Workplace Safety Analysis: A Case Study on Machine Accidents
VerifiedAdded on 2022/08/22
|4
|585
|28
Report
AI Summary
The assignment analyzes a workplace accident involving a faulty machine and a worker's injury. The report identifies the root causes of the accident, including unsafe conditions and actions, such as operating a faulty machine without proper safety measures. The worker's failure to switch off th...
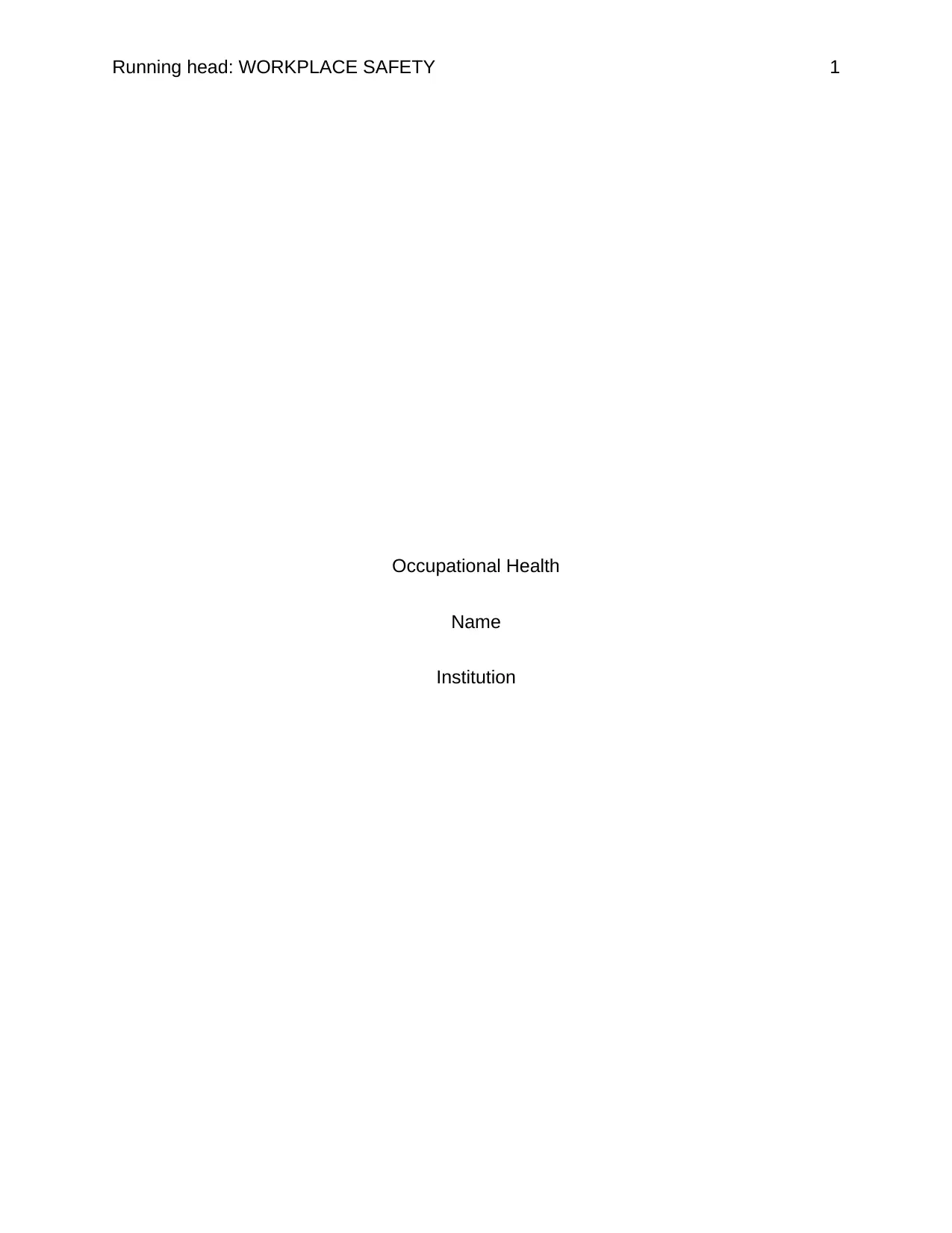
Running head: WORKPLACE SAFETY 1
Occupational Health
Name
Institution
Occupational Health
Name
Institution
Paraphrase This Document
Need a fresh take? Get an instant paraphrase of this document with our AI Paraphraser
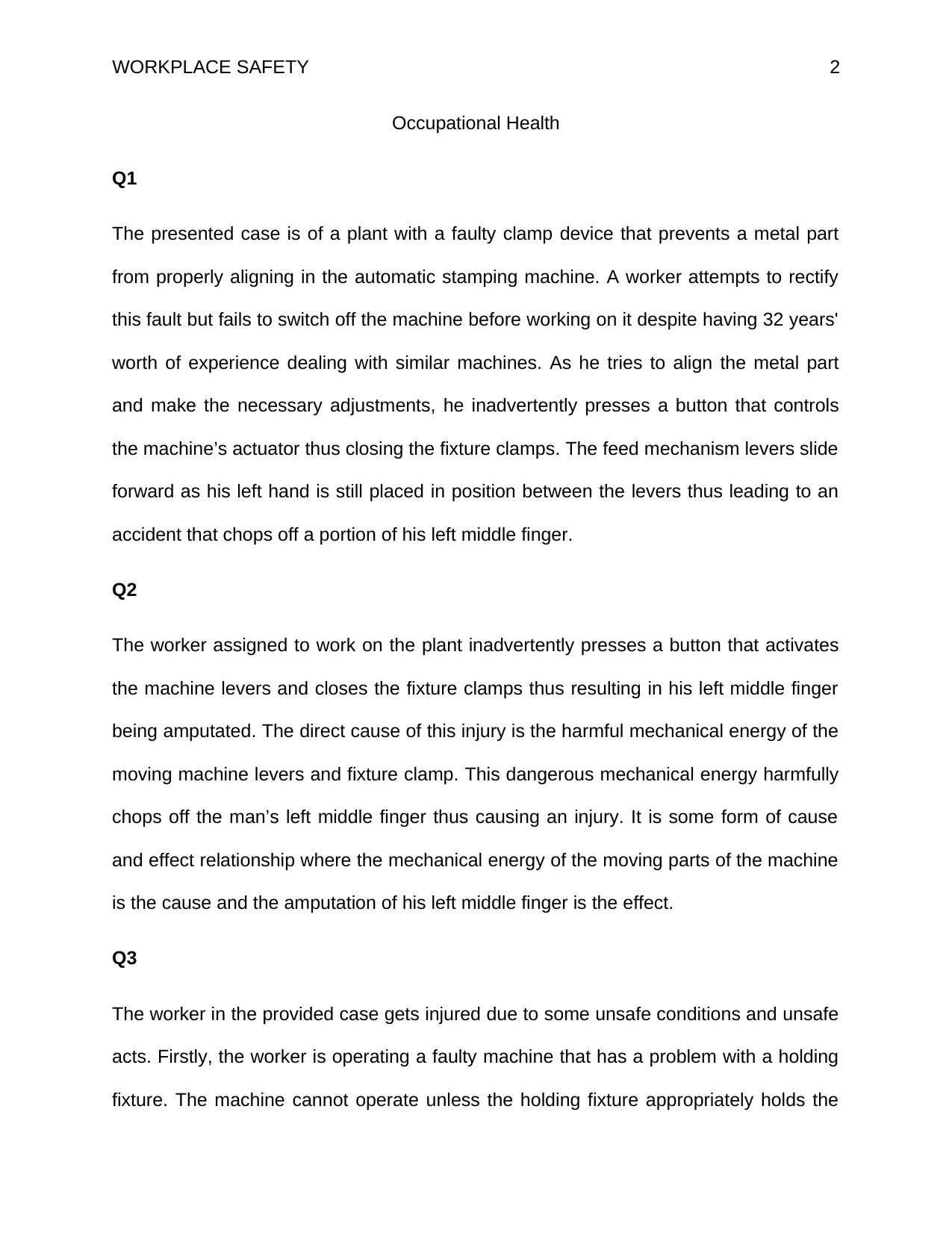
WORKPLACE SAFETY 2
Occupational Health
Q1
The presented case is of a plant with a faulty clamp device that prevents a metal part
from properly aligning in the automatic stamping machine. A worker attempts to rectify
this fault but fails to switch off the machine before working on it despite having 32 years'
worth of experience dealing with similar machines. As he tries to align the metal part
and make the necessary adjustments, he inadvertently presses a button that controls
the machine’s actuator thus closing the fixture clamps. The feed mechanism levers slide
forward as his left hand is still placed in position between the levers thus leading to an
accident that chops off a portion of his left middle finger.
Q2
The worker assigned to work on the plant inadvertently presses a button that activates
the machine levers and closes the fixture clamps thus resulting in his left middle finger
being amputated. The direct cause of this injury is the harmful mechanical energy of the
moving machine levers and fixture clamp. This dangerous mechanical energy harmfully
chops off the man’s left middle finger thus causing an injury. It is some form of cause
and effect relationship where the mechanical energy of the moving parts of the machine
is the cause and the amputation of his left middle finger is the effect.
Q3
The worker in the provided case gets injured due to some unsafe conditions and unsafe
acts. Firstly, the worker is operating a faulty machine that has a problem with a holding
fixture. The machine cannot operate unless the holding fixture appropriately holds the
Occupational Health
Q1
The presented case is of a plant with a faulty clamp device that prevents a metal part
from properly aligning in the automatic stamping machine. A worker attempts to rectify
this fault but fails to switch off the machine before working on it despite having 32 years'
worth of experience dealing with similar machines. As he tries to align the metal part
and make the necessary adjustments, he inadvertently presses a button that controls
the machine’s actuator thus closing the fixture clamps. The feed mechanism levers slide
forward as his left hand is still placed in position between the levers thus leading to an
accident that chops off a portion of his left middle finger.
Q2
The worker assigned to work on the plant inadvertently presses a button that activates
the machine levers and closes the fixture clamps thus resulting in his left middle finger
being amputated. The direct cause of this injury is the harmful mechanical energy of the
moving machine levers and fixture clamp. This dangerous mechanical energy harmfully
chops off the man’s left middle finger thus causing an injury. It is some form of cause
and effect relationship where the mechanical energy of the moving parts of the machine
is the cause and the amputation of his left middle finger is the effect.
Q3
The worker in the provided case gets injured due to some unsafe conditions and unsafe
acts. Firstly, the worker is operating a faulty machine that has a problem with a holding
fixture. The machine cannot operate unless the holding fixture appropriately holds the
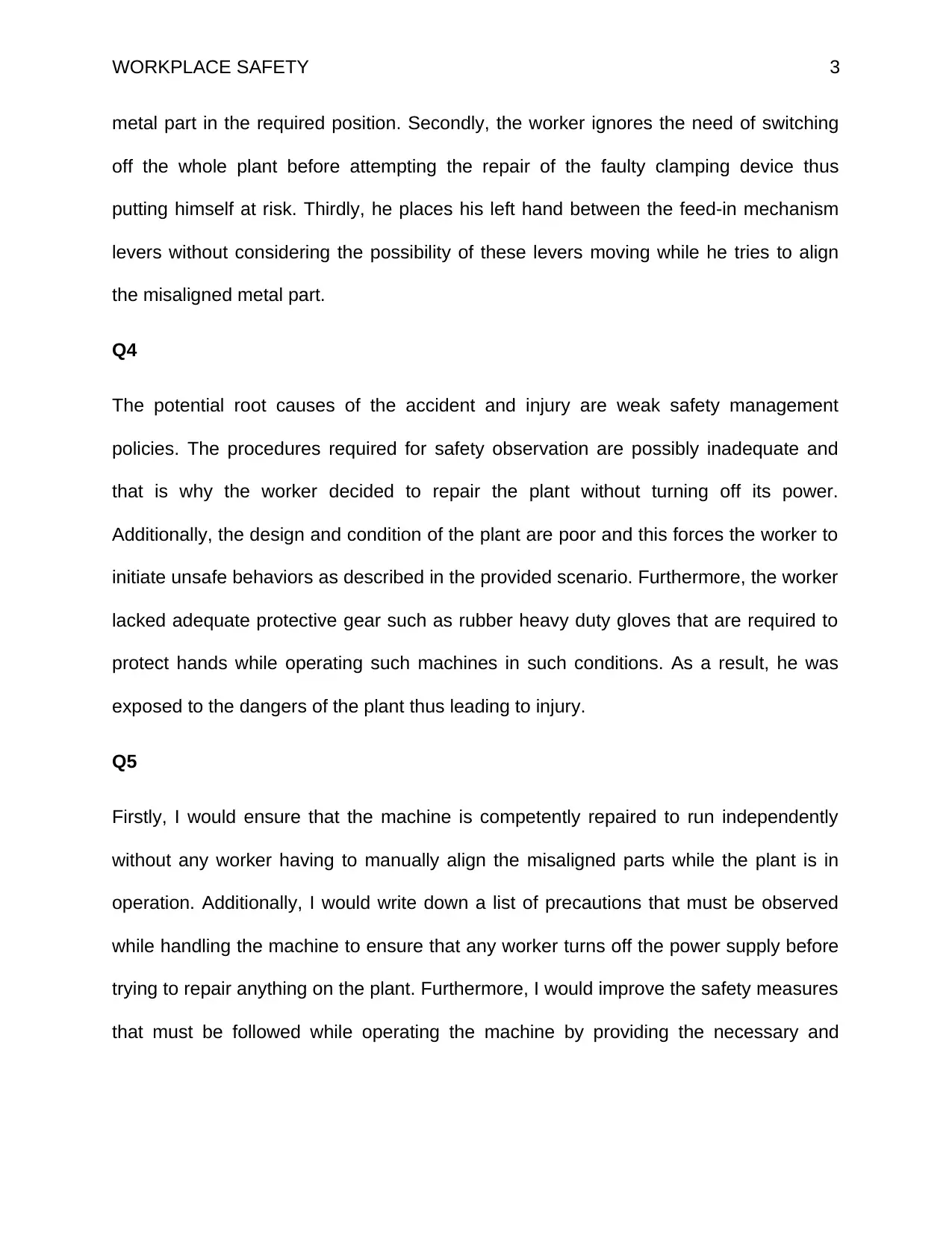
WORKPLACE SAFETY 3
metal part in the required position. Secondly, the worker ignores the need of switching
off the whole plant before attempting the repair of the faulty clamping device thus
putting himself at risk. Thirdly, he places his left hand between the feed-in mechanism
levers without considering the possibility of these levers moving while he tries to align
the misaligned metal part.
Q4
The potential root causes of the accident and injury are weak safety management
policies. The procedures required for safety observation are possibly inadequate and
that is why the worker decided to repair the plant without turning off its power.
Additionally, the design and condition of the plant are poor and this forces the worker to
initiate unsafe behaviors as described in the provided scenario. Furthermore, the worker
lacked adequate protective gear such as rubber heavy duty gloves that are required to
protect hands while operating such machines in such conditions. As a result, he was
exposed to the dangers of the plant thus leading to injury.
Q5
Firstly, I would ensure that the machine is competently repaired to run independently
without any worker having to manually align the misaligned parts while the plant is in
operation. Additionally, I would write down a list of precautions that must be observed
while handling the machine to ensure that any worker turns off the power supply before
trying to repair anything on the plant. Furthermore, I would improve the safety measures
that must be followed while operating the machine by providing the necessary and
metal part in the required position. Secondly, the worker ignores the need of switching
off the whole plant before attempting the repair of the faulty clamping device thus
putting himself at risk. Thirdly, he places his left hand between the feed-in mechanism
levers without considering the possibility of these levers moving while he tries to align
the misaligned metal part.
Q4
The potential root causes of the accident and injury are weak safety management
policies. The procedures required for safety observation are possibly inadequate and
that is why the worker decided to repair the plant without turning off its power.
Additionally, the design and condition of the plant are poor and this forces the worker to
initiate unsafe behaviors as described in the provided scenario. Furthermore, the worker
lacked adequate protective gear such as rubber heavy duty gloves that are required to
protect hands while operating such machines in such conditions. As a result, he was
exposed to the dangers of the plant thus leading to injury.
Q5
Firstly, I would ensure that the machine is competently repaired to run independently
without any worker having to manually align the misaligned parts while the plant is in
operation. Additionally, I would write down a list of precautions that must be observed
while handling the machine to ensure that any worker turns off the power supply before
trying to repair anything on the plant. Furthermore, I would improve the safety measures
that must be followed while operating the machine by providing the necessary and
⊘ This is a preview!⊘
Do you want full access?
Subscribe today to unlock all pages.

Trusted by 1+ million students worldwide
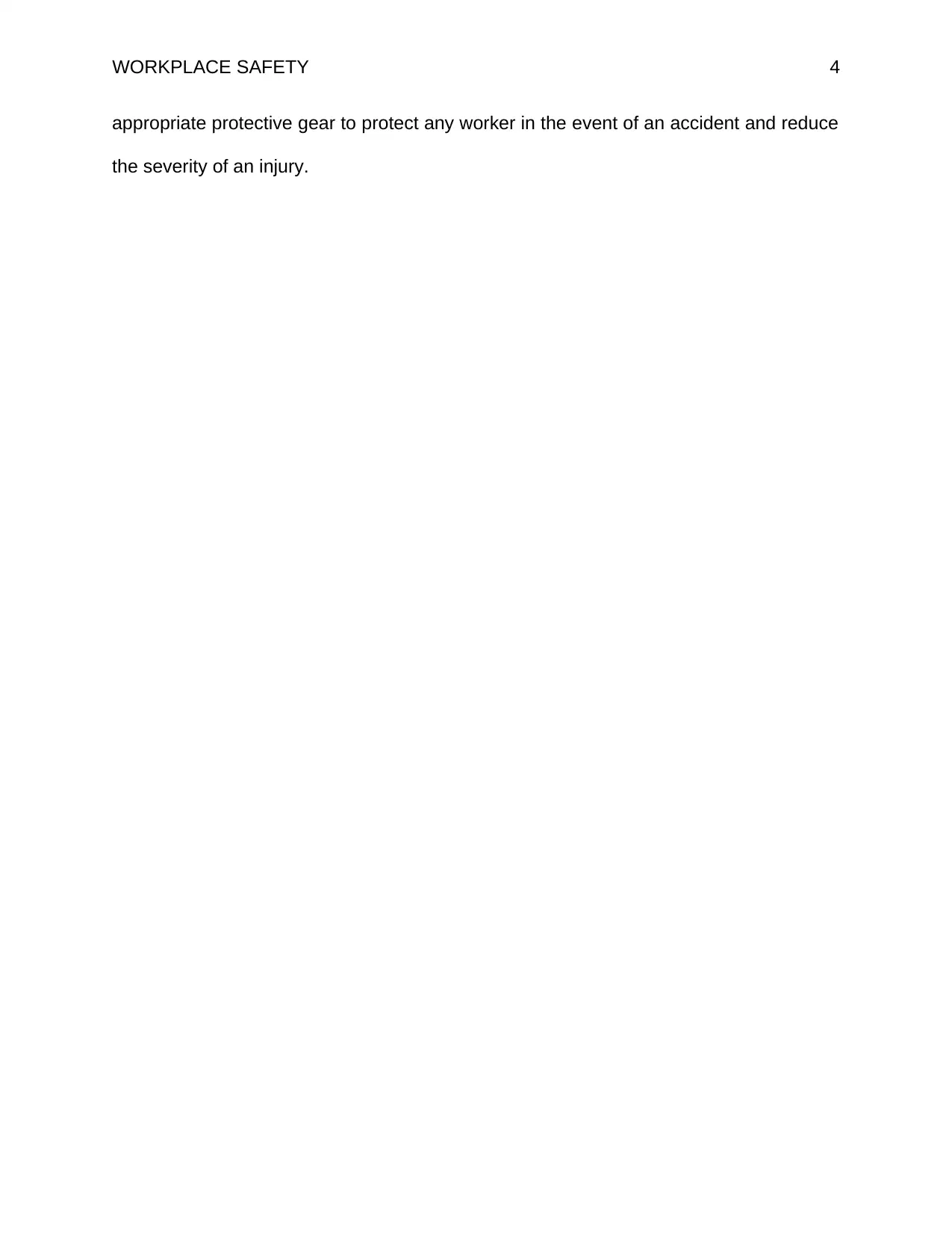
WORKPLACE SAFETY 4
appropriate protective gear to protect any worker in the event of an accident and reduce
the severity of an injury.
appropriate protective gear to protect any worker in the event of an accident and reduce
the severity of an injury.
1 out of 4

Your All-in-One AI-Powered Toolkit for Academic Success.
+13062052269
info@desklib.com
Available 24*7 on WhatsApp / Email
Unlock your academic potential
© 2024 | Zucol Services PVT LTD | All rights reserved.