HNBS 316: Operations and Project Management Report on M&S Company
VerifiedAdded on  2022/12/15
|18
|3501
|374
Report
AI Summary
This report provides a detailed analysis of operations and project management, focusing on the Marks & Spencer (M&S) company. It begins with an introduction to M&S, outlining its business operations and comparing operations with operations management. The report then reviews and critiques the implementation of operations management principles at M&S, including the application of Six Sigma and Lean techniques. It evaluates the extent to which operations management meets the company's requirements and discusses continuous improvement as a philosophy, describing Lean principles and presenting a continuous improvement plan. The report further explores continuous improvement principles and offers recommendations for improving operational functions. Part 2 of the report presents a case study overview, describing the project life cycle stages and evaluating each stage in the context of the case. It also examines the rationale behind project management methodologies, tools, and methods implemented in the project and critically evaluates the effectiveness of the project life cycle application. The report concludes with a summary of findings and recommendations.
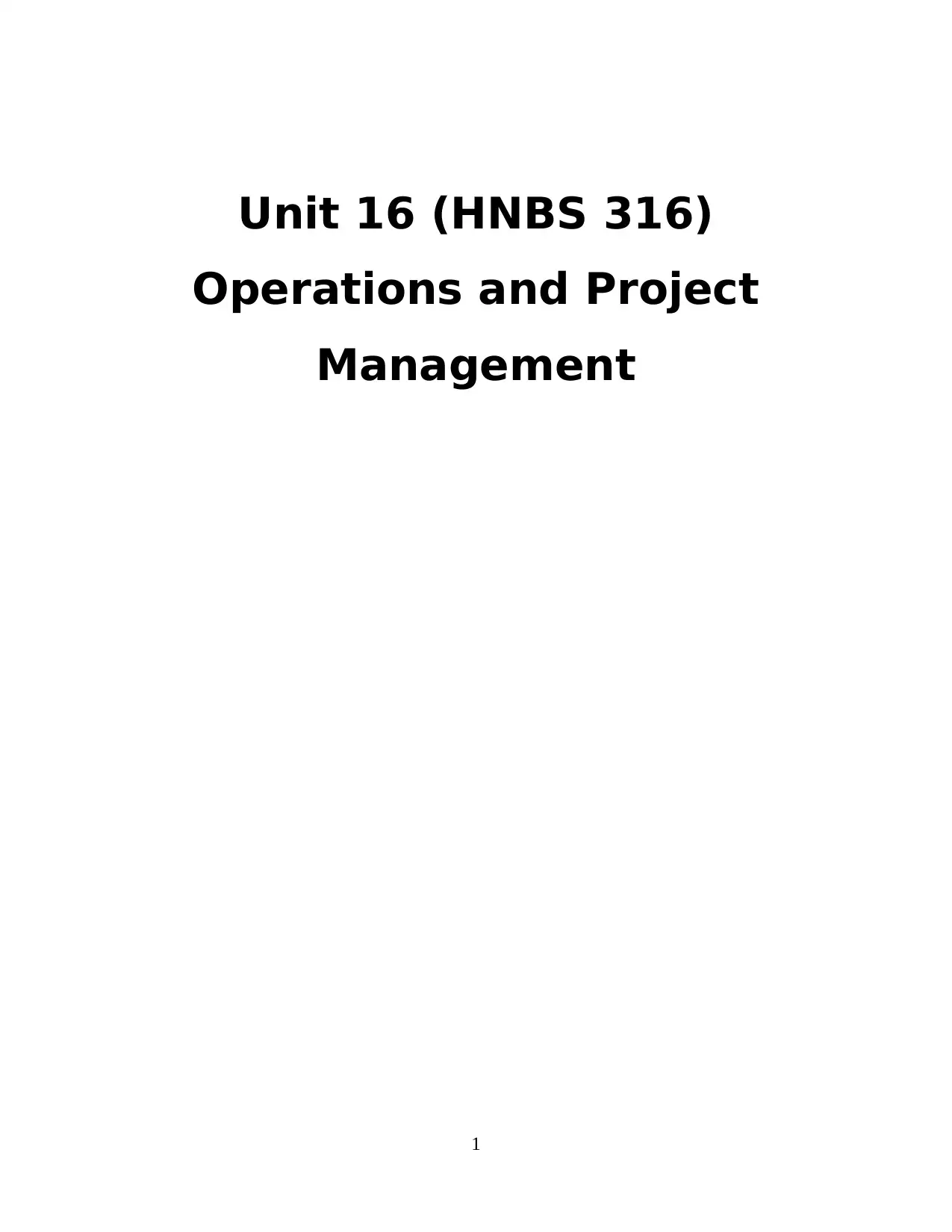
Unit 16 (HNBS 316)
Operations and Project
Management
1
Operations and Project
Management
1
Paraphrase This Document
Need a fresh take? Get an instant paraphrase of this document with our AI Paraphraser
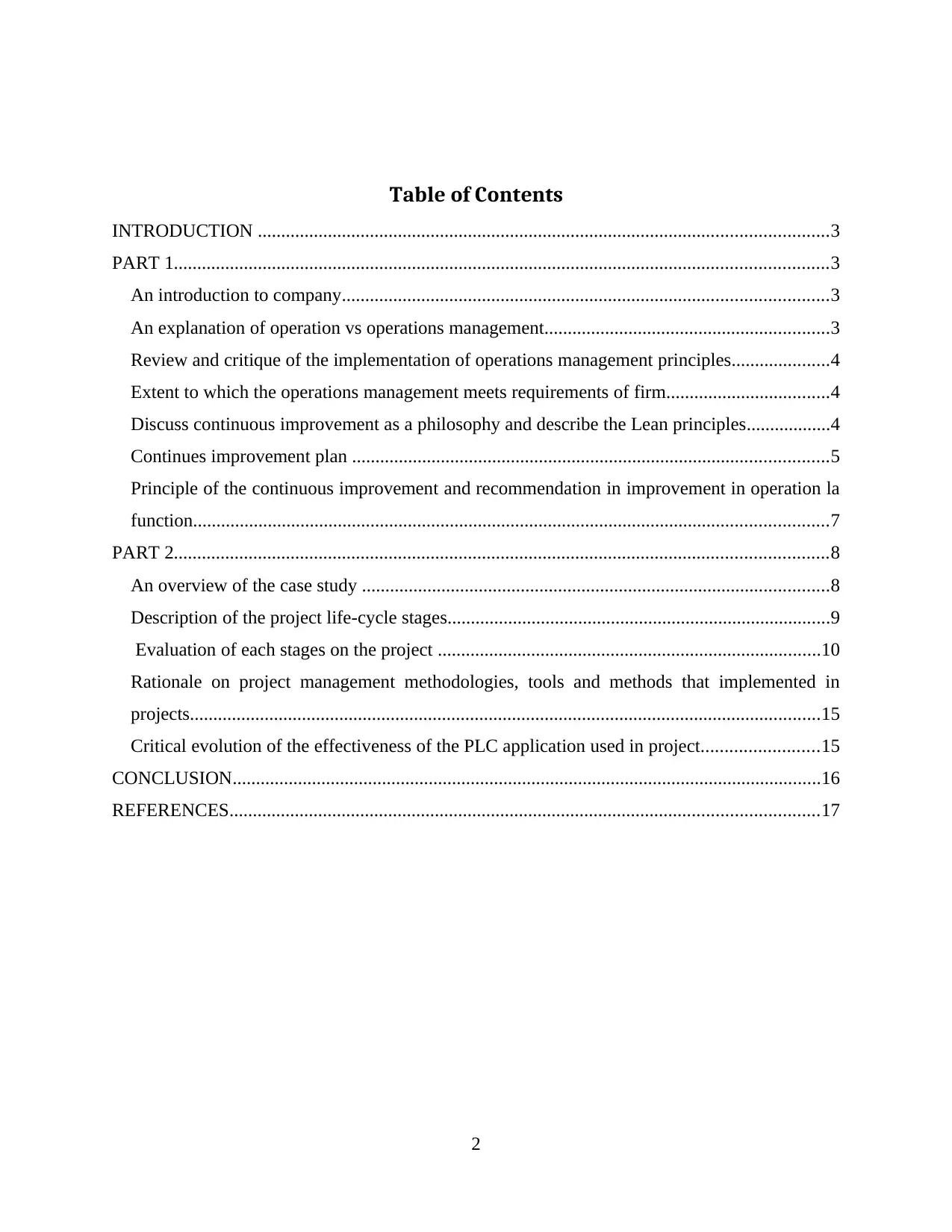
Table of Contents
INTRODUCTION ..........................................................................................................................3
PART 1............................................................................................................................................3
An introduction to company........................................................................................................3
An explanation of operation vs operations management.............................................................3
Review and critique of the implementation of operations management principles.....................4
Extent to which the operations management meets requirements of firm...................................4
Discuss continuous improvement as a philosophy and describe the Lean principles..................4
Continues improvement plan ......................................................................................................5
Principle of the continuous improvement and recommendation in improvement in operation la
function........................................................................................................................................7
PART 2............................................................................................................................................8
An overview of the case study ....................................................................................................8
Description of the project life-cycle stages..................................................................................9
Evaluation of each stages on the project ..................................................................................10
Rationale on project management methodologies, tools and methods that implemented in
projects.......................................................................................................................................15
Critical evolution of the effectiveness of the PLC application used in project.........................15
CONCLUSION..............................................................................................................................16
REFERENCES..............................................................................................................................17
2
INTRODUCTION ..........................................................................................................................3
PART 1............................................................................................................................................3
An introduction to company........................................................................................................3
An explanation of operation vs operations management.............................................................3
Review and critique of the implementation of operations management principles.....................4
Extent to which the operations management meets requirements of firm...................................4
Discuss continuous improvement as a philosophy and describe the Lean principles..................4
Continues improvement plan ......................................................................................................5
Principle of the continuous improvement and recommendation in improvement in operation la
function........................................................................................................................................7
PART 2............................................................................................................................................8
An overview of the case study ....................................................................................................8
Description of the project life-cycle stages..................................................................................9
Evaluation of each stages on the project ..................................................................................10
Rationale on project management methodologies, tools and methods that implemented in
projects.......................................................................................................................................15
Critical evolution of the effectiveness of the PLC application used in project.........................15
CONCLUSION..............................................................................................................................16
REFERENCES..............................................................................................................................17
2
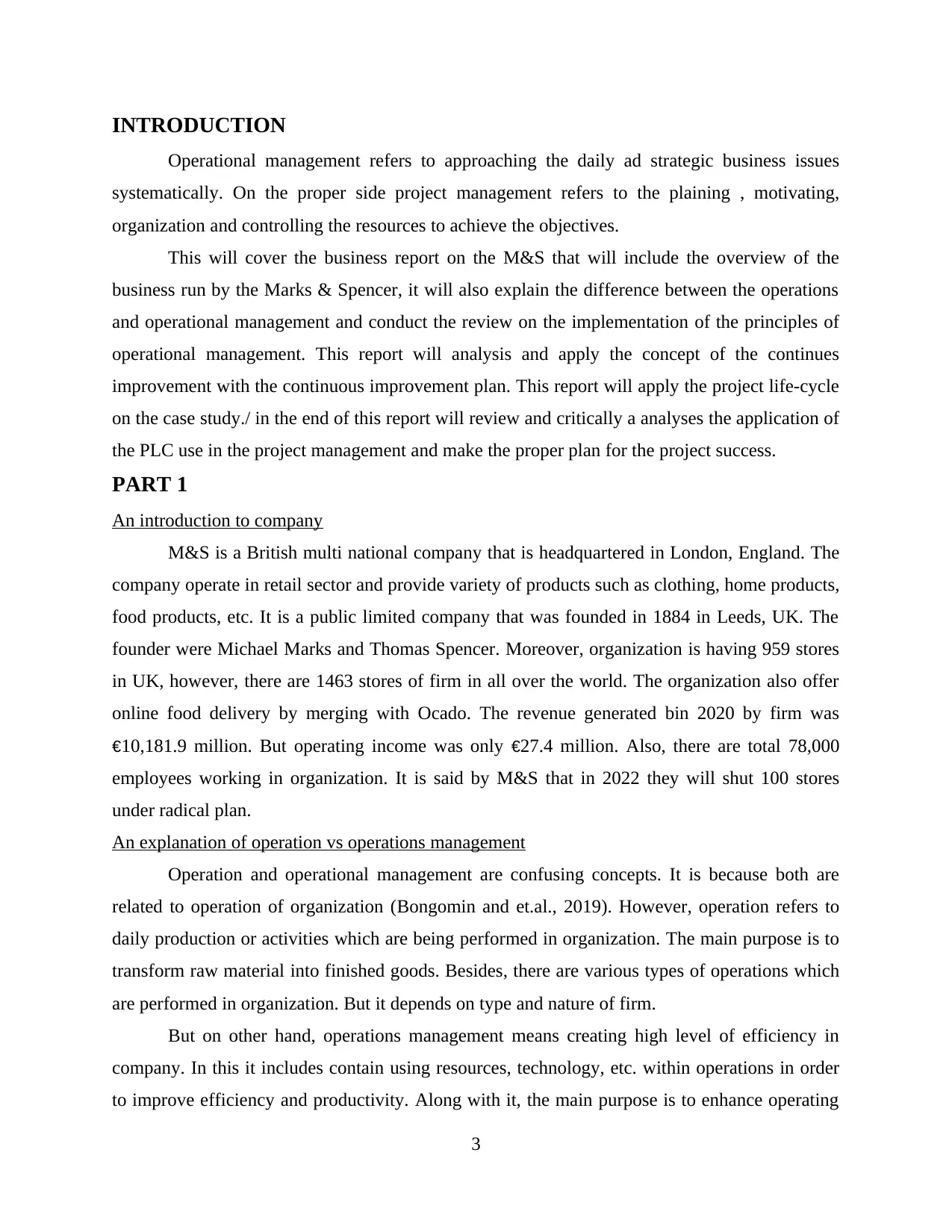
INTRODUCTION
Operational management refers to approaching the daily ad strategic business issues
systematically. On the proper side project management refers to the plaining , motivating,
organization and controlling the resources to achieve the objectives.
This will cover the business report on the M&S that will include the overview of the
business run by the Marks & Spencer, it will also explain the difference between the operations
and operational management and conduct the review on the implementation of the principles of
operational management. This report will analysis and apply the concept of the continues
improvement with the continuous improvement plan. This report will apply the project life-cycle
on the case study./ in the end of this report will review and critically a analyses the application of
the PLC use in the project management and make the proper plan for the project success.
PART 1
An introduction to company
M&S is a British multi national company that is headquartered in London, England. The
company operate in retail sector and provide variety of products such as clothing, home products,
food products, etc. It is a public limited company that was founded in 1884 in Leeds, UK. The
founder were Michael Marks and Thomas Spencer. Moreover, organization is having 959 stores
in UK, however, there are 1463 stores of firm in all over the world. The organization also offer
online food delivery by merging with Ocado. The revenue generated bin 2020 by firm was
€10,181.9 million. But operating income was only €27.4 million. Also, there are total 78,000
employees working in organization. It is said by M&S that in 2022 they will shut 100 stores
under radical plan.
An explanation of operation vs operations management
Operation and operational management are confusing concepts. It is because both are
related to operation of organization (Bongomin and et.al., 2019). However, operation refers to
daily production or activities which are being performed in organization. The main purpose is to
transform raw material into finished goods. Besides, there are various types of operations which
are performed in organization. But it depends on type and nature of firm.
But on other hand, operations management means creating high level of efficiency in
company. In this it includes contain using resources, technology, etc. within operations in order
to improve efficiency and productivity. Along with it, the main purpose is to enhance operating
3
Operational management refers to approaching the daily ad strategic business issues
systematically. On the proper side project management refers to the plaining , motivating,
organization and controlling the resources to achieve the objectives.
This will cover the business report on the M&S that will include the overview of the
business run by the Marks & Spencer, it will also explain the difference between the operations
and operational management and conduct the review on the implementation of the principles of
operational management. This report will analysis and apply the concept of the continues
improvement with the continuous improvement plan. This report will apply the project life-cycle
on the case study./ in the end of this report will review and critically a analyses the application of
the PLC use in the project management and make the proper plan for the project success.
PART 1
An introduction to company
M&S is a British multi national company that is headquartered in London, England. The
company operate in retail sector and provide variety of products such as clothing, home products,
food products, etc. It is a public limited company that was founded in 1884 in Leeds, UK. The
founder were Michael Marks and Thomas Spencer. Moreover, organization is having 959 stores
in UK, however, there are 1463 stores of firm in all over the world. The organization also offer
online food delivery by merging with Ocado. The revenue generated bin 2020 by firm was
€10,181.9 million. But operating income was only €27.4 million. Also, there are total 78,000
employees working in organization. It is said by M&S that in 2022 they will shut 100 stores
under radical plan.
An explanation of operation vs operations management
Operation and operational management are confusing concepts. It is because both are
related to operation of organization (Bongomin and et.al., 2019). However, operation refers to
daily production or activities which are being performed in organization. The main purpose is to
transform raw material into finished goods. Besides, there are various types of operations which
are performed in organization. But it depends on type and nature of firm.
But on other hand, operations management means creating high level of efficiency in
company. In this it includes contain using resources, technology, etc. within operations in order
to improve efficiency and productivity. Along with it, the main purpose is to enhance operating
3
You're viewing a preview
Unlock full access by subscribing today!
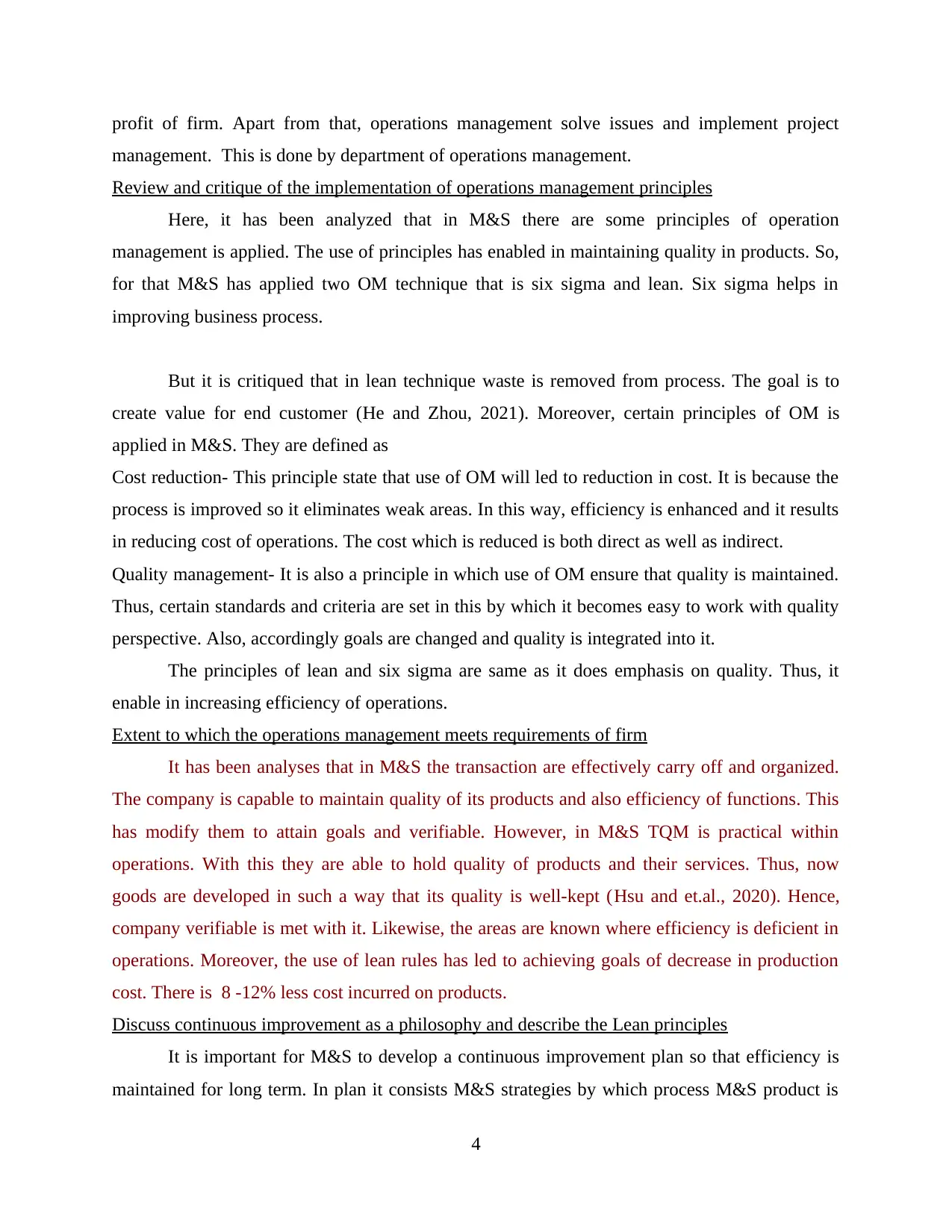
profit of firm. Apart from that, operations management solve issues and implement project
management. This is done by department of operations management.
Review and critique of the implementation of operations management principles
Here, it has been analyzed that in M&S there are some principles of operation
management is applied. The use of principles has enabled in maintaining quality in products. So,
for that M&S has applied two OM technique that is six sigma and lean. Six sigma helps in
improving business process.
But it is critiqued that in lean technique waste is removed from process. The goal is to
create value for end customer (He and Zhou, 2021). Moreover, certain principles of OM is
applied in M&S. They are defined as
Cost reduction- This principle state that use of OM will led to reduction in cost. It is because the
process is improved so it eliminates weak areas. In this way, efficiency is enhanced and it results
in reducing cost of operations. The cost which is reduced is both direct as well as indirect.
Quality management- It is also a principle in which use of OM ensure that quality is maintained.
Thus, certain standards and criteria are set in this by which it becomes easy to work with quality
perspective. Also, accordingly goals are changed and quality is integrated into it.
The principles of lean and six sigma are same as it does emphasis on quality. Thus, it
enable in increasing efficiency of operations.
Extent to which the operations management meets requirements of firm
It has been analyses that in M&S the transaction are effectively carry off and organized.
The company is capable to maintain quality of its products and also efficiency of functions. This
has modify them to attain goals and verifiable. However, in M&S TQM is practical within
operations. With this they are able to hold quality of products and their services. Thus, now
goods are developed in such a way that its quality is well-kept (Hsu and et.al., 2020). Hence,
company verifiable is met with it. Likewise, the areas are known where efficiency is deficient in
operations. Moreover, the use of lean rules has led to achieving goals of decrease in production
cost. There is 8 -12% less cost incurred on products.
Discuss continuous improvement as a philosophy and describe the Lean principles
It is important for M&S to develop a continuous improvement plan so that efficiency is
maintained for long term. In plan it consists M&S strategies by which process M&S product is
4
management. This is done by department of operations management.
Review and critique of the implementation of operations management principles
Here, it has been analyzed that in M&S there are some principles of operation
management is applied. The use of principles has enabled in maintaining quality in products. So,
for that M&S has applied two OM technique that is six sigma and lean. Six sigma helps in
improving business process.
But it is critiqued that in lean technique waste is removed from process. The goal is to
create value for end customer (He and Zhou, 2021). Moreover, certain principles of OM is
applied in M&S. They are defined as
Cost reduction- This principle state that use of OM will led to reduction in cost. It is because the
process is improved so it eliminates weak areas. In this way, efficiency is enhanced and it results
in reducing cost of operations. The cost which is reduced is both direct as well as indirect.
Quality management- It is also a principle in which use of OM ensure that quality is maintained.
Thus, certain standards and criteria are set in this by which it becomes easy to work with quality
perspective. Also, accordingly goals are changed and quality is integrated into it.
The principles of lean and six sigma are same as it does emphasis on quality. Thus, it
enable in increasing efficiency of operations.
Extent to which the operations management meets requirements of firm
It has been analyses that in M&S the transaction are effectively carry off and organized.
The company is capable to maintain quality of its products and also efficiency of functions. This
has modify them to attain goals and verifiable. However, in M&S TQM is practical within
operations. With this they are able to hold quality of products and their services. Thus, now
goods are developed in such a way that its quality is well-kept (Hsu and et.al., 2020). Hence,
company verifiable is met with it. Likewise, the areas are known where efficiency is deficient in
operations. Moreover, the use of lean rules has led to achieving goals of decrease in production
cost. There is 8 -12% less cost incurred on products.
Discuss continuous improvement as a philosophy and describe the Lean principles
It is important for M&S to develop a continuous improvement plan so that efficiency is
maintained for long term. In plan it consists M&S strategies by which process M&S product is
4
Paraphrase This Document
Need a fresh take? Get an instant paraphrase of this document with our AI Paraphraser
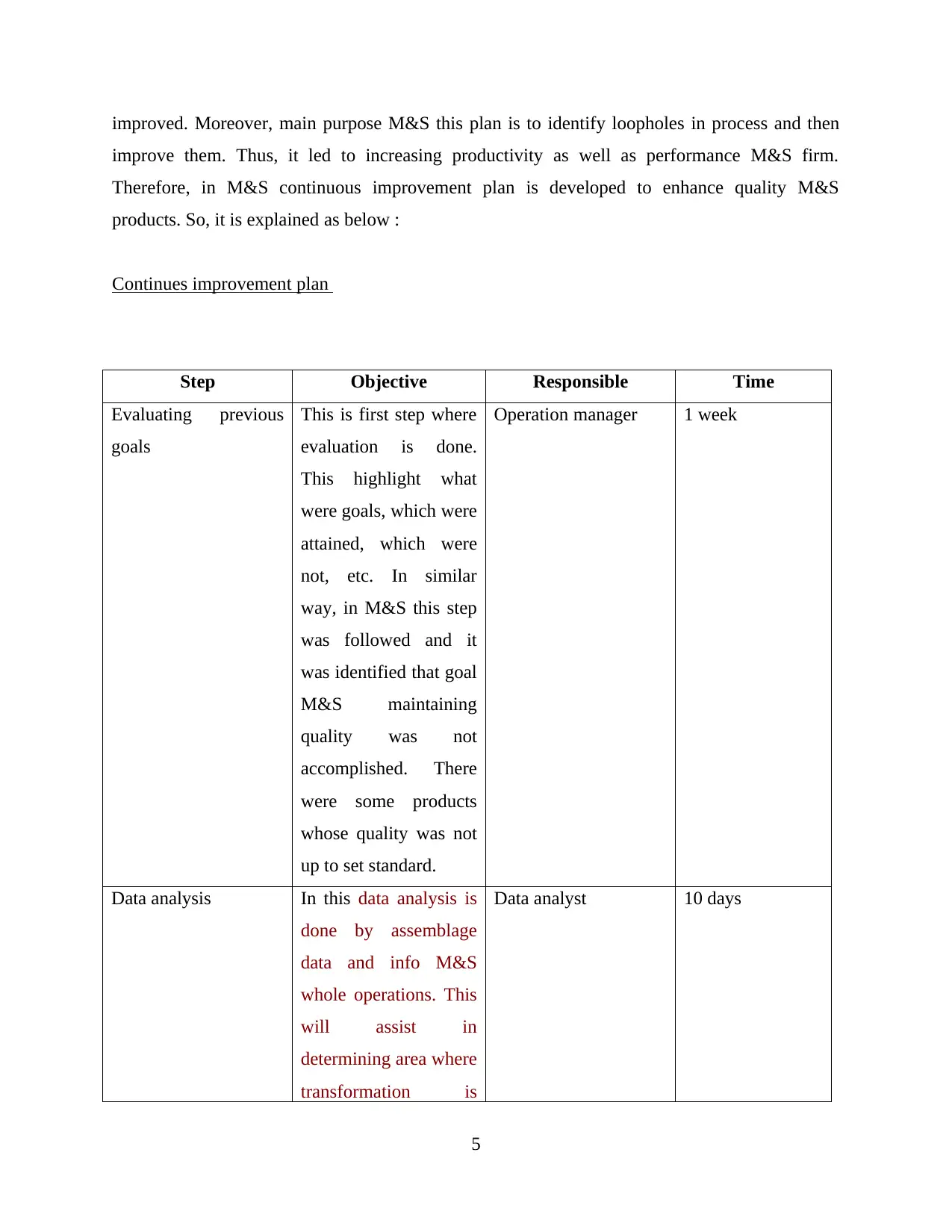
improved. Moreover, main purpose M&S this plan is to identify loopholes in process and then
improve them. Thus, it led to increasing productivity as well as performance M&S firm.
Therefore, in M&S continuous improvement plan is developed to enhance quality M&S
products. So, it is explained as below :
Continues improvement plan
Step Objective Responsible Time
Evaluating previous
goals
This is first step where
evaluation is done.
This highlight what
were goals, which were
attained, which were
not, etc. In similar
way, in M&S this step
was followed and it
was identified that goal
M&S maintaining
quality was not
accomplished. There
were some products
whose quality was not
up to set standard.
Operation manager 1 week
Data analysis In this data analysis is
done by assemblage
data and info M&S
whole operations. This
will assist in
determining area where
transformation is
Data analyst 10 days
5
improve them. Thus, it led to increasing productivity as well as performance M&S firm.
Therefore, in M&S continuous improvement plan is developed to enhance quality M&S
products. So, it is explained as below :
Continues improvement plan
Step Objective Responsible Time
Evaluating previous
goals
This is first step where
evaluation is done.
This highlight what
were goals, which were
attained, which were
not, etc. In similar
way, in M&S this step
was followed and it
was identified that goal
M&S maintaining
quality was not
accomplished. There
were some products
whose quality was not
up to set standard.
Operation manager 1 week
Data analysis In this data analysis is
done by assemblage
data and info M&S
whole operations. This
will assist in
determining area where
transformation is
Data analyst 10 days
5
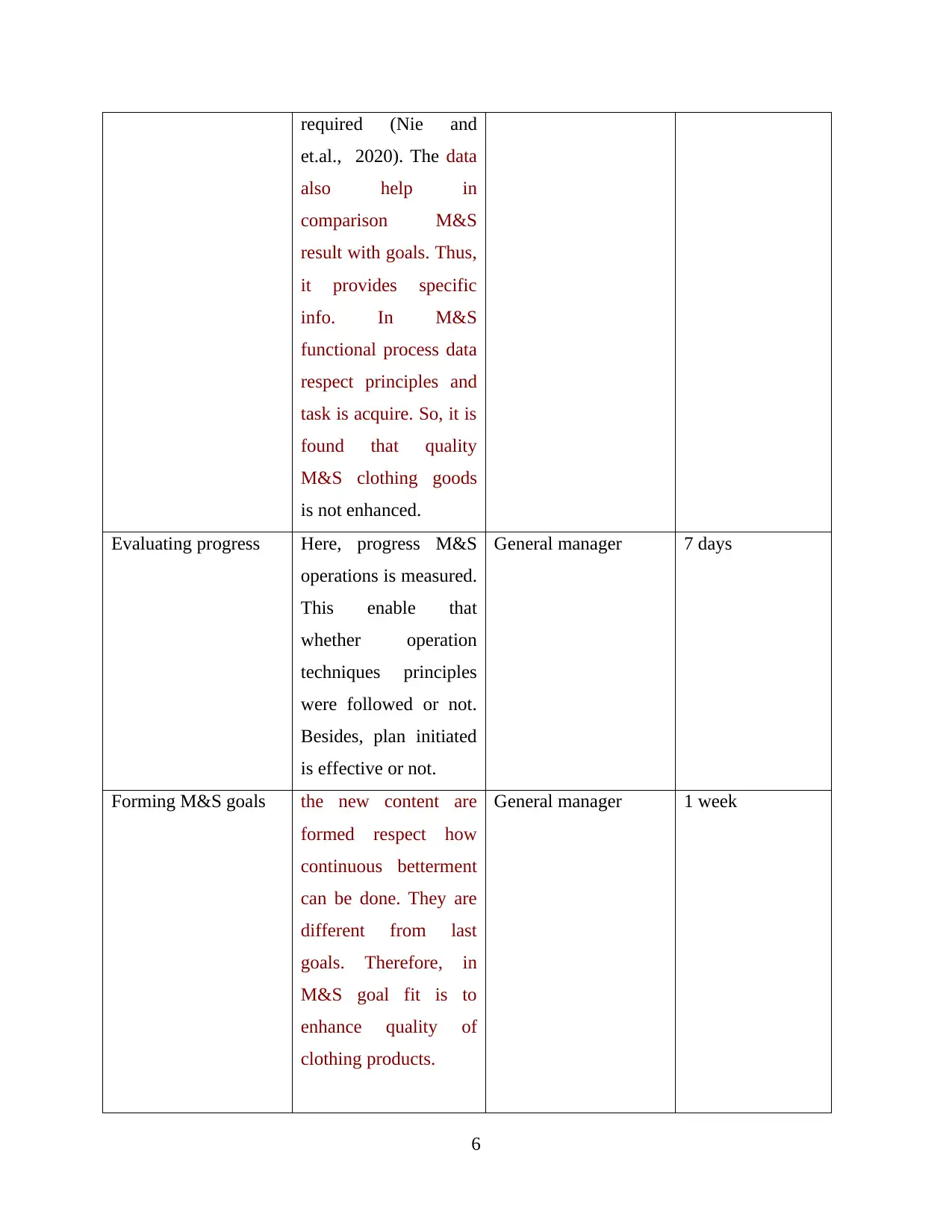
required (Nie and
et.al., 2020). The data
also help in
comparison M&S
result with goals. Thus,
it provides specific
info. In M&S
functional process data
respect principles and
task is acquire. So, it is
found that quality
M&S clothing goods
is not enhanced.
Evaluating progress Here, progress M&S
operations is measured.
This enable that
whether operation
techniques principles
were followed or not.
Besides, plan initiated
is effective or not.
General manager 7 days
Forming M&S goals the new content are
formed respect how
continuous betterment
can be done. They are
different from last
goals. Therefore, in
M&S goal fit is to
enhance quality of
clothing products.
General manager 1 week
6
et.al., 2020). The data
also help in
comparison M&S
result with goals. Thus,
it provides specific
info. In M&S
functional process data
respect principles and
task is acquire. So, it is
found that quality
M&S clothing goods
is not enhanced.
Evaluating progress Here, progress M&S
operations is measured.
This enable that
whether operation
techniques principles
were followed or not.
Besides, plan initiated
is effective or not.
General manager 7 days
Forming M&S goals the new content are
formed respect how
continuous betterment
can be done. They are
different from last
goals. Therefore, in
M&S goal fit is to
enhance quality of
clothing products.
General manager 1 week
6
You're viewing a preview
Unlock full access by subscribing today!
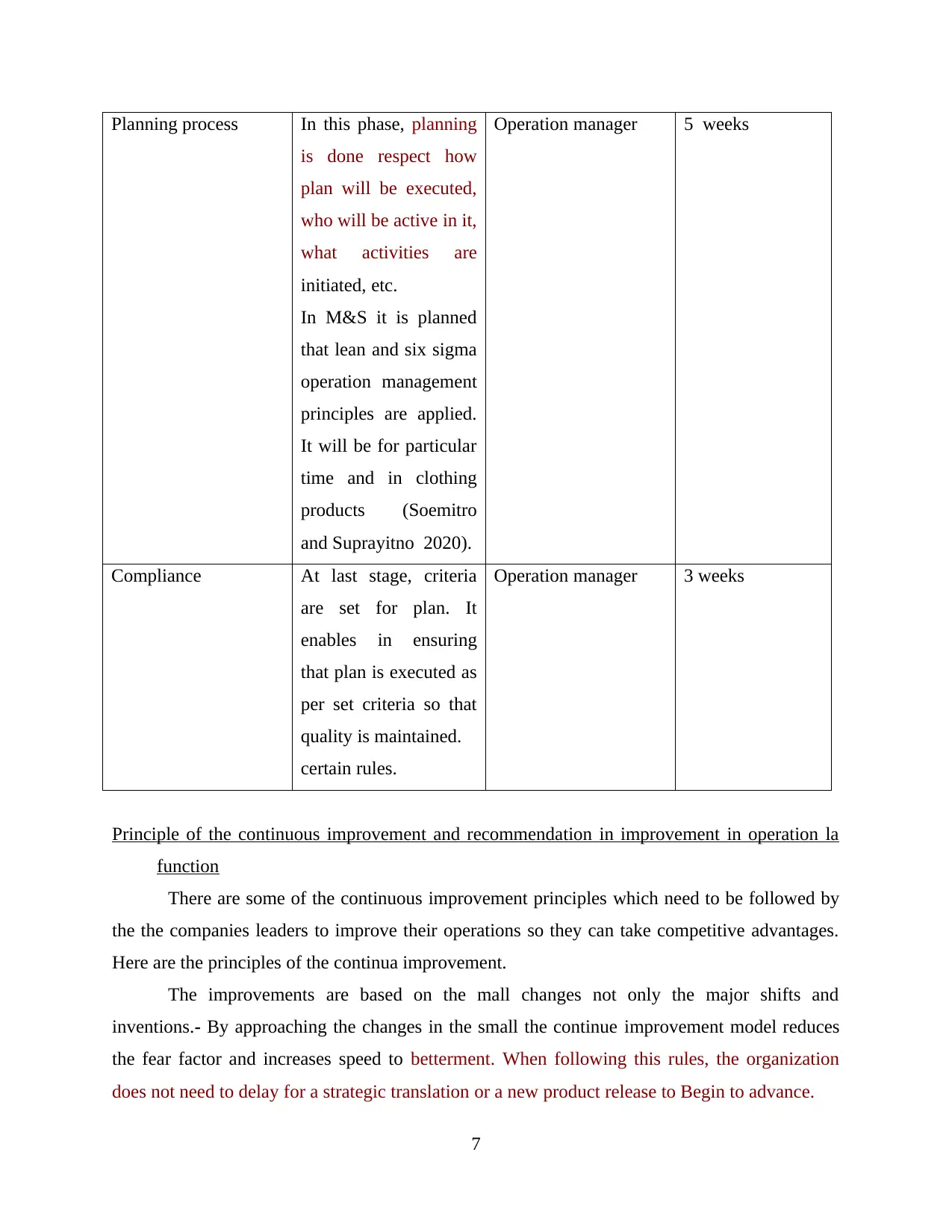
Planning process In this phase, planning
is done respect how
plan will be executed,
who will be active in it,
what activities are
initiated, etc.
In M&S it is planned
that lean and six sigma
operation management
principles are applied.
It will be for particular
time and in clothing
products (Soemitro
and Suprayitno 2020).
Operation manager 5 weeks
Compliance At last stage, criteria
are set for plan. It
enables in ensuring
that plan is executed as
per set criteria so that
quality is maintained.
certain rules.
Operation manager 3 weeks
Principle of the continuous improvement and recommendation in improvement in operation la
function
There are some of the continuous improvement principles which need to be followed by
the the companies leaders to improve their operations so they can take competitive advantages.
Here are the principles of the continua improvement.
The improvements are based on the mall changes not only the major shifts and
inventions.- By approaching the changes in the small the continue improvement model reduces
the fear factor and increases speed to betterment. When following this rules, the organization
does not need to delay for a strategic translation or a new product release to Begin to advance.
7
is done respect how
plan will be executed,
who will be active in it,
what activities are
initiated, etc.
In M&S it is planned
that lean and six sigma
operation management
principles are applied.
It will be for particular
time and in clothing
products (Soemitro
and Suprayitno 2020).
Operation manager 5 weeks
Compliance At last stage, criteria
are set for plan. It
enables in ensuring
that plan is executed as
per set criteria so that
quality is maintained.
certain rules.
Operation manager 3 weeks
Principle of the continuous improvement and recommendation in improvement in operation la
function
There are some of the continuous improvement principles which need to be followed by
the the companies leaders to improve their operations so they can take competitive advantages.
Here are the principles of the continua improvement.
The improvements are based on the mall changes not only the major shifts and
inventions.- By approaching the changes in the small the continue improvement model reduces
the fear factor and increases speed to betterment. When following this rules, the organization
does not need to delay for a strategic translation or a new product release to Begin to advance.
7
Paraphrase This Document
Need a fresh take? Get an instant paraphrase of this document with our AI Paraphraser
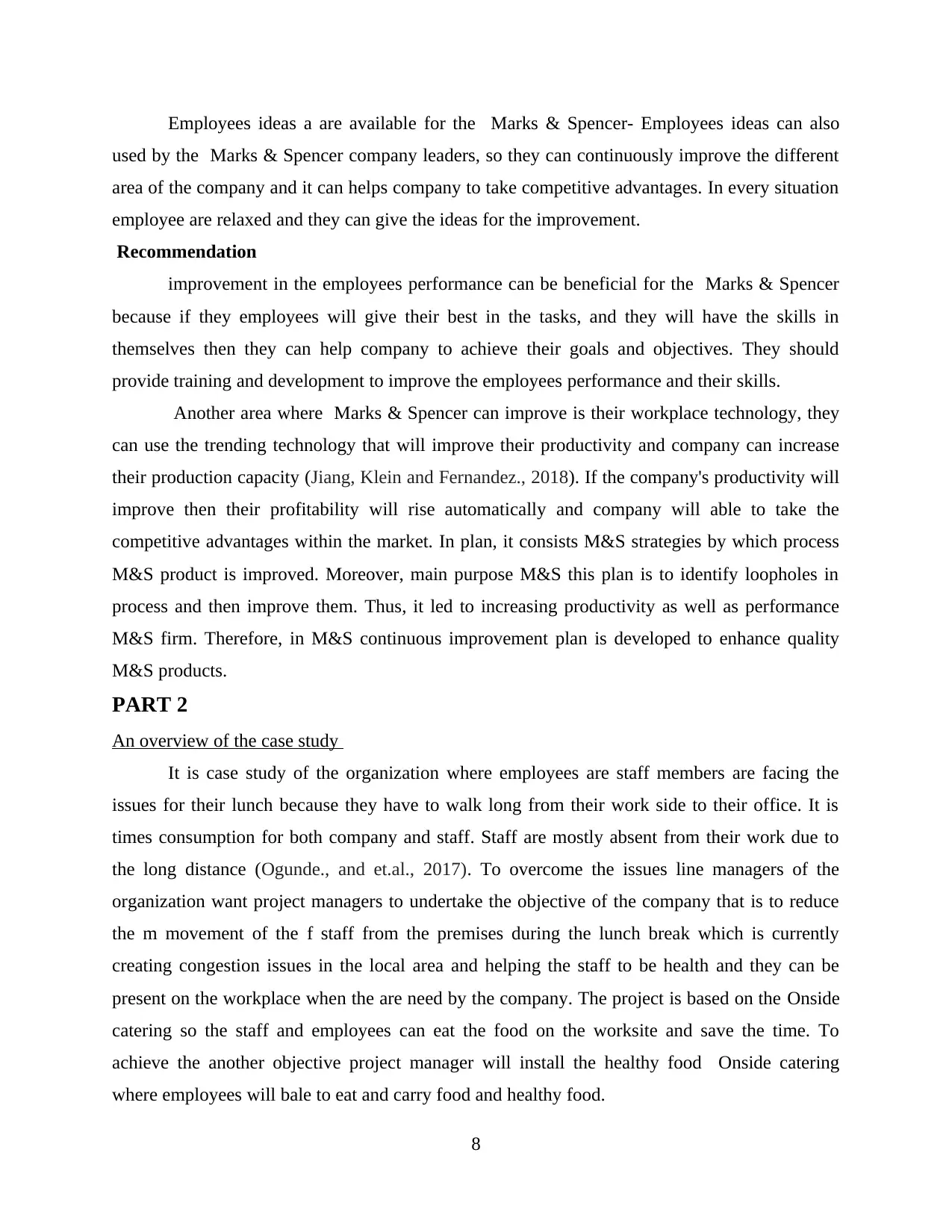
Employees ideas a are available for the Marks & Spencer- Employees ideas can also
used by the Marks & Spencer company leaders, so they can continuously improve the different
area of the company and it can helps company to take competitive advantages. In every situation
employee are relaxed and they can give the ideas for the improvement.
Recommendation
improvement in the employees performance can be beneficial for the Marks & Spencer
because if they employees will give their best in the tasks, and they will have the skills in
themselves then they can help company to achieve their goals and objectives. They should
provide training and development to improve the employees performance and their skills.
Another area where Marks & Spencer can improve is their workplace technology, they
can use the trending technology that will improve their productivity and company can increase
their production capacity (Jiang, Klein and Fernandez., 2018). If the company's productivity will
improve then their profitability will rise automatically and company will able to take the
competitive advantages within the market. In plan, it consists M&S strategies by which process
M&S product is improved. Moreover, main purpose M&S this plan is to identify loopholes in
process and then improve them. Thus, it led to increasing productivity as well as performance
M&S firm. Therefore, in M&S continuous improvement plan is developed to enhance quality
M&S products.
PART 2
An overview of the case study
It is case study of the organization where employees are staff members are facing the
issues for their lunch because they have to walk long from their work side to their office. It is
times consumption for both company and staff. Staff are mostly absent from their work due to
the long distance (Ogunde., and et.al., 2017). To overcome the issues line managers of the
organization want project managers to undertake the objective of the company that is to reduce
the m movement of the f staff from the premises during the lunch break which is currently
creating congestion issues in the local area and helping the staff to be health and they can be
present on the workplace when the are need by the company. The project is based on the Onside
catering so the staff and employees can eat the food on the worksite and save the time. To
achieve the another objective project manager will install the healthy food Onside catering
where employees will bale to eat and carry food and healthy food.
8
used by the Marks & Spencer company leaders, so they can continuously improve the different
area of the company and it can helps company to take competitive advantages. In every situation
employee are relaxed and they can give the ideas for the improvement.
Recommendation
improvement in the employees performance can be beneficial for the Marks & Spencer
because if they employees will give their best in the tasks, and they will have the skills in
themselves then they can help company to achieve their goals and objectives. They should
provide training and development to improve the employees performance and their skills.
Another area where Marks & Spencer can improve is their workplace technology, they
can use the trending technology that will improve their productivity and company can increase
their production capacity (Jiang, Klein and Fernandez., 2018). If the company's productivity will
improve then their profitability will rise automatically and company will able to take the
competitive advantages within the market. In plan, it consists M&S strategies by which process
M&S product is improved. Moreover, main purpose M&S this plan is to identify loopholes in
process and then improve them. Thus, it led to increasing productivity as well as performance
M&S firm. Therefore, in M&S continuous improvement plan is developed to enhance quality
M&S products.
PART 2
An overview of the case study
It is case study of the organization where employees are staff members are facing the
issues for their lunch because they have to walk long from their work side to their office. It is
times consumption for both company and staff. Staff are mostly absent from their work due to
the long distance (Ogunde., and et.al., 2017). To overcome the issues line managers of the
organization want project managers to undertake the objective of the company that is to reduce
the m movement of the f staff from the premises during the lunch break which is currently
creating congestion issues in the local area and helping the staff to be health and they can be
present on the workplace when the are need by the company. The project is based on the Onside
catering so the staff and employees can eat the food on the worksite and save the time. To
achieve the another objective project manager will install the healthy food Onside catering
where employees will bale to eat and carry food and healthy food.
8
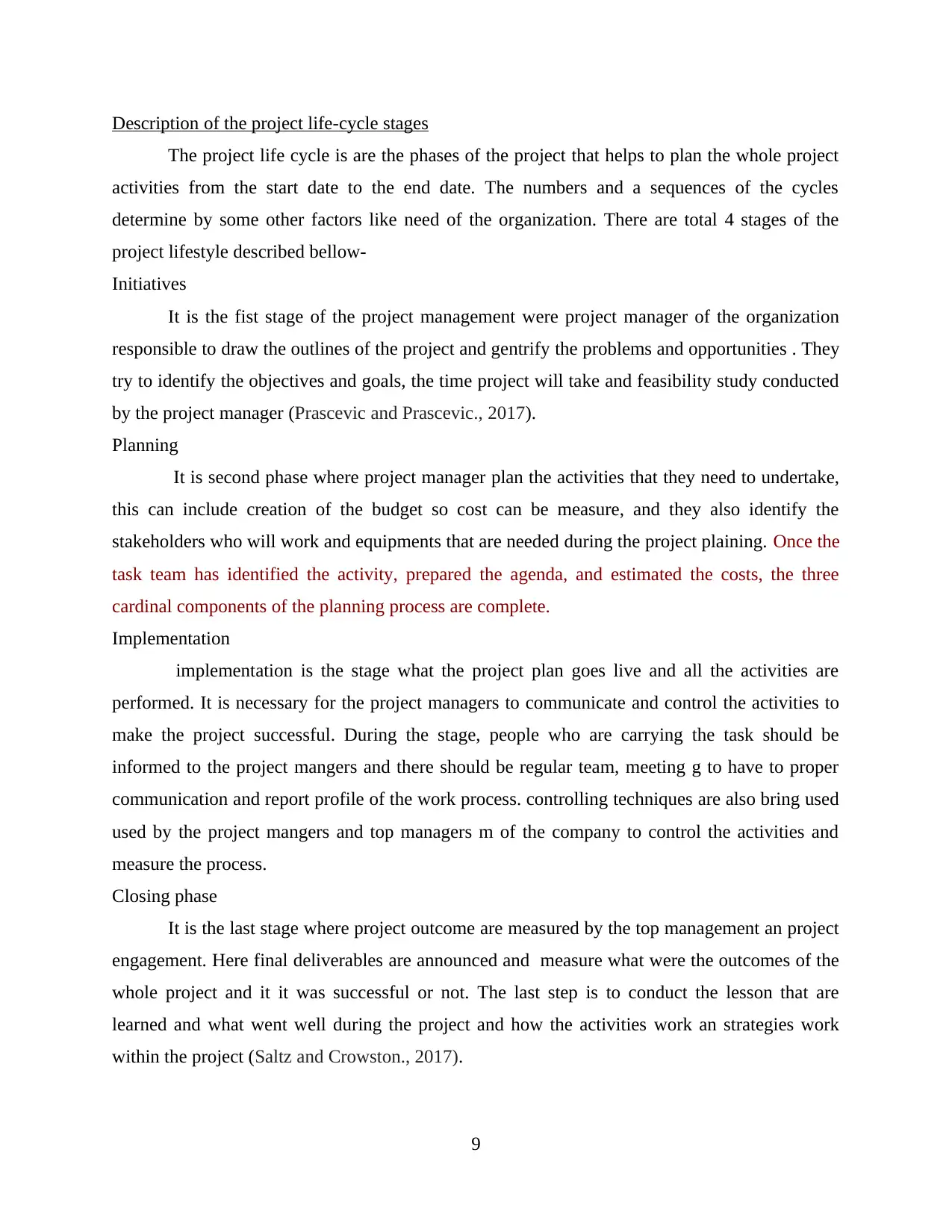
Description of the project life-cycle stages
The project life cycle is are the phases of the project that helps to plan the whole project
activities from the start date to the end date. The numbers and a sequences of the cycles
determine by some other factors like need of the organization. There are total 4 stages of the
project lifestyle described bellow-
Initiatives
It is the fist stage of the project management were project manager of the organization
responsible to draw the outlines of the project and gentrify the problems and opportunities . They
try to identify the objectives and goals, the time project will take and feasibility study conducted
by the project manager (Prascevic and Prascevic., 2017).
Planning
It is second phase where project manager plan the activities that they need to undertake,
this can include creation of the budget so cost can be measure, and they also identify the
stakeholders who will work and equipments that are needed during the project plaining. Once the
task team has identified the activity, prepared the agenda, and estimated the costs, the three
cardinal components of the planning process are complete.
Implementation
implementation is the stage what the project plan goes live and all the activities are
performed. It is necessary for the project managers to communicate and control the activities to
make the project successful. During the stage, people who are carrying the task should be
informed to the project mangers and there should be regular team, meeting g to have to proper
communication and report profile of the work process. controlling techniques are also bring used
used by the project mangers and top managers m of the company to control the activities and
measure the process.
Closing phase
It is the last stage where project outcome are measured by the top management an project
engagement. Here final deliverables are announced and measure what were the outcomes of the
whole project and it it was successful or not. The last step is to conduct the lesson that are
learned and what went well during the project and how the activities work an strategies work
within the project (Saltz and Crowston., 2017).
9
The project life cycle is are the phases of the project that helps to plan the whole project
activities from the start date to the end date. The numbers and a sequences of the cycles
determine by some other factors like need of the organization. There are total 4 stages of the
project lifestyle described bellow-
Initiatives
It is the fist stage of the project management were project manager of the organization
responsible to draw the outlines of the project and gentrify the problems and opportunities . They
try to identify the objectives and goals, the time project will take and feasibility study conducted
by the project manager (Prascevic and Prascevic., 2017).
Planning
It is second phase where project manager plan the activities that they need to undertake,
this can include creation of the budget so cost can be measure, and they also identify the
stakeholders who will work and equipments that are needed during the project plaining. Once the
task team has identified the activity, prepared the agenda, and estimated the costs, the three
cardinal components of the planning process are complete.
Implementation
implementation is the stage what the project plan goes live and all the activities are
performed. It is necessary for the project managers to communicate and control the activities to
make the project successful. During the stage, people who are carrying the task should be
informed to the project mangers and there should be regular team, meeting g to have to proper
communication and report profile of the work process. controlling techniques are also bring used
used by the project mangers and top managers m of the company to control the activities and
measure the process.
Closing phase
It is the last stage where project outcome are measured by the top management an project
engagement. Here final deliverables are announced and measure what were the outcomes of the
whole project and it it was successful or not. The last step is to conduct the lesson that are
learned and what went well during the project and how the activities work an strategies work
within the project (Saltz and Crowston., 2017).
9
You're viewing a preview
Unlock full access by subscribing today!
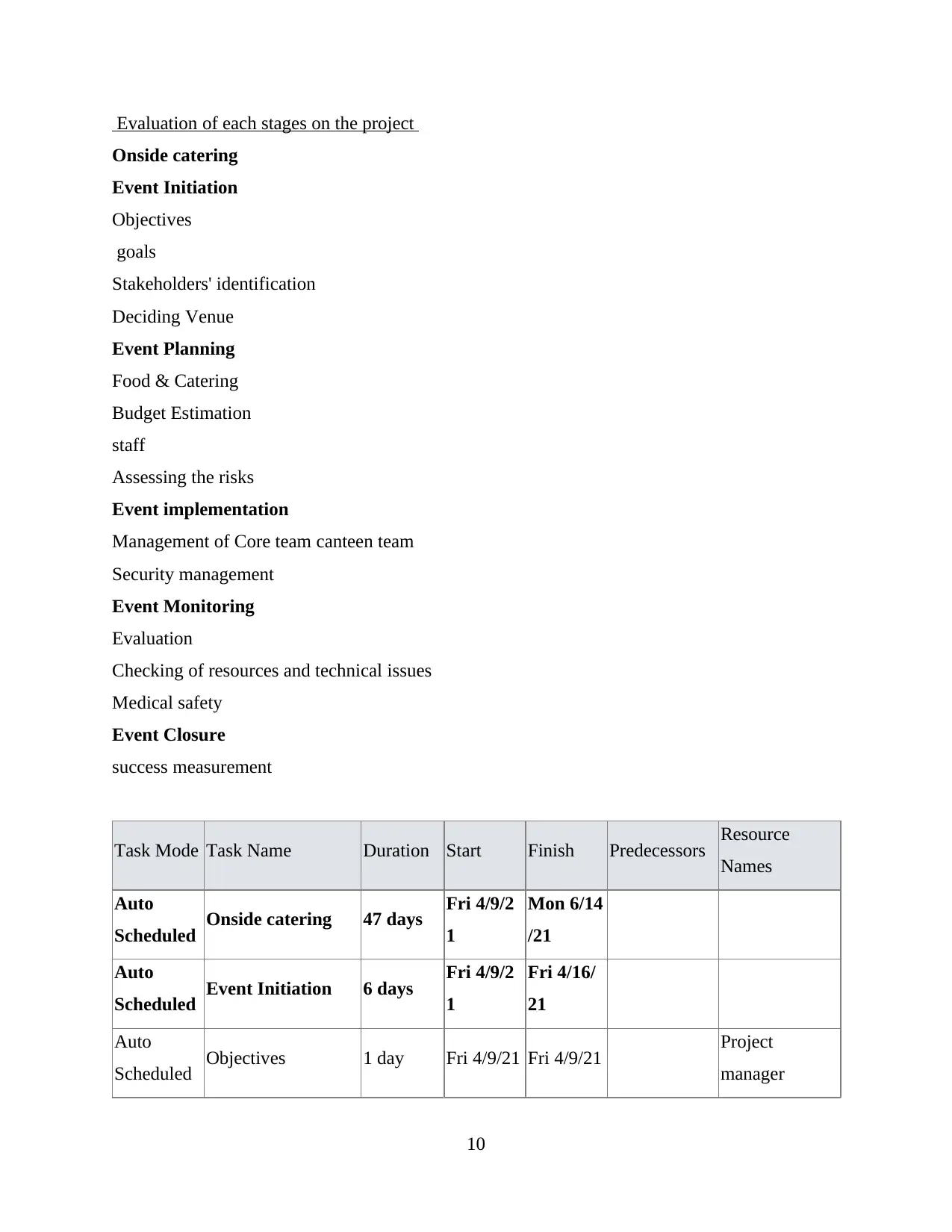
Evaluation of each stages on the project
Onside catering
Event Initiation
Objectives
goals
Stakeholders' identification
Deciding Venue
Event Planning
Food & Catering
Budget Estimation
staff
Assessing the risks
Event implementation
Management of Core team canteen team
Security management
Event Monitoring
Evaluation
Checking of resources and technical issues
Medical safety
Event Closure
success measurement
Task Mode Task Name Duration Start Finish Predecessors Resource
Names
Auto
Scheduled Onside catering 47 days Fri 4/9/2
1
Mon 6/14
/21
Auto
Scheduled Event Initiation 6 days Fri 4/9/2
1
Fri 4/16/
21
Auto
Scheduled Objectives 1 day Fri 4/9/21 Fri 4/9/21 Project
manager
10
Onside catering
Event Initiation
Objectives
goals
Stakeholders' identification
Deciding Venue
Event Planning
Food & Catering
Budget Estimation
staff
Assessing the risks
Event implementation
Management of Core team canteen team
Security management
Event Monitoring
Evaluation
Checking of resources and technical issues
Medical safety
Event Closure
success measurement
Task Mode Task Name Duration Start Finish Predecessors Resource
Names
Auto
Scheduled Onside catering 47 days Fri 4/9/2
1
Mon 6/14
/21
Auto
Scheduled Event Initiation 6 days Fri 4/9/2
1
Fri 4/16/
21
Auto
Scheduled Objectives 1 day Fri 4/9/21 Fri 4/9/21 Project
manager
10
Paraphrase This Document
Need a fresh take? Get an instant paraphrase of this document with our AI Paraphraser
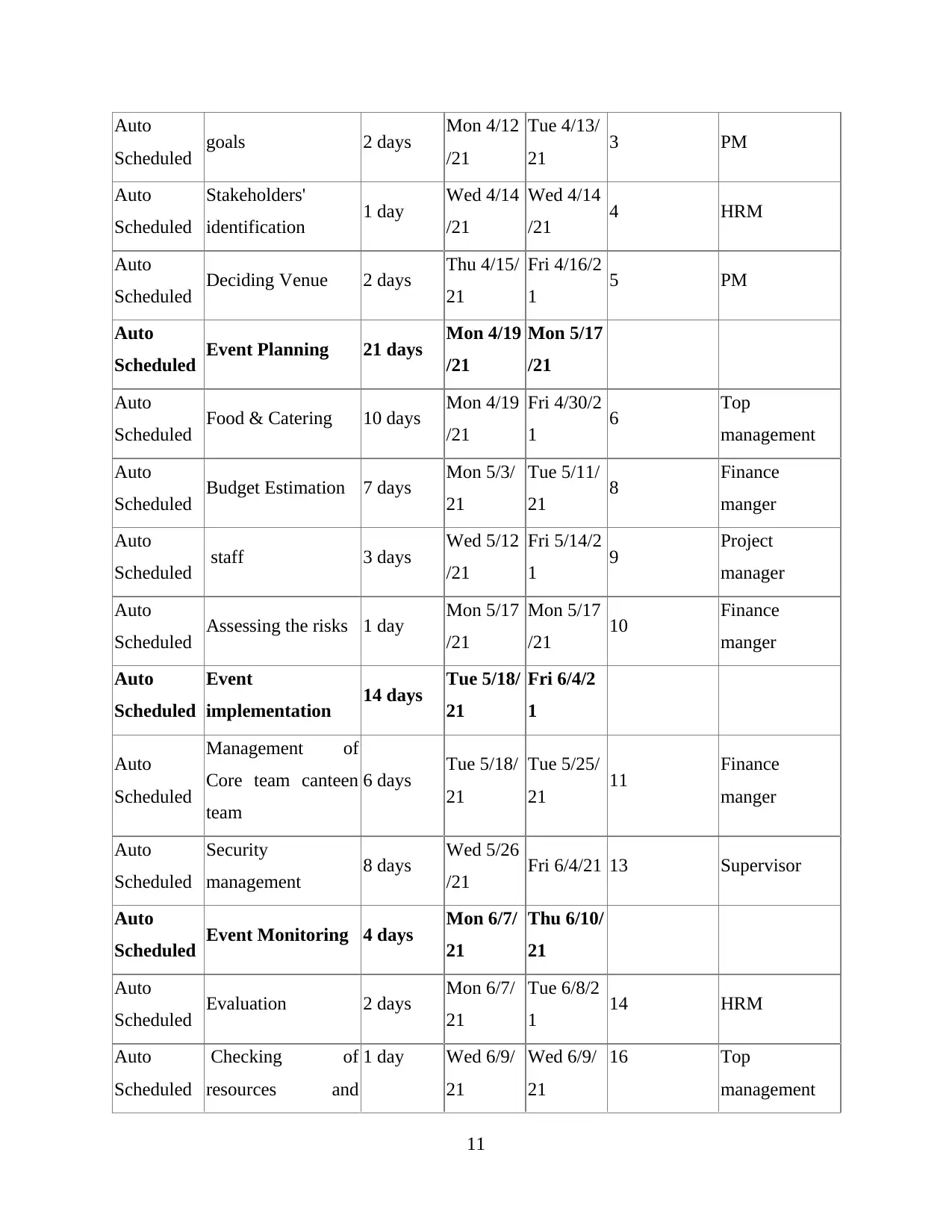
Auto
Scheduled goals 2 days Mon 4/12
/21
Tue 4/13/
21 3 PM
Auto
Scheduled
Stakeholders'
identification 1 day Wed 4/14
/21
Wed 4/14
/21 4 HRM
Auto
Scheduled Deciding Venue 2 days Thu 4/15/
21
Fri 4/16/2
1 5 PM
Auto
Scheduled Event Planning 21 days Mon 4/19
/21
Mon 5/17
/21
Auto
Scheduled Food & Catering 10 days Mon 4/19
/21
Fri 4/30/2
1 6 Top
management
Auto
Scheduled Budget Estimation 7 days Mon 5/3/
21
Tue 5/11/
21 8 Finance
manger
Auto
Scheduled staff 3 days Wed 5/12
/21
Fri 5/14/2
1 9 Project
manager
Auto
Scheduled Assessing the risks 1 day Mon 5/17
/21
Mon 5/17
/21 10 Finance
manger
Auto
Scheduled
Event
implementation 14 days Tue 5/18/
21
Fri 6/4/2
1
Auto
Scheduled
Management of
Core team canteen
team
6 days Tue 5/18/
21
Tue 5/25/
21 11 Finance
manger
Auto
Scheduled
Security
management 8 days Wed 5/26
/21 Fri 6/4/21 13 Supervisor
Auto
Scheduled Event Monitoring 4 days Mon 6/7/
21
Thu 6/10/
21
Auto
Scheduled Evaluation 2 days Mon 6/7/
21
Tue 6/8/2
1 14 HRM
Auto
Scheduled
Checking of
resources and
1 day Wed 6/9/
21
Wed 6/9/
21
16 Top
management
11
Scheduled goals 2 days Mon 4/12
/21
Tue 4/13/
21 3 PM
Auto
Scheduled
Stakeholders'
identification 1 day Wed 4/14
/21
Wed 4/14
/21 4 HRM
Auto
Scheduled Deciding Venue 2 days Thu 4/15/
21
Fri 4/16/2
1 5 PM
Auto
Scheduled Event Planning 21 days Mon 4/19
/21
Mon 5/17
/21
Auto
Scheduled Food & Catering 10 days Mon 4/19
/21
Fri 4/30/2
1 6 Top
management
Auto
Scheduled Budget Estimation 7 days Mon 5/3/
21
Tue 5/11/
21 8 Finance
manger
Auto
Scheduled staff 3 days Wed 5/12
/21
Fri 5/14/2
1 9 Project
manager
Auto
Scheduled Assessing the risks 1 day Mon 5/17
/21
Mon 5/17
/21 10 Finance
manger
Auto
Scheduled
Event
implementation 14 days Tue 5/18/
21
Fri 6/4/2
1
Auto
Scheduled
Management of
Core team canteen
team
6 days Tue 5/18/
21
Tue 5/25/
21 11 Finance
manger
Auto
Scheduled
Security
management 8 days Wed 5/26
/21 Fri 6/4/21 13 Supervisor
Auto
Scheduled Event Monitoring 4 days Mon 6/7/
21
Thu 6/10/
21
Auto
Scheduled Evaluation 2 days Mon 6/7/
21
Tue 6/8/2
1 14 HRM
Auto
Scheduled
Checking of
resources and
1 day Wed 6/9/
21
Wed 6/9/
21
16 Top
management
11
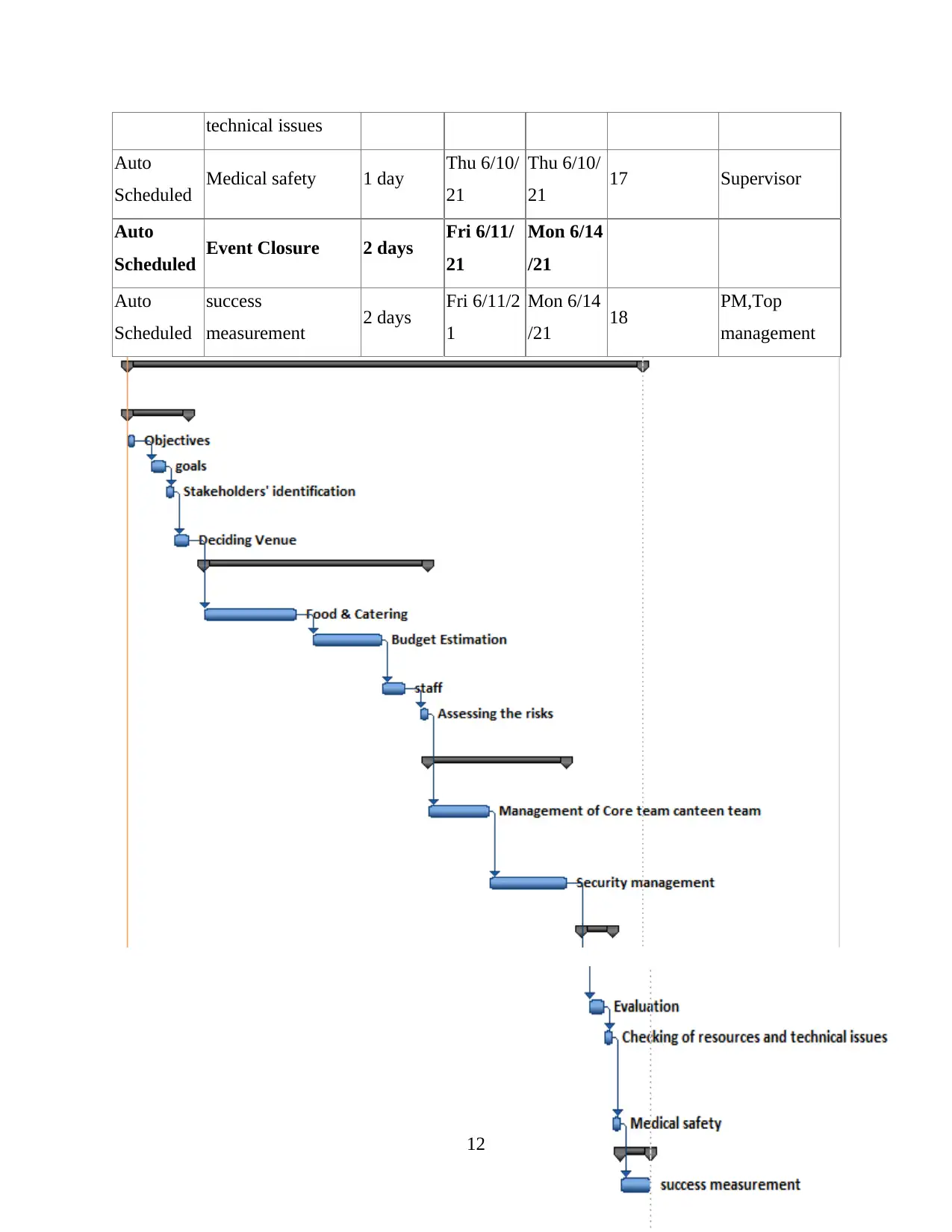
technical issues
Auto
Scheduled Medical safety 1 day Thu 6/10/
21
Thu 6/10/
21 17 Supervisor
Auto
Scheduled Event Closure 2 days Fri 6/11/
21
Mon 6/14
/21
Auto
Scheduled
success
measurement 2 days Fri 6/11/2
1
Mon 6/14
/21 18 PM,Top
management
12
Auto
Scheduled Medical safety 1 day Thu 6/10/
21
Thu 6/10/
21 17 Supervisor
Auto
Scheduled Event Closure 2 days Fri 6/11/
21
Mon 6/14
/21
Auto
Scheduled
success
measurement 2 days Fri 6/11/2
1
Mon 6/14
/21 18 PM,Top
management
12
You're viewing a preview
Unlock full access by subscribing today!
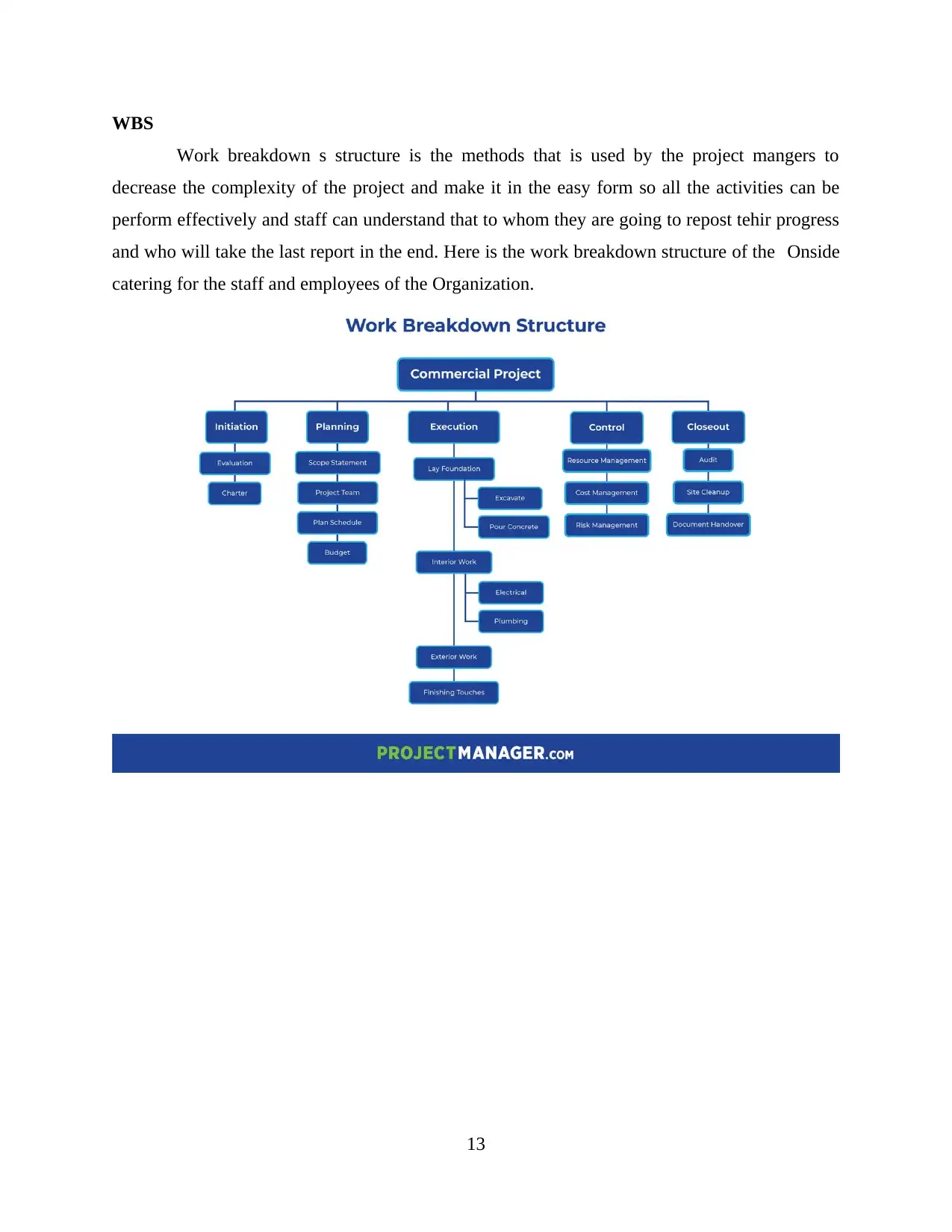
WBS
Work breakdown s structure is the methods that is used by the project mangers to
decrease the complexity of the project and make it in the easy form so all the activities can be
perform effectively and staff can understand that to whom they are going to repost tehir progress
and who will take the last report in the end. Here is the work breakdown structure of the Onside
catering for the staff and employees of the Organization.
13
Work breakdown s structure is the methods that is used by the project mangers to
decrease the complexity of the project and make it in the easy form so all the activities can be
perform effectively and staff can understand that to whom they are going to repost tehir progress
and who will take the last report in the end. Here is the work breakdown structure of the Onside
catering for the staff and employees of the Organization.
13
Paraphrase This Document
Need a fresh take? Get an instant paraphrase of this document with our AI Paraphraser
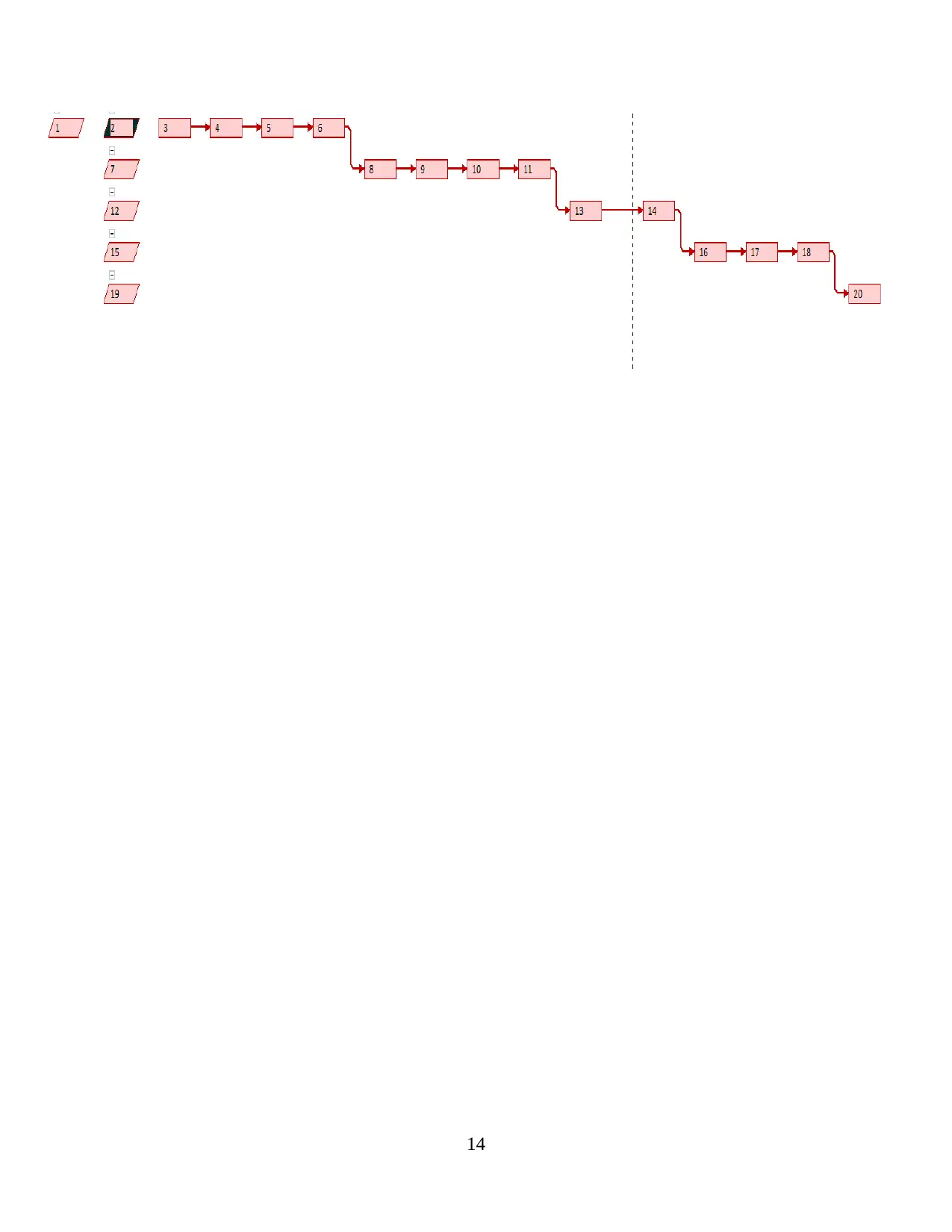
14
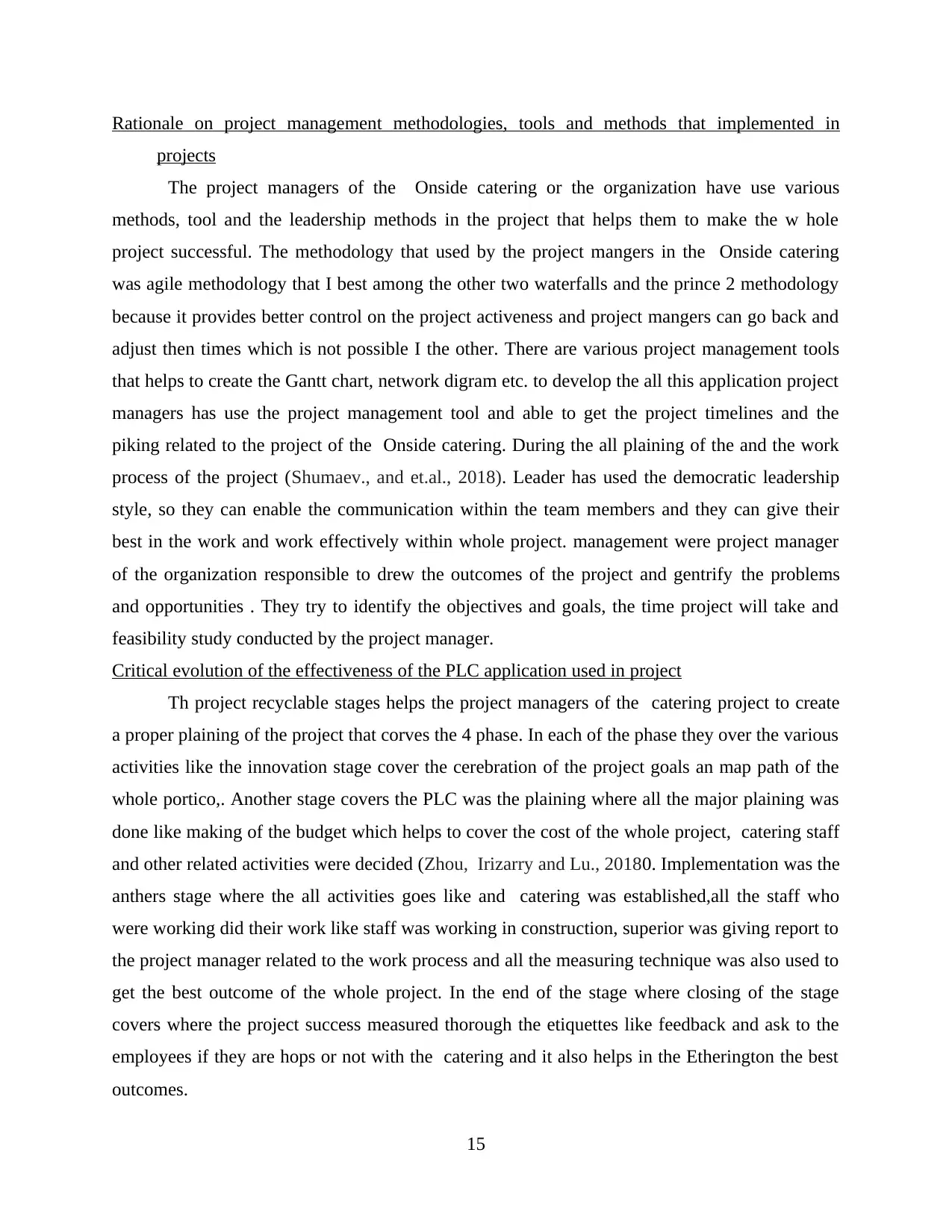
Rationale on project management methodologies, tools and methods that implemented in
projects
The project managers of the Onside catering or the organization have use various
methods, tool and the leadership methods in the project that helps them to make the w hole
project successful. The methodology that used by the project mangers in the Onside catering
was agile methodology that I best among the other two waterfalls and the prince 2 methodology
because it provides better control on the project activeness and project mangers can go back and
adjust then times which is not possible I the other. There are various project management tools
that helps to create the Gantt chart, network digram etc. to develop the all this application project
managers has use the project management tool and able to get the project timelines and the
piking related to the project of the Onside catering. During the all plaining of the and the work
process of the project (Shumaev., and et.al., 2018). Leader has used the democratic leadership
style, so they can enable the communication within the team members and they can give their
best in the work and work effectively within whole project. management were project manager
of the organization responsible to drew the outcomes of the project and gentrify the problems
and opportunities . They try to identify the objectives and goals, the time project will take and
feasibility study conducted by the project manager.
Critical evolution of the effectiveness of the PLC application used in project
Th project recyclable stages helps the project managers of the catering project to create
a proper plaining of the project that corves the 4 phase. In each of the phase they over the various
activities like the innovation stage cover the cerebration of the project goals an map path of the
whole portico,. Another stage covers the PLC was the plaining where all the major plaining was
done like making of the budget which helps to cover the cost of the whole project, catering staff
and other related activities were decided (Zhou, Irizarry and Lu., 20180. Implementation was the
anthers stage where the all activities goes like and catering was established,all the staff who
were working did their work like staff was working in construction, superior was giving report to
the project manager related to the work process and all the measuring technique was also used to
get the best outcome of the whole project. In the end of the stage where closing of the stage
covers where the project success measured thorough the etiquettes like feedback and ask to the
employees if they are hops or not with the catering and it also helps in the Etherington the best
outcomes.
15
projects
The project managers of the Onside catering or the organization have use various
methods, tool and the leadership methods in the project that helps them to make the w hole
project successful. The methodology that used by the project mangers in the Onside catering
was agile methodology that I best among the other two waterfalls and the prince 2 methodology
because it provides better control on the project activeness and project mangers can go back and
adjust then times which is not possible I the other. There are various project management tools
that helps to create the Gantt chart, network digram etc. to develop the all this application project
managers has use the project management tool and able to get the project timelines and the
piking related to the project of the Onside catering. During the all plaining of the and the work
process of the project (Shumaev., and et.al., 2018). Leader has used the democratic leadership
style, so they can enable the communication within the team members and they can give their
best in the work and work effectively within whole project. management were project manager
of the organization responsible to drew the outcomes of the project and gentrify the problems
and opportunities . They try to identify the objectives and goals, the time project will take and
feasibility study conducted by the project manager.
Critical evolution of the effectiveness of the PLC application used in project
Th project recyclable stages helps the project managers of the catering project to create
a proper plaining of the project that corves the 4 phase. In each of the phase they over the various
activities like the innovation stage cover the cerebration of the project goals an map path of the
whole portico,. Another stage covers the PLC was the plaining where all the major plaining was
done like making of the budget which helps to cover the cost of the whole project, catering staff
and other related activities were decided (Zhou, Irizarry and Lu., 20180. Implementation was the
anthers stage where the all activities goes like and catering was established,all the staff who
were working did their work like staff was working in construction, superior was giving report to
the project manager related to the work process and all the measuring technique was also used to
get the best outcome of the whole project. In the end of the stage where closing of the stage
covers where the project success measured thorough the etiquettes like feedback and ask to the
employees if they are hops or not with the catering and it also helps in the Etherington the best
outcomes.
15
You're viewing a preview
Unlock full access by subscribing today!
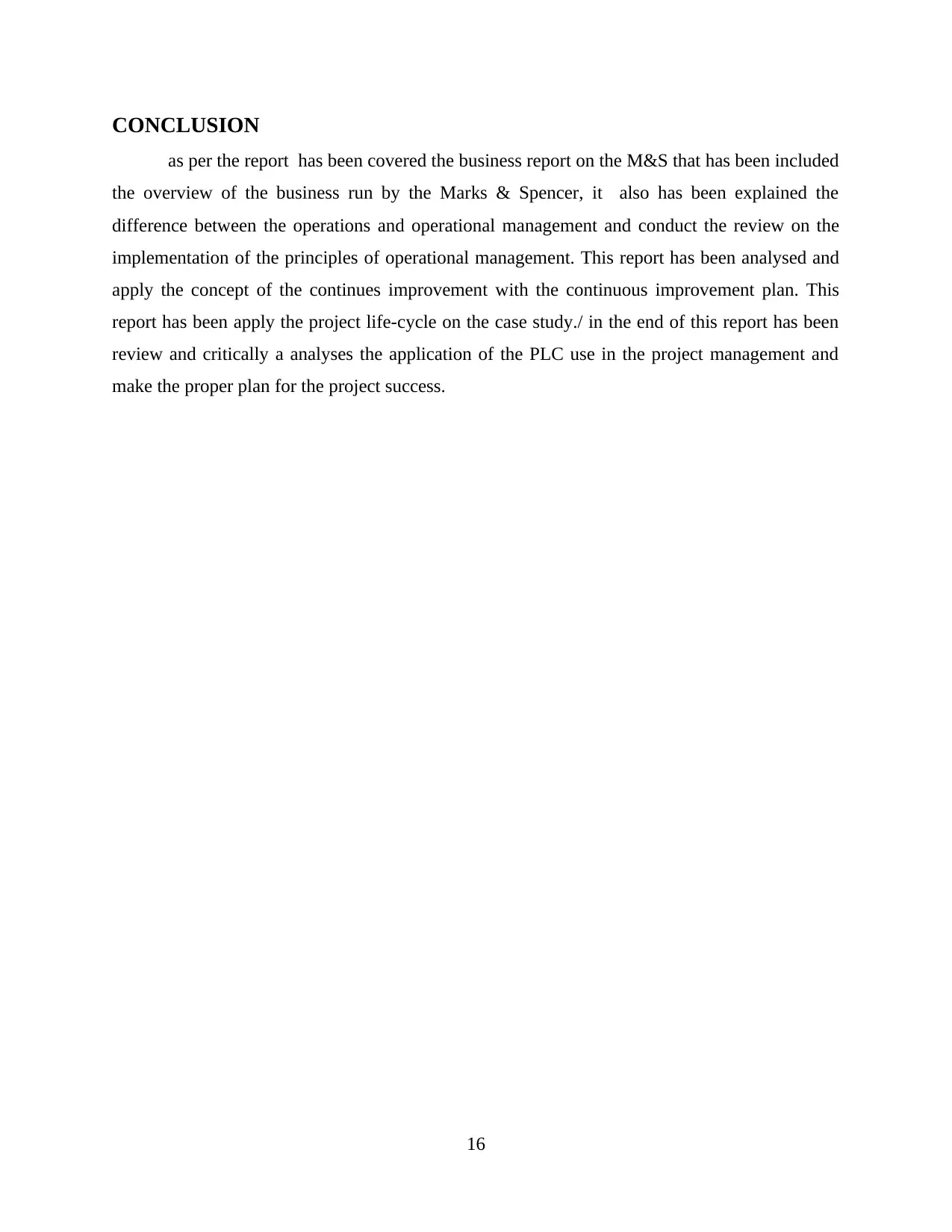
CONCLUSION
as per the report has been covered the business report on the M&S that has been included
the overview of the business run by the Marks & Spencer, it also has been explained the
difference between the operations and operational management and conduct the review on the
implementation of the principles of operational management. This report has been analysed and
apply the concept of the continues improvement with the continuous improvement plan. This
report has been apply the project life-cycle on the case study./ in the end of this report has been
review and critically a analyses the application of the PLC use in the project management and
make the proper plan for the project success.
16
as per the report has been covered the business report on the M&S that has been included
the overview of the business run by the Marks & Spencer, it also has been explained the
difference between the operations and operational management and conduct the review on the
implementation of the principles of operational management. This report has been analysed and
apply the concept of the continues improvement with the continuous improvement plan. This
report has been apply the project life-cycle on the case study./ in the end of this report has been
review and critically a analyses the application of the PLC use in the project management and
make the proper plan for the project success.
16
Paraphrase This Document
Need a fresh take? Get an instant paraphrase of this document with our AI Paraphraser
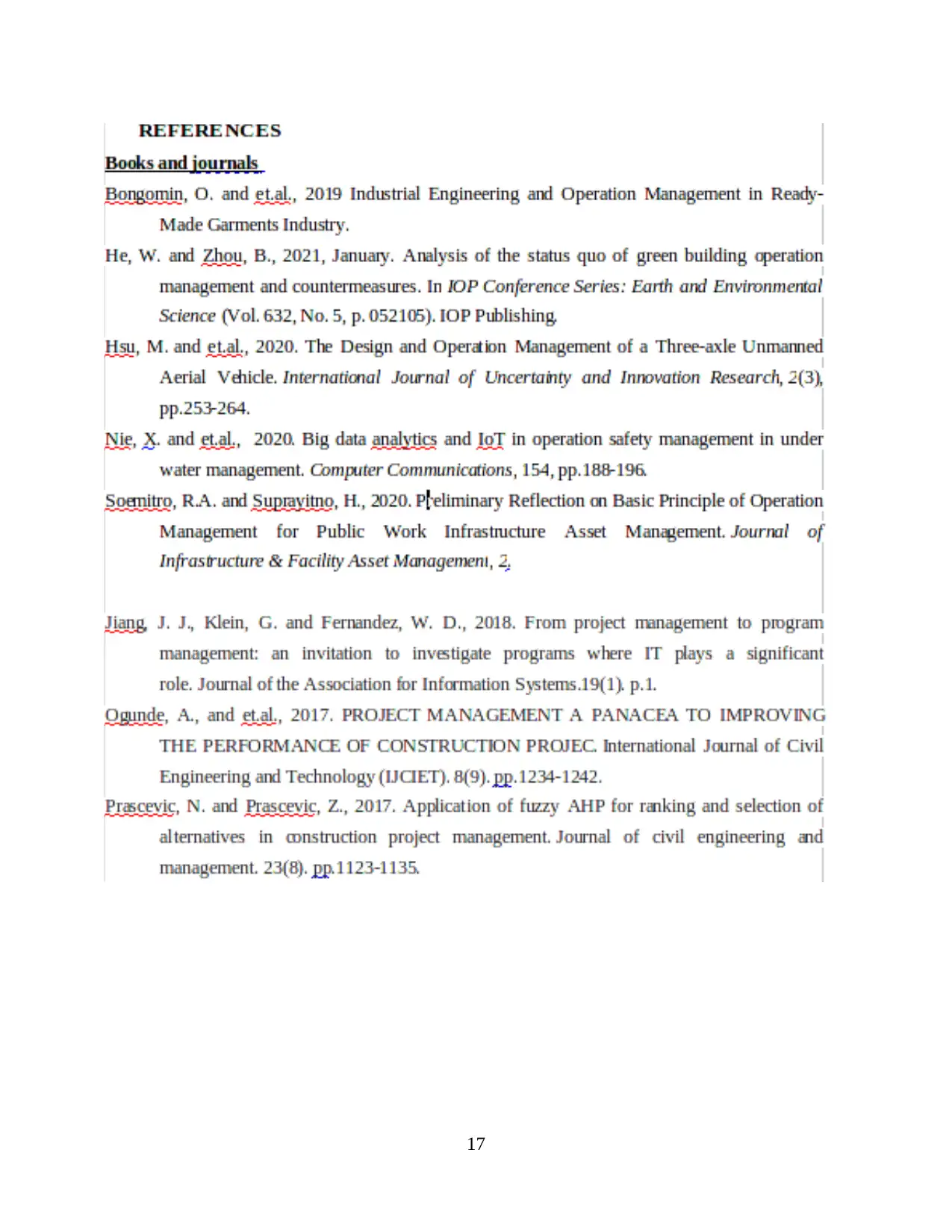
17
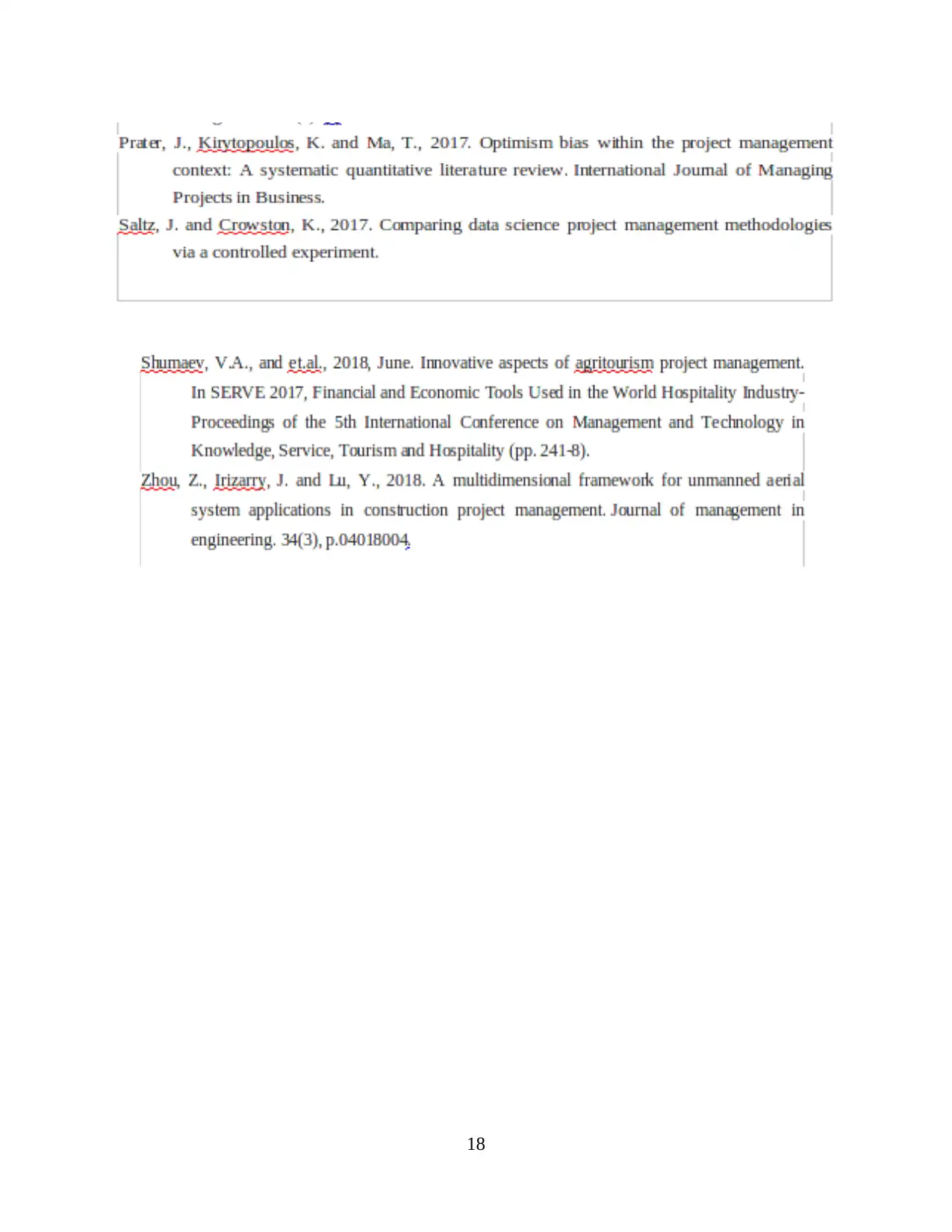
18
You're viewing a preview
Unlock full access by subscribing today!
1 out of 18
Related Documents

Your All-in-One AI-Powered Toolkit for Academic Success.
 +13062052269
info@desklib.com
Available 24*7 on WhatsApp / Email
Unlock your academic potential
© 2024  |  Zucol Services PVT LTD  |  All rights reserved.