
and socio political conditions to verify whether the trends are global or are governed
by region.
So far, the report has identified that a lot of the contributions of this technology as
well as their trends have been similar over the last few years signifying an
international similarity. This is important as it helps any willing investor to identify the
approaches they would require to take in order to jump into this industry. The
benefits and negatives as well as factors influencing their acceptability have been
documented in the report. These can be termed international as the two nations act
as a representative sample for the other nations in their socio economic categories.
i
EXECUTIVE SUMMARY:
Modular construction has been growing over the past few generations as
construction market has been evolving. As such, it has been the interest of investors
all over the world to identify the entry requirements, facilitators and barriers to the
market as well as the adoptability of this technique. Presently, it has had the benefits
of saving construction costs, time and maintaining a high level of environmental
preservation. To understand the extent of these factors, benefits and negatives, a
comparative study has been done between two nations of varying socio economic
and socio political conditions to verify whether the trends are global or are governed
by region.
So far, the report has identified that a lot of the contributions of this technology as
well as their trends have been similar over the last few years signifying an
international similarity. This is important as it helps any willing investor to identify the
approaches they would require to take in order to jump into this industry. The
benefits and negatives as well as factors influencing their acceptability have been
documented in the report. These can be termed international as the two nations act
as a representative sample for the other nations in their socio economic categories.
i
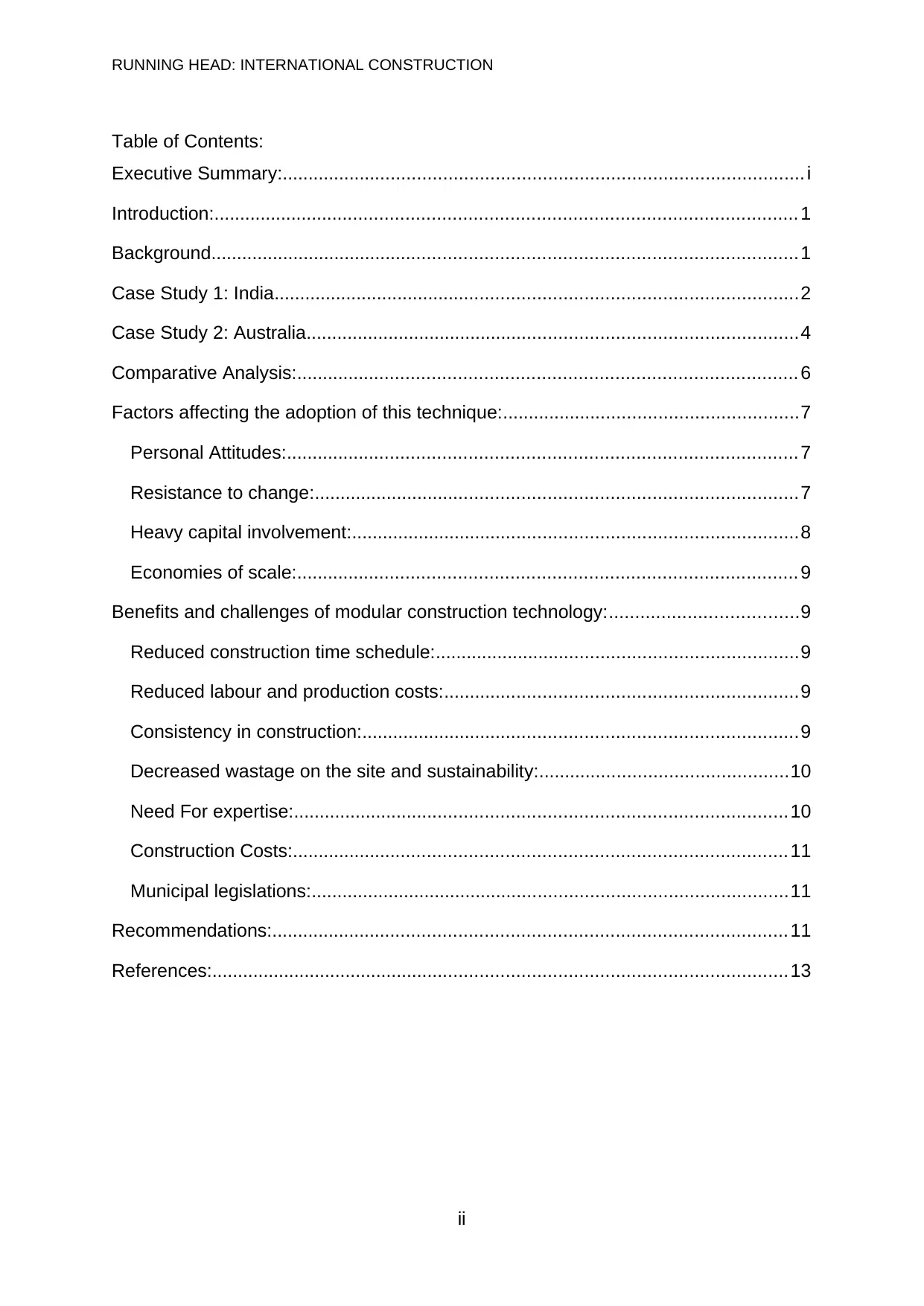
RUNNING HEAD: INTERNATIONAL CONSTRUCTION
Table of Contents:
Executive Summary:.................................................................................................... i
Introduction:................................................................................................................ 1
Background.................................................................................................................1
Case Study 1: India.....................................................................................................2
Case Study 2: Australia...............................................................................................4
Comparative Analysis:................................................................................................ 6
Factors affecting the adoption of this technique:.........................................................7
Personal Attitudes:.................................................................................................. 7
Resistance to change:.............................................................................................7
Heavy capital involvement:......................................................................................8
Economies of scale:................................................................................................ 9
Benefits and challenges of modular construction technology:....................................9
Reduced construction time schedule:......................................................................9
Reduced labour and production costs:....................................................................9
Consistency in construction:....................................................................................9
Decreased wastage on the site and sustainability:................................................10
Need For expertise:...............................................................................................10
Construction Costs:............................................................................................... 11
Municipal legislations:............................................................................................11
Recommendations:................................................................................................... 11
References:...............................................................................................................13
ii
Table of Contents:
Executive Summary:.................................................................................................... i
Introduction:................................................................................................................ 1
Background.................................................................................................................1
Case Study 1: India.....................................................................................................2
Case Study 2: Australia...............................................................................................4
Comparative Analysis:................................................................................................ 6
Factors affecting the adoption of this technique:.........................................................7
Personal Attitudes:.................................................................................................. 7
Resistance to change:.............................................................................................7
Heavy capital involvement:......................................................................................8
Economies of scale:................................................................................................ 9
Benefits and challenges of modular construction technology:....................................9
Reduced construction time schedule:......................................................................9
Reduced labour and production costs:....................................................................9
Consistency in construction:....................................................................................9
Decreased wastage on the site and sustainability:................................................10
Need For expertise:...............................................................................................10
Construction Costs:............................................................................................... 11
Municipal legislations:............................................................................................11
Recommendations:................................................................................................... 11
References:...............................................................................................................13
ii
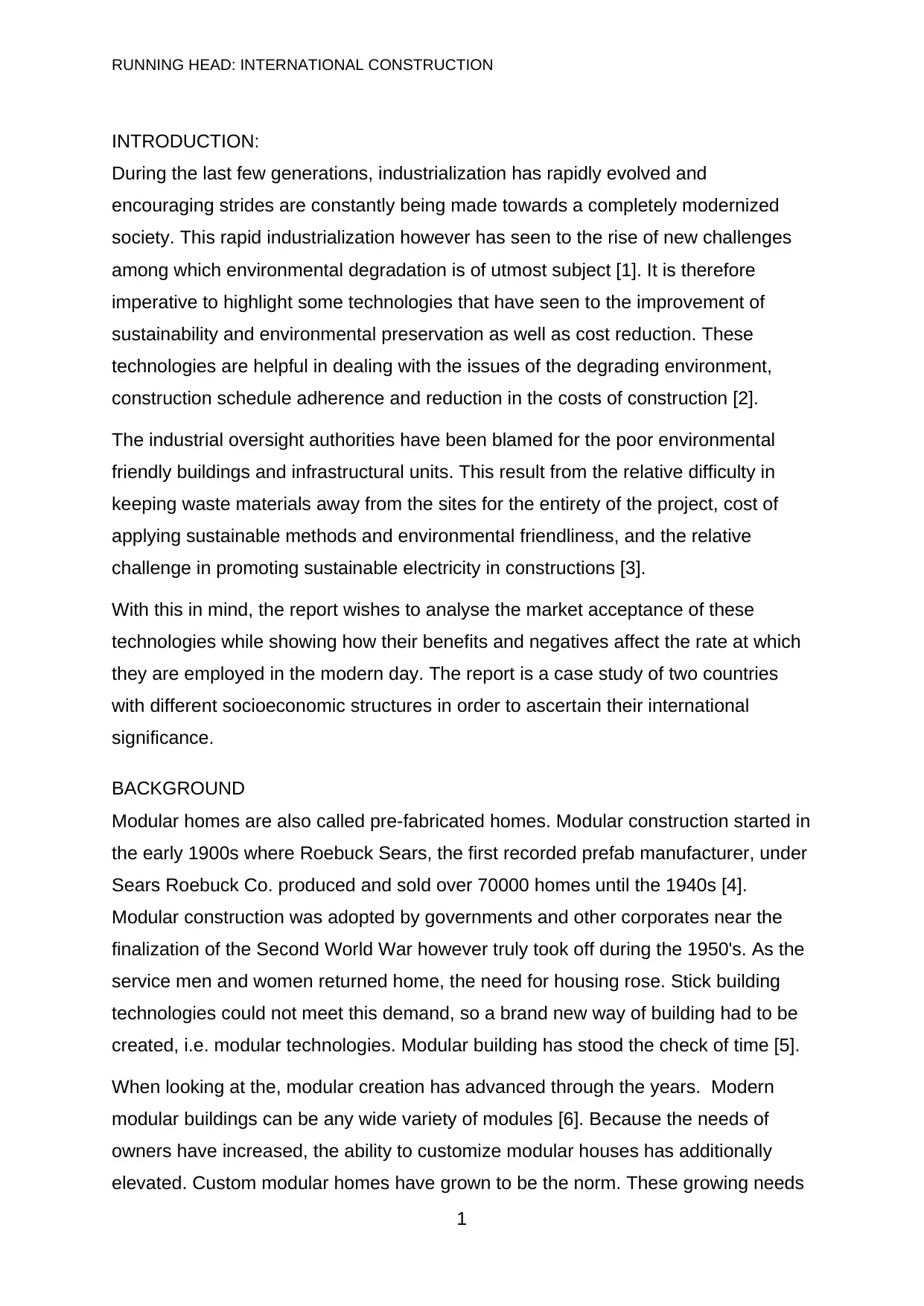
RUNNING HEAD: INTERNATIONAL CONSTRUCTION
INTRODUCTION:
During the last few generations, industrialization has rapidly evolved and
encouraging strides are constantly being made towards a completely modernized
society. This rapid industrialization however has seen to the rise of new challenges
among which environmental degradation is of utmost subject [1]. It is therefore
imperative to highlight some technologies that have seen to the improvement of
sustainability and environmental preservation as well as cost reduction. These
technologies are helpful in dealing with the issues of the degrading environment,
construction schedule adherence and reduction in the costs of construction [2].
The industrial oversight authorities have been blamed for the poor environmental
friendly buildings and infrastructural units. This result from the relative difficulty in
keeping waste materials away from the sites for the entirety of the project, cost of
applying sustainable methods and environmental friendliness, and the relative
challenge in promoting sustainable electricity in constructions [3].
With this in mind, the report wishes to analyse the market acceptance of these
technologies while showing how their benefits and negatives affect the rate at which
they are employed in the modern day. The report is a case study of two countries
with different socioeconomic structures in order to ascertain their international
significance.
BACKGROUND
Modular homes are also called pre-fabricated homes. Modular construction started in
the early 1900s where Roebuck Sears, the first recorded prefab manufacturer, under
Sears Roebuck Co. produced and sold over 70000 homes until the 1940s [4].
Modular construction was adopted by governments and other corporates near the
finalization of the Second World War however truly took off during the 1950's. As the
service men and women returned home, the need for housing rose. Stick building
technologies could not meet this demand, so a brand new way of building had to be
created, i.e. modular technologies. Modular building has stood the check of time [5].
When looking at the, modular creation has advanced through the years. Modern
modular buildings can be any wide variety of modules [6]. Because the needs of
owners have increased, the ability to customize modular houses has additionally
elevated. Custom modular homes have grown to be the norm. These growing needs
1
INTRODUCTION:
During the last few generations, industrialization has rapidly evolved and
encouraging strides are constantly being made towards a completely modernized
society. This rapid industrialization however has seen to the rise of new challenges
among which environmental degradation is of utmost subject [1]. It is therefore
imperative to highlight some technologies that have seen to the improvement of
sustainability and environmental preservation as well as cost reduction. These
technologies are helpful in dealing with the issues of the degrading environment,
construction schedule adherence and reduction in the costs of construction [2].
The industrial oversight authorities have been blamed for the poor environmental
friendly buildings and infrastructural units. This result from the relative difficulty in
keeping waste materials away from the sites for the entirety of the project, cost of
applying sustainable methods and environmental friendliness, and the relative
challenge in promoting sustainable electricity in constructions [3].
With this in mind, the report wishes to analyse the market acceptance of these
technologies while showing how their benefits and negatives affect the rate at which
they are employed in the modern day. The report is a case study of two countries
with different socioeconomic structures in order to ascertain their international
significance.
BACKGROUND
Modular homes are also called pre-fabricated homes. Modular construction started in
the early 1900s where Roebuck Sears, the first recorded prefab manufacturer, under
Sears Roebuck Co. produced and sold over 70000 homes until the 1940s [4].
Modular construction was adopted by governments and other corporates near the
finalization of the Second World War however truly took off during the 1950's. As the
service men and women returned home, the need for housing rose. Stick building
technologies could not meet this demand, so a brand new way of building had to be
created, i.e. modular technologies. Modular building has stood the check of time [5].
When looking at the, modular creation has advanced through the years. Modern
modular buildings can be any wide variety of modules [6]. Because the needs of
owners have increased, the ability to customize modular houses has additionally
elevated. Custom modular homes have grown to be the norm. These growing needs
1
Secure Best Marks with AI Grader
Need help grading? Try our AI Grader for instant feedback on your assignments.
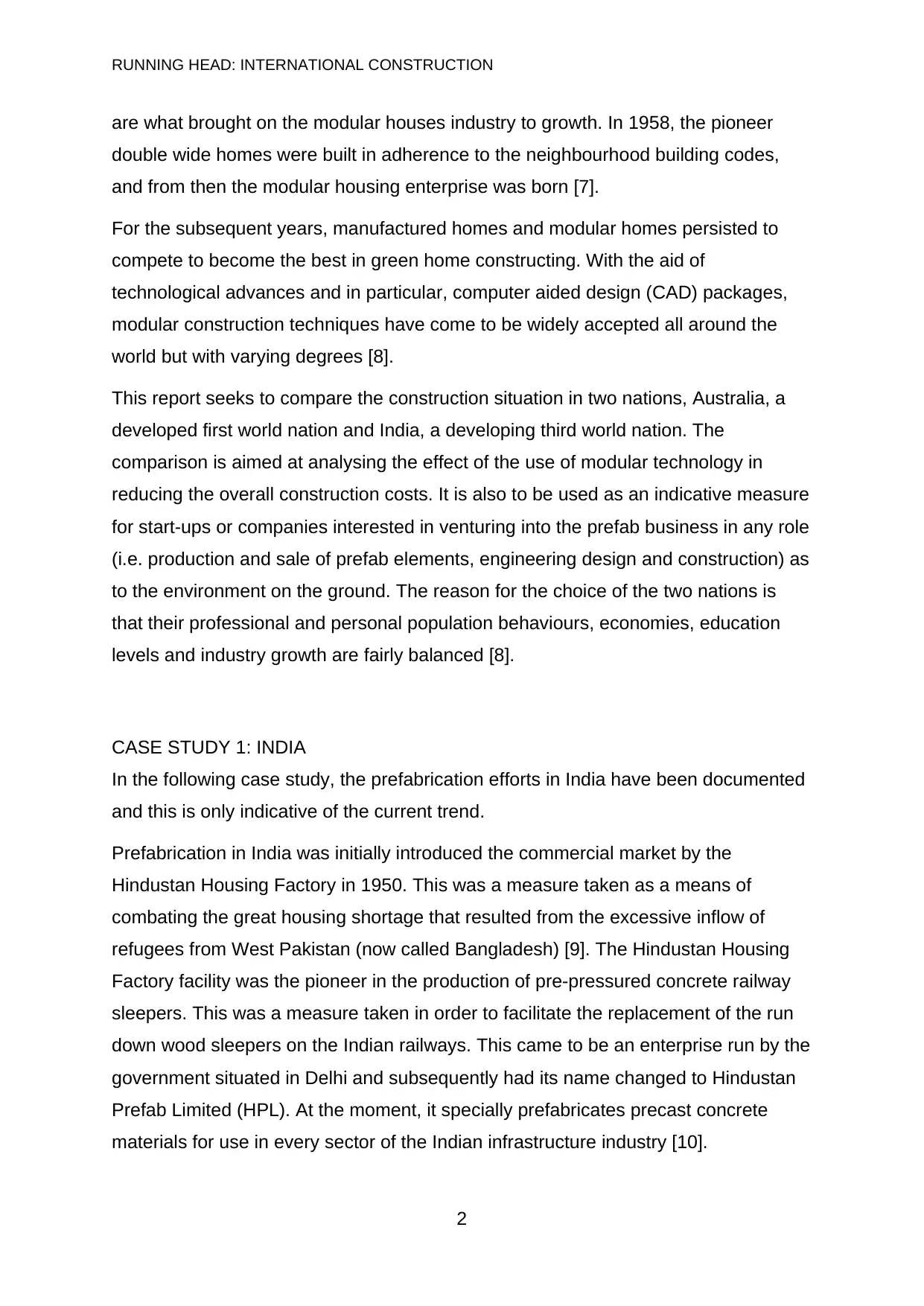
RUNNING HEAD: INTERNATIONAL CONSTRUCTION
are what brought on the modular houses industry to growth. In 1958, the pioneer
double wide homes were built in adherence to the neighbourhood building codes,
and from then the modular housing enterprise was born [7].
For the subsequent years, manufactured homes and modular homes persisted to
compete to become the best in green home constructing. With the aid of
technological advances and in particular, computer aided design (CAD) packages,
modular construction techniques have come to be widely accepted all around the
world but with varying degrees [8].
This report seeks to compare the construction situation in two nations, Australia, a
developed first world nation and India, a developing third world nation. The
comparison is aimed at analysing the effect of the use of modular technology in
reducing the overall construction costs. It is also to be used as an indicative measure
for start-ups or companies interested in venturing into the prefab business in any role
(i.e. production and sale of prefab elements, engineering design and construction) as
to the environment on the ground. The reason for the choice of the two nations is
that their professional and personal population behaviours, economies, education
levels and industry growth are fairly balanced [8].
CASE STUDY 1: INDIA
In the following case study, the prefabrication efforts in India have been documented
and this is only indicative of the current trend.
Prefabrication in India was initially introduced the commercial market by the
Hindustan Housing Factory in 1950. This was a measure taken as a means of
combating the great housing shortage that resulted from the excessive inflow of
refugees from West Pakistan (now called Bangladesh) [9]. The Hindustan Housing
Factory facility was the pioneer in the production of pre-pressured concrete railway
sleepers. This was a measure taken in order to facilitate the replacement of the run
down wood sleepers on the Indian railways. This came to be an enterprise run by the
government situated in Delhi and subsequently had its name changed to Hindustan
Prefab Limited (HPL). At the moment, it specially prefabricates precast concrete
materials for use in every sector of the Indian infrastructure industry [10].
2
are what brought on the modular houses industry to growth. In 1958, the pioneer
double wide homes were built in adherence to the neighbourhood building codes,
and from then the modular housing enterprise was born [7].
For the subsequent years, manufactured homes and modular homes persisted to
compete to become the best in green home constructing. With the aid of
technological advances and in particular, computer aided design (CAD) packages,
modular construction techniques have come to be widely accepted all around the
world but with varying degrees [8].
This report seeks to compare the construction situation in two nations, Australia, a
developed first world nation and India, a developing third world nation. The
comparison is aimed at analysing the effect of the use of modular technology in
reducing the overall construction costs. It is also to be used as an indicative measure
for start-ups or companies interested in venturing into the prefab business in any role
(i.e. production and sale of prefab elements, engineering design and construction) as
to the environment on the ground. The reason for the choice of the two nations is
that their professional and personal population behaviours, economies, education
levels and industry growth are fairly balanced [8].
CASE STUDY 1: INDIA
In the following case study, the prefabrication efforts in India have been documented
and this is only indicative of the current trend.
Prefabrication in India was initially introduced the commercial market by the
Hindustan Housing Factory in 1950. This was a measure taken as a means of
combating the great housing shortage that resulted from the excessive inflow of
refugees from West Pakistan (now called Bangladesh) [9]. The Hindustan Housing
Factory facility was the pioneer in the production of pre-pressured concrete railway
sleepers. This was a measure taken in order to facilitate the replacement of the run
down wood sleepers on the Indian railways. This came to be an enterprise run by the
government situated in Delhi and subsequently had its name changed to Hindustan
Prefab Limited (HPL). At the moment, it specially prefabricates precast concrete
materials for use in every sector of the Indian infrastructure industry [10].
2
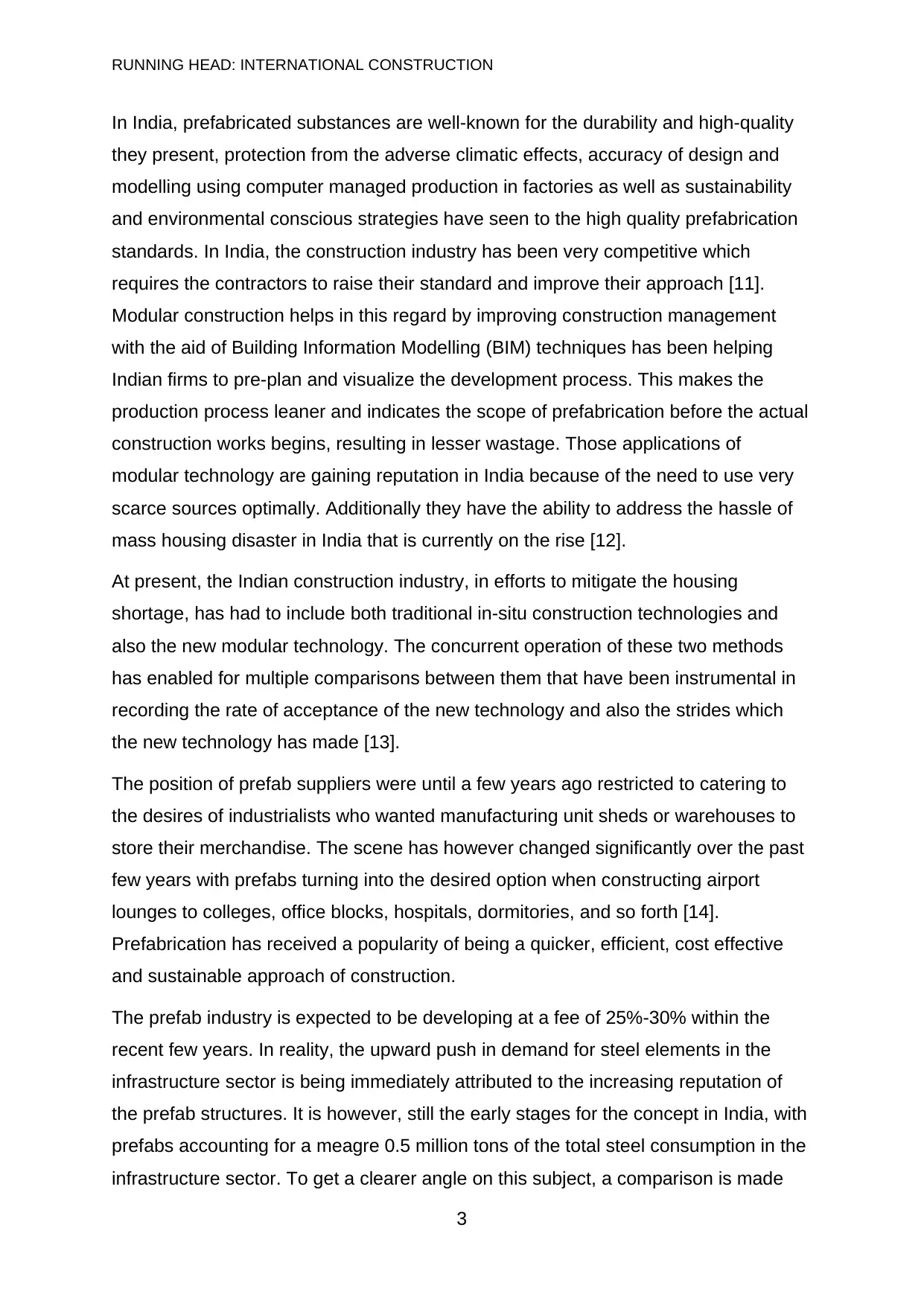
RUNNING HEAD: INTERNATIONAL CONSTRUCTION
In India, prefabricated substances are well-known for the durability and high-quality
they present, protection from the adverse climatic effects, accuracy of design and
modelling using computer managed production in factories as well as sustainability
and environmental conscious strategies have seen to the high quality prefabrication
standards. In India, the construction industry has been very competitive which
requires the contractors to raise their standard and improve their approach [11].
Modular construction helps in this regard by improving construction management
with the aid of Building Information Modelling (BIM) techniques has been helping
Indian firms to pre-plan and visualize the development process. This makes the
production process leaner and indicates the scope of prefabrication before the actual
construction works begins, resulting in lesser wastage. Those applications of
modular technology are gaining reputation in India because of the need to use very
scarce sources optimally. Additionally they have the ability to address the hassle of
mass housing disaster in India that is currently on the rise [12].
At present, the Indian construction industry, in efforts to mitigate the housing
shortage, has had to include both traditional in-situ construction technologies and
also the new modular technology. The concurrent operation of these two methods
has enabled for multiple comparisons between them that have been instrumental in
recording the rate of acceptance of the new technology and also the strides which
the new technology has made [13].
The position of prefab suppliers were until a few years ago restricted to catering to
the desires of industrialists who wanted manufacturing unit sheds or warehouses to
store their merchandise. The scene has however changed significantly over the past
few years with prefabs turning into the desired option when constructing airport
lounges to colleges, office blocks, hospitals, dormitories, and so forth [14].
Prefabrication has received a popularity of being a quicker, efficient, cost effective
and sustainable approach of construction.
The prefab industry is expected to be developing at a fee of 25%-30% within the
recent few years. In reality, the upward push in demand for steel elements in the
infrastructure sector is being immediately attributed to the increasing reputation of
the prefab structures. It is however, still the early stages for the concept in India, with
prefabs accounting for a meagre 0.5 million tons of the total steel consumption in the
infrastructure sector. To get a clearer angle on this subject, a comparison is made
3
In India, prefabricated substances are well-known for the durability and high-quality
they present, protection from the adverse climatic effects, accuracy of design and
modelling using computer managed production in factories as well as sustainability
and environmental conscious strategies have seen to the high quality prefabrication
standards. In India, the construction industry has been very competitive which
requires the contractors to raise their standard and improve their approach [11].
Modular construction helps in this regard by improving construction management
with the aid of Building Information Modelling (BIM) techniques has been helping
Indian firms to pre-plan and visualize the development process. This makes the
production process leaner and indicates the scope of prefabrication before the actual
construction works begins, resulting in lesser wastage. Those applications of
modular technology are gaining reputation in India because of the need to use very
scarce sources optimally. Additionally they have the ability to address the hassle of
mass housing disaster in India that is currently on the rise [12].
At present, the Indian construction industry, in efforts to mitigate the housing
shortage, has had to include both traditional in-situ construction technologies and
also the new modular technology. The concurrent operation of these two methods
has enabled for multiple comparisons between them that have been instrumental in
recording the rate of acceptance of the new technology and also the strides which
the new technology has made [13].
The position of prefab suppliers were until a few years ago restricted to catering to
the desires of industrialists who wanted manufacturing unit sheds or warehouses to
store their merchandise. The scene has however changed significantly over the past
few years with prefabs turning into the desired option when constructing airport
lounges to colleges, office blocks, hospitals, dormitories, and so forth [14].
Prefabrication has received a popularity of being a quicker, efficient, cost effective
and sustainable approach of construction.
The prefab industry is expected to be developing at a fee of 25%-30% within the
recent few years. In reality, the upward push in demand for steel elements in the
infrastructure sector is being immediately attributed to the increasing reputation of
the prefab structures. It is however, still the early stages for the concept in India, with
prefabs accounting for a meagre 0.5 million tons of the total steel consumption in the
infrastructure sector. To get a clearer angle on this subject, a comparison is made
3
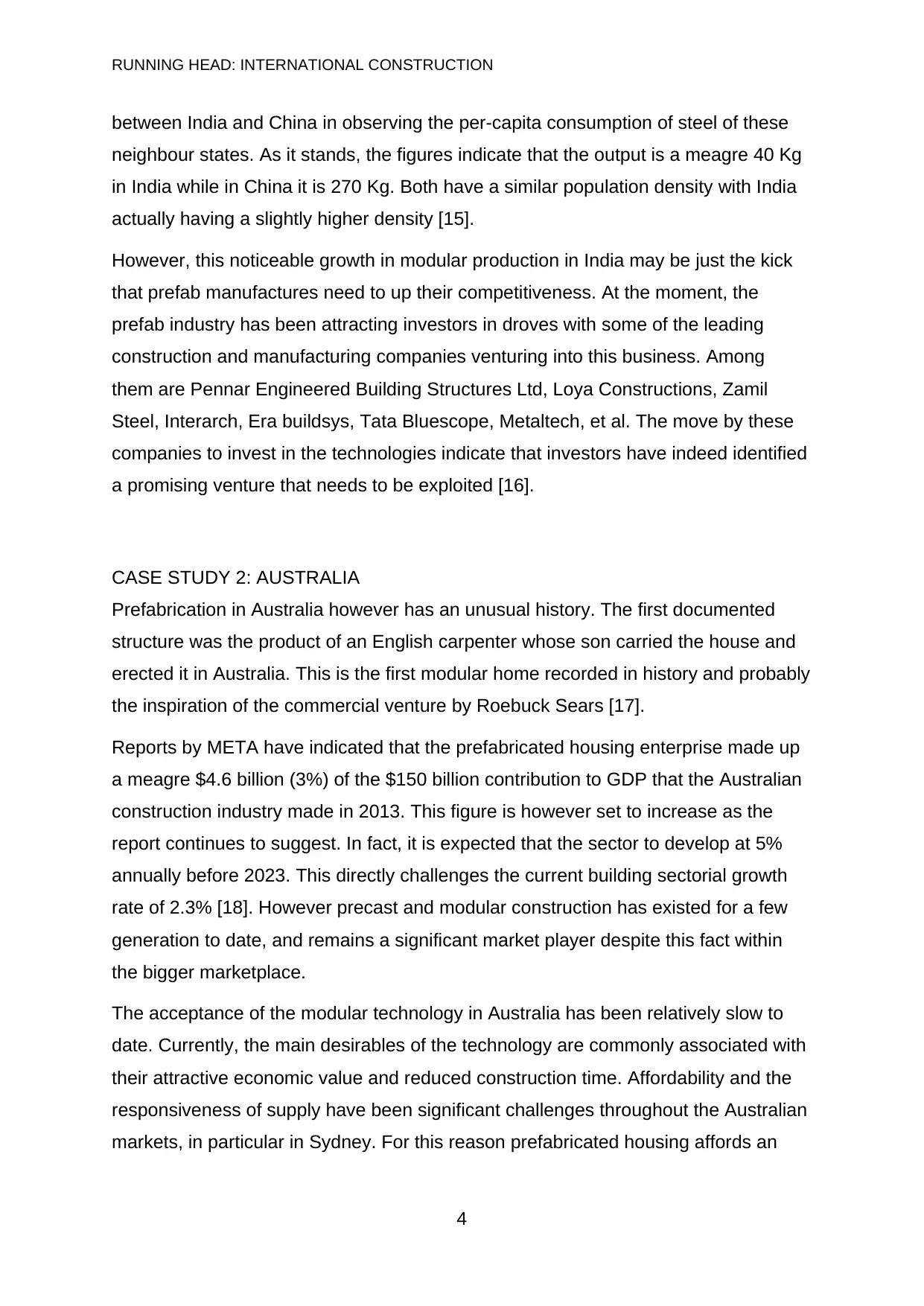
RUNNING HEAD: INTERNATIONAL CONSTRUCTION
between India and China in observing the per-capita consumption of steel of these
neighbour states. As it stands, the figures indicate that the output is a meagre 40 Kg
in India while in China it is 270 Kg. Both have a similar population density with India
actually having a slightly higher density [15].
However, this noticeable growth in modular production in India may be just the kick
that prefab manufactures need to up their competitiveness. At the moment, the
prefab industry has been attracting investors in droves with some of the leading
construction and manufacturing companies venturing into this business. Among
them are Pennar Engineered Building Structures Ltd, Loya Constructions, Zamil
Steel, Interarch, Era buildsys, Tata Bluescope, Metaltech, et al. The move by these
companies to invest in the technologies indicate that investors have indeed identified
a promising venture that needs to be exploited [16].
CASE STUDY 2: AUSTRALIA
Prefabrication in Australia however has an unusual history. The first documented
structure was the product of an English carpenter whose son carried the house and
erected it in Australia. This is the first modular home recorded in history and probably
the inspiration of the commercial venture by Roebuck Sears [17].
Reports by META have indicated that the prefabricated housing enterprise made up
a meagre $4.6 billion (3%) of the $150 billion contribution to GDP that the Australian
construction industry made in 2013. This figure is however set to increase as the
report continues to suggest. In fact, it is expected that the sector to develop at 5%
annually before 2023. This directly challenges the current building sectorial growth
rate of 2.3% [18]. However precast and modular construction has existed for a few
generation to date, and remains a significant market player despite this fact within
the bigger marketplace.
The acceptance of the modular technology in Australia has been relatively slow to
date. Currently, the main desirables of the technology are commonly associated with
their attractive economic value and reduced construction time. Affordability and the
responsiveness of supply have been significant challenges throughout the Australian
markets, in particular in Sydney. For this reason prefabricated housing affords an
4
between India and China in observing the per-capita consumption of steel of these
neighbour states. As it stands, the figures indicate that the output is a meagre 40 Kg
in India while in China it is 270 Kg. Both have a similar population density with India
actually having a slightly higher density [15].
However, this noticeable growth in modular production in India may be just the kick
that prefab manufactures need to up their competitiveness. At the moment, the
prefab industry has been attracting investors in droves with some of the leading
construction and manufacturing companies venturing into this business. Among
them are Pennar Engineered Building Structures Ltd, Loya Constructions, Zamil
Steel, Interarch, Era buildsys, Tata Bluescope, Metaltech, et al. The move by these
companies to invest in the technologies indicate that investors have indeed identified
a promising venture that needs to be exploited [16].
CASE STUDY 2: AUSTRALIA
Prefabrication in Australia however has an unusual history. The first documented
structure was the product of an English carpenter whose son carried the house and
erected it in Australia. This is the first modular home recorded in history and probably
the inspiration of the commercial venture by Roebuck Sears [17].
Reports by META have indicated that the prefabricated housing enterprise made up
a meagre $4.6 billion (3%) of the $150 billion contribution to GDP that the Australian
construction industry made in 2013. This figure is however set to increase as the
report continues to suggest. In fact, it is expected that the sector to develop at 5%
annually before 2023. This directly challenges the current building sectorial growth
rate of 2.3% [18]. However precast and modular construction has existed for a few
generation to date, and remains a significant market player despite this fact within
the bigger marketplace.
The acceptance of the modular technology in Australia has been relatively slow to
date. Currently, the main desirables of the technology are commonly associated with
their attractive economic value and reduced construction time. Affordability and the
responsiveness of supply have been significant challenges throughout the Australian
markets, in particular in Sydney. For this reason prefabricated housing affords an
4
Paraphrase This Document
Need a fresh take? Get an instant paraphrase of this document with our AI Paraphraser
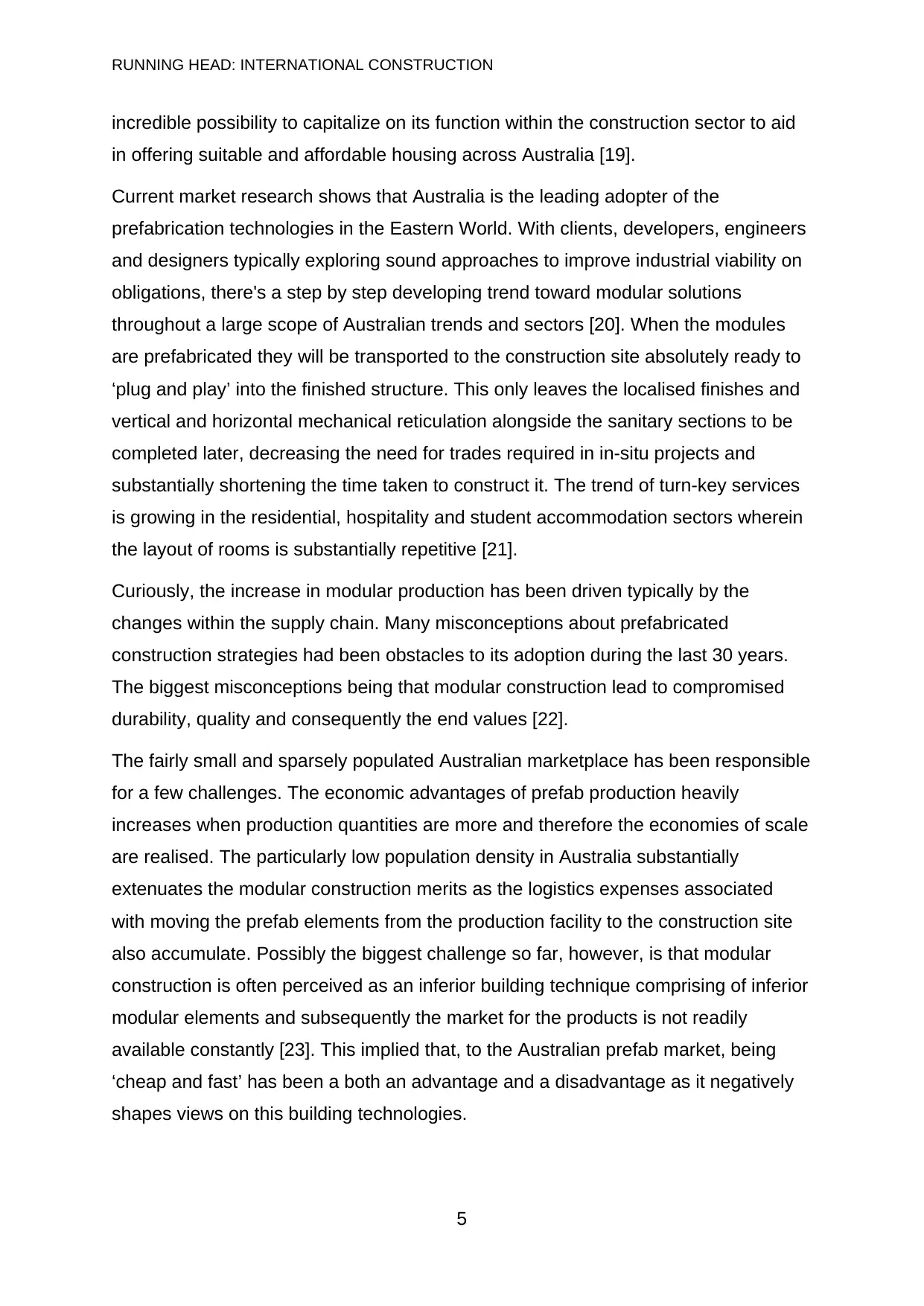
RUNNING HEAD: INTERNATIONAL CONSTRUCTION
incredible possibility to capitalize on its function within the construction sector to aid
in offering suitable and affordable housing across Australia [19].
Current market research shows that Australia is the leading adopter of the
prefabrication technologies in the Eastern World. With clients, developers, engineers
and designers typically exploring sound approaches to improve industrial viability on
obligations, there's a step by step developing trend toward modular solutions
throughout a large scope of Australian trends and sectors [20]. When the modules
are prefabricated they will be transported to the construction site absolutely ready to
‘plug and play’ into the finished structure. This only leaves the localised finishes and
vertical and horizontal mechanical reticulation alongside the sanitary sections to be
completed later, decreasing the need for trades required in in-situ projects and
substantially shortening the time taken to construct it. The trend of turn-key services
is growing in the residential, hospitality and student accommodation sectors wherein
the layout of rooms is substantially repetitive [21].
Curiously, the increase in modular production has been driven typically by the
changes within the supply chain. Many misconceptions about prefabricated
construction strategies had been obstacles to its adoption during the last 30 years.
The biggest misconceptions being that modular construction lead to compromised
durability, quality and consequently the end values [22].
The fairly small and sparsely populated Australian marketplace has been responsible
for a few challenges. The economic advantages of prefab production heavily
increases when production quantities are more and therefore the economies of scale
are realised. The particularly low population density in Australia substantially
extenuates the modular construction merits as the logistics expenses associated
with moving the prefab elements from the production facility to the construction site
also accumulate. Possibly the biggest challenge so far, however, is that modular
construction is often perceived as an inferior building technique comprising of inferior
modular elements and subsequently the market for the products is not readily
available constantly [23]. This implied that, to the Australian prefab market, being
‘cheap and fast’ has been a both an advantage and a disadvantage as it negatively
shapes views on this building technologies.
5
incredible possibility to capitalize on its function within the construction sector to aid
in offering suitable and affordable housing across Australia [19].
Current market research shows that Australia is the leading adopter of the
prefabrication technologies in the Eastern World. With clients, developers, engineers
and designers typically exploring sound approaches to improve industrial viability on
obligations, there's a step by step developing trend toward modular solutions
throughout a large scope of Australian trends and sectors [20]. When the modules
are prefabricated they will be transported to the construction site absolutely ready to
‘plug and play’ into the finished structure. This only leaves the localised finishes and
vertical and horizontal mechanical reticulation alongside the sanitary sections to be
completed later, decreasing the need for trades required in in-situ projects and
substantially shortening the time taken to construct it. The trend of turn-key services
is growing in the residential, hospitality and student accommodation sectors wherein
the layout of rooms is substantially repetitive [21].
Curiously, the increase in modular production has been driven typically by the
changes within the supply chain. Many misconceptions about prefabricated
construction strategies had been obstacles to its adoption during the last 30 years.
The biggest misconceptions being that modular construction lead to compromised
durability, quality and consequently the end values [22].
The fairly small and sparsely populated Australian marketplace has been responsible
for a few challenges. The economic advantages of prefab production heavily
increases when production quantities are more and therefore the economies of scale
are realised. The particularly low population density in Australia substantially
extenuates the modular construction merits as the logistics expenses associated
with moving the prefab elements from the production facility to the construction site
also accumulate. Possibly the biggest challenge so far, however, is that modular
construction is often perceived as an inferior building technique comprising of inferior
modular elements and subsequently the market for the products is not readily
available constantly [23]. This implied that, to the Australian prefab market, being
‘cheap and fast’ has been a both an advantage and a disadvantage as it negatively
shapes views on this building technologies.
5
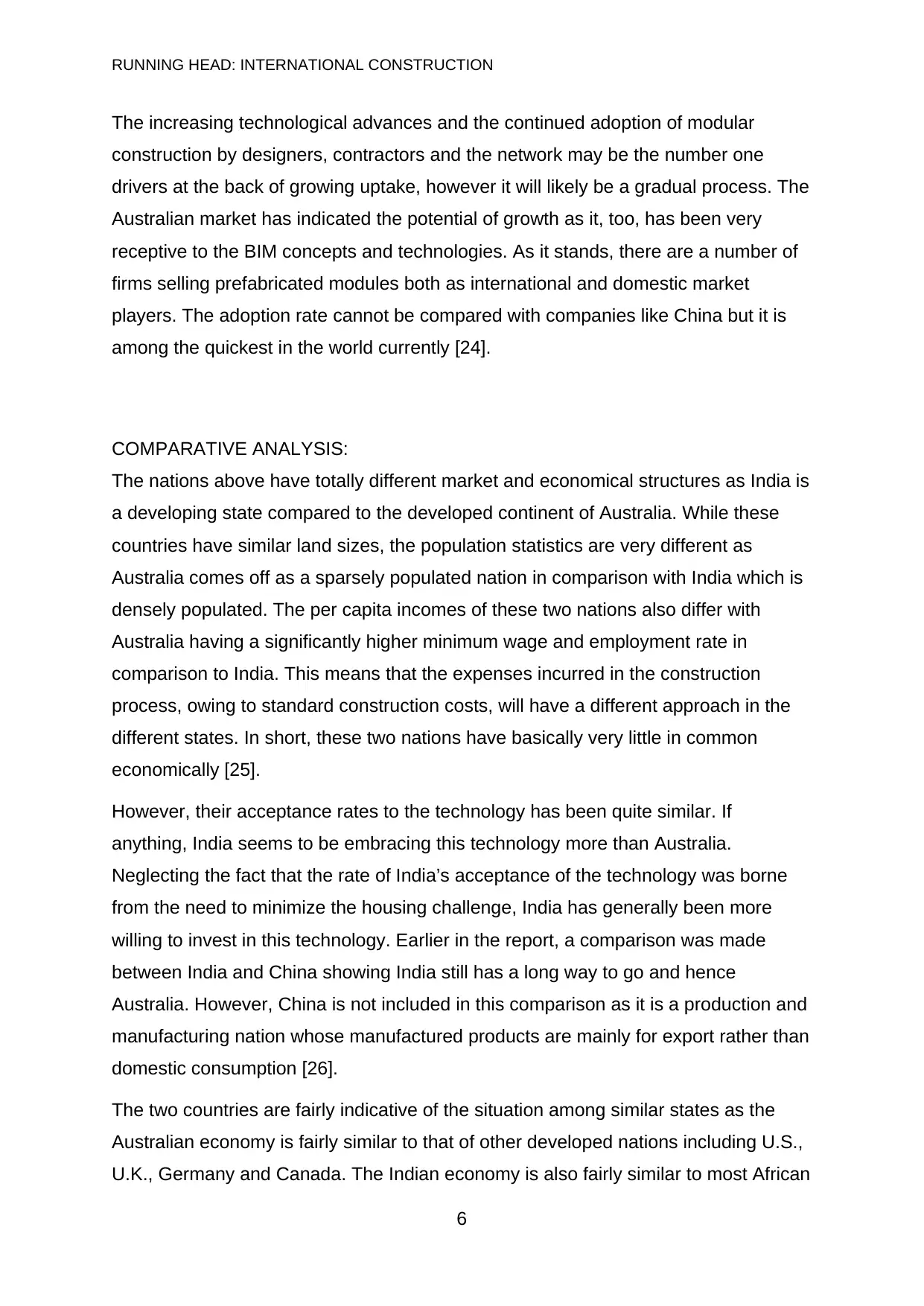
RUNNING HEAD: INTERNATIONAL CONSTRUCTION
The increasing technological advances and the continued adoption of modular
construction by designers, contractors and the network may be the number one
drivers at the back of growing uptake, however it will likely be a gradual process. The
Australian market has indicated the potential of growth as it, too, has been very
receptive to the BIM concepts and technologies. As it stands, there are a number of
firms selling prefabricated modules both as international and domestic market
players. The adoption rate cannot be compared with companies like China but it is
among the quickest in the world currently [24].
COMPARATIVE ANALYSIS:
The nations above have totally different market and economical structures as India is
a developing state compared to the developed continent of Australia. While these
countries have similar land sizes, the population statistics are very different as
Australia comes off as a sparsely populated nation in comparison with India which is
densely populated. The per capita incomes of these two nations also differ with
Australia having a significantly higher minimum wage and employment rate in
comparison to India. This means that the expenses incurred in the construction
process, owing to standard construction costs, will have a different approach in the
different states. In short, these two nations have basically very little in common
economically [25].
However, their acceptance rates to the technology has been quite similar. If
anything, India seems to be embracing this technology more than Australia.
Neglecting the fact that the rate of India’s acceptance of the technology was borne
from the need to minimize the housing challenge, India has generally been more
willing to invest in this technology. Earlier in the report, a comparison was made
between India and China showing India still has a long way to go and hence
Australia. However, China is not included in this comparison as it is a production and
manufacturing nation whose manufactured products are mainly for export rather than
domestic consumption [26].
The two countries are fairly indicative of the situation among similar states as the
Australian economy is fairly similar to that of other developed nations including U.S.,
U.K., Germany and Canada. The Indian economy is also fairly similar to most African
6
The increasing technological advances and the continued adoption of modular
construction by designers, contractors and the network may be the number one
drivers at the back of growing uptake, however it will likely be a gradual process. The
Australian market has indicated the potential of growth as it, too, has been very
receptive to the BIM concepts and technologies. As it stands, there are a number of
firms selling prefabricated modules both as international and domestic market
players. The adoption rate cannot be compared with companies like China but it is
among the quickest in the world currently [24].
COMPARATIVE ANALYSIS:
The nations above have totally different market and economical structures as India is
a developing state compared to the developed continent of Australia. While these
countries have similar land sizes, the population statistics are very different as
Australia comes off as a sparsely populated nation in comparison with India which is
densely populated. The per capita incomes of these two nations also differ with
Australia having a significantly higher minimum wage and employment rate in
comparison to India. This means that the expenses incurred in the construction
process, owing to standard construction costs, will have a different approach in the
different states. In short, these two nations have basically very little in common
economically [25].
However, their acceptance rates to the technology has been quite similar. If
anything, India seems to be embracing this technology more than Australia.
Neglecting the fact that the rate of India’s acceptance of the technology was borne
from the need to minimize the housing challenge, India has generally been more
willing to invest in this technology. Earlier in the report, a comparison was made
between India and China showing India still has a long way to go and hence
Australia. However, China is not included in this comparison as it is a production and
manufacturing nation whose manufactured products are mainly for export rather than
domestic consumption [26].
The two countries are fairly indicative of the situation among similar states as the
Australian economy is fairly similar to that of other developed nations including U.S.,
U.K., Germany and Canada. The Indian economy is also fairly similar to most African
6
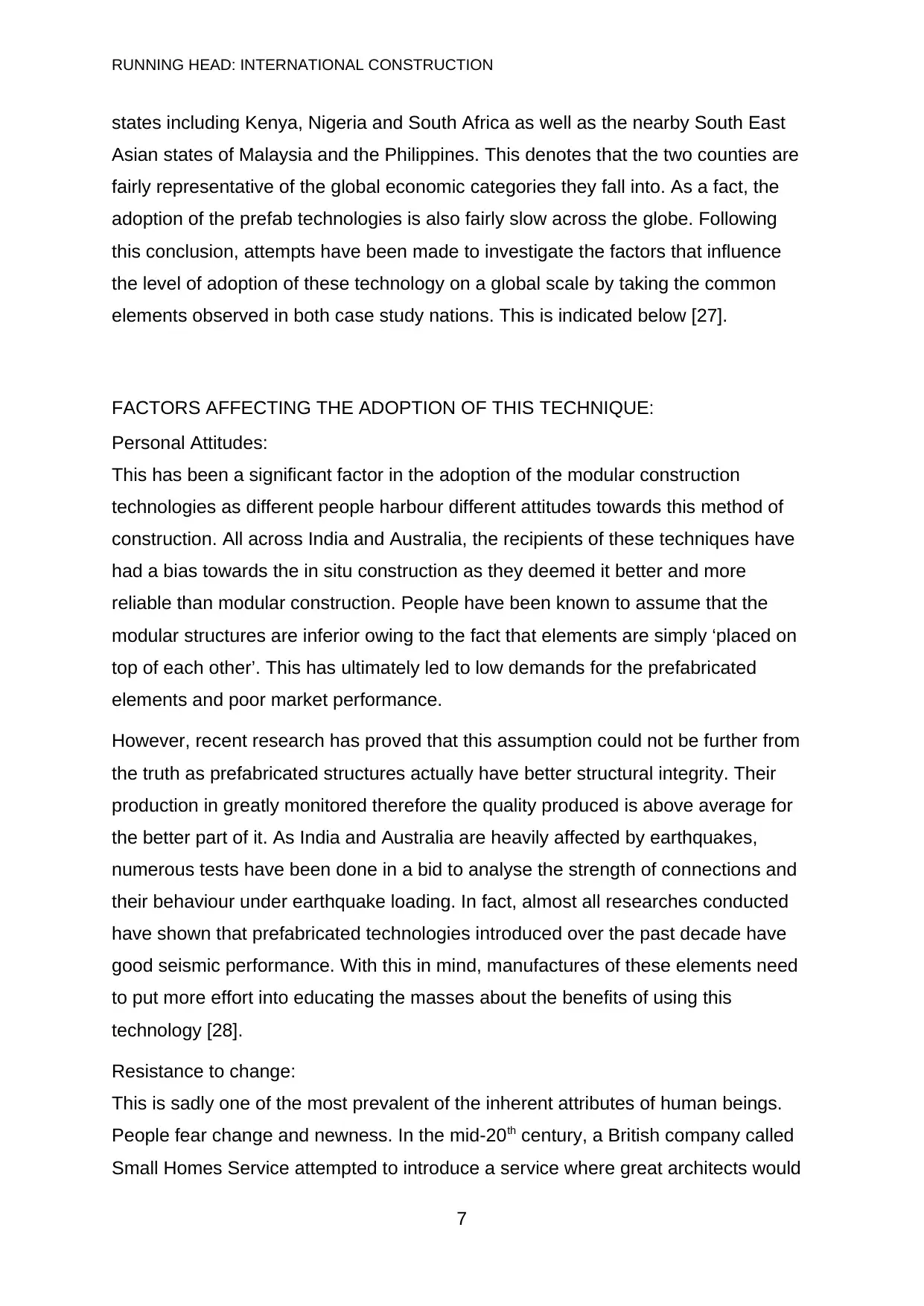
RUNNING HEAD: INTERNATIONAL CONSTRUCTION
states including Kenya, Nigeria and South Africa as well as the nearby South East
Asian states of Malaysia and the Philippines. This denotes that the two counties are
fairly representative of the global economic categories they fall into. As a fact, the
adoption of the prefab technologies is also fairly slow across the globe. Following
this conclusion, attempts have been made to investigate the factors that influence
the level of adoption of these technology on a global scale by taking the common
elements observed in both case study nations. This is indicated below [27].
FACTORS AFFECTING THE ADOPTION OF THIS TECHNIQUE:
Personal Attitudes:
This has been a significant factor in the adoption of the modular construction
technologies as different people harbour different attitudes towards this method of
construction. All across India and Australia, the recipients of these techniques have
had a bias towards the in situ construction as they deemed it better and more
reliable than modular construction. People have been known to assume that the
modular structures are inferior owing to the fact that elements are simply ‘placed on
top of each other’. This has ultimately led to low demands for the prefabricated
elements and poor market performance.
However, recent research has proved that this assumption could not be further from
the truth as prefabricated structures actually have better structural integrity. Their
production in greatly monitored therefore the quality produced is above average for
the better part of it. As India and Australia are heavily affected by earthquakes,
numerous tests have been done in a bid to analyse the strength of connections and
their behaviour under earthquake loading. In fact, almost all researches conducted
have shown that prefabricated technologies introduced over the past decade have
good seismic performance. With this in mind, manufactures of these elements need
to put more effort into educating the masses about the benefits of using this
technology [28].
Resistance to change:
This is sadly one of the most prevalent of the inherent attributes of human beings.
People fear change and newness. In the mid-20th century, a British company called
Small Homes Service attempted to introduce a service where great architects would
7
states including Kenya, Nigeria and South Africa as well as the nearby South East
Asian states of Malaysia and the Philippines. This denotes that the two counties are
fairly representative of the global economic categories they fall into. As a fact, the
adoption of the prefab technologies is also fairly slow across the globe. Following
this conclusion, attempts have been made to investigate the factors that influence
the level of adoption of these technology on a global scale by taking the common
elements observed in both case study nations. This is indicated below [27].
FACTORS AFFECTING THE ADOPTION OF THIS TECHNIQUE:
Personal Attitudes:
This has been a significant factor in the adoption of the modular construction
technologies as different people harbour different attitudes towards this method of
construction. All across India and Australia, the recipients of these techniques have
had a bias towards the in situ construction as they deemed it better and more
reliable than modular construction. People have been known to assume that the
modular structures are inferior owing to the fact that elements are simply ‘placed on
top of each other’. This has ultimately led to low demands for the prefabricated
elements and poor market performance.
However, recent research has proved that this assumption could not be further from
the truth as prefabricated structures actually have better structural integrity. Their
production in greatly monitored therefore the quality produced is above average for
the better part of it. As India and Australia are heavily affected by earthquakes,
numerous tests have been done in a bid to analyse the strength of connections and
their behaviour under earthquake loading. In fact, almost all researches conducted
have shown that prefabricated technologies introduced over the past decade have
good seismic performance. With this in mind, manufactures of these elements need
to put more effort into educating the masses about the benefits of using this
technology [28].
Resistance to change:
This is sadly one of the most prevalent of the inherent attributes of human beings.
People fear change and newness. In the mid-20th century, a British company called
Small Homes Service attempted to introduce a service where great architects would
7
Secure Best Marks with AI Grader
Need help grading? Try our AI Grader for instant feedback on your assignments.
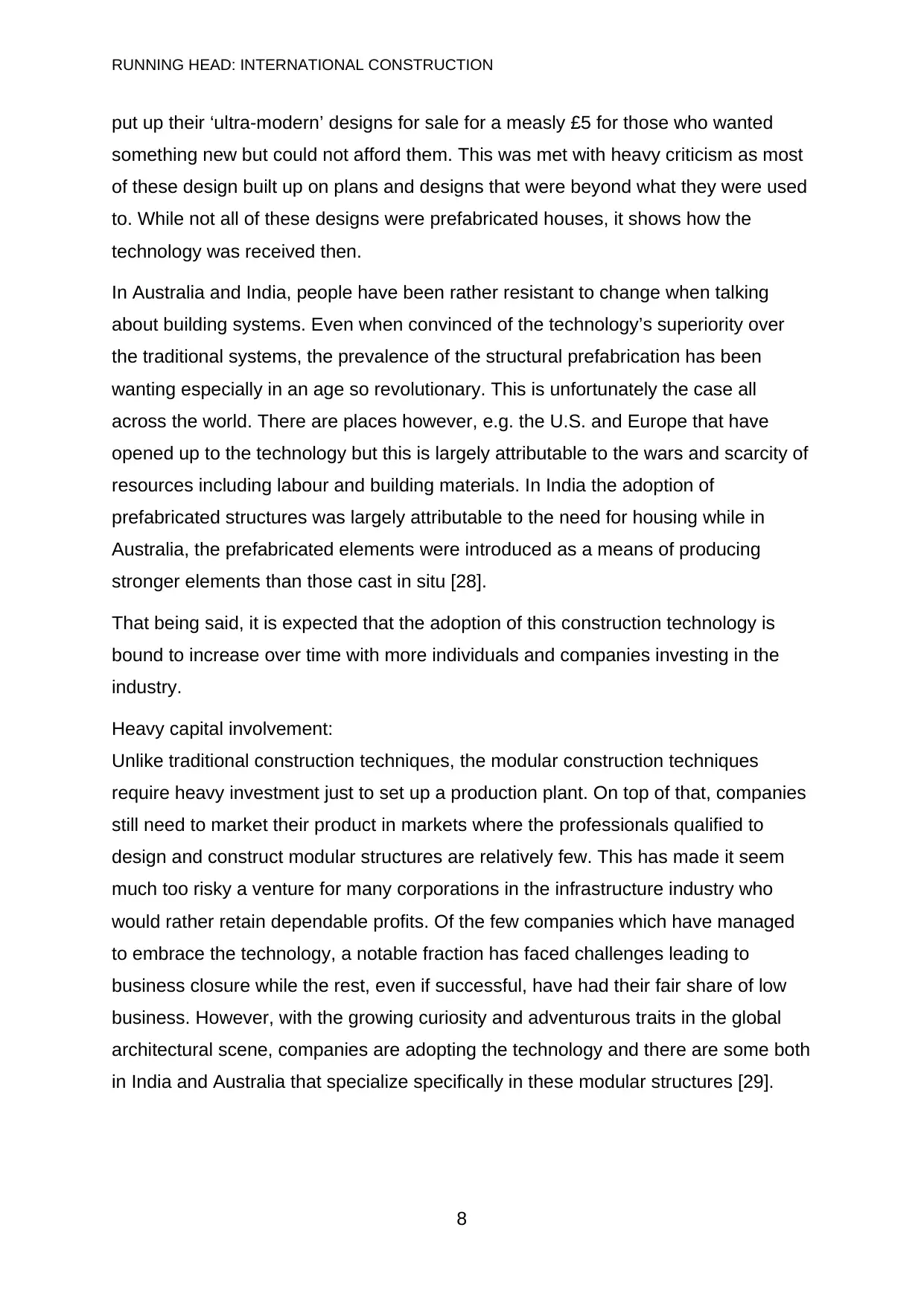
RUNNING HEAD: INTERNATIONAL CONSTRUCTION
put up their ‘ultra-modern’ designs for sale for a measly £5 for those who wanted
something new but could not afford them. This was met with heavy criticism as most
of these design built up on plans and designs that were beyond what they were used
to. While not all of these designs were prefabricated houses, it shows how the
technology was received then.
In Australia and India, people have been rather resistant to change when talking
about building systems. Even when convinced of the technology’s superiority over
the traditional systems, the prevalence of the structural prefabrication has been
wanting especially in an age so revolutionary. This is unfortunately the case all
across the world. There are places however, e.g. the U.S. and Europe that have
opened up to the technology but this is largely attributable to the wars and scarcity of
resources including labour and building materials. In India the adoption of
prefabricated structures was largely attributable to the need for housing while in
Australia, the prefabricated elements were introduced as a means of producing
stronger elements than those cast in situ [28].
That being said, it is expected that the adoption of this construction technology is
bound to increase over time with more individuals and companies investing in the
industry.
Heavy capital involvement:
Unlike traditional construction techniques, the modular construction techniques
require heavy investment just to set up a production plant. On top of that, companies
still need to market their product in markets where the professionals qualified to
design and construct modular structures are relatively few. This has made it seem
much too risky a venture for many corporations in the infrastructure industry who
would rather retain dependable profits. Of the few companies which have managed
to embrace the technology, a notable fraction has faced challenges leading to
business closure while the rest, even if successful, have had their fair share of low
business. However, with the growing curiosity and adventurous traits in the global
architectural scene, companies are adopting the technology and there are some both
in India and Australia that specialize specifically in these modular structures [29].
8
put up their ‘ultra-modern’ designs for sale for a measly £5 for those who wanted
something new but could not afford them. This was met with heavy criticism as most
of these design built up on plans and designs that were beyond what they were used
to. While not all of these designs were prefabricated houses, it shows how the
technology was received then.
In Australia and India, people have been rather resistant to change when talking
about building systems. Even when convinced of the technology’s superiority over
the traditional systems, the prevalence of the structural prefabrication has been
wanting especially in an age so revolutionary. This is unfortunately the case all
across the world. There are places however, e.g. the U.S. and Europe that have
opened up to the technology but this is largely attributable to the wars and scarcity of
resources including labour and building materials. In India the adoption of
prefabricated structures was largely attributable to the need for housing while in
Australia, the prefabricated elements were introduced as a means of producing
stronger elements than those cast in situ [28].
That being said, it is expected that the adoption of this construction technology is
bound to increase over time with more individuals and companies investing in the
industry.
Heavy capital involvement:
Unlike traditional construction techniques, the modular construction techniques
require heavy investment just to set up a production plant. On top of that, companies
still need to market their product in markets where the professionals qualified to
design and construct modular structures are relatively few. This has made it seem
much too risky a venture for many corporations in the infrastructure industry who
would rather retain dependable profits. Of the few companies which have managed
to embrace the technology, a notable fraction has faced challenges leading to
business closure while the rest, even if successful, have had their fair share of low
business. However, with the growing curiosity and adventurous traits in the global
architectural scene, companies are adopting the technology and there are some both
in India and Australia that specialize specifically in these modular structures [29].
8
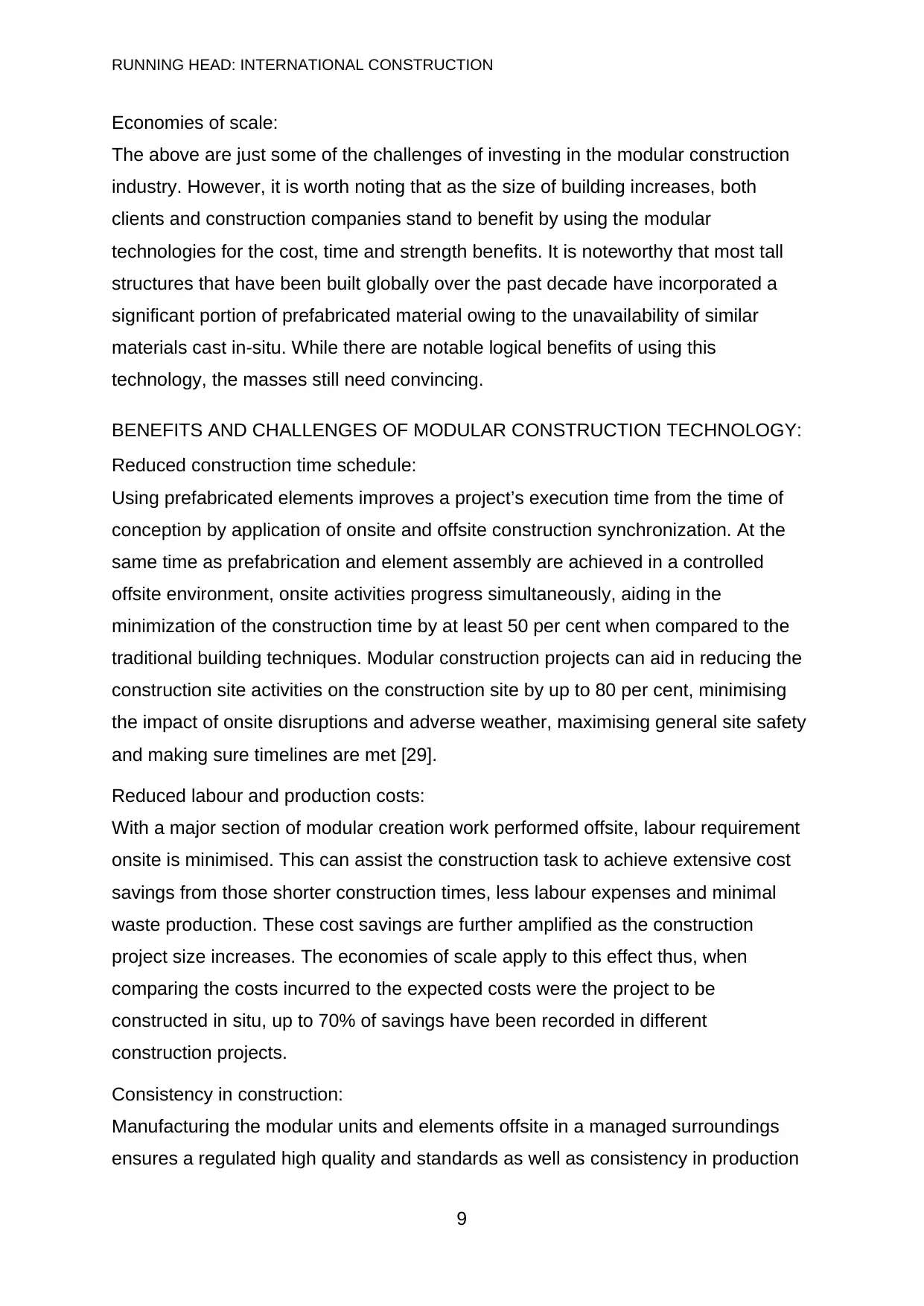
RUNNING HEAD: INTERNATIONAL CONSTRUCTION
Economies of scale:
The above are just some of the challenges of investing in the modular construction
industry. However, it is worth noting that as the size of building increases, both
clients and construction companies stand to benefit by using the modular
technologies for the cost, time and strength benefits. It is noteworthy that most tall
structures that have been built globally over the past decade have incorporated a
significant portion of prefabricated material owing to the unavailability of similar
materials cast in-situ. While there are notable logical benefits of using this
technology, the masses still need convincing.
BENEFITS AND CHALLENGES OF MODULAR CONSTRUCTION TECHNOLOGY:
Reduced construction time schedule:
Using prefabricated elements improves a project’s execution time from the time of
conception by application of onsite and offsite construction synchronization. At the
same time as prefabrication and element assembly are achieved in a controlled
offsite environment, onsite activities progress simultaneously, aiding in the
minimization of the construction time by at least 50 per cent when compared to the
traditional building techniques. Modular construction projects can aid in reducing the
construction site activities on the construction site by up to 80 per cent, minimising
the impact of onsite disruptions and adverse weather, maximising general site safety
and making sure timelines are met [29].
Reduced labour and production costs:
With a major section of modular creation work performed offsite, labour requirement
onsite is minimised. This can assist the construction task to achieve extensive cost
savings from those shorter construction times, less labour expenses and minimal
waste production. These cost savings are further amplified as the construction
project size increases. The economies of scale apply to this effect thus, when
comparing the costs incurred to the expected costs were the project to be
constructed in situ, up to 70% of savings have been recorded in different
construction projects.
Consistency in construction:
Manufacturing the modular units and elements offsite in a managed surroundings
ensures a regulated high quality and standards as well as consistency in production
9
Economies of scale:
The above are just some of the challenges of investing in the modular construction
industry. However, it is worth noting that as the size of building increases, both
clients and construction companies stand to benefit by using the modular
technologies for the cost, time and strength benefits. It is noteworthy that most tall
structures that have been built globally over the past decade have incorporated a
significant portion of prefabricated material owing to the unavailability of similar
materials cast in-situ. While there are notable logical benefits of using this
technology, the masses still need convincing.
BENEFITS AND CHALLENGES OF MODULAR CONSTRUCTION TECHNOLOGY:
Reduced construction time schedule:
Using prefabricated elements improves a project’s execution time from the time of
conception by application of onsite and offsite construction synchronization. At the
same time as prefabrication and element assembly are achieved in a controlled
offsite environment, onsite activities progress simultaneously, aiding in the
minimization of the construction time by at least 50 per cent when compared to the
traditional building techniques. Modular construction projects can aid in reducing the
construction site activities on the construction site by up to 80 per cent, minimising
the impact of onsite disruptions and adverse weather, maximising general site safety
and making sure timelines are met [29].
Reduced labour and production costs:
With a major section of modular creation work performed offsite, labour requirement
onsite is minimised. This can assist the construction task to achieve extensive cost
savings from those shorter construction times, less labour expenses and minimal
waste production. These cost savings are further amplified as the construction
project size increases. The economies of scale apply to this effect thus, when
comparing the costs incurred to the expected costs were the project to be
constructed in situ, up to 70% of savings have been recorded in different
construction projects.
Consistency in construction:
Manufacturing the modular units and elements offsite in a managed surroundings
ensures a regulated high quality and standards as well as consistency in production
9

RUNNING HEAD: INTERNATIONAL CONSTRUCTION
to satisfy overall performance and compliance requirements specific to the various
industry requirements. Also, when it comes to the onsite assembly, the elements
have special tailor made links that are in most cases much stronger that those cast
in situ while maintaining the right level of rigidity to resist the effects of seismic action
which is prevalent in not just India and Australia but a lot of other countries too. Due
to the material consistency, the wear and tear is balanced over the design life of the
material and the evenness of this wear is important in reducing weakness and
subsequent fracture in the various elements used in the construction [29].
Decreased wastage on the site and sustainability:
Made-to-measure homes and factory produced construction elements ensure waste
production is minimised on the on the site. Building and demolition waste from
conventional constructing techniques are accountable for more than 38 per cent of
Australia’s overall waste sent to landfill. This has a positive effect on the environment
as it reduces the footprint. The waste in this case can also be recycled, reused or
reclaimed enabling further sustainability and reducing the pressure on the earth’s
natural resources. This is important especially in India and other developing nations
seeking to reduce this pressure as more materials is readily available for
construction at a cheaper price [30].
Need For expertise:
Attributable to their notably one of a kind production approach, the whole machine of
precast concrete utilization has extra operational requirements that the conventional
on website construction. The necessities stem from member layout and manufacture
to the development process. By way of design, they may be surprisingly different in
comparison to bricks and other concrete members which necessitates a more
technical manufacturing technique. Additionally they require a variety of research
and testing so as for a producer to provide you with a precast member that satisfies
the monetary, safe, environmentally friendly and structural soundness necessities
[30].
Modular structures additionally require a higher degree of understanding of the
construction site because element assembly greatly varies from other ordinary brick
and mortar, and on the ground construction works. Even as they only require
technician to assemble the structural member at the right positions, the connections
among individual elements are more complex than in the conventional tactics.
10
to satisfy overall performance and compliance requirements specific to the various
industry requirements. Also, when it comes to the onsite assembly, the elements
have special tailor made links that are in most cases much stronger that those cast
in situ while maintaining the right level of rigidity to resist the effects of seismic action
which is prevalent in not just India and Australia but a lot of other countries too. Due
to the material consistency, the wear and tear is balanced over the design life of the
material and the evenness of this wear is important in reducing weakness and
subsequent fracture in the various elements used in the construction [29].
Decreased wastage on the site and sustainability:
Made-to-measure homes and factory produced construction elements ensure waste
production is minimised on the on the site. Building and demolition waste from
conventional constructing techniques are accountable for more than 38 per cent of
Australia’s overall waste sent to landfill. This has a positive effect on the environment
as it reduces the footprint. The waste in this case can also be recycled, reused or
reclaimed enabling further sustainability and reducing the pressure on the earth’s
natural resources. This is important especially in India and other developing nations
seeking to reduce this pressure as more materials is readily available for
construction at a cheaper price [30].
Need For expertise:
Attributable to their notably one of a kind production approach, the whole machine of
precast concrete utilization has extra operational requirements that the conventional
on website construction. The necessities stem from member layout and manufacture
to the development process. By way of design, they may be surprisingly different in
comparison to bricks and other concrete members which necessitates a more
technical manufacturing technique. Additionally they require a variety of research
and testing so as for a producer to provide you with a precast member that satisfies
the monetary, safe, environmentally friendly and structural soundness necessities
[30].
Modular structures additionally require a higher degree of understanding of the
construction site because element assembly greatly varies from other ordinary brick
and mortar, and on the ground construction works. Even as they only require
technician to assemble the structural member at the right positions, the connections
among individual elements are more complex than in the conventional tactics.
10
Paraphrase This Document
Need a fresh take? Get an instant paraphrase of this document with our AI Paraphraser
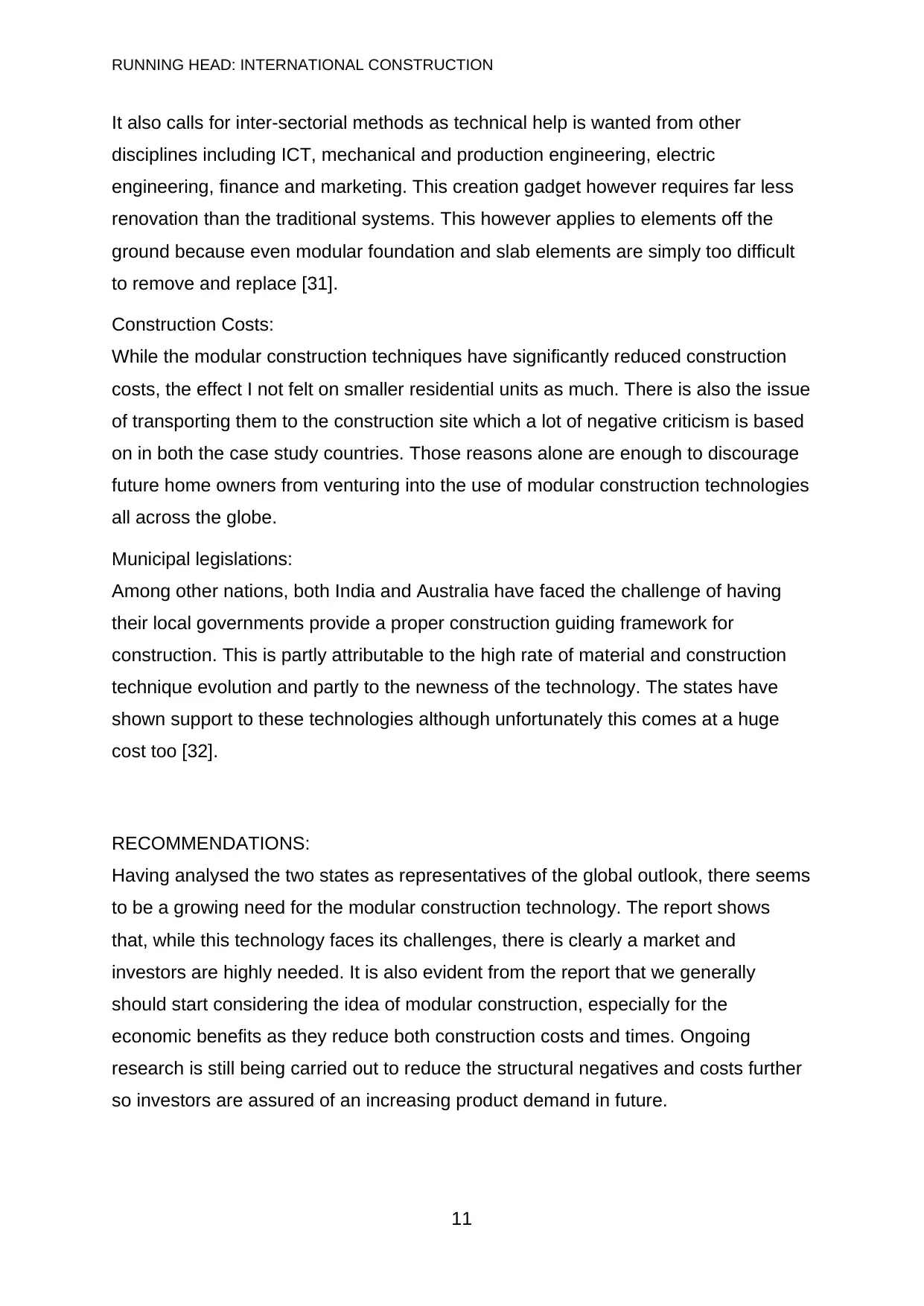
RUNNING HEAD: INTERNATIONAL CONSTRUCTION
It also calls for inter-sectorial methods as technical help is wanted from other
disciplines including ICT, mechanical and production engineering, electric
engineering, finance and marketing. This creation gadget however requires far less
renovation than the traditional systems. This however applies to elements off the
ground because even modular foundation and slab elements are simply too difficult
to remove and replace [31].
Construction Costs:
While the modular construction techniques have significantly reduced construction
costs, the effect I not felt on smaller residential units as much. There is also the issue
of transporting them to the construction site which a lot of negative criticism is based
on in both the case study countries. Those reasons alone are enough to discourage
future home owners from venturing into the use of modular construction technologies
all across the globe.
Municipal legislations:
Among other nations, both India and Australia have faced the challenge of having
their local governments provide a proper construction guiding framework for
construction. This is partly attributable to the high rate of material and construction
technique evolution and partly to the newness of the technology. The states have
shown support to these technologies although unfortunately this comes at a huge
cost too [32].
RECOMMENDATIONS:
Having analysed the two states as representatives of the global outlook, there seems
to be a growing need for the modular construction technology. The report shows
that, while this technology faces its challenges, there is clearly a market and
investors are highly needed. It is also evident from the report that we generally
should start considering the idea of modular construction, especially for the
economic benefits as they reduce both construction costs and times. Ongoing
research is still being carried out to reduce the structural negatives and costs further
so investors are assured of an increasing product demand in future.
11
It also calls for inter-sectorial methods as technical help is wanted from other
disciplines including ICT, mechanical and production engineering, electric
engineering, finance and marketing. This creation gadget however requires far less
renovation than the traditional systems. This however applies to elements off the
ground because even modular foundation and slab elements are simply too difficult
to remove and replace [31].
Construction Costs:
While the modular construction techniques have significantly reduced construction
costs, the effect I not felt on smaller residential units as much. There is also the issue
of transporting them to the construction site which a lot of negative criticism is based
on in both the case study countries. Those reasons alone are enough to discourage
future home owners from venturing into the use of modular construction technologies
all across the globe.
Municipal legislations:
Among other nations, both India and Australia have faced the challenge of having
their local governments provide a proper construction guiding framework for
construction. This is partly attributable to the high rate of material and construction
technique evolution and partly to the newness of the technology. The states have
shown support to these technologies although unfortunately this comes at a huge
cost too [32].
RECOMMENDATIONS:
Having analysed the two states as representatives of the global outlook, there seems
to be a growing need for the modular construction technology. The report shows
that, while this technology faces its challenges, there is clearly a market and
investors are highly needed. It is also evident from the report that we generally
should start considering the idea of modular construction, especially for the
economic benefits as they reduce both construction costs and times. Ongoing
research is still being carried out to reduce the structural negatives and costs further
so investors are assured of an increasing product demand in future.
11
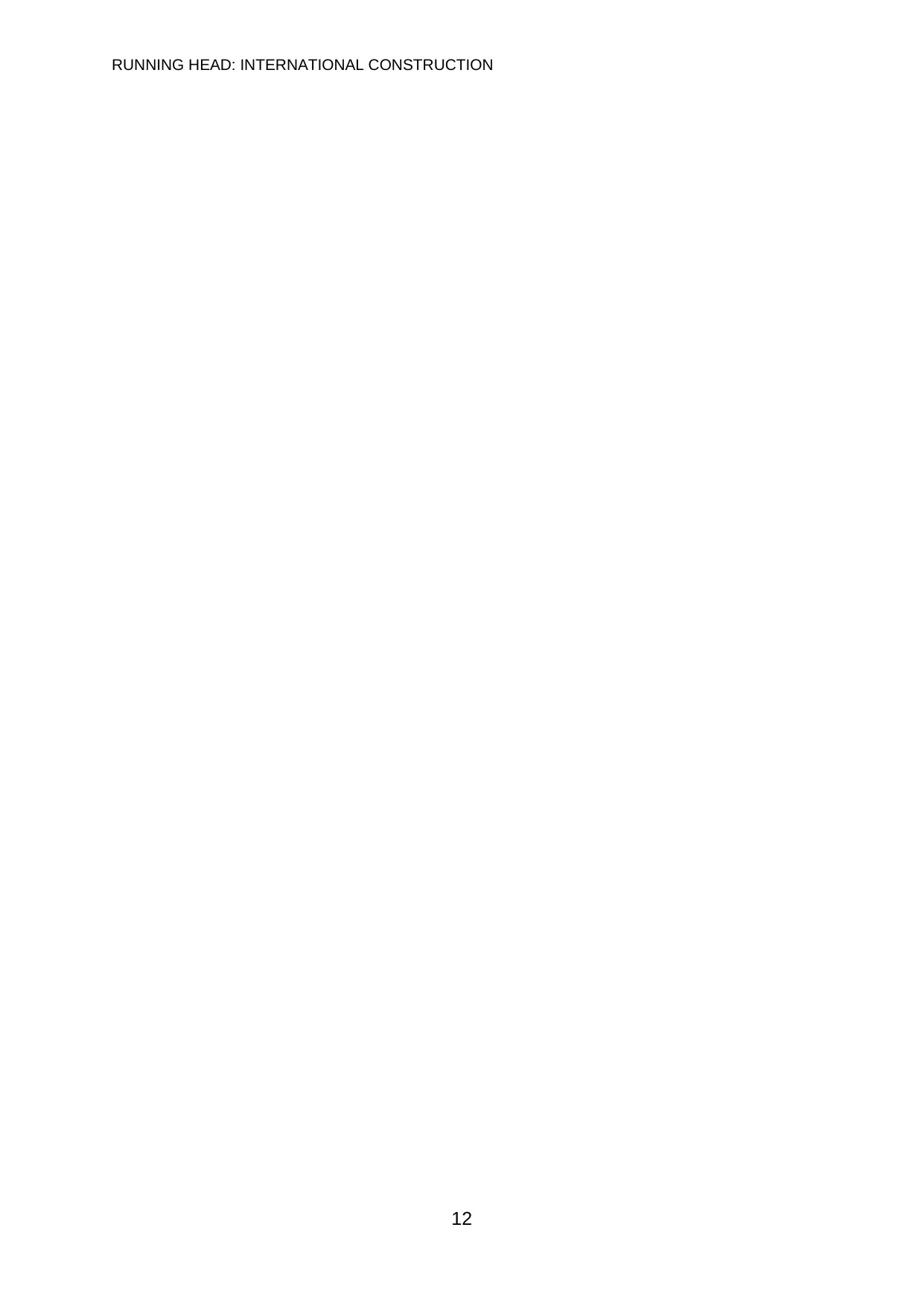
RUNNING HEAD: INTERNATIONAL CONSTRUCTION
12
12
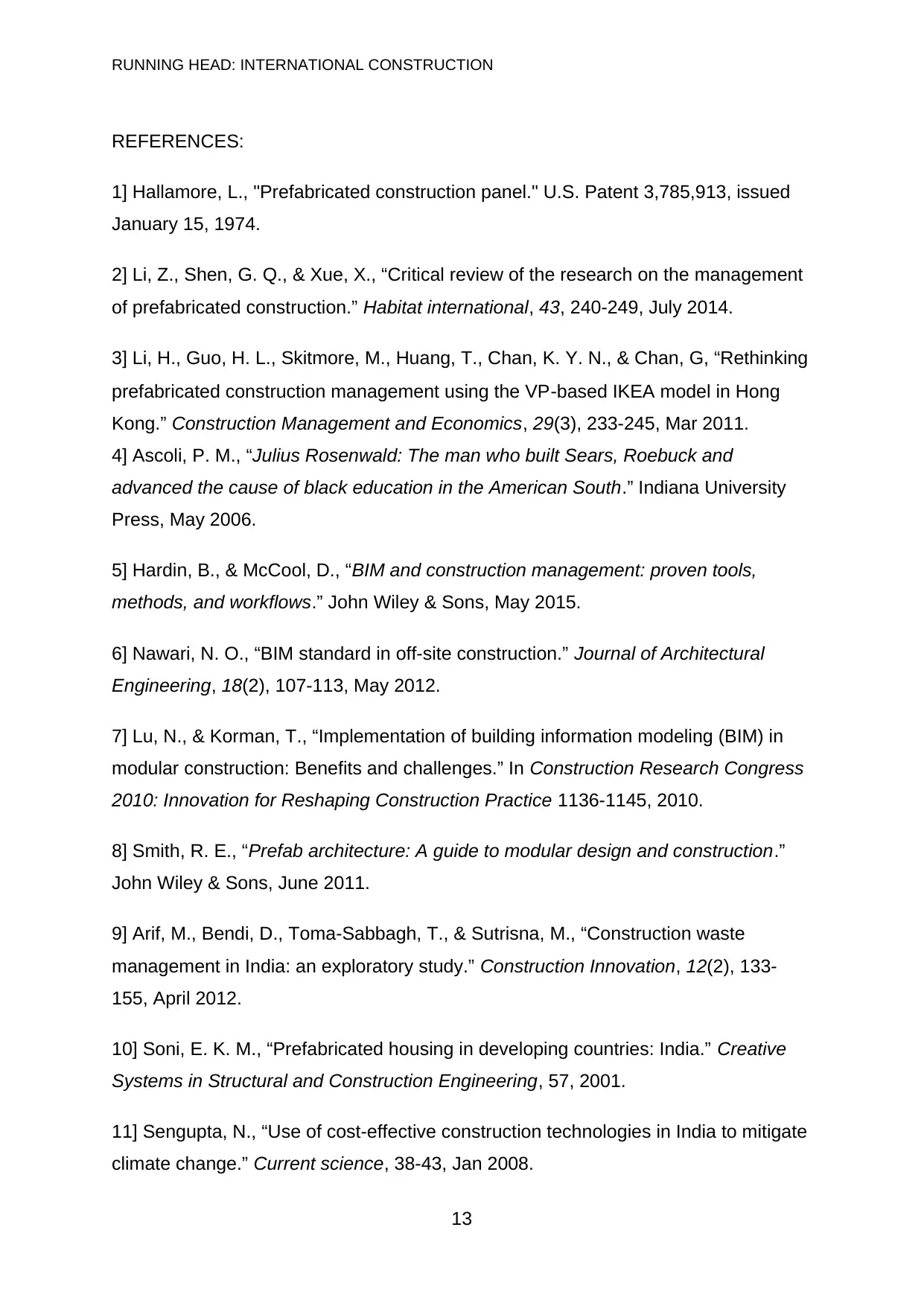
RUNNING HEAD: INTERNATIONAL CONSTRUCTION
REFERENCES:
1] Hallamore, L., "Prefabricated construction panel." U.S. Patent 3,785,913, issued
January 15, 1974.
2] Li, Z., Shen, G. Q., & Xue, X., “Critical review of the research on the management
of prefabricated construction.” Habitat international, 43, 240-249, July 2014.
3] Li, H., Guo, H. L., Skitmore, M., Huang, T., Chan, K. Y. N., & Chan, G, “Rethinking
prefabricated construction management using the VP‐based IKEA model in Hong
Kong.” Construction Management and Economics, 29(3), 233-245, Mar 2011.
4] Ascoli, P. M., “Julius Rosenwald: The man who built Sears, Roebuck and
advanced the cause of black education in the American South.” Indiana University
Press, May 2006.
5] Hardin, B., & McCool, D., “BIM and construction management: proven tools,
methods, and workflows.” John Wiley & Sons, May 2015.
6] Nawari, N. O., “BIM standard in off-site construction.” Journal of Architectural
Engineering, 18(2), 107-113, May 2012.
7] Lu, N., & Korman, T., “Implementation of building information modeling (BIM) in
modular construction: Benefits and challenges.” In Construction Research Congress
2010: Innovation for Reshaping Construction Practice 1136-1145, 2010.
8] Smith, R. E., “Prefab architecture: A guide to modular design and construction.”
John Wiley & Sons, June 2011.
9] Arif, M., Bendi, D., Toma-Sabbagh, T., & Sutrisna, M., “Construction waste
management in India: an exploratory study.” Construction Innovation, 12(2), 133-
155, April 2012.
10] Soni, E. K. M., “Prefabricated housing in developing countries: India.” Creative
Systems in Structural and Construction Engineering, 57, 2001.
11] Sengupta, N., “Use of cost-effective construction technologies in India to mitigate
climate change.” Current science, 38-43, Jan 2008.
13
REFERENCES:
1] Hallamore, L., "Prefabricated construction panel." U.S. Patent 3,785,913, issued
January 15, 1974.
2] Li, Z., Shen, G. Q., & Xue, X., “Critical review of the research on the management
of prefabricated construction.” Habitat international, 43, 240-249, July 2014.
3] Li, H., Guo, H. L., Skitmore, M., Huang, T., Chan, K. Y. N., & Chan, G, “Rethinking
prefabricated construction management using the VP‐based IKEA model in Hong
Kong.” Construction Management and Economics, 29(3), 233-245, Mar 2011.
4] Ascoli, P. M., “Julius Rosenwald: The man who built Sears, Roebuck and
advanced the cause of black education in the American South.” Indiana University
Press, May 2006.
5] Hardin, B., & McCool, D., “BIM and construction management: proven tools,
methods, and workflows.” John Wiley & Sons, May 2015.
6] Nawari, N. O., “BIM standard in off-site construction.” Journal of Architectural
Engineering, 18(2), 107-113, May 2012.
7] Lu, N., & Korman, T., “Implementation of building information modeling (BIM) in
modular construction: Benefits and challenges.” In Construction Research Congress
2010: Innovation for Reshaping Construction Practice 1136-1145, 2010.
8] Smith, R. E., “Prefab architecture: A guide to modular design and construction.”
John Wiley & Sons, June 2011.
9] Arif, M., Bendi, D., Toma-Sabbagh, T., & Sutrisna, M., “Construction waste
management in India: an exploratory study.” Construction Innovation, 12(2), 133-
155, April 2012.
10] Soni, E. K. M., “Prefabricated housing in developing countries: India.” Creative
Systems in Structural and Construction Engineering, 57, 2001.
11] Sengupta, N., “Use of cost-effective construction technologies in India to mitigate
climate change.” Current science, 38-43, Jan 2008.
13
Secure Best Marks with AI Grader
Need help grading? Try our AI Grader for instant feedback on your assignments.
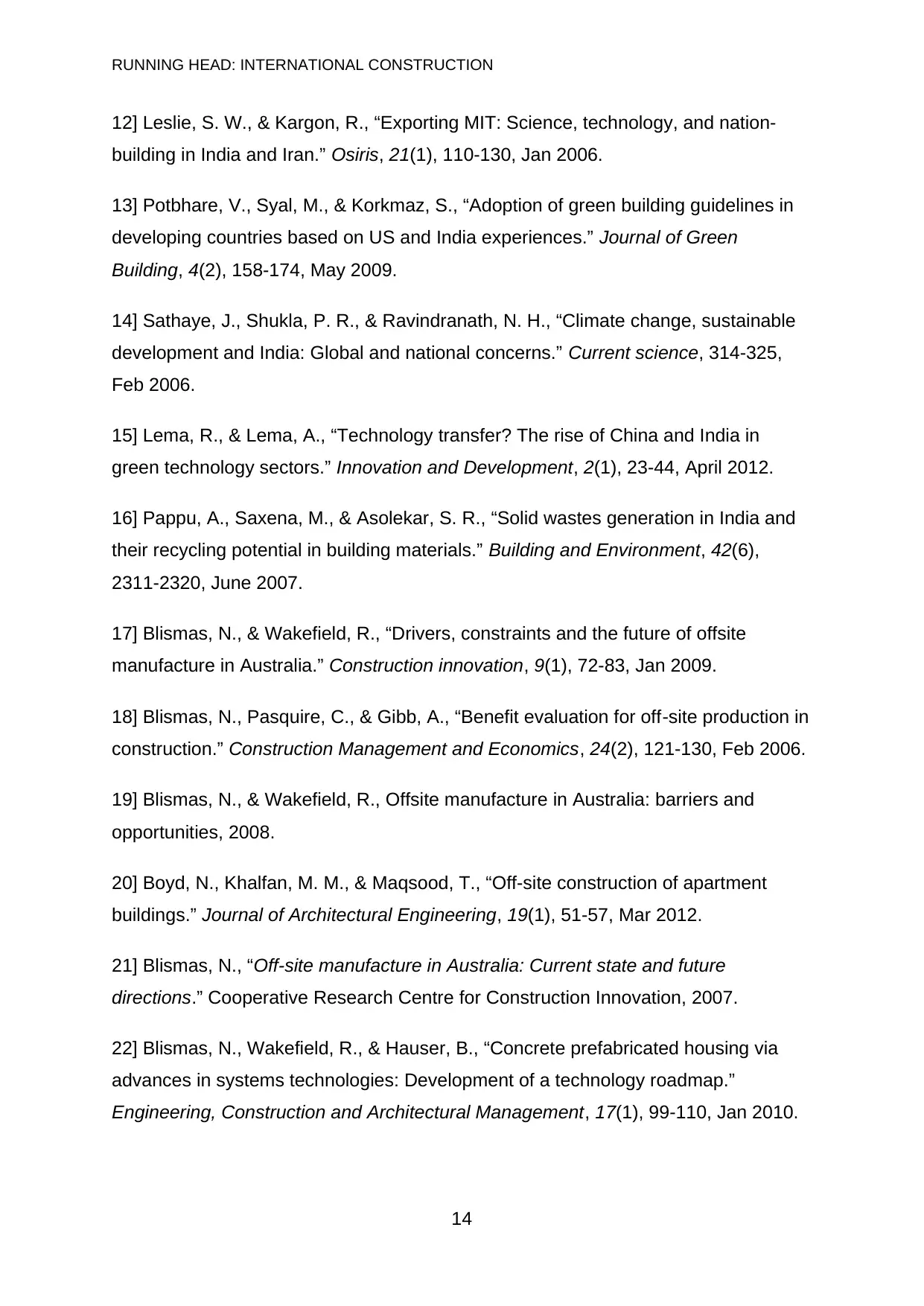
RUNNING HEAD: INTERNATIONAL CONSTRUCTION
12] Leslie, S. W., & Kargon, R., “Exporting MIT: Science, technology, and nation-
building in India and Iran.” Osiris, 21(1), 110-130, Jan 2006.
13] Potbhare, V., Syal, M., & Korkmaz, S., “Adoption of green building guidelines in
developing countries based on US and India experiences.” Journal of Green
Building, 4(2), 158-174, May 2009.
14] Sathaye, J., Shukla, P. R., & Ravindranath, N. H., “Climate change, sustainable
development and India: Global and national concerns.” Current science, 314-325,
Feb 2006.
15] Lema, R., & Lema, A., “Technology transfer? The rise of China and India in
green technology sectors.” Innovation and Development, 2(1), 23-44, April 2012.
16] Pappu, A., Saxena, M., & Asolekar, S. R., “Solid wastes generation in India and
their recycling potential in building materials.” Building and Environment, 42(6),
2311-2320, June 2007.
17] Blismas, N., & Wakefield, R., “Drivers, constraints and the future of offsite
manufacture in Australia.” Construction innovation, 9(1), 72-83, Jan 2009.
18] Blismas, N., Pasquire, C., & Gibb, A., “Benefit evaluation for off‐site production in
construction.” Construction Management and Economics, 24(2), 121-130, Feb 2006.
19] Blismas, N., & Wakefield, R., Offsite manufacture in Australia: barriers and
opportunities, 2008.
20] Boyd, N., Khalfan, M. M., & Maqsood, T., “Off-site construction of apartment
buildings.” Journal of Architectural Engineering, 19(1), 51-57, Mar 2012.
21] Blismas, N., “Off-site manufacture in Australia: Current state and future
directions.” Cooperative Research Centre for Construction Innovation, 2007.
22] Blismas, N., Wakefield, R., & Hauser, B., “Concrete prefabricated housing via
advances in systems technologies: Development of a technology roadmap.”
Engineering, Construction and Architectural Management, 17(1), 99-110, Jan 2010.
14
12] Leslie, S. W., & Kargon, R., “Exporting MIT: Science, technology, and nation-
building in India and Iran.” Osiris, 21(1), 110-130, Jan 2006.
13] Potbhare, V., Syal, M., & Korkmaz, S., “Adoption of green building guidelines in
developing countries based on US and India experiences.” Journal of Green
Building, 4(2), 158-174, May 2009.
14] Sathaye, J., Shukla, P. R., & Ravindranath, N. H., “Climate change, sustainable
development and India: Global and national concerns.” Current science, 314-325,
Feb 2006.
15] Lema, R., & Lema, A., “Technology transfer? The rise of China and India in
green technology sectors.” Innovation and Development, 2(1), 23-44, April 2012.
16] Pappu, A., Saxena, M., & Asolekar, S. R., “Solid wastes generation in India and
their recycling potential in building materials.” Building and Environment, 42(6),
2311-2320, June 2007.
17] Blismas, N., & Wakefield, R., “Drivers, constraints and the future of offsite
manufacture in Australia.” Construction innovation, 9(1), 72-83, Jan 2009.
18] Blismas, N., Pasquire, C., & Gibb, A., “Benefit evaluation for off‐site production in
construction.” Construction Management and Economics, 24(2), 121-130, Feb 2006.
19] Blismas, N., & Wakefield, R., Offsite manufacture in Australia: barriers and
opportunities, 2008.
20] Boyd, N., Khalfan, M. M., & Maqsood, T., “Off-site construction of apartment
buildings.” Journal of Architectural Engineering, 19(1), 51-57, Mar 2012.
21] Blismas, N., “Off-site manufacture in Australia: Current state and future
directions.” Cooperative Research Centre for Construction Innovation, 2007.
22] Blismas, N., Wakefield, R., & Hauser, B., “Concrete prefabricated housing via
advances in systems technologies: Development of a technology roadmap.”
Engineering, Construction and Architectural Management, 17(1), 99-110, Jan 2010.
14
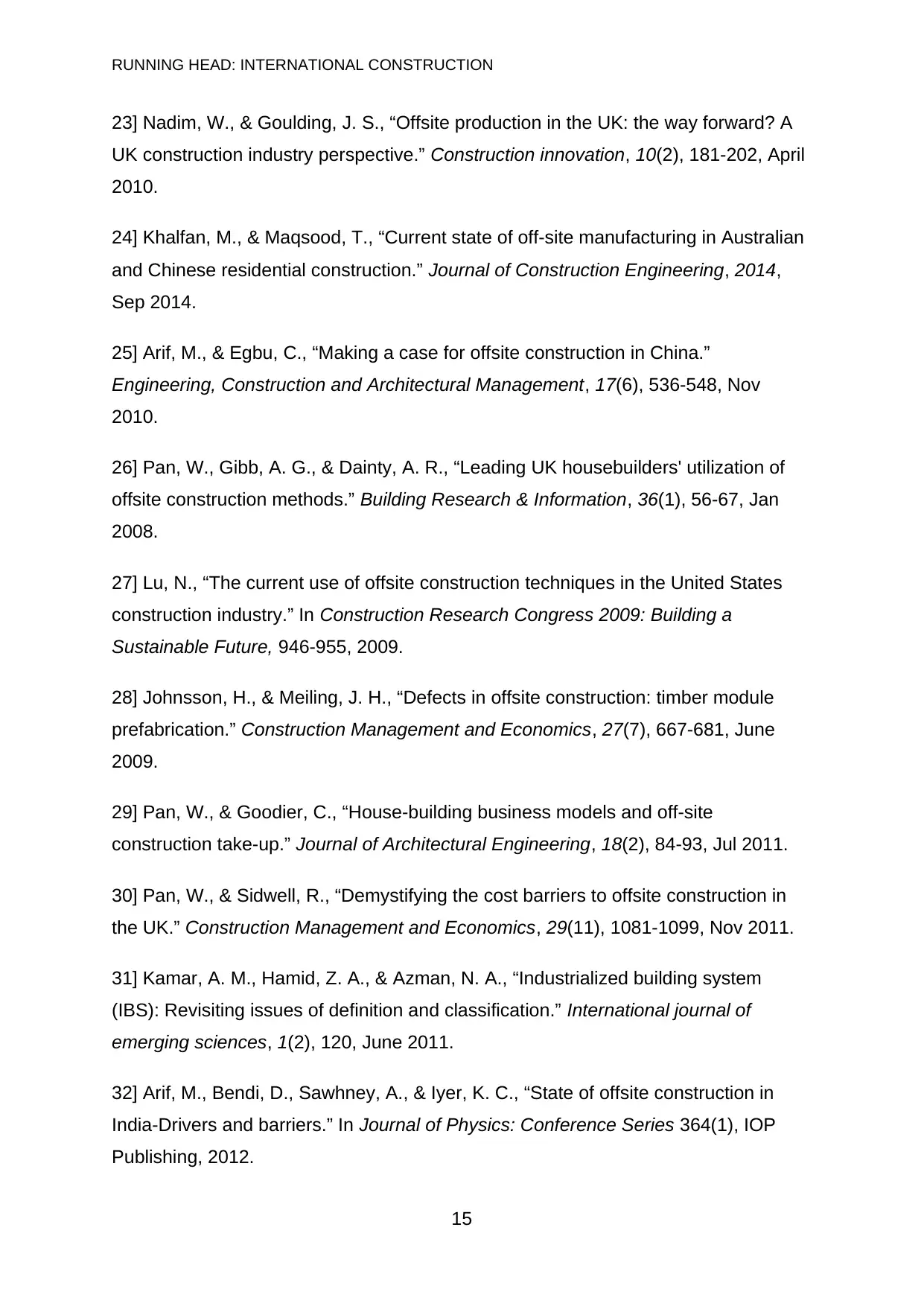
RUNNING HEAD: INTERNATIONAL CONSTRUCTION
23] Nadim, W., & Goulding, J. S., “Offsite production in the UK: the way forward? A
UK construction industry perspective.” Construction innovation, 10(2), 181-202, April
2010.
24] Khalfan, M., & Maqsood, T., “Current state of off-site manufacturing in Australian
and Chinese residential construction.” Journal of Construction Engineering, 2014,
Sep 2014.
25] Arif, M., & Egbu, C., “Making a case for offsite construction in China.”
Engineering, Construction and Architectural Management, 17(6), 536-548, Nov
2010.
26] Pan, W., Gibb, A. G., & Dainty, A. R., “Leading UK housebuilders' utilization of
offsite construction methods.” Building Research & Information, 36(1), 56-67, Jan
2008.
27] Lu, N., “The current use of offsite construction techniques in the United States
construction industry.” In Construction Research Congress 2009: Building a
Sustainable Future, 946-955, 2009.
28] Johnsson, H., & Meiling, J. H., “Defects in offsite construction: timber module
prefabrication.” Construction Management and Economics, 27(7), 667-681, June
2009.
29] Pan, W., & Goodier, C., “House-building business models and off-site
construction take-up.” Journal of Architectural Engineering, 18(2), 84-93, Jul 2011.
30] Pan, W., & Sidwell, R., “Demystifying the cost barriers to offsite construction in
the UK.” Construction Management and Economics, 29(11), 1081-1099, Nov 2011.
31] Kamar, A. M., Hamid, Z. A., & Azman, N. A., “Industrialized building system
(IBS): Revisiting issues of definition and classification.” International journal of
emerging sciences, 1(2), 120, June 2011.
32] Arif, M., Bendi, D., Sawhney, A., & Iyer, K. C., “State of offsite construction in
India-Drivers and barriers.” In Journal of Physics: Conference Series 364(1), IOP
Publishing, 2012.
15
23] Nadim, W., & Goulding, J. S., “Offsite production in the UK: the way forward? A
UK construction industry perspective.” Construction innovation, 10(2), 181-202, April
2010.
24] Khalfan, M., & Maqsood, T., “Current state of off-site manufacturing in Australian
and Chinese residential construction.” Journal of Construction Engineering, 2014,
Sep 2014.
25] Arif, M., & Egbu, C., “Making a case for offsite construction in China.”
Engineering, Construction and Architectural Management, 17(6), 536-548, Nov
2010.
26] Pan, W., Gibb, A. G., & Dainty, A. R., “Leading UK housebuilders' utilization of
offsite construction methods.” Building Research & Information, 36(1), 56-67, Jan
2008.
27] Lu, N., “The current use of offsite construction techniques in the United States
construction industry.” In Construction Research Congress 2009: Building a
Sustainable Future, 946-955, 2009.
28] Johnsson, H., & Meiling, J. H., “Defects in offsite construction: timber module
prefabrication.” Construction Management and Economics, 27(7), 667-681, June
2009.
29] Pan, W., & Goodier, C., “House-building business models and off-site
construction take-up.” Journal of Architectural Engineering, 18(2), 84-93, Jul 2011.
30] Pan, W., & Sidwell, R., “Demystifying the cost barriers to offsite construction in
the UK.” Construction Management and Economics, 29(11), 1081-1099, Nov 2011.
31] Kamar, A. M., Hamid, Z. A., & Azman, N. A., “Industrialized building system
(IBS): Revisiting issues of definition and classification.” International journal of
emerging sciences, 1(2), 120, June 2011.
32] Arif, M., Bendi, D., Sawhney, A., & Iyer, K. C., “State of offsite construction in
India-Drivers and barriers.” In Journal of Physics: Conference Series 364(1), IOP
Publishing, 2012.
15
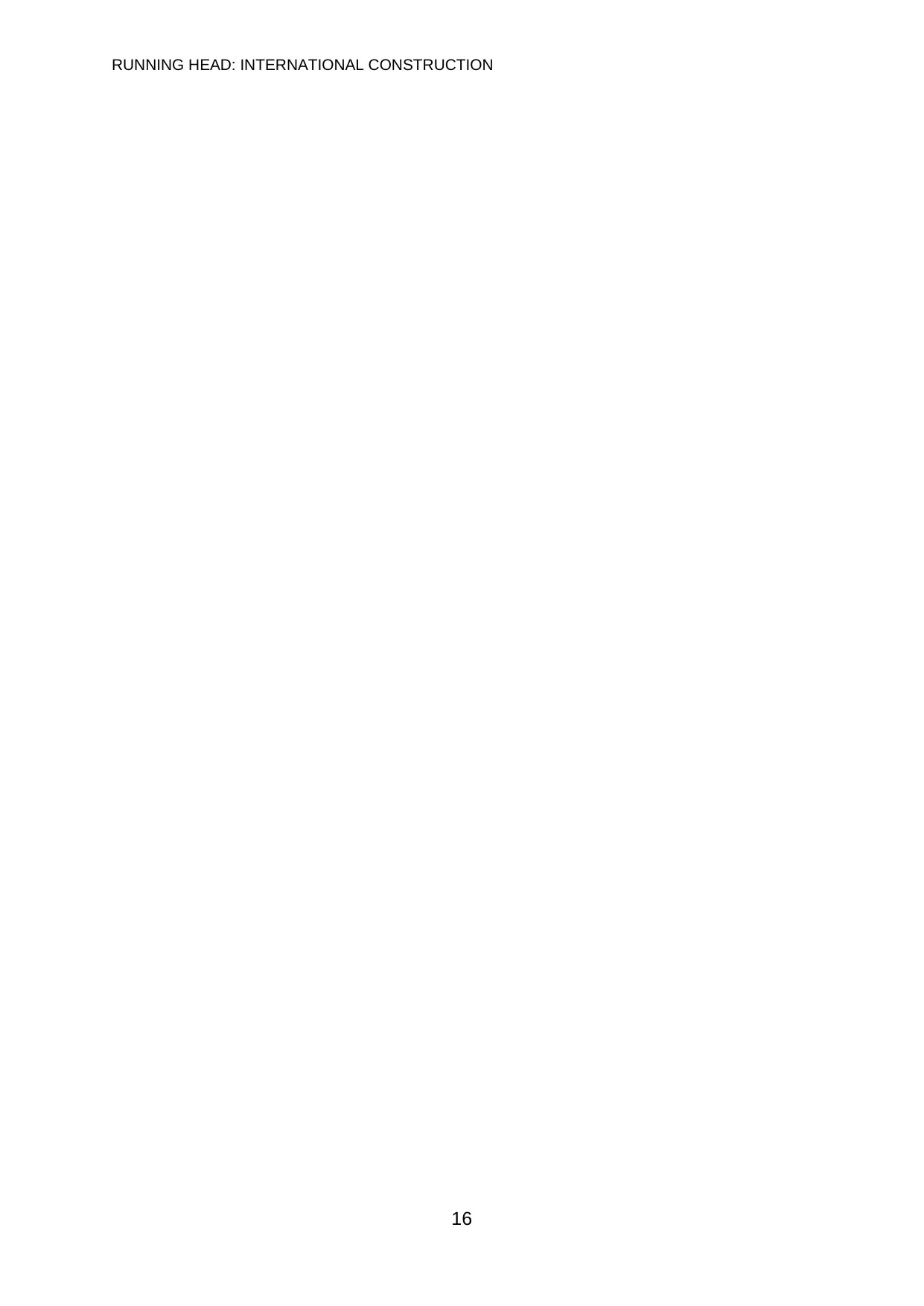
RUNNING HEAD: INTERNATIONAL CONSTRUCTION
16
16
1 out of 19
Related Documents

Your All-in-One AI-Powered Toolkit for Academic Success.
+13062052269
info@desklib.com
Available 24*7 on WhatsApp / Email
Unlock your academic potential
© 2024 | Zucol Services PVT LTD | All rights reserved.