OHSMS Essay: Interrelation of Safety Systems, Culture, and PDCA Cycle
VerifiedAdded on 2023/06/09
|10
|2714
|265
Essay
AI Summary
This essay delves into the intricate relationship between Occupational Health and Safety Management Systems (OHSMS), safety culture, and continual improvement, particularly focusing on how the implementation of a safety management system can drive improvements through the five stages of Hudson's Maturity Model. It explains how the Hudson Model elucidates the progression of safety culture maturity within organizations, from pathological to generative stages, and how safety management systems play a crucial role in this evolution. Furthermore, the essay describes how utilizing the Plan-Do-Check-Act (PDCA) cycle, a continual improvement methodology, aids in developing a robust OHS management system, ultimately fostering a mature safety culture within the workplace. The discussion encompasses the principles of OHS, various approaches to safety management including legislation, enforcement, education, and motivators, and concludes by emphasizing the importance of linking safety management systems with safety culture and continuous improvement for ensuring a safe and healthy work environment. Desklib provides access to this and many other solved assignments for students.
Contribute Materials
Your contribution can guide someone’s learning journey. Share your
documents today.
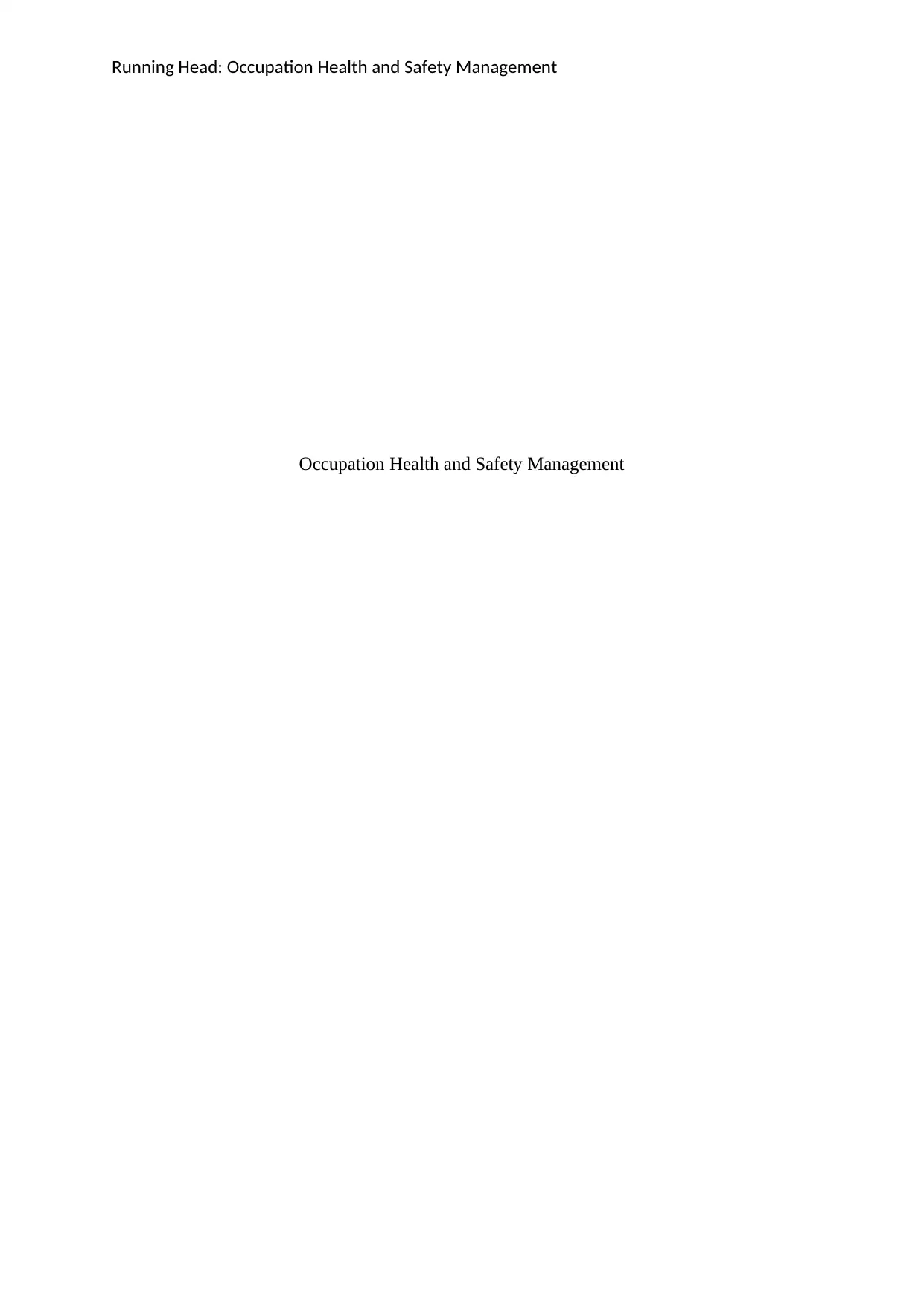
Running Head: Occupation Health and Safety Management
Occupation Health and Safety Management
Occupation Health and Safety Management
Secure Best Marks with AI Grader
Need help grading? Try our AI Grader for instant feedback on your assignments.
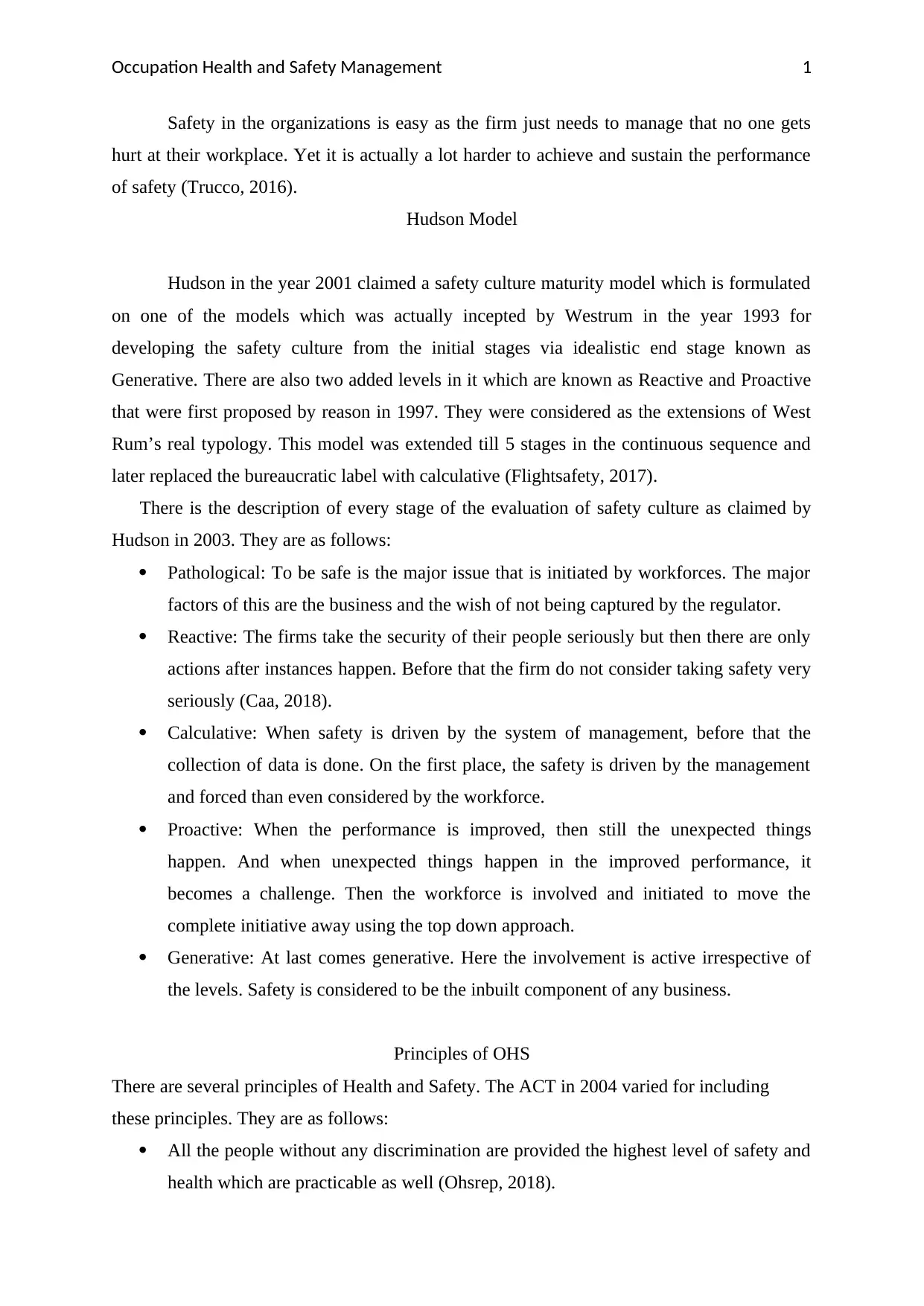
Occupation Health and Safety Management
Safety in the organizations is easy as the firm just needs to manage that no one gets
hurt at their workplace. Yet it is actually a lot harder to achieve and sustain the performance
of safety (Trucco, 2016).
Hudson Model
Hudson in the year 2001 claimed a safety culture maturity model which is formulated
on one of the models which was actually incepted by Westrum in the year 1993 for
developing the safety culture from the initial stages via idealistic end stage known as
Generative. There are also two added levels in it which are known as Reactive and Proactive
that were first proposed by reason in 1997. They were considered as the extensions of West
Rum’s real typology. This model was extended till 5 stages in the continuous sequence and
later replaced the bureaucratic label with calculative (Flightsafety, 2017).
There is the description of every stage of the evaluation of safety culture as claimed by
Hudson in 2003. They are as follows:
Pathological: To be safe is the major issue that is initiated by workforces. The major
factors of this are the business and the wish of not being captured by the regulator.
Reactive: The firms take the security of their people seriously but then there are only
actions after instances happen. Before that the firm do not consider taking safety very
seriously (Caa, 2018).
Calculative: When safety is driven by the system of management, before that the
collection of data is done. On the first place, the safety is driven by the management
and forced than even considered by the workforce.
Proactive: When the performance is improved, then still the unexpected things
happen. And when unexpected things happen in the improved performance, it
becomes a challenge. Then the workforce is involved and initiated to move the
complete initiative away using the top down approach.
Generative: At last comes generative. Here the involvement is active irrespective of
the levels. Safety is considered to be the inbuilt component of any business.
Principles of OHS
There are several principles of Health and Safety. The ACT in 2004 varied for including
these principles. They are as follows:
All the people without any discrimination are provided the highest level of safety and
health which are practicable as well (Ohsrep, 2018).
1
Safety in the organizations is easy as the firm just needs to manage that no one gets
hurt at their workplace. Yet it is actually a lot harder to achieve and sustain the performance
of safety (Trucco, 2016).
Hudson Model
Hudson in the year 2001 claimed a safety culture maturity model which is formulated
on one of the models which was actually incepted by Westrum in the year 1993 for
developing the safety culture from the initial stages via idealistic end stage known as
Generative. There are also two added levels in it which are known as Reactive and Proactive
that were first proposed by reason in 1997. They were considered as the extensions of West
Rum’s real typology. This model was extended till 5 stages in the continuous sequence and
later replaced the bureaucratic label with calculative (Flightsafety, 2017).
There is the description of every stage of the evaluation of safety culture as claimed by
Hudson in 2003. They are as follows:
Pathological: To be safe is the major issue that is initiated by workforces. The major
factors of this are the business and the wish of not being captured by the regulator.
Reactive: The firms take the security of their people seriously but then there are only
actions after instances happen. Before that the firm do not consider taking safety very
seriously (Caa, 2018).
Calculative: When safety is driven by the system of management, before that the
collection of data is done. On the first place, the safety is driven by the management
and forced than even considered by the workforce.
Proactive: When the performance is improved, then still the unexpected things
happen. And when unexpected things happen in the improved performance, it
becomes a challenge. Then the workforce is involved and initiated to move the
complete initiative away using the top down approach.
Generative: At last comes generative. Here the involvement is active irrespective of
the levels. Safety is considered to be the inbuilt component of any business.
Principles of OHS
There are several principles of Health and Safety. The ACT in 2004 varied for including
these principles. They are as follows:
All the people without any discrimination are provided the highest level of safety and
health which are practicable as well (Ohsrep, 2018).
1
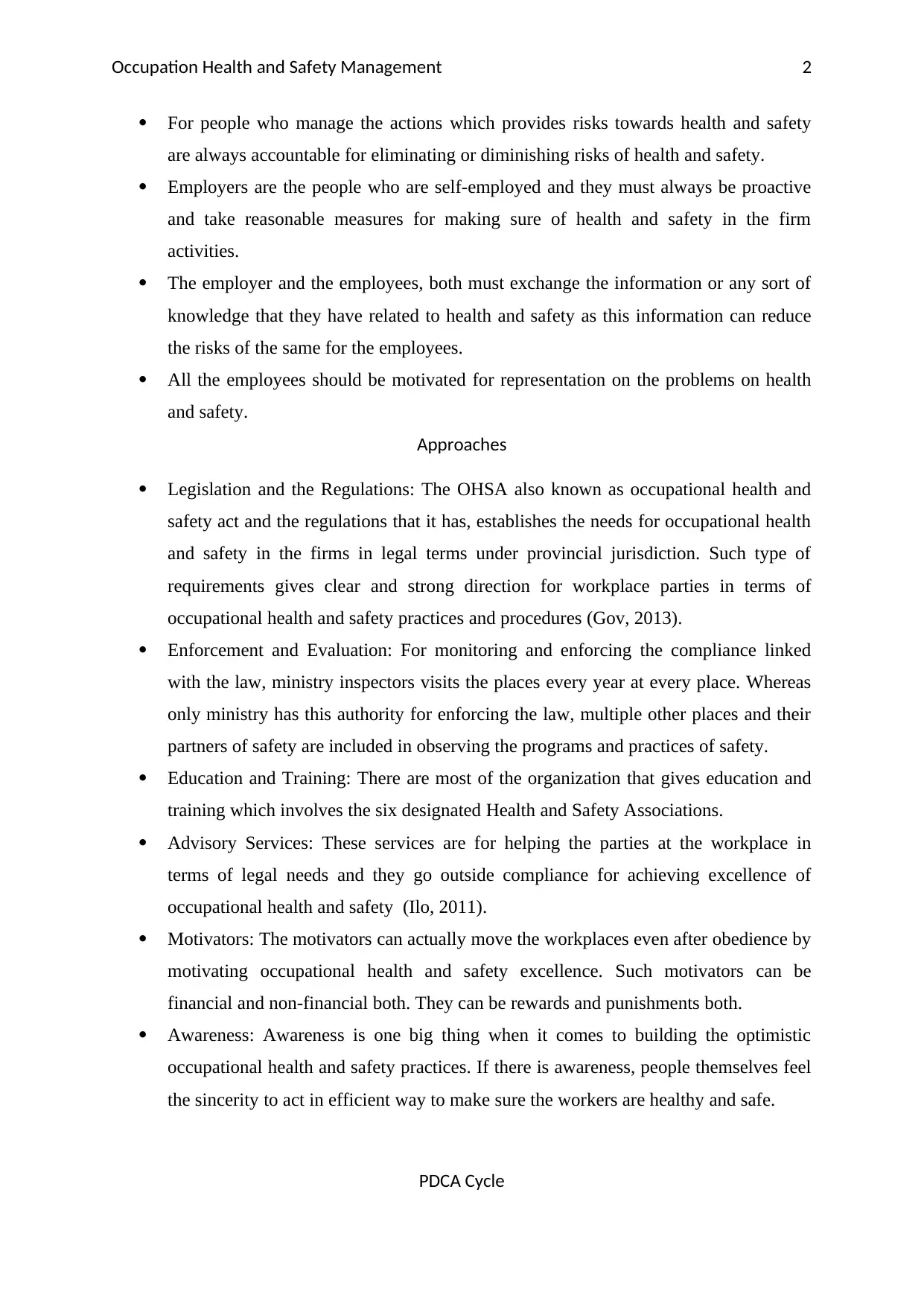
Occupation Health and Safety Management
For people who manage the actions which provides risks towards health and safety
are always accountable for eliminating or diminishing risks of health and safety.
Employers are the people who are self-employed and they must always be proactive
and take reasonable measures for making sure of health and safety in the firm
activities.
The employer and the employees, both must exchange the information or any sort of
knowledge that they have related to health and safety as this information can reduce
the risks of the same for the employees.
All the employees should be motivated for representation on the problems on health
and safety.
Approaches
Legislation and the Regulations: The OHSA also known as occupational health and
safety act and the regulations that it has, establishes the needs for occupational health
and safety in the firms in legal terms under provincial jurisdiction. Such type of
requirements gives clear and strong direction for workplace parties in terms of
occupational health and safety practices and procedures (Gov, 2013).
Enforcement and Evaluation: For monitoring and enforcing the compliance linked
with the law, ministry inspectors visits the places every year at every place. Whereas
only ministry has this authority for enforcing the law, multiple other places and their
partners of safety are included in observing the programs and practices of safety.
Education and Training: There are most of the organization that gives education and
training which involves the six designated Health and Safety Associations.
Advisory Services: These services are for helping the parties at the workplace in
terms of legal needs and they go outside compliance for achieving excellence of
occupational health and safety (Ilo, 2011).
Motivators: The motivators can actually move the workplaces even after obedience by
motivating occupational health and safety excellence. Such motivators can be
financial and non-financial both. They can be rewards and punishments both.
Awareness: Awareness is one big thing when it comes to building the optimistic
occupational health and safety practices. If there is awareness, people themselves feel
the sincerity to act in efficient way to make sure the workers are healthy and safe.
PDCA Cycle
2
For people who manage the actions which provides risks towards health and safety
are always accountable for eliminating or diminishing risks of health and safety.
Employers are the people who are self-employed and they must always be proactive
and take reasonable measures for making sure of health and safety in the firm
activities.
The employer and the employees, both must exchange the information or any sort of
knowledge that they have related to health and safety as this information can reduce
the risks of the same for the employees.
All the employees should be motivated for representation on the problems on health
and safety.
Approaches
Legislation and the Regulations: The OHSA also known as occupational health and
safety act and the regulations that it has, establishes the needs for occupational health
and safety in the firms in legal terms under provincial jurisdiction. Such type of
requirements gives clear and strong direction for workplace parties in terms of
occupational health and safety practices and procedures (Gov, 2013).
Enforcement and Evaluation: For monitoring and enforcing the compliance linked
with the law, ministry inspectors visits the places every year at every place. Whereas
only ministry has this authority for enforcing the law, multiple other places and their
partners of safety are included in observing the programs and practices of safety.
Education and Training: There are most of the organization that gives education and
training which involves the six designated Health and Safety Associations.
Advisory Services: These services are for helping the parties at the workplace in
terms of legal needs and they go outside compliance for achieving excellence of
occupational health and safety (Ilo, 2011).
Motivators: The motivators can actually move the workplaces even after obedience by
motivating occupational health and safety excellence. Such motivators can be
financial and non-financial both. They can be rewards and punishments both.
Awareness: Awareness is one big thing when it comes to building the optimistic
occupational health and safety practices. If there is awareness, people themselves feel
the sincerity to act in efficient way to make sure the workers are healthy and safe.
PDCA Cycle
2

Occupation Health and Safety Management
Figure 1: PDCA Cycle
Source: (Google, 2018).
Plan: The approach A+ starts with the Plan step which is known as analyse. This is the step in
which the needs of the student are analysed by monitoring the range of availability of data in
Pearl River’s electronic data warehouse from the grades till performance in tests.
Do: This phase has two steps:
1. Align: It inquires about the standards of national and state, their needs and ways in
which they will be assessed. The staffs also plans the program by seeking as to what
exactly is imparted at first and later grade levels and in other fields for making sure a
clear continuousness of instructions all through the schooling of the students (Foster,
2013).
2. The second step is known as the act. It is actual the step when the instructions are
given by the following the teaching goals and curriculum.
Check: This step is known as assess. The assessments, whether formal or informal, takes
place in a continuous manner from the teacher dipstick assessments up to a progress of every
six weeks reports to per annum standardized tests.
Act: In this simple step which is known as Standardize, the objectives are accomplished when
the curriculum teaching ways and design are taken to be as standardized (Muttu, 2016).
Safety management systems are interrelated with the safety culture and also with continual
improvement. The safety management systems are made for people to be safe and be healthy.
These systems ensure that people are safe at their workplace and they have no danger related
to their health. Imbibing the culture of safety will always make people follow it with
compliance or if it is any sort of rule. And to imbibe the culture in any workplace to ensure
health and safety, one has to continually improve the trends and measures of health and
3
Figure 1: PDCA Cycle
Source: (Google, 2018).
Plan: The approach A+ starts with the Plan step which is known as analyse. This is the step in
which the needs of the student are analysed by monitoring the range of availability of data in
Pearl River’s electronic data warehouse from the grades till performance in tests.
Do: This phase has two steps:
1. Align: It inquires about the standards of national and state, their needs and ways in
which they will be assessed. The staffs also plans the program by seeking as to what
exactly is imparted at first and later grade levels and in other fields for making sure a
clear continuousness of instructions all through the schooling of the students (Foster,
2013).
2. The second step is known as the act. It is actual the step when the instructions are
given by the following the teaching goals and curriculum.
Check: This step is known as assess. The assessments, whether formal or informal, takes
place in a continuous manner from the teacher dipstick assessments up to a progress of every
six weeks reports to per annum standardized tests.
Act: In this simple step which is known as Standardize, the objectives are accomplished when
the curriculum teaching ways and design are taken to be as standardized (Muttu, 2016).
Safety management systems are interrelated with the safety culture and also with continual
improvement. The safety management systems are made for people to be safe and be healthy.
These systems ensure that people are safe at their workplace and they have no danger related
to their health. Imbibing the culture of safety will always make people follow it with
compliance or if it is any sort of rule. And to imbibe the culture in any workplace to ensure
health and safety, one has to continually improve the trends and measures of health and
3
Secure Best Marks with AI Grader
Need help grading? Try our AI Grader for instant feedback on your assignments.
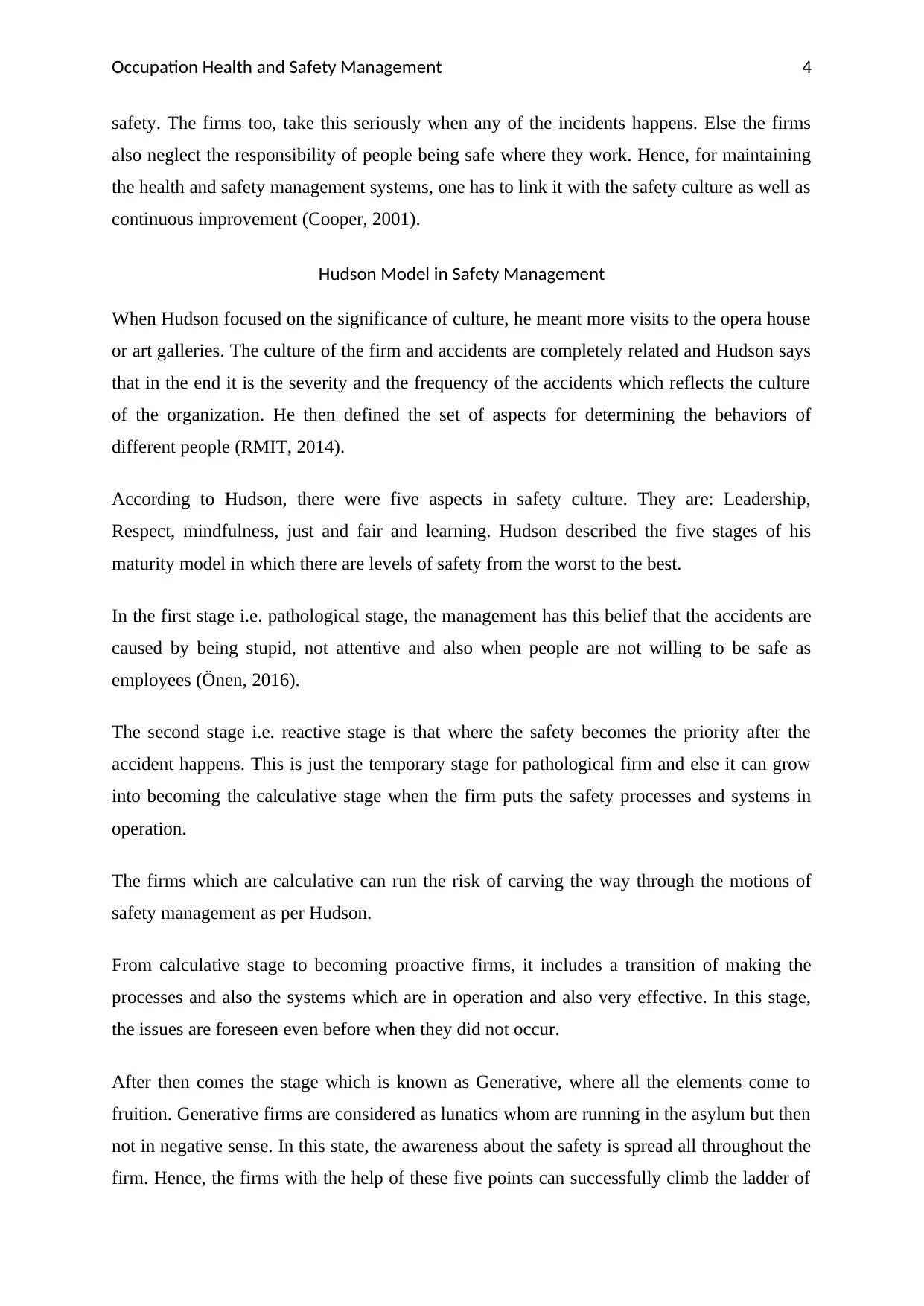
Occupation Health and Safety Management
safety. The firms too, take this seriously when any of the incidents happens. Else the firms
also neglect the responsibility of people being safe where they work. Hence, for maintaining
the health and safety management systems, one has to link it with the safety culture as well as
continuous improvement (Cooper, 2001).
Hudson Model in Safety Management
When Hudson focused on the significance of culture, he meant more visits to the opera house
or art galleries. The culture of the firm and accidents are completely related and Hudson says
that in the end it is the severity and the frequency of the accidents which reflects the culture
of the organization. He then defined the set of aspects for determining the behaviors of
different people (RMIT, 2014).
According to Hudson, there were five aspects in safety culture. They are: Leadership,
Respect, mindfulness, just and fair and learning. Hudson described the five stages of his
maturity model in which there are levels of safety from the worst to the best.
In the first stage i.e. pathological stage, the management has this belief that the accidents are
caused by being stupid, not attentive and also when people are not willing to be safe as
employees (Önen, 2016).
The second stage i.e. reactive stage is that where the safety becomes the priority after the
accident happens. This is just the temporary stage for pathological firm and else it can grow
into becoming the calculative stage when the firm puts the safety processes and systems in
operation.
The firms which are calculative can run the risk of carving the way through the motions of
safety management as per Hudson.
From calculative stage to becoming proactive firms, it includes a transition of making the
processes and also the systems which are in operation and also very effective. In this stage,
the issues are foreseen even before when they did not occur.
After then comes the stage which is known as Generative, where all the elements come to
fruition. Generative firms are considered as lunatics whom are running in the asylum but then
not in negative sense. In this state, the awareness about the safety is spread all throughout the
firm. Hence, the firms with the help of these five points can successfully climb the ladder of
4
safety. The firms too, take this seriously when any of the incidents happens. Else the firms
also neglect the responsibility of people being safe where they work. Hence, for maintaining
the health and safety management systems, one has to link it with the safety culture as well as
continuous improvement (Cooper, 2001).
Hudson Model in Safety Management
When Hudson focused on the significance of culture, he meant more visits to the opera house
or art galleries. The culture of the firm and accidents are completely related and Hudson says
that in the end it is the severity and the frequency of the accidents which reflects the culture
of the organization. He then defined the set of aspects for determining the behaviors of
different people (RMIT, 2014).
According to Hudson, there were five aspects in safety culture. They are: Leadership,
Respect, mindfulness, just and fair and learning. Hudson described the five stages of his
maturity model in which there are levels of safety from the worst to the best.
In the first stage i.e. pathological stage, the management has this belief that the accidents are
caused by being stupid, not attentive and also when people are not willing to be safe as
employees (Önen, 2016).
The second stage i.e. reactive stage is that where the safety becomes the priority after the
accident happens. This is just the temporary stage for pathological firm and else it can grow
into becoming the calculative stage when the firm puts the safety processes and systems in
operation.
The firms which are calculative can run the risk of carving the way through the motions of
safety management as per Hudson.
From calculative stage to becoming proactive firms, it includes a transition of making the
processes and also the systems which are in operation and also very effective. In this stage,
the issues are foreseen even before when they did not occur.
After then comes the stage which is known as Generative, where all the elements come to
fruition. Generative firms are considered as lunatics whom are running in the asylum but then
not in negative sense. In this state, the awareness about the safety is spread all throughout the
firm. Hence, the firms with the help of these five points can successfully climb the ladder of
4
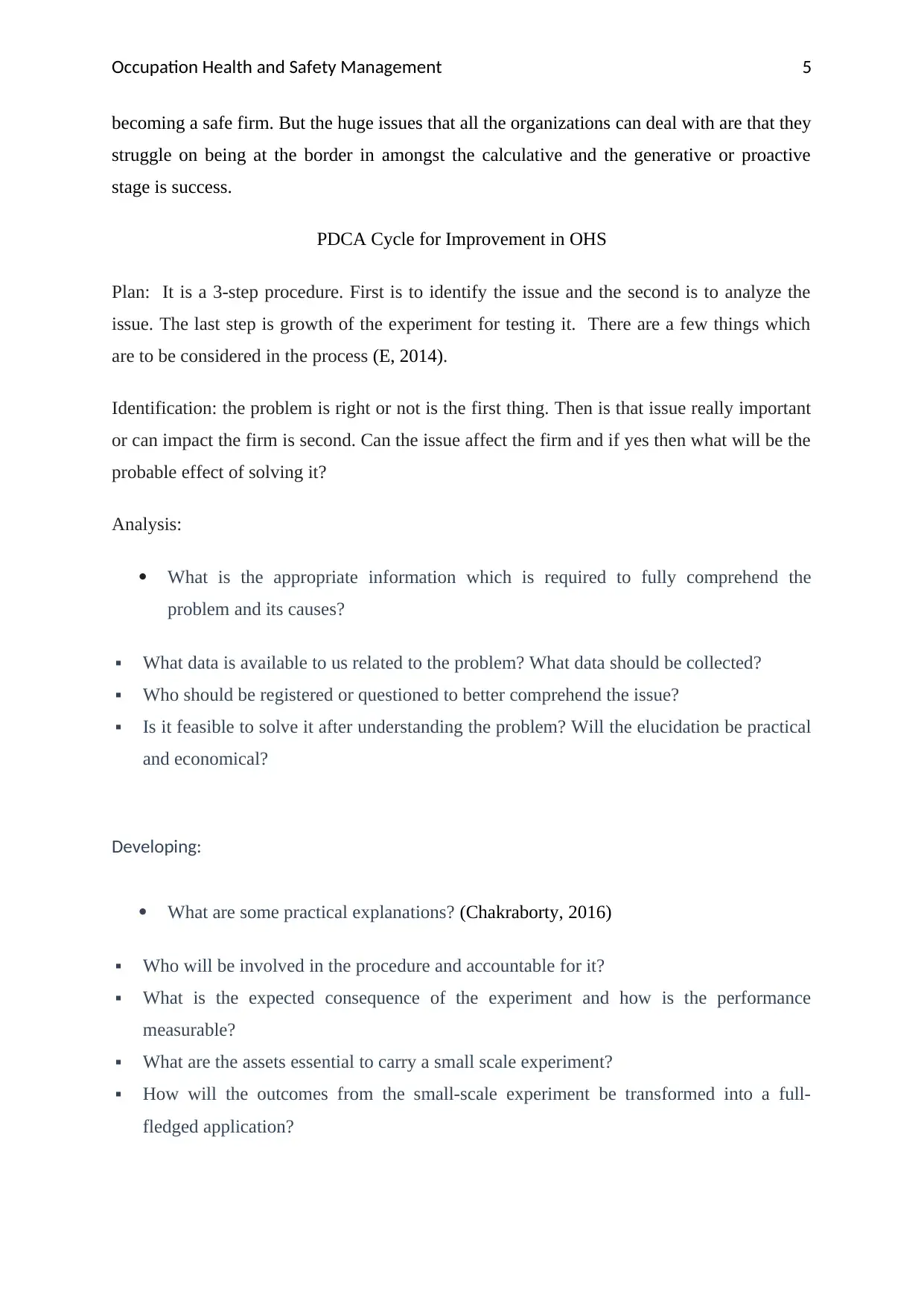
Occupation Health and Safety Management
becoming a safe firm. But the huge issues that all the organizations can deal with are that they
struggle on being at the border in amongst the calculative and the generative or proactive
stage is success.
PDCA Cycle for Improvement in OHS
Plan: It is a 3-step procedure. First is to identify the issue and the second is to analyze the
issue. The last step is growth of the experiment for testing it. There are a few things which
are to be considered in the process (E, 2014).
Identification: the problem is right or not is the first thing. Then is that issue really important
or can impact the firm is second. Can the issue affect the firm and if yes then what will be the
probable effect of solving it?
Analysis:
What is the appropriate information which is required to fully comprehend the
problem and its causes?
What data is available to us related to the problem? What data should be collected?
Who should be registered or questioned to better comprehend the issue?
Is it feasible to solve it after understanding the problem? Will the elucidation be practical
and economical?
Developing:
What are some practical explanations? (Chakraborty, 2016)
Who will be involved in the procedure and accountable for it?
What is the expected consequence of the experiment and how is the performance
measurable?
What are the assets essential to carry a small scale experiment?
How will the outcomes from the small-scale experiment be transformed into a full-
fledged application?
5
becoming a safe firm. But the huge issues that all the organizations can deal with are that they
struggle on being at the border in amongst the calculative and the generative or proactive
stage is success.
PDCA Cycle for Improvement in OHS
Plan: It is a 3-step procedure. First is to identify the issue and the second is to analyze the
issue. The last step is growth of the experiment for testing it. There are a few things which
are to be considered in the process (E, 2014).
Identification: the problem is right or not is the first thing. Then is that issue really important
or can impact the firm is second. Can the issue affect the firm and if yes then what will be the
probable effect of solving it?
Analysis:
What is the appropriate information which is required to fully comprehend the
problem and its causes?
What data is available to us related to the problem? What data should be collected?
Who should be registered or questioned to better comprehend the issue?
Is it feasible to solve it after understanding the problem? Will the elucidation be practical
and economical?
Developing:
What are some practical explanations? (Chakraborty, 2016)
Who will be involved in the procedure and accountable for it?
What is the expected consequence of the experiment and how is the performance
measurable?
What are the assets essential to carry a small scale experiment?
How will the outcomes from the small-scale experiment be transformed into a full-
fledged application?
5

Occupation Health and Safety Management
Do: It is the phase where there should be test done or certain transformations should be
carried out. This can be done on small scale studies.
. Small-scale experiments permit us to quickly adjust and learn as needed, and are typically
economical to commence. Make sure that the performance is measured and data is collected
necessary to make an evaluation later on.
Check
In this stage, experiment is reviewed, the results are analysed and identified regarding my
learning. Consider the following questions:
Did the application of the transformations accomplish the desired outcomes?
What did not work?
What was learned from the application?
Is there enough statistics to show that the change was operative?
Do you need to carry another research?
How can the small scale experiment measure the larger picture?
Is the proposed solution still feasible and useful?
Act
In this stage, take the actions which are based on what you have acquired in the study. If the
transformation did not work, go through the cycle again with an altered strategy. If you were
successful, integrate what you have acquired from the test into wider changes. New
improvements would be planned and cycle would start again. If your plan has worked, the
processes would be standardized and implemented throughout the business. During this phase
of the PDCA cycle, you should ask the following questions:
What resources would be required to apply the solution company-wise?
What kind of training is required for full application of the improvement?
How can the alteration be upheld and sustained?
How can we evaluate and monitor the influence of the solution?
6
Do: It is the phase where there should be test done or certain transformations should be
carried out. This can be done on small scale studies.
. Small-scale experiments permit us to quickly adjust and learn as needed, and are typically
economical to commence. Make sure that the performance is measured and data is collected
necessary to make an evaluation later on.
Check
In this stage, experiment is reviewed, the results are analysed and identified regarding my
learning. Consider the following questions:
Did the application of the transformations accomplish the desired outcomes?
What did not work?
What was learned from the application?
Is there enough statistics to show that the change was operative?
Do you need to carry another research?
How can the small scale experiment measure the larger picture?
Is the proposed solution still feasible and useful?
Act
In this stage, take the actions which are based on what you have acquired in the study. If the
transformation did not work, go through the cycle again with an altered strategy. If you were
successful, integrate what you have acquired from the test into wider changes. New
improvements would be planned and cycle would start again. If your plan has worked, the
processes would be standardized and implemented throughout the business. During this phase
of the PDCA cycle, you should ask the following questions:
What resources would be required to apply the solution company-wise?
What kind of training is required for full application of the improvement?
How can the alteration be upheld and sustained?
How can we evaluate and monitor the influence of the solution?
6
Paraphrase This Document
Need a fresh take? Get an instant paraphrase of this document with our AI Paraphraser
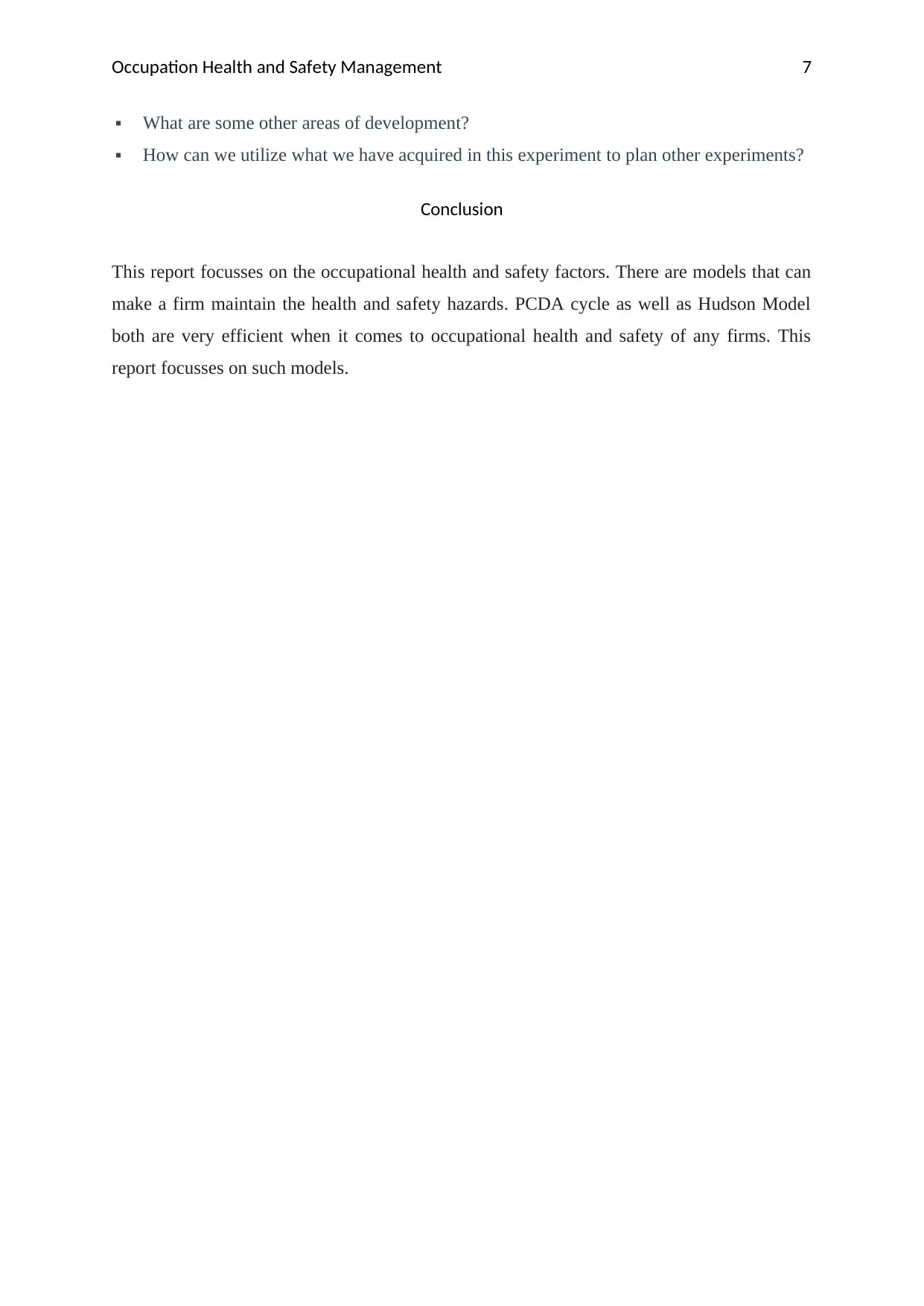
Occupation Health and Safety Management
What are some other areas of development?
How can we utilize what we have acquired in this experiment to plan other experiments?
Conclusion
This report focusses on the occupational health and safety factors. There are models that can
make a firm maintain the health and safety hazards. PCDA cycle as well as Hudson Model
both are very efficient when it comes to occupational health and safety of any firms. This
report focusses on such models.
7
What are some other areas of development?
How can we utilize what we have acquired in this experiment to plan other experiments?
Conclusion
This report focusses on the occupational health and safety factors. There are models that can
make a firm maintain the health and safety hazards. PCDA cycle as well as Hudson Model
both are very efficient when it comes to occupational health and safety of any firms. This
report focusses on such models.
7
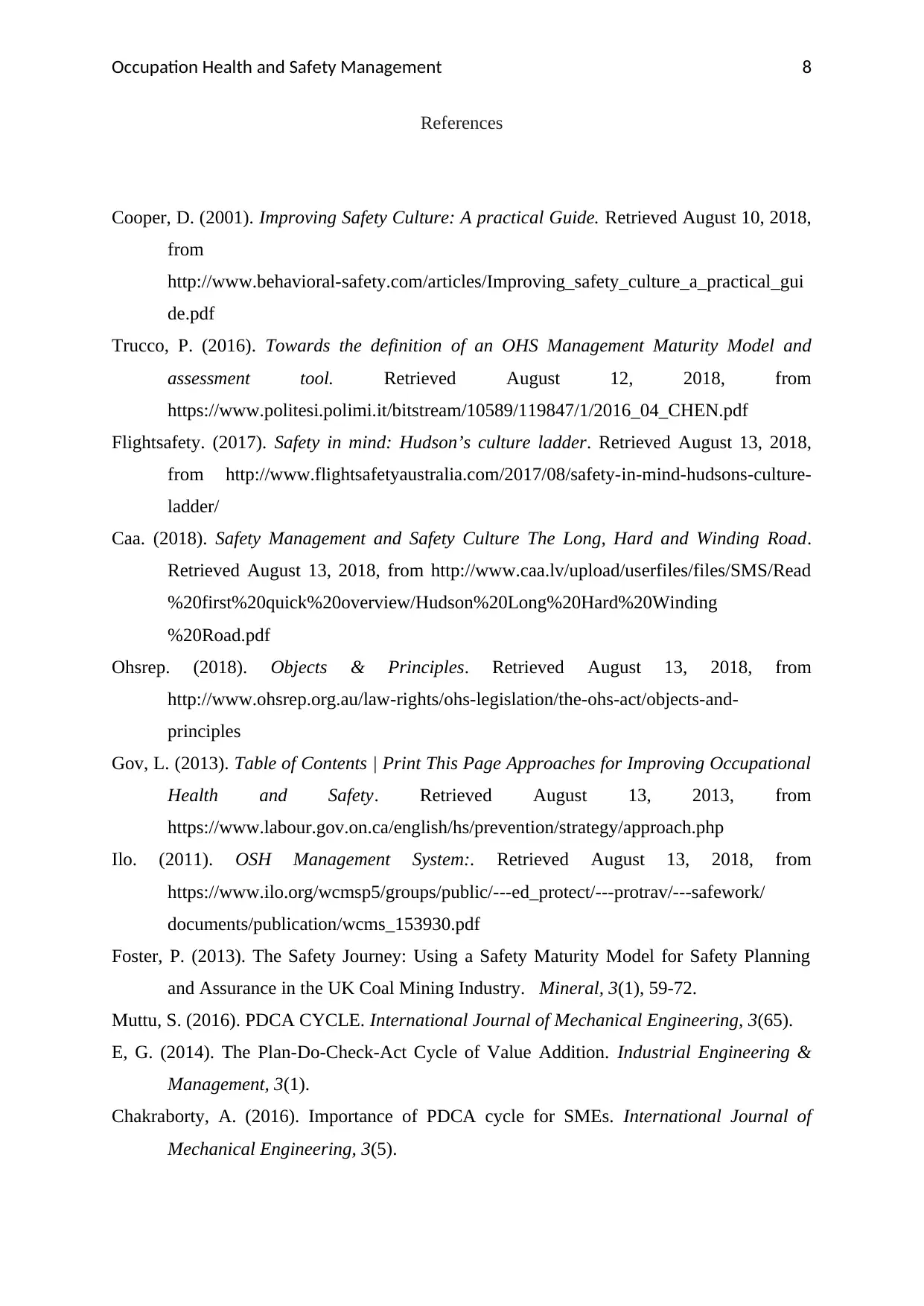
Occupation Health and Safety Management
References
Cooper, D. (2001). Improving Safety Culture: A practical Guide. Retrieved August 10, 2018,
from
http://www.behavioral-safety.com/articles/Improving_safety_culture_a_practical_gui
de.pdf
Trucco, P. (2016). Towards the definition of an OHS Management Maturity Model and
assessment tool. Retrieved August 12, 2018, from
https://www.politesi.polimi.it/bitstream/10589/119847/1/2016_04_CHEN.pdf
Flightsafety. (2017). Safety in mind: Hudson’s culture ladder. Retrieved August 13, 2018,
from http://www.flightsafetyaustralia.com/2017/08/safety-in-mind-hudsons-culture-
ladder/
Caa. (2018). Safety Management and Safety Culture The Long, Hard and Winding Road.
Retrieved August 13, 2018, from http://www.caa.lv/upload/userfiles/files/SMS/Read
%20first%20quick%20overview/Hudson%20Long%20Hard%20Winding
%20Road.pdf
Ohsrep. (2018). Objects & Principles. Retrieved August 13, 2018, from
http://www.ohsrep.org.au/law-rights/ohs-legislation/the-ohs-act/objects-and-
principles
Gov, L. (2013). Table of Contents | Print This Page Approaches for Improving Occupational
Health and Safety. Retrieved August 13, 2013, from
https://www.labour.gov.on.ca/english/hs/prevention/strategy/approach.php
Ilo. (2011). OSH Management System:. Retrieved August 13, 2018, from
https://www.ilo.org/wcmsp5/groups/public/---ed_protect/---protrav/---safework/
documents/publication/wcms_153930.pdf
Foster, P. (2013). The Safety Journey: Using a Safety Maturity Model for Safety Planning
and Assurance in the UK Coal Mining Industry. Mineral, 3(1), 59-72.
Muttu, S. (2016). PDCA CYCLE. International Journal of Mechanical Engineering, 3(65).
E, G. (2014). The Plan-Do-Check-Act Cycle of Value Addition. Industrial Engineering &
Management, 3(1).
Chakraborty, A. (2016). Importance of PDCA cycle for SMEs. International Journal of
Mechanical Engineering, 3(5).
8
References
Cooper, D. (2001). Improving Safety Culture: A practical Guide. Retrieved August 10, 2018,
from
http://www.behavioral-safety.com/articles/Improving_safety_culture_a_practical_gui
de.pdf
Trucco, P. (2016). Towards the definition of an OHS Management Maturity Model and
assessment tool. Retrieved August 12, 2018, from
https://www.politesi.polimi.it/bitstream/10589/119847/1/2016_04_CHEN.pdf
Flightsafety. (2017). Safety in mind: Hudson’s culture ladder. Retrieved August 13, 2018,
from http://www.flightsafetyaustralia.com/2017/08/safety-in-mind-hudsons-culture-
ladder/
Caa. (2018). Safety Management and Safety Culture The Long, Hard and Winding Road.
Retrieved August 13, 2018, from http://www.caa.lv/upload/userfiles/files/SMS/Read
%20first%20quick%20overview/Hudson%20Long%20Hard%20Winding
%20Road.pdf
Ohsrep. (2018). Objects & Principles. Retrieved August 13, 2018, from
http://www.ohsrep.org.au/law-rights/ohs-legislation/the-ohs-act/objects-and-
principles
Gov, L. (2013). Table of Contents | Print This Page Approaches for Improving Occupational
Health and Safety. Retrieved August 13, 2013, from
https://www.labour.gov.on.ca/english/hs/prevention/strategy/approach.php
Ilo. (2011). OSH Management System:. Retrieved August 13, 2018, from
https://www.ilo.org/wcmsp5/groups/public/---ed_protect/---protrav/---safework/
documents/publication/wcms_153930.pdf
Foster, P. (2013). The Safety Journey: Using a Safety Maturity Model for Safety Planning
and Assurance in the UK Coal Mining Industry. Mineral, 3(1), 59-72.
Muttu, S. (2016). PDCA CYCLE. International Journal of Mechanical Engineering, 3(65).
E, G. (2014). The Plan-Do-Check-Act Cycle of Value Addition. Industrial Engineering &
Management, 3(1).
Chakraborty, A. (2016). Importance of PDCA cycle for SMEs. International Journal of
Mechanical Engineering, 3(5).
8
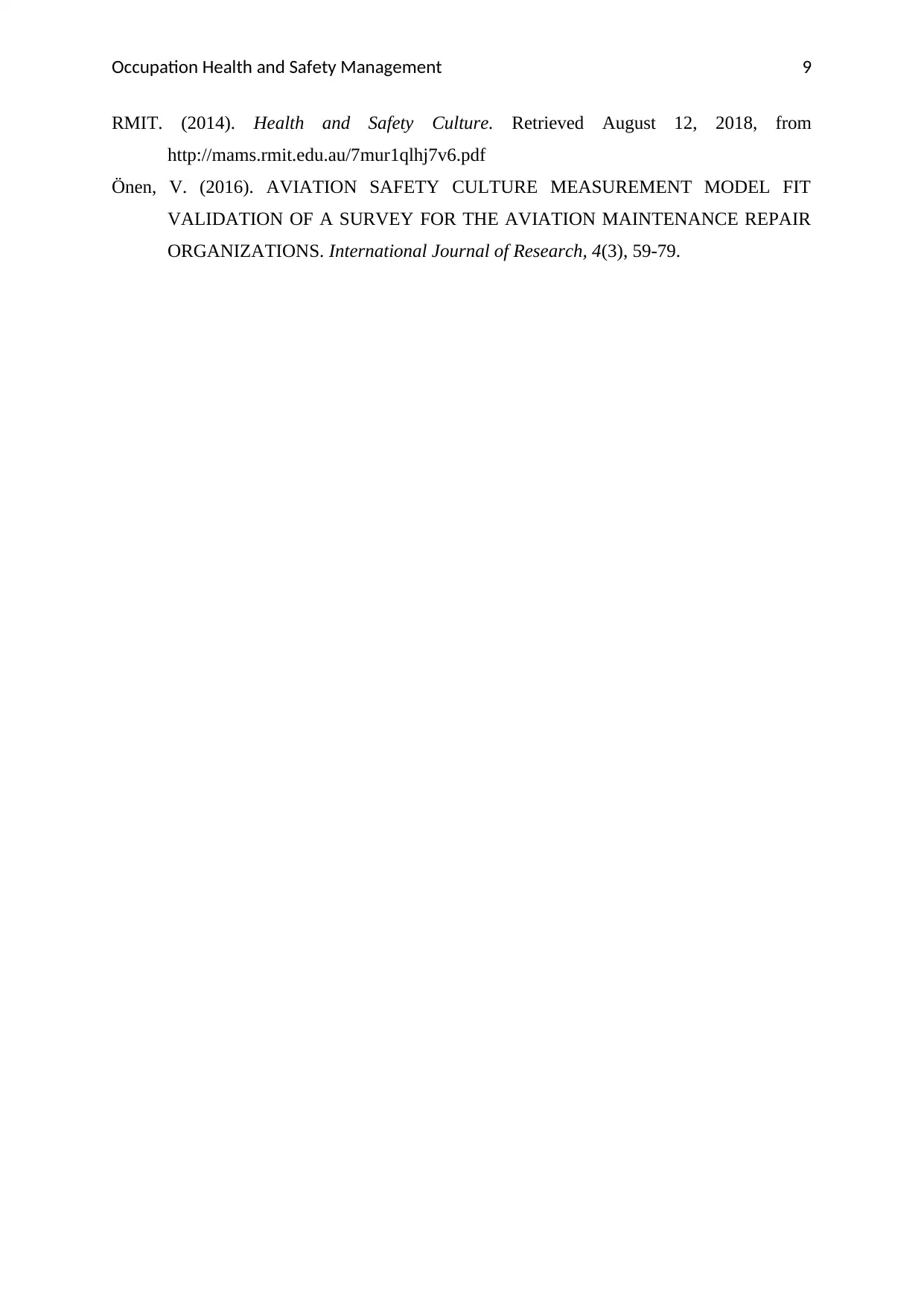
Occupation Health and Safety Management
RMIT. (2014). Health and Safety Culture. Retrieved August 12, 2018, from
http://mams.rmit.edu.au/7mur1qlhj7v6.pdf
Önen, V. (2016). AVIATION SAFETY CULTURE MEASUREMENT MODEL FIT
VALIDATION OF A SURVEY FOR THE AVIATION MAINTENANCE REPAIR
ORGANIZATIONS. International Journal of Research, 4(3), 59-79.
9
RMIT. (2014). Health and Safety Culture. Retrieved August 12, 2018, from
http://mams.rmit.edu.au/7mur1qlhj7v6.pdf
Önen, V. (2016). AVIATION SAFETY CULTURE MEASUREMENT MODEL FIT
VALIDATION OF A SURVEY FOR THE AVIATION MAINTENANCE REPAIR
ORGANIZATIONS. International Journal of Research, 4(3), 59-79.
9
1 out of 10

Your All-in-One AI-Powered Toolkit for Academic Success.
+13062052269
info@desklib.com
Available 24*7 on WhatsApp / Email
Unlock your academic potential
© 2024 | Zucol Services PVT LTD | All rights reserved.