Case Study: Risk Analysis with FMEA, FTA, and RBD Tools
VerifiedAdded on 2022/08/26
|23
|5038
|22
Report
AI Summary
This report presents a detailed analysis of risk prioritization methodologies, focusing on the application of Failure Mode and Effects Analysis (FMEA), Fault Tree Analysis (FTA), and Reliability Block Diagram (RBD). It explores the integration of these tools to enhance the objectivity and effectiveness of risk assessment, particularly in the context of equipment maintenance within an electric power facility. The study introduces a quantitative approach that incorporates factors such as downtime percentage, failure costs, and occurrence rates to prioritize failure modes. A case study is analyzed to demonstrate the practical application of this three-step ranking strategy, offering insights into the identification and mitigation of critical failures. The report also reviews literature on risk identification and prioritization, comparing traditional FMEA approaches with cost-based FMEA methods. It emphasizes the importance of data-driven decision-making for improving reliability and optimizing maintenance functions within an organization, aligning with industry standards such as ISO 9001 and ISO/TS 16949.
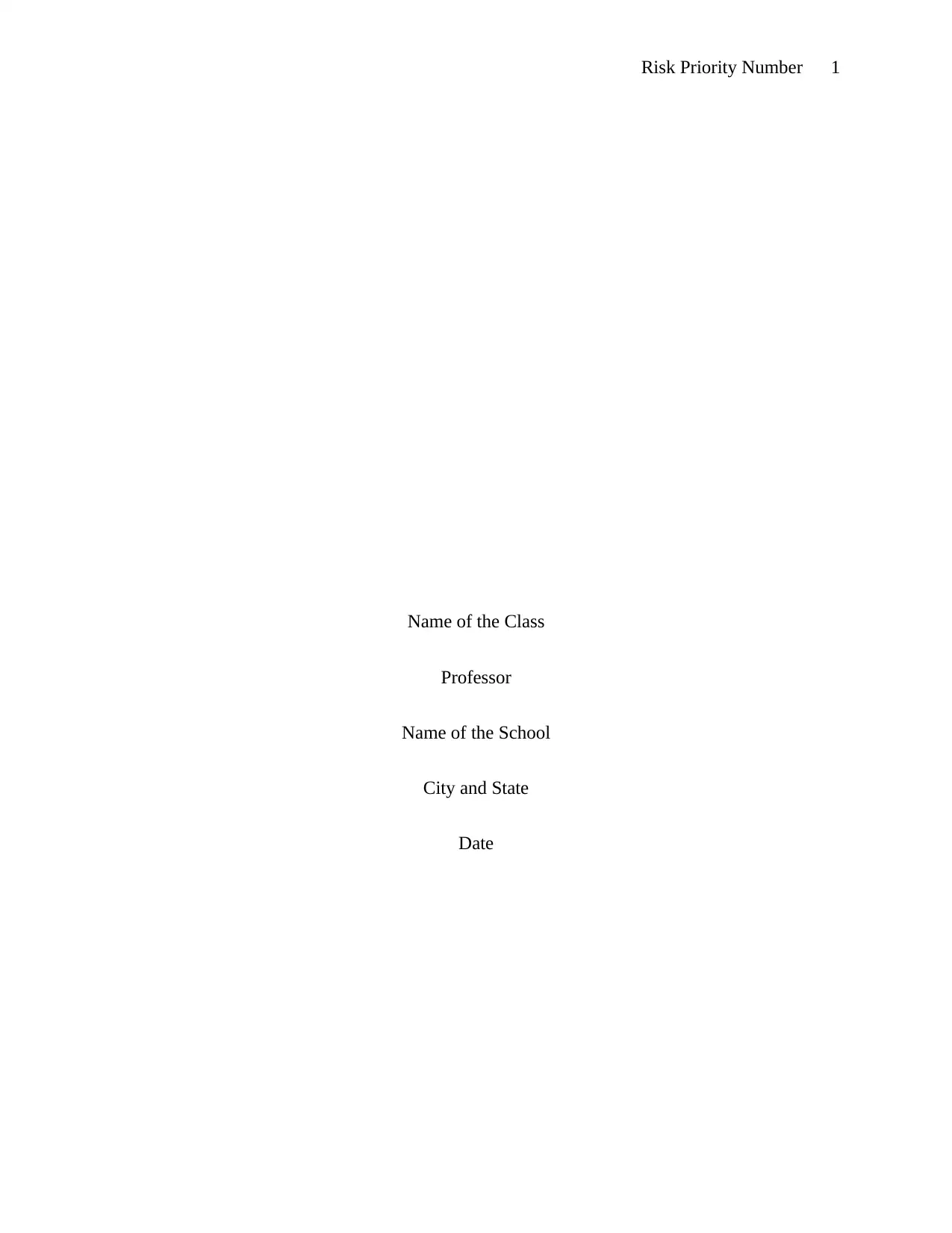
Risk Priority Number 1
Name of the Class
Professor
Name of the School
City and State
Date
Name of the Class
Professor
Name of the School
City and State
Date
Paraphrase This Document
Need a fresh take? Get an instant paraphrase of this document with our AI Paraphraser
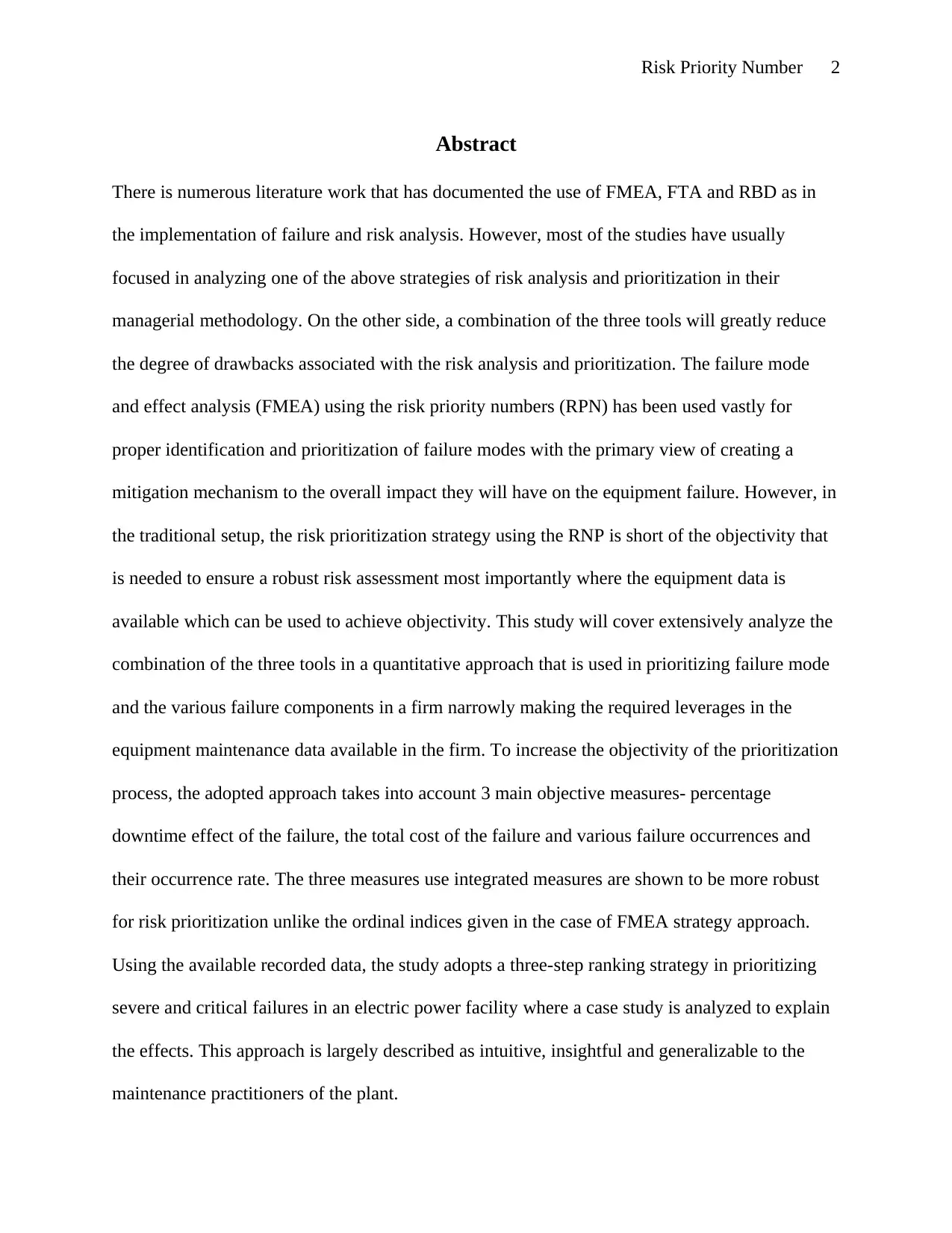
Risk Priority Number 2
Abstract
There is numerous literature work that has documented the use of FMEA, FTA and RBD as in
the implementation of failure and risk analysis. However, most of the studies have usually
focused in analyzing one of the above strategies of risk analysis and prioritization in their
managerial methodology. On the other side, a combination of the three tools will greatly reduce
the degree of drawbacks associated with the risk analysis and prioritization. The failure mode
and effect analysis (FMEA) using the risk priority numbers (RPN) has been used vastly for
proper identification and prioritization of failure modes with the primary view of creating a
mitigation mechanism to the overall impact they will have on the equipment failure. However, in
the traditional setup, the risk prioritization strategy using the RNP is short of the objectivity that
is needed to ensure a robust risk assessment most importantly where the equipment data is
available which can be used to achieve objectivity. This study will cover extensively analyze the
combination of the three tools in a quantitative approach that is used in prioritizing failure mode
and the various failure components in a firm narrowly making the required leverages in the
equipment maintenance data available in the firm. To increase the objectivity of the prioritization
process, the adopted approach takes into account 3 main objective measures- percentage
downtime effect of the failure, the total cost of the failure and various failure occurrences and
their occurrence rate. The three measures use integrated measures are shown to be more robust
for risk prioritization unlike the ordinal indices given in the case of FMEA strategy approach.
Using the available recorded data, the study adopts a three-step ranking strategy in prioritizing
severe and critical failures in an electric power facility where a case study is analyzed to explain
the effects. This approach is largely described as intuitive, insightful and generalizable to the
maintenance practitioners of the plant.
Abstract
There is numerous literature work that has documented the use of FMEA, FTA and RBD as in
the implementation of failure and risk analysis. However, most of the studies have usually
focused in analyzing one of the above strategies of risk analysis and prioritization in their
managerial methodology. On the other side, a combination of the three tools will greatly reduce
the degree of drawbacks associated with the risk analysis and prioritization. The failure mode
and effect analysis (FMEA) using the risk priority numbers (RPN) has been used vastly for
proper identification and prioritization of failure modes with the primary view of creating a
mitigation mechanism to the overall impact they will have on the equipment failure. However, in
the traditional setup, the risk prioritization strategy using the RNP is short of the objectivity that
is needed to ensure a robust risk assessment most importantly where the equipment data is
available which can be used to achieve objectivity. This study will cover extensively analyze the
combination of the three tools in a quantitative approach that is used in prioritizing failure mode
and the various failure components in a firm narrowly making the required leverages in the
equipment maintenance data available in the firm. To increase the objectivity of the prioritization
process, the adopted approach takes into account 3 main objective measures- percentage
downtime effect of the failure, the total cost of the failure and various failure occurrences and
their occurrence rate. The three measures use integrated measures are shown to be more robust
for risk prioritization unlike the ordinal indices given in the case of FMEA strategy approach.
Using the available recorded data, the study adopts a three-step ranking strategy in prioritizing
severe and critical failures in an electric power facility where a case study is analyzed to explain
the effects. This approach is largely described as intuitive, insightful and generalizable to the
maintenance practitioners of the plant.
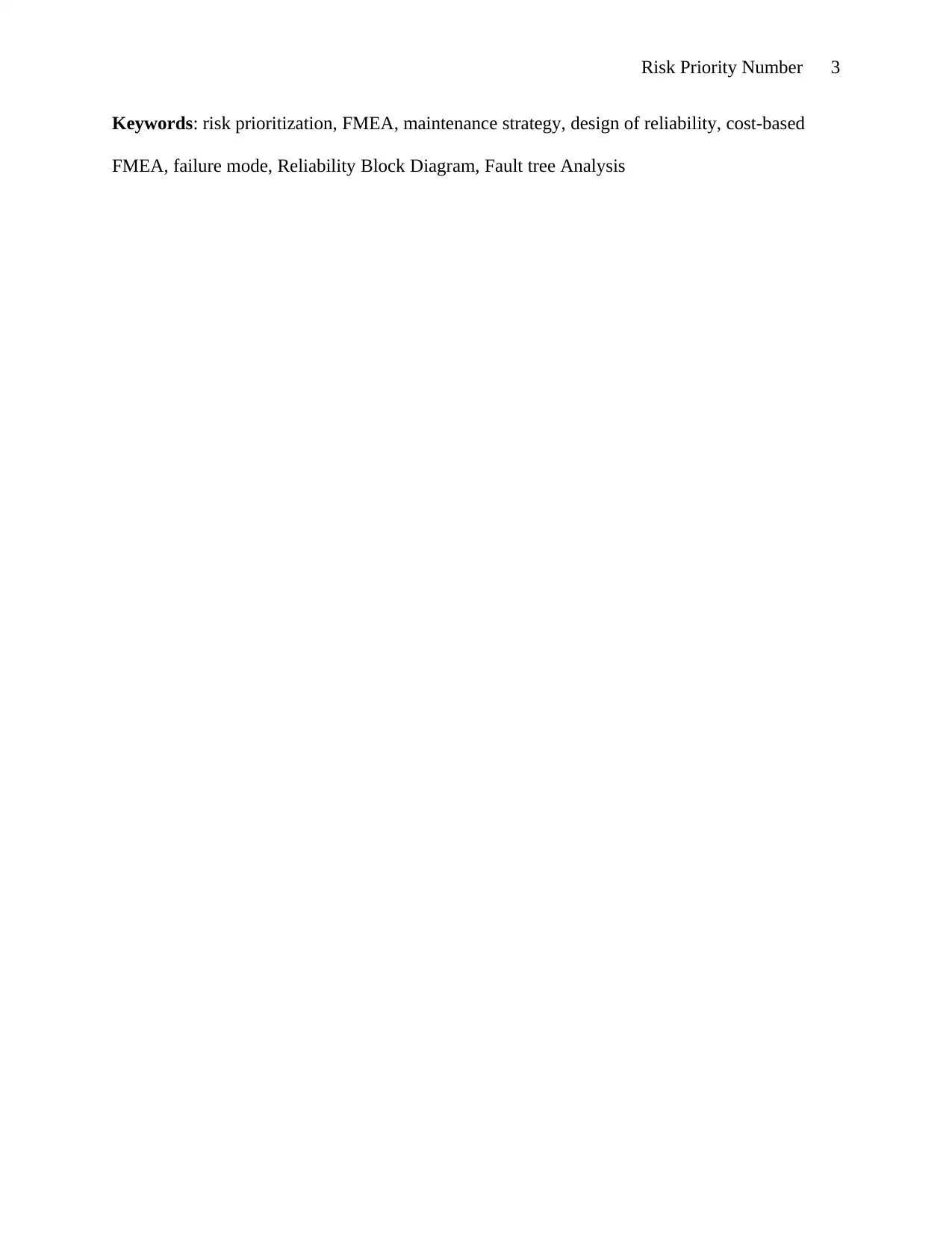
Risk Priority Number 3
Keywords: risk prioritization, FMEA, maintenance strategy, design of reliability, cost-based
FMEA, failure mode, Reliability Block Diagram, Fault tree Analysis
Keywords: risk prioritization, FMEA, maintenance strategy, design of reliability, cost-based
FMEA, failure mode, Reliability Block Diagram, Fault tree Analysis
You're viewing a preview
Unlock full access by subscribing today!
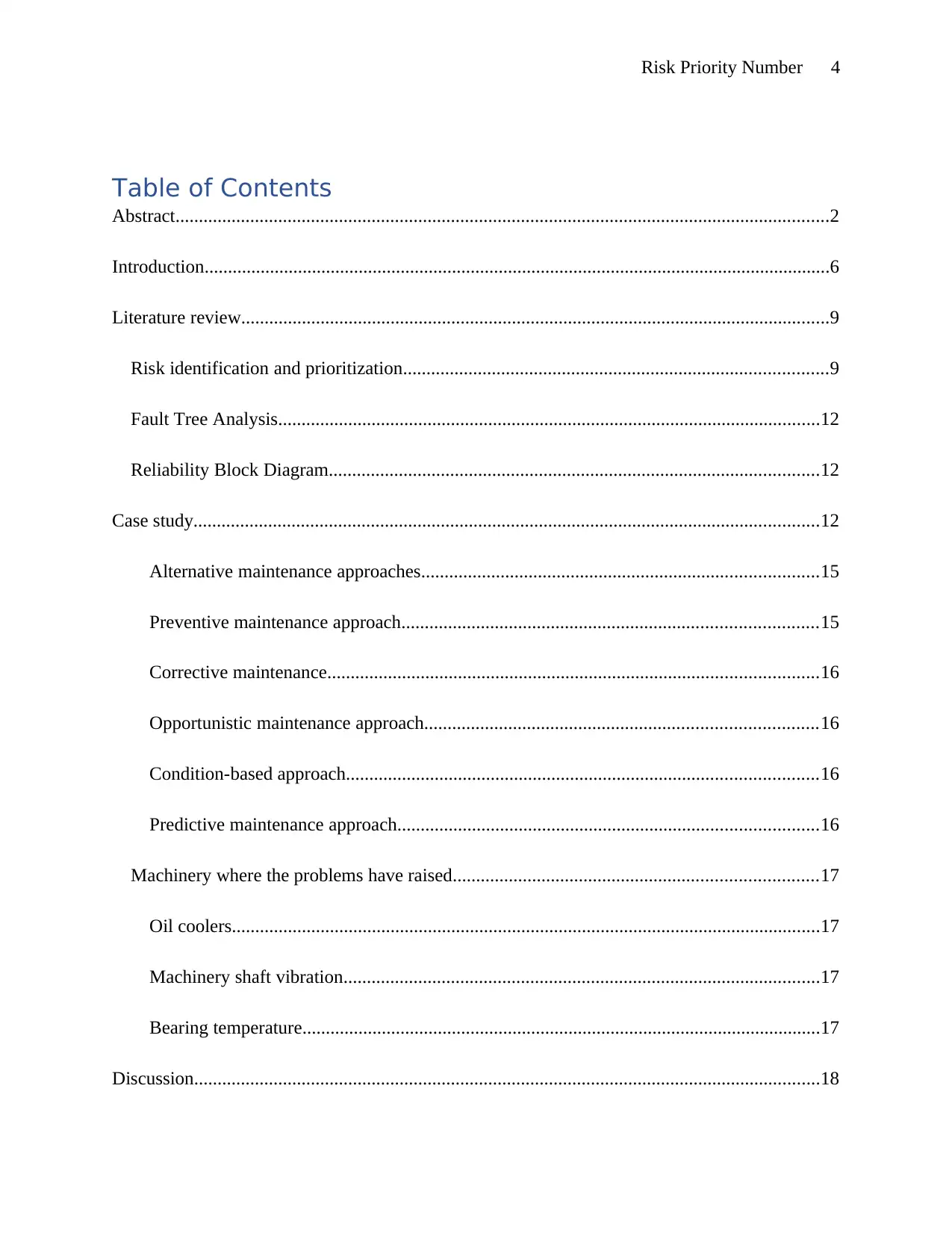
Risk Priority Number 4
Table of Contents
Abstract............................................................................................................................................2
Introduction......................................................................................................................................6
Literature review..............................................................................................................................9
Risk identification and prioritization...........................................................................................9
Fault Tree Analysis....................................................................................................................12
Reliability Block Diagram.........................................................................................................12
Case study......................................................................................................................................12
Alternative maintenance approaches.....................................................................................15
Preventive maintenance approach.........................................................................................15
Corrective maintenance.........................................................................................................16
Opportunistic maintenance approach....................................................................................16
Condition-based approach.....................................................................................................16
Predictive maintenance approach..........................................................................................16
Machinery where the problems have raised..............................................................................17
Oil coolers..............................................................................................................................17
Machinery shaft vibration......................................................................................................17
Bearing temperature...............................................................................................................17
Discussion......................................................................................................................................18
Table of Contents
Abstract............................................................................................................................................2
Introduction......................................................................................................................................6
Literature review..............................................................................................................................9
Risk identification and prioritization...........................................................................................9
Fault Tree Analysis....................................................................................................................12
Reliability Block Diagram.........................................................................................................12
Case study......................................................................................................................................12
Alternative maintenance approaches.....................................................................................15
Preventive maintenance approach.........................................................................................15
Corrective maintenance.........................................................................................................16
Opportunistic maintenance approach....................................................................................16
Condition-based approach.....................................................................................................16
Predictive maintenance approach..........................................................................................16
Machinery where the problems have raised..............................................................................17
Oil coolers..............................................................................................................................17
Machinery shaft vibration......................................................................................................17
Bearing temperature...............................................................................................................17
Discussion......................................................................................................................................18
Paraphrase This Document
Need a fresh take? Get an instant paraphrase of this document with our AI Paraphraser
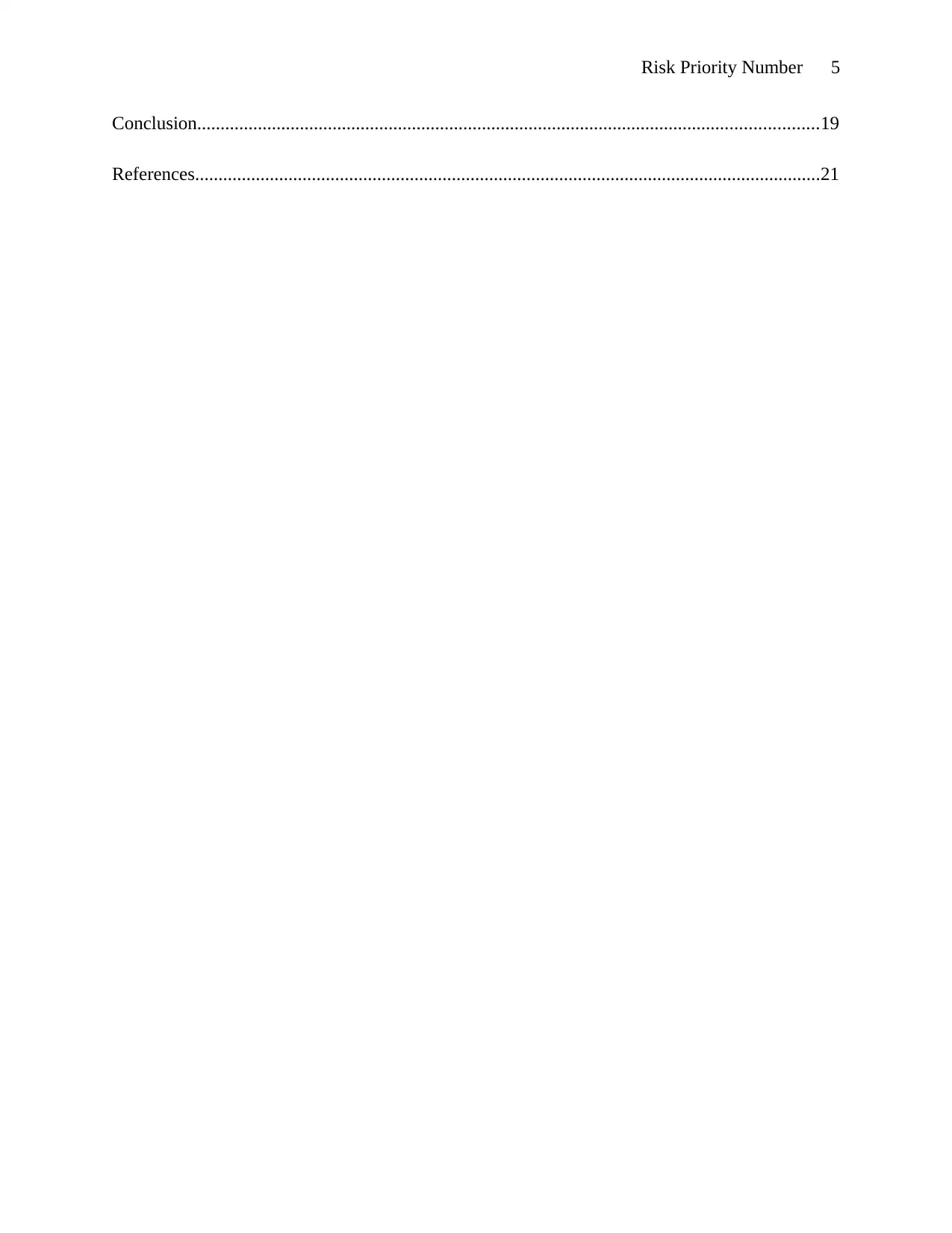
Risk Priority Number 5
Conclusion.....................................................................................................................................19
References......................................................................................................................................21
Conclusion.....................................................................................................................................19
References......................................................................................................................................21
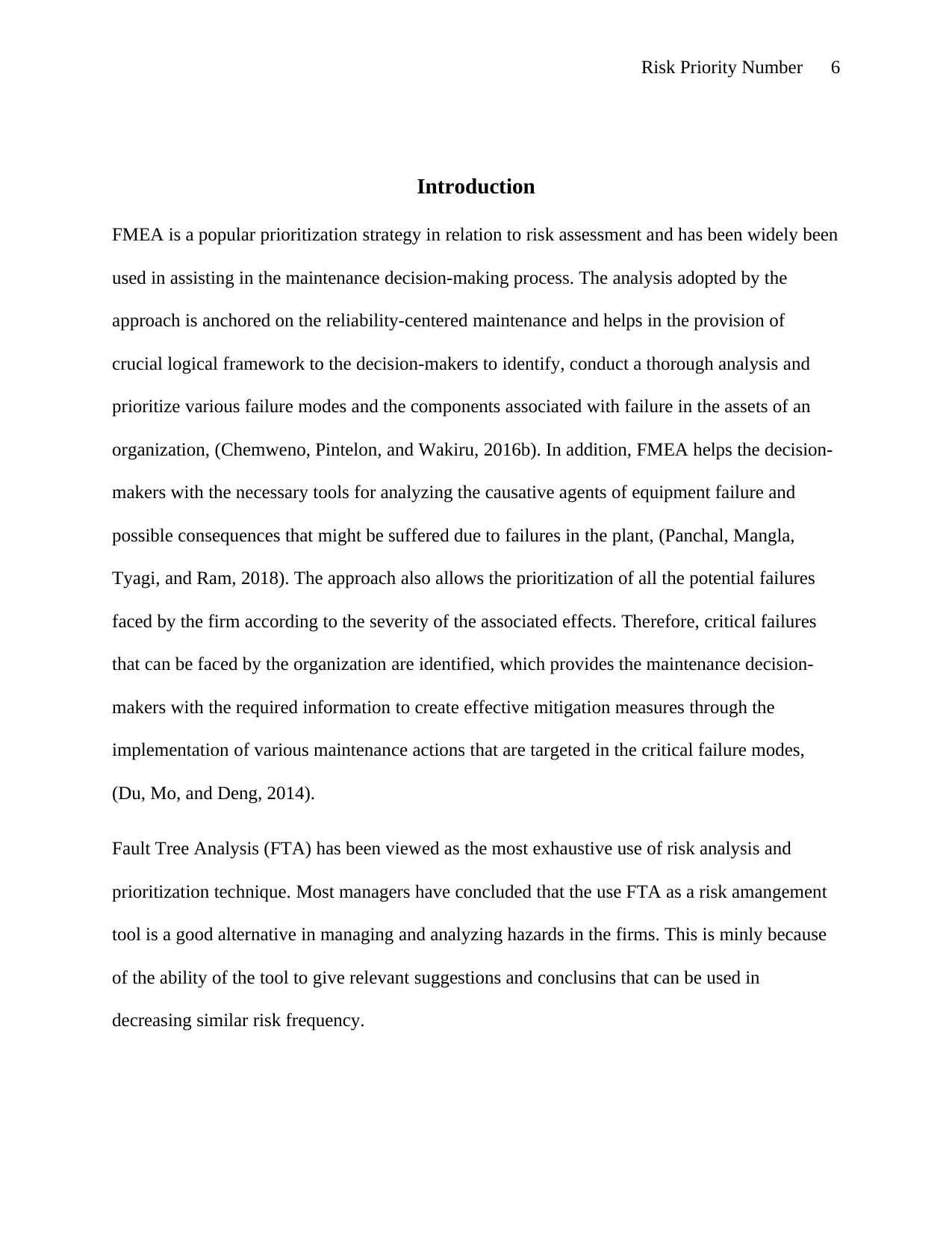
Risk Priority Number 6
Introduction
FMEA is a popular prioritization strategy in relation to risk assessment and has been widely been
used in assisting in the maintenance decision-making process. The analysis adopted by the
approach is anchored on the reliability-centered maintenance and helps in the provision of
crucial logical framework to the decision-makers to identify, conduct a thorough analysis and
prioritize various failure modes and the components associated with failure in the assets of an
organization, (Chemweno, Pintelon, and Wakiru, 2016b). In addition, FMEA helps the decision-
makers with the necessary tools for analyzing the causative agents of equipment failure and
possible consequences that might be suffered due to failures in the plant, (Panchal, Mangla,
Tyagi, and Ram, 2018). The approach also allows the prioritization of all the potential failures
faced by the firm according to the severity of the associated effects. Therefore, critical failures
that can be faced by the organization are identified, which provides the maintenance decision-
makers with the required information to create effective mitigation measures through the
implementation of various maintenance actions that are targeted in the critical failure modes,
(Du, Mo, and Deng, 2014).
Fault Tree Analysis (FTA) has been viewed as the most exhaustive use of risk analysis and
prioritization technique. Most managers have concluded that the use FTA as a risk amangement
tool is a good alternative in managing and analyzing hazards in the firms. This is minly because
of the ability of the tool to give relevant suggestions and conclusins that can be used in
decreasing similar risk frequency.
Introduction
FMEA is a popular prioritization strategy in relation to risk assessment and has been widely been
used in assisting in the maintenance decision-making process. The analysis adopted by the
approach is anchored on the reliability-centered maintenance and helps in the provision of
crucial logical framework to the decision-makers to identify, conduct a thorough analysis and
prioritize various failure modes and the components associated with failure in the assets of an
organization, (Chemweno, Pintelon, and Wakiru, 2016b). In addition, FMEA helps the decision-
makers with the necessary tools for analyzing the causative agents of equipment failure and
possible consequences that might be suffered due to failures in the plant, (Panchal, Mangla,
Tyagi, and Ram, 2018). The approach also allows the prioritization of all the potential failures
faced by the firm according to the severity of the associated effects. Therefore, critical failures
that can be faced by the organization are identified, which provides the maintenance decision-
makers with the required information to create effective mitigation measures through the
implementation of various maintenance actions that are targeted in the critical failure modes,
(Du, Mo, and Deng, 2014).
Fault Tree Analysis (FTA) has been viewed as the most exhaustive use of risk analysis and
prioritization technique. Most managers have concluded that the use FTA as a risk amangement
tool is a good alternative in managing and analyzing hazards in the firms. This is minly because
of the ability of the tool to give relevant suggestions and conclusins that can be used in
decreasing similar risk frequency.
You're viewing a preview
Unlock full access by subscribing today!
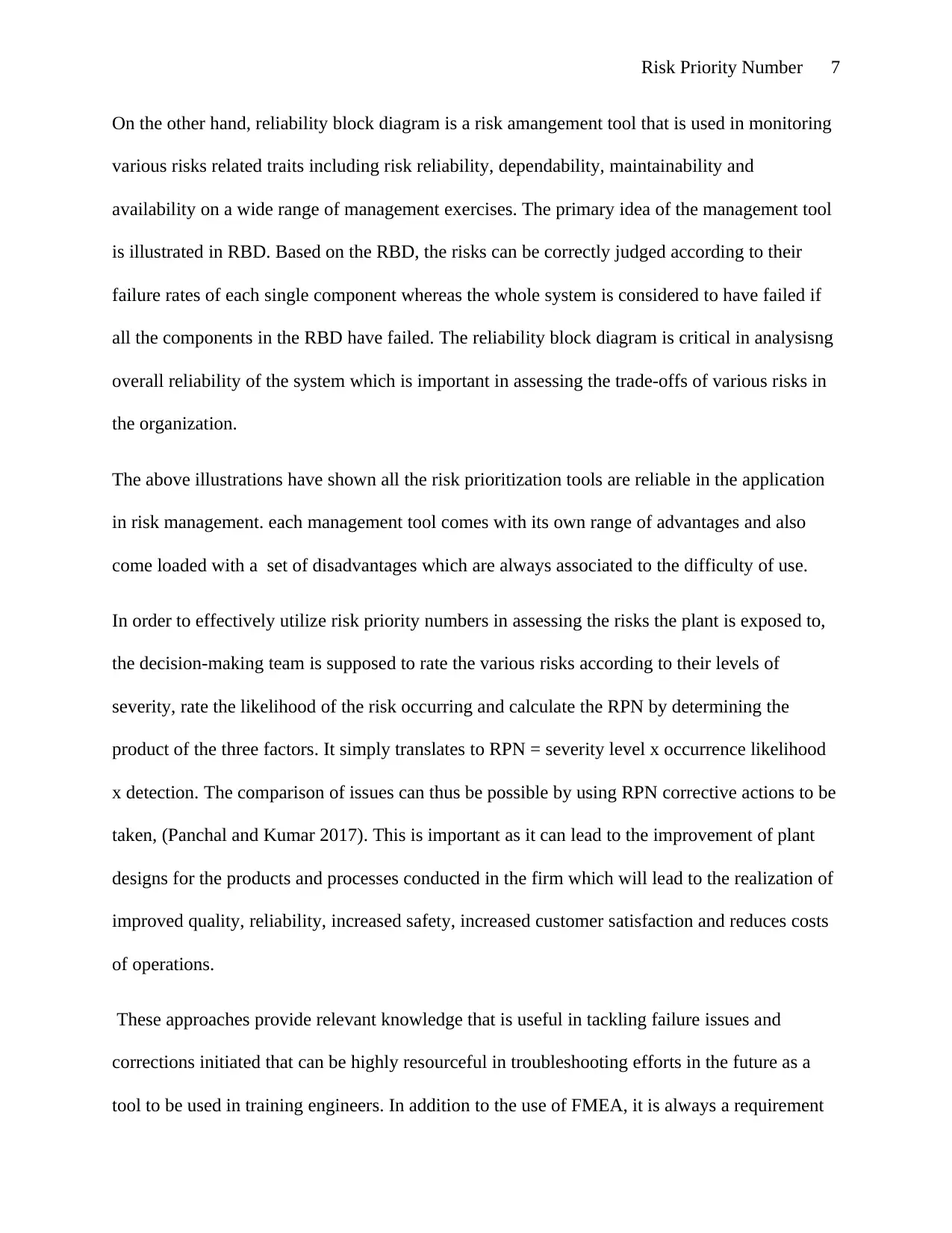
Risk Priority Number 7
On the other hand, reliability block diagram is a risk amangement tool that is used in monitoring
various risks related traits including risk reliability, dependability, maintainability and
availability on a wide range of management exercises. The primary idea of the management tool
is illustrated in RBD. Based on the RBD, the risks can be correctly judged according to their
failure rates of each single component whereas the whole system is considered to have failed if
all the components in the RBD have failed. The reliability block diagram is critical in analysisng
overall reliability of the system which is important in assessing the trade-offs of various risks in
the organization.
The above illustrations have shown all the risk prioritization tools are reliable in the application
in risk management. each management tool comes with its own range of advantages and also
come loaded with a set of disadvantages which are always associated to the difficulty of use.
In order to effectively utilize risk priority numbers in assessing the risks the plant is exposed to,
the decision-making team is supposed to rate the various risks according to their levels of
severity, rate the likelihood of the risk occurring and calculate the RPN by determining the
product of the three factors. It simply translates to RPN = severity level x occurrence likelihood
x detection. The comparison of issues can thus be possible by using RPN corrective actions to be
taken, (Panchal and Kumar 2017). This is important as it can lead to the improvement of plant
designs for the products and processes conducted in the firm which will lead to the realization of
improved quality, reliability, increased safety, increased customer satisfaction and reduces costs
of operations.
These approaches provide relevant knowledge that is useful in tackling failure issues and
corrections initiated that can be highly resourceful in troubleshooting efforts in the future as a
tool to be used in training engineers. In addition to the use of FMEA, it is always a requirement
On the other hand, reliability block diagram is a risk amangement tool that is used in monitoring
various risks related traits including risk reliability, dependability, maintainability and
availability on a wide range of management exercises. The primary idea of the management tool
is illustrated in RBD. Based on the RBD, the risks can be correctly judged according to their
failure rates of each single component whereas the whole system is considered to have failed if
all the components in the RBD have failed. The reliability block diagram is critical in analysisng
overall reliability of the system which is important in assessing the trade-offs of various risks in
the organization.
The above illustrations have shown all the risk prioritization tools are reliable in the application
in risk management. each management tool comes with its own range of advantages and also
come loaded with a set of disadvantages which are always associated to the difficulty of use.
In order to effectively utilize risk priority numbers in assessing the risks the plant is exposed to,
the decision-making team is supposed to rate the various risks according to their levels of
severity, rate the likelihood of the risk occurring and calculate the RPN by determining the
product of the three factors. It simply translates to RPN = severity level x occurrence likelihood
x detection. The comparison of issues can thus be possible by using RPN corrective actions to be
taken, (Panchal and Kumar 2017). This is important as it can lead to the improvement of plant
designs for the products and processes conducted in the firm which will lead to the realization of
improved quality, reliability, increased safety, increased customer satisfaction and reduces costs
of operations.
These approaches provide relevant knowledge that is useful in tackling failure issues and
corrections initiated that can be highly resourceful in troubleshooting efforts in the future as a
tool to be used in training engineers. In addition to the use of FMEA, it is always a requirement
Paraphrase This Document
Need a fresh take? Get an instant paraphrase of this document with our AI Paraphraser
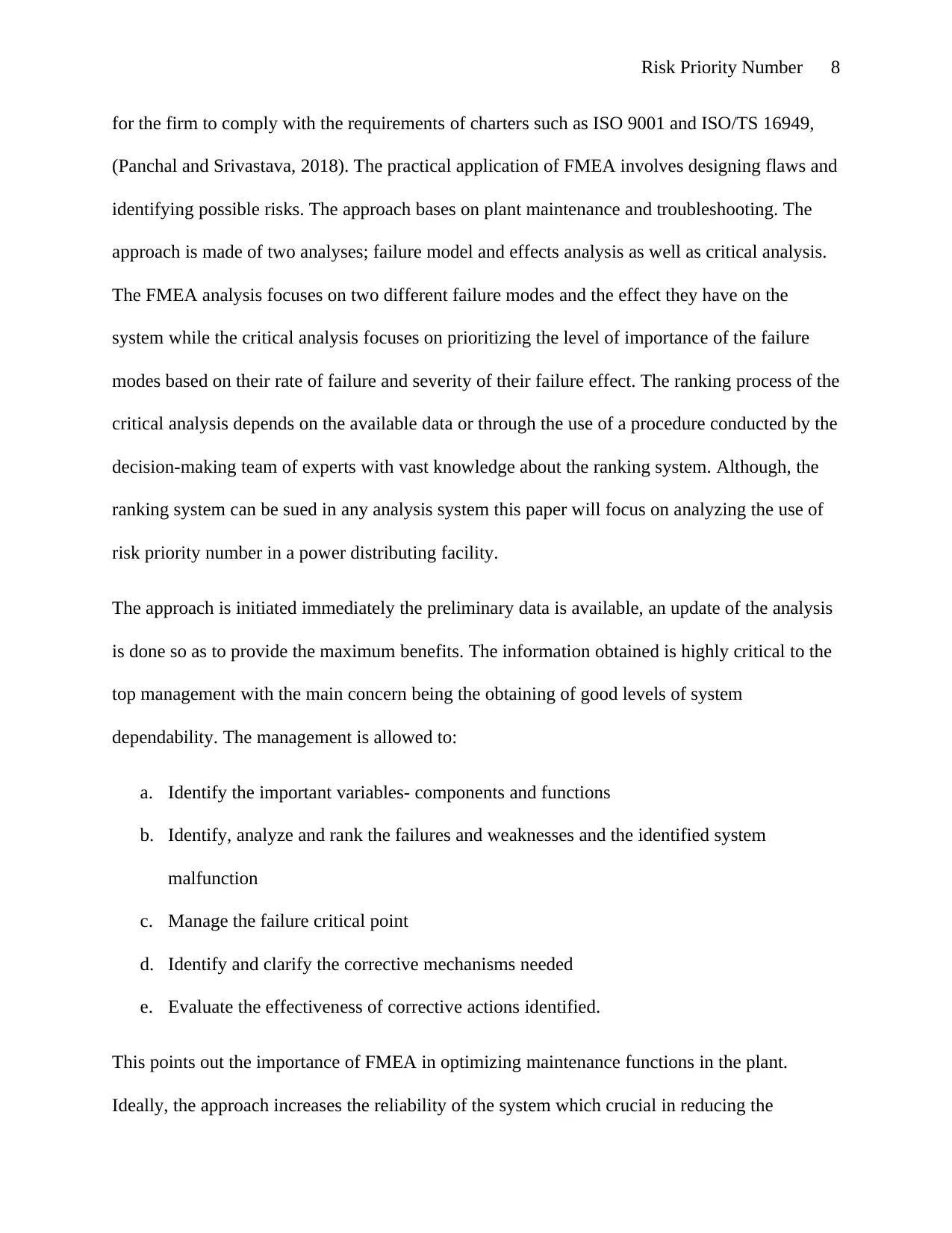
Risk Priority Number 8
for the firm to comply with the requirements of charters such as ISO 9001 and ISO/TS 16949,
(Panchal and Srivastava, 2018). The practical application of FMEA involves designing flaws and
identifying possible risks. The approach bases on plant maintenance and troubleshooting. The
approach is made of two analyses; failure model and effects analysis as well as critical analysis.
The FMEA analysis focuses on two different failure modes and the effect they have on the
system while the critical analysis focuses on prioritizing the level of importance of the failure
modes based on their rate of failure and severity of their failure effect. The ranking process of the
critical analysis depends on the available data or through the use of a procedure conducted by the
decision-making team of experts with vast knowledge about the ranking system. Although, the
ranking system can be sued in any analysis system this paper will focus on analyzing the use of
risk priority number in a power distributing facility.
The approach is initiated immediately the preliminary data is available, an update of the analysis
is done so as to provide the maximum benefits. The information obtained is highly critical to the
top management with the main concern being the obtaining of good levels of system
dependability. The management is allowed to:
a. Identify the important variables- components and functions
b. Identify, analyze and rank the failures and weaknesses and the identified system
malfunction
c. Manage the failure critical point
d. Identify and clarify the corrective mechanisms needed
e. Evaluate the effectiveness of corrective actions identified.
This points out the importance of FMEA in optimizing maintenance functions in the plant.
Ideally, the approach increases the reliability of the system which crucial in reducing the
for the firm to comply with the requirements of charters such as ISO 9001 and ISO/TS 16949,
(Panchal and Srivastava, 2018). The practical application of FMEA involves designing flaws and
identifying possible risks. The approach bases on plant maintenance and troubleshooting. The
approach is made of two analyses; failure model and effects analysis as well as critical analysis.
The FMEA analysis focuses on two different failure modes and the effect they have on the
system while the critical analysis focuses on prioritizing the level of importance of the failure
modes based on their rate of failure and severity of their failure effect. The ranking process of the
critical analysis depends on the available data or through the use of a procedure conducted by the
decision-making team of experts with vast knowledge about the ranking system. Although, the
ranking system can be sued in any analysis system this paper will focus on analyzing the use of
risk priority number in a power distributing facility.
The approach is initiated immediately the preliminary data is available, an update of the analysis
is done so as to provide the maximum benefits. The information obtained is highly critical to the
top management with the main concern being the obtaining of good levels of system
dependability. The management is allowed to:
a. Identify the important variables- components and functions
b. Identify, analyze and rank the failures and weaknesses and the identified system
malfunction
c. Manage the failure critical point
d. Identify and clarify the corrective mechanisms needed
e. Evaluate the effectiveness of corrective actions identified.
This points out the importance of FMEA in optimizing maintenance functions in the plant.
Ideally, the approach increases the reliability of the system which crucial in reducing the
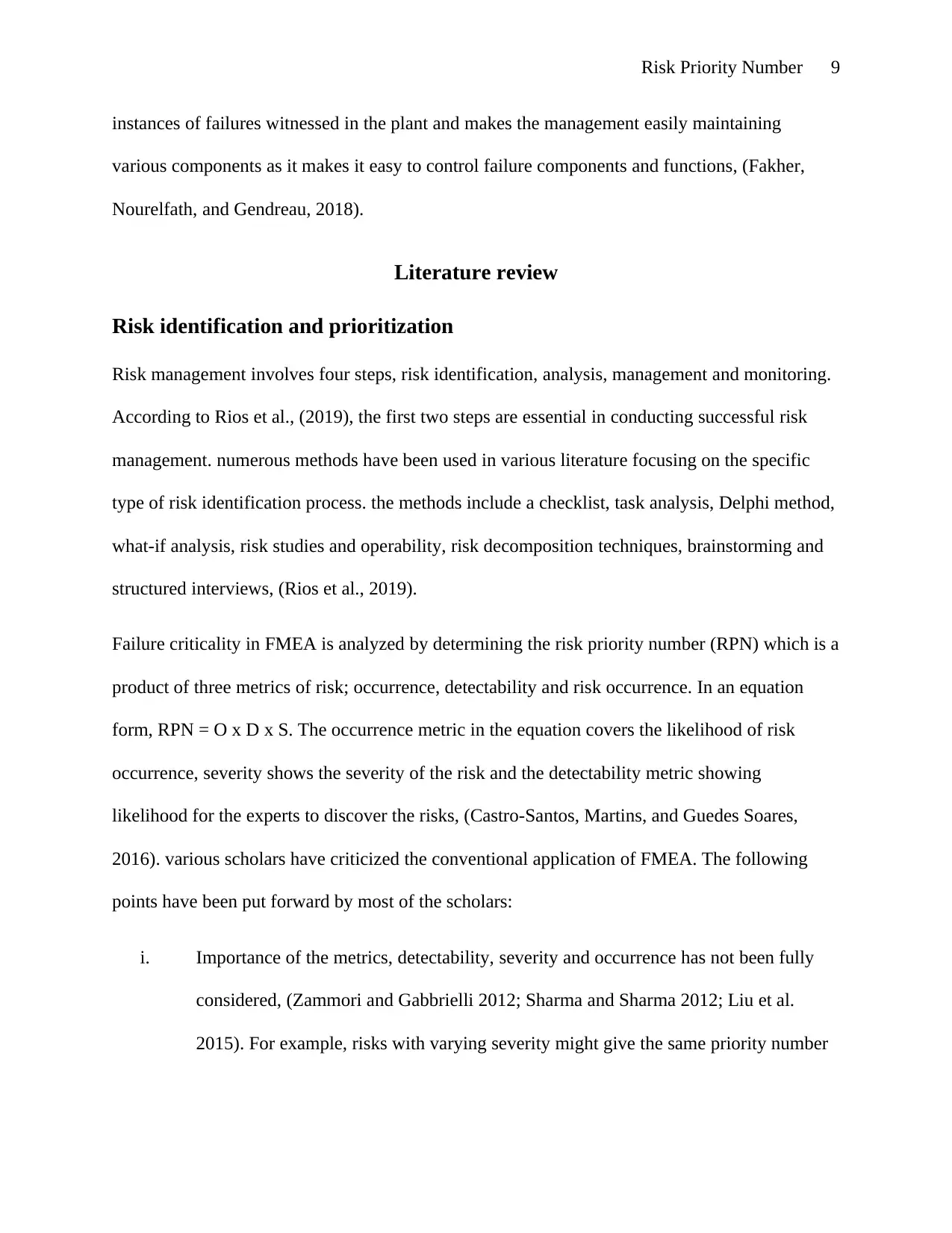
Risk Priority Number 9
instances of failures witnessed in the plant and makes the management easily maintaining
various components as it makes it easy to control failure components and functions, (Fakher,
Nourelfath, and Gendreau, 2018).
Literature review
Risk identification and prioritization
Risk management involves four steps, risk identification, analysis, management and monitoring.
According to Rios et al., (2019), the first two steps are essential in conducting successful risk
management. numerous methods have been used in various literature focusing on the specific
type of risk identification process. the methods include a checklist, task analysis, Delphi method,
what-if analysis, risk studies and operability, risk decomposition techniques, brainstorming and
structured interviews, (Rios et al., 2019).
Failure criticality in FMEA is analyzed by determining the risk priority number (RPN) which is a
product of three metrics of risk; occurrence, detectability and risk occurrence. In an equation
form, RPN = O x D x S. The occurrence metric in the equation covers the likelihood of risk
occurrence, severity shows the severity of the risk and the detectability metric showing
likelihood for the experts to discover the risks, (Castro-Santos, Martins, and Guedes Soares,
2016). various scholars have criticized the conventional application of FMEA. The following
points have been put forward by most of the scholars:
i. Importance of the metrics, detectability, severity and occurrence has not been fully
considered, (Zammori and Gabbrielli 2012; Sharma and Sharma 2012; Liu et al.
2015). For example, risks with varying severity might give the same priority number
instances of failures witnessed in the plant and makes the management easily maintaining
various components as it makes it easy to control failure components and functions, (Fakher,
Nourelfath, and Gendreau, 2018).
Literature review
Risk identification and prioritization
Risk management involves four steps, risk identification, analysis, management and monitoring.
According to Rios et al., (2019), the first two steps are essential in conducting successful risk
management. numerous methods have been used in various literature focusing on the specific
type of risk identification process. the methods include a checklist, task analysis, Delphi method,
what-if analysis, risk studies and operability, risk decomposition techniques, brainstorming and
structured interviews, (Rios et al., 2019).
Failure criticality in FMEA is analyzed by determining the risk priority number (RPN) which is a
product of three metrics of risk; occurrence, detectability and risk occurrence. In an equation
form, RPN = O x D x S. The occurrence metric in the equation covers the likelihood of risk
occurrence, severity shows the severity of the risk and the detectability metric showing
likelihood for the experts to discover the risks, (Castro-Santos, Martins, and Guedes Soares,
2016). various scholars have criticized the conventional application of FMEA. The following
points have been put forward by most of the scholars:
i. Importance of the metrics, detectability, severity and occurrence has not been fully
considered, (Zammori and Gabbrielli 2012; Sharma and Sharma 2012; Liu et al.
2015). For example, risks with varying severity might give the same priority number
You're viewing a preview
Unlock full access by subscribing today!
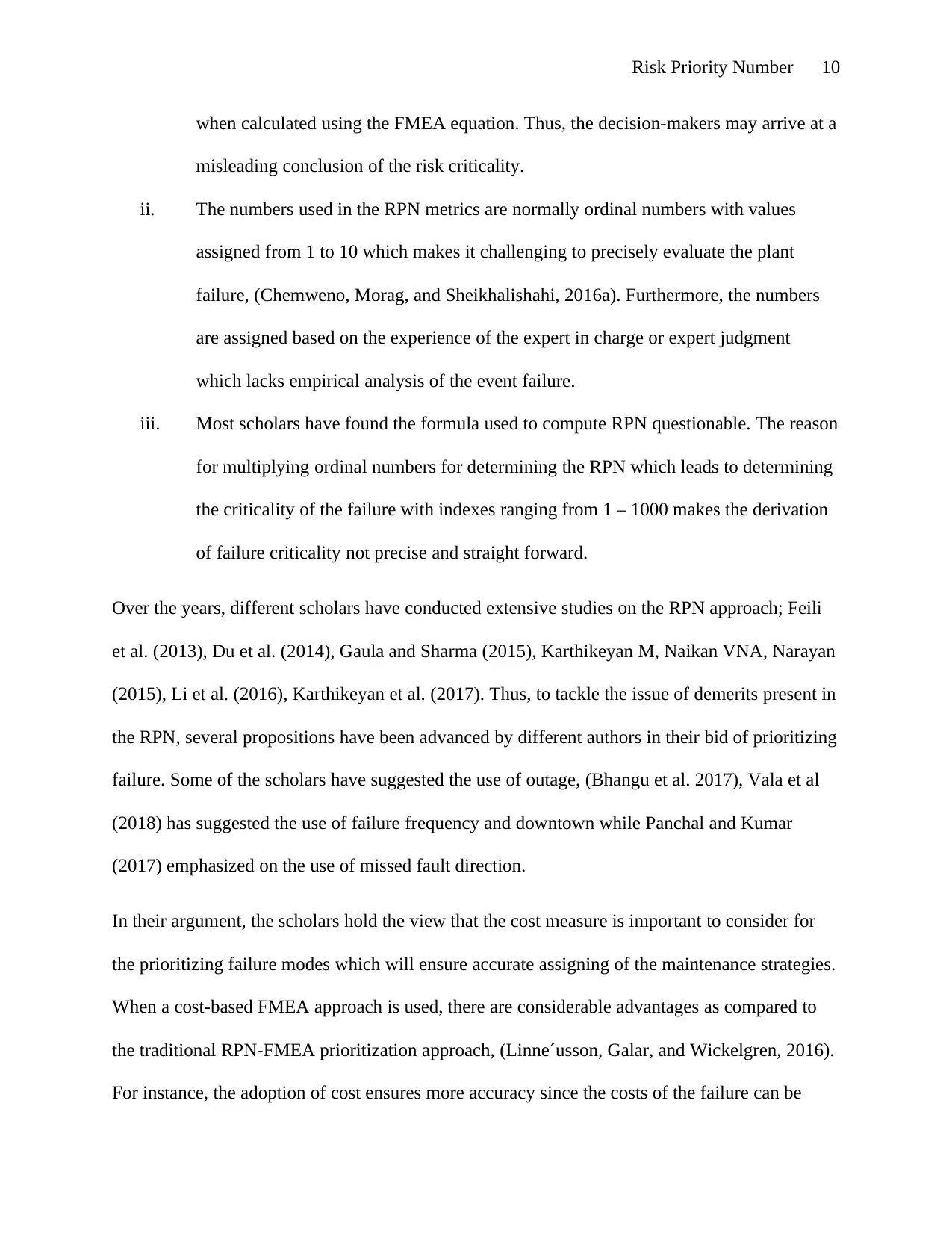
Risk Priority Number 10
when calculated using the FMEA equation. Thus, the decision-makers may arrive at a
misleading conclusion of the risk criticality.
ii. The numbers used in the RPN metrics are normally ordinal numbers with values
assigned from 1 to 10 which makes it challenging to precisely evaluate the plant
failure, (Chemweno, Morag, and Sheikhalishahi, 2016a). Furthermore, the numbers
are assigned based on the experience of the expert in charge or expert judgment
which lacks empirical analysis of the event failure.
iii. Most scholars have found the formula used to compute RPN questionable. The reason
for multiplying ordinal numbers for determining the RPN which leads to determining
the criticality of the failure with indexes ranging from 1 – 1000 makes the derivation
of failure criticality not precise and straight forward.
Over the years, different scholars have conducted extensive studies on the RPN approach; Feili
et al. (2013), Du et al. (2014), Gaula and Sharma (2015), Karthikeyan M, Naikan VNA, Narayan
(2015), Li et al. (2016), Karthikeyan et al. (2017). Thus, to tackle the issue of demerits present in
the RPN, several propositions have been advanced by different authors in their bid of prioritizing
failure. Some of the scholars have suggested the use of outage, (Bhangu et al. 2017), Vala et al
(2018) has suggested the use of failure frequency and downtown while Panchal and Kumar
(2017) emphasized on the use of missed fault direction.
In their argument, the scholars hold the view that the cost measure is important to consider for
the prioritizing failure modes which will ensure accurate assigning of the maintenance strategies.
When a cost-based FMEA approach is used, there are considerable advantages as compared to
the traditional RPN-FMEA prioritization approach, (Linne´usson, Galar, and Wickelgren, 2016).
For instance, the adoption of cost ensures more accuracy since the costs of the failure can be
when calculated using the FMEA equation. Thus, the decision-makers may arrive at a
misleading conclusion of the risk criticality.
ii. The numbers used in the RPN metrics are normally ordinal numbers with values
assigned from 1 to 10 which makes it challenging to precisely evaluate the plant
failure, (Chemweno, Morag, and Sheikhalishahi, 2016a). Furthermore, the numbers
are assigned based on the experience of the expert in charge or expert judgment
which lacks empirical analysis of the event failure.
iii. Most scholars have found the formula used to compute RPN questionable. The reason
for multiplying ordinal numbers for determining the RPN which leads to determining
the criticality of the failure with indexes ranging from 1 – 1000 makes the derivation
of failure criticality not precise and straight forward.
Over the years, different scholars have conducted extensive studies on the RPN approach; Feili
et al. (2013), Du et al. (2014), Gaula and Sharma (2015), Karthikeyan M, Naikan VNA, Narayan
(2015), Li et al. (2016), Karthikeyan et al. (2017). Thus, to tackle the issue of demerits present in
the RPN, several propositions have been advanced by different authors in their bid of prioritizing
failure. Some of the scholars have suggested the use of outage, (Bhangu et al. 2017), Vala et al
(2018) has suggested the use of failure frequency and downtown while Panchal and Kumar
(2017) emphasized on the use of missed fault direction.
In their argument, the scholars hold the view that the cost measure is important to consider for
the prioritizing failure modes which will ensure accurate assigning of the maintenance strategies.
When a cost-based FMEA approach is used, there are considerable advantages as compared to
the traditional RPN-FMEA prioritization approach, (Linne´usson, Galar, and Wickelgren, 2016).
For instance, the adoption of cost ensures more accuracy since the costs of the failure can be
Paraphrase This Document
Need a fresh take? Get an instant paraphrase of this document with our AI Paraphraser
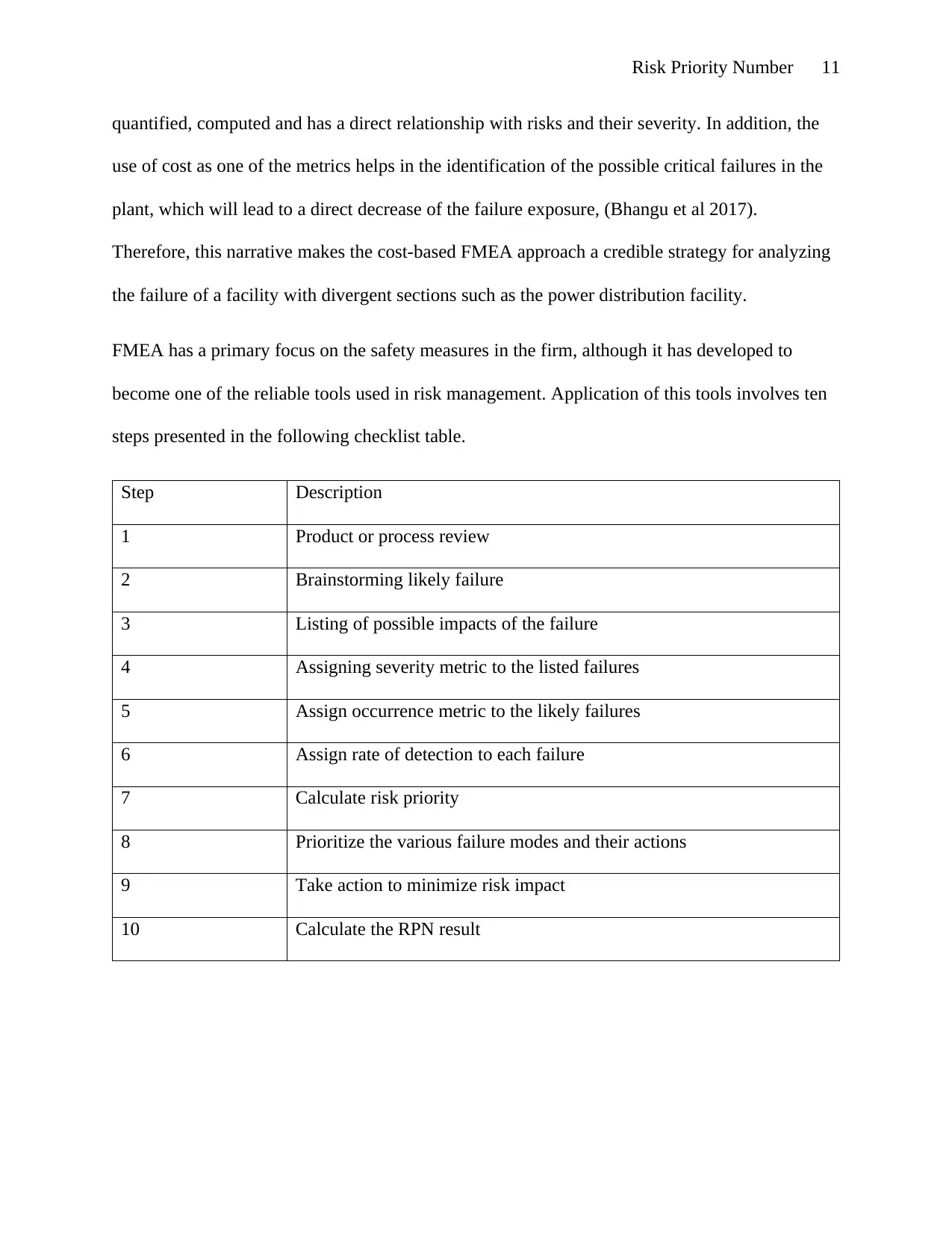
Risk Priority Number 11
quantified, computed and has a direct relationship with risks and their severity. In addition, the
use of cost as one of the metrics helps in the identification of the possible critical failures in the
plant, which will lead to a direct decrease of the failure exposure, (Bhangu et al 2017).
Therefore, this narrative makes the cost-based FMEA approach a credible strategy for analyzing
the failure of a facility with divergent sections such as the power distribution facility.
FMEA has a primary focus on the safety measures in the firm, although it has developed to
become one of the reliable tools used in risk management. Application of this tools involves ten
steps presented in the following checklist table.
Step Description
1 Product or process review
2 Brainstorming likely failure
3 Listing of possible impacts of the failure
4 Assigning severity metric to the listed failures
5 Assign occurrence metric to the likely failures
6 Assign rate of detection to each failure
7 Calculate risk priority
8 Prioritize the various failure modes and their actions
9 Take action to minimize risk impact
10 Calculate the RPN result
quantified, computed and has a direct relationship with risks and their severity. In addition, the
use of cost as one of the metrics helps in the identification of the possible critical failures in the
plant, which will lead to a direct decrease of the failure exposure, (Bhangu et al 2017).
Therefore, this narrative makes the cost-based FMEA approach a credible strategy for analyzing
the failure of a facility with divergent sections such as the power distribution facility.
FMEA has a primary focus on the safety measures in the firm, although it has developed to
become one of the reliable tools used in risk management. Application of this tools involves ten
steps presented in the following checklist table.
Step Description
1 Product or process review
2 Brainstorming likely failure
3 Listing of possible impacts of the failure
4 Assigning severity metric to the listed failures
5 Assign occurrence metric to the likely failures
6 Assign rate of detection to each failure
7 Calculate risk priority
8 Prioritize the various failure modes and their actions
9 Take action to minimize risk impact
10 Calculate the RPN result
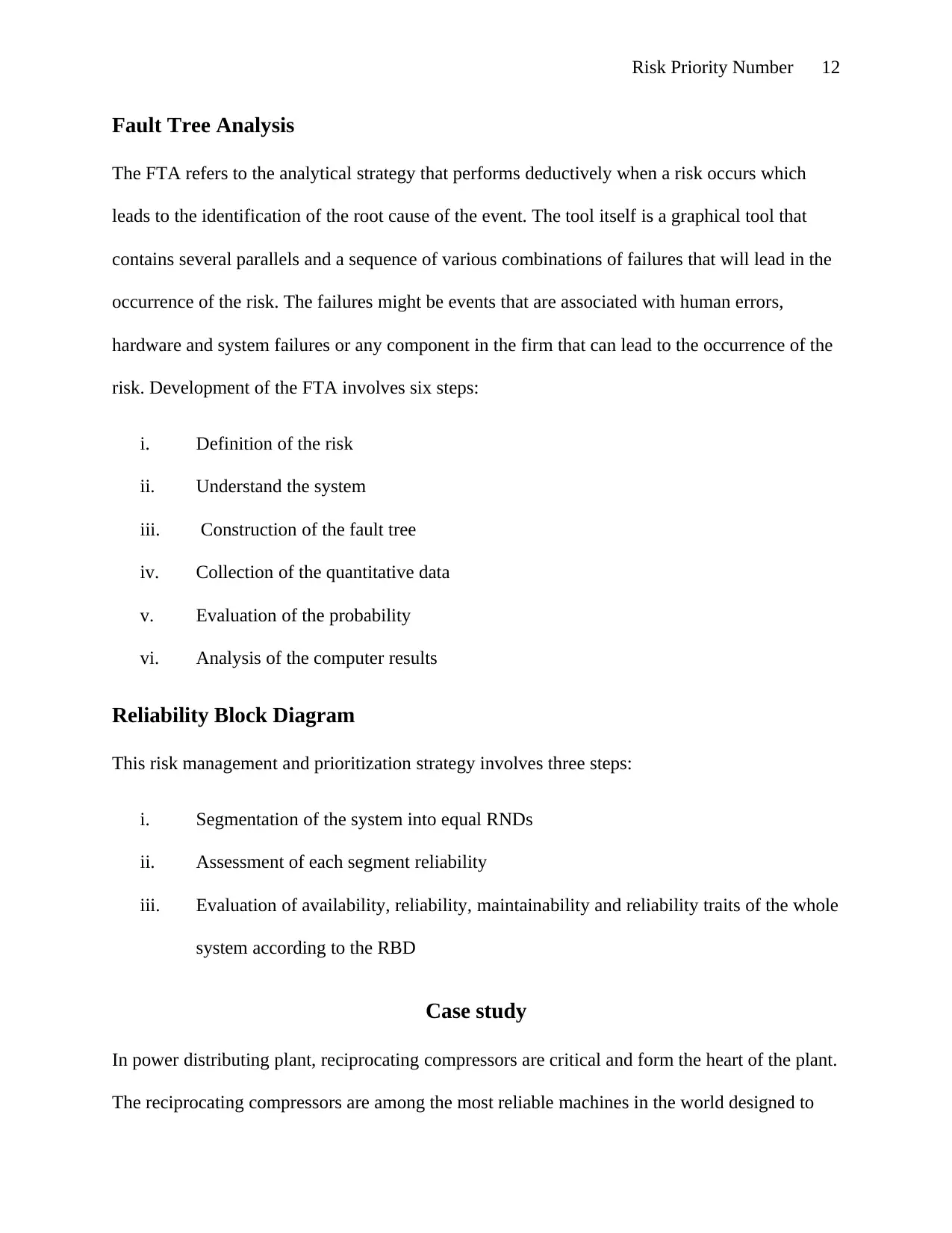
Risk Priority Number 12
Fault Tree Analysis
The FTA refers to the analytical strategy that performs deductively when a risk occurs which
leads to the identification of the root cause of the event. The tool itself is a graphical tool that
contains several parallels and a sequence of various combinations of failures that will lead in the
occurrence of the risk. The failures might be events that are associated with human errors,
hardware and system failures or any component in the firm that can lead to the occurrence of the
risk. Development of the FTA involves six steps:
i. Definition of the risk
ii. Understand the system
iii. Construction of the fault tree
iv. Collection of the quantitative data
v. Evaluation of the probability
vi. Analysis of the computer results
Reliability Block Diagram
This risk management and prioritization strategy involves three steps:
i. Segmentation of the system into equal RNDs
ii. Assessment of each segment reliability
iii. Evaluation of availability, reliability, maintainability and reliability traits of the whole
system according to the RBD
Case study
In power distributing plant, reciprocating compressors are critical and form the heart of the plant.
The reciprocating compressors are among the most reliable machines in the world designed to
Fault Tree Analysis
The FTA refers to the analytical strategy that performs deductively when a risk occurs which
leads to the identification of the root cause of the event. The tool itself is a graphical tool that
contains several parallels and a sequence of various combinations of failures that will lead in the
occurrence of the risk. The failures might be events that are associated with human errors,
hardware and system failures or any component in the firm that can lead to the occurrence of the
risk. Development of the FTA involves six steps:
i. Definition of the risk
ii. Understand the system
iii. Construction of the fault tree
iv. Collection of the quantitative data
v. Evaluation of the probability
vi. Analysis of the computer results
Reliability Block Diagram
This risk management and prioritization strategy involves three steps:
i. Segmentation of the system into equal RNDs
ii. Assessment of each segment reliability
iii. Evaluation of availability, reliability, maintainability and reliability traits of the whole
system according to the RBD
Case study
In power distributing plant, reciprocating compressors are critical and form the heart of the plant.
The reciprocating compressors are among the most reliable machines in the world designed to
You're viewing a preview
Unlock full access by subscribing today!
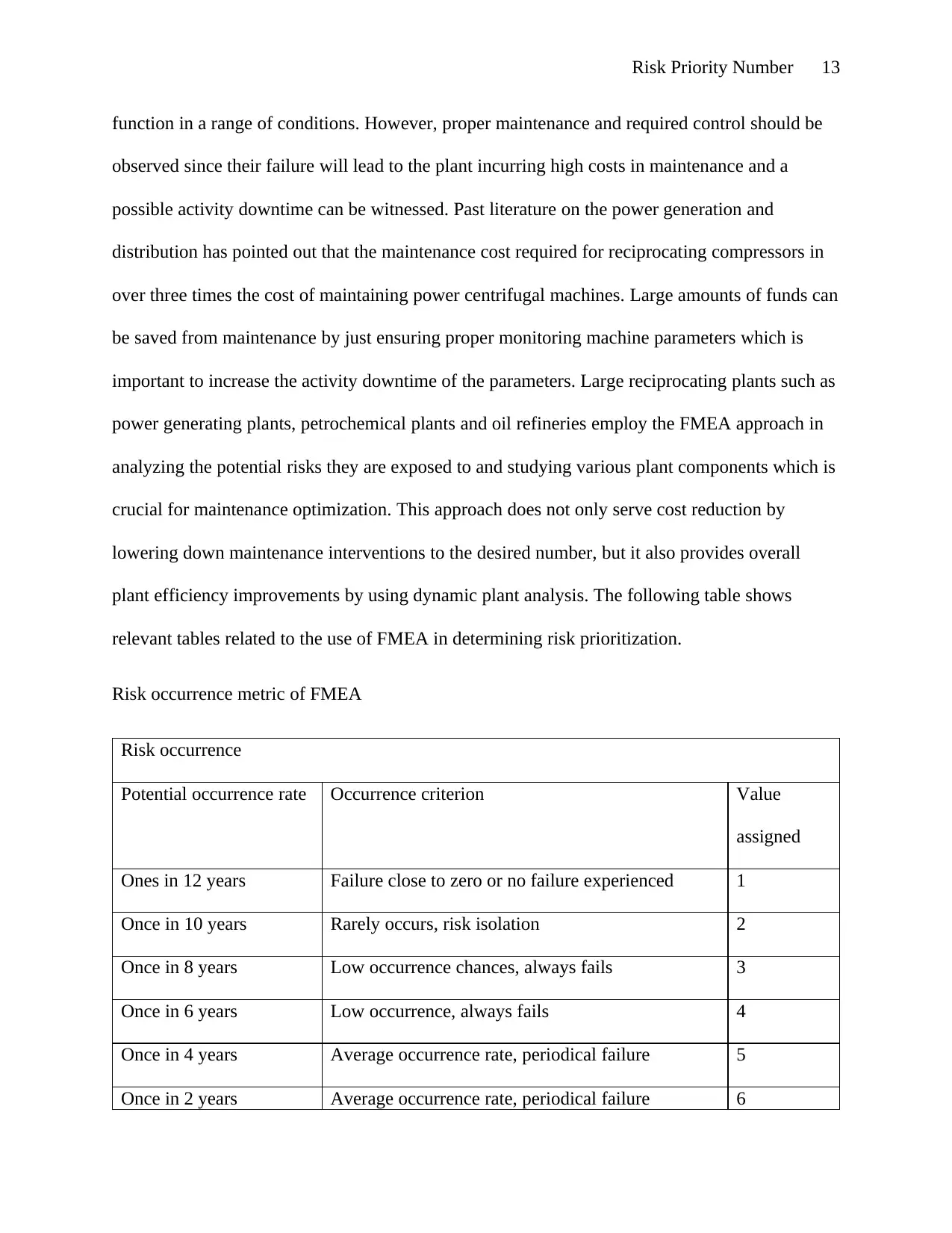
Risk Priority Number 13
function in a range of conditions. However, proper maintenance and required control should be
observed since their failure will lead to the plant incurring high costs in maintenance and a
possible activity downtime can be witnessed. Past literature on the power generation and
distribution has pointed out that the maintenance cost required for reciprocating compressors in
over three times the cost of maintaining power centrifugal machines. Large amounts of funds can
be saved from maintenance by just ensuring proper monitoring machine parameters which is
important to increase the activity downtime of the parameters. Large reciprocating plants such as
power generating plants, petrochemical plants and oil refineries employ the FMEA approach in
analyzing the potential risks they are exposed to and studying various plant components which is
crucial for maintenance optimization. This approach does not only serve cost reduction by
lowering down maintenance interventions to the desired number, but it also provides overall
plant efficiency improvements by using dynamic plant analysis. The following table shows
relevant tables related to the use of FMEA in determining risk prioritization.
Risk occurrence metric of FMEA
Risk occurrence
Potential occurrence rate Occurrence criterion Value
assigned
Ones in 12 years Failure close to zero or no failure experienced 1
Once in 10 years Rarely occurs, risk isolation 2
Once in 8 years Low occurrence chances, always fails 3
Once in 6 years Low occurrence, always fails 4
Once in 4 years Average occurrence rate, periodical failure 5
Once in 2 years Average occurrence rate, periodical failure 6
function in a range of conditions. However, proper maintenance and required control should be
observed since their failure will lead to the plant incurring high costs in maintenance and a
possible activity downtime can be witnessed. Past literature on the power generation and
distribution has pointed out that the maintenance cost required for reciprocating compressors in
over three times the cost of maintaining power centrifugal machines. Large amounts of funds can
be saved from maintenance by just ensuring proper monitoring machine parameters which is
important to increase the activity downtime of the parameters. Large reciprocating plants such as
power generating plants, petrochemical plants and oil refineries employ the FMEA approach in
analyzing the potential risks they are exposed to and studying various plant components which is
crucial for maintenance optimization. This approach does not only serve cost reduction by
lowering down maintenance interventions to the desired number, but it also provides overall
plant efficiency improvements by using dynamic plant analysis. The following table shows
relevant tables related to the use of FMEA in determining risk prioritization.
Risk occurrence metric of FMEA
Risk occurrence
Potential occurrence rate Occurrence criterion Value
assigned
Ones in 12 years Failure close to zero or no failure experienced 1
Once in 10 years Rarely occurs, risk isolation 2
Once in 8 years Low occurrence chances, always fails 3
Once in 6 years Low occurrence, always fails 4
Once in 4 years Average occurrence rate, periodical failure 5
Once in 2 years Average occurrence rate, periodical failure 6
Paraphrase This Document
Need a fresh take? Get an instant paraphrase of this document with our AI Paraphraser
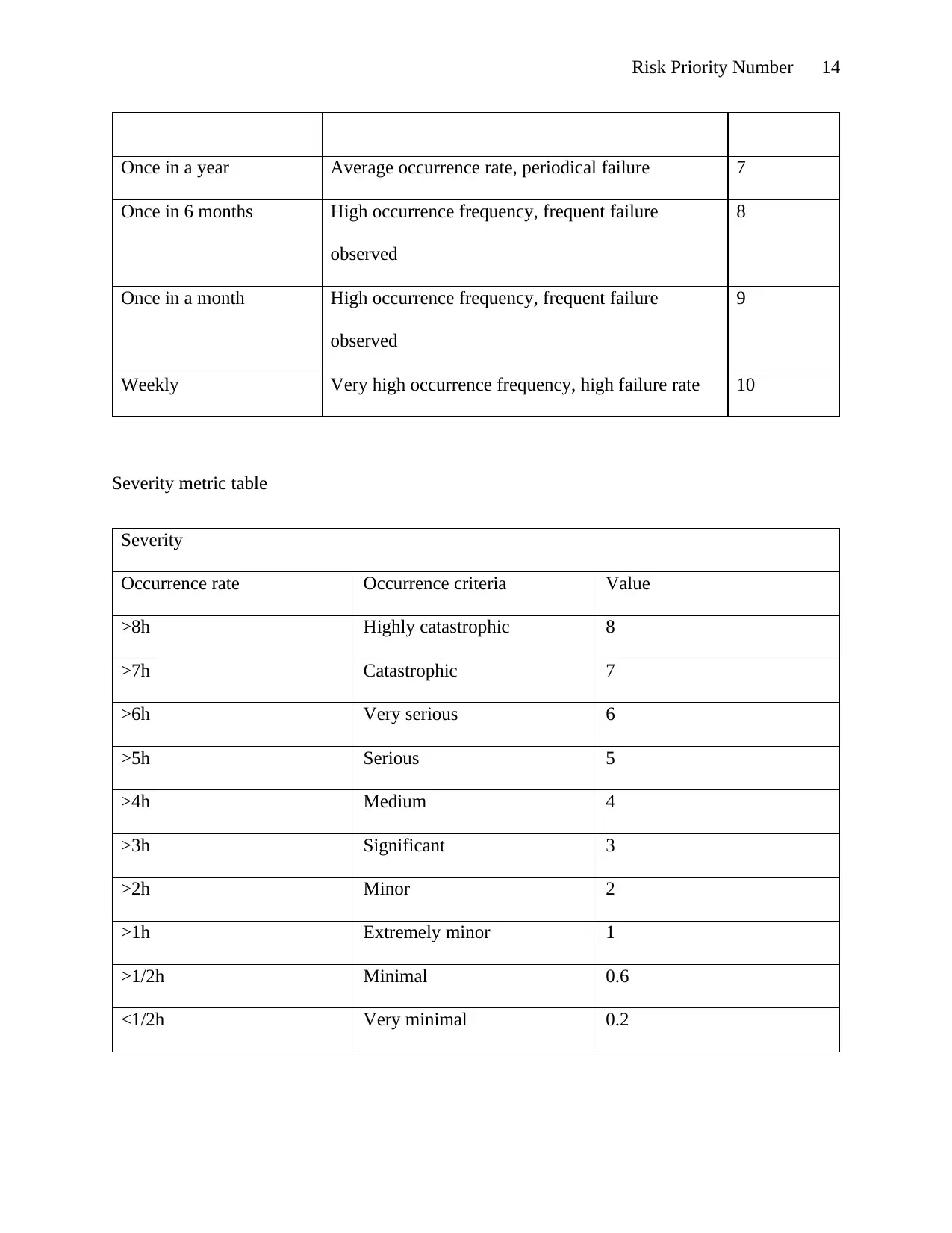
Risk Priority Number 14
Once in a year Average occurrence rate, periodical failure 7
Once in 6 months High occurrence frequency, frequent failure
observed
8
Once in a month High occurrence frequency, frequent failure
observed
9
Weekly Very high occurrence frequency, high failure rate 10
Severity metric table
Severity
Occurrence rate Occurrence criteria Value
>8h Highly catastrophic 8
>7h Catastrophic 7
>6h Very serious 6
>5h Serious 5
>4h Medium 4
>3h Significant 3
>2h Minor 2
>1h Extremely minor 1
>1/2h Minimal 0.6
<1/2h Very minimal 0.2
Once in a year Average occurrence rate, periodical failure 7
Once in 6 months High occurrence frequency, frequent failure
observed
8
Once in a month High occurrence frequency, frequent failure
observed
9
Weekly Very high occurrence frequency, high failure rate 10
Severity metric table
Severity
Occurrence rate Occurrence criteria Value
>8h Highly catastrophic 8
>7h Catastrophic 7
>6h Very serious 6
>5h Serious 5
>4h Medium 4
>3h Significant 3
>2h Minor 2
>1h Extremely minor 1
>1/2h Minimal 0.6
<1/2h Very minimal 0.2
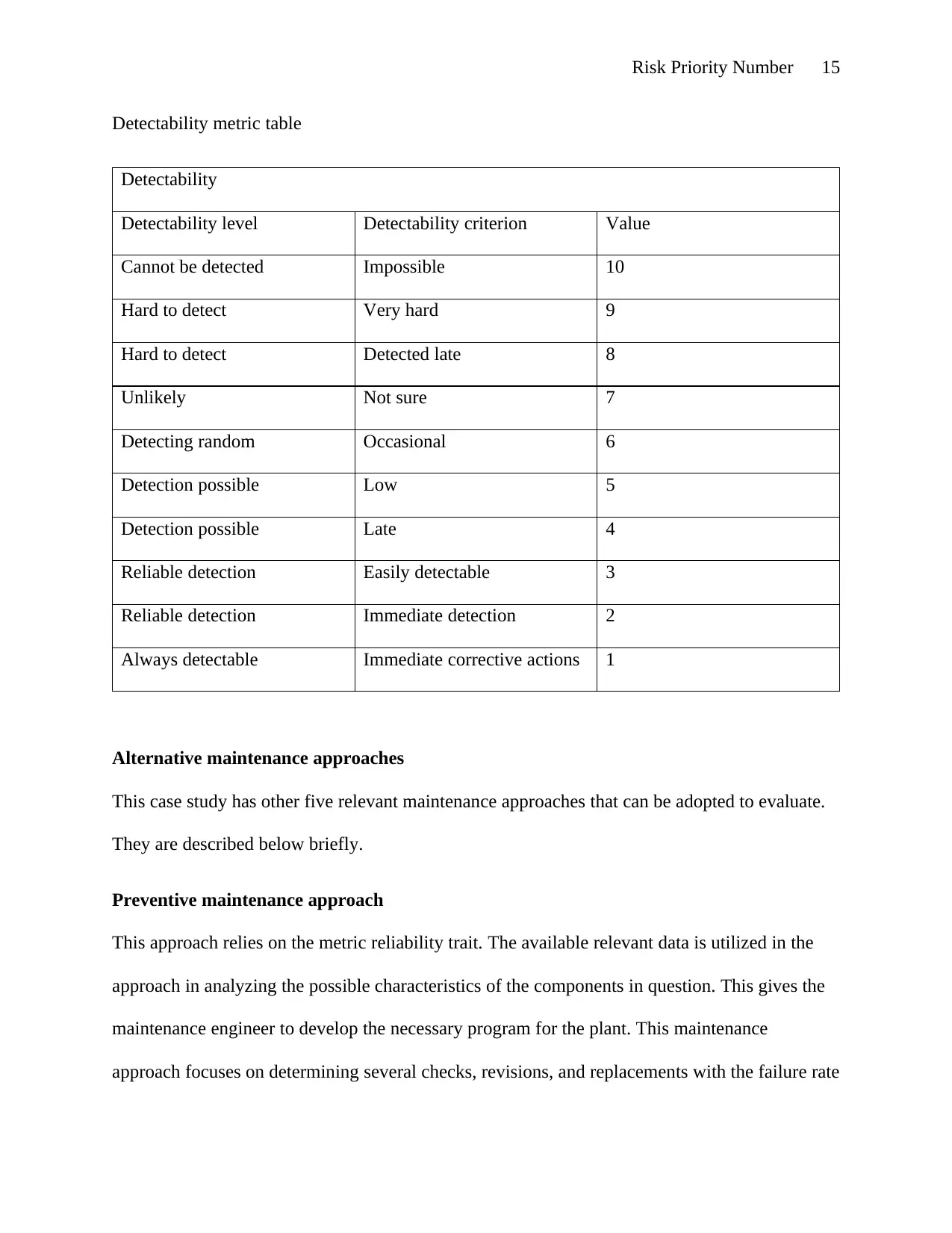
Risk Priority Number 15
Detectability metric table
Detectability
Detectability level Detectability criterion Value
Cannot be detected Impossible 10
Hard to detect Very hard 9
Hard to detect Detected late 8
Unlikely Not sure 7
Detecting random Occasional 6
Detection possible Low 5
Detection possible Late 4
Reliable detection Easily detectable 3
Reliable detection Immediate detection 2
Always detectable Immediate corrective actions 1
Alternative maintenance approaches
This case study has other five relevant maintenance approaches that can be adopted to evaluate.
They are described below briefly.
Preventive maintenance approach
This approach relies on the metric reliability trait. The available relevant data is utilized in the
approach in analyzing the possible characteristics of the components in question. This gives the
maintenance engineer to develop the necessary program for the plant. This maintenance
approach focuses on determining several checks, revisions, and replacements with the failure rate
Detectability metric table
Detectability
Detectability level Detectability criterion Value
Cannot be detected Impossible 10
Hard to detect Very hard 9
Hard to detect Detected late 8
Unlikely Not sure 7
Detecting random Occasional 6
Detection possible Low 5
Detection possible Late 4
Reliable detection Easily detectable 3
Reliable detection Immediate detection 2
Always detectable Immediate corrective actions 1
Alternative maintenance approaches
This case study has other five relevant maintenance approaches that can be adopted to evaluate.
They are described below briefly.
Preventive maintenance approach
This approach relies on the metric reliability trait. The available relevant data is utilized in the
approach in analyzing the possible characteristics of the components in question. This gives the
maintenance engineer to develop the necessary program for the plant. This maintenance
approach focuses on determining several checks, revisions, and replacements with the failure rate
You're viewing a preview
Unlock full access by subscribing today!
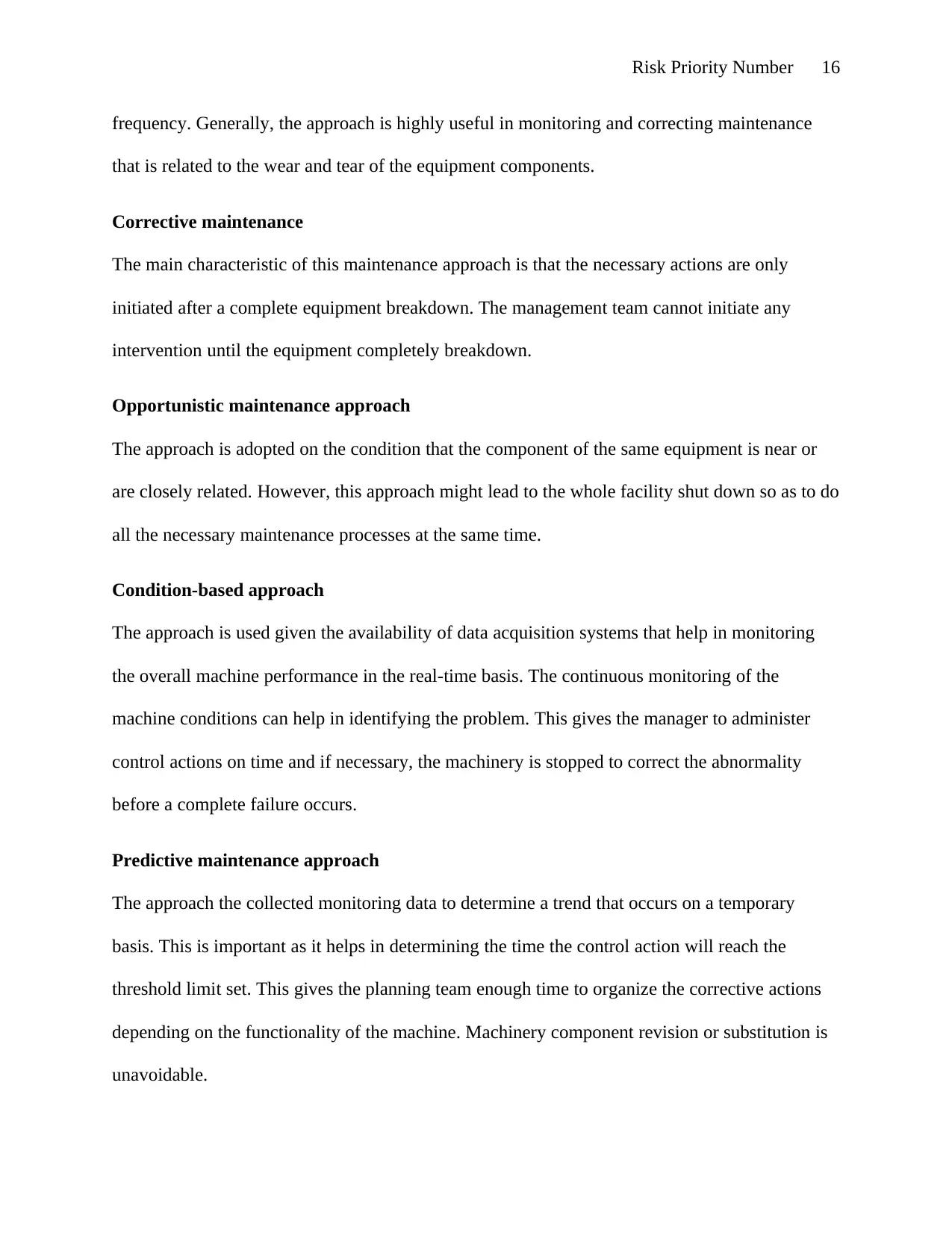
Risk Priority Number 16
frequency. Generally, the approach is highly useful in monitoring and correcting maintenance
that is related to the wear and tear of the equipment components.
Corrective maintenance
The main characteristic of this maintenance approach is that the necessary actions are only
initiated after a complete equipment breakdown. The management team cannot initiate any
intervention until the equipment completely breakdown.
Opportunistic maintenance approach
The approach is adopted on the condition that the component of the same equipment is near or
are closely related. However, this approach might lead to the whole facility shut down so as to do
all the necessary maintenance processes at the same time.
Condition-based approach
The approach is used given the availability of data acquisition systems that help in monitoring
the overall machine performance in the real-time basis. The continuous monitoring of the
machine conditions can help in identifying the problem. This gives the manager to administer
control actions on time and if necessary, the machinery is stopped to correct the abnormality
before a complete failure occurs.
Predictive maintenance approach
The approach the collected monitoring data to determine a trend that occurs on a temporary
basis. This is important as it helps in determining the time the control action will reach the
threshold limit set. This gives the planning team enough time to organize the corrective actions
depending on the functionality of the machine. Machinery component revision or substitution is
unavoidable.
frequency. Generally, the approach is highly useful in monitoring and correcting maintenance
that is related to the wear and tear of the equipment components.
Corrective maintenance
The main characteristic of this maintenance approach is that the necessary actions are only
initiated after a complete equipment breakdown. The management team cannot initiate any
intervention until the equipment completely breakdown.
Opportunistic maintenance approach
The approach is adopted on the condition that the component of the same equipment is near or
are closely related. However, this approach might lead to the whole facility shut down so as to do
all the necessary maintenance processes at the same time.
Condition-based approach
The approach is used given the availability of data acquisition systems that help in monitoring
the overall machine performance in the real-time basis. The continuous monitoring of the
machine conditions can help in identifying the problem. This gives the manager to administer
control actions on time and if necessary, the machinery is stopped to correct the abnormality
before a complete failure occurs.
Predictive maintenance approach
The approach the collected monitoring data to determine a trend that occurs on a temporary
basis. This is important as it helps in determining the time the control action will reach the
threshold limit set. This gives the planning team enough time to organize the corrective actions
depending on the functionality of the machine. Machinery component revision or substitution is
unavoidable.
Paraphrase This Document
Need a fresh take? Get an instant paraphrase of this document with our AI Paraphraser
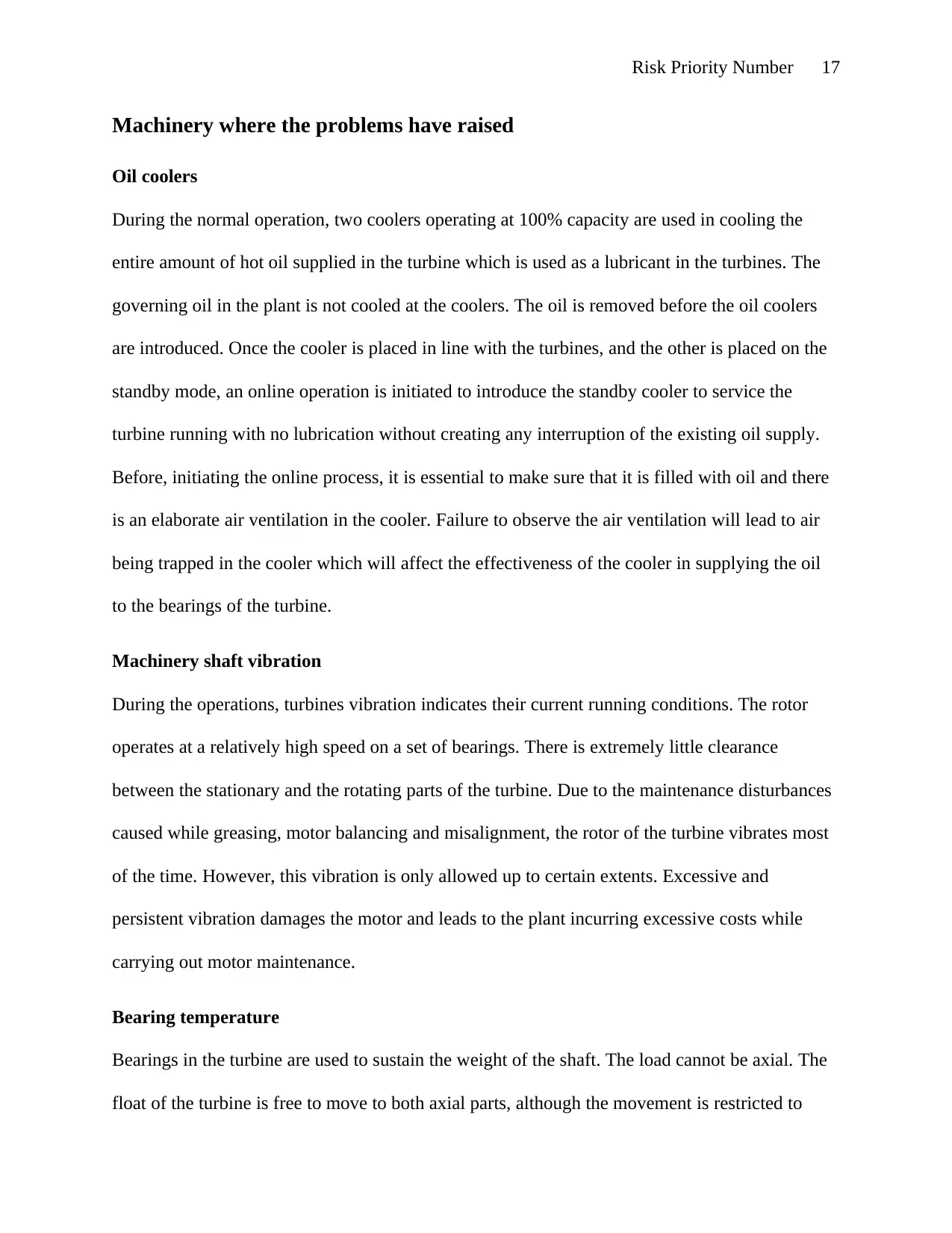
Risk Priority Number 17
Machinery where the problems have raised
Oil coolers
During the normal operation, two coolers operating at 100% capacity are used in cooling the
entire amount of hot oil supplied in the turbine which is used as a lubricant in the turbines. The
governing oil in the plant is not cooled at the coolers. The oil is removed before the oil coolers
are introduced. Once the cooler is placed in line with the turbines, and the other is placed on the
standby mode, an online operation is initiated to introduce the standby cooler to service the
turbine running with no lubrication without creating any interruption of the existing oil supply.
Before, initiating the online process, it is essential to make sure that it is filled with oil and there
is an elaborate air ventilation in the cooler. Failure to observe the air ventilation will lead to air
being trapped in the cooler which will affect the effectiveness of the cooler in supplying the oil
to the bearings of the turbine.
Machinery shaft vibration
During the operations, turbines vibration indicates their current running conditions. The rotor
operates at a relatively high speed on a set of bearings. There is extremely little clearance
between the stationary and the rotating parts of the turbine. Due to the maintenance disturbances
caused while greasing, motor balancing and misalignment, the rotor of the turbine vibrates most
of the time. However, this vibration is only allowed up to certain extents. Excessive and
persistent vibration damages the motor and leads to the plant incurring excessive costs while
carrying out motor maintenance.
Bearing temperature
Bearings in the turbine are used to sustain the weight of the shaft. The load cannot be axial. The
float of the turbine is free to move to both axial parts, although the movement is restricted to
Machinery where the problems have raised
Oil coolers
During the normal operation, two coolers operating at 100% capacity are used in cooling the
entire amount of hot oil supplied in the turbine which is used as a lubricant in the turbines. The
governing oil in the plant is not cooled at the coolers. The oil is removed before the oil coolers
are introduced. Once the cooler is placed in line with the turbines, and the other is placed on the
standby mode, an online operation is initiated to introduce the standby cooler to service the
turbine running with no lubrication without creating any interruption of the existing oil supply.
Before, initiating the online process, it is essential to make sure that it is filled with oil and there
is an elaborate air ventilation in the cooler. Failure to observe the air ventilation will lead to air
being trapped in the cooler which will affect the effectiveness of the cooler in supplying the oil
to the bearings of the turbine.
Machinery shaft vibration
During the operations, turbines vibration indicates their current running conditions. The rotor
operates at a relatively high speed on a set of bearings. There is extremely little clearance
between the stationary and the rotating parts of the turbine. Due to the maintenance disturbances
caused while greasing, motor balancing and misalignment, the rotor of the turbine vibrates most
of the time. However, this vibration is only allowed up to certain extents. Excessive and
persistent vibration damages the motor and leads to the plant incurring excessive costs while
carrying out motor maintenance.
Bearing temperature
Bearings in the turbine are used to sustain the weight of the shaft. The load cannot be axial. The
float of the turbine is free to move to both axial parts, although the movement is restricted to
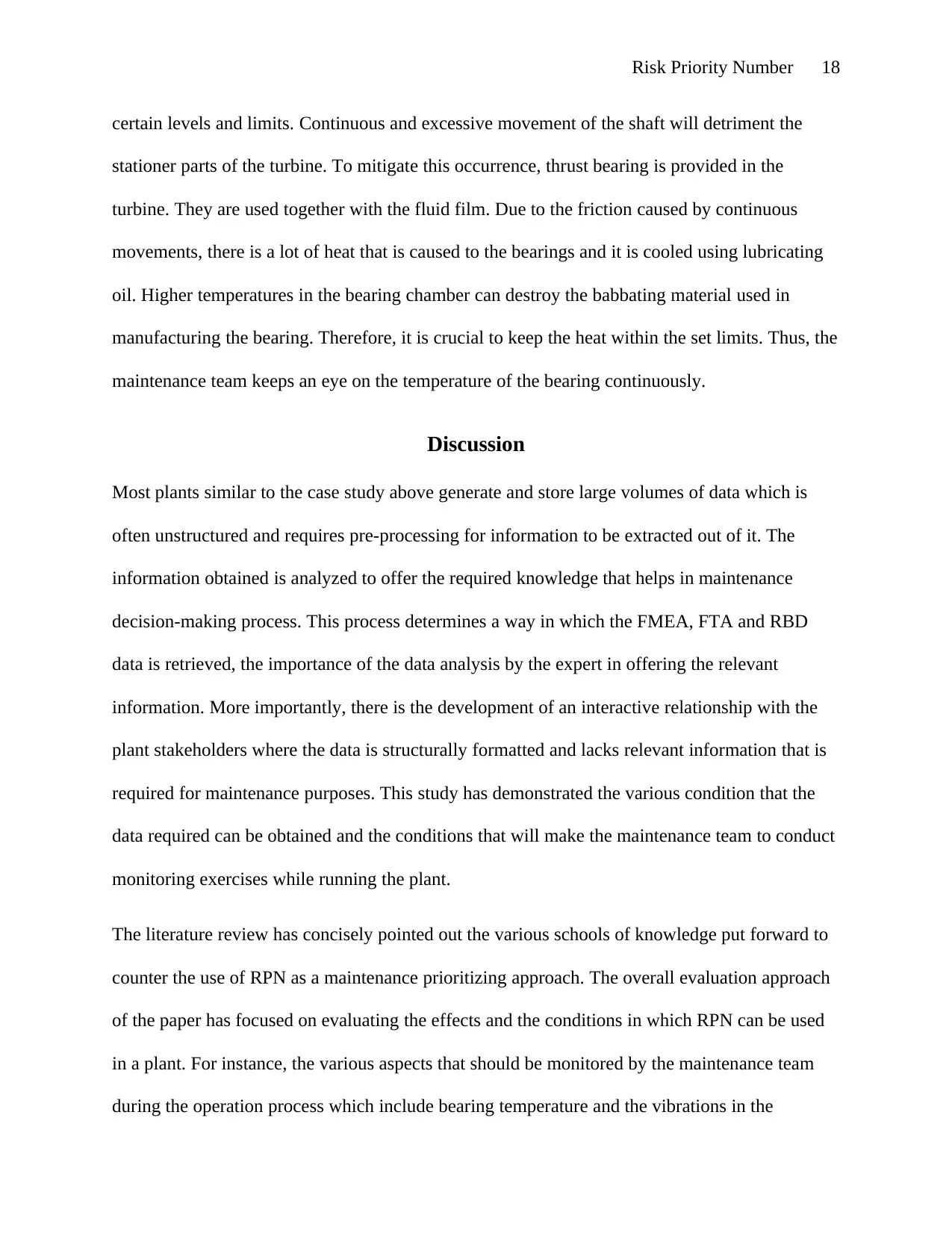
Risk Priority Number 18
certain levels and limits. Continuous and excessive movement of the shaft will detriment the
stationer parts of the turbine. To mitigate this occurrence, thrust bearing is provided in the
turbine. They are used together with the fluid film. Due to the friction caused by continuous
movements, there is a lot of heat that is caused to the bearings and it is cooled using lubricating
oil. Higher temperatures in the bearing chamber can destroy the babbating material used in
manufacturing the bearing. Therefore, it is crucial to keep the heat within the set limits. Thus, the
maintenance team keeps an eye on the temperature of the bearing continuously.
Discussion
Most plants similar to the case study above generate and store large volumes of data which is
often unstructured and requires pre-processing for information to be extracted out of it. The
information obtained is analyzed to offer the required knowledge that helps in maintenance
decision-making process. This process determines a way in which the FMEA, FTA and RBD
data is retrieved, the importance of the data analysis by the expert in offering the relevant
information. More importantly, there is the development of an interactive relationship with the
plant stakeholders where the data is structurally formatted and lacks relevant information that is
required for maintenance purposes. This study has demonstrated the various condition that the
data required can be obtained and the conditions that will make the maintenance team to conduct
monitoring exercises while running the plant.
The literature review has concisely pointed out the various schools of knowledge put forward to
counter the use of RPN as a maintenance prioritizing approach. The overall evaluation approach
of the paper has focused on evaluating the effects and the conditions in which RPN can be used
in a plant. For instance, the various aspects that should be monitored by the maintenance team
during the operation process which include bearing temperature and the vibrations in the
certain levels and limits. Continuous and excessive movement of the shaft will detriment the
stationer parts of the turbine. To mitigate this occurrence, thrust bearing is provided in the
turbine. They are used together with the fluid film. Due to the friction caused by continuous
movements, there is a lot of heat that is caused to the bearings and it is cooled using lubricating
oil. Higher temperatures in the bearing chamber can destroy the babbating material used in
manufacturing the bearing. Therefore, it is crucial to keep the heat within the set limits. Thus, the
maintenance team keeps an eye on the temperature of the bearing continuously.
Discussion
Most plants similar to the case study above generate and store large volumes of data which is
often unstructured and requires pre-processing for information to be extracted out of it. The
information obtained is analyzed to offer the required knowledge that helps in maintenance
decision-making process. This process determines a way in which the FMEA, FTA and RBD
data is retrieved, the importance of the data analysis by the expert in offering the relevant
information. More importantly, there is the development of an interactive relationship with the
plant stakeholders where the data is structurally formatted and lacks relevant information that is
required for maintenance purposes. This study has demonstrated the various condition that the
data required can be obtained and the conditions that will make the maintenance team to conduct
monitoring exercises while running the plant.
The literature review has concisely pointed out the various schools of knowledge put forward to
counter the use of RPN as a maintenance prioritizing approach. The overall evaluation approach
of the paper has focused on evaluating the effects and the conditions in which RPN can be used
in a plant. For instance, the various aspects that should be monitored by the maintenance team
during the operation process which include bearing temperature and the vibrations in the
You're viewing a preview
Unlock full access by subscribing today!
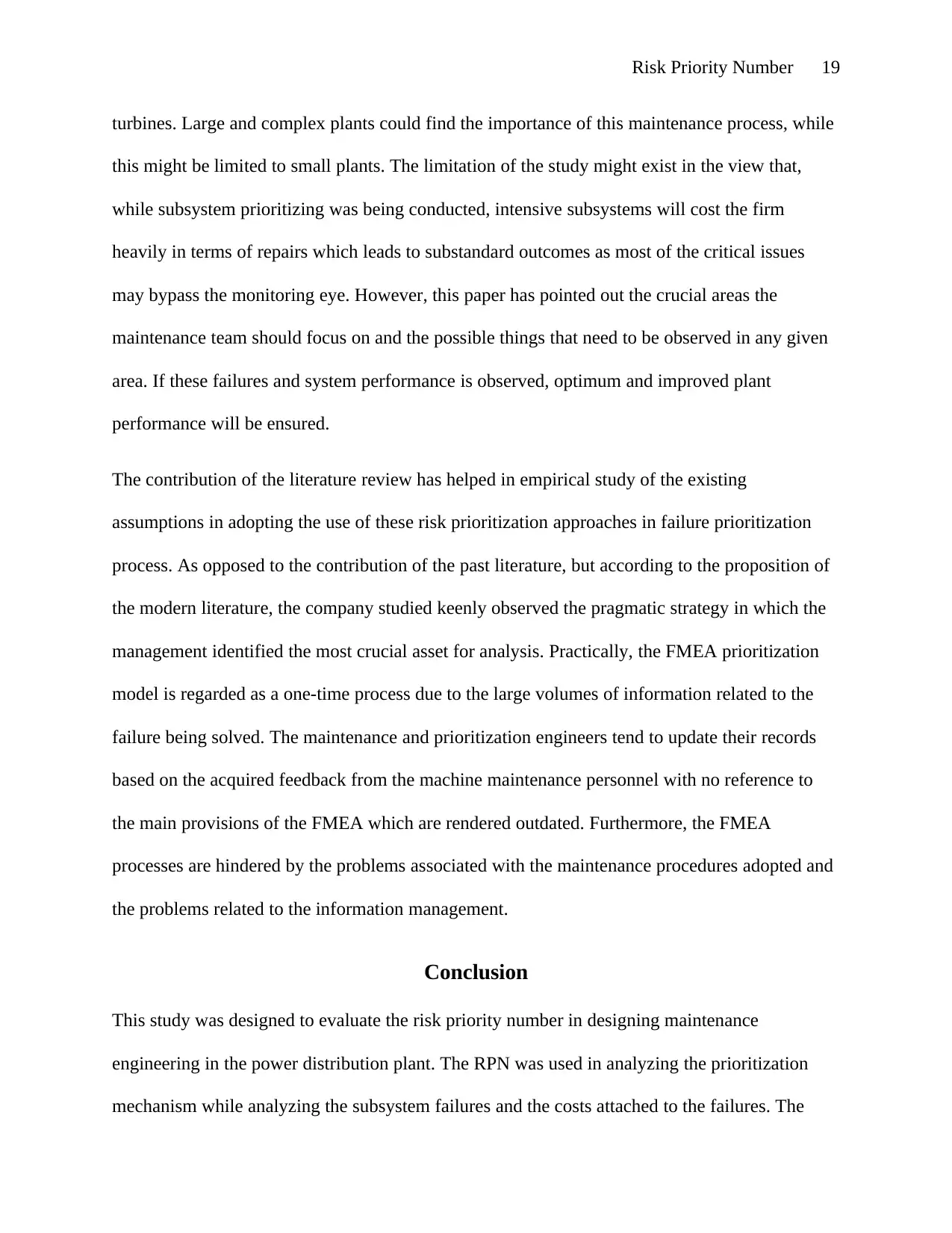
Risk Priority Number 19
turbines. Large and complex plants could find the importance of this maintenance process, while
this might be limited to small plants. The limitation of the study might exist in the view that,
while subsystem prioritizing was being conducted, intensive subsystems will cost the firm
heavily in terms of repairs which leads to substandard outcomes as most of the critical issues
may bypass the monitoring eye. However, this paper has pointed out the crucial areas the
maintenance team should focus on and the possible things that need to be observed in any given
area. If these failures and system performance is observed, optimum and improved plant
performance will be ensured.
The contribution of the literature review has helped in empirical study of the existing
assumptions in adopting the use of these risk prioritization approaches in failure prioritization
process. As opposed to the contribution of the past literature, but according to the proposition of
the modern literature, the company studied keenly observed the pragmatic strategy in which the
management identified the most crucial asset for analysis. Practically, the FMEA prioritization
model is regarded as a one-time process due to the large volumes of information related to the
failure being solved. The maintenance and prioritization engineers tend to update their records
based on the acquired feedback from the machine maintenance personnel with no reference to
the main provisions of the FMEA which are rendered outdated. Furthermore, the FMEA
processes are hindered by the problems associated with the maintenance procedures adopted and
the problems related to the information management.
Conclusion
This study was designed to evaluate the risk priority number in designing maintenance
engineering in the power distribution plant. The RPN was used in analyzing the prioritization
mechanism while analyzing the subsystem failures and the costs attached to the failures. The
turbines. Large and complex plants could find the importance of this maintenance process, while
this might be limited to small plants. The limitation of the study might exist in the view that,
while subsystem prioritizing was being conducted, intensive subsystems will cost the firm
heavily in terms of repairs which leads to substandard outcomes as most of the critical issues
may bypass the monitoring eye. However, this paper has pointed out the crucial areas the
maintenance team should focus on and the possible things that need to be observed in any given
area. If these failures and system performance is observed, optimum and improved plant
performance will be ensured.
The contribution of the literature review has helped in empirical study of the existing
assumptions in adopting the use of these risk prioritization approaches in failure prioritization
process. As opposed to the contribution of the past literature, but according to the proposition of
the modern literature, the company studied keenly observed the pragmatic strategy in which the
management identified the most crucial asset for analysis. Practically, the FMEA prioritization
model is regarded as a one-time process due to the large volumes of information related to the
failure being solved. The maintenance and prioritization engineers tend to update their records
based on the acquired feedback from the machine maintenance personnel with no reference to
the main provisions of the FMEA which are rendered outdated. Furthermore, the FMEA
processes are hindered by the problems associated with the maintenance procedures adopted and
the problems related to the information management.
Conclusion
This study was designed to evaluate the risk priority number in designing maintenance
engineering in the power distribution plant. The RPN was used in analyzing the prioritization
mechanism while analyzing the subsystem failures and the costs attached to the failures. The
Paraphrase This Document
Need a fresh take? Get an instant paraphrase of this document with our AI Paraphraser
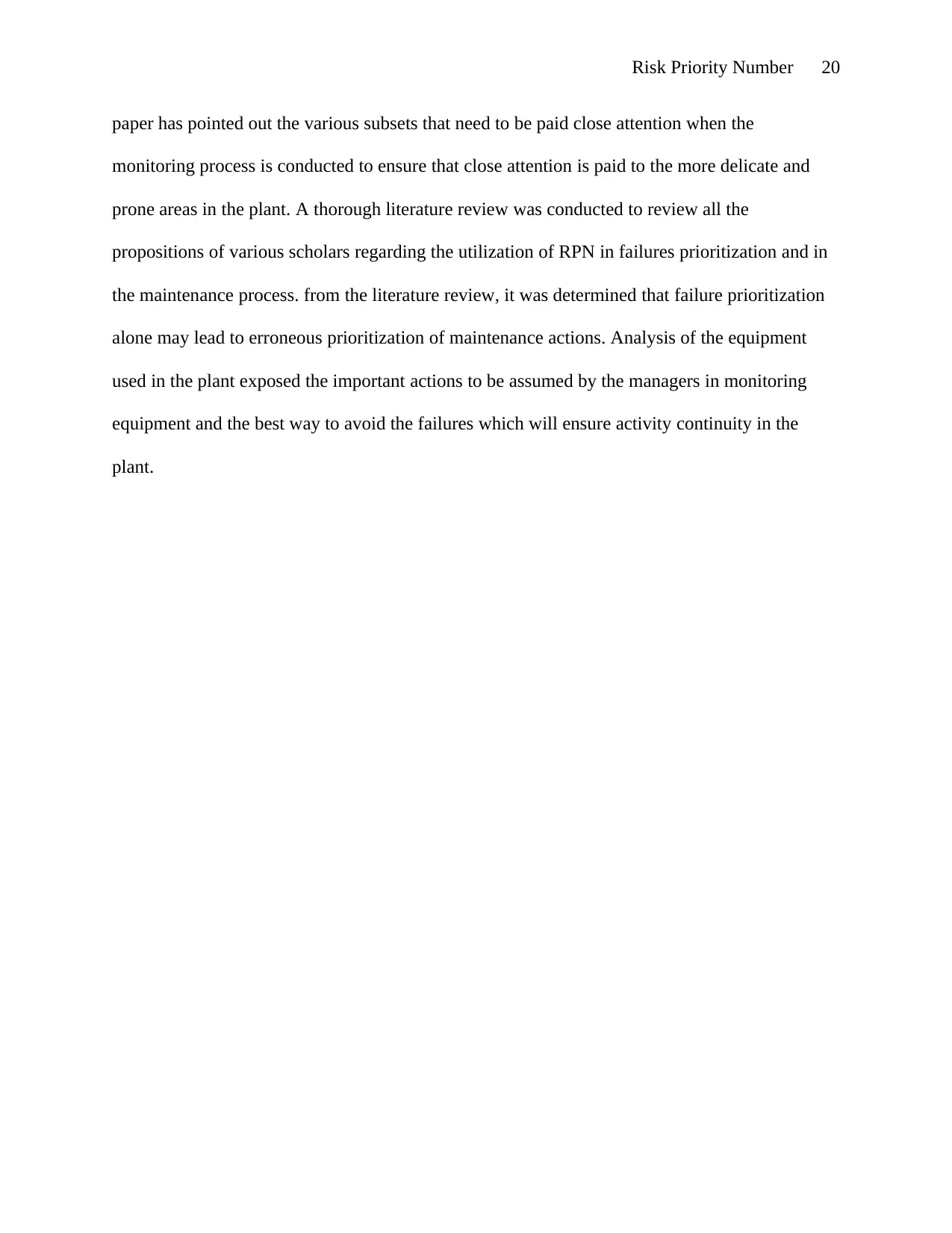
Risk Priority Number 20
paper has pointed out the various subsets that need to be paid close attention when the
monitoring process is conducted to ensure that close attention is paid to the more delicate and
prone areas in the plant. A thorough literature review was conducted to review all the
propositions of various scholars regarding the utilization of RPN in failures prioritization and in
the maintenance process. from the literature review, it was determined that failure prioritization
alone may lead to erroneous prioritization of maintenance actions. Analysis of the equipment
used in the plant exposed the important actions to be assumed by the managers in monitoring
equipment and the best way to avoid the failures which will ensure activity continuity in the
plant.
paper has pointed out the various subsets that need to be paid close attention when the
monitoring process is conducted to ensure that close attention is paid to the more delicate and
prone areas in the plant. A thorough literature review was conducted to review all the
propositions of various scholars regarding the utilization of RPN in failures prioritization and in
the maintenance process. from the literature review, it was determined that failure prioritization
alone may lead to erroneous prioritization of maintenance actions. Analysis of the equipment
used in the plant exposed the important actions to be assumed by the managers in monitoring
equipment and the best way to avoid the failures which will ensure activity continuity in the
plant.
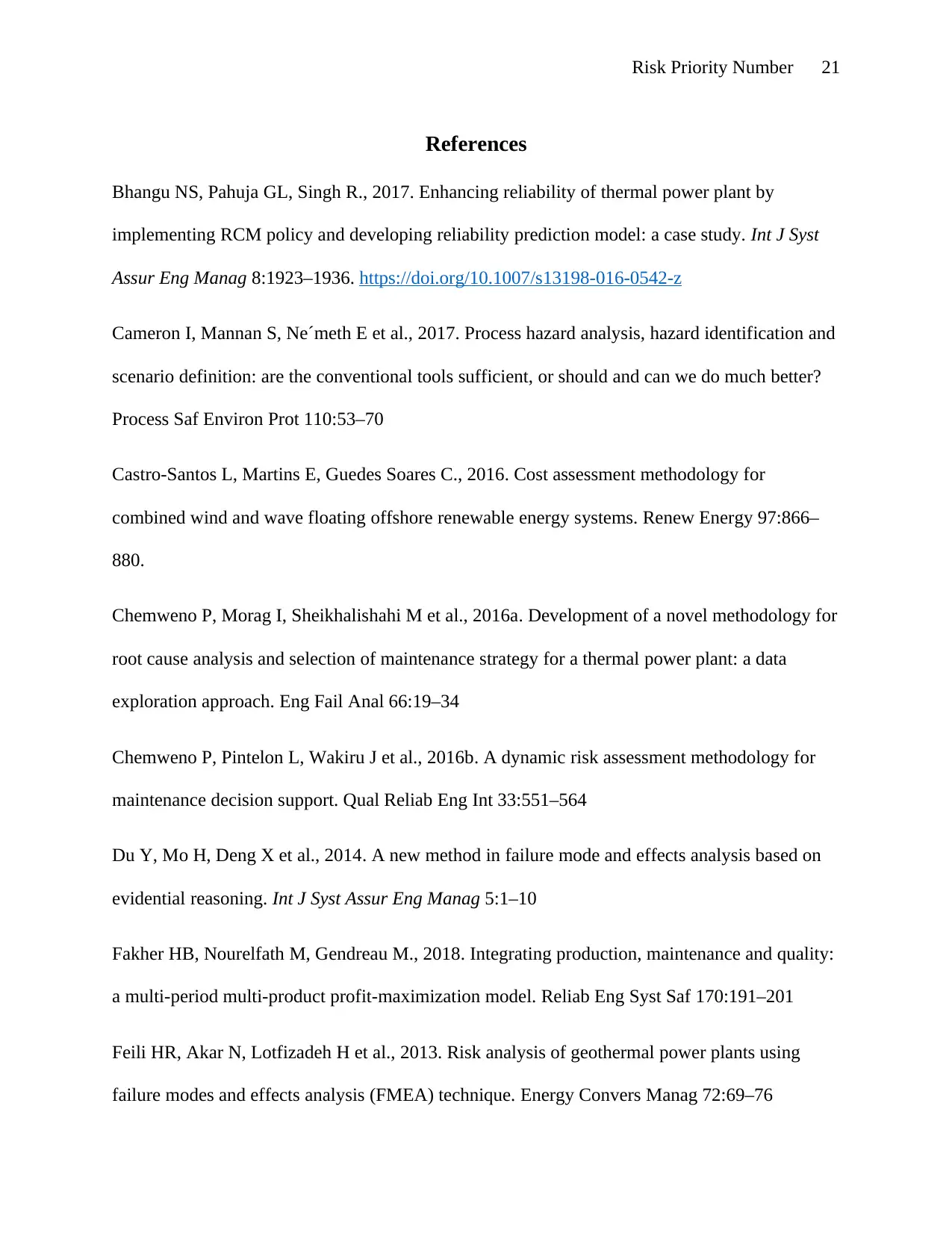
Risk Priority Number 21
References
Bhangu NS, Pahuja GL, Singh R., 2017. Enhancing reliability of thermal power plant by
implementing RCM policy and developing reliability prediction model: a case study. Int J Syst
Assur Eng Manag 8:1923–1936. https://doi.org/10.1007/s13198-016-0542-z
Cameron I, Mannan S, Ne´meth E et al., 2017. Process hazard analysis, hazard identification and
scenario definition: are the conventional tools sufficient, or should and can we do much better?
Process Saf Environ Prot 110:53–70
Castro-Santos L, Martins E, Guedes Soares C., 2016. Cost assessment methodology for
combined wind and wave floating offshore renewable energy systems. Renew Energy 97:866–
880.
Chemweno P, Morag I, Sheikhalishahi M et al., 2016a. Development of a novel methodology for
root cause analysis and selection of maintenance strategy for a thermal power plant: a data
exploration approach. Eng Fail Anal 66:19–34
Chemweno P, Pintelon L, Wakiru J et al., 2016b. A dynamic risk assessment methodology for
maintenance decision support. Qual Reliab Eng Int 33:551–564
Du Y, Mo H, Deng X et al., 2014. A new method in failure mode and effects analysis based on
evidential reasoning. Int J Syst Assur Eng Manag 5:1–10
Fakher HB, Nourelfath M, Gendreau M., 2018. Integrating production, maintenance and quality:
a multi-period multi-product profit-maximization model. Reliab Eng Syst Saf 170:191–201
Feili HR, Akar N, Lotfizadeh H et al., 2013. Risk analysis of geothermal power plants using
failure modes and effects analysis (FMEA) technique. Energy Convers Manag 72:69–76
References
Bhangu NS, Pahuja GL, Singh R., 2017. Enhancing reliability of thermal power plant by
implementing RCM policy and developing reliability prediction model: a case study. Int J Syst
Assur Eng Manag 8:1923–1936. https://doi.org/10.1007/s13198-016-0542-z
Cameron I, Mannan S, Ne´meth E et al., 2017. Process hazard analysis, hazard identification and
scenario definition: are the conventional tools sufficient, or should and can we do much better?
Process Saf Environ Prot 110:53–70
Castro-Santos L, Martins E, Guedes Soares C., 2016. Cost assessment methodology for
combined wind and wave floating offshore renewable energy systems. Renew Energy 97:866–
880.
Chemweno P, Morag I, Sheikhalishahi M et al., 2016a. Development of a novel methodology for
root cause analysis and selection of maintenance strategy for a thermal power plant: a data
exploration approach. Eng Fail Anal 66:19–34
Chemweno P, Pintelon L, Wakiru J et al., 2016b. A dynamic risk assessment methodology for
maintenance decision support. Qual Reliab Eng Int 33:551–564
Du Y, Mo H, Deng X et al., 2014. A new method in failure mode and effects analysis based on
evidential reasoning. Int J Syst Assur Eng Manag 5:1–10
Fakher HB, Nourelfath M, Gendreau M., 2018. Integrating production, maintenance and quality:
a multi-period multi-product profit-maximization model. Reliab Eng Syst Saf 170:191–201
Feili HR, Akar N, Lotfizadeh H et al., 2013. Risk analysis of geothermal power plants using
failure modes and effects analysis (FMEA) technique. Energy Convers Manag 72:69–76
You're viewing a preview
Unlock full access by subscribing today!
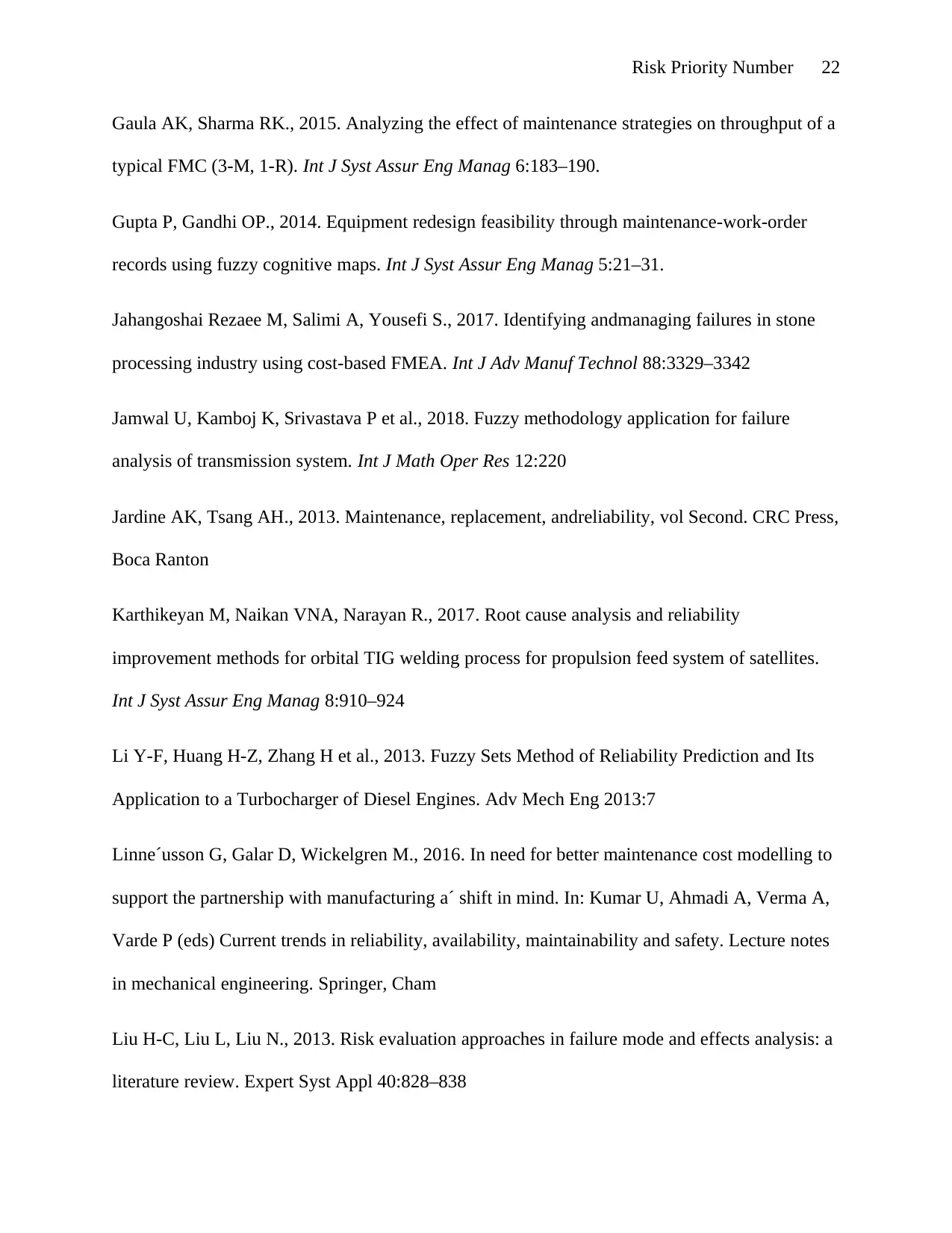
Risk Priority Number 22
Gaula AK, Sharma RK., 2015. Analyzing the effect of maintenance strategies on throughput of a
typical FMC (3-M, 1-R). Int J Syst Assur Eng Manag 6:183–190.
Gupta P, Gandhi OP., 2014. Equipment redesign feasibility through maintenance-work-order
records using fuzzy cognitive maps. Int J Syst Assur Eng Manag 5:21–31.
Jahangoshai Rezaee M, Salimi A, Yousefi S., 2017. Identifying andmanaging failures in stone
processing industry using cost-based FMEA. Int J Adv Manuf Technol 88:3329–3342
Jamwal U, Kamboj K, Srivastava P et al., 2018. Fuzzy methodology application for failure
analysis of transmission system. Int J Math Oper Res 12:220
Jardine AK, Tsang AH., 2013. Maintenance, replacement, andreliability, vol Second. CRC Press,
Boca Ranton
Karthikeyan M, Naikan VNA, Narayan R., 2017. Root cause analysis and reliability
improvement methods for orbital TIG welding process for propulsion feed system of satellites.
Int J Syst Assur Eng Manag 8:910–924
Li Y-F, Huang H-Z, Zhang H et al., 2013. Fuzzy Sets Method of Reliability Prediction and Its
Application to a Turbocharger of Diesel Engines. Adv Mech Eng 2013:7
Linne´usson G, Galar D, Wickelgren M., 2016. In need for better maintenance cost modelling to
support the partnership with manufacturing a´ shift in mind. In: Kumar U, Ahmadi A, Verma A,
Varde P (eds) Current trends in reliability, availability, maintainability and safety. Lecture notes
in mechanical engineering. Springer, Cham
Liu H-C, Liu L, Liu N., 2013. Risk evaluation approaches in failure mode and effects analysis: a
literature review. Expert Syst Appl 40:828–838
Gaula AK, Sharma RK., 2015. Analyzing the effect of maintenance strategies on throughput of a
typical FMC (3-M, 1-R). Int J Syst Assur Eng Manag 6:183–190.
Gupta P, Gandhi OP., 2014. Equipment redesign feasibility through maintenance-work-order
records using fuzzy cognitive maps. Int J Syst Assur Eng Manag 5:21–31.
Jahangoshai Rezaee M, Salimi A, Yousefi S., 2017. Identifying andmanaging failures in stone
processing industry using cost-based FMEA. Int J Adv Manuf Technol 88:3329–3342
Jamwal U, Kamboj K, Srivastava P et al., 2018. Fuzzy methodology application for failure
analysis of transmission system. Int J Math Oper Res 12:220
Jardine AK, Tsang AH., 2013. Maintenance, replacement, andreliability, vol Second. CRC Press,
Boca Ranton
Karthikeyan M, Naikan VNA, Narayan R., 2017. Root cause analysis and reliability
improvement methods for orbital TIG welding process for propulsion feed system of satellites.
Int J Syst Assur Eng Manag 8:910–924
Li Y-F, Huang H-Z, Zhang H et al., 2013. Fuzzy Sets Method of Reliability Prediction and Its
Application to a Turbocharger of Diesel Engines. Adv Mech Eng 2013:7
Linne´usson G, Galar D, Wickelgren M., 2016. In need for better maintenance cost modelling to
support the partnership with manufacturing a´ shift in mind. In: Kumar U, Ahmadi A, Verma A,
Varde P (eds) Current trends in reliability, availability, maintainability and safety. Lecture notes
in mechanical engineering. Springer, Cham
Liu H-C, Liu L, Liu N., 2013. Risk evaluation approaches in failure mode and effects analysis: a
literature review. Expert Syst Appl 40:828–838
Paraphrase This Document
Need a fresh take? Get an instant paraphrase of this document with our AI Paraphraser
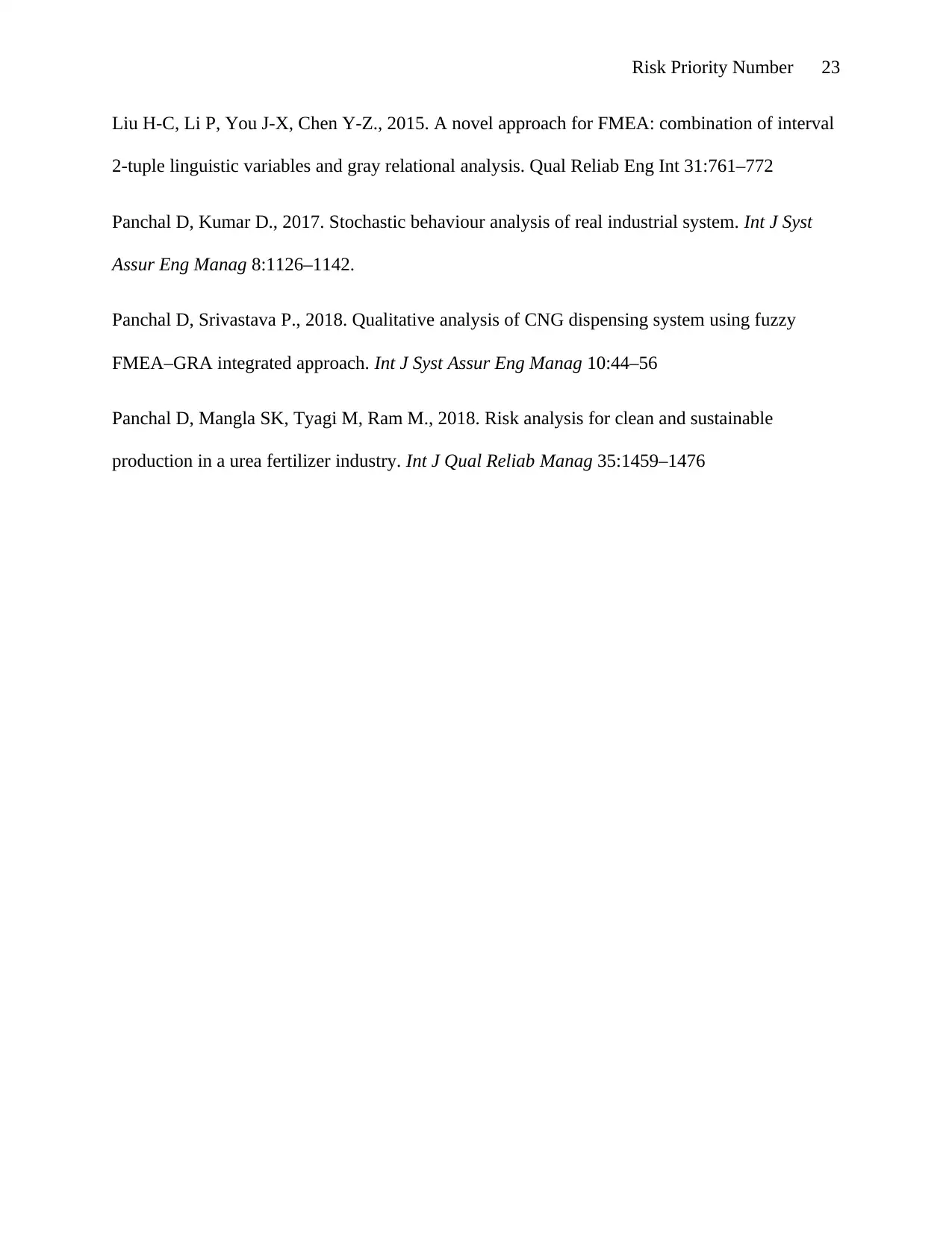
Risk Priority Number 23
Liu H-C, Li P, You J-X, Chen Y-Z., 2015. A novel approach for FMEA: combination of interval
2-tuple linguistic variables and gray relational analysis. Qual Reliab Eng Int 31:761–772
Panchal D, Kumar D., 2017. Stochastic behaviour analysis of real industrial system. Int J Syst
Assur Eng Manag 8:1126–1142.
Panchal D, Srivastava P., 2018. Qualitative analysis of CNG dispensing system using fuzzy
FMEA–GRA integrated approach. Int J Syst Assur Eng Manag 10:44–56
Panchal D, Mangla SK, Tyagi M, Ram M., 2018. Risk analysis for clean and sustainable
production in a urea fertilizer industry. Int J Qual Reliab Manag 35:1459–1476
Liu H-C, Li P, You J-X, Chen Y-Z., 2015. A novel approach for FMEA: combination of interval
2-tuple linguistic variables and gray relational analysis. Qual Reliab Eng Int 31:761–772
Panchal D, Kumar D., 2017. Stochastic behaviour analysis of real industrial system. Int J Syst
Assur Eng Manag 8:1126–1142.
Panchal D, Srivastava P., 2018. Qualitative analysis of CNG dispensing system using fuzzy
FMEA–GRA integrated approach. Int J Syst Assur Eng Manag 10:44–56
Panchal D, Mangla SK, Tyagi M, Ram M., 2018. Risk analysis for clean and sustainable
production in a urea fertilizer industry. Int J Qual Reliab Manag 35:1459–1476
1 out of 23
Related Documents

Your All-in-One AI-Powered Toolkit for Academic Success.
+13062052269
info@desklib.com
Available 24*7 on WhatsApp / Email
Unlock your academic potential
© 2024 | Zucol Services PVT LTD | All rights reserved.