Construction Site: Managing Occupational Health and Safety Project
VerifiedAdded on 2022/10/17
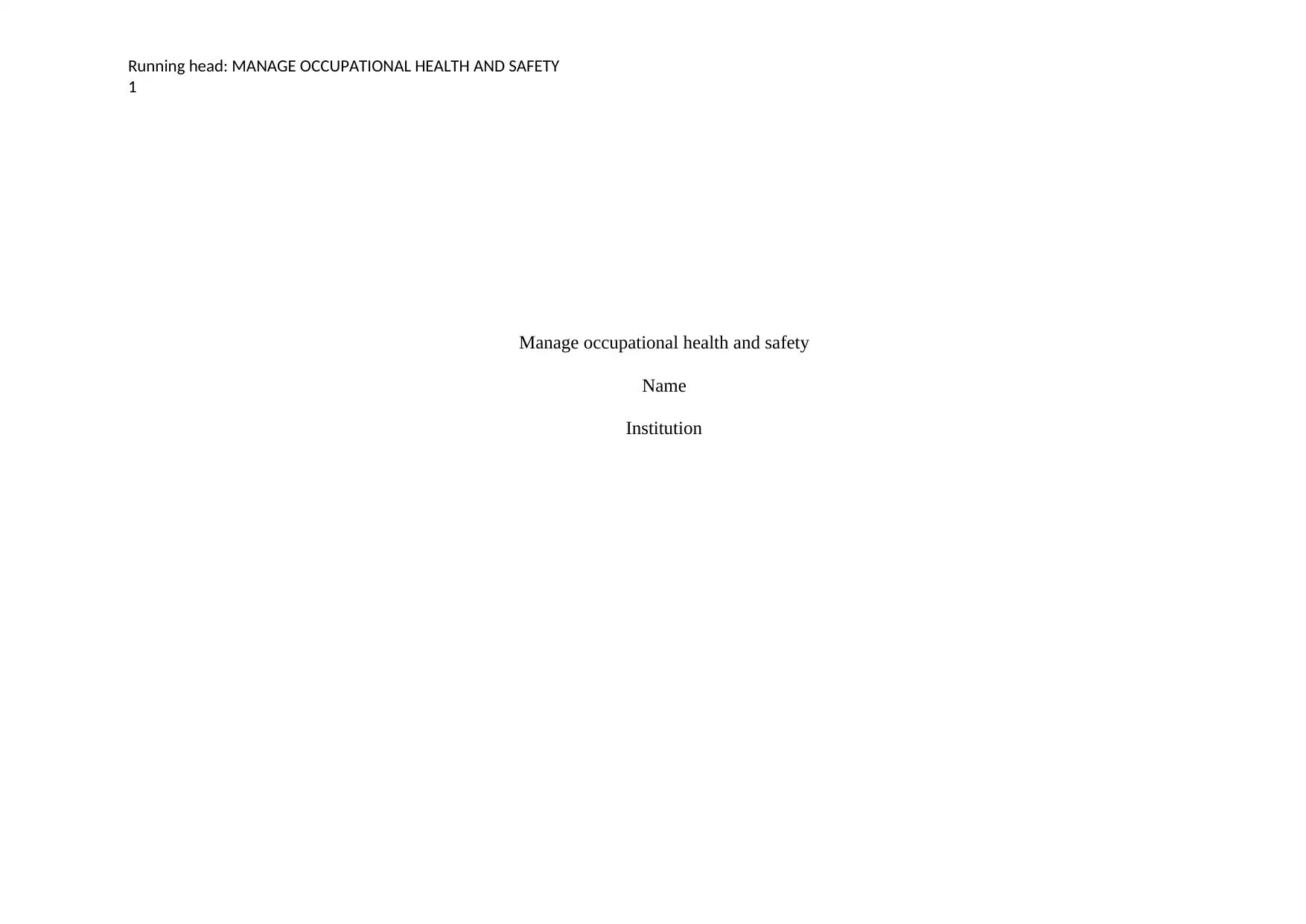
1
Manage occupational health and safety
Name
Institution
Paraphrase This Document
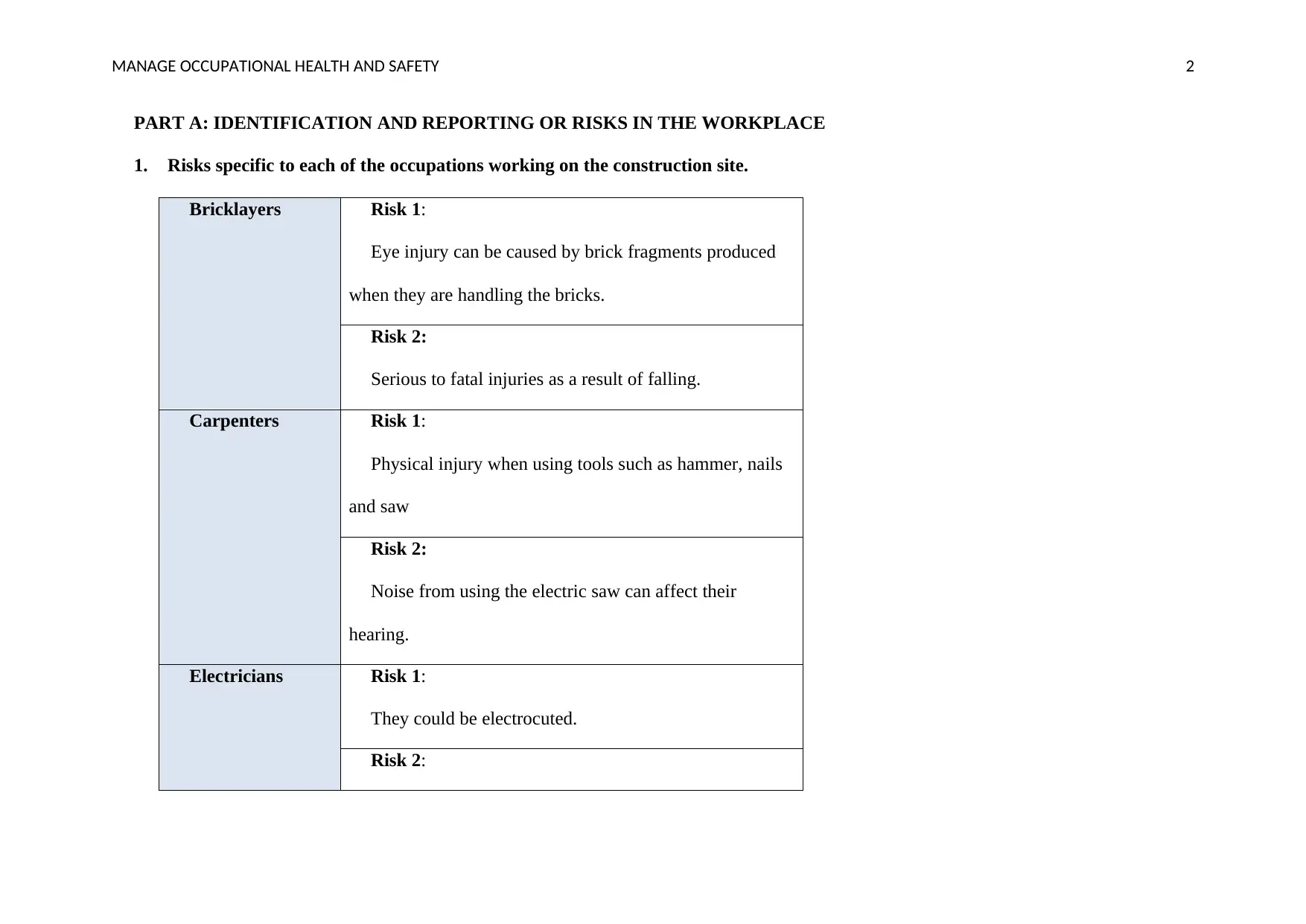
PART A: IDENTIFICATION AND REPORTING OR RISKS IN THE WORKPLACE
1. Risks specific to each of the occupations working on the construction site.
Bricklayers Risk 1:
Eye injury can be caused by brick fragments produced
when they are handling the bricks.
Risk 2:
Serious to fatal injuries as a result of falling.
Carpenters Risk 1:
Physical injury when using tools such as hammer, nails
and saw
Risk 2:
Noise from using the electric saw can affect their
hearing.
Electricians Risk 1:
They could be electrocuted.
Risk 2:
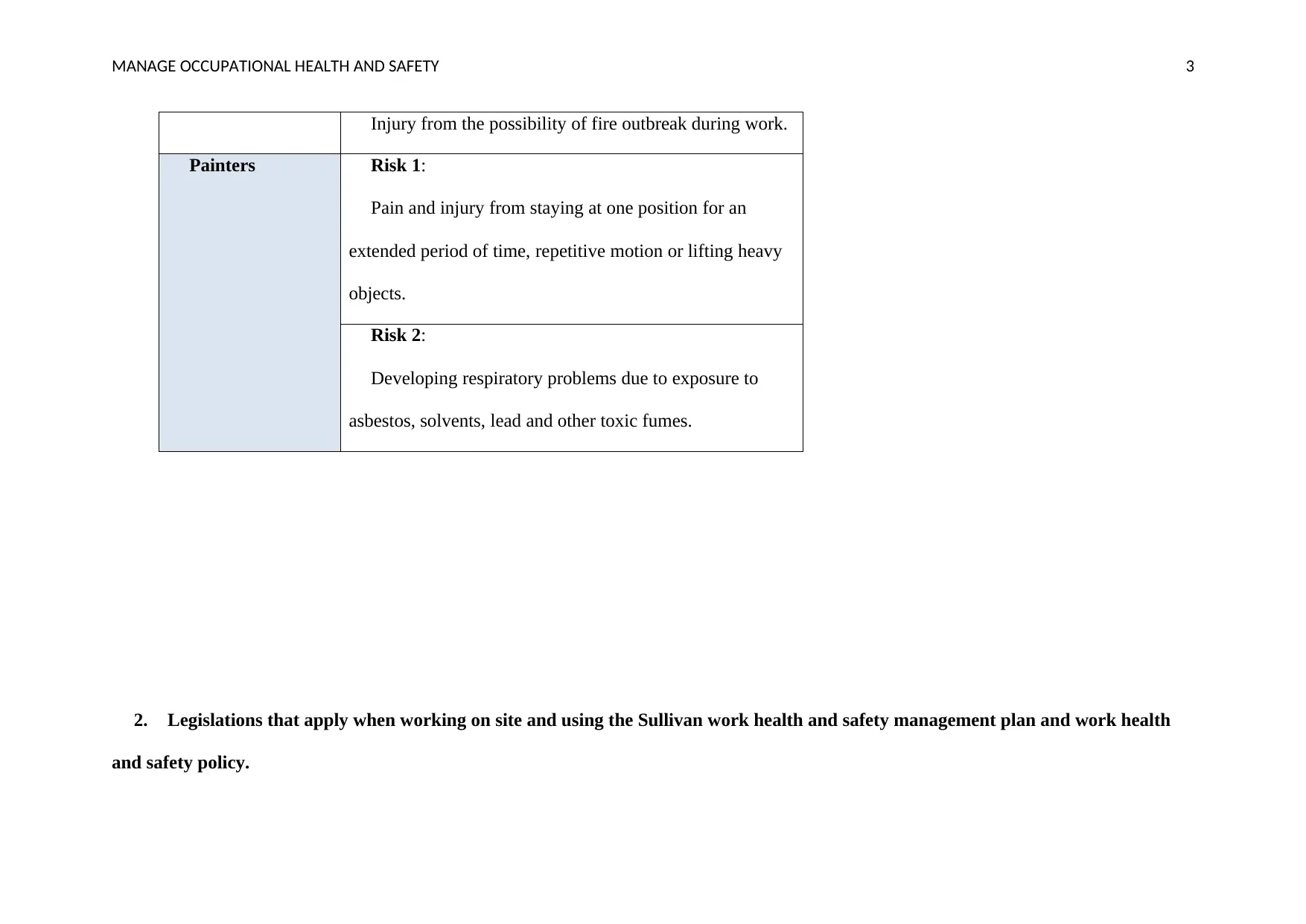
Injury from the possibility of fire outbreak during work.
Painters Risk 1:
Pain and injury from staying at one position for an
extended period of time, repetitive motion or lifting heavy
objects.
Risk 2:
Developing respiratory problems due to exposure to
asbestos, solvents, lead and other toxic fumes.
2. Legislations that apply when working on site and using the Sullivan work health and safety management plan and work health
and safety policy.
⊘ This is a preview!⊘
Do you want full access?
Subscribe today to unlock all pages.

Trusted by 1+ million students worldwide
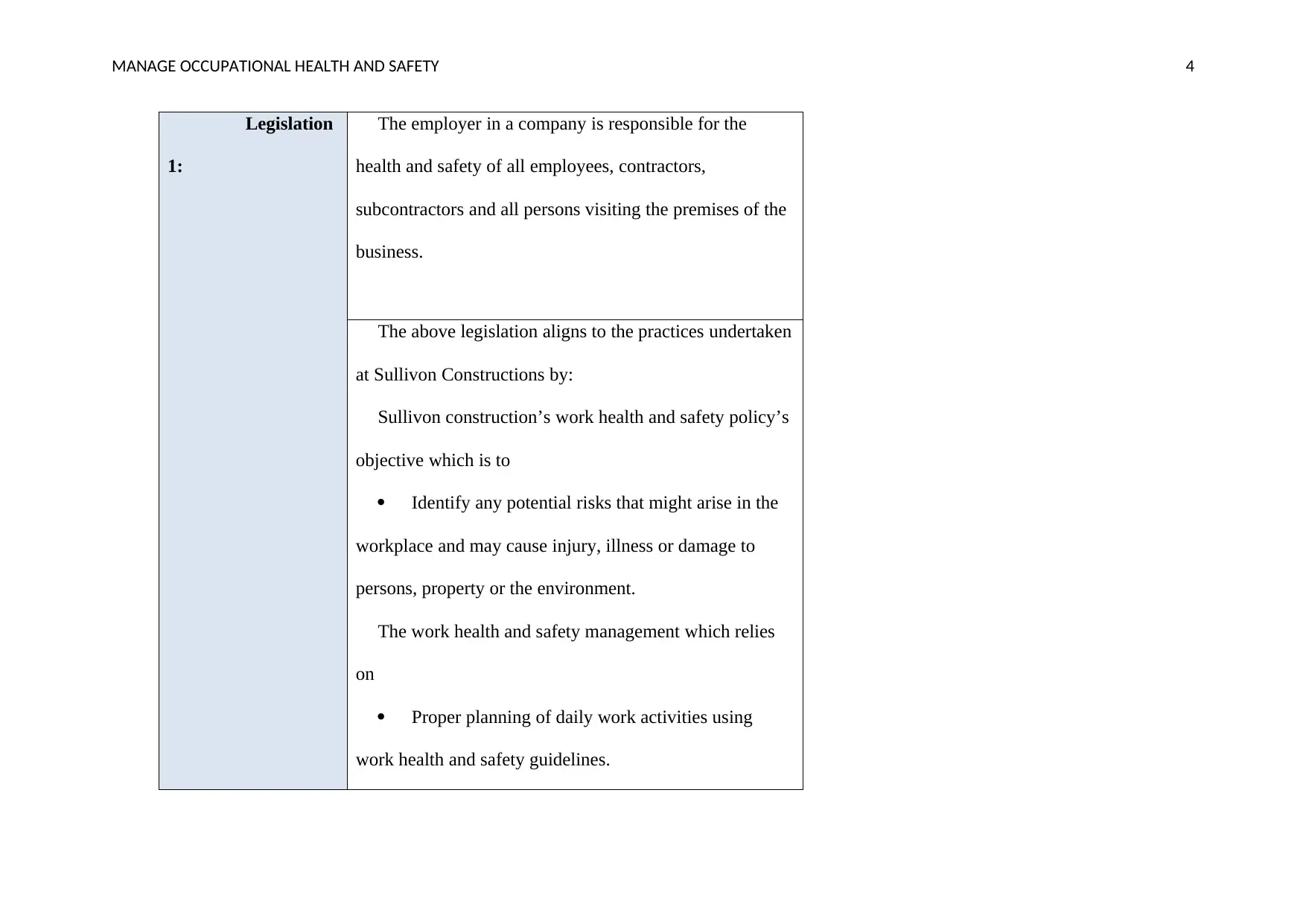
Legislation
1:
The employer in a company is responsible for the
health and safety of all employees, contractors,
subcontractors and all persons visiting the premises of the
business.
The above legislation aligns to the practices undertaken
at Sullivon Constructions by:
Sullivon construction’s work health and safety policy’s
objective which is to
Identify any potential risks that might arise in the
workplace and may cause injury, illness or damage to
persons, property or the environment.
The work health and safety management which relies
on
Proper planning of daily work activities using
work health and safety guidelines.
Paraphrase This Document
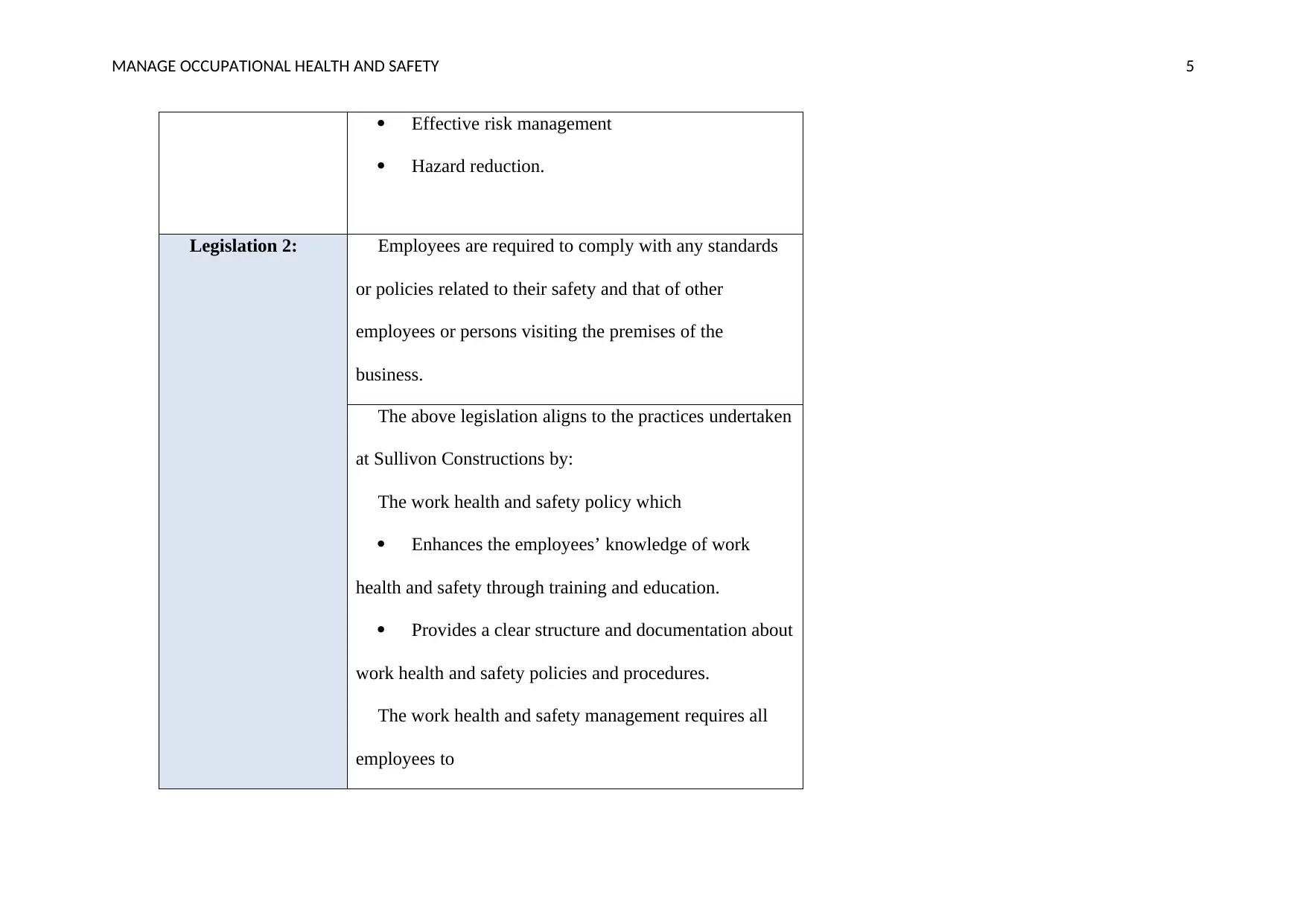
Effective risk management
Hazard reduction.
Legislation 2: Employees are required to comply with any standards
or policies related to their safety and that of other
employees or persons visiting the premises of the
business.
The above legislation aligns to the practices undertaken
at Sullivon Constructions by:
The work health and safety policy which
Enhances the employees’ knowledge of work
health and safety through training and education.
Provides a clear structure and documentation about
work health and safety policies and procedures.
The work health and safety management requires all
employees to
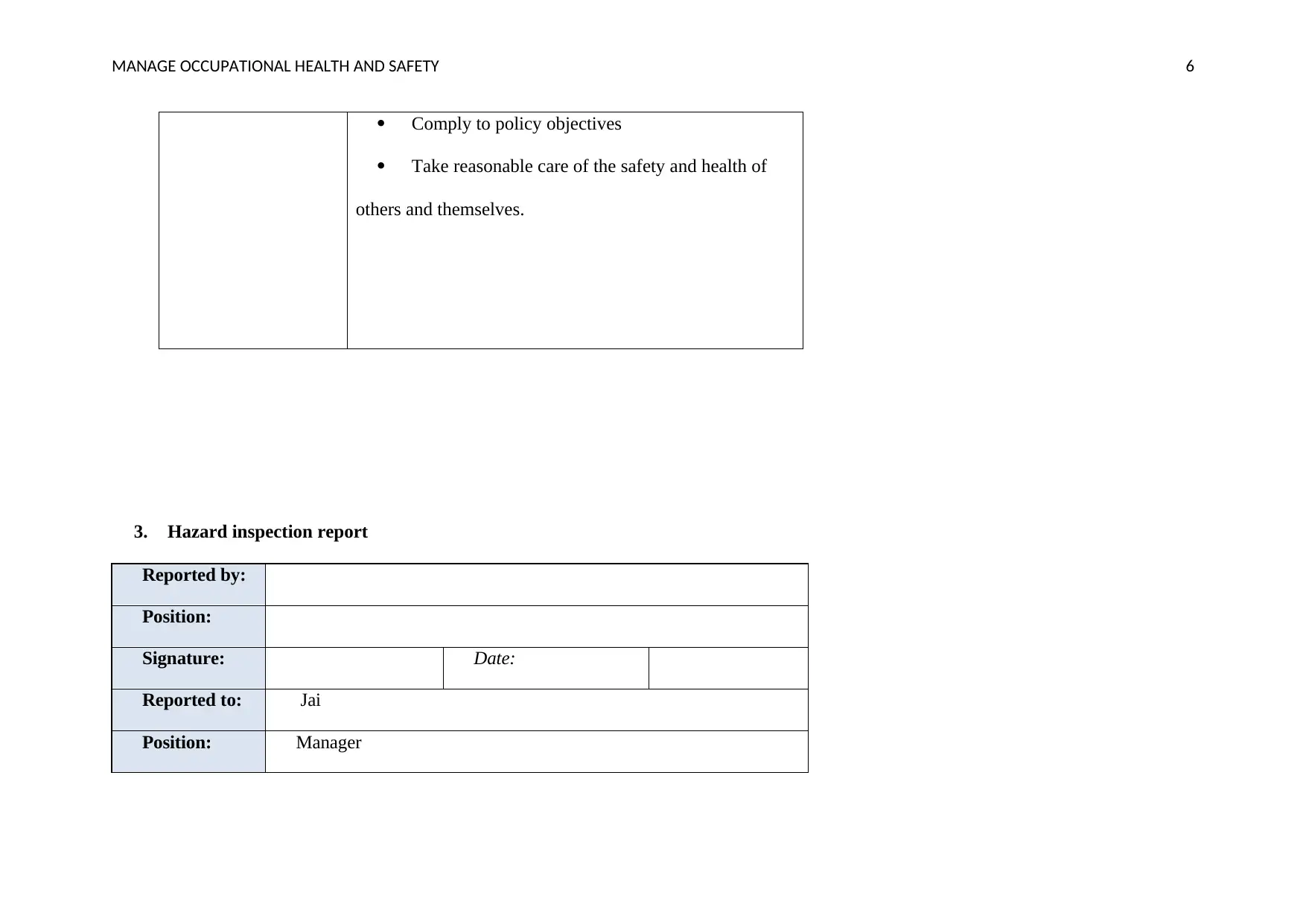
Comply to policy objectives
Take reasonable care of the safety and health of
others and themselves.
3. Hazard inspection report
Reported by:
Position:
Signature: Date:
Reported to: Jai
Position: Manager
⊘ This is a preview!⊘
Do you want full access?
Subscribe today to unlock all pages.

Trusted by 1+ million students worldwide
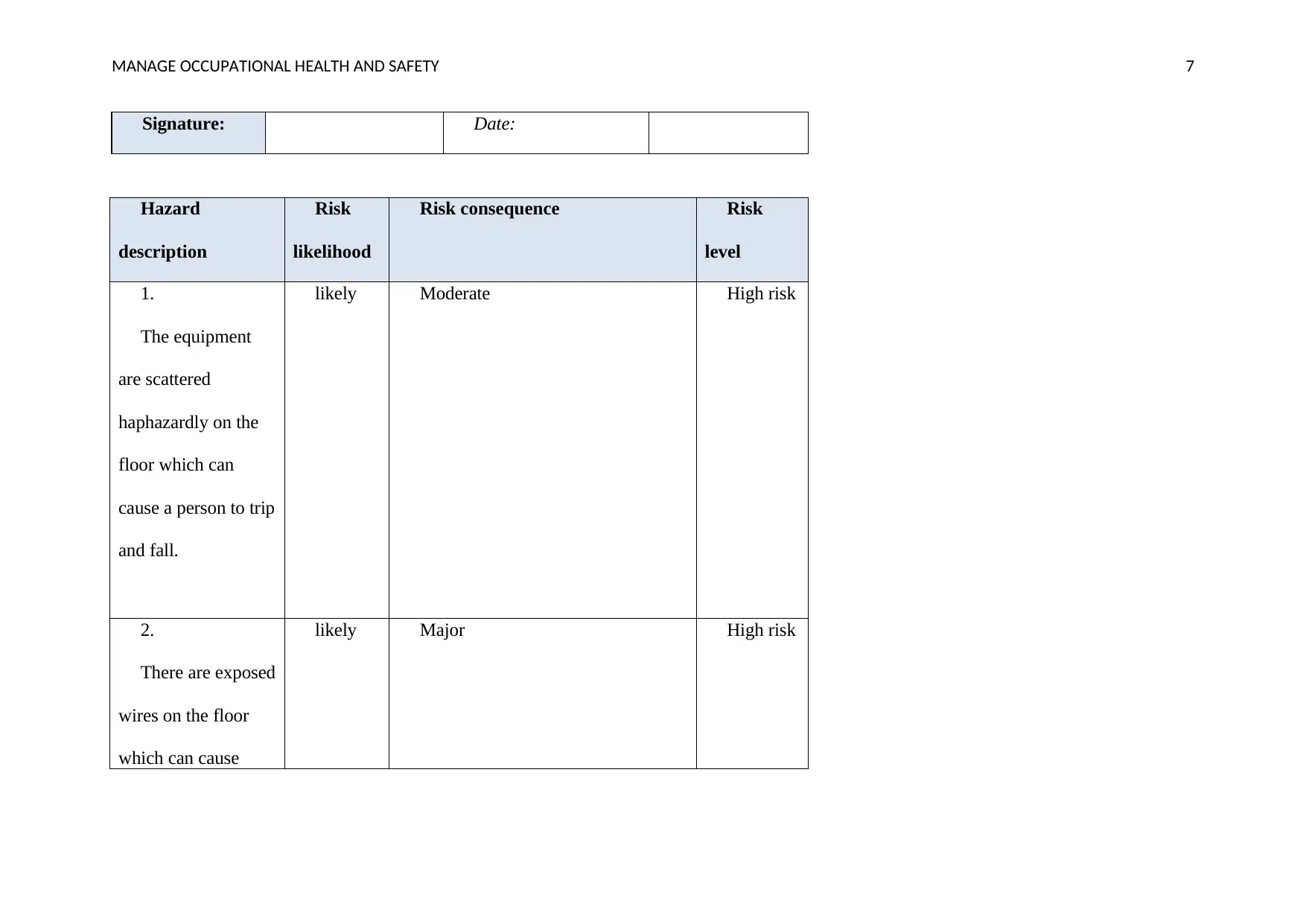
Signature: Date:
Hazard
description
Risk
likelihood
Risk consequence Risk
level
1.
The equipment
are scattered
haphazardly on the
floor which can
cause a person to trip
and fall.
likely Moderate High risk
2.
There are exposed
wires on the floor
which can cause
likely Major High risk
Paraphrase This Document
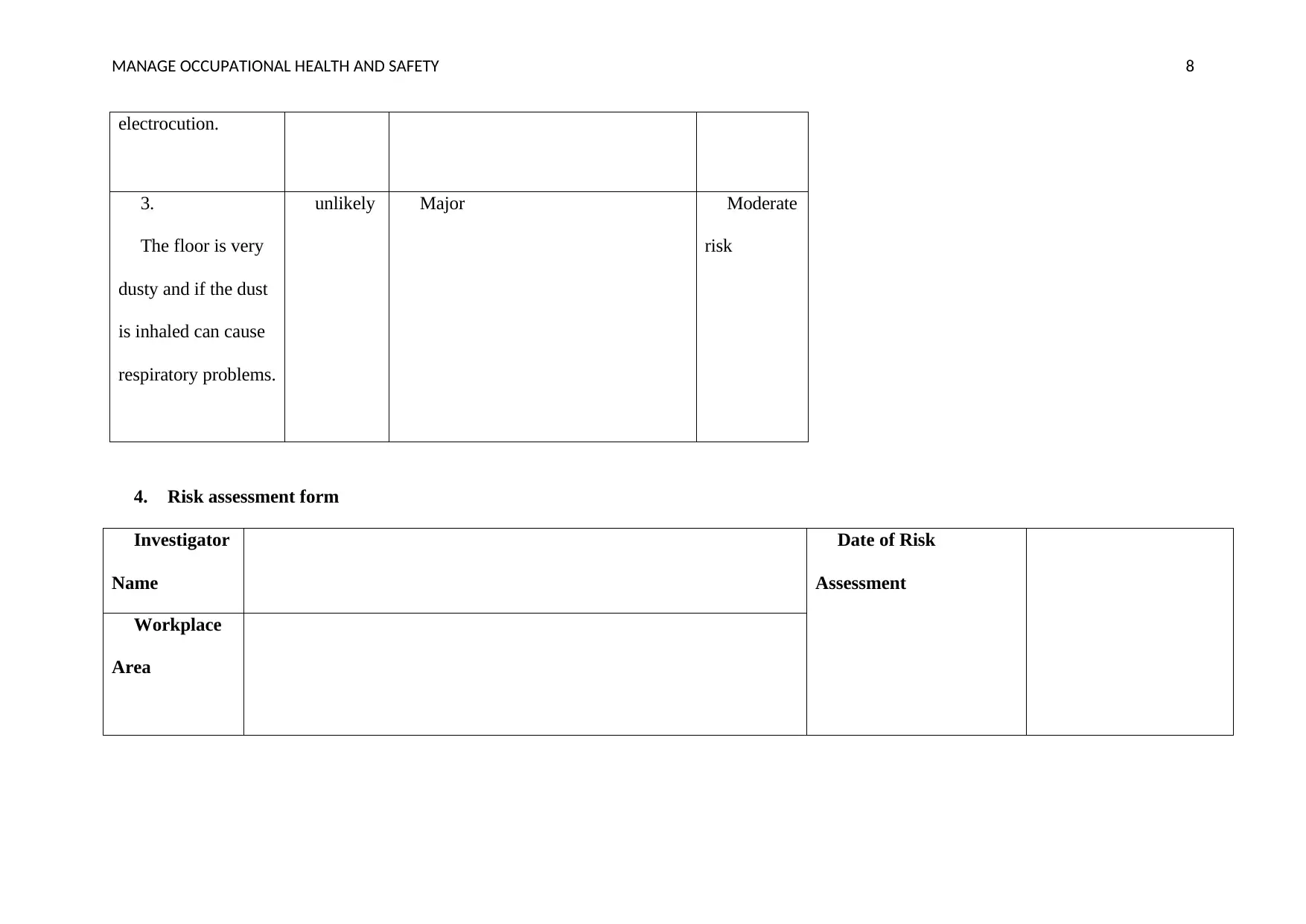
electrocution.
3.
The floor is very
dusty and if the dust
is inhaled can cause
respiratory problems.
unlikely Major Moderate
risk
4. Risk assessment form
Investigator
Name
Date of Risk
Assessment
Workplace
Area
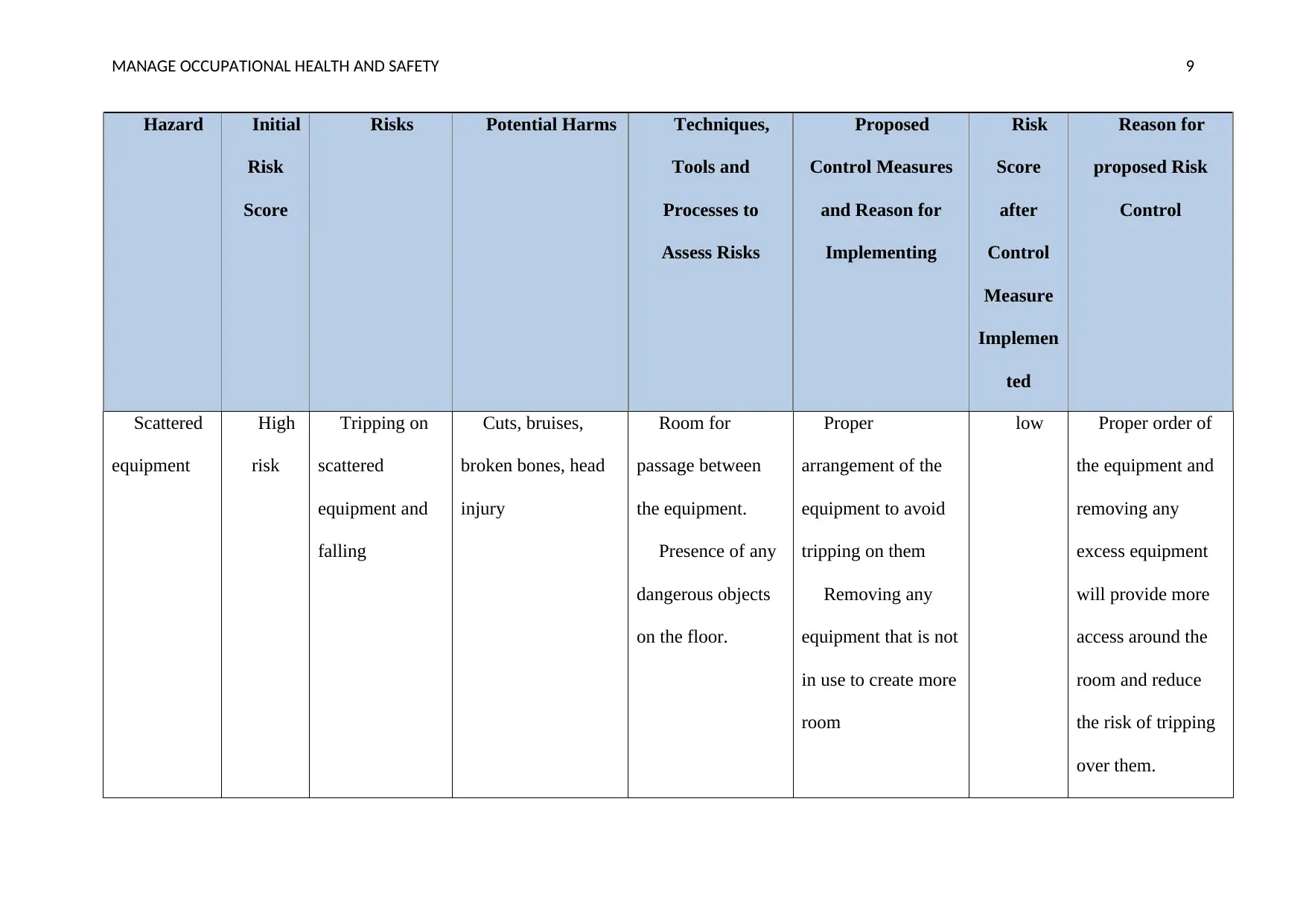
Hazard Initial
Risk
Score
Risks Potential Harms Techniques,
Tools and
Processes to
Assess Risks
Proposed
Control Measures
and Reason for
Implementing
Risk
Score
after
Control
Measure
Implemen
ted
Reason for
proposed Risk
Control
Scattered
equipment
High
risk
Tripping on
scattered
equipment and
falling
Cuts, bruises,
broken bones, head
injury
Room for
passage between
the equipment.
Presence of any
dangerous objects
on the floor.
Proper
arrangement of the
equipment to avoid
tripping on them
Removing any
equipment that is not
in use to create more
room
low Proper order of
the equipment and
removing any
excess equipment
will provide more
access around the
room and reduce
the risk of tripping
over them.
⊘ This is a preview!⊘
Do you want full access?
Subscribe today to unlock all pages.

Trusted by 1+ million students worldwide
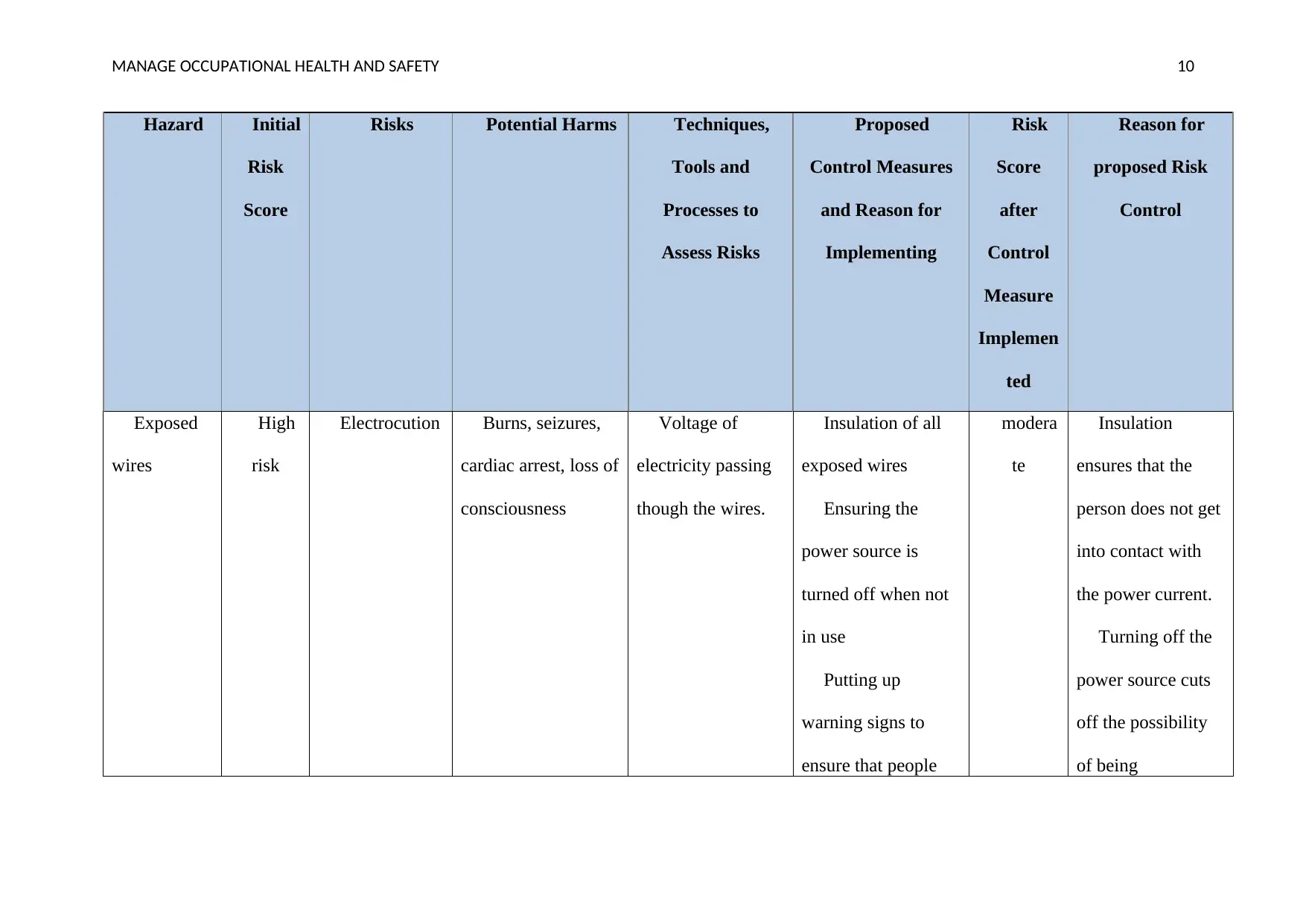
Hazard Initial
Risk
Score
Risks Potential Harms Techniques,
Tools and
Processes to
Assess Risks
Proposed
Control Measures
and Reason for
Implementing
Risk
Score
after
Control
Measure
Implemen
ted
Reason for
proposed Risk
Control
Exposed
wires
High
risk
Electrocution Burns, seizures,
cardiac arrest, loss of
consciousness
Voltage of
electricity passing
though the wires.
Insulation of all
exposed wires
Ensuring the
power source is
turned off when not
in use
Putting up
warning signs to
ensure that people
modera
te
Insulation
ensures that the
person does not get
into contact with
the power current.
Turning off the
power source cuts
off the possibility
of being
Paraphrase This Document
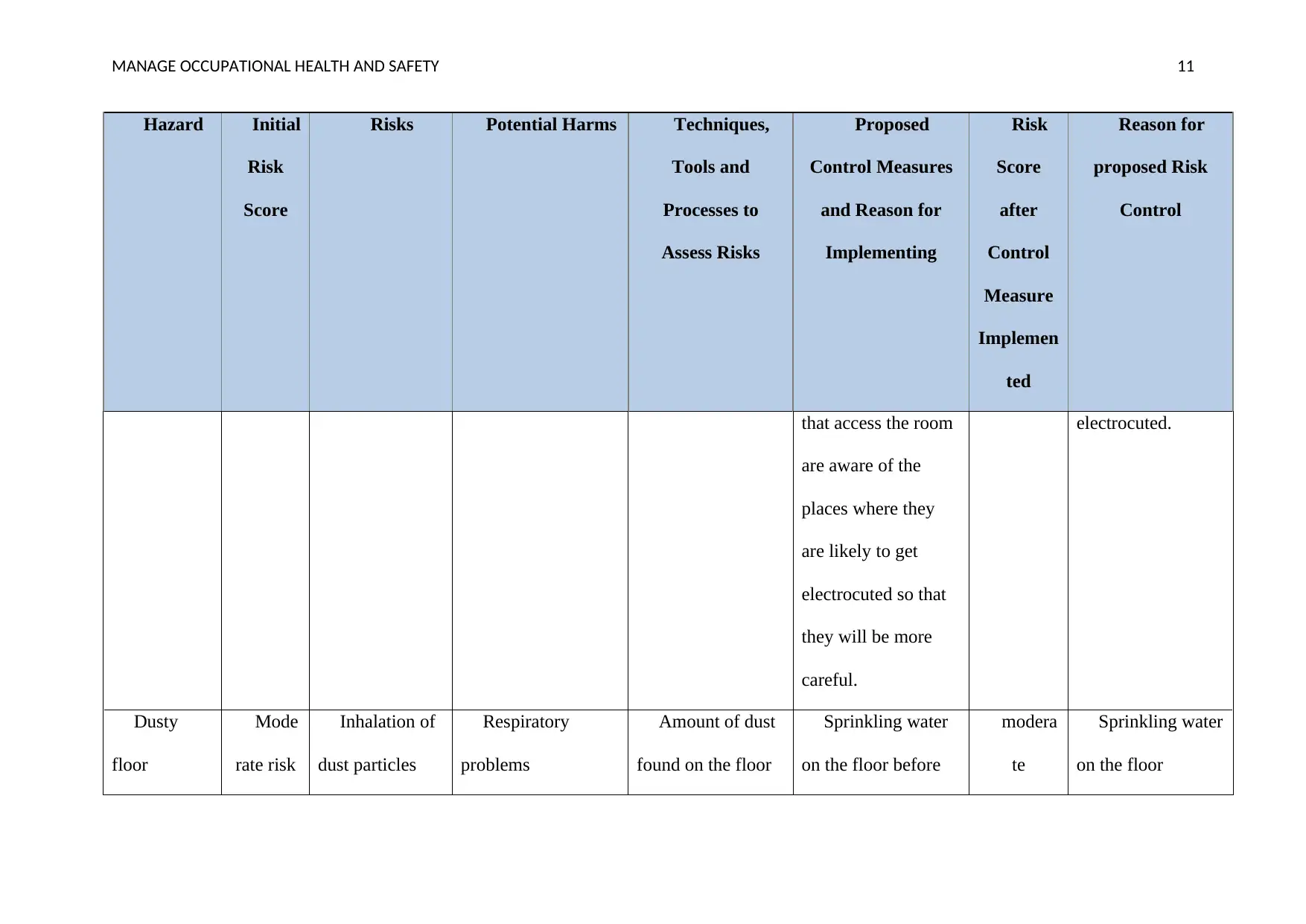
Hazard Initial
Risk
Score
Risks Potential Harms Techniques,
Tools and
Processes to
Assess Risks
Proposed
Control Measures
and Reason for
Implementing
Risk
Score
after
Control
Measure
Implemen
ted
Reason for
proposed Risk
Control
that access the room
are aware of the
places where they
are likely to get
electrocuted so that
they will be more
careful.
electrocuted.
Dusty
floor
Mode
rate risk
Inhalation of
dust particles
Respiratory
problems
Amount of dust
found on the floor
Sprinkling water
on the floor before
modera
te
Sprinkling water
on the floor
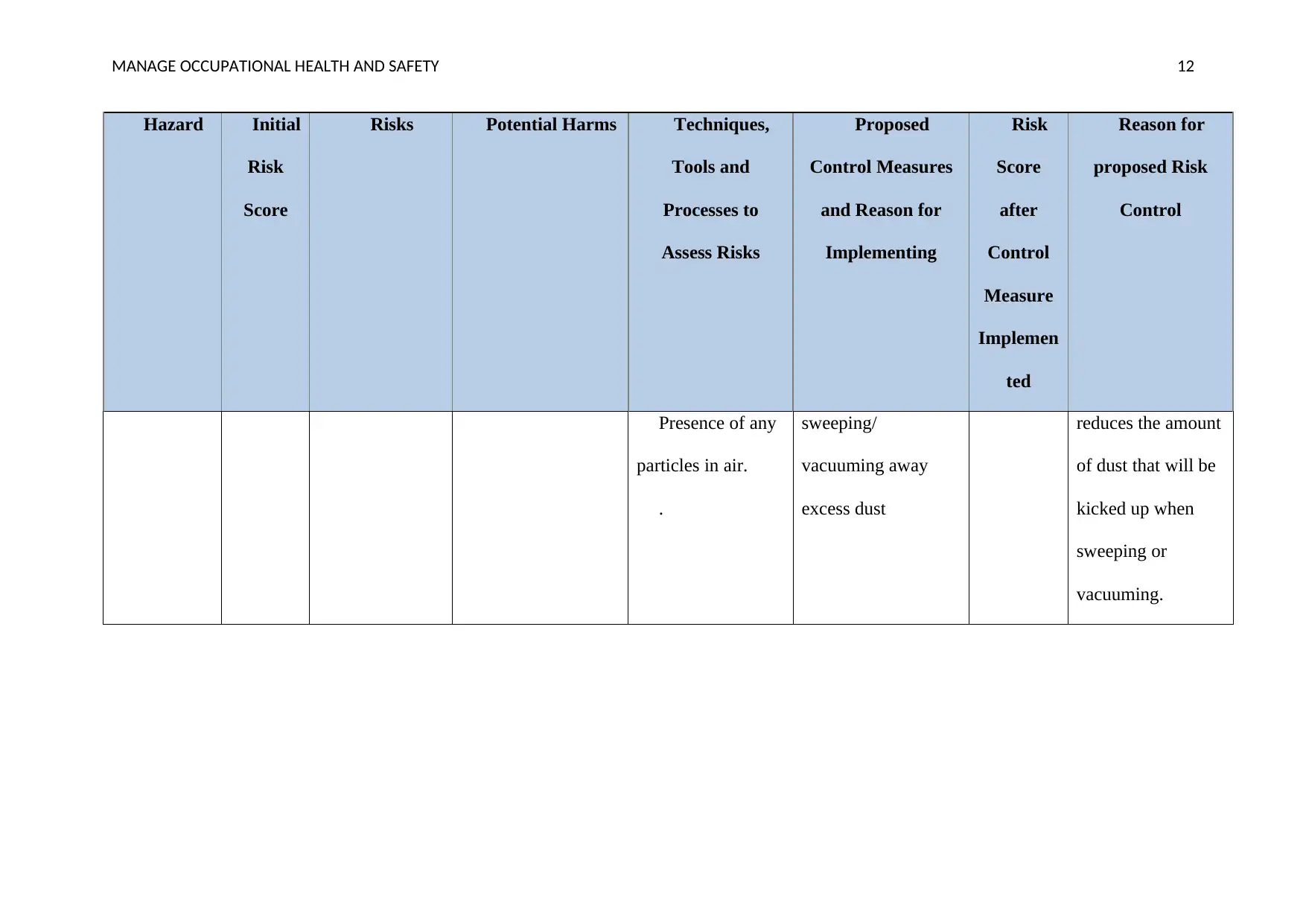
Hazard Initial
Risk
Score
Risks Potential Harms Techniques,
Tools and
Processes to
Assess Risks
Proposed
Control Measures
and Reason for
Implementing
Risk
Score
after
Control
Measure
Implemen
ted
Reason for
proposed Risk
Control
Presence of any
particles in air.
.
sweeping/
vacuuming away
excess dust
reduces the amount
of dust that will be
kicked up when
sweeping or
vacuuming.
⊘ This is a preview!⊘
Do you want full access?
Subscribe today to unlock all pages.

Trusted by 1+ million students worldwide
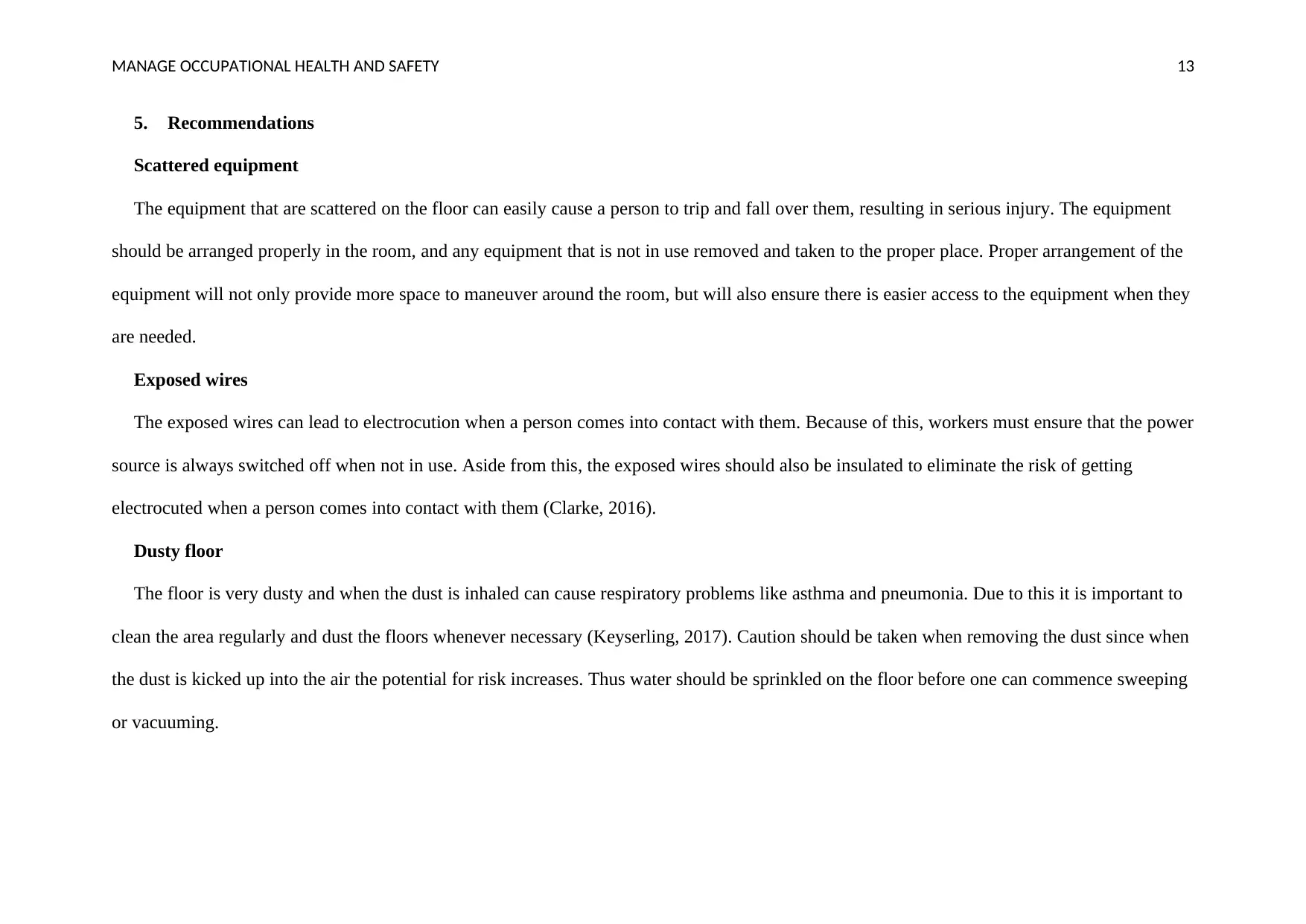
5. Recommendations
Scattered equipment
The equipment that are scattered on the floor can easily cause a person to trip and fall over them, resulting in serious injury. The equipment
should be arranged properly in the room, and any equipment that is not in use removed and taken to the proper place. Proper arrangement of the
equipment will not only provide more space to maneuver around the room, but will also ensure there is easier access to the equipment when they
are needed.
Exposed wires
The exposed wires can lead to electrocution when a person comes into contact with them. Because of this, workers must ensure that the power
source is always switched off when not in use. Aside from this, the exposed wires should also be insulated to eliminate the risk of getting
electrocuted when a person comes into contact with them (Clarke, 2016).
Dusty floor
The floor is very dusty and when the dust is inhaled can cause respiratory problems like asthma and pneumonia. Due to this it is important to
clean the area regularly and dust the floors whenever necessary (Keyserling, 2017). Caution should be taken when removing the dust since when
the dust is kicked up into the air the potential for risk increases. Thus water should be sprinkled on the floor before one can commence sweeping
or vacuuming.
Paraphrase This Document
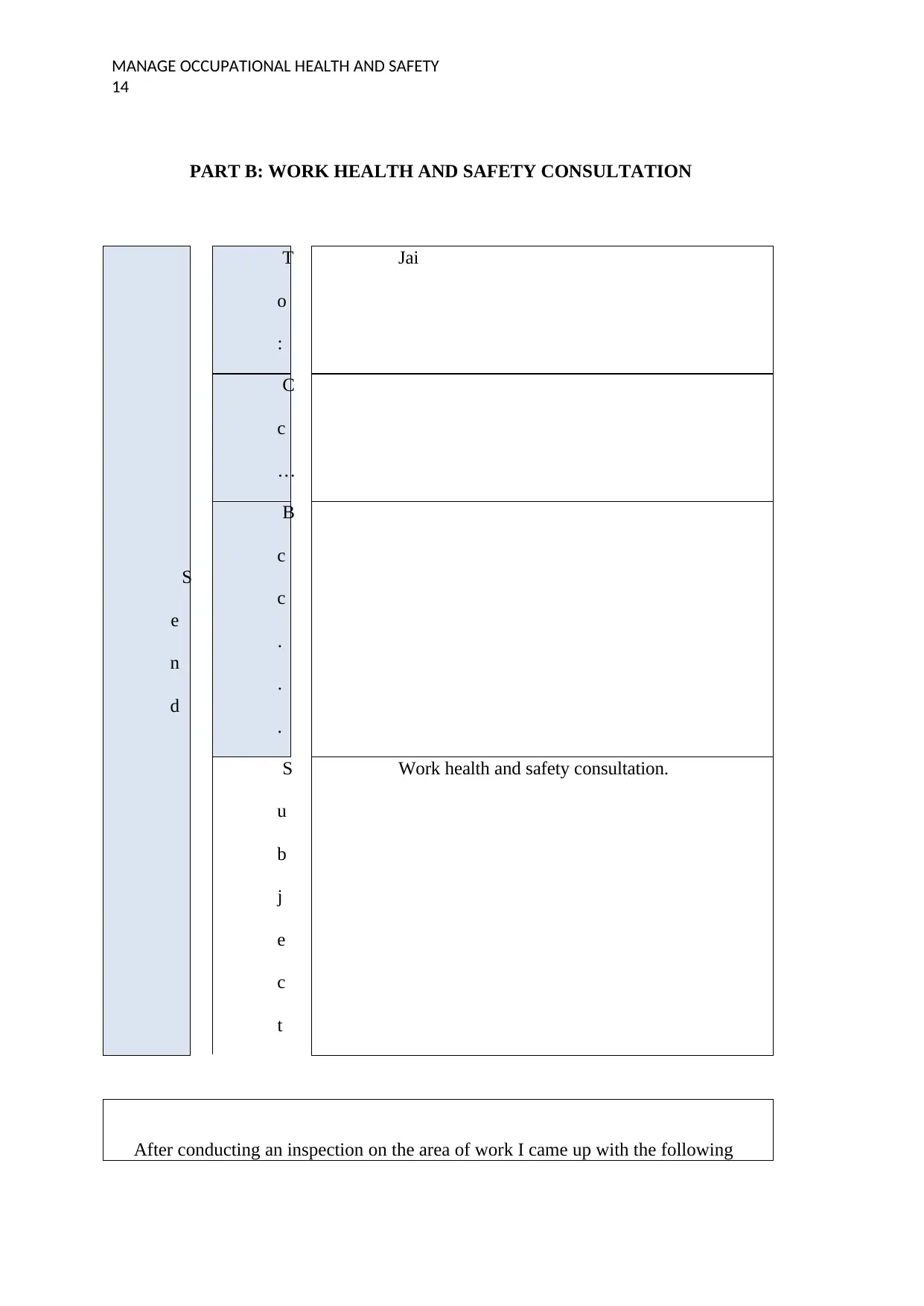
14
PART B: WORK HEALTH AND SAFETY CONSULTATION
S
e
n
d
T
o
:
Jai
C
c
…
B
c
c
.
.
.
S
u
b
j
e
c
t
Work health and safety consultation.
After conducting an inspection on the area of work I came up with the following
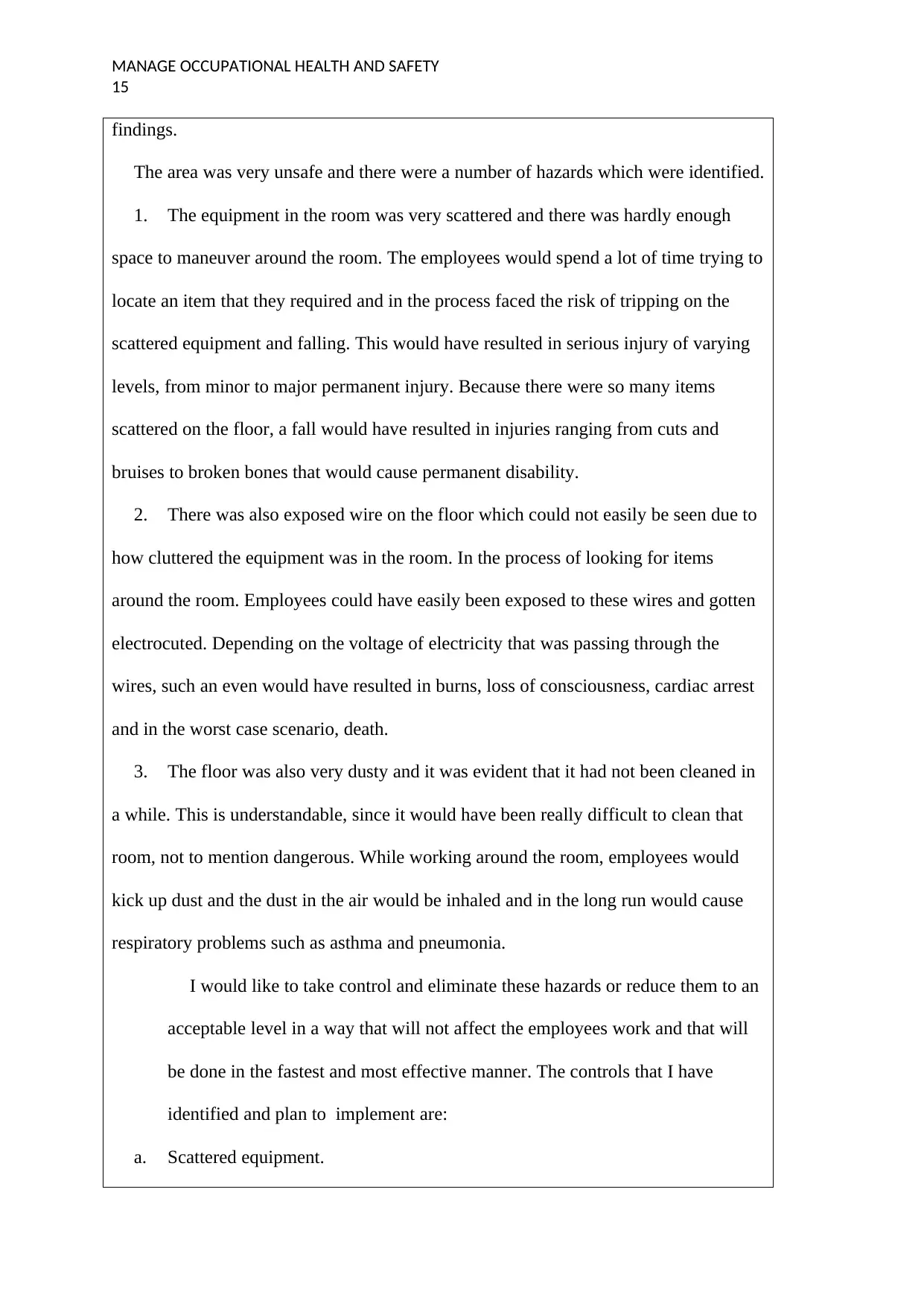
15
findings.
The area was very unsafe and there were a number of hazards which were identified.
1. The equipment in the room was very scattered and there was hardly enough
space to maneuver around the room. The employees would spend a lot of time trying to
locate an item that they required and in the process faced the risk of tripping on the
scattered equipment and falling. This would have resulted in serious injury of varying
levels, from minor to major permanent injury. Because there were so many items
scattered on the floor, a fall would have resulted in injuries ranging from cuts and
bruises to broken bones that would cause permanent disability.
2. There was also exposed wire on the floor which could not easily be seen due to
how cluttered the equipment was in the room. In the process of looking for items
around the room. Employees could have easily been exposed to these wires and gotten
electrocuted. Depending on the voltage of electricity that was passing through the
wires, such an even would have resulted in burns, loss of consciousness, cardiac arrest
and in the worst case scenario, death.
3. The floor was also very dusty and it was evident that it had not been cleaned in
a while. This is understandable, since it would have been really difficult to clean that
room, not to mention dangerous. While working around the room, employees would
kick up dust and the dust in the air would be inhaled and in the long run would cause
respiratory problems such as asthma and pneumonia.
I would like to take control and eliminate these hazards or reduce them to an
acceptable level in a way that will not affect the employees work and that will
be done in the fastest and most effective manner. The controls that I have
identified and plan to implement are:
a. Scattered equipment.
⊘ This is a preview!⊘
Do you want full access?
Subscribe today to unlock all pages.

Trusted by 1+ million students worldwide
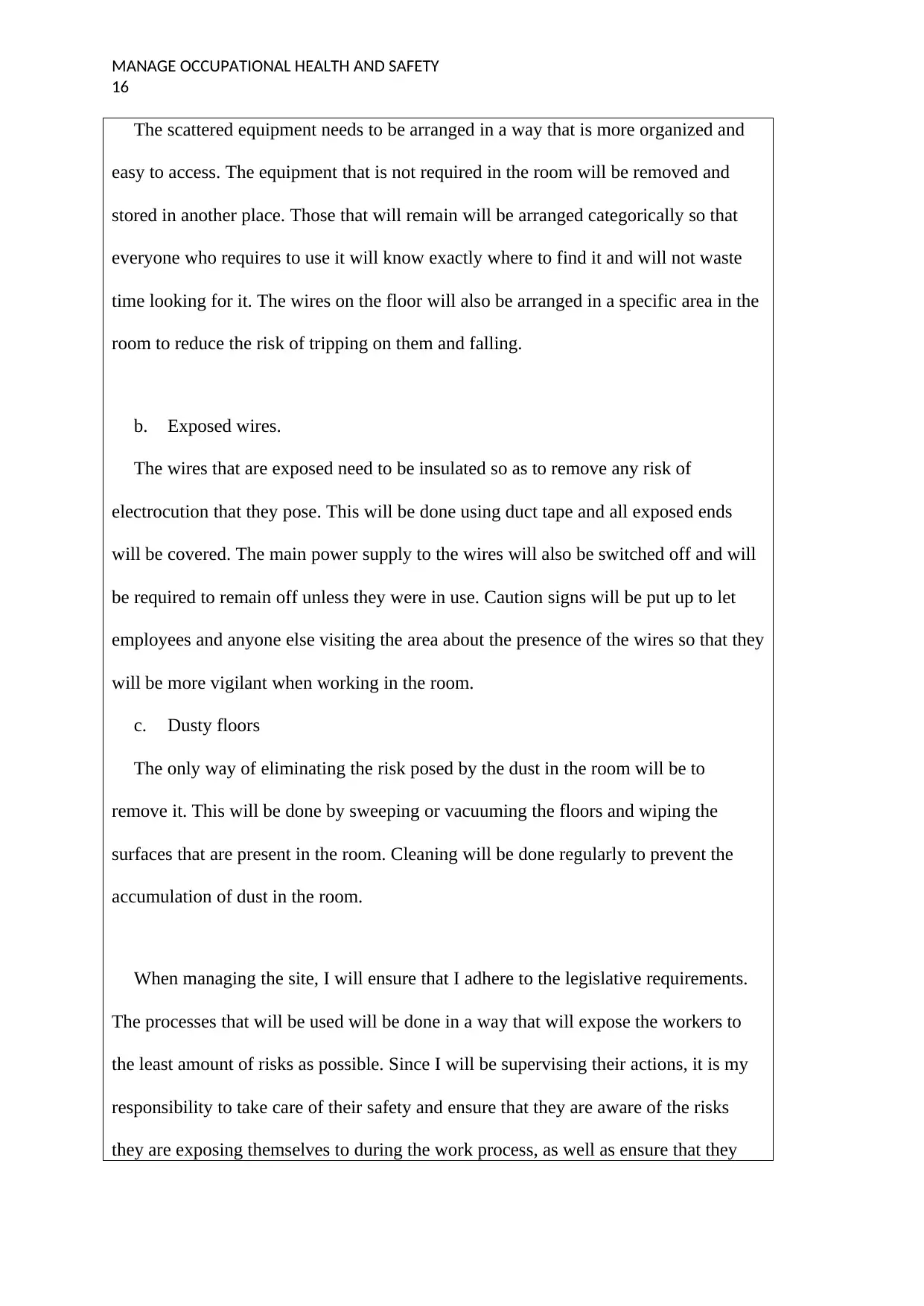
16
The scattered equipment needs to be arranged in a way that is more organized and
easy to access. The equipment that is not required in the room will be removed and
stored in another place. Those that will remain will be arranged categorically so that
everyone who requires to use it will know exactly where to find it and will not waste
time looking for it. The wires on the floor will also be arranged in a specific area in the
room to reduce the risk of tripping on them and falling.
b. Exposed wires.
The wires that are exposed need to be insulated so as to remove any risk of
electrocution that they pose. This will be done using duct tape and all exposed ends
will be covered. The main power supply to the wires will also be switched off and will
be required to remain off unless they were in use. Caution signs will be put up to let
employees and anyone else visiting the area about the presence of the wires so that they
will be more vigilant when working in the room.
c. Dusty floors
The only way of eliminating the risk posed by the dust in the room will be to
remove it. This will be done by sweeping or vacuuming the floors and wiping the
surfaces that are present in the room. Cleaning will be done regularly to prevent the
accumulation of dust in the room.
When managing the site, I will ensure that I adhere to the legislative requirements.
The processes that will be used will be done in a way that will expose the workers to
the least amount of risks as possible. Since I will be supervising their actions, it is my
responsibility to take care of their safety and ensure that they are aware of the risks
they are exposing themselves to during the work process, as well as ensure that they
Paraphrase This Document
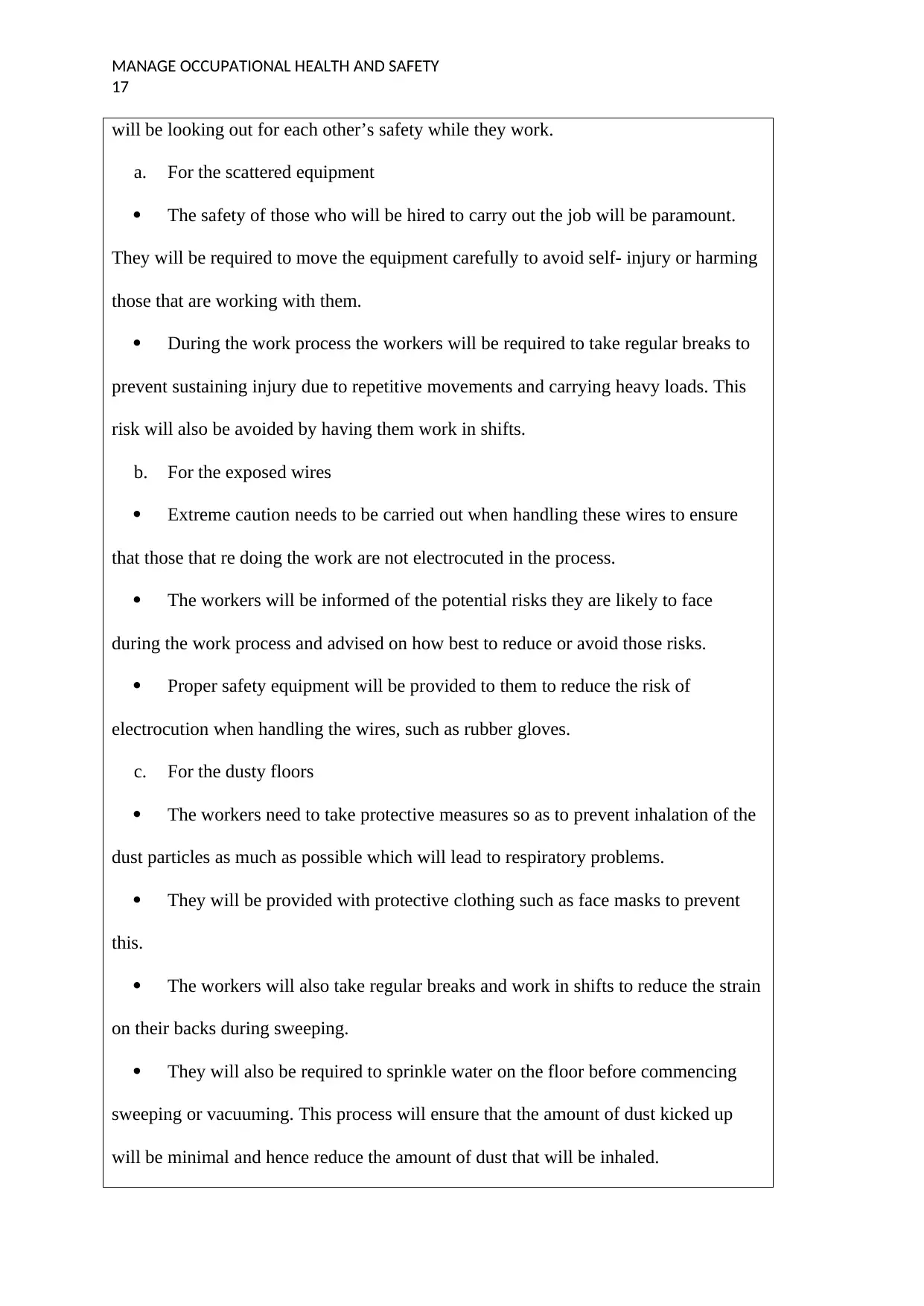
17
will be looking out for each other’s safety while they work.
a. For the scattered equipment
The safety of those who will be hired to carry out the job will be paramount.
They will be required to move the equipment carefully to avoid self- injury or harming
those that are working with them.
During the work process the workers will be required to take regular breaks to
prevent sustaining injury due to repetitive movements and carrying heavy loads. This
risk will also be avoided by having them work in shifts.
b. For the exposed wires
Extreme caution needs to be carried out when handling these wires to ensure
that those that re doing the work are not electrocuted in the process.
The workers will be informed of the potential risks they are likely to face
during the work process and advised on how best to reduce or avoid those risks.
Proper safety equipment will be provided to them to reduce the risk of
electrocution when handling the wires, such as rubber gloves.
c. For the dusty floors
The workers need to take protective measures so as to prevent inhalation of the
dust particles as much as possible which will lead to respiratory problems.
They will be provided with protective clothing such as face masks to prevent
this.
The workers will also take regular breaks and work in shifts to reduce the strain
on their backs during sweeping.
They will also be required to sprinkle water on the floor before commencing
sweeping or vacuuming. This process will ensure that the amount of dust kicked up
will be minimal and hence reduce the amount of dust that will be inhaled.
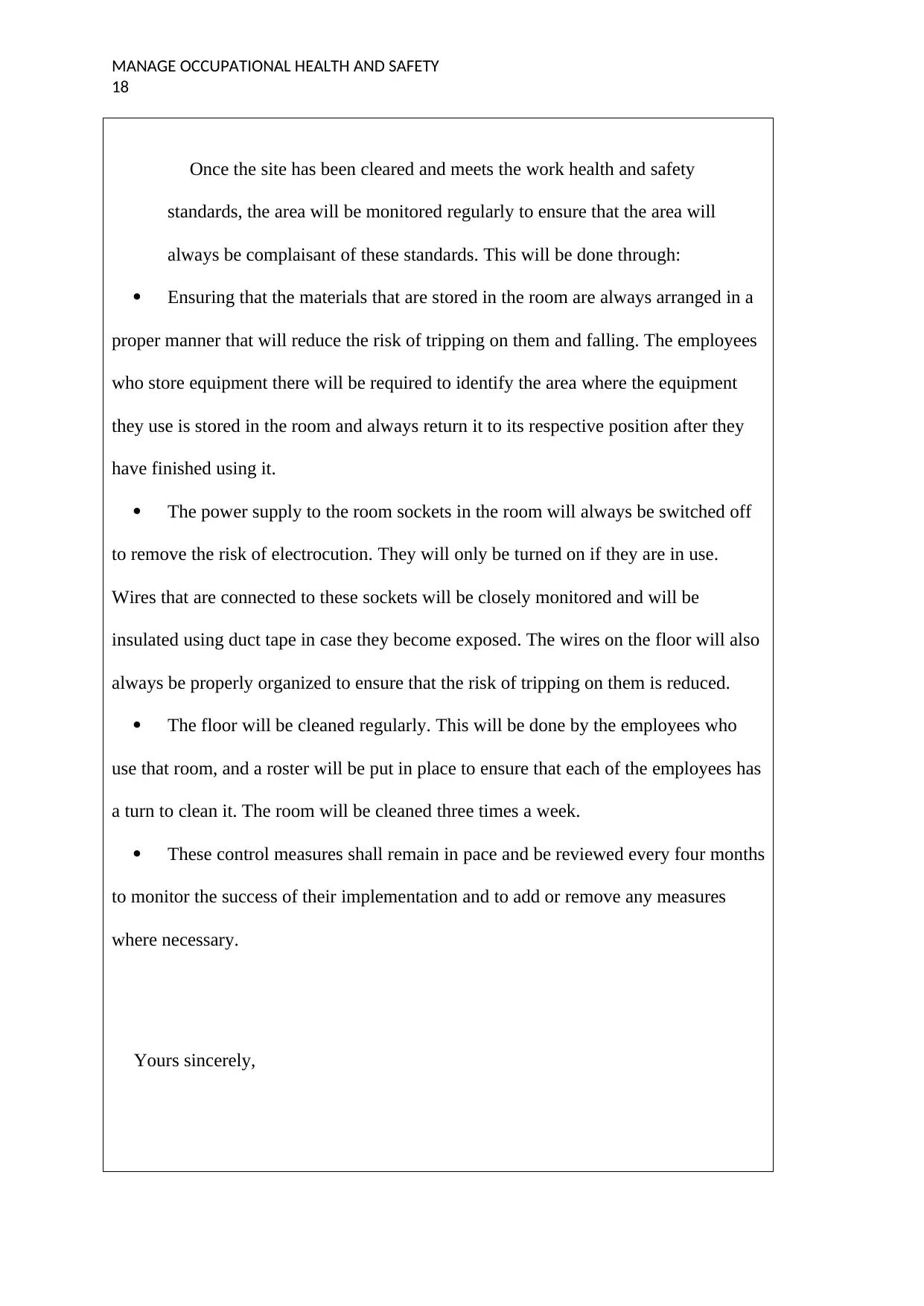
18
Once the site has been cleared and meets the work health and safety
standards, the area will be monitored regularly to ensure that the area will
always be complaisant of these standards. This will be done through:
Ensuring that the materials that are stored in the room are always arranged in a
proper manner that will reduce the risk of tripping on them and falling. The employees
who store equipment there will be required to identify the area where the equipment
they use is stored in the room and always return it to its respective position after they
have finished using it.
The power supply to the room sockets in the room will always be switched off
to remove the risk of electrocution. They will only be turned on if they are in use.
Wires that are connected to these sockets will be closely monitored and will be
insulated using duct tape in case they become exposed. The wires on the floor will also
always be properly organized to ensure that the risk of tripping on them is reduced.
The floor will be cleaned regularly. This will be done by the employees who
use that room, and a roster will be put in place to ensure that each of the employees has
a turn to clean it. The room will be cleaned three times a week.
These control measures shall remain in pace and be reviewed every four months
to monitor the success of their implementation and to add or remove any measures
where necessary.
Yours sincerely,
⊘ This is a preview!⊘
Do you want full access?
Subscribe today to unlock all pages.

Trusted by 1+ million students worldwide
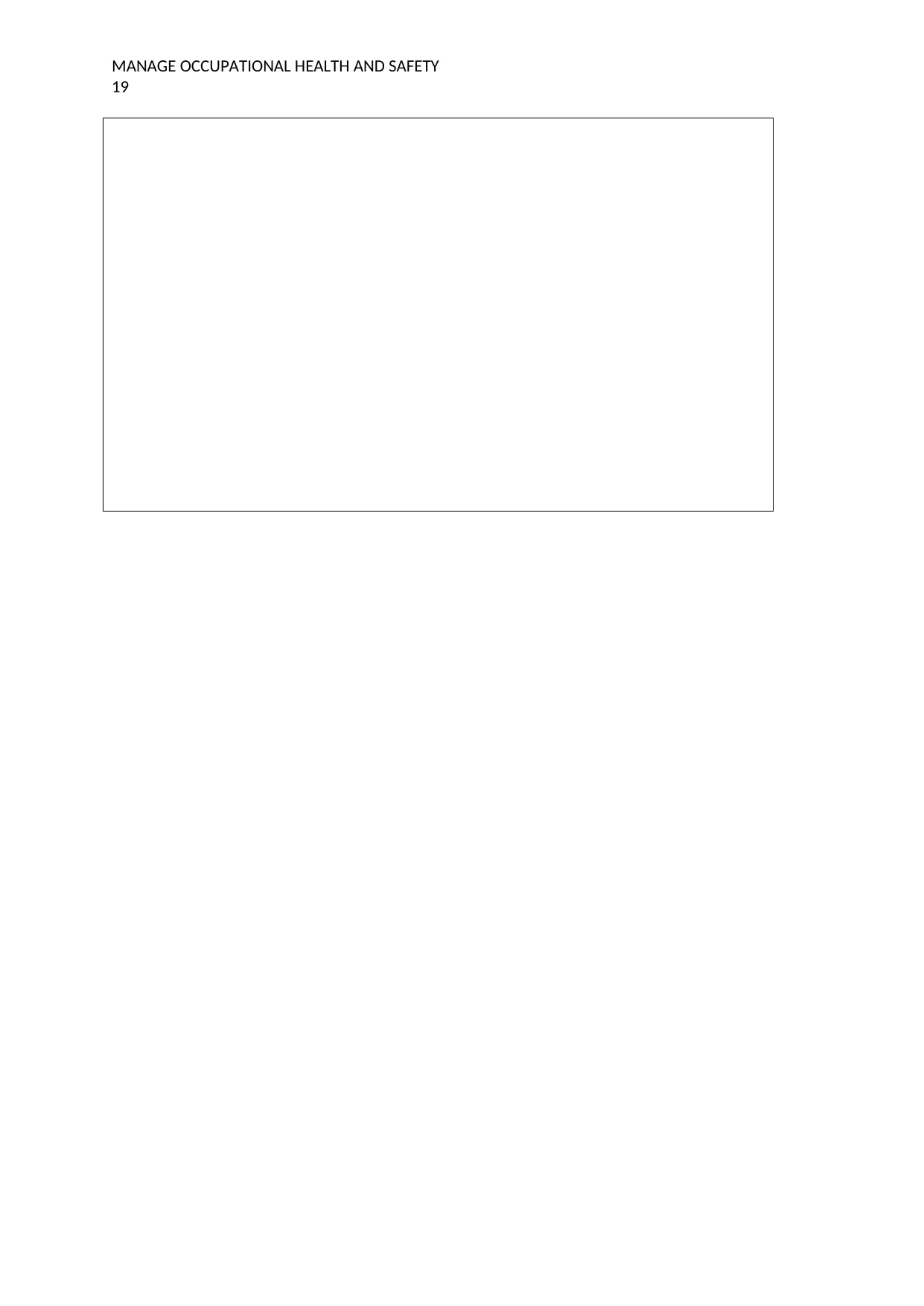
19
Paraphrase This Document
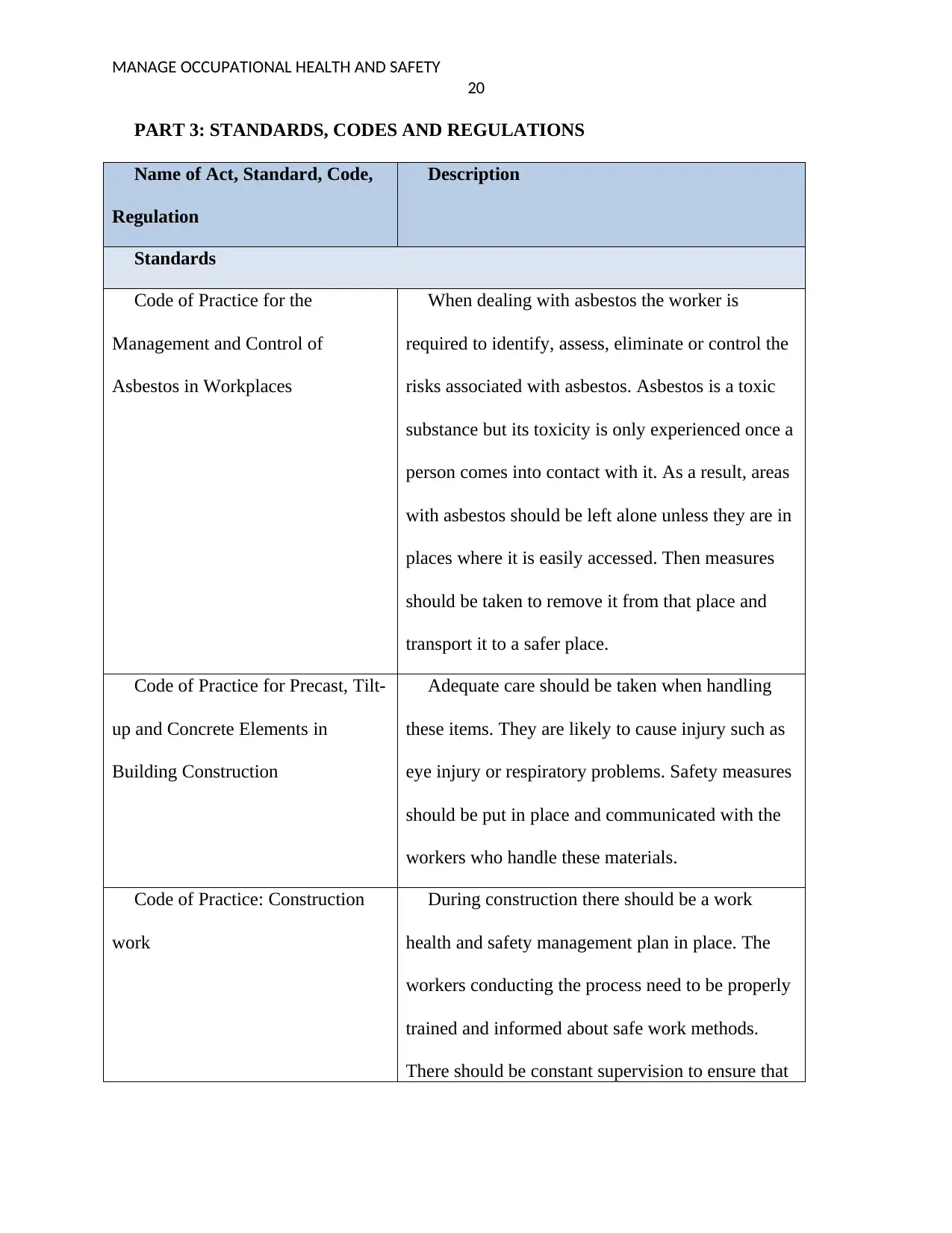
20
PART 3: STANDARDS, CODES AND REGULATIONS
Name of Act, Standard, Code,
Regulation
Description
Standards
Code of Practice for the
Management and Control of
Asbestos in Workplaces
When dealing with asbestos the worker is
required to identify, assess, eliminate or control the
risks associated with asbestos. Asbestos is a toxic
substance but its toxicity is only experienced once a
person comes into contact with it. As a result, areas
with asbestos should be left alone unless they are in
places where it is easily accessed. Then measures
should be taken to remove it from that place and
transport it to a safer place.
Code of Practice for Precast, Tilt-
up and Concrete Elements in
Building Construction
Adequate care should be taken when handling
these items. They are likely to cause injury such as
eye injury or respiratory problems. Safety measures
should be put in place and communicated with the
workers who handle these materials.
Code of Practice: Construction
work
During construction there should be a work
health and safety management plan in place. The
workers conducting the process need to be properly
trained and informed about safe work methods.
There should be constant supervision to ensure that
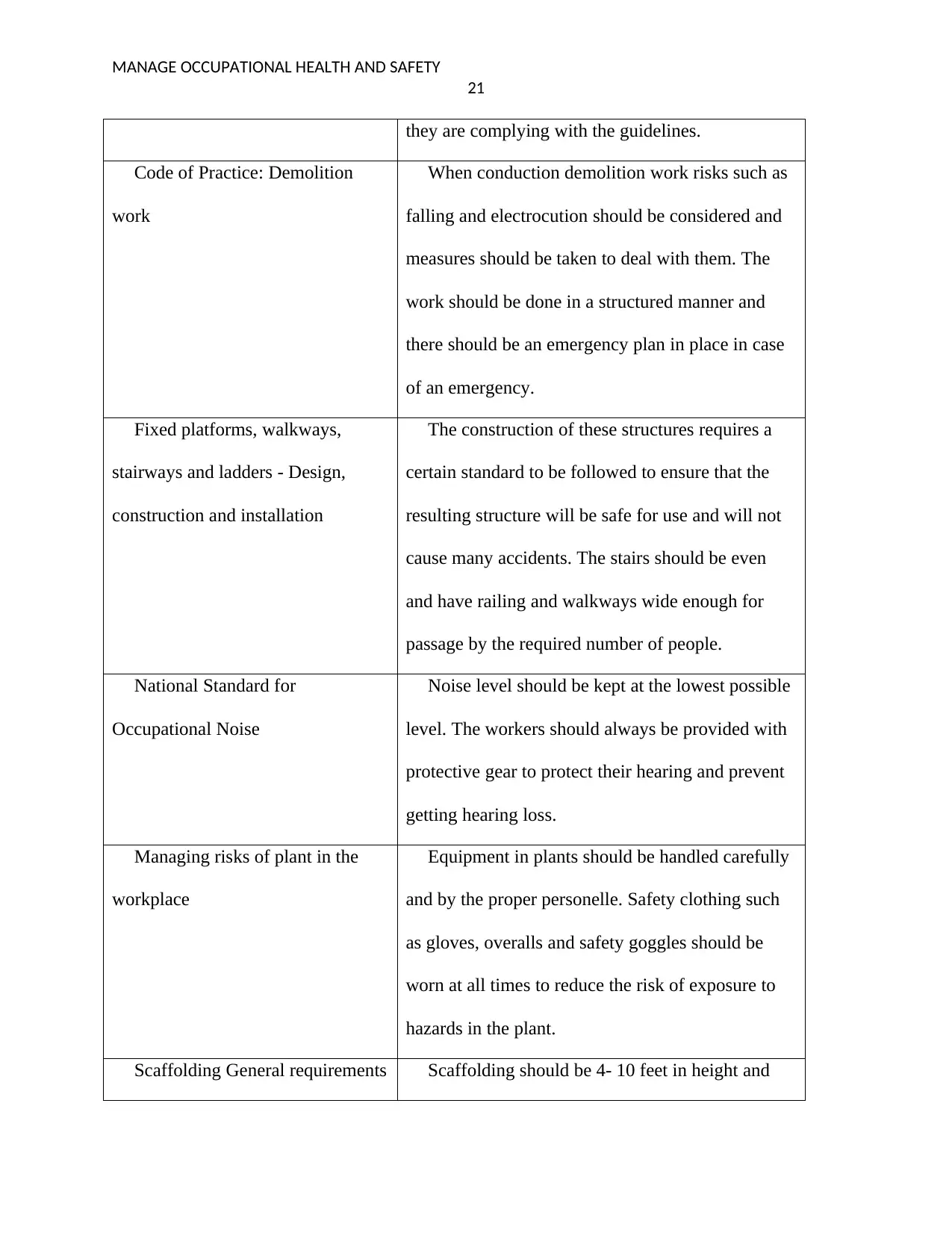
21
they are complying with the guidelines.
Code of Practice: Demolition
work
When conduction demolition work risks such as
falling and electrocution should be considered and
measures should be taken to deal with them. The
work should be done in a structured manner and
there should be an emergency plan in place in case
of an emergency.
Fixed platforms, walkways,
stairways and ladders - Design,
construction and installation
The construction of these structures requires a
certain standard to be followed to ensure that the
resulting structure will be safe for use and will not
cause many accidents. The stairs should be even
and have railing and walkways wide enough for
passage by the required number of people.
National Standard for
Occupational Noise
Noise level should be kept at the lowest possible
level. The workers should always be provided with
protective gear to protect their hearing and prevent
getting hearing loss.
Managing risks of plant in the
workplace
Equipment in plants should be handled carefully
and by the proper personelle. Safety clothing such
as gloves, overalls and safety goggles should be
worn at all times to reduce the risk of exposure to
hazards in the plant.
Scaffolding General requirements Scaffolding should be 4- 10 feet in height and
⊘ This is a preview!⊘
Do you want full access?
Subscribe today to unlock all pages.

Trusted by 1+ million students worldwide
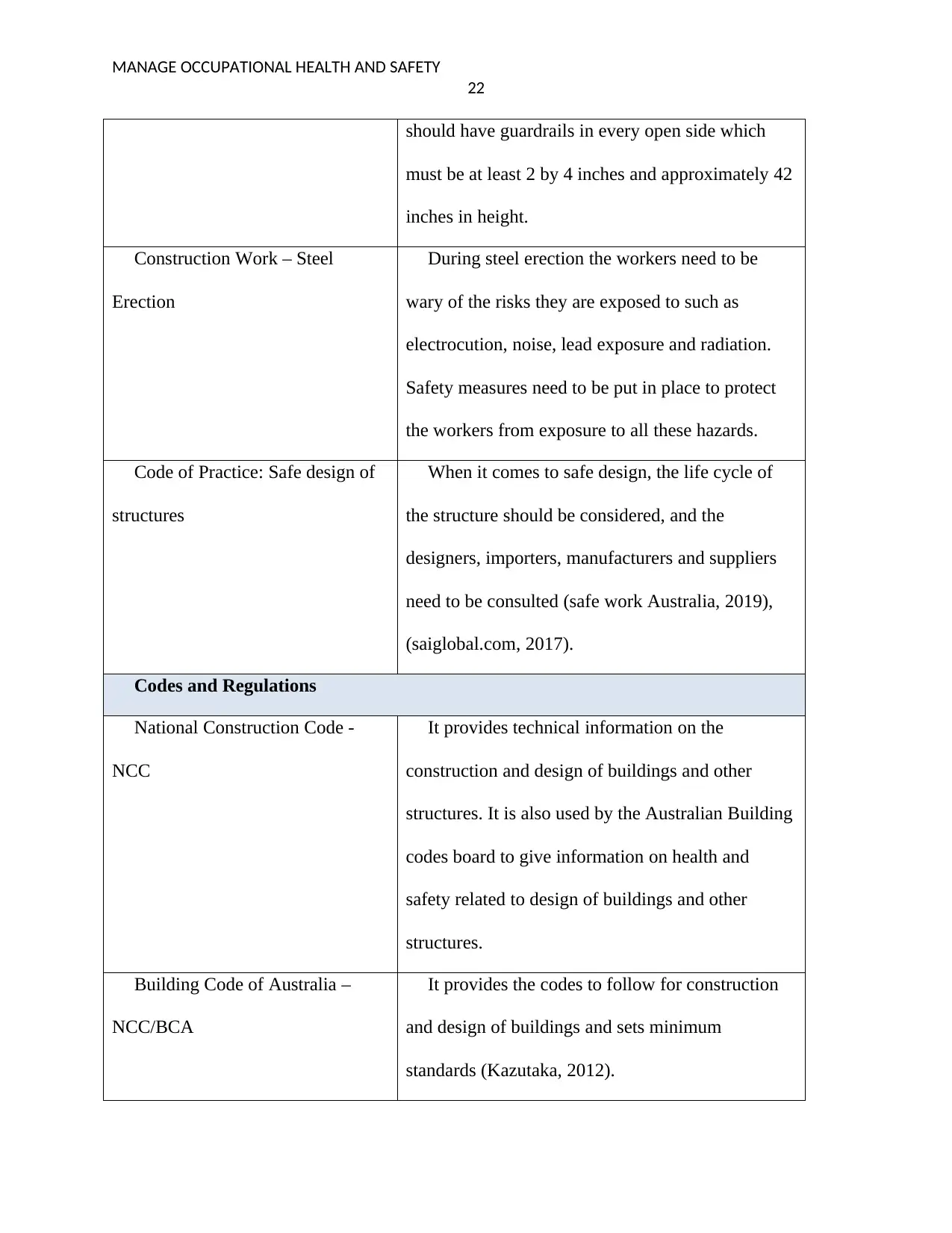
22
should have guardrails in every open side which
must be at least 2 by 4 inches and approximately 42
inches in height.
Construction Work – Steel
Erection
During steel erection the workers need to be
wary of the risks they are exposed to such as
electrocution, noise, lead exposure and radiation.
Safety measures need to be put in place to protect
the workers from exposure to all these hazards.
Code of Practice: Safe design of
structures
When it comes to safe design, the life cycle of
the structure should be considered, and the
designers, importers, manufacturers and suppliers
need to be consulted (safe work Australia, 2019),
(saiglobal.com, 2017).
Codes and Regulations
National Construction Code -
NCC
It provides technical information on the
construction and design of buildings and other
structures. It is also used by the Australian Building
codes board to give information on health and
safety related to design of buildings and other
structures.
Building Code of Australia –
NCC/BCA
It provides the codes to follow for construction
and design of buildings and sets minimum
standards (Kazutaka, 2012).
Paraphrase This Document
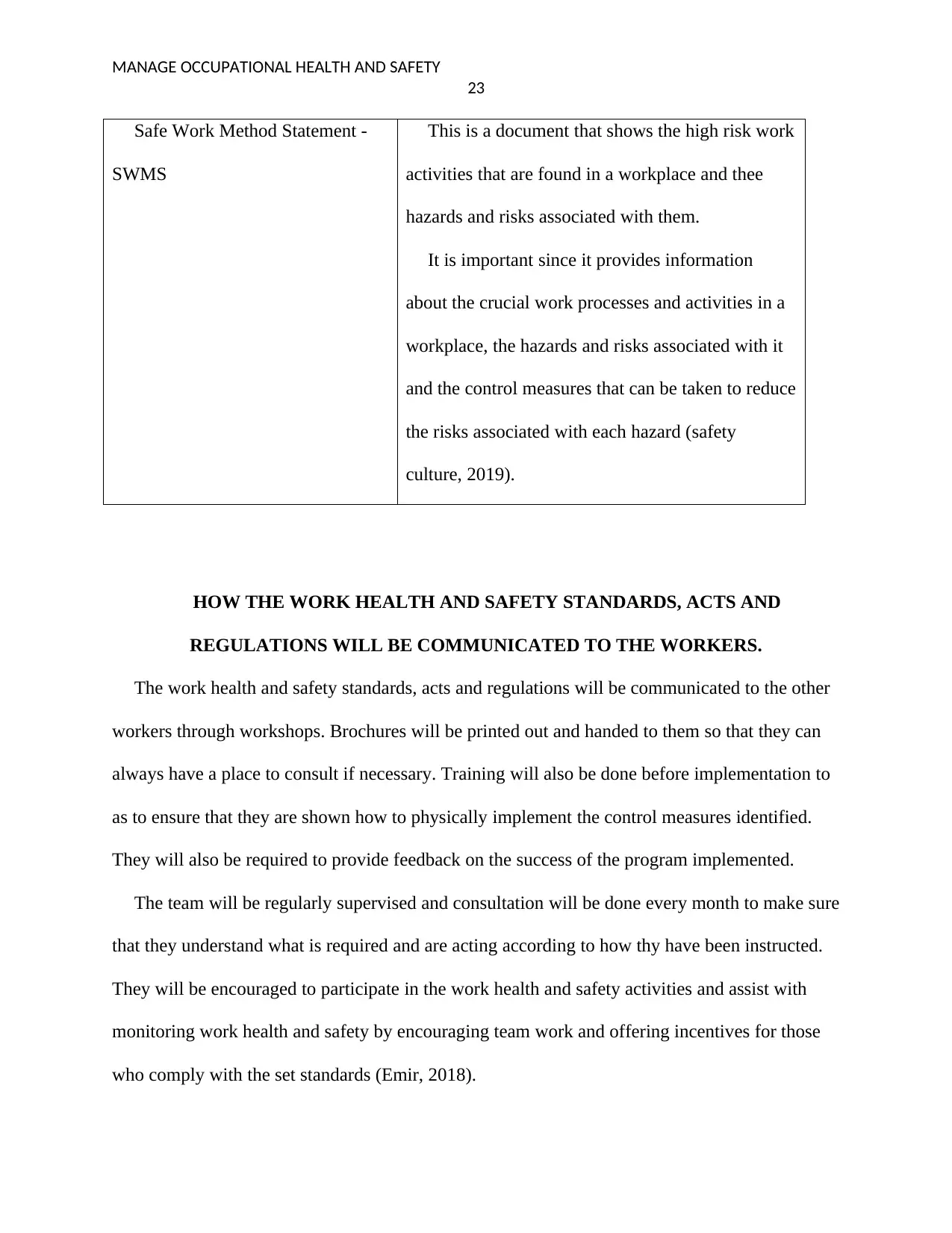
23
Safe Work Method Statement -
SWMS
This is a document that shows the high risk work
activities that are found in a workplace and thee
hazards and risks associated with them.
It is important since it provides information
about the crucial work processes and activities in a
workplace, the hazards and risks associated with it
and the control measures that can be taken to reduce
the risks associated with each hazard (safety
culture, 2019).
HOW THE WORK HEALTH AND SAFETY STANDARDS, ACTS AND
REGULATIONS WILL BE COMMUNICATED TO THE WORKERS.
The work health and safety standards, acts and regulations will be communicated to the other
workers through workshops. Brochures will be printed out and handed to them so that they can
always have a place to consult if necessary. Training will also be done before implementation to
as to ensure that they are shown how to physically implement the control measures identified.
They will also be required to provide feedback on the success of the program implemented.
The team will be regularly supervised and consultation will be done every month to make sure
that they understand what is required and are acting according to how thy have been instructed.
They will be encouraged to participate in the work health and safety activities and assist with
monitoring work health and safety by encouraging team work and offering incentives for those
who comply with the set standards (Emir, 2018).
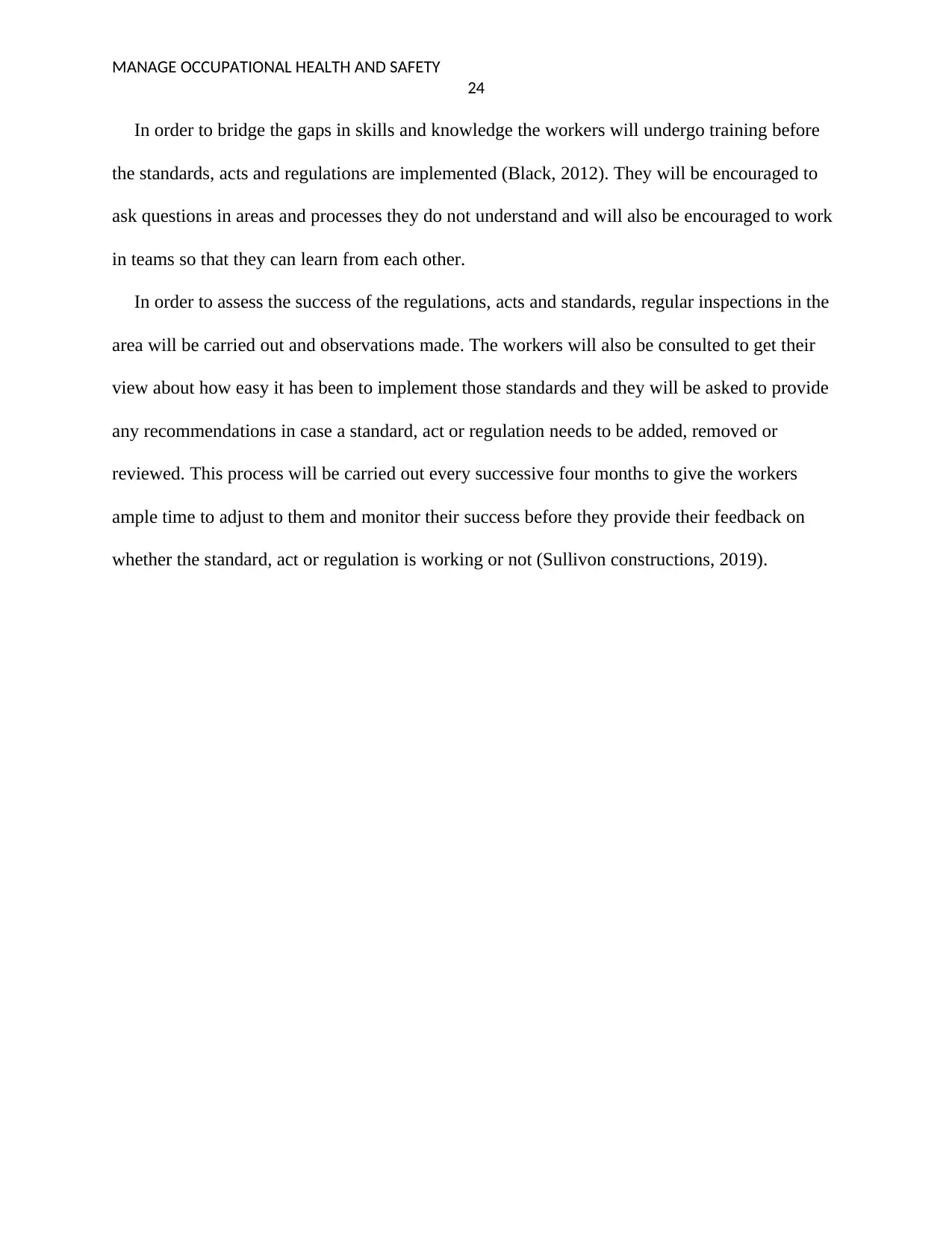
24
In order to bridge the gaps in skills and knowledge the workers will undergo training before
the standards, acts and regulations are implemented (Black, 2012). They will be encouraged to
ask questions in areas and processes they do not understand and will also be encouraged to work
in teams so that they can learn from each other.
In order to assess the success of the regulations, acts and standards, regular inspections in the
area will be carried out and observations made. The workers will also be consulted to get their
view about how easy it has been to implement those standards and they will be asked to provide
any recommendations in case a standard, act or regulation needs to be added, removed or
reviewed. This process will be carried out every successive four months to give the workers
ample time to adjust to them and monitor their success before they provide their feedback on
whether the standard, act or regulation is working or not (Sullivon constructions, 2019).
⊘ This is a preview!⊘
Do you want full access?
Subscribe today to unlock all pages.

Trusted by 1+ million students worldwide
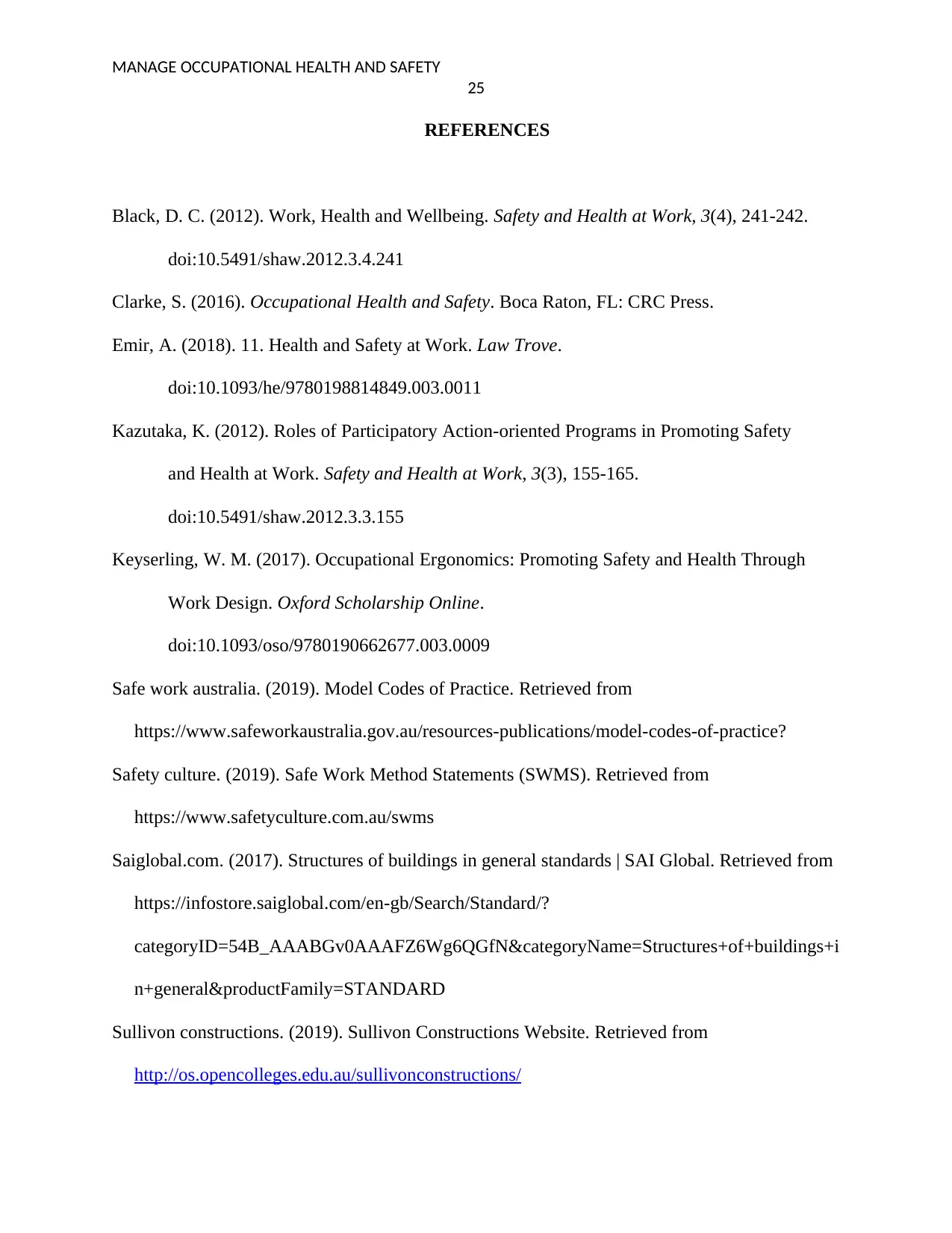
25
REFERENCES
Black, D. C. (2012). Work, Health and Wellbeing. Safety and Health at Work, 3(4), 241-242.
doi:10.5491/shaw.2012.3.4.241
Clarke, S. (2016). Occupational Health and Safety. Boca Raton, FL: CRC Press.
Emir, A. (2018). 11. Health and Safety at Work. Law Trove.
doi:10.1093/he/9780198814849.003.0011
Kazutaka, K. (2012). Roles of Participatory Action-oriented Programs in Promoting Safety
and Health at Work. Safety and Health at Work, 3(3), 155-165.
doi:10.5491/shaw.2012.3.3.155
Keyserling, W. M. (2017). Occupational Ergonomics: Promoting Safety and Health Through
Work Design. Oxford Scholarship Online.
doi:10.1093/oso/9780190662677.003.0009
Safe work australia. (2019). Model Codes of Practice. Retrieved from
https://www.safeworkaustralia.gov.au/resources-publications/model-codes-of-practice?
Safety culture. (2019). Safe Work Method Statements (SWMS). Retrieved from
https://www.safetyculture.com.au/swms
Saiglobal.com. (2017). Structures of buildings in general standards | SAI Global. Retrieved from
https://infostore.saiglobal.com/en-gb/Search/Standard/?
categoryID=54B_AAABGv0AAAFZ6Wg6QGfN&categoryName=Structures+of+buildings+i
n+general&productFamily=STANDARD
Sullivon constructions. (2019). Sullivon Constructions Website. Retrieved from
http://os.opencolleges.edu.au/sullivonconstructions/
Related Documents

Your All-in-One AI-Powered Toolkit for Academic Success.
+13062052269
info@desklib.com
Available 24*7 on WhatsApp / Email
© 2024 | Zucol Services PVT LTD | All rights reserved.